
A powder coating plant is a complex system where a part is coated and cured with automation. As a powder coating plant manufacturer, we design and build the best for our customers.
Powder coating is a dry finishing process that uses finely ground dry particles of pigment and resin to create a durable, hard, protective finish on a wide variety of surfaces. The powder is electrostatically charged and applied to the surface of the object to be coated, where it adheres and then cures under heat to form a hard, durable finish.
Powder coating plants are used to manufacture powder coating products. They typically include a number of different components, including:
- A powder coating booth: This is where the powder is applied to the object to be coated.
- A curing oven: This is where the powder is cured under heat to form a hard, durable finish.
- A powder recovery system: This system is used to recover any powder that does not adhere to the object to be coated.
- A pretreatment system: This system is used to clean and prepare the surface of the object to be coated for powder coating.
The specific components of a powder coating plant will vary depending on the type of products being manufactured and the desired production output.
Powder coating plants are typically used to manufacture products such as:
- Appliances: Powder coating is a popular choice for finishing appliances because it is durable, scratch-resistant, and easy to clean.
- Auto parts: Powder coating is also used to finish auto parts because it is resistant to corrosion and UV rays.
- Furniture: Powder coating is a good choice for finishing furniture because it is durable and easy to clean.
- Industrial equipment: Powder coating is used to finish industrial equipment because it is durable and can withstand harsh conditions.
Powder coating plants are a vital part of the manufacturing process for a variety of products. They offer a number of advantages over traditional liquid painting methods, including:
- Environmentally friendly: Powder coating does not use solvents, so it is more environmentally friendly than traditional liquid painting methods.
- Durable: Powder coating is a durable finish that is resistant to scratches, chipping, and fading.
- Easy to clean: Powder coating is easy to clean and maintain.
- Cost-effective: Powder coating can be a cost-effective way to finish a product.
If you are considering using powder coating to finish your products, you should contact a powder coating plant manufacturer to discuss your specific needs.
The electrostatic application of powder coating to a part begins with fluidization. Fluidization is a process where powder being sprayed mixes with compressed air, enabling it to be pumped from a container and supplied to the spray guns. The powder flow is regulated by controlling the air supplied to the pump. The powder supplied to the spray gun is charged using either a corona or tribocharging gun.
Charged powder moves to the grounded workpiece with the help of air supplied to the guns and the airflow in the booth. When the powder particles come close to the part, an electrostatic attraction between the charged powder particles and the grounded part adheres the powder to the part. The coated part then passes through an oven and is cured. The oversprayed powder is contained within an enclosure and drawn into the primary filter cartridges by a centrifugal fan.
Circulating air, now free of powder, is discharged through high-efficiency final filters into the plant as clean air. The primary filter cartridges are periodically reverse-pulsed to remove oversprayed powder. The powder is then sieved and supplied back to the guns to provide extremely efficient material for use again. A simple diagram showing how these process works is shown in Figure 1
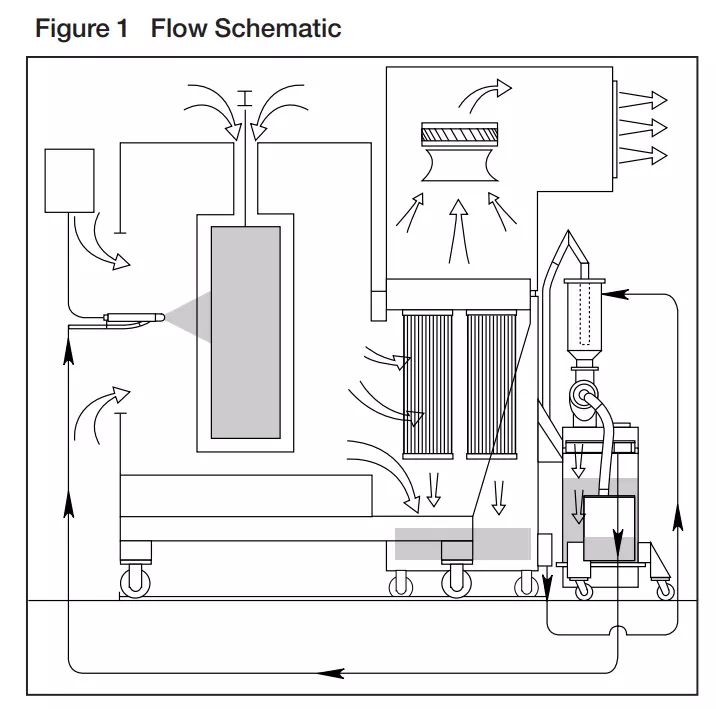
Powder coating is increasingly accepted as the preferred finishing process for many applications. Increasingly stringent environmental regulations, rising costs in all areas, and demands by consumers for better quality and more durable products are among the challenges facing today’s finishers. Powder coatings provide a solution to these challenges and others. Powder coating is the technique of applying dry paint to the component.
The powdered paint is normally applied by using a powder feed system and gun to electrostatically charge and spray the powder onto the part. For some applications, the part being coated is dipped into a fluidized bed of powder. The coated part is then heated in an oven, or via infrared panels, to melt and cure the paint. During the curing process, a chemical cross-linking reaction is triggered and it is this chemical reaction that gives the powder coatings many of their desirable properties.
Powder Coating Plant Manufacturer
A powder coating plant is a facility that houses the equipment and processes necessary to apply powder coating to various substrates, such as metals, plastics, and composites. These plants typically consist of several stages, including pre-treatment, powder application, curing, and post-treatment.
Key Components of a Powder Coating Plant
- Pre-Treatment System: This system prepares the workpiece surface for powder adhesion by removing contaminants like grease, oil, and rust. It may involve degreasing, etching, phosphating, and rinsing.
- Powder Booth: The powder booth provides a controlled environment for applying the powder coating, preventing overspray and contamination of the surrounding environment. It typically includes walls, a ceiling, a floor grate, an exhaust system, and powder coating guns.
- Powder Coating Guns: These guns apply the powder onto the workpieces using electrostatic or mechanical principles. Electrostatic guns impart a charge to the powder particles, attracting them to the grounded workpiece, while mechanical guns rely on air pressure to atomize and propel the powder.
- Reciprocator or Robot Arm: This device moves the powder coating guns back and forth over the workpieces, ensuring uniform and consistent powder distribution. Reciprocators are typically used for flat or evenly shaped workpieces, while robot arms offer greater flexibility for complex shapes.
- Curing Oven: The curing oven cures the applied powder coating, transforming it into a durable and hard finish. It heats the powder particles to a specific temperature for a specified time, allowing them to melt, flow, and crosslink.
- Workpiece Handling System: This system transports the workpieces through the various stages of the powder coating process, maintaining proper positioning and orientation. It may involve conveyor belts, rotating turntables, or automated robotic systems.
- Control System: The control system oversees the entire powder coating process, coordinating the operation of the different components, regulating the powder application, and monitoring the curing parameters.
- Powder Recovery System: This system collects overspray powder, reducing waste and allowing for powder reuse. It may involve cyclones, filters, or a combination of both.
Stages of the Powder Coating Process
- Pre-Treatment: The workpiece surface is cleaned and prepared to ensure proper powder adhesion.
- Powder Application: Electrostatic or mechanical guns apply a thin layer of powder coating to the pre-treated workpiece.
- Curing: The powder-coated workpiece is heated in an oven to cure the powder, transforming it into a durable and hard finish.
- Post-Treatment: The cured workpiece may undergo additional processing, such as inspection, packaging, or shipping.
Applications of Powder Coating Plants
Powder coating is widely used in various industries, including:
- Automotive: Coating car parts, such as bumpers, wheels, and frames, with durable and corrosion-resistant powder coatings.
- Appliance Industry: Providing a high-quality finish and protection for appliances, such as refrigerators, stoves, and washing machines.
- Furniture Industry: Enhancing the aesthetic appeal and durability of furniture pieces, such as chairs, tables, and cabinets.
- Electronics Industry: Protecting electronic components from corrosion and providing a smooth aesthetic finish.
- Construction Industry: Coating metal components, such as railings, pipes, and fittings, with durable and weather-resistant powder coatings.
- Aerospace Industry: Applying high-performance powder coatings to aircraft parts that demand exceptional strength and corrosion resistance.
Benefits of Powder Coating Plants
Powder coating offers several advantages over traditional liquid painting methods:
- Durable and Protective Finish: Powder coating provides a superior level of durability compared to paint, withstanding chipping, scratches, and fading.
- Environmentally Friendly: Powder coating is a solvent-free process, minimizing environmental impact.
- Efficient Powder Utilization: Powder recovery systems collect overspray powder, reducing waste and allowing for powder reuse.
- Consistent Coating Quality: Automated powder coating systems ensure uniform and consistent powder distribution, resulting in high-quality finishes.
- Versatility: Powder coating can be applied to a wide range of substrates and can achieve a variety of finishes.
Conclusion
Powder coating plants play a crucial role in various industries, providing a versatile and environmentally friendly method for applying durable and protective coatings to a wide range of products. By utilizing advanced technology and efficient processes, powder coating plants contribute to enhanced product quality, sustainability, and environmental protection.
Powder Application Transfer Efficiency of a Powder Coating Plant
Powder application transfer efficiency (PATE) is the percentage of powder that is transferred from the delivery system to the substrate. It is an important factor in determining the cost-effectiveness of powder coating, as it affects the amount of powder that is wasted.
There are a number of factors that can affect PATE, including:
- Powder properties: The properties of the powder, such as particle size, shape, and density, can affect how well it transfers to the substrate.
- Delivery system: The type of delivery system used, such as a spray gun or electrostatic applicator, can also affect PATE.
- Substrate properties: The properties of the substrate, such as its surface roughness and porosity, can also affect PATE.
- Application parameters: The application parameters, such as spray distance, air pressure, and voltage, can also affect PATE.
In general, a PATE of 60-80% is considered to be good. However, PATE can be as low as 40% for some applications.
There are a number of things that can be done to improve PATE, including:
- Using a high-quality powder: A high-quality powder will have a more uniform particle size and shape, which will improve transfer efficiency.
- Using a properly maintained delivery system: A properly maintained delivery system will help to ensure that the powder is applied consistently and evenly.
- Pretreating the substrate: Pretreating the substrate will help to improve surface adhesion and reduce the amount of powder that is wasted.
- Using the correct application parameters: Using the correct application parameters will help to ensure that the powder is applied evenly and that the correct amount of powder is used.
By improving PATE, you can reduce the amount of powder that is wasted, improve the quality of the finish, and save money.
Here are some additional tips for improving PATE:
- Use a backstop: A backstop will help to prevent overspray and reduce the amount of powder that is wasted.
- Use a powder recovery system: A powder recovery system will collect any powder that does not adhere to the substrate and recycle it for reuse.
- Train your employees: Make sure that your employees are trained on the proper powder coating techniques.
- Monitor your results: Regularly monitor your PATE to identify areas for improvement.
By following these tips, you can improve the PATE of your powder coating plant and save money.
What is first-pass transfer efficiency? It is defined as the amount of powder applied to the part compared to the total amount of powder sprayed by the application equipment. There are many variables to consider in achieving first-pass transfer efficiency. These variables and the applications that can affect first-pass transfer efficiency are discussed in the following pages of this article.
Powder Coating Gun and Nozzle Design
Powder coating gun and nozzle design plays a crucial role in achieving uniform powder deposition and a high-quality finish. The nozzle, in particular, influences the powder flow, atomization, and transfer efficiency. Here’s a detailed overview of powder coating gun and nozzle design:
Powder Coating Gun Design
A powder coating gun consists of several components that work together to deliver and apply powder particles to a substrate. These components include:
- Feed hopper: The feed hopper holds the powder and feeds it into the gun.
- Fluidized bed: The fluidized bed agitates the powder particles, preventing them from clumping and ensuring a consistent flow.
- Injection nozzle: The injection nozzle introduces the powder particles into the air stream.
- Air cap: The air cap shapes and directs the air stream, influencing the powder atomization and spray pattern.
- Electrostatic charge unit: The electrostatic charge unit applies a positive or negative charge to the powder particles, enhancing their attraction to the grounded substrate.
- Trigger mechanism: The trigger mechanism controls the flow of powder and air.
Nozzle Design
The nozzle plays a critical role in achieving the desired powder deposition and finish. Nozzle design considerations include:
- Nozzle shape: The shape of the nozzle, such as round, fan, or deflected, determines the spray pattern and the thickness of the powder coat.
- Nozzle orifice size: The orifice size affects the amount of powder being delivered and the powder particle size after atomization.
- Nozzle material: The nozzle material should be durable, wear-resistant, and compatible with the powder being used.
- Nozzle positioning: The nozzle should be positioned correctly relative to the substrate to ensure uniform powder deposition and avoid overspray.
Factors Affecting Powder Coating Gun and Nozzle Performance
Several factors influence the performance of powder coating guns and nozzles, including:
- Powder properties: Particle size, shape, and density of the powder affect its flow behavior and atomization.
- Air pressure: Air pressure controls the velocity of the air stream, influencing powder atomization and transfer efficiency.
- Electrostatic voltage: Electrostatic voltage enhances powder attraction to the substrate, reducing overspray and improving transfer efficiency.
- Spray distance: Spray distance affects the powder deposition pattern and the thickness of the powder coat.
- Substrate properties: Surface roughness, porosity, and cleanliness of the substrate influence powder adhesion and finish quality.
Optimizing Powder Coating Gun and Nozzle Performance
To achieve optimal performance from powder coating guns and nozzles, consider the following practices:
- Regular maintenance: Clean and maintain the gun and nozzle regularly to prevent clogging and ensure consistent performance.
- Proper powder selection: Select powder with appropriate particle size and properties for the desired finish and application.
- Fine-tune spray parameters: Adjust air pressure, electrostatic voltage, and spray distance to achieve the desired powder deposition and transfer efficiency.
- Monitor nozzle wear: Replace nozzles regularly to maintain consistent performance and prevent defects.
- Train operators: Provide proper training to operators on powder coating techniques, gun maintenance, and spray parameter optimization.
By carefully considering the design, selection, and maintenance of powder coating guns and nozzles, manufacturers can achieve consistent high-quality finishes and optimize their powder coating processes.
Corona and tribo charging are two methods widely used in commercial electrostatic powder spray equipment. The most popular method used in North America today is the electrostatic spray process which is comprised of three main components.
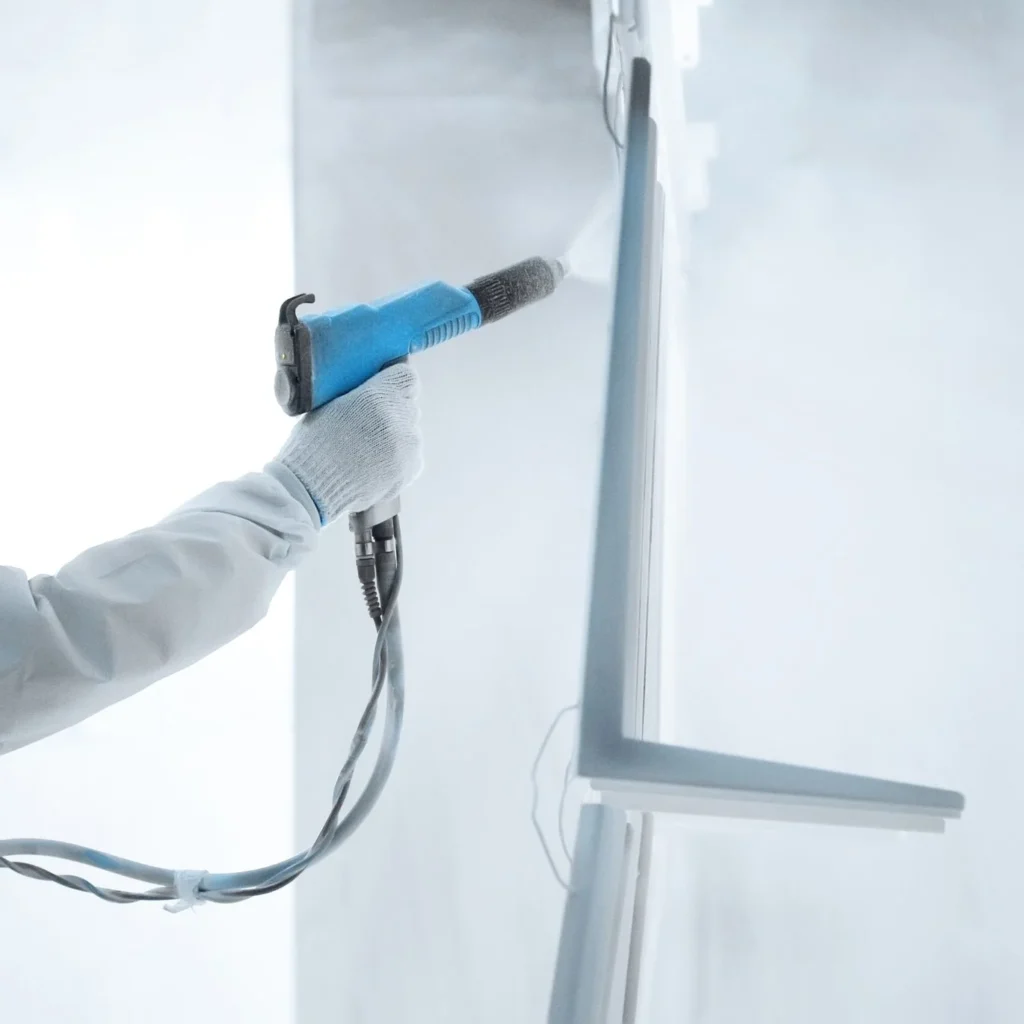
Electrostatic Powder Spray Guns
Electrostatic powder spray guns are a crucial component of the powder coating process, imparting an electrostatic charge to powder particles and attracting them to the grounded workpiece, ensuring uniform and efficient powder distribution. These guns are widely used in various industries due to their ability to produce high-quality finishes with minimal powder waste.
Principle of Operation of Electrostatic Powder Spray Guns
- Powder Feed: Powder is fed from a hopper into the powder gun through a metering device that controls the powder flow rate.
- Electrostatic Charging: The powder particles are passed through an electrostatic field generated by a high-voltage corona discharge. This imparts a positive charge to the powder particles.
- Air Atomization: Compressed air is used to atomize the powder particles into a fine mist, ensuring consistent particle size and distribution.
- Powder Spraying: The charged powder particles are sprayed towards the grounded workpiece. The electrostatic attraction between the charged particles and the grounded workpiece causes the particles to adhere to the workpiece surface.
Types of Electrostatic Powder Spray Guns
- Corona Discharge Guns: These guns utilize a corona discharge electrode to generate the electrostatic field. They are commonly used for general-purpose powder coating applications.
- Tribostatic Guns: These guns generate the electrostatic charge through friction between the powder particles and the gun components. They are suitable for high-volume powder coating applications.
- Electrostatic Rotary Disc Guns: These guns employ a rotating disc to generate the electrostatic charge. They are particularly effective for applying powder to complex shapes and recesses.
Advantages of Electrostatic Powder Spray Guns
- Uniform Coating: Electrostatic attraction ensures uniform powder distribution, minimizing overspray and reducing powder waste.
- Efficient Powder Utilization: The high transfer efficiency of electrostatic guns maximizes powder utilization, reducing costs and environmental impact.
- High-Quality Finish: Uniform powder distribution and minimal overspray contribute to high-quality, consistent finishes.
- Versatility: Electrostatic powder spray guns can be used with a wide range of powder types and workpiece shapes.
- Environmentally Friendly: Reduced powder waste and solvent-free operation promote environmental sustainability.
Applications of Electrostatic Powder Spray Guns
Electrostatic powder spray guns are widely used in various industries, including:
- Automotive Industry: Coating car parts, such as bumpers, wheels, and trim, with durable and aesthetically pleasing powder coatings.
- Appliance Industry: Providing a high-quality finish and protection for appliances, such as refrigerators, stoves, and washing machines.
- Furniture Industry: Enhancing the aesthetic appeal and durability of furniture pieces, such as chairs, tables, and cabinets.
- Electronics Industry: Protecting electronic components from corrosion and providing a smooth aesthetic finish.
- Construction Industry: Coating metal components, such as railings, pipes, and fittings, with durable and weather-resistant powder coatings.
- Aerospace Industry: Applying high-performance powder coatings to aircraft parts that demand exceptional strength and corrosion resistance.
Conclusion
Electrostatic powder spray guns have revolutionized the powder coating industry, enabling efficient, high-quality, and environmentally friendly powder application. By utilizing electrostatic principles, these guns minimize powder waste, enhance coating uniformity, and promote sustainability, making them an essential tool for a wide range of powder coating applications.
The functions of the electrostatic powder spray gun are to:
• Shape and direct the flow of powder.
• Control the pattern size, shape, and density of powder.
• Impart the electrostatic charge to the powder being
sprayed.
• Control the deposition of powder onto the parts being
sprayed.
Electrostatic Charging System in a Powder Coating Plant
The electrostatic charging system in a powder coating plant is a critical component of the overall coating process. It is responsible for applying a charge to the powder particles, which helps to ensure that they are evenly distributed and adhere to the substrate.
There are two main types of electrostatic charging systems: corona and friction.
Corona charging systems use high voltage to ionize the air around the powder particles. The ionized air molecules then attach to the powder particles, giving them a positive or negative charge.
Friction charging systems use friction to generate a charge on the powder particles. The powder particles are rubbed against a surface, which transfers electrons from the surface to the particles.
Once the powder particles are charged, they are attracted to the grounded substrate. This helps to ensure that the powder is evenly distributed and that it adheres to the substrate.
The electrostatic charging system is typically located in the powder coating booth. The powder is fed into the booth from a hopper, and it is then passed through the electrostatic charging system. The charged powder particles are then attracted to the substrate, and they form a coating on the surface.
The electrostatic charging system is an essential component of the powder coating process. It helps to ensure that the powder is evenly distributed and that it adheres to the substrate. This results in a high-quality, durable finish.
Here are some of the benefits of using an electrostatic charging system in a powder coating plant:
- Improved powder transfer efficiency: The electrostatic charge helps to attract the powder particles to the substrate, which reduces the amount of overspray.
- More uniform powder coating: The electrostatic charge helps to distribute the powder particles evenly, which results in a more uniform coating.
- Reduced waste: The improved powder transfer efficiency and uniform powder coating reduce the amount of waste powder.
- Improved durability: The electrostatic charge helps to create a stronger bond between the powder and the substrate, which results in a more durable finish.
If you are considering using a powder coating system, it is important to choose an electrostatic charging system that is right for your application. There are a number of factors to consider, such as the type of powder being used, the size and shape of the substrate, and the desired finish.
With proper care and maintenance, an electrostatic charging system can provide years of trouble-free operation.
The purpose of the charging system is to create a force within the sprayed powder particles enabling them to cling or attach themselves to bare, grounded metal parts
Electrostatic Corona Gun
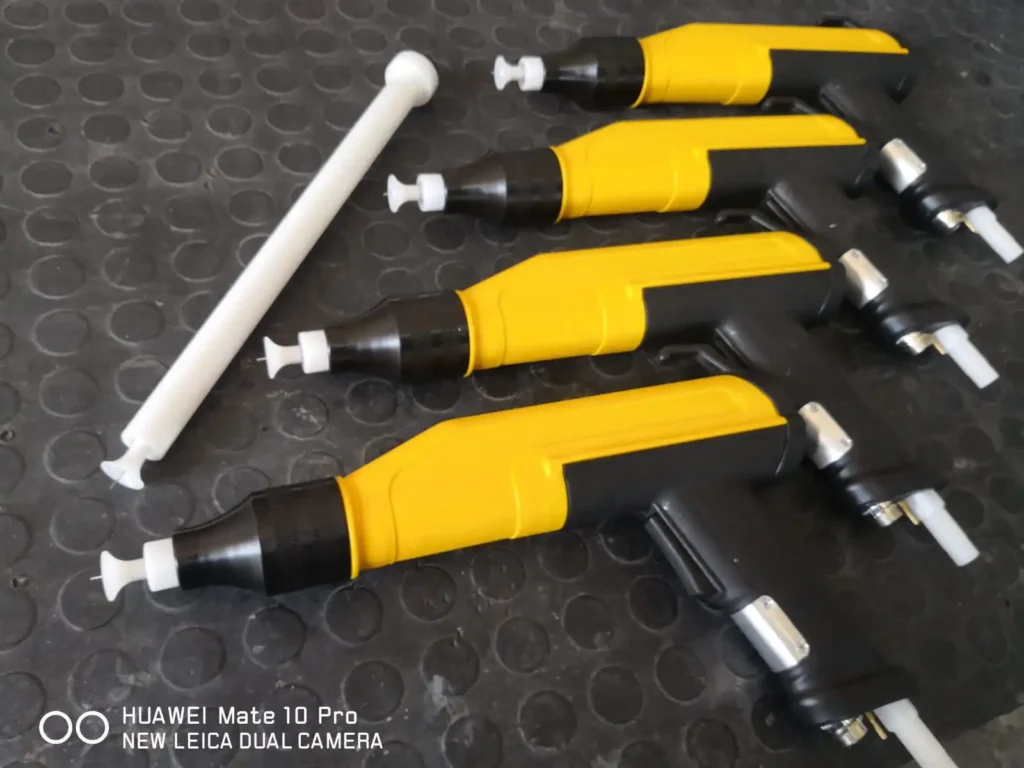
High voltage or low voltage cables are the two basic ways that the voltage source is currently applied to the tip of a corona-charged powder spray gun. The type of cable depends on whether the high-voltage generator is an external or internal power supply gun. Both come in negative or positive polarity. Generally, corona charging uses a negative polarity on the electrode as negative polarity produces more ions and is less prone to arcing than positive polarity.
The charging electrode is held at a very high negative potential, requiring a power supply rated from 30,000 to 100,000 volts. Positive polarity guns are used when spraying nylon or touching up in an automatic tribo system. Figure 5 illustrates an external power supply gun and an internal power supply gun for voltage generation
Corona Gun Design Criteria
- Charge in a region of high field strength.
- Charge where air velocities are low.
- Charge where the powder is well dispersed.
- Arrange the geometry of the charging electrode so the ions flow through the powder stream and the electrode is in the direct line of sight of the ground.
The above design features should be consolidated with
the pattern of powder flow, equipment cost(s), ease of maintenance, and durability.
Tribo Gun Charging in a Powder Coating Plant
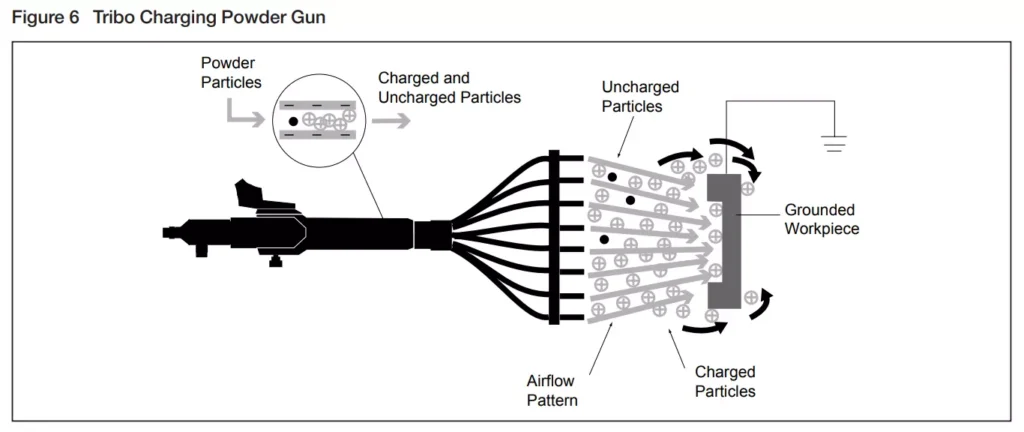
The word tribo is derived from the Greek word tribune, meaning to rub or produce friction. In tribo charging, the powder particles are charged by causing them to rub at a high velocity on a surface and thereby, transferring the charge. Without an external power supply and a
charging field in front of the gun, tribo charging virtually eliminates the problem of the “faraday cage effect.”
The powder particles take on a positive charge inside the gun due to the loss of electrons. The particles are now free to be directed to where they are needed. The powder flows into recessed and difficult-to-reach areas by nozzle direction and airflow. Because the particles are charged in the gun and there are no lines of force, it is less likely that the powder particles will build up on the leading edge of the part being coated. The advantage to this is the near elimination of “fatty edges” resulting in a uniform coating and even film build on the product.
One thing to note is that tribo charging is much more dependent on correct powder formulation (chemically) and particle grind size than corona-charging equipment. It is imperative that all powders be tested in tribo equipment to ensure good results.
Powder Spray Guns

The two major gun categories are manual and automatic. Manual guns can be used in stand-alone units, applications not requiring automatic guns, or with automatic systems that are generally used for difficult-to-reach and/or complex parts. Since the hand painter uses the spray gun for long periods of time, the flexibility, weight, efficiency and durability of the spray gun are important.
When considering the added mass of the hose and cable, keep in mind that most painters will hold the hose and cable with the other hand so that only three or four feet of hose and cable weight are added to the gun.
Also, depending on where the hose and cable are attached to the gun, the added weight may improve or degrade the overall balance. (Note: Work with your equipment supplier to help determine the right nozzle type for your application.) Automatic guns may be fixed, on gun movers, or a combination of both. In many cases, systems may be totally automatic without handguns for touch up.
Here are six things to consider before you purchase your next powder gun:
- Is the gun easy to disassemble and reassemble?
- Is there a variety of nozzles?
- Ease of cleaning for a color change?
- How many worn parts?
- Where is the manufacturing facility?
- Test the gun on your parts.
- Each type of gun has its place in the market depending on the application. The justification for each has to do with its specific design and overall chargeability. The most important thing to remember is the powder gun is just one piece of the application pie.
Powder Coating: An In-Depth Guide to Equipment and Processes
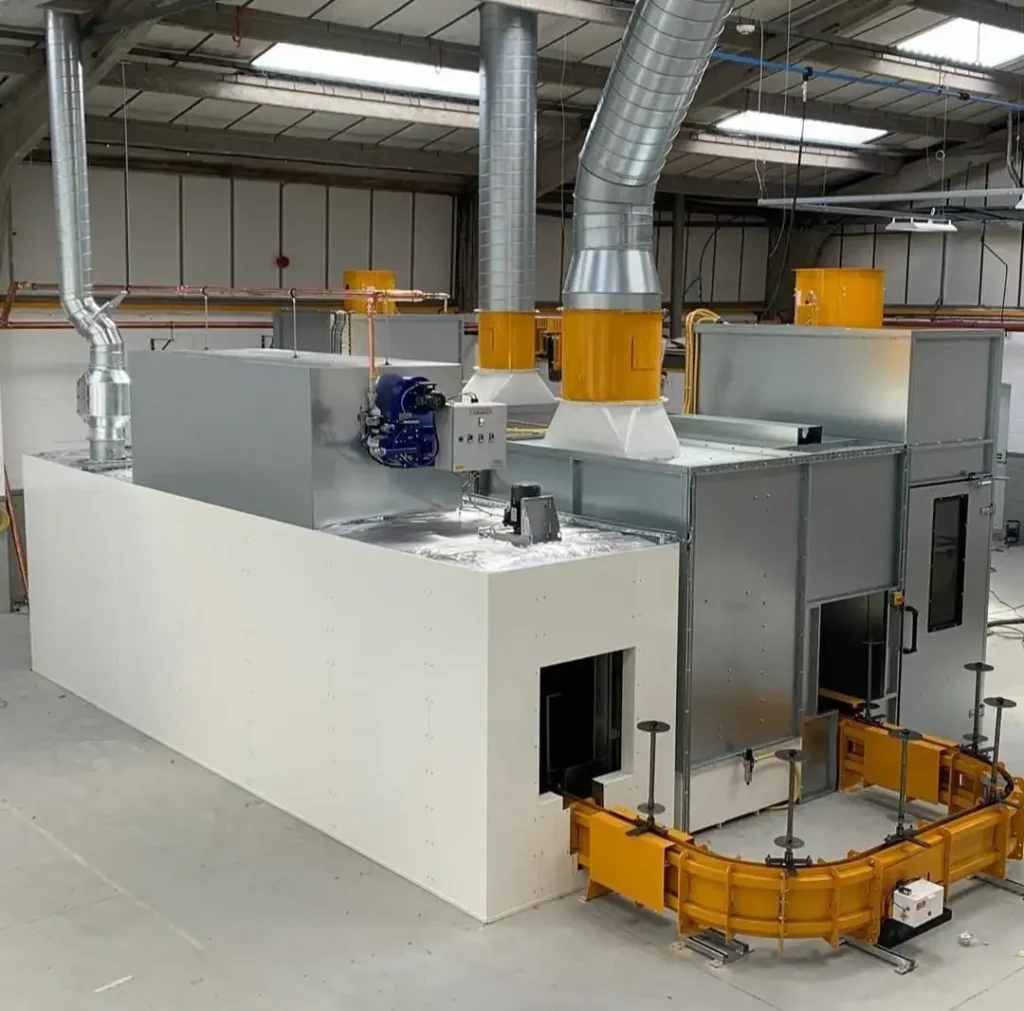
Introduction
Powder coating is a popular finishing process used across various industries to apply a durable and protective layer to metal surfaces. Unlike traditional liquid paint, powder coating uses a dry powder that is electrostatically charged and applied to the surface, which is then cured in a high-temperature oven. This process results in a hard finish that is more resistant to chipping, scratching, and fading.
In this guide, we’ll explore the different components of a powder coating system, including ovens, machines, equipment, and entire production lines. Understanding these elements is crucial for businesses looking to enhance their production capabilities with powder coating technology.
Powder Coating Ovens
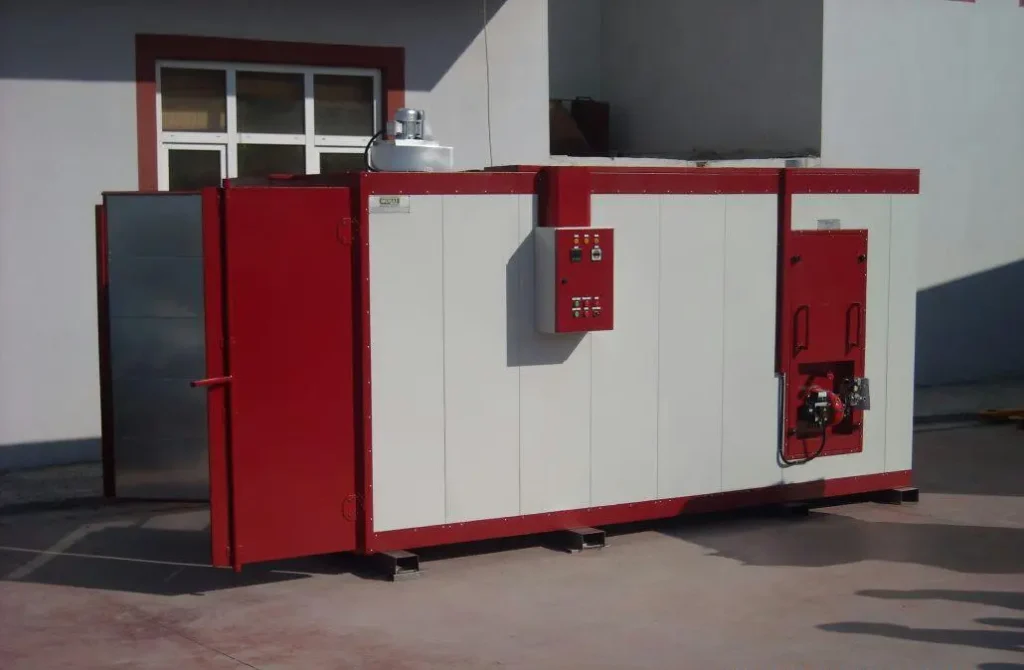
Definition and Purpose:
Powder coating ovens are essential for the curing process, where the powder adheres to the surface and forms a smooth, hard finish. These ovens provide the necessary heat to melt the powder, ensuring even and thorough coating.
Types of Powder Coating Ovens:
- Batch Ovens:
- Ideal for small to medium-sized production runs
- Flexibility to handle various part sizes
- Suitable for businesses with diverse product lines
- Conveyor Ovens:
- Designed for continuous production
- Higher throughput and efficiency
- Suitable for large-scale operations
Features and Specifications:
- Temperature Range: Typically between 325°F to 450°F
- Heating Source: Options include electric, gas, or infrared
- Size and Capacity: Varies based on production needs
- Energy Efficiency: Consider models with advanced insulation and airflow systems
How to Choose the Right Oven:
- Evaluate production volume and part sizes
- Consider energy consumption and operating costs
- Assess available space and installation requirements
- Consult with manufacturers for customized solutions
Powder Coating Machines
Overview of Different Machines Used:
Powder coating machines are used to apply the powder to the surface. They vary in complexity and functionality, catering to different production needs.
Manual vs. Automated Machines:
- Manual Machines:
- Suitable for small-scale operations
- Offers flexibility and control
- Requires skilled operators
- Automated Machines:
- Ideal for high-volume production
- Consistent and uniform application
- Reduced labor costs
Key Features and Specifications:
- Voltage and Power Requirements: Ensure compatibility with your facility
- Control Systems: Look for user-friendly interfaces and programmable settings
- Spray Gun Options: Different nozzles and gun types for various applications
Selecting the Right Machine for Your Needs:
- Determine the scale and complexity of your operations
- Evaluate budget constraints and long-term ROI
- Seek advice from industry experts and suppliers
Powder Coating Equipment
Essential Equipment for Powder Coating:
- Powder Coating Booths: Enclosed areas for applying powder
- Powder Recovery Systems: Capture and reuse overspray powder
- Air Compressors and Dryers: Ensure consistent airflow for optimal coating
Optional Equipment for Enhanced Performance:
- Pre-Treatment Systems: Clean and prepare surfaces before coating
- Curing Lamps: Speed up the curing process with infrared or UV lamps
Maintenance and Safety Considerations:
- Regularly inspect and clean equipment
- Train staff on proper handling and safety protocols
- Adhere to industry standards and regulations
Powder Coating Lines and Plants
Explanation of Powder Coating Lines:
Powder coating lines are integrated systems that automate the entire powder coating process, from pre-treatment to curing.
Components of a Powder Coating Line:
- Conveyor Systems: Move parts through the line efficiently
- Pre-Treatment Stations: Clean and prepare surfaces
- Powder Application Booths: Enclosed areas for powder coating
- Curing Ovens: Finalize the coating process
Design and Layout Considerations:
- Optimize workflow and space utilization
- Consider future scalability and expansion
- Ensure compliance with safety and environmental regulations
Scalability and Customization Options:
- Modular designs for easy expansion
- Custom configurations to meet specific production needs
Benefits of Powder Coating
Environmental Advantages:
- Low VOC emissions compared to liquid paints
- Overspray can be recycled, reducing waste
- Complies with environmental regulations
Durability and Longevity:
- Resistant to corrosion, fading, and wear
- Suitable for outdoor and high-traffic applications
- Provides a high-quality, professional finish
Cost-Effectiveness:
- Reduces long-term maintenance and repainting costs
- Efficient use of materials minimizes waste
- High throughput and automation lower labor expenses
Considerations for Setting Up a Powder Coating Plant
Initial Investment and ROI:
- Assess capital requirements for equipment and infrastructure
- Calculate potential returns based on production capacity and demand
- Explore financing options and incentives
Regulatory Compliance:
- Adhere to industry standards and local regulations
- Implement safety protocols and employee training
- Monitor environmental impact and waste management
Market Trends and Future Outlook:
- Growing demand for eco-friendly coatings
- Advancements in automation and technology
- Increasing adoption in automotive, aerospace, and consumer goods sectors
Conclusion
Powder coating offers numerous advantages over traditional liquid painting methods, making it an attractive option for industries seeking durable and environmentally friendly finishes. By investing in the right equipment and understanding the intricacies of powder coating processes, businesses can enhance their production capabilities and meet the growing demand for high-quality coated products.
When setting up a powder coating plant, it’s essential to carefully consider your needs, budget, and long-term goals. Collaborating with experienced suppliers and industry experts can help you make informed decisions and achieve success in the competitive world of powder coating.
This comprehensive guide should provide valuable insights for your website visitors and help position your business as a knowledgeable and reliable source in the powder coating industry.
Installation process steps
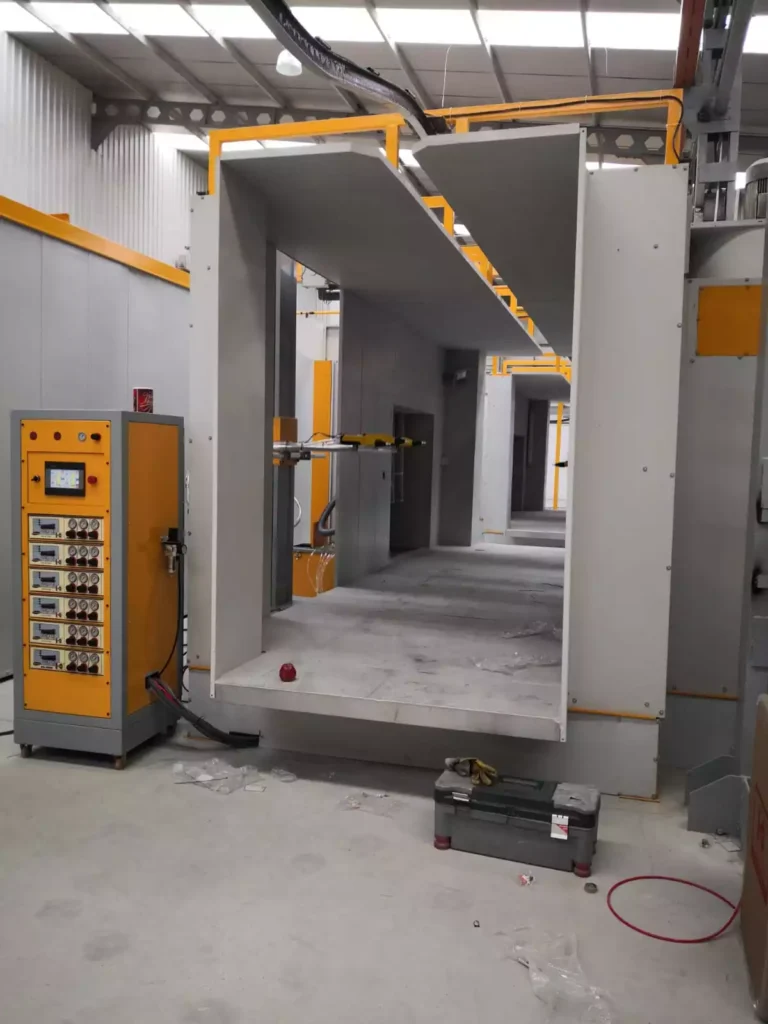
To provide a comprehensive guide on the installation process for powder coating systems, we’ll cover each step involved in setting up a powder coating plant. This includes planning, selecting equipment, site preparation, installation, testing, and staff training. Here’s a detailed outline and content for this section:
Outline for Installation Process Steps
- Planning and Design
- Assessing needs and capacity
- Layout and design considerations
- Budget and timeline
- Equipment Selection
- Choosing the right ovens, machines, and equipment
- Consulting with manufacturers and suppliers
- Site Preparation
- Preparing the facility for installation
- Ensuring compliance with regulations
- Installation Process
- Step-by-step installation guide
- Safety protocols and considerations
- System Testing and Calibration
- Testing each component
- Ensuring optimal performance
- Training and Support
- Staff training on operation and safety
- Ongoing maintenance and support
- Post-Installation Considerations
- Regular inspections and maintenance
- Upgrades and scalability
Installation Process Steps for Powder Coating Systems
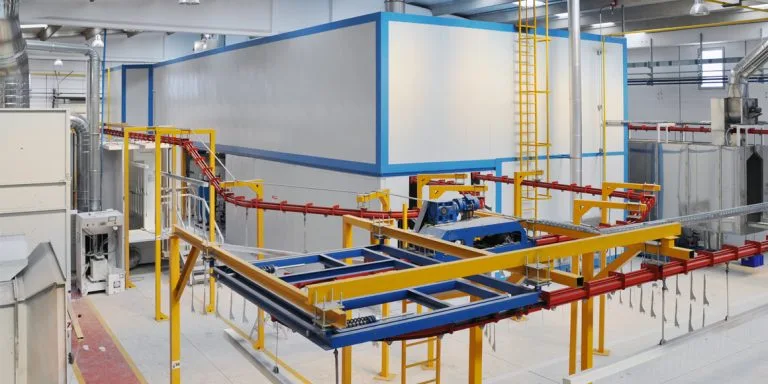
Setting up a powder coating plant involves careful planning and execution to ensure a successful installation. Here’s a step-by-step guide to help you navigate the process:
1. Planning and Design
Assessing Needs and Capacity:
- Identify Production Requirements: Determine the types and sizes of parts you will be coating, and estimate your production volume.
- Analyze Workflow: Consider how materials will move through the plant, from pre-treatment to curing.
- Evaluate Space Requirements: Ensure adequate space for equipment, storage, and workflow efficiency.
Layout and Design Considerations:
- Optimize Workflow: Design a layout that minimizes bottlenecks and maximizes efficiency.
- Future Scalability: Plan for potential expansion or upgrades.
- Compliance with Safety Standards: Ensure the layout meets all safety and regulatory requirements.
Budget and Timeline:
- Create a Detailed Budget: Account for equipment, installation, training, and operational costs.
- Establish a Timeline: Set realistic milestones for each phase of the installation process.
2. Equipment Selection
Choosing the Right Ovens, Machines, and Equipment:
- Powder Coating Ovens: Select between batch or conveyor ovens based on production needs.
- Powder Coating Machines: Choose manual or automated systems that match your operational scale.
- Additional Equipment: Consider powder booths, recovery systems, and pre-treatment stations.
Consulting with Manufacturers and Suppliers:
- Leverage Expertise: Work with manufacturers to choose equipment tailored to your specific requirements.
- Request Demonstrations: Evaluate equipment performance through demos or site visits.
- Negotiate Contracts: Ensure favorable terms and warranties with suppliers.
3. Site Preparation
Preparing the Facility for Installation:
- Infrastructure Readiness: Ensure adequate power supply, ventilation, and environmental controls.
- Space Optimization: Clear and organize the installation area for easy access and efficient workflow.
Ensuring Compliance with Regulations:
- Local Permits and Licenses: Obtain necessary permits and ensure compliance with zoning regulations.
- Safety Standards: Adhere to occupational health and safety standards.
4. Installation Process
Step-by-Step Installation Guide:
- Site Inspection: Conduct a final inspection of the site to verify readiness.
- Delivery and Unpacking: Receive and unpack equipment carefully, checking for any damage.
- Positioning Equipment: Install each piece of equipment according to the layout plan.
- Electrical and Plumbing Connections: Ensure all electrical and plumbing connections are correctly made and tested.
- Calibration and Setup: Configure equipment settings and calibrate machinery to specifications.
Safety Protocols and Considerations:
- Install Safety Features: Implement necessary safety features such as emergency stops and protective barriers.
- Personal Protective Equipment (PPE): Ensure that all personnel have access to required PPE.
5. System Testing and Calibration
Testing Each Component:
- Conduct Trial Runs: Test each component individually and as part of the integrated system.
- Check for Performance Issues: Identify and resolve any performance or operational issues.
Ensuring Optimal Performance:
- Fine-Tune Settings: Adjust equipment settings for optimal coating quality.
- Document Results: Record all testing results and adjustments for future reference.
6. Training and Support
Staff Training on Operation and Safety:
- Conduct Training Sessions: Provide comprehensive training on equipment operation and safety protocols.
- Create Training Materials: Develop manuals and guides for ongoing staff reference.
Ongoing Maintenance and Support:
- Establish a Maintenance Schedule: Set up regular maintenance checks to ensure equipment longevity.
- Vendor Support: Engage with suppliers for ongoing support and troubleshooting.
7. Post-Installation Considerations
Regular Inspections and Maintenance:
- Implement Routine Inspections: Regularly inspect equipment and systems for wear and tear.
- Schedule Maintenance: Adhere to the maintenance schedule to prevent downtime and extend equipment life.
Upgrades and Scalability:
- Monitor Technological Advancements: Stay informed about new technologies and equipment improvements.
- Plan for Upgrades: Budget for future upgrades and expansion as business needs grow.
Conclusion
The installation of a powder coating system is a multi-step process that requires meticulous planning and execution. By following these steps, businesses can ensure a smooth setup and operation, maximizing efficiency and product quality. It’s crucial to work closely with experienced manufacturers and suppliers to tailor the installation process to your specific needs and to provide ongoing training and support for staff.
Installation cost estimate
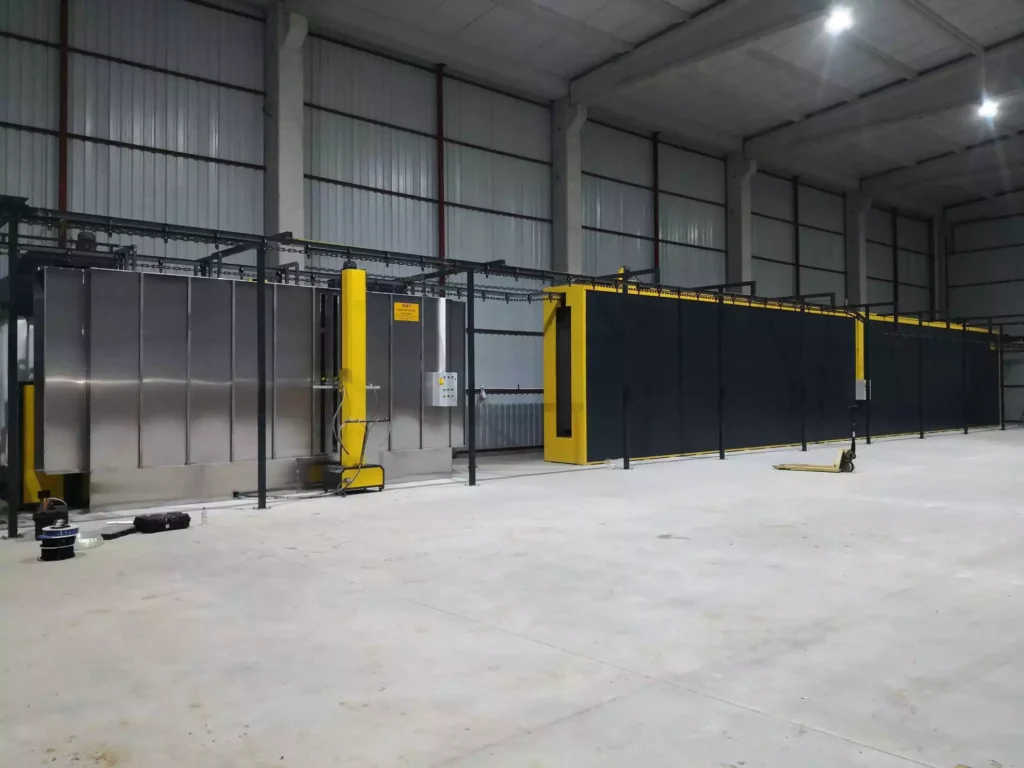
Estimating the installation cost of a powder coating system involves considering various factors, such as the size of the operation, the type of equipment, facility modifications, labor, and additional costs like permits and training. Here’s a detailed breakdown to help you understand the potential costs involved in setting up a powder coating plant.
Installation Cost Estimate for Powder Coating Systems
Factors Influencing Costs
- Type of Equipment and Technology
- Powder coating ovens (batch vs. conveyor)
- Coating machines (manual vs. automated)
- Auxiliary equipment (booths, recovery systems, pre-treatment stations)
- Scale and Capacity of the Operation
- Production volume
- Facility size and space requirements
- Facility Modifications
- Infrastructure updates (electrical, ventilation, plumbing)
- Space optimization and layout design
- Labor and Installation Services
- Skilled labor for installation
- Equipment calibration and testing
- Additional Costs
- Permits and regulatory compliance
- Staff training and support
- Maintenance and contingency expenses
Estimated Costs
Below is a general estimate of the costs associated with installing a powder coating system. Note that prices can vary significantly based on location, vendor, and specific requirements.
1. Equipment Costs
- Powder Coating Ovens:
- Batch Ovens: $1,000 – $50,000
- Conveyor Ovens: $10,000 – $200,000
- Powder Coating Machines:
- Manual Machines: $1,000 – $20,000
- Automated Systems: $20,000 – $100,000
- Auxiliary Equipment:
- Powder Booths: $2,000 – $30,000
- Recovery Systems: $3,000 – $15,000
- Pre-Treatment Systems: $10,000 – $50,000
2. Facility Modifications
- Electrical and Ventilation Upgrades: $10,000 – $50,000
- Space Optimization and Layout Design: $5,000 – $20,000
3. Labor and Installation Services
- Installation Labor: $10,000 – $30,000
- Calibration and Testing: $5,000 – $10,000
4. Additional Costs
- Permits and Compliance: $2,000 – $10,000
- Training and Support: $2,000 – $5,000
- Maintenance and Contingency: $5,000 – $15,000
Total Estimated Cost
The total estimated cost for installing a powder coating system can range from $70,000 to $500,000, depending on the size, complexity, and specific requirements of the operation. Here’s a breakdown by scale:
- Small-Scale Operations: $20,000 – $50,000
- Medium-Scale Operations: $50,000 – $100,000
- Large-Scale Operations: $100,000 – $500,000
Tips for Cost Management
- Conduct a Detailed Assessment:
- Evaluate your specific needs and choose equipment accordingly.
- Consider future scalability to avoid unnecessary upgrades later.
- Get Multiple Quotes:
- Request quotes from multiple vendors to compare prices and services.
- Negotiate terms and warranties to get the best deal.
- Plan for Contingencies:
- Set aside a contingency budget for unexpected expenses during installation.
- Regularly review and adjust your budget as the project progresses.
- Focus on Energy Efficiency:
- Invest in energy-efficient equipment to reduce long-term operational costs.
- Evaluate the potential return on investment (ROI) for each piece of equipment.
- Leverage Financing Options:
- Explore financing options, grants, or incentives available for industrial upgrades.
Conclusion
Setting up a powder coating plant requires a significant investment, but careful planning and strategic decision-making can help manage costs effectively. By considering your specific needs, working with experienced suppliers, and planning for the future, you can ensure a successful installation and operation of your powder coating system.
Let me know if you need further details or specific cost estimates tailored to your project!
Components of a Powder Coating Plant
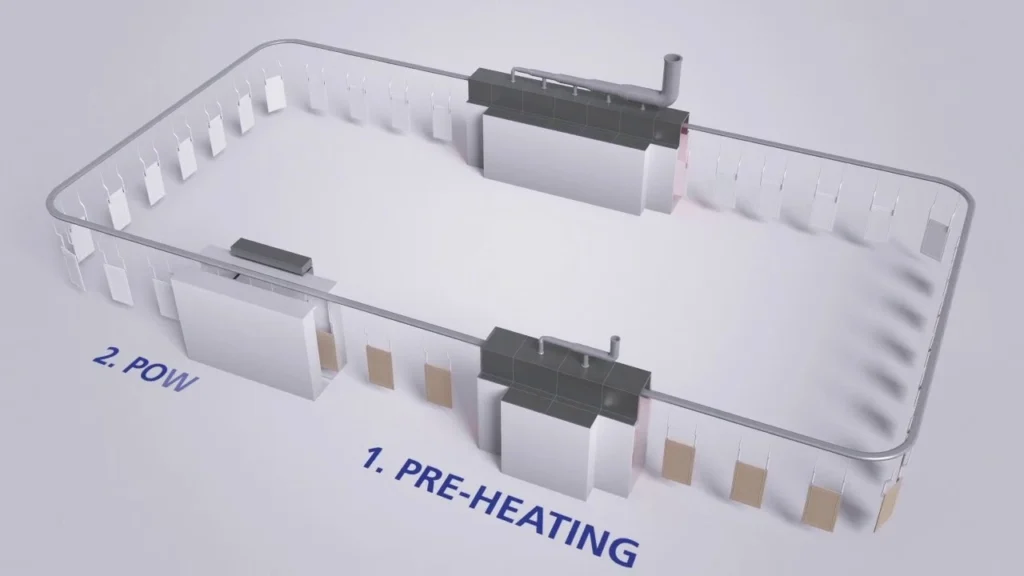
A powder coating plant consists of various components that work together to facilitate the coating process, from preparation to application and curing. Understanding these components is crucial for designing an efficient and effective system tailored to specific production needs. Below is a detailed overview of the key components of a powder coating plant:
Key Components of a Powder Coating Plant
- Pre-Treatment System
- Purpose: Cleans and prepares surfaces for powder coating to ensure adhesion and finish quality.
- Components:
- Washing Stations: Use chemical solutions to remove contaminants like grease, oil, dirt, and rust.
- Rinse Stations: Remove residual chemicals from the surface.
- Drying Ovens: Dry the parts after washing and rinsing to prepare them for powder application.
- Powder Coating Booths
- Purpose: Enclosed area where the powder is applied to the parts.
- Types:
- Manual Booths: Operators manually apply powder using spray guns. Ideal for small or custom jobs.
- Automatic Booths: Equipped with automated spray guns and reciprocators for high-volume production.
- Features:
- Ventilation Systems: Ensure proper airflow to capture overspray and maintain a clean environment.
- Powder Recovery Systems: Collect overspray powder for reuse, improving material efficiency.
- Powder Application Equipment
- Purpose: Applies the powder to the surfaces using electrostatic spray guns.
- Components:
- Electrostatic Spray Guns: Charge the powder particles and spray them onto the grounded parts.
- Control Units: Adjust settings like voltage, powder flow rate, and air pressure to ensure uniform coverage.
- Conveyor System
- Purpose: Transports parts through various stages of the powder coating process.
- Types:
- Overhead Conveyors: Hang parts from hooks or racks for continuous production.
- Floor Conveyors: Suitable for heavier or larger parts that cannot be suspended.
- Features:
- Variable Speed Control: Adjusts the speed of the conveyor to match production needs and curing times.
- Loading and Unloading Stations: Facilitate the movement of parts onto and off the conveyor system.
- Powder Coating Ovens
- Purpose: Cures the powder coating by melting and fusing it to the surface, forming a durable finish.
- Types:
- Batch Ovens: Suitable for smaller production runs and varied part sizes.
- Conveyor Ovens: Designed for continuous, high-volume production.
- Features:
- Temperature Control Systems: Ensure precise and consistent heating for optimal curing.
- Energy Efficiency: Incorporate insulation and heat recovery systems to minimize energy consumption.
- Cooling and Inspection Stations
- Purpose: Cool the parts after curing and inspect them for quality assurance.
- Components:
- Cooling Zones: Allow parts to cool gradually to avoid warping or defects.
- Inspection Areas: Check for coating consistency, thickness, and finish quality before packaging or assembly.
- Control and Monitoring Systems
- Purpose: Manage and monitor the entire powder coating process for efficiency and quality control.
- Components:
- PLC Systems (Programmable Logic Controllers): Automate and synchronize various plant operations.
- Data Logging and Analysis Tools: Record production metrics and identify areas for improvement.
- Safety and Environmental Controls
- Purpose: Ensure the safety of workers and compliance with environmental regulations.
- Components:
- Fire Suppression Systems: Protect against powder fires or explosions in booths and ovens.
- Ventilation and Filtration Systems: Maintain air quality by removing dust, fumes, and volatile organic compounds (VOCs).
- Personal Protective Equipment (PPE): Provide workers with necessary safety gear, such as masks, gloves, and goggles.
Optional and Auxiliary Components
- Advanced Pre-Treatment Systems: Utilize additional technologies like ultrasonic cleaning or nanotechnology for improved surface preparation.
- Curing Lamps: Use infrared or UV lamps for faster curing times and energy savings.
- Automated Robotic Systems: Enhance precision and efficiency in powder application and handling.
- Quality Control Instruments: Use advanced tools like thickness gauges, gloss meters, and adhesion testers for detailed quality assessment.
Layout and Design Considerations
- Workflow Optimization: Design the plant layout to minimize bottlenecks and ensure smooth transitions between stages.
- Space Utilization: Efficiently allocate space for equipment, storage, and movement of materials.
- Scalability: Plan for future expansion or upgrades to accommodate growing production demands.
Conclusion
A well-designed powder coating plant integrates these components to create an efficient, high-quality coating process. Understanding each element and its role in the system is crucial for businesses looking to enhance their powder coating capabilities. By investing in the right equipment and technology, companies can achieve superior finishes, increased productivity, and long-term success in the powder coating industry.
Detailed Components of a Powder Coating Plant
Certainly! To provide a detailed understanding of each component within a powder coating plant, we’ll delve into the technical specifications, functions, types, and key considerations for each element. This comprehensive breakdown will cover everything from the initial pre-treatment to the final inspection.
1. Pre-Treatment System
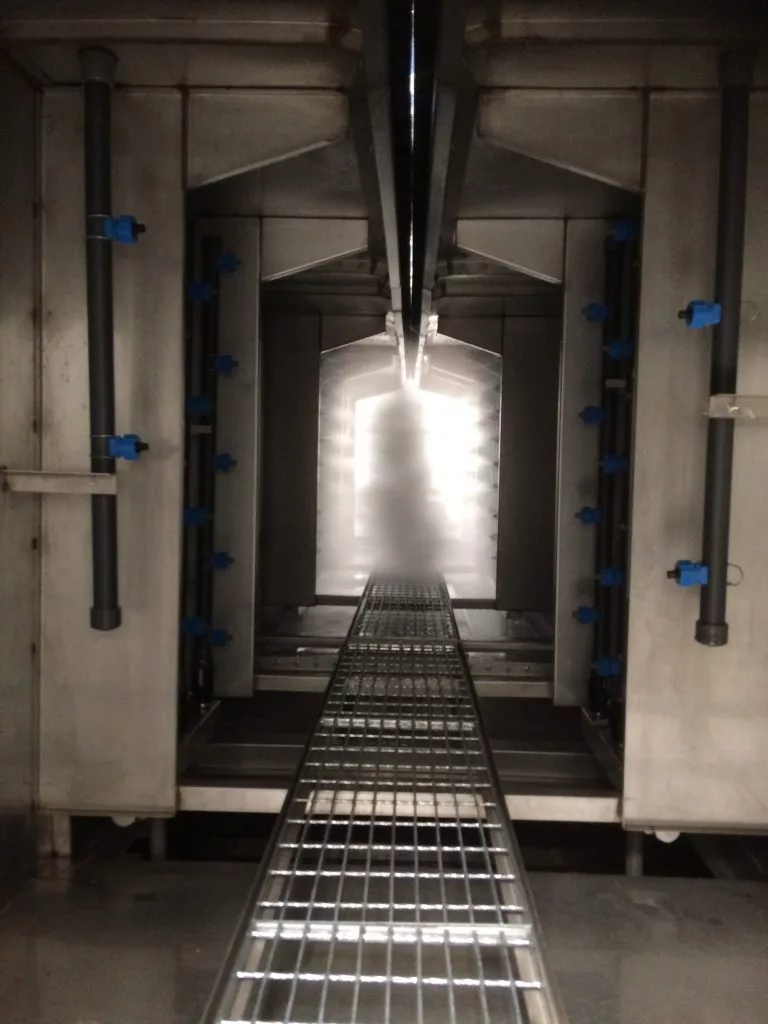
Overview
The pre-treatment system is crucial in ensuring that surfaces are properly cleaned and prepared for powder coating. This step enhances adhesion, improves finish quality, and increases the longevity of the coating.
Components and Process
1.1. Cleaning and Degreasing Stations
- Purpose: Remove oils, grease, and other contaminants from the surface.
- Methods:
- Alkaline Cleaning: Uses alkaline solutions to break down grease and oils.
- Solvent Cleaning: Employs organic solvents to dissolve contaminants.
- Ultrasonic Cleaning: Utilizes high-frequency sound waves for deep cleaning, especially effective for complex shapes.
- Equipment:
- Tanks and spray systems
- Heating elements to improve cleaning efficiency
- Agitation systems for even cleaning
1.2. Rinse Stations
- Purpose: Eliminate residual chemicals and contaminants from the cleaning stage.
- Types of Rinse:
- Freshwater Rinse: Basic water rinse to remove chemicals.
- Deionized Water Rinse: Prevents mineral deposits and spots on surfaces.
- Equipment:
- Spray bars and nozzles for thorough rinsing
- Closed-loop systems to recycle water and reduce waste
1.3. Surface Conditioning
- Purpose: Prepare the surface for subsequent conversion coating.
- Processes:
- Acid Etching: Removes oxides and prepares metal surfaces.
- Descaling: Removes scale and rust from the surface.
- Equipment:
- Immersion tanks or spray booths
- Automated dosing systems for precise chemical application
1.4. Conversion Coating
- Purpose: Apply a chemical layer that enhances powder adhesion and corrosion resistance.
- Types:
- Phosphate Coating: Iron or zinc phosphate for steel surfaces.
- Chromate Coating: Used for aluminum and zinc surfaces.
- Nano-Ceramic Coatings: Environmentally friendly option with superior adhesion and corrosion resistance.
- Equipment:
- Spray or immersion systems
- Temperature control for optimal reaction conditions
1.5. Drying Ovens
- Purpose: Remove moisture from parts to prevent defects in the powder coating.
- Features:
- Adjustable temperature settings
- Air circulation systems for even drying
- Equipment:
- Batch ovens for smaller production
- Conveyor ovens for continuous processing
Key Considerations
- Chemical Management: Ensure proper handling, storage, and disposal of chemicals used in pre-treatment.
- Environmental Compliance: Adhere to local regulations for effluent discharge and waste management.
- Maintenance: Regular cleaning and inspection of tanks and nozzles to prevent contamination.
