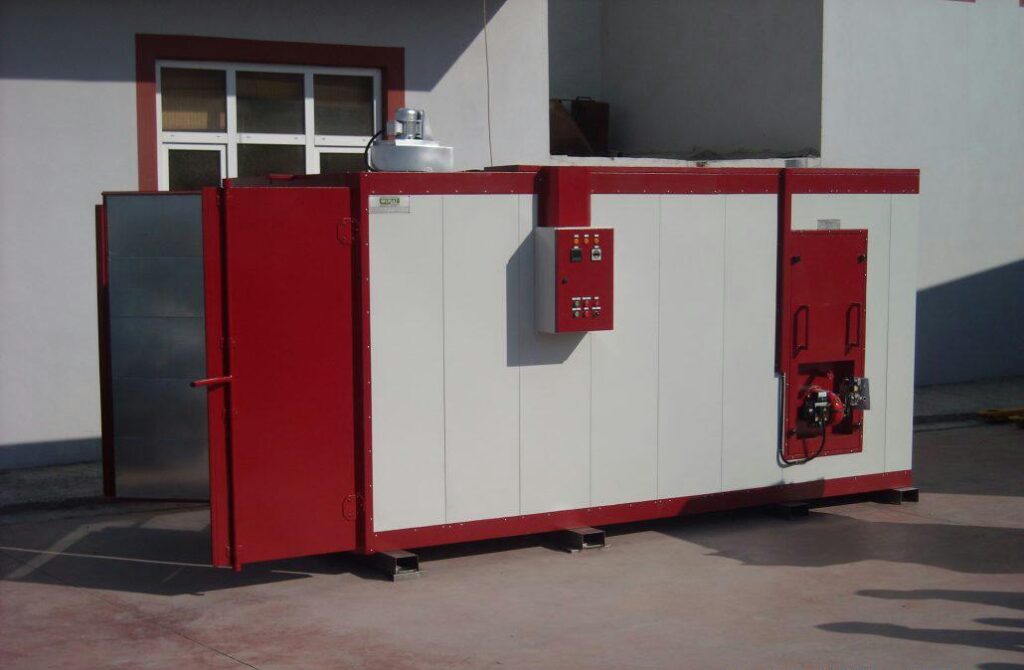
Gas Powder Coating Oven
Powder coating of metals is often favored by manufacturers because its finish is tougher than conventional paint. Powder coating is abrasion resistant and will not crack, chip, or peel as conventional paint will. Powder coating is typically done through a two-step process: First, the coating is applied to the part electrostatically with powder coating equipment, and then the newly powdered part is cured in an industrial gas powder coating oven under heat to form a skin.
This process is very efficient since the powder wraps around the back of the part for better coverage and ensures 95% material usage of the powder. The powder coating is a dust-like substance that behaves quasi-fluid. with the help of this material property, the powder coating flows through the hoses and gun of powder coating equipment and reaches the part already ionized with – ion. This helps the particle hang on the part and stay there till the part is grounded again. The parts that are coated with powder are either manually, or automatically with the help of a conveyor are taken into the gas oven, of which inside there is a 200 C temperature to melt the powder coating on the parts
Benefits of powder coating and curing in an oven: Heavy-duty construction and quality components Excellent uniformity and heating rates for consistent, high-quality curing results No powder blow-off – reduces rework Uniform heat distribution provides quality cured finishes and optimum cure cycles Quick heat-up rates so you can cure more loads per day Roof-mounted blowers conserve valuable floor space at your facility Fully adjusted and factory tested prior to shipment to reduce installation and start-up times Available with our exclusive energy-efficient oven upgrade
Small Gas Powder Coating Oven
The dimensions of our small powder coating oven start from 1,2m x 1,2m x 1,2m. This is for lab powder coating applications. The lab type oven is used to cure powder coating for samples and small items in small number
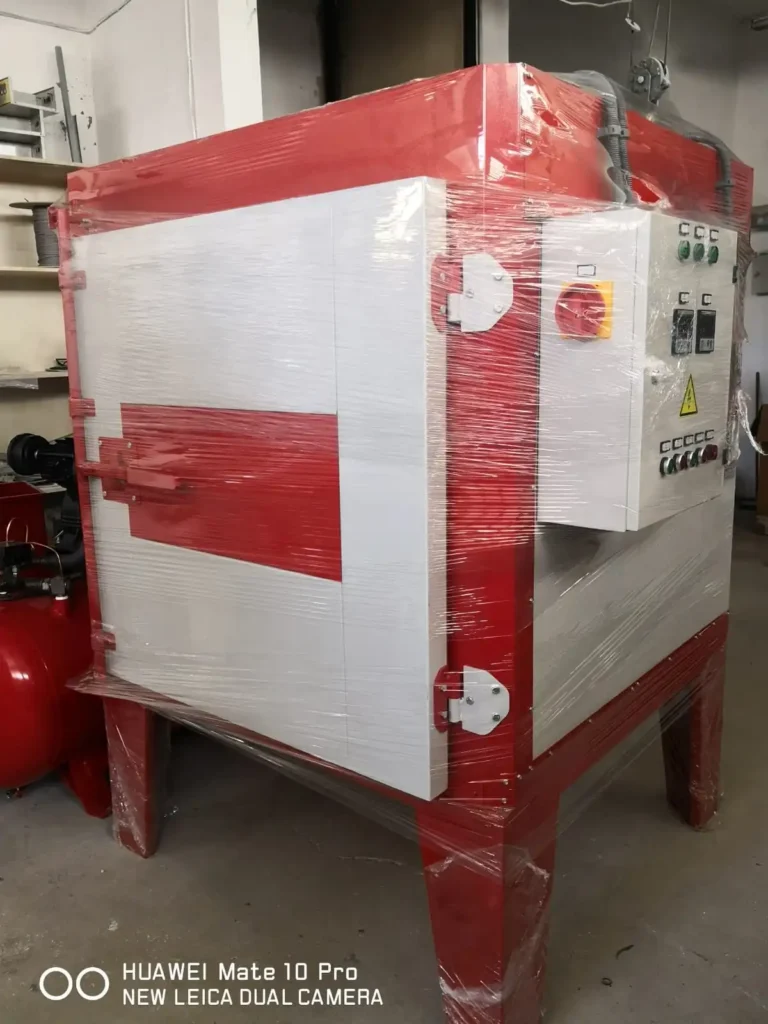
Powder coating companies that are doing custom coating can have some special requests for small items and samples. They don’t want to heat up a big oven for this and require a small lab-type box oven. This small oven can also be used for powder coating at home. Some people try to make their own DIY powder coating oven but this usually takes a long time for construction and can have some serious mistakes in manufacturing that can cause inefficiency and even danger to human life.
The powder coating cost usually increases in such DIY powder coating oven types. If the curing won’t be effective, you will need to use a powder coat remover to get the powder off the powder-coated metal has the entire powder coating process once again. The powder coating prices are not that low to let you repeat the same process again and again.
Gas Powder Coating Oven Characteristics
A gas powder coating oven is a crucial component of the powder coating process, responsible for curing the applied powder coating, transforming it into a durable and hard finish. The curing process involves heating the powder particles to a specific temperature for a specified time, allowing them to melt, flow, and crosslink, forming a continuous film on the substrate. Gas powder coating ovens utilize natural gas or propane as the fuel source for the heating process.
Components of a Gas Powder Coating Oven
A typical gas powder coating oven comprises several key components:
- Gas Burner System: The gas burner system provides the heat source for the curing process. It includes gas valves, regulators, and burners that efficiently combust natural gas or propane to generate hot air.
- Heat Exchanger: The heat exchanger transfers heat from the combustion gases to the circulating air, ensuring uniform heat distribution within the oven. It may be a finned tube heat exchanger or a plate-type heat exchanger.
- Air Circulation System: The air circulation system ensures consistent heat transfer to all parts of the workpiece. It includes fans, ducts, and distribution plenums that circulate hot air throughout the oven chamber.
- Temperature Control System: The temperature control system regulates the temperature within the curing oven, ensuring the powder particles are heated to the correct temperature range for optimal curing. It may involve thermocouples, controllers, and feedback loops.
- Workpiece Handling System: The workpiece handling system transports the powder-coated workpieces through the curing oven, maintaining proper positioning and exposure to the heat source. It may involve conveyor belts, rotating turntables, or automated robotic systems.
- Exhaust System: The exhaust system removes fumes and gases generated during the curing process, maintaining a safe and comfortable working environment. It may include fans, ducts, and filtration systems.
Types of Gas Powder Coating Ovens
The specific type of gas powder coating oven used depends on the production volume, workpiece size and shape, desired coating properties, and available space:
- Batch Ovens: Batch ovens are suitable for low-volume production and allow for manual loading and unloading of workpieces. They may be heated by gas burners, infrared (IR) emitters, or a combination of both.
- Continuous Ovens: Continuous ovens are designed for high-volume production and incorporate conveyor systems to transport workpieces through the curing process. They offer efficient and consistent curing results.
- Specialty Ovens: Specialty ovens are designed for specific applications, such as curing complex shapes or achieving high-gloss finishes. They may incorporate specialized heating elements, air circulation patterns, or atmosphere control systems.
Factors Affecting Gas Powder Curing
Several factors influence the effectiveness of gas powder curing:
- Powder Type: Different powder formulations require specific curing temperatures and times.
- Substrate Material: The substrate material’s thermal conductivity can affect the heating and curing process.
- Workpiece Thickness: Thinner workpieces may cure faster than thicker ones.
- Oven Temperature: Maintaining consistent temperature throughout the oven is crucial for uniform curing.
- Air Circulation: Proper air circulation ensures even heat distribution and prevents uneven curing.
- Curing Time: Insufficient curing time can lead to incomplete crosslinking and poor coating performance.
Conclusion
Gas powder coating ovens play a critical role in achieving durable and high-quality powder coatings. By selecting the appropriate curing oven, optimizing curing parameters, and maintaining proper operating conditions, manufacturers can ensure consistent and effective powder curing, resulting in long-lasting, protective, and aesthetically pleasing finishes.
Additional Considerations for Gas Powder Coating Ovens
- Fuel Efficiency: Choose an oven that utilizes fuel efficiently to minimize operating costs and environmental impact.
- Maintenance Requirements: Consider the ease of maintenance and availability of spare parts for the oven.
- Safety Features: Ensure the oven incorporates adequate safety features, such as emergency stop mechanisms and gas leak detection systems.
- Integration with Existing Systems: Ensure the oven can integrate seamlessly with existing equipment and processes.
- Compliance with Regulations: Verify the oven complies with relevant safety and environmental regulations.
Temperature Controller
A temperature controller is an essential component of a gas powder coating oven, ensuring that the powder particles are heated to the correct temperature range for optimal curing. This precision control is crucial for achieving consistent and high-quality powder coating results.
Functions of a Temperature Controller
The primary functions of a temperature controller in a gas powder coating oven include:
- Temperature Monitoring: Continuously monitors the temperature within the oven chamber using thermocouples or other temperature sensors.
- Temperature Regulation: Adjusts the operation of the gas burners or other heating elements to maintain the desired temperature setpoint.
- Alarm System: Triggers alarms if the temperature deviates from the setpoint, preventing potential damage to the powder coating or the workpiece.
- Data Logging: Records temperature data over time, providing valuable insights into oven performance and curing consistency.
Types of Temperature Controllers
Temperature controllers vary in complexity and features, ranging from simple analog controllers to sophisticated digital controllers with advanced control algorithms. The choice of controller depends on the specific requirements of the powder coating oven and the desired level of control accuracy.
- Analog Temperature Controllers: These controllers utilize mechanical or electrical components to regulate temperature. They are generally less expensive but offer limited control capabilities.
- PID Temperature Controllers: These controllers employ Proportional-Integral-Derivative (PID) control algorithms, providing more precise and responsive temperature regulation. They are widely used in industrial applications due to their effectiveness.
- Programmable Temperature Controllers: These controllers offer advanced features like programming temperature profiles, ramp rates, and dwell times, enabling optimized curing processes. They are particularly suitable for complex applications or production lines with varying requirements.
Selection Criteria for Temperature Controllers
When selecting a temperature controller for a gas powder coating oven, consider the following factors:
- Temperature Range: Ensure the controller can handle the desired curing temperature range for the powder coating being used.
- Accuracy Requirements: Choose a controller with the necessary accuracy to achieve consistent curing results.
- Control Algorithm: Select a controller with an appropriate control algorithm, such as PID, for precise temperature regulation.
- Communication Protocols: Consider if the controller supports communication protocols for integration with other systems or data logging purposes.
- Safety Features: Ensure the controller incorporates safety features, such as over-temperature alarms and fail-safe mechanisms.
Safety Considerations for Temperature Controller Operation
- Regular Calibration: Regularly calibrate the temperature controller to maintain accuracy and prevent deviations from the setpoint.
- Sensor Maintenance: Ensure the temperature sensors are properly installed, maintained, and calibrated for accurate temperature readings.
- Alarm Monitoring: Pay attention to temperature alarms and promptly address any deviations to prevent potential hazards.
- Emergency Procedures: Establish clear emergency procedures in case of temperature-related malfunctions or safety incidents.
Conclusion
A temperature controller plays a critical role in ensuring the quality and consistency of powder coating results. By selecting the appropriate controller, maintaining its operation, and adhering to safety guidelines, manufacturers can achieve optimal curing, extend the lifespan of their powder coating equipment, and maintain a safe working environment.
An Electronic Temperature Controller controls temperature conditions. It is a non-profiling type 1/16 DIN single channel controller that features automatic control. Either a time proportioned heat output or a 4-20 ma control signal is used for precise temperature control
Overtemperature Protection
An Electronic Temperature Controller is provided for temperature protection. The Electronic Temperature Controller will remove power to the heating system when an over-temperature condition is detected. Alarm circuitry may be included as an option.
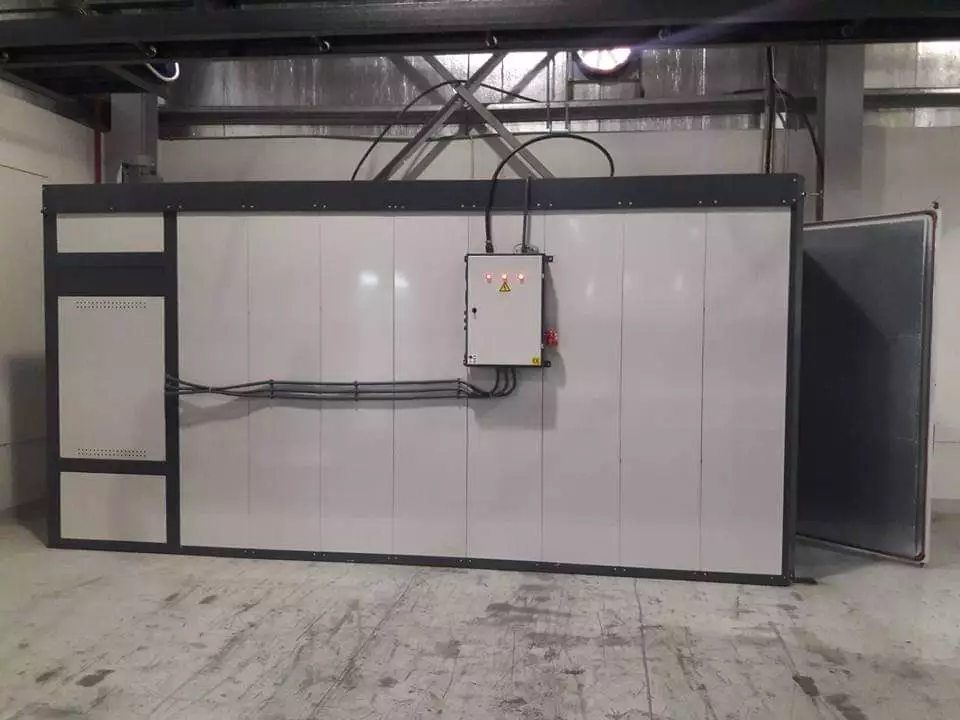
Overtemperature protection is a crucial safety mechanism in various industrial and commercial applications, including powder coating ovens, electrical systems, and machinery. It prevents overheating and potential damage to equipment, materials, and surrounding environments by automatically triggering corrective actions when temperatures exceed safe limits.
Principles of Overtemperature Protection
Overtemperature protection systems utilize various principles to monitor and regulate temperature, including:
- Temperature Sensors: These sensors, such as thermocouples or RTDs, detect temperature changes and convert them into electrical signals.
- Control Systems: These systems receive temperature signals from the sensors, compare them to preset thresholds, and initiate appropriate actions when temperatures exceed safe limits.
- Actuators: These devices, such as valves, switches, or relays, perform the necessary actions to reduce or prevent overheating, such as shutting down heating elements, activating cooling systems, or triggering alarms.
