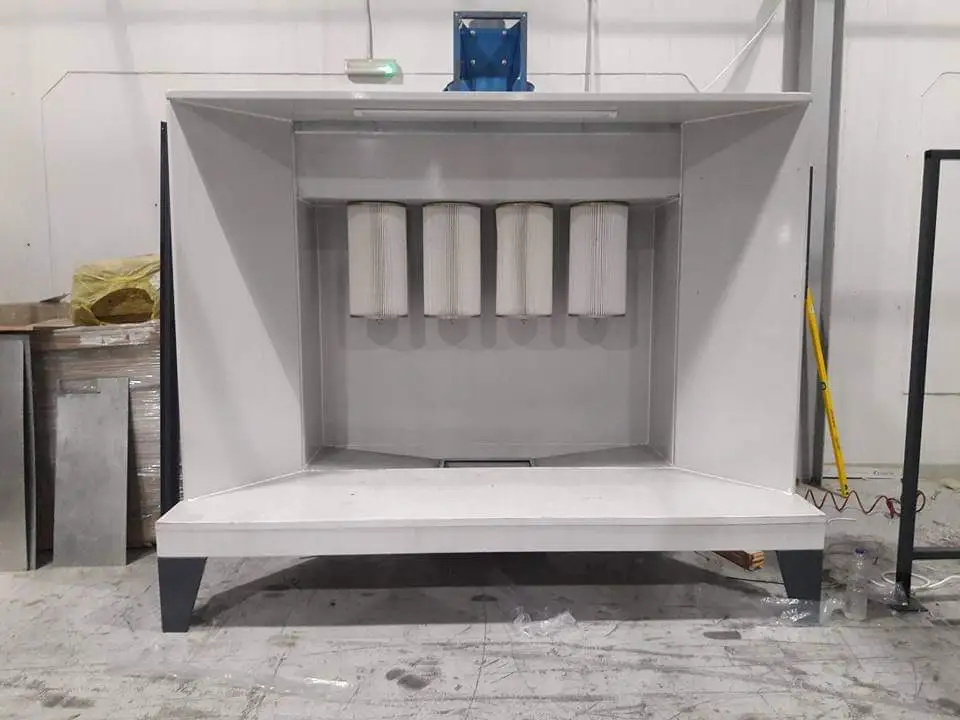
Powder Coating Booth Manufacturers. We design and manufacture Powder Coating booths with cartridge filters and automatic spray booths. High quality and low price
The powder coating booth is equipment, which is manufactured by welding galvanized or mild steel sheet metals in order to form a closed chamber. The closed chamber here is a vital parameter as the filter unit works with suction. The cartridge filters suck the air inside the powder spray booth by an electrical fan so that the unused powder coating flying inside the booth gets caught and sucked into the filters.
This unused powder coating powder can be reused by the blow-off purge of the filters. The recuperation of the booth is very important as this way you lose so less of the powder coating powder.
Powder coating is increasingly accepted as the preferred finishing process for many applications. Increasingly stringent environmental regulations, rising costs in all areas, and demands by consumers for better quality and more durable products are among the challenges facing today’s finishers. Powder coatings provide a solution to these challenges and others. Powder coating is the technique of applying dry paint to the component.
The powdered paint is normally applied by using a powder feed system and gun to electrostatically charge and spray the powder onto the part. For some applications, the part being coated is dipped into a fluidized bed of powder. The coated part is then heated in an oven, or via infrared panels, to melt and cure the paint. During the curing process, a chemical cross-linking reaction is triggered and it is this chemical reaction that gives the powder coatings many of their desirable properties.
Powder Coating Booth Manufacturers in Europe
There are so many powder coating booth manufacturers in Europe, and some of them have the most sales in the market.
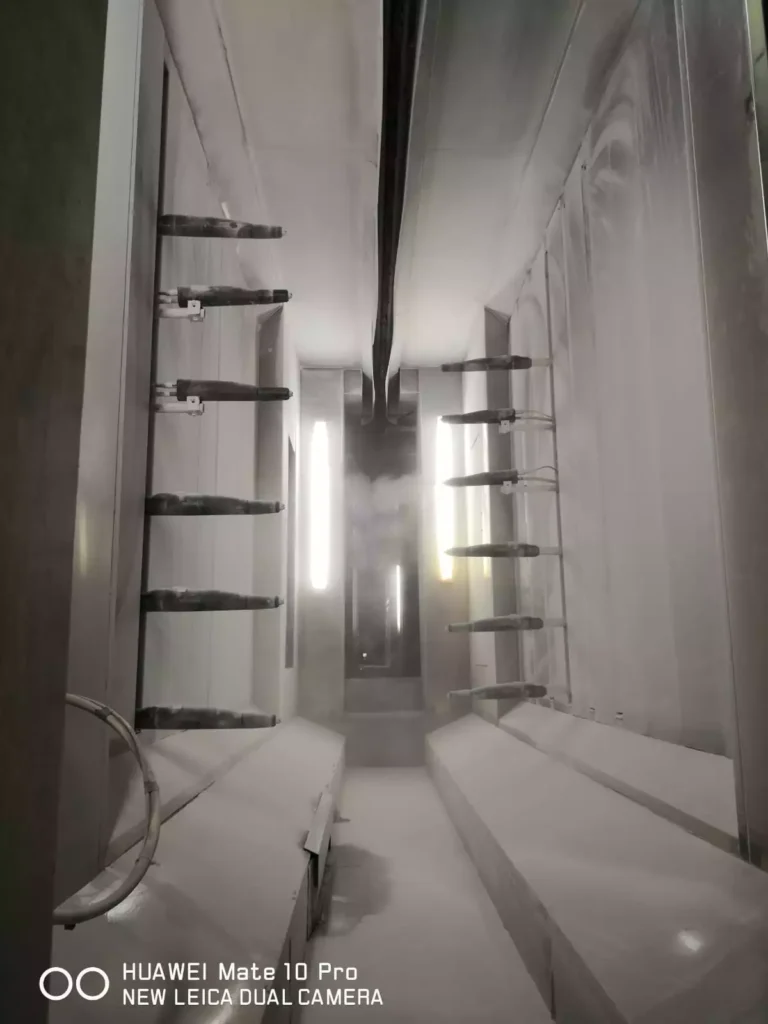
EMS Powder Coating Equipment is one of the main powder coating booth manufacturers in the EU. We have powder spray booths in Austria, Germany, and other countries.
In Atex booths, customers demand powder coating booth fire protection. Here the protection is carried out by using atex motors and fans which don’t carry risks of creating sparks in the mediums where powder coating exists.
Powder paint spray booths can be manual or automatic. The manual coating booth operates with cartridge filters whereas the automatic one works with cyclone and a powder coating filter system.

Building a powder coating spray booth is not an easy task and we do not advise our customers to build their own booths as the efficiency can be low and in the end, they may spend more money than buying a booth from a manufacturer.
A powder coating booth, also known as a powder coating spray booth or powder coating cabin, is a specialized enclosure used in the powder coating process. Powder coating is a surface finishing technique where a fine powder is electrostatically applied to a workpiece, and then heat-cured to create a durable and protective coating. The powder coating booth plays a crucial role in this process by providing a controlled environment for the application of the powder. Here are key features and components of a typical powder coating booth:
Components of a Powder Coating Booth:
- Enclosure: The booth is typically a closed or partially enclosed structure designed to contain the powder overspray and prevent it from escaping into the surrounding area. The enclosure may have walls, a ceiling, and a floor, or it may be an open-front booth.
- Exhaust System: A ventilation or exhaust system is a critical component of the booth. It is designed to capture and remove excess powder particles, fumes, and airborne contaminants generated during the coating process. The exhaust air may pass through filters to trap and collect the powder overspray.
- Airflow Control: The booth is designed with an airflow pattern that helps direct the powder particles towards the target workpiece and away from the operator. This controlled airflow is often achieved through the use of exhaust fans, ductwork, and strategically placed airfoils.
- Lighting: Adequate lighting is essential to ensure proper visibility during the coating process. Booths are equipped with lighting fixtures, typically located above the work area, to illuminate the workpiece.
- Powder Application Equipment: Inside the booth, there are components for powder application. This includes electrostatic spray guns or powder guns, which apply an electrostatic charge to the powder particles and direct them toward the grounded workpiece.