2. Powder Coating Booths
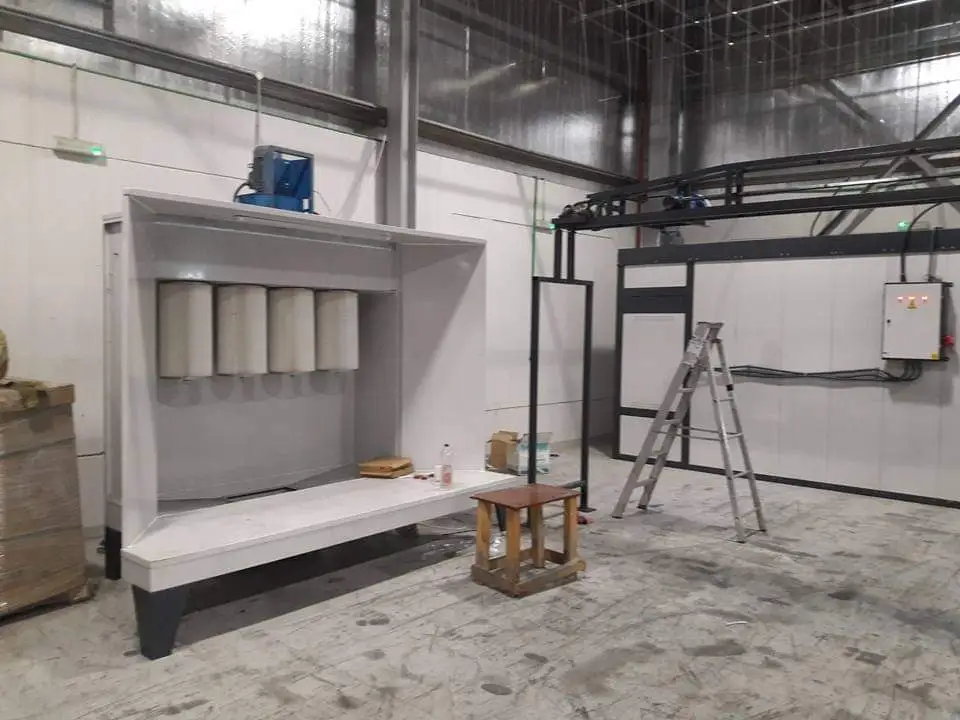
Overview
Powder coating booths provide a controlled environment for applying the powder. They ensure that the powder is applied evenly and that any overspray is efficiently managed and collected for reuse.
Types and Features
2.1. Manual Powder Coating Booths
- Purpose: Allow operators to manually apply powder using handheld spray guns.
- Applications: Suitable for small batches, custom jobs, and intricate parts.
- Features:
- Ventilation Systems: Maintain air quality and remove overspray.
- Lighting: Ensure visibility for precise application.
- Ergonomic Design: Facilitate operator comfort and efficiency.
2.2. Automatic Powder Coating Booths
- Purpose: Use automated systems to apply powder to parts, ideal for high-volume production.
- Applications: Suitable for standard parts and large-scale operations.
- Features:
- Robotic Arms and Reciprocators: Ensure consistent application across parts.
- Programmable Settings: Customize application parameters for different parts.
- Rapid Color Change Systems: Allow quick and efficient color changes with minimal downtime.
2.3. Powder Recovery Systems
- Purpose: Capture and recycle overspray powder to improve efficiency and reduce waste.
- Types:
- Cyclone Separators: Use centrifugal force to separate powder from the air.
- Cartridge Filters: Trap fine powder particles for reuse.
- Baghouse Filters: Employ fabric bags to capture powder, suitable for larger particles.
Key Considerations
- Airflow Management: Ensure proper ventilation to prevent contamination and maintain a clean environment.
- Color Change Efficiency: Invest in systems that allow quick and easy color changes to minimize downtime.
- Safety: Implement explosion-proof designs and fire suppression systems to prevent hazards.
3. Powder Application Equipment
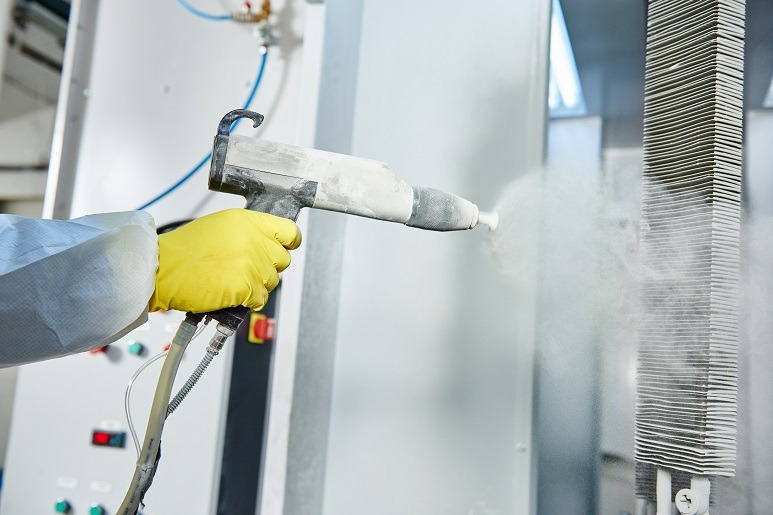
Overview
Powder application equipment is responsible for applying the powder coating to the parts. This equipment uses electrostatic principles to ensure uniform coverage and strong adhesion.
Components and Features
3.1. Electrostatic Spray Guns
- Purpose: Apply powder to the parts using an electrostatic charge.
- Types:
- Corona Guns: Use a high-voltage electrode to charge the powder.
- Tribo Guns: Charge the powder through friction, suitable for specific applications.
- Features:
- Adjustable Voltage and Current: Control the electrostatic charge for optimal coverage.
- Interchangeable Nozzles: Provide different spray patterns for various applications.
- Lightweight and Ergonomic Design: Ensure operator comfort during manual application.
3.2. Control Units
- Purpose: Manage and adjust the settings of the powder application equipment.
- Features:
- Digital Displays: Provide real-time feedback on settings and performance.
- Programmable Settings: Allow customization for different parts and powder types.
- Data Logging: Record application parameters for quality control and traceability.
3.3. Fluidized Bed Systems
- Purpose: Coat parts by dipping them into a bed of fluidized powder, typically used for thicker coatings.
- Applications: Suitable for specific applications requiring a thick and even coating.
- Features:
- Uniform Airflow: Ensure consistent fluidization of powder particles.
- Temperature Control: Maintain optimal conditions for coating.
Key Considerations
- Powder Compatibility: Ensure equipment is compatible with different powder formulations.
- Operator Training: Provide comprehensive training for operators to ensure efficient and safe use.
- Maintenance: Regularly clean and maintain spray guns and control units to prevent clogging and ensure consistent performance.
4. Conveyor System
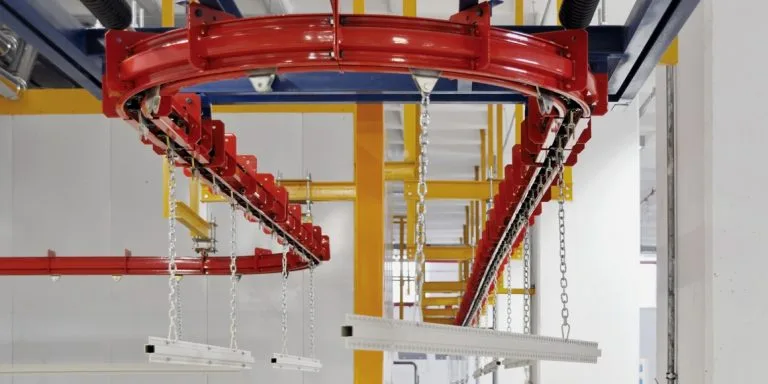
Overview
The conveyor system is the backbone of the powder coating plant, transporting parts through each stage of the process, from pre-treatment to curing.
Types and Features
4.1. Overhead Conveyors
- Purpose: Transport parts by suspending them from hooks or racks, ideal for continuous production.
- Types:
- Monorail Systems: Simple looped tracks for straightforward applications.
- Power and Free Systems: Offer more flexibility with multiple paths and stopping points.
- Features:
- Variable Speed Control: Adjust the speed to match production needs and curing times.
- Load Capacity: Designed to handle different part sizes and weights.
- Integration with Other Systems: Seamlessly integrate with pre-treatment, application, and curing systems.
4.2. Floor Conveyors
- Purpose: Transport heavier or larger parts that cannot be suspended, suitable for specific applications.
- Types:
- Belt Conveyors: Use belts to move parts horizontally or on an incline.
- Roller Conveyors: Employ rollers to facilitate the movement of parts.
- Features:
- Heavy-Duty Construction: Designed to support large or heavy parts.
- Customizable Configurations: Adapt to different plant layouts and processes.
Key Considerations
- Layout Design: Plan the conveyor layout to optimize workflow and minimize bottlenecks.
- Load and Speed Requirements: Ensure the conveyor system meets production demands for speed and capacity.
- Safety Features: Implement safety measures such as guards, emergency stops, and regular inspections.
5. Powder Coating Ovens
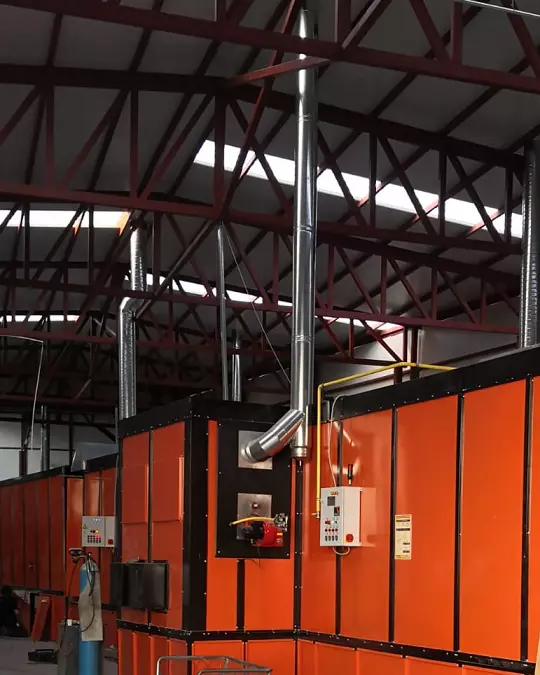
Overview
Powder coating ovens are responsible for curing the powder coating by melting and fusing it to the surface, resulting in a durable and attractive finish.
Types and Features
5.1. Batch Ovens
- Purpose: Cure parts in small batches, suitable for varied part sizes and low-volume production.
- Applications: Ideal for custom jobs, small businesses, and prototyping.
- Features:
- Adjustable Temperature Control: Precise control of curing conditions.
- Flexible Configuration: Accommodate different part sizes and shapes.
- Insulated Construction: Minimize heat loss and improve energy efficiency.
5.2. Conveyor Ovens
- Purpose: Designed for continuous production, curing parts as they move through the oven.
- Applications: Suitable for high-volume production and standardized parts.
- Features:
- Consistent Temperature Distribution: Ensure even curing across all parts.
- Variable Conveyor Speed: Match curing times with production speed.
- Energy Efficiency: Incorporate heat recovery systems and advanced insulation.
Key Considerations
- Oven Size and Capacity: Choose an oven that meets production demands without excessive energy use.
- Heating Source: Decide between electric, gas, or infrared heating based on cost and efficiency.
- Temperature Uniformity: Ensure consistent heat distribution to prevent defects in the finish.
6. Cooling and Inspection Stations
Overview
Cooling and inspection stations are crucial for ensuring the quality and consistency of the finished products. Cooling prevents defects, while inspection verifies the coating quality.
Components and Features
6.1. Cooling Zones
- Purpose: Gradually cool parts after curing to prevent warping or defects.
- Features:
- Controlled Airflow: Ensure even cooling and avoid thermal shock.
- Adjustable Cooling Rates: Customize settings for different materials and part sizes.
6.2. Inspection Areas
- Purpose: Conduct quality checks on coated parts to ensure consistency and adherence to standards.
- Features:
- Lighting and Magnification: Facilitate detailed visual inspections.
- Measurement Tools: Use instruments like thickness gauges and gloss meters for precise evaluation.
- Defect Detection Systems: Implement automated systems for detecting coating defects, such as thin spots or uneven coverage.
Key Considerations
- Quality Assurance Protocols: Establish standards and procedures for inspections to ensure consistent product quality.
- Training for Inspectors: Provide training to staff on recognizing defects and using inspection tools effectively.
- Feedback Loop: Use inspection data to inform process improvements and address recurring issues.
7. Control and Monitoring Systems
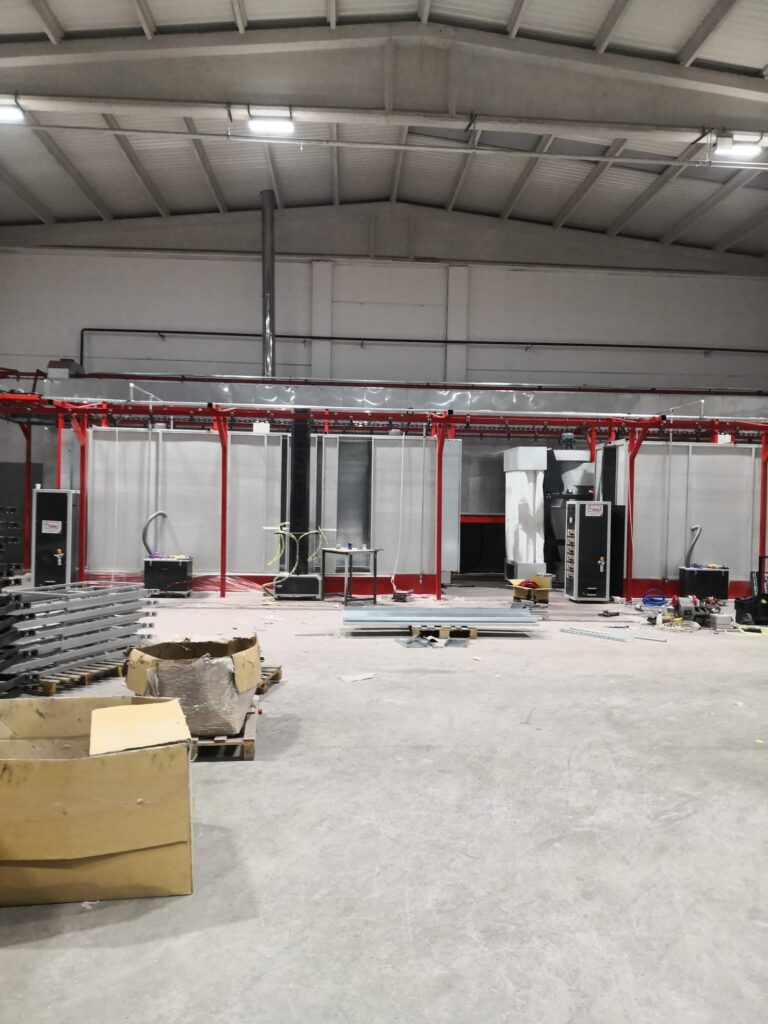
Overview
Control and monitoring systems automate and synchronize various plant operations, ensuring efficiency, consistency, and quality in the powder coating process.
Components and Features
7.1. PLC Systems (Programmable Logic Controllers)
- Purpose: Automate and control equipment functions throughout the plant.
- Features:
- Centralized Control: Manage multiple systems from a single interface.
- Real-Time Monitoring: Track performance metrics and adjust settings as needed.
- Data Logging: Record operational data for analysis and process optimization.
7.2. Data Logging and Analysis Tools
- Purpose: Collect and analyze production data to improve efficiency and quality.
- Features:
- Trend Analysis: Identify patterns and trends in production metrics.
- Performance Dashboards: Visualize key performance indicators (KPIs) for easy monitoring.
- Predictive Maintenance: Use data to anticipate equipment maintenance needs and prevent downtime.
Key Considerations
- System Integration: Ensure seamless integration with existing equipment and software.
- User Interface: Provide intuitive and user-friendly interfaces for operators.
- Cybersecurity: Implement security measures to protect sensitive data and control systems.
8. Safety and Environmental Controls
Overview
Safety and environmental controls are essential for protecting workers and ensuring compliance with regulations. These systems manage hazards and minimize environmental impact.
Components and Features
8.1. Fire Suppression Systems
- Purpose: Prevent and control powder fires or explosions in booths and ovens.
- Features:
- Automatic Detection and Suppression: Quickly identify and extinguish fires.
- Integration with Control Systems: Automatically shut down equipment in case of fire.
- Regular Testing and Maintenance: Ensure systems are operational and compliant with safety standards.
8.2. Ventilation and Filtration Systems
- Purpose: Maintain air quality by removing dust, fumes, and volatile organic compounds (VOCs).
- Features:
- High-Efficiency Particulate Air (HEPA) Filters: Capture fine particles and contaminants.
- Exhaust Fans and Ductwork: Ensure proper airflow and ventilation.
- Regular Filter Replacement: Maintain efficiency and prevent clogs.
8.3. Personal Protective Equipment (PPE)
- Purpose: Provide workers with necessary safety gear to protect against hazards.
- Components:
- Respirators and Masks: Protect against inhalation of powder particles and fumes.
- Safety Glasses and Goggles: Shield eyes from dust and chemical splashes.
- Gloves and Protective Clothing: Prevent skin contact with chemicals and powders.
Key Considerations
- Compliance with Regulations: Adhere to local and international safety and environmental standards.
- Safety Training: Conduct regular training sessions on safety protocols and emergency procedures.
- Continuous Improvement: Regularly review and update safety measures to address emerging risks and regulations.
Conclusion
Each component of a powder coating plant plays a vital role in ensuring a successful and efficient coating process. By understanding the details and functions of these components, businesses can design and operate a plant that meets their specific needs and production goals. Investing in the right equipment and systems, along with proper training and maintenance, will lead to high-quality finishes, increased productivity, and long-term success in the powder coating industry.
Installation time estimate
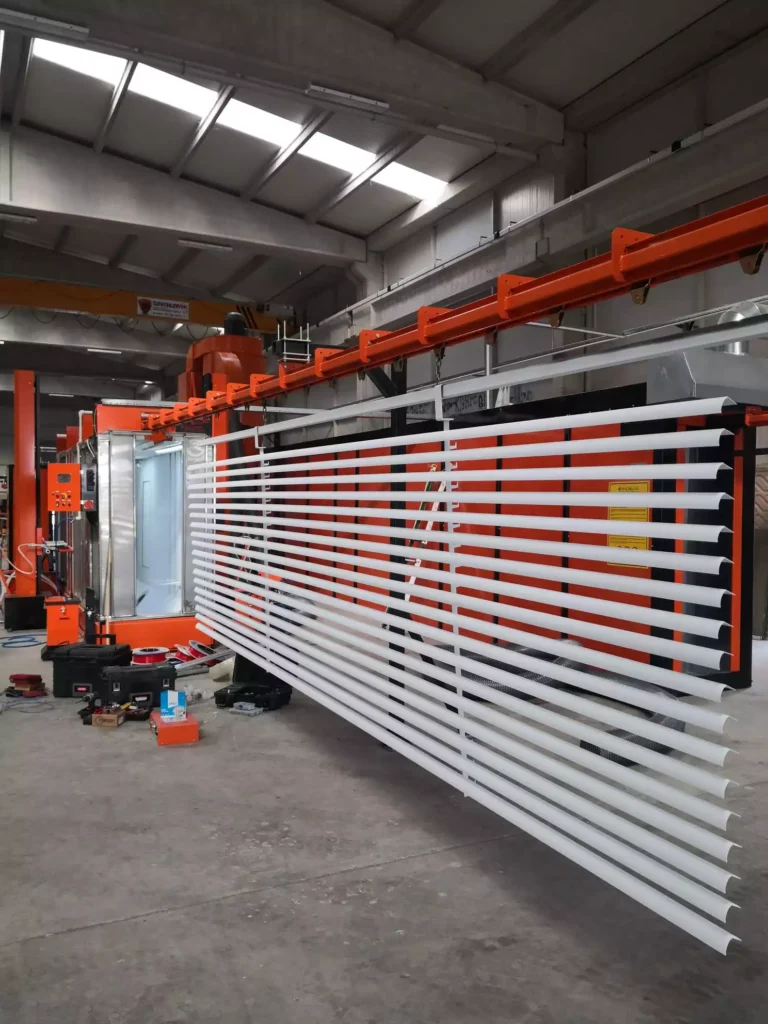
Estimating the installation time for a powder coating plant involves considering several factors such as the size of the operation, complexity of the equipment, facility preparation, and the efficiency of the installation team. Below is a detailed breakdown of the installation time estimate, including factors that can influence the timeline and strategies to ensure a smooth installation process.
Installation Time Estimate for a Powder Coating Plant
Factors Influencing Installation Time
- Scale and Complexity of the Plant
- Size and layout of the facility
- Number and type of equipment components
- Type of Equipment
- Manual vs. automated systems
- Batch vs. continuous production lines
- Site Preparation
- Existing infrastructure readiness
- Facility modifications needed
- Installation Team and Expertise
- Experience and skills of the installation crew
- Availability of necessary resources and tools
- Regulatory Compliance and Inspections
- Time required for permits and approvals
- Safety inspections and certifications
- Coordination and Scheduling
- Coordination between vendors, contractors, and stakeholders
- Availability of equipment and personnel
Estimated Installation Time by Component
Here is an approximate installation timeline for each major component of a powder coating plant. These estimates are generalized and may vary depending on specific project requirements.
1. Pre-Treatment System
- Time Estimate: 1 to 3 weeks
- Activities:
- Delivery and setup of washing, rinsing, and drying stations
- Plumbing and drainage installations
- Testing and calibration of chemical dosing systems
2. Powder Coating Booths
- Time Estimate: 1 to 2 weeks
- Activities:
- Assembly and installation of booth structures
- Integration of ventilation and powder recovery systems
- Setup of lighting and electrical connections
3. Powder Application Equipment
- Time Estimate: 1 to 2 weeks
- Activities:
- Installation of electrostatic spray guns and control units
- Calibration of application settings and nozzles
- Testing for uniform powder distribution
4. Conveyor System
- Time Estimate: 2 to 4 weeks
- Activities:
- Layout design and track installation
- Assembly of conveyor components and drives
- Testing for load capacity and speed control
5. Powder Coating Ovens
- Time Estimate: 2 to 3 weeks
- Activities:
- Installation of oven structures and insulation
- Setup of heating systems and temperature controls
- Testing for temperature uniformity and energy efficiency
6. Cooling and Inspection Stations
- Time Estimate: 1 to 2 weeks
- Activities:
- Installation of cooling systems and airflow management
- Setup of inspection stations and quality control tools
- Training staff on inspection procedures
7. Control and Monitoring Systems
- Time Estimate: 1 to 2 weeks
- Activities:
- Installation of PLC systems and control panels
- Integration with other equipment components
- Testing and validation of automation processes
8. Safety and Environmental Controls
- Time Estimate: 1 to 2 weeks
- Activities:
- Installation of fire suppression and ventilation systems
- Setup of safety barriers and emergency stops
- Safety audits and compliance checks
Total Estimated Installation Time
The total estimated installation time for a powder coating plant can range from 8 to 18 weeks, depending on the scale and complexity of the project. Here’s a breakdown by plant size:
- Small-Scale Operations: 8 to 10 weeks
- Medium-Scale Operations: 10 to 14 weeks
- Large-Scale Operations: 14 to 18 weeks
Strategies for Reducing Installation Time
- Detailed Planning and Coordination
- Develop a comprehensive project plan with clear timelines and milestones.
- Coordinate with vendors, contractors, and stakeholders to align schedules and resources.
- Pre-Fabrication and Pre-Assembly
- Opt for pre-fabricated components to reduce on-site assembly time.
- Pre-assemble equipment off-site where possible to minimize installation complexity.
- Experienced Installation Team
- Hire experienced professionals familiar with powder coating systems and processes.
- Conduct regular training and briefings to ensure the team is well-prepared.
- Efficient Site Preparation
- Ensure the facility is ready for installation before equipment arrives.
- Complete necessary infrastructure upgrades and modifications in advance.
- Streamlined Permitting and Inspections
- Obtain permits and approvals early in the project timeline.
- Schedule inspections and certifications to avoid delays.
- Contingency Planning
- Identify potential risks and develop contingency plans to address unforeseen issues.
- Allocate buffer time in the schedule for unexpected challenges.
Conclusion
The installation of a powder coating plant is a complex process that requires careful planning and coordination. By understanding the factors that influence installation time and implementing strategies to streamline the process, businesses can achieve a successful setup that meets their production goals and timelines.
Maintenance schedule tips
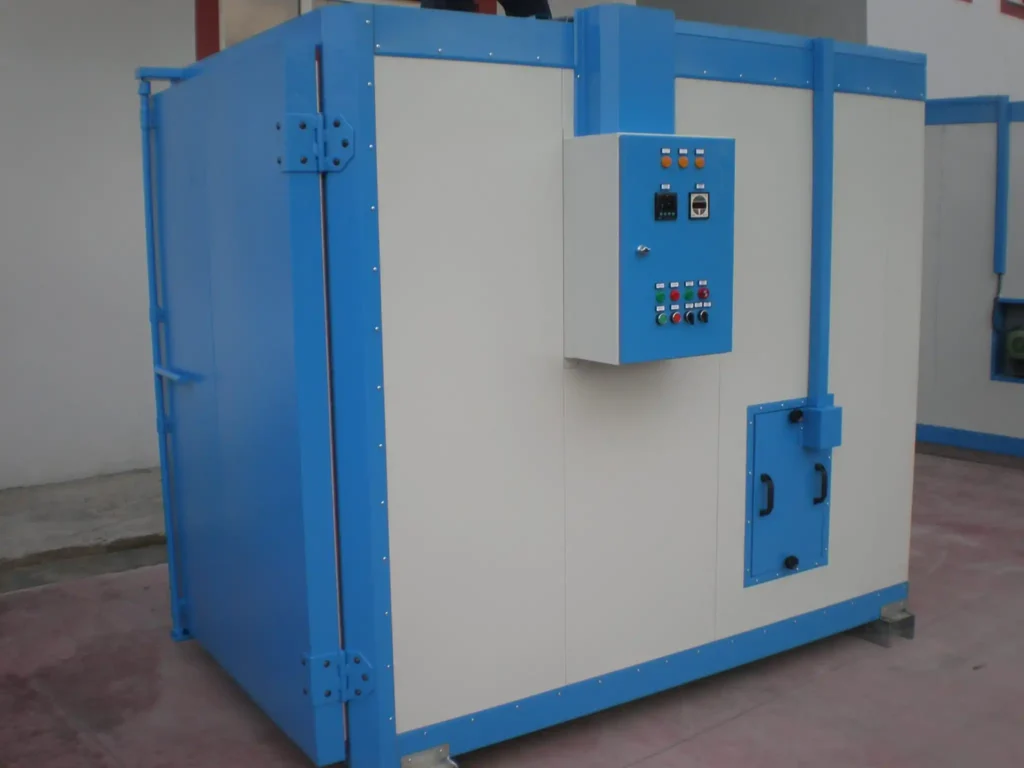
Creating a maintenance schedule for a powder coating plant is essential for ensuring efficient operation, minimizing downtime, and extending the lifespan of your equipment. A well-structured maintenance plan should address the needs of each component, including pre-treatment systems, powder coating booths, application equipment, conveyors, ovens, and safety controls. Here are some tips and guidelines to help you develop an effective maintenance schedule.
Tips for Creating a Maintenance Schedule for a Powder Coating Plant
1. Understand Equipment Requirements
- Read Manufacturer Guidelines: Start by reviewing the maintenance recommendations provided by the equipment manufacturers. These guidelines offer valuable insights into the specific needs and intervals for each component.
- Identify Critical Components: Prioritize maintenance for critical components that directly impact production quality and efficiency, such as spray guns, ovens, and conveyors.
2. Develop a Comprehensive Maintenance Plan
- Routine Inspections: Schedule regular inspections to identify wear and tear, leaks, or potential issues before they escalate. Inspections should cover all plant components, including electrical, mechanical, and safety systems.
- Preventive Maintenance: Implement a preventive maintenance schedule that includes tasks such as cleaning, lubrication, calibration, and parts replacement. This helps prevent unexpected breakdowns and maintains optimal performance.
- Predictive Maintenance: Utilize data analytics and monitoring tools to predict equipment failures and schedule maintenance based on condition and usage patterns.
3. Create a Detailed Maintenance Schedule
- Daily Maintenance Tasks:
- Check air pressure and filtration systems.
- Inspect spray guns and nozzles for clogs or wear.
- Clean work areas and remove powder buildup.
- Weekly Maintenance Tasks:
- Inspect conveyor systems for alignment and wear.
- Lubricate moving parts such as bearings and chains.
- Check temperature settings and calibrate sensors.
- Monthly Maintenance Tasks:
- Conduct a thorough inspection of pre-treatment systems.
- Inspect and clean ventilation and exhaust systems.
- Test and recalibrate control systems.
- Quarterly Maintenance Tasks:
- Perform a detailed inspection of the ovens for heat distribution and insulation integrity.
- Replace worn-out components such as belts and filters.
- Review and update safety protocols.
- Annual Maintenance Tasks:
- Conduct a comprehensive review of the entire plant.
- Audit compliance with safety and environmental regulations.
- Plan for equipment upgrades or replacements as needed.
4. Document Maintenance Activities
- Record Keeping: Maintain detailed records of all maintenance activities, including dates, tasks performed, and any issues identified. This documentation helps track equipment performance and identifies recurring problems.
- Use Digital Tools: Consider using computerized maintenance management systems (CMMS) to schedule, track, and analyze maintenance activities. Digital tools can provide reminders, automate scheduling, and generate reports.
5. Train and Empower Staff
- Employee Training: Train employees on the importance of maintenance and proper procedures. Ensure they understand how to identify and report issues and perform routine tasks.
- Empowerment: Encourage staff to take ownership of their equipment and be proactive in reporting potential problems.
6. Monitor Key Performance Indicators (KPIs)
- Track KPIs: Monitor KPIs such as equipment uptime, mean time between failures (MTBF), and maintenance costs to evaluate the effectiveness of your maintenance program.
- Continuous Improvement: Use KPI data to identify areas for improvement and make data-driven decisions to enhance maintenance strategies.
7. Plan for Spare Parts and Inventory
- Spare Parts Management: Maintain an inventory of critical spare parts to minimize downtime during repairs. Track usage patterns to ensure adequate stock levels.
- Vendor Relationships: Build strong relationships with equipment suppliers to ensure quick access to parts and technical support.
8. Evaluate and Adjust the Maintenance Plan
- Regular Reviews: Periodically review and update the maintenance schedule based on equipment performance, technological advancements, and changing production needs.
- Feedback Loop: Encourage feedback from maintenance staff and operators to identify pain points and improve processes.
Sample Maintenance Schedule Template
Here’s a sample template to help you structure your maintenance schedule:
Frequency | Task | Details |
---|---|---|
Daily | Check air pressure | Ensure proper airflow for spray guns and equipment. |
Inspect spray guns | Look for clogs, wear, and powder buildup. | |
Clean work areas | Remove excess powder and debris from booths and equipment. | |
Weekly | Inspect conveyor systems | Check alignment and wear of belts and chains. |
Lubricate moving parts | Apply lubrication to bearings, chains, and gears. | |
Calibrate temperature settings | Ensure accurate temperature readings in ovens. | |
Monthly | Inspect pre-treatment systems | Check tanks, pumps, and chemical levels. |
Clean ventilation systems | Remove dust and powder buildup in filters and ducts. | |
Test control systems | Verify functionality and accuracy of control units. | |
Quarterly | Inspect oven heat distribution | Check for even heat distribution and insulation integrity. |
Replace worn components | Swap out belts, filters, and other wear-prone parts. | |
Review safety protocols | Update safety measures and conduct training if needed. | |
Annually | Conduct plant-wide inspection | Evaluate overall condition and performance. |
Audit compliance with regulations | Ensure adherence to safety and environmental standards. | |
Plan equipment upgrades | Assess the need for new equipment or technology upgrades. |
Conclusion
Implementing a well-structured maintenance schedule is vital for the smooth operation and longevity of your powder coating plant. By focusing on preventive and predictive maintenance, documenting activities, and involving your team, you can reduce downtime, improve efficiency, and maintain high-quality production standards.
Powder Coating Oven Types
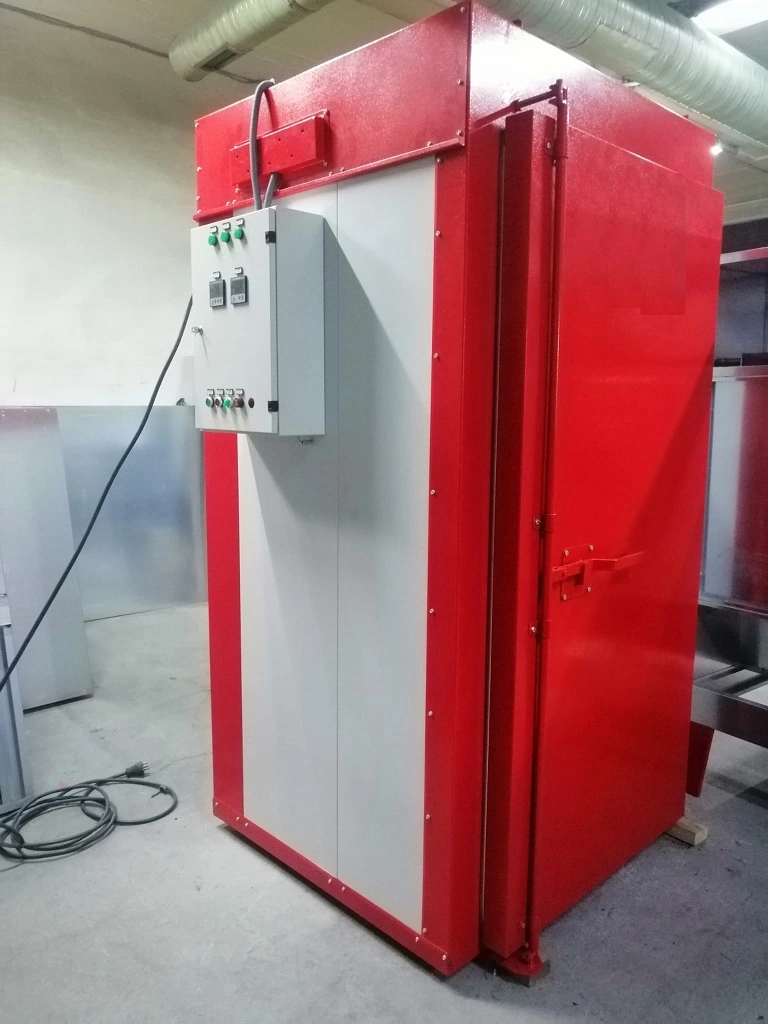
Powder coating ovens are a critical component of the powder coating process, providing the heat necessary to cure the powder and ensure a durable finish. There are several types of powder coating ovens, each designed to meet different production needs and efficiency levels. This guide will cover the various types of powder coating ovens, their features, benefits, and applications, helping you choose the right oven for your specific requirements.
Types of Powder Coating Ovens
1. Batch Ovens
Batch ovens are designed to cure powder coatings for small to medium-sized production runs. They are ideal for operations that require flexibility in coating different part sizes and types.
Features:
- Flexibility: Accommodates various part sizes and shapes.
- Energy Efficiency: Often includes insulation and heat recovery systems to reduce energy consumption.
- Manual or Semi-Automatic Operation: Suitable for low to moderate production volumes.
Benefits:
- Cost-Effective: Lower initial investment compared to continuous ovens.
- Versatile: Can handle a variety of coating tasks, including custom and complex shapes.
- Ease of Use: Simple to operate and maintain.
Applications:
- Small businesses and job shops
- Custom and prototype work
- Low to medium production volumes
Common Types of Batch Ovens:
- Walk-In Ovens: Large enough for operators to enter and load parts, suitable for oversized items.
- Cabinet Ovens: Smaller units ideal for small parts or lower-volume production.
- Truck-In Ovens: Designed for loading parts on racks or carts that can be rolled into the oven.
2. Conveyor Ovens
Conveyor ovens are designed for high-volume production and continuous processing. They automate the curing process, improving efficiency and consistency.
Features:
- Continuous Operation: Ideal for high production rates and large-scale operations.
- Automated Conveyor Systems: Transport parts through the oven for consistent curing.
- Variable Speed Control: Allows adjustment of conveyor speed to match curing requirements.
Benefits:
- High Throughput: Capable of processing large quantities of parts quickly.
- Consistent Quality: Ensures uniform curing across all parts.
- Reduced Labor Costs: Automation reduces the need for manual intervention.
Applications:
- Automotive and aerospace industries
- High-volume manufacturing plants
- Standardized parts production
Common Types of Conveyor Ovens:
- Monorail Ovens: Parts are hung from an overhead conveyor and pass through the oven in a linear path.
- Chain-On-Edge Ovens: Parts are attached to fixtures on a conveyor chain, suitable for heavier items.
- Flat-Belt Ovens: Use a flat conveyor belt to transport parts, ideal for lightweight or flat components.
3. Infrared Ovens
Infrared ovens use infrared radiation to cure powder coatings, offering a fast and energy-efficient alternative to conventional ovens. They are often used in combination with other oven types to optimize curing.
Features:
- Fast Heating: Infrared radiation provides rapid heat-up and curing times.
- Energy Efficiency: Direct heating reduces energy consumption compared to convection ovens.
- Compact Size: Smaller footprint compared to traditional ovens.
Benefits:
- Quick Curing: Significantly reduces curing times, increasing throughput.
- Targeted Heating: Infrared heat can be focused on specific areas, reducing overall energy use.
- Improved Finish: Provides smooth and even curing, minimizing defects.
Applications:
- Automotive and consumer electronics
- Applications requiring quick turnaround
- Parts with complex shapes or heat-sensitive materials
Common Types of Infrared Ovens:
- Short-Wave Infrared Ovens: Provide intense heat for fast curing, suitable for thicker coatings.
- Medium-Wave Infrared Ovens: Balance between heat intensity and penetration, ideal for general applications.
- Long-Wave Infrared Ovens: Gentle heat suitable for heat-sensitive substrates.
4. Gas-Fired Ovens
Gas-fired ovens use natural gas or propane as a heat source. They are popular for large-scale operations due to their efficiency and cost-effectiveness.
Features:
- High Heat Output: Efficiently generates high temperatures for rapid curing.
- Cost-Effective: Generally lower operating costs compared to electric ovens.
- Robust Construction: Designed to handle heavy-duty industrial use.
Benefits:
- Reduced Operating Costs: Lower energy costs compared to electric ovens, especially for large volumes.
- Reliable Performance: Consistent heating for uniform curing.
- Scalability: Suitable for large-scale production and expansion.
Applications:
- Automotive and heavy equipment manufacturing
- Large industrial operations
- High-volume powder coating lines
Common Types of Gas-Fired Ovens:
- Direct-Fired Ovens: Burners directly heat the air inside the oven chamber, providing fast and efficient heating.
- Indirect-Fired Ovens: Heat exchangers separate combustion gases from the oven air, offering cleaner operation.
5. Electric Ovens
Electric ovens use electrical heating elements to generate heat for curing powder coatings. They are commonly used in smaller operations due to their ease of use and installation.
Features:
- Precise Temperature Control: Offers accurate and consistent temperature settings.
- Easy Installation: No need for gas lines or combustion venting.
- Low Maintenance: Fewer moving parts compared to gas-fired ovens.
Benefits:
- Safe and Clean: No combustion gases, reducing emissions and improving air quality.
- Consistent Performance: Stable temperature control ensures uniform curing.
- Versatile: Suitable for various applications and materials.
Applications:
- Small to medium-sized businesses
- Custom and low-volume production
- Applications with strict environmental regulations
Common Types of Electric Ovens:
- Forced-Air Convection Ovens: Use fans to circulate heated air for uniform temperature distribution.
- Static Ovens: Rely on natural convection, suitable for delicate or sensitive parts.
6. Combination Ovens
Combination ovens integrate multiple heating methods, such as infrared and convection, to provide flexibility and optimize curing processes.
Features:
- Multi-Mode Operation: Allows switching between or combining different heating methods.
- Optimized Curing: Adjusts curing methods based on part size, shape, and material.
- Flexible Configuration: Customizable to meet specific production needs.
Benefits:
- Versatility: Capable of handling a wide range of parts and coatings.
- Improved Efficiency: Combines the strengths of different heating methods for optimal results.
- Enhanced Finish Quality: Provides tailored curing conditions to minimize defects.
Applications:
- Complex parts with varying geometries
- Industries requiring rapid production changes
- Specialized coating applications
Considerations for Choosing the Right Powder Coating Oven
When selecting a powder coating oven, consider the following factors:
- Production Volume:
- Choose batch ovens for low to medium production and conveyor ovens for high-volume operations.
- Part Size and Shape:
- Consider the size, weight, and geometry of the parts to determine the appropriate oven type.
- Energy Efficiency:
- Evaluate energy consumption and costs, especially for large-scale operations.
- Temperature Requirements:
- Ensure the oven can maintain consistent temperatures for your specific powder coatings.
- Space and Layout:
- Consider the available space and how the oven will fit into your production line layout.
- Budget and Cost:
- Balance initial investment with long-term operating costs and return on investment.
- Regulatory Compliance:
- Ensure the oven meets local safety and environmental regulations.
Conclusion
Selecting the right powder coating oven is crucial for achieving high-quality finishes and efficient production. By understanding the features, benefits, and applications of each oven type, businesses can make informed decisions that align with their production needs and goals. Investing in the right oven will enhance productivity, reduce costs, and ensure a durable, attractive finish on your coated products.
Powder coating oven maintenance tips
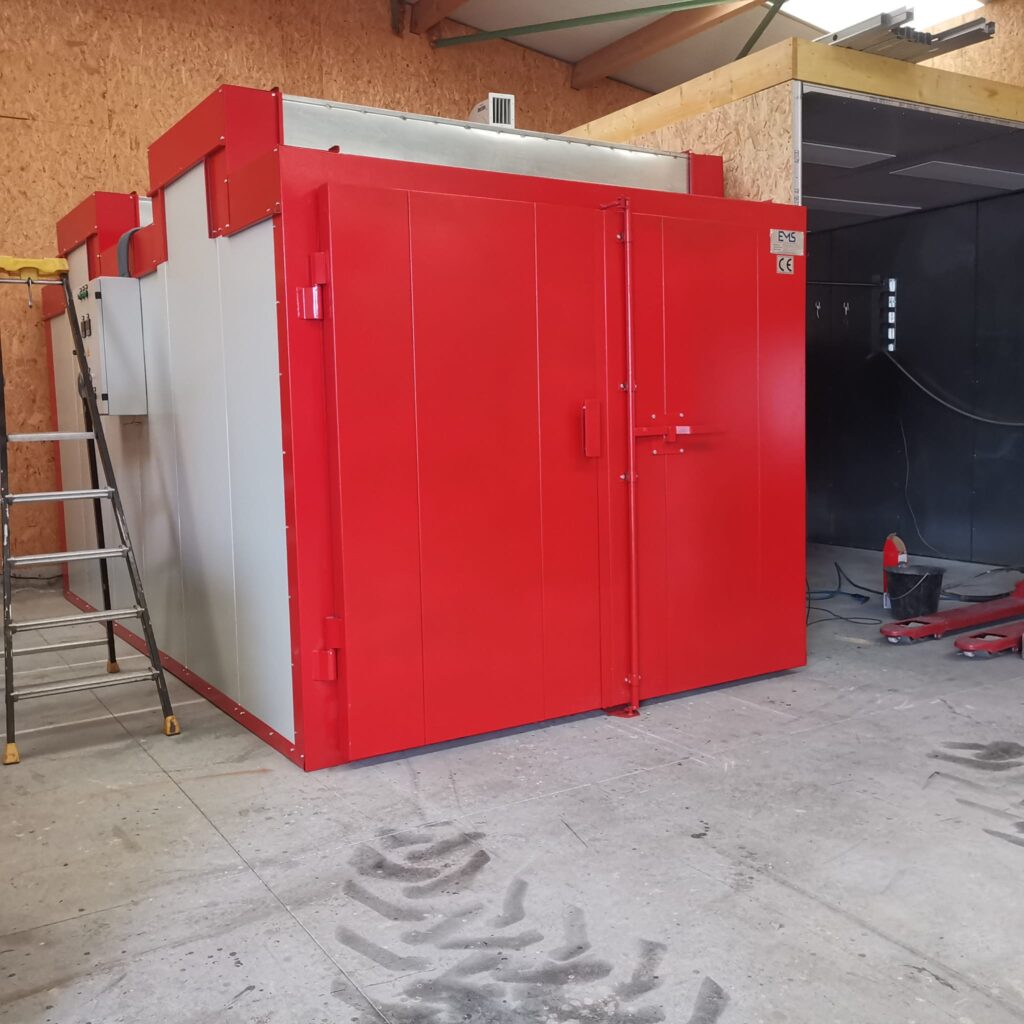
Proper maintenance of powder coating ovens is crucial to ensure efficient operation, consistent curing quality, and the longevity of the equipment. A well-maintained oven minimizes downtime, reduces energy consumption, and prevents costly repairs. Below are comprehensive tips and guidelines for maintaining powder coating ovens effectively.
Powder Coating Oven Maintenance Tips
1. Regular Cleaning
Keeping the oven clean is essential to prevent powder buildup, which can affect performance and finish quality.
Cleaning Tips:
- Daily Cleaning:
- Inspect and Clean Interior Surfaces: Remove any powder buildup on oven walls, floors, and ceilings.
- Clean Heating Elements: Check and clean heating elements to ensure efficient heat transfer.
- Vacuum or Sweep the Floor: Remove any loose powder or debris from the oven floor.
- Weekly Cleaning:
- Clean Air Ducts and Vents: Ensure proper airflow and ventilation by cleaning ducts and vents regularly.
- Wipe Down Doors and Seals: Clean door seals and check for any damage that could affect insulation.
- Monthly Cleaning:
- Deep Clean Oven Interior: Use a non-abrasive cleaner to deep clean the oven interior and remove any stubborn residue.
- Inspect and Clean Exhaust Systems: Check and clean exhaust fans and filters to prevent blockages.
2. Routine Inspections
Regular inspections help identify potential issues before they become major problems, ensuring the oven operates at peak efficiency.
Inspection Tips:
- Daily Inspections:
- Check Temperature Settings: Verify that the oven reaches and maintains the correct curing temperature.
- Monitor Airflow: Ensure that fans and blowers are functioning correctly for even heat distribution.
- Inspect Doors and Seals: Check for gaps or damage that could lead to heat loss.
- Weekly Inspections:
- Inspect Electrical Components: Check wiring, connections, and control panels for signs of wear or damage.
- Check for Unusual Noises: Listen for any unusual noises that might indicate mechanical issues.
- Monthly Inspections:
- Inspect Insulation: Check oven insulation for any damage or wear that could reduce energy efficiency.
- Examine Conveyor Systems: For conveyor ovens, inspect belts, chains, and rollers for wear and alignment.
3. Calibration and Testing
Regular calibration and testing ensure that the oven operates at the correct temperature and settings, maintaining coating quality.
Calibration Tips:
- Temperature Calibration:
- Use Thermocouples: Place thermocouples at various points in the oven to verify temperature uniformity.
- Adjust Temperature Controllers: Calibrate controllers to maintain consistent curing temperatures across the oven.
- Testing Performance:
- Conduct Cure Tests: Perform test runs with sample parts to ensure that coatings are cured properly.
- Check Heating Elements: Test heating elements for consistent output and replace any that are faulty.
4. Preventive Maintenance
Implementing a preventive maintenance schedule helps prevent unexpected breakdowns and extends the life of the oven.
Preventive Maintenance Tips:
- Lubrication:
- Lubricate Moving Parts: Apply lubrication to bearings, chains, and other moving parts to reduce friction and wear.
- Component Replacement:
- Replace Worn Parts: Regularly check and replace parts like belts, seals, and filters that show signs of wear.
- Fan and Blower Maintenance:
- Inspect and Clean Fans: Check fans for balance and clean them to prevent vibration and noise.
- Replace Worn Bearings: Replace any bearings that are noisy or show signs of wear.
5. Safety and Compliance
Ensuring safety and regulatory compliance is critical for protecting workers and meeting industry standards.
Safety Tips:
- Fire Safety:
- Check Fire Suppression Systems: Ensure that fire suppression systems are operational and regularly serviced.
- Install Smoke Detectors: Regularly test smoke detectors and alarms to ensure they are functional.
- Electrical Safety:
- Inspect Wiring and Connections: Regularly check electrical wiring and connections for signs of wear or damage.
- Conduct Safety Audits: Perform regular safety audits to ensure compliance with safety regulations.
6. Documentation and Record Keeping
Keeping detailed records of maintenance activities helps track oven performance and identify trends or recurring issues.
Documentation Tips:
- Maintain a Maintenance Log: Record all maintenance activities, including inspections, cleaning, and repairs.
- Track Performance Metrics: Monitor metrics such as energy consumption, downtime, and repair frequency.
7. Staff Training and Awareness
Proper training ensures that staff are equipped to perform maintenance tasks safely and effectively.
Training Tips:
- Provide Comprehensive Training: Train staff on oven operation, maintenance procedures, and safety protocols.
- Encourage Proactive Maintenance: Empower staff to identify and report potential issues promptly.
Sample Maintenance Schedule for Powder Coating Ovens
Below is a sample maintenance schedule to help you organize and plan oven maintenance tasks:
Frequency | Task | Details |
---|---|---|
Daily | Clean interior surfaces | Remove powder buildup from oven walls, floors, and ceilings. |
Check temperature settings | Verify that the oven reaches the correct curing temperature. | |
Inspect doors and seals | Look for gaps or damage that could lead to heat loss. | |
Weekly | Clean air ducts and vents | Ensure proper airflow and ventilation. |
Inspect electrical components | Check wiring, connections, and control panels for wear. | |
Lubricate moving parts | Apply lubrication to bearings, chains, and other components. | |
Monthly | Deep clean oven interior | Use non-abrasive cleaner to remove stubborn residue. |
Calibrate temperature controllers | Verify and adjust temperature settings for consistency. | |
Inspect insulation and conveyor systems | Check insulation integrity and conveyor alignment. | |
Quarterly | Test heating elements and fans | Ensure consistent output and replace faulty components. |
Review safety protocols and systems | Update safety measures and test fire suppression systems. | |
Annually | Conduct comprehensive performance review | Evaluate overall condition and plan for upgrades. |
Audit compliance with regulations | Ensure adherence to safety and environmental standards. |
Conclusion
Regular maintenance of powder coating ovens is essential for achieving high-quality finishes, maintaining production efficiency, and ensuring equipment longevity. By implementing a structured maintenance plan, conducting regular inspections, and training staff, businesses can minimize downtime, reduce costs, and maintain a safe working environment.
Powder Coating Spray Booth: Achieving Clean, Efficient, and High-Quality Coating Results
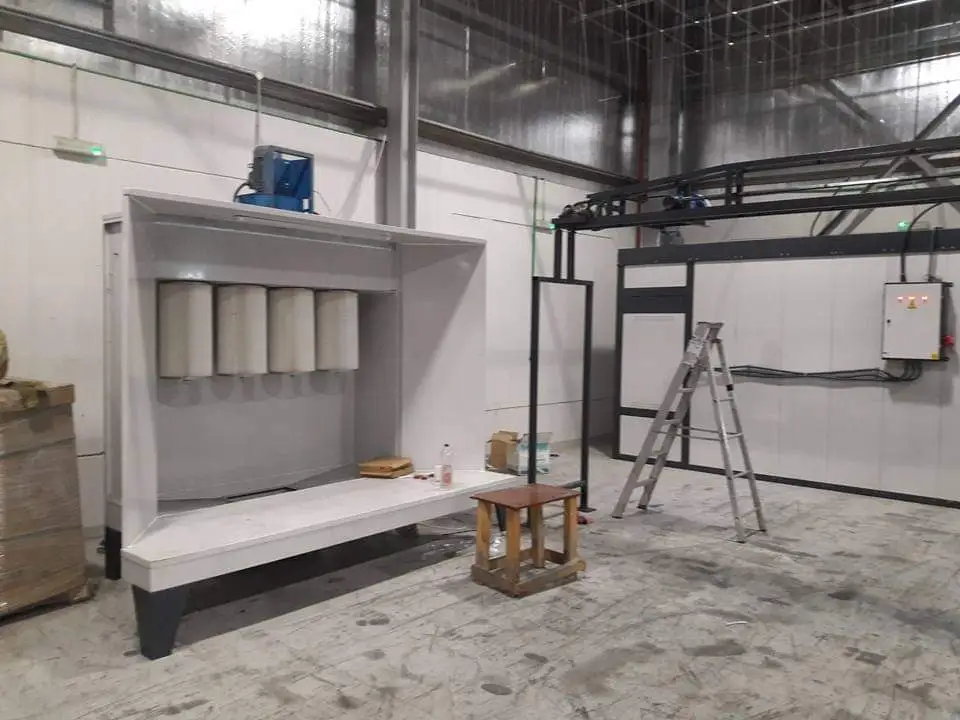
The powder coating process requires a controlled environment to ensure consistent and high-quality finishes. One of the most critical components in this process is the powder coating spray booth, where the actual application of powder takes place. Spray booths provide a dedicated space for applying powder, preventing contamination, capturing overspray, and ensuring that the process is both efficient and environmentally friendly.
Powder coating spray booths are designed to contain the powder within a specific area, keeping it from escaping into the surrounding workspace. These booths are typically equipped with air filtration and extraction systems that capture excess powder particles, reducing waste, minimizing health risks to workers, and maintaining a clean workspace. Additionally, the booth’s environment is controlled to ensure that no contaminants interfere with the powder coating process, resulting in smooth, durable finishes.
EMS Powder Coating Equipment is a trusted manufacturer of powder coating spray booths, offering a wide range of booths equipped with advanced filtration and ventilation systems. EMS spray booths are designed for optimal efficiency, safety, and cleanliness, making them an ideal choice for businesses looking to enhance their powder coating operations. In this guide, we’ll explore how powder coating spray booths work, their benefits, and why EMS Powder Coating Equipment is the best option for businesses seeking high-performance booths.
What is a Powder Coating Spray Booth?
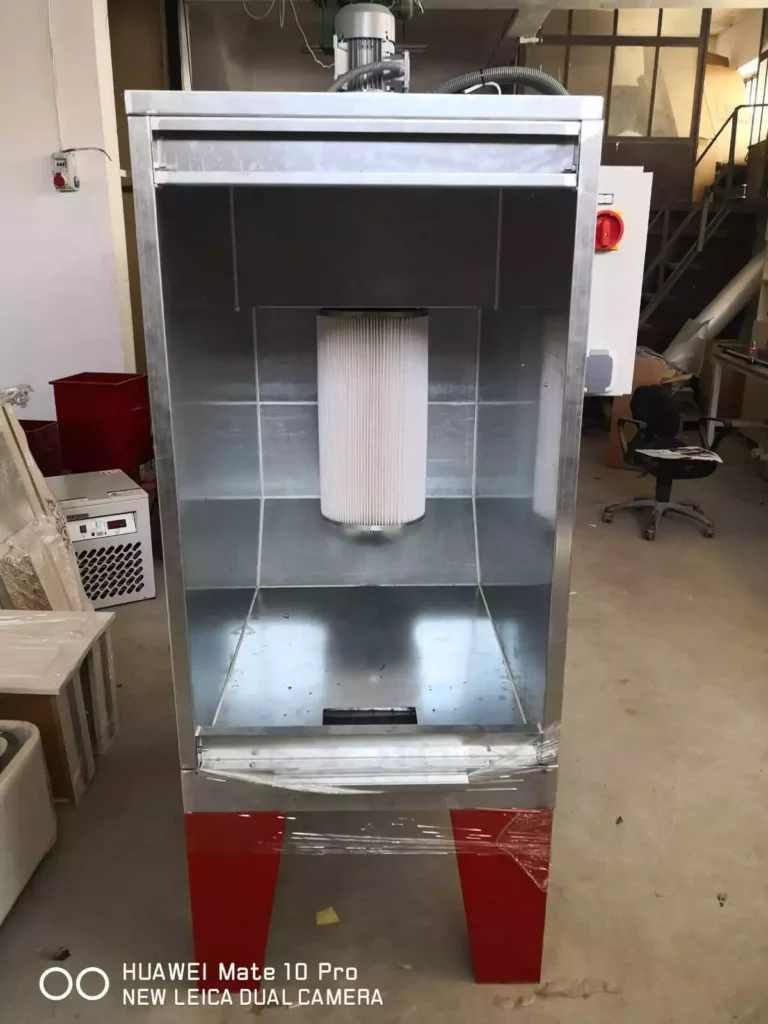
A powder coating spray booth is an enclosed space where powder is applied to products during the powder coating process. The booth provides a controlled environment that prevents external contaminants from affecting the coating process while also containing the powder within a specific area to prevent it from spreading throughout the workspace. These booths are an essential part of any powder coating system, as they ensure a clean, safe, and efficient application process.
How Powder Coating Spray Booths Work
In a powder coating spray booth, products are placed inside the booth and coated using electrostatic spray guns. These guns charge the powder particles, which are then attracted to the grounded surface of the product. This electrostatic attraction ensures that the powder adheres evenly to the product, providing a smooth and consistent coat.
As the powder is applied, some particles may not adhere to the product and become airborne. To prevent these excess particles from escaping into the surrounding workspace, the booth is equipped with an air extraction and filtration system. This system draws air through filters that capture the excess powder, keeping the air inside the booth clean and free from harmful particulates.
Many powder coating spray booths are equipped with features like adjustable airflow, which allows operators to control the speed and direction of air movement within the booth. This helps ensure that the powder is applied evenly and that overspray is efficiently captured and recycled, minimizing waste.
EMS Powder Coating Equipment manufactures spray booths with advanced air filtration and extraction systems that maximize efficiency and cleanliness. Their booths are designed to handle the demands of industrial powder coating operations, ensuring consistent and high-quality results.
The Benefits of Powder Coating Spray Booths
Powder coating spray booths are essential for businesses looking to improve the efficiency, safety, and quality of their powder coating process. Here are some of the key benefits of using a high-quality spray booth:
1. Improved Product Quality
A controlled environment is essential for achieving consistent, high-quality finishes in powder coating. In an open workspace, contaminants such as dust, dirt, or debris can settle on the product during the coating process, leading to defects like uneven finishes or poor adhesion. A powder coating spray booth provides a clean, enclosed space where products can be coated without the risk of contamination from the outside environment.
In addition to preventing contamination, the airflow and filtration system inside the booth ensure that overspray is effectively captured, preventing it from interfering with the final finish. The result is a smooth, even coating that meets the highest standards of quality and durability.
EMS Powder Coating Equipment designs its spray booths to provide a clean, controlled environment that enhances the quality of the finished product. Their booths are engineered for precision, ensuring that each product receives a flawless coating.
2. Reduced Powder Waste and Cost Savings
Powder waste is a common issue in powder coating operations, especially when the excess powder is not properly captured and recycled. Without a spray booth, much of the overspray can be lost, leading to higher material costs and environmental waste. Powder coating spray booths are designed to capture excess powder, allowing it to be collected and reused.
The filtration system in a spray booth traps airborne powder particles and prevents them from escaping into the workspace. This captured powder can then be reclaimed and reintroduced into the coating process, reducing material waste and cutting costs.
EMS Powder Coating Equipment offers spray booths with advanced powder recovery systems that maximize powder reuse and minimize waste. Their booths are designed to reduce material costs by ensuring that as much powder as possible is captured and recycled.
3. Enhanced Worker Safety
Worker safety is a top priority in any industrial setting, and powder coating operations are no exception. During the powder coating process, airborne powder particles can pose a respiratory hazard to workers if they are not properly contained. Inhaling these particles over time can lead to respiratory issues and other health problems.
Powder coating spray booths are equipped with ventilation and filtration systems that remove harmful particulates from the air, ensuring that the workspace remains clean and safe for operators. The booth’s design prevents airborne powder from escaping into the surrounding environment, reducing the risk of exposure for workers.
EMS Powder Coating Equipment designs its spray booths with safety in mind, offering advanced filtration and ventilation systems that protect workers from inhaling harmful particles. Their booths are built to meet the highest safety standards, ensuring a safe and healthy work environment.
4. Environmental Compliance
Many industries are subject to strict environmental regulations regarding air quality and emissions. Powder coating is an environmentally friendly process compared to liquid painting, as it produces minimal volatile organic compounds (VOCs). However, without proper containment and filtration, excess powder can still be released into the atmosphere, contributing to air pollution.
Powder coating spray booths are designed to contain and capture overspray, preventing it from being released into the environment. The booth’s filtration system ensures that any excess powder is collected and safely disposed of or recycled, helping businesses meet environmental regulations and reduce their overall environmental impact.
EMS Powder Coating Equipment offers spray booths with high-performance filtration systems that help businesses comply with environmental standards. Their booths are designed to minimize emissions and improve sustainability in powder coating operations.
5. Flexibility and Customization
Powder coating spray booths come in a variety of sizes and configurations, making them suitable for different types of products and production volumes. Whether you’re coating small parts or large industrial components, spray booths can be customized to meet the specific needs of your operation. This flexibility allows businesses to optimize their coating process for efficiency and quality.
Spray booths can also be equipped with additional features, such as adjustable airflow controls, automated powder recovery systems, and more, to enhance performance and meet the unique requirements of each production line.
EMS Powder Coating Equipment provides customizable spray booths that can be tailored to the specific needs of your business. Whether you need a small batch booth or a large conveyorized system, EMS offers solutions that ensure optimal performance and efficiency.
6. Easy Maintenance and Long-Term Reliability
A high-quality spray booth is a long-term investment that can provide years of reliable performance with proper maintenance. Regularly replacing filters and cleaning the booth ensures that it continues to operate efficiently and that air quality remains high. High-quality spray booths are built to withstand the demands of continuous industrial use, providing businesses with a durable solution for their powder coating needs.
EMS Powder Coating Equipment manufactures spray booths that are designed for ease of maintenance and long-lasting reliability. Their booths are constructed from high-quality materials that resist wear and tear, ensuring that your investment will continue to deliver top-tier performance for years to come.
Why Choose EMS Powder Coating Equipment for Spray Booths?
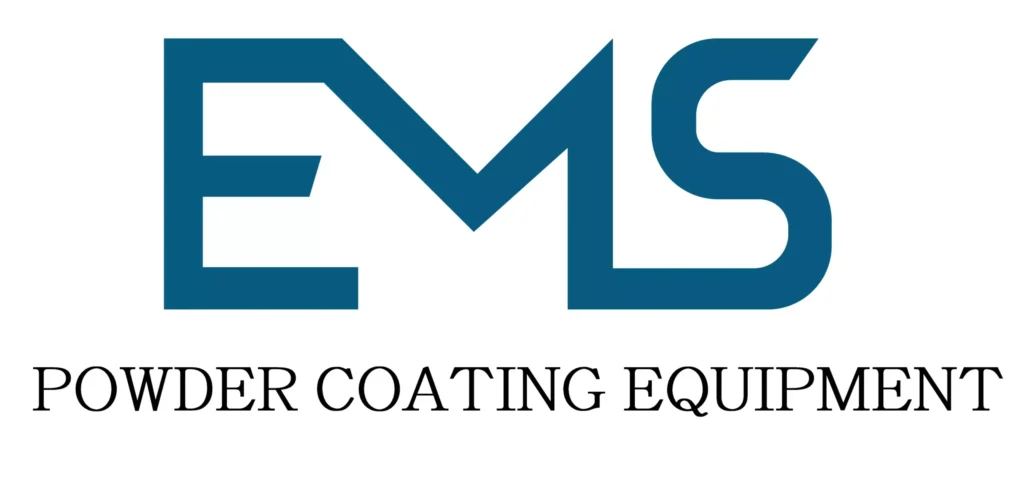
When selecting a powder coating spray booth, businesses need equipment that offers precision, efficiency, and durability. EMS Powder Coating Equipment is the industry leader in providing advanced spray booths that meet the highest standards of performance and safety. Here’s why EMS is the best choice for businesses looking to invest in high-quality spray booths:
1. Advanced Filtration and Ventilation Technology
EMS spray booths are equipped with cutting-edge filtration and ventilation systems that ensure a clean, safe environment for both workers and products. Their booths are designed to capture excess powder with maximum efficiency, preventing contamination and improving air quality in the workspace.
2. Customizable Solutions for Different Industries
Every production line has unique requirements, and EMS offers customizable solutions to meet those needs. Whether you’re working with small parts or large industrial components, EMS provides spray booths that can be tailored to fit your specific production environment. Their booths are available in a range of sizes and configurations, ensuring that businesses get the right solution for their needs.
3. Energy Efficiency and Cost Savings
EMS Powder Coating Equipment understands the importance of efficiency in today’s manufacturing environments. Their spray booths are designed to minimize powder waste and reduce energy consumption, helping businesses lower their operational costs without sacrificing performance.
4. Durability and Long-Lasting Performance
Built to withstand the rigors of industrial use, EMS spray booths are constructed from high-quality materials that ensure long-lasting performance. Their booths require minimal maintenance and are designed to provide reliable operation for years, making them a sound investment for any business.
5. Superior Customer Support and Service
In addition to providing top-tier equipment, EMS offers exceptional customer support and after-sales service. From installation and setup to ongoing maintenance and troubleshooting, EMS’s team of experts is dedicated to ensuring that your spray booth operates at peak efficiency.
Conclusion
A powder coating spray booth is an essential part of any powder coating system, providing a clean, controlled environment that ensures high-quality finishes, worker safety, and environmental compliance. By capturing and filtering overspray, these booths help businesses improve efficiency, reduce waste, and lower costs.
EMS Powder Coating Equipment is the industry leader in providing advanced spray booths with state-of-the-art filtration and ventilation systems. Whether you’re looking to upgrade your existing system or invest in new equipment, EMS offers customizable solutions that ensure your powder coating operations are optimized for maximum productivity and quality.
By choosing EMS powder coating spray booths, businesses can enhance their coating process, improve product quality, and reduce their environmental impact. With a proven track record of innovation and customer satisfaction, EMS is the best choice for businesses seeking reliable and efficient spray booths.
