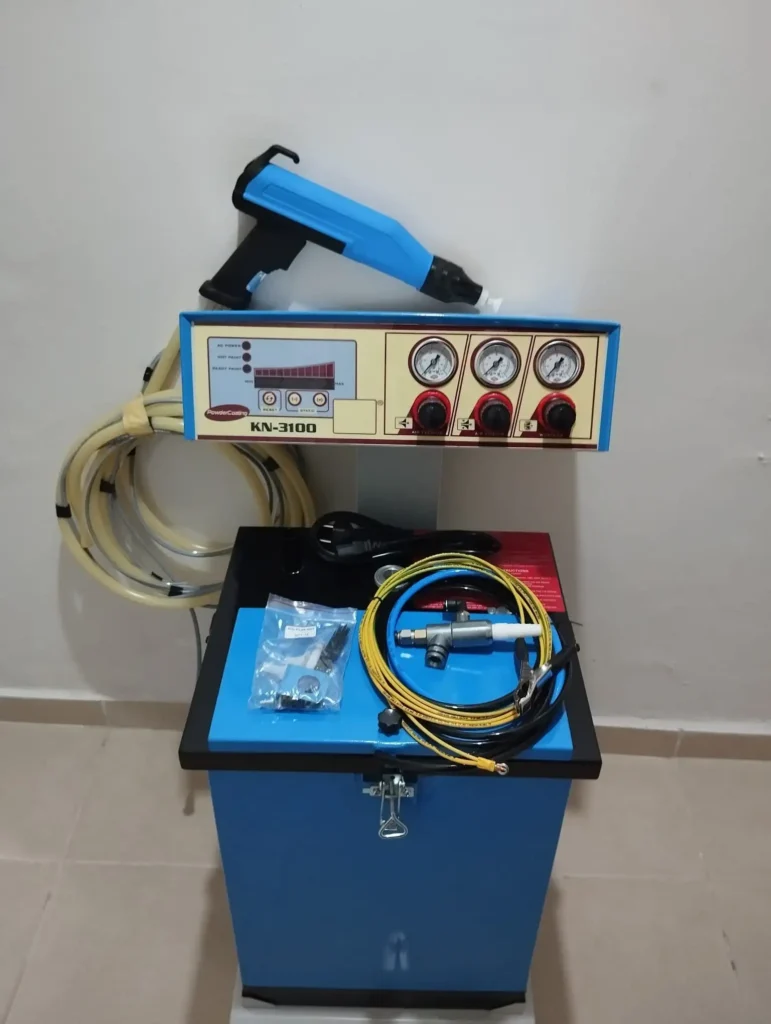
Powder Coating Spray Equipment: A powder coating system is a process used to apply a dry powder to a surface, usually metal, to create a durable and attractive finish. Unlike traditional liquid paint, powder coating does not require solvents to keep the binder and filler parts in a liquid suspension form. Instead, it uses a dry powder that is electrostatically applied to the surface. The coating is then cured under heat to form a hard, protective layer. This method is commonly used for both functional and aesthetic purposes, offering superior resistance to scratches, corrosion, fading, and wearing compared to other finishing techniques.
The powder coating process begins with the preparation of the surface. Proper surface preparation is crucial for achieving strong adhesion and ensuring the longevity of the coating. The surface must be cleaned of dirt, oil, grease, and any other contaminants that could interfere with the coating’s bond. Common methods for cleaning include abrasive blasting, chemical cleaning, or using a combination of both. After cleaning, the surface is usually treated with a conversion coating or a primer to further enhance adhesion and corrosion resistance.
Once the surface is ready, the powder is applied using a spray gun that electrostatically charges the powder particles. The charged particles are attracted to the grounded workpiece, ensuring that the powder sticks to the surface evenly. The spray gun can be adjusted to control the flow and pattern of the powder to achieve the desired finish. After the powder has been applied, the object is placed in an oven where the heat causes the powder to melt and flow, fusing into a smooth, solid coating. The curing process typically occurs at temperatures ranging from 160 to 200°C (320 to 390°F) and lasts for 10 to 30 minutes, depending on the thickness of the coating and the type of powder used.
The result is a tough, uniform coating that is resistant to chipping, scratching, fading, and wearing. The powder coating can also be used to create various textures, such as matte, gloss, or satin finishes. In addition to providing an attractive appearance, powder coatings are environmentally friendly. They release no volatile organic compounds (VOCs) into the air during application, making the process safer and more eco-friendly than traditional liquid coatings.
One of the main advantages of powder coating is its durability. Powder-coated surfaces are highly resistant to corrosion, chemicals, and harsh weather conditions, making it an ideal choice for outdoor applications such as automotive parts, aluminum windows, fences, and furniture. In industrial and commercial settings, powder coating is often used for machinery, equipment, and metal components that require a tough, long-lasting finish. Additionally, powder coating is also popular in the home improvement industry for items like appliances, door hardware, and light fixtures.
Another benefit of powder coating is its efficiency and cost-effectiveness. The powder coating process generates little waste since the powder overspray can often be recycled and reused. This makes the process more efficient than traditional liquid paint systems, which generate more waste and require extensive cleanup. The lack of solvents in powder coatings also reduces the need for hazardous waste disposal, which can be costly and regulated by environmental standards.
Powder coating systems come in various configurations, depending on the size and scale of the operation. Small businesses or home users may use manual or hand-held spray guns, while larger industrial applications typically rely on automated systems, such as conveyorized systems or batch ovens. These automated systems are designed to handle high volumes and ensure consistency in the application and curing of the coating. Automated powder coating systems can be highly efficient, reducing labor costs and improving the overall quality of the finish.
While powder coating offers many advantages, it does have some limitations. For instance, it is difficult to apply powder coatings to non-metal surfaces, such as wood or plastic, although there are specialty powders that can be used for these materials. Additionally, the powder coating process requires precise control of temperature and curing time, which can be challenging for smaller operations with less sophisticated equipment. Moreover, some colors and finishes may require more complex techniques or specialized equipment to achieve the desired effect, adding to the overall cost and complexity of the process.
Despite these challenges, the powder coating industry continues to grow due to the numerous benefits it offers in terms of both performance and environmental impact. Innovations in powder coating technology have led to the development of powders that can be applied to a wider range of materials and that offer improved functionality, such as anti-microbial properties, UV resistance, and even self-healing coatings. These advancements continue to expand the applications of powder coating, making it an increasingly popular choice in a wide variety of industries, including automotive, aerospace, furniture manufacturing, and consumer products. The ability to provide a durable, aesthetically pleasing, and environmentally friendly finish ensures that powder coating will remain a popular choice for surface finishing for many years to come.
Small Powder Coating System
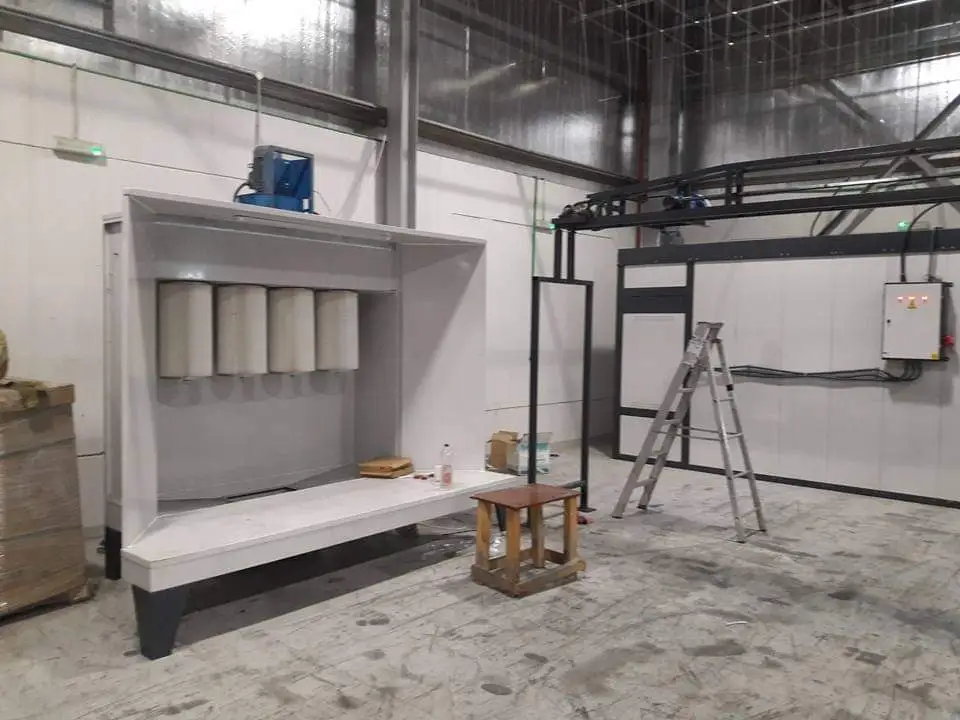
As the demand for more sustainable and efficient manufacturing processes increases, the powder coating industry is evolving with the introduction of new technologies and innovations. One such advancement is the development of low-temperature curing powders, which allow for energy savings and broader application possibilities. These new formulations enable manufacturers to use lower oven temperatures, reducing both energy consumption and the risk of warping or damaging sensitive substrates. Additionally, the increased use of advanced curing technologies such as infrared and ultraviolet (UV) light has further enhanced the precision and speed of the curing process, making powder coating even more efficient and adaptable for various applications.
Another significant development in the powder coating industry is the advent of hybrid coatings that combine the benefits of both liquid and powder coatings. These hybrid systems offer improved flexibility in terms of application and performance, combining the aesthetic qualities of liquid coatings with the durability and environmental benefits of powder coatings. Hybrid coatings can be particularly useful for industries where both visual appeal and long-lasting performance are critical, such as in consumer electronics or high-end appliances.
In the automotive sector, where durability and finish quality are paramount, powder coating is becoming an increasingly popular option for both interior and exterior vehicle parts. Manufacturers are using advanced powder coatings to improve resistance to heat, corrosion, and UV damage, allowing vehicles to maintain their appearance and performance for longer periods. Furthermore, powder coatings can be applied in a wide range of colors, textures, and finishes, offering manufacturers greater design flexibility and the ability to meet diverse consumer preferences.
The use of powder coating is also expanding in the renewable energy sector, particularly for components in wind turbines, solar panels, and other green technologies. Powder coatings offer enhanced protection against the elements, ensuring that these components remain effective and durable over extended periods. The eco-friendly nature of powder coatings aligns with the sustainability goals of the renewable energy industry, where reducing environmental impact is a key focus. Furthermore, as technology advances, the potential for powder coating to incorporate additional features, such as anti-reflective properties for solar panels, is being explored.
In addition to technological advancements, there is a growing emphasis on automation and digitalization in powder coating systems. Automated systems not only improve consistency and efficiency but also enhance the ability to monitor and control the coating process more precisely. Real-time data analytics and machine learning can be integrated into powder coating systems to optimize the application, curing, and inspection stages. For example, sensors and smart cameras can detect inconsistencies in the coating application, allowing operators to make immediate adjustments to ensure high-quality results. This integration of digital technologies enhances both the quality control process and overall operational efficiency.
Environmental sustainability remains a key driver in the growth of powder coating. As environmental regulations around the world become stricter, manufacturers are increasingly looking for ways to minimize waste and reduce their carbon footprint. Powder coating fits these goals well, as it produces minimal waste, does not require hazardous solvents, and is often more energy-efficient than other finishing methods. The fact that the powder overspray can be recovered and reused further reduces the amount of material wasted in the process. Additionally, some powder coatings are now formulated with recycled materials, offering even greater sustainability benefits.
The growing interest in circular economy practices has also contributed to the adoption of powder coating, particularly in industries such as automotive and electronics, where the ability to refurbish and reuse parts is becoming more important. Powder-coated surfaces can often be repainted or repaired if they become damaged, making it easier to extend the life of products and reduce the need for new materials. This focus on sustainability and product longevity is driving further innovation in the powder coating field, as manufacturers explore ways to make coatings even more durable, repairable, and environmentally friendly.
Despite its numerous advantages, there are some challenges that remain for the powder coating industry. For instance, the initial investment in equipment and facilities can be significant, especially for businesses that are transitioning from traditional liquid coating methods. Additionally, achieving a uniform finish on complex geometries or intricate parts can still be difficult, requiring careful control over application techniques. Furthermore, the powder coating industry must continue to address the issue of color matching, as achieving consistent color throughout large production runs or across different batches can be tricky, particularly when using specialty or metallic powders.
Overall, the powder coating system has emerged as one of the most effective, versatile, and eco-friendly finishing techniques available today. With its ability to provide superior durability, a wide range of aesthetic finishes, and environmental benefits, powder coating continues to play a crucial role in a variety of industries. From automotive and construction to electronics and consumer goods, powder coating has proven its value as a reliable and innovative solution for protecting and enhancing surfaces. As the industry continues to evolve, the combination of new materials, advanced technologies, and sustainability initiatives will ensure that powder coating remains at the forefront of surface finishing techniques for years to come.
As the powder coating industry advances, its applications are expanding into new areas that were previously not associated with this method. One such area is the medical and healthcare sector, where powder coatings are gaining attention for their ability to create hygienic, durable surfaces. Powder coatings with antimicrobial properties are being developed to minimize the growth of bacteria and other pathogens on medical equipment, hospital furniture, and devices. These coatings are particularly valuable in environments where sanitation is critical, as they help reduce the spread of infections and maintain a sterile environment. As healthcare standards become more stringent, powder coatings with specialized properties, such as resistance to harsh chemicals and frequent cleaning, are becoming increasingly sought after.
Another exciting frontier for powder coatings is the electronics industry, where coatings are being used to protect sensitive electronic components from moisture, dust, and static electricity. Powder coatings can be applied to a wide range of electronic devices, including casings for smartphones, laptops, televisions, and other consumer electronics. The protective coating helps extend the life of these devices by providing an additional layer of protection against environmental factors that can damage the delicate internal components. Furthermore, the aesthetic appeal of powder coatings allows for sleek, smooth finishes, which are often desired in high-end electronic products.
The trend toward more complex, multi-functional coatings is also gaining momentum. Manufacturers are exploring ways to incorporate additional features into powder coatings, such as self-healing properties, UV resistance, and even anti-fingerprint coatings. These innovations are particularly useful in industries where the appearance of the finished product is critical, such as in automotive design and high-end appliances. Self-healing coatings, for example, can recover from minor scratches or scuffs, maintaining the appearance and functionality of the coated surface over time. UV-resistant coatings help prevent fading or discoloration caused by prolonged exposure to sunlight, while anti-fingerprint coatings make it easier to maintain clean surfaces, enhancing both durability and aesthetics.
In addition to enhancing the functional properties of the coatings, there is also a growing demand for coatings that contribute to energy efficiency. For example, powder coatings with reflective properties can be used in architectural applications to reduce the absorption of heat, thereby lowering energy costs for buildings by improving their energy efficiency. These coatings can be applied to roofs, windows, and exterior walls to reflect sunlight and reduce the need for air conditioning, providing both environmental and economic benefits.
The customizability of powder coatings is another factor contributing to their widespread adoption. Powder coating systems allow manufacturers to create a broad spectrum of finishes, from smooth and glossy to textured or matte surfaces. These coatings can be formulated to match specific color schemes, textures, and finishes required for a particular application. With the increasing demand for personalized or unique designs, powder coatings provide a versatile and cost-effective way to meet these needs. For example, in the furniture industry, custom powder coatings can be applied to metal furniture to match interior design trends, providing a distinct and customized look.
As industries become more globalized, the importance of consistent quality control in the powder coating process has grown. International standards and certifications, such as ISO 9001, are helping to ensure that manufacturers maintain high levels of quality and consistency in their powder coating systems. This is particularly important for industries such as aerospace, automotive, and medical devices, where the integrity of the coating directly affects the safety and performance of the product. Standardization of the process ensures that manufacturers can meet customer expectations, comply with environmental regulations, and reduce defects or failures due to improper application or curing.
Moreover, as regulations surrounding environmental sustainability and waste reduction become more stringent, powder coating offers an ideal solution. Many manufacturers are turning to powder coating systems to comply with these regulations because the process generates minimal waste and avoids the need for hazardous chemicals. The ability to recycle overspray material not only reduces waste but also lowers material costs, making powder coating a more cost-effective solution than traditional liquid paint processes. Furthermore, as the global focus on reducing carbon emissions intensifies, the eco-friendly nature of powder coating aligns with the sustainability goals of many businesses.
The automation of powder coating systems has also seen significant improvements. Automated processes, such as robotic spray arms and conveyorized curing ovens, have made the application of powder coating faster and more consistent. These systems are particularly useful for large-scale industrial applications, where efficiency and throughput are critical. Automated systems reduce labor costs and improve the overall precision of the coating process, ensuring that each part receives an even and uniform finish. Moreover, with the integration of advanced sensors, AI, and machine learning algorithms, manufacturers can monitor the entire coating process in real time, enabling quick detection of any deviations from the desired outcome and minimizing defects.
In terms of future developments, researchers and manufacturers continue to explore new types of powders and curing techniques to expand the capabilities of powder coating systems. Innovations include powders made from renewable resources, such as bio-based polymers, and coatings with enhanced thermal conductivity for use in electronics and heat-sensitive applications. The integration of nanotechnology into powder coatings is also an exciting area of development, as it could enable the creation of coatings with highly specialized properties, such as improved water repellency, anti-corrosion capabilities, or enhanced strength.
In conclusion, powder coating is an advanced, versatile, and sustainable surface finishing technique that offers a wide range of benefits, including durability, aesthetic appeal, and environmental friendliness. With continuous technological advancements, it is becoming an increasingly attractive option across numerous industries, from automotive and aerospace to electronics and healthcare. As innovations in materials, application methods, and automation continue to shape the industry, powder coating will likely play an even more significant role in meeting the diverse and evolving needs of manufacturers and consumers. Its ability to provide high-quality, long-lasting finishes with minimal environmental impact ensures that powder coating will remain a crucial part of modern manufacturing processes for years to come.
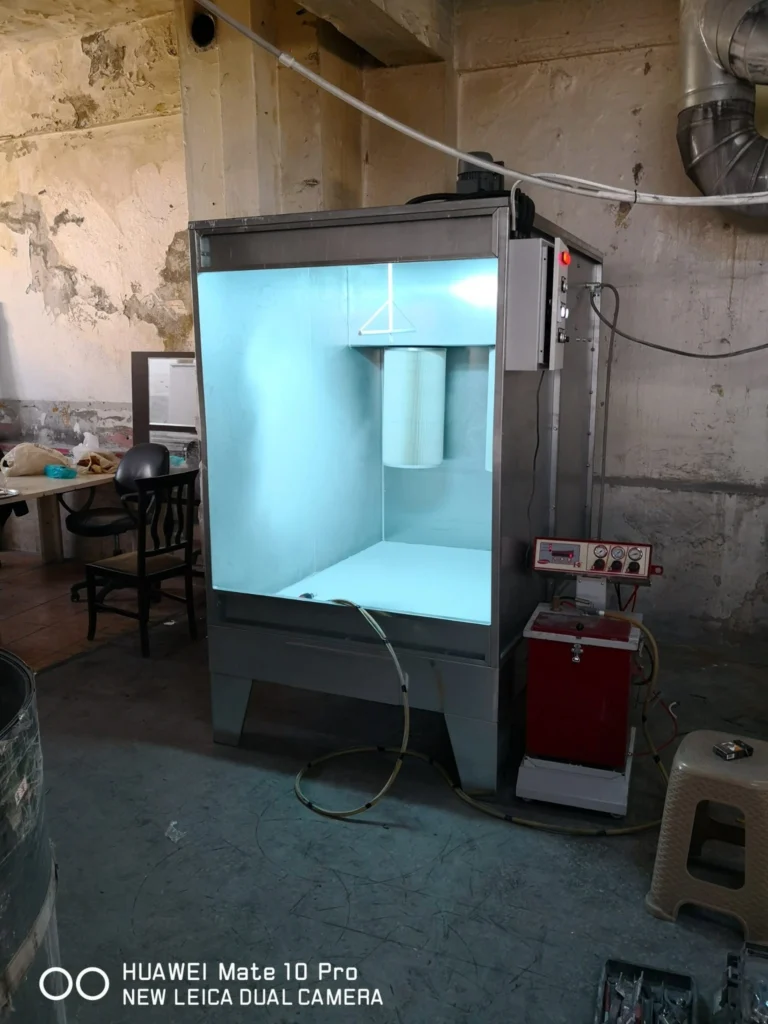
As the powder coating industry continues to evolve, it’s clear that the focus is not only on expanding the functional capabilities of the coatings themselves but also on improving the entire coating process, from application to end-use performance. One area where significant progress is being made is in the development of multi-layer powder coating systems. These systems combine different types of powders to create more advanced coatings that offer specific benefits, such as enhanced wear resistance, improved corrosion protection, and better aesthetics. For example, a multi-layer system might include a base layer that provides corrosion resistance, a middle layer that offers color and texture, and a top layer designed for increased durability or gloss retention. This approach allows manufacturers to tailor coatings for more demanding applications while still maintaining the efficiency and eco-friendliness that powder coatings are known for.
Additionally, with the increasing demand for coatings that can adapt to changing environments and requirements, smart coatings are beginning to emerge in the powder coating space. Smart coatings are those that respond to environmental changes or external stimuli. For example, some powder coatings can be designed to change color based on temperature, offering applications in industries where temperature monitoring is critical. These intelligent coatings could be used in transportation, infrastructure, and even consumer products, adding another layer of functionality to traditional coatings.
The trend toward sustainable practices in the powder coating industry continues to grow. The demand for coatings that help meet global sustainability targets is pushing manufacturers to find even more environmentally friendly solutions. This includes not only creating powders with lower environmental impacts but also improving the energy efficiency of the curing process. Powder coatings that cure at lower temperatures are more energy-efficient and contribute to reducing the carbon footprint of manufacturing operations. Research is also ongoing into reducing the carbon intensity of the manufacturing process for powder coatings themselves, with some companies exploring the use of renewable energy sources and the development of bio-based or recycled materials for the powder formulations.
The global shift toward circular economies is influencing the powder coating industry as well. In a circular economy, the focus is on maximizing the lifecycle of products by encouraging reuse, repair, and recycling. This has a direct connection to powder coating, as many components and products that are powder-coated can be easily refurbished and re-coated, helping to extend their useful life. This is especially important in industries such as automotive and appliances, where parts can be refurbished rather than discarded, offering both environmental and economic benefits. The ability to strip and re-coat parts with powder coating reduces waste and ensures that valuable materials are kept in circulation for longer.
One area where the powder coating industry is seeing rapid growth is in the architectural and construction sectors, particularly for products like windows, doors, fencing, and outdoor furniture. Powder coatings offer a durable, weather-resistant finish that can withstand the harsh outdoor elements, making them ideal for buildings and structures exposed to extreme conditions. The increasing focus on sustainable construction practices, coupled with the desire for aesthetically pleasing, low-maintenance finishes, is contributing to the rise of powder coatings in this sector. Coatings that provide additional functionalities, such as thermal insulation or reflective properties, are becoming more popular as they contribute to energy-efficient buildings and help reduce the overall environmental impact of construction projects.
The consumer goods sector is also seeing a surge in the use of powder coatings. With the growing desire for personalized, unique, and high-quality finishes on everyday products, powder coating offers an attractive solution. Items such as kitchen appliances, furniture, lighting fixtures, and even decorative objects can benefit from powder coating’s versatility in terms of texture, finish, and color. The ability to customize products with specialized finishes that match a consumer’s preferences or a brand’s design goals has made powder coating a popular choice for manufacturers looking to offer more distinctive, personalized products.
In the automotive industry, powder coating is increasingly being used for more than just exterior parts. With vehicles becoming more advanced and sophisticated, components such as engine parts, wheels, and suspension components are benefiting from the protective properties of powder coatings. These coatings provide excellent resistance to heat, abrasion, and corrosion, making them ideal for parts that are subjected to extreme conditions. Furthermore, advancements in the formulation of high-performance powder coatings have made it possible to create finishes that can withstand not only physical wear but also the chemical exposure typical of automotive environments, including oils, fuels, and road salts.
The development of specialty powder coatings is another area driving innovation in the industry. These coatings cater to specific needs and industries where the standard powder coatings might not be sufficient. For example, coatings with fire-retardant properties are used in industries like construction, where building materials must meet strict fire safety standards. Similarly, anti-graffiti powder coatings are becoming more common for outdoor structures like public transit infrastructure, where resistance to vandalism and ease of cleaning are critical. Coatings with anti-static properties are also gaining traction in electronics and cleanroom environments, where protection against static electricity is paramount.
Advances in application technologies are helping to streamline the powder coating process, further improving efficiency and reducing waste. For example, tribo charging technology has made it possible to apply powder more efficiently and with fewer environmental impacts. Traditional powder coating systems rely on electrostatic charging to attract powder particles to a surface, but tribo charging uses friction to charge the powder particles. This method can result in a more even distribution of powder, better coverage in complex geometries, and less powder waste overall. Tribo-charged systems are also often faster and more cost-effective than traditional electrostatic methods, especially for manufacturers with high-volume production lines.
The powder coating market is also expanding due to the growing adoption of digital technologies in manufacturing. From enhanced automation and robotics to machine learning and artificial intelligence, digital tools are being used to improve quality control, optimize curing cycles, and predict and prevent coating defects. These technologies are enabling manufacturers to monitor the coating process in real time, adjusting parameters as needed to ensure the best possible results. As digital technologies continue to improve, the powder coating industry is likely to see even greater efficiency, consistency, and cost-effectiveness.
Finally, global expansion of powder coating technologies is allowing the process to be used in markets around the world. With industries in emerging economies growing and modernization accelerating in developed markets, powder coating is increasingly seen as a cost-effective, high-quality finishing method that meets environmental regulations. The ability to use powder coatings in remote or harsh environments, where traditional liquid coatings may not be feasible, is also driving adoption in industries such as oil and gas, infrastructure, and marine applications.
In summary, the future of powder coating is bright and full of opportunities for innovation. With advancements in materials, technologies, and applications, powder coating is set to remain a key player in surface finishing. Its ability to meet the growing demand for durable, sustainable, and customizable finishes, combined with continuous improvements in efficiency and environmental performance, ensures that it will continue to be a favored solution across a wide range of industries. As the industry adapts to new challenges and opportunities, powder coating will undoubtedly continue to shape the future of manufacturing and design for years to come.
As the powder coating industry looks toward the future, several emerging trends are poised to reshape its landscape and drive even greater innovation. These trends reflect a combination of technological advancements, environmental considerations, and shifts in consumer preferences that will continue to influence how powder coatings are applied, formulated, and integrated into modern manufacturing processes.
One of the most significant trends in the powder coating sector is the growing demand for advanced functional coatings. Beyond just improving aesthetics, powder coatings are increasingly being engineered to provide specialized functional benefits. For example, self-cleaning coatings that utilize hydrophobic or photocatalytic properties are gaining traction, particularly in the construction and automotive industries. These coatings are designed to repel dirt, water, and other contaminants, reducing the need for frequent maintenance and ensuring that products maintain their appearance and performance over time. Similarly, anti-fouling coatings, which are often used in marine applications, are becoming more sophisticated, offering enhanced protection against the accumulation of biological growth such as algae, barnacles, and other marine organisms.
Nanotechnology is another area of interest in the development of powder coatings. By incorporating nanoparticles into the coating formulations, manufacturers can create surfaces with superior mechanical properties, enhanced corrosion resistance, and increased durability. Nanoparticles can also impart unique characteristics to the coating, such as antimicrobial properties or improved optical qualities. For example, coatings that incorporate nanoparticles of silver or copper can provide antibacterial protection, making them suitable for applications in healthcare, food processing, and high-traffic public spaces.
At the same time, the trend toward high-performance coatings is growing, particularly in industries that require coatings to withstand extreme conditions. High-temperature resistant powders are being developed for use in the aerospace, automotive, and industrial sectors, where components are exposed to temperatures far beyond the capabilities of traditional coatings. These coatings not only provide exceptional heat resistance but also maintain their color and integrity under high heat and mechanical stress. The development of coatings that are resistant to both heat and chemicals will likely drive the adoption of powder coatings in more specialized applications, such as in the oil and gas, petrochemical, and power generation industries.
The ongoing push for more sustainable coatings remains a central focus. Manufacturers are increasingly formulating low-VOC (volatile organic compound) powders and working to reduce the environmental impact of the powder coating process. This shift is aligned with growing regulatory pressures in many regions, where governments are imposing stricter environmental standards on manufacturing processes. In response to these challenges, the industry is embracing green technologies, including the use of renewable resources, low-energy curing systems, and water-based powders that offer more environmentally friendly alternatives to traditional solvent-based finishes.
To further improve sustainability, bio-based powder coatings made from renewable materials are starting to enter the market. These coatings use plant-derived polymers and resins instead of petroleum-based ingredients, helping to reduce the carbon footprint of the coating process. As the demand for sustainable products increases, bio-based and other eco-friendly powder coatings are expected to become more widely available, offering consumers and manufacturers a greener solution without sacrificing performance.
Along with sustainability, energy efficiency is also a critical consideration for future powder coating developments. The energy consumption associated with the curing process—particularly in large-scale manufacturing environments—can represent a significant portion of production costs. To address this, new curing technologies are being explored that require less energy. For instance, UV curing systems that use ultraviolet light instead of heat to cure the coating are gaining popularity. UV curing is faster, consumes less energy, and can be used on substrates that are sensitive to heat, broadening the scope of powder coating applications.
The growing trend of customization and personalization in consumer products is influencing the powder coating industry as well. As more consumers demand products that reflect their unique tastes and preferences, manufacturers are leveraging the flexibility of powder coatings to offer a wide range of finishes, colors, and textures. With the ability to apply customized designs on various substrates, powder coating is playing an increasingly important role in sectors such as furniture design, home decor, and personalized automotive parts. Advances in color-matching technologies, which allow for highly accurate reproduction of custom hues and finishes, are enabling manufacturers to offer even greater options for customization.
Another significant trend is the increasing use of digital technologies in the powder coating industry, particularly in the realm of smart manufacturing. As companies continue to integrate Industry 4.0 technologies into their operations, the powder coating process is becoming more connected, automated, and data-driven. For example, real-time monitoring of coating thickness, application consistency, and curing parameters is now possible through the use of advanced sensors and machine learning algorithms. These technologies allow manufacturers to track and adjust the coating process dynamically, ensuring optimal performance and reducing defects.
Moreover, augmented reality (AR) and virtual reality (VR) are starting to play a role in powder coating, especially in the training and maintenance sectors. By using AR or VR, operators can receive real-time visual guidance on how to apply coatings or troubleshoot issues during production. This technology can be particularly useful for training new workers, reducing human error, and increasing overall productivity.
The globalization of the powder coating market is also a key trend. As manufacturing continues to move to different regions and industries in developing economies continue to grow, the demand for high-quality, durable finishes is increasing. In particular, Asia-Pacific and Latin America are becoming key regions for powder coating adoption, driven by the rapid expansion of industries such as construction, automotive, and electronics. This shift is creating new opportunities for manufacturers to tap into emerging markets, expand their customer bases, and drive innovation tailored to specific regional needs.
With these trends, the powder coating industry is poised for continued growth and transformation. The ongoing pursuit of greater efficiency, sustainability, and functional advancements ensures that powder coating will remain a vital and evolving technology. As new applications emerge and industries continue to explore innovative ways to use coatings, the powder coating industry will need to remain agile and adaptable. The next several years will likely see further refinements in coating formulas, application technologies, and environmental practices that will expand the boundaries of what powder coatings can achieve.
In conclusion, powder coating remains a powerful, versatile solution for a wide range of industrial and consumer applications. As the industry evolves, it will continue to offer cutting-edge solutions to meet the increasing demands for durability, aesthetic appeal, and sustainability. The exciting trends of functional coatings, nanotechnology, energy efficiency, and smart manufacturing suggest that powder coating will not only continue to be an essential finishing technique but will also play a significant role in the future of manufacturing across various sectors.
As the powder coating industry progresses, additional areas of focus will continue to shape the future trajectory of this versatile technology. One of the most notable is the integration of advanced automation and robotics in the powder coating process. With the rapid development of robotic technologies and artificial intelligence (AI), manufacturers are optimizing the coating process to be faster, more precise, and cost-efficient. Robotics allows for uniform application of coatings across complex shapes and sizes, ensuring consistency and reducing the likelihood of human error. The use of robotic arms equipped with advanced spray nozzles and sensors enables precise control of the powder spray pattern, improving coating thickness uniformity and reducing overspray.
Moreover, the flexibility of robotic systems allows manufacturers to quickly adapt to different coating requirements, whether they involve varying batch sizes, product shapes, or complex geometries. This adaptability is particularly valuable in industries where production volumes can fluctuate, such as in custom manufacturing, automotive parts, and consumer electronics. By reducing the need for manual labor and improving the precision of the application process, robots help drive operational efficiency, reduce costs, and improve the overall quality of the coating.
Another area poised for growth is powder coating in additive manufacturing (3D printing). As 3D printing continues to gain traction in various industries, powder coating is being explored as a post-processing solution to enhance the surface finish of 3D-printed parts. 3D-printed components, while highly customizable, often require additional surface treatment to improve their durability, aesthetics, and functionality. Powder coating offers a cost-effective solution to add protective layers to 3D-printed metal, plastic, and composite parts. This integration of powder coating and additive manufacturing is particularly useful in sectors like aerospace, automotive, and medical devices, where the combination of custom 3D-printed designs and durable, high-performance finishes is becoming increasingly common.
As the demand for sustainability in manufacturing processes intensifies, the powder coating industry will increasingly prioritize life cycle assessments (LCAs) and eco-labeling as part of their sustainability efforts. Life cycle assessments provide a comprehensive view of the environmental impact of a coating from raw material extraction through production, use, and disposal. This holistic approach helps manufacturers identify opportunities to reduce waste, energy consumption, and carbon emissions throughout the coating’s life cycle. Eco-labeling programs that certify environmentally friendly products will be important for manufacturers looking to meet consumer expectations and differentiate themselves in an increasingly environmentally-conscious market. By utilizing recyclable powders, low-energy curing systems, and minimal waste technologies, the industry can continue to position powder coating as a sustainable alternative to traditional liquid coatings.
Furthermore, customer demand for transparency and traceability in the production process is growing. Consumers, particularly in industries like food processing, pharmaceuticals, and high-end electronics, are becoming more concerned about the safety and sustainability of the materials used in products. As such, the powder coating industry will need to invest in transparent supply chains that ensure the materials used in their coatings are responsibly sourced, compliant with health and safety regulations, and traceable throughout the production process. This will likely lead to increased collaboration between powder coating manufacturers, material suppliers, and certification bodies to maintain high standards for quality, safety, and environmental stewardship.
In parallel with these technological and sustainability advancements, there is also an increasing emphasis on training, education, and skill development within the powder coating industry. As automation and digital technologies become more integrated into coating processes, workers will need to acquire new skills to manage these advanced systems. Continuous training in robotic programming, quality control using AI, and troubleshooting automation issues will become increasingly important to ensure that manufacturing operations run smoothly and efficiently. Industry certifications and specialized training programs will also help ensure that the workforce is equipped to handle the evolving needs of the industry. As more skilled workers enter the field, they will play a crucial role in driving innovation and improving the quality of powder coating applications.
The powder coating market will also see a continued expansion in niche applications, driven by the diversification of industries seeking specialized coating solutions. Construction remains a major area for growth, particularly in exterior applications where coatings need to withstand weather extremes, pollution, and UV exposure. Powder coatings offer excellent performance for architectural metal surfaces, such as railings, windows, and building facades. Coatings that provide additional features like self-healing capabilities, anti-bacterial finishes, and light-reflecting properties will cater to the demands of the green building and infrastructure markets.
The transportation sector, including not only automotive but also rail, aerospace, and marine industries, will continue to drive innovation in powder coatings. As transportation systems become more aerodynamic, efficient, and sustainable, the need for coatings that can improve fuel efficiency, provide corrosion protection, and withstand environmental stresses will increase. For example, the aerospace industry is looking for lightweight, high-performance coatings that can resist the extreme conditions of flight, such as high pressures, temperatures, and UV radiation. This has led to the development of specialized coatings that balance performance with weight reduction.
Finally, the global shift toward electric vehicles (EVs) and sustainable transportation methods will drive further demand for advanced powder coatings. EV manufacturers require durable, lightweight coatings that offer protection against the elements and add to the aesthetic appeal of the vehicles. Powder coatings are particularly well-suited to EV parts, such as battery casings, chargers, motors, and interior components, because of their corrosion resistance, energy efficiency, and ability to be customized to meet unique design requirements.
As supply chains become more interconnected and the global demand for high-quality, low-impact products increases, the role of powder coating will likely continue to expand across various sectors. Its versatility, coupled with its inherent environmental benefits, will solidify its place as a primary method of surface finishing in the manufacturing world. Industry collaboration, continued research and development, and investment in new technologies will be critical to meeting the evolving needs of both manufacturers and consumers in the coming years.
In conclusion, powder coating stands at the crossroads of several evolving trends—technological innovation, sustainability, industry diversification, and increasing consumer demands for high-performance finishes. Its continued growth and development will not only be driven by advancements in materials and application techniques but also by its ability to meet the changing needs of industries focused on durability, aesthetic quality, and environmental responsibility. By adapting to the future demands of manufacturing and consumer markets, powder coating will remain an integral part of modern production and continue to offer reliable, efficient, and eco-friendly solutions.
Painting Systems Equipment
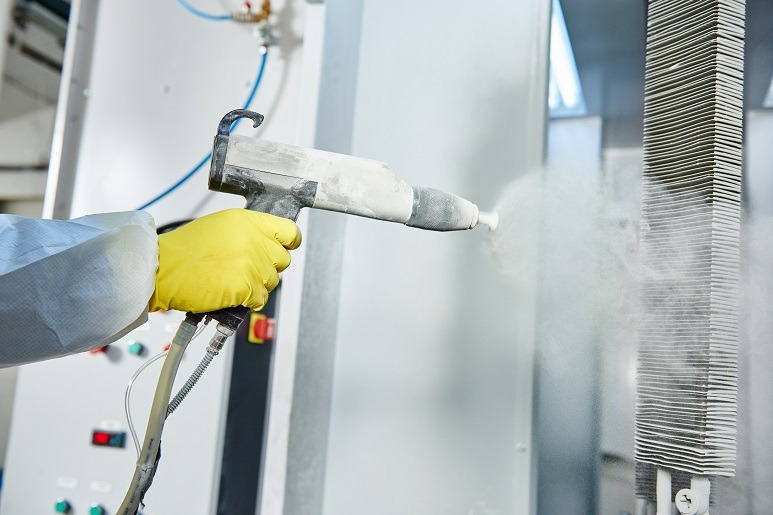
The painting systems equipment industry plays a critical role in a broad range of sectors, from manufacturing and construction to automotive and aerospace. As with many other industries, painting systems are undergoing significant innovation, driven by the need for greater efficiency, sustainability, and performance. The evolution of painting systems equipment is shaping how industries approach surface finishing, enhancing their ability to deliver high-quality, durable coatings while meeting increasingly stringent environmental standards. This transformation is influenced by advancements in technology, materials, application methods, and automation, all of which are working in tandem to improve the speed, quality, and cost-effectiveness of industrial painting.
At the core of modern painting systems is the growing focus on automation and robotics. Robotic painting systems, which automate the application of coatings, are becoming more prevalent due to their ability to enhance precision, reduce waste, and streamline the overall coating process. These automated systems are equipped with advanced sensors and controllers that allow for consistent application of coatings across complex geometries. Robotic arms, for instance, can reach difficult-to-access areas, ensuring uniform coverage even on intricate components. This technology is especially beneficial in industries like automotive and aerospace, where high-quality and uniform finishes are crucial, and where the complexity of parts requires advanced equipment for optimal performance.
The increasing adoption of artificial intelligence (AI) and machine learning is another game-changing trend in the painting systems equipment sector. These technologies are enhancing the efficiency of painting processes by enabling real-time monitoring and adaptive adjustments. AI systems can analyze data from sensors installed on the painting equipment to track parameters like coating thickness, spray pattern consistency, and environmental factors such as temperature and humidity. By continuously adjusting the application process based on this data, these smart systems can significantly reduce defects and improve the consistency of the final finish, leading to higher productivity and lower waste. Furthermore, AI is also used in predictive maintenance, helping identify potential issues in the equipment before they lead to costly downtime.
Alongside these innovations in automation and AI, the painting systems equipment industry is responding to growing environmental concerns by adopting more sustainable practices. This includes the development and integration of low-VOC (volatile organic compound) and waterborne paints, which produce fewer harmful emissions compared to traditional solvent-based coatings. These advances have become particularly important as governments and regulatory bodies around the world continue to impose stricter environmental regulations on industrial processes. As a result, painting equipment is being designed to accommodate these newer types of coatings while ensuring that application methods are still efficient and cost-effective. Water-based and UV-curable coatings are gaining traction due to their reduced environmental impact and fast curing times, which are beneficial in high-volume production environments.
In line with the drive for sustainability, the industry is also focusing on reducing energy consumption. The energy required to cure paint during the application process is one of the most significant operational costs for many manufacturing facilities. New painting equipment is being developed with low-energy curing technologies, such as infrared (IR) curing, UV curing, and electron beam curing. These technologies reduce the amount of energy needed to achieve optimal curing temperatures and can even cure coatings at ambient temperatures, which lowers overall energy consumption. For example, UV curing technology uses UV light to rapidly cure coatings, allowing for faster processing times and reduced energy use. These innovations are helping manufacturers lower their carbon footprints while maintaining high-quality finishes.
The demand for customization and personalization in consumer products is also influencing the painting systems equipment market. With industries such as consumer electronics, automotive, and home goods increasingly looking for unique finishes to meet individual customer preferences, painting equipment is being adapted to accommodate a wider variety of colors, textures, and finishes. In particular, automotive manufacturers are investing in advanced painting systems that offer greater flexibility in terms of color-matching, finish consistency, and the ability to apply multiple layers of coatings in one pass. The use of multi-layer coating systems, which can incorporate base coats, clear coats, and special effects coatings in a single process, is becoming more common as it allows manufacturers to achieve a wide range of visual and functional properties with minimal process changes.
Precision in coating thickness has also become a focal point in the development of painting systems. The ability to apply coatings of consistent thickness is crucial for ensuring that coatings perform as expected in terms of durability, corrosion resistance, and aesthetic appearance. As such, modern painting systems are equipped with advanced thickness measurement technologies, such as laser or electromagnetic sensors, that provide real-time feedback to operators. These technologies ensure that the applied coating meets the required specifications, reducing material waste and the risk of rework or defects.
In addition to these technological advancements, painting systems equipment is increasingly being designed with user-friendly interfaces and intuitive controls. Modern systems often include touchscreen interfaces, graphical displays, and data analytics tools that make it easier for operators to monitor the process, make adjustments, and track performance metrics. These user-friendly interfaces reduce the learning curve for new operators and improve overall process control, which is especially valuable in high-volume production environments where consistency and efficiency are critical. The ability to track and visualize data on parameters like spray patterns, coating thickness, and curing times helps operators make real-time adjustments to optimize performance.
Another major trend shaping the future of painting systems equipment is the rise of modular systems. Modular systems allow manufacturers to tailor their painting equipment to their specific needs, making it easier to scale operations and integrate new technologies as they emerge. For example, a modular painting system may consist of separate, customizable modules for spraying, curing, and inspection, allowing for flexibility in design and operation. This approach not only enables manufacturers to adjust their systems based on production volume and product complexity but also makes it easier to upgrade or replace components without overhauling the entire system.
In addition, the demand for high-quality coatings that offer both aesthetic appeal and enhanced functionality is pushing the painting systems equipment sector to explore new coating formulations. Anti-corrosion coatings, scratch-resistant finishes, antimicrobial coatings, and coatings with heat resistance or chemical resistance are becoming more prevalent, especially in industries like automotive, construction, and consumer goods. These coatings must be applied precisely and consistently, which in turn places higher demands on the equipment used for their application. Manufacturers are responding by developing specialized painting systems that are capable of applying these advanced coatings efficiently while ensuring that they retain their functional properties.
The rise of Industry 4.0 and the ongoing digital transformation in manufacturing are also impacting the painting systems equipment market. By incorporating IoT (Internet of Things) technologies, painting systems are becoming smarter and more connected, enabling real-time monitoring of equipment performance, coating quality, and process efficiency. This connectivity allows manufacturers to collect valuable data that can be analyzed to improve performance and reduce waste. Predictive analytics, powered by AI and machine learning, can provide insights into how the system will perform in the future, allowing for proactive maintenance and process optimization.
Finally, global market expansion and the rise of emerging economies are providing new opportunities for the painting systems equipment industry. As industries in regions such as Asia-Pacific, Africa, and Latin America continue to grow, the demand for high-quality painting systems is increasing. These regions are experiencing rapid industrialization, and as local manufacturers seek to improve their production processes, the need for advanced, cost-effective painting equipment becomes more pronounced. As a result, painting systems manufacturers are exploring ways to meet the demands of these emerging markets while maintaining high standards of quality, efficiency, and environmental responsibility.
In conclusion, the painting systems equipment market is undergoing rapid transformation, driven by technological advancements, environmental considerations, and evolving consumer demands. As industries continue to focus on efficiency, sustainability, and high-performance coatings, painting systems equipment will play an increasingly important role in delivering these goals. The rise of automation, AI, energy-efficient technologies, and customizable systems ensures that the painting equipment of the future will be more intelligent, adaptable, and sustainable than ever before. These innovations will continue to help manufacturers meet the challenges of a fast-paced, ever-evolving marketplace, providing them with the tools to achieve high-quality, cost-effective, and environmentally responsible finishes.
As the painting systems equipment industry evolves, there are several other emerging trends and factors that will continue to shape its future. These include innovations in surface preparation, advanced coating materials, and cross-industry integration, all of which are driving the development of more efficient, versatile, and sustainable painting technologies.
One of the critical areas of focus for painting systems equipment is improving surface preparation techniques. The quality of the final coating is highly dependent on how well the substrate is prepared before painting. Traditional methods, such as abrasive blasting and chemical etching, are being enhanced by newer, more efficient technologies that reduce material waste and improve surface adhesion. For example, plasma treatment and laser cleaning technologies are gaining traction as they offer precise, environmentally friendly alternatives to traditional surface preparation methods. These technologies remove contaminants and create a roughened surface that enhances coating adhesion, without using abrasive materials or harsh chemicals. Such advancements reduce environmental impact while increasing coating durability and longevity.
Advanced coating materials are also pushing the boundaries of what painting systems equipment can achieve. New generations of high-performance coatings are being developed that offer improved durability, corrosion resistance, and functionality, even in the harshest environments. These include superhydrophobic coatings, which repel water and contaminants, anti-fingerprint coatings used in electronics and high-touch surfaces, and conductive coatings for electronic and automotive applications. Painting systems equipment must be designed to handle these specialized materials, which often require precise application methods to achieve the desired performance characteristics. Equipment capable of handling nanostructured coatings, which offer unique properties such as self-healing or enhanced UV resistance, is also becoming more common. As the demand for specialized coatings grows, painting systems equipment will continue to evolve to support these new formulations.
Another critical development in painting systems equipment is the integration of painting processes with other manufacturing steps. As industries like automotive, aerospace, and electronics continue to push for more efficient and flexible manufacturing workflows, the need for integrated systems that combine painting with other processes, such as assembly, inspection, and packaging, is becoming more pronounced. For example, inline painting systems are being designed to operate seamlessly alongside other automated production lines, allowing for continuous, high-speed production without the need for additional handling or processing steps. This reduces downtime and improves overall productivity. Such integration also helps improve quality control, as the entire production process can be monitored and optimized in real time.
Customization and flexibility will continue to be significant drivers of innovation in painting systems equipment. Industries, especially automotive, consumer goods, and electronics, are demanding a wider range of custom finishes and coating options. Painting systems are adapting to meet these demands by becoming more modular and adjustable, enabling manufacturers to quickly switch between different coating formulations, textures, and colors. Advanced equipment is also being developed that can apply multi-coat systems in a single pass, further increasing production speed and flexibility. These systems are capable of applying a variety of coating types, such as base coats, clear coats, and special-effect finishes, on the same production line without compromising quality or requiring extended downtime for system reconfiguration.
In the context of quality control and inspection, significant strides are being made in automated defect detection and real-time monitoring. Advances in machine vision and optical inspection systems are enabling painting systems to automatically detect coating defects such as runs, sags, or uneven coverage, as well as inconsistencies in color or finish. These systems use high-resolution cameras and advanced algorithms to identify defects and ensure that only products meeting the required standards move forward in the production process. This real-time feedback loop allows for immediate corrections to be made, reducing the risk of defective products reaching the end-user. Automated inspection systems are also capable of measuring coating thickness and evaluating adhesion strength, ensuring that coatings meet the required technical specifications.
The move toward more sustainable production methods is also pushing the painting systems equipment industry to rethink the traditional processes used in coating application. The concept of a closed-loop system, which minimizes waste and optimizes the use of resources, is gaining traction. In these systems, overspray is collected, filtered, and recycled for future use, reducing material waste and helping manufacturers meet their sustainability targets. Some systems now come with integrated filtering and recycling units that capture excess paint and solvents from the spray booths and reclaim them for reuse, lowering overall consumption and cutting down on the need for hazardous waste disposal. This trend is not only driven by environmental regulations but also by the financial benefits of reducing waste and improving resource efficiency.
E-commerce and supply chain challenges are also influencing the painting systems equipment sector. The rise of e-commerce, particularly in industries such as consumer electronics and appliances, has created demand for faster and more flexible production systems. Consumers expect fast delivery times, and manufacturers need to accommodate shorter production cycles and custom orders. This has led to an increased need for lean manufacturing systems and agile production lines that can accommodate varying order sizes and customization requests. Additionally, supply chain disruptions, such as those caused by global events or trade issues, are prompting manufacturers to build more resilient and adaptive systems, ensuring that they can continue to deliver high-quality products despite external challenges.
