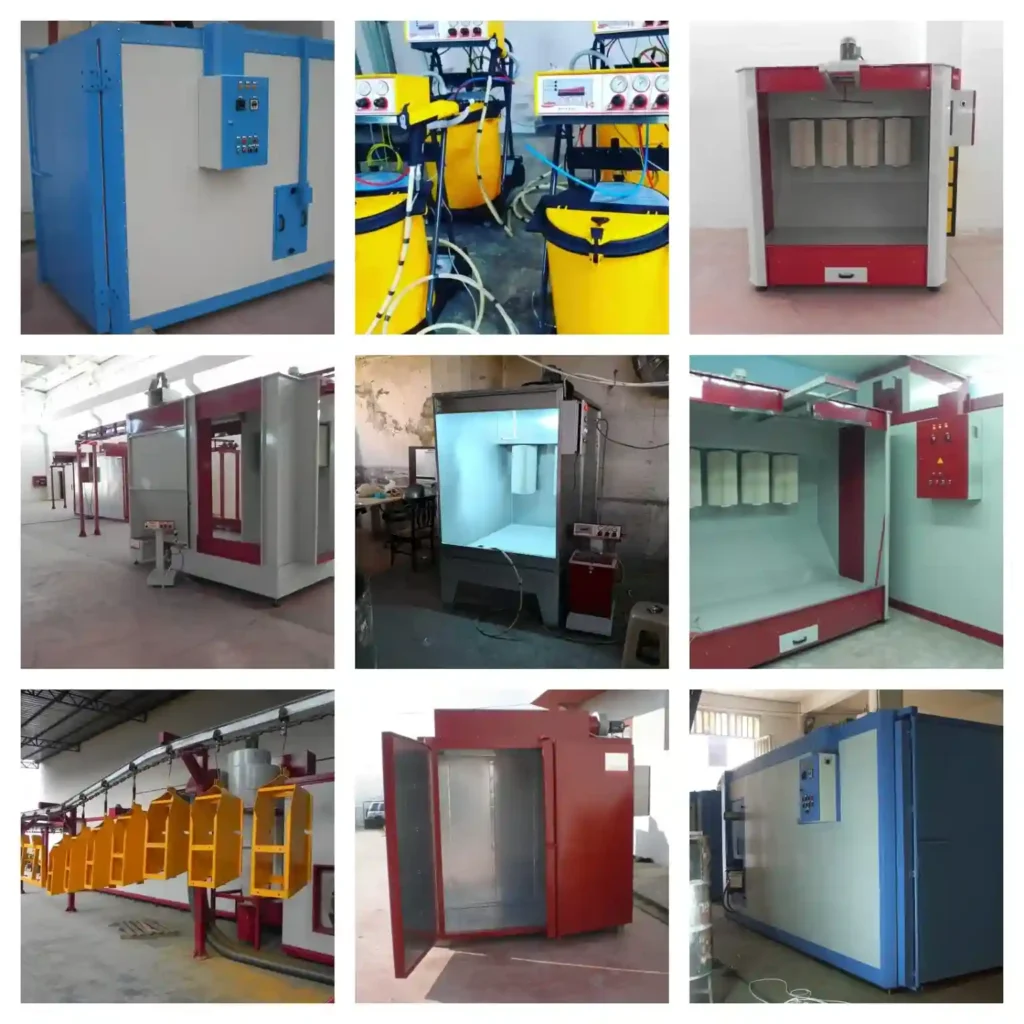
Powder Coating Equipment – Oven, Spray Booth, Powder coating gun – and High-Quality Powder Coating Machinery At Competitive Prices
Powder coating equipment is used to apply a thin layer of powder over a metal surface. This type of coating is applied by an electrostatic process and is a very popular method for finishing metal parts.
This type of equipment can be divided into two main categories: automatic and manual. Automatic booths are more popular because they provide better production rates, but they are also more expensive.
A powder booth is an enclosure in which the powder-coating process takes place. Powder-coating equipment includes an oven where the parts are heated to activate the powder, a gun that sprays or brushes on the powder, a conveyor belt that moves parts through the oven, and cartridge-type guns for applying thicker coatings with less overspray.
Powder coating is a technique that is used to provide a finish to metal parts. This technique has been in use for many years and it is still one of the most popular techniques today.
Powder coating equipment consists of booths, ovens, guns, machines, lines and conveyors. A booth can be either automatic or manual. An automatic booth is more expensive than a manual booth but it is also faster and more efficient.
Thermoset powder: Thermoset powders are the most common type of powder coating. They undergo an irreversible chemical reaction during the curing process, forming a hard, crosslinked network that is highly resistant to heat, chemicals, and scratches.
Thermoplastic powder: Thermoplastic powders do not undergo a chemical reaction during the curing process. Instead, they simply melt and fuse together when heated. This makes them less durable than thermoset powders, but they are also more re-flowable, which can be useful for certain applications.
Epoxy powder: Epoxy powders are known for their excellent corrosion resistance and chemical resistance. They are also very hard and durable. However, they can be brittle and are not as UV resistant as some other types of powder coating.
Polyester powder: Polyester powders are the most versatile type of powder coating. They offer a good balance of properties, including durability, corrosion resistance, UV resistance, and chemical resistance. They are also available in a wide range of colors and finishes.
Polyurethane powder: Polyurethane powders are known for their flexibility and toughness. They are also very resistant to abrasion and impact. However, they are not as heat resistant as some other types of powder coating.
Acrylic powder: Acrylic powders are known for their excellent UV resistance and weather resistance. They are also very glossy and have a high scratch resistance. However, they are not as chemically resistant as some other types of powder coating.
Nylon powder: Nylon powders are known for their excellent chemical resistance and abrasion resistance. They are also very flexible and impact resistant. However, they are not as heat resistant as some other types of powder coating.
Fluorocarbon powder: Fluorocarbon powders are known for their excellent chemical resistance, UV resistance, and non-stick properties. They are also very durable and easy to clean. However, they are relatively expensive.
Silica powder: Silica powders are used as fillers and extenders in powder coatings. They can help to improve the adhesion, flow, and leveling of the coating.
Metal flake powder: Metal flake powders are used to create decorative finishes. They can be used to add sparkle, shine, or a metallic look to a powder coating.
Powder Coating Equipment for Alloy Wheels and Rims
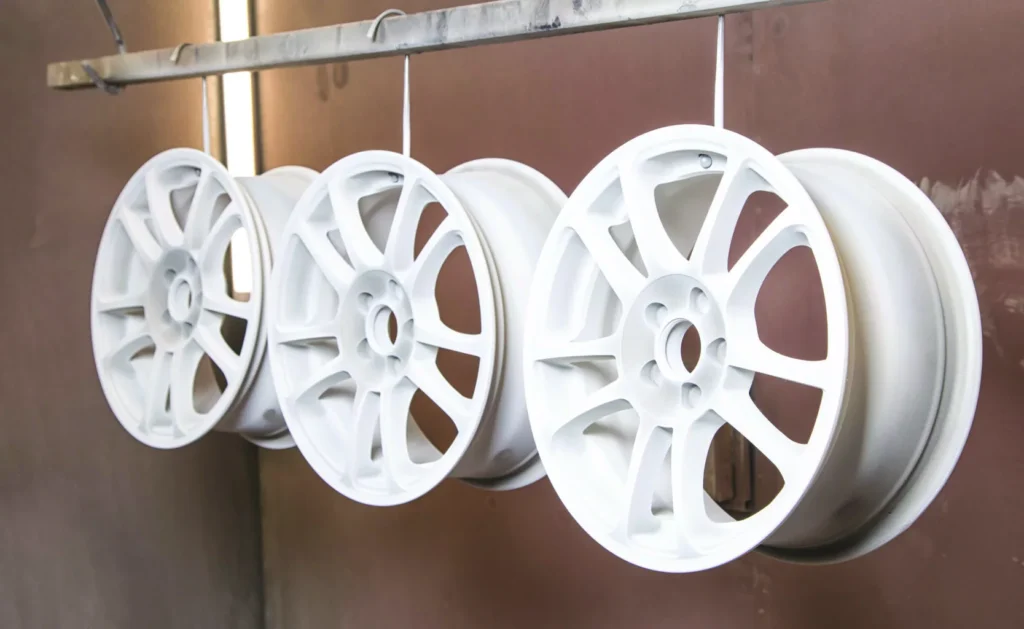
Transform Your Alloy Wheels with Powder Coating Ovens
Elevate your vehicle’s aesthetics and protect your alloy wheels from wear and tear with the power of powder coating. Our versatile alloy wheel powder coating ovens offer a user-friendly and efficient solution for achieving a durable, long-lasting finish that will make your wheels stand out.
Airflow Powder Coating Ovens: Ensuring Consistent Results
Our airflow powder coating ovens feature innovative air circulation systems that guarantee even heat distribution throughout the oven chamber. This consistent curing process ensures a uniform finish and optimal results for your alloy wheels.
Affordable Powder Coating Ovens: Quality at a Competitive Price
Experience the transformative power of powder coating without breaking the bank. Our affordable powder coating ovens provide exceptional value for money, delivering professional-grade results without compromising on quality or performance.
EMS Powder Coating Ovens: Your One-Stop Powder Coating Solution
Discover the convenience of our comprehensive EMS powder coating ovens. These ovens include everything you need for a seamless and efficient powder coating process, from the oven itself to the spray booth and all the necessary tools and accessories.
Aluminium Powder Coating Ovens: Tailored for Aluminum Alloys
Our aluminium powder coating ovens are specifically designed to handle the unique properties of aluminum alloys. These ovens offer precisely controlled temperature settings and optimized curing times to ensure a flawless finish on your aluminum wheels.
Australia Powder Coating Ovens: Designed for Australian Conditions
Enjoy the peace of mind that comes with choosing Australia-specific powder coating ovens. Our ovens are built to withstand the harsh Australian climate and meet all local safety and performance standards.
How Hot Does a Powder Coating Oven Get?
Powder coating ovens typically operate between 300 and 450 degrees Fahrenheit. The exact temperature will depend on the type of powder being used and the object being coated.
How Much Is a Powder Coating Oven?
Powder coating ovens range in price from a few hundred dollars to several thousand dollars. The price depends on the size, features, and quality of the oven.
How Does a Powder Coating Oven Work?
Powder coating ovens work by baking a dry powder onto the surface of the metal object. The powder melts and fuses to the metal surface, creating a hard, protective layer.
Powder Coating Oven Professional Installation
If you have the necessary skills and tools, you can build a powder coating oven yourself. However, for most people, it is more cost-effective and time-efficient to purchase a pre-built oven from a reputable supplier.
Powder Coating Oven Burner: The Heart of the Curing Process
The powder coating oven burner is responsible for heating the oven to the desired temperature. Choose a burner that is powerful enough for the size of your oven and the type of powder you are using.
Powder Coating Oven Blower: Ensuring Even Powder Distribution
The powder coating oven blower helps to evenly distribute the powder inside the oven. Choose a blower with the appropriate CFM rating for the size of your oven.
Powder Coat Oven BTU Calculator: Sizing Your Oven
Use a powder coat oven BTU calculator to determine the appropriate BTU rating for your oven. The BTU rating is based on the size of the oven and the type of powder you are using.
Powder Coat Oven Build Kit: A Complete Solution for Powder Coating Enthusiasts
Consider purchasing a powder coat oven build kit if you want to build your own oven. These kits typically include all of the components you need, as well as instructions on how to assemble the oven.
Powder Coat Oven BTU: Understanding Thermal Efficiency
The BTU rating of a powder coating oven measures its thermal efficiency. A higher BTU rating indicates that the oven is more efficient at heating the powder.
Unlock the Potential of Your Alloy Wheels with Powder Coating
Transform your alloy wheels and elevate your vehicle’s appearance with our versatile and easy-to-use powder coating ovens. Visit our website today to discover the perfect oven for your needs and experience the transformative power of powder coating.
Powder coating equipment can be broadly classified into cartridge-type and non-cartridge-type equipment. Cartridge-type powder coating equipment usually has an automated system for loading the powder from cartridges into the gun while non-cartridge-type powder coating equipment usually has an automated system for loading the powder from containers into the gun.
Powder coating is a type of paint that is applied by blowing powder from a gun to the surface to be coated. It is used for corrosion protection and decoration.
The powder coating equipment includes booth, oven, machine, line and conveyor. Powder coating machines are divided into cartridge-type and automatic booth. Automatic booths are more popular because they can process more products in one cycle.
Our range of powder coating machinery has been developed over the more than 30 years we have been serving the powder coating industry. In our factory in Turkey, we manufacture technically advanced, heavy-duty powder coating machinery to provide powder coaters with the equipment they need to produce a high volume of high-quality work as efficiently as possible. Our expertise in this area and adherence to value engineering principles has allowed us to build up a loyal customer base in countries around the world.
In order to provide our customers with the most competitively priced equipment, we manufacture our machinery in a range of standard sizes.
All of our machines are CE marked, guaranteed, and available to view in person by potential customers. There are also pictures and videos throughout this site showing the machinery in use.
We design, manufacture, and assembly powder coating ovens, automatic and manual booths, automatic and manual powder coating equipment, guns, automatic and bar transfer powder coating lines, powder coating filters, and spare parts for powder coating guns
Powder Coating Booth
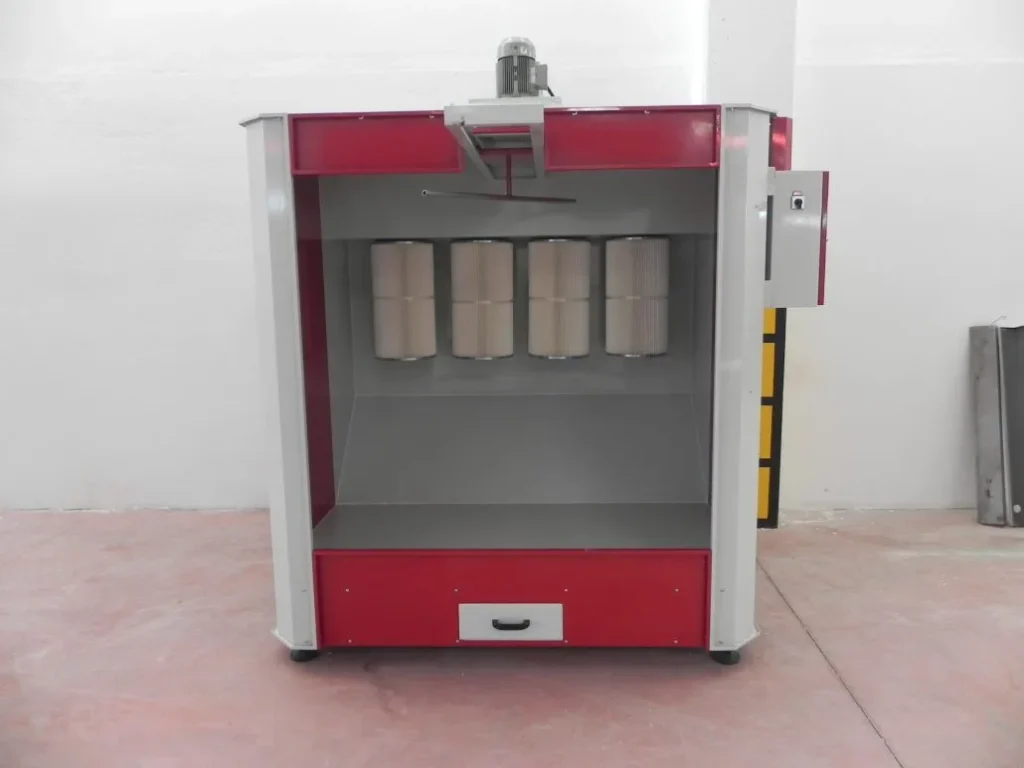
A powder coating booth is a specialized enclosure used to apply and cure powder coating finishes. Powder coating is a dry finishing process that uses finely ground powder particles that are electrostatically charged and sprayed onto a metal substrate. The powder particles are then cured using heat or UV light to form a durable, long-lasting finish.
Elevate Your Powder Coating Process with Our Versatile Booths
Transform your powder coating workspace with our comprehensive range of powder coating booths, designed to enhance efficiency, safety, and environmental compliance. From compact booths for enthusiasts to industrial-grade systems for large-scale production, we have the perfect solution to meet your unique needs.
Powder Coating Booth: A Crucial Component for Flawless Results
Powder coating booths are essential for controlling overspray and ensuring a dust-free environment during the powder coating process. Our booths feature innovative filtration systems that capture airborne powder particles, preventing them from spreading into the workspace and protecting your health.
Powder Coating Booth and Oven: A Complete Powder Coating Solution
Our integrated powder coating booth and oven combinations provide a complete solution for a seamless and efficient powder coating process. These systems eliminate the need for multiple pieces of equipment, saving you time and space.
Powder Coating Booth for Sale: Discover Affordable Options
Explore our wide selection of powder coating booths for sale, catering to a range of budgets and project requirements. We offer both new and used booths, ensuring you can find the perfect fit for your needs.
Nordson Powder Coating Booth: Renowned Quality for Professional Applications
Experience the exceptional performance and reliability of Nordson powder coating booths, trusted by professionals worldwide. These booths are designed to meet the demands of high-volume production environments.
Small Powder Coating Booth: Ideal for your Projects and Limited Spaces
Our compact powder coating booths are perfect for the enthusiasts and hobbyists who work in smaller spaces. These booths provide the essential functionality for effective powder coating without compromising on quality.
Wagner Powder Coating Booth: German Engineering for Exceptional Performance
Discover the superior engineering and craftsmanship of Wagner powder coating booths. These booths are renowned for their durability, efficiency, and ease of use.
Gema Powder Coating Booth: Advanced Technology for Optimal Results
Experience the cutting-edge technology of Gema powder coating booths. These booths feature innovative filtration systems and advanced control panels for precise operation.
Used Powder Coating Booth for Sale: Sustainable and Cost-Effective Solutions
Consider purchasing a used powder coating booth for a more eco-friendly and budget-conscious approach. Our selection of used booths undergoes thorough inspections and refurbishments to ensure optimal performance.
Powder Coating Booth Filters: Maintaining a Clean and Healthy Work Environment
Regularly replace your powder coating booth filters to maintain a clean and healthy work environment. We offer a wide range of filters to suit different booth models and powder types.
Powder Coating Booth and Oven for Sale: Complete Systems at Competitive Prices
Discover our exceptional deals on powder coating booth and oven combinations. These complete systems offer everything you need for a seamless powder coating process at a competitive price.
Powder Coating Equipment Australia: Your Local Source for Quality Equipment
Enjoy the convenience and expertise of our dedicated Australian team. We understand the unique needs of our Australian customers and provide tailored support and guidance, ensuring you have the knowledge and resources to succeed in your powder coating endeavors.
Powder Coating Equipment Auctions: Opportunities for Savvy Buyers
Explore powder coating equipment auctions for the chance to acquire high-quality equipment at even more affordable prices. Carefully inspect the equipment before bidding to ensure it meets your needs.
Powder Coating Agricultural Equipment: Protecting Farm Implements
Enhance the durability and appearance of your agricultural equipment with powder coating. Our booths are designed to accommodate a wide range of equipment sizes and shapes.
Powder Coating Booth for Sale Australia: Find the Perfect Booth for Your Australian Workshop
Browse our extensive selection of powder coating booths for sale in Australia, catering to the diverse needs of Australian businesses and individuals.
Transform Your Powder Coating Process Today
Visit our website today to discover the perfect powder coating booth for your needs and elevate your powder coating process to new heights of efficiency, safety, and quality.
Powder coating booths are typically equipped with a number of features to ensure a safe and efficient operation, including:
- Ventilation system: A ventilation system removes powder coating fumes and dust from the booth, protecting workers from respiratory problems.
- Grounding system: A grounding system prevents static electricity buildup, which can cause sparks and fires.
- Overspray recovery system: An overspray recovery system collects excess powder coating particles and returns them to the powder coating system for reuse.
- Lighting system: A lighting system provides good visibility inside the booth, making it easier for workers to apply the powder coating finish evenly.
Powder coating booths can be classified into two main types:
- Batch-type booths: Batch-type booths are designed for coating small to medium-sized batches of parts. Parts are typically loaded onto racks or hangers and then placed inside the booth for coating.
- Conveyorized booths: Conveyorized booths are designed for coating high volumes of parts. Parts are typically loaded onto a conveyor belt and then transported through the booth for coating.
Powder coating booths are used in a variety of industries, including automotive, aerospace, electronics, and consumer goods manufacturing.
Here are some additional tips for using a powder coating booth safely and effectively:
- Always wear appropriate personal protective equipment (PPE), such as gloves, safety glasses, and a respirator, when operating a powder coating booth.
- Make sure the booth is properly ventilated to remove powder coating fumes.
- Ground the booth and all equipment to prevent static electricity buildup.
- Clean the booth regularly to remove dust and debris.
- Follow the manufacturer’s instructions for operating the powder coating booth and equipment.
By following these tips, you can help to ensure that your powder coating booth is used safely and efficiently.
Powder coating spray booth for manual powder coating. We have a unique powder coating booth design, dedicated for an economical and fast powder spray. Our powder booth can have as small as 1 cartridge filter up to 8 filters. A manual powder coating booth is used for small capacities and small parts. Kindly send your request by mail to get a price for the powder coating booth for sale
Electrostatic spray gun:
An electrostatic spray gun is a specialized tool used to apply powder coatings. It utilizes an electrostatic charge to attract the powder particles to the substrate, ensuring even coverage and minimizing overspray. This method offers several advantages over traditional wet paint application, including reduced VOC emissions, enhanced efficiency, and a more durable finish.
Fluidized bed:
A fluidized bed is a container filled with finely ground powder particles that are kept in a suspended state by an upward airflow. This turbulent environment allows the powder particles to move freely and become electrically charged, making them ready for application using an electrostatic spray gun.
Spray booth:
A spray booth is an enclosed workspace designed to contain and filter overspray during the powder coating process. It typically features ventilation systems that extract and remove airborne particles, ensuring a clean and safe working environment. Spray booths can be customized to accommodate various product sizes and production volumes.
Curing oven:
A curing oven is a critical component in the powder coating process. It exposes the coated substrate to elevated temperatures, triggering the curing process. During curing, the powder particles melt and fuse together, forming a continuous, hard, and durable film. Curing ovens come in various configurations, including batch ovens, conveyor ovens, and infrared ovens.
Primer:
A primer is a thin layer applied to a substrate before applying a topcoat. Its primary function is to enhance the adhesion between the substrate and the topcoat, ensuring a strong and long-lasting bond. Primers also play a role in protecting the substrate from corrosion and providing a uniform base for the topcoat.
Topcoat:
The topcoat is the final layer applied in the powder coating process. It provides the desired finish, including color, texture, and gloss. Topcoats are designed to withstand various environmental factors, such as UV radiation, weathering, and chemicals. They also contribute to the overall durability and protective properties of the powder coating system.
Adhesion:
Adhesion refers to the strength of the bond between the powder coating and the substrate. Proper surface preparation and primer application are crucial for achieving optimal adhesion. Strong adhesion ensures that the coating will not peel, chip, or delaminate over time.
Durability:
Durability is the ability of a powder coating to resist wear, abrasion, and damage from various environmental factors. Durable powder coatings can withstand harsh conditions and maintain their integrity over extended periods. Factors that influence durability include the type of powder, the curing process, and the substrate material.
Corrosion resistance:
Corrosion resistance is the ability of a powder coating to protect a substrate from corrosion, which is the gradual deterioration of a material due to chemical reactions. Corrosion-resistant powder coatings are formulated with particular resins and pigments that provide enhanced protection against rust, oxidation, and other forms of corrosion.
Chemical resistance:
Chemical resistance is the ability of a powder coating to withstand exposure to various chemicals, including solvents, acids, and alkalis. Chemically resistant powder coatings are designed to maintain their integrity and performance in environments where chemical exposure is a concern.
Powder Coating Spray Booth
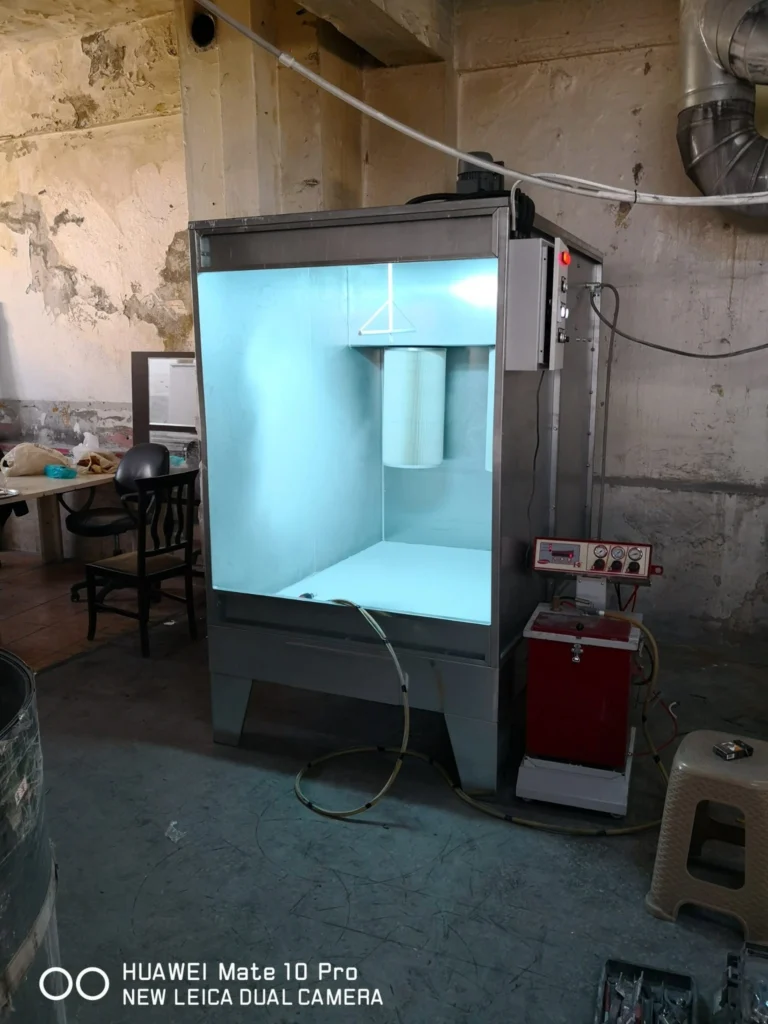
A powder coating spray booth is a specialized enclosure used to apply and cure powder coating finishes. It is a critical piece of equipment for any powder coating operation, as it provides a clean and controlled environment for applying the powder coating and curing it.
