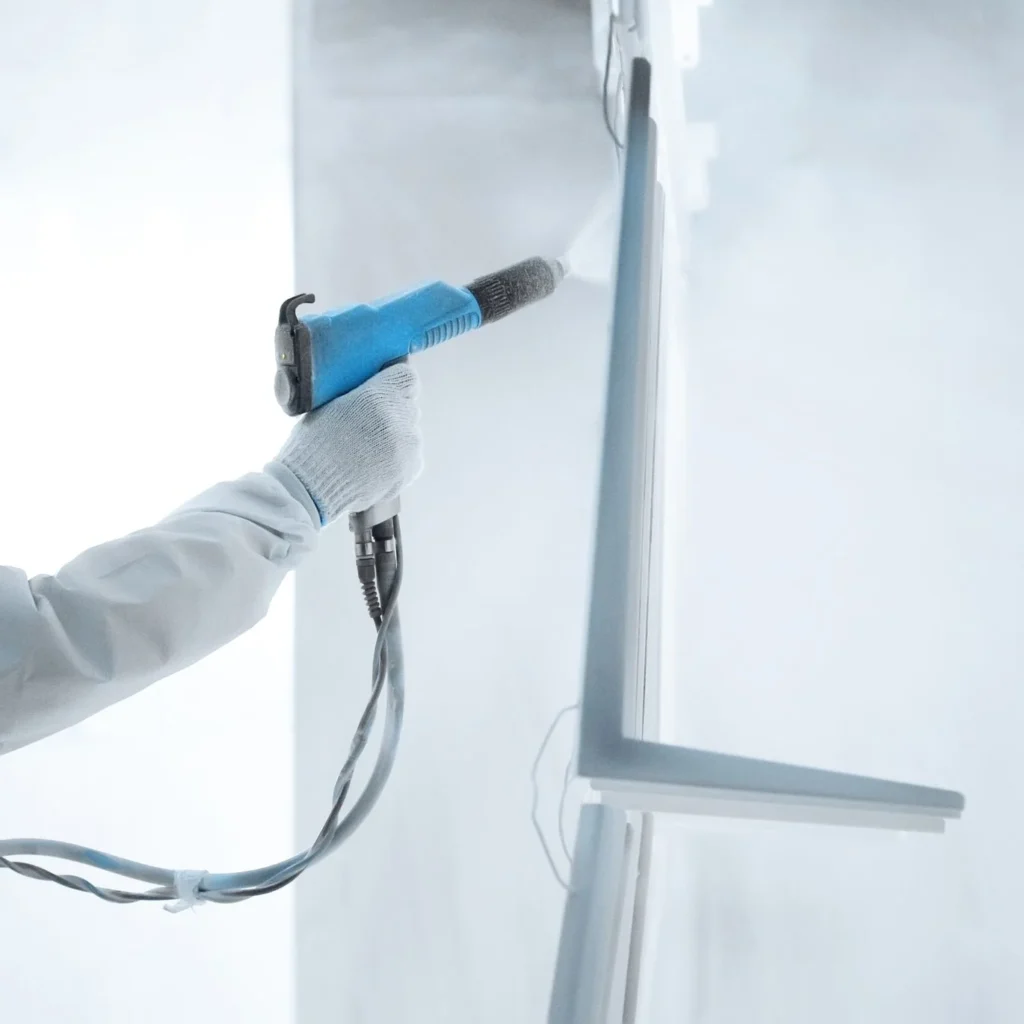
Powder coating is a special finishing application, carried out by electrostatically charged powder coating powder and an applicator such as a powder coating equipment.
Powder coating is increasingly accepted as the preferred finishing process for many applications. Increasingly stringent environmental regulations, rising costs in all areas, and demands by consumers for better quality and more durable products are among the challenges facing today’s finishers. Powder coatings provide a solution to these challenges and others. Powder coating is the technique of applying dry paint to the component.
The powdered paint is normally applied by using a powder feed system and gun to electrostatically charge and spray the powder onto the part. For some applications, the part being coated is dipped into a fluidized bed of powder. The coated part is then heated in an oven, or via infrared panels, to melt and cure the paint. During the curing process, a chemical cross-linking reaction is triggered and it is this chemical reaction that gives the powder coatings many of their desirable properties.
How is Powder Coating done – electrostatic spray?
The powder is applied with an electrostatic spray gun to a part that is at earth (or ground) potential. Before the powder is sent to the gun it is fluidized:
- To separate the individual grains of powder and so improve the electrostatic charge that can be applied to the powder and
- So that the powder flows more easily to the gun. Because the powder particles are electrostatically charged the powder wraps around to the back of the part as it passes by towards the air-off take system. By collecting the powder, which passes by the job and filtering it the efficiency of the process can be increased to 95% material usage.
The powder will remain attached to the part as long as some of the electrostatic charges remain on the powder. To obtain the final solid, tough, abrasion-resistant coating the powder-coated items are placed in an oven and heated to temperatures that range from 160 to 210 degrees C (depending on the powder).