Components of Overtemperature Protection Systems
A typical overtemperature protection system comprises several key components:
- Temperature Sensors: Strategically placed temperature sensors monitor the temperature of critical components, such as heating elements, bearings, or electrical conductors.
- Signal Conditioning Units: These units amplify, filter, or convert the raw temperature signals from the sensors into a format compatible with the control system.
- Control Logic: The control logic, implemented in a programmable logic controller (PLC) or other control device, receives temperature signals, compares them to setpoints, and activates the appropriate actuators.
- Actuators: Actuators, such as relays, valves, or contactors, perform the necessary actions to prevent overheating, such as shutting down heating elements, opening cooling valves, or triggering alarms.
- Alarms and Indicators: Alarms and indicators provide visual or audible warnings when temperatures approach or exceed safe limits, alerting operators to take corrective actions.
Applications of Overtemperature Protection
Overtemperature protection systems are widely used in various applications, including:
- Powder Coating Ovens: Prevent overheating of powder coating materials and substrates, ensuring consistent curing results and minimizing fire hazards.
- Electrical Systems: Protect electrical components, such as transformers, motors, and cables, from damage caused by excessive temperatures, preventing electrical failures and fire hazards.
- Machinery: Safeguard machinery components, such as bearings, gears, and engines, from overheating, preventing premature wear, tear, and breakdowns.
- Industrial Processes: Protect industrial processes, such as chemical reactions, distillation, and polymerization, from runaway conditions that could lead to explosions or hazardous releases.
- Commercial Appliances: Prevent overheating in appliances such as ovens, stoves, and dryers, minimizing fire risks and ensuring user safety.
Benefits of Overtemperature Protection
Overtemperature protection systems offer several significant benefits:
- Equipment Protection: Prevent damage to equipment, extending its lifespan and reducing maintenance costs.
- Safety Enhancement: Minimize fire hazards and protect workers from potential injuries caused by overheating.
- Process Control: Maintain stable and safe operating conditions for industrial processes, preventing costly disruptions and ensuring product quality.
- Environmental Protection: Prevent environmental pollution and hazardous releases caused by overheating or uncontrolled reactions.
- Insurance Compliance: Meet insurance requirements and safety regulations, reducing liability and risk.
Conclusion
Overtemperature protection is an essential safety measure that safeguards equipment, personnel, and the environment from the adverse consequences of overheating. By implementing effective overtemperature protection systems, industries and businesses can prevent costly damages, ensure safe operations, and maintain their reputation for reliability and safety.
Process Timer
A process timer is an essential component of a gas powder coating oven, ensuring that the powder particles are heated for the correct duration to achieve optimal curing. This precise control of curing time is crucial for consistent and high-quality powder coating results.
Functions of a Process Timer
The primary functions of a process timer in a gas powder coating oven include:
- Time Monitoring: Continuously tracks the elapsed time since the curing process began.
- Time Regulation: Controls the operation of the gas burners or other heating elements to maintain the desired curing time.
- Alarm System: Triggers alarms if the curing time exceeds or falls below the setpoint, preventing incomplete or over-curing of the powder coating.
- Data Logging: Records curing time data over time, providing valuable insights into process consistency and reproducibility.
Types of Process Timers
Process timers vary in complexity and features, ranging from simple mechanical timers to sophisticated digital timers with advanced control algorithms. The choice of timer depends on the specific requirements of the powder coating oven and the desired level of control accuracy.
- Mechanical Process Timers: These timers utilize mechanical components, such as gears and springs, to track and regulate curing time. They are generally less expensive but offer limited control capabilities.
- Electronic Process Timers: These timers employ electronic circuits and microcontrollers to provide precise time measurement and control. They are widely used in industrial applications due to their reliability and accuracy.
- Programmable Process Timers: These timers offer advanced features like programming curing time profiles, ramp rates, and dwell times, enabling optimized curing processes. They are particularly suitable for complex applications or production lines with varying requirements.
Selection Criteria for Process Timers
When selecting a process timer for a gas powder coating oven, consider the following factors:
- Time Range: Ensure the timer can handle the desired curing time range for the powder coating being used.
- Accuracy Requirements: Choose a timer with the necessary accuracy to achieve consistent curing results.
- Control Algorithm: Select a timer with an appropriate control algorithm, such as a proportional-integral-derivative (PID) algorithm, for precise time regulation.
- Communication Protocols: Consider if the timer supports communication protocols for integration with other systems or data logging purposes.
- Safety Features: Ensure the timer incorporates safety features, such as over-time alarms and fail-safe mechanisms.
Safety Considerations for Process Timer Operation
- Regular Calibration: Regularly calibrate the process timer to maintain accuracy and prevent deviations from the setpoint.
- Alarm Monitoring: Pay attention to time alarms and promptly address any deviations to prevent potential defects or inconsistent curing.
- Emergency Procedures: Establish clear emergency procedures in case of time-related malfunctions or safety incidents.
Conclusion
A process timer plays a critical role in ensuring the quality and consistency of powder coating results. By selecting the appropriate timer, maintaining its operation, and adhering to safety guidelines, manufacturers can achieve optimal curing, extend the lifespan of their powder coating equipment, and maintain a safe and efficient production process.
A Process Timer is provided, which has five user-selectable timing ranges from 0.01 seconds to 9999 hours. The timer will automatically start timing once the process setpoint temperature is reached. When the total preset time has elapsed, power to the heat control circuitry will be disabled.
Additional Features
EMS Powder Coating Equipment ovens are designed with the capability to incorporate many other optional features for safety purposes, enhanced process control, and a simplified operator interface. Consult a Gruenberg Applications Engineer or our Service Department for more information or questions.
Operating Parameters and Requirements
This equipment is designed to operate safely when the following environmental conditions are met:
- Indoor use only.
- Within a temperature range of 5°C to 30°C (max).
- Maximum relative humidity 90%.
The listed chamber specifications are based on operation at 24° C ambient temperature, the altitude at sea level, and a 60 Hz power supply. Chamber operation utilizing a 50 Hz power supply may derate the listed performance specifications. Equipment damage, personal injury, or death may result if this equipment is operated or maintained by untrained personnel.
Operators and service personnel must be familiar with the location and function of all controls and the inherent dangers of the equipment before operating or maintaining it. TPS shall not be liable for any damages, including incidental and/or consequential damages, regardless of the legal theory asserted, including negligence and/or strict liability.
Observe all safety warnings and operating parameters listed in this manual, as well as all Caution, Danger, and Warning signs or labels mounted on the equipment to reduce the risk of equipment damage and personal injury.
Location and Installation of the Gas Powder Coating Oven

Oven Classification – Electric Heated Units: NFPA 86 Class B ovens are heat utilization equipment operating at approximately atmospheric pressure wherein there are no flammable volatiles or combustible material being heated in the oven.
Oven Classification – Gas Heated Units: NFPA 86 Class A: “Class A ovens and furnaces are heat utilization equipment operating at approximately atmospheric pressure wherein there is a potential explosion or fire hazard that could be occasioned by the presence of flammable volatiles or combustible materials processed or heated in the furnace.”
Do not locate units in areas of wide ambient temperature variation such as near vents or outdoor entrances.
Do not place the unit near combustible materials or hazardous fumes or vapors.
Do not install the unit in a corrosive environment. A corrosive environment may lead to poor performance and deterioration of the unit.
Ventilation: The oven should be installed in an area where there is good air ventilation. Allow a minimum of 5 inches between any wall and any oven side.
Do not position the oven in a manner that would make it difficult to operate your main power disconnect switch.
Make sure the oven is leveled when set up. The floor of the chamber should be leveled with a Spirit Level to +/- 1/8” (3.175 mm) front to back and side to side.
Sometimes control panels are removed to facilitate shipment. When required, replace the panel securely and reconnect numbered electrical wires to matching numbered terminal blocks.
Very Important! Upon completion of the initial installation of the chamber and upon completion of any maintenance procedure, make sure that all access panels that have been removed are reinstalled securely before operating the unit.

Exhaust Connection for Gas Powder Coating Oven
The exhaust connection for a gas powder coating oven is a crucial component of the system, ensuring the safe and efficient removal of fumes, gases, and combustion byproducts generated during the curing process. Proper ventilation is essential for maintaining a healthy and comfortable working environment, preventing fire hazards, and complying with environmental regulations.
Design Considerations for Exhaust Connections
The design of the exhaust connection should take into account several factors:
- Fume and Gas Generation Rate: The size and capacity of the exhaust system should be proportional to the rate at which fumes and gases are generated during the powder coating process. This ensures effective removal of airborne contaminants.
- Oven Configuration: The exhaust connection should be positioned strategically to capture fumes and gases effectively from all parts of the oven chamber. This may involve multiple exhaust ports or strategically placed ducts.
- Fan Capacity: The exhaust fan should be sized appropriately to provide sufficient airflow for the removal of fumes and gases. This ensures proper ventilation and prevents recirculation of contaminants.
- Ducting System: The ductwork should be designed to minimize pressure drops and ensure smooth airflow from the oven to the exhaust outlet. This optimizes the efficiency of the exhaust system.
- Filtration System: A filtration system may be necessary to remove particulate matter and other contaminants from the exhaust stream before it is discharged into the atmosphere. This depends on the specific requirements of the powder coating application and environmental regulations.
Safety Considerations for Exhaust Connections
- Regular Maintenance: Regularly inspect and clean the exhaust system, including ducts, fans, and filters, to maintain optimal performance and prevent fire hazards.
- Electrical Safety: Ensure proper grounding and electrical safety procedures for the exhaust system components.
- Emergency Stops: Install and maintain emergency stop mechanisms to halt operations in case of unexpected hazards.
- Gas Detection Systems: Consider installing gas detection systems to monitor for potentially hazardous concentrations of fumes or gases.
- Personal Protective Equipment (PPE): Provide PPE, such as respirators, gloves, and safety glasses, when necessary for handling powder coating materials or working near the exhaust system.
- Training and Documentation: Provide thorough training to operators on proper exhaust system operation and safety procedures. Maintain comprehensive safety documentation.
Conclusion
The exhaust connection plays a vital role in maintaining a safe and environmentally compliant powder coating operation. By designing and maintaining an effective exhaust system, manufacturers can protect their employees, minimize environmental impact, and safeguard their facilities from potential fire hazards.
An exhaust port connection consisting of a 6” O.D. collar is installed with the exhaust blower assembly at the top of the oven. The exhaust housing includes a manual damper. A vent duct should be connected to the exhaust port collar and run to a location outside of the building (as necessary). This should be done in accordance with all local code regulations. Make sure the connection is secure.
Gas Supply Connection for Gas Powder Coating Oven
The gas supply connection for a gas powder coating oven is a critical component that ensures a safe and regulated flow of natural gas or propane to the oven’s burners. Proper gas supply connection is essential for achieving consistent curing results, maintaining equipment efficiency, and preventing potential hazards.
Design Considerations for Gas Supply Connections
The design of the gas supply connection should adhere to several guidelines:
- Gas Pressure Requirements: The gas supply line must be designed to withstand the pressure requirements of the oven’s burners. Excessive pressure can lead to safety hazards, while insufficient pressure can compromise curing performance.
- Gas Flow Rate: The gas supply system should be sized to provide the required flow rate for the oven’s burners. This ensures adequate heat generation for proper curing.
- Pipe Materials: The gas supply piping should be made from appropriate materials that can withstand the pressure, temperature, and potential corrosion associated with natural gas or propane.
- Valves and Regulators: Install pressure regulators and shut-off valves at appropriate points in the gas supply line to control gas flow and isolate the oven in case of emergencies.
- Leak Detection: Implement leak detection systems, such as pressure gauges, gas detectors, or soap bubble testing, to identify and promptly address gas leaks.
- Regular Maintenance: Maintain the gas supply system regularly to ensure its integrity, prevent leaks, and optimize performance.
Safety Considerations for Gas Supply Connections
- Compliance with Gas Codes: Ensure the gas supply system complies with local, national, and international gas codes and regulations.
- Qualified Personnel: Only trained and qualified personnel should handle the installation, maintenance, and repair of the gas supply system.
- Training and Documentation: Provide thorough training to operators on proper gas supply system operation, safety procedures, and emergency response protocols. Maintain comprehensive documentation of gas system installation, maintenance, and inspections.
- Ventilation: Ensure adequate ventilation in the vicinity of the gas supply system to prevent the accumulation of flammable gases.
- Emergency Procedures: Establish clear emergency procedures in case of gas leaks, fires, or other gas-related hazards.
- Personal Protective Equipment (PPE): Provide PPE, such as gloves, safety glasses, and gas detectors, when necessary for working near the gas supply system.
Conclusion
The gas supply connection plays a crucial role in the safe and efficient operation of a gas powder coating oven. By adhering to proper design principles, implementing robust safety measures, and maintaining regular maintenance, manufacturers can ensure the reliability and safety of their powder coating operations.
Gas-fired ovens may use either natural gas or liquid propane for combustion to heat the oven. You must follow your specific supply specifications listed on your General Arrangement Drawing D001 and when listed here.
Important! Please read the entire Gas Heating System section and all vendor manuals / cut sheets to familiarize yourself with all gas components before making your gas supply connection. The gas supply connection is made to a ball valve with a ½” FPT type connection. Make sure the connection is secure and is checked for leaks before operation.
Gas Supply – Liquid Propane: Pressure = xxx PSIG, xxxx CFH
Gas Supply – Natural Gas: Pressure = xxx PSIG, xxxx CFH
Air Circulation of Gas Powder Coating Oven
Gas-fired heating systems are normally installed in walk-in modular ovens. A high-volume airflow system is employed to provide maximum temperature uniformity. The type of air circulation system used depends on the configuration of the unit. Single module units can only employ a horizontal front-to-back airflow type pattern using centrifugal type blower wheels to generate air circulation. Double module units can employ two different types of air circulation systems, as listed below.
• Horizontal front-to-back pattern using centrifugal type blower wheels.
• Compound horizontal pattern using propeller-type fans.
The heating and generation of airflow occur in the conditioning plenum, which is normally located on the right side wall of the oven. Blower wheels or fans are driven with extended shafts by motors mounted in the
control cabinet. Heating is achieved by a gas burner that directs a flame down into a vertical perforated flame tube mounted in the manifold next to the conditioning plenum. Thermocouples used for temperature sensing
are normally mounted in the workspace on the plenum panel.
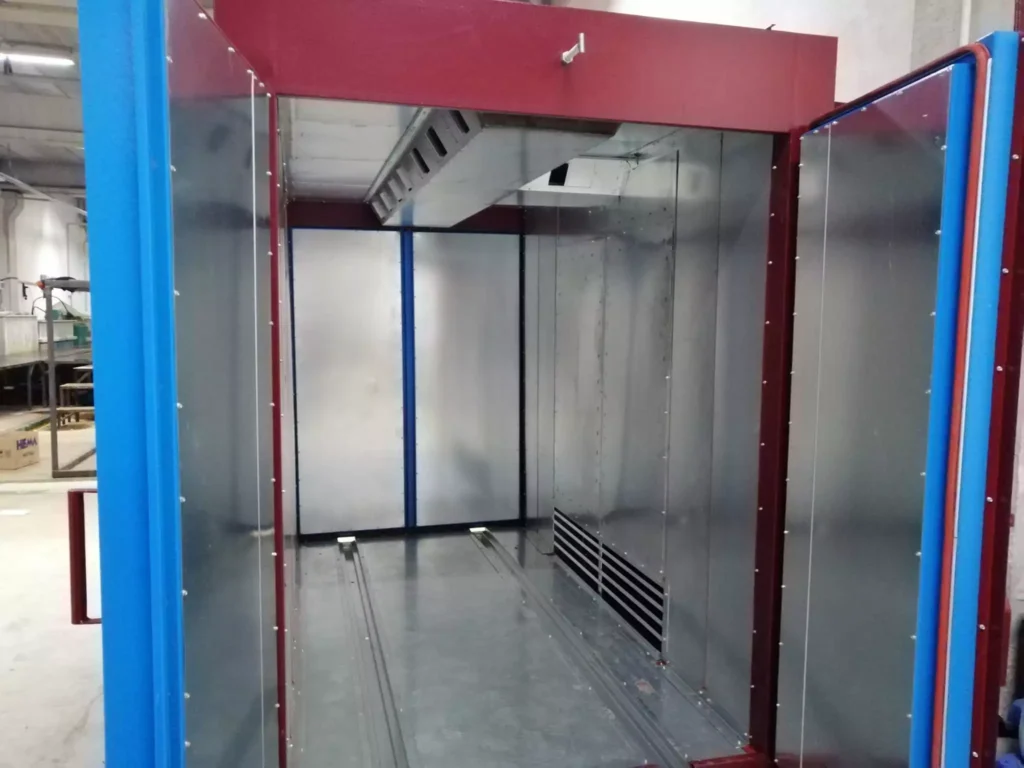
Airflow Description
Gas ovens using centrifugal type blower wheels for airflow generation employ a horizontal front-to-back type airflow system. The burner manifold is designed with a vertically mounted flame tube along with perforations on the back side of the manifold. Processed air is drawn into the burner manifold and conditioning plenum, and is heated as it mixes with hot air emitted from the flame tube.