Powder Coating Booth: The Key to High-Quality Finishes and Efficiency in Coating Processes
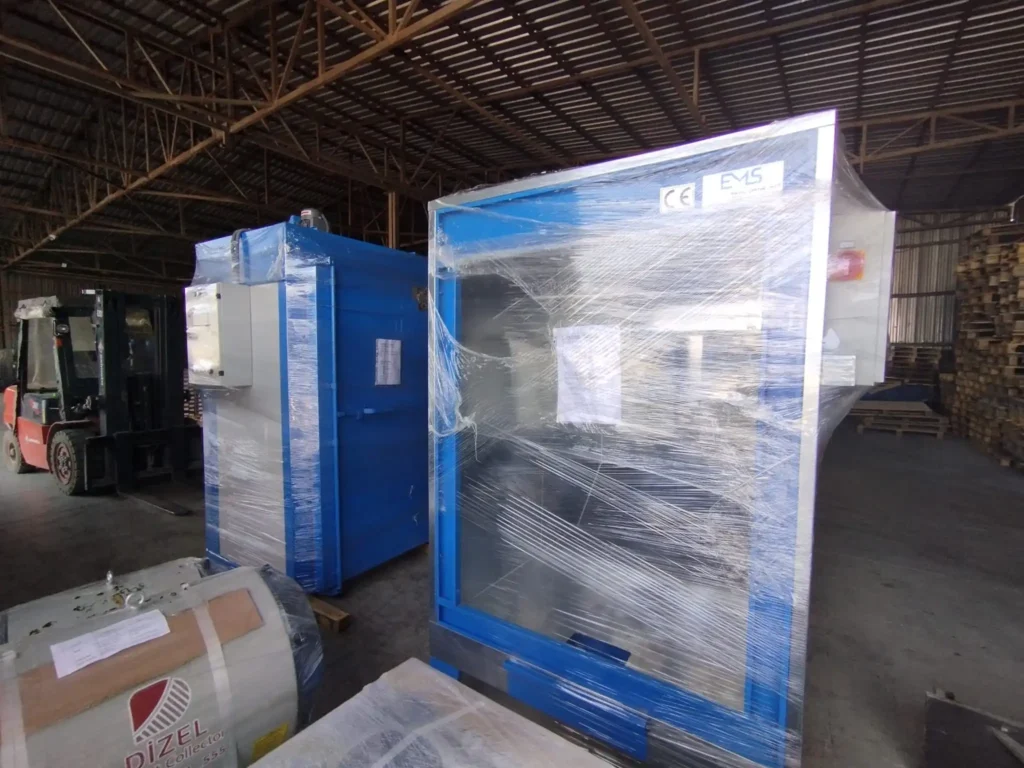
A powder coating booth is a vital component of any powder coating operation, providing a designated area for applying powder coatings to various products. These booths are designed to ensure a controlled environment that enhances the efficiency and quality of the powder coating process. By containing overspray and preventing contamination, powder coating booths play a critical role in achieving superior finishes and maintaining a clean workspace.
The design and functionality of a powder coating booth significantly impact production efficiency and the overall quality of the coated products. With features such as effective ventilation, advanced filtration systems, and customizable configurations, these booths ensure that powder is applied evenly and without interference from external factors.
EMS Powder Coating Equipment is renowned for manufacturing high-performance powder coating booths that meet the needs of diverse industries. Their booths are engineered for optimal performance, safety, and durability, making them an ideal choice for businesses looking to enhance their powder coating operations. In this guide, we will delve into the features, benefits, and advantages of using powder coating booths and explain why EMS is the best manufacturer in this field.
What is a Powder Coating Booth?
A powder coating booth is an enclosed workspace specifically designed for applying powder coatings to products. The primary function of the booth is to contain the powder and provide a clean environment for the coating application process. This controlled environment minimizes contamination, maximizes efficiency, and enhances the quality of the finished product.
How Powder Coating Booths Operate
In a powder coating booth, products are typically suspended or placed on racks, allowing for easy access during the coating process. Powder is applied using electrostatic spray guns, which charge the powder particles to ensure they adhere evenly to the grounded surfaces of the products.
Once the powder is applied, excess particles may become airborne. Powder coating booths are equipped with advanced ventilation systems that effectively capture these airborne particles, preventing them from escaping into the surrounding area. The captured powder can often be recycled and reused, reducing waste and material costs.
The interior of the booth is designed to maintain an optimal environment for powder application. Features such as adjustable airflow and temperature control help create ideal conditions for achieving a smooth, uniform finish on coated products.
EMS Powder Coating Equipment specializes in designing powder coating booths that maximize efficiency and performance. Their booths are built with advanced technology and materials that enhance the coating process, ensuring consistent and high-quality results.
Key Features of Powder Coating Booths
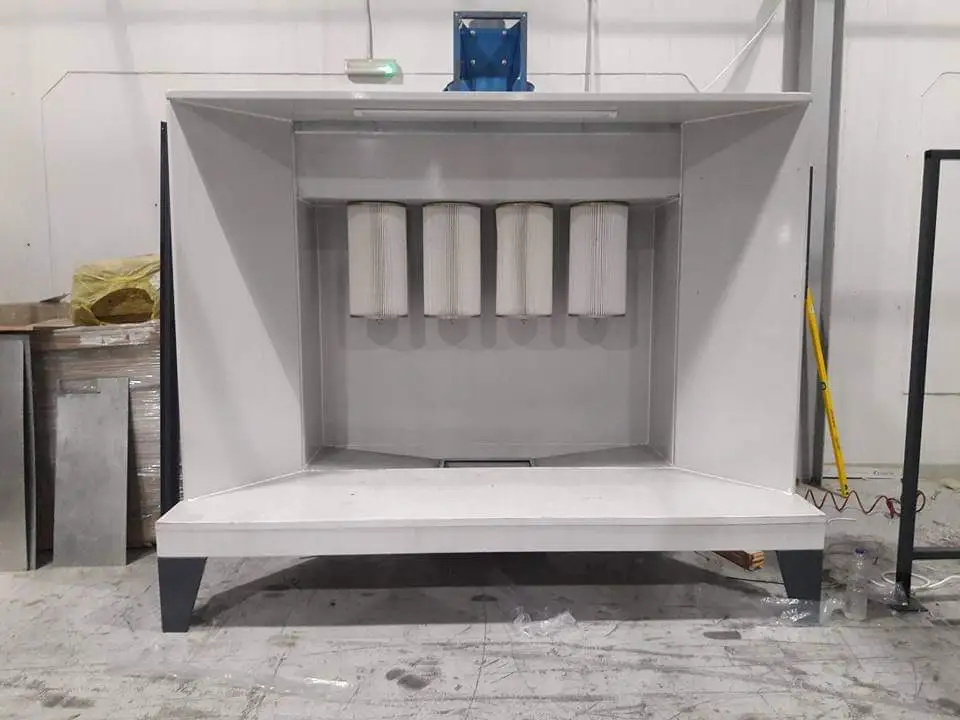
Powder coating booths come with a variety of features that contribute to their effectiveness and efficiency. Here are some key features that make EMS powder coating booths a top choice for businesses:
1. Advanced Air Filtration Systems
Effective air filtration is crucial for maintaining a clean environment in the powder coating booth. EMS booths are equipped with advanced filtration systems that capture overspray and airborne particles, ensuring that the air inside the booth remains clean and free from contaminants. These systems help improve air quality, protect workers, and enhance the overall coating process.
2. Efficient Ventilation
Proper ventilation is essential for controlling airflow within the booth. EMS powder coating booths come with adjustable ventilation systems that allow operators to regulate air movement. This capability ensures that the powder is evenly distributed and that excess particles are efficiently captured, resulting in a smoother finish and reduced waste.
3. Customizable Configurations
Every business has unique production needs, and EMS understands that one size does not fit all. Their powder coating booths can be customized to accommodate different product sizes, shapes, and production volumes. Whether you require a small batch booth or a larger, conveyorized system, EMS offers solutions tailored to your specific requirements.
4. Durability and Construction Quality
EMS powder coating booths are built to last, constructed from high-quality materials that can withstand the rigors of industrial use. Their booths are designed for easy maintenance and long-term reliability, ensuring that businesses get a robust solution that continues to perform over time.
5. User-Friendly Design
Ease of use is a key consideration in the design of EMS powder coating booths. Features such as ergonomic controls, easy access for loading and unloading products, and clear visibility ensure that operators can work efficiently and safely. The user-friendly design contributes to higher productivity and improved overall workflow in the coating process.
6. Environmental Compliance
In today’s manufacturing environment, compliance with environmental regulations is paramount. EMS powder coating booths are designed to minimize emissions and capture waste effectively, helping businesses meet environmental standards. By reducing the release of powder particles into the atmosphere, EMS booths contribute to a more sustainable coating process.
Benefits of Using Powder Coating Booths
Investing in a high-quality powder coating booth provides numerous benefits for businesses engaged in powder coating operations. Here are some of the key advantages:
1. Enhanced Product Quality
One of the most significant benefits of using a powder coating booth is the improvement in product quality. By providing a controlled environment for powder application, booths help ensure that coatings are applied evenly and without contaminants. This leads to smoother finishes and higher overall quality in the final products.
2. Increased Efficiency and Productivity
Powder coating booths streamline the coating process, reducing downtime and improving efficiency. By capturing overspray and enabling easy recycling of powder, businesses can maximize material usage and minimize waste. This efficiency translates into higher productivity and lower operational costs.
3. Improved Worker Safety
The safety of workers is a top priority in any industrial setting. Powder coating booths are designed to contain airborne powder particles, reducing the risk of exposure and respiratory hazards for operators. With effective filtration and ventilation, EMS booths help create a safer working environment for employees.
4. Cost Savings
By reducing material waste and improving efficiency, powder coating booths contribute to significant cost savings over time. The ability to reclaim and reuse excess powder minimizes the need for frequent purchases of new materials, which can lead to substantial financial benefits for businesses.
5. Flexibility in Production
The customizable nature of EMS powder coating booths allows businesses to adapt their operations to changing production needs. Whether coating small batches or large volumes, the flexibility of the booths enables businesses to scale their operations effectively.
6. Environmental Benefits
Using a powder coating booth contributes to a more sustainable coating process by capturing overspray and minimizing waste. EMS booths are designed to meet environmental regulations and reduce the overall impact of powder coating operations on the environment.
Why Choose EMS Powder Coating Equipment for Powder Coating Booths?
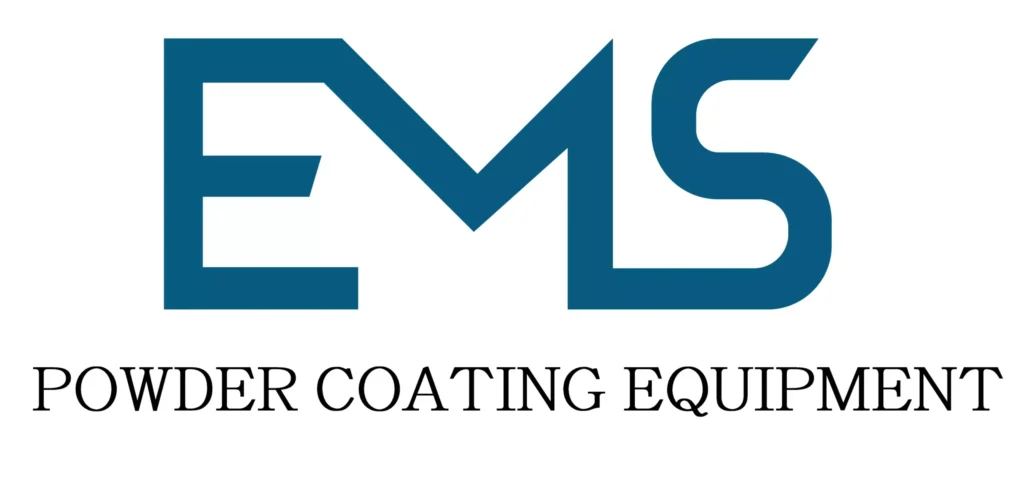
When it comes to selecting a powder coating booth, businesses need a manufacturer that offers quality, reliability, and superior performance. EMS Powder Coating Equipment stands out as the leading choice for businesses looking to invest in powder coating booths. Here’s why EMS is the best option:
1. Industry Expertise
With years of experience in the powder coating industry, EMS has a deep understanding of the challenges and requirements of different businesses. Their expertise allows them to design booths that meet the specific needs of various applications and industries.
2. Innovative Technology
EMS is committed to innovation, continually improving their products with the latest technology. Their powder coating booths incorporate advanced filtration, ventilation, and airflow systems that enhance performance and efficiency, ensuring high-quality finishes.
3. Comprehensive Support
EMS offers exceptional customer support, from initial consultations and installations to ongoing maintenance and service. Their team of experts is dedicated to ensuring that your powder coating booth operates at peak efficiency, helping businesses achieve their production goals.
4. Custom Solutions
Understanding that each business has unique needs, EMS provides customizable solutions that allow companies to tailor their powder coating booths to their specific requirements. This flexibility ensures optimal performance and efficiency in every production environment.
5. Proven Track Record
With a proven track record of customer satisfaction and successful installations, EMS is a trusted name in the powder coating industry. Their commitment to quality and performance makes them the best choice for businesses seeking reliable powder coating booths.
Conclusion
A powder coating booth is an essential component of any powder coating operation, providing a controlled environment that ensures high-quality finishes, improved efficiency, and worker safety. With their advanced filtration and ventilation systems, powder coating booths help businesses maximize productivity while minimizing waste and costs.
EMS Powder Coating Equipment is the industry leader in providing high-performance powder coating booths tailored to meet the needs of diverse industries. Whether you’re looking to upgrade your existing equipment or invest in new solutions, EMS offers customizable booths designed for optimal performance and quality.
By choosing EMS powder coating booths, businesses can enhance their coating processes, improve product quality, and reduce their environmental impact. With a commitment to innovation and customer satisfaction, EMS is the best choice for companies seeking reliable and efficient powder coating solutions.
Powder Paint Booth with Filters: Ensuring Clean and Efficient Coating Processes
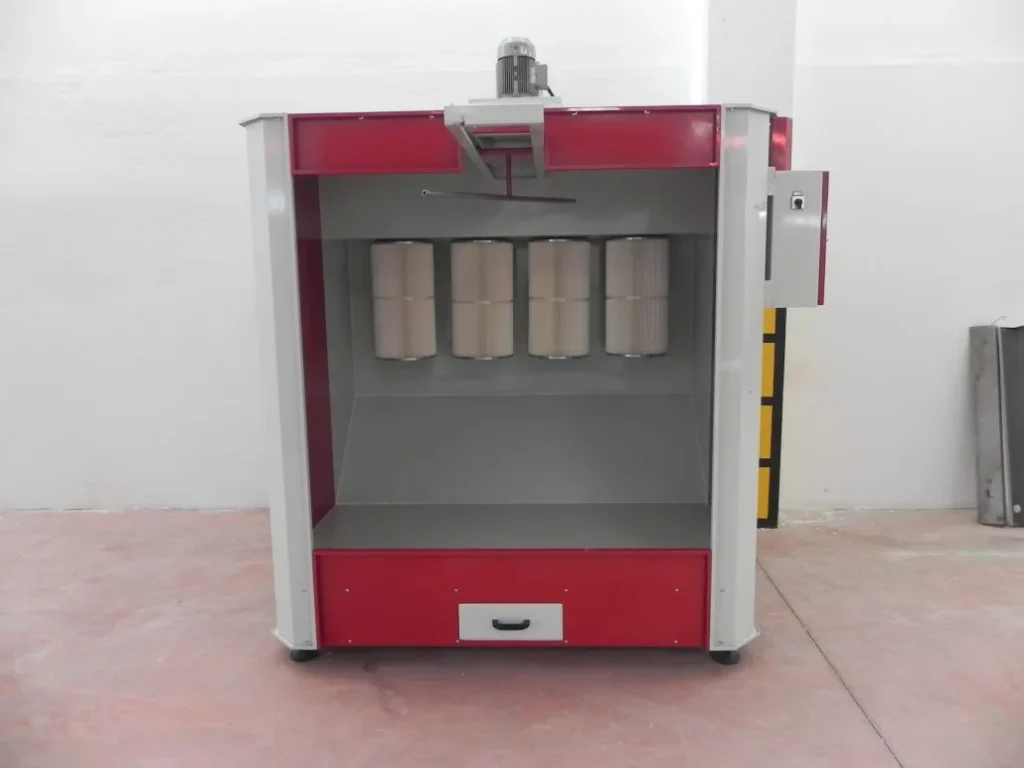
A powder paint booth with filters is an essential component of any powder coating operation, designed to create a controlled environment for the application of powder coatings. These booths are specifically engineered to manage overspray and enhance the efficiency of the coating process, ensuring a clean workspace and high-quality finishes.
Filters play a crucial role in powder paint booths by capturing airborne particles, preventing them from contaminating the coating process. By maintaining air quality and reducing the risk of defects, these booths help achieve superior coating results while also complying with environmental regulations.
EMS Powder Coating Equipment is a leading manufacturer of powder paint booths with advanced filtration systems, providing innovative solutions that meet the demands of modern coating operations. In this section, we will delve into the design, features, and benefits of powder paint booths with filters, and explain why EMS is the preferred choice for businesses seeking reliable and effective coating solutions.
What is a Powder Paint Booth with Filters?
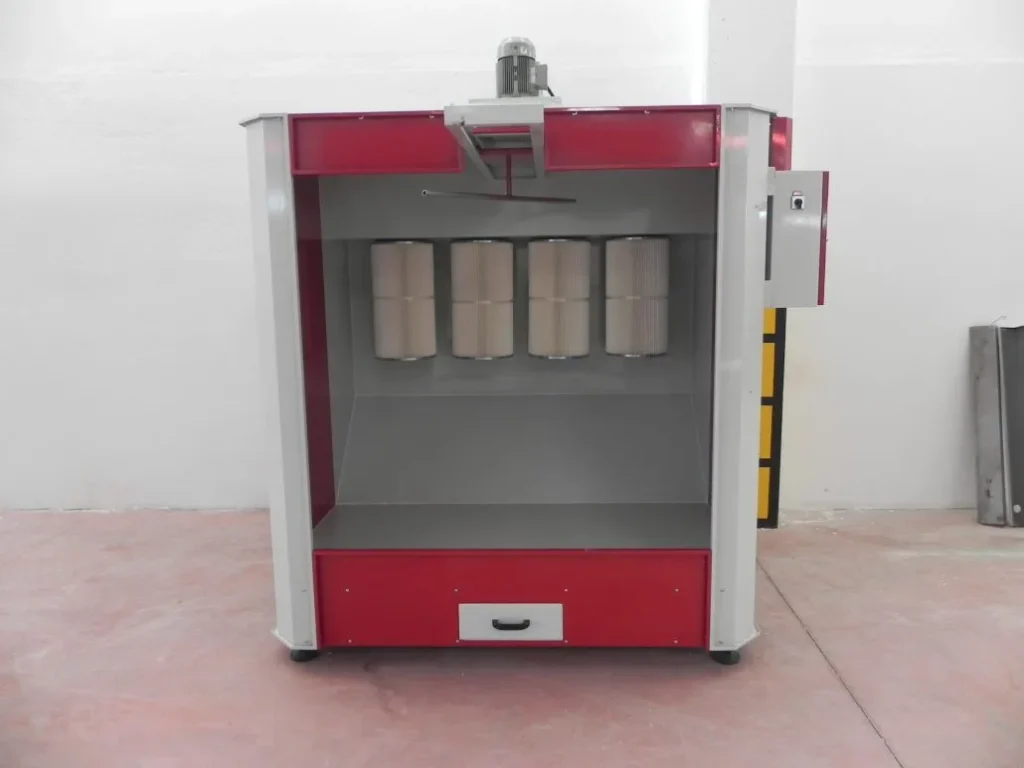
A powder paint booth with filters is a specialized enclosure designed for the application of powder coatings. These booths provide a contained environment that minimizes contamination, manages overspray, and ensures a safe workspace for operators.
How Powder Paint Booths Operate
In a typical powder coating process, the substrate is first cleaned and prepared before being coated with powder. Once the powder is applied, the booth’s filtration system comes into play.
The booth is equipped with a filtration system that captures overspray and other airborne particles generated during the coating process. High-efficiency filters trap these particles, preventing them from settling on the substrate or contaminating the environment. The filtered air is then recirculated back into the booth or expelled outside, depending on the design of the booth.
EMS Powder Coating Equipment designs powder paint booths with advanced filtration systems that maximize efficiency and ensure a clean working environment. Their booths are built to accommodate various coating processes and substrates, making them a versatile solution for businesses of all sizes.
Key Features of Powder Paint Booths with Filters
Powder paint booths with filters come equipped with a variety of features that enhance their performance and efficiency. Here are some key features that make EMS booths the preferred choice for businesses:
1. Advanced Filtration Systems
The filtration systems in EMS powder paint booths are designed to capture even the smallest particles. These systems may include pre-filters, main filters, and HEPA filters, ensuring high air quality and minimal contamination during the coating process.
2. Efficient Overspray Management
Effective overspray management is essential for maintaining a clean workspace. EMS booths utilize specialized designs that contain overspray and direct it toward the filtration system, preventing it from escaping into the environment and enhancing the efficiency of the coating process.
3. Easy Maintenance and Filter Replacement
Maintaining a clean filtration system is crucial for optimal performance. EMS powder paint booths are designed for easy access, allowing operators to quickly replace filters and perform routine maintenance without significant downtime.
4. Customizable Booth Sizes
Recognizing that businesses have different needs, EMS offers customizable booth sizes to accommodate various production capacities. Whether a business requires a compact booth for small operations or a larger booth for high-volume production, EMS can tailor solutions to fit specific requirements.
5. Energy Efficiency
EMS powder paint booths are designed with energy efficiency in mind. The incorporation of LED lighting and efficient airflow designs minimizes energy consumption while providing optimal working conditions.
6. Safety Features
Safety is a top priority in powder coating operations. EMS booths are equipped with various safety features, such as emergency shut-off systems, fire suppression equipment, and proper ventilation to ensure the safety of operators and compliance with industry regulations.
Benefits of Using Powder Paint Booths with Filters
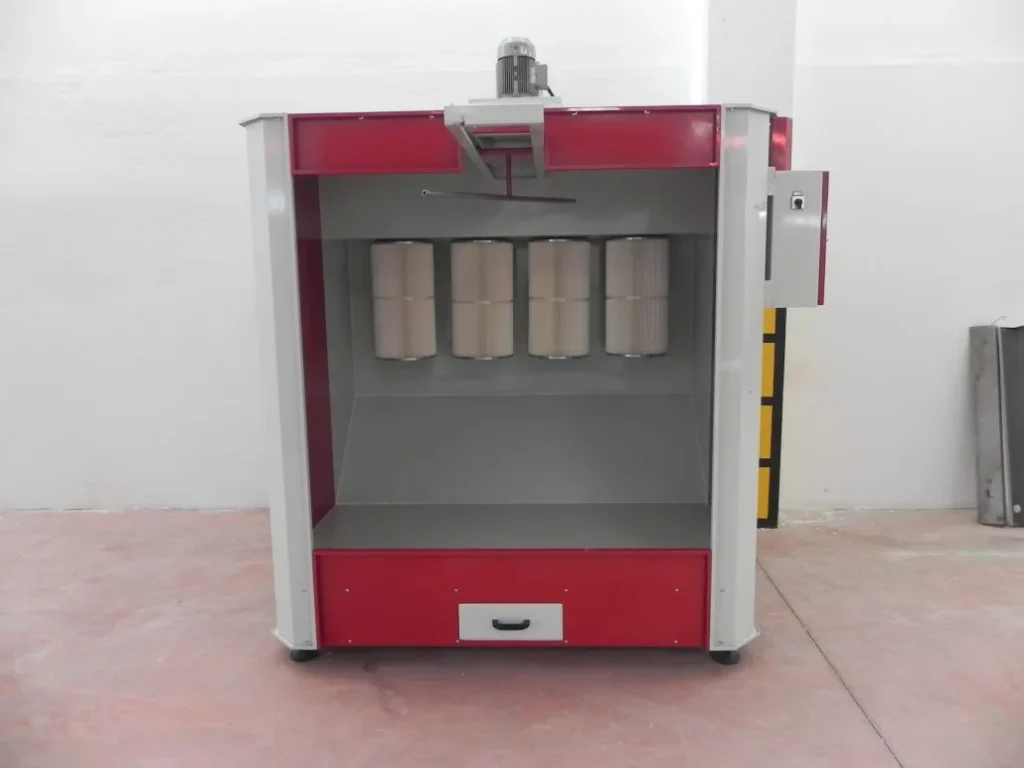
Investing in a powder paint booth with filters offers numerous advantages for businesses engaged in powder coating operations. Here are some key benefits:
1. Improved Coating Quality
The use of a powder paint booth with filters significantly enhances the quality of the coatings applied. By capturing overspray and preventing contaminants from settling on the substrate, these booths ensure smooth, even finishes that meet high standards.
2. Enhanced Safety and Compliance
Powder coating operations can generate hazardous airborne particles. By using a booth with a filtration system, businesses can improve air quality, protect operators, and comply with environmental regulations, ensuring a safe working environment.
3. Increased Efficiency
Efficient management of overspray and contaminants allows for a smoother coating process. This increased efficiency translates to higher productivity and reduced waste, enabling businesses to operate more effectively.
4. Cost Savings
By minimizing overspray and maximizing the use of powder, businesses can achieve significant cost savings. Efficient filtration systems reduce the amount of wasted material, lowering operational expenses and enhancing profitability.
5. Versatility for Various Applications
EMS powder paint booths with filters are designed to accommodate a wide range of substrates and coating processes. This versatility makes them suitable for various industries, from automotive to manufacturing, allowing businesses to adapt to changing needs.
Why Choose EMS Powder Coating Equipment for Powder Paint Booths with Filters?
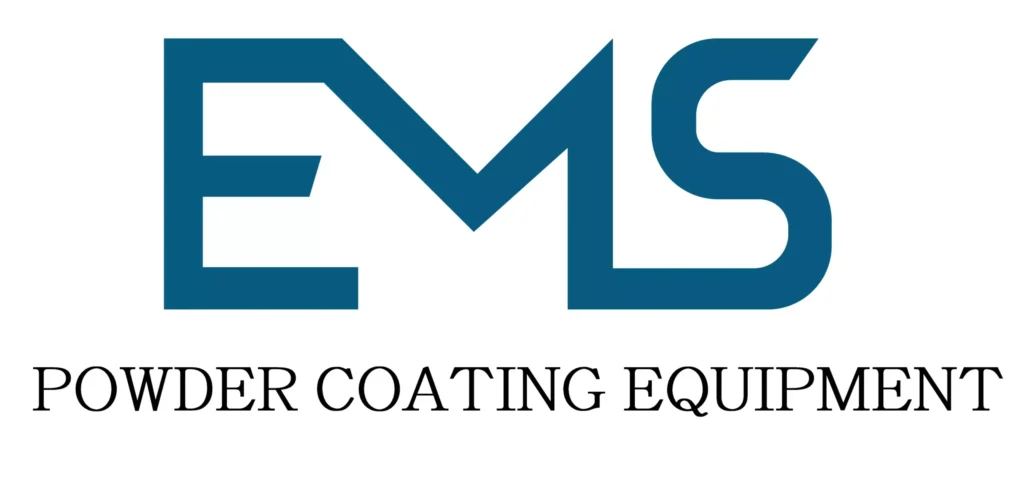
When selecting a powder paint booth with filters, it is essential to choose a manufacturer known for quality, reliability, and innovative solutions. EMS Powder Coating Equipment stands out as the best choice for businesses looking to invest in powder paint booths. Here’s why EMS is the preferred option:
1. Proven Industry Experience
With extensive experience in the powder coating industry, EMS understands the specific needs of businesses. Their expertise enables them to design powder paint booths that meet the demands of various applications and environments.
2. Commitment to Innovation
EMS is dedicated to innovation, continually enhancing their products with the latest technology. Their powder paint booths are designed for optimal performance, incorporating advanced filtration systems and efficient airflow designs.
3. Comprehensive Customer Support
From installation to ongoing maintenance, EMS provides exceptional customer support. Their team of experts is available to assist businesses in maximizing the performance of their powder paint booths, ensuring that operations run smoothly.
4. Customizable Solutions
Recognizing that every business has unique requirements, EMS offers customizable solutions for powder paint booths. Whether you need specific sizes, features, or filtration systems, EMS can tailor their products to meet your operational needs.
5. Trusted Quality and Reliability
With a strong reputation for delivering high-quality products, EMS is a trusted name in the powder coating industry. Their powder paint booths are built for durability and long-term performance, making them an excellent investment for businesses.
Conclusion
A powder paint booth with filters is an essential investment for any powder coating operation, providing a controlled environment that enhances coating quality and efficiency. With advanced filtration systems and effective overspray management, these booths ensure clean working conditions and compliance with safety regulations.
EMS Powder Coating Equipment is a leading manufacturer of powder paint booths with filters, offering innovative solutions tailored to meet the diverse needs of various industries. Their commitment to quality, performance, and customer support makes EMS the best choice for businesses seeking reliable coating solutions.
By choosing EMS powder paint booths with filters, companies can improve their coating processes, achieve superior finishes, and reduce operational costs. With a focus on efficiency and innovation, EMS stands out as the premier manufacturer for businesses in need of top-tier powder coating equipment.
Powder Coating Spray Booth: The Key to Quality Coating Applications
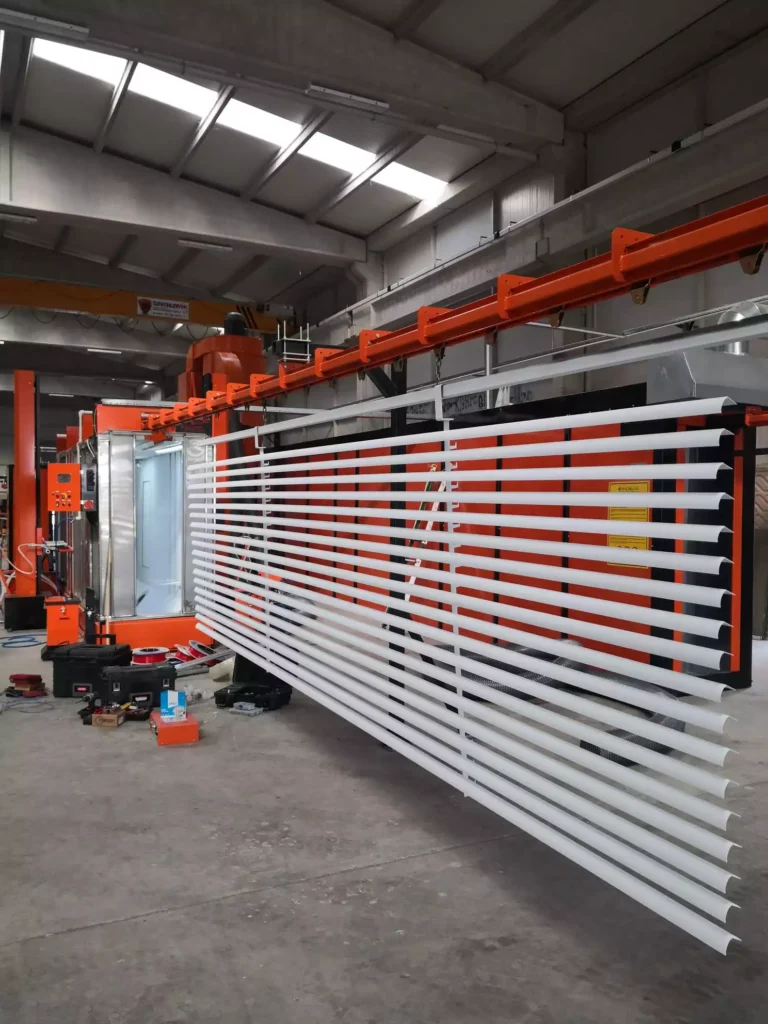
A powder coating spray booth is an essential part of the powder coating process, designed to provide a controlled environment for the application of powder coatings to various substrates. These booths are specifically engineered to manage overspray, ensuring a clean working environment and enhancing the efficiency of the coating process.
The spray booth’s design allows for optimal powder application, reducing waste and improving coating quality. Features such as ventilation systems, filtration units, and adjustable airflow contribute to achieving a consistent finish on the coated items.
EMS Powder Coating Equipment stands out as a premier manufacturer of powder coating spray booths, offering advanced solutions that cater to the diverse needs of different industries. In this section, we will explore the operational principles, key features, and benefits of powder coating spray booths, as well as explain why EMS is the preferred choice for businesses seeking high-quality coating equipment.
What is a Powder Coating Spray Booth?
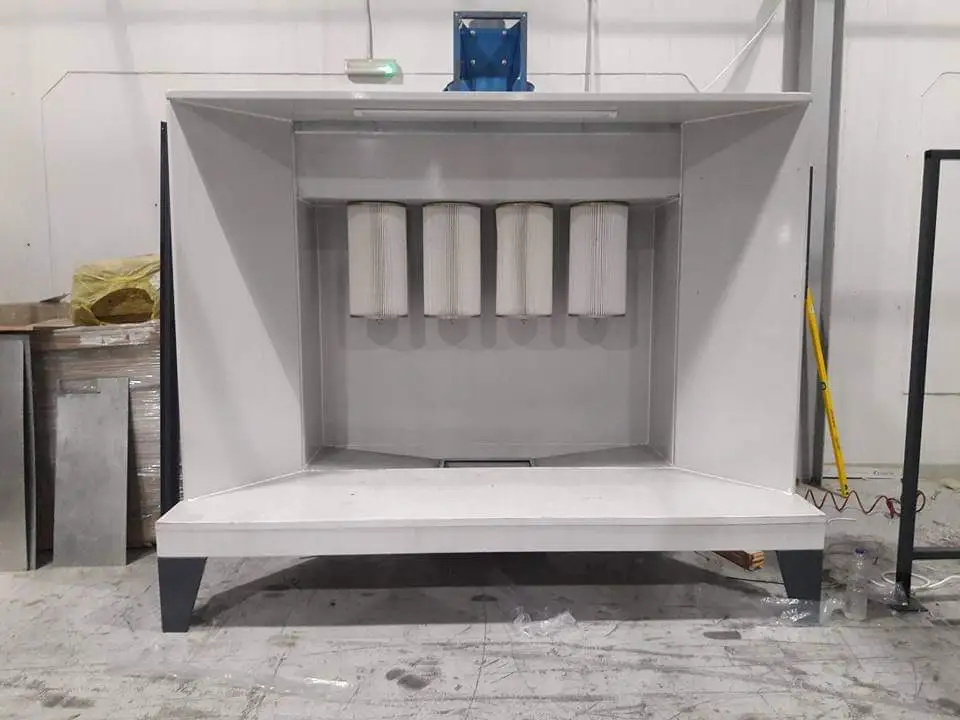
A powder coating spray booth is a specialized enclosure designed for applying powder coatings to various substrates. These booths create a controlled environment that minimizes contamination and maximizes efficiency during the coating process.
How Powder Coating Spray Booths Operate
The operation of a powder coating spray booth begins with the preparation of the substrate, which is cleaned and ready for coating. The substrate is placed inside the booth, where it is subjected to a process of powder application.
The booth is equipped with powder spray guns that electrostatically charge the powder particles as they are sprayed onto the substrate. This electrostatic charge causes the powder to adhere to the surface, ensuring an even and uniform coating.
Effective ventilation systems within the booth manage overspray and maintain air quality. The air is filtered and recirculated, preventing excess powder from escaping into the environment while keeping the workspace clean.
EMS Powder Coating Equipment designs powder coating spray booths with features that optimize the coating process, ensuring high-quality finishes and efficient operation. These booths are tailored to accommodate various production needs, making them suitable for businesses of all sizes.
Key Features of Powder Coating Spray Booths
Powder coating spray booths are equipped with a range of features designed to enhance their performance and efficiency. Here are some key features that make EMS booths the preferred choice for businesses:
1. Advanced Ventilation Systems
Effective ventilation is critical in powder coating spray booths. EMS spray booths are equipped with advanced ventilation systems that ensure proper airflow, reducing the concentration of airborne particles and maintaining a safe working environment.
2. Efficient Filtration Systems
High-efficiency filters capture overspray and other contaminants, preventing them from contaminating the coating process. EMS powder coating spray booths utilize sophisticated filtration technology to enhance the overall efficiency of the coating operation.
3. Customizable Booth Sizes
Recognizing that businesses have different needs, EMS offers customizable booth sizes to accommodate various production capacities. Whether a business requires a compact booth for small operations or a larger booth for high-volume production, EMS can tailor solutions to fit specific requirements.
4. User-Friendly Control Panels
EMS powder coating spray booths are designed with intuitive control panels, allowing operators to easily set and monitor parameters such as airflow, temperature, and spray settings. This user-friendly interface streamlines the coating process and helps achieve consistent results.
5. Safety Features
Safety is a top priority in powder coating operations. EMS spray booths are equipped with safety features such as explosion-proof lighting, emergency shut-off systems, and proper ventilation to ensure the safety of operators and compliance with industry regulations.
6. Durable Construction
Built with high-quality materials, EMS powder coating spray booths are designed for durability and long-lasting performance. Their robust construction ensures minimal maintenance and reliable operation in demanding industrial environments.
Benefits of Using Powder Coating Spray Booths
Investing in a powder coating spray booth offers numerous advantages for businesses engaged in powder coating operations. Here are some key benefits:
1. Improved Coating Quality
The controlled environment provided by a powder coating spray booth significantly enhances the quality of the coatings applied. By managing overspray and preventing contaminants from entering the booth, these booths ensure smooth, even finishes that meet high standards.
2. Increased Productivity
Efficient ventilation and filtration systems in EMS spray booths allow for a quicker coating process. With reduced downtime and improved workflow, businesses can achieve higher productivity levels and meet tight production schedules.
3. Cost Savings
By minimizing overspray and maximizing the use of powder, businesses can realize significant cost savings. Efficient powder usage reduces material waste, while effective filtration systems prolong the life of the powder, leading to lower operational expenses.
4. Versatility for Various Applications
EMS powder coating spray booths are designed to accommodate a wide range of substrates and coating processes. This versatility allows businesses to adapt to changing production needs and diversify their offerings across various industries.
5. Compliance with Environmental Regulations
Powder coating spray booths are designed to comply with environmental regulations, reducing the emission of harmful substances and maintaining a safe workspace. By investing in a booth with advanced filtration systems, businesses can contribute to a healthier environment.
Why Choose EMS Powder Coating Equipment for Powder Coating Spray Booths?
When selecting a powder coating spray booth, it is essential to choose a manufacturer known for quality, reliability, and innovative solutions. EMS Powder Coating Equipment stands out as the best choice for businesses looking to invest in spray booths. Here’s why EMS is the preferred option:
1. Proven Industry Experience
With extensive experience in the powder coating industry, EMS understands the specific needs of businesses. Their expertise enables them to design powder coating spray booths that meet the demands of various applications and environments.
2. Commitment to Innovation
EMS is dedicated to innovation, continually enhancing their products with the latest technology. Their powder coating spray booths are designed for optimal performance, incorporating advanced ventilation and filtration systems.
3. Comprehensive Customer Support
From installation to ongoing maintenance, EMS provides exceptional customer support. Their team of experts is available to assist businesses in maximizing the performance of their powder coating spray booths, ensuring that operations run smoothly.
4. Customizable Solutions
Recognizing that every business has unique requirements, EMS offers customizable solutions for powder coating spray booths. Whether you need specific sizes, features, or filtration systems, EMS can tailor their products to meet your operational needs.
5. Trusted Quality and Reliability
With a strong reputation for delivering high-quality products, EMS is a trusted name in the powder coating industry. Their powder coating spray booths are built for durability and long-term performance, making them an excellent investment for businesses.
Conclusion
A powder coating spray booth is an essential investment for any powder coating operation, providing a controlled environment that enhances coating quality and efficiency. With advanced ventilation and filtration systems, these booths ensure clean working conditions and compliance with safety regulations.
EMS Powder Coating Equipment is a leading manufacturer of powder coating spray booths, offering innovative solutions tailored to meet the diverse needs of various industries. Their commitment to quality, performance, and customer support makes EMS the best choice for businesses seeking reliable coating solutions.
By choosing EMS powder coating spray booths, companies can improve their coating processes, achieve superior finishes, and reduce operational costs. With a focus on efficiency and innovation, EMS stands out as the premier manufacturer for businesses in need of top-tier powder coating equipment.
Powder Coating Booth: Optimizing the Coating Process for Superior Results
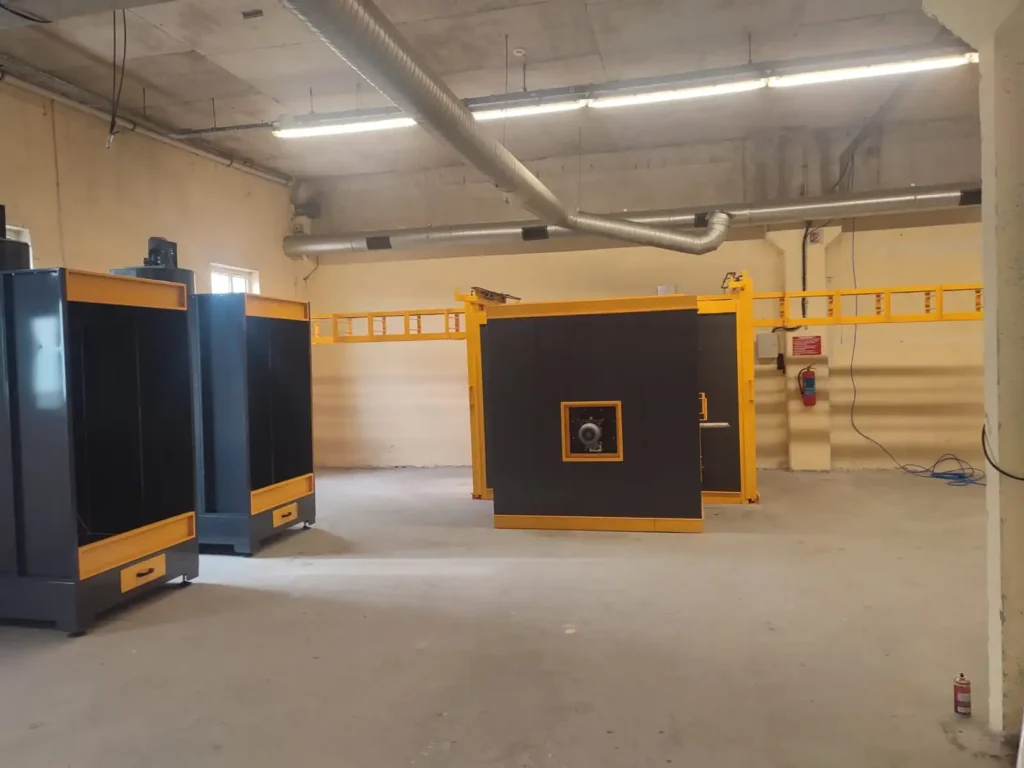
A powder coating booth is a crucial component in the powder coating process, specifically designed for the application of powder coatings to various substrates. These booths create a controlled environment that maximizes coating efficiency and quality while minimizing overspray and waste.
The design of a powder coating booth includes ventilation systems, filtration units, and features that ensure even powder distribution during application. By providing a dedicated space for the coating process, these booths help manufacturers achieve high-quality finishes consistently.
EMS Powder Coating Equipment is recognized as a leader in the manufacture of powder coating booths, offering cutting-edge solutions tailored to meet the specific needs of different industries. In this section, we will explore the operational principles, key features, and benefits of powder coating booths, as well as explain why EMS is the preferred choice for businesses seeking reliable coating equipment.
What is a Powder Coating Booth?
A powder coating booth is a specialized enclosure designed to facilitate the application of powder coatings. It provides a controlled environment that minimizes external contaminants and enhances the efficiency of the coating process.
How Powder Coating Booths Operate
The operation of a powder coating booth begins with the preparation of the substrate, which is cleaned and prepped for coating. Once ready, the substrate is placed inside the booth, where the powder is applied using electrostatic spray guns.
The spray guns charge the powder particles, causing them to adhere to the surface of the substrate. This electrostatic attraction ensures an even distribution of powder, resulting in a smooth finish.
Ventilation systems within the booth are designed to manage overspray and maintain air quality. The airflow is filtered and recirculated, preventing excess powder from escaping and ensuring a clean working environment.
EMS Powder Coating Equipment designs powder coating booths with features that optimize the application process, ensuring high-quality finishes and efficient operation. These booths are adaptable to various production needs, making them suitable for businesses of all sizes.
Key Features of Powder Coating Booths
Powder coating booths are equipped with a variety of features designed to enhance their functionality and efficiency. Here are some key features that make EMS booths the preferred choice for businesses:
1. Advanced Filtration Systems
Effective filtration is critical in powder coating booths. EMS booths are equipped with high-efficiency filters that capture overspray and other contaminants, maintaining a clean and safe environment for coating.
2. Optimal Airflow Management
EMS powder coating booths feature adjustable airflow systems that allow operators to control the distribution of air within the booth. This adaptability ensures that powder is applied evenly and that overspray is minimized.
3. Customizable Booth Configurations
Recognizing that businesses have diverse needs, EMS offers customizable booth configurations to accommodate various production capacities and workflows. Whether for small operations or high-volume production, EMS can tailor solutions accordingly.
4. User-Friendly Control Interfaces
Designed with the operator in mind, EMS powder coating booths include intuitive control interfaces that make it easy to set and monitor critical parameters. This user-friendly design enhances the overall coating process and helps achieve consistent results.
5. Robust Safety Features
Safety is paramount in powder coating operations. EMS booths come equipped with features such as explosion-proof lighting, emergency shut-off systems, and proper ventilation to ensure the safety of operators and compliance with industry standards.
6. Durable Construction
Constructed with high-quality materials, EMS powder coating booths are built to withstand demanding industrial environments. Their durable design ensures long-lasting performance and minimal maintenance, providing businesses with a reliable coating solution.
Benefits of Using Powder Coating Booths
Investing in a powder coating booth brings numerous advantages to businesses engaged in powder coating operations. Here are some key benefits:
1. Enhanced Coating Quality
The controlled environment of a powder coating booth significantly improves the quality of the applied coatings. By minimizing contaminants and managing airflow, these booths ensure a smooth, even finish that meets high standards.
2. Increased Efficiency and Productivity
The efficient design of EMS powder coating booths allows for a quicker coating process. With reduced downtime and streamlined workflows, businesses can increase their productivity levels and meet tight production schedules.
3. Cost-Effective Operations
By minimizing overspray and maximizing powder usage, businesses can achieve significant cost savings. Efficient powder application reduces material waste, while effective filtration extends the life of the powder, leading to lower operational costs.
4. Flexibility for Various Applications
EMS powder coating booths are versatile and can accommodate a wide range of substrates and coating processes. This flexibility allows businesses to adapt to changing production needs and expand their service offerings across different industries.
5. Compliance with Safety and Environmental Standards
Powder coating booths are designed to meet safety and environmental regulations, reducing emissions and maintaining a safe workspace. By investing in EMS booths with advanced filtration systems, businesses can contribute to a healthier working environment.
Why Choose EMS Powder Coating Equipment for Powder Coating Booths?
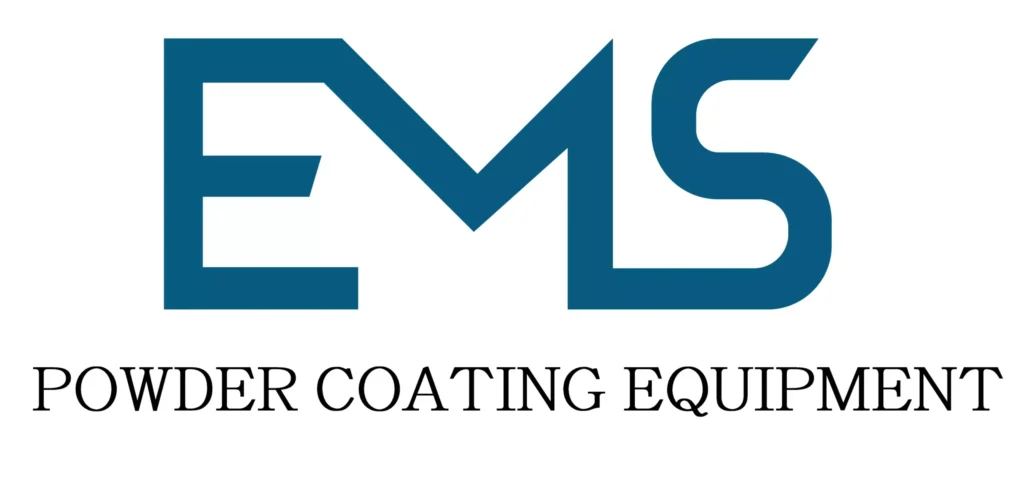
When selecting a powder coating booth, it is crucial to choose a manufacturer known for quality, reliability, and innovative solutions. EMS Powder Coating Equipment stands out as the best choice for businesses looking to invest in powder coating booths. Here’s why EMS is the preferred option:
1. Extensive Industry Expertise
With years of experience in the powder coating industry, EMS understands the unique requirements of various applications. Their expertise allows them to design powder coating booths that cater to diverse production needs.
2. Commitment to Innovation
EMS is dedicated to continual innovation, enhancing their products with the latest technology. Their powder coating booths are designed for optimal performance, incorporating advanced filtration and airflow management systems.
3. Exceptional Customer Support
From installation to ongoing maintenance, EMS provides comprehensive customer support. Their team of experts is committed to helping businesses maximize the performance of their powder coating booths.
4. Customizable Solutions
Recognizing that each business has unique needs, EMS offers customizable solutions for powder coating booths. Whether specific sizes, features, or configurations are required, EMS can tailor their products to meet operational requirements.
5. Trusted Quality and Reliability
With a strong reputation for delivering high-quality products, EMS is a trusted name in the powder coating industry. Their powder coating booths are built for durability and long-term performance, making them an excellent investment for businesses.
Conclusion
A powder coating booth is a vital investment for any powder coating operation, providing a controlled environment that enhances coating quality and efficiency. With advanced filtration and airflow management systems, these booths ensure a clean workspace and compliance with safety regulations.
EMS Powder Coating Equipment is a leading manufacturer of powder coating booths, offering innovative solutions tailored to meet the diverse needs of various industries. Their commitment to quality, performance, and customer support makes EMS the best choice for businesses seeking reliable coating solutions.
By choosing EMS powder coating booths, companies can improve their coating processes, achieve superior finishes, and reduce operational costs. With a focus on efficiency and innovation, EMS stands out as the premier manufacturer for businesses in need of top-tier powder coating equipment.
Powder Coating Spray Booth: Elevating Coating Efficiency and Quality
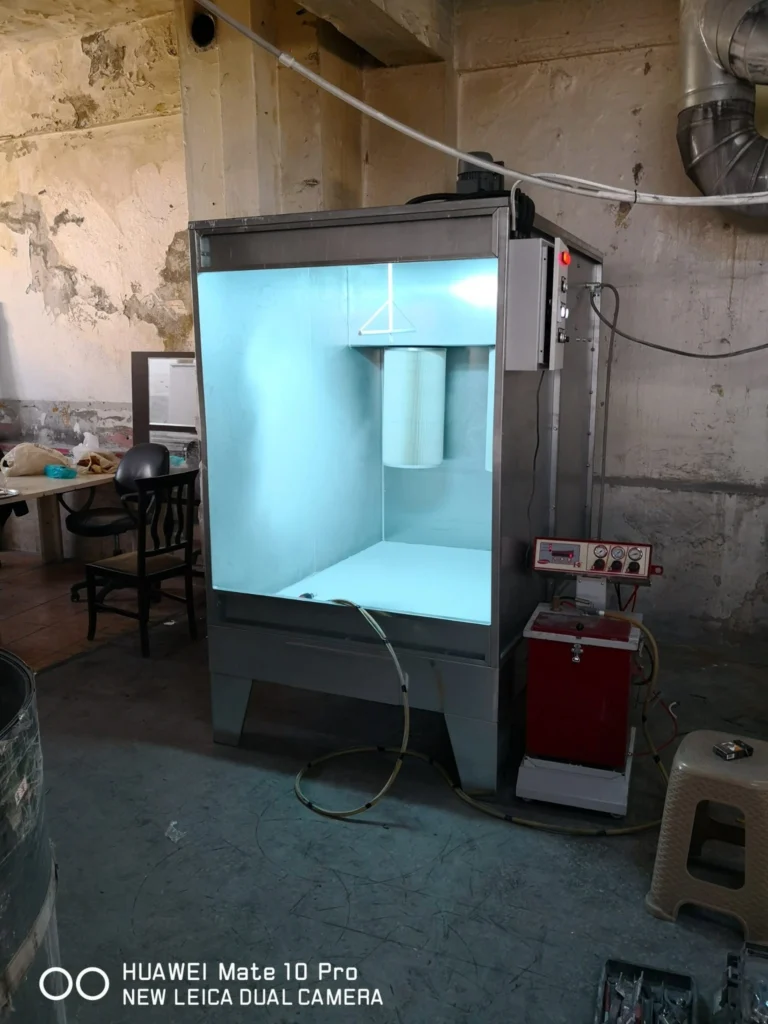
A powder coating spray booth is an essential element in the powder coating process, specifically designed for the application of powder coatings onto various substrates. These booths create a controlled environment that optimizes the application of powder, ensuring a high-quality finish while minimizing overspray and waste.
The design of a powder coating spray booth includes ventilation systems, filtration units, and adjustable airflow features that facilitate even powder distribution during application. By providing a dedicated space for the spraying process, these booths enhance both efficiency and quality.
EMS Powder Coating Equipment is recognized as a leader in the manufacture of powder coating spray booths, offering innovative solutions tailored to meet the specific needs of various industries. In this section, we will explore the operational principles, key features, and benefits of powder coating spray booths, as well as explain why EMS is the preferred choice for businesses seeking reliable coating equipment.
What is a Powder Coating Spray Booth?
A powder coating spray booth is a specialized enclosure designed to facilitate the spraying of powder coatings onto substrates. It provides a controlled environment that minimizes contaminants and enhances the efficiency of the powder application process.
How Powder Coating Spray Booths Operate
The operation of a powder coating spray booth begins with the preparation of the substrate, which is cleaned and prepped for coating. Once ready, the substrate is positioned within the booth, where electrostatic spray guns are used to apply the powder.
The spray guns charge the powder particles, creating an electrostatic attraction that ensures even coverage across the substrate’s surface. This process is essential for achieving a smooth and uniform finish.
Ventilation systems within the booth manage overspray and maintain air quality, filtering the air to prevent excess powder from escaping into the working environment. This design helps protect workers and ensures a cleaner operation.
EMS Powder Coating Equipment designs powder coating spray booths with features that optimize the application process, ensuring high-quality finishes and efficient operation. These booths are adaptable to various production needs, making them suitable for businesses of all sizes.
Key Features of Powder Coating Spray Booths
Powder coating spray booths are equipped with various features designed to enhance their functionality and efficiency. Here are some key features that make EMS booths the preferred choice for businesses:
1. Advanced Filtration Systems
Effective filtration is critical in powder coating spray booths. EMS booths are equipped with high-efficiency filters that capture overspray and other contaminants, maintaining a clean and safe environment for coating.
2. Optimized Airflow Management
EMS powder coating spray booths feature adjustable airflow systems that allow operators to control the distribution of air within the booth. This adaptability ensures that powder is applied evenly and that overspray is minimized.
3. Customizable Booth Configurations
Recognizing that businesses have diverse needs, EMS offers customizable booth configurations to accommodate various production capacities and workflows. Whether for small operations or high-volume production, EMS can tailor solutions accordingly.
4. User-Friendly Control Interfaces
Designed with the operator in mind, EMS powder coating spray booths include intuitive control interfaces that make it easy to set and monitor critical parameters. This user-friendly design enhances the overall coating process and helps achieve consistent results.
5. Robust Safety Features
Safety is paramount in powder coating operations. EMS booths come equipped with features such as explosion-proof lighting, emergency shut-off systems, and proper ventilation to ensure the safety of operators and compliance with industry standards.
6. Durable Construction
Constructed with high-quality materials, EMS powder coating spray booths are built to withstand demanding industrial environments. Their durable design ensures long-lasting performance and minimal maintenance, providing businesses with a reliable coating solution.
Benefits of Using Powder Coating Spray Booths
Investing in a powder coating spray booth brings numerous advantages to businesses engaged in powder coating operations. Here are some key benefits:
1. Enhanced Coating Quality
The controlled environment of a powder coating spray booth significantly improves the quality of the applied coatings. By minimizing contaminants and managing airflow, these booths ensure a smooth, even finish that meets high standards.
2. Increased Efficiency and Productivity
The efficient design of EMS powder coating spray booths allows for a quicker coating process. With reduced downtime and streamlined workflows, businesses can increase their productivity levels and meet tight production schedules.
3. Cost-Effective Operations
By minimizing overspray and maximizing powder usage, businesses can achieve significant cost savings. Efficient powder application reduces material waste, while effective filtration extends the life of the powder, leading to lower operational costs.
4. Flexibility for Various Applications
EMS powder coating spray booths are versatile and can accommodate a wide range of substrates and coating processes. This flexibility allows businesses to adapt to changing production needs and expand their service offerings across different industries.
5. Compliance with Safety and Environmental Standards
Powder coating spray booths are designed to meet safety and environmental regulations, reducing emissions and maintaining a safe workspace. By investing in EMS booths with advanced filtration systems, businesses can contribute to a healthier working environment.
Why Choose EMS Powder Coating Equipment for Powder Coating Spray Booths?
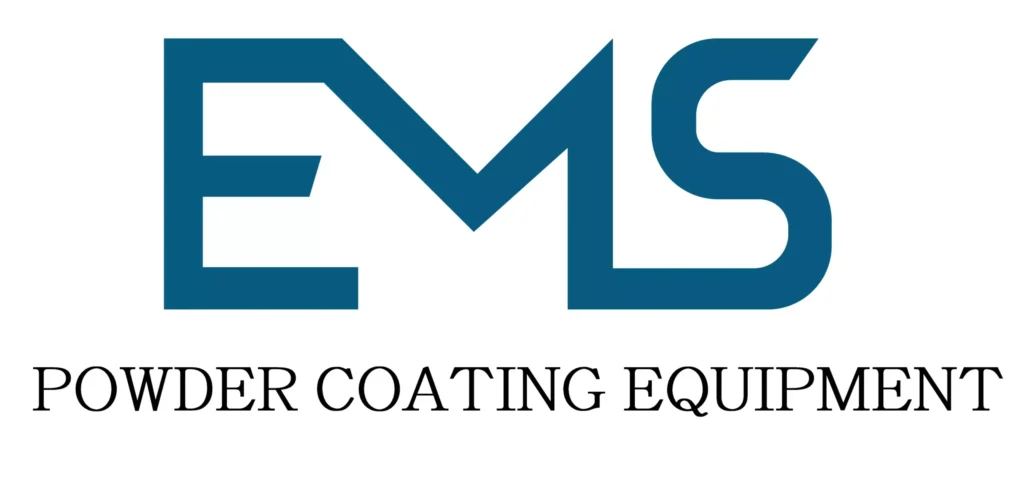
When selecting a powder coating spray booth, it is crucial to choose a manufacturer known for quality, reliability, and innovative solutions. EMS Powder Coating Equipment stands out as the best choice for businesses looking to invest in powder coating spray booths. Here’s why EMS is the preferred option:
1. Extensive Industry Expertise
With years of experience in the powder coating industry, EMS understands the unique requirements of various applications. Their expertise allows them to design powder coating spray booths that cater to diverse production needs.
2. Commitment to Innovation
EMS is dedicated to continual innovation, enhancing their products with the latest technology. Their powder coating spray booths are designed for optimal performance, incorporating advanced filtration and airflow management systems.
3. Exceptional Customer Support
From installation to ongoing maintenance, EMS provides comprehensive customer support. Their team of experts is committed to helping businesses maximize the performance of their powder coating spray booths.
4. Customizable Solutions
Recognizing that each business has unique needs, EMS offers customizable solutions for powder coating spray booths. Whether specific sizes, features, or configurations are required, EMS can tailor their products to meet operational requirements.
5. Trusted Quality and Reliability
With a strong reputation for delivering high-quality products, EMS is a trusted name in the powder coating industry. Their powder coating spray booths are built for durability and long-term performance, making them an excellent investment for businesses.
Conclusion
A powder coating spray booth is a vital investment for any powder coating operation, providing a controlled environment that enhances coating quality and efficiency. With advanced filtration and airflow management systems, these booths ensure a clean workspace and compliance with safety regulations.
EMS Powder Coating Equipment is a leading manufacturer of powder coating spray booths, offering innovative solutions tailored to meet the diverse needs of various industries. Their commitment to quality, performance, and customer support makes EMS the best choice for businesses seeking reliable coating solutions.
By choosing EMS powder coating spray booths, companies can improve their coating processes, achieve superior finishes, and reduce operational costs. With a focus on efficiency and innovation, EMS stands out as the premier manufacturer for businesses in need of top-tier powder coating equipment.
Powder Coating Booth: Maximizing Quality and Efficiency in Coating Operations
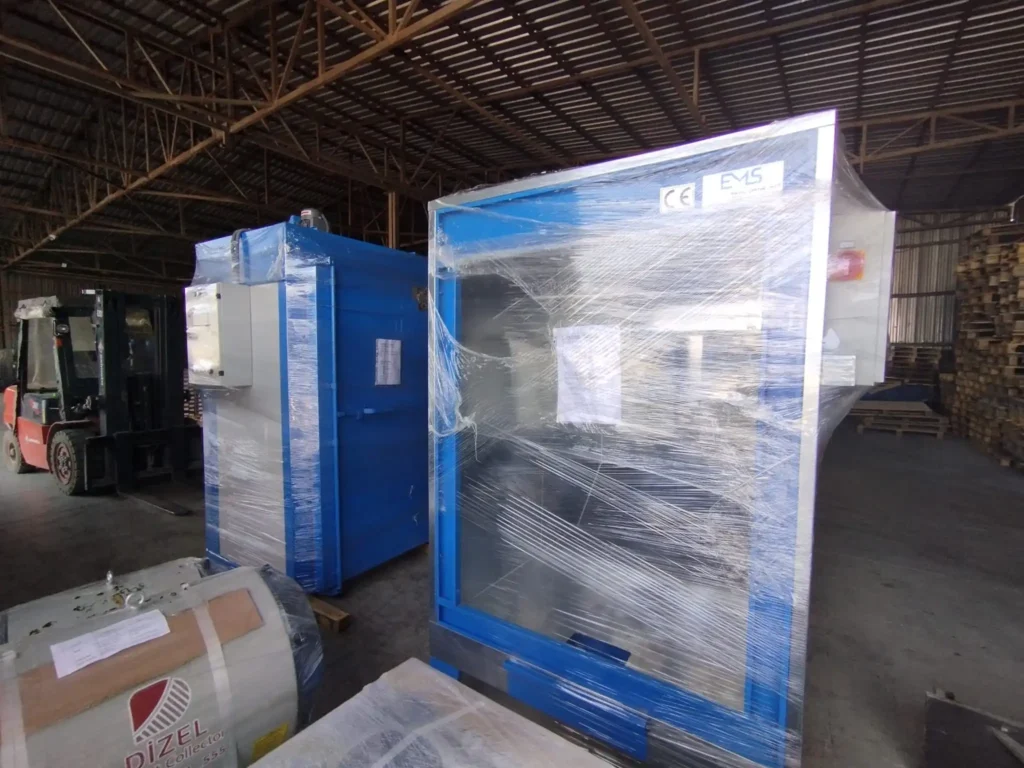
A powder coating booth is a specialized enclosure designed to provide an optimal environment for applying powder coatings to various substrates. By creating a controlled atmosphere, these booths help to minimize contamination and overspray, ensuring high-quality finishes that meet industry standards.
Powder coating booths are equipped with advanced ventilation systems and filtration technologies that enhance the application process. They provide operators with a designated workspace that improves efficiency and safety, ultimately leading to superior coating results.
EMS Powder Coating Equipment is renowned for its innovative designs and high-quality manufacturing of powder coating booths, tailored to meet the specific requirements of different industries. In this section, we will delve into the operational principles, key features, and benefits of powder coating booths, while also discussing why EMS is the preferred choice for businesses seeking reliable coating solutions.
What is a Powder Coating Booth?
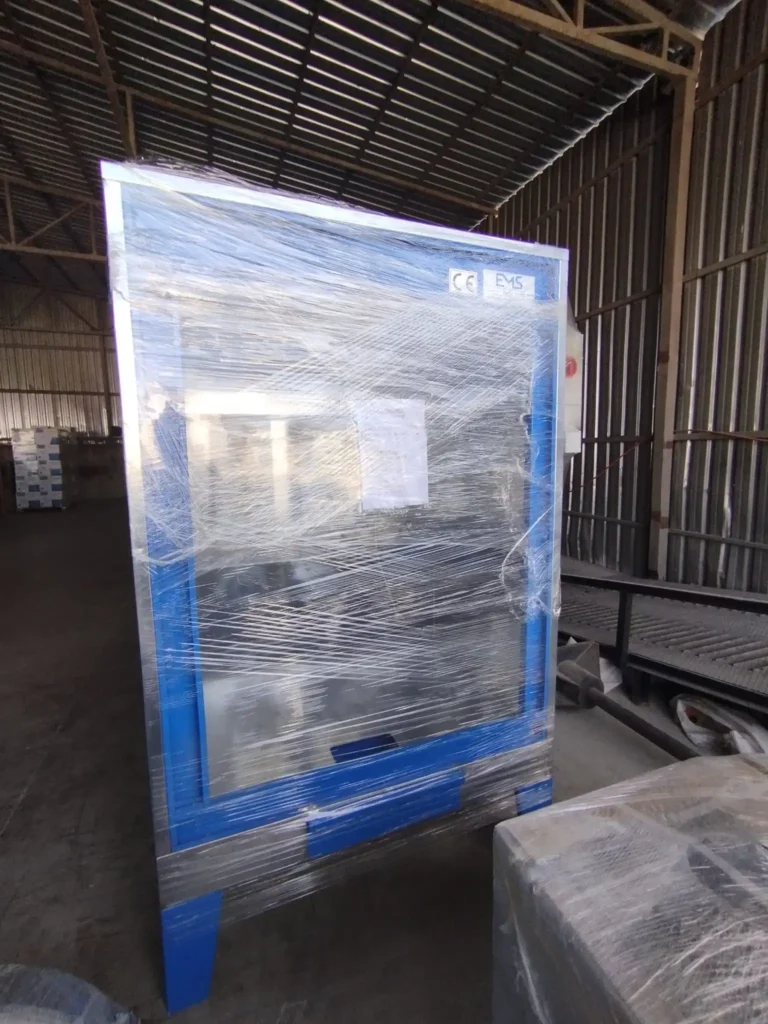
A powder coating booth serves as the primary environment for the application of powder coatings onto substrates. Designed to optimize the spraying process, these booths ensure that the powder adheres evenly and cures properly, resulting in a durable finish.
