
A powder coating booth is a specialized enclosure that is used to apply a dry powder coating to a variety of surfaces. The booth is designed to contain the powder and prevent it from spreading into the surrounding environment.
The booth is typically equipped with a ventilation system that removes overspray and fumes from the booth. The powder coating is applied using a spray gun, which is connected to a hopper that contains the powder. The spray gun is used to apply the powder to the surface in a uniform and even layer.
Once the powder is applied, it is cured in an oven to harden the coating. The curing process can be done at a variety of temperatures and for different lengths of time, depending on the type of powder being used.
Powder coating is a durable and long-lasting finish that can be used on a variety of materials, including metal, wood, and plastic. It is a popular choice for applications that require a high level of durability and resistance to scratches, chips, and fading.
Here you can find some brief information about the powder coating booth price and powder coating booth manufacturers
Powder Coating Booth Types
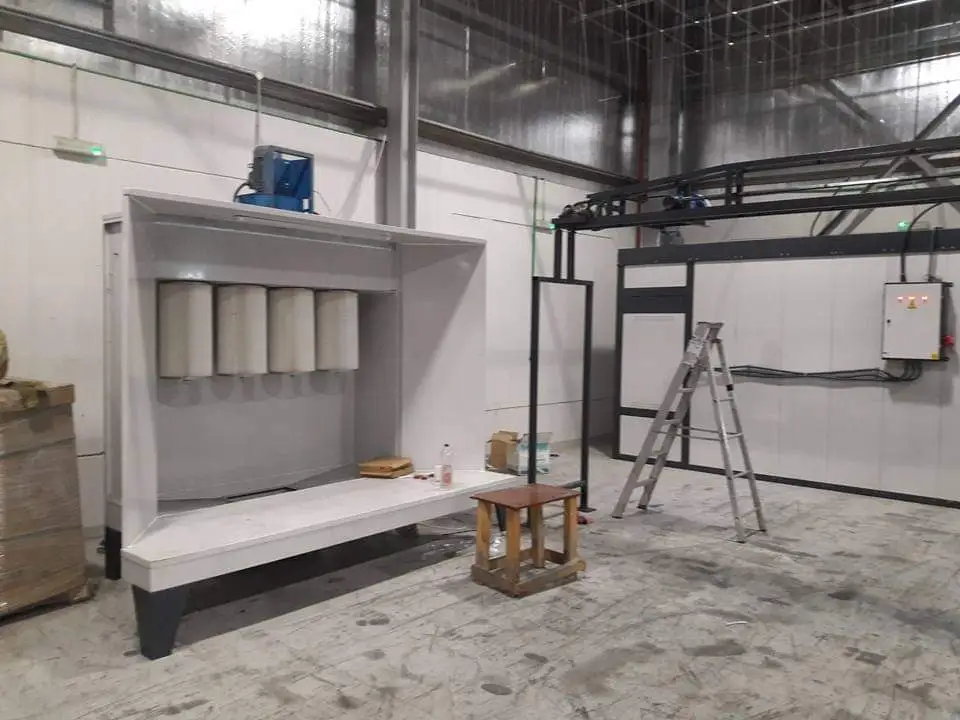
There are several types of powder coating booths, each with its own advantages and disadvantages. Some of the most common types include:
- Open-faced booths: These booths are open on one or more sides, which allows for easy access to the object being coated. However, open-faced booths are not as effective at containing overspray as other types of booths.
- Downward draft booths: These booths have a downward draft of air that helps to keep overspray from escaping the booth. Downward draft booths are more effective at containing overspray than open-faced booths, but they can be more expensive.
- Tunnel booths: These booths are enclosed on all sides and are used for coating large objects. Tunnel booths are the most effective at containing overspray, but they are also the most expensive.
- Robot booths: These booths are used to automate the powder coating process. Robot booths are more efficient and consistent than traditional booths, but they can be more expensive.
- Manual booths: These booths are operated by hand and are typically used for small objects. Manual booths are the least expensive type of booth, but they can be less efficient and consistent than other types of booths.
The type of powder coating booth that is right for you will depend on your specific needs and budget. If you are unsure of which type of booth to choose, you should consult with a powder coating expert.
Here is a table summarizing the different types of powder coating booths:
Type of booth | Advantages | Disadvantages |
---|---|---|
Open-faced booth | Easy access to object being coated | Not as effective at containing overspray |
Downward draft booth | More effective at containing overspray | More expensive |
Tunnel booth | Most effective at containing overspray | Most expensive |
Robot booth | More efficient and consistent | More expensive |
Manual booth | Least expensive | Less efficient and consistent |
Open-faced booths
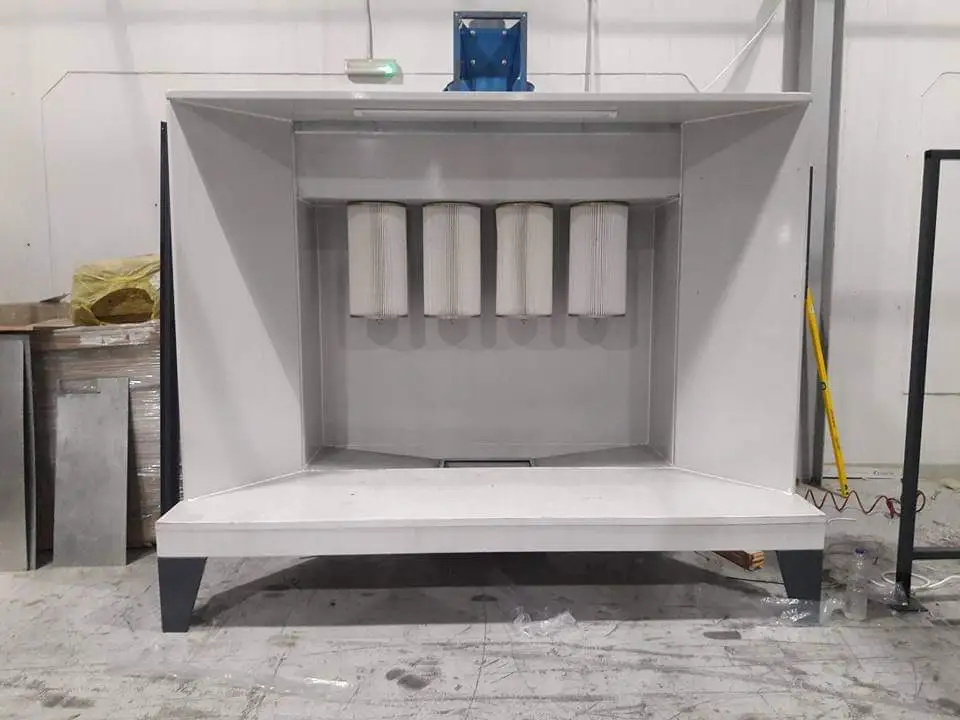
Open-faced powder coating booths are a type of powder coating enclosure that is typically used for small to medium-sized objects. They are open on one or more sides, which allows for easy access to the object being coated. However, open-faced booths are not as effective at containing overspray as other types of booths.
Advantages of open-faced powder coating booths:
- Easy access to the object being coated
- Less expensive than other types of booths
- Can be used for a variety of objects
- Easy to install and maintain
Disadvantages of open-faced powder coating booths:
- Not as effective at containing overspray
- Overspray can settle on nearby surfaces
- May not be suitable for use in high-traffic areas
Applications of open-faced powder coating booths:
- Coating small to medium-sized objects
- Coating objects with complex shapes
- Coating objects that are difficult to move
- Coating objects that require frequent access
Tips for using open-faced powder coating booths:
- Use a drop cloth or other protective covering to protect nearby surfaces from overspray.
- Make sure the booth is well-ventilated to prevent overspray from settling on nearby surfaces.
- Use a respirator or other personal protective equipment when using a powder coating booth.
Overall, open-faced powder coating booths are a versatile and affordable option for a variety of powder coating applications. However, it is important to be aware of their limitations and take steps to minimize overspray.
Tunnel booths
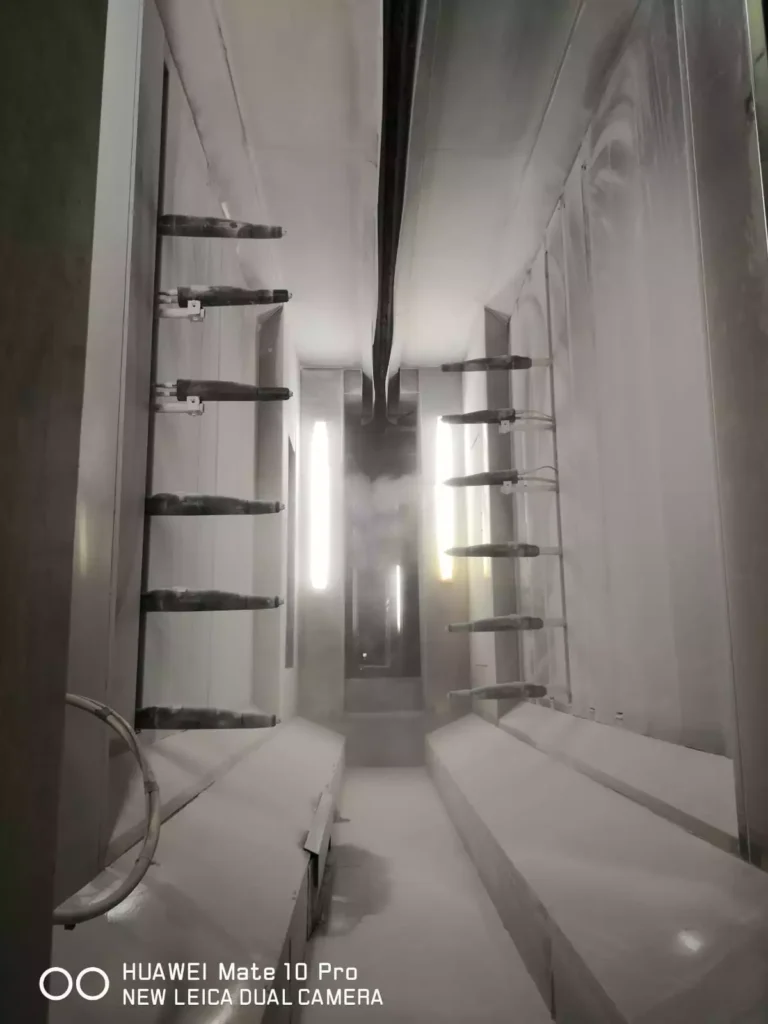
Tunnel powder coating booths are a type of powder coating enclosure that is typically used for coating large objects. They are enclosed on all sides and have an airflow system that removes overspray and fumes from the booth. Tunnel booths are the most effective type of booth at containing overspray, making them ideal for high-volume production.
Advantages of tunnel powder coating booths:
- Highly effective containment of overspray and fumes
- Suitable for coating large objects
- Efficient and consistent operation
- Can be automated for continuous production
- Minimal environmental impact
Disadvantages of tunnel powder coating booths:
- More expensive than other types of booths
- Larger footprint
- Requires more maintenance
- Not suitable for all objects (complex shapes or difficult access)
Applications of tunnel powder coating booths:
- Coating large metal objects such as automotive parts, appliances, and furniture
- Coating long or narrow objects such as pipes, beams, and shelving
- Coating objects with complex shapes or difficult access
- High-volume production environments
Tips for using tunnel powder coating booths:
- Ensure proper airflow and filtration to maintain containment efficiency.
- Regularly clean and maintain filters to optimize performance and prevent blockages.
- Implement quality control measures to monitor coating thickness and consistency.
- Use automated systems for continuous operation and minimize human error.
Overall, tunnel powder coating booths are a highly effective and efficient solution for large-scale powder coating applications. Their ability to contain overspray, automate the process, and minimize environmental impact makes them a valuable investment for businesses seeking consistent, high-quality results.
Manual Booths
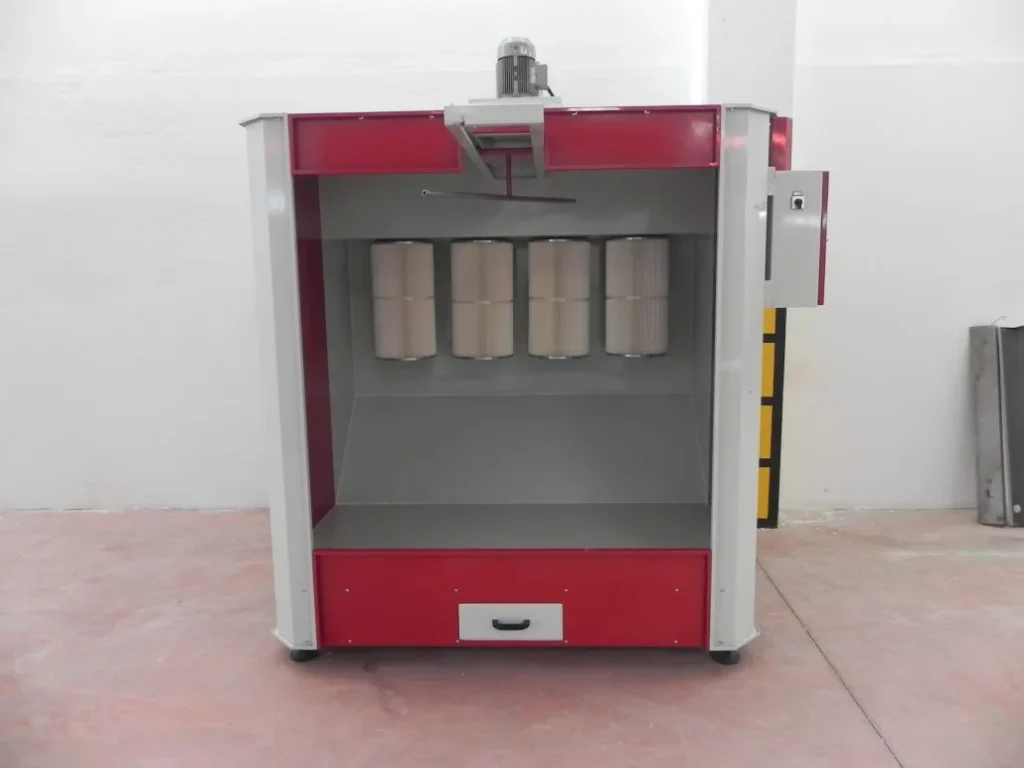
Manual powder coating booths, also known as spray booths, are enclosed workspaces used to apply dry powder coatings to various objects. They are typically smaller and less expensive than other types of powder coating booths, making them a popular choice for small-scale operations or hobbyists
Components of a Manual Powder Coating Booth:
- Booth Enclosure: The booth structure provides containment for overspray and fumes, ensuring a clean and safe working environment.
- Ventilation System: A fan or blower draws air through filters to remove overspray particles and fumes, maintaining air quality within the booth.
- Powder Feed System: A hopper or reservoir supplies powder to the spray gun, ensuring a consistent supply for coating application.
- Spray Gun: A manual or automatic spray gun applies the powder evenly onto the object being coated.
- Recovery System: Filters or a cyclone separator capture overspray particles, minimizing powder waste and environmental impact.
- Lighting System: Adequate lighting ensures proper visibility for the operator during the coating process.
Advantages of Manual Powder Coating Booths:
- Cost-effectiveness: Manual booths are generally less expensive than larger or automated booths, making them a budget-friendly option.
- Versatility: Manual booths can accommodate a variety of object sizes and shapes, suitable for various applications.
- Ease of Use: Manual booths are relatively easy to set up and operate, making them accessible to beginners or hobbyists.
- Flexibility: Manual booths can be adapted to various powder coating techniques, including electrostatic spraying and fluidized bed coating.
Disadvantages of Manual Powder Coating Booths:
- Labor Intensive: Manual booths require more operator involvement compared to automated systems, potentially increasing labor costs.
- Consistency: Manual application may result in variations in coating thickness and quality, requiring more operator skill and attention to detail.
- Lower Containment Efficiency: Manual booths may have slightly lower overspray containment compared to enclosed or tunnel booths.
Applications of Manual Powder Coating Booths:
- Small-scale Production: Manual booths are ideal for small production runs or custom coating projects.
- Hobbyist Use: DIY enthusiasts and hobbyists often use manual booths for personal projects due to their affordability and ease of operation.
- Coating Complex Shapes: Manual booths are suitable for coating objects with intricate designs or difficult access points.