Streamline Your Powder Coating Process with Automated Booths
Experience the transformative power of automated powder coating booths and revolutionize your production workflow. Our innovative booths seamlessly integrate powder application and curing, offering unparalleled efficiency, consistency, and operator safety.
Automatic Powder Coating Booth: Enhance Efficiency and Precision
Embrace the automation advantage with our automatic powder coating booths. These booths feature robotic arms and advanced control systems, automating the powder application process for consistent, high-quality results.
Automated Powder Coating Booth: Optimize Production and Reduce Labor Costs
Automated powder coating booths streamline production by eliminating manual powder application, reducing labor costs, and increasing output. This automation also minimizes the risk of human error, ensuring consistent and defect-free results.
Powder Coating Oven and Spray Booth: A Complete Solution
Our integrated powder coating oven and spray booth combinations provide a comprehensive solution for a seamless and efficient powder coating process. These systems eliminate the need for multiple pieces of equipment, saving you time and space.
How to Ground a Powder Coating Booth: Ensuring Electrical Safety
Proper grounding is essential for preventing electrical hazards in powder coating booths. Our detailed instructions and diagrams will guide you through the grounding process for optimal safety.
Setting Up a Powder Coating Booth: A Step-by-Step Guide
Our comprehensive setup guide will walk you through the process of installing and configuring your powder coating booth, ensuring it is properly positioned, connected, and ready for operation.
Powder Coating Equipment for Beginners: Essential Tools for Success
Embark on your powder coating journey with our essential equipment guide for beginners. Discover the tools and accessories you need to achieve professional-grade results at home.
Do You Need a Spray Booth for Powder Coating?: Understanding the Essentials
A spray booth is essential for capturing and filtering overspray during the powder coating process. Our guide explains the importance of a spray booth and helps you choose the right one for your needs.
Best Filter for Powder Coating Booth: Maintaining Clean Air and a Healthy Environment
Choose the best filter for your powder coating booth to ensure clean air circulation and protect your respiratory health. Our guide discusses different filter types and their effectiveness.
Batch Powder Coating Booth: Efficient Solutions for Medium-Sized Projects
Our batch powder coating booths are designed for medium-sized projects and offer a balance of efficiency, versatility, and ease of use. These booths are ideal for both home enthusiasts and industrial applications.
Benchtop Powder Coating Booth: Convenience and Versatility for Your Workbench
Our compact benchtop powder coating booths provide the perfect combination of convenience and versatility for your workbench. These booths are ideal for small projects and offer a user-friendly experience.
Building a Powder Coating Spray Booth: A Challenge for Experienced Enthusiasts
For experienced enthusiasts, building a powder coating spray booth can be a rewarding challenge. Our comprehensive resources and expert guidance will equip you with the knowledge and skills to tackle this project.
Spray Booth Powder Coating Booth: Optimizing Overspray Control
Our spray booth powder coating booths feature advanced filtration systems and optimized airflow designs to effectively capture overspray, ensuring a clean and healthy work environment.
Powder Coating Booth Cyclone: Enhanced Overspray Collection
Incorporate a powder coating booth cyclone into your setup to enhance overspray collection and reduce the risk of airborne contaminants. Our guide explains the benefits and selection of cyclones.
Powder Coating Booth Cost: Finding the Right Fit for Your Budget
Our diverse range of powder coating booths caters to a wide spectrum of budget requirements. Explore our affordable options for enthusiasts and discover our high-performance booths for professional applications.
Powder Coating Booth Cleaning: Maintaining Optimal Performance
Maintain the longevity and performance of your powder coating booth with regular cleaning. Our comprehensive cleaning guidelines will help you keep your booth in top condition.
Transform Your Powder Coating Experience Today
Visit our website today to discover the perfect powder coating booth for your needs and experience the transformative power of automation and efficiency in your powder coating process.
Powder coating spray booths are typically equipped with a number of features to ensure a safe and efficient operation, including:
- Ventilation system: A ventilation system removes powder coating fumes and dust from the booth, protecting workers from respiratory problems.
- Grounding system: A grounding system prevents static electricity buildup, which can cause sparks and fires.
- Overspray recovery system: An overspray recovery system collects excess powder coating particles and returns them to the powder coating system for reuse.
- Lighting system: A lighting system provides good visibility inside the booth, making it easier for workers to apply the powder coating finish evenly.
- Spray gun: A spray gun is used to apply the powder coating to the parts.
- Curing system: A curing system is used to cure the powder coating, melting it and fusing it to the substrate.
Powder coating spray booths can be classified into two main types:
- Batch-type booths: Batch-type booths are designed for coating small to medium-sized batches of parts. Parts are typically loaded onto racks or hangers and then placed inside the booth for coating.
- Conveyorized booths: Conveyorized booths are designed for coating high volumes of parts. Parts are typically loaded onto a conveyor belt and then transported through the booth for coating.
Powder coating spray booths are used in a variety of industries, including automotive, aerospace, electronics, and consumer goods manufacturing.
Here are some additional tips for using a powder coating spray booth safely and effectively:
- Always wear appropriate personal protective equipment (PPE), such as gloves, safety glasses, and a respirator, when operating a powder coating spray booth.
- Make sure the booth is properly ventilated to remove powder coating fumes.
- Ground the booth and all equipment to prevent static electricity buildup.
- Clean the booth regularly to remove dust and debris.
- Follow the manufacturer’s instructions for operating the powder coating spray booth and equipment.
By following these tips, you can help to ensure that your powder coating spray booth is used safely and efficiently.
Powder coating spray booth for small items like rims or wheels. The powder booth can be made of galvanized sheets or painted mild steel. The powder spray booth has powder recuperation with a filter cleaning system (blow-off). The booth system can be also operated with an afterfilter group if more than 2 colors will be applied.
UV resistance:
UV resistance is the ability of a material to withstand damage from ultraviolet (UV) radiation from the sun. UV radiation can cause fading, cracking, and chalking of materials, especially plastics and polymers. Powder coatings with high UV resistance are designed to maintain their color, gloss, and integrity when exposed to sunlight, ensuring long-lasting performance.
Weather resistance:
Weather resistance refers to the ability of a material to withstand the effects of various weather conditions, including rain, snow, wind, and temperature fluctuations. Weather-resistant powder coatings are formulated with resins and pigments that can withstand these harsh conditions without deteriorating or losing their protective properties.
VOC emissions:
VOC (volatile organic compound) emissions are gases emitted from certain substances, including some solvents and paints, that can contribute to air pollution and smog. Powder coatings offer a significant advantage over traditional wet paint application in terms of VOC emissions. Since powder coatings are applied in a dry state, they emit virtually no VOCs, making them a more environmentally friendly option.
Environmentally friendly:
Environmentally friendly products and processes are designed to minimize their negative impact on the environment. Powder coatings are considered environmentally friendly due to their low VOC emissions, reduced energy consumption during curing, and minimal waste generation. Additionally, many powder coating formulations are solvent-free and contain recycled materials, further enhancing their environmental profile.
Cost-effective:
Cost-effectiveness refers to the balance between the cost of a product or process and its benefits. Powder coatings are considered cost-effective due to several factors:
- Reduced material costs: Powder coatings have a high utilization rate, meaning that a significant portion of the applied powder adheres to the substrate, minimizing waste.
- Efficient application process: Powder coating application is relatively fast and requires less labor compared to traditional wet paint application.
- Long-lasting durability: Powder coatings offer superior durability and longevity, reducing the need for frequent repainting or maintenance.
Wide range of colors:
Powder coatings are available in a vast array of colors, enabling manufacturers and designers to create visually appealing and customized products. The color range encompasses various shades, tints, and tones, catering to diverse aesthetic preferences and industry requirements.
Customizable finishes:
Powder coatings can be formulated to achieve a variety of finishes, including matte, gloss, textured, and metallic. This versatility allows manufacturers to create unique and customized products that align with their specific design goals and market demands.
Versatile applications:
Powder coatings can be applied to a wide range of substrates, including metals, plastics, and composites. This versatility makes them suitable for a diverse array of applications across various industries.
Automotive industry:
Powder coatings are extensively used in the automotive industry due to their excellent durability, corrosion resistance, and chemical resistance. They are applied to various automotive components, including car bodies, wheels, bumpers, and interior trim.
Appliance industry:
Powder coatings are also widely used in the appliance industry, providing a durable and aesthetically pleasing finish for refrigerators, ovens, dishwashers, and other appliances. They offer superior protection against scratches, chipping, and fading, ensuring long-lasting performance.
Powder Coating Oven with Gas
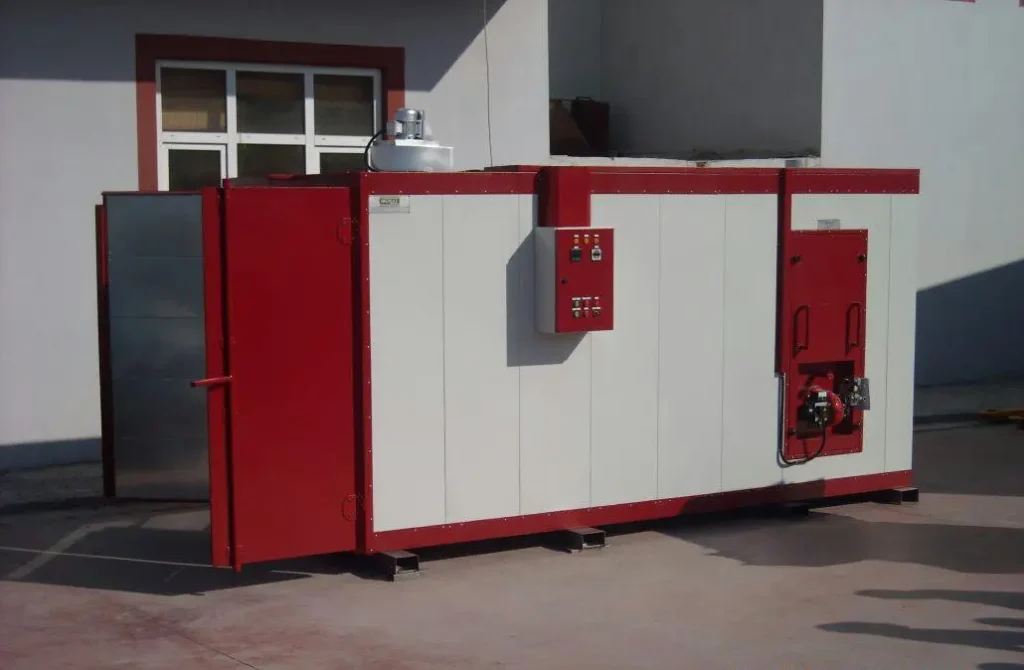
Unlock the Power of Powder Coating with Our Versatile Ovens
Transform your projects and elevate your professional work with our cutting-edge powder coating ovens. Experience the transformative power of powder coating and achieve a durable, long-lasting finish on a wide range of metal objects.
Powder Coat Oven Bake: Effortless Curing for Flawless Results
Our powder coating ovens feature innovative baking systems that ensure consistent and even heat distribution throughout the curing process. This guarantees a uniform, flawless finish on your powder-coated objects.
Powder Coating Batch Oven: Efficient Powder Coating for Small to Medium-Sized Projects
Our powder coating batch ovens are the perfect solution for small to medium-sized projects. These ovens provide a balance of efficiency, versatility, and ease of use, making them ideal for both home enthusiasts and industrial applications.
Powder Coating Batch Oven for Sale: Unmatched Value for Your Investment
Discover our exceptional range of powder coating batch ovens available for sale. Our ovens are meticulously designed to provide exceptional results while offering unmatched value for your investment.
Powder Coating Box Oven: Compact and Powerful for Space-Conscious Environments
Our compact powder coating box ovens are designed to fit seamlessly into space-conscious environments. These ovens pack a punch, delivering exceptional performance without compromising on quality or efficiency.
Build a Powder Coating Oven: A Rewarding Challenge for Experienced Enthusiasts
For experienced enthusiasts, building a powder coating oven can be a rewarding challenge. Our comprehensive resources and expert guidance will equip you with the knowledge and skills to tackle this project.
Bench Top Powder Coating Oven: Convenience and Versatility for Your Workbench
Our bench top powder coating ovens offer the perfect combination of convenience and versatility for your workbench. These compact ovens are ideal for small projects and provide a user-friendly experience.
Best Powder Coating Oven: Discover the Perfect Fit for Your Needs
With our diverse range of powder coating ovens, you’re sure to find the perfect fit for your specific needs. Our ovens cater to a wide range of project sizes, skill levels, and budget requirements.
Big Powder Coating Oven: Tackle Large-Scale Projects with Confidence
Our big powder coating ovens are designed to handle large-scale projects with ease. These ovens offer ample capacity and powerful heating capabilities, ensuring efficient and consistent curing for even the most demanding applications.
Burner for Powder Coating Oven: The Heart of the Curing Process
Choose the right burner for your powder coating oven to ensure optimal curing performance. Our selection of burners offers a range of BTU ratings to suit different oven sizes and powder types.
Blue M Powder Coating Oven: Renowned Quality for Professional Results
Experience the renowned quality and performance of Blue M powder coating ovens. These ovens are trusted by professionals worldwide for their reliability, durability, and consistent results.
Best Heating Element for Powder Coating Oven: Optimal Heat Distribution for a Flawless Finish
Select the best heating element for your powder coating oven to achieve optimal heat distribution and a flawless finish. Our range of heating elements offers various options to suit specific oven specifications.
Bumper Powder Coating Oven: Restore and Protect Your Vehicle’s Bumpers
Revamp your vehicle’s appearance and protect your bumpers from wear and tear with our specialized bumper powder coating ovens. These ovens provide the ideal environment for coating bumpers with a durable, long-lasting finish.
Powder Coating Booth and Oven: A Complete Solution for Seamless Powder Coating
Our integrated powder coating booth and oven combinations provide a complete solution for a seamless and efficient powder coating process. These systems ensure a dust-free environment and optimal results.
Powder Coating Oven Controller: Precise Control for Consistent Curing
Achieve precise temperature control with our advanced powder coating oven controllers. These controllers ensure consistent curing and eliminate the risk of inconsistencies or defects.
Powder Coating Oven Circulation Fan: Optimizing Heat Distribution for Even Curing
Our high-performance powder coating oven circulation fans optimize heat distribution throughout the oven chamber, ensuring even curing and a flawless finish on your powder-coated objects.
Embark on Your Powder Coating Journey Today
Transform your projects, enhance your professional work, and elevate your creativity with our versatile and easy-to-use powder coating ovens. Visit our website today to discover the perfect oven for your needs and experience the transformative power of powder coating.
A powder coating oven with gas uses natural gas or propane to heat the oven chamber and cure the powder coating finish. This type of oven is typically less expensive to purchase than an electric powder coating oven, but it has higher operating costs and produces more emissions.
Gas powder coating ovens typically consist of a large chamber that is heated by a series of gas burners. The parts to be coated are placed on racks or hangers and loaded into the oven chamber. The oven door is then closed and the gas burners are ignited. The heat from the gas burners melts the powder coating and fuses it to the parts. The curing time will vary depending on the type of powder coating and the desired finish.
Once the curing process is complete, the oven is turned off and the parts are removed. The parts are now coated with a durable, long-lasting powder coating finish.
Here are some of the advantages of using a gas powder coating oven:
- Lower initial cost: Gas powder coating ovens are typically less expensive to purchase than electric powder coating ovens.
- Greater flexibility: Gas powder coating ovens can be used to cure a wide variety of powder coatings, including epoxies, polyesters, and acrylics. They can also be used to coat a wide range of parts, from small electronic components to large automotive parts.
- Ease of use: Gas powder coating ovens are relatively easy to use. The ovens typically have programmable controllers that make it easy to set the curing temperature and time.
Here are some of the disadvantages of using a gas powder coating oven:
- Higher operating costs: Gas powder coating ovens have higher operating costs than electric powder coating ovens. This is because natural gas and propane are more expensive than electricity.
- Higher emissions: Gas powder coating ovens produce more emissions than electric powder coating ovens. This is because natural gas and propane combust to produce carbon monoxide, nitrogen oxides, and volatile organic compounds (VOCs).
Safety guidelines for using a gas powder coating oven:
- Make sure the oven is properly ventilated to remove powder coating fumes and exhaust gases.
- Ground the oven and all equipment to prevent static electricity buildup.
- Inspect the oven and gas lines regularly for leaks or damage.
- Have a fire extinguisher nearby.
- Train employees on the safe operation of the oven and gas lines.
By following these safety guidelines, you can help to ensure that your gas powder coating oven is used safely and efficiently.
Additional safety tips:
- Wear appropriate personal protective equipment (PPE), such as gloves, safety glasses, and a respirator.
- Be aware of the signs of carbon monoxide poisoning, such as headache, dizziness, nausea, and vomiting.
- If you experience any of these symptoms, leave the area immediately and seek medical attention.
By following these safety tips, you can help to protect yourself and your employees from the potential hazards of using a gas powder coating oven.
Powder coating curing oven is used to burn the powder on the parts. For small oven for powder coating, we mostly offer electric powder coating oven. As a bigger industrial oven fo powder coating, we offer gas powder coating oven. The powder oven can be made in any dimension, given by the customer
Powder Coating Booth with Filters

A powder coating booth with filters is a specialized enclosure used to apply and cure powder coating finishes, while also removing powder coating fumes and dust from the booth. This type of booth is essential for creating a safe and healthy work environment for powder coating operators.
Powder coating booth filters are essential components of powder coating booths, capturing overspray and preventing powder particles from spreading into the air. They are typically made of cellulose or polyester materials and come in various sizes and configurations to suit different booth sizes and powder types.
Powder booth filters are another name for powder coating booth filters.
Powder coating spray booth filters are specifically designed for use in powder coating spray booths, where they face higher levels of overspray and require more stringent filtration capabilities.
Automatic powder coating booths are advanced systems that automate the powder application process, offering increased efficiency, consistency, and operator safety. They typically feature robotic arms and sophisticated control systems.
Powder coating recovery booth filter systems are specialized filtration systems designed to capture and reclaim powder from overspray, reducing waste and maximizing powder utilization.
Do you need a spray booth for powder coating? Yes, a spray booth is essential for powder coating, as it captures and filters overspray, preventing powder particles from spreading into the air and protecting the health of workers and the environment.
How to build a powder coating booth Building a powder coating booth requires careful planning, construction skills, and knowledge of electrical and ventilation systems. It is recommended to consult with experienced professionals or purchase a pre-fabricated booth.
Used powder coating booths for sale offer a cost-effective option for those looking to acquire a powder coating booth. However, it is important to thoroughly inspect used booths to ensure they are in good working condition and meet safety requirements.
Here is some additional information that may be helpful:
- Powder coating booth filters should be replaced regularly to maintain optimal performance and prevent clogging.
- The type of filter media used in a powder coating booth filter will depend on the specific powder being used.
- Automatic powder coating booths are typically more expensive than manual booths, but they can save money in labor costs over time.
- Powder coating recovery booth filter systems can be a worthwhile investment for businesses that use large quantities of powder coating.
Benefits of using a powder coating booth with filters:
- Improved air quality: Powder coating booths with filters remove powder coating fumes and dust from the air, improving air quality for workers and reducing the risk of respiratory problems.
- Extended equipment life: Powder coating fumes and dust can damage equipment, such as spray guns and ovens. Using a booth with filters helps to extend the life of this equipment.
- Reduced cleanup: Powder coating booths with filters help to reduce the amount of cleanup required after powder coating operations. This can save time and money.
Types of filters used in powder coating booths:
There are two main types of filters used in powder coating booths:
- Primary filters: Primary filters are typically made of polyester or cellulose and are used to remove large particles of powder coating overspray from the air.
- HEPA filters: HEPA filters are high-efficiency particulate air filters that are used to remove very small particles of powder coating overspray from the air. HEPA filters are typically used in conjunction with primary filters to provide the highest level of filtration.
How to choose the right powder coating booth with filters:
When choosing a powder coating booth with filters, it is important to consider the following factors:
- The size of the booth: The booth should be large enough to accommodate the parts that will be coated.
- The type of powder coating that will be used: Some powder coatings produce more fumes than others. Choose a booth with filters that are rated to remove the type of fumes that will be produced.
- The air quality requirements of the workplace: Some workplaces have more stringent air quality requirements than others. Choose a booth with filters that meet the air quality requirements of your workplace.
Safety guidelines for using a powder coating booth with filters:
- Inspect the filters regularly and replace them when necessary.
- Make sure the booth is properly ventilated to remove powder coating fumes and exhaust gases.
- Ground the booth and all equipment to prevent static electricity buildup.
- Train employees on the safe operation of the booth and filter system.
By following these safety guidelines, you can help to ensure that your powder coating booth with filters is used safely and efficiently.
Besides the powder coating booth manufacturers, we have the best powder coating booth design, which enables the easiest coating. Closed by 5 sides, our powder spray booth is able to have a great recuperation in the coating booth range available.
Electric Powder Coating Oven

An electric powder coating oven is a type of oven that uses electricity to heat the oven chamber and cure the powder coating finish. This type of oven is more expensive to purchase than a gas powder coating oven, but it has lower operating costs and produces fewer emissions.
Electric Powder Coating Ovens: A Clean and Efficient Solution
Electric powder coating ovens offer a clean, energy-efficient, and user-friendly solution for achieving a durable, long-lasting finish on metal objects. These ovens provide precise temperature control and consistent heat distribution, ensuring optimal curing results.
Small Electric Powder Coating Ovens for Sale:
Discover a wide range of small electric powder coating ovens for sale, ideal for enthusiasts and small-scale projects. These compact ovens provide the essential functionality for effective powder coating without compromising on quality.
Electric Powder Coating Ovens for Sale UK:
Explore our comprehensive selection of electric powder coating ovens available for sale in the UK. We cater to a diverse range of needs, from hobbyists to professional businesses, offering ovens of various sizes and specifications.
Powder Coating Oven Gas vs Electric:
Electric powder coating ovens are preferred over gas ovens for several reasons:
- Cleanliness: Electric ovens eliminate the need for gas hookups, reducing the risk of carbon monoxide emissions and promoting a cleaner, healthier work environment.
- Energy Efficiency: Electric ovens typically offer better energy efficiency compared to gas ovens, resulting in lower operating costs and a reduced environmental impact.
- Ease of Use: Electric ovens are generally easier to operate and maintain than gas ovens, with simpler controls and fewer safety concerns.
Electric Heating Element for Powder Coating Oven:
The electric heating element is the heart of an electric powder coating oven, responsible for generating the heat necessary to cure the powder coating. Choose an element with the appropriate wattage to suit the size of your oven and the type of powder you are using.
Large Electric Oven for Powder Coating:
For larger projects and industrial applications, consider our range of large electric powder coating ovens. These ovens provide ample capacity, powerful heating capabilities, and automated features for streamlined operation.
Can You Use an Electric Oven for Powder Coating?
While it is technically possible to use a household electric oven for powder coating, it is not recommended for several reasons:
- Temperature Control: Household ovens often lack the precise temperature control required for proper powder coating curing.
- Ventilation: Household ovens are not designed for the dust and fumes generated during powder coating, potentially posing health risks.
- Safety: Household ovens are not intended for industrial use and may not meet safety standards for powder coating applications.
How Does a Powder Coating Oven Work?
Powder coating ovens operate on the principle of convection heating. The heating element warms the air inside the oven, which then circulates throughout the chamber, transferring heat to the metal object being coated. The powder coating particles melt and fuse to the metal surface, creating a hard, protective layer.
Safety Guidelines for Powder Coating:
- Wear protective gear: Always wear gloves, safety glasses, and a respirator when working with powder coating materials.
- Ventilate your workspace: Ensure adequate ventilation to remove dust and fumes during powder coating.
- Handle powder safely: Avoid inhaling or ingesting powder coating materials.
- Store powder properly: Keep powder coating materials in a cool, dry place, away from heat sources and ignition sources.
- Follow oven safety instructions: Carefully read and follow the manufacturer’s instructions for your powder coating oven.