Predictive maintenance is another area where innovation is playing a significant role in the future of painting systems equipment. The traditional approach of scheduled maintenance is being replaced by data-driven systems that predict when equipment will need maintenance based on usage patterns and sensor data. This approach can significantly reduce unexpected downtime and improve the reliability of painting equipment. Predictive maintenance systems rely on IoT sensors that monitor key components of painting systems, such as spray guns, curing ovens, and pumps. By analyzing this data, manufacturers can anticipate issues before they cause failures, enabling more efficient use of resources and minimizing the risk of production delays.
As manufacturers continue to prioritize global competitiveness, they will also increasingly look for painting systems that can support a diverse range of industries and applications. This trend will lead to further cross-industry innovation, where painting systems designed for one sector can be adapted to meet the needs of others. For example, a painting system originally designed for automotive applications might be modified for use in the aerospace industry, where precision and durability are paramount. Similarly, advancements in cleanroom painting systems used in semiconductor manufacturing are likely to inspire new equipment solutions for industries with stringent cleanliness requirements, such as medical devices or pharmaceuticals.
Lastly, training and workforce development will continue to be essential in ensuring that painting systems are operated efficiently and effectively. As technologies evolve, so too must the skill sets of the operators and technicians who manage these systems. Training programs focused on advanced painting technologies, robotic operations, and quality control methods will be crucial in equipping the workforce with the knowledge and expertise needed to keep pace with the changing landscape of painting systems equipment. Additionally, virtual reality (VR) and augmented reality (AR) are beginning to play a role in training and troubleshooting, offering hands-on, immersive learning experiences that can help operators gain proficiency in new technologies quickly.
In conclusion, the future of painting systems equipment will be shaped by a combination of technological advancements, environmental pressures, and changing industry demands. As manufacturers seek to improve the efficiency, sustainability, and quality of their coatings, painting systems equipment will continue to evolve to meet these challenges. The growing emphasis on automation, energy efficiency, sustainability, customization, and integrated manufacturing systems is paving the way for more advanced, flexible, and intelligent painting solutions. By embracing these trends, the painting systems equipment industry will not only address the needs of today’s manufacturing environments but also position itself for continued success in an ever-evolving global market.
Looking ahead, the continued evolution of painting systems equipment will also be influenced by broader industry-wide trends, such as digital transformation, global supply chain shifts, and the increasing focus on consumer-driven innovation. As painting systems equipment becomes more interconnected with Industry 4.0 and smart manufacturing trends, we are seeing an increased integration of data-driven technologies, cloud computing, and predictive analytics into the operational landscape. These innovations will drive the next wave of advancements in painting technology, offering manufacturers even greater levels of precision, efficiency, and customization.
The digitalization of manufacturing processes is enabling the creation of smart factories where painting systems are interconnected with other production equipment, providing seamless communication across the entire production line. This interconnectedness allows for more real-time monitoring and optimization of the painting process. For instance, with cloud-based platforms, manufacturers can remotely monitor the performance of their painting systems, access performance analytics, and track key performance indicators (KPIs) like throughput, coating quality, and material usage. This real-time data collection allows for immediate corrective actions, ensuring that quality is maintained and production continues without interruption.
Furthermore, as industries face growing supply chain challenges, including disruptions caused by global events, cost volatility, and logistical bottlenecks, painting systems equipment will need to be adaptable and resilient. The ability to pivot between different materials, substrates, and coating formulations will be essential in maintaining high levels of production continuity. For example, multi-functional coating systems that can easily switch between various types of coatings (e.g., powder coatings, liquid paints, UV-cured coatings) will become more in demand as manufacturers seek to mitigate the impact of supply chain volatility. These systems are designed to accommodate different materials while maintaining high performance and quality standards.
Additive manufacturing (3D printing) will also continue to influence the painting systems equipment market, especially as industries look to produce more customized and lightweight products. 3D-printed parts often require post-processing treatments to achieve a smooth, durable, and aesthetically pleasing finish, and painting systems equipment will evolve to cater to these needs. Advances in selective laser sintering (SLS), fused deposition modeling (FDM), and other 3D printing methods are leading to new coating applications that can enhance part performance and appearance. Painting equipment will need to be adapted to handle the unique surfaces and geometries of 3D-printed parts, while still delivering a high-quality finish.
Consumer-driven innovation is also an increasingly significant force shaping the development of painting systems equipment. Consumers are more informed and more demanding than ever before, expecting products with highly customized finishes, aesthetic appeal, and superior performance. The demand for personalized and unique finishes is becoming a central driver for industries like automotive, electronics, and home appliances. Manufacturers are responding by investing in painting systems that can support a wide variety of finishes—whether that involves custom colors, textures, or special effects coatings. As these markets demand shorter lead times for customized products, painting systems equipment will need to be able to quickly switch between different coating formulations and application techniques without sacrificing quality or efficiency.
Moreover, the demand for high-performance coatings that offer durability, resilience, and sustainability will continue to push the boundaries of painting systems technology. Coatings that provide anti-corrosion properties, heat resistance, chemical resistance, and self-healing capabilities are increasingly in demand, particularly in industries like aerospace, automotive, construction, and electronics. To meet these needs, painting systems equipment will have to support the application of these advanced coatings, ensuring they are applied in a way that preserves their unique properties and performs under harsh conditions.
In addition to functionality, the importance of aesthetics in product design is also a major driver of innovation in the painting systems equipment market. Cosmetic coatings used in industries like automotive and consumer electronics must be applied with a high level of precision and consistency to achieve the desired finish quality. This includes everything from mirror finishes and high-gloss clear coats to coatings with textured or matte surfaces. Painting systems equipment is evolving to provide highly flexible solutions for these applications, incorporating technologies like multi-layer coating systems, precision spraying, and automated defect detection to achieve the highest standards of visual appeal.
Training and workforce development will remain a critical component of the painting systems equipment market. As new technologies and equipment continue to emerge, manufacturers will need to ensure that their workers are equipped with the skills required to operate advanced painting systems. The adoption of robotics, AI-driven systems, and advanced data analytics will require a new generation of technicians who can not only operate these systems but also understand how to troubleshoot, maintain, and optimize them. Virtual reality (VR) and augmented reality (AR) are already playing an increasing role in training programs by offering workers simulated experiences that can help them learn how to operate complex equipment before working on the production floor. The ability to provide hands-on, immersive training experiences will ensure that operators are better prepared to work with cutting-edge painting technologies and equipment.
Moreover, as more global markets continue to emerge, particularly in developing regions, the demand for affordable yet high-performance painting systems will rise. Painting systems that are cost-effective, energy-efficient, and easy to maintain will be essential for manufacturers in emerging economies who are looking to build up their industrial capabilities. Localized solutions that consider specific regional needs—such as the availability of raw materials, environmental regulations, and local market demands—will be increasingly important. Customizable, modular systems will enable manufacturers to scale their operations quickly and cost-effectively while maintaining flexibility in production.
The demand for sustainability will also continue to shape the painting systems equipment market, particularly as consumers and regulatory agencies place increasing pressure on manufacturers to adopt environmentally friendly practices. The transition to waterborne coatings, low-VOC paints, and eco-friendly solvents will drive further innovations in painting systems equipment. Additionally, systems designed to minimize material waste and energy consumption will gain traction, with closed-loop recycling and energy-efficient curing methods becoming key components of sustainable painting processes.
In conclusion, the future of painting systems equipment is incredibly promising, with advancements in automation, sustainability, customization, and integration with smart manufacturing technologies driving the next wave of innovation. As industries increasingly prioritize precision, efficiency, and environmental responsibility, painting systems equipment will evolve to meet these challenges, providing manufacturers with the tools they need to remain competitive in a rapidly changing global marketplace. By embracing new technologies, improving the versatility of painting processes, and focusing on sustainability and customization, the painting systems equipment industry will continue to play a pivotal role in shaping the future of manufacturing across various sectors. The ongoing development of painting systems will empower manufacturers to deliver high-quality, innovative, and sustainable coatings that meet the ever-evolving needs of consumers and industries worldwide.
The ongoing evolution of painting systems equipment will continue to be shaped by a host of interconnected trends, particularly in the realms of technological advancements, environmental sustainability, and industry-specific innovations. As these factors converge, the industry will adapt to meet the growing demands of manufacturers, consumers, and regulatory bodies, driving further progress in painting systems technology.
The Role of Smart Technologies in Painting Systems
One of the most transformative influences on the future of painting systems equipment is the integration of smart technologies. The next generation of painting systems will be equipped with advanced sensors and artificial intelligence (AI) to enhance the overall efficiency and quality of the coating process. These systems will leverage real-time data to continuously adjust variables such as spray pressure, spray distance, and environmental conditions, ensuring that the coating is applied in the most effective way possible.
For example, smart robots equipped with AI can adapt to changes in production requirements, learning from past applications to fine-tune the coating process for different substrates, product geometries, or environmental conditions. AI-driven systems will also be able to predict potential defects by analyzing data from various stages of the process, allowing manufacturers to proactively address issues before they affect product quality. The predictive capabilities of AI are also expanding into maintenance and equipment optimization, where predictive analytics can forecast when a part or system component will need attention, reducing downtime and enhancing system longevity.
Furthermore, IoT (Internet of Things)-enabled equipment will enable seamless integration with enterprise-level ERP (Enterprise Resource Planning) systems, allowing manufacturers to collect and analyze data from multiple production lines in real-time. The data collected from painting systems can provide insights into everything from production rates to material usage, enabling manufacturers to make data-driven decisions that improve overall plant efficiency and product quality.
Energy-Efficient and Sustainable Coating Solutions
As environmental concerns intensify globally, painting systems equipment will be driven toward more energy-efficient and sustainable solutions. Beyond the shift toward low-VOC (volatile organic compound) and waterborne coatings, the industry will need to further explore methods to minimize the overall energy footprint of the painting process. UV-curing and electron beam curing systems, which cure coatings faster than traditional heat-based methods, are expected to gain further adoption due to their low energy consumption.
Energy-efficient ovens, infrared curing technologies, and fast-drying paint formulations are being developed to shorten curing times while reducing energy consumption. These innovations will reduce the carbon footprint of industrial coating processes, which is becoming an increasingly important factor for manufacturers looking to align with global sustainability goals. Additionally, the growing trend toward circular manufacturing will drive the adoption of closed-loop systems that capture and recycle paint overspray, enabling the reuse of materials and reducing waste. These efforts will help manufacturers meet both regulatory requirements and consumer demand for more sustainable products.
Advanced Coatings and Functional Coatings
The demand for advanced functional coatings will continue to increase across a wide variety of industries, such as aerospace, automotive, medical, and electronics. Functional coatings, which not only provide a decorative finish but also offer enhanced performance, are becoming more important as industries seek to improve the durability, corrosion resistance, and functional capabilities of their products.
For example, in automotive manufacturing, the application of scratch-resistant, anti-fingerprint, and self-healing coatings is becoming increasingly common. In the aerospace industry, coatings that provide heat resistance, chemical resistance, and anti-corrosion properties are critical for ensuring the safety and longevity of components exposed to extreme conditions. Painting systems will need to be designed to apply these advanced coatings effectively while maintaining the exacting performance standards required by these industries.
Additionally, the rise of smart coatings—such as those capable of detecting environmental changes (e.g., temperature, humidity) or those that can change properties in response to external stimuli—will drive innovation in painting equipment. These types of coatings will require precise application methods to ensure their functionality is not compromised during the application process, requiring painting systems to incorporate advanced technologies that can handle these complex materials.
Customization and Personalization
Consumer-driven demand for personalized products will be a key driver of innovation in painting systems equipment. The ability to offer custom finishes, unique colors, and bespoke patterns is becoming increasingly important across a range of industries, especially in consumer goods, electronics, and automotive manufacturing.
In particular, automotive manufacturers are pushing the boundaries of custom color matching and aesthetic effects, such as metallic finishes, pearlescent coatings, and color-shifting paints. To accommodate these needs, painting systems equipment will continue to evolve to provide high flexibility, enabling manufacturers to quickly switch between different formulations, textures, and finishes without requiring extensive downtime for reconfiguration.
Additionally, multi-layer coating systems that can apply base coats, clear coats, and special-effect finishes in a single pass will become more widespread. These systems allow manufacturers to achieve more complex and intricate designs without the need for multiple passes through the equipment, improving efficiency and throughput while providing highly customized results.
Automation and Robotics
The role of automation in the painting systems equipment industry will continue to expand, especially in high-volume production environments. The integration of robotic painting arms, automated conveyors, and smart inspection systems will enable manufacturers to increase productivity, consistency, and quality control. Automated systems are particularly useful in industries like automotive manufacturing, where high-volume, high-quality finishes are required across many different parts with minimal variability.
Robotic painting systems are especially beneficial when working with complex geometries or in situations that require precise, consistent coating applications. For example, robotic arms can reach difficult-to-access areas of a part, ensuring even coverage across intricate shapes. AI-powered robotic systems can adapt to changes in part positioning, coating types, and environmental conditions, leading to better efficiency and reduced defects.
Additionally, automated inspection and quality control systems will continue to evolve, with technologies such as machine vision and deep learning algorithms enabling automated defect detection. These systems can identify irregularities such as uneven coating thickness, color inconsistencies, and imperfections in the finish. By catching defects early in the process, these systems will help manufacturers improve product quality, reduce waste, and ensure that only the highest-quality products reach the consumer.
Global Market Expansion and Industry Adaptation
As painting systems equipment manufacturers look to expand into new markets, especially in developing regions, they will need to adapt their products to the specific needs of local industries. As global supply chains become more interconnected, manufacturers will face pressure to provide more flexible, scalable solutions that can adapt to regional variations in materials, substrates, and regulations.
For example, in emerging markets, the focus will often be on producing affordable, easy-to-maintain systems that can handle high volumes of production. At the same time, advanced systems capable of applying cutting-edge coatings with high performance will be essential in more mature markets, such as the automotive and aerospace industries, where quality, durability, and specialized finishes are paramount.
The expansion of global manufacturing networks will also drive demand for more versatile and modular painting systems that can accommodate a wide range of applications, coatings, and production needs. Modular systems allow manufacturers to scale their operations as needed and customize their equipment to meet the changing demands of a dynamic global market.
Looking Forward: The Future of Painting Systems Equipment
In the future, painting systems equipment will likely become more intelligent, sustainable, and customizable than ever before. The combination of smart technologies, robotic automation, advanced coating materials, and energy-efficient processes will ensure that painting systems continue to evolve in response to the growing demands of industries and consumers alike.
The global push for sustainability will further accelerate the development of technologies that reduce energy consumption, material waste, and environmental impact while still delivering high-quality finishes. At the same time, the increasing demand for personalized and innovative coatings will drive the continued evolution of painting systems that are both flexible and precise, enabling manufacturers to meet diverse customer needs.
Ultimately, the painting systems equipment industry is positioned to play a central role in shaping the future of high-quality manufacturing across a wide range of sectors, driving progress toward a more sustainable, efficient, and innovative industrial landscape. By embracing cutting-edge technologies, automation, and smart manufacturing solutions, painting systems will continue to push the boundaries of what is possible in coating applications, setting new standards for quality, precision, and sustainability in the years to come.
Powder Coating Spray Equipment

The evolution of powder coating spray equipment is driven by numerous advancements across industries that require high-performance finishes, sustainability, and efficiency in the application process. As manufacturers strive to meet growing demands for customized, durable coatings and adhere to environmental regulations, powder coating systems have become an integral part of the industrial coating process, particularly in sectors like automotive, appliances, construction, and furniture.
Technological Advancements in Powder Coating Spray Equipment
One of the most significant trends in powder coating spray equipment is the integration of advanced technologies that improve efficiency, precision, and finish quality. For example, electrostatic spray guns are now designed to offer improved charge-to-particle efficiency, which enhances the transfer of powder to the surface, ensuring that more powder adheres to the workpiece and less is wasted. These advanced spray guns incorporate features like automatic charge control, adjustable powder flow rates, and digital controls, allowing operators to fine-tune the application process for different materials and product shapes. This increased control improves the finish uniformity and quality while reducing the overall cost of coating materials.
In addition to spray guns, the powder coating equipment market has seen a surge in the development of automated powder coating systems. Robotic arms equipped with high-efficiency powder spray guns allow for the automation of the powder coating process, providing consistent, high-quality finishes across large production volumes. These systems can be programmed to handle different geometries and complex shapes, which is particularly beneficial for industries such as automotive manufacturing, where parts with intricate designs require precise powder application. The integration of motion control systems and feedback loops ensures that spray guns maintain optimal distance and angle from the workpiece, reducing overspray and improving the quality of the coating.
Another area of innovation is the use of smart powder coating equipment. Advanced spray booths, curing ovens, and material handling systems are increasingly being integrated with IoT (Internet of Things) technologies that enable real-time monitoring and process optimization. By collecting data from various stages of the coating process, manufacturers can identify potential issues early, allowing for timely interventions that prevent defects and downtime. Additionally, predictive analytics can forecast the performance of spray equipment and materials, helping manufacturers optimize their processes, reduce waste, and improve operational efficiency.
Sustainability in Powder Coating Spray Equipment
Sustainability continues to be a major driver of change in the powder coating industry, as both regulatory pressures and consumer preferences push for more environmentally friendly manufacturing practices. Powder coating itself is inherently more sustainable than traditional liquid coating methods because it produces no VOCs (volatile organic compounds) and minimal hazardous waste. However, the equipment used in the powder coating process has also seen improvements in energy efficiency, material utilization, and waste reduction.
For example, modern powder coating spray booths are equipped with recycling systems that allow for the reuse of oversprayed powder, reducing material waste. Some systems include dedicated filtration and recovery units, which capture unused powder particles from the air and filter them back into the system for reapplication. This process not only cuts down on waste but also reduces the overall cost of powder, which can be significant for high-volume manufacturers.
Further improvements in energy-efficient curing ovens have made the powder coating process even more environmentally friendly. Technologies such as infrared curing, convection ovens, and UV-cured powders reduce the amount of energy required for the curing process, speeding up production times and lowering the carbon footprint. The continued adoption of LED curing systems is also contributing to sustainability, as these systems consume significantly less energy than traditional heat-based curing methods while providing faster, more consistent results.
As manufacturers are increasingly required to meet global sustainability standards, powder coating spray equipment is also evolving to support coatings that are not only high-performance but also eco-friendly. This includes the development of water-based powders, bio-based resins, and low-temperature curing systems, all of which align with green chemistry principles. Powder coating manufacturers are also investing in closed-loop systems, which reduce waste and conserve resources by continuously recycling both powder and energy throughout the coating process.
Customization and Versatility in Powder Coating Spray Equipment
The trend toward customization and personalization is another factor that influences the development of powder coating spray equipment. In industries like automotive, electronics, and furniture manufacturing, there is increasing demand for coatings that offer unique finishes, textures, and aesthetic effects. To accommodate these demands, powder coating systems are becoming more versatile and capable of applying a wide range of coatings, from standard colors to special-effect finishes, such as metallics, pearlescent coatings, and glitter finishes.
Powder coating equipment manufacturers are responding to this demand by developing multi-functional spray systems that can handle multiple types of powders and coatings with minimal changeover time. This is particularly important for high-mix low-volume manufacturing environments, where producers need to switch between different colors or finishes quickly without compromising on quality. Advanced automated color change systems now allow manufacturers to easily switch between powder types, reducing downtime and waste. Some systems are also equipped with automatic cleaning features that ensure the spray guns and booths remain free from contamination when switching between different coatings.
Batch production flexibility has become a significant focus for powder coating systems. Manufacturers now offer customizable solutions that allow for easy adaptation to different batch sizes, whether it’s a high-volume production run or a small batch of highly specialized parts. The ability to easily scale production to meet varying demand is essential in today’s fast-paced, on-demand manufacturing environment.
Robotic Automation and Powder Coating Spray Equipment
Robotic automation continues to play an increasingly important role in powder coating spray systems, especially as manufacturers look to enhance production efficiency, consistency, and quality. Robotic spray arms offer significant advantages over traditional manual powder coating methods. They provide greater precision, can apply coatings consistently across complex shapes and parts, and reduce the risk of human error. Furthermore, robotic arms can operate in more hazardous or difficult-to-reach environments, allowing operators to focus on higher-level tasks and ensuring better safety.
Robotic systems are also being enhanced by AI (artificial intelligence) and machine learning algorithms, which allow them to adapt and optimize the spray process based on real-time data. These smart systems can automatically adjust the spray gun’s position, angle, and powder flow depending on the part geometry, size, and other environmental factors. By minimizing overspray and ensuring uniform coverage, robotic automation leads to improved product quality and reduced powder consumption.
In addition to robotic arms, automated handling systems are also being integrated with powder coating lines to streamline the process. Automated conveyors, part loading/unloading robots, and intelligent transport systems ensure that products are moved seamlessly through the spray booth, curing oven, and quality control stages, reducing the potential for errors and delays in production.
Improved Coating Performance and Durability
Powder coating spray equipment is also evolving to meet the growing demand for higher-performance coatings that offer superior durability, resilience, and aesthetic appeal. As industries such as automotive, construction, and appliances increasingly require coatings that can withstand harsh environmental conditions, powder coating systems must be capable of applying advanced coatings that offer corrosion resistance, scratch resistance, UV stability, and chemical resistance.
Innovations in polymer chemistry have led to the development of new, high-performance powders that offer exceptional durability and are suitable for applications in even the most challenging environments. In response, powder coating spray equipment has been adapted to handle these specialized formulations, ensuring that they are applied uniformly and without defects. The development of thermoplastic powders, which can be remelted and reused, also opens up new possibilities in applications where reworkability and repairability are crucial.
For example, in automotive manufacturing, powder coating systems are now being used to apply high-gloss, high-durability finishes to metal parts, such as wheels and chassis components. These coatings not only improve the appearance of the parts but also protect them from the damaging effects of corrosion, weathering, and wear.
Global Market and Industry Adaptation
As the demand for powder coating systems continues to rise globally, manufacturers will need to adapt their equipment to meet the specific needs of local markets. For example, emerging economies in Asia-Pacific, Latin America, and Africa are witnessing rapid industrial growth and urbanization, leading to greater demand for powder coating solutions across a variety of sectors. Powder coating spray equipment will need to be tailored to local requirements in terms of production capacity, cost-efficiency, and regulatory compliance.
In more mature markets, such as Europe and North America, there is an increasing emphasis on adopting high-tech solutions that improve efficiency and sustainability. Manufacturers in these regions are investing heavily in automated, energy-efficient powder coating systems that can support the growing demand for personalized and high-performance finishes.
The Future of Powder Coating Spray Equipment
Looking ahead, the future of powder coating spray equipment will be defined by smarter, more sustainable, and more flexible systems that support a wide range of coating applications and meet the evolving needs of industries worldwide. As manufacturers push for higher-quality coatings, faster production times, and lower environmental impact, powder coating equipment will continue to evolve to support these goals.
With the continued integration of smart technologies, automated systems, and advanced powder formulations, the powder coating spray equipment industry will remain at the forefront of industrial coating innovations, offering manufacturers the tools they need to create durable, aesthetically pleasing, and eco-friendly products at scale.
As the powder coating spray equipment industry continues to evolve, several additional trends and advancements will play a significant role in shaping the future of coating technologies. These trends include further automation, integration of eco-friendly practices, and greater adaptability to accommodate a wide range of industries and applications.
Further Automation and Industry 4.0 Integration
The automation of powder coating systems is expected to become even more advanced, as the Industry 4.0 revolution continues to influence manufacturing processes. Smart factories and connected production lines will incorporate technologies such as artificial intelligence (AI), machine learning, and big data analytics to create highly efficient, real-time production environments. Powder coating systems will become part of larger cyber-physical systems, where machines, sensors, and software collaborate to optimize performance.
In practice, this means spray booths, robotic arms, and curing ovens will be able to make real-time adjustments to the coating process based on data from production schedules, weather conditions, and even material types. For example, AI-powered systems can anticipate the exact amount of powder required for a given part based on historical data and machine learning algorithms, adjusting spray rates and speeds to reduce waste and improve uniformity.
Furthermore, collaborative robots (cobots) will continue to be integrated into powder coating lines, working alongside human operators to increase productivity and safety. Cobots will handle routine, repetitive tasks such as loading and unloading parts, while humans focus on tasks that require greater precision and decision-making. This collaboration between humans and machines will create more flexible, adaptable production systems capable of handling a variety of products with varying complexity and finish requirements.
Smart Powder Coating Systems for Predictive Maintenance
Predictive maintenance is another key area where powder coating equipment is likely to see significant improvement. Through the integration of sensors and IoT technologies, powder coating systems will be able to monitor the health of critical components, such as spray guns, filters, and conveyors, in real time. The data collected by these sensors will be analyzed using predictive analytics to forecast when parts or systems need maintenance before they fail.
This shift toward predictive maintenance not only reduces the likelihood of unplanned downtime but also lowers overall maintenance costs by preventing unnecessary part replacements and repairs. With the ability to track the performance and wear of individual components, manufacturers can ensure that powder coating systems remain in optimal working condition, even under high-demand production schedules.
Moreover, cloud-based platforms will enable manufacturers to access real-time data and performance insights from multiple production lines, ensuring a higher level of consistency across operations. By tracking trends and anomalies in equipment performance, plant managers will be able to make informed decisions about system improvements, staff training, and process optimizations.
Energy-Efficient Systems and Low-Emission Solutions
Energy efficiency and low-emission technologies will remain a focal point for the powder coating industry. As sustainability becomes more critical for businesses aiming to meet both regulatory requirements and consumer expectations, energy-efficient curing systems and spray booths will be integral to reducing the environmental impact of powder coating processes.
Innovative curing technologies such as infrared (IR) heating, ultraviolet (UV) curing, and electromagnetic induction will continue to be optimized for faster curing times and lower energy consumption. These technologies work by directly targeting the part being coated, reducing the need for energy-intensive ovens and cutting down on overall production costs. Furthermore, LED-based curing systems will see increased adoption, as they offer low power consumption, longer lifespan, and faster curing times, all of which contribute to a greener, more cost-effective production process.
Powder coating systems will also incorporate improved filtering technologies to reduce emissions from the spray booths, preventing airborne particles from escaping into the environment. These filtration systems will capture not only oversprayed powder but also any toxic substances that may be released during the coating process. Enhanced ventilation and dust control technologies will help ensure that the coating process adheres to both environmental and worker safety standards.
Enhanced Powder Coating Materials
The materials used in powder coating are also undergoing significant transformation to meet the needs of more demanding industries. Thermoplastic powders will continue to gain traction due to their reworkability and repairability. Unlike traditional thermoset powders, thermoplastics can be remelted and reused, offering significant advantages in situations where parts may need to be reworked or repaired after initial coating. These powders are also more adaptable, offering improved flexibility for applications in sectors like automotive, construction, and electrical components.
Additionally, the development of high-performance powder formulations will enable coatings to withstand even more extreme environments. Nano-coatings, which use particles at the nanoscale to provide enhanced properties such as self-healing, anti-corrosion, and anti-microbial capabilities, will become increasingly important in applications requiring advanced durability. These coatings are particularly valuable in industries like aerospace, marine, and medical device manufacturing, where exposure to extreme conditions or contamination is a concern.
Custom powder formulations are also becoming more common, as industries demand coatings with specific characteristics. Whether it’s a unique color, finish, or effect, manufacturers are looking for more flexibility from their powder coating systems to create truly bespoke results. Powder coating systems will increasingly need to support a variety of custom powder formulations that are both performance-driven and aesthetically appealing.
Global Market Expansion and Local Adaptation
As powder coating systems continue to expand globally, manufacturers must adapt their equipment to meet the unique needs of different markets. In emerging economies, where industrial growth is accelerating, demand will rise for cost-effective, easy-to-maintain powder coating systems that can handle high-volume production while minimizing downtime. These markets will benefit from more modular and scalable powder coating systems, which can be customized and expanded as production needs grow.
Meanwhile, in mature markets, there will be an increasing demand for more specialized and high-tech systems that offer better performance, greater precision, and efficiency. In these markets, the focus will be on advanced automation, sustainability, and smart integration. Manufacturers in North America and Europe will continue to push the envelope with high-efficiency, low-emission, and zero-waste solutions to meet stricter environmental regulations and sustainability goals.
Adapting to Diverse Industry Needs
As industries evolve, the versatility of powder coating systems will be tested. For instance, automotive manufacturers are moving toward lightweight materials such as aluminum and plastics, which require different application techniques and powder formulations. Powder coating systems will need to accommodate these changes by incorporating specialized equipment that can handle non-traditional materials without compromising finish quality or coating durability.
Similarly, aerospace manufacturers are seeking powder coatings that can withstand extreme temperatures, UV radiation, and harsh environmental conditions. High-performance, heat-resistant coatings will become more common, and powder coating systems will need to be designed to apply these specialized coatings efficiently and effectively.
The furniture industry is also seeing an increasing demand for unique finishes such as matte, satin, and glossy effects, which will require more specialized equipment capable of applying multi-layer coatings and decorative effects. Powder coating spray equipment will need to offer flexibility for complex designs, while still delivering durability and long-lasting finishes.
Future Trends: Smart, Sustainable, and Precise
The future of powder coating spray equipment will be driven by the increasing demand for smarter, sustainable, and precise solutions. As industries continue to demand greater performance, customization, and eco-friendliness from coating systems, powder coating technology will evolve to provide greater automation, energy efficiency, and flexibility. From AI-driven spray guns to high-performance, eco-friendly coatings, manufacturers will have access to an expanding suite of technologies that will enable them to meet the challenges of a rapidly changing marketplace.
Looking ahead, we can expect powder coating systems to become more intelligent, autonomous, and adaptive to meet the specific needs of manufacturers, ensuring high-quality finishes, sustainability, and greater productivity. With advances in material science, automation, and energy-efficient technologies, powder coating will continue to be a critical process for a wide range of industries, supporting innovative designs, eco-friendly practices, and superior performance in the years to come.
As we continue to explore the future of powder coating spray equipment, the ongoing developments across various technological, environmental, and market trends will further solidify the role of powder coating systems as a critical element in modern manufacturing. These systems will not only support the demand for high-performance, high-quality finishes but also align with broader goals in sustainability, efficiency, and adaptability. Below, we look into additional avenues of growth and innovation that will define the next stages of powder coating technologies.
Advanced Materials and Coating Innovations
The demand for advanced materials continues to rise across industries, pushing the boundaries of what powder coatings can achieve. Manufacturers are constantly looking for coatings that provide enhanced thermal resistance, electromagnetic shielding, anti-corrosion, anti-fingerprint, and self-cleaning properties. These advanced functionalities can significantly extend the life of parts, improve their performance, and offer unique aesthetic finishes.
Nano-coatings, in particular, are gaining attention due to their ability to provide high levels of durability, resistance, and protection with a minimal thickness. Nano-structured coatings can improve the hardness, scratch resistance, and chemical resistance of the coated surfaces, which is especially valuable for industries such as aerospace, electronics, and medical devices. Powder coating systems will evolve to support the precise application of these cutting-edge materials while maintaining the quality of the finish.
Moreover, powder coating formulations that combine the best properties of both thermoplastic and thermoset materials are becoming increasingly popular. These hybrid powders provide the reworkability of thermoplastics with the chemical resistance and high-temperature tolerance of thermosets, making them ideal for industries that need coatings that perform well under both high-performance and aesthetic demands.
Automation and Artificial Intelligence in Process Control
The integration of artificial intelligence (AI) and machine learning will continue to revolutionize the powder coating spray equipment sector. AI-driven powder coating systems will be capable of adjusting application parameters based on real-time feedback, improving consistency and reducing material waste. By leveraging historical data, AI can predict coating behaviors for different substrates and environmental conditions, helping operators optimize parameters such as powder flow rates, spray angles, and distance from the part.
For example, machine learning algorithms will analyze the interaction between the spray gun and various materials, refining the coating process to ensure even distribution and maximum adhesion while minimizing overspray and defects. Furthermore, AI systems will enable real-time defect detection, identifying inconsistencies or imperfections during the application and alerting operators for corrective action.
Robotic systems integrated with AI can independently adjust their movements, speed, and coating patterns to accommodate various part geometries and sizes. This reduces human error, improves production speed, and ensures precise application, even for intricate designs or complex product shapes. In high-volume manufacturing environments, robots equipped with AI and advanced powder spray equipment will be able to handle continuous production runs with minimal downtime and high efficiency.
Sustainability Beyond the Coating Process
Sustainability will continue to be a significant focus not just in the final coating but throughout the entire powder coating process. Manufacturers are increasingly looking for ways to reduce the environmental impact of their operations, and this includes making improvements in material recovery, energy use, and waste management.
Closed-loop systems that recover excess powder, reuse it, and reduce waste will become even more sophisticated, helping manufacturers reclaim more powder and minimize disposal. Additionally, advanced filtration systems will be further developed to capture not only the oversprayed powder but also airborne contaminants, ensuring compliance with stricter environmental regulations. These systems will help improve air quality in the working environment and reduce emissions from the powder coating process.
One exciting development is the growing use of eco-friendly powder coatings that utilize renewable raw materials or bio-based resins. These coatings reduce reliance on petroleum-based materials and contribute to the overall reduction of environmental footprint. Companies are also exploring low-temperature curing powders, which require significantly less energy to cure compared to traditional powder coatings, contributing to energy savings and reducing the carbon footprint.
As environmental regulations become stricter worldwide, particularly in Europe and North America, powder coating systems will have to evolve to meet new regulatory standards regarding VOCs (volatile organic compounds), waste reduction, and energy consumption. Manufacturers will be required to invest in technologies that align with both local regulations and global sustainability goals, particularly those tied to the Paris Agreement and circular economy principles.
Customization and Industry-Specific Solutions
As customer demands for customized products grow across industries, powder coating systems will continue to offer greater flexibility and versatility. Industries such as automotive, furniture, electronics, and consumer goods are increasingly adopting personalized finishes, colors, textures, and patterns. Manufacturers will demand powder coating systems that can easily switch between different types of powder materials, colors, and effects with minimal downtime, ensuring that they can respond quickly to market trends.
This demand for customization is driving the need for multi-functional systems capable of handling various types of coatings, including metallics, pearlescents, glossy and matte finishes, and even textured or patterned coatings. Specialized equipment, such as customizable spray guns, automatic color change systems, and advanced curing solutions, will be designed to support these variations while ensuring that the quality of the coating remains consistent across different batch sizes.
Additionally, small-batch manufacturers and startups are seeking scalable solutions that allow them to apply high-quality powder coatings to products of varying shapes and sizes. Powder coating equipment manufacturers are responding by creating modular systems that can be adapted to the needs of smaller production runs while offering the efficiency and precision typically associated with high-volume manufacturing.
Smart Coatings and IoT-Enabled Systems
The rise of the Internet of Things (IoT) in manufacturing is another exciting trend shaping the future of powder coating equipment. IoT-enabled powder coating systems will allow manufacturers to monitor and control their coating process remotely, offering real-time insights into key performance metrics such as powder usage, spray gun efficiency, and oven curing times.
With connected systems, powder coating manufacturers can collect data from various stages of production, allowing them to track product quality, equipment performance, and environmental conditions in real time. This continuous flow of data will be essential for making data-driven decisions that improve operational efficiency, reduce waste, and optimize production schedules. It will also help detect performance issues early, allowing for predictive maintenance and minimizing downtime.
For example, operators will be able to monitor powder usage and make adjustments remotely to ensure that spray guns are applying the optimal amount of powder, avoiding waste. They can also track the temperature and curing times in real-time, ensuring that parts are fully cured without overexposure to heat.
Furthermore, smart coatings will continue to emerge as a growing trend. These coatings have the potential to interact with their environment, offering enhanced performance. For instance, self-healing coatings will be able to repair minor scratches or chips automatically, while anti-microbial coatings will prevent the growth of bacteria and fungi on the surface. As these smart coatings become more widely available, powder coating systems will need to adapt to ensure precise application of these advanced materials.
Global Market Expansion and Adaptation to Regional Needs
As the global demand for powder coating systems grows, manufacturers will need to tailor their products to meet the unique requirements of different regions and industries. In emerging markets, such as Asia-Pacific, Africa, and Latin America, the focus will be on cost-effective, energy-efficient systems that can handle high-volume production without compromising on quality. These regions are likely to see a rise in demand for entry-level systems with scalable capabilities that allow manufacturers to grow their operations over time.
Conversely, in established markets such as North America and Europe, the emphasis will be on high-performance systems that support greater customization, sustainability, and advanced coatings. These markets are becoming increasingly aware of the need for energy-efficient, low-emission, and sustainable coating solutions, which will drive the development of more advanced curing systems, eco-friendly powders, and energy recovery technologies.
The Future Outlook for Powder Coating Spray Equipment
As the powder coating industry continues to evolve, the focus will be on creating more efficient, cost-effective, sustainable, and customizable systems. Manufacturers will increasingly rely on advanced technologies such as artificial intelligence, robotic automation, and IoT-enabled equipment to improve quality, reduce waste, and enhance production flexibility. At the same time, the push for environmental sustainability and energy efficiency will shape the development of coating materials and equipment, helping to create greener production processes.
The next decade promises to bring about even more innovative breakthroughs in smart coatings, automated powder application, and advanced curing technologies. These developments will help manufacturers across industries achieve higher performance, greater customization, and enhanced environmental compliance, ensuring that powder coating systems remain a critical component of modern manufacturing for years to come.
Electrostatic spray powder coating is a widely used and efficient method for applying powder coatings to a variety of substrates. Over the years, this technology has advanced significantly, incorporating innovations in spray equipment, automation, and material development. The future of electrostatic spray powder coating equipment will see more intelligent, efficient, and sustainable solutions that cater to the growing demands of diverse industries. The following outlines the key developments expected in this area.
Electrostatic Spray Powder Coating Technology: Current State and Future Trends
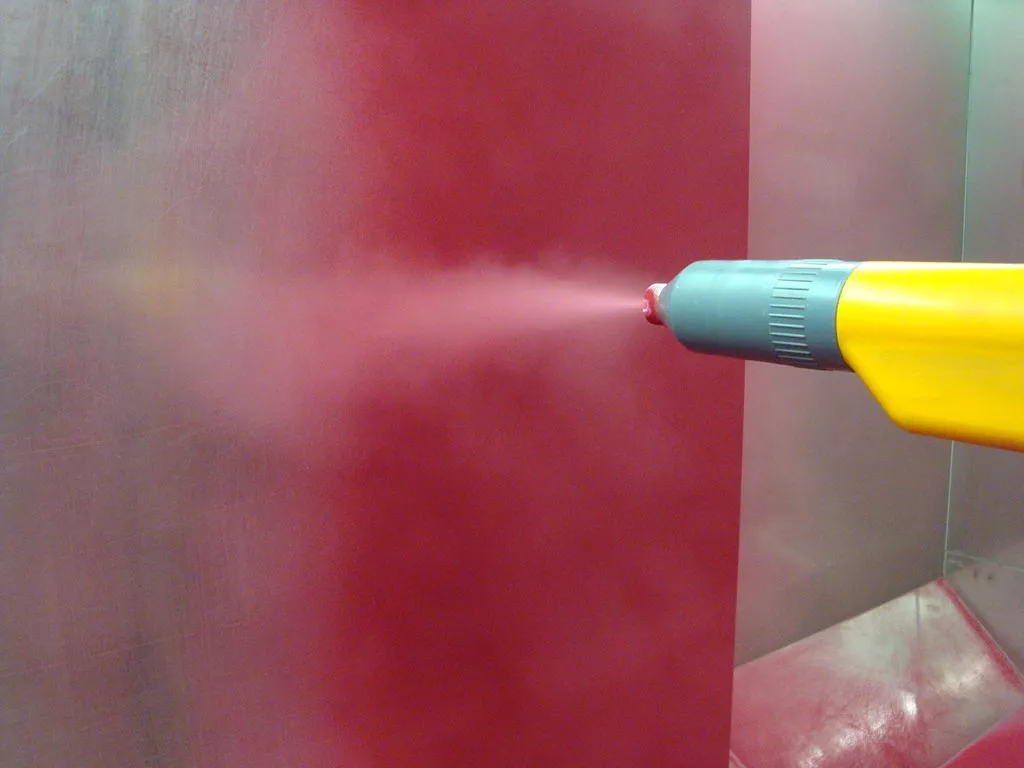
Electrostatic spray powder coating works by charging the powdered material with an electrostatic charge, which attracts it to a grounded substrate. This process ensures that the powder adheres evenly to the surface, and once applied, the powder is cured in an oven, forming a smooth, durable coating. The key benefits of this process include environmental sustainability, cost-effectiveness, and high-quality finishes. Electrostatic spray powder coating is commonly used in industries such as automotive, appliances, furniture, metal fabrication, and architectural applications.
Looking toward the future, electrostatic spray powder coating equipment is expected to evolve in response to several important trends, including automation, smart technologies, sustainability, and advances in materials.
Automation and Integration of Industry 4.0
The integration of automation and Industry 4.0 principles into electrostatic spray powder coating systems will continue to shape the future of this technology. Automated powder coating systems allow for consistent application, improved efficiency, and reduced labor costs. The introduction of robotic arms and automated guided vehicles (AGVs) in powder coating lines will enhance production speed and ensure uniform coating on parts of varying sizes and geometries.
Electrostatic spray systems are likely to become increasingly intelligent, with artificial intelligence (AI) and machine learning algorithms optimizing the coating process in real-time. These intelligent systems can analyze substrate types, surface imperfections, and environmental factors to adjust application parameters such as spray gun distance, air pressure, powder flow rates, and spray angles.
Data analytics will play a pivotal role in optimizing spray operations, helping manufacturers monitor the efficiency of their equipment, track coating quality, and detect faults early. With smart sensors embedded in the equipment, operators will receive real-time insights into key performance metrics, such as powder usage, coating thickness, and air flow, which will help streamline operations and reduce waste.
Additionally, robotic spraying will allow for high-speed, automated, and precise powder coating, particularly in high-volume industries like automotive manufacturing. Robots equipped with electrostatic spray guns will be able to adjust their spray patterns and coverage based on the part’s shape and size, reducing overspray and improving material usage efficiency.
Increased Use of IoT-Enabled Systems
The future of electrostatic spray powder coating equipment will also see the widespread adoption of Internet of Things (IoT) technologies. IoT-enabled spray coating systems will allow for the continuous monitoring of all components involved in the coating process. Sensors integrated into the equipment will track parameters such as temperature, humidity, powder flow rates, electrostatic charge levels, and gun position.
These systems will send real-time data to a centralized system, enabling remote monitoring and diagnostics. Manufacturers will be able to track system performance from anywhere, leading to better decision-making and more effective maintenance. IoT technology will also facilitate predictive maintenance, alerting operators when equipment needs attention before breakdowns occur, reducing downtime and ensuring the longevity of the equipment.
Furthermore, cloud-based platforms will allow for data aggregation from multiple coating systems, offering detailed insights into system performance across different production lines and facilities. This data can be analyzed to improve operational efficiency, minimize waste, and increase consistency in the application process.
Customization and Adaptation to Different Industries
As demand for customized products and finishes increases, electrostatic spray powder coating systems will evolve to provide more flexibility in their application. Multi-functional equipment will become more prevalent, enabling manufacturers to switch between different powder formulations, colors, and finishes with minimal downtime.
Electrostatic spray systems will need to support a wider range of coating options, including metallic, matte, glossy, textured, and multi-layered finishes. These customizable systems will offer greater adaptability to industries such as furniture, appliance manufacturing, electronics, and automotive, where varied finishes and high levels of design aesthetics are critical.
For example, automotive manufacturers may require electrostatic spray systems that can apply premium finishes like pearlescent, chromatic, or multi-tonal colors, while electronics manufacturers may need precision applications of coatings for components with intricate geometries. The ability to easily switch between these custom finishes without sacrificing application quality will be a major focus for future electrostatic spray powder coating systems.
Environmental Sustainability and Energy Efficiency
Environmental concerns will continue to drive the development of greener, more sustainable powder coating technologies. Powder coatings themselves are inherently environmentally friendly compared to traditional liquid coatings because they produce no volatile organic compounds (VOCs), minimal waste, and require less energy during application and curing. However, there is still room for improvement in terms of energy consumption and waste management.
Low-temperature curing is one area where electrostatic spray powder coating systems will see advancements. Traditional curing ovens can consume a significant amount of energy to reach high temperatures. The development of low-temperature curing powders, which cure at lower temperatures (often in the range of 120-180°C), will reduce the overall energy consumption of the coating process, making it more sustainable and cost-effective, especially for manufacturers with large-scale production facilities.
Additionally, the implementation of closed-loop powder recovery systems will ensure that excess powder can be collected and reused, reducing waste and making the powder coating process more resource-efficient. These systems will be designed to capture not just overspray but also powder that has fallen off parts or clung to surfaces during the coating process. By recycling powder, manufacturers can minimize material loss and maximize the use of each batch of powder.
Energy-efficient spray booths will also become standard in the industry. These booths will be equipped with advanced ventilation systems that capture and filter air particles while ensuring that energy consumption is kept to a minimum. LED lighting and variable-speed fans will be commonly used in these booths to further reduce energy use.
Technological Innovations in Powder Coating Materials
The continuous improvement of powder coating materials will play a key role in the development of electrostatic spray powder coating equipment. Manufacturers are increasingly seeking high-performance coatings that not only provide durable, long-lasting finishes but also offer additional functionalities such as self-healing, anti-microbial, and UV resistance.
The development of nano-powders will provide coatings with superior properties, such as enhanced hardness, scratch resistance, and anti-corrosion capabilities. These new powder formulations will require advanced electrostatic spray systems that can apply the powder with high precision while maintaining uniformity.
Hybrid powder formulations combining both thermoset and thermoplastic materials will also become more common. These hybrid powders offer a balance of high chemical resistance and reworkability, making them ideal for applications where parts need to be coated and then later reworked or repaired.
Additionally, bio-based and eco-friendly powders are expected to become more prevalent. These powders are made from renewable raw materials, reducing the dependency on petroleum-based ingredients and contributing to a more sustainable manufacturing process. Manufacturers will increasingly turn to powder coating systems capable of handling these new formulations, ensuring compatibility with the equipment and maintaining high-quality finishes.
Enhanced Safety and Ergonomics
Safety and ergonomics will continue to be a priority in the design and development of electrostatic spray powder coating equipment. Manufacturers are increasingly focused on creating user-friendly systems that reduce operator exposure to potentially harmful powders and ensure a safe working environment.
Advanced filtration systems will help capture airborne powders in the coating booth, preventing workers from inhaling potentially hazardous particles. These filtration systems will be more effective in powder capture and air quality management, contributing to better workplace safety.
In addition, ergonomic spray guns will be designed to reduce the physical strain on operators. Lightweight and easy-to-handle spray guns will provide better control and comfort during long application sessions, reducing operator fatigue and improving overall productivity.
Furthermore, systems will include automated cleaning functions that reduce manual labor. Self-cleaning spray guns and automatic booth cleaning systems will minimize the need for frequent manual cleaning, improving both efficiency and safety.
Global Market Expansion
The demand for electrostatic spray powder coating equipment will continue to expand globally, with particularly strong growth expected in emerging markets in regions such as Asia-Pacific, Latin America, and Africa. As manufacturing capacity increases in these regions, the need for affordable and scalable electrostatic powder coating systems will rise.
Simultaneously, mature markets like North America and Europe will continue to prioritize advanced systems that offer high levels of precision, sustainability, and customization. Manufacturers in these regions will seek systems that can handle complex parts and provide superior finishes while complying with stricter environmental regulations.
Conclusion
The future of electrostatic spray powder coating equipment lies in smarter, more automated, and more environmentally friendly systems. As industries continue to demand high-quality, customizable finishes, electrostatic spray systems will evolve to provide greater flexibility, higher efficiency, and enhanced sustainability. With advancements in robotic automation, AI integration, and eco-friendly materials, electrostatic spray powder coating will remain a critical component of modern manufacturing, offering an efficient and sustainable solution for a wide range of industries.
As electrostatic spray powder coating technology continues to evolve, the industry is witnessing significant advancements in both equipment and application processes. The future of this technology is marked by a strong focus on automation, sustainability, intelligent systems, and high-performance coatings. These developments are being driven by increasing demands for more efficient production, reduced environmental impact, and the ability to handle a diverse range of materials and products. Automation plays a critical role in this transformation. With the integration of robotics and advanced spray systems, manufacturers can automate much of the powder coating process, improving speed, precision, and consistency. Automated systems reduce the need for manual labor, resulting in higher throughput, fewer errors, and improved product quality.
At the same time, robotic arms and automated guided vehicles (AGVs) are being deployed in coating lines to handle parts of varying sizes and geometries, enabling precise application of coatings with minimal waste. The use of intelligent spray systems equipped with artificial intelligence (AI) will also play a central role. These systems will adapt to real-time conditions, optimizing key parameters such as powder flow rates, spray angles, and distance from the part based on feedback from sensors and analytics platforms. This capability will ensure that the coating process is always optimized, leading to greater consistency and quality in the final product.
Additionally, machine learning will enable coating systems to predict and adjust for variations in materials, environmental factors, and substrate types, ensuring that the coating process is always tailored for the best results. As electrostatic spray powder coating systems become more intelligent, they will also become more connected. With the advent of the Internet of Things (IoT), equipment will be able to send real-time data to central monitoring systems, enabling manufacturers to track key performance metrics such as powder usage, coating thickness, and oven curing times. This data will be invaluable for optimizing operations, predicting maintenance needs, and reducing downtime.
Manufacturers will also be able to collect valuable insights from connected systems, allowing for better decision-making and more efficient resource management. Furthermore, the rise of cloud-based platforms will enable remote monitoring of equipment, facilitating predictive maintenance and continuous improvements across production lines. Another significant trend shaping the future of electrostatic spray powder coating equipment is the emphasis on sustainability. As environmental concerns grow, both manufacturers and customers are increasingly prioritizing eco-friendly solutions. Powder coatings, by nature, already offer significant environmental benefits, such as the absence of volatile organic compounds (VOCs) and minimal waste.