- Recovery System: Many powder coating booths feature a powder recovery system. This system collects and recycles excess powder that doesn’t adhere to the workpiece. It can include filters, cyclone separators, or other devices for powder reclamation.
Key Features and Considerations:
- Operator Safety: Booths are designed with operator safety in mind. They may include features like protective clothing, gloves, and proper grounding to prevent electrostatic discharge.
- Environmental Compliance: Properly designed and maintained booths help prevent powder overspray from escaping into the environment, ensuring compliance with environmental regulations.
- Size and Configuration: Powder coating booths come in various sizes and configurations, from small batch booths to large conveyorized systems for high-volume production.
- Material Compatibility: The booth materials must be compatible with the powders and chemicals used in the coating process to prevent corrosion or contamination.
- Cleanliness and Maintenance: Regular cleaning and maintenance of the booth components, including filters, are necessary to ensure consistent coating quality.
- Powder Recovery Efficiency: The efficiency of the powder recovery system affects material usage and operating costs. High-efficiency systems can save on powder consumption.
Powder coating booths are essential for achieving high-quality, durable finishes on a wide range of products, including automotive parts, appliances, furniture, and more. Properly designed and maintained booths help ensure the efficiency, safety, and environmental compliance of the powder coating process.
Enclosed Environment:
An enclosed environment in a powder coating booth refers to a sealed workspace designed to confine the powder coating process within a controlled area. This feature is fundamental to powder coating operations as it ensures that the coating process remains contained, preventing overspray and airborne particles from escaping into the surrounding workspace or environment. Here’s a detailed exploration of the enclosed environment in a powder coating booth:
The enclosure typically consists of walls, a ceiling, and a floor, constructed from sturdy materials such as steel or aluminum. These materials provide structural integrity and durability to withstand the demands of powder coating operations. The walls and ceiling may be lined with soundproofing and insulation materials to dampen noise and maintain a comfortable working environment for operators.
One of the primary functions of the enclosed environment is to contain overspray generated during the powder coating process. Overspray occurs when powdered coating material is applied to a workpiece and any excess powder is not adhered to the surface. By confining the overspray within the booth, the enclosed environment prevents contamination of surrounding surfaces, machinery, and equipment.
Moreover, the enclosed environment facilitates the effective capture and extraction of overspray through the booth’s ventilation system. Negative pressure ventilation systems are commonly employed in powder coating booths, wherein exhaust fans draw air and overspray particles out of the booth and into filtration systems for removal. This ensures that the air inside the booth remains clean and free of contaminants, maintaining a safe and healthy working environment for operators.
In addition to containing overspray, the enclosed environment also serves to protect operators and surrounding areas from exposure to potentially harmful chemicals and particulates. Powder coating materials may contain volatile organic compounds (VOCs) or hazardous substances, which, if released into the atmosphere, can pose health risks to individuals and the environment. By confining these substances within the booth, the enclosed environment helps mitigate these risks and ensures compliance with safety regulations and environmental standards.
Furthermore, the enclosed environment provides a controlled atmosphere for the powder coating process, minimizing external factors that could impact coating quality and consistency. Factors such as temperature, humidity, and airflow can affect the performance of powder coating materials and the curing process. By maintaining stable environmental conditions within the booth, operators can achieve optimal coating results and ensure uniform adhesion and finish quality across all coated surfaces.
In summary, an enclosed environment is a critical feature of a powder coating booth, providing a controlled and contained workspace for powder coating operations. It prevents overspray contamination, protects operators from exposure to hazardous substances, and ensures consistent coating quality by maintaining stable environmental conditions. By confining the powder coating process within a sealed enclosure, the booth facilitates efficient and safe coating operations in various industrial applications.
Ventilation System:
A ventilation system in a powder coating booth plays a crucial role in maintaining a safe, clean, and controlled environment for powder coating operations. It consists of various components and mechanisms designed to regulate airflow, control air quality, and extract contaminants generated during the coating process. Here’s an in-depth exploration of the ventilation system in a powder coating booth:
- Airflow Regulation: The ventilation system controls the flow of air within the powder coating booth, ensuring proper circulation and distribution of air throughout the workspace. Adjustable dampers, louvers, or vents allow operators to regulate airflow rates and patterns to suit specific coating requirements, workpiece geometries, and environmental conditions.
- Negative Pressure Design: Many powder coating booths employ a negative pressure ventilation design, where exhaust fans create a slight vacuum or negative pressure inside the booth relative to the surrounding environment. This design helps contain overspray and airborne contaminants within the booth, preventing their escape into adjacent areas and minimizing the risk of contamination or exposure to surrounding equipment and personnel.
- Positive Pressure Option: Alternatively, some powder coating booths may utilize a positive pressure ventilation system, where filtered air is supplied into the booth at a higher pressure than the surrounding environment. Positive pressure booths help prevent the ingress of external contaminants, such as dust, dirt, or airborne pollutants, into the workspace, maintaining a cleaner and more controlled coating environment.
- Exhaust Fans: Exhaust fans are the primary components of the ventilation system responsible for extracting air and contaminants from the powder coating booth. These fans create airflow within the booth, drawing in contaminated air and directing it through ductwork to filtration systems or exhaust vents for removal from the workspace. Variable speed fans may be employed to adjust airflow rates according to coating requirements and production demands.
- Filtration Systems: Filtration systems are integral to the ventilation system, tasked with removing airborne contaminants, particulates, and VOCs generated during the powder coating process. High-efficiency particulate air (HEPA) filters, activated carbon filters, or combination filter media capture and trap overspray particles, fumes, and odors, ensuring clean, breathable air inside the booth and preventing pollution of the external environment.
- Air Recirculation: In some powder coating booths, air recirculation systems may be implemented to improve energy efficiency and reduce operating costs. These systems recirculate filtered air back into the booth after removing contaminants, rather than exhausting it outside. Air recirculation helps maintain stable environmental conditions within the booth, such as temperature and humidity, while minimizing energy consumption and HVAC load.
- Environmental Compliance: The ventilation system in a powder coating booth is designed to meet regulatory requirements and environmental standards governing air quality, emissions, and workplace safety. By effectively capturing and containing airborne contaminants, the system ensures compliance with local, state, and federal regulations, mitigating the risk of environmental pollution and protecting the health and safety of workers and the surrounding community.
- Operator Safety: A well-designed ventilation system enhances operator safety by minimizing exposure to hazardous substances, airborne particulates, and VOCs present in the coating environment. Proper airflow patterns, filtration efficiency, and containment measures reduce the concentration of contaminants in the air, preventing respiratory hazards, irritation, or adverse health effects among personnel working in the booth.
In summary, the ventilation system is a critical component of a powder coating booth, essential for maintaining a safe, clean, and controlled environment for coating operations. Its advanced features, including airflow regulation, negative pressure design, exhaust fans, filtration systems, air recirculation, environmental compliance, and operator safety measures, contribute to the efficiency, reliability, and sustainability of powder coating processes in various industrial applications.
Airflow Control:
Airflow control is a vital aspect of powder coating booth operation, ensuring optimal coating quality, process efficiency, and operator safety. It involves regulating the direction, velocity, and distribution of air within the booth to achieve desired coating outcomes and maintain a clean, controlled environment. Here’s a detailed exploration of airflow control in a powder coating booth:
- Directional Control: Airflow direction is crucial for guiding overspray particles away from the operator and toward the filtration system for containment and removal. Adjustable louvers, dampers, or vents strategically positioned within the booth allow operators to direct airflow patterns according to specific coating requirements and workpiece geometries. By controlling airflow direction, operators can minimize overspray drift, ensure uniform coating coverage, and prevent contamination of surrounding areas.
- Velocity Adjustment: Airflow velocity plays a critical role in powder dispersion, coating application, and overspray capture efficiency. Adjustable fan speeds or variable frequency drives (VFDs) enable operators to control airflow velocities within the booth, optimizing powder atomization, deposition rates, and transfer efficiency. Higher airflow velocities may be required for dense workpieces or intricate shapes to ensure proper powder penetration and coverage, while lower velocities may be suitable for delicate parts or thin coatings to prevent powder bounce-back or overspray.