- Repair and Restoration: Manual booths can be used for powder coating repairs, restorations, and touch-ups.
Tips for Using Manual Powder Coating Booths:
- Proper Ventilation: Ensure adequate ventilation to remove overspray particles and fumes, maintaining air quality and safety.
- Powder Preparation: Properly prepare the powder by mixing and sieving to ensure consistent particle size and prevent clogging.
- Spray Gun Technique: Practice proper spray gun technique, maintaining a consistent distance and angle to achieve even coating thickness.
- Clean and Maintenance: Regularly clean and maintain the booth, filters, and spray gun to prevent contamination and ensure optimal performance.
- Safety Precautions: Follow safety precautions, wear appropriate personal protective equipment, and handle powder with care to avoid inhalation or skin contact.
Powder Coating Booth Price
The powder coating booth price is our own manufacturing, made in our own production in Turkey. As a powder coating spray booth manufacturer, we can divide the powder coating booths into 2 main commercial categories.
- Commercial Powder Spray Booth
- DIY Powder Coating Booth
Companies make a commercial powder spray booth and they have some specific traditional values such as dimensions, material, and working power. DIY powder coating booth is made by amateurs or companies not related to the powder coating industry. DIY powder coating booths are made with galvanized or stainless steel sheets. The spray booths can be made with cartridge filters for dust collection.
The powder coating booth for sale can be a manual booth or an automatic spray booth. The difference between the manual and automatic paint systems is in the number of parts to be coated. Manual powder spray booths also have a recovery system with cartridge filters.
The manual coating booths can also be portable. They can be moved on their wheels in the production hall according to their needs. The manual powder coating spray booth have an exhaust fan on their top. These exhaust fans suck the air through the spray filters for cleaning and recuperation.
Powder Coating Booth Price Ranges

Cartridge System/Powder Collection Booths are typically used in batch and low/medium production applications. This booth features a cartridge filtration system using the module, which re-circulates clean, filtered air. The powder module includes a high-performance non-sparking fan, six high-efficiency primary cartridge filters, reverse pulse jet solenoids, and four final filters.
The deluxe control panel features a Photohelic pressure gauge that monitors pressure drop and initiates the high-velocity pulse of air that is automatically injected into each filter sequentially. This means that you change filters less often.
FEATURES
• White pre-coated galvanized steel panels
• Energy efficient inside access light fixture(s)
• Collector Module features high-efficiency cartridge filters and air solenoid for filter maintenance
• Standard differential pressure gauge with a safety interlock for automatic shut down when air pressure exceeds its normal operating range.
OPTIONS
• Fluidized bed for powder recovery (pump not included).
• Powder modules can be purchased separately
• Conveyor openings
• Booth extensions
• Control panel (UL listed) factory assembled, pre-wired, and numbered with motor starter, fuse disconnect – on/off switch, and a solid-state timer for adjustments of sequential pulse cleaning
Powder Coating Spray Booth Characteristics
OPTIONS
• Fluidized bed for powder recovery (pump not included).
• Powder modules can be purchased separately
• Conveyor openings
• Booth extensions
• Control panel (UL listed) factory assembled, pre-wired, and numbered with motor starter, fuse disconnect – on/off switch, and a solid-state timer for adjustments of sequential pulse cleaning
- Fluorescent lighting
- Central air manifold with required regulators
- 2-speed fan control with operating & cleaning modes
- Roll on/off track system
- Flame detection system
Request for product quality and performance has resulted in a full line of accessories that have been designed and manufactured for durability and long-lasting, trouble-free service. Great emphasis is placed on our engineering and workmanship so that GFS customers will receive the best products at competitive prices. Approved Replacement Parts and Filters GFS is also your approved full-line supplier for Parts and Filters for:
• Binks Booths
• DeVilbiss Booths
• JBI Booths & Ovens
• Blu-Surf Systems
• Milbanks Systems
• Other Spray Booth Manufacturers
• Filters (all Makes & Models)
• Electrical Components
• Oven Components
• Lighting
• Motors
• Fans
• Exhaust Ductwork
• Doors
• Grates and Pans
• Panels
• Filter Racks
• Insulation
• Hardware
• Spray Booth Accessories
• Other Miscellaneous
A powder coating booth is a controlled environment designed for the application of powder coating onto surfaces of various materials. The booth serves to contain and control the powder overspray, ensuring an efficient and clean coating process. Here are the key components and considerations for a powder coating booth:
- Enclosure:
- The booth is enclosed with walls, a ceiling, and a floor to contain the powder overspray and prevent it from escaping into the surrounding environment.
- The construction materials should be durable, easy to clean, and resistant to the build-up of powder residue.
- Ventilation System:
- An effective ventilation system is crucial to remove airborne powder particles and maintain a safe working environment.
- Exhaust fans are used to create airflow that captures overspray and directs it to the filtration system.
- Filtration System:
- The filtration system captures and filters out powder particles from the air before it is released into the environment.
- Primary and secondary filters are commonly used to achieve efficient filtration.
- Lighting:
- Adequate lighting is essential for operators to see and inspect workpieces during the coating process.
- Light fixtures are strategically positioned to minimize shadows and provide uniform illumination.
- Grounding and Static Control:
- Grounding measures, including grounding wires and rods, are implemented to dissipate static electricity and prevent electrostatic discharge.
- Anti-static flooring or grounding straps for personnel may be used to further control static.
- Powder Application Equipment:
- Powder coating guns and related equipment are used to apply the dry powder to the workpieces.
- The equipment should be properly maintained to ensure consistent and high-quality coatings.
- Recovery System:
- A powder recovery system captures overspray for reuse, minimizing waste and optimizing the use of powder materials.
- This system may include collector modules, filters, and a reclaiming hopper.
- Control Panel:
- A central control panel allows operators to manage various aspects of the powder coating process, such as fan speed, temperature, and safety features.
- Personnel Protection:
- Operators should be provided with personal protective equipment (PPE) including gloves, masks, and aprons to ensure their safety during the coating process.
- Access Doors:
- Access doors provide entry and exit points for operators and are designed to prevent powder leakage.
- Powder Storage Area (if applicable):
- Some booths may include a designated area for storing different types and colors of powder.
- Fire Suppression System:
- In case of a fire, a fire suppression system may be installed to quickly and effectively control and extinguish flames.
- Compliance with Regulations:
- The powder coating booth should comply with local environmental and safety regulations related to powder coating operations.
- Monitoring Systems:
- Monitoring systems may be integrated to track and display various parameters, ensuring the booth operates within specified parameters.
- Cleanout System:
- A system for cleaning and maintaining the booth, such as vacuum systems for removing accumulated powder.
Properly designing, installing, and maintaining a powder coating booth is crucial for achieving consistent, high-quality coatings and ensuring the safety of the operators and the environment. It’s important to consider the specific needs of the coating operation, including the type of workpieces, the volume of production, and compliance with industry regulations. Regular maintenance and operator training contribute to the successful and safe operation of the powder coating booth.
Enclosure
The enclosure of a powder coating booth is a critical component that provides a controlled environment for the powder coating process, containing overspray and maintaining a clean working space. Here are key aspects of the enclosure in a powder coating booth:
- Materials:
- The enclosure is constructed using materials that are durable, corrosion-resistant, and easy to clean. Common materials include galvanized steel, stainless steel, or other non-porous surfaces.
- Walls, Ceiling, and Floor:
- The booth is enclosed by walls, a ceiling, and a floor to create a contained space.
- The walls and ceiling are typically made of panels that form a smooth and seamless surface, preventing the accumulation of powder particles.
- Seals and Gaskets:
- Seals and gaskets are used at joints, access doors, and other openings to ensure an airtight seal.
- Proper seals prevent the escape of powder particles and maintain the efficiency of the ventilation system.
- Access Doors:
- Access doors provide entry and exit points for operators and equipment.
- Doors should be equipped with proper sealing mechanisms to prevent powder leakage.
- Windows or Viewing Panels:
- Some booths may include windows or viewing panels to allow operators to monitor the coating process without opening doors.
- These panels are typically made of materials that are easy to clean.
- Lighting:
- Adequate lighting is essential for operators to see and inspect workpieces during the coating process.
- Light fixtures are strategically placed to minimize shadows and provide uniform illumination.
- Grounding Points:
- Grounding points are installed throughout the enclosure to dissipate static electricity and prevent electrostatic discharge.
- Proper grounding is essential for the safety of operators and the effectiveness of the coating process.
- Anti-Static Flooring (Optional):
- In some cases, the booth floor may be equipped with anti-static or conductive flooring materials to enhance static dissipation.
- Anti-static flooring contributes to a safer working environment.
- Modular Construction (Optional):
- Some booths are designed with a modular construction, allowing for flexibility in size and configuration.
- Modular booths can be easily expanded or reconfigured to accommodate changing production needs.
- Cleanout Accessibility:
- The enclosure should be designed with features that facilitate easy cleaning and maintenance.
- Removable panels or access points allow operators to clean all areas effectively.
- Fire-Resistant Materials (Optional):
- Depending on safety regulations and requirements, certain components of the enclosure may be constructed using fire-resistant materials.
- Fire-resistant materials help contain and minimize the spread of fire in case of an emergency.
- Environmental Compliance:
- The enclosure design and materials should comply with local environmental regulations governing powder coating operations.
When designing a powder coating booth enclosure, it’s crucial to consider the type of workpieces, the volume of production, and adherence to safety and environmental regulations. Regular maintenance and cleaning of the enclosure contribute to the overall efficiency and safety of the powder coating process.
Ventilation System
The ventilation system in a powder coating booth is a crucial component that plays a key role in maintaining a controlled environment, removing airborne powder particles, and ensuring the safety of operators. Here are the key aspects of a ventilation system in a powder coating booth:
- Exhaust Fans:
- Powerful exhaust fans are installed to create controlled airflow within the booth.
- These fans draw in air containing overspray and direct it toward the filtration system for removal.
- Airflow Design:
- The ventilation system is designed to establish a consistent and controlled airflow pattern within the booth.
- Proper airflow ensures the capture of overspray and prevents the escape of powder particles.
- Ductwork:
- Ducts are used to transport air from the booth to the exterior or to a filtration system.
- Well-designed ductwork ensures efficient and effective removal of contaminants.
- Air Intake System:
- An intake system is incorporated to balance the airflow within the booth.
- It helps prevent negative pressure, which can affect the performance of the exhaust system.
- Balancing Airflow:
- The ventilation system is designed to balance the airflow, avoiding turbulence and ensuring consistent coating application.
- Variable Airflow Control:
- Some systems may have variable speed controls to adjust the airflow based on specific coating requirements and workpiece sizes.
- Air Velocity Control:
- Control mechanisms may be in place to adjust the speed and direction of the airflow, allowing for optimization based on the coating process.
- Exhaust Openings:
- Exhaust openings or outlets are strategically positioned to capture overspray and direct it out of the booth.
- These openings are connected to the ductwork leading to the exhaust fan(s).
- Air Filters:
- Air filters are an integral part of the ventilation system, capturing and removing powder particles from the air.
- Primary and secondary filters are commonly used and should be regularly checked and replaced to maintain efficiency.
- Positive Pressure Zones:
- In some systems, positive pressure zones may be created to prevent outside air, contaminants, or ambient humidity from entering the booth.
- Environmentally Controlled Systems:
- Some advanced systems may include features to control temperature and humidity within the booth for optimal coating conditions.
- Monitoring Systems:
- Monitoring systems may be implemented to track the performance of the ventilation system, including airflow, pressure, and filter status.
- Alarms or indicators may alert operators if issues arise.
- Emergency Stop Controls:
- Emergency stop controls should be in place to quickly shut down the ventilation system in case of an emergency.
- Compliance with Regulations:
- The design and operation of the ventilation system should comply with local environmental and safety regulations governing powder coating operations.
A well-designed and maintained ventilation system is essential for creating a safe and efficient powder coating environment. It ensures the removal of airborne contaminants, provides a clean working space, and contributes to the overall quality of powder coating applications. Regular inspections, cleaning, and filter replacements are necessary to maintain the effectiveness of the ventilation system.
Filtration System
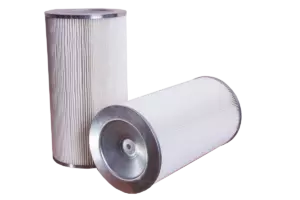
The filtration system in a powder coating booth is a critical component designed to capture and remove powder particles from the air, ensuring a clean and safe working environment. Here are the key components and considerations for a filtration system in a powder coating booth:
- Primary Filters:
- Primary filters are the first line of defense and capture larger particles of overspray.
- They prevent these particles from reaching the more sensitive secondary filters, extending the life of the entire filtration system.
- Secondary Filters:
- Secondary filters are designed to capture finer particles that may pass through the primary filters.
- These filters provide higher efficiency in removing smaller particles from the air.
- Filter Housing and Frames:
- The filtration system includes housings and frames to securely hold the filters in place.
- Well-designed frames ensure a proper seal to prevent air bypass and maximize filtration efficiency.
- Filter Media:
- Filters are made of media that is specifically designed to capture and retain powder particles.
- Common filter media includes polyester, fiberglass, or other materials with high particle retention capabilities.
- Filter Replacement Indicators:
- Some systems are equipped with indicators to signal when filters need replacement.
- Regularly replacing filters is essential for maintaining optimal airflow and filtration efficiency.
- Accessibility for Maintenance:
- The filtration system should be designed for easy access to facilitate regular maintenance tasks such as filter replacement and cleaning.
- Air-to-Cloth Ratio:
- The air-to-cloth ratio is a key consideration in filter design and refers to the volume of air that can be filtered per unit of filter surface area.
- Properly balancing this ratio is crucial for efficient filtration.
- Filter Efficiency Rating:
- Filters are assigned an efficiency rating based on their ability to capture particles of a certain size.
- High-efficiency filters are important for maintaining air quality and complying with environmental regulations.
- Filter Type:
- Depending on the specific requirements and regulations, different types of filters may be used, such as bag filters, cartridge filters, or panel filters.
- Environmental Compliance:
- The filtration system must comply with local environmental regulations regarding the control of airborne contaminants generated during powder coating.
- Filter Disposal:
- Proper disposal methods for used filters must be followed to adhere to environmental guidelines.
- Filter Cleaning or Replacement Schedule:
- Establishing a regular schedule for filter maintenance, cleaning, or replacement is essential to ensure consistent performance.
- Pressure Drop Monitoring:
- Monitoring the pressure drop across the filters helps identify when they are becoming clogged and need replacement.
Regular inspection and maintenance of the filtration system are crucial to the overall performance of the powder coating booth. It not only ensures a clean working environment but also contributes to the longevity and efficiency of the entire powder coating system.
Powder Coating Booth Types
Powder coating booths come in various types, each designed to meet specific application needs and production requirements. The choice of a powder coating booth depends on factors such as the type of workpieces, production volume, available space, and the desired level of automation. Here are some common types of powder coating booths:
- Open-Front Powder Booths:
- Open-front booths are the most basic type, featuring an open front where operators manually load and unload workpieces.
- They are suitable for small-scale operations and manual powder coating applications.
- Recovery Powder Booths:
- Recovery booths are equipped with a powder recovery system to collect oversprayed powder for reuse.
- These booths help minimize powder waste and optimize material usage.
- Batch Powder Booths:
- Batch booths are designed for small to medium-sized production runs where workpieces are coated in batches.
- Operators manually load and unload the workpieces for each coating cycle.
- Continuous Powder Booths:
- Continuous booths are designed for high-volume production with a continuous conveyor system.
- Workpieces move through the booth on a conveyor, ensuring a continuous and efficient coating process.
- Powder Coating Rooms:
- Powder coating rooms are fully enclosed spaces that provide a controlled environment for the coating process.
- These rooms may have multiple booths, dedicated air handling systems, and environmental controls.
- Automated Powder Booths:
- Automated booths feature robotic or automated systems for powder application and workpiece handling.
- They are suitable for high-volume production lines with a focus on efficiency and precision.
- Compact Powder Booths:
- Compact booths are designed for limited space applications where a smaller footprint is required.
- They are suitable for small workshops or facilities with space constraints.
- Custom Powder Booths:
- Custom booths are designed to meet specific requirements and can be tailored to accommodate unique workpieces or production processes.
- Customization may include size, configuration, and additional features.
- Fast Color Change Booths:
- Fast color change booths are designed to facilitate quick and efficient color changes.
