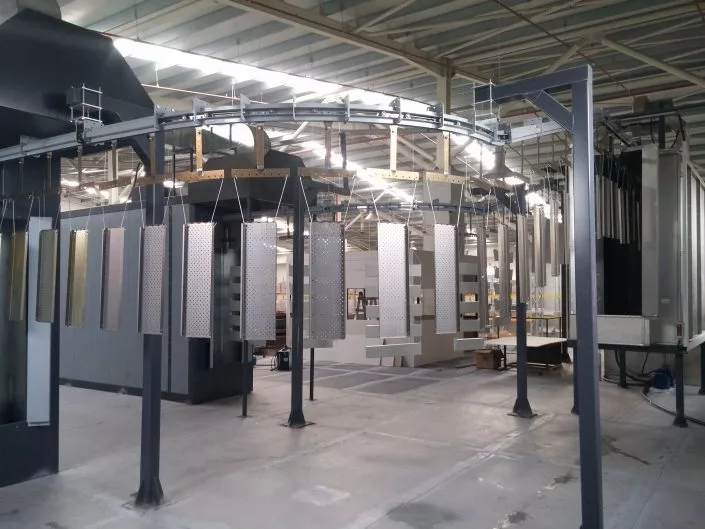
The Powder Coating Equipment for Steel Doors is one of the main areas where we manufacture powder coating plants for serial metal doors production.
Steel doors are manufactured with sheet metals made from steel coils. These coils are cut into square parts and they are needed to paint with powder coating powder before the assembly
Powder Coating for Steel Doors
The metal doors including security door set, steel door, commercial or exterial steel doors are mostly painted with powder coating. The powder coating is a much more durable solution for the steel doors finishing.
The metal door frame of the steel front dorst are also powder coated. The steel front doors and metal exterior doors are one of the main products, the doors manufacturers manufacture. Here below you can find information about the technical process about the powder coating equipment for steel doors and their pricing.
The Steps of the Powder Coating Equipment for Metal Doors
The powder coating process for metal doors involves several steps to ensure proper adhesion, uniform coverage, and a durable finish. Here are the key steps in the powder coating process for metal doors:
1. Surface Preparation:
- Cleaning: The first step is to clean the metal door’s surface thoroughly to remove any contaminants, oils, dirt, or rust. This is typically done using a combination of cleaning solutions, degreasers, and a rinse or wash process.
- Chemical Pre-Treatment: Some metal doors may undergo chemical pre-treatment, such as phosphating or chromate conversion coating. This treatment enhances adhesion and corrosion resistance.
- Drying: After cleaning and pre-treatment, the doors are dried to ensure there is no moisture on the surface.
Surface preparation: The metal surface to be coated must be clean and free of rust, grease, and other contaminants. The surface can be cleaned using a variety of methods, such as sandblasting, solvent cleaning, or alkaline cleaning.
- Sandblasting: Sandblasting is a process that uses compressed air to propel abrasive material against a surface to remove rust, paint, and other contaminants. This is the most effective method for surface preparation, but it can also be the most expensive.
- Solvent cleaning: Solvent cleaning is a process that uses a solvent to dissolve and remove contaminants from a surface. This method is less effective than sandblasting, but it is also less expensive.
- Alkaline cleaning: Alkaline cleaning is a process that uses an alkaline solution to remove contaminants from a surface. This method is effective for removing grease and oil, but it is not as effective for removing rust.
- Degreasing: Degreasing is a process that uses a solvent to remove grease and oil from a surface. This method is often used as a pre-treatment step before another cleaning method, such as sandblasting or alkaline cleaning.
- Pickling: Pickling is a process that uses an acid to remove rust and other contaminants from a surface. This method is effective for removing rust, but it can also damage the surface of the metal.
- Passivating: Passivating is a process that creates a protective layer on the surface of a metal to prevent corrosion. This method is often used on aluminum and stainless steel.
The best method for surface preparation will depend on the specific application. For example, if you are coating a metal surface that will be exposed to the weather, then you will need to use a more aggressive cleaning method, such as sandblasting. However, if you are coating a metal surface that will be indoors, then you may be able to use a less aggressive cleaning method, such as solvent cleaning.
Here are some additional tips for surface preparation before powder coating:
- Make sure that the surface is clean and dry. Any contaminants on the surface will interfere with the adhesion of the powder coat.
- Remove any sharp edges or burrs. These can damage the powder coat during the curing process.
- Mask off any areas that you do not want to coat. This will help to prevent overspray.
By following these tips, you can ensure that your powder coating project will be a success.
2. Masking (Optional):
- Masking or Taping: If there are areas of the door that should not be coated, such as hinges, handles, or glass panels, these areas are masked or taped off to protect them from the powder coating.
3. Powder Application:
- Electrostatic Application: An electrostatic powder coating gun is used to apply the dry powder coating material. The gun imparts an electrostatic charge to the powder particles, which are then attracted to the grounded metal door surface.
- Spray Booth: The metal door is typically placed in a spray booth to contain overspray and ensure a controlled environment for powder application.
- Uniform Coating: The operator carefully applies the powder, ensuring even coverage on all surfaces of the metal door.
Powder coating equipment is used to apply a protective layer of powder to metal surfaces. The powder is applied using an electrostatic gun, which applies a negative charge to the powder particles. The metal surface is then grounded, which attracts the negatively charged powder particles. The powder is then cured using heat, which melts the powder and forms a smooth, durable coating.
There are many different types of powder coating equipment available, including manual guns, automated guns, booths, and ovens. The type of equipment you need will depend on the size and complexity of your project.
Manual guns are the simplest and most affordable type of powder coating equipment. They are typically used for small projects or for touch-ups.
Powder Coating Application
- Surface preparation: The metal surface to be coated must be clean and free of rust, grease, and other contaminants. The surface can be cleaned using a variety of methods, such as sandblasting, solvent cleaning, or alkaline cleaning.
- Powder application: The powder is applied to the metal surface using an electrostatic gun. The gun applies a negative charge to the powder particles, which are then attracted to the grounded metal surface.
- Curing: The powder is cured using heat, which melts the powder and forms a smooth, durable coating. The curing time and temperature will vary depending on the type of powder being used.
Benefits of Powder Coating
- Durability: Powder coating is a very durable finish that can withstand harsh weather conditions and abrasion.
- Environmental friendliness: Powder coating is a very environmentally friendly finish, as it does not use any solvents or VOCs.
- Versatility: Powder coating is a very versatile finish that can be used on a variety of different materials, including metal, plastic, and wood.
- Cost-effectiveness: Powder coating is a very cost-effective finish, as it can be applied quickly and easily.
Drawbacks of Powder Coating
- Initial investment: Powder coating equipment can be expensive to purchase.
- Learning curve: There is a learning curve associated with using powder coating equipment.
- Limited color selection: The color selection for powder coating is not as wide as the color selection for other types of finishes, such as paint.
Overall, powder coating is a great option for those who are looking for a durable, environmentally friendly, and versatile finish.
Here are some additional things to keep in mind when choosing powder coating equipment:
- The size and complexity of your project: If you are only going to be coating small projects, then a manual gun may be all you need. However, if you are going to be coating larger projects, then you will need an automated gun.
- The type of material you are coating: Powder coating can be used on a variety of different materials, but some materials are more difficult to coat than others. For example, aluminum can be difficult to coat with powder coating because it is a heat-sensitive material.
- The budget: Powder coating equipment can range in price from a few hundred dollars to several thousand dollars. It is important to set a budget before you start shopping for equipment.
- The learning curve: There is a learning curve associated with using powder coating equipment. It is important to be willing to take the time to learn how to use the equipment properly before you start using it on your project.
4. Powder Collection:
- Excess Powder Removal: After powder application, any excess powder that did not adhere to the door is collected in a powder collection booth or system. This collected powder can be recycled for future use.
5. Curing:
- Transfer to Curing Oven: The metal doors are transferred to a curing oven immediately after powder application. The oven is preheated to the appropriate curing temperature, typically between 300°F (150°C) and 450°F (232°C), depending on the powder material.
- Curing Process: The doors remain in the curing oven for a specific duration, allowing the powder particles to melt and fuse together, forming a continuous and durable coating.
- Even Heating: The curing oven is designed to ensure even heating across the entire surface of the metal door to achieve a uniform finish.
Powder coating ovens are essential equipment for any powder coating operation. They are used to cure powder coating finishes on metal parts. Curing ovens melt and fuse the powder coating particles to the metal surface, creating a durable and long-lasting finish.
There are two main types of curing ovens: batch ovens and conveyor ovens.
Batch ovens
Batch ovens are used to cure small batches of parts. Parts are loaded into the oven and cured for a set period of time. Batch ovens are typically less expensive than conveyor ovens, but they are also less efficient.
Conveyor ovens
Conveyor ovens are used to cure large batches of parts. Parts are placed on a conveyor belt and moved through the oven. Conveyor ovens are more expensive than batch ovens, but they are also more efficient.
How curing ovens work
Curing ovens work by heating the powder coating finish to a specific temperature. The temperature required will vary depending on the type of powder coating being used. Once the powder coating has reached the correct temperature, it will melt and fuse to the metal surface.
Features of a curing oven
The following are some of the key features of a curing oven:
- Temperature control: The curing oven must be able to maintain a consistent temperature throughout the curing process. This is important to ensure that the powder coating finish is cured properly.
- Air circulation: The curing oven must have good air circulation to remove powder coating fumes and dust. This is important to protect workers from exposure to powder coating fumes and dust, and it also helps to prevent fires and explosions.
- Safety features: The curing oven should be equipped with safety features such as a fire extinguisher and a smoke alarm.
How to choose a curing oven
When choosing a curing oven, there are a number of factors to consider, including:
- Size: The size of the oven will depend on the size and quantity of parts that you will be curing.
- Type of powder coating: The type of powder coating that you will be using will also affect your choice of oven. For example, some powder coatings require a higher curing temperature than others.
- Features: Consider the features that are important to you, such as temperature control, air circulation, and safety features.
- Budget: Curing ovens can range in price from a few thousand dollars to tens of thousands of dollars. Set a budget before you start shopping so that you can find an oven that fits your needs and your budget.
How to use a curing oven safely and effectively
Here are some tips for using a curing oven safely and effectively:
- Always wear appropriate personal protective equipment (PPE), such as gloves, safety glasses, and a respirator, when using a curing oven.
- Make sure the oven is properly ventilated to remove powder coating fumes and dust.
- Follow the manufacturer’s instructions for operating the oven.
- Inspect the oven regularly for signs of wear or damage.
Troubleshooting common curing oven problems
Here are some common curing oven problems and how to troubleshoot them:
- Problem: The powder coating finish is not curing properly.
- Possible solutions: Increase the curing temperature or curing time. Make sure the oven is properly ventilated. Clean the oven regularly to remove powder coating dust and debris.
- Problem: The powder coating finish is peeling or chipping.
- Possible solutions: Make sure the metal surface is properly prepared before applying the powder coating finish. Use a primer to improve the adhesion of the powder coating finish. Increase the curing temperature or curing time.
Safety guidelines
- Follow all safety precautions outlined in the curing oven manufacturer’s instructions.
- Wear appropriate personal protective equipment (PPE), such as gloves, safety glasses, and a respirator, when using a curing oven.
- Do not operate a curing oven if it is damaged or malfunctioning.
- Keep flammable materials away from the curing oven.
- Be aware of the fire hazards associated with powder coating.
6. Cooling:
- Cooling Zone: After curing, the doors may pass through a cooling zone to reduce their temperature before further handling or packaging.
7. Inspection and Quality Control:
- Visual Inspection: Each coated metal door is visually inspected for defects, uniformity, and quality of the finish. Any imperfections are addressed before further processing.
8. Unmasking (If Applicable):
- Removing Masks or Tapes: If masking was applied earlier, it is now removed to reveal the finished, coated areas.
9. Packaging and Shipping:
- Packaging: The finished metal doors are packaged and prepared for shipment to customers or installation sites.
The powder coating process for metal doors requires careful attention to detail to ensure a high-quality finish. Proper surface preparation, even powder application, precise curing, and thorough inspection are crucial steps in achieving a durable and attractive coating that enhances the appearance and performance of the doors.
Powder Coating Equipment For Steel Doors
Powder coating equipment for steel doors is specialized equipment designed to efficiently and effectively apply powder coating finishes to steel door surfaces. Steel doors are commonly used in various applications, including residential, commercial, and industrial settings. Powder coating provides a durable, attractive, and long-lasting finish that enhances the appearance and performance of steel doors. Here are the key components and considerations for powder coating equipment used for steel doors:
1. Powder Coating Gun:
- Electrostatic Powder Coating Gun: An electrostatic powder coating gun is used to apply the dry powder coating material to the steel door. The gun imparts an electrostatic charge to the powder particles, which are attracted to the grounded steel door surface, ensuring an even and consistent coating.
- Nozzles and Applicators: The gun is equipped with various nozzles and applicators, such as fan nozzles or round nozzles, to control the spray pattern and ensure proper coverage.
2. Powder Feed System:
- Powder Hopper: The powder hopper holds the powder coating material and provides a controlled supply to the powder coating gun during the application process.
- Powder Pumps: Powder pumps transport the powder from the hopper to the gun, ensuring a consistent and steady flow of material.
3. Pre-Treatment Equipment:
- Surface Preparation: Proper surface preparation is essential for adhesion and coating durability. Pre-treatment equipment may include cleaning stations, degreasers, and sandblasting equipment to prepare the steel door surface by removing contaminants, rust, and old coatings.
4. Powder Recovery System:
- Powder Collection Booth: After the powder is applied to the door, excess powder is collected in a powder collection booth or system. This collected powder can be recycled for future use, reducing material waste.
5. Curing Oven:
- Curing Oven: After the powder is applied, the steel door is placed in a curing oven. The oven provides the necessary heat to melt and fuse the powder particles, creating a durable and protective coating. The curing process typically involves temperatures between 300°F (150°C) and 450°F (232°C).
- Even Heating: The curing oven should have a uniform heat distribution system to ensure even curing across the entire door surface.
6. Cooling Zone:
- Cooling Zone: After curing, the steel door may pass through a cooling zone to reduce its temperature before further handling or packaging.
7. Conveyor System:
- Conveyor System: A conveyor system transports the steel doors through the various stages of the powder coating process, including pre-treatment, powder application, curing, and cooling.
8. Control Panel:
- Control Panel: The equipment is typically controlled through a user-friendly control panel that allows operators to set and monitor parameters such as conveyor speed, oven temperature, and curing time.
9. Safety Features:
- Safety Interlocks: Safety interlock systems may be in place to ensure that equipment, especially the curing oven, cannot be opened while it is operating at high temperatures.
- Safety Procedures: Proper safety procedures and personal protective equipment should be in place to protect operators and maintain a safe working environment.
Powder coating equipment for steel doors is essential for achieving a high-quality, uniform, and durable finish. It is commonly used in the manufacturing and finishing of steel doors for various applications, including residential entry doors, commercial building doors, and industrial security doors. Proper equipment and processes ensure that steel doors receive a protective coating that enhances their appearance and extends their lifespan.