However, the next generation of powder coating systems will place an even greater emphasis on reducing energy consumption, optimizing powder recovery, and using eco-friendly materials. For instance, low-temperature curing powders will become more common, as they allow for energy savings by reducing the curing temperature required for the powder to set. These innovations will be especially beneficial for industries with large-scale manufacturing operations, where energy consumption can be a significant cost. Closed-loop powder recovery systems will continue to improve, enabling manufacturers to collect and reuse oversprayed powder. This will not only reduce material waste but also increase operational efficiency by ensuring that more of the powder is used effectively.
Moreover, eco-friendly powders made from renewable raw materials will see wider adoption. These powders, often based on bio-based resins, help reduce the environmental footprint of the coating process. Additionally, as companies face stricter environmental regulations, the demand for equipment that is energy-efficient and capable of meeting the latest environmental standards will increase. Energy-efficient spray booths will become more prevalent, equipped with advanced ventilation systems and LED lighting that help reduce power consumption while maintaining high performance.
As powder coating technology advances, the demand for more customized finishes will continue to grow. Industries such as automotive, electronics, appliances, and furniture are increasingly seeking powder coatings that offer unique textures, colors, and finishes. Electrostatic spray powder coating systems will need to be adaptable to accommodate a wide variety of coatings, including metallic, glossy, matte, and pearlescent finishes. This trend is driven by the consumer preference for more personalized, aesthetically distinct products.
Manufacturers will demand systems that can quickly switch between different coating types with minimal downtime. Multi-functional spray equipment that can handle a wide range of powders and finishes will be essential. For example, automotive manufacturers may require specialized coatings for premium finishes like pearlescent or chromatic colors, while appliance manufacturers may seek durable coatings for metal or plastic components. The ability to apply multiple layers of coatings with consistent quality and minimal waste will be crucial as product complexity increases.
In addition, the development of nano-powders will offer coatings with superior properties, such as enhanced hardness, scratch resistance, and anti-corrosion performance. These advanced powders will require electrostatic spray systems capable of applying them with high precision and uniformity, ensuring that the final product meets the stringent quality standards demanded by industries such as aerospace and electronics.
At the same time, hybrid powder formulations combining both thermoset and thermoplastic materials will gain popularity. These hybrid powders provide the durability and chemical resistance of thermosets with the flexibility and reworkability of thermoplastics, making them ideal for applications where parts may need to be reworked or repaired after coating. To accommodate these advanced materials, electrostatic spray powder coating equipment will need to offer more precise control over the application process, ensuring that even the most complex coatings can be applied with consistent quality.
Safety and ergonomics will continue to be a priority in the development of electrostatic spray powder coating equipment. Manufacturers are increasingly focused on designing equipment that reduces operator exposure to hazardous powders and minimizes physical strain. Advanced filtration systems will be incorporated into spray booths to capture airborne particles, improving workplace air quality and ensuring a safer environment for workers. Additionally, ergonomically designed spray guns and automated cleaning systems will help reduce operator fatigue and improve the overall efficiency of the coating process.
Finally, as the global market for electrostatic spray powder coating continues to expand, manufacturers will need equipment that can meet the specific requirements of diverse industries and regions. In emerging markets, where cost-effectiveness is a priority, electrostatic spray powder coating systems will need to be more affordable, versatile, and capable of handling large-scale production runs. In contrast, in mature markets, the demand will be for systems that offer advanced capabilities, such as customization, sustainability, and high-quality finishes.
Electrostatic spray powder coating equipment will evolve to address these needs, ensuring that manufacturers have the tools they need to stay competitive in an increasingly complex and dynamic global marketplace. With ongoing advancements in automation, material development, sustainability, and technology integration, the future of electrostatic spray powder coating is bright, offering manufacturers more efficient, flexible, and environmentally friendly solutions for a wide range of applications.
Looking forward, the future of electrostatic spray powder coating technology is also expected to be significantly influenced by advancements in material science and coating innovation. Manufacturers are constantly pushing the boundaries of what is possible with coatings to meet the demands of industries such as automotive, aerospace, electronics, and construction, where surface protection, durability, and aesthetic quality are paramount. The ongoing development of specialty coatings, such as high-temperature resistant, scratch-proof, and self-healing coatings, will open new possibilities for electrostatic spray systems. Self-healing coatings, which are designed to automatically repair minor scratches or damages on the surface, will gain popularity in industries where parts are subject to harsh environmental conditions or frequent wear, such as in automotive or outdoor furniture applications.
These coatings will require electrostatic spray systems with the ability to apply uniform, thin, and precise layers that preserve the functional properties of the material while still offering exceptional durability. Furthermore, as manufacturers aim to enhance the aesthetic appeal of their products, customizable finishes will become an even more important aspect of electrostatic spray powder coating. The need for unique textures, patterns, and colors will drive the development of spray equipment capable of applying a wide range of effects, from smooth glossy finishes to more complex, multi-dimensional textures.
Increased automation will also play a key role in streamlining the coating process and reducing operational costs. The introduction of collaborative robots (cobots), which work alongside human operators, will further improve the efficiency and safety of powder coating systems. These robots will assist with tasks such as handling parts, adjusting spray guns, or fine-tuning application parameters in real-time, all while improving consistency and reducing the likelihood of human error. The automation of coating lines will not only lead to faster production cycles but also improve product quality by ensuring that coatings are applied uniformly and with minimal defects.
In addition to collaborative robots, the integration of augmented reality (AR) and virtual reality (VR) technologies into the training and operational aspects of electrostatic spray powder coating systems will allow operators to better understand system performance and troubleshoot issues. With AR and VR, operators can visualize the entire coating process in real-time, providing a more interactive and intuitive approach to training. This, in turn, will lead to faster adaptation to new systems, higher-quality coatings, and fewer application mistakes.
As smart technologies continue to evolve, electrostatic spray powder coating systems will become increasingly self-regulating. For example, advanced sensors embedded in the equipment will continuously monitor critical factors such as electrostatic charge, spray gun distance, coating thickness, and air quality. These sensors will automatically adjust the process parameters to optimize performance and ensure that the coating is applied correctly on the first pass. This self-regulation will reduce the need for human intervention, improve coating consistency, and reduce material waste.
The growing demand for sustainable solutions will also spur innovation in the development of eco-friendly powder coatings that are not only bio-based but also waterborne or made from recycled materials. Waterborne powder coatings, for example, use water as a carrier instead of traditional solvents, making them more environmentally friendly while still offering excellent performance. Recycled powder coatings will also become more common, where powder materials that did not adhere properly to substrates are collected, filtered, and reused in the coating process. These efforts are part of a broader movement toward reducing the environmental footprint of the manufacturing process by using renewable resources and minimizing waste.
In the realm of global supply chains, the demand for electrostatic spray powder coating equipment will continue to increase as Asia-Pacific regions, particularly China and India, see rapid industrialization. These regions will become key markets for powder coating systems due to their booming manufacturing sectors. The ability to apply high-quality coatings on everything from automotive parts to appliance components will drive growth in these areas. At the same time, the industry will need to adapt to the unique demands of these regions, including the need for affordable solutions that maintain a high level of performance, ensuring that local manufacturers can meet international standards.
As regulatory requirements continue to evolve, particularly in regions with strict environmental standards, the demand for electrostatic spray systems capable of handling low-VOC, non-toxic, and non-hazardous coatings will continue to grow. The ability to adhere to these regulations will be a critical factor for manufacturers looking to sell in markets with stringent environmental laws, such as Europe and North America.
With all of these changes in mind, the maintenance and serviceability of electrostatic spray powder coating equipment will also evolve. Predictive maintenance will become the norm, with systems capable of monitoring wear and tear on components and alerting operators to issues before they lead to downtime. The use of self-diagnosing systems, supported by cloud-based analytics, will provide real-time data that allows technicians to troubleshoot and repair equipment remotely, minimizing operational disruptions and extending the lifespan of the equipment.
Furthermore, the growth of globalization and e-commerce will drive increased demand for smaller, more localized production facilities that can cater to regional markets more effectively. This will push manufacturers to create modular and scalable coating systems that can be easily adapted to different production scales and customized to meet specific market needs. These systems will need to be versatile enough to handle a wide range of coating types, parts, and applications without compromising on quality or efficiency.
Finally, the overall user experience of electrostatic spray powder coating systems will be a major focus for future developments. Intuitive interfaces, easy-to-use controls, and automated calibration will make it easier for operators to achieve optimal results without extensive training. Manufacturers will increasingly invest in user-friendly equipment that can be easily operated by personnel with minimal experience, thus lowering the barrier to entry for businesses looking to adopt powder coating technologies.
In conclusion, the future of electrostatic spray powder coating equipment is set to be defined by innovation across multiple areas, including automation, sustainability, material science, and intelligent technologies. As manufacturers strive to meet the demands of a global, fast-paced market, the evolution of electrostatic spray systems will provide the tools necessary to produce high-quality, durable, and aesthetically pleasing finishes at an increasingly efficient and environmentally responsible pace. By adopting these advanced systems, industries can achieve greater productivity, meet growing consumer expectations, and reduce their environmental impact, all while maintaining a competitive edge in an ever-evolving marketplace.
Powder Coating Gun
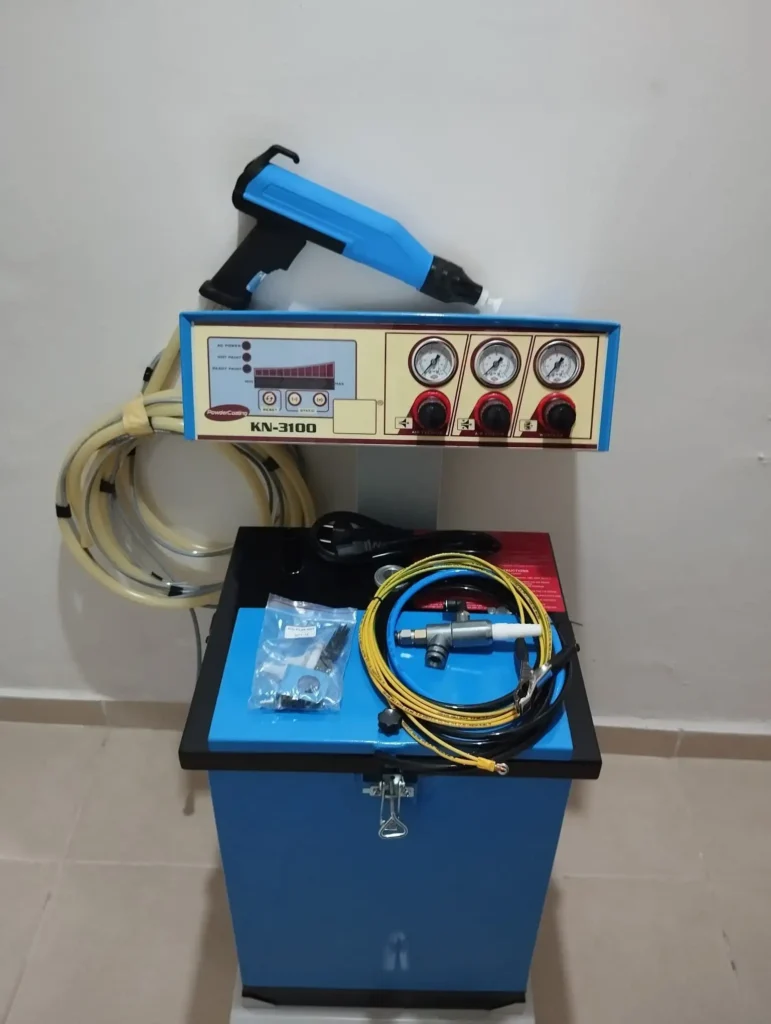
The future of powder coating guns is evolving rapidly, driven by advancements in technology, material science, and automation. As industries seek more efficient, sustainable, and high-quality coating processes, powder coating guns are becoming more sophisticated, offering better control, flexibility, and performance than ever before. The key trends shaping the future of powder coating guns include precision application, integration with automation, eco-friendly designs, and improved ergonomics.
One of the most notable advancements in powder coating gun technology is the increased precision and control over the application process. Electrostatic technology has long been a cornerstone of powder coating, but new developments in digital controls and sensor integration are taking the process to the next level. Modern powder coating guns are equipped with sensors that can monitor key factors such as electrostatic charge, powder flow rate, and spray pattern, providing operators with real-time feedback and enabling them to adjust settings on-the-fly for optimal results. These advancements reduce material waste, improve coating consistency, and ensure that coatings are applied evenly across complex geometries, regardless of the part size or shape.
Intelligent powder coating guns are becoming more prevalent, integrating with factory automation systems to enhance the coating process. These smart guns can communicate with other pieces of equipment, such as robotic arms and spray booths, adjusting parameters based on real-time conditions. For example, the guns may automatically adjust the spray voltage, powder flow rate, and spray distance based on the shape of the object being coated or the environmental conditions in the booth. This integration allows for higher throughput, greater consistency, and reduced human error.
In terms of automation, powder coating guns are being designed to work seamlessly with robotic systems. These automated systems can handle a wide range of components, adjusting spray angles and distances based on the geometry of the part being coated. The ability to quickly switch between different types of coatings, colors, and finishes is crucial for industries like automotive and electronics, where custom and high-quality finishes are in demand. Automated systems equipped with powder coating guns can drastically reduce downtime, optimize coating efficiency, and minimize human involvement, leading to cost savings and improved product quality.
Additionally, as sustainability continues to be a major focus in manufacturing, powder coating gun technology is being developed with a greater emphasis on eco-friendly operations. New designs are focused on reducing overspray and improving powder recovery. High-efficiency guns can achieve greater transfer efficiency, meaning more powder reaches the surface being coated rather than being wasted or oversprayed. This helps reduce material consumption and lowers operational costs. Furthermore, innovations in closed-loop recovery systems ensure that any oversprayed powder is captured and reused, reducing waste and the need for new powder. These advancements not only help manufacturers meet environmental regulations but also contribute to cost savings and a more sustainable production process.
The design of the powder coating gun itself is also evolving to improve operator comfort and safety. Advances in ergonomics have led to lighter, more balanced guns that reduce fatigue during extended use. The incorporation of vibration-reducing materials and adjustable handles helps operators maintain better control and reduce strain. Additionally, advanced filtration systems in the guns ensure that operators are not exposed to harmful dust or particles, improving workplace safety and comfort.
As the demand for customized finishes increases, powder coating guns will need to be more adaptable and versatile. Manufacturers are looking for guns that can handle a wide range of coatings, including metallic, textured, glossy, and matte finishes, with minimal setup changes. Multi-function guns that can easily switch between different powder types, colors, and finishes will be in high demand, particularly in industries like automotive and electronics, where custom designs are often required. The ability to apply coatings with varying thicknesses and effects will also require advanced control systems, ensuring that the coating is applied evenly and consistently across parts of different shapes and materials.
Another area of improvement is the precision of the electrostatic charge delivered by the gun. Advances in voltage control and charge distribution are allowing for more efficient coating application, even on complex geometries. The electrostatic force helps the powder adhere more effectively to the surface, reducing the chances of defects like runs, orange peel, or over-spraying. The more precise control over the electrostatic charge not only improves coating quality but also contributes to energy savings by reducing the amount of powder needed for each application.
As maintenance becomes a larger consideration, the future of powder coating guns will also include self-cleaning features and predictive maintenance capabilities. Self-cleaning mechanisms will help reduce downtime, ensuring that the guns remain operational for longer periods with minimal intervention. These systems will automatically clean the internal components, such as the powder flow paths and air filters, after each use or on a scheduled basis. Moreover, predictive maintenance algorithms will alert operators to potential issues before they lead to equipment failure. By monitoring the wear of critical components, such as the nozzle or the electrostatic charging system, the gun can predict when parts need to be replaced or serviced, thus reducing downtime and ensuring smooth operation.
Looking ahead, smart technologies such as Internet of Things (IoT) connectivity will be integrated into powder coating guns, enabling remote monitoring and real-time adjustments. IoT-enabled guns can send performance data directly to a cloud-based platform, where operators can analyze metrics such as powder usage, coating thickness, and transfer efficiency. This data can be used to optimize the coating process, adjust settings for different parts, and track the performance of multiple guns in a facility. IoT connectivity will also play a key role in remote diagnostics, allowing technicians to troubleshoot issues without needing to be physically present, reducing response times and improving overall system uptime.
As manufacturers continue to push for faster production cycles and higher throughput, powder coating guns will be developed to support high-speed operations without compromising on quality. Guns will need to apply coatings more quickly and efficiently, particularly in high-volume industries like automotive manufacturing, where parts move through the coating line at speeds that demand quick yet consistent application. Advanced guns with features like adjustable powder flow rates, optimized spray patterns, and quick-change nozzles will help meet these speed demands while still ensuring a high-quality finish.
The increasing complexity of coatings will also drive the development of multi-layer application systems, where different types of coatings are applied in a sequence to achieve specific performance characteristics. For example, a powder coating gun may be designed to apply a primer coat, followed by a top coat, and finally a clear coat in a seamless process. These systems will be particularly useful in industries like automotive and appliances, where multi-layer finishes are often required for both aesthetic and functional reasons, such as corrosion resistance and UV protection.
Finally, the global trend toward customization will push powder coating gun manufacturers to design systems that can easily accommodate a variety of part sizes, shapes, and materials. Whether it’s for small electronic components or large automotive parts, powder coating guns will need to be versatile enough to provide optimal results across a range of applications. The future of powder coating guns is set to be marked by flexibility, efficiency, sustainability, and intelligent systems, all of which will ensure that manufacturers can continue to meet the demands of an increasingly competitive and environmentally conscious marketplace.
As the powder coating industry continues to evolve, further innovations in material technology and equipment design will push the boundaries of what is possible with powder coating guns. The introduction of advanced coating materials, such as nano-coatings and composite powders, will require powder coating guns to handle new and often more challenging materials. These advanced coatings may require more precise application techniques, higher electrostatic charge control, and better flow regulation to ensure even coverage and optimal performance.
For instance, nano-powders offer superior properties such as increased scratch resistance, corrosion resistance, and enhanced heat resistance. The need to apply these coatings with the utmost precision will drive the development of more specialized guns capable of handling such demanding materials without compromising the final result. Powder coating guns will also need to adapt to the use of composite powders, which combine multiple materials to create coatings with enhanced mechanical properties or aesthetic finishes. The ability to apply these powders consistently across different substrates, without clumping or uneven distribution, will be essential.
Another area where powder coating guns are poised for improvement is in the realm of coating thickness control. Maintaining precise and uniform coat thickness is crucial for achieving the desired performance characteristics, such as durability, corrosion protection, and appearance. As the demand for more durable and high-performance coatings increases, especially in industries such as automotive and aerospace, the need for guns with better control over coating thickness will grow. Future powder coating guns will likely incorporate real-time monitoring systems that can adjust the powder flow rate, spray angle, and electrostatic charge to maintain consistent thickness throughout the application process.
Advances in automation will also enable powder coating guns to operate more autonomously. Guns may be equipped with auto-calibration systems that ensure they are always performing at their peak, even after a change in product type, powder material, or environmental conditions. These auto-calibration systems could adjust parameters like spray distance, powder flow, and spray pattern automatically, making it easier for operators to switch between different jobs without needing to manually reconfigure the equipment.
In addition, the growing demand for rapid changeover times will drive innovation in gun design to allow for quick swaps between different powder types, colors, and spray setups. The future of powder coating guns will likely include modular components that allow for easy customization and fast transitions, ensuring minimal downtime between jobs. This is especially important for industries that require frequent changes in product specifications, such as electronics manufacturers or furniture producers, where rapid adaptability can lead to increased productivity and cost savings.
The development of intelligent powder coating guns will go hand in hand with advancements in machine learning and artificial intelligence. Powder coating guns of the future could use AI-driven algorithms to optimize the coating process in real-time, analyzing variables such as part geometry, environmental conditions, and coating material to make adjustments on the fly. These intelligent systems would not only improve coating quality but also reduce material waste, as the guns could fine-tune the powder flow to match the specific needs of each part, ensuring that only the necessary amount of powder is applied.
The impact of sustainability on powder coating gun design will continue to be significant, particularly in the drive toward zero-waste operations. Powder coating guns will evolve to make better use of recycled powder and will be optimized for minimal powder loss. As environmental regulations become more stringent, manufacturers will demand guns that can operate efficiently with low-VOC powders and eco-friendly materials, such as biodegradable powders or powders derived from renewable sources. This will lead to the development of more energy-efficient guns, capable of applying these advanced powders while still maintaining high transfer efficiency and quality finishes.
Wireless technology and IoT integration will further transform powder coating guns by enabling them to become part of a connected network of equipment on the factory floor. Guns equipped with sensors and wireless connectivity will be able to send performance data to centralized monitoring systems, allowing operators to track and manage multiple coating lines simultaneously. These systems can provide real-time feedback on variables like powder usage, transfer efficiency, and gun performance, allowing manufacturers to optimize production processes and quickly address any issues that arise.
As part of this digital transformation, manufacturers will also have access to more advanced data analytics tools, which can analyze large datasets from the powder coating guns to uncover trends, inefficiencies, and opportunities for improvement. By harnessing this data, operators can make informed decisions about process adjustments, maintenance schedules, and even future investments in equipment upgrades.
The integration of augmented reality (AR) in the operation and maintenance of powder coating guns will also play a significant role in the future. AR technologies can assist operators by overlaying real-time visual information on the equipment, showing exactly how settings should be adjusted, or even providing step-by-step guides for troubleshooting and repairs. This will reduce training times and improve the accuracy of maintenance procedures, ensuring that the guns operate at peak performance.
Looking ahead, powder coating guns will continue to evolve to meet the challenges of an increasingly dynamic and competitive market. Advanced features such as higher transfer efficiency, better powder control, and integrated monitoring systems will drive improvements in quality, sustainability, and productivity. With innovations like AI-powered adjustments, modular designs, and sustainable materials, powder coating guns will play a critical role in helping manufacturers meet the growing demands for high-performance, environmentally friendly coatings.
In conclusion, the future of powder coating guns is bright, marked by technological advancements that not only improve efficiency and quality but also help manufacturers meet the growing demands for sustainability and versatility. As the industry continues to push for more precise, intelligent, and eco-friendly solutions, powder coating guns will remain an essential tool in the coating process, enabling manufacturers to produce high-quality finishes on a wide variety of products across diverse industries.
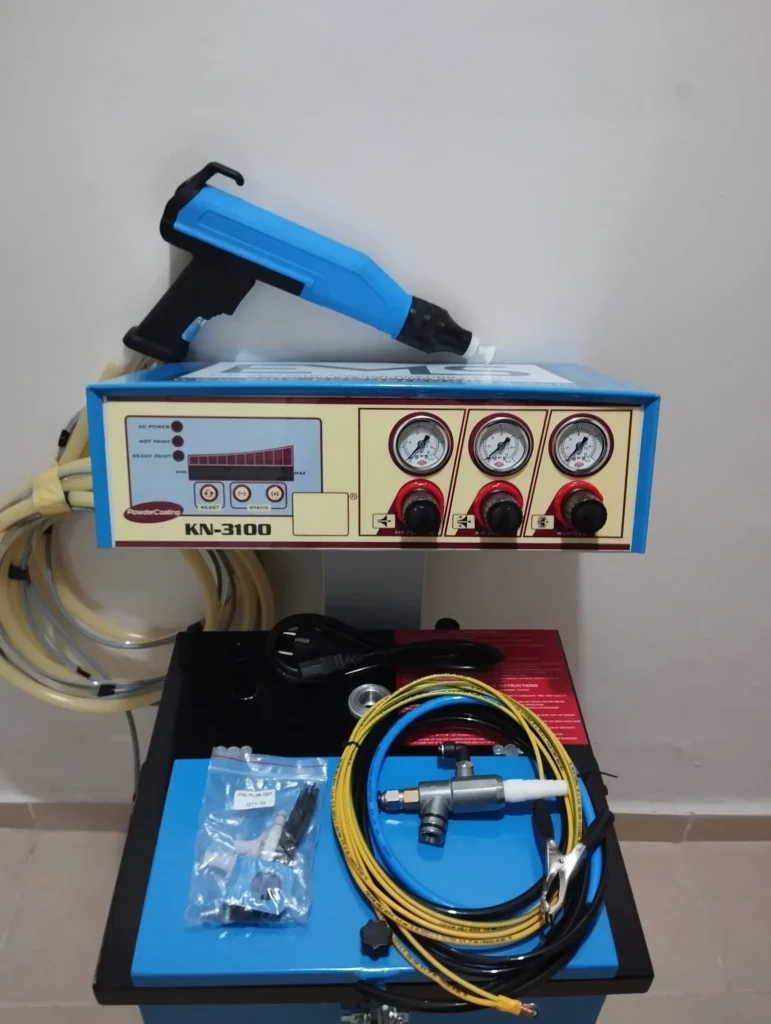
As we look further into the future, powder coating guns will likely evolve into even more automated and autonomous systems, significantly enhancing the manufacturing process. One of the key trends will be the integration of machine learning (ML) algorithms to optimize the coating process. These algorithms will enable the guns to continuously learn from past applications and adjust in real-time to achieve the best results for each specific job. For instance, machine learning models could predict and account for environmental changes, like humidity or temperature fluctuations, which can influence the coating’s performance. This adaptive capability will allow for consistent application quality, even in fluctuating conditions, thereby improving productivity and reducing the need for manual adjustments.
Moreover, future powder coating guns will likely be integrated with more advanced vision systems that can “see” and interpret the parts being coated. These vision systems could scan the object in real-time, recognize its shape, size, and features, and adjust the gun’s spray pattern and application technique accordingly. By doing so, these intelligent systems would ensure that every part receives the optimal amount of coating and at the correct angle, improving the uniformity of coatings on intricate geometries. This integration of computer vision with powder coating guns could significantly reduce waste by ensuring that the coating is applied only where it’s needed and in the precise amount required, further driving efficiency and reducing environmental impact.
The trend toward multi-functional and multi-material systems will also shape the future of powder coating guns. Powder coating technologies will need to handle a wide array of materials, including hybrid coatings that combine metallic powders, ceramic compounds, or even graphene-based powders for advanced applications. These next-generation powders could require adjustments in how the gun handles heat dissipation, powder flow, and electrostatic charging. Consequently, powder coating guns will need to be highly adaptable to a range of materials with varying particle sizes, shapes, and chemical compositions. The guns will likely incorporate advanced temperature control mechanisms to ensure that powders are applied in optimal conditions, regardless of their unique properties.
In line with the push for modularity and flexibility, the future of powder coating guns will likely involve customizable configurations that can be tailored for different industries or applications. Modular guns could allow for easy swapping of parts or nozzles, enabling companies to switch between coating different sizes and types of products without requiring significant downtime for reconfiguration. This modularity will be crucial for industries where fast changeovers and adaptability are essential, such as consumer electronics, automotive manufacturing, and appliance production.
Additionally, cloud-based technology will become a more integral part of powder coating systems. With cloud-connected powder coating guns, manufacturers will be able to monitor performance data and make real-time adjustments remotely. This will enable remote troubleshooting and predictive maintenance, reducing the need for on-site service calls and minimizing downtime. Predictive analytics can also forecast when maintenance is required, based on usage patterns, wear and tear, and other factors, thereby preventing potential malfunctions before they disrupt production.
The globalization of the manufacturing sector will drive further advancements in powder coating gun technology. With production facilities often operating in multiple regions or countries, there will be increasing demand for uniform performance standards across diverse environments. Powder coating guns will need to be equipped with systems that automatically adjust to regional differences in electricity supply, environmental conditions, and even regulatory standards related to coating materials and processes. This will make it easier for manufacturers to maintain consistent quality control across all their facilities, regardless of location.
Another area of focus will be user experience. Powder coating guns will become more intuitive to operate, with smart user interfaces that provide operators with real-time feedback and suggest the best settings for each specific task. These user interfaces could feature touchscreen controls, voice commands, or even gesture-based controls, making it easier for operators of all skill levels to achieve optimal results. Along with augmented reality (AR) tools, operators will be able to visually track the coating process, getting step-by-step guidance on setting adjustments, troubleshooting, and even maintenance procedures.
To address worker safety, especially in environments with high volumes of coating materials and volatile substances, future powder coating guns will likely incorporate advanced filtration and ventilation technologies. These systems will work to capture airborne particles and fumes, ensuring that workers are exposed to minimal risks. In addition to environmental safety, the design of powder coating guns will focus on enhancing the ergonomics to reduce strain during extended periods of use. Exoskeletal devices and wearable technology may even become commonplace, helping to reduce physical stress and fatigue, thus improving operator comfort and reducing the likelihood of injury.
The future of powder coating guns is also heavily influenced by a growing focus on customization in both industrial and consumer markets. As demand for personalized or specialized products rises, manufacturers will require highly flexible powder coating solutions capable of delivering unique finishes, patterns, and colors on a variety of substrates. Powder coating guns will need to provide precise control over things like color mixing, texture application, and finish variations, enabling manufacturers to create bespoke products that meet specific customer needs.
Finally, as regulatory pressures continue to mount globally, powder coating guns will increasingly be designed with environmental compliance in mind. Future innovations will include technologies that minimize energy consumption, improve air quality, and reduce hazardous emissions. Manufacturers will demand low-energy systems that can provide high-performance coatings while adhering to strict environmental standards. This trend will lead to the development of cleaner, greener powder coating solutions that have minimal impact on both the environment and workers’ health.
In conclusion, the evolution of powder coating guns is set to be characterized by a combination of intelligence, precision, automation, and sustainability. These advanced systems will allow manufacturers to improve coating quality, reduce waste, and increase operational efficiency, all while meeting the growing demand for more specialized, high-performance coatings. The integration of machine learning, AI, IoT, and cloud technologies will transform the powder coating process, enabling manufacturers to optimize every aspect of the coating operation from application to maintenance, leading to higher quality products, better environmental stewardship, and a more competitive edge in the marketplace.
As we look further into the future of powder coating guns, several other emerging technologies and trends will continue to shape their evolution, positioning these systems at the heart of advanced manufacturing. A key area of progress will be the development of adaptive coating systems that can automatically fine-tune application settings based on the material and geometry of the parts being coated. For example, powder coating guns could use advanced sensors to detect the type of substrate and adjust the electrostatic charge, powder flow, and spray pattern accordingly. This would ensure that no matter the material—be it aluminum, steel, plastics, or more delicate substrates—the powder is applied in the most efficient and optimal manner.
The trend toward intelligent systems will not only focus on real-time optimization but also on data-driven decision-making. Advanced powder coating guns will generate vast amounts of data, including powder consumption rates, application efficiency, environmental conditions, and coating results. This data will be continuously analyzed and used to predict and prevent common coating problems such as orange peel, wrinkles, or insufficient coverage. By leveraging big data analytics, manufacturers can develop better quality control practices, pinpoint inefficiencies, and make improvements without the need for manual intervention. This would enhance quality assurance across the entire production line, reducing defects and enhancing the overall reliability of the powder coating process.
The future of powder coating guns will also see the rise of collaborative robots (cobots) that work alongside human operators, providing an extra layer of efficiency and precision. Cobots, equipped with powder coating guns, will be able to work in tandem with human operators to coat intricate parts, ensuring that all the hard-to-reach areas are thoroughly covered. These robots will be capable of adjusting their movements and spray parameters based on feedback from integrated sensors and real-time adjustments, optimizing the coating process for each individual part. Cobots could also perform repetitive tasks such as cleaning or maintenance checks, freeing up human workers to focus on more complex activities.
Further, as manufacturers strive for greater sustainability, powder coating systems will evolve to meet circular economy principles. The concept of a circular economy encourages the reuse, recycling, and repurposing of materials rather than creating waste. This means that recycled powders will become an integral part of future systems, and powder recovery technologies will continue to improve. Advanced systems will capture virtually all oversprayed powder, even from intricate geometries, for recycling and reuse in future batches. Furthermore, powder coating guns will be designed to support eco-friendly powders that contain fewer volatile organic compounds (VOCs) and are made from renewable resources. These innovations will help meet global sustainability goals and ensure that the powder coating process remains environmentally responsible.
Another important development will be the ability of powder coating guns to apply multi-layer coatings in a single pass. In industries such as automotive, aerospace, and appliances, multi-layer coatings are essential for achieving complex finishes that offer both aesthetic appeal and functional performance. Future powder coating guns could be equipped with multi-material spray systems that allow different powders—each with its own properties and characteristics—to be applied simultaneously in different layers. This could streamline production, reduce material waste, and improve coating consistency, especially for high-performance coatings that require multiple distinct layers (such as primers, base coats, and clear coats).
The integration of augmented reality (AR) will also play a major role in improving both the operation and maintenance of powder coating guns. For example, AR glasses could be used by operators to receive real-time information directly overlaid onto the equipment as they work, including guidance on optimal settings, real-time adjustments, or maintenance schedules. This hands-free access to data will allow operators to make quicker decisions, troubleshoot problems more effectively, and enhance their overall productivity. Furthermore, AR could be used in training programs, enabling new operators to learn how to set up and maintain the equipment by following step-by-step virtual guides, reducing training time and improving skill levels.
Additionally, the growth of additive manufacturing (3D printing) will likely influence the development of powder coating guns, as new coating needs arise from increasingly complex and customized parts. 3D printing technologies often produce parts with intricate geometries that are difficult to coat using traditional methods. Powder coating guns will need to evolve to provide highly targeted and controlled application to accommodate these parts, ensuring uniform coverage while preventing overspray. The rise of 3D-printed parts also means that there will be a greater demand for coatings that provide advanced properties such as heat resistance, abrasion resistance, and electromagnetic shielding, driving the development of new powder formulations and coating techniques.
Modular and portable systems will become more common as manufacturers seek greater flexibility in their operations. In industries like construction, furniture manufacturing, and electronics, portable powder coating guns will enable coating applications in different locations, even in field conditions. These systems will be designed for ease of transport and quick setup, allowing for on-site powder coating without the need to bring parts back to a central facility. As powder coating becomes more flexible and accessible, companies will be able to coat parts directly where they are produced or used, reducing handling time and operational costs.
The push for faster production times will also influence the development of powder coating guns capable of high-speed applications. As industries demand faster turnaround times, especially in mass production environments like automotive and consumer goods, powder coating guns will need to apply coatings more rapidly without sacrificing quality. Future systems will likely incorporate advanced technologies such as high-efficiency nozzles, high-speed electrostatic charging, and fast-drying powders, enabling manufacturers to meet tighter production schedules while maintaining high-quality finishes.
Looking ahead, the evolution of powder coating guns will not only be driven by technological advancements but also by the ever-changing demands of the global marketplace. Manufacturers will continue to push for more customizable solutions, enhanced coating durability, and lower environmental impact. Powder coating guns will become essential tools in delivering innovative and sustainable solutions that can handle a diverse range of applications, from luxury finishes to high-performance industrial coatings. Their ability to adapt to emerging technologies, materials, and manufacturing trends will keep them at the forefront of coating technology for years to come.
In summary, the future of powder coating guns will be characterized by intelligent automation, customization, sustainability, and advanced technologies that cater to an increasingly complex and demanding manufacturing landscape. As industries embrace digitalization, new materials, and higher performance standards, powder coating guns will continue to evolve, delivering high-quality coatings in more efficient, adaptable, and environmentally friendly ways. These innovations will play a crucial role in helping manufacturers stay competitive, meet customer expectations, and achieve their sustainability goals.
Low-energy Painting Systems
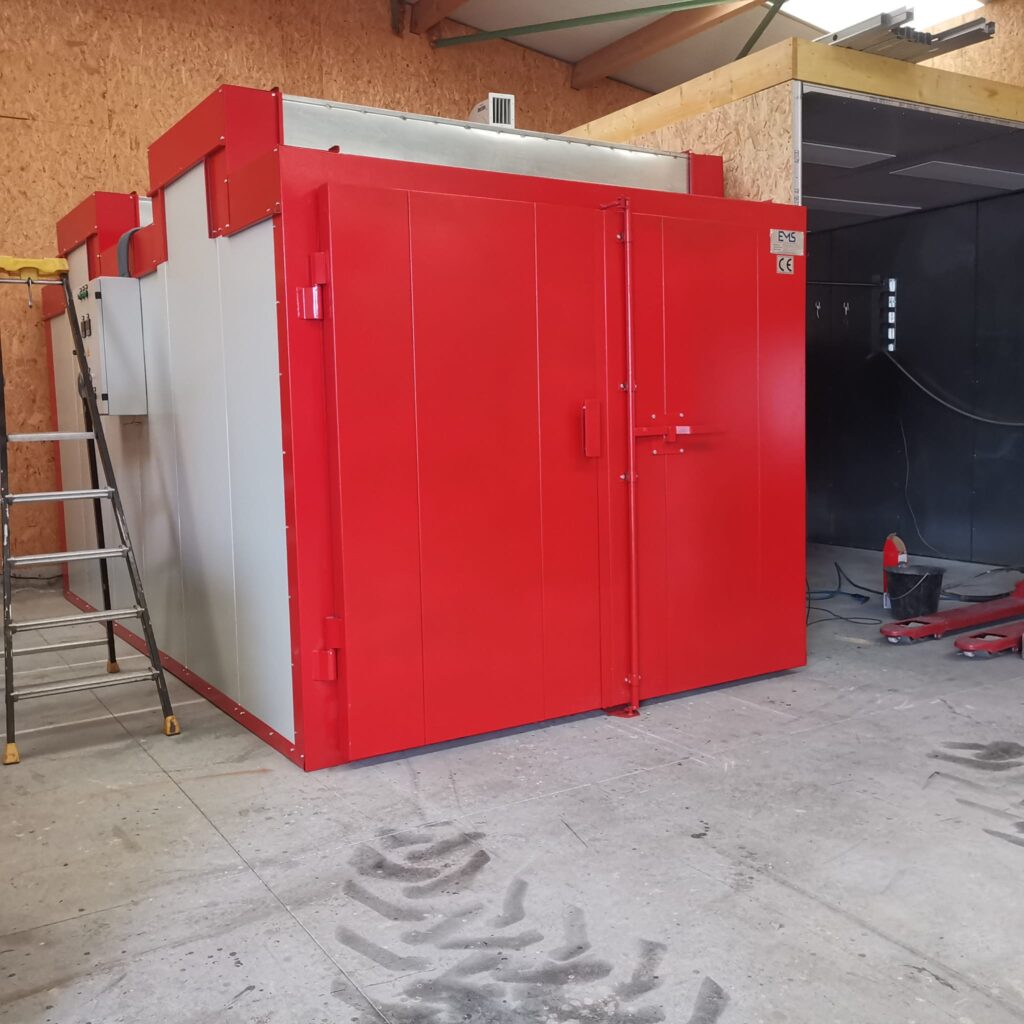
The future of low-energy painting systems is marked by a shift toward enhanced efficiency, sustainability, and automation, with a growing focus on reducing both energy consumption and environmental impact. As industries push for more eco-friendly solutions, these systems will incorporate advanced technologies and innovative materials designed to minimize energy use while maintaining high performance and quality finishes. Here’s a detailed look at what lies ahead for low-energy painting systems.
1. Energy-efficient technologies will be central to the development of low-energy painting systems. Traditional painting processes often involve significant energy consumption due to heating ovens, drying times, and the operation of equipment such as spray booths. The next generation of systems will integrate advanced heating techniques like infrared (IR) radiation or electromagnetic induction to provide localized, high-efficiency heating. These methods heat only the painted surface, reducing the amount of energy needed to dry or cure coatings. Infrared curing, for example, offers faster curing times at lower temperatures, helping to reduce energy consumption and improve throughput.
Additionally, low-energy drying systems will be improved. Traditional systems often require long drying times and high-temperature ovens to fully cure coatings. Future systems will leverage airflow optimization, infrared light, or ultraviolet (UV) curing technologies to drastically cut energy consumption while maintaining the high quality of finishes. UV curing, in particular, is gaining popularity in low-energy painting systems due to its speed and low heat output, reducing both energy costs and processing time.
2. The rise of eco-friendly coatings will significantly impact low-energy painting systems. The demand for low-VOC (volatile organic compound) and water-based coatings is on the rise due to increased environmental regulations and consumer demand for more sustainable products. These advanced coatings typically require lower curing temperatures, which makes them more compatible with energy-efficient technologies. Powder coatings are also becoming more prominent in low-energy systems because they can be applied without solvents, reducing harmful emissions and energy use. As eco-friendly coatings continue to evolve, they will be designed to cure more quickly and at lower temperatures, making them ideal for low-energy painting applications.
3. Automation and smart technologies will play a crucial role in optimizing the energy efficiency of painting systems. Future low-energy painting systems will integrate smart sensors and real-time monitoring systems that can adjust parameters such as temperature, spray pressure, and airflow based on the specific characteristics of each part. These systems will use machine learning algorithms to predict and adjust settings in real-time, optimizing energy usage and reducing waste. For instance, smart systems could automatically adjust the spray gun’s settings based on the part’s shape or material to minimize overspray and improve transfer efficiency, ensuring that energy and resources are used as efficiently as possible.
Additionally, predictive maintenance powered by data analytics will become a standard feature in low-energy painting systems. By monitoring equipment performance and identifying issues before they lead to downtime, manufacturers can ensure that their systems are always operating at peak efficiency, reducing energy waste and unplanned maintenance costs.
4. More energy-efficient pumps, fans, and air handling systems will be designed to reduce the overall energy footprint of low-energy painting systems. High-efficiency motors, variable-speed drives, and smart air recirculation systems will be integrated to minimize the energy used by equipment during the painting process. For example, airless spray guns will continue to improve, providing higher transfer efficiency and reducing the amount of compressed air needed. Meanwhile, automated air handling systems will recirculate air through the painting booth more efficiently, maintaining consistent temperature and humidity levels while using less energy.
5. Sustainable energy sources will increasingly be adopted to power low-energy painting systems. As the manufacturing sector continues to adopt greener practices, many painting systems will be powered by renewable energy sources like solar or wind power. In some cases, manufacturers may incorporate on-site energy generation or energy storage systems, reducing reliance on the grid and further lowering their environmental impact. This shift toward sustainable energy will be coupled with more energy-efficient machinery that can better integrate with these renewable energy systems, ensuring that painting operations remain energy efficient and cost-effective.
6. Integration with Industry 4.0 will continue to be a key factor in the evolution of low-energy painting systems. The increased use of connected devices and cloud computing will allow manufacturers to track energy consumption, detect inefficiencies, and optimize production processes remotely. By collecting data from painting systems and using advanced data analytics tools, manufacturers will be able to make more informed decisions about energy use and identify opportunities for energy savings. For example, painting systems could be programmed to use less energy during non-peak hours, further reducing costs and minimizing environmental impact.
7. Focus on lightweight, energy-efficient materials will drive new developments in low-energy painting systems. As industries like automotive and aerospace demand lighter materials for their products, low-energy painting systems will need to accommodate these changes. Lightweight materials, such as composite materials or aluminum, often require different coating techniques compared to traditional materials like steel. Low-energy systems will need to incorporate specialized spray techniques that optimize coating efficiency on these materials while keeping energy consumption low. Additionally, systems will need to adjust their curing processes to accommodate the unique properties of these lightweight materials, ensuring the coatings perform at the highest standards without using excessive energy.
8. Compact and mobile painting systems will gain traction in sectors where flexibility is key. The demand for on-the-go painting solutions will rise, especially in industries like construction, maintenance, and repair services. These mobile systems will be designed to be energy-efficient while offering flexibility in terms of location and application. Innovations in battery-powered painting systems and portable, low-energy curing technologies will allow companies to bring the painting process directly to the field, reducing setup times and cutting down on energy consumption associated with large, fixed paint booths.
9. Energy recovery systems will also play an increasing role in the future of low-energy painting systems. These systems capture and reuse heat that would otherwise be wasted, such as heat from exhaust air, to pre-heat incoming air or materials, thus reducing the overall energy load on the system. Waste heat recovery technologies can reduce the demand for external heating sources, making the entire painting process more energy-efficient and cost-effective. Furthermore, water-based cleaning technologies will be integrated into these systems to reduce water and chemical usage, ensuring that energy recovery systems are part of a broader zero-waste strategy.
10. Low-energy curing ovens will undergo significant advancements. New designs will incorporate modular ovens that are more energy-efficient and capable of quickly adapting to different part sizes and coating requirements. Hybrid curing ovens that combine both UV and infrared curing technologies will allow manufacturers to choose the most energy-efficient method based on the part they are coating. This flexibility will help optimize energy use, reduce curing times, and support a wider variety of coatings, from low-VOC to high-performance finishes.
In conclusion, the future of low-energy painting systems will focus on cutting-edge technologies, eco-friendly solutions, and intelligent automation to reduce energy consumption and environmental impact. By incorporating innovations such as advanced curing technologies, renewable energy sources, and smart sensors, low-energy painting systems will provide manufacturers with the tools they need to meet sustainability targets without compromising the quality of their coatings. As industries evolve and sustainability demands increase, low-energy painting systems will be at the forefront of a green revolution in manufacturing, providing cost-effective and environmentally responsible solutions for a wide range of applications.
As the demand for sustainable and cost-effective solutions continues to grow, low-energy painting systems will not only be driven by technological advancements but also by evolving regulatory frameworks and consumer expectations. These systems will increasingly be designed to meet stringent environmental standards and industry regulations while also offering flexibility to cater to a wide range of industries. Let’s explore further how these systems will evolve.
11. Integration of Artificial Intelligence (AI): In the future, AI will become integral to optimizing the operation of low-energy painting systems. AI-powered systems will continuously learn and adapt based on performance data, enabling them to autonomously optimize key variables such as temperature, flow rate, and spray patterns to achieve the desired coating quality while minimizing energy consumption. AI-driven process control will help predict when maintenance is required, ensuring that systems operate at peak efficiency and reduce downtime. Additionally, AI can analyze data from multiple sources across the production line, allowing manufacturers to fine-tune the entire coating process and identify patterns of energy waste or inefficiency, further reducing operational costs and environmental impact.
12. Advances in Coating Formulations: Coatings are likely to evolve further, becoming more energy-efficient themselves. For instance, self-curing coatings or high-solid content coatings could be developed, allowing for faster curing at lower temperatures. These coatings, which have a higher proportion of solids and less solvent content, require less energy to cure while offering superior performance. As coatings become more specialized for particular applications, manufacturers will also see more custom formulations that enhance the energy efficiency of low-energy painting systems. Coatings with enhanced adhesion properties will require fewer layers, further reducing energy use during the curing and drying processes.
13. Focus on Resource Recovery: Beyond energy, the next generation of low-energy painting systems will also focus on optimizing resource recovery in other areas. For example, systems will be developed to recycle excess paint and reclaim oversprayed material, reducing waste and minimizing the need for new resources. In systems where solvent-based paints are still in use, improved solvent recovery and regeneration systems will be implemented to clean and reuse solvents, minimizing the environmental impact of these substances. Similarly, systems will be designed to recover and filter air pollutants, such as volatile organic compounds (VOCs) and particulate matter, before they are released into the environment. These waste management solutions will enhance the sustainability profile of low-energy painting systems while reducing the operational costs of maintaining environmental compliance.
14. Enhanced Digital Connectivity: With the increasing adoption of Internet of Things (IoT) devices and cloud technologies, low-energy painting systems will become more interconnected, allowing manufacturers to monitor performance remotely and access real-time data on energy use, coating quality, and system efficiency. Cloud-based platforms will enable manufacturers to perform predictive maintenance, analyze historical data to optimize future operations, and ensure continuous improvement in energy efficiency. By integrating low-energy painting systems into broader smart factory ecosystems, manufacturers will be able to leverage data from various production stages to create more sustainable and energy-efficient processes across the entire production line. IoT-enabled systems will also facilitate remote troubleshooting and diagnostics, reducing the need for on-site service visits and minimizing downtime.
15. Smaller and Modular Systems for Custom Applications: As industries demand more flexibility, low-energy painting systems will be designed to be modular and easily adaptable to different production requirements. Smaller, modular systems will enable manufacturers to easily scale up or down, depending on production volume and part size. These systems will be highly customizable to accommodate the unique needs of industries such as aerospace, automotive, and consumer electronics, where precise control over coating thickness, finish, and curing time is critical. For example, modular spray booths could be designed for easy expansion, with integrated energy-saving features such as automated air recirculation and zone-specific heating controls to optimize energy consumption based on the size of the part being coated.
16. Low-energy Spray Technologies: In conjunction with the evolution of coating formulations, spray technologies will continue to improve to support low-energy painting systems. Electrostatic spray guns will become more advanced, with better charging efficiency, reduced overspray, and improved coating uniformity, allowing for less powder or paint to be wasted and ensuring a more efficient transfer to the surface. Additionally, technologies like airless spraying will become more refined, offering higher transfer efficiency and faster application, all while requiring less energy than traditional air-assisted spray systems. Furthermore, the development of low-pressure or HVLP (High Volume Low Pressure) spray equipment will enable lower energy consumption and reduced material waste, while still achieving a smooth, consistent finish.
17. Sustainable Facility Design: In parallel with technological innovations in the painting process itself, future low-energy painting systems will be part of a larger trend toward sustainable facility design. Painting booths, curing ovens, and related infrastructure will be optimized for energy efficiency, utilizing insulation materials, passive heating and cooling, and natural lighting to minimize reliance on artificial energy sources. For example, facilities may integrate green roofs or solar panels to reduce energy consumption and take advantage of renewable energy. Additionally, smart building technologies will be incorporated into painting facilities to monitor and control energy use in real-time, adjusting lighting, heating, and ventilation systems based on the needs of the production process.
18. Collaboration and Industry Standards: As the demand for low-energy solutions grows, the industry will likely see increased collaboration between equipment manufacturers, coating suppliers, and regulatory bodies to establish universal standards for energy-efficient painting processes. These standards will help ensure that low-energy painting systems meet the highest environmental performance benchmarks, promoting the adoption of best practices across industries. Furthermore, industry collaboration will drive knowledge-sharing, enabling manufacturers to stay ahead of regulatory changes, such as carbon emissions reduction goals and the implementation of circular economy principles, while benefiting from the latest innovations in low-energy coating technology.