- Uniform Distribution: Achieving uniform airflow distribution across the entire workpiece surface is essential for consistent coating quality and finish. Proper booth design, including strategically placed air distribution panels, baffles, or diffusers, helps ensure even airflow distribution and minimize turbulence within the booth. Uniform airflow prevents localized powder buildup, streaking, or uneven coating thicknesses, resulting in a smoother, more uniform finish across all coated surfaces.
- Negative Pressure Design: Many powder coating booths utilize a negative pressure ventilation design, where exhaust fans create a slight vacuum inside the booth relative to the surrounding environment. This negative pressure differential helps contain overspray and airborne contaminants within the booth, ensuring they are effectively captured and extracted by the ventilation system. Negative pressure design enhances overspray containment efficiency and operator safety by minimizing the risk of overspray drift or escape from the booth.
- Positive Pressure Option: Alternatively, some powder coating booths may employ a positive pressure ventilation system, where filtered air is supplied into the booth at a higher pressure than the surrounding environment. Positive pressure booths help prevent the ingress of external contaminants, maintain clean air quality within the booth, and create a controlled environment conducive to high-quality coating applications. Positive pressure design is particularly beneficial for sensitive or precision coating processes that require strict environmental control and contamination prevention.
- Variable Airflow Zones: Powder coating booths may feature variable airflow zones or adjustable airflow curtains to accommodate different coating requirements and workpiece configurations. These zones allow operators to create customized airflow patterns, such as concentrated airflow around complex geometries or uniform airflow across large flat surfaces, optimizing coating efficiency and quality. Variable airflow control enhances process flexibility, adaptability, and productivity in diverse coating applications.
- Environmental Control: Airflow control is essential for maintaining stable environmental conditions within the powder coating booth, including temperature, humidity, and air quality. Proper airflow management helps regulate heat distribution, moisture levels, and airborne contaminant concentrations, ensuring consistent coating performance and curing outcomes. By controlling environmental variables, operators can minimize coating defects, optimize process parameters, and achieve superior coating results across various operating conditions.
In summary, airflow control is a critical aspect of powder coating booth operation, essential for achieving optimal coating quality, process efficiency, and operator safety. Its advanced features, including directional control, velocity adjustment, uniform distribution, negative pressure design, positive pressure options, variable airflow zones, and environmental control capabilities, contribute to the effectiveness, reliability, and versatility of powder coating processes in various industrial applications.
Recovery System:
A recovery system in a powder coating booth is a critical component designed to reclaim and recycle overspray powder, minimizing material waste, and improving process efficiency. It consists of various mechanisms and equipment dedicated to capturing, separating, and reintroducing overspray powder into the powder coating process. Here’s an extensive exploration of the recovery system in a powder coating booth:
- Overspray Collection: The primary function of the recovery system is to collect overspray powder generated during the coating process and prevent its dispersion into the surrounding environment. As powdered coating material is sprayed onto the workpiece, a portion of the powder does not adhere and becomes airborne overspray. The recovery system captures this overspray before it escapes from the booth, ensuring efficient material utilization and waste reduction.
- Capture Mechanisms: Different capture mechanisms may be employed within the powder coating booth to capture overspray powder effectively. These mechanisms include cyclone separators, which utilize centrifugal force to separate overspray particles from the airflow, and cartridge collectors, which use filter media to trap and retain airborne powder particles. Additionally, electrostatic precipitators may be utilized to charge overspray particles and attract them to grounded collector plates for recovery.
- Separation Efficiency: The recovery system’s effectiveness depends on its ability to separate overspray powder from the airflow efficiently. High-efficiency separation mechanisms, such as cyclone separators with optimized geometry or cartridge collectors with advanced filter media, ensure maximum powder capture and retention while minimizing pressure drop and energy consumption. Efficient separation systems contribute to higher powder recovery rates and improved process performance.
- Powder Recycling: Once captured, overspray powder is reintroduced into the powder coating process for reuse, reducing material waste and lowering operating costs. The recovered powder is typically transferred to a fluidizing hopper or powder feeder, where it is mixed with fresh powder to maintain a consistent feedstock for coating operations. By recycling overspray powder, the recovery system maximizes material utilization and minimizes the need for additional powder replenishment, saving both cost and resources.
- Reintroduction Mechanisms: Various mechanisms may be employed to reintroduce recovered powder into the coating process. These include pneumatic conveyors, which transport powder from the collection system to the fluidizing hopper or powder feeder through a series of air ducts or pipelines. Vibratory feeders or rotary valves may also be used to meter and dispense recovered powder into the coating system, ensuring accurate and controlled powder delivery.
- Powder Conditioning: In some cases, recovered powder may undergo conditioning or treatment to maintain its flowability, consistency, and electrostatic properties. Conditioning processes such as sieving, deagglomeration, or electrostatic recharging may be employed to ensure that recovered powder performs effectively in the coating process and adheres to quality standards. Proper powder conditioning helps optimize coating performance and ensures consistent finish quality across all coated surfaces.
- Process Integration: The recovery system is integrated seamlessly into the powder coating booth’s workflow, operating in conjunction with powder application equipment, ventilation systems, and control systems. Automation features such as sensors, actuators, and programmable logic controllers (PLCs) enable the recovery system to synchronize with coating processes, adjust to changing operating conditions, and optimize powder recovery efficiency in real-time.
- Environmental Benefits: Beyond material savings and cost reduction, the recovery system offers environmental benefits by minimizing material waste and reducing the environmental footprint of powder coating operations. By recycling overspray powder, the system conserves natural resources, reduces energy consumption associated with powder production, and mitigates the environmental impact of waste disposal. Additionally, lower material consumption translates into reduced emissions and pollution, contributing to sustainable manufacturing practices and regulatory compliance.
In summary, the recovery system is a crucial component of a powder coating booth, essential for reclaiming and recycling overspray powder to minimize waste and improve process efficiency. Its advanced features, including overspray collection mechanisms, efficient separation systems, powder recycling mechanisms, reintroduction mechanisms, powder conditioning processes, process integration capabilities, and environmental benefits, contribute to the effectiveness, sustainability, and cost-effectiveness of powder coating processes in various industrial applications.
Recycling in Powder Coating Booths:
Recycling plays a pivotal role in powder coating operations, contributing to sustainability, cost-effectiveness, and environmental responsibility. Within the context of a powder coating booth, recycling primarily refers to the reuse of overspray powder generated during the coating process. Here’s an in-depth exploration of recycling in powder coating booths:
- Overspray Powder: In powder coating, overspray occurs when excess powder particles are not adhered to the workpiece during the application process and remain airborne within the booth. This overspray powder represents a valuable resource that can be recycled and reused in subsequent coating cycles, minimizing material waste and conserving resources.
- Collection and Recovery: Overspray powder is collected and recovered using specialized equipment and systems integrated into the powder coating booth. Cyclone separators, cartridge collectors, or electrostatic precipitators capture overspray particles from the airflow, separating them from the surrounding air. The recovered powder is then transferred to a recycling system for processing and reintroduction into the coating process.
- Powder Recycling System: A powder recycling system consists of various components and mechanisms designed to reclaim, condition, and reintroduce overspray powder into the powder coating process. Pneumatic conveyors, vibratory feeders, or rotary valves transport recovered powder from the collection system to a fluidizing hopper or powder feeder, where it is mixed with fresh powder for reuse.
- Material Savings: Recycling overspray powder enables powder coating operations to minimize material consumption and reduce the need for fresh powder replenishment. By reusing recovered powder, manufacturers can conserve raw materials, lower material costs, and optimize material utilization rates, leading to significant savings over time.
- Cost-Effectiveness: Powder recycling contributes to the cost-effectiveness of powder coating operations by reducing material waste and associated disposal costs. Instead of disposing of unused powder as waste, recycling allows manufacturers to maximize the value of their powder inventory and extend its lifecycle through multiple coating cycles. This results in cost savings and improved profitability for powder coating businesses.
- Quality Assurance: Recycled powder undergoes conditioning or treatment to maintain its flowability, consistency, and performance characteristics. Sieving, deagglomeration, or electrostatic recharging processes may be employed to ensure that recycled powder meets quality standards and performs effectively in the coating process. Quality assurance measures help maintain consistent coating quality and finish across all coated surfaces.
- Environmental Benefits: Powder recycling offers significant environmental benefits by reducing the environmental footprint of powder coating operations. By conserving raw materials, minimizing waste generation, and reducing energy consumption associated with powder production, recycling contributes to resource conservation and pollution prevention. Additionally, recycling helps mitigate the environmental impact of waste disposal and promotes sustainable manufacturing practices.