Powder Coating Equipment For Steel Doors
Powder coating is a popular and durable finishing option for steel doors, providing a protective and attractive surface. When setting up powder coating equipment for steel doors, consider the following key components and steps:
- Surface Preparation:
- Clean the steel doors thoroughly to remove any dirt, oil, rust, or other contaminants. This can be done through methods like sandblasting, chemical cleaning, or a combination of both.
- Powder Coating Booth:
- Use a powder coating booth to contain the overspray and ensure an even coating. The booth should have proper ventilation to exhaust airborne particles and fumes.
- Powder Coating Gun:
- Choose a high-quality powder coating gun that suits the size and shape of steel doors. Electrostatic guns are commonly used in powder coating for an efficient and even application.
- Powder Delivery System:
- Ensure that the powder delivery system, including the powder feeder and hopper, is functioning correctly. The powder should flow smoothly to the gun for consistent application.
- Curing Oven:
- After the powder is applied, the steel doors must be cured in a high-temperature oven. The curing process melts the powder, forming a durable coating. The oven should have adequate space for the doors and maintain a consistent temperature.
- Temperature and Humidity Control:
- Maintain control over the temperature and humidity in the powder coating area to ensure optimal conditions for coating adhesion and curing.
- Grounding System:
- Proper grounding is essential in the powder coating process to ensure the even distribution of the powder and minimize overspray. Ground the steel doors and the coating equipment.
- Quality Control:
- Implement quality control measures to check the thickness and uniformity of the powder coating. Consider using instruments like thickness gauges to ensure compliance with industry standards.
- Safety Measures:
- Implement safety measures to protect workers and equipment. This includes proper personal protective equipment (PPE), ventilation systems, and fire safety precautions.
- Cleaning and Maintenance:
- Regularly clean and maintain the powder coating equipment to ensure its longevity and optimal performance. This includes cleaning the booth, gun, and filters.
- Compliance with Regulations:
- Ensure that your powder coating process complies with environmental and safety regulations. Powder coating is often considered more environmentally friendly than traditional wet painting methods, but it’s important to follow local regulations.
Consulting with a powder coating equipment supplier or an expert in the field can provide additional guidance tailored to your specific requirements.
Surface Preparation
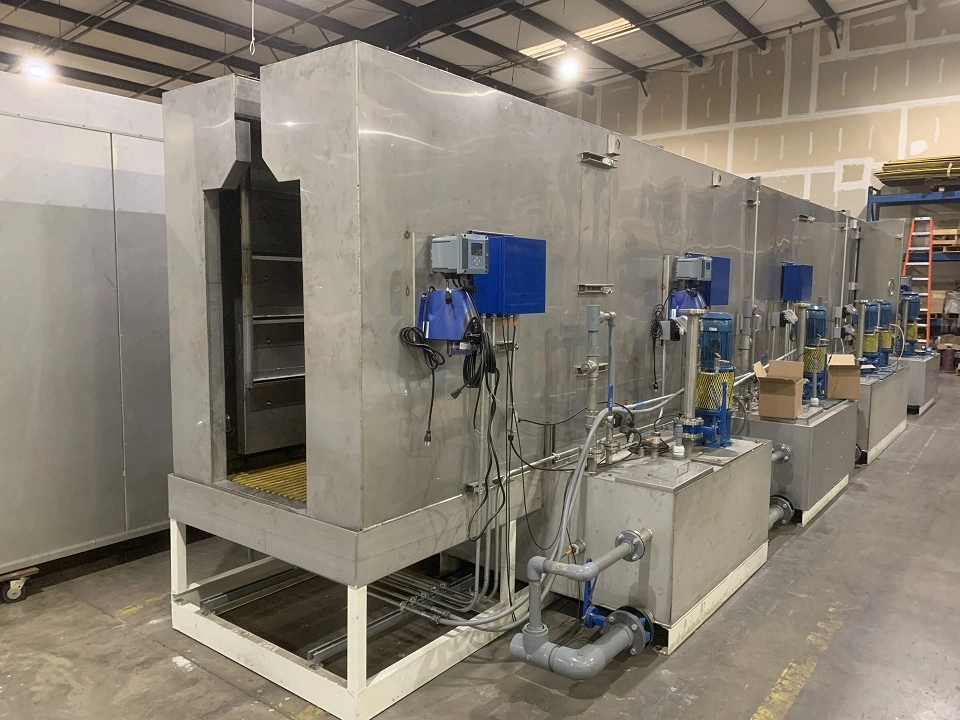
Surface preparation is a crucial step in the powder coating process, as it directly influences the adhesion and durability of the coating. Properly preparing the surface of steel doors before applying the powder coating involves several key steps:
- Cleaning:
- Remove all dirt, grease, oil, and other contaminants from the surface of the steel doors. Use a suitable cleaning solution and ensure that the doors are thoroughly cleaned. This can be done through methods such as pressure washing, solvent cleaning, or alkaline cleaning.
- Degreasing:
- Degrease the steel doors to eliminate any remaining oils or greases. This step is essential for ensuring good adhesion of the powder coating. Solvent-based or alkaline degreasers are commonly used for this purpose.
- Rust Removal:
- If there is any rust on the steel doors, it must be removed before coating. Use methods such as sandblasting, abrasive blasting, or chemical rust removers to achieve a clean, rust-free surface. After removing rust, it’s important to passivate or treat the steel to prevent further corrosion.
- Surface Profiling:
- Create a suitable surface profile on the steel doors to enhance adhesion. Abrasive blasting, sanding, or other mechanical methods can be used to achieve the desired level of surface roughness. The specific profile required may depend on the powder coating material being used.
- Phosphating or Chromating:
- Treat the steel doors with a phosphating or chromating solution to create a conversion coating. This coating enhances corrosion resistance and promotes better adhesion of the powder coating. Phosphating is a common process for preparing metal surfaces.
- Masking:
- If there are areas of the steel doors that should not be coated, such as hardware or specific design features, use masking materials to protect those areas during the coating process.
- Drying:
- Ensure that the steel doors are completely dry before applying the powder coating. Any moisture on the surface can affect adhesion and lead to coating defects. Use drying methods such as air drying, forced air, or ovens.
- Surface Inspection:
- After surface preparation, inspect the steel doors for any remaining contaminants, irregularities, or defects. Address any issues before proceeding with the powder coating process.
Remember that the effectiveness of the powder coating largely depends on the quality of surface preparation. Skipping or inadequately performing these steps can result in poor adhesion, coating failure, and reduced durability. Always follow the manufacturer’s guidelines for surface preparation and consider the specific requirements of the powder coating material being used.
Powder Coating Booth for Steel Doors
When setting up a powder coating booth for steel doors, it’s important to ensure that the booth provides a controlled environment for the application of powder coating, minimizes overspray, and allows for efficient curing. Here are key considerations for setting up a powder coating booth for steel doors:
- Size and Design:
- Choose a booth that is large enough to accommodate the size of steel doors you will be coating. The booth should have proper dimensions and design to allow easy movement and coating of the doors from different angles.
- Ventilation System:
- Install an effective ventilation system to capture and exhaust airborne particles, fumes, and overspray. Proper ventilation helps maintain a clean working environment and ensures the safety of operators.
- Airflow Management:
- Design the booth to have uniform airflow to ensure even distribution of the powder and prevent uneven coating. This may involve the use of proper air extraction and air replacement systems.
- Lighting:
- Install adequate lighting inside the booth to provide clear visibility of the steel doors during the coating process. Proper lighting helps operators identify any defects or areas that may need additional attention.
- Grounding System:
- Implement a grounding system to prevent the buildup of static electricity. Proper grounding helps in the efficient application of powder coating by preventing issues such as Faraday cage effects.
- Filters:
- Install high-quality filters in the powder coating booth to capture overspray and contaminants. Regularly check and replace filters to maintain optimal performance and prevent the risk of contamination in the coating process.
- Access Doors and Openings:
- Ensure that the booth has convenient access doors and openings for the introduction and removal of steel doors. This facilitates efficient workflow and minimizes the risk of contamination.
- Environmental Controls:
- Control the temperature and humidity within the booth to create an environment conducive to optimal powder coating application and curing. Maintain the recommended conditions for the specific powder coating material being used.
- Reclaim System (Optional):
- Consider incorporating a powder reclaim system if you want to recover and reuse excess powder. This can help reduce waste and improve efficiency.
- Safety Features:
- Incorporate safety features such as emergency stop buttons, fire suppression systems, and adequate ventilation to ensure a safe working environment for operators.
- Compliance with Regulations:
- Ensure that the powder coating booth complies with local environmental and safety regulations. This may include compliance with air quality standards and the installation of necessary safety features.
Before purchasing or installing a powder coating booth, consult with suppliers, manufacturers, or experts in the field to ensure that the equipment meets your specific requirements and local regulations. Following proper setup and maintenance procedures will contribute to the overall effectiveness and safety of the powder coating process for steel doors.
Powder Coating Gun
Choosing the right powder coating gun is crucial for achieving an even, high-quality finish on steel doors. Powder coating guns are electrostatic devices that charge the powder particles, allowing them to adhere to the grounded surface. Here are key factors to consider when selecting a powder coating gun for steel doors:
- Type of Powder Coating Gun:
- There are two main types of powder coating guns: corona guns and tribo guns. Corona guns are more common and use a high-voltage electrostatic charge to apply the powder. Tribo guns, on the other hand, use friction to charge the powder particles. Corona guns are generally more popular for steel door applications due to their efficiency.
- Adjustability and Controls:
- Choose a powder coating gun that provides adjustable settings for powder flow rate, air pressure, and voltage. This flexibility allows you to optimize the coating process based on the specific requirements of the steel doors and the powder being used.
- Gun Weight and Ergonomics:
- Consider the weight and ergonomics of the powder coating gun, as operators will be using it for extended periods. A lightweight and well-balanced gun can reduce operator fatigue and improve overall efficiency.
- Versatility:
- Opt for a gun that is versatile and suitable for various powder coating applications. This is especially important if you plan to coat different types of steel doors with different coating materials.
- Ease of Maintenance:
- Choose a powder coating gun that is easy to disassemble and clean. Regular maintenance is crucial for ensuring consistent performance and prolonging the lifespan of the gun.
- Powder Output Uniformity:
- Look for a gun that provides uniform and consistent powder output. This ensures an even coating thickness across the entire surface of the steel doors.
- Compatibility with Powder Coating Material:
- Ensure that the powder coating gun is compatible with the specific type of powder coating material you intend to use. Different materials may have varying particle sizes and charging characteristics.
- Grounding Features:
- The powder coating gun should have effective grounding features to prevent issues like Faraday cage effects, which can result in uneven coating. Proper grounding ensures that the charged particles reach all areas of the steel doors.
- Ease of Integration:
- Consider how easily the powder coating gun can be integrated into your overall powder coating system, including compatibility with the control system and other equipment such as the powder booth and curing oven.
- Brand Reputation and Support:
- Choose a reputable brand with a history of providing reliable powder coating equipment. Additionally, consider the availability of customer support, spare parts, and technical assistance from the manufacturer.
Before making a final decision, it’s advisable to consult with suppliers, review user feedback, and, if possible, test the powder coating gun to ensure it meets your specific requirements for coating steel doors effectively.
Powder Delivery System
A powder delivery system is a critical component of a powder coating setup, ensuring the efficient and controlled delivery of powder to the powder coating gun. The system typically consists of a powder feeder, powder hopper, and associated components. When selecting a powder delivery system for coating steel doors, consider the following factors:
- Powder Feeder:
- Choose a powder feeder that provides a consistent and reliable flow of powder to the gun. A properly functioning feeder is crucial for achieving uniform coating thickness on steel doors. The feeder should be adjustable to accommodate different powder types and application requirements.
- Powder Hopper:
- Select a powder hopper with sufficient capacity to hold an adequate amount of powder for the size of steel doors you are coating. The hopper should be designed to prevent powder contamination and promote efficient powder flow.
- Fluidization:
- Many powder hoppers use fluidization to ensure that the powder remains in a consistent and fluidized state, ready for delivery. Proper fluidization prevents powder clumping and ensures a smooth flow to the powder coating gun.
- Material Compatibility:
- Ensure that the materials used in the powder delivery system are compatible with the type of powder coating material you intend to use. This includes the construction of the feeder, hopper, and any other components that come in contact with the powder.
- Adjustability and Control:
- Look for a powder delivery system that offers adjustable settings for powder flow rate and other relevant parameters. This allows you to fine-tune the system based on the specific requirements of the steel doors and the powder coating material.
- Ease of Cleaning and Maintenance:
- Select a system that is easy to clean and maintain. Regular cleaning is essential to prevent cross-contamination between different powder colors or types. Quick disassembly and accessibility to components simplify maintenance tasks.
- Powder Recovery System (Optional):
- Consider whether you need a powder recovery system to reclaim and reuse excess powder. A recovery system can help reduce waste and improve overall efficiency. It typically includes features like cyclone separators and filters to separate reusable powder from overspray.
- Grounding:
- Ensure that the powder delivery system is properly grounded to prevent electrostatic issues. Grounding is essential for the efficient and uniform application of powder coating on steel doors.
- Integration with Powder Coating Equipment:
- The powder delivery system should integrate seamlessly with other components of your powder coating setup, such as the powder booth, gun, and curing oven. Compatibility ensures a smooth and coordinated coating process.
- Reliability and Durability:
- Choose a system from a reputable manufacturer known for producing reliable and durable equipment. A robust powder delivery system contributes to the overall efficiency and consistency of the powder coating process.
Before finalizing your choice, consult with suppliers, review product specifications, and consider any specific requirements related to the size and volume of steel doors you will be coating. Testing the system with your specific powder coating material and application conditions can also help ensure optimal performance.
Curing Oven
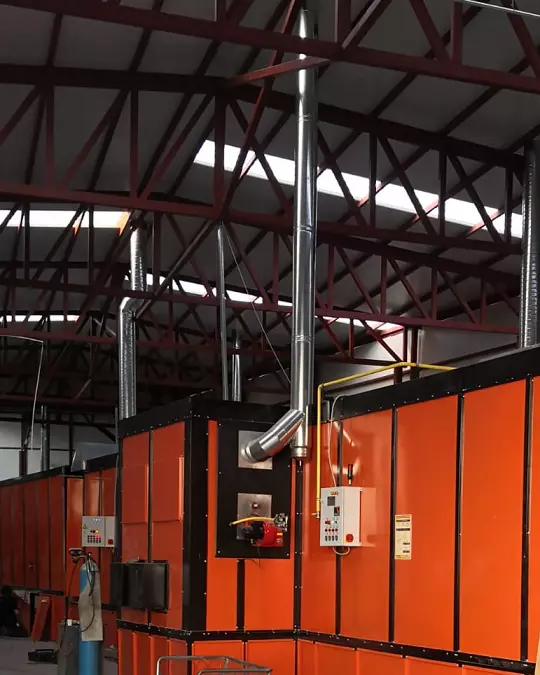
A curing oven is a crucial component in the powder coating process for steel doors, as it facilitates the curing or baking of the applied powder coating. The curing process melts the powder particles, allowing them to flow and form a smooth, durable finish on the steel surface. When selecting a curing oven for powder coating steel doors, consider the following key factors:
- Temperature Control:
- Choose an oven with precise temperature control capabilities. The curing temperature will depend on the specific powder coating material being used, so the oven should be able to reach and maintain the required temperature consistently.