Fresh ambient air is also drawn into the plenum where it mixes with the heated air. Conditioned air is discharged into the workspace through perforations near the front of the plenum housing. The air flows back through the workspace in a horizontal manner to condition the product and then returns to the plenum for reconditioning.
A portion of the processed air is exhausted through a port in the chamber ceiling by the exhaust blower. An air intake port with a manual slide damper is installed in the ceiling of each module to allow fresh ambient air to replenish the exhausted air. Slide dampers are mechanically locked to a predetermined minimum opening.
Heating System of Gas Powder Coating Oven
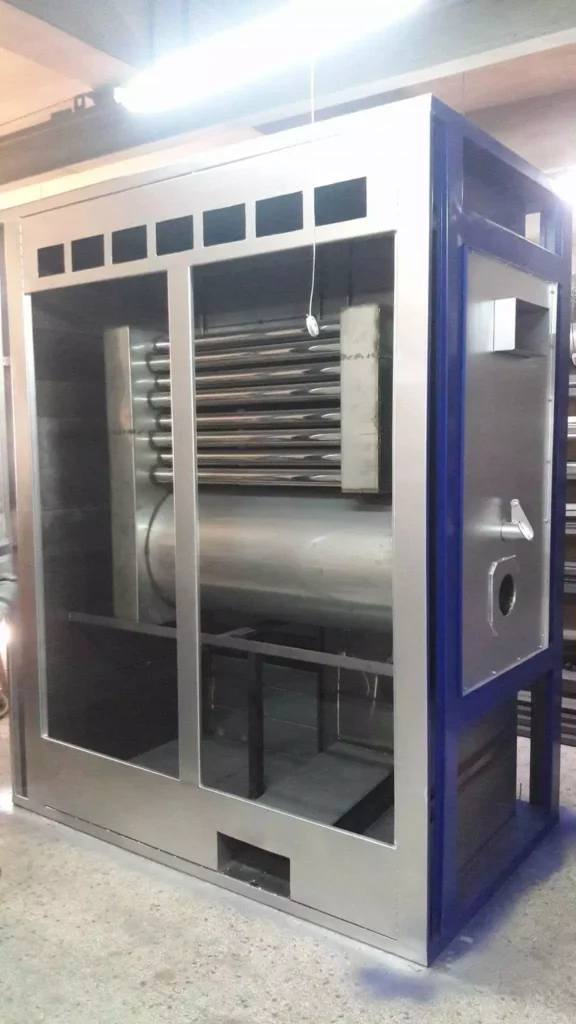
Important Note: Due to the diverse array of configurations available in a gas heating system, this section will describe basic system requirements, standard equipment used, and fundamental operation.
EMS Powder Coating gas heated ovens are designed to operate with either a natural gas supply or a liquid propane supply according to NFPA 86 (National Fire Protection Association) safety standards. To meet NFPA main gas train requirements, a Closed Position Indicator CPI is used for electrical indication of the safety valve’s closed position. A direct-fired type gas system is used in which the flame is shot through a burner manifold in the conditioning plenum.
Recirculating oven air is heated as it is drawn through the flame. Direct-fired systems are typically greater than 90% efficient. Since products of combustion enter the workspace with this type, it is reserved for those processes that are not emission sensitive. However, many safety precautions are employed with a direct-fired system to compensate for the presence of an open flame. The following sections detail the standard gas heating components used and their operation. The actual components used will vary with your application, so it’s important to check your oven specifications.
Exhaust Blower of the Gas Powder Coating Oven
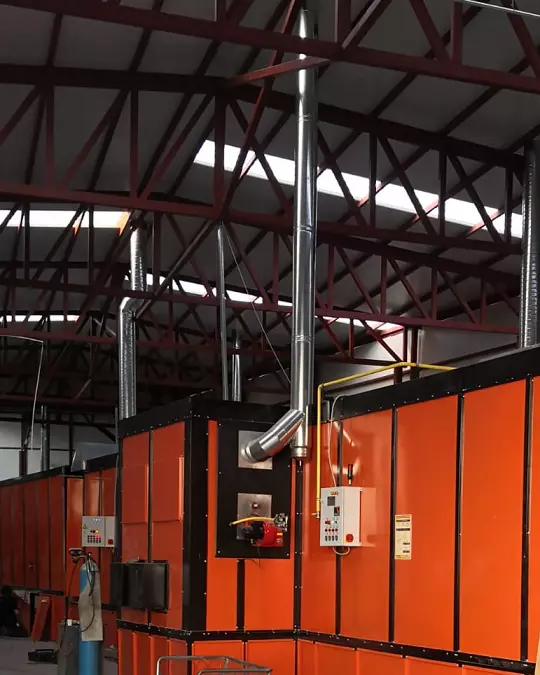
An exhaust blower is standard with all direct-fired systems to serve two purposes. Initially, the blower is used along with a purge air timer to purge oven air for a fixed time before the gas burner is fired. When the purge
cycle time is complete, the exhaust blower is used to maintain a constant exchange of oven air with fresh ambient air. Ambient air is drawn into the oven through slide dampers mounted atop each module.
A differential pressure switch is used to monitor airflow generation by the exhaust blower, and subsequently for correct operation of the blower motor. These devices use a diaphragm to sense pressure and to mechanically trigger a SPDT Snap Switch when the proper pressure is developed across the blower wheel (or fan). Correct rotation of the motor is necessary for the switch to operate properly. If a loss of pressure / airflow were detected, the switch would open and remove power from the gas burner.
Loss of airflow may result from a motor malfunction, a loose blower wheel (or fan), or constricted air intake or exhaust ports. Blower Spark-Proof Design: The blower housing is designed with a non-sparking type construction. The housing and inlet rings are made of aluminum while the blower wheel is made of stainless steel. Should the blower wheel come off its shaft and strike the blower housing or inlet ring, no sparks can be generated between the two metals.
Gas Burner – Combustion Blower
The three elements necessary for combustion are fuel, oxygen, and ignition. The combustion blower supplies a constant flow of fresh air to the burner. The air is mixed with gas by various methods in order to establish ignition and to sustain complete combustion. The combustion motor starts immediately when the OVEN ON switch is closed. A combustion airflow switch monitors airflow from the combustion blower. This is a differential air pressure type, which will shut down the burner if a loss of airflow is detected.
A burner is defined as a device used for the introduction of fuel and air into an oven at the required velocities, turbulence, and concentration to maintain ignition and combustion of fuel. A Blast type burner is normally
used. This burner delivers a combustible mixture under pressure, normally above 0.3 inch W.C. to the combustion zone. Various flame safety devices are installed within the burner.
EMS Powder Coating Equipment
Powder coating equipment is used to apply a thin layer of powder over a metal surface. This type of coating is applied by an electrostatic process and is a very popular method for finishing metal parts.
This type of equipment can be divided into two main categories: automatic and manual. Automatic booths are more popular because they provide better production rates, but they are also more expensive.
A powder booth is an enclosure in which the powder-coating process takes place. Powder-coating equipment includes an oven where the parts are heated to activate the powder, a gun that sprays or brushes on the powder, a conveyor belt that moves parts through the oven, and cartridge-type guns for applying thicker coatings with less overspray.
Powder coating is a technique that is used to provide a finish to metal parts. This technique has been in use for many years and it is still one of the most popular techniques today.
Powder coating equipment consists of booths, ovens, guns, machines, lines and conveyors. A booth can be either automatic or manual. An automatic booth is more expensive than a manual booth but it is also faster and more efficient.
What is a Gas Powder Coating Oven? (450-500 words)
A gas powder coating oven is an industrial curing oven that uses natural gas or propane as its primary energy source to generate the heat needed to cure powder coatings. These ovens are designed to create a controlled environment where the coated product is exposed to consistent, high temperatures, allowing the powder to melt, flow, and bond to the surface. The result is a hard, smooth, and durable finish that protects the product from wear, corrosion, and environmental damage.
Gas ovens are particularly effective for curing large quantities of products quickly, thanks to their fast heat-up times and ability to maintain steady temperatures over long periods. They are commonly used in industries such as automotive manufacturing, metal fabrication, and industrial equipment production, where high volumes of parts need to be coated and cured efficiently.
How Gas Ovens Work
Gas powder coating ovens operate by burning natural gas or propane in a combustion chamber, which generates heat that is then circulated throughout the curing chamber. The combustion process is controlled by a burner system that regulates the flow of gas to maintain the desired temperature. Fans or blowers distribute the heated air evenly across the chamber, ensuring that the temperature remains consistent throughout the curing process.
The temperature inside the oven is typically controlled by a digital system that allows operators to set and monitor the curing temperature and time. This precise control is crucial for ensuring that the powder coating cures properly, achieving the desired finish and durability.
Gas powder coating ovens can be configured as batch ovens, where products are loaded into the oven in groups, or as conveyorized systems, where products move through the oven on a conveyor belt. Conveyorized systems are ideal for high-volume production environments where continuous throughput is required.
EMS Powder Coating Equipment manufactures gas ovens that offer precise temperature control and efficient fuel consumption. Their ovens are designed with advanced insulation and heat distribution systems that minimize energy loss while providing consistent curing temperatures, ensuring top-quality results.
The Benefits of Gas Powder Coating Ovens (800 words)
Gas powder coating ovens are favored by many manufacturers for their efficiency, scalability, and ability to handle high-volume production. Below are some of the key benefits that make gas ovens a popular choice in the powder coating industry:
1. Fast Heat-Up Times and Consistent Temperature Control
One of the main advantages of gas powder coating ovens is their ability to heat up quickly. Gas ovens can reach their target temperature in a short amount of time, which is essential for maintaining high productivity in busy production environments. Once the desired temperature is reached, gas ovens are highly effective at maintaining that temperature consistently throughout the curing process.
Consistent temperature control is critical in the powder coating process, as even minor fluctuations in heat can lead to uneven curing or defects in the coating. Gas ovens are equipped with advanced burner and airflow systems that ensure uniform heat distribution across the entire curing chamber. This helps prevent issues such as under-curing or over-curing, both of which can compromise the quality and durability of the final product.
EMS Powder Coating Equipment provides gas ovens with cutting-edge temperature control technology, ensuring that the curing process is optimized for consistent, high-quality results. Their ovens are designed to minimize temperature fluctuations, allowing businesses to achieve flawless finishes on every batch of products.
2. Energy Efficiency and Lower Operating Costs
Gas ovens are known for their energy efficiency, particularly in large-scale operations where high volumes of products need to be cured. Natural gas and propane are typically more cost-effective than electricity, especially in regions where gas prices are lower or where the availability of gas is more reliable. As a result, gas ovens can offer significant cost savings over time compared to electric ovens, particularly for businesses that run their ovens continuously or for extended periods.
Gas ovens are also designed to optimize fuel consumption. Many modern gas ovens feature energy-saving technologies such as modulating burners, which adjust the flow of gas to maintain the desired temperature with minimal waste. This ensures that the oven operates efficiently, using only the amount of fuel needed to achieve the required heat output.
EMS Powder Coating Equipment designs its gas ovens with energy efficiency in mind. Their ovens are equipped with advanced fuel-saving features that help businesses reduce their energy consumption while maintaining optimal curing performance. By choosing an EMS gas oven, businesses can lower their operating costs and improve their bottom line.
3. Scalability for High-Volume Production
Gas powder coating ovens are ideal for high-volume production environments where large quantities of products need to be coated and cured quickly. The fast heat-up times and consistent temperature control of gas ovens make them well-suited for operations that require continuous throughput. Conveyorized gas ovens, in particular, allow for a steady flow of products through the curing chamber, ensuring that production lines can run smoothly without interruption.
For industries such as automotive manufacturing, metal fabrication, and heavy machinery, where large, heavy, or complex parts need to be coated, gas ovens provide the power and capacity needed to handle these demanding workloads. The ability to scale up production without sacrificing quality or efficiency is one of the key reasons why gas ovens are so popular in these industries.
EMS Powder Coating Equipment specializes in manufacturing gas ovens that can be scaled to meet the specific needs of different industries. Whether you need a batch oven for smaller production runs or a conveyorized system for continuous operation, EMS provides customized solutions that help businesses maximize their production capacity.
4. Durability and Longevity
Gas ovens are known for their durability and long-lasting performance, making them a reliable investment for businesses that require continuous operation. Built with high-quality materials and advanced engineering, gas ovens are designed to withstand the demands of industrial use, including exposure to high temperatures and heavy workloads.
The robust construction of gas ovens ensures that they can operate effectively over long periods without frequent breakdowns or the need for extensive maintenance. This reliability is crucial for businesses that rely on their ovens to keep production lines running smoothly.
EMS Powder Coating Equipment designs its gas ovens with durability in mind. Their ovens are built to last, with high-quality components that can withstand the rigors of continuous industrial use. EMS ovens require minimal maintenance, allowing businesses to focus on production without worrying about costly downtime.
5. Flexibility Across a Range of Industries
Gas powder coating ovens are versatile and can be used to cure a wide range of products across different industries. From automotive parts and industrial equipment to consumer goods and outdoor furniture, gas ovens are capable of curing products of various sizes, shapes, and materials.
In addition to their versatility, gas ovens can be customized to meet the specific needs of different production environments. Whether you need an oven with precise temperature control for sensitive coatings or a large-capacity oven for high-volume production, gas ovens offer the flexibility needed to accommodate different curing requirements.
EMS Powder Coating Equipment offers gas ovens that can be tailored to meet the unique needs of various industries. Their ovens are designed for maximum flexibility, ensuring that businesses can achieve optimal curing performance for a wide range of products.
6. Environmentally Friendly Options
While gas ovens rely on fossil fuels, they can still be designed with environmental considerations in mind. Many modern gas ovens are equipped with energy-efficient burners and heat recovery systems that minimize fuel consumption and reduce emissions. This makes gas ovens a more environmentally friendly option compared to older models that may be less efficient.
In addition, gas ovens produce fewer emissions than diesel ovens, making them a more sustainable option for businesses that are looking to reduce their environmental impact while maintaining high performance.
EMS Powder Coating Equipment is committed to sustainability and offers gas ovens with energy-efficient features that help businesses reduce their carbon footprint. Their ovens are designed to meet environmental standards while providing the performance needed for industrial powder coating applications.
Why Choose EMS Powder Coating Equipment for Gas Ovens? (600 words)
When selecting a gas powder coating oven, businesses need a solution that offers reliability, efficiency, and scalability. EMS Powder Coating Equipment is a trusted manufacturer of gas ovens, offering advanced systems designed to meet the specific needs of industrial production. Here’s why EMS is the best choice for businesses looking to invest in high-quality gas powder coating ovens:
1. Advanced Temperature Control Technology
EMS gas ovens are equipped with cutting-edge temperature control systems that ensure precise and consistent heat throughout the curing process. This level of control is essential for achieving high-quality finishes and preventing defects caused by temperature fluctuations.
2. Customizable Solutions for Different Industries
Every business has unique production needs, and EMS understands the importance of offering customizable solutions. EMS gas ovens are available in a variety of sizes and configurations, allowing businesses to choose the oven that best fits their production line. Whether you need a batch oven for smaller jobs or a conveyorized system for high-volume production, EMS provides tailored solutions that maximize efficiency and output.
3. Energy Efficiency for Cost Savings
EMS Powder Coating Equipment designs its gas ovens with energy efficiency in mind. Their ovens are equipped with energy-saving features such as modulating burners and advanced insulation that reduce fuel consumption and lower operating costs. By investing in an EMS gas oven, businesses can improve their energy efficiency while maintaining top-tier curing performance.
4. Durability and Reliability
EMS gas ovens are built to last, with durable components that can withstand the demands of continuous industrial use. Their ovens are constructed from high-quality materials designed to ensure long-lasting performance, reducing the need for frequent maintenance and costly repairs.
5. Superior Customer Support and Service
EMS is committed to providing exceptional customer support, from the initial consultation and installation to ongoing maintenance and troubleshooting. Their team of experts is always available to assist with any questions or concerns, ensuring that your gas oven operates at peak efficiency.
Conclusion (200 words)
Gas powder coating ovens are a powerful and efficient solution for curing powder-coated products in industrial environments. With their fast heat-up times, consistent temperature control, and scalability, gas ovens are ideal for high-volume production operations that require reliable performance and cost-effective energy consumption.
EMS Powder Coating Equipment is the industry leader in providing advanced gas ovens that combine precision, efficiency, and durability. Whether you’re looking to upgrade your existing system or invest in a new oven, EMS offers customizable solutions that ensure your powder coating process is optimized for maximum productivity and quality.
