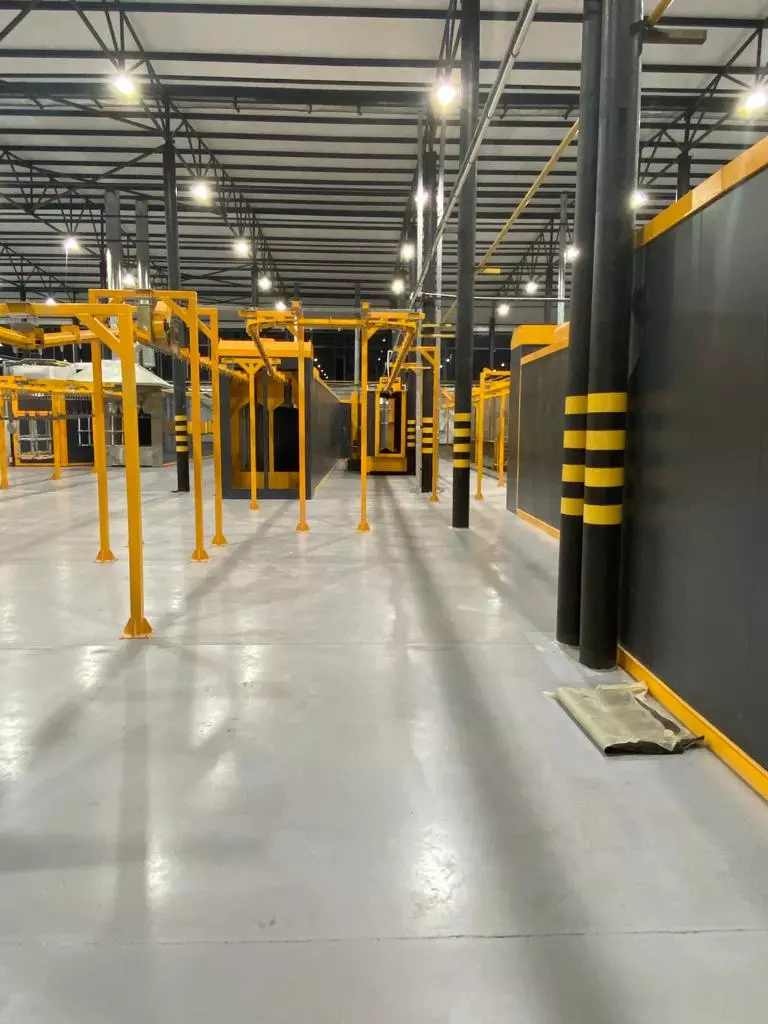
Used Powder Coating Conveyor Systems: Electrocoating, often referred to as e-coating, is a process widely used in industries requiring high-quality, uniform coatings on metal surfaces. A key component of the e-coating process is the conveyor system, which plays a critical role in the efficiency, consistency, and quality of the overall operation. Electrocoating conveyors are engineered to transport parts through each stage of the process, ensuring precise control and consistency in application. These conveyors are designed to handle various shapes, sizes, and weights of components, enabling their seamless movement through pre-treatment, coating, and curing stages.
The conveyor system in an electrocoating operation is typically automated and designed to move parts at a controlled speed to ensure optimal exposure to the coating bath. The design of the conveyor must account for the specific requirements of the e-coating line, such as the dimensions of the coating tanks, the distance between stages, and the need for immersion or spray treatment in certain phases of the process. Overhead conveyors are commonly used in e-coating systems, as they allow for the efficient transport of parts while minimizing floor space requirements. The overhead configuration also prevents contamination of the parts by keeping them away from ground-level debris.
The materials used to construct the conveyor system must be resistant to the chemicals and temperatures involved in the e-coating process. Corrosion resistance is a critical factor, as the conveyor is exposed to cleaning agents, electrocoating solutions, and curing ovens. Stainless steel and other corrosion-resistant materials are often used for components that come into direct contact with these substances. Additionally, the conveyor system must be designed to accommodate varying weights and sizes of parts while maintaining stability and alignment throughout the process.
One of the key advantages of a well-designed electrocoating conveyor system is its ability to integrate with other automation technologies. Sensors, robotics, and control systems can be used to monitor the position and movement of parts, ensuring precise control over the coating process. This integration enhances efficiency, reduces waste, and ensures consistent quality across batches. Conveyor speed and part orientation can also be adjusted dynamically to meet the specific requirements of different production runs, providing flexibility in manufacturing.
The maintenance and reliability of the conveyor system are crucial to the success of the electrocoating process. Regular inspections and preventive maintenance help to identify and address potential issues before they lead to downtime. Proper lubrication, tension adjustment, and cleaning of the conveyor system are essential to ensure smooth operation. Furthermore, modern conveyor systems are often equipped with diagnostic tools that provide real-time feedback on performance, enabling operators to make informed decisions and maintain optimal functionality.
In conclusion, the electrocoating conveyor system is an indispensable component of the e-coating process, offering precise control, integration capabilities, and durability. Its design and maintenance significantly impact the efficiency and quality of the electrocoating line, making it a critical area of focus for manufacturers aiming to achieve high standards in their coating operations.
Electrocoating Conveyor
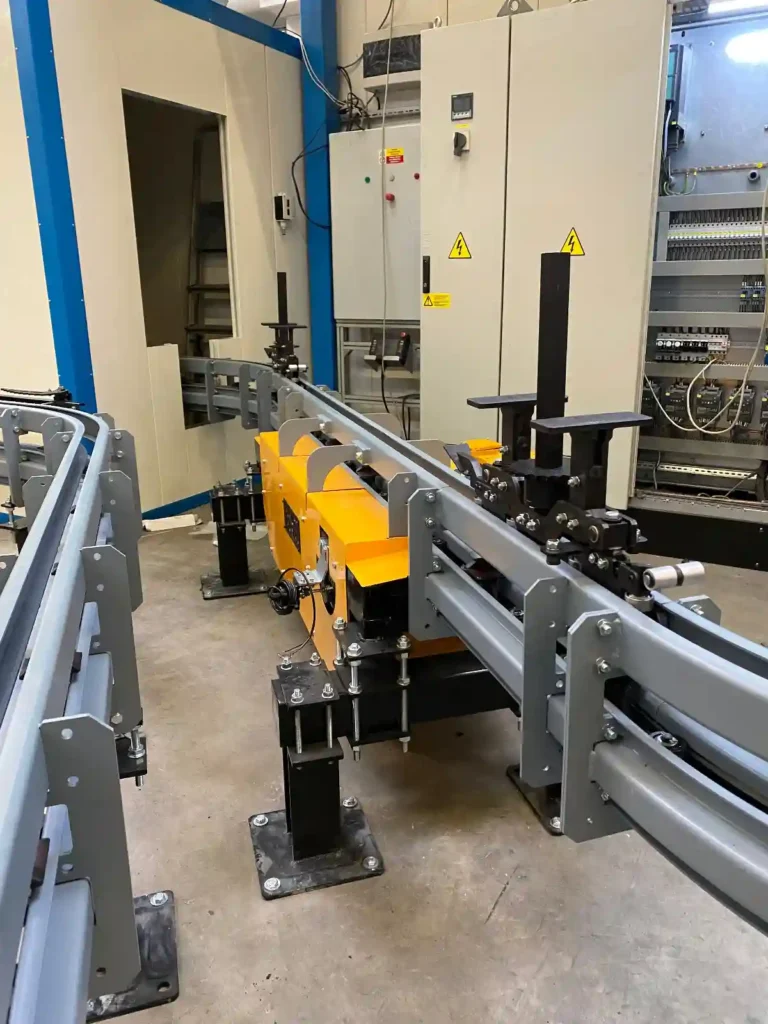
As the electrocoating process has evolved, so too have the designs and technologies used in the conveyor systems that support it. Modern electrocoating conveyors are increasingly designed to maximize energy efficiency and reduce environmental impact. For instance, energy-efficient motors, regenerative braking systems, and advanced control systems are now common features that help minimize power consumption. Additionally, the use of conveyor systems that can operate at variable speeds further enhances energy savings, allowing for the optimization of flow rates based on production needs.