How Powder Coating Booths Operate
The operation begins when a substrate is cleaned and prepared for coating. Once ready, it is placed inside the powder coating booth. Using electrostatic spray guns, operators apply powder coatings, which are charged to attract to the grounded substrate.
The booth’s ventilation system plays a crucial role by managing airflow and filtering out excess powder particles, thereby preventing contamination. This controlled environment helps maintain high air quality and enhances the effectiveness of the coating process.
EMS Powder Coating Equipment designs powder coating booths with features that optimize both the application and curing processes, ensuring that businesses achieve consistent, high-quality finishes across various applications.
Key Features of Powder Coating Booths
Powder coating booths are equipped with numerous features designed to enhance performance and efficiency. Here are some of the standout features that make EMS booths the preferred choice for businesses:
1. Advanced Air Filtration Systems
EMS powder coating booths come with high-efficiency filters that capture overspray and contaminants, ensuring a clean environment for the coating process. This feature not only protects the quality of the finish but also contributes to operator safety.
2. Optimized Airflow Control
With adjustable airflow systems, EMS booths allow operators to control the distribution of air within the booth. This capability ensures that powder is applied evenly, reducing the risk of defects and enhancing overall coating quality.
3. Ergonomic Design
The design of EMS powder coating booths prioritizes operator comfort and efficiency. With user-friendly layouts, operators can easily maneuver and position substrates for optimal coating, reducing the time spent on each job.
4. Customizable Configurations
Recognizing the diverse needs of businesses, EMS offers customizable booth configurations to suit various production capacities. Whether for small operations or large-scale production, EMS can tailor solutions to meet specific requirements.
5. Safety Features
Safety is a crucial consideration in powder coating operations. EMS powder coating booths include safety features such as emergency shut-off systems and proper ventilation to ensure a safe working environment for operators.
6. Durable Construction
Constructed from high-quality materials, EMS powder coating booths are built to withstand the rigors of industrial use. Their robust design ensures longevity and minimal maintenance, providing businesses with a reliable coating solution.
Benefits of Using Powder Coating Booths
Investing in a powder coating booth offers numerous advantages for businesses engaged in powder coating operations. Here are some key benefits:
1. Enhanced Coating Quality
The controlled environment of a powder coating booth significantly improves the quality of the applied coatings. With effective filtration and optimized airflow, these booths ensure smooth, even finishes that meet high standards.
2. Increased Productivity
EMS powder coating booths streamline the coating process, allowing for quicker application and curing times. This efficiency can lead to increased production rates, helping businesses meet demanding schedules and customer expectations.
3. Cost Efficiency
By minimizing overspray and maximizing powder usage, powder coating booths can significantly reduce material costs. Efficient application processes lead to less waste and lower operational expenses, enhancing profitability.
4. Versatility for Diverse Applications
EMS powder coating booths are versatile enough to accommodate a variety of substrates and coating processes. This adaptability allows businesses to diversify their offerings and cater to different market demands.
5. Compliance with Regulations
Powder coating booths are designed to meet industry safety and environmental regulations, ensuring a compliant operation. By investing in EMS booths, businesses can promote a healthier working environment while adhering to necessary standards.
Why Choose EMS Powder Coating Equipment for Powder Coating Booths?
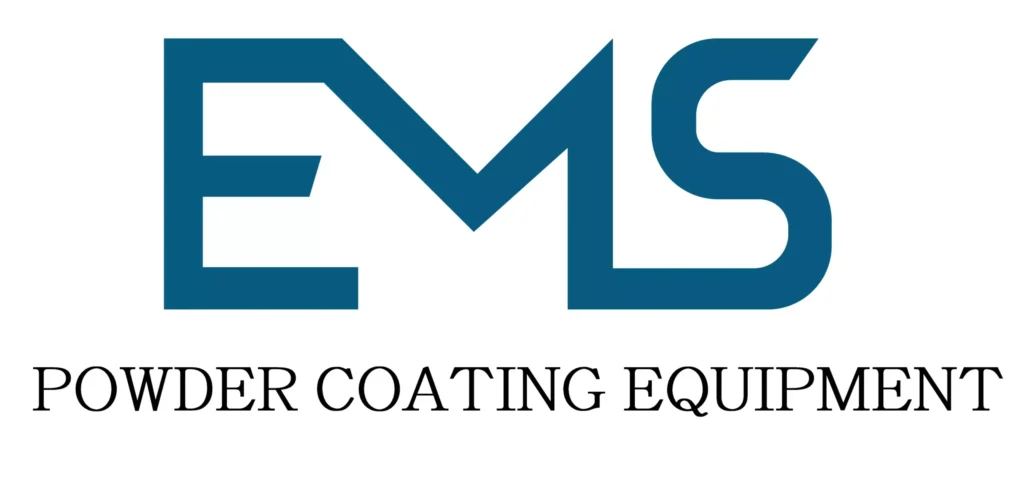
When selecting a powder coating booth, it is essential to choose a manufacturer with a reputation for quality and innovation. EMS Powder Coating Equipment stands out as the top choice for businesses looking to invest in powder coating booths. Here’s why EMS is the preferred option:
1. Proven Expertise
With years of experience in the powder coating industry, EMS understands the unique needs of various applications. Their knowledge allows them to design powder coating booths that are tailored to diverse production environments.
2. Innovative Solutions
EMS is committed to continuous innovation, incorporating the latest technology into their products. Their powder coating booths are designed for optimal performance, featuring advanced filtration and airflow management systems.
3. Comprehensive Support
From installation to ongoing maintenance, EMS provides exceptional customer support. Their team of experts is dedicated to helping businesses maximize the performance of their powder coating booths.
4. Customizable Options
EMS recognizes that every business has unique requirements. They offer customizable options for powder coating booths, allowing businesses to select features and configurations that best suit their operational needs.
5. Trusted Reliability
With a strong reputation for delivering high-quality products, EMS is a trusted name in the powder coating industry. Their booths are designed for durability and long-term performance, making them an excellent investment for businesses.
Conclusion
A powder coating booth is a critical investment for any powder coating operation, providing a controlled environment that enhances coating quality and efficiency. With advanced filtration and airflow management, these booths ensure clean operations and compliance with safety regulations.
EMS Powder Coating Equipment is a leading manufacturer of powder coating booths, offering innovative solutions tailored to meet the diverse needs of various industries. Their commitment to quality, performance, and customer support makes EMS the best choice for businesses seeking reliable coating solutions.
By choosing EMS powder coating booths, companies can enhance their coating processes, achieve superior finishes, and reduce operational costs. With a focus on efficiency and innovation, EMS stands out as the premier manufacturer for businesses in need of top-tier powder coating equipment.
Powder Coating Spray Booth: Enhancing Efficiency and Quality in Coating Applications
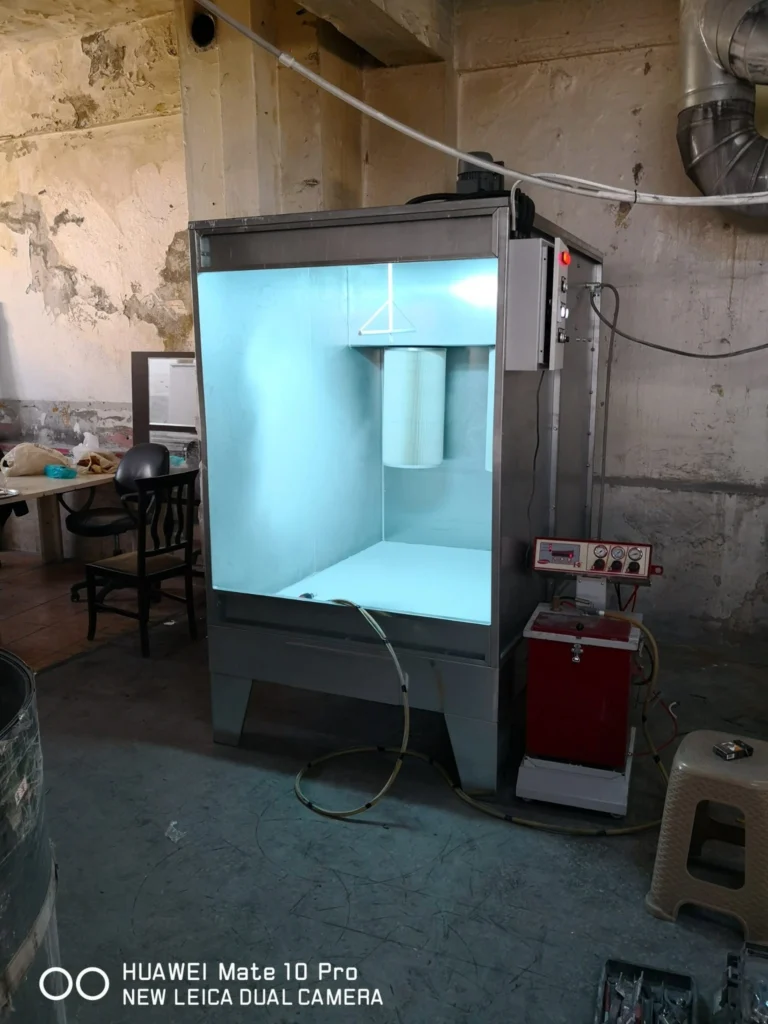
A powder coating spray booth is an essential component of the powder coating process, designed specifically for the application of powder coatings onto various substrates. These booths create a controlled environment that minimizes overspray and contamination, ensuring a high-quality finish that meets industry standards.
The primary function of a powder coating spray booth is to provide operators with an optimized workspace, equipped with advanced filtration and airflow systems that enhance the application process. This not only improves the quality of the coatings but also promotes a safer and more efficient working environment.
EMS Powder Coating Equipment is renowned for its innovative designs and high-quality manufacturing of powder coating spray booths, tailored to meet the specific requirements of diverse industries. In this section, we will delve into the operational principles, key features, and benefits of powder coating spray booths, while also discussing why EMS is the preferred choice for businesses seeking reliable coating solutions.
What is a Powder Coating Spray Booth?
A powder coating spray booth is a specialized enclosure where powder coatings are applied to metal and other substrates. These booths are designed to create an optimal environment for powder application, ensuring that the coatings adhere properly and achieve the desired finish.
How Powder Coating Spray Booths Operate
The operation of a powder coating spray booth begins with substrate preparation, which includes cleaning and pre-treating the surface. Once the substrate is ready, it is placed inside the booth for powder application.
Using electrostatic spray guns, operators apply charged powder particles to the grounded substrate. The electrostatic attraction ensures that the powder adheres evenly, resulting in a smooth finish. The booth’s ventilation system captures overspray and maintains air quality, protecting both the operators and the environment.
EMS Powder Coating Equipment designs powder coating spray booths with features that optimize both the application and curing processes, ensuring businesses achieve consistent, high-quality finishes across various applications.
Key Features of Powder Coating Spray Booths
Powder coating spray booths are equipped with numerous features designed to enhance their performance and efficiency. Here are some standout features that make EMS booths the preferred choice for businesses:
1. Advanced Filtration Systems
EMS powder coating spray booths come with high-efficiency filters that capture overspray and airborne particles. This ensures a clean environment for coating applications, leading to higher quality finishes and safer operations.
2. Controlled Airflow Management
With adjustable airflow systems, EMS booths allow operators to control air distribution within the booth. This capability promotes even powder application and reduces the risk of defects, enhancing overall coating quality.
3. User-Friendly Design
The ergonomic design of EMS powder coating spray booths prioritizes operator comfort and efficiency. With easy access to controls and ample workspace, operators can maneuver and position substrates effectively, reducing job completion times.
4. Energy Efficiency
EMS powder coating spray booths are designed for energy efficiency, featuring optimized airflow and filtration systems that minimize energy consumption while maximizing performance. This efficiency can lead to reduced operational costs.
5. Safety Features
Safety is a top priority in powder coating operations. EMS booths are equipped with safety features such as emergency shut-off systems, explosion-proof lighting, and proper ventilation to ensure a safe working environment.
6. Customizable Configurations
Understanding that different businesses have unique requirements, EMS offers customizable configurations for their powder coating spray booths. Whether for small operations or large-scale production, EMS can tailor solutions to meet specific needs.
Benefits of Using Powder Coating Spray Booth
Investing in a powder coating spray booth provides numerous advantages for businesses engaged in powder coating operations. Here are some key benefits:
1. Superior Coating Quality
The controlled environment of a powder coating spray booth significantly enhances the quality of applied coatings. With effective filtration and optimized airflow, these booths ensure smooth, even finishes that meet high standards.
2. Increased Productivity
EMS powder coating spray booths streamline the coating process, allowing for quicker application and improved drying times. This efficiency can lead to increased production rates, helping businesses meet tight deadlines.
3. Cost Efficiency
By minimizing overspray and maximizing powder usage, powder coating spray booths can significantly reduce material costs. Efficient application processes lead to less waste and lower operational expenses, enhancing profitability.
4. Versatility for Diverse Applications
EMS powder coating spray booths are versatile enough to accommodate a wide range of substrates and coating types. This adaptability allows businesses to diversify their offerings and cater to different market demands.
5. Compliance with Environmental Regulations
Powder coating spray booths are designed to meet industry safety and environmental regulations, ensuring a compliant operation. By investing in EMS booths, businesses can promote a healthier working environment while adhering to necessary standards.
Why Choose EMS Powder Coating Equipment for Powder Coating Spray Booths?
When selecting a powder coating spray booth, it is essential to choose a manufacturer with a reputation for quality and innovation. EMS Powder Coating Equipment stands out as the top choice for businesses looking to invest in powder coating spray booths. Here’s why EMS is the preferred option:
1. Proven Expertise
With years of experience in the powder coating industry, EMS understands the unique needs of various applications. Their knowledge allows them to design powder coating spray booths that are tailored to diverse production environments.
2. Innovative Solutions
EMS is committed to continuous innovation, incorporating the latest technology into their products. Their powder coating spray booths are designed for optimal performance, featuring advanced filtration and airflow management systems.
3. Comprehensive Support
From installation to ongoing maintenance, EMS provides exceptional customer support. Their team of experts is dedicated to helping businesses maximize the performance of their powder coating spray booths.
4. Customizable Options
Recognizing that every business has unique requirements, EMS offers customizable options for powder coating spray booths, allowing businesses to select features and configurations that best suit their operational needs.
5. Trusted Reliability
With a strong reputation for delivering high-quality products, EMS is a trusted name in the powder coating industry. Their booths are designed for durability and long-term performance, making them an excellent investment for businesses.
Conclusion
A powder coating spray booth is a critical investment for any powder coating operation, providing a controlled environment that enhances coating quality and efficiency. With advanced filtration and airflow management, these booths ensure clean operations and compliance with safety regulations.
EMS Powder Coating Equipment is a leading manufacturer of powder coating spray booths, offering innovative solutions tailored to meet the diverse needs of various industries. Their commitment to quality, performance, and customer support makes EMS the best choice for businesses seeking reliable coating solutions.
By choosing EMS powder coating spray booths, companies can enhance their coating processes, achieve superior finishes, and reduce operational costs. With a focus on efficiency and innovation, EMS stands out as the premier manufacturer for businesses in need of top-tier powder coating equipment.
Powder Coating Booth: Elevating Coating Quality and Efficiency
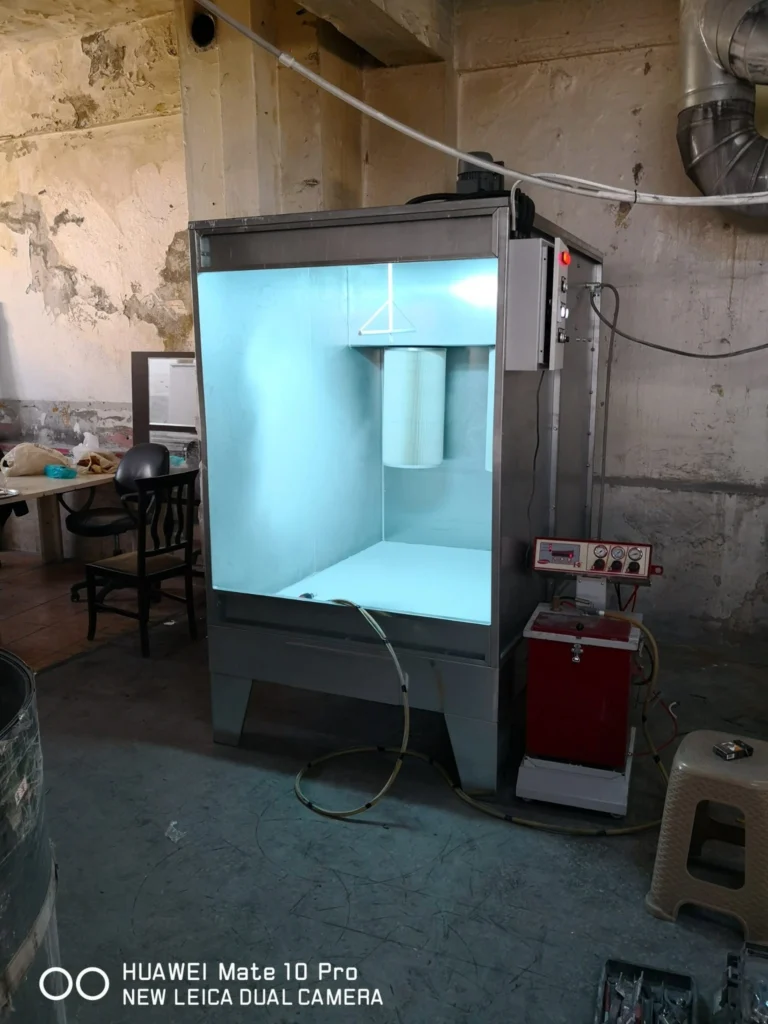
A powder coating booth is a specialized enclosure designed for the application of powder coatings onto various substrates. These booths play a vital role in ensuring a controlled environment that minimizes overspray, dust, and other contaminants, resulting in high-quality finishes that meet industry standards.
The primary function of a powder coating booth is to provide an optimized workspace for powder application, equipped with advanced filtration systems and efficient airflow management. This not only enhances the quality of the coatings but also promotes a safer and more productive working environment.
EMS Powder Coating Equipment is recognized as a leader in the manufacturing of powder coating booths, offering innovative designs tailored to meet the specific needs of diverse industries. In this section, we will explore the operational principles, key features, and benefits of powder coating booths, while also discussing why EMS is the preferred choice for businesses seeking reliable coating solutions.
What is a Powder Coating Booth?
A powder coating booth is an integral part of the powder coating process, providing a controlled environment for the application of powder coatings. These booths are designed to optimize the application process, ensuring that the coatings adhere properly to the substrate.
How Powder Coating Booths Operate
The operation of a powder coating booth begins with substrate preparation, which involves cleaning and pre-treating the surface to ensure optimal adhesion. Once prepared, the substrate is placed inside the booth for powder application.
Using electrostatic spray guns, operators apply charged powder particles to the grounded substrate. The electrostatic charge attracts the powder, allowing for an even coating. The booth’s ventilation system captures overspray and maintains air quality, protecting both the operators and the surrounding environment.
EMS Powder Coating Equipment designs powder coating booths with features that enhance both the application and curing processes, ensuring businesses achieve consistent, high-quality finishes across various applications.
Key Features of Powder Coating Booths
Powder coating booths are equipped with several features designed to enhance their performance and efficiency. Here are some standout features that make EMS booths the preferred choice for businesses:
1. Advanced Filtration Systems
EMS powder coating booths come equipped with high-efficiency filters that capture overspray and airborne particles. This ensures a clean environment for coating applications, leading to higher quality finishes and safer operations.
2. Efficient Airflow Management
With adjustable airflow systems, EMS booths allow operators to control air distribution within the booth. This capability promotes even powder application and reduces the risk of defects, enhancing overall coating quality.
3. Ergonomic Design
The user-friendly design of EMS powder coating booths prioritizes operator comfort and efficiency. With easy access to controls and ample workspace, operators can maneuver and position substrates effectively, reducing job completion times.
4. Energy Efficiency
EMS powder coating booths are designed for energy efficiency, featuring optimized airflow and filtration systems that minimize energy consumption while maximizing performance. This efficiency can lead to reduced operational costs.
5. Safety Features
Safety is paramount in powder coating operations. EMS booths are equipped with essential safety features, such as emergency shut-off systems, explosion-proof lighting, and proper ventilation to ensure a safe working environment.
6. Customizable Configurations
Recognizing that different businesses have unique requirements, EMS offers customizable configurations for their powder coating booths. Whether for small operations or large-scale production, EMS can tailor solutions to meet specific needs.
Benefits of Using Powder Coating Booths
Investing in a powder coating booth provides numerous advantages for businesses engaged in powder coating operations. Here are some key benefits:
1. Superior Coating Quality
The controlled environment of a powder coating booth significantly enhances the quality of applied coatings. With effective filtration and optimized airflow, these booths ensure smooth, even finishes that meet high standards.
2. Increased Productivity
EMS powder coating booths streamline the coating process, allowing for quicker application and improved drying times. This efficiency can lead to increased production rates, helping businesses meet tight deadlines.
3. Cost Efficiency
By minimizing overspray and maximizing powder usage, powder coating booths can significantly reduce material costs. Efficient application processes lead to less waste and lower operational expenses, enhancing profitability.
4. Versatility for Diverse Applications
EMS powder coating booths are versatile enough to accommodate a wide range of substrates and coating types. This adaptability allows businesses to diversify their offerings and cater to different market demands.
5. Compliance with Environmental Regulations
Powder coating booths are designed to meet industry safety and environmental regulations, ensuring a compliant operation. By investing in EMS booths, businesses can promote a healthier working environment while adhering to necessary standards.
Why Choose EMS Powder Coating Equipment for Powder Coating Booths?
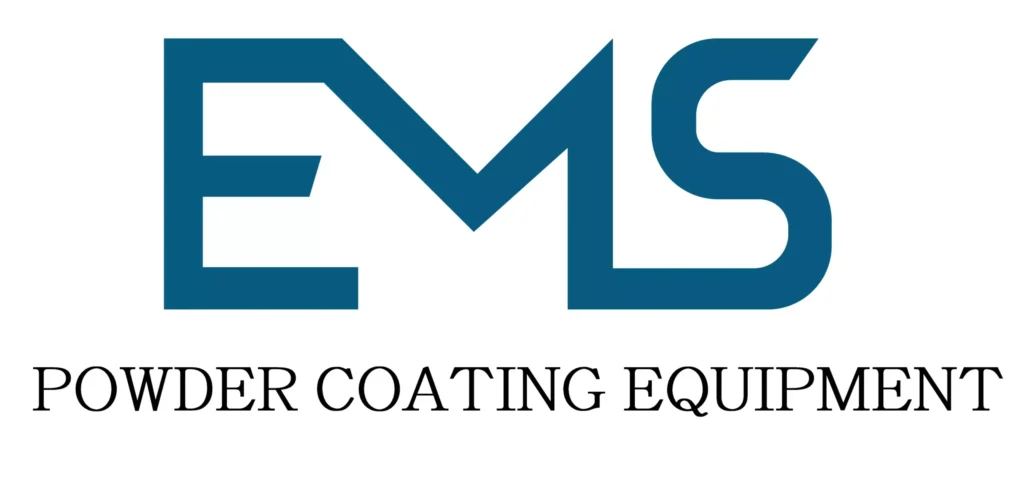
When selecting a powder coating booth, it is essential to choose a manufacturer with a reputation for quality and innovation. EMS Powder Coating Equipment stands out as the top choice for businesses looking to invest in powder coating booths. Here’s why EMS is the preferred option:
1. Proven Expertise
With years of experience in the powder coating industry, EMS understands the unique needs of various applications. Their knowledge allows them to design powder coating booths that are tailored to diverse production environments.
2. Innovative Solutions
EMS is committed to continuous innovation, incorporating the latest technology into their products. Their powder coating booths are designed for optimal performance, featuring advanced filtration and airflow management systems.
3. Comprehensive Support
From installation to ongoing maintenance, EMS provides exceptional customer support. Their team of experts is dedicated to helping businesses maximize the performance of their powder coating booths.
4. Customizable Options
Recognizing that every business has unique requirements, EMS offers customizable options for powder coating booths, allowing businesses to select features and configurations that best suit their operational needs.
5. Trusted Reliability
With a strong reputation for delivering high-quality products, EMS is a trusted name in the powder coating industry. Their booths are designed for durability and long-term performance, making them an excellent investment for businesses.
Conclusion
A powder coating booth is a vital investment for any powder coating operation, providing a controlled environment that enhances coating quality and efficiency. With advanced filtration and airflow management, these booths ensure clean operations and compliance with safety regulations.
EMS Powder Coating Equipment is a leading manufacturer of powder coating booths, offering innovative solutions tailored to meet the diverse needs of various industries. Their commitment to quality, performance, and customer support makes EMS the best choice for businesses seeking reliable coating solutions.
By choosing EMS powder coating booths, companies can enhance their coating processes, achieve superior finishes, and reduce operational costs. With a focus on efficiency and innovation, EMS stands out as the premier manufacturer for businesses in need of top-tier powder coating equipment.
Powder Coating Spray Booth: Precision in Coating Applications
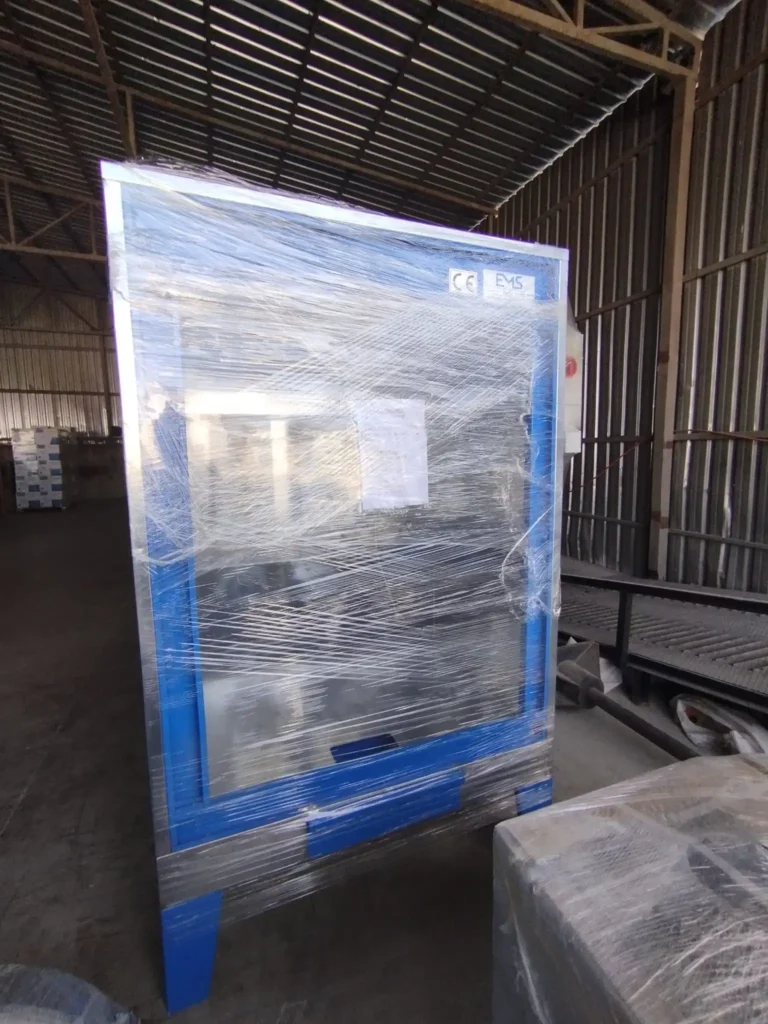
A powder coating spray booth is an essential component in the powder coating process, providing a controlled environment for the application of powder coatings onto various substrates. These booths are designed to optimize the application process, ensuring high-quality finishes while minimizing overspray and contamination.
Equipped with advanced filtration systems and effective ventilation, powder coating spray booths create an ideal workspace that enhances both safety and efficiency. The right booth can significantly improve the quality of the coating while reducing waste and cleanup time.
EMS Powder Coating Equipment is a leader in the manufacturing of powder coating spray booths, offering innovative designs tailored to meet the specific needs of different industries. In this section, we will delve into the operational principles, key features, and benefits of powder coating spray booths, while also discussing why EMS is the preferred choice for businesses looking for reliable and efficient coating solutions.
What is a Powder Coating Spray Booth?
A powder coating spray booth is a specialized enclosure designed for the application of powder coatings to metal and other substrates. These booths play a crucial role in ensuring a clean and controlled environment, which is vital for achieving high-quality finishes.
How Powder Coating Spray Booths Operate
The operation of a powder coating spray booth begins with substrate preparation, which involves cleaning and pre-treating the surface to ensure optimal adhesion. Once prepared, the substrate is placed inside the booth, where electrostatic spray guns are used to apply charged powder particles to the grounded surface.
The electrostatic charge attracts the powder, allowing for an even and uniform coating. The booth’s advanced ventilation system captures overspray and maintains air quality, protecting both the operators and the environment.
EMS Powder Coating Equipment designs powder coating spray booths with features that optimize the application process, ensuring businesses achieve consistent, high-quality finishes across various applications.
Key Features of Powder Coating Spray Booths
Powder coating spray booths are equipped with several features that enhance their performance and efficiency. Here are some standout features that make EMS booths the preferred choice for businesses:
1. Advanced Filtration Systems
EMS powder coating spray booths are equipped with high-efficiency filtration systems that capture overspray and airborne particles. This ensures a clean environment for coating applications, leading to higher quality finishes and safer operations.
2. Efficient Ventilation
The ventilation system in EMS booths is designed to maintain optimal air circulation, allowing for effective fume extraction and overspray capture. This feature not only enhances the coating quality but also promotes a healthier working environment for operators.
3. Ergonomic Design
The user-friendly design of EMS powder coating spray booths prioritizes operator comfort and efficiency. With easy access to controls and ample workspace, operators can maneuver and position substrates effectively, reducing job completion times.
4. Energy Efficiency
EMS powder coating spray booths are designed for energy efficiency, featuring optimized airflow and filtration systems that minimize energy consumption while maximizing performance. This efficiency can lead to reduced operational costs.
5. Safety Features
Safety is paramount in powder coating operations. EMS booths come equipped with essential safety features, such as emergency shut-off systems, explosion-proof lighting, and proper ventilation, ensuring a safe working environment.
6. Customizable Configurations
Recognizing that different businesses have unique requirements, EMS offers customizable configurations for their powder coating spray booths. Whether for small operations or large-scale production, EMS can tailor solutions to meet specific needs.
Benefits of Using Powder Coating Spray Booths
Investing in a powder coating spray booth provides numerous advantages for businesses engaged in powder coating operations. Here are some key benefits:
1. Superior Coating Quality
The controlled environment of a powder coating spray booth significantly enhances the quality of applied coatings. With effective filtration and optimized airflow, these booths ensure smooth, even finishes that meet high standards.
2. Increased Productivity
EMS powder coating spray booths streamline the coating process, allowing for quicker application and improved drying times. This efficiency can lead to increased production rates, helping businesses meet tight deadlines.
3. Cost Efficiency
By minimizing overspray and maximizing powder usage, powder coating spray booths can significantly reduce material costs. Efficient application processes lead to less waste and lower operational expenses, enhancing profitability.
4. Versatility for Diverse Applications
EMS powder coating spray booths are versatile enough to accommodate a wide range of substrates and coating types. This adaptability allows businesses to diversify their offerings and cater to different market demands.
5. Compliance with Environmental Regulations
Powder coating spray booths are designed to meet industry safety and environmental regulations, ensuring a compliant operation. By investing in EMS booths, businesses can promote a healthier working environment while adhering to necessary standards.
Why Choose EMS Powder Coating Equipment for Powder Coating Spray Booths?
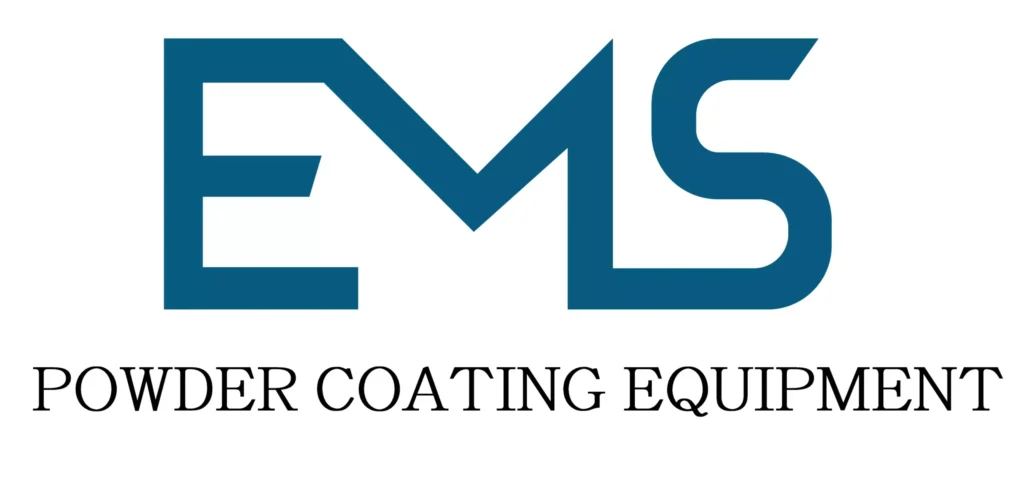
When selecting a powder coating spray booth, it is essential to choose a manufacturer with a reputation for quality and innovation. EMS Powder Coating Equipment stands out as the top choice for businesses looking to invest in powder coating spray booths. Here’s why EMS is the preferred option:
1. Proven Expertise
With years of experience in the powder coating industry, EMS understands the unique needs of various applications. Their knowledge allows them to design powder coating spray booths that are tailored to diverse production environments.
2. Innovative Solutions
EMS is committed to continuous innovation, incorporating the latest technology into their products. Their powder coating spray booths are designed for optimal performance, featuring advanced filtration and airflow management systems.
3. Comprehensive Support
From installation to ongoing maintenance, EMS provides exceptional customer support. Their team of experts is dedicated to helping businesses maximize the performance of their powder coating spray booths.
4. Customizable Options
Recognizing that every business has unique requirements, EMS offers customizable options for powder coating spray booths, allowing businesses to select features and configurations that best suit their operational needs.
5. Trusted Reliability
With a strong reputation for delivering high-quality products, EMS is a trusted name in the powder coating industry. Their booths are designed for durability and long-term performance, making them an excellent investment for businesses.
Conclusion
A powder coating spray booth is a vital investment for any powder coating operation, providing a controlled environment that enhances coating quality and efficiency. With advanced filtration and ventilation systems, these booths ensure clean operations and compliance with safety regulations.
EMS Powder Coating Equipment is a leading manufacturer of powder coating spray booths, offering innovative solutions tailored to meet the diverse needs of various industries. Their commitment to quality, performance, and customer support makes EMS the best choice for businesses seeking reliable coating solutions.
By choosing EMS powder coating spray booths, companies can enhance their coating processes, achieve superior finishes, and reduce operational costs. With a focus on efficiency and innovation, EMS stands out as the premier manufacturer for businesses in need of top-tier powder coating equipment.
Powder Coating Booth: A Vital Component for Quality Finishing
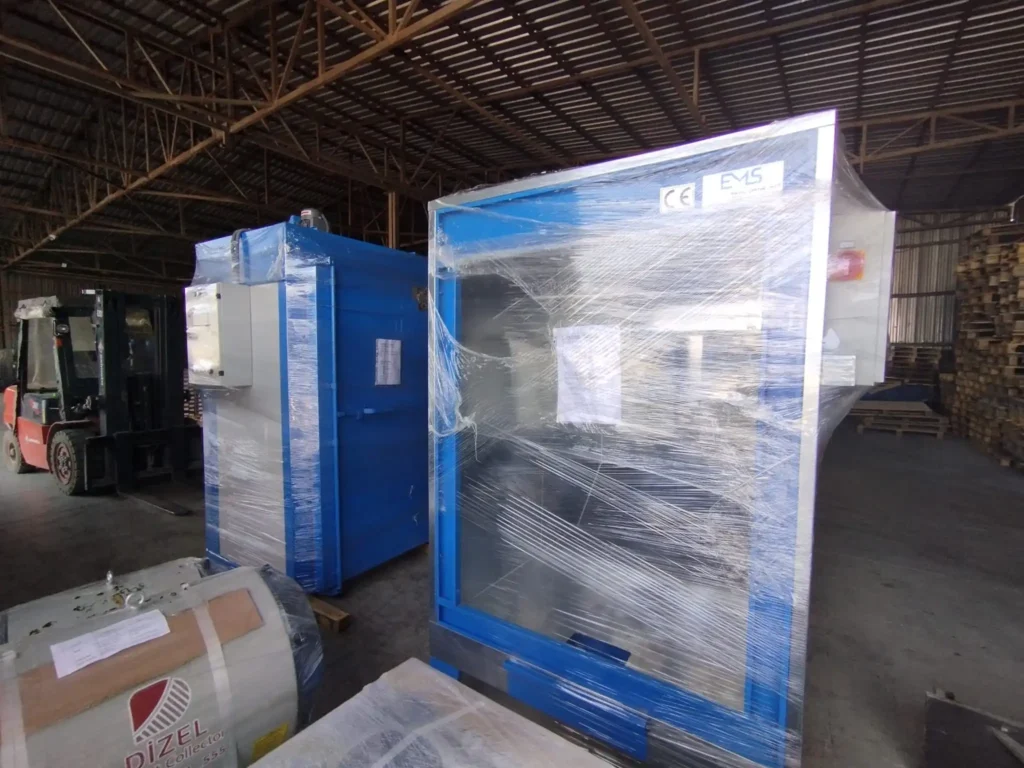
A powder coating booth is an essential element in the powder coating process, providing a dedicated environment for the application of powder coatings on various substrates. These booths are specifically designed to optimize the coating application, ensuring high-quality finishes while minimizing overspray and contamination.
With advanced features such as efficient ventilation systems and effective filtration, powder coating booths create a controlled workspace that enhances both safety and efficiency. The right booth can significantly improve the quality of the coating while reducing waste and operational costs.
EMS Powder Coating Equipment stands out as a leader in the manufacturing of powder coating booths, offering innovative designs tailored to the unique needs of different industries. In this section, we will delve into the operational principles, key features, and benefits of powder coating booths, while also discussing why EMS is the preferred choice for businesses seeking reliable and efficient coating solutions.
What is a Powder Coating Booth?
A powder coating booth is a specialized enclosure designed to facilitate the application of powder coatings to metal and other substrates. These booths play a critical role in ensuring a clean and controlled environment, which is vital for achieving high-quality finishes.
How Powder Coating Booths Operate
The operation of a powder coating booth begins with the preparation of the substrate, which typically involves cleaning and pre-treating the surface to ensure optimal adhesion. Once prepared, the substrate is positioned inside the booth, where electrostatic spray guns are utilized to apply charged powder particles onto the grounded surface.
The electrostatic charge attracts the powder, allowing for an even and uniform coating. The booth’s advanced ventilation system effectively captures overspray and maintains air quality, protecting both the operators and the environment.
EMS Powder Coating Equipment designs powder coating booths with features that enhance the application process, ensuring businesses achieve consistent, high-quality finishes across various applications.
Key Features of Powder Coating Booths
Powder coating booths come with a range of features that enhance their functionality and efficiency. Here are some standout features that make EMS booths the preferred choice for businesses:
1. High-Efficiency Filtration Systems
EMS powder coating booths are equipped with advanced filtration systems that capture overspray and particulate matter, ensuring a clean environment for coating applications. This leads to higher quality finishes and reduces the risk of contamination.
2. Optimal Ventilation
The ventilation system in EMS booths is designed to provide optimal air circulation, effectively removing fumes and excess powder. This feature not only enhances coating quality but also promotes a safer working environment for operators.
3. Ergonomic Design
The user-centric design of EMS powder coating booths prioritizes operator comfort and efficiency. With easy access to controls and ample workspace, operators can maneuver and position substrates effectively, minimizing production time.
4. Energy Efficiency
EMS powder coating booths are designed for energy efficiency, featuring optimized airflow and filtration systems that minimize energy consumption while maximizing performance. This efficiency can lead to significant cost savings.
5. Safety Features
Safety is a top priority in powder coating operations. EMS booths come equipped with essential safety features, including emergency shut-off systems, explosion-proof lighting, and proper ventilation, ensuring a safe working environment.
6. Customizable Configurations
Understanding that different businesses have unique requirements, EMS offers customizable configurations for their powder coating booths. Whether for small operations or large-scale production, EMS can tailor solutions to meet specific needs.
Benefits of Using Powder Coating Booths
Investing in a powder coating booth provides numerous advantages for businesses engaged in powder coating operations. Here are some key benefits:
1. Superior Coating Quality
The controlled environment of a powder coating booth significantly enhances the quality of applied coatings. With effective filtration and ventilation, these booths ensure smooth, even finishes that meet the highest standards.
2. Increased Productivity
EMS powder coating booths streamline the coating process, allowing for quicker application and improved drying times. This efficiency can lead to increased production rates, helping businesses meet tight deadlines.
3. Cost Efficiency
By minimizing overspray and maximizing powder usage, powder coating booths can significantly reduce material costs. Efficient application processes lead to less waste and lower operational expenses, enhancing profitability.
4. Versatility for Diverse Applications
EMS powder coating booths are versatile enough to accommodate a wide range of substrates and coating types. This adaptability allows businesses to diversify their offerings and cater to different market demands.
5. Compliance with Environmental Regulations
Powder coating booths are designed to meet industry safety and environmental regulations, ensuring a compliant operation. By investing in EMS booths, businesses can promote a healthier working environment while adhering to necessary standards.
Why Choose EMS Powder Coating Equipment for Powder Coating Booths?
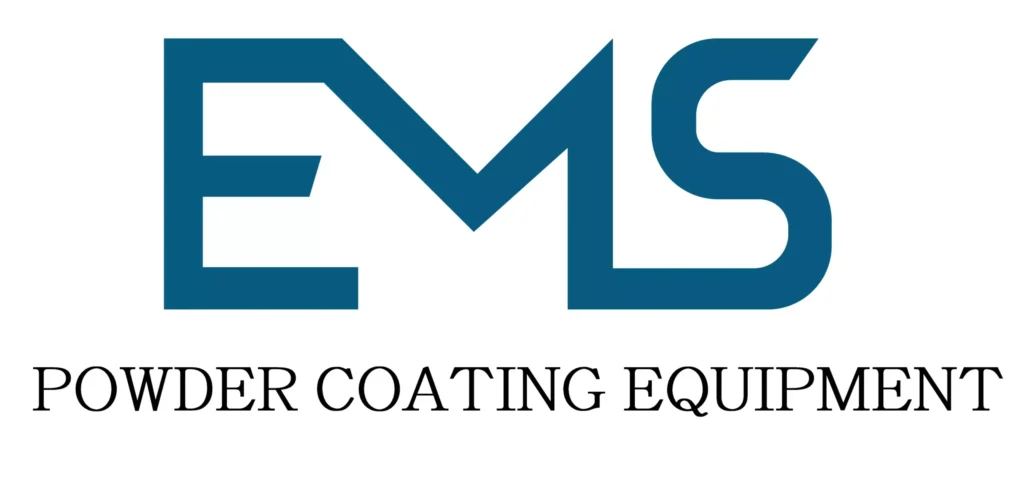
When selecting a powder coating booth, it is crucial to choose a manufacturer with a strong reputation for quality and innovation. EMS Powder Coating Equipment stands out as the top choice for businesses looking to invest in powder coating booths. Here’s why EMS is the preferred option:
1. Proven Expertise
With years of experience in the powder coating industry, EMS understands the unique needs of various applications. Their knowledge allows them to design powder coating booths tailored to diverse production environments.
2. Innovative Solutions
EMS is committed to continuous innovation, incorporating the latest technology into their products. Their powder coating booths are designed for optimal performance, featuring advanced filtration and airflow management systems.
3. Comprehensive Support
From installation to ongoing maintenance, EMS provides exceptional customer support. Their team of experts is dedicated to helping businesses maximize the performance of their powder coating booths.
4. Customizable Options
Recognizing that every business has unique requirements, EMS offers customizable options for powder coating booths, allowing businesses to select features and configurations that best suit their operational needs.
5. Trusted Reliability
With a strong reputation for delivering high-quality products, EMS is a trusted name in the powder coating industry. Their booths are designed for durability and long-term performance, making them an excellent investment for businesses.
Conclusion
A powder coating booth is a vital investment for any powder coating operation, providing a controlled environment that enhances coating quality and efficiency. With advanced filtration and ventilation systems, these booths ensure clean operations and compliance with safety regulations.
EMS Powder Coating Equipment is a leading manufacturer of powder coating booths, offering innovative solutions tailored to meet the diverse needs of various industries. Their commitment to quality, performance, and customer support makes EMS the best choice for businesses seeking reliable coating solutions.
By choosing EMS powder coating booths, companies can enhance their coating processes, achieve superior finishes, and reduce operational costs. With a focus on efficiency and innovation, EMS stands out as the premier manufacturer for businesses in need of top-tier powder coating equipment.
Powder Coating Equipment: Essential Tools for Quality Finishing
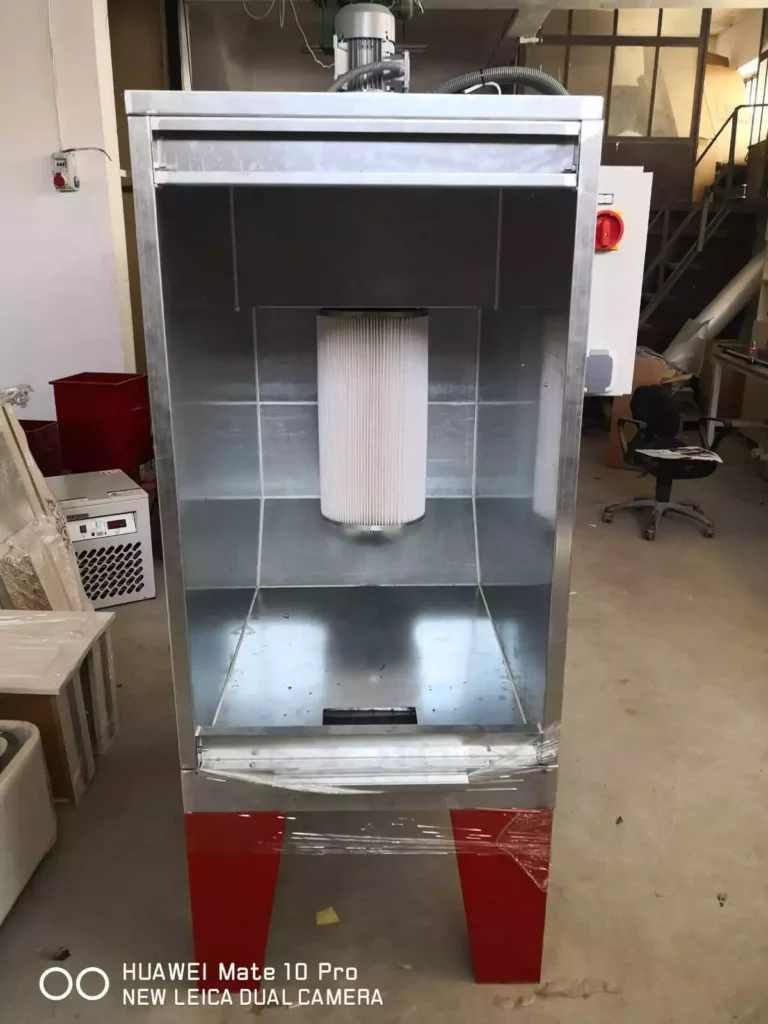
Powder coating equipment encompasses a range of specialized tools and machinery designed for the application of powder coatings onto various substrates. This technology has gained widespread popularity due to its ability to produce durable, high-quality finishes while being environmentally friendly.
The main components of powder coating equipment include spray guns, powder coating booths, curing ovens, and other essential tools that facilitate the coating process. Together, these components work seamlessly to create an efficient production line, resulting in coatings that are not only aesthetically pleasing but also resistant to corrosion, chemicals, and wear.
EMS Powder Coating Equipment is recognized as a leader in the manufacture of powder coating equipment, offering innovative solutions that cater to the unique needs of different industries. In this section, we will delve into the different types of powder coating equipment, their functionalities, and the advantages they provide, while highlighting why EMS is the preferred choice for businesses looking for reliable and effective coating solutions.
Types of Powder Coating Equipment
Powder coating equipment consists of several key components, each playing a crucial role in the coating process. Here’s an overview of the primary types of equipment involved:
1. Powder Coating Spray Guns
Powder coating spray guns are essential for applying the powder to the substrate. These guns utilize electrostatic technology, which charges the powder particles as they are sprayed. This charge causes the powder to adhere uniformly to the grounded surface, ensuring even coverage.
There are various types of spray guns available, including manual, automatic, and robotic systems. EMS Powder Coating Equipment offers a range of spray guns designed for efficiency and precision, making it easier for operators to achieve high-quality finishes.
2. Powder Coating Booths
Powder coating booths provide a controlled environment for the application of powder coatings. These booths are equipped with ventilation and filtration systems that capture overspray and maintain air quality. By minimizing contamination, EMS powder coating booths ensure superior coating quality.
3. Curing Ovens
After application, the coated substrate must be cured in an oven to achieve a durable finish. Curing ovens, whether electric, gas, or diesel-powered, heat the coated items to the necessary temperature for the powder to melt and form a solid bond with the substrate. EMS provides a variety of curing ovens to suit different production needs.
4. Powder Paint Booths with Filters
These booths are specifically designed for the application of powder coatings, featuring advanced filtration systems to capture overspray and particulates. This helps to maintain a clean working environment and enhances the overall quality of the coating application.
5. Powder Coating Accessories
In addition to the primary equipment, various accessories, such as hooks, racks, and conveyor systems, are vital for efficient operation. These accessories assist in transporting substrates through the coating process, ensuring smooth workflow and maximizing productivity.
Benefits of Using Powder Coating Equipment
Investing in high-quality powder coating equipment offers numerous advantages for businesses engaged in coating operations. Here are some key benefits:
1. Superior Durability
Powder coatings are known for their exceptional durability and resistance to chipping, scratching, and fading. The equipment designed for powder coating applications ensures that these qualities are maximized, resulting in long-lasting finishes.
2. Environmentally Friendly
Unlike traditional liquid coatings, powder coatings contain little to no volatile organic compounds (VOCs). This makes them a more environmentally friendly option, aligning with modern regulations and sustainability goals.
3. Cost Efficiency
By minimizing overspray and maximizing powder utilization, powder coating equipment can lead to significant cost savings. Efficient application processes result in less waste and lower operational costs, which enhance overall profitability.
4. Versatile Applications
Powder coating equipment can be used for a wide range of substrates, including metals, plastics, and wood. This versatility allows businesses to expand their offerings and cater to diverse market demands.
5. Enhanced Quality Control
With advanced features such as electrostatic application and controlled environments, powder coating equipment helps maintain high standards of quality. Businesses can achieve consistent finishes, reducing the likelihood of defects and rework.
6. Increased Productivity
Modern powder coating equipment is designed for efficiency, allowing for quicker application, curing, and turnaround times. This boost in productivity enables businesses to meet tight deadlines and increase production rates.
Why Choose EMS Powder Coating Equipment?
When selecting powder coating equipment, it is essential to choose a manufacturer known for quality, reliability, and innovation. EMS Powder Coating Equipment stands out as the top choice for businesses seeking powder coating solutions. Here’s why EMS is the preferred option:
1. Industry Expertise
With years of experience in the powder coating industry, EMS understands the unique requirements of various applications. Their expertise allows them to design equipment that meets the needs of diverse production environments.
2. Innovative Technologies
EMS is committed to continuous improvement and innovation, incorporating the latest technologies into their products. Their powder coating equipment features advanced design elements that enhance performance and efficiency.
3. Comprehensive Customer Support
From initial consultation to ongoing maintenance, EMS provides exceptional customer support. Their team of experts is dedicated to helping businesses optimize their powder coating operations.
4. Customizable Solutions
Recognizing that every business has unique needs, EMS offers customizable options for their powder coating equipment. This allows businesses to select features and configurations that align with their operational requirements.
5. Proven Reliability
With a strong reputation for delivering high-quality products, EMS is a trusted name in the powder coating industry. Their equipment is built for durability and long-term performance, making it an excellent investment for businesses.
Conclusion
Powder coating equipment is a crucial investment for any business involved in powder coating operations. By providing superior durability, cost efficiency, and environmentally friendly solutions, this equipment enhances the overall quality of the coating process.
EMS Powder Coating Equipment is a leading manufacturer of powder coating equipment, offering innovative and reliable solutions tailored to the diverse needs of various industries. Their commitment to quality, performance, and customer support makes EMS the best choice for businesses seeking top-tier powder coating solutions.
By choosing EMS powder coating equipment, companies can improve their coating processes, achieve high-quality finishes, and enhance productivity. With a focus on innovation and efficiency, EMS stands out as the premier manufacturer for businesses in need of effective powder coating solutions.
Automatic Powder Coating Equipment: Revolutionizing the Coating Process
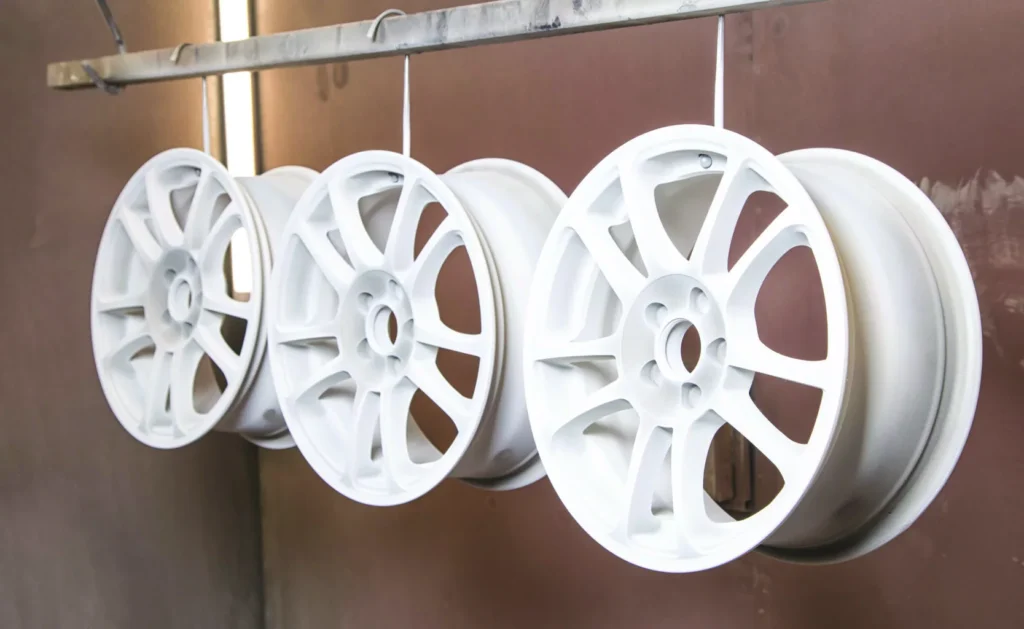
Automatic powder coating equipment represents a significant advancement in the field of surface finishing. Designed to automate the powder coating process, this equipment enhances efficiency, consistency, and quality, making it a preferred choice for manufacturers across various industries.
By utilizing automation technologies, businesses can significantly reduce labor costs and improve production speed while maintaining high standards of quality. Automatic systems include components such as robotic spray arms, automated conveyor systems, and sophisticated controls that ensure precise application of powder coatings.
EMS Powder Coating Equipment has established itself as a leader in the manufacture of automatic powder coating systems, offering innovative solutions that cater to diverse operational needs. In this section, we will delve into the key components of automatic powder coating equipment, its advantages, and the reasons why EMS is the go-to choice for businesses looking to enhance their coating processes.
Key Components of Automatic Powder Coating Equipment
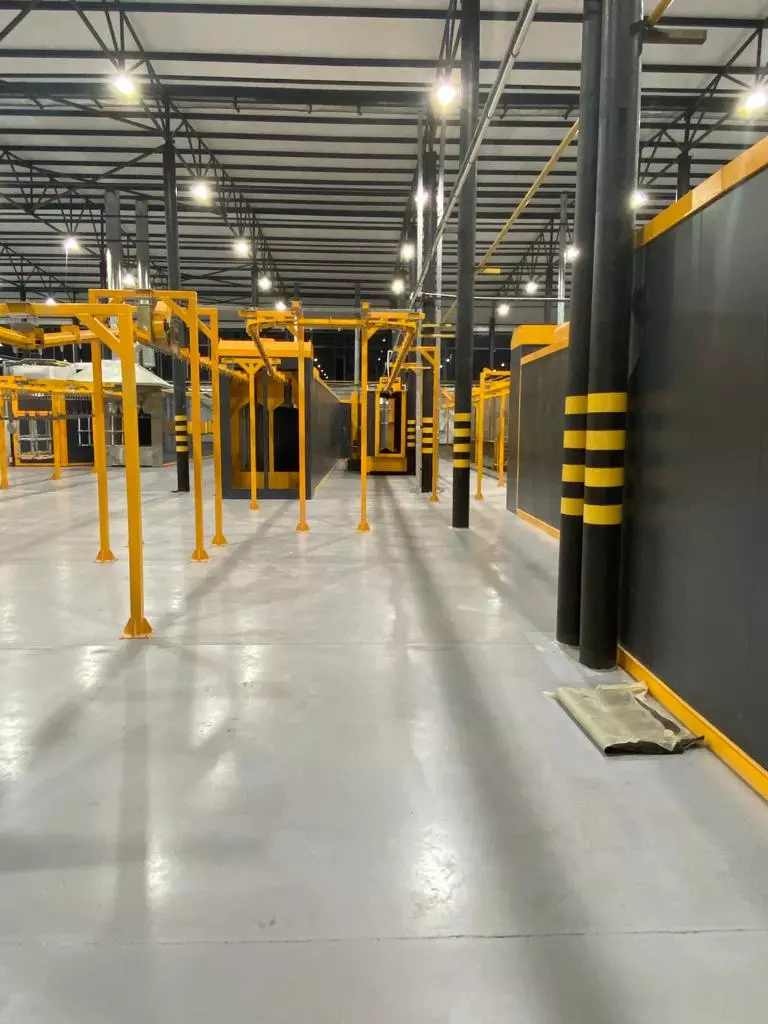
Automatic powder coating equipment consists of several critical components that work together to streamline the coating process. Here’s an overview of these essential elements:
1. Robotic Spray Guns
Robotic spray guns are a cornerstone of automatic powder coating systems. These devices are programmed to apply powder coatings uniformly and efficiently. The use of robotics allows for precise control over the application process, resulting in consistent and high-quality finishes.
2. Automated Conveyor Systems
Automated conveyor systems transport substrates through various stages of the powder coating process, from cleaning to coating and curing. This continuous movement minimizes manual handling and increases productivity by reducing downtime.
3. Powder Coating Booths
Automatic powder coating systems typically include dedicated booths designed to contain overspray and enhance air quality. These booths are equipped with advanced filtration and ventilation systems to ensure a clean environment for coating applications.
4. Curing Ovens
Curing ovens are essential for achieving durable finishes in automatic powder coating systems. These ovens are engineered to provide consistent heat distribution, ensuring that the powder melts and bonds effectively with the substrate.
5. Control Systems
Advanced control systems in automatic powder coating equipment allow for precise adjustments and monitoring of the coating process. Operators can easily program parameters such as application thickness, speed, and curing times, optimizing performance and quality.
Benefits of Automatic Powder Coating Equipment
Investing in automatic powder coating equipment offers numerous advantages for manufacturers. Here are some key benefits:
1. Enhanced Efficiency
Automatic systems significantly improve production efficiency by minimizing manual labor and reducing cycle times. The integration of robotic spray arms and conveyor systems allows for continuous operation, resulting in higher output rates.
2. Consistent Quality
One of the primary benefits of automatic powder coating equipment is the ability to achieve consistent and uniform coatings. Automated systems eliminate variations caused by human operators, ensuring high-quality finishes across all products.
3. Cost Savings
By reducing labor costs and improving material utilization, automatic powder coating equipment can lead to substantial cost savings. Efficient application processes minimize waste, enhancing the overall profitability of operations.
4. Flexibility and Scalability
Automatic powder coating systems can be easily adapted to accommodate different substrates and coating types. This flexibility allows manufacturers to diversify their product offerings and scale operations as demand increases.
5. Improved Safety
Automating the powder coating process enhances workplace safety by minimizing human exposure to potentially hazardous materials. Advanced control systems and robotics reduce the need for manual handling, creating a safer working environment.
6. Advanced Monitoring and Control
Modern automatic powder coating equipment includes sophisticated monitoring and control features that provide real-time data on the coating process. This capability allows operators to quickly identify and address any issues, ensuring optimal performance.
Why Choose EMS Powder Coating Equipment?
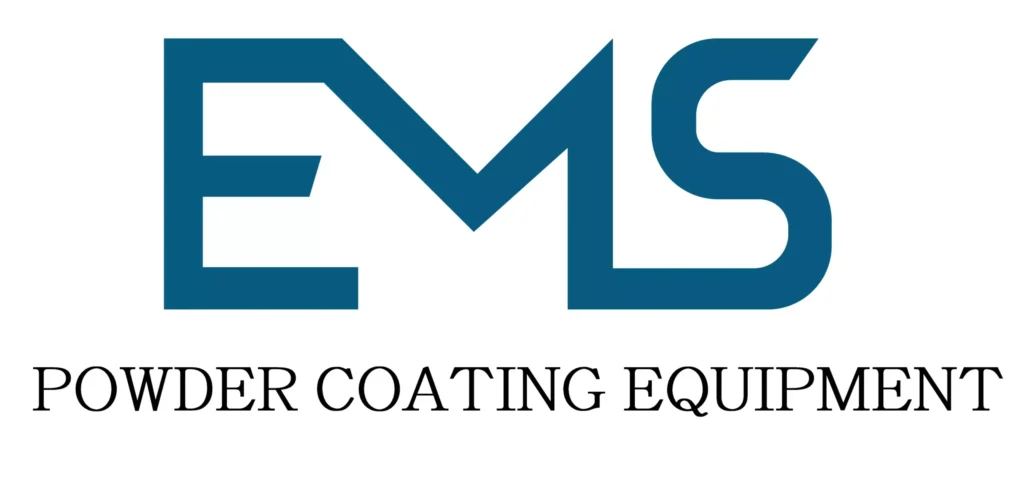
When selecting automatic powder coating equipment, it’s essential to choose a manufacturer known for quality, innovation, and reliability. EMS Powder Coating Equipment stands out as the top choice for businesses looking to enhance their powder coating processes. Here’s why EMS is the preferred option:
1. Proven Industry Expertise
With extensive experience in the powder coating sector, EMS understands the unique challenges and requirements of different applications. Their expertise allows them to design automatic systems that meet diverse operational needs.
2. Innovative Technologies
EMS is committed to innovation, continuously integrating the latest technologies into their automatic powder coating equipment. Their systems are designed for optimal performance, featuring advanced robotics and control systems that enhance efficiency.
3. Comprehensive Customer Support
From initial consultation through installation and ongoing maintenance, EMS provides exceptional customer support. Their team of experts is dedicated to helping businesses maximize the performance of their automatic systems.
4. Customizable Solutions
Recognizing that every business has distinct requirements, EMS offers customizable options for their automatic powder coating equipment. This allows companies to tailor solutions to their specific production needs.
5. Trusted Reliability
With a strong reputation for delivering high-quality products, EMS is a trusted name in the powder coating industry. Their automatic equipment is built for durability and long-term performance, making it an excellent investment for businesses.
Conclusion
Automatic powder coating equipment is a game-changer for manufacturers looking to enhance their coating processes. By improving efficiency, consistency, and quality, these systems provide a competitive edge in today’s fast-paced market.
EMS Powder Coating Equipment is a leading manufacturer of automatic powder coating systems, offering innovative solutions tailored to the diverse needs of various industries. Their commitment to quality, performance, and customer support makes EMS the best choice for businesses seeking reliable and effective coating solutions.
By choosing EMS automatic powder coating equipment, companies can optimize their operations, achieve superior finishes, and enhance productivity. With a focus on innovation and efficiency, EMS stands out as the premier manufacturer for businesses in need of top-tier powder coating solutions.
Powder Coating Reciprocator: Precision in Coating Application

A powder coating reciprocator is a specialized piece of equipment designed to apply powder coatings efficiently and uniformly to various surfaces. By utilizing a mechanical arm that moves in a back-and-forth motion, reciprocators ensure that every part of the substrate receives an even application of powder. This technology is crucial for achieving high-quality finishes and is widely used in industries ranging from automotive to furniture manufacturing.
The primary advantage of using a reciprocator lies in its ability to automate the powder coating process, resulting in improved consistency and reduced labor costs. Unlike manual application methods, which can lead to variations in coating thickness and quality, reciprocators provide precise control over the application process.
EMS Powder Coating Equipment is renowned for manufacturing high-quality powder coating reciprocators that meet the diverse needs of various industries. In this section, we will delve into the key features of powder coating reciprocators, their benefits, and the reasons why EMS is the go-to choice for businesses seeking reliable and effective coating solutions.
Key Features of Powder Coating Reciprocators
Powder coating reciprocators consist of several essential components that work together to ensure precise application of powder coatings. Here are the key features of these machines:
1. Mechanical Arm Design
The mechanical arm of a powder coating reciprocator is engineered for smooth and controlled movement. This design allows for consistent coverage across the substrate, minimizing the risk of missed spots or uneven application.
