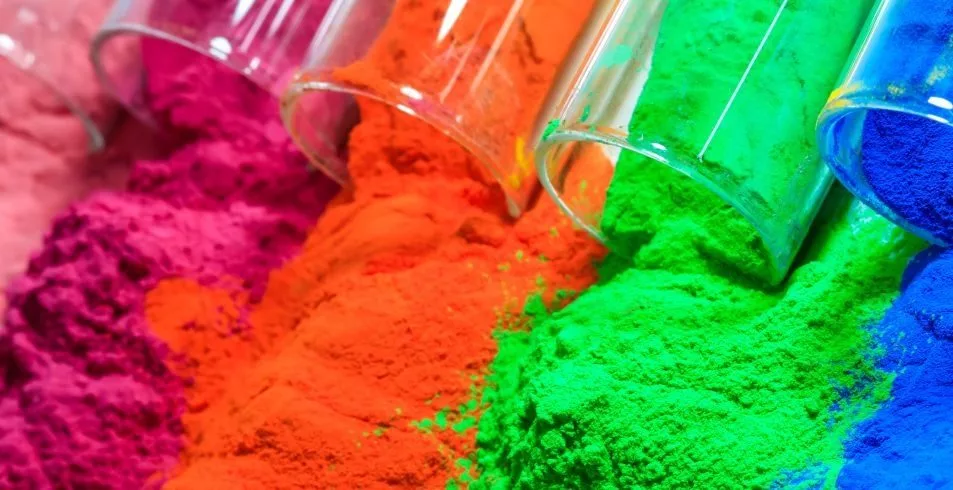
What is Powder Coating? Powder coating is by far the youngest of the surface finishing techniques in common use today. It was used in Australia about 1967. Powder coating is the technique of applying dry paint to a part. The final cured coating is the same as a 2-pack wet paint.
Powder coating is increasingly accepted as the preferred finishing process for many applications. Increasingly stringent environmental regulations, rising costs in all areas, and demands by consumers for better quality and more durable products are among the challenges facing today’s finishers. Powder coatings provide a solution to these challenges and others. Powder coating is the technique of applying dry paint to the component.
The powdered paint is normally applied by using a powder feed system and gun to electrostatically charge and spray the powder onto the part. For some applications, the part being coated is dipped into a fluidized bed of powder. The coated part is then heated in an oven, or via infrared panels, to melt and cure the paint. During the curing process, a chemical cross-linking reaction is triggered and it is this chemical reaction that gives the powder coatings many of their desirable properties.
In normal wet painting such as house paints, the solids are in suspension in a liquid carrier, which must evaporate before the solid paint coating is produced. Powder coating is a dry finishing process, using finely ground particles of pigment and resin that are generally electrostatically charged and sprayed onto electrically grounded parts.
The charged powder particles adhere to the parts and are held there until melted and fused into a smooth coating in a curing oven. Before coating the part to be coated are first pre-treated similarly to conventional liquid-coated parts. The pre-treatment process is normally conducted in series with the coating and curing operations
Powder coating is a finishing process in which a metal object is coated with powdered paint. This process can be done in an oven or booth, and the powder is electrostatically charged to stick to the metal. The paint is applied dry and can be sprayed or the heated part can be dipped into a powder tank.
Powder coatings are typically used on objects with a smooth surface but can be applied to rough surfaces like chains and gears. The powder is electrostatically charged and can be applied in an oven, booth, or by spraying. Powder coating provides multiple benefits over traditional methods of painting. It’s more economical, better quality, and has a longer life than other finishes such as wet paint.
Powder coating is a process that is more economical and better than wet paint. It is also more durable and has a better finish, that provides an economical, better, and more durable finish to the object being coated. It can be applied to any type of object from small items like tools to large items like cars or buses.
What is Powder Coating?