One of the emerging trends in the electrocoating conveyor systems is the integration of Industry 4.0 technologies. Smart conveyors equipped with sensors, artificial intelligence, and machine learning capabilities can monitor and analyze the operational conditions in real-time. These systems collect data such as temperature, humidity, part speed, and coating thickness, and use it to adjust parameters automatically, ensuring consistent quality while reducing the need for manual intervention. Predictive maintenance is another benefit of these advanced systems, where data analytics can predict potential failures or wear, enabling proactive repairs and minimizing unplanned downtime.
In addition to technological advancements, the design of electrocoating conveyors continues to prioritize sustainability. The use of recyclable materials for the construction of conveyor components, as well as the ability to minimize waste and rework during the coating process, are key considerations in reducing the overall environmental footprint. Some manufacturers are also incorporating closed-loop systems that recycle coating solutions, reducing the need for fresh chemicals and minimizing waste disposal. Such initiatives are not only beneficial for the environment but can also lead to significant cost savings in the long term.
Furthermore, the versatility of electrocoating conveyors allows them to support a wide range of industries beyond automotive and industrial applications. For instance, they are increasingly being used in the production of electronics, appliances, and even decorative metal products. The ability to provide a high-quality finish that is both durable and corrosion-resistant makes electrocoating a popular choice for a variety of applications. The flexibility of conveyor systems enables them to handle the unique demands of these diverse industries, offering tailored solutions that meet specific coating requirements.
From a design perspective, the choice of conveyor type and configuration is influenced by several factors, including the layout of the plant, the nature of the products being coated, and the desired throughput. Automated shuttle conveyors, roller conveyors, or chain conveyors may all be used, depending on the space available and the complexity of the operation. Some e-coating lines use modular conveyor systems, which allow for easy expansion or reconfiguration to meet changing production needs. These systems are particularly advantageous for companies with fluctuating demand or those looking to scale up operations in the future.
In addition to material handling, the electrocoating conveyor system also plays a role in ensuring part cleanliness and preventing contamination. The conveyor must be designed to allow for easy access to cleaning stations, ensuring that parts are free of oils, dust, and other contaminants before they enter the coating process. Some systems incorporate automated cleaning functions to help maintain the cleanliness of the conveyor itself, reducing the likelihood of contamination from the conveyor system transferring to the coated parts.
In conclusion, the electrocoating conveyor system is a vital part of the e-coating process, offering key advantages in terms of efficiency, consistency, and adaptability. The continual development of more advanced, energy-efficient, and automated conveyor technologies is helping to drive improvements in the electrocoating process, enabling manufacturers to meet higher standards of quality and sustainability. Whether used in automotive production, industrial manufacturing, or consumer goods production, the electrocoating conveyor remains an essential piece of equipment in achieving high-quality, durable coatings with minimal environmental impact.
As industries continue to push for higher efficiency, lower costs, and improved environmental performance, the role of the electrocoating conveyor system is expected to grow even more critical. Emerging technologies in automation, robotics, and artificial intelligence are playing a central role in shaping the future of electrocoating conveyor systems, further enhancing their capabilities and driving greater levels of productivity.
One of the most significant advancements in conveyor technology is the ability to incorporate more sophisticated robotic systems for handling and positioning parts. Robots integrated into the conveyor lines can pick and place parts with extreme precision, reducing the need for human intervention and minimizing the risk of contamination. These robotic arms are often designed to work seamlessly with conveyor systems, ensuring smooth, continuous production flows and greater precision in part handling. They can also adjust the orientation of parts automatically to ensure the most effective coating application, especially in cases where complex geometries are involved.
Robotic automation also plays a critical role in ensuring consistency throughout the coating process. By precisely controlling the speed, pressure, and movement of parts as they move along the conveyor, robotic systems help maintain uniform coating thickness, which is vital for the durability and functionality of the final product. The ability to adapt the speed of the conveyor based on real-time sensor data ensures that the parts spend the optimal amount of time in each stage of the electrocoating process, whether it’s the immersion stage, drying, or curing phase.
Furthermore, with the advancement of machine vision technologies, electrocoating conveyors are increasingly able to detect defects or inconsistencies in the parts being processed. Vision systems mounted along the conveyor can scan parts for signs of improper coating, scratches, or other issues before they move further along the production line. These systems can automatically flag problematic parts and remove them from the line for further inspection or correction, reducing the likelihood of defective parts reaching the final stage and minimizing waste.
The introduction of smart sensors is another area where conveyor systems are becoming more sophisticated. These sensors monitor everything from environmental conditions to conveyor alignment and the speed of part movement. They can detect changes in the process, such as temperature fluctuations or deviations from the desired coating thickness, and make real-time adjustments to maintain optimal conditions. This reduces the need for manual intervention and helps operators fine-tune the system for maximum efficiency and quality.
Beyond operational benefits, the integration of Industry 4.0 principles is contributing to a more connected and transparent production environment. By linking electrocoating conveyors to a central control system or a cloud-based platform, operators can monitor key performance indicators (KPIs) from anywhere within the facility or remotely. Real-time monitoring helps identify bottlenecks, track production progress, and make data-driven decisions to improve throughput and reduce downtime. These systems also provide valuable insights into long-term performance trends, enabling predictive maintenance and more accurate forecasting for spare parts and supplies.
In terms of sustainability, many modern electrocoating conveyors are designed with closed-loop water and air systems to minimize energy and resource consumption. For example, water used in the pre-treatment and rinsing stages of electrocoating can be treated and recycled through filtration systems, reducing the need for fresh water and limiting wastewater generation. Similarly, exhaust systems that capture overspray and volatile organic compounds (VOCs) are becoming more common to help reduce air pollution and ensure compliance with increasingly strict environmental regulations.
The ongoing evolution of electrocoating conveyor systems is also supporting a shift toward more environmentally friendly and sustainable coatings. The use of water-based coatings, for example, is on the rise, as they are less toxic and generate fewer emissions compared to solvent-based coatings. Electrocoating conveyors that are optimized for these types of coatings ensure that the process is not only efficient but also aligned with environmental best practices.
Manufacturers are also exploring the potential of alternative materials and innovative designs in conveyor construction. Lightweight, corrosion-resistant materials such as composite metals or plastics are being utilized to reduce weight and improve durability, further extending the lifespan of conveyor systems and reducing maintenance costs. Modular conveyor systems that can be easily reconfigured or expanded are also gaining traction, offering flexibility in adapting to new production requirements or scaling operations up or down with minimal investment.
In conclusion, the electrocoating conveyor system is evolving at a rapid pace, driven by advancements in automation, sensor technologies, and sustainable practices. These innovations are enhancing the overall efficiency, quality, and environmental performance of electrocoating operations. As industries demand more versatile, energy-efficient, and cost-effective solutions, electrocoating conveyors will continue to be a key enabler of high-quality coatings, providing manufacturers with the tools they need to meet the challenges of a rapidly changing market. Whether through greater automation, smarter systems, or more sustainable processes, the future of electrocoating conveyors is one of continued innovation and optimization.
