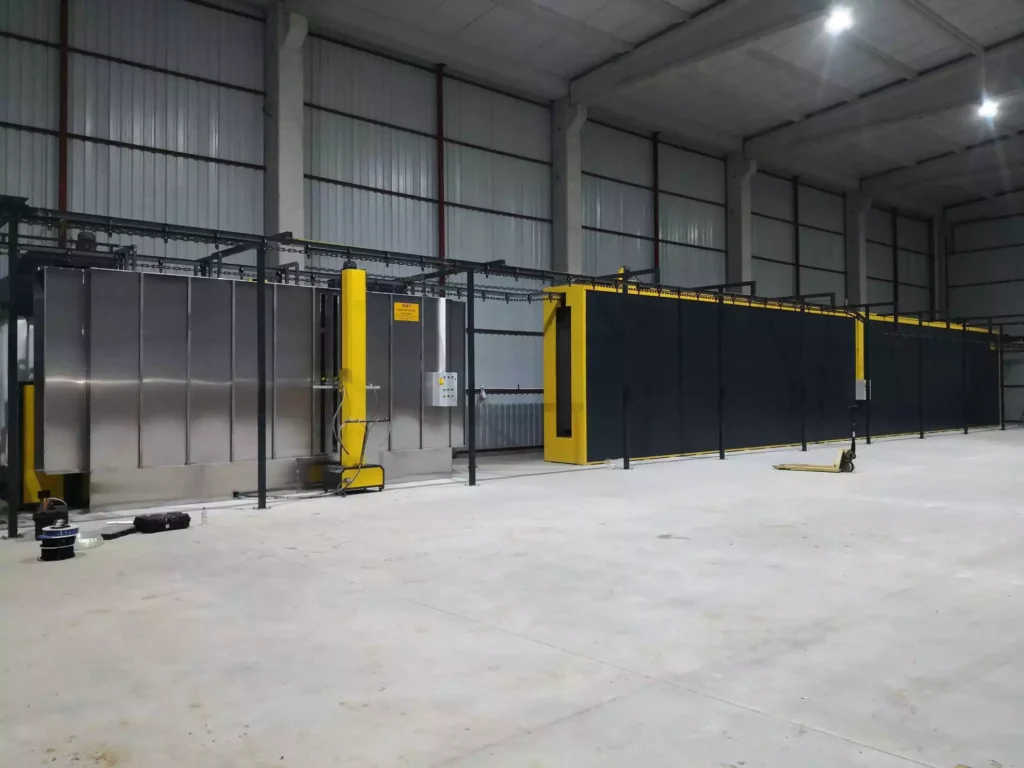
We manufacture Powder coat booth and oven as well as Cartridge Filter booths, Batch ovens, Gas fired and Electric Powder Curing ovens, and Powder Spray Guns.
A powder coat booth is a ventilated enclosure used to apply powder coating to metal objects. The booth is typically made of a metal frame with a plastic liner and contains a high-efficiency particulate air (HEPA) filter system.
Powder coating is a dry powder coating process that uses electrostatics to apply a powder coating to a metal object. The powder coating is then cured in an oven to melt and bond to the metal surface.
The powder coat booth helps to collect excess powder coating that is not applied to the object. The collected powder coating can be recycled and reused.
Powder Coat Oven
A powder coat oven is a heated chamber used to cure powder coating on metal objects. The oven typically reaches temperatures of 400-450 degrees Fahrenheit, which is hot enough to melt and bond the powder coating to the metal surface.
Powder coat ovens are typically made of a metal cabinet with a heating element and a fan. The fan circulates hot air around the object being cured, ensuring that the powder coating is evenly cured.
Powder coat ovens are an essential part of the powder coating process. They provide a controlled environment in which the powder coating can be cured properly.
Powder Coat Booth and Oven Combos
Some powder coating booths come with integrated ovens. This can be a convenient option for small businesses and hobbyists who need a complete powder coating system.
Powder coat booth and oven combos typically have a smaller footprint than separate booth and oven systems. They are also less expensive to purchase and operate.
However, powder coat booth and oven combos may not be suitable for large-scale production applications. They may also not be able to cure large or heavy objects.
Conclusion
Powder coat booths and ovens are essential tools for powder coating metal objects. They help to collect excess powder coating and cure the powder coating to the metal surface.
Powder coat booth and oven combos can be a convenient and affordable option for small businesses and hobbyists. However, they may not be suitable for large-scale production applications.
Powder Paint Booth in Powder Coat Booth and Oven
Powder-coating booth manufacturers produce various types of powder-coating spray booths for sale. Here below you can find some brief information about our powder paint spray booth types
A powder coating booth is a specialized enclosure that is used to apply a dry powder coating to a variety of surfaces. The booth is designed to contain the powder and prevent it from spreading into the surrounding environment.
The booth is typically equipped with a ventilation system that removes overspray and fumes from the booth. The powder coating is applied using a spray gun, which is connected to a hopper that contains the powder. The spray gun is used to apply the powder to the surface in a uniform and even layer.
Once the powder is applied, it is cured in an oven to harden the coating. The curing process can be done at a variety of temperatures and for different lengths of time, depending on the type of powder being used.
Powder coating is a durable and long-lasting finish that can be used on a variety of materials, including metal, wood, and plastic. It is a popular choice for applications that require a high level of durability and resistance to scratches, chips, and fading.
1 Filter Powder Coating Spray Booth
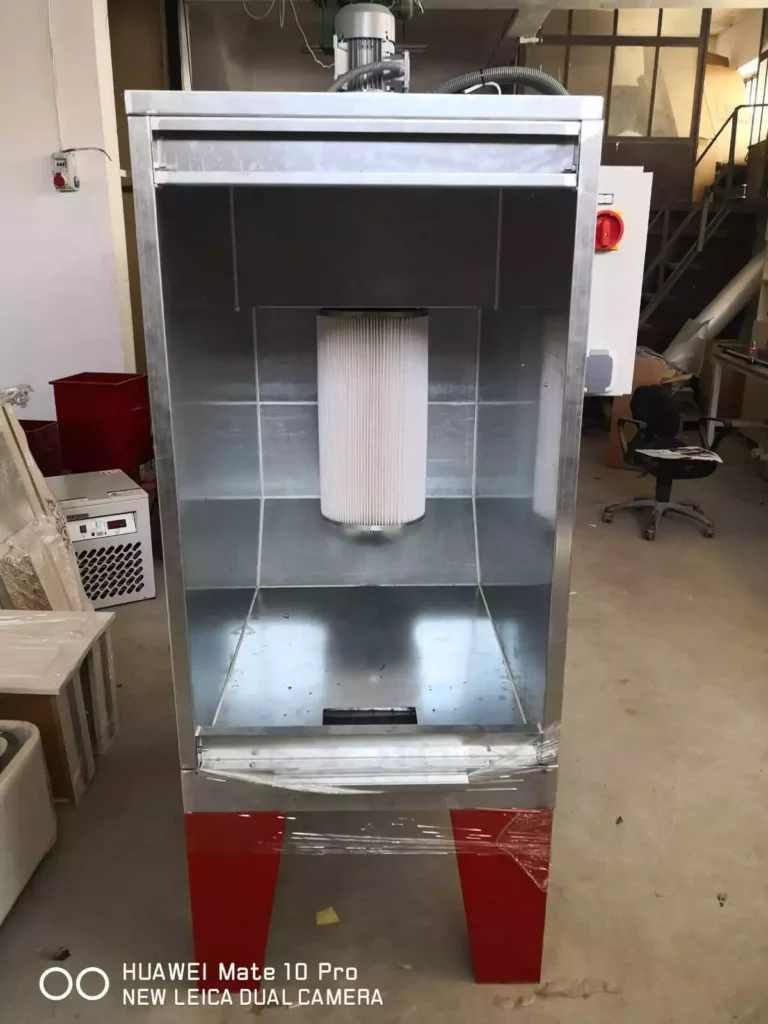
The 1 Filter Powder Coating Booth has 1 cartridge filter of 32×60 cm. The filter is made of cellulose and sucks the flying powder around in the booth.
Filters for powder coating spray booths are essential for trapping airborne powder particles and preventing them from escaping into the environment. Filters can be made from a variety of materials, including polyester, fiberglass, and nanofibre. They are typically rated according to their efficiency at removing particles of a certain size.
Types of powder coating spray booth filters:
- Panel filters: These are the most common type of powder coating spray booth filter. They are made up of a series of pleated sheets of filter media that are sandwiched between metal frames. Panel filters are relatively inexpensive and easy to replace.
- Cartridge filters: These filters are made up of a series of cylindrical filter cartridges that are stacked together. Cartridge filters are more efficient than panel filters at removing particles, but they are also more expensive and more difficult to replace.
- Pulsating filters: Pulsating filters use compressed air to shake loose powder particles from the filter media. This helps to extend the life of the filter and improve its efficiency.
How to choose a powder coating spray booth filter:
- Consider the type of powder coating booth you have: Some booths use a single filter, while others use multiple filters. You will need to choose a filter that is compatible with your booth.
- Determine the efficiency rating you need: The efficiency rating of a filter tells you how well it can remove particles of a certain size. For most powder coating applications, a filter with an efficiency rating of MERV 8 or higher is recommended.
- Factor in the cost and ease of replacement: Panel filters are the most affordable and easy to replace, while cartridge filters are more efficient but more expensive and difficult to replace.
Maintenance of powder coating spray booth filters:
- Inspect the filters regularly: Inspect the filters for signs of wear and tear, such as tears or holes in the filter media. If you see any damage, replace the filter immediately.
- Clean the filters regularly: Powder coating spray booth filters can become clogged with powder particles over time. This can reduce the efficiency of the filter and allow particles to escape into the environment. To clean the filters, use a vacuum cleaner or compressed air to remove the powder particles.
- Replace the filters regularly: Most powder coating spray booth filters should be replaced every 6-12 months, depending on the level of use.
By following these tips, you can ensure that your powder coating spray booth filters are working properly and that you are minimizing the environmental impact of your powder coating operations.
2 Filter Powder Coating Spray Booth
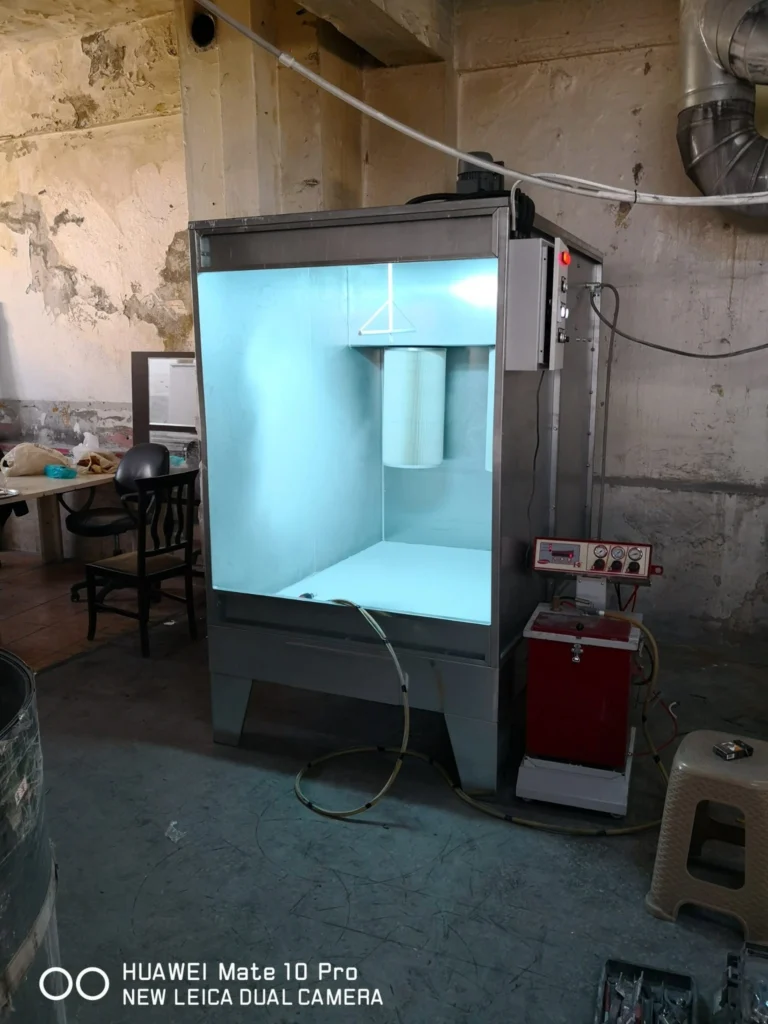
The 2 Filter Powder Coating Booth has 2 cartridge filters of 32×60 cm. The filter is made of cellulose and sucks the flying powder around in the booth.
3 and 4 Filter Powder Coating Spray Booth
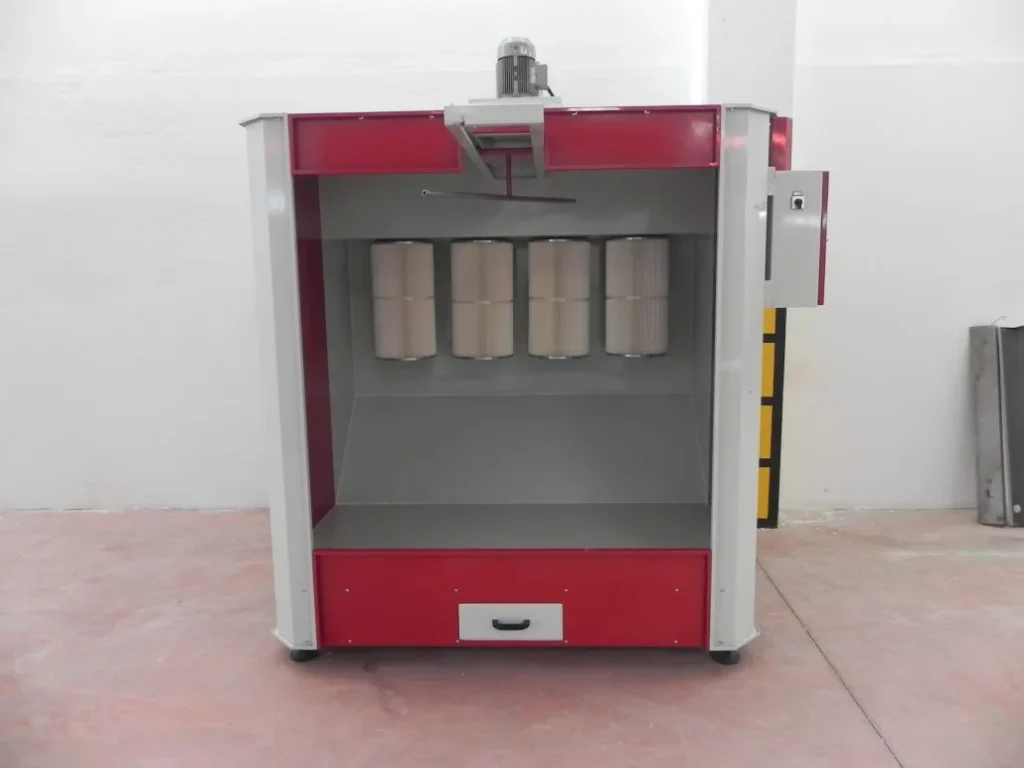
The 3 and 4 Filter Powder Coating Booth has 3 and 4 cartridge filters of 32×60 cm. The filter is made of cellulose and sucks the flying powder around in the booth.
For any powder coating booth price, kindly send a request by e-mail.
Besides the powder coating spray booth for sale, we also manufacture powder coat oven for powder curing. The ovens for powder coating usually have 2 types
- Electric Powder Coating Oven
- Gas Powder Coating Oven
Electric Powder Coating Ovens
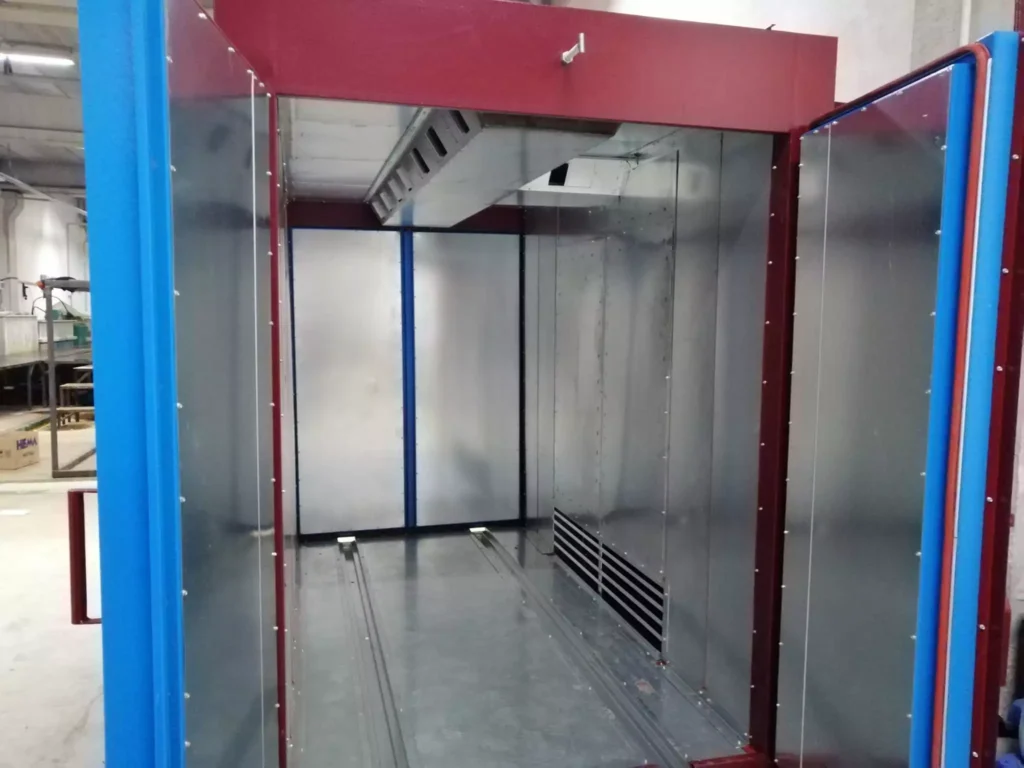
We manufacture electric powder coating ovens in various dimensions where our standard width is 1,5 m and standard height is 1,8 m. These ovens have air circulation.
An electric powder coating oven is a specialized oven used to cure powder coatings. Powder coating is a finishing process that uses electrostatic powder to apply a tough, durable coating to a variety of surfaces. The powder is then cured in an oven at a high temperature, which melts the powder and binds it to the surface.
Electric powder coating ovens use electric resistance heaters to heat the air inside the chamber. Gas-fired powder coating ovens are also available, but electric ovens are becoming increasingly popular due to their lower operating costs and environmental benefits.
Electric powder coating ovens come in a variety of sizes and configurations to suit the needs of different applications. Some ovens are designed for small parts, while others can accommodate large items such as car bumpers or furniture.
The most important features of an electric powder coating oven are its insulation and temperature control system. The insulation helps to maintain a uniform temperature within the oven, which is essential for curing the powder coating evenly. The temperature control system ensures that the oven reaches the desired temperature and maintains it for the required time.
Other features to consider when selecting an electric powder coating oven include its safety features, ease of use, and maintenance requirements.
Gas Powder Coating Ovens
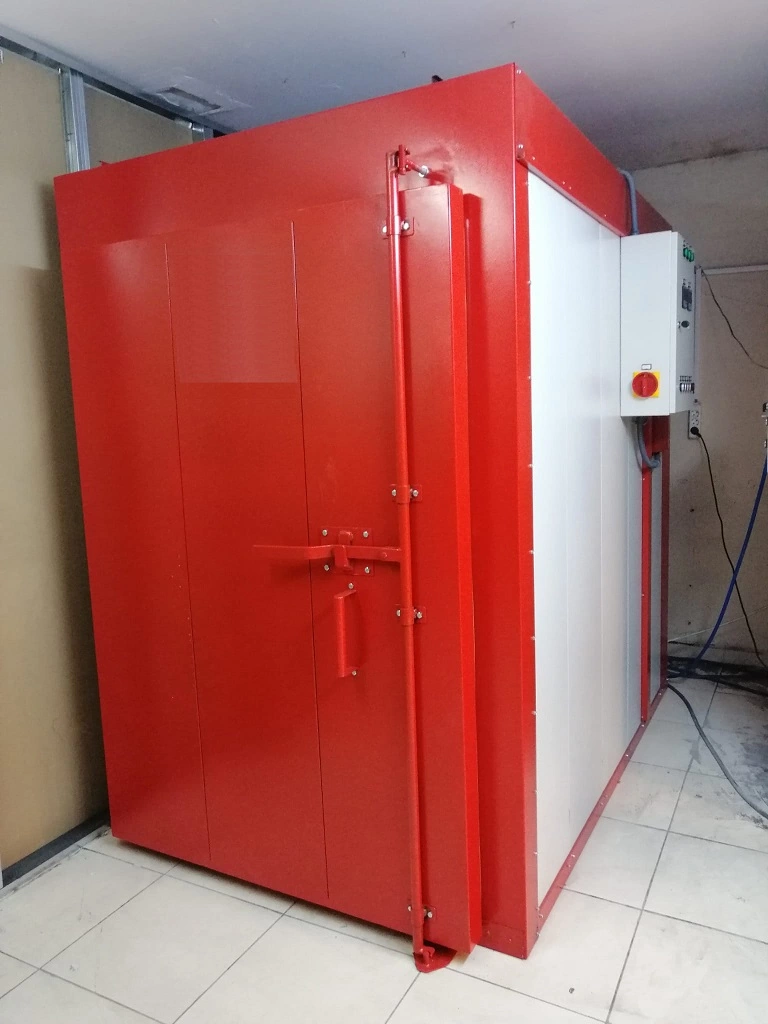
We manufacture gas powder coating ovens in various dimensions where our standard width is 1,5 m and standard height is 1,8 m. These ovens have air circulation.
For a large powder coating oven or a small powder coating oven but a cheap powder coating oven, kindly send us your request by mail. Our sales team will contact you in a short time
A gas-type powder coating curing oven is a specialized piece of equipment used in the powder coating industry to cure powder coatings onto metal substrates. It utilizes gas combustion to heat the interior chamber to a high temperature, typically between 150°C and 200°C, where the powder particles melt, flow, and fuse to form a continuous, hard, and durable coating.
Key Components of a Gas-Type Powder Coating Curing Oven:
- Heating Chamber: The heart of the oven is the heating chamber, which is typically constructed from high-temperature-resistant materials like stainless steel or refractory bricks.
- Gas Burners: Gas burners are the primary source of heat, typically utilizing propane, natural gas, or liquefied petroleum gas (LPG). They are positioned strategically within the chamber to ensure even heat distribution.
- Circulation Fans: Circulation fans help to circulate the heated air throughout the chamber, ensuring that all surfaces of the coated parts receive uniform curing temperatures.
- Temperature Control System: A precise temperature control system regulates the oven’s temperature, ensuring that the curing process occurs within the specified range for optimal coating adhesion and performance.
- Conveyor System (Optional): For batch curing, conveyor systems are employed to transport the coated parts through the oven at a controlled speed, ensuring that they spend the appropriate time at the desired temperature for curing.
Benefits of Gas-Type Powder Coating Curing Ovens:
- Quick Heating: Gas burners provide rapid heating, allowing for faster curing cycles compared to electric ovens.
- Uniform Heating: Circulation fans ensure even heat distribution across the chamber, preventing hot spots and potential coating defects.
- Cost-Effectiveness: Gas is generally a more cost-effective fuel source than electricity.
- Versatility: Gas-type ovens can accommodate a wide range of workpiece sizes and shapes.
- Environmental Considerations: Gas-fired ovens can be equipped with pollution control systems to minimize emissions.
Applications of Gas-Type Powder Coating Curing Ovens:
- Manufacturing of metal parts: Automotive, appliance, furniture, and machinery industries extensively use powder coating for corrosion protection and aesthetic enhancement.
- Construction and building products: Gas-cured powder coatings are employed for architectural applications like railings, fences, and facades.
- Industrial equipment: Powder coating is prevalent in industries like agriculture, mining, and heavy machinery for durability and corrosion resistance.
Safety Precautions:
- Proper ventilation: Ensure adequate ventilation to remove fumes and prevent the buildup of harmful gases.
- Extinguishing systems: Equip the oven with fire extinguishers and emergency shut-off valves in case of fire hazards.
- Regular maintenance: Conduct regular inspections and maintenance to maintain the oven’s safety and efficiency.
- Training and certification: Operators should undergo training and obtain relevant certifications to handle gas-fired equipment safely.
Powder Coat Booth and Oven
A powder coat booth and oven are two essential pieces of equipment for powder coating. The booth is where the powder is applied to the part, and the oven is where the powder is cured.
Powder Coat Booth
A powder coat booth is a ventilated enclosure where the powder is applied to the part. The booth is typically equipped with a spray gun that is used to apply the powder, as well as a system for collecting and filtering the excess powder.
There are two main types of powder coat booths: manual and automatic. Manual booths are operated by hand, while automatic booths are controlled by a computer.
Powder Coat Oven
A powder coat oven is a heated enclosure where the powder is cured. The oven is typically equipped with a conveyor belt that carries the parts through the oven.
There are two main types of powder coat ovens: batch and conveyor. Batch ovens are used to cure small batches of parts, while conveyor ovens are used to cure large volumes of parts.
Choosing a Powder Coat Booth and Oven
When choosing a powder coat booth and oven, it is important to consider the following factors:
- The size and type of parts you will be coating
- The volume of parts you will be coating
- Your budget
If you are only coating a small number of parts, you may be able to get away with using a manual booth and a batch oven. However, if you are coating a large number of parts, you will need to invest in an automatic booth and a conveyor oven.
It is also important to make sure that the booth and oven you choose are compatible with the type of powder coating you will be using.
Safety
Powder coating can be a hazardous process if not done properly. It is important to follow all safety precautions when using a powder coat booth and oven.
Here are some safety tips:
- Wear appropriate personal protective equipment (PPE), such as gloves, goggles, and a respirator.
- Follow the manufacturer’s instructions for operating the booth and oven.
- Keep the booth and oven clean and free of debris.
- Inspect the booth and oven regularly for any signs of damage or wear and tear.
By following these safety tips, you can help to prevent accidents and injuries when operating a powder coat booth and oven.
Powder Coating: An In-Depth Guide to Equipment and Processes
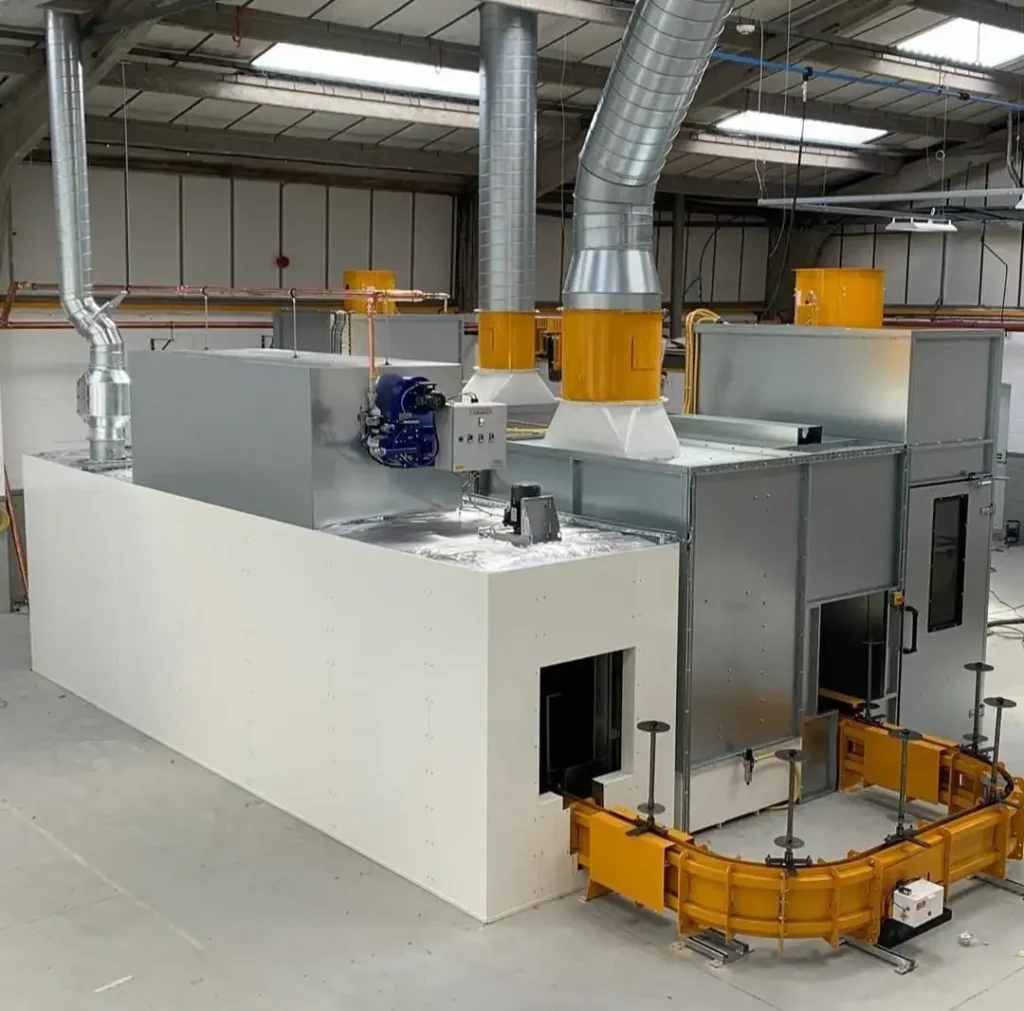
Introduction
Powder coating is a popular finishing process used across various industries to apply a durable and protective layer to metal surfaces. Unlike traditional liquid paint, powder coating uses a dry powder that is electrostatically charged and applied to the surface, which is then cured in a high-temperature oven. This process results in a hard finish that is more resistant to chipping, scratching, and fading.