- Size and Capacity:
- Select an oven with sufficient interior space to accommodate the size and quantity of steel doors you plan to coat. The doors should be arranged in the oven to ensure even heat distribution and uniform curing.
- Airflow and Ventilation:
- Opt for an oven with a well-designed airflow system to ensure uniform heating. Adequate ventilation helps remove any volatiles released during the curing process and prevents the accumulation of fumes.
- Heating Source:
- Common heating sources for curing ovens include electric elements, gas burners, or infrared radiation. Choose a heating source that aligns with your facility’s infrastructure and energy requirements.
- Insulation:
- The oven should have effective insulation to retain heat and improve energy efficiency. Proper insulation also contributes to temperature stability and uniform curing.
- Conveyor System (if applicable):
- If you have a conveyorized powder coating system, ensure that the oven is equipped with a suitable conveyor system. The conveyor should be designed to move the steel doors through the oven at a consistent speed for uniform curing.
- Controls and Monitoring:
- Look for an oven with user-friendly controls and monitoring features. Digital controllers with programmable settings allow you to set precise curing profiles for different powder coating materials.
- Safety Features:
- Ensure that the oven is equipped with safety features such as over-temperature protection, emergency shut-off controls, and proper ventilation to protect operators and prevent accidents.
- Exhaust System:
- A well-designed exhaust system is essential for removing fumes and ensuring a safe working environment. It also helps in maintaining the cleanliness of the oven interior.
- Compliance with Standards:
- Verify that the curing oven complies with relevant industry standards and safety regulations. Adhering to standards ensures the quality and safety of the curing process.
- Cooling Zone (if needed):
- Some powder coating processes may benefit from a cooling zone after the curing process. Ensure that your curing oven setup allows for adequate cooling time if necessary.
- Ease of Maintenance:
- Choose an oven that is easy to clean and maintain. Accessible components and features that simplify maintenance tasks contribute to the longevity and efficiency of the curing oven.
Before making a final decision, consult with suppliers or manufacturers to ensure that the curing oven meets your specific requirements and adheres to industry standards. Testing the oven with sample steel doors and your chosen powder coating material can help verify its performance in real-world conditions.
Powder Coating: An In-Depth Guide to Equipment and Processes
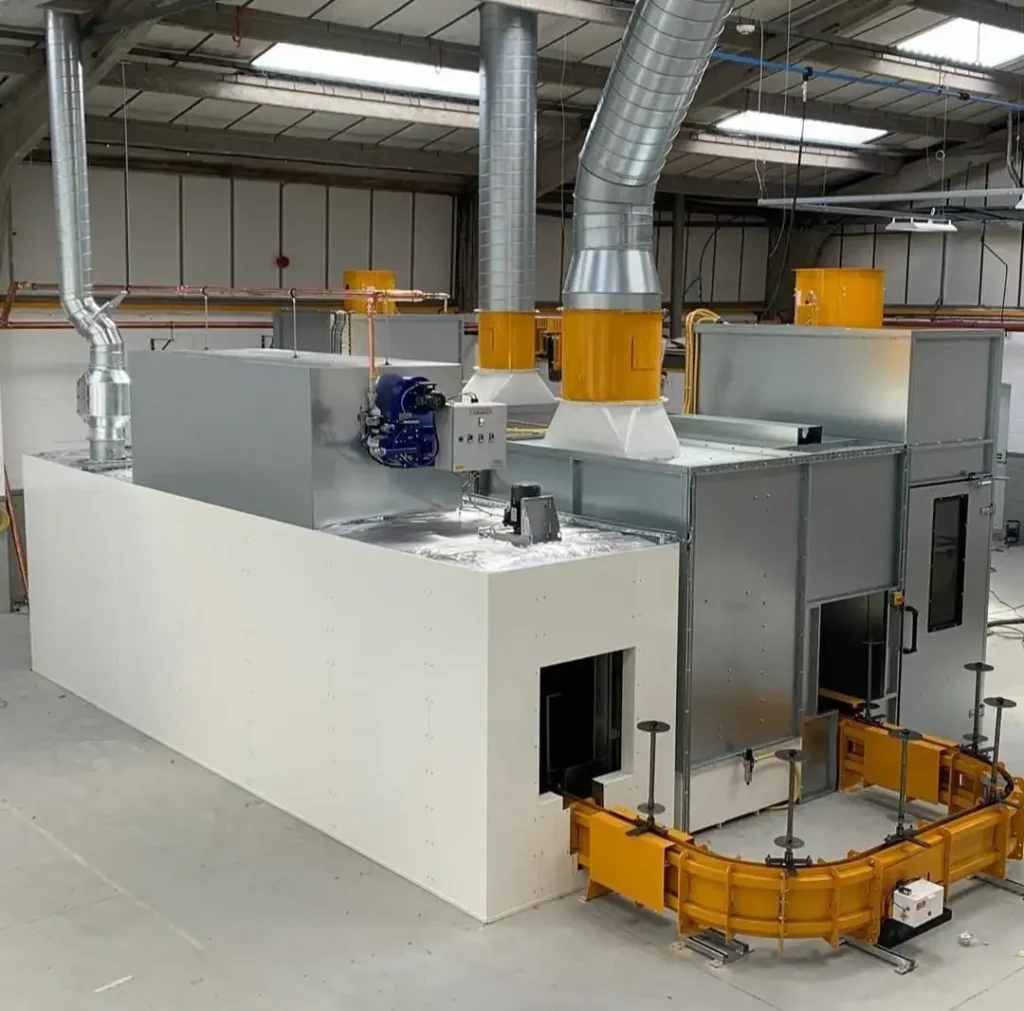
Introduction
Powder coating is a popular finishing process used across various industries to apply a durable and protective layer to metal surfaces. Unlike traditional liquid paint, powder coating uses a dry powder that is electrostatically charged and applied to the surface, which is then cured in a high-temperature oven. This process results in a hard finish that is more resistant to chipping, scratching, and fading.
In this guide, we’ll explore the different components of a powder coating system, including ovens, machines, equipment, and entire production lines. Understanding these elements is crucial for businesses looking to enhance their production capabilities with powder coating technology.
Powder Coating Ovens
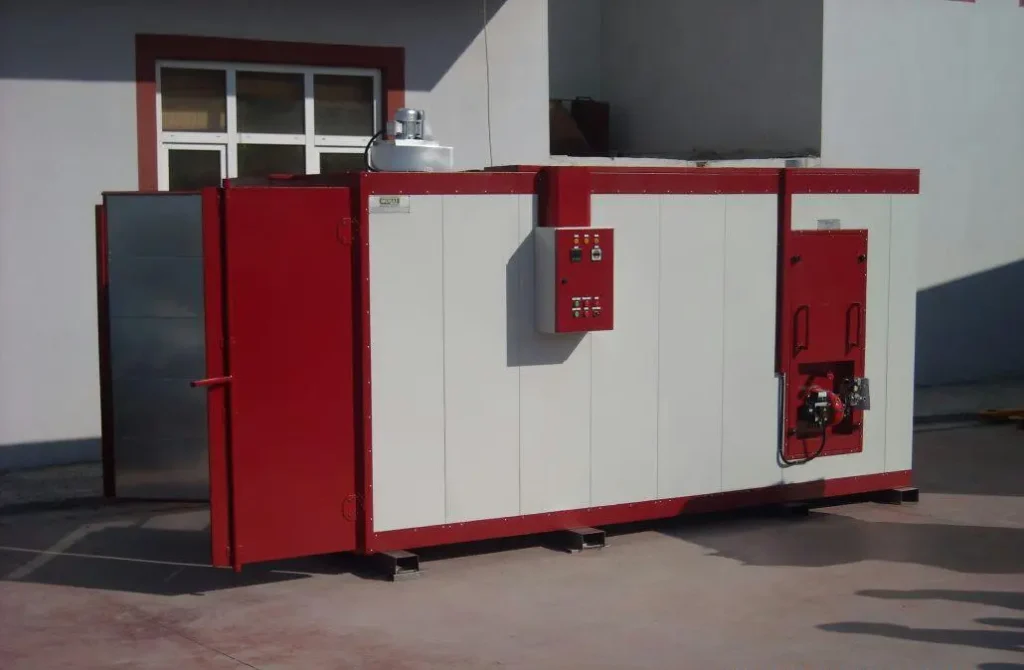
Definition and Purpose:
Powder coating ovens are essential for the curing process, where the powder adheres to the surface and forms a smooth, hard finish. These ovens provide the necessary heat to melt the powder, ensuring even and thorough coating.
Types of Powder Coating Ovens:
- Batch Ovens:
- Ideal for small to medium-sized production runs
- Flexibility to handle various part sizes
- Suitable for businesses with diverse product lines
- Conveyor Ovens:
- Designed for continuous production
- Higher throughput and efficiency
- Suitable for large-scale operations
Features and Specifications:
- Temperature Range: Typically between 325°F to 450°F
- Heating Source: Options include electric, gas, or infrared
- Size and Capacity: Varies based on production needs
- Energy Efficiency: Consider models with advanced insulation and airflow systems
How to Choose the Right Oven:
- Evaluate production volume and part sizes
- Consider energy consumption and operating costs
- Assess available space and installation requirements
- Consult with manufacturers for customized solutions
Powder Coating Machines
Overview of Different Machines Used:
Powder coating machines are used to apply the powder to the surface. They vary in complexity and functionality, catering to different production needs.
Manual vs. Automated Machines:
- Manual Machines:
- Suitable for small-scale operations
- Offers flexibility and control
- Requires skilled operators
- Automated Machines:
- Ideal for high-volume production
- Consistent and uniform application
- Reduced labor costs
Key Features and Specifications:
- Voltage and Power Requirements: Ensure compatibility with your facility
- Control Systems: Look for user-friendly interfaces and programmable settings
- Spray Gun Options: Different nozzles and gun types for various applications
Selecting the Right Machine for Your Needs:
- Determine the scale and complexity of your operations
- Evaluate budget constraints and long-term ROI
- Seek advice from industry experts and suppliers
Powder Coating Equipment
Essential Equipment for Powder Coating:
- Powder Coating Booths: Enclosed areas for applying powder
- Powder Recovery Systems: Capture and reuse overspray powder
- Air Compressors and Dryers: Ensure consistent airflow for optimal coating
Optional Equipment for Enhanced Performance:
- Pre-Treatment Systems: Clean and prepare surfaces before coating
- Curing Lamps: Speed up the curing process with infrared or UV lamps
Maintenance and Safety Considerations:
- Regularly inspect and clean equipment
- Train staff on proper handling and safety protocols
- Adhere to industry standards and regulations
Powder Coating Lines and Plants
Explanation of Powder Coating Lines:
Powder coating lines are integrated systems that automate the entire powder coating process, from pre-treatment to curing.
Components of a Powder Coating Line:
- Conveyor Systems: Move parts through the line efficiently
- Pre-Treatment Stations: Clean and prepare surfaces
- Powder Application Booths: Enclosed areas for powder coating
- Curing Ovens: Finalize the coating process
Design and Layout Considerations:
- Optimize workflow and space utilization
- Consider future scalability and expansion
- Ensure compliance with safety and environmental regulations
Scalability and Customization Options:
- Modular designs for easy expansion
- Custom configurations to meet specific production needs
Benefits of Powder Coating
Environmental Advantages:
- Low VOC emissions compared to liquid paints
- Overspray can be recycled, reducing waste
- Complies with environmental regulations
Durability and Longevity:
- Resistant to corrosion, fading, and wear
- Suitable for outdoor and high-traffic applications
- Provides a high-quality, professional finish
Cost-Effectiveness:
- Reduces long-term maintenance and repainting costs
- Efficient use of materials minimizes waste
- High throughput and automation lower labor expenses
Considerations for Setting Up a Powder Coating Plant
Initial Investment and ROI:
- Assess capital requirements for equipment and infrastructure
- Calculate potential returns based on production capacity and demand
- Explore financing options and incentives
Regulatory Compliance:
- Adhere to industry standards and local regulations
- Implement safety protocols and employee training
- Monitor environmental impact and waste management
Market Trends and Future Outlook:
- Growing demand for eco-friendly coatings
- Advancements in automation and technology
- Increasing adoption in automotive, aerospace, and consumer goods sectors
Conclusion
Powder coating offers numerous advantages over traditional liquid painting methods, making it an attractive option for industries seeking durable and environmentally friendly finishes. By investing in the right equipment and understanding the intricacies of powder coating processes, businesses can enhance their production capabilities and meet the growing demand for high-quality coated products.
When setting up a powder coating plant, it’s essential to carefully consider your needs, budget, and long-term goals. Collaborating with experienced suppliers and industry experts can help you make informed decisions and achieve success in the competitive world of powder coating.
This comprehensive guide should provide valuable insights for your website visitors and help position your business as a knowledgeable and reliable source in the powder coating industry.