Used Powder Coating Conveyor Systems
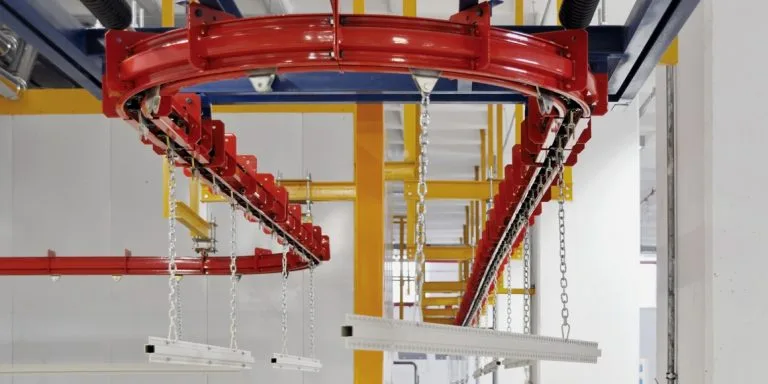
Used powder coating conveyor systems are a popular choice for manufacturers looking for a cost-effective solution to transport parts through the powder coating process. These systems, often acquired from companies upgrading their operations or from those who no longer need them, can still offer excellent performance if properly maintained and refurbished. Powder coating conveyors play an integral role in the efficiency and consistency of the coating process, helping to ensure a uniform application of powder to metal, plastic, or other material substrates. Despite being pre-owned, many used systems come equipped with the same essential features and functionality as new systems, offering a viable alternative for businesses seeking to maintain productivity while managing costs.
The primary function of a powder coating conveyor system is to transport parts through various stages of the coating process, including pre-treatment, coating, curing, and cooling. These systems are generally designed for automated operation, which helps to increase throughput, reduce human error, and ensure that parts are consistently coated. Overhead conveyors are typically used in powder coating lines, allowing for better space utilization and helping to keep parts suspended and free from contamination. The overhead configuration minimizes the risk of debris or dirt coming into contact with the parts during transport, a key consideration for maintaining high-quality finishes.
Used powder coating conveyor systems come in a variety of designs, including chain-driven, roller, and monorail conveyors. The choice of system depends on several factors, such as the size, weight, and complexity of the parts being coated, as well as the available floor space. Chain-driven conveyors are particularly common, as they can transport heavier parts and are robust enough to handle the demanding conditions of the powder coating process. Roller conveyors are suitable for parts that can be easily moved using wheels or rollers, and monorail systems are often used when parts require specialized handling or need to be rotated during the coating process.
The materials used in the construction of used powder coating conveyors are critical to ensuring their longevity and performance. These systems are typically made from durable, corrosion-resistant materials such as stainless steel, which can withstand exposure to the high temperatures and harsh chemicals used in powder coating. Since powder coating involves electrostatic charges, the conveyor must also be designed to ensure that parts are safely transported without discharging the static electricity that could interfere with the coating process. The conveyor should also be capable of handling the rigors of moving parts through powder booths, ovens, and cooling stations.
The condition of a used powder coating conveyor system depends on its age, previous usage, and the level of maintenance it has received. Many companies that sell used systems will offer to refurbish or upgrade the conveyors before resale, ensuring that they meet the necessary operational standards. Refurbishing a used conveyor can involve replacing worn-out components, such as bearings, rollers, or motors, as well as cleaning and re-coating the system to ensure it is free from any contaminants that could affect the parts being coated. Regular maintenance, including lubrication and tensioning of the conveyor chain or components, ensures smooth operation and prevents unnecessary downtime.
One of the key advantages of purchasing a used powder coating conveyor system is the significant cost savings. New systems can be quite expensive, especially for larger or more complex conveyor setups, while used systems typically offer a more affordable option without sacrificing too much in terms of functionality. For businesses operating on a tighter budget or those seeking to expand their coating capabilities without a large capital expenditure, buying a used system can be an attractive option.
Used powder coating conveyors also come with the benefit of being readily available. Since many used systems are sold by businesses that have upgraded their equipment, they are often in stock and can be quickly shipped, allowing manufacturers to get their operations up and running with minimal lead time. Furthermore, many suppliers offer warranties or service agreements on used systems, providing additional peace of mind and assurance of their quality and functionality.
The integration of a used powder coating conveyor system into an existing production line is another important consideration. Depending on the configuration and layout of the plant, the conveyor may need to be customized or re-engineered to fit within the available space or to accommodate specific product handling requirements. In some cases, companies may need to invest in additional equipment, such as curing ovens, powder booths, or cooling systems, to complete the powder coating process. When purchasing a used conveyor system, it is essential to ensure that the entire powder coating line is properly integrated, which may require the assistance of professionals with expertise in coating system design and layout.
As with any pre-owned equipment, it is important to thoroughly assess the condition and functionality of a used powder coating conveyor system before making a purchase. This includes checking for any signs of wear and tear, verifying the operational status of key components (such as motors, chains, and bearings), and ensuring that the system can handle the specific requirements of the coating operation. It is also crucial to confirm that the used system meets industry safety standards and complies with any relevant regulations, such as those governing electrical equipment or environmental emissions.
The continued use of powder coating conveyor systems, whether new or used, is driven by the many advantages that powder coating offers over traditional liquid coatings. Powder coating provides a more durable, consistent, and environmentally friendly finish, with minimal VOC emissions and less waste. The ability to apply a uniform coating with minimal overspray further improves the efficiency of the process, making it an attractive option for manufacturers in industries such as automotive, electronics, appliances, and metal fabrication.
In conclusion, used powder coating conveyor systems can offer an efficient and cost-effective solution for businesses looking to streamline their coating processes. With proper maintenance and occasional refurbishment, these systems can perform effectively for many years, offering the same benefits as new systems without the high upfront cost. Their flexibility, durability, and compatibility with various types of powder coating applications make them an essential tool for manufacturers looking to maintain high-quality finishes while managing operational costs. Whether for a small-scale operation or a large manufacturing line, used powder coating conveyors continue to play a vital role in optimizing production processes and ensuring consistent, high-quality coatings.
As the demand for powder coating continues to rise across various industries, used powder coating conveyor systems are likely to become even more valuable to manufacturers seeking ways to enhance their operations while maintaining cost-efficiency. In addition to offering affordability, these systems can be adapted to meet the unique needs of diverse manufacturing environments, making them a flexible and practical solution for businesses of all sizes.
One area where used powder coating conveyors can particularly shine is in industries with fluctuating production volumes. Since the used systems are often available at a lower initial investment, companies with seasonal or variable production demands can benefit from the ability to quickly expand their coating capabilities without the significant financial commitment of purchasing new equipment. This flexibility is crucial for businesses that need to adjust production capacity based on customer demand or market conditions.
Additionally, used powder coating conveyor systems are often an excellent solution for small to mid-sized manufacturers that may not require the advanced features found in brand-new systems. While new systems may come with the latest technology, such as automated coating adjustment and real-time monitoring, many smaller businesses find that a well-maintained, used conveyor system offers everything they need to achieve consistent and high-quality finishes without the complexity or cost associated with state-of-the-art models. For these manufacturers, used systems can still provide a significant return on investment by enabling more efficient workflows and reducing the need for manual labor.
The ability to refurbish and upgrade used powder coating conveyors is another compelling reason why they are an attractive option for manufacturers. Companies specializing in used conveyor systems often offer customizable solutions, where the conveyors can be modified to fit the specific needs of the buyer. This might involve extending the conveyor length, adjusting the height, or even upgrading the drive mechanisms to improve performance. Refurbishment can also include the replacement of outdated electrical components or the addition of automation features that make the system more efficient and adaptable to modern production processes.
Used conveyor systems also present an opportunity for businesses to adopt more sustainable practices. In many cases, acquiring a pre-owned system helps extend the life cycle of the equipment, reducing the demand for new materials and the energy required to produce them. By reusing and refurbishing existing conveyor systems, manufacturers contribute to a circular economy model that minimizes waste and promotes resource conservation. Moreover, many of the companies that sell used systems provide eco-friendly refurbishment options, such as the use of non-toxic coatings and energy-efficient components, further supporting sustainability goals.