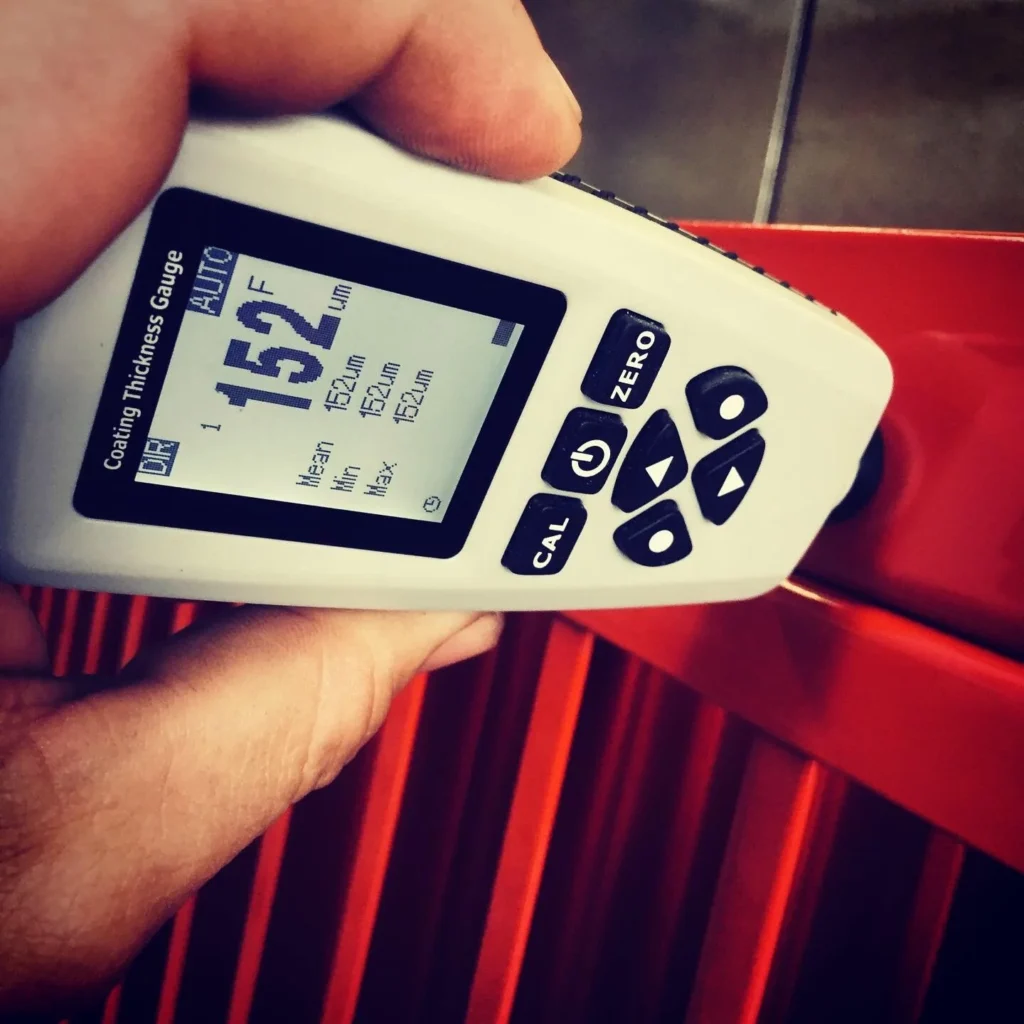
Powder coatings is a great industry. The powder has ran through our veins for over 16 years, it is not new to us and we have literally done every single job associated with this industry with the exception of the raw material side. Our contributors have formulated, manufactured, developed, managed, troubleshoot, applied and consulted.
The powder can make you laugh and it can make you cry. This manual is targeted at the person who wants to do it right. The person who is tired of getting rejects and field failures on their parts.
Where applicable, shortcuts and money-saving tips are incorporated. However, at no time do we cut out safety or quality. These are the traits of a successful manufacturer. If you want to do it cheaply and don’t care about safety or quality, then we suggest you read no further. We wish you good luck.
Over the years we have seen entrepreneurs with barely enough money for rent and a powder gun become millionaires and seen millionaires with huge facilities go bankrupt. Where you end up is directly proportional to how seriously (and at times – unserious) you take this business. Regardless of your current skill level in the industry, you will find this manual will serve your needs. From the novice hobby coater to the OEM applying millions of pounds annually, this manual has valuable information for you. Powder Coating can fall into the following categories:
- Powder coating for hobby
- Powder coating job shop
- Powder coating for an OEM
Eventually, we end up crossing into each category. Every single powder coating line at one time or another is used for hobby or ‘government’ work. Job shops may end up making certain parts for sale which they sell outright becoming OEM”s. OEMs may have excess line capacity which they end up using to do job shop work.