- Regulatory Compliance: Recycling overspray powder aligns with regulatory requirements and environmental standards governing waste management and pollution prevention. By implementing recycling practices, powder coating facilities demonstrate environmental responsibility and compliance with applicable regulations, reducing the risk of fines, penalties, or legal liabilities associated with improper waste management.
- Continuous Improvement: Powder recycling fosters a culture of continuous improvement and innovation within the powder coating industry. Manufacturers are continually developing and implementing advanced recycling technologies, processes, and equipment to enhance powder recovery efficiency, optimize material utilization, and improve overall process performance. Continuous improvement initiatives drive sustainability, competitiveness, and growth in the powder coating sector.
In summary, recycling is a cornerstone of sustainable powder coating practices, enabling manufacturers to minimize waste, conserve resources, and reduce environmental impact. Within powder coating booths, recycling overspray powder contributes to cost-effectiveness, quality assurance, environmental responsibility, and regulatory compliance. By embracing recycling initiatives, powder coating businesses can achieve economic, environmental, and social sustainability while maintaining competitiveness in the global marketplace.
Exhaust Fans in Powder Coating Booths:
Exhaust fans are essential components of powder coating booths, playing a critical role in maintaining a clean, safe, and efficient working environment. These fans are responsible for extracting air and overspray particles from the booth, ensuring proper ventilation, contaminant removal, and operator safety. Here’s a detailed exploration of exhaust fans in powder coating booths:
- Air Extraction: Exhaust fans create airflow within the powder coating booth, drawing in contaminated air and overspray particles generated during the coating process. This airflow carries overspray away from the workpiece and operator, directing it towards filtration systems or exhaust vents for removal from the booth.
- Negative Pressure Design: Many powder coating booths utilize a negative pressure ventilation design, where exhaust fans create a slight vacuum or negative pressure inside the booth relative to the surrounding environment. This negative pressure helps contain overspray and airborne contaminants within the booth, preventing their escape into adjacent areas and minimizing the risk of contamination or exposure.
- High Efficiency: Exhaust fans are designed for high efficiency and performance, capable of moving large volumes of air and overspray particles to ensure effective contaminant capture and extraction. Variable speed fans or fan arrays may be employed to adjust airflow rates according to coating requirements, production demands, and booth size, optimizing fan performance and energy consumption.
- Filtration Compatibility: Exhaust fans are compatible with various filtration systems commonly used in powder coating booths, including cartridge collectors, cyclone separators, and electrostatic precipitators. These filtration systems capture overspray particles from the airflow, allowing exhaust fans to efficiently remove contaminants and maintain clean air quality within the booth.
- Ductwork and Ventilation Networks: Exhaust fans are connected to ductwork and ventilation networks that distribute airflow throughout the powder coating booth. Ductwork channels contaminated air from the booth to filtration systems or exhaust vents located outside the facility, ensuring proper contaminant removal and environmental compliance.
- Ductwork Design: Proper ductwork design is essential for optimizing airflow distribution, minimizing pressure drop, and preventing turbulence within the ventilation system. Smooth, well-insulated ducts with minimal bends and obstructions facilitate efficient airflow and reduce energy consumption, enhancing fan performance and overall booth efficiency.
- Noise Reduction: Exhaust fans may be equipped with noise-reducing features such as soundproof enclosures, vibration dampeners, or acoustical baffles to minimize noise levels and ensure a quieter working environment for operators. Noise reduction measures enhance operator comfort and productivity while maintaining ventilation system performance.
- Maintenance and Inspection: Regular maintenance and inspection of exhaust fans are essential to ensure continued performance and reliability. Routine tasks such as cleaning fan blades, lubricating bearings, and inspecting motor components help prevent equipment breakdowns, optimize fan efficiency, and extend equipment lifespan.
- Safety Features: Exhaust fans incorporate safety features to protect operators and equipment from potential hazards. Overload protection, thermal sensors, and automatic shut-off mechanisms prevent overheating and motor failure, while safety guards and covers prevent accidental contact with moving parts.
In summary, exhaust fans are integral components of powder coating booths, essential for maintaining proper ventilation, contaminant removal, and operator safety. Their high efficiency, compatibility with filtration systems, ductwork design, noise reduction capabilities, maintenance requirements, and safety features contribute to the overall performance, reliability, and effectiveness of powder coating operations in various industrial applications.
Filters in Powder Coating Booths:
Filters are crucial components of powder coating booths, responsible for capturing overspray particles and contaminants generated during the coating process. They play a vital role in maintaining air quality, protecting equipment, and ensuring compliance with environmental regulations. Here’s a detailed exploration of filters in powder coating booths:
- Filtration Efficiency: Filters in powder coating booths are designed to effectively capture overspray particles, preventing them from escaping into the surrounding environment. High-efficiency filters, such as cartridge filters, HEPA filters, or electrostatic precipitators, are capable of trapping even the smallest particles, ensuring clean air quality and minimizing pollution.
- Overspray Capture: As powdered coating material is sprayed onto the workpiece, a portion of the powder does not adhere and becomes airborne overspray. Filters capture this overspray, preventing it from settling on surfaces or escaping from the booth. Proper filtration ensures that overspray particles are retained within the booth and can be reclaimed for reuse or properly disposed of.
- Types of Filters: Powder coating booths may utilize various types of filters, each with specific characteristics and applications:
- Cartridge Filters: These cylindrical filters consist of pleated media housed in a cartridge structure. They offer high surface area for particle capture and are commonly used in dry powder coating booths.
- HEPA Filters: High-efficiency particulate air (HEPA) filters are capable of capturing particles as small as 0.3 microns with 99.97% efficiency. They are ideal for capturing fine overspray particles and maintaining clean air quality.
- Electrostatic Precipitators: These filters use electrostatic charges to attract and capture overspray particles onto collector plates. They are effective for high-volume overspray capture and are often used in combination with other filtration systems.
- Placement and Configuration: Filters are strategically placed within the powder coating booth to capture overspray particles as air passes through them. They may be positioned in exhaust ducts, filter walls, or filtration units located at the exhaust outlet of the booth. Proper filter placement ensures efficient overspray capture and prevents contamination of downstream equipment or the surrounding environment.
- Filter Maintenance: Regular maintenance of filters is essential to ensure optimal performance and longevity. Routine tasks such as cleaning, replacement, or reconditioning help prevent filter clogging, maintain airflow rates, and extend filter lifespan. Filter maintenance schedules should be established based on operating conditions, coating volumes, and manufacturer recommendations.
- Pressure Drop: As filters capture overspray particles, they may experience a build-up of material, leading to an increase in pressure drop across the filter media. Monitoring pressure drop levels is essential to assess filter performance and determine when maintenance or replacement is required. Excessive pressure drop can impact airflow rates, booth efficiency, and coating quality.
- Environmental Compliance: Filters play a critical role in ensuring compliance with environmental regulations governing air quality and emissions from powder coating operations. By effectively capturing overspray particles, filters prevent pollution of the surrounding environment and mitigate the risk of fines, penalties, or legal liabilities associated with non-compliance.
- Quality Assurance: Clean filters are essential for maintaining consistent coating quality and finish. Properly functioning filters prevent overspray contamination, minimize coating defects, and ensure uniform deposition of powder onto workpieces. Regular filter maintenance and replacement contribute to quality assurance and customer satisfaction.
In summary, filters are indispensable components of powder coating booths, essential for capturing overspray particles, maintaining air quality, and ensuring environmental compliance. Their high filtration efficiency, strategic placement, maintenance requirements, and role in quality assurance make them critical elements of successful powder coating operations in various industrial settings.
Air Recirculation in Powder Coating Booths:
Air recirculation is a process commonly employed in powder coating booths to improve energy efficiency, enhance coating quality, and reduce environmental impact. By recirculating air within the booth, operators can optimize airflow patterns, maintain consistent environmental conditions, and minimize heat loss. Here’s an in-depth exploration of air recirculation in powder coating booths:
- Principle of Operation: Air recirculation involves the reuse of air that has already been circulated within the powder coating booth. Instead of exhausting all the air outside the booth and replacing it with fresh air, a portion of the air is recirculated back into the booth after undergoing filtration and conditioning processes. This recirculated air is blended with fresh makeup air to maintain desired airflow rates and environmental conditions.