In terms of operational benefits, the integration of used powder coating conveyor systems into existing lines helps companies maintain high levels of consistency and quality in their coating processes. Since these systems are designed to automatically transport parts through various stages of the powder coating process, they reduce the potential for human error and minimize the chances of inconsistent powder application. Whether the goal is to apply an even coat, reduce overspray, or optimize curing times, used powder coating conveyors can deliver predictable results, enhancing product quality and production reliability.
Furthermore, the maintenance and repair costs associated with used powder coating conveyors are often lower than those of new systems. Many suppliers offer maintenance services, parts replacements, and troubleshooting support for used systems, ensuring that businesses can keep their operations running smoothly without excessive downtime or costly repairs. For companies that lack the resources to maintain a fleet of new equipment, used systems provide a more manageable and cost-effective alternative that still meets production needs.
One of the greatest advantages of acquiring a used powder coating conveyor system is the opportunity to experience immediate operational benefits. Since these systems have been previously used in real-world applications, many buyers can rely on the experience and performance data from previous owners. This offers a level of confidence that the system will meet the buyer’s operational goals. Many used systems come with detailed maintenance records and a history of performance, which can be valuable in assessing their condition and expected lifespan.
The size and capacity of the used conveyor system should also be considered when making a purchase. Larger systems may be more suitable for high-volume operations, while smaller conveyors are ideal for businesses with limited space or lower throughput requirements. Some manufacturers even specialize in providing compact and modular systems that can be easily customized and reconfigured based on changing production needs. Whether a business requires a small conveyor for a niche product line or a larger system for mass production, there are used solutions that can be tailored to fit.
When it comes to integrating used powder coating conveyors into the production line, it’s essential to ensure that the system is compatible with other equipment and the specific coating process requirements. This includes checking that the used system aligns with the dimensions of the powder coating booths and ovens, as well as ensuring that the transport system can handle the weight and size of the products being coated. For some businesses, the purchase of a used system may require the addition of certain modifications, such as retrofitting the system to accommodate specific parts or adjusting the speed to meet throughput requirements. In these cases, working with an experienced supplier or technician who can assist with installation and setup can ensure that the system integrates seamlessly into the existing operation.
In conclusion, used powder coating conveyor systems present manufacturers with an excellent opportunity to enhance their operations while keeping costs under control. These systems offer a wide range of benefits, including affordability, flexibility, and the ability to refurbish or customize according to specific needs. By selecting a well-maintained and properly upgraded system, businesses can enjoy the advantages of consistent and high-quality powder coating, increased production efficiency, and a more sustainable approach to equipment usage. As manufacturing industries continue to seek ways to optimize their processes and reduce expenses, used powder coating conveyor systems will remain a key solution in maintaining competitive advantage and operational success.
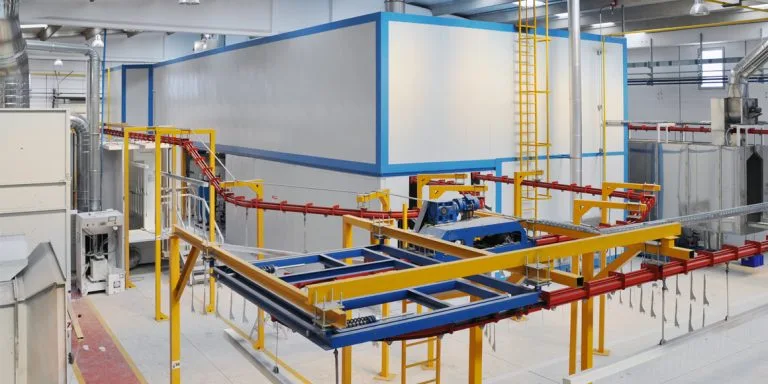
The demand for used powder coating conveyor systems is likely to remain strong as industries seek to maximize the lifespan of existing equipment and reduce upfront costs. However, businesses must be mindful of certain considerations when opting for a used system to ensure they make a sound investment. Thoroughly evaluating the system’s condition, understanding the maintenance history, and verifying compatibility with existing production lines are essential steps in the purchasing process. With careful selection, a used powder coating conveyor system can provide manufacturers with the performance and reliability they need to compete in the market while keeping operational costs in check.
Additionally, the expanding trend toward automation in powder coating processes presents a further opportunity for used conveyor systems. Many manufacturers are moving toward fully automated powder coating lines that can run with minimal human intervention, offering both cost savings and efficiency gains. Even though these systems are typically more expensive when new, purchasing a used conveyor system that can be integrated with automation technology can be a smart way to modernize operations. Used systems can be retrofitted with automation components such as robotics, sensors, and smart controllers to increase throughput and improve process control. This means manufacturers can benefit from the efficiency of automation without the prohibitive costs of buying a completely new system.
The potential for technological upgrades is another advantage of used powder coating conveyor systems. As new advancements emerge in powder coating technology, older systems can be retrofitted with upgraded components, improving overall performance. For example, older conveyors can be fitted with advanced energy-efficient motors, state-of-the-art powder coating booths, or precision curing ovens that align with the latest environmental standards. These upgrades can extend the life of a used system while improving its operational efficiency, making it more suitable for modern production demands. For manufacturers focused on reducing their environmental impact, upgrading a used system to improve energy efficiency or reduce emissions can also support sustainability goals and help meet regulatory requirements.
Maintenance and spare parts availability are critical factors in ensuring that a used powder coating conveyor system continues to operate smoothly. Many used systems are sold with warranties or service agreements, and it’s crucial to ensure that spare parts for the system are still readily available from the manufacturer or third-party suppliers. Some manufacturers may provide ongoing support for older systems, while others may offer dedicated service teams to ensure that components are replaced quickly and efficiently. Establishing a reliable maintenance routine and keeping track of wear and tear on key components, such as conveyor chains, motors, and bearings, can prevent costly breakdowns and extend the system’s lifespan.
For businesses that prioritize flexibility in their operations, used powder coating conveyor systems offer the benefit of scalability. As production volumes increase or the types of products being coated change, a used system can be reconfigured or expanded to meet new requirements. Modular conveyor systems, for example, can be adapted to handle different product sizes, weight capacities, or process stages. Some systems may be designed with adjustable conveyor speeds or conveyor paths that allow for more precise control over the coating process. This level of flexibility enables manufacturers to continue using the system effectively as their production needs evolve over time.
Another consideration when purchasing used powder coating conveyor systems is their ability to meet specific industry requirements, such as compliance with safety standards, environmental regulations, and industry certifications. For example, many industries, particularly those in the automotive and aerospace sectors, require that equipment meet specific safety or environmental performance standards. When purchasing a used system, it’s important to verify that the equipment complies with relevant industry regulations to avoid costly delays or compliance issues. It may also be necessary to assess the system’s ability to handle special coating requirements, such as high-performance coatings or coatings with specific durability or heat resistance.
The quality of the used powder coating conveyor system should always be prioritized. Even though a used system may be more affordable, it is essential that the equipment can still perform reliably over the long term. Evaluating the reputation of the seller, ensuring the system has been well-maintained, and confirming that the system has passed any necessary inspections are important steps in verifying quality. Additionally, many suppliers of used systems offer reconditioning or refurbishing services that ensure the system is in good working order before it is sold. When selecting a supplier, it is beneficial to work with a company that provides clear documentation on the system’s history and any refurbishments or upgrades that have been made.