Research is imperative when deciding which industry you will serve with powder coating. Find your niche, do quality work at a reasonable price and you will be successful. Some areas which are hot right now include refinishing wheels, coating temperature sensitive parts such as wood or plastic, and doing OEM work.
Powder Coating is basically a dry paint. Instead of being dissolved or suspended in a liquid medium: such as, solvent or water, powder is applied in its dry form, finer than ground pepper, courser than flour, directly to the surface to be coated.
Each powder particle contains resin, pigments, modifiers, extenders and if it is a reactive system, a curing agent. Most powder coatings are reactive and contain curing agents. The term for these reactive powder coatings is: Thermoset The term for the non-reactive powder coatings is: Thermoplastic

Why should we use powder coatings?
- Powder Coating offers a number of significant advantages:
- Absence of solvents
- Applied in one coat – high standard of finish with good edge coverage
- Few rejects
- Resistant to chipping, scratching, abrasion and bending
- Easy to apply
- Cleaner working conditions
- Virtually no atmospheric pollution, very little or 0% VOC!
- Safety in use and on storage, low fire hazard
- Insurance premiums may be lower
- No viscosity adjustments
Savings in overall costs are possible
Powder coatings are electrostatically applied to parts using either a fluidized bed or electrostatic spray. The part to be powder coated is grounded and the powder is charged, this attracts the powder to the part, much like a magnet attracts steel.
This charge holds the powder to the part and the part is then cured (baked) in an oven. A typical cure cycle would be 15 minutes at 380 F. Cure cycles always refer to the amount of time the part is at the temperature specified, not how long it is in the oven Due to the significant advances in formulating, manufacturing, and application technologies over the past 15 years powder is used in many areas previously not thought possible.
Powder coatings are daily applied in shops ranging from custom job shops to the world’s largest manufacturers. Metal, plastic, wood, composite, and glass substrates can be coated provided the part does not deteriorate or distort at the cure temperature of the powder. Current low-temperature technology allows for cures in the 250F range.
Office Furniture, General Metals, Engine Parts, Light Fixtures, Industrial Shelving, Computer Cases, Toolboxes, Medical Equipment, Barbeque and Gas Grills, Appliances, Ceramic bottles, Ceramic flash/instrument bulbs, Ceramic roofing tile, Wooden toilet seats, Kitchen cabinets, Home-office furniture, Outdoor grill tables, Children’s furniture and many other items can be successfully powder coated.
How are Powder Coatings made?
Powder coatings are manufactured using an extruder, or compounder, which melt and mixes the raw materials together. This mixed material is then flattened and cooled and then subsequently ground down to the appropriate particle size for the application.
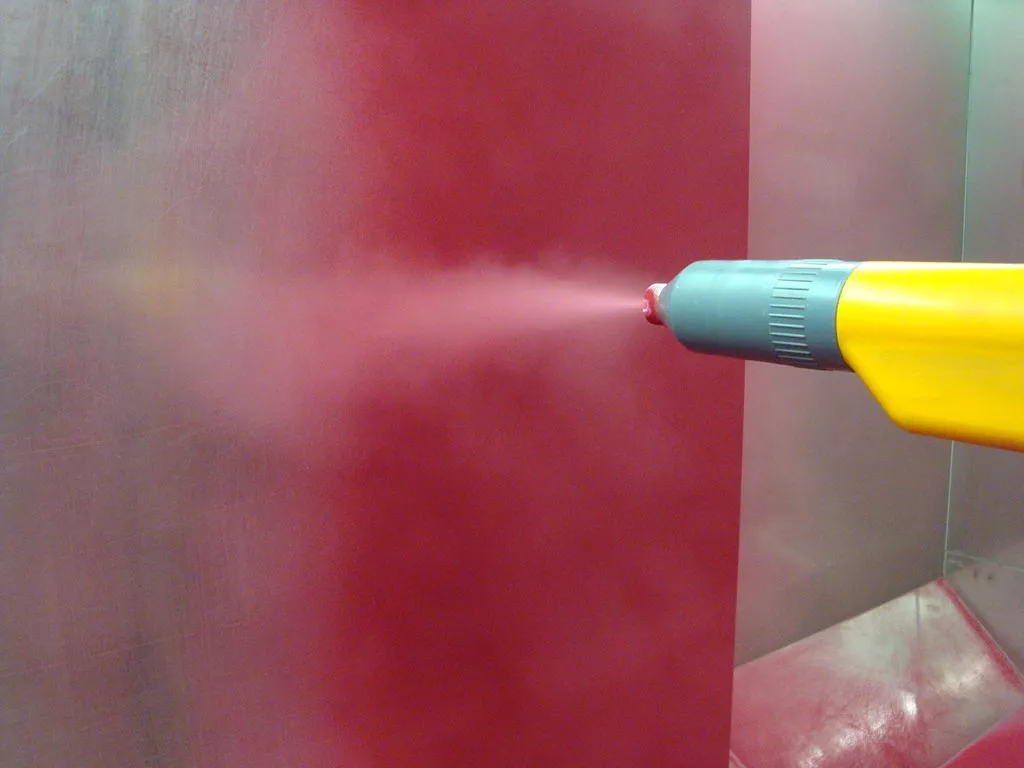
Powder Coating Types: Thermoset Powder Coating
Thermosetting powders are primarily composed of relatively high molecular