In this guide, we’ll explore the different components of a powder coating system, including ovens, machines, equipment, and entire production lines. Understanding these elements is crucial for businesses looking to enhance their production capabilities with powder coating technology.
Powder Coating Ovens
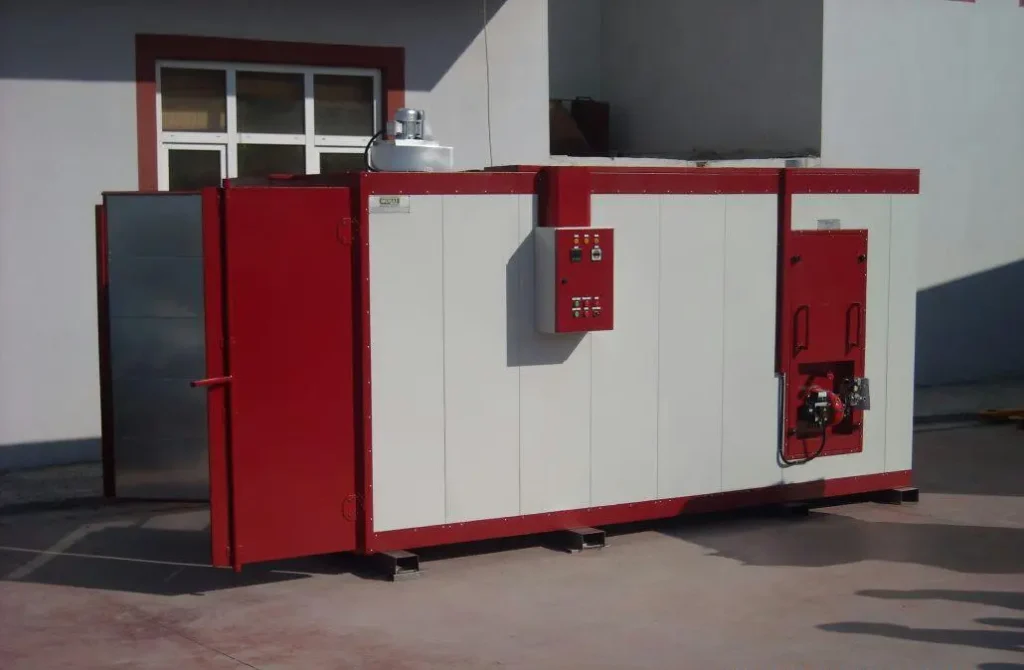
Definition and Purpose:
Powder coating ovens are essential for the curing process, where the powder adheres to the surface and forms a smooth, hard finish. These ovens provide the necessary heat to melt the powder, ensuring even and thorough coating.
Types of Powder Coating Ovens:
- Batch Ovens:
- Ideal for small to medium-sized production runs
- Flexibility to handle various part sizes
- Suitable for businesses with diverse product lines
- Conveyor Ovens:
- Designed for continuous production
- Higher throughput and efficiency
- Suitable for large-scale operations
Features and Specifications:
- Temperature Range: Typically between 325°F to 450°F
- Heating Source: Options include electric, gas, or infrared
- Size and Capacity: Varies based on production needs
- Energy Efficiency: Consider models with advanced insulation and airflow systems
How to Choose the Right Oven:
- Evaluate production volume and part sizes
- Consider energy consumption and operating costs
- Assess available space and installation requirements
- Consult with manufacturers for customized solutions
Powder Coating Machines
Overview of Different Machines Used:
Powder coating machines are used to apply the powder to the surface. They vary in complexity and functionality, catering to different production needs.
Manual vs. Automated Machines:
- Manual Machines:
- Suitable for small-scale operations
- Offers flexibility and control
- Requires skilled operators
- Automated Machines:
- Ideal for high-volume production
- Consistent and uniform application
- Reduced labor costs
Key Features and Specifications:
- Voltage and Power Requirements: Ensure compatibility with your facility
- Control Systems: Look for user-friendly interfaces and programmable settings
- Spray Gun Options: Different nozzles and gun types for various applications
Selecting the Right Machine for Your Needs:
- Determine the scale and complexity of your operations
- Evaluate budget constraints and long-term ROI
- Seek advice from industry experts and suppliers
Powder Coating Equipment
Essential Equipment for Powder Coating:
- Powder Coating Booths: Enclosed areas for applying powder
- Powder Recovery Systems: Capture and reuse overspray powder
- Air Compressors and Dryers: Ensure consistent airflow for optimal coating
Optional Equipment for Enhanced Performance:
- Pre-Treatment Systems: Clean and prepare surfaces before coating
- Curing Lamps: Speed up the curing process with infrared or UV lamps
Maintenance and Safety Considerations:
- Regularly inspect and clean equipment
- Train staff on proper handling and safety protocols
- Adhere to industry standards and regulations
Powder Coating Lines and Plants
Explanation of Powder Coating Lines:
Powder coating lines are integrated systems that automate the entire powder coating process, from pre-treatment to curing.
Components of a Powder Coating Line:
- Conveyor Systems: Move parts through the line efficiently
- Pre-Treatment Stations: Clean and prepare surfaces
- Powder Application Booths: Enclosed areas for powder coating
- Curing Ovens: Finalize the coating process
Design and Layout Considerations:
- Optimize workflow and space utilization
- Consider future scalability and expansion
- Ensure compliance with safety and environmental regulations
Scalability and Customization Options:
- Modular designs for easy expansion
- Custom configurations to meet specific production needs
Benefits of Powder Coating
Environmental Advantages:
- Low VOC emissions compared to liquid paints
- Overspray can be recycled, reducing waste
- Complies with environmental regulations
Durability and Longevity:
- Resistant to corrosion, fading, and wear
- Suitable for outdoor and high-traffic applications
- Provides a high-quality, professional finish
Cost-Effectiveness:
- Reduces long-term maintenance and repainting costs
- Efficient use of materials minimizes waste
- High throughput and automation lower labor expenses
Considerations for Setting Up a Powder Coating Plant
Initial Investment and ROI:
- Assess capital requirements for equipment and infrastructure
- Calculate potential returns based on production capacity and demand
- Explore financing options and incentives
Regulatory Compliance:
- Adhere to industry standards and local regulations
- Implement safety protocols and employee training
- Monitor environmental impact and waste management
Market Trends and Future Outlook:
- Growing demand for eco-friendly coatings
- Advancements in automation and technology
- Increasing adoption in automotive, aerospace, and consumer goods sectors
Conclusion
Powder coating offers numerous advantages over traditional liquid painting methods, making it an attractive option for industries seeking durable and environmentally friendly finishes. By investing in the right equipment and understanding the intricacies of powder coating processes, businesses can enhance their production capabilities and meet the growing demand for high-quality coated products.
When setting up a powder coating plant, it’s essential to carefully consider your needs, budget, and long-term goals. Collaborating with experienced suppliers and industry experts can help you make informed decisions and achieve success in the competitive world of powder coating.
This comprehensive guide should provide valuable insights for your website visitors and help position your business as a knowledgeable and reliable source in the powder coating industry.
Installation process steps
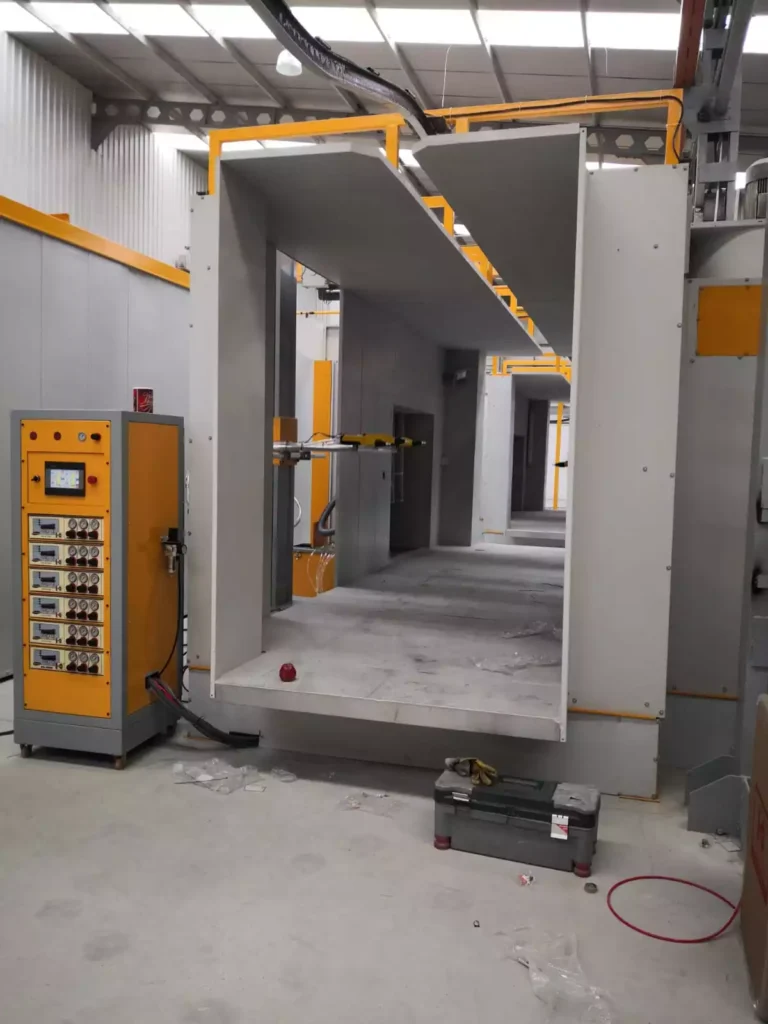
To provide a comprehensive guide on the installation process for powder coating systems, we’ll cover each step involved in setting up a powder coating plant. This includes planning, selecting equipment, site preparation, installation, testing, and staff training. Here’s a detailed outline and content for this section:
Outline for Installation Process Steps
- Planning and Design
- Assessing needs and capacity
- Layout and design considerations
- Budget and timeline
- Equipment Selection
- Choosing the right ovens, machines, and equipment
- Consulting with manufacturers and suppliers
- Site Preparation
- Preparing the facility for installation
- Ensuring compliance with regulations
- Installation Process
- Step-by-step installation guide
- Safety protocols and considerations
- System Testing and Calibration
- Testing each component
- Ensuring optimal performance
- Training and Support
- Staff training on operation and safety
- Ongoing maintenance and support
- Post-Installation Considerations
- Regular inspections and maintenance
- Upgrades and scalability
Installation Process Steps for Powder Coating Systems
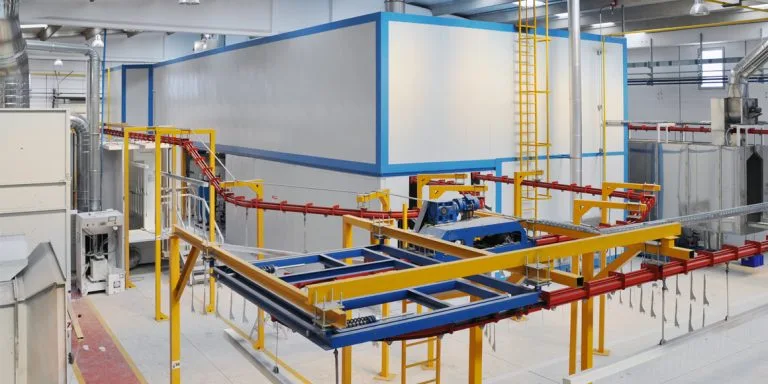
Setting up a powder coating plant involves careful planning and execution to ensure a successful installation. Here’s a step-by-step guide to help you navigate the process:
1. Planning and Design
Assessing Needs and Capacity:
- Identify Production Requirements: Determine the types and sizes of parts you will be coating, and estimate your production volume.
- Analyze Workflow: Consider how materials will move through the plant, from pre-treatment to curing.
- Evaluate Space Requirements: Ensure adequate space for equipment, storage, and workflow efficiency.
Layout and Design Considerations:
- Optimize Workflow: Design a layout that minimizes bottlenecks and maximizes efficiency.
- Future Scalability: Plan for potential expansion or upgrades.
- Compliance with Safety Standards: Ensure the layout meets all safety and regulatory requirements.
Budget and Timeline:
- Create a Detailed Budget: Account for equipment, installation, training, and operational costs.
- Establish a Timeline: Set realistic milestones for each phase of the installation process.
2. Equipment Selection
Choosing the Right Ovens, Machines, and Equipment:
- Powder Coating Ovens: Select between batch or conveyor ovens based on production needs.
- Powder Coating Machines: Choose manual or automated systems that match your operational scale.
- Additional Equipment: Consider powder booths, recovery systems, and pre-treatment stations.
Consulting with Manufacturers and Suppliers:
- Leverage Expertise: Work with manufacturers to choose equipment tailored to your specific requirements.
- Request Demonstrations: Evaluate equipment performance through demos or site visits.
- Negotiate Contracts: Ensure favorable terms and warranties with suppliers.
3. Site Preparation
Preparing the Facility for Installation:
- Infrastructure Readiness: Ensure adequate power supply, ventilation, and environmental controls.
- Space Optimization: Clear and organize the installation area for easy access and efficient workflow.
Ensuring Compliance with Regulations:
- Local Permits and Licenses: Obtain necessary permits and ensure compliance with zoning regulations.
- Safety Standards: Adhere to occupational health and safety standards.
4. Installation Process
Step-by-Step Installation Guide:
- Site Inspection: Conduct a final inspection of the site to verify readiness.
- Delivery and Unpacking: Receive and unpack equipment carefully, checking for any damage.
- Positioning Equipment: Install each piece of equipment according to the layout plan.
- Electrical and Plumbing Connections: Ensure all electrical and plumbing connections are correctly made and tested.
- Calibration and Setup: Configure equipment settings and calibrate machinery to specifications.
Safety Protocols and Considerations:
- Install Safety Features: Implement necessary safety features such as emergency stops and protective barriers.
- Personal Protective Equipment (PPE): Ensure that all personnel have access to required PPE.
5. System Testing and Calibration
Testing Each Component:
- Conduct Trial Runs: Test each component individually and as part of the integrated system.
- Check for Performance Issues: Identify and resolve any performance or operational issues.
Ensuring Optimal Performance:
- Fine-Tune Settings: Adjust equipment settings for optimal coating quality.
- Document Results: Record all testing results and adjustments for future reference.
6. Training and Support
Staff Training on Operation and Safety:
- Conduct Training Sessions: Provide comprehensive training on equipment operation and safety protocols.
- Create Training Materials: Develop manuals and guides for ongoing staff reference.
Ongoing Maintenance and Support:
- Establish a Maintenance Schedule: Set up regular maintenance checks to ensure equipment longevity.
- Vendor Support: Engage with suppliers for ongoing support and troubleshooting.
7. Post-Installation Considerations
Regular Inspections and Maintenance:
- Implement Routine Inspections: Regularly inspect equipment and systems for wear and tear.
- Schedule Maintenance: Adhere to the maintenance schedule to prevent downtime and extend equipment life.
Upgrades and Scalability:
- Monitor Technological Advancements: Stay informed about new technologies and equipment improvements.
- Plan for Upgrades: Budget for future upgrades and expansion as business needs grow.
Conclusion
The installation of a powder coating system is a multi-step process that requires meticulous planning and execution. By following these steps, businesses can ensure a smooth setup and operation, maximizing efficiency and product quality. It’s crucial to work closely with experienced manufacturers and suppliers to tailor the installation process to your specific needs and to provide ongoing training and support for staff.
Installation cost estimate
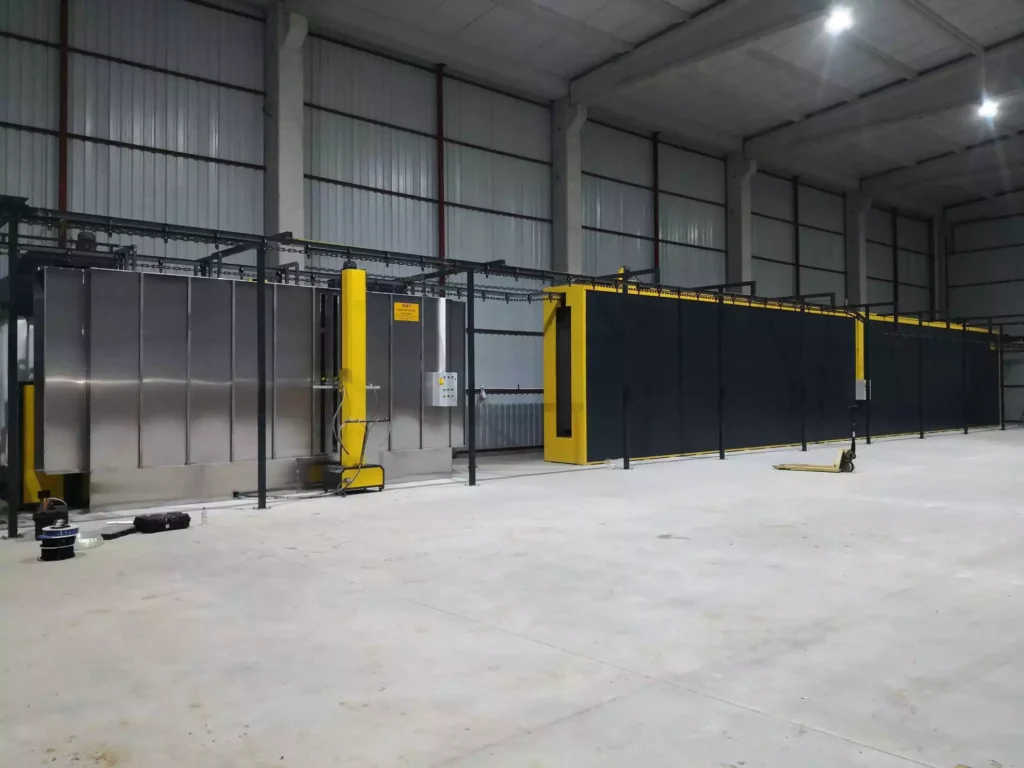
Estimating the installation cost of a powder coating system involves considering various factors, such as the size of the operation, the type of equipment, facility modifications, labor, and additional costs like permits and training. Here’s a detailed breakdown to help you understand the potential costs involved in setting up a powder coating plant.
Installation Cost Estimate for Powder Coating Systems
Factors Influencing Costs
- Type of Equipment and Technology
- Powder coating ovens (batch vs. conveyor)
- Coating machines (manual vs. automated)
- Auxiliary equipment (booths, recovery systems, pre-treatment stations)
- Scale and Capacity of the Operation
- Production volume
- Facility size and space requirements
- Facility Modifications
- Infrastructure updates (electrical, ventilation, plumbing)
- Space optimization and layout design
- Labor and Installation Services
- Skilled labor for installation
- Equipment calibration and testing
- Additional Costs
- Permits and regulatory compliance
- Staff training and support
- Maintenance and contingency expenses
Estimated Costs
Below is a general estimate of the costs associated with installing a powder coating system. Note that prices can vary significantly based on location, vendor, and specific requirements.
1. Equipment Costs
- Powder Coating Ovens:
- Batch Ovens: $1,000 – $50,000
- Conveyor Ovens: $10,000 – $200,000
- Powder Coating Machines:
- Manual Machines: $1,000 – $20,000
- Automated Systems: $20,000 – $100,000
- Auxiliary Equipment:
- Powder Booths: $2,000 – $30,000
- Recovery Systems: $3,000 – $15,000
- Pre-Treatment Systems: $10,000 – $50,000
2. Facility Modifications
- Electrical and Ventilation Upgrades: $10,000 – $50,000
- Space Optimization and Layout Design: $5,000 – $20,000
3. Labor and Installation Services
- Installation Labor: $10,000 – $30,000
- Calibration and Testing: $5,000 – $10,000
4. Additional Costs
- Permits and Compliance: $2,000 – $10,000
- Training and Support: $2,000 – $5,000
- Maintenance and Contingency: $5,000 – $15,000
Total Estimated Cost
The total estimated cost for installing a powder coating system can range from $70,000 to $500,000, depending on the size, complexity, and specific requirements of the operation. Here’s a breakdown by scale:
- Small-Scale Operations: $20,000 – $50,000
- Medium-Scale Operations: $50,000 – $100,000
- Large-Scale Operations: $100,000 – $500,000
Tips for Cost Management
- Conduct a Detailed Assessment:
- Evaluate your specific needs and choose equipment accordingly.
- Consider future scalability to avoid unnecessary upgrades later.
- Get Multiple Quotes:
- Request quotes from multiple vendors to compare prices and services.
- Negotiate terms and warranties to get the best deal.
- Plan for Contingencies:
- Set aside a contingency budget for unexpected expenses during installation.
- Regularly review and adjust your budget as the project progresses.
- Focus on Energy Efficiency:
- Invest in energy-efficient equipment to reduce long-term operational costs.
- Evaluate the potential return on investment (ROI) for each piece of equipment.
- Leverage Financing Options:
- Explore financing options, grants, or incentives available for industrial upgrades.
Conclusion
Setting up a powder coating plant requires a significant investment, but careful planning and strategic decision-making can help manage costs effectively. By considering your specific needs, working with experienced suppliers, and planning for the future, you can ensure a successful installation and operation of your powder coating system.
Let me know if you need further details or specific cost estimates tailored to your project!
Components of a Powder Coating Plant
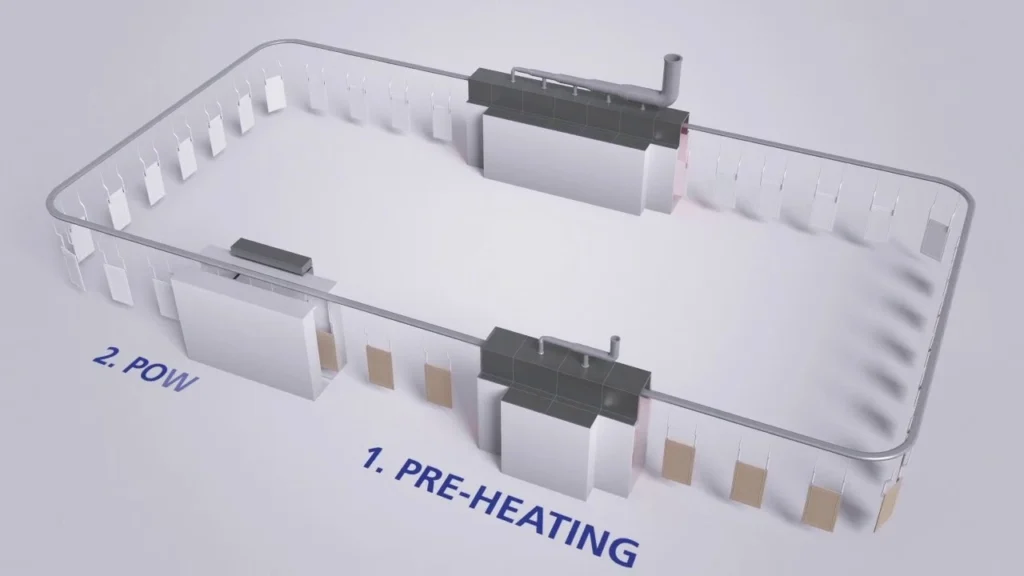
A powder coating plant consists of various components that work together to facilitate the coating process, from preparation to application and curing. Understanding these components is crucial for designing an efficient and effective system tailored to specific production needs. Below is a detailed overview of the key components of a powder coating plant:
Key Components of a Powder Coating Plant
- Pre-Treatment System
- Purpose: Cleans and prepares surfaces for powder coating to ensure adhesion and finish quality.
- Components:
- Washing Stations: Use chemical solutions to remove contaminants like grease, oil, dirt, and rust.
- Rinse Stations: Remove residual chemicals from the surface.
- Drying Ovens: Dry the parts after washing and rinsing to prepare them for powder application.
- Powder Coating Booths
- Purpose: Enclosed area where the powder is applied to the parts.
- Types:
- Manual Booths: Operators manually apply powder using spray guns. Ideal for small or custom jobs.
- Automatic Booths: Equipped with automated spray guns and reciprocators for high-volume production.
- Features:
- Ventilation Systems: Ensure proper airflow to capture overspray and maintain a clean environment.
- Powder Recovery Systems: Collect overspray powder for reuse, improving material efficiency.
- Powder Application Equipment
- Purpose: Applies the powder to the surfaces using electrostatic spray guns.
- Components:
- Electrostatic Spray Guns: Charge the powder particles and spray them onto the grounded parts.
- Control Units: Adjust settings like voltage, powder flow rate, and air pressure to ensure uniform coverage.
- Conveyor System
- Purpose: Transports parts through various stages of the powder coating process.
- Types:
- Overhead Conveyors: Hang parts from hooks or racks for continuous production.
- Floor Conveyors: Suitable for heavier or larger parts that cannot be suspended.
- Features:
- Variable Speed Control: Adjusts the speed of the conveyor to match production needs and curing times.
- Loading and Unloading Stations: Facilitate the movement of parts onto and off the conveyor system.
- Powder Coating Ovens
- Purpose: Cures the powder coating by melting and fusing it to the surface, forming a durable finish.
- Types:
- Batch Ovens: Suitable for smaller production runs and varied part sizes.
- Conveyor Ovens: Designed for continuous, high-volume production.
- Features:
- Temperature Control Systems: Ensure precise and consistent heating for optimal curing.
- Energy Efficiency: Incorporate insulation and heat recovery systems to minimize energy consumption.
- Cooling and Inspection Stations
- Purpose: Cool the parts after curing and inspect them for quality assurance.
- Components:
- Cooling Zones: Allow parts to cool gradually to avoid warping or defects.
- Inspection Areas: Check for coating consistency, thickness, and finish quality before packaging or assembly.
- Control and Monitoring Systems
- Purpose: Manage and monitor the entire powder coating process for efficiency and quality control.
- Components:
- PLC Systems (Programmable Logic Controllers): Automate and synchronize various plant operations.
- Data Logging and Analysis Tools: Record production metrics and identify areas for improvement.
- Safety and Environmental Controls
- Purpose: Ensure the safety of workers and compliance with environmental regulations.
- Components:
- Fire Suppression Systems: Protect against powder fires or explosions in booths and ovens.
- Ventilation and Filtration Systems: Maintain air quality by removing dust, fumes, and volatile organic compounds (VOCs).
- Personal Protective Equipment (PPE): Provide workers with necessary safety gear, such as masks, gloves, and goggles.
Optional and Auxiliary Components
- Advanced Pre-Treatment Systems: Utilize additional technologies like ultrasonic cleaning or nanotechnology for improved surface preparation.
- Curing Lamps: Use infrared or UV lamps for faster curing times and energy savings.
- Automated Robotic Systems: Enhance precision and efficiency in powder application and handling.
- Quality Control Instruments: Use advanced tools like thickness gauges, gloss meters, and adhesion testers for detailed quality assessment.
Layout and Design Considerations
- Workflow Optimization: Design the plant layout to minimize bottlenecks and ensure smooth transitions between stages.
- Space Utilization: Efficiently allocate space for equipment, storage, and movement of materials.
- Scalability: Plan for future expansion or upgrades to accommodate growing production demands.
