
Powder Coating Application is basically carried out either by dipping a heated or grounded part into the powder paint, or by fluidizing (mixing powder with air) the powder and then spraying it to a heated or grounded part.
Powder coating is increasingly accepted as the preferred finishing process for many applications. Increasingly stringent environmental regulations, rising costs in all areas, and demands by consumers for better quality and more durable products are among the challenges facing today’s finishers. Powder coatings provide a solution to these challenges and others. Powder coating is the technique of applying dry paint to the component.
The powdered paint is normally applied by using a powder feed system and gun to electrostatically charge and spray the powder onto the part. For some applications, the part being coated is dipped into a fluidized bed of powder. The coated part is then heated in an oven, or via infrared panels, to melt and cure the paint. During the curing process, a chemical cross-linking reaction is triggered and it is this chemical reaction that gives the powder coatings many of their desirable properties.
Powder Coatings Application: Application Equipment
Powder Coating: A Comprehensive Overview
Introduction
Powder coating is a versatile and durable finishing technique that utilizes dry, finely ground powder particles to create a hard and protective layer on a variety of substrates, including metals, plastics, and composites. This process offers numerous advantages over traditional liquid painting methods, including enhanced durability, environmental friendliness, and improved application efficiency.
Key Components of Powder Coating
- Powder Coating Gun: The heart of the powder coating process, responsible for atomizing the powder particles into a fine mist that can be applied to the workpiece. Electrostatic guns impart a charge to the powder particles for better adhesion, while mechanical guns rely on air pressure for atomization.
- Powder Coating Booth: A controlled environment for applying the powder coating, preventing overspray and contamination of the surrounding environment. It typically includes walls, a ceiling, a floor grate, an exhaust system, and powder coating guns.
- Powder Hopper: Stores the powder before it is fed to the gun. It may include a hopper lid to prevent spills and a powder feed mechanism to regulate the flow of powder to the gun.
- Curing Oven: Cures the applied powder coating, transforming it into a durable finish. It heats the powder particles to a specific temperature for a specific time to allow them to melt, flow, and crosslink.
- Pre-Treatment: Prepares the workpiece surface for optimal powder adhesion by removing contaminants like grease, oil, and rust. It may involve degreasing, etching, and phosphating.
- Electrostatic Powder Coating: Utilizes electrostatic charge to attract powder particles to the grounded workpiece, ensuring uniform coating and reducing overspray. It is particularly suitable for complex geometries and recessed areas.
- Mechanical Powder Coating: Relies on air pressure to atomize the powder particles and propel them onto the workpiece. It is often used for larger workpieces with simpler geometries.
- Powder Feed System: Regulates the flow of powder from the hopper to the powder coating gun, ensuring a consistent and controlled application. It may involve mechanical or pneumatic systems.
- Powder Recovery System: Collects overspray powder, minimizing waste and allowing for powder reuse, promoting sustainability. It may involve cyclones, filters, or electrostatic precipitators.
- Grounding: Connects the workpiece to an electrical ground, ensuring that the charged powder particles are attracted and adhere to the surface. Proper grounding is crucial for effective electrostatic powder coating.
Advantages of Powder Coating
- Durability: Powder coating produces a durable and hard finish that is resistant to chipping, scratching, fading, and corrosion. It can withstand harsh environments and extended use.
- Environmental Friendliness: Powder coating is a solvent-free process, reducing the release of volatile organic compounds (VOCs) and environmental pollutants. It contributes to a more sustainable finishing method.
- Uniform Coating: Electrostatic powder coating ensures even and consistent coverage on the workpiece, minimizing thickness variations and imperfections.
- Wide Color and Finish Options: Powder coating offers a vast range of colors, gloss levels, and textures, catering to diverse aesthetic preferences and functional requirements.
- Cost-Effectiveness: Powder coating can be more cost-effective than traditional liquid painting methods, especially for large-scale production runs.
- Improved Efficiency: The powder coating process can be faster and more efficient than liquid painting, reducing production time and labor costs.