Under the influence of heat, a thermosetting powder goes through 4 stages to full cure. Melt, Flow Gel, Cure. The final coating is continuous and will vary from high gloss to flat matt depending on the design of the powder by the supplier.
Powder Coating Guns
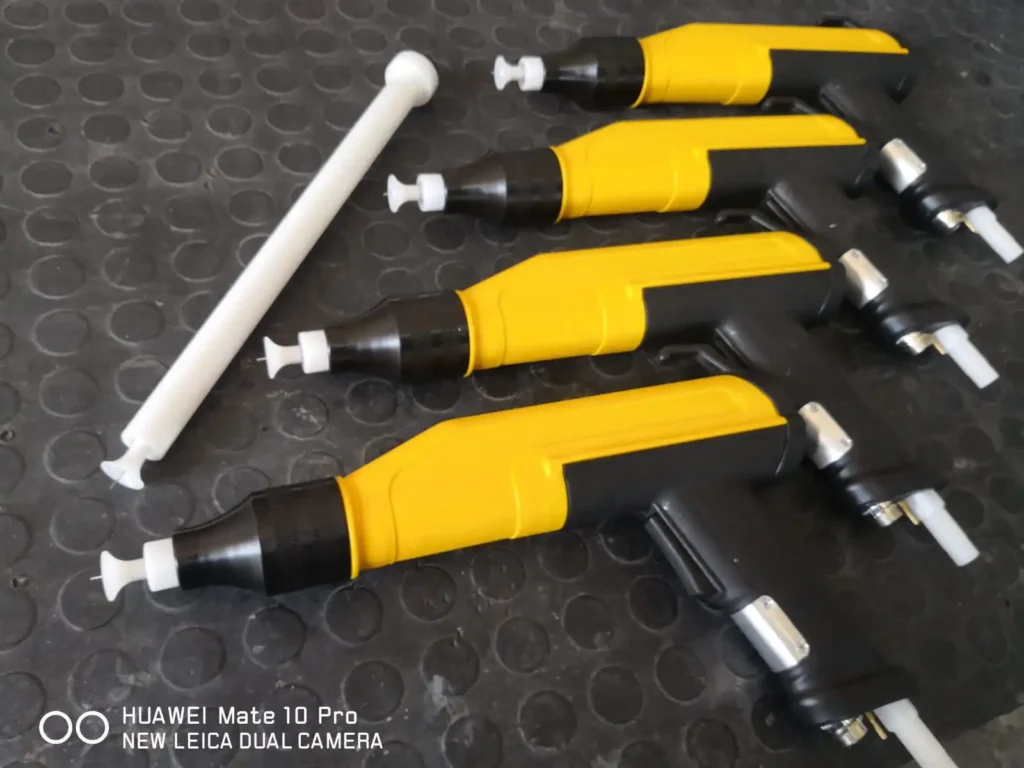
There are at least three types of electrostatic guns in use:
- Corona charging guns where electric power is used to generate the electrostatic charge. Corona guns are either internal or external charging.
- Tribo charging guns where the electrostatic charge is generated by friction between the powder and the gun barrel.
- “Bell” charging guns where the powder is charged by being “flung” from the perimeter of the “bell”
- Not all powder is applied using guns. One system makes use of electrostatic tunnels.
How is color introduced?
Colour is added to powder coating during the manufacturing process, i.e. before the powder reaches the powder coater. There is little that can be done to change the color consistently, once the powder leaves the manufacturing plant.
Why powder coat?
Powder coating produces a high specification coating that is relatively hard, abrasion resistant (depending on the specification), and tough. Thin powder coating can be bent but this is not recommended for exterior applications. The choice of colors and finishes is almost limitless if you have the time and money to have the powder produced by the powder manufacturer. Powder coating can be applied over a wide range of thicknesses.
The new Australian Standard, “AS/NZS 4506 – Thermoset powder coating” will recommend a 25-micron minimum for mild interior applications and up to 60 micron minimum for exterior applications. Care must be exercised when quoting minimum thickness because some powder will not give “coverage” below 60 or even 80 microns. “Coverage” is the
ability to cove the color of the metal with the powder. Some of the white colors require about 75 microns to give full “coverage”. One of the orange colors must be applied at 80 microns. Colour matching is quite acceptable from batch to batch.