Conclusion
A well-designed powder coating plant integrates these components to create an efficient, high-quality coating process. Understanding each element and its role in the system is crucial for businesses looking to enhance their powder coating capabilities. By investing in the right equipment and technology, companies can achieve superior finishes, increased productivity, and long-term success in the powder coating industry.
Detailed Components of a Powder Coating Plant
Certainly! To provide a detailed understanding of each component within a powder coating plant, we’ll delve into the technical specifications, functions, types, and key considerations for each element. This comprehensive breakdown will cover everything from the initial pre-treatment to the final inspection.
1. Pre-Treatment System
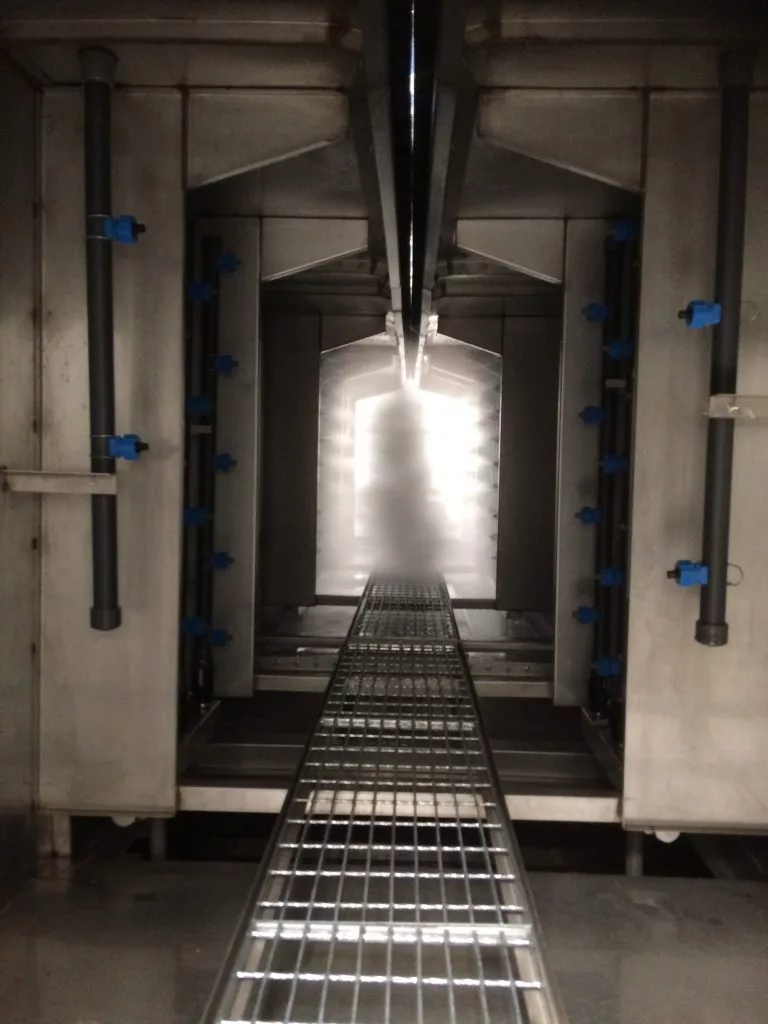
Overview
The pre-treatment system is crucial in ensuring that surfaces are properly cleaned and prepared for powder coating. This step enhances adhesion, improves finish quality, and increases the longevity of the coating.
Components and Process
1.1. Cleaning and Degreasing Stations
- Purpose: Remove oils, grease, and other contaminants from the surface.
- Methods:
- Alkaline Cleaning: Uses alkaline solutions to break down grease and oils.
- Solvent Cleaning: Employs organic solvents to dissolve contaminants.
- Ultrasonic Cleaning: Utilizes high-frequency sound waves for deep cleaning, especially effective for complex shapes.
- Equipment:
- Tanks and spray systems
- Heating elements to improve cleaning efficiency
- Agitation systems for even cleaning
1.2. Rinse Stations
- Purpose: Eliminate residual chemicals and contaminants from the cleaning stage.
- Types of Rinse:
- Freshwater Rinse: Basic water rinse to remove chemicals.
- Deionized Water Rinse: Prevents mineral deposits and spots on surfaces.
- Equipment:
- Spray bars and nozzles for thorough rinsing
- Closed-loop systems to recycle water and reduce waste
1.3. Surface Conditioning
- Purpose: Prepare the surface for subsequent conversion coating.
- Processes:
- Acid Etching: Removes oxides and prepares metal surfaces.
- Descaling: Removes scale and rust from the surface.
- Equipment:
- Immersion tanks or spray booths
- Automated dosing systems for precise chemical application
1.4. Conversion Coating
- Purpose: Apply a chemical layer that enhances powder adhesion and corrosion resistance.
- Types:
- Phosphate Coating: Iron or zinc phosphate for steel surfaces.
- Chromate Coating: Used for aluminum and zinc surfaces.
- Nano-Ceramic Coatings: Environmentally friendly option with superior adhesion and corrosion resistance.
- Equipment:
- Spray or immersion systems
- Temperature control for optimal reaction conditions
1.5. Drying Ovens
- Purpose: Remove moisture from parts to prevent defects in the powder coating.
- Features:
- Adjustable temperature settings
- Air circulation systems for even drying
- Equipment:
- Batch ovens for smaller production
- Conveyor ovens for continuous processing
Key Considerations
- Chemical Management: Ensure proper handling, storage, and disposal of chemicals used in pre-treatment.
- Environmental Compliance: Adhere to local regulations for effluent discharge and waste management.
- Maintenance: Regular cleaning and inspection of tanks and nozzles to prevent contamination.
2. Powder Coating Booths
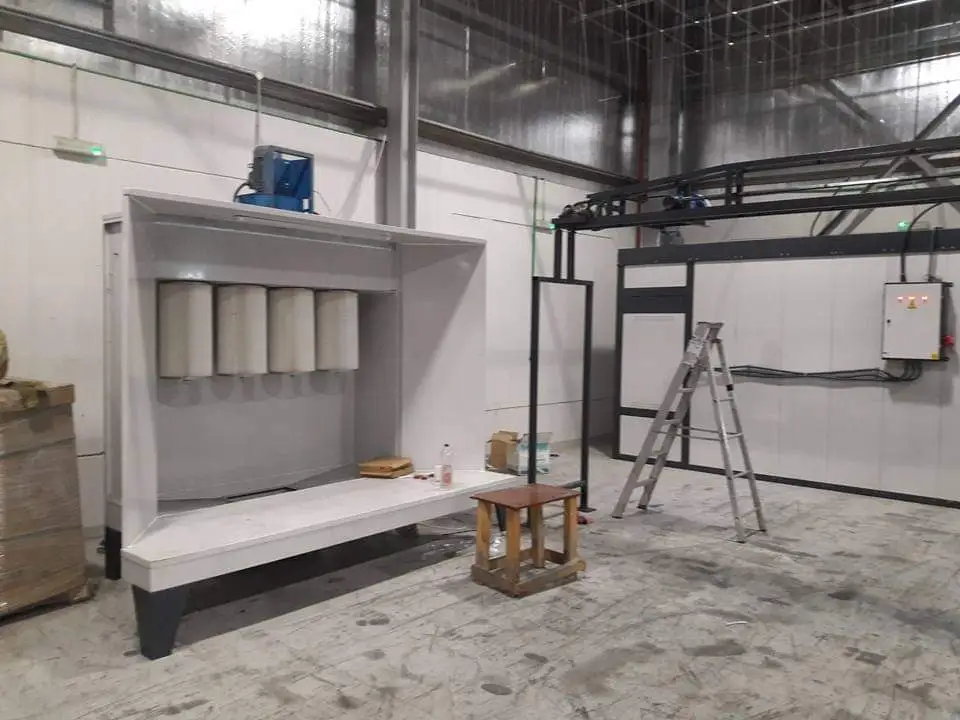
Overview
Powder coating booths provide a controlled environment for applying the powder. They ensure that the powder is applied evenly and that any overspray is efficiently managed and collected for reuse.
Types and Features
2.1. Manual Powder Coating Booths
- Purpose: Allow operators to manually apply powder using handheld spray guns.
- Applications: Suitable for small batches, custom jobs, and intricate parts.
- Features:
- Ventilation Systems: Maintain air quality and remove overspray.
- Lighting: Ensure visibility for precise application.
- Ergonomic Design: Facilitate operator comfort and efficiency.
2.2. Automatic Powder Coating Booths
- Purpose: Use automated systems to apply powder to parts, ideal for high-volume production.
- Applications: Suitable for standard parts and large-scale operations.
- Features:
- Robotic Arms and Reciprocators: Ensure consistent application across parts.
- Programmable Settings: Customize application parameters for different parts.
- Rapid Color Change Systems: Allow quick and efficient color changes with minimal downtime.
2.3. Powder Recovery Systems
- Purpose: Capture and recycle overspray powder to improve efficiency and reduce waste.
- Types:
- Cyclone Separators: Use centrifugal force to separate powder from the air.
- Cartridge Filters: Trap fine powder particles for reuse.
- Baghouse Filters: Employ fabric bags to capture powder, suitable for larger particles.
Key Considerations
- Airflow Management: Ensure proper ventilation to prevent contamination and maintain a clean environment.
- Color Change Efficiency: Invest in systems that allow quick and easy color changes to minimize downtime.
- Safety: Implement explosion-proof designs and fire suppression systems to prevent hazards.
3. Powder Application Equipment
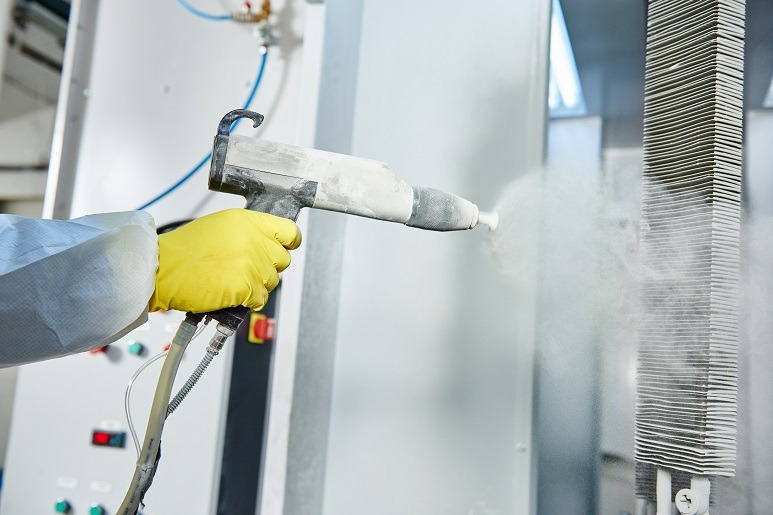
Overview
Powder application equipment is responsible for applying the powder coating to the parts. This equipment uses electrostatic principles to ensure uniform coverage and strong adhesion.
Components and Features
3.1. Electrostatic Spray Guns
- Purpose: Apply powder to the parts using an electrostatic charge.
- Types:
- Corona Guns: Use a high-voltage electrode to charge the powder.
- Tribo Guns: Charge the powder through friction, suitable for specific applications.
- Features:
- Adjustable Voltage and Current: Control the electrostatic charge for optimal coverage.
- Interchangeable Nozzles: Provide different spray patterns for various applications.
- Lightweight and Ergonomic Design: Ensure operator comfort during manual application.
3.2. Control Units
- Purpose: Manage and adjust the settings of the powder application equipment.
- Features:
- Digital Displays: Provide real-time feedback on settings and performance.
- Programmable Settings: Allow customization for different parts and powder types.
- Data Logging: Record application parameters for quality control and traceability.
3.3. Fluidized Bed Systems
- Purpose: Coat parts by dipping them into a bed of fluidized powder, typically used for thicker coatings.
- Applications: Suitable for specific applications requiring a thick and even coating.
- Features:
- Uniform Airflow: Ensure consistent fluidization of powder particles.
- Temperature Control: Maintain optimal conditions for coating.
Key Considerations
- Powder Compatibility: Ensure equipment is compatible with different powder formulations.
- Operator Training: Provide comprehensive training for operators to ensure efficient and safe use.
- Maintenance: Regularly clean and maintain spray guns and control units to prevent clogging and ensure consistent performance.
4. Conveyor System
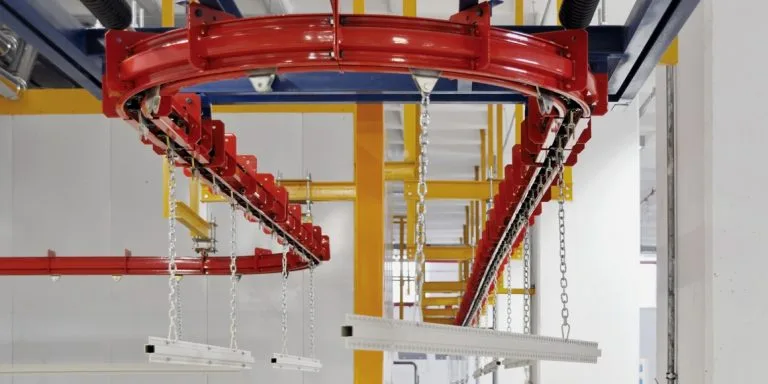
Overview
The conveyor system is the backbone of the powder coating plant, transporting parts through each stage of the process, from pre-treatment to curing.
Types and Features
4.1. Overhead Conveyors
- Purpose: Transport parts by suspending them from hooks or racks, ideal for continuous production.
- Types:
- Monorail Systems: Simple looped tracks for straightforward applications.
- Power and Free Systems: Offer more flexibility with multiple paths and stopping points.
- Features:
- Variable Speed Control: Adjust the speed to match production needs and curing times.
- Load Capacity: Designed to handle different part sizes and weights.
- Integration with Other Systems: Seamlessly integrate with pre-treatment, application, and curing systems.
4.2. Floor Conveyors
- Purpose: Transport heavier or larger parts that cannot be suspended, suitable for specific applications.
- Types:
- Belt Conveyors: Use belts to move parts horizontally or on an incline.
- Roller Conveyors: Employ rollers to facilitate the movement of parts.
- Features:
- Heavy-Duty Construction: Designed to support large or heavy parts.
- Customizable Configurations: Adapt to different plant layouts and processes.
Key Considerations
- Layout Design: Plan the conveyor layout to optimize workflow and minimize bottlenecks.
- Load and Speed Requirements: Ensure the conveyor system meets production demands for speed and capacity.
- Safety Features: Implement safety measures such as guards, emergency stops, and regular inspections.
5. Powder Coating Ovens
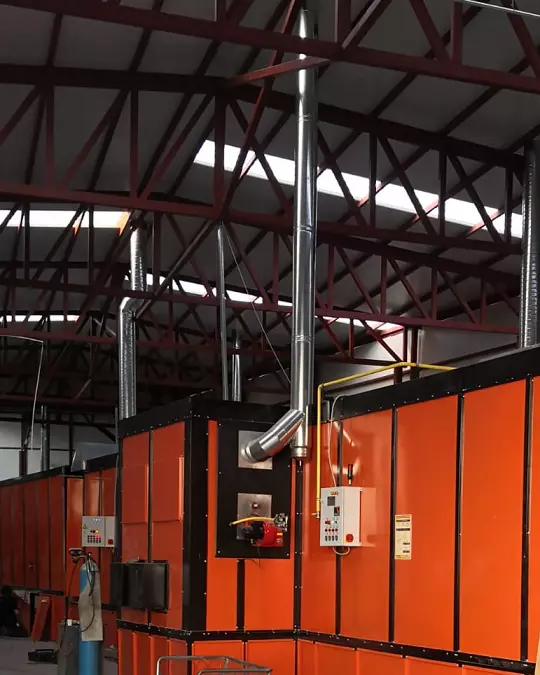
Overview
Powder coating ovens are responsible for curing the powder coating by melting and fusing it to the surface, resulting in a durable and attractive finish.
Types and Features
5.1. Batch Ovens
- Purpose: Cure parts in small batches, suitable for varied part sizes and low-volume production.
- Applications: Ideal for custom jobs, small businesses, and prototyping.
- Features:
- Adjustable Temperature Control: Precise control of curing conditions.
- Flexible Configuration: Accommodate different part sizes and shapes.
- Insulated Construction: Minimize heat loss and improve energy efficiency.
5.2. Conveyor Ovens
- Purpose: Designed for continuous production, curing parts as they move through the oven.
- Applications: Suitable for high-volume production and standardized parts.
- Features:
- Consistent Temperature Distribution: Ensure even curing across all parts.
- Variable Conveyor Speed: Match curing times with production speed.
- Energy Efficiency: Incorporate heat recovery systems and advanced insulation.
Key Considerations
- Oven Size and Capacity: Choose an oven that meets production demands without excessive energy use.
- Heating Source: Decide between electric, gas, or infrared heating based on cost and efficiency.
- Temperature Uniformity: Ensure consistent heat distribution to prevent defects in the finish.
6. Cooling and Inspection Stations
Overview
Cooling and inspection stations are crucial for ensuring the quality and consistency of the finished products. Cooling prevents defects, while inspection verifies the coating quality.
Components and Features
6.1. Cooling Zones
- Purpose: Gradually cool parts after curing to prevent warping or defects.
- Features:
- Controlled Airflow: Ensure even cooling and avoid thermal shock.
- Adjustable Cooling Rates: Customize settings for different materials and part sizes.
6.2. Inspection Areas
- Purpose: Conduct quality checks on coated parts to ensure consistency and adherence to standards.
- Features:
- Lighting and Magnification: Facilitate detailed visual inspections.
- Measurement Tools: Use instruments like thickness gauges and gloss meters for precise evaluation.
- Defect Detection Systems: Implement automated systems for detecting coating defects, such as thin spots or uneven coverage.
Key Considerations
- Quality Assurance Protocols: Establish standards and procedures for inspections to ensure consistent product quality.
- Training for Inspectors: Provide training to staff on recognizing defects and using inspection tools effectively.
- Feedback Loop: Use inspection data to inform process improvements and address recurring issues.
7. Control and Monitoring Systems
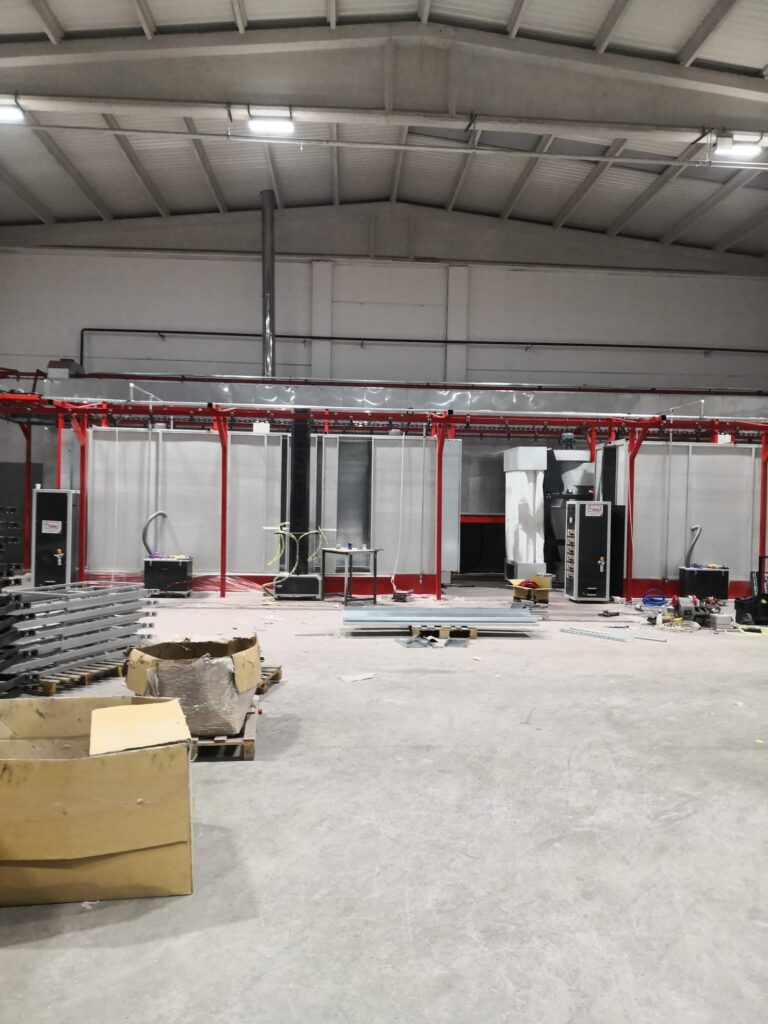
Overview
Control and monitoring systems automate and synchronize various plant operations, ensuring efficiency, consistency, and quality in the powder coating process.
Components and Features
7.1. PLC Systems (Programmable Logic Controllers)
- Purpose: Automate and control equipment functions throughout the plant.
- Features:
- Centralized Control: Manage multiple systems from a single interface.
- Real-Time Monitoring: Track performance metrics and adjust settings as needed.
- Data Logging: Record operational data for analysis and process optimization.
7.2. Data Logging and Analysis Tools
- Purpose: Collect and analyze production data to improve efficiency and quality.
- Features:
- Trend Analysis: Identify patterns and trends in production metrics.
- Performance Dashboards: Visualize key performance indicators (KPIs) for easy monitoring.
- Predictive Maintenance: Use data to anticipate equipment maintenance needs and prevent downtime.
Key Considerations
- System Integration: Ensure seamless integration with existing equipment and software.
- User Interface: Provide intuitive and user-friendly interfaces for operators.
- Cybersecurity: Implement security measures to protect sensitive data and control systems.
8. Safety and Environmental Controls
Overview
Safety and environmental controls are essential for protecting workers and ensuring compliance with regulations. These systems manage hazards and minimize environmental impact.
Components and Features
8.1. Fire Suppression Systems
- Purpose: Prevent and control powder fires or explosions in booths and ovens.
- Features:
- Automatic Detection and Suppression: Quickly identify and extinguish fires.
- Integration with Control Systems: Automatically shut down equipment in case of fire.
- Regular Testing and Maintenance: Ensure systems are operational and compliant with safety standards.
8.2. Ventilation and Filtration Systems
- Purpose: Maintain air quality by removing dust, fumes, and volatile organic compounds (VOCs).
- Features:
- High-Efficiency Particulate Air (HEPA) Filters: Capture fine particles and contaminants.
- Exhaust Fans and Ductwork: Ensure proper airflow and ventilation.
- Regular Filter Replacement: Maintain efficiency and prevent clogs.
8.3. Personal Protective Equipment (PPE)
- Purpose: Provide workers with necessary safety gear to protect against hazards.
- Components:
- Respirators and Masks: Protect against inhalation of powder particles and fumes.
- Safety Glasses and Goggles: Shield eyes from dust and chemical splashes.
- Gloves and Protective Clothing: Prevent skin contact with chemicals and powders.
Key Considerations
- Compliance with Regulations: Adhere to local and international safety and environmental standards.
- Safety Training: Conduct regular training sessions on safety protocols and emergency procedures.
- Continuous Improvement: Regularly review and update safety measures to address emerging risks and regulations.
Conclusion
Each component of a powder coating plant plays a vital role in ensuring a successful and efficient coating process. By understanding the details and functions of these components, businesses can design and operate a plant that meets their specific needs and production goals. Investing in the right equipment and systems, along with proper training and maintenance, will lead to high-quality finishes, increased productivity, and long-term success in the powder coating industry.
Installation time estimate
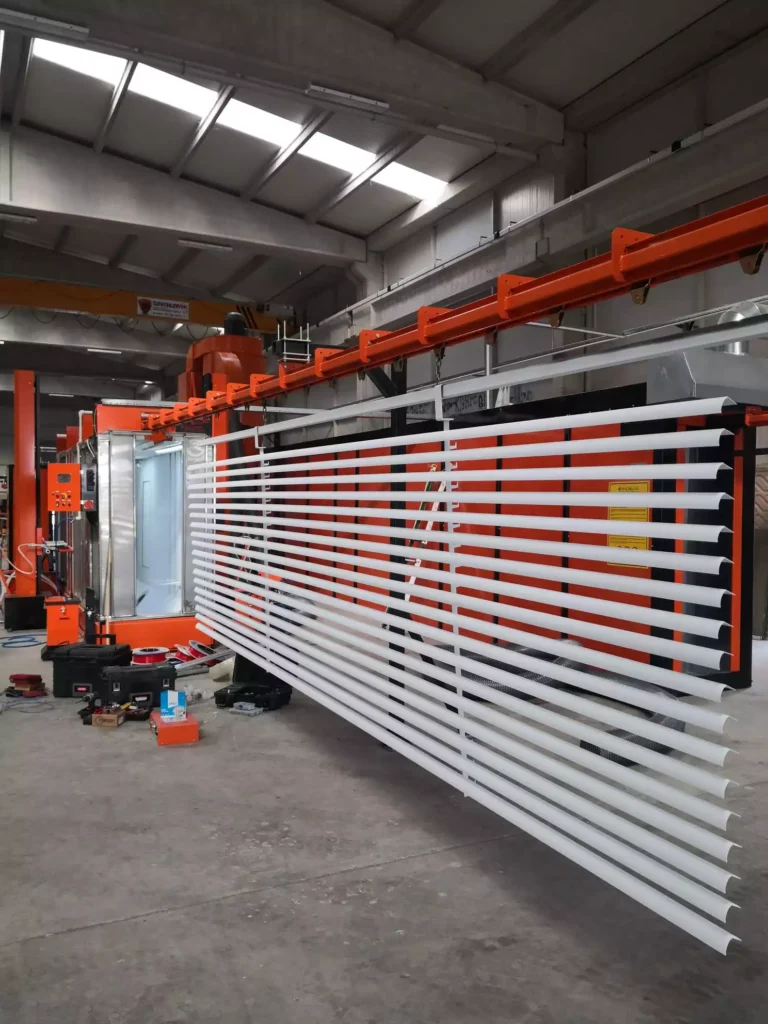
Estimating the installation time for a powder coating plant involves considering several factors such as the size of the operation, complexity of the equipment, facility preparation, and the efficiency of the installation team. Below is a detailed breakdown of the installation time estimate, including factors that can influence the timeline and strategies to ensure a smooth installation process.
Installation Time Estimate for a Powder Coating Plant
Factors Influencing Installation Time
- Scale and Complexity of the Plant
- Size and layout of the facility
- Number and type of equipment components
- Type of Equipment
- Manual vs. automated systems
- Batch vs. continuous production lines
- Site Preparation
- Existing infrastructure readiness
- Facility modifications needed
- Installation Team and Expertise
- Experience and skills of the installation crew
- Availability of necessary resources and tools
- Regulatory Compliance and Inspections
- Time required for permits and approvals
- Safety inspections and certifications
- Coordination and Scheduling
- Coordination between vendors, contractors, and stakeholders
- Availability of equipment and personnel
Estimated Installation Time by Component
Here is an approximate installation timeline for each major component of a powder coating plant. These estimates are generalized and may vary depending on specific project requirements.
1. Pre-Treatment System
- Time Estimate: 1 to 3 weeks
- Activities:
- Delivery and setup of washing, rinsing, and drying stations
- Plumbing and drainage installations
- Testing and calibration of chemical dosing systems
2. Powder Coating Booths
- Time Estimate: 1 to 2 weeks
- Activities:
- Assembly and installation of booth structures
- Integration of ventilation and powder recovery systems
- Setup of lighting and electrical connections
3. Powder Application Equipment
- Time Estimate: 1 to 2 weeks
- Activities:
- Installation of electrostatic spray guns and control units
- Calibration of application settings and nozzles
- Testing for uniform powder distribution
4. Conveyor System
- Time Estimate: 2 to 4 weeks
- Activities:
- Layout design and track installation
- Assembly of conveyor components and drives
- Testing for load capacity and speed control
5. Powder Coating Ovens
- Time Estimate: 2 to 3 weeks
- Activities:
- Installation of oven structures and insulation
- Setup of heating systems and temperature controls
- Testing for temperature uniformity and energy efficiency
6. Cooling and Inspection Stations
- Time Estimate: 1 to 2 weeks
- Activities:
- Installation of cooling systems and airflow management
- Setup of inspection stations and quality control tools
- Training staff on inspection procedures
7. Control and Monitoring Systems
- Time Estimate: 1 to 2 weeks
- Activities:
- Installation of PLC systems and control panels
- Integration with other equipment components
- Testing and validation of automation processes
8. Safety and Environmental Controls
- Time Estimate: 1 to 2 weeks
- Activities:
- Installation of fire suppression and ventilation systems
- Setup of safety barriers and emergency stops
- Safety audits and compliance checks
Total Estimated Installation Time
The total estimated installation time for a powder coating plant can range from 8 to 18 weeks, depending on the scale and complexity of the project. Here’s a breakdown by plant size:
- Small-Scale Operations: 8 to 10 weeks
- Medium-Scale Operations: 10 to 14 weeks
- Large-Scale Operations: 14 to 18 weeks
Strategies for Reducing Installation Time
- Detailed Planning and Coordination
- Develop a comprehensive project plan with clear timelines and milestones.