Installation process steps
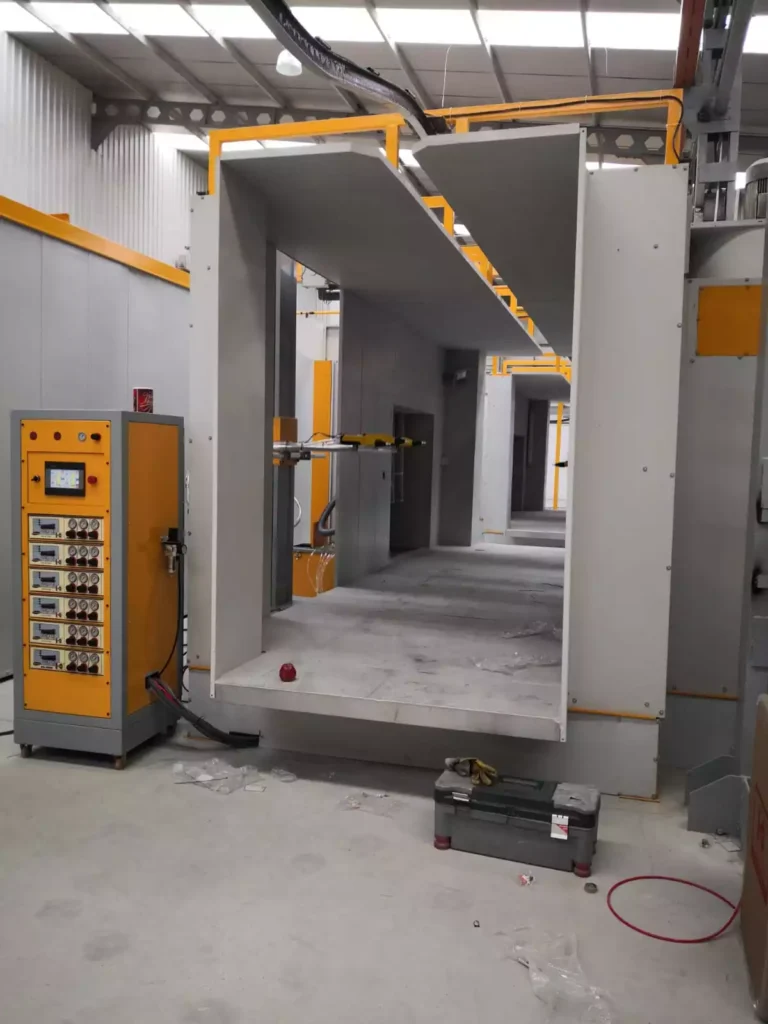
To provide a comprehensive guide on the installation process for powder coating systems, we’ll cover each step involved in setting up a powder coating plant. This includes planning, selecting equipment, site preparation, installation, testing, and staff training. Here’s a detailed outline and content for this section:
Outline for Installation Process Steps
- Planning and Design
- Assessing needs and capacity
- Layout and design considerations
- Budget and timeline
- Equipment Selection
- Choosing the right ovens, machines, and equipment
- Consulting with manufacturers and suppliers
- Site Preparation
- Preparing the facility for installation
- Ensuring compliance with regulations
- Installation Process
- Step-by-step installation guide
- Safety protocols and considerations
- System Testing and Calibration
- Testing each component
- Ensuring optimal performance
- Training and Support
- Staff training on operation and safety
- Ongoing maintenance and support
- Post-Installation Considerations
- Regular inspections and maintenance
- Upgrades and scalability
Installation Process Steps for Powder Coating Systems
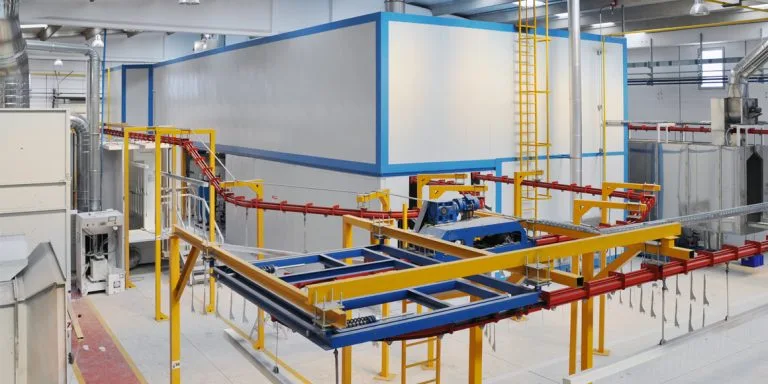
Setting up a powder coating plant involves careful planning and execution to ensure a successful installation. Here’s a step-by-step guide to help you navigate the process:
1. Planning and Design
Assessing Needs and Capacity:
- Identify Production Requirements: Determine the types and sizes of parts you will be coating, and estimate your production volume.
- Analyze Workflow: Consider how materials will move through the plant, from pre-treatment to curing.
- Evaluate Space Requirements: Ensure adequate space for equipment, storage, and workflow efficiency.
Layout and Design Considerations:
- Optimize Workflow: Design a layout that minimizes bottlenecks and maximizes efficiency.
- Future Scalability: Plan for potential expansion or upgrades.
- Compliance with Safety Standards: Ensure the layout meets all safety and regulatory requirements.
Budget and Timeline:
- Create a Detailed Budget: Account for equipment, installation, training, and operational costs.
- Establish a Timeline: Set realistic milestones for each phase of the installation process.
2. Equipment Selection
Choosing the Right Ovens, Machines, and Equipment:
- Powder Coating Ovens: Select between batch or conveyor ovens based on production needs.
- Powder Coating Machines: Choose manual or automated systems that match your operational scale.
- Additional Equipment: Consider powder booths, recovery systems, and pre-treatment stations.
Consulting with Manufacturers and Suppliers:
- Leverage Expertise: Work with manufacturers to choose equipment tailored to your specific requirements.
- Request Demonstrations: Evaluate equipment performance through demos or site visits.
- Negotiate Contracts: Ensure favorable terms and warranties with suppliers.
3. Site Preparation
Preparing the Facility for Installation:
- Infrastructure Readiness: Ensure adequate power supply, ventilation, and environmental controls.
- Space Optimization: Clear and organize the installation area for easy access and efficient workflow.
Ensuring Compliance with Regulations:
- Local Permits and Licenses: Obtain necessary permits and ensure compliance with zoning regulations.
- Safety Standards: Adhere to occupational health and safety standards.
4. Installation Process
Step-by-Step Installation Guide:
- Site Inspection: Conduct a final inspection of the site to verify readiness.
- Delivery and Unpacking: Receive and unpack equipment carefully, checking for any damage.
- Positioning Equipment: Install each piece of equipment according to the layout plan.
- Electrical and Plumbing Connections: Ensure all electrical and plumbing connections are correctly made and tested.
- Calibration and Setup: Configure equipment settings and calibrate machinery to specifications.
Safety Protocols and Considerations:
- Install Safety Features: Implement necessary safety features such as emergency stops and protective barriers.
- Personal Protective Equipment (PPE): Ensure that all personnel have access to required PPE.
5. System Testing and Calibration
Testing Each Component:
- Conduct Trial Runs: Test each component individually and as part of the integrated system.
- Check for Performance Issues: Identify and resolve any performance or operational issues.
Ensuring Optimal Performance:
- Fine-Tune Settings: Adjust equipment settings for optimal coating quality.
- Document Results: Record all testing results and adjustments for future reference.
6. Training and Support
Staff Training on Operation and Safety:
- Conduct Training Sessions: Provide comprehensive training on equipment operation and safety protocols.
- Create Training Materials: Develop manuals and guides for ongoing staff reference.
Ongoing Maintenance and Support:
- Establish a Maintenance Schedule: Set up regular maintenance checks to ensure equipment longevity.
- Vendor Support: Engage with suppliers for ongoing support and troubleshooting.
7. Post-Installation Considerations
Regular Inspections and Maintenance:
- Implement Routine Inspections: Regularly inspect equipment and systems for wear and tear.
- Schedule Maintenance: Adhere to the maintenance schedule to prevent downtime and extend equipment life.
Upgrades and Scalability:
- Monitor Technological Advancements: Stay informed about new technologies and equipment improvements.
- Plan for Upgrades: Budget for future upgrades and expansion as business needs grow.
Conclusion
The installation of a powder coating system is a multi-step process that requires meticulous planning and execution. By following these steps, businesses can ensure a smooth setup and operation, maximizing efficiency and product quality. It’s crucial to work closely with experienced manufacturers and suppliers to tailor the installation process to your specific needs and to provide ongoing training and support for staff.
Installation cost estimate
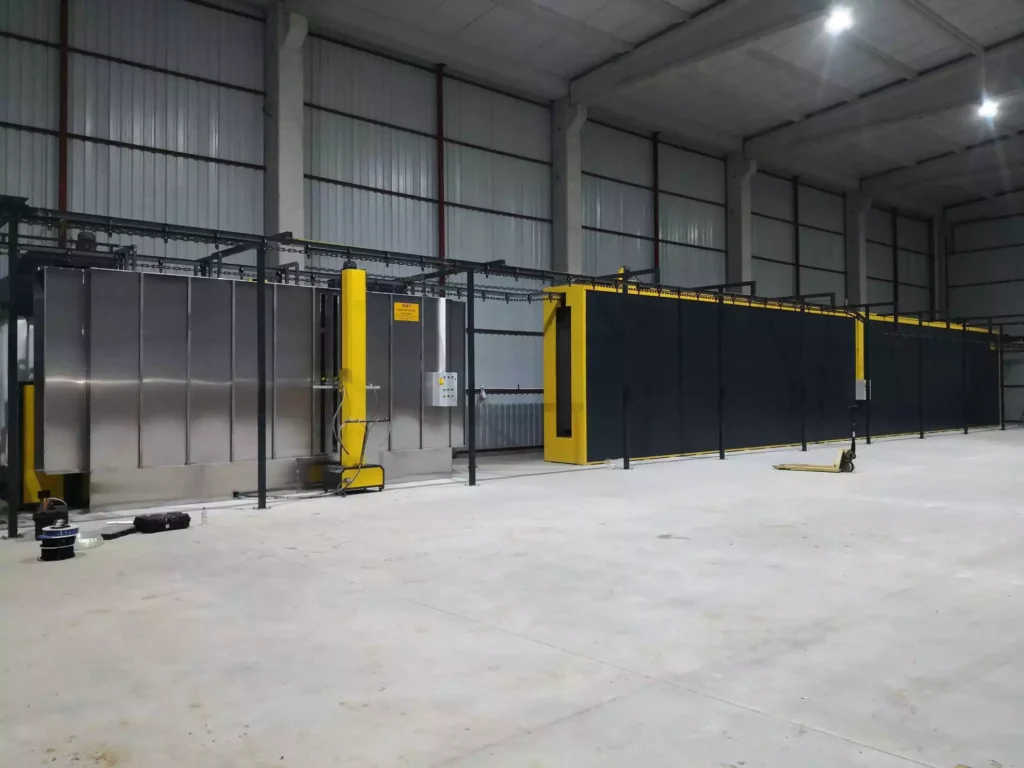
Estimating the installation cost of a powder coating system involves considering various factors, such as the size of the operation, the type of equipment, facility modifications, labor, and additional costs like permits and training. Here’s a detailed breakdown to help you understand the potential costs involved in setting up a powder coating plant.
Installation Cost Estimate for Powder Coating Systems
Factors Influencing Costs
- Type of Equipment and Technology
- Powder coating ovens (batch vs. conveyor)
- Coating machines (manual vs. automated)
- Auxiliary equipment (booths, recovery systems, pre-treatment stations)
- Scale and Capacity of the Operation
- Production volume
- Facility size and space requirements
- Facility Modifications
- Infrastructure updates (electrical, ventilation, plumbing)
- Space optimization and layout design
- Labor and Installation Services
- Skilled labor for installation
- Equipment calibration and testing
- Additional Costs
- Permits and regulatory compliance
- Staff training and support
- Maintenance and contingency expenses
Estimated Costs
Below is a general estimate of the costs associated with installing a powder coating system. Note that prices can vary significantly based on location, vendor, and specific requirements.
1. Equipment Costs
- Powder Coating Ovens:
- Batch Ovens: $1,000 – $50,000
- Conveyor Ovens: $10,000 – $200,000
- Powder Coating Machines:
- Manual Machines: $1,000 – $20,000
- Automated Systems: $20,000 – $100,000
- Auxiliary Equipment:
- Powder Booths: $2,000 – $30,000
- Recovery Systems: $3,000 – $15,000
- Pre-Treatment Systems: $10,000 – $50,000
2. Facility Modifications
- Electrical and Ventilation Upgrades: $10,000 – $50,000
- Space Optimization and Layout Design: $5,000 – $20,000
3. Labor and Installation Services
- Installation Labor: $10,000 – $30,000
- Calibration and Testing: $5,000 – $10,000
4. Additional Costs
- Permits and Compliance: $2,000 – $10,000
- Training and Support: $2,000 – $5,000
- Maintenance and Contingency: $5,000 – $15,000
Total Estimated Cost
The total estimated cost for installing a powder coating system can range from $70,000 to $500,000, depending on the size, complexity, and specific requirements of the operation. Here’s a breakdown by scale:
- Small-Scale Operations: $20,000 – $50,000
- Medium-Scale Operations: $50,000 – $100,000
- Large-Scale Operations: $100,000 – $500,000
Tips for Cost Management
- Conduct a Detailed Assessment:
- Evaluate your specific needs and choose equipment accordingly.
- Consider future scalability to avoid unnecessary upgrades later.
- Get Multiple Quotes:
- Request quotes from multiple vendors to compare prices and services.
- Negotiate terms and warranties to get the best deal.
- Plan for Contingencies:
- Set aside a contingency budget for unexpected expenses during installation.
- Regularly review and adjust your budget as the project progresses.
- Focus on Energy Efficiency:
- Invest in energy-efficient equipment to reduce long-term operational costs.
- Evaluate the potential return on investment (ROI) for each piece of equipment.
- Leverage Financing Options:
- Explore financing options, grants, or incentives available for industrial upgrades.
Conclusion
Setting up a powder coating plant requires a significant investment, but careful planning and strategic decision-making can help manage costs effectively. By considering your specific needs, working with experienced suppliers, and planning for the future, you can ensure a successful installation and operation of your powder coating system.
Let me know if you need further details or specific cost estimates tailored to your project!
Components of a Powder Coating Plant
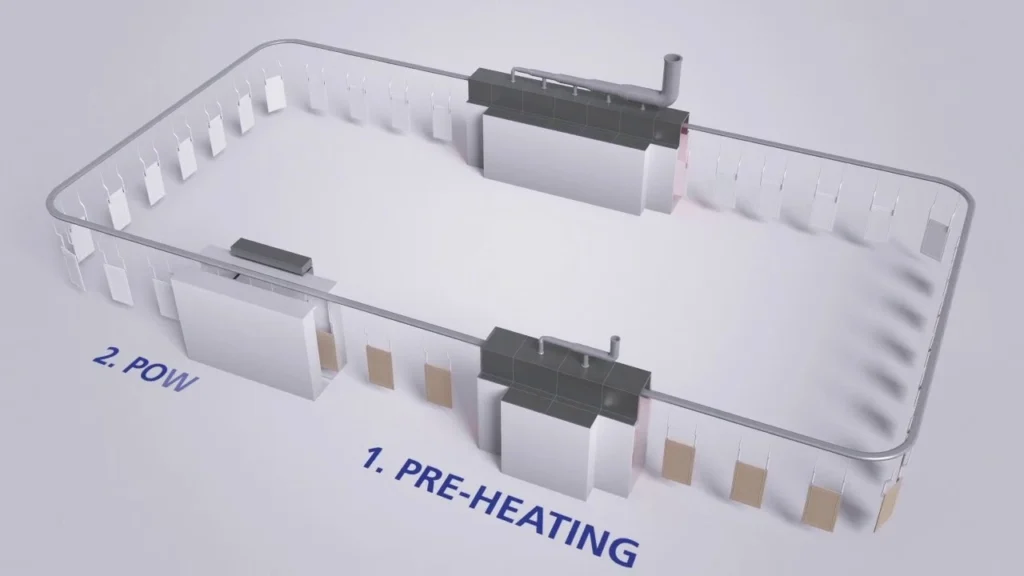
A powder coating plant consists of various components that work together to facilitate the coating process, from preparation to application and curing. Understanding these components is crucial for designing an efficient and effective system tailored to specific production needs. Below is a detailed overview of the key components of a powder coating plant:
Key Components of a Powder Coating Plant
- Pre-Treatment System
- Purpose: Cleans and prepares surfaces for powder coating to ensure adhesion and finish quality.
- Components:
- Washing Stations: Use chemical solutions to remove contaminants like grease, oil, dirt, and rust.
- Rinse Stations: Remove residual chemicals from the surface.
- Drying Ovens: Dry the parts after washing and rinsing to prepare them for powder application.
- Powder Coating Booths
- Purpose: Enclosed area where the powder is applied to the parts.