- Reduced Overspray: Electrostatic powder coating minimizes overspray, resulting in less waste and material consumption.
- Versatility: Powder coating can be applied to a wide range of substrates, including metals, plastics, and composites, making it a versatile finishing technique.
- Enhanced Safety: Powder coating eliminates the use of hazardous solvents, reducing the risk of exposure to harmful chemicals.
- Sustainability: Powder recovery systems minimize powder waste, promoting resource conservation and environmental sustainability.
Applications of Powder Coating
- Automotive Industry: Powder coating is widely used in the automotive industry to apply durable and aesthetically pleasing finishes to car parts, such as bumpers, wheels, and trim.
- Appliance Industry: Powder coating provides a high-quality finish and protection for appliances, such as refrigerators, stoves, and washing machines.
- Furniture Industry: Powder coating enhances the aesthetic appeal and durability of furniture pieces, such as chairs, tables, and cabinets.
- Electronics Industry: Powder coating protects electronic components from corrosion and provides a smooth aesthetic finish.
- Construction Industry: Powder coating is used to apply durable and weather-resistant coatings to metal components, such as railings, pipes, and fittings.
- Aerospace Industry: Powder coating provides high-performance finishes for aircraft parts that demand exceptional strength and corrosion resistance.
- DIY and Small-Scale Production: Powder coating kits are readily available for DIY enthusiasts and small
Powder coatings are applied using one of three standard methods:
- Fluidized Bed
- Electrostatic spray, Corona charge
- Electrostatic spray, Tribo charge
Fluidized Bed for Powder Coating Application
In this process, the combination of the fluidized bed and electrostatic electrodes create a cloud of charged powder particles above the powder bed. As in any fluidized bed, the powder material is fluidized by introducing compressed air through a porous membrane into the powder bed.
The depth of powder material in the bed is usually 2″ to 4″ (50 mm to 101 MM) Electrostatic charged electrodes, are so located in the powder bed as to charge the air used to fluidize when high voltage DC potential is applied to them. Ionizing this air results in electrostatically charged powder particles, having relatively identical high electrical charges These particles thus repel each other and move upward.
Having different electrical potentials, the powder particles and the parts to be coated or grounded, produce an electrical field of attraction. Basically, only the electrostatic field produced in this process is used to apply the powder material to the parts being coated. In contrast to electrostatic spray methods, little air is used to control the volume and velocity of the powder material. The electrostatic fluidized bed is ideally suited to substrates that have a relatively small vertical dimension, such as flat sheets, expanded metal, wire mesh, screen, cable, tubing and small parts on a conveyorized line.
The electrostatic fluidized bed offers the advantage of being able to coat some objects such as flat sheets on one side only as opposed to the conventional fluidized bed that requires dipping of the entire part. The electrostatic fluidized bed includes an integral control panel and utilizes the same powder supply unit as the manual electrostatic spray system.
The preheating of parts is not necessary with this method. The electrical forces — positive to negative — will cause the deposition of the powder on the surface whether that surface is hot or cold. Preheated parts used with electrostatics will result in a thicker coating than otherwise.