weight solid resins and a crosslinker. The primary resins used in the formulation
of thermosetting powder are:
- Epoxy
- Polyester
- Acrylic
These primary resins are used with different crosslinkers to produce a variety of powder coatings. There are many crosslinkers used in powder coatings, including amines, anhydrides, melamines, and blocked or non-blocked isocyanates. Some formulations also use more than one resin in hybrid formulations. When a thermoset powder is applied and subjected to heat it will melt, flow and chemically crosslink to form a finished film. Chemical reactions during the curing cycle create a polymer network which provides excellent resistance to coating
breakdown. Once cured and crosslinked, this polymer network will not melt and flow again if heat is applied.
Powder Coating Chemistry: Thermoplastic Powder Coating Thermoplastic Powders do not chemically crosslink upon application of heat, but melt and flow over the part in the oven. As the part cools, after exiting the oven, the film hardens but will remelt upon application of sufficient heat. The primary types of thermoplastic powders are: - Polyethylene
- Polypropylene
- Nylon
- Polyvinyl Chloride
- Polyester
- Polyvinyledene flurides/fluorcarbons
Thermoplastic powder coatings are based on thermoplastic resins of high molecular weight. The properties of these coatings are dependent on the basic properties of the resin. These tough and resistant resins tend to be difficult, as well as expensive, to grind to the very fine particles necessary for the spray application and fusing of thin films. These systems are used more as thicker coatings of many mils thickness and are applied mainly by fluidized bed technique. Most powder coaters do not apply these.
Thermoset Powder Coating Types: Epoxy Powder Coatings
The epoxy family of powder coatings is the most prominent type of thermosetting powder in use today. The listing of available epoxy formulations is quite extensive because of the wide formulating latitude that exists. These materials, as is all thermoset powder coatings, consist of resins, crosslinker or hardener, reinforcing fillers, pigments, processing aids, flow agents, and other modifiers.
A change in the type or the amount of any one of these constituents can noticeably change the properties and performance characteristics of the final product. Epoxy powder coatings are generally custom formulated to the specific decorative and performance requirements of a given end-use. Unfortunately, the epoxy resin-based powder coatings have two major deficiencies – they discolor if overbaked and chalk on exterior exposure.
Typical Applications include Fire Extinguishers, Toys, Mixers & Blenders, Oil Filters, Shelving, Dryer Drums, Fertilizer Spreaders, Refrigerator Racks, and Microwave Ovens, Primers, Tools, and Kitchen Furniture.
Thermoset Powder Coating Types: Epoxy Hybrid Powder Coatings This group of powder coatings could be considered part of the epoxy family except that the high percentage of polyester (or Acrylic) utilized (often in excess of half of the resin) makes that classification misleading. Property-wise, however, these hybrid coatings are more closely akin to epoxies than polyesters, with a few notable exceptions.