- They may include features such as quick-release components and automatic cleaning systems.
- Manual Powder Booths:
- Manual booths are operated by personnel who manually apply the powder coating using handheld powder coating guns.
- They are suitable for smaller operations or situations where manual control is preferred.
- Pass-Through Powder Booths:
- Pass-through booths have openings on both ends, allowing workpieces to pass through the booth.
- They are suitable for integration into existing production lines.
- Curing Booths:
- Curing booths are designed to include curing ovens within the booth structure.
- After powder application, workpieces move directly into the curing section for the curing process.
- Reciprocator Booths:
- Reciprocator booths feature a reciprocating system that moves the powder coating gun back and forth, providing more uniform coverage.
- They are often used in automated systems for precise and consistent coating.
When selecting a powder coating booth, it’s essential to consider the specific requirements of the application, production goals, and available resources. The chosen booth type should align with the workflow and efficiency goals of the powder coating operation.
Open-Front Powder Booths
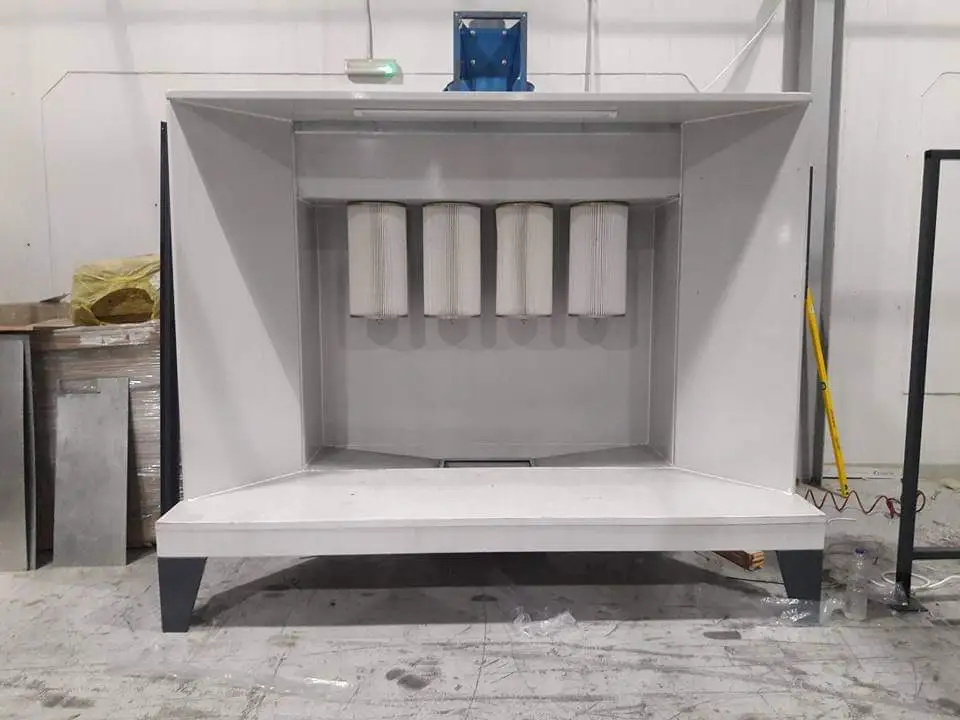
Open-front powder booths are a type of powder coating booth that features an open front, allowing for manual loading and unloading of workpieces by operators. These booths are commonly used in small-scale operations, workshops, or situations where the coating process is primarily manual. Here are key characteristics and considerations for open-front powder booths:
- Design and Structure:
- Open-front booths are typically enclosed on three sides (back and sides) with an open front where operators have direct access to the workpieces.
- The structure may consist of panels made of durable materials such as galvanized steel, stainless steel, or other corrosion-resistant materials.
- Manual Operation:
- Workpieces are manually loaded onto hangers or racks, coated with powder by operators using handheld powder coating guns, and then manually unloaded after coating.
- This manual operation is suitable for small production volumes or custom workpieces.
- Powder Application Equipment:
- Open-front booths are compatible with handheld powder coating guns.
- Operators use these guns to apply the dry powder coating to the surfaces of the workpieces.
- Operator Access:
- The open front provides easy access for operators to visually inspect the workpieces during the coating process.
- Operators can move around the booth to ensure thorough and uniform powder application.
- Flexible Workpiece Handling:
- Workpieces of various shapes and sizes can be accommodated in open-front booths.
- The flexibility of manual handling allows for customization and adaptation to different workpiece geometries.
- Space Requirements:
- Open-front booths may have a smaller footprint compared to larger automated booths.
- They are suitable for facilities with limited space.
- Limited Automation:
- While open-front booths are manually operated, they can still be integrated with basic automation, such as conveyors for moving workpieces in and out of the booth.
- Color Change:
- Changing colors in open-front booths involves purging the powder coating gun and may require manual cleaning or changing of hoses.
- Color change times may be longer compared to more automated systems.
- Ventilation System:
- The booth should be equipped with a ventilation system to capture overspray and maintain a clean working environment.
- Exhaust fans help direct overspray to the filtration system.
- Operator Safety:
- Personal protective equipment (PPE) should be provided to operators, including gloves, masks, and appropriate clothing.
- Adequate ventilation ensures that operators are not exposed to high concentrations of airborne powder.
- Powder Recovery System (Optional):
- Some open-front booths may include a powder recovery system to collect and reclaim oversprayed powder for reuse.
- This helps minimize waste and optimize material usage.
Open-front powder booths are suitable for applications where manual control and flexibility are important, such as small-batch production, custom workpieces, or situations with limited automation requirements. While they may have limitations in terms of production volume and speed, open-front booths offer simplicity, affordability, and adaptability to a variety of coating needs.
Recovery Powder Booths
Recovery powder booths, also known as powder recovery booths or powder reclamation booths, are specialized types of powder coating booths equipped with a powder recovery system. The primary purpose of these booths is to capture oversprayed powder particles, reclaim them, and then reuse the recovered powder. Here are key features and considerations for recovery powder booths:
- Powder Recovery System:
- The distinguishing feature of recovery powder booths is the inclusion of a powder recovery system.
- This system collects and separates oversprayed powder particles from the air, allowing for the reclamation and reuse of the powder.
- Collector Modules or Filters:
- Collector modules or filters are positioned within the booth to capture oversprayed powder.
- These filters are designed to allow clean air to pass through while retaining the powder particles.
- Reclaiming Hopper or Cyclone Separator:
- The collected powder is directed to a reclaiming hopper or a cyclone separator where separation of the powder from the air occurs.
- Gravity or centrifugal force is used to separate the powder, allowing it to be reclaimed for reuse.
- Powder Recovery Pump:
- Some systems may incorporate a powder recovery pump to assist in transporting the collected powder from the booth to the reclaiming hopper.
- Fluidizing System:
- A fluidizing system within the reclaiming hopper ensures that the collected powder remains in a fluid-like state for ease of transport and application.
- Powder Storage System:
- The recovered powder is directed to a storage system, which may include bins or containers.
- Properly designed storage systems allow for easy retrieval and reuse of the reclaimed powder.
- Filter Cleaning Mechanism (Optional):
- Some recovery powder booths may include a filter cleaning mechanism to enhance the efficiency of the filtration system.
- This mechanism may involve automatic cleaning of filters to prevent clogging and maintain optimal performance.
- Powder Sieve:
- A powder sieve may be used in the recovery system to remove any impurities or larger particles from the reclaimed powder.
- This step ensures that the recovered powder is of high quality and suitable for reuse.
- Powder Recirculation (Optional):
- In some setups, recovered powder may be recirculated back into the powder delivery system for application.
- Recirculation helps maximize the utilization of powder and minimize waste.
- Monitoring and Control Systems:
- Monitoring systems may be integrated to track the performance of the recovery system.
- Control systems may adjust parameters to optimize powder recovery efficiency.
- Compliance with Environmental Regulations:
- Recovery powder booths should comply with local environmental regulations related to the handling and reuse of powder materials.
- Proper disposal methods for used filters and waste powder must be followed.
- Maintenance and Cleaning:
- Regular maintenance and cleaning of the recovery system components are crucial for its efficient operation and longevity.
Recovery powder booths are especially beneficial in reducing powder waste, optimizing material usage, and improving the overall sustainability of powder coating processes. They are suitable for applications where efficient powder recovery and reuse are priorities.
Batch Powder Booths
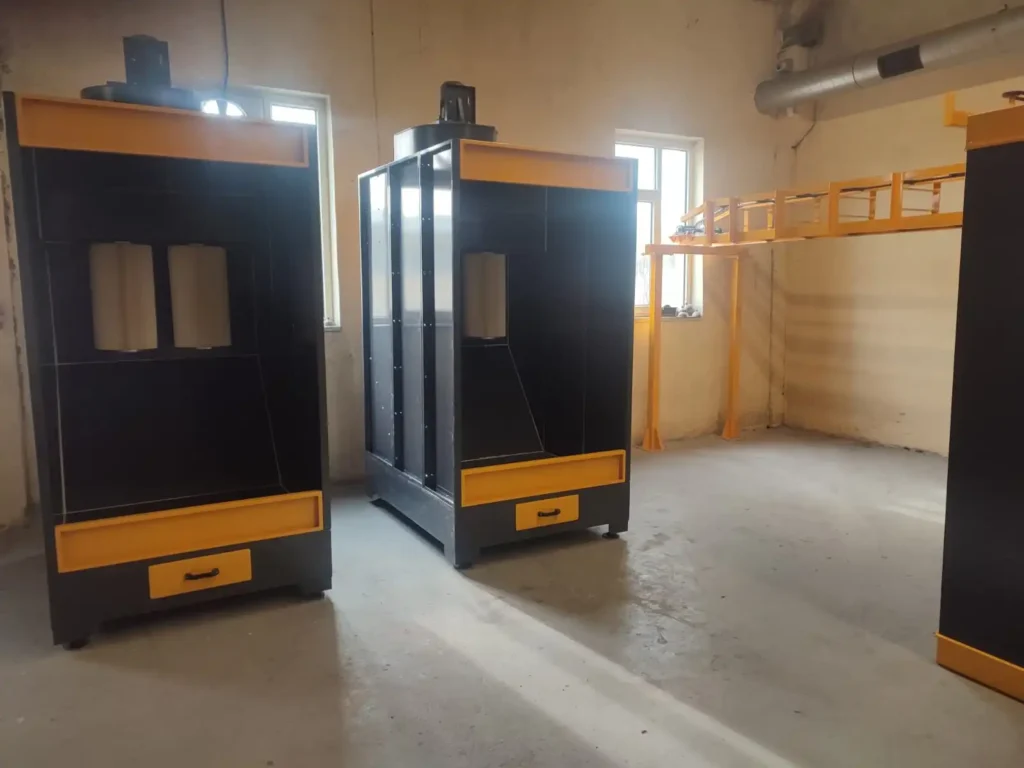
Batch powder booths are designed for small to medium-sized powder coating operations where workpieces are coated in batches. These booths are characterized by their manual loading and unloading processes, making them suitable for situations where customization, flexibility, and smaller production volumes are priorities. Here are key features and considerations for batch powder booths:
- Manual Operation:
- Batch powder booths are manually operated, and workpieces are loaded onto hangers or racks by operators.
- Operators apply the powder coating manually using handheld powder coating guns.
- Enclosed Structure:
- These booths are fully enclosed structures with walls, a ceiling, and typically three sides (back and sides), providing a controlled environment for the coating process.
- Open Front:
- Batch powder booths have an open front, allowing operators to have direct access to the workpieces during loading, coating, and unloading.
- Flexibility in Workpiece Handling:
- Workpieces of various shapes and sizes can be accommodated in batch powder booths.
- The manual loading process allows for flexibility in handling different types of workpieces.
- Powder Application Equipment:
- Handheld powder coating guns are used for the application of dry powder coating to the surfaces of the workpieces.
- Operators have control over the coating process to ensure even and uniform coverage.
- Ventilation System:
- Batch powder booths are equipped with a ventilation system to capture overspray and maintain a clean working environment.
- Exhaust fans direct overspray to the filtration system.
- Powder Recovery System (Optional):
- Some batch powder booths may include a powder recovery system to collect and reclaim oversprayed powder for reuse.
- Recovery systems help minimize powder waste and optimize material usage.
- Accessibility for Maintenance:
- The booth design should allow easy access for maintenance tasks, such as cleaning or replacing filters, and checking the overall condition of the booth.
- Operator Safety:
- Personal protective equipment (PPE), including gloves, masks, and appropriate clothing, should be provided to operators.
- Adequate ventilation ensures that operators are not exposed to high concentrations of airborne powder.
- Color Change:
- Changing colors in batch powder booths involves purging the powder coating gun and may require manual cleaning or changing of hoses.
- Color change times may be longer compared to more automated systems.
- Powder Sieve (Optional):
- Some batch powder booths may include a powder sieve in the recovery system to remove impurities and larger particles from the reclaimed powder.
- Compliance with Regulations:
- Batch powder booths should comply with local environmental and safety regulations governing powder coating operations.
Batch powder booths are suitable for applications where manual control, customization, and flexibility are essential. They are commonly found in small to medium-sized job shops, custom coating facilities, and situations where production volumes do not justify continuous or automated powder coating lines
Continuous Powder Booths

Continuous powder booths are designed for high-volume powder coating operations where workpieces move through the booth on a continuous conveyor system. These booths provide an efficient and automated solution for large-scale production, ensuring a continuous flow of workpieces through the coating process. Here are key features and considerations for continuous powder booths:
- Conveyor System:
- Continuous powder booths are integrated with a conveyor system that moves workpieces through the booth.
- The conveyor system ensures a constant and controlled flow of workpieces, optimizing production efficiency.
- Automatic Loading and Unloading:
- Workpieces are typically loaded onto the conveyor automatically at the entrance of the booth and unloaded at the exit.
- This automation reduces the need for manual handling and increases production throughput.
- Enclosed Structure:
- Continuous powder booths have enclosed structures with walls, a ceiling, and three sides (back and sides) to contain overspray and maintain a controlled environment.
- Powder Application Equipment:
- Automated powder application equipment, such as robotic arms or reciprocators, is commonly used for the precise and uniform application of powder coating.
- This automation ensures consistent coating quality across a large volume of workpieces.
- Ventilation System:
- A ventilation system is integral to continuous powder booths, capturing overspray and directing it to the filtration system.
- Proper airflow design ensures effective overspray capture and containment.
- Powder Recovery System:
- Continuous booths often include a powder recovery system to collect and reclaim oversprayed powder for reuse.
- Recovery systems contribute to minimizing powder waste and optimizing material usage.
- Automatic Color Change Systems:
- Continuous powder booths may feature automatic color change systems that streamline the process of switching between different powder colors.
- Automated purging and cleaning processes reduce downtime associated with color changes.
- Environmental Controls:
- Some continuous booths may incorporate environmental controls, such as temperature and humidity regulation, to optimize coating conditions.
- Maintaining controlled environmental conditions contributes to consistent coating quality.
- Operator Monitoring and Control:
- Operators may have control panels for monitoring and adjusting various parameters, ensuring the booth operates within specified parameters.
- Automatic monitoring systems enhance process control and efficiency.
- Powder Sieve and Reclaiming Systems:
- Continuous booths may include powder sieves and advanced reclaiming systems to remove impurities and ensure the quality of the reclaimed powder.
- Customizable Configurations:
- Continuous powder booths can be customized based on the specific requirements of the production line, including size, configuration, and automation levels.
- Compliance with Regulations:
- Continuous powder booths must comply with local environmental and safety regulations governing powder coating operations.
Continuous powder booths are ideal for large-scale manufacturing environments where high production volumes and efficiency are paramount. The automation and continuous conveyor system contribute to consistent coating quality, reduced labor requirements, and increased overall productivity.
