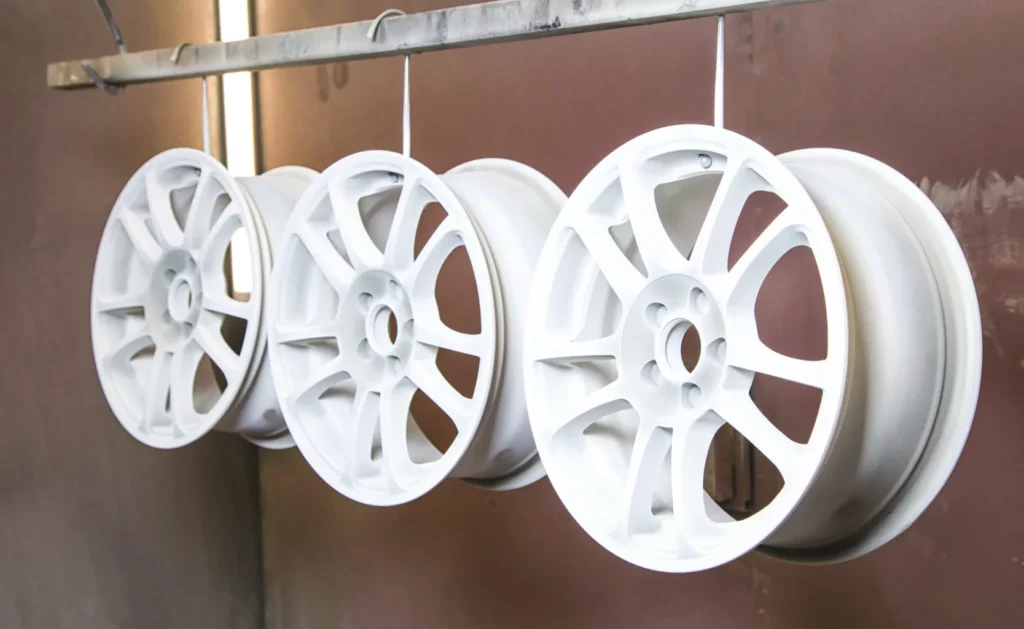
We manufacture the Chicago Powder Coating System for our customers in the US. High Quality & Cheap Prices & 2 years Guaranty and Free Consultation
Our Chicago electric powder coating system includes:
- Chicago electric powder coating gun
- Chicago electric powder coating oven
A Chicago Powder Coating System typically refers to a comprehensive setup or installation used for the process of powder coating in various industrial and manufacturing applications. This system encompasses a range of equipment and components designed to apply a protective and decorative powder coating to surfaces, typically made of metal, but also used on other materials like plastics or ceramics. Here’s an overview of the key components and features commonly found in a Chicago Powder Coating System:
1. Powder Coating Booth:
- Enclosed Workspace: The heart of the system is the powder coating booth or spray booth, which provides a controlled and enclosed environment for the coating process.
- Exhaust and Ventilation: The booth is equipped with exhaust systems and ventilation to remove overspray, fumes, and airborne particles created during the coating process.
2. Powder Coating Guns:
- Electrostatic Spray Guns: These guns apply the powder coating material using an electrostatic charge, ensuring even and efficient coverage.
- Automatic and Manual Guns: Systems may include both automatic (robotic) and manual powder coating guns to accommodate different production needs and part sizes.
3. Powder Supply System:
- Powder Hoppers: Containers for holding and delivering the powder coating material to the guns.
- Fluidization: Many systems use fluidization to maintain a consistent flow of powder, preventing clumping and ensuring a smooth application.
4. Powder Recovery System:
- Cartridge Filters or Cyclone Collectors: These components capture and recover excess powder particles, minimizing waste and facilitating reuse.
5. Conveyor System:
- Conveyor Line: In many industrial applications, a conveyor system is used to transport workpieces through the coating process. These can be manual or automated conveyor systems.
6. Curing Oven:
- Batch or Continuous Ovens: A curing oven is used to heat and cure the powder coating material onto the workpieces. Systems may include batch ovens for smaller production runs or continuous ovens for larger-scale operations.
- Precise Temperature Control: Modern ovens have precise temperature control systems to ensure uniform curing and high-quality finishes.
7. Control System:
- PLC (Programmable Logic Controller): The control system manages and monitors the entire powder coating process, including gun settings, conveyor speed, and temperature control.
- Touchscreen Interface: Many systems feature user-friendly touchscreen interfaces for easy operation and monitoring.
8. Safety Features:
- Safety Interlocks: To prevent accidents, access doors and hatches are often equipped with safety interlock systems that shut down the system when opened during operation.
- Emergency Stop Buttons: Easily accessible emergency stop buttons are provided for immediate shutdown in case of emergencies.
9. Environmental Compliance:
- Exhaust and Filtration: Compliance with environmental regulations is ensured through efficient exhaust and filtration systems that capture and treat fumes and particles generated during the process.
10. Quality Control:
- Inspection and Quality Assurance: Systems may include quality control stations where operators inspect finished workpieces for defects and ensure adherence to quality standards.
11. Customization and Integration:
- Custom Solutions: Chicago Powder Coating Systems can be customized to fit specific production needs, including the integration of robotics for automated handling.
These systems are used in various industries, including automotive, aerospace, furniture, and general manufacturing, to apply durable and attractive powder-coated finishes to a wide range of products. The choice of a Chicago Powder Coating System depends on the specific production requirements and the types of workpieces to be coated.
Key Components of the Chicago Powder Coating System
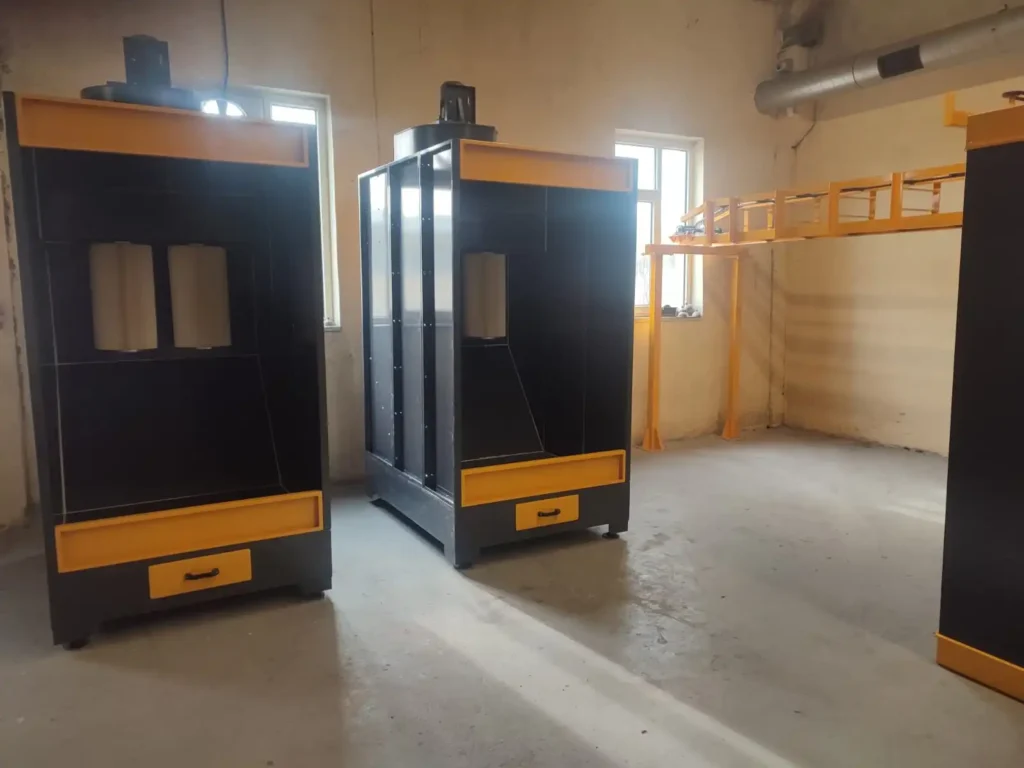
1. Powder Coating Booth:
- Enclosed Workspace: The powder coating booth provides a controlled and enclosed environment for the coating process, preventing contamination and overspray from escaping.
- Lighting: Proper booth lighting is crucial for visibility during the coating process. Booths typically feature bright, evenly distributed lighting to ensure accurate and consistent coating application.
- Powder Recovery System: The booth includes a powder recovery system that captures overspray. It often consists of cartridge filters or cyclone collectors to separate and collect excess powder for reuse.
- Airflow and Ventilation: Adequate ventilation and exhaust systems are integrated into the booth to remove fumes, airborne particles, and excess powder from the workspace. Proper airflow management helps maintain a clean and safe environment.
2. Powder Coating Guns:
- Electrostatic Spray Guns: These guns use electrostatic principles to impart an electric charge to the powder particles, ensuring they adhere uniformly to the grounded workpiece. This electrostatic effect leads to efficient and even coverage.
- Automatic and Manual Guns: Powder coating systems may include both automatic and manual guns. Automatic guns are often used in high-volume production, while manual guns provide more precise control for complex or custom work.
- Nozzles and Tips: Powder guns are equipped with interchangeable nozzles and tips to control the spray pattern and powder flow rate. Different workpiece shapes and sizes may require specific nozzle configurations.
3. Powder Supply System:
- Powder Hoppers: These containers hold the powder coating material and supply it to the spray guns. They are designed to prevent powder clumping and ensure a consistent flow.
- Fluidization: Many powder hoppers incorporate fluidization systems, which use air to create a fluidized bed of powder. This prevents agglomeration and maintains a smooth and consistent powder feed.
4. Conveyor System:
- Conveyor Line: In industrial applications, a conveyor system is often used to move workpieces through the coating process. Conveyors can be manual or fully automated, and their design may include indexing for precise positioning and efficient throughput.
- Variable Speed Control: Conveyor systems usually offer variable speed control to accommodate different production rates and curing times.
5. Curing Oven:
- Batch or Continuous Ovens: Powder coating systems are equipped with curing ovens to heat and cure the powder-coated finish. Batch ovens are suitable for smaller production runs, while continuous ovens are designed for larger-scale operations.
- Precise Temperature Control: Ovens incorporate advanced temperature control systems, often utilizing PID controllers, to ensure that curing temperatures are maintained within tight tolerances for consistent and durable coatings.
- Heating Elements: Ovens use heating elements, such as resistance wires or infrared panels, to provide controlled and evenly distributed heat within the oven chamber.
6. Control System:
- PLC (Programmable Logic Controller): The control system manages and coordinates the entire powder coating process. It controls various parameters, including gun settings, conveyor speed, oven temperature, and curing time.
- Touchscreen Interface: User-friendly touchscreen interfaces are common in modern systems, enabling operators to monitor and adjust settings with ease.
7. Safety Features:
- Safety Interlocks: Access doors and hatches are equipped with safety interlock systems to prevent them from being opened during operation. This minimizes the risk of accidents and exposure to high temperatures.
- Emergency Stop Buttons: Easily accessible emergency stop buttons or switches are provided for immediate shutdown in case of emergencies or equipment malfunctions.
8. Environmental Compliance:
- Exhaust and Filtration: Compliance with environmental regulations is achieved through efficient exhaust and filtration systems. These systems capture and treat fumes and airborne particles, ensuring compliance with air quality standards.
- Emissions Control: Powder coating systems often incorporate emissions control technologies, such as afterburners or thermal oxidizers, to further reduce emissions and environmental impact.
These key components work together seamlessly in a Chicago Powder Coating System to deliver precise, efficient, and environmentally friendly powder-coated finishes on a wide range of products across various industries. The proper selection and configuration of these components are essential to achieving high-quality and consistent results.
Powder Coating: An In-Depth Guide to Equipment and Processes
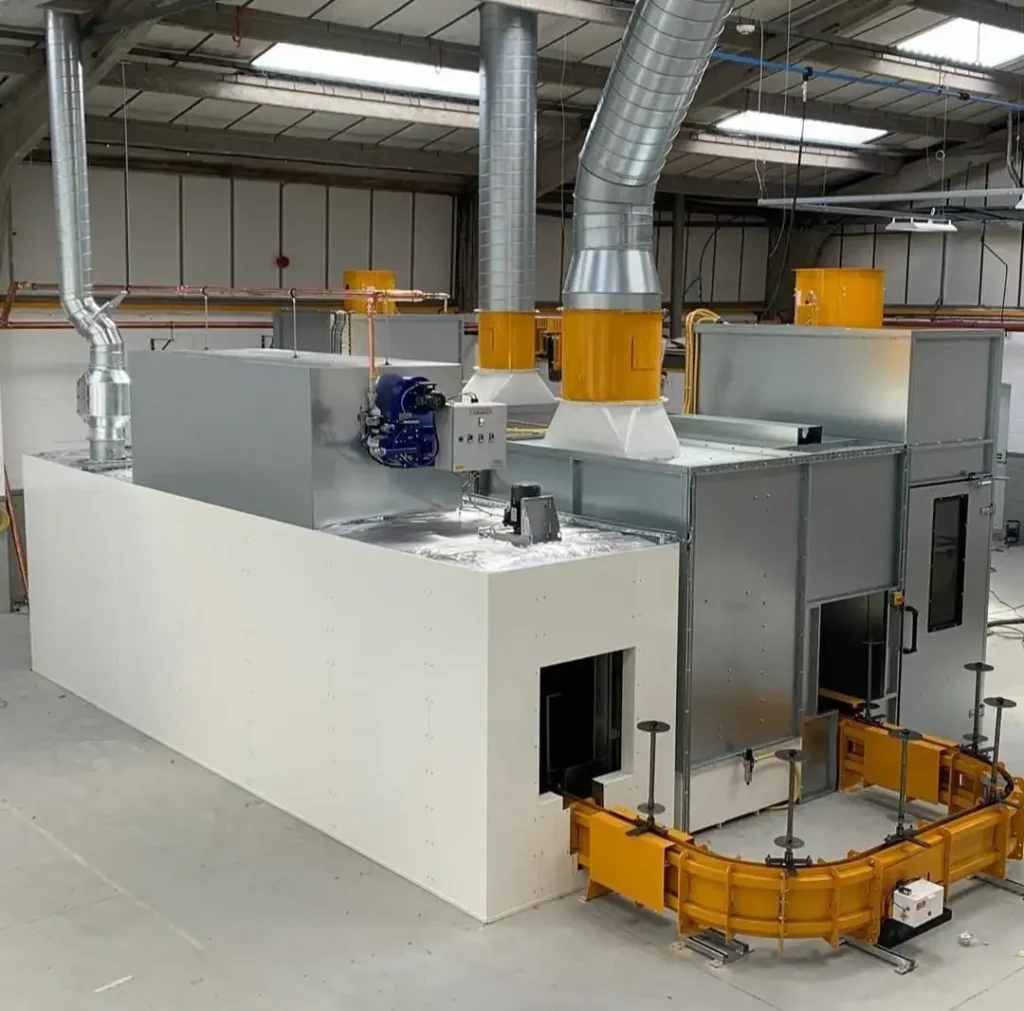
Introduction
Powder coating is a popular finishing process used across various industries to apply a durable and protective layer to metal surfaces. Unlike traditional liquid paint, powder coating uses a dry powder that is electrostatically charged and applied to the surface, which is then cured in a high-temperature oven. This process results in a hard finish that is more resistant to chipping, scratching, and fading.
In this guide, we’ll explore the different components of a powder coating system, including ovens, machines, equipment, and entire production lines. Understanding these elements is crucial for businesses looking to enhance their production capabilities with powder coating technology.
Powder Coating Ovens
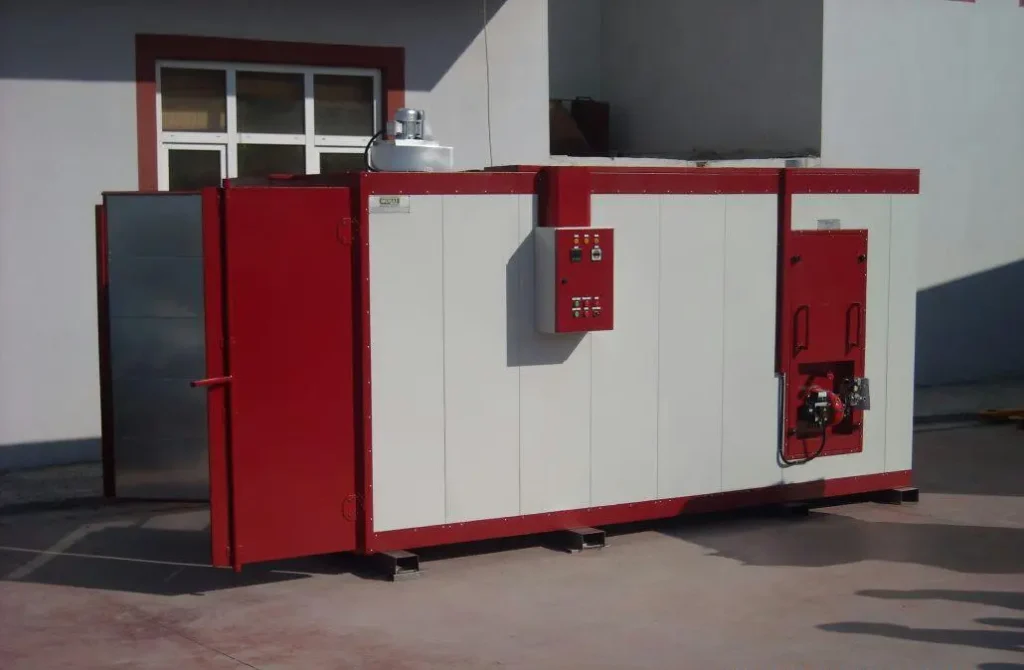
Definition and Purpose:
Powder coating ovens are essential for the curing process, where the powder adheres to the surface and forms a smooth, hard finish. These ovens provide the necessary heat to melt the powder, ensuring even and thorough coating.
Types of Powder Coating Ovens:
- Batch Ovens:
- Ideal for small to medium-sized production runs
- Flexibility to handle various part sizes
- Suitable for businesses with diverse product lines
- Conveyor Ovens:
- Designed for continuous production
- Higher throughput and efficiency
- Suitable for large-scale operations
Features and Specifications:
- Temperature Range: Typically between 325°F to 450°F
- Heating Source: Options include electric, gas, or infrared
- Size and Capacity: Varies based on production needs
- Energy Efficiency: Consider models with advanced insulation and airflow systems
How to Choose the Right Oven:
- Evaluate production volume and part sizes
- Consider energy consumption and operating costs
- Assess available space and installation requirements
- Consult with manufacturers for customized solutions
Powder Coating Machines
Overview of Different Machines Used:
Powder coating machines are used to apply the powder to the surface. They vary in complexity and functionality, catering to different production needs.
Manual vs. Automated Machines:
- Manual Machines:
- Suitable for small-scale operations
- Offers flexibility and control
- Requires skilled operators
- Automated Machines:
- Ideal for high-volume production
- Consistent and uniform application
- Reduced labor costs
Key Features and Specifications:
- Voltage and Power Requirements: Ensure compatibility with your facility
- Control Systems: Look for user-friendly interfaces and programmable settings
- Spray Gun Options: Different nozzles and gun types for various applications
Selecting the Right Machine for Your Needs:
- Determine the scale and complexity of your operations
- Evaluate budget constraints and long-term ROI
- Seek advice from industry experts and suppliers
Powder Coating Equipment
Essential Equipment for Powder Coating:
- Powder Coating Booths: Enclosed areas for applying powder
- Powder Recovery Systems: Capture and reuse overspray powder
- Air Compressors and Dryers: Ensure consistent airflow for optimal coating
Optional Equipment for Enhanced Performance:
- Pre-Treatment Systems: Clean and prepare surfaces before coating
- Curing Lamps: Speed up the curing process with infrared or UV lamps
Maintenance and Safety Considerations:
- Regularly inspect and clean equipment
- Train staff on proper handling and safety protocols
- Adhere to industry standards and regulations
Powder Coating Lines and Plants
Explanation of Powder Coating Lines:
Powder coating lines are integrated systems that automate the entire powder coating process, from pre-treatment to curing.
