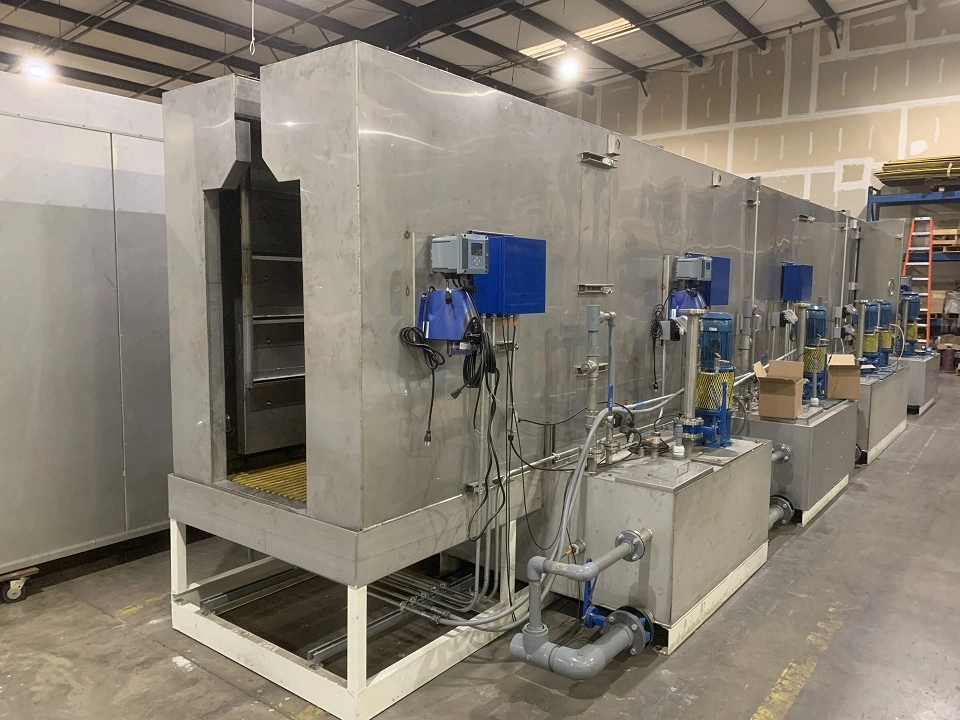
Zinc phosphate pretreatment is essential in powder coating pretreatment when higher performance and quality are required.
Zinc Phosphatizing or Zinc phosphate pretreatment
After iron phosphatizing, the most versatile and popular system with powder coating would be zinc phosphatizing. It achieves the quality performance expected from powder coating. Zinc phosphatizing not only converts the surface of the substrate but also overlays a crystalline structure.
It actually grows a zinc phosphate crystal on the surface of the metal. Under the examination of an electron microscope, iron phosphate coating appears smooth while zinc phosphate coating leaves an intricate matrix to which the powder coating can adhere. This gives the metal a heavier coating than iron which in turn also offers superior corrosion resistance. The same substrates pretreated with iron phosphate coating can be pretreated with a zinc phosphate coating.
Zinc phosphatizing is harder to maintain and there are more critical controls. Zinc is less tolerant to changes in time, temperature, concentration, and pH. It is more expensive. Zinc phosphatizing requires a higher capital expense in that tanks have to be stainless steel or acid resistant. The zinc content also renders it more difficult to dispose of.
Where absolute maximum corrosion resistance is required, zinc phosphatizing would be our recommended approach. Even though powder coatings exhibit very high corrosion resistance as opposed to conventional liquid coatings, zinc phosphate will further improve upon those corrosion resistance characteristics. Products which require long service life or which must endure the torture of harsh environmental or atmospheric conditions are probably best pretreated with a zinc phosphate coating.
How to Phosphatize
Iron phosphate coating can be applied in all three chemical cleaning systems (1. immersion or soak tank, 2. spray wash, or 3. pressure wand.)
The cleaning and conversion coating is typically accomplished in stages.
There can be as few as two stages.
1- Clean & Conversion Coat
2- Rinse
Three Stages
1-Clean & Conversion Coat
2-Rinse
3- Seal
Or a five-stage system:
1-Clean
2-Rinse
3-Conversion Coat
4- Rinse
5- Seal
Additional stages can be used in custom-designed systems. Zinc phosphatizing must be done in a five-stage operation.
In pretreating powder-coated products, we recommend the use of a five-stage system in which the cleaning stage is separated from the phosphatizing stage. The overwhelming importance of a thorough cleaning prior to powder coating has led us to conclude that a five-stage system works best.
Rinsing
While cleaning and phosphatizing are the principal units of operation in the pretreatment process, the importance of thorough rinsing cannot be overlooked. It is very important that the rinse stages be kept clean to avoid recontamination of the parts.
Any chemical remaining on the part becomes soil which must be removed prior to proceeding to the next stage of the system. The rinsing stage cannot be overlooked. There are two types of final rinses: chromated and non-chromate. The chromated final rinse has always been known as the standard of the industry, but it has come under increasing scrutiny from environmental and occupational safety regulators.