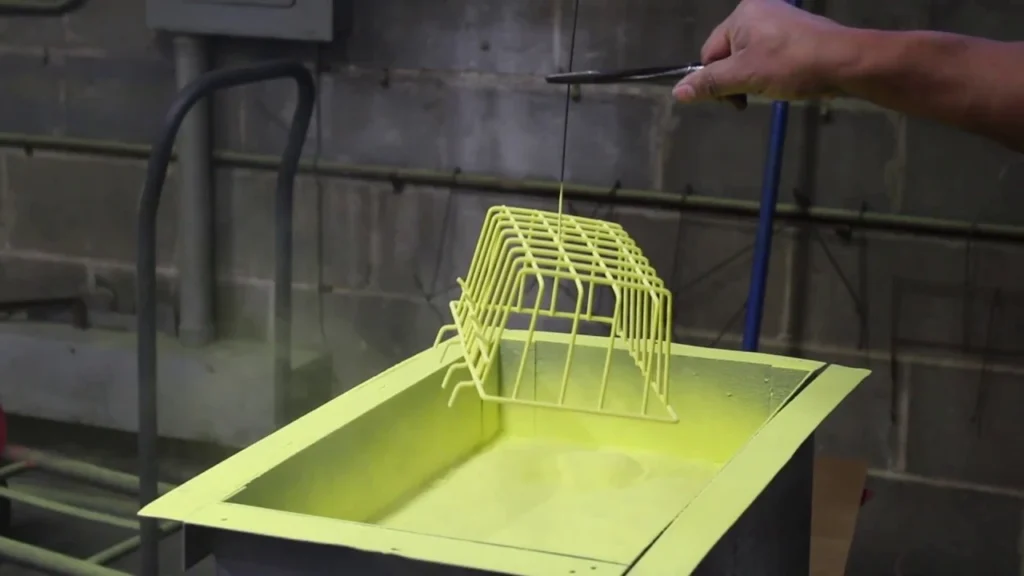
Electrostatic Powder Spray Coating
To apply powder coating materials with the electrostatic powder spray process, five basic pieces of equipment are needed:
- The powder feeder unit. Feed Hopper.
- The electrostatic spray gun. Corona or Tribo.
- The electrostatic voltage source. For Corona only.
- A powder recovery unit. Reclaim and/or Filter module.
- The spray booth. In the operation of an electrostatic powder spray system, the powder is supplied to the spray gun from a feeder unit, where the powder is stored for use. The powder is siphoned or pumped from the feeder unit through the powder feed hose to the spray guns. Spray guns direct the powder toward the part to be sprayed in the form of a diffused cloud. Propelling force is provided both by air used to transport the powder from the feeder unit to the spray gun and by the electrostatic charge imparted to the powder at the gun. This electrostatic charge is generated in any of the following methods: Internal Corona, Remote
Corona and Tribo
Electrostatic Powder Spray Coating, Corona Gun for Powder Coating Application

Powder coating is a versatile and durable finishing technique that utilizes dry, finely ground powder particles to create a hard and protective layer on a variety of substrates, including metals, plastics, and composites. This process offers numerous advantages over traditional liquid painting methods, including enhanced durability, environmental friendliness, and improved application efficiency.
Key Components of Powder Coating
- Powder Coating Gun: The heart of the powder coating process, responsible for atomizing the powder particles into a fine mist that can be applied to the workpiece. Electrostatic guns impart a charge to the powder particles for better adhesion, while mechanical guns rely on air pressure for atomization.
- Powder Coating Booth: A controlled environment for applying the powder coating, preventing overspray and contamination of the surrounding environment. It typically includes walls, a ceiling, a floor grate, an exhaust system, and powder coating guns.
- Powder Hopper: Stores the powder before it is fed to the gun. It may include a hopper lid to prevent spills and a powder feed mechanism to regulate the flow of powder to the gun.
- Curing Oven: Cures the applied powder coating, transforming it into a durable finish. It heats the powder particles to a specific temperature for a specific time to allow them to melt, flow, and crosslink.
- Pre-Treatment: Prepares the workpiece surface for optimal powder adhesion by removing contaminants like grease, oil, and rust. It may involve degreasing, etching, and phosphating.
Electrostatic Powder Coating:
Electrostatic powder coating is the most common method of applying powder coating. It utilizes electrostatic charge to attract powder particles to the grounded workpiece, ensuring uniform coating and reducing overspray. This method is particularly suitable for complex geometries and recessed areas.
Principle of Electrostatic Powder Coating:
- Electrostatic Charging: The powder particles are charged with a positive or negative electrostatic charge using a corona discharge gun.
- Grounded Workpiece: The workpiece is electrically grounded, creating an opposite charge to the powder particles.
- Electrostatic Attraction: The charged powder particles are attracted to the grounded workpiece, ensuring even and consistent coverage.