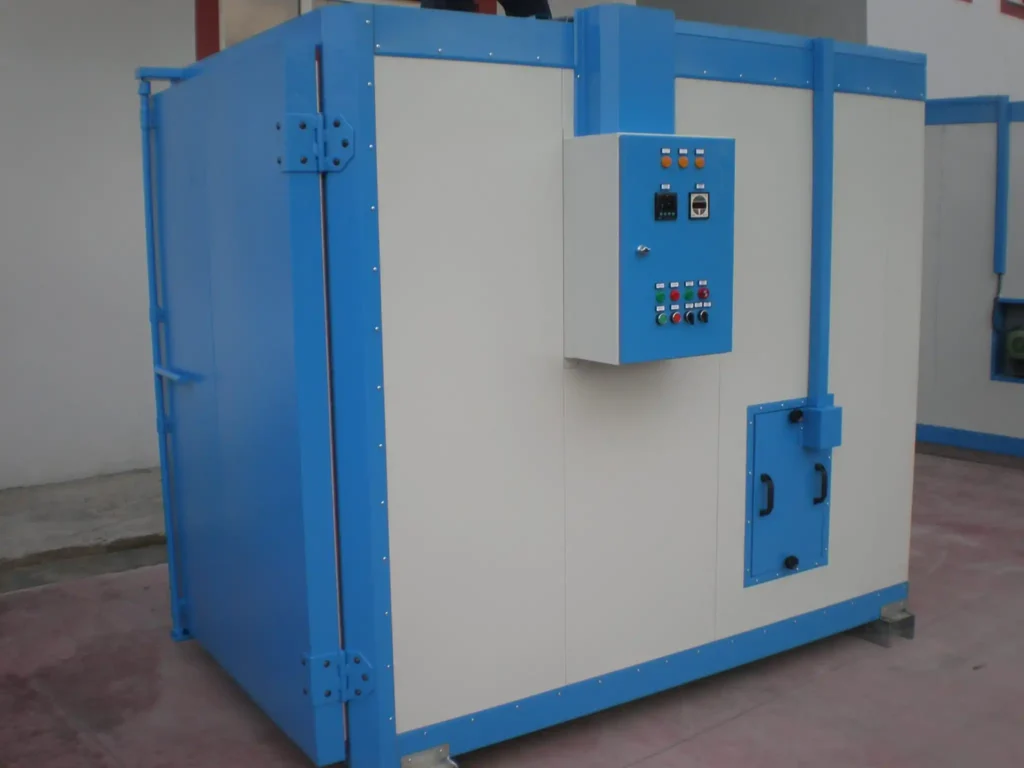
A powder coating oven is a specialized piece of equipment used to cure powder coating, a type of finishing that applies a dry powder to a metal object. The oven heats the powder, causing it to melt and flow onto the metal surface, creating a hard, durable finish.
Powder Coating Oven Process
- Surface Preparation: Before applying powder coating, the metal object must be thoroughly cleaned to remove dirt, grease, and rust. This may involve sandblasting, chemical etching, or other surface preparation techniques.
- Powder Application: The powder coating is applied to the prepared metal surface using various methods, such as electrostatic spraying, fluidized bed dipping, or electrostatic flocking. The powder particles adhere to the metal surface due to electrostatic attraction.
- Curing: The coated object is placed in the powder coating oven, where it is heated to a specific temperature for a predetermined time. This process melts and fuses the powder particles onto the metal surface, creating a hard, protective layer.
- Cooling: After curing, the object is allowed to cool completely. The powder coating will have solidified into a durable finish that is resistant to scratches, corrosion, and chemicals.
Powder Coating Electric Oven
Electric powder coating ovens are commonly used due to their cleanliness, energy efficiency, and ease of use. They provide precise temperature control and consistent heat distribution, ensuring optimal curing results.
Convection Oven for Powder Coating
While convection ovens can technically be used for powder coating, they are not ideal due to several limitations:
- Temperature Control: Household convection ovens often lack the precise temperature control required for proper powder coating curing.
- Ventilation: Convection ovens are not designed for the dust and fumes generated during powder coating, potentially posing health risks.
- Safety: Convection ovens are not intended for industrial use and may not meet safety standards for powder coating applications.
Electric Oven Powder Coating
Using a household electric oven for powder coating is not recommended for safety reasons. Household ovens are not designed for powder coating and may not provide the proper temperature control, ventilation, or safety features.
Gas or Electric Oven for Powder Coating
Electric powder coating ovens are generally preferred over gas ovens due to their cleanliness, energy efficiency, and ease of use. Gas ovens pose potential carbon monoxide emission risks and require additional safety precautions.
Regular Oven for Powder Coating
Regular household ovens are not suitable for powder coating due to their lack of precise temperature control, ventilation, and safety features. Using a regular oven for powder coating can pose health and safety hazards.
Gas Oven for Powder Coating
Gas ovens can be used for powder coating, but they are not as common as electric ovens. Gas ovens require additional safety precautions due to the potential for carbon monoxide emissions.
Electric Powder Coating Ovens
Electric powder coating ovens offer a clean, energy-efficient, and user-friendly solution for powder coating. They provide precise temperature control and consistent heat distribution, ensuring optimal curing results.
Remember to always follow the manufacturer’s instructions and safety guidelines when using a powder coating oven.
Electric Large Powder Coating Ovens: Powerful Solutions for Large Projects
Tackle large-scale powder coating projects with the power and efficiency of electric large powder coating ovens. These ovens offer ample capacity, powerful heating capabilities, and automated features to streamline your operation and achieve exceptional results.
Power Coating Oven Time:
The time required for powder coating curing depends on the size and complexity of the object, the type of powder being used, and the oven temperature. Generally, curing times range from 10 to 30 minutes.
Electric Smoker Powder Coat Oven:
While electric smokers can technically be used for powder coating, they are not recommended due to several limitations:
- Temperature Control: Electric smokers often lack the precise temperature control required for proper powder coating curing.
- Ventilation: Electric smokers are not designed for the dust and fumes generated during powder coating, potentially posing health risks.
- Safety: Electric smokers are not intended for industrial use and may not meet safety standards for powder coating applications.
Electric vs Gas Powder Coating Oven:
Electric powder coating ovens are generally preferred over gas ovens due to several advantages:
- Cleanliness: Electric ovens eliminate the need for gas hookups, reducing the risk of carbon monoxide emissions and promoting a cleaner, healthier work environment.
- Energy Efficiency: Electric ovens typically offer better energy efficiency compared to gas ovens, resulting in lower operating costs and a reduced environmental impact.
- Ease of Use: Electric ovens are generally easier to operate and maintain than gas ovens, with simpler controls and fewer safety concerns.
3x3x6 Powder Coat Oven:
A 3x3x6 powder coat oven measures 3 feet in width, 3 feet in depth, and 6 feet in height. This size is suitable for a variety of medium-sized projects, such as automotive wheels, bicycle frames, and small appliances.
Safety Guidelines for Powder Coating:
- Wear protective gear: Always wear gloves, safety glasses, and a respirator when working with powder coating materials.
- Ventilate your workspace: Ensure adequate ventilation to remove dust and fumes during powder coating.
- Handle powder safely: Avoid inhaling or ingesting powder coating materials.
- Store powder properly: Keep powder coating materials in a cool, dry place, away from heat sources and ignition sources.
- Follow oven safety instructions: Carefully read and follow the manufacturer’s instructions for your powder coating oven.
Remember to always prioritize safety when working with powder coating equipment and materials.
Unleash the Power of Powder Coating with Our Versatile and Affordable Ovens
Transform your projects and professional work with our cutting-edge powder coating ovens, offering exceptional performance at a competitive cost. Embrace the transformative power of powder coating and achieve a durable, long-lasting finish on a wide range of metal objects.
Powder Coating Oven Cost: Find the Perfect Fit for Your Budget
Our diverse range of powder coating ovens caters to a wide spectrum of budget requirements. Explore our affordable options for enthusiasts and discover our high-performance ovens for professional applications.
Powder Coating Oven Canada: Your Local Source for Quality Ovens
Enjoy the convenience of our dedicated Canadian team and extensive network of distributors across the country. We understand the unique needs of our Canadian customers and provide tailored support and guidance, ensuring you have the knowledge and resources to succeed in your powder coating endeavors.
Powder Coating Oven Calibration: Precision and Reliability for Optimal Results
Our powder coating ovens feature advanced calibration systems that ensure precise temperature control and consistent curing. This guarantees a uniform, high-quality finish on your powder-coated objects.
Powder Coating Oven Control Box Wiring: A Guide for Powder Coating Enthusiasts
For the powder coating enthusiasts, our comprehensive wiring diagrams and instructional guides simplify the process of connecting the control box to your powder coating oven.
Powder Coating Oven Calculator: Determine the Right Oven Size for Your Needs
Utilize our user-friendly powder coating oven calculator to determine the appropriate oven size for your project requirements and workspace dimensions.
Powder Coating Oven China: Quality and Value from Global Manufacturers
We partner with reputable powder coating oven manufacturers in China to bring you high-quality ovens at competitive prices. Our rigorous quality control procedures ensure that only the best products reach our customers.
Powder Coating Oven Container: Safe and Efficient Shipping for Your Oven
Our secure and durable powder coating oven containers protect your oven from damage during shipping and ensure it arrives in perfect condition for immediate use.
Powder Coat Oven Cleaning: Maintain Optimal Performance
Maintain the longevity and performance of your powder coating oven with regular cleaning. Our comprehensive cleaning guidelines will help you keep your oven in top condition.
Cheap Powder Coating Oven: Exceptional Value Without Compromising Quality
Discover our range of affordable powder coating ovens that provide exceptional value for money. These ovens deliver professional-grade results without breaking the bank.
Commercial Powder Coating Oven: High-Volume Production with Unmatched Efficiency
Our commercial powder coating ovens are designed to handle high-volume production with ease. These ovens offer ample capacity, powerful heating capabilities, and automated features for streamlined operation.
Chicago Electric Powder Coating Oven: A Trusted Brand for the Enthusiasts
Explore our selection of Chicago Electric powder coating ovens, renowned for their ease of use and affordability. These ovens are ideal for the enthusiasts and small-scale projects.
Chicago Powder Coating Oven: Professional-Grade Performance for Demanding Applications
Our Chicago powder coating ovens are designed to meet the demands of professional powder coating applications. These ovens offer superior performance, durability, and reliability for consistent results.
Control Panel for Powder Coating Oven: Intuitive Control for Precise Curing
Our user-friendly control panels provide intuitive control over the powder coating process, allowing you to adjust temperature, time, and other parameters with ease.
Can You Make a Powder Coating Oven?: Embark on a Challenge
For experienced enthusiasts, building a powder coating oven can be a rewarding challenge. Our comprehensive resources and expert guidance will equip you with the knowledge and skills to tackle this project.
Can You Start Powder Coating with our oven?: Unleash Your Creativity
Express your creativity and customize your powder coating oven by building your own. Our detailed instructions and helpful tips will guide you through the process.
Transform Your Projects and Professional Work with Our Powder Coating Ovens
Visit our website today to discover the perfect powder coating oven for your needs and experience the transformative power of powder coating.
Electric powder coating ovens are typically equipped with a number of features to ensure a safe and efficient operation, including:
- Overheating protection: Overheating protection systems automatically shut down the oven if it overheats.
- Fire suppression system: Fire suppression systems automatically extinguish fires in the oven chamber.
- Ventilation system: Ventilation systems remove powder coating fumes and dust from the oven chamber.
- Digital controls: Digital controls allow operators to set the curing temperature and time precisely.
Electric powder coating ovens can be used to cure a wide variety of powder coatings, including epoxies, polyesters, and acrylics. They can also be used to coat a wide range of parts, from small electronic components to large automotive parts.
Here are some of the advantages of using an electric powder coating oven:
- Lower operating costs: Electric powder coating ovens have lower operating costs than gas powder coating ovens. This is because electricity is typically less expensive than natural gas and propane.
- Lower emissions: Electric powder coating ovens produce fewer emissions than gas powder coating ovens. This is because electricity does not combust to produce carbon monoxide, nitrogen oxides, or volatile organic compounds (VOCs).
- Greater precision: Electric powder coating ovens allow for more precise control of the curing temperature and time. This can help to improve the quality and consistency of the powder coating finish.
Here are some of the disadvantages of using an electric powder coating oven:
- Higher initial cost: Electric powder coating ovens are typically more expensive to purchase than gas powder coating ovens.
- Lower power efficiency: Electric powder coating ovens are less power-efficient than gas powder coating ovens. This means that they will use more electricity to operate.
Safety guidelines for using an electric powder coating oven:
- Wear appropriate personal protective equipment (PPE), such as gloves, safety glasses, and a respirator.
- Make sure the oven is properly ventilated to remove powder coating fumes.
- Ground the oven and all equipment to prevent static electricity buildup.
- Inspect the oven regularly for damage or wear and tear.
- Have a fire extinguisher nearby.
By following these safety guidelines, you can help to ensure that your electric powder coating oven is used safely and efficiently.
Powder curing oven can be electrical, gas or diesel operated. The coating oven is best to operate with electricity when the capacity is small. The coating oven has walls made of sandwich panels, with Rockwool and glasswool pressed with galvanized sheets.
As one of the powder coating oven manufacturers, we offer our electrical powder coating oven in any dimensions and design, that our customers need. The oven powder is cured at 180 C for 20 mins. The time for the powder coating in oven also depends on the parts weight and material type.
Diesel Powder Coating Oven

A diesel powder coating oven is a type of powder coating oven that uses diesel fuel to heat the oven chamber and cure the powder coating finish. This type of oven is typically less expensive to purchase than an electric or gas powder coating oven, but it has higher operating costs and produces more emissions.
Diesel powder coating ovens typically consist of a large chamber that is heated by a diesel burner. The parts to be coated are placed on racks or hangers and loaded into the oven chamber. The oven door is then closed and the diesel burner is ignited. The heat from the diesel burner melts the powder coating and fuses it to the parts. The curing time will vary depending on the type of powder coating and the desired finish.
Once the curing process is complete, the oven is turned off and the parts are removed. The parts are now coated with a durable, long-lasting powder coating finish.
Advantages of using a diesel powder coating oven:
- Lower initial cost: Diesel powder coating ovens are typically less expensive to purchase than electric or gas powder coating ovens.
- Greater flexibility: Diesel powder coating ovens can be used to cure a wide variety of powder coatings, including epoxies, polyesters, and acrylics. They can also be used to coat a wide range of parts, from small electronic components to large automotive parts.
- Ease of use: Diesel powder coating ovens are relatively easy to use. The ovens typically have programmable controllers that make it easy to set the curing temperature and time.
Disadvantages of using a diesel powder coating oven:
- Higher operating costs: Diesel powder coating ovens have higher operating costs than electric or gas powder coating ovens. This is because diesel fuel is typically more expensive than electricity or natural gas.
- Higher emissions: Diesel powder coating ovens produce more emissions than electric or gas powder coating ovens. This is because diesel fuel combusts to produce carbon monoxide, nitrogen oxides, and particulate matter (PM).
Safety guidelines for using a diesel powder coating oven:
- Make sure the oven is properly ventilated to remove powder coating fumes and exhaust gases.
- Ground the oven and all equipment to prevent static electricity buildup.
- Inspect the oven and fuel lines regularly for leaks or damage.
- Have a fire extinguisher nearby.
- Train employees on the safe operation of the oven and fuel lines.
Additional safety tips:
- Wear appropriate personal protective equipment (PPE), such as gloves, safety glasses, and a respirator.
- Be aware of the signs of carbon monoxide poisoning, such as headache, dizziness, nausea, and vomiting.
- If you experience any of these symptoms, leave the area immediately and seek medical attention.
By following these safety guidelines, you can help to ensure that your diesel powder coating oven is used safely and efficiently.
Powder curing oven can be electrical, gas or diesel operated. The coating oven is best to operate with gas or diesel when the capacity is hight. The diesel powder coating oven is required for powder coaters, where the electrical setup is low and there is no natural gas connection.
Our coating oven has walls made of sandwich panels, with Rockwool and glasswool pressed with galvanized sheets. As one of the powder coating oven manufacturers, we offer our diesel powder coating oven in any dimensions and design, that our customers need. The oven powder is cured at 180 C for 20 mins. The time for the powder coating in oven also depends on the parts weight and material type.
Powder Coating Reciprocator
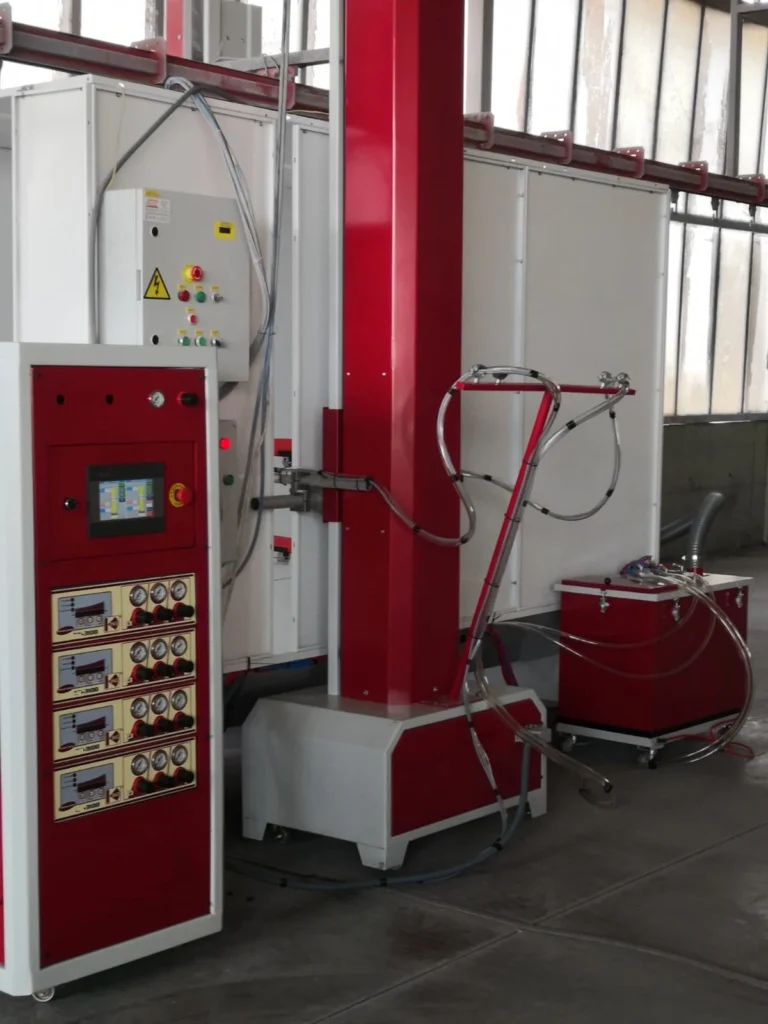
A powder coating reciprocator is a machine that moves powder coating guns back and forth over the parts being coated. This helps to ensure that the powder coating is applied evenly and consistently.
Powder coating reciprocators are typically used in high-volume powder coating operations, such as in the automotive and electronics industries. They can be used to coat a wide variety of parts, from small electronic components to large automotive parts.
Powder coating reciprocators are typically equipped with a number of features to ensure a safe and efficient operation, including:
- Adjustable speed: The speed of the reciprocator can be adjusted to match the curing speed of the powder coating.
- Overload protection: Overload protection systems automatically shut down the reciprocator if it is overloaded.
- Emergency stop: Emergency stop buttons allow operators to quickly stop the reciprocator in the event of an emergency.
Advantages of using a powder coating reciprocator:
- Improved efficiency: Powder coating reciprocators can help to improve the efficiency of powder coating operations by automating the movement of the powder coating guns.
- Consistent finish: Powder coating reciprocators can help to ensure that the powder coating is applied evenly and consistently, resulting in a high-quality finish.
- Reduced labor costs: Powder coating reciprocators can help to reduce labor costs by eliminating the need for manual workers to move the powder coating guns.
Disadvantages of using a powder coating reciprocator:
- High initial cost: Powder coating reciprocators can be expensive to purchase.
- Requires skilled operators: Powder coating reciprocators require skilled operators to set up and operate them.
- Maintenance requirements: Powder coating reciprocators require regular maintenance to ensure that they operate properly.
Safety guidelines for using a powder coating reciprocator:
- Wear appropriate personal protective equipment (PPE), such as gloves, safety glasses, and a respirator.
- Make sure the reciprocator is properly grounded to prevent static electricity buildup.
- Inspect the reciprocator regularly for damage or wear and tear.
- Train employees on the safe operation of the reciprocator.
By following these safety guidelines, you can help to ensure that your powder coating reciprocator is used safely and efficiently.
Reciprocator for powder coating is used in automatic powder coating applications. The reciprocator (or the powder coating robot) is used to make a reciprocating movement in the vertical plane to move the powder coating guns in accordance with the moving conveyor.
Automatic Powder Coating Equipment

Automatic powder coating equipment is a system of machines and devices that work together to apply and cure powder coating to parts in a high-volume, automated environment. This type of equipment is typically used in large manufacturing facilities such as automotive plants and electronics factories.
Automatic powder coating equipment has revolutionized the industry by streamlining the process, enhancing efficiency, and ensuring consistent, high-quality results. These systems incorporate advanced automation technology to automate various stages of powder coating, from powder application to curing.
What Equipment Is Needed for Powder Coating?
A basic powder coating setup typically includes:
- Powder Coating Booth: A ventilated enclosure to contain and filter overspray, ensuring a clean and healthy work environment.
- Powder Coating Gun: An electrostatic device that applies powder particles to the object being coated.
- Powder Coating Oven: A heated chamber that cures the powder coating, fusing it onto the metal surface.
- Compressor: Provides compressed air for the powder coating gun.
- Control Panel: Regulates the powder coating process, including powder application, oven temperature, and curing time.
Powder Coating Equipment Cost
The cost of powder coating equipment varies depending on the size, features, and automation level of the components. Basic setups can be acquired for a few thousand dollars, while advanced automated systems can cost tens of thousands of dollars or more.
How Does a Powder Coating System Work?
The powder coating system operates through a series of steps:
- Surface Preparation: The metal object is thoroughly cleaned to remove impurities and ensure proper powder adhesion.
- Preheating: The object is preheated to eliminate moisture and enhance powder flow.
- Powder Application: Electrostatically charged powder particles are sprayed onto the preheated object, adhering to the surface due to electrostatic attraction.
- Curing: The coated object is transferred to the powder coating oven, where it is heated to a specific temperature for a predetermined time. This process melts and fuses the powder particles onto the metal surface, creating a durable finish.
- Cooling: The object is allowed to cool completely, allowing the powder coating to solidify into a hard, protective layer.
Automated Powder Coating Systems
Automated powder coating systems incorporate robotic arms, advanced control systems, and conveyor belts to automate various stages of the powder coating process, including:
- Powder Application: Robotic arms precisely apply powder to the object, ensuring consistent coverage and minimizing overspray.
- Object Handling: Conveyor belts transport the objects through the various stages of the process, eliminating manual handling and reducing labor costs.
- Process Monitoring: Automated systems monitor and control powder application parameters, oven temperature, and curing time, ensuring consistent results.
Automatic Powder Coating Line
An automatic powder coating line consists of a series of interconnected machines and equipment that perform the entire powder coating process in a continuous automated flow. This includes automated booths, conveyor belts, robotic arms, and control systems.
Automatic Powder Coating
Automatic powder coating refers to the use of automated equipment to streamline and automate the powder coating process. This includes automated powder application, object handling, and process monitoring.
Powder Coating Automation
Powder coating automation encompasses the integration of various automated technologies into the powder coating process to enhance efficiency, consistency, and productivity. It involves automated powder application, object handling, process control, and data management.
Benefits of Automatic Powder Coating Equipment:
- Increased Efficiency: Automation significantly reduces labor costs and processing time, leading to increased production output.
- Improved Consistency: Automated systems ensure consistent powder application, oven temperature control, and curing time, resulting in uniform, high-quality finishes.
- Reduced Overspray: Automated systems minimize overspray, reducing powder waste and environmental impact.
- Enhanced Safety: Automated systems eliminate manual handling of hazardous materials, improving worker safety.
- Data-Driven Optimization: Automated systems collect and analyze process data, enabling continuous improvement and optimization.
Automatic powder coating equipment typically consists of the following components:
- Powder coating gun: A powder coating gun is a device that applies the powder coating to the parts.
- Reciprocator: A reciprocator is a machine that moves the powder coating gun back and forth over the parts being coated.
- Curing oven: A curing oven is an oven that heats the powder coating to melt it and fuse it to the parts.
- Conveyor system: A conveyor system transports the parts through the powder coating process, from the powder coating gun to the reciprocator to the curing oven.
Automatic powder coating equipment is typically programmed to follow a specific set of steps. The steps may vary depending on the type of powder coating being used and the desired finish, but they typically include the following:
- The parts are cleaned and pre-treated.
- The powder coating is applied to the parts using the powder coating gun.
- The parts are moved through the reciprocator to ensure that the powder coating is applied evenly and consistently.
- The parts are cured in the curing oven.
- The parts are inspected and packaged.
Gema automatic powder coating refers to automatic powder coating systems manufactured by Gema, a renowned manufacturer of powder coating equipment. Gema’s automatic systems are known for their reliability, precision, and efficiency.
Automatic powder coating machine price can vary widely depending on the size, features, and automation level of the machine. Basic automatic powder coating machines can cost around $10,000, while more advanced systems can cost $100,000 or more.