19. Cost Savings and Return on Investment (ROI): As low-energy painting systems continue to evolve, manufacturers will increasingly recognize the long-term cost savings associated with these technologies. While the initial investment in energy-efficient equipment may be higher, the return on investment (ROI) will be driven by the reduced energy consumption, lower maintenance costs, and improved material usage efficiency. Additionally, the ability to meet sustainability goals and reduce carbon footprints will become a key differentiator in competitive markets, further enhancing the financial and reputational benefits of adopting low-energy painting systems.
20. Focus on Global Impact and Supply Chain Sustainability: Lastly, as the pressure to address climate change and reduce environmental impact intensifies, the adoption of low-energy painting systems will play an essential role in meeting global sustainability targets. Manufacturers will need to consider not only the energy consumption of their painting processes but also the entire supply chain’s environmental footprint, from the sourcing of raw materials to the disposal of waste. By implementing low-energy systems, manufacturers can contribute to a greener supply chain, reduce their environmental liabilities, and align their operations with global sustainability initiatives, such as the Paris Agreement or United Nations Sustainable Development Goals (SDGs).
In summary, the future of low-energy painting systems will be shaped by cutting-edge technologies, sustainable practices, and intelligent automation. These systems will help manufacturers achieve higher levels of efficiency, quality, and environmental responsibility, offering a holistic approach to reducing energy consumption and waste while meeting the diverse needs of modern industries. Through innovations in smart technologies, eco-friendly coatings, and energy recovery, low-energy painting systems will play a critical role in the future of sustainable manufacturing.
As we look even further into the future of low-energy painting systems, several additional trends and emerging technologies are likely to shape their continued evolution. These advancements will address the increasing need for automation, cost reduction, and environmental responsibility across industries. Here’s a deeper dive into how these systems will continue to evolve:
21. Advances in Coating Material Development: The development of novel coating materials will further impact low-energy painting systems. With growing interest in biodegradable and natural material-based coatings, there will be an emphasis on producing environmentally friendly formulations that not only reduce energy use but also have a lower environmental footprint throughout their lifecycle. Bio-based coatings, for example, will leverage materials like plant oils or natural resins, offering a more sustainable alternative to petroleum-based coatings. These materials will require less energy to manufacture and apply, contributing to a more efficient and green painting process.
22. Hybrid Systems for Diverse Coating Applications: The future of low-energy painting systems will likely involve hybrid technologies that combine different coating methods to optimize energy efficiency. For instance, a hybrid system might combine powder coating with liquid spray or UV curing, depending on the specific requirements of the part being coated. Hybrid systems will provide the flexibility to handle a wider range of coatings with varying curing requirements while still keeping energy consumption low. This will be especially important in industries like automotive manufacturing or consumer electronics, where different finishes and functionalities are required for various parts.
23. Enhanced Recycling and Waste Reduction: In addition to reducing energy consumption, low-energy painting systems will increasingly focus on minimizing waste across the entire coating process. The development of closed-loop systems will ensure that oversprayed paint, solvents, and even the air used in spray booths are captured, filtered, and either recycled or repurposed. New recycling technologies will allow manufacturers to reclaim more material than ever before, reducing reliance on raw materials and minimizing disposal costs. Zero-waste systems will become more prevalent as part of the ongoing push toward sustainability and responsible resource management.
24. Automation and Robotics for Precision: The integration of robotics and automation into low-energy painting systems will continue to grow. Robotic arms equipped with advanced vision systems will precisely apply coatings to parts with intricate shapes, ensuring even coverage with minimal waste. These robots can be programmed to adapt to different part sizes and configurations, further optimizing energy use by adjusting spray parameters based on the shape and material of the workpiece. Automated systems will also improve the precision of curing times and temperatures, reducing energy use by ensuring parts are only subjected to the exact amount of heat needed for optimal curing.
25. Integration with Sustainability Standards: The increasing demand for green certifications and adherence to international environmental standards will push manufacturers to adopt low-energy painting systems that not only reduce energy consumption but also meet increasingly stringent regulatory requirements. This includes certifications such as ISO 14001 (Environmental Management) and LEED (Leadership in Energy and Environmental Design). These standards ensure that the entire coating process, from materials to energy use, meets global sustainability benchmarks. In the future, low-energy painting systems will be required to integrate seamlessly with sustainability reporting tools, enabling manufacturers to easily track and report their environmental impact.
26. Advanced Simulation Tools for Process Optimization: The role of simulation software will continue to grow in the design and optimization of low-energy painting systems. Using computer-aided design (CAD) and finite element analysis (FEA), manufacturers will be able to simulate the painting process to optimize energy usage before actual production begins. These tools will enable more precise simulations of coating thickness, curing time, and spray patterns, ensuring that energy consumption is minimized while achieving the desired quality. By optimizing the process upfront, manufacturers will avoid unnecessary energy expenditure during the actual production phase.
27. Energy Efficiency through Supply Chain Collaboration: The future of low-energy painting systems will involve more collaborative efforts between manufacturers, coating suppliers, and equipment providers. Manufacturers will increasingly work closely with coating suppliers to ensure that the coatings they choose are optimized for energy-efficient application methods. In turn, coating suppliers will develop formulations that are compatible with low-energy systems, ensuring that they can be applied with minimal energy input and still achieve high-quality results. By aligning the entire supply chain around the goal of energy efficiency, manufacturers will be able to further streamline their operations and reduce overall environmental impact.
28. Real-time Performance Monitoring and Feedback: The increasing prevalence of real-time data monitoring and feedback loops in low-energy painting systems will enable manufacturers to quickly adjust processes to maintain energy efficiency. Advanced sensors embedded in spray booths, curing systems, and booths will collect data on variables like temperature, humidity, spray rate, and energy consumption. This data will be analyzed by machine learning algorithms to provide dynamic recommendations for reducing energy consumption, improving coating quality, and minimizing waste. Operators will receive instant feedback on their processes, enabling them to make immediate adjustments to optimize efficiency without sacrificing performance.
29. Carbon Capture and Offset Solutions: As part of the broader commitment to carbon neutrality, some low-energy painting systems will integrate carbon capture technologies to further reduce their environmental impact. These systems will capture carbon dioxide (CO2) emissions generated during the coating process and either store or repurpose them for use in other processes, such as manufacturing biofuels or chemicals. Additionally, carbon offset programs will play an important role in helping manufacturers achieve carbon neutrality by investing in projects that absorb or offset the environmental impact of their operations.
30. Global Expansion of Energy-Efficient Standards: As global pressure to combat climate change increases, there will be a global push for more energy-efficient industrial practices, including painting processes. Countries and regions around the world will introduce stricter energy efficiency standards for industrial processes. As these regulations expand, low-energy painting systems will become increasingly essential for businesses seeking to comply with local and international environmental laws. This trend will drive the global adoption of energy-efficient systems, pushing manufacturers to adopt cutting-edge technologies and best practices to stay competitive and compliant.
31. Green Building Initiatives in Construction: With the rise of sustainable construction and the growing focus on green building initiatives, low-energy painting systems will find an increasing role in the construction industry. These systems will be used to coat building materials such as metal cladding, pre-painted panels, and concrete surfaces, contributing to the overall energy efficiency and sustainability of buildings. The coatings applied in construction will be designed to minimize energy use, improve the insulation properties of surfaces, and reduce the environmental impact of the building’s life cycle.
32. Reduction in Total Cost of Ownership (TCO): As low-energy painting systems become more advanced, the overall total cost of ownership (TCO) will decrease. The reduction in energy use, maintenance costs, and material waste will result in lower operational expenses for manufacturers. Moreover, as energy-efficient technologies become more widely adopted, the initial investment costs of these systems will likely decrease as economies of scale take effect. Over time, manufacturers will see improved profit margins due to reduced energy bills, fewer maintenance costs, and more efficient production cycles.
33. Collaborative Industry Research and Development: The future of low-energy painting systems will also be shaped by collaborative R&D between industrial companies, research institutions, and government agencies. As the demand for low-energy, eco-friendly solutions grows, public and private sector players will increasingly invest in developing new technologies and materials that will help reduce energy consumption in coating applications. Collaborative R&D initiatives will focus on everything from coating formulations and spray technologies to the energy recovery systems that power painting operations, creating a more innovative and sustainable industry.
In conclusion, the future of low-energy painting systems will be driven by continuous innovation, environmental responsibility, and technological integration. These systems will play a central role in creating more sustainable manufacturing practices and reducing the overall environmental impact of the coating process. By leveraging advanced technologies like AI, automation, renewable energy, and eco-friendly materials, low-energy painting systems will not only reduce energy consumption but also contribute to a more circular economy, ensuring that resources are used efficiently and sustainably throughout their lifecycle.
Powder Spraying Production Line
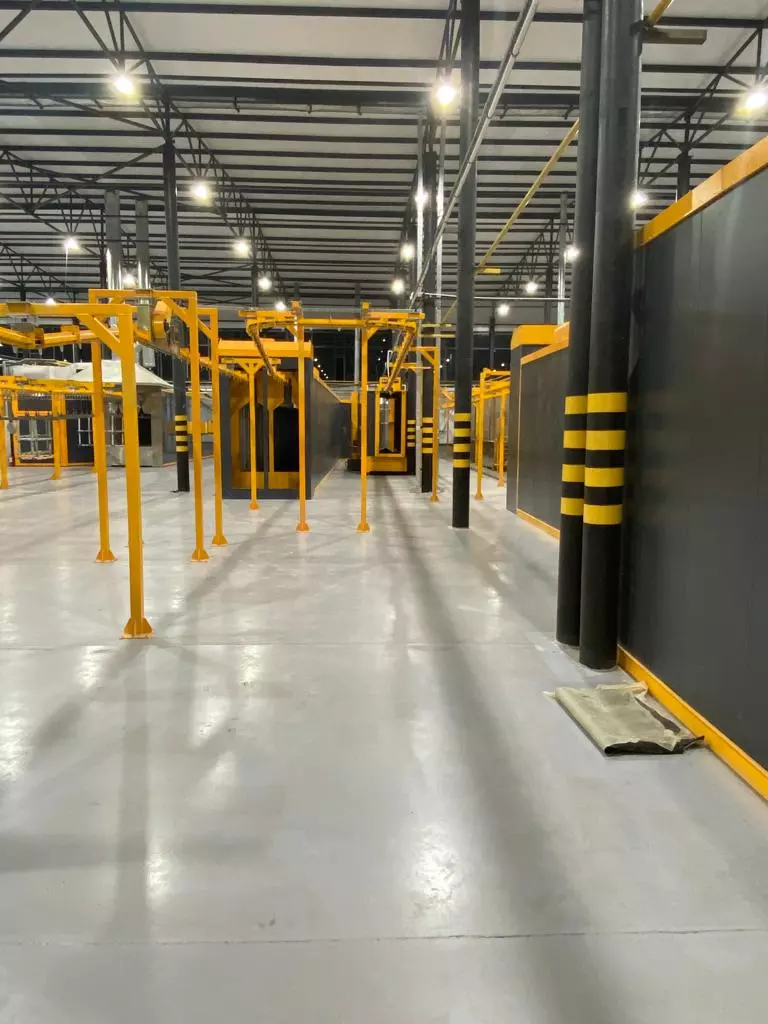
The future of the powder spraying production line is characterized by an ongoing transformation driven by advancements in technology, environmental concerns, and the demand for higher productivity and efficiency. These production lines are critical in industries such as automotive, aerospace, furniture, electronics, and heavy machinery, where a durable and high-quality finish is required. As with other manufacturing processes, the evolution of powder spraying production lines is being influenced by a need for sustainability, cost-effectiveness, and technological innovations.
1. Energy Efficiency and Sustainability: The demand for energy-efficient systems will continue to grow as industries and governments focus on reducing carbon footprints and minimizing energy consumption. Modern powder spraying production lines will incorporate energy-saving features such as recuperative heat systems, smart control panels, and energy-efficient curing ovens. These systems will operate at optimized levels of energy consumption, reducing the operational cost for manufacturers. Furthermore, the use of renewable energy sources, such as solar or wind power, to power these systems will become more widespread. The implementation of waste recovery systems to reclaim and reuse powder overspray and other materials will also play a key role in reducing environmental impact and improving efficiency.
2. Advanced Powder Recovery Systems: Powder recovery and reuse will become an increasingly important part of the powder spraying production line. New technologies in cyclonic powder recovery systems, fluidized bed recovery, and electrostatic powder collection will make it possible to reclaim up to 99% of the powder that would otherwise be wasted. These advanced systems will help manufacturers reduce costs by minimizing material waste and providing a more economical way to use powder materials. Additionally, automated cleaning systems will help ensure that recovery systems remain highly effective without needing frequent manual intervention, further optimizing production efficiency.
3. Automation and Robotics: The integration of robotics and automation will continue to be a defining feature of the powder spraying production line of the future. Robotic arms equipped with advanced vision systems will be able to precisely and consistently apply powder coatings to a wide variety of parts, from small components to large industrial items. Robots will be capable of adjusting their application parameters based on the shape and size of the part, which will significantly reduce material waste and improve transfer efficiency. Automation in powder spraying production lines will also enhance repeatability and consistency in coating quality, which is critical in high-precision industries like aerospace and electronics. Furthermore, automated systems will optimize curing times and temperatures, ensuring the coatings achieve maximum performance while minimizing energy consumption.
4. Real-time Monitoring and Control: Future powder spraying production lines will rely heavily on real-time monitoring systems to ensure optimal performance throughout the entire coating process. Sensors and smart controllers will gather data on key factors such as spray gun performance, powder application rates, humidity, temperature, and oven efficiency. This data will be analyzed in real-time to adjust processes on-the-fly, ensuring consistent coating quality and minimizing energy use. This data-driven approach will help operators identify issues early, reducing the risk of defects and rework, and improving overall system reliability and uptime.
5. Improved Powder Coating Materials: The powder coating industry will see significant advancements in coating formulations designed for specific applications. New materials will be developed to offer enhanced durability, aesthetic appeal, and environmental performance. For instance, thermoplastic powders that can be re-melted and re-formed will gain popularity due to their ability to be recycled. Furthermore, low-cure powder coatings will become more common, as they allow for energy savings during the curing process by requiring lower temperatures to achieve the desired finish. Additionally, nano-coatings and specialty powders with enhanced corrosion resistance, scratch resistance, or UV protection will be developed, offering manufacturers more versatile and sustainable options.
6. Integration with Smart Factory and Industry 4.0: As industries adopt Industry 4.0 practices, powder spraying production lines will become increasingly interconnected within the broader smart factory ecosystem. This will involve the integration of Internet of Things (IoT) sensors, cloud computing, and big data analytics to provide comprehensive insights into production processes. The ability to monitor and control multiple production lines remotely will allow manufacturers to make real-time adjustments, reducing downtime and increasing overall operational efficiency. With predictive maintenance, powered by AI and machine learning algorithms, production lines will be able to forecast when components need servicing, reducing unplanned breakdowns and increasing the longevity of equipment.
7. Multi-Stage Coating Systems: In response to growing customer demand for more complex finishes, future powder spraying production lines will increasingly feature multi-stage coating processes. These systems will apply multiple layers of powder coatings with varying properties, such as adhesion, anti-corrosion, and aesthetic appeal, to ensure the final product meets the required specifications. For example, an initial epoxy powder layer might be followed by a polyester topcoat for enhanced UV resistance and color retention. Multi-stage coating systems will be optimized for energy efficiency, ensuring each layer is applied and cured with minimal waste and energy consumption.
8. Enhanced User Interface and Control Systems: As the complexity of powder spraying production lines increases, so will the need for more intuitive and user-friendly control interfaces. These systems will feature touchscreen panels, augmented reality (AR) interfaces, and voice control to allow operators to easily monitor and control multiple production parameters. Additionally, operators will be able to access data remotely via cloud-based platforms, which will enable them to adjust processes, troubleshoot issues, and access real-time feedback from any location. This shift towards more accessible control systems will improve operator efficiency and reduce the chances of human error during the coating process.
9. Customization and Flexibility: Manufacturers will increasingly demand flexible powder spraying production lines that can be easily customized to meet the unique needs of different industries and parts. Future lines will feature modular components that can be easily reconfigured to handle different types of products, coating requirements, and production volumes. For instance, a line could be adapted to coat automotive parts one day and electronics enclosures the next. Quick-change systems will enable the rapid adjustment of spray guns, curing ovens, and conveyor systems, reducing downtime between runs and enabling manufacturers to be more responsive to customer needs.
10. Advanced Curing Technologies: The curing process plays a pivotal role in determining the quality and durability of powder coatings. The future of curing will involve the integration of ultraviolet (UV) curing and infrared (IR) heating systems to further reduce energy consumption. UV curing systems, for example, will provide instant curing capabilities, especially for thinner coatings, while IR heaters will target specific areas of the part to reduce heat loss and energy use. These technologies will provide faster curing times, greater energy savings, and superior coating performance.
11. Smart Logistics and Workflow Optimization: Future powder spraying production lines will be highly integrated with smart logistics systems that enable seamless workflows from material handling to coating and curing. Automated material transport systems (e.g., conveyors, AGVs) will ensure that parts are moved efficiently through each stage of production. These systems will be dynamically adjusted based on real-time data, optimizing production flow and reducing bottlenecks. Additionally, inventory management systems will be tied directly to the production line, ensuring that powder materials, tools, and parts are always available when needed, reducing downtime caused by material shortages.
12. Focus on Worker Safety and Ergonomics: With the increasing complexity of powder spraying production lines, the need for worker safety and ergonomics will become even more important. New advancements in personal protective equipment (PPE), such as smart suits that monitor worker health, will help reduce exposure to harmful chemicals and improve worker safety. Additionally, ergonomic design of workstations and automated material handling systems will reduce worker fatigue and injury, ensuring that operators can work more efficiently and safely. The goal will be to create a more sustainable working environment, promoting the health and well-being of employees.
13. Global Adoption of Lean Manufacturing Practices: Lean manufacturing principles, such as just-in-time (JIT) production, kaizen (continuous improvement), and 5S (organization), will be widely adopted within powder spraying production lines to reduce waste, improve efficiency, and enhance product quality. The future lines will feature highly automated, data-driven systems that are continuously fine-tuned to improve productivity while reducing material waste and energy consumption. The focus will be on producing high-quality products in the most resource-efficient way possible, ensuring manufacturers stay competitive in an increasingly globalized market.
14. Industry Collaboration and Standardization: As powder coating technologies evolve, industry players—including equipment manufacturers, material suppliers, and research institutions—will collaborate to establish best practices and universal standards for powder spraying production lines. These standards will ensure that energy-efficient systems meet rigorous quality and environmental benchmarks, providing consistency across industries. With standardization, manufacturers will have clearer guidelines for designing and implementing powder spraying lines that meet global sustainability and quality expectations.
In conclusion, the future of powder spraying production lines will be marked by technological advancements, environmental sustainability, and operational efficiency. The integration of automation, robotics, real-time data monitoring, and energy-efficient systems will drive down costs, increase productivity, and reduce environmental impact. These innovations will allow manufacturers to produce high-quality, durable finishes in a more cost-effective and sustainable manner, making powder spraying production lines an essential part of the next generation of industrial manufacturing.
As we continue to look ahead, several more factors will influence the ongoing development and expansion of powder spraying production lines. With an increasing focus on industry-specific applications, supply chain integration, and advanced control systems, the industry will witness further evolution in both the technology and business models behind these systems. Below are some of the key additional developments expected in the future:
15. Industry-Specific Customization: The demand for tailored solutions will continue to grow in the powder spraying industry. Various industries such as automotive, aerospace, consumer electronics, and furniture have distinct coating needs that require customized powder spraying solutions. Future powder spraying production lines will be designed with more specific features and capabilities tailored to meet the unique challenges and requirements of different sectors. For example, the automotive industry will require production lines capable of applying highly durable coatings with both aesthetic appeal and long-term protection against weathering. For the aerospace industry, powder spraying systems will increasingly focus on applying coatings that can withstand extreme temperatures and corrosive environments. This trend towards sector-specific customization will be supported by modular production lines that can be adjusted or reconfigured for different products.
16. Expansion of Powder Coating for Architectural Applications: As architectural trends move toward more sustainable building practices, powder coating will play an increasingly important role in the construction and design of building materials. Powder coating is well-suited for architectural applications because it provides a durable, weather-resistant finish that is suitable for metal cladding, windows, doors, and fencing. In the future, powder spraying production lines will be designed with the capacity to coat larger architectural elements while still maintaining high-quality finishes. This includes the adoption of advanced curing methods, such as infrared curing, to handle large items and improve energy efficiency during the coating process.
17. Increased Integration with Artificial Intelligence (AI): Artificial Intelligence (AI) will play an even greater role in the operation of powder spraying production lines in the future. AI will be used to enhance predictive maintenance by analyzing historical data from equipment sensors to predict potential breakdowns before they occur. This will enable manufacturers to perform maintenance only when needed, reducing downtime and improving productivity. AI will also assist in optimizing coating applications by analyzing variables such as spray parameters, part geometry, and ambient conditions. The AI system will automatically adjust the spray settings to ensure maximum efficiency and consistent coating quality, further reducing energy consumption and material waste.
18. Cross-Industry Collaborations and Partnerships: The future success of powder spraying production lines will depend on collaborative partnerships across industries. Coating manufacturers, equipment suppliers, material producers, and industrial end-users will collaborate to create systems that offer greater versatility, energy efficiency, and sustainability. For example, partnerships between powder coating suppliers and equipment manufacturers could result in the development of coating materials that are specifically formulated for use in low-energy or high-speed production systems. Such collaborations will help drive innovation and provide the tools manufacturers need to stay competitive in an ever-changing marketplace.
19. Integration with Advanced Supply Chain Management Systems: The future powder spraying production line will be tightly integrated with advanced supply chain management (SCM) systems. These integrations will allow for better synchronization between the manufacturing floor and supply chain logistics, enabling more efficient handling of materials, timely deliveries, and optimized inventory levels. Real-time tracking of materials, work-in-progress items, and finished products will allow manufacturers to make faster decisions, reduce production delays, and improve overall efficiency. Additionally, automated inventory management will reduce manual labor and ensure that the required quantities of powder and parts are always available when needed, reducing the risk of production stoppages.
20. Integration with Augmented Reality (AR) for Maintenance and Training: Augmented Reality (AR) will become an increasingly valuable tool in the operation and maintenance of powder spraying production lines. AR-enabled devices, such as smart glasses, will allow technicians to receive real-time, context-sensitive instructions while performing maintenance or troubleshooting tasks. By overlaying digital information onto physical equipment, AR can guide technicians through complex procedures and assist with problem identification. Moreover, AR will be used for remote assistance, allowing experts to provide live guidance to operators or maintenance workers, regardless of location. AR will also play a key role in operator training, enabling new employees to simulate and practice powder coating tasks in a controlled, virtual environment before working on live production lines.
21. Enhanced Coating Durability and Functionality: In response to more demanding applications, future powder spraying production lines will focus on producing coatings with superior functional properties. This includes coatings with self-healing capabilities, enhanced corrosion resistance, thermal management, and antimicrobial properties. Advances in nanotechnology will enable the development of coatings that not only provide aesthetic finishes but also enhance product performance. For instance, self-healing coatings could automatically repair minor scratches and chips, extending the lifespan of coated products. The ability to apply coatings with unique functional properties will open up new markets, especially in sectors like electronics, automotive, and medical devices.
22. Advanced Curing Systems and Reduced Energy Consumption: The energy consumption associated with curing powder coatings is a significant part of the overall energy demand in powder spraying production lines. As part of the trend toward sustainability, advanced curing systems will reduce energy consumption by making curing processes more efficient. UV curing technologies, for example, will become more widely used, especially for thin-film coatings that require quick curing at lower temperatures. LED curing will also see broader adoption, offering even lower energy consumption compared to traditional curing methods. These energy-efficient curing solutions will help manufacturers meet stringent environmental standards while still achieving high-quality coatings with excellent adhesion, durability, and aesthetics.
23. Global Expansion of Powder Coating Markets: As environmental regulations tighten and industries shift toward more sustainable practices, the global demand for powder coating will continue to increase. Emerging economies, particularly in Asia, Latin America, and Africa, will witness significant growth in powder coating applications as these regions develop their industrial infrastructure. In these regions, powder spraying production lines will be tailored to accommodate the specific needs of local industries, ensuring cost-effective and sustainable solutions. As a result, the powder coating industry will become more globalized, with increased cross-border collaboration and international standards emerging to ensure quality and sustainability across regions.
24. Digital Twins for Production Line Simulation: The concept of a digital twin, which is a virtual representation of a physical production line, will gain traction in the powder spraying industry. Manufacturers will use digital twins to simulate the entire powder spraying process, from material handling to coating and curing. These virtual models will allow manufacturers to test new coating materials, processes, and configurations before applying them to the real production line. By simulating changes in a digital environment, manufacturers can identify potential inefficiencies, test different scenarios, and optimize the line for better performance. Digital twins will also be instrumental in troubleshooting and predictive maintenance by offering real-time simulations that reflect the actual performance of the physical system.
25. Continuous Improvement and Lean Manufacturing: The focus on lean manufacturing principles will continue to evolve in powder spraying production lines. The emphasis will be on reducing waste, improving workflow efficiency, and enhancing the quality of finished products. Techniques like value stream mapping, Kaizen (continuous improvement), and Six Sigma will help identify and eliminate inefficiencies in the coating process. By optimizing material usage, reducing defects, and improving the speed of production, manufacturers can reduce costs, minimize environmental impact, and increase the overall profitability of their operations.
26. Increased Demand for High-Throughput Production Lines: As industries demand faster production speeds, powder spraying production lines will be designed to handle high-throughput manufacturing without compromising on coating quality. The future lines will feature faster conveyor systems, multiple spray booths, and rapid curing ovens that can apply coatings to large volumes of products in a shorter time. Batch processing systems will also be optimized to handle higher quantities of parts with more flexible configurations. This increased capacity will help manufacturers meet growing demand while improving the overall throughput and efficiency of production.
In conclusion, the future of powder spraying production lines will be shaped by ongoing technological advancements, environmental goals, and market demands for greater efficiency, customization, and sustainability. From the integration of advanced technologies like AI, robotics, and real-time monitoring systems to the development of eco-friendly materials and energy-efficient curing methods, powder spraying production lines will continue to evolve and meet the increasingly complex demands of modern industries. The key to success will lie in adopting a holistic approach that combines cutting-edge technology, sustainability, and operational efficiency to create production systems that are not only capable of delivering high-quality results but also contribute to the global push for a more sustainable and efficient manufacturing future.
Powder Coating Machine
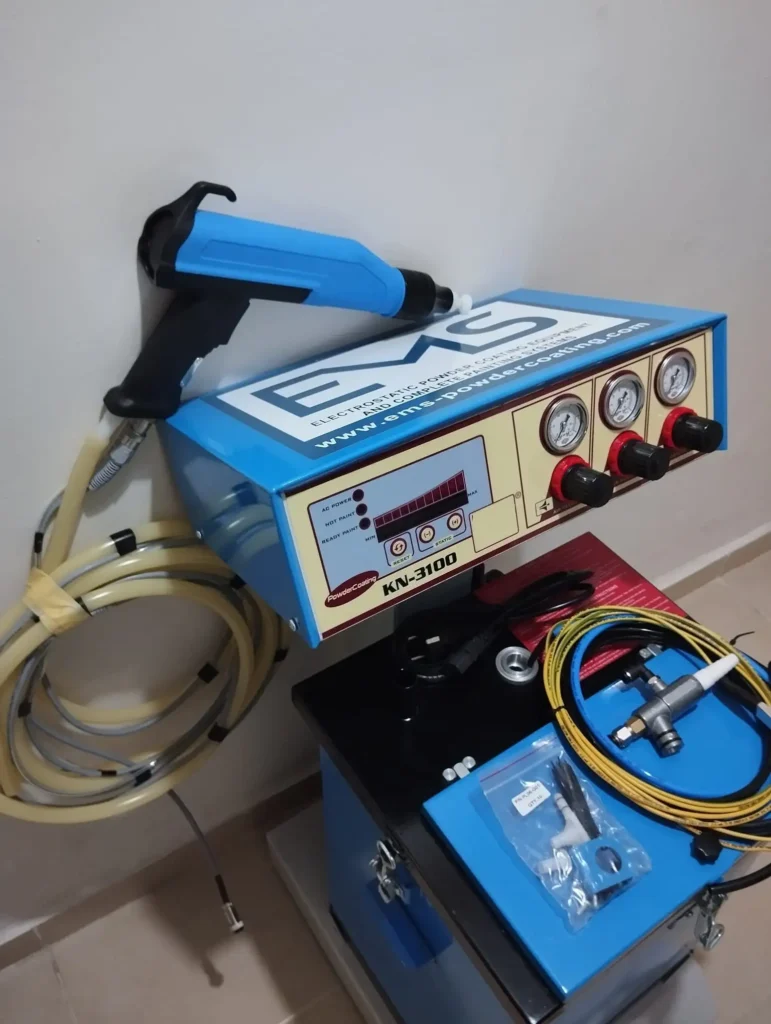
The future of powder coating machines is expected to evolve rapidly, driven by innovations in automation, energy efficiency, sustainability, and customization to meet the increasingly diverse needs of industries such as automotive, aerospace, consumer electronics, and architecture. These machines are essential in the application of powder coatings, offering several advantages, including durability, smooth finishes, and environmental benefits. However, the powder coating industry continues to push the boundaries of technology to enhance machine performance and production efficiency. Here’s what we can expect for powder coating machines in the future:
1. Energy Efficiency and Reduced Environmental Impact:
As industries face rising energy costs and stricter environmental regulations, energy-efficient powder coating machines will become more widespread. These machines will feature optimized curing ovens, such as infrared (IR) and ultraviolet (UV) curing systems, to reduce energy consumption. LED curing technologies are expected to be integrated into powder coating machines, offering lower energy requirements, faster curing times, and more consistent results. In addition to curing innovations, the machines will include features to minimize waste and improve material recovery, such as advanced cyclonic recovery systems and overspray recycling. By reclaiming and reusing powders more effectively, manufacturers will reduce operational costs and minimize the environmental footprint of the powder coating process.
2. Automation and Robotics Integration:
The integration of robots and automation systems into powder coating machines will become more prevalent as manufacturers seek higher productivity and consistency. Automated spray guns will be programmed to apply coatings more accurately and with greater efficiency. Robots equipped with advanced vision systems will be able to adjust the spray pattern and coating thickness based on the shape and size of the part, ensuring uniform application and reducing material waste. Automated powder coating machines will be able to handle a broader range of products, from small parts to large industrial components, without requiring frequent manual adjustments. Additionally, robotic arms will perform automated part handling, significantly reducing labor costs and enhancing throughput.
3. Advanced Control Systems and Real-Time Monitoring:
The future of powder coating machines will be marked by smart technology and real-time monitoring systems. These systems will monitor various parameters during the coating process, including spray gun performance, powder feed rates, ambient conditions, and curing temperatures. Sensors embedded in the machine will gather data and send it to a central control system where it can be analyzed to ensure optimal performance. This will allow operators to make adjustments on the fly to maintain coating quality and reduce defects. Machine interfaces will become more user-friendly, with touchscreens, augmented reality (AR) systems, and even voice control to improve ease of operation and provide on-demand feedback. Data from the machines will be integrated with cloud-based platforms, enabling remote monitoring and maintenance.
4. Improved Coating Quality and Consistency:
Future powder coating machines will incorporate high-precision technologies to improve coating quality and ensure a more consistent finish. Electrostatic spray systems will become more sophisticated, providing better control over the coating application and improving transfer efficiency. The latest machines will be equipped with advanced spray guns capable of creating a uniform coating layer, even on complex geometries. Additionally, in-line inspection systems will be implemented to detect defects during the coating process, ensuring that only properly coated parts move to the next stage of production. The machines will also feature automatic adjustment of spray parameters based on the size, shape, and material of the part being coated.
5. Customization and Versatility:
As industries demand more tailored solutions, powder coating machines will become increasingly versatile and customizable. The future machines will allow for the quick adjustment of spray settings and curing parameters to accommodate different materials, part sizes, and production volumes. Modular designs will enable manufacturers to configure powder coating machines to meet specific production requirements, whether they need a line for small batch runs or high-volume production. Quick-change systems will allow for the rapid switching of spray guns, nozzles, and curing ovens, reducing downtime between runs and providing greater flexibility in handling a wide range of coatings.
6. Smarter Powder Management Systems:
Powder management will be another key focus area for future powder coating machines. Advanced powder feed systems will ensure consistent and reliable powder delivery, minimizing interruptions during the coating process. Machines will feature auto-adjustment mechanisms that fine-tune the powder flow based on real-time feedback, ensuring a stable and consistent spray. Additionally, automated powder recirculation and overspray recovery systems will reclaim excess powder and feed it back into the system, minimizing waste and reducing material costs. These smarter systems will enhance production efficiency, improve coating uniformity, and reduce material costs.
7. Integration with Industry 4.0:
The concept of Industry 4.0, which focuses on smart factories and interconnected systems, will become a significant factor in the future of powder coating machines. These machines will be equipped with IoT (Internet of Things) sensors that communicate with other machines, systems, and control platforms within the factory. This interconnectivity will allow for real-time data exchange, enabling operators to make informed decisions, optimize workflows, and improve overall production efficiency. For example, when a machine requires maintenance or a part needs replacing, the system will alert the operator or initiate corrective actions automatically. Additionally, cloud-based analytics will provide manufacturers with insights into machine performance, helping identify areas for improvement and increasing overall uptime.
8. Faster Curing and Drying Times:
Future powder coating machines will focus on reducing curing and drying times to increase throughput. Hybrid curing systems combining UV, IR, and LED technologies will allow for faster and more efficient curing. These systems will also be capable of handling thicker coatings, which are becoming increasingly popular in industries requiring high-performance finishes. Machines will automatically adjust curing times and temperatures based on the thickness of the coating, part material, and other parameters, ensuring the coatings achieve the desired durability without wasting energy or time.
9. High-Throughput and Continuous Production:
To meet the growing demand for faster production, powder coating machines will be designed for high-throughput manufacturing. These machines will feature high-speed conveyors, multi-stage coating systems, and advanced curing ovens to process large quantities of parts without compromising on coating quality. Continuous production lines will allow for seamless handling of products, and batch production capabilities will also be enhanced to accommodate shorter production runs with minimal setup time. This high-speed operation will reduce costs and lead times while maintaining the high standards of powder coating finishes.
10. Smart Maintenance and Predictive Analytics:
Predictive maintenance technologies will be integrated into powder coating machines to minimize downtime and extend the life of equipment. Sensors and machine learning algorithms will be used to monitor machine health in real-time, identifying potential issues before they cause a breakdown. These systems will predict when components such as motors, spray guns, or curing ovens need servicing or replacement, enabling manufacturers to perform maintenance only when necessary, rather than on a fixed schedule. Remote diagnostics and troubleshooting will become more accessible, enabling experts to guide operators through problem-solving processes without the need for on-site visits.
11. Enhanced Coating Materials:
The advancement of coating materials will continue to impact powder coating machines. New high-performance powders that offer improved durability, UV resistance, and chemical resistance will be developed, requiring machines to adapt to new powder types. Additionally, the formulation of eco-friendly powders, including those that contain fewer solvents and are free of harmful substances, will be prioritized. Powder coating machines will be designed to handle these innovative materials, with systems capable of precise application and curing to ensure maximum performance.
12. Ergonomics and Operator Safety:
As powder coating machines become more complex, the importance of operator safety and ergonomics will increase. Machines will be designed with safety features such as automated safety shutdowns, dust extraction systems, and advanced PPE (Personal Protective Equipment) for operators. Ergonomic considerations will also be incorporated into the design of the machines to ensure operators work in a comfortable and efficient environment, reducing fatigue and improving overall productivity.
13. Modular Design for Flexibility:
The future of powder coating machines will see an increase in modular designs, allowing manufacturers to customize and scale their production lines as needed. Modular components such as spray booths, powder feeders, curing systems, and conveyors can be added or reconfigured without disrupting the entire production process. This flexibility allows manufacturers to adapt to changing production demands, whether they need to scale up for large orders or scale down for smaller, more specialized runs.
14. Globalization and Cross-Border Standards:
As the demand for powder coating grows globally, particularly in emerging markets, powder coating machines will be designed to meet international standards for quality, sustainability, and safety. Manufacturers will need to comply with a range of local regulations and market demands, which will drive the development of machines capable of handling a broad range of products, materials, and environmental conditions. These globalized standards will ensure that powder coating machines provide reliable, high-quality finishes regardless of location, ensuring manufacturers can compete in international markets.
15. Advanced Safety and Environmental Features:
As part of the push towards sustainability, future powder coating machines will be equipped with advanced safety features to protect both operators and the environment. These features will include enhanced filtration systems to reduce airborne particles, automated shutdown mechanisms for emergency situations, and advanced fire suppression systems. Environmental regulations will push machines to use fewer chemicals and reduce harmful emissions, while still maintaining the desired coating performance.
Conclusion:
The future of powder coating machines is bright, driven by technological advancements and the push for more sustainable, efficient, and flexible manufacturing processes. Automation, energy efficiency, smarter control systems, and the ability to handle a wider variety of coating materials will position powder coating machines as key components in modern manufacturing lines. With increased focus on sustainability, customization, and productivity, powder coating machines will continue to evolve to meet the diverse needs of industries worldwide.
As we continue to look ahead, several more emerging trends and technologies will further shape the future of powder coating machines. These innovations aim to enhance productivity, reduce environmental impact, improve coating performance, and meet the evolving needs of industries across the globe.
16. Integration with Artificial Intelligence (AI) and Machine Learning (ML):
The role of artificial intelligence (AI) and machine learning (ML) in powder coating machines will grow significantly. These technologies will enable the machines to make real-time decisions about the application process. AI-powered systems will continuously analyze variables such as spray patterns, coat thickness, material flow, and humidity, adjusting the parameters for optimal performance. Machine learning algorithms will learn from previous coatings and adapt the spray gun settings to improve the coating process over time, further reducing defects and material waste. Additionally, AI will assist with predictive maintenance, identifying potential mechanical failures before they occur, which reduces downtime and extends the lifespan of the equipment.
17. Integration with Virtual Reality (VR) for Training:
Virtual reality (VR) will be increasingly used in training operators to handle powder coating machines. With VR simulations, operators can practice and learn how to adjust spray parameters, handle different materials, and troubleshoot common issues without interacting with the actual equipment. This immersive training method allows operators to gain experience in a safe, controlled environment, minimizing the risk of accidents on the production floor. VR training can also be useful for remote assistance, where experts can guide operators through troubleshooting steps using virtual representations of the machinery and process.
18. Enhanced Powder Coating Machine Flexibility for Small Batch Runs:
As markets increasingly demand customized products in smaller batches, powder coating machines will evolve to handle smaller production volumes without sacrificing speed or quality. Batch production capabilities will improve, allowing for the quick changeover of colors and coatings between runs. Systems will feature automatic color change technologies that minimize downtime and reduce the need for manual cleaning between batch changes. The machines will also be designed to efficiently handle low-volume production runs, making them suitable for industries that require shorter production cycles and higher product customization. This flexibility will be particularly valuable in industries such as furniture, consumer electronics, and specialized automotive parts, where product diversity and customer demands are high.
19. Hybrid Coating Systems:
Hybrid coating systems combining liquid paint and powder coating technologies will gain popularity, offering the best of both worlds. These systems allow manufacturers to apply a powder coating base for durability and liquid topcoats for a glossy or high-performance finish. Hybrid powder coating machines will be designed to switch seamlessly between both types of coatings, offering more versatile and varied applications for a broader range of products. For example, manufacturers could use this combination to apply powder coatings for weather resistance and liquid coatings for enhanced aesthetic appeal. These hybrid systems will expand the range of applications for powder coating while reducing the need for separate machines and systems for different types of coatings.
20. Electrostatic Powder Coating Gun Advancements:
The development of electrostatic powder coating guns will continue to improve, providing better control over the charge and flow of the powder particles. Future guns will feature multi-charge systems that allow for the application of more complex coatings, ensuring uniformity even on parts with complex geometries. Improved airflow control will allow for more precise powder application, reducing overspray and improving transfer efficiency. These advanced powder coating guns will also be more ergonomically designed, making them easier to handle for operators over long periods, reducing fatigue and improving productivity.
21. Use of Biodegradable and Sustainable Powders:
The industry will continue to focus on sustainable materials by developing biodegradable powders and eco-friendly coatings. Advances in powder coating formulations will lead to powders made from renewable resources, such as plant-based ingredients or recycled materials, that do not compromise on performance. These sustainable powders will be increasingly used in industries such as automotive, furniture, and electronics, where the environmental impact of production processes is under close scrutiny. Powder coating machines will be designed to handle these new types of coatings without compromising on efficiency or quality, while simultaneously contributing to reducing the carbon footprint of the manufacturing process.
22. Advanced Coating for Additive Manufacturing (3D Printing):
As additive manufacturing (3D printing) becomes more widespread, there will be growing demand for powder coating in post-printing processes. 3D-printed parts often require coatings to enhance their durability, appearance, or surface finish. Powder coating machines will be designed to handle the unique challenges of coating 3D-printed components, such as irregular geometries or porous surfaces. New powder coating machines will integrate technologies that ensure uniform coating application even on complex or delicate 3D-printed surfaces, offering manufacturers the ability to improve the mechanical properties and visual appeal of their printed products.
23. Real-Time Data Analytics for Quality Control:
Future powder coating machines will be equipped with advanced data analytics systems that perform continuous quality checks throughout the coating process. In-line sensors will detect any inconsistencies in the coating, such as variations in thickness, texture, or color. These real-time data systems will alert operators if a deviation occurs, allowing for immediate corrections before the part moves further down the line. This closed-loop quality control system will enable manufacturers to achieve higher levels of consistency and minimize defects, thus reducing rework and waste. Data will be stored and analyzed over time to identify patterns and optimize production settings, improving overall machine performance and reducing the likelihood of future errors.
24. Increased Customization for Coating Materials:
As industries demand more specialized coatings with unique properties, powder coating machines will offer more flexibility in handling a variety of custom coatings. Machines will be designed to accommodate specialized powder formulations that offer properties such as heat resistance, corrosion resistance, scratch resistance, or antimicrobial properties. This demand for customization will lead to the development of machines with more precise material handling systems that can handle unique powders without clogging or disrupting the flow. The machines will allow operators to easily switch between different types of coatings, ensuring consistent application even when dealing with non-standard formulations.
25. Integration with Digital Twins for Production Optimization:
The concept of the digital twin will be increasingly applied to powder coating machines. A digital twin is a virtual replica of a physical machine or production line that allows for real-time monitoring and simulation of performance. By using a digital twin, manufacturers will be able to simulate different coating scenarios, test new material formulations, or optimize production workflows without disrupting the actual manufacturing process. This technology will help identify inefficiencies, troubleshoot problems, and predict performance outcomes, allowing for more efficient production planning and cost savings.
26. Global Standards and Certification Compliance:
As global demand for powder coating continues to rise, powder coating machines will be designed to meet a broader range of international standards and certification requirements. These standards will ensure that machines comply with the environmental, safety, and performance regulations in different regions. Future machines will be equipped with features that make them easier to certify for compliance with global standards, including ISO certifications, REACH (Registration, Evaluation, Authorisation and Restriction of Chemicals) compliance, and LEED (Leadership in Energy and Environmental Design) ratings. This will allow manufacturers to easily export their coated products to global markets, ensuring that they meet the necessary regulatory and quality standards.
27. Collaboration with Supply Chain Technology:
To improve the efficiency and traceability of the coating process, powder coating machines will be increasingly integrated with supply chain management systems. This integration will enable manufacturers to track the entire flow of materials, from powder procurement to final product delivery. Real-time data on production schedules, inventory levels, and part status will allow for more accurate planning and better management of resources. The ability to synchronize production with other supply chain activities will improve overall lead times and reduce bottlenecks, enabling manufacturers to respond more quickly to changing market demands.
Conclusion:
The future of powder coating machines is poised to be shaped by cutting-edge innovations that drive efficiency, sustainability, automation, and customization. By integrating technologies like artificial intelligence, machine learning, robotics, and virtual reality, powder coating machines will become more intelligent, adaptable, and capable of meeting the diverse demands of industries worldwide. The emphasis on energy efficiency, predictive maintenance, and real-time data analysis will help manufacturers optimize their operations and reduce waste, while the integration of advanced curing systems and eco-friendly powders will contribute to a more sustainable future for powder coating. As these technologies continue to develop, powder coating machines will play an increasingly central role in creating high-quality finishes across a wide variety of applications.
As we look even further into the future of powder coating machines, there are a few more key developments and trends that are likely to emerge. These will continue to advance the capabilities of powder coating technology, drive innovation in the manufacturing sector, and improve the overall sustainability and efficiency of production processes.
28. 3D Powder Coating for Complex Shapes:
With the continued rise of 3D printing, we can expect the emergence of 3D powder coating techniques. These techniques will be tailored to handle the unique challenges presented by 3D-printed parts, such as non-uniform surfaces, complex geometries, and layered structures. Advanced powder coating machines will incorporate 3D scanning and AI-based pattern recognition systems to ensure that coatings are applied evenly and uniformly across all surfaces. This will open up new possibilities in industries such as aerospace, automotive, and medical device manufacturing, where parts with intricate designs require a precise and durable finish. Additionally, the ability to coat small-scale, highly detailed 3D-printed objects will support innovation in product development and prototyping.
29. Advanced Heat Management Systems:
With the increasing complexity of powder coating systems and the higher performance demands, advanced heat management systems will play a crucial role in maintaining optimal operating conditions. Innovations in temperature regulation will enable more precise control over the curing and drying processes, particularly as manufacturers work with new, high-performance materials that require specific curing conditions. Automated temperature monitoring and adaptive heating systems will be integrated into machines to provide consistent and energy-efficient operation. These systems will ensure that the powder coating process is carried out within the ideal temperature range, preventing issues such as under-curing, over-curing, or color inconsistency.
30. Advanced Coating Texture Control:
Future powder coating machines will feature enhanced control over the texture of the finished product. The development of texture-controlled spray systems will allow manufacturers to apply coatings that achieve specific surface finishes, such as matte, glossy, hammered, or wrinkled effects. These systems will incorporate precision nozzle design and advanced electrostatic control to ensure that texture patterns are consistently applied across different part surfaces. This level of control will allow for more sophisticated finishes, which are especially desirable in industries such as consumer electronics, furniture, and luxury automotive parts, where aesthetics are as important as functionality.
31. Continuous Innovation in Powder Coating Materials:
As material science continues to evolve, the range of powder coating materials will expand. Manufacturers will develop more specialized powders, such as those with heat-resistant properties, anti-corrosive coatings, or even antimicrobial finishes. Future powder coating machines will be engineered to work with these new materials, ensuring precise application and efficient curing. The development of functional powders that offer multiple benefits, such as conductive or anti-fingerprint coatings, will offer new possibilities in fields like electronics, automotive, and medical device manufacturing. Machines will be equipped with the flexibility to switch between different materials without compromising coating quality, providing manufacturers with a competitive edge in delivering specialized products.
32. Zero-Waste Powder Coating Systems:
The increasing focus on sustainability will lead to the development of zero-waste powder coating systems. These systems will be designed to minimize or eliminate any overspray, reduce energy consumption, and utilize advanced technologies to recycle unused powder back into the system for reuse. Closed-loop systems will enable powders to be collected, filtered, and reintroduced into the application process without degradation, ensuring that no powder is wasted. This will drastically reduce both material costs and environmental impact. Additionally, advanced dust extraction and filtering systems will ensure that any airborne particles are captured and recycled, contributing to cleaner production environments and compliance with health and safety standards.
33. Enhanced Color Accuracy and Customization:
Future powder coating machines will offer even greater color accuracy and customization. The machines will integrate with digital color matching systems, ensuring that the exact shade, hue, and finish required by customers are achieved with minimal deviation. This could include computer-controlled color mixing systems that automatically adjust the formula to match customer specifications or ensure consistent results across batches. Color prediction and matching software will also become more advanced, reducing the need for manual adjustments and improving efficiency. The ability to precisely match custom colors and textures will be particularly important in sectors like automotive, consumer goods, and interior design, where personalized finishes are in high demand.
34. Collaboration with Advanced Coating Testing Equipment:
As powder coating technologies evolve, they will increasingly be integrated with advanced testing equipment designed to evaluate the quality and durability of coatings. These tools will provide real-time analysis of adhesion strength, hardness, corrosion resistance, and surface uniformity. By incorporating testing systems into the coating machine itself, manufacturers will be able to perform in-line quality control to ensure that every part meets the required standards without the need for additional testing steps. Automated testing systems will evaluate the coating’s performance under real-world conditions, ensuring that the end product is ready for use without requiring additional steps or delays.
35. Self-Cleaning Coating Systems:
A significant trend that will impact the future of powder coating is the development of self-cleaning powder coating systems. These systems will utilize nanotechnology and smart materials that allow the coating equipment to be self-cleaning or easier to maintain. For example, self-healing materials could be integrated into the machine components, such as nozzles and spray guns, to automatically remove any buildup of powder or residue during the coating process. This would minimize the need for downtime between runs and improve overall operational efficiency. Additionally, these self-cleaning technologies could be used to maintain coating consistency and reduce the time required for machine maintenance.
36. Enhanced Integration with Post-Coating Processes:
To streamline the overall production process, powder coating machines will be increasingly integrated with post-coating processes. This could include automatic systems for inspection, packaging, labeling, and even storage. These integrated solutions will reduce the time and labor required for post-coating steps, improve throughput, and help to optimize inventory management. For example, in automated systems, after the coating is applied and cured, the parts could automatically be moved to inspection stations where machine vision systems assess quality and identify defects. If necessary, parts could be rerouted for correction or finishing before packaging. This seamless workflow will increase productivity and reduce the risk of human error.
37. Localized Powder Coating Systems for Custom Markets:
As manufacturing becomes more decentralized and localized, compact, modular powder coating systems designed for smaller, specialized production environments will become more common. These systems will be smaller, more flexible, and adaptable to localized market needs. Manufacturers will be able to install these systems in smaller workshops or remote areas where larger, industrial-scale machines might not be feasible. Such systems will allow manufacturers to meet demand for custom or niche products quickly and efficiently, without relying on large central factories. This will also reduce shipping costs and lead times for parts that require custom powder coatings.