- Curing: The coated workpiece is then transferred to a curing oven, where the powder melts, flows, and crosslinks to form a durable finish.
Advantages of Electrostatic Powder Coating:
- Uniform Coating: Electrostatic attraction ensures even and consistent coverage, minimizing thickness variations and imperfections.
- Reduced Overspray: Charged powder particles adhere to the workpiece, reducing overspray and minimizing powder waste.
- Suitable for Complex Geometries: Electrostatic attraction allows for coating complex shapes and recessed areas effectively.
- Environmentally Friendly: Minimized overspray reduces environmental impact and promotes sustainability.
Applications of Electrostatic Powder Coating:
- Automotive Industry: Electrostatic powder coating is widely used in the automotive industry to coat car components, such as bumpers, wheels, and trim.
- Appliance Industry: It is used to provide a high-quality finish and protection for appliances, such as refrigerators, stoves, and washing machines.
- Electronics Industry: Electrostatic powder coating is used to protect electronic components from corrosion and provide a smooth aesthetic finish.
- Construction Industry: It is used to apply durable and weather-resistant coatings to metal components, such as railings, pipes, and fittings.
- DIY and Small-Scale Production: Electrostatic powder coating kits are available for DIY enthusiasts and small-scale production runs.
Mechanical Powder Coating:
Mechanical powder coating relies on air pressure to atomize the powder particles and propel them onto the workpiece. It is often used for larger workpieces with simpler geometries.
Principle of Mechanical Powder Coating:
- Compressed Air: Compressed air is used to atomize the powder particles into a fine mist.
- Powder Feed System: The powder is fed from a hopper into the air stream, where it is mixed with compressed air.
- Powder Nozzle: The atomized powder is directed towards the workpiece using a powder nozzle.
- Impact Coating: The powder particles impact the workpiece and adhere due to the force of the air stream.
- Curing: The coated workpiece is then transferred to a curing oven, where the powder melts, flows, and crosslinks to form a durable finish.
Advantages of Mechanical Powder Coating:
- Simple Operation: Mechanical powder coating systems are relatively simple to operate and maintain.
- Suitable for Large Workpieces: Mechanical powder coating is suitable for larger workpieces with simpler geometries.
- High Production Rates: Mechanical powder coating systems can achieve high production rates for large-scale applications.
- Cost-Effective: Mechanical powder coating systems are often less expensive than electrostatic powder coating systems.
There are two types of corona guns
- Internally charged (Low Voltage) Corona gun
- Remotely charged (High Voltage) Corona guns
Each type comes in negative or positive polarity, although corona charging generally uses negative polarity at the electrode.
This is because negative polarity produces more ions and is less prone to arcing. Positive charging guns are mostly used in tribo touch up applications and with some thermoset materials. This very high voltage potential at the electrode requires a power supply rated between 30,000 and 100,000 volts.
This creates an field of electrical attraction between the gun and the grounded part. The particles stick to the part much like a magnet to steel, creating a layer of powder on the part. Over spray, or powder not adhering to the part, is collected for re-use. In the collector unit, powder is separated from the conveying airflow.