Automated powder coating is the process of using automated equipment to apply powder coating to metal objects. Automated powder coating systems can significantly improve efficiency, consistency, and safety compared to manual powder coating methods.
Automated powder coating line is a series of interconnected machines and equipment that perform the entire powder coating process in a continuous automated flow. Automated powder coating lines are typically used for high-volume production applications.
Quality control powder coating is the process of ensuring that powder coating is applied and cured correctly to achieve the desired quality standards. Quality control measures can include visual inspection, thickness testing, and adhesion testing.
Automatic powder coating spray gun is an automated device that applies powder coating to metal objects. Automatic powder coating spray guns can be programmed to apply powder with precision and consistency, reducing overspray and improving coating quality.
Can powder coating be done on site? Yes, powder coating can be done on site using portable powder coating equipment. However, for high-volume production or large-scale projects, it is typically more cost-effective to use an off-site powder coating facility.
Cost to set up powder coating can vary depending on the size and complexity of the setup. The cost of basic powder coating equipment and supplies can be around $5,000, while the cost of a complete automated powder coating system can be $100,000 or more.
Automatic powder coating machine is a general term for any machine that automatically applies powder coating to metal objects. There are many different types of automatic powder coating machines, ranging from simple manual machines to complex robotic systems.
Automatic powder coating gun is a type of automatic powder coating machine that applies powder coating using an electrostatic spray gun. Automatic powder coating guns can be programmed to apply powder with precision and consistency, reducing overspray and improving coating quality.
Automated powder coating equipment refers to machinery that automatically applies powder coating to metal objects. This equipment can significantly improve efficiency, consistency, and safety compared to manual powder coating methods.
Automated powder coating machine is another term for automated powder coating equipment. These machines can be programmed to apply powder coating with precision and consistency, reducing overspray and improving coating quality.
Automated powder coating gun is a type of automated powder coating machine that applies powder coating using an electrostatic spray gun. These guns can be programmed to apply powder with precision and consistency, reducing overspray and improving coating quality.
Nordson automatic powder coating system is a specific brand of automated powder coating equipment manufactured by Nordson. Nordson is a leading manufacturer of powder coating equipment, and their automatic systems are known for their reliability, performance, and innovation.
Color automatic powder coating gun is a type of automated powder coating gun that can apply multiple colors of powder coating to an object. These guns are typically used for complex applications where multiple colors are required.
A to Z powder coating is a comprehensive term that encompasses all aspects of powder coating, from surface preparation to curing. It refers to the entire powder coating process, from start to finish.
2 coat powder coating process involves applying two layers of powder coating to an object. The first coat is typically a primer coat, which provides adhesion and corrosion protection. The second coat is the top coat, which provides the desired color and finish.
Automatic powder coating equipment offers a number of advantages over manual powder coating, including:
- Increased efficiency: Automatic powder coating equipment can significantly increase the efficiency of powder coating operations.
- Improved quality: Automatic powder coating equipment can help to improve the quality of the powder coating finish by ensuring that the powder coating is applied evenly and consistently.
- Reduced costs: Automatic powder coating equipment can help to reduce labor costs and improve overall cost-effectiveness.
However, automatic powder coating equipment can also be expensive to purchase and maintain. It is important to carefully consider the needs of your business before investing in automatic powder coating equipment.
Here are some additional tips for using automatic powder coating equipment safely and efficiently:
- Wear appropriate personal protective equipment (PPE), such as gloves, safety glasses, and a respirator.
- Make sure the equipment is properly grounded to prevent static electricity buildup.
- Inspect the equipment regularly for damage or wear and tear.
- Train employees on the safe operation of the equipment.
- Follow the manufacturer’s instructions for operating the equipment.
By following these tips, you can help to ensure that your automatic powder coating equipment is used safely and efficiently to produce high-quality powder coated products.
The automatic powder coating equipment is used in automatic electrostatic powder paint systems. Each automatic powder coating machine is controlled by a powder coating control unit located in the electrical board. The powder coating system is equipped with powder paint robots.
Powder Coating Equipment
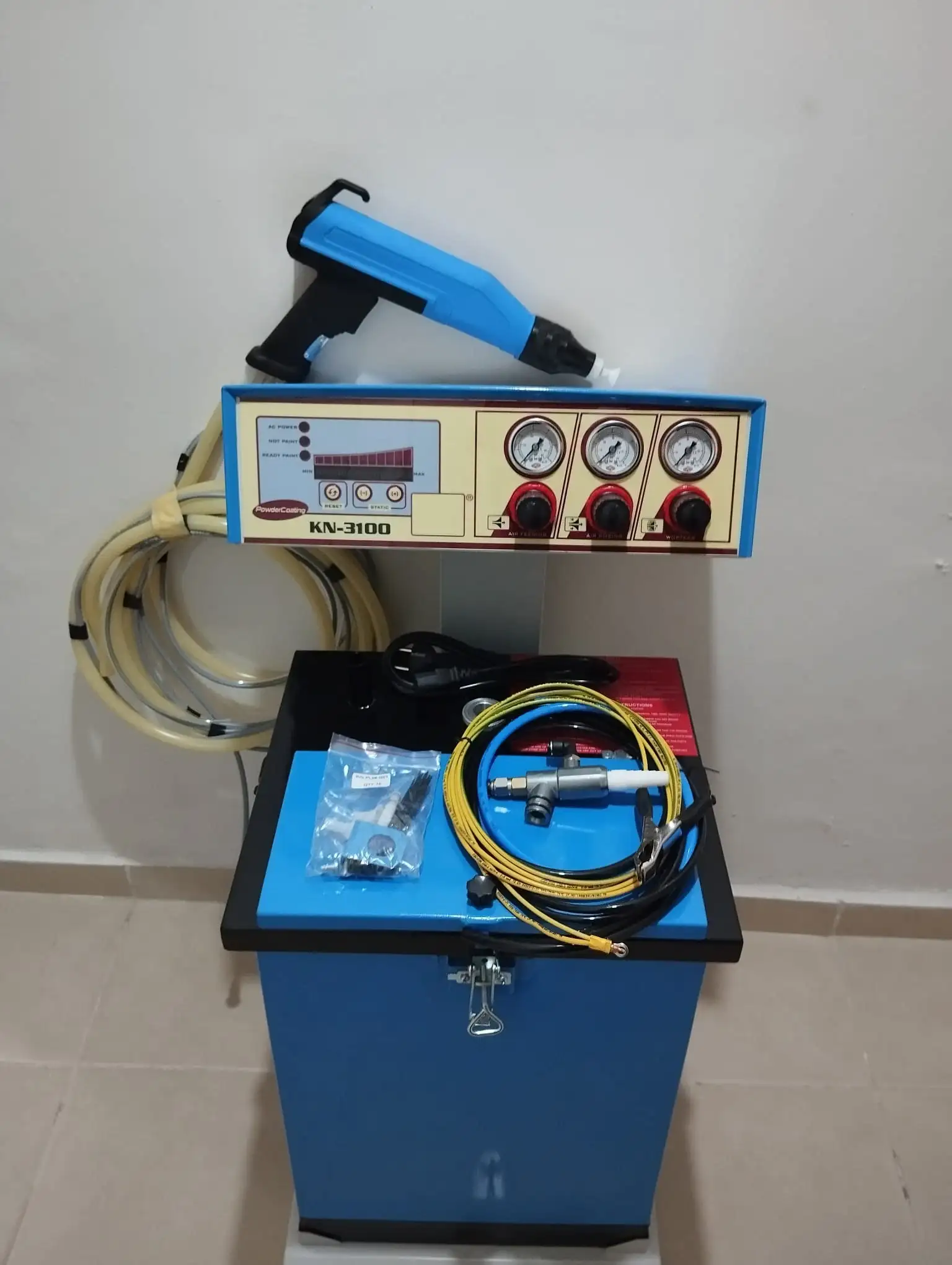
Powder Coating Equipment
Powder coating equipment encompasses a range of machines and tools used to apply powder coating to metal surfaces. It includes booths, ovens, guns, compressors, and accessories.
Industrial Powder Coating Equipment
Industrial powder coating equipment is designed for high-volume production environments and typically features larger capacities, automated systems, and advanced features to handle demanding applications.
Small Scale Powder Coating Equipment
Small-scale powder coating equipment is suitable for smaller projects, enthusiasts, or businesses with limited production needs. It offers compact setups and manual operation.
Wagner Powder Coating Equipment
Wagner is a renowned manufacturer of powder coating equipment, offering a wide range of booths, ovens, guns, and accessories for various applications.
Powder Coating Equipment Australia
Numerous suppliers in Australia offer powder coating equipment, including booths, ovens, guns, and accessories, to cater to the needs of Australian businesses.
Powder Coating Machine and Oven
A powder coating machine, also known as a powder coating gun, applies powder particles to the metal surface using electrostatic principles. A powder coating oven cures the powder coating, melting it and fusing it to the metal surface.
Powder Coating Gun Australia
Various suppliers in Australia offer powder coating guns, including manual and automatic options, to suit different production needs and budgets.
Powder Coating Gun Air Pressure
The recommended air pressure for a powder coating gun typically ranges from 60 to 80 PSI. The specific pressure may vary depending on the gun model, powder type, and desired spray pattern.
Powder Coating Gun Accessories
Powder coating gun accessories include nozzles, electrodes, filters, o-rings, and cleaning kits to maintain optimal gun performance and prevent overspray.
Powder Coating Agricultural Equipment
Powder coating is a popular choice for protecting and beautifying agricultural equipment due to its durability, corrosion resistance, and aesthetic appeal.
Alloy Wheel Powder Coating Equipment
Specialized powder coating equipment is available for alloy wheel coating, ensuring proper application and adhesion to the specific surface characteristics of alloy wheels.
Auction Powder Coating Equipment
Used powder coating equipment can be found at auctions, offering potential cost savings for businesses or individuals looking for affordable options.
Automatic Powder Coating Equipment
Automatic powder coating equipment utilizes robotic arms, conveyor belts, and advanced control systems to automate various stages of the powder coating process, improving efficiency, reducing labor costs, and ensuring consistent results.
American Equipment Powder Coating
Several American manufacturers produce powder coating equipment, including booths, ovens, guns, and accessories, known for their quality, durability, and innovation.
Equipment Needed to Start a Powder Coating Business
Essential equipment to start a powder coating business includes:
- Powder Coating Booth: Provides a controlled environment for powder application and overspray containment.
- Powder Coating Gun: Electrostatically applies powder particles to the metal surface.
- Compressor: Provides compressed air for the powder coating gun.
- Powder Coating Oven: Cures the powder coating, fusing it to the metal surface.
- Safety Gear: Includes gloves, respirator, and safety glasses.
Powder Coat Gun Best
The best powder coat gun for a specific application depends on factors such as production volume, desired spray pattern, powder type, and budget. Popular brands include Wagner, Nordson, and Gema.
Here are some of the most common types of powder coating equipment, along with an image of each:
- Powder coating gun: A powder coating gun is a device that applies the powder coating to the parts. It is typically connected to a powder coating machine, which supplies the powder to the gun.
- Reciprocator: A reciprocator is a machine that moves the powder coating gun back and forth over the parts being coated. This helps to ensure that the powder coating is applied evenly and consistently.
- Powder coating machine: A powder coating machine is a machine that supplies the powder coating to the powder coating gun. It typically has a hopper that holds the powder and a pump that feeds the powder to the gun.
Powder Coating Equipment for Beginners
For beginners, a basic powder coating setup includes:
- Powder Coating Booth: Encloses the powder coating process to contain overspray and protect the work environment.
- Powder Coating Gun: Applies powder particles to the metal surface using electrostatic principles.
- Compressor: Provides compressed air for the powder coating gun.
- Powder Coating Oven: Cures the powder coating, melting it and fusing it to the metal surface.
- Safety Gear: Includes gloves, respirator, and safety glasses.
What Equipment Is Needed for Powder Coating
The specific equipment needed for powder coating depends on the size and complexity of the projects. However, essential equipment typically includes:
- Powder Coating Booth: A controlled environment for powder application and overspray containment.
- Powder Coating Gun: Electrostatically applies powder particles to the metal surface.
- Compressor: Provides compressed air for the powder coating gun.
- Powder Coating Oven: Cures the powder coating, fusing it to the metal surface.
- Safety Gear: Includes gloves, respirator, and safety glasses.
Powder Coating Equipment Cost
The cost of powder coating equipment varies depending on the size, features, and automation level of the equipment. Basic manual setups can start around $10,000, while automated systems with advanced features can cost $100,000 or more.
Powder Coating Examples
Powder coating is widely used in various industries, including:
Automotive: Protecting and beautifying car parts, rims, and accessories.
Appliance: Enhancing the durability and appearance of appliances, such as refrigerators, stoves, and washing machines.
Architectural: Protecting and decorating metal components in buildings, such as railings, frames, and doors.
Industrial: Coating machinery, tools, and equipment for corrosion resistance and durability.
Consumer Goods: Enhancing the finish and durability of products like bicycles, electronics, and furniture.
Best Powder Coating Equipment
The best powder coating equipment depends on specific needs and budget considerations. Popular brands include Wagner, Nordson, and Gema.
Powder Coating Equipment Brisbane
Numerous suppliers in Brisbane offer powder coating equipment, including booths, ovens, guns, and accessories, catering to the needs of businesses and individuals in the region.
Fluidized Bed Powder Coating Equipment
Fluidized bed powder coating equipment is a specialized system that utilizes a bed of air-suspended powder to coat objects. It is particularly suitable for complex shapes and intricate details.
Powder Coating Equipment Canada
Many suppliers in Canada offer powder coating equipment, including booths, ovens, guns, and accessories, to meet the requirements of Canadian businesses.
Powder Coating Gun Canada
Powder coating guns are readily available in Canada through authorized distributors and online retailers, catering to various production needs and budgets.
Powder Coating Machine Cost
The cost of a powder coating machine depends on its size, features, and automation level. Basic manual machines can start around $2,000, while advanced automated systems can cost upwards of $50,000.
Powder Coating Gun Cascade
A powder coating gun cascade is a type of electrostatic powder coating gun that utilizes multiple nozzles to create a wider and more uniform spray pattern.
Powder Coating Gun Circuit Diagram
A powder coating gun circuit diagram illustrates the electrical components and connections within the gun, including the power supply, transformer, and control circuitry.
Powder Coating Machine China
Several Chinese manufacturers produce powder coating equipment, offering cost-effective options for businesses seeking affordable solutions.
Commercial Powder Coating Equipment
Commercial powder coating equipment is designed for high-volume production environments and typically features larger capacities, robust construction, and advanced features to handle demanding applications.
Cost of Powder Coating Equipment
The overall cost of powder coating equipment can vary significantly depending on the size, features, automation level, and capacity of the system. Factors such as booth dimensions, ventilation capacity, and automation features significantly impact the total cost.
A powder coat paint gun is a manual powder coating device. The device has a control unit, to adjust the voltage and current for the coating, a powder spraying gun, the injector and the stand unit. The powder coating gun has a cascade in it to increase the voltage going through the powder.
Powder and Talc Coating Machine for Cable
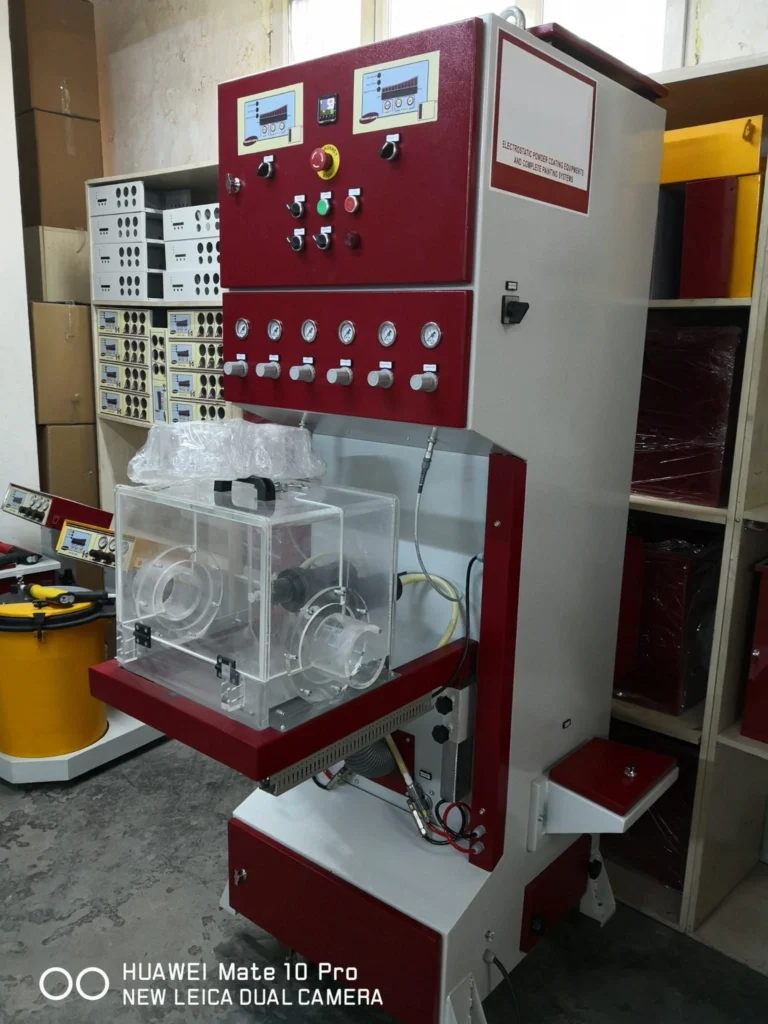
A powder and talc coating machine for cable is a specialized machine that applies a thin layer of powder or talcum powder to the surface of electrical cables. This coating has a number of benefits, including:
- Insulation: The coating helps to insulate the cable and protect it from electrical shorts.
- Corrosion protection: The coating helps to protect the cable from corrosion caused by moisture and other environmental factors.
- Abrasion resistance: The coating helps to protect the cable from abrasion and wear.
- Lubrication: The coating can help to lubricate the cable and reduce friction.
The coating process typically involves the following steps:
- The cable is cleaned and pre-treated to ensure that the coating will adhere properly.
- The powder or talcum powder is applied to the cable using an electrostatic spray gun.
- The cable is cured in an oven to melt and fuse the coating to the surface of the cable.
The specific type of powder or talcum powder that is used will vary depending on the desired properties of the coating. For example, some powders are designed to provide superior insulation, while others are designed to provide corrosion protection.
Powder and talc coating machines for cable are used in a variety of industries, including:
- Electrical: Powder and talc coating machines are used to coat electrical cables used in power plants, substations, and other electrical installations.
- Automotive: Powder and talc coating machines are used to coat electrical cables used in automobiles.
- Aerospace: Powder and talc coating machines are used to coat electrical cables used in aircraft and spacecraft.
- Telecommunications: Powder and talc coating machines are used to coat electrical cables used in telecommunications networks.
Powder and talc coating machines for cable are an important tool for protecting electrical cables from damage and ensuring their reliable performance.
Electrostatic powder or talc coating for cables, hoses and wires is essential in the cable, wire, and hose industry. Our talcum coating machine for cables is the best in its field with an efficient coating of cables
Powder Coating Filter
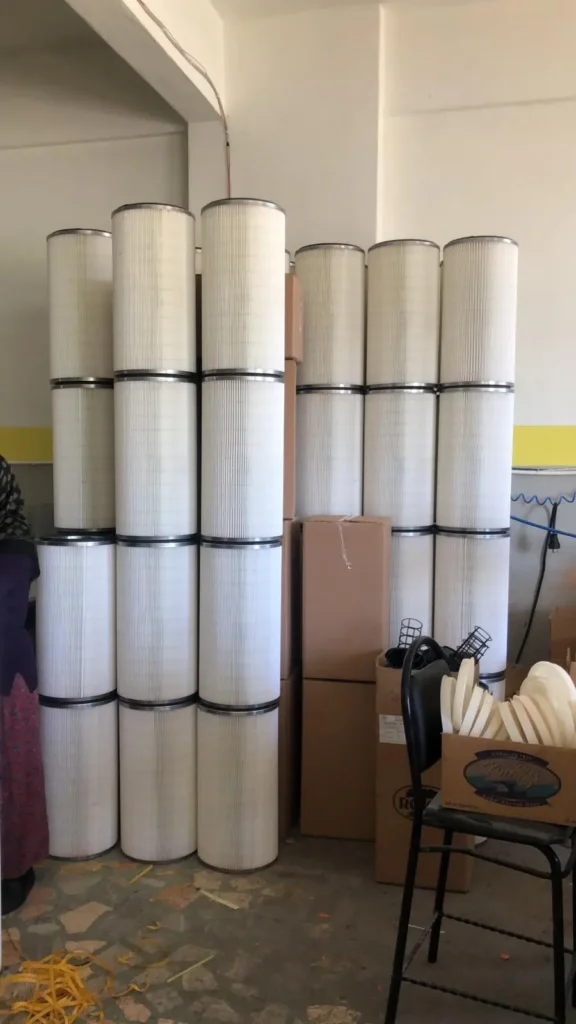
A powder coating filter is a device that removes powder coating particles from the air. This is important because powder coating particles can be harmful to human health if inhaled. Powder coating filters are typically used in powder coating booths and ovens to remove powder coating particles from the air before it is released into the environment.
There are two main types of powder coating filters:
- Primary filters: Primary filters are typically made of polyester or cellulose and are used to remove large particles of powder coating overspray from the air.
- HEPA filters: HEPA filters are high-efficiency particulate air filters that are used to remove very small particles of powder coating overspray from the air. HEPA filters are typically used in conjunction with primary filters to provide the highest level of filtration.
Powder coating filters are typically rated by their MERV (Minimum Efficiency Reporting Value) rating. The MERV rating is a measure of how well a filter can remove particles of different sizes. The higher the MERV rating, the more efficient the filter is at removing small particles.
When choosing a powder coating filter, it is important to consider the following factors:
- The size of the powder coating booth or oven: The filter should be large enough to handle the airflow volume of the booth or oven.
- The type of powder coating being used: Some powder coatings produce more fumes than others. Choose a filter that is rated to remove the type of fumes that will be produced.
- The desired level of filtration: If you need to achieve the highest level of filtration, choose a filter with a high MERV rating.
Powder coating filters should be inspected and replaced regularly to ensure that they are operating properly.
Here are some additional tips for using powder coating filters safely and efficiently:
- Wear appropriate personal protective equipment (PPE), such as gloves, safety glasses, and a respirator.
- Make sure the filter is properly installed and maintained.
- Inspect the filter regularly for damage or wear and tear.
- Replace the filter when it is dirty or damaged.
By following these tips, you can help to ensure that your powder coating filters are used safely and efficiently to protect your workers and the environment.
Powder Coating Filter
Powder coating filters are essential components of powder coating booths, responsible for capturing overspray particles and preventing them from escaping into the environment. They play a crucial role in maintaining a clean and healthy work environment and ensuring compliance with environmental regulations.
Powder Coating Filters
Powder coating filters come in various types, including cartridge filters, pleated filters, and bag filters. Each type offers different advantages and is suitable for specific applications.
Powder Coating Filter System
The powder coating filter system is an integrated component of the powder coating booth, encompassing the filters, housing, and airflow mechanisms. It works in conjunction with the booth’s ventilation system to capture and remove overspray particles.
Industrial Powder Coating Filter
Industrial powder coating filters are designed to handle high-volume powder coating operations and are typically larger, more robust, and more efficient than filters for smaller setups.
Powder Coating Filter Cleaning
Regular cleaning of powder coating filters is essential to maintain their effectiveness and prevent clogging. Cleaning methods vary depending on the filter type but typically involve manual or automated techniques.
Powder Coating Filters Suppliers
Numerous suppliers worldwide provide powder coating filters, offering a wide range of options to suit various booth sizes, production volumes, and budget considerations.
Best Filter for Powder Coating Booth
The best filter for a powder coating booth depends on factors such as booth size, overspray volume, powder type, and desired efficiency. Cartridge filters are a common and versatile choice, while pleated filters offer higher efficiency for finer particles.
Cartridge Filter Powder Coating Booth
Cartridge filters are widely used in powder coating booths due to their efficiency, ease of maintenance, and ability to capture a wide range of particle sizes. They come in various sizes and configurations to fit different booth requirements.
Powder Coating Cartridge Filters
Powder coating cartridge filters are designed specifically for capturing overspray particles in powder coating booths. They offer high efficiency, long service life, and easy replacement.
Air Filter for Powder Coating
Air filters are essential components of powder coating booths, preventing dust and debris from entering the ventilation system and potentially damaging the equipment. They are typically installed upstream of the powder coating filters.
Pocket Filters for Powder Coating
Pocket filters are a type of air filter that utilizes pockets of filter media to capture dust and debris. They are often used in combination with cartridge filters for a layered filtration system.
Powder Coating Recovery Booth Filter Systems
Powder coating recovery booth filter systems are designed to capture overspray particles and reclaim usable powder, reducing waste and minimizing environmental impact.
Powder Coating Gun Filter
Powder coating gun filters are installed within the powder coating gun, protecting the gun’s internal components from overspray particles and ensuring smooth operation.
Cartridge Filter for Powder Coating
Cartridge filters are commonly used in powder coating booths due to their efficient filtration, ease of maintenance, and versatility. They come in various sizes and configurations to suit different booth requirements.