38. Artificial Intelligence for Process Optimization:
The future of powder coating systems will increasingly incorporate artificial intelligence (AI) to optimize the entire coating process. AI algorithms will analyze various parameters, including spray gun settings, powder flow, and curing times, and adjust them in real time based on continuous feedback. This will help minimize waste, improve coating quality, and reduce human error. Over time, the AI system will learn from past coating processes and become better at predicting the best conditions for applying coatings to different parts, materials, or shapes. AI-driven systems will also improve workflow management, enabling manufacturers to streamline their operations and reduce downtime.
39. Machine-to-Machine Communication:
As powder coating machines become more interconnected, machine-to-machine (M2M) communication will become crucial for coordinating production activities. These machines will be able to share data, automatically adjust production schedules, and monitor the health of one another in real time. For example, if one part of the powder coating line is delayed due to maintenance, the system can automatically reroute work to another line or adjust the schedule for the entire system. M2M communication will enable greater synchronization between different stages of the production process, improving overall efficiency and flexibility in manufacturing workflows.
40. Collaboration with Digital Manufacturing Platforms:
Future powder coating machines will be closely linked to digital manufacturing platforms. These platforms will allow for better collaboration between design, engineering, and production teams, enabling real-time feedback on product designs and coating requirements. Manufacturers will be able to track the status of powder coating jobs, review coating specifications, and share performance data across the entire production chain. With access to real-time data and remote monitoring capabilities, production managers will be able to make data-driven decisions to optimize workflows, reduce costs, and maintain high product quality.
Conclusion:
As powder coating machines continue to evolve, the future will bring innovations that enhance their capabilities, flexibility, and performance. The integration of AI, robotics, smart materials, and advanced automation will revolutionize the way powder coating systems are designed and operated, improving efficiency, quality, and sustainability. Future machines will be more energy-efficient, faster, and capable of handling a wider variety of products and coating requirements. By focusing on reducing waste, improving the precision of coatings, and providing more customized solutions, the powder coating industry will continue to meet the growing demands of a rapidly changing global marketplace.
Large Scale Powder Coating
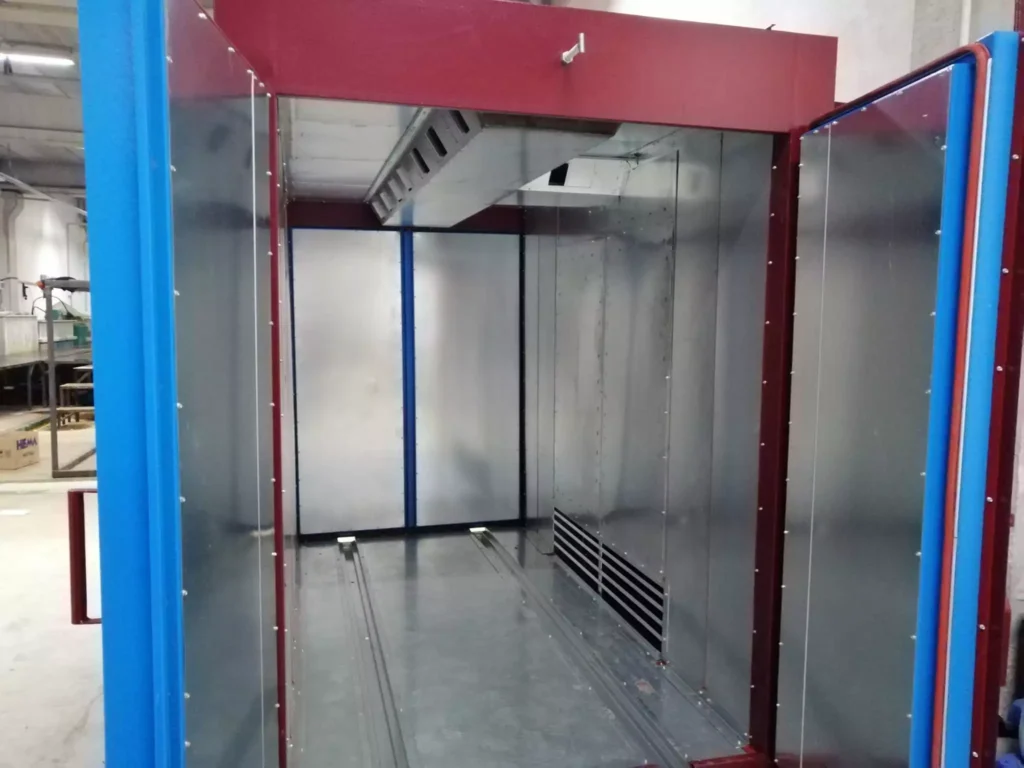
The future of large-scale powder coating systems is poised for significant transformation, driven by advancements in technology, automation, and sustainability. As industries increasingly demand high-quality, durable finishes for a wide range of applications, large-scale powder coating systems are evolving to meet these needs. These systems, which are critical in sectors such as automotive, construction, appliances, metal manufacturing, and furniture production, will continue to adapt to the growing demands for efficiency, customization, and environmental responsibility.
1. Increased Automation and Robotics:
As automation becomes more prevalent, large-scale powder coating lines will see the integration of robotics and automated handling systems. Robots will take over repetitive tasks such as part loading and unloading, as well as precise spray gun movements. These robots will be programmed to adjust spray angles, coating thickness, and other parameters based on the specific shape and size of each part. Automation will reduce human intervention, which leads to more consistent and precise coatings while increasing overall throughput. Additionally, robots can work continuously with minimal breaks, boosting productivity.
2. AI-Driven Process Optimization:
Incorporating artificial intelligence (AI) into large-scale powder coating operations will enable real-time monitoring and optimization of the entire process. AI algorithms will analyze various parameters, such as coating thickness, cure times, powder flow rates, and humidity, and adjust settings for optimal performance. The system will learn from previous operations and improve its ability to predict and prevent defects such as inconsistent coating, overspray, or uneven curing. This predictive approach to process optimization will reduce waste, improve material efficiency, and minimize the chance of defects in the final product.
3. Energy Efficiency and Sustainable Practices:
The pressure to reduce environmental impact will lead to major improvements in the energy efficiency of large-scale powder coating systems. Machines will become more energy-efficient, using lower temperatures or shorter curing times without compromising the quality of the finish. This will be achieved through innovations such as advanced heat recovery systems, which capture and reuse energy during the curing process. Additionally, there will be a push toward eco-friendly powder formulations, including low-VOC (volatile organic compound) and zero-VOC powders, which will be safer for both operators and the environment.
4. Real-Time Data Monitoring and Analytics:
The future of large-scale powder coating will involve greater integration with real-time data analytics and Internet of Things (IoT) technologies. Sensors embedded within the coating line will continuously monitor critical parameters, such as temperature, humidity, and powder flow, and send this data to central control systems. These systems will use advanced analytics to detect trends, predict potential issues, and optimize the process to ensure consistent coating quality. The ability to monitor and adjust the coating process remotely will also allow for quicker responses to any issues that arise, reducing downtime and improving overall throughput.
5. Modular and Flexible System Design:
To meet the ever-changing demands of manufacturers, large-scale powder coating systems will become more modular and flexible. Manufacturers will be able to easily adjust and reconfigure their coating lines to accommodate different product types, sizes, and production volumes. Modular systems allow for easy integration of additional equipment or the reconfiguration of existing setups without a major overhaul. This flexibility will be particularly valuable in industries that produce a wide variety of products or experience frequent changes in production schedules or batch sizes.
6. Increased Customization and Color Matching:
As consumer preferences shift towards personalization and customization, large-scale powder coating systems will become better equipped to handle unique colors and finishes. Digital color matching systems will allow manufacturers to achieve perfect color consistency across different parts, batches, and even shifts. This will be crucial for industries like automotive, where specific colors and finishes are a key part of branding. Customization options will also extend to special effects like metallic, gloss, matte, or textured finishes, enabling brands to offer more unique and differentiated products.
7. Integrated Coating and Curing Technology:
In large-scale powder coating operations, the integration of advanced curing systems will become increasingly important. The development of high-efficiency curing ovens will reduce energy consumption while improving throughput and ensuring consistent curing across all parts. Electromagnetic induction curing, infrared curing, and UV curing technologies are examples of advanced curing methods that will help reduce curing times, lower energy usage, and improve the overall quality of the coating. The integration of these advanced curing technologies with the powder coating system will enable smoother production and faster turnaround times for large runs.
8. Predictive Maintenance and Smart Diagnostics:
In large-scale powder coating systems, predictive maintenance will become the norm. Advanced sensors and diagnostic tools will monitor the health of critical components like spray guns, conveyors, and curing ovens. The system will provide real-time alerts about potential issues, such as wear and tear on components or deviations in performance. This predictive capability will allow manufacturers to perform maintenance before a failure occurs, reducing unexpected downtime and extending the life of the equipment. Smart diagnostics will also provide operators with detailed insights into the performance of the coating line, making it easier to troubleshoot and resolve problems.
9. Advanced Powder Recycling Systems:
As sustainability continues to be a priority, large-scale powder coating systems will feature advanced powder recycling systems to minimize waste. These systems will capture and filter overspray powder, allowing it to be reused in subsequent coating applications without significant degradation. Modern powder recovery systems, such as cyclone recovery and air filtration technologies, will be able to filter out contaminants and ensure that the recycled powder is as effective as newly applied powder. This not only reduces material costs but also minimizes environmental impact, as less powder is discarded and fewer raw materials are needed.
10. Customizable Coating Thickness Control:
One of the key features of future large-scale powder coating systems will be precise control over coating thickness. Automated thickness measurement technologies will be integrated into the line to continuously monitor and adjust the amount of powder being applied to each part. This level of precision will ensure that the coating thickness is within the desired specifications, improving the quality of the finish and reducing the chances of defects or inconsistencies. This will be particularly important for industries such as automotive, where even slight variations in coating thickness can affect both appearance and durability.
11. Advanced Coating Texture and Finish Control:
As coating technologies evolve, large-scale systems will offer better control over the texture and finish of powder coatings. Manufacturers will be able to achieve a variety of surface finishes, including smooth, textured, matte, or glossy, with even greater precision. Innovations in nozzle design, airflow control, and electrostatic charge will ensure that the powder is applied uniformly across the surface, regardless of the geometry or complexity of the part. Advanced systems will also be capable of applying special textures, such as wrinkle finishes or hammered effects, in a consistent manner.
12. Integration with ERP and MES Systems:
As the manufacturing sector moves toward more digitally integrated operations, large-scale powder coating lines will become increasingly connected with Enterprise Resource Planning (ERP) and Manufacturing Execution Systems (MES). These systems will allow manufacturers to track the flow of materials, monitor production schedules, and optimize inventory management. By connecting the powder coating line to other parts of the manufacturing process, manufacturers will gain better visibility and control over the entire production workflow, improving efficiency and reducing the chances of errors or delays.
13. Expansion of Powder Coating Applications:
The capabilities of large-scale powder coating systems will expand to accommodate a broader range of materials and applications. For example, future systems will be designed to apply coatings to non-metal surfaces, such as plastics and wood. Additionally, more specialized coatings will be available for use in extreme environments, such as high-temperature or chemical-resistant coatings for industrial and aerospace applications. These expanded capabilities will allow manufacturers to offer more versatile products that meet the growing demands for specialized finishes.
14. Zero Defects Philosophy:
The future of large-scale powder coating systems will involve a more proactive approach to quality control, often referred to as the zero defects philosophy. The system will use a combination of real-time sensors, machine vision systems, and AI-driven analysis to detect and correct defects immediately. The coating process will be constantly adjusted to ensure that any inconsistencies—such as uneven thickness, color variation, or surface imperfections—are eliminated before the part moves forward. This approach will reduce the need for rework and improve overall product quality, which will be critical for industries where consistency and durability are paramount.
15. Global Expansion of Powder Coating Facilities:
As global markets expand, there will be an increased demand for large-scale powder coating systems capable of handling higher volumes and greater complexity. Manufacturers will need to build more regional production facilities that are equipped with state-of-the-art powder coating lines. These facilities will be designed for high-volume production and will serve markets where demand for finished parts is growing rapidly. The need for highly efficient and automated systems will be key to meeting this demand while maintaining quality and reducing operational costs.
Conclusion:
Large-scale powder coating systems will continue to evolve in response to the demands for greater efficiency, customization, sustainability, and quality control. Automation, AI-driven optimization, and real-time data analytics will play crucial roles in transforming the way these systems operate, while innovations in coating materials and curing technology will open up new possibilities for product finishes. Sustainability and environmental responsibility will remain a driving force, with advancements in powder recycling, energy efficiency, and eco-friendly coatings leading the way. Ultimately, these developments will position large-scale powder coating systems as an essential tool for high-quality, high-efficiency manufacturing across a range of industries.
Large-scale powder coating systems are continuously evolving to meet the increasing demands of modern industries for high-quality, durable finishes. These systems are becoming more automated, energy-efficient, and adaptable, which is essential for high-volume production in sectors like automotive, construction, appliances, and metal manufacturing. The integration of robotics and automation is playing a major role in increasing productivity and consistency in large-scale powder coating operations. Robots handle tasks such as loading, unloading, and spray gun movement, ensuring more accurate coatings and reducing human intervention, which minimizes errors and improves efficiency. Automation also allows for 24/7 operation, contributing to increased throughput.
Artificial intelligence (AI) is becoming an integral part of these systems, enabling real-time process optimization. AI algorithms can adjust parameters such as powder flow rates, curing times, and spray angles based on continuous feedback, ensuring consistent coating quality and reducing material waste. As AI learns from past operations, it can predict potential issues before they arise, which leads to fewer defects and enhanced operational efficiency. This predictive approach also helps improve the overall sustainability of the powder coating process, as it reduces energy consumption, material waste, and downtime.
Sustainability is a key driver in the development of large-scale powder coating systems. These systems are becoming more energy-efficient, with innovations such as advanced heat recovery systems that capture and reuse energy during the curing process. Furthermore, the use of eco-friendly powder formulations, including low-VOC and zero-VOC powders, is gaining popularity, contributing to a reduction in the environmental impact of manufacturing processes. The trend toward eco-conscious solutions is also leading to the development of advanced powder recovery systems that allow for the recycling of overspray, significantly reducing material waste and costs.
Real-time data monitoring and IoT integration are helping manufacturers keep track of various factors that impact the coating process, such as temperature, humidity, and powder flow. This data is processed and analyzed, allowing for immediate adjustments to be made and ensuring that the coatings meet the desired quality standards. Additionally, the ability to monitor and control the system remotely helps operators troubleshoot and resolve issues more efficiently, reducing downtime and enhancing overall productivity.
As manufacturers face increasing demand for more customized products, large-scale powder coating systems are becoming more flexible. Modular and reconfigurable systems allow for quick adaptation to different product types and sizes, enabling manufacturers to meet changing market needs without significant downtime. These flexible systems also facilitate better management of product variants, improving operational efficiency and enabling a more responsive production environment.
Color consistency and customization are other areas where large-scale powder coating systems are advancing. Digital color matching and control systems ensure that the right color is achieved every time, and manufacturers can quickly switch between different color options without disrupting the production flow. This is particularly important in industries like automotive and consumer goods, where color accuracy and custom finishes are critical. These systems also allow for the application of special effects, such as metallic finishes, matte, glossy, or textured coatings, expanding the aesthetic possibilities for manufacturers.
Advanced curing technologies are also playing a significant role in large-scale powder coating systems. Modern curing ovens are becoming more efficient, reducing energy consumption while improving throughput. Techniques like electromagnetic induction curing, infrared curing, and UV curing are gaining traction as they offer faster curing times and more energy-efficient operations, helping to reduce the overall environmental footprint of powder coating.
As manufacturers seek to reduce the risk of defects and improve product quality, large-scale powder coating systems are incorporating enhanced quality control measures. Automated inspection systems that use machine vision technology are now capable of identifying and correcting defects such as uneven coating thickness or color variations before the parts move further along the production line. This approach significantly reduces the need for rework and enhances product consistency, which is essential for industries where quality is a top priority.
Another key area of development is predictive maintenance. Sensors and diagnostic tools embedded within the powder coating system help monitor the condition of critical components, such as spray guns, conveyors, and curing ovens. These systems can alert operators to potential maintenance needs before a failure occurs, minimizing unplanned downtime and extending the lifespan of equipment. This proactive approach to maintenance ensures that the coating line remains operational with minimal disruptions, further improving efficiency.
With the growing emphasis on digital integration, large-scale powder coating systems are becoming increasingly connected to other parts of the manufacturing process. By linking these systems to ERP and MES platforms, manufacturers can monitor production schedules, manage inventory, and track performance metrics across different stages of production. This integrated approach helps to streamline operations, reduce errors, and improve overall throughput, making large-scale powder coating systems an essential part of the modern manufacturing environment.
Looking toward the future, large-scale powder coating systems will continue to expand their capabilities to handle more complex coatings and materials. Advances in coating technology will allow these systems to apply powder coatings to a broader range of materials, including plastics and even wood, while offering specialized finishes for products exposed to extreme environments, such as high temperatures or corrosive chemicals. This versatility will open up new opportunities for manufacturers across a wide range of industries.
Finally, the trend of global expansion in manufacturing facilities will drive the need for large-scale powder coating systems that are not only efficient but also able to operate in different regions with varying requirements. These systems will be designed for scalability, allowing companies to meet growing demand in regional markets while maintaining high levels of quality and efficiency.
In conclusion, the future of large-scale powder coating systems is one of continuous innovation. These systems will become more automated, sustainable, flexible, and connected, enabling manufacturers to meet the challenges of modern production while enhancing product quality and reducing costs. Through advancements in AI, energy efficiency, customization, and predictive maintenance, large-scale powder coating systems will play a critical role in the manufacturing sector for years to come.
As large-scale powder coating systems continue to evolve, further breakthroughs are expected in areas such as smart coatings and advanced surface treatments. Manufacturers are exploring new methods to improve the durability, functionality, and performance of the powder coatings they apply. For example, self-healing coatings and anti-microbial finishes are being developed to provide additional value for industries like healthcare, automotive, and food processing. These coatings could be especially useful for protecting surfaces from environmental damage or wear and tear, enhancing the longevity and resilience of coated products.
Moreover, the integration of augmented reality (AR) and virtual reality (VR) tools into the operation of powder coating systems will become increasingly common. These technologies will allow operators to visualize the coating process in real-time, providing an interactive way to detect and troubleshoot problems. AR could also be used for remote support, allowing experts to guide operators through complex adjustments or maintenance procedures without being physically present. This technology will reduce training time for new operators and increase the overall efficiency of the workforce.
Another major development in the future of large-scale powder coating systems is the potential for collaborative manufacturing environments. As manufacturing plants become more connected, powder coating systems may operate in tandem with other manufacturing processes like 3D printing, additive manufacturing, and precision machining. For example, in industries where parts are produced using additive manufacturing, powder coating will become an essential final step to ensure the parts have the required aesthetic appearance and functional durability. This integration will allow for a more streamlined, interconnected production process, reducing the need for separate workstations and improving the flow of materials between different production stages.
The rise of industrial Internet of Things (IIoT) devices will enable even more granular monitoring and data collection from powder coating systems. IIoT sensors will collect data not only from the machines themselves but also from the production environment. This will help monitor factors such as air quality, temperature, and humidity, providing additional insights into how environmental conditions affect the coating process. Real-time environmental monitoring will help operators make adjustments on the fly, ensuring that the coatings are applied under optimal conditions and that any external factors influencing the process can be controlled.
The development of more advanced materials for powder coating will also play a significant role in shaping the future of large-scale systems. New powders with enhanced properties, such as greater resistance to corrosion, UV degradation, or high temperatures, will open up new application areas, especially in demanding industries like aerospace and marine. There may also be innovations in multi-layer powder coating systems, where different powders are applied in succession to achieve specific mechanical or aesthetic properties. This approach will offer manufacturers more flexibility in designing finishes that meet unique requirements.
Large-scale powder coating lines will increasingly incorporate end-of-line inspection technologies such as 3D scanning and laser-based measurement systems. These technologies will provide a detailed analysis of the surface geometry of the coated parts, ensuring that the coating adheres evenly to the entire surface. For parts with intricate shapes, 3D scanning will ensure that the coating process is uniform, which will be especially important in industries such as electronics and automotive, where precision and quality are paramount.
The evolving trend toward customized and small-batch production will also impact large-scale powder coating systems. While powder coating is traditionally associated with high-volume production runs, more manufacturers are now seeking systems that can easily accommodate smaller batches of custom-colored or specially finished parts. The development of quick-change technologies, which allow for fast switching between powder types, colors, and curing conditions, will be a critical factor in meeting these demands. This flexibility will enable manufacturers to stay competitive in a market where short lead times and customized solutions are increasingly in demand.
Moreover, cloud-based platforms will be leveraged to store, analyze, and share the performance data generated by large-scale powder coating systems. Cloud technology will allow manufacturers to access detailed reports, performance trends, and real-time alerts from anywhere in the world, offering enhanced support for multi-location operations. Cloud-based systems can also assist in remote diagnostics, allowing maintenance teams to troubleshoot issues with minimal downtime. This connectivity between coating systems and cloud platforms will provide deeper insights into machine performance and maintenance needs, leading to more efficient and responsive operations.
As the global push for sustainability continues, further innovations in waste reduction and material recovery will be integral to the future of large-scale powder coating systems. Manufacturers are focusing on eliminating waste throughout the coating process, from raw materials to production line inefficiencies. Advanced powder reclamation systems that can separate and reuse mixed or oversprayed powders will become more sophisticated, helping to reduce the environmental footprint of the process. Innovations in solvent recovery and more efficient powder application techniques will also contribute to the push for a circular economy in powder coating.
Lastly, global supply chains will continue to play a crucial role in shaping the development of large-scale powder coating systems. As manufacturers expand their operations worldwide, these systems will need to adapt to regional requirements and local environmental standards. The flexibility of these systems to meet different regulatory demands, handle varying supply chain conditions, and accommodate diverse customer specifications will be essential for global competitiveness. Large-scale systems will need to integrate not just with local production facilities but also with supplier networks and logistics providers, ensuring seamless and efficient operations across all geographies.
In conclusion, the future of large-scale powder coating systems will be characterized by a blend of automation, sustainability, innovation, and digital connectivity. These systems will continue to evolve to meet the changing demands of modern manufacturing, offering improved quality, flexibility, and cost-efficiency. From AI-driven process control to advanced curing technologies and environmental monitoring, the ongoing advancements in powder coating systems will empower manufacturers to produce higher-quality products faster, while reducing waste and energy consumption. The continued development of flexible, interconnected, and intelligent coating systems will be key to ensuring that powder coating remains a critical part of the manufacturing process for years to come.
Automated Coating Machines Manufacturer
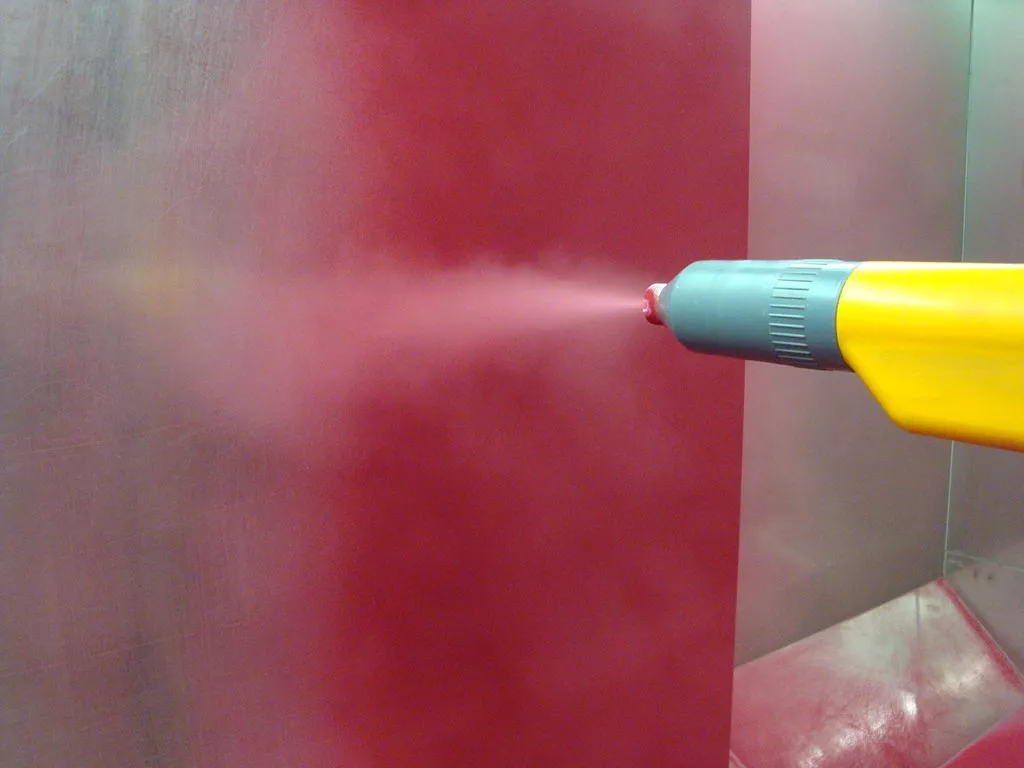
The future of automated coating machines manufacturing is driven by a range of factors including technological advancements, the demand for higher efficiency, greater precision, and environmental sustainability. Automated coating machines, which are widely used in industries like automotive, aerospace, electronics, and construction, are being designed to meet these evolving needs. As industries increasingly require faster turnaround times, reduced waste, and customizable finishes, the role of automated coating machines has become more integral to modern manufacturing processes.
The evolution of automated coating machines is focused on increased automation and intelligent control systems. As manufacturing environments move toward more flexible production lines, automated coating systems are incorporating advanced robotics, AI, and machine learning technologies. Robotic arms, conveyors, and automated spray guns are programmed to handle intricate coating tasks with minimal human intervention, leading to greater precision, consistency, and throughput. These robotic systems can work continuously, adjusting the coating process in real-time based on the shape, size, and material of the product being coated. This enables manufacturers to achieve uniform coatings with higher efficiency, reducing human error and the risk of defects.
AI-driven process optimization is becoming a crucial component of automated coating machines. AI algorithms are increasingly integrated into the systems to optimize key parameters such as spray patterns, powder flow, and curing temperatures. The AI learns from each cycle of coating and adapts to changing conditions, adjusting the parameters to achieve the best results every time. With predictive analytics, these systems can identify potential issues before they occur, reducing downtime and ensuring consistent quality. The ability to continuously monitor and analyze the coating process allows for better control over coating thickness, curing time, and material usage, leading to more efficient and sustainable operations.
In parallel with automation and AI, sustainability is a significant driving force behind the development of automated coating machines. Manufacturers are under increasing pressure to adopt eco-friendly practices and reduce waste. Automated coating systems are now equipped with advanced powder recovery systems that capture overspray and recycle the unused powder, significantly reducing material waste and cost. Innovations in low-VOC (volatile organic compounds) and zero-VOC coatings are also being integrated into automated systems to minimize harmful emissions during the coating process. Additionally, energy-efficient curing systems are being adopted to reduce the overall environmental impact of the coating process. These systems allow for faster curing with lower energy consumption, thus contributing to a greener manufacturing process.
Flexibility and customization are becoming key features in automated coating machines. With the increasing demand for personalized and short-run production, manufacturers need systems that can quickly adapt to different product sizes, coating materials, and finishes. Automated machines are now being designed to handle a wide range of coatings, from standard finishes to specialized textures or custom colors. Quick-changeover technologies, such as automated color change systems, are allowing manufacturers to transition between coating formulations without significant downtime. This ability to handle diverse product lines and quickly adjust to changing market demands enhances the efficiency and adaptability of manufacturing facilities.
As manufacturing continues to shift towards smart factories, automated coating machines are becoming more connected and integrated with other production systems. The use of IoT (Internet of Things) devices enables real-time monitoring and control of coating lines, allowing operators to track the performance of machines and materials. IoT sensors can monitor everything from coating thickness to temperature and humidity, providing operators with data that helps optimize the coating process. This connectivity also facilitates predictive maintenance, where machine components are continuously monitored, and data is used to anticipate when maintenance is needed. This helps to prevent unexpected breakdowns, ensuring that the coating lines remain operational and productive.
Modular design is becoming more prevalent in automated coating machines, allowing manufacturers to scale their operations and integrate new technologies with ease. Modular systems enable the addition or reconfiguration of components to meet specific production requirements without requiring a complete redesign of the entire system. This flexibility is crucial for industries where production demands can change rapidly. For example, manufacturers in the automotive or electronics sectors may need to adjust their coating processes to accommodate new products or production volumes. Modular designs allow for seamless upgrades and integration with existing equipment, ensuring that manufacturers can maintain their competitive edge as market conditions evolve.
Advanced surface treatment capabilities are also being incorporated into automated coating systems. With the increasing demand for coatings that offer enhanced durability, resistance to corrosion, and specialized surface properties, automated machines are now being equipped to handle a variety of surface treatments. These treatments include processes like plasma coating, anodizing, and nanocoatings, which add specific properties to the substrate material. These systems can be programmed to apply these advanced coatings in precise layers, ensuring uniform application and optimal performance of the final product. This expansion of capabilities opens new avenues for manufacturers to produce highly specialized products for demanding industries such as aerospace, defense, and electronics.
The rise of additive manufacturing (3D printing) is also influencing the development of automated coating machines. As 3D printing continues to grow in use for manufacturing complex and custom parts, automated coating machines will need to handle a broader range of geometries and material types. These systems will be adapted to coat 3D-printed parts with high precision, ensuring that coatings are applied effectively to intricate designs. Coating systems capable of handling the unique challenges posed by additive manufacturing, such as variable part sizes and geometries, will be essential as industries like automotive and aerospace increasingly adopt 3D printing for production.
End-of-line inspection systems are another important aspect of the future of automated coating machines. As the demand for high-quality, defect-free coatings grows, manufacturers are integrating advanced inspection technologies into their coating lines. Machine vision systems and AI-based quality control solutions are being used to detect defects, such as inconsistencies in coating thickness, color variation, or surface imperfections. These systems can flag issues in real-time, ensuring that faulty products are identified before they reach the final stages of production. By incorporating these inspection technologies, automated coating systems can achieve zero-defect manufacturing, enhancing product quality and reducing rework.
As the global market becomes more interconnected, manufacturers of automated coating machines are focusing on creating systems that can handle the needs of global supply chains. These systems need to be adaptable to various regulatory environments and capable of handling different product specifications across regions. The ability to integrate with diverse manufacturing systems, supply chains, and logistics networks is becoming increasingly important as manufacturers expand their operations globally. Automated coating machines are designed to be flexible and scalable, able to accommodate regional production requirements while maintaining high levels of efficiency and product consistency.
In summary, the future of automated coating machines manufacturing is one of continual innovation. Automation, AI, sustainability, flexibility, and digital connectivity are key themes that will define the next generation of coating systems. As manufacturers face increasing demands for higher quality, lower costs, and faster production times, automated coating machines will become more advanced, efficient, and capable of handling a wider range of applications. The incorporation of advanced materials, AI-driven process control, robotic automation, and sustainable practices will ensure that these machines remain at the forefront of modern manufacturing, providing manufacturers with the tools they need to meet the evolving needs of global markets.
Looking ahead, the future of automated coating machines will continue to be shaped by advancements in technology, sustainability, and the demand for highly specialized finishes. Customization and personalization will remain at the core of the next wave of innovation, driven by the rise of mass customization in industries such as automotive, consumer electronics, and consumer goods. Automated coating systems will become more capable of quickly adapting to a wide variety of customer specifications, whether for unique colors, textures, or special performance properties like anti-scratch, anti-corrosion, or UV resistance.
One key development will be the integration of additive manufacturing with automated coating systems. As additive manufacturing (AM) becomes more prevalent in industries such as aerospace, automotive, and medical devices, there is an increasing need for automated coating machines that can handle the challenges of coating complex, three-dimensional parts. This will require coating systems that can ensure a uniform and high-quality finish across intricate geometries, a capability that is critical for products with specialized needs such as lightweight structures or customized medical devices. The integration of 3D printing technologies with coating systems will also reduce the need for multiple separate processes, streamlining production workflows and improving efficiency.
In addition, the need for precise, multi-layer coatings will drive further innovations in automated coating systems. More industries are relying on multi-layer coatings to provide the optimal balance of appearance, protection, and performance, such as in the automotive and aerospace sectors. For instance, a base coat may be applied to provide adhesion and corrosion resistance, followed by a topcoat for aesthetic purposes and durability. To maintain efficiency and product consistency, future automated coating machines will need to apply multiple layers with exact precision while controlling thickness, curing times, and chemical bonding between layers.
The rise of smart coatings will also contribute to the evolution of automated coating systems. These coatings offer additional functional benefits, such as self-healing properties, corrosion resistance, or the ability to change color based on environmental conditions. For example, self-healing coatings could repair minor scratches or damages over time, ensuring that products maintain their appearance and functionality longer. Automated coating machines will need to integrate with innovative materials and processes that can apply these advanced coatings with precise control. Manufacturers will be able to produce not only aesthetically pleasing products but also highly functional ones that offer enhanced performance in extreme environments.
Another significant trend will be the increased use of predictive analytics in automated coating systems. Predictive maintenance, powered by real-time data collected from sensors and monitoring devices, will help manufacturers anticipate when components of their coating machines may need repair or replacement, thus minimizing costly downtime. Through continuous monitoring of machine performance, temperature, humidity, and material usage, predictive analytics will allow for optimal maintenance scheduling, improving both the reliability and efficiency of automated coating machines. By predicting potential failures before they happen, these systems will prevent costly disruptions, extend machine lifespans, and increase productivity.
The growing demand for sustainable manufacturing processes will continue to influence the development of automated coating machines. Manufacturers are under increasing pressure to adopt environmentally friendly solutions, including the use of eco-friendly coatings and reducing material waste. In response, automated coating systems are being designed to integrate closed-loop systems that recover overspray and reuse materials, ensuring that the powder used in coating is efficiently recovered and recycled. This approach reduces the need for excess materials, lowers production costs, and minimizes the environmental impact of the coating process.
Moreover, the use of biodegradable coatings and water-based solutions will be explored to replace traditional solvent-based coatings that can emit harmful VOCs (volatile organic compounds). Automated systems that can work with these new materials will need to accommodate different application methods, drying times, and curing processes to ensure high-quality finishes while complying with environmental regulations.
In line with the move toward more data-driven manufacturing, the integration of cloud-based systems will offer manufacturers enhanced flexibility in monitoring and managing their automated coating machines. These systems can aggregate performance data from multiple machines across different locations, providing operators and management with a centralized view of production and real-time insights into system performance. Cloud-based systems will also enable remote diagnostics and troubleshooting, reducing the need for on-site intervention and allowing companies to manage their operations more efficiently from anywhere in the world. This capability will be especially important as manufacturers expand globally and require a unified system for tracking operations in various regions.
Additionally, digital twins will become a critical tool in the development and operation of automated coating machines. Digital twins are virtual replicas of physical systems that allow manufacturers to simulate, analyze, and optimize machine performance before physical adjustments are made. In coating systems, digital twins will be used to simulate the coating process, identify potential issues in design or operation, and optimize machine parameters for specific products or production environments. The ability to test and fine-tune the system virtually will significantly reduce trial-and-error in the development phase and improve system performance once deployed.
In response to growing consumer demand for fast production cycles, automated coating machines will also evolve to incorporate faster coating and curing technologies. High-speed curing ovens, as well as innovations like infrared curing and microwave curing, are set to revolutionize how quickly products can be coated and dried. This is particularly beneficial in industries where speed to market is critical, such as in electronics or automotive production. Advanced curing technologies will allow manufacturers to increase throughput, reduce energy costs, and maintain the same high level of coating quality.
The increased focus on global supply chains will necessitate the development of automated coating systems that are versatile enough to meet the demands of diverse markets. This could involve designing machines that can quickly accommodate different regional regulations, coatings formulations, and production schedules. Manufacturers will require machines that are capable of scaling up or down based on varying demand and that can adapt to rapidly changing supply chain conditions. Automated coating machines will thus need to be both flexible and scalable to support a globalized manufacturing network.
As the automated coating machine industry evolves, there will also be an increasing need for manufacturers to collaborate with material suppliers, equipment designers, and software developers to stay at the cutting edge. This ecosystem of partnerships will drive innovations in coating technologies, machine capabilities, and software solutions that help manufacturers stay competitive. Coating machine manufacturers will need to offer tailored solutions that meet the specific needs of different industries and production environments, ensuring that their products remain relevant and effective in an ever-changing marketplace.
In conclusion, the future of automated coating machines is one of continual growth and transformation. As the demand for highly specialized, sustainable, and customizable coatings increases, automated coating systems will become more sophisticated and adaptable. Through advancements in robotics, AI, sustainability, and connectivity, manufacturers will be able to achieve greater efficiency, higher product quality, and reduced costs. Automated coating machines will play a critical role in meeting the challenges of modern manufacturing, supporting industries ranging from automotive and aerospace to electronics and consumer goods. The next generation of coating machines will offer unmatched precision, flexibility, and sustainability, helping manufacturers meet the evolving needs of a dynamic global market.
As automated coating machines continue to evolve, the integration of advanced coating techniques and innovative technologies will become increasingly critical in maintaining their competitive edge. For example, new multi-functional coatings will push the boundaries of what is possible with automated coating machines. These coatings may include features like self-cleaning, heat resistance, anti-fingerprint properties, and more, creating demand for coating systems that can handle the precise application of these advanced materials. Automated systems will need to adapt quickly to these novel coating formulations, requiring continuous R&D and system updates.
Another key area of development will be increased machine intelligence. Automation and AI will not just optimize the coating process but will also enable automated systems to learn from real-world conditions. Machine learning algorithms can now analyze large amounts of data, from material properties to environmental conditions, and apply these insights to improve machine performance in real-time. This will result in even higher-quality coatings with minimal waste, and operators will be able to set up and adjust coating processes with much greater ease, increasing overall efficiency.
Collaborative robots (cobots) will also play a larger role in the future of automated coating machines. Unlike traditional robots that work in isolation, cobots are designed to work alongside human operators, allowing for a safer and more efficient workflow. In the context of coating systems, cobots could be used for tasks like loading and unloading parts, setting up equipment, or adjusting machine parameters, while the human operators focus on overseeing the system and making decisions. This collaboration can improve the overall ergonomics of the process and increase the versatility of coating machines in complex or high-mix production environments.
Moreover, the rise of customized, on-demand manufacturing will require coating machines to be more flexible than ever before. As consumers and businesses continue to demand products tailored to their needs, coating systems will need to handle a broader range of specifications. This might include providing personalized colors, textures, and finishes for everything from electronics to furniture. Manufacturers of automated coating systems will need to focus on creating machines that can quickly and efficiently adapt to these personalized demands, with features like fast color changes, automated viscosity adjustments, and customizable spray patterns.
The adoption of digital manufacturing techniques will also continue to shape the future of automated coating systems. With the rise of Industry 4.0 and the digital twin concept, automated coating systems will be linked to a comprehensive digital infrastructure. In a fully digitalized factory, coating machines can share data across different systems, such as quality control, production planning, and logistics. This interconnectivity will enable the entire manufacturing process to be optimized in real-time, ensuring that the right materials, equipment, and resources are always available when needed. The use of digital twins will allow manufacturers to simulate the entire coating process, predicting potential issues and providing data-driven recommendations for process improvements.
As part of this transition to digital and interconnected manufacturing, cloud-based monitoring systems will provide more comprehensive oversight of coating operations. Through cloud computing, manufacturers will be able to track the performance of multiple automated coating machines across different sites, allowing for better coordination of maintenance schedules, remote diagnostics, and access to real-time production data. This will help optimize machine uptime and reduce the complexity of managing large, geographically dispersed manufacturing operations.
The increasing use of flexible substrates and novel materials will challenge automated coating systems to accommodate non-traditional surfaces. For example, flexible electronics, wearable technology, and lightweight composite materials are becoming more prominent in industries like consumer electronics, automotive, and healthcare. Automated coating machines will need to handle these materials delicately, applying coatings that not only enhance performance but also maintain the integrity of the substrate. This may require developing new application techniques or incorporating precision coating systems that can handle softer or thinner materials without damaging them.
Furthermore, high-throughput testing will become more common, particularly in industries where batch-to-batch consistency is paramount. The ability to rapidly test small batches of products during the coating process will enable manufacturers to make on-the-fly adjustments, ensuring that every product meets the required specifications. This means the automated coating system must be capable of incorporating inline testing and real-time adjustments without interrupting production. The ability to immediately adjust parameters such as spray volume, speed, and curing time based on real-time data will be a significant advantage in ensuring product quality.
Another important future development will be the use of environmentally friendly, biodegradable coatings. As consumers become more environmentally conscious, manufacturers will increasingly seek out coatings that are non-toxic, biodegradable, and derived from sustainable materials. Automated coating systems will need to be capable of handling these new, eco-friendly materials, which may have different properties compared to traditional coatings. The equipment will need to be designed to work with formulations that are both environmentally safe and effective in providing the required protective and aesthetic properties.
The future of automated coating machines will also see greater integration with other advanced manufacturing technologies. For example, combining coating machines with laser processing or plasma surface treatment could allow for a more efficient and precise approach to coating applications. Laser processing could be used to prepare the surface of a part before coating, improving adhesion and overall finish. Similarly, plasma treatment could enhance the bonding of coatings to difficult-to-coat surfaces, such as those made of certain plastics or metals. These hybrid technologies could help improve both the functionality and efficiency of coating processes, especially for products that require a high degree of precision or special coatings.
In conclusion, automated coating machines are evolving rapidly to meet the demands of modern manufacturing. The next generation of coating systems will be marked by greater flexibility, efficiency, and adaptability, driven by innovations in AI, robotics, sustainability, and digital connectivity. As manufacturers seek to create more complex, customized, and eco-friendly products, automated coating systems will play a critical role in streamlining production processes, reducing waste, and ensuring the highest quality finishes. With advancements in machine intelligence, smart coatings, and digital manufacturing, the future of automated coating machines will offer manufacturers the tools they need to stay competitive in a dynamic and increasingly complex global marketplace.
Automated Coating Machines Manufacturer
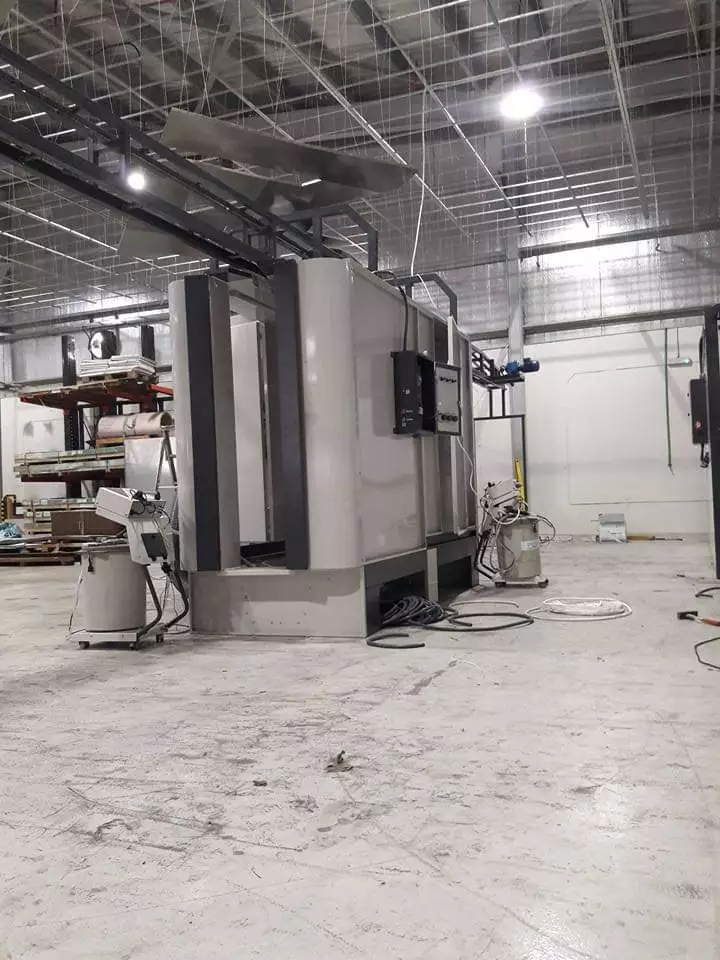
The future of automated coating machine manufacturing is being shaped by the evolving demands of industries that require high-quality, efficient, and sustainable coating solutions. Automated coating machines have become essential in various sectors such as automotive, aerospace, electronics, consumer goods, and more, as they provide consistent, precise, and high-throughput production capabilities. As manufacturers face pressures to improve quality, reduce costs, and enhance sustainability, the role of automated coating machine manufacturers is becoming more critical in driving innovation and meeting these evolving requirements.
The development of automated coating machines is heavily influenced by advancements in robotics, AI, and machine learning. Manufacturers of automated coating machines are incorporating cutting-edge robotics to handle complex tasks like spray coating, powder coating, and liquid application with unparalleled precision. Robots, often equipped with multi-axis arms, allow for highly flexible coating applications, ensuring uniformity and consistency even in complex geometries. This is particularly important in industries like automotive, where intricate surfaces and parts must be coated consistently and efficiently. AI-driven systems are increasingly being integrated into automated coating machines, providing real-time process optimization, defect detection, and adjustments based on feedback from sensors and data analytics. These AI systems can help maintain the highest quality standards by continuously analyzing production data and adapting machine parameters to minimize waste and errors.
Another important trend in the automated coating machine sector is enhanced sustainability. Manufacturers are under significant pressure to reduce the environmental impact of their production processes. As a result, coating machines are being designed with energy-efficient features, low-emission technologies, and material recycling systems. Automated machines equipped with powder recovery systems allow for the recycling of excess powder during coating processes, which helps reduce material waste and lower costs. In addition, eco-friendly coatings, such as water-based or solvent-free coatings, are becoming more common, and automated coating machine manufacturers are increasingly developing machines that can apply these advanced materials effectively. These machines help manufacturers meet environmental regulations and the growing consumer demand for sustainable products.
Customization is another key driver of change in automated coating machine manufacturing. With industries such as electronics, automotive, and consumer goods increasingly demanding personalized or niche products, coating machines need to be adaptable to various materials, sizes, and shapes. Automated coating machine manufacturers are responding by developing more flexible systems that can be easily adjusted for different production needs. Features like fast color change capabilities, adjustable spray patterns, and multi-functional coating heads are becoming more common. This flexibility allows manufacturers to quickly switch between different types of coatings, reduce downtime, and respond to shifting market demands for personalized finishes.
Manufacturers of automated coating machines are also focusing on integrating smart technologies into their systems. As part of the Industry 4.0 revolution, automated coating machines are becoming part of a larger digital ecosystem. These machines are being connected through Internet of Things (IoT) devices, enabling real-time monitoring, predictive maintenance, and performance analysis. With IoT connectivity, operators can track machine performance remotely, ensuring better control over coating quality, machine efficiency, and resource usage. These smart machines collect data on every aspect of the coating process, allowing for data-driven decision-making and ensuring that the machines operate at peak efficiency.
Modularity is a significant trend in the design of automated coating machines, allowing manufacturers to customize and upgrade machines to meet specific production requirements. Modular machines can be easily adapted for different coating processes, including powder coating, liquid coating, and electrostatic spraying, offering flexibility across various industries. Modular components can be added or removed to accommodate different part sizes, coating materials, and production speeds, reducing the need for completely new machines as production needs evolve. This scalability is particularly beneficial for manufacturers who need to quickly respond to changing market demands and are looking for cost-effective ways to upgrade their equipment.
In terms of precision and quality, automated coating machine manufacturers are focused on creating systems that can achieve high levels of consistency and accuracy. Coating thickness, uniformity, adhesion, and surface quality are critical factors, particularly in industries like aerospace and automotive, where product performance and appearance are paramount. As such, manufacturers are incorporating advanced sensors, laser scanners, and vision systems into their machines to ensure that each coating layer is applied perfectly. These technologies enable real-time inspection and adjustment, reducing defects and ensuring that each product meets strict quality standards.
Innovation in coating technologies is another driving factor for automated coating machine manufacturers. As new materials and coating techniques continue to emerge, coating machine manufacturers are continuously improving their designs to accommodate these innovations. For example, new smart coatings are being developed that offer enhanced performance properties, such as self-healing, anti-corrosion, or heat-resistant capabilities. Automated coating machines will need to be able to apply these advanced coatings with precision, ensuring that their benefits are fully realized. Additionally, emerging techniques like plasma treatment and nano-coatings are expected to become more prevalent in the future, requiring automated coating systems to apply coatings at the microscopic level to achieve specific performance attributes.
The globalization of supply chains is influencing automated coating machine manufacturing by driving the need for systems that are adaptable to different market conditions. Manufacturers are increasingly designing machines that can work in diverse environments and meet international standards. These systems need to handle different types of coatings, comply with various regulatory requirements, and be able to accommodate diverse product types. The ability to offer customized, localized solutions will be crucial as manufacturers expand into new regions or work with a wide variety of clients with unique production needs.
Additionally, the move toward high-throughput production is driving innovation in automated coating machine designs. Manufacturers in industries such as automotive and electronics are under pressure to produce large quantities of high-quality products in shorter timeframes. Automated coating machines are being designed with faster cycle times, allowing for higher production speeds without compromising the quality of the coating. Features such as high-speed curing ovens, automated conveyor systems, and advanced spray guns are being incorporated to improve throughput while maintaining consistent results.
The increased focus on predictive maintenance will play a significant role in the future of automated coating machines. By incorporating sensors and IoT devices into the machines, manufacturers will be able to gather data on machine performance and detect issues before they cause breakdowns. Predictive maintenance reduces downtime and allows manufacturers to schedule repairs and parts replacements more effectively. This capability can be integrated with cloud-based monitoring systems that allow operators to manage machines remotely and make adjustments to optimize production, maintenance schedules, and machine performance across multiple sites.