Components of a Powder Coating Line:
- Conveyor Systems: Move parts through the line efficiently
- Pre-Treatment Stations: Clean and prepare surfaces
- Powder Application Booths: Enclosed areas for powder coating
- Curing Ovens: Finalize the coating process
Design and Layout Considerations:
- Optimize workflow and space utilization
- Consider future scalability and expansion
- Ensure compliance with safety and environmental regulations
Scalability and Customization Options:
- Modular designs for easy expansion
- Custom configurations to meet specific production needs
Benefits of Powder Coating
Environmental Advantages:
- Low VOC emissions compared to liquid paints
- Overspray can be recycled, reducing waste
- Complies with environmental regulations
Durability and Longevity:
- Resistant to corrosion, fading, and wear
- Suitable for outdoor and high-traffic applications
- Provides a high-quality, professional finish
Cost-Effectiveness:
- Reduces long-term maintenance and repainting costs
- Efficient use of materials minimizes waste
- High throughput and automation lower labor expenses
Considerations for Setting Up a Powder Coating Plant
Initial Investment and ROI:
- Assess capital requirements for equipment and infrastructure
- Calculate potential returns based on production capacity and demand
- Explore financing options and incentives
Regulatory Compliance:
- Adhere to industry standards and local regulations
- Implement safety protocols and employee training
- Monitor environmental impact and waste management
Market Trends and Future Outlook:
- Growing demand for eco-friendly coatings
- Advancements in automation and technology
- Increasing adoption in automotive, aerospace, and consumer goods sectors
Conclusion
Powder coating offers numerous advantages over traditional liquid painting methods, making it an attractive option for industries seeking durable and environmentally friendly finishes. By investing in the right equipment and understanding the intricacies of powder coating processes, businesses can enhance their production capabilities and meet the growing demand for high-quality coated products.
When setting up a powder coating plant, it’s essential to carefully consider your needs, budget, and long-term goals. Collaborating with experienced suppliers and industry experts can help you make informed decisions and achieve success in the competitive world of powder coating.
This comprehensive guide should provide valuable insights for your website visitors and help position your business as a knowledgeable and reliable source in the powder coating industry.
Installation process steps
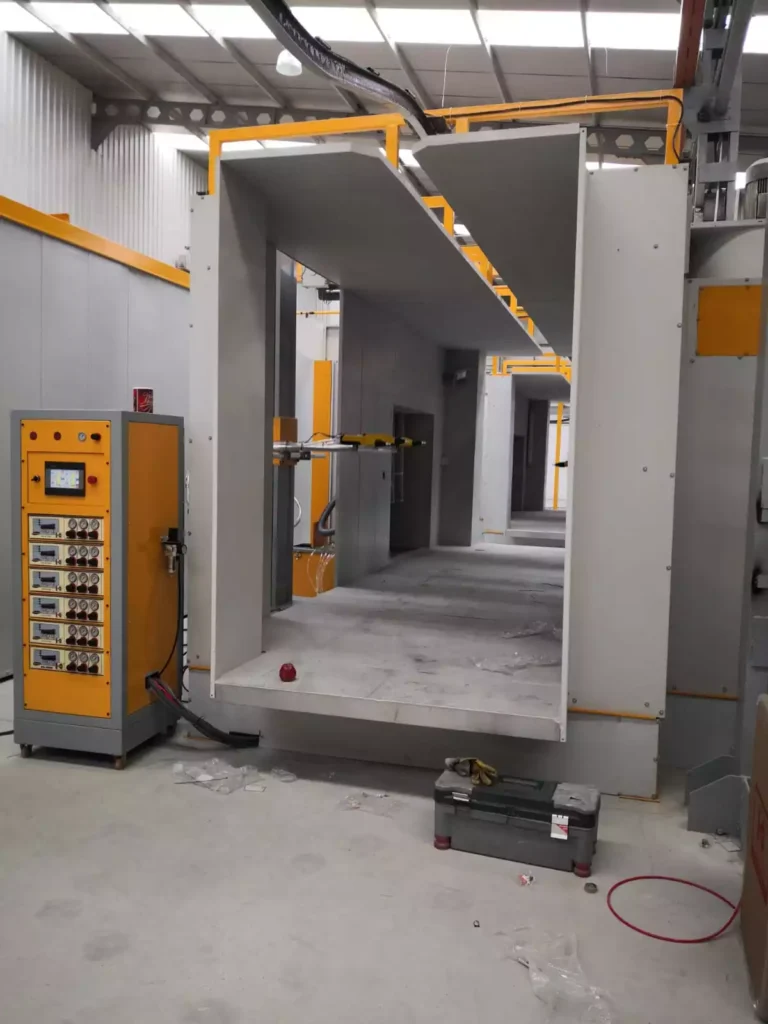
To provide a comprehensive guide on the installation process for powder coating systems, we’ll cover each step involved in setting up a powder coating plant. This includes planning, selecting equipment, site preparation, installation, testing, and staff training. Here’s a detailed outline and content for this section:
Outline for Installation Process Steps
- Planning and Design
- Assessing needs and capacity
- Layout and design considerations
- Budget and timeline
- Equipment Selection
- Choosing the right ovens, machines, and equipment
- Consulting with manufacturers and suppliers
- Site Preparation
- Preparing the facility for installation
- Ensuring compliance with regulations
- Installation Process
- Step-by-step installation guide
- Safety protocols and considerations
- System Testing and Calibration
- Testing each component
- Ensuring optimal performance
- Training and Support
- Staff training on operation and safety
- Ongoing maintenance and support
- Post-Installation Considerations
- Regular inspections and maintenance
- Upgrades and scalability
Installation Process Steps for Powder Coating Systems
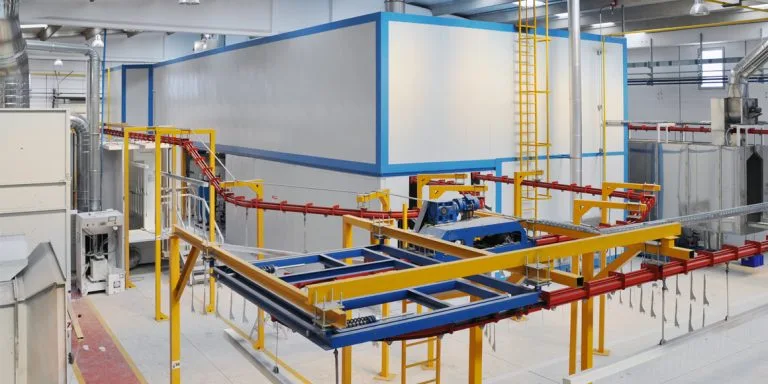
Setting up a powder coating plant involves careful planning and execution to ensure a successful installation. Here’s a step-by-step guide to help you navigate the process:
1. Planning and Design
Assessing Needs and Capacity:
- Identify Production Requirements: Determine the types and sizes of parts you will be coating, and estimate your production volume.
- Analyze Workflow: Consider how materials will move through the plant, from pre-treatment to curing.
- Evaluate Space Requirements: Ensure adequate space for equipment, storage, and workflow efficiency.
Layout and Design Considerations:
- Optimize Workflow: Design a layout that minimizes bottlenecks and maximizes efficiency.
- Future Scalability: Plan for potential expansion or upgrades.
- Compliance with Safety Standards: Ensure the layout meets all safety and regulatory requirements.
Budget and Timeline:
- Create a Detailed Budget: Account for equipment, installation, training, and operational costs.
- Establish a Timeline: Set realistic milestones for each phase of the installation process.
2. Equipment Selection
Choosing the Right Ovens, Machines, and Equipment:
- Powder Coating Ovens: Select between batch or conveyor ovens based on production needs.
- Powder Coating Machines: Choose manual or automated systems that match your operational scale.
- Additional Equipment: Consider powder booths, recovery systems, and pre-treatment stations.
Consulting with Manufacturers and Suppliers:
- Leverage Expertise: Work with manufacturers to choose equipment tailored to your specific requirements.
- Request Demonstrations: Evaluate equipment performance through demos or site visits.
- Negotiate Contracts: Ensure favorable terms and warranties with suppliers.
3. Site Preparation
Preparing the Facility for Installation:
- Infrastructure Readiness: Ensure adequate power supply, ventilation, and environmental controls.
- Space Optimization: Clear and organize the installation area for easy access and efficient workflow.
Ensuring Compliance with Regulations:
- Local Permits and Licenses: Obtain necessary permits and ensure compliance with zoning regulations.
- Safety Standards: Adhere to occupational health and safety standards.
4. Installation Process
Step-by-Step Installation Guide:
- Site Inspection: Conduct a final inspection of the site to verify readiness.
- Delivery and Unpacking: Receive and unpack equipment carefully, checking for any damage.
- Positioning Equipment: Install each piece of equipment according to the layout plan.
- Electrical and Plumbing Connections: Ensure all electrical and plumbing connections are correctly made and tested.
- Calibration and Setup: Configure equipment settings and calibrate machinery to specifications.
Safety Protocols and Considerations:
- Install Safety Features: Implement necessary safety features such as emergency stops and protective barriers.
- Personal Protective Equipment (PPE): Ensure that all personnel have access to required PPE.
5. System Testing and Calibration
Testing Each Component:
- Conduct Trial Runs: Test each component individually and as part of the integrated system.
- Check for Performance Issues: Identify and resolve any performance or operational issues.
Ensuring Optimal Performance:
- Fine-Tune Settings: Adjust equipment settings for optimal coating quality.
- Document Results: Record all testing results and adjustments for future reference.
6. Training and Support
Staff Training on Operation and Safety:
- Conduct Training Sessions: Provide comprehensive training on equipment operation and safety protocols.
- Create Training Materials: Develop manuals and guides for ongoing staff reference.
Ongoing Maintenance and Support:
- Establish a Maintenance Schedule: Set up regular maintenance checks to ensure equipment longevity.
- Vendor Support: Engage with suppliers for ongoing support and troubleshooting.
7. Post-Installation Considerations
Regular Inspections and Maintenance:
- Implement Routine Inspections: Regularly inspect equipment and systems for wear and tear.
- Schedule Maintenance: Adhere to the maintenance schedule to prevent downtime and extend equipment life.
Upgrades and Scalability:
- Monitor Technological Advancements: Stay informed about new technologies and equipment improvements.
- Plan for Upgrades: Budget for future upgrades and expansion as business needs grow.
Conclusion
The installation of a powder coating system is a multi-step process that requires meticulous planning and execution. By following these steps, businesses can ensure a smooth setup and operation, maximizing efficiency and product quality. It’s crucial to work closely with experienced manufacturers and suppliers to tailor the installation process to your specific needs and to provide ongoing training and support for staff.
Installation cost estimate
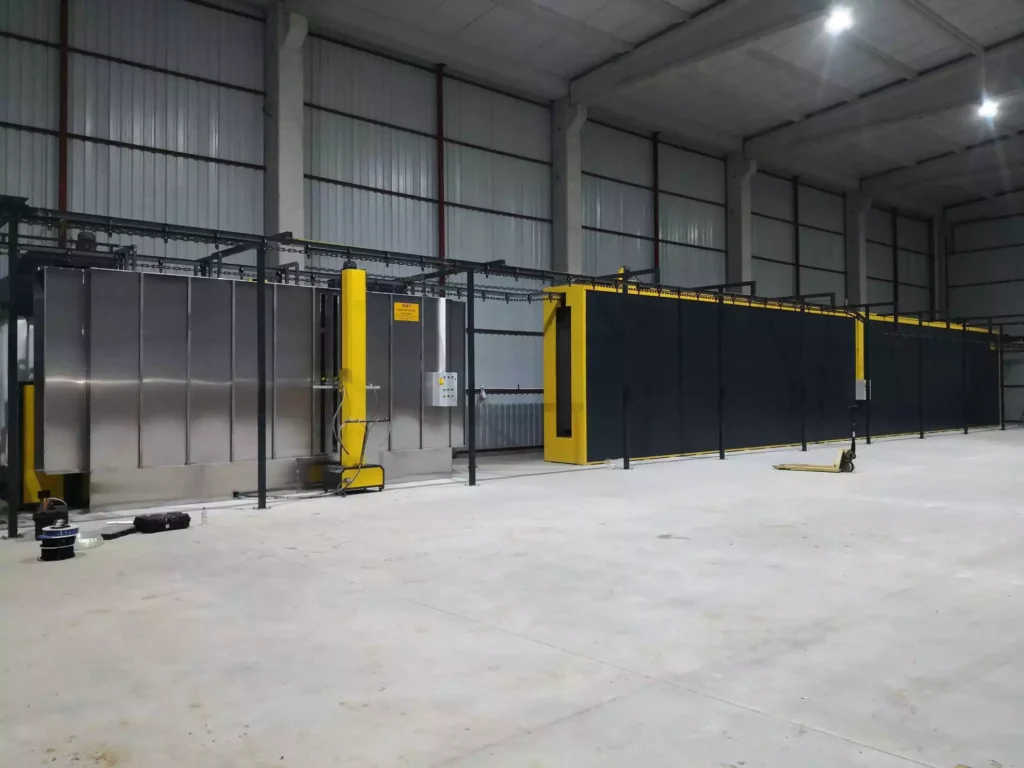
Estimating the installation cost of a powder coating system involves considering various factors, such as the size of the operation, the type of equipment, facility modifications, labor, and additional costs like permits and training. Here’s a detailed breakdown to help you understand the potential costs involved in setting up a powder coating plant.
Installation Cost Estimate for Powder Coating Systems
Factors Influencing Costs
- Type of Equipment and Technology
- Powder coating ovens (batch vs. conveyor)
- Coating machines (manual vs. automated)
- Auxiliary equipment (booths, recovery systems, pre-treatment stations)
- Scale and Capacity of the Operation
- Production volume
- Facility size and space requirements
- Facility Modifications
- Infrastructure updates (electrical, ventilation, plumbing)
- Space optimization and layout design
- Labor and Installation Services
- Skilled labor for installation
- Equipment calibration and testing
- Additional Costs
- Permits and regulatory compliance
- Staff training and support
- Maintenance and contingency expenses
Estimated Costs
Below is a general estimate of the costs associated with installing a powder coating system. Note that prices can vary significantly based on location, vendor, and specific requirements.
1. Equipment Costs
- Powder Coating Ovens:
- Batch Ovens: $1,000 – $50,000
- Conveyor Ovens: $10,000 – $200,000
- Powder Coating Machines:
- Manual Machines: $1,000 – $20,000
- Automated Systems: $20,000 – $100,000
- Auxiliary Equipment:
- Powder Booths: $2,000 – $30,000
- Recovery Systems: $3,000 – $15,000
- Pre-Treatment Systems: $10,000 – $50,000
2. Facility Modifications
- Electrical and Ventilation Upgrades: $10,000 – $50,000
- Space Optimization and Layout Design: $5,000 – $20,000
3. Labor and Installation Services
- Installation Labor: $10,000 – $30,000
- Calibration and Testing: $5,000 – $10,000
4. Additional Costs
- Permits and Compliance: $2,000 – $10,000
- Training and Support: $2,000 – $5,000
- Maintenance and Contingency: $5,000 – $15,000
Total Estimated Cost
The total estimated cost for installing a powder coating system can range from $70,000 to $500,000, depending on the size, complexity, and specific requirements of the operation. Here’s a breakdown by scale:
- Small-Scale Operations: $20,000 – $50,000
- Medium-Scale Operations: $50,000 – $100,000
- Large-Scale Operations: $100,000 – $500,000
Tips for Cost Management
- Conduct a Detailed Assessment:
- Evaluate your specific needs and choose equipment accordingly.
- Consider future scalability to avoid unnecessary upgrades later.
- Get Multiple Quotes:
- Request quotes from multiple vendors to compare prices and services.
- Negotiate terms and warranties to get the best deal.
- Plan for Contingencies:
- Set aside a contingency budget for unexpected expenses during installation.
- Regularly review and adjust your budget as the project progresses.
- Focus on Energy Efficiency:
- Invest in energy-efficient equipment to reduce long-term operational costs.
- Evaluate the potential return on investment (ROI) for each piece of equipment.
- Leverage Financing Options:
- Explore financing options, grants, or incentives available for industrial upgrades.
Conclusion
Setting up a powder coating plant requires a significant investment, but careful planning and strategic decision-making can help manage costs effectively. By considering your specific needs, working with experienced suppliers, and planning for the future, you can ensure a successful installation and operation of your powder coating system.
Let me know if you need further details or specific cost estimates tailored to your project!
Components of a Powder Coating Plant
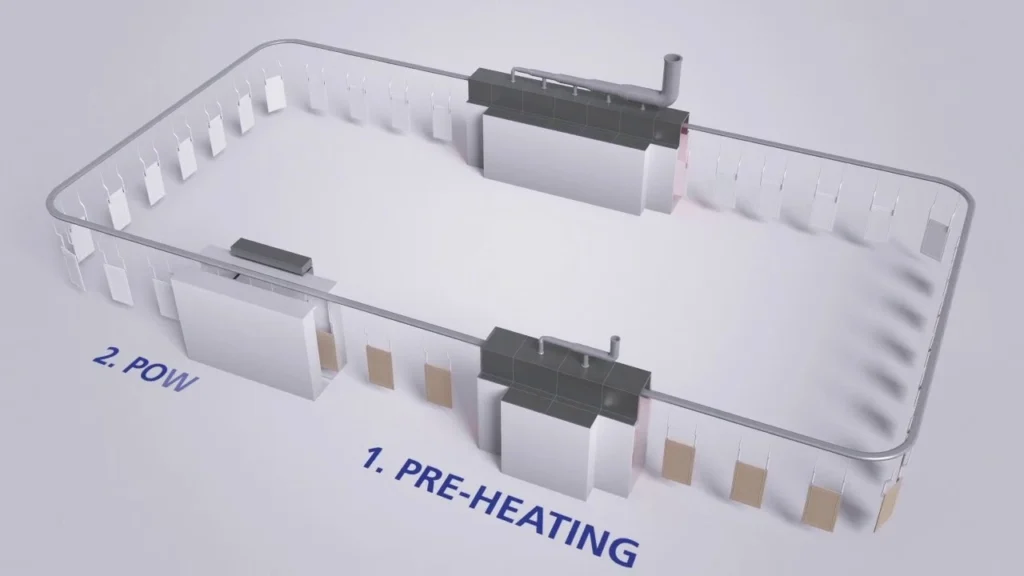
A powder coating plant consists of various components that work together to facilitate the coating process, from preparation to application and curing. Understanding these components is crucial for designing an efficient and effective system tailored to specific production needs. Below is a detailed overview of the key components of a powder coating plant:
Key Components of a Powder Coating Plant
- Pre-Treatment System
- Purpose: Cleans and prepares surfaces for powder coating to ensure adhesion and finish quality.
- Components:
- Washing Stations: Use chemical solutions to remove contaminants like grease, oil, dirt, and rust.
- Rinse Stations: Remove residual chemicals from the surface.
- Drying Ovens: Dry the parts after washing and rinsing to prepare them for powder application.
- Powder Coating Booths
- Purpose: Enclosed area where the powder is applied to the parts.
- Types:
- Manual Booths: Operators manually apply powder using spray guns. Ideal for small or custom jobs.
- Automatic Booths: Equipped with automated spray guns and reciprocators for high-volume production.
- Features:
- Ventilation Systems: Ensure proper airflow to capture overspray and maintain a clean environment.
- Powder Recovery Systems: Collect overspray powder for reuse, improving material efficiency.
- Powder Application Equipment
- Purpose: Applies the powder to the surfaces using electrostatic spray guns.
- Components:
- Electrostatic Spray Guns: Charge the powder particles and spray them onto the grounded parts.
- Control Units: Adjust settings like voltage, powder flow rate, and air pressure to ensure uniform coverage.
- Conveyor System
- Purpose: Transports parts through various stages of the powder coating process.
- Types:
- Overhead Conveyors: Hang parts from hooks or racks for continuous production.
- Floor Conveyors: Suitable for heavier or larger parts that cannot be suspended.
- Features:
- Variable Speed Control: Adjusts the speed of the conveyor to match production needs and curing times.
- Loading and Unloading Stations: Facilitate the movement of parts onto and off the conveyor system.
- Powder Coating Ovens
- Purpose: Cures the powder coating by melting and fusing it to the surface, forming a durable finish.
- Types:
- Batch Ovens: Suitable for smaller production runs and varied part sizes.
- Conveyor Ovens: Designed for continuous, high-volume production.
- Features:
- Temperature Control Systems: Ensure precise and consistent heating for optimal curing.
- Energy Efficiency: Incorporate insulation and heat recovery systems to minimize energy consumption.
- Cooling and Inspection Stations
- Purpose: Cool the parts after curing and inspect them for quality assurance.