The trend is away from chrome to safer, nonchromated rinses. Without an absolutely clean part, conversion coating will not perform to the extent that offers the subsequently powder-coated parts to realize optimum adhesion and corrosion resistance. A commitment to thorough cleaning is key to maximizing powder coating performance
Zinc phosphate pretreatment
Zinc phosphate pretreatment is a surface treatment process used to prepare metal surfaces, primarily steel and iron, for subsequent coating or painting. This process involves the application of a zinc phosphate coating to the metal surface to improve adhesion, corrosion resistance, and overall paint performance. Here are the key aspects of zinc phosphate pretreatment:
1. Surface Preparation:
- Before the zinc phosphate coating is applied, the metal surface must be thoroughly cleaned and prepared. This involves removing any contaminants, such as rust, oil, grease, and scale, through processes like degreasing and pickling.
2. Phosphating Process:
- The metal part is immersed in a phosphating solution that contains zinc phosphate chemicals. This solution typically consists of zinc phosphate, water, accelerators, and other additives.
- The process can be carried out at different temperatures, ranging from ambient temperature to elevated temperatures (usually 120-160°C or 250-320°F), depending on the specific requirements of the application.
3. Chemical Reaction:
- During the phosphating process, a chemical reaction occurs between the metal surface and the phosphate solution. This results in the formation of a thin, crystalline layer of zinc phosphate on the metal’s surface.
4. Benefits of Zinc Phosphate Pretreatment:
- Improved Adhesion: The zinc phosphate coating provides a roughened surface with excellent adhesion properties, allowing paint or coatings to bond effectively.
- Corrosion Resistance: Zinc phosphate acts as a corrosion inhibitor, providing a protective barrier between the metal substrate and the surrounding environment.
- Enhanced Paint Performance: Surfaces treated with zinc phosphate exhibit improved paint and coating performance, including better resistance to chipping, peeling, and blistering.
- Surface Finish: The process can also contribute to a smoother surface finish, reducing imperfections in the final painted or coated surface.
5. Post-Treatment Rinse:
- After phosphating, the metal part is typically rinsed with clean water to remove any residual phosphate solution.
6. Drying:
- The treated metal part is dried to remove excess moisture, ensuring that it is ready for the application of paint or coatings.
7. Painting or Coating Application:
- Once the metal surface has been phosphated, it is ready for the application of paint, powder coating, or other protective coatings.
Zinc phosphate pretreatment is commonly used in various industries, including automotive manufacturing, aerospace, construction, and industrial equipment production. It is valued for its ability to improve the longevity and performance of painted or coated metal parts, especially in harsh environments where corrosion resistance is crucial. Different formulations of zinc phosphate solutions may be used depending on the specific application and desired performance characteristics.
Phosphating Process
The phosphating process is a surface treatment method used to prepare metal surfaces for subsequent coating, painting, or to enhance corrosion resistance. This process typically involves the formation of a phosphate coating on the metal’s surface. Here is an overview of the phosphating process:
1. Surface Preparation:
- Before phosphating can begin, the metal surface must be thoroughly cleaned to remove any contaminants such as rust, oil, grease, scale, and other impurities. Common cleaning methods include degreasing and pickling.
2. Phosphate Bath Preparation:
- A phosphate solution is prepared, which typically contains chemicals such as phosphoric acid, zinc phosphate, or iron phosphate, depending on the specific application and desired properties of the coating.
- The phosphate solution may also include additives such as accelerators and surfactants to enhance the process.
3. Immersion or Spray Application:
- The metal parts are either immersed in the phosphate bath or sprayed with the phosphate solution. Immersion is more common for bulk processing, while spraying is used for smaller or more intricate parts.
4. Chemical Reaction:
- When the metal surface comes into contact with the phosphate solution, a chemical reaction occurs between the metal and the phosphates. This chemical reaction results in the formation of a thin, crystalline phosphate layer on the metal surface.
5. Phosphate Coating Types:
- Depending on the specific formulation of the phosphate solution and the application, different types of phosphate coatings can be formed. Common types include zinc phosphate, iron phosphate, and manganese phosphate.
6. Rinse Stage:
- After the phosphate treatment, the metal parts are rinsed with clean water to remove any residual phosphate solution.
7. Post-Phosphating Treatment (Optional):
- In some cases, the phosphate-coated metal parts may undergo additional treatments, such as passivation or chromating, to further enhance corrosion resistance or adhesion properties.
8. Drying:
- The treated metal parts are typically dried to remove excess moisture before proceeding to the next manufacturing step.
9. Coating Application:
- Once phosphated and dried, the metal parts are ready for the application of paint, powder coating, or other protective coatings. The phosphate coating serves as a primer layer that enhances the adhesion of subsequent coatings.
The phosphating process is widely used in various industries, including automotive, aerospace, construction, and industrial manufacturing, where improved corrosion resistance and better adhesion of coatings are essential. The choice of phosphate type and process parameters depends on the specific requirements of the application and the type of metal being treated.
EMS Powder Coating Equipment
Powder coating equipment is used to apply a thin layer of powder over a metal surface. This type of coating is applied by an electrostatic process and is a very popular method for finishing metal parts.
This type of equipment can be divided into two main categories: automatic and manual. Automatic booths are more popular because they provide better production rates, but they are also more expensive.
A powder booth is an enclosure in which the powder-coating process takes place. Powder-coating equipment includes an oven where the parts are heated to activate the powder, a gun that sprays or brushes on the powder, a conveyor belt that moves parts through the oven, and cartridge-type guns for applying thicker coatings with less overspray.
Powder coating is a technique that is used to provide a finish to metal parts. This technique has been in use for many years and it is still one of the most popular techniques today.
Powder coating equipment consists of booths, ovens, guns, machines, lines and conveyors. A booth can be either automatic or manual. An automatic booth is more expensive than a manual booth but it is also faster and more efficient.