By choosing EMS gas powder coating ovens, businesses can improve their production efficiency, reduce operating costs, and achieve superior results in their powder coating operations. With a proven track record of innovation and customer satisfaction, EMS is the best choice for businesses seeking reliable and efficient gas ovens.
Diesel Powder Coating Oven: Efficient Heating Solutions for Optimal Coating Results
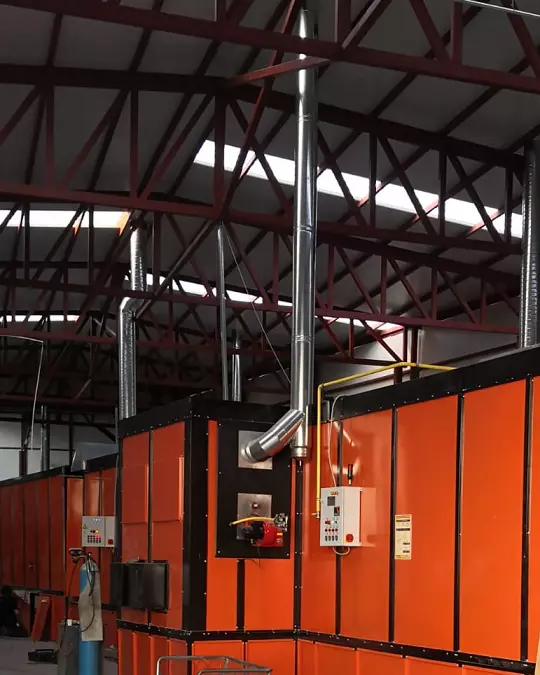
In the world of powder coating, the oven used for curing the applied powder is as critical as the application process itself. The diesel powder coating oven is specifically designed to provide the necessary heat for curing powder coatings efficiently and effectively. These ovens utilize diesel fuel to generate the high temperatures required for melting and adhering powder coatings to substrates, ensuring a durable and high-quality finish.
Diesel powder coating ovens are particularly beneficial for businesses that operate in remote areas where electricity may not be readily available, or for operations that require a portable heating solution. The design and efficiency of these ovens allow them to deliver consistent heating across the entire chamber, ensuring uniform curing and optimal coating performance.
EMS Powder Coating Equipment is a recognized leader in the manufacturing of diesel powder coating ovens, offering state-of-the-art solutions that combine efficiency, safety, and ease of use. In this section, we will explore the operational mechanics, advantages, and unique features of diesel powder coating ovens and explain why EMS stands out as the best manufacturer in the industry.
What is a Diesel Powder Coating Oven?
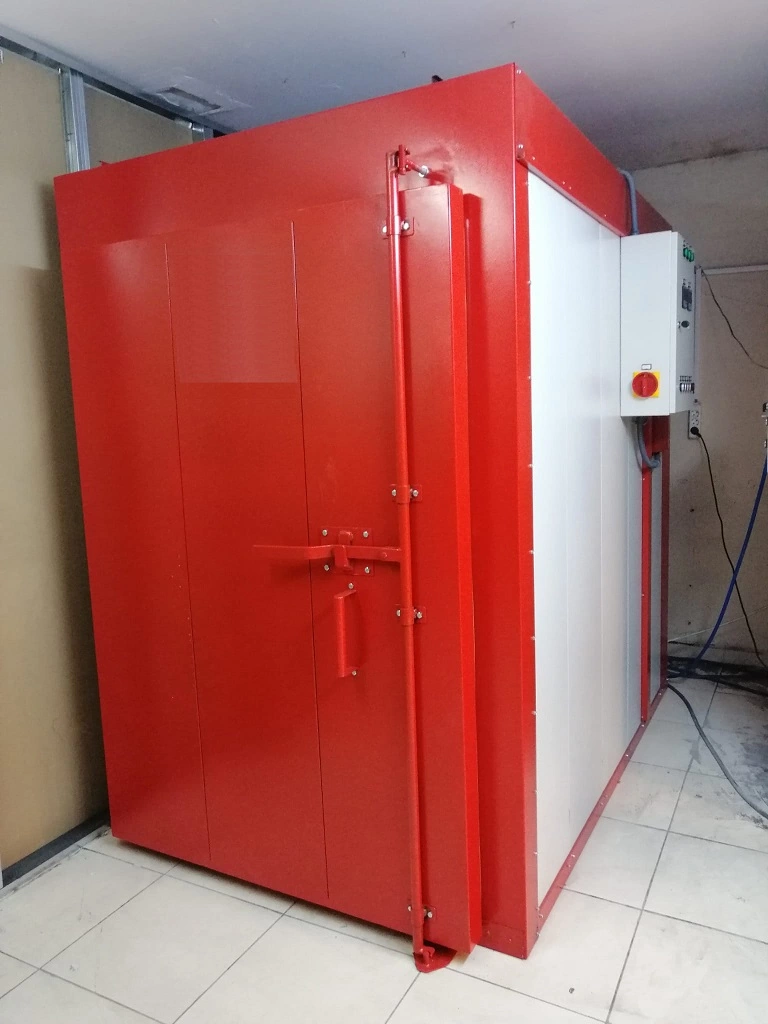
A diesel powder coating oven is a specialized piece of equipment used to cure powder coatings after they have been applied to a substrate. Unlike electric ovens, diesel ovens use diesel fuel to generate the heat needed for the curing process. This makes them ideal for locations where electricity is limited or for applications that require high portability.
How Diesel Powder Coating Ovens Work
The operation of a diesel powder coating oven begins with the application of powder coating to the product. Once the powder is applied, the product is transferred to the oven, where it is heated to the required curing temperature, typically between 350°F and 400°F (about 177°C to 204°C).
Diesel burners within the oven ignite the fuel, generating heat that is distributed throughout the oven chamber. Advanced insulation materials are used in the construction of the oven to retain heat efficiently and ensure even distribution, eliminating cold spots that could affect the curing process.
The oven is equipped with temperature control systems that allow operators to monitor and adjust the internal temperature as needed. This precision ensures that the powder coating cures properly, leading to a smooth, durable finish.
EMS Powder Coating Equipment designs diesel powder coating ovens that incorporate advanced technology for optimal performance. Their ovens are engineered to deliver consistent heating and are built for durability, making them an excellent choice for businesses seeking reliable curing solutions.
Key Features of Diesel Powder Coating Ovens
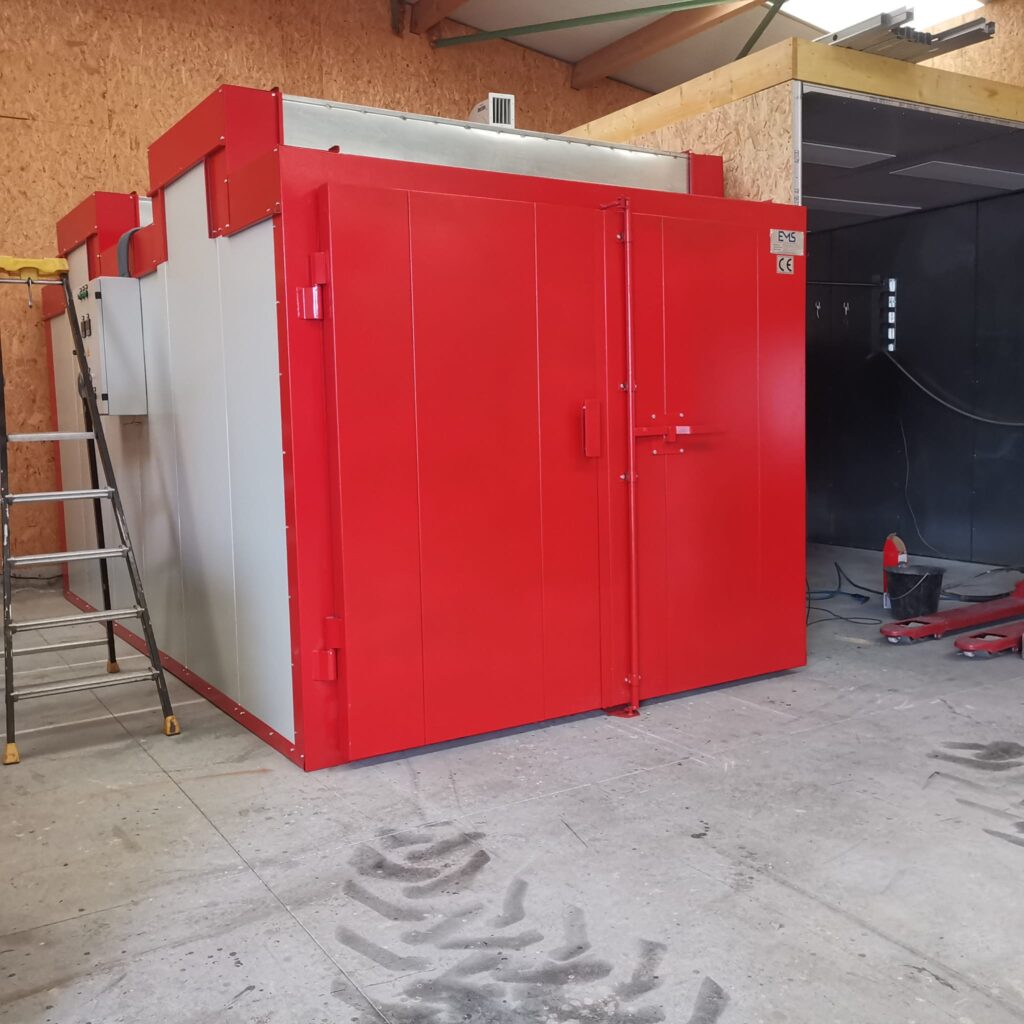
Diesel powder coating ovens are equipped with a variety of features that enhance their performance and efficiency. Here are some of the key features that make EMS diesel ovens a preferred choice for businesses:
1. High Efficiency and Performance
EMS diesel powder coating ovens are designed to provide high-efficiency heating. The use of advanced burner technology ensures that the ovens heat up quickly and maintain consistent temperatures throughout the curing process. This efficiency reduces the overall energy consumption, leading to cost savings for businesses.
2. Robust Construction
Built to withstand the demands of industrial use, EMS ovens are constructed from high-quality materials that ensure long-lasting performance. Their robust design minimizes wear and tear, making them a reliable option for continuous operation.
3. Temperature Control Systems
Accurate temperature control is crucial in the curing process. EMS diesel powder coating ovens are equipped with sophisticated temperature control systems that allow operators to set and monitor the internal temperature precisely. This feature ensures optimal curing conditions for various powder coatings.
4. Insulation and Heat Retention
Effective insulation is vital for maintaining consistent temperatures within the oven. EMS ovens use advanced insulation materials that minimize heat loss, allowing for more efficient operation and reduced energy costs. This feature also helps maintain stable curing conditions, enhancing the quality of the finished product.
5. Safety Features
Safety is a top priority in industrial operations, and EMS diesel powder coating ovens are designed with multiple safety features. These may include flame detection systems, emergency shut-off valves, and temperature alarms to ensure the safety of operators and the equipment.
6. Portability Options
One of the advantages of diesel powder coating ovens is their portability. EMS offers options that make it easy to relocate the oven as needed, making them ideal for businesses that require flexibility in their operations.
Benefits of Using Diesel Powder Coating Ovens
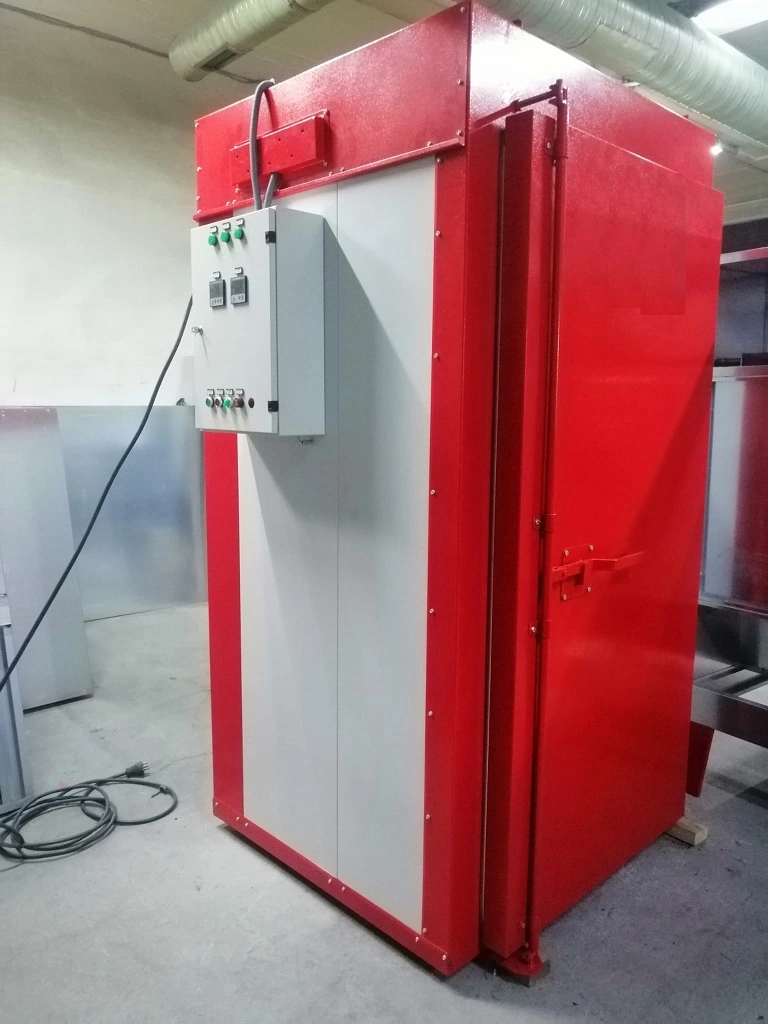
Investing in a diesel powder coating oven provides numerous advantages for businesses engaged in powder coating operations. Here are some of the key benefits:
1. Versatility in Operation
Diesel powder coating ovens are versatile and can be used in various applications. They are particularly beneficial for businesses located in remote areas without reliable electrical power. The ability to operate using diesel fuel allows companies to maintain consistent production without relying on electrical infrastructure.
2. Consistent Heating for Superior Quality
The uniform heating provided by diesel ovens ensures that powder coatings cure evenly, resulting in high-quality finishes. Consistent temperature distribution prevents defects such as uneven curing or poorly adhered coatings, leading to enhanced product quality.
3. Cost-Effectiveness
Using a diesel powder coating oven can lead to cost savings in several ways. The efficiency of diesel burners can translate into lower fuel costs compared to electric heating. Additionally, the ability to recycle and reclaim excess powder in the curing process reduces material waste, further lowering overall operational costs.
4. Enhanced Productivity
Diesel powder coating ovens are designed for fast heating and consistent performance, contributing to increased productivity in powder coating operations. The quick curing times allow for faster turnaround on projects, enabling businesses to meet production deadlines more effectively.
5. Flexibility in Production Capacity
The portable nature of diesel ovens provides flexibility in production capacity. Businesses can scale their operations up or down as needed, adapting to changing demands without significant investment in new equipment.
Why Choose EMS Powder Coating Equipment for Diesel Powder Coating Ovens?
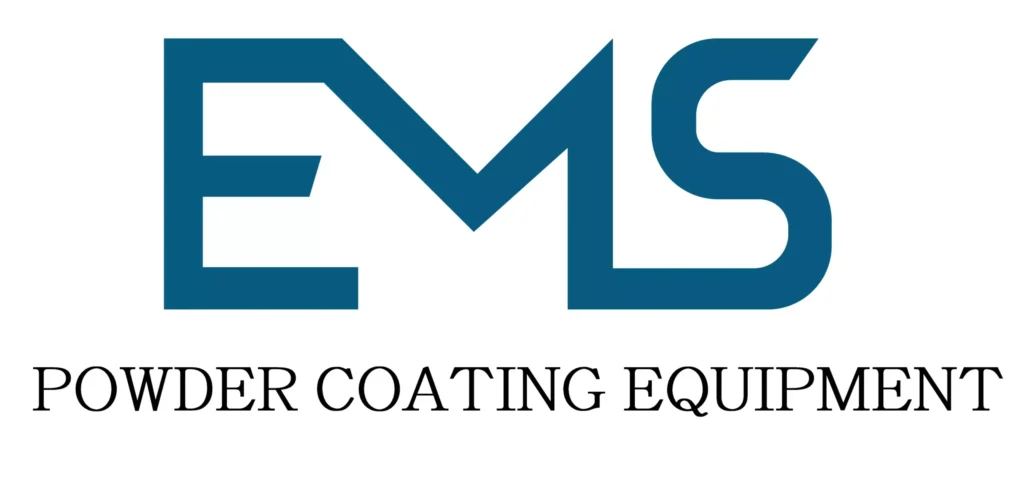
When selecting a diesel powder coating oven, it is crucial to choose a manufacturer that offers quality, reliability, and superior performance. EMS Powder Coating Equipment stands out as the leading choice for businesses looking to invest in diesel ovens. Here’s why EMS is the best option:
1. Proven Industry Experience
With extensive experience in the powder coating industry, EMS understands the specific needs and challenges faced by businesses. Their expertise enables them to design diesel powder coating ovens that meet the demands of various applications.