Powder Coating Rooms
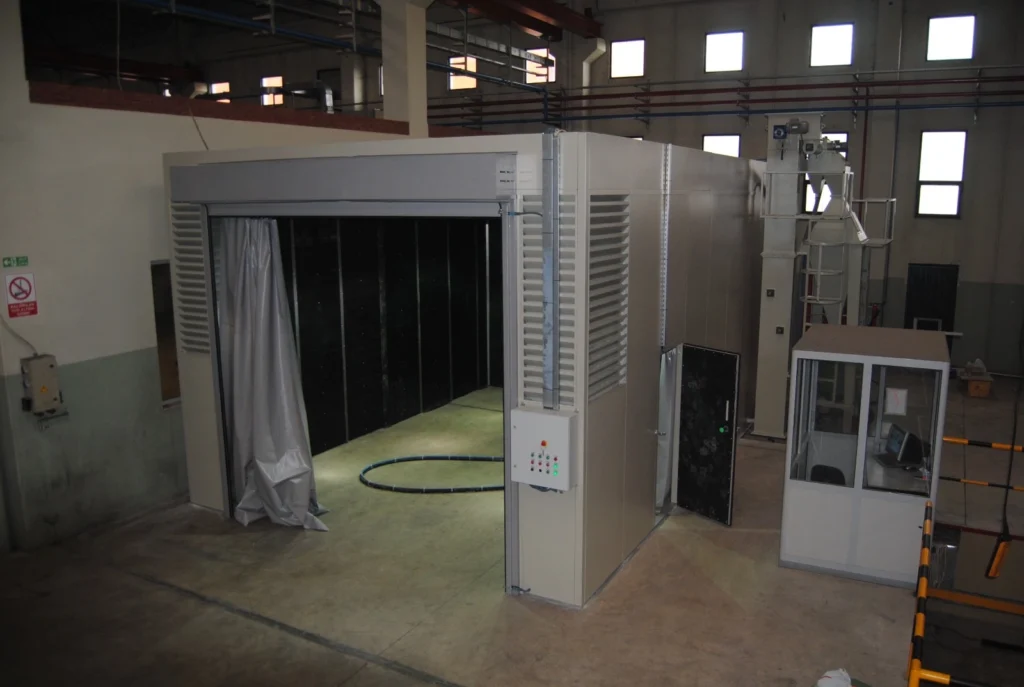
Powder coating rooms, also known as powder coating enclosures or powder coating environments, are fully enclosed spaces designed to provide a controlled and clean environment for powder coating processes. Unlike individual booths, powder coating rooms are larger structures that can accommodate multiple workstations or booths within the same enclosed space. Here are key features and considerations for powder coating rooms:
- Enclosed Structure:
- Powder coating rooms are fully enclosed structures with walls, a ceiling, and often a floor to create a controlled and contained environment.
- Walls are typically made of durable and smooth materials to prevent the accumulation of powder particles.
- Size and Configurations:
- Powder coating rooms vary in size and can be customized to fit the specific needs of the operation.
- They can be designed with multiple booths or workstations to accommodate different coating processes simultaneously.
- Operator Workstations:
- Workstations within the powder coating room may include manual or automated powder application equipment, such as handheld guns, robotic arms, or reciprocators.
- Operator workstations are strategically arranged to optimize workflow and efficiency.
- Powder Application Equipment:
- Powder coating rooms can accommodate various types of powder application equipment, depending on the production requirements.
- The choice of equipment may include manual guns, automatic guns, or a combination of both.
- Conveyor Systems (Optional):
- In larger powder coating rooms, conveyor systems may be integrated to facilitate the movement of workpieces through the coating process.
- Conveyors enhance efficiency and reduce the need for manual handling.
- Ventilation System:
- Powder coating rooms are equipped with a robust ventilation system to capture overspray and maintain a clean working environment.
- Exhaust fans direct overspray to the filtration system for efficient removal.
- Filtration System:
- A filtration system is essential for removing powder particles from the air to maintain air quality within the room.
- Primary and secondary filters are commonly used in conjunction with a powder recovery system.
- Powder Recovery System:
- Powder recovery systems within the room collect and reclaim oversprayed powder for reuse.
- These systems contribute to minimizing powder waste and optimizing material usage.
- Color Change Systems:
- Powder coating rooms may incorporate automatic color change systems to streamline the process of switching between different powder colors.
- Automated purging and cleaning processes reduce downtime associated with color changes.
- Temperature and Humidity Control (Optional):
- Depending on the coating requirements, some powder coating rooms may include environmental controls for temperature and humidity regulation.
- Controlled environmental conditions contribute to consistent coating quality.
- Operator Safety Measures:
- Personal protective equipment (PPE) should be provided to operators working within the powder coating room.
- Adequate ventilation and grounding measures contribute to a safe working environment.
- Monitoring and Control Systems:
- Powder coating rooms may include monitoring and control systems for overseeing various parameters, ensuring the coating process operates within specified conditions.
- Accessibility and Maintenance:
- The room design should allow for easy access and maintenance of equipment, filters, and other components.
- Accessibility is crucial for regular cleaning and upkeep.
- Compliance with Regulations:
- Powder coating rooms must comply with local environmental and safety regulations governing powder coating operations.
Powder coating rooms are suitable for larger-scale manufacturing operations that require simultaneous processing of multiple workpieces or different coating processes. Their customization options, environmental controls, and integration with advanced equipment make them versatile for various industrial applications.
Automated Powder Booths
Automated powder booths represent a high-tech and efficient approach to powder coating processes. These booths are designed to minimize manual intervention and optimize production throughput by incorporating automated systems for powder application, workpiece handling, and other key functions. Here are key features and considerations for automated powder booths:
- Robotic Powder Application:
- Automated powder booths often feature robotic arms equipped with powder coating guns for precise and consistent powder application.
- Robotic systems allow for programmable and repeatable coating processes.
- Reciprocators:
- Reciprocators are automated systems that move powder coating guns back and forth horizontally or vertically.
- They contribute to uniform coating coverage and are often used in conjunction with robotic arms.
- Automatic Workpiece Handling:
- Automated booths incorporate systems for the automatic loading and unloading of workpieces onto the conveyor or processing line.
- Conveyors, robots, or other material handling equipment move workpieces through the coating process without manual intervention.
- Conveyor Systems:
- Conveyor systems are commonly integrated into automated powder booths to facilitate the continuous movement of workpieces through the coating process.
- Automated conveyors contribute to increased production efficiency.
- Automatic Color Change Systems:
- Automated powder booths often include systems for rapid and efficient color changes.
- These systems may automate the purging, cleaning, and transitioning between different powder colors, reducing downtime.
- Controlled Environmental Conditions:
- Some automated booths may include environmental controls such as temperature and humidity regulation to optimize coating conditions.
- Controlled environments contribute to consistent coating quality.
- Monitoring and Control Systems:
- Automated powder booths are equipped with advanced monitoring and control systems.
- These systems oversee various parameters, ensuring the booth operates within specified conditions and can be controlled remotely.
- Powder Recovery Systems:
- Automated booths include efficient powder recovery systems that capture and reclaim oversprayed powder for reuse.
- Powder recovery systems contribute to minimizing waste and optimizing material usage.
- Integration with ERP Systems:
- In some advanced setups, automated powder booths may be integrated with enterprise resource planning (ERP) systems for seamless production management.
- Integration enhances data tracking, reporting, and overall process efficiency.
- Powder Sieve and Reclaiming Systems:
- Automated booths may incorporate advanced powder sieve and reclaiming systems to ensure the quality of the reclaimed powder.
- These systems remove impurities and larger particles from the reclaimed powder.
- Operator Interface:
- Automated powder booths typically feature user-friendly interfaces for operators to program, monitor, and control the coating process.
- Touchscreens or other interface technologies streamline operation.
- Safety Features:
- Automated booths prioritize operator safety with features such as safety sensors, emergency stop controls, and compliance with safety standards.
- Automated systems may be equipped with built-in safety protocols.
- Custom Configurations:
- Automated powder booths can be customized based on specific production requirements, including size, layout, and level of automation.
Automated powder booths are well-suited for high-volume manufacturing environments where efficiency, precision, and consistent coating quality are essential. The integration of robotics, conveyors, and advanced control systems allows for a streamlined and optimized powder coating process.
Compact Powder Booths
Compact powder booths are designed to provide a space-efficient solution for powder coating applications, particularly in situations where limited space is available. These booths are characterized by their smaller footprint while still maintaining the necessary features for effective powder coating. Here are key features and considerations for compact powder booths:
- Space-Efficient Design:
- Compact powder booths are specifically designed to occupy a smaller footprint, making them suitable for workshops or facilities with limited space.
- Enclosed Structure:
- Like larger powder booths, compact booths are fully enclosed structures with walls, a ceiling, and typically three sides (back and sides) to contain overspray.
- Manual Operation:
- Compact powder booths are often manually operated, with operators loading and unloading workpieces onto hangers or racks.
- Handheld powder coating guns are typically used for the application of dry powder coating.
- Ventilation System:
- These booths are equipped with a ventilation system that captures overspray and directs it to the filtration system for removal.
- Proper airflow design ensures effective overspray capture and containment.
- Filtration System:
- Compact booths include a filtration system with primary and secondary filters to remove powder particles from the air.
- Some may include a powder recovery system for the collection and reclamation of oversprayed powder.
- Powder Recovery System (Optional):
- Depending on the design, compact powder booths may feature a powder recovery system to collect and reclaim oversprayed powder for reuse.
- Recovery systems contribute to minimizing powder waste.
- Color Change:
- Color changes in compact powder booths typically involve purging the powder coating gun and may require manual cleaning or changing of hoses.
- Color change times may be longer compared to more automated systems.
- Operator Safety:
- Personal protective equipment (PPE), including gloves, masks, and appropriate clothing, should be provided to operators.
- Adequate ventilation ensures that operators are not exposed to high concentrations of airborne powder.
- Powder Sieve (Optional):
- Some compact powder booths may include a powder sieve in the recovery system to remove impurities and ensure the quality of the reclaimed powder.
- Simple Controls:
- Compact booths typically feature simple and easy-to-use controls for manual operation.
- Basic control panels may be used for adjusting parameters such as airflow and powder application settings.
- Accessibility and Maintenance:
- The compact design should allow for easy access to components for maintenance tasks, such as cleaning or replacing filters.
- Accessibility is crucial for regular cleaning and upkeep.
- Customization Options:
- While compact powder booths are generally designed with a smaller footprint, they can still be customized based on specific requirements, such as size and configuration.
Compact powder booths are suitable for smaller workshops, job shops, or facilities with limited space where manual operation is acceptable and the production volume may not justify a larger booth. They provide a cost-effective and efficient solution for powder coating applications in constrained environments.
Fast Color Change Booths
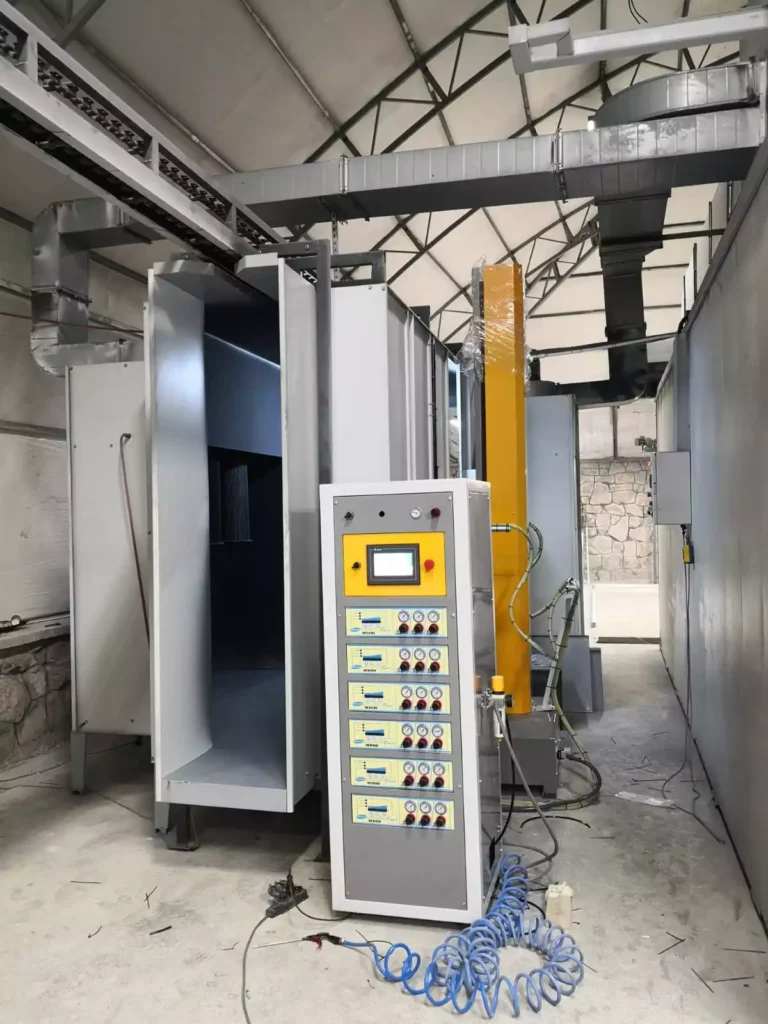
Fast color change booths are specialized powder coating booths designed to minimize downtime during the transition between different powder colors. These booths incorporate features and technologies that streamline the color change process, allowing for quick and efficient adjustments. Here are key features and considerations for fast color change booths:
- Color Change Modules:
- Fast color change booths are equipped with dedicated color change modules or systems that facilitate the quick transition between different powder colors.
- These modules may include components for powder purging, cleaning, and transitioning to a new color.
- Automatic Powder Purging:
- The booth may feature automatic powder purging systems that remove the existing powder from the application equipment, such as the powder coating guns.
- Purging helps prevent color contamination during the transition.
- Quick-Release Components:
- Fast color change booths are designed with quick-release mechanisms for various components, including powder hoses, nozzles, and other parts.
- Quick-release features enable rapid disassembly and reassembly during color changes.
- Powder Recovery System Design:
- The powder recovery system is optimized for quick and efficient color changes.
- Reclaiming systems should be designed to handle different powder types without extensive cleaning between color transitions.
- Color Change Carts or Modules:
- Some systems use color change carts or modules that can be quickly swapped in and out.
- These carts may contain pre-loaded powder and associated equipment for specific colors.
- Programmable Control Systems:
- Fast color change booths often feature programmable control systems that allow operators to pre-program color change sequences.
- Automated sequences can include purging, cleaning, and adjusting parameters for the new color.
- Powder Sieving and Quality Checks:
- Color change booths may include integrated powder sieving systems to ensure the quality of the reclaimed powder.
- Quality checks and monitoring systems may be incorporated to verify color consistency.
- Rapid Cleaning Systems:
- Cleaning systems within the booth are designed for speed and efficiency.
- Automated or semi-automated cleaning processes may be employed to reduce manual intervention.
- Color Change Time Reduction:
- The primary goal of fast color change booths is to significantly reduce the time required for color changes.
- This reduction in changeover time improves overall production efficiency.
- Operator Training and Ergonomics:
- Training programs and ergonomic designs are implemented to help operators efficiently execute color changes.
- User-friendly interfaces and controls contribute to ease of operation.
- Compatibility with Various Powder Types:
- Fast color change booths should be adaptable to different types of powders, including various colors, chemistries, and particle sizes.
- Compatibility ensures versatility in coating applications.
- Maintenance and Reliability:
- The booth design should facilitate easy maintenance and ensure reliable performance during color changeovers.
- Regular maintenance tasks should be straightforward and not contribute to extended downtime.
Fast color change booths are particularly valuable in production environments where frequent color changes are required. These booths contribute to increased operational efficiency, reduced waste, and improved overall productivity in powder coating processes.
Manual Powder Booths
Manual powder booths are powder coating booths where the application of the dry powder coating is carried out manually by operators. These booths are suitable for small to medium-scale operations where a high level of customization and manual control over the coating process is desired. Here are key features and considerations for manual powder booths:
- Manual Operation:
- In manual powder booths, operators are responsible for loading workpieces onto hangers or racks, applying the powder coating using handheld powder coating guns, and unloading the coated workpieces.
- Handheld Powder Coating Guns:
- Manual powder booths use handheld powder coating guns, allowing operators to have direct control over the application process.
- These guns are operated manually to apply the dry powder coating to the surfaces of the workpieces.
- Enclosed Structure:
- Manual powder booths are fully enclosed structures with walls, a ceiling, and typically three sides (back and sides) to contain overspray and create a controlled environment.
- Open Front:
- These booths have an open front, providing easy access for operators to load, coat, and unload workpieces.
- The open front design facilitates manual handling and visual inspection of the workpieces during the coating process.
- Ventilation System:
- Manual powder booths are equipped with a ventilation system to capture overspray and maintain a clean working environment.
- Exhaust fans help direct overspray to the filtration system for efficient removal.
- Filtration System:
- The booth includes a filtration system with primary and secondary filters to remove powder particles from the air.