- Components:
- Cooling Zones: Allow parts to cool gradually to avoid warping or defects.
- Inspection Areas: Check for coating consistency, thickness, and finish quality before packaging or assembly.
- Control and Monitoring Systems
- Purpose: Manage and monitor the entire powder coating process for efficiency and quality control.
- Components:
- PLC Systems (Programmable Logic Controllers): Automate and synchronize various plant operations.
- Data Logging and Analysis Tools: Record production metrics and identify areas for improvement.
- Safety and Environmental Controls
- Purpose: Ensure the safety of workers and compliance with environmental regulations.
- Components:
- Fire Suppression Systems: Protect against powder fires or explosions in booths and ovens.
- Ventilation and Filtration Systems: Maintain air quality by removing dust, fumes, and volatile organic compounds (VOCs).
- Personal Protective Equipment (PPE): Provide workers with necessary safety gear, such as masks, gloves, and goggles.
Optional and Auxiliary Components
- Advanced Pre-Treatment Systems: Utilize additional technologies like ultrasonic cleaning or nanotechnology for improved surface preparation.
- Curing Lamps: Use infrared or UV lamps for faster curing times and energy savings.
- Automated Robotic Systems: Enhance precision and efficiency in powder application and handling.
- Quality Control Instruments: Use advanced tools like thickness gauges, gloss meters, and adhesion testers for detailed quality assessment.
Layout and Design Considerations
- Workflow Optimization: Design the plant layout to minimize bottlenecks and ensure smooth transitions between stages.
- Space Utilization: Efficiently allocate space for equipment, storage, and movement of materials.
- Scalability: Plan for future expansion or upgrades to accommodate growing production demands.
Conclusion
A well-designed powder coating plant integrates these components to create an efficient, high-quality coating process. Understanding each element and its role in the system is crucial for businesses looking to enhance their powder coating capabilities. By investing in the right equipment and technology, companies can achieve superior finishes, increased productivity, and long-term success in the powder coating industry.
Detailed Components of a Powder Coating Plant
Certainly! To provide a detailed understanding of each component within a powder coating plant, we’ll delve into the technical specifications, functions, types, and key considerations for each element. This comprehensive breakdown will cover everything from the initial pre-treatment to the final inspection.
1. Pre-Treatment System
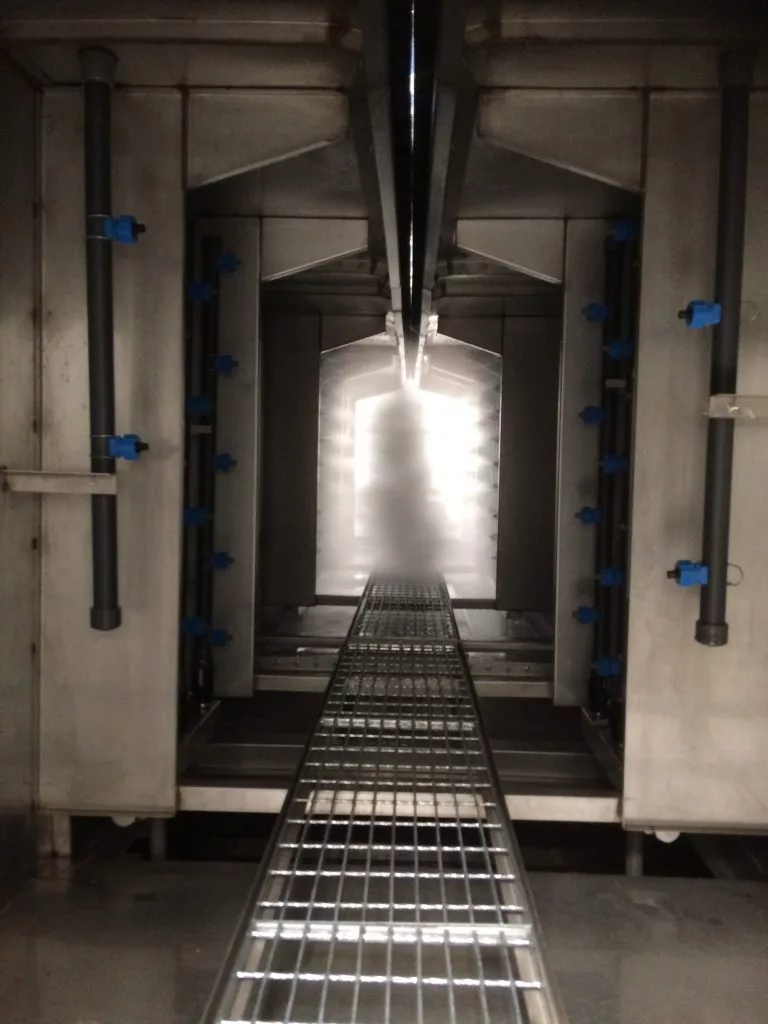
Overview
The pre-treatment system is crucial in ensuring that surfaces are properly cleaned and prepared for powder coating. This step enhances adhesion, improves finish quality, and increases the longevity of the coating.
Components and Process
1.1. Cleaning and Degreasing Stations
- Purpose: Remove oils, grease, and other contaminants from the surface.
- Methods:
- Alkaline Cleaning: Uses alkaline solutions to break down grease and oils.
- Solvent Cleaning: Employs organic solvents to dissolve contaminants.
- Ultrasonic Cleaning: Utilizes high-frequency sound waves for deep cleaning, especially effective for complex shapes.
- Equipment:
- Tanks and spray systems
- Heating elements to improve cleaning efficiency
- Agitation systems for even cleaning
1.2. Rinse Stations
- Purpose: Eliminate residual chemicals and contaminants from the cleaning stage.
- Types of Rinse:
- Freshwater Rinse: Basic water rinse to remove chemicals.
- Deionized Water Rinse: Prevents mineral deposits and spots on surfaces.
- Equipment:
- Spray bars and nozzles for thorough rinsing
- Closed-loop systems to recycle water and reduce waste
1.3. Surface Conditioning
- Purpose: Prepare the surface for subsequent conversion coating.
- Processes:
- Acid Etching: Removes oxides and prepares metal surfaces.
- Descaling: Removes scale and rust from the surface.
- Equipment:
- Immersion tanks or spray booths
- Automated dosing systems for precise chemical application
1.4. Conversion Coating
- Purpose: Apply a chemical layer that enhances powder adhesion and corrosion resistance.
- Types:
- Phosphate Coating: Iron or zinc phosphate for steel surfaces.
- Chromate Coating: Used for aluminum and zinc surfaces.
- Nano-Ceramic Coatings: Environmentally friendly option with superior adhesion and corrosion resistance.
- Equipment:
- Spray or immersion systems
- Temperature control for optimal reaction conditions
1.5. Drying Ovens
- Purpose: Remove moisture from parts to prevent defects in the powder coating.
- Features:
- Adjustable temperature settings
- Air circulation systems for even drying
- Equipment:
- Batch ovens for smaller production
- Conveyor ovens for continuous processing
Key Considerations
- Chemical Management: Ensure proper handling, storage, and disposal of chemicals used in pre-treatment.
- Environmental Compliance: Adhere to local regulations for effluent discharge and waste management.
- Maintenance: Regular cleaning and inspection of tanks and nozzles to prevent contamination.
2. Powder Coating Booths
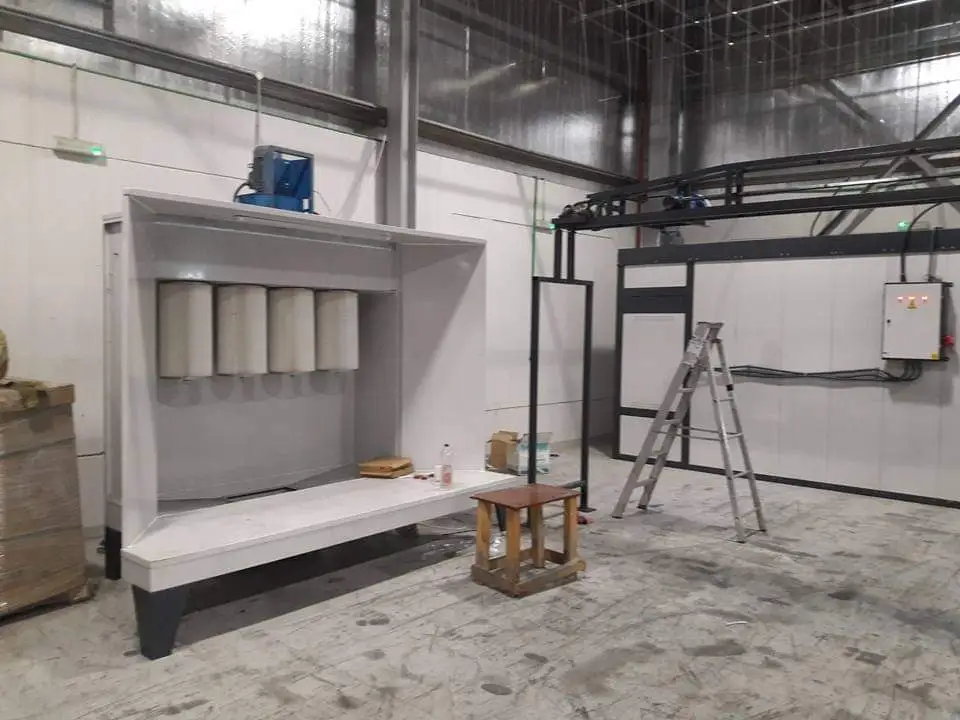
Overview
Powder coating booths provide a controlled environment for applying the powder. They ensure that the powder is applied evenly and that any overspray is efficiently managed and collected for reuse.
Types and Features
2.1. Manual Powder Coating Booths
- Purpose: Allow operators to manually apply powder using handheld spray guns.
- Applications: Suitable for small batches, custom jobs, and intricate parts.
- Features:
- Ventilation Systems: Maintain air quality and remove overspray.
- Lighting: Ensure visibility for precise application.
- Ergonomic Design: Facilitate operator comfort and efficiency.
2.2. Automatic Powder Coating Booths
- Purpose: Use automated systems to apply powder to parts, ideal for high-volume production.
- Applications: Suitable for standard parts and large-scale operations.
- Features:
- Robotic Arms and Reciprocators: Ensure consistent application across parts.
- Programmable Settings: Customize application parameters for different parts.
- Rapid Color Change Systems: Allow quick and efficient color changes with minimal downtime.
2.3. Powder Recovery Systems
- Purpose: Capture and recycle overspray powder to improve efficiency and reduce waste.
- Types:
- Cyclone Separators: Use centrifugal force to separate powder from the air.
- Cartridge Filters: Trap fine powder particles for reuse.
- Baghouse Filters: Employ fabric bags to capture powder, suitable for larger particles.
Key Considerations
- Airflow Management: Ensure proper ventilation to prevent contamination and maintain a clean environment.
- Color Change Efficiency: Invest in systems that allow quick and easy color changes to minimize downtime.
- Safety: Implement explosion-proof designs and fire suppression systems to prevent hazards.
3. Powder Application Equipment
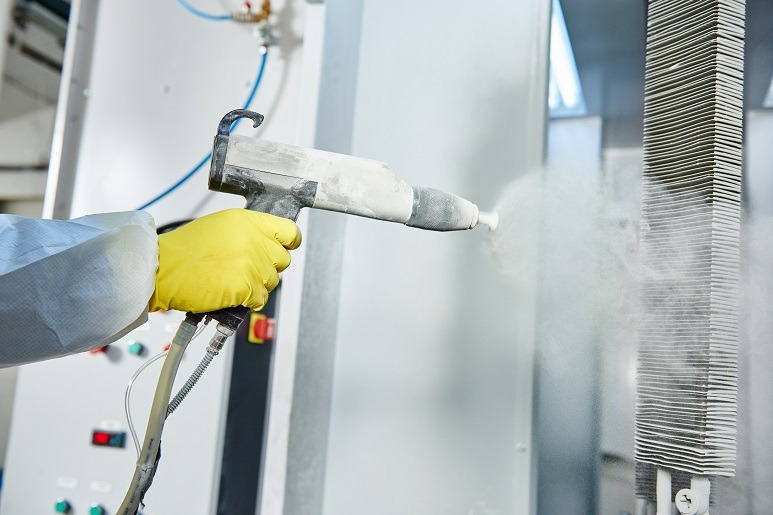
Overview
Powder application equipment is responsible for applying the powder coating to the parts. This equipment uses electrostatic principles to ensure uniform coverage and strong adhesion.
Components and Features
3.1. Electrostatic Spray Guns
- Purpose: Apply powder to the parts using an electrostatic charge.
- Types:
- Corona Guns: Use a high-voltage electrode to charge the powder.
- Tribo Guns: Charge the powder through friction, suitable for specific applications.
- Features:
- Adjustable Voltage and Current: Control the electrostatic charge for optimal coverage.
- Interchangeable Nozzles: Provide different spray patterns for various applications.
- Lightweight and Ergonomic Design: Ensure operator comfort during manual application.
3.2. Control Units
- Purpose: Manage and adjust the settings of the powder application equipment.
- Features:
- Digital Displays: Provide real-time feedback on settings and performance.
- Programmable Settings: Allow customization for different parts and powder types.
- Data Logging: Record application parameters for quality control and traceability.
3.3. Fluidized Bed Systems
- Purpose: Coat parts by dipping them into a bed of fluidized powder, typically used for thicker coatings.
- Applications: Suitable for specific applications requiring a thick and even coating.
- Features:
- Uniform Airflow: Ensure consistent fluidization of powder particles.
- Temperature Control: Maintain optimal conditions for coating.
Key Considerations
- Powder Compatibility: Ensure equipment is compatible with different powder formulations.
- Operator Training: Provide comprehensive training for operators to ensure efficient and safe use.
- Maintenance: Regularly clean and maintain spray guns and control units to prevent clogging and ensure consistent performance.
4. Conveyor System
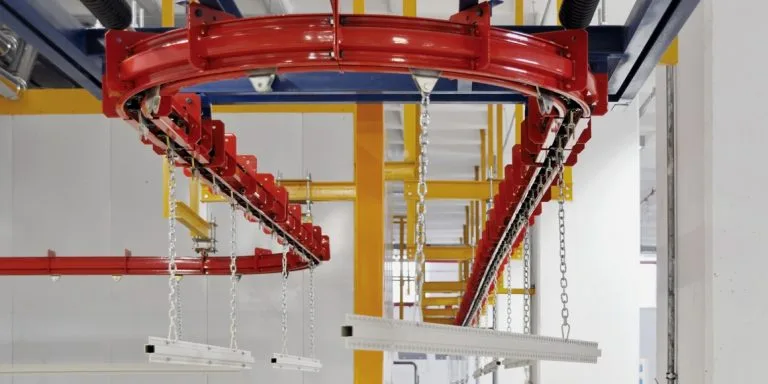
Overview
The conveyor system is the backbone of the powder coating plant, transporting parts through each stage of the process, from pre-treatment to curing.
Types and Features
4.1. Overhead Conveyors
- Purpose: Transport parts by suspending them from hooks or racks, ideal for continuous production.
- Types:
- Monorail Systems: Simple looped tracks for straightforward applications.
- Power and Free Systems: Offer more flexibility with multiple paths and stopping points.
- Features:
- Variable Speed Control: Adjust the speed to match production needs and curing times.
- Load Capacity: Designed to handle different part sizes and weights.
- Integration with Other Systems: Seamlessly integrate with pre-treatment, application, and curing systems.
4.2. Floor Conveyors
- Purpose: Transport heavier or larger parts that cannot be suspended, suitable for specific applications.
- Types:
- Belt Conveyors: Use belts to move parts horizontally or on an incline.
- Roller Conveyors: Employ rollers to facilitate the movement of parts.
- Features:
- Heavy-Duty Construction: Designed to support large or heavy parts.
- Customizable Configurations: Adapt to different plant layouts and processes.
Key Considerations
- Layout Design: Plan the conveyor layout to optimize workflow and minimize bottlenecks.
- Load and Speed Requirements: Ensure the conveyor system meets production demands for speed and capacity.
- Safety Features: Implement safety measures such as guards, emergency stops, and regular inspections.
5. Powder Coating Ovens
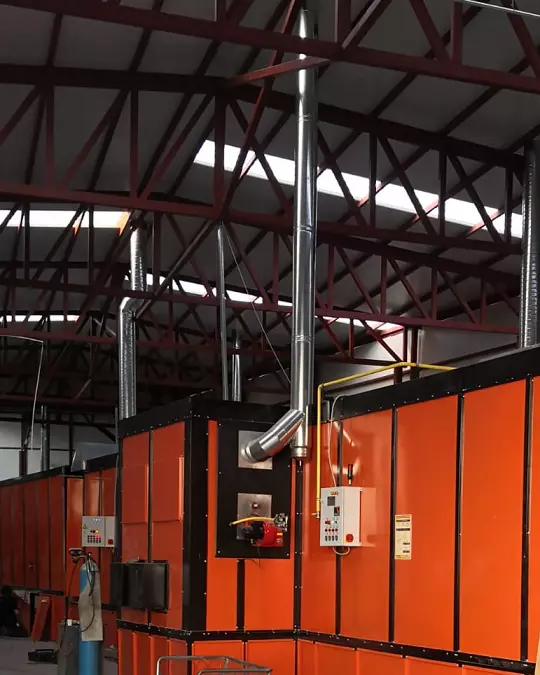
Overview
Powder coating ovens are responsible for curing the powder coating by melting and fusing it to the surface, resulting in a durable and attractive finish.
Types and Features
5.1. Batch Ovens
- Purpose: Cure parts in small batches, suitable for varied part sizes and low-volume production.
- Applications: Ideal for custom jobs, small businesses, and prototyping.
- Features:
- Adjustable Temperature Control: Precise control of curing conditions.
- Flexible Configuration: Accommodate different part sizes and shapes.
- Insulated Construction: Minimize heat loss and improve energy efficiency.
5.2. Conveyor Ovens
- Purpose: Designed for continuous production, curing parts as they move through the oven.
- Applications: Suitable for high-volume production and standardized parts.
- Features:
- Consistent Temperature Distribution: Ensure even curing across all parts.
- Variable Conveyor Speed: Match curing times with production speed.
- Energy Efficiency: Incorporate heat recovery systems and advanced insulation.
Key Considerations
- Oven Size and Capacity: Choose an oven that meets production demands without excessive energy use.
- Heating Source: Decide between electric, gas, or infrared heating based on cost and efficiency.
- Temperature Uniformity: Ensure consistent heat distribution to prevent defects in the finish.
6. Cooling and Inspection Stations
Overview
Cooling and inspection stations are crucial for ensuring the quality and consistency of the finished products. Cooling prevents defects, while inspection verifies the coating quality.
Components and Features
6.1. Cooling Zones
- Purpose: Gradually cool parts after curing to prevent warping or defects.
- Features:
- Controlled Airflow: Ensure even cooling and avoid thermal shock.
- Adjustable Cooling Rates: Customize settings for different materials and part sizes.
6.2. Inspection Areas
- Purpose: Conduct quality checks on coated parts to ensure consistency and adherence to standards.
- Features:
- Lighting and Magnification: Facilitate detailed visual inspections.
- Measurement Tools: Use instruments like thickness gauges and gloss meters for precise evaluation.
- Defect Detection Systems: Implement automated systems for detecting coating defects, such as thin spots or uneven coverage.
Key Considerations
- Quality Assurance Protocols: Establish standards and procedures for inspections to ensure consistent product quality.
- Training for Inspectors: Provide training to staff on recognizing defects and using inspection tools effectively.
- Feedback Loop: Use inspection data to inform process improvements and address recurring issues.