- Energy Efficiency: Air recirculation offers significant energy savings compared to constant fresh air ventilation systems. By recirculating a portion of the air, the need for heating or cooling makeup air is reduced, resulting in lower energy consumption and operating costs. Energy-efficient recirculation systems may incorporate heat recovery units or air-to-air heat exchangers to further optimize energy utilization and reduce environmental impact.
- Air Filtration: Recirculated air undergoes filtration to remove overspray particles, contaminants, and airborne pollutants generated during the coating process. Filters such as cartridge filters, HEPA filters, or electrostatic precipitators capture overspray particles before the air is recirculated back into the booth. Proper filtration ensures clean air quality, minimizes contamination, and maintains coating integrity.
- Temperature and Humidity Control: Air recirculation allows for precise control of temperature and humidity levels within the powder coating booth. Recirculated air can be conditioned using heating or cooling systems to maintain optimal operating conditions for the coating process. Temperature and humidity sensors, along with automated control systems, regulate air recirculation rates to achieve desired environmental parameters.
- Airflow Management: Recirculation systems enable operators to optimize airflow patterns within the powder coating booth, ensuring uniform distribution of air and overspray particles. Adjustable louvers, dampers, or variable frequency drives (VFDs) control airflow direction, velocity, and distribution, enhancing coating efficiency and quality. Proper airflow management minimizes overspray drift, prevents coating defects, and improves transfer efficiency.
- Environmental Compliance: Air recirculation systems contribute to environmental sustainability by reducing energy consumption, greenhouse gas emissions, and resource depletion associated with powder coating operations. By minimizing the need for fresh makeup air and optimizing energy utilization, recirculation systems help mitigate the environmental impact of industrial processes and ensure compliance with regulatory requirements.
- Process Flexibility: Recirculation systems offer greater flexibility in powder coating operations, allowing operators to adapt to changing production demands, environmental conditions, and coating requirements. Variable airflow control, temperature adjustment, and humidity regulation enable process optimization and customization to meet specific application needs while maintaining efficiency and quality.
- Noise Reduction: Air recirculation systems may incorporate noise-reducing features such as soundproof enclosures, acoustic insulation, or vibration dampeners to minimize noise levels within the powder coating booth. Noise reduction measures enhance operator comfort, reduce workplace distractions, and improve overall working conditions.
In summary, air recirculation is a highly effective strategy for optimizing energy efficiency, enhancing coating quality, and reducing environmental impact in powder coating booths. Its benefits include energy savings, improved air quality, precise environmental control, process flexibility, noise reduction, and environmental compliance. By incorporating air recirculation systems into powder coating operations, manufacturers can achieve cost savings, operational efficiency, and sustainability goals while maintaining high standards of product quality and performance.
HEPA Filters in Powder Coating Booths:
High-Efficiency Particulate Air (HEPA) filters are critical components of powder coating booths, designed to effectively capture fine overspray particles and ensure clean air quality within the working environment. HEPA filters play a vital role in maintaining operator safety, protecting equipment, and achieving regulatory compliance. Here’s an extensive exploration of HEPA filters in powder coating booths:
- Filtration Efficiency: HEPA filters are renowned for their exceptional filtration efficiency, capable of capturing airborne particles as small as 0.3 microns with 99.97% efficiency. This high level of filtration ensures that even the finest overspray particles generated during the powder coating process are effectively captured and retained within the booth, preventing their release into the surrounding environment.
- Overspray Capture: As powdered coating material is sprayed onto workpieces within the booth, a portion of the powder becomes airborne overspray. HEPA filters capture this overspray, preventing it from escaping into the atmosphere or settling on surfaces outside the booth. By maintaining clean air quality, HEPA filters help minimize contamination, ensure product quality, and protect the health and safety of workers.
- Comprehensive Filtration: HEPA filters offer comprehensive filtration capabilities, capturing not only overspray particles but also various other airborne contaminants, including dust, pollen, mold spores, and bacteria. This broad spectrum of filtration ensures that the air within the powder coating booth remains clean and free of harmful pollutants, creating a safe and healthy working environment for operators.
- Filter Construction: HEPA filters are constructed using a dense network of microscopic fibers arranged in a pleated configuration. This design maximizes surface area for particle capture while maintaining low airflow resistance, ensuring efficient filtration without compromising booth airflow rates. The filter media is typically enclosed within a sturdy frame made of metal or plastic to provide structural support and durability.
- Placement and Configuration: HEPA filters are strategically placed within the powder coating booth to intercept overspray particles as air passes through them. They may be installed in dedicated filtration units located at the exhaust outlet of the booth or integrated into the booth’s ventilation system. Proper placement and configuration ensure optimal filtration performance and prevent overspray contamination of downstream equipment or the surrounding environment.
- Filter Maintenance: Regular maintenance of HEPA filters is essential to ensure continued performance and longevity. Routine tasks such as periodic inspection, cleaning, or replacement help prevent filter clogging, maintain airflow rates, and extend filter lifespan. Filter maintenance schedules should be established based on operating conditions, coating volumes, and manufacturer recommendations.
- Environmental Compliance: HEPA filters play a crucial role in ensuring compliance with environmental regulations governing air quality and emissions from powder coating operations. By effectively capturing overspray particles and contaminants, HEPA filters prevent pollution of the surrounding environment and help mitigate the risk of fines, penalties, or legal liabilities associated with non-compliance.
- Quality Assurance: Clean HEPA filters are essential for maintaining consistent coating quality and finish. Properly functioning filters prevent overspray contamination, minimize coating defects, and ensure uniform deposition of powder onto workpieces. Regular filter maintenance and replacement contribute to quality assurance and customer satisfaction.
In summary, HEPA filters are indispensable components of powder coating booths, providing superior filtration efficiency, comprehensive contaminant capture, and regulatory compliance. Their advanced filtration capabilities, strategic placement, maintenance requirements, and role in quality assurance make them essential for ensuring clean air quality and operator safety in powder coating operations.
Activated Carbon Filters in Powder Coating Booths:
Activated carbon filters are specialized filtration media used in powder coating booths to effectively remove volatile organic compounds (VOCs), odors, and other gaseous contaminants from the air. These filters play a crucial role in maintaining clean air quality, protecting the environment, and ensuring operator safety. Here’s a detailed exploration of activated carbon filters in powder coating booths:
- Adsorption Principle: Activated carbon filters operate on the principle of adsorption, where gaseous contaminants are trapped or adhered to the porous surface of activated carbon particles. Activated carbon has a large internal surface area and high adsorption capacity, making it highly effective at capturing a wide range of VOCs and odorous compounds present in the air.
- Removal of VOCs: During the powder coating process, VOCs may be released from coating materials, solvents, or substrates, contributing to air pollution and potential health hazards. Activated carbon filters efficiently adsorb VOC molecules as air passes through them, effectively removing these contaminants and preventing their release into the atmosphere.
- Odor Control: Activated carbon filters are particularly effective at controlling odors generated during powder coating operations, such as those from curing ovens or chemical processes. The porous structure of activated carbon provides ample surface area for odor molecules to adsorb, neutralizing unpleasant smells and improving air quality within the booth.
- Complementary Filtration: Activated carbon filters are often used in conjunction with other filtration media, such as HEPA filters or pre-filters, to provide comprehensive air purification in powder coating booths. HEPA filters capture solid particulate matter, while activated carbon filters target gaseous pollutants, ensuring thorough contaminant removal and clean air recirculation.
- Filter Construction: Activated carbon filters consist of activated carbon particles impregnated onto a substrate material, such as foam, pleated paper, or granular media. The substrate provides structural support and uniform airflow distribution, while the activated carbon adsorbs gaseous contaminants as air passes through the filter. Activated carbon filters may be housed in specialized filter cartridges, panels, or canisters for easy installation and replacement.
- Replacement Interval: The adsorption capacity of activated carbon filters is finite, and they must be replaced periodically to maintain effective filtration performance. The replacement interval depends on various factors, including the concentration of contaminants, airflow rates, operating conditions, and filter size. Regular monitoring and maintenance are essential to ensure timely replacement and optimal filter performance.
- Environmental Benefits: Activated carbon filters contribute to environmental sustainability by reducing air pollution and minimizing the release of harmful VOCs into the atmosphere. By effectively capturing gaseous contaminants, these filters help protect air quality, mitigate health risks, and promote eco-friendly powder coating practices.