- Coordinate with vendors, contractors, and stakeholders to align schedules and resources.
- Pre-Fabrication and Pre-Assembly
- Opt for pre-fabricated components to reduce on-site assembly time.
- Pre-assemble equipment off-site where possible to minimize installation complexity.
- Experienced Installation Team
- Hire experienced professionals familiar with powder coating systems and processes.
- Conduct regular training and briefings to ensure the team is well-prepared.
- Efficient Site Preparation
- Ensure the facility is ready for installation before equipment arrives.
- Complete necessary infrastructure upgrades and modifications in advance.
- Streamlined Permitting and Inspections
- Obtain permits and approvals early in the project timeline.
- Schedule inspections and certifications to avoid delays.
- Contingency Planning
- Identify potential risks and develop contingency plans to address unforeseen issues.
- Allocate buffer time in the schedule for unexpected challenges.
Conclusion
The installation of a powder coating plant is a complex process that requires careful planning and coordination. By understanding the factors that influence installation time and implementing strategies to streamline the process, businesses can achieve a successful setup that meets their production goals and timelines.
Maintenance schedule tips
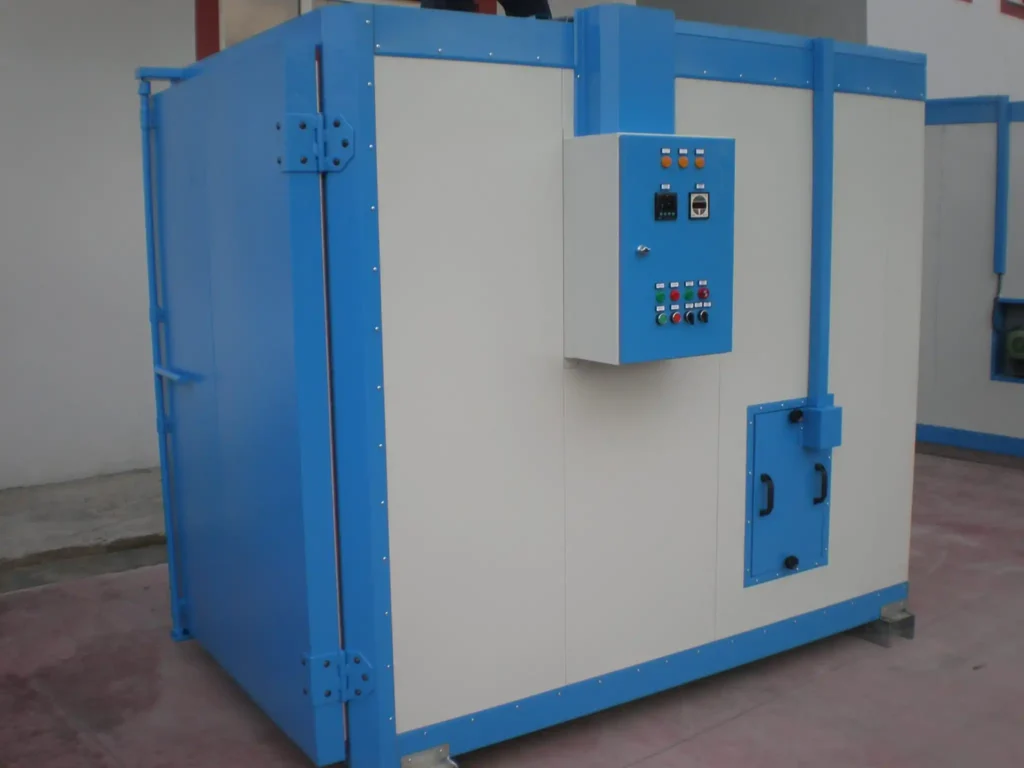
Creating a maintenance schedule for a powder coating plant is essential for ensuring efficient operation, minimizing downtime, and extending the lifespan of your equipment. A well-structured maintenance plan should address the needs of each component, including pre-treatment systems, powder coating booths, application equipment, conveyors, ovens, and safety controls. Here are some tips and guidelines to help you develop an effective maintenance schedule.
Tips for Creating a Maintenance Schedule for a Powder Coating Plant
1. Understand Equipment Requirements
- Read Manufacturer Guidelines: Start by reviewing the maintenance recommendations provided by the equipment manufacturers. These guidelines offer valuable insights into the specific needs and intervals for each component.
- Identify Critical Components: Prioritize maintenance for critical components that directly impact production quality and efficiency, such as spray guns, ovens, and conveyors.
2. Develop a Comprehensive Maintenance Plan
- Routine Inspections: Schedule regular inspections to identify wear and tear, leaks, or potential issues before they escalate. Inspections should cover all plant components, including electrical, mechanical, and safety systems.
- Preventive Maintenance: Implement a preventive maintenance schedule that includes tasks such as cleaning, lubrication, calibration, and parts replacement. This helps prevent unexpected breakdowns and maintains optimal performance.
- Predictive Maintenance: Utilize data analytics and monitoring tools to predict equipment failures and schedule maintenance based on condition and usage patterns.
3. Create a Detailed Maintenance Schedule
- Daily Maintenance Tasks:
- Check air pressure and filtration systems.
- Inspect spray guns and nozzles for clogs or wear.
- Clean work areas and remove powder buildup.
- Weekly Maintenance Tasks:
- Inspect conveyor systems for alignment and wear.
- Lubricate moving parts such as bearings and chains.
- Check temperature settings and calibrate sensors.
- Monthly Maintenance Tasks:
- Conduct a thorough inspection of pre-treatment systems.
- Inspect and clean ventilation and exhaust systems.
- Test and recalibrate control systems.
- Quarterly Maintenance Tasks:
- Perform a detailed inspection of the ovens for heat distribution and insulation integrity.
- Replace worn-out components such as belts and filters.
- Review and update safety protocols.
- Annual Maintenance Tasks:
- Conduct a comprehensive review of the entire plant.
- Audit compliance with safety and environmental regulations.
- Plan for equipment upgrades or replacements as needed.
4. Document Maintenance Activities
- Record Keeping: Maintain detailed records of all maintenance activities, including dates, tasks performed, and any issues identified. This documentation helps track equipment performance and identifies recurring problems.
- Use Digital Tools: Consider using computerized maintenance management systems (CMMS) to schedule, track, and analyze maintenance activities. Digital tools can provide reminders, automate scheduling, and generate reports.
5. Train and Empower Staff
- Employee Training: Train employees on the importance of maintenance and proper procedures. Ensure they understand how to identify and report issues and perform routine tasks.
- Empowerment: Encourage staff to take ownership of their equipment and be proactive in reporting potential problems.
6. Monitor Key Performance Indicators (KPIs)
- Track KPIs: Monitor KPIs such as equipment uptime, mean time between failures (MTBF), and maintenance costs to evaluate the effectiveness of your maintenance program.
- Continuous Improvement: Use KPI data to identify areas for improvement and make data-driven decisions to enhance maintenance strategies.
7. Plan for Spare Parts and Inventory
- Spare Parts Management: Maintain an inventory of critical spare parts to minimize downtime during repairs. Track usage patterns to ensure adequate stock levels.
- Vendor Relationships: Build strong relationships with equipment suppliers to ensure quick access to parts and technical support.
8. Evaluate and Adjust the Maintenance Plan
- Regular Reviews: Periodically review and update the maintenance schedule based on equipment performance, technological advancements, and changing production needs.
- Feedback Loop: Encourage feedback from maintenance staff and operators to identify pain points and improve processes.
Sample Maintenance Schedule Template
Here’s a sample template to help you structure your maintenance schedule:
Frequency | Task | Details |
---|---|---|
Daily | Check air pressure | Ensure proper airflow for spray guns and equipment. |
Inspect spray guns | Look for clogs, wear, and powder buildup. | |
Clean work areas | Remove excess powder and debris from booths and equipment. | |
Weekly | Inspect conveyor systems | Check alignment and wear of belts and chains. |
Lubricate moving parts | Apply lubrication to bearings, chains, and gears. | |
Calibrate temperature settings | Ensure accurate temperature readings in ovens. | |
Monthly | Inspect pre-treatment systems | Check tanks, pumps, and chemical levels. |
Clean ventilation systems | Remove dust and powder buildup in filters and ducts. | |
Test control systems | Verify functionality and accuracy of control units. | |
Quarterly | Inspect oven heat distribution | Check for even heat distribution and insulation integrity. |
Replace worn components | Swap out belts, filters, and other wear-prone parts. | |
Review safety protocols | Update safety measures and conduct training if needed. | |
Annually | Conduct plant-wide inspection | Evaluate overall condition and performance. |
Audit compliance with regulations | Ensure adherence to safety and environmental standards. | |
Plan equipment upgrades | Assess the need for new equipment or technology upgrades. |
Conclusion
Implementing a well-structured maintenance schedule is vital for the smooth operation and longevity of your powder coating plant. By focusing on preventive and predictive maintenance, documenting activities, and involving your team, you can reduce downtime, improve efficiency, and maintain high-quality production standards.
Powder Coating Oven Types
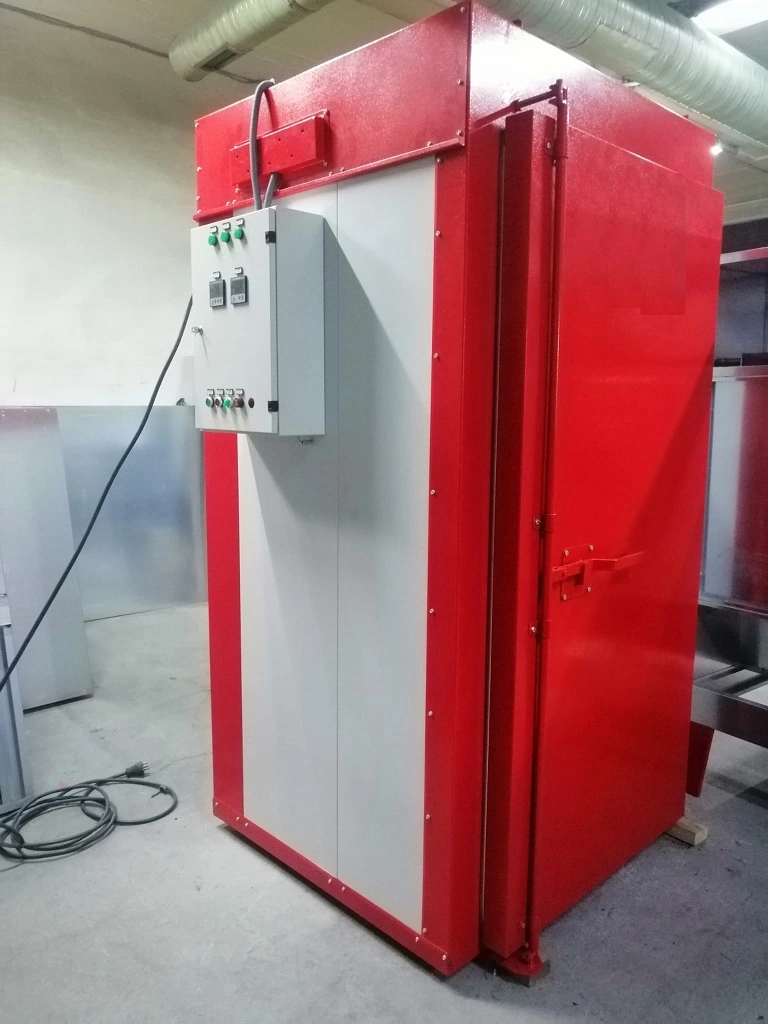
Powder coating ovens are a critical component of the powder coating process, providing the heat necessary to cure the powder and ensure a durable finish. There are several types of powder coating ovens, each designed to meet different production needs and efficiency levels. This guide will cover the various types of powder coating ovens, their features, benefits, and applications, helping you choose the right oven for your specific requirements.
Types of Powder Coating Ovens
1. Batch Ovens
Batch ovens are designed to cure powder coatings for small to medium-sized production runs. They are ideal for operations that require flexibility in coating different part sizes and types.
Features:
- Flexibility: Accommodates various part sizes and shapes.
- Energy Efficiency: Often includes insulation and heat recovery systems to reduce energy consumption.
- Manual or Semi-Automatic Operation: Suitable for low to moderate production volumes.
Benefits:
- Cost-Effective: Lower initial investment compared to continuous ovens.
- Versatile: Can handle a variety of coating tasks, including custom and complex shapes.
- Ease of Use: Simple to operate and maintain.
Applications:
- Small businesses and job shops
- Custom and prototype work
- Low to medium production volumes
Common Types of Batch Ovens:
- Walk-In Ovens: Large enough for operators to enter and load parts, suitable for oversized items.
- Cabinet Ovens: Smaller units ideal for small parts or lower-volume production.
- Truck-In Ovens: Designed for loading parts on racks or carts that can be rolled into the oven.
2. Conveyor Ovens
Conveyor ovens are designed for high-volume production and continuous processing. They automate the curing process, improving efficiency and consistency.
Features:
- Continuous Operation: Ideal for high production rates and large-scale operations.
- Automated Conveyor Systems: Transport parts through the oven for consistent curing.
- Variable Speed Control: Allows adjustment of conveyor speed to match curing requirements.
Benefits:
- High Throughput: Capable of processing large quantities of parts quickly.
- Consistent Quality: Ensures uniform curing across all parts.
- Reduced Labor Costs: Automation reduces the need for manual intervention.
Applications:
- Automotive and aerospace industries
- High-volume manufacturing plants
- Standardized parts production
Common Types of Conveyor Ovens:
- Monorail Ovens: Parts are hung from an overhead conveyor and pass through the oven in a linear path.
- Chain-On-Edge Ovens: Parts are attached to fixtures on a conveyor chain, suitable for heavier items.
- Flat-Belt Ovens: Use a flat conveyor belt to transport parts, ideal for lightweight or flat components.
3. Infrared Ovens
Infrared ovens use infrared radiation to cure powder coatings, offering a fast and energy-efficient alternative to conventional ovens. They are often used in combination with other oven types to optimize curing.
Features:
- Fast Heating: Infrared radiation provides rapid heat-up and curing times.
- Energy Efficiency: Direct heating reduces energy consumption compared to convection ovens.
- Compact Size: Smaller footprint compared to traditional ovens.
Benefits:
- Quick Curing: Significantly reduces curing times, increasing throughput.
- Targeted Heating: Infrared heat can be focused on specific areas, reducing overall energy use.
- Improved Finish: Provides smooth and even curing, minimizing defects.
Applications:
- Automotive and consumer electronics
- Applications requiring quick turnaround
- Parts with complex shapes or heat-sensitive materials
Common Types of Infrared Ovens:
- Short-Wave Infrared Ovens: Provide intense heat for fast curing, suitable for thicker coatings.
- Medium-Wave Infrared Ovens: Balance between heat intensity and penetration, ideal for general applications.
- Long-Wave Infrared Ovens: Gentle heat suitable for heat-sensitive substrates.
4. Gas-Fired Ovens
Gas-fired ovens use natural gas or propane as a heat source. They are popular for large-scale operations due to their efficiency and cost-effectiveness.
Features:
- High Heat Output: Efficiently generates high temperatures for rapid curing.
- Cost-Effective: Generally lower operating costs compared to electric ovens.
- Robust Construction: Designed to handle heavy-duty industrial use.
Benefits:
- Reduced Operating Costs: Lower energy costs compared to electric ovens, especially for large volumes.
- Reliable Performance: Consistent heating for uniform curing.
- Scalability: Suitable for large-scale production and expansion.
Applications:
- Automotive and heavy equipment manufacturing
- Large industrial operations
- High-volume powder coating lines
Common Types of Gas-Fired Ovens:
- Direct-Fired Ovens: Burners directly heat the air inside the oven chamber, providing fast and efficient heating.
- Indirect-Fired Ovens: Heat exchangers separate combustion gases from the oven air, offering cleaner operation.
5. Electric Ovens
Electric ovens use electrical heating elements to generate heat for curing powder coatings. They are commonly used in smaller operations due to their ease of use and installation.
Features:
- Precise Temperature Control: Offers accurate and consistent temperature settings.
- Easy Installation: No need for gas lines or combustion venting.
- Low Maintenance: Fewer moving parts compared to gas-fired ovens.
Benefits:
- Safe and Clean: No combustion gases, reducing emissions and improving air quality.
- Consistent Performance: Stable temperature control ensures uniform curing.
- Versatile: Suitable for various applications and materials.
Applications:
- Small to medium-sized businesses
- Custom and low-volume production
- Applications with strict environmental regulations
Common Types of Electric Ovens:
- Forced-Air Convection Ovens: Use fans to circulate heated air for uniform temperature distribution.
- Static Ovens: Rely on natural convection, suitable for delicate or sensitive parts.
6. Combination Ovens
Combination ovens integrate multiple heating methods, such as infrared and convection, to provide flexibility and optimize curing processes.
Features:
- Multi-Mode Operation: Allows switching between or combining different heating methods.
- Optimized Curing: Adjusts curing methods based on part size, shape, and material.
- Flexible Configuration: Customizable to meet specific production needs.
Benefits:
- Versatility: Capable of handling a wide range of parts and coatings.
- Improved Efficiency: Combines the strengths of different heating methods for optimal results.
- Enhanced Finish Quality: Provides tailored curing conditions to minimize defects.
Applications:
- Complex parts with varying geometries
- Industries requiring rapid production changes
- Specialized coating applications
Considerations for Choosing the Right Powder Coating Oven
When selecting a powder coating oven, consider the following factors:
- Production Volume:
- Choose batch ovens for low to medium production and conveyor ovens for high-volume operations.
- Part Size and Shape:
- Consider the size, weight, and geometry of the parts to determine the appropriate oven type.
- Energy Efficiency:
- Evaluate energy consumption and costs, especially for large-scale operations.
- Temperature Requirements:
- Ensure the oven can maintain consistent temperatures for your specific powder coatings.
- Space and Layout:
- Consider the available space and how the oven will fit into your production line layout.
- Budget and Cost:
- Balance initial investment with long-term operating costs and return on investment.
- Regulatory Compliance:
- Ensure the oven meets local safety and environmental regulations.
Conclusion
Selecting the right powder coating oven is crucial for achieving high-quality finishes and efficient production. By understanding the features, benefits, and applications of each oven type, businesses can make informed decisions that align with their production needs and goals. Investing in the right oven will enhance productivity, reduce costs, and ensure a durable, attractive finish on your coated products.
Powder coating oven maintenance tips
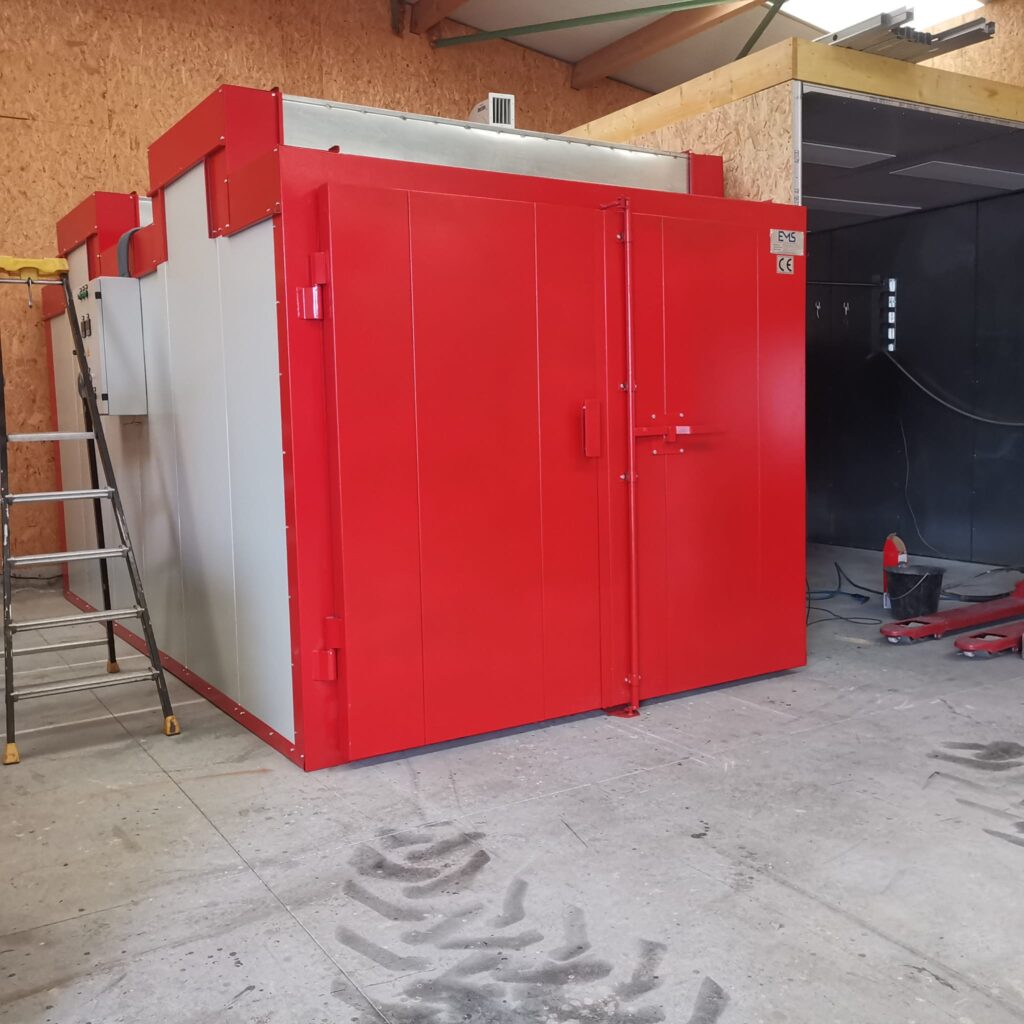
Proper maintenance of powder coating ovens is crucial to ensure efficient operation, consistent curing quality, and the longevity of the equipment. A well-maintained oven minimizes downtime, reduces energy consumption, and prevents costly repairs. Below are comprehensive tips and guidelines for maintaining powder coating ovens effectively.
Powder Coating Oven Maintenance Tips
1. Regular Cleaning
Keeping the oven clean is essential to prevent powder buildup, which can affect performance and finish quality.
Cleaning Tips:
- Daily Cleaning:
- Inspect and Clean Interior Surfaces: Remove any powder buildup on oven walls, floors, and ceilings.
- Clean Heating Elements: Check and clean heating elements to ensure efficient heat transfer.
- Vacuum or Sweep the Floor: Remove any loose powder or debris from the oven floor.
- Weekly Cleaning:
- Clean Air Ducts and Vents: Ensure proper airflow and ventilation by cleaning ducts and vents regularly.
- Wipe Down Doors and Seals: Clean door seals and check for any damage that could affect insulation.
- Monthly Cleaning:
- Deep Clean Oven Interior: Use a non-abrasive cleaner to deep clean the oven interior and remove any stubborn residue.
- Inspect and Clean Exhaust Systems: Check and clean exhaust fans and filters to prevent blockages.
2. Routine Inspections
Regular inspections help identify potential issues before they become major problems, ensuring the oven operates at peak efficiency.
Inspection Tips:
- Daily Inspections:
- Check Temperature Settings: Verify that the oven reaches and maintains the correct curing temperature.
- Monitor Airflow: Ensure that fans and blowers are functioning correctly for even heat distribution.
- Inspect Doors and Seals: Check for gaps or damage that could lead to heat loss.
- Weekly Inspections:
- Inspect Electrical Components: Check wiring, connections, and control panels for signs of wear or damage.
- Check for Unusual Noises: Listen for any unusual noises that might indicate mechanical issues.
- Monthly Inspections:
- Inspect Insulation: Check oven insulation for any damage or wear that could reduce energy efficiency.
- Examine Conveyor Systems: For conveyor ovens, inspect belts, chains, and rollers for wear and alignment.
3. Calibration and Testing
Regular calibration and testing ensure that the oven operates at the correct temperature and settings, maintaining coating quality.
Calibration Tips:
- Temperature Calibration:
- Use Thermocouples: Place thermocouples at various points in the oven to verify temperature uniformity.
- Adjust Temperature Controllers: Calibrate controllers to maintain consistent curing temperatures across the oven.
- Testing Performance:
- Conduct Cure Tests: Perform test runs with sample parts to ensure that coatings are cured properly.
- Check Heating Elements: Test heating elements for consistent output and replace any that are faulty.
4. Preventive Maintenance
Implementing a preventive maintenance schedule helps prevent unexpected breakdowns and extends the life of the oven.
Preventive Maintenance Tips:
- Lubrication:
- Lubricate Moving Parts: Apply lubrication to bearings, chains, and other moving parts to reduce friction and wear.
- Component Replacement:
- Replace Worn Parts: Regularly check and replace parts like belts, seals, and filters that show signs of wear.
- Fan and Blower Maintenance:
- Inspect and Clean Fans: Check fans for balance and clean them to prevent vibration and noise.
- Replace Worn Bearings: Replace any bearings that are noisy or show signs of wear.
5. Safety and Compliance
Ensuring safety and regulatory compliance is critical for protecting workers and meeting industry standards.
Safety Tips:
- Fire Safety:
- Check Fire Suppression Systems: Ensure that fire suppression systems are operational and regularly serviced.
- Install Smoke Detectors: Regularly test smoke detectors and alarms to ensure they are functional.
- Electrical Safety:
- Inspect Wiring and Connections: Regularly check electrical wiring and connections for signs of wear or damage.
- Conduct Safety Audits: Perform regular safety audits to ensure compliance with safety regulations.
6. Documentation and Record Keeping
Keeping detailed records of maintenance activities helps track oven performance and identify trends or recurring issues.
Documentation Tips:
- Maintain a Maintenance Log: Record all maintenance activities, including inspections, cleaning, and repairs.
- Track Performance Metrics: Monitor metrics such as energy consumption, downtime, and repair frequency.
7. Staff Training and Awareness
Proper training ensures that staff are equipped to perform maintenance tasks safely and effectively.
Training Tips:
- Provide Comprehensive Training: Train staff on oven operation, maintenance procedures, and safety protocols.
- Encourage Proactive Maintenance: Empower staff to identify and report potential issues promptly.
Sample Maintenance Schedule for Powder Coating Ovens
Below is a sample maintenance schedule to help you organize and plan oven maintenance tasks:
Frequency | Task | Details |
---|---|---|
Daily | Clean interior surfaces | Remove powder buildup from oven walls, floors, and ceilings. |
Check temperature settings | Verify that the oven reaches the correct curing temperature. | |
Inspect doors and seals | Look for gaps or damage that could lead to heat loss. | |
Weekly | Clean air ducts and vents | Ensure proper airflow and ventilation. |
Inspect electrical components | Check wiring, connections, and control panels for wear. | |
Lubricate moving parts | Apply lubrication to bearings, chains, and other components. | |
Monthly | Deep clean oven interior | Use non-abrasive cleaner to remove stubborn residue. |
Calibrate temperature controllers | Verify and adjust temperature settings for consistency. | |
Inspect insulation and conveyor systems | Check insulation integrity and conveyor alignment. | |
Quarterly | Test heating elements and fans | Ensure consistent output and replace faulty components. |
Review safety protocols and systems | Update safety measures and test fire suppression systems. | |
Annually | Conduct comprehensive performance review | Evaluate overall condition and plan for upgrades. |
Audit compliance with regulations | Ensure adherence to safety and environmental standards. |
Conclusion
Regular maintenance of powder coating ovens is essential for achieving high-quality finishes, maintaining production efficiency, and ensuring equipment longevity. By implementing a structured maintenance plan, conducting regular inspections, and training staff, businesses can minimize downtime, reduce costs, and maintain a safe working environment.
