Alloy Wheels Powder Coating Machinery: Alloy wheel powder coating is a popular process used to improve the appearance and durability of alloy wheels. It involves applying a fine powder to the wheel’s surface, followed by curing in an oven. The powder coating creates a hard, durable finish that is resistant to corrosion, scratches, and chips. Here’s a general overview of the powder coating system for alloy wheels:
Key Steps in Alloy Wheel Powder Coating System:
- Preparation:
- Cleaning: The wheels are thoroughly cleaned to remove dirt, grease, and contaminants. This may involve abrasive blasting or using chemicals like acid or caustic solutions to clean the surface.
- Pre-treatment: A chemical pre-treatment, such as phosphating or anodizing, can be applied to improve adhesion and corrosion resistance.
- Surface Inspection: Any imperfections, such as scratches or dents, are fixed during this step to ensure a smooth and even coating.
- Powder Application:
- The wheels are electrostatically sprayed with a powder coating material. The powder is charged so that it adheres to the metal surface. The most common powder materials include epoxy, polyester, and hybrid formulations.
- Different colors and finishes (such as matte, glossy, or textured) can be applied depending on the desired outcome.
- Curing:
- After the powder is applied, the wheels are placed in a curing oven where the powder melts and forms a smooth, durable coating. The curing process involves heating the coated wheels to a specific temperature (usually around 180–200°C or 356–392°F) for a set amount of time to ensure the coating fully bonds to the wheel.
- Cooling and Inspection:
- Once the wheels are cured, they are allowed to cool down. After cooling, they undergo a quality inspection to ensure the coating is smooth, even, and free of defects like bubbles or streaks.
- Any imperfections may be corrected by re-coating or polishing.
- Finishing Touches:
- The final product may undergo additional steps such as polishing, applying decals or logos, or adding a clear coat for additional protection and shine.
Benefits of Powder Coating Alloy Wheels:
- Durability: Powder coating creates a tough finish that resists chips, scratches, fading, and corrosion.
- Aesthetic Flexibility: Various colors, textures, and finishes can be applied to create a custom look for the wheels.
- Environmentally Friendly: Unlike traditional liquid paints, powder coating doesn’t require solvents, reducing the release of harmful VOCs (Volatile Organic Compounds).
- Cost-Effective: Once the system is set up, powder coating can be more cost-effective compared to other finishing techniques like wet painting.
Equipment Used in the System:
- Powder Spray Gun: The tool used to apply the powder to the surface of the alloy wheel. The gun uses electrostatic charge to make the powder stick to the wheel.
- Curing Oven: A large oven used to bake the coated wheels at high temperatures to cure the powder coating.
- Blast Cabinet: A machine used to clean and prepare the wheels using abrasive materials before coating.
- Powder Booth: A spray booth where the powder coating process takes place, often equipped with filters to capture excess powder.
Maintenance of the Coating:
To maintain the powder-coated finish, regular cleaning is recommended. Wheels should be washed with mild soap and water, avoiding harsh chemicals or abrasive tools that could damage the finish. Proper maintenance helps ensure the longevity of the coating.
The alloy wheel powder coating system involves several critical steps to ensure a durable and visually appealing finish. First, the wheels are thoroughly cleaned to remove any dirt, oil, or other contaminants. This is typically done through abrasive blasting, chemical cleaning, or a combination of both. Pre-treatment steps like phosphating or anodizing might be applied to enhance the adhesion of the powder coating and increase the overall corrosion resistance. Once cleaned and prepped, the wheels are ready for the application of the powder. Using an electrostatic spray gun, the powder, which is made of finely ground particles, is charged and sprayed onto the wheel’s surface. The electrostatic charge ensures that the powder adheres to the wheel before it is cured.
After applying the powder, the wheels are placed in a curing oven, where they are heated to a specific temperature, usually between 180-200°C, to melt and bond the powder to the wheel’s surface. The curing process causes the powder particles to fuse into a uniform, smooth, and durable layer. Once the wheels have cooled, they undergo a final inspection to ensure that the coating is consistent and free of defects such as runs, unevenness, or bubbles. Depending on the desired finish, the wheels may undergo further processes like polishing or applying additional coatings. This process not only improves the aesthetics of the wheels, offering a wide range of colors and finishes but also enhances their longevity by making them resistant to scratches, chips, and corrosion.
The system typically requires equipment like spray guns for applying the powder, a curing oven to bake the powder, and blast cabinets for preparing the wheels before coating. Powder coating is a more eco-friendly option than traditional painting because it doesn’t involve solvents or hazardous chemicals, reducing environmental impact. Additionally, it’s cost-effective due to lower material waste and faster curing times compared to conventional wet paint systems. Proper maintenance of the powder-coated wheels involves regular washing with mild soap and water to prevent dirt buildup and ensure the finish stays in top condition.
In addition to the fundamental steps and equipment already discussed, several other considerations can impact the overall quality and efficiency of the alloy wheel powder coating system. One key factor is the choice of powder material. The most commonly used powders are epoxy-based, polyester-based, and hybrid formulations, each with its own set of characteristics. Epoxy powders are known for their excellent adhesion and corrosion resistance, making them ideal for parts exposed to harsh environments. However, they may not be as UV resistant as other types, which is why polyester powders are often used for exterior applications, offering better protection against fading caused by sunlight.
Another critical factor in the powder coating process is the environmental control within the spray booth and curing oven. The booth must be well-ventilated to ensure that excess powder is safely captured and not released into the air. This helps reduce wastage and keeps the environment clean. Additionally, the curing oven’s temperature must be precisely controlled to ensure that the powder cures evenly and effectively, which is key to achieving a durable and smooth finish. Over or under-curing can result in poor adhesion, inconsistent texture, or a weakened coating.
The quality of the finish also depends on the curing time. It’s essential to follow the manufacturer’s guidelines for the appropriate curing time to ensure a strong bond between the powder and the alloy surface. Typically, this will range from 10 to 20 minutes at the target temperature, but it can vary based on the size of the wheels and the specific type of powder used.
To further enhance the durability of the coating, some systems offer the option of applying a clear coat on top of the powder layer. This adds an additional layer of protection, particularly against abrasions, environmental contaminants, and chemicals like road salt. It also enhances the overall finish, providing a glossy or matte look, depending on customer preferences.
The efficiency of the entire system can also be influenced by factors like throughput, the setup time for each batch of wheels, and the overall automation of the process. Many modern powder coating systems are designed to be highly automated, reducing labor costs and increasing consistency. Automated systems allow for precise control over powder application, curing time, and other variables, ensuring high-quality results while improving speed.
While the powder coating process is highly effective for protecting alloy wheels and improving their appearance, it’s important to maintain the equipment properly. This includes regularly cleaning the spray guns, curing ovens, and spray booths to prevent contamination, build-up, or clogging of the equipment. Routine maintenance helps ensure the system runs smoothly, reducing downtime and increasing overall productivity.
A high-efficiency alloy wheel powder coating line is designed to maximize productivity, minimize energy consumption, and ensure consistent, high-quality results in the coating of alloy wheels. These systems integrate advanced technologies, automation, and optimized workflows to streamline the powder coating process while maintaining top-tier quality standards. Here’s an outline of how a high-efficiency alloy wheel powder coating line operates:
Key Features of a High-Efficiency Alloy Wheel Powder Coating Line:
- Automated Loading and Unloading:
- Automated systems are used to load and unload the alloy wheels into and out of the powder coating line, reducing manual labor and increasing throughput. Robotic arms or conveyors are commonly used for this purpose.
- The automation allows for consistent handling of wheels, reducing the risk of human error and improving the speed of production.
- Pre-treatment and Surface Preparation:
- High-efficiency systems often incorporate state-of-the-art pre-treatment technology to ensure the wheels are properly cleaned and prepared for coating.
- This can include automated blast cabinets, ultrasonic cleaning systems, or chemical cleaning stations to remove contaminants like oils, dirt, and rust.
- Advanced pre-treatment methods like multi-stage phosphate coating are also used to enhance the adhesion of the powder and prevent corrosion.
- Electrostatic Powder Application:
- The heart of a high-efficiency system is the electrostatic powder application. High-quality, automated powder spray guns apply the coating in a precise, controlled manner.
- These systems feature advanced electrostatic technology, where the powder is charged as it leaves the gun, ensuring even coverage and maximum adhesion.
- Automatic powder recovery systems are integrated into the spray booths to collect overspray, reducing waste and increasing efficiency.
- Advanced Curing Technology:
- The curing oven in a high-efficiency system is optimized for energy consumption and consistency. These ovens often use energy-efficient technologies like convection heating or infrared radiation to reduce the time and energy required for curing.
- Advanced temperature and humidity controls ensure that the coating is uniformly cured, preventing defects like bubbles or streaks.
- Some systems incorporate conveyorized ovens that move the wheels through a set curing zone, allowing for continuous production without the need for manual handling.
- Automation and Process Control:
- A high-efficiency powder coating line often includes advanced process control systems, which monitor variables like temperature, spray pressure, and coating thickness in real-time.
- These systems adjust the parameters automatically to ensure the coating process remains within the specified limits, improving consistency and quality.
- Real-time feedback allows operators to quickly identify and address issues, reducing downtime and defects.
- Energy Recovery and Waste Reduction:
- High-efficiency systems are designed to minimize waste by using powder recovery systems that capture unused powder and return it to the application process.
- Energy recovery systems within the curing oven or spray booth can further optimize energy use, cutting down on operational costs and reducing the carbon footprint of the process.
- Post-Coating Inspection and Quality Control:
- After the wheels have been coated and cured, they go through automated inspection stations where machines inspect the coating for imperfections such as color consistency, thickness, and adhesion.
- Some systems employ robotic arms or vision systems equipped with cameras to conduct this inspection, ensuring that only wheels that meet the quality standards move to the next stage of production.
- In cases where defects are detected, the system may trigger an automatic rejection mechanism or notify operators for manual inspection.
- Automated Packaging:
- Once the wheels are coated and inspected, they are automatically packaged using robotic arms or conveyors. This reduces manual handling and speeds up the process.
- Packaging can include wrapping, labeling, and boxing the finished wheels in preparation for shipment or storage.
- Integration with ERP Systems:
- Many high-efficiency lines are integrated with Enterprise Resource Planning (ERP) systems, allowing for real-time monitoring of production data, inventory, and supply chain management.
- This integration allows manufacturers to track production rates, order quantities, and material usage efficiently, helping to improve overall operational efficiency and customer satisfaction.
Advantages of High-Efficiency Alloy Wheel Powder Coating Lines:
- Increased Throughput: Automation and optimized processes result in faster cycle times, enabling more wheels to be coated in less time.
- Consistent Quality: Real-time monitoring and automated adjustments help ensure that each wheel receives an even coating, resulting in high-quality finishes.
- Reduced Waste and Lower Costs: Powder recovery systems, energy-efficient curing ovens, and automated material handling reduce waste and lower operational costs, making the process more sustainable.
- Flexibility: Modern high-efficiency systems are often adaptable, allowing manufacturers to easily change color, finish, or powder type depending on customer requirements without significant downtime.
- Minimal Labor Requirements: Automation reduces the need for manual labor, which decreases human error, enhances consistency, and allows workers to focus on other value-added tasks.
- Reduced Environmental Impact: By reducing powder waste and energy consumption, high-efficiency systems are more environmentally friendly compared to traditional coating systems.
A high-efficiency alloy wheel powder coating line is ideal for manufacturers looking to boost production capacity while maintaining high standards of quality, reducing operational costs, and supporting sustainable practices. Such a system is particularly advantageous in industries where large volumes of wheels need to be coated with high consistency, such as in automotive manufacturing, aftermarket wheel production, and large-scale remanufacturing operations.
A high-efficiency alloy wheel powder coating line focuses on streamlining the coating process by integrating advanced technologies and automation to enhance productivity, reduce energy consumption, and maintain consistent high-quality results. In these systems, automated loading and unloading systems are often employed to quickly and efficiently handle wheels, minimizing manual labor and improving throughput. This automation extends to various stages of the coating process, from pre-treatment and surface preparation to the application of powder and the curing process.
In terms of pre-treatment, high-efficiency lines often include automated blast cabinets or ultrasonic cleaning systems to ensure thorough surface cleaning before powder application. These systems are designed to remove all contaminants like oil, dirt, and rust, ensuring that the powder adheres properly. The electrostatic powder application process uses high-quality spray guns that apply the coating evenly across the wheel’s surface. These guns employ electrostatic charging, ensuring that the powder sticks to the surface, even in hard-to-reach areas. Additionally, advanced powder recovery systems capture overspray, reducing waste and making the process more sustainable.
The curing process is optimized in high-efficiency systems with energy-saving features like convection heating or infrared radiation, ensuring that the powder cures quickly and uniformly. The curing ovens are equipped with precise temperature and humidity controls to ensure that the wheels are properly baked, avoiding defects like uneven coating or incomplete curing. Some systems even use conveyorized ovens that allow continuous production, reducing manual handling and increasing output.
Automation plays a key role in ensuring consistent quality, with process control systems continuously monitoring variables like temperature, spray pressure, and coating thickness. These systems make real-time adjustments, reducing the chances of defects and maintaining high standards. Once the wheels are coated, they undergo automated inspection, often using robotic arms or vision systems that check for any imperfections in the coating, such as inconsistent color or thickness. Defective wheels are automatically rejected or flagged for manual inspection, ensuring that only high-quality wheels proceed to the next stage.
Energy recovery and waste reduction are central to high-efficiency systems, where technologies like powder recovery systems and energy-efficient ovens help cut down on operational costs. By capturing unused powder and reintroducing it into the process, these systems minimize material waste. Additionally, advanced curing ovens and spray booths help conserve energy, further reducing the system’s environmental impact. After coating and inspection, the wheels are automatically packaged, often with robotic arms that handle the wrapping and boxing of the finished products for shipment.
Integration with Enterprise Resource Planning (ERP) systems allows manufacturers to monitor production rates, manage inventory, and track material usage in real time. This integration enhances overall efficiency and provides a clearer view of the production process, allowing for better planning and decision-making. The high-efficiency alloy wheel powder coating line is designed not only to maximize throughput but also to maintain a level of flexibility, allowing manufacturers to easily switch between different colors, finishes, or powder types depending on customer needs.
By reducing manual labor, improving consistency, and minimizing waste, these systems offer a significant advantage for manufacturers looking to increase their production capacity while maintaining a sustainable approach. They are especially beneficial in industries with high-volume production needs, such as automotive manufacturing or large-scale wheel remanufacturing operations, where the need for both speed and quality is critical. The result is a process that not only meets but often exceeds the expectations for durability, appearance, and environmental responsibility.
A key aspect of high-efficiency alloy wheel powder coating lines is their ability to handle varying production volumes while maintaining high quality. These lines can be designed to accommodate both small and large runs, offering flexibility in production. They are ideal for manufacturers who need to quickly shift from one production batch to another, whether it’s for custom orders or different wheel models. The system’s automation allows it to scale efficiently, meaning that even during peak demand, production can continue without compromising the consistency or quality of the finished products.
Advanced features like automatic color change systems further enhance the flexibility of high-efficiency lines. These systems allow manufacturers to switch between different powder colors or finishes with minimal downtime. Automatic flushing systems ensure that the previous color does not mix with the new one, ensuring a flawless finish every time. This capability is particularly useful in industries where customers demand a variety of colors or finishes on their wheels, such as the automotive aftermarket, where customizations are a major selling point.
High-efficiency powder coating lines also support increased throughput by optimizing every step of the process. For example, automated curing ovens reduce the cycle time for each wheel, enabling faster production rates. Conveyorized systems move the wheels seamlessly through each stage, from pre-treatment to curing, while maintaining consistent speed and efficiency. This integration of processes helps eliminate bottlenecks and ensures a smooth, continuous flow from start to finish.
The integration of machine learning and artificial intelligence (AI) in some high-efficiency lines takes quality control to the next level. AI-based systems can analyze data in real-time, predicting potential issues in the coating process before they become major problems. These systems can learn from previous production cycles and optimize parameters like powder application pressure, curing temperature, and speed for each batch. As a result, manufacturers benefit from predictive maintenance, reducing unexpected downtime and extending the lifespan of critical equipment.
Another advantage of high-efficiency systems is their focus on sustainability. Not only do powder coating lines significantly reduce the use of volatile organic compounds (VOCs) by eliminating the need for solvent-based coatings, but they also optimize energy usage, reducing the carbon footprint of the operation. The energy recovery features within the curing ovens ensure that heat is reused rather than wasted, further reducing energy consumption and cost.
Maintaining a clean and safe work environment is another priority of high-efficiency systems. Automated cleaning stations or systems that use minimal water and chemicals for pre-treatment and cleaning reduce the environmental impact of waste disposal. These cleaning systems are often closed-loop, meaning that the water or chemicals can be reused, minimizing waste. Additionally, modern spray booths are designed with filtration systems that capture excess powder, preventing it from being released into the environment and improving air quality in the workplace.
Moreover, the efficiency of the system makes it highly cost-effective in the long run. While the initial investment in a high-efficiency coating line may be higher, the reduction in material waste, lower energy consumption, and decreased labor costs lead to a quicker return on investment. The ability to produce high-quality, durable wheels at a faster rate also boosts overall profitability. These lines are particularly advantageous for manufacturers who need to stay competitive in industries that demand both volume and customization, such as automotive, industrial equipment, and aftermarket products.
Finally, the continuous development of high-efficiency alloy wheel powder coating lines reflects broader trends in manufacturing, where the focus is not only on maximizing output but also on improving precision and reducing environmental impacts. As manufacturers face increasing pressure to meet sustainability goals while maintaining competitive pricing, investing in such high-efficiency systems becomes a strategic decision to stay ahead of the curve in both quality and environmental responsibility.
Alloy Wheel Powder Coating Machine Line
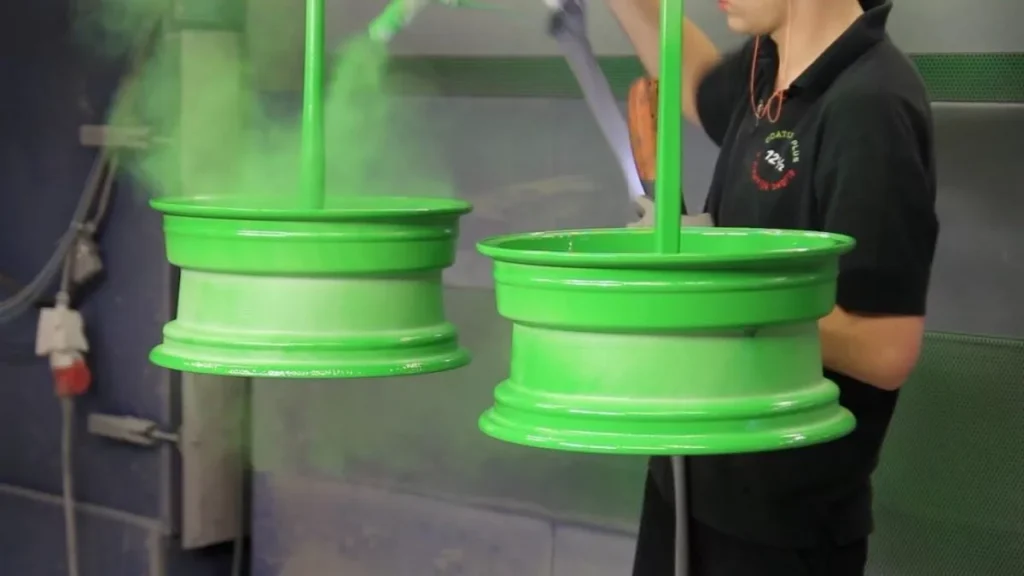
An alloy wheel powder coating machine line is a fully automated or semi-automated system designed for the efficient coating of alloy wheels with powder-based finishes. The line integrates several machines and technologies to ensure high-quality coatings while maximizing production speed, reducing waste, and improving the overall efficiency of the coating process. These lines are used extensively in industries like automotive manufacturing, aftermarket wheel customization, and large-scale wheel remanufacturing.
Key Components of an Alloy Wheel Powder Coating Machine Line:
- Loading and Unloading Systems:
- Automated Conveyors: These are used to transport wheels throughout the coating process, from pre-treatment to finishing. They are typically designed for smooth, continuous movement, ensuring that wheels are moved quickly and efficiently through the entire system.
- Robotic Arms or Manual Stations: Depending on the level of automation, either robotic arms or manual stations handle the loading of wheels onto conveyors, ensuring proper placement and minimizing the risk of contamination or damage.
- Pre-treatment Stations:
- Blast Cabinets: These are used for cleaning the wheels by blasting them with abrasive materials like sand or shot. This removes rust, old paint, or any surface contaminants, preparing the wheels for a clean and consistent powder coating.
- Chemical Cleaning and Phosphating: In addition to abrasive blasting, chemical cleaning stations or phosphating baths may be employed. Phosphating creates a microscopic layer that improves the adhesion of the powder coating and helps prevent corrosion.
- Ultrasonic Cleaning: For more sensitive or detailed cleaning, ultrasonic cleaning systems use high-frequency sound waves to clean wheels without damaging the surface.
- Powder Application Booth:
- Electrostatic Powder Spraying: Powder is applied to the wheel using electrostatic spray guns, which charge the powder particles. This charge causes the powder to adhere to the wheel’s surface evenly. The electrostatic application ensures that even hard-to-reach areas are coated effectively.
- Powder Recovery Systems: Excess powder is collected through air filtration systems and returned to the powder hopper, reducing waste and improving cost efficiency. The recovery system captures overspray and recycles it back into the process, ensuring minimal powder wastage.
- Multiple Powder Booths: Some systems feature multiple powder booths for different color or texture applications. Automated color change systems can switch between powder colors with minimal downtime, making these lines ideal for custom or batch orders.
- Curing Oven:
- Conveyorized Curing Ovens: After the powder is applied, the wheels are moved into a curing oven where the powder is heated to around 180-200°C (356-392°F) for a set amount of time. The heat causes the powder to melt and bond to the wheel’s surface, creating a durable, protective coating.
- Infrared or Convection Heating: Some advanced systems use infrared or convection heating to cure the powder more efficiently. These technologies reduce the time required to cure the coating while using less energy.
- Energy-efficient Systems: High-efficiency curing ovens are designed to minimize energy consumption. Features like heat recovery systems allow the reuse of heat, cutting down on overall energy costs.
- Cooling System:
- Cooling Chambers: After the wheels are cured, they are moved into cooling chambers where they are cooled down to ambient temperature. The cooling process ensures that the coating solidifies properly and prevents warping or distortion of the wheels.
- Airflow or Water Cooling: Depending on the design of the system, either forced airflow or water cooling can be used to accelerate the cooling process, ensuring that the wheels are ready for handling quickly.
- Inspection and Quality Control Stations:
- Automated Vision Systems: High-end systems may include automated vision inspection stations that use cameras and sensors to check for coating defects such as uneven thickness, bubbling, or imperfections in the color finish. These systems provide real-time feedback to the operators, ensuring that only defect-free wheels proceed to the next stage.
- Manual Inspection: In addition to automated inspection, some lines may include manual inspection stations where workers check the wheels for any defects that the automated system may have missed.
- Packaging and Unloading:
- Automated Unloading: After the wheels are coated and inspected, they are moved by the system to unloading stations. This may involve robotic arms or conveyors that place the wheels in packaging stations.
- Packaging Systems: Wheels are wrapped and packaged in boxes or other protective materials to prevent damage during transit. In some systems, packaging is fully automated to minimize labor costs and speed up the process.
- Control System and Monitoring:
- PLC (Programmable Logic Controller): A PLC-based control system is used to monitor and control every stage of the powder coating line. It ensures that parameters like temperature, coating thickness, curing time, and conveyor speed are adjusted for optimal results.
- Real-time Data Tracking: Many systems come with data logging capabilities that allow manufacturers to track production data, quality control metrics, and maintenance schedules in real-time. This helps improve overall production efficiency and ensures consistency.
- Safety and Environmental Features:
- Dust Extraction and Filtration: Powder coating lines are equipped with dust extraction systems to remove airborne powder and ensure a safe working environment. These systems filter out excess powder from the air to keep the workplace clean and minimize exposure to hazardous materials.
- Environmental Considerations: Many alloy wheel powder coating machines are designed with sustainability in mind. Features like energy-efficient curing ovens, powder recovery systems, and low-VOC materials help reduce environmental impact while maintaining high efficiency.
Advantages of Alloy Wheel Powder Coating Machine Lines:
- High Productivity: Automation and streamlined processes allow for rapid production, which is essential for high-volume manufacturers or those with large orders.
- Consistency and Quality: The use of electrostatic powder spraying ensures an even, uniform coating, while automated inspection systems guarantee consistent quality.
- Cost-Effectiveness: Powder recovery systems and energy-efficient curing ovens help reduce waste and energy consumption, making these systems cost-effective in the long term.
- Environmental Benefits: Powder coating is an eco-friendly process that generates little to no hazardous waste compared to traditional liquid paint methods. Additionally, modern systems incorporate energy-saving technologies that reduce the carbon footprint.
- Customization: With automated color change systems and multiple powder booths, manufacturers can easily produce custom colors and finishes to meet specific customer requirements.
- Reduced Downtime: Automated processes and predictive maintenance capabilities help minimize downtime and keep production running smoothly.
Overall, an alloy wheel powder coating machine line is an advanced, efficient, and eco-friendly system that meets the growing demands for high-quality, durable, and customizable wheel finishes. If you’re interested in specific technical details, like a particular machine’s capabilities or how the automation works, feel free to ask!
Alloy wheel powder coating machine lines are designed for efficiency, speed, and high-quality finishes. These systems automate much of the process, from loading wheels to applying powder and curing the coating, allowing manufacturers to achieve high throughput without sacrificing quality. The advanced automation not only increases production speed but also ensures consistency in the coating application, reducing human error and maintaining uniformity across all finished products. The pre-treatment stage, which cleans the wheels before powder application, is a crucial part of the process. Whether through abrasive blasting or chemical cleaning, this stage ensures that the wheels are free from contaminants, which helps the powder adhere better and creates a more durable finish. The electrostatic powder application is one of the defining features of the line. The powder is charged as it is sprayed, which helps it cling to the wheel’s surface even in hard-to-reach areas, ensuring an even and uniform coating. The powder recovery system is another essential part of these lines. As powder is sprayed, excess material that does not adhere to the wheel is captured and sent back to the hopper for reuse. This helps reduce material waste and contributes to cost efficiency.
The curing process is also optimized in these systems, using either convection heating or infrared radiation to heat the coated wheels at precise temperatures. This step ensures that the powder bonds properly to the wheel, forming a durable and protective layer. The curing ovens are designed to be energy-efficient, often using heat recovery systems to minimize energy consumption, which helps reduce operational costs. Once the wheels are coated and cured, they are cooled either through forced air or water cooling, which solidifies the coating and prepares the wheels for inspection. Automated inspection systems using cameras or sensors check for imperfections like uneven coating, color inconsistencies, or bubbles. These systems quickly detect any defects, ensuring that only perfectly coated wheels proceed to packaging. After inspection, wheels are unloaded and moved to packaging stations, where they are wrapped and boxed for shipment or storage.
The entire system is controlled through a central PLC-based control system, which monitors every step of the process, adjusting parameters like temperature, spray pressure, and curing time to optimize performance. The system also tracks production data in real-time, providing insights into efficiency, quality control, and maintenance needs. These powder coating lines are designed to be environmentally friendly by reducing waste, energy consumption, and the release of harmful VOCs. Features like dust extraction systems help maintain a clean working environment by capturing airborne powder particles, ensuring that the air quality remains safe for workers. Additionally, the systems are designed to be customizable, with options for switching powder colors or finishes quickly, making them suitable for manufacturers that need to fulfill custom or diverse customer orders.
Overall, an alloy wheel powder coating machine line offers significant benefits in terms of speed, quality, cost-effectiveness, and environmental sustainability. By automating key stages of the process and incorporating advanced technologies like powder recovery and predictive maintenance, these systems allow manufacturers to meet the growing demands for high-quality, customizable, and durable wheel finishes while also minimizing operational costs and waste.
As the demand for customized and durable alloy wheels continues to rise, manufacturers are increasingly turning to fully integrated powder coating lines that can accommodate both high-volume production and frequent design changes. These systems are engineered for scalability, allowing production lines to expand or adjust in capacity based on market demands without significant reconfiguration. Many lines now incorporate modular components, so additional stations can be added for extra curing capacity, specialized finishes, or new colors with minimal disruption to ongoing operations. This adaptability is particularly valuable in markets where consumer preferences shift rapidly and product variety is a competitive advantage.
One of the standout features of advanced powder coating machine lines is their ability to manage high-mix, low-volume production efficiently. Thanks to fast color change systems and intelligent process controls, manufacturers can transition between different product specifications without long setup times or contamination issues. Automated systems clean and purge lines rapidly, allowing for nearly seamless shifts from one wheel type or finish to another. This flexibility not only supports customization but also helps reduce downtime and material waste, improving overall equipment effectiveness.
Digital integration is another important development in modern coating lines. The use of Industry 4.0 technologies such as IoT sensors, real-time analytics, and cloud-based monitoring provides operators with unprecedented control and insight into every phase of production. These systems can detect wear in components, anticipate maintenance needs, and even recommend operational adjustments to optimize output. This data-driven approach ensures the coating process remains consistent and efficient, even as production loads and environmental conditions vary.
The environmental performance of these systems has also improved significantly. Closed-loop water systems in pre-treatment stages reduce water consumption and the release of effluents. Low-energy curing ovens and high-efficiency filtration units not only reduce electricity usage but also meet stringent emissions standards. The result is a process that supports both regulatory compliance and corporate sustainability goals, which are increasingly important in today’s global manufacturing landscape.
Additionally, powder coating lines contribute to product durability. Compared to liquid paints, powder coatings offer superior resistance to corrosion, chipping, and fading, which is particularly important for wheels exposed to harsh road and weather conditions. The robust finish achieved through precise application and curing enhances the product’s lifespan and reduces warranty claims or returns due to cosmetic damage. This reliability builds customer confidence and strengthens brand reputation.
On the labor side, automation has also improved workplace safety and reduced the need for highly specialized manual skills. By automating tasks like spraying, curing, and handling heavy wheels, these systems reduce physical strain and exposure to hazardous substances. Operators are instead trained to oversee systems, monitor data, and perform routine maintenance, shifting the labor profile toward safer and more technically skilled roles.
In conclusion, alloy wheel powder coating machine lines have evolved into highly sophisticated systems that integrate mechanical efficiency, digital intelligence, environmental responsibility, and user-focused design. Their ability to deliver high-quality, consistent results across a wide range of product types makes them an essential part of modern wheel manufacturing operations. Whether serving OEM production lines or high-end custom shops, these systems are key to meeting the twin goals of operational excellence and superior product performance. Would you like help drafting specifications or selecting equipment for a particular facility?
Alloy Wheel Powder Coating Robotic Line
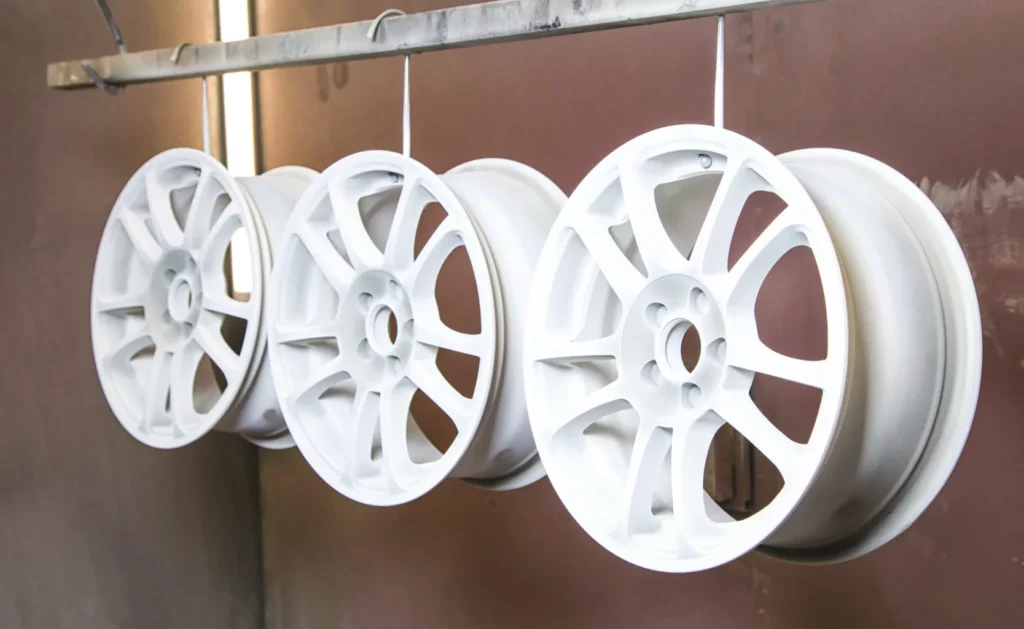
An alloy wheel powder coating robotic line represents the most advanced and automated solution for applying powder coatings to alloy wheels, combining robotics, intelligent control systems, and precision engineering to deliver unmatched consistency, speed, and efficiency. These lines are designed for manufacturers aiming for high production volumes with minimal human intervention while maintaining exceptional finish quality and operational flexibility.
In this setup, robotic arms perform many critical tasks such as wheel loading and unloading, powder application, and even real-time inspection. The use of industrial robots ensures repeatable precision in every cycle, which is especially important when dealing with complex wheel geometries and intricate designs. Robotic sprayers can follow precise paths around the wheel, adjusting spray angles and distances dynamically, which results in uniform coating thickness even in deep recesses or tight corners. These robots are typically programmed with 3D models of the wheels, allowing them to adapt to various wheel sizes and designs without manual recalibration.
The pre-treatment phase in a robotic line is also highly automated. Wheels are fed through automated cleaning tunnels or robotic blast stations where contaminants like oils, oxides, and old coatings are removed. This preparation is vital for ensuring proper adhesion of the powder. In some lines, robots handle wheel orientation during this phase to expose all surfaces uniformly to the blasting media or chemicals.
After pre-treatment, the wheels move via conveyor to the robotic powder spray booth. Here, multiple robotic arms equipped with electrostatic spray guns apply the powder coating. These arms move in perfectly synchronized paths to ensure 360-degree coverage, and they adjust parameters like powder flow rate, gun voltage, and air pressure in real time based on sensor feedback. Advanced systems use AI-driven vision or laser scanning to verify that the coating is even and within specified thickness tolerances before the wheel exits the booth.
The coated wheels then enter a precisely controlled curing oven. In robotic lines, conveyor systems often use indexing or continuous flow to ensure accurate timing and temperature exposure for each wheel. Some systems also include robotic handling at oven entry and exit points to maintain a completely touchless workflow. The ovens themselves are equipped with energy-saving technologies like heat recovery and zone-based heating to optimize power use without sacrificing curing quality.
Post-curing, robotic arms may also carry out visual inspection using high-resolution cameras and AI-powered defect detection. These systems can identify flaws like orange peel texture, pinholes, or uneven gloss and immediately sort defective parts for rework or rejection. In many cases, this step replaces the need for manual quality control, speeding up throughput and reducing labor costs.
A robotic powder coating line also integrates with MES (Manufacturing Execution Systems) or ERP platforms to provide real-time tracking of production data, coating performance, equipment status, and material usage. This level of digital integration enables predictive maintenance, minimizes unplanned downtime, and supports lean manufacturing strategies. It also allows for seamless product changeovers; with robotic programming stored digitally, switching from one wheel model or color to another takes only moments, reducing production lag between batches.
From an environmental perspective, robotic lines are designed for minimal waste and emissions. Powder recovery systems are more efficient due to the precise application by robots, reducing overspray. Closed-loop air systems and advanced filtration reduce the escape of fine particulates into the work environment, making the system both cleaner and safer.
Overall, an alloy wheel powder coating robotic line is the pinnacle of coating technology in the wheel industry. It offers unmatched consistency, speed, and adaptability, making it ideal for high-end OEMs, performance wheel brands, and any operation where quality and efficiency are non-negotiable. Would you like a breakdown of cost considerations or the technical configuration of a standard robotic cell in such a line?
The continuous evolution of alloy wheel powder coating robotic lines is driving the wheel manufacturing industry toward higher levels of automation, precision, and sustainability. These systems operate with a seamless flow of operations, where every stage—from surface preparation to final inspection—is managed by coordinated robotic units and intelligent software. The result is a streamlined process that significantly reduces human involvement while delivering flawless, repeatable quality across thousands of wheels. Each robotic arm is calibrated for exact motion paths that follow the contours of each wheel design, with sensors constantly feeding back data to adjust for variables like coating buildup or ambient temperature changes. This dynamic control leads to better transfer efficiency, meaning less powder is wasted and fewer defects occur during the application process.
The integration of vision systems and laser-guided positioning ensures that each wheel is identified, aligned, and coated with high accuracy regardless of its specific geometry or size. These systems allow robots to perform at a level of consistency that manual labor cannot match, reducing scrap rates and improving the overall finish. The shift toward such fully robotic lines is also reducing the need for highly skilled coating operators and replacing it with system supervisors and maintenance technicians who ensure the line runs optimally. Maintenance is largely predictive, based on data collected from the robotic components, powder delivery systems, and conveyor drives, which reduces downtime and extends equipment life.
Color changeovers, once a major source of production delay and contamination, are now executed by automated cleaning and purging systems within the powder booths. These systems can switch from one color to another in under five minutes, flushing out lines, cleaning spray nozzles, and resetting spray parameters—all without manual input. This functionality is especially critical for manufacturers that produce small batches or offer customized finishes, enabling them to fulfill diverse orders without sacrificing efficiency. The robotic nature of these lines also makes it easier to track and trace every wheel through the production process. Each wheel can be tagged with a barcode or RFID chip, allowing the system to log which batch, settings, and powder type were used for every individual item. This provides manufacturers with complete traceability and quality assurance documentation, which is increasingly important in the OEM and aftermarket supply chains.
The environmental performance of robotic powder coating lines is not only superior in terms of emissions and energy efficiency but also in how they handle raw materials. Overspray is minimized due to the precise targeting of robotic sprayers, and the powder that is recovered can often be immediately reused without compromising finish quality. Energy consumption is further reduced through the use of intelligent curing ovens that regulate their output based on the load, adjusting heat zones to avoid wasting energy when fewer wheels are being processed. These ovens can also integrate with the robotic line’s schedule to ensure that only wheels that meet all pre-curing requirements are admitted, preventing under- or over-cured coatings.
In terms of scalability, robotic lines are modular and can be expanded to include additional robots, inspection systems, or ovens as production demand increases. This makes them a future-proof investment for manufacturers who anticipate growing volumes or shifting product types. The user interface for operating these systems is typically centralized through an HMI or SCADA platform, providing real-time visualization of every station along the line. This central control also allows for remote diagnostics, system updates, and even cloud-based optimization in facilities connected to digital factory networks. With fewer physical touchpoints, there is also a significant improvement in cleanliness, safety, and product handling. Wheels remain untouched by human hands throughout most of the process, reducing contamination and physical damage. For manufacturers that prioritize high-end finishes or serve luxury automotive brands, this kind of handling is critical to maintaining a flawless surface throughout production.
Altogether, a robotic powder coating line for alloy wheels offers a compelling combination of precision, speed, flexibility, and long-term cost efficiency. It enables manufacturers to respond quickly to market changes, deliver premium products consistently, and meet ever-tightening environmental regulations without compromise. As more companies seek to modernize their facilities, these systems represent the benchmark for fully automated wheel finishing technology.
These robotic powder coating lines are also instrumental in maintaining consistent production output during labor shortages or fluctuations in workforce availability. Since they rely on automation rather than manual labor for critical functions such as spraying, quality control, and material handling, they provide operational stability regardless of external staffing issues. This level of resilience is particularly valuable in markets with tight delivery timelines or just-in-time manufacturing requirements, where any delay can disrupt the entire supply chain. Moreover, robots can operate continuously across multiple shifts without fatigue or performance degradation, making them ideal for high-volume production environments that demand uninterrupted output.
Another key advantage is the ability of these systems to adapt to increasingly complex wheel designs. With growing consumer demand for multi-spoke, concave, and machined-face wheels, manual coating techniques often fall short in achieving even coverage in intricate or recessed areas. Robotic arms equipped with multi-axis movement and precision-programmed paths can navigate these geometries flawlessly, ensuring that every surface receives a uniform layer of powder. This ensures not only visual appeal but also complete corrosion protection, even in hard-to-reach spots that would otherwise be vulnerable to environmental wear.
In facilities where high customization is a selling point, robotic lines offer mass customization without compromising efficiency. Each wheel can be processed with a different coating formula, gloss level, or texture by simply updating the robot’s program and powder feed system. This on-the-fly adjustability allows manufacturers to offer a wide range of styles and finishes—from satin blacks and hyper silvers to metallic flakes and transparent topcoats—without retooling or manual masking. It also opens opportunities for limited editions or customer-specified colors, supporting a business model focused on differentiation rather than pure volume.
The upstream and downstream integration of robotic coating lines further enhances their value. They are commonly linked with CNC machining centers, automated polishing stations, or laser engraving systems to form a complete manufacturing cell. Wheels can move directly from shaping and surface prep to coating and final inspection without manual transfers, reducing the risk of handling damage and further accelerating lead times. At the end of the line, robotic packing stations can also be included to wrap, label, and palletize wheels for immediate shipment. This end-to-end automation simplifies logistics and provides a clear path for tracking every unit from raw casting to finished product.
Training and support for these systems have also improved with virtual simulation tools and digital twins. Operators and technicians can now train on simulated versions of the line to learn how to adjust settings, troubleshoot faults, or optimize workflows without disrupting actual production. Digital twins also enable predictive analytics, where the system can model how wear and process drift might affect coating quality over time and alert teams to take corrective action before issues arise. These tools contribute not just to productivity, but to a more controlled, intelligent, and proactive manufacturing environment.
Ultimately, the robotic alloy wheel powder coating line represents a fusion of mechanical precision, software intelligence, and material science. It meets the rising expectations of consumers and OEMs for premium quality, color diversity, and long-term durability—while also addressing the manufacturer’s need for reliability, cost control, and sustainable practices. As wheel designs continue to evolve and global standards for environmental compliance become stricter, the adoption of these systems will only accelerate. They are not just a technology upgrade; they are becoming a strategic necessity for any forward-looking wheel production operation.