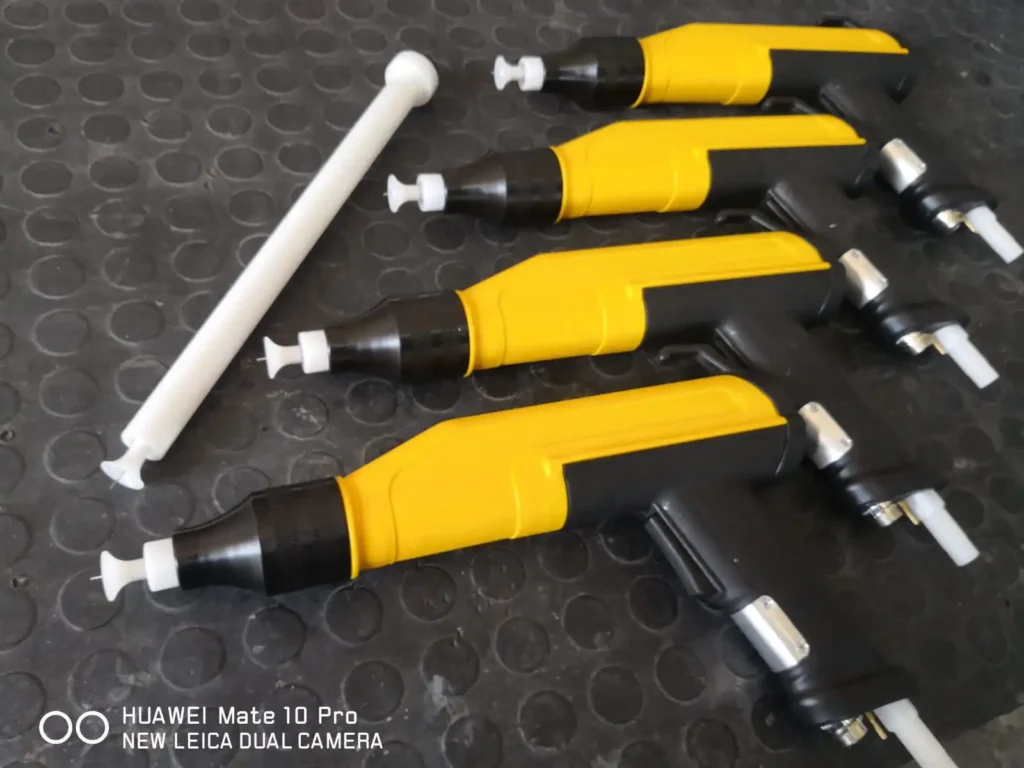
Collected powder is then recycled, either automatically or manually, back to the feeder unit to be resprayed. Air is passed through a filter media device into a clean air plenum and then through a final or absolute filter back into the plant environment as clean air. The coated part is then carried from the application area and subjected to heat, which results in the flow out and curing of the powder material.
Electrostatic Powder Spray Coating
Electrostatic powder spray guns function to shape and direct the flow of the powder as supplied from the feed hopper; control the pattern size, shape, and density of powder, as it is emitted from the spray gun; impart the electrostatic charge to the powder being sprayed, and control the deposition of powder on parts being sprayed through gun position, pattern shape, and electrostatic levels.
The charging electrode we mentioned earlier is located at the front of the spray gun. When the powder passes by the electrode, it picks up a charge – which is variable, and deposits on the part. The thickness of this deposition can be controlled by the position of the spray gun, length of spray time, level of electrostatic charge and velocity of the powder flow from gun to part, part aperture, etc.
Thickness of the applied powder to the part also can be controlled by affected characteristics inherent to the powder being sprayed; such as particle size, shape, type of powder material and distribution of the powder particle size range.
These factors are all covered in out troubleshooting guide.
Electrostatic Powder Spray Coating, Corona Gun
The two types of Corona guns are very similar. The difference is where the high voltage power supply is located. The cable between gun control and gun will therefore be of low voltage (internal) or high voltage (remote). Corona gun technology has evolved greatly over the past ten years and two advances are becoming prevalent throughout the industry.
Automatic Current Control: Allows for automatic adjustment of gun voltage to maintain the gun current and field strength between the gun and part at an optimum level. This allows for more uniformity in the coating since the gun logic compensates for operator and part configuration variations as well as faraday cage effect problems.
Free-Ion Collectors: Is a device which extracts free ions from the space between a gun and a part, drawing them to a grounded collector electrode behind the gun tip. An inexpensive retrofit to existing equipment, these also permit for greater uniformity and greatly improved faraday cage penetration abilities.
