
We manufacture the Tribo Powder Coating Gun for the powder coating industry. The Tribo Powder Coating Gun has no cascade to charge the powder coating powder.
EMS Powder Coating Gun
- Powder Feed Hopper: The gun houses a hopper that stores the powdered coating material.
- Powder Injection System: Inside the hopper, a mechanism agitates and feeds the powder towards the application nozzle. This can be achieved with air pressure or a mechanical auger system.
- Electrostatic Charging: The powder particles receive an electrical charge as they pass through a corona electrode within the gun. This charge can be positive or negative depending on the gun’s design and the type of powder being used.
- Powder Delivery Nozzle: The charged powder particles travel through a nozzle towards the grounded target object. The nozzle design helps shape and direct the powder spray for optimal coverage.
- Air Assist: Compressed air is often used in conjunction with the powder flow to help break up clumps, improve atomization (separation of particles), and ensure proper application onto the surface.
Types of Powder Coating Guns:
There are two main types of powder coating guns:
- Tribo Gun: This type uses friction to electrically charge the powder particles as they rub against the interior walls of the gun. Tribo guns are generally simpler and less expensive, but they may not offer the same level of control and efficiency compared to the other type.
- Electrostatic Gun: This type utilizes a dedicated electrode within the gun to directly charge the powder particles. Electrostatic guns provide more precise control over the charging process, leading to a more consistent and uniform finish.
Choosing the Right Powder Coating Gun:
The selection of a powder coating gun depends on several factors, including:
- Application size and complexity: Larger projects or those requiring high precision might benefit from a high-end electrostatic gun.
- Production volume: For high-volume operations, a robust and efficient gun is essential.
- Powder type: Different powder formulations may have specific compatibility requirements with the gun’s charging mechanism.
- Budget: Powder coating guns range in price from basic models for hobbyists to advanced industrial systems.
By understanding the function and types of powder coating guns, you can make an informed decision when choosing the right tool for your specific needs.sharemore_vert
Powder Feed Hopper
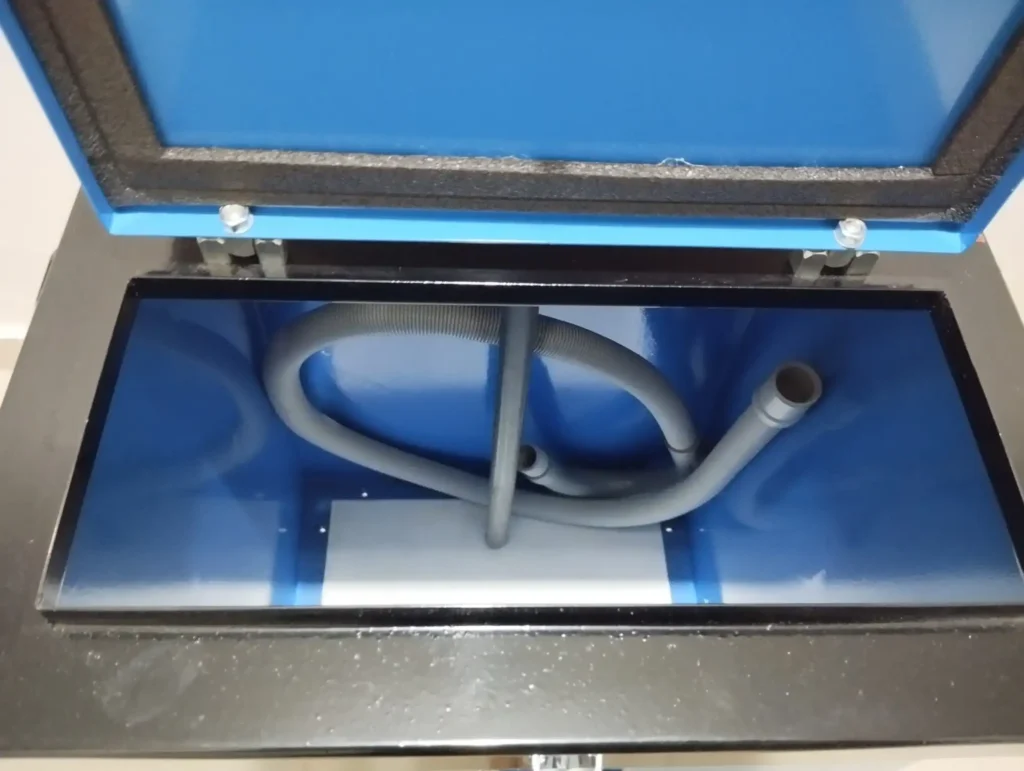
The powder feed hopper is a crucial component of a powder coating gun, acting as the reservoir for the powdered coating material. It ensures a steady and controlled flow of powder towards the application nozzle. Here’s a closer look at its key features and functions:
- Design:
- Typically made of stainless steel for durability and ease of cleaning.
- Often cylindrical or conical in shape to promote smooth powder flow towards the bottom.
- May have a transparent window for monitoring powder level.
- Capacity:
- Varies depending on the gun and application needs.
- Larger hoppers allow for longer operation times between refills.
- Powder Agitation:
- A mechanism within the hopper keeps the powder fluidized. This prevents caking and ensures a consistent flow.
- Air Fluidization: Compressed air is introduced from the bottom of the hopper through a porous membrane. The air bubbles up through the powder, keeping the particles suspended and mobile.
- Mechanical Agitation: In some cases, a rotating paddle or auger system mixes the powder to prevent settling and promote flow.
- A mechanism within the hopper keeps the powder fluidized. This prevents caking and ensures a consistent flow.
- Powder Feed Control:
- A valve or other mechanism regulates the amount of powder entering the delivery system.
- This allows for adjustments to the powder flow rate, which ultimately affects the coating thickness.
Benefits of a Powder Feed Hopper:
- Consistent Powder Flow: Proper agitation prevents clumping and ensures a smooth, even delivery of powder to the nozzle.
- Application Control: The ability to adjust the powder flow rate allows for precise control over the coating thickness.
- Efficiency: Minimizes downtime by allowing for extended operation before needing refilling.
- Powder Protection: The enclosed design protects the powder from contamination and moisture absorption.
Additional Points:
- Some powder coating systems utilize pressurized hoppers. These hoppers rely on compressed air to not only fluidize the powder but also propel it towards the gun.
- For small jobs or hobbyist applications, mini hoppers may be available that attach directly to the gun.
By understanding the function and importance of the powder feed hopper, you can appreciate its role in achieving a successful and efficient powder coating process.s
Powder Injection System
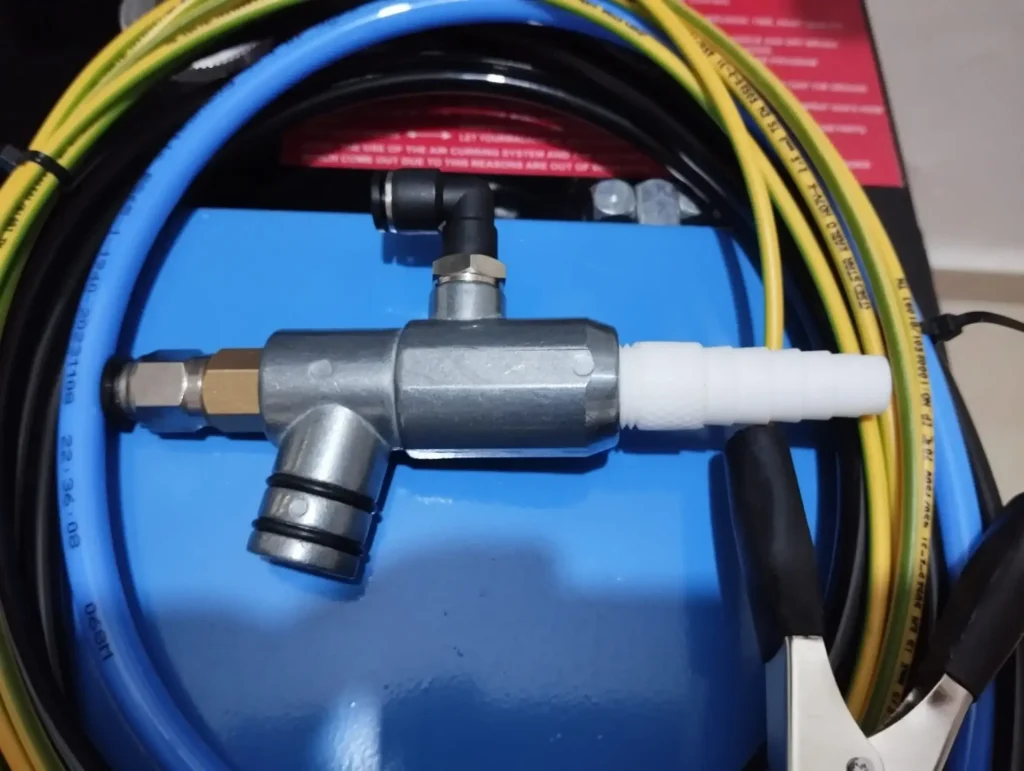
The powder injection system in a powder coating gun plays a critical role in delivering a steady and controlled flow of charged powder particles towards the application nozzle. Here’s a breakdown of its components and operation:
Components:
- Powder Pickup: This can be a simple opening at the bottom of the hopper or a dedicated mechanism like a venturi injector.
- Venturi Injector (if used): This utilizes the Bernoulli principle, where a high-velocity airflow creates a low-pressure zone. This low pressure draws powder from the hopper into the airflow.
- Delivery System: This system transports the powder from the pickup point towards the nozzle. It can be:
- Air-fed: Compressed air is used to convey the powder through the system. The air pressure needs to be carefully controlled to ensure proper powder movement without causing excessive turbulence or damage to the particles.
- Auger-fed: A mechanical auger screw continuously moves the powder from the hopper towards the nozzle. This method offers more precise control over the powder flow rate compared to air-fed systems.
Charging Mechanism:
- Regardless of the delivery system type (air or auger), the powder typically encounters a charging mechanism before reaching the nozzle.
- Tribo Gun: In this type, the powder particles receive an electrical charge through friction as they rub against the walls of the delivery system or dedicated charging elements.
- Electrostatic Gun: A dedicated electrode, often a high-voltage corona electrode, is present within the system. This electrode ionizes the surrounding air, creating charged ions that collide with the powder particles and transfer their charge.
Benefits of a Powder Injection System:
- Controlled Flow: The system ensures a consistent and adjustable flow of powder, allowing for precise control over the coating thickness.
- Efficient Powder Delivery: Minimizes powder waste and optimizes the coating process.
- Charging Integration: Seamlessly integrates the powder charging process within the delivery system.
- Compatibility: Different types of injection systems cater to various powder types and application needs (air-fed for simpler setups, auger-fed for more precise control).
Additional Points:
- The design and complexity of the powder injection system vary depending on the gun type (Tribo vs. Electrostatic).
- Some systems may incorporate additional features like flow rate adjusters or powder level sensors.
By understanding the function of the powder injection system, you can appreciate its role in achieving a consistent, efficient, and well-controlled powder coating application.
Electrostatic Charging

In powder coating, electrostatic charging is the magic ingredient that makes the whole process work. It transforms the dry powder particles into tiny, attracted magnets, ensuring they efficiently coat the target object. Here’s a deeper dive into this fascinating process:
The Science Behind It:
Electrostatic charging relies on the fundamental principle of opposite charges attracting. The process involves giving the powder particles an electrical charge, either positive or negative depending on the gun and powder type.
Two Main Charging Methods:
- Tribo Charging (Friction Charging): This method utilizes friction to impart a charge on the powder particles. As the powder flows through the gun, it rubs against the interior walls or dedicated charging elements. This friction transfers electrons between the powder and the contact surfaces, resulting in charged particles.
- Advantages: Simpler design, generally less expensive guns.
- Disadvantages: Less control over the charging process, can lead to inconsistencies in the final coating.
- Corona Charging: This method utilizes a high-voltage corona electrode within the gun. This electrode ionizes the surrounding air, creating charged ions (positive or negative depending on the polarity). These ions then collide with the powder particles, transferring their charge.
- Advantages: More precise control over the charging process, leading to a more consistent and uniform finish.
- Disadvantages: Generally more complex and expensive guns compared to Tribo systems.
Benefits of Electrostatic Charging:
- Enhanced Coating Efficiency: Charged particles are attracted to the grounded object, significantly improving the transfer rate and reducing powder waste.
- Uniform Coverage: The electrostatic forces help distribute the powder particles more evenly, resulting in a smooth and consistent finish.
- Reduced Overspray: By attracting the powder to the target object, electrostatic charging minimizes the amount of powder lost as overspray, improving environmental efficiency.
- Penetration into Recessed Areas: The electrostatic attraction helps the charged powder particles reach and coat even recessed areas on the object.
Additional Points:
- The strength of the electrical charge plays a crucial role. Too weak, and the particles won’t adhere well. Too strong, and they can repel each other, impacting coating quality.
- Modern powder coating guns often allow for adjustments to the charging parameters for optimal results with different powder types and applications.
By understanding the principles of electrostatic charging, you can appreciate its vital role in achieving a high-quality, efficient, and environmentally friendly powder coating process.
Powder Delivery Nozzle
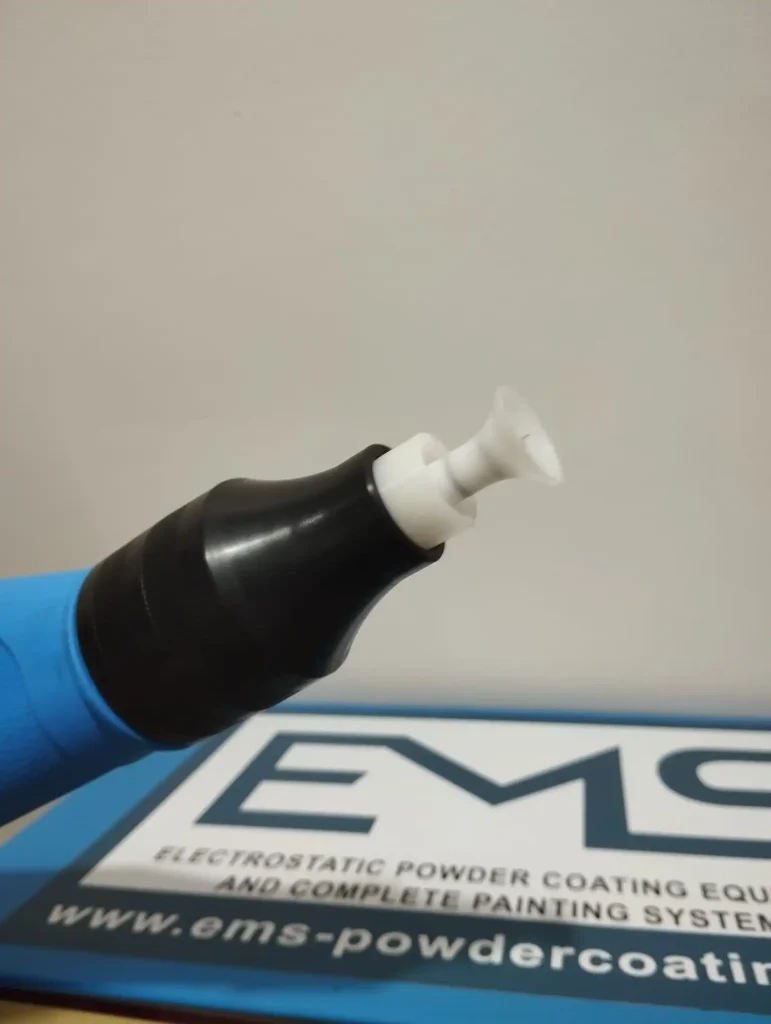
The powder delivery nozzle in a powder coating gun acts as the final frontier for the powder particles before they land on the target object. It plays a critical role in shaping the powder spray pattern and ensuring optimal application for a smooth, even finish.
Design and Functionality:
- Typically made of a durable and lightweight material like aluminum or stainless steel.
- May have a simple round opening or a more complex design with internal shaping to achieve specific spray patterns (flat fan, round, angled).
- Often features an orifice (opening) size that can be adjusted to control the powder flow rate at the nozzle exit.
Types of Powder Delivery Nozzles:
- Standard Round Nozzle: Offers a basic, circular spray pattern suitable for general applications.
- Flat Fan Nozzle: Creates a wide, flat fan-shaped spray pattern, ideal for covering large flat surfaces. May come in different fan angles to suit specific needs.
- Angled Nozzle: Designed to deliver the powder at an angle, useful for reaching recessed areas or coating complex shapes.
- Specialty Nozzles: Some manufacturers offer specialized nozzles with unique shapes or features for specific applications, like coating pipes or internal surfaces.
Factors Affecting Nozzle Selection:
- Desired Spray Pattern: The type of object being coated will dictate the most suitable spray pattern (round, flat, angled).
- Application Complexity: For complex shapes, angled nozzles or nozzles with specialized designs might be necessary.
- Powder Flow Rate: The nozzle orifice size should be compatible with the desired powder flow rate for optimal application efficiency.
- Environmental Considerations: In settings with limited ventilation, a more focused spray pattern might be preferred to minimize overspray.
Benefits of a Well-Chosen Powder Delivery Nozzle:
- Uniform Coating: The right nozzle helps achieve a smooth, even distribution of powder across the target surface.
- Application Efficiency: Optimized spray patterns minimize powder waste and improve coating coverage.
- Reduced Overspray: Focused nozzles help direct the powder towards the object, reducing the amount of overspray lost to the environment.
- Versatility: A range of nozzle options allows for adapting the gun to different coating tasks.
Additional Points:
- Some powder coating guns offer quick-change nozzle systems for easy swapping between different spray patterns.
- Proper cleaning and maintenance of the nozzle are crucial to prevent clogging and ensure consistent performance.
By understanding the function and importance of the powder delivery nozzle, you can select the right one for your specific application and achieve professional-looking powder coating results.
Powder coating is increasingly accepted as the preferred finishing process for many applications. Increasingly stringent environmental regulations, rising costs in all areas, and demands by consumers for better quality and more durable products are among the challenges facing today’s finishers. Powder coatings provide a solution to these challenges and others. Powder coating is the technique of applying dry paint to the component.
The powdered paint is normally applied by using a powder feed system and gun to electrostatically charge and spray the powder onto the part. For some applications, the part being coated is dipped into a fluidized bed of powder. The coated part is then heated in an oven, or via infrared panels, to melt and cure the paint. During the curing process, a chemical cross-linking reaction is triggered and it is this chemical reaction that gives the powder coatings many of their desirable properties.
Not only do we manufacture our powder coating equipment, we also ship them worldwide to your facility with care
We’re not just the manufacturers of your powder coating equipment, we’re also your worldwide delivery partners.
At EMS Powder Coating Equipment, we understand that getting your powder coating equipment to you quickly and safely is just as important as manufacturing it to the highest standards. That’s why we offer worldwide delivery services to all of our customers.
We work with a network of experienced and reliable shipping partners to ensure that your equipment arrives on time and in perfect condition. We also offer a variety of shipping options to fit your budget and needs.
Whether you need your equipment shipped to a local address or to an international destination, we can help. We’ll work with you to choose the best shipping option for your needs and to keep you updated on the status of your shipment every step of the way.
So when you choose EMS for your powder coating equipment, you’re not just getting the best products on the market, you’re also getting the best possible delivery experience.
Contact us today to learn more about our worldwide delivery services.