7. Control and Monitoring Systems
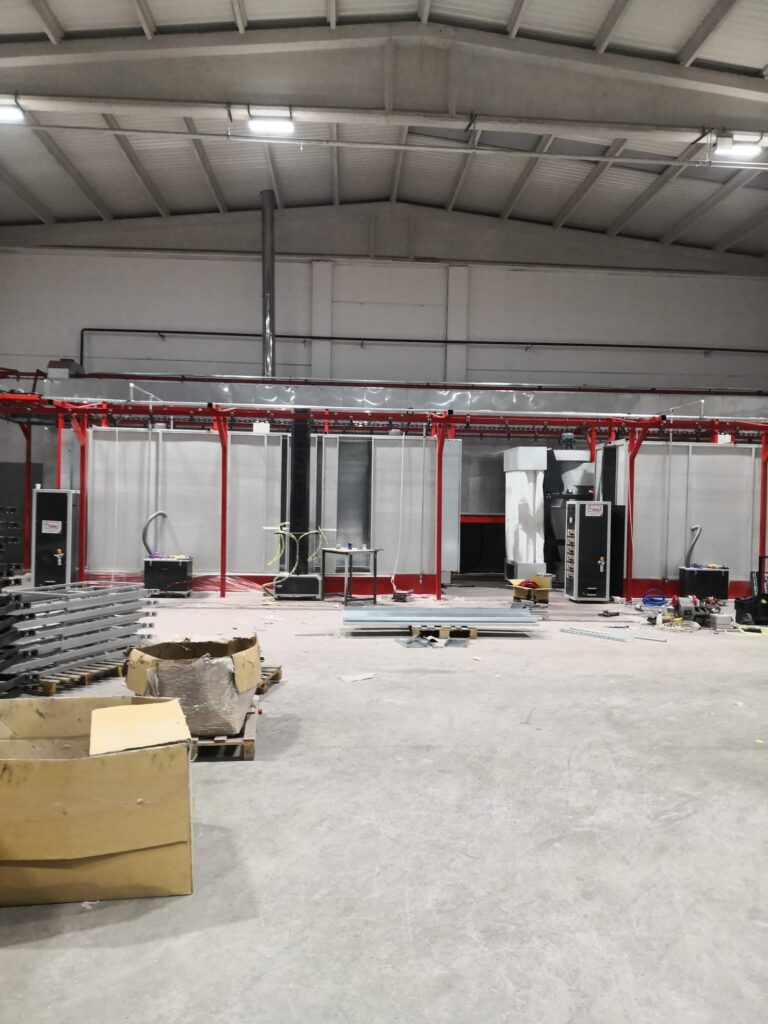
Overview
Control and monitoring systems automate and synchronize various plant operations, ensuring efficiency, consistency, and quality in the powder coating process.
Components and Features
7.1. PLC Systems (Programmable Logic Controllers)
- Purpose: Automate and control equipment functions throughout the plant.
- Features:
- Centralized Control: Manage multiple systems from a single interface.
- Real-Time Monitoring: Track performance metrics and adjust settings as needed.
- Data Logging: Record operational data for analysis and process optimization.
7.2. Data Logging and Analysis Tools
- Purpose: Collect and analyze production data to improve efficiency and quality.
- Features:
- Trend Analysis: Identify patterns and trends in production metrics.
- Performance Dashboards: Visualize key performance indicators (KPIs) for easy monitoring.
- Predictive Maintenance: Use data to anticipate equipment maintenance needs and prevent downtime.
Key Considerations
- System Integration: Ensure seamless integration with existing equipment and software.
- User Interface: Provide intuitive and user-friendly interfaces for operators.
- Cybersecurity: Implement security measures to protect sensitive data and control systems.
8. Safety and Environmental Controls
Overview
Safety and environmental controls are essential for protecting workers and ensuring compliance with regulations. These systems manage hazards and minimize environmental impact.
Components and Features
8.1. Fire Suppression Systems
- Purpose: Prevent and control powder fires or explosions in booths and ovens.
- Features:
- Automatic Detection and Suppression: Quickly identify and extinguish fires.
- Integration with Control Systems: Automatically shut down equipment in case of fire.
- Regular Testing and Maintenance: Ensure systems are operational and compliant with safety standards.
8.2. Ventilation and Filtration Systems
- Purpose: Maintain air quality by removing dust, fumes, and volatile organic compounds (VOCs).
- Features:
- High-Efficiency Particulate Air (HEPA) Filters: Capture fine particles and contaminants.
- Exhaust Fans and Ductwork: Ensure proper airflow and ventilation.
- Regular Filter Replacement: Maintain efficiency and prevent clogs.
8.3. Personal Protective Equipment (PPE)
- Purpose: Provide workers with necessary safety gear to protect against hazards.
- Components:
- Respirators and Masks: Protect against inhalation of powder particles and fumes.
- Safety Glasses and Goggles: Shield eyes from dust and chemical splashes.
- Gloves and Protective Clothing: Prevent skin contact with chemicals and powders.
Key Considerations
- Compliance with Regulations: Adhere to local and international safety and environmental standards.
- Safety Training: Conduct regular training sessions on safety protocols and emergency procedures.
- Continuous Improvement: Regularly review and update safety measures to address emerging risks and regulations.
Conclusion
Each component of a powder coating plant plays a vital role in ensuring a successful and efficient coating process. By understanding the details and functions of these components, businesses can design and operate a plant that meets their specific needs and production goals. Investing in the right equipment and systems, along with proper training and maintenance, will lead to high-quality finishes, increased productivity, and long-term success in the powder coating industry.
Installation time estimate
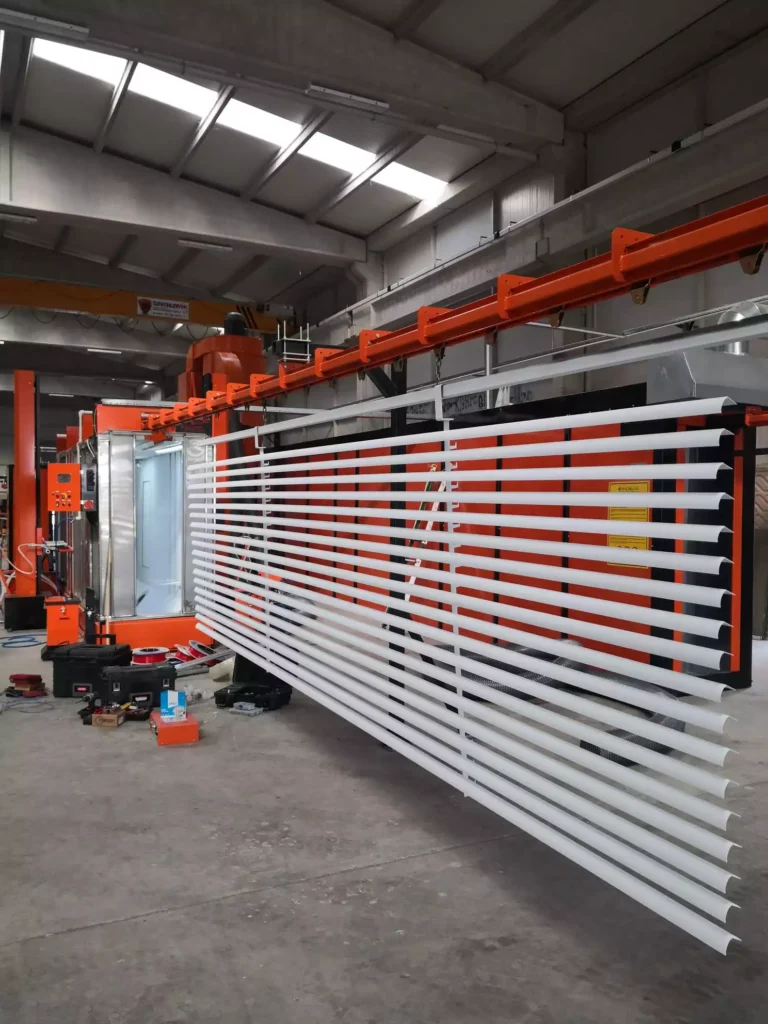
Estimating the installation time for a powder coating plant involves considering several factors such as the size of the operation, complexity of the equipment, facility preparation, and the efficiency of the installation team. Below is a detailed breakdown of the installation time estimate, including factors that can influence the timeline and strategies to ensure a smooth installation process.
Installation Time Estimate for a Powder Coating Plant
Factors Influencing Installation Time
- Scale and Complexity of the Plant
- Size and layout of the facility
- Number and type of equipment components
- Type of Equipment
- Manual vs. automated systems
- Batch vs. continuous production lines
- Site Preparation
- Existing infrastructure readiness
- Facility modifications needed
- Installation Team and Expertise
- Experience and skills of the installation crew
- Availability of necessary resources and tools
- Regulatory Compliance and Inspections
- Time required for permits and approvals
- Safety inspections and certifications
- Coordination and Scheduling
- Coordination between vendors, contractors, and stakeholders
- Availability of equipment and personnel
Estimated Installation Time by Component
Here is an approximate installation timeline for each major component of a powder coating plant. These estimates are generalized and may vary depending on specific project requirements.
1. Pre-Treatment System
- Time Estimate: 1 to 3 weeks
- Activities:
- Delivery and setup of washing, rinsing, and drying stations
- Plumbing and drainage installations
- Testing and calibration of chemical dosing systems
2. Powder Coating Booths
- Time Estimate: 1 to 2 weeks
- Activities:
- Assembly and installation of booth structures
- Integration of ventilation and powder recovery systems
- Setup of lighting and electrical connections
3. Powder Application Equipment
- Time Estimate: 1 to 2 weeks
- Activities:
- Installation of electrostatic spray guns and control units
- Calibration of application settings and nozzles
- Testing for uniform powder distribution
4. Conveyor System
- Time Estimate: 2 to 4 weeks
- Activities:
- Layout design and track installation
- Assembly of conveyor components and drives
- Testing for load capacity and speed control
5. Powder Coating Ovens
- Time Estimate: 2 to 3 weeks
- Activities:
- Installation of oven structures and insulation
- Setup of heating systems and temperature controls
- Testing for temperature uniformity and energy efficiency
6. Cooling and Inspection Stations
- Time Estimate: 1 to 2 weeks
- Activities:
- Installation of cooling systems and airflow management
- Setup of inspection stations and quality control tools
- Training staff on inspection procedures
7. Control and Monitoring Systems
- Time Estimate: 1 to 2 weeks
- Activities:
- Installation of PLC systems and control panels
- Integration with other equipment components
- Testing and validation of automation processes
8. Safety and Environmental Controls
- Time Estimate: 1 to 2 weeks
- Activities:
- Installation of fire suppression and ventilation systems
- Setup of safety barriers and emergency stops
- Safety audits and compliance checks
Total Estimated Installation Time
The total estimated installation time for a powder coating plant can range from 8 to 18 weeks, depending on the scale and complexity of the project. Here’s a breakdown by plant size:
- Small-Scale Operations: 8 to 10 weeks
- Medium-Scale Operations: 10 to 14 weeks
- Large-Scale Operations: 14 to 18 weeks
Strategies for Reducing Installation Time
- Detailed Planning and Coordination
- Develop a comprehensive project plan with clear timelines and milestones.
- Coordinate with vendors, contractors, and stakeholders to align schedules and resources.
- Pre-Fabrication and Pre-Assembly
- Opt for pre-fabricated components to reduce on-site assembly time.
- Pre-assemble equipment off-site where possible to minimize installation complexity.
- Experienced Installation Team
- Hire experienced professionals familiar with powder coating systems and processes.
- Conduct regular training and briefings to ensure the team is well-prepared.
- Efficient Site Preparation
- Ensure the facility is ready for installation before equipment arrives.
- Complete necessary infrastructure upgrades and modifications in advance.
- Streamlined Permitting and Inspections
- Obtain permits and approvals early in the project timeline.
- Schedule inspections and certifications to avoid delays.
- Contingency Planning
- Identify potential risks and develop contingency plans to address unforeseen issues.
- Allocate buffer time in the schedule for unexpected challenges.
Conclusion
The installation of a powder coating plant is a complex process that requires careful planning and coordination. By understanding the factors that influence installation time and implementing strategies to streamline the process, businesses can achieve a successful setup that meets their production goals and timelines.
Maintenance schedule tips
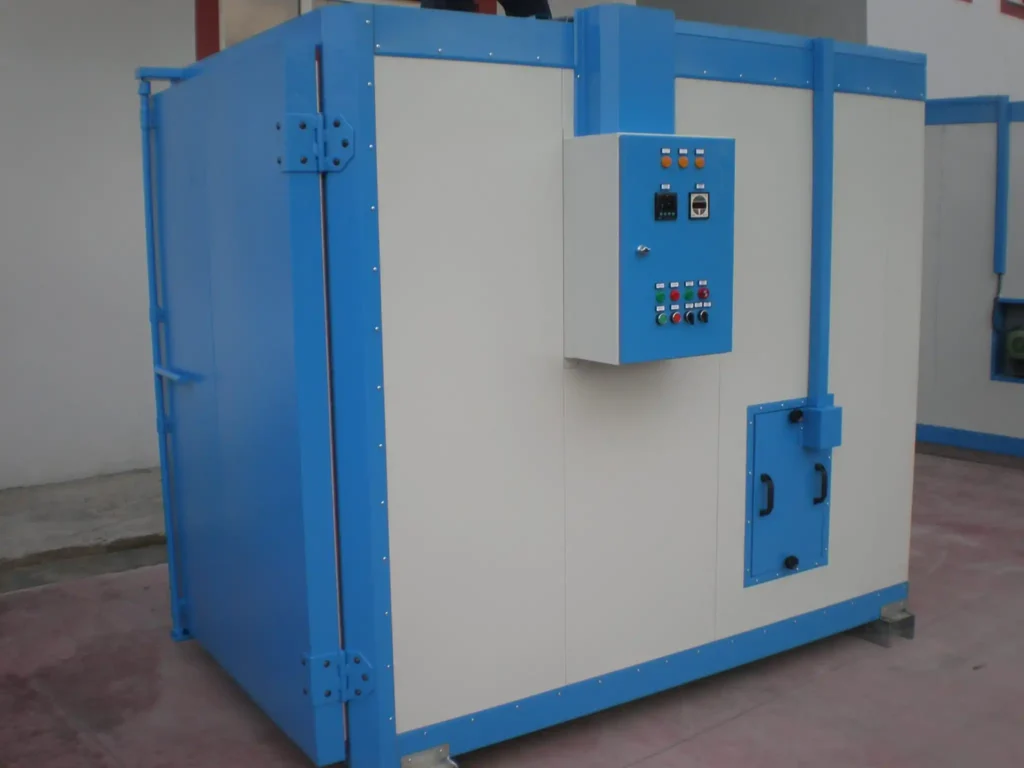
Creating a maintenance schedule for a powder coating plant is essential for ensuring efficient operation, minimizing downtime, and extending the lifespan of your equipment. A well-structured maintenance plan should address the needs of each component, including pre-treatment systems, powder coating booths, application equipment, conveyors, ovens, and safety controls. Here are some tips and guidelines to help you develop an effective maintenance schedule.
Tips for Creating a Maintenance Schedule for a Powder Coating Plant
1. Understand Equipment Requirements
- Read Manufacturer Guidelines: Start by reviewing the maintenance recommendations provided by the equipment manufacturers. These guidelines offer valuable insights into the specific needs and intervals for each component.
- Identify Critical Components: Prioritize maintenance for critical components that directly impact production quality and efficiency, such as spray guns, ovens, and conveyors.
2. Develop a Comprehensive Maintenance Plan
- Routine Inspections: Schedule regular inspections to identify wear and tear, leaks, or potential issues before they escalate. Inspections should cover all plant components, including electrical, mechanical, and safety systems.
- Preventive Maintenance: Implement a preventive maintenance schedule that includes tasks such as cleaning, lubrication, calibration, and parts replacement. This helps prevent unexpected breakdowns and maintains optimal performance.
- Predictive Maintenance: Utilize data analytics and monitoring tools to predict equipment failures and schedule maintenance based on condition and usage patterns.
3. Create a Detailed Maintenance Schedule
- Daily Maintenance Tasks:
- Check air pressure and filtration systems.
- Inspect spray guns and nozzles for clogs or wear.
- Clean work areas and remove powder buildup.
- Weekly Maintenance Tasks:
- Inspect conveyor systems for alignment and wear.
- Lubricate moving parts such as bearings and chains.
- Check temperature settings and calibrate sensors.
- Monthly Maintenance Tasks:
- Conduct a thorough inspection of pre-treatment systems.
- Inspect and clean ventilation and exhaust systems.
- Test and recalibrate control systems.
- Quarterly Maintenance Tasks:
- Perform a detailed inspection of the ovens for heat distribution and insulation integrity.
- Replace worn-out components such as belts and filters.
- Review and update safety protocols.
- Annual Maintenance Tasks:
- Conduct a comprehensive review of the entire plant.
- Audit compliance with safety and environmental regulations.
- Plan for equipment upgrades or replacements as needed.
4. Document Maintenance Activities
- Record Keeping: Maintain detailed records of all maintenance activities, including dates, tasks performed, and any issues identified. This documentation helps track equipment performance and identifies recurring problems.
- Use Digital Tools: Consider using computerized maintenance management systems (CMMS) to schedule, track, and analyze maintenance activities. Digital tools can provide reminders, automate scheduling, and generate reports.
5. Train and Empower Staff
- Employee Training: Train employees on the importance of maintenance and proper procedures. Ensure they understand how to identify and report issues and perform routine tasks.
- Empowerment: Encourage staff to take ownership of their equipment and be proactive in reporting potential problems.
6. Monitor Key Performance Indicators (KPIs)
- Track KPIs: Monitor KPIs such as equipment uptime, mean time between failures (MTBF), and maintenance costs to evaluate the effectiveness of your maintenance program.
- Continuous Improvement: Use KPI data to identify areas for improvement and make data-driven decisions to enhance maintenance strategies.
7. Plan for Spare Parts and Inventory
- Spare Parts Management: Maintain an inventory of critical spare parts to minimize downtime during repairs. Track usage patterns to ensure adequate stock levels.
- Vendor Relationships: Build strong relationships with equipment suppliers to ensure quick access to parts and technical support.
8. Evaluate and Adjust the Maintenance Plan
- Regular Reviews: Periodically review and update the maintenance schedule based on equipment performance, technological advancements, and changing production needs.
- Feedback Loop: Encourage feedback from maintenance staff and operators to identify pain points and improve processes.
Sample Maintenance Schedule Template
Here’s a sample template to help you structure your maintenance schedule:
Frequency | Task | Details |
---|---|---|
Daily | Check air pressure | Ensure proper airflow for spray guns and equipment. |
Inspect spray guns | Look for clogs, wear, and powder buildup. | |
Clean work areas | Remove excess powder and debris from booths and equipment. | |
Weekly | Inspect conveyor systems | Check alignment and wear of belts and chains. |
Lubricate moving parts | Apply lubrication to bearings, chains, and gears. | |
Calibrate temperature settings | Ensure accurate temperature readings in ovens. | |
Monthly | Inspect pre-treatment systems | Check tanks, pumps, and chemical levels. |
Clean ventilation systems | Remove dust and powder buildup in filters and ducts. | |
Test control systems | Verify functionality and accuracy of control units. | |
Quarterly | Inspect oven heat distribution | Check for even heat distribution and insulation integrity. |
Replace worn components | Swap out belts, filters, and other wear-prone parts. | |
Review safety protocols | Update safety measures and conduct training if needed. | |
Annually | Conduct plant-wide inspection | Evaluate overall condition and performance. |
Audit compliance with regulations | Ensure adherence to safety and environmental standards. | |
Plan equipment upgrades | Assess the need for new equipment or technology upgrades. |
Conclusion
Implementing a well-structured maintenance schedule is vital for the smooth operation and longevity of your powder coating plant. By focusing on preventive and predictive maintenance, documenting activities, and involving your team, you can reduce downtime, improve efficiency, and maintain high-quality production standards.