- Some booths may also feature a powder recovery system to collect and reclaim oversprayed powder.
- Color Change:
- Changing colors in manual powder booths involves purging the powder coating gun and may require manual cleaning or changing of hoses.
- Color change times are generally longer compared to more automated systems.
- Operator Safety:
- Personal protective equipment (PPE), including gloves, masks, and appropriate clothing, should be provided to operators.
- Adequate ventilation ensures that operators are not exposed to high concentrations of airborne powder.
- Flexibility in Workpiece Handling:
- Workpieces of various shapes and sizes can be accommodated in manual powder booths.
- The flexibility of manual handling allows for customization and adaptation to different workpiece geometries.
- Powder Sieve (Optional):
- Some manual powder booths may include a powder sieve in the recovery system to remove impurities and ensure the quality of the reclaimed powder.
- Accessibility and Maintenance:
- The booth design should allow easy access for maintenance tasks, such as cleaning or replacing filters, and checking the overall condition of the booth.
- Regular maintenance tasks should be straightforward.
- Cost-Effective Solution:
- Manual powder booths are often a cost-effective solution for smaller operations or applications with lower production volumes.
- They require less upfront investment compared to automated systems.
Manual powder booths are suitable for applications where manual control, customization, and flexibility are important considerations. They are commonly found in smaller job shops, custom coating facilities, or situations where the coating process is more artisanal in nature.
Powder coating is a dry finishing process where an electrostatically charged powder is sprayed onto a metal surface and then cured in an oven to form a durable, smooth, and uniform coating. It is commonly used on automotive parts, furniture, and industrial equipment.
2. Gather the Necessary Equipment
To start powder coating, you’ll need the following equipment:
Essential Equipment:
- Powder Coating Gun – A spray gun that applies the powder using electrostatic charge.
- Powder Coating Booth – An enclosed space to contain overspray.
- Curing Oven – An oven that heats the coated parts to fuse the powder.
- Air Compressor – Supplies air for the spray gun.
- Powder Coating Powder – Available in different colors and finishes.
- Grounding System – Ensures proper adhesion and safety.
- Cleaning and Pre-Treatment Supplies – Degreasers, phosphate coatings, or sandblasters for surface preparation.
Optional but Useful Equipment:
- Spray Booth Ventilation System – Helps remove excess powder.
- Infrared Curing Lamps – For small projects or touch-ups.
- Masking Materials – For areas that should not be coated.
3. Prepare the Metal Surface
Proper surface preparation is critical for adhesion and durability.
- Cleaning – Remove dirt, grease, and oil using a degreaser or alkaline cleaner.
- Media Blasting – Use sandblasting or bead blasting to remove rust, old paint, or oxidation.
- Chemical Pre-Treatment – Apply a phosphate or chromate coating for corrosion resistance.
- Drying – Ensure the surface is completely dry before applying powder.
4. Apply the Powder
- Ground the Part – Attach the grounding clamp to prevent powder from repelling.
- Use the Powder Gun – Fill the spray gun with powder and set the right voltage (typically 10-100 kV).
- Apply an Even Coat – Move the gun in smooth, overlapping motions.
- Inspect the Coating – Ensure even coverage before curing.
5. Cure the Powder
- Preheat the Oven – Typically, powder coatings cure at 350–450°F (175–230°C).
- Bake the Coated Part – Place the item in the oven and cure according to the powder manufacturer’s specifications (usually 10-20 minutes after reaching the required temperature).
- Cool Down – Let the part cool before handling.
6. Quality Inspection
- Check for uniformity, adhesion, and gloss.
- Perform a scratch or adhesion test if needed.
- If necessary, reapply and re-cure for touch-ups.
7. Safety Precautions
- Wear Personal Protective Equipment (PPE) (gloves, respirator, safety glasses).
- Ensure Proper Ventilation to avoid inhaling powder.
- Keep Electrical Equipment Grounded to prevent static discharge.
- Follow Fire Safety Rules, as some powders are flammable before curing.
8. Start Small and Expand
If you’re a beginner, start with small projects and practice on scrap metal before coating important parts. Once you’re confident, consider expanding into custom projects, automotive parts, or even a professional powder coating business.
Starting powder coating requires understanding the process and gathering the right equipment. Powder coating is a dry finishing technique where electrostatically charged powder is sprayed onto a metal surface and cured in an oven to create a durable finish. To begin, you’ll need a powder coating gun, a spray booth, a curing oven, an air compressor, grounding equipment, and cleaning supplies like degreasers and sandblasting tools. The process starts with surface preparation, which involves cleaning, media blasting, and sometimes applying a phosphate or chromate coating for better adhesion and corrosion resistance.
Once the surface is prepped and dried, the part is grounded, and powder is applied using the spray gun, ensuring even coverage with smooth, overlapping strokes. After coating, the part is cured in an oven at temperatures ranging from 350–450°F for 10-20 minutes, depending on the powder type. After curing, the part is left to cool, and a quality inspection is performed to check adhesion, gloss, and uniformity. Safety is crucial, so always wear PPE like gloves, a respirator, and safety glasses, and ensure good ventilation. If you’re starting as a hobby, practicing on scrap metal helps improve technique before tackling important projects. If you’re considering a business, investing in better equipment and marketing your services can help expand your operations.
To achieve professional results in powder coating, mastering different techniques and understanding material properties is essential. Various powders, such as epoxy, polyester, polyurethane, and hybrid formulations, offer unique characteristics suited for specific applications. Epoxy powders provide excellent corrosion resistance but degrade under UV exposure, making them ideal for indoor use. Polyester powders are more versatile, offering durability and weather resistance for outdoor applications. Hybrid powders combine epoxy and polyester properties for balanced performance, while polyurethane powders provide superior chemical resistance and gloss retention.
Controlling application parameters significantly affects coating quality. Adjusting the gun’s voltage, air pressure, and distance from the surface ensures proper powder adhesion and even coverage. Too much voltage can cause back-ionization, leading to defects, while too little may result in poor coverage. Properly grounding the workpiece prevents powder repulsion and ensures a strong electrostatic charge for uniform coating. Layering techniques, such as using multiple coats for added thickness or combining different powder types for aesthetic effects, enhance final results.
Curing plays a critical role in powder performance. Factors like oven temperature consistency, heat distribution, and cure time must be closely monitored. Uneven curing can lead to poor adhesion, chipping, or inconsistent gloss. Using an infrared thermometer or data logger helps verify temperature accuracy. Infrared curing systems offer faster heat-up times compared to conventional convection ovens, making them ideal for high-volume production.
As you gain experience, experimenting with specialty powders like metallics, textures, or candy finishes can add visual appeal to projects. Custom masking techniques allow for multi-color designs and precise detailing. If scaling up operations, investing in automated conveyor systems and industrial spray booths improves efficiency and consistency. Whether for personal projects or commercial applications, refining your process through practice and continuous learning leads to high-quality, durable finishes that stand out.
As you refine your powder coating process, understanding troubleshooting techniques becomes essential for maintaining high-quality finishes. Common defects include orange peel, fisheyes, pinholes, and poor adhesion, each caused by specific issues in surface preparation, application, or curing. Orange peel, a rough texture resembling an orange’s skin, often results from incorrect gun settings, excessive powder thickness, or uneven curing. Adjusting the gun’s voltage, air pressure, and coating distance can help achieve a smoother finish. Fisheyes, small craters in the coating, are typically caused by contaminants like oil or silicone.
Thorough cleaning and degreasing, as well as avoiding cross-contamination, help prevent this issue. Pinholes occur due to trapped gases escaping during curing, often from porous substrates or improper surface preparation. Pre-baking metal parts to outgas contaminants before applying powder can reduce pinholes. Poor adhesion usually stems from inadequate cleaning, insufficient grounding, or incorrect curing. Ensuring a properly prepped surface and following the correct cure cycle improves adhesion and durability.
Expanding your knowledge of different substrates and coating challenges is also important. While powder coating is primarily used for metal, advances in technology allow for coating heat-sensitive materials like MDF wood and plastics using low-temperature curing powders. For aluminum, applying a chromate or non-chromate conversion coating enhances corrosion resistance and adhesion. Galvanized steel requires special pre-treatments to prevent adhesion failures due to zinc oxidation. Understanding these substrate-specific requirements ensures reliable performance across diverse applications.
If considering a business venture, optimizing workflow and marketing services can help establish a strong presence. Efficient workspace layout, proper ventilation, and well-organized equipment reduce downtime and increase productivity. Offering specialized coatings, such as high-temperature powders for exhaust systems or anti-microbial coatings for medical equipment, can attract niche markets. Developing an online presence through a website, social media, and before-and-after project showcases helps build credibility and attract customers. Providing additional services like sandblasting, custom color matching, and on-site coating for large structures can further differentiate your business.
Continuous learning through industry forums, training courses, and supplier recommendations keeps you updated on the latest trends and technologies in powder coating. Investing in high-quality equipment, understanding the science behind the process, and maintaining a commitment to quality will set you apart in the industry. Whether for personal projects or professional applications, mastering powder coating opens the door to a world of creative and functional possibilities.
Portable Powder Coating Booth
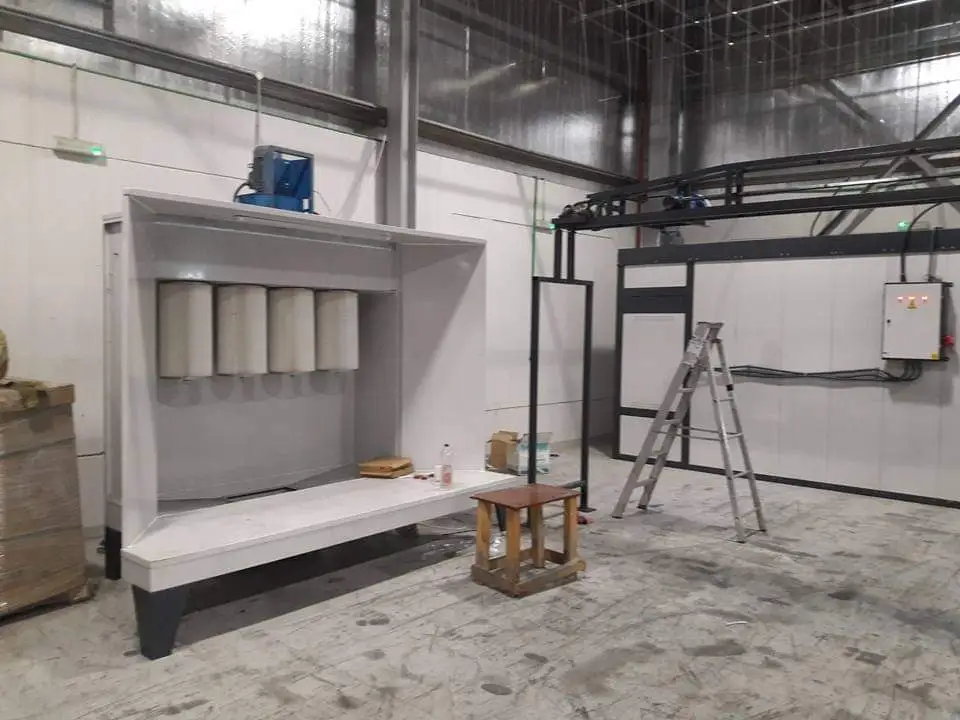
A portable powder coating booth is a compact, movable enclosure designed to contain overspray, improve coating efficiency, and ensure a clean working environment. It is ideal for small-scale operations, DIY enthusiasts, or businesses with limited space. These booths provide a controlled area for powder application while preventing contamination and maintaining proper airflow.
Key Features of a Portable Powder Coating Booth
- Compact and Movable Design – Typically made with lightweight yet durable materials like aluminum frames and fire-resistant panels. Some models have wheels for easy relocation.
- Built-in Ventilation System – Equipped with fans and filters to remove airborne powder particles, improving air quality and reducing contamination.
- Easy Assembly and Disassembly – Many designs use a modular approach, allowing users to set up and pack away the booth quickly.
- Electrostatic Safe Grounding – Ensures proper grounding to enhance powder adhesion and prevent static buildup.
- LED Lighting – Integrated lighting helps in better visibility while coating parts.
- Adjustable Size Options – Available in various dimensions to accommodate small to medium-sized parts.
- Recirculating or Exhaust Filtration – Some booths feature a cartridge-style filter system that collects and recirculates air, reducing powder waste and maintaining a cleaner workspace.
Advantages of a Portable Powder Coating Booth
- Space-Saving – Perfect for garages, small workshops, and mobile businesses.
- Cost-Effective – More affordable than full-scale industrial booths.
- Versatility – Can be used for various coating projects, including automotive, furniture, and custom metalwork.
- Reduced Overspray Contamination – Helps maintain a clean workspace and improves powder utilization.
Considerations When Choosing a Portable Powder Coating Booth
- Booth Size – Ensure it fits the largest parts you plan to coat.
- Filtration System – A high-efficiency filtration system improves safety and air quality.
- Mobility – If you need to move the booth frequently, opt for a model with wheels.
- Airflow Efficiency – Proper airflow is critical for removing excess powder without affecting the application.
A portable powder coating booth is a compact and mobile enclosure designed to control overspray, improve coating efficiency, and provide a cleaner working environment. These booths are ideal for small workshops, DIY enthusiasts, or businesses that need flexibility without investing in a full-scale industrial setup. They typically feature a lightweight yet durable frame, fire-resistant panels, and an integrated ventilation system to remove airborne powder particles. Many models come with wheels for easy relocation and modular designs for quick assembly and disassembly. Proper electrostatic grounding is essential for safety and ensuring effective powder adhesion, while built-in LED lighting enhances visibility during coating. Some booths use recirculating filtration systems with high-efficiency filters to capture excess powder and maintain air quality, reducing waste and contamination.
Portable powder coating booths offer several advantages, including space-saving designs, cost-effectiveness, and versatility for coating automotive parts, furniture, and custom metalwork. They prevent overspray contamination, improve powder utilization, and make cleanup easier. When choosing a booth, it’s important to consider factors like size, filtration efficiency, airflow control, and mobility. A well-designed booth should accommodate the largest parts you plan to coat while maintaining efficient ventilation. If mobility is a priority, opting for a model with wheels or a collapsible structure makes transportation and storage more convenient. Airflow must be optimized to remove excess powder without interfering with the application process.
For those interested in a DIY approach, building a portable powder coating booth can be an affordable and customizable option. Using materials like PVC pipes or aluminum frames, fire-resistant sheeting, and an exhaust fan with a filter system can create an effective workspace. A grounding system is necessary to prevent static buildup, and adding proper lighting improves coating precision. Whether purchasing a ready-made booth or constructing one, ensuring adequate ventilation and safety measures is key to achieving high-quality powder-coated finishes.
When setting up a portable powder coating booth, airflow management is critical to achieving consistent results and maintaining a clean workspace. A well-designed booth should have a controlled air intake and exhaust system that prevents excess powder from settling on coated parts while ensuring proper ventilation. Many portable booths use high-efficiency particulate air (HEPA) filters or cartridge filters to capture airborne powder and prevent contamination. Some models recirculate filtered air back into the workspace, reducing the need for external venting, while others require an exhaust duct to remove air outside. Proper airflow balance prevents turbulence that could disrupt powder application and ensures even coating distribution.
The choice between a recirculating vs. exhaust ventilation system depends on your workspace and safety requirements. Recirculating systems are ideal for enclosed areas without external venting options, but they require regular filter maintenance to avoid clogging. Exhaust systems, on the other hand, directly vent powder-laden air outside, preventing buildup inside the booth but may require compliance with local environmental regulations. If working in a small garage or mobile setup, a recirculating system with replaceable filters offers convenience and flexibility.
Another important factor in optimizing a portable booth is lighting. LED lighting provides bright, energy-efficient illumination, allowing for better visibility of powder coverage and identifying areas that may need reapplication. Placing lights outside the booth behind clear, dust-resistant panels prevents contamination and extends their lifespan.
For efficiency and workflow, organizing the booth with dedicated areas for coating, drying, and cooling streamlines the process. Using turntables or hanging racks allows for easier part rotation and access to all surfaces, reducing the chances of missed spots. If coating multiple parts, a well-ventilated drying area helps prevent airborne powder from settling on freshly coated surfaces before curing.