Electrostatic Alloy Wheel Powder Coating Line
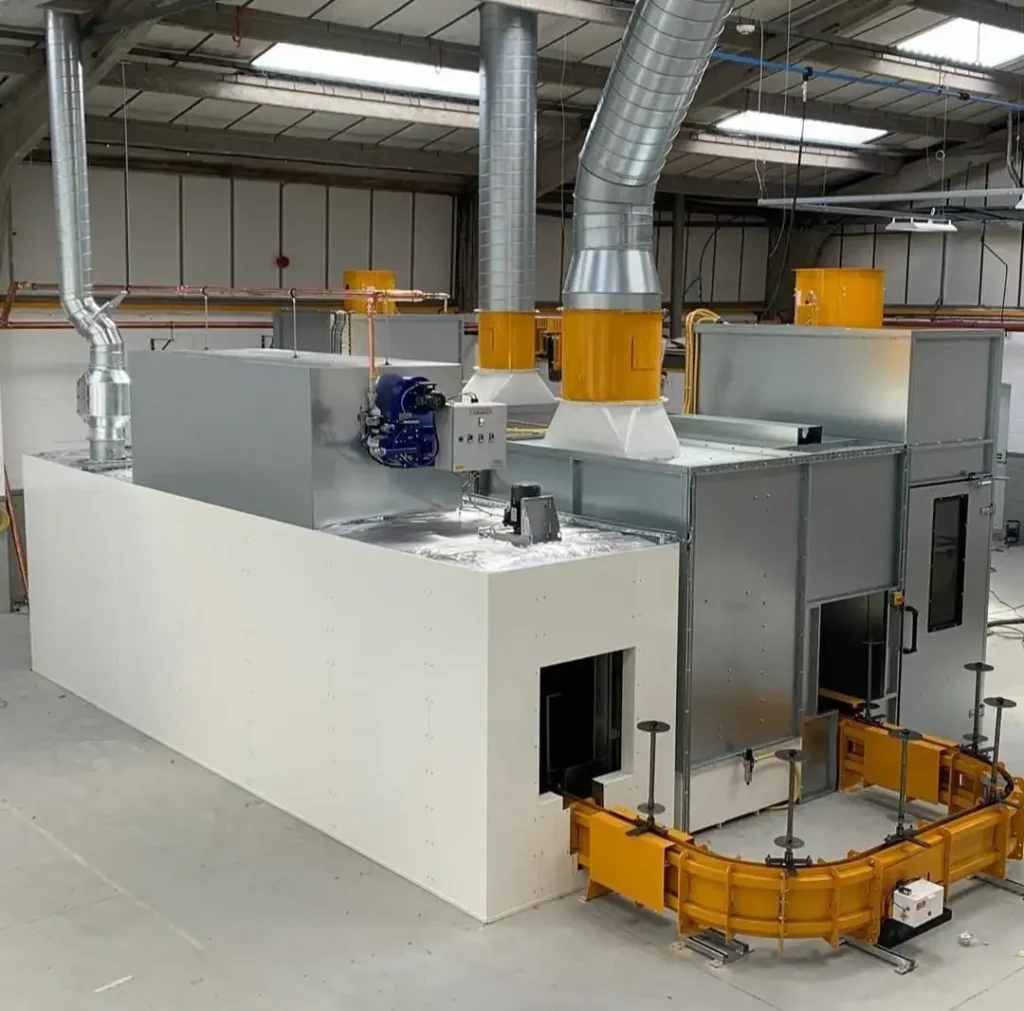
An electrostatic alloy wheel powder coating line is a specialized production system designed to apply powder coatings onto alloy wheels using electrostatic principles. This method is highly effective in achieving a durable, uniform, and aesthetically appealing finish while maximizing material efficiency and minimizing environmental impact. The line typically consists of sequentially arranged stations, each contributing to surface preparation, powder application, curing, and finishing, all synchronized for high-throughput production.
The core of the system is the electrostatic spray booth, where the powder coating is applied. Here, finely ground powder particles—usually made of thermoset polymers with additives for color, gloss, and durability—are electrostatically charged as they exit the spray gun. The alloy wheels, which are grounded, attract the charged particles, allowing the powder to adhere evenly across the wheel’s complex geometry. This process enables excellent coverage, even in recessed or intricate areas, reducing the need for touch-ups or multiple passes. Robotic or manually operated guns may be used, but in high-capacity lines, automatic reciprocators or multi-axis robots are preferred for precision and consistency.
Before powder application, wheels pass through a critical pre-treatment process, which removes oils, dirt, and oxides. This may involve degreasing, alkaline cleaning, rinsing, and sometimes conversion coatings such as zirconium or phosphate to enhance corrosion resistance. A clean and chemically activated surface ensures that the powder coating bonds effectively, leading to improved durability and finish quality. Depending on plant design, wheels may be pre-heated after pretreatment to improve powder adhesion by creating a slightly tacky surface.
Once coated, the wheels are conveyed into a curing oven. The powder melts and chemically reacts to form a solid, cross-linked film when heated to temperatures typically between 160°C and 200°C. This cured coating provides a hard, resilient surface that resists chipping, UV degradation, corrosion, and road chemicals. Convection ovens are most common, but infrared or hybrid ovens may be used for faster heat-up and energy efficiency. Cure times and temperatures are tightly controlled to ensure consistent film formation across all wheels.
A key advantage of electrostatic powder coating lines is the material efficiency. Overspray—powder that doesn’t land on the wheel—is collected by high-efficiency recovery systems, filtered, and often reused. This closed-loop setup significantly reduces waste and contributes to cost savings, especially for expensive custom colors or finishes. Moreover, because powder coatings are solvent-free, these systems emit virtually no volatile organic compounds (VOCs), helping manufacturers meet strict environmental regulations and sustainability goals.
After curing, wheels are cooled and may pass through quality inspection stations equipped with vision systems, thickness gauges, or human inspectors. Any imperfections—such as under-coverage, drips, or inclusions—can be flagged for rework. The final stage may include packing, labeling, and palletizing, depending on the production setup.
Electrostatic powder coating lines are scalable and can be configured for batch or continuous production. With digital control systems, operators can monitor temperature profiles, line speed, and spray parameters in real time, ensuring process stability and repeatability. These systems also support fast color changes, ideal for facilities handling custom finishes or varied production runs.
In summary, an electrostatic alloy wheel powder coating line delivers a combination of high performance, cost efficiency, and environmental compliance. Its ability to apply consistent, attractive, and long-lasting finishes makes it a vital solution for both OEM and aftermarket wheel manufacturers aiming to meet modern performance and design standards. Would you like to explore specific system components or layout configurations for such a line?
In modern manufacturing environments, the electrostatic alloy wheel powder coating line is increasingly integrated with digital process controls that enhance both efficiency and traceability. Every wheel entering the system can be tracked using barcode or RFID identification, allowing the control software to adjust parameters such as spray duration, powder type, and oven dwell time automatically. This individualized process control ensures that even mixed production batches—wheels of different designs or color specifications—can be coated uniformly without stopping or reconfiguring the line. The system’s flexibility allows for rapid adaptation to changing customer demands, making it suitable for both high-volume OEM contracts and specialized aftermarket orders.
The electrostatic method is not only more environmentally sustainable but also yields a finish that is harder and more resistant to wear than traditional liquid paints. Because the powder particles are drawn to the grounded metal by electrostatic attraction, they coat the surface evenly without sagging or dripping. Once cured, the coating becomes a dense, impermeable layer that resists corrosion, stone chips, brake dust, UV degradation, and salt exposure. This is particularly important for wheels that face harsh road conditions, seasonal temperature extremes, or prolonged sunlight exposure. The consistent film build achieved through electrostatic application also improves the aesthetic quality of the wheel by eliminating thin spots, orange peel, or uneven gloss, which are common issues in other coating techniques.
For manufacturers pursuing lean operations and reduced material waste, the electrostatic line offers clear advantages. Overspray is minimal due to the directional nature of the electric field, and any powder that does not adhere to the wheel is collected through cyclone recovery and filtration units. This reclaimed powder is often reintegrated into the process without significant loss of performance, further reducing material costs. In high-volume facilities, this can translate into thousands of dollars saved each year, alongside a lower environmental footprint due to reduced powder disposal.
The electrostatic powder coating process also simplifies compliance with safety and air quality standards. Because no solvents are involved, there is no release of volatile organic compounds into the air, and explosion hazards are significantly reduced. Air handling systems within the spray booths are designed to maintain clean working environments and prevent operator exposure to airborne particulates. In addition, many facilities use programmable logic controllers and sensors to monitor airflow, booth pressure, and humidity, all of which can affect powder performance. This data-driven approach ensures that conditions remain optimal regardless of external environmental changes, such as seasonal humidity fluctuations or shifts in line temperature.
Another key benefit is the reduction in labor and operator dependency. Once installed and commissioned, electrostatic powder coating lines require minimal human intervention aside from maintenance and oversight. Routine tasks such as gun cleaning, powder refills, and conveyor checks can be scheduled and even automated in some systems. The system’s reliability allows manufacturers to maintain production throughput without worrying about inconsistent manual application or staffing gaps. Furthermore, with advanced HMI touchscreens and remote diagnostics, line operators can quickly troubleshoot issues or perform system adjustments with minimal training, reducing downtime and improving overall equipment efficiency.
As industry expectations shift toward greater customization and faster turnaround times, electrostatic lines are also evolving to include rapid color change hoppers, automated booth cleaning systems, and dual-gun or multi-gun arrays that can handle complex wheel designs in a single pass. The combination of high transfer efficiency, low material waste, and robust coating quality makes these lines ideal for demanding production environments. Whether the end goal is a high-gloss show finish, a rugged matte look, or a multi-layered appearance with topcoats and clear finishes, the electrostatic powder coating line delivers with precision and repeatability.
Overall, the electrostatic alloy wheel powder coating line represents a sophisticated convergence of materials science, automation, and sustainable design. It addresses the dual demand for premium finish quality and manufacturing efficiency, while also aligning with stricter regulatory standards and rising consumer expectations. In a competitive industry where visual impact and product lifespan matter, this technology provides manufacturers with the tools to differentiate their wheels not just by design, but by durability and finish excellence.
The continuous advancement of electrostatic alloy wheel powder coating technology is also paving the way for increased integration with other smart manufacturing tools and techniques. The industry is increasingly adopting Industry 4.0 technologies, enabling real-time data collection and analysis across the entire coating process. By embedding sensors into critical points of the coating line—such as the spray booth, curing oven, and recovery systems—manufacturers gain valuable insights into process variables like temperature, humidity, coating thickness, and powder consumption. This information is processed through central control systems, enabling operators to fine-tune conditions on the fly and optimize the application process, ensuring that each wheel receives the ideal amount of coating without waste.
One significant development is the ability to perform predictive maintenance on these systems. By analyzing data trends over time, manufacturers can predict when components are likely to fail or require servicing. For example, sensors can detect slight changes in spray patterns that may indicate a clogged nozzle or issues with the electrostatic charge, prompting maintenance before a full breakdown occurs. This predictive approach reduces unplanned downtime and helps extend the life of both robotic arms and electrostatic spray guns, ensuring that the line continues to run smoothly with minimal interruptions.
The digital integration of the coating line also allows for seamless remote monitoring and control. Plant managers and technical teams can access the system from anywhere, providing real-time status updates, performance analytics, and troubleshooting assistance. This ability to manage the process remotely can improve operational efficiency, particularly for manufacturers operating multiple shifts or facilities in different locations. The same digital systems can track the performance of individual wheels, ensuring consistent quality and streamlining production reporting for traceability or regulatory compliance.
Another exciting trend is the customization of finishes. With advancements in both powder chemistry and application technology, electrostatic coating lines are now capable of achieving more varied and complex finishes. Manufacturers can offer a wide array of effects, from metallic and pearlescent finishes to textured or matte surfaces, all while maintaining the core benefits of powder coating—durability, uniformity, and resistance to the elements. These specialized finishes are achieved by adjusting the electrostatic charge and applying multiple layers of powder, with some lines incorporating advanced processes like multi-coat applications or clear-coat finishes to enhance gloss, depth, and protection.
The integration of robotic arms with electrostatic spray guns is also improving. Robots can now apply powder coatings with precision, ensuring that the spray gun moves along predetermined paths that cover all parts of the wheel, even in hard-to-reach areas. The robot’s precise control also reduces overspray and improves transfer efficiency, which is particularly important in reducing waste and minimizing the environmental impact. With these robotic systems, manufacturers can rapidly change between different wheel designs or sizes without manual adjustments, increasing the versatility of the line.
Additionally, fast-change powder delivery systems have made significant strides. These systems enable powder color changes in a matter of minutes, reducing the downtime typically associated with purging and cleaning between color shifts. This is particularly beneficial for manufacturers producing limited edition runs or responding to market trends that require rapid adjustments in coating color. The improved efficiency and speed of these color changes have become a major competitive advantage for businesses that prioritize customer satisfaction and fast delivery times.
Beyond speed and efficiency, electrostatic powder coating lines also focus on improving sustainability. With growing environmental concerns and stringent regulations on manufacturing processes, many systems now include features designed to reduce energy consumption and environmental impact. Advanced energy recovery systems help to reduce the amount of energy required for curing, while closed-loop water systems in the pre-treatment stations minimize water usage. The closed-loop recovery systems in the powder booths allow the collected overspray to be cleaned, filtered, and returned to the process, ensuring that little to no powder is wasted.
Moreover, these systems often come with automated environmental controls that adjust parameters based on real-time feedback from the environment. For example, humidity and temperature are monitored continuously to prevent deviations that could affect coating quality. In doing so, the systems not only ensure optimal performance but also enhance environmental compliance, contributing to manufacturers’ sustainability initiatives.
Electrostatic powder coating lines are becoming more adaptable, with some lines now being able to handle a broader range of wheel sizes and designs. This adaptability is particularly valuable for businesses that offer custom wheels or work with high-end performance vehicles, where unique designs are often required. These flexible lines can handle wheels with different profiles, from standard flat-faced designs to more complex multi-spoke and deep-dish configurations, all while maintaining the highest standards of coating quality.
As consumer demand for customized finishes grows, these systems will only become more refined, with manufacturers constantly innovating to meet the new aesthetic and performance requirements. This makes the electrostatic alloy wheel powder coating line not only a technological solution but also a strategic tool for businesses looking to differentiate their products in a competitive market. The system’s ability to deliver premium quality, minimize waste, and operate with minimal environmental impact positions it as a key player in the future of wheel manufacturing.
Alloy Wheel Powder Coating Automation Line
An alloy wheel powder coating automation line is an advanced manufacturing system designed to automate the entire powder coating process for alloy wheels. This automation not only increases production speed and efficiency but also ensures consistent quality and reduces labor costs. By integrating various automated processes—from pre-treatment to powder application, curing, and quality control—the system streamlines the production workflow and enhances overall operational performance.
The automation line begins with wheel loading and handling, where either robots or conveyor systems take the wheels from the storage area and move them through the various stages of the coating process. In high-volume facilities, automated systems can load, orient, and transfer wheels to specific stations without human intervention. For example, wheels might be indexed into a pre-treatment station, where they undergo a series of cleaning processes, such as chemical degreasing, abrasive blasting, or phosphating, to ensure the surface is clean and ready for coating. This is a critical step, as surface preparation directly impacts the adhesion and durability of the powder coating.
Once pre-treated, the wheels are transferred to an electrostatic powder coating booth, which is the core of the coating line. In this stage, automated robotic arms or electrostatic spray guns apply the powder coating to the wheels. The use of robotic sprayers allows for precise control of the powder application process. The robots follow pre-programmed paths, ensuring that each wheel is coated uniformly, even in intricate or recessed areas. This is especially important in alloy wheel production, where designs often feature complex shapes and multi-spoke configurations that require a high level of precision for complete coverage.
The electrostatic charge applied to the powder particles helps them adhere to the grounded wheel surface, resulting in a consistent and even coating. Additionally, powder recovery systems built into the spray booth ensure that any overspray is collected, filtered, and recycled back into the system, minimizing waste and reducing material costs.
Following powder application, the wheels move to a curing oven. Here, the powder is heated to a high temperature (typically between 160°C and 200°C) to melt and fuse, creating a smooth, durable, and chemically resistant finish. The curing process is automated, with the oven temperature and curing time precisely controlled to ensure a consistent result across all wheels. Conveyor systems, often integrated with the curing oven, move the wheels through the oven at a controlled pace, ensuring each wheel receives the appropriate level of heat exposure.
After curing, the wheels exit the oven and enter a cooling station. Here, automated systems cool the wheels to room temperature before they move on to quality inspection and finishing. Automated vision systems can be employed to detect defects such as uneven coverage, bubbles, or imperfections in the finish. Some systems even incorporate laser scanning or high-definition cameras to check the thickness and uniformity of the powder coating. If any defects are detected, the affected wheels are flagged for rework, ensuring that only wheels meeting the required standards continue through the line.
For higher levels of automation, post-inspection handling can be further automated. Robotic arms or automated packing systems may be used to unload the wheels from the inspection area, move them to final packaging, and palletize them for shipment. This further minimizes human labor while maintaining a smooth and efficient workflow, reducing the potential for damage or contamination during the final stages of production.
The entire automation line is typically controlled by a centralized control system that allows operators to monitor and adjust various parameters, such as temperature, conveyor speed, and coating thickness. Many modern systems are integrated with Industrial Internet of Things (IIoT) technologies, which provide real-time data on the performance of the entire line, including energy consumption, material usage, and equipment health. These insights enable predictive maintenance, helping prevent downtime and ensuring optimal system performance.
One of the biggest advantages of an alloy wheel powder coating automation line is consistency and repeatability. The use of robots and automated equipment ensures that each wheel is coated exactly the same way, with no variation in thickness or finish. This leads to higher quality products and fewer defects, making the line ideal for high-volume production environments where uniformity is key. It also allows for rapid changeovers between different wheel sizes or colors without the need for manual adjustments, which increases overall flexibility.
Energy efficiency is another key benefit of automated systems. By optimizing the curing process, reducing overspray, and reclaiming powder, these lines use less material and energy compared to traditional manual methods. This not only reduces costs but also aligns with sustainability goals, as manufacturers can meet stricter environmental regulations regarding waste and emissions.
In terms of flexibility, modern automated alloy wheel powder coating lines are adaptable to a variety of wheel designs and sizes. Automated handling systems can accommodate wheels of different profiles, from simple flat designs to complex multi-spoke or deep-dish configurations. The electrostatic spray systems can also be easily adjusted to accommodate different powder types, finishes, or colors, making the line suitable for both mass production and more specialized, custom orders.
Overall, an alloy wheel powder coating automation line is an efficient, scalable, and cost-effective solution for manufacturers looking to improve quality, reduce labor costs, and meet growing market demands for precision-engineered finishes. With its ability to handle high volumes, maintain consistent product quality, and minimize waste, it is a key technology for modern alloy wheel production.
The automation of the alloy wheel powder coating line not only elevates production efficiency but also significantly enhances the ability to respond to market dynamics. As customer preferences shift towards more personalized or limited-edition wheels, automated systems can easily accommodate quick changes in design, color, or finish without causing production delays. Advanced software allows operators to adjust the powder application parameters, curing times, and even coating layers with minimal downtime, enabling manufacturers to fulfill diverse customer requests while maintaining high throughput.
One of the most remarkable aspects of these automated lines is their ability to scale. Whether the factory is producing a few hundred or tens of thousands of alloy wheels daily, the automation ensures that each product meets stringent quality standards. Manufacturers can scale operations without significantly increasing labor costs, thanks to the automation of wheel handling, coating application, and even post-production inspection and packing. This scalability is particularly advantageous in industries like automotive manufacturing, where demand can fluctuate based on seasonality, model updates, or the introduction of new trends. Automated systems can quickly adjust to these fluctuations, ensuring that production meets demand without compromising on quality or speed.
In addition to its core functions, automation can also be integrated with advanced analytics and predictive modeling to improve the overall efficiency of the coating line. Sensors installed throughout the system can collect data on every aspect of production, from powder consumption to the curing process. This data is then analyzed to identify any areas of inefficiency or potential equipment failures before they occur. For example, if a sensor detects an anomaly in the curing process, the system can alert operators in real time and adjust the oven settings to correct the issue, preventing defective products from reaching the end of the line. This proactive approach helps manufacturers maintain a steady, uninterrupted flow of high-quality wheels, reducing waste and minimizing costly rework.
Moreover, these automation lines are designed with sustainability in mind. Many systems incorporate energy-efficient technologies, such as heat recovery units in curing ovens, that help lower energy consumption while maintaining the required process temperatures. The efficient use of materials is another critical aspect. Powder coating is a dry process, and any excess powder is typically reclaimed and reused in the system, reducing the need for new powder and minimizing waste. In addition, the electrostatic nature of the coating process ensures that the powder is applied directly to the wheel surface with minimal overspray, further reducing material usage. Combined with the absence of volatile organic compounds (VOCs) in the coating process, this makes the automation line a more environmentally friendly option compared to traditional liquid painting methods.
With advanced robotic arms or automated conveyors, the entire post-coating process is streamlined as well. After curing, automated systems can handle the unloading, cooling, inspection, and packing of the wheels. For example, once the wheels are cooled, they can be automatically transferred to quality inspection stations where vision systems or other automated detection technologies assess the coating’s uniformity and finish. This ensures that only wheels with perfect coatings move forward to the packaging stage, reducing the chance of human error or oversight in the inspection process. After inspection, robotic arms or automated packaging stations can handle the wheels without risk of damage, placing them in protective packaging or palletizing them for shipment.
The adoption of smart technologies further enhances the capabilities of these systems. Manufacturers can use cloud-based platforms or local servers to monitor real-time data from the production line, analyze performance metrics, and adjust workflows remotely. This centralized monitoring not only makes troubleshooting more efficient but also allows for continuous optimization of the coating process based on feedback from previous production runs. Additionally, integrated systems can track inventory, powder usage, and curing cycles to maintain optimal stock levels, ensuring that the coating process runs without interruptions due to supply chain issues.
For manufacturers seeking to differentiate themselves in a competitive market, the integration of customization options is a game changer. Automation allows for quick, flexible changes in the production process. Customers can request a variety of finishes—from matte, gloss, or satin to textured or metallic—and these can be achieved with little disruption to the production line. The ability to seamlessly switch between different colors, textures, and effects without requiring significant downtime is a major advantage in industries where variety and personalization are key selling points.
Ultimately, the alloy wheel powder coating automation line provides a comprehensive solution that meets the challenges of modern manufacturing, from high-volume production to intricate custom designs. By embracing automation, manufacturers can ensure consistent quality, reduce waste, and increase efficiency while staying adaptable to changing consumer demands. Whether for mass production or specialized orders, automated lines offer the flexibility, precision, and sustainability needed to remain competitive in the rapidly evolving market for alloy wheels.
The future of alloy wheel powder coating automation lines is poised for even greater advancements as artificial intelligence (AI) and machine learning (ML) technologies continue to make their way into the manufacturing process. These technologies can help further optimize the line’s operations by analyzing vast amounts of data from the entire coating process. AI algorithms can predict issues before they occur, suggest corrective actions, and automatically adjust system settings for peak efficiency. This predictive capability can be especially valuable in high-variability environments where quick responses are needed to address production challenges without halting the entire line.
Another exciting development in the field is the integration of augmented reality (AR) and virtual reality (VR) for maintenance and training purposes. Technicians can wear AR glasses to receive real-time, step-by-step instructions for equipment repairs or troubleshooting while working on the system. This hands-free guidance enhances the speed and accuracy of maintenance tasks, reducing the likelihood of errors or unnecessary downtime. VR training modules could also be used to educate new operators or technicians about how to operate, maintain, and troubleshoot the automated line. These innovations will make it easier for companies to keep their workforce skilled and minimize downtime during training or maintenance activities.
The growing demand for smart manufacturing is also driving further automation integration. IoT-enabled devices are capable of collecting and transmitting real-time data from every point in the production process, which can be aggregated and analyzed in cloud-based platforms. This data provides detailed insights into machine performance, cycle times, and quality control metrics. By harnessing this data, manufacturers can make more informed decisions about everything from system upgrades to production schedules, ensuring optimal uptime and resource utilization. These insights also help manufacturers identify trends in powder usage, curing efficiency, and coating quality, which can contribute to continuous improvement over time.
Another significant area of innovation is the use of robotic process automation (RPA) for repetitive tasks that go beyond the coating process itself. For example, automated systems can take over functions like parts inspection, cleaning, or post-coating touch-ups, further reducing the need for manual labor and allowing human workers to focus on higher-value tasks. As the complexity of wheel designs increases, RPA can help ensure that even intricate areas receive the appropriate level of coating without compromising speed or quality.
Additionally, the future of alloy wheel powder coating automation will likely see further improvements in material science. Newer, more advanced powder formulations—such as powders with improved adhesion properties, faster curing times, and enhanced durability—are continually being developed. These innovations not only contribute to better aesthetics and performance but also help streamline the coating process, reducing cycle times and further improving overall efficiency. Future powder coatings may also have enhanced characteristics, like better heat resistance, improved scratch resistance, or even self-healing properties, opening up new possibilities for alloy wheel finishes.
Sustainability will also continue to be a driving force in the development of these automated systems. As regulations around emissions, waste management, and energy consumption become stricter, the integration of energy-efficient solutions will be a priority for manufacturers. This could include everything from low-energy curing technologies to the adoption of renewable energy sources in the manufacturing process. Moreover, advances in material recycling and waste reduction will allow for even more sustainable operations, with powder reclaim systems becoming more efficient, reducing the overall material waste associated with the process.
In terms of design and flexibility, the next generation of automated alloy wheel coating lines will increasingly be able to handle a broader variety of wheel designs and sizes with minimal reconfiguration. This increased flexibility will be important as customers demand more customized and unique wheel designs for everything from luxury cars to performance vehicles. The ability to quickly switch between different finishes and handle complex geometries—such as deep-dish or multi-piece wheels—without significant setup times will allow manufacturers to remain agile in a competitive market.
Lastly, the integration of digital twins—virtual replicas of the production line—could offer manufacturers real-time simulation capabilities. This technology would enable them to test different configurations, powder formulations, and curing processes in a virtual environment before applying them on the actual line. By simulating and analyzing various production scenarios, manufacturers can optimize their coating process even before making physical changes to the system, reducing trial-and-error and improving the overall efficiency and effectiveness of the coating operation.
As the demand for customization, speed, and quality continues to grow in the automotive and aftermarket sectors, the evolution of alloy wheel powder coating automation lines will play a crucial role in meeting these expectations. The integration of cutting-edge technologies like AI, robotics, and digitalization will make these lines faster, more adaptable, and more efficient, ensuring that manufacturers can stay ahead of industry trends and deliver superior products to customers at competitive prices. The future of alloy wheel powder coating automation is bright, with ongoing innovations ensuring that the process remains a cornerstone of high-performance, high-quality manufacturing.
Alloy Wheel Powder Coating Production System
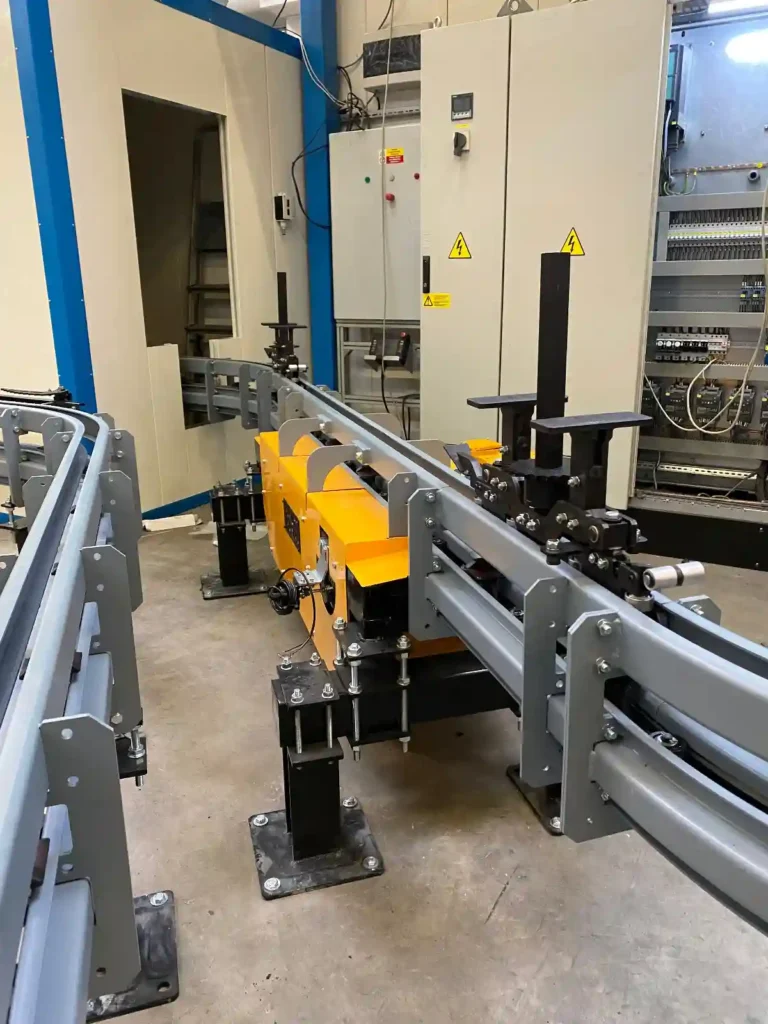
An alloy wheel powder coating production system is a comprehensive manufacturing setup designed to coat alloy wheels with a powder-based coating that provides superior durability, finish quality, and environmental benefits. The system encompasses all stages from wheel preparation to final inspection, often incorporating automation, advanced coating techniques, and precise control over the entire production process to ensure consistent quality, efficiency, and sustainability.
The process typically begins with the pre-treatment of alloy wheels, which is a critical stage for ensuring that the coating adheres properly and lasts over time. Pre-treatment involves a series of cleaning and surface preparation steps to remove contaminants like oil, dirt, and rust. This can include chemical cleaning, abrasive blasting (shot blasting or grit blasting), and phosphating or chromate conversion to create a surface that promotes better adhesion for the powder coating. Pre-treatment is essential because any remaining contaminants can interfere with the bond between the coating and the wheel surface, leading to defects like peeling or poor adhesion.
After pre-treatment, the wheels are transferred to the electrostatic powder coating booth. In this booth, the wheels are charged electrostatically, and a fine powder coating is applied to the surface using electrostatic spray guns or robotic arms. The electrostatic charge causes the powder particles to stick to the grounded metal surface of the wheel. This process is highly efficient as it minimizes overspray, ensuring that most of the powder ends up on the wheel. The precise control over the coating application allows for uniform coverage, even in hard-to-reach areas, such as between spokes or deep contours, which can be challenging for manual spraying.
The powder used in the coating system is typically made from a combination of resins, pigments, and curing agents. Powder coatings offer several advantages over traditional liquid coatings, including a wide range of finishes, such as matte, gloss, metallic, and textured, as well as enhanced durability and resistance to UV light, scratches, and chemicals. The coatings are free of solvents, making them more environmentally friendly compared to liquid paints that emit volatile organic compounds (VOCs) during application.
After the powder is applied, the wheels are transferred to the curing oven. This is where the powder coating is melted and chemically cured, forming a hard, durable finish. The curing process typically involves heating the coated wheels to a temperature between 160°C and 200°C (320°F and 390°F) for a set period of time, depending on the powder formulation. The curing oven is typically conveyorized, allowing for continuous movement of the wheels through the oven to maintain consistent processing times for each wheel. The controlled heating ensures that the powder coating properly fuses to the wheel surface, resulting in a smooth, hard, and resistant finish.
Once the curing process is complete, the wheels are removed from the oven and move to a cooling station where they are cooled to room temperature. Automated cooling systems may be used to speed up the process, ensuring that the wheels do not remain in the oven too long, which could affect the coating’s properties.
The next stage is quality control and inspection. Automated visual inspection systems, often equipped with cameras and sensors, are employed to check for defects such as uneven coating thickness, chips, bubbles, or other imperfections. These systems can detect flaws that are difficult for human inspectors to spot and can flag any defective wheels for rework. Some systems also use laser or ultrasonic technology to measure coating thickness to ensure that it falls within the desired range. Any wheels that pass inspection are then moved to the next step, while those that do not meet quality standards are separated for rework.
Post-coating finishing can include additional steps like touch-ups or additional layers of coating if required for specific finishes, such as gloss or metallic effects. In some cases, a clear coat is applied over the powder coating to enhance the appearance and provide additional protection against scratches and environmental damage.
Once the wheels have passed inspection and finished all necessary coating steps, they move to the packaging station. At this stage, automated systems can be used to load the wheels into packaging materials or onto pallets for transport. Packaging is a critical step to ensure that the coated wheels remain undamaged during transit and handling, and the use of automation in this stage further streamlines the production process, reducing manual labor.
Throughout the entire process, a central control system manages the production line, allowing operators to monitor key parameters such as temperature, spray gun settings, and conveyor speed. Advanced systems may also include real-time data collection to monitor production efficiency, powder usage, energy consumption, and quality control metrics. These systems can be integrated with Industry 4.0 technologies, enabling remote monitoring and predictive maintenance, ensuring that the production line runs smoothly without unexpected downtime.
One of the key benefits of a modern alloy wheel powder coating production system is its energy efficiency. Powder coating requires less energy compared to traditional liquid coatings, as there is no need for solvents to evaporate during application. The curing ovens also typically feature energy-efficient designs, such as heat recovery systems, that capture and reuse heat from the exhaust air, reducing the overall energy consumption of the system.
Sustainability is also a major focus in modern powder coating production. As powder coatings are solvent-free and can be reclaimed and reused, waste is minimized. Powder recovery systems collect overspray powder and filter it for reuse, ensuring that only a small amount of powder is wasted during production. This recycling capability contributes to the system’s environmental benefits, making powder coating an attractive alternative to traditional paint methods in terms of both cost and environmental impact.
The automation and precision offered by modern alloy wheel powder coating production systems also provide enhanced customization options. These systems can be programmed to handle various wheel designs, sizes, and finishes, offering manufacturers the flexibility to cater to specific customer demands, whether for mass production or custom, limited-edition orders. Automated color changes can also be quickly executed without significant downtime, allowing for greater variety in the finished products.
In summary, an alloy wheel powder coating production system integrates cutting-edge technologies to provide high-efficiency, high-quality, and environmentally friendly solutions for coating alloy wheels. From pre-treatment and electrostatic powder application to curing and quality control, every stage of the process is optimized for performance, consistency, and sustainability, making it a crucial part of modern wheel manufacturing.
The alloy wheel powder coating production system is designed to optimize every phase of the process, from loading and handling wheels to final inspection and packaging. Automation plays a crucial role in enhancing production speed, reducing labor costs, and maintaining consistent quality throughout the entire manufacturing cycle. Automated conveyors transport wheels seamlessly through different stages, reducing human error and maintaining a continuous flow. With each wheel moving through the system, robotic arms or automated spray guns apply the powder precisely, ensuring even coverage and minimal overspray. As powder coating is applied electrostatically, it adheres uniformly to the wheels’ surface, ensuring a flawless finish even in the most intricate wheel designs.
The curing process, essential for creating a durable and hard finish, is precisely controlled to prevent inconsistencies in quality. Advanced heating systems ensure that the powder coating is heated to the ideal temperature and duration, resulting in a uniform bond that provides excellent resistance to chips, scratches, and environmental wear. The cooling phase follows, allowing the wheels to return to ambient temperature before they are subject to any inspection or finishing touches. During this cooling phase, controlled systems ensure that the wheels maintain their integrity and prevent warping or other defects that could occur due to uneven cooling.
Quality control is an essential part of the process. Automated systems equipped with high-resolution cameras or laser scanners inspect each wheel for any imperfections, such as uneven coating thickness, surface bubbles, or other defects. This enables immediate detection of issues, which can then be addressed quickly through automated rework or adjustments to the system settings. In many cases, the system can perform detailed checks on coating consistency, including measuring thickness and uniformity across the wheel’s surface. These real-time inspections ensure that only wheels meeting the highest standards move on to the packaging stage, minimizing defects and reducing waste.
After inspection, wheels proceed to the packaging stage, where automated systems further streamline the process. Robotic arms or conveyor systems may carefully place wheels into packaging materials or onto pallets. This step is crucial to protect the delicate powder-coated finish from damage during transport and ensures that the wheels reach their final destination in pristine condition. Additionally, automated packaging systems can optimize material usage, reducing waste and improving efficiency by precisely sizing packaging materials to fit the products.
Energy efficiency and sustainability are key considerations in the design of these production systems. As manufacturers look for ways to reduce their environmental footprint, the ability to recycle powder overspray is an important advantage. Recovery systems are built into the coating booths to collect unused powder, which is then filtered and reused, making the process more cost-effective and reducing material waste. Moreover, the energy efficiency of curing ovens is often enhanced through heat recovery systems, which recapture and reuse heat, reducing the overall energy consumption of the line.
Smart technologies and data-driven insights further increase the capabilities of alloy wheel powder coating production systems. Sensors and IoT devices embedded throughout the system collect vast amounts of data, providing valuable information on machine performance, temperature fluctuations, powder consumption, and even wear and tear on equipment. This data is used to monitor system performance in real time and can be analyzed to predict when maintenance is needed, preventing costly downtime and improving the overall reliability of the system. By utilizing cloud-based platforms, manufacturers can access this data remotely, allowing them to make adjustments and optimize processes without being physically present on the factory floor.
Customization is another area where the system excels. Modern systems are highly adaptable, allowing manufacturers to handle a variety of wheel sizes, designs, and finishes with ease. Whether the job requires simple monochrome finishes or intricate, multi-layered custom designs, the system can be adjusted to meet the specific requirements without significant reconfiguration. This flexibility enables manufacturers to respond quickly to customer demands for unique or limited-edition designs, while maintaining the high throughput and efficiency expected from an automated production system.
With the rise of consumer demand for more personalized products, the integration of advanced coating technologies, including metallic, textured, and gloss finishes, allows manufacturers to offer a wide range of aesthetic options. This capability is enhanced by the automation of color changes and finish options, which can be quickly implemented with minimal downtime. As customer preferences shift toward more customized, high-end finishes for their vehicles, manufacturers who embrace these technologies can cater to these needs without sacrificing speed or quality.
As the industry moves toward further automation, it’s also expected that the role of artificial intelligence (AI) and machine learning (ML) will increase. These technologies can analyze data from every stage of the production line, identifying patterns and suggesting improvements for operational efficiency. AI can be employed to monitor real-time conditions, detect anomalies in coating consistency, and adjust parameters autonomously, making the system more self-sufficient and reducing the need for human intervention. Furthermore, AI and ML can predict potential failures based on historical data, allowing manufacturers to take preventative measures before issues arise, enhancing the longevity and reliability of the entire system.
The future of alloy wheel powder coating production systems will likely see continued improvements in automation and integration, with more factories implementing interconnected systems that allow for seamless data exchange across different stages of the production process. This integration could lead to smart factories where every aspect of production—from pre-treatment to final packaging—is optimized for efficiency, energy savings, and minimal waste. This will ultimately help manufacturers meet both consumer demand and environmental standards, positioning them for long-term success in an increasingly competitive marketplace.
In the realm of global production, such systems are increasingly capable of being scaled to meet large-scale demands while maintaining the flexibility to adjust for different regional requirements. Whether producing large volumes for mainstream vehicle models or low-volume runs for niche markets, the alloy wheel powder coating production system can adapt to handle the intricacies of various market needs, ensuring that manufacturers can stay competitive in both mass production and specialized, high-quality offerings.
In summary, alloy wheel powder coating production systems represent a vital advancement in the manufacturing process, combining cutting-edge automation, precision, energy efficiency, and customization to meet the demands of the modern automotive industry. These systems not only provide superior quality finishes but also offer flexibility, sustainability, and adaptability, making them a key component of modern wheel manufacturing. With future advancements in AI, machine learning, and smart manufacturing, these systems will continue to evolve, driving improvements in efficiency, quality, and customer satisfaction across the industry.
Fully Integrated Alloy Wheel Powder Coating Line

A fully integrated alloy wheel powder coating line is a highly advanced and automated production system that encompasses all the necessary stages of alloy wheel coating, from pre-treatment to final packaging. The system is designed to maximize efficiency, quality, and sustainability while ensuring that every step of the process is seamlessly connected. This integration improves operational speed, reduces the potential for errors, and enables real-time monitoring and adjustments across the entire production line.
The first stage in a fully integrated powder coating line is typically the pre-treatment process. This includes thorough cleaning, degreasing, and surface preparation of the alloy wheels to ensure that the coating adheres properly. Pre-treatment is often done through automated systems that clean the wheels using chemical baths or abrasive blasting, followed by rinsing and drying. Some systems also include a phosphating or chromating step to improve adhesion and corrosion resistance. This is crucial for ensuring the longevity and durability of the final powder coating. By integrating this stage into the overall line, manufacturers can eliminate the need for separate manual cleaning stations, reducing human error and speeding up the process.
After pre-treatment, the wheels are automatically transported to the powder coating station, where the electrostatic coating process begins. Using robotic arms or automated electrostatic spray guns, a precise, even layer of powder is applied to the wheel’s surface. The electrostatic process ensures that the powder adheres evenly and efficiently, covering even the most complex geometries. Because powder coating is a dry process, it is more environmentally friendly than traditional liquid coatings, which release solvents and volatile organic compounds (VOCs). The application of the powder can be automated to adjust the thickness, uniformity, and even color changes based on real-time data or customer specifications.
Once the powder is applied, the wheels are transferred to the curing oven, which is also part of the integrated system. This oven is where the powder coating is heated to a temperature of around 160°C to 200°C (320°F to 390°F), allowing it to melt, flow, and chemically bond to the surface of the alloy wheel. The curing process is typically controlled by advanced automated systems that monitor and adjust temperature and time parameters to ensure consistent, high-quality results. The use of energy-efficient ovens with heat recovery systems is also becoming more common, allowing manufacturers to reduce energy consumption during the curing phase.
Following the curing process, the wheels are moved to the cooling station. In a fully integrated system, the cooling process is automated to ensure the wheels are cooled uniformly and without any issues like warping or cracking. After cooling, the wheels proceed to the quality control stage, which is often one of the most crucial parts of the entire system. Here, automated visual inspection systems equipped with cameras or laser scanners check for coating defects, including uneven coverage, bubbles, or scratches. This allows for the identification of issues that could affect the appearance or durability of the wheel. If defects are detected, the system can either alert operators for manual inspection or automatically rework the affected wheels.
Once the wheels pass quality control, they move to the finishing station. This may involve touch-ups for any minor defects, additional coatings (such as clear coats), or the application of specific finishes like matte, glossy, or metallic effects. Automated systems can handle these tasks with high precision, ensuring consistency in the final appearance of the wheels. In some advanced systems, additional layers of coating can be applied to provide extra protection against scratches, UV degradation, or harsh weather conditions.
The next step is the packaging stage, where wheels are automatically packaged to protect their surface during storage and shipment. Robotic arms or automated conveyors handle the wheels, placing them into custom-designed packaging materials, such as foam or protective wraps, and ensuring that the wheels are securely packaged to prevent any damage during transportation. In an integrated system, the packaging process is synchronized with other stages, ensuring that wheels are efficiently moved from one phase to the next without any unnecessary delays.