Installation and Maintenance
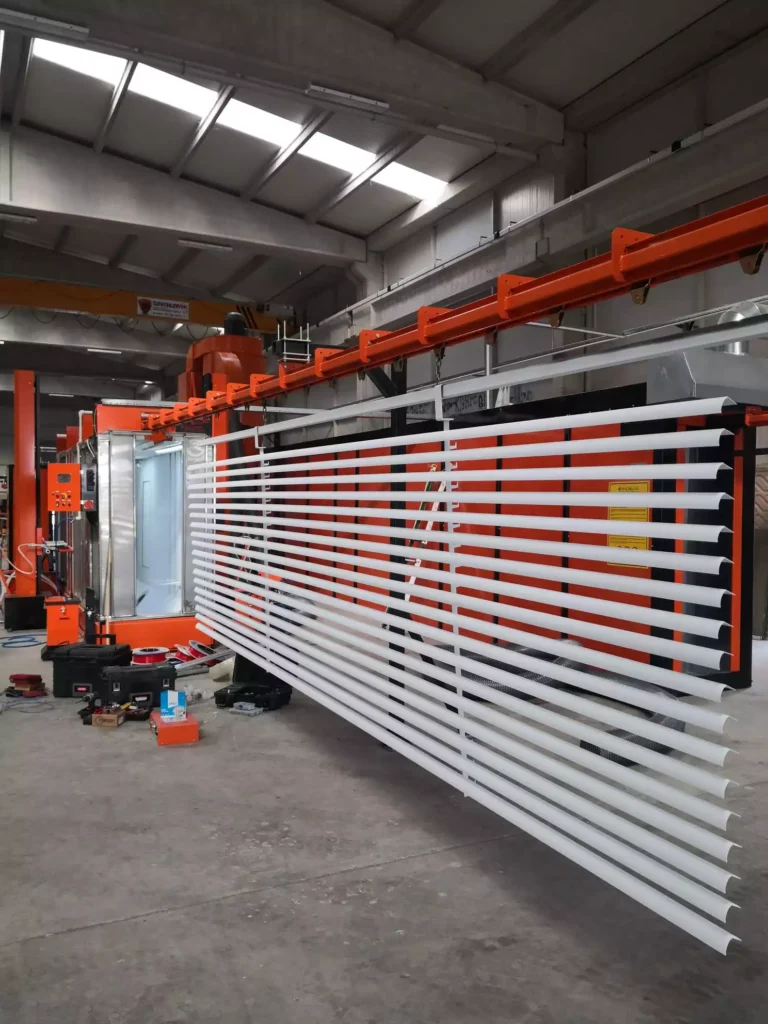
During installation, the powder coating should be protected from damage due to abrasion and materials of construction such as mortar and brick cleaning chemicals. Once installed, maintaining the initial appearance of a powder coating is a simple matter. The soot and grime which builds up on surfaces from time to time contain moisture and salts which will adversely affect the powder coating and must be removed.
The powder coating should be washed down regularly (at least once each 6 months in less severe applications and more often in marine and industrial environments) the coating should be washed down with soapy water – use a neutral detergent – and rinsed off with clean water. When powder-coated items are installed without damage to the powder coating they are maintained regularly, they should be relatively permanent. The correctly applied coating, although not metallurgically bonded to the metal will not crack, chip, or peel as with conventional paint films
Moisture Separator for Powder Coating
Putting down a nice paint job on that project car you have been working on is hard enough without having the aggravation of air line contaminants ruining it. Preventing moisture and oil from contaminating your airline and subsequently your pain job is all a matter of having the right equipment and using it properly. The key to keeping moisture out of your airline is to separate the moisture from the air entering your paint gun with an in-line air water separator and filter.
Instructions for Powder Coating
Locate a suitable position to mount the wall-mounted in-line air water separator and filter unit in your air supply line a few feet from the air compressor itself. This unit will remove most of the moisture from your air supply line and will also remove all other contaminants and leave you with a nice, clean air supply to not only your spray gun but your other tools. Mount the tool-mounted mini in-line air water separator between your paint gun and the clean, dry air hose you will use only for painting.
This mini air water separator will remove the last traces of moisture that may be in the air supply line just before it enters your spray gun. Open the drain petcock value on your compressor to drain any water from your compressor tank. Close the valve when the water is drained. Test your new moisture-free air supply line to make sure it’s leak-free and that the filters and separators work properly according to their instructions. Begin painting.
Different treatment steps in powder coating:
Pre-treatment of profiles is usually carried out by dipping the profiles (a jig) into a sequence of tanks containing different chemical solutions. Most producers use chromating as conversion coating and therefore chromatin will be discussed in this manual. The following sequence of stems is normally used to pre-treat aluminum prior to powder coating.
Degreasing: In the degreasing step oil, grease, and other surface contaminations are removed from the profile surface to obtain a clean surface prior to etching. Inhibitors are often added to protect the metal surface from attack during this cleaning operation.
Rinsing:
There is usually a rinsing step (or more) after each process step to remove chemicals from the profile surface and prevent carryover and contamination of the solution. Mains water is normally good enough after the first pre-treatment steps, but in the final rinsing step, the water should be very clean to avoid adhesion and corrosion problems. In this case, the conductivity of the rinsing water (do-ionized water) should not exceed 30 μS/cm.
This de-ionized water rinse is extremely important, as salts (calcium) caused by hard water dried on the extrusion surface can be the starting point of corrosion and lacquer blistering. There are no limits regarding the rinsing temperature of the first rinsing baths, but the temperature of the water in the rinsing steps after chromatin should not exceed 50ƒC. If the rinsing water is too hot the chromate layer could be washed off. The rinsing time is usually a few minutes. Agitation of the jig (profiles) and/or air agitation of the water is an advantage to get better rinsing.