For those interested in scaling up their powder coating setup, investing in an automated turnkey portable booth system can improve efficiency. Some advanced portable booths integrate an automated gun and conveyor system, allowing for a higher volume of parts to be coated consistently. If mobility is a priority, collapsible designs with quick-folding frames make transport and storage more convenient for mobile powder coating services.
Whether building a DIY setup or purchasing a professional-grade portable booth, ensuring proper ventilation, lighting, and workspace organization will significantly improve coating quality and efficiency. With the right setup, a portable powder coating booth can provide professional results while offering flexibility and affordability for small-scale or mobile operations.
When operating a portable powder coating booth, maintaining cleanliness and filter efficiency is essential for consistent results and prolonged equipment lifespan. Accumulated powder residue can interfere with airflow, reduce filtration effectiveness, and create contamination issues that affect coating quality. Regularly replacing or cleaning filters, depending on the system type, ensures proper ventilation and prevents airborne particles from settling on freshly coated parts. High-efficiency cartridge filters are commonly used in portable booths, and some systems include pulse-cleaning mechanisms that extend filter life by periodically removing excess powder buildup. If working in a confined space, a well-maintained recirculating system prevents excessive powder accumulation while keeping air quality within safe limits.
To further enhance efficiency, integrating dedicated grounding points inside the booth helps maintain a strong electrostatic charge for better powder adhesion. Proper grounding minimizes overspray waste and reduces the risk of uneven coating due to powder repulsion. Using adjustable airflow controls allows fine-tuning of the booth’s ventilation to suit different part sizes and coating thicknesses, preventing unwanted turbulence that can disrupt powder application.
For mobile operations, a collapsible or modular booth design provides the flexibility to transport and set up quickly at different locations. Mobile powder coating businesses benefit from compact, lightweight booths that fit inside a trailer or workshop while still offering adequate airflow and containment. Some advanced portable booths incorporate HEPA filtration and self-contained exhaust systems, making them suitable for use in enclosed spaces without external venting. Battery-powered lighting and compact air compressor setups further improve portability, allowing on-site coating for automotive parts, metal gates, and industrial components.
Safety remains a top priority in any powder coating setup, especially in confined workspaces. Proper grounding, fire-resistant booth materials, and well-ventilated areas prevent static discharge and reduce fire hazards from airborne powder particles. Storing powders in a dry, temperature-controlled environment prevents moisture absorption, which can affect application quality. Wearing appropriate personal protective equipment (PPE), such as respirators, gloves, and anti-static footwear, ensures a safe working environment, particularly when handling fine powders in enclosed booths.
For those looking to optimize production and scale their powder coating process, upgrading to automated extraction fans, multi-stage filtration, and modular booth expansions can improve efficiency and accommodate larger projects. Customizing a portable booth with adjustable height and width panels allows for greater versatility when coating different-sized parts. Whether operating a small DIY setup or a mobile business, refining booth design, filtration, and workflow practices leads to professional-grade powder coating results with minimal overspray and waste.
A powder coating system is a complete setup designed to apply a dry powder finish to metal surfaces, offering a durable and smooth coating. The system includes several components that work together to ensure efficient and high-quality application, from powder preparation to curing. A typical powder coating system consists of the following parts:
Powder Coating Gun
The powder coating gun is the core tool used to apply the powder to a part. It works by electrostatically charging the powder particles as they pass through the gun, which then adhere to the grounded metal surface. The gun typically offers adjustable settings for voltage, airflow, and spray pattern, allowing you to fine-tune the application based on the part’s size and shape. The two main types of guns are manual spray guns and automatic spray guns, with the latter being used in larger, more industrial applications where consistent coating on high volumes of parts is necessary.
Powder Coating Powder
Powder coating powder comes in various formulations, such as epoxy, polyester, urethane, and hybrid blends. The choice of powder depends on the intended application, the desired finish, and environmental conditions. Epoxy powders offer excellent corrosion resistance, making them suitable for indoor use, while polyester powders provide superior UV resistance for outdoor applications. The powder is usually supplied in fine particles that can be loaded into the powder coating gun.
Powder Coating Booth
The booth is the enclosed space where powder is sprayed onto the parts. It is designed to contain overspray, reduce contamination, and provide a clean environment for coating. The booth may come with integrated exhaust systems or recirculating filtration to manage air quality by filtering out airborne powder particles. Many powder coating booths also feature a grounding system to ensure proper adhesion and avoid static build-up. Depending on the operation’s scale, booths may be small, portable units for DIY and small jobs or large, industrial-grade units for mass production.
Curing Oven
Once the powder is applied, the coated part needs to be baked in a curing oven to fuse the powder and create a smooth, hard finish. The oven heats the part to the manufacturer’s recommended temperature (typically 350–450°F or 175–230°C) for a set period, usually between 10 and 20 minutes, depending on the powder’s type and thickness. Curing is a critical step for ensuring durability, adhesion, and finish quality. The oven should have a consistent temperature and even heat distribution for optimal results.
Powder Recovery System
A powder recovery system helps minimize waste by collecting and recycling oversprayed powder from the booth. It typically includes a cyclone separator or filter unit that captures the powder and returns it to the hopper for reuse. These systems can be either manual or automatic, depending on the scale of the operation. For small-scale applications, a simple recovery system with a filter may suffice, while large-scale systems use sophisticated equipment to ensure efficient powder capture and reuse.
Air Compressor
An air compressor is required to provide the air pressure needed to operate the powder coating gun. It supplies consistent airflow to help atomize the powder, ensuring smooth application onto the workpiece. The air compressor should have enough capacity to meet the demands of the system, especially if using an automatic coating setup.
Powder Coating Accessories
Other accessories can enhance the performance and flexibility of the powder coating system:
- Turntables or Hanging Racks: Used to rotate parts during coating for even coverage.
- Grounding Equipment: Ensures proper electrical connection between the part and the booth to achieve good powder adhesion.
- Masking Materials: Prevents powder from coating areas that shouldn’t be coated.
- Filters: In the gun and booth to ensure clean air supply and reduce contamination.
Choosing the Right System
Selecting the appropriate powder coating system depends on several factors, including the scale of the operation, types of parts being coated, and the environment. For a small-scale operation or hobbyist, a portable powder coating system with a manual gun, small booth, and basic curing oven will suffice. For larger-scale or industrial operations, a fully automated powder coating system with an automatic spray gun, conveyor belt, industrial booth, and a large curing oven will be necessary to achieve high throughput and consistency.
In all cases, it’s essential to consider:
- Application type: Whether you’re coating small, intricate parts or large, heavy-duty items.
- Powder type: Different powders have unique properties, so select the one that suits your needs.
- Equipment size and capacity: Ensure the system fits your workspace and meets production volume needs.
A well-designed powder coating system offers excellent durability, finish quality, and environmental benefits (since it produces fewer emissions than traditional liquid coatings). Regular maintenance and proper setup of the system components ensure smooth operation and long-lasting results.
A powder coating system works as a cohesive unit to apply durable and high-quality finishes to metal parts. The system’s core component is the powder coating gun, which applies the electrostatically charged powder onto the metal surface. The powder adheres to the surface due to the charge and the part’s grounded nature, creating an even coating. Depending on the operation’s size, you can choose between manual or automatic spray guns, with the latter being ideal for high-volume or industrial applications where consistency and speed are crucial.
The powder itself plays a significant role in the final result. Powders come in different types, such as epoxy, polyester, and hybrid blends, each offering specific characteristics like corrosion resistance or UV protection. Epoxy powders are ideal for indoor applications due to their superior adhesion and chemical resistance, while polyester powders are better for outdoor use because of their weather resistance. The powder is typically stored in a hopper connected to the powder gun, which feeds it through a delivery system and onto the part.
Once the powder is applied, the part needs to be cured in an oven. The curing process involves heating the coated part to a specific temperature (typically 350–450°F), where the powder melts and bonds to the metal, forming a hard, durable finish. A well-calibrated oven with consistent heat distribution is critical to achieving uniform curing, as uneven temperatures can cause defects like soft spots or uneven gloss.
After the part is coated, powder recovery systems are often used to minimize waste. These systems capture overspray and recycle the unused powder back into the hopper for reuse, which is both cost-effective and environmentally friendly. The recovery system typically includes cyclonic separators or filter units that remove excess powder, ensuring that only the powder that adheres to the part is cured, while the rest is recaptured.
Air compressors are another essential part of the system, supplying the necessary airflow to operate the powder coating gun. A reliable compressor is required to provide consistent air pressure, ensuring that the powder is atomized properly and applied evenly onto the parts.
Incorporating accessories like turntables, racks for hanging parts, and grounding equipment further enhances the powder coating process. Turntables and hanging racks help ensure uniform coverage by rotating or suspending parts during the application. Grounding equipment ensures proper electrical contact between the parts and the booth, improving powder adhesion.
Choosing the right powder coating system depends on your specific needs, such as the type of parts you’re coating, the size of the operation, and the production volume. For small operations or DIY projects, a portable setup with a small booth and manual gun may be sufficient. For large-scale industrial applications, an automated system with high-capacity guns, a conveyor system for continuous operation, and a larger curing oven will be necessary to meet high throughput and consistency.
No matter the scale of the operation, regular maintenance and calibration of the system components are key to ensuring quality results. With the right equipment, powder coating provides a long-lasting, attractive, and environmentally friendly finish to a wide range of products.
When expanding or fine-tuning your powder coating system, it’s important to focus on process optimization and ensuring consistency across all components. The effectiveness of the system relies not just on the equipment, but also on the environmental conditions and the attention to detail in each step. For example, maintaining proper humidity and temperature levels in the workspace is crucial, as high moisture levels can cause the powder to clump or degrade, while extreme temperatures may affect curing times or powder application consistency.
Proper maintenance of the powder coating gun is essential for achieving smooth, uniform finishes. Regularly cleaning the nozzle and checking for wear ensures that the gun is working at peak efficiency. Fine-tuning the air pressure and voltage settings on the gun also plays a significant role in improving the coating’s consistency. If too much voltage is applied, the powder can start repelling from the part, causing defects like uneven application or overspray. On the other hand, insufficient voltage results in poor adhesion and a patchy finish. Therefore, experimenting with settings based on the part’s material and shape is key to achieving the desired result.
The booth is another critical area to focus on. A well-maintained booth with clean filters will ensure optimal airflow and reduce contamination. In industrial environments, a more advanced system with multi-stage filtration or cyclonic separators may be necessary to handle larger volumes of overspray and ensure high-quality finishes. In small-scale setups, portable powder coating booths that use compact filtration systems can still be effective for achieving professional results, but regular maintenance is important to prevent clogging and reduce the risk of contamination.
A more advanced feature to consider in a larger setup is the use of automated coating systems. Automated systems, which integrate robotic arms or conveyors, allow for consistent, repeatable application of powder, reducing human error and improving throughput. These systems are ideal for large-scale operations that require high-volume production. In contrast, smaller operations or hobbyists may find that manual powder coating guns provide enough control for achieving precision finishes.
The curing process also plays a major role in the quality of the finish. An oven with even temperature distribution is essential for ensuring that the coating properly bonds to the substrate, providing a durable, scratch-resistant finish. Regularly calibrating the oven to maintain consistent temperature settings, checking the oven’s airflow, and ensuring it is clean will help prevent defects such as soft spots or uneven finishes. Some advanced curing systems use infrared heat technology, which offers faster curing times compared to traditional convection ovens and can be more energy-efficient. However, infrared systems require careful monitoring to avoid overheating parts or uneven curing.
Additionally, choosing the right powder formulation for your specific application will have a significant impact on the end result. Polyester powder coatings are ideal for outdoor use due to their superior UV resistance, while epoxy powders are often used for their excellent adhesion and chemical resistance, but they aren’t as durable under direct sunlight. There are also urethane powders for extra toughness, and hybrid options that offer a balance of epoxy and polyester benefits. Each formulation has its advantages and should be selected based on the environment the finished part will be exposed to.
Lastly, workflow efficiency is an essential factor when scaling your operation. Efficiently organizing the coating process, from loading parts into the booth to curing and unloading, can drastically improve productivity. Using automated conveyors can reduce manual handling time and ensure consistent and controlled application across high volumes of parts. Moreover, incorporating custom racking systems for different part shapes and sizes helps maintain organization and speeds up the overall process.
In conclusion, optimizing your powder coating system comes down to maintaining and fine-tuning each part of the process. Whether you are working on small batches or large-scale industrial production, focusing on equipment maintenance, controlling environmental factors, and selecting the right materials can greatly enhance the quality, efficiency, and consistency of your powder-coated finishes.
When further refining and expanding your powder coating system, it’s important to think about long-term scalability and flexibility in your setup. For businesses or hobbyists looking to increase production without compromising quality, investing in specialized equipment and advanced techniques can help ensure consistent, high-quality finishes over time. One such consideration is the ability to scale the curing process. In large setups, moving from batch ovens to conveyorized curing systems can significantly increase throughput. Conveyorized systems allow parts to be coated and cured in a continuous flow, eliminating the need for manual handling after application and speeding up the production process.
For high-volume applications, some businesses use multi-zone curing ovens, which offer precise temperature control across different sections of the oven, allowing parts to pass through multiple temperature zones for optimal curing. These ovens can be fine-tuned based on the specific requirements of the coating material and the thickness of the parts. Advanced curing systems can even incorporate gas-assisted heating for improved energy efficiency, reducing operational costs while maintaining excellent coating performance.
Powder recovery and waste management also become increasingly important as production volumes grow. As you scale, you might consider more sophisticated automated powder recovery systems that use cyclonic air separators, pulse jet filters, or vacuum recovery systems to capture oversprayed powder. These systems can be set up to reclaim powder with a high degree of efficiency, which helps to minimize material costs and reduce environmental waste. In some advanced setups, digital powder recovery monitoring systems can track the amount of powder used and recovered, providing real-time data to improve efficiency and reduce waste.
To maintain high-quality finishes, quality control measures should be implemented throughout the process. This can include using UV light to check for uniform powder distribution or using thickness gauges to ensure that the powder layer is within the desired range. Implementing in-line inspections or automated inspection systems that use cameras or sensors to detect defects can prevent issues like orange peel, pinholes, or over-sprayed areas from affecting production. These systems can be integrated into the process flow, providing immediate feedback to the operator for necessary adjustments.
It’s also crucial to keep up with technological advancements in the powder coating industry. New materials, equipment, and processes are constantly being developed to improve performance, efficiency, and environmental impact. For instance, low-temperature cure powders allow for coating heat-sensitive materials like plastics or wood without the risk of warping or damage. Similarly, nano-coatings or ceramic powders provide specialized finishes that enhance properties like heat resistance, corrosion resistance, or abrasion resistance, offering unique solutions for specific industries, such as automotive or aerospace.
Another evolving aspect of powder coating is the increased demand for customization and color matching. Offering custom powder colors or finishes can set your business apart from competitors. Many powder coating systems now integrate with digital color matching systems, allowing you to replicate colors more accurately and improve customer satisfaction. For more artistic or high-end applications, textured finishes or metallic coatings can be used to create distinct visual effects, opening the door for more diverse applications in furniture, architecture, and consumer products.
Finally, in terms of environmental impact, the powder coating process is already more eco-friendly than many traditional liquid coatings. However, further steps can be taken to minimize waste and energy consumption. For example, using eco-friendly powders with lower volatile organic compound (VOC) emissions can reduce environmental impact. Some businesses are also looking into energy-efficient LED curing systems or solar-powered booths, which can cut down on energy use and further align with sustainability goals.
In essence, expanding and improving your powder coating system involves careful consideration of efficiency, scalability, technological advancements, and quality control. Whether you’re scaling up for higher production volume, improving the environmental footprint of your process, or offering more customization, embracing new technologies and methods will keep your powder coating system competitive and capable of meeting diverse customer needs. By constantly refining your system, you ensure that your setup delivers high-quality finishes, operational efficiency, and a sustainable future.
Small Scale Powder Coating Equipment
Small-scale powder coating equipment is designed to provide professional-quality finishes on a smaller scale, making it ideal for hobbyists, small business owners, or DIY enthusiasts. These systems are more compact and affordable compared to industrial setups, yet they can still deliver durable and attractive finishes for a variety of metal parts, such as automotive components, furniture, home accessories, and small machinery.
Powder Coating Gun
At the heart of any small-scale powder coating system is the powder coating gun. For small operations, a manual powder coating gun is typically used, which is portable and affordable while still providing control over the coating process. These guns are easy to use and can be adjusted for voltage, airflow, and spray pattern. More advanced models offer features like adjustable spray settings, allowing you to fine-tune the application based on the part’s size, shape, and the type of powder being used. Electrostatic guns charge the powder as it is sprayed, ensuring a strong bond to the grounded part.