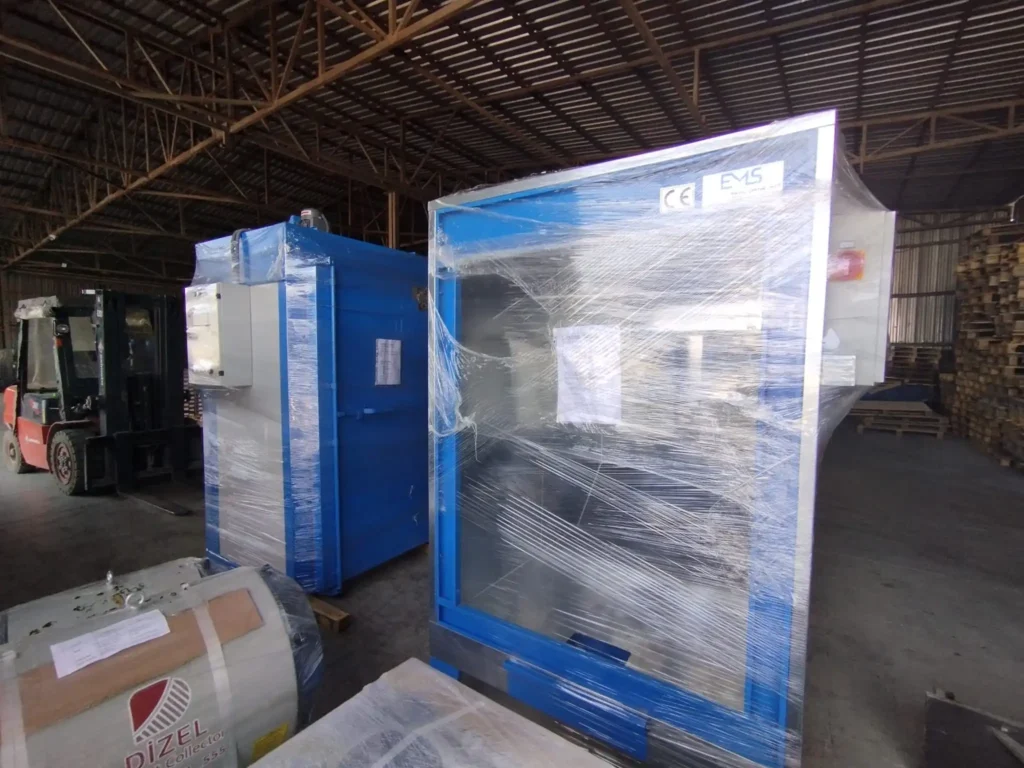
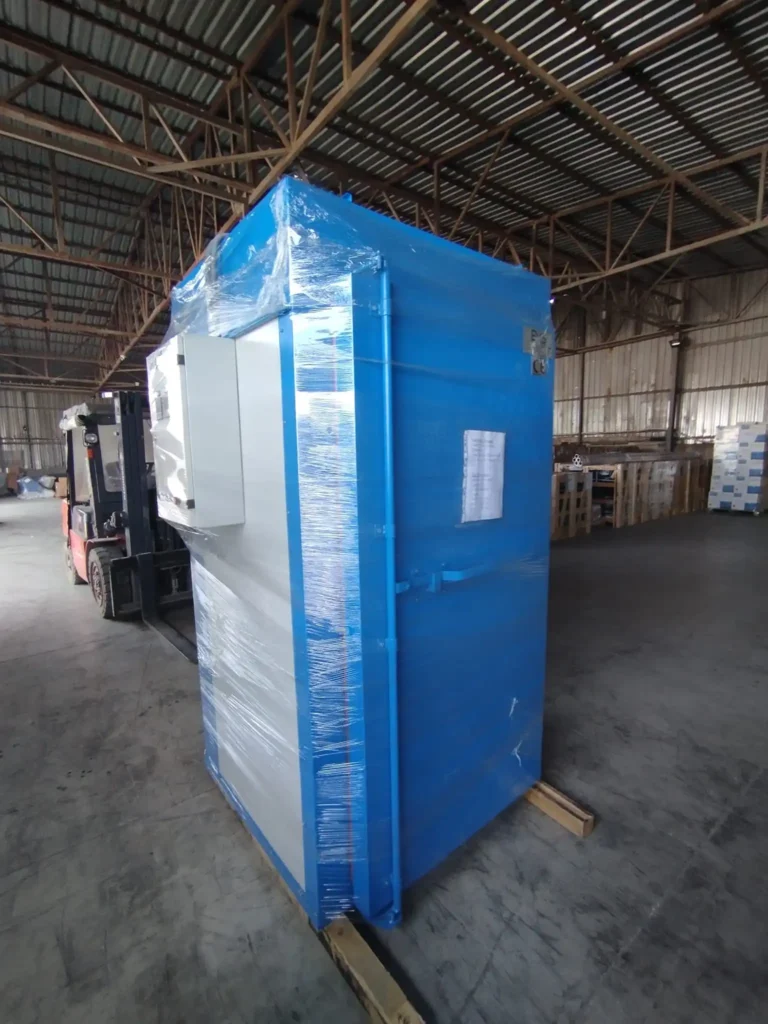
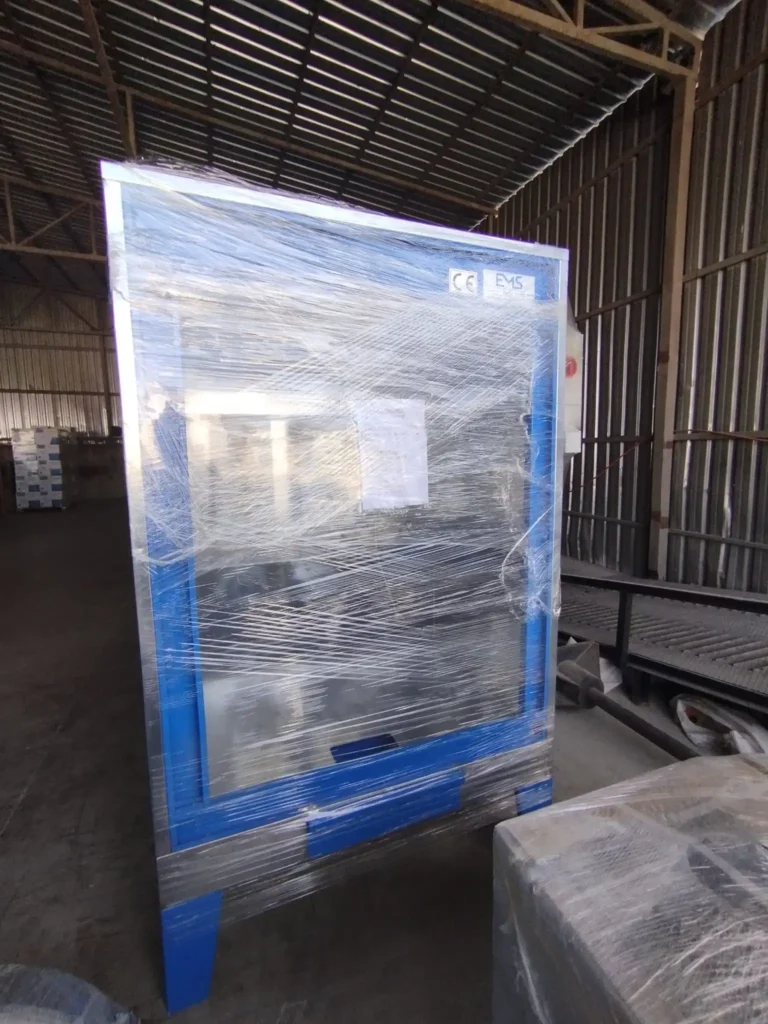
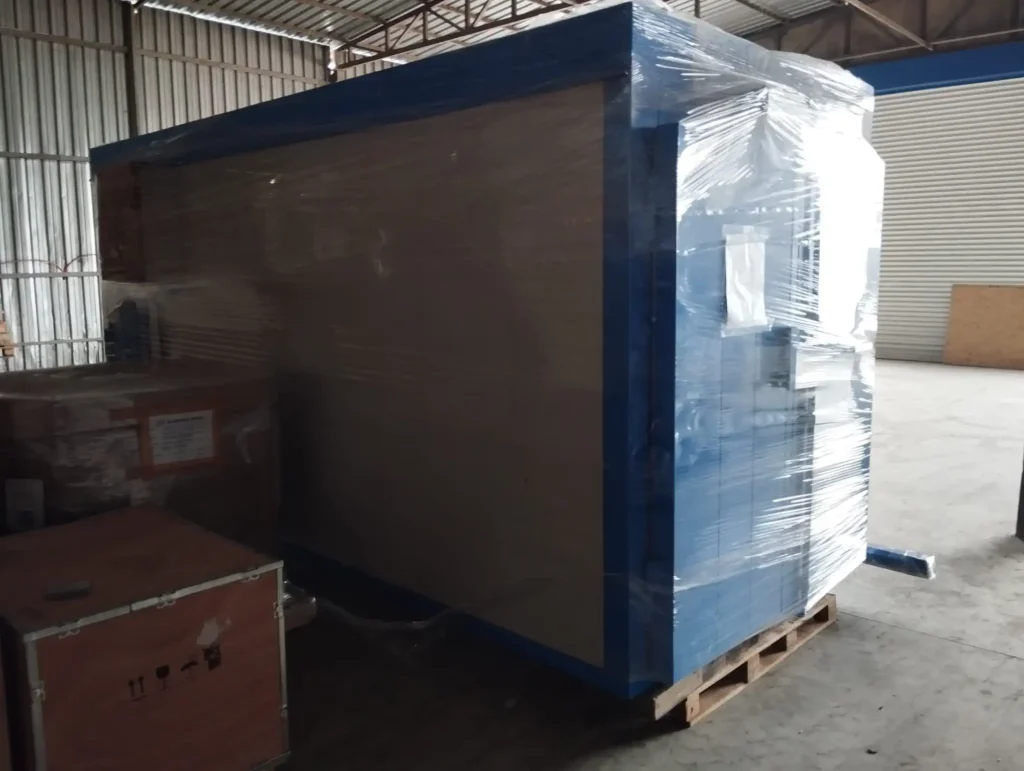
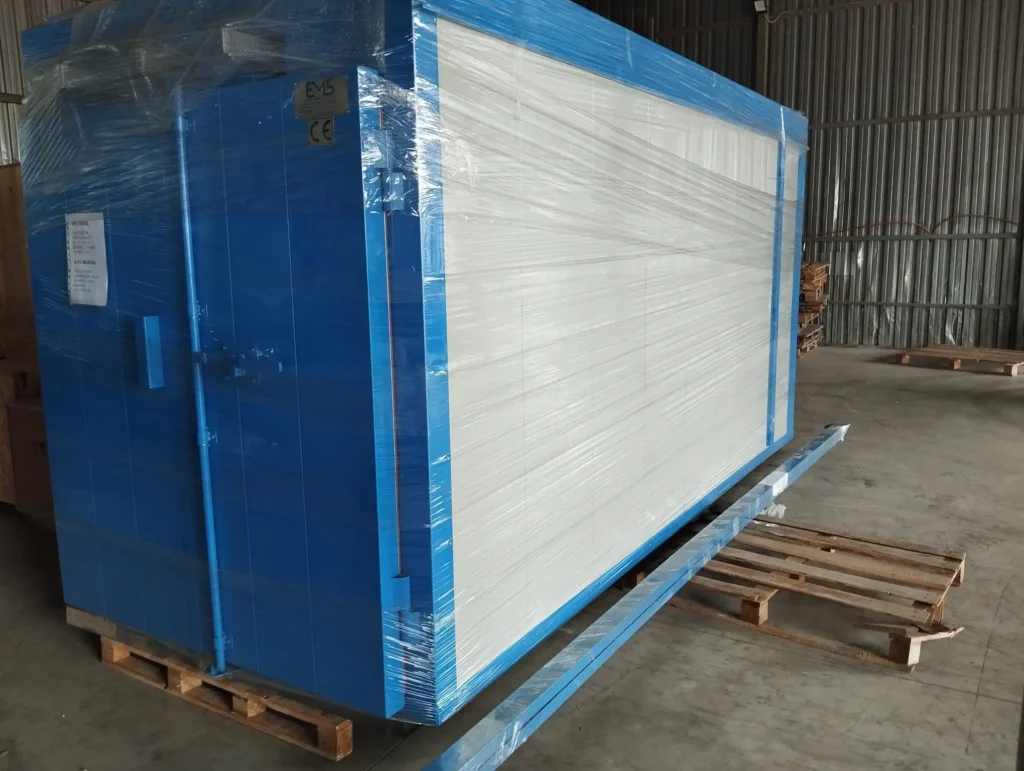
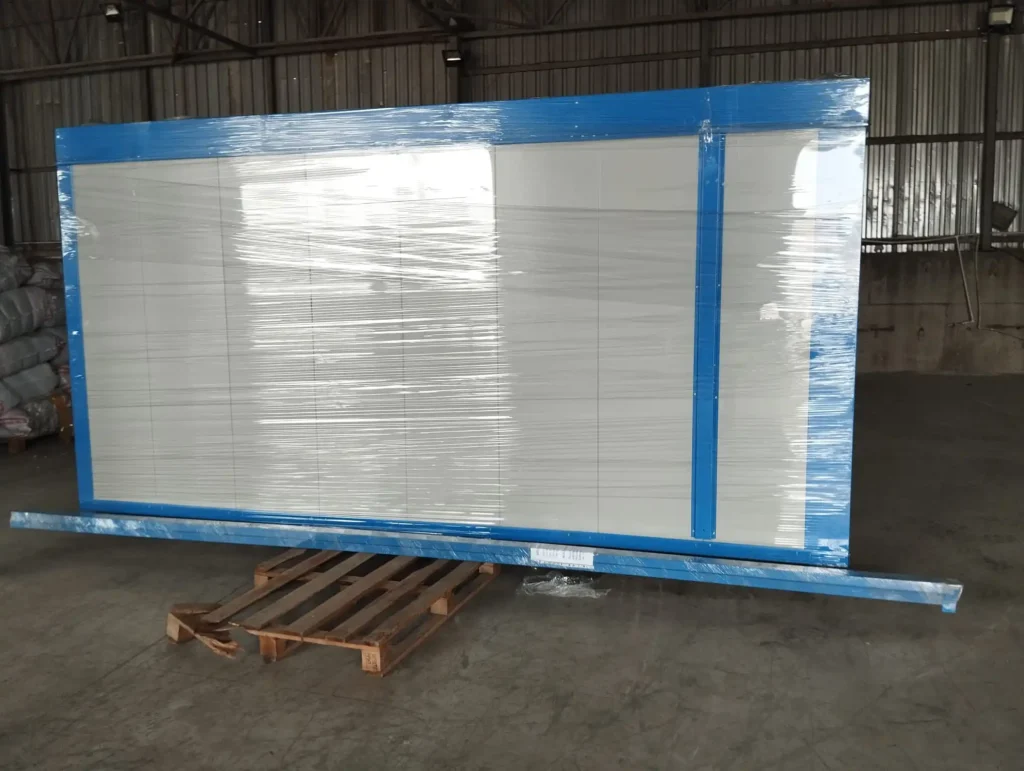
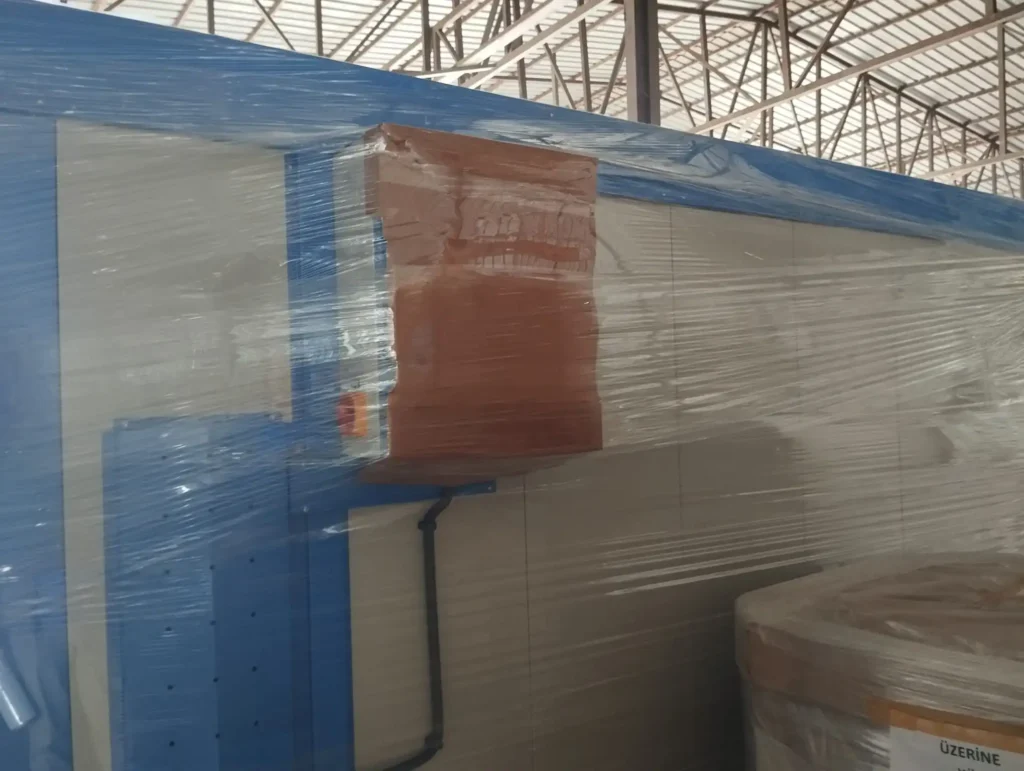
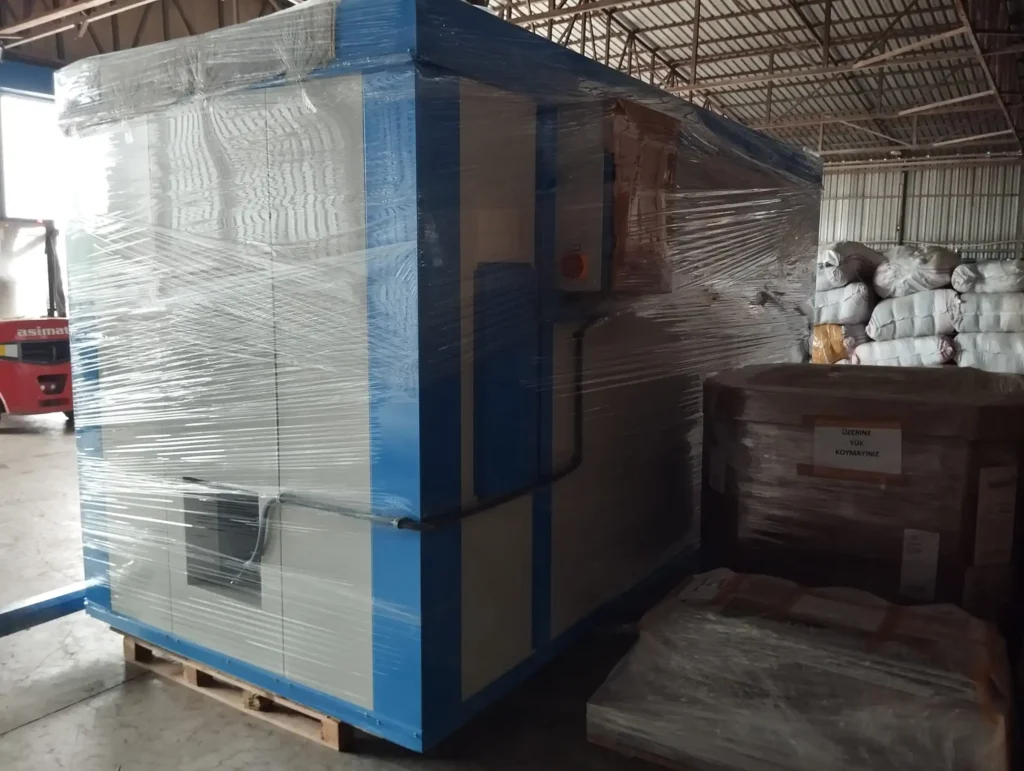
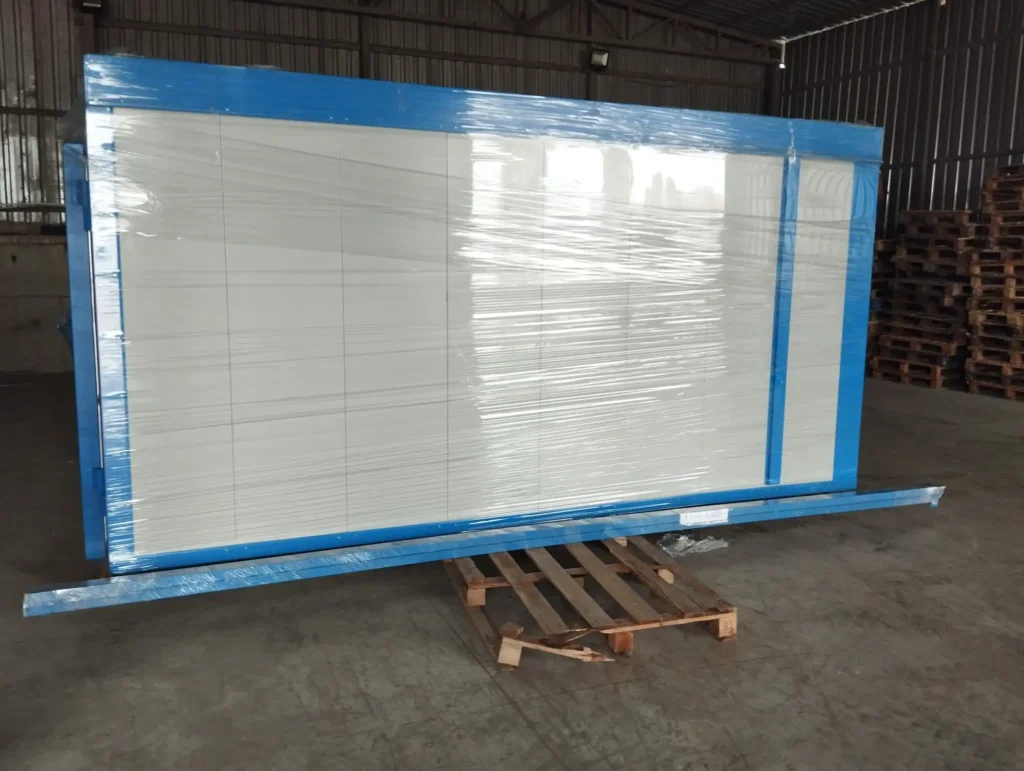
A tribo powder coating gun is a type of powder coating gun that uses friction to charge powder particles. This is in contrast to corona powder coating guns, which use electricity to charge the powder particles.