2. Adjustable Speed and Stroke Length
Reciprocators offer adjustable speed settings and stroke lengths, allowing operators to customize the application process according to the specific needs of different substrates. This flexibility enhances the overall efficiency of the coating operation.
3. Integrated Spray Gun Systems
Most powder coating reciprocators come equipped with integrated spray gun systems, ensuring that the powder is applied uniformly. These systems are often designed to utilize electrostatic technology, which helps the powder adhere better to the substrate.
4. Control Panels
Modern reciprocators feature user-friendly control panels that allow operators to easily adjust settings such as speed, stroke length, and application thickness. These controls provide the ability to monitor the coating process in real time.
5. Safety Features
Safety is a key consideration in any manufacturing environment. Powder coating reciprocators are equipped with various safety features, such as emergency stop buttons and protective enclosures, to ensure safe operation for workers.
Benefits of Using Powder Coating Reciprocators
Investing in a powder coating reciprocator offers numerous advantages for businesses involved in powder coating operations. Here are some key benefits:
1. Improved Application Efficiency
Powder coating reciprocators significantly enhance the efficiency of the coating process. By automating the application, businesses can reduce cycle times and increase throughput, ultimately improving production rates.
2. Consistent Quality
One of the main advantages of using reciprocators is the ability to achieve consistent and uniform coatings. This level of precision minimizes defects and ensures high-quality finishes, which is crucial for customer satisfaction.
3. Reduced Labor Costs
Automating the powder coating process with reciprocators allows businesses to reduce their reliance on manual labor. This not only lowers labor costs but also minimizes the potential for human error in the application process.
4. Enhanced Material Utilization
Powder coating reciprocators are designed to optimize powder utilization. By applying the powder evenly and efficiently, businesses can reduce waste and lower material costs.
5. Flexibility in Application
Reciprocators can be adjusted to accommodate various substrate shapes and sizes. This flexibility allows businesses to diversify their offerings and cater to different market needs.
6. Minimal Maintenance Requirements
Modern powder coating reciprocators are built with durability in mind, requiring minimal maintenance. This reduces downtime and helps businesses maintain consistent production levels.
Why Choose EMS Powder Coating Equipment?
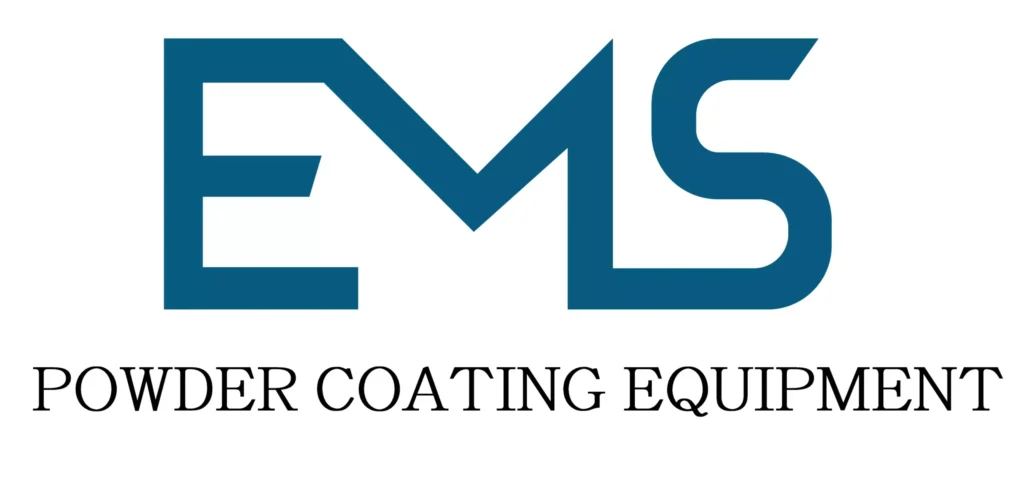
When selecting a powder coating reciprocator, it’s essential to choose a manufacturer known for quality, reliability, and innovation. EMS Powder Coating Equipment stands out as the preferred choice for businesses looking to enhance their powder coating processes. Here’s why EMS is the best option:
1. Proven Industry Experience
With extensive experience in the powder coating industry, EMS understands the unique challenges and requirements of various applications. Their expertise enables them to design reciprocators that cater to diverse operational needs.
2. Innovative Solutions
EMS is committed to innovation, continuously integrating the latest technologies into their powder coating reciprocators. Their systems are designed for optimal performance and efficiency, enhancing overall productivity.
3. Comprehensive Customer Support
From the initial consultation through installation and ongoing maintenance, EMS provides exceptional customer support. Their team of experts is dedicated to helping businesses maximize the performance of their reciprocators.
4. Customizable Options
Recognizing that every business has distinct requirements, EMS offers customizable options for their powder coating reciprocators. This allows companies to tailor solutions to their specific production needs.
5. Trusted Quality
With a strong reputation for delivering high-quality products, EMS is a trusted name in the powder coating industry. Their reciprocators are built for durability and long-term performance, making them an excellent investment for businesses.
Conclusion
Powder coating reciprocators play a vital role in modern manufacturing, providing precision and efficiency in the coating application process. By automating this process, businesses can achieve consistent quality, improve productivity, and reduce labor costs.
EMS Powder Coating Equipment is a leading manufacturer of powder coating reciprocators, offering innovative solutions tailored to the diverse needs of various industries. Their commitment to quality, performance, and customer support makes EMS the best choice for businesses seeking reliable and effective coating solutions.
By choosing EMS powder coating reciprocators, companies can optimize their coating processes, achieve superior finishes, and enhance overall productivity. With a focus on innovation and efficiency, EMS stands out as the premier manufacturer for businesses in need of top-tier powder coating solutions.
What is a Gas Powder Coating Oven?
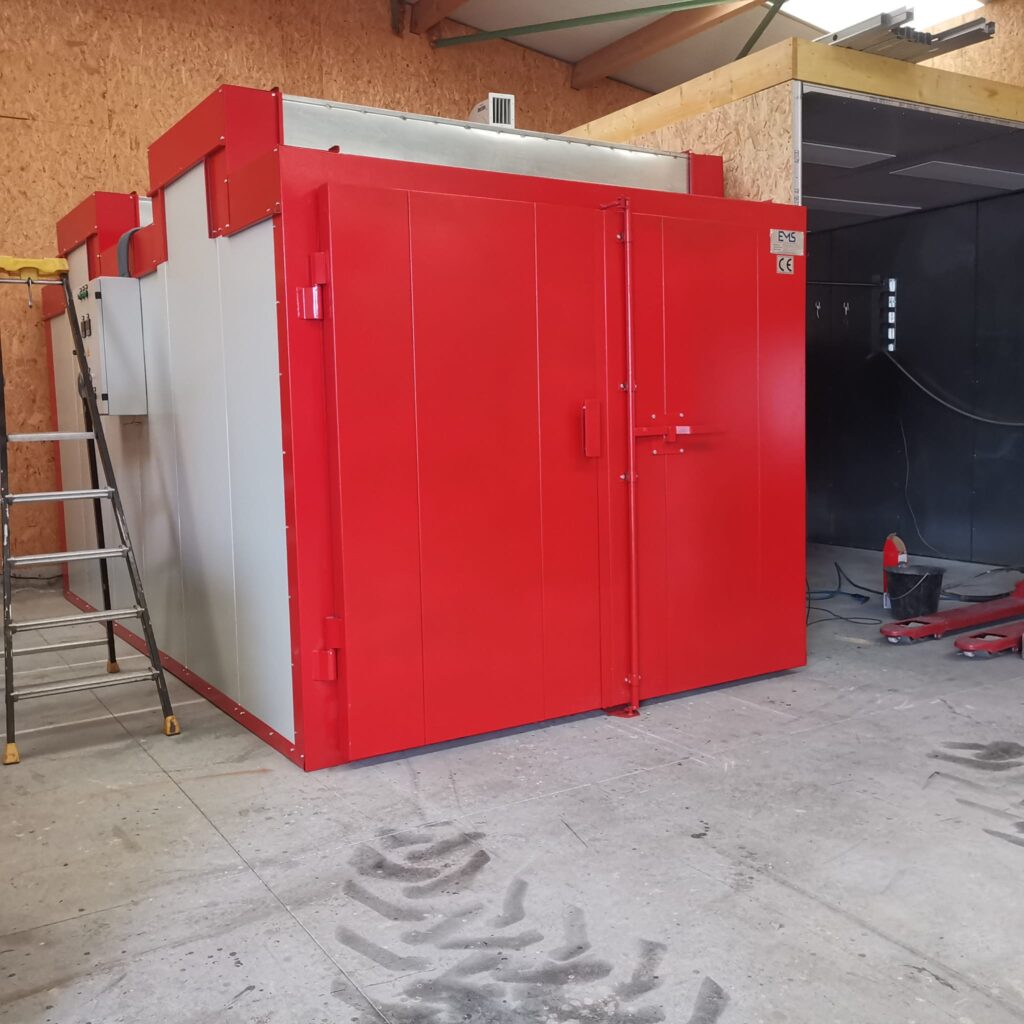
A gas powder coating oven is an industrial curing oven that uses natural gas or propane as its primary energy source to generate the heat needed to cure powder coatings. These ovens are designed to create a controlled environment where the coated product is exposed to consistent, high temperatures, allowing the powder to melt, flow, and bond to the surface. The result is a hard, smooth, and durable finish that protects the product from wear, corrosion, and environmental damage.
Gas ovens are particularly effective for curing large quantities of products quickly, thanks to their fast heat-up times and ability to maintain steady temperatures over long periods. They are commonly used in industries such as automotive manufacturing, metal fabrication, and industrial equipment production, where high volumes of parts need to be coated and cured efficiently.
How Gas Ovens Work
Gas powder coating ovens operate by burning natural gas or propane in a combustion chamber, which generates heat that is then circulated throughout the curing chamber. The combustion process is controlled by a burner system that regulates the flow of gas to maintain the desired temperature. Fans or blowers distribute the heated air evenly across the chamber, ensuring that the temperature remains consistent throughout the curing process.
The temperature inside the oven is typically controlled by a digital system that allows operators to set and monitor the curing temperature and time. This precise control is crucial for ensuring that the powder coating cures properly, achieving the desired finish and durability.
Gas powder coating ovens can be configured as batch ovens, where products are loaded into the oven in groups, or as conveyorized systems, where products move through the oven on a conveyor belt. Conveyorized systems are ideal for high-volume production environments where continuous throughput is required.
EMS Powder Coating Equipment manufactures gas ovens that offer precise temperature control and efficient fuel consumption. Their ovens are designed with advanced insulation and heat distribution systems that minimize energy loss while providing consistent curing temperatures, ensuring top-quality results.
The Benefits of Gas Powder Coating Ovens
Gas powder coating ovens are favored by many manufacturers for their efficiency, scalability, and ability to handle high-volume production. Below are some of the key benefits that make gas ovens a popular choice in the powder coating industry:
1. Fast Heat-Up Times and Consistent Temperature Control
One of the main advantages of gas powder coating ovens is their ability to heat up quickly. Gas ovens can reach their target temperature in a short amount of time, which is essential for maintaining high productivity in busy production environments. Once the desired temperature is reached, gas ovens are highly effective at maintaining that temperature consistently throughout the curing process.
Consistent temperature control is critical in the powder coating process, as even minor fluctuations in heat can lead to uneven curing or defects in the coating. Gas ovens are equipped with advanced burner and airflow systems that ensure uniform heat distribution across the entire curing chamber. This helps prevent issues such as under-curing or over-curing, both of which can compromise the quality and durability of the final product.
EMS Powder Coating Equipment provides gas ovens with cutting-edge temperature control technology, ensuring that the curing process is optimized for consistent, high-quality results. Their ovens are designed to minimize temperature fluctuations, allowing businesses to achieve flawless finishes on every batch of products.
2. Energy Efficiency and Lower Operating Costs
Gas ovens are known for their energy efficiency, particularly in large-scale operations where high volumes of products need to be cured. Natural gas and propane are typically more cost-effective than electricity, especially in regions where gas prices are lower or where the availability of gas is more reliable. As a result, gas ovens can offer significant cost savings over time compared to electric ovens, particularly for businesses that run their ovens continuously or for extended periods.
Gas ovens are also designed to optimize fuel consumption. Many modern gas ovens feature energy-saving technologies such as modulating burners, which adjust the flow of gas to maintain the desired temperature with minimal waste. This ensures that the oven operates efficiently, using only the amount of fuel needed to achieve the required heat output.
EMS Powder Coating Equipment designs its gas ovens with energy efficiency in mind. Their ovens are equipped with advanced fuel-saving features that help businesses reduce their energy consumption while maintaining optimal curing performance. By choosing an EMS gas oven, businesses can lower their operating costs and improve their bottom line.
3. Scalability for High-Volume Production
Gas powder coating ovens are ideal for high-volume production environments where large quantities of products need to be coated and cured quickly. The fast heat-up times and consistent temperature control of gas ovens make them well-suited for operations that require continuous throughput. Conveyorized gas ovens, in particular, allow for a steady flow of products through the curing chamber, ensuring that production lines can run smoothly without interruption.
For industries such as automotive manufacturing, metal fabrication, and heavy machinery, where large, heavy, or complex parts need to be coated, gas ovens provide the power and capacity needed to handle these demanding workloads. The ability to scale up production without sacrificing quality or efficiency is one of the key reasons why gas ovens are so popular in these industries.
EMS Powder Coating Equipment specializes in manufacturing gas ovens that can be scaled to meet the specific needs of different industries. Whether you need a batch oven for smaller production runs or a conveyorized system for continuous operation, EMS provides customized solutions that help businesses maximize their production capacity.
4. Durability and Longevity
Gas ovens are known for their durability and long-lasting performance, making them a reliable investment for businesses that require continuous operation. Built with high-quality materials and advanced engineering, gas ovens are designed to withstand the demands of industrial use, including exposure to high temperatures and heavy workloads.
The robust construction of gas ovens ensures that they can operate effectively over long periods without frequent breakdowns or the need for extensive maintenance. This reliability is crucial for businesses that rely on their ovens to keep production lines running smoothly.
EMS Powder Coating Equipment designs its gas ovens with durability in mind. Their ovens are built to last, with high-quality components that can withstand the rigors of continuous industrial use. EMS ovens require minimal maintenance, allowing businesses to focus on production without worrying about costly downtime.
5. Flexibility Across a Range of Industries
Gas powder coating ovens are versatile and can be used to cure a wide range of products across different industries. From automotive parts and industrial equipment to consumer goods and outdoor furniture, gas ovens are capable of curing products of various sizes, shapes, and materials.
In addition to their versatility, gas ovens can be customized to meet the specific needs of different production environments. Whether you need an oven with precise temperature control for sensitive coatings or a large-capacity oven for high-volume production, gas ovens offer the flexibility needed to accommodate different curing requirements.
EMS Powder Coating Equipment offers gas ovens that can be tailored to meet the unique needs of various industries. Their ovens are designed for maximum flexibility, ensuring that businesses can achieve optimal curing performance for a wide range of products.
6. Environmentally Friendly Options
While gas ovens rely on fossil fuels, they can still be designed with environmental considerations in mind. Many modern gas ovens are equipped with energy-efficient burners and heat recovery systems that minimize fuel consumption and reduce emissions. This makes gas ovens a more environmentally friendly option compared to older models that may be less efficient.
In addition, gas ovens produce fewer emissions than diesel ovens, making them a more sustainable option for businesses that are looking to reduce their environmental impact while maintaining high performance.
EMS Powder Coating Equipment is committed to sustainability and offers gas ovens with energy-efficient features that help businesses reduce their carbon footprint. Their ovens are designed to meet environmental standards while providing the performance needed for industrial powder coating applications.
Why Choose EMS Powder Coating Equipment for Gas Ovens?
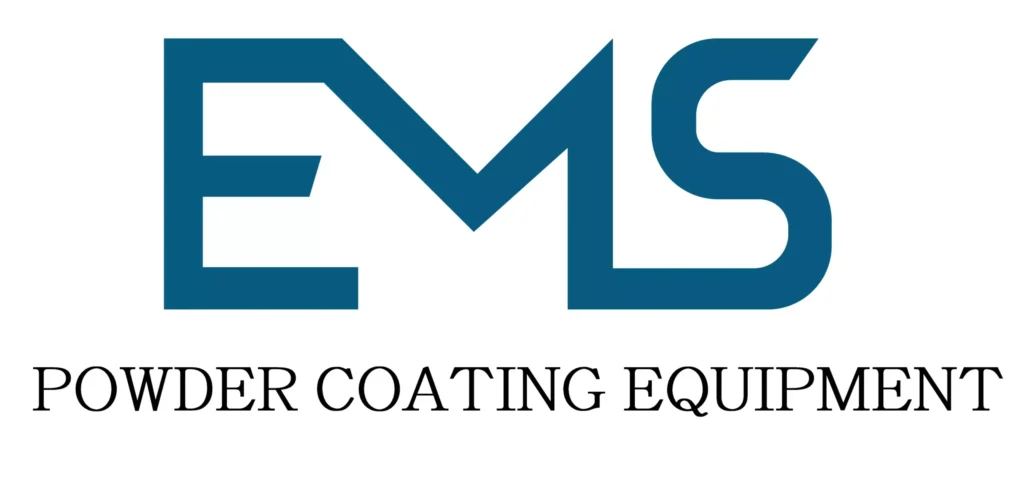
When selecting a gas powder coating oven, businesses need a solution that offers reliability, efficiency, and scalability. EMS Powder Coating Equipment is a trusted manufacturer of gas ovens, offering advanced systems designed to meet the specific needs of industrial production. Here’s why EMS is the best choice for businesses looking to invest in high-quality gas powder coating ovens:
1. Advanced Temperature Control Technology
EMS gas ovens are equipped with cutting-edge temperature control systems that ensure precise and consistent heat throughout the curing process. This level of control is essential for achieving high-quality finishes and preventing defects caused by temperature fluctuations.
2. Customizable Solutions for Different Industries
Every business has unique production needs, and EMS understands the importance of offering customizable solutions. EMS gas ovens are available in a variety of sizes and configurations, allowing businesses to choose the oven that best fits their production line. Whether you need a batch oven for smaller jobs or a conveyorized system for high-volume production, EMS provides tailored solutions that maximize efficiency and output.
3. Energy Efficiency for Cost Savings
EMS Powder Coating Equipment designs its gas ovens with energy efficiency in mind. Their ovens are equipped with energy-saving features such as modulating burners and advanced insulation that reduce fuel consumption and lower operating costs. By investing in an EMS gas oven, businesses can improve their energy efficiency while maintaining top-tier curing performance.
4. Durability and Reliability
EMS gas ovens are built to last, with durable components that can withstand the demands of continuous industrial use. Their ovens are constructed from high-quality materials designed to ensure long-lasting performance, reducing the need for frequent maintenance and costly repairs.
5. Superior Customer Support and Service
EMS is committed to providing exceptional customer support, from the initial consultation and installation to ongoing maintenance and troubleshooting. Their team of experts is always available to assist with any questions or concerns, ensuring that your gas oven operates at peak efficiency.
Conclusion
Gas powder coating ovens are a powerful and efficient solution for curing powder-coated products in industrial environments. With their fast heat-up times, consistent temperature control, and scalability, gas ovens are ideal for high-volume production operations that require reliable performance and cost-effective energy consumption.
EMS Powder Coating Equipment is the industry leader in providing advanced gas ovens that combine precision, efficiency, and durability. Whether you’re looking to upgrade your existing system or invest in a new oven, EMS offers customizable solutions that ensure your powder coating process is optimized for maximum productivity and quality.
By choosing EMS gas powder coating ovens, businesses can improve their production efficiency, reduce operating costs, and achieve superior results in their powder coating operations. With a proven track record of innovation and customer satisfaction, EMS is the best choice for businesses seeking reliable and efficient gas ovens.
Diesel Powder Coating Oven: Efficient Heating Solutions for Optimal Coating Results
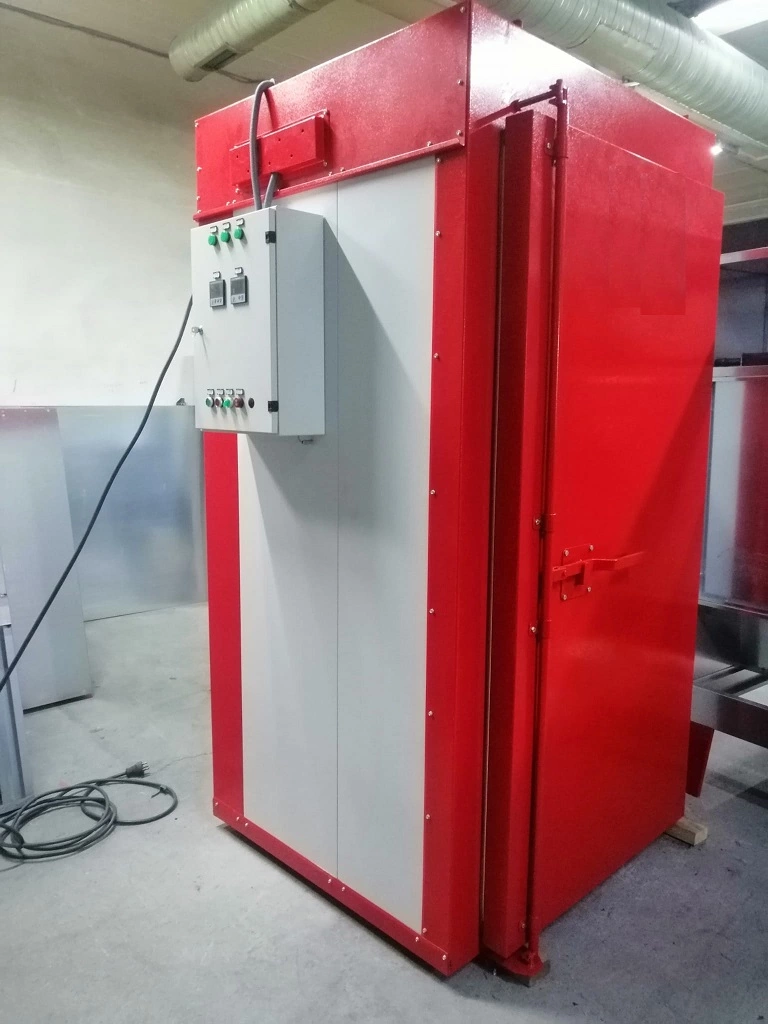
In the world of powder coating, the oven used for curing the applied powder is as critical as the application process itself. The diesel powder coating oven is specifically designed to provide the necessary heat for curing powder coatings efficiently and effectively. These ovens utilize diesel fuel to generate the high temperatures required for melting and adhering powder coatings to substrates, ensuring a durable and high-quality finish.
Diesel powder coating ovens are particularly beneficial for businesses that operate in remote areas where electricity may not be readily available, or for operations that require a portable heating solution. The design and efficiency of these ovens allow them to deliver consistent heating across the entire chamber, ensuring uniform curing and optimal coating performance.
EMS Powder Coating Equipment is a recognized leader in the manufacturing of diesel powder coating ovens, offering state-of-the-art solutions that combine efficiency, safety, and ease of use. In this section, we will explore the operational mechanics, advantages, and unique features of diesel powder coating ovens and explain why EMS stands out as the best manufacturer in the industry.
What is a Diesel Powder Coating Oven?
A diesel powder coating oven is a specialized piece of equipment used to cure powder coatings after they have been applied to a substrate. Unlike electric ovens, diesel ovens use diesel fuel to generate the heat needed for the curing process. This makes them ideal for locations where electricity is limited or for applications that require high portability.
How Diesel Powder Coating Ovens Work
The operation of a diesel powder coating oven begins with the application of powder coating to the product. Once the powder is applied, the product is transferred to the oven, where it is heated to the required curing temperature, typically between 350°F and 400°F (about 177°C to 204°C).
Diesel burners within the oven ignite the fuel, generating heat that is distributed throughout the oven chamber. Advanced insulation materials are used in the construction of the oven to retain heat efficiently and ensure even distribution, eliminating cold spots that could affect the curing process.
The oven is equipped with temperature control systems that allow operators to monitor and adjust the internal temperature as needed. This precision ensures that the powder coating cures properly, leading to a smooth, durable finish.
EMS Powder Coating Equipment designs diesel powder coating ovens that incorporate advanced technology for optimal performance. Their ovens are engineered to deliver consistent heating and are built for durability, making them an excellent choice for businesses seeking reliable curing solutions.
Key Features of Diesel Powder Coating Ovens
Diesel powder coating ovens are equipped with a variety of features that enhance their performance and efficiency. Here are some of the key features that make EMS diesel ovens a preferred choice for businesses:
1. High Efficiency and Performance
EMS diesel powder coating ovens are designed to provide high-efficiency heating. The use of advanced burner technology ensures that the ovens heat up quickly and maintain consistent temperatures throughout the curing process. This efficiency reduces the overall energy consumption, leading to cost savings for businesses.
2. Robust Construction
Built to withstand the demands of industrial use, EMS ovens are constructed from high-quality materials that ensure long-lasting performance. Their robust design minimizes wear and tear, making them a reliable option for continuous operation.
3. Temperature Control Systems
Accurate temperature control is crucial in the curing process. EMS diesel powder coating ovens are equipped with sophisticated temperature control systems that allow operators to set and monitor the internal temperature precisely. This feature ensures optimal curing conditions for various powder coatings.
4. Insulation and Heat Retention
Effective insulation is vital for maintaining consistent temperatures within the oven. EMS ovens use advanced insulation materials that minimize heat loss, allowing for more efficient operation and reduced energy costs. This feature also helps maintain stable curing conditions, enhancing the quality of the finished product.
5. Safety Features
Safety is a top priority in industrial operations, and EMS diesel powder coating ovens are designed with multiple safety features. These may include flame detection systems, emergency shut-off valves, and temperature alarms to ensure the safety of operators and the equipment.
6. Portability Options
One of the advantages of diesel powder coating ovens is their portability. EMS offers options that make it easy to relocate the oven as needed, making them ideal for businesses that require flexibility in their operations.
Benefits of Using Diesel Powder Coating Ovens
Investing in a diesel powder coating oven provides numerous advantages for businesses engaged in powder coating operations. Here are some of the key benefits:
1. Versatility in Operation
Diesel powder coating ovens are versatile and can be used in various applications. They are particularly beneficial for businesses located in remote areas without reliable electrical power. The ability to operate using diesel fuel allows companies to maintain consistent production without relying on electrical infrastructure.
2. Consistent Heating for Superior Quality
The uniform heating provided by diesel ovens ensures that powder coatings cure evenly, resulting in high-quality finishes. Consistent temperature distribution prevents defects such as uneven curing or poorly adhered coatings, leading to enhanced product quality.
3. Cost-Effectiveness
Using a diesel powder coating oven can lead to cost savings in several ways. The efficiency of diesel burners can translate into lower fuel costs compared to electric heating. Additionally, the ability to recycle and reclaim excess powder in the curing process reduces material waste, further lowering overall operational costs.
4. Enhanced Productivity
Diesel powder coating ovens are designed for fast heating and consistent performance, contributing to increased productivity in powder coating operations. The quick curing times allow for faster turnaround on projects, enabling businesses to meet production deadlines more effectively.
5. Flexibility in Production Capacity
The portable nature of diesel ovens provides flexibility in production capacity. Businesses can scale their operations up or down as needed, adapting to changing demands without significant investment in new equipment.
Why Choose EMS Powder Coating Equipment for Diesel Powder Coating Ovens?
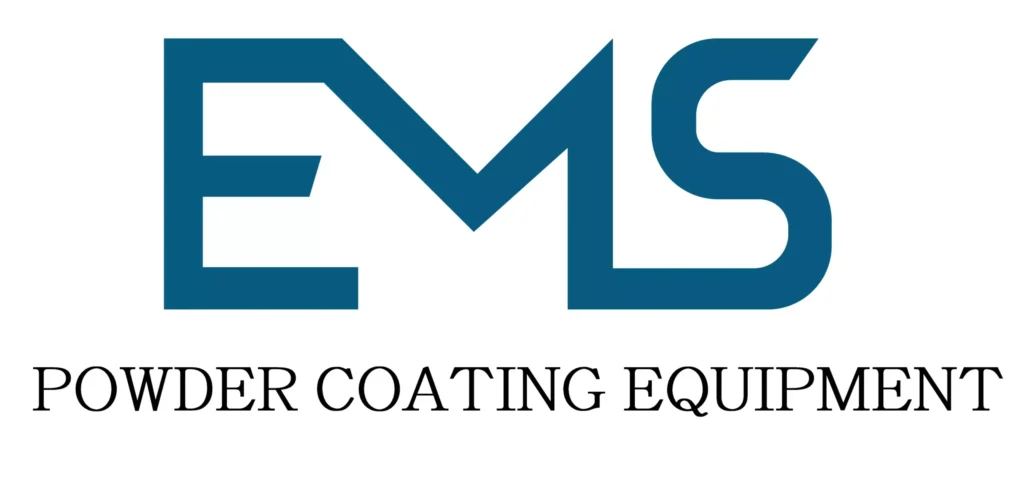
When selecting a diesel powder coating oven, it is crucial to choose a manufacturer that offers quality, reliability, and superior performance. EMS Powder Coating Equipment stands out as the leading choice for businesses looking to invest in diesel ovens. Here’s why EMS is the best option:
1. Proven Industry Experience
With extensive experience in the powder coating industry, EMS understands the specific needs and challenges faced by businesses. Their expertise enables them to design diesel powder coating ovens that meet the demands of various applications.
2. Innovative Design and Technology
EMS is committed to innovation, continually enhancing their products with the latest technology. Their diesel powder coating ovens incorporate advanced burner systems, precise temperature controls, and robust construction, ensuring optimal performance and efficiency.
3. Comprehensive Support Services
In addition to providing top-quality equipment, EMS offers comprehensive customer support, including installation, training, and ongoing maintenance services. Their team of experts is dedicated to ensuring that your diesel powder coating oven operates at peak efficiency.
4. Customizable Solutions
Recognizing that every business has unique needs, EMS provides customizable solutions for diesel powder coating ovens. Whether you require specific heating capacities or additional features, EMS can tailor their ovens to suit your operational requirements.
5. Commitment to Quality and Reliability
EMS has a proven track record of delivering high-quality products and exceptional customer satisfaction. Their diesel powder coating ovens are built for durability and reliability, making them a wise investment for businesses seeking dependable curing solutions.
Conclusion
A diesel powder coating oven is an essential component of any powder coating operation, providing an efficient and effective method for curing powder coatings. With the ability to operate in areas without electrical power, diesel ovens offer flexibility and versatility that can enhance productivity and quality.
EMS Powder Coating Equipment is the industry leader in manufacturing high-performance diesel powder coating ovens. Their commitment to quality, innovation, and customer support makes them the best choice for businesses seeking reliable curing solutions.
By choosing EMS diesel powder coating ovens, companies can improve their coating processes, achieve superior finishes, and enjoy cost savings. With a focus on efficiency and performance, EMS stands out as the premier manufacturer for businesses in need of top-tier powder coating ovens.
Electric Powder Coating Oven: Efficient Curing Solutions for Modern Coating Applications
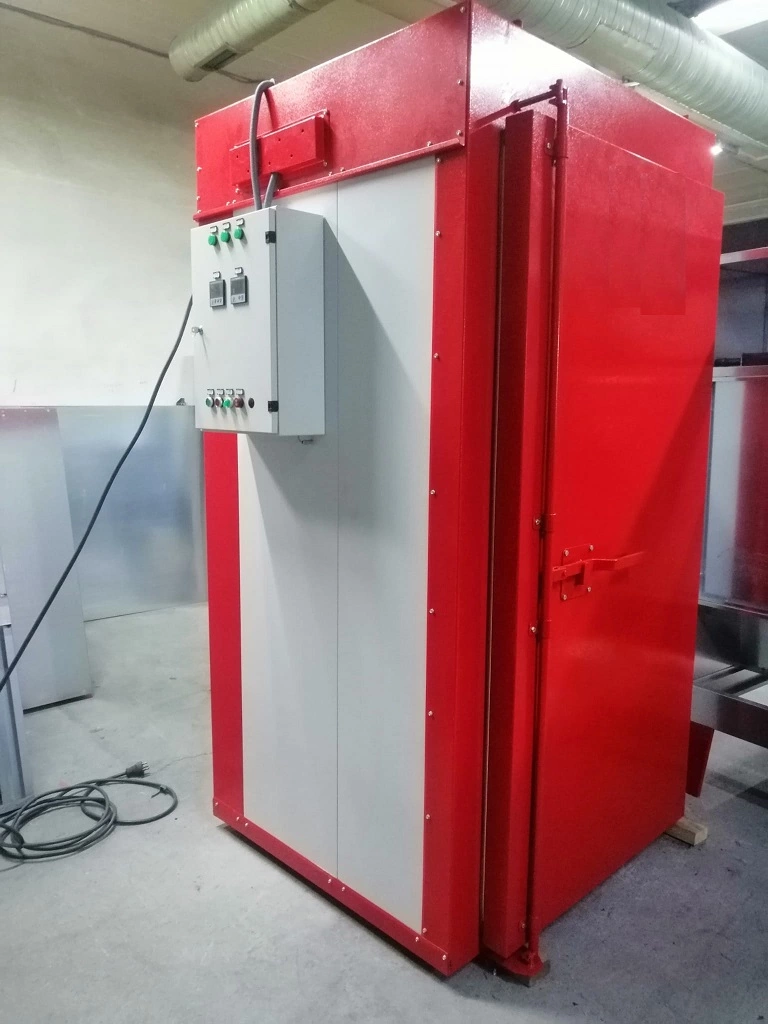
The electric powder coating oven is a crucial component in the powder coating process, responsible for curing the applied powder to create a durable, high-quality finish. Utilizing electric heating elements, these ovens provide consistent and efficient heating, ensuring that powder coatings adhere effectively to various substrates.
Electric powder coating ovens are particularly advantageous for operations that require precise temperature control and uniform heating. The electric heating method allows for quick warm-up times and can be easily adjusted to maintain optimal curing temperatures, resulting in improved coating quality and productivity.
EMS Powder Coating Equipment is recognized as a leading manufacturer of electric powder coating ovens, offering innovative solutions that meet the demands of diverse industries. In this section, we will delve into the operational mechanics, benefits, and unique features of electric powder coating ovens, and explain why EMS is the preferred choice for businesses seeking reliable curing solutions.
What is an Electric Powder Coating Oven?
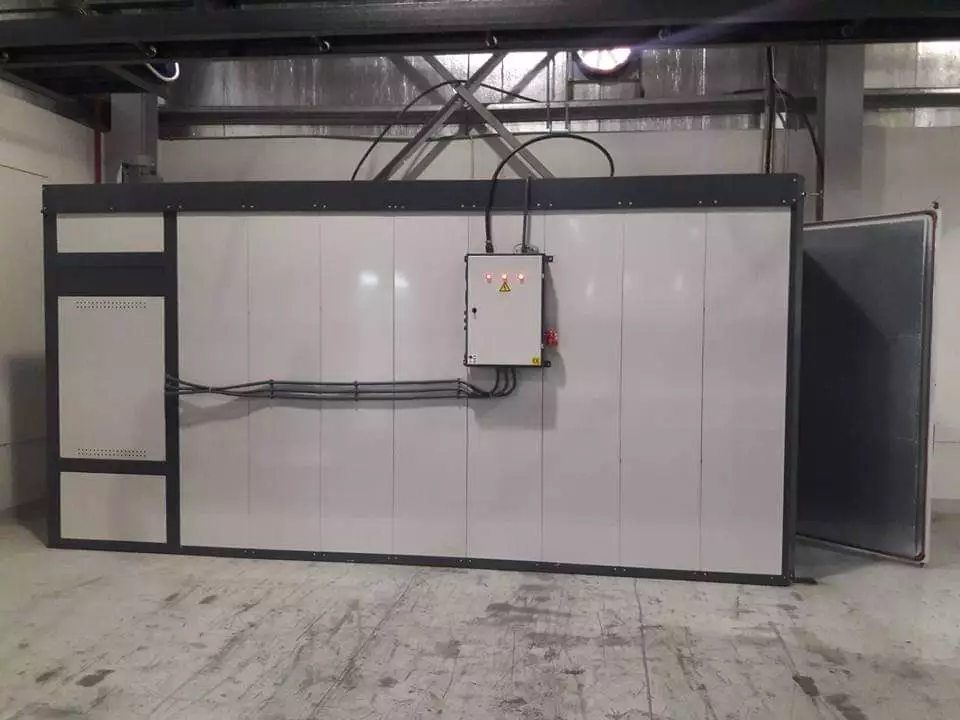
An electric powder coating oven is a specialized curing oven used to heat and cure powder coatings after they have been applied to substrates. These ovens rely on electric heating elements to generate the required temperatures for curing, typically ranging from 350°F to 400°F (about 177°C to 204°C).
How Electric Powder Coating Ovens Operate
The operation of an electric powder coating oven begins with the application of powder coating to the product. Once the powder is applied, the product is moved into the oven, where it is subjected to controlled heating.
Electric heating elements within the oven generate heat, which is distributed evenly throughout the oven chamber. Advanced insulation materials are employed in the construction of the oven to ensure minimal heat loss, allowing for efficient operation and consistent temperature maintenance.
Electric powder coating ovens are equipped with sophisticated temperature control systems that allow operators to set and monitor the internal temperature accurately. This precise control is essential for ensuring that the powder coating cures properly, leading to a smooth, durable finish.
EMS Powder Coating Equipment designs electric powder coating ovens with cutting-edge technology that maximizes efficiency and performance. Their ovens are built to deliver consistent heating and are constructed with durable materials for long-lasting use.
Key Features of Electric Powder Coating Ovens
Electric powder coating ovens come with a variety of features that enhance their performance and efficiency. Here are some of the key features that make EMS electric ovens a top choice for businesses:
1. Precision Temperature Control
EMS electric powder coating ovens are equipped with advanced temperature control systems, allowing for accurate monitoring and adjustment of internal temperatures. This precision is crucial for achieving optimal curing conditions for various powder coatings, ensuring consistent quality in the finished product.
2. Quick Warm-Up Times
One of the advantages of electric ovens is their quick warm-up times. EMS ovens are designed to heat up rapidly, reducing downtime between batches and enhancing overall productivity in the coating process.
3. Energy Efficiency
Electric powder coating ovens are designed for energy efficiency. By using electric heating elements and advanced insulation materials, EMS ovens minimize energy consumption while maintaining optimal heating performance, resulting in cost savings for businesses.
4. Uniform Heating
The design of EMS electric powder coating ovens ensures uniform heat distribution throughout the oven chamber. This consistent heating is vital for preventing cold spots that can lead to uneven curing, ultimately improving the quality of the coated products.
5. Durable Construction
EMS electric powder coating ovens are built to withstand the rigors of industrial use. Constructed from high-quality materials, these ovens are designed for long-lasting performance and minimal maintenance, making them a reliable choice for businesses.
6. User-Friendly Interface
Ease of use is a key consideration in the design of EMS electric powder coating ovens. With intuitive controls and clear displays, operators can easily monitor and adjust settings, streamlining the coating process and improving workflow efficiency.
Benefits of Using Electric Powder Coating Ovens
Investing in an electric powder coating oven provides numerous advantages for businesses engaged in powder coating operations. Here are some of the key benefits:
1. Consistent Coating Quality
One of the primary benefits of using electric powder coating ovens is the consistent quality of the coatings achieved. The precise temperature control and uniform heating contribute to smooth, durable finishes, enhancing the overall quality of the final products.
2. Increased Productivity
Electric powder coating ovens are designed for efficiency, with quick warm-up times and minimal downtime. This increased productivity allows businesses to meet tight deadlines and improve their overall throughput.
3. Cost-Effective Operation
The energy-efficient design of EMS electric ovens translates to lower operational costs. By minimizing energy consumption and optimizing the curing process, businesses can reduce their overall expenses while maintaining high-quality outputs.
4. Flexibility in Production
Electric powder coating ovens offer flexibility in production capacity, allowing businesses to scale their operations as needed. Whether coating small batches or larger volumes, EMS ovens can be tailored to accommodate varying production demands.
5. Environmentally Friendly
Electric ovens produce fewer emissions compared to their diesel counterparts, making them a more environmentally friendly option for powder coating operations. By using electric heating, businesses can reduce their carbon footprint and contribute to sustainability efforts.
Why Choose EMS Powder Coating Equipment for Electric Powder Coating Ovens?
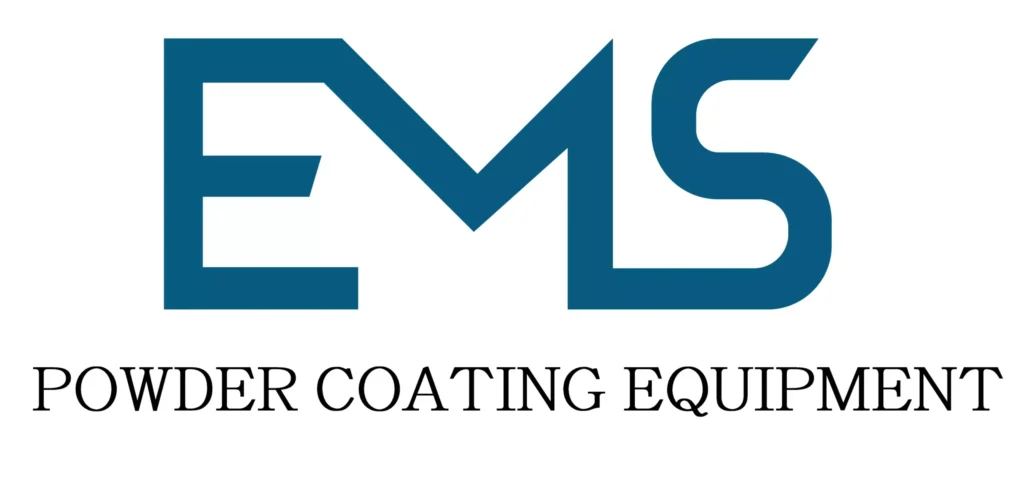
When it comes to selecting an electric powder coating oven, businesses need a manufacturer that offers quality, reliability, and superior performance. EMS Powder Coating Equipment stands out as the best choice for businesses looking to invest in electric ovens. Here’s why EMS is the preferred option:
1. Extensive Industry Experience
With years of experience in the powder coating industry, EMS understands the unique needs and challenges faced by businesses. Their expertise allows them to design electric powder coating ovens that cater to various applications and industries.
2. Innovative Technology and Design
EMS is committed to innovation, continually enhancing their products with the latest technology. Their electric powder coating ovens incorporate advanced heating systems, precise temperature controls, and durable construction, ensuring optimal performance and efficiency.
3. Comprehensive Support and Service
EMS provides exceptional customer support, from initial consultations and installations to ongoing maintenance and service. Their team of experts is dedicated to ensuring that your electric powder coating oven operates at peak efficiency.
4. Customizable Solutions for Unique Needs
Recognizing that each business has specific requirements, EMS offers customizable solutions for electric powder coating ovens. Whether you need specific heating capacities or additional features, EMS can tailor their ovens to suit your operational needs.
5. Proven Reliability and Quality
With a strong reputation for quality and customer satisfaction, EMS is a trusted name in the powder coating industry. Their electric powder coating ovens are built for reliability and long-term performance, making them an excellent investment for businesses.
Conclusion
An electric powder coating oven is an essential part of any powder coating operation, providing an efficient and effective method for curing powder coatings. With precise temperature control and uniform heating, electric ovens enhance productivity and ensure high-quality finishes.
EMS Powder Coating Equipment is the leading manufacturer of electric powder coating ovens, offering innovative solutions tailored to meet the diverse needs of various industries. Their commitment to quality, performance, and customer support makes EMS the best choice for businesses seeking reliable curing solutions.
By investing in EMS electric powder coating ovens, companies can improve their coating processes, achieve superior finishes, and reduce operational costs. With a focus on efficiency and innovation, EMS stands out as the premier manufacturer for businesses in need of top-tier powder coating ovens.
Gas Powder Coating Oven: Efficient and Versatile Curing Solutions
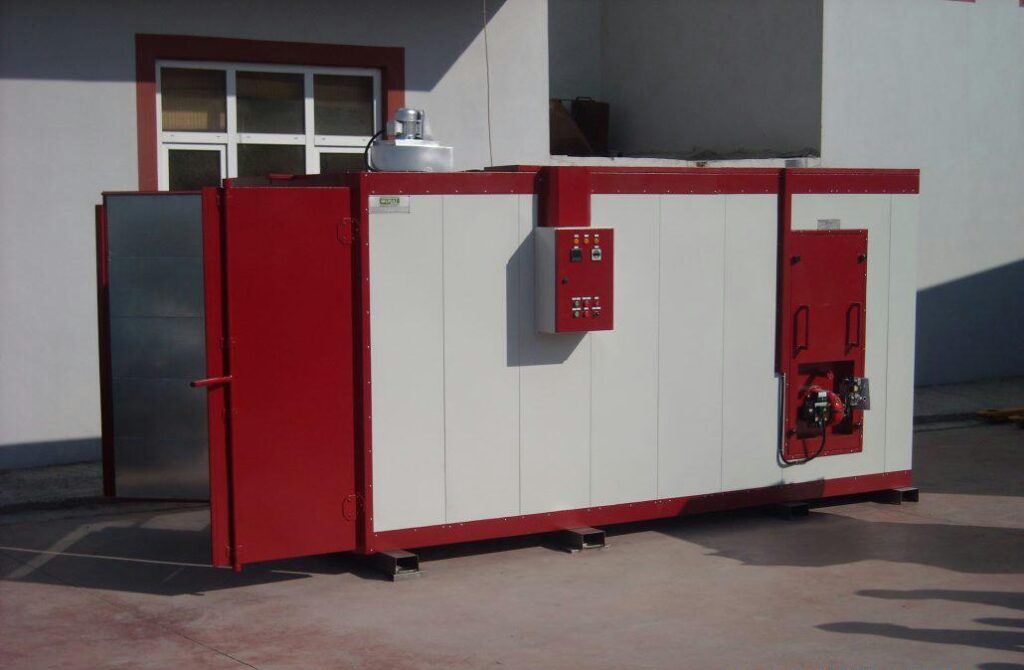
A gas powder coating oven is a vital component in the powder coating process, utilizing gas as a heat source to cure powder coatings applied to various substrates. Known for their efficiency and rapid heating capabilities, gas ovens provide consistent temperatures essential for achieving high-quality finishes.
Gas powder coating ovens are particularly advantageous in environments where electricity costs are high or where fast heat-up times are essential for productivity. These ovens are designed to deliver uniform heat distribution, ensuring that the powder coating cures evenly across the entire surface of the substrate.
EMS Powder Coating Equipment is a recognized leader in the manufacture of gas powder coating ovens, offering innovative solutions tailored to meet the diverse needs of industries. In this section, we will explore the operational mechanics, key features, and benefits of gas powder coating ovens while explaining why EMS is the top choice for businesses seeking reliable curing solutions.
What is a Gas Powder Coating Oven?
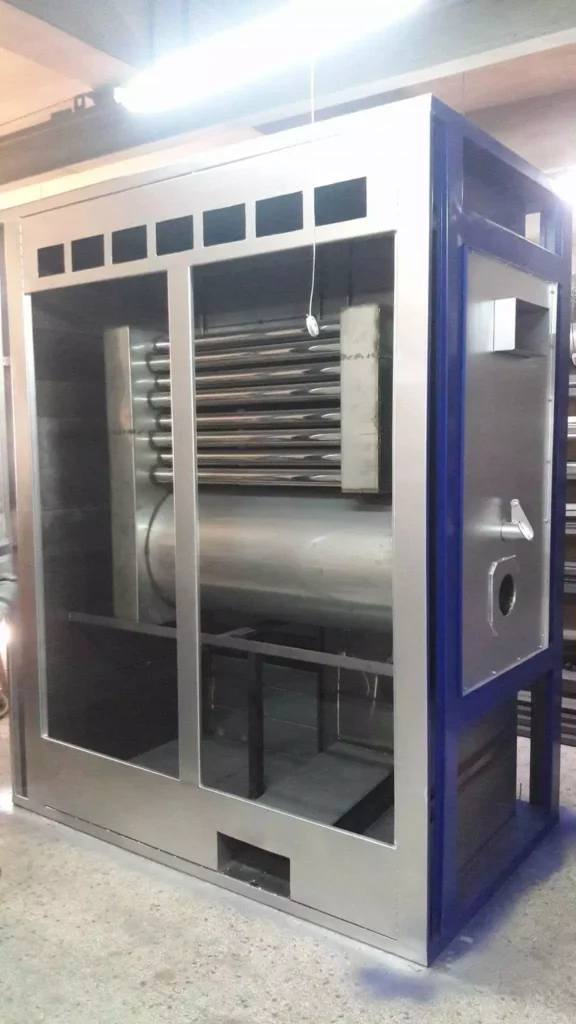
A gas powder coating oven is a specialized curing oven designed to heat and cure powder coatings using natural gas or propane as the primary energy source. This type of oven is essential for ensuring that the applied powder adheres properly to the substrate, resulting in a durable and aesthetically pleasing finish.
How Gas Powder Coating Ovens Operate
The operation of a gas powder coating oven begins after the powder coating has been applied to the substrate. The product is placed inside the oven, where it is subjected to controlled heating.
Gas burners located within the oven generate heat, which is distributed evenly throughout the oven chamber. This uniform heating is critical for preventing cold spots that can lead to uneven curing. Advanced insulation materials are used in the construction of gas ovens to minimize heat loss, ensuring efficient operation.
The gas powder coating ovens manufactured by EMS Powder Coating Equipment feature sophisticated temperature control systems, allowing operators to set and monitor internal temperatures accurately. This precision ensures that the powder coating cures optimally, producing a smooth, durable finish.
Key Features of Gas Powder Coating Ovens
Gas powder coating ovens are equipped with various features that enhance their performance and efficiency. Here are some key features that make EMS ovens the preferred choice for businesses:
1. Rapid Heat-Up Times
One of the standout benefits of gas powder coating ovens is their rapid heat-up times. EMS ovens are designed to reach optimal curing temperatures quickly, reducing downtime and improving overall productivity in the coating process.
2. Consistent Temperature Control
EMS gas ovens are equipped with advanced temperature control systems that provide precise monitoring and adjustments. This consistent temperature control is crucial for achieving high-quality finishes and preventing defects in the coating.
3. Energy Efficiency
Gas powder coating ovens are often more energy-efficient than electric counterparts, especially in regions with high electricity costs. EMS ovens are designed to optimize fuel consumption while delivering superior heating performance.
4. Durable Construction
Built with high-quality materials, EMS gas powder coating ovens are designed for long-lasting performance and durability. Their robust construction ensures minimal maintenance and reliable operation in demanding industrial environments.
5. User-Friendly Interface
EMS ovens feature intuitive controls that allow operators to easily set and monitor heating parameters. This user-friendly interface streamlines the coating process, making it easier for staff to achieve consistent results.
6. Safety Features
Safety is a top priority in the design of gas powder coating ovens. EMS ovens are equipped with various safety features, including flame detection systems, emergency shut-off valves, and proper ventilation to ensure the safety of operators.
Benefits of Using Gas Powder Coating Ovens
Investing in a gas powder coating oven provides numerous advantages for businesses involved in powder coating operations. Here are some key benefits:
1. Enhanced Coating Quality
Gas powder coating ovens deliver consistent and uniform heat, ensuring that powder coatings cure evenly. This enhances the quality of the final product, resulting in smooth and durable finishes.
2. Increased Production Efficiency
The rapid heat-up times of gas ovens enable businesses to reduce downtime between batches. This increased efficiency leads to higher productivity, allowing companies to meet tighter production deadlines.
3. Cost-Effective Operation
Gas ovens often result in lower operational costs, particularly in areas where gas prices are competitive. The efficient use of fuel contributes to overall cost savings for businesses.
4. Flexibility for Various Applications
Gas powder coating ovens are versatile and can accommodate a wide range of substrates and coating processes. This flexibility allows businesses to adapt to changing production needs and diversify their offerings.
5. Environmentally Friendly Options
Modern gas ovens are designed to minimize emissions, making them an environmentally friendly option for powder coating operations. By utilizing efficient combustion systems, EMS ovens reduce their carbon footprint while maintaining high performance.
Why Choose EMS Powder Coating Equipment for Gas Powder Coating Ovens?
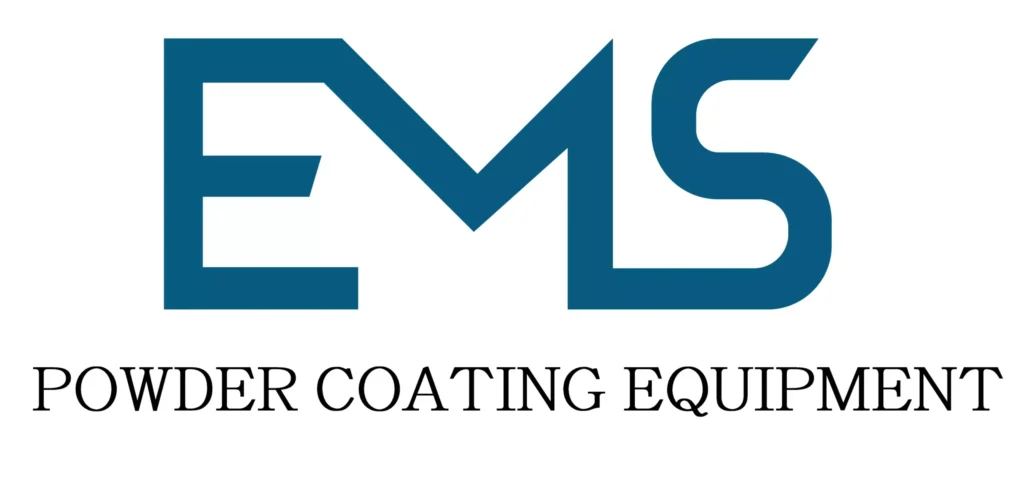
When selecting a gas powder coating oven, businesses need a manufacturer that offers reliability, quality, and innovative solutions. EMS Powder Coating Equipment stands out as the best choice for businesses looking to invest in gas ovens. Here’s why EMS is the preferred option:
1. Extensive Industry Experience
With years of experience in the powder coating industry, EMS understands the unique requirements of various applications. Their expertise enables them to design gas powder coating ovens that cater to diverse industries and operational needs.
2. Innovative Design and Technology
EMS is committed to innovation, continually enhancing their products with the latest technology. Their gas powder coating ovens incorporate advanced heating systems, precise temperature controls, and robust construction for optimal performance.
3. Exceptional Customer Support
From initial consultations to ongoing maintenance, EMS provides comprehensive customer support. Their team of experts is dedicated to ensuring that your gas powder coating oven operates at peak efficiency.
4. Custom Solutions for Unique Needs
Recognizing that every business has specific requirements, EMS offers customizable solutions for gas powder coating ovens. Whether you need tailored heating capacities or additional features, EMS can design ovens to fit your operational needs.
5. Proven Reliability and Quality
With a strong reputation for delivering high-quality products, EMS is a trusted name in the powder coating industry. Their gas powder coating ovens are built for reliability and long-term performance, making them an excellent investment for businesses.
Conclusion
A gas powder coating oven is an essential component of any powder coating operation, providing efficient and effective heating solutions for curing coatings. With rapid heat-up times and precise temperature control, gas ovens enhance productivity and ensure high-quality finishes.
EMS Powder Coating Equipment is a leading manufacturer of gas powder coating ovens, offering innovative solutions tailored to meet the diverse needs of various industries. Their commitment to quality, performance, and customer support makes EMS the best choice for businesses seeking reliable curing solutions.
By investing in EMS gas powder coating ovens, companies can improve their coating processes, achieve superior finishes, and reduce operational costs. With a focus on efficiency and innovation, EMS stands out as the premier manufacturer for businesses in need of top-tier powder coating equipment.
Gas Powder Coating Oven: Efficiency and Performance in Coating Applications
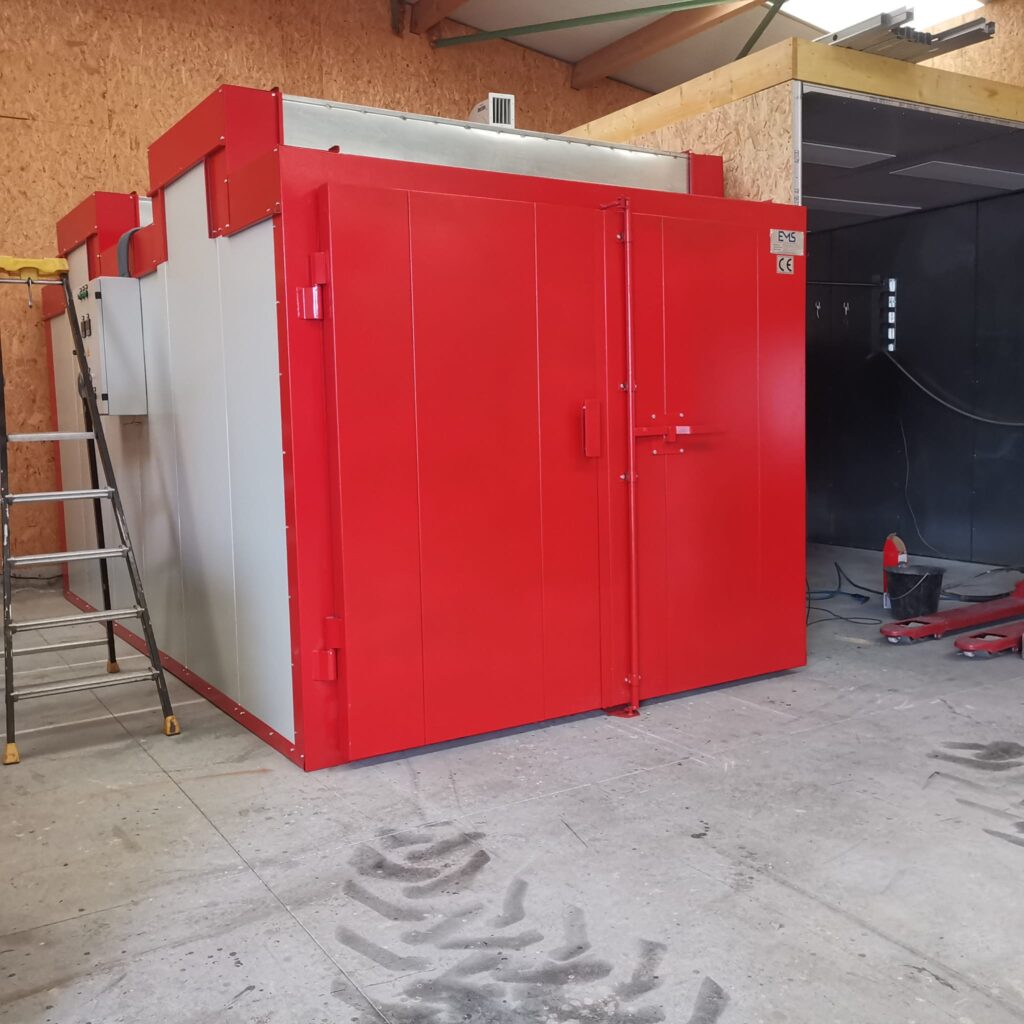
A gas powder coating oven is a vital component in the powder coating process, designed to cure powder coatings efficiently. Utilizing gas as a heating source, these ovens provide an optimal environment for achieving high-quality finishes on coated substrates.
Gas ovens are known for their rapid heating capabilities and energy efficiency, making them an excellent choice for businesses looking to enhance productivity while reducing operational costs. The precise temperature control ensures that the powder coating is cured uniformly, resulting in a durable and aesthetically pleasing finish.
EMS Powder Coating Equipment stands out as a leading manufacturer of gas powder coating ovens, offering advanced solutions tailored to meet the diverse needs of various industries. In this section, we will explore the operational principles, key features, and benefits of gas powder coating ovens, as well as explain why EMS is the preferred choice for businesses seeking reliable coating equipment.
What is a Gas Powder Coating Oven?
A gas powder coating oven is an industrial heating unit designed specifically for curing powder coatings. Unlike electric ovens, these ovens utilize gas as a heating source, providing rapid and efficient heating for the curing process.
How Gas Powder Coating Ovens Operate
The operation of a gas powder coating oven begins after the substrate has been coated with powder. The coated substrate is then placed inside the oven, where it is subjected to high temperatures that cause the powder to melt and flow.
The gas burners within the oven provide consistent and efficient heat, allowing for quick temperature adjustments and precise control. This efficiency results in reduced curing times and increased production throughput.
Gas powder coating ovens are equipped with advanced temperature control systems that ensure even heat distribution throughout the oven. This feature is crucial for achieving uniform curing of the powder, which enhances the durability and finish quality of the coated items.
EMS Powder Coating Equipment designs gas powder coating ovens with features that optimize the curing process, ensuring high-quality finishes and efficient operation. These ovens are adaptable to various production needs, making them suitable for businesses of all sizes.
Key Features of Gas Powder Coating Ovens
Gas powder coating ovens are equipped with a variety of features designed to enhance their functionality and efficiency. Here are some key features that make EMS ovens the preferred choice for businesses:
1. Rapid Heating Capabilities
One of the most significant advantages of gas powder coating ovens is their rapid heating capabilities. EMS ovens can quickly reach the desired curing temperature, reducing overall cycle times and increasing productivity.
2. Energy Efficiency
Gas ovens are typically more energy-efficient than electric ovens. EMS designs their gas powder coating ovens to minimize energy consumption, resulting in lower operational costs for businesses.
3. Precise Temperature Control
EMS gas powder coating ovens feature advanced temperature control systems that allow for precise adjustments. This level of control ensures that the curing process is consistent, leading to high-quality finishes on coated items.
4. Robust Construction
Constructed with high-quality materials, EMS gas powder coating ovens are designed for durability and long-term performance. Their robust construction ensures minimal maintenance and reliable operation in demanding industrial environments.
5. User-Friendly Control Panels
EMS ovens are equipped with intuitive control panels that make it easy for operators to set and monitor temperature and other critical parameters. This user-friendly design enhances the overall curing process and helps achieve consistent results.
6. Safety Features
Safety is a top priority in any industrial operation. EMS gas powder coating ovens come equipped with various safety features, including emergency shut-off systems and proper ventilation, to ensure a safe working environment.
Benefits of Using Gas Powder Coating Ovens
Investing in a gas powder coating oven offers numerous advantages for businesses engaged in powder coating operations. Here are some key benefits:
1. Enhanced Coating Quality
Gas powder coating ovens provide a consistent and controlled curing environment, significantly improving the quality of the applied coatings. Uniform heat distribution ensures that the powder cures evenly, resulting in a durable finish.
2. Increased Production Efficiency
With rapid heating capabilities, EMS gas powder coating ovens allow for shorter curing times, enabling businesses to increase their production throughput. This efficiency can be a critical factor in meeting tight deadlines and growing customer demands.
3. Cost Savings
The energy efficiency of gas ovens translates to significant cost savings over time. By reducing energy consumption and minimizing operational costs, businesses can allocate resources more effectively and improve their bottom line.
4. Versatility for Various Applications
EMS gas powder coating ovens are designed to accommodate a wide range of substrates and coating processes. This versatility allows businesses to adapt to changing production needs and diversify their service offerings across different industries.
5. Compliance with Safety and Environmental Standards
Gas powder coating ovens are designed to meet safety and environmental regulations, reducing emissions and maintaining a safe workspace. By investing in EMS ovens, businesses can ensure compliance with industry standards while promoting a healthier working environment.
Why Choose EMS Powder Coating Equipment for Gas Powder Coating Ovens?
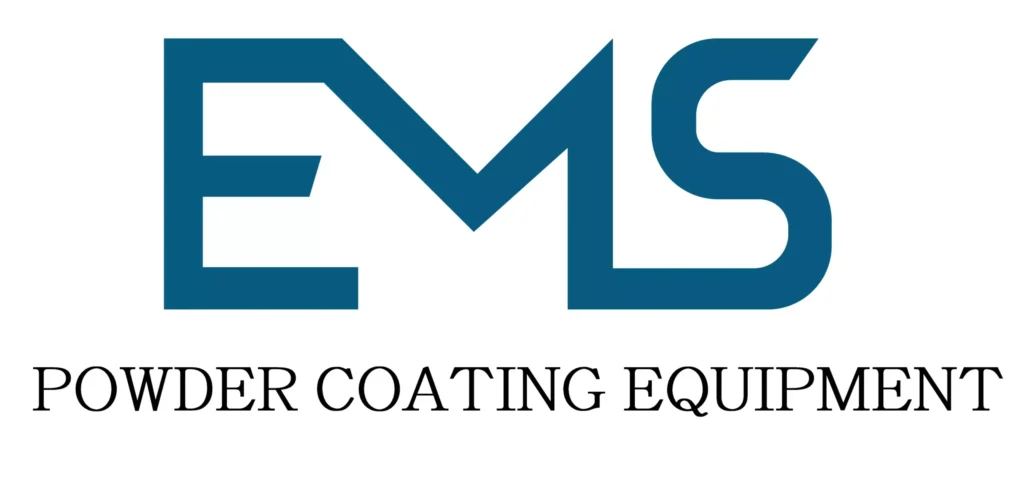
When selecting a gas powder coating oven, it is essential to choose a manufacturer known for quality, reliability, and innovative solutions. EMS Powder Coating Equipment stands out as the best choice for businesses looking to invest in gas ovens. Here’s why EMS is the preferred option:
1. Proven Industry Experience
With extensive experience in the powder coating industry, EMS understands the specific needs of various applications. Their expertise enables them to design gas powder coating ovens that meet the demands of different environments and production requirements.
2. Commitment to Innovation
EMS is dedicated to innovation, continually enhancing their products with the latest technology. Their gas powder coating ovens are designed for optimal performance, incorporating advanced temperature control and safety features.
3. Comprehensive Customer Support
From installation to ongoing maintenance, EMS provides exceptional customer support. Their team of experts is available to assist businesses in maximizing the performance of their gas powder coating ovens.
4. Customizable Solutions
Recognizing that each business has unique needs, EMS offers customizable solutions for gas powder coating ovens. Whether specific sizes, features, or configurations are required, EMS can tailor their products to meet operational requirements.