Powder Coating Powder
The powder is typically supplied in plastic bags or containers, and it can be either epoxy, polyester, urethane, or a hybrid blend. Small-scale systems often use the same types of powders as industrial systems, but the quantity and application are scaled down. Choosing the right powder depends on the part’s intended use. Epoxy powders are great for indoor items due to their excellent adhesion and chemical resistance, while polyester powders are better suited for outdoor items due to their UV resistance.
Powder Coating Booth
A powder coating booth is a critical component in a small-scale setup. The booth is designed to contain the overspray of powder, ensuring a clean work environment and preventing contamination of other parts. Small booths are often portable, lightweight, and can fit in a home garage or small workspace. They can be set up with a basic ventilation system or filter units to remove excess powder from the air. Many small booths include a recovering system that helps to recycle oversprayed powder, reducing material waste.
Curing Oven
After the powder is applied, the part needs to be cured in an oven to bond the powder to the metal surface. For small-scale applications, compact curing ovens are used, often with adjustable temperature settings to ensure proper curing. These ovens typically reach temperatures between 350-450°F (175-230°C) and can accommodate smaller parts. Curing time usually ranges from 10 to 20 minutes, depending on the size and material of the part. Many small-scale curing ovens are electric-powered and come with digital controls for precise temperature regulation.
Air Compressor
An air compressor is necessary to supply air pressure to the powder coating gun. Small-scale setups often use compact, portable compressors with a sufficient air delivery rate to ensure that the powder is properly atomized and applied evenly to the parts. Air compressors for small powder coating systems typically have a pressure range of 10-30 psi and a tank size that is appropriate for the coating process.
Powder Recovery System
For small-scale operations, a manual powder recovery system is usually sufficient to capture oversprayed powder and return it to the hopper for reuse. These systems may include simple filters, cyclonic separators, or catch trays to collect the unused powder. By recycling the powder, these recovery systems help reduce waste and save money in the long term.
Other Accessories
Additional accessories can improve the quality and efficiency of small-scale powder coating setups. For instance, turntables or racking systems can be used to rotate or hang parts, ensuring even coating on all sides. Masking tape or plugs can be applied to areas that should not be coated, preventing unwanted coverage. Grounding equipment is essential to ensure that the electrostatic charge from the powder coating gun properly adheres to the metal parts, preventing powder repulsion or weak adhesion.
Portable Powder Coating System
Some small-scale powder coating systems are designed for ultimate portability and can be used in various locations, such as a home workshop, garage, or even outdoors. These systems are often lightweight, easy to set up, and can be moved around with ease. Portable booths can fold up for storage, and smaller curing ovens with digital temperature controls offer flexibility for different types of projects.
In summary, small-scale powder coating equipment offers a cost-effective solution for achieving high-quality finishes on smaller batches of metal parts. By selecting the right components—powder coating gun, booth, curing oven, and compressor—you can build a system that provides professional results for DIY projects, custom coatings, or small business applications. Regular maintenance and proper setup of each component are essential for ensuring consistent finishes and efficient operation.
Small-scale powder coating equipment is designed to offer an efficient and cost-effective solution for achieving high-quality finishes on smaller batches of metal parts. These systems are perfect for hobbyists, small businesses, or DIY enthusiasts who need to coat items like automotive parts, furniture, or home accessories. The heart of the system is the powder coating gun, which applies the powder to the part through an electrostatic charge, ensuring a strong bond between the powder and the grounded surface. These guns are adjustable, allowing users to fine-tune spray patterns, airflow, and voltage to match the part’s size and the type of powder being used.
The powder itself comes in various formulations, such as epoxy, polyester, and hybrid blends, each suited for specific applications. Epoxy powders are ideal for indoor use due to their excellent adhesion and chemical resistance, while polyester powders are more suitable for outdoor use because of their superior UV resistance. Small-scale systems use the same types of powders as larger ones, but in smaller quantities that are easier to manage. Once the powder is applied, it needs to be cured in an oven. Small, compact curing ovens are typically used in these setups, allowing users to cure parts at the right temperature (usually between 350–450°F) for about 10 to 20 minutes, depending on the part’s material and thickness. These ovens often come with digital controls to maintain precise temperature settings, ensuring the powder bonds correctly to the part.
Air compressors are essential for providing the necessary airflow to the powder coating gun, atomizing the powder and helping it to adhere evenly to the metal part. In small-scale setups, portable compressors are used, which are easy to transport and store, providing enough air pressure to apply the powder effectively. Powder recovery systems are also an important part of small-scale operations, as they allow oversprayed powder to be collected and reused, reducing waste and saving money. These systems can be as simple as filters or catch trays to collect excess powder, or more advanced cyclonic separators that provide more efficient powder recovery.
Small powder coating booths are designed to contain overspray, ensuring a clean working environment and preventing contamination. These booths are often portable, lightweight, and compact, making them suitable for smaller workspaces like home garages or workshops. Many booths come equipped with basic filtration systems to remove excess powder from the air and help recycle oversprayed powder back into the system. Some setups also include racking or turntable systems that allow parts to be rotated during coating for even coverage. Grounding equipment is also essential in these systems to ensure that the electrostatic charge properly adheres the powder to the part, preventing any issues with adhesion or powder repulsion.
In essence, small-scale powder coating equipment provides a great way to achieve professional-quality coatings without the need for large, industrial setups. By choosing the right components, such as the gun, booth, curing oven, and recovery system, users can create a customized powder coating system that meets their needs. Whether it’s for personal projects or small business operations, these systems can produce durable, attractive finishes on a wide variety of metal parts, all while minimizing waste and being cost-effective. Proper maintenance and attention to each component are key to ensuring consistent and high-quality results with every coating project.
Expanding on small-scale powder coating systems, one important aspect is achieving the right balance between affordability and quality. As these systems are often used by individuals or small businesses, keeping costs manageable while ensuring the best possible results is crucial. This is why many small-scale setups are designed with versatility in mind, allowing users to coat a variety of items without needing a huge investment in specialized equipment. The compactness of these systems means they can be set up in a home workshop, garage, or smaller industrial spaces without taking up too much room.
In terms of powder coating guns, it’s important to select one with adjustable settings, allowing flexibility for different types of powder and part sizes. Some advanced models even offer digital controls, which can improve consistency and efficiency, especially when you need to fine-tune the application process. The use of electrostatic guns makes sure that the powder adheres effectively to the metal surface, resulting in a more uniform and durable coating. Investing in a gun with good ergonomics and ease of cleaning can make the process less tedious and help prolong the lifespan of the equipment.
When choosing a curing oven, one key consideration is its size and the type of heating it uses. Small-scale systems often feature electric ovens, which are ideal for handling smaller parts or batches. The temperature accuracy of the oven is essential to ensure the powder bonds correctly and cures evenly. Some curing ovens come with digital thermostats, making it easier to control the temperature and avoid inconsistencies. Additionally, ovens with ventilation systems help to maintain air quality and ensure that fumes or smoke are properly expelled during the curing process.
For air compressors, a small, portable unit that provides enough CFM (cubic feet per minute) and PSI (pounds per square inch) to efficiently run the powder coating gun is key. This doesn’t mean you need the most expensive compressor, but the air supply should be consistent to ensure the powder is sprayed evenly. Moisture filters can also be an essential addition, as excess moisture in the air can affect the powder application, leading to defects like poor adhesion or texture issues.
Another critical component in small-scale systems is the powder recovery unit. While industrial systems often have complex automated recovery systems, smaller setups use more manual options to recycle powder, which can help keep costs low. Cyclone separators or basic filtration systems are common and work by collecting and filtering out overspray, so it can be reused. This not only saves material costs but also reduces the environmental impact by minimizing waste. Additionally, using recovery systems allows users to work more efficiently, especially in situations where multiple layers of powder are applied.
To ensure a smooth workflow, organizing the work area is key. Many small-scale systems offer the option to hang or mount parts on racks or use turntables to rotate parts during application, ensuring even coverage. These types of solutions are simple but effective in improving coating consistency. If parts are large or have irregular shapes, custom racks or hooks can be used to position the items optimally for coating.
Moreover, masking materials are a simple but essential addition for preventing overspray on areas that don’t need coating, such as threaded parts, connectors, or areas that should remain free of powder. This can be achieved using masking tape, plugs, or other forms of protective covering. Masking ensures that the parts function as intended after the coating process and reduces the time needed for touch-ups or cleanup.
For those with limited space or budget, portable powder coating booths are an excellent choice. These booths are designed for easy setup and takedown, allowing users to coat parts in almost any environment. Many of these booths are equipped with basic filtration systems to capture overspray, and some even feature recirculating powder systems that allow for powder recovery during the process. Depending on your needs, portable booths can either be open-air setups for large, less delicate items or fully enclosed booths for more controlled applications.
Maintenance is also a key factor in ensuring the longevity of the equipment. Keeping the powder coating gun clean is essential to avoid clogs or buildup of powder in the nozzle, which can affect the spray pattern. Similarly, regular checks on the curing oven will help identify any temperature inconsistencies or faulty heating elements before they affect production. Powder booths should be cleaned periodically to avoid contamination, and filters in the booth and recovery systems should be replaced or cleaned as necessary to maintain airflow and prevent excess powder from circulating into the air.
Ultimately, small-scale powder coating systems are designed to provide flexibility, efficiency, and quality while remaining affordable for users with limited space or budget. With the right selection of equipment and regular maintenance, these systems can produce high-quality finishes on metal parts, making them an ideal solution for a range of applications—from custom projects to small business operations. By tailoring the setup to meet specific needs and ensuring the process is streamlined, users can achieve professional results without the need for large-scale industrial equipment.
When considering a small-scale powder coating system, it’s also essential to think about the versatility of the setup. One of the benefits of these systems is the ability to coat a wide variety of parts, from small components to larger items like automotive parts, outdoor furniture, and even custom home décor pieces. This flexibility allows users to tackle different projects and customer demands, making it ideal for both personal and business use.
For businesses that plan to take on more clients or higher volumes of work, the system can still be scaled up in a manageable way. Modular powder coating systems allow for expansion, meaning that as production needs grow, you can easily add components like additional booths, larger ovens, or even automated powder coating guns. Automated systems can help increase productivity by reducing labor costs and improving coating consistency, which is particularly beneficial for high-volume operations. Adding a conveyor system can streamline the process for larger batches, allowing parts to move automatically through the booth and curing oven, thereby saving time and increasing throughput.
Another aspect to consider is the energy efficiency of your equipment. In smaller setups, users often look for low-energy options that reduce overhead costs. LED curing lights are a great choice for energy efficiency, as they use far less power compared to traditional heating elements. For the curing oven, consider one with good insulation and an efficient heating mechanism that prevents heat loss and maintains stable temperatures, minimizing energy usage. Some ovens are designed with programmable timers and temperature controls to further optimize the curing process, ensuring that the parts are heated to the correct temperature without waste.
Environmental factors are also becoming a significant consideration for small-scale powder coating operations. While powder coating is generally more eco-friendly than liquid coatings, as it produces fewer volatile organic compounds (VOCs), further steps can be taken to reduce the environmental impact. Eco-friendly powders with low VOC content or those made from sustainable materials can be selected, helping meet environmental regulations and appeal to environmentally conscious customers. Additionally, implementing a waste management system for collecting and recycling overspray powder helps minimize waste and improves cost-effectiveness.
One trend in the industry is the development of DIY and home-based powder coating systems. These systems are designed for hobbyists and small-scale businesses who may not have access to a large workspace. Compact, portable booths that fold up for storage, combined with small but efficient curing ovens, are perfect for those who work from home or have limited space. These systems can be set up quickly and offer flexibility for part-time or weekend businesses that want to offer professional-quality finishes without a significant investment.
Moreover, it’s important to consider the long-term reliability and durability of the equipment. Small-scale powder coating equipment is typically built for lighter use than industrial systems, but investing in well-made, durable components will ensure a better return on investment and fewer issues in the long run. It’s also crucial to have technical support or access to replacement parts, as some components, like heating elements or spray guns, may wear out over time.
In addition to the functional aspects, training and skill development are vital for getting the most out of a small-scale powder coating system. While powder coating is a straightforward process, it does require some skill and experience to master. Many suppliers offer training videos or tutorials, and some even provide hands-on workshops to help users understand the nuances of powder application, curing, and troubleshooting. As you gain more experience, you’ll learn how to adjust your process to achieve the perfect finish, whether it’s a smooth, glossy coat or a textured, matte finish.
Another consideration is color customization. Powder coating allows for a wide range of colors, textures, and finishes, making it an attractive option for businesses looking to offer unique customizations. Many powder coating systems now feature color-matching technology, allowing users to accurately reproduce colors and achieve the exact shade that customers are looking for. Whether it’s creating vibrant custom finishes for automotive parts or offering trendy color options for furniture, the ability to mix and match different hues gives small businesses the edge when it comes to offering personalized, custom designs.
Lastly, health and safety should always be prioritized. Powder coating, like any coating process, involves handling chemicals and working with high temperatures. It’s important to ensure that your workspace is well-ventilated to avoid inhaling powder dust or fumes, especially in confined spaces. Using respirators or dust masks can further protect your health. Additionally, protective clothing such as gloves, goggles, and long sleeves should be worn to minimize exposure to the powder and other materials.
In conclusion, small-scale powder coating systems offer an excellent solution for hobbyists, small businesses, and DIY enthusiasts who want to produce high-quality, durable finishes on a range of metal parts. With the right equipment, maintenance, and attention to detail, users can achieve professional-level results without the need for large, expensive systems. As your needs grow, you can scale up the system by adding components like larger booths, curing ovens, or automated systems, making it a flexible choice that adapts to your specific requirements. By staying informed about new technologies, techniques, and eco-friendly practices, you can continue to improve your process and deliver top-notch finishes for your projects.
Powder Coating Booth
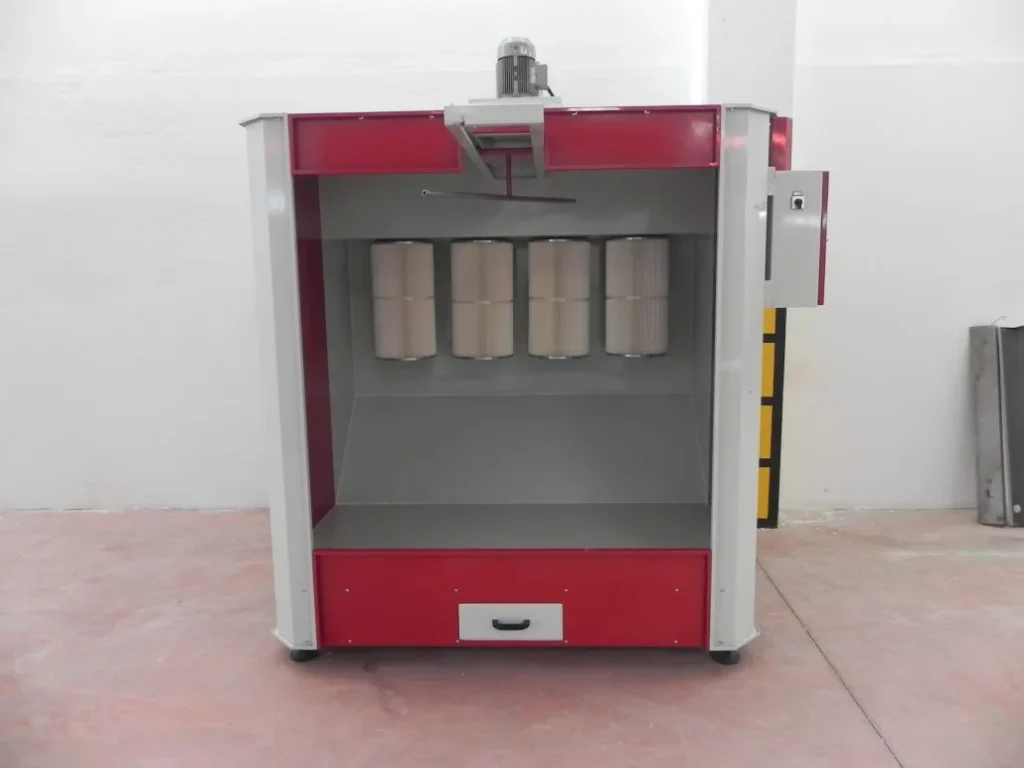
A powder coating booth is an essential part of any powder coating system. It is designed to contain the overspray of powder and direct it towards a collection system, ensuring that the workspace remains clean and the coating process remains efficient. The booth also helps in creating a controlled environment for applying the powder, reducing contaminants and ensuring the consistency of the finish. There are several types of powder coating booths, and choosing the right one depends on factors like workspace size, production volume, and specific needs.