Finally, while the cost-effectiveness of used powder coating conveyor systems is a significant advantage, businesses must also evaluate the long-term value of the system. Although the initial purchase price may be lower, the system’s total cost of ownership over its lifespan, including maintenance, energy consumption, and potential upgrades, should be considered. The savings on upfront costs should be weighed against factors such as reliability, longevity, and the potential for future growth. A well-maintained used system that has been properly refurbished and upgraded can provide substantial long-term value, but it’s important to ensure that it is capable of meeting future production demands without incurring excessive maintenance costs or operational inefficiencies.
In conclusion, used powder coating conveyor systems present a range of benefits for manufacturers looking to improve their coating processes without the substantial investment required for new equipment. These systems can offer reliable performance, flexibility, and cost savings, making them an attractive option for companies of all sizes. By carefully assessing the condition of the system, verifying compatibility with existing processes, and considering potential upgrades, businesses can maximize the value of their investment and improve the efficiency, quality, and sustainability of their powder coating operations. With the right selection and maintenance, used powder coating conveyor systems can continue to provide high performance and cost-effective solutions for years to come, supporting manufacturers in maintaining competitive advantage in an increasingly demanding market.
As the manufacturing landscape evolves, the role of used powder coating conveyor systems will likely become even more integral to cost-effective production strategies. These systems are particularly valuable in industries that prioritize flexibility, adaptability, and efficiency, and as companies continue to seek ways to optimize their operations, used conveyors provide an attractive solution. With the right modifications and upgrades, these systems can meet the demands of modern production environments, offering a versatile, reliable, and economical alternative to purchasing entirely new equipment.
Looking ahead, one of the most significant factors that could drive further adoption of used powder coating conveyor systems is the growing emphasis on sustainability and environmental responsibility within the manufacturing sector. As global regulations surrounding emissions, energy consumption, and waste disposal continue to tighten, companies will increasingly seek out ways to reduce their environmental footprint. The adoption of used equipment is one such way to reduce the environmental impact associated with manufacturing new products. By extending the lifecycle of conveyor systems and refurbishing existing machinery rather than discarding it, businesses contribute to the circular economy and minimize waste in a way that supports sustainable practices.
Moreover, as energy efficiency becomes a critical concern for industries worldwide, many companies are focusing on retrofitting their used systems with energy-saving technologies. For example, older conveyors may be updated with energy-efficient motors or sensors that optimize power consumption based on real-time demand, reducing both energy use and operating costs. Some systems can also be upgraded to improve the efficiency of powder coating booths, ovens, and curing stations, further enhancing the overall energy efficiency of the production line. By investing in energy-saving solutions, manufacturers can lower their carbon footprint and reduce utility expenses, helping them achieve sustainability goals while improving their bottom line.
In addition to energy efficiency, other technological advancements are likely to continue influencing the design and performance of used powder coating conveyor systems. With the growing integration of smart technologies across industries, the potential for adding IoT (Internet of Things) sensors and smart controls to used systems is significant. These technologies allow for real-time monitoring of conveyor performance, part tracking, and the detection of inefficiencies or issues in the coating process. IoT-connected systems provide operators with valuable insights into production performance, enabling predictive maintenance, proactive troubleshooting, and more precise process control. The integration of these technologies into used conveyor systems offers manufacturers a cost-effective way to achieve the benefits of Industry 4.0 without the need for a complete overhaul of their existing equipment.
Furthermore, as powder coating processes continue to evolve, the demand for more specialized and custom coating applications will increase. Industries such as automotive, aerospace, and electronics often require coatings with very specific properties, such as corrosion resistance, heat resistance, or advanced aesthetic finishes. Used powder coating conveyor systems can be adapted to meet these specific needs by incorporating additional features such as adjustable conveyor speeds, multi-stage curing zones, or special coatings for particular part shapes. By customizing used systems, manufacturers can create versatile, multi-functional lines that meet the evolving demands of their products.
For businesses operating in a competitive market, the ability to reduce downtime is crucial to maximizing productivity. Used powder coating conveyors, when properly maintained and upgraded, can offer reliable performance for extended periods. Regular inspections, routine maintenance, and strategic replacements of key components ensure that the system continues to operate smoothly, reducing the likelihood of unexpected breakdowns and minimizing costly downtime. For companies that rely on consistent throughput to meet customer deadlines, used systems that have been refurbished and properly maintained can provide a dependable solution without the need for frequent repairs.
Another key consideration for manufacturers purchasing used powder coating conveyor systems is the long-term impact on operational efficiency. Over time, a well-maintained conveyor system can become a significant asset to a business by enabling a smooth and streamlined production process. By ensuring that parts are moved consistently and efficiently through the coating process, conveyors reduce the time and effort required to handle products manually. This increases throughput, improves coating uniformity, and decreases labor costs. Additionally, with used systems, businesses may be able to scale production without the need for significant capital investment, allowing them to respond more quickly to market demands.
For companies with tight budgets or those looking to optimize their production lines without major capital expenditures, the option of purchasing a used powder coating conveyor system offers considerable financial benefits. Rather than waiting to accumulate funds for the purchase of new equipment, manufacturers can access a fully functional system at a fraction of the cost. This can be particularly important for small and medium-sized enterprises (SMEs) or startups that need to manage cash flow carefully. By acquiring a used conveyor system, these businesses can improve their operations and stay competitive without incurring the financial burden of purchasing new machinery.
The resale market for used powder coating conveyor systems is also expected to continue expanding as businesses look to sell or upgrade their equipment. Many suppliers of used systems specialize in sourcing high-quality used conveyors from companies that no longer require them. These systems often come with detailed records, maintenance histories, and refurbishing documentation, offering potential buyers reassurance regarding their condition and reliability. The increased availability of high-quality, pre-owned systems will continue to make them an attractive choice for manufacturers looking to expand or modernize their production lines at a lower cost.
Finally, for manufacturers considering the purchase of a used powder coating conveyor system, it’s essential to understand the specific needs of the business and the system’s capabilities. Ensuring that the conveyor is the right fit for the type of products being coated and that it meets the requirements of the production line is key to a successful implementation. Businesses should carefully assess the system’s size, capacity, speed, and compatibility with other equipment in their production line. Working with experienced suppliers and installation professionals can help ensure that the used system is set up correctly and optimized for the company’s needs.
In conclusion, used powder coating conveyor systems offer manufacturers a cost-effective and flexible solution to improve their coating operations. With the right maintenance, upgrades, and adaptations, these systems can provide long-term value, efficiency, and productivity gains. By investing in used equipment, businesses can enhance their competitiveness, reduce operating costs, and achieve sustainability goals, all while improving the quality and consistency of their powder coating processes. As the market for used systems continues to grow, manufacturers will have increasing opportunities to access high-quality, affordable equipment that meets their unique production needs, further solidifying the role of used powder coating conveyor systems as a key component of modern manufacturing operations.
Not only do we manufacture our powder coating equipment, we also ship them worldwide to your facility with care
We’re not just the manufacturers of your powder coating equipment, we’re also your worldwide delivery partners.
At EMS Powder Coating Equipment, we understand that getting your powder coating equipment to you quickly and safely is just as important as manufacturing it to the highest standards. That’s why we offer worldwide delivery services to all of our customers.
We work with a network of experienced and reliable shipping partners to ensure that your equipment arrives on time and in perfect condition. We also offer a variety of shipping options to fit your budget and needs.
Whether you need your equipment shipped to a local address or to an international destination, we can help. We’ll work with you to choose the best shipping option for your needs and to keep you updated on the status of your shipment every step of the way.
So when you choose EMS for your powder coating equipment, you’re not just getting the best products on the market, you’re also getting the best possible delivery experience.
Contact us today to learn more about our worldwide delivery services.