What Is the Powder in Powder Coating
Powder coating is a type of dry finishing process that utilizes finely ground particles of pigment and resin. These particles are electrostatically charged and applied to a metal surface, where they adhere and form a durable coating.
Can You Powder Coat Yourself
Yes, you can powder coat yourself with a basic setup of equipment and proper preparation. However, it is essential to follow safety guidelines, use appropriate ventilation, and ensure proper surface preparation for optimal results.
Can Powder Coating Be Removed
Yes, powder coating can be removed using various methods, including chemical strippers, heat, or mechanical abrasion. The removal method depends on the type of powder coating, the underlying metal surface, and the desired outcome.
How Do You Powder Coat Something
The powder coating process typically involves the following steps:
- Surface Preparation: Clean, degrease, and blast the metal surface to ensure proper adhesion and a durable finish.
- Preheating: Heat the object to remove moisture and enhance powder flow.
- Powder Application: Electrostatically apply powder particles to the preheated object.
- Curing: Bake the object in an oven at specific temperature and time for proper powder fusion.
- Cooling: Allow the object to cool completely, solidifying the powder coating.
Powder Coating Booth Filters
Powder coating booth filters play a crucial role in capturing overspray particles, maintaining a clean work environment, and preventing environmental pollution. Regularly cleaning and replacing filters are essential for optimal performance.
How Long Does Powder Coating Powder Last?
Powder coating powder has an indefinite shelf life if stored properly in a dry, airtight container away from direct sunlight and heat. The powder particles remain stable and retain their properties for extended periods.
How to Powder Coat Over Powder Coat
Powder coating over powder coat is possible, but it requires careful preparation to ensure proper adhesion. The existing powder coat surface may need to be lightly sanded or blasted to roughen it up, providing a better grip for the new powder coat layer.
Is Powder Coating Powder Toxic?
The toxicity of powder coating powder depends on the specific chemicals used in the formulation. Some powder coat formulations may contain hazardous ingredients, such as isocyanates or epoxy resins, which can pose health risks if inhaled or ingested. However, many powder coat manufacturers offer non-toxic or low-VOC (volatile organic compound) powder coat options that minimize these risks.
Can You Powder Coat Carbon Fiber?
Yes, you can powder coat carbon fiber. However, the process requires special considerations due to the unique properties of carbon fiber. Proper surface preparation is crucial, and the curing temperature must be carefully controlled to avoid damaging the carbon fiber material.
Can You Powder Coat Any Color?
Yes, powder coating is available in a vast range of colors, including standard colors, metallic colors, textured finishes, and custom colors. The choice of color depends on the desired aesthetic and the specific application.
Can You Powder Coat Carbon?
Yes, you can powder coat carbon fiber components. However, the process requires special considerations due to the unique properties of carbon fiber. Proper surface preparation is crucial, and the curing temperature must be carefully controlled to avoid damaging the carbon fiber material.
Can You Powder Coat Any Colour?
Yes, powder coating is available in a wide spectrum of colors, including standard colors, metallic colors, textured finishes, and custom colors. The selection of color depends on the desired aesthetic and the specific application.
What Colors Does Powder Coating Come In?
Powder coating offers a vast array of colors, encompassing standard RAL colors, metallic shades, textured finishes, and custom colors. The choice of color is determined by the desired aesthetic and the specific application.
E Powder Coating
E-powder coating, also known as electrostatic powder coating, is the standard method for applying powder coating. It utilizes electrostatic principles to charge the powder particles, allowing them to adhere to the grounded metal surface.
Powder Coating Filtration Systems
Powder coating filtration systems are essential components of powder coating booths, capturing overspray particles and preventing them from escaping into the environment. They play a crucial role in maintaining a clean work environment and ensuring compliance with environmental regulations.
Powder Coating for Filters
Powder coating can be used to protect and enhance the performance of filters in various applications. It can provide corrosion resistance, improve durability, and enhance filtration efficiency.
Filter for Powder Coating Booth
Powder coating booth filters are specifically designed to capture overspray particles generated during the powder coating process. They come in various types, including cartridge filters, pleated filters, and bag filters.
Can Powder Coating Be Glossy?
Yes, powder coating can achieve a wide range of finishes, including glossy, semi-gloss, and matte. The desired gloss level is determined by the choice of powder coat formulation and the application technique.
Is Powder Coating Powder Flammable?
Some powder coating powders may contain flammable ingredients, such as certain resins or additives. However, many powder coat formulations are designed to be non-flammable or have a low flash point, reducing the risk of fire hazards.
To find the best filter for powder coating booth is a critical task for powder coaters. We supply 325×600 , 325×900 cellulose and polyester filter for powder spray booths.
Cable Powder Coating Machine
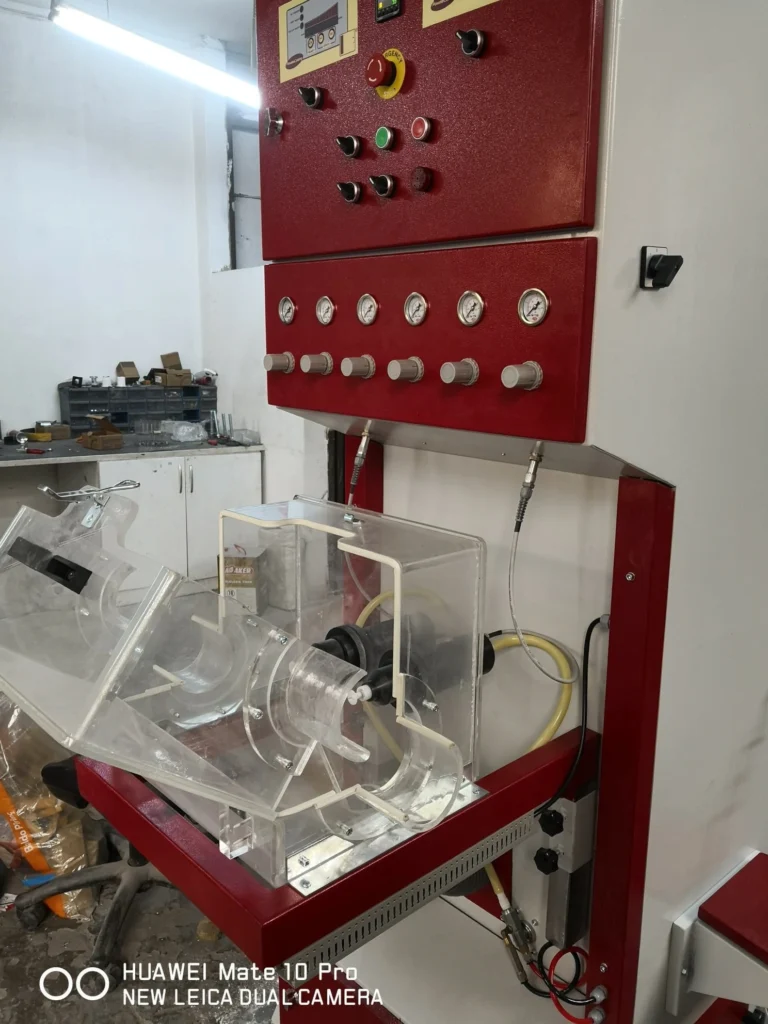
A cable powder coating machine is a specialized machine that applies a thin layer of powder coating to the surface of electrical cables.
The machine typically consists of the following components:
- Powder coating gun: The powder coating gun applies the powder coating to the cable.
- Reciprocator: The reciprocator moves the powder coating gun back and forth over the cable to ensure that the coating is applied evenly.
- Curing oven: The curing oven heats the powder coating to melt it and fuse it to the surface of the cable.
- Conveyor system: The conveyor system transports the cable through the powder coating process.
The machine can be programmed to coat the cable with a variety of different powder coatings, depending on the desired properties of the coating. For example, some powder coatings are designed to provide superior insulation, while others are designed to provide corrosion protection.
Cable powder coating machines are used in a variety of industries, including:
- Electrical: Cable powder coating machines are used to coat electrical cables used in power plants, substations, and other electrical installations.
- Automotive: Cable powder coating machines are used to coat electrical cables used in automobiles.
- Aerospace: Cable powder coating machines are used to coat electrical cables used in aircraft and spacecraft.
- Telecommunications: Cable powder coating machines are used to coat electrical cables used in telecommunications networks.
Cable powder coating machines are an important tool for protecting electrical cables from damage and ensuring their reliable performance.
Here are some of the benefits of using a cable powder coating machine:
- Improved insulation: The powder coating provides a barrier that helps to insulate the cable and protect it from electrical shorts.
- Corrosion protection: The powder coating helps to protect the cable from corrosion caused by moisture and other environmental factors.
- Abrasion resistance: The powder coating helps to protect the cable from abrasion and wear.
- Lubrication: The powder coating can help to lubricate the cable and reduce friction.
- Enhanced aesthetics: The powder coating can provide a more attractive and durable finish to the cable.
Cable powder coating machines are a versatile and cost-effective way to protect electrical cables from damage and extend their lifespan.Cable coating with talcum or powder is easy with our cable coating machine. Powder or Talcum is easily applied with our cable powder applicator machine.
Small Powder Coating Booth for Alloy Wheels
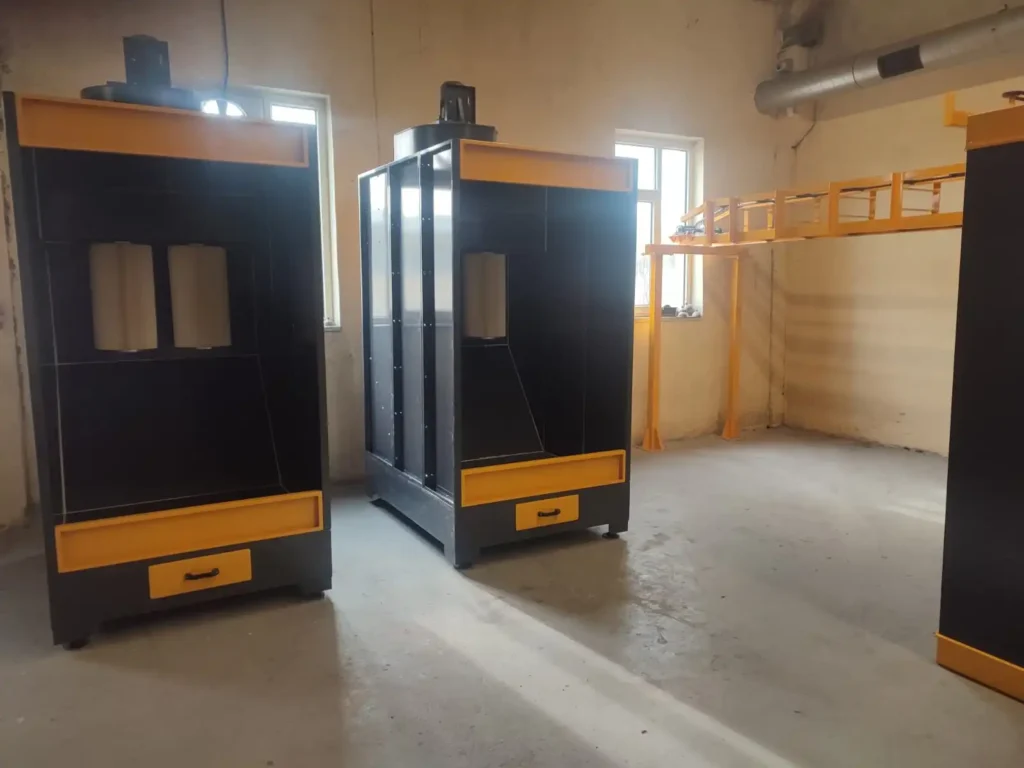
A small powder coating booth for alloy wheels is a specialized enclosure that is used to apply and cure powder coating finishes to alloy wheels. Powder coating is a dry finishing process that uses finely ground powder particles that are electrostatically charged and sprayed onto a metal substrate. The powder particles are then cured using heat or UV light to form a durable, long-lasting finish.
Small Powder Coating Booth for Alloy Wheels
Small powder coating booths are specifically designed for smaller projects, making them ideal for powder coating alloy wheels. These booths provide a controlled environment for applying powder coating and contain overspray, minimizing waste and protecting the work environment.
Can You Powder Coat Alloy Wheels Black?
Yes, you can powder coat alloy wheels black. Powder coating offers a wide range of colors, including black, and provides a durable, long-lasting finish that is resistant to chipping, fading, and corrosion.
Can Alloy Wheels Be Powder Coated?
Yes, alloy wheels can be powder coated. Powder coating is a common and effective method for protecting and beautifying alloy wheels. It enhances the wheels’ appearance, provides corrosion resistance, and can even improve brake performance by reducing heat transfer.
Can Alloy Rims Be Powder Coated?
Yes, alloy rims can be powder coated. The process for powder coating alloy rims is similar to that of powder coating alloy wheels. Proper surface preparation is essential to ensure good adhesion and a durable finish.
Can Aluminum Alloy Wheels Be Powder Coated?
Yes, aluminum alloy wheels can be powder coated. Aluminum alloys are well-suited for powder coating due to their good adhesion properties and ability to withstand the curing temperatures involved in the process.
Powder Coating Auto Wheels
Powder coating is a popular choice for auto wheels due to its durability, corrosion resistance, and aesthetically pleasing finish. It protects wheels from the harsh elements and enhances their appearance.
Wheels Powder Coating Near Me
Numerous companies offer powder coating services for alloy wheels. You can search online or ask local auto body shops for recommendations.
How to Powder Coat Aluminum Wheels
Powder coating aluminum wheels involves several steps:
- Surface Preparation: Thoroughly clean and degrease the wheels to remove dirt, grease, and contaminants.
- Blasting: Blast the wheels with an abrasive media to roughen the surface and enhance powder adhesion.
- Preheating: Preheat the wheels to remove moisture and improve powder flow.
- Powder Application: Electrostatically apply powder particles to the preheated wheels.
- Curing: Bake the wheels in an oven at a specific temperature and time to cure the powder coating.
- Cooling: Allow the wheels to cool completely for proper curing.
Can You Powder Coat Alloy Wheels Yourself?
Yes, you can powder coat alloy wheels yourself with the proper equipment, knowledge, and safety precautions. However, professional powder coating services offer expertise, consistency, and access to specialized equipment.
Powder Coating Alloy Wheels Problems
Potential problems with powder coating alloy wheels include:
- Improper Surface Preparation: Inadequate cleaning or blasting can lead to poor adhesion and peeling of the powder coat.
- Incorrect Curing: Overheating or underheating the wheels can affect the powder coat’s durability and appearance.
- Overspray: Poor application techniques can result in overspray, which can be difficult to remove and affect the overall finish.
- Contamination: Dust or debris in the booth can contaminate the powder and cause imperfections in the finish.
Rims Powder Coated
Powder coating rims provides a durable, protective, and aesthetically pleasing finish that enhances the appearance and performance of rims.
Titanium Powder Coat Wheels
Titanium powder coating is a specialized process that offers exceptional durability, corrosion resistance, and heat resistance. It is often used for high-performance wheels in motorsport and aerospace applications.
Can U Powder Coat Aluminum Rims?
Yes, aluminum rims can be powder coated. Aluminum is a common material for rims, and powder coating provides a long-lasting, protective finish.
Can You Powder Coat Your Own Wheels?
Yes, you can powder coat your own wheels with the proper equipment, knowledge, and safety precautions. However, professional powder coating services offer expertise, consistency, and access to specialized equipment.
Small powder coating booths for alloy wheels are typically designed to accommodate one or two wheels at a time. They are typically equipped with the following features:
- Ventilation system: A ventilation system removes powder coating fumes and dust from the booth, protecting workers from respiratory problems.
- Grounding system: A grounding system prevents static electricity buildup, which can cause sparks and fires.
- Overspray recovery system: An overspray recovery system collects excess powder coating particles and returns them to the powder coating system for reuse.
- Lighting system: A lighting system provides good visibility inside the booth, making it easier for workers to apply the powder coating finish evenly.
- Spray gun: A spray gun is used to apply the powder coating to the wheels.
- Curing system: A curing system is used to cure the powder coating, melting it and fusing it to the wheel.
Small powder coating booths for alloy wheels are typically used in automotive repair shops, custom wheel shops, and other businesses that specialize in powder coating alloy wheels.
Here are some tips for using a small powder coating booth for alloy wheels safely and effectively:
- Always wear appropriate personal protective equipment (PPE), such as gloves, safety glasses, and a respirator, when operating a powder coating booth.
- Make sure the booth is properly ventilated to remove powder coating fumes.
- Ground the booth and all equipment to prevent static electricity buildup.
- Clean the booth regularly to remove dust and debris.
- Follow the manufacturer’s instructions for operating the powder coating booth and equipment.
By following these tips, you can help to ensure that your small powder coating booth for alloy wheels is used safely and efficiently.
Small Powder Coating Oven for Alloy Wheels
Compact powder coating ovens are specifically designed for smaller projects, making them suitable for powder coating alloy wheels. These ovens provide a controlled environment for curing powder coating and ensure proper adhesion and a durable finish.
Small Powder Coating Oven for Sale
Numerous suppliers offer small powder coating ovens for sale, catering to various needs and budgets. Online retailers, hardware stores, and specialized powder coating equipment suppliers are common sources.
Oven for Powder Coating Wheels
Powder coating ovens specifically designed for curing powder coating on wheels are available. These ovens typically feature dimensions that accommodate common wheel sizes and provide the necessary heat distribution and temperature control.
Small Oven for Powder Coating
Small powder coating ovens are ideal for smaller projects or businesses with limited production volume. They offer compact size, ease of operation, and energy efficiency, making them a practical choice for various applications.
Alloy Wheel Powder Coating Oven
Alloy wheel powder coating ovens are designed to cure powder coating on alloy wheels, ensuring proper adhesion and a durable finish. They typically feature controlled heating and cooling cycles to optimize the curing process.
2 Tone Powder Coated Wheels
Achieving a two-tone finish on powder coated wheels involves applying different powder coat colors to specific areas of the wheel and curing them separately. This technique requires masking and careful application to create the desired effect.
4x4x6 Powder Coat Oven
4x4x6 powder coating ovens are compact ovens measuring 4 feet in length, 4 feet in width, and 6 feet in height. They are suitable for small to medium-sized projects and can accommodate various metal objects.
Small Powder Coating Ovens
Small powder coating ovens are designed for limited production volume or smaller projects. They offer compact size, ease of use, and energy efficiency, making them a practical choice for various applications.
6x6x8 Powder Coating Oven
6x6x8 powder coating ovens are larger ovens measuring 6 feet in length, 6 feet in width, and 8 feet in height. They can accommodate larger objects and handle higher production volumes.
Powder Coating Oven for Car Frame
Powder coating ovens specifically designed for curing powder coating on car frames are available. These ovens typically feature larger dimensions to accommodate the frame size and provide the necessary heat distribution and temperature control.
8x8x20 Powder Coating Oven
8x8x20 powder coating ovens are industrial-sized ovens measuring 8 feet in length, 8 feet in width, and 20 feet in height. They are designed for high-volume production and can accommodate large metal objects or multiple smaller items simultaneously.
The powder coating on alloy wheels is a popular application if you need to paint alloy wheels. Powder coating rims can be a good business idea. To paint a wheel, you need a powder spray booth and a curing oven. To spray paint the rim, you will also need a powder spray gun. The coated wheels have a longer surface life and cost more than standard rims
Small Powder Coating Oven for Alloy Wheels
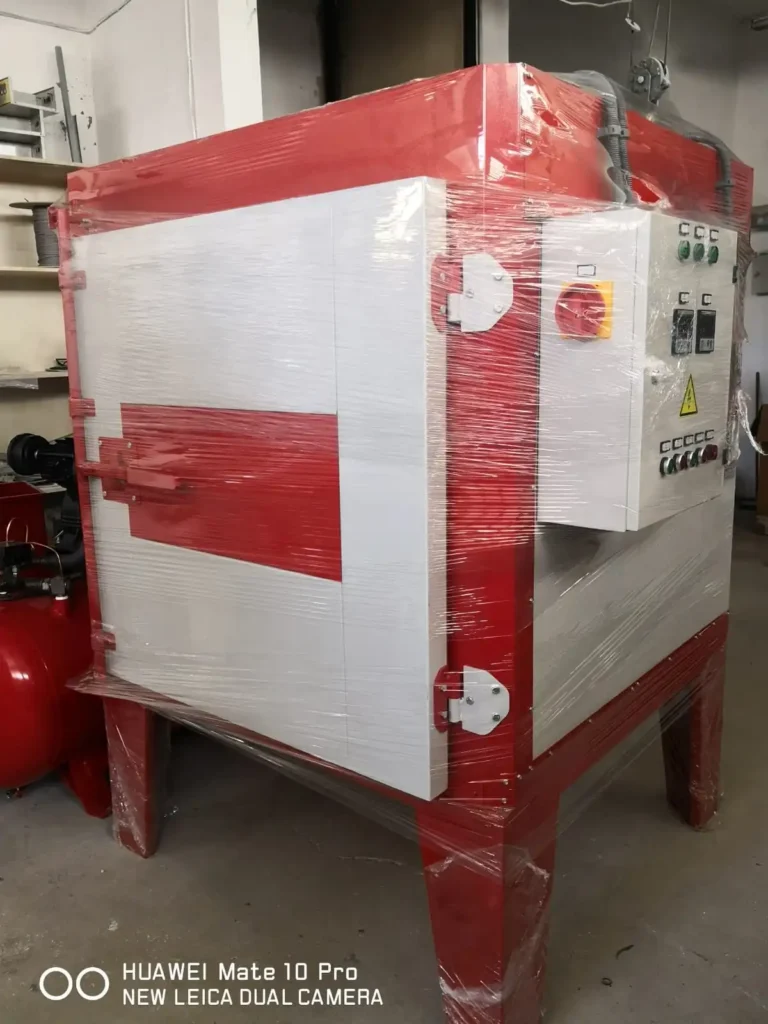
A small powder coating oven for alloy wheels is a specialized oven that is used to cure powder coating finishes on alloy wheels. Powder coating is a dry finishing process that uses finely ground powder particles that are electrostatically charged and sprayed onto a metal substrate. The powder particles are then cured using heat or UV light to form a durable, long-lasting finish.
Small powder coating ovens for alloy wheels are typically designed to accommodate one or two wheels at a time. They are typically equipped with the following features:
- Digital temperature controller: A digital temperature controller allows the user to set and precisely control the curing temperature.
- Overheating protection: Overheating protection systems automatically shut down the oven if it overheats.
- Fire suppression system: Fire suppression systems automatically extinguish fires in the oven chamber.
- Ventilation system: Ventilation systems remove powder coating fumes and exhaust gases from the oven chamber.
- Racks: Racks are used to hold the alloy wheels in place during the curing process.
Small powder coating ovens for alloy wheels are typically used in automotive repair shops, custom wheel shops, and other businesses that specialize in powder coating alloy wheels.
Here are some tips for using a small powder coating oven for alloy wheels safely and effectively:
- Always wear appropriate personal protective equipment (PPE), such as gloves, safety glasses, and a respirator, when operating a powder coating oven.
- Make sure the oven is properly ventilated to remove powder coating fumes and exhaust gases.
- Place the alloy wheels on the racks properly and follow the manufacturer’s instructions for setting the curing temperature and time.
- Do not overload the oven.
- Inspect the oven regularly for damage or wear and tear.
By following these tips, you can help to ensure that your small powder coating oven for alloy wheels is used safely and efficiently.
Additional tips:
- Make sure the alloy wheels are clean and dry before powder coating.
- Apply a thin, even coat of powder coating to the alloy wheels.
- Cure the powder coating according to the manufacturer’s instructions.
- Allow the alloy wheels to cool completely before handling them.
By following these tips, you can help to ensure that your powder coated alloy wheels have a durable, long-lasting finish.
For powder coating alloy wheels, we have a unique solution. A small powder coating oven for 4 alloy wheels. This small electric powder curing oven takes up to 4 rims inside and finishes curing of 4 wheels every half an hour.
Automatic Powder Coating Equipment
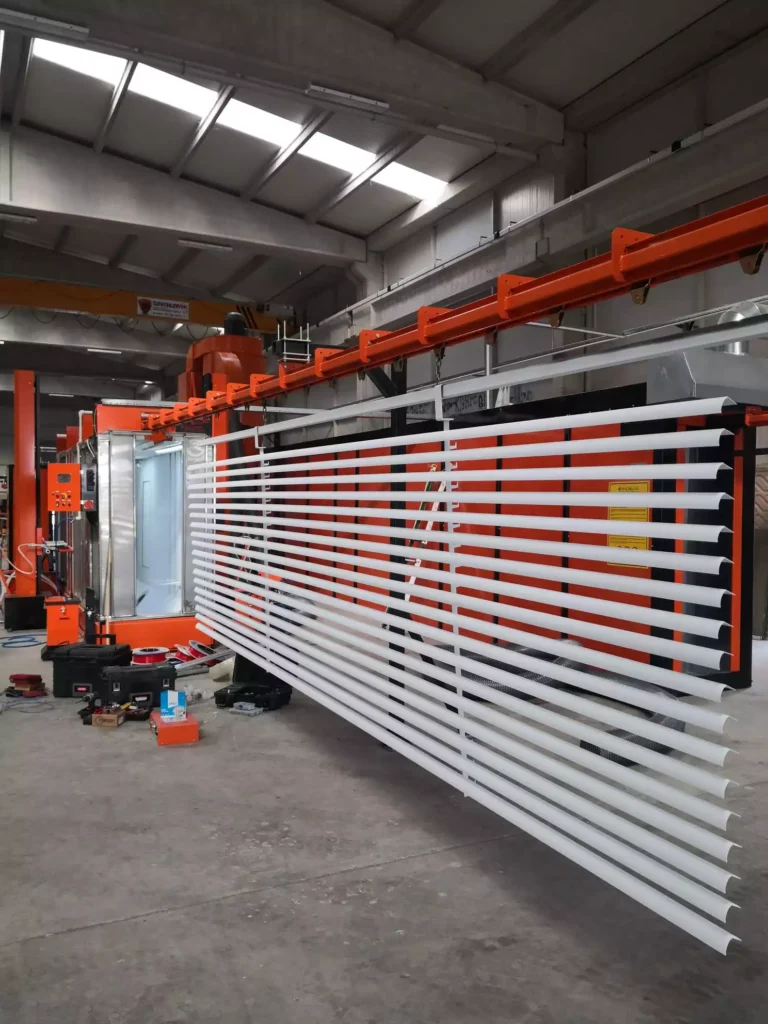
Automatic powder coating equipment is a system of machines and devices that work together to apply and cure powder coating to parts in a high-volume, automated environment. This type of equipment is typically used in large manufacturing facilities such as automotive plants and electronics factories.