5. Trusted Quality and Reliability
With a strong reputation for delivering high-quality products, EMS is a trusted name in the powder coating industry. Their gas powder coating ovens are built for durability and long-term performance, making them an excellent investment for businesses.
Conclusion
A gas powder coating oven is a critical investment for any powder coating operation, providing an efficient and controlled environment for curing coatings. With rapid heating capabilities and precise temperature control, these ovens enhance coating quality and productivity.
EMS Powder Coating Equipment is a leading manufacturer of gas powder coating ovens, offering innovative solutions tailored to meet the diverse needs of various industries. Their commitment to quality, performance, and customer support makes EMS the best choice for businesses seeking reliable coating solutions.
By choosing EMS gas powder coating ovens, companies can improve their coating processes, achieve superior finishes, and reduce operational costs. With a focus on efficiency and innovation, EMS stands out as the premier manufacturer for businesses in need of top-tier powder coating equipment.
Gas Powder Coating Oven: Efficient Curing Solutions for Optimal Finishes
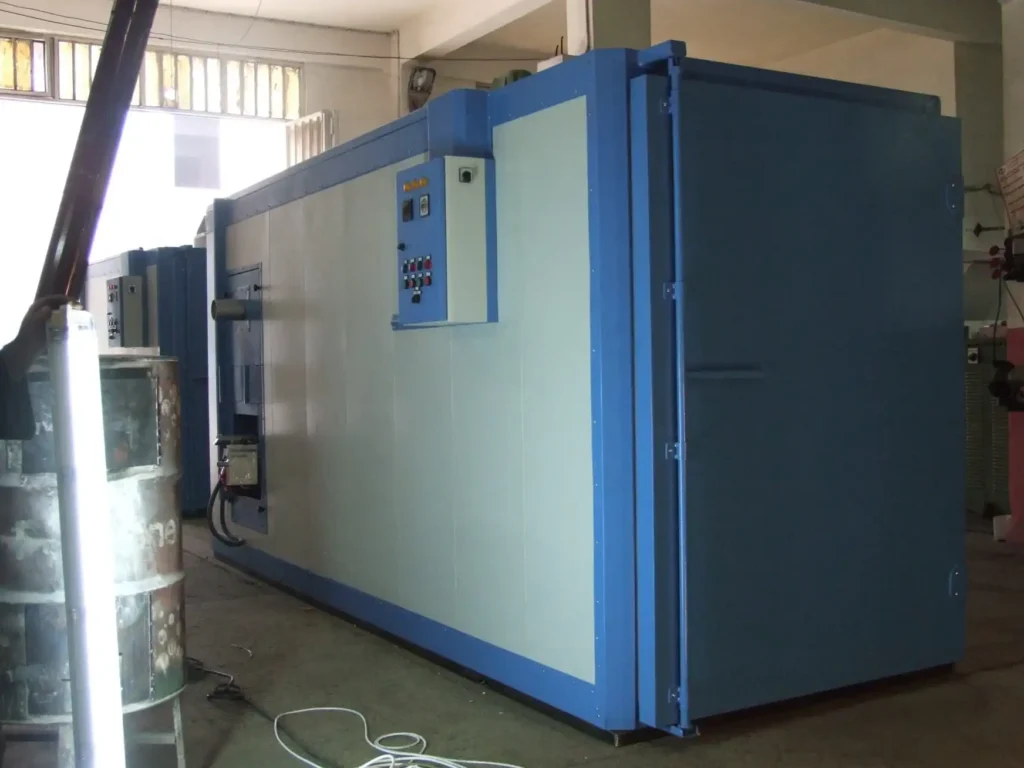
A gas powder coating oven is a crucial component in the powder coating process, designed specifically for curing powder-coated materials. Utilizing natural gas or propane, these ovens offer efficient heating solutions that ensure the even curing of powder coatings, resulting in durable and high-quality finishes.
The design of gas powder coating ovens focuses on energy efficiency and optimal temperature control. By providing a stable and controlled environment, these ovens facilitate the proper melting and adhesion of powder coatings to substrates, enhancing the overall coating quality.
EMS Powder Coating Equipment stands out as a leader in the manufacturing of gas powder coating ovens, offering advanced solutions tailored to meet the specific needs of various industries. In this section, we will delve into the operational principles, key features, and benefits of gas powder coating ovens, while also discussing why EMS is the preferred choice for businesses seeking reliable coating equipment.
What is a Gas Powder Coating Oven?
A gas powder coating oven is an industrial oven specifically designed to cure powder coatings applied to metal substrates. By utilizing gas as a heat source, these ovens provide rapid and efficient curing, ensuring a high-quality finish.
How Gas Powder Coating Ovens Operate
The operation of a gas powder coating oven begins after the substrate has been coated with powder. Once the application is complete, the substrate is placed inside the oven, where controlled temperatures are maintained.
Gas burners generate heat, which is evenly distributed throughout the oven. This uniform heat application ensures that the powder melts, flows, and adheres properly to the substrate. Curing times and temperatures can be adjusted to suit different types of powder coatings and substrate materials.
EMS Powder Coating Equipment designs gas powder coating ovens with features that optimize the curing process, ensuring that businesses achieve consistent, high-quality finishes across a variety of applications.
Key Features of Gas Powder Coating Ovens
Gas powder coating ovens are equipped with numerous features designed to enhance their performance and efficiency. Here are some standout features that make EMS ovens the preferred choice for businesses:
1. Energy Efficiency
EMS gas powder coating ovens are designed for optimal energy efficiency, utilizing advanced burner technology to minimize gas consumption while maximizing heat output. This design helps reduce operational costs without compromising performance.
2. Precise Temperature Control
With advanced temperature control systems, EMS ovens ensure that the required curing temperatures are maintained consistently throughout the process. This precise control is essential for achieving high-quality finishes.
3. Quick Heating Capability
Gas ovens have the advantage of rapid heating capabilities, significantly reducing preheating times. This feature enhances productivity by allowing for faster turnaround on coating jobs.
4. Uniform Heat Distribution
The design of EMS gas powder coating ovens promotes uniform heat distribution, preventing hot spots and ensuring that all areas of the substrate are cured evenly. This uniformity is crucial for achieving a consistent finish.
5. Safety Features
Safety is paramount in any industrial operation. EMS ovens come equipped with safety features such as flame monitoring systems, emergency shut-off valves, and proper ventilation to ensure a safe working environment for operators.
6. Customizable Sizes and Configurations
Recognizing that different businesses have varying needs, EMS offers customizable sizes and configurations for their gas powder coating ovens. This flexibility allows businesses to choose the right oven to fit their production capacities.
Benefits of Using Gas Powder Coating Ovens
Investing in a gas powder coating oven provides numerous advantages for businesses engaged in powder coating operations. Here are some key benefits:
1. Enhanced Coating Quality
Gas powder coating ovens promote optimal curing conditions, leading to high-quality finishes. The even application of heat ensures that the powder melts and adheres properly, resulting in durable coatings.
2. Increased Efficiency
The rapid heating capabilities of gas ovens reduce preheating and curing times, allowing for quicker production cycles. This increased efficiency can significantly enhance overall productivity.
3. Cost-Effective Operations
With their energy-efficient designs, gas powder coating ovens can reduce fuel costs compared to electric ovens. Additionally, the improved curing processes result in less rework and waste, contributing to lower operational costs.
4. Versatility for Different Applications
EMS gas powder coating ovens are versatile and can accommodate a wide range of powder coatings and substrate materials. This adaptability allows businesses to diversify their service offerings and meet various customer demands.
5. Compliance with Safety Standards
EMS gas powder coating ovens are designed to meet industry safety regulations, ensuring a safe working environment. Their robust safety features protect both operators and the surrounding environment.
Why Choose EMS Powder Coating Equipment for Gas Powder Coating Ovens?
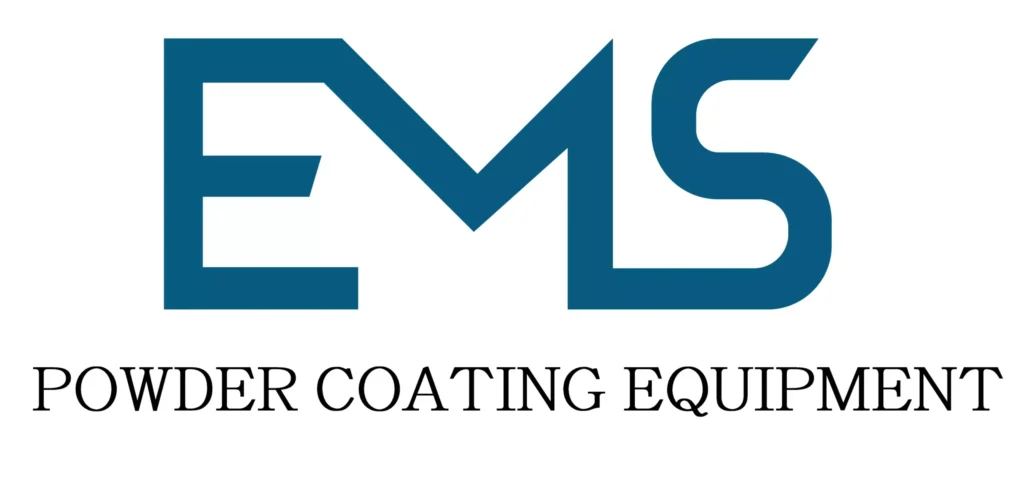
Selecting a gas powder coating oven requires careful consideration of the manufacturer’s reputation for quality and reliability. EMS Powder Coating Equipment is the top choice for businesses looking to invest in gas powder coating ovens. Here’s why EMS stands out:
1. Industry Expertise
With years of experience in the powder coating industry, EMS understands the unique requirements of various applications. Their expertise allows them to design gas powder coating ovens that are tailored to meet diverse production environments.
2. Commitment to Innovation
EMS is dedicated to continual innovation, integrating the latest technologies into their products. Their gas powder coating ovens are designed for optimal performance, featuring advanced controls and safety mechanisms.
3. Exceptional Customer Support
From installation to ongoing maintenance, EMS provides comprehensive customer support. Their team of experts is committed to helping businesses maximize the performance of their gas powder coating ovens.
4. Custom Solutions
Recognizing that every business has unique needs, EMS offers customizable solutions for gas powder coating ovens. This flexibility ensures that businesses can select the right features and configurations for their operations.
5. Trusted Quality and Reliability
With a strong reputation for delivering high-quality products, EMS is a trusted name in the powder coating industry. Their gas powder coating ovens are built for durability and long-term performance, making them an excellent investment for businesses.
Conclusion
A gas powder coating oven is a vital investment for any powder coating operation, providing efficient and controlled curing of powder coatings. With their advanced features and energy-efficient designs, these ovens enhance coating quality and productivity.
EMS Powder Coating Equipment is a leading manufacturer of gas powder coating ovens, offering innovative solutions tailored to meet the diverse needs of various industries. Their commitment to quality, performance, and customer support makes EMS the best choice for businesses seeking reliable coating equipment.
By choosing EMS gas powder coating ovens, companies can improve their coating processes, achieve superior finishes, and reduce operational costs. With a focus on efficiency and innovation, EMS stands out as the premier manufacturer for businesses in need of top-tier powder coating equipment.
Gas Powder Coating Oven: Efficiency and Precision in Coating Applications
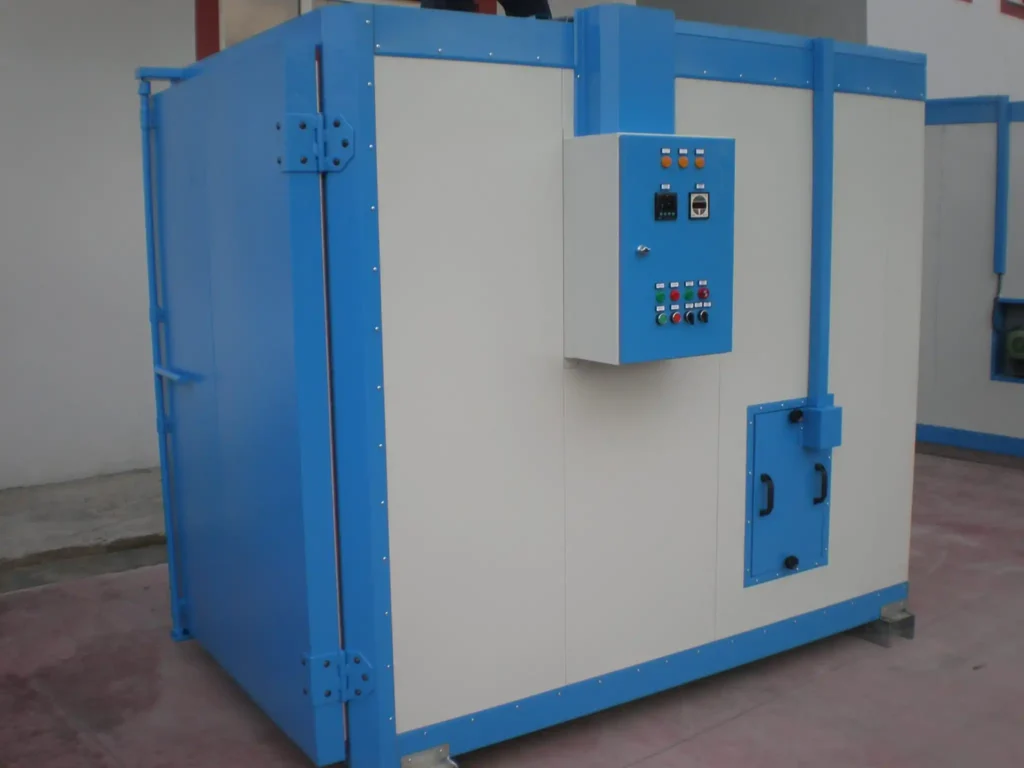
A gas powder coating oven is an essential component in the powder coating process, providing the necessary heat to cure powder coatings applied to various substrates. The curing process is crucial for achieving a durable, high-quality finish that adheres effectively to the surface.
These ovens are specifically designed to deliver uniform heat distribution, ensuring that the powder coating cures evenly and efficiently. With advancements in technology, modern gas powder coating ovens also incorporate features that enhance energy efficiency and operational safety.
EMS Powder Coating Equipment is recognized as a leader in the manufacturing of gas powder coating ovens, offering state-of-the-art solutions tailored to meet the diverse needs of various industries. In this section, we will delve into the operational principles, key features, and benefits of gas powder coating ovens, while also discussing why EMS is the preferred choice for businesses seeking reliable and efficient coating solutions.
What is a Gas Powder Coating Oven?
A gas powder coating oven is a specialized curing chamber used in the powder coating process. It employs gas as the primary heat source to cure the powder coatings applied to metal and other substrates.
How Gas Powder Coating Ovens Operate
The operation of a gas powder coating oven begins after the powder has been applied to the substrate in a spray booth. Once the substrate is ready, it is transferred to the oven, where precise heating elements deliver the required temperature for curing.
The oven’s design ensures uniform heat distribution, allowing the powder coating to melt and flow, ultimately bonding to the substrate. The curing process is crucial, as it transforms the powder into a hard, protective finish that is both aesthetically pleasing and durable.
EMS Powder Coating Equipment designs gas powder coating ovens with advanced features that optimize curing efficiency and performance, ensuring businesses achieve consistent, high-quality finishes across various applications.
Key Features of Gas Powder Coating Ovens
Gas powder coating ovens are equipped with several features that enhance their performance and efficiency. Here are some standout features that make EMS ovens the preferred choice for businesses:
1. Uniform Heat Distribution
EMS gas powder coating ovens are engineered to provide uniform heat distribution throughout the curing chamber. This feature ensures that every part of the substrate receives the same level of heat, resulting in even curing and high-quality finishes.
2. Energy Efficiency
Modern EMS gas ovens are designed for energy efficiency, utilizing advanced insulation and burner technology. This allows businesses to reduce energy consumption while maintaining optimal curing temperatures, leading to cost savings over time.
3. User-Friendly Controls
The intuitive control systems in EMS gas powder coating ovens allow operators to easily set and monitor temperatures and curing times. This user-friendly interface streamlines operations and enhances overall productivity.
4. Safety Features
Safety is paramount in any coating operation. EMS gas powder coating ovens come equipped with essential safety features, including flame safety devices, emergency shut-off systems, and proper ventilation, ensuring a safe working environment.
5. Customizable Configurations
Understanding that different businesses have unique requirements, EMS offers customizable configurations for their gas powder coating ovens. Whether for small operations or large-scale production, EMS can tailor solutions to meet specific needs.
6. Durable Construction
Built with high-quality materials, EMS gas powder coating ovens are designed for longevity and reliability. Their robust construction ensures consistent performance even in demanding production environments.
Benefits of Using Gas Powder Coating Ovens
Investing in a gas powder coating oven provides numerous advantages for businesses engaged in powder coating operations. Here are some key benefits:
1. Consistent Coating Quality
The precise temperature control and uniform heat distribution in gas powder coating ovens lead to consistent curing results. This ensures that the final finish meets the highest quality standards.
2. Faster Curing Times
Gas powder coating ovens typically offer faster curing times compared to electric ovens, enhancing production efficiency. This speed allows businesses to complete more jobs in less time, increasing overall output.
3. Cost Efficiency
By utilizing gas as an energy source, businesses can benefit from lower operational costs compared to electric ovens. The energy-efficient design of EMS ovens further enhances this cost-effectiveness.
4. Versatility for Diverse Applications
EMS gas powder coating ovens are versatile enough to handle a wide range of substrates and coating types, allowing businesses to expand their offerings and cater to different market demands.
5. Compliance with Environmental Regulations
Gas powder coating ovens are designed to meet industry safety and environmental regulations, ensuring a compliant operation. By investing in EMS ovens, businesses can promote a healthier working environment while adhering to necessary standards.
Why Choose EMS Powder Coating Equipment for Gas Powder Coating Ovens?
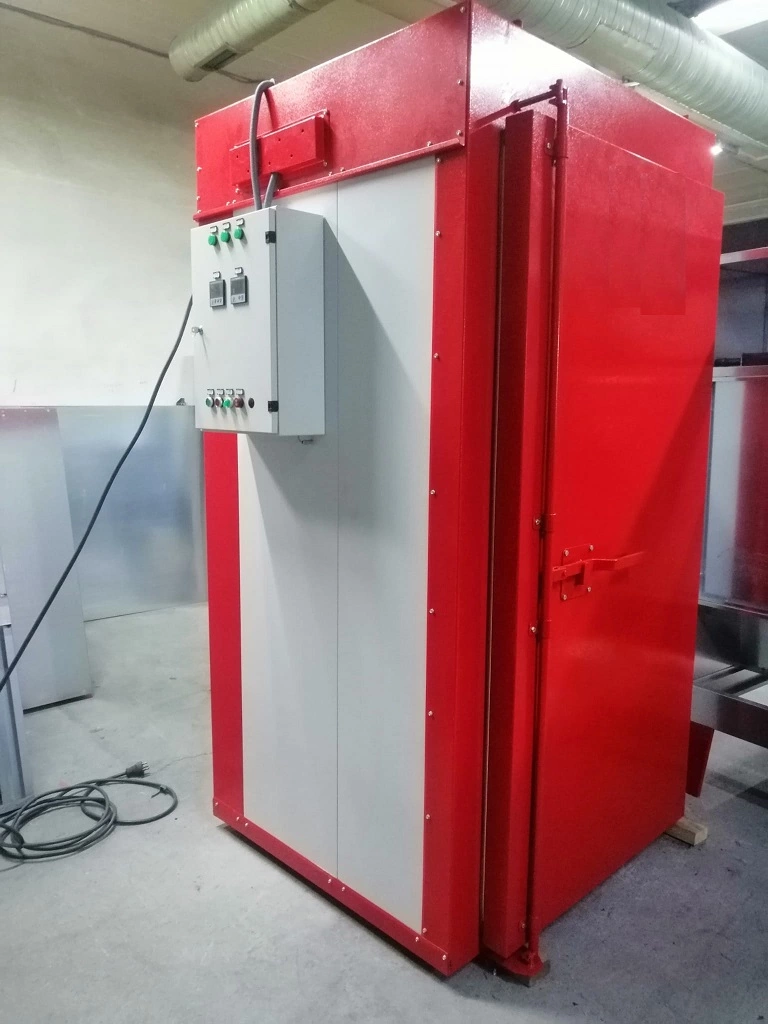
When selecting a gas powder coating oven, it is essential to choose a manufacturer with a reputation for quality and innovation. EMS Powder Coating Equipment stands out as the top choice for businesses looking to invest in gas powder coating ovens. Here’s why EMS is the preferred option:
1. Proven Expertise
With years of experience in the powder coating industry, EMS understands the unique needs of various applications. Their knowledge allows them to design gas powder coating ovens that are tailored to diverse production environments.
2. Innovative Solutions
EMS is committed to continuous innovation, incorporating the latest technology into their products. Their gas powder coating ovens are designed for optimal performance, featuring advanced temperature control and safety systems.
3. Comprehensive Support
From installation to ongoing maintenance, EMS provides exceptional customer support. Their team of experts is dedicated to helping businesses maximize the performance of their gas powder coating ovens.
4. Customizable Options
Recognizing that every business has unique requirements, EMS offers customizable options for gas powder coating ovens, allowing businesses to select features and configurations that best suit their operational needs.
5. Trusted Reliability
With a strong reputation for delivering high-quality products, EMS is a trusted name in the powder coating industry. Their ovens are designed for durability and long-term performance, making them an excellent investment for businesses.
Conclusion
A gas powder coating oven is a crucial investment for any powder coating operation, providing the necessary heat to cure powder coatings effectively. With uniform heat distribution and energy-efficient designs, these ovens ensure high-quality finishes while optimizing operational efficiency.
EMS Powder Coating Equipment is a leading manufacturer of gas powder coating ovens, offering innovative solutions tailored to meet the diverse needs of various industries. Their commitment to quality, performance, and customer support makes EMS the best choice for businesses seeking reliable coating solutions.
By choosing EMS gas powder coating ovens, companies can enhance their curing processes, achieve superior finishes, and reduce operational costs. With a focus on efficiency and innovation, EMS stands out as the premier manufacturer for businesses in need of top-tier powder coating equipment.
Powder coating is a popular method for applying a protective and decorative finish to metal surfaces. The process involves applying a dry powder that is then cured under heat to form a durable, high-quality coating. Here’s an overview of the equipment used in powder coating:
1. Powder Coating Gun
- Function: The gun is used to apply the powder onto the metal surface. It uses an electrostatic charge to attract the powder particles to the grounded workpiece.
- Types:
- Corona Guns: The most common type, which applies a high voltage to charge the powder.
- Triboelectric Guns: These use friction to charge the powder.
2. Powder Booth
- Function: The booth is where the powder is applied to the workpiece. It provides a controlled environment to minimize contamination and optimize the application process.
- Types:
- Open Face Booths: For simple, low-volume jobs.
- Enclosed Booths: These are more effective for high-efficiency powder recovery.
3. Powder Recovery System
- Function: This system recycles unused powder. It usually involves a combination of filters and cyclonic separation to capture the excess powder that didn’t stick to the workpiece.
- Key Components:
- Cyclone: Separates the powder from the air.
- Filters: Help remove any airborne powder particles.
4. Curing Oven
- Function: After the powder is applied, the workpiece must be heated to a specific temperature for the powder to cure and form a solid, durable finish.
- Types:
- Batch Ovens: Used for smaller volumes, where items are placed inside and baked.
- Conveyor Ovens: Used for high-volume production, where parts move through the oven on a conveyor belt.
5. Pre-treatment System
- Function: Prior to coating, surfaces must be cleaned to ensure the powder adheres properly. This system involves chemical cleaning or abrasive methods such as sandblasting.
- Components:
- Wash Stations: For removing grease, oils, and other contaminants.
- Phosphating: Adds a layer that enhances powder adhesion.
6. Air Compressor
- Function: Provides the necessary air pressure for the powder coating gun, recovery system, and curing oven. Proper air quality is important to avoid contamination of the coating process.
7. Powder Coating Curing Systems
- These include:
- Infrared (IR) Curing: Cures the powder using infrared radiation.
- Convection Ovens: Uses hot air to cure the coating.
- Hybrid Systems: Combines both infrared and convection methods for faster curing.
8. Cooling System
- After curing, parts may need to be cooled rapidly to prevent warping or distortion. A cooling system, such as a blow-off system or a cooling tunnel, is used for this purpose.
9. Control Systems
- Modern powder coating systems often come with digital controllers that monitor and adjust key parameters like temperature, humidity, powder flow, and oven speed. These ensure consistent quality and efficiency.
Maintenance and Safety
- Maintenance: Regular cleaning and maintenance of guns, booths, and recovery systems are critical to ensure smooth operation and high-quality finishes.
- Safety: Powder coating involves the use of chemicals and high temperatures, so personal protective equipment (PPE) like gloves, goggles, and proper ventilation is necessary.
Powder coating is a highly efficient and durable finishing process, widely used in industries like automotive, construction, and appliances. The equipment involved in powder coating ensures that the coating is applied uniformly and cures effectively to form a tough, resistant finish.
The powder coating gun is one of the essential pieces of equipment. It uses electrostatic forces to apply a dry powder to the surface of the item being coated. The powder is charged and then attracted to the grounded metal surface, ensuring even coverage. The process typically uses a high-voltage corona gun or, in some cases, a triboelectric gun that relies on friction for charging the powder. This application process is done inside a powder booth, a controlled environment designed to minimize contamination. These booths can range from simple open-faced models for small jobs to fully enclosed booths with advanced filtration systems for high-efficiency powder recovery.
To make sure the powder that doesn’t stick to the workpiece is not wasted, a recovery system is used. This system captures the excess powder and recycles it for future use, making the process more cost-effective. The recovery system typically involves cyclonic separation and filter systems to remove the powder from the air, preventing any loss of material and keeping the environment clean.
Once the powder is applied, the coated parts need to be cured in a curing oven. The heat causes the powder to melt and bond to the surface, forming a solid, durable coating. There are two primary types of curing ovens: batch ovens, which are used for smaller runs and where parts are placed individually for curing, and conveyor ovens, which are designed for high-volume production with parts moving through the oven continuously on a belt. The curing process must be precisely controlled, with attention to both temperature and time, to ensure a perfect finish. Some systems also use infrared radiation or convection to speed up the curing process.
Before powder coating can be applied, the parts must go through a pre-treatment process to ensure proper adhesion. This typically involves cleaning and surface preparation, which may include washing with chemicals or sandblasting to remove oils, grease, and rust. For some applications, a phosphate layer might also be applied to further enhance adhesion and corrosion resistance.
The air compressor plays a crucial role throughout the process, providing the necessary pressure for the gun, recovery system, and sometimes even the curing oven. The air quality must be carefully controlled to prevent contaminants from affecting the coating process.
After the parts are cured, they may require a cooling phase to avoid warping or distortion, which can be achieved through blow-off systems or cooling tunnels. Modern powder coating systems often come with advanced control systems, allowing operators to monitor and adjust parameters such as temperature, powder flow, and curing time to ensure consistent results.
Lastly, maintenance of the equipment is vital for consistent performance. This includes regular cleaning of the guns, booths, recovery systems, and ovens to avoid build-up that could affect the coating quality. In addition, safety is a key consideration. The process involves working with high-voltage equipment and high temperatures, so protective gear such as gloves, goggles, and proper ventilation is essential to ensure the safety of the operators.
In essence, the combination of precise application, efficient powder recovery, effective curing, and safety protocols makes powder coating a highly effective and sustainable finishing process.
Expanding further on the powder coating process, the equipment setup is designed to work harmoniously, ensuring both efficiency and quality in the final product. The key to the success of powder coating lies not just in the equipment but also in the operational environment, including temperature, humidity, and cleanliness of the workspace. Powder coating is known for its environmental benefits since it typically produces fewer VOCs (volatile organic compounds) than liquid paints, making it a more eco-friendly option.
Another important aspect of powder coating equipment is its adaptability to different production scales. In smaller operations or when custom work is required, batch ovens and manual powder application guns are often used. However, for large-scale manufacturing, automated systems with conveyor belts are more common. These systems allow continuous movement of parts through the powder application booth and curing oven, leading to faster turnaround times and higher volumes of production. Automated systems also reduce the chances of human error and provide consistent finishes, especially in environments where high precision is required, like in the automotive or appliance industries.
The evolution of powder coating technology has also led to more advanced methods of curing the powder. In addition to traditional convection ovens, some newer systems utilize infrared (IR) curing, which is more energy-efficient because it heats the parts directly, rather than relying on air circulation. This can reduce curing times, making the process even more efficient. Hybrid curing systems that combine IR and convection also exist, giving manufacturers the ability to balance speed and energy usage, depending on the specific needs of the job.
For some applications, especially in industries where aesthetics and durability are critical, custom finishes can be achieved by using various types of powders. These range from standard polyester and epoxy powders to more advanced options like urethane, hybrid, or epoxy-polyester powders. These variations allow for specific properties such as greater resistance to UV degradation, chemical exposure, or extreme temperatures. Additionally, powders can be customized to create different textures or effects, such as matte, gloss, or metallic finishes, to meet aesthetic demands.
Technology has also introduced sophisticated control and monitoring systems that make it easier for operators to maintain precise conditions throughout the process. These systems allow users to track parameters such as temperature, powder thickness, and air pressure in real-time, providing a high level of control over the final result. Some advanced systems can even adjust settings automatically to compensate for variations in temperature or powder flow, further enhancing the quality and consistency of the coating.
As the powder coating industry continues to evolve, the focus is also shifting toward sustainability. Many manufacturers are exploring ways to minimize waste, such as using more efficient powder recovery systems and ensuring that any overspray or waste materials are properly disposed of or recycled. Advances in powder formulation have also led to the development of low-temperature curing powders that can be used on a broader range of substrates, reducing energy consumption and making powder coating even more versatile.
Moreover, research into new types of powders has expanded the range of materials that can be coated, including plastics and other non-metal surfaces. This opens up new opportunities for industries that require coatings on a variety of substrates beyond metal, expanding the potential applications for powder coating across fields like furniture manufacturing, electronics, and even automotive parts that use plastic components.
Lastly, as industries demand greater customization and faster turnaround times, many companies are investing in digital powder coating solutions. These solutions include sophisticated software that allows operators to precisely control coating parameters, ensuring that each product meets specific requirements. The future of powder coating equipment likely includes even more automation and integration with Industry 4.0 technologies, where real-time data analysis, machine learning, and predictive maintenance systems will play a key role in optimizing the powder coating process.
In summary, powder coating equipment is at the heart of creating durable, high-quality finishes for a wide variety of industries. Its evolution continues to focus on efficiency, sustainability, and adaptability to meet the increasing demands for customization, precision, and speed in the production process.
Expanding on the advancements and trends in powder coating, the ongoing improvements in equipment and techniques continue to shape the industry. As manufacturing processes become more sophisticated and as demands for efficiency, quality, and sustainability increase, several key innovations are driving the future of powder coating.
One significant trend is the increasing emphasis on automation. Automated powder coating systems are becoming more common, particularly in high-volume manufacturing environments. These systems use robotic arms or conveyor systems to apply the powder and move the parts through the curing process. Robotic powder coating offers multiple advantages, such as consistency in application, the ability to handle complex geometries, and improved safety by reducing human exposure to high-voltage equipment and hot surfaces. Automated systems can also optimize the powder application process, reducing waste and ensuring that parts are coated uniformly.
In tandem with automation, there has been an increasing push toward integrating smart technology into powder coating processes. This includes the use of sensors and control systems to monitor and adjust various parameters in real-time. For example, humidity and temperature sensors can ensure that the environment inside the powder booth is ideal for coating, while automated systems can track and adjust the flow of powder to minimize overspray and waste. Additionally, many modern systems now include data logging and analysis capabilities, which provide manufacturers with detailed insights into the coating process. These insights can help operators identify and resolve issues quickly, leading to less downtime and higher-quality finishes.
Another exciting development is the advancement in coating materials. Powder manufacturers are continually innovating to offer powders with improved properties, including enhanced durability, better resistance to UV light, and improved chemical resistance. There has also been a rise in the use of customized powder formulations for specific applications. For example, coatings with improved adhesion properties are being developed for use on challenging surfaces such as plastics, wood, or non-ferrous metals. This broadens the potential applications for powder coating, allowing manufacturers to achieve a durable, consistent finish on a wider variety of substrates. Some coatings even include anti-microbial properties, making them suitable for medical or food industry applications where cleanliness is paramount.
In addition to these advancements, the sustainability of the powder coating process is continually being improved. A major benefit of powder coating is that it produces fewer volatile organic compounds (VOCs) compared to traditional liquid coatings, but companies are going further to minimize their environmental footprint. New low-temperature curing powders are being developed to reduce energy consumption in the curing phase, which can account for a significant portion of energy use in powder coating operations. These powders can be cured at lower temperatures, which not only saves energy but also allows for the coating of a broader range of materials, including heat-sensitive substrates.
Recycling and waste reduction are also critical areas of focus. Modern powder coating systems include improved recovery systems that capture nearly all overspray and recycle it back into the process. In addition, some companies have implemented closed-loop systems where excess powder is recovered, cleaned, and reused, significantly reducing material waste. The adoption of these systems not only lowers operating costs but also aligns with the growing emphasis on sustainable manufacturing practices.
There is also growing interest in the development of water-based powder coatings. While traditional powder coatings are solvent-free, water-based versions use water as the primary carrier for the powder, rather than relying on chemical solvents. These coatings are particularly attractive for use in industries where solvent emissions and health concerns are top priorities. While still relatively new, water-based powder coatings offer a promising solution to the need for even more eco-friendly coating options.
As the powder coating industry moves forward, high-efficiency powder recovery systems are being developed to further reduce waste and improve sustainability. These systems not only capture overspray more effectively but also help reclaim finer powders that would have traditionally been lost in the process. By using cyclonic separation, electrostatic filters, or more advanced air filtration systems, recovery rates have improved significantly, making the process even more economical and environmentally friendly.
Customization is another area where powder coating is advancing. In today’s market, many industries require a wide range of colors, textures, and finishes to meet customer demands. Manufacturers are now able to create specialty finishes that include unique effects such as metallic, textured, or hammertone finishes, giving products more aesthetic appeal. The ability to produce customized coatings is especially important in industries like automotive and consumer goods, where design and branding are essential.
The future of powder coating also lies in its potential to be integrated with smart factories. As part of Industry 4.0, powder coating systems are increasingly connected to larger manufacturing ecosystems. This allows manufacturers to monitor production in real-time, using predictive maintenance and remote diagnostics to minimize downtime and improve overall efficiency. By connecting powder coating systems with other processes like assembly or packaging, manufacturers can ensure smoother workflows and optimize the entire production line.
Lastly, innovation in curing technology continues to progress. Traditional convection ovens have been complemented by new curing technologies like infrared, ultraviolet (UV), and even induction curing. These methods provide faster curing times and reduced energy consumption, helping companies meet production deadlines while reducing operating costs.
In conclusion, the powder coating industry is on the brink of significant advancements, driven by technological innovation, sustainability goals, and a demand for more customization. As automated systems, smart technology, and more efficient materials continue to evolve, powder coating will remain a highly relevant and growing method of coating for industries ranging from automotive to electronics and beyond. The shift toward eco-friendly processes, faster production, and customization promises a bright future for powder coating in a wide variety of applications.
Automatic Powder Coating Equipment
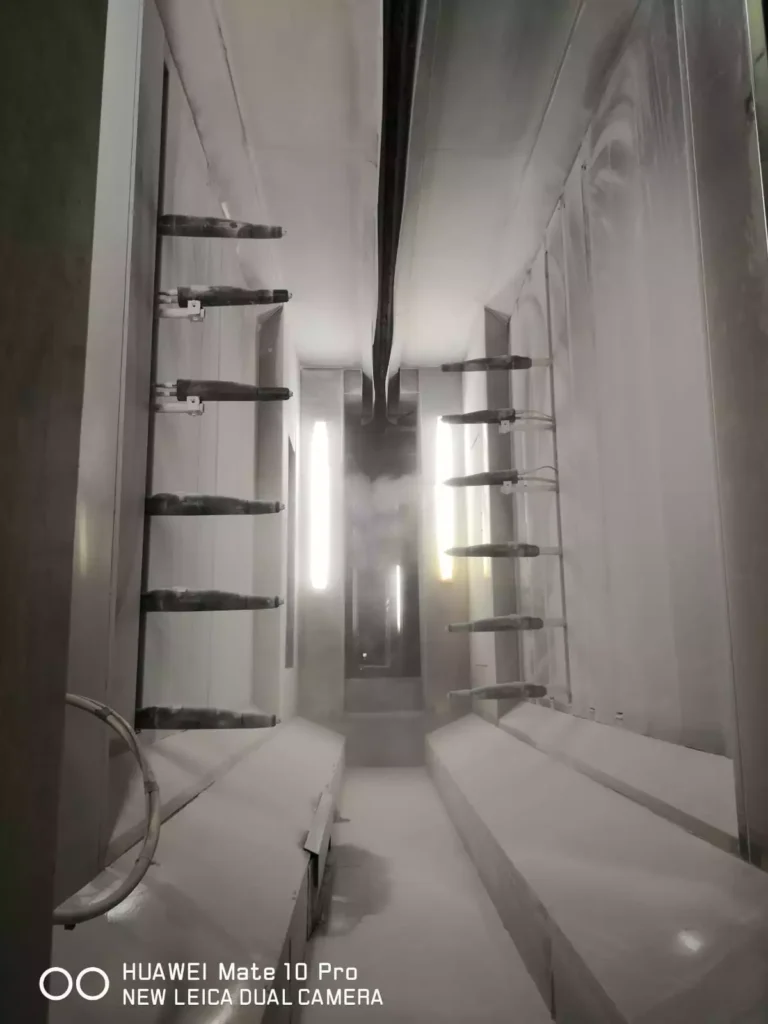
Automatic powder coating equipment is designed to streamline and enhance the powder coating process by using automation to apply powder and cure parts with minimal human intervention. These systems are especially beneficial for high-volume production, as they increase efficiency, ensure consistent quality, and reduce labor costs. Here’s an overview of the key components and features of automatic powder coating equipment:
Key Components of Automatic Powder Coating Equipment:
- Automated Powder Coating Guns:
- These guns are designed to apply powder to parts automatically. In an automated system, robotic arms or conveyors are used to move the workpieces to and from the coating area. The guns apply a uniform layer of powder, using an electrostatic charge to ensure the powder adheres to the grounded workpiece.
- Types of Guns:
- Corona guns: These are the most common type of automatic guns, applying high voltage to create an electrostatic charge that attracts the powder.
- Triboelectric guns: These use friction to charge the powder, which can be advantageous in certain applications where high-efficiency coating is required.
- Robotic Arms and Conveyors:
- Robotic arms: In an automated setup, robotic arms are often used to apply powder to parts in a controlled and precise manner. These robots can handle intricate geometries, ensuring even coverage and consistent coating thickness. Robotic arms also help in moving parts through different stages of the process, such as powder application, curing, and cooling.
- Conveyor systems: Conveyor belts are used to move parts through various stages of the coating process, including the application booth, curing oven, and cooling stations. Automated conveyors reduce manual handling and speed up the production process by allowing parts to be continuously processed.
- Automatic Powder Recovery Systems:
- An automatic powder recovery system captures the excess powder that doesn’t adhere to the part during the application process. The recovery system uses cyclonic separation or filtration to remove powder from the air, collect it, and return it to the powder hopper for reuse.
- The system ensures that there is minimal waste, as unused powder is cleaned and recycled. In automated systems, this process is fully integrated, allowing for continuous use of recovered powder without operator intervention.
- Automatic Pre-treatment Systems:
- Pre-treatment is an essential step in preparing parts for powder coating. Automatic pre-treatment systems typically consist of wash stations, chemical treatments, or sandblasting equipment that remove contaminants such as oils, grease, rust, and dirt.
- These systems ensure that the surface is clean and properly prepared for the powder coating process, improving adhesion and coating quality.
- Automated Curing Ovens:
- After the powder is applied, it needs to be cured in an oven to form a solid, durable finish. In automated systems, curing ovens are designed to handle multiple parts at once, with automated conveyor systems moving parts through the oven at the correct speed and temperature.
- Batch ovens: These are used for smaller, custom runs, where parts are placed individually in the oven.
- Conveyor ovens: These are more common in high-volume production, where parts move continuously through the oven.
- Advanced curing ovens may use technologies like infrared (IR) radiation or hybrid curing systems that combine infrared and convection methods for faster curing times and energy efficiency.
- Automatic Powder Coating Booths:
- Automatic powder coating booths are equipped with systems that apply powder uniformly to the workpiece. The booth is designed to create a controlled environment that minimizes contamination and powder waste. Some automatic systems are enclosed and equipped with advanced filtration and air management systems to capture and recycle powder.
- The booth is also typically designed with an efficient ventilation system to remove excess powder from the air, ensuring a clean working environment.
- Control Systems and Monitoring:
- Modern automatic powder coating systems include integrated control systems that manage various parameters such as powder flow, voltage, and coating thickness. These systems provide real-time data and feedback to operators, allowing them to monitor the performance of the system and ensure consistent results.
- In more advanced systems, the control system may feature a touchscreen interface that allows operators to adjust settings remotely, monitor equipment performance, and troubleshoot any issues that arise during the coating process.
Benefits of Automatic Powder Coating Equipment:
- Improved Efficiency:
- Automation reduces the need for manual intervention, speeding up the production process. Parts can be processed continuously, and the system can operate for longer periods without breaks, increasing throughput.
- Consistent Quality:
- Automatic systems ensure that each part receives a consistent, even coating, which is difficult to achieve with manual application. The automated powder guns and robotic arms are programmed to apply powder precisely, minimizing variations in coating thickness and finish.
- Reduced Waste:
- The recovery systems in automatic powder coating equipment significantly reduce the amount of powder waste, which is both environmentally friendly and cost-effective. Powder that does not adhere to the part is collected, cleaned, and reused, making the process more sustainable.
- Faster Turnaround:
- The use of automated systems, such as conveyors and robotic arms, reduces handling time and allows parts to move quickly through each stage of the process. This results in faster turnaround times, which is especially important in industries with tight production deadlines.
- Enhanced Safety:
- Automation reduces the need for human operators to be in direct contact with high-voltage equipment and high-temperature ovens, which improves overall safety in the work environment. Robots and automated systems handle the repetitive and potentially hazardous tasks.
- Reduced Labor Costs:
- With automation, the need for manual labor is significantly reduced, leading to lower labor costs. The system can operate with minimal human intervention, allowing operators to focus on overseeing the process rather than performing manual tasks.
- Scalability:
- Automatic powder coating systems are highly scalable. As production demands increase, the system can be expanded with additional guns, robots, or conveyors to accommodate higher volumes without compromising on quality.
- Flexibility:
- Many automated powder coating systems are adaptable, allowing manufacturers to adjust the powder application process for different types of parts and finishes. The system can handle a variety of sizes and shapes of parts, making it suitable for a wide range of industries, from automotive to electronics.
Conclusion:
Automatic powder coating equipment offers significant advantages in terms of speed, efficiency, quality, and cost-effectiveness. By integrating robotic arms, automated guns, conveyors, recovery systems, and curing ovens, manufacturers can achieve consistent and high-quality finishes while reducing waste and increasing production capacity. As technology continues to advance, the future of automatic powder coating systems will likely include even more sophisticated control systems, greater automation, and integration with Industry 4.0 technologies to further optimize the process.
Automatic powder coating equipment is designed to automate the entire powder coating process, making it faster, more efficient, and less dependent on manual labor. These systems are particularly beneficial in high-volume production environments where consistency and speed are critical. By automating the application of powder, the pre-treatment of parts, and the curing process, manufacturers can significantly improve the quality of the coating while reducing waste and production time.
The powder coating process begins with automated powder guns, which are equipped to apply a uniform layer of powder onto the workpiece. These guns are integrated with robotic arms or conveyor systems that transport parts through the process. The guns are often equipped with electrostatic charge technology to attract powder particles to the grounded surface, ensuring an even and consistent coating. These automated guns can be programmed to apply the right amount of powder in a controlled manner, reducing the likelihood of overspray and ensuring that the coating thickness is uniform across all parts.
Automated robotic arms are used to handle and move parts throughout the coating process. They can navigate complex part geometries, ensuring precise and accurate powder application. These robotic systems are programmed to follow a set path, which guarantees consistent coverage on each piece. Conveyor belts, on the other hand, transport parts automatically through different stages, such as the powder application booth and the curing oven. This continuous movement eliminates the need for manual intervention, allowing parts to be processed faster and more efficiently.
In addition to powder application, automated systems are equipped with powder recovery systems. These systems capture any powder that doesn’t adhere to the part during the application process and return it to the system for reuse. This is achieved through methods like cyclonic separation or filtration, which help remove the powder from the air and clean it so it can be recycled. The integration of these recovery systems is essential in reducing waste, lowering material costs, and improving the overall sustainability of the powder coating process.
The pre-treatment of parts, which is a crucial step in ensuring proper powder adhesion, is also automated in many advanced systems. This might involve washing stations that use chemical treatments or abrasive blasting to clean parts before coating. Automated pre-treatment systems ensure that the surface is properly prepared, leading to better adhesion of the powder and a more durable finish. The pre-treatment process is often monitored through sensors to ensure that it meets the required standards before the parts move to the coating stage.
Once the powder has been applied, parts are automatically transported to the curing oven, where the powder is heated to a high temperature, causing it to melt and bond to the surface. In automated systems, conveyor belts are used to move parts through the oven, ensuring a continuous process. The curing time and temperature are carefully controlled to ensure the coating forms a smooth, durable finish. Some automated systems use advanced curing technologies like infrared radiation or hybrid systems that combine convection and infrared heating. These technologies speed up the curing process, improve energy efficiency, and allow for more precise control over the curing process.
Automatic powder coating systems come equipped with sophisticated control and monitoring systems, which enable operators to oversee the entire process. These systems allow operators to monitor important variables like powder flow, temperature, and coating thickness in real-time. Some systems are even equipped with sensors that automatically adjust these parameters, ensuring optimal results with minimal intervention. The use of control systems also helps operators identify any issues or inconsistencies during the process, allowing them to quickly address problems and reduce downtime.
The benefits of automatic powder coating equipment are numerous. The most obvious advantage is the increased efficiency and speed of production. Automation significantly reduces the need for manual labor, which not only cuts down on labor costs but also reduces the potential for human error. Parts are moved through the coating process more quickly, and with robotic arms and automated systems applying the powder, the quality is consistent across all parts. This consistency is particularly important in industries where a high-quality finish is required, such as automotive, appliances, and electronics.
Another key benefit is the reduction of powder waste. Automatic recovery systems capture unused powder, which can be cleaned and recycled back into the process. This is both cost-effective and environmentally friendly, as it reduces the amount of waste generated and ensures that the material is used efficiently. By minimizing overspray and optimizing powder usage, automatic systems help to lower the overall cost of the coating process.
Automatic powder coating systems also improve safety. The use of robots and automated systems reduces human involvement in potentially hazardous tasks, such as handling high-voltage equipment or working near high-temperature ovens. This minimizes the risk of injury to workers and creates a safer work environment. Additionally, automated systems can operate for long periods with little downtime, ensuring that production can continue without interruption.
The scalability of automatic powder coating systems is another major advantage. As production demands increase, the system can be expanded with additional robotic arms, guns, and conveyor systems to meet the needs of larger production runs. This flexibility ensures that the system can grow with the business, providing the capacity to handle a variety of production volumes without compromising on quality or efficiency.
Customization is another area where automatic powder coating systems shine. These systems are adaptable and can be programmed to apply different types of powders, finishes, and colors depending on the specific requirements of the parts being coated. Whether it’s a glossy, matte, textured, or metallic finish, automated systems can handle the job with precision and consistency. This ability to customize finishes makes automatic powder coating systems particularly useful in industries that require specialized coatings, such as automotive or consumer electronics.
In conclusion, automatic powder coating equipment is transforming the way products are finished in a wide range of industries. The automation of powder application, pre-treatment, curing, and recovery systems not only boosts efficiency and reduces waste but also ensures a consistent, high-quality finish across all parts. By reducing manual labor, increasing safety, and offering greater flexibility and scalability, these systems provide manufacturers with a competitive edge, allowing them to meet growing demand while maintaining high standards of quality and sustainability.
The continued evolution of automatic powder coating equipment introduces even more advanced capabilities and refinements that further streamline the coating process. One major advancement is the increasing integration of Industry 4.0 technologies into automatic powder coating systems. This includes data-driven insights from sensors, automated monitoring systems, and the use of predictive analytics to optimize production schedules and improve quality control. By incorporating real-time data into the coating process, manufacturers can make immediate adjustments to improve efficiency, reduce downtime, and avoid production errors before they occur.
For example, sensors embedded in the system can detect any deviations from the optimal coating conditions, such as incorrect powder flow, temperature fluctuations, or curing inconsistencies. These sensors provide feedback to the central control system, which automatically adjusts the process parameters to compensate for any changes, ensuring that the coating is applied consistently across all parts. With the help of these technologies, predictive maintenance can also be implemented, enabling operators to identify and address potential issues with the equipment before they lead to failures or production stoppages.
Another exciting development is the further automation of the pre-treatment process. As surface preparation is crucial for the success of powder coating, the automation of this step can drastically improve efficiency and reduce human error. Automated pre-treatment systems are now being designed with enhanced robotic washing stations and chemical baths, capable of handling large batches of parts with minimal oversight. These systems can also monitor and adjust chemical concentrations in real time, ensuring that parts are treated optimally for adhesion, which can lead to a more durable finish.
Advanced powder coating guns are also becoming more sophisticated. Newer technologies in electrostatic application allow for better control of powder distribution, even in areas that are difficult to reach, such as deep cavities or complex geometries. These new-generation guns offer better powder adhesion, improved transfer efficiency, and the ability to apply coatings at much lower voltages, reducing the energy consumption of the system while maintaining high-quality finishes. The reduction in energy use is especially important in industries where energy efficiency is a key concern, such as in the automotive and appliance sectors.
Moreover, low-temperature curing technologies are increasingly integrated into automatic powder coating equipment. These advancements allow parts to be cured at lower temperatures, which can be advantageous for coating substrates that might be damaged by high heat, such as certain plastics or heat-sensitive materials. This allows for greater versatility in the range of materials that can be coated using powder coating, broadening the scope of applications. By curing at lower temperatures, manufacturers also see a reduction in overall energy consumption, aligning with sustainability goals.
The powder recovery systems in automatic setups are becoming even more efficient. As technology improves, recovery systems are able to capture smaller particles of powder that were once difficult to reuse, increasing overall powder utilization and further reducing material waste. New advanced filtration systems, such as nano-filtration and electrostatic filtering, are making these recovery systems even more effective at cleaning and reusing powder with minimal loss. These improvements not only save money but also contribute to a greener, more sustainable process by reducing the amount of excess powder that ends up in landfills.
In addition to operational enhancements, there has been a shift toward greater flexibility in coating finishes. Automated systems now support a broader range of finishes, from highly decorative to functional coatings, making it easier for manufacturers to produce parts with the specific visual or performance characteristics needed. The ability to apply multi-layer coatings with varying textures, colors, or even specialized finishes—like anti-microbial or UV-resistant coatings—has become easier through the automation of powder coating systems.
Furthermore, some systems now include the ability to handle dual or multi-color powder coatings, enabling manufacturers to create more intricate designs or customized color schemes without the need for extensive manual intervention. This is particularly useful in industries where aesthetic appeal is critical, such as the furniture, consumer electronics, and automotive sectors, where brands demand high-quality, unique finishes.
The integration of robotic finishing systems also extends to the post-coating process, where the parts are automatically cooled, inspected, and even packaged, ready for shipment. This is especially beneficial in industries that require high-throughput production, such as automotive parts or consumer goods. Cooling tunnels, for instance, can now be automated to ensure that parts cool down at an optimal rate, preventing warping or distortion of parts after curing. Automated inspection systems use cameras and sensors to assess the quality of the coating, ensuring that no defects—such as runs, sags, or missed spots—are present. This enhances product quality and reduces the need for manual inspection.
Additionally, integrating the entire powder coating process into a single automated line ensures a seamless workflow, from part loading to coating and curing, all the way through to packaging. This type of integrated system minimizes the need for manual handling, reduces potential contamination, and improves overall process speed. The entire process, from coating to curing to cooling, is executed in one continuous flow, making it more efficient and reducing downtime between steps.
The customizability of automatic powder coating systems is another key benefit that continues to evolve. Manufacturers can program their systems to handle specific coating requirements, including adjustments to the type of powder used, the speed of conveyor belts, curing temperature, and even the flow of recovery powder. This level of customization makes it possible to create highly specialized coatings tailored to the needs of a variety of industries, from aerospace to heavy machinery, to consumer products.
Looking to the future, the role of artificial intelligence (AI) and machine learning is likely to become more prominent in automatic powder coating systems. AI can be used to analyze data from sensors and monitoring systems to detect patterns, predict potential failures, and optimize system performance. Machine learning algorithms can analyze historical data to suggest improvements in the coating process, helping manufacturers make adjustments that improve efficiency, quality, and sustainability.
In summary, the future of automatic powder coating equipment is poised to be marked by greater integration of smart technology, more sophisticated materials and coatings, and an increasing focus on sustainability and energy efficiency. With automation continuing to play a central role in enhancing production speed and consistency, the industry is heading toward even more advanced, high-quality, and environmentally responsible coating solutions. As technology advances, automatic powder coating systems will become more versatile, efficient, and capable of meeting the evolving needs of industries around the world.
As automatic powder coating systems continue to evolve, manufacturers are placing a stronger emphasis on sustainability and resource efficiency, in response to growing environmental concerns and regulatory pressures. The future of these systems will see even greater strides toward eco-friendly practices, such as reduced energy consumption, improved powder recovery rates, and the use of biodegradable or non-toxic coatings. The need for a circular economy—where waste is minimized and materials are reused—is increasingly becoming a focal point, and advancements in powder coating technology align with this goal.
The integration of low-emission technologies is one area where significant improvements are expected. By using advanced curing methods that operate at lower temperatures, such as infrared (IR) and ultraviolet (UV) curing, manufacturers can reduce the energy required to heat the curing ovens. These technologies heat parts directly, bypassing the need to heat large volumes of air within the oven, which reduces both energy consumption and production time. This results in a lower carbon footprint for the powder coating process, contributing to sustainability goals and decreasing operating costs. For example, UV curing allows for faster curing times, meaning products are ready for use more quickly, increasing throughput while using less energy.
Waste reduction and recycling are also a major part of the drive for more sustainable powder coating systems. Modern powder recovery technologies have advanced to the point where almost all of the excess powder can be captured and reused. By utilizing techniques like cyclonic separation, filtration, and electrostatic powder recovery, automated systems can recover fine powder particles that would have previously been discarded, leading to minimal waste. The powder that is collected can be filtered, cleaned, and recycled back into the coating process, lowering material costs and reducing the environmental impact of discarded coatings. This is a huge benefit for manufacturers, as it not only lowers costs but also supports environmentally conscious practices.
Another promising trend in sustainability is the development of green powder coatings. These coatings are made from raw materials that are non-toxic, contain fewer harmful chemicals, and offer reduced emissions during curing. Manufacturers are increasingly shifting toward water-based or low-VOC (volatile organic compounds) powder coatings, which are safer for workers and more environmentally friendly. This reduces the release of harmful substances into the atmosphere and minimizes the need for hazardous waste disposal.
On the manufacturing floor, smarter inventory management will help further reduce waste. Automated systems can track and manage inventory in real time, ensuring that the right amount of powder is ordered, stored, and used. This reduces overstocking, which leads to wasted material, and ensures that the powder coating process is as efficient as possible. With precise tracking, manufacturers can minimize their environmental footprint by using only what is necessary and eliminating the need for excess stock or shipping.
In terms of improving operational performance, there is a trend toward incorporating augmented reality (AR) and virtual reality (VR) technologies to assist operators in troubleshooting and system maintenance. These immersive technologies allow workers to virtually inspect the coating process, identify potential issues in real time, and even simulate repairs or process adjustments. AR glasses or VR interfaces can provide detailed, on-the-spot information about equipment status, coating parameters, and predictive maintenance needs, helping to reduce downtime and keep the systems running at peak efficiency.
The next generation of automatic powder coating systems will likely feature more advanced process optimization algorithms that rely on AI and machine learning. These systems will analyze real-time data from the coating process to fine-tune application parameters such as powder flow rates, electrostatic charge levels, and curing temperatures. By continuously learning from each batch, the system can automatically adjust to ensure the best coating quality with minimal waste and downtime. This approach would allow for greater flexibility and adaptability to varying production runs, enabling manufacturers to maintain high standards of quality while optimizing their resources.
The smart factory concept will be fully integrated with automatic powder coating systems in the near future. This integration allows powder coating equipment to communicate with other manufacturing processes and machines, creating a seamless, fully automated production environment. Parts can be loaded, coated, cured, and packaged with minimal human involvement, all managed by an overarching central system that optimizes the entire workflow. This interconnected system enables manufacturers to synchronize their powder coating operations with other stages of production, such as assembly, quality control, and packaging, creating a just-in-time manufacturing environment that reduces inventory costs and accelerates time-to-market.
In addition to operational improvements, the introduction of robotic process automation (RPA) in powder coating systems will further drive the industry’s evolution. RPA systems can automate tasks that were previously considered too complex or detailed for traditional automation, such as adjusting the powder flow based on the surface geometry of the part being coated or handling the nuances of multi-color or multi-layer finishes. These advanced robotic systems will work in tandem with AI to provide precise, high-quality coatings on a wide range of products, from delicate electronic parts to heavy-duty industrial machinery.
There’s also the growing potential for 3D printing to complement or even replace traditional powder coating processes in certain applications. With 3D printing technologies improving rapidly, manufacturers are exploring the possibility of coating 3D-printed parts directly with powder to create a uniform and durable finish. This could revolutionize industries like aerospace or medical devices, where lightweight, complex parts require high-performance coatings.
Looking further ahead, personalized coating solutions may become more common in industries like consumer goods and automotive, where specific coatings are needed to achieve desired aesthetic effects or functional properties. With advanced customization capabilities, customers could have direct input into the coatings applied to their products, from colors and textures to special properties such as scratch resistance or thermal protection.
In summary, the future of automatic powder coating equipment will be defined by greater efficiency, sustainability, and smart technology integration. Manufacturers will continue to benefit from improved automation, energy-saving technologies, advanced recovery systems, and better process optimization. The adoption of AI, machine learning, AR/VR, and smart factory concepts will pave the way for increasingly flexible, scalable, and eco-friendly powder coating operations. These advancements will help manufacturers meet the growing demands for high-quality coatings while reducing their environmental footprint, ultimately driving a more sustainable and innovative future for the industry.
Powder Coating Reciprocator

A powder coating reciprocator is a key component in the automatic powder coating process. It is a mechanical or robotic device used to move powder coating guns back and forth across the surface of a part to ensure even and consistent application of the powder. The reciprocator’s movement is typically controlled by a computer or PLC (programmable logic controller) and is carefully programmed to ensure precise powder coverage, especially for complex or intricate part geometries.
How a Powder Coating Reciprocator Works:
The reciprocator is designed to move the powder coating spray guns in a controlled path, usually in horizontal or vertical directions, to ensure even distribution of the powder over the part. This movement can be linear, with the guns moving back and forth across the part, or in some cases, a more complex pattern is used depending on the design of the part being coated.
- Movement and Speed Control: The reciprocator’s movement can be precisely controlled in terms of speed, stroke length, and direction. This helps ensure that the powder coating is applied evenly and without overlap. By adjusting the speed and direction of the reciprocator, operators can optimize the coating process for different part shapes and sizes.
- Spray Guns: The powder coating guns are mounted on the reciprocator, and they can be adjusted to different angles or distances from the part being coated. These guns are typically electrostatic, charging the powder particles to attract them to the grounded part, ensuring even powder distribution.
- Control Systems: Modern reciprocators are often integrated with advanced control systems that can adjust the movement based on factors such as part size, geometry, or coating requirements. The control system may automatically adjust the speed and stroke length of the reciprocator to ensure the powder is applied correctly, and it can even stop or pause in certain areas where more coverage is required.
- Automated Functions: In fully automated powder coating systems, the reciprocator can be part of a continuous production line where parts are moved through various stages, including pre-treatment, coating, curing, and cooling. The reciprocator plays a crucial role in the coating step, as it moves the powder guns consistently and accurately to coat the parts.
Benefits of Powder Coating Reciprocators:
- Uniform Coating Application: The primary benefit of using a reciprocator is its ability to apply a uniform layer of powder over the surface of the part. The controlled, repetitive motion ensures that no spots are missed and that the powder adheres evenly across the part’s surface.
- Enhanced Speed and Efficiency: Reciprocators increase the speed and efficiency of the powder coating process, as they eliminate the need for manual application, which can be inconsistent and slow. The automated movement of the guns ensures faster cycle times, leading to higher production throughput.
- Improved Powder Recovery: As reciprocators are often part of a more sophisticated powder coating system, they are integrated with powder recovery technologies that allow unused powder to be captured and recycled. This reduces waste and lowers material costs, making the entire process more cost-effective and environmentally friendly.
- Better Finish Quality: Automated reciprocators can provide higher-quality finishes compared to manual methods, as the even distribution of powder leads to fewer imperfections, such as streaks, runs, or uneven thickness. This is particularly important in industries where aesthetics and durability are crucial.
- Flexibility for Complex Parts: Reciprocators are versatile enough to handle a wide range of part sizes and geometries, from flat surfaces to intricate shapes. Their adjustable parameters make them suitable for a variety of applications, whether it’s a simple part with few curves or a more complex shape with deep recesses or edges.
- Reduced Labor Costs: By automating the powder coating process with a reciprocator, the need for manual labor is greatly reduced. This not only cuts down on labor costs but also reduces the risk of human error, leading to a more consistent and predictable coating result.
- Customization: Modern reciprocators can be programmed to apply different types of powder coatings, whether it’s a single color or a multi-layer, textured, or special finish. The ability to easily switch between different coating styles adds to the system’s flexibility, especially for manufacturers that need to produce parts with varying aesthetic or functional coatings.
Types of Powder Coating Reciprocators:
- Manual Reciprocators: These are simple, basic systems where the operator manually adjusts the movement of the spray gun. They are typically less expensive but also less efficient and precise than automated systems.
- Semi-Automatic Reciprocators: These systems involve some level of automation, where the operator can set up the movement parameters, but the machine still requires some manual input, such as loading and unloading parts. Semi-automatic systems can provide better consistency and efficiency than manual ones.
- Fully Automatic Reciprocators: In fully automatic systems, the reciprocator is integrated into a complete automated powder coating line. These systems are programmable and are capable of adjusting to different part types and sizes automatically, ensuring optimal powder application without human intervention.
Maintenance of Powder Coating Reciprocators:
To maintain the proper functioning of a powder coating reciprocator, regular maintenance is essential. This includes:
- Cleaning: Powder buildup on the reciprocator’s moving parts can cause irregular motion or inefficient powder distribution. Regular cleaning of the spray guns, control mechanisms, and conveyor tracks is crucial.
- Lubrication: The reciprocator’s moving parts, such as gears, rails, and bearings, should be regularly lubricated to prevent wear and tear.
- Inspection: Routine inspections to check for wear on mechanical components and electrical systems help ensure that the reciprocator operates smoothly.
- Calibration: Over time, the reciprocator may require recalibration to ensure that the movement parameters remain accurate, which can be done using the machine’s control system or manual adjustments.
Applications of Powder Coating Reciprocators:
Powder coating reciprocators are widely used in various industries, including:
- Automotive: For coating car parts, rims, and other components.
- Appliances: Such as washers, dryers, refrigerators, and ovens.
- Metal Fabrication: Coating metal components in construction, agriculture, and industrial machinery.
- Furniture: Applying durable, aesthetic finishes to office furniture and outdoor furniture.
- Electronics: Coating parts like housings, cases, and panels for consumer electronics.
In conclusion, the powder coating reciprocator is an essential part of modern powder coating systems, providing consistency, speed, and high-quality finishes. Whether used in manual, semi-automatic, or fully automatic systems, it helps manufacturers achieve uniform powder distribution, reduce waste, and enhance overall process efficiency. With continued advancements in automation and control technology, the role of reciprocators in powder coating systems will only grow in importance, supporting industries that require high-quality and durable coatings.
Advanced Features of Powder Coating Reciprocators:
- Programmable Movement: Modern powder coating reciprocators are equipped with advanced controllers that allow for precise programming of the movement patterns. This means that users can set specific speed, stroke length, and direction for the spray guns based on the type of part being coated. These programmable settings allow for optimal coverage, ensuring that the part is coated uniformly and efficiently, reducing the chances of uneven powder application.
- Electrostatic Control Integration: Many powder coating reciprocators are integrated with electrostatic powder application technology. This system charges the powder particles, which are then attracted to the grounded part, allowing for a more consistent application. The reciprocator works in tandem with the electrostatic system to ensure that powder is distributed evenly and sticks to the surface of the part, even in areas that may otherwise be difficult to coat.
- Variable Speed Control: Some advanced reciprocators offer variable speed control, allowing users to adjust the speed of the reciprocator’s movement based on the specific part characteristics. Faster speeds may be ideal for simpler, flat parts, while slower speeds can ensure more coverage on complex or intricate parts with deep crevices or hard-to-reach areas. Variable speed control ensures that the coating process is optimized for each specific job, improving both the quality of the finish and the efficiency of the operation.
- Vertical and Horizontal Adjustments: For complex geometries, vertical and horizontal adjustments in the reciprocator’s movement may be necessary. This allows for greater flexibility in coating parts of different shapes, such as those with irregular contours or tall, narrow features. These adjustments can also optimize the angle of the powder spray, ensuring that every part of the part is coated uniformly, including undercuts and hard-to-reach areas.
- Multi-Gun Configuration: Some reciprocators allow for multi-gun configurations, where multiple spray guns can be mounted on the same reciprocator arm or on separate arms that work in parallel. This setup is particularly useful for large parts that need to be coated quickly. Multi-gun systems enable better coverage and speed up the process, as each gun applies a portion of the coating, allowing for a faster overall coating time.