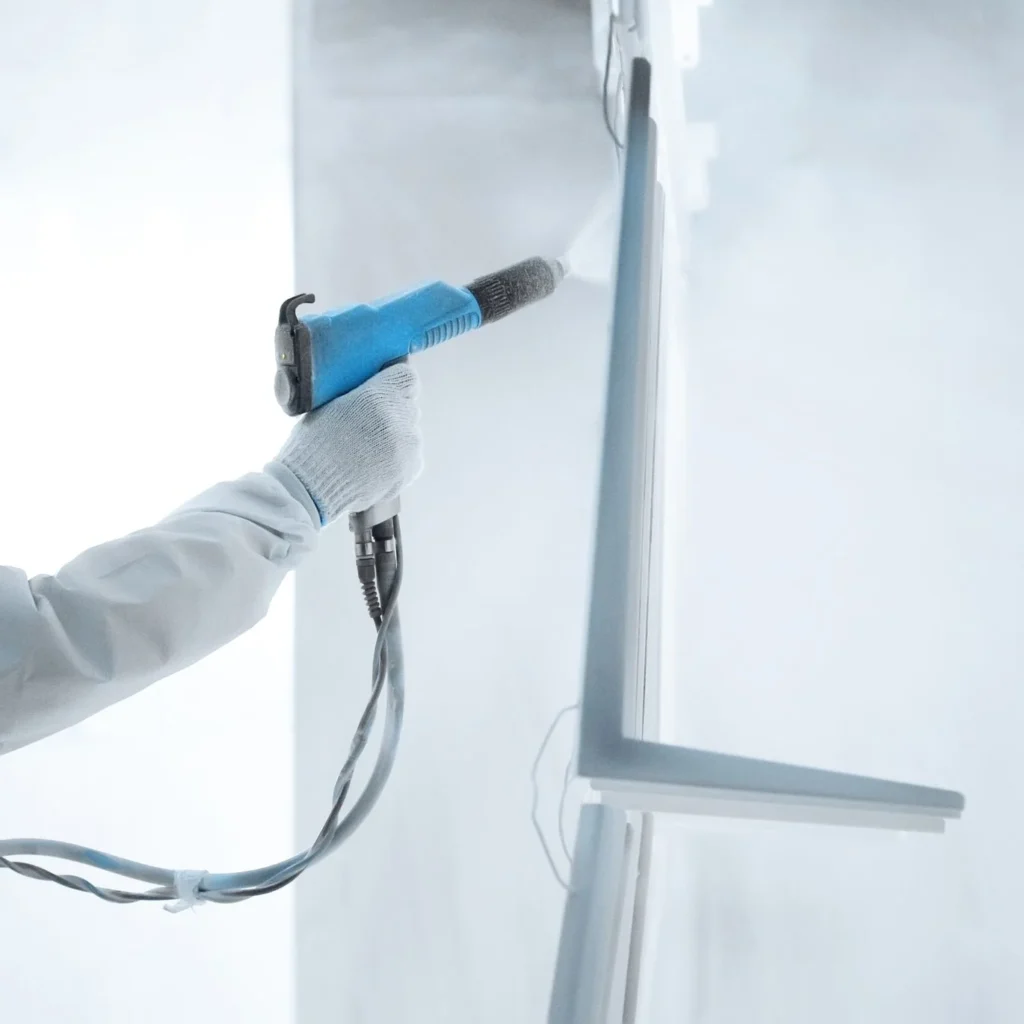
Electrostatic Powder Spray Coating, Tribo Gun for Powder Coating Application
The word tribo is derived from the Greek word tribune, meaning to rub or produce friction. With tribo charging the powder is charged by means of special materials(such as Teflon) which by stealing electrons from the powder particles impart a positive charge on the powder as it flows, and rubs, through the gun.
Tribo guns have no internal or remote power supply. This means no electrostatic field is created, virtually eliminating the faraday cage effect, making this the ideal approach for use in coating intricate parts such as detailed automotive rims and heatsinks.
These formulations are much more dependent upon the formulation and particle size as well as environment than corona powders are. High humidity or extremely dry environments can affect the amount of charge imparted upon the powder.