Integration of data analytics and real-time monitoring is another important feature of a fully integrated alloy wheel powder coating line. Sensors and IoT devices are embedded throughout the system to monitor every aspect of production, from temperature and humidity in the curing oven to powder consumption and coating thickness. This data is collected and analyzed in real time, allowing operators to track performance, identify inefficiencies, and make immediate adjustments to maintain the optimal conditions for each phase of the process. In some cases, the system can even adjust parameters automatically based on the data it collects, ensuring that production runs smoothly and consistently.
Advanced automation and control systems in a fully integrated line also improve workflow coordination. The entire production process is interconnected, meaning that the movement of materials, wheels, and products is automated and seamlessly controlled from one phase to the next. This reduces the need for manual intervention, eliminates bottlenecks, and ensures a continuous flow of production, leading to faster turnaround times and reduced lead times for orders.
Another key advantage of a fully integrated alloy wheel powder coating line is the reduction of waste. Powder coating is inherently more material-efficient compared to liquid coatings, as excess powder can be reclaimed and reused through automated recovery systems. In addition, the integrated system can be configured to optimize powder usage, reducing overspray and minimizing material waste. This, combined with more energy-efficient curing ovens and recycling capabilities, makes the system more environmentally sustainable. It also helps manufacturers reduce operational costs over time.
Customization is another benefit of an integrated system. The ability to easily switch between different finishes, colors, and coating types without significant downtime is a major advantage for manufacturers who need to cater to a variety of customer preferences. Automated systems can quickly adjust to different powder types or change spray parameters to achieve a wide range of finishes, whether it’s a matte, gloss, textured, or custom metallic effect.
Finally, the scalability of a fully integrated system is another major advantage. As customer demand grows or changes, the system can easily be expanded to accommodate increased production volumes. The flexibility of automated systems allows manufacturers to adapt quickly to changes in production needs, whether that involves handling larger batches or switching between various wheel sizes and designs without compromising on quality.
In conclusion, a fully integrated alloy wheel powder coating line represents the pinnacle of modern manufacturing technology. By combining automation, precision coating techniques, energy-efficient systems, and advanced data analytics, it offers manufacturers the ability to produce high-quality, customized alloy wheels at high volumes with minimal waste and maximum efficiency. With the continued advancements in automation and smart manufacturing, these systems are poised to become even more flexible, sustainable, and responsive to customer demands, helping manufacturers stay competitive in a fast-evolving market.
A fully integrated alloy wheel powder coating line ensures that all aspects of the production process, from wheel preparation to final packaging, are connected seamlessly. This integration enhances the efficiency of the entire operation, reduces the chances of human error, and allows for a smoother workflow. The automation within the system ensures that each phase of production operates at peak performance, with minimal downtime. This kind of system minimizes manual intervention, which not only speeds up production but also ensures consistency in the finished product, leading to high-quality output every time.
The ability to handle large volumes while maintaining high standards of customization is a significant benefit of a fully integrated line. Customization options are highly adaptable, enabling the system to produce wheels with various finishes, such as gloss, matte, or textured, with ease. The flexibility of the automation allows the system to handle different wheel sizes and designs without major adjustments. This capability is especially important for manufacturers catering to diverse customer demands, where quick changes in production requirements may be needed.
Data analytics is central to the integration of the system, providing real-time insights into various aspects of the production process. By collecting and analyzing data from different stages—such as coating thickness, curing temperature, and even air quality—operators can continuously monitor system performance and identify areas for improvement. The integration of data allows for predictive maintenance, ensuring that any issues are detected before they result in costly downtime or defects. This predictive approach minimizes disruptions and enhances overall operational efficiency.
Energy efficiency is another key factor driving the benefits of a fully integrated powder coating line. Many systems incorporate heat recovery technologies in their curing ovens, allowing the system to reuse energy and reduce overall consumption. This not only reduces costs but also minimizes the environmental impact of the manufacturing process. Additionally, powder recovery systems ensure that overspray is collected and reused, further reducing waste and enhancing the sustainability of the production process.
The integration of the various stages, from pre-treatment to final inspection and packaging, also ensures smoother logistics within the factory. Automated conveyors and robotic systems transport wheels from one station to the next, ensuring that each wheel is processed in a timely manner and reducing the risk of bottlenecks or delays. The synchronization of processes ensures that wheels move efficiently through the line, allowing for higher throughput while maintaining consistent quality.
The ability to achieve precise control over the coating process is one of the standout features of an integrated alloy wheel powder coating line. Automated spray guns, combined with robotic arms, ensure that the powder is applied evenly and consistently, even on complex geometries. This level of control reduces the chance of defects such as uneven coverage or undercoating, which can compromise the quality of the finished wheel. Furthermore, automated quality control systems detect issues like surface imperfections or coating thickness deviations, allowing for quick corrective actions.
As a result, fully integrated powder coating lines offer manufacturers the ability to produce alloy wheels that meet high standards of both aesthetics and functionality. The combination of automation, precision, and real-time monitoring leads to high throughput, consistent quality, and a more sustainable production process. Manufacturers can respond quickly to changes in customer demand while minimizing waste and maximizing resource utilization. Ultimately, the integration of these advanced systems positions companies to stay competitive in a market where efficiency, quality, and sustainability are increasingly important.
Continuous Alloy Wheel Powder Coating Line
A continuous alloy wheel powder coating line is an advanced manufacturing system designed for high-volume production of alloy wheels with powder coatings. Unlike traditional batch processes, a continuous line operates with an uninterrupted flow of wheels through each stage of production, from pre-treatment to coating application, curing, cooling, inspection, and packaging. This continuous nature allows for faster throughput, reduced production costs, and more consistent quality, making it ideal for manufacturers with high demand and a need for high-efficiency operations.
In a continuous powder coating line, the wheels are continuously loaded onto a conveyor system that moves them through different stages of production. The system is designed to handle large volumes of alloy wheels, providing a streamlined process that minimizes human intervention and maximizes operational efficiency.
The first step in a continuous line is the pre-treatment process, where wheels are automatically cleaned, degreased, and prepared for coating. This process ensures that the surface is free from contaminants such as dirt, oil, and rust, which could affect the adhesion and durability of the powder coating. In a continuous system, pre-treatment stations are integrated into the conveyor line, meaning wheels are automatically moved from one station to the next without any pauses. The pre-treatment process often includes chemical baths, abrasive blasting, and phosphating or chromate conversion, depending on the requirements of the coating. The use of automated cleaning systems improves consistency and reduces the potential for errors.
Once pre-treatment is completed, the wheels are transported to the powder coating station, where the actual coating is applied. This is typically done using electrostatic spray guns or robotic arms. The electrostatic charge applied during this process causes the powder particles to adhere to the wheel’s surface. In a continuous system, the application process is optimized for speed and precision, ensuring that powder is applied evenly and consistently across the entire wheel. The system can be adjusted to apply different types of coatings, such as glossy, matte, or metallic finishes, depending on the customer’s specifications. The advantage of the continuous approach is that it allows for minimal downtime between color changes or different coating types, which helps to maintain high production efficiency.
After the powder coating is applied, the wheels move to the curing oven for the next step in the process. This is where the powder is heated to a temperature of 160°C to 200°C (320°F to 390°F), causing it to melt, flow, and chemically bond to the surface of the wheel. The curing oven is designed for continuous operation, often featuring a conveyorized system that moves the wheels through the oven at a constant speed. The temperature and time in the curing oven are precisely controlled to ensure that the powder coating bonds properly to the wheel surface and forms a hard, durable finish.
After the curing process, the wheels are transferred to a cooling station, where they are cooled to room temperature. The cooling process is automated to ensure that the wheels do not experience any warping or other defects caused by uneven cooling. In some systems, the cooling phase may include forced air or water cooling to accelerate the process and prepare the wheels for the next stage.
Once cooled, the wheels are subjected to quality control and inspection. In a continuous line, this is often done through automated visual inspection systems. Cameras and sensors scan each wheel for defects such as uneven coating thickness, bubbles, scratches, or other imperfections. The system can automatically flag defective wheels for further inspection or rework, minimizing the risk of faulty products making it to the packaging stage. Automated thickness gauges may also be used to ensure that the powder coating meets the required specifications.
After passing the inspection process, the wheels move to the packaging station. In a continuous system, this stage is also automated. Robotic arms or conveyors carefully place the wheels into protective packaging, such as foam or bubble wrap, to prevent damage during shipping and handling. The packaging process is synchronized with the rest of the production line, so there is no delay in moving the wheels from one stage to the next.
One of the key advantages of a continuous alloy wheel powder coating line is its efficiency. Because the system operates without interruption, it can handle a large number of wheels in a short amount of time, making it ideal for manufacturers with high demand. The continuous nature of the line also reduces the potential for human error, improves consistency, and minimizes the need for rework or quality control failures. The system’s integration also ensures that each phase of production is tightly coordinated, with automated conveyors moving wheels seamlessly through each station.
Another important benefit of a continuous powder coating line is its cost-effectiveness. By automating most stages of production, manufacturers can reduce labor costs and improve throughput. Additionally, the continuous nature of the system allows for more efficient use of resources, such as energy and materials. For example, powder overspray is often collected and recycled back into the system, reducing waste and ensuring that the materials are used efficiently. Similarly, the use of energy-efficient curing ovens and heat recovery systems minimizes energy consumption, further reducing operational costs.
Customization is also achievable in a continuous powder coating system. The system can handle a variety of wheel sizes, designs, and finishes, offering manufacturers flexibility to meet the demands of different customers or products. The ability to quickly switch between different finishes or powder colors makes it ideal for manufacturers who need to produce customized or limited-edition wheels.
In terms of environmental benefits, the continuous alloy wheel powder coating line is also more sustainable than traditional coating methods. Powder coating is a dry process, meaning it does not emit solvents or volatile organic compounds (VOCs) into the atmosphere. The ability to reclaim overspray powder and the use of energy-efficient curing systems further reduce the environmental impact of the manufacturing process, making it a greener option compared to liquid coating methods.
Overall, a continuous alloy wheel powder coating line offers a high level of efficiency, flexibility, and quality control, making it a preferred solution for large-scale production of alloy wheels. Its integration of automation, energy-efficient processes, and waste reduction measures positions it as a cost-effective and sustainable option for manufacturers in the automotive industry. As demand for high-quality, customized alloy wheels continues to grow, the continuous powder coating line will remain a crucial part of the manufacturing process, driving innovation and operational excellence.
A continuous alloy wheel powder coating line provides a significant advantage in terms of high-volume production while maintaining the flexibility needed for varying customer demands. By integrating all steps into a seamless, continuous flow, this system ensures that wheels move efficiently from one stage to the next, minimizing downtime and maximizing throughput. The ability to handle large volumes of wheels without sacrificing quality makes it a highly effective solution for manufacturers looking to keep up with market demand while maintaining a high standard of craftsmanship.
The process, while automated, still allows for detailed monitoring and adjustments based on real-time feedback, ensuring that the system can adapt quickly to changes in production needs or to correct any issues that might arise. Automated systems that monitor temperature, pressure, coating thickness, and curing times ensure that each wheel receives the same level of precision and care. This is particularly crucial for products like alloy wheels, where even minor defects can compromise both aesthetics and performance.
Another key benefit of a continuous system is the reduction in material waste. Powder coating inherently reduces overspray compared to liquid coatings, and the continuous system is designed to capture and recycle powder overspray, allowing it to be reused in future batches. This waste-reduction process not only saves on material costs but also aligns with growing environmental demands to reduce waste and carbon footprints. Additionally, the continuous nature of the line ensures that wheels are always being worked on, without any idle time, which helps reduce unnecessary energy consumption and optimizes efficiency across the entire system.
Moreover, the system’s adaptability allows for customization without significant interruptions to production. Wheels of different sizes, designs, and finishes can all be processed on the same line, with minimal adjustments required between runs. This is important for manufacturers who need to respond quickly to varying customer preferences, such as producing different finishes for different vehicle models or creating limited-edition styles. The versatility of the continuous line helps manufacturers stay competitive by offering a wide range of options while still meeting tight deadlines.
In addition, automated quality control systems embedded throughout the line ensure that any defects in the powder coating are detected and addressed before the wheels move further down the production line. High-resolution cameras, laser scanners, and automated thickness gauges provide real-time feedback, allowing the system to identify imperfections such as inconsistent coating coverage, surface defects, or thickness discrepancies. This automated quality assurance process not only ensures that every wheel meets the highest standards but also prevents the need for rework or waste by identifying issues early on.
With the growing demand for customization and premium finishes in the automotive industry, continuous alloy wheel powder coating lines offer manufacturers the tools needed to provide customers with the exact specifications they desire. Whether it’s a high-gloss finish, a matte look, or a custom color, the system can quickly switch between different powders and finishes, making it possible to meet a wide range of customer requirements without significant downtime or delays in production. This level of flexibility, combined with the speed and efficiency of a continuous line, allows manufacturers to deliver high-quality, customized alloy wheels at scale.
Finally, the energy efficiency of the system plays an important role in reducing overall operating costs. The use of energy-efficient ovens for the curing process, coupled with heat recovery technologies that capture and reuse energy, helps minimize the environmental impact of the coating process. Additionally, the automation of most stages in the process eliminates the need for large amounts of labor, reducing operational costs while maintaining high standards of quality.
In summary, a continuous alloy wheel powder coating line represents a highly efficient and cost-effective solution for manufacturers looking to meet the demands of the modern automotive market. The integration of automation, real-time monitoring, and waste-reduction technologies ensures that the system operates with maximum efficiency while maintaining the highest quality standards. As the automotive industry continues to evolve, manufacturers equipped with these advanced production lines will be well-positioned to meet growing demands for customization, premium finishes, and sustainable manufacturing practices.
Alloy Wheel Powder Coating Automation System

An Alloy Wheel Powder Coating Automation System is a highly advanced, fully automated production line designed specifically to handle the process of applying powder coatings to alloy wheels. The goal of this system is to optimize efficiency, consistency, and quality by automating each stage of the powder coating process, from pre-treatment to the final packaging of the coated wheels. By leveraging automation, manufacturers can achieve higher throughput, reduced labor costs, minimized waste, and enhanced precision, all while maintaining a high standard of finish and durability.
The system typically begins with automated pre-treatment, where alloy wheels are cleaned and prepared for coating. This step is critical because the surface of the wheel must be free from contaminants such as dirt, grease, or rust, which could prevent the powder coating from adhering properly. Pre-treatment is usually carried out using a series of automated processes, such as chemical cleaning, abrasive blasting, or phosphating. The automated system ensures that each wheel undergoes the same rigorous cleaning process, improving consistency and reducing the chances of errors. Once cleaned, the wheels are automatically moved to the next stage without manual intervention, reducing labor and the possibility of contamination.
Following pre-treatment, the wheels are transported to the powder coating station. This is the core part of the automation system, where the powder is applied to the alloy wheel. The process usually involves electrostatic powder spraying, where an electrostatic charge is applied to the powder particles, causing them to be attracted to the wheel surface. Automated spray guns or robotic arms are often used in this stage to ensure that the powder is applied evenly and efficiently. These robotic systems can adjust the spray patterns and coverage based on the shape and size of each wheel, ensuring a consistent finish. The system can also be programmed to apply different types of coatings, such as gloss, matte, or textured finishes, providing flexibility for manufacturers to meet a wide range of customer requirements.
Once the powder is applied, the wheels are transferred to an automated curing oven. The oven is part of the automation system, with a conveyor that moves the wheels through a temperature-controlled environment, where the powder is heated to a specific temperature (usually between 160°C and 200°C). The heat causes the powder to melt, flow, and bond with the wheel’s surface, creating a durable, hard finish. The curing process is monitored by the automation system to ensure that the wheels spend the right amount of time at the correct temperature, resulting in a uniform and high-quality finish. In many systems, energy-efficient ovens with heat recovery are used to reduce energy consumption and operational costs, aligning with sustainability goals.
After the curing process, the wheels are moved to the cooling station, where they are cooled to room temperature. Automated cooling systems, such as forced air or water cooling, ensure that the wheels cool evenly and quickly, preventing any thermal shock or warping. The cooling phase is carefully controlled to maintain the integrity of the coating and ensure that the wheels retain their intended shape and finish.
Next, the wheels undergo automated quality control and inspection. This is a crucial part of the alloy wheel powder coating automation system, as it ensures that only wheels that meet quality standards are passed to the next stage. High-resolution cameras, laser sensors, and thickness gauges are integrated into the system to check for defects such as uneven coating, bubbles, scratches, or undercoating. The automated system scans each wheel, detecting any imperfections that could affect the performance or aesthetic quality of the coating. If defects are detected, the system can automatically flag the wheel for rework or alert operators for manual inspection.
Once the wheels pass the inspection stage, they are transferred to the packaging station, where they are automatically packaged for shipment. Robotic arms or conveyors place the wheels into protective packaging, such as foam, bubble wrap, or custom molds, ensuring that they are securely protected during transport. The automated system streamlines the packaging process, ensuring consistency and reducing handling time.
An important feature of the Alloy Wheel Powder Coating Automation System is its integration and synchronization. All stages of the process—pre-treatment, coating, curing, cooling, inspection, and packaging—are interconnected through a central control system. This ensures that wheels flow smoothly from one stage to the next without bottlenecks or delays. Automated conveyors, robots, and sensors work in harmony to ensure a seamless operation that maximizes production efficiency.
The system is also designed to be data-driven, with real-time monitoring and feedback systems that track performance metrics across the entire production process. Sensors embedded throughout the system continuously collect data on parameters such as temperature, coating thickness, and curing time. This data is analyzed in real time to identify any potential issues before they impact production. For example, if the system detects that the temperature in the curing oven is slightly off, it can automatically adjust the heating process to maintain consistency. The ability to collect and analyze this data allows operators to make informed decisions and maintain optimal performance.
Furthermore, waste reduction is a key benefit of automation. Powder overspray, which is often a concern in traditional coating methods, can be collected, filtered, and recycled in an automated system. This reduces material waste and increases the cost-effectiveness of the system. By reclaiming unused powder, the system also reduces the environmental impact of the manufacturing process. Additionally, the automation system minimizes human intervention, leading to fewer errors, less handling, and a more efficient use of resources.
In terms of flexibility, an alloy wheel powder coating automation system can be designed to accommodate different wheel sizes, designs, and finishes. The automated spray guns or robotic arms can be adjusted for different wheel geometries, ensuring that each wheel receives the correct coating application. Additionally, the system can be programmed to switch between different powder colors or finishes with minimal downtime, making it ideal for manufacturers who need to respond to changing customer demands or produce limited-edition designs.
Finally, maintenance is simplified in an automated system. Automated diagnostics and predictive maintenance features allow the system to identify potential issues before they cause downtime, ensuring that the production line operates smoothly. Regular monitoring of key components, such as spray guns, curing ovens, and conveyors, ensures that wear and tear are detected early, and necessary repairs or replacements can be made proactively.
In conclusion, an Alloy Wheel Powder Coating Automation System provides manufacturers with a highly efficient, cost-effective, and flexible solution for producing high-quality coated alloy wheels. The integration of automation in every stage of production—pre-treatment, coating, curing, cooling, inspection, and packaging—ensures that the system operates at optimal performance, delivering consistent, high-quality finishes while reducing labor costs, waste, and energy consumption. With real-time monitoring and predictive maintenance, these systems offer the scalability and flexibility needed to meet increasing customer demands while ensuring a sustainable and environmentally friendly manufacturing process.
The alloy wheel powder coating automation system offers substantial improvements in operational efficiency and product consistency, making it a valuable asset for manufacturers who need to scale up production while maintaining high-quality standards. By automating the various stages of the coating process, the system minimizes human error and enhances the ability to produce large volumes of wheels with minimal intervention. This not only increases throughput but also ensures that each wheel receives the same level of precision and attention to detail, regardless of the batch size.
One of the significant benefits of automation is the ability to optimize production time. With fewer manual interventions, the system operates more quickly, ensuring that the wheels move smoothly from one stage to the next with no unnecessary delays. This reduction in downtime is crucial for manufacturers who operate under tight schedules and need to meet the growing demand for high-quality, aesthetically pleasing alloy wheels. The automated system ensures that no time is wasted in the process, from cleaning and coating to curing and packaging.
Another key advantage is the reduced labor requirements. With much of the work being handled by robots, spray guns, sensors, and conveyors, the need for human labor is significantly reduced. This leads to a decrease in labor costs and can free up workers for more value-added tasks such as overseeing the system, conducting quality checks, and addressing any system anomalies. As labor costs continue to rise globally, reducing reliance on manual labor while increasing output is a critical competitive advantage for manufacturers.
Additionally, the precise control offered by the automation system ensures that the powder coating process is consistent, regardless of the complexity of the wheel’s design or finish. Automated spray guns can be adjusted to deliver a uniform coating, even on wheels with intricate shapes or curves. This level of precision ensures that the wheels receive an even layer of coating that meets the required thickness specifications. For customers demanding specific finishes, such as matte, gloss, or textured effects, the system can easily switch between different powder types or colors, delivering customized results with minimal downtime between runs.
The integration of data-driven systems further enhances the automation process by enabling real-time tracking and monitoring of every stage in the coating process. Sensors continuously measure and report on key parameters, such as coating thickness, temperature, and curing time. This data is analyzed to identify any potential issues, allowing operators to make adjustments in real-time to ensure that every wheel meets the desired specifications. Predictive maintenance capabilities also come into play, as the system can predict when parts are likely to wear out or require attention, helping to prevent unscheduled downtime and costly repairs.
The automation system also contributes to sustainability goals. Powder coating is a more environmentally friendly option compared to traditional liquid paints, as it does not release harmful solvents or volatile organic compounds (VOCs) into the atmosphere. Moreover, the system’s ability to collect and recycle overspray powder minimizes material waste, making the process more cost-effective and environmentally conscious. This closed-loop approach reduces the need for raw materials and minimizes the environmental impact of production, which is an increasingly important consideration for manufacturers in today’s eco-conscious marketplace.
Furthermore, the automation system is designed with scalability in mind. As demand for alloy wheels continues to rise, manufacturers can scale up production by simply increasing the number of automated stations or optimizing the line’s throughput. The system can easily handle higher production volumes without requiring major changes to the existing infrastructure, making it highly adaptable to changing market conditions or customer needs.
The ability to offer customization is also a significant advantage in the competitive alloy wheel market. Customers increasingly demand personalized products, such as custom colors or unique finishes. The automated system can handle these customizations quickly and accurately, enabling manufacturers to meet the needs of a diverse customer base. This ability to deliver highly personalized products while maintaining a consistent, high-quality finish is a critical differentiator in the industry.
In terms of quality control, the integration of automated inspection systems ensures that the wheels meet strict quality standards before they are packaged and shipped. High-resolution cameras and sensors scan the wheels for any imperfections, such as uneven coating, scratches, or bubbles. These automated systems ensure that only flawless products move forward, while defective wheels are flagged for rework or discarded. This high level of quality assurance ensures that customers receive products that meet or exceed their expectations every time.
Lastly, the easy integration of the system into existing production lines makes it a versatile solution for manufacturers looking to upgrade their operations without overhauling their entire infrastructure. The system can be tailored to fit the specific needs of the manufacturer, ensuring a smooth transition and minimal disruption to ongoing production.
In conclusion, an alloy wheel powder coating automation system represents a transformative shift in manufacturing practices for the automotive industry. It combines advanced robotics, precise control, real-time data analytics, and sustainability to deliver high-quality, customized products with maximum efficiency. As the demand for alloy wheels continues to grow, and as manufacturers seek ways to stay competitive, automation systems like this will play a crucial role in helping companies meet these challenges while maintaining high standards of production, cost-efficiency, and environmental responsibility.
Automated Alloy Wheel Powder Application Line
An Automated Alloy Wheel Powder Application Line is a state-of-the-art system designed to apply powder coatings to alloy wheels efficiently and with precision. This line is highly automated, using advanced technologies such as robotic arms, electrostatic spray guns, and automated conveyors to ensure that the coating process is as fast, consistent, and cost-effective as possible. The system is ideal for high-volume production environments, where speed and consistency are paramount.
The automated alloy wheel powder application line starts with wheel handling and transportation. Alloy wheels are typically loaded onto the line through an automated conveyor system that moves them seamlessly between each stage of the process. This minimizes human intervention, reducing labor costs and the potential for errors or contamination during handling. The system ensures that wheels are loaded quickly and efficiently, without unnecessary delays.
The first key step in the application line is the pre-treatment process. Before powder coating, alloy wheels must undergo a thorough cleaning process to remove any contaminants such as dirt, oil, rust, or previous coatings. This step is crucial for ensuring proper adhesion of the powder coating to the wheel’s surface. In an automated line, the pre-treatment process typically involves a series of cleaning stations, such as chemical baths, abrasive blasting, or phosphate coating. The wheels move automatically from one station to the next, ensuring a thorough and consistent cleaning process with minimal human involvement.
Once the wheels have been cleaned and prepped, they proceed to the powder coating station. This is where the coating is applied to the wheel’s surface. The system uses electrostatic spray guns or robotic arms that apply a finely powdered coating to the wheel. The electrostatic guns charge the powder particles, causing them to be attracted to the wheel’s surface, ensuring an even and uniform application. In automated systems, the robotic arms are programmed to adjust spray patterns based on the wheel’s geometry, ensuring that each wheel receives the proper amount of coating, regardless of shape or size.
An automated color change feature allows the system to switch between different powder types or colors without significant downtime. This is particularly beneficial for manufacturers who need to produce different finishes or customized wheels for various customer requirements. The ability to quickly switch between colors or finishes ensures that the production line remains flexible and efficient, reducing wait times and increasing throughput.
Once the powder is applied, the wheels are transferred to an automated curing oven where the powder is baked at high temperatures to form a durable, smooth finish. The oven is typically conveyorized, with the wheels moving through it at a controlled speed and temperature. The curing process ensures that the powder melts and bonds with the wheel, creating a hard, resilient finish that is resistant to wear, corrosion, and UV damage. The automated curing oven uses precise temperature control and monitoring systems to ensure that each wheel is properly cured, which is essential for ensuring the quality and durability of the final product.
After curing, the wheels are moved to a cooling station where they are allowed to cool to room temperature. Automated cooling systems use forced air or water to ensure that the wheels cool evenly and quickly, preventing any distortion or defects from developing. The cooling process is tightly controlled, as it is crucial to the final appearance and strength of the coating.
The wheels then proceed to the inspection and quality control stage, where they undergo thorough checks for any defects in the coating. Automated inspection systems using cameras, laser scanners, or ultrasonic sensors scan the wheels for imperfections such as uneven coating, air bubbles, scratches, or contamination. These systems can detect defects in real-time and flag any wheels that do not meet the required specifications. In some systems, defective wheels can be automatically rejected, while others may be sent to a manual inspection station for further examination or rework.
Once the wheels have passed inspection, they move to the packaging station, where they are automatically packaged for shipment. Robotic arms or conveyors move the wheels into protective packaging, such as foam, shrink wrap, or custom protective shells, ensuring that they are well-protected during transport and handling. This automated packaging process helps to speed up the final steps of production while ensuring that the wheels are securely packaged without human handling.
One of the most important features of an Automated Alloy Wheel Powder Application Line is its integration. The entire system is connected and controlled by a central control system that monitors and manages each stage of the process. This integration allows for real-time adjustments and optimizations, ensuring that the production line operates smoothly and efficiently. The system can automatically detect any issues or deviations in the process and make adjustments in real-time to maintain optimal performance.
Additionally, the line can be equipped with data collection and monitoring capabilities, which allow manufacturers to track production metrics such as throughput, coating thickness, curing time, and quality control results. This data is invaluable for optimizing the production process and identifying areas for improvement. The ability to analyze and act on production data also helps manufacturers make informed decisions about maintenance, quality assurance, and overall efficiency.
The sustainability aspect of an automated powder coating line is also significant. Powder coating itself is an eco-friendly method of applying finishes since it does not release solvents or volatile organic compounds (VOCs) into the atmosphere. Additionally, the automated system’s ability to recycle overspray powder minimizes waste, making the entire process more environmentally friendly. This feature helps manufacturers reduce material costs and their environmental impact, aligning with global trends toward more sustainable manufacturing practices.
In conclusion, an Automated Alloy Wheel Powder Application Line offers manufacturers an efficient, consistent, and high-quality method for coating alloy wheels. The system’s ability to handle the entire coating process—from pre-treatment to curing and packaging—automatically increases throughput, reduces labor costs, and improves product consistency. With the added benefits of quick color changes, precise quality control, and real-time monitoring, this system is ideal for high-volume production environments where efficiency, quality, and customization are key. By incorporating automation, the system not only improves production efficiency but also enhances the overall sustainability and environmental impact of the manufacturing process.
An Automated Alloy Wheel Powder Application Line offers a seamless, efficient, and highly precise way of applying powder coatings to alloy wheels. By automating the entire process, manufacturers can achieve consistent, high-quality finishes with significantly reduced labor costs. The system eliminates the need for manual handling, thereby reducing human error, contamination risks, and production delays. Automated conveyors, robotic arms, and spray guns work in harmony to ensure that each wheel receives the same level of care and attention, whether it’s the first wheel of a batch or the last.
At its core, the system operates on the principle of high efficiency. Alloy wheels are moved through each stage of the coating process—cleaning, powder application, curing, and cooling—without the need for manual intervention. This not only speeds up production but also ensures that each wheel is consistently treated in the same manner. The wheels are cleaned thoroughly using automated pre-treatment methods, ensuring that no dirt, grease, or contaminants remain that could affect the adhesion of the powder coating. This meticulous cleaning process ensures a stronger bond and longer-lasting finish for each wheel.
The powder application process itself is a highlight of the automated system. Using electrostatic spray guns or robotic arms, the system applies a finely controlled layer of powder to the wheels. The electrostatic charge helps the powder adhere perfectly to the wheel’s surface, creating an even coat without excessive waste. With automated color change capabilities, manufacturers can quickly switch between different powder types or colors, allowing for greater flexibility and customization in the products they offer. This feature makes it possible to meet the diverse needs of customers while keeping downtime to a minimum.
Once the powder is applied, the wheels are transferred to the curing ovens, where the powder is baked at precise temperatures to create a smooth and durable finish. The curing process is carefully monitored and controlled by the automated system, ensuring that the correct temperature and timing are maintained for each wheel. This results in a high-quality, resilient finish that is both visually appealing and functional. After curing, the wheels are cooled using automated cooling systems, ensuring an even temperature distribution and preventing any warping or damage that could occur if cooled unevenly.
Inspection is another area where automation shines. High-resolution cameras and sensors inspect each wheel for defects such as uneven coating, scratches, or imperfections in the powder layer. Automated defect detection systems can identify these issues in real-time and either flag the wheel for further inspection or automatically reject defective items. This continuous quality control process ensures that only the best products make it through to the final stage, eliminating the need for costly manual inspections and reducing the risk of defects reaching customers.
The final stage of the process is the automated packaging system. Once the wheels have passed inspection, they are moved to the packaging area, where robotic arms or conveyors place them into protective packaging. This automated process ensures that the wheels are packed securely and efficiently, reducing the chance of damage during shipping and handling. By eliminating human intervention in this final step, manufacturers further reduce labor costs and enhance overall throughput.
Moreover, the system’s integration with real-time data monitoring allows for ongoing optimization of the entire production process. Sensors embedded in various stages of the line collect data on variables like coating thickness, curing temperature, and wheel movement speed. This data is analyzed to identify inefficiencies or potential issues, enabling immediate corrective actions to be taken. The ability to track and analyze data at every step enhances decision-making, streamlines operations, and ensures that the entire process operates at peak efficiency.
From an environmental perspective, the automated powder coating line offers significant sustainability benefits. Powder coating itself is an eco-friendly alternative to traditional wet coatings since it doesn’t release harmful volatile organic compounds (VOCs) or solvents into the atmosphere. Additionally, the ability to reclaim and recycle overspray powder reduces material waste, further enhancing the sustainability of the manufacturing process. This makes the system an attractive choice for companies looking to reduce their environmental footprint while maintaining high production standards.
In conclusion, an Automated Alloy Wheel Powder Application Line revolutionizes the manufacturing process by combining speed, consistency, flexibility, and sustainability. The system’s ability to efficiently manage the coating process, from cleaning and application to curing, cooling, and packaging, leads to faster production times, reduced costs, and higher quality products. By minimizing manual handling and incorporating advanced technologies like robotic arms, electrostatic spray guns, and real-time monitoring, the system offers a significant competitive advantage to manufacturers in the alloy wheel industry. Whether producing standard finishes or custom-designed wheels, this automated line can help meet customer demand for high-quality, durable products while improving operational efficiency and sustainability.
Alloy Wheel Powder Coating Assembly Line
An Alloy Wheel Powder Coating Assembly Line is a highly efficient and automated production line specifically designed for coating alloy wheels with powder coatings. The assembly line combines several stages, from wheel pre-treatment to final packaging, ensuring each wheel is coated uniformly and to the highest quality standards. With automation, the system can handle large volumes of production while maintaining consistent, high-quality results throughout the process. The entire assembly line is designed for efficiency, minimizing downtime, reducing manual labor, and optimizing the coating process, ensuring a smooth workflow from start to finish.
The system typically begins with the wheel loading and pre-treatment process where the alloy wheels are automatically transferred to the cleaning stations. Pre-treatment is a crucial step in ensuring that the wheels are properly prepared for coating. Automated cleaning systems such as chemical baths, abrasive blasting, or phosphating are used to remove any dirt, oils, rust, or old coatings from the wheels. This ensures that the powder coating will adhere properly and creates a strong bond between the coating and the wheel surface. The pre-treatment process is closely monitored and regulated to ensure that all wheels are cleaned to the same standard, creating consistency across the entire production run. Once cleaned, the wheels are automatically conveyed to the next stage, where the powder coating process takes place.
At the powder application stage, the system uses robotic arms or electrostatic spray guns to apply a uniform layer of powder coating onto the surface of the alloy wheel. The powder is typically applied electrostatically, where a charge is applied to the powder particles, which are then attracted to the grounded wheel. This process ensures that the powder adheres evenly and covers the entire surface, even in hard-to-reach areas. Automated robots or spray arms are programmed to adjust their movements according to the shape and size of the wheel, ensuring that the powder is applied in the optimal pattern for each specific wheel design. This stage is important for achieving consistent coverage, and the system can handle different finishes, such as gloss, matte, or textured coatings. The system also allows for quick color changes, making it possible to switch between various colors or finishes with minimal downtime. This flexibility is crucial for meeting the diverse needs of customers and for offering customization options.
After the powder is applied, the wheels proceed to the curing oven, where they are heated to a specific temperature, typically between 160°C and 200°C, depending on the type of powder being used. The curing process allows the powder to melt, flow, and chemically bond to the surface of the wheel, creating a durable, hard coating. The curing oven is part of an automated conveyor system, moving the wheels through a temperature-controlled environment. The temperature and timing within the oven are closely monitored by the system to ensure uniform curing, preventing defects such as uneven coating or insufficient curing. The system typically uses energy-efficient ovens to reduce energy consumption and ensure consistent results, which is critical for maintaining the quality of the final product.
Once the curing process is complete, the wheels move to the cooling station, where they are cooled to room temperature. This cooling process is crucial because it prevents thermal shock, which could distort or crack the coating. Automated cooling systems, such as forced air or water cooling, ensure that the wheels cool evenly and quickly, maintaining the integrity of the powder coating. The cooling process is monitored and regulated to ensure the wheels reach the appropriate temperature before moving on to the next stage.
At the quality control and inspection station, the wheels undergo automated checks for any imperfections or defects. This step ensures that each wheel meets the required standards for coating thickness, surface finish, and overall quality. High-resolution cameras, laser sensors, and thickness gauges are integrated into the system to detect issues such as uneven coating, bubbles, or scratches. If defects are detected, the system flags the wheel for further inspection or rework. This automated inspection ensures that only high-quality wheels move forward in the production process, reducing the risk of defective products reaching the customers. The integration of automated inspection also helps speed up the process, as it eliminates the need for manual quality checks, which can be time-consuming and prone to human error.
Once the wheels pass the quality inspection, they move to the packaging station, where they are automatically packaged for shipment. Robotic arms or conveyors handle the packaging process, ensuring that the wheels are securely packed and protected during transport. The automated packaging system ensures that the wheels are wrapped in protective materials, such as foam or custom-fit packaging, to prevent damage during handling and shipping. By automating this final step, manufacturers can reduce labor costs and ensure that packaging is consistent across all products.
The entire system is controlled by a centralized control system, which coordinates and monitors each stage of the process. This allows for real-time adjustments and ensures that the entire assembly line operates efficiently. Data collection systems track key production metrics, such as coating thickness, curing time, and throughput, allowing manufacturers to optimize performance and make data-driven decisions. The system can detect and address issues before they result in downtime, ensuring continuous production.
An important aspect of the alloy wheel powder coating assembly line is its sustainability. Powder coating is an environmentally friendly alternative to traditional liquid coatings, as it doesn’t release harmful solvents or volatile organic compounds (VOCs) into the air. Furthermore, the automated system minimizes material waste by reclaiming and recycling overspray powder. This closed-loop approach not only reduces environmental impact but also makes the system more cost-effective by reducing the amount of powder material used in the process. The system’s energy-efficient ovens and precise control over temperature and curing time further enhance its sustainability by reducing energy consumption.
In conclusion, an Alloy Wheel Powder Coating Assembly Line offers manufacturers a highly efficient and automated solution for producing high-quality coated alloy wheels. By automating each stage of the coating process—from pre-treatment and powder application to curing, cooling, inspection, and packaging—this system optimizes throughput, reduces labor costs, and ensures consistent, high-quality results. The integration of advanced technologies such as robotic arms, electrostatic spray guns, and automated inspection systems enhances the precision and flexibility of the system, while real-time data monitoring allows for continuous optimization. Additionally, the environmental benefits of powder coating, along with the system’s ability to recycle overspray and reduce waste, make it a sustainable option for manufacturers.
The Alloy Wheel Powder Coating Assembly Line continues to be a game-changer in automotive manufacturing, combining automation, precision, and speed to create a seamless production process. The system’s ability to adapt to different production needs makes it versatile and highly efficient. As manufacturers look to meet increasing consumer demand for high-quality, customized, and durable alloy wheels, the system plays a critical role in ensuring high output without compromising quality.
One of the standout features of this assembly line is its flexibility in handling various wheel designs, sizes, and finishes. Whether producing wheels for luxury vehicles, sports cars, or everyday passenger cars, the system can easily adjust to accommodate different product requirements. Automated robotic arms are equipped with advanced sensors and programming, allowing them to modify their movements based on the wheel’s shape and complexity. This ensures that every wheel, no matter how intricate its design, is coated uniformly and to the exact specifications required.
Another important advantage of the assembly line is its high throughput capacity. The use of automated conveyors and robotic arms speeds up the movement of wheels between each station, reducing bottlenecks and increasing overall production capacity. This makes it ideal for high-volume production environments, where maintaining a fast production cycle is crucial to meeting deadlines and customer demands. The system can operate at a consistent speed, ensuring that each wheel is processed within the set time frame, without delays.
As the system uses advanced robotic technology for both powder application and inspection, it is not just about speed and consistency, but also precision. The electrostatic spray guns, in particular, ensure an even application of powder, covering even the most challenging areas of the wheel. The coating thickness can be controlled to extremely tight tolerances, ensuring that each wheel meets the required standards. This level of precision is crucial for maintaining the strength, appearance, and durability of the wheels, particularly since alloy wheels are often exposed to harsh conditions such as high temperatures, abrasions, and chemicals. The consistent application of powder also ensures a uniform finish, which is important for aesthetic reasons, especially for customers seeking custom finishes.
The automated inspection process, integrated within the assembly line, takes quality control to the next level. With the use of machine vision systems and advanced sensors, the line can detect even the smallest defects that could affect the quality of the final product. This includes issues like uneven powder distribution, imperfections, or any irregularities that might arise during the coating process. The automated quality control ensures that defective wheels are quickly identified and either flagged for rework or discarded, thereby reducing the chances of subpar products reaching the customer. By automating the inspection process, manufacturers can also ensure faster detection of any production issues, allowing for quicker resolution and reducing downtime.
Moreover, the ability of the assembly line to optimize energy usage helps manufacturers reduce operating costs. The system’s energy-efficient ovens not only cure the powder coating effectively but also reduce energy consumption during the heating and curing phases. As energy prices continue to rise, the importance of energy efficiency in manufacturing systems has become even more significant. Additionally, as sustainability becomes a growing concern, manufacturers are increasingly seeking solutions that reduce their carbon footprint. This system, with its reduced energy consumption and waste recycling capabilities, aligns well with these goals.
One of the innovative aspects of the alloy wheel powder coating assembly line is its ability to incorporate predictive maintenance. Sensors embedded throughout the system constantly monitor equipment conditions, detecting wear and tear before it leads to a breakdown. This allows manufacturers to perform maintenance at optimal times, reducing unplanned downtime and extending the life of the equipment. Predictive maintenance also improves overall system efficiency, as it helps prevent bottlenecks and disruptions in the production cycle. It ensures that maintenance activities are performed proactively rather than reactively, which can have a significant impact on operational efficiency and reduce costly repairs or replacements.
Another benefit of this assembly line is the customization options it offers. As demand for personalized products grows, the automated system can switch between different finishes, colors, and effects with ease. Whether it’s a matte, gloss, or metallic finish, or even a textured coating, the system can accommodate a wide range of coating requirements. This flexibility is crucial for catering to diverse customer preferences and trends in the automotive market, making the system highly adaptable to changes in consumer demand. The quick changeover capabilities also ensure that there is minimal downtime between production runs, increasing overall efficiency.
The integration of data analytics into the assembly line allows manufacturers to track and analyze key production metrics in real-time. This data can provide insights into aspects like production speed, coating thickness consistency, oven temperatures, and inspection results. By leveraging this data, manufacturers can optimize their processes, identify bottlenecks, and fine-tune the system for maximum productivity. The use of advanced analytics helps manufacturers make informed decisions about process improvements and resource allocation, contributing to more efficient production and a better bottom line.
In addition, the system’s scalability is another important factor. As the demand for alloy wheels grows or fluctuates, manufacturers can easily scale up the system by adding more robotic arms, curing stations, or inspection modules. This scalability ensures that manufacturers are not constrained by their production capabilities and can adapt to market changes or increased demand without having to invest in entirely new systems.
Finally, the sustainability of the Alloy Wheel Powder Coating Assembly Line should not be overlooked. The use of powder coating is already an environmentally friendly option compared to traditional liquid coatings because it does not release harmful chemicals into the atmosphere. The ability to reclaim and reuse powder overspray further minimizes waste and reduces the overall environmental impact of the manufacturing process. The automated system’s efficient use of resources, energy, and materials contributes to a more sustainable production process, which is an increasingly important consideration for manufacturers seeking to align with global environmental standards.