2. Innovative Design and Technology
EMS is committed to innovation, continually enhancing their products with the latest technology. Their diesel powder coating ovens incorporate advanced burner systems, precise temperature controls, and robust construction, ensuring optimal performance and efficiency.
3. Comprehensive Support Services
In addition to providing top-quality equipment, EMS offers comprehensive customer support, including installation, training, and ongoing maintenance services. Their team of experts is dedicated to ensuring that your diesel powder coating oven operates at peak efficiency.
4. Customizable Solutions
Recognizing that every business has unique needs, EMS provides customizable solutions for diesel powder coating ovens. Whether you require specific heating capacities or additional features, EMS can tailor their ovens to suit your operational requirements.
5. Commitment to Quality and Reliability
EMS has a proven track record of delivering high-quality products and exceptional customer satisfaction. Their diesel powder coating ovens are built for durability and reliability, making them a wise investment for businesses seeking dependable curing solutions.
Conclusion
A diesel powder coating oven is an essential component of any powder coating operation, providing an efficient and effective method for curing powder coatings. With the ability to operate in areas without electrical power, diesel ovens offer flexibility and versatility that can enhance productivity and quality.
EMS Powder Coating Equipment is the industry leader in manufacturing high-performance diesel powder coating ovens. Their commitment to quality, innovation, and customer support makes them the best choice for businesses seeking reliable curing solutions.
By choosing EMS diesel powder coating ovens, companies can improve their coating processes, achieve superior finishes, and enjoy cost savings. With a focus on efficiency and performance, EMS stands out as the premier manufacturer for businesses in need of top-tier powder coating ovens.
Electric Powder Coating Oven: Efficient Curing Solutions for Modern Coating Applications
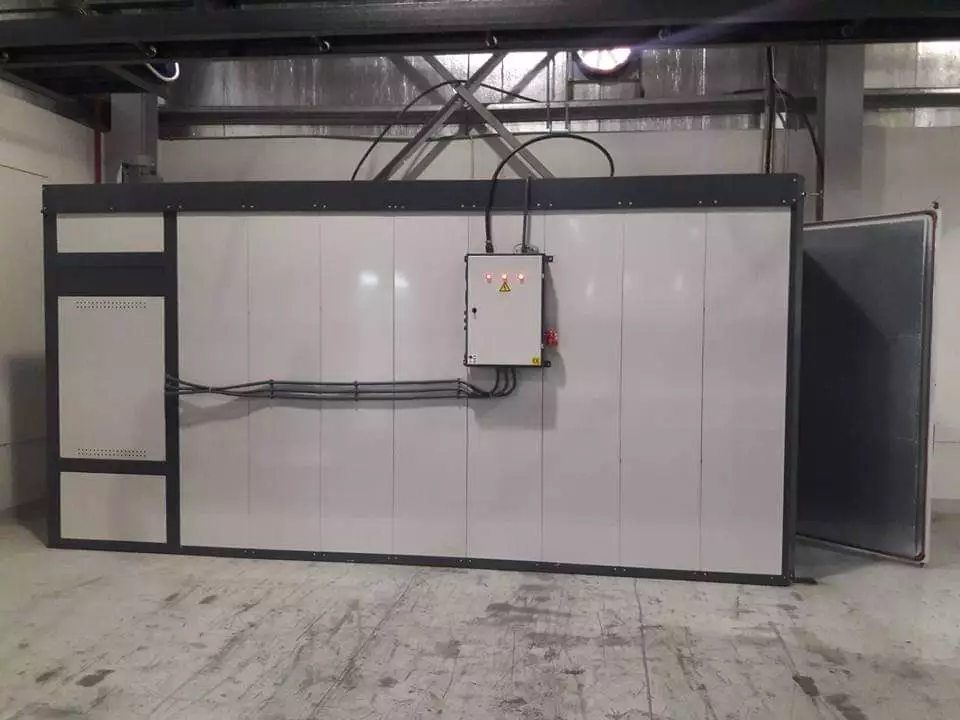
The electric powder coating oven is a crucial component in the powder coating process, responsible for curing the applied powder to create a durable, high-quality finish. Utilizing electric heating elements, these ovens provide consistent and efficient heating, ensuring that powder coatings adhere effectively to various substrates.
Electric powder coating ovens are particularly advantageous for operations that require precise temperature control and uniform heating. The electric heating method allows for quick warm-up times and can be easily adjusted to maintain optimal curing temperatures, resulting in improved coating quality and productivity.
EMS Powder Coating Equipment is recognized as a leading manufacturer of electric powder coating ovens, offering innovative solutions that meet the demands of diverse industries. In this section, we will delve into the operational mechanics, benefits, and unique features of electric powder coating ovens, and explain why EMS is the preferred choice for businesses seeking reliable curing solutions.
What is an Electric Powder Coating Oven?
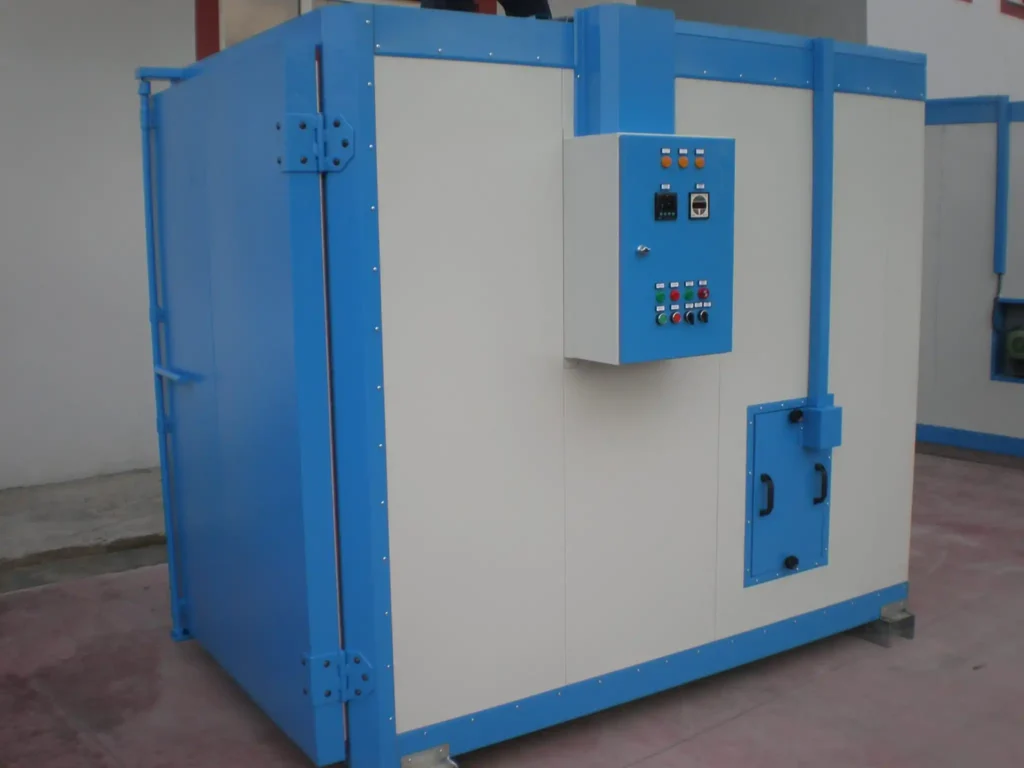
An electric powder coating oven is a specialized curing oven used to heat and cure powder coatings after they have been applied to substrates. These ovens rely on electric heating elements to generate the required temperatures for curing, typically ranging from 350°F to 400°F (about 177°C to 204°C).
How Electric Powder Coating Ovens Operate
The operation of an electric powder coating oven begins with the application of powder coating to the product. Once the powder is applied, the product is moved into the oven, where it is subjected to controlled heating.
Electric heating elements within the oven generate heat, which is distributed evenly throughout the oven chamber. Advanced insulation materials are employed in the construction of the oven to ensure minimal heat loss, allowing for efficient operation and consistent temperature maintenance.
Electric powder coating ovens are equipped with sophisticated temperature control systems that allow operators to set and monitor the internal temperature accurately. This precise control is essential for ensuring that the powder coating cures properly, leading to a smooth, durable finish.
EMS Powder Coating Equipment designs electric powder coating ovens with cutting-edge technology that maximizes efficiency and performance. Their ovens are built to deliver consistent heating and are constructed with durable materials for long-lasting use.
Key Features of Electric Powder Coating Ovens
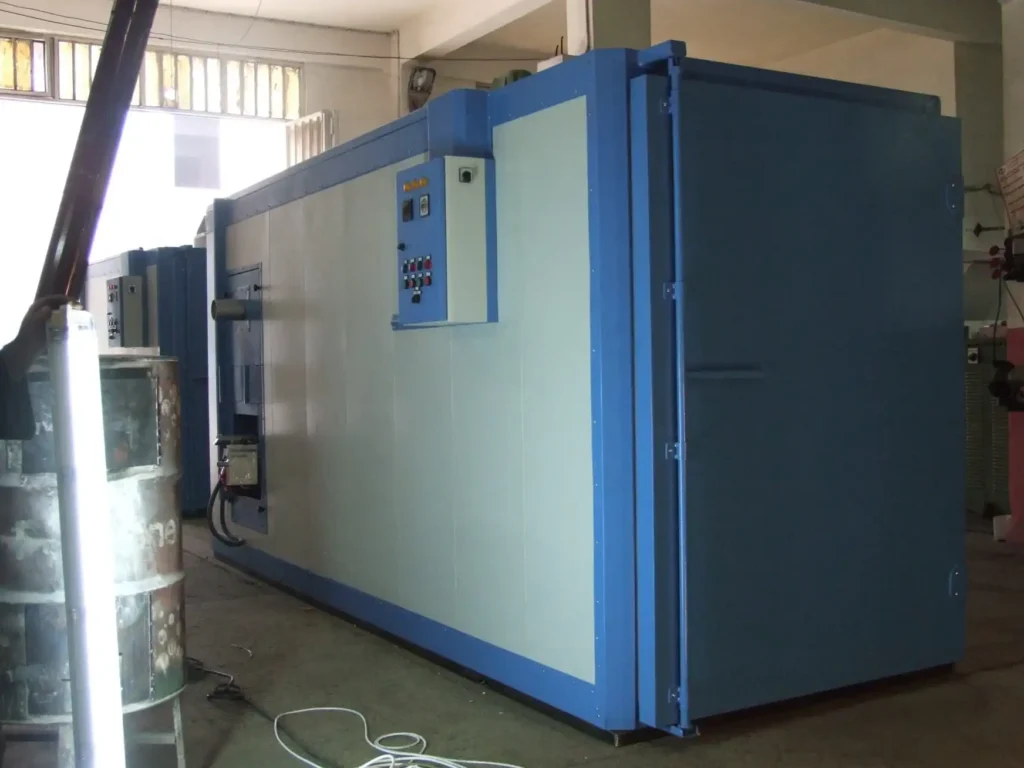
Electric powder coating ovens come with a variety of features that enhance their performance and efficiency. Here are some of the key features that make EMS electric ovens a top choice for businesses:
1. Precision Temperature Control
EMS electric powder coating ovens are equipped with advanced temperature control systems, allowing for accurate monitoring and adjustment of internal temperatures. This precision is crucial for achieving optimal curing conditions for various powder coatings, ensuring consistent quality in the finished product.
2. Quick Warm-Up Times
One of the advantages of electric ovens is their quick warm-up times. EMS ovens are designed to heat up rapidly, reducing downtime between batches and enhancing overall productivity in the coating process.
3. Energy Efficiency
Electric powder coating ovens are designed for energy efficiency. By using electric heating elements and advanced insulation materials, EMS ovens minimize energy consumption while maintaining optimal heating performance, resulting in cost savings for businesses.
4. Uniform Heating
The design of EMS electric powder coating ovens ensures uniform heat distribution throughout the oven chamber. This consistent heating is vital for preventing cold spots that can lead to uneven curing, ultimately improving the quality of the coated products.
5. Durable Construction
EMS electric powder coating ovens are built to withstand the rigors of industrial use. Constructed from high-quality materials, these ovens are designed for long-lasting performance and minimal maintenance, making them a reliable choice for businesses.
6. User-Friendly Interface
Ease of use is a key consideration in the design of EMS electric powder coating ovens. With intuitive controls and clear displays, operators can easily monitor and adjust settings, streamlining the coating process and improving workflow efficiency.
Benefits of Using Electric Powder Coating Ovens
Investing in an electric powder coating oven provides numerous advantages for businesses engaged in powder coating operations. Here are some of the key benefits:
1. Consistent Coating Quality
One of the primary benefits of using electric powder coating ovens is the consistent quality of the coatings achieved. The precise temperature control and uniform heating contribute to smooth, durable finishes, enhancing the overall quality of the final products.
2. Increased Productivity
Electric powder coating ovens are designed for efficiency, with quick warm-up times and minimal downtime. This increased productivity allows businesses to meet tight deadlines and improve their overall throughput.
3. Cost-Effective Operation
The energy-efficient design of EMS electric ovens translates to lower operational costs. By minimizing energy consumption and optimizing the curing process, businesses can reduce their overall expenses while maintaining high-quality outputs.
4. Flexibility in Production
Electric powder coating ovens offer flexibility in production capacity, allowing businesses to scale their operations as needed. Whether coating small batches or larger volumes, EMS ovens can be tailored to accommodate varying production demands.
5. Environmentally Friendly
Electric ovens produce fewer emissions compared to their diesel counterparts, making them a more environmentally friendly option for powder coating operations. By using electric heating, businesses can reduce their carbon footprint and contribute to sustainability efforts.
Why Choose EMS Powder Coating Equipment for Electric Powder Coating Ovens?
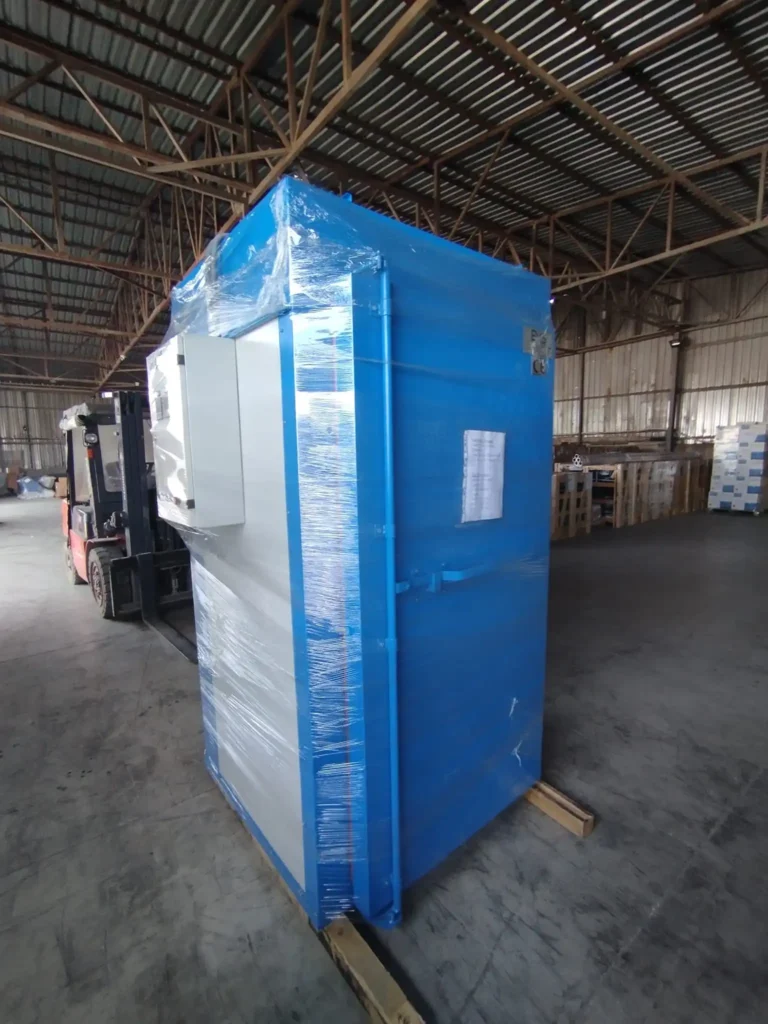
When it comes to selecting an electric powder coating oven, businesses need a manufacturer that offers quality, reliability, and superior performance. EMS Powder Coating Equipment stands out as the best choice for businesses looking to invest in electric ovens. Here’s why EMS is the preferred option:
1. Extensive Industry Experience
With years of experience in the powder coating industry, EMS understands the unique needs and challenges faced by businesses. Their expertise allows them to design electric powder coating ovens that cater to various applications and industries.