Powder Coating Spray Booth: Achieving Clean, Efficient, and High-Quality Coating Results
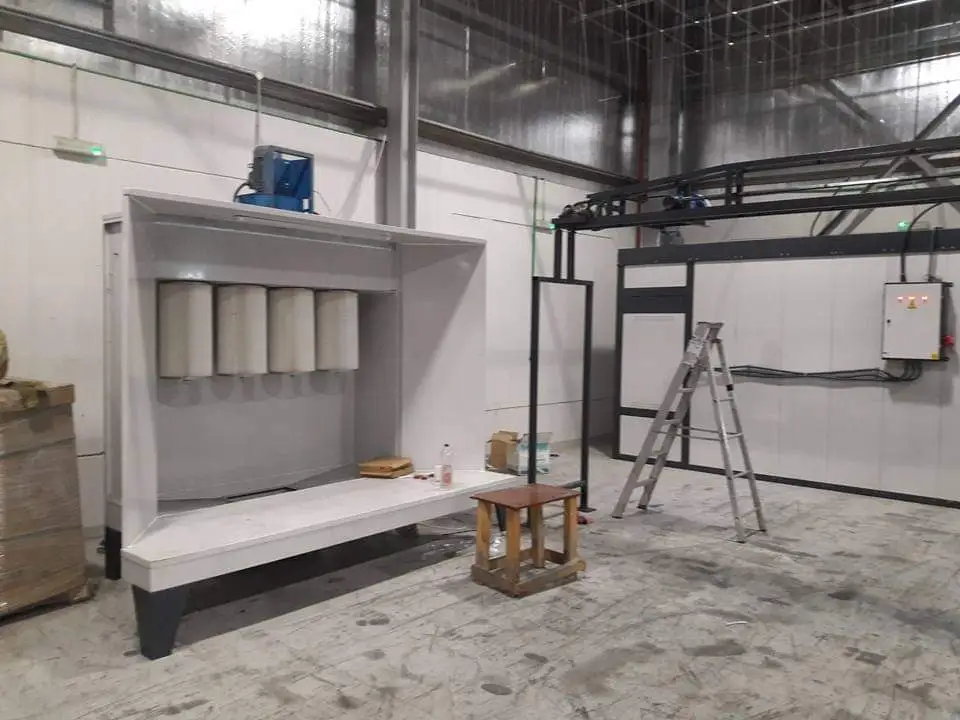
The powder coating process requires a controlled environment to ensure consistent and high-quality finishes. One of the most critical components in this process is the powder coating spray booth, where the actual application of powder takes place. Spray booths provide a dedicated space for applying powder, preventing contamination, capturing overspray, and ensuring that the process is both efficient and environmentally friendly.
Powder coating spray booths are designed to contain the powder within a specific area, keeping it from escaping into the surrounding workspace. These booths are typically equipped with air filtration and extraction systems that capture excess powder particles, reducing waste, minimizing health risks to workers, and maintaining a clean workspace. Additionally, the booth’s environment is controlled to ensure that no contaminants interfere with the powder coating process, resulting in smooth, durable finishes.
EMS Powder Coating Equipment is a trusted manufacturer of powder coating spray booths, offering a wide range of booths equipped with advanced filtration and ventilation systems. EMS spray booths are designed for optimal efficiency, safety, and cleanliness, making them an ideal choice for businesses looking to enhance their powder coating operations. In this guide, we’ll explore how powder coating spray booths work, their benefits, and why EMS Powder Coating Equipment is the best option for businesses seeking high-performance booths.
What is a Powder Coating Spray Booth?
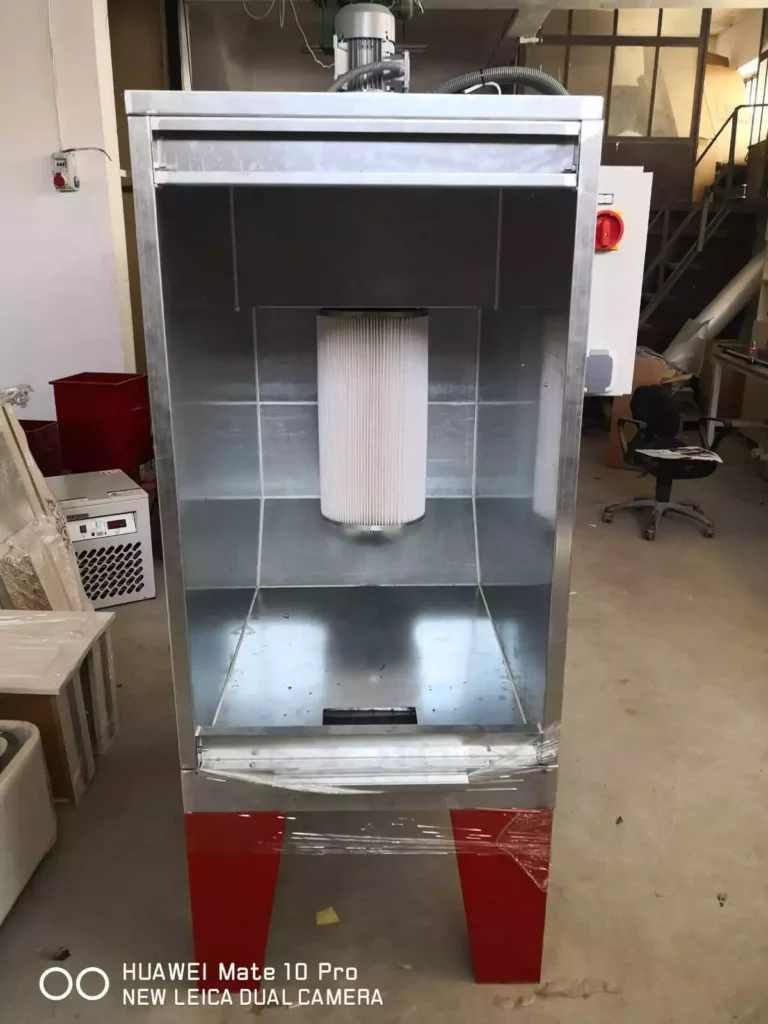
A powder coating spray booth is an enclosed space where powder is applied to products during the powder coating process. The booth provides a controlled environment that prevents external contaminants from affecting the coating process while also containing the powder within a specific area to prevent it from spreading throughout the workspace. These booths are an essential part of any powder coating system, as they ensure a clean, safe, and efficient application process.
How Powder Coating Spray Booths Work
In a powder coating spray booth, products are placed inside the booth and coated using electrostatic spray guns. These guns charge the powder particles, which are then attracted to the grounded surface of the product. This electrostatic attraction ensures that the powder adheres evenly to the product, providing a smooth and consistent coat.
As the powder is applied, some particles may not adhere to the product and become airborne. To prevent these excess particles from escaping into the surrounding workspace, the booth is equipped with an air extraction and filtration system. This system draws air through filters that capture the excess powder, keeping the air inside the booth clean and free from harmful particulates.
Many powder coating spray booths are equipped with features like adjustable airflow, which allows operators to control the speed and direction of air movement within the booth. This helps ensure that the powder is applied evenly and that overspray is efficiently captured and recycled, minimizing waste.
EMS Powder Coating Equipment manufactures spray booths with advanced air filtration and extraction systems that maximize efficiency and cleanliness. Their booths are designed to handle the demands of industrial powder coating operations, ensuring consistent and high-quality results.
The Benefits of Powder Coating Spray Booths
Powder coating spray booths are essential for businesses looking to improve the efficiency, safety, and quality of their powder coating process. Here are some of the key benefits of using a high-quality spray booth:
1. Improved Product Quality
A controlled environment is essential for achieving consistent, high-quality finishes in powder coating. In an open workspace, contaminants such as dust, dirt, or debris can settle on the product during the coating process, leading to defects like uneven finishes or poor adhesion. A powder coating spray booth provides a clean, enclosed space where products can be coated without the risk of contamination from the outside environment.
In addition to preventing contamination, the airflow and filtration system inside the booth ensure that overspray is effectively captured, preventing it from interfering with the final finish. The result is a smooth, even coating that meets the highest standards of quality and durability.
EMS Powder Coating Equipment designs its spray booths to provide a clean, controlled environment that enhances the quality of the finished product. Their booths are engineered for precision, ensuring that each product receives a flawless coating.
2. Reduced Powder Waste and Cost Savings
Powder waste is a common issue in powder coating operations, especially when the excess powder is not properly captured and recycled. Without a spray booth, much of the overspray can be lost, leading to higher material costs and environmental waste. Powder coating spray booths are designed to capture excess powder, allowing it to be collected and reused.
The filtration system in a spray booth traps airborne powder particles and prevents them from escaping into the workspace. This captured powder can then be reclaimed and reintroduced into the coating process, reducing material waste and cutting costs.
EMS Powder Coating Equipment offers spray booths with advanced powder recovery systems that maximize powder reuse and minimize waste. Their booths are designed to reduce material costs by ensuring that as much powder as possible is captured and recycled.
3. Enhanced Worker Safety
Worker safety is a top priority in any industrial setting, and powder coating operations are no exception. During the powder coating process, airborne powder particles can pose a respiratory hazard to workers if they are not properly contained. Inhaling these particles over time can lead to respiratory issues and other health problems.
Powder coating spray booths are equipped with ventilation and filtration systems that remove harmful particulates from the air, ensuring that the workspace remains clean and safe for operators. The booth’s design prevents airborne powder from escaping into the surrounding environment, reducing the risk of exposure for workers.
EMS Powder Coating Equipment designs its spray booths with safety in mind, offering advanced filtration and ventilation systems that protect workers from inhaling harmful particles. Their booths are built to meet the highest safety standards, ensuring a safe and healthy work environment.
4. Environmental Compliance
Many industries are subject to strict environmental regulations regarding air quality and emissions. Powder coating is an environmentally friendly process compared to liquid painting, as it produces minimal volatile organic compounds (VOCs). However, without proper containment and filtration, excess powder can still be released into the atmosphere, contributing to air pollution.
Powder coating spray booths are designed to contain and capture overspray, preventing it from being released into the environment. The booth’s filtration system ensures that any excess powder is collected and safely disposed of or recycled, helping businesses meet environmental regulations and reduce their overall environmental impact.
EMS Powder Coating Equipment offers spray booths with high-performance filtration systems that help businesses comply with environmental standards. Their booths are designed to minimize emissions and improve sustainability in powder coating operations.
5. Flexibility and Customization
Powder coating spray booths come in a variety of sizes and configurations, making them suitable for different types of products and production volumes. Whether you’re coating small parts or large industrial components, spray booths can be customized to meet the specific needs of your operation. This flexibility allows businesses to optimize their coating process for efficiency and quality.
Spray booths can also be equipped with additional features, such as adjustable airflow controls, automated powder recovery systems, and more, to enhance performance and meet the unique requirements of each production line.
EMS Powder Coating Equipment provides customizable spray booths that can be tailored to the specific needs of your business. Whether you need a small batch booth or a large conveyorized system, EMS offers solutions that ensure optimal performance and efficiency.
6. Easy Maintenance and Long-Term Reliability
A high-quality spray booth is a long-term investment that can provide years of reliable performance with proper maintenance. Regularly replacing filters and cleaning the booth ensures that it continues to operate efficiently and that air quality remains high. High-quality spray booths are built to withstand the demands of continuous industrial use, providing businesses with a durable solution for their powder coating needs.
EMS Powder Coating Equipment manufactures spray booths that are designed for ease of maintenance and long-lasting reliability. Their booths are constructed from high-quality materials that resist wear and tear, ensuring that your investment will continue to deliver top-tier performance for years to come.
Why Choose EMS Powder Coating Equipment for Spray Booths?
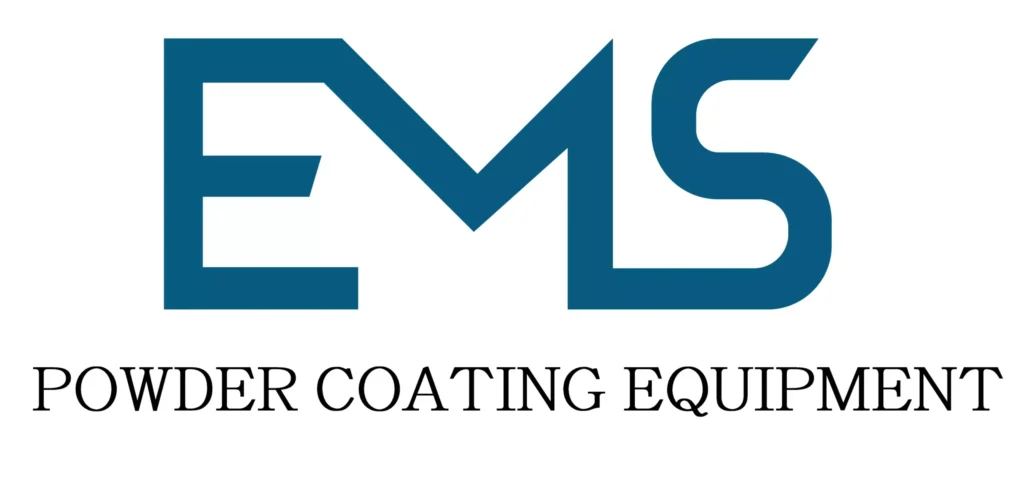
When selecting a powder coating spray booth, businesses need equipment that offers precision, efficiency, and durability. EMS Powder Coating Equipment is the industry leader in providing advanced spray booths that meet the highest standards of performance and safety. Here’s why EMS is the best choice for businesses looking to invest in high-quality spray booths:
1. Advanced Filtration and Ventilation Technology
EMS spray booths are equipped with cutting-edge filtration and ventilation systems that ensure a clean, safe environment for both workers and products. Their booths are designed to capture excess powder with maximum efficiency, preventing contamination and improving air quality in the workspace.
2. Customizable Solutions for Different Industries
Every production line has unique requirements, and EMS offers customizable solutions to meet those needs. Whether you’re working with small parts or large industrial components, EMS provides spray booths that can be tailored to fit your specific production environment. Their booths are available in a range of sizes and configurations, ensuring that businesses get the right solution for their needs.
3. Energy Efficiency and Cost Savings
EMS Powder Coating Equipment understands the importance of efficiency in today’s manufacturing environments. Their spray booths are designed to minimize powder waste and reduce energy consumption, helping businesses lower their operational costs without sacrificing performance.
4. Durability and Long-Lasting Performance
Built to withstand the rigors of industrial use, EMS spray booths are constructed from high-quality materials that ensure long-lasting performance. Their booths require minimal maintenance and are designed to provide reliable operation for years, making them a sound investment for any business.
5. Superior Customer Support and Service
In addition to providing top-tier equipment, EMS offers exceptional customer support and after-sales service. From installation and setup to ongoing maintenance and troubleshooting, EMS’s team of experts is dedicated to ensuring that your spray booth operates at peak efficiency.
Conclusion
A powder coating spray booth is an essential part of any powder coating system, providing a clean, controlled environment that ensures high-quality finishes, worker safety, and environmental compliance. By capturing and filtering overspray, these booths help businesses improve efficiency, reduce waste, and lower costs.
EMS Powder Coating Equipment is the industry leader in providing advanced spray booths with state-of-the-art filtration and ventilation systems. Whether you’re looking to upgrade your existing system or invest in new equipment, EMS offers customizable solutions that ensure your powder coating operations are optimized for maximum productivity and quality.
By choosing EMS powder coating spray booths, businesses can enhance their coating process, improve product quality, and reduce their environmental impact. With a proven track record of innovation and customer satisfaction, EMS is the best choice for businesses seeking reliable and efficient spray booths.
Powder Coating Booth: The Key to High-Quality Finishes and Efficiency in Coating Processes
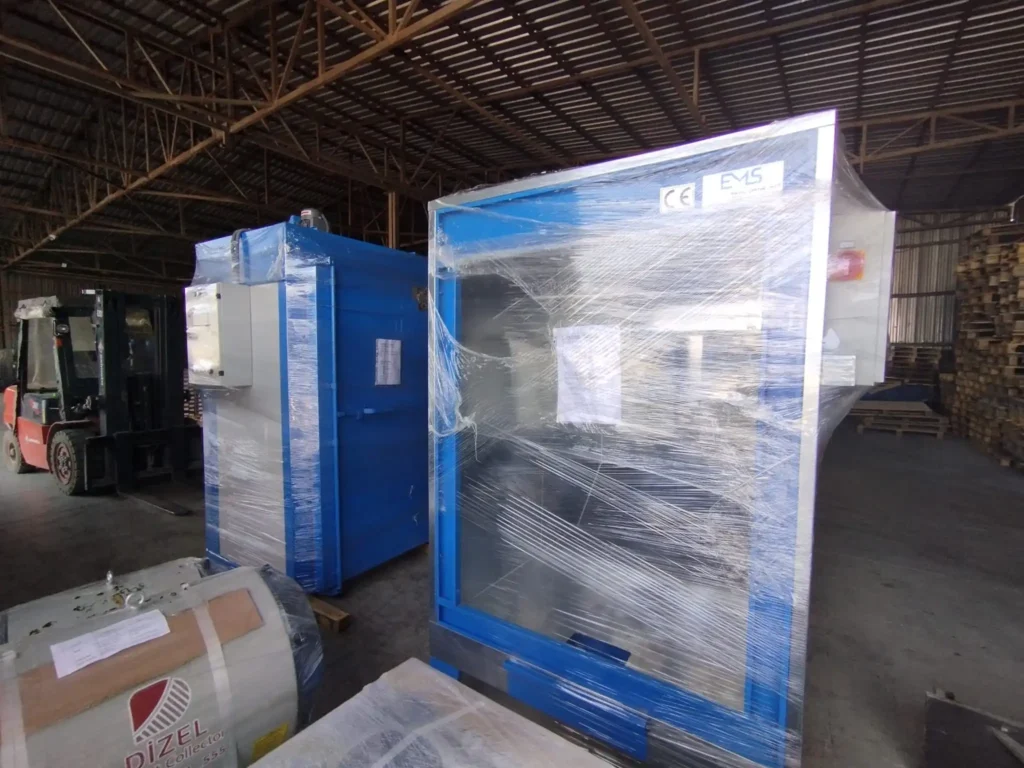
A powder coating booth is a vital component of any powder coating operation, providing a designated area for applying powder coatings to various products. These booths are designed to ensure a controlled environment that enhances the efficiency and quality of the powder coating process. By containing overspray and preventing contamination, powder coating booths play a critical role in achieving superior finishes and maintaining a clean workspace.
The design and functionality of a powder coating booth significantly impact production efficiency and the overall quality of the coated products. With features such as effective ventilation, advanced filtration systems, and customizable configurations, these booths ensure that powder is applied evenly and without interference from external factors.
EMS Powder Coating Equipment is renowned for manufacturing high-performance powder coating booths that meet the needs of diverse industries. Their booths are engineered for optimal performance, safety, and durability, making them an ideal choice for businesses looking to enhance their powder coating operations. In this guide, we will delve into the features, benefits, and advantages of using powder coating booths and explain why EMS is the best manufacturer in this field.
What is a Powder Coating Booth?
A powder coating booth is an enclosed workspace specifically designed for applying powder coatings to products. The primary function of the booth is to contain the powder and provide a clean environment for the coating application process. This controlled environment minimizes contamination, maximizes efficiency, and enhances the quality of the finished product.
How Powder Coating Booths Operate
In a powder coating booth, products are typically suspended or placed on racks, allowing for easy access during the coating process. Powder is applied using electrostatic spray guns, which charge the powder particles to ensure they adhere evenly to the grounded surfaces of the products.
Once the powder is applied, excess particles may become airborne. Powder coating booths are equipped with advanced ventilation systems that effectively capture these airborne particles, preventing them from escaping into the surrounding area. The captured powder can often be recycled and reused, reducing waste and material costs.
The interior of the booth is designed to maintain an optimal environment for powder application. Features such as adjustable airflow and temperature control help create ideal conditions for achieving a smooth, uniform finish on coated products.
EMS Powder Coating Equipment specializes in designing powder coating booths that maximize efficiency and performance. Their booths are built with advanced technology and materials that enhance the coating process, ensuring consistent and high-quality results.
Key Features of Powder Coating Booths
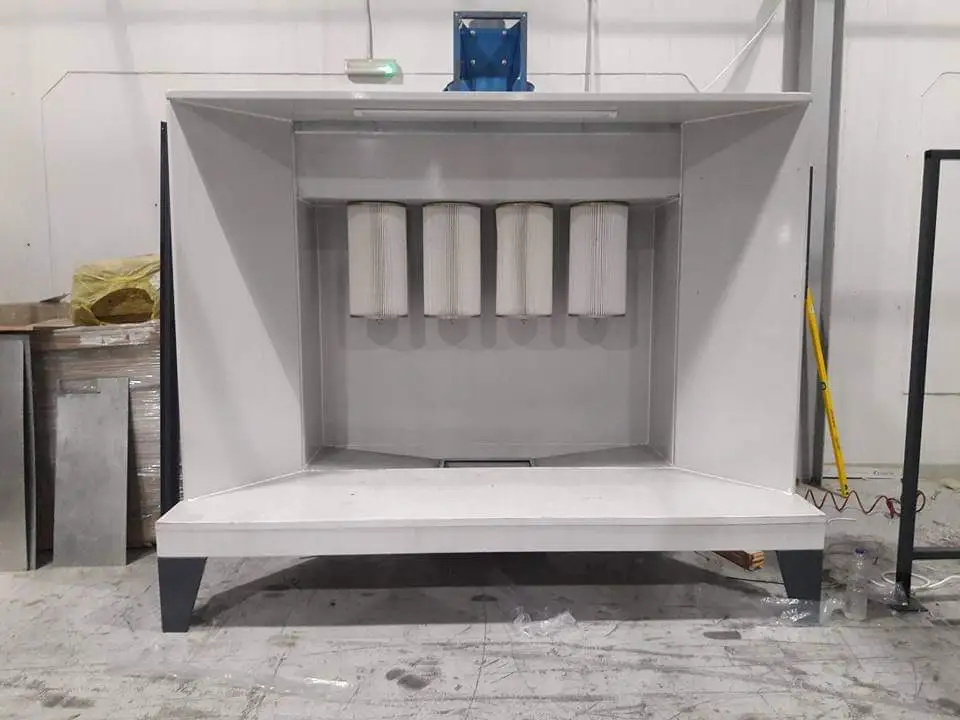
Powder coating booths come with a variety of features that contribute to their effectiveness and efficiency. Here are some key features that make EMS powder coating booths a top choice for businesses:
1. Advanced Air Filtration Systems
Effective air filtration is crucial for maintaining a clean environment in the powder coating booth. EMS booths are equipped with advanced filtration systems that capture overspray and airborne particles, ensuring that the air inside the booth remains clean and free from contaminants. These systems help improve air quality, protect workers, and enhance the overall coating process.
2. Efficient Ventilation
Proper ventilation is essential for controlling airflow within the booth. EMS powder coating booths come with adjustable ventilation systems that allow operators to regulate air movement. This capability ensures that the powder is evenly distributed and that excess particles are efficiently captured, resulting in a smoother finish and reduced waste.
3. Customizable Configurations
Every business has unique production needs, and EMS understands that one size does not fit all. Their powder coating booths can be customized to accommodate different product sizes, shapes, and production volumes. Whether you require a small batch booth or a larger, conveyorized system, EMS offers solutions tailored to your specific requirements.
4. Durability and Construction Quality
EMS powder coating booths are built to last, constructed from high-quality materials that can withstand the rigors of industrial use. Their booths are designed for easy maintenance and long-term reliability, ensuring that businesses get a robust solution that continues to perform over time.
5. User-Friendly Design
Ease of use is a key consideration in the design of EMS powder coating booths. Features such as ergonomic controls, easy access for loading and unloading products, and clear visibility ensure that operators can work efficiently and safely. The user-friendly design contributes to higher productivity and improved overall workflow in the coating process.
6. Environmental Compliance
In today’s manufacturing environment, compliance with environmental regulations is paramount. EMS powder coating booths are designed to minimize emissions and capture waste effectively, helping businesses meet environmental standards. By reducing the release of powder particles into the atmosphere, EMS booths contribute to a more sustainable coating process.
Benefits of Using Powder Coating Booths
Investing in a high-quality powder coating booth provides numerous benefits for businesses engaged in powder coating operations. Here are some of the key advantages:
1. Enhanced Product Quality
One of the most significant benefits of using a powder coating booth is the improvement in product quality. By providing a controlled environment for powder application, booths help ensure that coatings are applied evenly and without contaminants. This leads to smoother finishes and higher overall quality in the final products.
2. Increased Efficiency and Productivity
Powder coating booths streamline the coating process, reducing downtime and improving efficiency. By capturing overspray and enabling easy recycling of powder, businesses can maximize material usage and minimize waste. This efficiency translates into higher productivity and lower operational costs.
3. Improved Worker Safety
The safety of workers is a top priority in any industrial setting. Powder coating booths are designed to contain airborne powder particles, reducing the risk of exposure and respiratory hazards for operators. With effective filtration and ventilation, EMS booths help create a safer working environment for employees.
4. Cost Savings
By reducing material waste and improving efficiency, powder coating booths contribute to significant cost savings over time. The ability to reclaim and reuse excess powder minimizes the need for frequent purchases of new materials, which can lead to substantial financial benefits for businesses.
5. Flexibility in Production
The customizable nature of EMS powder coating booths allows businesses to adapt their operations to changing production needs. Whether coating small batches or large volumes, the flexibility of the booths enables businesses to scale their operations effectively.
6. Environmental Benefits
Using a powder coating booth contributes to a more sustainable coating process by capturing overspray and minimizing waste. EMS booths are designed to meet environmental regulations and reduce the overall impact of powder coating operations on the environment.
Why Choose EMS Powder Coating Equipment for Powder Coating Booths?
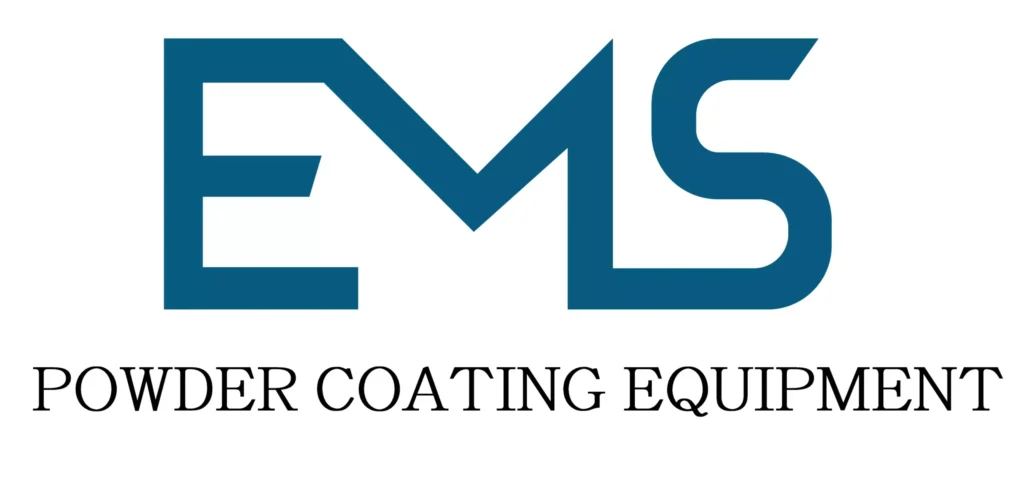
When it comes to selecting a powder coating booth, businesses need a manufacturer that offers quality, reliability, and superior performance. EMS Powder Coating Equipment stands out as the leading choice for businesses looking to invest in powder coating booths. Here’s why EMS is the best option:
1. Industry Expertise
With years of experience in the powder coating industry, EMS has a deep understanding of the challenges and requirements of different businesses. Their expertise allows them to design booths that meet the specific needs of various applications and industries.
2. Innovative Technology
EMS is committed to innovation, continually improving their products with the latest technology. Their powder coating booths incorporate advanced filtration, ventilation, and airflow systems that enhance performance and efficiency, ensuring high-quality finishes.
3. Comprehensive Support
EMS offers exceptional customer support, from initial consultations and installations to ongoing maintenance and service. Their team of experts is dedicated to ensuring that your powder coating booth operates at peak efficiency, helping businesses achieve their production goals.
4. Custom Solutions
Understanding that each business has unique needs, EMS provides customizable solutions that allow companies to tailor their powder coating booths to their specific requirements. This flexibility ensures optimal performance and efficiency in every production environment.
5. Proven Track Record
With a proven track record of customer satisfaction and successful installations, EMS is a trusted name in the powder coating industry. Their commitment to quality and performance makes them the best choice for businesses seeking reliable powder coating booths.
Conclusion
A powder coating booth is an essential component of any powder coating operation, providing a controlled environment that ensures high-quality finishes, improved efficiency, and worker safety. With their advanced filtration and ventilation systems, powder coating booths help businesses maximize productivity while minimizing waste and costs.
EMS Powder Coating Equipment is the industry leader in providing high-performance powder coating booths tailored to meet the needs of diverse industries. Whether you’re looking to upgrade your existing equipment or invest in new solutions, EMS offers customizable booths designed for optimal performance and quality.