They show similar flexibility in terms of impact and bend resistance, but are slightly softer in pencil hardness – H to 3H being characteristic. Their corrosion resistance is comparable to epoxies in many cases, but their resistance to solvents and alkali is generally inferior. A major advantage of these hybrids, due to the influence of the polyester or acrylic component, is a higher resistance to overbake yellowing in the cure oven.
This also translates to improved weatherablilty. These systems will begin to chalk almost as fast as epoxy, but the deterioration is slower and the discoloration less severe. These systems also have excellent electrostatic spray characteristics with high transfer efficiency and penetrate well into corners and recesses. Typical Applications include: the same end-use as epoxies, especially if a slight improvement in heat stability or weathering is required
Thermoset Powder Coating Types: Polyester Powder Coatings
Polyester powder coatings can be broken down in three groups:
- Polyester Urethane: Hydroxyl functional resin cured with a blocked Isocyanurate
- Polyester TGIC: Carboxyl functional resin cured with Triglycidyl Isocyanurate
- Polyester TGIC Free: Carboxyl functional resin cured either with Tetramethoxymethyl Glycoluril or with Beta- hydroxyalkylamide
All three types of Polyester powder coatings have very good exterior weathering properties and are generally used for outdoor applications.
Thermoset Powder Coating Types: Polyester Urethane Powder Coatings
The primary type which has been in use for the past number of years is a urethane cured polyester powder which is comparable chemically to the exterior quality urethane paints which have been used on aircraft, buses, trucks, and railroad cars for the past 17+ years. Coatings of this type combine outstanding thin film appearance and toughness with excellent weathering properties. They are true competitors to high-quality liquid paints, exhibiting superior chip, mar, and scuff resistance at 1.5 mils
thickness.
Adhesion to properly prepared ferrous and nonferrous metals is excellent, providing long-term resistance to humidity and salt spray. These formulations must reach a temperature of at least 360 F before crosslinking can occur. This is due to the fact that the curing agent is blocked with e-Caprolactam to prevent curing at ambient temperatures. These powders are sensitive to films thicker than 3 mills due to the fact that the e-Caprolactam evolution can cause outgassing at thicker films.
Thermoset Powder Coating Types: Polyester TGIC Powder Coatings
This type of polyester is based upon technology developed in Europe. These products can best be described as more exterior durable cousins of the epoxy-polyester hybrids – the difference being that instead of using a conventional epoxy resin to co-react with the polyester, a very low molecular weight glycidal or epoxy-functional, curing agent is used.
Overbake color stability, as with epoxy polyesters, is also excellent.
Their adhesion and corrosion-resistant properties are comparable to the urethane cured polyester, but their resistance to chemicals and solvents is lower. A significant advantage is a fact that these can typically be cured at lower temperatures, for shorter periods than urethane or TGIC Free systems.
Cure cycles as low as 6 minutes at 300 F are attainable. TGIC formulations also provide good overbake and outgassing characteristics making them friendly to apply. The higher melt viscosity of the TGIC crosslinker also results in good edge coverage and tough thick films but also results in a slight orange peel effect
Thermoset Powder Coating Types: Polyester TGIC Free Powder Coatings
These formulations were developed in response to industry concerns regarding the possible side effects of overexposure to the curative Triglycidyl Isocyanurate. These exhibit similar performance and application properties as TGIC formulations do. With TGIC Free formulations it is possible to develop the much desired ‘wrinkle’ texture effect. Increased resistance to film discoloration and yellowing of the coating is realized with these formulations
Thermoset Powder Coating Types: Acrylic Powder Coatings
Acrylic formulations give excellent exterior durability. There are two classifications of acrylic formulations. Urethane Acrylic and GMA Acrylic.
Thermoset Powder Coating Types: Urethane Acrylic
These formulations are similar in properties to Polyester Urethane products, offering excellent thin film appearance, good chemical resistance and hard durable films. The flexibility and impact of these is very poor due to the high crosslink density of the cured film.
Thermoset Powder Coating Types: GMA Acrylics
These are also similar in properties to Polyester Urethane products. They make excellent clear coats over brass and chrome, being ideal for bath fixtures and automotive wheels. These however also exhibit poor flexibility and more importantly are highly incompatible with all other powder chemistries. This requires the manufacturers and users to utilize isolated systems to prevent cross contamination.