Etching
The thin natural oxide coating on the aluminum surface has to be removed before the chromating. Inhibitors are often added to protect the metal surface from attack during this etching operation. Temperatures between 50ƒC and 70ƒC are normal. The cleaning time is from 3 to 4 minutes and higher depending on the surface conditions.
Rinsing
There is usually a rinsing step (or more) after the process steps to remove chemicals from the profile surface and prevent carryover and contamination of the solution. Mains water is normally good enough after the first pre-treatment steps, but in the final rinsing step, the water should be very clean to avoid adhesion and corrosion problems. In this case, the conductivity of the rinsing water (de-ionized water) should not exceed 30 μS/cm.
This de-ionized water rinse is extremely important, as salts (calcium) caused by hard water dried on the extrusion surface can be the starting point of corrosion and lacquer blistering. There are no limits regarding the rinsing temperature of the first rinsing baths, but if the temperature of the water is too hot the chromate layer could be washed off. The rinsing time is usually a few minutes. Agitation of the jig (profiles) and/or air agitation of the water is an advantage to get better rinsing.

Deoxidisation
In the deoxidization process, any smut resulting from insoluble etching is removed. This smut layer consists of oxides like magnesium oxide, intermetallics, silicon, etc. which are not soluble in alkaline solutions. Smut is removed by a dip in an acid solution such as nitric acid or sulphuric acid, but many producers of coated aluminum profiles use special deoxidization products from chemical suppliers in coated aluminum profiles that use special deoxidization products from the chemical supplier in addition to nitric acid.
These deoxidization products may consist of chromate in order to inhibit the deoxidization process on the aluminum surface and fluorides to remove silicon. The dipping time may vary from 30 seconds up to 5 minutes dependent on the smut layer the solution and the alloy. The deoxidization process is usually carried out at room temperature.
Rinsing (double rinsing)
There is usually a rinsing step (or more) after each process steps to remove chemicals from the profile surface and prevent carryover and contamination of the solution. Mains water is normally good enough after the first pre-treatment steps, but in the final rinsing step, the water should be very clean to avoid adhesion and corrosion problems. In this case, the conductivity of the rinsing water (de-ionized water) should not exceed 3μS/cm.
This de-ionized water rinse is extremely important, as salts (calcium) caused by hard water dried on the extrusion surface can be the starting point of corrosion and lacquer blistering. There are no limits regarding the rinsing temperature of the first rinsing baths, but the temperature of the water in the rinsing steps after chromating should not exceed 50ƒC. If the rinsing water is too hot, the chromate layer could be washed off. The rinsing time is usually a few minutes. Agitation of the jig (profiles) and/or air agitation of the water is an advantage to get better rinsing.
Drying
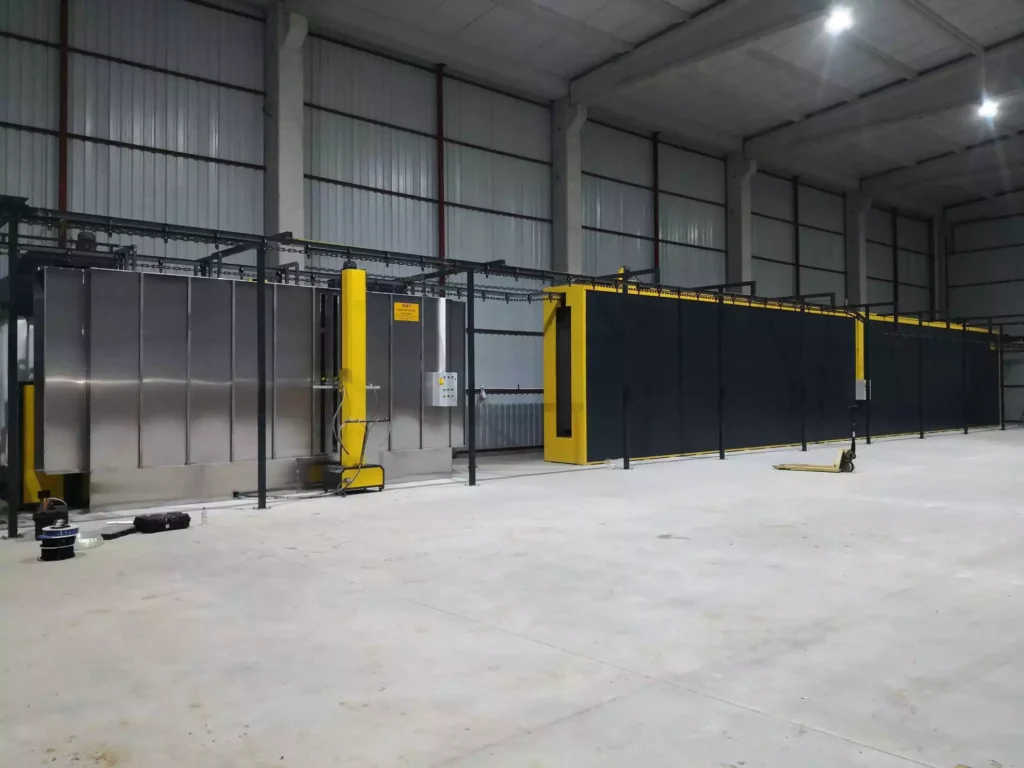
Prior to powder coating, the profiles have to be completely dry. Moisture on the surface will interfere with the coating process. The temperature of the profile surface should not be too high in the drying oven. The breakdown temperature for the yellow chromate coating is about 65ƒC and about for the green chromate coating. If the drying temperature exceeds these limits the conversion coatings may give an inferior
corrosion resistance.