Automatic Powder Coating Booth:
An automatic powder coating booth utilizes robotic arms to apply powder coating precisely and consistently, reducing overspray and enhancing the finish quality. These booths are ideal for high-volume production environments.
Automated Powder Coating Booth:
An automated powder coating booth employs a conveyor belt to transport objects through the powder coating process, streamlining production and increasing output. This type of booth is suitable for large-scale operations.
Powder Coating Oven and Spray Booth:
A powder coating oven is responsible for curing the powder coating, melting it and fusing it to the metal surface. A spray booth encloses the powder application process, capturing overspray and preventing it from spreading into the air.
How to Ground a Powder Coating Booth:
Proper grounding is crucial for electrical safety in powder coating booths. Follow these steps to ground your booth effectively:
- Identify a Grounding Source: Connect the booth to a grounding rod or a metal water pipe.
- Secure the Grounding Wire: Attach the grounding wire to the designated grounding point on the booth.
- Verify Grounding Continuity: Use a multimeter to test the continuity of the grounding connection.
Setting Up a Powder Coating Booth:
Setting up a powder coating booth involves careful planning and execution. Follow these guidelines:
- Choose an Appropriate Location: Ensure ample space for the booth and ventilation components.
- Install the Booth Properly: Follow the manufacturer’s instructions for precise installation.
- Connect Electrical Components: Hire a qualified electrician to connect electrical wiring safely.
- Establish Ventilation: Install ventilation fans and ducts to remove overspray and fumes.
Powder Coating Equipment for Beginners:
Essential equipment for beginners includes:
- Powder Coating Booth: Provides a controlled environment for powder application and overspray containment.
- Powder Coating Gun: Electrostatically applies powder particles to the metal surface.
- Compressor: Provides compressed air for the powder coating gun.
- Powder Coating Oven: Cures the powder coating, fusing it to the metal surface.
- Safety Gear: Includes gloves, respirator, and safety glasses.
Do You Need a Spray Booth for Powder Coating?
Yes, a spray booth is essential for powder coating to capture and filter overspray, preventing powder particles from spreading into the air and protecting the health of workers and the environment.
Best Filter for Powder Coating Booth:
The best filter for a powder coating booth depends on the specific powder being used. Generally, cellulose or polyester filters are effective for most powders. Consider factors like particle size and filtration efficiency when selecting a filter.
Batch Powder Coating Booth:
A batch powder coating booth is designed for medium-sized projects, offering efficiency, versatility, and ease of use. These booths are suitable for both hobbyists and industrial applications.
Benchtop Powder Coating Booth:
A benchtop powder coating booth is a compact and convenient option for small projects and enthusiasts. These booths provide a user-friendly experience within a limited workspace.
Building a Powder Coating Spray Booth:
Building a powder coating spray booth requires expertise in construction, electrical systems, and ventilation. If you lack experience, consult professionals or consider purchasing a pre-fabricated booth.
Automatic powder coating equipment offers a number of advantages over manual powder coating, including:
- Increased efficiency: Automatic powder coating equipment can significantly increase the efficiency of powder coating operations.
- Improved quality: Automatic powder coating equipment can help to improve the quality of the powder coating finish by ensuring that the powder coating is applied evenly and consistently.
- Reduced costs: Automatic powder coating equipment can help to reduce labor costs and improve overall cost-effectiveness.
However, automatic powder coating equipment can also be expensive to purchase and maintain. It is important to carefully consider the needs of your business before investing in automatic powder coating equipment.
Here are some additional tips for using automatic powder coating equipment safely and efficiently:
- Wear appropriate personal protective equipment (PPE), such as gloves, safety glasses, and a respirator.
- Make sure the equipment is properly grounded to prevent static electricity buildup.
- Inspect the equipment regularly for damage or wear and tear.
- Train employees on the safe operation of the equipment.
- Follow the manufacturer’s instructions for operating the equipment.
By following these tips, you can help to ensure that your automatic powder coating equipment is used safely and efficiently to produce high-quality powder coated products.
Automatic powder coating equipment is used for high capacities where the powder coating is applied on moving parts carried by a conveyor. The automatic powder coating equipment includes a surface pretreatment, a tunnel-type drying oven, an automatic powder spray booth, automatic powder coating equipment, and reciprocators, and a tunnel-type powder curing oven.
Automatic Powder Coating Booth
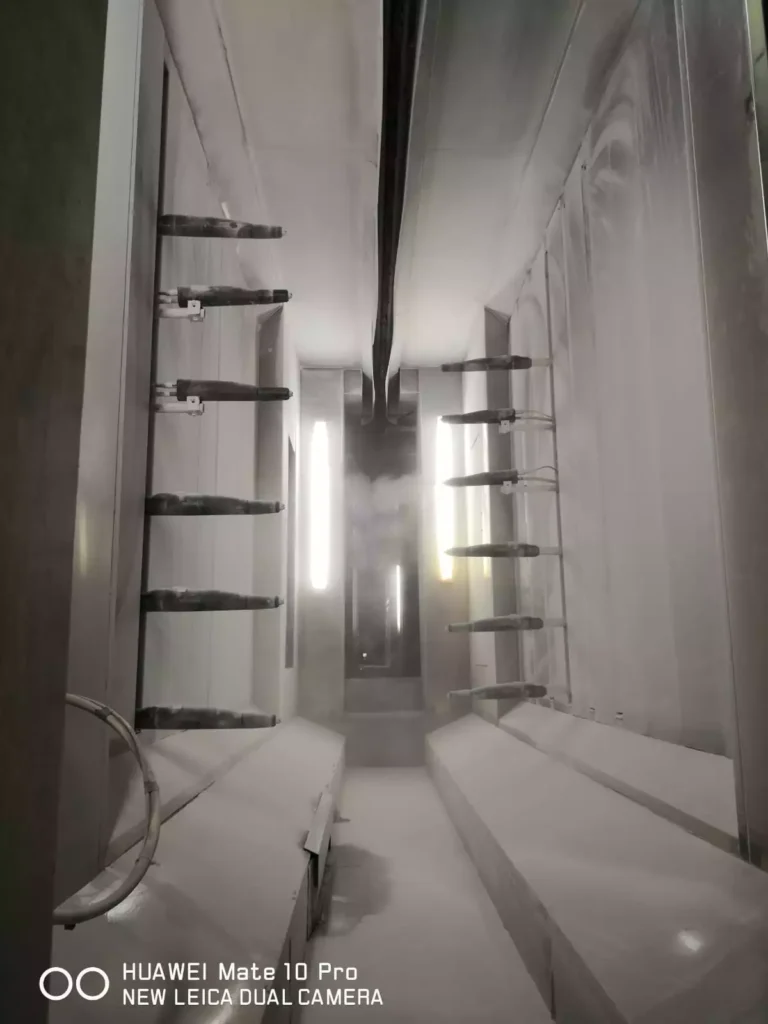
An automatic powder coating booth is a specialized enclosure that is used to apply and cure powder coating finishes to parts in a high-volume, automated environment. This type of booth is typically used in large manufacturing facilities such as automotive plants and electronics factories.
Spray Booth Powder Coating Booth
A powder coating booth is a specialized enclosure designed to contain and filter overspray during the powder coating process. It ensures a clean and safe environment for workers and prevents powder particles from spreading into the air.
Powder Coating Booth Cyclone
A cyclone is a type of dust collector that utilizes centrifugal force to separate powder particles from the airstream. It is an efficient and effective way to capture and collect overspray in powder coating booths.
Powder Coating Booth Cost
The cost of a powder coating booth can vary depending on the size, features, and automation level of the booth. Basic manual booths can start around $5,000, while automated booths with advanced features can cost $100,000 or more.
Powder Coating Booth Cleaning
Regular cleaning is essential to maintain the performance and longevity of a powder coating booth. This typically involves removing accumulated overspray, cleaning filters, and maintaining ventilation components.
Powder Coating Booth Cartridge
A cartridge filter is a type of dust collector that uses pleated filter media to capture powder particles. It is commonly used in powder coating booths due to its efficiency and ease of maintenance.
Powder Coating Equipment Canada
Numerous suppliers in Canada offer powder coating equipment, including booths, ovens, guns, and accessories. They provide a range of options to suit various needs and budgets.
Powder Coating Equipment Cost
The cost of powder coating equipment varies depending on the specific components and their quality. Basic equipment sets can start around $10,000, while comprehensive setups for industrial applications can cost significantly more.
Powder Coating Booth Dust Collector
A dust collector is an essential component of a powder coating booth, responsible for capturing and filtering overspray. Cyclones and cartridge filters are common types of dust collectors used in these booths.
Cartridge Filter Powder Coating Booth
A cartridge filter powder coating booth utilizes cartridge filters to capture overspray. These booths offer efficient filtration and are relatively easy to maintain.
Cyclone Powder Coating Booth
A cyclone powder coating booth employs a cyclone dust collector to separate powder particles from the airstream. These booths are known for their high efficiency and ability to handle large volumes of overspray.
Cost for Powder Coating Booth
The cost of a powder coating booth can vary widely depending on the size, features, and automation level. Factors such as booth dimensions, ventilation capacity, and automation features significantly impact the overall cost.
Compact Powder Coating Booth
A compact powder coating booth is a smaller and more space-efficient option, ideal for smaller projects and limited workspaces. These booths provide a versatile solution for enthusiasts or small businesses.
Cost of Small Powder Coating Booth
The cost of a small powder coating booth depends on its size, features, and included accessories. Basic compact booths can start around $2,000, while more advanced models with additional features can cost upwards of $5,000.
Automatic powder coating booths are typically equipped with the following features:
- Automatic powder coating guns: Automatic powder coating guns are used to apply the powder coating to the parts. They are typically controlled by a computer system, which allows for precise control of the powder coating application process.
- Reciprocators: Reciprocators are machines that move the parts back and forth over the powder coating guns. This helps to ensure that the powder coating is applied evenly and consistently.
- Curing ovens: Curing ovens are ovens that heat the powder coating to melt it and fuse it to the parts. The temperature and curing time will vary depending on the type of powder coating being used.
- Conveyor system: A conveyor system transports the parts through the powder coating booth, from the powder coating guns to the reciprocators to the curing ovens. This helps to automate the process and improve efficiency.
- Ventilation system: A ventilation system removes powder coating fumes and dust from the booth, protecting workers from respiratory problems.
- Grounding system: A grounding system prevents static electricity buildup, which can cause sparks and fires.
Automatic powder coating booths offer a number of advantages over manual powder coating booths, including:
- Increased efficiency: Automatic powder coating booths can significantly increase the efficiency of powder coating operations by automating the powder coating application process.
- Improved quality: Automatic powder coating booths can help to improve the quality of the powder coating finish by ensuring that the powder coating is applied evenly and consistently.
- Reduced costs: Automatic powder coating booths can help to reduce labor costs and improve overall cost-effectiveness.
However, automatic powder coating booths can also be expensive to purchase and maintain. It is important to carefully consider the needs of your business before investing in an automatic powder coating booth.
Here are some additional tips for using an automatic powder coating booth safely and efficiently:
- Wear appropriate personal protective equipment (PPE), such as gloves, safety glasses, and a respirator, when operating an automatic powder coating booth.
- Make sure the booth is properly ventilated to remove powder coating fumes.
- Ground the booth and all equipment to prevent static electricity buildup.
- Clean the booth regularly to remove dust and debris.
- Follow the manufacturer’s instructions for operating the automatic powder coating booth and equipment.
By following these tips, you can help to ensure that your automatic powder coating booth is used safely and efficiently to produce high-quality powder coated products.
An automatic powder coating booth is used for higher capacities and with automatic powder coating equipment. The automatic powder coating booth can be made of stainless steel sheets, painted sheet metals, or galvanized sheets and is equipped with a cyclone rather than filters
Powder Coating Line
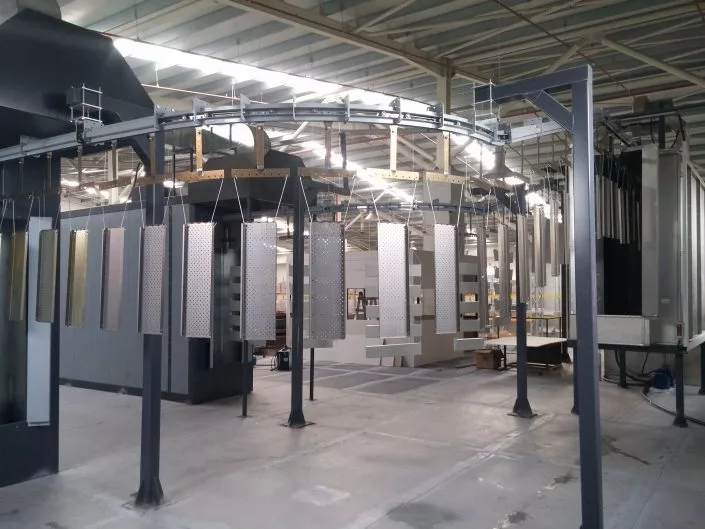
A powder coating line is a system of machines and devices that work together to apply and cure powder coating to parts in a high-volume, automated environment. This type of line is typically used in large manufacturing facilities such as automotive plants and electronics factories.
Powder Coating Line
A powder coating line is a series of interconnected machines and equipment that perform the entire powder coating process in a continuous automated flow. It streamlines production, improves efficiency, and ensures consistent results.
Automated Powder Coating Line
An automated powder coating line utilizes robotic arms, advanced control systems, and conveyor belts to automate various stages of the powder coating process, including powder application, object handling, and process monitoring.
Vertical Powder Coating Line
A vertical powder coating line is designed for coating objects that can be suspended vertically, such as pipes, tubes, and automotive parts. It offers efficient utilization of vertical space and is suitable for high-volume production.
Automatic Powder Coating Line
An automatic powder coating line is synonymous with an automated powder coating line. It refers to a system that automatically applies powder coating to objects, reducing manual labor and enhancing efficiency.
Horizontal Powder Coating Line
A horizontal powder coating line is designed for coating objects that can be conveyed horizontally, such as flat panels, metal sheets, and appliance components. It is suitable for handling a wide range of object shapes and sizes.
Manual Powder Coating Line
A manual powder coating line relies on manual labor for powder application, object handling, and process control. While less efficient than automated lines, manual lines may be suitable for small-scale operations or limited budgets.
Small Powder Coating Line
A small powder coating line is a compact and space-efficient setup, designed for smaller projects and limited workspaces. It is suitable for enthusiasts, small businesses, or low-volume production needs.
Powder Coating Line Cost
The cost of a powder coating line can vary significantly depending on the size, features, automation level, and capacity of the system. Basic manual lines can start around $10,000, while advanced automated lines with high-capacity can cost $100,000 or more.
Powder Coating Automated Line
An automated powder coating line, also known as an automatic powder coating line, utilizes automation technology to streamline the powder coating process. It enhances efficiency, reduces labor costs, and ensures consistent results.
Powder Coating Slogans
Here are some catchy powder coating slogans:
- Powder coating: The durable finish that lasts.
- Enhance your products with powder coating perfection.
- Powder coating: The versatile solution for a wide range of applications.
- Protect and beautify your metal surfaces with powder coating.
- Powder coating: The environmentally friendly choice for a long-lasting finish.
What Will Adhere to Powder Coating
Proper surface preparation is crucial for powder coating adhesion. Clean, dry, and grit-blasted metal surfaces ensure optimal adhesion and a durable finish.
Powder Coating Issues
Common powder coating issues include:
- Orange peel: A rough, textured finish caused by uneven powder distribution or improper curing.
- Fisheyes: Small, crater-like defects caused by contaminants or moisture on the surface.
- Chalking: A powdery surface condition caused by UV exposure or chemical degradation.
- Overspray: Excess powder that doesn’t adhere to the object, creating waste and potential environmental concerns.
Powder Coating Examples
Powder coating is widely used in various industries, including:
- Automotive: Protecting and beautifying car parts, rims, and accessories.
- Appliance: Enhancing the durability and appearance of appliances, such as refrigerators, stoves, and washing machines.
- Architectural: Protecting and decorating metal components in buildings, such as railings, frames, and doors.
- Industrial: Coating machinery, tools, and equipment for corrosion resistance and durability.
- Consumer Goods: Enhancing the finish and durability of products like bicycles, electronics, and furniture.
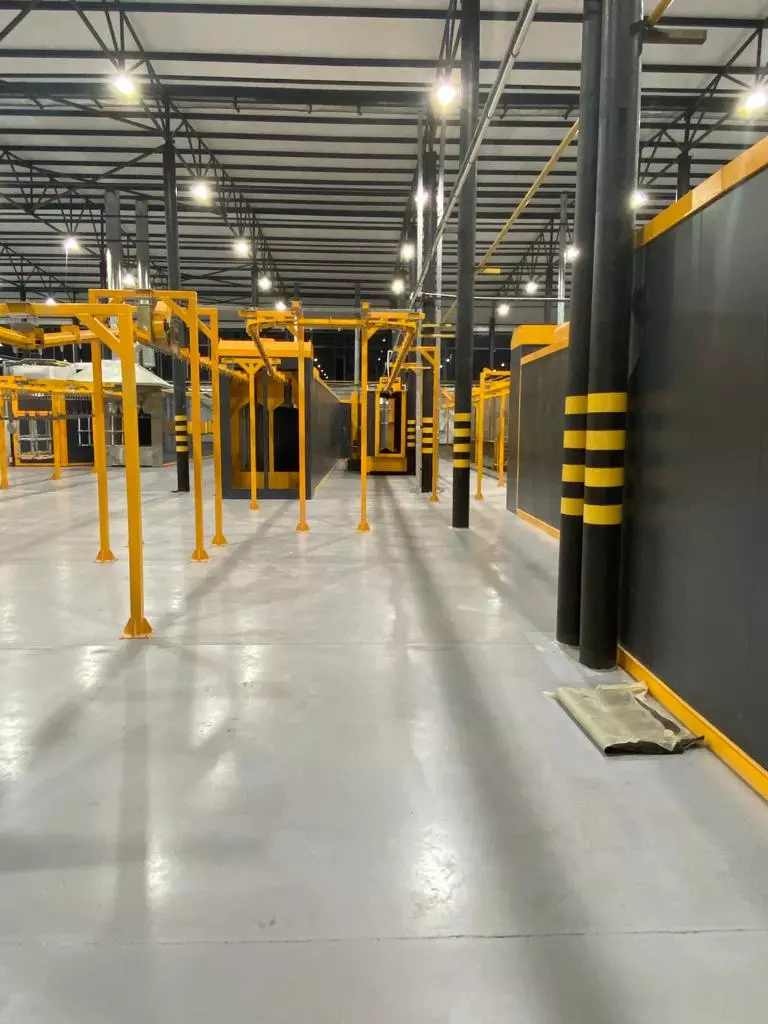
Powder Coating Line Conveyor Chain Suppliers
Numerous suppliers provide conveyor chains specifically designed for powder coating lines. These chains are engineered to withstand the rigors of the powder coating process, ensuring consistent movement and durability.
Powder Coating Conveyor System
The powder coating conveyor system is the backbone of the powder coating line, responsible for transporting objects through the various stages of the process, including preheating, powder application, curing, and cooling.
Powder Coating Control System
The powder coating control system regulates and monitors various aspects of the powder coating process, including powder application parameters, oven temperature, curing time, and conveyor speed.
Powder Coating Cube System
A powder coating cube system is a modular and compact powder coating setup that encloses the powder coating process in a self-contained unit. It offers space-efficiency and is suitable for smaller workspaces.
Powder Coating Coating Line
Powder coating coating line is another term for a powder coating line. It refers to the entire system that applies powder coating to objects in a continuous automated or manual flow.
Conveyor Chain for Powder Coating Line
Conveyor chains specifically designed for powder coating lines are essential to ensure smooth and consistent movement of objects through the powder coating process. These chains are durable and resistant to the effects of powder coating materials.
Cost of Powder for Powder Coating
The cost of powder for powder coating varies depending on the type of powder, quantity, and supplier. Generally, high-quality powders may cost more but offer superior performance and durability.
Powder Coated Price
The price of powder-coated products can vary depending on the complexity of the object, the type of powder used, and the desired finish. Powder coating typically adds a cost premium compared to traditional paint finishes.
Steps in Powder Coating
The basic steps in powder coating include:
- Surface Preparation: Cleaning, degreasing, and blasting to ensure a clean and adherent surface.
- Preheating: Heating the object to remove moisture and enhance powder flow.
- Powder Application: Electrostatically applying powder particles to the preheated object.
- Curing: Baking the object in an oven to melt and fuse the powder particles onto the surface.
- Cooling: Allowing the object to cool completely, solidifying the powder coating.
Powder Coating Step by Step Process
A more detailed step-by-step powder coating process involves:
- Hanging or placing the object on the conveyor or rack.
- Pre-cleaning to remove dirt, grease, and loose contaminants.
- Chemical cleaning to remove oxides, rust, and other impurities.
- Rinsing to remove cleaning agents and ensure a clean surface.
- Drying to completely remove moisture from the surface.
- Blasting to roughen the surface and enhance powder adhesion.
- Electrostatic powder application using a spray gun.
- Curing in an oven at specific temperature and time for proper powder fusion.
- Cooling to allow the powder coating to solidify and harden.
Powder Coating Exhaust System
A powder coating exhaust system is crucial for removing overspray, fumes, and particulates generated during the powder coating process. It ensures a clean and healthy work environment and prevents environmental contamination.
Powder Coated Pole Review
Powder coated poles offer several advantages over traditionally painted poles, including:
- Durability: Powder coating provides superior resistance to chipping, fading, and scratching.
- Corrosion Protection: Powder coating effectively protects metal poles from corrosion and rust.
- Low Maintenance: Powder coating requires minimal maintenance compared to painted poles.
- Aesthetic Appeal: Powder coating offers a wide range of colors and finishes to enhance the appearance of poles.
Electrostatic Powder Coating Line
An electrostatic powder coating line utilizes electrostatic principles to attract and apply powder particles to the object. This method ensures efficient and uniform powder distribution, minimizing overspray and waste.
Electral Powder Coating Line
Electral powder coating line is a synonym for electrostatic powder coating line. It refers to a system that uses electrostatic forces to apply powder coating, achieving consistent and even coverage.
Electrostatic Powder Coating Line for Sale
Numerous manufacturers and distributors offer electrostatic powder coating lines for sale. These lines are available in various sizes and configurations to suit different production needs and budgets.
A powder coating line typically consists of the following components:
- Pretreatment system: A pretreatment system prepares the parts for powder coating by cleaning and removing any contaminants. This is typically done using a series of tanks containing chemicals such as alkaline cleaners, acids, and rinses.
- Powder coating booth: A powder coating booth is an enclosure where the powder coating is applied to the parts. The booth is typically equipped with powder coating guns, reciprocators, and a ventilation system to remove powder coating fumes
- Curing oven: A curing oven is an oven that heats the powder coating to melt it and fuse it to the parts. The temperature and curing time will vary depending on the type of powder coating being used.
- Conveyor system: A conveyor system transports the parts through the powder coating line, from the pretreatment system to the powder coating booth to the curing oven. This helps to automate the process and improve efficiency.
Powder coating lines offer a number of advantages over other finishing processes, including:
- Durability: Powder coating is a very durable finish that can resist corrosion, abrasion, and chemicals.
- Environmental friendliness: Powder coating is a relatively environmentally friendly process that produces few emissions.
- Versatility: Powder coating can be applied to a wide variety of materials, including metals, plastics, and glass.
However, powder coating lines can also be expensive to purchase and maintain. It is important to carefully consider the needs of your business before investing in a powder coating line.
Here are some additional tips for using a powder coating line safely and efficiently:
- Wear appropriate personal protective equipment (PPE), such as gloves, safety glasses, and a respirator, when operating a powder coating line.
- Make sure the line is properly ventilated to remove powder coating fumes and dust.
- Ground the line and all equipment to prevent static electricity buildup.
- Clean the line regularly to remove dust and debris.
- Follow the manufacturer’s instructions for operating the powder coating line and equipment.