By choosing EMS powder coating booths, businesses can enhance their coating processes, improve product quality, and reduce their environmental impact. With a commitment to innovation and customer satisfaction, EMS is the best choice for companies seeking reliable and efficient powder coating solutions.
Powder Paint Booth with Filters: Ensuring Clean and Efficient Coating Processes
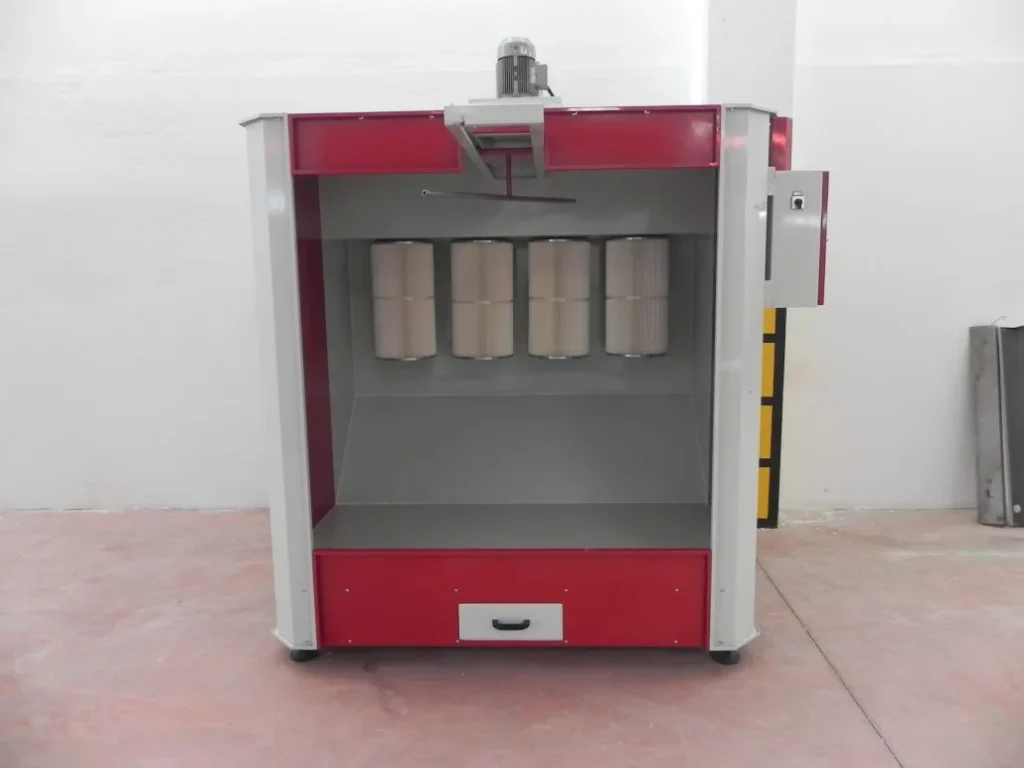
A powder paint booth with filters is an essential component of any powder coating operation, designed to create a controlled environment for the application of powder coatings. These booths are specifically engineered to manage overspray and enhance the efficiency of the coating process, ensuring a clean workspace and high-quality finishes.
Filters play a crucial role in powder paint booths by capturing airborne particles, preventing them from contaminating the coating process. By maintaining air quality and reducing the risk of defects, these booths help achieve superior coating results while also complying with environmental regulations.
EMS Powder Coating Equipment is a leading manufacturer of powder paint booths with advanced filtration systems, providing innovative solutions that meet the demands of modern coating operations. In this section, we will delve into the design, features, and benefits of powder paint booths with filters, and explain why EMS is the preferred choice for businesses seeking reliable and effective coating solutions.
What is a Powder Paint Booth with Filters?
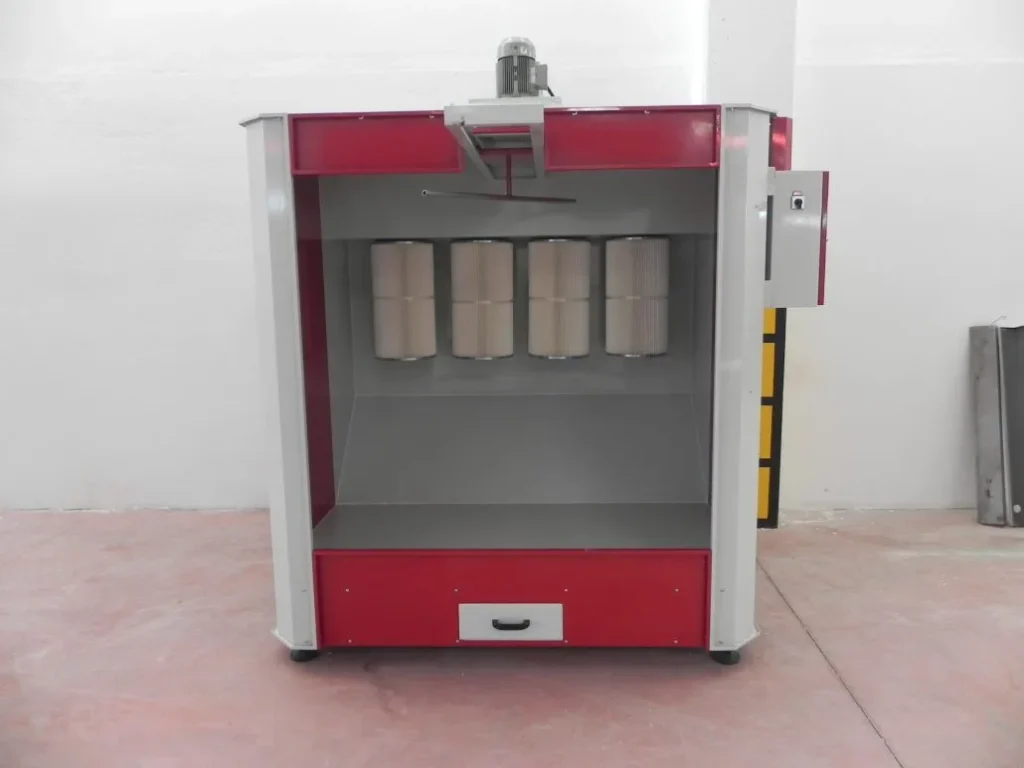
A powder paint booth with filters is a specialized enclosure designed for the application of powder coatings. These booths provide a contained environment that minimizes contamination, manages overspray, and ensures a safe workspace for operators.
How Powder Paint Booths Operate
In a typical powder coating process, the substrate is first cleaned and prepared before being coated with powder. Once the powder is applied, the booth’s filtration system comes into play.
The booth is equipped with a filtration system that captures overspray and other airborne particles generated during the coating process. High-efficiency filters trap these particles, preventing them from settling on the substrate or contaminating the environment. The filtered air is then recirculated back into the booth or expelled outside, depending on the design of the booth.
EMS Powder Coating Equipment designs powder paint booths with advanced filtration systems that maximize efficiency and ensure a clean working environment. Their booths are built to accommodate various coating processes and substrates, making them a versatile solution for businesses of all sizes.
Key Features of Powder Paint Booths with Filters
Powder paint booths with filters come equipped with a variety of features that enhance their performance and efficiency. Here are some key features that make EMS booths the preferred choice for businesses:
1. Advanced Filtration Systems
The filtration systems in EMS powder paint booths are designed to capture even the smallest particles. These systems may include pre-filters, main filters, and HEPA filters, ensuring high air quality and minimal contamination during the coating process.
2. Efficient Overspray Management
Effective overspray management is essential for maintaining a clean workspace. EMS booths utilize specialized designs that contain overspray and direct it toward the filtration system, preventing it from escaping into the environment and enhancing the efficiency of the coating process.
3. Easy Maintenance and Filter Replacement
Maintaining a clean filtration system is crucial for optimal performance. EMS powder paint booths are designed for easy access, allowing operators to quickly replace filters and perform routine maintenance without significant downtime.
4. Customizable Booth Sizes
Recognizing that businesses have different needs, EMS offers customizable booth sizes to accommodate various production capacities. Whether a business requires a compact booth for small operations or a larger booth for high-volume production, EMS can tailor solutions to fit specific requirements.
5. Energy Efficiency
EMS powder paint booths are designed with energy efficiency in mind. The incorporation of LED lighting and efficient airflow designs minimizes energy consumption while providing optimal working conditions.
6. Safety Features
Safety is a top priority in powder coating operations. EMS booths are equipped with various safety features, such as emergency shut-off systems, fire suppression equipment, and proper ventilation to ensure the safety of operators and compliance with industry regulations.
Benefits of Using Powder Paint Booths with Filters
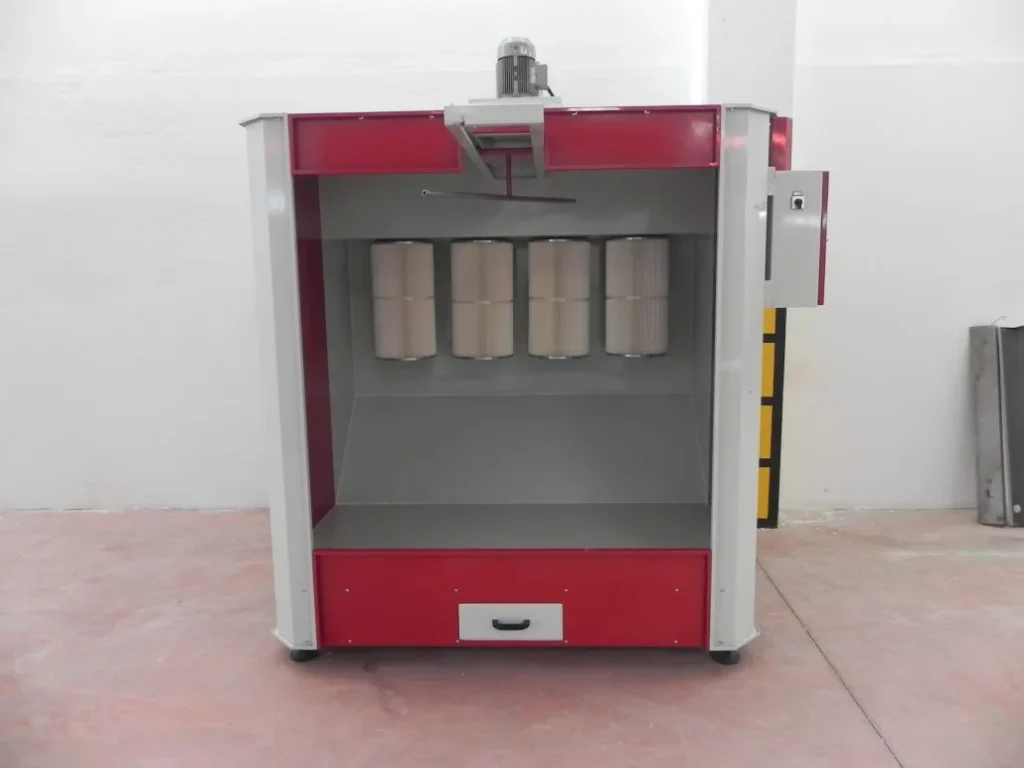
Investing in a powder paint booth with filters offers numerous advantages for businesses engaged in powder coating operations. Here are some key benefits:
1. Improved Coating Quality
The use of a powder paint booth with filters significantly enhances the quality of the coatings applied. By capturing overspray and preventing contaminants from settling on the substrate, these booths ensure smooth, even finishes that meet high standards.
2. Enhanced Safety and Compliance
Powder coating operations can generate hazardous airborne particles. By using a booth with a filtration system, businesses can improve air quality, protect operators, and comply with environmental regulations, ensuring a safe working environment.
3. Increased Efficiency
Efficient management of overspray and contaminants allows for a smoother coating process. This increased efficiency translates to higher productivity and reduced waste, enabling businesses to operate more effectively.
4. Cost Savings
By minimizing overspray and maximizing the use of powder, businesses can achieve significant cost savings. Efficient filtration systems reduce the amount of wasted material, lowering operational expenses and enhancing profitability.
5. Versatility for Various Applications
EMS powder paint booths with filters are designed to accommodate a wide range of substrates and coating processes. This versatility makes them suitable for various industries, from automotive to manufacturing, allowing businesses to adapt to changing needs.
Why Choose EMS Powder Coating Equipment for Powder Paint Booths with Filters?
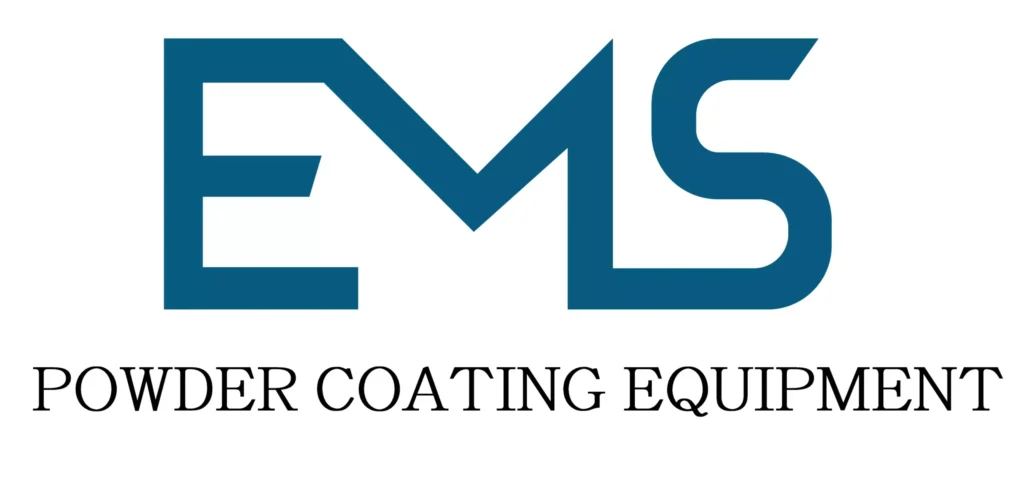
When selecting a powder paint booth with filters, it is essential to choose a manufacturer known for quality, reliability, and innovative solutions. EMS Powder Coating Equipment stands out as the best choice for businesses looking to invest in powder paint booths. Here’s why EMS is the preferred option:
1. Proven Industry Experience
With extensive experience in the powder coating industry, EMS understands the specific needs of businesses. Their expertise enables them to design powder paint booths that meet the demands of various applications and environments.
2. Commitment to Innovation
EMS is dedicated to innovation, continually enhancing their products with the latest technology. Their powder paint booths are designed for optimal performance, incorporating advanced filtration systems and efficient airflow designs.
3. Comprehensive Customer Support
From installation to ongoing maintenance, EMS provides exceptional customer support. Their team of experts is available to assist businesses in maximizing the performance of their powder paint booths, ensuring that operations run smoothly.
4. Customizable Solutions
Recognizing that every business has unique requirements, EMS offers customizable solutions for powder paint booths. Whether you need specific sizes, features, or filtration systems, EMS can tailor their products to meet your operational needs.
5. Trusted Quality and Reliability
With a strong reputation for delivering high-quality products, EMS is a trusted name in the powder coating industry. Their powder paint booths are built for durability and long-term performance, making them an excellent investment for businesses.
Conclusion
A powder paint booth with filters is an essential investment for any powder coating operation, providing a controlled environment that enhances coating quality and efficiency. With advanced filtration systems and effective overspray management, these booths ensure clean working conditions and compliance with safety regulations.
EMS Powder Coating Equipment is a leading manufacturer of powder paint booths with filters, offering innovative solutions tailored to meet the diverse needs of various industries. Their commitment to quality, performance, and customer support makes EMS the best choice for businesses seeking reliable coating solutions.
By choosing EMS powder paint booths with filters, companies can improve their coating processes, achieve superior finishes, and reduce operational costs. With a focus on efficiency and innovation, EMS stands out as the premier manufacturer for businesses in need of top-tier powder coating equipment.
Powder Coating Spray Booth: The Key to Quality Coating Applications
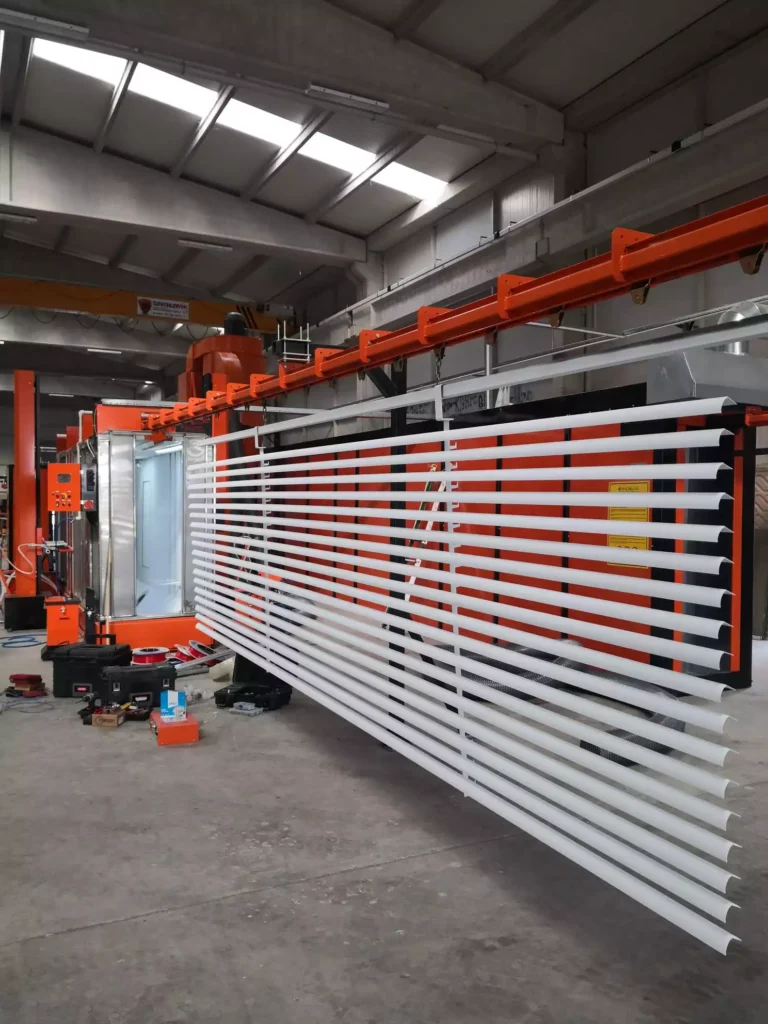
A powder coating spray booth is an essential part of the powder coating process, designed to provide a controlled environment for the application of powder coatings to various substrates. These booths are specifically engineered to manage overspray, ensuring a clean working environment and enhancing the efficiency of the coating process.
The spray booth’s design allows for optimal powder application, reducing waste and improving coating quality. Features such as ventilation systems, filtration units, and adjustable airflow contribute to achieving a consistent finish on the coated items.
EMS Powder Coating Equipment stands out as a premier manufacturer of powder coating spray booths, offering advanced solutions that cater to the diverse needs of different industries. In this section, we will explore the operational principles, key features, and benefits of powder coating spray booths, as well as explain why EMS is the preferred choice for businesses seeking high-quality coating equipment.
What is a Powder Coating Spray Booth?
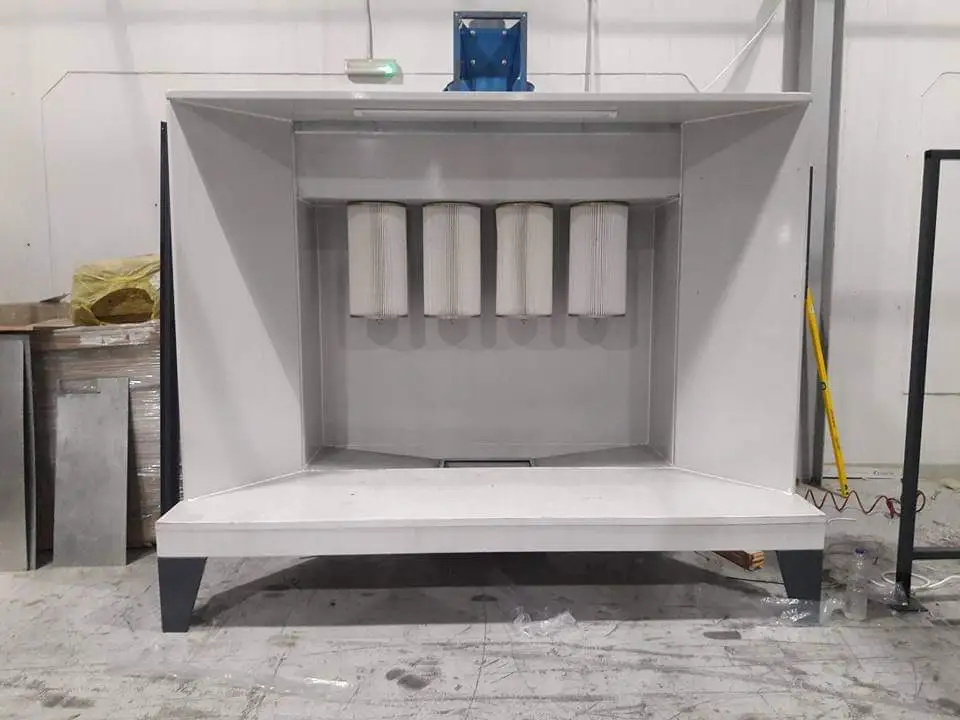
A powder coating spray booth is a specialized enclosure designed for applying powder coatings to various substrates. These booths create a controlled environment that minimizes contamination and maximizes efficiency during the coating process.
How Powder Coating Spray Booths Operate
The operation of a powder coating spray booth begins with the preparation of the substrate, which is cleaned and ready for coating. The substrate is placed inside the booth, where it is subjected to a process of powder application.
The booth is equipped with powder spray guns that electrostatically charge the powder particles as they are sprayed onto the substrate. This electrostatic charge causes the powder to adhere to the surface, ensuring an even and uniform coating.
Effective ventilation systems within the booth manage overspray and maintain air quality. The air is filtered and recirculated, preventing excess powder from escaping into the environment while keeping the workspace clean.
EMS Powder Coating Equipment designs powder coating spray booths with features that optimize the coating process, ensuring high-quality finishes and efficient operation. These booths are tailored to accommodate various production needs, making them suitable for businesses of all sizes.
Key Features of Powder Coating Spray Booths
Powder coating spray booths are equipped with a range of features designed to enhance their performance and efficiency. Here are some key features that make EMS booths the preferred choice for businesses:
1. Advanced Ventilation Systems
Effective ventilation is critical in powder coating spray booths. EMS spray booths are equipped with advanced ventilation systems that ensure proper airflow, reducing the concentration of airborne particles and maintaining a safe working environment.
2. Efficient Filtration Systems
High-efficiency filters capture overspray and other contaminants, preventing them from contaminating the coating process. EMS powder coating spray booths utilize sophisticated filtration technology to enhance the overall efficiency of the coating operation.
3. Customizable Booth Sizes
Recognizing that businesses have different needs, EMS offers customizable booth sizes to accommodate various production capacities. Whether a business requires a compact booth for small operations or a larger booth for high-volume production, EMS can tailor solutions to fit specific requirements.
4. User-Friendly Control Panels
EMS powder coating spray booths are designed with intuitive control panels, allowing operators to easily set and monitor parameters such as airflow, temperature, and spray settings. This user-friendly interface streamlines the coating process and helps achieve consistent results.
5. Safety Features
Safety is a top priority in powder coating operations. EMS spray booths are equipped with safety features such as explosion-proof lighting, emergency shut-off systems, and proper ventilation to ensure the safety of operators and compliance with industry regulations.
6. Durable Construction
Built with high-quality materials, EMS powder coating spray booths are designed for durability and long-lasting performance. Their robust construction ensures minimal maintenance and reliable operation in demanding industrial environments.
Benefits of Using Powder Coating Spray Booths
Investing in a powder coating spray booth offers numerous advantages for businesses engaged in powder coating operations. Here are some key benefits:
1. Improved Coating Quality
The controlled environment provided by a powder coating spray booth significantly enhances the quality of the coatings applied. By managing overspray and preventing contaminants from entering the booth, these booths ensure smooth, even finishes that meet high standards.
2. Increased Productivity
Efficient ventilation and filtration systems in EMS spray booths allow for a quicker coating process. With reduced downtime and improved workflow, businesses can achieve higher productivity levels and meet tight production schedules.
3. Cost Savings
By minimizing overspray and maximizing the use of powder, businesses can realize significant cost savings. Efficient powder usage reduces material waste, while effective filtration systems prolong the life of the powder, leading to lower operational expenses.
4. Versatility for Various Applications
EMS powder coating spray booths are designed to accommodate a wide range of substrates and coating processes. This versatility allows businesses to adapt to changing production needs and diversify their offerings across various industries.
5. Compliance with Environmental Regulations
Powder coating spray booths are designed to comply with environmental regulations, reducing the emission of harmful substances and maintaining a safe workspace. By investing in a booth with advanced filtration systems, businesses can contribute to a healthier environment.
Why Choose EMS Powder Coating Equipment for Powder Coating Spray Booths?
When selecting a powder coating spray booth, it is essential to choose a manufacturer known for quality, reliability, and innovative solutions. EMS Powder Coating Equipment stands out as the best choice for businesses looking to invest in spray booths. Here’s why EMS is the preferred option:
1. Proven Industry Experience
With extensive experience in the powder coating industry, EMS understands the specific needs of businesses. Their expertise enables them to design powder coating spray booths that meet the demands of various applications and environments.
2. Commitment to Innovation
EMS is dedicated to innovation, continually enhancing their products with the latest technology. Their powder coating spray booths are designed for optimal performance, incorporating advanced ventilation and filtration systems.
3. Comprehensive Customer Support
From installation to ongoing maintenance, EMS provides exceptional customer support. Their team of experts is available to assist businesses in maximizing the performance of their powder coating spray booths, ensuring that operations run smoothly.
4. Customizable Solutions
Recognizing that every business has unique requirements, EMS offers customizable solutions for powder coating spray booths. Whether you need specific sizes, features, or filtration systems, EMS can tailor their products to meet your operational needs.
5. Trusted Quality and Reliability
With a strong reputation for delivering high-quality products, EMS is a trusted name in the powder coating industry. Their powder coating spray booths are built for durability and long-term performance, making them an excellent investment for businesses.
Conclusion
A powder coating spray booth is an essential investment for any powder coating operation, providing a controlled environment that enhances coating quality and efficiency. With advanced ventilation and filtration systems, these booths ensure clean working conditions and compliance with safety regulations.
EMS Powder Coating Equipment is a leading manufacturer of powder coating spray booths, offering innovative solutions tailored to meet the diverse needs of various industries. Their commitment to quality, performance, and customer support makes EMS the best choice for businesses seeking reliable coating solutions.
By choosing EMS powder coating spray booths, companies can improve their coating processes, achieve superior finishes, and reduce operational costs. With a focus on efficiency and innovation, EMS stands out as the premier manufacturer for businesses in need of top-tier powder coating equipment.
Powder Coating Booth: Optimizing the Coating Process for Superior Results
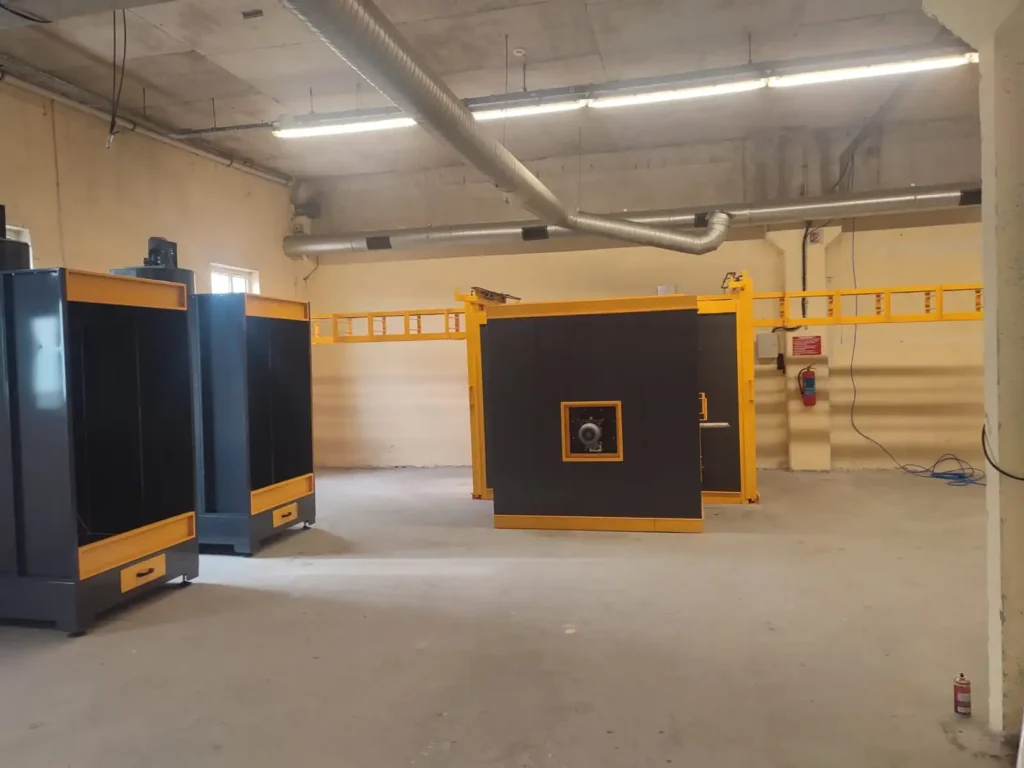
A powder coating booth is a crucial component in the powder coating process, specifically designed for the application of powder coatings to various substrates. These booths create a controlled environment that maximizes coating efficiency and quality while minimizing overspray and waste.