Powder Coating
Before powder coating, the profiles, which have been pre-treated by dipping, must be rejigged. The conveyor system in the powder coating/curing lines does not fit the jigging system in the pre-treatment lines. The profiles are jigged horizontally during powder coating, as they are in the pre-treatment process. The speed of the conveyor is related to powder application parameters and coring conditions (oven length and temperature).
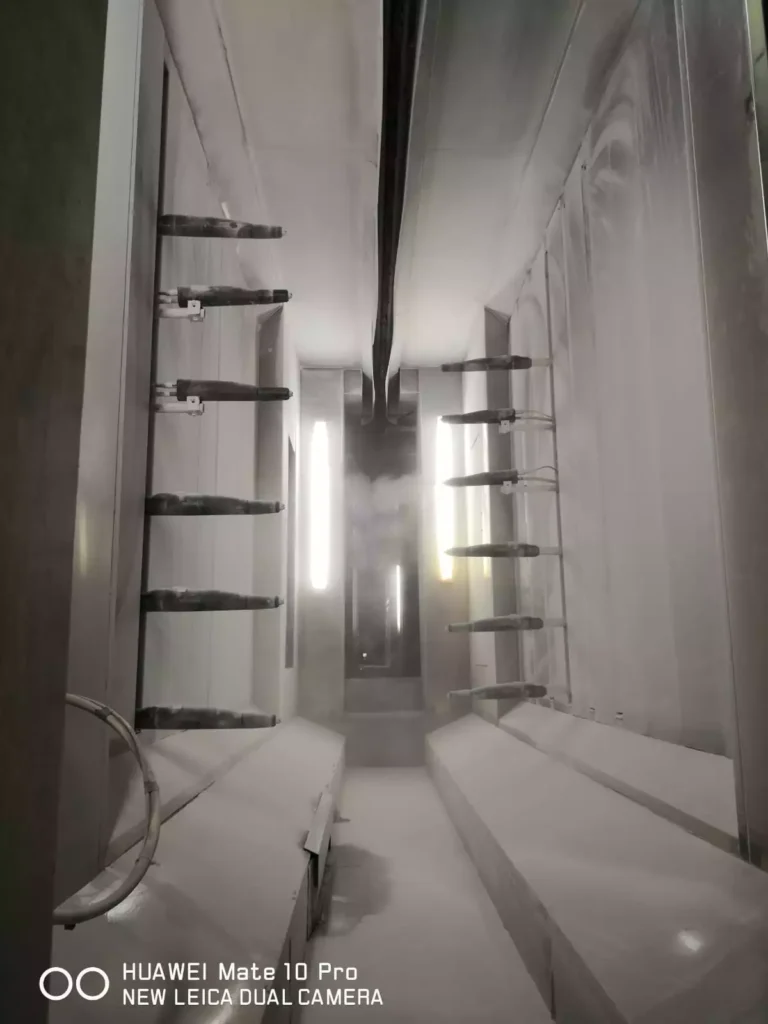
The powder coating operation is carried out in special spray booths. There are many types of spray booths on the market, but the two kinds more commonly used are cartridge filter booths and cyclone booths. The cartridge filter booth has the advantage of high recovery and of being gentler to the powder, producing fewer files.
On the other hand, it is practically impossible to clean, so a separate filter system for every color is needed. Colour changing is paramount in coating extrusions, so maybe the cyclone booth is more suitable. The losses in the cyclone are heavily reduced by using tribo guns, as these have a very high first pass transfer efficiency so that only a relatively small proportion of powder arrives at the cyclone at all.
It may be added that as cyclones lose the fines, there are no quality problems due to fines. There are powder guns placed on both sides of the booth, usually in the middle of the booth walls (see figures below). The number of guns is dependent on the shape of the profiles and the type of powder. Tribostatic powder coating needs at least twice as many guns as electrostatic powder coating.
But the number of guns is also dependent on demands regarding the surface finish of the profiles. When using a greater number of guns the air and powder pressure could be decreased. That will cause a raise in surface quality, but also less wear on the powder hoses. Powder coating line including pre-treatment steps
Normally some of the powder guns are in a fixed position, while most of the guns move automatically slowly up and down. Adjustment of the guns is – as mentioned above – dependent on the shape of the profile, but also dependent on which coating thickness and finish are requested.
Curing
The curing operation is carried out in curing ovens. A curing oven should:
- Be energy efficient
- Have the same temperature across the length or the height of the extrusion
- Not have too much turbulence, so that powder isn’t blown away.