In conclusion, the Alloy Wheel Powder Coating Assembly Line represents a leap forward in manufacturing technology. It combines automation, precision, speed, and flexibility to create a system that is capable of producing high-quality alloy wheels at scale. With its ability to customize finishes, optimize energy usage, maintain high levels of quality control, and offer predictive maintenance, this assembly line is designed to meet the demands of modern manufacturing while also reducing costs and environmental impact. By incorporating real-time data analytics and being adaptable to changes in demand, the system ensures that manufacturers can remain competitive in a rapidly changing market.
Alloy Wheel Powder Coating Finishing Line
An Alloy Wheel Powder Coating Finishing Line is a specialized production line designed to provide the final touches to alloy wheels after they have been coated with powder. The finishing process ensures that the coating is smooth, durable, and free from defects, providing both functional and aesthetic benefits. This line typically includes a combination of coating, curing, inspection, and post-coating processes, all aimed at achieving a high-quality, long-lasting finish on alloy wheels. Here’s an overview of the key stages involved in the finishing line:
- Powder Coating Application: This is the core step where the powder coating is applied to the alloy wheels. The powder is typically applied using electrostatic spray guns or robotic arms, which charge the powder particles and attract them to the grounded wheels. This ensures even coverage of the wheel’s surface, including intricate areas that may be hard to reach with traditional methods. The system can be adjusted to achieve different textures, gloss levels, or finishes, depending on the desired end result.
- Curing Process: After the powder is applied, the wheels are transferred to the curing oven, where the coating is baked at a controlled temperature (typically between 160°C to 200°C). The heat causes the powder particles to melt, fuse, and chemically bond to the surface of the alloy wheel, resulting in a smooth, hard coating. The curing time and temperature are critical factors in achieving a high-quality finish that is durable and resistant to scratches, chips, and corrosion.
- Cooling Stage: After the curing process, the wheels are moved to a cooling section. This allows the coating to solidify and cool down evenly. The cooling stage is critical to ensuring that the coating doesn’t warp or crack due to sudden temperature changes. Cooling is typically done with forced air or water-cooling systems. The temperature and speed at which the wheels are cooled can impact the final finish, so this step is carefully controlled.
- Inspection and Quality Control: Following the curing and cooling stages, the alloy wheels are carefully inspected for defects. This is done using automated vision systems or manual checks depending on the specific requirements. Automated systems can detect imperfections like uneven coating, bubbles, or scratches in real-time. The wheels that pass inspection move forward in the production line, while any defective wheels are either reworked or discarded. This ensures that only products with a flawless finish reach the final stages.
- Post-Coating Treatments: In some cases, additional processes are used to further enhance the finish of the coated wheels. These treatments can include:
- Polishing: For wheels that require a shiny, reflective surface, a polishing stage may be included after the powder coating. Polishing helps to bring out the shine and remove any remaining imperfections on the surface.
- Clear Coating: A layer of clear powder coating may be applied on top of the initial color or finish to provide additional protection against environmental factors such as UV rays, salt, or chemicals. This clear coat helps to enhance the durability and lifespan of the coating.
- Texture Application: For certain styles of wheels, a textured finish may be required. This can be achieved by using a textured powder or adjusting the application process to achieve the desired roughness or pattern.
- Final Inspection and Touch-Up: After the wheels go through all the coating and post-coating processes, a final inspection is conducted to ensure that the product meets all quality standards. Any minor defects or imperfections that might have been missed in the earlier stages can be addressed during this phase. Automated systems, such as robotic touch-up stations, can apply small repairs to areas with imperfections, ensuring that every wheel looks flawless.
- Packaging and Shipping: Once the wheels have passed inspection and any necessary touch-ups have been completed, the final step is packaging. Alloy wheels are typically packaged with care to prevent damage during shipping. Automated packaging systems, often using robotic arms or conveyor belts, securely place the wheels into protective packaging materials, such as foam inserts or custom-fit cardboard. The wheels are then ready for shipment to customers, ensuring they arrive in perfect condition.
Benefits of the Alloy Wheel Powder Coating Finishing Line:
- Consistency: The use of automated systems ensures that each wheel receives the same level of coating quality, producing consistent results across large production runs.
- High-Quality Finish: The controlled application, curing, and inspection processes help to ensure a smooth, durable, and visually appealing finish that enhances the wheel’s performance and aesthetics.
- Customization: The line can accommodate a wide range of finishes, including matte, glossy, metallic, or textured coatings, making it versatile for various customer preferences.
- Efficiency: Automation streamlines the process, improving throughput, reducing labor costs, and minimizing downtime. Automated inspection and rework systems further enhance production efficiency.
- Environmental Benefits: Powder coating is an eco-friendly alternative to liquid coatings, as it does not emit volatile organic compounds (VOCs) or hazardous chemicals. The system also reclaims and recycles overspray powder, reducing waste and material costs.
- Durability: The curing process creates a hard, scratch-resistant coating that protects the alloy wheels from corrosion, chipping, and other damage, ensuring they last longer under harsh conditions.
In conclusion, an Alloy Wheel Powder Coating Finishing Line offers a comprehensive solution for manufacturers looking to produce high-quality, durable, and aesthetically pleasing alloy wheels. By incorporating automated systems for powder application, curing, cooling, inspection, and post-coating treatments, manufacturers can achieve greater efficiency, consistency, and customization. The line’s flexibility, combined with its environmentally friendly and cost-effective features, makes it an essential part of modern alloy wheel production.
An Alloy Wheel Powder Coating Finishing Line is a critical part of the manufacturing process, focused on delivering high-quality, durable finishes on alloy wheels. The line is designed to efficiently apply powder coatings and ensure that each wheel achieves a consistent, smooth, and durable finish. The system begins with the application of the powder coating, where automated electrostatic spray guns or robotic arms apply the powder evenly to the wheel’s surface. This electrostatic process ensures that the powder adheres evenly, even in complex or intricate areas, providing a flawless coating. After the powder is applied, the wheels are moved into curing ovens where they are heated to specific temperatures, allowing the powder to melt and chemically bond to the wheel’s surface. This curing process creates a hard, scratch-resistant surface that ensures durability. After the curing stage, the wheels are allowed to cool at a controlled rate, often with the help of cooling systems like forced air or water, to prevent any distortion or cracking in the coating.
Once cooled, the wheels undergo a final inspection phase where any imperfections or defects in the coating, such as uneven surfaces or bubbles, are detected. Automated vision systems or manual inspection ensure that only high-quality products proceed to the next stage. If necessary, post-coating treatments like polishing, clear coating, or texture application may be applied to enhance the wheel’s appearance or provide additional protection. The final inspection is crucial for ensuring that every wheel meets stringent quality standards before moving to the packaging stage. Once the wheels pass the inspection, they are securely packaged to protect them during shipment, ensuring that they reach customers in perfect condition.
The use of automated systems throughout the finishing line improves efficiency, reduces labor costs, and allows for consistent quality control. The process is also environmentally friendly, as powder coating eliminates the need for solvents and reduces emissions. Additionally, the system can recycle powder overspray, reducing material waste. This finishing line is designed for flexibility, capable of accommodating various finishes, textures, and customizations, and is adaptable to meet the needs of different markets. The entire line ensures that the alloy wheels not only look good but also offer long-lasting performance, making them suitable for a variety of vehicles and driving conditions.
Automated Alloy Wheel Powder Coating Facility
An Automated Alloy Wheel Powder Coating Facility is a sophisticated production system designed to streamline and enhance the alloy wheel coating process. This facility utilizes automated equipment and technology to provide a high-efficiency, high-quality coating solution for alloy wheels, ensuring uniformity, durability, and consistency in the final product. The facility is composed of several integrated stages that handle different aspects of the coating process, from pre-treatment to final inspection and packaging, all of which are optimized to reduce labor, increase throughput, and minimize waste.
The process begins with automated wheel handling, where the alloy wheels are moved along a conveyor system to the first station. At this stage, pre-treatment processes are employed to prepare the wheel surface for powder coating. This typically involves automated cleaning systems such as chemical baths, abrasive blasting, or phosphating to remove contaminants like oil, rust, dirt, and old coatings. These steps ensure that the surface of the wheel is free from impurities that could affect the adhesion and quality of the powder coating.
Once the wheels are properly pre-treated, they move to the powder application stage, where automated systems apply the powder coating to the wheel’s surface. This process uses electrostatic spray guns or robotic arms that apply the powder evenly to the surface of the wheel. Electrostatic charging ensures that the powder particles are attracted to the grounded wheel, providing even coverage and preventing overspray. The robotic arms or spray guns are often equipped with sensors and advanced programming to adjust the coating process based on the wheel’s design, ensuring that even hard-to-reach areas are coated efficiently. Automated color change systems also allow for quick transitions between different powder colors or finishes without significant downtime, providing flexibility in production.
After the powder coating is applied, the wheels move to the curing ovens, which are an integral part of the facility. These ovens are designed to heat the wheels to a precise temperature, allowing the powder to melt, fuse, and chemically bond to the wheel surface. The temperature, time, and airflow in the oven are carefully controlled to achieve optimal curing conditions. This process ensures that the coating is durable, scratch-resistant, and able to withstand environmental factors such as UV rays, road salts, and chemical exposure.
Once the curing process is complete, the wheels move to the cooling stage. Cooling is a critical part of the process to prevent thermal shock, which could lead to cracks or imperfections in the coating. The cooling system, typically using forced air or water cooling, gradually reduces the temperature of the wheels to ambient conditions, allowing the coating to solidify evenly.
Next, the wheels enter the quality control and inspection stage. This step is essential to ensuring that each wheel meets the desired specifications for coating thickness, uniformity, and overall finish. Automated inspection systems using vision cameras, laser sensors, and thickness gauges check the coating for defects such as uneven coverage, air bubbles, or scratches. Any wheels that do not meet the required standards are flagged for rework or rejection, ensuring that only high-quality products proceed to the next stage.
If necessary, the wheels may undergo post-coating treatments such as polishing, clear coating, or additional texture application. Polishing may be used to enhance the wheel’s shine or remove any imperfections that remain after the curing process. Clear coating provides an extra layer of protection to improve the durability and appearance of the wheels, while textured finishes can be applied for a unique look or specific performance requirements.
The final stage of the process is packaging and shipment. Automated systems carefully package the wheels to prevent damage during transportation. Protective materials, such as foam or custom-fit packaging, are used to ensure the wheels are securely packed. Once packaged, the wheels are ready for shipment to customers, meeting the standards of quality and safety required for automotive applications.
Throughout the entire process, an advanced centralized control system oversees the operation of the entire facility. This system allows for real-time monitoring, adjusting parameters like curing time, powder application, and temperature to ensure the consistency and quality of the final product. Data analytics also provide insights into key performance metrics, such as cycle time, defect rates, and production efficiency, enabling continuous improvement and optimization.
The Automated Alloy Wheel Powder Coating Facility offers several advantages, including:
- Increased production efficiency due to automation, which reduces manual labor and operational costs.
- Consistency and quality control across all wheels, ensuring that each product meets the required standards.
- Reduced material waste thanks to the system’s ability to reclaim and recycle overspray powder, making the process more cost-effective and environmentally friendly.
- Customization capabilities that allow for different finishes, textures, and colors, providing flexibility to meet customer demands.
- Sustainability with minimal emissions and reduced use of hazardous chemicals, as powder coating does not require solvents and produces no volatile organic compounds (VOCs).
- Scalability to handle increasing production volumes without compromising quality or efficiency.
In conclusion, an Automated Alloy Wheel Powder Coating Facility is an advanced and highly efficient solution for producing high-quality, durable, and customized alloy wheels. By automating the coating process from start to finish, the facility ensures consistent product quality, reduces costs, and offers greater flexibility for meeting customer demands. The integration of advanced technologies, such as robotic arms, automated inspection systems, and centralized control systems, makes this facility an essential part of modern alloy wheel manufacturing.
An Automated Alloy Wheel Powder Coating Facility is a fully integrated system that streamlines the entire coating process, enhancing both efficiency and product quality. It starts with an automated conveyor system that transports the wheels through various stages of coating. The initial step involves pre-treatment, where automated cleaning systems ensure that each wheel is free of contaminants, such as dirt, oils, or rust, which could affect the adhesion of the powder coating. Once pre-treated, the wheels are ready for the powder application stage. Here, electrostatic spray guns or robotic arms apply the powder coating uniformly to the wheel surface. These advanced systems use electrostatic forces to ensure even coverage and minimize overspray, even on complex designs. With the ability to adjust to different finishes and colors quickly, these automated systems also reduce downtime and increase production flexibility.
Once the powder is applied, the wheels move into curing ovens. These ovens are meticulously controlled to heat the wheels to the precise temperature required for the powder to fuse and bond to the wheel’s surface, forming a durable, scratch-resistant coating. The curing process is critical, as it determines the quality and longevity of the coating. After the curing process, the wheels are carefully cooled, which helps solidify the coating and prevents any warping or cracking due to temperature fluctuations. The cooling system ensures that the wheels are brought down to ambient temperatures gradually and evenly.
Following the cooling stage, the wheels undergo a quality control process. Automated inspection systems with vision cameras, laser sensors, and thickness gauges scan each wheel for defects such as uneven coating, air bubbles, or scratches. The system is designed to detect even the smallest imperfections, ensuring that only flawless products move forward. Defective wheels are flagged for rework or disposal, maintaining high production standards. If required, the wheels may also go through post-coating treatments like polishing, clear coating, or texture application. These additional treatments improve the finish, enhance durability, or add custom design features. The final inspection checks for any residual issues before the wheels are packaged. Using automated packaging systems, the wheels are securely wrapped to prevent damage during transit, ensuring that they reach the customer in pristine condition.
Throughout the entire process, a centralized control system monitors and optimizes each stage of production. This system enables real-time adjustments and provides valuable data for performance analysis, allowing for continuous improvement and greater efficiency. The facility’s automation not only reduces labor costs but also enhances consistency and reduces material waste. Since powder coating is an environmentally friendly process, the facility’s automated systems are designed to reclaim overspray powder, minimizing waste and further improving sustainability. The ability to quickly switch between different colors and finishes without significant downtime makes the facility highly adaptable, catering to varying customer preferences and market demands. The scalability of the system also allows manufacturers to ramp up production as needed, ensuring that they can meet increasing demand without sacrificing quality.
In conclusion, the Automated Alloy Wheel Powder Coating Facility represents a modern, efficient, and eco-friendly approach to alloy wheel production. By automating every stage of the coating process, from pre-treatment and powder application to curing, cooling, inspection, and packaging, the facility ensures consistent, high-quality finishes that meet the highest industry standards. The use of advanced robotics, automated inspection, and centralized control systems improves production efficiency, reduces waste, and enhances customization, making it an invaluable asset for manufacturers looking to stay competitive in the automotive market.
Alloy Wheel Powder Coating Conveyor Line
An Alloy Wheel Powder Coating Conveyor Line is a specialized automated system designed to efficiently transport and process alloy wheels through various stages of powder coating. This conveyor line integrates several stages, from pre-treatment and powder application to curing and cooling, ensuring that each wheel receives a consistent and high-quality coating. The primary goal of the conveyor system is to streamline the production process, reducing labor, increasing throughput, and maintaining consistent product quality.
The process begins when alloy wheels are loaded onto the conveyor system, which automatically transports them through different stations. The first station typically involves pre-treatment, where the wheels are cleaned and prepared for coating. This could include automated stages such as washing, chemical baths, abrasive blasting, or phosphating to remove any contaminants that might affect the adhesion of the powder coating. Proper pre-treatment is essential for ensuring that the powder bonds effectively to the wheel surface, resulting in a durable, high-quality finish.
Once the wheels are pre-treated, they are transported to the powder coating application stage. The conveyor line moves the wheels into position for automated electrostatic powder spraying, where electrostatic guns or robotic arms apply the powder coating evenly across the surface of the wheel. The powder is electrostatically charged, causing it to adhere to the grounded wheel, ensuring an even and uniform coating even in hard-to-reach areas. The automated system can be adjusted for different finishes, such as matte, glossy, or textured, depending on the desired outcome. This system also allows for quick changes between different colors or finishes, minimizing downtime and maximizing production flexibility.
After the powder coating is applied, the wheels continue down the conveyor line to the curing oven. The curing process is critical for bonding the powder to the surface of the wheel. In the oven, the wheels are heated to a specific temperature (usually between 160°C to 200°C) for a set amount of time, causing the powder to melt and chemically bond to the wheel’s surface. The conveyor line ensures that each wheel is exposed to the correct temperature and time, providing a uniform cure and ensuring that the coating is hard, durable, and resistant to scratching, chipping, and corrosion.
Once the curing process is complete, the wheels move through a cooling stage. During cooling, the wheels are gradually brought to ambient temperature, ensuring that the coating sets properly and does not crack or warp due to rapid cooling. The cooling system could use forced air or water-cooled systems to control the temperature gradually and evenly, ensuring a smooth and stable finish.
Following the cooling stage, the wheels proceed to quality control and inspection. Automated vision systems, laser sensors, or manual inspection stations are used to check for defects in the coating, such as uneven coverage, air bubbles, or scratches. If any defects are detected, the system may automatically reject or mark the wheel for rework. The wheels that pass inspection are then ready for packaging.
The final step in the process is packaging and shipment. Automated packaging systems secure the wheels in protective materials such as foam or custom-fit packaging to prevent damage during transport. The conveyor system ensures that the wheels are packaged quickly and efficiently, reducing the chances of handling errors.
The Alloy Wheel Powder Coating Conveyor Line offers several advantages, including high production efficiency, consistent coating quality, reduced labor costs, and minimal waste. The automated nature of the system ensures that each wheel receives the same level of quality and finish, providing a consistent product for customers. The system is also environmentally friendly, as powder coating does not release harmful solvents or chemicals, and overspray powder is typically reclaimed and reused. Additionally, the line’s ability to accommodate different finishes and colors, coupled with quick changeover capabilities, makes it highly versatile and able to meet varying customer demands.
Overall, an Alloy Wheel Powder Coating Conveyor Line is an essential part of modern alloy wheel manufacturing, offering speed, flexibility, and quality. By automating each stage of the process and integrating advanced technologies, the conveyor line ensures that wheels are coated efficiently, consistently, and to the highest standards, making it a key component in any alloy wheel production facility.
An Alloy Wheel Powder Coating Conveyor Line is designed to optimize the alloy wheel coating process, making it more efficient, consistent, and scalable. The conveyor system acts as the backbone of the facility, guiding the wheels through each step of the coating process, from preparation to packaging. As wheels enter the system, they are automatically conveyed through pre-treatment stages where they are cleaned and prepared. These stages often include automated washing, chemical cleaning, and abrasive blasting to remove contaminants like dirt, oils, and rust. The goal of pre-treatment is to ensure that the powder coating adheres properly and evenly to the wheel surface.
Once pre-treated, the wheels move to the powder coating application stage. The electrostatic spraying process, where powder is applied through electrostatic guns or robotic arms, ensures an even coating across the wheel’s surface, including difficult-to-reach areas. The powder particles are charged, which allows them to stick to the grounded surface of the wheel, creating an even and consistent layer. The system can be programmed to switch between different colors or finishes, ensuring versatility and reducing downtime between different batches of wheels.
After the powder is applied, the wheels continue down the conveyor line into the curing oven. Here, the wheels are heated to a specific temperature for a precise period, allowing the powder to melt and chemically bond with the wheel surface. This curing process is critical for achieving a durable, hard coating that is resistant to scratches, chips, and environmental damage. Following the curing process, the wheels are cooled using forced air or water-cooling systems to prevent rapid temperature changes that could damage the finish.
Once cooled, the wheels are subjected to quality control and inspection. Automated systems, including vision cameras and laser sensors, scan the wheels for defects such as uneven coating, air bubbles, or scratches. Wheels that do not meet quality standards are either reworked or discarded. Those that pass the inspection move to the packaging stage, where the conveyor system efficiently transports them to be packed for shipment. The packaging is designed to protect the wheels from damage during transport, using materials like foam inserts or custom-fit cartons.
Throughout the process, the conveyor line is controlled by an automated system that ensures every wheel moves through each stage with precision and consistency. Real-time monitoring allows operators to track the performance of each stage, adjusting parameters as necessary to maintain optimal results. This automated system reduces labor costs, minimizes human error, and enhances the overall efficiency of the production process.
In addition, the system is environmentally friendly. Powder coating eliminates the need for solvents and chemicals that are common in traditional liquid coatings, making it a safer, more eco-conscious choice. Furthermore, the overspray powder is usually collected and recycled, reducing material waste and improving the overall sustainability of the operation.
By integrating automation, the Alloy Wheel Powder Coating Conveyor Line ensures high product quality, faster production cycles, and the flexibility to adapt to changing customer demands. This streamlined, cost-effective process is a key advantage for manufacturers, helping them meet market demands for a consistent, high-quality product while maintaining operational efficiency.
Fully Automated Alloy Wheel Powder Coating Process
The Fully Automated Alloy Wheel Powder Coating Process is a highly efficient and precise manufacturing method that involves advanced automation at every stage of the alloy wheel coating process. This system integrates a series of automated machines and robotic technologies designed to improve productivity, ensure consistent quality, and reduce manual intervention. The process is streamlined from pre-treatment all the way through to packaging, ensuring high-quality finishes while optimizing throughput and reducing waste.
The process begins with automated wheel handling, where alloy wheels are automatically loaded onto the conveyor system, which transports them to the next stages of production. The first station in the process is pre-treatment, where the wheels undergo cleaning and surface preparation. Automated cleaning systems such as chemical baths, abrasive blasting, or ultrasonic cleaning are used to remove contaminants like oil, dirt, rust, and other residues from the wheel’s surface. This stage is crucial because proper cleaning ensures that the powder coating adheres uniformly and securely to the surface of the wheel.
Once the wheels are cleaned and prepared, they are transferred to the powder coating application station. Here, automated electrostatic powder spray guns or robotic arms are used to apply the powder coating. These systems are designed to evenly apply the powder to the surface of the wheel by using electrostatic charges that make the powder stick to the grounded surface. The powder application is carefully controlled by automated systems that can adjust the spray pattern to ensure that even the most complex wheel designs receive an even coat of powder. The electrostatic process minimizes overspray and ensures that the coating is consistent, creating a smooth, uniform finish.
After the powder is applied, the wheels move to the curing oven. The wheels are transported through the oven on the conveyor system, where they are heated to a specific temperature for a set duration. The curing process causes the powder to melt and chemically bond to the wheel’s surface, resulting in a durable, scratch-resistant coating. The temperature and time in the curing oven are closely monitored and controlled by automated systems to ensure optimal curing conditions for every wheel. The curing process gives the wheel its final finish, making it both aesthetically pleasing and durable enough to withstand the rigors of daily use, including exposure to UV light, road salts, and other environmental factors.
Once the wheels exit the curing oven, they are transferred to the cooling station. The cooling system is automated to regulate the temperature of the wheels and ensure that the coating sets evenly without distortion. The wheels are gradually cooled using forced air or water-cooling systems, which prevents any rapid temperature changes that could potentially crack or warp the coating.
After cooling, the wheels undergo automated quality control and inspection. Vision systems equipped with high-definition cameras or laser sensors automatically scan the wheels for defects such as uneven coating, bubbles, cracks, or imperfections. These systems can detect even the smallest issues, ensuring that only wheels with perfect finishes move forward to the next stage. If defects are detected, the system can either flag the wheel for rework or remove it from the production line entirely.
Once the wheels pass inspection, they proceed to the final stage: packaging. The wheels are automatically moved to the packaging area, where automated systems package them securely to prevent damage during shipping. The wheels may be placed in custom-fit boxes or wrapped in protective materials like foam or plastic to ensure they remain in pristine condition as they move through the logistics chain.
Throughout the entire process, a centralized control system monitors and manages all stages, from pre-treatment to packaging. This control system uses real-time data to optimize each phase of production, allowing for adjustments to be made instantly to maintain quality and efficiency. The data gathered from each stage of the process is analyzed to improve future operations, track production metrics, and reduce downtime.
The Fully Automated Alloy Wheel Powder Coating Process offers several benefits, including high levels of production efficiency, consistent quality, reduced labor costs, and minimal waste. Automated systems also contribute to environmental sustainability by reducing the use of solvents and chemicals, as powder coating does not require these materials. Moreover, any overspray from the powder coating process is typically collected and recycled, further reducing waste and improving the sustainability of the operation.
In conclusion, the Fully Automated Alloy Wheel Powder Coating Process is an advanced, high-performance system that ensures alloy wheels are coated with precision and consistency. The complete automation of each stage of the process—from cleaning and powder application to curing, cooling, and packaging—results in faster production cycles, higher-quality finishes, and reduced operational costs, making it a key solution for alloy wheel manufacturers seeking to stay competitive in the automotive market.
The fully automated alloy wheel powder coating process continues to provide unmatched consistency, scalability, and operational control across large-scale manufacturing environments. With automation overseeing each critical parameter—temperature, conveyor speed, powder spray rate, and curing time—manufacturers can maintain high standards of finish quality with minimal human error. As production requirements change, such as shifts in wheel size, shape, or coating type, modern automated systems can be rapidly reprogrammed or recalibrated, allowing the line to adapt quickly without prolonged downtime or manual reconfiguration. This flexibility is particularly valuable in custom or short-run production scenarios, where frequent changeovers are necessary.
Furthermore, advanced automation integrates seamlessly with digital manufacturing platforms and Industry 4.0 technologies. Each stage of the process can be tracked through sensors and software, producing detailed data logs for every wheel. This traceability ensures that manufacturers can quickly identify and isolate any issues in the production chain, enhancing quality assurance and facilitating regulatory compliance. Predictive maintenance systems monitor equipment health in real time, identifying potential mechanical failures or component wear before they lead to costly downtime. As a result, the system not only maximizes uptime and throughput but also prolongs the lifespan of expensive machinery through timely interventions and diagnostics.
Energy efficiency is another major benefit of fully automated systems. Curing ovens, for example, can be equipped with zoned heating elements that activate only when wheels are present, reducing unnecessary energy consumption. Similarly, powder spray booths often include intelligent reclaim systems that collect unused powder, filter it, and return it to the supply cycle, minimizing waste and reducing raw material costs. These sustainability-focused features align with modern environmental regulations and corporate goals to lower carbon footprints and improve eco-efficiency.
Automation also enhances worker safety. With minimal manual handling of wheels or direct interaction with high-temperature ovens, harsh chemicals, or airborne particulates, operators are removed from potentially hazardous environments. Instead, they can focus on system oversight, diagnostics, and process optimization from a centralized control station, improving working conditions and reducing the risk of accidents or exposure.
Ultimately, the fully automated alloy wheel powder coating process delivers significant advantages in speed, precision, consistency, and adaptability. Whether producing thousands of identical wheels or handling varied custom batches, the system ensures optimal coating quality while minimizing resource consumption and operational costs. As demand grows for more durable, corrosion-resistant, and visually appealing alloy wheels in both the OEM and aftermarket sectors, fully automated powder coating lines are increasingly becoming a cornerstone of competitive, future-ready manufacturing strategies.
Alloy Wheel Powder Coating Production Line
An Alloy Wheel Powder Coating Production Line is a comprehensive and streamlined system designed to handle high-volume, consistent, and high-quality finishing of alloy wheels using powder coating technology. This production line combines mechanical automation, robotic application, and process control to deliver a uniform, durable finish that meets both aesthetic and performance standards required by the automotive industry. The process begins with the wheels being loaded onto an automated conveyor system, which continuously moves them through each stage of the operation with precision timing and minimal manual handling.
The first phase in the production line is surface preparation, which typically includes a multi-stage cleaning and pre-treatment sequence. Here, alloy wheels are cleaned of oils, residues, oxidation, and other contaminants that would interfere with coating adhesion. This is achieved through automated washing, degreasing, and possibly chemical etching or phosphate treatments, all performed in enclosed, controlled chambers. The cleanliness and surface profile achieved in this phase are critical for the long-term performance of the powder coating.
Once pre-treated, the wheels enter the powder coating booth, where robotic arms or automated spray guns apply a fine, electrostatically charged powder. The powder particles are attracted to the grounded metal surface of the wheel, forming a uniform layer that wraps around complex contours and recessed areas. The application system can be finely tuned for various coating types, textures, and colors, enabling manufacturers to meet diverse product specifications. Multiple color lines or rapid changeover systems can also be integrated for increased production flexibility.
Following application, the wheels pass into an industrial curing oven where the powder melts and chemically bonds to the surface under precise temperature and time conditions. The curing oven is designed to maintain stable heat zones and energy efficiency while accommodating varying wheel sizes and profiles. As the wheels exit the oven, they undergo a controlled cooling phase to allow the coating to harden without defects like cracking or bubbling.
After cooling, wheels move to a quality inspection zone where automated systems with optical scanners and thickness gauges assess the coating for consistency, coverage, gloss level, and defects. Real-time feedback from these systems can be used to fine-tune upstream processes, ensuring each wheel meets stringent visual and performance criteria. Wheels that meet specifications are directed to automated packaging stations where they are wrapped and prepared for shipment, while any that do not pass inspection are flagged for rework.
The entire production line is governed by a centralized control system that monitors process variables such as line speed, oven temperature, powder usage, and equipment status. This data-driven approach allows for optimized throughput, reduced downtime, and predictable maintenance schedules. Additionally, powder recovery systems help reclaim overspray, making the process highly sustainable and cost-effective by reducing waste and environmental impact.
Incorporating automation, precision controls, and integrated diagnostics, the alloy wheel powder coating production line ensures a reliable, repeatable, and scalable operation. It enables manufacturers to deliver a premium finish that enhances both the appearance and durability of alloy wheels while maintaining production efficiency and environmental responsibility.
As the alloy wheel powder coating production line continues to operate, its performance relies heavily on synchronization between each segment of the process. The transition of wheels from one stage to another is controlled by programmable logic controllers (PLCs) and monitored in real time by sensors and software interfaces that adjust process parameters instantly to avoid bottlenecks or quality issues. These systems not only ensure continuous flow but also maintain critical tolerances across temperature, timing, and coating thickness to ensure every wheel matches specification. The efficiency gained through this level of automation allows for high-volume production with minimal human intervention, reducing labor costs and increasing throughput.
The coating process itself is designed to be both versatile and robust. Different formulations of powder—such as polyester for UV resistance, epoxy for corrosion resistance, or hybrid blends—can be used based on the end-use requirements of the wheels. The flexibility of the line allows quick changeovers, enabling manufacturers to switch between finishes or colors within a short time frame without compromising cleanliness or cross-contamination. Powder hoppers can be cleaned via automated purging systems, and spray guns can be flushed and reprogrammed with new parameters, all under centralized control. This adaptability is essential for serving both OEM contracts with strict color codes and custom aftermarket demands that may include metallic, matte, gloss, or textured finishes.
Environmental considerations are also deeply integrated into the design of the production line. Since powder coating is a dry finishing process, it eliminates the need for hazardous solvents and volatile organic compounds (VOCs), making it much more environmentally friendly than traditional liquid painting. The powder overspray is collected via recovery systems, filtered, and reused, which not only reduces waste but also lowers material costs significantly. Air filtration and ventilation systems ensure clean working environments and compliance with environmental safety standards, while energy-efficient curing ovens and modular process control minimize the carbon footprint of the operation.
The digital backbone of the production line allows for full traceability and quality documentation. Each wheel can be tagged and tracked through the system, linking back to a digital record of the process parameters it experienced. This is invaluable for quality assurance and customer satisfaction, as it provides verifiable evidence of compliance with specifications. It also facilitates continuous improvement by identifying recurring issues or process deviations that can be addressed through predictive maintenance or software updates.
In terms of operational reliability, the production line is built for uptime. Redundancies in key systems such as conveyors, temperature control loops, and powder feeders ensure that the line can continue running even in the event of localized equipment failure. Maintenance schedules are managed by automated alerts and diagnostics, with easy-access panels and modular components designed for rapid servicing. Staff are trained not for manual coating tasks, but for overseeing process stability and responding to any alerts or deviations reported by the system.
Ultimately, the alloy wheel powder coating production line represents the intersection of mechanical precision, chemical engineering, and digital control. It transforms raw alloy wheels into finished, ready-for-market products with remarkable speed and consistency, fulfilling the dual demands of aesthetic appeal and functional protection. Whether for high-performance sports cars, commercial fleets, or luxury sedans, the line delivers finishes that are both visually striking and capable of withstanding the harsh conditions of real-world driving. Its ability to scale output while maintaining environmental and quality standards makes it a cornerstone of modern wheel manufacturing.
Alloy Wheel Powder Coating Automated Line

An Alloy Wheel Powder Coating Automated Line is a technologically advanced manufacturing solution designed to apply durable, high-quality powder coatings to alloy wheels with minimal human intervention. This automated line integrates robotic application systems, intelligent conveyors, precision-controlled curing ovens, and real-time monitoring tools into a continuous, high-efficiency workflow. The core objective is to increase throughput, maintain consistent coating quality, reduce labor costs, and minimize environmental impact.
The process starts with automated wheel loading onto a conveyor system that transports each wheel through a series of programmed steps. In the pre-treatment stage, the wheels are cleaned in enclosed chambers using high-pressure sprays, chemical solutions, or shot blasting equipment, depending on the desired surface profile. This automated cleaning ensures every wheel has a contamination-free surface to optimize powder adhesion.
After surface preparation, the wheels move seamlessly into the powder coating booth, where robotic arms or automated electrostatic spray guns apply the powder with extreme accuracy. These systems adjust spray patterns, flow rates, and angles in real time to match the design and geometry of each wheel. Advanced systems can detect surface conditions and dynamically optimize coating thickness, ensuring full and even coverage with minimal waste.
Once coated, the wheels enter a high-precision curing oven where the powder is thermally bonded to the surface. Temperature zones within the oven are carefully regulated by a central control system that tracks each wheel’s progress, ensuring consistent heat application across all batches. The resulting finish is both aesthetically uniform and functionally resistant to scratches, corrosion, UV light, and harsh environmental exposure.
After curing, wheels are cooled in a controlled environment to prevent thermal shock and are then automatically routed to inspection stations. Vision systems and sensors inspect the finish for defects such as uneven coating, pinholes, or foreign particles. Non-conforming items are flagged for rework or removal without disrupting the production line. Approved wheels are labeled, sorted, and packaged for delivery—all without manual handling.
Throughout the entire process, the automated line is monitored by integrated software platforms that collect and analyze data in real time. These platforms enable predictive maintenance, automatic fault detection, and production optimization. The system supports rapid changeovers between coating types or colors, allowing for efficient handling of varied production orders without extended downtime.
This automated approach significantly reduces human exposure to chemicals and high-temperature environments, improving workplace safety. It also contributes to sustainability by reclaiming unused powder, reducing emissions, and conserving energy. The Alloy Wheel Powder Coating Automated Line offers a competitive edge by delivering consistent product quality, operational efficiency, and adaptability in a market that demands speed, precision, and high aesthetic standards.
The integration of automation in the alloy wheel powder coating line enhances not only efficiency but also overall product consistency and traceability. Each wheel, once entered into the line, is assigned a digital identifier that allows its progress to be monitored through every step of the process. This identifier is linked to a centralized control system that logs environmental conditions, process parameters, and inspection outcomes. Such traceability is invaluable for maintaining quality assurance standards, fulfilling compliance requirements, and providing accountability in the event of warranty claims or product audits. It also allows for in-depth analytics on production performance, revealing opportunities to fine-tune cycle times, reduce energy consumption, and minimize scrap rates.
Robotic application units play a central role in ensuring repeatability and finish uniformity, especially on wheels with complex designs or deep recesses. These robotic systems can be programmed to follow precise spray paths, adjusting speed and angle dynamically to prevent overspray and ensure full coverage even on intricate geometries. Adaptive feedback mechanisms further refine the application process, allowing for real-time corrections based on visual or sensor input. This level of precision would be extremely difficult to replicate manually and leads to significantly reduced powder usage per part, thereby lowering material costs while improving environmental sustainability.
The automated curing phase is equally critical. Modern ovens are designed with zoning technology, allowing different sections of the oven to operate at varying temperatures based on the wheel’s location and coating type. This not only ensures optimal curing conditions but also conserves energy by reducing unnecessary heating. Conveyor speed is also adjustable in real-time to match throughput needs and guarantee the powder coating reaches its full mechanical and chemical properties before cooling begins. The temperature data and dwell time for each wheel are recorded and stored automatically, ensuring process integrity and making it easier to pinpoint any deviations if issues arise later.
Once cooled, automated inspection stations use high-resolution cameras and laser profiling tools to scan the entire surface of each wheel. These systems detect flaws such as surface roughness, insufficient coverage, or color inconsistencies with a level of detail far beyond what manual inspection could achieve. If a wheel fails inspection, it is automatically diverted from the main line into a rework loop or quality quarantine area. This automated inspection system dramatically increases the reliability and speed of defect detection, allowing for immediate feedback to upstream processes if a pattern of errors is detected.
The packaging phase at the end of the line is equally optimized for automation. Robotic arms lift finished wheels onto packing conveyors, where they are automatically bagged, cushioned with protective material, and boxed according to size and customer specifications. Barcodes and RFID tags are applied for inventory tracking and shipping coordination. This reduces human handling, which not only improves worker safety but also minimizes the risk of damaging the freshly coated surfaces. The automated packaging station can also be configured to integrate with logistics software, ensuring seamless synchronization between production output and shipping schedules.
The modularity of the entire line means it can be scaled or reconfigured based on production demands. Whether producing a limited batch of custom wheels or fulfilling a large-scale OEM order, the same automated system can adapt by adjusting cycle times, powder formulas, or curing profiles with minimal downtime. Cloud-based integration allows remote access to performance dashboards and maintenance scheduling, enabling plant managers and engineers to oversee operations from virtually anywhere.
In addition to operational benefits, the automated line significantly enhances the facility’s environmental footprint. Powder coating generates no hazardous air pollutants and very little waste, especially when paired with recovery systems that reclaim and recycle unused powder. The elimination of solvents and volatile organic compounds also simplifies regulatory compliance and reduces the need for expensive emissions control systems. Energy-efficient curing ovens and smart climate control within enclosed process areas further contribute to sustainability goals and operating cost reductions.
Ultimately, the Alloy Wheel Powder Coating Automated Line represents a convergence of material science, robotics, and digital manufacturing. It allows for superior coating quality, faster production speeds, fewer defects, and greater flexibility in responding to market trends or customer needs. For manufacturers looking to stay competitive in a demanding automotive sector, investing in a fully automated powder coating line is no longer just a strategic advantage—it’s rapidly becoming an operational necessity.
Automated Alloy Wheel Powder Coating System
An Automated Alloy Wheel Powder Coating System is a fully integrated, intelligent solution designed to apply high-performance powder coatings to alloy wheels with exceptional speed, precision, and consistency. This system combines advanced robotics, electrostatic spray technology, real-time process monitoring, and conveyor automation to deliver flawless finishes on wheels while significantly reducing manual labor and material waste. As demand grows for higher quality, durability, and aesthetic variation in alloy wheels, such systems are increasingly central to modern manufacturing strategies.
The automation begins the moment wheels enter the system, typically via a programmable conveyor that moves each unit through a pre-defined sequence. The first step is surface preparation, which may include multi-stage chemical cleaning, shot blasting, or phosphate treatment, depending on the type of wheel and required finish. These cleaning processes are executed inside enclosed chambers with automated dosing, spraying, and rinsing systems that ensure perfect surface condition for powder adhesion. Consistent surface prep is crucial to achieving strong coating durability, corrosion resistance, and an even final appearance.
Once cleaned and dried, the wheels proceed into the powder coating booth, where robotic arms equipped with electrostatic spray guns apply the powder. These robots are calibrated to follow complex 3D paths that accommodate different wheel designs and sizes, ensuring every crevice and contour receives even coverage. The electrostatic nature of the spray means that the powder clings tightly to the grounded metal surface, improving application efficiency and minimizing overspray. Integrated sensors measure powder thickness in real time, adjusting spray parameters automatically to meet exact specifications.
After coating, the wheels enter an energy-efficient curing oven that melts and bonds the powder to the metal surface. Temperature and conveyor speed are managed by a central control system to guarantee optimal curing cycles for each wheel. These ovens are often designed with multiple heating zones and airflow controls to ensure uniform curing, regardless of wheel size or design complexity. Precise control of this step is essential for achieving the desired finish performance, such as gloss, hardness, chip resistance, and weatherability.
The system continues with automated cooling stations that gradually reduce the temperature of each wheel in a controlled environment. Once cooled, each wheel is inspected by automated vision systems and thickness sensors. These tools detect imperfections like inconsistent coating, under- or over-application, or foreign particles, and immediately flag any defective products. Defective wheels are diverted for reprocessing, while those meeting specifications are automatically labeled, tracked, and routed for packaging or further processing.
All operational data—ranging from powder usage and conveyor speed to oven temperature and inspection results—is logged by a centralized software platform. This digital layer enables live process monitoring, predictive maintenance alerts, and production analytics that help engineers and operators refine performance over time. The data can also be used to meet traceability requirements for OEM customers, allowing every wheel to be traced back through the exact conditions it experienced during production.
This level of automation not only boosts output and product quality but also dramatically reduces waste. Unused powder is collected via high-efficiency recovery systems, filtered, and recycled back into the process with minimal material loss. Energy-efficient ovens and minimal reliance on solvents or water make the system environmentally responsible, often exceeding compliance standards for emissions and resource use.
In summary, the Automated Alloy Wheel Powder Coating System offers manufacturers a streamlined, cost-effective, and scalable approach to finishing wheels. It replaces variable manual processes with repeatable precision, shortens production cycles, increases yield, and supports both large-batch and customized production needs. As customer expectations rise and environmental regulations tighten, this system stands as a future-ready solution for competitive, high-quality alloy wheel finishing.
The automated alloy wheel powder coating system is not only about mechanical efficiency but also about intelligent process integration. At the core of the system is a centralized control unit, often supported by industrial IoT platforms, which continuously collects data from every sensor, robotic arm, and conveyor motor. This digital infrastructure allows for real-time diagnostics, adaptive process control, and instant decision-making. If a robotic spray arm detects slight deviations in wheel geometry, it can immediately adjust its spray path. If a conveyor sensor picks up a jam or a misaligned wheel, the system can halt, alert operators, and reroute tasks without derailing the entire line. These features dramatically reduce downtime and make the entire operation more resilient to errors and inefficiencies.
The use of robotics in the powder booth extends beyond basic motion control. Vision-guided robotic systems can scan each incoming wheel to detect any minor variation in design or orientation and adjust spray parameters accordingly. This allows a single automated system to handle a wide variety of wheel models without requiring lengthy manual changeovers. The robots also maintain a level of repeatability and precision that ensures every wheel receives the exact amount of powder coating, minimizing defects like orange peel, thin spots, or buildup. Because the powder is applied electrostatically, the system achieves excellent wrap-around coverage, meaning even areas that aren’t directly sprayed receive an even coat due to the natural attraction of the charged powder to the metal surface. This contributes significantly to both the visual appeal and the long-term durability of the finished wheel.