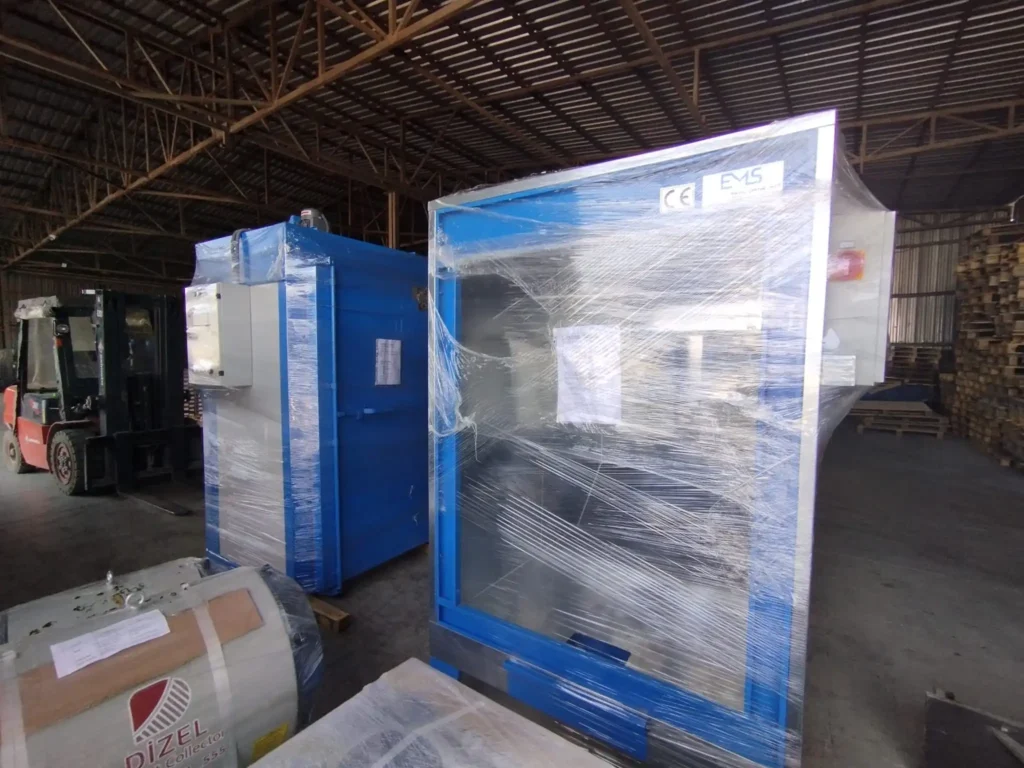
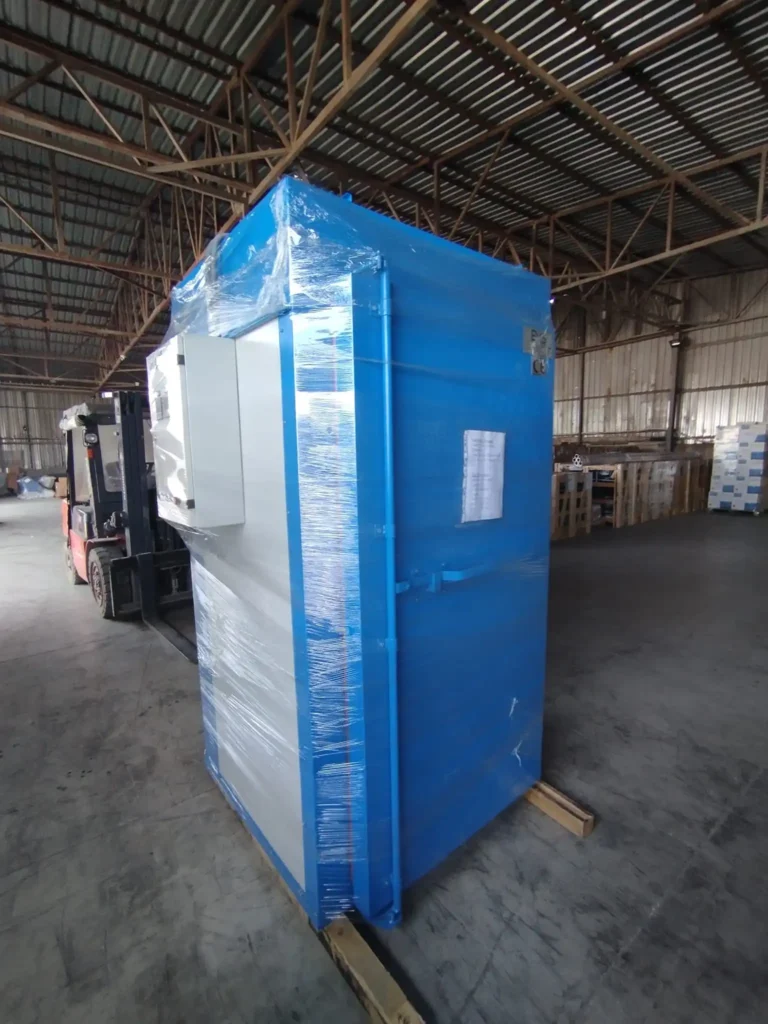
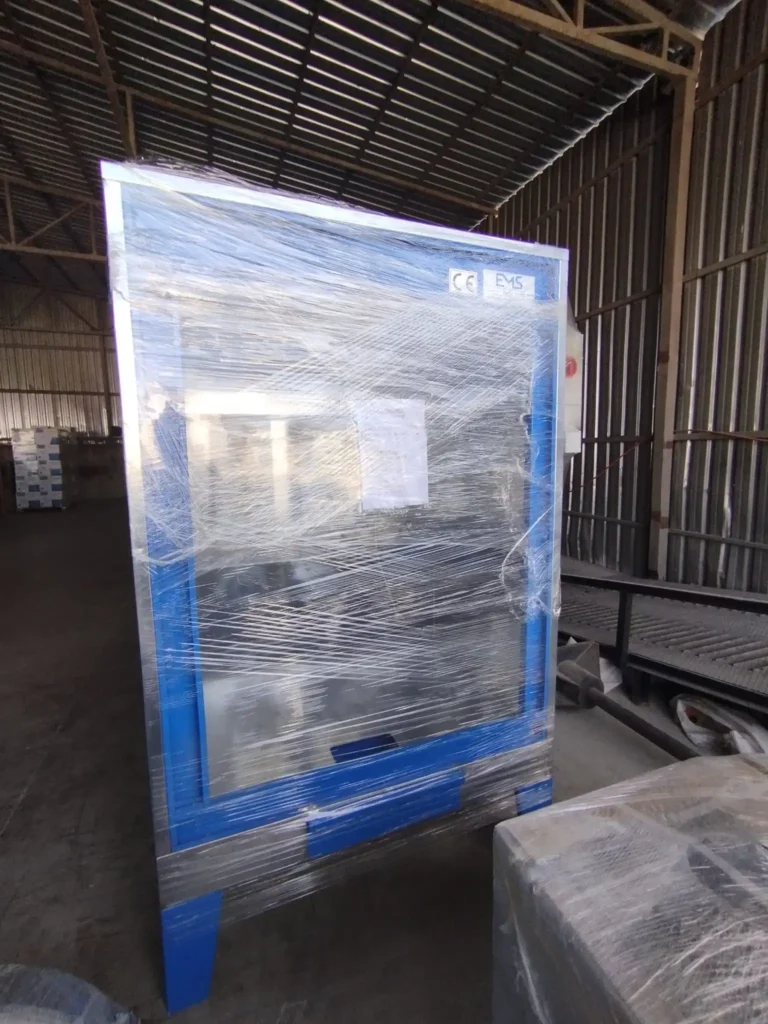