The two last conditions are contrasting, as uniformity of temperature is often obtained by strong air recirculation. This means that air speeds in the oven must be well calculated. The energy required for the curing operation is given by supplying heat in two different ways:
Hot air convection heating
IR (infra-red) radiation
Some producers of powder-coated profiles use both hot air convection heating and IR radiation. The IR elements are placed at the entrance of the curing oven in order to give a rapid and effective energy transfer in the reaction of the powder coating. Thereby minimizing the chance of powder being blown off Normally the temperature to get proper coring of a powder coating is around 200ƒC, and the curing time may be 10-1 minute.
To obtain a powder coating with a good level or flow properties – that means without any orange peel – the temperature has to be at the correct level at the entrance of the oven to ensure a proper melting of the powder. After melting there is a reaction between the resin and the cross-linking agent and a chemical bonding takes place between molecules.
This is the reason for the good wear resistance and surfaces hardness of the thermosetting powder lacquers compared with the thermoplastic powders, where only a fusion of powder particles occurs during the curing reaction
What is Powder Coating?
The powder is a dry coating. Instead of being dissolved or suspended in a the liquid medium, such as solvent or water, the powder is applied in a granular form. This material is finer than ground pepper but coarser than flour and is applied directly to the surface to be coated. The powder is created by blending the various components (binders, resins, pigments, fillers, and additives) and processing them through an extruder into a continuous mass.
This homogenous mass is cooled and broken into small chips, which are then ground into the powder. Each powder particle contains within it the necessary components for reforming into the finished coating. After the powder is applied to the part, typically using an electrostatic spray process, the part passes through an oven and cures, melting into a smooth film on the surface of the part.
Powder Formulation
There are two distinct types of powder, Thermoset, and Thermoplastic. The Thermoset powders are reactive, which means that under cure conditions there is a chemical “crosslinking”, so that, once cured, the coating will not remelt. Epoxies, acrylics, and most hybrids are examples of Thermoset powders, making up over 90% of the current powder market.
Thermoplastic powders do not “crosslink” when cured, but simply melt and flow over the surface of the part. The film hardens on cooling, but if it is reheated it will remelt. Vinyls, nylons, and fluorocarbons are examples of thermoplastic powders. Enamel powder is a specialized formulation used in applications that previously used liquid porcelain enamel.
It utilizes glass in its formulation and is cured, or fired, at
very high heat. The result is a finish that is particularly resistant to heat, scratching, and harsh chemicals and is typically used in appliances, such as washers, dryers, ovens, and ranges.
How is the powder applied?
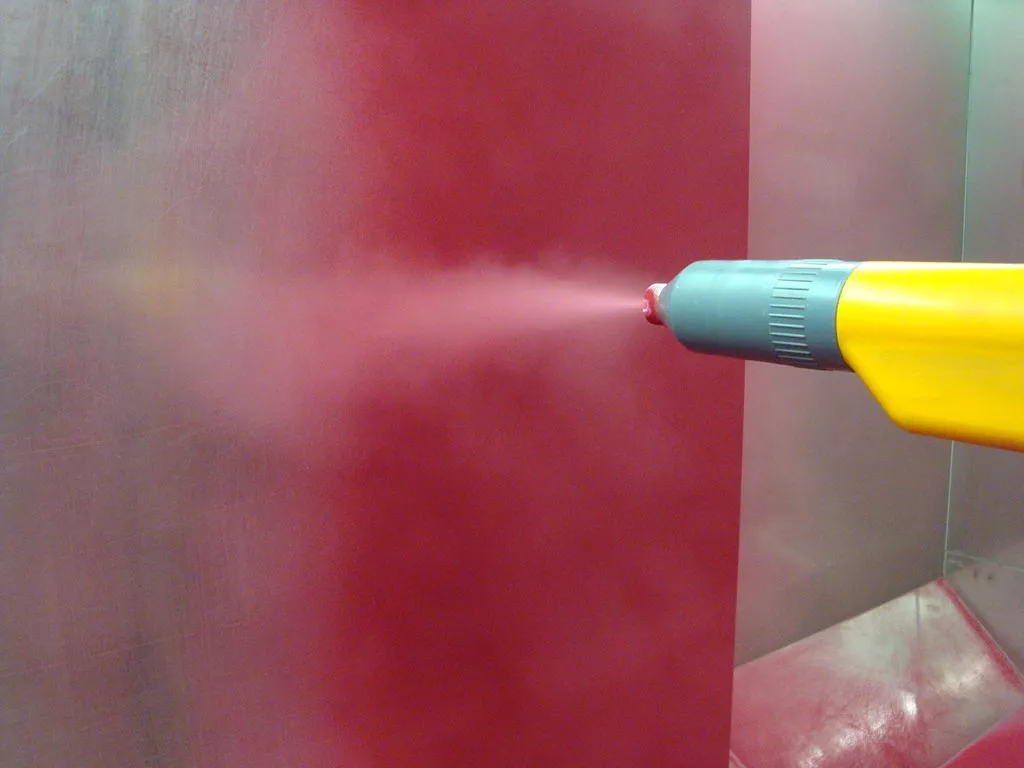
The application process involves applying a charge to the dry powder particles and spraying them onto a grounded substrate. The substrate, or part, is typically grounded through the conveyor or hanger holding the part. The powder once attracted to the part, is then held on the surface
until it is melted and cured into a smooth coating film in the bake oven. The spray process takes place inside a booth designed to contain the oversprayed powder and makes it possible to collect the overspray and ultimately reclaim it for reuse.