Energy consumption is another area where the system excels due to its design for sustainability. Curing ovens are optimized with insulated panels, variable-speed fans, and heat recovery loops to retain and redistribute thermal energy, reducing fuel or electricity usage. Similarly, the automated pre-treatment and drying sections operate in enclosed circuits with minimal water or chemical loss, and filtration systems ensure that discharge meets or exceeds environmental standards. Many modern systems now include integrated carbon footprint tracking and emissions reporting modules to support green manufacturing initiatives and satisfy customer ESG (Environmental, Social, Governance) reporting requirements.
A significant advantage of this system lies in its flexibility and scalability. Facilities equipped with such automation can handle both small custom runs and large-scale OEM orders with little operational adjustment. Software-defined production recipes make it easy to switch from one wheel model or finish type to another, enabling just-in-time manufacturing with fewer delays and inventory costs. Furthermore, maintenance routines are largely automated—lubrication schedules, wear-and-tear monitoring, and predictive part replacement alerts are built into the system—reducing the need for extensive manual inspections and allowing technical teams to focus on higher-level oversight.
From a quality standpoint, the end product consistently meets the stringent demands of automotive OEMs and high-end aftermarket suppliers. Powder coating not only provides a premium finish but also offers superior protection against road salts, UV exposure, and mechanical wear, ensuring the wheels retain their appearance and function over many years of use. With automated inspection and thickness verification built into the line, every wheel leaving the facility meets defined tolerances without relying on subjective human judgment. This consistency is critical in industries where brand reputation is tied closely to product finish and performance.
Finally, the fully automated system improves workplace safety and ergonomics by removing workers from exposure to powders, chemicals, heat, and repetitive tasks. Operators instead manage the system via user-friendly interfaces, often with touchscreens or remote access dashboards, where they can monitor performance, make adjustments, or review output without needing to physically interact with hazardous environments. Training requirements are also streamlined, as technicians focus more on process oversight than manual labor.
Overall, the automated alloy wheel powder coating system represents a convergence of advanced manufacturing technologies aimed at improving speed, consistency, sustainability, and safety. It is a strategic investment for manufacturers seeking to future-proof their operations, reduce waste, and deliver high-quality products that stand out in a competitive market.
Powder Coating Equipment for Wheel Coating
Powder coating equipment for wheel coating is specifically engineered to apply durable, high-performance finishes to alloy wheels in a consistent, efficient, and environmentally friendly manner. This equipment includes a combination of pre-treatment systems, powder spray booths, electrostatic spray guns, recovery units, and curing ovens, all of which are designed to work in harmony to deliver flawless coating results. The core component is the electrostatic powder spray gun, which charges powder particles and directs them toward the grounded wheel, ensuring strong adhesion and uniform coverage, even on intricate wheel designs. These guns often feature programmable settings for voltage, flow rate, and spray pattern, allowing operators or automated systems to customize the coating process for different wheel types or finish requirements.
The spray booth is another critical element and is typically constructed with anti-static materials and integrated filtration systems to maintain clean air and reduce powder contamination. These booths can be manual, semi-automatic, or fully robotic, depending on production scale and automation level. Robotic booths, often used in high-volume operations, use multiple axis-controlled arms and vision systems to precisely target each surface, ensuring repeatability and minimizing waste.
Powder recovery systems are essential for maximizing efficiency and reducing cost. These systems capture overspray through cyclone separators or cartridge filters and return the reclaimed powder back to the feed system for reuse, significantly cutting down on material loss. They are designed to handle frequent color changes with minimal contamination, using fast-cleaning mechanisms to purge the system between batches.
Curing ovens are used to heat the coated wheels to a temperature where the powder melts and chemically bonds to the surface. These ovens can be batch-type or continuous, with precise control over temperature and airflow to ensure even curing. Infrared, convection, or hybrid heating technologies may be used depending on the specific powder formulation and throughput needs.
Together, these systems form a complete powder coating solution tailored for wheel production, offering fast cycle times, reduced labor, superior coating performance, and compliance with modern environmental and safety standards.
In a modern powder coating setup for wheel coating, each piece of equipment plays a specialized role in maintaining process integrity and achieving a flawless finish. The pre-treatment phase typically involves a multi-stage process that may include degreasing, rinsing, phosphating, and drying. This is crucial because any residual oil, dirt, or oxidation on the wheel surface can interfere with the powder’s ability to adhere and cure properly. These pre-treatment systems are often integrated into conveyor-based lines where wheels are automatically guided through spray tunnels or immersion tanks, and drying ovens are used to ensure moisture-free surfaces before coating.
The powder delivery system is engineered for consistent material flow, incorporating fluidizing hoppers and precise feed pumps that maintain a steady supply of powder to the spray guns. These systems are adjustable for different powder chemistries, including epoxy, polyester, or hybrid formulations, depending on the desired finish properties such as corrosion resistance, gloss level, and UV durability. Advanced control units regulate the electrostatic charging process and allow operators to fine-tune settings in real-time to match wheel geometry, ensuring that even deep recesses and spokes receive a full, even coat.
Manual powder booths are commonly used in small batch or custom operations where flexibility is key, while automated booths with robotic arms and programmable logic controllers dominate high-volume production lines. These robotic systems follow programmed paths with micron-level accuracy, optimizing transfer efficiency and greatly reducing powder waste. Integrated sensors monitor booth conditions such as humidity, air pressure, and powder flow rate, sending alerts if deviations occur that could affect quality. This real-time feedback enables adjustments before defects are introduced, protecting both productivity and output quality.
The curing process is critical, as incomplete or uneven curing can result in poor adhesion, reduced hardness, and compromised weather resistance. Curing ovens are often equipped with zoned heating elements and digital PID controllers that adjust temperatures based on wheel mass and coating type. Convection ovens provide uniform air circulation, while infrared ovens offer rapid heat-up times and are ideal for fast-paced lines. Some systems use a hybrid of both to balance speed and thermal uniformity. Conveyor systems within the oven are synchronized with the upstream coating process to ensure proper dwell times for each wheel, avoiding under- or over-curing.
Once wheels are cured and cooled, inspection systems are used to verify the coating’s quality. In many advanced setups, high-resolution cameras, laser sensors, and colorimeters are used to detect inconsistencies in color, thickness, and surface smoothness. These systems can instantly reject wheels that fall outside tolerance and send them back for rework without disrupting the main line. This level of automation not only ensures that every wheel meets customer specifications but also significantly reduces the reliance on manual quality checks, thereby improving throughput and traceability.
Reclaim and recovery systems are particularly important for operations seeking to minimize environmental impact and reduce material costs. These systems use cyclones, sieves, and filters to separate usable powder from contaminants, allowing operators to reuse the powder without compromising finish quality. Many of these systems are designed for rapid color change, with automatic cleaning sequences that minimize downtime between production runs. This is especially valuable in production environments where multiple finishes are applied in short succession.
The software and control interface used to coordinate all these systems is typically centralized, allowing supervisors to monitor, adjust, and analyze the entire coating process from a single dashboard. Key metrics such as powder consumption, oven temperature profiles, equipment utilization, and defect rates are recorded in real-time and used for process optimization and maintenance planning. This level of oversight enables proactive problem-solving and contributes to long-term improvements in yield and quality.
Overall, powder coating equipment for wheel coating is a sophisticated ecosystem where each component contributes to a high-efficiency, high-precision, and environmentally conscious operation. Whether for custom wheel shops or large-scale OEM production, this equipment ensures a durable, attractive finish that meets the strict performance and aesthetic demands of the automotive industry.
Alloy Wheel Powder Coating Machinery Setup
An Alloy Wheel Powder Coating Machinery Setup is a purpose-built assembly of interconnected machines designed to automate and streamline the powder coating process for alloy wheels, ensuring consistent quality, efficient production, and reduced labor dependence. This setup typically starts with a loading station where raw or pre-machined wheels are placed onto a motorized conveyor or rotating hanger system. These conveyors move wheels through each processing stage with precision timing and synchronized flow, eliminating manual handling and minimizing production delays.
The first active stage is surface pre-treatment, which usually involves a multi-stage cleaning tunnel. This machinery uses high-pressure sprays or immersion tanks filled with degreasers, phosphate solutions, and rinsing agents to remove contaminants and enhance powder adhesion. Integrated drying ovens with forced hot air ensure every wheel is moisture-free before entering the coating booth. Sensors monitor chemical concentrations and temperature to maintain optimal pre-treatment conditions with minimal human intervention.
Following pre-treatment, the wheels enter the powder coating booth where robotic arms equipped with electrostatic spray guns apply the powder. These robots are programmed to adapt to various wheel shapes and sizes, adjusting their path, distance, and spray rate accordingly. The booth itself is equipped with powder recovery systems—such as cyclones and cartridge filters—that capture overspray and automatically recycle it into the system, maximizing material usage and minimizing waste. The powder feed system delivers a continuous, fluidized supply of coating material, ensuring stable output and color consistency.
Next, the wheels are transported into a curing oven, typically a continuous-conveyor infrared or convection type, depending on the coating requirements. These ovens are precisely controlled to maintain a consistent thermal profile that allows the powder to melt, flow, and chemically bond to the wheel surface. The conveyor speed and zone temperatures are digitally synchronized with the rest of the setup, ensuring each wheel receives the correct dwell time and heat exposure for complete curing without risking under- or over-processing.
After curing, the wheels pass through a cooling station where ambient or conditioned air gradually reduces the temperature. Automated inspection machinery may then scan the wheel for defects using high-resolution cameras, laser thickness gauges, or color sensors. Non-conforming parts are automatically flagged and diverted for rework, while accepted wheels move on to labeling, packaging, or further finishing processes. All machinery in the setup is linked to a central control system, often operated through an HMI (Human-Machine Interface) that provides real-time process monitoring, diagnostics, and recipe management.
This integrated machinery setup not only accelerates production and enhances finish uniformity, but it also minimizes environmental impact through powder reclamation, energy-efficient ovens, and reduced VOC emissions. It is an essential investment for manufacturers looking to scale alloy wheel production while meeting high standards for quality, throughput, and sustainability.
In an alloy wheel powder coating machinery setup, the automation is designed to seamlessly integrate each part of the process, ensuring a high level of consistency and precision across the entire production line. As the wheels enter the conveyor system, sensors track their movement and position, ensuring that each wheel moves through the entire process without any misalignment. The pre-treatment phase, which is essential for preparing the surface, is carried out in automated spray or immersion tunnels that deliver cleaning and etching solutions precisely as needed. Once the surface is properly prepared, it is critical that the wheel is dried thoroughly to prevent moisture from interfering with the powder coating process, and this step is achieved with high-efficiency drying ovens that reduce energy consumption while maintaining the desired conditions for fast drying.
The powder coating booth utilizes advanced robotics to apply a uniform layer of coating. These robotic arms are equipped with electrostatic spray guns that charge the powder particles and direct them toward the grounded wheel. The electrostatic charge ensures excellent powder adhesion even to complex wheel geometries, ensuring that all areas, including difficult-to-reach recesses and deep spokes, receive a consistent coat. The spray booth is designed to minimize powder waste by utilizing efficient recovery systems, which separate excess powder from the air and return it to the system for reuse. This minimizes material costs while contributing to a cleaner, more sustainable process. Additionally, the systems are designed to handle frequent color changes, allowing for flexibility in meeting diverse customer demands without significant downtime.
Once the coating is applied, the wheels move through the curing process, which is a critical step in ensuring the durability and strength of the powder coating. Curing ovens, typically using infrared or convection heating, are designed with multiple heating zones that can be adjusted to match the needs of each batch. These ovens maintain precise temperature control to ensure that the powder bonds properly to the wheel, providing the desired mechanical and chemical properties such as hardness, corrosion resistance, and a glossy finish. The conveyor speed in the oven is synchronized with the wheel’s coating needs, ensuring that each wheel is exposed to the correct temperature and duration for optimal results.
After curing, the wheels pass through a cooling system, often equipped with controlled air circulation, to gradually bring down their temperature. This helps to stabilize the finish and ensure that the wheels are fully set before inspection. Automated inspection systems then check the wheels for any defects such as uneven coating, color discrepancies, or surface imperfections. High-definition cameras, laser scanners, and thickness gauges are typically used in these systems to detect even the smallest flaws, ensuring that only high-quality products are sent forward in the production process. If a defect is detected, the system will automatically divert the wheel for rework or recycling, while acceptable wheels continue on to packaging or further finishing processes.
The entire production line is controlled through a centralized system that provides operators with real-time monitoring and diagnostic tools. This allows for quick adjustments to be made if any part of the process deviates from the preset parameters, minimizing downtime and maintaining high throughput. Data from each stage, including powder usage, curing times, inspection results, and conveyor speeds, are logged for quality control purposes, ensuring full traceability for each wheel produced. Additionally, the system’s software enables predictive maintenance by tracking the health of equipment and alerting operators to any potential issues before they lead to downtime or quality failures.
Overall, the alloy wheel powder coating machinery setup is designed to create an efficient, sustainable, and high-quality coating process. By automating each stage—from surface preparation to coating application, curing, inspection, and packaging—the setup minimizes human error, improves throughput, and consistently delivers finished wheels that meet the high standards of the automotive industry. This level of automation also reduces operational costs, enhances product quality, and supports scalability for both small custom batches and large-scale production runs.
Industrial Alloy Wheel Powder Coating Equipment
Industrial alloy wheel powder coating equipment is designed for high-efficiency, large-scale production, offering advanced technologies to apply durable and aesthetically appealing finishes to alloy wheels. The primary goal of this equipment is to provide uniform, long-lasting coatings while minimizing material waste, reducing labor costs, and maintaining high throughput. This equipment integrates several advanced systems, including automated pre-treatment, electrostatic powder application, curing, and inspection processes, each optimized for alloy wheel production.
At the start of the process, pre-treatment equipment prepares the wheels by cleaning and treating the surfaces to ensure proper powder adhesion. This typically involves multi-stage chemical cleaning systems, which include degreasing, phosphate coating, and rinsing stages. Pre-treatment tunnels or spray booths use high-pressure jets to remove grease, dirt, and oxidation from the wheels. In some setups, the wheels are also subjected to a shot-blasting process, which adds a layer of abrasion to the wheel surface, improving adhesion properties. The wheels are then dried in high-efficiency drying ovens that remove all moisture, ensuring the coating bonds properly.
Following pre-treatment, the wheels move into the powder coating booth where an electrostatic spray process is used to apply the powder. Robotic arms or automated spray guns are typically used to apply the powder evenly across the wheel’s surface. These spray systems charge the powder particles, which are attracted to the grounded metal of the wheel, ensuring uniform coverage even on complex wheel designs with intricate spokes and contours. The electrostatic process minimizes overspray, reducing powder waste and improving efficiency. The booth is often equipped with powder recovery systems (e.g., cyclones or cartridge filters), which capture excess powder and send it back into the system for reuse, further minimizing material waste and cost.
The wheels then move into curing ovens where the powder is heated to its curing temperature. The curing process ensures that the powder bonds properly to the surface of the wheel, providing a durable, resistant finish. The curing oven typically uses convection heating, infrared heating, or a hybrid of both, depending on the speed and material requirements. The oven’s temperature is precisely controlled to ensure even curing, while the conveyor speed ensures that wheels are exposed to the heat for the proper amount of time. The curing process not only melts and bonds the powder but also enhances the coating’s mechanical properties such as hardness, corrosion resistance, and UV stability.
After curing, the wheels are cooled using controlled cooling systems, typically featuring air circulation to gradually bring down the temperature to ambient levels. Once cooled, automated inspection systems use advanced vision technologies like high-definition cameras, laser sensors, and thickness gauges to check for defects in the coating. These systems detect issues such as uneven coating, color variation, surface imperfections, or powder under- or over-application. Defective wheels are automatically diverted for reprocessing, while quality wheels move on to further finishing or packaging.
The entire system is often controlled through a centralized control system that enables operators to monitor and adjust parameters in real time, ensuring optimal production efficiency. Software integrated into the control system allows for recipe management, quality tracking, and data logging, ensuring traceability for each wheel and improving overall process transparency. The system also features predictive maintenance capabilities, allowing operators to identify potential issues before they lead to downtime, ensuring consistent production.
Additionally, many industrial powder coating systems for alloy wheels incorporate energy-efficient technologies. These can include heat recovery systems that capture and reuse thermal energy in curing ovens, reducing overall energy consumption. Ventilation and filtration systems also play a critical role in maintaining clean air quality by capturing airborne powders and ensuring compliance with environmental standards. By reducing the need for solvents, water, and reducing VOC emissions, these systems support sustainability goals.
The end result is a high-quality, durable, and aesthetically pleasing coating that is resistant to corrosion, chipping, and UV degradation, ideal for use on alloy wheels exposed to harsh road conditions and extreme weather. Industrial alloy wheel powder coating equipment helps manufacturers meet the demands of high-volume production while maintaining superior quality control and minimizing costs.
Industrial alloy wheel powder coating equipment is specifically designed to handle the demanding requirements of large-scale production while ensuring consistent quality and efficiency. This equipment integrates advanced automation and precision technologies, enabling manufacturers to produce high-performance alloy wheels that meet automotive industry standards for durability, appearance, and resistance to environmental stressors. The pre-treatment system plays a critical role in ensuring that wheels are clean, free from contaminants, and properly prepared to accept the powder coating. This process eliminates any oils, residues, or oxides that may be present on the surface, which could impair the adhesion of the coating. By utilizing automated spray systems, immersion tanks, or ultrasonic cleaning systems, manufacturers can ensure a thorough, repeatable cleaning process that sets the stage for a flawless finish.
Once the wheels are properly prepared, they enter the powder coating booth where robotic arms or automated spray guns apply the powder coating material to the wheels. These spray guns use electrostatic charges to ensure a uniform application of powder across all areas of the wheel, including hard-to-reach spots, ensuring a smooth, even coating that bonds to the metal surface. The electrostatic process not only ensures better adhesion but also minimizes waste by reducing overspray. Powder recovery systems within the booth capture unused powder and return it to the system, reducing material costs and minimizing environmental impact. This reclaimed powder can be reused in future applications, reducing overall waste and improving cost-effectiveness.
After the coating is applied, the wheels are transported to the curing oven, where the powder is heated to the required temperature, causing it to melt, flow, and chemically bond to the surface of the wheel. The curing process is critical in ensuring that the finish is durable, smooth, and resistant to wear and corrosion. The curing ovens are typically equipped with precise temperature controls, airflow management systems, and thermal insulation to ensure that the heat is evenly distributed and maintained at the correct temperature for the required duration. This guarantees a consistent, high-quality finish for every wheel processed through the system.
Once the curing process is complete, the wheels are cooled gradually using air circulation systems to avoid thermal shock and ensure the coating sets properly. Cooling systems help control the temperature drop to prevent any distortion or cracking in the finish. Automated inspection systems, often integrated into the production line, scan each wheel for defects in coating thickness, color consistency, or surface imperfections. These inspection systems utilize advanced technologies such as laser sensors, high-resolution cameras, or even 3D imaging to detect any anomalies. If any issues are detected, the wheel is automatically flagged for rework or discarded, ensuring that only products that meet the stringent quality standards move forward.
The centralized control system that oversees the entire process provides operators with real-time monitoring and diagnostic capabilities, allowing for precise control over every stage of the coating process. This control system can store different process recipes for various types of finishes or wheel designs, making it easy to switch between different jobs without extensive downtime. The system also gathers valuable data about material usage, equipment performance, and production rates, which can be used for continuous process improvement and predictive maintenance. By analyzing trends in this data, operators can identify potential issues before they lead to downtime or defects, improving overall system reliability and production efficiency.
In addition to providing a high-quality finish, industrial alloy wheel powder coating equipment is designed with energy efficiency and sustainability in mind. Features such as heat recovery systems, energy-efficient curing ovens, and advanced filtration and ventilation systems help reduce energy consumption and limit the environmental impact of the production process. These systems capture and reuse thermal energy from the curing ovens, reducing the need for additional energy inputs, while filtration systems help prevent the release of harmful powders and chemicals into the environment, ensuring compliance with environmental regulations.
Overall, industrial alloy wheel powder coating equipment enables manufacturers to produce large volumes of high-quality, durable alloy wheels with a consistent, attractive finish. The integration of automated systems, energy-efficient technologies, and precise quality control ensures that each wheel meets the strictest performance and aesthetic standards while maximizing productivity and minimizing waste. This makes it an essential investment for manufacturers looking to improve their production capabilities, reduce operational costs, and maintain a competitive edge in the automotive industry.
Alloy Wheel Coating Production Equipment
Alloy wheel coating production equipment is specialized machinery designed to apply protective and decorative coatings to alloy wheels, ensuring they are durable, aesthetically pleasing, and resistant to harsh environments. This equipment integrates several stages of the coating process, including surface preparation, coating application, curing, cooling, and quality control, all of which are optimized for high-volume production while maintaining superior quality.
The process begins with surface preparation equipment, which is crucial to ensuring proper adhesion of the coating. This equipment typically includes automated pre-treatment systems that involve washing, degreasing, and sometimes shot blasting or sandblasting to clean and roughen the wheel surface. This ensures that any contaminants, such as oils, dirt, or rust, are removed before the coating is applied. In some setups, phosphating or other surface treatment chemicals may be used to enhance corrosion resistance. The pre-treated wheels are then dried using high-efficiency drying systems to remove any residual moisture.
Once the wheels are adequately prepared, they enter the powder coating application booth, where the coating material is applied using electrostatic spray guns or robotic arms. The powder coating booth uses electrostatic forces to apply charged powder particles to the grounded wheel surface, ensuring a uniform layer of coating. These systems are highly automated, with robotic arms programmed to adjust their movement and spray patterns based on the geometry of the wheel. The booths often feature advanced powder recovery systems, such as cyclones or filters, which capture any overspray and return it to the system for reuse, minimizing waste and reducing operating costs.
After the powder is applied, the wheels move into curing ovens, where the coating is baked to cure and chemically bond to the wheel surface. Curing ovens are equipped with precise temperature controls and airflow management systems to ensure even heat distribution and optimal curing conditions. These ovens can be convection-based, infrared, or a combination of both, depending on the production needs. The curing process is critical to ensuring the coating achieves the necessary hardness, resistance to UV degradation, and overall durability. The temperature and duration of the curing process are carefully controlled to prevent under-curing or over-curing, both of which can affect the final finish.
Once cured, the wheels pass through cooling systems, where ambient or controlled air is used to gradually bring down the temperature of the wheels. This step helps ensure that the coating solidifies properly and prevents any potential defects, such as cracking or warping, that might occur due to rapid temperature changes.
The next step in the production process is automated inspection, which typically involves advanced camera systems, laser sensors, or other quality control technologies. These inspection systems check for coating uniformity, color consistency, thickness, and any visible defects such as bubbles or runs. Defective wheels are automatically rejected or sent for rework, ensuring that only high-quality products move on to the next stage. The inspection systems are often integrated into the production line, providing real-time feedback and allowing for rapid adjustments if issues are detected.
Finally, the finished wheels may undergo additional finishing operations, such as polishing, labeling, or packaging. These final steps help enhance the appearance of the wheels and prepare them for shipment or further use. The entire production system is typically controlled through a centralized control panel or software system, which allows operators to monitor, adjust, and optimize each stage of the process. These systems provide real-time data on machine performance, production rates, and quality metrics, allowing for quick decision-making and improved process efficiency.
Overall, alloy wheel coating production equipment is designed to provide a high level of automation, efficiency, and quality control, enabling manufacturers to produce large volumes of alloy wheels with consistent, durable coatings. The integration of advanced technologies at each stage—pre-treatment, powder application, curing, inspection, and finishing—ensures that the final product meets the strictest standards for performance and aesthetics, making it suitable for a wide range of automotive and industrial applications.
Alloy wheel coating production equipment is engineered to ensure a seamless, high-quality coating process, aimed at both enhancing the aesthetic appeal and extending the lifespan of alloy wheels. The system begins with automated pre-treatment systems that thoroughly clean the wheels. This is done through processes such as degreasing, washing, or abrasive blasting, which remove contaminants like oils, dirt, rust, and oxidation, preparing the surface for optimal powder adhesion. By incorporating robotic handling or automated conveyors, these systems reduce the risk of human error and enhance consistency across large production volumes. After cleaning, the wheels are heated or dried to remove any residual moisture, which is critical to preventing defects during the coating process.
The next phase involves applying the powder coating, which is achieved through electrostatic spray guns or automated robotic arms that precisely apply the coating to the wheel. The powder is electrostatically charged to ensure an even and consistent layer of coating. The automated spray systems are highly adaptable, adjusting to different wheel geometries to ensure even coverage of all surfaces, including intricate spokes and recesses. Advanced powder recovery systems help minimize waste by capturing overspray, allowing it to be reused in subsequent applications. This reduces material costs and ensures a more environmentally friendly process by cutting down on powder wastage.
Once the powder is applied, the wheels enter the curing ovens, where they are subjected to controlled heat to melt the powder and enable it to bond permanently to the surface of the wheel. The curing process ensures the coating achieves its required hardness, durability, and resistance to corrosion, UV degradation, and other environmental factors. Temperature and time are closely monitored and controlled to ensure optimal curing, as both under-curing and over-curing can result in a compromised finish. The curing ovens are often designed with advanced temperature management systems that provide consistent heat distribution, which is crucial for maintaining uniform coating quality across all wheels.
After curing, the wheels move to the cooling stage, where controlled air circulation ensures the temperature is gradually lowered to prevent any thermal shock that could damage the coating. This controlled cooling ensures that the coating solidifies properly and adheres securely to the wheel surface, preserving its durability and appearance. Once cooled, the wheels are ready for inspection. Automated inspection systems, equipped with advanced imaging and laser technologies, examine each wheel for defects such as uneven coating, color inconsistencies, or surface imperfections. Any wheels that fail inspection are either rejected or diverted for rework, ensuring only the highest quality products make it to the final stages.
The inspection process is often coupled with data collection, where each wheel’s performance and quality metrics are logged. This data helps operators track efficiency, monitor equipment performance, and identify any potential issues before they cause major disruptions in production. With real-time monitoring, the system can alert operators to any irregularities, allowing for swift corrective actions to maintain optimal production rates.
After inspection, the wheels are ready for final finishing processes such as labeling, polishing, or packaging. These steps prepare the wheels for shipment or further customization. The entire production line is often controlled by a centralized system, allowing operators to oversee the process, make adjustments, and optimize machine performance. The system can store different operational parameters for various coating jobs, making it easy to switch between product batches without causing significant downtime. This level of automation, coupled with data-driven insights, helps maintain a continuous production flow, reducing lead times and ensuring a consistent, high-quality product.
The overall design of alloy wheel coating production equipment also focuses on energy efficiency and sustainability. Modern systems often include features such as heat recovery in curing ovens to reduce energy consumption, advanced filtration systems to capture overspray, and powder recycling systems to minimize material waste. These energy-saving and environmentally conscious features contribute to a more cost-effective and sustainable manufacturing process, reducing the environmental footprint of production while ensuring a consistent, high-quality finish on every wheel produced.
Powder Coating Technology for Alloy Wheels
Powder coating technology for alloy wheels is an advanced finishing process that provides durable, aesthetically pleasing, and environmentally friendly coatings for automotive and industrial applications. This process uses dry powder, rather than liquid paint, to coat alloy wheels, providing a tough, long-lasting finish that is resistant to corrosion, scratches, and UV degradation. The technology behind powder coating is highly efficient, cost-effective, and environmentally conscious, making it an ideal choice for the high demands of alloy wheel finishing.
The process begins with surface preparation, which is crucial for achieving strong adhesion and ensuring the longevity of the coating. Alloy wheels are cleaned and treated to remove any contaminants, oils, dirt, or oxidation. This step typically involves a series of automated cleaning methods such as degreasing, shot blasting, or chemical etching. In some cases, wheels are subjected to a phosphate treatment, which not only cleans but also adds a layer of corrosion resistance to the surface. After cleaning, the wheels are dried to remove any residual moisture, preventing any defects in the coating process.
Once the wheels are prepped, the next step involves the powder application process, where the powder is electrostatically charged and sprayed onto the wheel’s surface. Electrostatic spray guns or automated robotic arms are commonly used to apply the powder. The powder is made up of finely ground particles of resin and pigments, which are electrically charged as they pass through the gun. The charged particles are attracted to the grounded wheel surface, ensuring that the coating is applied evenly and uniformly across all areas, even in difficult-to-reach spots such as deep spokes. The electrostatic charge also helps minimize overspray, improving efficiency and reducing material waste.
One of the key benefits of powder coating is its ability to create a uniform, smooth finish that adheres strongly to the wheel. The powder itself is a combination of resin, curing agents, pigments, and fillers, which, when heated, melt and fuse together to form a solid, durable layer. This process takes place in the curing oven, where the coated wheels are heated to a specific temperature, typically between 160°C and 200°C (320°F to 390°F). The heat causes the powder particles to melt and bond to the wheel’s surface, forming a strong chemical bond that ensures the coating is hard, resistant to corrosion, and resistant to wear and tear. The curing time and temperature are precisely controlled to ensure that the coating achieves the desired mechanical properties without damaging the wheel or the finish.
Once the wheels are fully cured, they pass through a cooling system to bring the temperature down gradually. This prevents thermal shock, which could lead to cracking or distortion of the coating. The wheels are then subject to a quality inspection process, where automated systems using advanced camera technology, laser scanners, and thickness gauges ensure that the coating is applied evenly, without defects such as bubbles, uneven thickness, or color inconsistencies. Any wheels that fail inspection are automatically diverted for rework or scrapping, ensuring that only high-quality products move forward.
In addition to the standard coating process, there are also advanced powder coating technologies that enhance the functionality and aesthetics of the finish. For example, metallic, matte, and glossy finishes can be achieved by adjusting the powder formulation, while special effects like textures or color-shifting pigments can be used to create custom looks. This gives manufacturers the flexibility to offer a wide variety of finishes that cater to different customer preferences in the automotive industry.
The advantages of using powder coating technology for alloy wheels include superior durability, reduced environmental impact, and improved cost-effectiveness. Since powder coatings are free of solvents, they release fewer volatile organic compounds (VOCs), making the process more environmentally friendly than traditional liquid coating methods. Additionally, the powder coating process generates minimal waste, as excess powder can be captured and reused through recovery systems, further reducing material costs and improving sustainability.
Overall, powder coating technology offers alloy wheel manufacturers a high-performance, cost-effective, and environmentally friendly solution for producing wheels that are not only visually appealing but also resistant to the harsh conditions encountered on the road. With its combination of excellent adhesion, durability, and versatility in finish options, powder coating remains one of the most popular and effective coating technologies for alloy wheels.
Alloy Wheel Finishing Equipment
Alloy wheel finishing equipment is designed to give alloy wheels their final aesthetic and functional qualities after the primary coating process has been completed. This equipment focuses on enhancing the visual appearance, durability, and performance of the wheels, ensuring they meet the quality standards required for automotive and industrial applications. Finishing equipment can range from simple polishing machines to highly automated systems that add specific textures, patterns, or protective layers to the wheels. The goal is to provide a flawless final product that is both attractive and capable of withstanding the harsh conditions alloy wheels are exposed to.
The first type of finishing operation is polishing. After the wheels have been coated and cured, polishing is often used to achieve a high-gloss finish, removing any imperfections, light scratches, or minor defects from the surface. Automated polishing machines use abrasive wheels, buffing pads, or rotary brushes that rotate at high speeds to smooth the surface of the wheel. These machines are designed to handle various wheel sizes and geometries, and their operation can be controlled through programmable settings that adjust the pressure, speed, and duration of the polishing process to ensure a consistent finish.
Surface texturing is another type of finishing operation that can be applied to alloy wheels, especially those that require a matte or satin finish rather than a high-gloss appearance. Texturing can be done using abrasive blasting, shot blasting, or sandblasting machines, which use high-pressure air to propel small abrasive particles onto the wheel’s surface. These processes create a uniform texture or matte finish that not only enhances the appearance but also provides additional resistance to scratches and minor abrasions. Vibratory finishing is another technique used for creating smooth or textured surfaces. It involves placing the wheels in a large vibrating chamber with abrasive media that polishes or roughens the surface, depending on the desired result.
Once the wheels have been polished or textured, they may undergo additional protective coating processes, such as applying a clear coat or lacquer to enhance the finish and improve the durability of the coating. Clear coating equipment typically uses spray booths equipped with electrostatic spray systems or automated robotic arms that apply a transparent layer over the wheel’s primary coating. This clear coat not only improves the appearance by enhancing the gloss but also provides extra protection against environmental factors like UV radiation, road salts, and water, helping to preserve the wheel’s finish over time.
Laser engraving or etching equipment can also be used in the finishing process, allowing manufacturers to add branding, logos, or intricate designs to the alloy wheel’s surface. Laser systems use focused beams of light to vaporize small areas of the wheel’s coating, creating precise, durable markings without the need for physical contact. This process offers a high degree of accuracy and can be used to add detailed designs or even batch numbers for traceability purposes.
In some cases, wheels may require quality control inspection at the finishing stage to ensure the final product meets the required standards. Automated inspection systems use advanced vision systems, cameras, and sensors to detect any defects in the coating or surface. These systems can check for issues such as uneven coating, color variations, scratches, or other imperfections that could affect the quality or aesthetic appeal of the wheels. Defective wheels are automatically diverted for rework or rejected, ensuring only flawless products continue in the production process.
Finally, packaging and labeling equipment is used at the end of the finishing process. Automated systems carefully pack the finished wheels to protect them from damage during shipping and storage. Labeling systems may also be used to apply brand labels, product codes, or other identifying information to the packaging or the wheels themselves.
Alloy wheel finishing equipment plays a crucial role in delivering high-quality wheels that meet customer expectations for both aesthetics and performance. By incorporating automated polishing, surface texturing, clear coating, laser engraving, and advanced inspection systems, manufacturers can produce wheels with superior finishes that offer durability, visual appeal, and functionality. This equipment ensures that every alloy wheel that leaves the production line is both attractive and capable of withstanding the rigors of automotive use.
In addition to the core processes, automated handling systems are often integrated with alloy wheel finishing equipment to improve production efficiency and ensure smooth transitions between stages. These systems typically include conveyors, robotic arms, or gantries that transport wheels from one process to the next without the need for manual labor. Automated handling ensures that wheels are precisely positioned for each operation, minimizing the risk of damage or defects during the transition between stages. This not only boosts throughput but also reduces the likelihood of human error, ensuring a more consistent and reliable process.
For added versatility, multi-stage finishing systems are sometimes used to combine several operations into one integrated line. For example, a system may include a combination of polishing, texturing, and clear coating in a single sequence. This setup reduces downtime by eliminating the need for separate machines for each operation, streamlining the production flow, and allowing for faster turnaround times. These multi-stage systems can also be programmed to handle different finishes or to adapt to various types of wheel designs, making them more flexible for manufacturers who need to produce a wide range of styles and finishes.
Another innovative addition to alloy wheel finishing lines is the use of robotic polishing and laser finishing systems. These robotic systems, typically equipped with precision grinding or polishing tools, can be programmed to follow the complex contours of alloy wheels, ensuring an even and high-quality finish that would be difficult to achieve with manual labor. The integration of robotic arms in polishing and coating tasks reduces labor costs, increases throughput, and ensures the wheels maintain uniformity across production batches. Additionally, laser finishing technology can be used to create intricate designs or textured surfaces that add unique visual appeal to the wheels. It can also provide functional finishes such as heat dissipation patterns or customizable designs tailored to customer specifications.
To further enhance sustainability and energy efficiency, many modern alloy wheel finishing systems incorporate advanced technologies such as energy-efficient curing ovens, recycling powder recovery systems, and low-emission coating systems. Energy-efficient curing ovens reduce the amount of energy needed to cure the coatings, while powder recovery systems capture overspray and unused powder for reuse, reducing material waste and lowering operating costs. Moreover, newer coating systems may use low-VOC (volatile organic compound) or water-based coatings to improve environmental performance, aligning with stricter regulations and industry standards on emissions and hazardous materials.
Advanced automation and control systems are essential for managing these complex production lines. These systems allow operators to monitor the entire coating process in real time, adjusting parameters such as temperature, pressure, and application speed to optimize efficiency and ensure consistent quality. Data collected from each stage of the production process can be stored and analyzed to provide valuable insights into machine performance, production rates, and product quality. Predictive maintenance features can be incorporated into the control systems to monitor the health of the equipment, alerting operators to any potential issues before they cause machine breakdowns or production delays.
Finally, finish customization has become a key aspect of alloy wheel production, with consumers increasingly seeking unique and personalized designs for their wheels. Alloy wheel finishing equipment can be designed to accommodate a range of finishing options, from high-gloss and matte to textured, metallic, or even color-shifting effects. This flexibility is achieved through specialized coating formulations, application techniques, and equipment that can handle various types of finishes, providing a broad range of possibilities for manufacturers to meet consumer demands for customization and innovation.
In conclusion, alloy wheel finishing equipment is a critical part of the production process, ensuring that the final product not only looks aesthetically appealing but also performs well under the demanding conditions of everyday use. The combination of automated systems, advanced finishing techniques, and energy-efficient technologies helps manufacturers produce high-quality alloy wheels in an efficient, cost-effective, and sustainable manner. These systems also allow for greater flexibility and customization, making it easier for manufacturers to meet changing market demands and customer preferences. By investing in state-of-the-art finishing equipment, manufacturers can maintain a competitive edge in the market while delivering superior products that satisfy the expectations of both consumers and industry standards.
Powder Coating Solutions for Alloy Wheels
Powder coating solutions for alloy wheels are designed to provide a durable, attractive, and long-lasting finish that enhances both the aesthetic appeal and performance of the wheels. The powder coating process involves applying a dry powder, typically composed of resin, pigments, curing agents, and additives, which is then electrostatically charged and applied to the alloy wheel surface. The wheels are then heated in a curing oven, where the powder melts and forms a strong, chemical bond to the wheel surface. This process offers numerous benefits, including superior resistance to corrosion, abrasion, UV degradation, and environmental elements, making it ideal for alloy wheel coatings that are exposed to harsh road conditions.
Key Benefits of Powder Coating for Alloy Wheels
- Durability and Protection: Powder coating forms a tough, impact-resistant finish that protects alloy wheels from damage caused by road debris, rocks, and chemicals such as road salts. The coating is highly resistant to scratching, chipping, and fading, ensuring that the wheels maintain their appearance for a long time.
- Corrosion Resistance: One of the most important advantages of powder coating for alloy wheels is its ability to resist corrosion. The coating creates a protective barrier against moisture, salts, and other environmental factors that could cause rust or deterioration of the metal surface, especially in harsh climates with heavy snowfall or salty roads.
- UV Stability: Powder coating provides excellent UV stability, which prevents the finish from fading or discoloring over time. This makes it an ideal solution for wheels that will be exposed to constant sunlight, maintaining the visual appeal of the wheels even in harsh, sunny environments.
- Aesthetic Variety: Powder coating offers a wide range of color options and finishes, including matte, gloss, satin, metallic, and even custom effects. Manufacturers can achieve unique and personalized looks, including color-shifting effects, pearlescent finishes, and textured surfaces. This versatility allows car owners and manufacturers to choose finishes that complement the vehicle’s style.
- Environmentally Friendly: Unlike traditional liquid paint, powder coating is free of solvents and VOCs (volatile organic compounds), making it a more eco-friendly solution. The process generates less waste, as any overspray or excess powder can be recovered and reused. This reduces the environmental impact of the coating process, making it a sustainable option for manufacturers and consumers.
- Cost-Effective: Powder coating is a cost-effective solution in the long term due to its durability and the reduced need for maintenance or touch-ups. The process itself is efficient, and the ability to reuse excess powder reduces material costs. Additionally, the high-quality finish achieved with powder coating can increase the value of the alloy wheels and make them more attractive to buyers.
Powder Coating Process for Alloy Wheels
- Surface Preparation: The first step in the powder coating process is preparing the alloy wheel surface. This is a critical stage to ensure proper adhesion of the powder coating. Alloy wheels are typically cleaned using methods such as shot blasting, sandblasting, or chemical treatments to remove oils, dirt, corrosion, and other contaminants. Some processes may also include a phosphate treatment to enhance corrosion resistance. The wheels are then dried to eliminate any moisture that might interfere with the coating process.
- Powder Application: After the surface is prepped, the wheels are placed into an electrostatic powder application booth. In this booth, the wheels are grounded, and an electrostatic spray gun is used to apply a charged powder to the wheel’s surface. The electrostatic charge causes the powder particles to be attracted to the wheel, ensuring an even and consistent coat across all areas, including hard-to-reach sections like spokes. The powder can be applied in different thicknesses, depending on the desired finish.
- Curing: Once the powder is applied, the wheels are moved into a curing oven. The curing process involves heating the wheels to a specific temperature (usually between 160°C to 200°C or 320°F to 390°F) for a predetermined amount of time. During this stage, the powder particles melt and chemically bond with the surface of the wheel, forming a durable, smooth, and hard coating. The curing oven is carefully controlled to ensure even heat distribution, ensuring the coating is properly cured and fully bonded.
- Cooling and Inspection: After curing, the wheels are allowed to cool down gradually, which helps solidify the coating and prevents thermal shock. Once cooled, the wheels undergo a thorough inspection to ensure the finish is even and free from defects. Advanced automated inspection systems may be used to check for issues such as color inconsistencies, uneven coating thickness, or surface imperfections. Any wheels that do not meet the quality standards are either rejected or reworked.
- Finishing Touches: Once the wheels pass inspection, they may undergo additional finishing steps such as polishing, labeling, or applying protective layers such as clear coats. Clear coating adds an extra layer of protection and enhances the finish’s gloss and UV stability, while also providing additional resistance to corrosion and fading.
Types of Powder Coatings for Alloy Wheels
- Polyester Powder Coatings: These coatings are among the most commonly used for alloy wheels due to their excellent outdoor durability, resistance to weathering, and ability to provide a smooth finish. Polyester coatings are available in a wide range of colors and finishes, making them ideal for producing aesthetically pleasing results.
- Epoxy Powder Coatings: Epoxy coatings provide superior adhesion and corrosion resistance, making them suitable for wheels exposed to harsh conditions. However, they are less UV stable than polyester coatings, so they are typically used for applications where the wheels are less likely to be exposed to prolonged sunlight.
- Hybrid Powder Coatings: Hybrid coatings combine the benefits of both epoxy and polyester resins, offering a balance of good corrosion resistance and UV stability. These coatings are often used for alloy wheels that require both durability and resistance to outdoor elements.
- Polyurethane Powder Coatings: Polyurethane coatings are known for their high abrasion resistance and excellent gloss retention. They are often used in automotive and industrial applications where a tough, long-lasting finish is required.