How Tribo Powder Coating Guns Work
Tribo powder coating guns work by rubbing the powder particles against a surface, such as a Teflon or ceramic tube. This friction creates a static charge on the powder particles, which causes them to be attracted to the surface being coated.
Advantages of Tribo Powder Coating Guns
There are several advantages to using tribo powder coating guns, including:
- No need for electricity: Tribo powder coating guns do not require electricity to operate, which can be a safety advantage in certain environments.
- Less susceptible to Faraday cage effects: Tribo powder coating guns are less susceptible to Faraday cage effects, which can occur when the surface being coated is surrounded by metal.
- Can be used with a wider range of powders: Tribo powder coating guns can be used with a wider range of powders than corona powder coating guns.
Disadvantages of Tribo Powder Coating Guns
There are also some disadvantages to using tribo powder coating guns, including:
- Lower transfer efficiency: Tribo powder coating guns typically have a lower transfer efficiency than corona powder coating guns. This means that more powder is wasted.
- Not as suitable for complex shapes: Tribo powder coating guns are not as suitable for coating complex shapes as corona powder coating guns.
Applications of Tribo Powder Coating Guns
Tribo powder coating guns are a good choice for a variety of applications, including:
- Coating metal parts: Tribo powder coating guns are often used to coat metal parts, such as automotive parts, appliances, and machinery.
- Coating wood furniture: Tribo powder coating guns can also be used to coat wood furniture.
- Coating plastic parts: Tribo powder coating guns can be used to coat plastic parts, but they are not as well-suited for this application as corona powder coating guns.
Overall, tribo powder coating guns are a versatile and effective way to apply powder coatings. They are a good choice for a variety of applications, and they offer several advantages over corona powder coating guns.
Here are some additional tips for using a tribo powder coating gun:
- Use the correct air pressure: The air pressure should be adjusted according to the type of powder being used.
- Hold the gun at the correct distance from the surface: The gun should be held at a distance of 6-8 inches from the surface.
- Move the gun back and forth slowly: The gun should be moved back and forth slowly to ensure even coverage.
By following these tips, you can help to ensure that your tribo powder coating gun is operating properly and delivering consistent results.
The tribo process utilizes charging through friction. We know that when 2 plastic foils are pulled apart, they mutually attract each other again. Both separating surfaces have charged themselves with an opposite polarity electrical charge, which after separation attract each other again. Tribo charging uses this phenomenon, only that the charge is drawn off.
The powder particles are brought into contact with another plastic material and immediately separated again. This process can take place in a tube, hose or on a plate. Ideally, it should take place at a high air velocity because turbulence is created in the tube, which increases the number of contacts.
Tribo Powder Coating Gun
A tribo powder coating gun is a type of powder coating gun that utilizes tribocharging to apply powder coating to workpieces. Unlike traditional electrostatic powder coating guns, which rely on an electrostatic field to attract powder particles to the grounded workpiece, tribo guns use friction between the powder particles and the gun’s nozzle to induce a charge on the particles. This tribocharging technique has several advantages over electrostatic charging, including:
- Reduced Overspray: Triboguns produce less overspray than electrostatic guns because the powder particles are not attracted to the gun’s nozzle as strongly. This can lead to significant cost savings in powder consumption and reduced airborne powder contamination.
- Better Coating Coverage: Triboguns can produce more uniform coating coverage than electrostatic guns because the tribocharging process does not depend on the workpiece’s surface conductivity. This is beneficial for coating intricate or complex shapes.
- Improved Workpiece Finish: Triboguns can produce a smoother and more even finish than electrostatic guns because the tribocharging process does not create as much electrostatic attraction between the powder particles. This can be especially beneficial for applications where a high-quality cosmetic finish is required.
- Increased Powder Flow Rate: Triboguns can operate at higher powder flow rates than electrostatic guns because the powder particles are not as strongly attracted to the gun’s nozzle. This can lead to increased production rates and reduced cycle times.
- Versatility with Different Powders: Triboguns can be used with a wider range of powder types than electrostatic guns, including some that are not compatible with electrostatic charging. This can expand the range of applications for powder coating.
In addition to these advantages, tribo powder coating guns are also simpler to operate and maintain than electrostatic guns. They do not require as much fine-tuning and are less sensitive to changes in humidity or temperature.
Comparison of Tribo and Electrostatic Powder Coating Guns
Feature | Tribo Powder Coating Gun | Electrostatic Powder Coating Gun |
---|---|---|
Charging Mechanism | Tribocharging | Electrostatic charging |
Overspray | Less | More |
Coating Coverage | Better | Less consistent |
Workpiece Finish | Smoother, more even | Less consistent |
Powder Flow Rate | Higher | Lower |
Powder Compatibility | Wider range | Narrower range |
Operation | Simpler | More complex |
Maintenance | Easier | More difficult |
Applications of Tribo Powder Coating Guns
Tribo powder coating guns are used in a wide variety of applications, including:
- Automotive: Coating car bodies, exterior trim, interior components, and wheels
- Electronics: Coating enclosures, casings, and components for electronic devices
- Appliance: Coating refrigerators, stoves, dishwashers, and washing machines
- Furniture: Coating metal and plastic furniture components
- Industrial: Coating machinery parts, tools, pipes, and other industrial components
- Aerospace: Coating aircraft components for corrosion protection and aesthetic enhancement
- Medical Equipment: Coating medical devices for durability, biocompatibility, and aesthetic appeal
The Principle of the Tribo Powder Coating Gun

Powder coating is increasingly accepted as the preferred finishing process for many applications. Increasingly stringent environmental regulations, rising costs in all areas, and demands by consumers for better quality and more durable products are among the challenges facing today’s finishers. Powder coatings provide a solution to these challenges and others. Powder coating is the technique of applying dry paint to the component.
The powdered paint is normally applied by using a powder feed system and gun to electrostatically charge and spray the powder onto the part. For some applications, the part being coated is dipped into a fluidized bed of powder. The coated part is then heated in an oven, or via infrared panels, to melt and cure the paint. During the curing process, a chemical cross-linking reaction is triggered and it is this chemical reaction that gives the powder coatings many of their desirable properties.
Difference between a Corona and a Tribo Gun
Both corona and tribo powder coating guns are used to apply powder coatings to surfaces. However, they differ in the way they charge the powder particles.
Corona guns use electricity to charge the powder particles. An electrode inside the gun generates a high-voltage corona discharge, which ionizes the air around it. These ions then attach to the powder particles, giving them a positive charge. The positively charged powder particles are then attracted to the grounded surface being coated.
Tribo guns use friction to charge the powder particles. The powder particles are rubbed against a surface, such as a Teflon or ceramic tube, which generates a static charge on the powder particles. The positively charged powder particles are then attracted to the grounded surface being coated.
Here is a table summarizing the key differences between corona and tribo powder coating guns:
Feature | Corona Gun | Tribo Gun |
---|---|---|
Powder charging method | Electricity | Friction |
Need for electricity | Yes | No |
Susceptibility to Faraday cage effects | Yes | No |
Transfer efficiency | Higher | Lower |
Suitability for complex shapes | Good | Fair |
Powder compatibility | Narrower | Wider |
Here is a more detailed comparison of the two types of guns:
Corona guns are the more common type of powder coating gun. They are more efficient at transferring powder to the surface, and they are better suited for coating complex shapes. However, they require electricity to operate, and they are more susceptible to Faraday cage effects.
Tribo guns are a good choice for applications where electricity is not available or where Faraday cage effects are a concern. They are also a good choice for coating a wider range of powders. However, they are not as efficient as corona guns, and they are not as well-suited for coating complex shapes.
Ultimately, the best type of powder coating gun for you will depend on your specific needs and application. If you are not sure which type of gun is right for you, you should consult with a powder coating expert.
Parts of the Tribo Gun
Here are the main parts of a tribo powder coating gun:
Powder hopper: This is the container that holds the powder that is to be sprayed.
Feed mechanism: This mechanism controls the flow of powder from the hopper to the nozzle.
Nozzle: This is the opening through which the powder is released.
Injector: This is the device that transports powder from the hopper to the nozzle.
Electrode: This is the charged metal rod that is located near the nozzle. The electrode charges the powder particles as they pass through the air, so that they are attracted to the surface being coated.
Control system: This controls the operation of the gun, including the powder feed rate, air pressure, and voltage.
Air supply system: This supplies the air that is used to atomize the powder.
Barrel: This is the long, cylindrical part of the gun that houses the injector, electrode, and nozzle.
Trigger: This is the lever that is used to activate the gun.
Hose: This is the flexible tube that connects the gun to the powder hopper and air supply system.
Ground clamp: This is the clamp that connects the gun to the grounded surface being coated.
Safety switch: This is the switch that prevents the gun from operating unless it is properly grounded.
These are the main parts of a tribo powder coating gun. The specific design of the gun may vary depending on the manufacturer and model.
Here are some additional tips for using a tribo powder coating gun:
- Keep the gun clean: Regularly clean the gun to prevent the buildup of powder, which can interfere with its performance.
- Inspect the gun regularly: Regularly inspect the gun for signs of wear or damage.
- Calibrate the gun regularly: Regularly calibrate the gun to ensure that it is delivering the correct amount of powder.
By following these tips, you can help to ensure that your tribo powder coating gun is operating properly and delivering consistent results.
The plastic material used is Teflon. The tribo charging only has a limited adjustment. As with electrostatic charging the powder is fed through an injector to the powder gun. Because the conveying velocity of the powder is not sufficient to charge the powder with the required charge in the gun, the transit velocity of the powder through the gun is increased with supplementary air.
Because of this, regulation of the air volume and with it the charging of the powder, regulation is only limited. The advantage of tribo charging lies in its good depth of penetration. Tribo-charging does not create excess ions in the air. The space charge is insignificant. This is why the penetration of powder in cavities, such as post boxes, and wheel rims is better than with the Corona gun.
The charge on fresh powder is higher than with electrostatic charging. The coated surfaces are smoother, and the ‘orange peel’ effect is less marked. The disadvantage of tribo charging is its limited flexibility and the recovery of the powder.
Not every powder can be used with tribo guns, it requires a special Tribo additive (aluminum oxide). Today, of course, powder manufacturers can make most powders suitable for tribo use. Fresh powder charges best, and powder that has been recovered a number of times can no longer be used. The higher the fine particle content in the powder the less tribo capable it is.
Tribo Powder Coating Gun
A tribo powder coating gun is a specialized type of powder coating gun used in the powder coating process. It operates based on a different principle than conventional corona charging powder coating guns. Tribocharging is an alternative method for electrically charging powder particles before they are applied to a workpiece. Here’s how a tribo powder coating gun works and its key features:
How a Tribo Powder Coating Gun Works:
- In a tribocharging process, the powder coating gun doesn’t rely on an electrostatic field generated by a high-voltage electrode (corona charging) to charge the powder particles.
- Instead, it uses friction to charge the powder particles. When the powder flows through the gun, it rubs against a non-metallic material within the gun’s interior (usually a Teflon or PTFE material). This friction causes the powder particles to acquire a static charge.
- The charged powder particles are then directed toward the grounded workpiece, where they adhere due to the electrostatic attraction between the charged particles and the grounded surface.
Key Features of a Tribo Powder Coating Gun:
- Friction-Based Charging: The distinguishing feature of a tribo powder coating gun is its friction-based charging mechanism. This makes it well-suited for certain powder types that may not charge effectively using corona charging.
- Compatibility with Specialty Powders: Tribo guns are often used with specialty powder coatings, such as metallic or textured powders, that may not respond well to corona charging.
- Uniform Coating: Tribo guns are known for producing a uniform and consistent powder application, which can result in high-quality finishes with minimal orange peel or other imperfections.
- Reduced Faraday Cage Effect: The tribocharging process is less susceptible to the Faraday cage effect, a phenomenon where powder particles do not coat recessed or complex shapes effectively. This can be an advantage when coating intricate workpieces.
- Lower Voltage Requirements: Unlike corona guns, tribo guns typically operate at lower voltage levels, which may reduce the risk of electrostatic discharge and offer some safety advantages.
- Complex Geometry: Tribo guns are often used in situations where the workpiece has complex geometry or when coating sharp edges, as they can provide better coverage in these cases.
- Maintenance: Tribo guns may have different maintenance requirements compared to corona guns due to the friction-based charging mechanism. Regular cleaning and inspection are necessary to ensure consistent performance.
It’s important to note that the choice between a tribo powder coating gun and a corona charging gun depends on several factors, including the type of powder being used, the desired finish quality, and the specific requirements of the coating project. Tribo guns are particularly valuable when working with certain specialty powders, but corona charging guns are still widely used in many powder coating applications.
Powder coating has revolutionized the way industries apply finishes to their products, offering a highly durable, long-lasting, and environmentally friendly alternative to traditional liquid paint. This process involves applying a dry powder — typically composed of finely ground resins and pigments — which is electrostatically charged before being sprayed onto a surface. Once applied, the powder is cured under heat, forming a strong bond that resists corrosion, weathering, and wear.
At the heart of this process is powder coating equipment, which plays a critical role in ensuring the quality and efficiency of the coating process. Whether for small-scale workshops or large industrial plants, choosing the right equipment can significantly impact production outcomes, energy consumption, and the final appearance of the coated product.
For businesses looking to achieve the best results, EMS Powder Coating Equipment stands out as a leader in the field, providing innovative, high-performance systems that are built to last. With a strong focus on precision, reliability, and ease of use, EMS has earned a reputation for manufacturing the industry’s most trusted powder coating equipment. In this guide, we’ll explore the different components of powder coating systems, their benefits, and why EMS Powder Coating Equipment is the top choice for any powder coating needs.
What is Powder Coating?
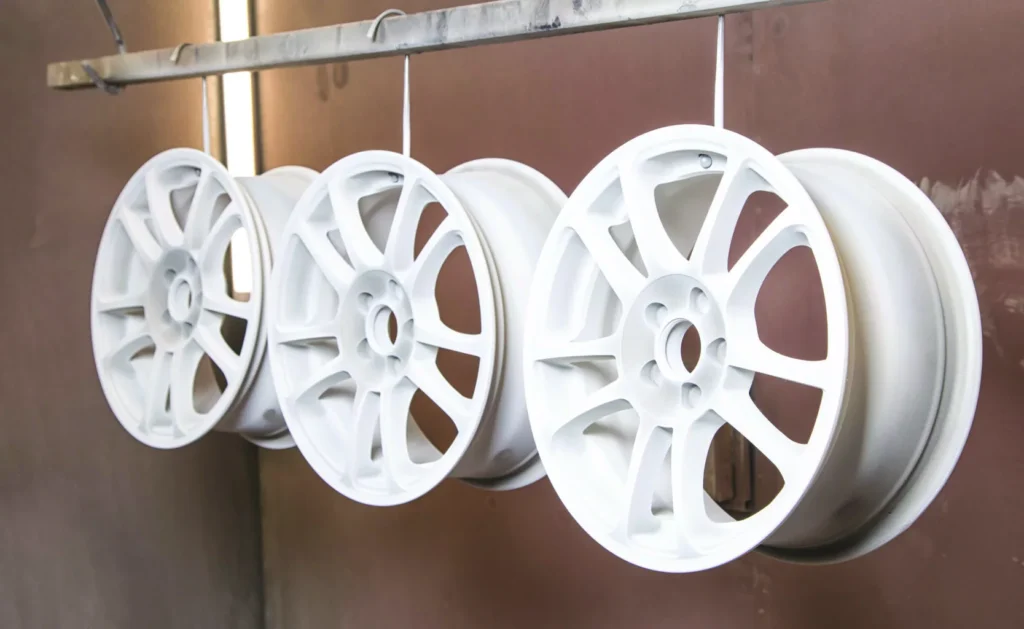
Powder coating is a dry finishing process that has gained widespread popularity due to its durability, versatility, and eco-friendly nature. Unlike liquid paint, which requires a solvent to keep the binder and filler in liquid form, powder coating is applied as a free-flowing, dry powder. This powder is usually composed of thermoplastic or thermoset polymer resins mixed with curatives, pigments, leveling agents, flow modifiers, and other additives to ensure a smooth and protective finish.
One of the biggest advantages of powder coating is its ability to create a thicker and more consistent finish without running or sagging. This results in a more uniform appearance and a stronger bond with the material being coated. Powder coating is particularly favored in industrial applications, where components need to withstand heavy use, exposure to the elements, or high temperatures. Surfaces that can be coated include metal, aluminum, steel, glass, and even some plastics.
There are several benefits to using powder coating over traditional paint. Powder coatings are extremely durable and resistant to corrosion, UV rays, and wear, making them ideal for both indoor and outdoor applications. Additionally, because no solvents are used, powder coating emits negligible volatile organic compounds (VOCs), making it much safer for workers and the environment. The overspray can be easily collected and reused, contributing to minimal waste.
With the right equipment, companies can achieve these outstanding benefits. EMS Powder Coating Equipment offers the most advanced systems, ensuring maximum efficiency in the application process and superior finish quality.
Key Components of Powder Coating Equipment
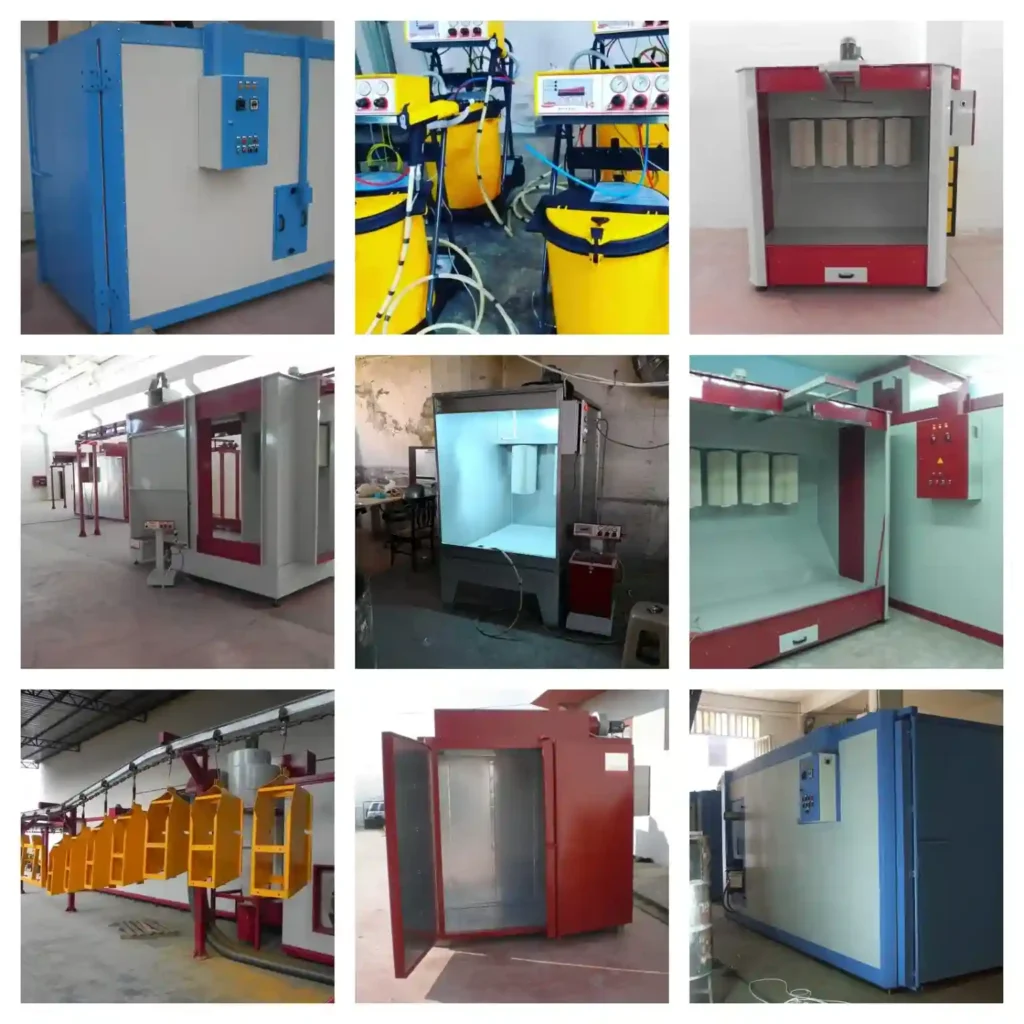
Powder coating equipment consists of several essential components that work together to ensure a flawless, durable finish. Each piece of equipment plays a specific role in the powder coating process, and the quality of each component directly affects the overall performance and efficiency of the coating line.