The powder is fed pneumatically out of the powder container, or hopper, into the powder applicator, or gun. As the powder exits the gun, a low amperage, high voltage charge is applied to the powder particles, causing them to be attracted to the grounded workpiece. This attraction may even cause the powder to “wrap” around the piece, coating the back side.
The oversprayed powder, suspended in the air contained inside the powder booth, is then passed through a separation process that permits the powder particles to be retrieved from the air. The clean air is fed back to the work environment, eliminating the need for air make-up. The reclaimed powder is mixed with a proportionate amount of fresh, virgin powder for reuse achieving consistent results and up to 98% material utilization.
How Will Powder Coating Benefit My Operation?
Reviewing the potential benefits of powder coating will give you an incentive to proceed with the quest for the best finish for your operation. So let’s look at the three “E’s” of powder coating in more detail.
Economy
- Material utilization is much higher with powder, making your material costs much lower. 92% to 98% of the powder you buy will be applied to the parts you are finishing versus an average of 60% with an electrostatic liquid system (the other 40% is waste and must be disposed of!)
- Since most of the material is used on the part, there is very little waste to be disposed of. And the powder is not considered hazardous waste, so the cost of disposal is minimal compared to the high cost of toxic waste disposal.
- Air used to exhaust the powder in a spray booth is returned directly to the plant, eliminating heating and cooling costs for the make-up air required when air is vented outside the plant.
- Air loss from the curing oven is minimized as there is only a very small amount of volatile substance that must be exhausted. The cost of maintaining oven temperatures is therefore minimized also.
- The powder is simpler to spray, so less skilled labor is needed, training is easily done and fewer errors are made in the coating. All of which saves scrap, labor, and, ultimately, operating costs.
- Most powders require no primer, providing more savings in time and materials.
Excellence
- The cured powder finish is less susceptible to damage than a liquid finish. There is less need for repair work on the finished item, and packaging is less elaborate, saving time and cost on rework and packaging.
- Epoxy, acrylic, and hybrid powders provide excellent adhesion and hardness for improved resistance to chipping, abrasion, corrosion, and chemicals; and it’s flexible enough to be formable without cracking.
- Polyester powders provide additional advantages in ultraviolet and weathering resistance.
Ecology
The powder is the overwhelming preference of the EPA, eliminating:
- Solvent fumes and VOCs from spray booth and oven exhausts that pollute the air.
- Potentially toxic sludge and water that can contaminate the earth and must be disposed of as hazardous waste.
How Will a Powder System Work in My Operation?
Powder systems are available in all degrees of technical sophistication, and can be designed to meet a wide range of requirements for
performance, cost, and space constraints. From a basic manual, one gun
operation with a batch booth, to a highly complex multi-gun, totally automated configuration, there are guns, booths and other peripherals
for all occasions.
Powder Coating Equipment
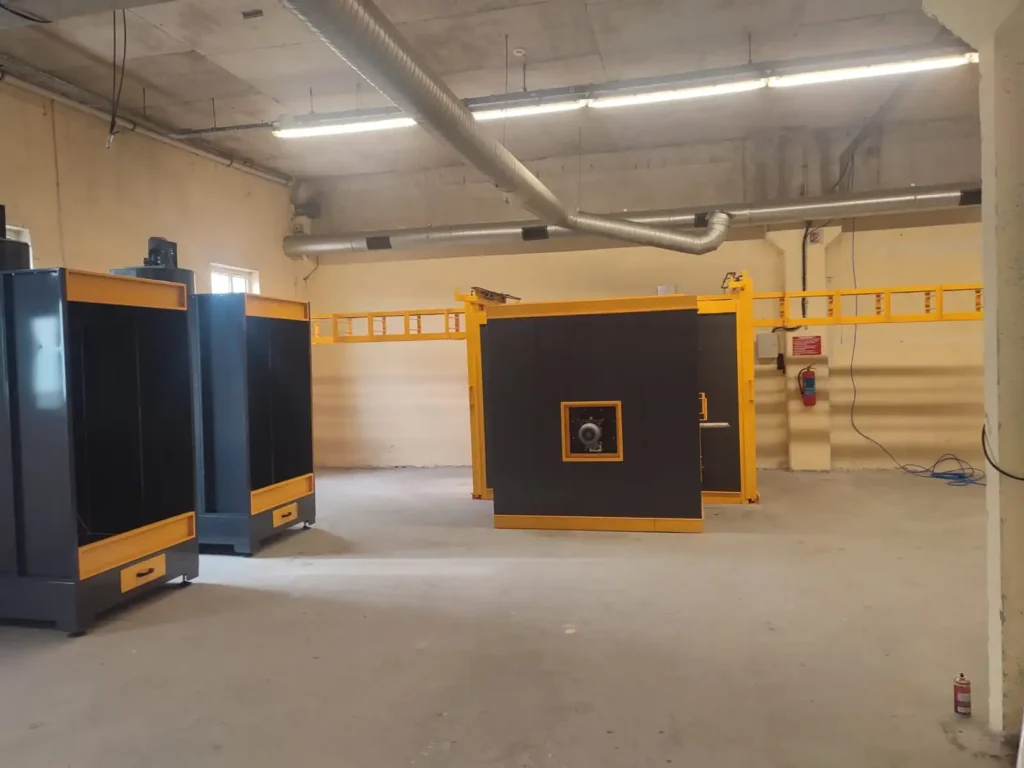
The guns are all essentially similar in their function of spraying the powder.