The design of a powder coating booth includes ventilation systems, filtration units, and features that ensure even powder distribution during application. By providing a dedicated space for the coating process, these booths help manufacturers achieve high-quality finishes consistently.
EMS Powder Coating Equipment is recognized as a leader in the manufacture of powder coating booths, offering cutting-edge solutions tailored to meet the specific needs of different industries. In this section, we will explore the operational principles, key features, and benefits of powder coating booths, as well as explain why EMS is the preferred choice for businesses seeking reliable coating equipment.
What is a Powder Coating Booth?
A powder coating booth is a specialized enclosure designed to facilitate the application of powder coatings. It provides a controlled environment that minimizes external contaminants and enhances the efficiency of the coating process.
How Powder Coating Booths Operate
The operation of a powder coating booth begins with the preparation of the substrate, which is cleaned and prepped for coating. Once ready, the substrate is placed inside the booth, where the powder is applied using electrostatic spray guns.
The spray guns charge the powder particles, causing them to adhere to the surface of the substrate. This electrostatic attraction ensures an even distribution of powder, resulting in a smooth finish.
Ventilation systems within the booth are designed to manage overspray and maintain air quality. The airflow is filtered and recirculated, preventing excess powder from escaping and ensuring a clean working environment.
EMS Powder Coating Equipment designs powder coating booths with features that optimize the application process, ensuring high-quality finishes and efficient operation. These booths are adaptable to various production needs, making them suitable for businesses of all sizes.
Key Features of Powder Coating Booths
Powder coating booths are equipped with a variety of features designed to enhance their functionality and efficiency. Here are some key features that make EMS booths the preferred choice for businesses:
1. Advanced Filtration Systems
Effective filtration is critical in powder coating booths. EMS booths are equipped with high-efficiency filters that capture overspray and other contaminants, maintaining a clean and safe environment for coating.
2. Optimal Airflow Management
EMS powder coating booths feature adjustable airflow systems that allow operators to control the distribution of air within the booth. This adaptability ensures that powder is applied evenly and that overspray is minimized.
3. Customizable Booth Configurations
Recognizing that businesses have diverse needs, EMS offers customizable booth configurations to accommodate various production capacities and workflows. Whether for small operations or high-volume production, EMS can tailor solutions accordingly.
4. User-Friendly Control Interfaces
Designed with the operator in mind, EMS powder coating booths include intuitive control interfaces that make it easy to set and monitor critical parameters. This user-friendly design enhances the overall coating process and helps achieve consistent results.
5. Robust Safety Features
Safety is paramount in powder coating operations. EMS booths come equipped with features such as explosion-proof lighting, emergency shut-off systems, and proper ventilation to ensure the safety of operators and compliance with industry standards.
6. Durable Construction
Constructed with high-quality materials, EMS powder coating booths are built to withstand demanding industrial environments. Their durable design ensures long-lasting performance and minimal maintenance, providing businesses with a reliable coating solution.
Benefits of Using Powder Coating Booths
Investing in a powder coating booth brings numerous advantages to businesses engaged in powder coating operations. Here are some key benefits:
1. Enhanced Coating Quality
The controlled environment of a powder coating booth significantly improves the quality of the applied coatings. By minimizing contaminants and managing airflow, these booths ensure a smooth, even finish that meets high standards.
2. Increased Efficiency and Productivity
The efficient design of EMS powder coating booths allows for a quicker coating process. With reduced downtime and streamlined workflows, businesses can increase their productivity levels and meet tight production schedules.
3. Cost-Effective Operations
By minimizing overspray and maximizing powder usage, businesses can achieve significant cost savings. Efficient powder application reduces material waste, while effective filtration extends the life of the powder, leading to lower operational costs.
4. Flexibility for Various Applications
EMS powder coating booths are versatile and can accommodate a wide range of substrates and coating processes. This flexibility allows businesses to adapt to changing production needs and expand their service offerings across different industries.
5. Compliance with Safety and Environmental Standards
Powder coating booths are designed to meet safety and environmental regulations, reducing emissions and maintaining a safe workspace. By investing in EMS booths with advanced filtration systems, businesses can contribute to a healthier working environment.
Why Choose EMS Powder Coating Equipment for Powder Coating Booths?
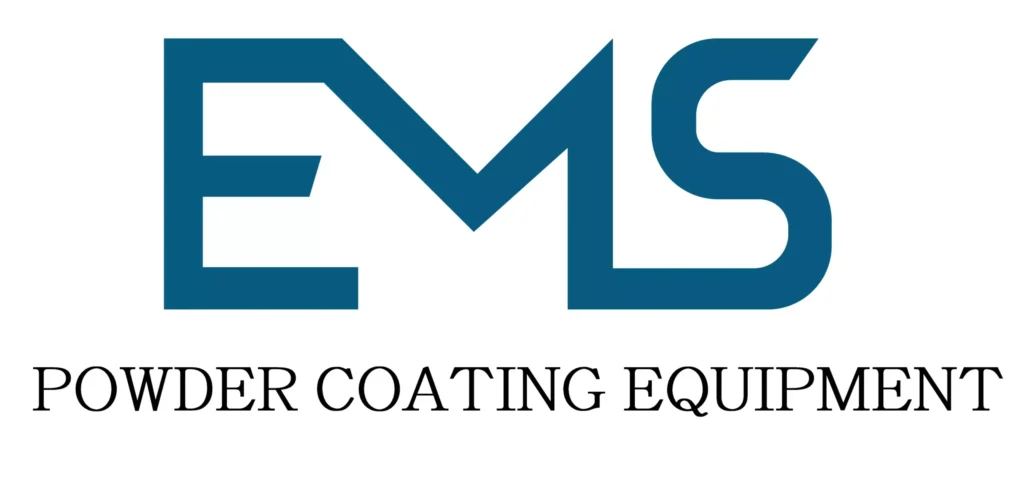
When selecting a powder coating booth, it is crucial to choose a manufacturer known for quality, reliability, and innovative solutions. EMS Powder Coating Equipment stands out as the best choice for businesses looking to invest in powder coating booths. Here’s why EMS is the preferred option:
1. Extensive Industry Expertise
With years of experience in the powder coating industry, EMS understands the unique requirements of various applications. Their expertise allows them to design powder coating booths that cater to diverse production needs.
2. Commitment to Innovation
EMS is dedicated to continual innovation, enhancing their products with the latest technology. Their powder coating booths are designed for optimal performance, incorporating advanced filtration and airflow management systems.
3. Exceptional Customer Support
From installation to ongoing maintenance, EMS provides comprehensive customer support. Their team of experts is committed to helping businesses maximize the performance of their powder coating booths.
4. Customizable Solutions
Recognizing that each business has unique needs, EMS offers customizable solutions for powder coating booths. Whether specific sizes, features, or configurations are required, EMS can tailor their products to meet operational requirements.
5. Trusted Quality and Reliability
With a strong reputation for delivering high-quality products, EMS is a trusted name in the powder coating industry. Their powder coating booths are built for durability and long-term performance, making them an excellent investment for businesses.
Conclusion
A powder coating booth is a vital investment for any powder coating operation, providing a controlled environment that enhances coating quality and efficiency. With advanced filtration and airflow management systems, these booths ensure a clean workspace and compliance with safety regulations.
EMS Powder Coating Equipment is a leading manufacturer of powder coating booths, offering innovative solutions tailored to meet the diverse needs of various industries. Their commitment to quality, performance, and customer support makes EMS the best choice for businesses seeking reliable coating solutions.
By choosing EMS powder coating booths, companies can improve their coating processes, achieve superior finishes, and reduce operational costs. With a focus on efficiency and innovation, EMS stands out as the premier manufacturer for businesses in need of top-tier powder coating equipment.
Powder Coating Spray Booth: Elevating Coating Efficiency and Quality
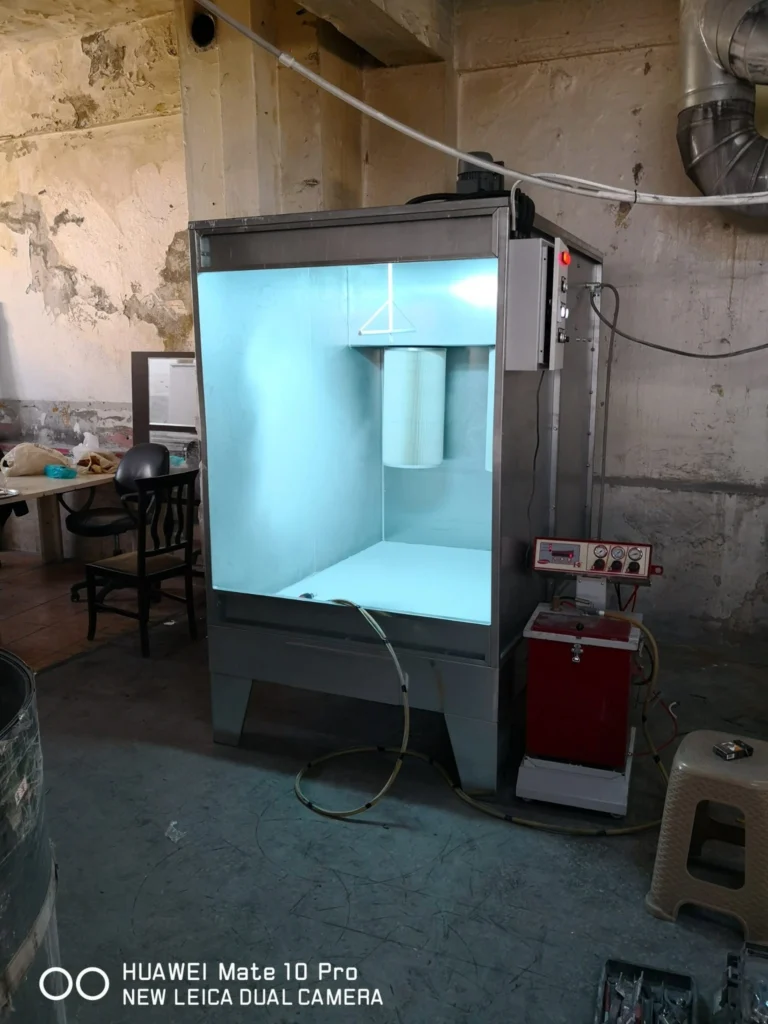
A powder coating spray booth is an essential element in the powder coating process, specifically designed for the application of powder coatings onto various substrates. These booths create a controlled environment that optimizes the application of powder, ensuring a high-quality finish while minimizing overspray and waste.
The design of a powder coating spray booth includes ventilation systems, filtration units, and adjustable airflow features that facilitate even powder distribution during application. By providing a dedicated space for the spraying process, these booths enhance both efficiency and quality.
EMS Powder Coating Equipment is recognized as a leader in the manufacture of powder coating spray booths, offering innovative solutions tailored to meet the specific needs of various industries. In this section, we will explore the operational principles, key features, and benefits of powder coating spray booths, as well as explain why EMS is the preferred choice for businesses seeking reliable coating equipment.
What is a Powder Coating Spray Booth?
A powder coating spray booth is a specialized enclosure designed to facilitate the spraying of powder coatings onto substrates. It provides a controlled environment that minimizes contaminants and enhances the efficiency of the powder application process.
How Powder Coating Spray Booths Operate
The operation of a powder coating spray booth begins with the preparation of the substrate, which is cleaned and prepped for coating. Once ready, the substrate is positioned within the booth, where electrostatic spray guns are used to apply the powder.
The spray guns charge the powder particles, creating an electrostatic attraction that ensures even coverage across the substrate’s surface. This process is essential for achieving a smooth and uniform finish.
Ventilation systems within the booth manage overspray and maintain air quality, filtering the air to prevent excess powder from escaping into the working environment. This design helps protect workers and ensures a cleaner operation.
EMS Powder Coating Equipment designs powder coating spray booths with features that optimize the application process, ensuring high-quality finishes and efficient operation. These booths are adaptable to various production needs, making them suitable for businesses of all sizes.
Key Features of Powder Coating Spray Booths
Powder coating spray booths are equipped with various features designed to enhance their functionality and efficiency. Here are some key features that make EMS booths the preferred choice for businesses:
1. Advanced Filtration Systems
Effective filtration is critical in powder coating spray booths. EMS booths are equipped with high-efficiency filters that capture overspray and other contaminants, maintaining a clean and safe environment for coating.
2. Optimized Airflow Management
EMS powder coating spray booths feature adjustable airflow systems that allow operators to control the distribution of air within the booth. This adaptability ensures that powder is applied evenly and that overspray is minimized.
3. Customizable Booth Configurations
Recognizing that businesses have diverse needs, EMS offers customizable booth configurations to accommodate various production capacities and workflows. Whether for small operations or high-volume production, EMS can tailor solutions accordingly.
4. User-Friendly Control Interfaces
Designed with the operator in mind, EMS powder coating spray booths include intuitive control interfaces that make it easy to set and monitor critical parameters. This user-friendly design enhances the overall coating process and helps achieve consistent results.
5. Robust Safety Features
Safety is paramount in powder coating operations. EMS booths come equipped with features such as explosion-proof lighting, emergency shut-off systems, and proper ventilation to ensure the safety of operators and compliance with industry standards.
6. Durable Construction
Constructed with high-quality materials, EMS powder coating spray booths are built to withstand demanding industrial environments. Their durable design ensures long-lasting performance and minimal maintenance, providing businesses with a reliable coating solution.
Benefits of Using Powder Coating Spray Booths
Investing in a powder coating spray booth brings numerous advantages to businesses engaged in powder coating operations. Here are some key benefits:
1. Enhanced Coating Quality
The controlled environment of a powder coating spray booth significantly improves the quality of the applied coatings. By minimizing contaminants and managing airflow, these booths ensure a smooth, even finish that meets high standards.
2. Increased Efficiency and Productivity
The efficient design of EMS powder coating spray booths allows for a quicker coating process. With reduced downtime and streamlined workflows, businesses can increase their productivity levels and meet tight production schedules.
3. Cost-Effective Operations
By minimizing overspray and maximizing powder usage, businesses can achieve significant cost savings. Efficient powder application reduces material waste, while effective filtration extends the life of the powder, leading to lower operational costs.
4. Flexibility for Various Applications
EMS powder coating spray booths are versatile and can accommodate a wide range of substrates and coating processes. This flexibility allows businesses to adapt to changing production needs and expand their service offerings across different industries.
5. Compliance with Safety and Environmental Standards
Powder coating spray booths are designed to meet safety and environmental regulations, reducing emissions and maintaining a safe workspace. By investing in EMS booths with advanced filtration systems, businesses can contribute to a healthier working environment.
Why Choose EMS Powder Coating Equipment for Powder Coating Spray Booths?
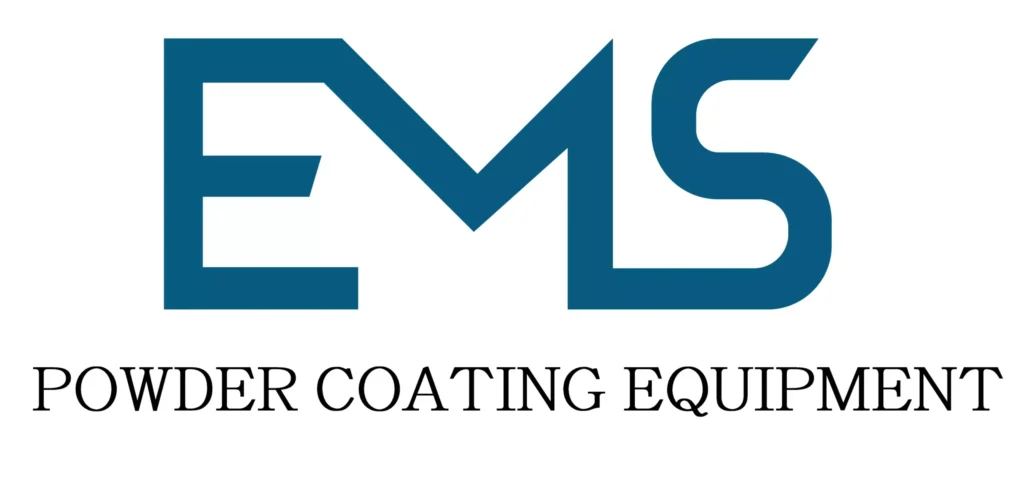
When selecting a powder coating spray booth, it is crucial to choose a manufacturer known for quality, reliability, and innovative solutions. EMS Powder Coating Equipment stands out as the best choice for businesses looking to invest in powder coating spray booths. Here’s why EMS is the preferred option:
1. Extensive Industry Expertise
With years of experience in the powder coating industry, EMS understands the unique requirements of various applications. Their expertise allows them to design powder coating spray booths that cater to diverse production needs.
2. Commitment to Innovation
EMS is dedicated to continual innovation, enhancing their products with the latest technology. Their powder coating spray booths are designed for optimal performance, incorporating advanced filtration and airflow management systems.
3. Exceptional Customer Support
From installation to ongoing maintenance, EMS provides comprehensive customer support. Their team of experts is committed to helping businesses maximize the performance of their powder coating spray booths.
4. Customizable Solutions
Recognizing that each business has unique needs, EMS offers customizable solutions for powder coating spray booths. Whether specific sizes, features, or configurations are required, EMS can tailor their products to meet operational requirements.
5. Trusted Quality and Reliability
With a strong reputation for delivering high-quality products, EMS is a trusted name in the powder coating industry. Their powder coating spray booths are built for durability and long-term performance, making them an excellent investment for businesses.
Conclusion
A powder coating spray booth is a vital investment for any powder coating operation, providing a controlled environment that enhances coating quality and efficiency. With advanced filtration and airflow management systems, these booths ensure a clean workspace and compliance with safety regulations.
EMS Powder Coating Equipment is a leading manufacturer of powder coating spray booths, offering innovative solutions tailored to meet the diverse needs of various industries. Their commitment to quality, performance, and customer support makes EMS the best choice for businesses seeking reliable coating solutions.
By choosing EMS powder coating spray booths, companies can improve their coating processes, achieve superior finishes, and reduce operational costs. With a focus on efficiency and innovation, EMS stands out as the premier manufacturer for businesses in need of top-tier powder coating equipment.
Powder Coating Booth: Maximizing Quality and Efficiency in Coating Operations
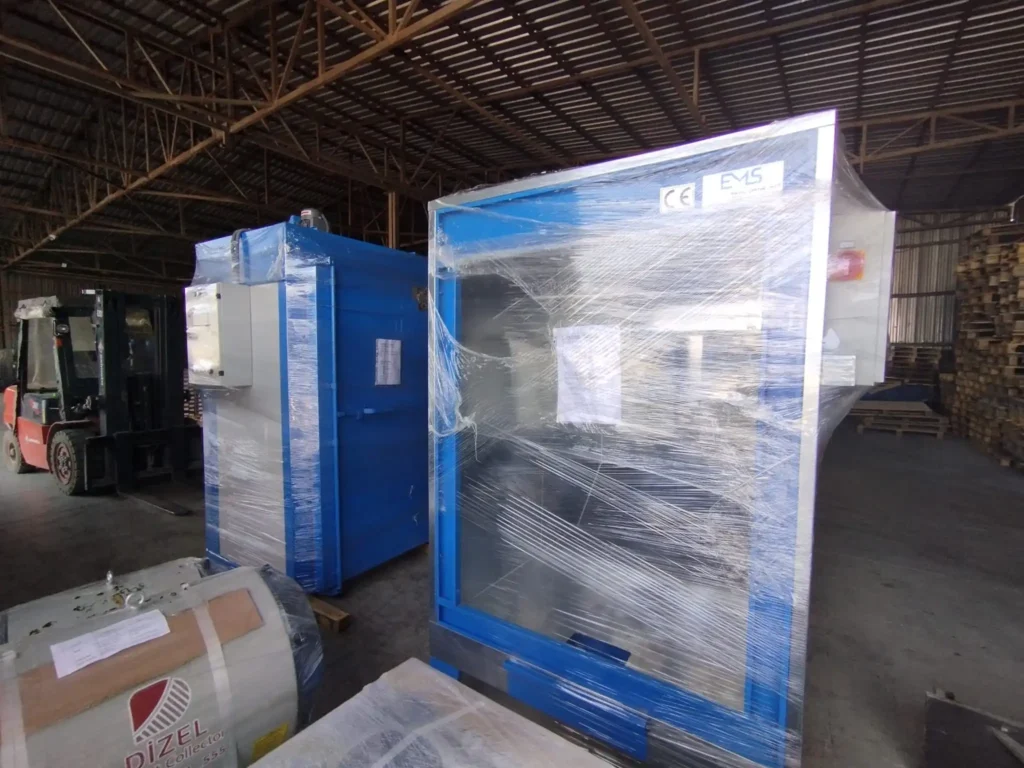
A powder coating booth is a specialized enclosure designed to provide an optimal environment for applying powder coatings to various substrates. By creating a controlled atmosphere, these booths help to minimize contamination and overspray, ensuring high-quality finishes that meet industry standards.
Powder coating booths are equipped with advanced ventilation systems and filtration technologies that enhance the application process. They provide operators with a designated workspace that improves efficiency and safety, ultimately leading to superior coating results.
EMS Powder Coating Equipment is renowned for its innovative designs and high-quality manufacturing of powder coating booths, tailored to meet the specific requirements of different industries. In this section, we will delve into the operational principles, key features, and benefits of powder coating booths, while also discussing why EMS is the preferred choice for businesses seeking reliable coating solutions.
What is a Powder Coating Booth?
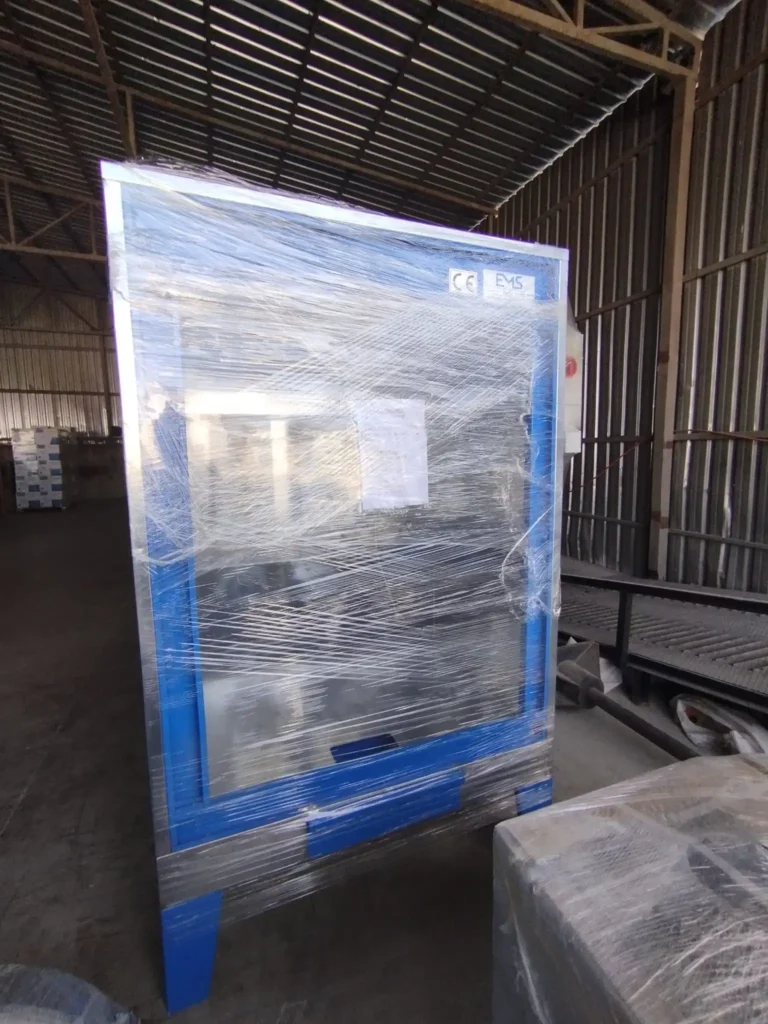
A powder coating booth serves as the primary environment for the application of powder coatings onto substrates. Designed to optimize the spraying process, these booths ensure that the powder adheres evenly and cures properly, resulting in a durable finish.
How Powder Coating Booths Operate
The operation begins when a substrate is cleaned and prepared for coating. Once ready, it is placed inside the powder coating booth. Using electrostatic spray guns, operators apply powder coatings, which are charged to attract to the grounded substrate.
The booth’s ventilation system plays a crucial role by managing airflow and filtering out excess powder particles, thereby preventing contamination. This controlled environment helps maintain high air quality and enhances the effectiveness of the coating process.
EMS Powder Coating Equipment designs powder coating booths with features that optimize both the application and curing processes, ensuring that businesses achieve consistent, high-quality finishes across various applications.
Key Features of Powder Coating Booths
Powder coating booths are equipped with numerous features designed to enhance performance and efficiency. Here are some of the standout features that make EMS booths the preferred choice for businesses:
1. Advanced Air Filtration Systems
EMS powder coating booths come with high-efficiency filters that capture overspray and contaminants, ensuring a clean environment for the coating process. This feature not only protects the quality of the finish but also contributes to operator safety.
2. Optimized Airflow Control
With adjustable airflow systems, EMS booths allow operators to control the distribution of air within the booth. This capability ensures that powder is applied evenly, reducing the risk of defects and enhancing overall coating quality.
3. Ergonomic Design
The design of EMS powder coating booths prioritizes operator comfort and efficiency. With user-friendly layouts, operators can easily maneuver and position substrates for optimal coating, reducing the time spent on each job.
4. Customizable Configurations
Recognizing the diverse needs of businesses, EMS offers customizable booth configurations to suit various production capacities. Whether for small operations or large-scale production, EMS can tailor solutions to meet specific requirements.
5. Safety Features
Safety is a crucial consideration in powder coating operations. EMS powder coating booths include safety features such as emergency shut-off systems and proper ventilation to ensure a safe working environment for operators.
6. Durable Construction
Constructed from high-quality materials, EMS powder coating booths are built to withstand the rigors of industrial use. Their robust design ensures longevity and minimal maintenance, providing businesses with a reliable coating solution.
Benefits of Using Powder Coating Booths
Investing in a powder coating booth offers numerous advantages for businesses engaged in powder coating operations. Here are some key benefits:
1. Enhanced Coating Quality
The controlled environment of a powder coating booth significantly improves the quality of the applied coatings. With effective filtration and optimized airflow, these booths ensure smooth, even finishes that meet high standards.
2. Increased Productivity
EMS powder coating booths streamline the coating process, allowing for quicker application and curing times. This efficiency can lead to increased production rates, helping businesses meet demanding schedules and customer expectations.
3. Cost Efficiency
By minimizing overspray and maximizing powder usage, powder coating booths can significantly reduce material costs. Efficient application processes lead to less waste and lower operational expenses, enhancing profitability.
4. Versatility for Diverse Applications
EMS powder coating booths are versatile enough to accommodate a variety of substrates and coating processes. This adaptability allows businesses to diversify their offerings and cater to different market demands.
5. Compliance with Regulations
Powder coating booths are designed to meet industry safety and environmental regulations, ensuring a compliant operation. By investing in EMS booths, businesses can promote a healthier working environment while adhering to necessary standards.
Why Choose EMS Powder Coating Equipment for Powder Coating Booths?