Conclusion
Powder coating solutions for alloy wheels offer numerous advantages, including enhanced durability, corrosion resistance, aesthetic flexibility, and environmental sustainability. By applying powder coatings to alloy wheels, manufacturers and consumers alike can achieve a high-quality finish that enhances the wheels’ appearance and performance. The process of powder coating provides long-term protection against wear, weathering, and UV degradation, while offering a wide range of customizable options in terms of colors and finishes. With its cost-effectiveness, ease of maintenance, and superior protection, powder coating remains a top choice for alloy wheel coatings in the automotive industry.
Powder coating for alloy wheels is a cutting-edge technology that offers a multitude of benefits, combining aesthetics, durability, and environmental responsibility. The process, as previously explained, uses a dry powder, which is electrostatically applied and then cured to form a durable coating. This not only enhances the appearance of alloy wheels but also provides a high level of protection against environmental factors such as UV radiation, road salts, moisture, and road debris.
The powder coating process offers significant advantages over traditional liquid painting, including a tougher finish that is more resistant to scratching, chipping, and fading. The ability to apply a smooth, uniform coat across intricate wheel designs ensures that even the most complex wheel shapes can be coated effectively. Additionally, the powder can be customized to create a variety of finishes, from high gloss to matte, metallic, and even textured or custom effects like color-shifting pigments, offering consumers a broad range of options to match their vehicle’s style.
The process of powder coating begins with precise surface preparation, which is essential for optimal adhesion. Alloy wheels are cleaned and treated to remove contaminants, such as oils, dust, and rust. Various techniques like shot blasting or sandblasting are used to prepare the surface for the powder application, ensuring that the coating adheres properly and lasts for a long time. Once the wheel is prepared, the powder is electrostatically charged and applied using a specialized spray gun. The charged powder is attracted to the wheel’s surface, forming an even and consistent layer that covers the entire wheel, including hard-to-reach areas like spokes.
After the powder is applied, the wheels are moved into a curing oven, where they are heated to a specific temperature for a set time. This process causes the powder to melt and chemically bond to the surface of the alloy wheel, creating a solid and uniform layer. The heat also helps to remove any remaining moisture and ensures that the coating cures properly, forming a finish that is resistant to the rigors of road conditions, from exposure to dirt and grime to harsh weather.
In addition to the protective qualities of powder coating, the process is highly efficient and environmentally friendly. Unlike traditional liquid paints, powder coating contains no solvents and emits fewer volatile organic compounds (VOCs), making it a more sustainable option. Excess powder can be reclaimed and reused, reducing waste and improving cost-effectiveness. The powder coating process also produces less overspray compared to liquid painting, which means less material is wasted.
Powder coating offers various customization options, including the ability to achieve unique effects such as metallic, glossy, satin, or matte finishes. Manufacturers can produce alloy wheels that fit a wide range of aesthetic preferences, from subtle and sophisticated to bold and attention-grabbing. Additionally, specialized coatings can be applied to achieve textures, patterns, or even custom logos and designs, further increasing the appeal of alloy wheels. The versatility of powder coating allows manufacturers to cater to a diverse range of customers, whether they are looking for high-performance wheels, luxury designs, or custom finishes for show vehicles.
Another benefit of powder coating is its long-term performance. Once applied and cured, the coating forms a tough, durable finish that helps protect alloy wheels from the elements. Exposure to saltwater, UV rays, dirt, and brake dust can degrade wheel finishes over time, but powder coating offers superior resistance to these elements. It helps prevent the wheels from corroding, fading, or losing their visual appeal, even after extended exposure to harsh conditions. This makes it particularly beneficial for alloy wheels used in vehicles that are regularly exposed to challenging driving environments, such as off-road vehicles or cars in coastal regions with salty air.
For high-volume manufacturers, powder coating is also a more efficient and cost-effective option in terms of both time and resources. The equipment required for the powder coating process, including the spray guns, curing ovens, and powder recovery systems, can be automated to optimize production throughput. Automated systems are often integrated with robotic arms or conveyors, ensuring that wheels move efficiently between different stages of the process and reducing labor costs. Additionally, the ability to reclaim and reuse powder ensures that material waste is minimized, further driving down production costs.
As the automotive industry continues to embrace sustainability and eco-friendly solutions, powder coating remains a leading choice for alloy wheel finishes. The process aligns with increasingly stringent environmental regulations, helping manufacturers reduce their carbon footprint. The absence of solvents, low emissions, and efficient use of materials all contribute to a more sustainable manufacturing process, making it an attractive option for both manufacturers and consumers.
Ultimately, powder coating solutions for alloy wheels are a combination of advanced technology, durability, and customization options that cater to both functional and aesthetic needs. By providing a tough, long-lasting finish that resists wear, corrosion, and UV damage, powder coating helps extend the life of alloy wheels while enhancing their appearance. Whether used for standard automotive applications or high-end custom designs, powder coating provides a reliable, sustainable, and visually appealing solution for alloy wheel manufacturers and consumers alike.
Alloy Wheel Powder Coating Units

Alloy wheel powder coating units are specialized systems designed to apply powder coatings to alloy wheels, ensuring that they achieve a durable and visually appealing finish. These units combine various stages of preparation, application, curing, and finishing, all tailored to the specific needs of alloy wheels. The goal is to create a high-quality, protective coating that enhances the wheels’ aesthetic appeal while offering superior resistance to environmental factors like corrosion, UV exposure, road salts, and abrasion. These systems are typically automated to ensure consistency, efficiency, and reduced human error in the coating process.
An alloy wheel powder coating unit typically consists of the following key components:
- Surface Preparation Station: Before applying the powder, the alloy wheels must be cleaned and prepped to ensure that the coating adheres properly. Surface preparation typically involves processes like shot blasting, sandblasting, or chemical cleaning to remove contaminants such as grease, dirt, oxidation, and any previous coatings. The wheels are often subjected to a cleaning bath or abrasive treatment to provide a rough surface profile that helps the powder adhere more effectively.
- Powder Application Booth: After surface preparation, the next step is the application of the powder coating. In the application booth, the wheels are placed on a conveyor system or in a rotary fixture. An electrostatic spray gun is used to charge the powder particles, which are then sprayed onto the grounded wheels. The electrostatic charge ensures that the powder sticks evenly to the wheel’s surface, even on complex geometries like spokes. The powder can be selected in various colors, finishes (e.g., matte, gloss, satin), or even special effects like metallic or textured coatings.
- Curing Oven: Once the powder is applied, the wheels are moved into a curing oven, where they are heated to the required temperature for a specified amount of time. This process allows the powder to melt and chemically bond to the alloy wheel surface, creating a hard, durable finish. The curing process ensures that the coating is uniform and smooth, offering resistance to scratches, corrosion, and fading. The temperature and curing time are controlled based on the specific powder coating material being used.
- Cooling Station: After the wheels are cured, they are cooled down in a controlled manner to allow the coating to harden and set properly. Cooling is important because it prevents thermal shock, which could cause defects like cracking or warping in the finish. This stage can involve an air-cooled system or even a water-cooled setup, depending on the specifications of the powder coating unit.
- Inspection and Quality Control: After cooling, the wheels are thoroughly inspected for defects such as uneven coating, color inconsistencies, or surface imperfections. Automated inspection systems equipped with cameras, sensors, or vision systems can detect common issues, such as thin or thick areas of coating, incomplete coverage, or physical defects in the finish. Wheels that do not meet the quality standards are typically removed from the line for rework or rejection.
- Post-Coating Treatment: In some cases, wheels may undergo additional treatments after the powder coating process. This could involve applying a clear coat for added protection and gloss enhancement or using polishing equipment to improve the appearance of the finish. Some units may also include the option for laser engraving or etching to add branding or design elements to the wheels, further enhancing the customization options.
- Packaging and Handling: Once the wheels pass inspection and any final treatments, they are ready for packaging and shipment. Automated packaging systems ensure that the wheels are properly handled and protected during transportation. In addition, labeling systems may be employed to identify the specific wheel type, color, finish, and batch number for traceability purposes.
Types of Alloy Wheel Powder Coating Units
- Manual or Semi-Automatic Units: These units typically involve more manual intervention during the application and curing stages. Operators might manually apply the powder or place the wheels on conveyor systems for coating and curing. While these systems are less expensive than fully automated lines, they require skilled operators to ensure consistent quality and efficiency.
- Fully Automated Powder Coating Units: Fully automated units are ideal for high-volume production and are designed to streamline the coating process from start to finish. These systems include fully automated conveyors, robotic arms, and automated spray guns, reducing the need for human intervention and improving consistency across all coated wheels. These units can be programmed for different wheel sizes, shapes, and coating specifications, ensuring flexibility and scalability in production.
- Compact Powder Coating Units: Smaller or compact units are designed for lower-volume production or for businesses with limited space. These units typically integrate several key stages of the powder coating process into a single, space-efficient system. Compact units are ideal for small-scale manufacturers or custom wheel shops that focus on niche markets.
Advantages of Alloy Wheel Powder Coating Units
- Efficiency: Powder coating units, especially automated ones, can handle high volumes of alloy wheels with minimal downtime. The speed and consistency of the process make them ideal for meeting production deadlines and reducing lead times.
- Durability: The powder coating process results in a tough, long-lasting finish that provides superior protection against scratches, chips, corrosion, and UV degradation. Alloy wheels coated with powder have a significantly longer lifespan compared to those finished with traditional paint.
- Customization: The flexibility in selecting different types of powders, colors, and finishes allows manufacturers to create a wide range of aesthetic options for alloy wheels. Customization options such as matte, glossy, metallic, and textured finishes can cater to a variety of consumer preferences.
- Environmental Benefits: Powder coating is more eco-friendly compared to traditional liquid coatings. It produces no volatile organic compounds (VOCs) or hazardous solvents, making it safer for both the environment and workers. Furthermore, powder overspray can be collected and reused, reducing material waste.
- Cost-Effectiveness: Although the initial setup for a powder coating unit can be costly, the long-term cost savings from reduced labor, material waste, and maintenance make it a cost-effective solution. The durable finish reduces the need for frequent touch-ups or replacements, further lowering maintenance costs.
- Consistency: Automated powder coating units ensure that each alloy wheel receives an even, consistent coating, regardless of its design or complexity. This consistency improves the overall quality of the finished product, making it easier to meet stringent industry standards.
Conclusion
Alloy wheel powder coating units are an essential part of the production process for automotive manufacturers, custom wheel shops, and any business involved in wheel finishes. These units provide a highly efficient, durable, and customizable solution for applying high-quality powder coatings to alloy wheels. By incorporating surface preparation, powder application, curing, and quality control stages into a streamlined system, manufacturers can produce alloy wheels with excellent finishes that enhance the visual appeal and performance of vehicles while offering long-lasting protection against environmental factors. Whether for high-volume manufacturing or custom designs, alloy wheel powder coating units help ensure that wheels are finished to the highest standards of quality, durability, and aesthetics.
Alloy wheel powder coating units are specialized systems engineered to apply powder coatings to alloy wheels, ensuring they achieve a durable and visually appealing finish. These units combine various stages like surface preparation, powder application, curing, and finishing, all tailored to alloy wheels. The purpose is to create a high-quality, protective coating that enhances the wheels’ aesthetic appeal and provides resistance to environmental factors such as corrosion, UV exposure, road salts, and abrasion. Many of these units are automated to ensure consistency, efficiency, and minimal human error throughout the coating process.
The surface preparation is the first and crucial step in the coating process. Alloy wheels are cleaned and prepped to guarantee proper adhesion. Methods like shot blasting, sandblasting, or chemical cleaning are often used to remove contaminants such as oils, dirt, rust, or any old paint. The surface is then conditioned to provide a rough profile that helps the powder adhere better to the wheel surface. After preparation, the wheels enter the powder application booth, where an electrostatic spray gun applies the powder coating. The powder particles are charged electrostatically and sprayed onto the grounded wheel surface. The powder adheres evenly, ensuring the entire wheel surface, even in hard-to-reach areas, is coated with precision.
Following the application, the wheels move to the curing oven, where the powder is heated at a specific temperature, typically between 160°C to 200°C (320°F to 390°F), to allow it to melt and chemically bond with the alloy wheel. This creates a hard, durable finish that offers superior protection against wear, UV degradation, and corrosion. The curing process ensures the coating cures evenly and remains smooth, resulting in a finish that can withstand the wear and tear from road conditions, dirt, and harsh environmental factors.
Once the wheels are cured, they need to cool down properly to avoid defects like cracking or warping. Cooling systems typically allow the wheels to cool gradually, ensuring the finish hardens without compromising its structural integrity. After cooling, the wheels undergo a thorough inspection to check for defects such as uneven coating, color inconsistencies, or surface imperfections. Advanced inspection systems equipped with cameras or sensors may be used to identify any issues with the coating quality. If the wheels do not meet the required standards, they are reworked or discarded.
Some units include additional finishing options, such as clear coats for added protection and gloss or polishing systems to improve the final appearance. Clear coats provide an extra layer of UV protection and enhance the glossiness and durability of the finish. In some cases, wheels may undergo branding or custom logo application as part of the finishing touches, adding an extra layer of personalization to the finished product. The wheels are then packaged for delivery, ensuring they are properly protected during transit. Automated packaging systems ensure the wheels are handled with care and ready for shipment to customers.
Alloy wheel powder coating units come in various configurations, including manual, semi-automatic, or fully automated systems, depending on production needs and scale. Manual units involve more human intervention during the powder application and curing stages, while semi-automatic systems may use robotic arms or conveyors to enhance efficiency. Fully automated systems integrate all stages, from surface preparation to curing, ensuring a highly efficient and consistent process. These automated units are ideal for high-volume production as they reduce labor costs, minimize errors, and improve overall productivity.
The fully automated systems in particular are optimized for speed and consistency, allowing manufacturers to coat hundreds or thousands of wheels per day. These units can accommodate different wheel sizes and types, offering flexibility in meeting various customer demands. Automated powder coating units typically have automated conveyors, robotic arms for applying the powder, and integrated curing ovens to streamline the entire process.
Compact powder coating units are often designed for smaller-scale operations or businesses with limited space. These units combine multiple stages of the powder coating process into one compact system, making them ideal for small shops or custom wheel manufacturers who do not need high-volume production. Even though these units are smaller, they can still produce high-quality finishes, offering an efficient solution for those who focus on niche markets or custom-designed wheels.
The efficiency of powder coating units translates into lower operating costs, as the powder used can often be recycled and reused. This reduces material waste, ensuring cost savings over time. Additionally, the durability of the powder-coated finish reduces the need for frequent touch-ups or replacements, further lowering maintenance costs in the long run. The eco-friendly nature of powder coating also plays a significant role, as the process generates fewer emissions compared to traditional liquid painting, and it does not require the use of solvents or VOCs (volatile organic compounds), making it a cleaner alternative for both manufacturers and the environment.
Customization is another major advantage offered by alloy wheel powder coating units. With a wide range of powder options, manufacturers can produce wheels with different textures, colors, and finishes. From matte to high-gloss, metallic to textured, and even custom effects like color-shifting pigments, powder coating allows for diverse design options. This flexibility enables manufacturers to meet consumer demands for unique and personalized finishes, whether for high-performance vehicles or luxury cars.
The long-term benefits of powder coating are clear—wheels that undergo the powder coating process are highly resistant to scratches, chips, UV degradation, and corrosion. This increased durability makes powder coating an attractive option for consumers who want their wheels to maintain their appearance over time, particularly in challenging environments where exposure to harsh weather conditions, road salts, and chemicals can accelerate wear and tear.
In conclusion, alloy wheel powder coating units are integral to producing high-quality, durable, and aesthetically pleasing finishes for alloy wheels. These systems ensure efficiency, consistency, and customization in the coating process, making them ideal for high-volume manufacturers and custom wheel makers alike. Whether used for automotive applications or specialized custom projects, powder coating provides wheels with a long-lasting protective finish, reducing maintenance costs and enhancing the visual appeal and performance of alloy wheels. As technology continues to evolve, alloy wheel powder coating units will remain a reliable and sustainable solution for the automotive industry, offering improved production capabilities and environmental benefits.
Alloy Wheel Coating System
An alloy wheel coating system refers to the entire process and set of equipment used to apply a protective and decorative finish to alloy wheels. This system ensures that alloy wheels are treated with high-quality coatings that not only enhance their appearance but also offer durability and protection against environmental factors like corrosion, UV degradation, road salts, and scratches. Alloy wheel coating systems are typically composed of various stages, including surface preparation, application of the coating, curing, inspection, and finishing. These systems can be manual, semi-automatic, or fully automated, depending on the scale of production and the level of customization required.
The alloy wheel coating process involves several critical steps to achieve a durable and aesthetically pleasing finish:
- Surface Preparation: Alloy wheels need to be thoroughly cleaned and prepared before applying the coating. This stage typically involves removing any contaminants like grease, dirt, oils, and rust. Methods such as shot blasting, sandblasting, or chemical cleaning are used to clean the wheels, ensuring that the surface is free of any impurities that could hinder adhesion. Surface preparation is vital to achieving a long-lasting, smooth finish.
- Coating Application: Once the wheels are properly prepared, the coating is applied. This can be done through various methods, with powder coating being the most common choice. In this process, the coating powder is sprayed onto the wheel using an electrostatic spray gun, which charges the powder particles so that they stick to the wheel surface. The powder is then applied evenly to ensure that all areas of the wheel, including spokes and edges, are covered. Other coating methods may include liquid coating, but powder coating is preferred for its durability, efficiency, and environmental friendliness. With powder coating, there are no solvents or volatile organic compounds (VOCs), making it a safer and cleaner process for both workers and the environment.
- Curing: After the powder coating is applied, the wheels are placed in a curing oven. The heat from the oven melts the powder, causing it to chemically bond to the wheel’s surface, forming a hard, durable coating. This curing process is essential to achieve the desired thickness and strength of the coating. The temperature and curing time must be carefully controlled to ensure uniformity and durability.
- Cooling: Once the wheels have been cured, they need to cool down gradually. This cooling phase helps the coating harden properly and prevents defects such as cracking or warping. Cooling can be done using either air or water-cooled systems, depending on the design of the alloy wheel coating system.
- Inspection and Quality Control: After cooling, the coated wheels undergo a thorough inspection to ensure that the coating is even and free from defects. Automated systems may be used for visual inspection, checking for inconsistencies in coating thickness, coverage, or color. Any wheels that fail the inspection are typically removed from the line for rework.
- Finishing: In some cases, a clear coat may be applied on top of the powder-coated layer for added protection and gloss enhancement. The clear coat further strengthens the finish and provides a layer of UV protection, preventing the wheels from fading over time. Additional finishing steps may include polishing or adding custom designs or logos to the wheel surface.
- Packaging and Shipping: Once the wheels pass inspection and any additional finishing steps, they are packaged and prepared for shipment. Automated packaging systems ensure the wheels are safely handled and protected during transport.
Types of Alloy Wheel Coating Systems
- Manual Coating Systems: Manual coating systems typically involve operators applying the coating using spray guns. These systems are more labor-intensive but can be suitable for small-scale operations or highly customized work where individual attention is required for each wheel. However, the quality and consistency of the coating can vary, and it may not be as efficient for large-scale production.
- Semi-Automatic Coating Systems: These systems use a combination of manual and automated processes. While operators may still apply the coating manually or oversee certain stages, some parts of the process, such as curing and conveyor handling, are automated. Semi-automatic systems are more efficient than manual systems and can handle higher volumes of wheels, offering a good balance between customization and automation.
- Fully Automated Coating Systems: Fully automated alloy wheel coating systems are designed for high-volume production. These systems handle the entire coating process, from surface preparation to curing, with minimal human intervention. Robots and conveyors move the wheels through the various stages of the process, and automated spray guns apply the coating uniformly. These systems offer the highest level of consistency, speed, and efficiency, making them ideal for large-scale manufacturers.
Benefits of Alloy Wheel Coating Systems
- Durability: Coating systems, especially powder coating, provide a highly durable finish that resists chipping, scratching, and fading. This makes alloy wheels more resistant to wear and tear, extending their lifespan and maintaining their appearance for longer.
- Aesthetic Appeal: Alloy wheel coating systems allow for a wide range of finishes, from glossy and metallic to matte or satin. This flexibility makes it possible to create custom-designed wheels that complement the look of various vehicles, whether for standard production models or high-end custom builds.
- Environmental Sustainability: Powder coating is an eco-friendly option because it does not release harmful solvents or volatile organic compounds (VOCs). The powder used can also be reclaimed and reused, reducing material waste and improving overall sustainability. This makes alloy wheel coating systems an environmentally responsible choice for manufacturers.
- Cost-Effectiveness: Although the initial investment in coating equipment may be high, powder coating systems are cost-effective in the long run. They offer faster processing times, reduced waste, and lower maintenance costs compared to traditional liquid coatings. Additionally, the durability of the finished wheels reduces the need for frequent rework or replacements, which further lowers costs over time.
- Customization: The ability to apply various finishes and colors, including metallics, matte, gloss, and custom effects, allows manufacturers to meet the diverse demands of customers. This makes alloy wheel coating systems ideal for both standard and custom wheel production.
- Efficiency: Automated systems streamline the coating process, increasing production speed and reducing labor costs. This ensures a high output of consistently coated wheels, which is crucial for manufacturers dealing with large volumes of products.
Conclusion
Alloy wheel coating systems are integral to the automotive and aftermarket wheel industries, offering a reliable, durable, and aesthetically pleasing finish for alloy wheels. With a variety of coating methods and system configurations available—ranging from manual to fully automated processes—these systems are designed to meet the specific needs of different manufacturers, from small custom shops to large-scale production facilities. The benefits of alloy wheel coating systems include improved wheel protection, enhanced visual appeal, eco-friendliness, and long-term cost savings, making them a vital component in modern wheel manufacturing. Whether for mass production or bespoke designs, alloy wheel coating systems provide a comprehensive solution that ensures high-quality finishes that withstand the test of time and the elements.
An alloy wheel coating system is a comprehensive solution designed to apply protective and decorative finishes to alloy wheels. These systems are engineered to enhance the visual appeal of the wheels while also providing durability and resistance to environmental factors such as corrosion, UV damage, road salts, and abrasion. The system typically involves several stages: surface preparation, coating application, curing, inspection, and finishing. These stages are carefully integrated to ensure that the alloy wheels receive an even, smooth, and long-lasting coating. While manual systems are suitable for smaller-scale or custom work, automated systems are designed for large-scale production, offering higher efficiency, consistency, and speed.
The process begins with surface preparation, where the alloy wheels are cleaned and treated to ensure proper adhesion of the coating. This can include sandblasting, shot blasting, or chemical cleaning to remove contaminants such as oils, dirt, rust, and any old paint. Without proper surface preparation, the coating might fail to bond properly, leading to defects and reduced durability. Once the wheels are prepped, the coating is applied. Powder coating is the most commonly used method, where an electrostatic spray gun charges the powder particles, allowing them to adhere evenly to the wheel’s surface. This electrostatic process ensures that the coating is applied uniformly, even in intricate areas like spokes and edges.
After the powder coating is applied, the wheels move to a curing oven. The heat from the oven melts the powder, allowing it to bond chemically with the surface of the alloy wheel, creating a tough, durable finish. The curing process is crucial for ensuring that the coating hardens correctly and maintains a uniform appearance. Once the curing process is complete, the wheels are cooled, either through air or water-cooled systems. This cooling stage ensures that the coating hardens properly and prevents the wheels from warping or cracking due to thermal stress.
Once cooled, the coated wheels undergo a thorough inspection to check for defects such as uneven coating, color inconsistencies, or surface imperfections. Automated inspection systems are often employed to detect such issues, ensuring that only wheels that meet the quality standards are passed along. After passing inspection, additional finishing processes may be carried out. This could involve applying a clear coat to enhance gloss and provide extra UV protection, or polishing the wheels to improve the final appearance. Some systems also allow for custom designs, logos, or branding to be added to the wheels at this stage.
Finally, once the wheels are finished, they are packaged and prepared for shipment. Packaging systems ensure that the wheels are safely handled and protected during transit to prevent any damage to the coating. Alloy wheel coating systems can vary in complexity, from manual or semi-automatic systems to fully automated, high-volume production lines. Fully automated systems, typically used for large-scale manufacturing, use robots and conveyor belts to move wheels through the coating process, ensuring consistency and high efficiency.
Alloy wheel coating systems offer numerous advantages, including enhanced durability, improved visual appeal, environmental sustainability, and cost-effectiveness. The powder coating process, in particular, is eco-friendly because it generates no harmful solvents or volatile organic compounds (VOCs), making it safer for workers and the environment. The coatings themselves are highly durable, offering excellent resistance to scratching, fading, and corrosion. This durability helps to reduce maintenance costs over time, as the coated wheels remain in good condition for longer periods.
Customization options are also a key benefit of alloy wheel coating systems. With a wide range of finishes available, such as matte, gloss, metallic, and custom textures, manufacturers can meet customer preferences for unique or personalized wheel designs. The ability to apply custom coatings allows businesses to cater to a variety of markets, from luxury vehicle manufacturers to aftermarket wheel suppliers.
Moreover, alloy wheel coating systems improve overall production efficiency. Automated systems streamline the entire coating process, reducing the need for manual labor and speeding up production times. This leads to a more consistent product output, which is essential for meeting high demand in industries like automotive manufacturing. By reducing the chances of defects and ensuring uniformity in coating application, these systems help manufacturers meet high-quality standards consistently.
The initial investment in alloy wheel coating systems can be significant, particularly for high-end automated units. However, the long-term savings in material waste reduction, labor costs, and maintenance make these systems a cost-effective solution. Powder coating systems, in particular, allow for the reuse of powder overspray, reducing material waste and making the coating process more economical. Additionally, the long-lasting nature of the coatings means that wheels need less frequent touch-ups or replacements, leading to further cost savings over time.
In conclusion, alloy wheel coating systems are essential for producing high-quality, durable, and aesthetically pleasing finishes on alloy wheels. Whether for large-scale manufacturers or custom shops, these systems provide the necessary technology to apply consistent and efficient coatings, improving both the appearance and performance of alloy wheels. With options for manual, semi-automatic, or fully automated systems, businesses can choose the best configuration based on their production needs. Alloy wheel coating systems offer numerous advantages, from improved durability and aesthetic flexibility to enhanced efficiency and environmental benefits, making them an indispensable part of modern wheel manufacturing processes.
Powder Coating Stations for Alloy Wheels
Powder coating stations for alloy wheels are specialized areas within a manufacturing facility where alloy wheels undergo the powder coating process. These stations are equipped with the necessary technology and tools to ensure that the wheels are properly coated with powder and cured to form a durable and aesthetically pleasing finish. Powder coating is a popular method for finishing alloy wheels because it provides superior protection against scratches, corrosion, and UV degradation compared to traditional liquid paints.
Key Components of Powder Coating Stations for Alloy Wheels:
- Surface Preparation Area: Before applying the powder coating, it is essential that the alloy wheels undergo thorough surface preparation. This is the first step in the powder coating process and involves cleaning the wheels to remove contaminants such as grease, dirt, rust, and old coatings. Surface preparation can be done using methods like:
- Shot Blasting: A process where high-velocity steel shot or grit is blasted onto the wheel’s surface to remove contaminants and create a rough texture for better adhesion.
- Sandblasting: Similar to shot blasting, sandblasting uses sand or other abrasive materials to clean the wheel surface.
- Chemical Cleaning: This involves using chemical agents or cleaners to dissolve dirt, oils, or rust from the wheel surface.
Proper surface preparation is essential for ensuring that the powder coating adheres properly to the wheel, which helps achieve a durable finish.
- Powder Coating Application Booth: After the wheels are prepared, they move to the application booth, where the powder coating is applied. In this stage:
- Electrostatic Spray Guns: These are used to spray the coating powder onto the wheel. The electrostatic spray gun charges the powder particles, which are then attracted to the grounded wheel surface. This ensures an even and uniform coating of the powder.
- Manual or Automatic Application: Powder coating stations may be either manually operated or automated. In manual systems, operators apply the powder coating using handheld spray guns, while automated systems use robotic arms or conveyors to apply the powder evenly across the wheel’s surface.
- Booth Design: The booth is typically equipped with a filtration system to remove excess powder from the air, which is then recycled to prevent wastage. The application booth is often enclosed to ensure safety and minimize exposure to the powder particles.
- Curing Oven: Once the powder has been applied, the wheels are moved into a curing oven. The oven is preheated to a specific temperature, usually between 160°C and 200°C (320°F to 390°F), depending on the type of powder being used. In the oven:
- The heat causes the powder to melt and chemically bond to the surface of the alloy wheel.
- This curing process results in a hard, durable, and smooth finish that is resistant to scratches, fading, and corrosion.
- The curing time and temperature are critical to ensuring that the powder coating cures uniformly and properly.
- Cooling Area: After the curing process, the wheels must be cooled down before they can be handled further. This cooling phase allows the coating to harden and settle, ensuring that it maintains its integrity. Cooling can be done using air or water-cooling systems, depending on the design of the powder coating station.
- Inspection Station: After cooling, the wheels are inspected for defects such as uneven coating, color inconsistencies, or surface imperfections. This is an important step to ensure that the final product meets quality standards. Automated inspection systems may use cameras or sensors to detect defects, or it may be done manually by operators. Wheels that fail inspection are typically sent back for rework or are discarded if they cannot be salvaged.
- Finishing and Touch-up: If necessary, additional finishing steps can be applied, such as adding a clear coat for extra protection, gloss enhancement, or UV resistance. In some cases, the wheels may be polished, buffed, or even branded with logos or custom designs. These final touches ensure the wheels not only perform well but also look visually appealing.
- Packaging and Shipping: Once the powder-coated wheels are inspected and finished, they are packaged for shipment. Proper packaging is important to prevent any damage to the finish during transport. Alloy wheel powder coating stations often incorporate automated packaging systems to ensure that the wheels are carefully handled and securely packaged for delivery.
Benefits of Powder Coating Stations for Alloy Wheels:
- Durability: Powder coating provides a tough, long-lasting finish that is resistant to chips, scratches, corrosion, and UV degradation. This makes it ideal for alloy wheels, which are exposed to harsh road conditions, salt, and weathering.
- Efficiency: The process is efficient, especially with automated powder coating stations. Automated systems streamline the coating application and curing process, reducing labor costs and increasing production capacity.
- Customization: Powder coating allows for a variety of finishes, including gloss, matte, satin, metallic, and even custom effects such as color-shifting pigments. This gives manufacturers the ability to produce unique and personalized wheels for their customers.
- Eco-Friendly: Powder coating is an environmentally friendly process since it does not use solvents or release volatile organic compounds (VOCs). Additionally, overspray powder can be reclaimed and reused, reducing material waste.
- Cost-Effective: Although the initial investment in powder coating stations may be high, the long-term savings are significant. The durability of the powder coating reduces the need for frequent touch-ups or replacements, and the process itself is more cost-effective than liquid coating methods.
- Improved Aesthetic: Powder coating provides a consistent, high-quality finish that enhances the appearance of alloy wheels. Whether for standard production or custom designs, powder coating offers a smooth, even coating that meets the aesthetic demands of customers.
- Reduced Maintenance: Powder-coated wheels require less maintenance and are easier to clean compared to other coatings. The durable finish resists dirt and grime, helping the wheels maintain their visual appeal over time.
Conclusion:
Powder coating stations for alloy wheels are vital for producing high-quality, durable, and aesthetically pleasing finishes. These stations ensure that the wheels are properly prepared, coated, cured, and inspected, offering a superior alternative to traditional liquid painting methods. Whether for mass production or custom projects, powder coating stations provide the efficiency, customization, and durability needed to meet the demands of the automotive and aftermarket wheel industries. With advances in automation and technology, these systems continue to improve, making them a key part of modern wheel manufacturing processes.
Powder coating stations for alloy wheels are critical components of the wheel manufacturing process, designed to apply protective and decorative finishes that enhance both the performance and appearance of the wheels. The powder coating process involves applying a fine powder to the surface of the wheel, which is then cured in a high-temperature oven to create a durable and smooth finish. These stations are equipped with various specialized tools and systems that ensure the coating is applied evenly and consistently, producing a high-quality result. Alloy wheel powder coating stations can be set up in a variety of ways, depending on the size and scale of the operation, ranging from manual to fully automated systems.
In powder coating stations, the first and foremost step is surface preparation. The alloy wheels are cleaned to remove any contaminants, such as oils, dirt, rust, or old paint, that could affect the adhesion of the powder coating. Surface preparation methods like shot blasting or sandblasting are commonly used, where abrasive materials are blasted onto the wheel’s surface to ensure it’s free of contaminants and to create a textured surface that enhances powder adhesion. Chemical cleaning is another common method, where wheels are immersed in a bath of cleaning agents to remove impurities. Proper preparation is essential for achieving a high-quality finish and ensuring that the powder bonds well to the wheel surface.
After the wheels are prepped, they move to the powder coating application booth. This is where the powder coating is applied using electrostatic spray guns that charge the powder particles, causing them to stick to the wheel surface. The application booth is designed to ensure that the coating is applied evenly, and it often includes systems to collect and reuse overspray powder, reducing waste. Automated systems use robotic arms or conveyors to move the wheels through the application process, while manual systems rely on operators to apply the powder by hand. The electrostatic process allows for an even distribution of powder over complex wheel shapes, including spokes and edges, which can be challenging to coat with traditional liquid paint.
Once the powder is applied, the wheels are transferred to a curing oven, where they are heated to a specific temperature. The heat causes the powder particles to melt and chemically bond to the alloy wheel surface, forming a hard and durable finish. The curing process is essential for creating a smooth, even coating that is resistant to wear, corrosion, and fading. After curing, the wheels are allowed to cool, solidifying the coating and preparing them for the next steps.
Once cooled, the wheels undergo a thorough inspection to ensure that the coating has been applied evenly and that no defects, such as color inconsistencies, uneven coating, or surface imperfections, are present. Automated inspection systems may be used to detect defects, or operators may visually inspect the wheels to check for quality. Wheels that fail inspection are typically removed from the production line and either reworked or discarded if they cannot be salvaged.
Additional finishing steps may be applied to further enhance the appearance and performance of the coated wheels. Some powder coating stations include a clear coating step, which provides a glossy finish and additional protection against UV degradation and environmental damage. The clear coat can also help preserve the coating’s appearance over time, ensuring that the wheels maintain their visual appeal. Polishing or buffing may also be applied to achieve a high-shine finish, and in some cases, custom designs or logos may be added to the wheels for branding purposes.
After finishing, the powder-coated wheels are packaged for shipment. The packaging process is carefully designed to protect the wheels during transportation, as the coated finish must be kept free from scratches and damage. Alloy wheel powder coating stations often include automated packaging systems to handle the wheels with care and ensure they are securely packed for delivery.
Overall, alloy wheel powder coating stations offer a reliable, efficient, and eco-friendly method for producing high-quality wheel finishes. Powder coating provides several benefits, including increased durability, resistance to fading and corrosion, and a more aesthetically pleasing result compared to traditional liquid coatings. These stations are vital for both mass production and custom alloy wheel projects, offering versatility and the ability to create a wide range of finishes. Whether for standard production runs or custom, bespoke wheel designs, powder coating stations play an essential role in the modern wheel manufacturing process, providing a durable and visually appealing solution for alloy wheels.
Equipment for Alloy Wheel Powder Coating
Equipment for alloy wheel powder coating is designed to efficiently apply a durable, protective finish to alloy wheels, ensuring both performance and aesthetic appeal. The equipment involved in this process is tailored to ensure that wheels are properly prepped, coated, cured, and finished. These systems can range from simple manual setups to fully automated, high-throughput production lines. Here’s an overview of the key equipment used in alloy wheel powder coating:
1. Surface Preparation Equipment:
- Shot Blasting Machines: These machines use high-velocity steel shot or grit to clean the alloy wheel surface by removing contaminants such as rust, old paint, dirt, and oil. Shot blasting also creates a rough texture on the surface, which helps the powder adhere better to the wheel.
- Sandblasting Cabinets: Similar to shot blasting, sandblasting uses fine sand or abrasive materials to clean and roughen the wheel surface. This step is crucial for ensuring that the powder coating bonds effectively.
- Chemical Cleaning Systems: These systems use solvents or chemical agents to clean and degrease the wheels, ensuring that no contaminants interfere with the coating process.
- Pre-Treatment Stations: Some setups include pre-treatment baths or systems that apply a protective layer to the wheel surface to prevent corrosion before powder coating. This process may involve phosphating or chromating the wheels to enhance the durability of the coating.
2. Powder Coating Application Equipment:
- Electrostatic Spray Guns: These are the primary tools for applying powder coating to alloy wheels. The guns charge the powder particles electrostatically, causing them to adhere to the grounded wheel surface. This method ensures even coverage and efficient use of the powder.
- Automatic Powder Coating Systems: In large-scale production lines, robots or automated spray systems apply the powder coating to the wheels. These systems can move the wheels into position and use spray nozzles to apply the powder uniformly across the wheel’s surface, ensuring consistent coverage, even in complex shapes like spokes.
- Manual Spray Guns: In smaller or custom setups, operators use handheld electrostatic spray guns to apply the powder coating. These guns give operators flexibility in applying coatings to wheels with intricate designs or unique specifications.
- Powder Feeders and Conveyors: These devices help deliver a steady, controlled flow of powder to the spray guns, ensuring that the right amount of powder is applied. Conveyors are used to move the wheels through the coating station, making the process more efficient.
3. Curing Equipment:
- Curing Ovens: After the powder coating is applied, the wheels are moved into curing ovens where they are heated to a specific temperature (usually between 160°C and 200°C) to melt and bond the powder to the surface of the wheel. The curing process is critical for creating a tough, durable, and consistent finish. The oven can be electric or gas-powered, with designs ranging from batch ovens to continuous conveyorized systems.
- Infrared Curing Systems: For faster curing, some systems use infrared (IR) radiation to heat the powder coating. This method allows for quicker cycle times and is often used in high-volume production settings.
4. Cooling Systems:
- Cooling Conveyors: After curing, the wheels need to cool before they can be handled. Cooling conveyors, often equipped with fans or water sprays, are used to bring the temperature of the coated wheels down to room temperature in a controlled manner, ensuring that the coating hardens properly.
- Air Cooling Stations: In some setups, wheels are placed in air-cooled chambers where fans blow ambient air over the wheels to cool them. This process ensures that the coating does not deform due to rapid cooling.
5. Inspection and Quality Control Equipment:
- Visual Inspection Stations: After curing and cooling, the wheels undergo visual inspection to check for defects such as color inconsistencies, coating thickness issues, or surface imperfections. Manual inspection or automated camera systems are used to detect these issues.
- Thickness Gauges: These tools are used to measure the thickness of the powder coating to ensure it meets specifications. Excessively thick coatings can result in bubbling or cracking, while too thin a coating may not provide adequate protection.
- Gloss Meters: These are used to check the level of gloss or sheen on the coated wheels. Different types of finishes (e.g., matte, satin, gloss) can be measured and controlled using these instruments to maintain the desired appearance.
6. Finishing Equipment:
- Polishing Machines: Some alloy wheels may undergo a polishing process after coating to enhance their shine and smoothness. This is particularly common for high-end or custom wheels where aesthetic appeal is important.
- Clear Coat Application Systems: To provide additional protection against UV radiation and scratches, a clear coat may be applied over the base powder coating. This system is typically automated and can be integrated into the main powder coating line.
- Decal and Branding Machines: Custom branding or logos can be applied to the wheels after powder coating, often using UV printing or other forms of ink application.
7. Waste Management and Recovery Systems:
- Powder Recovery Systems: These systems capture overspray powder and allow it to be reclaimed and reused in the coating process. This reduces waste and ensures that the powder is used efficiently. The recovery system typically includes cyclonic separators, filters, and pneumatic conveyors.
- Ventilation and Filtration Systems: Powder coating stations generate airborne dust and fumes, so effective ventilation and filtration systems are essential for maintaining a clean, safe working environment. These systems help capture airborne powder and prevent contamination of the work area.
8. Packaging and Shipping Equipment:
- Automated Packaging Systems: After the wheels are coated and finished, they are moved to packaging stations where they are carefully packed for shipping. Automated systems may use conveyors, robots, or packaging machines to secure the wheels for transport, minimizing handling and reducing the risk of damage to the coating.
- Protective Wrapping Machines: These machines wrap the alloy wheels in protective materials such as bubble wrap or plastic to prevent any damage during transportation.
Conclusion:
The equipment used in alloy wheel powder coating is vital for producing a high-quality, durable finish that meets the aesthetic and performance requirements of the automotive industry. From surface preparation to curing and finishing, each piece of equipment plays a crucial role in ensuring the powder coating is applied effectively and consistently. Advanced systems, including automated spray guns, curing ovens, and powder recovery units, enhance production efficiency and help minimize waste, making powder coating an eco-friendly and cost-effective choice for manufacturers.
The equipment used for alloy wheel powder coating is essential for delivering high-quality finishes that meet the durability and aesthetic standards required in the automotive industry. These systems work together to ensure that alloy wheels are properly prepared, coated, cured, and inspected for defects, while also allowing for customization and efficiency in the production process. The first step involves surface preparation, where the wheels are cleaned using shot blasting, sandblasting, or chemical cleaning. These methods remove contaminants like rust, dirt, oil, or previous coatings, ensuring that the powder will adhere correctly to the surface. After the wheels are cleaned and prepped, they move on to the application phase, where electrostatic spray guns apply the powder coating evenly to the surface of the wheel. This process uses electrostatic charge to ensure the powder adheres uniformly to the wheel, even in areas with complex geometry like spokes.
Once the powder is applied, the wheels are transferred to curing ovens, where they are heated to melt the powder and bond it to the alloy wheel surface. This curing process is critical for creating a durable and smooth finish. Some systems also employ infrared curing to speed up the process. After curing, the wheels are cooled to room temperature, typically using air-cooling systems or cooling conveyors. This ensures the coating solidifies and hardens properly.
Quality control plays a significant role in ensuring the final product meets the required standards. After curing, wheels are visually inspected for defects, and automated systems may assist in identifying color inconsistencies or coating imperfections. Thickness gauges measure the coating’s uniformity, ensuring it meets specified requirements for performance and durability. For certain designs, polishing or clear coating may be added to enhance the aesthetic or provide extra protection against UV rays and scratching. Finally, the wheels are packaged for shipment using automated systems that secure the wheels in protective materials to prevent any damage during transit.
Additionally, powder recovery systems and filtration systems are employed to minimize material waste and maintain a clean work environment. These systems capture overspray powder and recycle it for future use, reducing operational costs and environmental impact. Ventilation and filtration ensure that airborne powder particles are effectively captured, maintaining air quality and safety in the workspace.
The combination of surface preparation, coating application, curing, finishing, inspection, and packaging equipment ensures that alloy wheel powder coating is done efficiently and to the highest standards. These technologies not only improve the aesthetic appeal of the wheels but also enhance their durability, offering protection against scratches, fading, corrosion, and wear from harsh environmental conditions. The integration of automated systems in large-scale production lines also increases throughput, reduces labor costs, and enhances consistency across production batches, making powder coating a cost-effective and reliable solution for alloy wheel finishing.