Each gun has a control unit that regulates the voltage being generated
and the rate at which the powder is delivered from the hopper. Areas to
review when selecting the application equipment are the efficiency of the
charge, the consistency of the powder flow, and the accuracy with which
both can be adjusted to provide the right level of performance. Once the
optimal settings have been established it is important that they can be repeated systematically each time they are used.
Booths and Recovery

Powder booths are also basically similar, but use two distinct types of
recovery equipment, cartridge filters or a cyclone separator. Each style is
particularly suitable for a different type of application. To select the
appropriate system you should consider the production batch size,
the number of different types or colors of powder being used, and the
frequency with which they are changed.
The finished quality of the desired coating should also be considered when making the selection. Therefore, prior to starting your search for the perfect powder system, you should have a clear picture of what you need and what factors are important to your operation. If you expect to change powders frequently, then a fast color change time will be high on the list of necessary features; if, however, you do long runs using the same powder throughout, then a highly efficient reclaim system will be more critical. If the parts are all the same then automatic guns may be cost effective, but if they are intricate structures that are difficult to coat, manual operators may make more sense.
Now that we have covered the basics you should have a better idea of what powder is all about. On the following pages are some worksheets that will show you just how powder can deliver savings to your operating costs. After working through them, you may be surprised at how quickly a powder system may pay for itself — and it will keep you in compliance, no matter how much more stringent the regulations become!
Common Powder Coating Terms
Back Ionization: An excessive build-up of charged powder particles which
may limit further powder being deposited on the substrate. The electrical charge on the surface layer may be reversed, repelling additional powder.
Bulk Density: Mass per unit of volume in powder form including the
air trapped between particles.
Cartridge Filter: A cylindrical filter unit used to separate oversprayed powder from air for recovery and reuse.
Corona Charge: The process of inducing a static electric charge on
powder particles by passing the powder through an electrostatic field
generated by a high-voltage device.
Cure Schedule: The time/temperature relationship required to properly fuse a powder coating.
Cyclone: A type of recovery unit using a centrifugal process to separate
oversprayed powder particles from an air flow.
Delivery: The process of moving the powder through the application
equipment to the end product.
Edge Coverage: A powder’s ability to flow over, build and adhere to sharp
corners, angles and edges.
Electrostatic Spray Technique: A deposition method of spraying and
charging powder so that it is deposited on a grounded substrate.
(See Corona charging and Tribo charging.)
Faraday Cage Effect: A condition that may exist on a substrate due to
its geometric configuration that may inhibit the electrostatic deposition of
powder particles at a specific localized area.
Film Formation: The forming of a continuous film by melting powder
particles and fusing them together by the application of energy.
Fluidizing: The process of suspending the powder in a continuous stream of air giving it “fluid” characteristics. Used to facilitate the transfer of the powder to the application device.
Fusion: The melting and flow of individual powder particles when
heated to form a continuous film.
Grounding: The electrical grounding of the item to be coated.
Impact Fusion: The combining of powder particles to form a solid mass
during the delivery and application process.
Lower Explosive Limit (LEL): The lower point for a range of concentrations of organic particles suspended in air that can be ignited
by a sufficient energy source.
Micron/Mils: Common unit of measurement of coating thickness. 25.4μ (microns or micrometers) = 1 mil (one-thousandth of an inch)
Particle Size: Average diameter of an individual, irregular powder particle.
Recovery: The process of removing non-deposited powder from the air
prior to reclaiming it for reuse.
Spray Booth: A specially designed enclosure in which powders are
introduced, contained, and recovered during the coating process.
Surface Appearance: Generally refers to the smoothness and gloss of
powder coating films and the presence and degree of surface
defects.
System Utilization or System Efficiency: The combined efficiencies
of each component in the powder coating system resulting in total
material usage compared to the amount of material entered into the
system.
Transfer Efficiency: The ratio of the powder deposited on the workpiece
compared to the amount of powder sprayed during a fixed time period.
Tribo Charging: Process of creating a static electrical charge on powder
particles by creating friction between them and non-conductive material.
Virgin Powder: Powder that has not been previously sprayed as opposed
to reclaimed powder.
Wrap: A characteristic of electrostatic application for the powder to seek out and adhere to parts of the substrate, not in direct line of sight of the delivery point.