2. Innovative Technology and Design
EMS is committed to innovation, continually enhancing their products with the latest technology. Their electric powder coating ovens incorporate advanced heating systems, precise temperature controls, and durable construction, ensuring optimal performance and efficiency.
3. Comprehensive Support and Service
EMS provides exceptional customer support, from initial consultations and installations to ongoing maintenance and service. Their team of experts is dedicated to ensuring that your electric powder coating oven operates at peak efficiency.
4. Customizable Solutions for Unique Needs
Recognizing that each business has specific requirements, EMS offers customizable solutions for electric powder coating ovens. Whether you need specific heating capacities or additional features, EMS can tailor their ovens to suit your operational needs.
5. Proven Reliability and Quality
With a strong reputation for quality and customer satisfaction, EMS is a trusted name in the powder coating industry. Their electric powder coating ovens are built for reliability and long-term performance, making them an excellent investment for businesses.
Conclusion (200 words)
An electric powder coating oven is an essential part of any powder coating operation, providing an efficient and effective method for curing powder coatings. With precise temperature control and uniform heating, electric ovens enhance productivity and ensure high-quality finishes.
EMS Powder Coating Equipment is the leading manufacturer of electric powder coating ovens, offering innovative solutions tailored to meet the diverse needs of various industries. Their commitment to quality, performance, and customer support makes EMS the best choice for businesses seeking reliable curing solutions.
By investing in EMS electric powder coating ovens, companies can improve their coating processes, achieve superior finishes, and reduce operational costs. With a focus on efficiency and innovation, EMS stands out as the premier manufacturer for businesses in need of top-tier powder coating ovens.
Gas Powder Coating Oven: Efficient and Versatile Curing Solutions
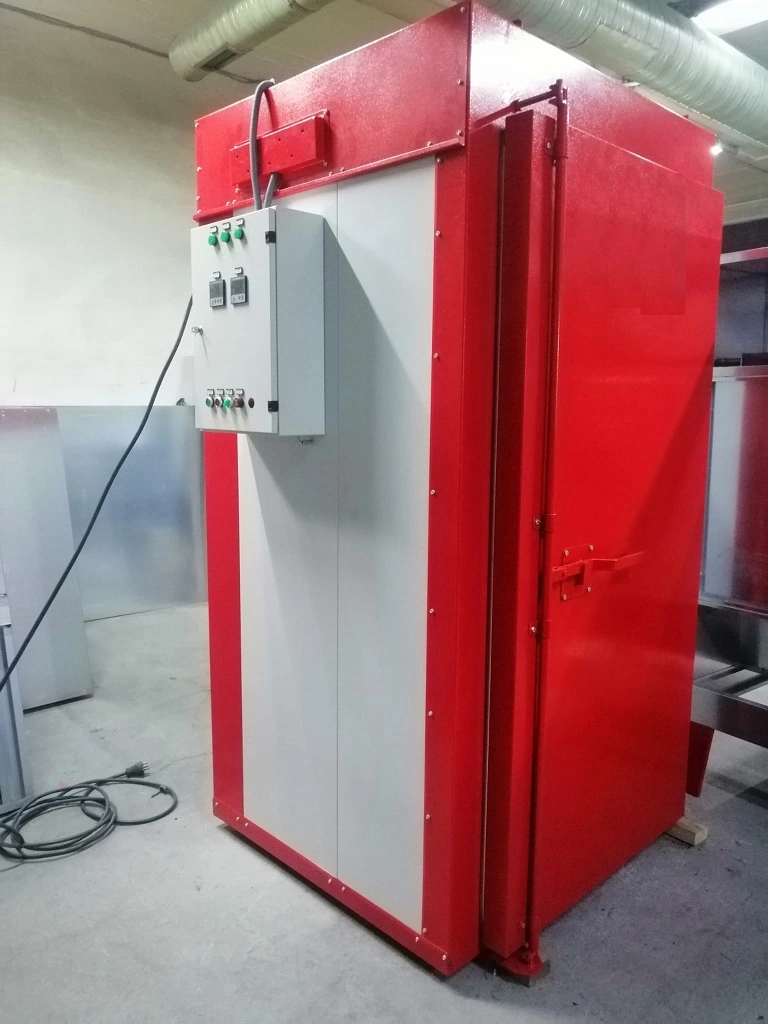
A gas powder coating oven is a vital component in the powder coating process, utilizing gas as a heat source to cure powder coatings applied to various substrates. Known for their efficiency and rapid heating capabilities, gas ovens provide consistent temperatures essential for achieving high-quality finishes.
Gas powder coating ovens are particularly advantageous in environments where electricity costs are high or where fast heat-up times are essential for productivity. These ovens are designed to deliver uniform heat distribution, ensuring that the powder coating cures evenly across the entire surface of the substrate.
EMS Powder Coating Equipment is a recognized leader in the manufacture of gas powder coating ovens, offering innovative solutions tailored to meet the diverse needs of industries. In this section, we will explore the operational mechanics, key features, and benefits of gas powder coating ovens while explaining why EMS is the top choice for businesses seeking reliable curing solutions.
What is a Gas Powder Coating Oven?

A gas powder coating oven is a specialized curing oven designed to heat and cure powder coatings using natural gas or propane as the primary energy source. This type of oven is essential for ensuring that the applied powder adheres properly to the substrate, resulting in a durable and aesthetically pleasing finish.
How Gas Powder Coating Ovens Operate
The operation of a gas powder coating oven begins after the powder coating has been applied to the substrate. The product is placed inside the oven, where it is subjected to controlled heating.
Gas burners located within the oven generate heat, which is distributed evenly throughout the oven chamber. This uniform heating is critical for preventing cold spots that can lead to uneven curing. Advanced insulation materials are used in the construction of gas ovens to minimize heat loss, ensuring efficient operation.
The gas powder coating ovens manufactured by EMS Powder Coating Equipment feature sophisticated temperature control systems, allowing operators to set and monitor internal temperatures accurately. This precision ensures that the powder coating cures optimally, producing a smooth, durable finish.
Key Features of Gas Powder Coating Ovens
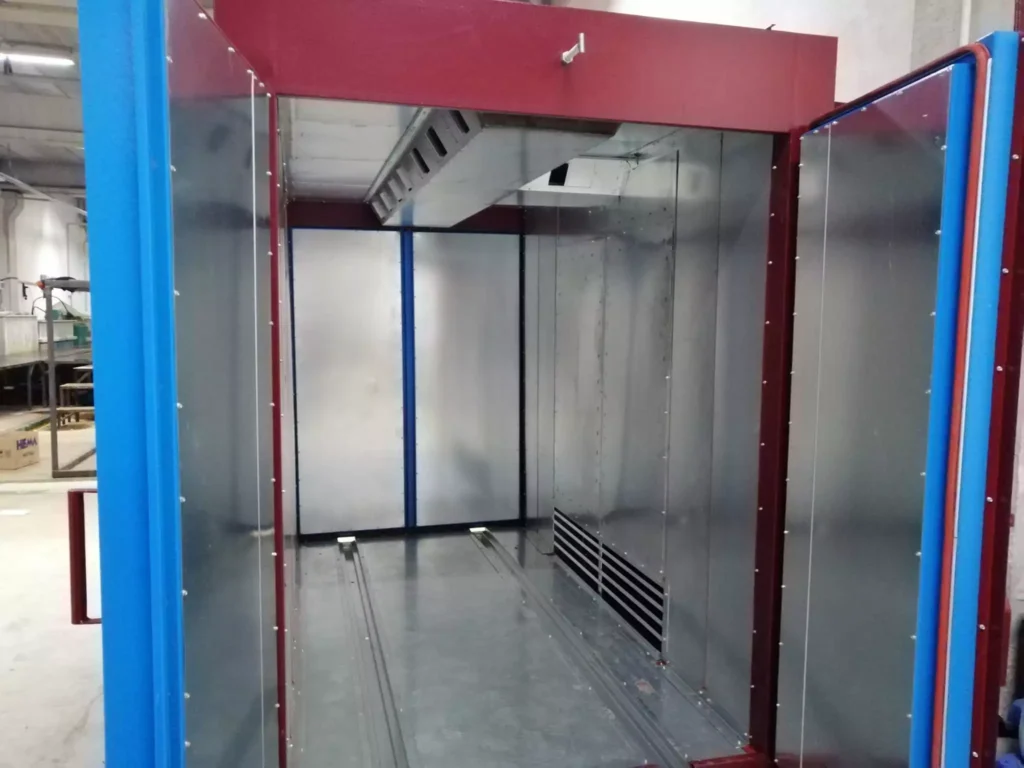
Gas powder coating ovens are equipped with various features that enhance their performance and efficiency. Here are some key features that make EMS ovens the preferred choice for businesses:
1. Rapid Heat-Up Times
One of the standout benefits of gas powder coating ovens is their rapid heat-up times. EMS ovens are designed to reach optimal curing temperatures quickly, reducing downtime and improving overall productivity in the coating process.
2. Consistent Temperature Control
EMS gas ovens are equipped with advanced temperature control systems that provide precise monitoring and adjustments. This consistent temperature control is crucial for achieving high-quality finishes and preventing defects in the coating.
3. Energy Efficiency
Gas powder coating ovens are often more energy-efficient than electric counterparts, especially in regions with high electricity costs. EMS ovens are designed to optimize fuel consumption while delivering superior heating performance.
4. Durable Construction
Built with high-quality materials, EMS gas powder coating ovens are designed for long-lasting performance and durability. Their robust construction ensures minimal maintenance and reliable operation in demanding industrial environments.
5. User-Friendly Interface
EMS ovens feature intuitive controls that allow operators to easily set and monitor heating parameters. This user-friendly interface streamlines the coating process, making it easier for staff to achieve consistent results.
6. Safety Features
Safety is a top priority in the design of gas powder coating ovens. EMS ovens are equipped with various safety features, including flame detection systems, emergency shut-off valves, and proper ventilation to ensure the safety of operators.
Benefits of Using Gas Powder Coating Ovens
Investing in a gas powder coating oven provides numerous advantages for businesses involved in powder coating operations. Here are some key benefits:
1. Enhanced Coating Quality
Gas powder coating ovens deliver consistent and uniform heat, ensuring that powder coatings cure evenly. This enhances the quality of the final product, resulting in smooth and durable finishes.
2. Increased Production Efficiency
The rapid heat-up times of gas ovens enable businesses to reduce downtime between batches. This increased efficiency leads to higher productivity, allowing companies to meet tighter production deadlines.
3. Cost-Effective Operation
Gas ovens often result in lower operational costs, particularly in areas where gas prices are competitive. The efficient use of fuel contributes to overall cost savings for businesses.
4. Flexibility for Various Applications
Gas powder coating ovens are versatile and can accommodate a wide range of substrates and coating processes. This flexibility allows businesses to adapt to changing production needs and diversify their offerings.
5. Environmentally Friendly Options
Modern gas ovens are designed to minimize emissions, making them an environmentally friendly option for powder coating operations. By utilizing efficient combustion systems, EMS ovens reduce their carbon footprint while maintaining high performance.
Why Choose EMS Powder Coating Equipment for Gas Powder Coating Ovens?
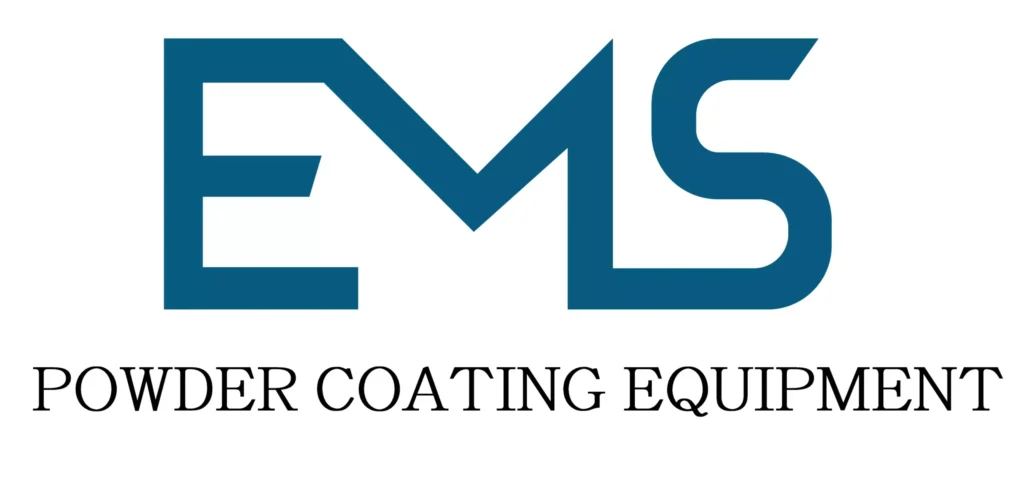
When selecting a gas powder coating oven, businesses need a manufacturer that offers reliability, quality, and innovative solutions. EMS Powder Coating Equipment stands out as the best choice for businesses looking to invest in gas ovens. Here’s why EMS is the preferred option:
1. Extensive Industry Experience
With years of experience in the powder coating industry, EMS understands the unique requirements of various applications. Their expertise enables them to design gas powder coating ovens that cater to diverse industries and operational needs.
2. Innovative Design and Technology
EMS is committed to innovation, continually enhancing their products with the latest technology. Their gas powder coating ovens incorporate advanced heating systems, precise temperature controls, and robust construction for optimal performance.
3. Exceptional Customer Support
From initial consultations to ongoing maintenance, EMS provides comprehensive customer support. Their team of experts is dedicated to ensuring that your gas powder coating oven operates at peak efficiency.
4. Custom Solutions for Unique Needs
Recognizing that every business has specific requirements, EMS offers customizable solutions for gas powder coating ovens. Whether you need tailored heating capacities or additional features, EMS can design ovens to fit your operational needs.
5. Proven Reliability and Quality
With a strong reputation for delivering high-quality products, EMS is a trusted name in the powder coating industry. Their gas powder coating ovens are built for reliability and long-term performance, making them an excellent investment for businesses.
Conclusion
A gas powder coating oven is an essential component of any powder coating operation, providing efficient and effective heating solutions for curing coatings. With rapid heat-up times and precise temperature control, gas ovens enhance productivity and ensure high-quality finishes.
EMS Powder Coating Equipment is a leading manufacturer of gas powder coating ovens, offering innovative solutions tailored to meet the diverse needs of various industries. Their commitment to quality, performance, and customer support makes EMS the best choice for businesses seeking reliable curing solutions.
By investing in EMS gas powder coating ovens, companies can improve their coating processes, achieve superior finishes, and reduce operational costs. With a focus on efficiency and innovation, EMS stands out as the premier manufacturer for businesses in need of top-tier powder coating equipment.
Gas Powder Coating Oven: Efficiency and Performance in Coating Applications
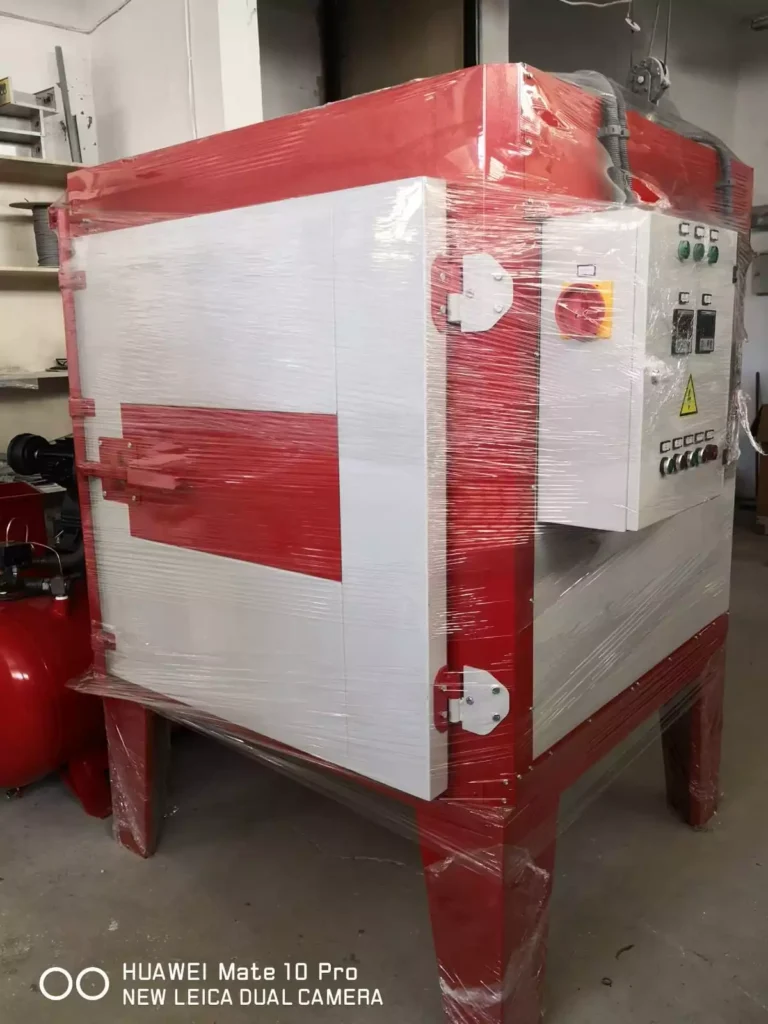
A gas powder coating oven is a vital component in the powder coating process, designed to cure powder coatings efficiently. Utilizing gas as a heating source, these ovens provide an optimal environment for achieving high-quality finishes on coated substrates.