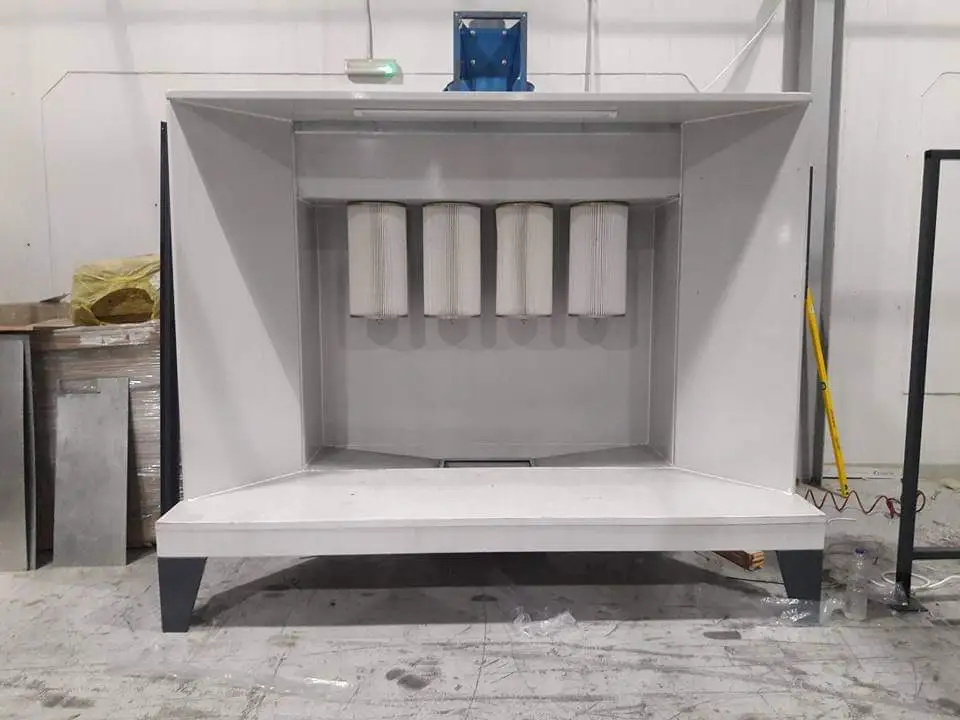
The powder coating process starts when the object being coated enters a booth with an oven at one end, which heats up to 400 degrees Fahrenheit (200 degrees Celsius). Once heated, the powder-coated part can be put in the oven and wait for 30 mins.
Is it better than wet paint?
Powder coating is a process that is often used to finish metal surfaces. It’s a process that can be done in an oven or by hand, and it’s also more economical than wet paint.
There are many advantages of powder coating over wet paint. Powder coatings are more durable, they have better color retention, and they don’t require laborious preparation time.
Powder coatings also offer some environmental benefits over wet paint because they don’t produce any vapors or fumes when applied and cured in an oven or booth.
Powder coating is a finishing process that is often used to provide a smooth and durable surface. It is typically applied by spraying the powder onto the surface, which melts and adheres to the substrate. Powder coating can be applied to many different types of materials, such as metals, plastics, concrete, and wood.
Do you need a spray booth for powder coating?
The advantages of powder coating are that it can be applied at higher temperatures than wet paint, which means it provides better durability. It also provides better corrosion resistance than wet paint because of its electrostatic properties. Another advantage is that it has lower costs than wet paint because it does not require an oven or booth for drying. Powder coating also reduces waste because there isn’t any solvent-based material being sprayed over the surface like there would be with wet paint.
Powder coating is the process of applying a dry powder to a surface and then baking it to form a solid coating. The dry powder is typically aluminum oxide but can be made from other materials, such as titanium dioxide. Powder coating has many advantages over wet paint including being more economical, better finishing, and more durable.
Powder coating is applied by electrostatic spraying or by dipping the article into the powder. It is also possible to apply powder with an air gun or mechanical sprayer. The article may be heated before applying the powder in order to fuse the particles together and reduce porosity (air bubbles).
Ways of Powder Coating Applying
There is essentially two common ways of applying powder coating: electrostatic spray and by fluidized bed powder coating. There are several other processes that have been developed, but they are far less used. These include flame spraying, spraying with a plasma gun, airless hot spray, and coating by electrophoretic deposition. The fluidized bed is the original powder coating technique. It is still the primary technique used for the application of thermoplastic powder.