Powder Coating Oven Types
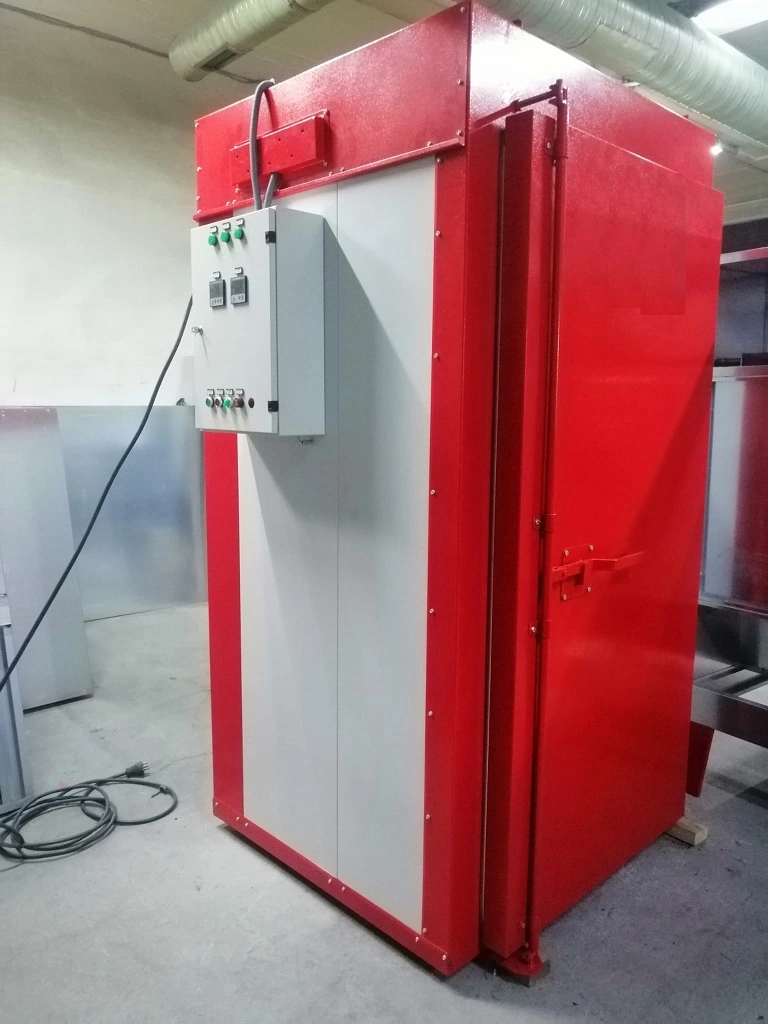
Powder coating ovens are a critical component of the powder coating process, providing the heat necessary to cure the powder and ensure a durable finish. There are several types of powder coating ovens, each designed to meet different production needs and efficiency levels. This guide will cover the various types of powder coating ovens, their features, benefits, and applications, helping you choose the right oven for your specific requirements.
Types of Powder Coating Ovens
1. Batch Ovens
Batch ovens are designed to cure powder coatings for small to medium-sized production runs. They are ideal for operations that require flexibility in coating different part sizes and types.
Features:
- Flexibility: Accommodates various part sizes and shapes.
- Energy Efficiency: Often includes insulation and heat recovery systems to reduce energy consumption.
- Manual or Semi-Automatic Operation: Suitable for low to moderate production volumes.
Benefits:
- Cost-Effective: Lower initial investment compared to continuous ovens.
- Versatile: Can handle a variety of coating tasks, including custom and complex shapes.
- Ease of Use: Simple to operate and maintain.
Applications:
- Small businesses and job shops
- Custom and prototype work
- Low to medium production volumes
Common Types of Batch Ovens:
- Walk-In Ovens: Large enough for operators to enter and load parts, suitable for oversized items.
- Cabinet Ovens: Smaller units ideal for small parts or lower-volume production.
- Truck-In Ovens: Designed for loading parts on racks or carts that can be rolled into the oven.
2. Conveyor Ovens
Conveyor ovens are designed for high-volume production and continuous processing. They automate the curing process, improving efficiency and consistency.
Features:
- Continuous Operation: Ideal for high production rates and large-scale operations.
- Automated Conveyor Systems: Transport parts through the oven for consistent curing.
- Variable Speed Control: Allows adjustment of conveyor speed to match curing requirements.
Benefits:
- High Throughput: Capable of processing large quantities of parts quickly.
- Consistent Quality: Ensures uniform curing across all parts.
- Reduced Labor Costs: Automation reduces the need for manual intervention.
Applications:
- Automotive and aerospace industries
- High-volume manufacturing plants
- Standardized parts production
Common Types of Conveyor Ovens:
- Monorail Ovens: Parts are hung from an overhead conveyor and pass through the oven in a linear path.
- Chain-On-Edge Ovens: Parts are attached to fixtures on a conveyor chain, suitable for heavier items.
- Flat-Belt Ovens: Use a flat conveyor belt to transport parts, ideal for lightweight or flat components.
3. Infrared Ovens
Infrared ovens use infrared radiation to cure powder coatings, offering a fast and energy-efficient alternative to conventional ovens. They are often used in combination with other oven types to optimize curing.
Features:
- Fast Heating: Infrared radiation provides rapid heat-up and curing times.
- Energy Efficiency: Direct heating reduces energy consumption compared to convection ovens.
- Compact Size: Smaller footprint compared to traditional ovens.
Benefits:
- Quick Curing: Significantly reduces curing times, increasing throughput.
- Targeted Heating: Infrared heat can be focused on specific areas, reducing overall energy use.
- Improved Finish: Provides smooth and even curing, minimizing defects.
Applications:
- Automotive and consumer electronics
- Applications requiring quick turnaround
- Parts with complex shapes or heat-sensitive materials
Common Types of Infrared Ovens:
- Short-Wave Infrared Ovens: Provide intense heat for fast curing, suitable for thicker coatings.
- Medium-Wave Infrared Ovens: Balance between heat intensity and penetration, ideal for general applications.
- Long-Wave Infrared Ovens: Gentle heat suitable for heat-sensitive substrates.
4. Gas-Fired Ovens
Gas-fired ovens use natural gas or propane as a heat source. They are popular for large-scale operations due to their efficiency and cost-effectiveness.
Features:
- High Heat Output: Efficiently generates high temperatures for rapid curing.
- Cost-Effective: Generally lower operating costs compared to electric ovens.
- Robust Construction: Designed to handle heavy-duty industrial use.
Benefits:
- Reduced Operating Costs: Lower energy costs compared to electric ovens, especially for large volumes.
- Reliable Performance: Consistent heating for uniform curing.
- Scalability: Suitable for large-scale production and expansion.
Applications:
- Automotive and heavy equipment manufacturing
- Large industrial operations
- High-volume powder coating lines
Common Types of Gas-Fired Ovens:
- Direct-Fired Ovens: Burners directly heat the air inside the oven chamber, providing fast and efficient heating.
- Indirect-Fired Ovens: Heat exchangers separate combustion gases from the oven air, offering cleaner operation.
5. Electric Ovens
Electric ovens use electrical heating elements to generate heat for curing powder coatings. They are commonly used in smaller operations due to their ease of use and installation.
Features:
- Precise Temperature Control: Offers accurate and consistent temperature settings.
- Easy Installation: No need for gas lines or combustion venting.
- Low Maintenance: Fewer moving parts compared to gas-fired ovens.
Benefits:
- Safe and Clean: No combustion gases, reducing emissions and improving air quality.
- Consistent Performance: Stable temperature control ensures uniform curing.
- Versatile: Suitable for various applications and materials.
Applications:
- Small to medium-sized businesses
- Custom and low-volume production
- Applications with strict environmental regulations
Common Types of Electric Ovens:
- Forced-Air Convection Ovens: Use fans to circulate heated air for uniform temperature distribution.
- Static Ovens: Rely on natural convection, suitable for delicate or sensitive parts.
6. Combination Ovens
Combination ovens integrate multiple heating methods, such as infrared and convection, to provide flexibility and optimize curing processes.
Features:
- Multi-Mode Operation: Allows switching between or combining different heating methods.
- Optimized Curing: Adjusts curing methods based on part size, shape, and material.
- Flexible Configuration: Customizable to meet specific production needs.
Benefits:
- Versatility: Capable of handling a wide range of parts and coatings.
- Improved Efficiency: Combines the strengths of different heating methods for optimal results.
- Enhanced Finish Quality: Provides tailored curing conditions to minimize defects.
Applications:
- Complex parts with varying geometries
- Industries requiring rapid production changes
- Specialized coating applications
Considerations for Choosing the Right Powder Coating Oven
When selecting a powder coating oven, consider the following factors:
- Production Volume:
- Choose batch ovens for low to medium production and conveyor ovens for high-volume operations.
- Part Size and Shape:
- Consider the size, weight, and geometry of the parts to determine the appropriate oven type.
- Energy Efficiency:
- Evaluate energy consumption and costs, especially for large-scale operations.
- Temperature Requirements:
- Ensure the oven can maintain consistent temperatures for your specific powder coatings.
- Space and Layout:
- Consider the available space and how the oven will fit into your production line layout.
- Budget and Cost:
- Balance initial investment with long-term operating costs and return on investment.
- Regulatory Compliance:
- Ensure the oven meets local safety and environmental regulations.
Conclusion
Selecting the right powder coating oven is crucial for achieving high-quality finishes and efficient production. By understanding the features, benefits, and applications of each oven type, businesses can make informed decisions that align with their production needs and goals. Investing in the right oven will enhance productivity, reduce costs, and ensure a durable, attractive finish on your coated products.
Powder coating oven maintenance tips
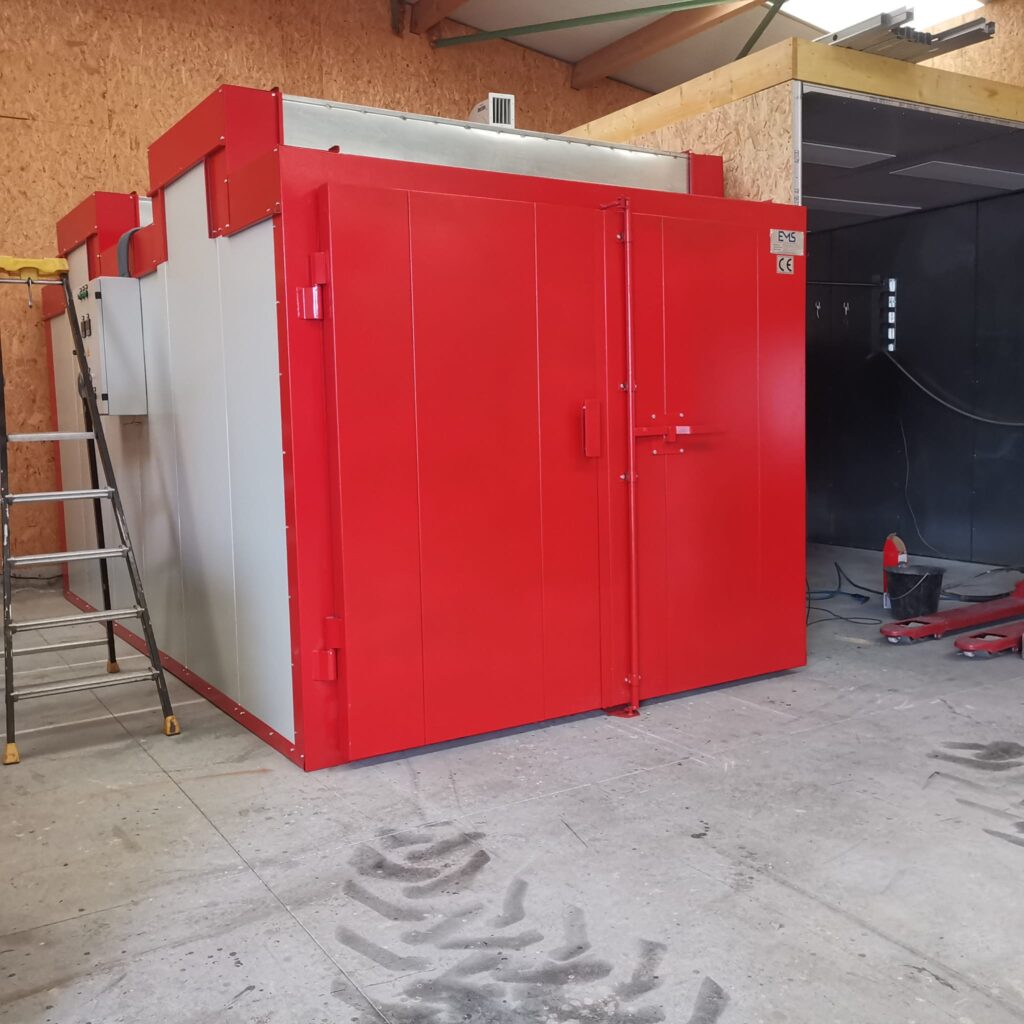
Proper maintenance of powder coating ovens is crucial to ensure efficient operation, consistent curing quality, and the longevity of the equipment. A well-maintained oven minimizes downtime, reduces energy consumption, and prevents costly repairs. Below are comprehensive tips and guidelines for maintaining powder coating ovens effectively.
Powder Coating Oven Maintenance Tips
1. Regular Cleaning
Keeping the oven clean is essential to prevent powder buildup, which can affect performance and finish quality.
Cleaning Tips:
- Daily Cleaning:
- Inspect and Clean Interior Surfaces: Remove any powder buildup on oven walls, floors, and ceilings.
- Clean Heating Elements: Check and clean heating elements to ensure efficient heat transfer.
- Vacuum or Sweep the Floor: Remove any loose powder or debris from the oven floor.
- Weekly Cleaning:
- Clean Air Ducts and Vents: Ensure proper airflow and ventilation by cleaning ducts and vents regularly.
- Wipe Down Doors and Seals: Clean door seals and check for any damage that could affect insulation.
- Monthly Cleaning:
- Deep Clean Oven Interior: Use a non-abrasive cleaner to deep clean the oven interior and remove any stubborn residue.
- Inspect and Clean Exhaust Systems: Check and clean exhaust fans and filters to prevent blockages.
2. Routine Inspections
Regular inspections help identify potential issues before they become major problems, ensuring the oven operates at peak efficiency.
Inspection Tips:
- Daily Inspections:
- Check Temperature Settings: Verify that the oven reaches and maintains the correct curing temperature.
- Monitor Airflow: Ensure that fans and blowers are functioning correctly for even heat distribution.
- Inspect Doors and Seals: Check for gaps or damage that could lead to heat loss.
- Weekly Inspections:
- Inspect Electrical Components: Check wiring, connections, and control panels for signs of wear or damage.
- Check for Unusual Noises: Listen for any unusual noises that might indicate mechanical issues.
- Monthly Inspections:
- Inspect Insulation: Check oven insulation for any damage or wear that could reduce energy efficiency.
- Examine Conveyor Systems: For conveyor ovens, inspect belts, chains, and rollers for wear and alignment.
3. Calibration and Testing
Regular calibration and testing ensure that the oven operates at the correct temperature and settings, maintaining coating quality.
Calibration Tips:
- Temperature Calibration:
- Use Thermocouples: Place thermocouples at various points in the oven to verify temperature uniformity.
- Adjust Temperature Controllers: Calibrate controllers to maintain consistent curing temperatures across the oven.
- Testing Performance:
- Conduct Cure Tests: Perform test runs with sample parts to ensure that coatings are cured properly.
- Check Heating Elements: Test heating elements for consistent output and replace any that are faulty.
4. Preventive Maintenance
Implementing a preventive maintenance schedule helps prevent unexpected breakdowns and extends the life of the oven.
Preventive Maintenance Tips:
- Lubrication:
- Lubricate Moving Parts: Apply lubrication to bearings, chains, and other moving parts to reduce friction and wear.
- Component Replacement:
- Replace Worn Parts: Regularly check and replace parts like belts, seals, and filters that show signs of wear.
- Fan and Blower Maintenance:
- Inspect and Clean Fans: Check fans for balance and clean them to prevent vibration and noise.
- Replace Worn Bearings: Replace any bearings that are noisy or show signs of wear.
5. Safety and Compliance
Ensuring safety and regulatory compliance is critical for protecting workers and meeting industry standards.
Safety Tips:
- Fire Safety:
- Check Fire Suppression Systems: Ensure that fire suppression systems are operational and regularly serviced.
- Install Smoke Detectors: Regularly test smoke detectors and alarms to ensure they are functional.
- Electrical Safety:
- Inspect Wiring and Connections: Regularly check electrical wiring and connections for signs of wear or damage.
- Conduct Safety Audits: Perform regular safety audits to ensure compliance with safety regulations.
6. Documentation and Record Keeping
Keeping detailed records of maintenance activities helps track oven performance and identify trends or recurring issues.
Documentation Tips:
- Maintain a Maintenance Log: Record all maintenance activities, including inspections, cleaning, and repairs.
- Track Performance Metrics: Monitor metrics such as energy consumption, downtime, and repair frequency.
7. Staff Training and Awareness
Proper training ensures that staff are equipped to perform maintenance tasks safely and effectively.
Training Tips:
- Provide Comprehensive Training: Train staff on oven operation, maintenance procedures, and safety protocols.
- Encourage Proactive Maintenance: Empower staff to identify and report potential issues promptly.
Sample Maintenance Schedule for Powder Coating Ovens
Below is a sample maintenance schedule to help you organize and plan oven maintenance tasks:
Frequency | Task | Details |
---|---|---|
Daily | Clean interior surfaces | Remove powder buildup from oven walls, floors, and ceilings. |
Check temperature settings | Verify that the oven reaches the correct curing temperature. | |
Inspect doors and seals | Look for gaps or damage that could lead to heat loss. | |
Weekly | Clean air ducts and vents | Ensure proper airflow and ventilation. |
Inspect electrical components | Check wiring, connections, and control panels for wear. | |
Lubricate moving parts | Apply lubrication to bearings, chains, and other components. | |
Monthly | Deep clean oven interior | Use non-abrasive cleaner to remove stubborn residue. |
Calibrate temperature controllers | Verify and adjust temperature settings for consistency. | |
Inspect insulation and conveyor systems | Check insulation integrity and conveyor alignment. | |
Quarterly | Test heating elements and fans | Ensure consistent output and replace faulty components. |
Review safety protocols and systems | Update safety measures and test fire suppression systems. | |
Annually | Conduct comprehensive performance review | Evaluate overall condition and plan for upgrades. |
Audit compliance with regulations | Ensure adherence to safety and environmental standards. |
Powder coating is a dry finishing process where an electrostatically charged powder is sprayed onto a metal surface and then cured in an oven to form a durable, smooth, and uniform coating. It is commonly used on automotive parts, furniture, and industrial equipment.
2. Gather the Necessary Equipment
To start powder coating, you’ll need the following equipment:
Essential Equipment:
- Powder Coating Gun – A spray gun that applies the powder using electrostatic charge.
- Powder Coating Booth – An enclosed space to contain overspray.
- Curing Oven – An oven that heats the coated parts to fuse the powder.
- Air Compressor – Supplies air for the spray gun.
- Powder Coating Powder – Available in different colors and finishes.
- Grounding System – Ensures proper adhesion and safety.
- Cleaning and Pre-Treatment Supplies – Degreasers, phosphate coatings, or sandblasters for surface preparation.
Optional but Useful Equipment:
- Spray Booth Ventilation System – Helps remove excess powder.
- Infrared Curing Lamps – For small projects or touch-ups.
- Masking Materials – For areas that should not be coated.
3. Prepare the Metal Surface
Proper surface preparation is critical for adhesion and durability.
- Cleaning – Remove dirt, grease, and oil using a degreaser or alkaline cleaner.
- Media Blasting – Use sandblasting or bead blasting to remove rust, old paint, or oxidation.
- Chemical Pre-Treatment – Apply a phosphate or chromate coating for corrosion resistance.
- Drying – Ensure the surface is completely dry before applying powder.
4. Apply the Powder
- Ground the Part – Attach the grounding clamp to prevent powder from repelling.
- Use the Powder Gun – Fill the spray gun with powder and set the right voltage (typically 10-100 kV).
- Apply an Even Coat – Move the gun in smooth, overlapping motions.
- Inspect the Coating – Ensure even coverage before curing.
5. Cure the Powder
- Preheat the Oven – Typically, powder coatings cure at 350–450°F (175–230°C).
- Bake the Coated Part – Place the item in the oven and cure according to the powder manufacturer’s specifications (usually 10-20 minutes after reaching the required temperature).
- Cool Down – Let the part cool before handling.
6. Quality Inspection
- Check for uniformity, adhesion, and gloss.
- Perform a scratch or adhesion test if needed.
- If necessary, reapply and re-cure for touch-ups.
7. Safety Precautions
- Wear Personal Protective Equipment (PPE) (gloves, respirator, safety glasses).
- Ensure Proper Ventilation to avoid inhaling powder.
- Keep Electrical Equipment Grounded to prevent static discharge.
- Follow Fire Safety Rules, as some powders are flammable before curing.
8. Start Small and Expand
If you’re a beginner, start with small projects and practice on scrap metal before coating important parts. Once you’re confident, consider expanding into custom projects, automotive parts, or even a professional powder coating business.
Starting powder coating requires understanding the process and gathering the right equipment. Powder coating is a dry finishing technique where electrostatically charged powder is sprayed onto a metal surface and cured in an oven to create a durable finish. To begin, you’ll need a powder coating gun, a spray booth, a curing oven, an air compressor, grounding equipment, and cleaning supplies like degreasers and sandblasting tools. The process starts with surface preparation, which involves cleaning, media blasting, and sometimes applying a phosphate or chromate coating for better adhesion and corrosion resistance.