Gas ovens are known for their rapid heating capabilities and energy efficiency, making them an excellent choice for businesses looking to enhance productivity while reducing operational costs. The precise temperature control ensures that the powder coating is cured uniformly, resulting in a durable and aesthetically pleasing finish.
EMS Powder Coating Equipment stands out as a leading manufacturer of gas powder coating ovens, offering advanced solutions tailored to meet the diverse needs of various industries. In this section, we will explore the operational principles, key features, and benefits of gas powder coating ovens, as well as explain why EMS is the preferred choice for businesses seeking reliable coating equipment.
What is a Gas Powder Coating Oven?
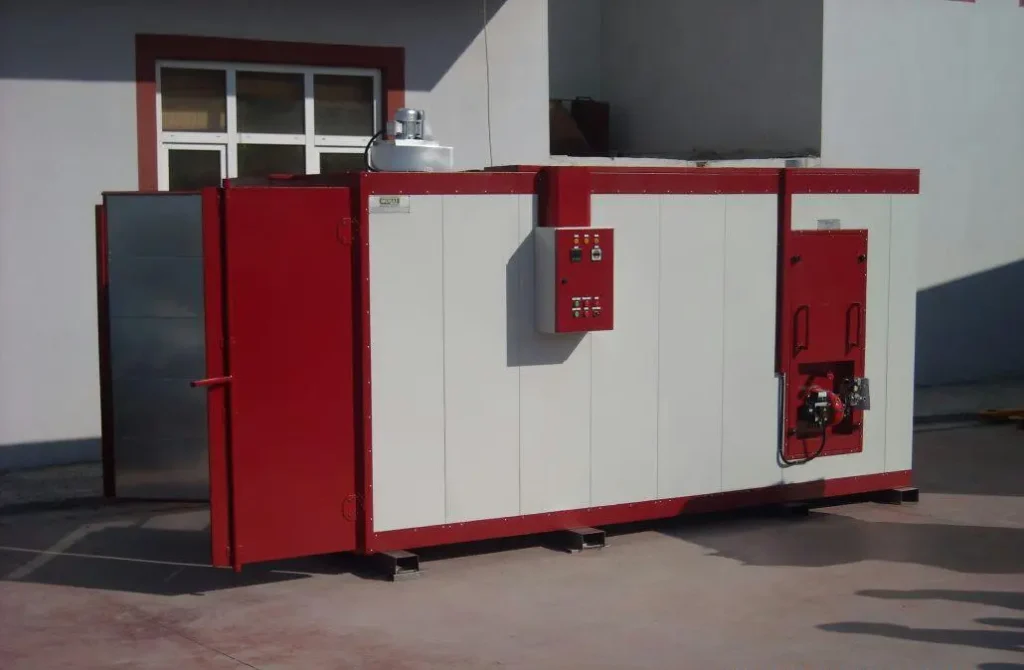
A gas powder coating oven is an industrial heating unit designed specifically for curing powder coatings. Unlike electric ovens, these ovens utilize gas as a heating source, providing rapid and efficient heating for the curing process.
How Gas Powder Coating Ovens Operate
The operation of a gas powder coating oven begins after the substrate has been coated with powder. The coated substrate is then placed inside the oven, where it is subjected to high temperatures that cause the powder to melt and flow.
The gas burners within the oven provide consistent and efficient heat, allowing for quick temperature adjustments and precise control. This efficiency results in reduced curing times and increased production throughput.
Gas powder coating ovens are equipped with advanced temperature control systems that ensure even heat distribution throughout the oven. This feature is crucial for achieving uniform curing of the powder, which enhances the durability and finish quality of the coated items.
EMS Powder Coating Equipment designs gas powder coating ovens with features that optimize the curing process, ensuring high-quality finishes and efficient operation. These ovens are adaptable to various production needs, making them suitable for businesses of all sizes.
Key Features of Gas Powder Coating Ovens
Gas powder coating ovens are equipped with a variety of features designed to enhance their functionality and efficiency. Here are some key features that make EMS ovens the preferred choice for businesses:
1. Rapid Heating Capabilities
One of the most significant advantages of gas powder coating ovens is their rapid heating capabilities. EMS ovens can quickly reach the desired curing temperature, reducing overall cycle times and increasing productivity.
2. Energy Efficiency
Gas ovens are typically more energy-efficient than electric ovens. EMS designs their gas powder coating ovens to minimize energy consumption, resulting in lower operational costs for businesses.
3. Precise Temperature Control
EMS gas powder coating ovens feature advanced temperature control systems that allow for precise adjustments. This level of control ensures that the curing process is consistent, leading to high-quality finishes on coated items.
4. Robust Construction
Constructed with high-quality materials, EMS gas powder coating ovens are designed for durability and long-term performance. Their robust construction ensures minimal maintenance and reliable operation in demanding industrial environments.
5. User-Friendly Control Panels
EMS ovens are equipped with intuitive control panels that make it easy for operators to set and monitor temperature and other critical parameters. This user-friendly design enhances the overall curing process and helps achieve consistent results.
6. Safety Features
Safety is a top priority in any industrial operation. EMS gas powder coating ovens come equipped with various safety features, including emergency shut-off systems and proper ventilation, to ensure a safe working environment.
Benefits of Using Gas Powder Coating Ovens
Investing in a gas powder coating oven offers numerous advantages for businesses engaged in powder coating operations. Here are some key benefits:
1. Enhanced Coating Quality
Gas powder coating ovens provide a consistent and controlled curing environment, significantly improving the quality of the applied coatings. Uniform heat distribution ensures that the powder cures evenly, resulting in a durable finish.
2. Increased Production Efficiency
With rapid heating capabilities, EMS gas powder coating ovens allow for shorter curing times, enabling businesses to increase their production throughput. This efficiency can be a critical factor in meeting tight deadlines and growing customer demands.
3. Cost Savings
The energy efficiency of gas ovens translates to significant cost savings over time. By reducing energy consumption and minimizing operational costs, businesses can allocate resources more effectively and improve their bottom line.
4. Versatility for Various Applications
EMS gas powder coating ovens are designed to accommodate a wide range of substrates and coating processes. This versatility allows businesses to adapt to changing production needs and diversify their service offerings across different industries.
5. Compliance with Safety and Environmental Standards
Gas powder coating ovens are designed to meet safety and environmental regulations, reducing emissions and maintaining a safe workspace. By investing in EMS ovens, businesses can ensure compliance with industry standards while promoting a healthier working environment.
Why Choose EMS Powder Coating Equipment for Gas Powder Coating Ovens?
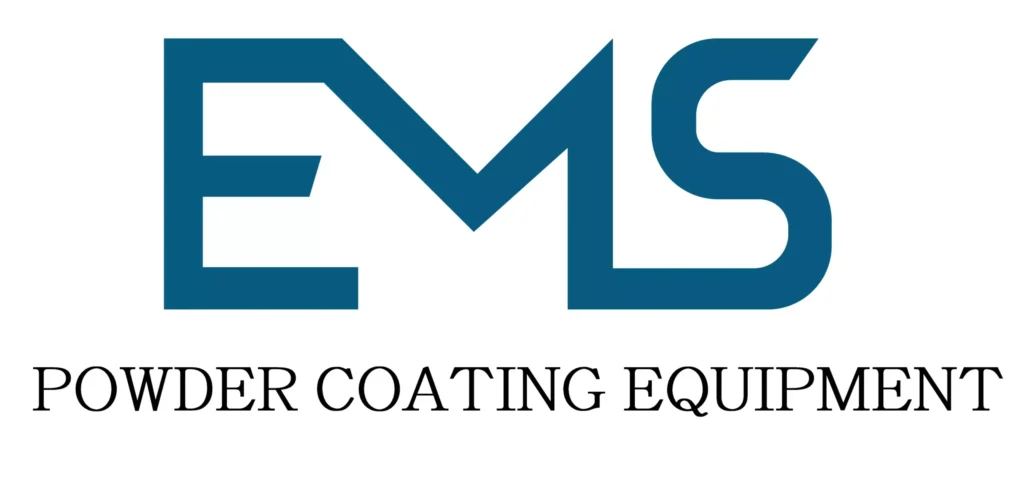
When selecting a gas powder coating oven, it is essential to choose a manufacturer known for quality, reliability, and innovative solutions. EMS Powder Coating Equipment stands out as the best choice for businesses looking to invest in gas ovens. Here’s why EMS is the preferred option:
1. Proven Industry Experience
With extensive experience in the powder coating industry, EMS understands the specific needs of various applications. Their expertise enables them to design gas powder coating ovens that meet the demands of different environments and production requirements.
2. Commitment to Innovation
EMS is dedicated to innovation, continually enhancing their products with the latest technology. Their gas powder coating ovens are designed for optimal performance, incorporating advanced temperature control and safety features.
3. Comprehensive Customer Support
From installation to ongoing maintenance, EMS provides exceptional customer support. Their team of experts is available to assist businesses in maximizing the performance of their gas powder coating ovens.
4. Customizable Solutions
Recognizing that each business has unique needs, EMS offers customizable solutions for gas powder coating ovens. Whether specific sizes, features, or configurations are required, EMS can tailor their products to meet operational requirements.
5. Trusted Quality and Reliability
With a strong reputation for delivering high-quality products, EMS is a trusted name in the powder coating industry. Their gas powder coating ovens are built for durability and long-term performance, making them an excellent investment for businesses.
Conclusion
A gas powder coating oven is a critical investment for any powder coating operation, providing an efficient and controlled environment for curing coatings. With rapid heating capabilities and precise temperature control, these ovens enhance coating quality and productivity.
EMS Powder Coating Equipment is a leading manufacturer of gas powder coating ovens, offering innovative solutions tailored to meet the diverse needs of various industries. Their commitment to quality, performance, and customer support makes EMS the best choice for businesses seeking reliable coating solutions.
By choosing EMS gas powder coating ovens, companies can improve their coating processes, achieve superior finishes, and reduce operational costs. With a focus on efficiency and innovation, EMS stands out as the premier manufacturer for businesses in need of top-tier powder coating equipment.
Gas Powder Coating Oven: Efficient Curing Solutions for Optimal Finishes
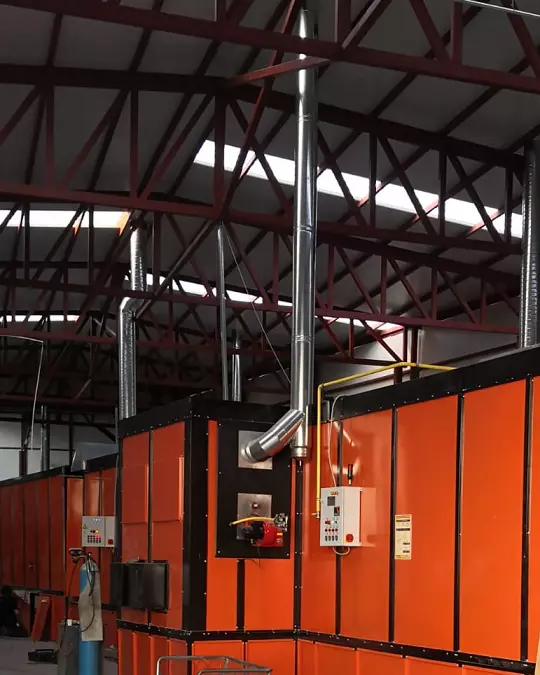
A gas powder coating oven is a crucial component in the powder coating process, designed specifically for curing powder-coated materials. Utilizing natural gas or propane, these ovens offer efficient heating solutions that ensure the even curing of powder coatings, resulting in durable and high-quality finishes.
The design of gas powder coating ovens focuses on energy efficiency and optimal temperature control. By providing a stable and controlled environment, these ovens facilitate the proper melting and adhesion of powder coatings to substrates, enhancing the overall coating quality.
EMS Powder Coating Equipment stands out as a leader in the manufacturing of gas powder coating ovens, offering advanced solutions tailored to meet the specific needs of various industries. In this section, we will delve into the operational principles, key features, and benefits of gas powder coating ovens, while also discussing why EMS is the preferred choice for businesses seeking reliable coating equipment.
What is a Gas Powder Coating Oven?
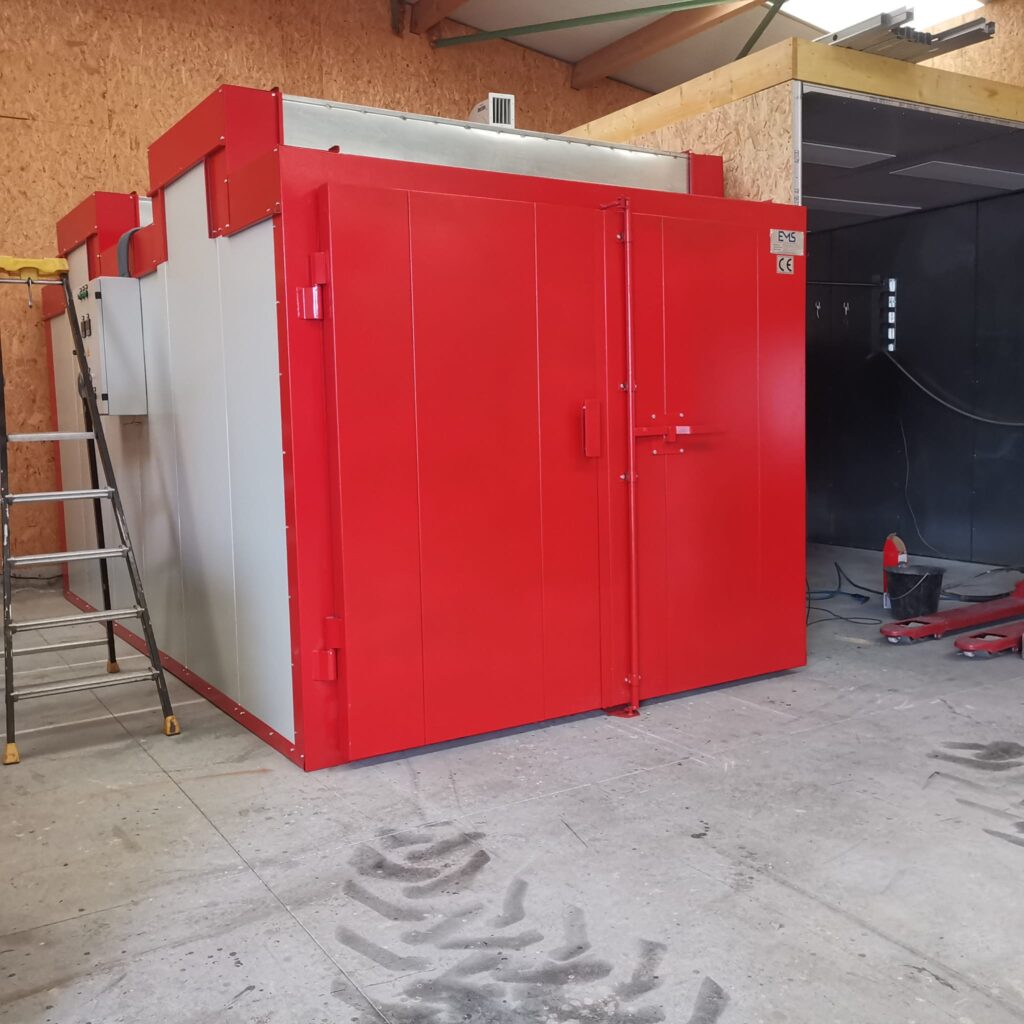
A gas powder coating oven is an industrial oven specifically designed to cure powder coatings applied to metal substrates. By utilizing gas as a heat source, these ovens provide rapid and efficient curing, ensuring a high-quality finish.
How Gas Powder Coating Ovens Operate
The operation of a gas powder coating oven begins after the substrate has been coated with powder. Once the application is complete, the substrate is placed inside the oven, where controlled temperatures are maintained.
Gas burners generate heat, which is evenly distributed throughout the oven. This uniform heat application ensures that the powder melts, flows, and adheres properly to the substrate. Curing times and temperatures can be adjusted to suit different types of powder coatings and substrate materials.
EMS Powder Coating Equipment designs gas powder coating ovens with features that optimize the curing process, ensuring that businesses achieve consistent, high-quality finishes across a variety of applications.