In conclusion, automated coating machine manufacturers are at the forefront of a significant transformation in the manufacturing industry. As demand grows for faster, more efficient, and sustainable coating solutions, manufacturers of automated coating machines will need to focus on flexibility, precision, and adaptability. Innovations in robotics, AI, and connectivity, along with advances in sustainable materials and customizable features, will help drive the evolution of automated coating systems. By integrating cutting-edge technologies like AI, IoT, and predictive maintenance, these manufacturers will be able to provide solutions that help companies stay competitive in a rapidly changing global marketplace. With an emphasis on smart manufacturing, sustainability, and efficiency, the future of automated coating machine manufacturing looks promising, offering manufacturers the tools they need to meet the growing demands of modern industries.
As the demand for advanced coating technologies continues to grow, automated coating machine manufacturers are also focusing on enhancing production flexibility to address the needs of different industries. One of the most significant changes in the industry will be the shift toward multi-functionality in coating machines. These systems are being designed to not only perform traditional coating tasks but also to support advanced treatments such as nano-coating, electroplating, and functional coatings. This versatility will allow manufacturers to cater to an increasingly diverse range of applications, from protective coatings for industrial components to specialized finishes for consumer electronics. The ability to combine multiple coating technologies within one system will provide manufacturers with the flexibility to meet both short-term and long-term production goals.
The growing need for real-time quality control and immediate adjustments in the coating process is prompting the integration of advanced sensors and visual inspection systems into automated coating machines. These sensors can detect subtle variations in coating thickness, surface uniformity, and gloss levels, alerting operators to potential defects as they occur. This allows for immediate corrective actions, preventing waste and ensuring that only high-quality products are shipped out. Manufacturers are also exploring machine vision systems that can monitor every stage of the coating process, from part preparation to curing, providing detailed feedback on quality metrics and facilitating real-time decision-making.
Automation in coating systems extends beyond the coating process itself. Manufacturers are increasingly designing fully integrated, automated production lines that combine coating machines with other manufacturing processes such as assembly, packaging, and quality testing. The combination of automated coating systems with end-to-end manufacturing workflows offers significant advantages in terms of efficiency, reduced labor costs, and shorter lead times. The ability to automate the entire production cycle—from part handling to coating and final inspection—will continue to drive improvements in production speed and consistency, leading to faster time-to-market for products across various industries.
In parallel, remote operation and diagnostics will become more prevalent in the automated coating machine sector. With the growing trend of global manufacturing operations and a more distributed workforce, manufacturers will continue to adopt cloud-based platforms that allow operators and maintenance personnel to monitor and control machines from virtually anywhere in the world. These platforms can provide real-time insights into machine performance, efficiency, and health, allowing for proactive maintenance, better resource management, and faster troubleshooting. Remote diagnostics and troubleshooting will also reduce the need for on-site visits, lowering maintenance costs and minimizing production downtime.
To improve the cost-effectiveness of automated coating systems, manufacturers are increasingly designing machines with modular components that can be customized and upgraded based on specific production needs. These systems offer the ability to scale up or down depending on demand, allowing manufacturers to adapt quickly to changes in production volume or coating complexity. Modular systems also allow for more cost-effective solutions by enabling the use of existing equipment for different types of coatings, reducing the need for extensive capital investment in entirely new machines. This flexibility is especially crucial for companies in rapidly evolving industries, where production requirements can shift frequently.
As environmental concerns become more pressing, the demand for sustainable coating processes will continue to influence the design and manufacturing of automated coating machines. Manufacturers are focusing on reducing energy consumption, minimizing waste, and lowering emissions during the coating process. Energy-efficient systems, such as infrared curing and low-temperature spray technologies, are being incorporated into new machine designs to minimize the environmental impact. Additionally, closed-loop systems are being developed that allow for the recycling of unused coating materials, reducing waste and ensuring that no material is lost during production. These eco-friendly systems align with stricter regulations on VOCs (volatile organic compounds) and carbon emissions, ensuring that manufacturers can comply with environmental standards while delivering high-quality products.
The trend towards smart factories and Industry 4.0 is also driving innovation in the automated coating machine sector. The integration of big data analytics, machine learning, and IoT technologies allows manufacturers to optimize their coating systems based on real-time data. This data-driven approach enables manufacturers to gain deep insights into operational efficiency, track key performance indicators (KPIs), and make informed decisions that reduce costs, improve quality, and increase throughput. By implementing data analytics at every stage of the production process, coating machine manufacturers can help their clients reduce material waste, identify bottlenecks, and improve overall system performance.
With global supply chains continuing to evolve, automated coating machine manufacturers are also focusing on making their machines adaptable to different international markets. As manufacturers expand operations in new regions, there is a growing need for coating machines that can handle a wide range of coatings, comply with varying environmental regulations, and operate in diverse production environments. By designing machines that are both flexible and scalable, manufacturers can cater to the specific needs of their clients across different geographic locations, offering customized solutions that meet regional regulatory and market demands.
Furthermore, manufacturers of automated coating machines are embracing collaboration with material suppliers and industry partners to stay ahead of the competition. As new coating materials and technologies are constantly emerging, partnerships between coating machine manufacturers and material suppliers are essential for ensuring that coating machines can handle the latest innovations. By staying closely aligned with material trends, machine manufacturers can develop equipment that is compatible with new coatings and treatment methods, offering their customers cutting-edge solutions that enhance performance and efficiency.
Another significant development in the field of automated coating systems will be the rise of robotic spray applications and advanced spray guns. Robotic systems equipped with specialized spray guns can provide more precise control over the coating process, ensuring uniform coverage even on complex surfaces. The latest robotic spray systems are designed with advanced algorithms that adapt the spray pattern, spray distance, and application speed based on the part’s geometry and coating requirements. This technology allows for more efficient use of coating materials and minimizes overspray, leading to a reduction in waste and production costs.
The demand for high-precision and multi-layer coatings is expected to rise in the coming years, especially in industries such as aerospace, electronics, and automotive. Automated coating systems will increasingly be designed to apply multiple coatings in a single pass, creating more durable, functional, and visually appealing products. Multi-layer coatings can offer a combination of properties such as corrosion resistance, abrasion resistance, and aesthetic appeal. As manufacturers continue to push for enhanced coating durability and performance, automated coating systems will need to integrate precise control over each coating layer, ensuring that all layers are applied uniformly and effectively.
In conclusion, the future of automated coating machine manufacturing is focused on precision, flexibility, sustainability, and innovation. As industries continue to demand more sophisticated, customized, and efficient coating solutions, manufacturers of automated coating machines must adapt by integrating cutting-edge technologies, developing modular and scalable systems, and incorporating eco-friendly practices into their designs. With advancements in AI, robotics, IoT, and data analytics, the next generation of automated coating systems will enable manufacturers to produce high-quality, customizable products at faster speeds and lower costs, while meeting stringent environmental standards. By embracing these trends, automated coating machine manufacturers will remain at the forefront of the industry, providing solutions that meet the evolving needs of global markets.
Powder Coat Sprayer
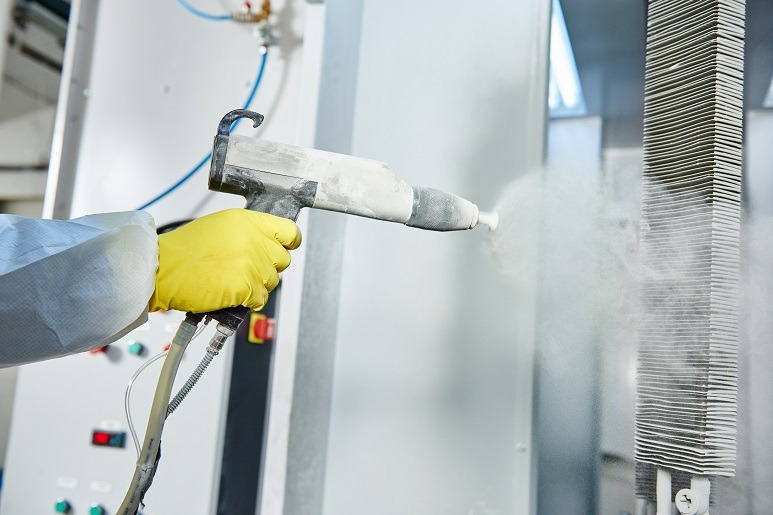
A powder coat sprayer is an essential tool in the powder coating process, which involves applying a dry powder to a substrate, typically metal, and curing it under heat to form a durable and even finish. These sprayers are designed to apply powdered coating materials using electrostatic spray technology, ensuring that the powder adheres to the surface of the object before being baked in an oven. The development of powder coat sprayers has significantly advanced, and they are now available in a wide range of models and features tailored to specific coating needs.
One of the key components of a powder coat sprayer is the electrostatic charging system, which uses an electric field to impart a charge to the powder particles as they are sprayed. The charged particles are attracted to the grounded substrate, allowing for a uniform coating that minimizes overspray and waste. This charging process is crucial for achieving high-quality finishes, especially on complex or intricate parts. Some sprayers also come with adjustable voltage controls to fine-tune the level of charge applied to the powder, enhancing the ability to coat difficult shapes and surfaces.
The spray gun of a powder coat sprayer is the primary tool used to apply the powder. Modern spray guns are typically lightweight, ergonomic, and designed for ease of use, reducing operator fatigue and increasing productivity. They offer precise control over the flow of powder and air, allowing the operator to achieve a consistent coat. Some models come with digital controls that enable operators to adjust settings like airflow, powder feed rate, and electrostatic voltage at the touch of a button. This level of control is essential in industries where high-quality, consistent finishes are a must, such as automotive, furniture, and appliance manufacturing.
Powder delivery systems are another critical aspect of powder coat sprayers. These systems ensure a steady and controlled flow of powder from the supply hopper to the spray gun. The powder is usually stored in a hopper and transported to the spray gun via a combination of compressed air and vacuum suction. Advanced delivery systems are designed to minimize powder clumping and ensure that the powder remains dry and free-flowing, ensuring a smooth and even application. Some systems even include automatic cleaning features to prevent powder build-up, reducing maintenance time and improving overall efficiency.
In terms of performance, modern powder coat sprayers are designed to offer high transfer efficiency—meaning a higher percentage of the powder is applied to the workpiece rather than lost to overspray. This efficiency not only reduces waste but also helps to improve the cost-effectiveness of the coating process. Many powder coat sprayers also offer adjustable spray patterns, allowing operators to choose from a variety of spray shapes (such as circular, fan, or oval) to optimize coverage for different shapes and sizes of parts.
A significant development in powder coat sprayers is the incorporation of advanced technology such as automated spray systems and robotic arms. These technologies improve consistency and speed, making them particularly useful in high-volume production settings. Robotic powder coating systems, for example, are capable of automating the spraying process, which not only speeds up production but also reduces the risk of human error and variation. Robotic sprayers can follow precise paths and apply coatings evenly, even on complex geometries, making them ideal for industries like automotive manufacturing, where uniformity and efficiency are key.
The versatility of powder coat sprayers is another key factor driving their adoption. They can be used for a wide range of substrates, including metal, plastic, and even some ceramics, making them suitable for various industries beyond just metal coating. They are commonly used in automotive, aerospace, appliances, and industrial equipment sectors, but they are also finding applications in industries such as electronics and furniture, where customized finishes and protective coatings are needed.
Powder coat sprayers also contribute to environmental sustainability by offering a more eco-friendly coating process compared to traditional liquid coatings. Since powder coating does not contain solvents, it eliminates the need for VOCs (volatile organic compounds) that are harmful to both the environment and human health. Additionally, the powder used in these sprayers is often reclaimable, making the process more resource-efficient and reducing waste. This aligns with the growing emphasis on green manufacturing and sustainable practices within the coatings industry.
Maintenance and care of powder coat sprayers are crucial for ensuring their longevity and optimal performance. The most common maintenance tasks include cleaning the spray guns and delivery systems to prevent powder clogs and ensure smooth operation. Manufacturers often provide cleaning kits designed specifically for this purpose, making it easier for operators to maintain the equipment. Regular maintenance also involves checking the electrical components, such as the electrostatic charging system, to ensure consistent performance and quality finishes.
Training and expertise are also essential for maximizing the potential of a powder coat sprayer. While these systems are designed for ease of use, proper training ensures that operators can efficiently adjust settings, troubleshoot potential issues, and maintain consistent, high-quality results. Many manufacturers offer specialized training programs to help users optimize their use of powder coat sprayers, covering everything from powder selection to spraying techniques and maintenance practices.
Another important consideration in the selection of a powder coat sprayer is the cost. While these systems can be a significant investment, they often provide substantial long-term savings due to their efficiency, reduced material waste, and the durability of powder coatings. Many manufacturers offer a range of sprayers to suit different budgets and production scales, from more basic manual sprayers for smaller operations to high-tech automated sprayers for large-scale, high-volume production lines. The return on investment (ROI) for a powder coat sprayer can be realized over time through lower operational costs and higher throughput, making them a cost-effective option for many manufacturers.
The future of powder coat sprayers is also tied to ongoing advancements in materials and coatings. With the development of new powder formulations—such as those with enhanced heat resistance, corrosion protection, and UV stability—the capabilities of powder coat sprayers will continue to expand. Manufacturers will need to adapt their sprayers to handle new formulations, including those with different flow characteristics, particle sizes, or curing requirements. Additionally, the rise of smart sprayers integrated with sensor technologies will allow operators to collect real-time data on the coating process, helping to fine-tune performance and reduce variability in coating applications.
The integration of digital technologies into powder coat sprayers is also on the horizon. The use of machine learning and AI could enable sprayers to automatically adjust parameters such as airflow, pressure, and voltage based on real-time feedback from sensors. This could further enhance the precision and consistency of the coating process, leading to even higher-quality finishes and more efficient production lines. Moreover, automated diagnostics could provide alerts about potential issues before they become problems, minimizing downtime and improving overall equipment reliability.
In conclusion, powder coat sprayers have become indispensable tools in modern coating applications, providing efficient, environmentally friendly, and high-quality finishes across a wide range of industries. As technology continues to evolve, these sprayers will become even more precise, adaptable, and cost-effective, meeting the growing demands for customization, sustainability, and performance. Whether in manual, semi-automated, or fully automated systems, powder coat sprayers will continue to play a crucial role in the future of coating applications, offering manufacturers the ability to meet the challenges of an increasingly complex and competitive marketplace.
The development of smart powder coat sprayers is expected to continue transforming the powder coating industry. As Industry 4.0 principles become more integrated into manufacturing processes, powder coat sprayers will likely evolve to incorporate features such as advanced sensors, data analytics, and remote monitoring. These smart sprayers can collect real-time data on key variables like coating thickness, application efficiency, and even environmental factors such as temperature and humidity, which can all influence the final coating quality. By analyzing this data, manufacturers can optimize settings for every part and adjust parameters in real time to ensure consistency and reduce waste.
The introduction of predictive maintenance is another exciting development in the world of powder coating sprayers. Using sensor data and machine learning algorithms, predictive maintenance tools can monitor the performance of the sprayer in real time and predict when parts might need maintenance or replacement. This proactive approach can significantly reduce downtime and maintenance costs, as it allows manufacturers to address potential issues before they cause disruptions in production. For example, a sprayer that detects unusual wear on the nozzle can alert operators ahead of time to perform maintenance, minimizing unplanned halts in the coating process.
Furthermore, user interface innovations will continue to improve in smart sprayers. The development of intuitive touchscreen controls, voice-activated systems, and mobile apps for controlling and monitoring powder coat sprayers will enhance the user experience. These advancements will allow operators to quickly adjust settings, view real-time performance reports, and even troubleshoot issues remotely. With a growing emphasis on user-friendly technology, operators will spend less time training on complex systems, and more time focusing on optimizing coating applications.
Energy efficiency is another area where powder coat sprayers are expected to advance. Modern systems are already designed to be more energy-efficient than older models, but as energy costs rise and sustainability goals become more critical, manufacturers are pushing to further reduce energy consumption in sprayers. Technologies like low-energy electrostatic charging, reduced air consumption, and energy-efficient curing systems are already being explored. Manufacturers will likely continue to innovate in this area, offering solutions that help companies save on energy while still achieving the same high-quality results.
Customization and flexibility are increasingly important in powder coating applications, as many industries require coatings tailored to specific needs. For example, automotive manufacturers may require coatings with specific color profiles, texture finishes, or weather-resistant properties, while electronics companies might focus on coatings that offer better thermal management or conductivity. Powder coat sprayers are being designed with greater versatility, capable of handling a variety of powder materials and adjusting settings for specific types of finishes. This flexibility allows manufacturers to meet the exacting demands of customers in a wide range of sectors, from aerospace and marine to furniture and architectural finishes.
Another innovation in the powder coating sector is the development of advanced powder materials that can be applied with the latest powder coat sprayers. Thermoplastic powders, flame-retardant powders, and high-gloss finishes are examples of specialized powders that are becoming more common. These materials require sprayers that are equipped with features that can handle the unique properties of each powder type. For instance, some powders may require higher temperatures or specialized curing processes to achieve the desired performance, and powder coat sprayers must be able to accommodate these requirements without compromising quality or efficiency.
In addition, the integration of robotic automation in powder coating lines has allowed for the increased use of powder coat sprayers in high-volume production environments. Automated systems can control the movement of the sprayer, adjust its position, and apply coatings more precisely than human operators. These robots, often equipped with advanced sensors and machine vision, can ensure even coverage on parts with complex geometries and can consistently apply coatings to the same high standard, even over extended periods. This has led to faster production speeds, lower labor costs, and greater consistency in finished products.
The application of powder coatings in non-traditional industries is also expanding. For example, the construction industry is increasingly adopting powder coating for architectural elements like window frames, facades, and building panels due to the durability and aesthetic appeal of the finish. In electronics, where heat management is critical, powder coatings that provide thermal conductivity are being applied to components such as heatsinks and circuit boards. Similarly, consumer goods like kitchen appliances, furniture, and sports equipment are benefiting from the versatility and durability of powder coatings, which are applied using advanced powder coat sprayers to achieve finishes that are resistant to scratches, UV degradation, and environmental wear.
In the future, powder coat sprayers will likely become even more integrated with the overall production environment, thanks to advancements in IIoT (Industrial Internet of Things). By connecting sprayers to the factory’s central control system, manufacturers will be able to track powder consumption, monitor machine health, and optimize coating schedules in real time. This level of connectivity will lead to a more data-driven approach to powder coating, enabling manufacturers to adjust production plans on the fly and make real-time adjustments to the coating process to ensure that each job is completed efficiently and at the highest standard.
As powder coat sprayers continue to evolve, the coating industry as a whole will see increased automation, precision, and efficiency. The convergence of advanced technologies such as AI, robotics, and smart factory solutions will result in sprayers that can adapt to a wider variety of applications, deliver more consistent results, and operate with minimal waste. The evolution of powder coating systems will continue to meet the demands of industries seeking greater customization, sustainability, and cost-effectiveness in their coating processes.
Ultimately, the powder coat sprayer will remain a crucial component in the world of coating technologies, offering manufacturers the tools they need to produce high-quality, durable, and aesthetically pleasing finishes on a wide range of materials. With the ongoing advancements in automation, smart technologies, and energy-efficient designs, these sprayers will continue to drive innovation and improve the overall powder coating process for years to come.
As the powder coating industry continues to evolve, further innovations in powder coat sprayers will focus on achieving greater precision, enhanced user experience, and sustainability. The integration of digitalization will be a significant trend, as sprayers become part of a larger, more interconnected system of machines and processes. Machine learning and AI-based algorithms will enable sprayers to learn from previous applications, adjusting parameters like spray pressure, powder flow rate, and electrostatic charge to optimize results with each use. By analyzing the feedback from sensors and real-time data, these smart sprayers will not only improve their performance over time but also anticipate challenges such as surface irregularities, helping to maintain high standards of finish consistency.
One of the ongoing challenges in powder coating is ensuring uniform coverage over complex or irregularly shaped parts. Advancements in spray gun design will continue to improve this aspect, with new guns featuring enhanced adjustable spray patterns and more precise air delivery. The ability to easily customize spray patterns will allow operators to coat parts of various shapes and sizes more efficiently. Enhanced robotic arms equipped with multi-axis movement will also allow sprayers to reach hard-to-coat areas, reducing the need for manual labor and ensuring that the entire part receives an even, high-quality finish.
Additionally, the integration of machine vision systems with powder coat sprayers will play a critical role in the future of automated coating lines. By using high-definition cameras and advanced imaging technology, these systems will be able to inspect the part in real time and assess whether the coating is being applied uniformly. This feedback will be relayed to the sprayer, which can then make immediate adjustments to optimize application and ensure that the coating process is as efficient and precise as possible.
The use of robotic powder coat sprayers will also expand in the future, especially in industries requiring high-precision or high-volume production, such as the automotive, aerospace, and electronics sectors. These robots are capable of maintaining consistent spraying speed, pressure, and distance from the part, reducing human error and ensuring uniformity in the final finish. This level of automation can be especially beneficial in situations where consistency is critical, such as in the production of automotive body panels or high-performance electronic enclosures that require highly durable coatings. By using robots equipped with artificial intelligence, manufacturers can implement systems that continuously learn from previous coatings and adapt to the specific needs of each production run.
Another area where the powder coat sprayer is likely to see advancements is in application to a wider variety of materials. As the demand for more diverse substrates increases, powder coating sprayers will need to handle materials beyond traditional metals, such as plastics, ceramics, and composites. For these materials, customized coating formulations and sprayer adjustments will be needed to ensure proper adhesion, curing, and finish quality. Specialized sprayers that can handle these unique materials with precision will open up new applications in industries such as consumer goods, construction, and electronics.
The rise of eco-friendly and sustainable coating solutions will continue to drive innovation in powder coating systems. Manufacturers are increasingly focusing on developing low-emission powders and systems that reduce the environmental impact of the coating process. The elimination of VOCs and solvents in the powder coating process already sets it apart from traditional liquid coatings in terms of environmental impact. However, further innovations in sustainable powder formulations will make the process even greener, allowing manufacturers to reduce waste, increase recycling, and lower their carbon footprint. Some of the newer powders being developed are based on biodegradable or renewable materials, offering an even more environmentally friendly solution for a wide range of applications.
Energy consumption remains a major factor in the operation of powder coat sprayers. As energy costs continue to rise and sustainability goals become more stringent, manufacturers are expected to focus on reducing the energy requirements of the coating process. New techniques in infrared curing, lower temperature curing, and advanced curing ovens will reduce energy consumption without compromising the quality of the final finish. Moreover, more efficient electrostatic charging systems and air management features will lower energy use, making powder coating an even more cost-effective and environmentally friendly option for manufacturers.
Another area where advancements are expected is in the ease of cleaning and maintenance of powder coat sprayers. Given the nature of powder coating materials, cleaning can be a challenging and time-consuming process. Many powder coat sprayers now feature self-cleaning mechanisms or easy-to-remove components that simplify the maintenance process. Future sprayers may feature automated cleaning cycles, which reduce downtime and the need for manual intervention. This would not only increase the efficiency of the coating process but also extend the lifespan of the equipment.
The market for high-performance coatings will continue to expand, driven by the need for greater durability, resistance to harsh environments, and longer-lasting finishes. Industries such as automotive, construction, appliance, and electronics will demand coatings that offer superior abrasion resistance, UV stability, chemical resistance, and anti-corrosion properties. To meet these requirements, powder coat sprayers will be designed to apply these specialty coatings with greater consistency, even on complex geometries. With advancements in spray technologies and precision control systems, manufacturers will be able to apply these high-performance coatings more effectively, reducing the need for multiple coats and minimizing waste.
The rise of customized finishes is another trend that will drive innovation in powder coat sprayers. With growing demand for unique and specialized finishes, from matte and glossy to textured and metallic, sprayers will be developed to allow for precise control over the coating texture and visual effects. Advanced sprayers will provide the ability to create coatings with distinct visual qualities that match the needs of specific applications, offering both aesthetic appeal and functional performance.
Smart connectivity will be a crucial aspect of the next generation of powder coat sprayers. Manufacturers will increasingly adopt cloud-based systems that allow operators to monitor and control sprayers remotely. These systems will provide operators with real-time insights into performance metrics, coating quality, and machine health, even allowing for predictive diagnostics and remote troubleshooting. Additionally, these connected systems will enable real-time feedback to improve processes and make adjustments on the fly, leading to better overall productivity and quality control.
Lastly, as the demand for high-throughput production lines grows, integrated systems combining powder coat sprayers with other processes such as cleaning, pre-treatment, and curing will become more common. These integrated systems will streamline the production process, reducing cycle times and improving efficiency. By combining multiple coating processes into a seamless, automated production line, manufacturers can achieve faster turnaround times, lower operational costs, and higher-quality results.
In summary, the future of powder coat sprayers is incredibly exciting, with continuous developments in automation, sustainability, precision, and smart technology. As industries demand more customized, eco-friendly, and durable coatings, sprayers will evolve to meet these needs, providing manufacturers with the tools to remain competitive and efficient. Whether through advancements in robotics, AI, machine vision, or energy efficiency, the role of the powder coat sprayer in modern manufacturing will only grow more significant, ensuring that it continues to be a crucial tool for creating high-quality finishes across a wide range of industries.
Powder Coat Spray Gun
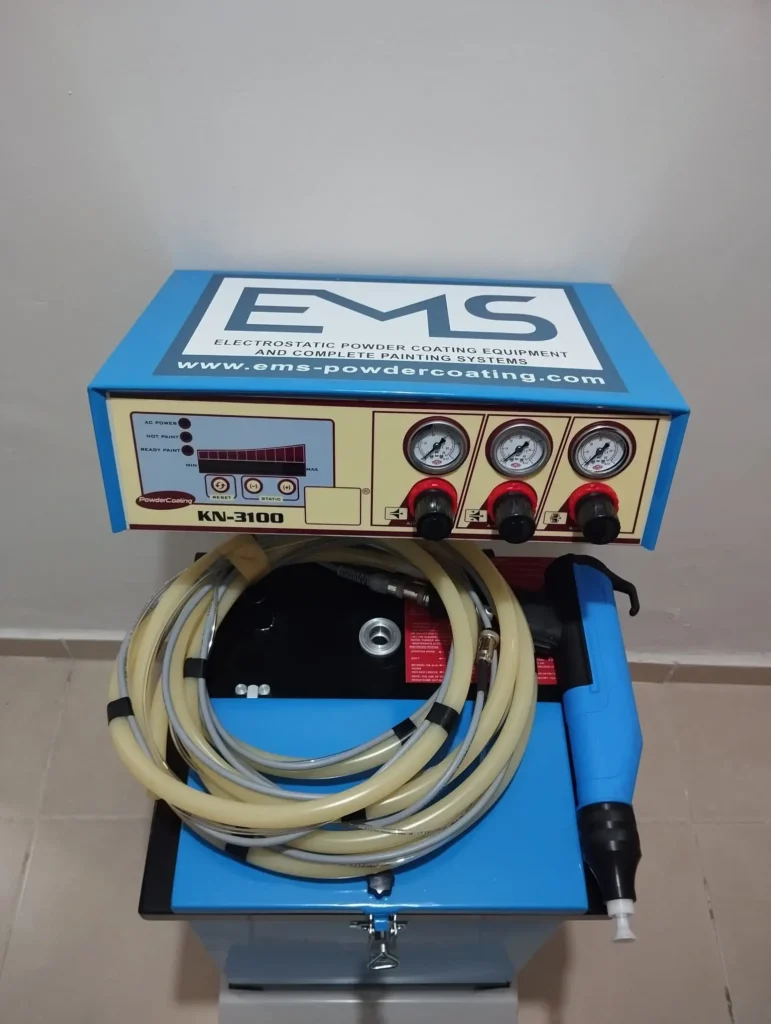
The powder coat spray gun is a pivotal tool in the powder coating process, playing a central role in applying a consistent, even layer of powder to various substrates. As the demand for higher-quality finishes and more efficient production methods grows, powder coat spray guns are evolving to incorporate new technologies that improve performance, precision, and energy efficiency.
One of the key advancements in powder coat spray guns is the incorporation of electrostatic charging systems. These systems give the sprayed powder an electrical charge, causing it to be attracted to the grounded substrate. This process ensures that powder adheres more effectively to the surface, reducing overspray and waste, and providing a smoother, more uniform finish. As the technology advances, these electrostatic systems will continue to become more efficient, allowing spray guns to provide higher transfer efficiencies, which translates into reduced powder consumption and lower material costs.
The design of powder coat spray guns is also evolving to improve ergonomics and ease of use. Lightweight materials, adjustable spray settings, and user-friendly interfaces are becoming standard features in modern spray guns. These enhancements allow operators to work longer hours without fatigue while ensuring precise and controlled powder application. Adjustable flow rates and spray patterns help operators optimize the gun for different coating applications, whether they are dealing with large flat surfaces or intricate geometries that require fine detail. Customizable settings allow operators to apply the right amount of powder for each job, minimizing waste and ensuring uniform coverage.
Another important development is the integration of advanced nozzle technology. The nozzle is a critical component of the spray gun, and new innovations are enabling more uniform powder flow and improved control over the spray pattern. Innovations such as multi-nozzle configurations and variable angle nozzles allow spray guns to handle a broader range of applications, providing greater flexibility in coating parts with complex shapes and varied surface textures. The ability to fine-tune the nozzle configuration to match specific job requirements ensures that the coating process is both efficient and precise.
The ability of powder coat spray guns to handle various types of powders is also improving. Modern spray guns are being designed to work with an increasingly diverse range of powders, including low-temperature curing, thermoplastic, and heat-sensitive powders. This versatility is important as industries seek coatings that offer specific properties, such as chemical resistance, abrasion resistance, or high-gloss finishes. Advanced spray guns can now handle these specialized powders without compromising performance, ensuring a high-quality finish on a variety of materials.
To enhance application consistency, some powder coat spray guns now feature automatic adjustment systems that monitor key parameters such as powder flow, air pressure, and electrostatic charge. These systems can make real-time adjustments to maintain consistent coating thickness and even coverage, reducing the likelihood of defects. This automation not only improves the quality of the coating but also reduces the need for constant manual adjustments, increasing operational efficiency.
Self-cleaning mechanisms in modern powder coat spray guns are becoming more common, addressing one of the more time-consuming aspects of powder coating—cleaning. Powder coating is a dry process, and if the equipment isn’t properly cleaned, powder can build up and cause blockages or inefficiencies. Self-cleaning features, such as automated nozzle cleaning, easy-to-remove parts, and air purging systems, help operators maintain the gun’s performance without spending excessive time on maintenance. These innovations also reduce downtime and help keep production lines running smoothly.
Smart technology is also making its way into powder coat spray guns. These “smart” spray guns incorporate sensors and data analytics to optimize the coating process. For example, spray guns equipped with pressure sensors or flow meters can detect when the spray pattern is beginning to deteriorate due to clogged nozzles or insufficient powder flow. When these issues are detected, the system can notify the operator or automatically adjust settings to maintain optimal performance. This capability reduces the chances of defects or inconsistencies in the coating, ensuring that each application is of the highest quality.
As sustainability becomes a larger concern in manufacturing, eco-friendly powder coating solutions are driving innovations in spray gun design. Many modern powder coat spray guns are designed to work with low-emission powders that reduce harmful effects on the environment. The ability to apply coatings with minimal waste is also a focus of modern spray gun design. Improved transfer efficiency and air management systems ensure that more powder adheres to the part, reducing overspray and the environmental impact of the coating process.
Durability is another area where powder coat spray guns are improving. With the constant need for reliability in high-volume production environments, manufacturers are designing guns with enhanced resistance to wear and tear. Durable, abrasion-resistant materials ensure that spray guns continue to perform well, even in harsh working conditions. These guns can withstand the rigors of industrial environments and maintain consistent performance over longer periods of time, reducing the need for frequent replacements.
The growth of robotic automation in coating systems is also influencing powder coat spray gun technology. Robotic systems equipped with spray guns are increasingly used in high-throughput industries like automotive manufacturing, where precision and efficiency are essential. These systems can position the spray gun more accurately and consistently than human operators, ensuring even coating across all parts. Additionally, robotic arms can apply coatings to parts with complex shapes or difficult-to-reach areas, expanding the possibilities for powder coating applications. Machine vision systems combined with robotic spray guns also enable real-time feedback to ensure that the coating is applied correctly, with uniform thickness and no defects.
In the future, integrated coating systems that combine the powder coat spray gun with other technologies such as surface pre-treatment, curing ovens, and post-coating inspection systems will become more common. These systems will streamline the coating process, improving both speed and quality. By combining multiple processes into one seamless system, manufacturers can reduce cycle times, lower labor costs, and increase throughput without sacrificing coating quality.
In summary, powder coat spray guns are becoming increasingly sophisticated, with advancements focused on improving precision, efficiency, and ease of use. The integration of smart technology, advanced nozzles, self-cleaning features, and automated systems will help to optimize the powder coating process, reduce waste, and ensure high-quality finishes across a wide range of industries. As powder coating continues to be a preferred method for achieving durable, high-performance coatings, powder coat spray guns will play a crucial role in the ongoing evolution of coating technologies, providing manufacturers with the tools they need to meet the demands of sustainability, customization, and efficiency.
As powder coating technologies continue to advance, powder coat spray guns will become even more integrated and smart, offering additional benefits to manufacturers. Future developments are likely to focus on further enhancing the automation of the coating process, as well as improving the efficiency and sustainability of the systems.
A growing trend is the integration of AI-based control systems into powder coat spray guns. These systems will allow the guns to analyze the surface of the part in real-time and adjust the spray settings accordingly. For example, if the gun detects irregularities in the part’s geometry or surface profile, it could automatically adjust the spray angle, distance, or pressure to ensure that the coating is applied uniformly. This adaptive behavior would greatly reduce the possibility of human error and ensure that every part, regardless of its shape or condition, receives the best possible coating.
In terms of quality control, future powder coat spray guns will likely feature more advanced sensor technologies that can not only monitor the coating process but also inspect the finished coat. These sensors could detect issues like powder buildup, uneven coating thickness, or overspray, and alert the operator immediately. Some systems might even be able to self-correct by adjusting the spray parameters, such as powder flow or electrostatic charge, to ensure a consistent finish.
The continued evolution of mobile connectivity will also have a profound impact on the future of powder coat spray guns. Operators and managers will be able to monitor the performance of the spray guns remotely through mobile apps or web-based interfaces, receiving real-time data on key performance indicators like material consumption, spray uniformity, and machine status. This level of connectivity will allow operators to make adjustments on the go and enable managers to make data-driven decisions about process improvements, maintenance schedules, and production optimization.
Additionally, the flexibility of powder coat spray guns will continue to improve, especially when it comes to working with different types of powders. Advances in powder technology mean that the range of powders being used is expanding, from those offering better durability and corrosion resistance to those with unique aesthetic finishes, such as metallic, textured, or matte coatings. As the variety of available powder types grows, so will the need for spray guns that can apply these powders effectively and consistently. New spray gun models are likely to be more adaptable, capable of handling multiple powder types with ease, without sacrificing the quality of the finish or requiring frequent adjustments.
In high-volume production environments, speed and efficiency will remain essential, driving the development of high-throughput powder coat spray guns. These guns will be optimized for faster material flow, allowing for quicker coverage of larger parts without compromising coating quality. Features such as automated powder loading, fast-charging electrostatic systems, and variable-speed powder delivery will further streamline the process. In these environments, reducing cycle times while maintaining precise control over powder deposition will be a critical focus.
Another area of growth will be in the design of modular spray systems. These systems will allow manufacturers to customize their equipment based on their specific needs, whether that’s for different part sizes, coating requirements, or production volumes. The modular design will enable manufacturers to easily swap out spray guns, nozzles, and other components based on the job at hand. This flexibility will increase the lifespan of the equipment and make it easier to adjust production lines for changing customer demands or product specifications.
Energy efficiency will continue to be a driving force in the development of powder coat spray guns. As the industry faces increasing pressure to reduce energy consumption and lower operating costs, manufacturers will focus on creating guns that are more energy-efficient without sacrificing performance. Spray guns equipped with low-energy electrostatic charging systems, improved air flow management, and optimized powder delivery systems will minimize energy use, reduce waste, and cut down on production costs. Additionally, solar-powered systems or guns that integrate with energy-saving coating ovens could become more common, especially in industries focused on sustainability and green manufacturing practices.
One key aspect of future powder coat spray gun development will be making them more user-friendly. Innovations in ergonomics and interface design will simplify operation, allowing operators to adjust settings with ease and ensuring that even those new to powder coating can achieve high-quality results. Touchscreen controls, intuitive menus, and pre-set programming will make it easier for operators to handle the equipment, reducing the training time required and making powder coating a more accessible option for businesses of all sizes.
The adoption of advanced materials in the construction of spray guns will also play a role in improving durability and long-term performance. As spray guns are subjected to abrasive powders, exposure to high air pressures, and extended use, the materials used in their construction must be able to withstand these conditions. In the future, manufacturers will likely use more corrosion-resistant, abrasion-resistant, and lightweight materials in spray guns, reducing wear and tear and extending the equipment’s lifespan. Ceramic coatings, stainless steel components, and reinforced polymers may become standard materials for spray gun construction.
With robotic and automated coating systems becoming more common, powder coat spray guns will increasingly be designed to work seamlessly with automated systems. These advanced systems, which can apply coatings at high speed with little or no human intervention, require spray guns that can be controlled remotely or integrated with robotic arms. Robotic arms with precise movements can apply coatings to parts that are difficult to reach, while advanced machine vision systems can inspect the parts to ensure the coating is applied consistently and uniformly. In these systems, the spray guns will need to be highly adaptive, able to respond to changes in the part’s position or surface texture and adjust settings in real-time.
In terms of environmental sustainability, powder coat spray guns will be designed to work with eco-friendly powders that are increasingly being developed from biodegradable or renewable sources. These advancements align with the broader trend toward reducing the carbon footprint of manufacturing processes. As regulations around environmental impact become stricter, manufacturers will need to implement coating systems that meet these demands without compromising performance. Spray guns will continue to evolve to handle these new materials efficiently, ensuring that coatings are applied correctly while adhering to sustainability standards.
In conclusion, the future of the powder coat spray gun will be shaped by technological advancements that enhance its performance, efficiency, and adaptability. As industries move toward more automated, smart, and energy-efficient systems, spray guns will evolve to meet these needs, offering enhanced precision, flexibility, and ease of use. Whether it’s through the integration of AI-based technologies, advanced materials, or eco-friendly solutions, the powder coat spray gun will remain a critical tool in achieving high-quality coatings across a wide range of industries. The ongoing innovation in this field promises to increase productivity, reduce waste, and ensure that finish quality continues to meet the highest standards.
Powder Coating Gun Machine
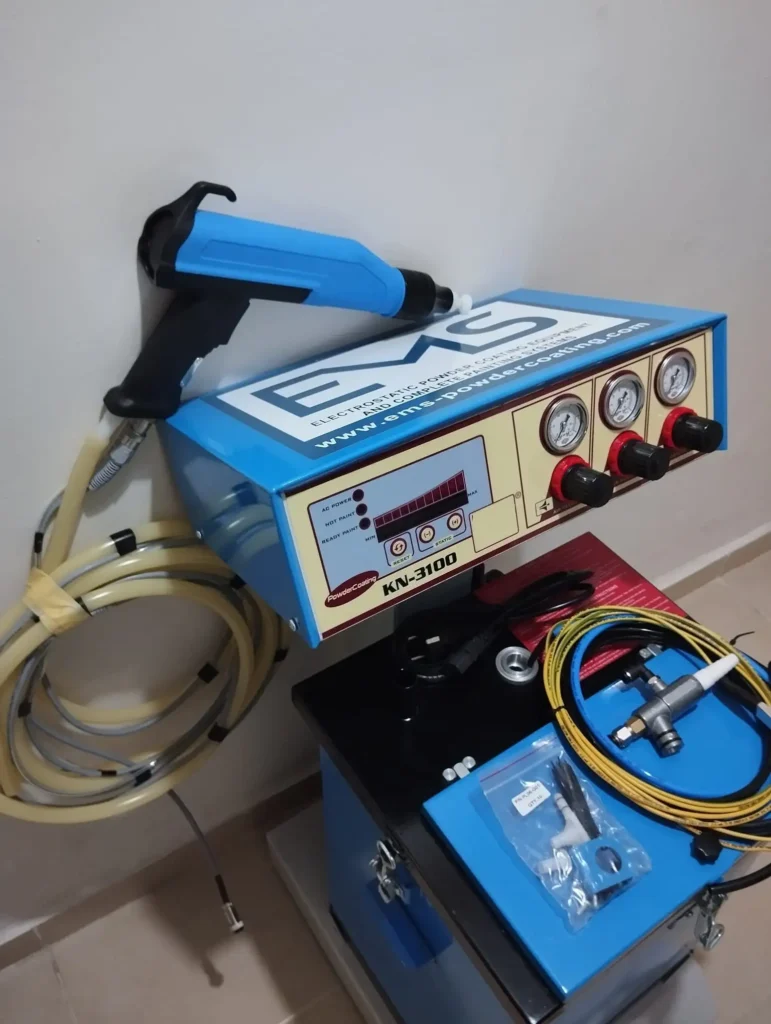
The powder coating gun machine is a crucial component in the powder coating process, designed to apply a fine layer of electrostatically charged powder to a substrate. This machine is used across a variety of industries to achieve durable, high-quality finishes on metal, plastic, and other materials. As the demand for more efficient, precise, and sustainable coating solutions grows, the technology behind powder coating gun machines continues to advance. The future of these machines is set to be defined by improvements in automation, energy efficiency, and coating precision.
At the core of the powder coating gun machine is its electrostatic application system, which imparts a charge to the powder particles, making them adhere to the grounded substrate. This system not only improves the efficiency of the coating process by reducing powder wastage but also ensures a smooth, uniform coating. As technology advances, electrostatic charging systems are becoming more efficient, providing better transfer efficiency and improving the overall quality of the coating. With these enhancements, powder coating gun machines can now work with a wider range of powders, including low-temperature curing powders, specialized finishes, and even heat-sensitive powders without compromising performance.
The design of the powder coating gun machine is becoming increasingly sophisticated, with a focus on improving ergonomics and ease of use. These machines are now often built with lightweight materials and adjustable features that allow operators to customize the settings based on the specific needs of each job. Adjustable spray patterns, spray volume controls, and user-friendly interfaces make it easier for operators to achieve the desired coating thickness and uniformity, whether applying powder to large flat surfaces or intricate, geometrically complex parts. These adjustments ensure that the coating process is as efficient and precise as possible, reducing material waste and increasing overall productivity.
Automation is another key development in powder coating gun machines. Automated systems that include robotic arms or conveyor belts integrated with powder coating guns are becoming increasingly common in industries such as automotive manufacturing and industrial coating. These robotic systems allow for more consistent application of coatings, reducing the likelihood of human error and improving throughput. The robots can apply coatings to parts with complex shapes or difficult-to-reach areas that might be challenging for manual operators, ensuring that every part receives an even, high-quality finish. Additionally, automated systems can work continuously without breaks, increasing productivity and reducing labor costs.
Powder coating gun machines are also evolving to meet the growing demand for eco-friendly and sustainable solutions. As sustainability becomes a priority for manufacturers, the focus is shifting toward machines that are more energy-efficient and use less material. For example, many modern powder coating gun machines are designed with low-energy electrostatic systems and advanced powder delivery mechanisms that ensure minimal energy consumption while maintaining high-quality application. Efficient air management systems help reduce the amount of compressed air required during operation, which lowers the overall energy usage and reduces operational costs.
The development of self-cleaning systems is another significant advancement in powder coating gun machines. Cleaning a powder coating gun traditionally involves manually disassembling and wiping the machine to remove any residual powder. This can be time-consuming and disruptive to production. Self-cleaning features, such as automated nozzle cleaning, air purging systems, and easy-to-remove components, significantly reduce the amount of downtime required for maintenance, allowing operators to quickly prepare the machine for the next coating job. These features also help ensure that the machine operates at peak efficiency, minimizing the risk of clogged nozzles or uneven powder application due to buildup.
An important advancement is the integration of smart technology into powder coating gun machines. These systems use sensors to monitor the performance of the machine in real time, automatically adjusting key parameters such as powder flow, air pressure, and electrostatic charge. These automatic adjustments ensure that the coating is applied consistently, regardless of variations in part size, shape, or surface conditions. For example, if a sensor detects a decrease in powder flow, the system can increase the flow rate to maintain the desired coating thickness. This level of automation reduces the need for manual intervention, increases process reliability, and ensures that each part receives the correct coating every time.
Robustness and durability are also crucial considerations in the design of powder coating gun machines. In high-volume production environments, where machines are running continuously, equipment must be able to withstand wear and tear. The construction of modern powder coating gun machines uses high-quality materials that are abrasion-resistant, corrosion-resistant, and capable of handling the harsh environments created by the constant application of dry powder. Components made from stainless steel, ceramic coatings, and reinforced polymers extend the lifespan of the machine and help reduce the need for frequent replacements or repairs.
The versatility of powder coating gun machines is also improving. Newer models are capable of working with a wider range of substrates and powder types, including textured, metallic, and glossy finishes. This versatility is key as industries seek coatings that offer specific functional or aesthetic properties. For example, some powder coating gun machines are designed to work with specialty powders that provide high chemical resistance, UV protection, or abrasion resistance. The machines can handle these different powders without compromising the quality or efficiency of the application, offering manufacturers greater flexibility in their coating options.
Additionally, modular designs in powder coating gun machines are becoming more common, allowing manufacturers to easily adapt their systems to different needs. Modular machines can be equipped with different nozzles, spray guns, or even powder types to meet specific coating requirements. This adaptability helps manufacturers increase production capacity or modify their coating systems to accommodate changes in customer demands or new product lines without investing in entirely new equipment.
The evolution of data analytics is also playing a role in the advancement of powder coating gun machines. These machines can now collect and store data on key performance metrics such as material consumption, coating thickness, and production throughput. This data can be analyzed to identify trends, monitor machine performance, and pinpoint areas for improvement. For example, data analysis may reveal that certain adjustments lead to more efficient powder application, which can be implemented across the entire production line to improve consistency and reduce waste.
Looking ahead, wireless communication will likely become a standard feature in powder coating gun machines. This would allow operators and managers to monitor and control the machines remotely, ensuring that any issues are quickly identified and addressed. Wireless connectivity also enables the integration of powder coating systems with smart factory systems, facilitating real-time data sharing and enabling more effective coordination between different stages of the production process.
The future of powder coating gun machines will be driven by innovations that make them more efficient, flexible, and sustainable. As the need for high-quality finishes grows across a wide range of industries, powder coating gun machines will continue to evolve to meet these demands, offering enhanced precision, user-friendly operation, and improved eco-performance. Advances in automation, smart technology, and data analytics will enable manufacturers to further optimize their coating processes, improve throughput, and reduce waste, contributing to a more sustainable and cost-effective coating solution for a variety of industries.
The future of powder coating gun machines will also be deeply influenced by advancements in customization and personalization of coating finishes. As industries demand more unique and tailored coatings to meet aesthetic or functional requirements, powder coating gun machines will be designed to handle specialized finishes more efficiently. These may include multicolor effects, gradient finishes, textured coatings, and variegated effects that can give products a distinct look and feel. To achieve this, machines will increasingly be able to handle more complex applications, where multiple powders or colors are applied in a single pass without the need for manual intervention or long changeover times. This level of precision will allow manufacturers to produce products with unique designs or patterns more easily.
Another exciting development will be in sustainability and recycling. As environmental concerns become more prominent, powder coating gun machines will increasingly be designed to operate with zero-waste systems. For example, recycling systems integrated into the powder coating machines could capture overspray powder and return it to the coating process, reducing material waste and lowering operational costs. These systems could use air filtration, reclamation chambers, or cyclonic separation technologies to reclaim unused powder, ensuring that as much of the powder as possible is used in the coating process rather than being discarded. Moreover, biodegradable and non-toxic powders will likely become more widely available, and machines will be adapted to work with these more environmentally friendly materials.
The trend toward smart manufacturing is likely to integrate powder coating gun machines with IoT (Internet of Things) technology. Through IoT integration, powder coating systems can share data across various stages of production, providing real-time feedback to operators, maintenance teams, and managers. This can enable predictive maintenance, where the machine can analyze its own performance and notify operators about the need for maintenance before a breakdown occurs. Additionally, these systems will allow operators to track usage patterns, optimizing for maximum efficiency, reducing downtime, and improving the quality of the final product. By collecting performance data, operators can fine-tune the coating process to achieve more consistent results and reduce the variability associated with manual application techniques.
Multi-functional coating gun machines are also on the horizon. These machines could be designed to apply not just powder coatings but also liquid coatings, depending on the needs of the production line. The ability to switch between powder and liquid coating seamlessly would enhance the versatility of these machines, allowing manufacturers to handle a broader range of coating applications without requiring different equipment setups. For instance, certain industries may need a combination of both powder coatings for durability and liquid coatings for more precise color applications. Machines that can seamlessly perform both types of coating would eliminate the need for multiple machines and reduce overall capital investment.
In high-volume production facilities, speed and throughput will be increasingly prioritized. Manufacturers will continue to seek out powder coating gun machines that allow for faster coating cycles without sacrificing quality. Machines equipped with advanced powder delivery systems, capable of maintaining consistent powder flow at high speeds, will become essential. Faster curing ovens and infrared curing systems will also complement these machines, enabling faster turnaround times and allowing the production process to move more efficiently.
The globalization of supply chains will further drive demand for versatile and adaptable powder coating gun machines. Manufacturers in diverse regions will require machines that can handle a variety of powder formulations, from those produced locally to those sourced internationally. These machines will need to accommodate the differing properties of powders, ensuring that the coating process remains consistent regardless of the material’s origin. Additionally, manufacturers will seek equipment that can be easily adapted for use with local regulations, ensuring that their powder coating processes comply with varying environmental standards.