For small-scale or DIY setups, powder coating booths are typically compact, portable, and easy to set up and use. These booths can be either open-air or enclosed with filters and air circulation systems to collect the oversprayed powder and maintain a clean environment. A small powder coating booth often includes a basic filtration system to prevent the powder from circulating in the air and contaminating the surroundings.
In larger industrial applications, powder coating booths are often equipped with advanced air filtration systems, including high-efficiency particulate air (HEPA) filters and cyclonic separators. These systems work by using a combination of airflow patterns, negative pressure, and filters to ensure that the oversprayed powder is captured and can be recycled, reducing waste and saving on material costs. The booth is usually designed with airflow systems that draw air in from the surrounding environment and push the air out through filters to ensure safe and efficient operation.
Powder coating booths typically have adjustable spray zones or spray guns to allow the operator to apply the powder evenly on the part. The booth is designed to directly funnel the overspray into a collection area, such as a cyclone or recovery system, where it can be filtered and reused. This reduces waste and helps in achieving an even coating on each part.
When choosing a powder coating booth, there are a few key factors to keep in mind:
- Size: The booth should be large enough to accommodate the parts you intend to coat. A booth that is too small can limit the size of parts, while a booth that is too large can be inefficient and take up unnecessary space.
- Ventilation: Proper ventilation is crucial for a safe and effective coating process. The booth should be equipped with a fan or exhaust system to ensure that the air is drawn into the booth and filtered, preventing the build-up of dust and powder in the workspace. Good airflow also helps ensure an even coating and prevents over-spray from settling outside the booth.
- Powder Recovery System: Many powder coating booths come with built-in recovery systems, which collect the oversprayed powder and allow it to be recycled. This helps reduce waste and saves on material costs. There are cyclonic recovery systems that use centrifugal force to separate the powder from the air and filter it out, and manual recovery systems where powder is collected in catch trays or bags.
- Cleaning and Maintenance: A good powder coating booth should be easy to clean and maintain. The powder residue can build up over time, so having a booth that is designed for easy access to filters and recovery systems can save time and effort in the long run. Look for booths with smooth, non-porous surfaces that are easy to wipe down.
- Cost: The cost of a powder coating booth varies depending on the size, features, and type of equipment. Basic booths for small-scale or DIY applications are relatively affordable, while industrial-grade booths with advanced filtration and recovery systems can be more expensive. When purchasing a booth, it’s important to consider the return on investment in terms of efficiency, reduced waste, and improved coating quality.
- Portability: For small-scale operations, portable powder coating booths are an excellent choice. These booths are lightweight, foldable, and easy to store. They can be set up in garages, workshops, or other small spaces without the need for permanent installation.
When using a powder coating booth, it’s important to follow the safety guidelines. Always ensure the booth is well-ventilated to avoid inhaling powder particles or fumes, which can be harmful to your health. Wear appropriate protective gear such as gloves, goggles, and a respirator to prevent exposure to powder dust. Make sure that the booth is free of any flammable materials, as powder coatings can create sparks when applied to metal surfaces.
In summary, a powder coating booth is an essential piece of equipment for anyone involved in powder coating, whether for personal, hobby, or small business use. By choosing the right booth that fits your workspace, production needs, and budget, you can ensure an efficient, clean, and safe powder coating process, while also reducing waste and improving the overall quality of your finishes.
A powder coating booth plays a pivotal role in the powder coating process by containing overspray and helping create a controlled environment for even and efficient application. It directs excess powder into recovery systems to minimize waste, ensuring that the process is more cost-effective while also keeping the work area clean and free of contaminants. Whether you’re working with small parts or larger items, a well-designed booth is essential for achieving consistent results and maintaining a safe working environment.
For small-scale or DIY setups, powder coating booths are typically compact and portable. These booths are ideal for home workshops or limited spaces because they can easily be assembled and disassembled. Smaller booths usually come with basic filtration systems to keep the overspray contained, but they might not have advanced recovery systems like industrial-sized booths. While these smaller setups are budget-friendly, they still offer an efficient way to apply coatings on metal parts without the need for large, expensive systems.
For larger operations, industrial-grade powder coating booths offer higher efficiency, especially in terms of powder recovery and air filtration. These booths are typically equipped with advanced systems that utilize cyclonic separators, which remove powder from the air and return it to the hopper for reuse. This reduces material waste and ensures that the powder coating process is more sustainable. The air filtration systems in these larger booths often include high-efficiency particulate air (HEPA) filters to capture fine particles and prevent them from escaping into the environment. These systems create a cleaner, safer working environment, especially when working with large volumes of parts.
When choosing a powder coating booth, it’s essential to consider your needs, such as the size of the parts you’ll be coating and the volume of work you’re planning to do. A booth that’s too small may limit the size of the items you can coat, while a booth that’s too large can take up unnecessary space and may be less energy-efficient. Ensuring proper ventilation is critical in any booth setup to help exhaust fumes and maintain a safe environment. Having a fan or exhaust system that draws air into the booth and pushes it out through filters is a basic yet essential feature in any powder coating booth, whether it’s small or industrial.
Another factor to keep in mind is the booth’s ease of cleaning and maintenance. Powder residue can build up quickly, so it’s important to select a booth that makes it easy to access and clean filters, powder recovery systems, and the general structure of the booth. A booth that’s designed with smooth surfaces and fewer hard-to-reach areas will reduce cleaning time and improve overall maintenance. Additionally, look for booths that offer simple access to parts that need regular maintenance or replacement, such as filters, fans, and exhaust components.
The cost of a powder coating booth varies widely depending on its size, features, and intended use. For DIY projects or small business applications, a basic booth may be more affordable, while larger systems with advanced air filtration and recovery capabilities will come at a higher price point. It’s important to consider the long-term savings that come from using a booth with a recovery system, as it helps reduce powder waste and makes the coating process more efficient. In small operations, a portable booth can provide the flexibility to coat parts in various locations, allowing for easy setup and storage. Portable booths are particularly useful for small shops or businesses that need to move their equipment between workspaces or need to coat different types of items.
In addition to saving material costs, a well-designed booth can improve the overall coating quality. Properly capturing overspray ensures that the powder is applied to the parts with more precision, leading to a more uniform finish. Powder coating booths equipped with recovery systems can help keep the air cleaner, prevent contaminants from affecting the coating, and ensure that excess powder is effectively recycled. This not only saves on material costs but also helps maintain the environmental standards by reducing the amount of powder that escapes into the air.
Overall, a powder coating booth is an essential investment for anyone involved in powder coating, from hobbyists and small business owners to larger manufacturers. Whether you’re applying a glossy finish to automotive parts or coating furniture for sale, a high-quality booth helps ensure that the process is smooth, efficient, and safe. A booth that suits your specific needs will improve the quality of your work, reduce waste, and increase productivity, making it an indispensable part of any powder coating operation.
As you continue exploring powder coating booths, it’s also important to consider customization options for your specific requirements. Many powder coating booths can be tailored to suit particular projects, whether it’s large or intricate items. For example, some booths come with adjustable walls or internal dividers to create separate areas for different part sizes. If you are working with parts of varying shapes or dimensions, adjustable shelving or turntable systems within the booth can help with coating even the most complex parts.
The environmental impact of powder coating booths is another area to consider. While powder coating itself is already an eco-friendly option compared to traditional liquid paints, a booth that incorporates green technologies can enhance sustainability. Some powder coating booths feature energy-efficient heating systems or LED curing lights that consume less electricity than conventional methods. Additionally, certain booths are designed to be more energy-efficient, using insulated panels and heat-recirculating ovens to maintain a consistent temperature while reducing overall energy consumption. These energy-efficient features can lead to significant long-term savings and reduce your carbon footprint.
Noise control can also be a consideration in some powder coating operations, especially in small or home-based workshops. Powder coating booths with sound-dampening features can help reduce the noise generated by air compressors, fans, and other machinery. This is particularly important in settings where noise could be a disturbance or in more densely populated areas. Some booths come with noise reduction packages, such as soundproofing materials on walls or quieter air circulation systems, which make the working environment more comfortable.
When it comes to workflow efficiency, a well-organized booth setup can dramatically speed up your coating process. For example, having a turntable or rotating rack system inside the booth allows parts to be evenly coated as they rotate, ensuring a smooth and uniform finish on all sides. This eliminates the need for the operator to manually reposition the parts, saving time and ensuring consistency in the coating. For larger parts, oversize booths or booths with adjustable features allow for optimal maneuverability and positioning of items, making it easier to coat larger or bulkier objects.
Maintenance and longevity of the booth are critical for ongoing productivity. The lifespan of powder coating booths is often determined by the materials used in construction and the quality of the filtration system. Many booths are built with sturdy, corrosion-resistant materials such as galvanized steel or powder-coated metal to ensure durability and long-term performance. Regular inspection of the booth, particularly the air filters, powder recovery units, and airflow components, is essential to ensure smooth operation and to prevent costly downtime. The filters, in particular, should be cleaned or replaced according to the manufacturer’s recommendations to maintain optimal airflow and prevent the buildup of powder residue in the system.
Another key point is safety features. Since powder coating involves working with flammable materials, it is crucial to choose a booth that offers adequate fire prevention measures. Many modern booths are equipped with fire suppression systems that can detect any signs of a fire and activate automatically to put it out. Additionally, booths should be equipped with grounding equipment to prevent static buildup, which can also pose a fire hazard. The booth should also be designed with sufficient exhaust capacity to ensure that any fumes or particles are safely directed away from the work area.
As businesses expand, automation in powder coating booths is becoming more common. Automated systems can help improve efficiency, reduce human error, and increase throughput. For example, automated spray guns or robotic arms can be integrated into powder coating booths for high-volume applications, allowing for precise and consistent coating even for complex or detailed parts. These systems can be programmed to move around the part in specific patterns, ensuring uniform coverage without the need for manual operation. Automated powder coating systems also provide a level of consistency that can be difficult to achieve manually, making them ideal for larger production runs where quality and uniformity are critical.
For high-demand businesses or those aiming to produce large quantities of parts, conveyorized powder coating systems can significantly improve productivity. These systems use conveyor belts or automated tracks to move parts through the booth and curing oven, ensuring that parts are coated and cured without requiring manual intervention. Conveyor systems can be adapted to work with various booth sizes and configurations, allowing for seamless integration into existing production lines.
Lastly, training and expertise are essential for operating a powder coating booth efficiently. While the process itself is relatively simple, achieving a high-quality finish consistently requires skill and knowledge. Proper training will ensure that operators understand how to adjust settings for different powder types, manage the curing process, and troubleshoot common issues. Many manufacturers offer training or support services to help businesses get the most out of their powder coating booths, whether it’s about application techniques, equipment setup, or ongoing maintenance.
Ultimately, the right powder coating booth for your operation will depend on factors like the scale of your production, part sizes, budget, and specific application needs. Whether you’re just starting out with a small, portable setup or running a larger, automated production line, investing in a quality booth can enhance both the quality and efficiency of your powder coating process. With the right equipment, attention to detail, and a well-maintained booth, you can achieve high-quality finishes while optimizing your workflow and minimizing material waste.
As you continue refining your powder coating setup, it’s important to focus on optimizing workflow and part handling. Efficient part handling is crucial to achieving high-quality, consistent results. One way to streamline this process is by using hanging racks or fixtures that can support multiple parts at once. For example, a vertical hanging system can help maximize the use of space within the booth, allowing you to coat multiple parts simultaneously without overcrowding. This method can be particularly useful for small parts or components that require less time to coat. For larger items, horizontal racks or custom fixtures can help ensure they remain stable and properly aligned during the coating process, which can prevent uneven application.
In addition to part handling, material management is an important consideration. Different powder coatings have different application requirements, including varying flow rates, particle sizes, and curing times. It’s important to have a clear organizational system for powder storage to ensure that different colors and types of powders are properly segregated and easy to access. Some businesses implement color change systems, which allow for quick transitions between different powder colors without having to clean the entire system. This system is especially useful in high-volume production environments where frequent color changes are necessary.
For automated powder coating booths, additional features such as color monitoring systems and coating thickness sensors can enhance the overall quality control process. These systems ensure that each part receives an even layer of powder and that the correct thickness is maintained throughout the coating process. This is particularly useful for industries that require strict adherence to quality standards, such as automotive or aerospace, where even the slightest inconsistency can lead to defects.
Customization of coatings is another area where businesses can differentiate themselves. Many powder coating systems now allow for the application of specialty powders that give parts unique finishes, such as metallic, textured, or gloss coatings. Custom finishes are popular in markets like automotive restoration, home furnishings, and decorative products. Being able to offer these unique options requires not only a powder coating booth capable of applying various powders but also the knowledge of how to adjust settings to get the desired effect. As part of your investment in equipment, consider learning how to mix powders or apply different textures for a range of results.
Energy consumption is a significant cost factor in large-scale powder coating operations, especially with the use of curing ovens. Efficient heat recovery systems and low-energy ovens are an excellent way to reduce operational costs. Some powder coating ovens come with pre-heat zones or variable temperature controls, allowing you to control the temperature precisely and avoid energy waste. Thermal insulation is another important feature that can help maintain oven temperature, further reducing energy consumption.
To achieve the best possible results, it’s critical to maintain an ideal application environment. Temperature and humidity levels play a large role in the quality of the powder coating. If the ambient temperature is too high or low, it can affect the powder’s ability to adhere to the part or cure properly. High humidity can lead to issues such as condensation on parts before they’re coated, which may cause adhesion issues or uneven coating. Keeping your powder coating booth in a controlled environment with proper air conditioning or ventilation is key to achieving consistently high-quality finishes.
As businesses grow, having a scalable powder coating system becomes more important. If you start with a small-scale setup and later decide to expand, look for equipment that is easy to upgrade. For example, a powder coating booth with a modular design can allow for future expansion, whether that means adding more spray guns, extending the booth, or integrating more automated features. Some systems can grow with your needs by adding additional curing ovens, conveyor systems, or powder recovery units, allowing you to keep up with increasing demand while minimizing disruptions.
Moreover, automation plays a key role in scaling up production. For businesses looking to increase output while maintaining consistent quality, automated spray guns and robotic arms can be integrated into the powder coating process. These robotic systems can handle repetitive tasks such as spraying powder onto parts, ensuring uniformity and precision. This level of automation reduces the risk of human error, increases speed, and improves coating consistency. Robotic arms can be programmed to handle complex shapes and adjust spraying patterns based on the part’s contours, which would be difficult to achieve manually.
Industry standards and certifications are also important to consider when operating a powder coating business. Some industries, such as aerospace or automotive manufacturing, require powder coating processes to meet specific performance and safety standards. These standards often include requirements for coating thickness, durability, and environmental considerations. Keeping up with certifications or regulatory compliance can help ensure that your coating processes meet customer expectations and industry norms.
The maintenance of powder coating booths requires attention to detail to ensure smooth operations. Regularly inspecting components such as spray guns, filters, airflow systems, and recovery units is vital to maintaining equipment performance. Cleaning is a critical part of this maintenance process. Over time, the buildup of powder residue can affect the coating process, leading to clogged filters or poor application. A good cleaning routine can prevent downtime and costly repairs. It’s also important to monitor air quality in the booth to ensure that the ventilation systems are functioning properly and that the work environment remains safe for operators.
Lastly, keeping customer satisfaction at the forefront of your operation is essential. Whether you’re coating automotive parts, industrial equipment, or decorative pieces, providing a consistently high-quality finish will keep your customers returning. Offering fast turnaround times, excellent customer service, and the ability to accommodate custom orders can set your business apart from competitors. Ensuring that your powder coating booth and system are well-maintained, and that you continue to upgrade your processes with new technologies, will help you stay ahead in the market.
In conclusion, a successful powder coating operation, whether small-scale or large, requires not only the right equipment but also a well-organized, efficient system that ensures high-quality results. By focusing on workflow optimization, energy efficiency, maintenance, and customer satisfaction, you can maximize the potential of your powder coating booth and build a thriving business.