By following these tips, you can help to ensure that your powder coating line is used safely and efficiently to produce high-quality powder coated products.
The automatic powder coating line is used when the capacity of painting is high. This way the parts are coated in an automatic powder coating booth and they are transferred into the booth with a conveyor line. The parts that are coated in the booth are later transferred into the powder curing oven.
Furniture industry:
Powder coatings are increasingly popular in the furniture industry due to their durability, scratch resistance, and wide range of colors and finishes. They are used on various furniture components, including frames, legs, tabletops, and chairs. Powder coatings provide a durable finish that can withstand everyday wear and tear, and they can be easily cleaned and maintained.
Construction industry:
Powder coatings are used in the construction industry for a variety of applications, including protecting metal railings, frames, and supports from corrosion and weathering. They are also used to coat architectural panels, metal roofing, and other exterior components. Powder coatings provide a durable and long-lasting finish that can withstand harsh weather conditions and UV radiation.
Aerospace industry:
Powder coatings are used in the aerospace industry for a variety of applications, including protecting aircraft components from corrosion, wear, and abrasion. They are also used to coat aerospace parts that need to be lightweight and resistant to extreme temperatures. Powder coatings provide a durable and high-performance finish that is essential for the safety and reliability of aircraft.
Medical device industry:
Powder coatings are used in the medical device industry for a variety of applications, including coating implants, surgical instruments, and medical equipment. They are used to provide a biocompatible surface that is resistant to corrosion, wear, and sterilization processes. Powder coatings also provide a smooth and easy-to-clean surface that is important for preventing the spread of infection.
Powder coating process:
The powder coating process is a multi-step process that involves surface preparation, powder application, curing, and quality control.
- Surface preparation: The surface of the substrate must be clean and free of contaminants before powder coating can be applied. This may involve degreasing, etching, and blasting.
- Powder application: The powder is applied to the substrate using an electrostatic spray gun. The powder particles are charged, which causes them to be attracted to the grounded substrate.
- Curing: The coated substrate is placed in a curing oven, where it is heated to a specific temperature for a specific amount of time. This causes the powder particles to melt and fuse together, forming a continuous film.
- Quality control: The finished product is inspected to ensure that the coating is uniform, durable, and free of defects.
Powder coating safety:
Powder coating is a safe process when used properly. However, it is important to take precautions to avoid inhaling powder particles or exposure to solvents. Workers should wear appropriate personal protective equipment (PPE), such as gloves, safety glasses, and respirators. They should also work in a well-ventilated area.
Powder Coating Safety:
Powder coating is a safe process when used properly, but it is important to take precautions to avoid inhaling powder particles or exposure to solvents. Here are some safety tips for powder coating:
- Wear appropriate personal protective equipment (PPE): This includes gloves, safety glasses, and a respirator to protect your eyes, skin, and lungs from powder particles and solvents.
- Work in a well-ventilated area: This will help to remove dust and fumes from the work area.
- Handle hazardous materials safely: This includes reading safety data sheets (SDSs) for all materials used, using proper storage and handling procedures, and disposing of hazardous waste properly.
Powder Coating Benefits:
Powder coating offers several benefits over traditional wet paint application, including:
- Environmentally friendly: Powder coating emits virtually no VOCs (volatile organic compounds), which are harmful air pollutants.
- Durable and long-lasting: Powder coatings are resistant to scratches, chipping, fading, and corrosion.
- Wide range of colors and finishes: Powder coatings are available in a wide variety of colors, finishes, and textures.
- Cost-effective: Powder coating can be a more cost-effective option than traditional wet paint application in the long run, due to its durability and reduced waste.
Powder Coating Limitations:
Powder coating also has some limitations, including:
- Thinner film thickness: Powder coatings typically have a thinner film thickness than wet paint, which may not be suitable for all applications.
- Potential for overspray: Overspray can occur if the powder application is not done properly. This can waste powder and create a mess.
Potential Hazards of Powder Coating:
The main potential hazards of powder coating are:
- Inhalation of powder particles: Inhalation of powder particles can cause respiratory problems, such as asthma.
- Exposure to solvents: Some powder coating processes use solvents, which can be harmful to your health if you are exposed to them for too long.
- Fire: Powder coating dust is combustible, so it is important to take precautions to prevent fires.
By following proper safety precautions, you can safely enjoy the many benefits of powder coating.
Surface Pretreatment for Powder Coating Equipment
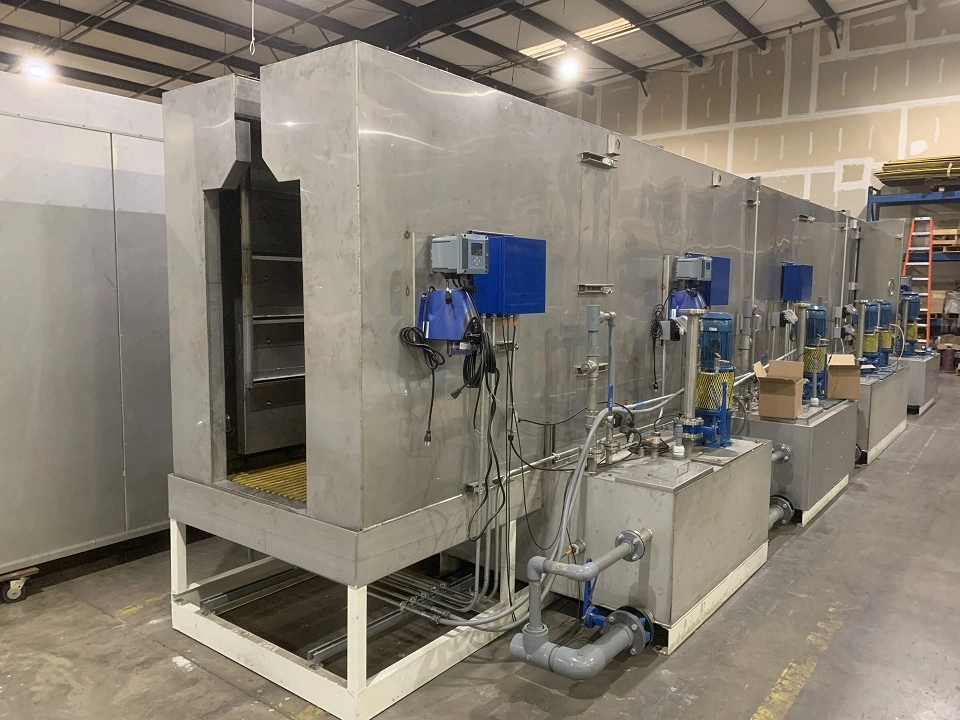
Surface pretreatment is an important step in the powder coating process. It helps to prepare the surface of the part to be coated by cleaning and removing any contaminants. This ensures that the powder coating will adhere properly and create a durable finish.
Surface Pretreatment for Powder Coating Equipment
Surface pretreatment is a crucial step in the powder coating process, ensuring optimal adhesion and a durable finish. Various pretreatment equipment and methods are available to prepare different types of metal surfaces for powder coating.
Surface Preparation for Powder Coating
Surface preparation involves cleaning, degreasing, and roughening the metal surface to remove contaminants, oxides, and impurities. This enhances powder adhesion and creates a favorable surface for powder bonding.
Surface Prep for Powder Coating
Surface prep is a shortened term for surface preparation for powder coating. It refers to the process of cleaning, degreasing, and roughening the metal surface to ensure proper adhesion of the powder coating.
Surface Preparation and Coating
Surface preparation and coating are two interconnected processes. Proper surface preparation is essential to achieve a high-quality, durable powder coating finish.
Powder Coating Pretreatment Equipment
Powder coating pretreatment equipment encompasses a range of machines and tools used to prepare metal surfaces for powder coating. These include cleaning tanks, blasting booths, and surface conditioning equipment.
Pretreatment for Powder Coating
Pretreatment for powder coating is the overall process of preparing the metal surface for powder application. It includes cleaning, degreasing, etching, and rinsing to ensure optimal adhesion and a durable finish.
Coating Surface Preparation
Coating surface preparation refers to the specific steps involved in preparing the metal surface for powder coating. These steps may vary depending on the type of metal, the desired finish, and the powder coating system being used.
Surface Pretreatment
Surface pretreatment is a broader term that encompasses surface preparation techniques for various applications, including powder coating, painting, and other surface finishing processes.
Laser Surface Preparation
Laser surface preparation utilizes laser technology to clean, ablate, and modify metal surfaces. It is a precise and efficient method for preparing complex geometries and hard-to-reach areas.
Metal Surface Preparation
Metal surface preparation specifically refers to the pretreatment methods used for preparing various metal substrates for powder coating and other surface finishing processes.
Quality Surface Processing
Quality surface processing is essential for achieving a high-quality powder coating finish. It involves careful control of pretreatment parameters, surface inspection, and ensuring proper cleaning and conditioning of the metal surface.
Zirconium Pretreatment for Powder Coating
Zirconium pretreatment is a type of chemical pretreatment that utilizes zirconium compounds to create a conversion coating on the metal surface. It is particularly effective for aluminum and its alloys.
Surface Treatment Technologies
Surface treatment technologies encompass a wide range of methods used to modify and enhance the properties of metal surfaces. These include pretreatment for powder coating, anodizing, galvanizing, and other surface finishing techniques.
Powder Coating Pretreatment Chemicals
Powder coating pretreatment chemicals are specialized formulations used to clean, degrease, and etch metal surfaces for powder coating. They are designed to remove contaminants, improve adhesion, and create a favorable surface for powder bonding.
Powder Coating Pretreatment
Powder coating pretreatment encompasses the entire process of preparing the metal surface for powder coating, including cleaning, degreasing, etching, and rinsing. It is essential for achieving a durable and high-quality powder coating finish.
5 Stage Pretreatment Washer
A 5-stage pretreatment washer is a type of automated pretreatment system that utilizes five stages of cleaning, degreasing, etching, and rinsing to prepare metal surfaces for powder coating. It offers efficiency and consistency in surface preparation.
Aluminum Pretreatment for Powder Coating
Aluminum pretreatment involves specific cleaning and etching processes designed to remove the oxide layer and prepare the aluminum surface for powder coating. It ensures optimal adhesion and a durable finish.
There are a variety of surface pretreatment processes that can be used for powder coating. The specific process that is used will depend on the type of substrate being coated and the desired finish. Some common surface pretreatment processes for powder coating include:
- Alkaline cleaning: Alkaline cleaning is a process that uses alkaline detergents to remove dirt, grease, and oil from the surface of the substrate.
- Acid etching: Acid etching is a process that uses acid to remove oxides and other contaminants from the surface of the substrate.
- Conversion coatings: Conversion coatings are a type of coating that reacts with the surface of the substrate to form a protective layer. This layer helps to improve the adhesion of the powder coating.
Once the surface pretreatment process is complete, the substrate is ready to be powder coated.
Here are some of the benefits of using surface pretreatment for powder coating:
- Improved adhesion: Surface pretreatment helps to improve the adhesion of the powder coating to the substrate. This results in a more durable and long-lasting finish.
- Enhanced corrosion resistance: Surface pretreatment can also help to enhance the corrosion resistance of the powder coating. This is because the surface pretreatment process removes contaminants that can act as focal points for corrosion.
- Improved appearance: Surface pretreatment can also help to improve the appearance of the powder coating. This is because it removes contaminants that can cause the powder coating to look dull or uneven.
Powder coating equipment can also be used to apply surface pretreatment coatings to substrates. This can be done using a variety of different application methods, such as spraying, dipping, and electroplating.
Safety tips for using surface pretreatment equipment:
- Wear appropriate personal protective equipment (PPE), such as gloves, safety glasses, and a respirator, when operating surface pretreatment equipment.
- Follow the manufacturer’s instructions for operating the equipment safely.
- Store surface pretreatment chemicals in a safe and secure location.
- Dispose of surface pretreatment chemicals properly.
By following these safety tips, you can help to ensure that surface pretreatment equipment is used safely and effectively.
The surface pretreatment for powder coating is a chemical cleaning process, used to degrease and wash the parts with basic or alkaline chemicals. These chemicals remove the rust, dust, and oil from the surface of the parts that are later going to be painted. The process of surface pretreatment is determined according to the surface quality and dirеyness of the parts.
Gema Spare Parts
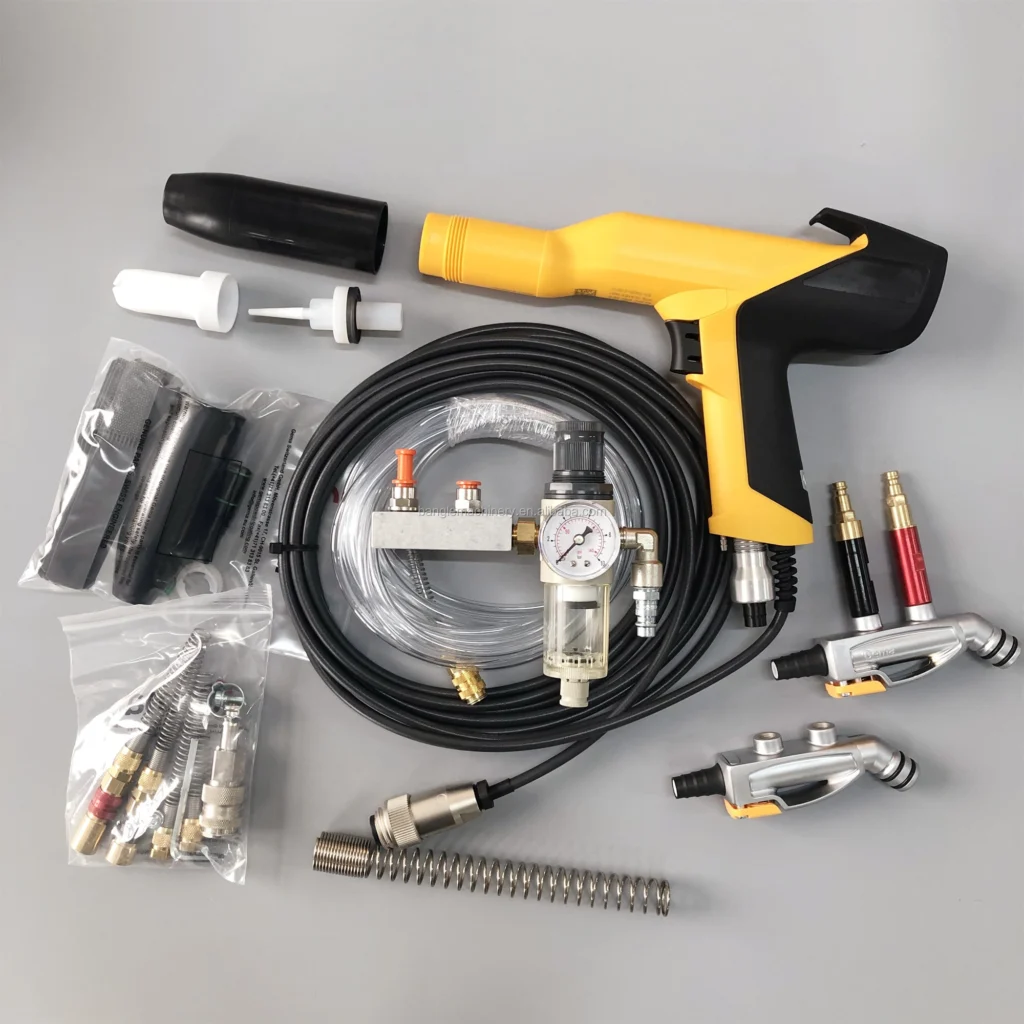
We are a leading supplier of powder coating equipment spare parts and offer a wide range of spare parts for all major powder coating brands, including Gema, Nordson, and Ionbond.
Gema Spare Parts
Gema is a renowned manufacturer of powder coating equipment, including booths, ovens, guns, and accessories. They offer a comprehensive range of spare parts to maintain and repair their equipment.
Gema Spare Parts List
Gema provides detailed spare parts lists for all their equipment models. These lists include part numbers, descriptions, and compatibility information.
Gema Powder Coating Gun Spare Parts
Gema offers a wide range of spare parts for their powder coating guns, including nozzles, electrodes, filters, and o-rings. These parts are essential for maintaining optimal gun performance and preventing overspray.
Gema Optiflex 2 Spare Parts
The Optiflex 2 is a popular powder coating gun model from Gema. Spare parts for the Optiflex 2 include nozzles, electrodes, filters, and seals.
Gema Powder Coating Spare Parts
Gema powder coating spare parts are designed to ensure the longevity and performance of Gema equipment. They are manufactured from high-quality materials and undergo rigorous testing to meet Gema’s standards.
Gema Optiflex Spare Parts
Spare parts for Gema Optiflex powder coating guns are readily available from authorized Gema distributors and online retailers.
Gema Replacement Parts
Gema replacement parts are original manufacturer parts that meet the exact specifications of Gema equipment. They are the preferred choice for maintaining optimal performance and ensuring compatibility.
Gema Parts List
Gema provides comprehensive parts lists for all their equipment models, allowing users to easily identify and order the necessary spare parts.
Gema Parts
Gema parts are known for their reliability, durability, and compatibility with Gema equipment. They are backed by Gema’s warranty and support.
Our Non-OEM Gema Spare Parts spare parts are made to the highest quality standards and are backed by a satisfaction guarantee. They offer fast and reliable shipping worldwide, so you can get the spare parts you need when you need them.
Here are some of the most popular Gema spare parts:
- Powder coating guns: Powder coating guns are the most important part of any powder coating system. Gema Spare Parts offers a wide range of powder coating guns to suit all needs, from small hobby guns to large industrial guns.
- Powder coating nozzles: Powder coating nozzles are responsible for atomizing the powder coating and spraying it onto the substrate. Gema Spare Parts offers a wide range of powder coating nozzles to suit all needs, from general-purpose nozzles to specialized nozzles for specific applications.
- Powder coating filters: Powder coating filters remove impurities from the powder coating before it is sprayed onto the substrate. Gema Spare Parts offers a wide range of powder coating filters to suit all needs, from standard filters to high-efficiency filters for demanding applications.
- Powder coating hoses: Powder coating hoses transport the powder coating from the powder coating machine to the powder coating gun. Gema Spare Parts offers a wide range of powder coating hoses to suit all needs, from standard hoses to high-pressure hoses for demanding applications.
- Powder coating pumps: Powder coating pumps deliver the powder coating to the powder coating gun. Gema Spare Parts offers a wide range of powder coating pumps to suit all needs, from small hobby pumps to large industrial pumps.
If you need a Gema spare part, EMS is the place to go. We offer a wide range of spare parts for all major powder coating brands, and our spare parts are made to the highest quality standards.
Wagner Spare Parts

Wagner Spare Parts is a leading supplier of spare parts for Wagner powder coating equipment. They offer a wide range of spare parts for all major Wagner powder coating systems, including powder coating guns, reciprocators, curing ovens, and conveyor systems.
Wagner Spare Parts
Wagner is a well-established manufacturer of paint sprayers and powder coating equipment. They offer a comprehensive range of spare parts to maintain and repair their equipment.
Where to Buy Wagner Spare Parts
Wagner spare parts can be purchased from authorized Wagner distributors, online retailers, and directly from Wagner’s website.
Wagner Spare Parts UK
Wagner has a strong presence in the UK market, with a network of authorized distributors and a dedicated online store for UK customers.
Wagner Spare Parts Australia
Wagner offers a wide range of spare parts for their Australian customers through their authorized distributors and online store.
Wagner Spare Parts NZ
Wagner’s spare parts are also readily available in New Zealand through a network of authorized distributors and online retailers.
Wagner Paint Sprayer Parts Australia
Wagner provides a comprehensive range of spare parts for their paint sprayers, including nozzles, filters, pumps, and repair kits.
Wagner Airless Spare Parts
Wagner offers a specialized range of spare parts for their airless paint sprayers, including pumps, diaphragms, packings, and filters.
Wagner Sprayer Parts List
Wagner provides detailed spare parts lists for all their sprayer models, allowing users to easily identify the necessary parts.
Where to Buy Wagner Spray Gun Spare Parts
Wagner spray gun spare parts can be purchased from authorized Wagner distributors, online retailers, or directly from Wagner’s website.
Wagner Replacement Parts Canada
Wagner offers a comprehensive range of replacement parts for their Canadian customers through their authorized distributors and online store.
Wagner Paint Sprayer Parts Canada
Wagner provides a wide range of spare parts for their paint sprayers in Canada, including nozzles, filters, pumps, and repair kits.
Wagner Control 150M Spare Parts
Wagner offers a dedicated range of spare parts for their Control 150M paint sprayer, including hoses, filters, nozzles, and repair kits.
Wagner Powder Coating Gun Spare Parts
Wagner provides a range of spare parts for their powder coating guns, including nozzles, electrodes, filters, and seals.
Wagner Control Pro 250M Spare Parts
Wagner offers a comprehensive range of spare parts for their Control Pro 250M paint sprayer, including hoses, filters, nozzles, and repair kits.
Wagner Spare Parts spare parts are made to the highest quality standards and are backed by a satisfaction guarantee. They offer fast and reliable shipping worldwide, so you can get the spare parts you need when you need them.
Here are some of the most popular Wagner spare parts:
- Powder coating guns: Wagner Spare Parts offers a wide range of powder coating guns to suit all needs, from small hobby guns to large industrial guns. Some of the most popular Wagner powder coating guns include the Control Pro 130, the Control Pro 150, and the Control Pro 190.
- Reciprocators: Wagner Spare Parts offers a wide range of reciprocators to suit all needs, from small manual reciprocators to large automated reciprocators. Some of the most popular Wagner reciprocators include the CompactReciprocator and the PowerReciprocator.
- Curing ovens: Wagner Spare Parts offers a wide range of curing ovens to suit all needs, from small batch ovens to large continuous flow ovens. Some of the most popular Wagner curing ovens include the Universal oven and the PowerCuring oven.
- Conveyor systems: Wagner Spare Parts offers a wide range of conveyor systems to suit all needs, from simple overhead conveyor systems to complex automated conveyor systems. Some of the most popular Wagner conveyor systems include the PowerConveyor and the FlexConveyor.
If you need a Wagner spare part, Wagner Spare Parts is the place to go. They offer a wide range of spare parts for all major Wagner powder coating systems, and their spare parts are made to the highest quality standards.
Here are some tips for using Wagner spare parts safely and effectively:
- Always wear appropriate personal protective equipment (PPE), such as gloves, safety glasses, and a respirator, when working with Wagner powder coating equipment and spare parts.
- Follow the manufacturer’s instructions for installing and using Wagner spare parts.
- Inspect Wagner spare parts regularly for signs of wear or damage.
- Replace Wagner spare parts immediately if they are worn or damaged.
By following these tips, you can help to ensure that Wagner spare parts are used safely and effectively to maintain and repair Wagner powder coating equipment.
Nordson Spare Parts

Nordson Spare Parts is a leading supplier of spare parts for Nordson powder coating equipment. They offer a wide range of spare parts for all major Nordson powder coating systems, including powder coating guns, reciprocators, curing ovens, and conveyor systems.
Nordson Spare Parts
Nordson is a leading manufacturer of industrial dispensing and coating systems. They offer a wide range of spare parts to maintain and repair their equipment.
Nordson Spare Parts UK
Nordson provides a comprehensive range of spare parts for their UK customers through their authorized distributors and online store.
Nordson Powder Coating Gun Spare Parts
Nordson offers a wide range of spare parts for their powder coating guns, including nozzles, electrodes, filters, and seals. These parts are essential for maintaining optimal gun performance and preventing overspray.
Nordson Parts List
Nordson provides detailed spare parts lists for all their equipment models, allowing users to easily identify and order the necessary spare parts.
Nordson Spare Parts Catalog
Nordson offers comprehensive spare parts catalogs for their various equipment lines, providing detailed information on part numbers, descriptions, and compatibility.
Nordson Replacement Parts
Nordson replacement parts are original manufacturer parts that meet the exact specifications of Nordson equipment. They are the preferred choice for maintaining optimal performance and ensuring compatibility.
Nordson Replacement Parts Catalog
Nordson provides a dedicated replacement parts catalog, listing all the replacement parts available for their equipment, along with detailed part numbers, descriptions, and compatibility information.
What Does Nordson Do?
Nordson is a global leader in precision dispensing and coating systems. They provide a wide range of equipment and solutions for various industries, including:
- Adhesive Dispensing: Precise application of adhesives, sealants, and lubricants for various applications.
- Electronic Solutions: Dispensing and coating systems for electronics assembly and manufacturing.
- Industrial Coating Systems: Application of protective coatings for industrial products and components.
- Polymer Processing Systems: Equipment for extrusion, melt filtration, and pellet production.
Nordson’s products are used in a wide range of industries, including automotive, electronics, aerospace, medical, and packaging. Their commitment to innovation and quality has made them a trusted partner for manufacturers worldwide.
Nordson Spare Parts spare parts are made to the highest quality standards and are backed by a satisfaction guarantee. They offer fast and reliable shipping worldwide, so you can get the spare parts you need when you need them.
Here are some of the most popular Nordson spare parts:
- Powder coating guns: Nordson Spare Parts offers a wide range of powder coating guns to suit all needs, from small hobby guns to large industrial guns. Some of the most popular Nordson powder coating guns include the ProBlue, the DuraBlue, and the Encore series guns.