Once the surface is prepped and dried, the part is grounded, and powder is applied using the spray gun, ensuring even coverage with smooth, overlapping strokes. After coating, the part is cured in an oven at temperatures ranging from 350–450°F for 10-20 minutes, depending on the powder type. After curing, the part is left to cool, and a quality inspection is performed to check adhesion, gloss, and uniformity. Safety is crucial, so always wear PPE like gloves, a respirator, and safety glasses, and ensure good ventilation. If you’re starting as a hobby, practicing on scrap metal helps improve technique before tackling important projects. If you’re considering a business, investing in better equipment and marketing your services can help expand your operations.
To achieve professional results in powder coating, mastering different techniques and understanding material properties is essential. Various powders, such as epoxy, polyester, polyurethane, and hybrid formulations, offer unique characteristics suited for specific applications. Epoxy powders provide excellent corrosion resistance but degrade under UV exposure, making them ideal for indoor use. Polyester powders are more versatile, offering durability and weather resistance for outdoor applications. Hybrid powders combine epoxy and polyester properties for balanced performance, while polyurethane powders provide superior chemical resistance and gloss retention.
Controlling application parameters significantly affects coating quality. Adjusting the gun’s voltage, air pressure, and distance from the surface ensures proper powder adhesion and even coverage. Too much voltage can cause back-ionization, leading to defects, while too little may result in poor coverage. Properly grounding the workpiece prevents powder repulsion and ensures a strong electrostatic charge for uniform coating. Layering techniques, such as using multiple coats for added thickness or combining different powder types for aesthetic effects, enhance final results.
Curing plays a critical role in powder performance. Factors like oven temperature consistency, heat distribution, and cure time must be closely monitored. Uneven curing can lead to poor adhesion, chipping, or inconsistent gloss. Using an infrared thermometer or data logger helps verify temperature accuracy. Infrared curing systems offer faster heat-up times compared to conventional convection ovens, making them ideal for high-volume production.
As you gain experience, experimenting with specialty powders like metallics, textures, or candy finishes can add visual appeal to projects. Custom masking techniques allow for multi-color designs and precise detailing. If scaling up operations, investing in automated conveyor systems and industrial spray booths improves efficiency and consistency. Whether for personal projects or commercial applications, refining your process through practice and continuous learning leads to high-quality, durable finishes that stand out.
As you refine your powder coating process, understanding troubleshooting techniques becomes essential for maintaining high-quality finishes. Common defects include orange peel, fisheyes, pinholes, and poor adhesion, each caused by specific issues in surface preparation, application, or curing. Orange peel, a rough texture resembling an orange’s skin, often results from incorrect gun settings, excessive powder thickness, or uneven curing. Adjusting the gun’s voltage, air pressure, and coating distance can help achieve a smoother finish. Fisheyes, small craters in the coating, are typically caused by contaminants like oil or silicone.
Thorough cleaning and degreasing, as well as avoiding cross-contamination, help prevent this issue. Pinholes occur due to trapped gases escaping during curing, often from porous substrates or improper surface preparation. Pre-baking metal parts to outgas contaminants before applying powder can reduce pinholes. Poor adhesion usually stems from inadequate cleaning, insufficient grounding, or incorrect curing. Ensuring a properly prepped surface and following the correct cure cycle improves adhesion and durability.
Expanding your knowledge of different substrates and coating challenges is also important. While powder coating is primarily used for metal, advances in technology allow for coating heat-sensitive materials like MDF wood and plastics using low-temperature curing powders. For aluminum, applying a chromate or non-chromate conversion coating enhances corrosion resistance and adhesion. Galvanized steel requires special pre-treatments to prevent adhesion failures due to zinc oxidation. Understanding these substrate-specific requirements ensures reliable performance across diverse applications.
If considering a business venture, optimizing workflow and marketing services can help establish a strong presence. Efficient workspace layout, proper ventilation, and well-organized equipment reduce downtime and increase productivity. Offering specialized coatings, such as high-temperature powders for exhaust systems or anti-microbial coatings for medical equipment, can attract niche markets. Developing an online presence through a website, social media, and before-and-after project showcases helps build credibility and attract customers. Providing additional services like sandblasting, custom color matching, and on-site coating for large structures can further differentiate your business.
Continuous learning through industry forums, training courses, and supplier recommendations keeps you updated on the latest trends and technologies in powder coating. Investing in high-quality equipment, understanding the science behind the process, and maintaining a commitment to quality will set you apart in the industry. Whether for personal projects or professional applications, mastering powder coating opens the door to a world of creative and functional possibilities.
Portable Powder Coating Booth
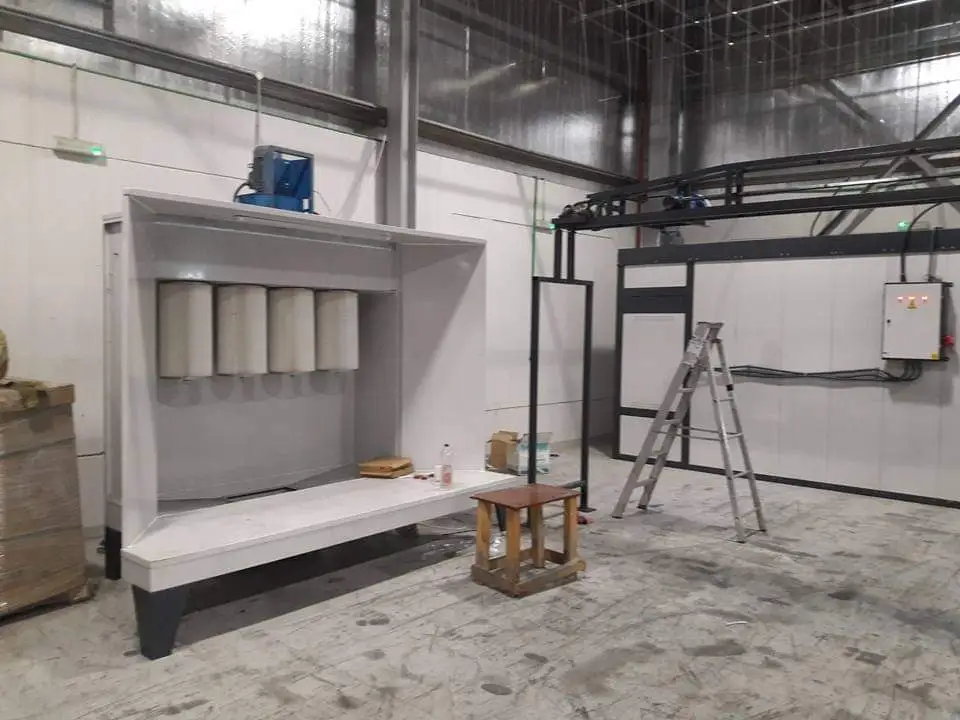
A portable powder coating booth is a compact, movable enclosure designed to contain overspray, improve coating efficiency, and ensure a clean working environment. It is ideal for small-scale operations, DIY enthusiasts, or businesses with limited space. These booths provide a controlled area for powder application while preventing contamination and maintaining proper airflow.
Key Features of a Portable Powder Coating Booth
- Compact and Movable Design – Typically made with lightweight yet durable materials like aluminum frames and fire-resistant panels. Some models have wheels for easy relocation.
- Built-in Ventilation System – Equipped with fans and filters to remove airborne powder particles, improving air quality and reducing contamination.
- Easy Assembly and Disassembly – Many designs use a modular approach, allowing users to set up and pack away the booth quickly.
- Electrostatic Safe Grounding – Ensures proper grounding to enhance powder adhesion and prevent static buildup.
- LED Lighting – Integrated lighting helps in better visibility while coating parts.
- Adjustable Size Options – Available in various dimensions to accommodate small to medium-sized parts.
- Recirculating or Exhaust Filtration – Some booths feature a cartridge-style filter system that collects and recirculates air, reducing powder waste and maintaining a cleaner workspace.
Advantages of a Portable Powder Coating Booth
- Space-Saving – Perfect for garages, small workshops, and mobile businesses.
- Cost-Effective – More affordable than full-scale industrial booths.
- Versatility – Can be used for various coating projects, including automotive, furniture, and custom metalwork.
- Reduced Overspray Contamination – Helps maintain a clean workspace and improves powder utilization.
Considerations When Choosing a Portable Powder Coating Booth
- Booth Size – Ensure it fits the largest parts you plan to coat.
- Filtration System – A high-efficiency filtration system improves safety and air quality.
- Mobility – If you need to move the booth frequently, opt for a model with wheels.
- Airflow Efficiency – Proper airflow is critical for removing excess powder without affecting the application.
A portable powder coating booth is a compact and mobile enclosure designed to control overspray, improve coating efficiency, and provide a cleaner working environment. These booths are ideal for small workshops, DIY enthusiasts, or businesses that need flexibility without investing in a full-scale industrial setup. They typically feature a lightweight yet durable frame, fire-resistant panels, and an integrated ventilation system to remove airborne powder particles. Many models come with wheels for easy relocation and modular designs for quick assembly and disassembly. Proper electrostatic grounding is essential for safety and ensuring effective powder adhesion, while built-in LED lighting enhances visibility during coating. Some booths use recirculating filtration systems with high-efficiency filters to capture excess powder and maintain air quality, reducing waste and contamination.
Portable powder coating booths offer several advantages, including space-saving designs, cost-effectiveness, and versatility for coating automotive parts, furniture, and custom metalwork. They prevent overspray contamination, improve powder utilization, and make cleanup easier. When choosing a booth, it’s important to consider factors like size, filtration efficiency, airflow control, and mobility. A well-designed booth should accommodate the largest parts you plan to coat while maintaining efficient ventilation. If mobility is a priority, opting for a model with wheels or a collapsible structure makes transportation and storage more convenient. Airflow must be optimized to remove excess powder without interfering with the application process.
For those interested in a DIY approach, building a portable powder coating booth can be an affordable and customizable option. Using materials like PVC pipes or aluminum frames, fire-resistant sheeting, and an exhaust fan with a filter system can create an effective workspace. A grounding system is necessary to prevent static buildup, and adding proper lighting improves coating precision. Whether purchasing a ready-made booth or constructing one, ensuring adequate ventilation and safety measures is key to achieving high-quality powder-coated finishes.
When setting up a portable powder coating booth, airflow management is critical to achieving consistent results and maintaining a clean workspace. A well-designed booth should have a controlled air intake and exhaust system that prevents excess powder from settling on coated parts while ensuring proper ventilation. Many portable booths use high-efficiency particulate air (HEPA) filters or cartridge filters to capture airborne powder and prevent contamination. Some models recirculate filtered air back into the workspace, reducing the need for external venting, while others require an exhaust duct to remove air outside. Proper airflow balance prevents turbulence that could disrupt powder application and ensures even coating distribution.
The choice between a recirculating vs. exhaust ventilation system depends on your workspace and safety requirements. Recirculating systems are ideal for enclosed areas without external venting options, but they require regular filter maintenance to avoid clogging. Exhaust systems, on the other hand, directly vent powder-laden air outside, preventing buildup inside the booth but may require compliance with local environmental regulations. If working in a small garage or mobile setup, a recirculating system with replaceable filters offers convenience and flexibility.
Another important factor in optimizing a portable booth is lighting. LED lighting provides bright, energy-efficient illumination, allowing for better visibility of powder coverage and identifying areas that may need reapplication. Placing lights outside the booth behind clear, dust-resistant panels prevents contamination and extends their lifespan.
For efficiency and workflow, organizing the booth with dedicated areas for coating, drying, and cooling streamlines the process. Using turntables or hanging racks allows for easier part rotation and access to all surfaces, reducing the chances of missed spots. If coating multiple parts, a well-ventilated drying area helps prevent airborne powder from settling on freshly coated surfaces before curing.
For those interested in scaling up their powder coating setup, investing in an automated turnkey portable booth system can improve efficiency. Some advanced portable booths integrate an automated gun and conveyor system, allowing for a higher volume of parts to be coated consistently. If mobility is a priority, collapsible designs with quick-folding frames make transport and storage more convenient for mobile powder coating services.
Whether building a DIY setup or purchasing a professional-grade portable booth, ensuring proper ventilation, lighting, and workspace organization will significantly improve coating quality and efficiency. With the right setup, a portable powder coating booth can provide professional results while offering flexibility and affordability for small-scale or mobile operations.
When operating a portable powder coating booth, maintaining cleanliness and filter efficiency is essential for consistent results and prolonged equipment lifespan. Accumulated powder residue can interfere with airflow, reduce filtration effectiveness, and create contamination issues that affect coating quality. Regularly replacing or cleaning filters, depending on the system type, ensures proper ventilation and prevents airborne particles from settling on freshly coated parts. High-efficiency cartridge filters are commonly used in portable booths, and some systems include pulse-cleaning mechanisms that extend filter life by periodically removing excess powder buildup. If working in a confined space, a well-maintained recirculating system prevents excessive powder accumulation while keeping air quality within safe limits.
To further enhance efficiency, integrating dedicated grounding points inside the booth helps maintain a strong electrostatic charge for better powder adhesion. Proper grounding minimizes overspray waste and reduces the risk of uneven coating due to powder repulsion. Using adjustable airflow controls allows fine-tuning of the booth’s ventilation to suit different part sizes and coating thicknesses, preventing unwanted turbulence that can disrupt powder application.
For mobile operations, a collapsible or modular booth design provides the flexibility to transport and set up quickly at different locations. Mobile powder coating businesses benefit from compact, lightweight booths that fit inside a trailer or workshop while still offering adequate airflow and containment. Some advanced portable booths incorporate HEPA filtration and self-contained exhaust systems, making them suitable for use in enclosed spaces without external venting. Battery-powered lighting and compact air compressor setups further improve portability, allowing on-site coating for automotive parts, metal gates, and industrial components.
Safety remains a top priority in any powder coating setup, especially in confined workspaces. Proper grounding, fire-resistant booth materials, and well-ventilated areas prevent static discharge and reduce fire hazards from airborne powder particles. Storing powders in a dry, temperature-controlled environment prevents moisture absorption, which can affect application quality. Wearing appropriate personal protective equipment (PPE), such as respirators, gloves, and anti-static footwear, ensures a safe working environment, particularly when handling fine powders in enclosed booths.
For those looking to optimize production and scale their powder coating process, upgrading to automated extraction fans, multi-stage filtration, and modular booth expansions can improve efficiency and accommodate larger projects. Customizing a portable booth with adjustable height and width panels allows for greater versatility when coating different-sized parts. Whether operating a small DIY setup or a mobile business, refining booth design, filtration, and workflow practices leads to professional-grade powder coating results with minimal overspray and waste.
A powder coating system is a complete setup designed to apply a dry powder finish to metal surfaces, offering a durable and smooth coating. The system includes several components that work together to ensure efficient and high-quality application, from powder preparation to curing. A typical powder coating system consists of the following parts:
Powder Coating Gun
The powder coating gun is the core tool used to apply the powder to a part. It works by electrostatically charging the powder particles as they pass through the gun, which then adhere to the grounded metal surface. The gun typically offers adjustable settings for voltage, airflow, and spray pattern, allowing you to fine-tune the application based on the part’s size and shape. The two main types of guns are manual spray guns and automatic spray guns, with the latter being used in larger, more industrial applications where consistent coating on high volumes of parts is necessary.
Powder Coating Powder
Powder coating powder comes in various formulations, such as epoxy, polyester, urethane, and hybrid blends. The choice of powder depends on the intended application, the desired finish, and environmental conditions. Epoxy powders offer excellent corrosion resistance, making them suitable for indoor use, while polyester powders provide superior UV resistance for outdoor applications. The powder is usually supplied in fine particles that can be loaded into the powder coating gun.
Powder Coating Booth
The booth is the enclosed space where powder is sprayed onto the parts. It is designed to contain overspray, reduce contamination, and provide a clean environment for coating. The booth may come with integrated exhaust systems or recirculating filtration to manage air quality by filtering out airborne powder particles. Many powder coating booths also feature a grounding system to ensure proper adhesion and avoid static build-up. Depending on the operation’s scale, booths may be small, portable units for DIY and small jobs or large, industrial-grade units for mass production.
Curing Oven
Once the powder is applied, the coated part needs to be baked in a curing oven to fuse the powder and create a smooth, hard finish. The oven heats the part to the manufacturer’s recommended temperature (typically 350–450°F or 175–230°C) for a set period, usually between 10 and 20 minutes, depending on the powder’s type and thickness. Curing is a critical step for ensuring durability, adhesion, and finish quality. The oven should have a consistent temperature and even heat distribution for optimal results.
Powder Recovery System
A powder recovery system helps minimize waste by collecting and recycling oversprayed powder from the booth. It typically includes a cyclone separator or filter unit that captures the powder and returns it to the hopper for reuse. These systems can be either manual or automatic, depending on the scale of the operation. For small-scale applications, a simple recovery system with a filter may suffice, while large-scale systems use sophisticated equipment to ensure efficient powder capture and reuse.
Air Compressor
An air compressor is required to provide the air pressure needed to operate the powder coating gun. It supplies consistent airflow to help atomize the powder, ensuring smooth application onto the workpiece. The air compressor should have enough capacity to meet the demands of the system, especially if using an automatic coating setup.
Powder Coating Accessories
Other accessories can enhance the performance and flexibility of the powder coating system:
- Turntables or Hanging Racks: Used to rotate parts during coating for even coverage.
- Grounding Equipment: Ensures proper electrical connection between the part and the booth to achieve good powder adhesion.
- Masking Materials: Prevents powder from coating areas that shouldn’t be coated.
- Filters: In the gun and booth to ensure clean air supply and reduce contamination.
Choosing the Right System
Selecting the appropriate powder coating system depends on several factors, including the scale of the operation, types of parts being coated, and the environment. For a small-scale operation or hobbyist, a portable powder coating system with a manual gun, small booth, and basic curing oven will suffice. For larger-scale or industrial operations, a fully automated powder coating system with an automatic spray gun, conveyor belt, industrial booth, and a large curing oven will be necessary to achieve high throughput and consistency.
In all cases, it’s essential to consider:
- Application type: Whether you’re coating small, intricate parts or large, heavy-duty items.
- Powder type: Different powders have unique properties, so select the one that suits your needs.
- Equipment size and capacity: Ensure the system fits your workspace and meets production volume needs.
A well-designed powder coating system offers excellent durability, finish quality, and environmental benefits (since it produces fewer emissions than traditional liquid coatings). Regular maintenance and proper setup of the system components ensure smooth operation and long-lasting results.
A powder coating system works as a cohesive unit to apply durable and high-quality finishes to metal parts. The system’s core component is the powder coating gun, which applies the electrostatically charged powder onto the metal surface. The powder adheres to the surface due to the charge and the part’s grounded nature, creating an even coating. Depending on the operation’s size, you can choose between manual or automatic spray guns, with the latter being ideal for high-volume or industrial applications where consistency and speed are crucial.
The powder itself plays a significant role in the final result. Powders come in different types, such as epoxy, polyester, and hybrid blends, each offering specific characteristics like corrosion resistance or UV protection. Epoxy powders are ideal for indoor applications due to their superior adhesion and chemical resistance, while polyester powders are better for outdoor use because of their weather resistance. The powder is typically stored in a hopper connected to the powder gun, which feeds it through a delivery system and onto the part.
Once the powder is applied, the part needs to be cured in an oven. The curing process involves heating the coated part to a specific temperature (typically 350–450°F), where the powder melts and bonds to the metal, forming a hard, durable finish. A well-calibrated oven with consistent heat distribution is critical to achieving uniform curing, as uneven temperatures can cause defects like soft spots or uneven gloss.
After the part is coated, powder recovery systems are often used to minimize waste. These systems capture overspray and recycle the unused powder back into the hopper for reuse, which is both cost-effective and environmentally friendly. The recovery system typically includes cyclonic separators or filter units that remove excess powder, ensuring that only the powder that adheres to the part is cured, while the rest is recaptured.
Air compressors are another essential part of the system, supplying the necessary airflow to operate the powder coating gun. A reliable compressor is required to provide consistent air pressure, ensuring that the powder is atomized properly and applied evenly onto the parts.
Incorporating accessories like turntables, racks for hanging parts, and grounding equipment further enhances the powder coating process. Turntables and hanging racks help ensure uniform coverage by rotating or suspending parts during the application. Grounding equipment ensures proper electrical contact between the parts and the booth, improving powder adhesion.