Below are the most important components of a powder coating system:
1. Application System: Electrostatic Spray Guns
At the core of any powder coating operation is the application system, which includes the electrostatic spray gun. The spray gun is responsible for applying the powder to the surface of the object, ensuring an even coat and strong adherence. The powder is electrostatically charged as it is released from the gun, and it is attracted to the grounded object. This creates a uniform layer of powder across the surface.
Spray guns can vary in sophistication, from manual models for smaller operations to fully automatic systems used in large-scale industrial applications. Automatic spray guns ensure greater consistency and higher efficiency, making them an essential component for companies that need to coat large volumes of products.
EMS Powder Coating Equipment offers state-of-the-art electrostatic spray guns designed for optimal performance. Whether you need manual or automatic systems, EMS ensures that each piece of equipment is engineered for precision and ease of use. Their spray guns offer smooth application with minimal overspray, reducing waste and improving operational efficiency.
2. Powder Coating Booth
A powder coating booth is essential for creating a controlled environment in which the powder can be applied to the product without contamination. The booth prevents the powder from spreading into other areas of the facility, which not only keeps the workspace clean but also ensures that the powder is fully contained for collection and reuse. Most powder coating booths are equipped with a ventilation system that helps filter out airborne particles, protecting both the workers and the environment.
Powder coating booths can be categorized into two main types: open-front and closed-front booths. Open-front booths are typically used for smaller projects and are easy to set up and operate. On the other hand, closed-front booths are often used in high-volume industrial settings because they provide more controlled conditions and reduce the risk of contamination.
EMS Powder Coating Equipment provides high-quality powder coating booths tailored to the specific needs of your operation. Their booths are designed for maximum efficiency, with advanced filtration systems that keep the workspace safe and reduce powder loss. EMS booths are also easy to clean and maintain, ensuring minimal downtime between shifts.
3. Curing Ovens
Once the powder has been applied to the surface, the object must be cured in an oven to allow the powder to melt, flow, and form a continuous coating. Curing ovens are vital to the powder coating process, as they ensure that the powder bonds correctly to the substrate, resulting in a hard, smooth, and durable finish. There are several types of curing ovens available, including convection ovens, infrared ovens, and hybrid ovens.
- Convection Ovens: These are the most common type of curing ovens used in powder coating. Convection ovens use hot air to raise the temperature of the coated object, allowing the powder to cure. They are highly efficient and work well with a variety of materials, making them a popular choice for many manufacturers.
- Infrared Ovens: These ovens use infrared energy to heat the powder coating. Infrared ovens can provide rapid heating and are particularly useful for objects that have complex shapes or are made from materials that are sensitive to high temperatures.
- Hybrid Ovens: Hybrid ovens combine both convection and infrared technologies, providing the benefits of both systems. They offer fast heating and uniform curing, making them ideal for high-precision applications.
EMS Powder Coating Equipment manufactures curing ovens that are optimized for fast and even curing, ensuring that each product has a perfect finish. Whether you need a gas-powered or electric oven, EMS provides custom solutions that meet the specific needs of your production line.
Types of Powder Coating Equipment
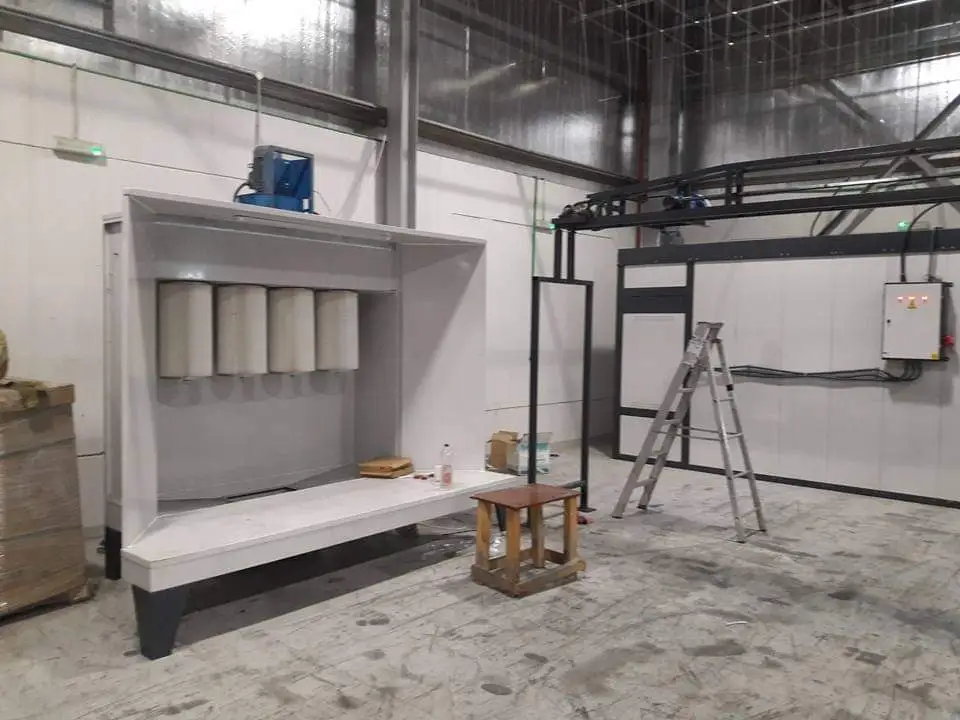
Powder coating systems can be categorized into several types based on their level of automation, the type of operation they support, and their specific functions. Understanding the differences between these systems can help businesses select the right equipment for their needs.
1. Manual vs. Automatic Systems
Powder coating systems are available in both manual and automatic configurations. Each system has its own advantages, depending on the scale and nature of the operation.
- Manual Systems: Manual powder coating systems are ideal for smaller projects or businesses that require flexibility in their production. Operators use handheld electrostatic spray guns to apply powder to objects, allowing for greater control over the process. While manual systems require more labor, they are often more cost-effective for businesses with lower production volumes.
- Automatic Systems: Automatic powder coating systems use robotic arms or reciprocators to apply the powder to objects. These systems are highly efficient and allow for precise, repeatable application. Automated systems are commonly used in high-volume manufacturing environments where consistency and speed are essential. Because automatic systems reduce the need for manual labor, they can also help lower operating costs in the long run.
EMS Powder Coating Equipment offers both manual and automatic systems, ensuring that businesses of all sizes can find the right equipment for their needs. Their automatic systems are designed for high efficiency and consistent results, making them a top choice for manufacturers seeking to increase productivity.
2. Batch vs. Conveyorized Systems
Another important distinction in powder coating equipment is between batch and conveyorized systems.
- Batch Systems: In a batch system, objects are coated one at a time or in small groups. After the powder is applied, the objects are placed in a curing oven. Batch systems are ideal for smaller production runs or when flexibility is required. They allow operators to handle various parts and products in small quantities.
- Conveyorized Systems: Conveyorized systems are used in large-scale production environments. In this system, objects move through the powder coating line on a conveyor belt, passing through the spray booth and curing oven without the need for manual handling. Conveyorized systems are highly efficient and are the best choice for high-volume operations that need to coat large quantities of parts consistently and quickly.
EMS Powder Coating Equipment provides robust batch and conveyorized systems tailored to different production needs. Whether you need a flexible batch system for custom work or a conveyorized system for high-speed production, EMS offers solutions that enhance productivity and ensure high-quality finishes.
Why Choose EMS Powder Coating Equipment?
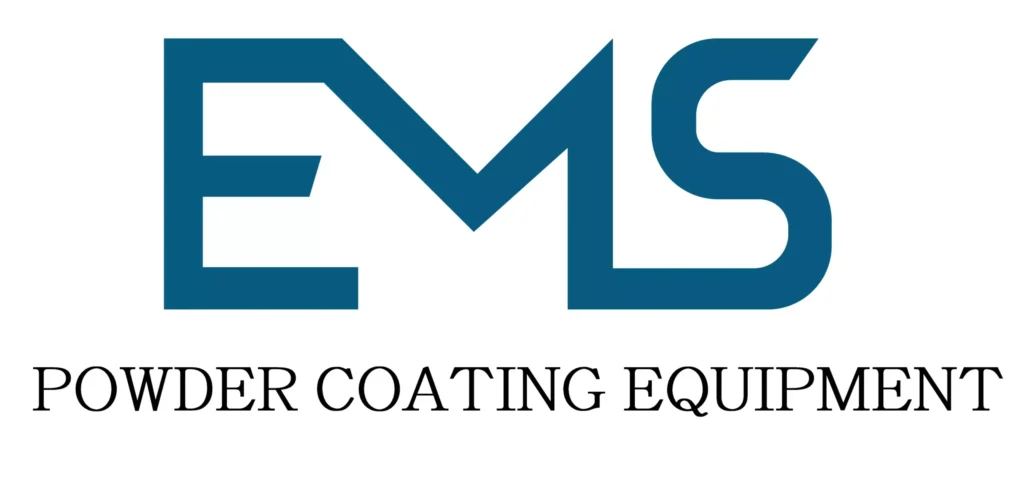
When it comes to selecting powder coating equipment, businesses must consider multiple factors such as efficiency, reliability, ease of use, and cost-effectiveness. EMS Powder Coating Equipment excels in all of these areas, offering top-of-the-line solutions that meet the needs of various industries. Below are several reasons why EMS is regarded as the best manufacturer of powder coating equipment.
1. Cutting-Edge Technology and Innovation
EMS Powder Coating Equipment has built its reputation on a foundation of innovation and cutting-edge technology. The company continuously invests in research and development to ensure that its equipment stays ahead of the competition. EMS systems are designed with the latest advancements in electrostatic application technology, providing users with superior precision and control.
From advanced automatic reciprocators to highly efficient curing ovens, EMS equipment incorporates state-of-the-art features that ensure smooth and reliable operation. The company’s commitment to technological innovation ensures that customers receive equipment that is not only efficient but also future-proof, capable of adapting to evolving industry demands.
For instance, EMS’s automated spray systems are equipped with sophisticated controls that allow for fine-tuning of the powder application process, ensuring that the coating is applied consistently across all surfaces, regardless of shape or size. These systems can be programmed for different jobs, making them ideal for high-volume operations where efficiency is paramount.
2. Customization and Versatility
Every business has unique needs, and EMS Powder Coating Equipment understands the importance of providing customizable solutions. Whether you’re running a small-scale operation or a large industrial plant, EMS offers a variety of equipment configurations tailored to your specific requirements.
One of the standout features of EMS is its ability to deliver both standard and customized powder coating systems. If your production line has particular space constraints or operational needs, EMS can provide specialized configurations to maximize your space while optimizing performance. This level of flexibility sets EMS apart from many competitors who only offer off-the-shelf solutions.
Moreover, EMS equipment is versatile and adaptable across a wide range of industries. Whether you’re working in automotive manufacturing, furniture production, or consumer goods, EMS’s systems can handle different materials and product sizes with ease. This versatility ensures that businesses investing in EMS Powder Coating Equipment are making a long-term investment that will pay dividends across various projects.
3. Durability and Reliability
Powder coating equipment represents a significant investment for any business, so it’s crucial that the systems you choose are built to last. EMS Powder Coating Equipment is renowned for the durability and reliability of its products. All equipment is designed with high-quality materials that can withstand the rigors of daily industrial use, ensuring minimal maintenance and long service life.
EMS takes pride in manufacturing powder coating systems that are not only highly efficient but also reliable under continuous operation. This means fewer breakdowns, less downtime, and reduced maintenance costs, all of which contribute to increased productivity and profitability for businesses.
The reliability of EMS systems is backed by rigorous quality control measures. Each piece of equipment undergoes thorough testing before being delivered to customers, ensuring that it meets the highest standards of performance and safety.
4. Energy Efficiency
Energy consumption is a critical consideration for any business, particularly in industries with high operational costs. EMS Powder Coating Equipment is designed to maximize energy efficiency without compromising performance. This focus on energy conservation helps businesses reduce their operational expenses while also minimizing their environmental footprint.
EMS offers high-efficiency curing ovens that use innovative technology to ensure uniform heat distribution and rapid curing times. These ovens consume less energy compared to traditional models, helping businesses cut down on utility costs. Additionally, EMS systems are designed to reduce powder waste, allowing operators to reclaim and reuse powder that is not deposited on the substrate, further boosting cost savings and sustainability.
5. Exceptional Customer Support and After-Sales Service
Another significant factor that sets EMS Powder Coating Equipment apart is the company’s commitment to customer support. Purchasing industrial equipment is a long-term investment, and EMS ensures that customers receive ongoing support throughout the life of their equipment.
From the initial consultation to installation and training, EMS offers comprehensive support to ensure that businesses get the most out of their systems. The company also provides maintenance and repair services, ensuring that any issues are addressed promptly to avoid prolonged downtime. This dedication to after-sales service gives EMS customers peace of mind, knowing that their equipment is backed by a team of experts ready to assist at any time.
6. Proven Track Record and Global Reach
With years of experience and a global client base, EMS Powder Coating Equipment has established itself as a leading manufacturer in the industry. The company has successfully partnered with businesses across the world, delivering equipment that has helped manufacturers improve their processes and quality.
EMS’s extensive portfolio of clients includes companies from a wide range of industries, including automotive, aerospace, furniture, and consumer goods. This broad industry experience ensures that EMS understands the specific needs of different sectors and can tailor solutions accordingly.
Trends and Innovations in Powder Coating Equipment
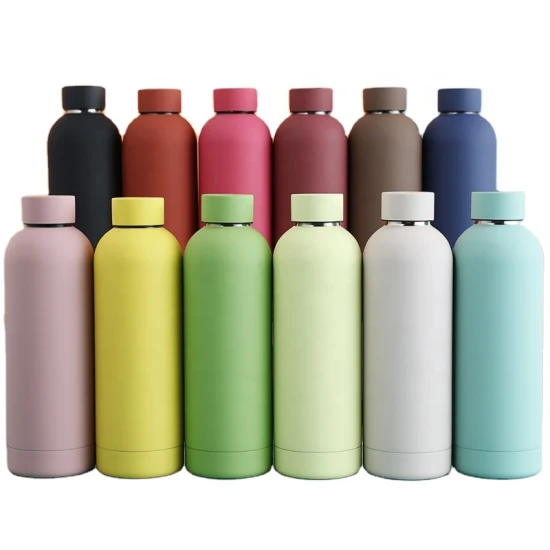
The powder coating industry is constantly evolving, with new technologies and trends shaping the way businesses operate. EMS Powder Coating Equipment stays at the forefront of these developments, ensuring that its customers benefit from the latest innovations in the field. Below are some of the key trends currently influencing powder coating technology:
1. Automation and Industry 4.0 Integration
Automation is becoming increasingly prevalent in the powder coating industry, with businesses looking for ways to improve efficiency and reduce labor costs. Automated systems, such as EMS’s powder coating reciprocators, allow for more consistent application and faster production times. Industry 4.0 integration, including the use of smart sensors and data analytics, is also making it easier for manufacturers to monitor and optimize their powder coating operations in real-time.
EMS has embraced these trends by offering equipment that can be fully integrated into modern manufacturing systems. This allows businesses to streamline their operations and improve overall productivity while maintaining high levels of quality.
2. Sustainability and Eco-Friendly Solutions
As industries become more focused on sustainability, the demand for environmentally friendly powder coating solutions continues to grow. Powder coating is inherently eco-friendly because it produces minimal waste and contains no solvents, which reduces VOC emissions. However, EMS has taken sustainability a step further by designing energy-efficient systems that consume less power while maintaining optimal performance.
These innovations make EMS Powder Coating Equipment the ideal choice for businesses seeking to reduce their environmental impact without sacrificing quality or efficiency.
3. Advanced Material Compatibility
New advances in powder coating materials are allowing manufacturers to coat a wider range of substrates, including plastics and composites. EMS’s powder coating systems are designed to handle these advanced materials, providing businesses with the flexibility to expand their product offerings.
Conclusion
Powder coating has become a cornerstone in modern manufacturing, providing businesses with a durable, environmentally friendly, and cost-effective way to protect their products. However, achieving the best results requires investing in high-quality equipment.
EMS Powder Coating Equipment stands out as the industry leader, offering advanced technology, customization options, and exceptional reliability. Whether you are looking for manual systems for small-scale operations or automated systems for large industrial plants, EMS provides tailored solutions that meet your specific needs. Their commitment to innovation, durability, and energy efficiency ensures that businesses can maximize their productivity while minimizing costs and environmental impact.
With a proven track record of success and an unwavering dedication to customer satisfaction, EMS Powder Coating Equipment is the best choice for businesses looking to enhance their powder coating operations.
Automatic Powder Coating Equipment: A Revolution in Efficiency and Precision

The powder coating industry has experienced significant advancements in recent years, with automation playing a key role in improving production efficiency, consistency, and overall quality. Automatic powder coating equipment has transformed the way manufacturers apply powder coatings, enabling them to increase throughput while maintaining precise control over the application process. This technology is particularly valuable in high-volume production environments, where consistent quality and reduced operational costs are critical for success.
Automatic powder coating systems use advanced robotic systems, reciprocators, and intelligent controls to streamline the coating process. These systems are designed to apply powder evenly and consistently, reducing waste, improving the quality of the finish, and lowering labor costs. By removing the human element from most stages of the coating process, automatic systems provide a higher level of accuracy and reproducibility.
EMS Powder Coating Equipment is at the forefront of this revolution, offering state-of-the-art automatic systems that cater to the needs of industries around the globe. Known for their advanced technology, reliability, and customizable solutions, EMS’s automatic powder coating equipment is trusted by manufacturers who require high precision and efficiency in their production lines. In this guide, we’ll explore the features of automatic powder coating systems, their benefits, and why EMS Powder Coating Equipment is the best choice for businesses looking to automate their powder coating process.
What is Automatic Powder Coating Equipment?
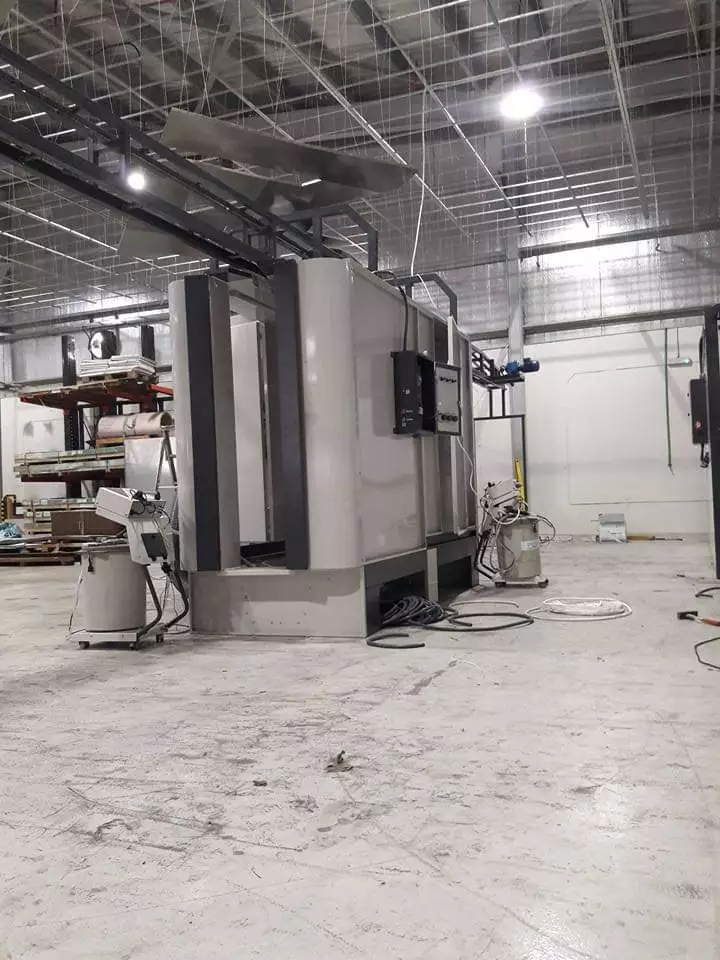
Automatic powder coating equipment refers to a fully automated system that applies powder coatings to products with minimal human intervention. These systems typically consist of several key components, including automatic spray guns, reciprocators, conveyors, and curing ovens. Each of these components works together seamlessly to ensure that powder is applied uniformly and efficiently.