- Occupational Safety: Activated carbon filters play a crucial role in safeguarding the health and safety of powder coating booth operators by removing hazardous VOCs and odors from the air. Clean air quality within the booth reduces the risk of respiratory irritation, chemical exposure, and long-term health effects associated with airborne contaminants.
In summary, activated carbon filters are essential components of powder coating booths, providing efficient removal of VOCs, odors, and gaseous pollutants to ensure clean air quality and operator safety. Their adsorption capabilities, complementary filtration with other media, filter construction, replacement requirements, environmental benefits, and role in occupational safety make them indispensable for maintaining a healthy and sustainable working environment in powder coating operations.
Hooks in Powder Coating Booths:
Hooks are essential components used in powder coating booths to suspend workpieces during the coating process. They play a critical role in facilitating efficient coating application, ensuring uniform coverage, and maximizing production throughput. Here’s an in-depth exploration of hooks in powder coating booths:
- Fixture Attachment: Hooks serve as attachment points for workpieces, allowing them to be securely suspended from overhead conveyor systems or racks within the powder coating booth. Workpieces are typically hung from hooks by their designated attachment points, such as holes, tabs, or handles, ensuring stable positioning during the coating process.
- Versatility: Hooks come in various shapes, sizes, and configurations to accommodate a wide range of workpiece shapes, sizes, and weights. Common hook designs include straight hooks, J-hooks, C-hooks, S-hooks, and specialized hooks tailored to specific applications or workpiece geometries. This versatility allows operators to effectively coat diverse product types with minimal setup or adjustments.
- Material Compatibility: Hooks are constructed from materials compatible with the powder coating process, such as stainless steel, aluminum, or high-temperature plastics. These materials offer durability, corrosion resistance, and heat resistance required for continuous exposure to powder coating materials, curing temperatures, and cleaning chemicals.
- Coating Accessibility: Hooks are designed to ensure optimal coating accessibility for all surfaces of the workpiece, including recessed areas, corners, and edges. Proper hook placement and spacing allow for uniform powder deposition and coverage, minimizing the risk of coating defects such as runs, drips, or uneven finishes.
- Conveyor Integration: Hooks are often integrated with overhead conveyor systems or racks that transport workpieces through the powder coating booth. The design of hooks and conveyor systems must be coordinated to ensure compatibility, smooth movement, and proper spacing between workpieces to prevent contact or interference during coating application.
- Loading and Unloading Efficiency: Hooks facilitate efficient loading and unloading of workpieces onto and off of the conveyor system or rack within the powder coating booth. Quick-release mechanisms, adjustable hook positions, and ergonomic designs streamline the handling process, minimizing downtime and maximizing production throughput.
- Grounding Considerations: In electrostatic powder coating systems, hooks may be electrically grounded to prevent electrostatic discharge and ensure uniform powder deposition. Grounding hooks effectively dissipate electrostatic charges from workpieces, reducing the risk of powder migration, Faraday cage effects, or coating inconsistencies.
- Cleaning and Maintenance: Hooks require regular cleaning and maintenance to remove accumulated powder residue, coatings, or contaminants that may affect coating quality or interfere with conveyor operation. Cleaning methods may include manual wiping, chemical cleaning, abrasive blasting, or automated cleaning systems integrated into the powder coating line.
- Compatibility with Hanging Systems: Hooks must be compatible with hanging systems or fixtures used to suspend workpieces within the powder coating booth. These hanging systems may include conveyor hooks, rack hangers, masking fixtures, or specialized suspension devices tailored to specific workpiece geometries or handling requirements.
- Safety Considerations: Hooks should be designed with safety features to prevent workpiece slippage, tipping, or dislodgment during handling or coating processes. Load capacity ratings, secure attachment points, and anti-slip coatings or grips enhance operator safety and prevent accidents or damage to workpieces.
In summary, hooks are indispensable components of powder coating booths, providing efficient suspension and handling of workpieces during the coating process. Their versatility, material compatibility, coating accessibility, conveyor integration, loading efficiency, grounding considerations, cleaning requirements, compatibility with hanging systems, and safety features contribute to the overall efficiency, productivity, and quality of powder coating operations in various industrial applications.
Conveyor Systems in Powder Coating Booths:
Conveyor systems play a vital role in powder coating operations by facilitating the movement of workpieces through the coating process. These systems enable efficient handling, precise positioning, and consistent coating application, ultimately contributing to increased productivity and quality in powder coating booths. Here’s an in-depth exploration of conveyor systems in powder coating booths:
- Continuous Material Flow: Conveyor systems provide a continuous flow of workpieces through the powder coating booth, ensuring a consistent and uninterrupted coating process. Workpieces are loaded onto the conveyor at the entrance of the booth and transported along a predetermined path, passing through various stages of the coating process before exiting the booth.
- Customizable Configurations: Conveyor systems can be customized to meet the specific requirements of powder coating operations, including workpiece size, shape, weight, and production volume. Common conveyor configurations include overhead conveyors, floor-mounted conveyors, monorail systems, power and free conveyors, and indexing conveyors, each offering unique advantages in terms of space utilization, flexibility, and throughput.
- Material Handling Efficiency: Conveyor systems streamline material handling tasks by automating the movement of workpieces through the coating process. Automated loading and unloading stations, adjustable conveyor speeds, and synchronized operation with other equipment optimize material flow, minimize manual labor, and reduce cycle times, leading to increased efficiency and productivity.
- Precision Positioning: Conveyor systems ensure precise positioning of workpieces within the powder coating booth, allowing for accurate coating application and uniform coverage. Workpiece spacing, orientation, and alignment can be controlled to minimize overspray, prevent contact between adjacent parts, and maximize coating efficiency.
- Integration with Coating Equipment: Conveyor systems are integrated with various coating equipment, such as spray guns, powder booths, curing ovens, and cooling stations, to create a cohesive and efficient coating line. Proper alignment, synchronization, and coordination between conveyor components and coating equipment ensure smooth material flow and consistent processing parameters throughout the production line.
- Versatility and Flexibility: Conveyor systems offer versatility and flexibility to adapt to different production requirements, product types, and coating processes. Modular conveyor sections, adjustable conveyor speeds, and programmable control systems allow for quick setup, reconfiguration, and customization to accommodate changing production demands or product specifications.
- Cleaning and Maintenance: Conveyor systems require regular cleaning and maintenance to ensure optimal performance and longevity. Routine maintenance tasks may include cleaning conveyor belts, lubricating moving parts, inspecting drive mechanisms, and replacing worn or damaged components. Proper maintenance practices minimize downtime, prevent equipment failures, and prolong the service life of conveyor systems.
- Safety Features: Conveyor systems are equipped with safety features to protect operators and prevent accidents during material handling operations. Safety guards, emergency stop buttons, interlocks, and sensors ensure safe operation and compliance with occupational health and safety regulations. Conveyor safety training and regular safety inspections further enhance workplace safety and reduce the risk of injuries.
- Environmental Considerations: Conveyor systems contribute to environmental sustainability by optimizing material flow, reducing energy consumption, and minimizing waste generation in powder coating operations. Efficient material handling, precise coating application, and controlled process parameters help conserve resources, reduce emissions, and promote eco-friendly manufacturing practices.
In summary, conveyor systems are integral components of powder coating booths, providing continuous material flow, efficient material handling, precision positioning, versatility, flexibility, and environmental sustainability. Their customizable configurations, integration with coating equipment, maintenance requirements, safety features, and role in enhancing productivity and quality make them indispensable for optimizing powder coating operations in various industrial applications.
Curing Optimization in Powder Coating Booths:
Curing optimization is a critical aspect of powder coating operations, ensuring that coated workpieces achieve the desired finish, durability, and performance characteristics. Proper curing enhances coating adhesion, hardness, chemical resistance, and appearance, ultimately maximizing product quality and customer satisfaction. Here’s a comprehensive exploration of curing optimization in powder coating booths:
- Curing Process Overview: Curing is the final stage of the powder coating process, where the applied powder coating is transformed into a durable, fully cured finish. This transformation occurs when the coated workpieces are exposed to elevated temperatures for a specified time, allowing the powder particles to melt, flow, and chemically crosslink to form a continuous, uniform coating.