Alloy Wheel Powder Coating Setup
An alloy wheel powder coating setup involves a series of interconnected equipment and processes designed to prepare, apply, cure, and finish the powder coating on alloy wheels. The entire system is carefully designed to ensure high efficiency, consistent quality, and minimal waste while achieving the desired aesthetic and protective qualities for the wheels. Here’s a breakdown of the typical components involved in an alloy wheel powder coating setup:
- Pre-Treatment and Surface Preparation:
The first step in the setup is to prepare the alloy wheels by removing any contaminants, such as dirt, oil, rust, and old coatings. This is done through a combination of cleaning and abrasive processes:- Shot Blasting/Sand Blasting: These processes use abrasive materials to clean and roughen the surface of the wheels, ensuring better powder adhesion.
- Chemical Cleaning: Wheels may be dipped or sprayed with chemicals to remove grease, oil, or any other contaminants that may interfere with the powder’s ability to bond to the wheel surface.
- Phosphating or Chromating: In some cases, pre-treatment involves applying a thin protective layer to the surface to enhance the corrosion resistance of the alloy wheels.
- Powder Coating Application:
Once the wheels are cleaned, they are moved to the powder coating application station. This is where the actual powder coating is applied to the wheels using electrostatic spray guns. The powder coating process typically involves:- Electrostatic Spray Guns: These guns charge the powder particles, causing them to adhere to the grounded surface of the alloy wheel. The application is highly efficient, ensuring an even coating even on complex wheel designs.
- Automatic or Manual Application: The system can be either manual, where operators apply the powder by hand, or automatic, where robotic arms or automated spray booths apply the powder coating to the wheels in a consistent and repeatable manner.
- Powder Feed System: The powder is fed to the spray guns from a central hopper, and the system controls the amount and flow of powder to ensure optimal coating.
- Curing and Baking:
After the powder coating is applied, the wheels need to be heated to a high temperature to cure the powder. This is done in a curing oven:- Curing Ovens: The wheels are transferred to a curing oven, where they are heated to a specific temperature (usually between 160°C and 200°C). This process melts the powder and causes it to chemically bond with the surface of the wheel, creating a durable, hard finish.
- Continuous or Batch Ovens: Depending on the scale of production, curing ovens can be either batch-style (where wheels are placed individually) or continuous (where wheels are moved through the oven on a conveyor system).
- Cooling:
After curing, the wheels need to be cooled to solidify the coating:- Cooling Conveyors: A cooling conveyor system helps lower the temperature of the wheels after they exit the curing oven. This is done by either circulating air or using fans to speed up the cooling process.
- Air Cooling Stations: Some systems use dedicated air-cooling stations to cool the wheels more rapidly, ensuring that the coating solidifies evenly and prevents defects.
- Inspection and Quality Control:
Quality control is an essential part of the setup to ensure the finished wheels meet the required standards. The wheels are inspected for any defects, such as color inconsistencies, uneven coating thickness, or surface imperfections. Tools used in the quality control phase include:- Visual Inspection: Operators or automated systems visually inspect the wheels to check for defects.
- Thickness Gauges: These tools measure the thickness of the powder coating to ensure it meets the specifications.
- Gloss Meters: Gloss meters are used to check the finish’s gloss level, ensuring it meets the desired aesthetic, whether matte, satin, or glossy.
- Finishing and Additional Coating:
After the primary powder coating is applied and cured, some additional finishing steps may be performed:- Clear Coating: In some cases, a clear topcoat is applied to add extra protection to the finish and provide a glossy appearance. This step helps protect against UV degradation, scratches, and other environmental factors.
- Polishing or Buffing: The wheels may be polished or buffed to achieve a high-shine finish, especially in cases where the wheel requires a premium aesthetic.
- Custom Designs or Branding: Custom logos or designs can be added through various printing or engraving techniques after the powder coating is finished.
- Packaging and Shipping:
After the wheels are fully coated and inspected, they are ready for packaging and shipping. The packaging process ensures that the wheels are protected from scratches or damage during transport:- Automated Packaging Systems: These systems may include conveyors and robots that place the wheels into protective wrapping or boxes, ready for delivery.
- Protective Wrapping: The wheels are often wrapped in materials such as bubble wrap or foam to prevent any damage during shipping.
- Powder Recovery and Waste Management:
To minimize waste and ensure the efficient use of materials, powder recovery and recycling systems are incorporated into the setup:- Powder Recovery Systems: These systems collect overspray powder that is not applied to the wheel, filter it, and return it to the hopper for reuse, reducing waste and operating costs.
- Filtration Systems: The powder coating process can create dust and airborne particles, so ventilation and filtration systems are installed to capture the powder particles and ensure a clean, safe working environment.
Overall, the alloy wheel powder coating setup is a combination of various specialized equipment working in harmony to produce high-quality, durable, and aesthetically appealing alloy wheels. From surface preparation to curing and final inspection, each step is vital to achieving the desired outcome and ensuring that the wheels meet the standards required for automotive use. The setup can be customized depending on the scale of production, with fully automated lines being ideal for high-volume manufacturers and smaller setups suitable for custom or lower-volume operations.
An alloy wheel powder coating setup is designed to efficiently apply a durable, high-quality finish to alloy wheels, enhancing both their appearance and protection. The process begins with surface preparation, where the wheels are thoroughly cleaned and prepped to ensure that the powder will adhere properly. This includes removing any contaminants, such as dirt, oil, rust, or old coatings, typically using shot blasting, sandblasting, or chemical cleaning techniques. After the wheels are cleaned, they move to the powder coating application stage. In this stage, the powder coating is applied to the wheels using electrostatic spray guns. The guns charge the powder particles, causing them to stick to the grounded surface of the alloy wheel. This process ensures that the powder is evenly distributed, even on intricate or complex wheel shapes. The powder feed system controls the flow of powder, ensuring that the right amount is applied to achieve the desired finish.
Once the powder coating is applied, the wheels are placed in curing ovens, where they are heated to a specific temperature to cure the powder. The curing process melts the powder and bonds it to the wheel’s surface, creating a durable, hard finish. The curing ovens can either be batch-style or continuous, depending on the scale of the operation. After curing, the wheels are moved to cooling stations, where they are cooled to solidify the coating and ensure that the finish hardens evenly. Cooling systems, such as cooling conveyors or air cooling stations, are used to bring the temperature of the wheels down in a controlled manner.
Quality control is an essential part of the powder coating setup. After curing and cooling, the wheels are inspected for defects such as color inconsistencies, uneven coating thickness, or surface imperfections. Visual inspections are conducted, and tools like thickness gauges and gloss meters are used to ensure the coating meets the required specifications. If any issues are found, the wheels are removed from the production line for rework or scrapping.
Additional finishing steps may be applied to enhance the appearance and performance of the wheels. Clear coating can be applied as an extra layer of protection against UV degradation, scratches, and environmental damage. In some cases, wheels are polished or buffed to create a high-shine finish. Custom logos or designs can also be added to the wheels after the powder coating process to give them a unique or branded look. After finishing, the wheels are packaged for shipment. Packaging systems ensure that the wheels are protected from damage during transport, and automated systems are often used to handle the packaging process efficiently.
To minimize material waste and improve sustainability, powder recovery systems are included in the setup. These systems collect overspray powder, filter it, and return it to the powder hopper for reuse, reducing waste and operating costs. Ventilation and filtration systems help maintain air quality in the production area by capturing airborne powder particles, ensuring a clean and safe work environment.
Overall, an alloy wheel powder coating setup combines a variety of equipment and processes to ensure that wheels are coated with precision, durability, and consistency. The setup can range from manual systems for small-scale or custom operations to fully automated lines for high-volume production. Regardless of the scale, the goal is to produce wheels that not only meet aesthetic demands but also provide superior protection against wear, corrosion, and environmental elements.
Automated Alloy Wheel Powder Coating Equipment
Automated alloy wheel powder coating equipment is designed to streamline the entire powder coating process for alloy wheels, ensuring consistency, efficiency, and high-quality finishes. These systems use automation to handle tasks like surface preparation, coating application, curing, and finishing, which are crucial to achieving a durable and aesthetically pleasing result. The key components of automated alloy wheel powder coating equipment include:
The system starts with surface preparation, where alloy wheels are cleaned to remove contaminants such as rust, dirt, oil, and old coatings. Automated shot blasting or sandblasting machines are used for this purpose. These systems are equipped with robotic arms or conveyors that ensure each wheel is thoroughly cleaned and prepped. Additionally, chemical cleaning stations may be integrated to ensure that the wheels are free of oils and grease before the powder coating process begins. Automated systems can also apply pre-treatment coatings, such as phosphating or chromating, to improve corrosion resistance.
After surface preparation, the wheels move to the powder coating application stage. Automated electrostatic powder spray guns or robotic arms are used to apply the powder coating evenly across the wheel’s surface. These systems are programmed to move the spray guns in such a way that the powder is applied to every part of the wheel, including hard-to-reach areas like spokes and rims. Powder feed systems are also automated to ensure consistent powder flow, allowing for precise control over the application and thickness of the coating. The electrostatic charge applied to the powder particles ensures they stick to the grounded wheel surface, creating a uniform and durable finish.
Once the powder coating is applied, the wheels are transferred to a curing oven. Automated conveyor systems move the wheels through the oven, where they are heated to the required temperature to cure the powder coating. Curing ovens can be either batch or continuous, depending on the production scale. Automated systems ensure the wheels are moved through the oven at the right speed and are exposed to consistent heat for the correct duration to ensure the powder melts and bonds to the wheel’s surface. After curing, the wheels pass through cooling conveyors or air cooling stations, where they are cooled to room temperature in a controlled manner.
Inspection and quality control are integrated into automated powder coating systems to ensure that the wheels meet required specifications. Automated visual inspection systems using cameras or sensors are employed to detect defects such as uneven coating, color variations, or surface imperfections. These systems can also measure the coating thickness and gloss levels to ensure that the finish is uniform and meets industry standards. If any defects are found, the system can automatically remove the defective wheels from the line for rework or scrapping.
For finishing, automated systems can be used to apply additional coatings, such as a clear coat, which provides extra protection and enhances the gloss of the wheel. Some systems also include polishing or buffing stages to improve the shine and smoothness of the finished product. Custom branding or logos can be added using automated UV printing or laser engraving equipment after the coating process.
The final step is packaging and shipping. Automated packaging systems move the wheels through protective wrapping stations, where they are wrapped in materials like bubble wrap or foam. These systems help secure the wheels for shipping and ensure that they are protected from damage during transport.
In addition to these core stages, powder recovery systems are integrated into automated equipment setups. These systems capture any overspray powder from the application process, filter it, and return it to the powder hopper for reuse. This helps reduce waste, lower operational costs, and improve sustainability. Ventilation and filtration systems also ensure that the workspace remains clean and safe by capturing airborne powder particles.
Automated alloy wheel powder coating equipment offers significant benefits, including increased efficiency, consistent quality, reduced labor costs, and improved safety. These systems are ideal for high-volume production environments where speed and precision are essential. With automation, manufacturers can produce alloy wheels that meet the highest standards of durability, aesthetic appeal, and performance, while also maintaining cost-effectiveness and sustainability.
Automated alloy wheel powder coating equipment is designed to fully automate the coating process, ensuring precise, high-quality finishes and significantly increasing production efficiency. The entire setup streamlines the stages from surface preparation to final inspection, reducing labor costs and enhancing consistency. The process begins with cleaning the alloy wheels, using automated shot blasting or sandblasting equipment to remove rust, dirt, oil, and old coatings. These machines use robotic arms or conveyor systems to ensure that each wheel is thoroughly cleaned and prepped for the coating. Chemical cleaning stations are also included to eliminate oils and grease from the wheels, ensuring proper adhesion of the powder coating.
Once cleaned, the wheels are moved to the powder coating application area. Automated electrostatic spray guns or robotic arms apply the powder coating evenly over the wheel’s surface. These automated systems are programmed to move with precision, ensuring that the powder is applied uniformly, even to hard-to-reach areas such as spokes or rims. The electrostatic charge attracts the powder to the grounded wheel, ensuring a durable, consistent coating. Automated powder feed systems are also integrated to ensure a steady flow of powder, controlling the application rate and thickness to meet the desired specifications.
After powder application, the wheels are transferred to curing ovens where the powder coating is heat-cured to bond with the wheel’s surface. Conveyor systems are used to move the wheels through the oven at a controlled speed and temperature, ensuring that each wheel is fully cured and that the powder melts and bonds properly to the wheel surface. Curing ovens can be continuous or batch-type, depending on the production setup. Once cured, the wheels pass through cooling stations, where air or cooling conveyors bring the temperature of the wheels down, allowing the coating to solidify evenly.
Quality control is a key feature of automated powder coating systems. Automated inspection systems using cameras, sensors, or vision systems are deployed to inspect the wheels for any defects such as uneven coatings, color variations, or surface imperfections. These systems can automatically detect issues like gloss inconsistencies or uneven thickness, ensuring that only the highest quality wheels continue through the process. If defects are detected, the system can reject the faulty wheels or direct them for rework.
Automated finishing systems may include steps like clear coating to add an extra layer of protection and enhance the gloss or polish of the wheel. Some setups also include robotic polishing or buffing stations to provide a smooth, high-shine finish. In addition, custom designs or logos can be applied to the wheels using automated printing or laser engraving technologies.
After finishing, the wheels are moved through automated packaging stations where they are wrapped in protective materials like bubble wrap or foam to prevent any damage during shipping. Packaging systems can also automate the process of boxing or securing the wheels for delivery, ensuring that each product is handled carefully and efficiently.
To minimize waste and improve operational efficiency, automated powder recovery systems are integrated into the process. These systems capture any overspray powder, filter it, and return it to the powder feed hopper for reuse, reducing waste and operating costs. Additionally, advanced filtration and ventilation systems ensure a clean working environment by capturing airborne powder particles and maintaining air quality.
The integration of automation into alloy wheel powder coating systems improves both the speed and consistency of production. These systems are capable of handling high volumes of alloy wheels with minimal manual intervention, making them ideal for large-scale manufacturers. The result is a highly efficient, cost-effective production process that delivers alloy wheels with superior durability, aesthetic appeal, and performance. Automated powder coating equipment provides significant benefits in terms of product quality, operational efficiency, and environmental sustainability.
Alloy Wheel Coating Machinery
Alloy wheel coating machinery is a specialized set of equipment designed to apply a protective and aesthetic coating to alloy wheels, typically using powder coating techniques. These machines are crucial in ensuring that the wheels not only look visually appealing but also gain a layer of protection that enhances their durability, corrosion resistance, and longevity. Here’s an overview of the machinery involved in the alloy wheel coating process:
The first piece of equipment in the process is surface preparation machinery. This is where the alloy wheels are cleaned and prepped for coating. Surface preparation is essential to ensure proper adhesion of the coating. This stage typically involves shot blasting or sandblasting machines, which use high-velocity abrasive particles to clean the wheels of contaminants such as rust, grease, or old coatings. Additionally, chemical cleaning stations may be incorporated into the setup to remove oils and grease that cannot be removed by blasting. These machines ensure that the surface is free of impurities that could interfere with the coating process.
After surface cleaning, the next stage is powder coating application machinery. The most common method for applying the powder coating is through electrostatic spray guns, which charge the powder particles and make them adhere to the grounded alloy wheel. In automated setups, robotic arms are used to move the spray guns around the wheel, ensuring uniform application across all surfaces, including complex areas like spokes. Automatic powder feed systems deliver a consistent flow of powder to the spray guns, allowing for precise control over the amount of powder applied. These systems are designed to provide a uniform coating thickness, which is crucial for achieving a high-quality finish.
Following the powder application, the wheels move to the curing oven. Curing ovens are specialized chambers where the coated wheels are heated to a specific temperature, usually between 160°C and 200°C, to cure the powder. This heating process melts the powder, which then bonds chemically to the wheel surface, creating a hard, durable finish. Conveyor systems are used to transport the wheels through the curing oven in a consistent and controlled manner, ensuring that the temperature and curing time are optimized for the best result. The curing ovens can be either batch-type or continuous, depending on the production requirements.
After curing, the wheels are moved to cooling conveyors or cooling stations, where they are allowed to cool down to room temperature. This ensures that the coating solidifies and hardens evenly. Cooling fans or cooling conveyors help speed up the cooling process, allowing the wheels to be handled more quickly and efficiently.
Once cooled, inspection and quality control machinery come into play. This machinery includes visual inspection stations with cameras or sensors that can detect defects like uneven coatings, color inconsistencies, or surface imperfections. Coating thickness gauges measure the uniformity of the coating, ensuring that the wheels meet required specifications. Some systems also use gloss meters to check the finish’s gloss level. Automated quality control ensures that any defects are identified and the wheels are removed from the production line for rework or rejection.
In the finishing stage, additional machinery might be used to apply a clear coat or add a polishing step. Clear coat machinery applies an extra protective layer on top of the base powder coating, enhancing its durability and providing extra UV protection. Polishing machines can be used to achieve a high-gloss finish, especially for premium wheel designs. For custom branding or logos, UV printers or laser engraving machines can be used to add markings or designs to the wheels after the coating process.
Finally, after all finishing steps are complete, the wheels move to packaging machinery, which ensures the wheels are securely wrapped and ready for shipment. This can include automated systems that wrap the wheels in protective materials such as bubble wrap or foam and place them into shipping boxes. The packaging process is streamlined for high-volume production, ensuring that the wheels are protected from damage during transport.
To improve operational efficiency and sustainability, powder recovery systems are incorporated into the machinery setup. These systems capture any overspray powder during the coating process and filter it, returning it to the powder hopper for reuse. This reduces material waste, helps cut down on costs, and ensures that the operation is more environmentally friendly.
Alloy wheel coating machinery is designed for high throughput and can be fully automated for large-scale production. The equipment ensures that the wheels are coated consistently, with a durable finish that enhances both their visual appeal and longevity. By integrating advanced technologies such as robotic arms, automated spray systems, curing ovens, cooling systems, and quality control mechanisms, alloy wheel coating machinery can deliver high-quality wheels at scale while maintaining cost-effectiveness and sustainability.
Alloy wheel coating machinery is designed to provide an efficient and high-quality process for applying protective and decorative coatings to alloy wheels. The process begins with the surface preparation, where alloy wheels are cleaned to remove any contaminants that could interfere with the coating’s adhesion. This is typically done using shot blasting or sandblasting equipment, which cleans the wheels by blasting them with abrasive particles. Chemical cleaning stations may also be used to remove oils and grease that are difficult to eliminate through blasting alone. After the cleaning process, the wheels are thoroughly inspected to ensure that the surface is free of any contaminants, as a clean surface is essential for a successful coating application.
Next comes the powder coating application stage. This is typically achieved using electrostatic spray guns, which apply a charged powder to the grounded alloy wheel. In an automated system, robotic arms are used to precisely control the application of the powder, ensuring that every part of the wheel, including hard-to-reach areas, receives an even coating. The electrostatic charge ensures that the powder particles adhere to the wheel’s surface, which is crucial for achieving a consistent, smooth finish. The powder application system is equipped with an automatic powder feed to ensure a steady and uniform powder supply, which helps maintain the consistency of the coating.
Once the powder has been applied, the wheels are moved to a curing oven, where they are heated to a specific temperature to allow the powder to melt and bond with the surface of the wheel. The curing process forms a strong, durable, and resistant coating. The curing oven uses conveyor systems to move the wheels through the oven, ensuring they are heated evenly and consistently, and remain in the optimal temperature range for the correct amount of time. After the curing process is complete, the wheels are transferred to cooling stations or cooling conveyors, where they are cooled to room temperature in a controlled manner. The cooling phase allows the coating to harden, ensuring that it sets and becomes fully solidified.
The quality control and inspection process ensures that the finished product meets the required standards. Automated visual inspection systems, often utilizing cameras or sensors, detect any defects such as uneven coating, color inconsistencies, or surface imperfections. Specialized equipment like thickness gauges and gloss meters is used to measure the uniformity of the coating and the level of gloss, ensuring that the wheels meet the desired specifications. Any defects are flagged, and the affected wheels are separated for rework or rejection.
In some cases, the finishing step involves additional processes like applying a clear coat to provide extra protection and enhance the visual finish. Polishing machines may also be used to create a high-gloss shine, which is particularly common for premium or decorative wheel designs. If custom branding or logos are required, UV printing or laser engraving machines can be incorporated into the process to add these features after the coating has been applied.
Once the wheels have been coated, cured, cooled, and finished, they are moved to packaging systems, which securely wrap the wheels in protective materials like bubble wrap or foam, ensuring they are safe for transport. Automated packaging systems are used to handle the wheels efficiently and ensure that they are properly secured for shipment to customers.
To enhance sustainability and reduce costs, powder recovery systems are incorporated into the machinery setup. These systems collect overspray powder, filter it, and return it to the powder hopper for reuse. This helps to minimize waste, reduce material costs, and promote a more environmentally friendly process by reusing the powder rather than discarding it.
Alloy wheel coating machinery is designed to handle large volumes of wheels with precision and efficiency, often in a fully automated process. The integration of advanced technologies like robotic arms, electrostatic coating systems, automated curing and cooling systems, and quality control mechanisms ensures that the wheels are coated to the highest standards of durability and appearance. By automating these processes, manufacturers can produce high-quality alloy wheels at a faster rate, reduce labor costs, and maintain consistency across large production runs. The combination of automation, precision, and quality control in alloy wheel coating machinery not only improves operational efficiency but also ensures that the final product meets the aesthetic and performance standards required by consumers.
Powder Coating Tools for Alloy Wheels
Powder coating tools for alloy wheels are specialized equipment used to apply durable and high-quality coatings to wheels, providing them with both aesthetic appeal and enhanced protection against corrosion, scratches, and other environmental factors. These tools ensure that the powder coating process is carried out efficiently, with consistent results across all the wheels being coated. Here’s an overview of the main powder coating tools used for alloy wheels:
Electrostatic Spray Guns: These are one of the most essential tools in powder coating. Electrostatic spray guns work by applying an electrostatic charge to the powder particles, which are then attracted to the grounded alloy wheel. The electrostatic charge ensures an even coating, even on complex wheel designs. These spray guns are available in manual or automatic versions, with the latter often being used in robotic applications for high-volume production. The guns can be adjusted for spray patterns, airflow, and powder output to achieve the desired coverage and coating thickness.
Powder Feed Systems: The powder feed system supplies the electrostatic spray guns with a steady flow of powder. These systems are crucial for maintaining a consistent coating application. They include powder hoppers, pumps, and filters that regulate the flow and prevent clogs. High-efficiency powder feed systems ensure minimal wastage and smooth operation throughout the coating process.
Powder Coating Booths: These booths are designed to contain the powder coating process and ensure a clean, controlled environment. The booths typically include exhaust systems that remove airborne powder particles, improving air quality and reducing the risk of contamination. They also feature recirculation systems that capture overspray powder, filter it, and return it to the powder hopper, which helps reduce material waste and enhance sustainability.
Curing Ovens: After the powder is applied to the wheels, it needs to be cured to form a strong and durable finish. Curing ovens are designed to heat the coated wheels to the required temperature (usually between 160°C and 200°C), allowing the powder to melt and chemically bond to the wheel surface. These ovens can be batch-style or continuous conveyor ovens, depending on the scale of production. Temperature and time controls within the ovens ensure that each wheel receives consistent heat, which is vital for the quality and durability of the coating.
Cooling Systems: Once the wheels are cured in the oven, they need to cool down to room temperature. Cooling systems, such as cooling conveyors or cooling tunnels, are used to speed up the cooling process and ensure that the coating hardens uniformly. This step is critical in preventing any defects that could arise from uneven cooling.
Powder Recovery Systems: These systems are essential for minimizing waste in the powder coating process. Powder recovery tools capture overspray powder from the application area, filter it, and return it to the powder feed system for reuse. This not only helps in reducing material costs but also improves the overall efficiency of the coating process, making it more environmentally friendly.
Thickness Gauges: These tools are used to measure the coating thickness on the alloy wheels. Ensuring that the coating is applied at the correct thickness is crucial for achieving optimal durability and performance. Thickness gauges can be either mechanical or digital and provide feedback on whether the coating is within the desired range.
Masking Tools: Masking tools are used to cover areas of the wheel that should not be coated, such as the wheel hub or areas where custom designs or logos will be applied later. These tools include masking tapes, plugs, and caps, which prevent powder from being deposited on certain parts of the wheel. Masking is essential for maintaining precise areas of coating and achieving high-quality finishes.
UV Printers: For custom branding or logos, UV printing tools can be used after the powder coating process. UV printers allow for the application of logos, designs, or text onto the wheels with high precision and durability. The prints are cured instantly using ultraviolet light, which bonds the ink to the surface without affecting the underlying powder coating.
Polishing Tools: For finishing the wheels after they are powder coated, polishing machines are often used to achieve a high-gloss finish. These tools are designed to smooth out the coating and remove any minor imperfections, giving the wheels a polished and shiny appearance. Polishing can also enhance the visual depth and quality of the coating.
Quality Control Tools: To ensure that the powder coating is applied correctly and the wheels meet the desired standards, a variety of quality control tools are used. These include visual inspection tools, color spectrometers, and gloss meters to check for even coverage, color accuracy, and gloss levels. Additionally, adhesion testing tools may be used to ensure that the coating adheres properly to the wheel surface and doesn’t peel or chip easily.
Safety Equipment: Powder coating processes can generate airborne particles, so safety tools are important to protect workers. These include respirators or dust masks, protective gloves, and eye protection to prevent inhalation of powder particles or contact with chemicals. Proper ventilation and filtration systems within the coating booths also play a key role in maintaining a safe working environment.
Together, these powder coating tools form an integrated system that allows for the efficient, high-quality coating of alloy wheels. Each tool plays a specific role in ensuring that the wheels are properly coated, cured, finished, and inspected, all while minimizing waste and maximizing productivity. These tools are particularly important for manufacturers looking to streamline their production processes and produce alloy wheels that meet the highest standards of durability, performance, and aesthetics.
Powder coating tools for alloy wheels are specialized devices that enable the precise application of protective coatings, ensuring durability, corrosion resistance, and an appealing finish. The most essential tool in this process is the electrostatic spray gun. This device works by applying an electrostatic charge to the powder particles, which are then attracted to the grounded wheel surface. The electrostatic force helps to ensure even coverage, even in complex areas like wheel spokes. Automated systems, including robotic arms, can move these spray guns with high precision, ensuring uniform coating distribution on every part of the wheel. To optimize the process, powder feed systems deliver a consistent flow of powder to the spray guns, ensuring smooth application. The powder feed system includes hoppers and pumps that regulate the powder flow and prevent clogs, maintaining an efficient coating process.
Once the powder is applied, the wheels are moved into curing ovens. Curing ovens are essential in the process as they heat the coated wheels to a temperature that allows the powder to melt and chemically bond to the wheel’s surface. The ovens can be batch-style or continuous, depending on the production scale, and they use conveyor systems to move wheels through the oven at a controlled pace, ensuring consistent heating and curing. After the curing stage, the wheels are transferred to cooling systems, which are often cooling conveyors, to rapidly bring the temperature of the wheels down, allowing the coating to solidify evenly. This ensures that no defects are created due to uneven cooling and that the coating remains intact.
During the coating process, powder recovery systems play a crucial role in efficiency and sustainability. These systems capture overspray powder and filter it for reuse, minimizing waste and reducing material costs. By ensuring that excess powder is recycled, manufacturers can reduce operational expenses and make the process more environmentally friendly. Once the coating process is complete, quality control tools like thickness gauges, gloss meters, and adhesion testers are used to verify the final finish. These tools measure the coating thickness, gloss level, and adhesion strength to ensure the product meets industry standards. Any defective wheels can be flagged for rework or rejection, helping to maintain product consistency.
Masking tools are used to protect areas of the wheel that should not be coated, such as wheel hubs or areas reserved for custom logos. Masking tapes, plugs, and caps are applied to these areas to prevent the powder from being deposited. Once the powder is applied and cured, some systems may include polishing tools to enhance the gloss and smoothness of the final finish. These polishing machines smooth out any imperfections in the coating and can create a high-gloss shine, which is often desired for premium or custom-designed wheels. UV printing and laser engraving tools are sometimes used for adding custom logos or designs to the wheels, ensuring that the branding is applied after the coating process without damaging the finish.
For high-volume production, automation tools like robotic arms and conveyor systems are integrated into the coating line to streamline the process, reduce labor costs, and increase efficiency. These automated systems can handle multiple wheels simultaneously, applying coatings and moving them through the various stages of preparation, coating, curing, and finishing with minimal human intervention. Additionally, safety equipment such as dust masks, respirators, gloves, and protective eyewear are essential for workers to avoid inhalation of powder particles or contact with chemicals during the process. Proper ventilation and filtration systems are also crucial for maintaining a safe working environment and minimizing airborne particles.
These powder coating tools and systems combine to ensure that alloy wheels are coated efficiently, with a durable, aesthetically pleasing finish. The entire process, from surface preparation to final inspection, is designed to produce high-quality results with minimal waste and high throughput, making alloy wheel powder coating a reliable and cost-effective solution for manufacturers.
Alloy Wheel Powder Coating Systems
Alloy wheel powder coating systems are comprehensive setups designed to apply a durable, high-quality powder coating finish to alloy wheels. These systems integrate various machines and technologies to ensure that wheels are coated with precision and efficiency while providing an attractive finish and long-lasting protection. These systems typically consist of several key components working together to provide the necessary surface preparation, powder application, curing, cooling, and quality control. Below is a breakdown of the essential parts of an alloy wheel powder coating system:
The process begins with surface preparation equipment, which is crucial for ensuring that the alloy wheels are free of contaminants, oils, rust, and old coatings. Commonly used machines include shot blasting or sandblasting machines, which use abrasive particles to clean the surface of the wheels. This is followed by chemical cleaning processes, where the wheels are washed with cleaning agents to remove oils, grease, and other residues. The cleaning process is vital because it ensures proper adhesion of the powder coating to the wheel surface.
After cleaning, the wheels are ready for powder coating application, which is typically done using electrostatic spray guns. These guns charge the powder particles, which are then attracted to the grounded alloy wheel. Electrostatic guns allow for a uniform and consistent powder coating, even on complex wheel shapes. For larger production runs, automated systems often incorporate robotic arms that move the spray guns around the wheel, ensuring even coating on all surfaces. Additionally, automatic powder feed systems help maintain a steady and controlled flow of powder to the spray guns, optimizing the application process.
Once the powder has been applied, the wheels move to the curing ovens. These ovens are heated to specific temperatures (usually between 160°C and 200°C), which causes the powder to melt and chemically bond with the wheel surface. Conveyor systems are used to transport the wheels through the oven at a consistent speed, ensuring that the powder coating is properly cured. The curing process is crucial because it hardens the coating, giving it the durability and resistance to scratches, corrosion, and other wear and tear.
After curing, the wheels are moved to cooling systems, where they are allowed to cool to room temperature. Cooling systems, such as cooling tunnels or cooling conveyors, help the wheels cool down in a controlled manner. This is important to avoid any defects or warping that might occur if the cooling process is uneven or too rapid.
The next step in the powder coating system involves inspection and quality control. Automated visual inspection systems equipped with cameras or sensors are used to check for defects like uneven coating, color inconsistencies, or surface imperfections. Coating thickness gauges are also employed to ensure that the coating is applied to the proper thickness, which is critical for both aesthetics and durability. Additionally, adhesion testing tools are used to ensure the powder coating properly bonds to the wheel surface.
Finishing equipment may be used to further enhance the appearance of the coated wheels. For example, polishing machines can be used to create a high-gloss finish, while UV printers or laser engraving machines may be used to add custom logos, designs, or other markings to the wheels.
To optimize the process and minimize material waste, powder recovery systems are incorporated. These systems capture any overspray powder, filter it, and return it to the powder hopper for reuse. This recycling process reduces the amount of powder wasted, helping to lower material costs and improve environmental sustainability.
Finally, once the coating process is complete, the wheels are moved to packaging stations, where they are carefully packaged to prevent damage during shipping. This can include wrapping the wheels in protective materials such as bubble wrap or foam, and placing them into sturdy shipping boxes.
Overall, alloy wheel powder coating systems are designed to offer high-efficiency, high-quality production for coating wheels in large volumes. By automating the coating process and integrating advanced technologies for surface preparation, coating application, curing, cooling, and quality control, these systems allow manufacturers to produce wheels with a durable, attractive finish while maintaining cost-effectiveness and minimizing waste.
Alloy wheel powder coating systems are designed to optimize the coating process, ensuring alloy wheels are finished with both aesthetic appeal and enhanced protection. The system begins with surface preparation, which is essential to ensure proper adhesion of the powder coating. This includes abrasive blasting, chemical cleaning, and sometimes acid treatments to remove contaminants, oils, and rust from the wheel surfaces. The cleaning process is critical because any residue left on the wheel can affect the finish and durability of the powder coating.
Once cleaned, the wheels are moved to the powder coating stage. This is typically done using electrostatic spray guns, which charge the powder particles so that they are attracted to the grounded wheel surface. This ensures an even coating, even on intricate wheel designs. The spray guns are often mounted on robotic arms, allowing for precise control and the ability to coat multiple wheels simultaneously. The powder coating is typically applied in multiple layers to achieve the desired finish, with each layer being evenly distributed to create a smooth, consistent surface.
After application, the wheels are moved to curing ovens, where they are heated to temperatures ranging from 160°C to 200°C. The heat melts the powder, allowing it to bond chemically with the wheel surface. Conveyor systems are used to transport the wheels through the oven at a consistent pace, ensuring that each wheel receives an even amount of heat. The curing process is essential because it transforms the powder into a durable, hard coating that provides resistance to scratches, chemicals, and weathering.
Once the curing process is completed, the wheels are transferred to cooling systems, where they are allowed to cool down in a controlled environment. Cooling tunnels or cooling conveyors are often used to ensure that the cooling is uniform, which prevents any warping or defects in the coating. This phase is important for allowing the coating to solidify and gain its full strength.
Quality control is an essential part of the alloy wheel powder coating system. This is where defects are identified and corrective actions are taken. Automated inspection systems, equipped with cameras or sensors, detect any inconsistencies in the coating, such as uneven distribution, color discrepancies, or surface imperfections. Coating thickness gauges are used to ensure the powder has been applied at the correct thickness, which is critical for both aesthetics and performance. Adhesion testing ensures that the coating is firmly bonded to the wheel surface, and that it will withstand wear and tear over time.
Once the wheels are fully coated, cured, and cooled, finishing processes like polishing or adding custom logos are sometimes applied. Polishing machines are used to give the wheels a high-gloss finish, enhancing their appearance, while UV printers or laser engravers can apply branding, designs, or other decorative elements onto the surface without damaging the coating.
To ensure sustainability and reduce material waste, powder recovery systems are incorporated into the system. These systems capture overspray powder, filter it, and recycle it back into the application process. This not only reduces the amount of powder wasted but also cuts down on material costs and helps create an environmentally friendly process.
Finally, once all the processes are complete, the coated wheels are carefully packaged to prevent damage during shipping. The wheels are typically wrapped in protective materials like foam or bubble wrap before being placed into shipping containers. This step ensures that the finished product reaches its destination without any defects caused by handling or transportation.
In essence, alloy wheel powder coating systems are designed to combine advanced technologies for coating application, curing, cooling, quality control, and finishing, providing manufacturers with a streamlined, efficient process for creating high-quality, durable alloy wheels. The automation involved in the process reduces labor costs and increases production capacity, while advanced inspection and quality control systems ensure that every wheel meets the desired standards of performance and aesthetics.
Powder Coating Machines for Alloy Wheels
Powder coating machines for alloy wheels are specialized systems designed to efficiently and uniformly apply powder coatings to the surface of alloy wheels. These machines are crucial for ensuring the coating is durable, smooth, and aesthetically appealing, offering protection against corrosion, scratches, and wear. Powder coating machines for alloy wheels typically involve a combination of various technologies to handle surface preparation, powder application, curing, and post-coating finishing. Below is an overview of the main types of machines used in the powder coating process for alloy wheels:
1. Powder Coating Spray Guns: These are the core tools used to apply the powder coating to alloy wheels. Powder coating spray guns operate by using electrostatic principles. The powder particles are given an electrostatic charge, which attracts them to the grounded wheel. This electrostatic attraction ensures a uniform and smooth application, even on complex wheel surfaces. These guns come in manual or automatic versions, with the automatic models often being used in robotic systems for high-volume production. Adjustable settings on the guns allow for control over the powder flow, spray pattern, and air pressure to achieve the desired coating thickness and quality.
2. Powder Feed Systems: The powder feed system is essential for supplying the electrostatic spray guns with a consistent and controlled flow of powder. These systems typically include a powder hopper, pump, and filter to deliver the powder in an efficient manner. The powder is stored in a hopper, where it is constantly fed into the spray guns using a pump, which ensures that the powder flows steadily. Filters are used to remove any contaminants from the powder, preventing blockages or defects in the coating. Advanced powder feed systems improve the efficiency of the coating process by minimizing powder wastage and ensuring consistent application.
3. Powder Coating Booths: These specialized booths contain the powder application process and ensure that the environment remains clean and free from contamination. Powder coating booths are equipped with ventilation and exhaust systems that capture overspray and airborne powder particles. This not only helps to maintain air quality but also ensures that any excess powder is collected and filtered for reuse. The booths also help to prevent contamination by keeping the coating area isolated from external dust and debris.
4. Curing Ovens: After the powder has been applied to the alloy wheels, it needs to be cured to create a durable, high-quality finish. Curing ovens are heated to a specific temperature (usually between 160°C and 200°C) to allow the powder to melt and chemically bond to the wheel surface. The ovens can be batch-style or continuous conveyor ovens, depending on the scale of production. A conveyor system is typically used in larger setups to move the wheels through the oven at a controlled speed, ensuring an even cure. The curing process is vital for ensuring that the powder coating forms a hard, scratch-resistant, and corrosion-resistant finish.
5. Cooling Systems: After the wheels have been cured in the oven, they are often subjected to cooling systems to bring them down to room temperature. Cooling conveyors or cooling tunnels are commonly used to speed up the cooling process and ensure that the coating solidifies evenly. Rapid and uniform cooling is important to avoid any warping, cracking, or defects in the coating.
6. Powder Recovery Systems: One of the key components of powder coating machines for alloy wheels is the powder recovery system. These systems capture overspray powder from the spray booths, filter it, and return it to the powder feed system for reuse. Powder recovery is essential for reducing material waste, lowering costs, and improving the sustainability of the coating process. These systems typically use cyclonic separators, filters, and hoppers to capture the excess powder and ensure that it can be reused without contamination.
7. Automated Robotic Arms and Conveyors: In large-scale production lines, robotic arms and automated conveyor systems are often integrated into the powder coating machines. Robotic arms are used to move the spray guns around the wheels, ensuring an even and consistent coating application. These systems are programmed to handle complex wheel designs and high production volumes, reducing the need for manual labor. Conveyors are used to move the wheels between different stages of the coating process, such as moving them from surface preparation to powder application, then to curing, and finally to cooling and packaging. The integration of automation increases the speed, accuracy, and efficiency of the powder coating process.
8. Masking Tools: Masking tools are used to cover parts of the alloy wheel that should not be coated, such as the wheel hub or areas that will be left uncoated for custom designs. Masking tape, plugs, and caps are applied to these areas before powder application, ensuring that powder is only applied where desired. Masking tools help to create precise, clean lines in the finished product.
9. Finishing and Polishing Machines: After the powder coating process is complete, some systems include finishing and polishing machines to enhance the appearance of the coated wheels. These machines are used to smooth out any imperfections in the coating and achieve a high-gloss, polished finish. Polishing can significantly improve the visual quality of the wheels, especially in cases where a mirror-like shine is desired.
10. Inspection and Testing Equipment: Quality control is crucial in any powder coating process, and this is especially true for alloy wheels. Automated inspection equipment is used to check for defects such as uneven coating, color inconsistencies, or surface imperfections. Common inspection tools include visual inspection systems, gloss meters, and thickness gauges, which ensure that the coating is uniform and meets the required standards. Adhesion testing is also performed to confirm that the powder coating adheres properly to the wheel surface and will not peel or chip easily.
Incorporating all of these machines and systems into a single alloy wheel powder coating line helps manufacturers produce high-quality, durable, and visually appealing products at scale. By utilizing automated systems, robotic arms, powder recovery technologies, and advanced curing ovens, these powder coating machines ensure that alloy wheels receive a consistent and high-performance coating that will last for years under various environmental conditions.
Powder coating machines for alloy wheels combine various technologies to create a seamless, efficient, and high-quality process. The primary component of these systems is the electrostatic spray gun, which charges the powder particles as they are sprayed onto the alloy wheel. This electrostatic charge causes the powder to be attracted to the grounded wheel surface, ensuring a uniform and even coating. The spray guns are typically mounted on robotic arms in high-volume operations, allowing for precise movement and coating of intricate wheel designs. Powder feed systems are integral to the spray guns, ensuring a consistent flow of powder to maintain a steady application rate, which helps in reducing waste and ensuring a smooth finish.
After the powder is applied, the coated wheels are moved into curing ovens where the powder coating is heated to a specific temperature, typically around 180°C, to melt and bond with the surface of the wheel. This curing process is essential to achieving a durable, hard finish that resists scratches, weathering, and corrosion. Conveyor systems are commonly used to move the wheels through the ovens, allowing them to pass through the heat source at a consistent rate to ensure even curing. Once the curing process is complete, the wheels are transferred to cooling systems, which may involve cooling tunnels or conveyors designed to gradually lower the temperature of the wheels to prevent warping or cracking.
A significant feature of powder coating systems is the powder recovery system, which captures any overspray from the powder application process. This system is designed to filter and collect the excess powder, which can then be reused, reducing material waste and operational costs. This feature is especially important for ensuring sustainability and efficiency in a high-production environment. Additionally, many systems include masking tools that are used to cover areas of the wheel that should not be coated. Masking is essential for creating clean lines and precise coatings, especially around areas like the wheel hub or where custom designs are intended to remain uncovered.
Once the powder has been cured and the wheels have cooled, the final steps involve inspection and quality control to ensure the finished product meets the desired standards. This often includes automated inspection systems that check for imperfections like uneven coating, defects in the finish, or color inconsistencies. Tools like thickness gauges and adhesion testers are used to measure the coating’s uniformity and durability, ensuring that the powder is properly adhered to the wheel surface. If any defects are found, the wheels may be flagged for rework or rejected, maintaining high-quality output throughout the production process.
Finally, finishing touches such as polishing machines can be used to smooth out the surface, enhancing the aesthetic quality and creating a high-gloss, mirror-like finish. In some systems, UV printers or laser engravers may be used to add logos, designs, or custom branding to the wheels, allowing for unique, personalized finishes without damaging the coating. After all these processes are completed, the wheels are carefully packaged to prevent damage during transport. The entire process, from surface preparation to final inspection, is designed to ensure that alloy wheels are coated with a finish that not only looks great but also provides excellent protection from the elements and wear.