1. Automatic Spray Guns
The core of any automatic powder coating system is the spray gun. In an automated setup, multiple spray guns are mounted on robotic arms or reciprocators that move in precise, pre-programmed patterns. These guns are electrostatically charged, allowing the powder particles to adhere to the product surface through an electrostatic field. The guns can adjust their position and angle to coat even complex or irregular shapes with ease.
One of the primary advantages of automatic spray guns is their ability to apply powder coatings with extreme consistency. Since they follow pre-programmed patterns, there is no variation in the application process, resulting in a uniform coat every time. Additionally, these systems reduce overspray and powder wastage, leading to cost savings.
EMS Powder Coating Equipment offers some of the most advanced automatic spray gun systems in the industry. Their spray guns are designed for maximum precision and can be programmed to handle different product sizes and shapes, ensuring a consistent finish across the entire production run.
2. Reciprocators
Reciprocators are the components that control the vertical movement of the spray guns, allowing them to cover the full height of the object being coated. Reciprocators are typically used in conjunction with conveyorized systems, where parts move through the spray booth at a constant speed. The reciprocators move the spray guns up and down, ensuring even coverage over the entire surface of the product.
Automatic reciprocators are crucial in high-speed production environments, where consistency and speed are essential. These systems can be programmed to adjust their speed and range of motion depending on the size and shape of the product, making them ideal for complex parts or large quantities of products.
EMS Powder Coating Equipment specializes in advanced reciprocators that can be customized to fit any production line. Their systems are known for their reliability and smooth operation, ensuring that products are evenly coated without any gaps or inconsistencies.
3. Conveyor Systems
In an automatic powder coating setup, the conveyor system moves products through the various stages of the coating process, including the spray booth and curing oven. Conveyorized systems allow for continuous production, increasing throughput and reducing the need for manual handling.
Conveyors can be programmed to adjust their speed based on the complexity of the parts being coated or the specific requirements of the coating process. This flexibility makes automatic powder coating systems highly adaptable to different production environments.
EMS Powder Coating Equipment offers conveyor systems that integrate seamlessly with their automatic spray guns and reciprocators. Their conveyor systems are designed for high efficiency and can handle a wide range of product sizes and weights, making them ideal for industries such as automotive, furniture, and appliance manufacturing.
The Benefits of Automatic Powder Coating Equipment
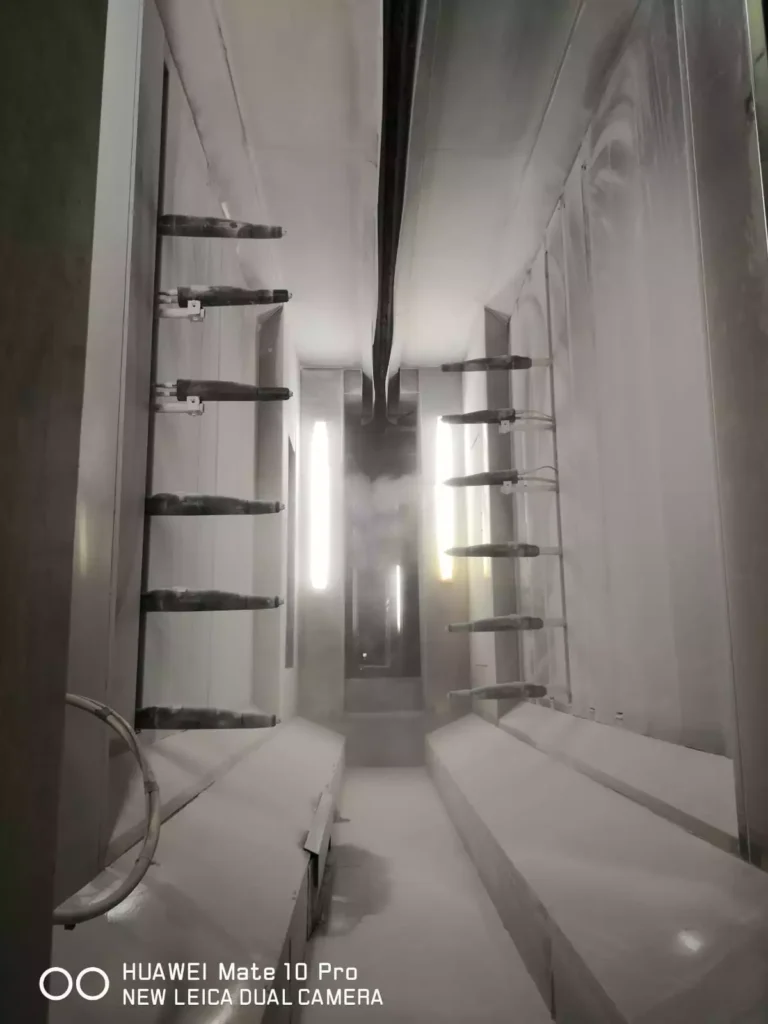
Automation in powder coating has introduced several key advantages that have revolutionized the industry. Below are some of the most significant benefits of automatic powder coating equipment:
1. Improved Consistency and Quality
One of the biggest challenges in manual powder coating is achieving consistent results. Human operators, while skilled, are prone to variability in their application methods, which can lead to uneven coating thickness, poor adhesion, or defects in the finish. Automatic powder coating systems eliminate these issues by providing consistent, repeatable application.
Since automatic spray guns and reciprocators follow precise, pre-programmed instructions, every product receives the same level of coating, ensuring a high-quality finish on each item. This consistency is especially important for industries that produce large quantities of parts and need to meet strict quality standards.
EMS Powder Coating Equipment ensures that their automatic systems deliver uniform coating results, with even powder distribution and minimal overspray. This results in a durable, high-quality finish that meets or exceeds industry standards.
2. Increased Production Efficiency
Automatic powder coating equipment is designed to optimize the entire coating process, significantly increasing production efficiency. By automating the application process, businesses can coat more parts in less time, resulting in higher throughput. This is particularly beneficial for industries with high production volumes, where speed and efficiency are critical to meeting demand.
The integration of conveyor systems into automatic setups also reduces the need for manual handling of parts, minimizing downtime and labor costs. Products move seamlessly from the spray booth to the curing oven without interruption, further streamlining the process.
For manufacturers that need to maximize output, EMS Powder Coating Equipment offers fully integrated automatic systems that work in harmony to reduce bottlenecks and improve production flow.
3. Reduced Labor Costs
Automation reduces the need for manual labor in the powder coating process, leading to significant cost savings for businesses. In manual setups, skilled operators are required to oversee the application of the powder, adjust the equipment, and ensure that each product is coated evenly. In contrast, automatic systems can handle these tasks without the need for constant supervision.
By reducing labor requirements, businesses can allocate their workforce to other areas of production or reduce overall labor costs. Automatic systems also reduce the likelihood of human error, further decreasing the need for rework or repairs.
With EMS Powder Coating Equipment, manufacturers can implement automatic systems that not only reduce labor costs but also improve overall operational efficiency.
4. Enhanced Flexibility and Adaptability
One of the misconceptions about automatic powder coating systems is that they are rigid and inflexible. However, modern automatic systems, like those provided by EMS Powder Coating Equipment, are highly adaptable and can be configured to handle a wide range of products.
These systems can be programmed to adjust the speed, powder flow rate, and gun positioning to accommodate different shapes, sizes, and coating requirements. This makes them suitable for a variety of industries, from automotive parts to consumer electronics. Additionally, with programmable systems, businesses can quickly switch between different product lines, allowing for greater flexibility in production.
5. Lower Powder Waste
Powder waste is a common issue in manual powder coating processes. Overspray and uneven application often result in excess powder being lost, leading to higher material costs. Automatic systems are designed to minimize waste by ensuring that the powder is applied evenly and only where it is needed.
Many automatic systems also include powder recovery systems that capture unused powder and recycle it back into the process. This not only reduces material costs but also contributes to a more sustainable, environmentally friendly operation.
EMS Powder Coating Equipment offers advanced powder recovery systems that integrate seamlessly with their automatic equipment, ensuring that businesses can operate efficiently while minimizing waste.
6. Scalability and Future-Proofing
Automatic powder coating equipment is highly scalable, making it an excellent long-term investment for businesses looking to grow. As production volumes increase, automatic systems can be expanded or upgraded to handle larger workloads without sacrificing quality or efficiency. This scalability ensures that businesses can continue to meet demand as they grow, without the need to completely overhaul their equipment.
Furthermore, the technology behind automatic powder coating systems is constantly evolving. By investing in high-quality equipment from manufacturers like EMS Powder Coating Equipment, businesses can future-proof their operations and stay competitive in an increasingly automated industry.
Why EMS Powder Coating Equipment is the Best Choice for Automatic Systems
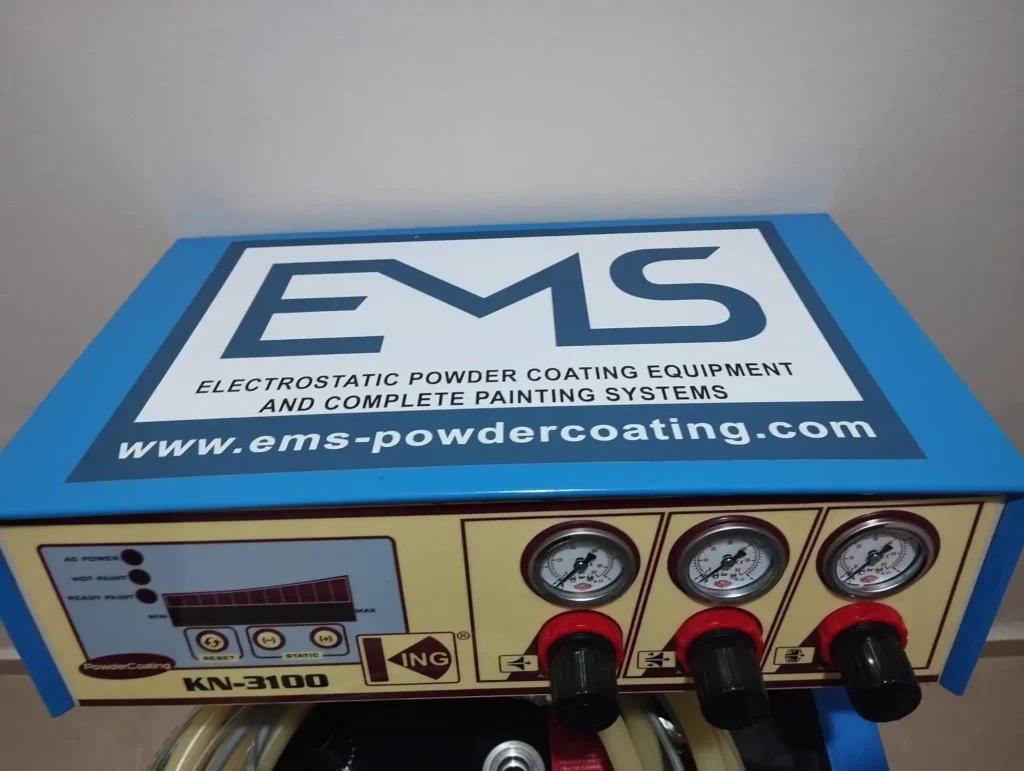
When selecting automatic powder coating equipment, it’s essential to choose a manufacturer that not only offers advanced technology but also understands the unique needs of your business. EMS Powder Coating Equipment stands out as the best choice for several reasons:
1. Industry-Leading Technology
EMS Powder Coating Equipment is known for its cutting-edge technology, offering some of the most advanced automatic systems available. Their equipment is designed to maximize efficiency, reduce waste, and provide consistent, high-quality finishes across all products. With features such as programmable spray guns, intelligent reciprocators, and high-efficiency conveyor systems, EMS equipment ensures that businesses can achieve superior results with minimal effort.
2. Customization and Flexibility
Every manufacturing operation is different, and EMS understands the importance of providing equipment that meets the specific needs of each customer. EMS offers customizable automatic systems that can be tailored to your production line, whether you’re coating small parts or large, complex products. This level of flexibility ensures that businesses get the most out of their investment, with equipment that can adapt to changing needs.
3. Reliability and Durability
EMS Powder Coating Equipment is renowned for the reliability and durability of its products. Built with high-quality materials and engineered for long-term performance, EMS systems are designed to withstand the rigors of continuous industrial use. This means fewer breakdowns, less downtime, and lower maintenance costs, all of which contribute to increased productivity and profitability.
4. Superior Support and Service
In addition to offering top-tier equipment, EMS provides exceptional customer support and after-sales service. From installation and training to ongoing maintenance and troubleshooting, EMS is committed to ensuring that customers get the most out of their automatic systems. Their team of experts is always available to provide guidance and assistance, making them a trusted partner for businesses around the world.
Conclusion
Automatic powder coating equipment represents a significant advancement in the manufacturing industry, offering businesses improved efficiency, consistency, and cost savings. With the ability to handle high-volume production while maintaining precise control over the coating process, automatic systems are an essential tool for any manufacturer looking to stay competitive.
EMS Powder Coating Equipment is the industry leader in automatic powder coating systems, providing advanced technology, customizable solutions, and unmatched reliability. Whether you’re seeking to automate your production line for the first time or upgrade your existing equipment, EMS offers the expertise and products needed to take your powder coating operation to the next level.
By investing in EMS automatic powder coating equipment, businesses can increase productivity, reduce costs, and ensure a consistently high-quality finish for their products. With a proven track record of success and a commitment to innovation, EMS is the best choice for manufacturers looking to optimize their powder coating process.
Powder Coating Reciprocators: Precision and Efficiency for Perfect Coating Applications

In the powder coating process, ensuring consistent coverage across a product’s surface is essential for both aesthetic appeal and functional protection. While spray guns deliver the powder to the product, powder coating reciprocators are the backbone of automation, enabling the precise, efficient movement of the guns. These devices move spray guns in vertical or horizontal patterns, ensuring that the powder is applied evenly over the entire surface of the object being coated.
Powder coating reciprocators are vital for operations where large volumes of parts must be coated consistently and quickly, such as in automotive, electronics, and industrial manufacturing. They automate the repetitive movements required during powder coating, reducing labor, increasing throughput, and improving the overall quality of the finished product.
EMS Powder Coating Equipment is a trusted manufacturer of advanced reciprocator systems designed to meet the rigorous demands of industrial coating applications. EMS reciprocators are known for their reliability, precision, and adaptability, making them the ideal solution for businesses looking to optimize their powder coating processes. In this guide, we’ll delve into the functionality of powder coating reciprocators, explore their benefits, and discuss why EMS Powder Coating Equipment provides the best reciprocators on the market.
What is a Powder Coating Reciprocator?
A powder coating reciprocator is a piece of automated equipment designed to move spray guns in a controlled, repetitive motion to ensure consistent powder application across the entire surface of a product. The reciprocator is typically used in conjunction with automated spray guns and conveyor systems, forming an essential part of an automated powder coating line.
The movement of the reciprocator is typically either vertical or horizontal, depending on the shape and size of the object being coated. The spray guns, mounted on the reciprocator, move in synchronized patterns to cover every area of the object evenly. This motion is particularly useful for coating large or complex objects, as it ensures that no areas are missed and that the powder is applied at the correct thickness.
Reciprocators can be used for a wide range of applications, from flat surfaces like panels to intricate shapes with multiple contours. They are commonly used in industries where precision and consistency are critical, such as:
- Automotive parts: Car bodies, frames, and other components require even coating to ensure durability and corrosion resistance.
- Metal fabrication: Industrial equipment, furniture, and appliances benefit from uniform powder coating for both aesthetics and performance.
- Electronics: Certain electronics components require protective powder coatings that can only be applied evenly with the help of a reciprocator.
While manual powder coating requires operators to control the movement of the spray gun, reciprocators automate this process, ensuring that the application is performed with extreme accuracy. This eliminates human error and ensures that every part coated meets strict quality standards.
EMS Powder Coating Equipment provides advanced reciprocator systems that offer precision control, robust construction, and flexibility for different production needs. Their reciprocators can be programmed to handle a variety of objects, making them ideal for businesses that produce different parts on the same line.
How Powder Coating Reciprocators Work
Powder coating reciprocators work by automating the repetitive motion required to coat parts evenly. Below is an overview of the main components and how they function together to ensure consistent powder application:
1. Spray Gun Movement
The primary function of the reciprocator is to control the movement of the spray guns. These guns are mounted onto the reciprocator’s arms, which move in a vertical or horizontal motion to coat the product evenly. The speed and range of motion can be adjusted based on the size, shape, and complexity of the object being coated.
Spray guns release powder through an electrostatic process, where the powder particles are charged and attracted to the grounded object. This ensures that the powder adheres to every part of the object, even in difficult-to-reach areas like corners or crevices.
EMS Powder Coating Equipment manufactures reciprocators that provide precise control over spray gun movement. Their systems allow for easy adjustment of the speed and stroke length, ensuring that the coating is applied with maximum efficiency and minimal overspray. This not only improves the quality of the finish but also reduces powder wastage, leading to significant cost savings.
2. Synchronization with Conveyor Systems
In most automated powder coating lines, reciprocators work alongside conveyor systems. As parts move through the spray booth on a conveyor belt, the reciprocator moves the spray guns in sync with the parts, ensuring that every object receives uniform coating. The reciprocator’s movement is programmed to match the speed of the conveyor, ensuring that no areas are missed or over-coated.
This synchronization is critical for maintaining production efficiency and consistency. In high-speed production environments, such as automotive or appliance manufacturing, even slight misalignment between the reciprocator and conveyor can lead to defects or uneven coatings.
EMS Powder Coating Equipment integrates their reciprocators seamlessly with conveyor systems. Their reciprocators are equipped with advanced sensors and controls that ensure perfect synchronization, even in high-speed operations. This allows businesses to maintain consistent quality without slowing down production.
3. Programmable Motion and Flexibility
Modern reciprocators offer a high degree of flexibility, allowing manufacturers to program their motion patterns based on the specific needs of the product being coated. For instance, some objects may require more complex coating patterns, especially if they have intricate shapes or multiple surfaces that need to be coated at different angles.
Reciprocators can be programmed to adjust the speed of their movement, the distance between the spray guns and the object, and even the number of passes the guns make over the surface. This ensures that each product receives the correct amount of powder, regardless of its shape or size.
EMS Powder Coating Equipment provides reciprocators that are fully programmable, allowing businesses to adjust their settings based on production requirements. Whether coating flat panels or more complex parts, EMS reciprocators deliver the precision needed to achieve perfect results.
4. Maintenance and Durability
Given that reciprocators are a crucial part of any automated powder coating system, their durability and ease of maintenance are important factors to consider. High-quality reciprocators should be built to withstand continuous operation in demanding industrial environments without frequent breakdowns or downtime.
EMS Powder Coating Equipment designs their reciprocators with robust materials and engineering to ensure long-lasting performance. Their systems require minimal maintenance, and any routine servicing is made easy by their user-friendly design. This reliability reduces the risk of costly downtime, allowing businesses to keep their production lines running smoothly.
The Benefits of Using Powder Coating Reciprocators
Powder coating reciprocators offer numerous benefits that make them indispensable in modern manufacturing environments. Here are some of the key advantages:
1. Improved Coating Consistency
Manual powder coating relies heavily on the skill and experience of the operator. While experienced workers can achieve excellent results, manual coating is inherently prone to variability. Even slight inconsistencies in movement or technique can lead to uneven coating thickness, overspray, or missed areas.
Powder coating reciprocators eliminate these issues by providing precise, repeatable motion. Once programmed, the reciprocator applies the powder in the exact same way every time, ensuring uniform coverage across all parts. This consistency leads to better overall product quality and reduces the risk of rework.
EMS Powder Coating Equipment is known for its high-precision reciprocators that deliver flawless results. Their systems ensure that every part receives the same level of coating, leading to a more durable and attractive finish.
2. Increased Production Efficiency
Automating the movement of the spray guns allows businesses to significantly increase their production speed. Manual powder coating requires operators to move the spray gun around the part, a process that can be slow and labor-intensive. Reciprocators, on the other hand, can coat parts at a much faster rate, especially when used in conjunction with conveyor systems.
In high-volume production environments, this increase in efficiency can lead to significant cost savings. More parts can be coated in less time, allowing businesses to meet customer demand without compromising on quality.