Electrostatic effectiveness: For all powder applications
The effectiveness of any of these types of powder spray guns is not totally dependent on the gun alone. Characteristics of the powder material also affect the transfer efficiencies realized in the process. The powder particles must, of course, be capable of accepting the electrostatic charge imparted by the spray gun. A compromise between high conductivity and low conductivity is necessary, to ensure both acceptance of the electrostatic charge and adhesion to the part sprayed.
The nature of the particle material likewise has an influence upon the possibility of it obtaining a maximum charge. The particle must first be able to accept the maximum charge as it passes through the ion cloud. The degree of acceptance is directly related to the electrical conductivity of the particle.
The charge upon the particle likewise has great influence upon the manner in which the material collects upon the surface and the rate at which the film of material builds. A charged layer accumulates upon the surface with the material and has the effect of building a force that opposes further deposition.
The rate of film growth must be related to other factors such as the velocity at which the charged powder is projected toward the surface, the distance of the gun from the surface, the particle size, the time of exposure of the surface in the spray, the voltage on the gun and the quantity of powder being delivered from the gun.
Increasing the voltage applied to the spray gun while keeping other factors constant will result in more film being collected on the part in equal exposure times. The rate at which powder collects on the part at the beginning of the exposure increases as the voltage increases. As exposure increases, the accumulation rate tends to become the same for all voltages, when using a corona discharge gun.
Generally, as the distance from the gun outlet increases, the film accumulated on the part in a given time decreases. Film accumulation is much more rapid initially when the distance is small. The effects of the air velocity gradient at the part upon the deposition of powder are similar to those of distance from the gun.
As the air velocity increases, the accumulation in a given time decreases. The ultimate film thickness obtained is independent of the rate of powder delivery in the absence of air velocity gradient interference. The rate of film build which occurs initially is approximately proportional to the quantity of powder delivered per unit of time at a constant voltage.
As spraying time increases, the effect of powder output on the rate of film growth becomes less pronounced. The initial rate of growth of the film thickness is approximately proportional to the particle size; the rate of growth depends upon the particle size over a wide range of spraying time, and the limiting value of the film thickness is greater with smaller-sized powders.
By proper understanding of the manner in which these variables generally influence the deposition of the material, an applicator can take into consideration the characteristics of equipment, methods, and materials which will result in a satisfactory application.
Powder Coating Application Conditions
For electrostatic spray guns to function properly and safely, the following conditions should be maintained:
- Fixed powder spray guns must be adequately grounded at their points of support, if metallic, to reduce the possibility of static charge buildup on the gun and the possible discharge of this static charge to a part or component in the spray area.
- Manual powder spray gun operators must be adequately grounded (usually through the gun handle) to prevent the buildup of a static charge on the operator’s body during spray operations.
- Powder spray gun parts that come into physical contact with moving
powder must be inspected and cleaned on a regular basis. Parts which contact powder during the movement of powder are prone to wear (especially if the powder material is abrasive) at high velocity and form impact fusion. Worn parts result in poor control of powder flow, accentuated impact fusion and more frequent cleaning is required. If a part is worn, it should be replaced Electrostatic spray guns, manual and automatic, should be checked periodically to determine the level of electrostatic charge being imparted to the powder material being sprayed. The lack of, or decrease in, expected electrostatic charge indicates a problem in the electrostatic system and should be corrected as soon as possible. Troubleshooting guides should be utilized when inspecting or repairing any component within the electrostatic system to reduce the possibility of electric shock. - When using fixed or automatic powder spray guns, interlocks should be provided which will rapidly de-energize the high-voltage elements involved with electrostatic spray under any of the following conditions: stoppage of ventilating fans or failure of ventilating equipment from any cause; stoppage of conveyor carrying goods through the electrostatic spray, upon trigger from spark detection modules in booth, and other conditions as prescribed by regulatory agencies.
Yes, Powder booths can go up in flames despite the lack of solvents used. With no detection modules, the fire will burn fast with terrible results. We know of a few of these fires over the past few years, one at a customer who disabled their detection system.