Benefits of Advanced Features:
- Increased Flexibility and Precision: The combination of programmable movement, electrostatic control, and multi-gun configurations allows for higher precision in the powder coating process, especially when dealing with complex part shapes and sizes.
- Enhanced Speed and Throughput: With variable speed control and multi-gun configurations, reciprocators can apply coatings faster, allowing for higher throughput in manufacturing operations. This is particularly valuable in high-volume industries such as automotive and appliances.
- Reduced Waste: Advanced systems with optimized movement and electrostatic charge help reduce the amount of powder that misses the part or is over-applied. This minimizes waste, reduces material costs, and contributes to more sustainable operations by ensuring maximum powder efficiency.
Integration with Other Systems:
Powder coating reciprocators can also be integrated with automated handling systems to create fully integrated powder coating lines. These systems can automatically load and unload parts, move them through pre-treatment stages, and transport them through the coating and curing process without requiring manual intervention. When combined with robotic arms or conveyor systems, the reciprocator can ensure that each part receives consistent coverage as it moves through the coating process.
For example, in a fully automated powder coating line, the part is loaded onto a conveyor belt, where it moves into the coating zone. Here, the reciprocator moves the powder spray guns over the part while adjusting the spray pattern and coverage area to match the part’s shape. After coating, the part is moved into a curing oven where it is baked at a specific temperature, and then cooled before being unloaded and packaged.
Impact on Quality Control:
Quality control is a critical aspect of powder coating, and the reciprocator plays a key role in ensuring consistent and high-quality finishes. Automated systems with built-in monitoring features can provide real-time feedback on coating thickness, uniformity, and powder usage. For example:
- Coating Thickness Measurement: Some systems are equipped with sensors that measure the thickness of the applied powder layer in real-time, ensuring that it meets specified standards.
- Automated Inspection: Vision systems or cameras can be integrated with the reciprocator to monitor the application process and ensure there are no defects, such as powder streaks, inconsistencies, or missed areas. If an issue is detected, the system can automatically adjust the movement or pause the process to prevent further defects.
- Feedback Loops: In some advanced systems, real-time data collected from the coating process can be fed back to the system’s control software. If irregularities are detected, adjustments can be made on the fly to optimize the coating process, ensuring that defects are minimized and quality is maintained.
Conclusion:
The powder coating reciprocator is a crucial part of modern powder coating systems, offering significant advantages in terms of speed, efficiency, precision, and quality. With continued advancements in technology, reciprocators are becoming more versatile and adaptable to a wide range of applications. Whether it’s for small, intricate parts or large-scale, high-volume production, the reciprocator ensures that powder coatings are applied consistently and evenly. By integrating with automated lines, multi-gun systems, and advanced control technologies, reciprocators help manufacturers meet the growing demands for high-quality, durable finishes while reducing waste, improving throughput, and contributing to sustainability.
The integration of powder coating reciprocators into automated systems has further enhanced their capabilities. These advancements not only improve coating consistency but also enable a more seamless and efficient workflow across the entire coating process. By automating the movement of the spray guns, the reciprocator removes much of the human error that can occur in manual applications. This level of consistency is critical in industries where appearance and durability are paramount, such as automotive and appliance manufacturing.
As the powder coating industry continues to evolve, the demand for greater precision and faster processing speeds is pushing the boundaries of what reciprocators can achieve. Some of the latest systems include features like motion sensors and adaptive learning algorithms that allow the reciprocator to adjust its movements based on the specific shape and orientation of each part. This adaptive feature helps ensure that even the most complex parts are coated evenly, regardless of their geometry.
Moreover, the modern reciprocator’s role in improving overall resource efficiency cannot be overlooked. By fine-tuning the powder flow rate and minimizing overspray, it contributes significantly to reducing material waste. The electrostatic process already ensures that most of the powder is attracted to the part, but by optimizing the reciprocator’s path and speed, companies can reclaim a larger portion of the unused powder for reuse, thus reducing costs and minimizing environmental impact.
Another important consideration is the relationship between reciprocators and energy consumption. In powder coating, the curing process typically requires the part to be baked in an oven, and the energy used in this stage can account for a significant portion of the overall energy consumption. While the reciprocator itself doesn’t directly affect the curing process, its role in streamlining the coating stage helps shorten cycle times. This reduction in time spent on coating parts can lead to a decrease in the total energy required for each part, as the oven can process parts more quickly. Additionally, with improved automation and synchronization between coating and curing, manufacturers can optimize their oven loads, further improving energy efficiency.
Advancements in smart manufacturing technologies are also beginning to integrate with reciprocator systems. These systems, powered by the Internet of Things (IoT), allow for real-time monitoring and remote diagnostics, making it easier to spot potential issues and fix them before they become major problems. Operators can access detailed performance data on the reciprocator, such as movement patterns, speed, and coating coverage, from a central control room or via mobile devices, allowing them to make adjustments on the fly. This level of connectivity ensures that the powder coating process remains agile and responsive to changing production requirements.
The flexibility of modern reciprocators is also increasing. These machines can be easily adapted to handle various part sizes and shapes. The ability to adjust the coating path or the number of guns used allows for a wider range of applications, from simple geometries to highly complex, custom parts. In industries like aerospace or medical device manufacturing, where part designs can be highly intricate, the ability to use a reciprocator that can adjust its path dynamically ensures that the coating is applied uniformly, regardless of the part’s complexity.
Lastly, the continued push toward sustainability in manufacturing means that powder coating reciprocators are being designed with eco-friendly features. As the coating process moves toward greener solutions, such as low-VOC or water-based powders, reciprocators are being engineered to work with these new materials. The improved powder recovery systems built into these devices also play a critical role in reducing waste and conserving materials. As environmental regulations become stricter, the powder coating industry is increasingly focusing on ways to minimize its environmental footprint, and reciprocators are key to meeting these goals.
In conclusion, the evolution of powder coating reciprocators reflects a broader trend in manufacturing toward higher precision, greater automation, and improved sustainability. As they continue to integrate advanced technologies like adaptive control systems, energy-efficient designs, and smart monitoring, reciprocators are becoming even more essential to industries seeking efficient, high-quality, and environmentally friendly coating solutions. These machines are no longer just part of the process; they are the backbone of modern powder coating lines that help businesses meet the growing demands of speed, quality, and sustainability.
The next generation of powder coating reciprocators will likely see even more profound shifts, influenced by ongoing advancements in robotics, artificial intelligence (AI), and machine learning (ML). These technologies will significantly enhance the precision and flexibility of reciprocators, making them even more adaptable to complex manufacturing needs and pushing the boundaries of what is possible in terms of coating quality and process optimization.
One of the most exciting prospects is the integration of AI-driven predictive analytics into reciprocator systems. This would allow for the monitoring of various variables—such as part geometry, powder flow, and environmental factors—that can influence the coating process. By analyzing real-time data, AI systems can predict and correct potential inconsistencies in the coating application before they occur, reducing the likelihood of defects and ensuring that every part meets the desired quality standards. For instance, if the system detects a slight variation in powder thickness or flow rate, it could automatically adjust the reciprocator’s speed, spray angle, or distance from the part to compensate.
With the combination of machine learning and advanced computer vision, powder coating reciprocators could be equipped with the ability to “see” the parts they are coating in real time. Cameras or imaging systems would allow the reciprocator to scan the part’s surface and identify areas that may require more powder or areas where the application is excessive. By continuously analyzing the part’s shape and surface, the system could adjust in real time, ensuring that every nook and cranny is evenly coated without overspray or missed spots. This technology would be especially beneficial for highly intricate or geometrically complex parts, where traditional reciprocators might struggle to achieve consistent coverage.
In addition to quality control, AI and machine learning could also contribute to process optimization by analyzing historical data to determine the most efficient coating parameters. For example, based on the past performance of specific powder types or part geometries, the system could automatically adjust the reciprocator’s settings to optimize the application process, reducing waste, energy consumption, and curing time. Over time, the system would “learn” the ideal settings for a variety of production scenarios, continuously improving the coating process as more data is collected.
The integration of robotic arms and collaborative robots (cobots) with powder coating reciprocators is another area of significant growth. These advanced robots would provide even greater flexibility and precision in powder coating applications. Cobots, in particular, are designed to work alongside human operators, providing added support while ensuring safety. These systems could be used to coat parts with irregular shapes, move components through different stages of the process, or even handle delicate items with minimal risk of damage. Their ability to adapt to different tasks and environments would make them invaluable for industries that produce diverse parts requiring varied coating techniques.
The future of powder coating reciprocators will also likely feature increased integration with other manufacturing technologies within the factory. This includes the ability to communicate seamlessly with automated guided vehicles (AGVs) that transport parts, as well as integration with Enterprise Resource Planning (ERP) systems that help manage production schedules, inventory, and overall factory workflow. Such connectivity would ensure that the coating process is always synchronized with the rest of the manufacturing line, enhancing overall operational efficiency and reducing downtime.
Sustainability will continue to be a key driving factor in the evolution of reciprocator technology. Future designs will likely emphasize energy efficiency, utilizing lower-power motors and advanced power management systems. This is important not only to reduce operational costs but also to align with global efforts to reduce carbon footprints. Additionally, improvements in powder recovery and waste management technologies will further minimize the environmental impact of powder coating. New methods for capturing and reusing overspray, for example, could lead to even higher recovery rates, ensuring that powder material is utilized to its fullest potential.
In terms of coating materials, we are seeing the development of more sustainable and specialized powder formulations that offer better performance with less environmental impact. These include water-based powders, low-VOC coatings, and biodegradable materials. Reciprocators will need to adapt to these new materials, ensuring they can apply them efficiently while maintaining the high-quality finish expected in industries such as automotive, architecture, and consumer goods.
Furthermore, customization will become more important as consumers and businesses alike demand more tailored solutions. Reciprocators of the future will likely offer even more flexible capabilities, allowing for custom color blending, texture creation, and the application of multiple coating layers in a single pass. This could revolutionize sectors like high-end consumer goods and luxury products, where the ability to offer bespoke finishes can set brands apart.
The ongoing development of smart factories will also shape the future of reciprocators. In these advanced environments, manufacturing equipment is interconnected through IoT sensors, creating a highly responsive and data-driven production system. In such settings, reciprocators will play a crucial role in ensuring that the powder coating process is seamlessly integrated with other steps, from material handling to packaging, and that the entire production line operates with maximum efficiency. For instance, real-time data from the reciprocator can be used to dynamically adjust oven temperatures, curing times, or conveyor speeds to optimize the overall process.
Finally, the concept of remote monitoring and control will become even more prominent. Manufacturers will be able to oversee and control their powder coating systems from virtually anywhere, thanks to cloud-based interfaces and mobile applications. This would allow operators to monitor performance, adjust settings, and troubleshoot issues without needing to be physically present on the factory floor, improving flexibility and response times.
In conclusion, the future of powder coating reciprocators is incredibly exciting, with developments in AI, robotics, sustainability, and smart manufacturing technologies shaping the next generation of systems. These advancements will not only improve the quality and efficiency of the coating process but also contribute to a more sustainable and agile manufacturing environment. As these technologies continue to evolve, reciprocators will become even more integral to the success of modern manufacturing, enabling companies to meet the growing demands for high-quality, customized, and environmentally responsible products.
Powder Coating Machine
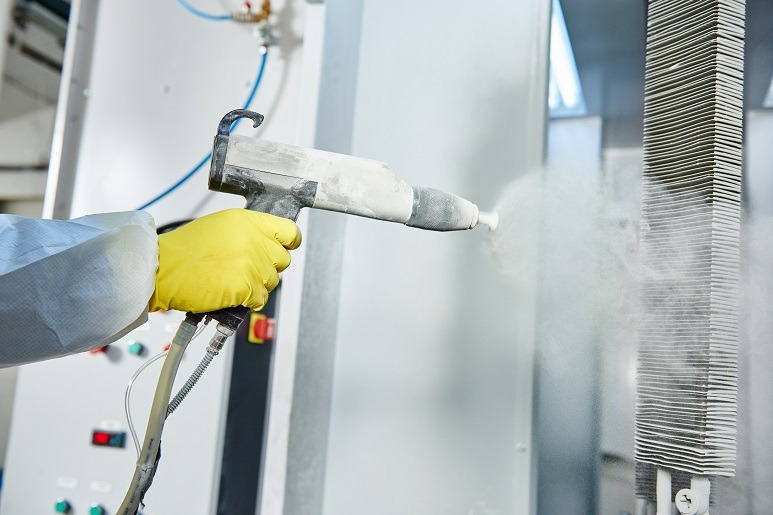
A powder coating machine is a critical piece of equipment in the powder coating process, used to apply a dry powder to metal or other materials in order to create a durable, high-quality finish. Powder coating is a more environmentally friendly alternative to traditional liquid paints because it doesn’t require solvents and produces fewer emissions. The machine works by spraying electrostatically charged powder particles onto a part, which is then cured in an oven to form a solid, long-lasting coating.
Key Components of a Powder Coating Machine:
- Powder Spray Gun: The spray gun is the heart of the powder coating machine, used to apply the powder to the surface of the object being coated. The gun works by charging the powder particles electrostatically, causing them to be attracted to the grounded part. This process ensures even coverage and efficient use of the powder. Spray guns may come in different types:
- Corona guns: The most common type, where the powder is charged by the corona discharge created by a high-voltage electrode.
- Tribo guns: These work by using friction to charge the powder particles as they move through the gun.
- Powder Booth: The powder booth is the enclosed area where the coating process takes place. It is designed to contain the overspray powder, ensuring that it doesn’t contaminate the surrounding environment. Powder booths may include features like:
- Filtered airflow to prevent the escape of powder particles.
- Recirculation systems to collect and reuse unused powder.
- Efficient ventilation to capture and filter out excess powder and maintain a clean working environment.
- Powder Recovery System: One of the advantages of powder coating is the ability to reclaim unused powder, reducing waste and material costs. The recovery system consists of:
- Cyclone separators or filters that capture airborne powder particles.
- Suction and vacuum systems to remove the excess powder from the air within the booth and direct it into storage containers for reuse.
- Curing Oven: Once the powder has been applied to the part, it needs to be cured to form a solid coating. The curing oven is heated to a specific temperature (typically between 160°C and 200°C, depending on the powder material), which causes the powder to melt, flow, and chemically bond to the substrate, creating a hard, durable finish. There are different types of curing ovens:
- Convection ovens, where hot air circulates around the parts.
- Infrared ovens, which use radiant heat to cure the powder more quickly.
- Hybrid ovens, which combine convection and infrared technologies.
- Conveyor System: In larger systems, parts are often transported through the powder coating process via a conveyor system. This helps to automate the process and ensures parts are consistently moved through the spray booth and curing oven. Conveyor systems can be manual or automated, depending on the size and requirements of the production line.
- Control Panel: A control panel is used to adjust the settings for the powder coating machine. It includes controls for the spray gun settings (such as voltage and airflow), curing oven temperature and time, and conveyor speed. The control panel allows operators to fine-tune the process based on the specific material and type of finish required.
Types of Powder Coating Machines:
- Manual Powder Coating Machine: A manual powder coating system involves a spray gun operated by an individual who manually applies the powder to the part. This system is often used for small batches or customized items. Manual machines are typically more affordable but may be less efficient and consistent compared to automated systems.
- Automatic Powder Coating Machine: In an automatic system, the spray guns and other components of the powder coating process are automated to improve efficiency and consistency. Parts are usually loaded onto a conveyor system, where they are transported through the powder booth and curing oven. Automatic machines are ideal for high-volume production and larger manufacturing facilities, where consistency, speed, and quality are crucial.
- Robotic Powder Coating Machine: Robotic powder coating systems are highly advanced, using robotic arms to move spray guns over parts. These systems can be programmed to coat complex parts with high precision, ensuring an even coat and reducing the chances of human error. Robotic systems are commonly used in industries such as automotive and aerospace, where part geometries are complex, and high-quality finishes are required.
Powder Coating Process with a Powder Coating Machine:
- Preparation: Before the powder coating can be applied, the part must be cleaned and pretreated to ensure proper adhesion of the powder. This may involve processes such as:
- Cleaning: Removing oils, dirt, or other contaminants from the surface.
- Pretreatment: Applying a phosphate or chromate coating to enhance powder adhesion and corrosion resistance.
- Drying: Ensuring that the part is dry before powder application.
- Powder Application: The part is placed in the powder booth, where it is sprayed with an electrostatically charged powder from the spray gun. The charged powder particles adhere to the grounded part, forming a thin, uniform layer. The amount of powder applied is controlled by adjusting the settings on the gun, such as voltage, airflow, and the distance from the part.
- Curing: After the powder is applied, the part is moved into the curing oven, where heat causes the powder to melt, flow, and chemically bond to the surface of the part. The curing process typically lasts for 10-20 minutes, depending on the type of powder and the part’s size and thickness.
- Cooling: Once the curing process is complete, the part is removed from the oven and allowed to cool. This cooling period solidifies the coating, giving the part a durable, smooth, and uniform finish.
- Inspection and Finishing: After cooling, the coated part may undergo inspection for quality control purposes. If necessary, touch-ups can be made to address any imperfections. Some machines may have automated inspection systems that check for coating thickness and consistency, ensuring that each part meets the required specifications.
Advantages of Powder Coating Machines:
- Durability: Powder coatings are highly durable, providing resistance to scratches, chipping, fading, and corrosion. This makes powder coating machines ideal for industrial applications where long-lasting finishes are required.
- Environmentally Friendly: Powder coating does not require solvents or chemicals, which reduces the environmental impact associated with traditional liquid coatings. The process produces fewer emissions and waste, making it a more sustainable option.
- Efficiency: Powder coating is more efficient than liquid painting because it produces less waste and allows for faster application. The electrostatic process ensures that most of the powder sticks to the part, and unused powder can be recycled.
- Variety of Finishes: Powder coating machines can produce a wide range of finishes, including matte, gloss, textured, and even custom colors. The flexibility in finish types makes it suitable for various industries, from automotive to home appliances to architectural elements.
- Cost-Effective: While initial setup costs for a powder coating system can be higher, the reduced need for solvents, faster curing times, and the ability to recycle unused powder make the process cost-effective in the long run.
Applications of Powder Coating Machines:
- Automotive: Powder coating is widely used to coat car parts, wheels, bumpers, and trim components due to its durability and resistance to the elements.
- Appliances: Items such as refrigerators, washing machines, and ovens often receive powder coatings for their durability and aesthetic appeal.
- Architectural Components: Aluminum window frames, door handles, and other exterior components are often powder-coated for both aesthetic and protective reasons.
- Metal Furniture: Furniture pieces like tables, chairs, and filing cabinets benefit from the durable finish offered by powder coating.
Conclusion:
Powder coating machines are essential for achieving high-quality, durable finishes on a wide variety of materials, particularly metals. They offer numerous advantages, such as durability, environmental sustainability, efficiency, and cost-effectiveness. Whether used in manual, automatic, or robotic systems, powder coating machines have become indispensable in industries that require long-lasting, aesthetically pleasing coatings on metal parts. As technology continues to improve, the capabilities of powder coating machines will continue to evolve, providing even better performance and flexibility for manufacturers.
Powder coating machines play a crucial role in providing high-quality, durable finishes for a wide range of materials, particularly metals, by utilizing a process that is both efficient and environmentally friendly. These machines ensure that products like automotive parts, appliances, and metal furniture receive a uniform and lasting coat that not only enhances their appearance but also protects them from the elements, wear, and tear.
The process begins with a thorough cleaning and pretreatment of the part to ensure that the coating adheres properly. This step may involve the removal of oils, grease, and contaminants, followed by the application of a chemical treatment to improve adhesion. Once the surface is prepped, the powder coating machine applies the dry powder using an electrostatic spray gun. The powder particles are electrically charged and then attracted to the grounded part. This application method helps ensure even coverage, reducing the amount of waste powder that would otherwise be lost in the air. The excess powder that doesn’t stick to the part is captured by the powder recovery system and can be recycled for future use, which helps reduce material costs and environmental impact.
After the powder is applied, the part is transferred to a curing oven where it is heated to the required temperature. This heat causes the powder to melt, flow, and chemically bond to the surface, creating a smooth, hard finish that provides excellent durability and resistance to scratches, corrosion, fading, and chipping. The curing process is critical to ensuring the final product meets the desired quality standards. Once the part has been properly cured, it is allowed to cool, solidifying the coating and making the part ready for inspection.
The ability to recycle unused powder is a major advantage of the powder coating process. Not only does this reduce waste, but it also minimizes the cost of materials, which can be a significant expense for high-volume production lines. Additionally, because powder coatings do not require solvents or chemicals, the environmental impact is much lower than that of traditional liquid coatings. This makes powder coating an attractive option for manufacturers seeking sustainable solutions.
Powder coating machines are versatile, and their use extends across a variety of industries. In the automotive sector, they are used to coat car parts such as wheels, bumpers, and trim components, where durability and resistance to harsh conditions are critical. The appliance industry also benefits from powder coating technology, as items like refrigerators, ovens, and washing machines often require tough, long-lasting finishes to withstand everyday use and exposure to moisture. The architectural industry relies on powder coating for items like window frames, door handles, and other exterior components, as the coating provides both aesthetic appeal and protection against the elements. Similarly, metal furniture manufacturers use powder coating to ensure their products are both attractive and durable.
One of the advantages of powder coating machines is their ability to produce a variety of finishes, including matte, glossy, textured, and even custom colors. This flexibility allows manufacturers to meet the demands of different applications and consumer preferences. While the initial investment in a powder coating system may be higher than traditional liquid painting equipment, the long-term savings in material costs, environmental compliance, and energy efficiency make it a cost-effective solution in high-volume production settings.
As technology continues to advance, powder coating machines are becoming more sophisticated, with improvements in automation and robotic systems. Automated systems, in particular, increase efficiency and ensure consistent application, especially in high-volume settings. Robotic powder coating machines can be programmed to move spray guns over parts with great precision, ensuring that even complex geometries receive an even coat of powder. This level of automation allows for faster turnaround times and reduces the potential for human error.
The ongoing integration of IoT and AI technologies into powder coating systems is transforming how these machines operate. Real-time monitoring of the process allows for predictive maintenance, and advanced sensors can detect variations in powder thickness, ensuring that the finish is consistently applied to meet stringent quality standards. Smart systems can automatically adjust spray gun settings, curing times, and oven temperatures, ensuring that every part is coated according to the exact specifications required.
The flexibility of powder coating machines continues to grow, allowing them to handle a wider range of part shapes and sizes. With innovations in conveyor systems, robotic arms, and automated processes, these machines can accommodate a variety of production environments, from small-batch custom work to large-scale manufacturing operations. As industries continue to push for higher quality, faster production times, and more sustainable practices, the powder coating machine will remain a key player in achieving these goals.
In conclusion, powder coating machines are essential for delivering high-performance finishes across many industries, from automotive and appliances to architectural components and metal furniture. Their ability to produce durable, high-quality coatings, combined with their environmental benefits and efficiency, makes them a preferred solution for many manufacturers. As technology continues to advance, these machines will only become more powerful, capable, and adaptable, further solidifying their role in modern manufacturing processes.
As the powder coating industry continues to evolve, the technology behind powder coating machines is advancing to meet the increasing demands for higher precision, better efficiency, and more eco-friendly solutions. One of the most notable trends in the development of powder coating machines is the integration of automation and robotics, which is transforming the powder coating process across various industries. The automation of tasks like powder application, part handling, and curing significantly reduces labor costs while improving consistency and throughput. Automated powder coating systems can quickly adjust to changes in part size or shape, making them ideal for high-volume manufacturing environments where consistent quality is essential.
Moreover, robotic powder coating machines offer an unprecedented level of control and precision. These systems utilize robotic arms that can be programmed to coat parts in complex or difficult-to-reach areas, ensuring an even and consistent coating across the entire surface. Robotic systems can be paired with advanced vision systems, enabling the machine to “see” the part, evaluate its geometry, and adjust the spray pattern accordingly. This level of adaptability ensures that parts with intricate shapes, such as automotive components or custom-designed products, receive a uniform coat that traditional manual or non-robotic systems might struggle to achieve.
Alongside robotic automation, there is also a growing focus on data-driven technologies in powder coating systems. With the advent of smart manufacturing, powder coating machines are increasingly equipped with sensors, cameras, and IoT connectivity to monitor and adjust the coating process in real-time. This allows manufacturers to track every stage of the coating process, from powder application to curing, ensuring that parts are coated consistently and defects are minimized. By collecting and analyzing this data, manufacturers can identify trends, optimize their processes, and even predict when maintenance is required, reducing downtime and increasing operational efficiency.
Incorporating AI into powder coating systems further enhances their capabilities. For instance, AI-driven algorithms can optimize powder usage, automatically adjusting the spray gun settings based on part geometry, powder type, and environmental conditions. By improving the accuracy of powder application and reducing waste, these intelligent systems help manufacturers cut costs and reduce their environmental footprint. The use of machine learning also enables the system to adapt to new materials and processes as they are introduced, making it highly versatile and future-proof.
As environmental concerns continue to rise, powder coating systems are becoming more sustainable. The demand for greener manufacturing practices is driving the development of energy-efficient powder coating machines that minimize power consumption while maintaining high-quality finishes. New technologies in curing ovens, such as infrared curing, have made it possible to reduce the energy required for the curing process. This is particularly important in industries with strict sustainability goals, as energy-efficient systems can significantly lower operating costs and reduce the carbon footprint of production lines.
Another environmentally friendly development in powder coating is the use of low-VOC (volatile organic compound) or water-based powders, which produce fewer harmful emissions compared to traditional solvents. These innovations are part of a broader trend toward eco-friendly coating materials, which are less harmful to workers and the environment while maintaining the same high standards of finish and durability. The powder coating process itself, which eliminates the need for solvents, already offers a greener alternative to liquid coatings, and these new materials further enhance the environmental benefits of the process.
As the global market for customized products continues to grow, powder coating machines are also becoming more adaptable to the needs of diverse industries. From high-end automotive finishes to customized metal furniture and appliances, the ability to create unique colors, textures, and finishes is in high demand. Powder coating machines are now capable of producing specialized effects, such as metallic finishes, textured coatings, and multi-layered coatings, giving manufacturers the flexibility to meet these bespoke requirements. This customization capability is particularly beneficial for industries like luxury goods, where product differentiation is key to attracting consumers.
At the same time, the growing trend of shorter production cycles and on-demand manufacturing is also influencing powder coating technologies. Manufacturers are increasingly expected to produce smaller batches of products, often with quick turnaround times. To accommodate this, powder coating systems are being designed to be more flexible, allowing for fast changeovers between different parts and finishes. Quick color change systems and automated part loading/unloading systems are examples of technologies that enable powder coating machines to be more versatile and responsive to rapidly changing production schedules.
As demand for higher throughput continues to grow, manufacturers are also looking for ways to streamline the powder coating process. Innovations in conveyor systems and batch processing allow parts to be coated more quickly and efficiently. For instance, modular conveyor systems can be configured to handle various part sizes and shapes, optimizing part flow and reducing the time it takes for parts to go through the entire coating process. This flexibility is essential for industries that deal with a wide range of parts, from small custom components to large mass-produced items.
In addition to improving efficiency and sustainability, the powder coating industry is also benefiting from innovations in advanced coating materials. New formulations of powder coatings are offering improved properties, such as better corrosion resistance, increased UV stability, and greater flexibility for demanding applications. These new coatings are enabling manufacturers to expand the range of products that can be powder-coated, including those exposed to harsher environmental conditions, such as marine and outdoor applications.
As the technology behind powder coating systems advances, the cost of ownership for manufacturers continues to decrease. Automation, energy-efficient systems, and material recovery technologies are all contributing to a lower total cost of ownership. Furthermore, the recyclability of powder coating material itself reduces waste and makes the process more cost-effective in the long term. Manufacturers who invest in these advanced systems benefit from improved quality, reduced waste, and enhanced operational efficiencies, making powder coating a more attractive option for a wide variety of industries.
In conclusion, the future of powder coating machines is marked by advancements in automation, sustainability, data-driven optimization, and customization. As these machines continue to evolve, they will offer even greater precision, efficiency, and flexibility, enabling manufacturers to meet the increasing demands of modern production environments. With improvements in energy efficiency, environmental sustainability, and the ability to handle customized finishes, powder coating systems are poised to remain a crucial part of manufacturing processes across a broad range of industries. As technology progresses, powder coating machines will continue to play an integral role in delivering high-quality, durable finishes while meeting the growing need for eco-friendly, cost-effective solutions.
The next wave of advancements in powder coating machines will likely focus on further enhancing automation and digital integration, which will continue to drive the evolution of the industry toward higher efficiency and greater precision. Smart factories equipped with interconnected systems and data-sharing capabilities will be able to monitor every aspect of the powder coating process in real-time, leading to more intelligent decision-making and less human intervention.
Predictive maintenance is one of the key benefits of this digital transformation. With the integration of IoT sensors, machines will be able to detect anomalies in real-time and predict when certain components, such as motors or spray guns, will need maintenance or replacement. By analyzing historical data and recognizing patterns, these systems can help prevent breakdowns, extend the life of equipment, and minimize downtime. Manufacturers will no longer have to rely on a fixed maintenance schedule or wait for an issue to arise before making repairs. This predictive approach reduces costs and boosts operational uptime, making powder coating machines more reliable and cost-effective over the long term.
Additionally, the use of artificial intelligence (AI) and machine learning will enable powder coating machines to continuously learn from the data they collect during the production process. AI algorithms will be able to automatically adjust key variables, such as spray gun settings, airflow, and oven curing times, based on real-time performance data. This means that the machines can continuously improve their own efficiency and output without the need for human intervention. This will lead to a new era of self-optimizing systems where the machines themselves are responsible for fine-tuning their processes to achieve the best possible results. The increased accuracy will not only improve product quality but will also reduce material waste and energy consumption.
Another exciting development in the future of powder coating systems will be the advancement of powder materials themselves. Innovations in powder formulations will continue to improve the quality and performance of powder coatings. For instance, nano-coatings could provide an even more durable and resistant finish, offering additional benefits such as enhanced corrosion resistance, higher scratch resistance, or even self-healing properties. This is particularly important in industries where parts are exposed to extreme environments, such as marine, automotive, or industrial applications. New materials may also enable powder coatings to be used on a broader range of substrates, expanding their potential applications even further.
In addition to improved performance characteristics, new powder coatings will likely focus on expanding the color and texture options available to manufacturers. Custom color-matching technologies, using advanced spectrophotometers and AI algorithms, will enable manufacturers to more easily replicate specific color shades, offering greater precision in meeting client demands. In addition to color, textured finishes like metallic, matte, and satin coatings will continue to gain popularity. New technologies may even allow for the creation of interactive finishes that change appearance depending on the angle of the light, offering a dynamic visual appeal.
The future of powder coating machines will also be shaped by advances in sustainability. With the continued push toward greener manufacturing practices, there will be more demand for low-emission powder coating systems that limit harmful pollutants and reduce the environmental impact of industrial operations. Emerging trends in zero-waste and circular manufacturing will influence the design of powder coating systems, encouraging greater recycling of excess powder, water-based and non-toxic powder formulations, and more energy-efficient curing processes. Powder coating machines will become key enablers of circular economies where waste and by-products are minimized, and materials are reused as much as possible.
Energy-efficient curing technologies will play a significant role in making powder coating systems more sustainable. New infrared curing ovens and hybrid curing systems, which combine infrared radiation with conventional convection heating, are expected to reduce energy consumption and increase throughput. Infrared curing, for example, can heat parts more quickly by directly applying heat to the substrate, making the process faster and more energy-efficient. With the rise of renewable energy sources, manufacturers will also have the opportunity to power their powder coating systems with cleaner energy, further reducing their carbon footprint.
Moreover, the growing trend of customization in manufacturing will continue to shape the powder coating market. As consumers increasingly demand unique and personalized products, powder coating systems will need to accommodate small batch runs and quick changes between coatings. The rise of on-demand manufacturing and just-in-time production means that manufacturers will require machines that can quickly adjust to different parts, finishes, and colors, all while maintaining consistent quality. This increased demand for flexibility will push powder coating systems to evolve, with more modular systems and fast-changeover technologies that make switching between coatings faster and more efficient.
The integration of robotics and artificial intelligence will also enable even more precise and intricate designs to be coated. With advancements in 3D printing and additive manufacturing, there will be an increase in the use of powder coating for parts with complex geometries and detailed surfaces. Robotic arms and automated spray guns will be able to follow the contours of these parts with a high degree of accuracy, ensuring that the coating is applied evenly and consistently, even on intricate or non-standard shapes. This will open up new possibilities for industries such as aerospace, medical devices, and custom automotive, where precision is critical, and the need for customization is high.
In summary, the future of powder coating machines is full of potential. Advances in automation, artificial intelligence, energy efficiency, and sustainable practices will continue to transform how powder coating systems operate. As manufacturers demand more customized solutions and faster production cycles, these machines will evolve to meet these challenges, with better precision, improved material handling, and greater adaptability. With the continued development of new powder formulations, smarter technologies, and environmentally friendly innovations, powder coating will remain a cutting-edge solution for achieving high-performance, durable finishes across a wide range of industries.
Powder Coating Equipment
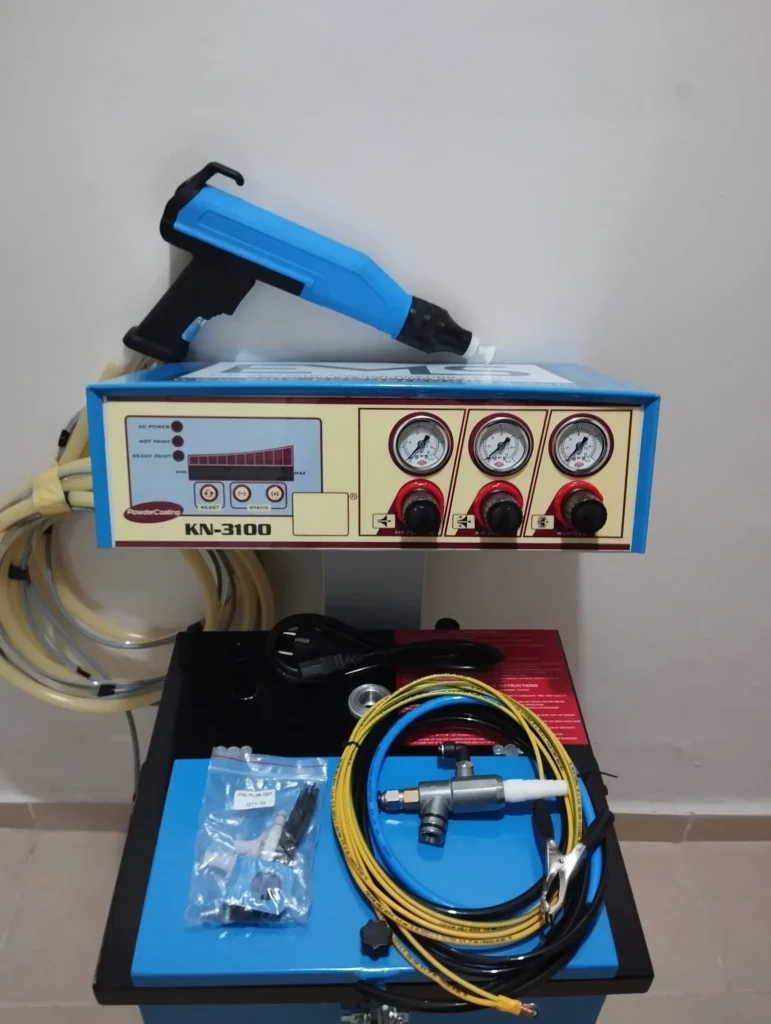
Powder coating equipment is a key component in the powder coating process, which is used to apply a durable, high-quality finish to various products, particularly metal parts, while minimizing environmental impact. Powder coating equipment ensures that the powder is evenly applied and properly cured, resulting in a smooth, durable finish. Below is an overview of the main components and types of powder coating equipment used in industrial applications:
Key Components of Powder Coating Equipment
- Powder Coating Spray Gun
- The spray gun is the central tool in powder coating equipment. It uses electrostatic charging to apply powder to the surface of the part. The powder particles are given a negative charge, while the part is grounded, causing the powder to be attracted to the surface. There are different types of spray guns, such as manual, automatic, and robotic spray guns, each suited for different production needs.
- Manual spray guns are used in smaller operations and for custom parts. Operators manually direct the spray nozzle over the part.
- Automatic spray guns are used in automated systems and are designed to apply powder coatings with precision for consistent finishes.
- Robotic spray guns provide high precision and can handle complex geometries, typically found in large-scale manufacturing settings.
- Powder Booth
- The powder booth is where the parts are coated with powder. It provides a controlled environment to ensure that the powder is applied evenly. Powder booths come with an integrated airflow system to keep the powder in suspension and prevent overspray.
- These booths are designed with filters to capture excess powder, which can be reused, ensuring efficient use of materials and reducing waste.
- Advanced booths may include recapture systems to collect the unused powder and send it back to the powder feed system for reuse.
- Powder Recovery System
- A powder recovery system captures excess or oversprayed powder that doesn’t adhere to the part. This system typically includes filters, cyclonic separators, and sieving equipment. The recovered powder is sent back into the powder supply for reuse, reducing waste and improving cost-efficiency.
- These systems are essential in high-volume manufacturing environments, where minimizing material waste is crucial for profitability and environmental sustainability.
- Curing Oven
- The curing oven is used to bake the coated parts at a specific temperature to melt the powder and bond it to the surface. Curing is a critical step in powder coating, as it ensures that the coating hardens to form a tough, durable finish.
- There are various types of curing ovens, such as convection ovens, infrared ovens, and hybrid ovens. The choice of oven depends on the type of powder coating used, part size, and production requirements.
- Modern curing ovens are often designed for energy efficiency, reducing operating costs while maintaining uniform heat distribution for consistent results.
- Conveyor System
- The conveyor system is responsible for moving parts through the powder coating process. Conveyor systems can be manual, automated, or robotically controlled, depending on the scale of production.
- Automated conveyor systems improve efficiency by providing consistent part movement, reducing handling time, and minimizing errors.
- Overhead conveyors and flat-bed conveyors are commonly used to transport parts from one stage of the process to another, such as from pre-treatment to coating and then to curing.
- Pre-Treatment System
- Before powder coating, parts must be pre-treated to ensure proper adhesion of the coating. Pre-treatment systems are used to clean, degrease, and sometimes chemically etch the surface of parts.
- Common pre-treatment methods include phosphating, abrasive blasting, or acid pickling, which remove oils, dirt, and rust from metal surfaces.
- Pre-treatment is critical in industries such as automotive and aerospace, where durability and adhesion are vital for product performance.
- Powder Feed System
- The powder feed system is responsible for delivering the correct amount of powder to the spray gun. The system ensures a constant flow of powder, which is important for achieving uniform coating coverage.
- The powder can be supplied through gravity-fed hoppers, pressure pots, or fluidized beds, each providing a different method for maintaining a steady powder supply.
- Control and Automation Systems
- Advanced powder coating systems often include automated control systems that monitor and adjust various aspects of the process, including spray gun parameters, oven temperature, and curing times.
- PLC (Programmable Logic Controllers) and HMI (Human Machine Interface) systems are used to integrate and control the entire powder coating line. These systems ensure that the coating process remains consistent, reducing human error and improving overall productivity.
Types of Powder Coating Equipment
- Manual Powder Coating Equipment
- Manual powder coating equipment includes handheld spray guns, powder booths, and basic curing ovens. It is typically used in smaller-scale operations, custom work, and low-volume production.
- This type of equipment offers flexibility and lower upfront costs but may not be as efficient for large-scale production runs due to the higher labor requirements.
- Automatic Powder Coating Equipment
- Automatic systems are ideal for high-volume production and large part runs. These systems use robotic arms, automatic spray guns, and conveyor belts to coat parts without the need for human intervention during the application process.
- Automatic equipment can increase throughput, improve consistency, and reduce labor costs, making it ideal for industries like automotive and appliance manufacturing.
- Batch Powder Coating Systems
- Batch systems are used for small to medium-sized parts that are coated in smaller quantities or in a non-continuous manner. These systems are highly customizable and can be configured for a variety of parts with different geometries.
- While not as high-output as automated systems, batch powder coating systems are efficient for custom or low-volume production.
- Robotic Powder Coating Systems
- Robotic systems are used in applications that require high precision and flexibility in coating complex geometries. These systems are highly automated and use robotic arms to apply powder to parts with consistent and accurate results.
- Robotic systems are especially useful in industries like automotive, aerospace, and electronics, where parts have intricate shapes or where the need for a uniform coating is paramount.
- Hybrid Powder Coating Systems
- Hybrid systems combine the benefits of both manual and automatic systems, allowing manufacturers to switch between batch processing and continuous production. This adaptability is useful for companies that need both flexibility and efficiency in their powder coating processes.
- Hybrid systems can be customized to meet specific production needs, making them suitable for medium to high-volume runs that involve different part types and coatings.
Benefits of Powder Coating Equipment
- Durability: Powder-coated surfaces are resistant to scratches, fading, corrosion, and chipping, making them ideal for harsh environments and heavy-use applications.
- Environmental Benefits: Powder coating produces less waste compared to traditional liquid coatings. Additionally, the process doesn’t require solvents, making it more environmentally friendly.
- Cost-Effectiveness: The ability to recycle unused powder reduces material costs, and the durability of powder coatings extends the life of products, reducing long-term replacement costs.
- Customization: Powder coating equipment allows for a wide variety of textures, finishes, and colors, making it suitable for many industries where aesthetics are important.
- High Efficiency: Automated systems and robotic arms improve throughput, minimize downtime, and ensure consistency across large production runs.
In conclusion, powder coating equipment is crucial for ensuring the efficient, high-quality, and environmentally friendly application of durable coatings to various parts. The choice of equipment, whether manual, automatic, or robotic, depends on the scale of production, type of parts, and specific requirements of the industry. With ongoing advancements in technology, powder coating equipment is becoming more efficient, customizable, and eco-friendly, ensuring that it remains a popular choice in manufacturing across many sectors.
Powder coating equipment plays a crucial role in ensuring that a wide range of products, particularly metal parts, receive durable and high-quality finishes. These systems are designed to efficiently apply powder coatings to products while minimizing waste and environmental impact. One of the most important components in powder coating equipment is the spray gun. This tool uses electrostatic charge to apply powder to a part, ensuring that the powder adheres evenly to the surface. Powder coating systems typically come with either manual or automated spray guns, depending on the scale and precision required. For large-scale operations, automatic and robotic spray guns are increasingly being used as they provide high precision and consistency, allowing for faster and more efficient coating with minimal human intervention.
The powder is applied inside a powder booth, where a controlled airflow helps keep the powder suspended and ensures an even distribution. Advanced booths come with integrated systems to capture oversprayed powder, which is then recycled for reuse, reducing waste and making the process more cost-effective. The recovered powder is directed back to the powder feed system, which supplies the spray gun with a constant stream of powder during the application process. These systems can include gravity-fed hoppers, pressure pots, or fluidized beds, each chosen based on the production requirements.
After the powder is applied to the parts, they are moved into a curing oven. The oven heats the parts to a specific temperature, causing the powder to melt and bond to the surface, resulting in a smooth and durable coating. Infrared ovens and hybrid curing ovens are becoming more popular as they provide energy-efficient solutions and faster curing times. The choice of oven depends on the type of powder coating being used and the specific needs of the production process.
To facilitate smooth movement through the process, a conveyor system is often used to transport parts between different stages, such as pre-treatment, coating, and curing. These conveyor systems can be manual or automated, with overhead conveyors and flat-bed conveyors being the most common types. The use of automated conveyors increases efficiency and ensures parts are handled consistently throughout the coating process.
Before the powder is applied, parts must go through a pre-treatment process, which may involve cleaning, degreasing, and sometimes etching the surface to ensure proper adhesion. Common pre-treatment methods include phosphating and abrasive blasting, which remove dirt, oils, and rust from the metal surface. The pre-treatment ensures that the powder adheres properly, resulting in a high-quality and durable finish that can withstand environmental stresses such as corrosion, fading, and wear.
As manufacturers seek greater efficiency, more powder coating systems are being integrated with advanced control and automation technologies. Programmable controllers (PLCs) and human-machine interfaces (HMIs) allow operators to control and monitor the coating process from start to finish, ensuring that the machines run smoothly and consistently. These systems can adjust spray parameters, curing times, and oven temperatures based on real-time data, further enhancing the efficiency and quality of the finished product.
One of the key advantages of powder coating equipment is the ability to recycle excess powder, which significantly reduces waste. With powder recovery systems that capture overspray, manufacturers can reuse powder that does not adhere to the part, making the process more sustainable and cost-effective. This recovery system is often integrated into the powder booth, where filters and cyclonic separators collect unused powder for reintroduction into the process.
Powder coating equipment is highly customizable, and there are systems available for different production volumes and part types. Manual systems are ideal for smaller production runs, offering flexibility for custom parts, while automatic systems are better suited for large-scale, high-volume production. Automated systems use robotic arms and conveyors to move parts through the coating process, improving throughput and consistency. Hybrid systems allow manufacturers to combine manual and automated processes, providing flexibility for small to medium-sized runs with varying part types and finishes.
The powder coating process itself is highly efficient and environmentally friendly compared to traditional liquid coatings. Since it doesn’t require solvents, powder coating generates fewer volatile organic compounds (VOCs) and reduces the environmental impact. Additionally, the durability of powder coatings means that parts require less frequent maintenance or replacement, further contributing to sustainability.
In terms of energy efficiency, the development of more advanced curing ovens has made it possible to reduce the energy consumption of the powder coating process. Infrared curing ovens, for example, directly apply heat to the parts, allowing for faster curing times and reducing the overall energy required to achieve a high-quality finish. This energy-efficient technology is particularly beneficial for manufacturers looking to lower operating costs and reduce their carbon footprint.
Looking forward, the trend in powder coating equipment will continue to focus on automation and smart technologies. The integration of IoT sensors, AI, and machine learning into powder coating systems will allow for more precise control of the coating process. These technologies will be able to monitor the process in real time, making adjustments to optimize powder application, curing time, and temperature, ensuring a consistent, high-quality finish every time. Predictive maintenance capabilities powered by AI will also reduce downtime by anticipating equipment failures before they happen, extending the life of machines and minimizing the risk of production delays.
Powder coating equipment is also becoming more flexible and adaptable to meet the increasing demand for custom finishes. As industries require more specialized coatings—such as metallic, textured, or multi-layer finishes—powder coating systems are evolving to accommodate these diverse needs. Advances in color-matching technology and interactive finishes that change appearance depending on lighting or viewing angle will enable manufacturers to create unique and high-end products that appeal to modern consumers.
With growing demand for eco-friendly manufacturing practices, powder coating systems will continue to embrace sustainability. New powder formulations that are low-VOC or even water-based will reduce harmful emissions, while increased focus on material recovery will ensure that waste is minimized. These systems will also be designed to handle shorter production cycles and on-demand manufacturing, which are increasingly important in industries that need flexibility and speed in response to customer demands.
Overall, the evolution of powder coating equipment is focused on improving efficiency, quality, sustainability, and customization. With innovations in automation, smart technologies, and energy-efficient systems, powder coating is becoming an even more attractive solution for a wide variety of industries, from automotive to appliance manufacturing, offering durable, eco-friendly, and cost-effective finishes. As technology advances, the future of powder coating equipment looks set to deliver even greater precision, speed, and sustainability.
As powder coating equipment continues to evolve, there will be a further push toward intelligent manufacturing with an emphasis on data integration and real-time monitoring. The adoption of smart systems that are interconnected within the production line will enhance the ability to collect, analyze, and leverage data throughout the entire coating process. By integrating technologies like Internet of Things (IoT) sensors and cloud computing, manufacturers can gain deep insights into every step of the coating process—from powder application to curing—and make instant adjustments to optimize efficiency and quality.
The implementation of predictive analytics will take the maintenance and operational performance of powder coating equipment to the next level. Using historical data and sensor inputs, these systems will be able to predict when a machine or part is likely to fail, allowing for proactive maintenance that reduces unplanned downtime and minimizes production disruptions. These predictive systems will also help identify inefficiencies in the coating process, allowing manufacturers to fine-tune their operations and reduce waste, which will further lower costs and improve overall sustainability.
One of the major areas of innovation in powder coating equipment will be in the development of next-generation powder formulations. New powders with improved adhesion properties, enhanced resistance to UV degradation, and superior chemical resistance will enable manufacturers to meet the increasingly complex demands of industries like automotive, aerospace, and electronics. These advanced formulations may also offer benefits such as self-healing capabilities, allowing the coating to recover from minor scratches or damage without requiring touch-ups.
There will also be an increased demand for specialized finishes that go beyond traditional solid colors. As design aesthetics become more important, manufacturers will look for ways to incorporate metallic, pearlescent, and textured finishes with greater precision. Powder coating systems will need to adapt to these demands, allowing for easy customization and the ability to seamlessly switch between different powder types and finishes without sacrificing efficiency. Automated systems will be able to detect the specific coating requirements for each batch, ensuring that the correct powder is applied, and the coating is consistent.
Another significant area of focus will be in improving the energy efficiency of the entire powder coating process. Hybrid ovens, which combine traditional convection with advanced infrared or UV curing technologies, are being developed to reduce energy consumption and curing times. By applying energy more directly to the parts being coated, these systems will enable faster throughput and a reduced environmental footprint, helping manufacturers meet increasingly stringent sustainability goals. Moreover, the integration of solar power and other renewable energy sources into the curing process could help reduce the reliance on conventional energy, making powder coating even more eco-friendly.
The industry will also continue to explore automated robotic solutions that enhance both the precision and efficiency of the powder coating process. With advancements in robotics, systems are now capable of coating highly complex or delicate parts with intricate geometries, which was once difficult to achieve with traditional manual or automated spray methods. Collaborative robots (cobots), which work alongside human operators, will become more common in powder coating lines. These cobots can be deployed to assist in delicate tasks, such as fine-tuning spray patterns or handling smaller, custom-coated components that require human oversight.
In addition to increased automation, there will be a growing trend toward customized powder coating systems tailored to meet the needs of specific industries. Modular systems will allow manufacturers to configure their equipment based on the requirements of each job. Whether it’s a batch system for smaller runs, an automated conveyor system for high-volume production, or a hybrid solution that combines both, manufacturers will be able to tailor their powder coating equipment for maximum flexibility and efficiency.
Sustainability will continue to be a major driver of change within the powder coating industry. As consumers and governments place greater emphasis on environmental responsibility, powder coating will see further advancements in reduced environmental impact and resource efficiency. From low-emission curing ovens to waterborne and non-toxic powder formulations, the focus on creating coatings that are safer for both the environment and human health will shape the direction of the industry.
The future of powder coating also holds the potential for faster production cycles and just-in-time manufacturing. As industries demand quicker turnaround times and more agile production lines, powder coating equipment will need to adapt to meet these challenges. Future systems will likely feature enhanced fast-changeover capabilities that allow for quick switches between colors and coatings, minimizing downtime and maximizing throughput. This is particularly important in industries like automotive, where rapid customization of parts and finishes is key to meeting consumer demand.
Another important aspect of the future of powder coating equipment will be enhanced precision and quality control. Advances in machine vision, automated inspection systems, and augmented reality (AR) technologies will be integrated into the powder coating process to ensure that every part is coated to the highest standards. These systems will use advanced sensors and cameras to detect any coating defects, such as missed spots, uneven application, or contamination. This data will be fed into automated systems, allowing for immediate adjustments to the coating process and preventing defects before they occur.
Finally, as powder coating technology continues to advance, the market for powder-coated products will expand. More industries are adopting powder coating for its combination of durability, environmental friendliness, and aesthetic appeal. Consumer goods, such as electronics, home appliances, and furniture, are increasingly being powder coated due to the unique finish options, long-lasting durability, and low environmental impact compared to traditional painting methods.
In conclusion, the future of powder coating equipment is poised for major advancements driven by automation, sustainability, customization, and digitalization. Manufacturers will benefit from systems that offer greater flexibility, improved efficiency, and the ability to meet the evolving needs of a diverse range of industries. With the continued development of innovative powder formulations, eco-friendly technologies, and cutting-edge robotic solutions, powder coating will remain a key process for producing high-quality, durable, and sustainable finishes on a wide range of products.
Automated Powder Coating System
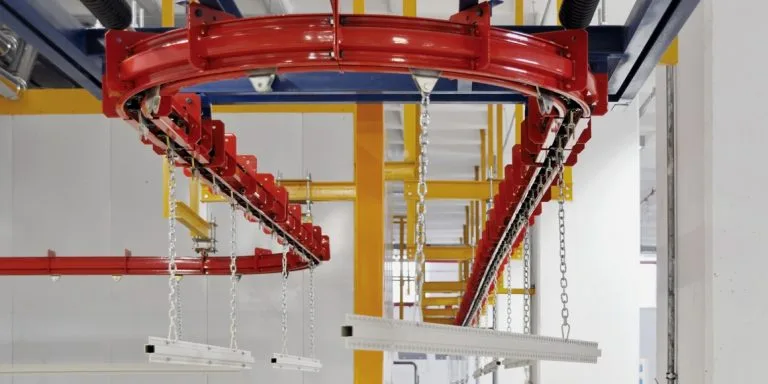
An Automated Powder Coating System is designed to apply a uniform, durable powder coating to parts with minimal manual intervention. This system is particularly valuable for high-volume production environments where efficiency, consistency, and quality are essential. Automated powder coating systems integrate advanced technologies to streamline the coating process, improving precision, reducing waste, and enhancing productivity. Below is a comprehensive overview of the components and benefits of automated powder coating systems.
Key Components of an Automated Powder Coating System
- Automatic Powder Coating Guns
- Automatic spray guns are central to the automated coating process. These guns are programmed to apply powder to parts with consistent coverage. They use electrostatic charge to ensure that the powder is attracted to the surface of the part, resulting in even coverage. The spray guns are controlled by robotic arms or conveyors that move them around the part to apply the powder uniformly.
- Spray gun types may include automatic reciprocators, which move back and forth, or robotic spray arms that allow for precise application over complex geometries.
- Robotic Systems
- Robotic arms are often integrated into automated powder coating systems to provide high precision in powder application. The robots are programmed to move the spray guns in a manner that ensures even and consistent powder deposition on every part, regardless of its shape.
- Articulated robotic arms can reach all areas of the part, ensuring that every surface is coated. Robots can work with multiple guns simultaneously to increase the speed of the process.
- These systems are capable of handling complex shapes and configurations, making them ideal for industries such as automotive, aerospace, and electronics.
- Powder Feed System
- The powder feed system delivers the powder to the spray guns in a controlled manner. It typically uses gravity-fed hoppers, pressure pots, or fluidized beds to provide a steady flow of powder to the guns.
- The system is integrated with the powder recovery unit, ensuring that any excess powder is collected and sent back into the feed system for reuse, reducing material waste and improving cost-effectiveness.
- Powder Booth
- The powder booth is a dedicated area where the powder is sprayed onto the parts. Automated powder coating booths are designed to minimize powder loss and ensure an even application across all parts. They typically feature airflow systems that keep the powder suspended, preventing overspray from settling in unwanted areas.
- Advanced booths come with recapture systems that collect unused powder and send it back into the system for reuse, making the process more environmentally friendly and economical.
- Filtration systems within the booth help keep the air clean by removing excess powder, which is important for worker safety and for maintaining a clean working environment.
- Conveyor System
- A conveyor system is used to move parts through the various stages of the powder coating process, from pre-treatment and coating to curing. Automated conveyors help reduce the need for manual handling, which increases throughput and reduces the potential for contamination or errors in handling.
- These conveyors can be overhead, flat-belt, or monorail systems, depending on the layout of the production line and the size of the parts being coated.
- Curing Oven
- After the powder is applied, the parts are moved into a curing oven, where the powder is baked at a specific temperature. The heat causes the powder to melt and form a durable, protective finish on the part.
- Infrared curing ovens and hybrid curing ovens are often used in automated systems to speed up the curing process and improve energy efficiency. These ovens ensure that all parts receive uniform heat to create a consistent finish.
- The curing oven can be integrated with automated conveyors, ensuring that parts are moved through the oven at the correct speed and temperature for optimal curing.
- Powder Recovery and Filtration System
- Powder recovery systems are designed to capture excess or oversprayed powder. The recovered powder is sent back to the powder feed system for reuse, reducing material waste and improving efficiency.
- The system typically includes cyclonic separators, filters, and sieving equipment to remove contaminants from the powder before it is reused.
- High-efficiency filters are crucial to maintaining clean air in the powder booth and ensuring that recovered powder meets the required quality standards.
- Control and Automation System
- A central control system is used to monitor and manage the entire automated powder coating process. This includes controlling the operation of spray guns, robotic arms, conveyor systems, curing ovens, and powder recovery systems.
- Programmable Logic Controllers (PLCs) and Human-Machine Interfaces (HMIs) are used to control and adjust key parameters such as spray gun speed, powder feed rates, oven temperature, and curing time.
- Modern systems often feature data logging and real-time monitoring capabilities, enabling manufacturers to track performance, detect issues, and make adjustments quickly to optimize the process.
Benefits of Automated Powder Coating Systems
- Increased Efficiency
- Automated systems significantly increase the speed and efficiency of the powder coating process. By reducing manual intervention, parts can be coated more quickly, allowing for faster production cycles and higher throughput. This is especially beneficial for industries with high-volume production needs, such as automotive or appliance manufacturing.
- Consistency and Quality Control
- Automation ensures that powder coating is applied uniformly, reducing the likelihood of defects such as inconsistent coverage, overspray, or uneven coating thickness. With robotic arms and automated spray guns, the system can apply coatings with a high degree of precision, resulting in a consistent finish across all parts.
- Cost Savings
- While the initial investment in automated powder coating equipment can be significant, the long-term savings are substantial. The ability to recycle unused powder, reduce labor costs, and minimize material waste makes automated systems a cost-effective solution over time.
- Reduced labor costs, faster production times, and fewer defects all contribute to overall cost savings in the production process.
- Environmental Benefits
- Automated systems are designed to minimize waste and improve material recovery. The use of powder recovery systems allows for the reuse of oversprayed powder, significantly reducing waste and lowering material costs.
- Moreover, powder coating is an environmentally friendly process compared to traditional liquid coating methods. It does not require solvents, reducing the emission of volatile organic compounds (VOCs) and creating a safer, more sustainable working environment.
- Improved Safety
- Automation reduces the amount of direct human involvement in the coating process, which can be hazardous due to the chemicals and heat involved. The use of robotic systems and automated conveyors minimizes the risk of worker exposure to harmful substances, improving workplace safety.
- Flexibility and Customization
- Automated systems can be programmed to coat parts of various sizes and shapes, providing flexibility for different types of production runs. Modern automated powder coating systems often feature easy changeover capabilities, allowing manufacturers to switch between different powder colors or finishes quickly and with minimal downtime.
- Increased Precision
- The integration of robotic arms and automatic spray guns enhances precision and enables the coating of complex geometries. Robotic systems are capable of adjusting their spray patterns and angles to ensure that every part is coated evenly, even in hard-to-reach areas.
- Reduced Downtime
- Automated powder coating systems can operate continuously, with minimal intervention required. This leads to reduced downtime and increased uptime in production. Furthermore, predictive maintenance systems powered by AI and IoT sensors can anticipate equipment failures before they happen, minimizing unplanned outages.
Applications of Automated Powder Coating Systems
Automated powder coating systems are used across various industries due to their efficiency and versatility. Some key applications include:
- Automotive Industry: Powder coating is used for car parts, including wheels, bumpers, and chassis components. The automated system ensures that these parts receive a durable, high-quality finish that withstands wear, corrosion, and exposure to the elements.
- Appliance Manufacturing: Household appliances such as refrigerators, washing machines, and ovens benefit from powder coating, as it provides a tough, attractive finish. Automated systems are ideal for coating large quantities of parts consistently.
- Metal Fabrication: Automated systems are used to coat metal furniture, structural components, and other metal products. The precision of robotic systems ensures a uniform finish on metal surfaces.
- Electronics: Some electronic components are coated with powder to enhance durability, protect against corrosion, and provide an aesthetic finish.
- Architectural Coatings: Powder coating is used to finish architectural components like window frames, door frames, and decorative metalwork. Automated systems provide a consistent and high-quality finish for these products, which are often exposed to harsh environmental conditions.
In conclusion, automated powder coating systems are a game-changer for industries looking to improve production efficiency, reduce costs, and maintain consistent quality. With their ability to handle complex geometries, provide precision coating, and recycle materials for minimal waste, these systems are essential for manufacturers aiming to meet the growing demands of high-volume production, sustainability, and product quality.
Automated powder coating systems have revolutionized the coating process by increasing efficiency, precision, and consistency, particularly for high-volume manufacturing. These systems are essential for industries that require rapid production cycles and top-notch finish quality, such as automotive, aerospace, and appliance manufacturing. By incorporating robotic systems, automated powder coating equipment can achieve unparalleled consistency in powder application, ensuring uniform coverage and reducing the risk of defects like missed spots or uneven coating thickness. Additionally, the use of advanced spray guns and robotic arms ensures that even parts with intricate shapes or difficult-to-reach areas receive a consistent, durable finish.
One of the most significant advantages of these automated systems is their ability to reduce material waste. Through the use of powder recovery systems, excess powder is captured and sent back into the system, allowing it to be reused. This closed-loop system minimizes waste, making powder coating a more environmentally friendly option than traditional liquid coatings that require solvents. The ability to recycle powder is a significant cost-saving feature for manufacturers, as it reduces the amount of new powder needed for production. Furthermore, automated systems often come with built-in filtration and separation systems, ensuring that only high-quality powder is applied to the parts, which further enhances the final product’s durability and finish.
Another key benefit of automated powder coating systems is their speed. These systems are designed to run continuously with minimal downtime, which is especially important for industries that rely on large-scale, high-volume production. Automated systems can also handle multiple parts simultaneously, dramatically increasing throughput while maintaining quality. The integration of robotic systems with conveyor systems ensures that parts move seamlessly through each stage of the coating process, from application to curing, without manual handling. This reduces the chances of contamination or defects caused by human error and significantly increases production efficiency.
Moreover, automated powder coating systems are increasingly integrated with smart technologies like IoT sensors and machine learning algorithms. These innovations allow manufacturers to monitor the process in real-time, track performance, and make immediate adjustments if necessary. For example, a system could automatically adjust spray parameters or curing times based on real-time data, ensuring optimal results every time. These systems can also provide valuable insights into maintenance needs, enabling predictive maintenance that helps reduce downtime by addressing issues before they cause equipment failure.
With the ability to customize the finish and adapt to various parts, automated systems can handle a wide range of coating requirements. Whether applying a simple solid color or a complex texture, automated powder coating systems offer the flexibility to meet diverse customer demands. In fact, many systems today feature easy changeover capabilities, allowing manufacturers to switch between colors or coatings quickly without significant downtime. This level of customization makes these systems ideal for industries that require both high-volume production and flexibility, such as automotive manufacturing, where part designs and finishes can vary.
The curing process is another area where automation adds value. After powder is applied, parts are moved to a curing oven, where the powder melts and bonds to the surface. Automated curing ovens are often equipped with advanced technologies, such as infrared heating and hybrid curing systems, that reduce energy consumption and speed up curing times. These ovens are often integrated with the automated conveyor system, ensuring that parts are heated to the correct temperature for the right amount of time, leading to consistent results.
In terms of cost-effectiveness, while the initial investment in automated systems may be high, the return on investment is significant due to reduced labor costs, faster production times, and lower material waste. The precision of automated systems minimizes the need for manual touch-ups or rework, which can be both time-consuming and costly. Additionally, by reducing waste and increasing throughput, automated systems help manufacturers achieve higher profit margins and remain competitive in a rapidly changing market.
Another notable advantage of automated systems is their environmental impact. Compared to traditional liquid coatings that contain solvents and volatile organic compounds (VOCs), powder coating is a much cleaner process. It produces little to no harmful emissions, making it an attractive option for companies looking to reduce their environmental footprint. The ability to recover and reuse powder further contributes to the system’s eco-friendliness, as it limits material waste and reduces the need for raw materials.
The versatility of automated powder coating systems means they can be used across a broad spectrum of industries. For example, in the automotive sector, powder coating is used for a variety of components, from chassis parts to wheels. The durability and corrosion resistance of the coating make it ideal for parts exposed to harsh weather conditions. In appliance manufacturing, products like refrigerators, washing machines, and microwaves benefit from the smooth, long-lasting finish that automated powder coating provides. Furthermore, the system’s ability to handle large volumes of parts at once ensures that manufacturers can meet the high demands of these industries.
Electronics is another area where automated powder coating systems have proven valuable. Components like circuit boards or metal enclosures require powder coatings that offer protection from wear, corrosion, and even electromagnetic interference (EMI). Automated systems ensure that these delicate components receive the proper coating thickness and uniformity, preventing defects and ensuring reliability.
In terms of future advancements, automated powder coating systems will likely continue to integrate more sophisticated technologies, such as machine vision for automated quality control. By using cameras and sensors, these systems can detect defects in real-time and make immediate adjustments to the coating process to ensure that all parts meet the required standards. In addition, artificial intelligence and big data analytics will play an increasingly important role in optimizing the powder coating process, predicting maintenance needs, and improving the overall quality and efficiency of the system.
Looking ahead, there will also be a greater emphasis on sustainability. With growing pressure to reduce environmental impact, the powder coating industry will likely see more innovations in low-emission systems, eco-friendly powders, and energy-efficient curing ovens. As demand for custom finishes continues to rise, automated systems will evolve to handle a broader range of finishes, such as textured coatings, metallic finishes, and specialty effects, without compromising speed or efficiency.
Overall, automated powder coating systems represent the future of coating technology, offering manufacturers an efficient, cost-effective, and sustainable solution for high-quality finishes. With their ability to handle large production runs, deliver consistent results, and minimize waste, these systems are essential in meeting the evolving demands of industries seeking to improve their operations and produce top-tier products. As technology continues to advance, automated powder coating systems will become even more precise, flexible, and energy-efficient, helping manufacturers stay competitive while achieving the highest standards of quality and sustainability.