Choosing the right powder coating system depends on your specific needs, such as the type of parts you’re coating, the size of the operation, and the production volume. For small operations or DIY projects, a portable setup with a small booth and manual gun may be sufficient. For large-scale industrial applications, an automated system with high-capacity guns, a conveyor system for continuous operation, and a larger curing oven will be necessary to meet high throughput and consistency.
No matter the scale of the operation, regular maintenance and calibration of the system components are key to ensuring quality results. With the right equipment, powder coating provides a long-lasting, attractive, and environmentally friendly finish to a wide range of products.
When expanding or fine-tuning your powder coating system, it’s important to focus on process optimization and ensuring consistency across all components. The effectiveness of the system relies not just on the equipment, but also on the environmental conditions and the attention to detail in each step. For example, maintaining proper humidity and temperature levels in the workspace is crucial, as high moisture levels can cause the powder to clump or degrade, while extreme temperatures may affect curing times or powder application consistency.
Proper maintenance of the powder coating gun is essential for achieving smooth, uniform finishes. Regularly cleaning the nozzle and checking for wear ensures that the gun is working at peak efficiency. Fine-tuning the air pressure and voltage settings on the gun also plays a significant role in improving the coating’s consistency. If too much voltage is applied, the powder can start repelling from the part, causing defects like uneven application or overspray. On the other hand, insufficient voltage results in poor adhesion and a patchy finish. Therefore, experimenting with settings based on the part’s material and shape is key to achieving the desired result.
The booth is another critical area to focus on. A well-maintained booth with clean filters will ensure optimal airflow and reduce contamination. In industrial environments, a more advanced system with multi-stage filtration or cyclonic separators may be necessary to handle larger volumes of overspray and ensure high-quality finishes. In small-scale setups, portable powder coating booths that use compact filtration systems can still be effective for achieving professional results, but regular maintenance is important to prevent clogging and reduce the risk of contamination.
A more advanced feature to consider in a larger setup is the use of automated coating systems. Automated systems, which integrate robotic arms or conveyors, allow for consistent, repeatable application of powder, reducing human error and improving throughput. These systems are ideal for large-scale operations that require high-volume production. In contrast, smaller operations or hobbyists may find that manual powder coating guns provide enough control for achieving precision finishes.
The curing process also plays a major role in the quality of the finish. An oven with even temperature distribution is essential for ensuring that the coating properly bonds to the substrate, providing a durable, scratch-resistant finish. Regularly calibrating the oven to maintain consistent temperature settings, checking the oven’s airflow, and ensuring it is clean will help prevent defects such as soft spots or uneven finishes. Some advanced curing systems use infrared heat technology, which offers faster curing times compared to traditional convection ovens and can be more energy-efficient. However, infrared systems require careful monitoring to avoid overheating parts or uneven curing.
Additionally, choosing the right powder formulation for your specific application will have a significant impact on the end result. Polyester powder coatings are ideal for outdoor use due to their superior UV resistance, while epoxy powders are often used for their excellent adhesion and chemical resistance, but they aren’t as durable under direct sunlight. There are also urethane powders for extra toughness, and hybrid options that offer a balance of epoxy and polyester benefits. Each formulation has its advantages and should be selected based on the environment the finished part will be exposed to.
Lastly, workflow efficiency is an essential factor when scaling your operation. Efficiently organizing the coating process, from loading parts into the booth to curing and unloading, can drastically improve productivity. Using automated conveyors can reduce manual handling time and ensure consistent and controlled application across high volumes of parts. Moreover, incorporating custom racking systems for different part shapes and sizes helps maintain organization and speeds up the overall process.
In conclusion, optimizing your powder coating system comes down to maintaining and fine-tuning each part of the process. Whether you are working on small batches or large-scale industrial production, focusing on equipment maintenance, controlling environmental factors, and selecting the right materials can greatly enhance the quality, efficiency, and consistency of your powder-coated finishes.
When further refining and expanding your powder coating system, it’s important to think about long-term scalability and flexibility in your setup. For businesses or hobbyists looking to increase production without compromising quality, investing in specialized equipment and advanced techniques can help ensure consistent, high-quality finishes over time. One such consideration is the ability to scale the curing process. In large setups, moving from batch ovens to conveyorized curing systems can significantly increase throughput. Conveyorized systems allow parts to be coated and cured in a continuous flow, eliminating the need for manual handling after application and speeding up the production process.
For high-volume applications, some businesses use multi-zone curing ovens, which offer precise temperature control across different sections of the oven, allowing parts to pass through multiple temperature zones for optimal curing. These ovens can be fine-tuned based on the specific requirements of the coating material and the thickness of the parts. Advanced curing systems can even incorporate gas-assisted heating for improved energy efficiency, reducing operational costs while maintaining excellent coating performance.
Powder recovery and waste management also become increasingly important as production volumes grow. As you scale, you might consider more sophisticated automated powder recovery systems that use cyclonic air separators, pulse jet filters, or vacuum recovery systems to capture oversprayed powder. These systems can be set up to reclaim powder with a high degree of efficiency, which helps to minimize material costs and reduce environmental waste. In some advanced setups, digital powder recovery monitoring systems can track the amount of powder used and recovered, providing real-time data to improve efficiency and reduce waste.
To maintain high-quality finishes, quality control measures should be implemented throughout the process. This can include using UV light to check for uniform powder distribution or using thickness gauges to ensure that the powder layer is within the desired range. Implementing in-line inspections or automated inspection systems that use cameras or sensors to detect defects can prevent issues like orange peel, pinholes, or over-sprayed areas from affecting production. These systems can be integrated into the process flow, providing immediate feedback to the operator for necessary adjustments.
It’s also crucial to keep up with technological advancements in the powder coating industry. New materials, equipment, and processes are constantly being developed to improve performance, efficiency, and environmental impact. For instance, low-temperature cure powders allow for coating heat-sensitive materials like plastics or wood without the risk of warping or damage. Similarly, nano-coatings or ceramic powders provide specialized finishes that enhance properties like heat resistance, corrosion resistance, or abrasion resistance, offering unique solutions for specific industries, such as automotive or aerospace.
Another evolving aspect of powder coating is the increased demand for customization and color matching. Offering custom powder colors or finishes can set your business apart from competitors. Many powder coating systems now integrate with digital color matching systems, allowing you to replicate colors more accurately and improve customer satisfaction. For more artistic or high-end applications, textured finishes or metallic coatings can be used to create distinct visual effects, opening the door for more diverse applications in furniture, architecture, and consumer products.
Finally, in terms of environmental impact, the powder coating process is already more eco-friendly than many traditional liquid coatings. However, further steps can be taken to minimize waste and energy consumption. For example, using eco-friendly powders with lower volatile organic compound (VOC) emissions can reduce environmental impact. Some businesses are also looking into energy-efficient LED curing systems or solar-powered booths, which can cut down on energy use and further align with sustainability goals.
In essence, expanding and improving your powder coating system involves careful consideration of efficiency, scalability, technological advancements, and quality control. Whether you’re scaling up for higher production volume, improving the environmental footprint of your process, or offering more customization, embracing new technologies and methods will keep your powder coating system competitive and capable of meeting diverse customer needs. By constantly refining your system, you ensure that your setup delivers high-quality finishes, operational efficiency, and a sustainable future.
Small Scale Powder Coating Equipment
Small-scale powder coating equipment is designed to provide professional-quality finishes on a smaller scale, making it ideal for hobbyists, small business owners, or DIY enthusiasts. These systems are more compact and affordable compared to industrial setups, yet they can still deliver durable and attractive finishes for a variety of metal parts, such as automotive components, furniture, home accessories, and small machinery.
Powder Coating Gun
At the heart of any small-scale powder coating system is the powder coating gun. For small operations, a manual powder coating gun is typically used, which is portable and affordable while still providing control over the coating process. These guns are easy to use and can be adjusted for voltage, airflow, and spray pattern. More advanced models offer features like adjustable spray settings, allowing you to fine-tune the application based on the part’s size, shape, and the type of powder being used. Electrostatic guns charge the powder as it is sprayed, ensuring a strong bond to the grounded part.
Powder Coating Powder
The powder is typically supplied in plastic bags or containers, and it can be either epoxy, polyester, urethane, or a hybrid blend. Small-scale systems often use the same types of powders as industrial systems, but the quantity and application are scaled down. Choosing the right powder depends on the part’s intended use. Epoxy powders are great for indoor items due to their excellent adhesion and chemical resistance, while polyester powders are better suited for outdoor items due to their UV resistance.
Powder Coating Booth
A powder coating booth is a critical component in a small-scale setup. The booth is designed to contain the overspray of powder, ensuring a clean work environment and preventing contamination of other parts. Small booths are often portable, lightweight, and can fit in a home garage or small workspace. They can be set up with a basic ventilation system or filter units to remove excess powder from the air. Many small booths include a recovering system that helps to recycle oversprayed powder, reducing material waste.
Curing Oven
After the powder is applied, the part needs to be cured in an oven to bond the powder to the metal surface. For small-scale applications, compact curing ovens are used, often with adjustable temperature settings to ensure proper curing. These ovens typically reach temperatures between 350-450°F (175-230°C) and can accommodate smaller parts. Curing time usually ranges from 10 to 20 minutes, depending on the size and material of the part. Many small-scale curing ovens are electric-powered and come with digital controls for precise temperature regulation.
Air Compressor
An air compressor is necessary to supply air pressure to the powder coating gun. Small-scale setups often use compact, portable compressors with a sufficient air delivery rate to ensure that the powder is properly atomized and applied evenly to the parts. Air compressors for small powder coating systems typically have a pressure range of 10-30 psi and a tank size that is appropriate for the coating process.
Powder Recovery System
For small-scale operations, a manual powder recovery system is usually sufficient to capture oversprayed powder and return it to the hopper for reuse. These systems may include simple filters, cyclonic separators, or catch trays to collect the unused powder. By recycling the powder, these recovery systems help reduce waste and save money in the long term.
Other Accessories
Additional accessories can improve the quality and efficiency of small-scale powder coating setups. For instance, turntables or racking systems can be used to rotate or hang parts, ensuring even coating on all sides. Masking tape or plugs can be applied to areas that should not be coated, preventing unwanted coverage. Grounding equipment is essential to ensure that the electrostatic charge from the powder coating gun properly adheres to the metal parts, preventing powder repulsion or weak adhesion.
Portable Powder Coating System
Some small-scale powder coating systems are designed for ultimate portability and can be used in various locations, such as a home workshop, garage, or even outdoors. These systems are often lightweight, easy to set up, and can be moved around with ease. Portable booths can fold up for storage, and smaller curing ovens with digital temperature controls offer flexibility for different types of projects.
In summary, small-scale powder coating equipment offers a cost-effective solution for achieving high-quality finishes on smaller batches of metal parts. By selecting the right components—powder coating gun, booth, curing oven, and compressor—you can build a system that provides professional results for DIY projects, custom coatings, or small business applications. Regular maintenance and proper setup of each component are essential for ensuring consistent finishes and efficient operation.
Small-scale powder coating equipment is designed to offer an efficient and cost-effective solution for achieving high-quality finishes on smaller batches of metal parts. These systems are perfect for hobbyists, small businesses, or DIY enthusiasts who need to coat items like automotive parts, furniture, or home accessories. The heart of the system is the powder coating gun, which applies the powder to the part through an electrostatic charge, ensuring a strong bond between the powder and the grounded surface. These guns are adjustable, allowing users to fine-tune spray patterns, airflow, and voltage to match the part’s size and the type of powder being used.
The powder itself comes in various formulations, such as epoxy, polyester, and hybrid blends, each suited for specific applications. Epoxy powders are ideal for indoor use due to their excellent adhesion and chemical resistance, while polyester powders are more suitable for outdoor use because of their superior UV resistance. Small-scale systems use the same types of powders as larger ones, but in smaller quantities that are easier to manage. Once the powder is applied, it needs to be cured in an oven. Small, compact curing ovens are typically used in these setups, allowing users to cure parts at the right temperature (usually between 350–450°F) for about 10 to 20 minutes, depending on the part’s material and thickness. These ovens often come with digital controls to maintain precise temperature settings, ensuring the powder bonds correctly to the part.
Air compressors are essential for providing the necessary airflow to the powder coating gun, atomizing the powder and helping it to adhere evenly to the metal part. In small-scale setups, portable compressors are used, which are easy to transport and store, providing enough air pressure to apply the powder effectively. Powder recovery systems are also an important part of small-scale operations, as they allow oversprayed powder to be collected and reused, reducing waste and saving money. These systems can be as simple as filters or catch trays to collect excess powder, or more advanced cyclonic separators that provide more efficient powder recovery.
Small powder coating booths are designed to contain overspray, ensuring a clean working environment and preventing contamination. These booths are often portable, lightweight, and compact, making them suitable for smaller workspaces like home garages or workshops. Many booths come equipped with basic filtration systems to remove excess powder from the air and help recycle oversprayed powder back into the system. Some setups also include racking or turntable systems that allow parts to be rotated during coating for even coverage. Grounding equipment is also essential in these systems to ensure that the electrostatic charge properly adheres the powder to the part, preventing any issues with adhesion or powder repulsion.
In essence, small-scale powder coating equipment provides a great way to achieve professional-quality coatings without the need for large, industrial setups. By choosing the right components, such as the gun, booth, curing oven, and recovery system, users can create a customized powder coating system that meets their needs. Whether it’s for personal projects or small business operations, these systems can produce durable, attractive finishes on a wide variety of metal parts, all while minimizing waste and being cost-effective. Proper maintenance and attention to each component are key to ensuring consistent and high-quality results with every coating project.
Expanding on small-scale powder coating systems, one important aspect is achieving the right balance between affordability and quality. As these systems are often used by individuals or small businesses, keeping costs manageable while ensuring the best possible results is crucial. This is why many small-scale setups are designed with versatility in mind, allowing users to coat a variety of items without needing a huge investment in specialized equipment. The compactness of these systems means they can be set up in a home workshop, garage, or smaller industrial spaces without taking up too much room.
In terms of powder coating guns, it’s important to select one with adjustable settings, allowing flexibility for different types of powder and part sizes. Some advanced models even offer digital controls, which can improve consistency and efficiency, especially when you need to fine-tune the application process. The use of electrostatic guns makes sure that the powder adheres effectively to the metal surface, resulting in a more uniform and durable coating. Investing in a gun with good ergonomics and ease of cleaning can make the process less tedious and help prolong the lifespan of the equipment.
When choosing a curing oven, one key consideration is its size and the type of heating it uses. Small-scale systems often feature electric ovens, which are ideal for handling smaller parts or batches. The temperature accuracy of the oven is essential to ensure the powder bonds correctly and cures evenly. Some curing ovens come with digital thermostats, making it easier to control the temperature and avoid inconsistencies. Additionally, ovens with ventilation systems help to maintain air quality and ensure that fumes or smoke are properly expelled during the curing process.
For air compressors, a small, portable unit that provides enough CFM (cubic feet per minute) and PSI (pounds per square inch) to efficiently run the powder coating gun is key. This doesn’t mean you need the most expensive compressor, but the air supply should be consistent to ensure the powder is sprayed evenly. Moisture filters can also be an essential addition, as excess moisture in the air can affect the powder application, leading to defects like poor adhesion or texture issues.
Another critical component in small-scale systems is the powder recovery unit. While industrial systems often have complex automated recovery systems, smaller setups use more manual options to recycle powder, which can help keep costs low. Cyclone separators or basic filtration systems are common and work by collecting and filtering out overspray, so it can be reused. This not only saves material costs but also reduces the environmental impact by minimizing waste. Additionally, using recovery systems allows users to work more efficiently, especially in situations where multiple layers of powder are applied.
To ensure a smooth workflow, organizing the work area is key. Many small-scale systems offer the option to hang or mount parts on racks or use turntables to rotate parts during application, ensuring even coverage. These types of solutions are simple but effective in improving coating consistency. If parts are large or have irregular shapes, custom racks or hooks can be used to position the items optimally for coating.
Moreover, masking materials are a simple but essential addition for preventing overspray on areas that don’t need coating, such as threaded parts, connectors, or areas that should remain free of powder. This can be achieved using masking tape, plugs, or other forms of protective covering. Masking ensures that the parts function as intended after the coating process and reduces the time needed for touch-ups or cleanup.
For those with limited space or budget, portable powder coating booths are an excellent choice. These booths are designed for easy setup and takedown, allowing users to coat parts in almost any environment. Many of these booths are equipped with basic filtration systems to capture overspray, and some even feature recirculating powder systems that allow for powder recovery during the process. Depending on your needs, portable booths can either be open-air setups for large, less delicate items or fully enclosed booths for more controlled applications.
Maintenance is also a key factor in ensuring the longevity of the equipment. Keeping the powder coating gun clean is essential to avoid clogs or buildup of powder in the nozzle, which can affect the spray pattern. Similarly, regular checks on the curing oven will help identify any temperature inconsistencies or faulty heating elements before they affect production. Powder booths should be cleaned periodically to avoid contamination, and filters in the booth and recovery systems should be replaced or cleaned as necessary to maintain airflow and prevent excess powder from circulating into the air.
Ultimately, small-scale powder coating systems are designed to provide flexibility, efficiency, and quality while remaining affordable for users with limited space or budget. With the right selection of equipment and regular maintenance, these systems can produce high-quality finishes on metal parts, making them an ideal solution for a range of applications—from custom projects to small business operations. By tailoring the setup to meet specific needs and ensuring the process is streamlined, users can achieve professional results without the need for large-scale industrial equipment.
When considering a small-scale powder coating system, it’s also essential to think about the versatility of the setup. One of the benefits of these systems is the ability to coat a wide variety of parts, from small components to larger items like automotive parts, outdoor furniture, and even custom home décor pieces. This flexibility allows users to tackle different projects and customer demands, making it ideal for both personal and business use.
For businesses that plan to take on more clients or higher volumes of work, the system can still be scaled up in a manageable way. Modular powder coating systems allow for expansion, meaning that as production needs grow, you can easily add components like additional booths, larger ovens, or even automated powder coating guns. Automated systems can help increase productivity by reducing labor costs and improving coating consistency, which is particularly beneficial for high-volume operations. Adding a conveyor system can streamline the process for larger batches, allowing parts to move automatically through the booth and curing oven, thereby saving time and increasing throughput.
Another aspect to consider is the energy efficiency of your equipment. In smaller setups, users often look for low-energy options that reduce overhead costs. LED curing lights are a great choice for energy efficiency, as they use far less power compared to traditional heating elements. For the curing oven, consider one with good insulation and an efficient heating mechanism that prevents heat loss and maintains stable temperatures, minimizing energy usage. Some ovens are designed with programmable timers and temperature controls to further optimize the curing process, ensuring that the parts are heated to the correct temperature without waste.
Environmental factors are also becoming a significant consideration for small-scale powder coating operations. While powder coating is generally more eco-friendly than liquid coatings, as it produces fewer volatile organic compounds (VOCs), further steps can be taken to reduce the environmental impact. Eco-friendly powders with low VOC content or those made from sustainable materials can be selected, helping meet environmental regulations and appeal to environmentally conscious customers. Additionally, implementing a waste management system for collecting and recycling overspray powder helps minimize waste and improves cost-effectiveness.
One trend in the industry is the development of DIY and home-based powder coating systems. These systems are designed for hobbyists and small-scale businesses who may not have access to a large workspace. Compact, portable booths that fold up for storage, combined with small but efficient curing ovens, are perfect for those who work from home or have limited space. These systems can be set up quickly and offer flexibility for part-time or weekend businesses that want to offer professional-quality finishes without a significant investment.
Moreover, it’s important to consider the long-term reliability and durability of the equipment. Small-scale powder coating equipment is typically built for lighter use than industrial systems, but investing in well-made, durable components will ensure a better return on investment and fewer issues in the long run. It’s also crucial to have technical support or access to replacement parts, as some components, like heating elements or spray guns, may wear out over time.
In addition to the functional aspects, training and skill development are vital for getting the most out of a small-scale powder coating system. While powder coating is a straightforward process, it does require some skill and experience to master. Many suppliers offer training videos or tutorials, and some even provide hands-on workshops to help users understand the nuances of powder application, curing, and troubleshooting. As you gain more experience, you’ll learn how to adjust your process to achieve the perfect finish, whether it’s a smooth, glossy coat or a textured, matte finish.