- Reciprocators: Nordson Spare Parts offers a wide range of reciprocators to suit all needs, from small manual reciprocators to large automated reciprocators. Some of the most popular Nordson reciprocators include the ProFlex and the DuraFlex series reciprocators.
- Curing ovens: Nordson Spare Parts offers a wide range of curing ovens to suit all needs, from small batch ovens to large continuous flow ovens. Some of the most popular Nordson curing ovens include the IRDry and the UVcure series ovens.
- Conveyor systems: Nordson Spare Parts offers a wide range of conveyor systems to suit all needs, from simple overhead conveyor systems to complex automated conveyor systems. Some of the most popular Nordson conveyor systems include the ProTrack and the DuraTrack series conveyor systems.
If you need a Nordson spare part, Nordson Spare Parts is the place to go. They offer a wide range of spare parts for all major Nordson powder coating systems, and their spare parts are made to the highest quality standards.
Here are some tips for using Nordson spare parts safely and effectively:
- Always wear appropriate personal protective equipment (PPE), such as gloves, safety glasses, and a respirator, when working with Nordson powder coating equipment and spare parts.
- Follow the manufacturer’s instructions for installing and using Nordson spare parts.
- Inspect Nordson spare parts regularly for signs of wear or damage.
- Replace Nordson spare parts immediately if they are worn or damaged.
By following these tips, you can help to ensure that Nordson spare parts are used safely and effectively to maintain and repair Nordson powder coating equipment.
In addition to the above, here are some additional tips for finding the right Nordson spare parts:
- Identify the model number of your Nordson powder coating equipment. This will help you to find the correct spare parts for your specific system.
- Contact Nordson customer support for assistance. Nordson customer support can help you to identify the correct spare parts for your needs and can also provide you with pricing and availability information.
- Purchase Nordson spare parts from a reputable supplier. This will help to ensure that you are getting high-quality parts that are compatible with your Nordson powder coating equipment.
Not only do we manufacture our powder coating equipment, we also ship them worldwide to your facility with care
We’re not just the manufacturers of your powder coating equipment, we’re also your worldwide delivery partners.
At EMS Powder Coating Equipment, we understand that getting your powder coating equipment to you quickly and safely is just as important as manufacturing it to the highest standards. That’s why we offer worldwide delivery services to all of our customers.
We work with a network of experienced and reliable shipping partners to ensure that your equipment arrives on time and in perfect condition. We also offer a variety of shipping options to fit your budget and needs.
Whether you need your equipment shipped to a local address or to an international destination, we can help. We’ll work with you to choose the best shipping option for your needs and to keep you updated on the status of your shipment every step of the way.
So when you choose EMS for your powder coating equipment, you’re not just getting the best products on the market, you’re also getting the best possible delivery experience.
Contact us today to learn more about our worldwide delivery services.
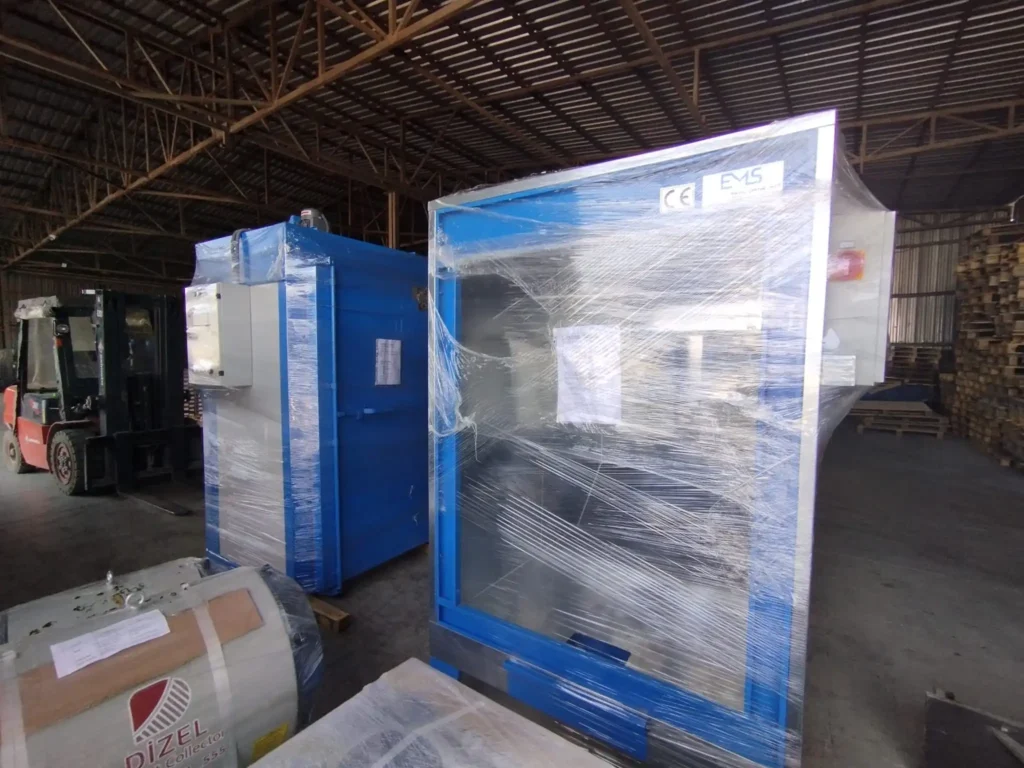
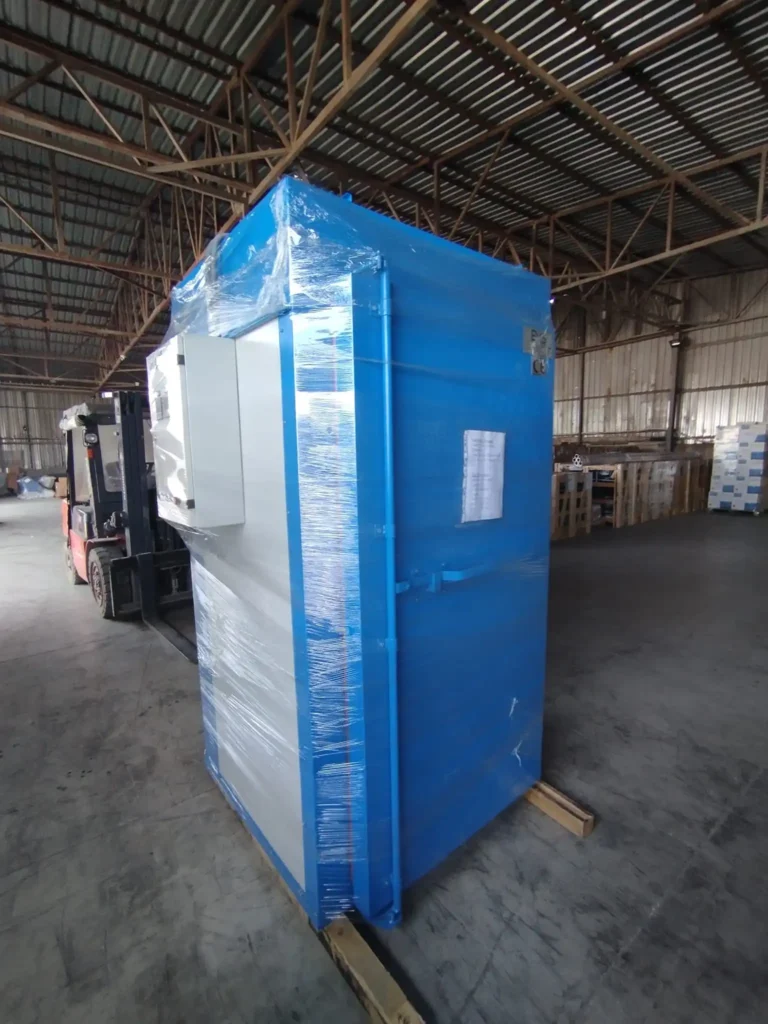
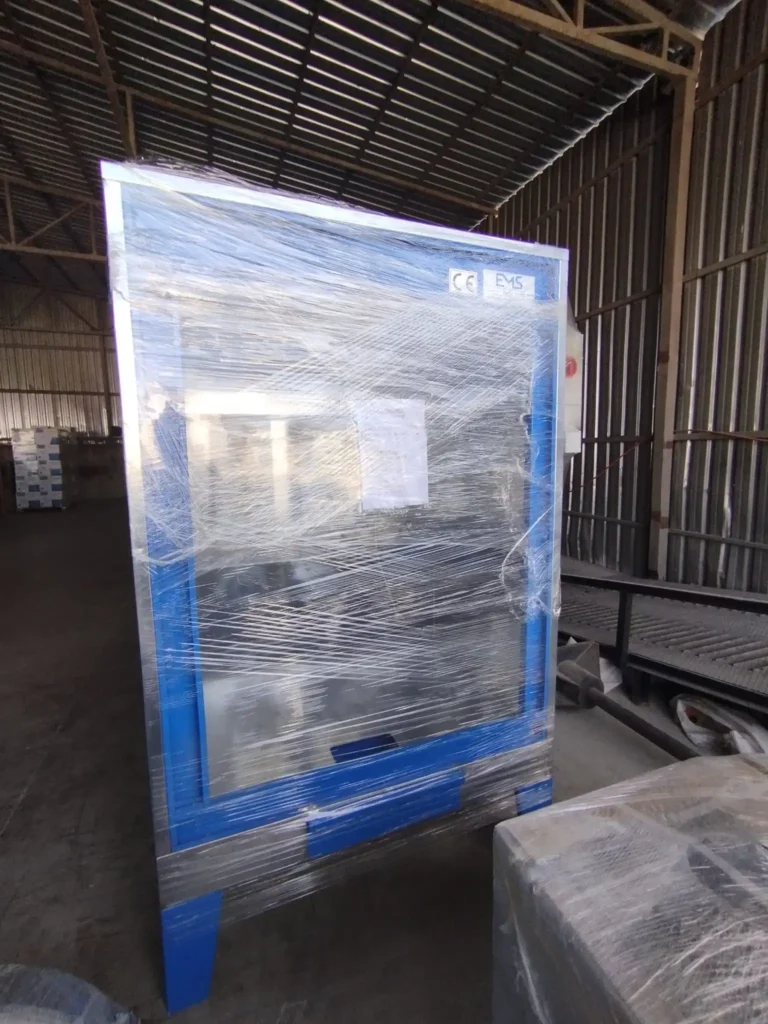
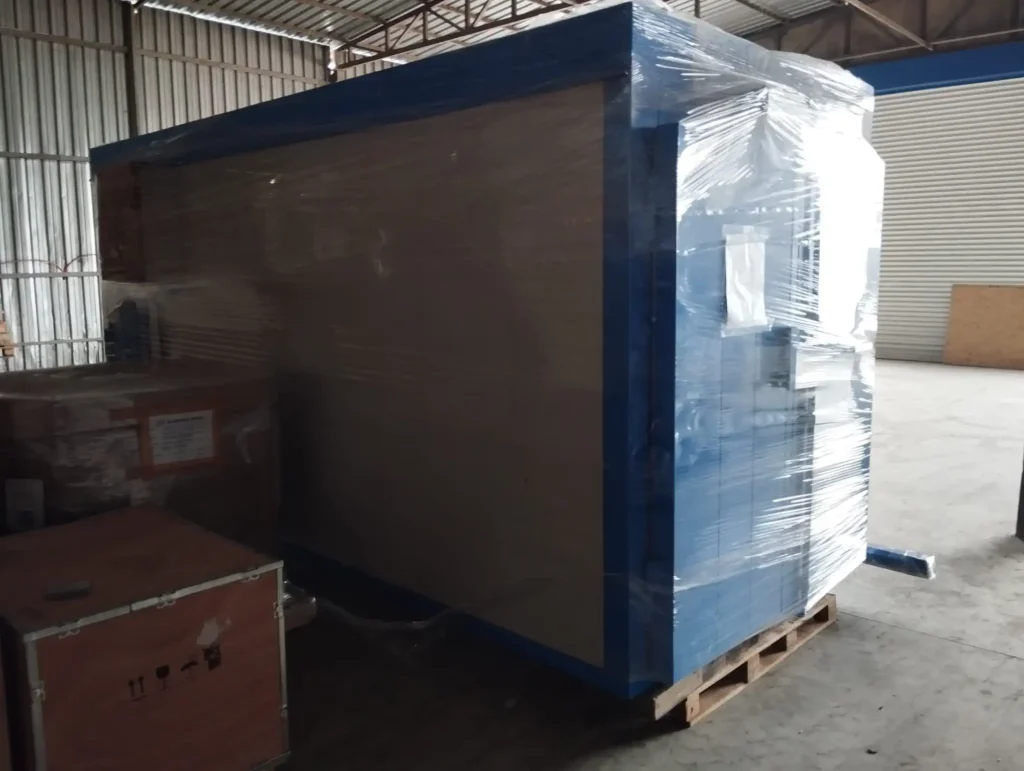
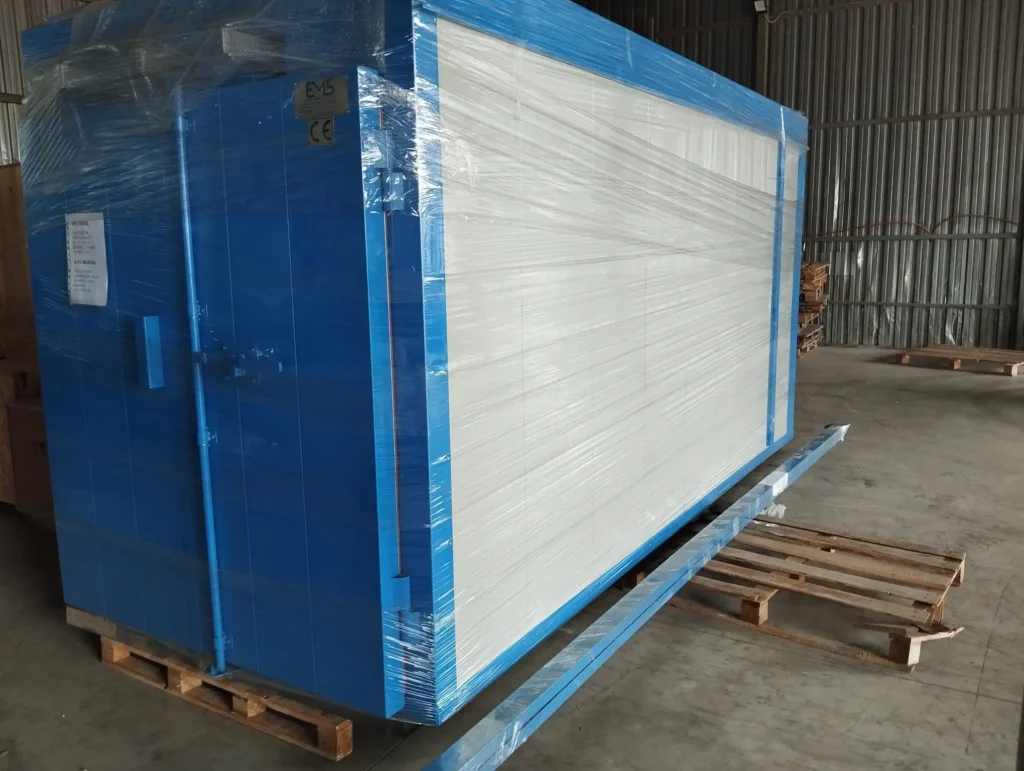
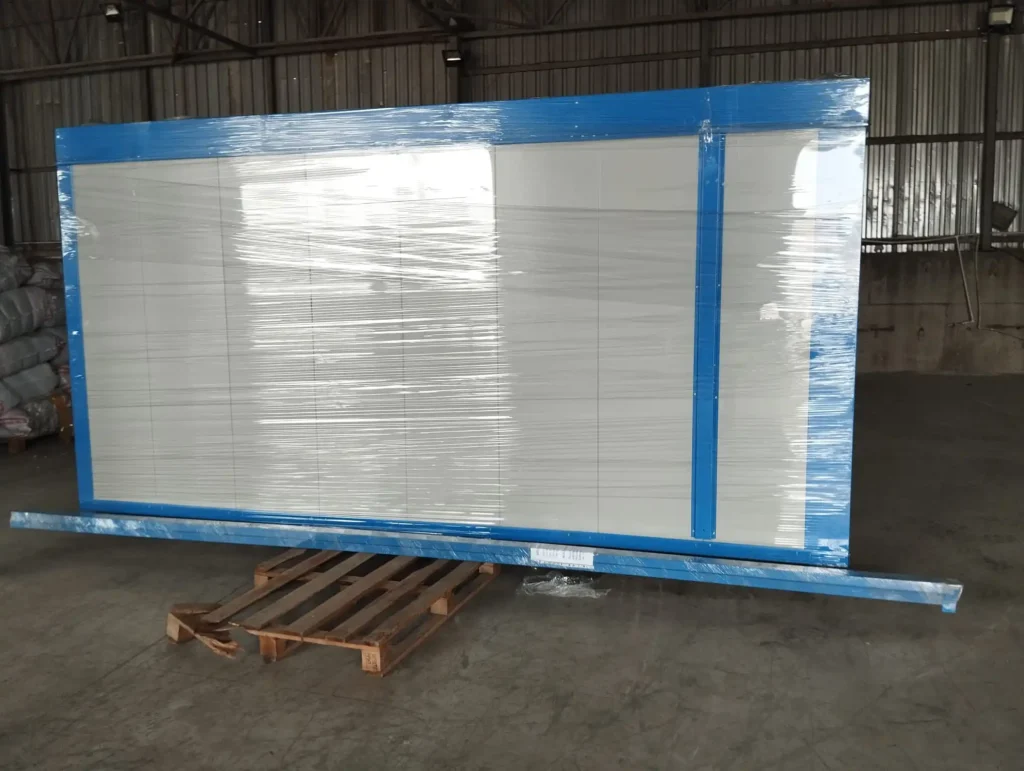
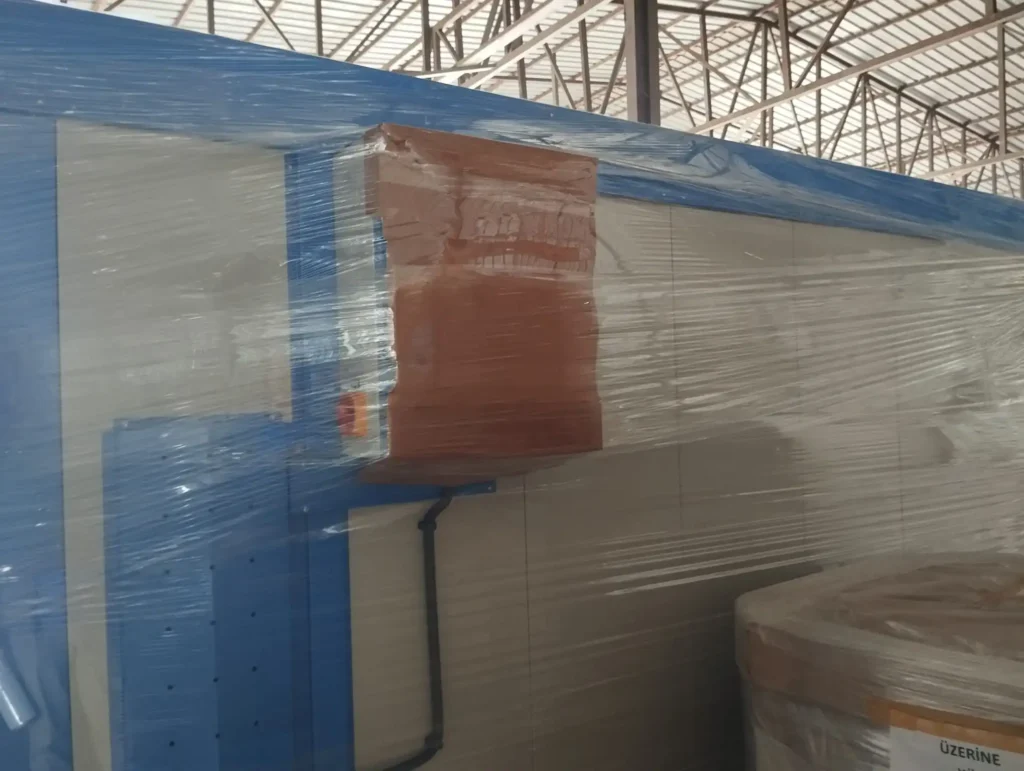
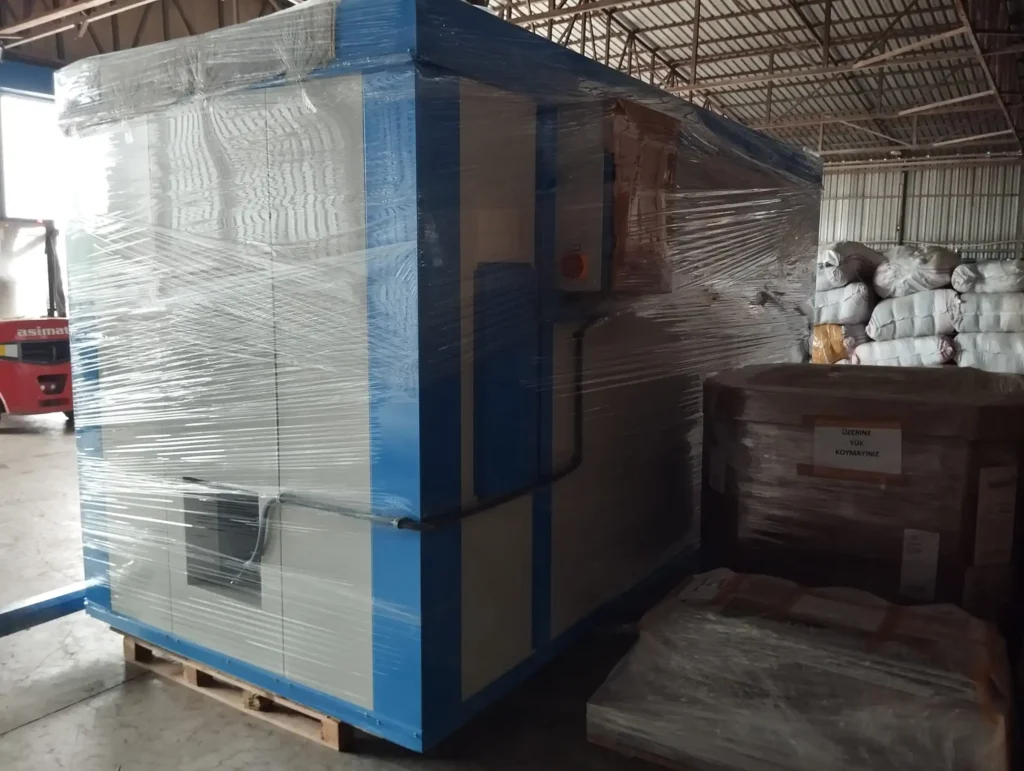
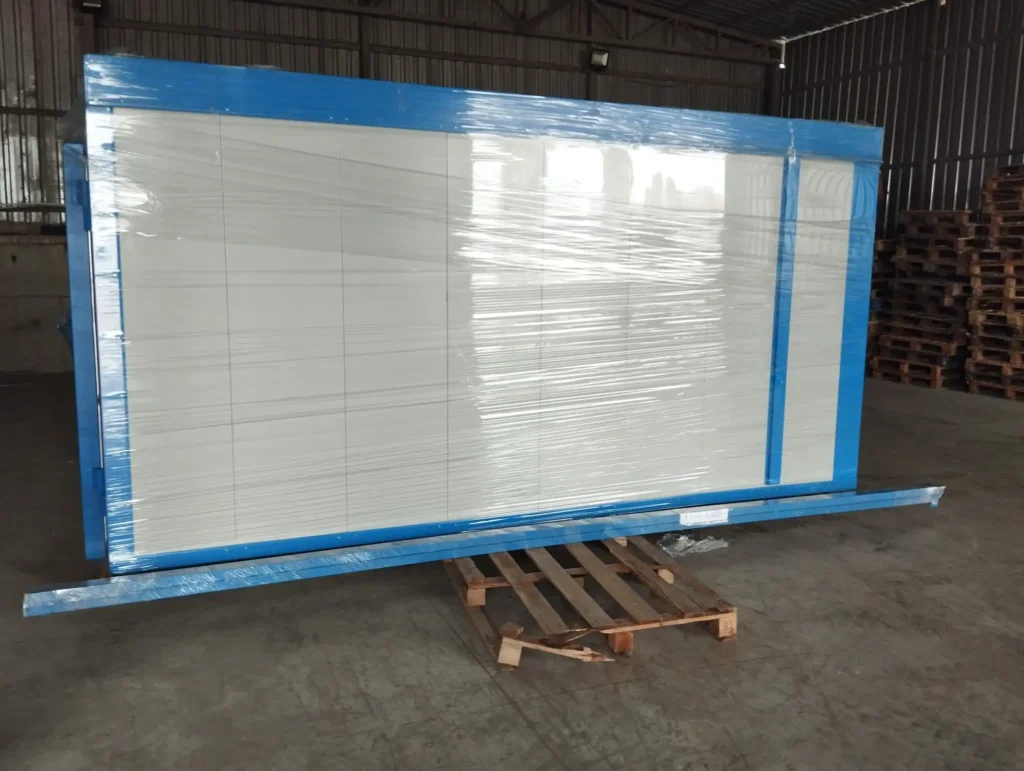