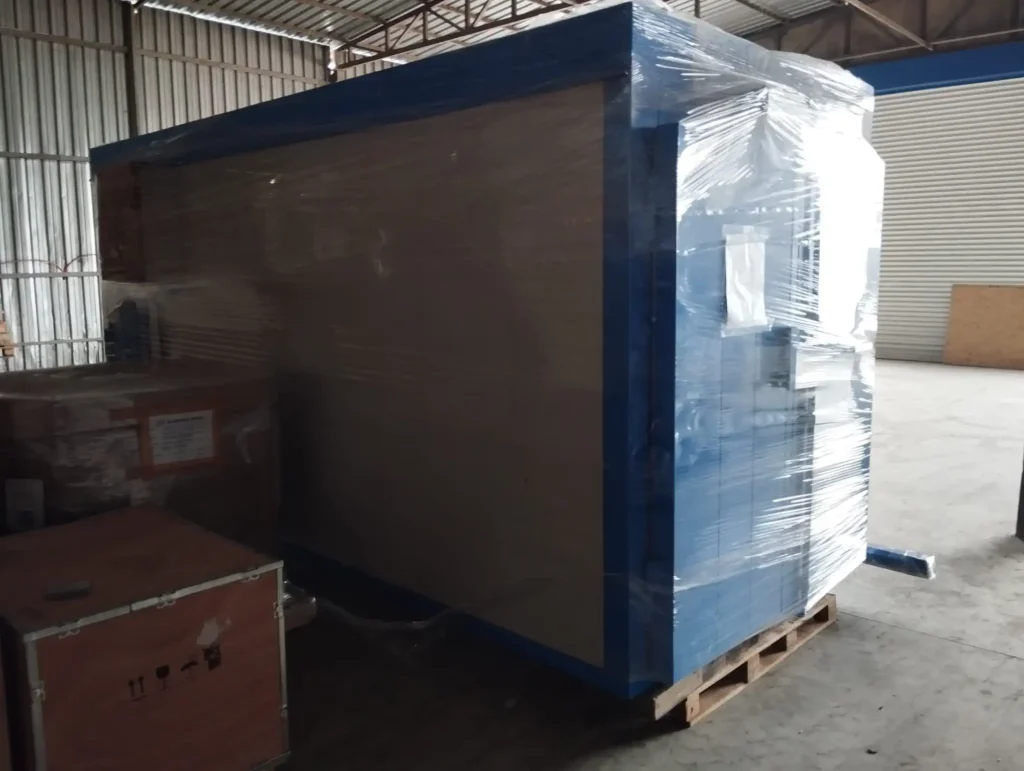
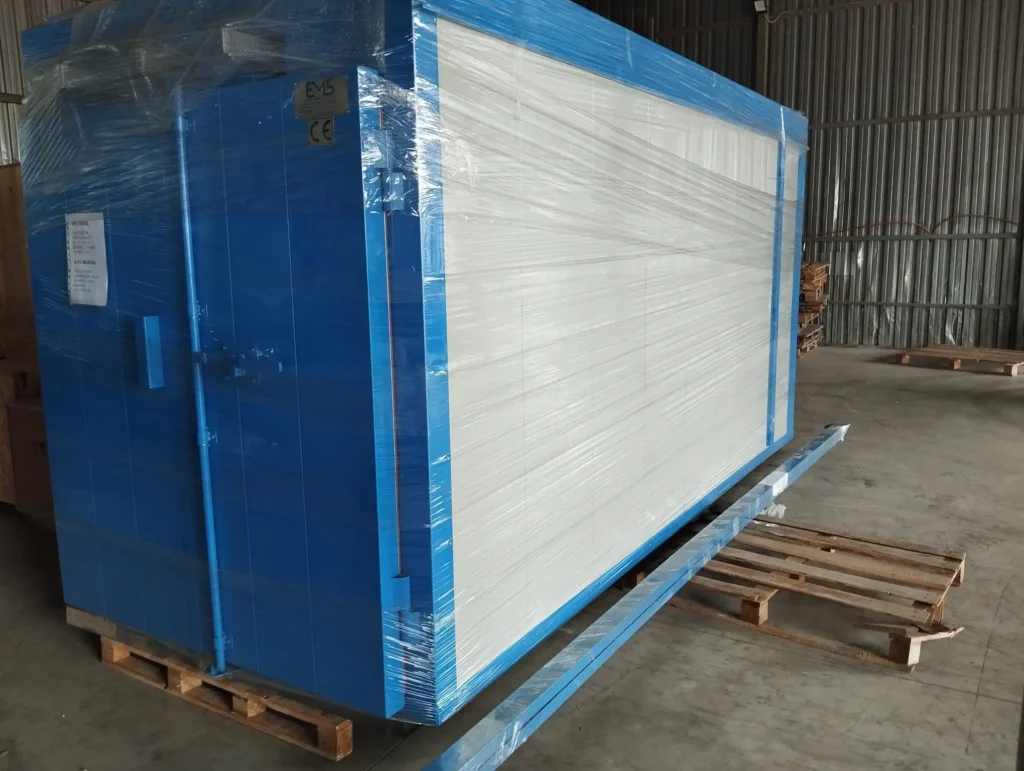
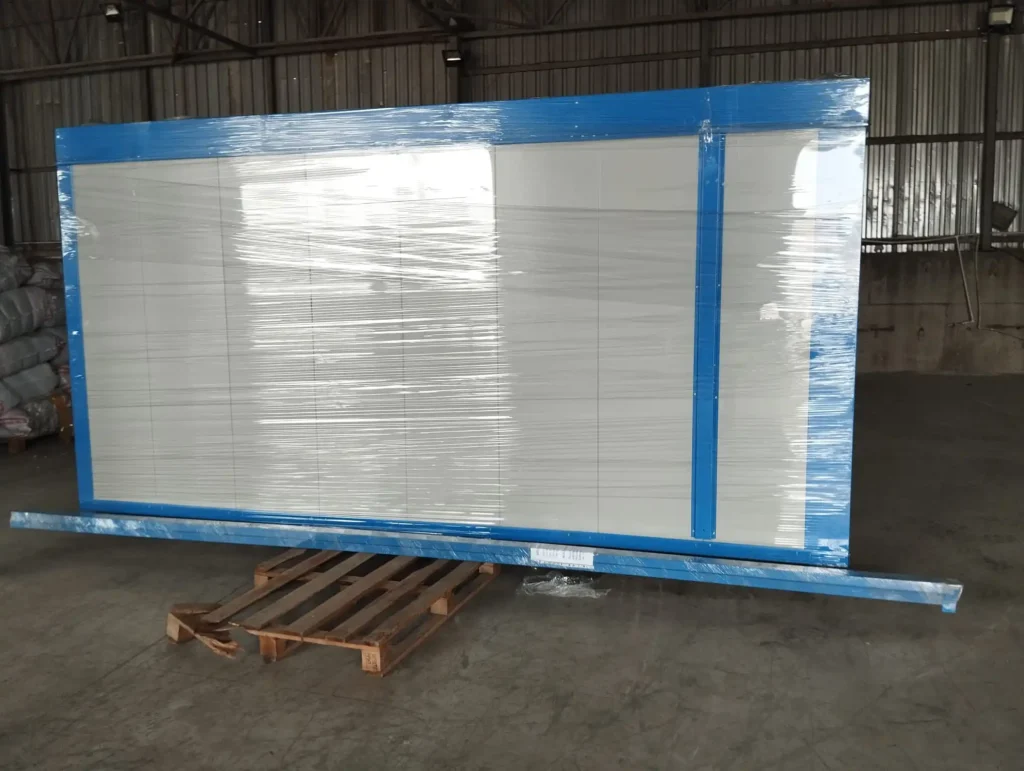