With EMS Powder Coating Equipment, manufacturers benefit from reciprocators designed to maximize efficiency. Their systems can be integrated into fast-paced production lines, enabling businesses to boost their output while maintaining excellent coating quality.
3. Reduced Labor Costs
Automating the powder coating process with reciprocators reduces the need for skilled labor. Manual powder coating requires operators to be trained in the correct application techniques, and businesses must rely on these operators to consistently produce high-quality results. By automating this process, businesses can reduce their reliance on manual labor and lower their overall labor costs.
Reciprocators allow businesses to allocate their workforce to other areas of production, improving overall efficiency. Additionally, because automated systems reduce the risk of human error, businesses can also reduce the costs associated with rework or defective products.
EMS Powder Coating Equipment provides advanced reciprocator systems that minimize the need for manual intervention, allowing businesses to lower labor costs while maintaining high-quality standards.
4. Versatility Across Different Products
One of the standout benefits of powder coating reciprocators is their versatility. These systems can be programmed to coat a wide variety of products, from flat panels to complex parts with multiple angles and surfaces. This flexibility makes reciprocators suitable for businesses that produce a diverse range of products or frequently change their production lines.
EMS Powder Coating Equipment’s reciprocators are highly adaptable, allowing manufacturers to coat different types of parts without needing to reconfigure the entire system. Whether coating small, intricate parts or large industrial components, EMS’s reciprocators ensure that every product is coated with precision and consistency.
5. Powder Efficiency and Waste Reduction
In manual powder coating, overspray and powder waste are common issues. Even skilled operators may have difficulty applying powder evenly, leading to excess powder being wasted. Reciprocators, on the other hand, are designed to apply the exact amount of powder needed, reducing overspray and improving overall efficiency.
Many reciprocator systems also include powder recovery systems, which capture any unused powder and recycle it back into the system. This not only reduces material costs but also makes the coating process more environmentally friendly.
EMS Powder Coating Equipment offers reciprocators with advanced powder recovery systems, ensuring that businesses can minimize waste and operate more sustainably. By reducing powder waste, EMS systems help businesses cut costs and lower their environmental impact.
Why Choose EMS Powder Coating Equipment for Reciprocators?
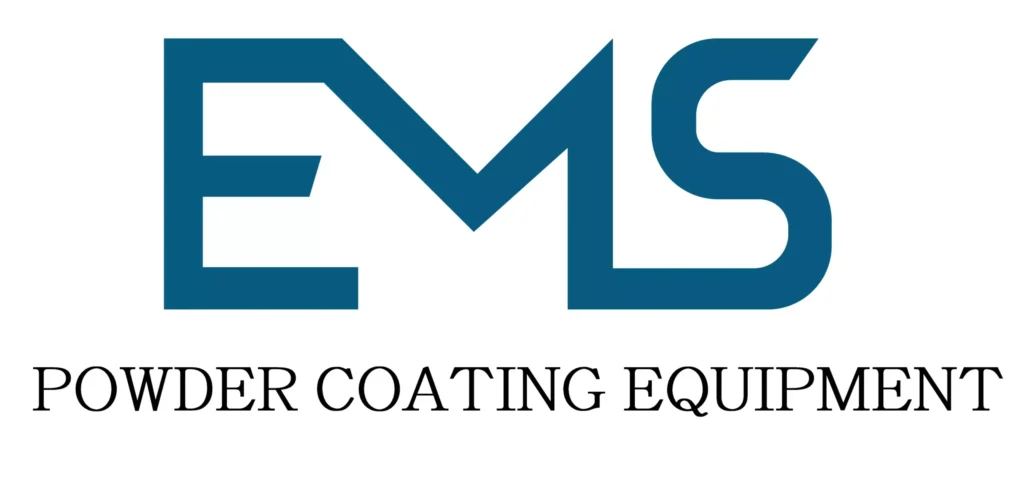
Choosing the right powder coating reciprocator is critical for achieving the best results in your production line. EMS Powder Coating Equipment is the industry leader in reciprocator technology, offering systems that are designed for precision, efficiency, and durability. Here’s why EMS is the best choice for businesses looking to invest in reciprocators:
1. Advanced Technology for Precision Control
EMS reciprocators are equipped with the latest technology, allowing for precise control over spray gun movement. Their systems can be programmed to meet the specific needs of your production line, ensuring that every part is coated evenly. Whether you’re coating flat panels or complex shapes, EMS reciprocators provide the accuracy needed to achieve perfect results.
2. Customization and Flexibility
Every business has unique coating requirements, and EMS understands the importance of providing customizable solutions. EMS reciprocators can be tailored to fit your specific production line, with adjustable stroke lengths, speeds, and motion patterns. This flexibility allows businesses to optimize their powder coating process and maximize efficiency.
3. Durability and Reliability
Built with high-quality materials and engineering, EMS reciprocators are designed for long-lasting performance. These systems are robust enough to withstand continuous operation in demanding industrial environments, ensuring that businesses can rely on them for years without frequent maintenance or breakdowns.
4. Seamless Integration with Existing Systems
EMS reciprocators are designed to integrate seamlessly with other equipment in your powder coating line, including conveyor systems and curing ovens. This ensures that your production line operates smoothly and efficiently, with minimal downtime or disruption.
Conclusion
Powder coating reciprocators are a key component of any automated coating system, providing the precision and efficiency needed to produce consistent, high-quality finishes. By automating the movement of spray guns, reciprocators ensure that every product is coated evenly, reducing the risk of defects and improving overall production efficiency.
EMS Powder Coating Equipment offers the best reciprocators on the market, designed to meet the needs of businesses in a wide range of industries. With advanced technology, customizable solutions, and a commitment to durability and reliability, EMS ensures that your powder coating process is optimized for maximum efficiency and quality.
Whether you’re looking to automate your production line for the first time or upgrade your existing equipment, EMS Powder Coating Equipment provides the expertise and products needed to take your powder coating operation to the next level.
Powder coating has revolutionized the way industries apply finishes to their products, offering a highly durable, long-lasting, and environmentally friendly alternative to traditional liquid paint. This process involves applying a dry powder — typically composed of finely ground resins and pigments — which is electrostatically charged before being sprayed onto a surface. Once applied, the powder is cured under heat, forming a strong bond that resists corrosion, weathering, and wear.
At the heart of this process is powder coating equipment, which plays a critical role in ensuring the quality and efficiency of the coating process. Whether for small-scale workshops or large industrial plants, choosing the right equipment can significantly impact production outcomes, energy consumption, and the final appearance of the coated product.
For businesses looking to achieve the best results, EMS Powder Coating Equipment stands out as a leader in the field, providing innovative, high-performance systems that are built to last. With a strong focus on precision, reliability, and ease of use, EMS has earned a reputation for manufacturing the industry’s most trusted powder coating equipment. In this guide, we’ll explore the different components of powder coating systems, their benefits, and why EMS Powder Coating Equipment is the top choice for any powder coating needs.
What is Powder Coating?
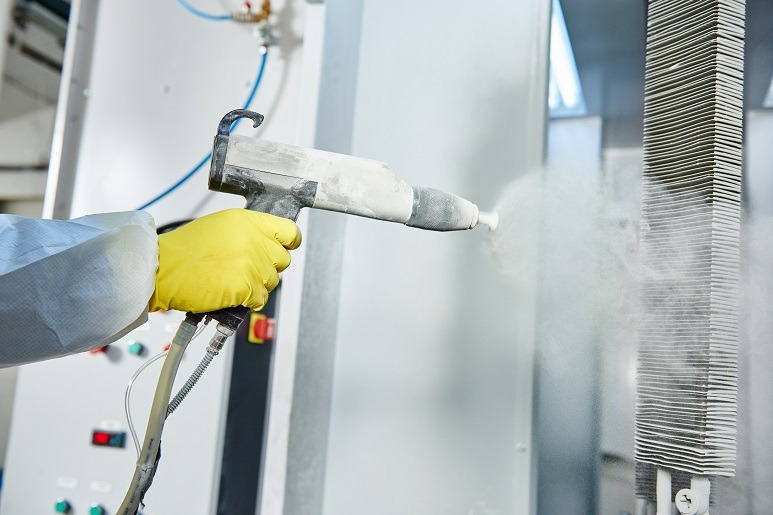
Powder coating is a dry finishing process that has gained widespread popularity due to its durability, versatility, and eco-friendly nature. Unlike liquid paint, which requires a solvent to keep the binder and filler in liquid form, powder coating is applied as a free-flowing, dry powder. This powder is usually composed of thermoplastic or thermoset polymer resins mixed with curatives, pigments, leveling agents, flow modifiers, and other additives to ensure a smooth and protective finish.
One of the biggest advantages of powder coating is its ability to create a thicker and more consistent finish without running or sagging. This results in a more uniform appearance and a stronger bond with the material being coated. Powder coating is particularly favored in industrial applications, where components need to withstand heavy use, exposure to the elements, or high temperatures. Surfaces that can be coated include metal, aluminum, steel, glass, and even some plastics.
There are several benefits to using powder coating over traditional paint. Powder coatings are extremely durable and resistant to corrosion, UV rays, and wear, making them ideal for both indoor and outdoor applications. Additionally, because no solvents are used, powder coating emits negligible volatile organic compounds (VOCs), making it much safer for workers and the environment. The overspray can be easily collected and reused, contributing to minimal waste.
With the right equipment, companies can achieve these outstanding benefits. EMS Powder Coating Equipment offers the most advanced systems, ensuring maximum efficiency in the application process and superior finish quality.
Key Components of Powder Coating Equipment
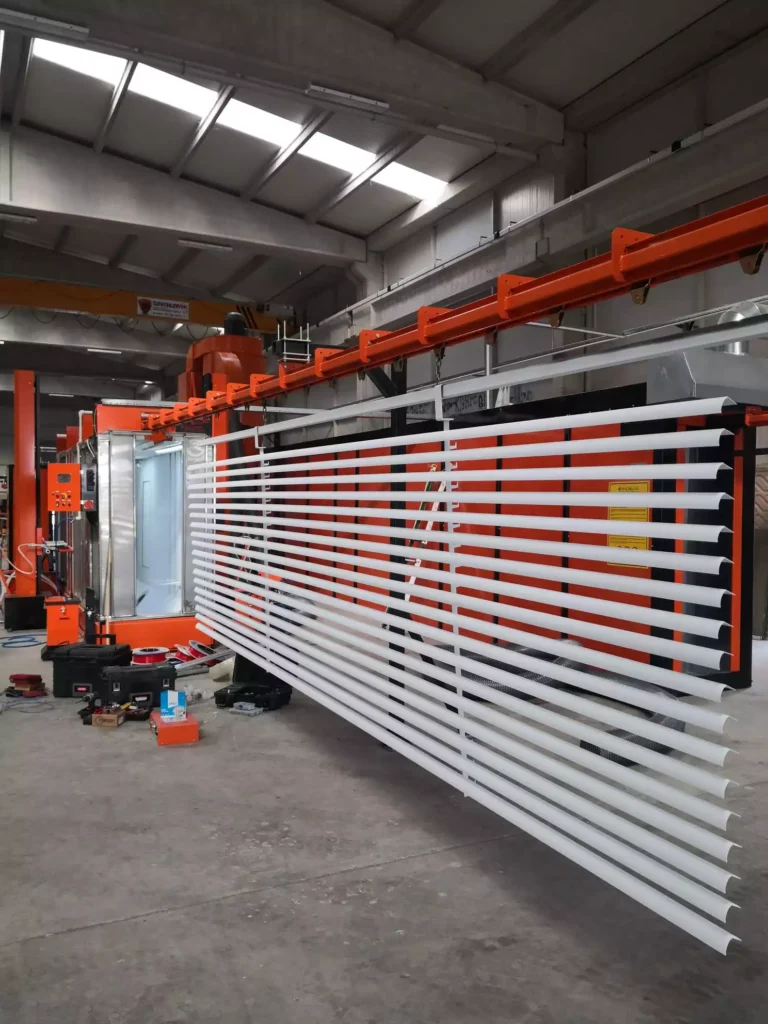
Powder coating equipment consists of several essential components that work together to ensure a flawless, durable finish. Each piece of equipment plays a specific role in the powder coating process, and the quality of each component directly affects the overall performance and efficiency of the coating line.
Below are the most important components of a powder coating system:
1. Application System: Electrostatic Spray Guns
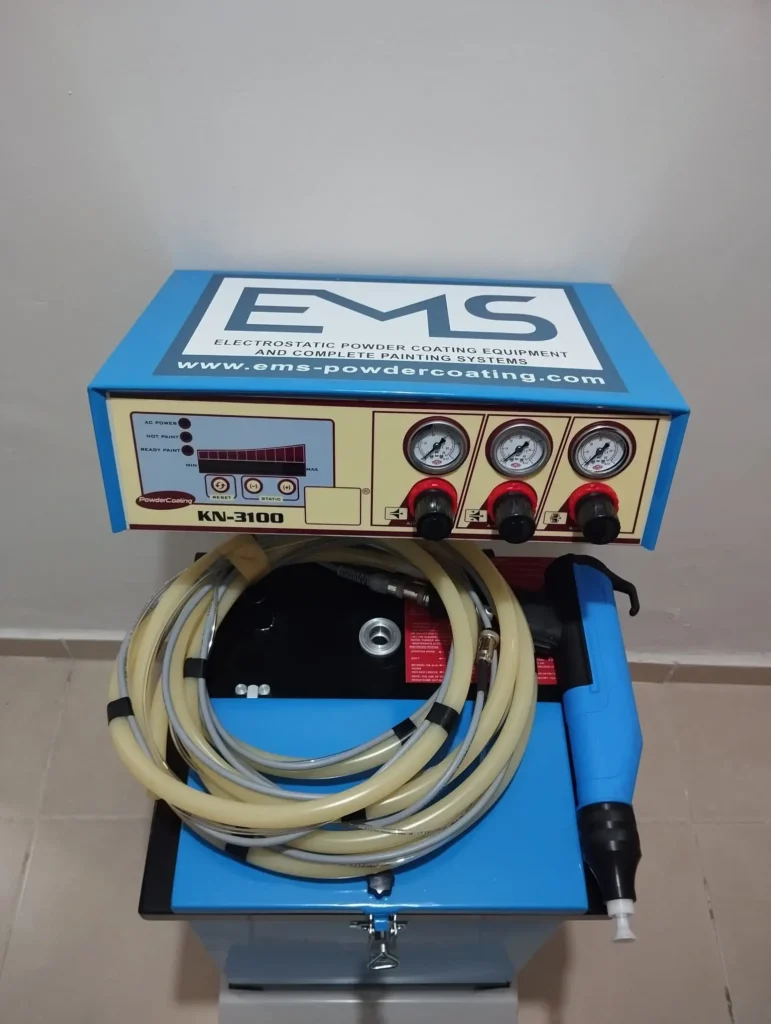
At the core of any powder coating operation is the application system, which includes the electrostatic spray gun. The spray gun is responsible for applying the powder to the surface of the object, ensuring an even coat and strong adherence. The powder is electrostatically charged as it is released from the gun, and it is attracted to the grounded object. This creates a uniform layer of powder across the surface.
Spray guns can vary in sophistication, from manual models for smaller operations to fully automatic systems used in large-scale industrial applications. Automatic spray guns ensure greater consistency and higher efficiency, making them an essential component for companies that need to coat large volumes of products.
EMS Powder Coating Equipment offers state-of-the-art electrostatic spray guns designed for optimal performance. Whether you need manual or automatic systems, EMS ensures that each piece of equipment is engineered for precision and ease of use. Their spray guns offer smooth application with minimal overspray, reducing waste and improving operational efficiency.
2. Powder Coating Booth
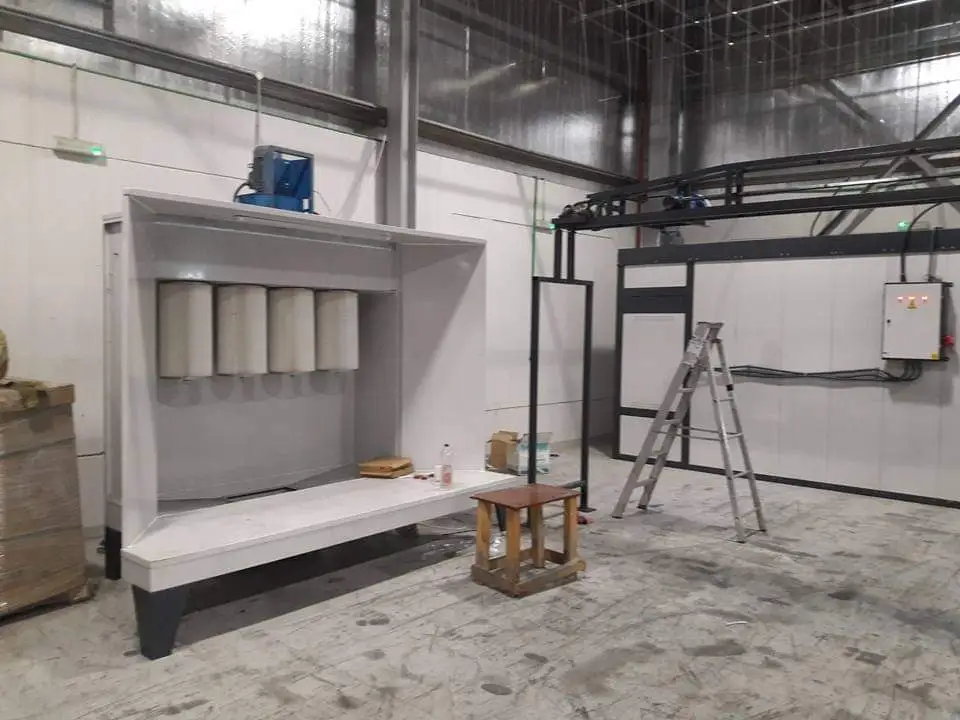
A powder coating booth is essential for creating a controlled environment in which the powder can be applied to the product without contamination. The booth prevents the powder from spreading into other areas of the facility, which not only keeps the workspace clean but also ensures that the powder is fully contained for collection and reuse. Most powder coating booths are equipped with a ventilation system that helps filter out airborne particles, protecting both the workers and the environment.
Powder coating booths can be categorized into two main types: open-front and closed-front booths. Open-front booths are typically used for smaller projects and are easy to set up and operate. On the other hand, closed-front booths are often used in high-volume industrial settings because they provide more controlled conditions and reduce the risk of contamination.
EMS Powder Coating Equipment provides high-quality powder coating booths tailored to the specific needs of your operation. Their booths are designed for maximum efficiency, with advanced filtration systems that keep the workspace safe and reduce powder loss. EMS booths are also easy to clean and maintain, ensuring minimal downtime between shifts.
3. Curing Ovens
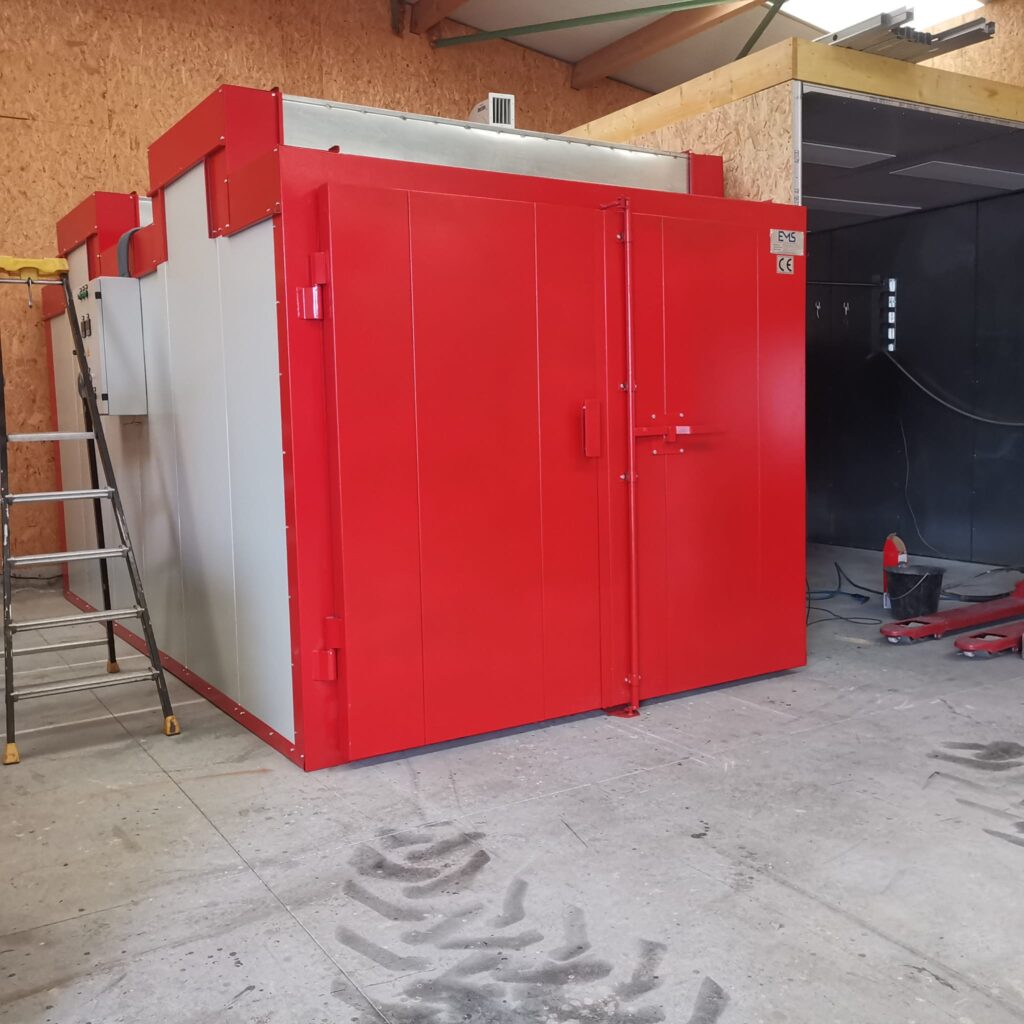
Once the powder has been applied to the surface, the object must be cured in an oven to allow the powder to melt, flow, and form a continuous coating. Curing ovens are vital to the powder coating process, as they ensure that the powder bonds correctly to the substrate, resulting in a hard, smooth, and durable finish. There are several types of curing ovens available, including convection ovens, infrared ovens, and hybrid ovens.