The fluidized bed is also used for the application of some thermoset powders where high film build is required. Thermo-set powders designed for electrical insulation often use the fluidized bed technique. The parts are preheated to a temperature significantly higher than the melting point of the powder.
The parts are then immersed into a “fluidized bed” of the coating powder where the plastic powder is melted onto the part. The electrostatic spray is the primary technique used for thermo set powder. The parties of powder are given an electrical charge in the powder coating gun. The target part is attached to a fixture that is grounded.
The electrically charged powder particles are attracted to the grounded part and attach themselves like little magnets to the part. The particles build up on the surface of the part until it is covered with charged particles and the part surface is charged. At this point, the oncoming particles are actually repelled by the charged particles on the part and the coating process stops. This provides an even film thickness.
Materials of Powder Coating
There are two types of powder coating thermoplastic and thermosetting A thermoplastic powder coating is one that melts and flows when heat is applied, but continues to have the same chemical composition once it cools and solidifies. Thermoplastic powder exhibit excellent chemical resistance, toughness, and flexibility.
They are applied mainly by the fluidized bed application technique, in which heated parts are dipped into a vat where the powders are fluidized by air and are used in many thick film applications.
They are generally applied to a surface that has been preheated to a temperature significantly higher than the melting point of the powder. As a thermoplastic powder material is applied to the hot surface it will melt and “fusion bond” to the surface and then “flow out” into a strong, continuous film. As the film cools it develops its physical properties.
Nylon powder coating materials are the most commonly used thermoplastic powder. Thermosetting powder coatings are based on lower molecular weight solid resins and melt when exposed to heat. After they flow into a uniform thin layer, however, they chemically crosslink within themselves or with other reactive components to form a reaction product of much higher molecular weight. These newly formed materials are heat stable and unlike the thermoplastic products after curing, will not soften back to the liquid phase when heated.
The Thermosetting Powder
The thermosetting powder is derived from three generic types of resins: epoxy, polyester, and acrylic. From these resin types, several coating systems are derived. Resins used in thermosetting powder can be ground into fine particles necessary for spray application and a thin film finish. Most of the technological advancements in recent years have been with thermosetting powder.