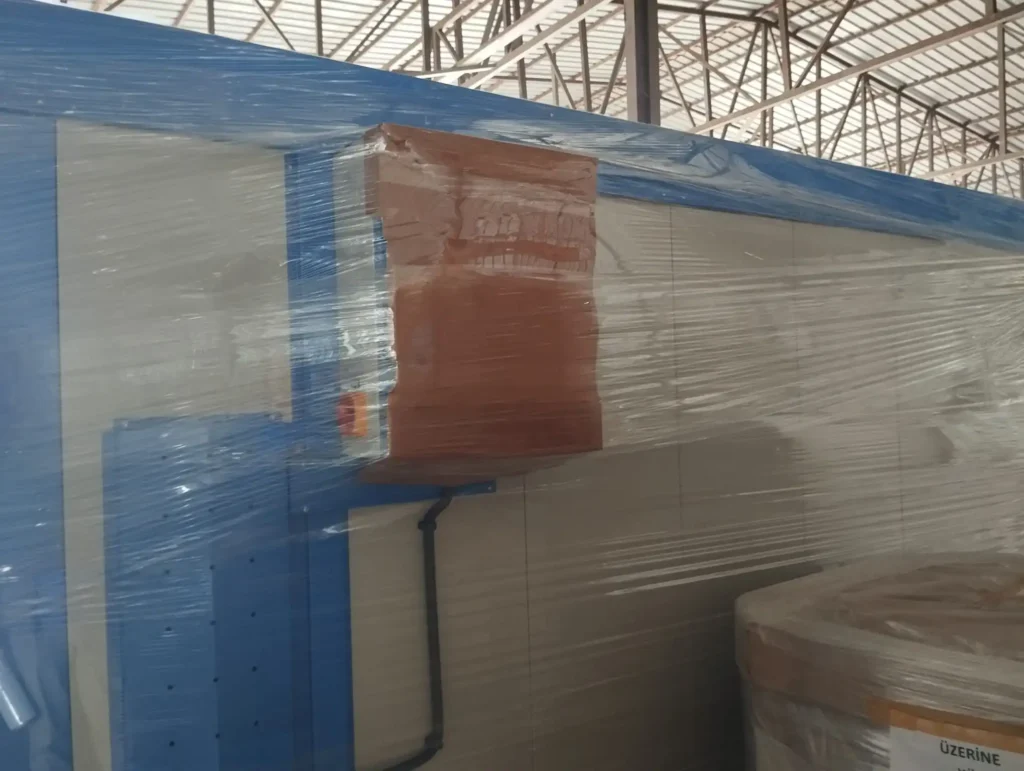
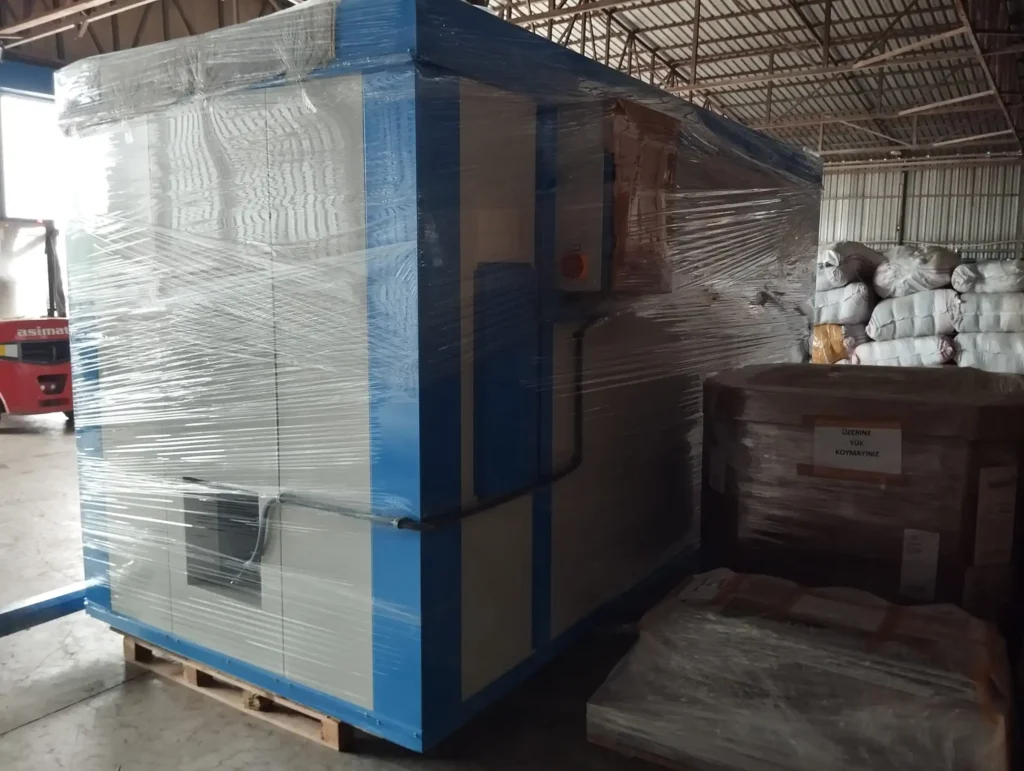
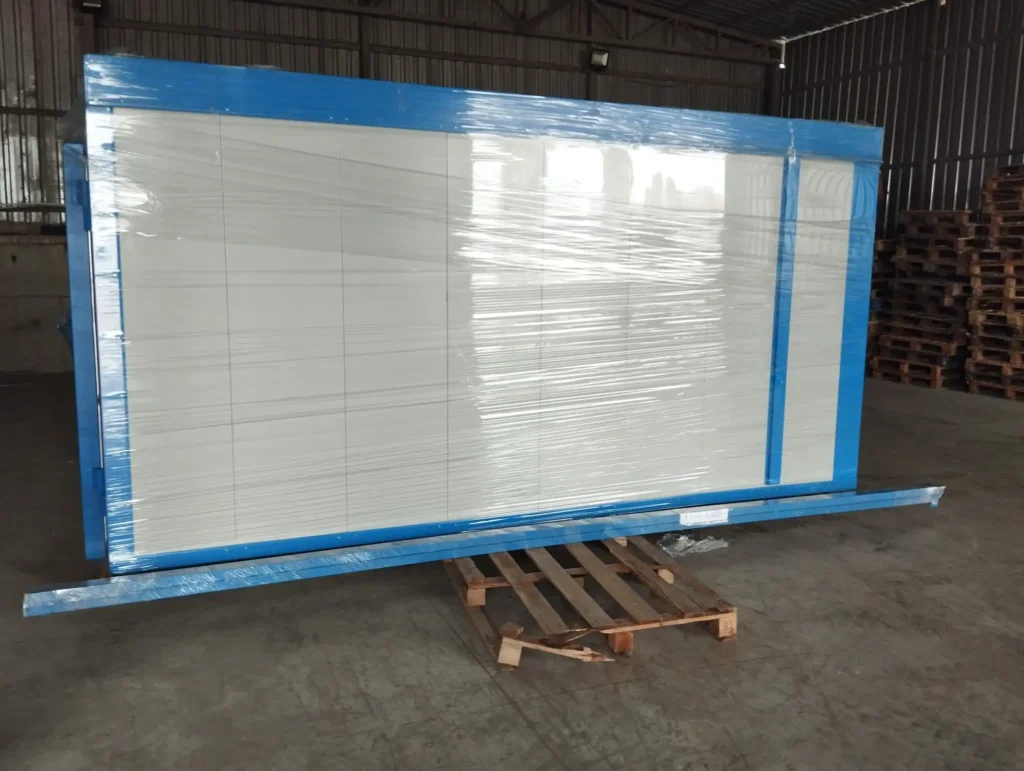