Another consideration is color customization. Powder coating allows for a wide range of colors, textures, and finishes, making it an attractive option for businesses looking to offer unique customizations. Many powder coating systems now feature color-matching technology, allowing users to accurately reproduce colors and achieve the exact shade that customers are looking for. Whether it’s creating vibrant custom finishes for automotive parts or offering trendy color options for furniture, the ability to mix and match different hues gives small businesses the edge when it comes to offering personalized, custom designs.
Lastly, health and safety should always be prioritized. Powder coating, like any coating process, involves handling chemicals and working with high temperatures. It’s important to ensure that your workspace is well-ventilated to avoid inhaling powder dust or fumes, especially in confined spaces. Using respirators or dust masks can further protect your health. Additionally, protective clothing such as gloves, goggles, and long sleeves should be worn to minimize exposure to the powder and other materials.
In conclusion, small-scale powder coating systems offer an excellent solution for hobbyists, small businesses, and DIY enthusiasts who want to produce high-quality, durable finishes on a range of metal parts. With the right equipment, maintenance, and attention to detail, users can achieve professional-level results without the need for large, expensive systems. As your needs grow, you can scale up the system by adding components like larger booths, curing ovens, or automated systems, making it a flexible choice that adapts to your specific requirements. By staying informed about new technologies, techniques, and eco-friendly practices, you can continue to improve your process and deliver top-notch finishes for your projects.
Powder Coating Booth
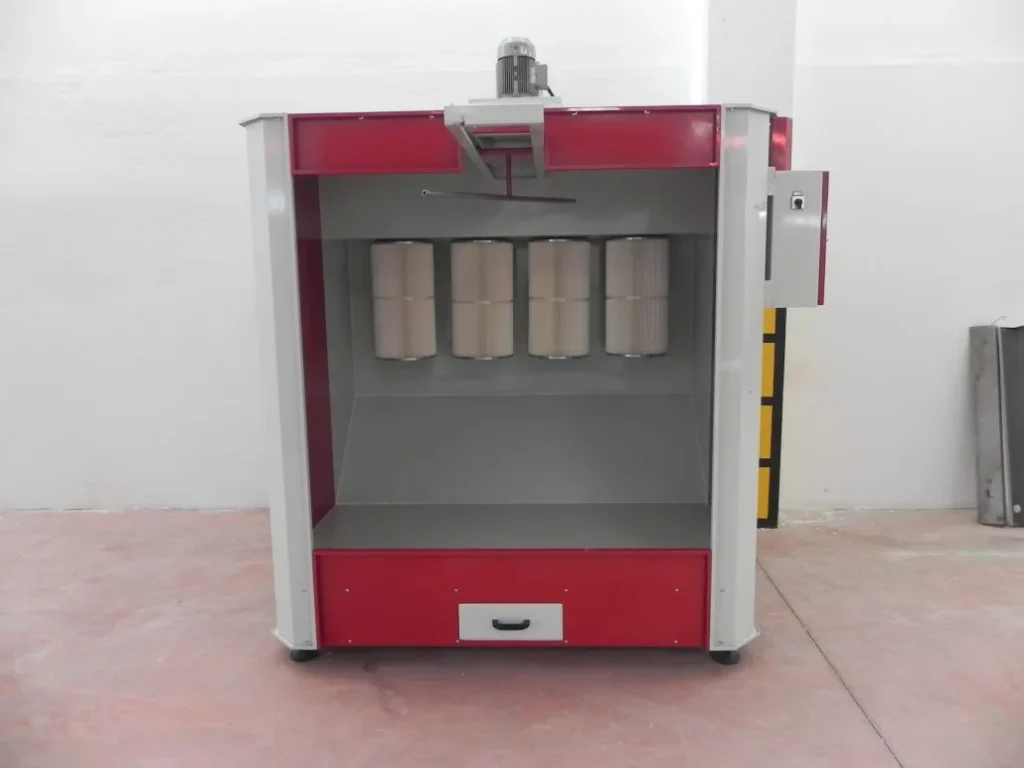
A powder coating booth is an essential part of any powder coating system. It is designed to contain the overspray of powder and direct it towards a collection system, ensuring that the workspace remains clean and the coating process remains efficient. The booth also helps in creating a controlled environment for applying the powder, reducing contaminants and ensuring the consistency of the finish. There are several types of powder coating booths, and choosing the right one depends on factors like workspace size, production volume, and specific needs.
For small-scale or DIY setups, powder coating booths are typically compact, portable, and easy to set up and use. These booths can be either open-air or enclosed with filters and air circulation systems to collect the oversprayed powder and maintain a clean environment. A small powder coating booth often includes a basic filtration system to prevent the powder from circulating in the air and contaminating the surroundings.
In larger industrial applications, powder coating booths are often equipped with advanced air filtration systems, including high-efficiency particulate air (HEPA) filters and cyclonic separators. These systems work by using a combination of airflow patterns, negative pressure, and filters to ensure that the oversprayed powder is captured and can be recycled, reducing waste and saving on material costs. The booth is usually designed with airflow systems that draw air in from the surrounding environment and push the air out through filters to ensure safe and efficient operation.
Powder coating booths typically have adjustable spray zones or spray guns to allow the operator to apply the powder evenly on the part. The booth is designed to directly funnel the overspray into a collection area, such as a cyclone or recovery system, where it can be filtered and reused. This reduces waste and helps in achieving an even coating on each part.
When choosing a powder coating booth, there are a few key factors to keep in mind:
- Size: The booth should be large enough to accommodate the parts you intend to coat. A booth that is too small can limit the size of parts, while a booth that is too large can be inefficient and take up unnecessary space.
- Ventilation: Proper ventilation is crucial for a safe and effective coating process. The booth should be equipped with a fan or exhaust system to ensure that the air is drawn into the booth and filtered, preventing the build-up of dust and powder in the workspace. Good airflow also helps ensure an even coating and prevents over-spray from settling outside the booth.
- Powder Recovery System: Many powder coating booths come with built-in recovery systems, which collect the oversprayed powder and allow it to be recycled. This helps reduce waste and saves on material costs. There are cyclonic recovery systems that use centrifugal force to separate the powder from the air and filter it out, and manual recovery systems where powder is collected in catch trays or bags.
- Cleaning and Maintenance: A good powder coating booth should be easy to clean and maintain. The powder residue can build up over time, so having a booth that is designed for easy access to filters and recovery systems can save time and effort in the long run. Look for booths with smooth, non-porous surfaces that are easy to wipe down.
- Cost: The cost of a powder coating booth varies depending on the size, features, and type of equipment. Basic booths for small-scale or DIY applications are relatively affordable, while industrial-grade booths with advanced filtration and recovery systems can be more expensive. When purchasing a booth, it’s important to consider the return on investment in terms of efficiency, reduced waste, and improved coating quality.
- Portability: For small-scale operations, portable powder coating booths are an excellent choice. These booths are lightweight, foldable, and easy to store. They can be set up in garages, workshops, or other small spaces without the need for permanent installation.
When using a powder coating booth, it’s important to follow the safety guidelines. Always ensure the booth is well-ventilated to avoid inhaling powder particles or fumes, which can be harmful to your health. Wear appropriate protective gear such as gloves, goggles, and a respirator to prevent exposure to powder dust. Make sure that the booth is free of any flammable materials, as powder coatings can create sparks when applied to metal surfaces.
In summary, a powder coating booth is an essential piece of equipment for anyone involved in powder coating, whether for personal, hobby, or small business use. By choosing the right booth that fits your workspace, production needs, and budget, you can ensure an efficient, clean, and safe powder coating process, while also reducing waste and improving the overall quality of your finishes.
A powder coating booth plays a pivotal role in the powder coating process by containing overspray and helping create a controlled environment for even and efficient application. It directs excess powder into recovery systems to minimize waste, ensuring that the process is more cost-effective while also keeping the work area clean and free of contaminants. Whether you’re working with small parts or larger items, a well-designed booth is essential for achieving consistent results and maintaining a safe working environment.
For small-scale or DIY setups, powder coating booths are typically compact and portable. These booths are ideal for home workshops or limited spaces because they can easily be assembled and disassembled. Smaller booths usually come with basic filtration systems to keep the overspray contained, but they might not have advanced recovery systems like industrial-sized booths. While these smaller setups are budget-friendly, they still offer an efficient way to apply coatings on metal parts without the need for large, expensive systems.
For larger operations, industrial-grade powder coating booths offer higher efficiency, especially in terms of powder recovery and air filtration. These booths are typically equipped with advanced systems that utilize cyclonic separators, which remove powder from the air and return it to the hopper for reuse. This reduces material waste and ensures that the powder coating process is more sustainable. The air filtration systems in these larger booths often include high-efficiency particulate air (HEPA) filters to capture fine particles and prevent them from escaping into the environment. These systems create a cleaner, safer working environment, especially when working with large volumes of parts.
When choosing a powder coating booth, it’s essential to consider your needs, such as the size of the parts you’ll be coating and the volume of work you’re planning to do. A booth that’s too small may limit the size of the items you can coat, while a booth that’s too large can take up unnecessary space and may be less energy-efficient. Ensuring proper ventilation is critical in any booth setup to help exhaust fumes and maintain a safe environment. Having a fan or exhaust system that draws air into the booth and pushes it out through filters is a basic yet essential feature in any powder coating booth, whether it’s small or industrial.
Another factor to keep in mind is the booth’s ease of cleaning and maintenance. Powder residue can build up quickly, so it’s important to select a booth that makes it easy to access and clean filters, powder recovery systems, and the general structure of the booth. A booth that’s designed with smooth surfaces and fewer hard-to-reach areas will reduce cleaning time and improve overall maintenance. Additionally, look for booths that offer simple access to parts that need regular maintenance or replacement, such as filters, fans, and exhaust components.
The cost of a powder coating booth varies widely depending on its size, features, and intended use. For DIY projects or small business applications, a basic booth may be more affordable, while larger systems with advanced air filtration and recovery capabilities will come at a higher price point. It’s important to consider the long-term savings that come from using a booth with a recovery system, as it helps reduce powder waste and makes the coating process more efficient. In small operations, a portable booth can provide the flexibility to coat parts in various locations, allowing for easy setup and storage. Portable booths are particularly useful for small shops or businesses that need to move their equipment between workspaces or need to coat different types of items.
In addition to saving material costs, a well-designed booth can improve the overall coating quality. Properly capturing overspray ensures that the powder is applied to the parts with more precision, leading to a more uniform finish. Powder coating booths equipped with recovery systems can help keep the air cleaner, prevent contaminants from affecting the coating, and ensure that excess powder is effectively recycled. This not only saves on material costs but also helps maintain the environmental standards by reducing the amount of powder that escapes into the air.
Overall, a powder coating booth is an essential investment for anyone involved in powder coating, from hobbyists and small business owners to larger manufacturers. Whether you’re applying a glossy finish to automotive parts or coating furniture for sale, a high-quality booth helps ensure that the process is smooth, efficient, and safe. A booth that suits your specific needs will improve the quality of your work, reduce waste, and increase productivity, making it an indispensable part of any powder coating operation.
As you continue exploring powder coating booths, it’s also important to consider customization options for your specific requirements. Many powder coating booths can be tailored to suit particular projects, whether it’s large or intricate items. For example, some booths come with adjustable walls or internal dividers to create separate areas for different part sizes. If you are working with parts of varying shapes or dimensions, adjustable shelving or turntable systems within the booth can help with coating even the most complex parts.
The environmental impact of powder coating booths is another area to consider. While powder coating itself is already an eco-friendly option compared to traditional liquid paints, a booth that incorporates green technologies can enhance sustainability. Some powder coating booths feature energy-efficient heating systems or LED curing lights that consume less electricity than conventional methods. Additionally, certain booths are designed to be more energy-efficient, using insulated panels and heat-recirculating ovens to maintain a consistent temperature while reducing overall energy consumption. These energy-efficient features can lead to significant long-term savings and reduce your carbon footprint.
Noise control can also be a consideration in some powder coating operations, especially in small or home-based workshops. Powder coating booths with sound-dampening features can help reduce the noise generated by air compressors, fans, and other machinery. This is particularly important in settings where noise could be a disturbance or in more densely populated areas. Some booths come with noise reduction packages, such as soundproofing materials on walls or quieter air circulation systems, which make the working environment more comfortable.
When it comes to workflow efficiency, a well-organized booth setup can dramatically speed up your coating process. For example, having a turntable or rotating rack system inside the booth allows parts to be evenly coated as they rotate, ensuring a smooth and uniform finish on all sides. This eliminates the need for the operator to manually reposition the parts, saving time and ensuring consistency in the coating. For larger parts, oversize booths or booths with adjustable features allow for optimal maneuverability and positioning of items, making it easier to coat larger or bulkier objects.
Maintenance and longevity of the booth are critical for ongoing productivity. The lifespan of powder coating booths is often determined by the materials used in construction and the quality of the filtration system. Many booths are built with sturdy, corrosion-resistant materials such as galvanized steel or powder-coated metal to ensure durability and long-term performance. Regular inspection of the booth, particularly the air filters, powder recovery units, and airflow components, is essential to ensure smooth operation and to prevent costly downtime. The filters, in particular, should be cleaned or replaced according to the manufacturer’s recommendations to maintain optimal airflow and prevent the buildup of powder residue in the system.
Another key point is safety features. Since powder coating involves working with flammable materials, it is crucial to choose a booth that offers adequate fire prevention measures. Many modern booths are equipped with fire suppression systems that can detect any signs of a fire and activate automatically to put it out. Additionally, booths should be equipped with grounding equipment to prevent static buildup, which can also pose a fire hazard. The booth should also be designed with sufficient exhaust capacity to ensure that any fumes or particles are safely directed away from the work area.
As businesses expand, automation in powder coating booths is becoming more common. Automated systems can help improve efficiency, reduce human error, and increase throughput. For example, automated spray guns or robotic arms can be integrated into powder coating booths for high-volume applications, allowing for precise and consistent coating even for complex or detailed parts. These systems can be programmed to move around the part in specific patterns, ensuring uniform coverage without the need for manual operation. Automated powder coating systems also provide a level of consistency that can be difficult to achieve manually, making them ideal for larger production runs where quality and uniformity are critical.
For high-demand businesses or those aiming to produce large quantities of parts, conveyorized powder coating systems can significantly improve productivity. These systems use conveyor belts or automated tracks to move parts through the booth and curing oven, ensuring that parts are coated and cured without requiring manual intervention. Conveyor systems can be adapted to work with various booth sizes and configurations, allowing for seamless integration into existing production lines.
Lastly, training and expertise are essential for operating a powder coating booth efficiently. While the process itself is relatively simple, achieving a high-quality finish consistently requires skill and knowledge. Proper training will ensure that operators understand how to adjust settings for different powder types, manage the curing process, and troubleshoot common issues. Many manufacturers offer training or support services to help businesses get the most out of their powder coating booths, whether it’s about application techniques, equipment setup, or ongoing maintenance.
Ultimately, the right powder coating booth for your operation will depend on factors like the scale of your production, part sizes, budget, and specific application needs. Whether you’re just starting out with a small, portable setup or running a larger, automated production line, investing in a quality booth can enhance both the quality and efficiency of your powder coating process. With the right equipment, attention to detail, and a well-maintained booth, you can achieve high-quality finishes while optimizing your workflow and minimizing material waste.
As you continue refining your powder coating setup, it’s important to focus on optimizing workflow and part handling. Efficient part handling is crucial to achieving high-quality, consistent results. One way to streamline this process is by using hanging racks or fixtures that can support multiple parts at once. For example, a vertical hanging system can help maximize the use of space within the booth, allowing you to coat multiple parts simultaneously without overcrowding. This method can be particularly useful for small parts or components that require less time to coat. For larger items, horizontal racks or custom fixtures can help ensure they remain stable and properly aligned during the coating process, which can prevent uneven application.
In addition to part handling, material management is an important consideration. Different powder coatings have different application requirements, including varying flow rates, particle sizes, and curing times. It’s important to have a clear organizational system for powder storage to ensure that different colors and types of powders are properly segregated and easy to access. Some businesses implement color change systems, which allow for quick transitions between different powder colors without having to clean the entire system. This system is especially useful in high-volume production environments where frequent color changes are necessary.
For automated powder coating booths, additional features such as color monitoring systems and coating thickness sensors can enhance the overall quality control process. These systems ensure that each part receives an even layer of powder and that the correct thickness is maintained throughout the coating process. This is particularly useful for industries that require strict adherence to quality standards, such as automotive or aerospace, where even the slightest inconsistency can lead to defects.
Customization of coatings is another area where businesses can differentiate themselves. Many powder coating systems now allow for the application of specialty powders that give parts unique finishes, such as metallic, textured, or gloss coatings. Custom finishes are popular in markets like automotive restoration, home furnishings, and decorative products. Being able to offer these unique options requires not only a powder coating booth capable of applying various powders but also the knowledge of how to adjust settings to get the desired effect. As part of your investment in equipment, consider learning how to mix powders or apply different textures for a range of results.
Energy consumption is a significant cost factor in large-scale powder coating operations, especially with the use of curing ovens. Efficient heat recovery systems and low-energy ovens are an excellent way to reduce operational costs. Some powder coating ovens come with pre-heat zones or variable temperature controls, allowing you to control the temperature precisely and avoid energy waste. Thermal insulation is another important feature that can help maintain oven temperature, further reducing energy consumption.
To achieve the best possible results, it’s critical to maintain an ideal application environment. Temperature and humidity levels play a large role in the quality of the powder coating. If the ambient temperature is too high or low, it can affect the powder’s ability to adhere to the part or cure properly. High humidity can lead to issues such as condensation on parts before they’re coated, which may cause adhesion issues or uneven coating. Keeping your powder coating booth in a controlled environment with proper air conditioning or ventilation is key to achieving consistently high-quality finishes.
As businesses grow, having a scalable powder coating system becomes more important. If you start with a small-scale setup and later decide to expand, look for equipment that is easy to upgrade. For example, a powder coating booth with a modular design can allow for future expansion, whether that means adding more spray guns, extending the booth, or integrating more automated features. Some systems can grow with your needs by adding additional curing ovens, conveyor systems, or powder recovery units, allowing you to keep up with increasing demand while minimizing disruptions.
Moreover, automation plays a key role in scaling up production. For businesses looking to increase output while maintaining consistent quality, automated spray guns and robotic arms can be integrated into the powder coating process. These robotic systems can handle repetitive tasks such as spraying powder onto parts, ensuring uniformity and precision. This level of automation reduces the risk of human error, increases speed, and improves coating consistency. Robotic arms can be programmed to handle complex shapes and adjust spraying patterns based on the part’s contours, which would be difficult to achieve manually.
Industry standards and certifications are also important to consider when operating a powder coating business. Some industries, such as aerospace or automotive manufacturing, require powder coating processes to meet specific performance and safety standards. These standards often include requirements for coating thickness, durability, and environmental considerations. Keeping up with certifications or regulatory compliance can help ensure that your coating processes meet customer expectations and industry norms.
The maintenance of powder coating booths requires attention to detail to ensure smooth operations. Regularly inspecting components such as spray guns, filters, airflow systems, and recovery units is vital to maintaining equipment performance. Cleaning is a critical part of this maintenance process. Over time, the buildup of powder residue can affect the coating process, leading to clogged filters or poor application. A good cleaning routine can prevent downtime and costly repairs. It’s also important to monitor air quality in the booth to ensure that the ventilation systems are functioning properly and that the work environment remains safe for operators.
Lastly, keeping customer satisfaction at the forefront of your operation is essential. Whether you’re coating automotive parts, industrial equipment, or decorative pieces, providing a consistently high-quality finish will keep your customers returning. Offering fast turnaround times, excellent customer service, and the ability to accommodate custom orders can set your business apart from competitors. Ensuring that your powder coating booth and system are well-maintained, and that you continue to upgrade your processes with new technologies, will help you stay ahead in the market.
In conclusion, a successful powder coating operation, whether small-scale or large, requires not only the right equipment but also a well-organized, efficient system that ensures high-quality results. By focusing on workflow optimization, energy efficiency, maintenance, and customer satisfaction, you can maximize the potential of your powder coating booth and build a thriving business.
Conclusion
Regular maintenance of powder coating ovens is essential for achieving high-quality finishes, maintaining production efficiency, and ensuring equipment longevity. By implementing a structured maintenance plan, conducting regular inspections, and training staff, businesses can minimize downtime, reduce costs, and maintain a safe working environment.