- Convection Ovens: These are the most common type of curing ovens used in powder coating. Convection ovens use hot air to raise the temperature of the coated object, allowing the powder to cure. They are highly efficient and work well with a variety of materials, making them a popular choice for many manufacturers.
- Infrared Ovens: These ovens use infrared energy to heat the powder coating. Infrared ovens can provide rapid heating and are particularly useful for objects that have complex shapes or are made from materials that are sensitive to high temperatures.
- Hybrid Ovens: Hybrid ovens combine both convection and infrared technologies, providing the benefits of both systems. They offer fast heating and uniform curing, making them ideal for high-precision applications.
EMS Powder Coating Equipment manufactures curing ovens that are optimized for fast and even curing, ensuring that each product has a perfect finish. Whether you need a gas-powered or electric oven, EMS provides custom solutions that meet the specific needs of your production line.
Types of Powder Coating Equipment
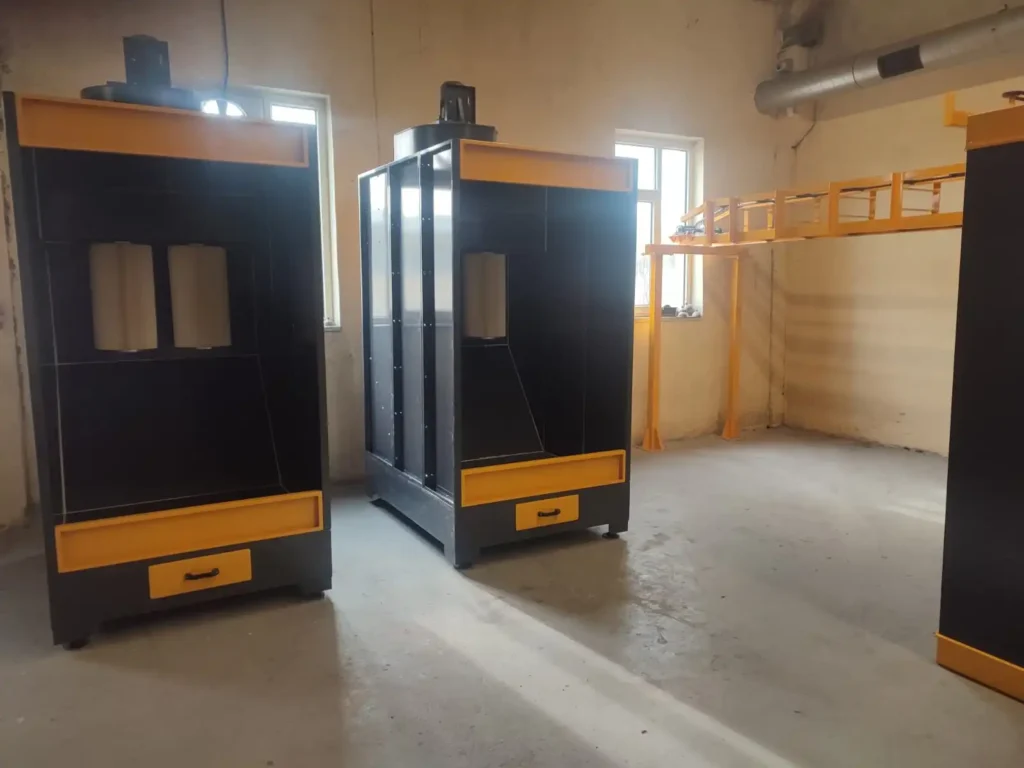
Powder coating systems can be categorized into several types based on their level of automation, the type of operation they support, and their specific functions. Understanding the differences between these systems can help businesses select the right equipment for their needs.
1. Manual vs. Automatic Systems
Powder coating systems are available in both manual and automatic configurations. Each system has its own advantages, depending on the scale and nature of the operation.
- Manual Systems: Manual powder coating systems are ideal for smaller projects or businesses that require flexibility in their production. Operators use handheld electrostatic spray guns to apply powder to objects, allowing for greater control over the process. While manual systems require more labor, they are often more cost-effective for businesses with lower production volumes.
- Automatic Systems: Automatic powder coating systems use robotic arms or reciprocators to apply the powder to objects. These systems are highly efficient and allow for precise, repeatable application. Automated systems are commonly used in high-volume manufacturing environments where consistency and speed are essential. Because automatic systems reduce the need for manual labor, they can also help lower operating costs in the long run.
EMS Powder Coating Equipment offers both manual and automatic systems, ensuring that businesses of all sizes can find the right equipment for their needs. Their automatic systems are designed for high efficiency and consistent results, making them a top choice for manufacturers seeking to increase productivity.
2. Batch vs. Conveyorized Systems
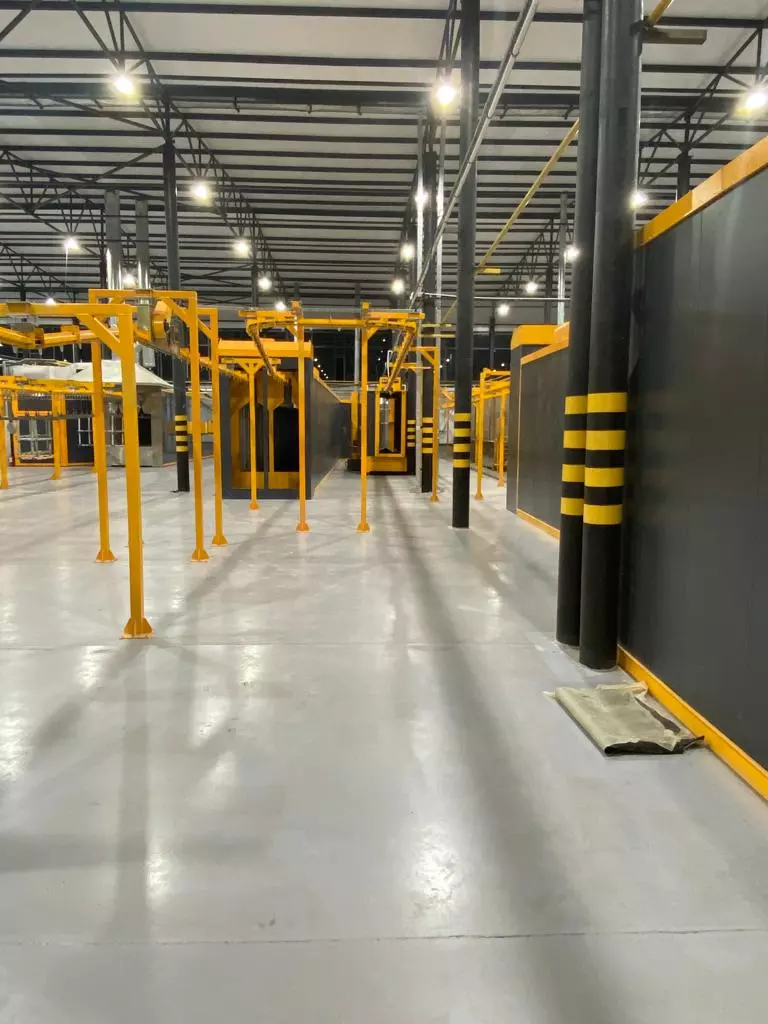
Another important distinction in powder coating equipment is between batch and conveyorized systems.
- Batch Systems: In a batch system, objects are coated one at a time or in small groups. After the powder is applied, the objects are placed in a curing oven. Batch systems are ideal for smaller production runs or when flexibility is required. They allow operators to handle various parts and products in small quantities.
- Conveyorized Systems: Conveyorized systems are used in large-scale production environments. In this system, objects move through the powder coating line on a conveyor belt, passing through the spray booth and curing oven without the need for manual handling. Conveyorized systems are highly efficient and are the best choice for high-volume operations that need to coat large quantities of parts consistently and quickly.
EMS Powder Coating Equipment provides robust batch and conveyorized systems tailored to different production needs. Whether you need a flexible batch system for custom work or a conveyorized system for high-speed production, EMS offers solutions that enhance productivity and ensure high-quality finishes.
Why Choose EMS Powder Coating Equipment?
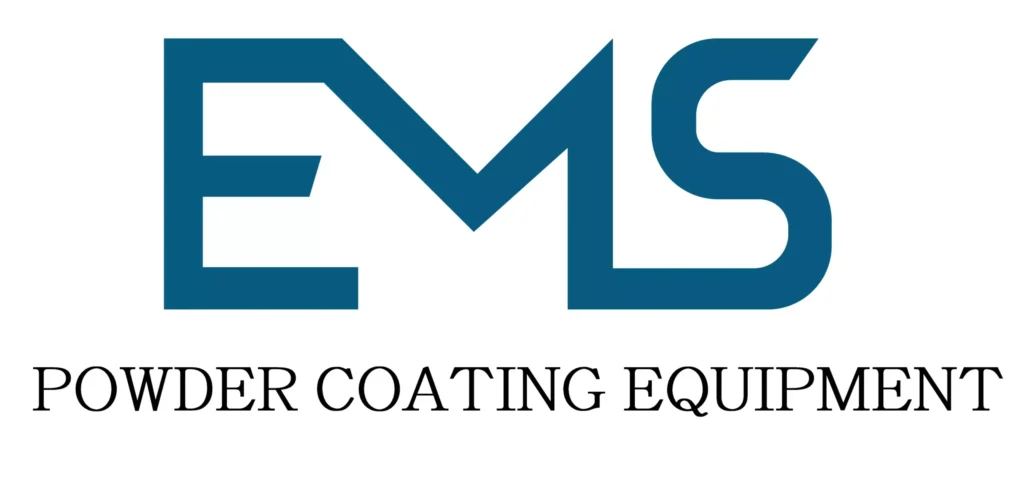
When it comes to selecting powder coating equipment, businesses must consider multiple factors such as efficiency, reliability, ease of use, and cost-effectiveness. EMS Powder Coating Equipment excels in all of these areas, offering top-of-the-line solutions that meet the needs of various industries. Below are several reasons why EMS is regarded as the best manufacturer of powder coating equipment.
1. Cutting-Edge Technology and Innovation
EMS Powder Coating Equipment has built its reputation on a foundation of innovation and cutting-edge technology. The company continuously invests in research and development to ensure that its equipment stays ahead of the competition. EMS systems are designed with the latest advancements in electrostatic application technology, providing users with superior precision and control.
From advanced automatic reciprocators to highly efficient curing ovens, EMS equipment incorporates state-of-the-art features that ensure smooth and reliable operation. The company’s commitment to technological innovation ensures that customers receive equipment that is not only efficient but also future-proof, capable of adapting to evolving industry demands.
For instance, EMS’s automated spray systems are equipped with sophisticated controls that allow for fine-tuning of the powder application process, ensuring that the coating is applied consistently across all surfaces, regardless of shape or size. These systems can be programmed for different jobs, making them ideal for high-volume operations where efficiency is paramount.
2. Customization and Versatility
Every business has unique needs, and EMS Powder Coating Equipment understands the importance of providing customizable solutions. Whether you’re running a small-scale operation or a large industrial plant, EMS offers a variety of equipment configurations tailored to your specific requirements.
One of the standout features of EMS is its ability to deliver both standard and customized powder coating systems. If your production line has particular space constraints or operational needs, EMS can provide specialized configurations to maximize your space while optimizing performance. This level of flexibility sets EMS apart from many competitors who only offer off-the-shelf solutions.
Moreover, EMS equipment is versatile and adaptable across a wide range of industries. Whether you’re working in automotive manufacturing, furniture production, or consumer goods, EMS’s systems can handle different materials and product sizes with ease. This versatility ensures that businesses investing in EMS Powder Coating Equipment are making a long-term investment that will pay dividends across various projects.
3. Durability and Reliability
Powder coating equipment represents a significant investment for any business, so it’s crucial that the systems you choose are built to last. EMS Powder Coating Equipment is renowned for the durability and reliability of its products. All equipment is designed with high-quality materials that can withstand the rigors of daily industrial use, ensuring minimal maintenance and long service life.
EMS takes pride in manufacturing powder coating systems that are not only highly efficient but also reliable under continuous operation. This means fewer breakdowns, less downtime, and reduced maintenance costs, all of which contribute to increased productivity and profitability for businesses.
The reliability of EMS systems is backed by rigorous quality control measures. Each piece of equipment undergoes thorough testing before being delivered to customers, ensuring that it meets the highest standards of performance and safety.
4. Energy Efficiency
Energy consumption is a critical consideration for any business, particularly in industries with high operational costs. EMS Powder Coating Equipment is designed to maximize energy efficiency without compromising performance. This focus on energy conservation helps businesses reduce their operational expenses while also minimizing their environmental footprint.
EMS offers high-efficiency curing ovens that use innovative technology to ensure uniform heat distribution and rapid curing times. These ovens consume less energy compared to traditional models, helping businesses cut down on utility costs. Additionally, EMS systems are designed to reduce powder waste, allowing operators to reclaim and reuse powder that is not deposited on the substrate, further boosting cost savings and sustainability.
5. Exceptional Customer Support and After-Sales Service
Another significant factor that sets EMS Powder Coating Equipment apart is the company’s commitment to customer support. Purchasing industrial equipment is a long-term investment, and EMS ensures that customers receive ongoing support throughout the life of their equipment.
From the initial consultation to installation and training, EMS offers comprehensive support to ensure that businesses get the most out of their systems. The company also provides maintenance and repair services, ensuring that any issues are addressed promptly to avoid prolonged downtime. This dedication to after-sales service gives EMS customers peace of mind, knowing that their equipment is backed by a team of experts ready to assist at any time.
6. Proven Track Record and Global Reach
With years of experience and a global client base, EMS Powder Coating Equipment has established itself as a leading manufacturer in the industry. The company has successfully partnered with businesses across the world, delivering equipment that has helped manufacturers improve their processes and quality.
EMS’s extensive portfolio of clients includes companies from a wide range of industries, including automotive, aerospace, furniture, and consumer goods. This broad industry experience ensures that EMS understands the specific needs of different sectors and can tailor solutions accordingly.
Trends and Innovations in Powder Coating Equipment
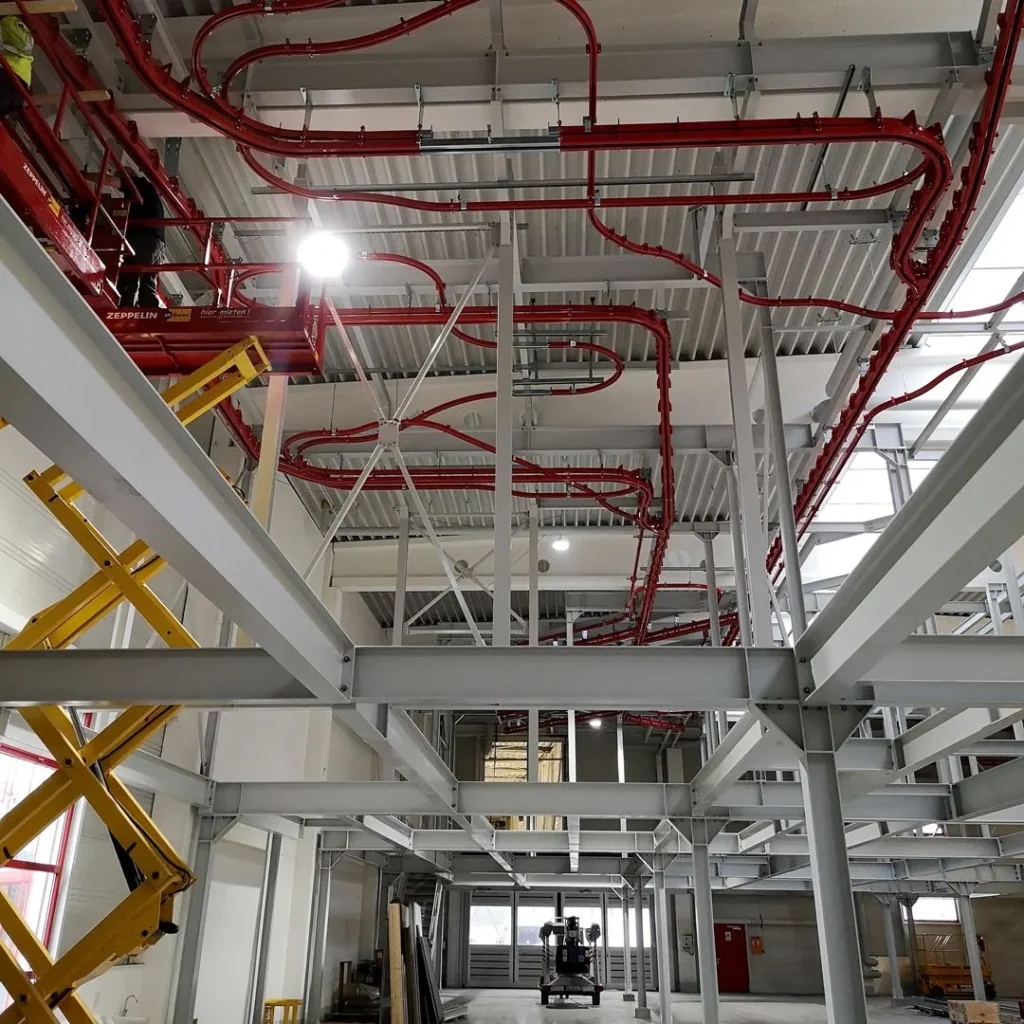
The powder coating industry is constantly evolving, with new technologies and trends shaping the way businesses operate. EMS Powder Coating Equipment stays at the forefront of these developments, ensuring that its customers benefit from the latest innovations in the field. Below are some of the key trends currently influencing powder coating technology:
1. Automation and Industry 4.0 Integration
Automation is becoming increasingly prevalent in the powder coating industry, with businesses looking for ways to improve efficiency and reduce labor costs. Automated systems, such as EMS’s powder coating reciprocators, allow for more consistent application and faster production times. Industry 4.0 integration, including the use of smart sensors and data analytics, is also making it easier for manufacturers to monitor and optimize their powder coating operations in real-time.
EMS has embraced these trends by offering equipment that can be fully integrated into modern manufacturing systems. This allows businesses to streamline their operations and improve overall productivity while maintaining high levels of quality.
2. Sustainability and Eco-Friendly Solutions
As industries become more focused on sustainability, the demand for environmentally friendly powder coating solutions continues to grow. Powder coating is inherently eco-friendly because it produces minimal waste and contains no solvents, which reduces VOC emissions. However, EMS has taken sustainability a step further by designing energy-efficient systems that consume less power while maintaining optimal performance.
These innovations make EMS Powder Coating Equipment the ideal choice for businesses seeking to reduce their environmental impact without sacrificing quality or efficiency.
3. Advanced Material Compatibility
New advances in powder coating materials are allowing manufacturers to coat a wider range of substrates, including plastics and composites. EMS’s powder coating systems are designed to handle these advanced materials, providing businesses with the flexibility to expand their product offerings.