As customization of consumer products continues to rise, manufacturers will increasingly rely on powder coating gun machines to offer a wide array of finishes that cater to specific consumer preferences. Automotive industries, for example, will look to powder coating gun machines to apply vibrant, durable coatings to car parts, such as rims or bumpers, while electronics manufacturers may require precise coatings for heat dissipation or protection from corrosion. Architectural coatings will demand machines capable of applying long-lasting finishes to metals or extrusions, ensuring that these parts can withstand exposure to harsh weather conditions while retaining their aesthetic appeal. The ability to meet these growing demands will push manufacturers to innovate and develop even more specialized coating guns with unique capabilities.
Moreover, advanced software systems will continue to play a role in enhancing the effectiveness of powder coating gun machines. These systems will not only control the machine’s operational parameters but also provide in-depth analytics on the performance metrics of every coating process. This data will be crucial for optimizing processes, identifying inefficiencies, and improving quality control. Software advancements will likely include features like automated color mixing, real-time adjustments, and performance tracking across multiple machines, ensuring that production lines run smoothly and consistently.
Training and user education will also evolve with these advances. As powder coating gun machines become more sophisticated, operators will require enhanced training to understand and manage the technologies involved. Augmented reality (AR) and virtual reality (VR) technologies may be integrated into training programs, offering immersive, hands-on learning experiences for operators without the risks associated with physical machines. These digital training tools will help new operators get up to speed quickly and ensure that all workers are equipped to maximize the performance of the powder coating gun machines.
As for maintenance, the future of powder coating gun machines will likely see the development of self-diagnosing machines. These machines will use sensors and diagnostic tools to assess the condition of key components, identifying potential issues before they become critical. The machine will then alert the operator or maintenance team, allowing for quicker and more targeted repairs, thus preventing downtime and extending the lifespan of the machine.
In terms of global supply chain integration, powder coating gun machines will likely include capabilities for remote troubleshooting and diagnostic support. Manufacturers in different parts of the world will be able to rely on a single, unified network of experts to provide real-time support, maintenance advice, and troubleshooting assistance. This level of connectivity will help keep machines running smoothly across different geographical regions, ensuring global production continuity.
In summary, the future of the powder coating gun machine is one of continued advancement, focusing on increased automation, sustainability, precision, and versatility. As industries demand more eco-friendly, efficient, and customizable coating solutions, the powder coating gun machine will evolve to meet these needs, incorporating the latest in smart technology, robotic systems, and energy-efficient designs. These machines will not only improve the quality and consistency of powder coating processes but also help manufacturers remain competitive in an increasingly complex and environmentally-conscious market.
As powder coating technology progresses, industry-specific adaptations of powder coating gun machines will also become more prominent. Aerospace, defense, and medical industries are increasingly demanding specialized coatings that offer enhanced protection against corrosion, extreme temperatures, and wear. In these sectors, powder coating gun machines will need to apply coatings that meet stringent regulatory standards while maintaining precision and durability. For example, the aerospace industry may require coatings that are high-temperature resistant or capable of withstanding pressure fluctuations during flight, while medical device manufacturers might need coatings that are biocompatible and non-reactive.
In parallel, industries dealing with high-performance finishes such as electronics, automotive, and furniture design will demand coatings that deliver exceptional surface finishes, greater color retention, and increased resistance to UV radiation. In this context, powder coating gun machines will need to adapt to different coating requirements, such as working with specialized formulations like nano-coatings that offer unique properties like self-cleaning surfaces or anti-microbial finishes.
An important factor driving the development of advanced powder coating guns will be their ability to manage complex materials. As manufacturers continue to seek out alternatives to traditional coatings, the demand for powder coating systems that can handle more advanced powder formulations will grow. This includes powders that are designed to offer unique effects, such as metallic, matte, and textured finishes that replicate wood grain or stone-like surfaces. Furthermore, high-performance powders, such as those based on fluoropolymers or epoxies, will require powder coating gun machines to possess more advanced features that enhance precision and application.
Another major trend will be the integration of sustainability into every stage of the coating process. With more companies focusing on their environmental impact, there is an increasing demand for solutions that are both resource-efficient and carbon-friendly. Powder coating gun machines will continue to be designed to reduce their environmental footprint, not just in terms of energy usage but also in terms of material waste and emissions. The trend toward closed-loop systems will increase, where overspray powder is fully reclaimed and reused, reducing material loss. Advances in air filtration technologies will ensure that minimal powder is lost during application, while water-based powder formulations will become more common to provide lower-VOC (volatile organic compound) solutions.
Moreover, technological advances in sensors and automation will allow powder coating machines to collect and analyze more granular data during each coating job. Machine learning algorithms could be integrated to adjust machine parameters automatically based on environmental conditions, part characteristics, or historical performance data. Over time, the system would learn the most efficient settings for each specific scenario, improving both the quality and efficiency of the coating process. For example, if a particular type of substrate requires a slight adjustment in powder flow or voltage, the machine can make those adjustments automatically, without the need for manual calibration.
The focus on user experience will continue to grow as manufacturers seek to make their powder coating equipment more operator-friendly. This includes intuitive interfaces that provide operators with immediate feedback on the coating process, automated diagnostics to detect faults early, and easy-to-understand maintenance schedules. Digital touchscreens and user interface design improvements will make machines easier to operate, while remote monitoring capabilities will allow operators to manage their coating lines from anywhere, improving flexibility and control.
In terms of cost-effectiveness, companies will continue to push for machines that deliver high throughput with lower operational costs. This could be achieved through improvements in powder efficiency, reduced energy consumption, and longer-lasting components that require less frequent maintenance. Powder coating gun machines that are designed to minimize the amount of energy consumed during curing and reduce operational downtime will be particularly attractive to industries aiming to keep operational costs low while maintaining high standards of quality.
Looking ahead, integrating robotics and AI-driven automation will increasingly define the powder coating process. AI will enhance the machine’s ability to predict when certain components need to be replaced, reducing the risk of unexpected breakdowns and optimizing performance. Robotics will further improve efficiency in terms of consistency and speed, and the combination of AI and robotics will provide even higher levels of precision, ensuring that the coating is applied evenly across complex geometries.
Collaboration across industries will also become a more significant factor. As manufacturers in various sectors work together to refine coating systems and improve the capabilities of their equipment, we may see the development of more modular powder coating solutions. These systems could be tailored to the unique requirements of each industry, allowing manufacturers to customize their powder coating equipment based on the specific needs of their production line. Such collaboration could also lead to standardization in key areas of the powder coating process, making it easier for different systems to integrate seamlessly.
The continued advancement of coating powders will be pivotal in shaping the future of powder coating gun machines. Future powder formulations may not only provide the same level of durability and protection as current coatings but will also introduce new characteristics such as self-healing properties, improved adhesion to non-metallic surfaces, and advanced resistance to harsh chemicals. This will drive the development of machines that can handle increasingly sophisticated materials, making powder coating solutions even more versatile and suitable for a wide range of applications.
Additionally, with the increasing adoption of digital manufacturing and 3D printing technologies, powder coating gun machines could integrate with additive manufacturing processes to create coated 3D-printed parts. The ability to apply coatings to 3D-printed objects will open up new opportunities for industries such as aerospace, medical devices, and consumer electronics, where customized, high-performance finishes are required for complex geometries.
As the global market for powder coating continues to grow, particularly in regions like Asia-Pacific, Latin America, and Eastern Europe, manufacturers will need to meet the demand for affordable, high-quality coating solutions. This global shift will likely lead to more localized production of powder coating gun machines, enabling manufacturers to offer cost-effective solutions tailored to specific regional requirements.
Ultimately, the future of powder coating gun machines will be shaped by the ongoing push for technological innovation, sustainability, and market-driven customization. As industries continue to evolve and demand more specialized coating solutions, these machines will become increasingly efficient, adaptable, and user-friendly, setting new standards for coating technology in a wide range of applications. The focus on eco-friendly processes, automated operations, and cost-effective production will ensure that powder coating remains a versatile and valuable finishing solution for decades to come.
Reciprocator Machine

The reciprocator machine plays a pivotal role in modern coating systems, especially in industries where high-quality finishes are required across various substrates. Used extensively in automated coating lines, the reciprocator machine is primarily responsible for moving coating spray guns, such as those used in liquid painting or powder coating, across parts in a controlled and precise manner. The machine’s ability to move in a back-and-forth (reciprocal) motion allows it to coat large and complex surfaces uniformly, making it indispensable for high-volume production, particularly in industries such as automotive manufacturing, appliance coating, metal fabrication, and furniture manufacturing.
At the core of the reciprocator machine is its mechanical drive system, which typically includes a motor and drive components (such as gears, belts, or rails) that facilitate smooth back-and-forth movement. These systems are designed to handle large-scale applications, ensuring that the spray guns cover a broad area while maintaining precision and consistency. This allows for uniform coating thickness across the entire surface, improving the overall aesthetic quality and performance of the finished product.
Automation is a key feature of modern reciprocator machines. These machines are frequently integrated into automated systems alongside robotic arms, conveyors, and curing ovens to create fully automated coating lines. With the ability to precisely control the speed, stroke length, and direction of the spray gun, the reciprocator ensures that coating is applied uniformly without any missed spots or uneven thickness. This level of precision is crucial for meeting quality standards in high-volume production environments. Additionally, the use of sensors and programming systems ensures that the machine adjusts its motion based on part size, shape, and the specific coating material being used, making the process more efficient and adaptable.
A significant advancement in the design of reciprocator machines is the development of high-precision controllers that allow operators to fine-tune various parameters, such as the speed of the machine, spray patterns, and coating thickness. These systems, often featuring digital interfaces or touchscreens, offer greater ease of operation and increased flexibility in programming. Operators can store different settings for different products or parts, allowing for quick adjustments and reducing the time spent setting up the machine for different jobs. This makes reciprocator machines ideal for companies that need to handle multiple product types or varying part sizes without significant downtime.
The motion control system of a reciprocator is often sophisticated, utilizing servo motors or stepper motors for precise control of movement. These systems enable the machine to achieve high-speed, smooth strokes, reducing the chances of any interruptions or coating defects. Additionally, feedback loops can be integrated into the control system, which provides real-time monitoring of the machine’s performance, ensuring optimal coating quality and enabling predictive maintenance to avoid equipment failure. For example, if a sensor detects a slight deviation in the movement or operation of the reciprocator, it can adjust the machine in real time or alert the operator to potential issues, minimizing downtime and improving consistency.
The benefits of reciprocator machines also extend to cost efficiency. Because these machines are typically integrated with spray booths and powder or liquid spray guns, they can maximize material usage by reducing overspray, waste, and the need for manual touch-ups. Additionally, the automation of the reciprocator reduces the reliance on labor, making it easier to scale production volumes without significantly increasing labor costs. This is particularly important in industries where profit margins are tight and demand for high-quality products is constant.
Energy efficiency is another consideration in the design and operation of reciprocator machines. As industries continue to prioritize sustainability and cost reduction, manufacturers are designing machines that consume less power and utilize more efficient motors and drive systems. Machines equipped with variable frequency drives (VFDs) can adjust the motor speed based on operational needs, ensuring that the system uses only the necessary amount of energy. Additionally, modern reciprocators may feature lightweight components and streamlined mechanical designs that minimize energy consumption during operation.
Another significant evolution in reciprocator machines is the integration of smart technologies. The future of these systems will likely be marked by increased connectivity and data-driven insights. Through the use of IoT sensors, manufacturers will be able to collect data on key performance indicators, such as spray coverage, system uptime, and powder usage. This data can be analyzed to identify inefficiencies or areas for improvement in the coating process. For example, if data shows that a certain spray gun is underperforming in a particular zone, the machine’s motion system can be adjusted to compensate for this or a more thorough inspection can be initiated. This level of data-driven control will lead to better process optimization, improved quality assurance, and real-time troubleshooting capabilities.
Maintenance is a critical aspect of the reciprocator machine’s operational efficiency. These machines are subject to wear and tear due to their frequent movement and exposure to harsh materials such as powder coatings or solvents used in liquid coatings. To minimize downtime and prolong the life of the machine, modern reciprocators are often equipped with self-diagnostics and predictive maintenance features. Sensors can detect irregularities in the machine’s motion, motor performance, or even the quality of coating applied, allowing for preemptive maintenance actions. This not only reduces the need for costly repairs but also ensures that the machine is always operating at peak performance.
The ongoing demand for versatility in coating applications is driving the development of multi-function reciprocator machines. These machines can now handle a variety of materials and coatings, from traditional powder coatings to liquid paints and even more specialized finishes like high-temperature coatings or anti-corrosive treatments. With the ability to switch between different coating materials and substrates quickly, these machines offer significant flexibility, enabling manufacturers to meet the specific needs of diverse industries, whether in aerospace, automotive, construction, or furniture production.
Customization options are becoming increasingly important for customers. As the demand for specific product finishes grows, reciprocator machines can now be tailored to suit the unique needs of a given production line. For example, coating lines that require spray guns to apply coatings in intricate patterns, curves, or hard-to-reach areas can benefit from articulating arms or variable-angle motion control systems in the reciprocator. These flexible designs enable precise control over the application of coatings, ensuring that each part, regardless of shape, receives a perfect finish.
An emerging trend is the focus on environmental sustainability in reciprocator machines. Modern systems are designed with low-emission and low-waste goals in mind, allowing companies to reduce their environmental footprint while still achieving the high-quality finishes demanded by their customers. This may involve the development of reclaim systems that capture overspray powder, advanced ventilation technologies that minimize solvent emissions, and more efficient curing methods that use less energy.
Robotics and artificial intelligence (AI) are also beginning to be incorporated into reciprocator machines. In combination with the basic reciprocator motion, AI-driven systems can adapt to real-time production conditions, automatically adjusting the motion of the spray guns or other application devices based on factors such as part size, surface texture, and even the type of coating. This adaptability can significantly improve both coating quality and productivity, making it possible for companies to meet higher demands while maintaining consistency and reducing material waste.
The integration of robotic arms with reciprocator machines also allows for even more complex and detailed coating tasks. Robotic arms can handle coatings on complex geometries, while the reciprocator ensures that every surface is coated evenly. This robotic solution can handle parts with intricate shapes or moving parts that would otherwise require multiple manual interventions.
In the coming years, cloud-based solutions will likely play an increasing role in reciprocator machines, providing centralized platforms for monitoring, diagnostics, and performance optimization. Cloud platforms can collect data from multiple machines across various production lines, enabling manufacturers to track system performance, compare efficiency metrics, and even remotely troubleshoot issues. This cloud-based approach enhances the ability to manage and scale production operations without the need for direct manual intervention at every stage of the process.
In summary, the future of reciprocator machines is promising, driven by the continued advancements in automation, precision, sustainability, and data integration. As the demands for more complex coatings, higher efficiency, and eco-friendly solutions increase, reciprocator machines will evolve to meet these challenges, providing manufacturers with greater control, flexibility, and productivity in the coating process. With their ability to handle diverse substrates and coating types, along with innovations in robotics, AI, and connectivity, reciprocator machines will remain integral to high-quality, high-throughput coating applications across a wide range of industries.
As reciprocator machines evolve further, the integration of advanced materials and innovative technologies will continue to redefine their capabilities and applications. The growing trend towards Industry 4.0 will see these machines becoming smarter and more interconnected within broader manufacturing systems. The use of cloud computing, big data, and predictive analytics will enable manufacturers to optimize coating processes based on real-time data collection and analysis. This will facilitate proactive adjustments to machine parameters, ensuring optimal coating quality and process efficiency across production lines. By utilizing data-driven insights, manufacturers can predict wear and tear, foresee potential downtime, and optimize operational schedules, leading to significant cost savings and reduced maintenance needs.
One major area of development is the ability to handle multi-layer coatings or complex finishing systems. In industries where coatings require more than one application layer (such as automotive, furniture, or architectural coatings), reciprocator machines will become more adaptable. These machines may feature multi-gun configurations, allowing simultaneous coating of different layers or application of specialized coatings in a single pass. This would drastically reduce the production time, improve coating consistency, and enable the efficient application of advanced finishes, such as textured or functional coatings like anti-fingerprint or self-cleaning layers.
Additionally, multi-coating systems could enable manufacturers to use different coating materials within a single operation, streamlining the process. For example, a reciprocator machine may be equipped with multiple spray heads that can apply both powder coatings and liquid coatings, ensuring compatibility with a wider range of products and customer requirements. This versatility makes reciprocator machines more attractive to industries that require high flexibility and the ability to meet varying customer demands.
A significant aspect of the next phase in reciprocator machine technology is the advancement of robotics. As robotic systems become more sophisticated, they will integrate seamlessly with reciprocators to offer precise control over every aspect of the coating process. Robots equipped with vision systems and 3D scanning technologies will be able to inspect and adapt to parts in real-time, ensuring that coatings are applied uniformly, even on irregularly shaped or moving parts. These intelligent systems will detect imperfections, adjust spray parameters, and improve process consistency.
Moreover, artificial intelligence (AI) will play a major role in enhancing the overall productivity and efficiency of reciprocator machines. AI algorithms can analyze vast amounts of data to detect patterns, optimize spray patterns, and ensure coatings are applied with minimal waste. For example, AI systems might adjust the speed or stroke of the reciprocator in real time, based on feedback from sensors that measure powder distribution, coating thickness, or surface finish. This will result in an even more efficient use of materials and a reduction in defects, leading to improved operational throughput and fewer rework cycles.
In addition to AI and robotics, augmented reality (AR) could further enhance the user experience and operational efficiency. With AR technology, operators could receive real-time instructions or feedback directly through smart glasses or displays, helping them make faster, more accurate decisions during machine setup and troubleshooting. This kind of technology would also assist in remote maintenance or training, allowing expert technicians to guide operators through repairs or setup procedures without being physically present. Remote troubleshooting capabilities will become more common, enabling manufacturers to address technical issues or adjust machine settings without having to send personnel to the site, thus improving response time and reducing service costs.
Another avenue for advancement in reciprocator machines will be the increased integration with supply chain management systems. By connecting reciprocator machines to enterprise resource planning (ERP) or manufacturing execution systems (MES), manufacturers can track the progress of parts through the entire production process. This connectivity will ensure that coating applications are synchronized with other manufacturing activities, reducing delays, bottlenecks, and production inefficiencies. These systems can also assist with inventory management, ensuring that the required materials, such as specific coatings or sprays, are always available and ready for use.
Additionally, as industries increasingly demand eco-friendly solutions, reciprocator machines will incorporate sustainable practices. Machines will be designed to reduce environmental impact by using energy-efficient components, reducing chemical emissions, and ensuring minimal waste through the recovery and reuse of overspray. Low-emission spray systems that use non-toxic, water-based coatings or low-VOC (volatile organic compound) formulations will become more widespread. This aligns with global sustainability trends, particularly in the automotive and consumer goods industries, where environmental responsibility is becoming a key driver of innovation.
One example of this eco-conscious shift is the use of closed-loop systems in coating operations, which allow for the efficient recovery and reuse of overspray powder. With better filtration and powder recovery systems, powder coating waste can be minimized, and powders can be recycled, reducing the cost of materials and the environmental footprint of the coating process.
Moreover, the growing focus on energy-efficient operations will drive the development of high-efficiency motors, advanced control systems, and automated systems that adjust to fluctuating production requirements. These systems can reduce energy consumption during machine startup, operation, and shutdown, which is crucial in industries that operate on tight margins and aim to reduce operating costs.
The scalability of reciprocator machines will also improve, as future systems are designed to handle greater throughput and the demands of larger-scale operations. This scalability will be particularly beneficial for businesses that need to scale up production for large orders, especially in industries like automotive manufacturing, construction, and consumer electronics. Manufacturers will be able to add more spray guns, expand their coating lines, or introduce additional stages to the coating process to meet increasing demand without compromising on quality or efficiency.
Customization will continue to be a driving factor in the development of reciprocator machines. Manufacturers will increasingly require coating solutions tailored to their specific production needs. Reciprocators with modular designs that allow easy reconfiguration or addition of components will become more common. This flexibility will allow manufacturers to adapt quickly to new product lines or market demands without requiring entirely new equipment.
Looking ahead, the role of reciprocator machines will continue to grow as industries push the boundaries of what’s possible with coatings. With advancements in automation, precision, flexibility, and sustainability, reciprocator machines will remain an integral part of the manufacturing landscape, driving improvements in quality, productivity, and cost-efficiency. As technology evolves, these machines will not only meet the growing demands of industries today but also adapt to the future needs of tomorrow, helping manufacturers stay ahead in an increasingly competitive global marketplace.
Powder Coating Booths
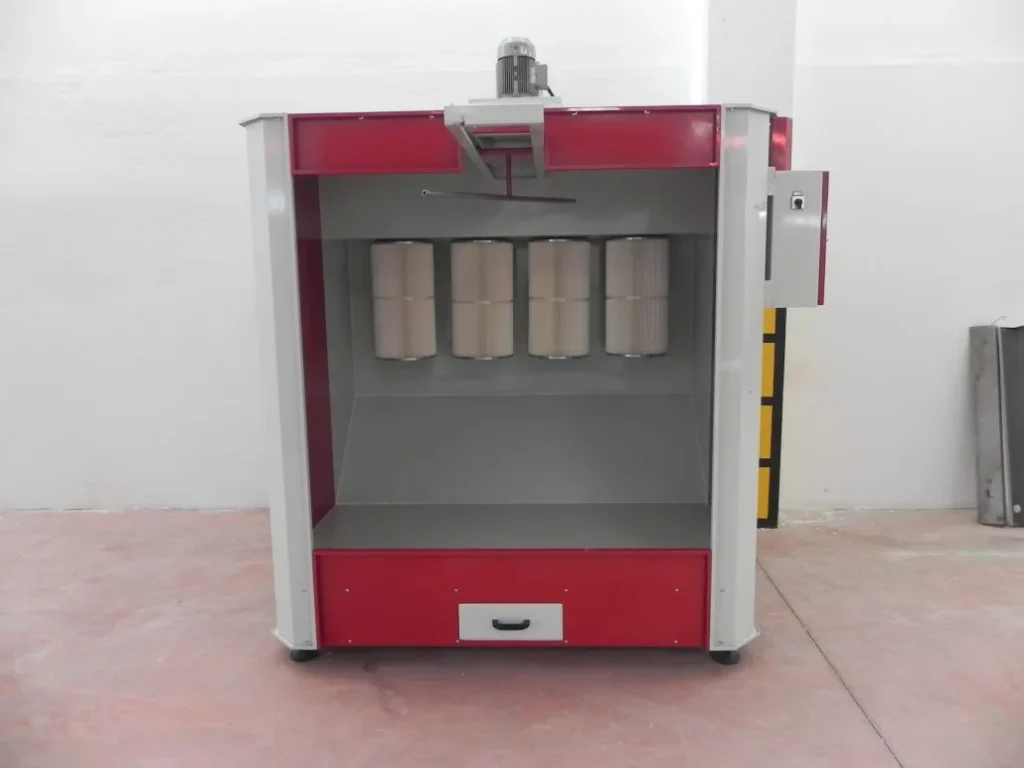
Powder coating booths are critical components in the powder coating process, providing a controlled environment where powdered coatings are applied to metal, plastic, and other materials. These booths are designed to ensure the even distribution of powder, prevent contamination, and optimize the coating process for efficiency, safety, and high-quality finishes. A powder coating booth is typically a fully enclosed or semi-enclosed space where the powder is applied using specialized equipment like spray guns, electrostatic sprayers, or fluidized beds.
The primary purpose of a powder coating booth is to create an environment where powder can be applied to parts while maintaining high levels of air quality and ensuring that powder is not wasted. The booth collects excess powder through extraction systems, such as dust collectors or air filtration units, and allows it to be recovered and reused, which helps minimize waste and reduce operating costs.
The design of a powder coating booth is crucial to achieving consistent coating quality. These booths typically feature controlled airflow systems, which direct the airflow in a way that prevents the powder from becoming airborne and settling on surfaces outside the booth. This system often uses high-efficiency particulate air (HEPA) filters or cyclonic collectors to capture excess powder, and ensure that it is returned to the powder reservoir for reuse.
At the heart of a powder coating booth is the airflow management system. The system is designed to provide uniform distribution of the powder, ensuring that parts receive a consistent coat without buildup of excess material or uneven spots. Most powder coating booths feature horizontal or vertical airflow, with a clean room environment to protect the coating from environmental contaminants, such as dust or moisture, which could negatively affect the finish.
A key feature of modern powder coating booths is electrostatic charging. The spray guns used in these booths charge the powder particles with an electrical charge, which is then attracted to the grounded workpieces. This electrostatic attraction ensures that the powder adheres to the surface of the workpiece more effectively, reducing overspray and improving coating efficiency. By using this technology, powder coating booths achieve high levels of material utilization, reducing waste and lowering costs associated with unused powder.
Exhaust systems in powder coating booths play a critical role in safety and operational efficiency. The air quality within the booth must be carefully controlled to prevent the buildup of flammable or toxic fumes that may be generated by the powder or the curing process. Booths are equipped with exhaust fans and air filtration units that remove these fumes, creating a safer work environment. Additionally, powder coating booths often use explosion-proof equipment in areas where flammable materials are used, in line with safety regulations and standards.
The design of a powder coating booth also includes provisions for easy cleaning and maintenance. Since powder coating can generate a significant amount of overspray, booths are designed with smooth, durable surfaces that are easy to wipe down and maintain. Washable filters and self-cleaning mechanisms are also common features, allowing for minimal downtime and efficient operation.
To ensure productivity and workflow efficiency, modern powder coating booths are equipped with automated material handling systems. These systems use conveyors, lift systems, and robots to move parts in and out of the booth, reducing the need for manual labor and increasing throughput. Robotic arms or automated spray systems within the booth allow for precise application of powder coatings, ensuring that every part is coated consistently.
There are several different types of powder coating booths designed to meet various production needs, such as manual booths, automatic booths, and hybrid booths. In manual booths, operators apply the powder coatings by hand using electrostatic guns, offering flexibility in the types of parts coated and the ability to adjust settings based on the specific product being coated. Automatic booths, on the other hand, use robotic arms or spray machines to apply the coating, providing high-speed, consistent finishes for large-volume production. Hybrid booths combine both manual and automated systems, offering the best of both worlds in terms of flexibility and automation.
Maintenance of powder coating booths is essential to keep the systems running smoothly and to avoid costly downtime. Regular cleaning and maintenance of the filtration systems, extraction fans, and spray guns help ensure optimal operation. Additionally, ensuring that the powder coating booth is regularly inspected for airflow consistency, filter replacement, and proper grounding is important to maintaining the quality of the coating and the safety of the workspace.
One important trend in powder coating booth technology is the increased emphasis on environmental sustainability. Manufacturers are looking for ways to reduce the environmental impact of the powder coating process. This includes using energy-efficient exhaust systems, recycling overspray powder, and ensuring that booths are designed to minimize powder waste. Furthermore, some booths now feature low-energy systems that consume less electricity during operation, helping businesses reduce their energy costs and environmental footprint.
Modular designs are also becoming more common in powder coating booth construction. This allows companies to scale their systems based on production demands. Modular booths can be expanded or reconfigured by adding additional booths or components as needed, allowing for greater flexibility in production. This flexibility is particularly valuable in industries where production runs are short or product specifications change frequently.
Another key development in powder coating booth technology is the integration of smart systems and monitoring technologies. These systems can track booth performance in real time, providing operators with important metrics such as powder usage, air quality, and energy consumption. IoT-enabled systems can also send alerts to operators when maintenance is required or when a system is underperforming. This allows businesses to identify potential issues early and reduce downtime, ensuring that production remains efficient and cost-effective.
As customization becomes increasingly important to customers, powder coating booths are being designed to accommodate a wide variety of parts and coating types. Booths can now be customized for specific types of products, such as automotive parts, kitchen appliances, or industrial machinery, by adjusting the size, configuration, and airflow system. This ensures that the booth provides the best possible results for each unique coating job, further enhancing the quality of the finished product.
In the future, powder coating booths will likely see further advancements in automation, data analytics, and sustainability. The integration of AI and machine learning could allow the booth to adjust its parameters in real-time based on environmental factors, material types, or coating thickness. This level of automation would increase the precision and speed of the coating process while reducing errors and waste.
Safety features will also continue to evolve. Powder coating booths will increasingly incorporate advanced fire suppression systems, gas detection for hazardous fumes, and automated shut-off mechanisms that reduce the risk of fires or explosions. These features are critical in ensuring the safety of workers and complying with strict industry safety regulations, especially as the use of highly flammable powders becomes more prevalent.
In conclusion, powder coating booths are an essential part of the powder coating process, offering a controlled environment that ensures the efficient application of high-quality coatings. As the demand for high-performance coatings and sustainable manufacturing processes grows, powder coating booths will continue to evolve, incorporating advanced technologies like automation, AI, and energy efficiency. With the ability to handle larger volumes, reduce waste, improve safety, and adapt to new coating types, modern powder coating booths will remain integral to the future of manufacturing and surface finishing across multiple industries.
Powder Coating Surface Finish

Powder coating surface finish refers to the final appearance, texture, and quality of a coating applied to a substrate using a powder coating process. The surface finish is an essential aspect of the powder coating process, as it directly influences both the aesthetic appeal and the functional performance of the coated product. A high-quality surface finish ensures that the product meets the desired specifications for durability, appearance, and texture, whether the item is a part for automotive, furniture, architectural, or industrial applications.
Powder coating involves applying a dry powder to a surface and then curing it under heat, which causes the powder to melt and form a hard, durable finish. The finish of a powder-coated surface can vary widely, depending on factors such as powder type, application techniques, curing parameters, and the substrate material. A wide variety of surface finishes can be achieved, including smooth, matte, glossy, textured, wrinkled, and hammered effects, each suited for different functional and aesthetic needs.
The texture of a powder coating finish is often determined by the type of powder used and the method of application. For example, powders with a fine particle size typically result in a smoother finish, while coarse powders or specific application techniques can create textured finishes. Textured finishes are commonly used in industries that require a more rugged, slip-resistant surface or where the finish must conceal imperfections in the substrate.
Gloss level is another crucial factor that influences the surface finish. Powder coating can achieve a wide range of gloss levels, from high-gloss, which gives a shiny and reflective surface, to matte or satin finishes, which provide a more subtle, low-sheen appearance. The gloss level is often selected based on aesthetic preferences, product functionality, and environmental considerations. High-gloss finishes are popular for applications like automotive parts and consumer electronics, while matte finishes are favored for architectural and industrial products, where glare reduction and a non-reflective surface are important.
The color and uniformity of the coating also contribute to the overall surface finish. Powder coatings are available in a broad spectrum of colors, and the application process must ensure that the powder adheres evenly across the surface. Uneven coating thickness can result in imperfections, such as orange peel or flow marks, that affect the surface finish. These imperfections can occur due to improper application techniques, insufficient powder coverage, or poor curing. In addition to uniformity, special effects can be incorporated into the powder coating to create unique surface finishes. Metallic, pearl, and chameleon finishes are examples of specialized coatings that offer a dynamic, changing appearance under different lighting conditions.
Durability and performance are key aspects of the powder coating surface finish, as the finish needs to be able to withstand the environment in which the coated product will be used. The finish must be resistant to abrasion, corrosion, UV degradation, chemical exposure, and impact. These factors are influenced by the choice of powder material and the curing process. Epoxy-based powder coatings are known for their superior corrosion resistance and chemical resistance, making them ideal for industrial applications. Polyester-based coatings, on the other hand, offer excellent UV resistance, which makes them suitable for outdoor applications such as automotive and architectural coatings.
The substrate material is also a key factor in determining the surface finish quality. Powder coatings adhere better to certain materials, and the smoothness or roughness of the substrate surface will influence how the powder coating settles and bonds. Proper surface preparation, such as cleaning, sanding, and pre-treating the substrate, is essential to achieving a high-quality finish. For example, aluminum and steel are commonly used substrates for powder coating, and each requires different surface treatments to achieve optimal adhesion and finish. Galvanized steel, for example, may require additional steps like zinc-phosphate treatments to ensure good coating adhesion.
Application techniques also play a significant role in the final surface finish. The use of electrostatic spray guns is common in powder coating, where the powder is charged and attracted to the grounded part. The application technique must be adjusted to ensure uniform powder deposition. Electrostatic coating produces a fine, even coat, but it requires precise control of powder flow, gun distance, and spray angle to avoid defects such as overspray or unwanted build-up of powder in corners or recessed areas. The application of powder can also be impacted by the spray booth environment, which must be free of contaminants and have proper airflow to ensure a clean finish.
Curing is the final critical step in the powder coating process, and it directly affects the surface finish. Once the powder is applied, the parts are placed in an oven and heated to the temperature required for the powder to melt, flow, and cure. The curing process transforms the powder into a hard, durable coating. The exact curing time and temperature depend on the powder formulation, but it is essential that the curing process is consistent and properly controlled to avoid under-curing or over-curing. Under-cured powder may result in a soft, easily damaged surface, while over-cured powder may lead to brittleness or discoloration. Both under-curing and over-curing can degrade the finish quality.
Powder coating finish quality can be measured through a variety of tests, such as adhesion tests, scratch resistance, impact resistance, and gloss measurements. These tests ensure that the finished product meets specific industry standards for quality and performance. For example, in the automotive industry, the surface finish must withstand stone chips, bird droppings, and chemical exposure, while for furniture or appliances, a more aesthetic finish is required, with emphasis on scratch resistance and UV stability.
Recent advancements in powder coating technology have also led to the development of low-temperature curing powders, which enable manufacturers to achieve a high-quality finish at lower temperatures. This development is particularly beneficial for substrates that may be sensitive to high heat, such as plastic parts or composite materials. Similarly, the use of polymer blends and hybrid powders has expanded the range of finishes that can be achieved with powder coating, providing additional flexibility in achieving specialized surface effects like textured or wrinkle finishes.
Environmental sustainability is also a growing concern in the powder coating industry. Unlike traditional liquid coatings, powder coatings produce minimal volatile organic compound (VOC) emissions and are generally considered more environmentally friendly. Additionally, the ability to recover and reuse overspray powder in powder coating booths makes this process highly efficient and waste-reducing. Manufacturers can achieve a more sustainable finish by using low-VOC, non-toxic, or water-based powder formulations that are designed to minimize environmental impact while maintaining high performance and aesthetics.
Powder coating finish trends are evolving as industries demand more customized solutions for both aesthetic and functional purposes. As new technologies emerge, manufacturers are able to offer more advanced surface finishes that provide a competitive edge in the marketplace. Whether it’s achieving a premium gloss, a unique texture, or a functional finish with superior corrosion resistance, the variety of powder coating surface finishes available ensures that companies can meet the specific needs of their customers, all while benefiting from the durability, sustainability, and cost-effectiveness that powder coating offers.
In conclusion, powder coating surface finishes are a vital component of the powder coating process, with the final result affecting both the appearance and performance of the coated product. The finish can be tailored to meet specific requirements in various industries, providing options for smooth, matte, textured, metallic, and specialized effects. Achieving the perfect surface finish depends on factors such as application technique, powder type, curing conditions, and substrate preparation. As advancements in powder coating technologies continue, manufacturers will have access to an even broader range of finishing options, while maintaining a focus on quality, durability, and sustainability.
As the powder coating industry continues to evolve, the demand for innovative surface finishes grows, driven by both aesthetic trends and functional requirements. The ability to customize the surface finish for specific applications is one of the key advantages of powder coating over other finishing methods. For instance, industries such as automotive, furniture, construction, appliances, and consumer electronics are increasingly seeking specialized powder coatings that provide enhanced performance in addition to appealing visual characteristics.
One of the most significant trends in the industry is the use of powder coating for architectural applications, particularly for outdoor and high-performance finishes. For exterior surfaces, such as metal panels, railings, and window frames, the surface finish must be resistant to UV rays, weathering, and abrasion. Polyester and hybrid powder coatings are particularly suited for such applications because of their high UV stability and color retention under harsh environmental conditions. These finishes not only provide an attractive and durable appearance but also contribute to energy efficiency when used in architectural coatings, helping to reflect heat and reduce cooling costs in buildings.
In the automotive industry, powder coating surface finishes have gained traction for their superior durability and resistance to scratches and corrosion. Powder coatings for automotive parts need to withstand demanding conditions such as stone chips, salt exposure, and high-temperature environments. This has led to the development of specialty powder coatings, such as thermoplastic and high-performance hybrid coatings, that offer excellent mechanical properties like abrasion resistance, flexibility, and impact strength. These finishes are essential for parts that are exposed to heavy wear, such as bumpers, wheels, grilles, and engine components. Furthermore, manufacturers are increasingly focused on providing custom finishes like textured, matte, or satin to meet consumer preferences for unique and stylish automotive aesthetics.
The furniture industry also benefits from powder coating finishes, as these provide both functional and decorative qualities. For furniture used in outdoor environments, such as patio furniture, the finish needs to offer weather resistance, scratch resistance, and easy maintenance. Outdoor powder coatings are engineered to withstand exposure to moisture, UV rays, and temperature extremes, maintaining their appearance over time. On the other hand, indoor furniture often requires smooth, high-gloss finishes for an upscale look or matte finishes for a more subdued, contemporary style. The versatility of powder coating allows for the creation of bold colors, metallic effects, and even custom designs that cater to varying aesthetic preferences.
The development of powder coatings with specialty effects is another exciting trend. The ability to create metallic finishes, pearlescent effects, and chameleon-style color-shifting coatings is becoming increasingly popular. These finishes not only enhance the aesthetic appeal but also provide a distinct, high-end look. Metallic powders, which contain small metallic particles, create a reflective surface that can simulate the appearance of brushed metal or chrome. Pearl and iridescent powders offer finishes that change color when viewed from different angles, adding an element of depth and movement to the product’s surface.
In addition to aesthetic finishes, there is a growing emphasis on eco-friendly and sustainable powder coatings. Manufacturers are increasingly focused on reducing the environmental impact of the powder coating process by developing low-VOC (volatile organic compound) powders, water-based formulations, and recyclable powders. The powder coating process is already inherently more sustainable compared to liquid coatings due to its ability to recycle overspray powder, reducing waste. New innovations in low-temperature curing powders have also contributed to energy savings, allowing for reduced curing temperatures and shorter curing times, which ultimately reduces energy consumption and improves overall production efficiency. Additionally, eco-friendly powder coatings are being formulated to meet various green building standards, such as LEED (Leadership in Energy and Environmental Design), further supporting sustainability in construction and design industries.
Advancements in technology and automation are also improving the precision and consistency of powder coating surface finishes. Automated systems are able to apply coatings more consistently, ensuring that every part receives an even coat, regardless of its size or shape. The integration of robotic arms, conveyor systems, and automated spray guns reduces the need for manual labor and minimizes human error. Automated curing systems can also be calibrated to ensure precise control over the temperature and time required for optimal curing, reducing the chances of over-curing or under-curing, both of which can affect the quality of the surface finish.
The quality control and inspection of powder coating finishes have become more sophisticated with the introduction of non-destructive testing (NDT) methods. Techniques like electrostatic charge testing, adhesion testing, and ultrasonic testing are used to ensure that the coating has bonded properly to the substrate and will perform well in the long term. Adhesion tests are particularly important to check whether the powder coating has adhered properly to the surface, as poor adhesion can lead to defects like peeling or flaking. Impact resistance tests measure the ability of the coating to withstand physical stress, while scratch resistance tests help ensure that the surface will maintain its appearance even after prolonged use.
Moreover, the integration of smart manufacturing techniques is enhancing the ability to monitor and adjust surface finish quality in real-time. IoT-enabled powder coating systems provide continuous data on variables such as airflow, temperature, and humidity, which are critical factors in ensuring a consistent finish. These systems allow manufacturers to detect potential issues early, reducing waste and improving overall product quality.
Surface finish performance is also enhanced by innovations in chemical formulations for specialized applications. For example, anti-graffiti coatings, anti-bacterial coatings, and anti-static finishes have been developed for applications that require more than just a decorative finish. These coatings serve a functional purpose, providing added protection against environmental contaminants, bacteria, or electrostatic discharge. In electronics, anti-static finishes help reduce the risk of damage to sensitive components, while in hospitals or public spaces, anti-bacterial coatings improve cleanliness and reduce the spread of germs.
As demand for customization increases, the ability to offer unique and highly specialized powder coating finishes will become a key differentiator in the market. Manufacturers who can deliver customized finishes with high precision and efficiency will likely find themselves in high demand, as industries seek out coatings that can enhance their products’ aesthetics, durability, and functionality.
In summary, the field of powder coating surface finishes continues to evolve, offering a wide range of aesthetic and functional finishes that meet the diverse needs of different industries. From high-performance coatings for automotive and architectural applications to innovative metallic, textured, and specialty effects, the technology and techniques available today allow for the creation of truly customized and durable finishes. The combination of advanced application methods, eco-friendly formulations, automation, and sophisticated quality control systems ensures that powder coating remains a leading choice for industries that require high-quality, durable, and sustainable finishes. As new innovations continue to emerge, the potential for even more specialized and high-performance coatings is limitless.
As the powder coating industry advances, several emerging trends and technologies are poised to shape its future, pushing the boundaries of surface finishes even further. These developments are driven by demands for higher performance, greater customization, improved sustainability, and efficiency in production processes.
One key trend is the increasing focus on functional coatings that offer more than just an aesthetic appeal. As industries demand more multifunctional coatings, manufacturers are responding with innovations that provide additional benefits, such as anti-corrosion, anti-fingerprint, self-healing, anti-slip, and heat-resistant finishes. For example, in the automotive industry, self-healing powder coatings have been developed to repair minor scratches or chips in the finish over time, maintaining the appearance and functionality of the product. These types of finishes have the potential to drastically reduce maintenance needs and increase the lifespan of products, making them highly attractive to industries that rely on products being exposed to wear and tear.
Smart coatings represent another exciting area of growth. These coatings are embedded with sensors or materials that respond to environmental changes, such as temperature, humidity, or chemical exposure. Smart powder coatings can offer additional layers of protection by signaling when a coating has degraded, allowing for proactive maintenance or replacement. For example, in infrastructure, such as bridges or rooftop panels, smart coatings could detect corrosion before it becomes visible, thereby reducing long-term repair costs and improving safety.
Additionally, high-performance coatings are being developed to withstand even more extreme environments. For example, high-temperature powder coatings for industrial applications are now capable of withstanding heat up to 1000°F (537°C) or more. These coatings are ideal for use in high-performance engines, machinery, and electrical components, where durability under extreme conditions is crucial. The development of fire-resistant and flame-retardant coatings also opens up new possibilities in construction and architecture, where fire safety is a major concern.
Another area where the powder coating industry is seeing innovation is in the development of lightweight coatings that can maintain the same high level of durability without adding significant weight to the final product. This is particularly relevant in industries like aerospace, where weight reduction can lead to increased fuel efficiency and overall performance. Advances in polymer chemistry and nanotechnology are enabling the development of these lightweight coatings, offering high-strength finishes that meet rigorous industry standards without compromising on performance or appearance.
The industrial automation trend is also continuing to reshape the powder coating landscape. Manufacturers are increasingly incorporating robotic spraying systems, automated curing ovens, and smart inspection technology into their powder coating lines. These advancements improve precision, speed, and efficiency while reducing human error and labor costs. By integrating artificial intelligence (AI) and machine learning, automated systems can learn from past applications, predict and adjust for possible inconsistencies, and ensure a consistent finish across large volumes of parts. This level of automation is particularly valuable in high-volume manufacturing environments where consistency and productivity are essential.
Moreover, robotic systems can handle complex geometries that would be challenging for human operators to coat uniformly. For instance, the use of multi-axis robotic arms in powder coating systems allows for the even application of powder to intricate shapes, such as automotive body parts, large equipment, or decorative architectural elements. These systems not only reduce manual labor but also ensure higher precision, as robots can spray from multiple angles, achieving complete coverage without any gaps or overspray.
In terms of environmental impact, the powder coating process has long been regarded as a more eco-friendly option compared to traditional liquid coatings. As a dry application, powder coating generates fewer volatile organic compounds (VOCs), contributing to a cleaner environment. However, the industry is going a step further by developing biodegradable and recyclable powder formulations, further reducing the ecological footprint. By utilizing more sustainable raw materials and ensuring that powders can be reclaimed and reused without compromising quality, the industry continues to improve its green credentials.
Powder coating systems are also becoming more energy-efficient, which is particularly important in an era of increasing environmental consciousness. Lower curing temperatures, as mentioned previously, are helping manufacturers save energy while still achieving optimal finishes. These low-energy powders require less heat during the curing process, leading to a reduction in carbon emissions. In addition, infrared curing and ultraviolet (UV) curing technologies are gaining traction, allowing for even more energy-efficient powder coating processes that reduce both energy consumption and costs.
Another important innovation is the development of low-temperature curing powders designed for substrates that are sensitive to heat. These powders cure at lower temperatures, which is beneficial for coating plastics and composite materials without compromising the performance of the coating or damaging the underlying material. This opens up new possibilities in industries such as electronics, furniture, and consumer goods, where non-metal substrates are often used.
In terms of market growth, the powder coating industry is expanding beyond its traditional strongholds into emerging markets, such as Asia-Pacific, Latin America, and parts of Africa, where industrialization and infrastructure development are on the rise. China and India, in particular, are becoming major consumers of powder coatings as they develop their manufacturing sectors and invest in modernizing infrastructure. The growing middle class in these regions is also driving demand for high-quality finishes in appliances, automotive, and consumer goods sectors.
This global expansion is creating opportunities for new manufacturing facilities, distribution networks, and regional powder coating suppliers. Local manufacturers are capitalizing on the need for more cost-effective, high-quality coatings and are starting to produce region-specific powders tailored to the unique needs of local industries. For example, in tropical climates, coatings with added humidity resistance and UV protection are in high demand, while in more temperate regions, energy-efficient coatings are favored.
Finally, as manufacturers continue to demand faster turnaround times, the development of rapid-cure and ultra-fast-curing powders is helping to increase productivity and efficiency in the powder coating industry. These innovations are particularly beneficial in high-volume manufacturing environments, where minimizing production time is crucial to meeting customer demands and maintaining competitive pricing.
In conclusion, the powder coating industry is undergoing a transformation, fueled by innovations in coating materials, technology, automation, and sustainability. The industry is advancing toward more specialized coatings, energy-efficient processes, and eco-friendly formulations, all while maintaining the high quality and performance standards that make powder coating a preferred choice for many industries. As new technologies continue to emerge, powder coatings will become even more versatile, customizable, and efficient, offering enhanced performance, longer lifespan, and reduced environmental impact. Whether for automotive, furniture, construction, or industrial applications, powder coating surface finishes will continue to evolve, meeting the demands of an ever-changing market.
Powder Coat Finishes for Doors
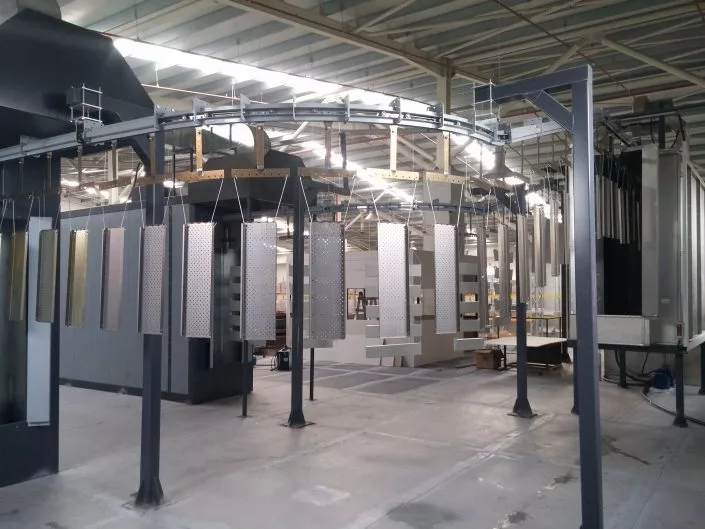
Powder coat finishes for doors have become increasingly popular due to their durability, aesthetic appeal, and versatility. These finishes are used on a variety of doors, including exterior doors, interior doors, security doors, and fire-rated doors, offering an array of benefits that traditional paint finishes cannot match. The powder coating process involves applying a dry powder to the door’s surface, which is then cured using heat to create a hard, durable finish. This finish is resistant to chipping, scratching, fading, and other types of wear, making it an ideal choice for doors exposed to heavy use and environmental factors.
The powder coating process provides a smooth, uniform finish on doors, which can be customized to suit a wide range of styles, colors, and effects. Manufacturers can create finishes that mimic the look of metallics, wood grains, textures, and even glossy or matte finishes, giving doors a unique and attractive appearance. This flexibility allows powder coating to meet the demands of different industries, from residential and commercial buildings to industrial and institutional applications.
One of the primary advantages of powder coating finishes for doors is their durability. Powder-coated doors are resistant to abrasion, corrosion, UV degradation, and chemical exposure, which makes them suitable for both indoor and outdoor applications. For exterior doors, particularly in regions with extreme weather conditions, powder coating provides superior protection against the elements. The finish prevents moisture and salt from penetrating the surface, which can lead to rust and corrosion in traditional metal doors. As a result, powder-coated doors have a longer lifespan compared to those painted with conventional liquid paints.
Another key benefit is the low maintenance required for powder-coated doors. The hard, smooth surface created by powder coating resists dirt buildup, making it easier to clean compared to other door finishes. This is particularly advantageous for doors that are exposed to high-traffic environments, such as commercial buildings, warehouses, or public spaces, where doors are frequently opened and closed and subject to dirt, fingerprints, and wear.
The energy efficiency of powder-coated doors is also a significant consideration, especially in applications where thermal insulation is important. In many cases, the powder coating process can be combined with other insulation techniques to create energy-efficient doors that help maintain temperature control within buildings. This is particularly useful for doors used in cold storage, refrigerated warehouses, or industrial facilities where maintaining a stable internal temperature is crucial for product preservation and energy savings.
For residential applications, powder-coated doors offer a wide variety of color options and finish textures, allowing homeowners to choose a door that complements the architectural style of their property. Whether it’s a traditional style with a wood-like finish, a modern design with a high-gloss, or a rustic appearance with a matte texture, powder coating offers endless customization possibilities. The long-lasting nature of the finish ensures that the door maintains its aesthetic appeal over time, even when exposed to harsh sunlight or frequent cleaning.