Epoxy: Epoxy powder coating exhibit inherent toughness, corrosion resistance, chemical resistance, flexibility, adhesion, and abrasion resistance. Epoxy powder is normally used where a tough durable film is required and the product will not be exposed to direct sunlight for a long period of time. An epoxy coating will form a chalk-like appearance on the surface with lengthy exposure to sunlight.
Typical Applications of Powder Coating
Appliances
Business machines
Electrical enclosures
Hospital equipment
Office furniture
Oil filters
Powder tools
Shelving
Toolboxes
Urethane powder coating feature characteristics of excellent gloss retention and long-term resistance to humidity and corrosion in thin film applications.
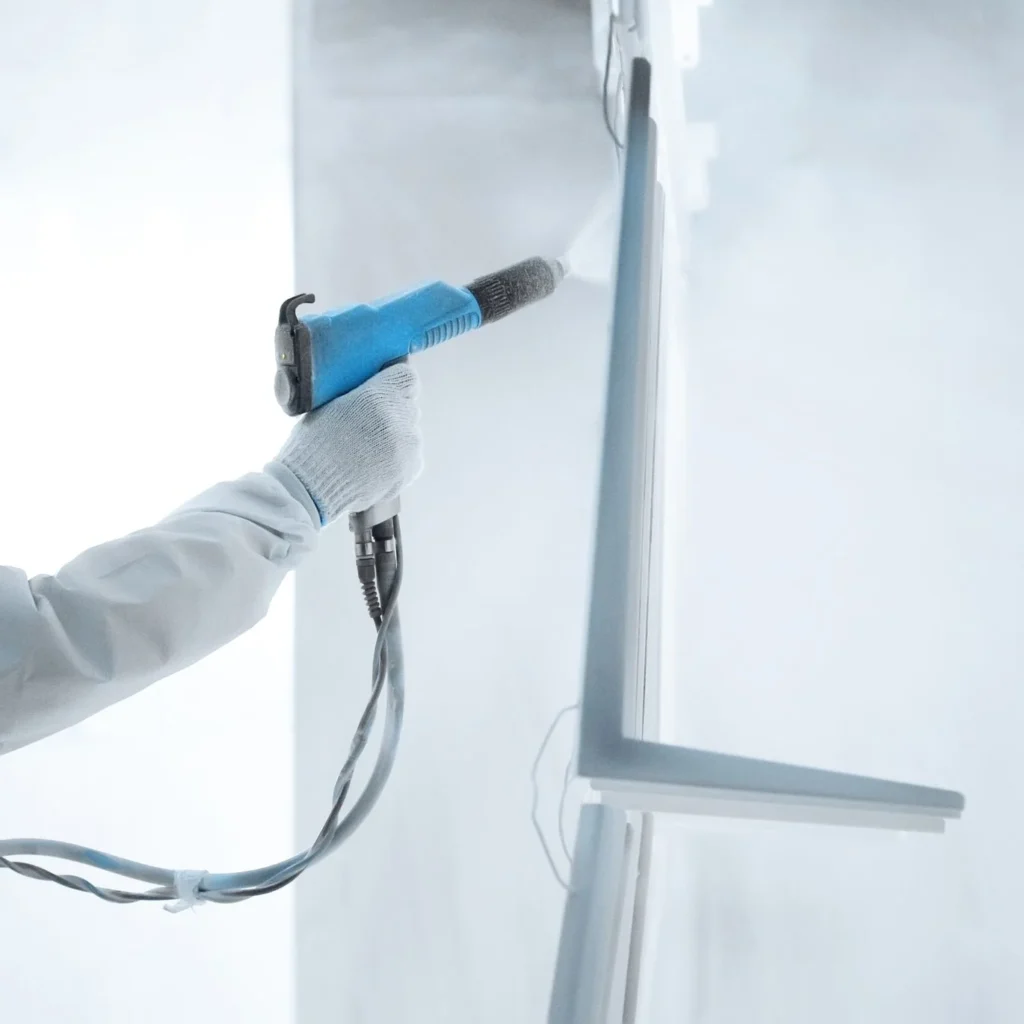
Typical applications include:
Agricultural Equipment
Air conditioners
Construction Equipment
Electrical Enclosures
Lawn and garden equipment
Lawn furniture
Light fixtures
Office furniture
Recreational Equipment
Under-hood Automotive
Wheel and Rims
Polyester Powder Coating features characteristics of long-term exterior durability, high-performance mechanical properties, and over-back resistance. Polyester powder is widely used for decorative components where good resistance to the ultraviolet rays from sunlight is important. Many automotive trim components and other exterior components are coated with polyester powder.
Typical applications include:
Agricultural Equipment
Appliances
Construction Equipment
Electrical Enclosures
Lawn and Garden Equipment
Lawn Furniture
Recreational Equipment
Under-hood Automotive
Wheel and Rims
Acrylic powder is specified where the decorative requirements and resistance to ultraviolet rays from sunlight for a longer period of time are critical. Many critical automotive trim components are coated with acrylic powder.
Preparation of Powder Coating
The basis of any good coating is preparation. The vast majority of powder coating failures can be traced to a lack of suitable preparation.
The preparation treatment is different for different materials. In general, for all applications the preparation treatment for aluminum is as follows:
- Clean or Clean
- Rinse Rinse
- Etch Etch
- Rinse Rinse
- Chromate Phosphate
- Rinse Rinse
- Demin Rinse Demin Rinse
Oil and greases are removed in weak alkali or neutral detergent solutions and the surface is etched to remove heavy oxide. After rinsing the aluminum is dipped into a chromate or phosphate solution to form a conversion coating on the aluminum. This film is chemically attached to aluminum. After rinsing the aluminum is finally rinsed in demineralized water. Some non-chrome, dried in place pre-treatment is beginning to come onto the market, currently, these are not recommended for exterior applications.
The conversion coating has two functions:
- The presents a surface to the powder which favors adhesion more than the oxides that vary readily on aluminum surfaces and
- It reduces the incidence of under-film corrosion, which may occur during holidays in the coating. The use of demineralized water reduces the presence of chemical salts on the aluminum surface. These salts have been found to cause fill form corrosion in humid conditions