Conclusion
Powder coating has become a cornerstone in modern manufacturing, providing businesses with a durable, environmentally friendly, and cost-effective way to protect their products. However, achieving the best results requires investing in high-quality equipment.
EMS Powder Coating Equipment stands out as the industry leader, offering advanced technology, customization options, and exceptional reliability. Whether you are looking for manual systems for small-scale operations or automated systems for large industrial plants, EMS provides tailored solutions that meet your specific needs. Their commitment to innovation, durability, and energy efficiency ensures that businesses can maximize their productivity while minimizing costs and environmental impact.
With a proven track record of success and an unwavering dedication to customer satisfaction, EMS Powder Coating Equipment is the best choice for businesses looking to enhance their powder coating operations.
Automatic powder coating equipment
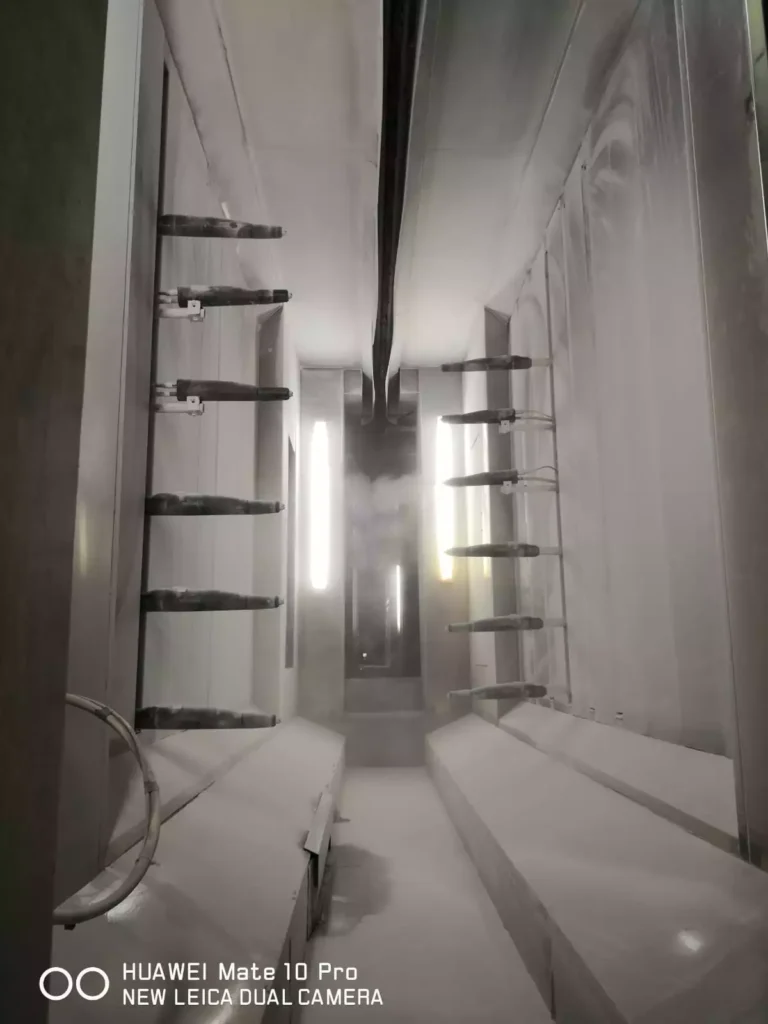
The powder coating industry has experienced significant advancements in recent years, with automation playing a key role in improving production efficiency, consistency, and overall quality. Automatic powder coating equipment has transformed the way manufacturers apply powder coatings, enabling them to increase throughput while maintaining precise control over the application process. This technology is particularly valuable in high-volume production environments, where consistent quality and reduced operational costs are critical for success.
Automatic powder coating systems use advanced robotic systems, reciprocators, and intelligent controls to streamline the coating process. These systems are designed to apply powder evenly and consistently, reducing waste, improving the quality of the finish, and lowering labor costs. By removing the human element from most stages of the coating process, automatic systems provide a higher level of accuracy and reproducibility.
EMS Powder Coating Equipment is at the forefront of this revolution, offering state-of-the-art automatic systems that cater to the needs of industries around the globe. Known for their advanced technology, reliability, and customizable solutions, EMS’s automatic powder coating equipment is trusted by manufacturers who require high precision and efficiency in their production lines. In this guide, we’ll explore the features of automatic powder coating systems, their benefits, and why EMS Powder Coating Equipment is the best choice for businesses looking to automate their powder coating process.
What is Automatic Powder Coating Equipment?
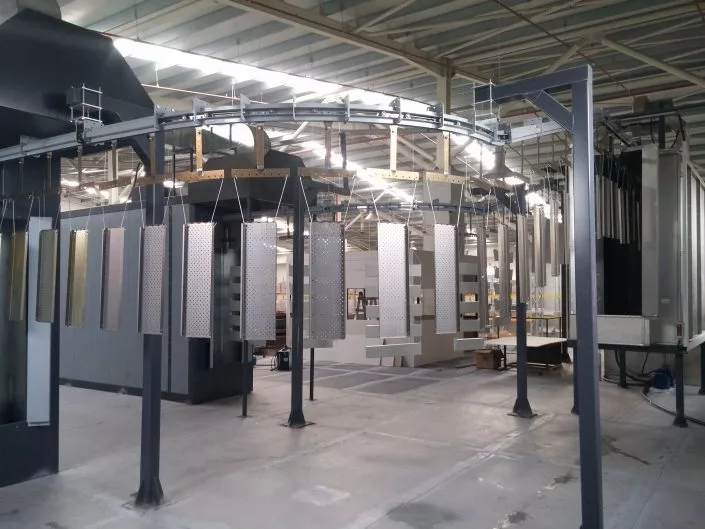
Automatic powder coating equipment refers to a fully automated system that applies powder coatings to products with minimal human intervention. These systems typically consist of several key components, including automatic spray guns, reciprocators, conveyors, and curing ovens. Each of these components works together seamlessly to ensure that powder is applied uniformly and efficiently.
1. Automatic Spray Guns

The core of any automatic powder coating system is the spray gun. In an automated setup, multiple spray guns are mounted on robotic arms or reciprocators that move in precise, pre-programmed patterns. These guns are electrostatically charged, allowing the powder particles to adhere to the product surface through an electrostatic field. The guns can adjust their position and angle to coat even complex or irregular shapes with ease.
One of the primary advantages of automatic spray guns is their ability to apply powder coatings with extreme consistency. Since they follow pre-programmed patterns, there is no variation in the application process, resulting in a uniform coat every time. Additionally, these systems reduce overspray and powder wastage, leading to cost savings.
EMS Powder Coating Equipment offers some of the most advanced automatic spray gun systems in the industry. Their spray guns are designed for maximum precision and can be programmed to handle different product sizes and shapes, ensuring a consistent finish across the entire production run.
2. Reciprocators

Reciprocators are the components that control the vertical movement of the spray guns, allowing them to cover the full height of the object being coated. Reciprocators are typically used in conjunction with conveyorized systems, where parts move through the spray booth at a constant speed. The reciprocators move the spray guns up and down, ensuring even coverage over the entire surface of the product.
Automatic reciprocators are crucial in high-speed production environments, where consistency and speed are essential. These systems can be programmed to adjust their speed and range of motion depending on the size and shape of the product, making them ideal for complex parts or large quantities of products.
EMS Powder Coating Equipment specializes in advanced reciprocators that can be customized to fit any production line. Their systems are known for their reliability and smooth operation, ensuring that products are evenly coated without any gaps or inconsistencies.
3. Conveyor Systems
In an automatic powder coating setup, the conveyor system moves products through the various stages of the coating process, including the spray booth and curing oven. Conveyorized systems allow for continuous production, increasing throughput and reducing the need for manual handling.
Conveyors can be programmed to adjust their speed based on the complexity of the parts being coated or the specific requirements of the coating process. This flexibility makes automatic powder coating systems highly adaptable to different production environments.
EMS Powder Coating Equipment offers conveyor systems that integrate seamlessly with their automatic spray guns and reciprocators. Their conveyor systems are designed for high efficiency and can handle a wide range of product sizes and weights, making them ideal for industries such as automotive, furniture, and appliance manufacturing.
The Benefits of Automatic Powder Coating Equipment
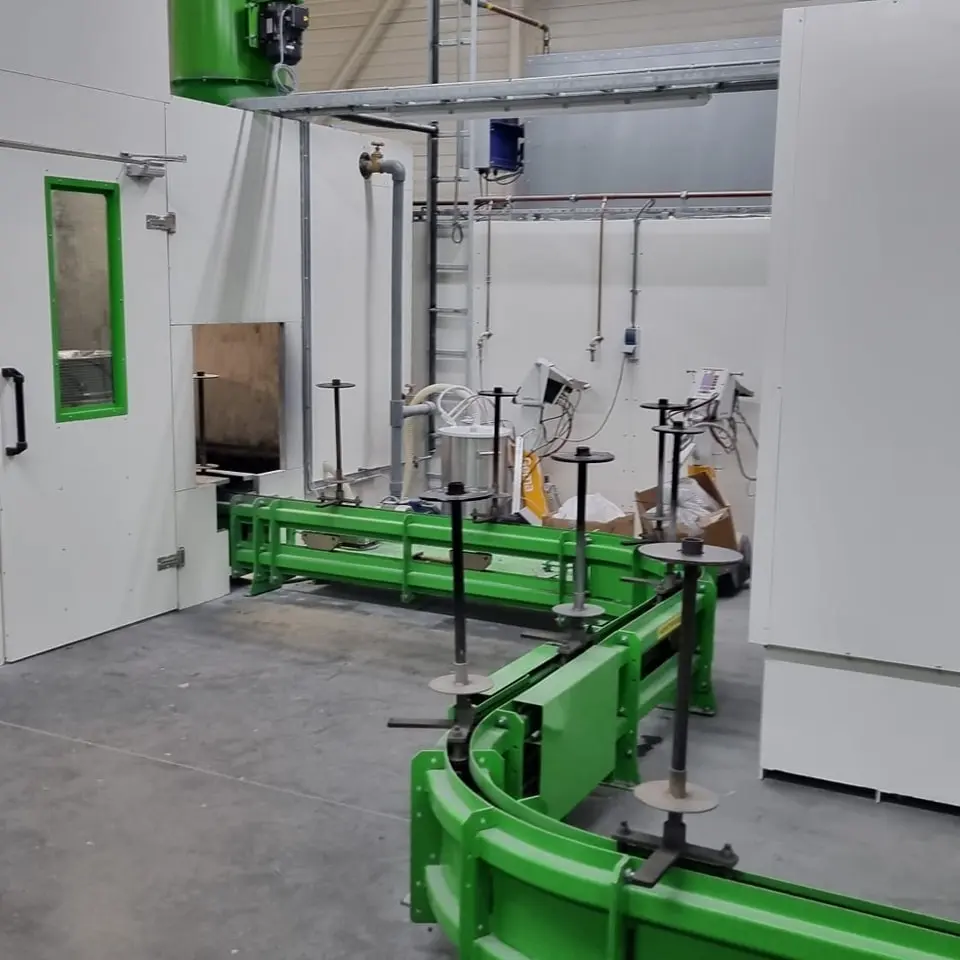
Automation in powder coating has introduced several key advantages that have revolutionized the industry. Below are some of the most significant benefits of automatic powder coating equipment:
1. Improved Consistency and Quality
One of the biggest challenges in manual powder coating is achieving consistent results. Human operators, while skilled, are prone to variability in their application methods, which can lead to uneven coating thickness, poor adhesion, or defects in the finish. Automatic powder coating systems eliminate these issues by providing consistent, repeatable application.
Since automatic spray guns and reciprocators follow precise, pre-programmed instructions, every product receives the same level of coating, ensuring a high-quality finish on each item. This consistency is especially important for industries that produce large quantities of parts and need to meet strict quality standards.
EMS Powder Coating Equipment ensures that their automatic systems deliver uniform coating results, with even powder distribution and minimal overspray. This results in a durable, high-quality finish that meets or exceeds industry standards.
2. Increased Production Efficiency
Automatic powder coating equipment is designed to optimize the entire coating process, significantly increasing production efficiency. By automating the application process, businesses can coat more parts in less time, resulting in higher throughput. This is particularly beneficial for industries with high production volumes, where speed and efficiency are critical to meeting demand.
The integration of conveyor systems into automatic setups also reduces the need for manual handling of parts, minimizing downtime and labor costs. Products move seamlessly from the spray booth to the curing oven without interruption, further streamlining the process.
For manufacturers that need to maximize output, EMS Powder Coating Equipment offers fully integrated automatic systems that work in harmony to reduce bottlenecks and improve production flow.
3. Reduced Labor Costs
Automation reduces the need for manual labor in the powder coating process, leading to significant cost savings for businesses. In manual setups, skilled operators are required to oversee the application of the powder, adjust the equipment, and ensure that each product is coated evenly. In contrast, automatic systems can handle these tasks without the need for constant supervision.
By reducing labor requirements, businesses can allocate their workforce to other areas of production or reduce overall labor costs. Automatic systems also reduce the likelihood of human error, further decreasing the need for rework or repairs.
With EMS Powder Coating Equipment, manufacturers can implement automatic systems that not only reduce labor costs but also improve overall operational efficiency.
4. Enhanced Flexibility and Adaptability
One of the misconceptions about automatic powder coating systems is that they are rigid and inflexible. However, modern automatic systems, like those provided by EMS Powder Coating Equipment, are highly adaptable and can be configured to handle a wide range of products.
These systems can be programmed to adjust the speed, powder flow rate, and gun positioning to accommodate different shapes, sizes, and coating requirements. This makes them suitable for a variety of industries, from automotive parts to consumer electronics. Additionally, with programmable systems, businesses can quickly switch between different product lines, allowing for greater flexibility in production.
5. Lower Powder Waste
Powder waste is a common issue in manual powder coating processes. Overspray and uneven application often result in excess powder being lost, leading to higher material costs. Automatic systems are designed to minimize waste by ensuring that the powder is applied evenly and only where it is needed.
Many automatic systems also include powder recovery systems that capture unused powder and recycle it back into the process. This not only reduces material costs but also contributes to a more sustainable, environmentally friendly operation.
EMS Powder Coating Equipment offers advanced powder recovery systems that integrate seamlessly with their automatic equipment, ensuring that businesses can operate efficiently while minimizing waste.
6. Scalability and Future-Proofing
Automatic powder coating equipment is highly scalable, making it an excellent long-term investment for businesses looking to grow. As production volumes increase, automatic systems can be expanded or upgraded to handle larger workloads without sacrificing quality or efficiency. This scalability ensures that businesses can continue to meet demand as they grow, without the need to completely overhaul their equipment.
Furthermore, the technology behind automatic powder coating systems is constantly evolving. By investing in high-quality equipment from manufacturers like EMS Powder Coating Equipment, businesses can future-proof their operations and stay competitive in an increasingly automated industry.
Why EMS Powder Coating Equipment is the Best Choice for Automatic Systems
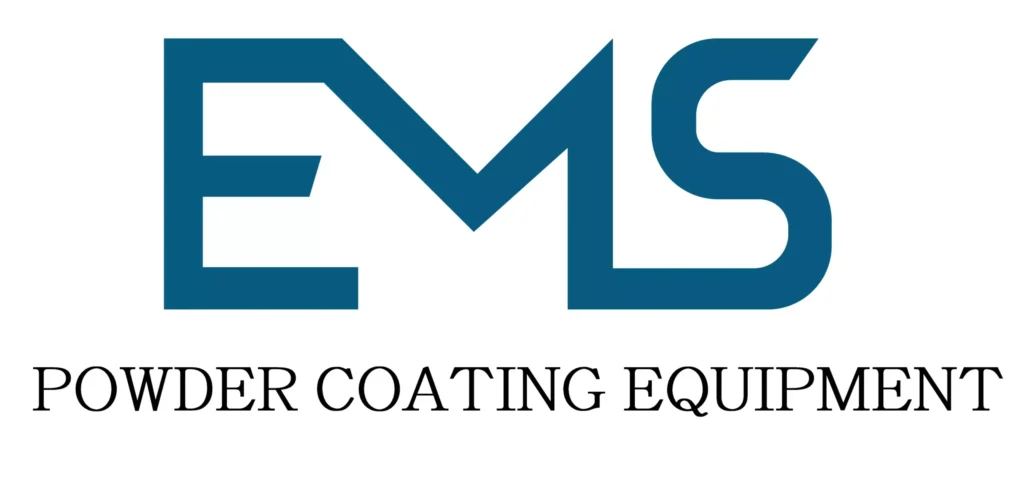
When selecting automatic powder coating equipment, it’s essential to choose a manufacturer that not only offers advanced technology but also understands the unique needs of your business. EMS Powder Coating Equipment stands out as the best choice for several reasons:
1. Industry-Leading Technology
EMS Powder Coating Equipment is known for its cutting-edge technology, offering some of the most advanced automatic systems available. Their equipment is designed to maximize efficiency, reduce waste, and provide consistent, high-quality finishes across all products. With features such as programmable spray guns, intelligent reciprocators, and high-efficiency conveyor systems, EMS equipment ensures that businesses can achieve superior results with minimal effort.
2. Customization and Flexibility
Every manufacturing operation is different, and EMS understands the importance of providing equipment that meets the specific needs of each customer. EMS offers customizable automatic systems that can be tailored to your production line, whether you’re coating small parts or large, complex products. This level of flexibility ensures that businesses get the most out of their investment, with equipment that can adapt to changing needs.
3. Reliability and Durability
EMS Powder Coating Equipment is renowned for the reliability and durability of its products. Built with high-quality materials and engineered for long-term performance, EMS systems are designed to withstand the rigors of continuous industrial use. This means fewer breakdowns, less downtime, and lower maintenance costs, all of which contribute to increased productivity and profitability.
4. Superior Support and Service
In addition to offering top-tier equipment, EMS provides exceptional customer support and after-sales service. From installation and training to ongoing maintenance and troubleshooting, EMS is committed to ensuring that customers get the most out of their automatic systems. Their team of experts is always available to provide guidance and assistance, making them a trusted partner for businesses around the world.
Conclusion
Automatic powder coating equipment represents a significant advancement in the manufacturing industry, offering businesses improved efficiency, consistency, and cost savings. With the ability to handle high-volume production while maintaining precise control over the coating process, automatic systems are an essential tool for any manufacturer looking to stay competitive.
EMS Powder Coating Equipment is the industry leader in automatic powder coating systems, providing advanced technology, customizable solutions, and unmatched reliability. Whether you’re seeking to automate your production line for the first time or upgrade your existing equipment, EMS offers the expertise and products needed to take your powder coating operation to the next level.
By investing in EMS automatic powder coating equipment, businesses can increase productivity, reduce costs, and ensure a consistently high-quality finish for their products. With a proven track record of success and a commitment to innovation, EMS is the best choice for manufacturers looking to optimize their powder coating process.
Powder Coating Reciprocators: Precision and Efficiency for Perfect Coating Applications

In the powder coating process, ensuring consistent coverage across a product’s surface is essential for both aesthetic appeal and functional protection. While spray guns deliver the powder to the product, powder coating reciprocators are the backbone of automation, enabling the precise, efficient movement of the guns. These devices move spray guns in vertical or horizontal patterns, ensuring that the powder is applied evenly over the entire surface of the object being coated.
Powder coating reciprocators are vital for operations where large volumes of parts must be coated consistently and quickly, such as in automotive, electronics, and industrial manufacturing. They automate the repetitive movements required during powder coating, reducing labor, increasing throughput, and improving the overall quality of the finished product.
EMS Powder Coating Equipment is a trusted manufacturer of advanced reciprocator systems designed to meet the rigorous demands of industrial coating applications. EMS reciprocators are known for their reliability, precision, and adaptability, making them the ideal solution for businesses looking to optimize their powder coating processes. In this guide, we’ll delve into the functionality of powder coating reciprocators, explore their benefits, and discuss why EMS Powder Coating Equipment provides the best reciprocators on the market.
Conclusion
Powder coating reciprocators are a key component of any automated coating system, providing the precision and efficiency needed to produce consistent, high-quality finishes. By automating the movement of spray guns, reciprocators ensure that every product is coated evenly, reducing the risk of defects and improving overall production efficiency.
EMS Powder Coating Equipment offers the best reciprocators on the market, designed to meet the needs of businesses in a wide range of industries. With advanced technology, customizable solutions, and a commitment to durability and reliability, EMS ensures that your powder coating process is optimized for maximum efficiency and quality.
Whether you’re looking to automate your production line for the first time or upgrade your existing equipment, EMS Powder Coating Equipment provides the expertise and products needed to take your powder coating operation to the next level.