In commercial and industrial applications, the demand for strong, secure, and long-lasting doors is paramount. Powder coating provides a finish that not only protects the door but also enhances its structural integrity. For security doors, fire-rated doors, and doors in high-traffic areas, powder coating offers enhanced protection against physical damage, rust, and weathering. These doors are often subjected to abrasion, scratching, and impact, and powder coating provides a superior finish that resists these types of damage.
Architectural doors are another category where powder coating is gaining popularity. Storefront doors, entrance doors, and sliding doors benefit from powder coating’s ability to provide a smooth, high-quality finish that maintains its integrity in both high-traffic areas and outdoor environments. The finish can be customized with various textures and colors to match the overall design scheme of the building, whether it’s a sleek, modern look for office buildings or a more traditional appearance for historical renovations.
For fire-rated doors, powder coating provides added protection without compromising the door’s fire resistance. Fire-rated doors are a critical part of a building’s fire safety plan, and applying a powder coating finish does not interfere with the door’s ability to perform under extreme heat. Some intumescent powder coatings can even be formulated to expand under heat, offering additional fire-resistant properties, making them ideal for applications where both safety and durability are necessary.
One of the main reasons powder-coated finishes are so highly regarded for doors is their environmental benefits. The powder coating process generates little to no waste, as any excess powder that does not adhere to the surface can be recycled and reused. Additionally, the absence of solvents in the powder means there are fewer volatile organic compounds (VOCs) released into the environment, making powder coating a more eco-friendly option compared to traditional liquid paints. Many powder coating systems also have energy-efficient curing ovens that reduce energy consumption during the finishing process.
In terms of color options, powder coatings offer a wide range of hues and shades, including standard colors, custom colors, and special effects like metallics, pearlescent, and textures. Whether a customer is looking for a bold, bright color for a modern building, or a more subtle, neutral tone for a traditional entrance, powder coatings can accommodate almost any design requirement. Textured finishes can provide a unique look and feel, with options like sand-textured, wrinkle, or hammered finishes that add depth and visual interest to the door’s surface.
Customization extends beyond color and texture to the type of powder coating itself. There are various formulations of powder coatings designed for specific applications. For example, epoxy powders offer excellent adhesion and corrosion resistance, making them ideal for indoor doors, while polyester and urethane-based powders are more commonly used for outdoor doors due to their resistance to UV degradation and weathering. Hybrid formulations combine the benefits of both to offer a well-rounded solution for doors that will be used both indoors and outdoors.
The application method of powder coating also plays a crucial role in ensuring a high-quality finish. Most powder coatings are applied using an electrostatic spray system, where the powder is charged and sprayed onto the grounded door surface. This ensures that the powder adheres evenly and consistently across the entire door, even in hard-to-reach areas. The door is then placed in a curing oven, where the heat causes the powder to melt and fuse into a continuous, durable layer.
In conclusion, powder coating finishes for doors provide a highly durable, customizable, and environmentally friendly solution for a wide range of applications. From residential to commercial, industrial to architectural, powder coating offers superior protection against the elements, wear and tear, and environmental factors, all while enhancing the aesthetic appeal of the door. The ability to achieve various colors, textures, and finishes, along with the longevity and low maintenance requirements, makes powder coating the preferred choice for modern door finishing. Whether for aesthetic purposes or functional performance, powder-coated doors offer a combination of form and function that ensures lasting beauty and durability.
Powder coating finishes for doors are increasingly being chosen not only for their aesthetic appeal and durability, but also for their ability to meet specific performance requirements in various industries. As the need for customized solutions grows, powder coating technologies continue to evolve, enabling more specialized and precise applications for doors across different sectors.
One of the main areas of growth is in the commercial sector, where the demand for high-performance doors continues to rise. For example, in hospitality and retail environments, powder-coated doors are used to create visually appealing entrances that withstand the demands of high foot traffic. Security doors in banks, government buildings, and retail stores require additional features, such as anti-theft or fire-resistant coatings. Powder coating provides a durable finish that can be combined with specialized coatings for added protection against vandalism, corrosion, and other forms of wear and tear.
In industrial applications, powder-coated doors are often used for heavy-duty environments where both functional durability and aesthetic appeal are important. Warehouse doors, loading bay doors, and factory entrances are frequently subjected to harsh conditions, including abrasion, chemical exposure, and extreme weather. Powder coating offers a level of protection against these environmental factors, while also ensuring that doors remain in good condition even after years of use. Furthermore, powder-coated finishes help prevent the accumulation of dirt and grime, making cleaning easier and less time-consuming for facility managers.
For industrial and automotive applications, powder-coated doors are often used for garage doors, entrance gates, and vehicle doors. In these cases, the durability of powder coating ensures that the doors maintain their finish and functionality over time, even in high-traffic areas exposed to extreme temperatures, chemical spills, and other contaminants. Powder coating is also used to create a high-gloss finish for vehicle doors, which helps to enhance the overall appearance of commercial fleets or automotive products.
Another growing trend is the increasing focus on sustainability and eco-friendly practices in the powder coating industry. With increasing awareness around the need for environmentally responsible practices, manufacturers are looking for ways to reduce their carbon footprint. One of the primary benefits of powder coating is that it is a low-VOC (volatile organic compound) process, which means it has a significantly lower environmental impact compared to traditional liquid coatings. This is especially important in public buildings, schools, and healthcare facilities, where both the environmental impact of the coatings and the health of the people within the buildings are key concerns.
Powder coating is also more energy-efficient compared to traditional painting techniques. The curing ovens used in powder coating require less energy than conventional paint drying methods, leading to lower operating costs and reduced carbon emissions. The ability to recycle excess powder further minimizes waste, which contributes to the process’s sustainability. This makes powder coating a top choice for architects and designers seeking to meet green building standards, such as LEED (Leadership in Energy and Environmental Design) certifications.
The technology behind powder coating systems is also improving. Advanced application methods such as electrostatic spraying allow for more efficient powder application. This technique uses an electric charge to ensure that powder particles are attracted to the surface of the door, minimizing overspray and ensuring uniform coverage. The high transfer efficiency of this method reduces material waste, improving both the environmental footprint and the cost-effectiveness of powder coating.
As the market for powder-coated doors expands, manufacturers are also focusing on improving the speed and efficiency of the powder coating process. Automated powder coating lines are now being used to streamline production, allowing manufacturers to coat larger quantities of doors in a shorter amount of time. This increases throughput while maintaining high levels of quality and finish consistency. Automation also reduces labor costs and ensures that the powder coating is applied evenly and precisely, even on complex door designs.
Further technological advancements in powder coating include the development of specialized powder formulations that are more environmentally friendly, more durable, and more adaptable to various types of doors. For example, epoxy-based powder coatings are highly resistant to corrosion and chemical exposure, making them ideal for industrial doors used in chemical plants, factories, or marine environments. Polyester-based powder coatings, on the other hand, provide excellent protection against UV radiation, making them a top choice for outdoor doors exposed to harsh sunlight.
Nanotechnology is also beginning to play a role in the development of advanced powder coatings. By incorporating nano-sized particles into powder coatings, manufacturers can enhance the performance characteristics of the finish. These particles can improve scratch resistance, anti-microbial properties, and even the self-cleaning capabilities of the coating. For example, nano-silver particles can be used in powder coatings to provide doors with anti-bacterial properties, which is especially beneficial in hospitals, schools, and public buildings.
In terms of design trends, powder-coated doors are increasingly being used to create modern and contemporary looks for both commercial and residential spaces. The ability to achieve a smooth, glossy finish or matte appearance with powder coating allows architects and designers to experiment with a range of visual styles, from sleek, minimalist aesthetics to more textured, rustic finishes. Additionally, metallic finishes or high-tech effects can give doors a unique, cutting-edge appearance, making them stand out in both modern homes and corporate buildings.
The design flexibility of powder-coated finishes extends to custom colors and even custom patterns. Designers can create bespoke finishes for doors that match specific color schemes or branding requirements, making powder coating ideal for projects where a distinct, tailored look is necessary. Architectural finishes like brushed metal or wood grain effects are also growing in popularity for use in commercial and high-end residential applications, offering a more sophisticated, natural look that is not easily achievable with traditional paint finishes.
Lastly, the popularity of smart homes and smart buildings is influencing the future of powder coating for doors. As smart technologies become more integrated into building designs, powder-coated doors are beginning to incorporate touch-sensitive or self-healing coatings. In the case of self-healing finishes, the powder coating can repair itself from minor scratches or abrasions, extending the door’s aesthetic life. As more doors are equipped with smart locks, access control systems, and sensors, powder-coated finishes will continue to evolve, ensuring that they are compatible with these advanced technologies while maintaining their visual appeal and performance.
In conclusion, powder-coated finishes for doors offer a combination of aesthetic flexibility, durability, and environmental responsibility that makes them the go-to choice for a wide range of applications. Whether for residential, commercial, industrial, or architectural purposes, powder coating provides long-lasting performance that resists the wear and tear of everyday use, all while offering customization options to fit specific design needs. With ongoing advancements in technology and a growing focus on sustainability, powder coating is poised to remain a leading solution for door finishes in the years to come.
Powder Blasting Equipment
Powder blasting equipment is essential for surface preparation, coating, and cleaning in a variety of industrial applications. This specialized equipment is used in processes like abrasive blasting, surface treatment, cleaning, and pre-coating. Powder blasting is a popular choice in industries where the quality of surface finishes and cleaning processes plays a critical role in the performance, longevity, and aesthetics of products.
At its core, powder blasting involves the use of finely ground abrasive materials, often referred to as powder abrasives, which are propelled at high velocities using compressed air. This method is commonly applied to surfaces like metal, wood, plastic, glass, and concrete to remove contaminants, roughen the surface, or prepare it for subsequent treatments such as powder coating or painting. Unlike traditional sandblasting, which typically uses sand as the abrasive material, powder blasting uses a variety of powder abrasives such as baking soda, plastic beads, aluminum oxide, or silicon carbide, allowing for more controlled and versatile applications.
Powder blasting equipment consists of several key components, each playing an important role in achieving the desired results. These include:
- Blasting Gun: The blasting gun is the primary tool used to direct the abrasive powder onto the surface. Typically, the gun uses compressed air or other propelling mechanisms to shoot the abrasive material at high speeds. The nozzle of the gun can be adjusted to control the pressure, spray pattern, and flow rate of the abrasive powder. Advanced airless and pressure-fed systems are also available for more precise control of the blasting process.
- Compressor: A high-capacity air compressor is essential for supplying the pressurized air needed to propel the powder abrasive material at high velocities. The compressor needs to deliver consistent airflow at high pressure to ensure a smooth and efficient blasting process. The size and power of the compressor will vary depending on the scale of the operation, with larger systems capable of handling continuous or industrial-scale blasting jobs.
- Blasting Cabinet or Enclosure: In many powder blasting applications, the blasting process is carried out in a controlled environment. A blasting cabinet or enclosure is used to contain the abrasive powder and ensure that it is directed onto the surface in a controlled manner. These cabinets also help collect and recycle the abrasive material, reducing waste and ensuring that it can be reused multiple times. The enclosure also serves to protect the operator from the dust and debris produced during the blasting process.
- Abrasive Powder: The choice of abrasive powder is critical for the success of powder blasting. The type of powder used depends on the material being treated and the desired outcome. Baking soda is often used for cleaning delicate surfaces without causing damage, while aluminum oxide or silicon carbide is ideal for more aggressive surface preparation. Plastic beads are used for gentle cleaning and surface finishing, while other abrasives are chosen based on their hardness and ability to remove contaminants effectively.
- Dust Collection System: Blasting generates dust, which is harmful to both the operator and the environment. A dust collection system is integrated into the powder blasting equipment to capture and filter out harmful particles. This system is essential for maintaining clean air in the workspace and ensuring compliance with safety and environmental regulations. The collection system uses a combination of filters and fans to remove airborne particles and keep the air quality safe.
- Powder Blasting Hose: The powder blasting hose connects the compressor and the blasting gun, carrying the pressurized air and abrasive material to the nozzle. The hose needs to be durable, flexible, and able to withstand the pressure and abrasiveness of the materials used in the blasting process. High-quality hoses are designed to be resistant to wear and tear, ensuring the equipment’s longevity and minimizing the need for frequent replacements.
- Control Panel: The control panel is the heart of the powder blasting system, allowing operators to adjust the settings, monitor performance, and manage the blasting process. It is typically equipped with controls for adjusting air pressure, powder flow, and nozzle distance. More advanced systems have digital interfaces that provide detailed feedback on the operation, such as powder consumption rates, air pressure, and cycle times.
Powder blasting can be used in various industrial sectors, including:
- Automotive: In the automotive industry, powder blasting is used to prepare metal surfaces for coating or painting. It is commonly used for cleaning and prepping car parts, such as engine components, chassis, and body panels, ensuring that these parts have the proper surface profile for powder coating or painting. This ensures that coatings adhere well and last longer.
- Aerospace: The aerospace industry relies heavily on powder blasting equipment for cleaning and prepping aircraft parts, including engine components, landing gears, and aircraft fuselages. Powder blasting is used to remove rust, scale, and other contaminants, which is essential for the safety and performance of aircraft.
- Marine: Powder blasting is commonly used to prepare boat hulls, propellers, and other marine components for protective coatings, ensuring they remain durable and resistant to corrosion from saltwater and other harsh conditions. The high pressure of powder blasting removes marine growth, barnacles, and rust, keeping these components clean and functioning properly.
- Metalworking: Powder blasting is often used in metalworking applications for surface preparation before welding, coating, or painting. It can be used to remove oxidation, rust, and other contaminants from metal surfaces, creating a clean and smooth surface ideal for powder coating or painting.
- Construction and Renovation: Powder blasting is used to clean and restore various materials used in construction, including brick, stone, and concrete. It can be used to remove dirt, moss, old paint, and other contaminants, giving surfaces a new, polished appearance.
One of the major benefits of powder blasting equipment is its environmental friendliness. Unlike traditional abrasive blasting, which often uses materials like sand or steel shot that can be harmful to the environment, powder blasting uses abrasive powders that are often eco-friendly, such as baking soda or plastic beads. These materials produce less dust and are less likely to cause environmental harm. Furthermore, the process itself produces less airborne debris and uses fewer hazardous chemicals, making it a more sustainable option in many industries.
Safety is a top priority when working with powder blasting equipment. As with any abrasive blasting process, proper personal protective equipment (PPE) must be worn to protect the operator from flying debris and dust. This includes wearing goggles, dust masks, protective clothing, and gloves. Adequate ventilation and dust collection systems are also necessary to maintain a safe and clean working environment.
Powder blasting systems are highly versatile and can be adjusted to meet the needs of different applications. The flexibility of the equipment allows operators to control the pressure, powder flow, and nozzle direction to achieve a wide range of surface treatments, from cleaning and preparation to polishing and finishing. This adaptability makes powder blasting a valuable tool across numerous industries, offering a reliable and efficient way to prepare surfaces for further treatment, coating, or use.
In conclusion, powder blasting equipment is an essential part of modern surface treatment, cleaning, and coating processes. Its versatility, effectiveness, and eco-friendly nature make it a popular choice in industries ranging from automotive and aerospace to construction and metalworking. With the ability to prepare surfaces for powder coating, painting, and other treatments, powder blasting ensures optimal adhesion and durability for various applications. As technologies continue to evolve, the efficiency, safety, and environmental benefits of powder blasting equipment are expected to improve, making it an increasingly important tool in industrial surface preparation.
Continuing from the previous discussion, advancements in powder blasting technology are driving the evolution of more efficient, precise, and eco-friendly systems. As industries increasingly prioritize sustainability, powder blasting equipment is adapting with innovative technologies that reduce waste, improve performance, and enhance operational safety.
One of the most notable advancements in powder blasting systems is the development of automated blasting solutions. Robotic blasting systems are being integrated into manufacturing lines to handle high-volume production with consistent precision. These automated systems can be programmed to handle complex blasting tasks, including specific surface profiles and controlled abrasiveness, which reduces the margin of error often seen with manual operations. By automating the blasting process, companies can achieve faster turnaround times and improve overall production efficiency.
Another area of significant development is the integration of smart technology into powder blasting equipment. Modern blasting systems now come equipped with digital controls and sensor technology that enable real-time monitoring and adjustments to ensure optimal blasting conditions. Pressure sensors, flow meters, and temperature gauges can continuously monitor the blasting process, allowing operators to adjust settings on the fly for more accurate results. The inclusion of data logging and diagnostic tools provides operators with insights into equipment performance, helping to prevent breakdowns, reduce downtime, and ensure consistent quality.
In addition to automation and smart technology, there is a growing emphasis on improving the recycling and reusability of abrasive powders. Traditional abrasive blasting methods often result in the waste of materials, leading to higher operational costs and environmental concerns. However, with the recycling systems built into modern powder blasting equipment, abrasives can be collected, filtered, and reused multiple times without sacrificing blasting quality. Closed-loop systems not only lower the need for frequent abrasive replenishment, but also reduce the environmental impact by minimizing material waste.
One of the advantages of powder blasting over traditional sandblasting or other forms of abrasive blasting is its ability to achieve a gentle yet effective cleaning process, making it suitable for a broader range of surfaces. For example, powder blasting can be used to clean delicate electronic components, glass, and plastic surfaces, where other methods might risk damaging the material. Powder blasting, when done correctly, allows for precise control over the application, ensuring that the substrate is cleaned without harming its integrity.
Powder blasting systems are also evolving to accommodate new eco-friendly abrasives. Traditional abrasives often contained toxic substances or were difficult to dispose of safely. As the demand for sustainable and non-toxic materials grows, powder blasting manufacturers have developed new abrasives made from natural, biodegradable materials such as walnut shells, corn cob granules, or crushed glass. These eco-friendly options ensure that the process is safer for both operators and the environment, while still providing effective cleaning and preparation for surface coatings.
The market for mobile powder blasting equipment is expanding, as well. With industries needing the flexibility to perform on-site blasting at remote locations, manufacturers are developing portable powder blasting systems that are compact, lightweight, and capable of operating in varied environments. These systems allow businesses to take powder blasting to construction sites, shipyards, and other locations, providing convenience and reducing the need for transporting large items to specialized facilities. For example, mobile powder blasting rigs are frequently used for cleaning large machinery, pipelines, and infrastructure components in places where it would be impractical to move the item to a fixed blasting station.
Furthermore, innovations in abrasive powder delivery systems are improving the precision and control of the blasting process. Air-assisted systems can ensure that the powder is mixed and delivered with greater consistency, reducing the chances of irregular application or overspray. Pressure-fed systems are becoming more common for high-volume applications, ensuring that the abrasive powder is propelled with uniform speed and force, allowing for faster and more effective blasting results.
In specialized applications, such as aerospace or electronics manufacturing, low-abrasion and highly controlled powder blasting are necessary to maintain the integrity of sensitive surfaces. For example, non-metallic abrasives such as sodium bicarbonate (baking soda) are used to clean delicate surfaces without causing scratches or other damage. These powders break down upon impact, ensuring that they do not create debris that might damage the surface. This makes powder blasting ideal for cleaning highly intricate parts, such as circuit boards, precision machinery, and optical components.
With increased regulations on environmental and safety standards across many industries, powder blasting systems are also incorporating features that ensure compliance with these laws. Advanced filtration systems and air purification technologies are incorporated into the design of modern equipment to capture any airborne particles during blasting, protecting both workers and the environment. Dustless blasting systems, for example, combine water and abrasives to minimize the amount of dust created during the blasting process, making them ideal for indoor applications or environments where air quality is critical.
Another growing trend in powder blasting is its use in art restoration and historic preservation. Museums and historical sites often rely on powder blasting to carefully clean delicate surfaces, such as stone sculptures, metal artifacts, and wooden objects, without causing harm. By using the proper abrasives, restoration experts can remove dirt, grime, and old coatings while preserving the integrity of the artwork or historical structure. This process is preferred in many cases over more aggressive methods like sandblasting, which may damage the surface over time.
Finally, the maintenance of powder blasting equipment is a key aspect of ensuring long-term, efficient performance. Regular inspections, part replacements, and proper cleaning of equipment components such as blasting nozzles, hoses, and filters are critical for preventing clogs, ensuring consistent powder delivery, and maintaining the system’s overall performance. As powder blasting technology advances, manufacturers are developing self-cleaning systems and parts that require less frequent maintenance, improving uptime and reducing operational costs.
In conclusion, powder blasting equipment has become an indispensable tool in many industries, offering versatility in surface cleaning, preparation, and coating. As technologies continue to evolve, powder blasting systems are becoming more efficient, eco-friendly, and precise. With advancements in automation, smart technology, recycling, and eco-friendly abrasives, powder blasting continues to improve in terms of both performance and sustainability. Its growing adoption across diverse sectors, from aerospace to art restoration, reflects its critical role in surface treatment and cleaning.
As powder blasting technology continues to advance, it is increasingly contributing to the development of more sustainable and cost-effective industrial processes. With a heightened focus on environmental responsibility, the latest innovations aim to reduce both the environmental impact and the energy consumption of powder blasting systems, addressing the growing demands for sustainability in industries across the globe.
One area where powder blasting is seeing significant improvements is in energy efficiency. Traditional abrasive blasting systems often require substantial energy to operate, especially when using high-powered compressors and large blasting units. However, advancements in energy-efficient compressor technology are allowing for a reduction in energy consumption while still maintaining the required blasting performance. Newer systems feature variable-speed drives (VSD) that adjust compressor speed according to demand, ensuring that energy is used only when necessary. This not only lowers operating costs but also reduces the carbon footprint of powder blasting operations.
The incorporation of electric-powered and battery-operated systems is also gaining traction in certain markets. These systems provide greater flexibility for remote operations and are more sustainable, reducing the reliance on fossil fuels. For example, portable powder blasting machines designed for smaller jobs or mobile applications can now be powered by rechargeable battery packs, allowing operators to perform work in areas where traditional power sources might not be available.
Additionally, the development of closed-loop abrasive recycling systems is playing a key role in making powder blasting more environmentally friendly. Traditional systems often result in significant waste of abrasive materials, as once the abrasives are used, they are discarded. However, the latest recycling systems allow for the collection, cleaning, and reuse of abrasives within the blasting system, minimizing material waste. These closed-loop systems feature advanced filtration units that can filter out contaminants from the used abrasives, extending their lifespan and improving the overall cost-effectiveness of the process.
In industries where safety is paramount, such as aerospace, automotive, and marine applications, safety innovations in powder blasting equipment are improving operator protection and reducing workplace hazards. Ergonomically designed equipment is becoming more common, ensuring that operators can perform tasks safely and comfortably. For instance, blasting nozzles are designed to be lightweight and easy to handle, reducing operator strain and the risk of repetitive motion injuries. In addition, improvements in dust control systems, such as HEPA filters and abrasive recovery units, ensure that operators are protected from inhaling potentially harmful dust and particles generated during the blasting process.
As industries increasingly embrace digitalization, powder blasting equipment is also benefiting from the integration of Internet of Things (IoT) technologies. IoT-enabled powder blasting systems allow for remote monitoring and predictive maintenance, ensuring that equipment is always functioning optimally. Sensors embedded in the equipment can collect data on operational performance, such as air pressure, powder flow, and abrasive usage, and send this information to centralized systems. This data is then analyzed to detect patterns and potential issues, enabling operators to schedule maintenance before problems occur. Predictive maintenance reduces downtime, extends the lifespan of equipment, and lowers overall maintenance costs.
Another innovative trend in powder blasting technology is the use of robotic systems that perform tasks such as precision cleaning or surface preparation. These robotic systems are designed to work in environments where human operators might face risks, such as in hazardous materials handling or extreme temperature conditions. Robots equipped with advanced sensors and artificial intelligence (AI) capabilities are able to carry out complex blasting tasks with high accuracy, reducing human error and improving the quality of results. They can be programmed to work around-the-clock, significantly increasing production efficiency, particularly in high-demand industries.
Automation in powder blasting is especially valuable in industries that require high-volume, repetitive surface preparation tasks. For instance, metalworking, automotive assembly lines, and manufacturers of household appliances can all benefit from robotic systems that perform blasting operations with minimal supervision. These systems not only reduce labor costs but also ensure that the blasting process is consistent, resulting in uniform surface finishes that meet stringent quality standards.
The use of advanced coatings in conjunction with powder blasting technology is also an emerging trend. As companies strive to create products that are both durable and visually appealing, powder coating is becoming increasingly popular in conjunction with powder blasting. In many cases, powder blasting is used as a preparatory step before applying a protective powder coat on metal, plastic, or other substrates. This ensures that the substrate has an optimal surface profile for coating adhesion. As the powder coating industry evolves, innovations in eco-friendly powder coatings, such as those with low volatile organic compounds (VOCs), are being paired with powder blasting systems to create sustainable products that are not only functional but also contribute to a greener environment.
Beyond traditional industrial applications, the growing demand for architectural finishes is driving the use of powder blasting for decorative finishes and surface texturing. In the construction and interior design sectors, powder blasting is used to prepare surfaces for the application of unique finishes such as matte textures, metallic finishes, and patinas. For example, architectural metal panels, stone facades, and concrete surfaces can be treated with powder blasting to achieve specific textures or remove unwanted layers, such as old paint or corrosion. This capability is transforming the way designers approach material finishes and providing new creative possibilities for architects and builders.
Powder blasting technology is also being increasingly used in environmental remediation projects. For example, lead paint removal, asbestos abatement, and the cleaning of contaminated surfaces benefit from the use of environmentally friendly and non-toxic powder abrasives. By using soda blasting or similar powder abrasives, hazardous substances can be safely removed without the need for harmful chemicals or abrasive materials that can pollute the surrounding environment.
Research and development in powder blasting technology is focused on creating more effective and efficient systems that meet the needs of modern manufacturing and industrial processes. As manufacturers push for greater productivity, performance, and cost-effectiveness, continued advancements in materials science, automation, and energy efficiency will shape the future of powder blasting equipment. Additionally, innovations in multi-functional equipment, which can handle both abrasive blasting and other surface treatment processes, are helping industries to streamline operations and reduce the need for multiple pieces of equipment.
As industries seek solutions that address both performance and sustainability, the future of powder blasting looks promising, with improvements in energy use, material waste reduction, automation, and process control. These advancements will ensure that powder blasting remains a critical component in industries where high-quality, reliable surface preparation and cleaning are essential. Whether for preparing surfaces for coatings, cleaning delicate components, or restoring historical artifacts, powder blasting equipment will continue to evolve, providing smarter, more sustainable solutions for industrial and commercial applications.
Not only do we manufacture our powder coating equipment, we also ship them worldwide to your facility with care
We’re not just the manufacturers of your powder coating equipment, we’re also your worldwide delivery partners.
At EMS Powder Coating Equipment, we understand that getting your powder coating equipment to you quickly and safely is just as important as manufacturing it to the highest standards. That’s why we offer worldwide delivery services to all of our customers.
We work with a network of experienced and reliable shipping partners to ensure that your equipment arrives on time and in perfect condition. We also offer a variety of shipping options to fit your budget and needs.
Whether you need your equipment shipped to a local address or to an international destination, we can help. We’ll work with you to choose the best shipping option for your needs and to keep you updated on the status of your shipment every step of the way.
So when you choose EMS for your powder coating equipment, you’re not just getting the best products on the market, you’re also getting the best possible delivery experience.
Contact us today to learn more about our worldwide delivery services.
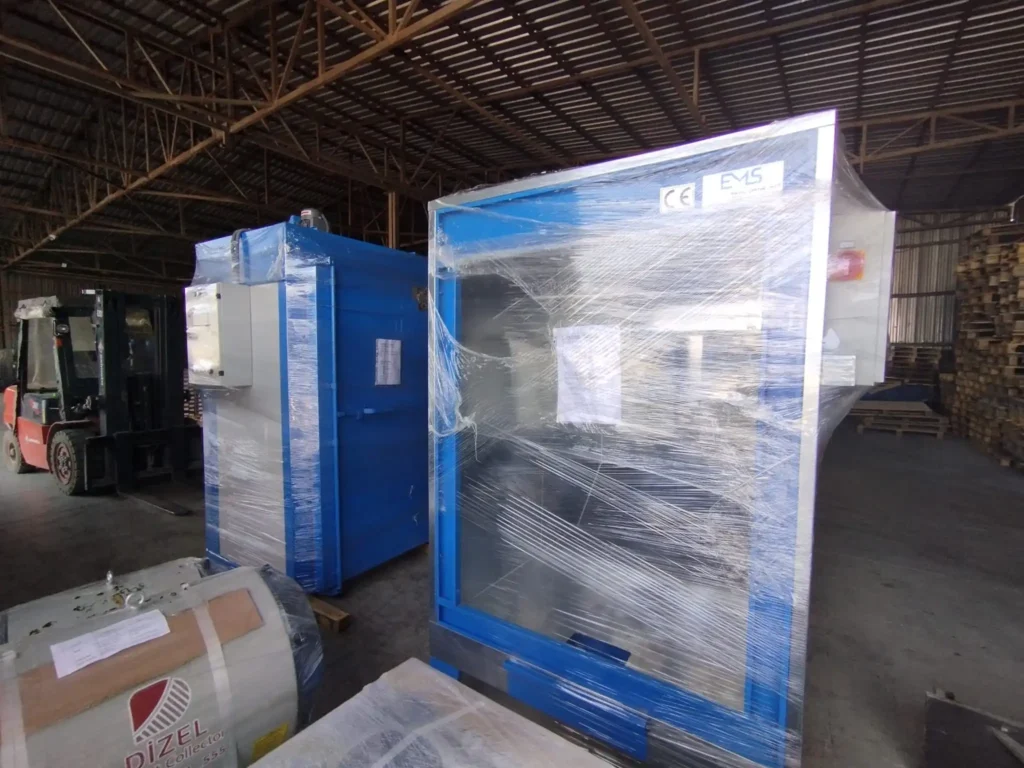
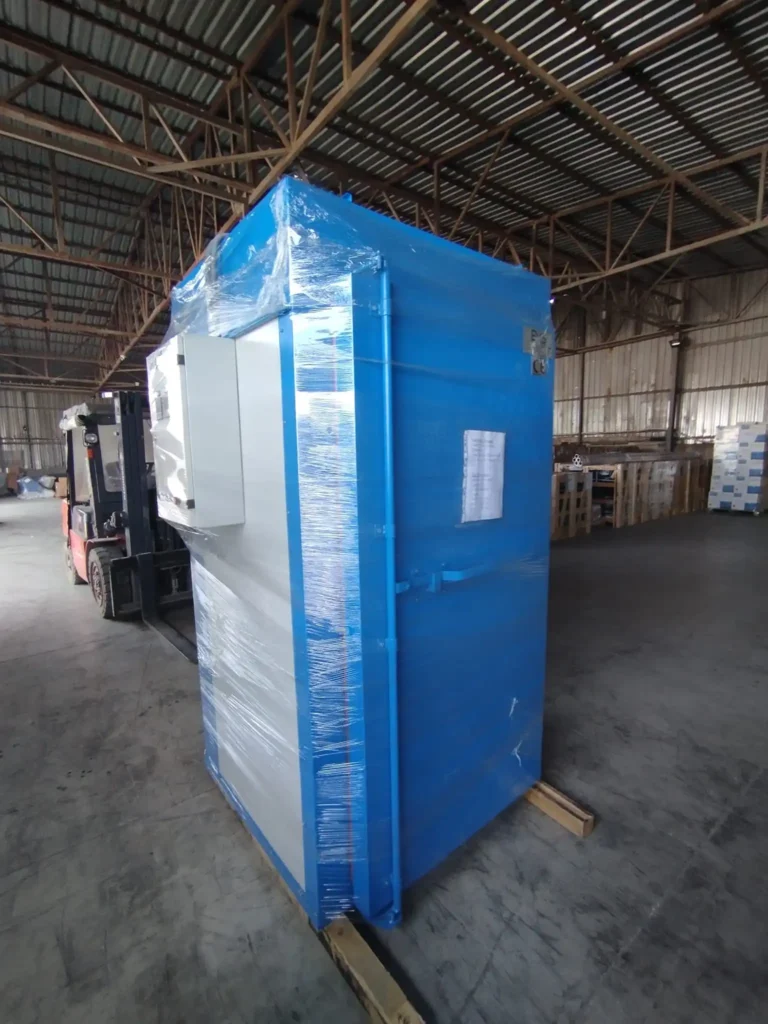
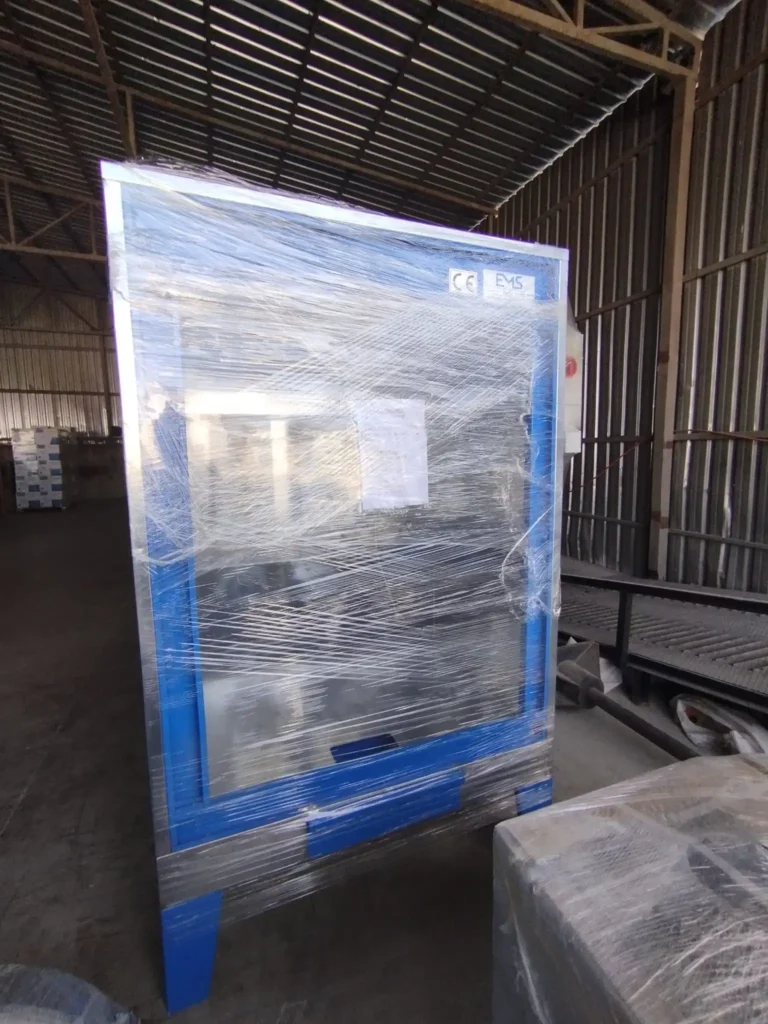
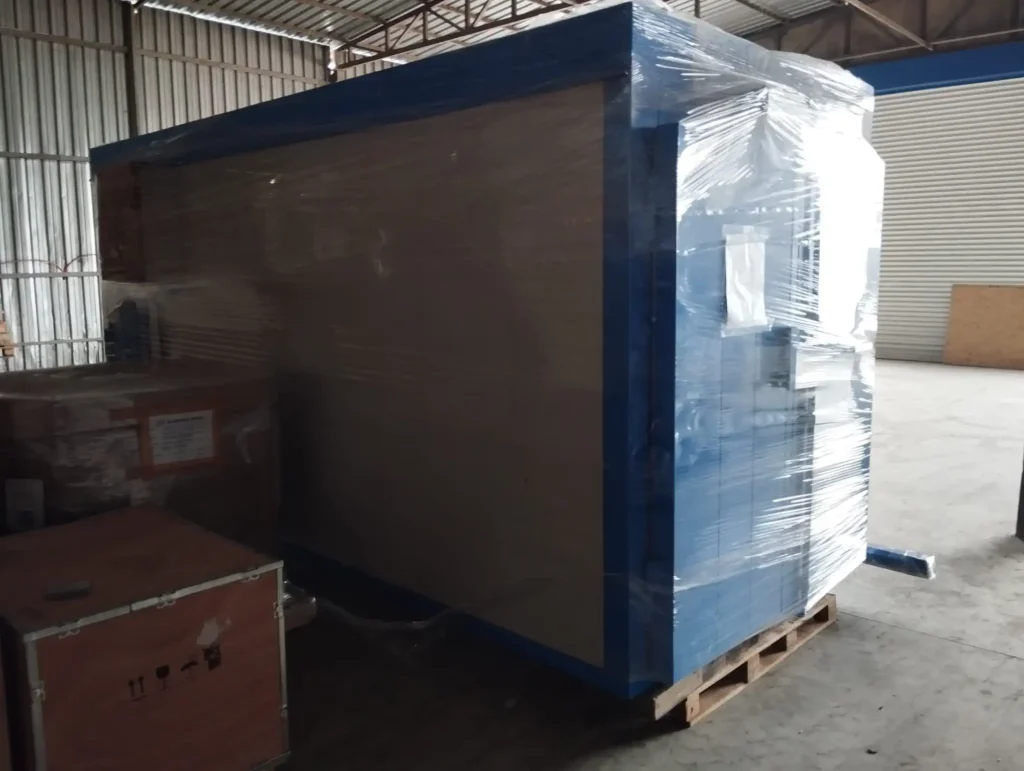
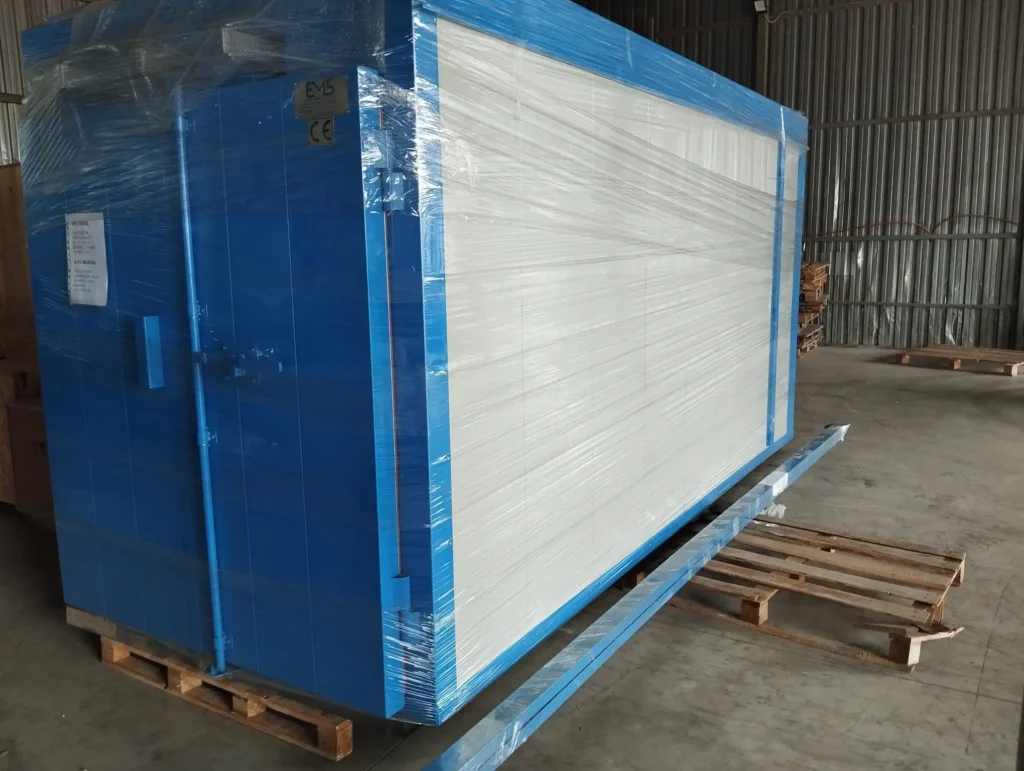
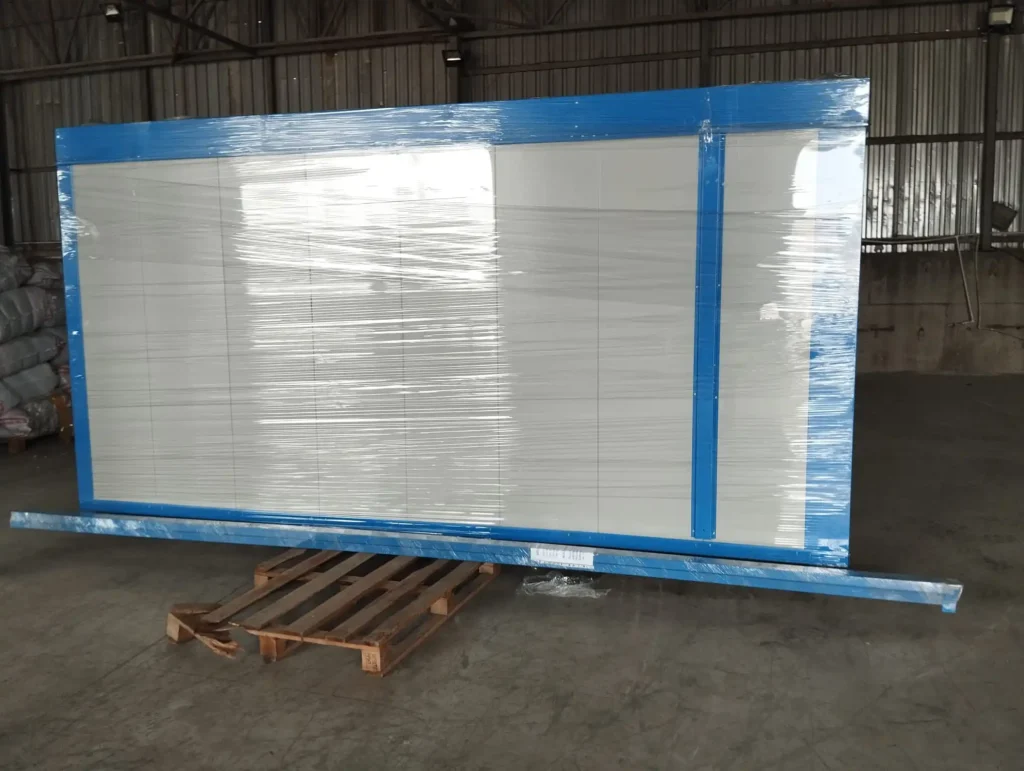
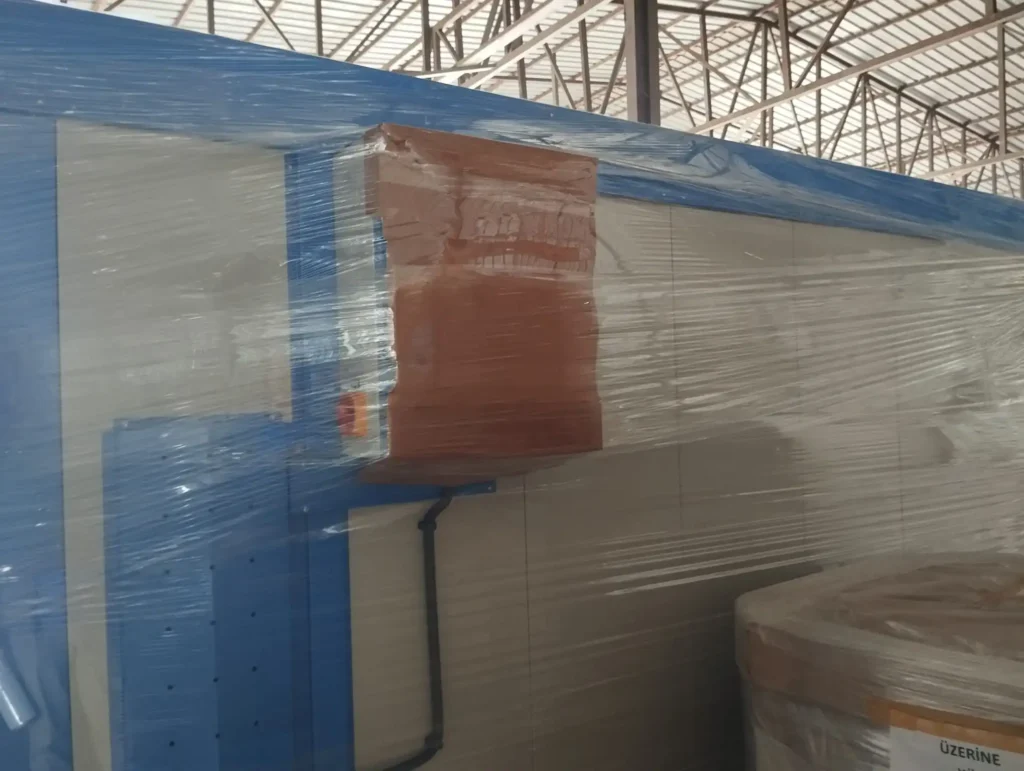
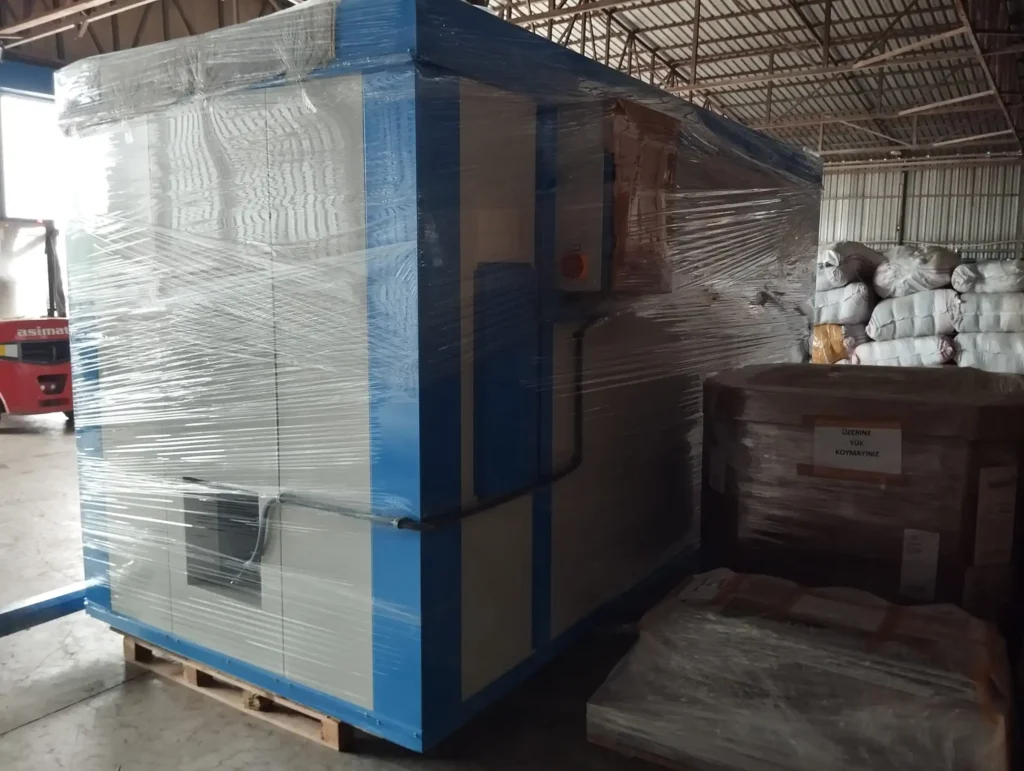
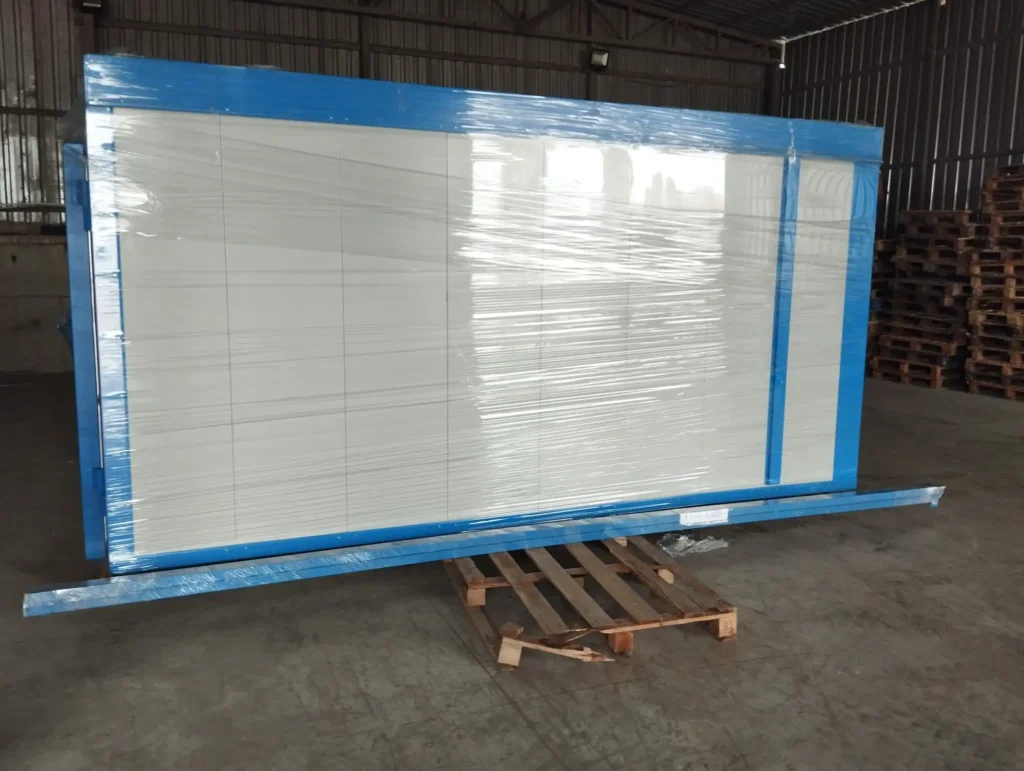