- Types:
- Manual Booths: Operators manually apply powder using spray guns. Ideal for small or custom jobs.
- Automatic Booths: Equipped with automated spray guns and reciprocators for high-volume production.
- Features:
- Ventilation Systems: Ensure proper airflow to capture overspray and maintain a clean environment.
- Powder Recovery Systems: Collect overspray powder for reuse, improving material efficiency.
- Powder Application Equipment
- Purpose: Applies the powder to the surfaces using electrostatic spray guns.
- Components:
- Electrostatic Spray Guns: Charge the powder particles and spray them onto the grounded parts.
- Control Units: Adjust settings like voltage, powder flow rate, and air pressure to ensure uniform coverage.
- Conveyor System
- Purpose: Transports parts through various stages of the powder coating process.
- Types:
- Overhead Conveyors: Hang parts from hooks or racks for continuous production.
- Floor Conveyors: Suitable for heavier or larger parts that cannot be suspended.
- Features:
- Variable Speed Control: Adjusts the speed of the conveyor to match production needs and curing times.
- Loading and Unloading Stations: Facilitate the movement of parts onto and off the conveyor system.
- Powder Coating Ovens
- Purpose: Cures the powder coating by melting and fusing it to the surface, forming a durable finish.
- Types:
- Batch Ovens: Suitable for smaller production runs and varied part sizes.
- Conveyor Ovens: Designed for continuous, high-volume production.
- Features:
- Temperature Control Systems: Ensure precise and consistent heating for optimal curing.
- Energy Efficiency: Incorporate insulation and heat recovery systems to minimize energy consumption.
- Cooling and Inspection Stations
- Purpose: Cool the parts after curing and inspect them for quality assurance.
- Components:
- Cooling Zones: Allow parts to cool gradually to avoid warping or defects.
- Inspection Areas: Check for coating consistency, thickness, and finish quality before packaging or assembly.
- Control and Monitoring Systems
- Purpose: Manage and monitor the entire powder coating process for efficiency and quality control.
- Components:
- PLC Systems (Programmable Logic Controllers): Automate and synchronize various plant operations.
- Data Logging and Analysis Tools: Record production metrics and identify areas for improvement.
- Safety and Environmental Controls
- Purpose: Ensure the safety of workers and compliance with environmental regulations.
- Components:
- Fire Suppression Systems: Protect against powder fires or explosions in booths and ovens.
- Ventilation and Filtration Systems: Maintain air quality by removing dust, fumes, and volatile organic compounds (VOCs).
- Personal Protective Equipment (PPE): Provide workers with necessary safety gear, such as masks, gloves, and goggles.
Optional and Auxiliary Components
- Advanced Pre-Treatment Systems: Utilize additional technologies like ultrasonic cleaning or nanotechnology for improved surface preparation.
- Curing Lamps: Use infrared or UV lamps for faster curing times and energy savings.
- Automated Robotic Systems: Enhance precision and efficiency in powder application and handling.
- Quality Control Instruments: Use advanced tools like thickness gauges, gloss meters, and adhesion testers for detailed quality assessment.
Layout and Design Considerations
- Workflow Optimization: Design the plant layout to minimize bottlenecks and ensure smooth transitions between stages.
- Space Utilization: Efficiently allocate space for equipment, storage, and movement of materials.
- Scalability: Plan for future expansion or upgrades to accommodate growing production demands.
Conclusion
A well-designed powder coating plant integrates these components to create an efficient, high-quality coating process. Understanding each element and its role in the system is crucial for businesses looking to enhance their powder coating capabilities. By investing in the right equipment and technology, companies can achieve superior finishes, increased productivity, and long-term success in the powder coating industry.
Detailed Components of a Powder Coating Plant
Certainly! To provide a detailed understanding of each component within a powder coating plant, we’ll delve into the technical specifications, functions, types, and key considerations for each element. This comprehensive breakdown will cover everything from the initial pre-treatment to the final inspection.
1. Pre-Treatment System
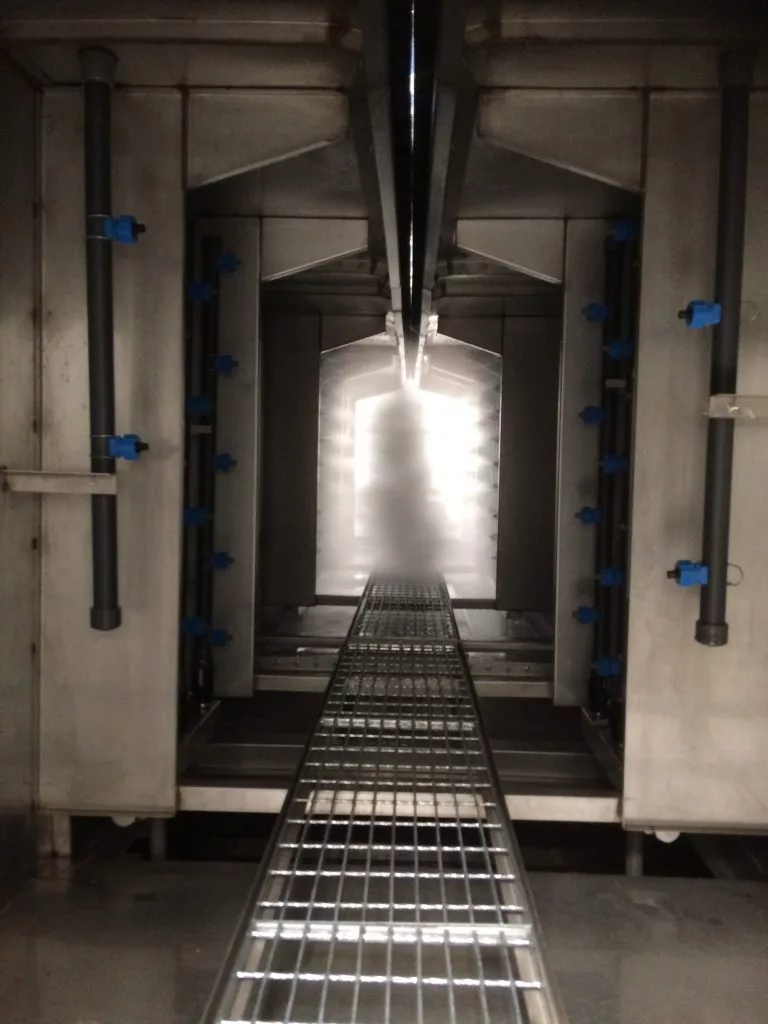
Overview
The pre-treatment system is crucial in ensuring that surfaces are properly cleaned and prepared for powder coating. This step enhances adhesion, improves finish quality, and increases the longevity of the coating.
Components and Process
1.1. Cleaning and Degreasing Stations
- Purpose: Remove oils, grease, and other contaminants from the surface.
- Methods:
- Alkaline Cleaning: Uses alkaline solutions to break down grease and oils.
- Solvent Cleaning: Employs organic solvents to dissolve contaminants.
- Ultrasonic Cleaning: Utilizes high-frequency sound waves for deep cleaning, especially effective for complex shapes.
- Equipment:
- Tanks and spray systems
- Heating elements to improve cleaning efficiency
- Agitation systems for even cleaning
1.2. Rinse Stations
- Purpose: Eliminate residual chemicals and contaminants from the cleaning stage.
- Types of Rinse:
- Freshwater Rinse: Basic water rinse to remove chemicals.
- Deionized Water Rinse: Prevents mineral deposits and spots on surfaces.
- Equipment:
- Spray bars and nozzles for thorough rinsing
- Closed-loop systems to recycle water and reduce waste
1.3. Surface Conditioning
- Purpose: Prepare the surface for subsequent conversion coating.
- Processes:
- Acid Etching: Removes oxides and prepares metal surfaces.
- Descaling: Removes scale and rust from the surface.
- Equipment:
- Immersion tanks or spray booths
- Automated dosing systems for precise chemical application
1.4. Conversion Coating
- Purpose: Apply a chemical layer that enhances powder adhesion and corrosion resistance.
- Types:
- Phosphate Coating: Iron or zinc phosphate for steel surfaces.
- Chromate Coating: Used for aluminum and zinc surfaces.
- Nano-Ceramic Coatings: Environmentally friendly option with superior adhesion and corrosion resistance.
- Equipment:
- Spray or immersion systems
- Temperature control for optimal reaction conditions
1.5. Drying Ovens
- Purpose: Remove moisture from parts to prevent defects in the powder coating.
- Features:
- Adjustable temperature settings
- Air circulation systems for even drying
- Equipment:
- Batch ovens for smaller production
- Conveyor ovens for continuous processing
Key Considerations
- Chemical Management: Ensure proper handling, storage, and disposal of chemicals used in pre-treatment.
- Environmental Compliance: Adhere to local regulations for effluent discharge and waste management.
- Maintenance: Regular cleaning and inspection of tanks and nozzles to prevent contamination.
2. Powder Coating Booths
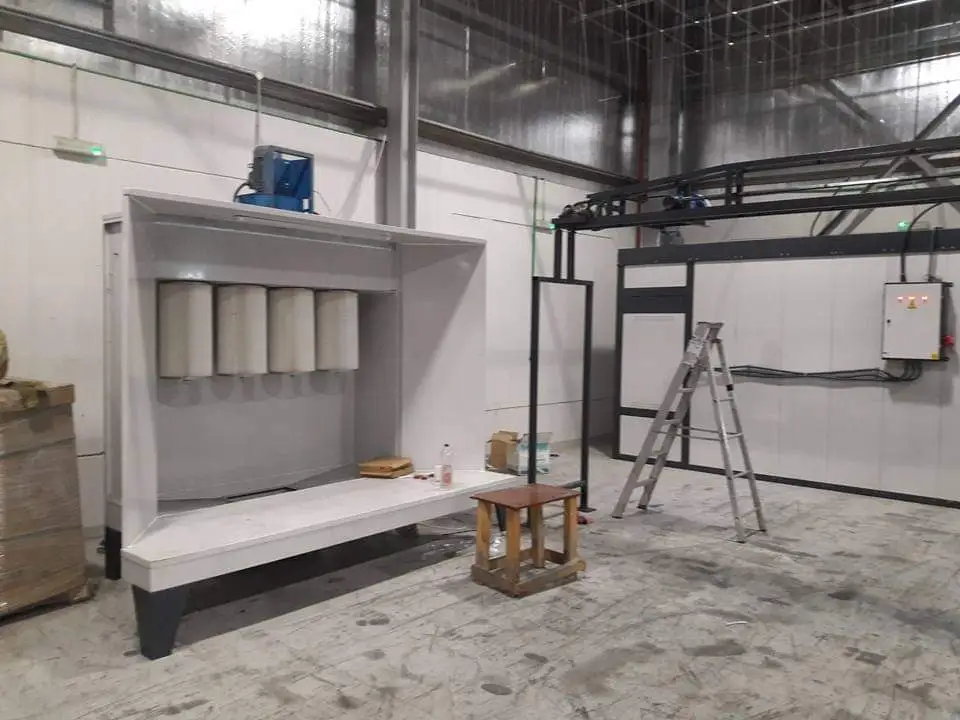
Overview
Powder coating booths provide a controlled environment for applying the powder. They ensure that the powder is applied evenly and that any overspray is efficiently managed and collected for reuse.
Types and Features
2.1. Manual Powder Coating Booths
- Purpose: Allow operators to manually apply powder using handheld spray guns.
- Applications: Suitable for small batches, custom jobs, and intricate parts.
- Features:
- Ventilation Systems: Maintain air quality and remove overspray.
- Lighting: Ensure visibility for precise application.
- Ergonomic Design: Facilitate operator comfort and efficiency.
2.2. Automatic Powder Coating Booths
- Purpose: Use automated systems to apply powder to parts, ideal for high-volume production.
- Applications: Suitable for standard parts and large-scale operations.
- Features:
- Robotic Arms and Reciprocators: Ensure consistent application across parts.
- Programmable Settings: Customize application parameters for different parts.
- Rapid Color Change Systems: Allow quick and efficient color changes with minimal downtime.
2.3. Powder Recovery Systems
- Purpose: Capture and recycle overspray powder to improve efficiency and reduce waste.
- Types:
- Cyclone Separators: Use centrifugal force to separate powder from the air.
- Cartridge Filters: Trap fine powder particles for reuse.
- Baghouse Filters: Employ fabric bags to capture powder, suitable for larger particles.
Key Considerations
- Airflow Management: Ensure proper ventilation to prevent contamination and maintain a clean environment.
- Color Change Efficiency: Invest in systems that allow quick and easy color changes to minimize downtime.
- Safety: Implement explosion-proof designs and fire suppression systems to prevent hazards.
3. Powder Application Equipment
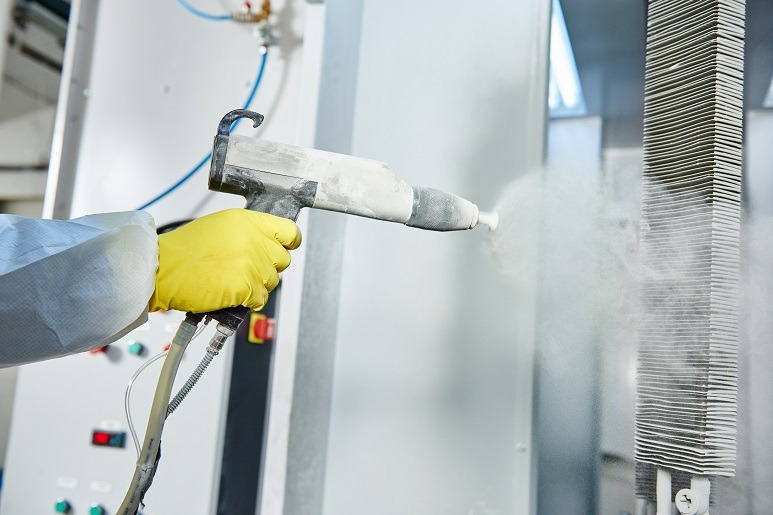
Overview
Powder application equipment is responsible for applying the powder coating to the parts. This equipment uses electrostatic principles to ensure uniform coverage and strong adhesion.
Components and Features
3.1. Electrostatic Spray Guns
- Purpose: Apply powder to the parts using an electrostatic charge.
- Types:
- Corona Guns: Use a high-voltage electrode to charge the powder.
- Tribo Guns: Charge the powder through friction, suitable for specific applications.
- Features:
- Adjustable Voltage and Current: Control the electrostatic charge for optimal coverage.
- Interchangeable Nozzles: Provide different spray patterns for various applications.
- Lightweight and Ergonomic Design: Ensure operator comfort during manual application.
3.2. Control Units
- Purpose: Manage and adjust the settings of the powder application equipment.
- Features:
- Digital Displays: Provide real-time feedback on settings and performance.
- Programmable Settings: Allow customization for different parts and powder types.
- Data Logging: Record application parameters for quality control and traceability.
3.3. Fluidized Bed Systems
- Purpose: Coat parts by dipping them into a bed of fluidized powder, typically used for thicker coatings.
- Applications: Suitable for specific applications requiring a thick and even coating.