Alloy Wheel Coating Equipment
Alloy wheel coating equipment is designed to apply durable and aesthetically pleasing finishes to alloy wheels, offering protection from corrosion, scratches, and environmental wear. These equipment setups are highly specialized and consist of several key machines and systems, each playing an essential role in ensuring a consistent, high-quality powder coating finish. The process typically includes surface preparation, coating application, curing, quality control, and post-coating finishing.
The core of alloy wheel coating equipment is the surface preparation machinery, which is crucial for cleaning the wheels and ensuring proper adhesion of the powder coating. Shot blasting machines or sandblasting units are often used to clean the wheels by using abrasive materials to remove contaminants, rust, and old coatings. This step is vital for achieving a smooth surface for coating. Following this, chemical cleaning processes or acid etching may be employed to ensure the removal of oils, grease, and any remaining residues.
Once the alloy wheels are properly cleaned, the powder coating application process begins. Electrostatic spray guns are typically used in the application process, where powder particles are given a positive charge, and the wheel is grounded, causing the powder to stick to the wheel’s surface. The electrostatic charge ensures an even and consistent application, even on complex shapes. In high-production systems, automated robotic arms are often employed to control the spray guns, providing precise application of the powder coating and increasing throughput. The automatic powder feed system ensures a constant supply of powder, improving application consistency and reducing waste.
The wheels are then moved to curing ovens, where the powder coating is heated to a temperature typically between 160°C and 200°C. The heat causes the powder to melt and bond with the surface of the wheel, forming a durable and smooth finish. Conveyor systems are commonly used to move the wheels through the oven, ensuring even exposure to heat for consistent curing. The ovens may be batch-type or continuous conveyor ovens, depending on the size of the production operation.
After curing, the coated wheels are moved to cooling systems to cool down at a controlled rate. Cooling tunnels or cooling conveyors help maintain the integrity of the coating by preventing rapid temperature changes that could cause defects or warping. The cooling process solidifies the coating, ensuring it becomes hard and scratch-resistant.
Powder recovery systems are an integral part of alloy wheel coating equipment, as they allow for the capture and reuse of excess powder. These systems collect any overspray from the electrostatic application process, filter it to remove contaminants, and return the powder to the hopper for reuse. This reduces material costs, minimizes waste, and contributes to environmental sustainability.
Masking equipment is also used in alloy wheel coating systems to cover specific areas of the wheel that should not be coated. For example, parts of the wheel’s hub or areas that require a different finish may be masked before powder coating. Masking ensures that only the desired areas receive the coating, creating clean lines and customized designs.
After the coating process is complete, the wheels undergo inspection and quality control. Automated systems or manual inspections check for defects such as uneven coating, color discrepancies, or surface imperfections. Thickness gauges are used to measure the powder coating’s thickness, ensuring it meets the required specifications for durability and performance. Adhesion tests are conducted to confirm that the coating has bonded properly to the alloy surface and will not peel or chip under normal usage.
In some cases, finishing equipment such as polishing machines may be used to add a high-gloss finish to the coated wheels. These machines help smooth out imperfections and enhance the visual appeal of the wheels. Laser engraving or UV printing may also be incorporated for adding custom logos, designs, or branding on the finished product without compromising the quality of the coating.
Once all the steps are complete, the wheels are carefully packaged to prevent damage during shipping. This final step may include wrapping the wheels in protective materials such as bubble wrap or foam before placing them in sturdy shipping boxes.
Alloy wheel coating equipment is an integrated system designed to streamline the entire coating process, from cleaning and application to curing and finishing. By automating many of the stages and incorporating advanced technologies like robotic arms, powder recovery systems, and quality control tools, manufacturers can ensure high-quality, consistent finishes that meet the aesthetic and performance requirements for alloy wheels.
Alloy wheel coating equipment is designed to ensure the effective and efficient application of powder coatings, which provide durability, aesthetic appeal, and protection against corrosion, wear, and environmental conditions. The process begins with surface preparation, where the wheels undergo cleaning to remove dirt, grease, rust, and old coatings. This cleaning stage is essential for ensuring proper adhesion of the new powder coating. Equipment like shot blasting machines, sandblasters, or chemical cleaning systems are commonly used to prepare the alloy surface, creating a rough profile that allows the coating to adhere better. Additionally, some systems use acid baths to etch the wheels for further preparation, ensuring a clean and optimal surface for the powder.
Following the surface preparation, the wheels move to the powder application stage, where the actual coating process occurs. Electrostatic spray guns are the most common technology used to apply powder coatings. These guns use electrostatic force to charge the powder particles, making them adhere to the grounded wheel surface. This method ensures a smooth, uniform coating, even on complex, intricate wheel designs. To enhance precision and consistency, robotic arms equipped with spray guns are often used, allowing for automated, high-volume production while maintaining high-quality standards. The automated systems allow for consistent application, reducing human error and the need for manual labor.
Once the powder is applied, the wheels are transferred to curing ovens. These ovens are heated to temperatures between 160°C and 200°C to melt the powder, allowing it to chemically bond with the wheel surface. Conveyor belts or automated handling systems are used to move the wheels through the oven at a controlled speed, ensuring they are evenly exposed to heat for the proper duration. The curing process is critical, as it transforms the powder into a hard, durable finish that provides resistance to scratches, chemical exposure, and other types of damage.
After curing, the wheels are cooled in cooling systems, which are designed to regulate the cooling process. This ensures that the coating solidifies correctly and avoids any defects or warping that may occur if the wheels cool too quickly or unevenly. Cooling tunnels or cooling conveyors are used to guide the wheels through a controlled cooling environment, helping them achieve optimal hardness and stability.
A crucial part of alloy wheel coating equipment is the powder recovery system. During the coating process, not all of the powder applied to the wheels stays on the surface. The excess powder that doesn’t adhere to the wheels can be captured by the recovery system. These systems use cyclonic separators, filters, and collecting hoppers to capture overspray, which can then be filtered and reused. This minimizes waste, reduces material costs, and promotes sustainability in the production process.
Masking equipment is used when specific areas of the wheel need to be left uncoated, such as the wheel hub or areas where different finishes are required. This masking ensures that only the desired sections of the wheel receive the coating, maintaining clean lines and preventing coating where it is not wanted. Various masking tools, such as masking tape, plugs, or caps, are used to protect parts of the wheel from the coating process.
After the wheels have been coated, they undergo inspection and quality control. These systems check the finished wheels for defects such as uneven coating, color variations, or surface imperfections. Automated inspection systems, including visual cameras and sensors, are often used to detect such flaws. Additionally, thickness gauges measure the coating’s thickness to ensure it meets required specifications. Adhesion tests are also conducted to verify that the powder coating is securely bonded to the alloy surface and will not peel or chip over time.
For finishing touches, some systems include polishing equipment, which helps to smooth out any minor imperfections in the coating and enhance the glossiness of the surface. UV printers or laser engraving machines can also be used to add custom designs, logos, or branding to the wheels, providing unique and personalized finishes without damaging the coating.
Finally, once the wheels pass all quality control checks, they are carefully packaged for shipping. This often involves wrapping the wheels in protective materials like foam or bubble wrap to prevent damage during transport. Packaging systems ensure that the wheels are securely packed to avoid scratches or dents, ensuring that they arrive at their destination in pristine condition.
Alloy wheel coating equipment is a highly integrated system that combines advanced technology to ensure the powder coating process is efficient, consistent, and produces high-quality results. From the initial cleaning and surface preparation to powder application, curing, cooling, and finishing, these machines are designed to handle high production volumes while maintaining the aesthetic and performance standards required for alloy wheels. The use of automated systems, robotic arms, and sophisticated recovery methods makes the process not only more efficient but also more environmentally friendly by reducing material waste.
Powder Coating Equipment for Alloy Wheels
Powder coating equipment for alloy wheels is designed to provide a durable, smooth, and high-quality finish that protects wheels from environmental damage, corrosion, and scratches. These systems integrate multiple machines and technologies to ensure the coating process is efficient and consistent, delivering a superior finish to alloy wheels. The main components of powder coating equipment for alloy wheels include surface preparation tools, powder application machines, curing systems, recovery systems, and quality control mechanisms.
The process begins with surface preparation equipment, which is essential for ensuring good adhesion between the powder coating and the alloy wheel. Commonly used equipment includes shot blasting machines, sandblasters, or chemical cleaning stations. These machines clean the wheel’s surface by removing any dirt, rust, oil, or previous coatings. The preparation stage may also involve acid etching to roughen the surface and improve the powder’s adherence to the wheel, which is especially important for ensuring the durability and longevity of the finish.
Once the wheels are prepped, the next stage is powder application, which is typically carried out using electrostatic spray guns. These guns use an electrostatic charge to attract powder particles to the grounded wheel, ensuring an even and smooth application. The powder is generally a mixture of finely ground particles of pigment and resin. In high-volume production, robotic arms or automated spray systems are often used to apply the powder uniformly to complex wheel shapes, improving consistency and speed. The automatic powder feed systems help maintain a consistent flow of powder to the spray guns, ensuring that there is minimal waste and that the powder application is uniform across the wheel surface.
After powder has been applied to the wheel, the next step is the curing process, where the coated wheels are placed in curing ovens. These ovens are typically heated to temperatures ranging from 160°C to 200°C. The heat causes the powder to melt, flow, and chemically bond to the wheel, forming a durable, hard finish. Conveyor systems are used to move the wheels through the oven, ensuring even exposure to heat. The wheels are moved at a controlled pace to ensure they remain in the oven long enough to cure properly. This stage is crucial for ensuring the powder coating is strong and resistant to wear and tear.
After curing, the wheels need to be cooled, and cooling systems are used to bring the temperature down gradually. These systems may consist of cooling tunnels or cooling conveyors that provide a controlled cooling environment, helping the coating solidify evenly and avoid issues like warping or cracking.
Powder recovery systems play a critical role in reducing waste and improving efficiency. During the application process, not all the powder applied to the wheel adheres to its surface. Excess powder, or overspray, is captured by the recovery system, filtered, and returned to the powder feed system for reuse. This reduces material costs and helps make the process more sustainable. The recovery system typically includes cyclonic separators, filters, and collecting hoppers, which help capture and filter excess powder while preventing contamination from dust or other debris.
To ensure precision, masking tools are often used to cover specific parts of the wheel that should not be coated, such as the hub or areas designed for a different finish. Masking tape, caps, and plugs are applied to these parts to protect them from the powder coating process, creating sharp boundaries for clean, precise coatings.
After the coating is complete, the wheels undergo inspection to ensure quality. This may include both manual and automated systems that check for defects such as uneven coating, color variations, or surface imperfections. Automated systems may include visual inspection cameras and sensors that detect inconsistencies, while thickness gauges measure the coating’s thickness to ensure it meets the required standards. Adhesion testing is also performed to ensure the coating adheres well to the alloy surface and will not peel or chip.
In some systems, polishing equipment or finishing machines are used to add a high-gloss or smooth finish to the coated wheels. These machines smooth out minor imperfections and enhance the visual appearance of the coating. Additionally, laser engraving or UV printing technologies can be integrated into the system to add custom designs, logos, or branding to the wheel surface, giving it a personalized touch without damaging the coating.
Once all stages are completed, the finished alloy wheels are carefully packaged to prevent damage during transport. Packaging systems ensure that the wheels are protected with foam or bubble wrap and placed in sturdy boxes for shipment.
Powder coating equipment for alloy wheels integrates these various systems to streamline the production process, ensuring high-quality, consistent results. By automating key stages, incorporating recovery systems, and using advanced curing and cooling technologies, manufacturers can achieve an efficient, environmentally-friendly, and cost-effective coating process that results in durable and visually appealing alloy wheels.
Powder coating equipment for alloy wheels is built to deliver a reliable, long-lasting finish while maintaining efficiency and quality throughout the production process. The systems begin with the essential step of surface preparation, which cleans the wheel surface and ensures optimal adhesion for the coating. Shot blasting, sandblasting, and chemical cleaning are commonly used methods that remove contaminants, rust, and old coatings, providing a clean foundation for the new finish. After surface preparation, the wheels are ready for powder application, where electrostatic spray guns apply a layer of powder. The powder is charged, ensuring it clings evenly to the wheel’s surface. In high-production environments, robotic arms are used to apply the powder uniformly to intricate wheel designs. These systems are paired with automatic powder feed systems to provide a consistent supply of powder, minimizing waste and maximizing efficiency. Once the wheels are coated, they move to curing ovens where the powder is heated to bond with the wheel surface, creating a durable finish that withstands harsh conditions. Conveyor systems carry the wheels through the oven at a controlled speed, ensuring uniform curing across all wheels. After curing, the wheels are moved to cooling systems that help solidify the coating at a controlled rate, avoiding defects from uneven cooling. Powder recovery systems capture excess powder, preventing waste and allowing for recycling, reducing costs and improving the sustainability of the process. Masking equipment is used to protect areas that should not be coated, ensuring clean lines and precise finishes. The wheels undergo quality control inspections, using automated systems to detect defects, measure coating thickness, and test adhesion. Polishing and finishing equipment is often incorporated to enhance the aesthetic appeal, providing a glossy finish or adding custom designs. Finally, after all steps are completed, the wheels are packaged for delivery, ensuring they arrive without damage. This integrated equipment setup ensures that alloy wheels are coated with a high-quality, durable finish that meets industry standards.
Alloy Wheel Powder Coating Machinery
Alloy wheel powder coating machinery is designed to ensure a durable, aesthetically pleasing, and high-performance finish on alloy wheels. These machines work together in an integrated system that includes several stages, each playing a crucial role in ensuring the best possible outcome. The core components of alloy wheel powder coating machinery include surface preparation equipment, powder application systems, curing and cooling systems, recovery units, and quality control mechanisms.
The process begins with surface preparation equipment, which is crucial for ensuring that the alloy wheel surface is clean and ready to accept the powder coating. Typically, shot blasting machines or sandblasters are used to clean the wheels by using abrasives that remove dirt, rust, oils, and any old coatings. This roughens the wheel surface, providing a better texture for the powder to adhere to. Chemical cleaning systems may also be used, especially when wheels have residual oils or other contaminants that require removal. After blasting or chemical cleaning, some systems may apply acid etching to further prepare the surface by creating a more textured and reactive finish.
Once the surface is prepped, the next step is powder application, where the powder is applied to the cleaned wheels using electrostatic spray guns. These guns charge the powder particles with an electrostatic charge, which allows them to adhere to the grounded wheel surface. This process ensures an even, consistent coating, even on complex shapes and designs. In automated systems, robotic arms are often used to precisely control the application of the powder, ensuring uniform coverage on every wheel. The powder itself is typically a mixture of pigment and resin that, when applied correctly, forms a durable and hard finish once cured. Automatic powder feed systems supply the powder to the spray guns, ensuring a consistent supply of material while minimizing waste.
The next stage is curing, which involves baking the powder-coated wheels in curing ovens. These ovens heat the wheels to temperatures typically ranging from 160°C to 200°C, causing the powder to melt, flow, and chemically bond to the alloy wheel surface. This step is critical, as the heat cures the powder into a hard, protective layer that provides resistance against corrosion, scratches, and other environmental factors. Conveyor systems are often used to carry the wheels through the oven, ensuring they are heated evenly and consistently throughout. The wheels may be exposed to the oven’s heat for a specified duration, depending on the type of powder used.
After curing, the wheels need to be cooled, and this is where cooling systems come into play. These systems ensure that the wheels cool down at a controlled rate, which helps the coating solidify properly and prevents defects such as cracking or warping. Cooling tunnels or cooling conveyors guide the wheels through a set temperature range, allowing them to cool evenly without causing stress to the newly applied coating.
An important part of alloy wheel powder coating machinery is the powder recovery system. During the coating process, some powder does not adhere to the wheel surface and becomes overspray. These recovery systems collect excess powder through cyclonic separators and filtering units, preventing it from becoming waste. The recovered powder is then filtered and returned to the hopper, where it can be reused in the next cycle, reducing material costs and improving the overall efficiency of the coating process. The recovery system ensures that the process remains cost-effective while also promoting environmental sustainability.
Additionally, masking systems are often used to cover specific areas of the wheel that should not be coated, such as the wheel hub or certain sections that require a different finish. Masking materials can include tape, caps, or plugs, which are carefully applied before powder coating to prevent those areas from being covered in the powder.
Once the coating process is complete, inspection and quality control systems are employed to ensure that the finished product meets the desired standards. Automated inspection systems may use cameras and sensors to detect any defects, such as uneven coating, imperfections, or color variations. Thickness gauges are used to measure the coating’s thickness, ensuring it falls within the required range. Adhesion tests are also performed to ensure the coating properly bonds to the alloy surface and will not peel off over time.
Finally, finishing equipment such as polishing machines or UV printers may be used to add a final touch to the wheels. Polishing equipment smooths out any imperfections in the coating and adds a glossy finish. UV printing systems may also be incorporated to add logos, designs, or custom text to the wheels without compromising the integrity of the coating.
Alloy wheel powder coating machinery is an essential component of the manufacturing process for high-quality, durable alloy wheels. The combination of surface preparation, powder application, curing, cooling, recovery, and finishing ensures that the wheels have a durable, aesthetically pleasing finish that can withstand the rigors of daily use, including exposure to harsh weather conditions, road salt, and abrasions. By automating many of these processes and utilizing advanced technology, manufacturers can achieve high-volume production while maintaining consistent quality.
Alloy wheel powder coating machinery is designed to provide a high-quality, durable finish that enhances the appearance and longevity of alloy wheels. The process starts with surface preparation, where the wheels are cleaned to remove contaminants such as dirt, oils, rust, and old coatings. This is typically achieved through shot blasting, sandblasting, or chemical cleaning, which helps to create a rough texture that improves the adhesion of the powder. After the surface is prepped, the next step is powder application, where electrostatic spray guns charge the powder particles, allowing them to adhere to the grounded wheel surface. Robotic arms or automated spray systems are often used to ensure even and precise application of the powder, especially for complex wheel designs. The powder is typically a mix of pigment and resin, providing both color and durability once cured.
After the powder is applied, the wheels are transferred to curing ovens, where they are heated to a specific temperature to melt the powder, causing it to bond to the wheel surface. Conveyor systems are commonly used to move the wheels through the oven, ensuring that each wheel receives uniform exposure to heat. Once the curing process is complete, the wheels are cooled in a controlled environment to allow the coating to solidify properly, preventing any deformation or defects. During the entire coating process, excess powder that doesn’t adhere to the wheels is collected through powder recovery systems, which use cyclonic separators and filters to capture the overspray. This recovered powder is then reused, minimizing waste and reducing costs.
Masking systems are also used to protect specific areas of the wheel, such as the hub or parts that require a different finish. After the wheels are coated and cooled, they undergo a final inspection to ensure the coating is even, free from defects, and adheres properly to the alloy surface. Automated inspection systems are often employed to detect any imperfections or inconsistencies, while thickness gauges ensure that the coating is within the required specifications. Polishing equipment can be used to give the wheels a smooth, glossy finish, and custom designs or logos can be added through UV printing or laser engraving. The fully coated wheels are then packaged for shipping, with careful protection to avoid damage during transport. This comprehensive machinery setup ensures that the alloy wheels are finished with a high-quality, durable powder coating that not only improves their appearance but also provides protection against environmental damage, making them long-lasting and visually appealing.
Not only do we manufacture our powder coating equipment, we also ship them worldwide to your facility with care
We’re not just the manufacturers of your powder coating equipment, we’re also your worldwide delivery partners.
At EMS Powder Coating Equipment, we understand that getting your powder coating equipment to you quickly and safely is just as important as manufacturing it to the highest standards. That’s why we offer worldwide delivery services to all of our customers.
We work with a network of experienced and reliable shipping partners to ensure that your equipment arrives on time and in perfect condition. We also offer a variety of shipping options to fit your budget and needs.
Whether you need your equipment shipped to a local address or to an international destination, we can help. We’ll work with you to choose the best shipping option for your needs and to keep you updated on the status of your shipment every step of the way.
So when you choose EMS for your powder coating equipment, you’re not just getting the best products on the market, you’re also getting the best possible delivery experience.
Contact us today to learn more about our worldwide delivery services.
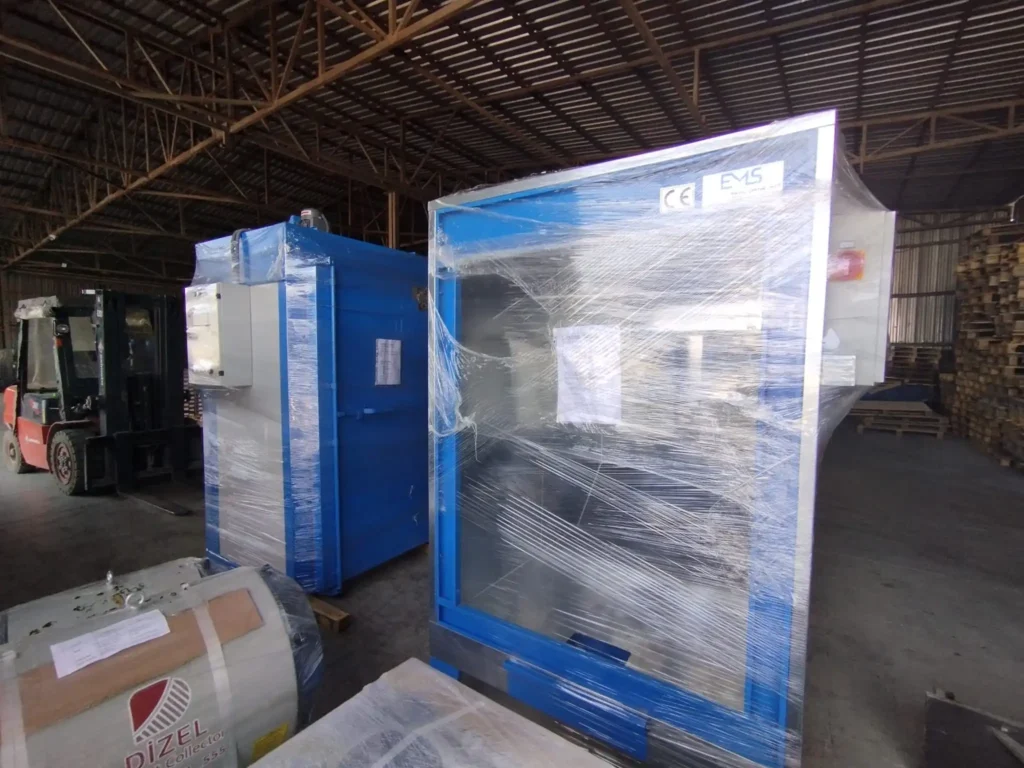
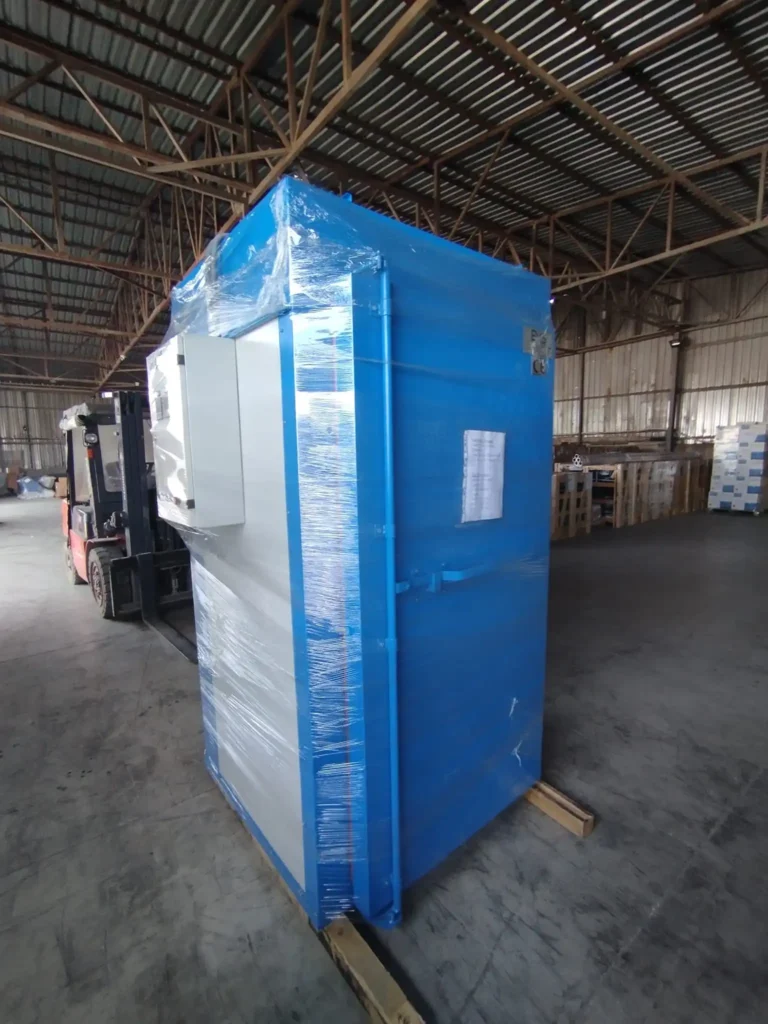
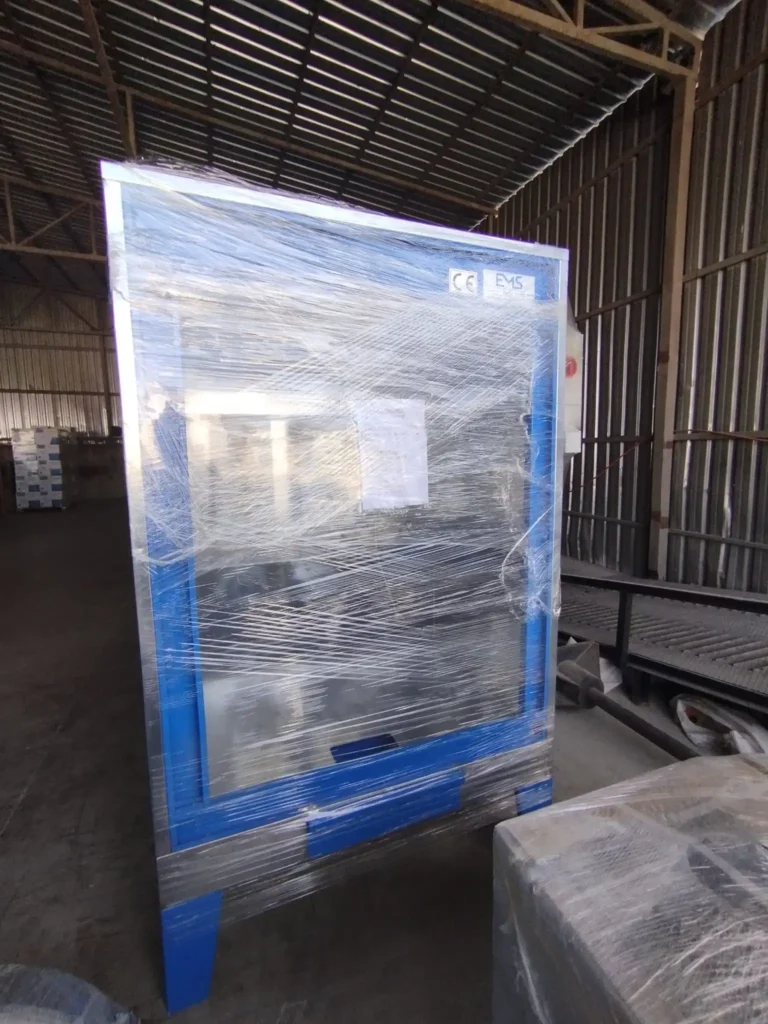
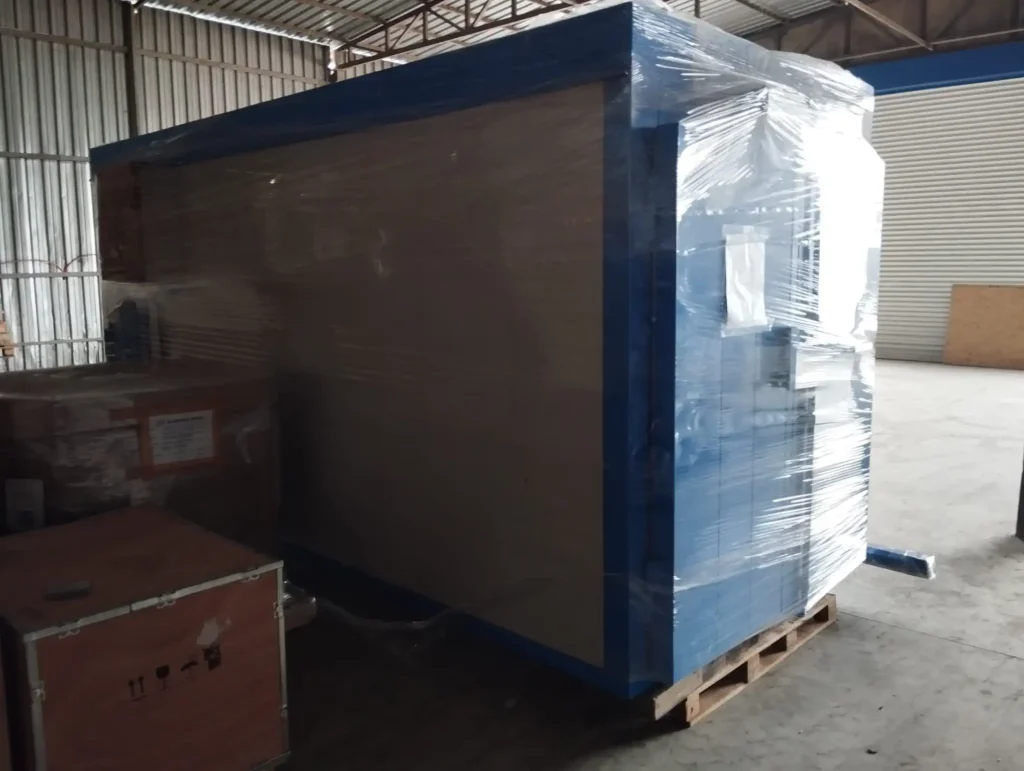
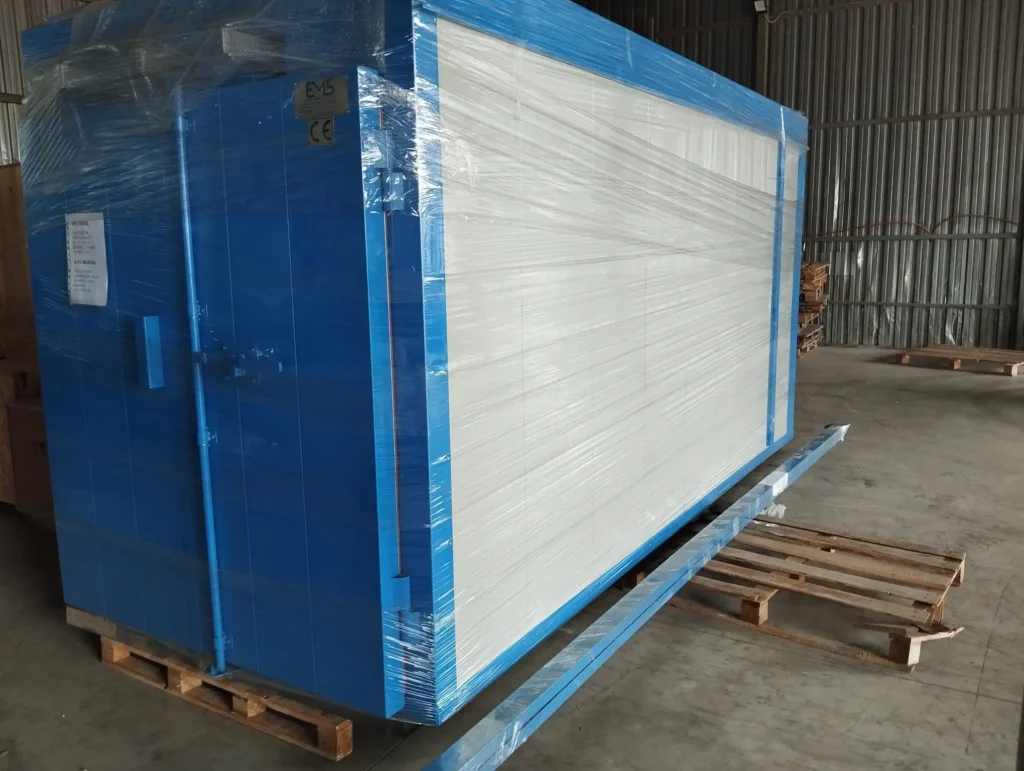
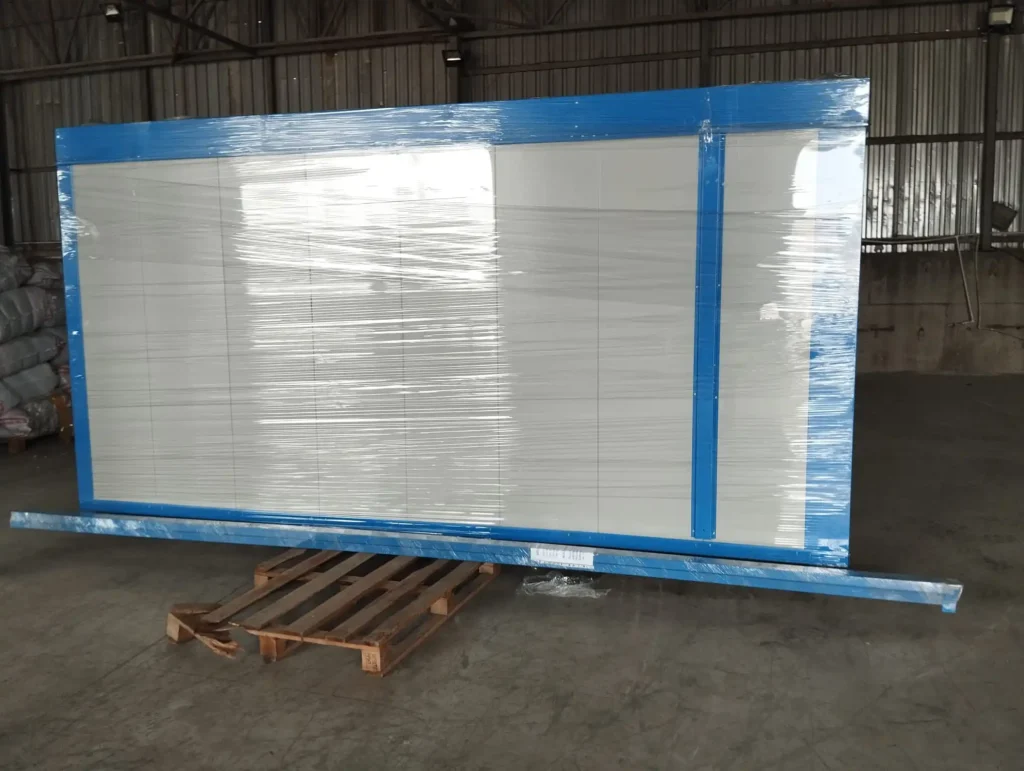
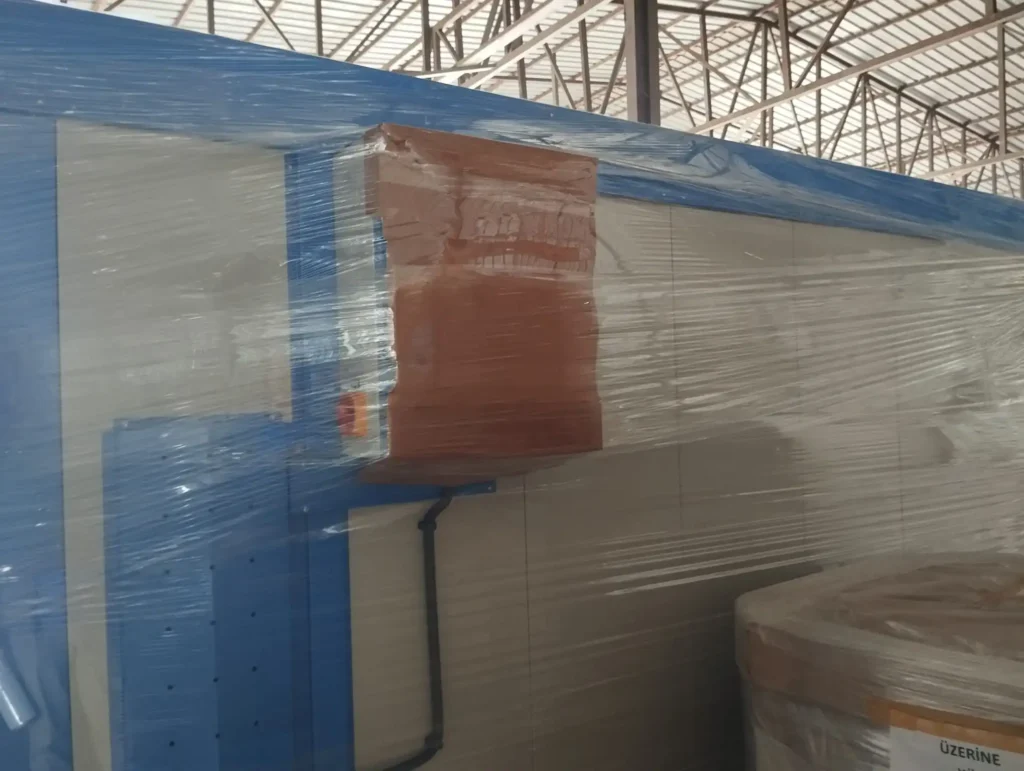
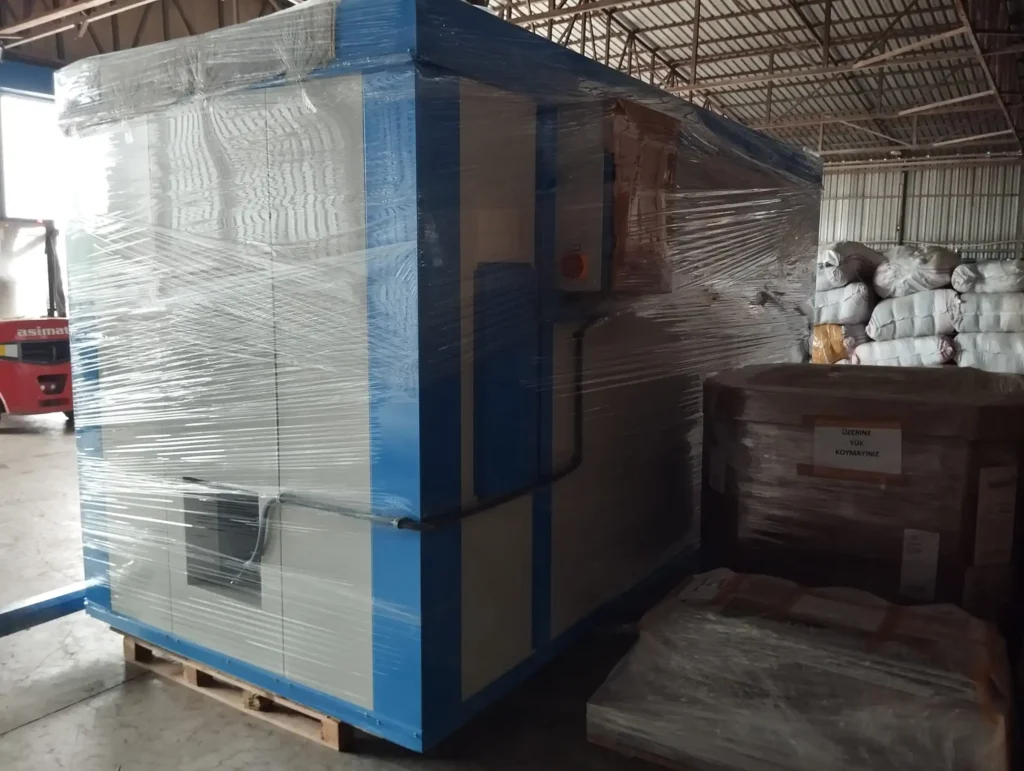
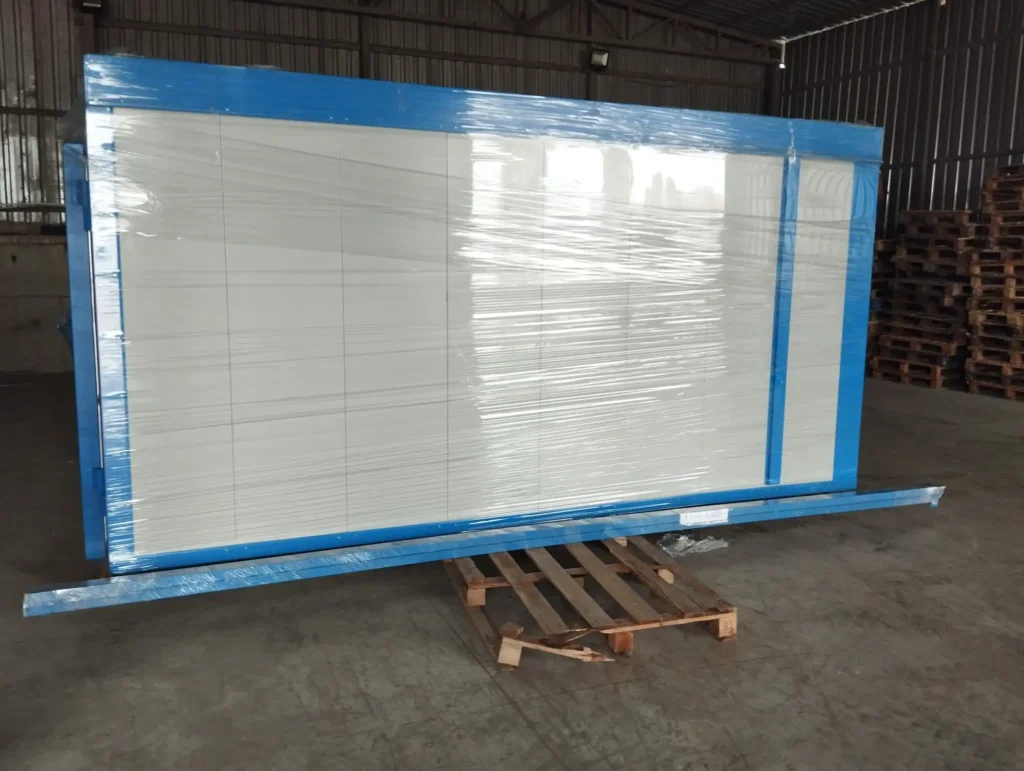