- Temperature Control: Proper temperature control is essential for achieving optimal curing results. Powder coating manufacturers specify recommended curing temperatures based on the type of powder, substrate material, coating thickness, and desired properties. Curing ovens in powder coating booths are equipped with precise temperature control systems, such as PID controllers, thermocouples, and heating elements, to maintain consistent and uniform temperatures throughout the curing process.
- Time Management: Curing time is another critical factor in achieving optimal coating performance. Powder coating manufacturers provide recommended curing times based on the specific formulation of the powder coating and substrate material. Curing times may vary depending on factors such as coating thickness, substrate geometry, oven airflow, and curing temperature. Operators must adhere to prescribed curing times to ensure sufficient crosslinking and curing of the powder coating.
- Temperature Ramp-Up and Ramp-Down: Proper temperature ramp-up and ramp-down procedures are essential for preventing coating defects and ensuring uniform curing. Gradual temperature ramp-up at the beginning of the curing cycle minimizes thermal shock and prevents substrate distortion, while controlled temperature ramp-down at the end of the curing cycle prevents coating defects such as orange peel, blistering, or adhesion failures.
- Heat Distribution: Uniform heat distribution within the curing oven is crucial for consistent curing results across all workpieces. Even airflow patterns, strategically placed air vents, and proper oven loading ensure uniform heat distribution and minimize temperature variations within the oven chamber. Monitoring and adjusting airflow rates, damper positions, and oven loading optimize heat distribution and improve curing efficiency.
- Substrate Preheating: Preheating the substrate before applying the powder coating can improve coating adhesion, reduce outgassing, and enhance curing efficiency. Substrate preheating removes moisture, solvents, and contaminants from the surface, allowing the powder coating to adhere more effectively and ensuring uniform curing throughout the coating layer. Preheating methods may include infrared heating, convection heating, or induction heating, depending on the substrate material and production requirements.
- Oven Atmosphere Control: Maintaining the proper atmosphere within the curing oven is essential for preventing coating defects and achieving optimal curing results. Inert gas injection or purging systems can be used to create an oxygen-free or reduced-oxygen atmosphere, minimizing the risk of coating oxidation, discoloration, or surface defects. Oxygen sensors, gas analyzers, and exhaust systems monitor and control the oven atmosphere to ensure consistent curing conditions.
- Post-Curing Inspection: After the curing process is complete, coated workpieces undergo thorough inspection to ensure proper curing and adherence to quality standards. Visual inspection, adhesion testing, hardness testing, and chemical resistance testing may be performed to assess coating performance and durability. Any defects or deficiencies identified during post-curing inspection are addressed promptly to maintain product quality and customer satisfaction.
By optimizing the curing process in powder coating booths, manufacturers can achieve superior coating performance, durability, and appearance, ultimately enhancing product quality, customer satisfaction, and competitiveness in the marketplace. Through meticulous temperature control, time management, temperature ramp-up and ramp-down procedures, heat distribution optimization, substrate preheating, oven atmosphere control, and post-curing inspection, operators can maximize the efficiency and effectiveness of the curing process, ensuring consistent and reliable results in powder coating operations.
Powder Recovery Efficiency in Powder Coating Booths:
Powder recovery efficiency is a critical parameter in powder coating operations, representing the percentage of overspray powder that is successfully captured and recycled for reuse. Maximizing powder recovery efficiency is essential for reducing material waste, minimizing environmental impact, and optimizing production costs. Here’s an in-depth exploration of powder recovery efficiency in powder coating booths:
- Overspray Collection System: Powder recovery efficiency depends on the design and effectiveness of the overspray collection system within the powder coating booth. This system typically consists of collection panels, filters, and recovery devices strategically positioned to capture overspray powder as it is expelled from the spray guns during the coating process.
- Collection Panel Design: The design of collection panels significantly influences powder recovery efficiency. Collection panels may be made of porous materials, such as expanded metal or perforated sheets, which allow overspray powder to pass through while trapping larger particles and preventing them from escaping into the surrounding environment. The size, shape, orientation, and spacing of collection panels are optimized to maximize powder capture and minimize air resistance.
- Filter Media Selection: Filters play a crucial role in capturing fine overspray particles and ensuring clean air recirculation within the powder coating booth. High-efficiency filters, such as HEPA (High-Efficiency Particulate Air) filters or cartridge filters, are commonly used to achieve optimal powder recovery efficiency. These filters have a high dust-holding capacity and can capture overspray particles as small as 0.3 microns with high efficiency, ensuring minimal powder loss during the collection process.
- Recovery Device Efficiency: Powder recovery devices, such as cyclone separators, electrostatic precipitators, or powder recovery booths, are employed to separate overspray powder from the airflow and facilitate its collection for recycling. These devices utilize various mechanisms, such as centrifugal force, electrostatic attraction, or gravitational settling, to separate powder particles from the air stream and deposit them into collection bins or hoppers for reuse.
- Powder Reclamation System: Once overspray powder is captured, it is transferred to a powder reclamation system for recycling. This system typically includes powder sieving, filtering, and blending equipment to remove contaminants, agglomerates, and impurities from the recovered powder and ensure its suitability for reuse in subsequent coating cycles. Efficient powder reclamation processes minimize material waste and maximize the utilization of recycled powder in powder coating operations.
- Optimized Airflow Management: Proper airflow management is essential for maximizing powder recovery efficiency in powder coating booths. Balanced airflow patterns, controlled air velocities, and strategically positioned exhaust fans ensure effective capture and containment of overspray powder within the booth. By directing airflow toward collection panels and filters, operators can enhance powder capture efficiency and minimize powder dispersion into the surrounding environment.
- Maintenance and Cleaning: Regular maintenance and cleaning of collection panels, filters, and powder recovery devices are essential for preserving their effectiveness and maximizing powder recovery efficiency over time. Routine cleaning tasks, such as filter replacement, panel washing, and equipment inspection, prevent clogging, maintain airflow rates, and extend the service life of powder recovery components.
- Performance Monitoring and Optimization: Continuous monitoring of powder recovery efficiency allows operators to identify potential inefficiencies or areas for improvement in the powder coating booth. Performance metrics, such as powder capture rates, air quality measurements, and powder reclamation yields, are monitored regularly to assess system performance and implement optimization strategies as needed.
By optimizing the design, operation, and maintenance of powder coating booths, manufacturers can achieve high powder recovery efficiency, minimize material waste, and enhance overall productivity and sustainability in powder coating operations. Through the strategic selection of collection panels, filters, recovery devices, airflow management techniques, and powder reclamation processes, operators can maximize the utilization of overspray powder and minimize environmental impact while maintaining consistent coating quality and performance.
Corrosion Resistance in Powder Coating Booths:
Corrosion resistance is a critical property of powder coating booths, ensuring long-term durability, performance, and reliability in harsh industrial environments. Powder coating booths are exposed to various corrosive agents, including chemicals, moisture, temperature fluctuations, and abrasive materials, which can degrade structural integrity and compromise coating quality over time. Here’s an in-depth exploration of corrosion resistance in powder coating booths:
- Material Selection: The choice of materials for constructing powder coating booths significantly impacts corrosion resistance. Corrosion-resistant materials such as stainless steel, aluminum, galvanized steel, and reinforced plastics are commonly used for booth components, including frame structures, panels, ductwork, and hardware. These materials offer superior resistance to rust, oxidation, chemical attack, and environmental degradation, ensuring long-term performance and reliability in corrosive industrial environments.
- Surface Preparation: Proper surface preparation is essential for enhancing the corrosion resistance of powder coating booth components. Before applying powder coatings, all metal surfaces should be thoroughly cleaned, degreased, and treated to remove contaminants, rust, and oxidation layers. Surface treatments such as chemical etching, phosphating, or mechanical abrasion create a clean, roughened surface that promotes adhesion and improves the durability of the powder coating.
- Powder Coating Application: Powder coatings themselves offer excellent corrosion resistance when applied correctly to properly prepared surfaces. Epoxy, polyester, polyurethane, and hybrid powder coatings are commonly used for booth components due to their outstanding resistance to chemicals, moisture, UV radiation, and mechanical abrasion. These coatings form a protective barrier that shields underlying substrates from corrosive agents and environmental damage, prolonging the service life of powder coating booths.