- Features:
- Uniform Airflow: Ensure consistent fluidization of powder particles.
- Temperature Control: Maintain optimal conditions for coating.
Key Considerations
- Powder Compatibility: Ensure equipment is compatible with different powder formulations.
- Operator Training: Provide comprehensive training for operators to ensure efficient and safe use.
- Maintenance: Regularly clean and maintain spray guns and control units to prevent clogging and ensure consistent performance.
4. Conveyor System
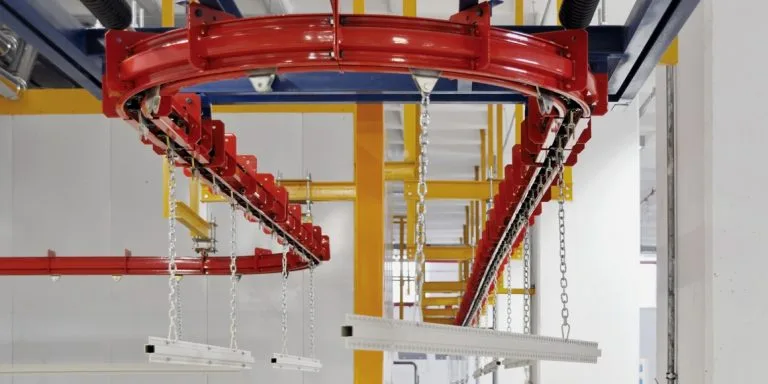
Overview
The conveyor system is the backbone of the powder coating plant, transporting parts through each stage of the process, from pre-treatment to curing.
Types and Features
4.1. Overhead Conveyors
- Purpose: Transport parts by suspending them from hooks or racks, ideal for continuous production.
- Types:
- Monorail Systems: Simple looped tracks for straightforward applications.
- Power and Free Systems: Offer more flexibility with multiple paths and stopping points.
- Features:
- Variable Speed Control: Adjust the speed to match production needs and curing times.
- Load Capacity: Designed to handle different part sizes and weights.
- Integration with Other Systems: Seamlessly integrate with pre-treatment, application, and curing systems.
4.2. Floor Conveyors
- Purpose: Transport heavier or larger parts that cannot be suspended, suitable for specific applications.
- Types:
- Belt Conveyors: Use belts to move parts horizontally or on an incline.
- Roller Conveyors: Employ rollers to facilitate the movement of parts.
- Features:
- Heavy-Duty Construction: Designed to support large or heavy parts.
- Customizable Configurations: Adapt to different plant layouts and processes.
Key Considerations
- Layout Design: Plan the conveyor layout to optimize workflow and minimize bottlenecks.
- Load and Speed Requirements: Ensure the conveyor system meets production demands for speed and capacity.
- Safety Features: Implement safety measures such as guards, emergency stops, and regular inspections.
5. Powder Coating Ovens
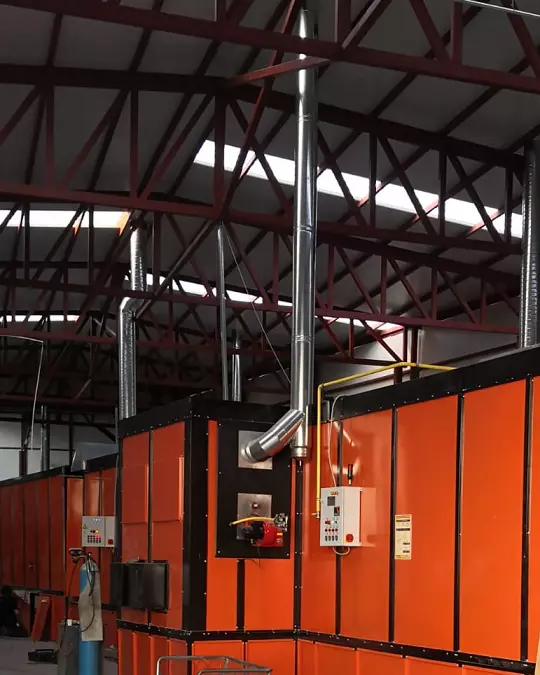
Overview
Powder coating ovens are responsible for curing the powder coating by melting and fusing it to the surface, resulting in a durable and attractive finish.
Types and Features
5.1. Batch Ovens
- Purpose: Cure parts in small batches, suitable for varied part sizes and low-volume production.
- Applications: Ideal for custom jobs, small businesses, and prototyping.
- Features:
- Adjustable Temperature Control: Precise control of curing conditions.
- Flexible Configuration: Accommodate different part sizes and shapes.
- Insulated Construction: Minimize heat loss and improve energy efficiency.
5.2. Conveyor Ovens
- Purpose: Designed for continuous production, curing parts as they move through the oven.
- Applications: Suitable for high-volume production and standardized parts.
- Features:
- Consistent Temperature Distribution: Ensure even curing across all parts.
- Variable Conveyor Speed: Match curing times with production speed.
- Energy Efficiency: Incorporate heat recovery systems and advanced insulation.
Key Considerations
- Oven Size and Capacity: Choose an oven that meets production demands without excessive energy use.
- Heating Source: Decide between electric, gas, or infrared heating based on cost and efficiency.
- Temperature Uniformity: Ensure consistent heat distribution to prevent defects in the finish.
6. Cooling and Inspection Stations
Overview
Cooling and inspection stations are crucial for ensuring the quality and consistency of the finished products. Cooling prevents defects, while inspection verifies the coating quality.
Components and Features
6.1. Cooling Zones
- Purpose: Gradually cool parts after curing to prevent warping or defects.
- Features:
- Controlled Airflow: Ensure even cooling and avoid thermal shock.
- Adjustable Cooling Rates: Customize settings for different materials and part sizes.
6.2. Inspection Areas
- Purpose: Conduct quality checks on coated parts to ensure consistency and adherence to standards.
- Features:
- Lighting and Magnification: Facilitate detailed visual inspections.
- Measurement Tools: Use instruments like thickness gauges and gloss meters for precise evaluation.
- Defect Detection Systems: Implement automated systems for detecting coating defects, such as thin spots or uneven coverage.
Key Considerations
- Quality Assurance Protocols: Establish standards and procedures for inspections to ensure consistent product quality.
- Training for Inspectors: Provide training to staff on recognizing defects and using inspection tools effectively.
- Feedback Loop: Use inspection data to inform process improvements and address recurring issues.
7. Control and Monitoring Systems
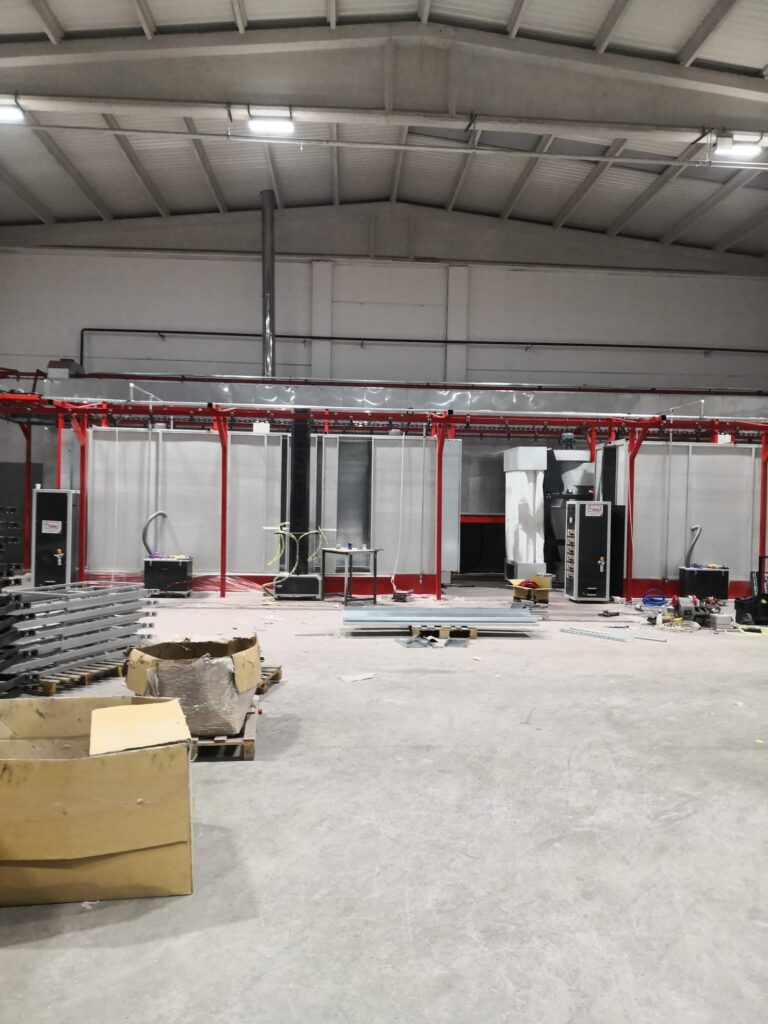
Overview
Control and monitoring systems automate and synchronize various plant operations, ensuring efficiency, consistency, and quality in the powder coating process.
Components and Features
7.1. PLC Systems (Programmable Logic Controllers)
- Purpose: Automate and control equipment functions throughout the plant.
- Features:
- Centralized Control: Manage multiple systems from a single interface.
- Real-Time Monitoring: Track performance metrics and adjust settings as needed.
- Data Logging: Record operational data for analysis and process optimization.
7.2. Data Logging and Analysis Tools
- Purpose: Collect and analyze production data to improve efficiency and quality.
- Features:
- Trend Analysis: Identify patterns and trends in production metrics.
- Performance Dashboards: Visualize key performance indicators (KPIs) for easy monitoring.
- Predictive Maintenance: Use data to anticipate equipment maintenance needs and prevent downtime.
Key Considerations
- System Integration: Ensure seamless integration with existing equipment and software.
- User Interface: Provide intuitive and user-friendly interfaces for operators.
- Cybersecurity: Implement security measures to protect sensitive data and control systems.
8. Safety and Environmental Controls
Overview
Safety and environmental controls are essential for protecting workers and ensuring compliance with regulations. These systems manage hazards and minimize environmental impact.
Components and Features
8.1. Fire Suppression Systems
- Purpose: Prevent and control powder fires or explosions in booths and ovens.
- Features:
- Automatic Detection and Suppression: Quickly identify and extinguish fires.
- Integration with Control Systems: Automatically shut down equipment in case of fire.
- Regular Testing and Maintenance: Ensure systems are operational and compliant with safety standards.
8.2. Ventilation and Filtration Systems
- Purpose: Maintain air quality by removing dust, fumes, and volatile organic compounds (VOCs).
- Features:
- High-Efficiency Particulate Air (HEPA) Filters: Capture fine particles and contaminants.
- Exhaust Fans and Ductwork: Ensure proper airflow and ventilation.
- Regular Filter Replacement: Maintain efficiency and prevent clogs.
8.3. Personal Protective Equipment (PPE)
- Purpose: Provide workers with necessary safety gear to protect against hazards.
- Components:
- Respirators and Masks: Protect against inhalation of powder particles and fumes.
- Safety Glasses and Goggles: Shield eyes from dust and chemical splashes.
- Gloves and Protective Clothing: Prevent skin contact with chemicals and powders.
Key Considerations
- Compliance with Regulations: Adhere to local and international safety and environmental standards.
- Safety Training: Conduct regular training sessions on safety protocols and emergency procedures.
- Continuous Improvement: Regularly review and update safety measures to address emerging risks and regulations.
Conclusion
Each component of a powder coating plant plays a vital role in ensuring a successful and efficient coating process. By understanding the details and functions of these components, businesses can design and operate a plant that meets their specific needs and production goals. Investing in the right equipment and systems, along with proper training and maintenance, will lead to high-quality finishes, increased productivity, and long-term success in the powder coating industry.
Installation time estimate
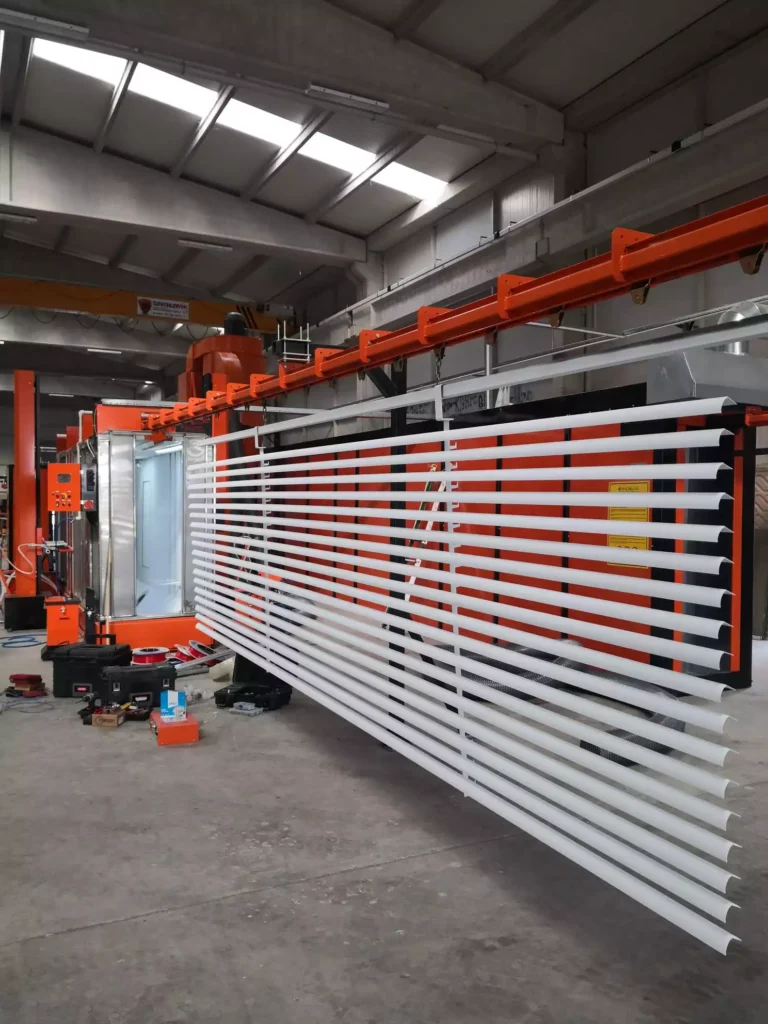
Estimating the installation time for a powder coating plant involves considering several factors such as the size of the operation, complexity of the equipment, facility preparation, and the efficiency of the installation team. Below is a detailed breakdown of the installation time estimate, including factors that can influence the timeline and strategies to ensure a smooth installation process.
Installation Time Estimate for a Powder Coating Plant
Factors Influencing Installation Time
- Scale and Complexity of the Plant
- Size and layout of the facility
- Number and type of equipment components
- Type of Equipment
- Manual vs. automated systems
- Batch vs. continuous production lines
- Site Preparation
- Existing infrastructure readiness
- Facility modifications needed
- Installation Team and Expertise
- Experience and skills of the installation crew
- Availability of necessary resources and tools
- Regulatory Compliance and Inspections
- Time required for permits and approvals
- Safety inspections and certifications
- Coordination and Scheduling
- Coordination between vendors, contractors, and stakeholders
- Availability of equipment and personnel
Estimated Installation Time by Component
Here is an approximate installation timeline for each major component of a powder coating plant. These estimates are generalized and may vary depending on specific project requirements.