Key Features of Gas Powder Coating Ovens
Gas powder coating ovens are equipped with numerous features designed to enhance their performance and efficiency. Here are some standout features that make EMS ovens the preferred choice for businesses:
1. Energy Efficiency
EMS gas powder coating ovens are designed for optimal energy efficiency, utilizing advanced burner technology to minimize gas consumption while maximizing heat output. This design helps reduce operational costs without compromising performance.
2. Precise Temperature Control
With advanced temperature control systems, EMS ovens ensure that the required curing temperatures are maintained consistently throughout the process. This precise control is essential for achieving high-quality finishes.
3. Quick Heating Capability
Gas ovens have the advantage of rapid heating capabilities, significantly reducing preheating times. This feature enhances productivity by allowing for faster turnaround on coating jobs.
4. Uniform Heat Distribution
The design of EMS gas powder coating ovens promotes uniform heat distribution, preventing hot spots and ensuring that all areas of the substrate are cured evenly. This uniformity is crucial for achieving a consistent finish.
5. Safety Features
Safety is paramount in any industrial operation. EMS ovens come equipped with safety features such as flame monitoring systems, emergency shut-off valves, and proper ventilation to ensure a safe working environment for operators.
6. Customizable Sizes and Configurations
Recognizing that different businesses have varying needs, EMS offers customizable sizes and configurations for their gas powder coating ovens. This flexibility allows businesses to choose the right oven to fit their production capacities.
Benefits of Using Gas Powder Coating Ovens
Investing in a gas powder coating oven provides numerous advantages for businesses engaged in powder coating operations. Here are some key benefits:
1. Enhanced Coating Quality
Gas powder coating ovens promote optimal curing conditions, leading to high-quality finishes. The even application of heat ensures that the powder melts and adheres properly, resulting in durable coatings.
2. Increased Efficiency
The rapid heating capabilities of gas ovens reduce preheating and curing times, allowing for quicker production cycles. This increased efficiency can significantly enhance overall productivity.
3. Cost-Effective Operations
With their energy-efficient designs, gas powder coating ovens can reduce fuel costs compared to electric ovens. Additionally, the improved curing processes result in less rework and waste, contributing to lower operational costs.
4. Versatility for Different Applications
EMS gas powder coating ovens are versatile and can accommodate a wide range of powder coatings and substrate materials. This adaptability allows businesses to diversify their service offerings and meet various customer demands.
5. Compliance with Safety Standards
EMS gas powder coating ovens are designed to meet industry safety regulations, ensuring a safe working environment. Their robust safety features protect both operators and the surrounding environment.
Why Choose EMS Powder Coating Equipment for Gas Powder Coating Ovens?
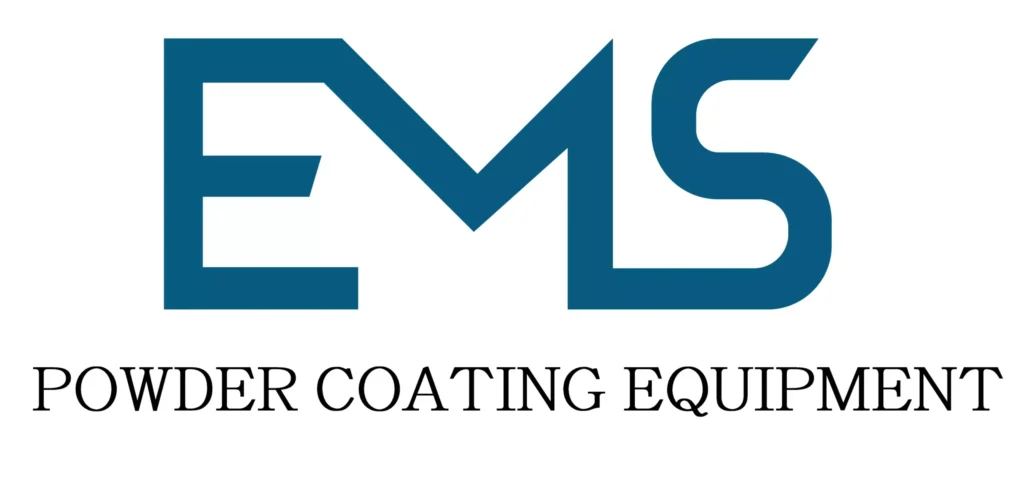
Selecting a gas powder coating oven requires careful consideration of the manufacturer’s reputation for quality and reliability. EMS Powder Coating Equipment is the top choice for businesses looking to invest in gas powder coating ovens. Here’s why EMS stands out:
1. Industry Expertise
With years of experience in the powder coating industry, EMS understands the unique requirements of various applications. Their expertise allows them to design gas powder coating ovens that are tailored to meet diverse production environments.
2. Commitment to Innovation
EMS is dedicated to continual innovation, integrating the latest technologies into their products. Their gas powder coating ovens are designed for optimal performance, featuring advanced controls and safety mechanisms.
3. Exceptional Customer Support
From installation to ongoing maintenance, EMS provides comprehensive customer support. Their team of experts is committed to helping businesses maximize the performance of their gas powder coating ovens.
4. Custom Solutions
Recognizing that every business has unique needs, EMS offers customizable solutions for gas powder coating ovens. This flexibility ensures that businesses can select the right features and configurations for their operations.
5. Trusted Quality and Reliability
With a strong reputation for delivering high-quality products, EMS is a trusted name in the powder coating industry. Their gas powder coating ovens are built for durability and long-term performance, making them an excellent investment for businesses.
Conclusion
A gas powder coating oven is a vital investment for any powder coating operation, providing efficient and controlled curing of powder coatings. With their advanced features and energy-efficient designs, these ovens enhance coating quality and productivity.
EMS Powder Coating Equipment is a leading manufacturer of gas powder coating ovens, offering innovative solutions tailored to meet the diverse needs of various industries. Their commitment to quality, performance, and customer support makes EMS the best choice for businesses seeking reliable coating equipment.
By choosing EMS gas powder coating ovens, companies can improve their coating processes, achieve superior finishes, and reduce operational costs. With a focus on efficiency and innovation, EMS stands out as the premier manufacturer for businesses in need of top-tier powder coating equipment.
Gas Powder Coating Oven: Efficiency and Precision in Coating Applications
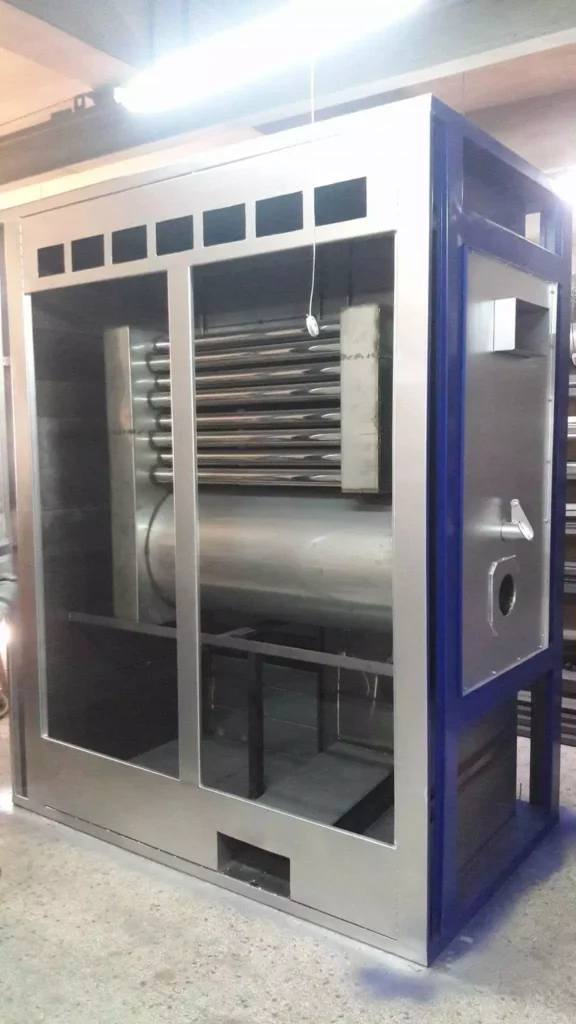
A gas powder coating oven is an essential component in the powder coating process, providing the necessary heat to cure powder coatings applied to various substrates. The curing process is crucial for achieving a durable, high-quality finish that adheres effectively to the surface.
These ovens are specifically designed to deliver uniform heat distribution, ensuring that the powder coating cures evenly and efficiently. With advancements in technology, modern gas powder coating ovens also incorporate features that enhance energy efficiency and operational safety.
EMS Powder Coating Equipment is recognized as a leader in the manufacturing of gas powder coating ovens, offering state-of-the-art solutions tailored to meet the diverse needs of various industries. In this section, we will delve into the operational principles, key features, and benefits of gas powder coating ovens, while also discussing why EMS is the preferred choice for businesses seeking reliable and efficient coating solutions.
What is a Gas Powder Coating Oven?
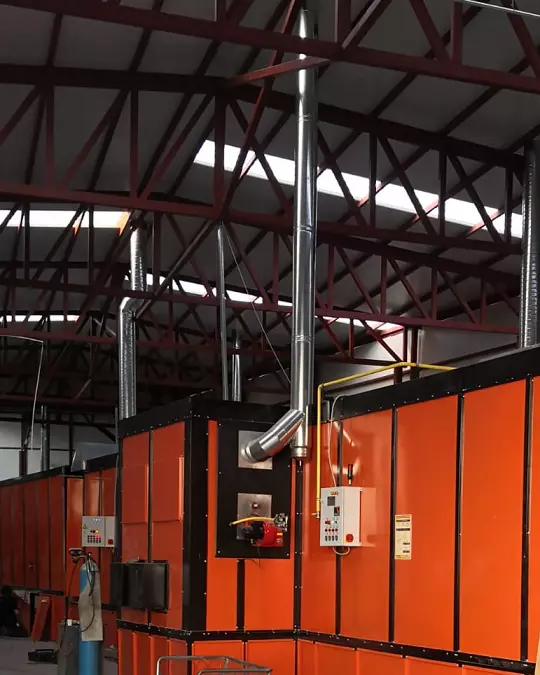
A gas powder coating oven is a specialized curing chamber used in the powder coating process. It employs gas as the primary heat source to cure the powder coatings applied to metal and other substrates.
How Gas Powder Coating Ovens Operate
The operation of a gas powder coating oven begins after the powder has been applied to the substrate in a spray booth. Once the substrate is ready, it is transferred to the oven, where precise heating elements deliver the required temperature for curing.
The oven’s design ensures uniform heat distribution, allowing the powder coating to melt and flow, ultimately bonding to the substrate. The curing process is crucial, as it transforms the powder into a hard, protective finish that is both aesthetically pleasing and durable.
EMS Powder Coating Equipment designs gas powder coating ovens with advanced features that optimize curing efficiency and performance, ensuring businesses achieve consistent, high-quality finishes across various applications.
Key Features of Gas Powder Coating Ovens
Gas powder coating ovens are equipped with several features that enhance their performance and efficiency. Here are some standout features that make EMS ovens the preferred choice for businesses:
1. Uniform Heat Distribution
EMS gas powder coating ovens are engineered to provide uniform heat distribution throughout the curing chamber. This feature ensures that every part of the substrate receives the same level of heat, resulting in even curing and high-quality finishes.
2. Energy Efficiency
Modern EMS gas ovens are designed for energy efficiency, utilizing advanced insulation and burner technology. This allows businesses to reduce energy consumption while maintaining optimal curing temperatures, leading to cost savings over time.
3. User-Friendly Controls
The intuitive control systems in EMS gas powder coating ovens allow operators to easily set and monitor temperatures and curing times. This user-friendly interface streamlines operations and enhances overall productivity.
4. Safety Features
Safety is paramount in any coating operation. EMS gas powder coating ovens come equipped with essential safety features, including flame safety devices, emergency shut-off systems, and proper ventilation, ensuring a safe working environment.
5. Customizable Configurations
Understanding that different businesses have unique requirements, EMS offers customizable configurations for their gas powder coating ovens. Whether for small operations or large-scale production, EMS can tailor solutions to meet specific needs.
6. Durable Construction
Built with high-quality materials, EMS gas powder coating ovens are designed for longevity and reliability. Their robust construction ensures consistent performance even in demanding production environments.
Benefits of Using Gas Powder Coating Ovens
Investing in a gas powder coating oven provides numerous advantages for businesses engaged in powder coating operations. Here are some key benefits:
1. Consistent Coating Quality
The precise temperature control and uniform heat distribution in gas powder coating ovens lead to consistent curing results. This ensures that the final finish meets the highest quality standards.
2. Faster Curing Times
Gas powder coating ovens typically offer faster curing times compared to electric ovens, enhancing production efficiency. This speed allows businesses to complete more jobs in less time, increasing overall output.
3. Cost Efficiency
By utilizing gas as an energy source, businesses can benefit from lower operational costs compared to electric ovens. The energy-efficient design of EMS ovens further enhances this cost-effectiveness.
4. Versatility for Diverse Applications
EMS gas powder coating ovens are versatile enough to handle a wide range of substrates and coating types, allowing businesses to expand their offerings and cater to different market demands.
5. Compliance with Environmental Regulations
Gas powder coating ovens are designed to meet industry safety and environmental regulations, ensuring a compliant operation. By investing in EMS ovens, businesses can promote a healthier working environment while adhering to necessary standards.
Why Choose EMS Powder Coating Equipment for Gas Powder Coating Ovens?
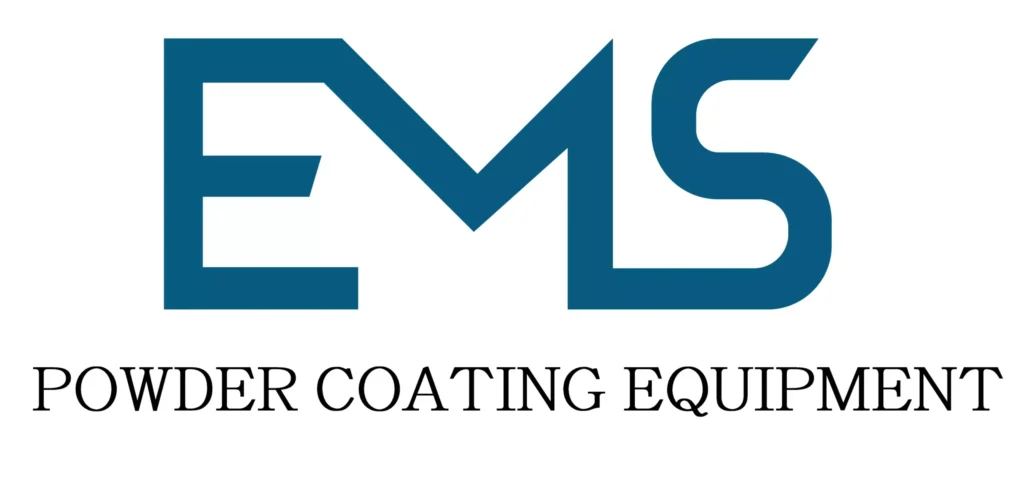
When selecting a gas powder coating oven, it is essential to choose a manufacturer with a reputation for quality and innovation. EMS Powder Coating Equipment stands out as the top choice for businesses looking to invest in gas powder coating ovens. Here’s why EMS is the preferred option:
1. Proven Expertise
With years of experience in the powder coating industry, EMS understands the unique needs of various applications. Their knowledge allows them to design gas powder coating ovens that are tailored to diverse production environments.
2. Innovative Solutions
EMS is committed to continuous innovation, incorporating the latest technology into their products. Their gas powder coating ovens are designed for optimal performance, featuring advanced temperature control and safety systems.
3. Comprehensive Support
From installation to ongoing maintenance, EMS provides exceptional customer support. Their team of experts is dedicated to helping businesses maximize the performance of their gas powder coating ovens.
4. Customizable Options
Recognizing that every business has unique requirements, EMS offers customizable options for gas powder coating ovens, allowing businesses to select features and configurations that best suit their operational needs.
5. Trusted Reliability
With a strong reputation for delivering high-quality products, EMS is a trusted name in the powder coating industry. Their ovens are designed for durability and long-term performance, making them an excellent investment for businesses.
Conclusion
A gas powder coating oven is a crucial investment for any powder coating operation, providing the necessary heat to cure powder coatings effectively. With uniform heat distribution and energy-efficient designs, these ovens ensure high-quality finishes while optimizing operational efficiency.
EMS Powder Coating Equipment is a leading manufacturer of gas powder coating ovens, offering innovative solutions tailored to meet the diverse needs of various industries. Their commitment to quality, performance, and customer support makes EMS the best choice for businesses seeking reliable coating solutions.
By choosing EMS gas powder coating ovens, companies can enhance their curing processes, achieve superior finishes, and reduce operational costs. With a focus on efficiency and innovation, EMS stands out as the premier manufacturer for businesses in need of top-tier powder coating equipment.