As automated powder coating systems continue to evolve, there will be an even greater push toward integration with Industry 4.0 technologies. The shift towards smart manufacturing will see automated powder coating systems leveraging big data analytics, cloud computing, and real-time data exchange to enable a fully connected production environment. These systems will not only monitor the coating process but also provide detailed insights into machine performance, environmental factors, and product quality throughout the entire production cycle. Manufacturers will be able to analyze data from the system in real-time, adjusting parameters to optimize output, prevent defects, and reduce waste without halting production.
In the near future, predictive maintenance will become even more sophisticated, utilizing AI-driven algorithms to predict potential failures or malfunctions before they happen. By analyzing patterns in sensor data, such as temperature, pressure, and powder usage, AI can forecast when parts or components of the system may need maintenance. This will reduce the risk of unexpected downtime, helping manufacturers avoid costly production interruptions. Predictive maintenance systems will also optimize service schedules, ensuring that parts are replaced or repaired only when necessary, further reducing costs and increasing the efficiency of the production line.
Furthermore, machine vision will play an increasingly important role in quality control within automated powder coating systems. Advanced visual inspection technologies will be able to detect even the smallest defects in the coating process, such as uneven powder distribution, inconsistent thickness, or contaminants in the coating. Cameras and imaging systems will work in real-time to provide instant feedback to the system, allowing for adjustments to the spray guns, curing temperatures, or conveyor speed. This will not only improve the consistency of the coating process but also reduce the need for manual inspection, which can be time-consuming and prone to human error.
To complement these advancements, augmented reality (AR) may be used to assist operators in monitoring and controlling the automated systems. By wearing AR glasses or using tablets, operators could access real-time data and analytics, viewing the status of various components, such as powder flow, gun settings, or oven temperatures, in an intuitive interface. AR could also provide troubleshooting guidance, with step-by-step visual instructions for maintenance or repair tasks, helping operators respond to issues more quickly and accurately.
The energy efficiency of automated powder coating systems will also continue to improve. As manufacturers look for ways to reduce their environmental footprint, the use of renewable energy sources, such as solar power, could become more common in curing ovens or auxiliary heating systems. Additionally, advanced energy recovery technologies will help optimize the use of energy during the curing process, reducing consumption and lowering operating costs. Some systems may even incorporate heat recovery systems to capture and reuse heat generated during the curing process, further improving overall energy efficiency.
Customization and flexibility will also be key drivers in the development of future automated powder coating systems. As consumer demands for personalized products increase, manufacturers will need systems that can easily switch between various powder types, colors, and finishes. Modular systems will allow manufacturers to reconfigure their powder coating setups based on the specific needs of a production run, providing a high degree of flexibility without sacrificing efficiency. These systems will be capable of handling a wide variety of finishes, including matte, glossy, metallic, and textured coatings, enabling manufacturers to meet diverse customer preferences.
Automation will also enable faster changeovers between production runs, reducing downtime and increasing the responsiveness of manufacturing operations. Automated powder coating systems will be equipped with quick-change features, such as powder delivery systems that can be rapidly cleaned and reconfigured, minimizing the time required to switch between different powder types. This is particularly important in industries where rapid turnaround times and custom finishes are required, such as the automotive and consumer electronics sectors.
Another potential development in automated powder coating is the integration of advanced coatings that offer enhanced performance characteristics, such as self-healing properties, anti-microbial coatings, or coatings with superhydrophobic (water-repellent) properties. These innovative coatings would open up new markets for automated powder coating systems, allowing manufacturers to meet the increasing demand for specialized finishes in industries like medical devices, food processing, and consumer goods. Automated systems would need to be adapted to handle these new types of powders, which may have different application requirements compared to traditional coatings.
The focus on sustainability will continue to drive innovations in powder coating technologies. As companies seek to meet stricter environmental regulations and achieve net-zero emissions goals, powder coating systems will evolve to become even more environmentally responsible. Water-based powder coatings, which are free from harmful solvents, will become more widely used, and manufacturers will look for ways to reduce the carbon footprint of their operations. For instance, systems may include features that enable the use of bio-based or recycled powders, further reducing the environmental impact of the coating process.
In conclusion, the future of automated powder coating systems is bright, with continued advancements that promise to improve efficiency, precision, flexibility, and sustainability. As manufacturers seek to meet the challenges of increasing production demands, customization, and environmental responsibility, automated powder coating systems will continue to evolve. With greater integration of smart technologies, energy efficiency improvements, and the ability to handle specialized coatings, these systems will remain a cornerstone of modern manufacturing, providing high-quality, cost-effective solutions for a wide range of industries. The continued development of these technologies will enable manufacturers to stay competitive in an increasingly demanding and environmentally conscious market.
As the demand for high-quality finishes and sustainable practices increases, the role of automated powder coating systems will expand further, enabling manufacturers to deliver precision-engineered products with greater consistency and lower environmental impact. Future developments in this field will increasingly focus on integrating cutting-edge technologies such as artificial intelligence (AI), machine learning (ML), and Internet of Things (IoT), which will further enhance the capabilities of automated systems in several ways.
One of the key advantages of AI and ML integration into automated powder coating systems will be the ability to optimize the application process in real-time. These systems will learn from historical data, environmental variables, and process feedback, adjusting settings like spray gun pressure, powder feed rates, and curing oven temperatures to ensure the most efficient and high-quality results with every application. The continuous learning capabilities of AI-powered systems will reduce the need for manual intervention and increase the adaptability of systems to handle a wider range of coatings, surfaces, and production demands. This kind of adaptive, data-driven approach will lead to minimized defects and optimized material usage, creating a smarter, more sustainable manufacturing process.
IoT integration will enable better communication between equipment and the central control system, providing real-time monitoring of production parameters such as humidity, temperature, and powder flow rates. The ability to collect and transmit data from connected sensors allows manufacturers to make proactive decisions on equipment maintenance, energy consumption, and operational adjustments. IoT will also facilitate better traceability and compliance reporting, as data collected throughout the powder coating process can be analyzed and stored for later review, ensuring quality assurance standards are met and products adhere to industry regulations.
Remote monitoring and control will become more prevalent in automated powder coating systems, offering manufacturers greater flexibility and control over their production lines. Operators will be able to access data and make adjustments from remote locations, reducing the need for on-site supervision. This could also help businesses scale production across multiple sites, allowing for centralized oversight of various manufacturing processes. Additionally, cloud-based platforms will play an important role in storing large amounts of production data, which can then be analyzed and accessed from anywhere in the world, fostering collaboration and informed decision-making.
As energy costs continue to rise and environmental concerns grow, energy-efficient technologies will be a major focus for automated powder coating systems. Future systems may incorporate more advanced heat recovery technologies in curing ovens, reducing energy consumption by capturing and reusing heat that would otherwise be wasted. Additionally, the use of low-energy curing methods such as infrared radiation or UV curing could reduce overall energy consumption and shorten curing times, further optimizing the process. Manufacturers will increasingly rely on sustainable energy sources, like solar or wind power, to fuel their operations, reducing the carbon footprint of powder coating systems.
Hybrid curing technologies will also gain traction, combining multiple curing methods to achieve superior results while reducing energy use. For example, a combination of infrared heat and convection ovens could allow for faster curing times and better energy efficiency, without compromising the quality of the finish. Manufacturers are likely to seek solutions that balance high-performance coating with sustainability goals, driving further innovations in curing technologies.
The demand for custom finishes will continue to grow as consumers seek more personalized products, leading to innovations in powder coating formulas. In the future, powder coatings may be designed to offer advanced properties such as scratch resistance, self-cleaning surfaces, or anti-fingerprint qualities. Automated powder coating systems will need to adapt to these more specialized formulations, which may require modifications in the powder delivery systems, spray techniques, and curing processes to accommodate new types of powder materials.
Customization in automated systems will not just be limited to finishes and formulations but will also extend to the flexibility of the equipment itself. As manufacturing processes become more diverse, automated systems will need to be reconfigurable to handle a range of part sizes, shapes, and materials. Modular systems will allow for easy reconfiguration of spray gun setups, curing oven temperatures, and conveyor speeds to adapt to changing production requirements. This level of flexibility will ensure that automated powder coating systems remain relevant in an ever-changing production landscape.
With the rise of global supply chains and just-in-time (JIT) manufacturing, automation will help meet the increasing pressure to deliver high-quality products quickly and efficiently. The future of powder coating will see systems designed to maximize throughput while maintaining consistency in the finish. As demand increases, especially for industries like automotive, electronics, and consumer goods, automated systems will need to scale up without sacrificing the precision and quality of the coating. The ability to quickly switch between different part types, colors, or finishes will allow manufacturers to stay agile in a competitive marketplace.
The shift toward eco-friendly coatings will continue to influence the design and development of powder coating equipment. Waterborne powder coatings and bio-based powders are gaining popularity for their reduced environmental impact. As the demand for non-toxic, low-VOC, and solvent-free coatings rises, manufacturers will need to adopt technologies that can handle these new formulations, ensuring compatibility with automated coating processes. Additionally, regulatory pressures to reduce environmental impact will push for further innovations in powder coatings that are not only high-performing but also sustainable.
Another area of development will be the integration of smart maintenance solutions. The ability to predict when maintenance is needed based on machine learning algorithms and real-time performance data will extend the life of equipment and reduce downtime. Automated powder coating systems will be equipped with self-diagnostic tools that can detect issues like wear and tear, clogged nozzles, or temperature fluctuations in real-time. These diagnostic tools will alert operators to potential issues before they become critical, allowing for preemptive action and minimizing disruptions to the production schedule.
Finally, collaboration between suppliers and manufacturers will play a critical role in advancing powder coating technologies. Suppliers of powders, curing equipment, and automation systems will continue to innovate together to create synergistic solutions that improve both the process and the final product. These partnerships will help manufacturers implement the most advanced powder coating solutions available, keeping them competitive while meeting the growing demand for high-quality, customizable, and sustainable coatings.
In conclusion, the future of automated powder coating systems is poised for continuous evolution, driven by advancements in AI, IoT, energy efficiency, and sustainability. Manufacturers will benefit from systems that are increasingly data-driven, customizable, and environmentally responsible, allowing them to meet the demands of a rapidly changing market. As automation becomes more integrated into smart manufacturing environments, powder coating systems will play a critical role in delivering high-quality, cost-effective, and eco-friendly coatings for a wide range of industries.
Alloy Wheel Powder Coating
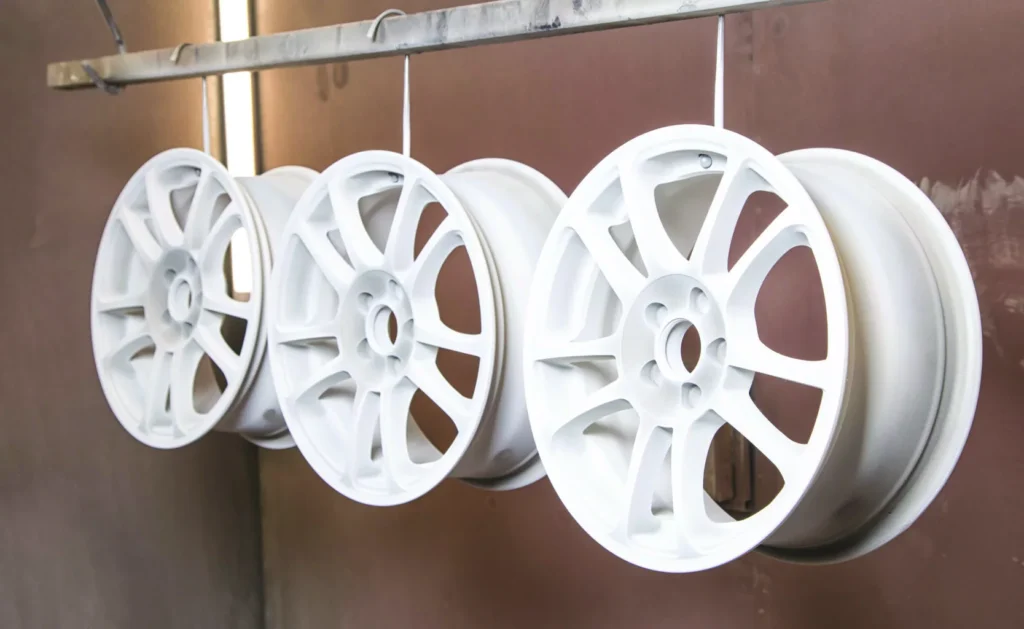
Alloy wheel powder coating is a popular and effective method used to enhance the appearance, durability, and protection of alloy wheels. The process involves applying a dry powder coating to the surface of the alloy wheels, which is then cured under heat to form a hard, protective finish. This method is preferred over traditional liquid painting for several reasons, including better durability, corrosion resistance, and a more uniform, smooth finish.
Key Benefits of Alloy Wheel Powder Coating
- Durability: Powder coating provides a more durable and long-lasting finish compared to traditional liquid paint. The coating forms a strong bond with the wheel surface, making it resistant to scratches, chips, fading, and wear. This is especially important for alloy wheels, which are exposed to harsh conditions such as road debris, salt, and UV rays.
- Corrosion Resistance: Alloy wheels are often exposed to moisture, salt, and chemicals, which can lead to corrosion and rusting. Powder coating acts as a protective barrier that prevents these elements from damaging the wheel’s surface, ensuring that the wheels maintain their appearance and structural integrity for a longer period.
- Aesthetic Appeal: Powder coating offers a wide range of finishes and colors, from matte and glossy to metallic and textured coatings. This allows car owners to customize their wheels to match the vehicle’s design and style. It also ensures a consistent and smooth finish, without the runs or sags that can occur with liquid paint.
- Eco-friendly: Powder coating is considered more environmentally friendly than traditional liquid painting because it contains no solvents and low levels of volatile organic compounds (VOCs). This makes it a safer and more sustainable option for both manufacturers and consumers.
- Cost-Effective: While the initial cost of powder coating may be higher than traditional painting, it is more cost-effective in the long run due to its durability and the fact that it requires fewer touch-ups or repairs. Additionally, the powder recovery system in many automated powder coating processes reduces material waste, making it more economical.
- Heat Resistance: Alloy wheels are exposed to high temperatures from the braking system. Powder coatings can withstand these higher temperatures without losing their structural integrity, unlike some traditional paints, which may break down or discolor under heat.
Powder Coating Process for Alloy Wheels
The process of powder coating alloy wheels is relatively straightforward, but it involves several key steps to ensure a high-quality finish:
- Cleaning and Preparation: The first step is to thoroughly clean the alloy wheel surface to remove any dirt, grease, or contaminants. This can be done using abrasive blasting (sandblasting), chemical cleaning agents, or other methods. The goal is to create a clean, smooth surface for the powder coating to adhere to.
- Surface Treatment: After cleaning, the wheels may undergo a treatment process to improve the adhesion of the powder coating. This often includes an acid etching or phosphating process that roughens the surface slightly, providing better bonding for the coating.
- Powder Application: Once the wheels are prepped, the powder is applied using an electrostatic spray gun. The powder particles are electrically charged and sprayed onto the wheel’s surface. The electrostatic charge ensures that the powder adheres evenly to the surface, creating a consistent layer of coating.
- Curing: After the powder is applied, the wheels are placed in a curing oven, where they are heated to a specific temperature (usually around 180-200°C or 356-392°F) for a set amount of time. During this process, the powder melts, flows, and chemically bonds to the surface, forming a hard, smooth finish. Curing is a critical step in ensuring the powder coating’s durability and performance.
- Cooling and Inspection: Once the curing process is complete, the wheels are allowed to cool down before being inspected for defects. Any imperfections, such as bubbles or inconsistencies, are identified and corrected. The wheels are then ready for reassembly and installation.
Types of Powder Coatings for Alloy Wheels
- Polyester Powder Coating: This is the most commonly used powder coating for alloy wheels due to its durability, weather resistance, and excellent finish. It is highly resistant to UV light, ensuring that the coating does not fade or discolor over time.
- Epoxy Powder Coating: Epoxy powder coatings offer excellent adhesion and corrosion resistance, making them ideal for wheels exposed to harsh conditions. However, they are not as resistant to UV degradation as polyester-based coatings, so they may be more prone to fading if exposed to direct sunlight over time.
- Hybrid Powder Coating: Hybrid powders combine the properties of both epoxy and polyester, offering a balance of durability, corrosion resistance, and UV stability. These coatings are well-suited for alloy wheels because they provide an excellent combination of protection and aesthetic appeal.
- Textured Finishes: In addition to glossy and matte finishes, alloy wheels can be powder-coated with textured finishes such as wrinkle, hammered, or pebble textures. These finishes not only enhance the visual appeal but also help to mask minor imperfections in the wheel’s surface.
- Metallic and Gloss Finishes: For a more striking look, metallic and gloss finishes can be applied. These finishes offer a high-shine effect and can include special metallic powders that add a glittering effect, giving the wheels a premium, customized look.
Common Applications of Alloy Wheel Powder Coating
- Automotive Industry: The most common application of powder coating is in the automotive industry, where it is used to coat alloy wheels of cars, trucks, and motorcycles. Powder-coated wheels offer superior protection against corrosion, road salts, and grime, which are particularly important for vehicles driven in areas with harsh winters or coastal climates.
- Motorcycle and Bicycle Wheels: Powder coating is also used on motorcycle and bicycle wheels, offering a durable finish that can withstand the wear and tear associated with outdoor use, including impacts, UV exposure, and moisture.
- Aftermarket Wheel Customization: Many aftermarket wheel suppliers offer powder coating as a customization service, allowing customers to choose from a range of colors, finishes, and textures. This allows vehicle owners to personalize their vehicles while also adding an extra layer of protection to their wheels.
- Off-Road Vehicles: Off-road vehicles, such as 4x4s and ATVs, often use powder-coated wheels due to the harsh conditions they are exposed to, including dirt, mud, and exposure to the elements. Powder coating helps to protect the wheels from corrosion, which is especially important when driving through water, snow, or off-road terrain.
Conclusion
Alloy wheel powder coating is an excellent way to enhance the durability, appearance, and longevity of wheels, offering significant advantages over traditional liquid paint. It provides superior protection against corrosion, chips, and UV degradation while offering a wide range of finishes and colors to suit various styles. Whether for OEM manufacturers or aftermarket customization, powder coating remains one of the most popular and effective ways to coat alloy wheels, ensuring they maintain their performance and aesthetic appeal for years.
Alloy wheel powder coating is a popular and effective way to enhance the appearance, durability, and protection of wheels, making them more resistant to corrosion, scratches, and wear. This method provides a superior finish compared to traditional liquid paint, making it the preferred choice for automotive, motorcycle, and bicycle wheels, as well as for off-road vehicles.
The powder coating process begins with thorough cleaning and preparation of the wheel’s surface. This ensures that any dirt, grease, or contaminants are removed, which could otherwise affect the adhesion of the coating. Once the wheel is clean, a surface treatment is applied to improve the bonding between the powder coating and the wheel. After this, the powder is applied using an electrostatic spray gun, where the powder particles are charged and adhere evenly to the wheel’s surface. The coating is then cured in an oven at high temperatures to form a hard, durable finish that is resistant to UV rays, weathering, and harsh chemicals.
Powder coating offers numerous advantages over traditional liquid paint. One of the main benefits is its durability; powder coating forms a much tougher bond with the wheel’s surface, making it more resistant to impacts, chips, and abrasions. Additionally, powder coating is less prone to fading or discoloration due to UV exposure, which is a common issue with liquid paints. Another significant advantage is corrosion resistance; alloy wheels are often exposed to water, road salts, and other environmental factors that can lead to rust and deterioration. Powder coating acts as a barrier, protecting the wheels from these elements and extending their lifespan.
Aesthetic appeal is another area where powder coating excels. With a variety of finishes and colors available, it allows car and bike owners to fully customize their wheels to match the look of their vehicles. Whether opting for a matte, glossy, or metallic finish, the powder coating process delivers a smooth and consistent surface. Custom finishes such as textured coatings are also available, offering unique visual effects and additional functionality, such as masking small imperfections on the wheel’s surface.
In terms of eco-friendliness, powder coating is a cleaner option compared to traditional liquid painting. It contains no solvents and emits little to no volatile organic compounds (VOCs), making it safer for both the environment and the workers applying the coating. Furthermore, powder coating produces less waste, as any excess powder can be collected and reused in the process.
Alloy wheel powder coating also provides a cost-effective long-term solution. While the initial investment may be higher than liquid painting, the durability of powder coating means fewer touch-ups or repaints are necessary. The overall life cycle of the coating is longer, which reduces maintenance costs and prolongs the overall performance and appearance of the wheels. This is particularly important for vehicles that are frequently exposed to harsh conditions, such as off-road vehicles or cars used in coastal areas with high salt content.
In the future, we can expect even more advancements in the alloy wheel powder coating process. With the integration of smart technologies, powder coating systems could become more efficient and adaptive, using data analytics and real-time monitoring to optimize the application and curing process. Additionally, the growing demand for sustainable practices may lead to further innovations, such as more eco-friendly powders, enhanced curing techniques that consume less energy, and further reduction in the environmental impact of powder coating systems.
Overall, alloy wheel powder coating remains one of the most effective and versatile methods for enhancing and protecting alloy wheels. Its combination of durability, aesthetic appeal, and environmental benefits makes it a preferred choice for both manufacturers and consumers alike. With continued innovation, it is likely that powder coating will continue to evolve, offering even greater protection and customization options in the future.
As alloy wheel powder coating continues to grow in popularity, several key advancements are on the horizon that will further enhance the performance and versatility of this coating method. One major trend is the development of advanced powder formulations that can offer even more specialized benefits. For instance, there is growing interest in self-healing powder coatings, which are designed to repair minor scratches or surface damage on their own when exposed to heat or sunlight. These coatings could significantly increase the longevity of powder-coated alloy wheels, as they would be able to “heal” from small chips and scratches that typically occur during everyday use.
Another area of focus is the advancement in color technology. While there are already numerous color options available for powder-coated wheels, manufacturers are increasingly pushing the boundaries to offer more sophisticated and unique color effects. Chameleon and pearlescent powders are becoming more popular, allowing for multi-dimensional finishes that change color depending on the angle of the light. This trend is being driven by consumer demand for highly customized and attention-grabbing designs. Additionally, metallic finishes that feature small reflective particles are being refined to offer a more brilliant, eye-catching shine without compromising durability.
Sustainability in powder coating is also expected to become a more prominent focus. As environmental regulations tighten and consumers become more eco-conscious, the powder coating industry is turning to bio-based and recycled powders. These alternatives use materials derived from renewable resources or recycled plastic and rubber to create the powders used in coating alloy wheels. This reduces the reliance on traditional raw materials and further diminishes the environmental impact of the coating process. Manufacturers may also begin to incorporate water-based powders as a greener alternative to conventional powder formulations, which are solvent-free but may still contain petrochemical components.
Additionally, with the increasing integration of digital technologies, powder coating processes are becoming more efficient and customizable. For example, 3D printing could allow for the production of custom powder-coated wheels with intricate patterns or shapes, enhancing the aesthetic appeal of the wheels and offering unique designs that were not previously possible. The use of artificial intelligence (AI) and machine learning (ML) could also play a role in automating the process of detecting imperfections or inconsistencies in the coating. AI could help fine-tune the application parameters, ensuring an even and flawless finish, while also monitoring the curing process to guarantee that the correct conditions are met.
The rise of smart manufacturing technologies will enable more flexible and automated powder coating systems that can adapt to a wide range of production needs. Automated systems equipped with sensors and machine vision could precisely monitor the wheel’s surface before, during, and after the coating application. These systems can detect small defects or contamination, alert operators in real time, and even make automatic adjustments to ensure the highest possible quality. Furthermore, IoT (Internet of Things) connectivity will allow real-time tracking of production data and remote monitoring of the powder coating process. Operators and managers will have access to key performance metrics and maintenance alerts, improving overall efficiency and reducing downtime.
Heat-resistant coatings will also continue to be a focal point for alloy wheel powder coating, especially as vehicles with performance-based needs become more prevalent. High-performance vehicles, such as sports cars and off-road trucks, generate more heat during driving, which can affect the integrity of traditional coatings. Advances in heat-resistant powder formulations will ensure that these wheels remain protected under high temperatures, preventing degradation, discoloration, or damage caused by the intense heat generated during high-speed driving or heavy braking.
In addition to improving the durability and appearance of alloy wheels, there is a growing trend to incorporate functional coatings. For example, powder coatings that include anti-microbial properties are being tested and could be incorporated into alloy wheels to offer additional benefits. This type of coating could be particularly useful for vehicles used in public transportation or shared vehicle fleets, where hygiene is a concern. Similarly, powder coatings with anti-fingerprint or hydrophobic properties are becoming more popular, as these finishes prevent oils and water from sticking to the surface, making the wheels easier to clean and maintain.
Energy-efficient curing processes are another key area for innovation. Traditional curing methods, which rely on large ovens, consume a significant amount of energy. However, newer methods, such as infrared curing or UV curing, can reduce energy consumption and cure the powder faster, improving the overall efficiency of the process. These alternative curing methods may also help reduce the environmental footprint of alloy wheel powder coating by lowering overall energy demand.
The global demand for customized and durable alloy wheels will continue to drive innovation in powder coating techniques. With an increasing number of car owners seeking personalized looks for their vehicles, powder coating offers an ideal solution for creating unique designs. Whether opting for a bold color, metallic finish, or a custom pattern, alloy wheels coated with high-quality powder provide the flexibility to meet diverse aesthetic preferences while maintaining their protective properties.
As technology advances and consumer demands shift, the future of alloy wheel powder coating promises to be even more exciting. With innovative materials, enhanced efficiency, eco-friendly practices, and customization options, the powder coating process will continue to evolve, offering better performance, improved sustainability, and even more beautiful results for alloy wheels in the years to come.
Looking ahead, the future of alloy wheel powder coating is poised to be shaped by further integration of advanced technologies, particularly in the areas of automation, sustainability, and customization. These innovations will not only improve the functional performance of the coating but also open up new possibilities for creativity and adaptability in the automotive industry.
One of the most promising areas of development is the continued refinement of automation in the powder coating process. Automation will likely take center stage in the evolution of alloy wheel coating, with increased use of robotic arms, automated conveyor systems, and AI-powered systems that can handle large-scale production with minimal human intervention. These technologies will enable manufacturers to coat wheels faster and more consistently, while reducing the likelihood of human error. Additionally, robots equipped with precision spray technology can ensure that each wheel receives a perfectly uniform coat, even in complex or intricate wheel designs.
With AI and machine learning, automated systems will be able to learn from past performance, optimizing the application process in real-time and adjusting parameters such as powder flow rate, spray gun position, and curing times to adapt to changing conditions or specific requirements. This increased precision will also reduce material waste, as the powder coating can be applied more efficiently, ensuring that only the necessary amount of coating is used. This is particularly important as manufacturers seek to meet sustainability goals while maintaining the quality of the product.
Sustainability will remain a driving force in the future of powder coating. As environmental concerns become more pressing and regulations around waste reduction and energy efficiency tighten, the industry will continue to innovate in ways that reduce its environmental footprint. In particular, low-energy curing technologies will become more widespread, allowing powder coatings to be cured at lower temperatures and in shorter times. This reduction in energy consumption will lower operational costs and minimize carbon emissions, aligning the powder coating process with global efforts to combat climate change.
Furthermore, recyclable and bio-based powder formulations will continue to gain traction. As the demand for more sustainable materials increases, powder coatings made from renewable resources or recycled materials will become more commonplace. These eco-friendly powders will help reduce reliance on petrochemical-derived products, offering manufacturers a greener alternative that aligns with sustainability goals. The development of closed-loop recycling systems for powder coatings could also reduce material waste, as excess powder can be reclaimed and reused in the production process.
Additionally, green chemistry innovations in the production of powder coatings will likely result in coatings with fewer hazardous chemicals, improving both the safety of workers and the environmental impact. This aligns with growing global concerns over harmful chemical exposure and the need for safer industrial processes. There is also potential for non-toxic additives to be developed, improving the safety and eco-friendliness of powder coatings without compromising performance.
The demand for customization in the automotive industry is expected to continue to rise, with consumers increasingly seeking more personalized designs for their vehicles. Powder coating offers a wide range of color options and finishes, but the future will see an even broader selection of unique textures, patterns, and finishes that can be applied to alloy wheels. Technologies like 3D printing and laser etching could be used to create intricate, custom designs on alloy wheels, allowing car owners to express their individuality in new ways. Matte, satin, and glossy finishes will continue to evolve, and new technologies may even enable the creation of dynamic finishes that change based on light exposure or viewing angle.
Smart coatings will also play an important role in the future of alloy wheel powder coating. These coatings, which are designed to respond to environmental changes, could offer enhanced functionalities such as self-cleaning, anti-fingerprint, or self-healing capabilities. For instance, wheels coated with hydrophobic (water-repellent) coatings will be easier to clean and maintain, while anti-fingerprint coatings will help keep wheels looking pristine for longer. Moreover, self-healing coatings could repair minor surface scratches, extending the lifespan of the coating and maintaining the appearance of the wheels even in the face of daily wear and tear.
Advanced curing techniques will continue to improve as well, with UV curing and infrared curing becoming more widely adopted. These methods allow for faster curing times and lower energy usage, making the coating process more efficient. As the technology matures, manufacturers may even be able to introduce localized curing methods that target specific areas of the wheel with precision, reducing overall curing times and energy consumption.
The globalization of the powder coating industry is another factor that will influence future trends. As more countries and regions adopt powder coating technology due to its cost-effectiveness, durability, and eco-friendly nature, the demand for high-quality coatings will increase. Manufacturers will need to ensure that their products meet a diverse set of standards and regulations in various markets while still offering a consistent, high-quality finish. This could drive the development of more universal powder coatings that are adaptable to different environmental conditions and requirements.
Moreover, the use of Internet of Things (IoT) technology in powder coating systems will allow for real-time monitoring and remote management. IoT sensors will track data points such as temperature, humidity, and curing times, providing operators with valuable insights that can help prevent defects and ensure optimal coating quality. Additionally, IoT-enabled systems will allow manufacturers to predict maintenance needs, reducing downtime and improving the overall efficiency of the powder coating process.
As the automotive and transportation industries continue to evolve, alloy wheel powder coating will play a central role in improving the performance and aesthetics of vehicles. Whether it’s through advancements in automation, the development of sustainable practices, the exploration of new textures and finishes, or the integration of smart technologies, the future of powder coating promises even more opportunities to create durable, high-quality, and customizable wheels. The combination of innovation, environmental consciousness, and consumer demand for personalization will drive this evolution, ensuring that alloy wheels continue to be coated with coatings that offer long-lasting protection and striking visual appeal.
Powder Coating Plant Manufacturing
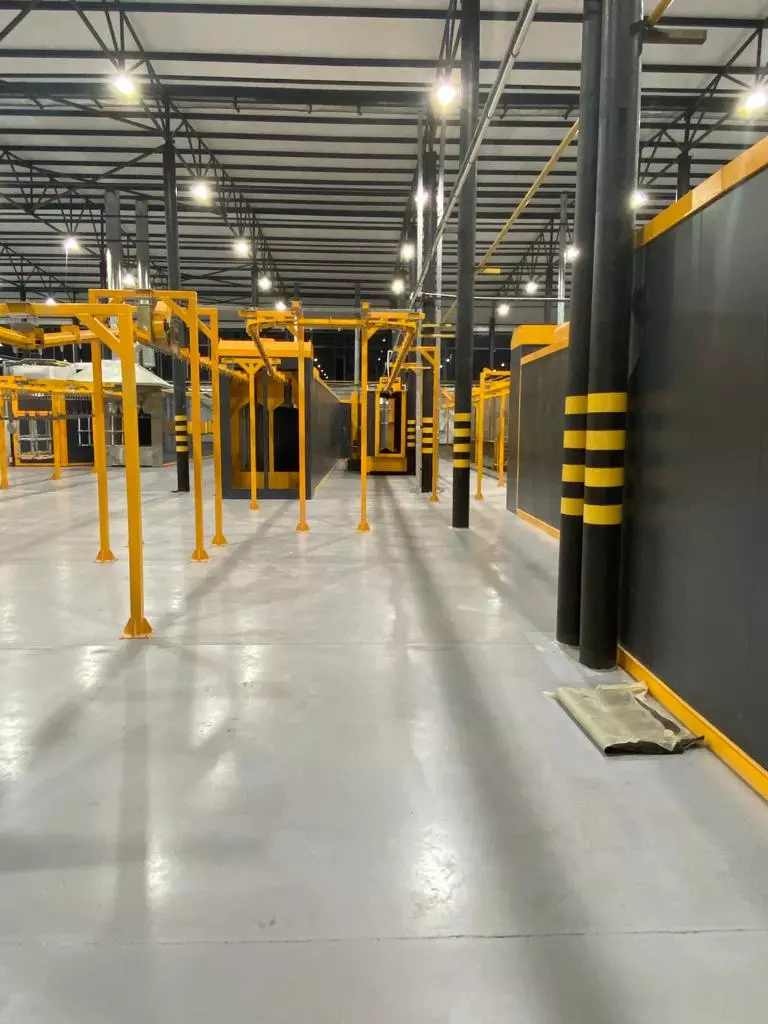
Powder coating plant manufacturing involves the design, construction, and operation of facilities dedicated to applying powder coatings to various products, such as metal parts, automotive components, and other substrates. A powder coating plant typically consists of a range of equipment, including application systems, curing ovens, and surface preparation tools, to ensure that the coating process is efficient, environmentally friendly, and produces high-quality finishes.
Here’s a detailed breakdown of the process involved in manufacturing a powder coating plant:
Key Components of a Powder Coating Plant
- Surface Preparation Equipment: The first step in any powder coating process is proper surface preparation. Clean surfaces are essential for good adhesion of the powder coating. Surface preparation equipment may include:
- Shot Blasting or Sand Blasting Machines: These machines are used to clean the metal surface by propelling abrasive particles at high speeds to remove contaminants like rust, dirt, and old coatings.
- Chemical Cleaning Stations: These systems use chemical solutions to clean and degrease the parts. This is often followed by a rinse to remove any residues and ensure the surface is clean.
- Phosphating or Chromating: Chemical treatment to increase corrosion resistance and improve the adhesion of the coating.
- Powder Application Systems: After surface preparation, the parts need to be coated with powder. This is typically done using electrostatic powder coating guns:
- Electrostatic Spray Guns: These are the primary tools used for applying the powder to the parts. The gun charges the powder particles electrostatically, causing them to adhere to the surface of the part. The powder is then evenly distributed over the object.
- Automatic and Manual Spray Booths: In an automated plant, robotic arms or conveyor systems may apply the coating, while manual spray booths are used for smaller or more intricate items. The powder is applied uniformly and evenly to achieve the desired finish.
- Curing Ovens: Once the powder is applied, it must be cured or baked to bond it to the surface of the part. Curing ovens are an essential component of a powder coating plant, where the coated items are subjected to heat to melt the powder and form a solid, durable coating. There are several types of curing ovens:
- Convection Ovens: These use hot air to cure the powder, providing an even distribution of heat throughout the oven.
- Infrared Ovens: These use infrared radiation to heat the surface of the parts more quickly than convection ovens, reducing curing times and energy consumption.
- Hybrid Ovens: Some modern systems use a combination of both convection and infrared heating to achieve more efficient curing.
- Cooling Systems: After the items are cured, they must be cooled to allow the coating to harden fully. Cooling systems typically use forced air or water cooling methods to rapidly lower the temperature of the coated items, ensuring they reach a stable, hardened state before handling or packaging.
- Powder Recovery and Filtration Systems: Powder coating systems are designed to minimize waste. Powder recovery systems are used to collect overspray, which can then be reused, reducing material costs and increasing efficiency. These systems generally include:
- Cyclone Systems: These are used to collect and separate excess powder from the air, returning it to the powder reservoir for reuse.
- Filters and Airflow Systems: These systems ensure that the powder particles do not pollute the environment, filtering out excess powder and maintaining a clean working atmosphere.
- Quality Control Stations: Ensuring a high-quality powder coating is crucial. A powder coating plant will typically include stations where finished parts are inspected for defects such as:
- Coating Thickness: Using tools like dry film thickness gauges to ensure the coating is applied evenly and to the correct thickness.
- Visual Inspection: Workers inspect the finished parts for imperfections such as runs, sags, or uneven coverage.
- Adhesion Tests: Methods like the crosshatch test or tape test may be used to assess how well the coating adheres to the surface.
- Material Handling Systems: Efficient movement of parts throughout the powder coating process is critical for both throughput and quality. Powder coating plants often use automated conveyor systems, hanging racks, and trolleys to transport parts from one station to the next, ensuring that the entire process runs smoothly and efficiently.
Design Considerations for Powder Coating Plant Manufacturing
- Capacity and Throughput: The design of a powder coating plant must be scalable to meet production demands. Whether it’s a small facility handling a limited volume of parts or a large operation processing thousands of items daily, the plant’s equipment should be sized to handle the required output.
- Space Planning and Layout: The layout of the powder coating plant is critical to ensuring efficient workflow and minimizing the risk of contamination. Equipment must be arranged in a logical flow, from surface preparation to powder application, curing, cooling, and final inspection. Adequate space for handling, storage, and inventory is also essential to maintain smooth operations.
- Energy Efficiency: Given that powder coating processes require significant energy, especially for curing, manufacturers focus on incorporating energy-efficient technologies into the plant. This includes using energy-saving ovens, optimizing airflow, and employing efficient powder recovery systems.
- Environmental Control: Powder coating plants must be designed to meet environmental regulations regarding emissions, waste disposal, and air quality. Ventilation systems, dust collection systems, and proper waste management are necessary to ensure that the plant operates in an environmentally responsible manner.
- Safety Considerations: The plant must comply with health and safety standards to protect workers from the potential hazards associated with powder coating. This includes proper ventilation to avoid inhalation of powder particles, fire safety measures due to the flammability of certain powders, and the use of personal protective equipment (PPE) for operators.
- Automation and Control Systems: Advanced powder coating plants may incorporate automated control systems to manage the entire process, from surface preparation to coating application and curing. These systems can monitor and adjust parameters in real-time, ensuring consistency, quality, and efficiency. Automation reduces human error and increases production speed, while also improving safety.
Trends in Powder Coating Plant Manufacturing
- Customization and Flexibility: As industries like automotive, aerospace, and consumer goods demand more customization, powder coating plants are increasingly incorporating flexible systems that can handle a wide range of part sizes, shapes, and finishes. Automated systems are becoming more adaptable, allowing for quick changes in production and customized coatings based on customer requirements.
- Sustainability: As companies strive to reduce their environmental footprint, many powder coating plants are being designed with sustainability in mind. This includes using eco-friendly powder formulations, reducing energy consumption through more efficient equipment, and recycling materials to minimize waste. Plants are also being built to comply with stricter environmental standards and regulations.
- Digitalization and Industry 4.0: The rise of digital technologies is having a significant impact on powder coating plant manufacturing. Sensors, IoT devices, and data analytics are being used to monitor equipment performance, track production efficiency, and predict maintenance needs. This approach allows for real-time data-driven decisions that improve quality control and reduce downtime.
- Advanced Curing Technologies: The demand for faster and more efficient curing processes has led to the development of new curing technologies, including UV curing and infrared curing, which use less energy and reduce curing times compared to traditional convection ovens.
- Lean Manufacturing Principles: Many powder coating plants are adopting lean manufacturing principles to optimize their operations. This includes improving workflows, reducing waste, and minimizing downtime by streamlining processes and implementing just-in-time production strategies.
Conclusion
Powder coating plant manufacturing is a complex, highly specialized field that requires advanced equipment, precise process control, and efficient operations to ensure the production of high-quality coated products. The plant’s design must accommodate the entire coating process, from surface preparation to final inspection, while also considering factors like automation, energy efficiency, and environmental responsibility. With the ongoing advancements in technology and growing demand for customizable, sustainable finishes, powder coating plant manufacturing will continue to evolve to meet the needs of various industries, offering solutions that improve both performance and aesthetic appeal.
Powder coating plant manufacturing is a highly specialized process that involves designing, constructing, and operating facilities dedicated to applying powder coatings to various products. The primary goal is to create durable, aesthetically appealing finishes that provide protection against corrosion, wear, and environmental exposure. Manufacturing a powder coating plant requires understanding the components of the coating process, including surface preparation, powder application, curing, and recovery systems, as well as the layout and design considerations necessary for efficient and effective operation.
At the heart of the process is the surface preparation phase, which is crucial for ensuring proper adhesion of the powder coating to the substrate. Surface preparation equipment, such as shot blasters or sandblasting machines, removes rust, dirt, grease, and old coatings, while chemical cleaning stations and phosphate treatments enhance corrosion resistance and coating adhesion. After cleaning, the powder application system takes over, where electrostatic spray guns charge the powder particles and apply them to the parts. Automated and manual spray booths help achieve even, uniform coverage. Once the powder is applied, the parts move to the curing ovens where heat is used to melt and bond the powder into a durable coating. These ovens can be convection, infrared, or hybrid, depending on the needs of the operation.
Following curing, a cooling system is used to lower the temperature of the parts to room temperature, ensuring the coating fully hardens. Powder recovery systems ensure efficiency and cost savings by collecting overspray, which can then be reused, reducing material waste. Filtration systems are also essential for maintaining a clean working environment and preventing contamination during the application process.
In terms of design, the layout of a powder coating plant is critical for ensuring smooth and efficient operation. The plant must be organized to allow for the logical flow of materials from surface preparation to application, curing, cooling, and inspection. Material handling systems, including automated conveyors, racks, and trolleys, are often incorporated to streamline the movement of parts and maintain workflow.
Another significant factor is energy efficiency, especially in curing processes, which can be energy-intensive. Incorporating energy-efficient ovens and optimizing energy use across the plant reduces operational costs and minimizes the plant’s environmental footprint. Moreover, with an increased emphasis on sustainability, many plants are moving toward eco-friendly powder formulations that are free from hazardous chemicals, while adopting practices that focus on minimizing waste and emissions.
The quality control process within a powder coating plant ensures that finished products meet the required standards. Tools for measuring coating thickness, performing visual inspections, and conducting adhesion tests are crucial for maintaining high product quality. New technologies, such as AI-powered systems, help improve consistency and reduce human error in the coating process by automating adjustments based on real-time data.
Advanced automation is increasingly becoming a defining feature of powder coating plants. Robotic arms and conveyors are used to apply powder coatings uniformly and efficiently, while automated curing systems and quality control stations help ensure that the process runs smoothly and consistently. The rise of Industry 4.0 technologies, such as IoT and data analytics, has also enabled powder coating plants to operate with greater precision. Real-time monitoring of equipment performance, predictive maintenance, and production data tracking help optimize operations and reduce downtime.
As environmental concerns continue to grow, the powder coating industry is embracing sustainable practices. Plants are incorporating systems that reduce energy consumption, recycle materials, and use environmentally friendly powders. The development of low-energy curing methods, such as UV and infrared curing, also helps reduce the plant’s environmental impact. Additionally, the use of bio-based powders and other sustainable materials will likely continue to increase, as manufacturers seek to reduce their carbon footprint and meet regulatory standards.
Customization is a growing trend in the automotive and consumer goods industries, and powder coating plants are evolving to meet the demand for more personalized finishes. Advances in coating technologies, such as self-healing, anti-fingerprint, and hydrophobic coatings, provide additional functionality and aesthetic appeal. Furthermore, innovations in color technology have opened up new possibilities for custom finishes, including metallic, pearlescent, and chameleon effects that change with light angles.
The future of powder coating plant manufacturing will continue to be influenced by advancements in automation, sustainability, and customization. As the industry evolves, the demand for more efficient, flexible, and environmentally friendly solutions will drive the development of innovative technologies that improve both product quality and production efficiency. The ongoing focus on energy efficiency, waste reduction, and customization will ensure that powder coating remains a vital and growing sector in manufacturing. With these improvements, the powder coating process will continue to deliver high-quality, durable finishes while meeting the ever-increasing demands for sustainability and performance.
Thermoplastic Powder Coating Equipment
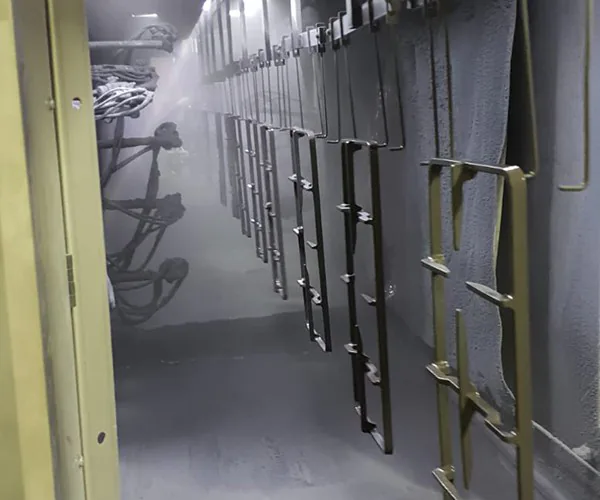
Thermoplastic powder coating equipment is specialized machinery designed to apply thermoplastic powder coatings to various substrates, primarily metals, to create durable, high-performance finishes. Unlike thermoset powders, which cure through chemical reactions during the baking process, thermoplastic powders melt and flow when heated and solidify again once cooled, without undergoing any chemical change. This characteristic makes thermoplastic powder coatings more suitable for products that require flexibility, high impact resistance, and the ability to be reworked or repaired.
The equipment used for thermoplastic powder coating is similar to that used for thermoset powder coating, but there are some distinct considerations given the different properties of thermoplastic materials. Here’s a breakdown of the essential components of thermoplastic powder coating equipment:
1. Powder Coating Application Systems
The application of thermoplastic powders typically involves an electrostatic spray gun that charges the powder particles, making them adhere to the surface of the part. The thermoplastic powder is applied in a manner similar to thermoset powder coating but requires careful control to ensure even coverage and the proper thickness of the coating. Some key considerations for thermoplastic powder application include:
- Electrostatic Spray Guns: These guns charge the powder particles and spray them onto the part, ensuring uniform coverage. In thermoplastic coatings, the gun setup must maintain a steady powder flow while avoiding over-spraying, as thermoplastic powders tend to be more prone to clumping compared to thermoset powders.
- Automatic and Manual Application: Depending on the production volume, thermoplastic powder coating can be applied using automatic robots or manual spray booths. Automated systems allow for faster, more uniform application, especially when parts have complex geometries.
2. Pre-Heating Systems
Thermoplastic powders need to be preheated before application to ensure they flow properly when they are sprayed onto the part. Pre-heating equipment, often integrated with the coating system, helps achieve the ideal temperature for the powder. This is an important step because if the powder is not heated sufficiently, it may not adhere well to the substrate.
3. Curing Ovens
Curing ovens are used to heat the coated parts after the thermoplastic powder has been applied. The key difference in curing for thermoplastic coatings is that it involves melt flow rather than a chemical curing reaction. As such, the oven must be carefully controlled to allow for uniform heat distribution and to achieve the desired thickness and finish. There are several considerations for thermoplastic powder curing:
- Temperature Control: The curing temperature must be sufficient to melt the thermoplastic powder but not so high as to degrade it. Typically, the curing temperature for thermoplastic coatings is lower than for thermoset coatings.
- Curing Time: Unlike thermoset coatings that require a longer time to cure, thermoplastic coatings usually cure more quickly once the material melts. Therefore, ovens are designed to ensure uniform heating and adequate time for the material to melt, flow, and bond to the substrate.
4. Cooling Systems
After the thermoplastic powder has been melted and adhered to the part, it must be cooled in order to solidify and form the final coating. Cooling systems use either forced air or water-cooling systems to quickly lower the temperature of the parts and solidify the thermoplastic material. Rapid cooling is necessary to maintain the desired coating finish and prevent defects like surface imperfections or an uneven finish.
5. Powder Recovery Systems
Thermoplastic powders are often more expensive than thermoset powders due to their properties and performance characteristics. To minimize waste, powder recovery systems are used to collect overspray during the application process. These systems include:
- Cyclone Recovery Units: These units separate excess powder from the air and funnel it back into the powder supply for reuse.
- Filters: The powder recovery system often includes filters that capture fine powder particles to ensure that the air remains clean and safe.
6. Surface Preparation Equipment
As with all powder coating processes, proper surface preparation is essential for ensuring a strong bond between the coating and the substrate. Thermoplastic powder coating equipment will typically include systems for cleaning, degreasing, and treating parts before they are coated. This may involve:
- Shot Blasting: To clean the surface and prepare it for coating by removing rust, scale, or old coatings.
- Chemical Cleaning Stations: These remove oils, dirt, or grease from the surface.
- Phosphating or Pretreatment: To enhance corrosion resistance and improve the bonding of the coating.
7. Quality Control Systems
The quality of thermoplastic powder coatings must be carefully monitored to ensure uniformity and durability. Key quality control features include:
- Thickness Measurement: Tools like dry film thickness gauges are used to measure the coating’s thickness, ensuring that it meets specifications for durability.
- Visual Inspection: To check for uniform coverage, color consistency, and the absence of defects like pinholes, runs, or sags.
- Adhesion Testing: Various methods such as crosshatch testing may be used to assess how well the coating adheres to the substrate.
8. Material Handling Systems
Efficient material handling systems are essential to move parts through the powder coating process. These systems include:
- Conveyor Systems: Automated conveyor systems move parts through different stages of the coating process, from cleaning to powder application and curing.
- Racking Systems: Racks are used to hold parts in place during coating and curing. In a thermoplastic powder coating system, these racks must be able to withstand the heat used during the curing process.
Advantages of Thermoplastic Powder Coating Equipment
Thermoplastic powder coating equipment offers several advantages, particularly when flexibility, impact resistance, and reworkability are essential:
- Reworkability: Since thermoplastic powders melt upon heating and solidify again once cooled, parts can be reheated and recoated if defects are found or if a different finish is required. This reworkability is ideal for applications where future modifications or repairs are necessary.
- Durability: Thermoplastic powder coatings are known for their high impact resistance, excellent flexibility, and better resistance to abrasion and wear compared to thermoset powders.
- Chemical Resistance: Thermoplastic coatings can provide better resistance to certain chemicals, making them suitable for applications in harsh environments.
- Environmental Benefits: Like thermoset powder coating, thermoplastic powder coatings do not require solvents, making the process cleaner and more environmentally friendly than traditional liquid coatings.
Challenges and Considerations
While thermoplastic powder coating has many benefits, there are challenges that need to be considered when designing and operating the equipment:
- Powder Flow and Application: Thermoplastic powders tend to be more challenging to apply uniformly compared to thermoset powders due to their tendency to clump together. Special care must be taken to ensure an even application without excess powder buildup.
- Curing Time: The curing time for thermoplastic powder coatings is typically shorter than thermoset powders, which may require more advanced or optimized curing systems to ensure the coating bonds properly.
- Material Costs: Thermoplastic powders tend to be more expensive than thermoset powders, so powder recovery systems must be well designed to reduce waste and make the process cost-effective.
Conclusion
Thermoplastic powder coating equipment is specialized for applying thermoplastic powders to substrates, providing products with enhanced flexibility, impact resistance, and reworkability. The key components of thermoplastic powder coating systems include surface preparation equipment, electrostatic spray guns, curing ovens, powder recovery systems, and material handling systems. While thermoplastic coatings offer excellent durability and resistance to wear and chemicals, the equipment must be designed to handle the unique challenges associated with their application, such as the need for uniform powder flow and effective curing. With the right setup, thermoplastic powder coating equipment can deliver high-quality finishes suitable for a wide range of applications in industries like automotive, industrial machinery, and consumer goods.
Thermoplastic powder coating equipment is designed to apply powder coatings that melt and fuse when heated, forming a durable, flexible, and long-lasting finish. The process involves several key steps to ensure uniform application and high-quality results. The equipment required for thermoplastic powder coating includes systems for surface preparation, powder application, curing, cooling, and powder recovery. Each of these components plays a crucial role in producing a reliable and aesthetically pleasing finish.
In the powder application phase, electrostatic spray guns are used to charge the thermoplastic powder particles, making them adhere to the surface of the part. This process ensures an even coat across the substrate, but special care must be taken to control the flow of powder, as thermoplastic powders can be more prone to clumping than thermoset powders. Whether the application is automated or manual depends on the scale of production, with automated systems offering faster, more consistent coverage for high-volume production.
Once the powder is applied, the parts are moved to the curing oven. The curing process for thermoplastic coatings is different from that of thermoset coatings; instead of chemical curing, thermoplastic powders melt and flow at a specific temperature. The oven must be calibrated to the correct temperature to allow the powder to melt and form a smooth, solid coating without causing any degradation to the material. Curing times are generally shorter for thermoplastic powders compared to thermoset powders, which makes temperature and time control in the oven critical for the proper adhesion and finish of the coating.
After curing, parts are cooled, often using air or water cooling systems, which helps the coating solidify quickly. This ensures that the finish is both durable and hard enough to withstand handling without marring the surface. The cooling process also ensures that the coating does not retain excess heat that could lead to deformation or other defects. Efficient cooling systems are designed to handle the volume of parts being processed and to ensure a smooth transition from the high heat of the curing oven to ambient temperatures.
One of the advantages of thermoplastic powder coating is its ability to be reworked. Because the coating simply melts and does not undergo a chemical curing process, damaged or imperfect parts can be reheated, and the coating can be reapplied. This makes it an ideal solution for products that may require future modifications or repairs. The reworkability aspect also means that overspray from the application process is not wasted. Powder recovery systems, which include cyclone recovery units and filtration systems, capture excess powder from the air and return it to the supply, ensuring minimal waste and reducing material costs.
The surface preparation phase, which includes cleaning and treating the substrate before the powder application, is crucial for achieving good adhesion and long-lasting performance of the coating. Equipment for shot blasting, chemical cleaning, and phosphating is used to remove dirt, grease, rust, and other contaminants from the part. This ensures that the thermoplastic powder bonds effectively to the surface, creating a strong and durable finish.
As with any industrial coating process, quality control is essential to ensuring that the finished products meet the required standards. Thickness gauges, visual inspections, and adhesion tests are performed to ensure uniform coating, good coverage, and the durability of the finished product. Thermoplastic coatings are often chosen for their impact resistance, flexibility, and ability to resist abrasion and wear. These coatings are also well-suited for applications where the coated parts will be exposed to chemicals or harsh environments.
Material handling systems, including conveyors, racks, and automated systems, are used to move parts through the various stages of the powder coating process. These systems ensure that the parts are consistently and efficiently processed, minimizing downtime and handling time. The design of the material handling system must accommodate the specific requirements of thermoplastic coating, such as the need for precise temperature control during curing and cooling.
Thermoplastic powders tend to be more expensive than thermoset powders, which makes the efficient use of materials critical. Powder recovery and recycling systems are employed to capture overspray, reducing waste and making the process more cost-effective. This is especially important in high-production environments where the cost of raw materials can significantly impact the overall production costs.
Overall, thermoplastic powder coating equipment must be designed to handle the unique properties of thermoplastic materials, including their melting point, flow characteristics, and reworkability. With proper application, curing, cooling, and recovery systems, thermoplastic powder coating provides a high-quality, durable finish suitable for a wide range of industries, including automotive, appliances, and industrial applications. The combination of flexibility, durability, and reworkability makes thermoplastic powder coating an attractive choice for products that require long-lasting performance under demanding conditions.
The thermoplastic powder coating process offers several unique advantages, which can make it particularly attractive for various industries. Since thermoplastic coatings can be re-melted and re-coated, they offer flexibility and a level of adaptability that is often not possible with thermoset coatings. This reworkability means that if a coating is damaged, it can simply be heated and re-applied, eliminating the need to strip off the old layer and start from scratch. This feature is valuable in situations where the coating might need to be adjusted or when parts are prone to wear and tear during their lifecycle.
Thermoplastic coatings also provide excellent impact resistance due to their inherent flexibility. The nature of the thermoplastic material means it can absorb impacts without cracking or chipping, making it ideal for high-wear environments like automotive parts, machinery components, and outdoor applications. Furthermore, thermoplastic coatings typically offer superior abrasion resistance, which is essential for items that are subjected to friction or rough handling.
Because thermoplastic powders do not cure chemically but instead undergo a melting process, they tend to exhibit better chemical resistance in many cases. This makes thermoplastic powder coatings ideal for parts that will be exposed to harsh chemicals, oils, or other corrosive materials. They also provide strong weather resistance, with many thermoplastic coatings performing well under UV exposure, temperature fluctuations, and extreme environmental conditions.
Thermoplastic coatings can be customized with various specialty additives to enhance certain properties. For example, thermoplastic coatings can be formulated with anti-static, anti-microbial, or fire-retardant properties, depending on the needs of the product or industry. Additives can also be incorporated to achieve a range of aesthetic finishes, including high gloss, matte, metallic, or textured looks.
In terms of sustainability, thermoplastic coatings offer some environmental advantages. Like all powder coatings, they are free from solvents, reducing the risk of harmful emissions. Furthermore, they typically involve minimal waste, as any overspray can be recovered and reused. This can be a significant benefit in reducing the environmental impact of the coating process. Given the rising demand for eco-friendly solutions in manufacturing, the ability to recover and reuse powder in thermoplastic systems contributes to a more sustainable and cost-efficient operation.
The powder recovery systems in thermoplastic powder coating processes are crucial for minimizing waste and maintaining consistent coating quality. Cyclone separators, filtration systems, and fluidized bed recovery units are commonly used to collect overspray and return it to the process. The ability to reuse excess powder significantly reduces material costs and waste, making the overall process more efficient. However, thermoplastic powder recovery systems must be carefully calibrated to handle the unique properties of thermoplastic powders, which may behave differently from thermoset powders in terms of flow and handling characteristics.
In terms of equipment considerations, thermoplastic powder coating systems must be designed with proper heat management. Since the powder requires careful temperature control during both the application and curing phases, having precise control systems for the curing oven is critical. Overheating can cause degradation of the coating material, while insufficient heating may result in poor adhesion or incomplete fusing. Customizable temperature zones within the curing oven, along with accurate thermostats, are essential for achieving the best results.
Automation also plays a key role in improving efficiency and consistency. Robotic arms and automated powder spray booths can achieve more consistent powder application, reducing human error and increasing throughput. Automated systems ensure that the coating is applied evenly across all parts, even those with complex geometries, which would be more challenging for manual operators to coat uniformly. Advanced technology also enables real-time monitoring, allowing for adjustments to be made to the coating process instantly. For instance, if the powder thickness is not within specification, automated systems can make adjustments to ensure that the required thickness is achieved.
For larger-scale operations, material handling becomes a crucial consideration. Conveyor systems, overhead tracks, and rotating racks are commonly used to move parts through the various stages of the powder coating process. Automated handling systems not only improve throughput but also reduce the physical strain on workers and minimize the chances of damage to parts during transit. Parts are often coated while suspended in racks or on conveyors, which must be designed to withstand the temperature of curing ovens and ensure the part is securely held during the entire coating cycle.
As demand for customization and aesthetic variety continues to grow, thermoplastic powder coatings can be tailored to achieve specific colors, textures, and finishes. Color consistency is critical, and with the right equipment, manufacturers can ensure that each batch of powder coating matches the desired hue and finish, whether it is for a matte, glossy, or even metallic look. Advances in powder formulation allow manufacturers to create a wide range of finishes, including highly reflective surfaces, textured coatings for improved grip, and even coatings that change appearance depending on the viewing angle.
The versatility of thermoplastic coatings makes them suitable for industries ranging from automotive manufacturing (where flexibility, impact, and chemical resistance are vital) to consumer electronics (where coatings may need to offer not only protection but also an appealing finish). Outdoor furniture, appliances, and industrial equipment also benefit from thermoplastic coatings’ ability to resist environmental wear and tear, ensuring products maintain their appearance and functionality for longer periods.
The future of thermoplastic powder coating is expected to continue evolving with advancements in automation, sustainability, and performance. Automation technologies will continue to reduce costs, increase precision, and improve the speed of production. At the same time, there is growing interest in eco-friendly alternatives and bio-based thermoplastic powders, which offer more sustainable coatings for industries looking to reduce their environmental footprint. These trends are driving the development of even more efficient and cost-effective powder coating systems that deliver high-quality results while meeting the increasing demands for sustainability and customization.
In conclusion, thermoplastic powder coating equipment is an integral part of a wide variety of manufacturing processes, providing a highly durable, flexible, and reworkable finish. By incorporating advanced technologies for application, curing, recovery, and quality control, manufacturers can produce parts with excellent impact resistance, chemical protection, and aesthetic appeal. As industries demand higher performance, more customization, and environmentally responsible solutions, thermoplastic powder coating will continue to evolve, offering new opportunities for manufacturers looking to enhance the durability and appearance of their products.
Thermoplastic powder coating continues to expand its reach and application across various industries, driven by the evolving demands for better performance, environmental sustainability, and aesthetic flexibility. As industries like automotive, aerospace, electronics, and consumer goods push for more durable and visually appealing coatings, thermoplastic powder coating systems are being adapted and optimized to meet these needs.
One of the key benefits of thermoplastic powder coatings is their superior adhesion properties. The ability of thermoplastic coatings to form strong bonds with substrates makes them especially useful in applications that require long-lasting finishes under extreme conditions. This characteristic is especially valuable in sectors such as automotive and industrial machinery, where parts are exposed to harsh environments, chemicals, and physical wear. In automotive manufacturing, thermoplastic coatings are used to provide durable finishes for both functional and aesthetic parts, including bumpers, trim pieces, and wheels. These coatings can withstand impact, resist abrasions, and maintain their appearance over time, even in outdoor conditions.
The flexibility of thermoplastic coatings makes them ideal for a variety of part geometries. Parts with intricate shapes or hard-to-reach areas can still receive uniform coverage, especially when automated systems like robotic arms or conveyor-based spray systems are used. These systems ensure that even complex shapes receive consistent and complete coating coverage, reducing the potential for imperfections that could arise from manual spraying. This capability is particularly important when coating parts with highly detailed surfaces or those that require specialized finishes.
In addition to their physical durability, thermoplastic coatings also offer aesthetic versatility. Manufacturers are increasingly focusing on providing customizable finishes to meet specific design requirements. Whether it’s a matte finish for a more industrial or understated look, a glossy finish for a high-end aesthetic, or a metallic finish for a premium appearance, thermoplastic powder coatings can be tailored to achieve a wide range of visual effects. The ability to incorporate metallic flake, pearlescent pigments, or color-shifting effects allows brands to offer products with unique looks that stand out in the marketplace.
Thermoplastic powder coating is also favored for its environmental benefits. Unlike liquid coatings, thermoplastic powders contain no solvents, which significantly reduces the emission of volatile organic compounds (VOCs). This is an important consideration as industries work to comply with increasingly stringent environmental regulations. The absence of solvents not only reduces harmful emissions but also enhances worker safety by minimizing exposure to toxic fumes that are typically released during the application of solvent-based coatings.
The ability to reuse oversprayed powder also contributes to the sustainability of the process. Advanced powder recovery systems, such as cyclone separators and fluidized bed systems, allow for the efficient capture and reuse of excess powder, minimizing waste and maximizing material utilization. This process makes thermoplastic powder coating more cost-effective, particularly in large-scale production environments, where the cost of raw materials can be a significant concern.
Energy efficiency is another area where thermoplastic powder coating has made strides. By optimizing curing ovens and controlling the temperature and duration of the curing cycle, manufacturers can reduce energy consumption while still achieving high-quality finishes. Innovations in oven technology, such as multi-zone ovens with precise temperature control, allow for better energy management, ensuring that the process uses only the necessary amount of energy while maintaining consistent coating quality.
Another trend in thermoplastic powder coating is the growing adoption of smart technologies to monitor and control the coating process. Real-time monitoring systems, which use sensors and data analytics, allow manufacturers to adjust variables like powder flow, spray gun settings, oven temperature, and curing time. These technologies enable manufacturers to maintain consistent product quality, reduce defects, and improve operational efficiency. Additionally, smart systems can collect data on the coating process, providing valuable insights that can help optimize workflows, troubleshoot issues, and predict maintenance needs.
Customization is becoming a more prominent feature of thermoplastic powder coatings. Manufacturers are increasingly using custom formulations to achieve specific performance characteristics in the coating. These formulations can include special additives that enhance corrosion resistance, increase chemical resistance, improve scratch resistance, or even add anti-bacterial properties. Customization also extends to the color matching process, which is essential for industries like consumer electronics and automotive manufacturing, where visual consistency and branding are critical.
As innovation in coating technologies continues to progress, bio-based and sustainable powder coatings are gaining traction. Companies are beginning to experiment with bio-derived resins and other environmentally friendly materials to create thermoplastic powders that are less reliant on petroleum-based products. These eco-friendly coatings offer similar performance characteristics as traditional thermoplastics but with a reduced environmental impact, aligning with global sustainability goals.
Thermoplastic coatings’ reparability is one of the key differentiators from thermoset powder coatings. This feature is particularly useful for industries that deal with parts that experience high wear or damage over time. For instance, in automotive and heavy equipment manufacturing, parts that are coated with thermoplastic powders can be repaired without the need for completely stripping and re-coating the surface. This ability to rework the coating by simply reheating the part allows manufacturers to maintain high-quality finishes while minimizing downtime and repair costs.
As the global focus on sustainability continues to grow, thermoplastic powder coating is well-positioned to benefit from these trends. The ability to produce low-VOC, solvent-free coatings that can be easily recycled makes thermoplastic powder coating an increasingly preferred choice for manufacturers committed to reducing their environmental impact. In industries like construction, furniture manufacturing, and consumer goods, where long-lasting, high-performance finishes are essential, the thermoplastic coating process offers an attractive combination of durability, aesthetics, and environmental friendliness.
The ongoing research and development efforts in the field of thermoplastic powder coatings will likely lead to even further innovations. As the demand for high-performance, eco-friendly coatings grows, manufacturers are likely to develop new formulations that offer enhanced properties, such as increased scratch resistance, self-healing capabilities, and advanced corrosion resistance. This continuous improvement will likely expand the applications of thermoplastic coatings into new industries and markets, making them an even more versatile and indispensable technology for modern manufacturing.
In conclusion, thermoplastic powder coating equipment is a key enabler in producing coatings that combine exceptional durability, flexibility, and aesthetic appeal. The combination of advanced application systems, customizable formulations, and sustainable practices makes thermoplastic powder coating an ideal choice for a wide range of industries, from automotive to industrial machinery. As technology continues to evolve and industries push for more sustainable, high-performance products, thermoplastic powder coating will undoubtedly remain a core technology in the future of surface finishing.