1. Pre-Treatment System
- Time Estimate: 1 to 3 weeks
- Activities:
- Delivery and setup of washing, rinsing, and drying stations
- Plumbing and drainage installations
- Testing and calibration of chemical dosing systems
2. Powder Coating Booths
- Time Estimate: 1 to 2 weeks
- Activities:
- Assembly and installation of booth structures
- Integration of ventilation and powder recovery systems
- Setup of lighting and electrical connections
3. Powder Application Equipment
- Time Estimate: 1 to 2 weeks
- Activities:
- Installation of electrostatic spray guns and control units
- Calibration of application settings and nozzles
- Testing for uniform powder distribution
4. Conveyor System
- Time Estimate: 2 to 4 weeks
- Activities:
- Layout design and track installation
- Assembly of conveyor components and drives
- Testing for load capacity and speed control
5. Powder Coating Ovens
- Time Estimate: 2 to 3 weeks
- Activities:
- Installation of oven structures and insulation
- Setup of heating systems and temperature controls
- Testing for temperature uniformity and energy efficiency
6. Cooling and Inspection Stations
- Time Estimate: 1 to 2 weeks
- Activities:
- Installation of cooling systems and airflow management
- Setup of inspection stations and quality control tools
- Training staff on inspection procedures
7. Control and Monitoring Systems
- Time Estimate: 1 to 2 weeks
- Activities:
- Installation of PLC systems and control panels
- Integration with other equipment components
- Testing and validation of automation processes
8. Safety and Environmental Controls
- Time Estimate: 1 to 2 weeks
- Activities:
- Installation of fire suppression and ventilation systems
- Setup of safety barriers and emergency stops
- Safety audits and compliance checks
Total Estimated Installation Time
The total estimated installation time for a powder coating plant can range from 8 to 18 weeks, depending on the scale and complexity of the project. Here’s a breakdown by plant size:
- Small-Scale Operations: 8 to 10 weeks
- Medium-Scale Operations: 10 to 14 weeks
- Large-Scale Operations: 14 to 18 weeks
Strategies for Reducing Installation Time
- Detailed Planning and Coordination
- Develop a comprehensive project plan with clear timelines and milestones.
- Coordinate with vendors, contractors, and stakeholders to align schedules and resources.
- Pre-Fabrication and Pre-Assembly
- Opt for pre-fabricated components to reduce on-site assembly time.
- Pre-assemble equipment off-site where possible to minimize installation complexity.
- Experienced Installation Team
- Hire experienced professionals familiar with powder coating systems and processes.
- Conduct regular training and briefings to ensure the team is well-prepared.
- Efficient Site Preparation
- Ensure the facility is ready for installation before equipment arrives.
- Complete necessary infrastructure upgrades and modifications in advance.
- Streamlined Permitting and Inspections
- Obtain permits and approvals early in the project timeline.
- Schedule inspections and certifications to avoid delays.
- Contingency Planning
- Identify potential risks and develop contingency plans to address unforeseen issues.
- Allocate buffer time in the schedule for unexpected challenges.
Conclusion
The installation of a powder coating plant is a complex process that requires careful planning and coordination. By understanding the factors that influence installation time and implementing strategies to streamline the process, businesses can achieve a successful setup that meets their production goals and timelines.
Maintenance schedule tips
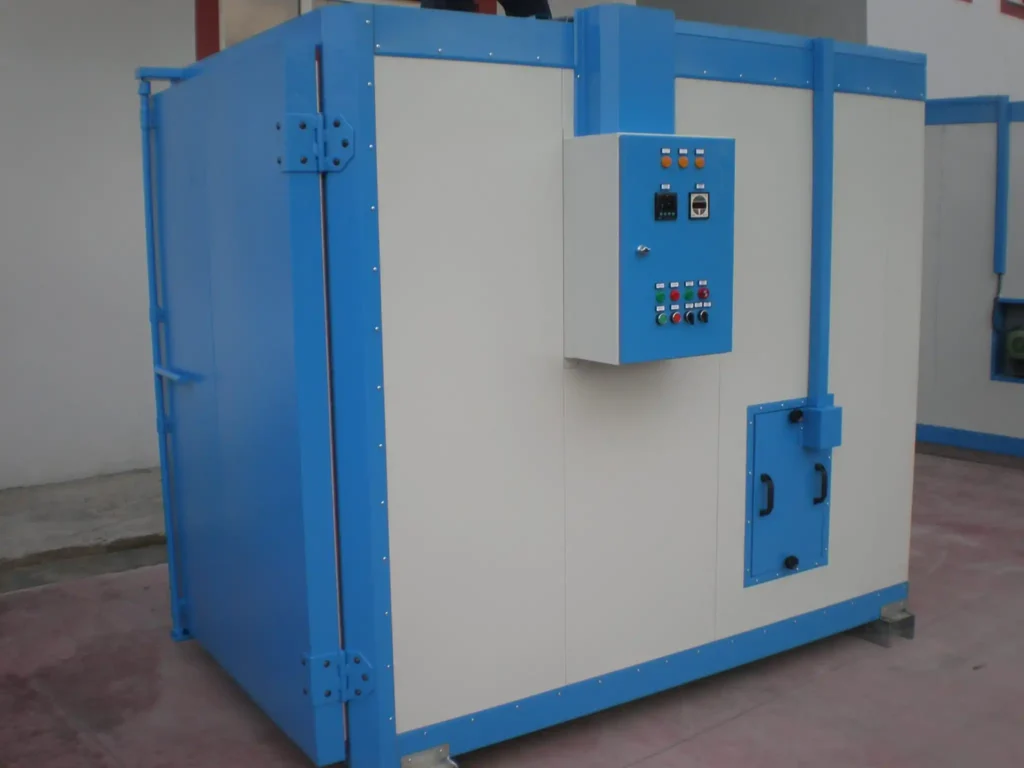
Creating a maintenance schedule for a powder coating plant is essential for ensuring efficient operation, minimizing downtime, and extending the lifespan of your equipment. A well-structured maintenance plan should address the needs of each component, including pre-treatment systems, powder coating booths, application equipment, conveyors, ovens, and safety controls. Here are some tips and guidelines to help you develop an effective maintenance schedule.
Tips for Creating a Maintenance Schedule for a Powder Coating Plant
1. Understand Equipment Requirements
- Read Manufacturer Guidelines: Start by reviewing the maintenance recommendations provided by the equipment manufacturers. These guidelines offer valuable insights into the specific needs and intervals for each component.
- Identify Critical Components: Prioritize maintenance for critical components that directly impact production quality and efficiency, such as spray guns, ovens, and conveyors.
2. Develop a Comprehensive Maintenance Plan
- Routine Inspections: Schedule regular inspections to identify wear and tear, leaks, or potential issues before they escalate. Inspections should cover all plant components, including electrical, mechanical, and safety systems.
- Preventive Maintenance: Implement a preventive maintenance schedule that includes tasks such as cleaning, lubrication, calibration, and parts replacement. This helps prevent unexpected breakdowns and maintains optimal performance.
- Predictive Maintenance: Utilize data analytics and monitoring tools to predict equipment failures and schedule maintenance based on condition and usage patterns.
3. Create a Detailed Maintenance Schedule
- Daily Maintenance Tasks:
- Check air pressure and filtration systems.
- Inspect spray guns and nozzles for clogs or wear.
- Clean work areas and remove powder buildup.
- Weekly Maintenance Tasks:
- Inspect conveyor systems for alignment and wear.
- Lubricate moving parts such as bearings and chains.
- Check temperature settings and calibrate sensors.
- Monthly Maintenance Tasks:
- Conduct a thorough inspection of pre-treatment systems.
- Inspect and clean ventilation and exhaust systems.
- Test and recalibrate control systems.
- Quarterly Maintenance Tasks:
- Perform a detailed inspection of the ovens for heat distribution and insulation integrity.
- Replace worn-out components such as belts and filters.
- Review and update safety protocols.
- Annual Maintenance Tasks:
- Conduct a comprehensive review of the entire plant.
- Audit compliance with safety and environmental regulations.
- Plan for equipment upgrades or replacements as needed.
4. Document Maintenance Activities
- Record Keeping: Maintain detailed records of all maintenance activities, including dates, tasks performed, and any issues identified. This documentation helps track equipment performance and identifies recurring problems.
- Use Digital Tools: Consider using computerized maintenance management systems (CMMS) to schedule, track, and analyze maintenance activities. Digital tools can provide reminders, automate scheduling, and generate reports.
5. Train and Empower Staff
- Employee Training: Train employees on the importance of maintenance and proper procedures. Ensure they understand how to identify and report issues and perform routine tasks.
- Empowerment: Encourage staff to take ownership of their equipment and be proactive in reporting potential problems.
6. Monitor Key Performance Indicators (KPIs)
- Track KPIs: Monitor KPIs such as equipment uptime, mean time between failures (MTBF), and maintenance costs to evaluate the effectiveness of your maintenance program.
- Continuous Improvement: Use KPI data to identify areas for improvement and make data-driven decisions to enhance maintenance strategies.
7. Plan for Spare Parts and Inventory
- Spare Parts Management: Maintain an inventory of critical spare parts to minimize downtime during repairs. Track usage patterns to ensure adequate stock levels.
- Vendor Relationships: Build strong relationships with equipment suppliers to ensure quick access to parts and technical support.
8. Evaluate and Adjust the Maintenance Plan
- Regular Reviews: Periodically review and update the maintenance schedule based on equipment performance, technological advancements, and changing production needs.
- Feedback Loop: Encourage feedback from maintenance staff and operators to identify pain points and improve processes.
Sample Maintenance Schedule Template
Here’s a sample template to help you structure your maintenance schedule:
Frequency | Task | Details |
---|---|---|
Daily | Check air pressure | Ensure proper airflow for spray guns and equipment. |
Inspect spray guns | Look for clogs, wear, and powder buildup. | |
Clean work areas | Remove excess powder and debris from booths and equipment. | |
Weekly | Inspect conveyor systems | Check alignment and wear of belts and chains. |
Lubricate moving parts | Apply lubrication to bearings, chains, and gears. | |
Calibrate temperature settings | Ensure accurate temperature readings in ovens. | |
Monthly | Inspect pre-treatment systems | Check tanks, pumps, and chemical levels. |
Clean ventilation systems | Remove dust and powder buildup in filters and ducts. | |
Test control systems | Verify functionality and accuracy of control units. | |
Quarterly | Inspect oven heat distribution | Check for even heat distribution and insulation integrity. |
Replace worn components | Swap out belts, filters, and other wear-prone parts. | |
Review safety protocols | Update safety measures and conduct training if needed. | |
Annually | Conduct plant-wide inspection | Evaluate overall condition and performance. |
Audit compliance with regulations | Ensure adherence to safety and environmental standards. | |
Plan equipment upgrades | Assess the need for new equipment or technology upgrades. |
Conclusion
Implementing a well-structured maintenance schedule is vital for the smooth operation and longevity of your powder coating plant. By focusing on preventive and predictive maintenance, documenting activities, and involving your team, you can reduce downtime, improve efficiency, and maintain high-quality production standards.
Powder Coating Oven Types
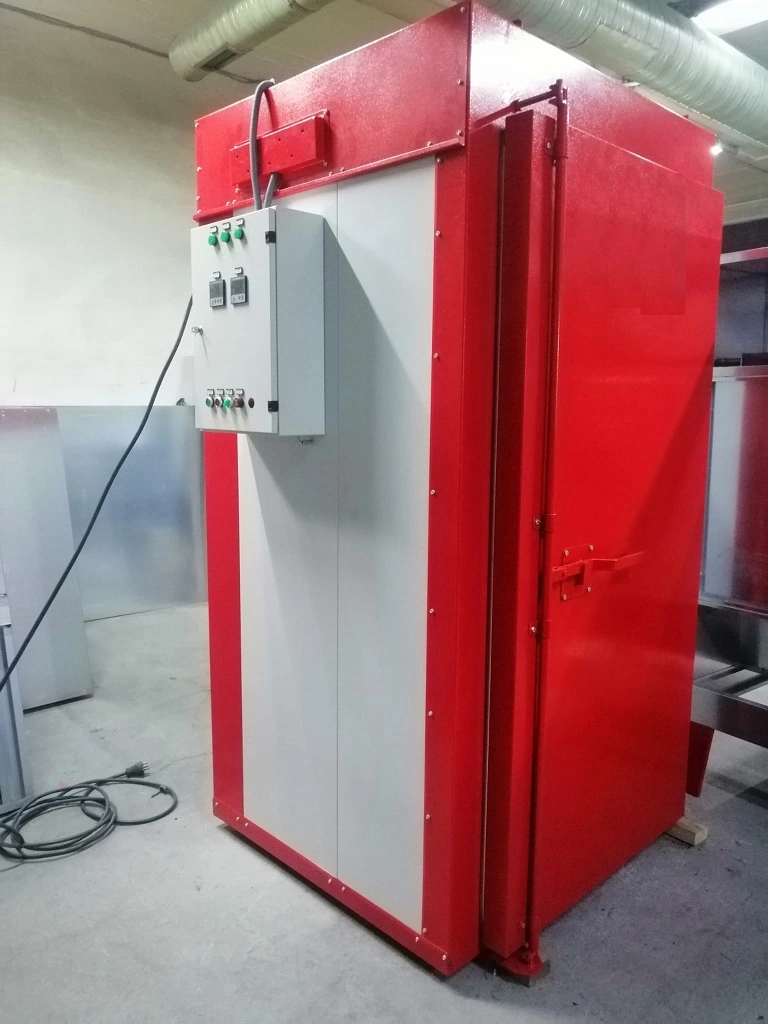
Powder coating ovens are a critical component of the powder coating process, providing the heat necessary to cure the powder and ensure a durable finish. There are several types of powder coating ovens, each designed to meet different production needs and efficiency levels. This guide will cover the various types of powder coating ovens, their features, benefits, and applications, helping you choose the right oven for your specific requirements.
Types of Powder Coating Ovens
1. Batch Ovens
Batch ovens are designed to cure powder coatings for small to medium-sized production runs. They are ideal for operations that require flexibility in coating different part sizes and types.
Features:
- Flexibility: Accommodates various part sizes and shapes.
- Energy Efficiency: Often includes insulation and heat recovery systems to reduce energy consumption.
- Manual or Semi-Automatic Operation: Suitable for low to moderate production volumes.
Benefits:
- Cost-Effective: Lower initial investment compared to continuous ovens.
- Versatile: Can handle a variety of coating tasks, including custom and complex shapes.
- Ease of Use: Simple to operate and maintain.
Applications:
- Small businesses and job shops
- Custom and prototype work
- Low to medium production volumes
Common Types of Batch Ovens:
- Walk-In Ovens: Large enough for operators to enter and load parts, suitable for oversized items.
- Cabinet Ovens: Smaller units ideal for small parts or lower-volume production.