- Coating Thickness: The thickness of the powder coating layer significantly influences its corrosion resistance properties. A thicker coating provides better protection against corrosion by increasing the barrier effect and reducing the permeability of corrosive agents. Powder coating thickness is carefully controlled during the application process to ensure uniform coverage and adequate protection of all booth components, including hard-to-reach areas and corners.
- Curing and Crosslinking: Proper curing and crosslinking of powder coatings are critical for achieving maximum corrosion resistance. Curing ovens in powder coating booths are equipped with precise temperature and time control systems to ensure thorough polymerization and crosslinking of the powder coating layer. This process creates a dense, chemically resistant film that effectively seals and protects the underlying substrate from corrosion, even under harsh operating conditions.
- Quality Control and Testing: Quality control measures, including coating thickness measurement, adhesion testing, salt spray testing, and accelerated weathering tests, are conducted to assess the corrosion resistance of powder coating booth components. These tests simulate real-world exposure conditions and evaluate the performance of powder coatings under various environmental stressors, helping manufacturers identify potential weaknesses and implement corrective actions to improve corrosion resistance.
- Maintenance and Inspection: Regular maintenance and inspection of powder coating booths are essential for preserving corrosion resistance and prolonging service life. Routine cleaning, lubrication, and corrosion protection treatments, such as periodic reapplication of powder coatings or corrosion inhibitors, prevent degradation and ensure continued performance in corrosive industrial environments.
- Environmental Considerations: Environmental factors such as humidity, temperature extremes, chemical exposure, and airborne contaminants can accelerate corrosion and degrade powder coating booth components over time. Proper environmental controls, including ventilation systems, humidity management, and corrosion-resistant coatings, help mitigate these factors and maintain optimal corrosion resistance in powder coating booths.
By incorporating corrosion-resistant materials, proper surface preparation techniques, high-quality powder coatings, precise curing processes, rigorous testing protocols, proactive maintenance practices, and environmental controls, manufacturers can enhance the corrosion resistance of powder coating booths and ensure long-term performance, durability, and reliability in industrial applications.
Powder Coating Process Optimization:
Process optimization is essential in powder coating operations to maximize efficiency, productivity, and quality while minimizing waste, energy consumption, and environmental impact. By fine-tuning various aspects of the powder coating process, manufacturers can achieve significant improvements in performance and profitability. Here’s a detailed exploration of powder coating process optimization:
- Workflow Analysis: Conduct a comprehensive analysis of the powder coating workflow to identify bottlenecks, inefficiencies, and opportunities for improvement. Evaluate each stage of the process, from substrate preparation to curing, to streamline operations, eliminate redundant steps, and optimize material flow.
- Material Selection: Choose high-quality powder coatings, substrates, and pre-treatment chemicals tailored to the specific requirements of the application. Select coatings with the desired performance characteristics, such as corrosion resistance, durability, and color stability, to meet customer specifications and regulatory standards effectively.
- Surface Preparation: Proper surface preparation is crucial for ensuring adhesion and durability of the powder coating. Implement effective cleaning, degreasing, and pretreatment processes to remove contaminants, oils, and oxidation layers from substrate surfaces. Optimize surface preparation methods to achieve the desired cleanliness and surface roughness for optimal coating adhesion.
- Powder Application Techniques: Evaluate and optimize powder application techniques to achieve uniform coverage, consistent thickness, and excellent finish quality. Adjust powder spray parameters, such as gun settings, spray distance, and airflow rates, to optimize transfer efficiency and minimize overspray. Explore advanced application technologies, such as electrostatic spray guns, automatic powder guns, and robotic systems, for precise and efficient coating application.
- Powder Recovery and Recycling: Maximize powder recovery efficiency to minimize material waste and reduce production costs. Implement effective overspray collection systems, filters, and recovery devices to capture and recycle overspray powder for reuse. Optimize powder reclamation processes, such as sieving, filtering, and blending, to maintain powder quality and maximize recycling rates.
- Curing Optimization: Fine-tune curing processes to achieve optimal coating performance and durability. Control curing oven temperature, time, and airflow to ensure thorough crosslinking and curing of the powder coating. Monitor and adjust temperature ramp-up and ramp-down rates to prevent coating defects and optimize energy efficiency.
- Quality Control Measures: Implement robust quality control measures to monitor and maintain coating quality throughout the production process. Conduct regular inspections, coating thickness measurements, adhesion tests, and visual evaluations to identify defects, inconsistencies, or deviations from specifications. Implement corrective actions promptly to address quality issues and prevent rework or scrap.
- Energy Efficiency: Optimize energy usage in powder coating operations to reduce operating costs and environmental impact. Implement energy-efficient equipment, such as low-energy curing ovens, LED lighting, and high-efficiency motors, to minimize energy consumption. Optimize production scheduling and batch sizes to maximize equipment utilization and minimize idle time.
- Process Monitoring and Data Analysis: Utilize advanced process monitoring and data analysis tools to track key performance metrics, identify trends, and make data-driven decisions for process optimization. Implement real-time monitoring systems, statistical process control (SPC) techniques, and predictive analytics to identify process variations, optimize parameters, and continuously improve process efficiency.
- Employee Training and Engagement: Invest in employee training and engagement initiatives to ensure that operators have the knowledge, skills, and motivation to perform their tasks effectively. Provide comprehensive training on powder coating processes, equipment operation, safety procedures, and quality standards. Encourage employee involvement in process improvement initiatives and empower them to suggest innovative solutions for optimization.
By systematically analyzing and optimizing the various aspects of the powder coating process, manufacturers can achieve significant improvements in efficiency, productivity, quality, and sustainability. Continuous process optimization efforts ensure that powder coating operations remain competitive, adaptive, and responsive to changing market demands and customer requirements.
Powder Coating Booth Types
Here are some additional details and considerations related to powder coating booths:
1. Booth Types:
- Batch Powder Coating Booths: These are designed for smaller-scale operations or custom work. Parts are typically hung on racks or hooks, manually coated, and then cured in an oven. Batch booths are versatile and suitable for various industries.
- Automated or Conveyorized Booths: These are designed for high-volume production. Parts move along a conveyor system through a series of powder application and curing stages. Conveyorized booths are common in industries like automotive manufacturing.
2. Airflow Control:
- Crossdraft vs. Downdraft: Powder coating booths can have crossdraft or downdraft airflow. Crossdraft booths have horizontal airflow, while downdraft booths have airflow moving vertically downward. Downdraft booths are more effective at capturing overspray and contaminants.
3. Filtration:
- Primary and Secondary Filters: Many powder coating booths use a combination of primary filters (e.g., polyester filters) to capture larger powder particles and secondary filters (e.g., HEPA filters) to capture finer particles, ensuring clean exhaust air.
4. Noise Control:
- Soundproofing: In large production facilities, noise from powder coating equipment can be a concern. Some booths are designed with soundproofing materials to reduce noise levels.
5. Lighting:
- LED Lighting: Many modern powder coating booths are equipped with LED lighting due to its energy efficiency and brightness.
6. Booth Size and Layout:
- Customization: Booths can be customized to suit the specific needs of a facility. This includes the size, layout, and the number of spray guns and curing ovens.
7. Maintenance and Cleaning:
- Regular Cleaning: Proper maintenance, including cleaning of booth components and changing filters, is essential to maintain booth efficiency and prevent cross-contamination of colors.
8. Safety:
- Operator Training: Operators must receive training on safe powder coating practices, including the use of personal protective equipment (PPE) and understanding the equipment’s safety features.
9. Environmental Compliance:
- Exhaust Air Treatment: Some facilities incorporate exhaust air treatment systems to further reduce emissions and ensure compliance with air quality regulations.
10. Energy Efficiency:
- Energy Recovery: Some powder coating booths are equipped with heat recovery systems to capture and reuse the heat generated during curing, improving energy efficiency.
11. Powder Management:
- Powder Handling Equipment: Powder coating booths are often complemented by equipment like powder hoppers and sieving machines for efficient powder handling and recycling.
12. Color Changeovers:
- Quick-Change Features: For facilities that frequently change colors, booths with quick-change features for spray gun and powder path cleaning can reduce downtime during color changeovers.
Choosing the right powder coating booth depends on the specific needs and production requirements of the facility. It’s important to consider factors such as throughput, part size and shape, available space, environmental regulations, and budget when selecting or designing a powder coating booth.