- Truck-In Ovens: Designed for loading parts on racks or carts that can be rolled into the oven.
2. Conveyor Ovens
Conveyor ovens are designed for high-volume production and continuous processing. They automate the curing process, improving efficiency and consistency.
Features:
- Continuous Operation: Ideal for high production rates and large-scale operations.
- Automated Conveyor Systems: Transport parts through the oven for consistent curing.
- Variable Speed Control: Allows adjustment of conveyor speed to match curing requirements.
Benefits:
- High Throughput: Capable of processing large quantities of parts quickly.
- Consistent Quality: Ensures uniform curing across all parts.
- Reduced Labor Costs: Automation reduces the need for manual intervention.
Applications:
- Automotive and aerospace industries
- High-volume manufacturing plants
- Standardized parts production
Common Types of Conveyor Ovens:
- Monorail Ovens: Parts are hung from an overhead conveyor and pass through the oven in a linear path.
- Chain-On-Edge Ovens: Parts are attached to fixtures on a conveyor chain, suitable for heavier items.
- Flat-Belt Ovens: Use a flat conveyor belt to transport parts, ideal for lightweight or flat components.
3. Infrared Ovens
Infrared ovens use infrared radiation to cure powder coatings, offering a fast and energy-efficient alternative to conventional ovens. They are often used in combination with other oven types to optimize curing.
Features:
- Fast Heating: Infrared radiation provides rapid heat-up and curing times.
- Energy Efficiency: Direct heating reduces energy consumption compared to convection ovens.
- Compact Size: Smaller footprint compared to traditional ovens.
Benefits:
- Quick Curing: Significantly reduces curing times, increasing throughput.
- Targeted Heating: Infrared heat can be focused on specific areas, reducing overall energy use.
- Improved Finish: Provides smooth and even curing, minimizing defects.
Applications:
- Automotive and consumer electronics
- Applications requiring quick turnaround
- Parts with complex shapes or heat-sensitive materials
Common Types of Infrared Ovens:
- Short-Wave Infrared Ovens: Provide intense heat for fast curing, suitable for thicker coatings.
- Medium-Wave Infrared Ovens: Balance between heat intensity and penetration, ideal for general applications.
- Long-Wave Infrared Ovens: Gentle heat suitable for heat-sensitive substrates.
4. Gas-Fired Ovens
Gas-fired ovens use natural gas or propane as a heat source. They are popular for large-scale operations due to their efficiency and cost-effectiveness.
Features:
- High Heat Output: Efficiently generates high temperatures for rapid curing.
- Cost-Effective: Generally lower operating costs compared to electric ovens.
- Robust Construction: Designed to handle heavy-duty industrial use.
Benefits:
- Reduced Operating Costs: Lower energy costs compared to electric ovens, especially for large volumes.
- Reliable Performance: Consistent heating for uniform curing.
- Scalability: Suitable for large-scale production and expansion.
Applications:
- Automotive and heavy equipment manufacturing
- Large industrial operations
- High-volume powder coating lines
Common Types of Gas-Fired Ovens:
- Direct-Fired Ovens: Burners directly heat the air inside the oven chamber, providing fast and efficient heating.
- Indirect-Fired Ovens: Heat exchangers separate combustion gases from the oven air, offering cleaner operation.
5. Electric Ovens
Electric ovens use electrical heating elements to generate heat for curing powder coatings. They are commonly used in smaller operations due to their ease of use and installation.
Features:
- Precise Temperature Control: Offers accurate and consistent temperature settings.
- Easy Installation: No need for gas lines or combustion venting.
- Low Maintenance: Fewer moving parts compared to gas-fired ovens.
Benefits:
- Safe and Clean: No combustion gases, reducing emissions and improving air quality.
- Consistent Performance: Stable temperature control ensures uniform curing.
- Versatile: Suitable for various applications and materials.
Applications:
- Small to medium-sized businesses
- Custom and low-volume production
- Applications with strict environmental regulations
Common Types of Electric Ovens:
- Forced-Air Convection Ovens: Use fans to circulate heated air for uniform temperature distribution.
- Static Ovens: Rely on natural convection, suitable for delicate or sensitive parts.
6. Combination Ovens
Combination ovens integrate multiple heating methods, such as infrared and convection, to provide flexibility and optimize curing processes.
Features:
- Multi-Mode Operation: Allows switching between or combining different heating methods.
- Optimized Curing: Adjusts curing methods based on part size, shape, and material.
- Flexible Configuration: Customizable to meet specific production needs.
Benefits:
- Versatility: Capable of handling a wide range of parts and coatings.
- Improved Efficiency: Combines the strengths of different heating methods for optimal results.
- Enhanced Finish Quality: Provides tailored curing conditions to minimize defects.
Applications:
- Complex parts with varying geometries
- Industries requiring rapid production changes
- Specialized coating applications
Considerations for Choosing the Right Powder Coating Oven
When selecting a powder coating oven, consider the following factors:
- Production Volume:
- Choose batch ovens for low to medium production and conveyor ovens for high-volume operations.
- Part Size and Shape:
- Consider the size, weight, and geometry of the parts to determine the appropriate oven type.
- Energy Efficiency:
- Evaluate energy consumption and costs, especially for large-scale operations.
- Temperature Requirements:
- Ensure the oven can maintain consistent temperatures for your specific powder coatings.
- Space and Layout:
- Consider the available space and how the oven will fit into your production line layout.
- Budget and Cost:
- Balance initial investment with long-term operating costs and return on investment.
- Regulatory Compliance:
- Ensure the oven meets local safety and environmental regulations.
Conclusion
Selecting the right powder coating oven is crucial for achieving high-quality finishes and efficient production. By understanding the features, benefits, and applications of each oven type, businesses can make informed decisions that align with their production needs and goals. Investing in the right oven will enhance productivity, reduce costs, and ensure a durable, attractive finish on your coated products.
Powder coating oven maintenance tips
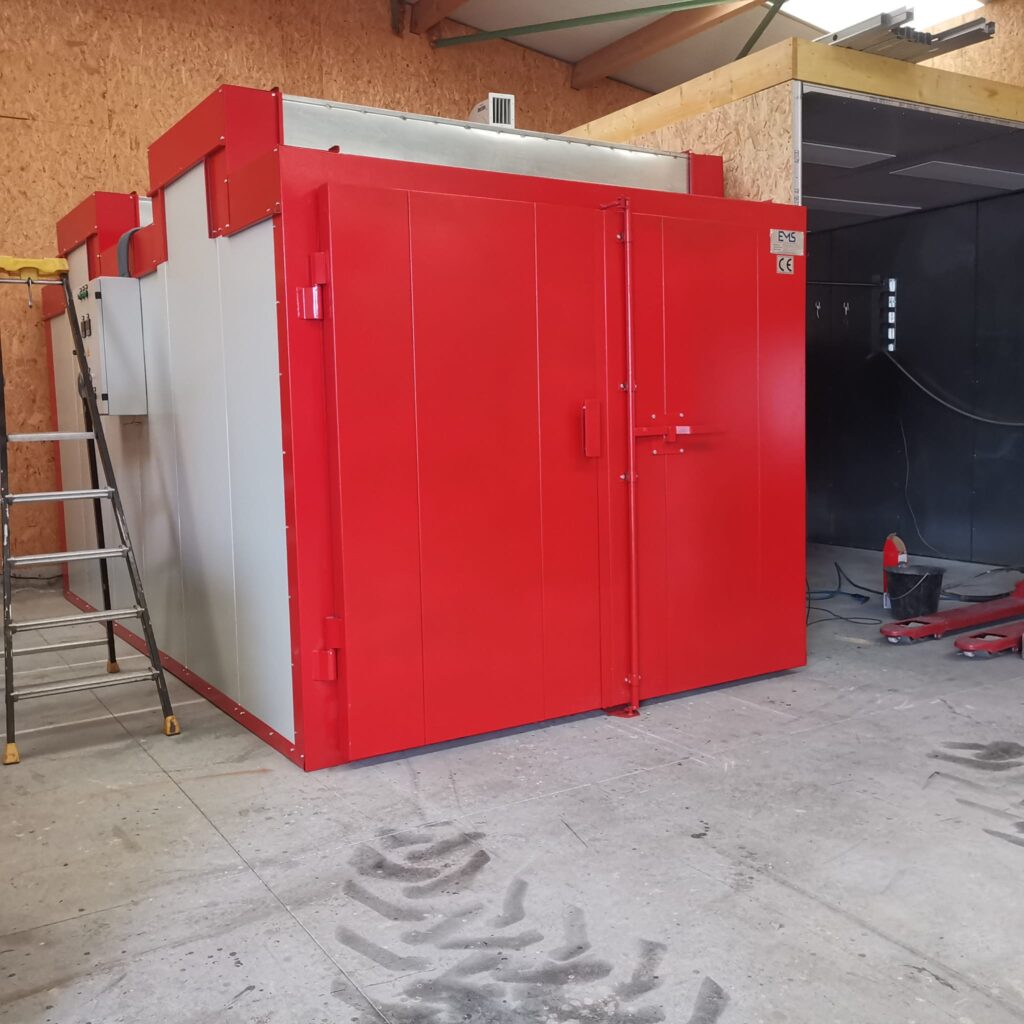
Proper maintenance of powder coating ovens is crucial to ensure efficient operation, consistent curing quality, and the longevity of the equipment. A well-maintained oven minimizes downtime, reduces energy consumption, and prevents costly repairs. Below are comprehensive tips and guidelines for maintaining powder coating ovens effectively.
Powder Coating Oven Maintenance Tips
1. Regular Cleaning
Keeping the oven clean is essential to prevent powder buildup, which can affect performance and finish quality.
Cleaning Tips:
- Daily Cleaning:
- Inspect and Clean Interior Surfaces: Remove any powder buildup on oven walls, floors, and ceilings.
- Clean Heating Elements: Check and clean heating elements to ensure efficient heat transfer.
- Vacuum or Sweep the Floor: Remove any loose powder or debris from the oven floor.
- Weekly Cleaning:
- Clean Air Ducts and Vents: Ensure proper airflow and ventilation by cleaning ducts and vents regularly.
- Wipe Down Doors and Seals: Clean door seals and check for any damage that could affect insulation.
- Monthly Cleaning:
- Deep Clean Oven Interior: Use a non-abrasive cleaner to deep clean the oven interior and remove any stubborn residue.
- Inspect and Clean Exhaust Systems: Check and clean exhaust fans and filters to prevent blockages.
2. Routine Inspections
Regular inspections help identify potential issues before they become major problems, ensuring the oven operates at peak efficiency.
Inspection Tips:
- Daily Inspections:
- Check Temperature Settings: Verify that the oven reaches and maintains the correct curing temperature.
- Monitor Airflow: Ensure that fans and blowers are functioning correctly for even heat distribution.
- Inspect Doors and Seals: Check for gaps or damage that could lead to heat loss.
- Weekly Inspections:
- Inspect Electrical Components: Check wiring, connections, and control panels for signs of wear or damage.
- Check for Unusual Noises: Listen for any unusual noises that might indicate mechanical issues.
- Monthly Inspections:
- Inspect Insulation: Check oven insulation for any damage or wear that could reduce energy efficiency.
- Examine Conveyor Systems: For conveyor ovens, inspect belts, chains, and rollers for wear and alignment.
3. Calibration and Testing
Regular calibration and testing ensure that the oven operates at the correct temperature and settings, maintaining coating quality.
Calibration Tips:
- Temperature Calibration:
- Use Thermocouples: Place thermocouples at various points in the oven to verify temperature uniformity.
- Adjust Temperature Controllers: Calibrate controllers to maintain consistent curing temperatures across the oven.
- Testing Performance:
- Conduct Cure Tests: Perform test runs with sample parts to ensure that coatings are cured properly.
- Check Heating Elements: Test heating elements for consistent output and replace any that are faulty.
4. Preventive Maintenance
Implementing a preventive maintenance schedule helps prevent unexpected breakdowns and extends the life of the oven.
Preventive Maintenance Tips:
- Lubrication:
- Lubricate Moving Parts: Apply lubrication to bearings, chains, and other moving parts to reduce friction and wear.
- Component Replacement:
- Replace Worn Parts: Regularly check and replace parts like belts, seals, and filters that show signs of wear.
- Fan and Blower Maintenance:
- Inspect and Clean Fans: Check fans for balance and clean them to prevent vibration and noise.
- Replace Worn Bearings: Replace any bearings that are noisy or show signs of wear.
5. Safety and Compliance
Ensuring safety and regulatory compliance is critical for protecting workers and meeting industry standards.
Safety Tips:
- Fire Safety:
- Check Fire Suppression Systems: Ensure that fire suppression systems are operational and regularly serviced.
- Install Smoke Detectors: Regularly test smoke detectors and alarms to ensure they are functional.
- Electrical Safety:
- Inspect Wiring and Connections: Regularly check electrical wiring and connections for signs of wear or damage.
- Conduct Safety Audits: Perform regular safety audits to ensure compliance with safety regulations.
6. Documentation and Record Keeping
Keeping detailed records of maintenance activities helps track oven performance and identify trends or recurring issues.
Documentation Tips:
- Maintain a Maintenance Log: Record all maintenance activities, including inspections, cleaning, and repairs.
- Track Performance Metrics: Monitor metrics such as energy consumption, downtime, and repair frequency.
7. Staff Training and Awareness
Proper training ensures that staff are equipped to perform maintenance tasks safely and effectively.
Training Tips:
- Provide Comprehensive Training: Train staff on oven operation, maintenance procedures, and safety protocols.
- Encourage Proactive Maintenance: Empower staff to identify and report potential issues promptly.
Sample Maintenance Schedule for Powder Coating Ovens
Below is a sample maintenance schedule to help you organize and plan oven maintenance tasks:
Frequency | Task | Details |
---|---|---|
Daily | Clean interior surfaces | Remove powder buildup from oven walls, floors, and ceilings. |
Check temperature settings | Verify that the oven reaches the correct curing temperature. | |
Inspect doors and seals | Look for gaps or damage that could lead to heat loss. | |
Weekly | Clean air ducts and vents | Ensure proper airflow and ventilation. |
Inspect electrical components | Check wiring, connections, and control panels for wear. | |
Lubricate moving parts | Apply lubrication to bearings, chains, and other components. | |
Monthly | Deep clean oven interior | Use non-abrasive cleaner to remove stubborn residue. |
Calibrate temperature controllers | Verify and adjust temperature settings for consistency. | |
Inspect insulation and conveyor systems | Check insulation integrity and conveyor alignment. | |
Quarterly | Test heating elements and fans | Ensure consistent output and replace faulty components. |
Review safety protocols and systems | Update safety measures and test fire suppression systems. | |
Annually | Conduct comprehensive performance review | Evaluate overall condition and plan for upgrades. |
Audit compliance with regulations | Ensure adherence to safety and environmental standards. |
Conclusion
Regular maintenance of powder coating ovens is essential for achieving high-quality finishes, maintaining production efficiency, and ensuring equipment longevity. By implementing a structured maintenance plan, conducting regular inspections, and training staff, businesses can minimize downtime, reduce costs, and maintain a safe working environment.