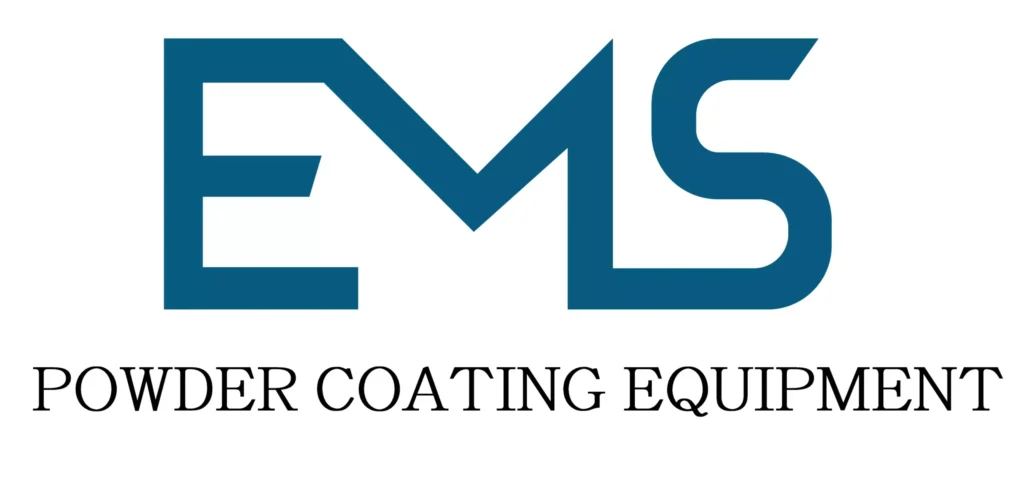
When selecting a powder coating booth, it is essential to choose a manufacturer with a reputation for quality and innovation. EMS Powder Coating Equipment stands out as the top choice for businesses looking to invest in powder coating booths. Here’s why EMS is the preferred option:
1. Proven Expertise
With years of experience in the powder coating industry, EMS understands the unique needs of various applications. Their knowledge allows them to design powder coating booths that are tailored to diverse production environments.
2. Innovative Solutions
EMS is committed to continuous innovation, incorporating the latest technology into their products. Their powder coating booths are designed for optimal performance, featuring advanced filtration and airflow management systems.
3. Comprehensive Support
From installation to ongoing maintenance, EMS provides exceptional customer support. Their team of experts is dedicated to helping businesses maximize the performance of their powder coating booths.
4. Customizable Options
EMS recognizes that every business has unique requirements. They offer customizable options for powder coating booths, allowing businesses to select features and configurations that best suit their operational needs.
5. Trusted Reliability
With a strong reputation for delivering high-quality products, EMS is a trusted name in the powder coating industry. Their booths are designed for durability and long-term performance, making them an excellent investment for businesses.
Conclusion
A powder coating booth is a critical investment for any powder coating operation, providing a controlled environment that enhances coating quality and efficiency. With advanced filtration and airflow management, these booths ensure clean operations and compliance with safety regulations.
EMS Powder Coating Equipment is a leading manufacturer of powder coating booths, offering innovative solutions tailored to meet the diverse needs of various industries. Their commitment to quality, performance, and customer support makes EMS the best choice for businesses seeking reliable coating solutions.
By choosing EMS powder coating booths, companies can enhance their coating processes, achieve superior finishes, and reduce operational costs. With a focus on efficiency and innovation, EMS stands out as the premier manufacturer for businesses in need of top-tier powder coating equipment.
Powder Coating Spray Booth: Enhancing Efficiency and Quality in Coating Applications
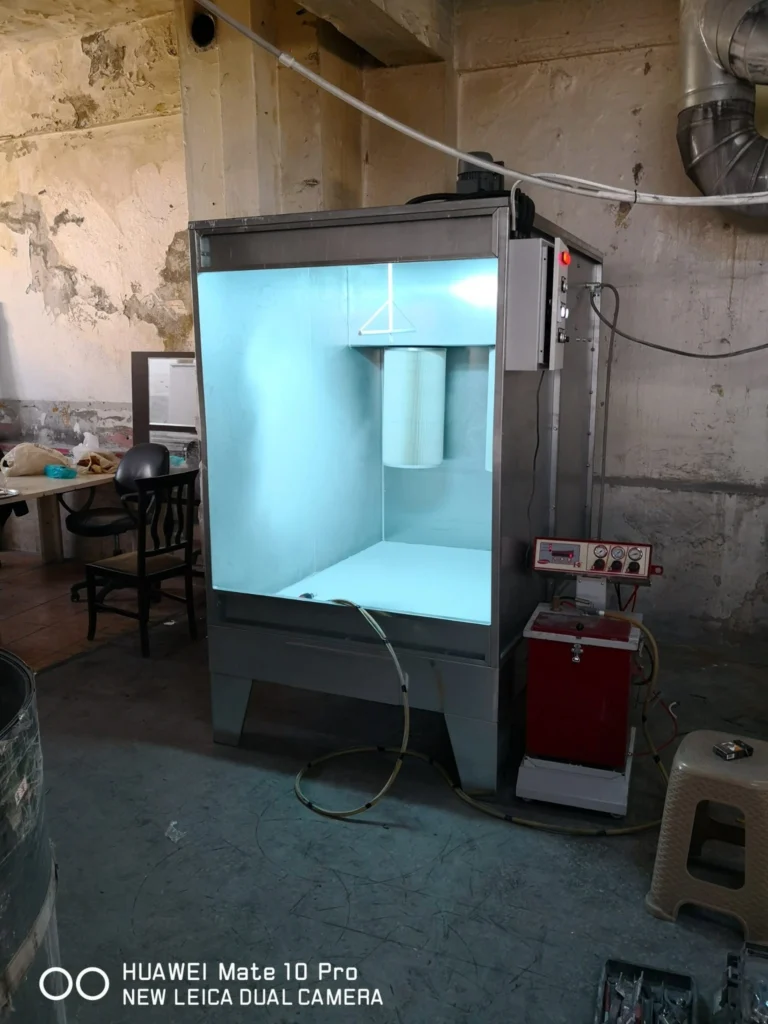
A powder coating spray booth is an essential component of the powder coating process, designed specifically for the application of powder coatings onto various substrates. These booths create a controlled environment that minimizes overspray and contamination, ensuring a high-quality finish that meets industry standards.
The primary function of a powder coating spray booth is to provide operators with an optimized workspace, equipped with advanced filtration and airflow systems that enhance the application process. This not only improves the quality of the coatings but also promotes a safer and more efficient working environment.
EMS Powder Coating Equipment is renowned for its innovative designs and high-quality manufacturing of powder coating spray booths, tailored to meet the specific requirements of diverse industries. In this section, we will delve into the operational principles, key features, and benefits of powder coating spray booths, while also discussing why EMS is the preferred choice for businesses seeking reliable coating solutions.
What is a Powder Coating Spray Booth?
A powder coating spray booth is a specialized enclosure where powder coatings are applied to metal and other substrates. These booths are designed to create an optimal environment for powder application, ensuring that the coatings adhere properly and achieve the desired finish.
How Powder Coating Spray Booths Operate
The operation of a powder coating spray booth begins with substrate preparation, which includes cleaning and pre-treating the surface. Once the substrate is ready, it is placed inside the booth for powder application.
Using electrostatic spray guns, operators apply charged powder particles to the grounded substrate. The electrostatic attraction ensures that the powder adheres evenly, resulting in a smooth finish. The booth’s ventilation system captures overspray and maintains air quality, protecting both the operators and the environment.
EMS Powder Coating Equipment designs powder coating spray booths with features that optimize both the application and curing processes, ensuring businesses achieve consistent, high-quality finishes across various applications.
Key Features of Powder Coating Spray Booths
Powder coating spray booths are equipped with numerous features designed to enhance their performance and efficiency. Here are some standout features that make EMS booths the preferred choice for businesses:
1. Advanced Filtration Systems
EMS powder coating spray booths come with high-efficiency filters that capture overspray and airborne particles. This ensures a clean environment for coating applications, leading to higher quality finishes and safer operations.
2. Controlled Airflow Management
With adjustable airflow systems, EMS booths allow operators to control air distribution within the booth. This capability promotes even powder application and reduces the risk of defects, enhancing overall coating quality.
3. User-Friendly Design
The ergonomic design of EMS powder coating spray booths prioritizes operator comfort and efficiency. With easy access to controls and ample workspace, operators can maneuver and position substrates effectively, reducing job completion times.
4. Energy Efficiency
EMS powder coating spray booths are designed for energy efficiency, featuring optimized airflow and filtration systems that minimize energy consumption while maximizing performance. This efficiency can lead to reduced operational costs.
5. Safety Features
Safety is a top priority in powder coating operations. EMS booths are equipped with safety features such as emergency shut-off systems, explosion-proof lighting, and proper ventilation to ensure a safe working environment.
6. Customizable Configurations
Understanding that different businesses have unique requirements, EMS offers customizable configurations for their powder coating spray booths. Whether for small operations or large-scale production, EMS can tailor solutions to meet specific needs.
Benefits of Using Powder Coating Spray Booth
Investing in a powder coating spray booth provides numerous advantages for businesses engaged in powder coating operations. Here are some key benefits:
1. Superior Coating Quality
The controlled environment of a powder coating spray booth significantly enhances the quality of applied coatings. With effective filtration and optimized airflow, these booths ensure smooth, even finishes that meet high standards.
2. Increased Productivity
EMS powder coating spray booths streamline the coating process, allowing for quicker application and improved drying times. This efficiency can lead to increased production rates, helping businesses meet tight deadlines.
3. Cost Efficiency
By minimizing overspray and maximizing powder usage, powder coating spray booths can significantly reduce material costs. Efficient application processes lead to less waste and lower operational expenses, enhancing profitability.
4. Versatility for Diverse Applications
EMS powder coating spray booths are versatile enough to accommodate a wide range of substrates and coating types. This adaptability allows businesses to diversify their offerings and cater to different market demands.
5. Compliance with Environmental Regulations
Powder coating spray booths are designed to meet industry safety and environmental regulations, ensuring a compliant operation. By investing in EMS booths, businesses can promote a healthier working environment while adhering to necessary standards.
Why Choose EMS Powder Coating Equipment for Powder Coating Spray Booths?
When selecting a powder coating spray booth, it is essential to choose a manufacturer with a reputation for quality and innovation. EMS Powder Coating Equipment stands out as the top choice for businesses looking to invest in powder coating spray booths. Here’s why EMS is the preferred option:
1. Proven Expertise
With years of experience in the powder coating industry, EMS understands the unique needs of various applications. Their knowledge allows them to design powder coating spray booths that are tailored to diverse production environments.
2. Innovative Solutions
EMS is committed to continuous innovation, incorporating the latest technology into their products. Their powder coating spray booths are designed for optimal performance, featuring advanced filtration and airflow management systems.
3. Comprehensive Support
From installation to ongoing maintenance, EMS provides exceptional customer support. Their team of experts is dedicated to helping businesses maximize the performance of their powder coating spray booths.
4. Customizable Options
Recognizing that every business has unique requirements, EMS offers customizable options for powder coating spray booths, allowing businesses to select features and configurations that best suit their operational needs.
5. Trusted Reliability
With a strong reputation for delivering high-quality products, EMS is a trusted name in the powder coating industry. Their booths are designed for durability and long-term performance, making them an excellent investment for businesses.
Conclusion
A powder coating spray booth is a critical investment for any powder coating operation, providing a controlled environment that enhances coating quality and efficiency. With advanced filtration and airflow management, these booths ensure clean operations and compliance with safety regulations.
EMS Powder Coating Equipment is a leading manufacturer of powder coating spray booths, offering innovative solutions tailored to meet the diverse needs of various industries. Their commitment to quality, performance, and customer support makes EMS the best choice for businesses seeking reliable coating solutions.
By choosing EMS powder coating spray booths, companies can enhance their coating processes, achieve superior finishes, and reduce operational costs. With a focus on efficiency and innovation, EMS stands out as the premier manufacturer for businesses in need of top-tier powder coating equipment.
Powder Coating Booth: Elevating Coating Quality and Efficiency
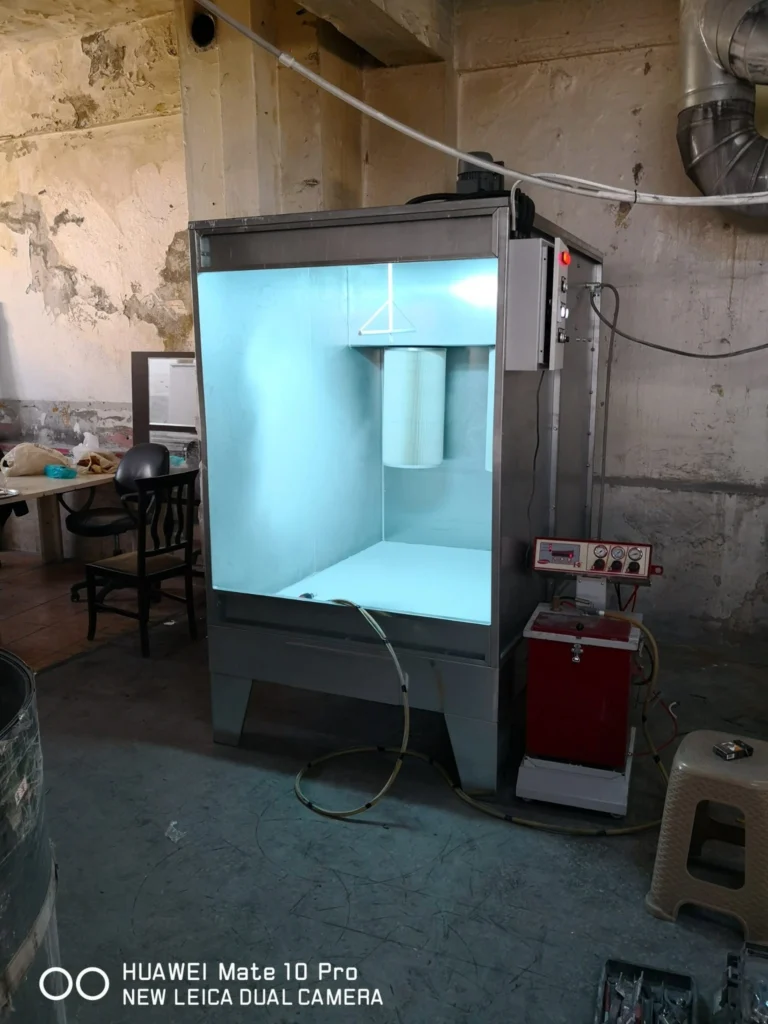
A powder coating booth is a specialized enclosure designed for the application of powder coatings onto various substrates. These booths play a vital role in ensuring a controlled environment that minimizes overspray, dust, and other contaminants, resulting in high-quality finishes that meet industry standards.
The primary function of a powder coating booth is to provide an optimized workspace for powder application, equipped with advanced filtration systems and efficient airflow management. This not only enhances the quality of the coatings but also promotes a safer and more productive working environment.
EMS Powder Coating Equipment is recognized as a leader in the manufacturing of powder coating booths, offering innovative designs tailored to meet the specific needs of diverse industries. In this section, we will explore the operational principles, key features, and benefits of powder coating booths, while also discussing why EMS is the preferred choice for businesses seeking reliable coating solutions.
What is a Powder Coating Booth?
A powder coating booth is an integral part of the powder coating process, providing a controlled environment for the application of powder coatings. These booths are designed to optimize the application process, ensuring that the coatings adhere properly to the substrate.
How Powder Coating Booths Operate
The operation of a powder coating booth begins with substrate preparation, which involves cleaning and pre-treating the surface to ensure optimal adhesion. Once prepared, the substrate is placed inside the booth for powder application.
Using electrostatic spray guns, operators apply charged powder particles to the grounded substrate. The electrostatic charge attracts the powder, allowing for an even coating. The booth’s ventilation system captures overspray and maintains air quality, protecting both the operators and the surrounding environment.
EMS Powder Coating Equipment designs powder coating booths with features that enhance both the application and curing processes, ensuring businesses achieve consistent, high-quality finishes across various applications.
Key Features of Powder Coating Booths
Powder coating booths are equipped with several features designed to enhance their performance and efficiency. Here are some standout features that make EMS booths the preferred choice for businesses:
1. Advanced Filtration Systems
EMS powder coating booths come equipped with high-efficiency filters that capture overspray and airborne particles. This ensures a clean environment for coating applications, leading to higher quality finishes and safer operations.
2. Efficient Airflow Management
With adjustable airflow systems, EMS booths allow operators to control air distribution within the booth. This capability promotes even powder application and reduces the risk of defects, enhancing overall coating quality.
3. Ergonomic Design
The user-friendly design of EMS powder coating booths prioritizes operator comfort and efficiency. With easy access to controls and ample workspace, operators can maneuver and position substrates effectively, reducing job completion times.
4. Energy Efficiency
EMS powder coating booths are designed for energy efficiency, featuring optimized airflow and filtration systems that minimize energy consumption while maximizing performance. This efficiency can lead to reduced operational costs.
5. Safety Features
Safety is paramount in powder coating operations. EMS booths are equipped with essential safety features, such as emergency shut-off systems, explosion-proof lighting, and proper ventilation to ensure a safe working environment.
6. Customizable Configurations
Recognizing that different businesses have unique requirements, EMS offers customizable configurations for their powder coating booths. Whether for small operations or large-scale production, EMS can tailor solutions to meet specific needs.
Benefits of Using Powder Coating Booths
Investing in a powder coating booth provides numerous advantages for businesses engaged in powder coating operations. Here are some key benefits:
1. Superior Coating Quality
The controlled environment of a powder coating booth significantly enhances the quality of applied coatings. With effective filtration and optimized airflow, these booths ensure smooth, even finishes that meet high standards.
2. Increased Productivity
EMS powder coating booths streamline the coating process, allowing for quicker application and improved drying times. This efficiency can lead to increased production rates, helping businesses meet tight deadlines.
3. Cost Efficiency
By minimizing overspray and maximizing powder usage, powder coating booths can significantly reduce material costs. Efficient application processes lead to less waste and lower operational expenses, enhancing profitability.
4. Versatility for Diverse Applications
EMS powder coating booths are versatile enough to accommodate a wide range of substrates and coating types. This adaptability allows businesses to diversify their offerings and cater to different market demands.
5. Compliance with Environmental Regulations
Powder coating booths are designed to meet industry safety and environmental regulations, ensuring a compliant operation. By investing in EMS booths, businesses can promote a healthier working environment while adhering to necessary standards.
Why Choose EMS Powder Coating Equipment for Powder Coating Booths?
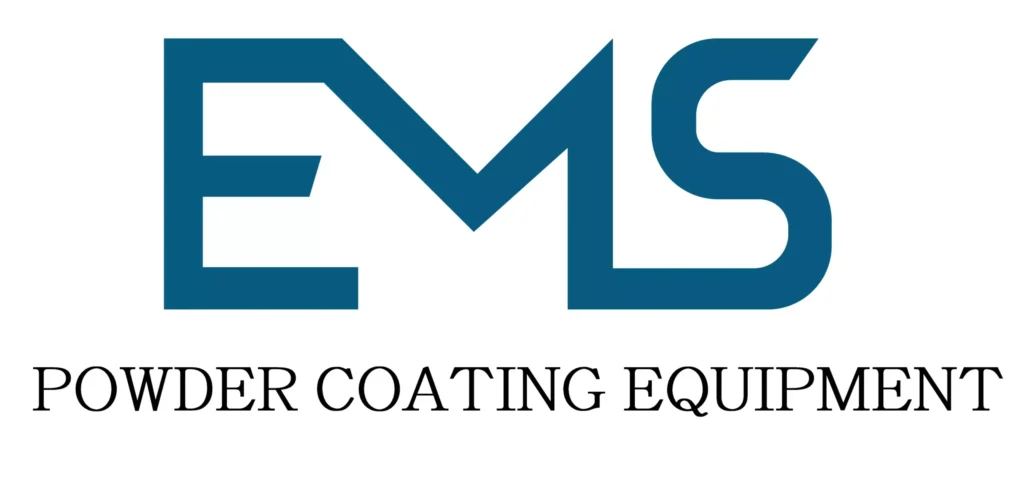
When selecting a powder coating booth, it is essential to choose a manufacturer with a reputation for quality and innovation. EMS Powder Coating Equipment stands out as the top choice for businesses looking to invest in powder coating booths. Here’s why EMS is the preferred option:
1. Proven Expertise
With years of experience in the powder coating industry, EMS understands the unique needs of various applications. Their knowledge allows them to design powder coating booths that are tailored to diverse production environments.
2. Innovative Solutions
EMS is committed to continuous innovation, incorporating the latest technology into their products. Their powder coating booths are designed for optimal performance, featuring advanced filtration and airflow management systems.
3. Comprehensive Support
From installation to ongoing maintenance, EMS provides exceptional customer support. Their team of experts is dedicated to helping businesses maximize the performance of their powder coating booths.
4. Customizable Options
Recognizing that every business has unique requirements, EMS offers customizable options for powder coating booths, allowing businesses to select features and configurations that best suit their operational needs.
5. Trusted Reliability
With a strong reputation for delivering high-quality products, EMS is a trusted name in the powder coating industry. Their booths are designed for durability and long-term performance, making them an excellent investment for businesses.
Conclusion
A powder coating booth is a vital investment for any powder coating operation, providing a controlled environment that enhances coating quality and efficiency. With advanced filtration and airflow management, these booths ensure clean operations and compliance with safety regulations.
EMS Powder Coating Equipment is a leading manufacturer of powder coating booths, offering innovative solutions tailored to meet the diverse needs of various industries. Their commitment to quality, performance, and customer support makes EMS the best choice for businesses seeking reliable coating solutions.
By choosing EMS powder coating booths, companies can enhance their coating processes, achieve superior finishes, and reduce operational costs. With a focus on efficiency and innovation, EMS stands out as the premier manufacturer for businesses in need of top-tier powder coating equipment.
Powder Coating Spray Booth: Precision in Coating Applications
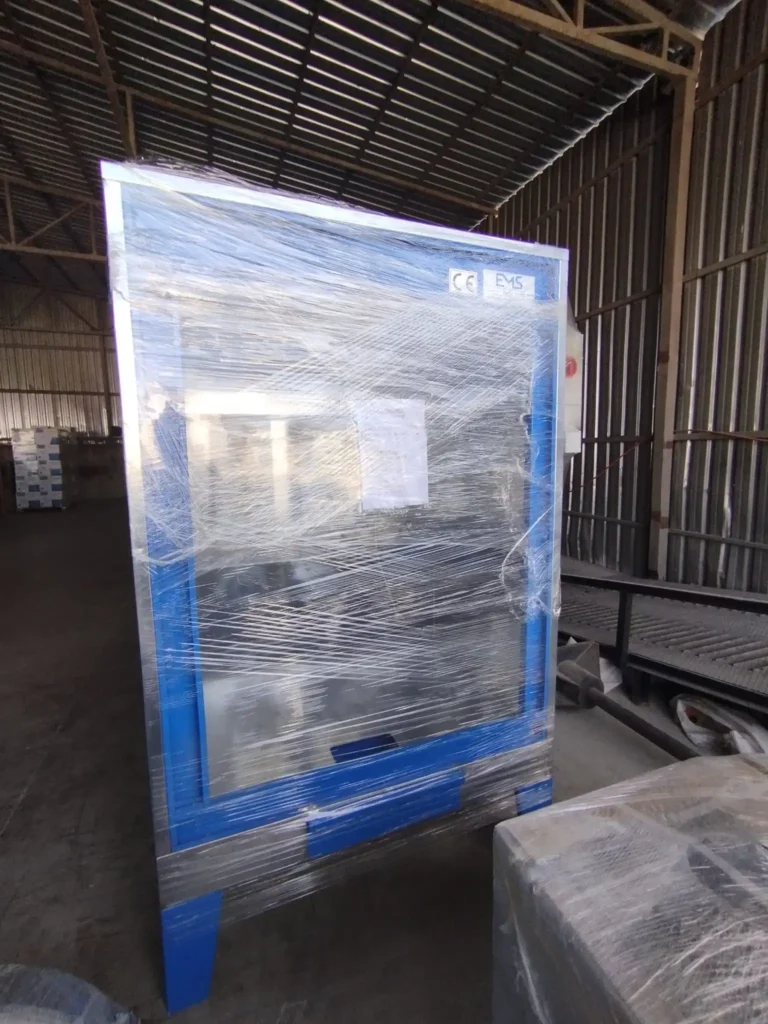
A powder coating spray booth is an essential component in the powder coating process, providing a controlled environment for the application of powder coatings onto various substrates. These booths are designed to optimize the application process, ensuring high-quality finishes while minimizing overspray and contamination.
Equipped with advanced filtration systems and effective ventilation, powder coating spray booths create an ideal workspace that enhances both safety and efficiency. The right booth can significantly improve the quality of the coating while reducing waste and cleanup time.
EMS Powder Coating Equipment is a leader in the manufacturing of powder coating spray booths, offering innovative designs tailored to meet the specific needs of different industries. In this section, we will delve into the operational principles, key features, and benefits of powder coating spray booths, while also discussing why EMS is the preferred choice for businesses looking for reliable and efficient coating solutions.
What is a Powder Coating Spray Booth?
A powder coating spray booth is a specialized enclosure designed for the application of powder coatings to metal and other substrates. These booths play a crucial role in ensuring a clean and controlled environment, which is vital for achieving high-quality finishes.
How Powder Coating Spray Booths Operate
The operation of a powder coating spray booth begins with substrate preparation, which involves cleaning and pre-treating the surface to ensure optimal adhesion. Once prepared, the substrate is placed inside the booth, where electrostatic spray guns are used to apply charged powder particles to the grounded surface.
The electrostatic charge attracts the powder, allowing for an even and uniform coating. The booth’s advanced ventilation system captures overspray and maintains air quality, protecting both the operators and the environment.
EMS Powder Coating Equipment designs powder coating spray booths with features that optimize the application process, ensuring businesses achieve consistent, high-quality finishes across various applications.
Key Features of Powder Coating Spray Booths
Powder coating spray booths are equipped with several features that enhance their performance and efficiency. Here are some standout features that make EMS booths the preferred choice for businesses:
1. Advanced Filtration Systems
EMS powder coating spray booths are equipped with high-efficiency filtration systems that capture overspray and airborne particles. This ensures a clean environment for coating applications, leading to higher quality finishes and safer operations.
2. Efficient Ventilation
The ventilation system in EMS booths is designed to maintain optimal air circulation, allowing for effective fume extraction and overspray capture. This feature not only enhances the coating quality but also promotes a healthier working environment for operators.
3. Ergonomic Design
The user-friendly design of EMS powder coating spray booths prioritizes operator comfort and efficiency. With easy access to controls and ample workspace, operators can maneuver and position substrates effectively, reducing job completion times.
4. Energy Efficiency
EMS powder coating spray booths are designed for energy efficiency, featuring optimized airflow and filtration systems that minimize energy consumption while maximizing performance. This efficiency can lead to reduced operational costs.
5. Safety Features
Safety is paramount in powder coating operations. EMS booths come equipped with essential safety features, such as emergency shut-off systems, explosion-proof lighting, and proper ventilation, ensuring a safe working environment.
6. Customizable Configurations
Recognizing that different businesses have unique requirements, EMS offers customizable configurations for their powder coating spray booths. Whether for small operations or large-scale production, EMS can tailor solutions to meet specific needs.
Benefits of Using Powder Coating Spray Booths
Investing in a powder coating spray booth provides numerous advantages for businesses engaged in powder coating operations. Here are some key benefits:
1. Superior Coating Quality
The controlled environment of a powder coating spray booth significantly enhances the quality of applied coatings. With effective filtration and optimized airflow, these booths ensure smooth, even finishes that meet high standards.
2. Increased Productivity
EMS powder coating spray booths streamline the coating process, allowing for quicker application and improved drying times. This efficiency can lead to increased production rates, helping businesses meet tight deadlines.
3. Cost Efficiency
By minimizing overspray and maximizing powder usage, powder coating spray booths can significantly reduce material costs. Efficient application processes lead to less waste and lower operational expenses, enhancing profitability.
4. Versatility for Diverse Applications
EMS powder coating spray booths are versatile enough to accommodate a wide range of substrates and coating types. This adaptability allows businesses to diversify their offerings and cater to different market demands.
5. Compliance with Environmental Regulations
Powder coating spray booths are designed to meet industry safety and environmental regulations, ensuring a compliant operation. By investing in EMS booths, businesses can promote a healthier working environment while adhering to necessary standards.
Why Choose EMS Powder Coating Equipment for Powder Coating Spray Booths?
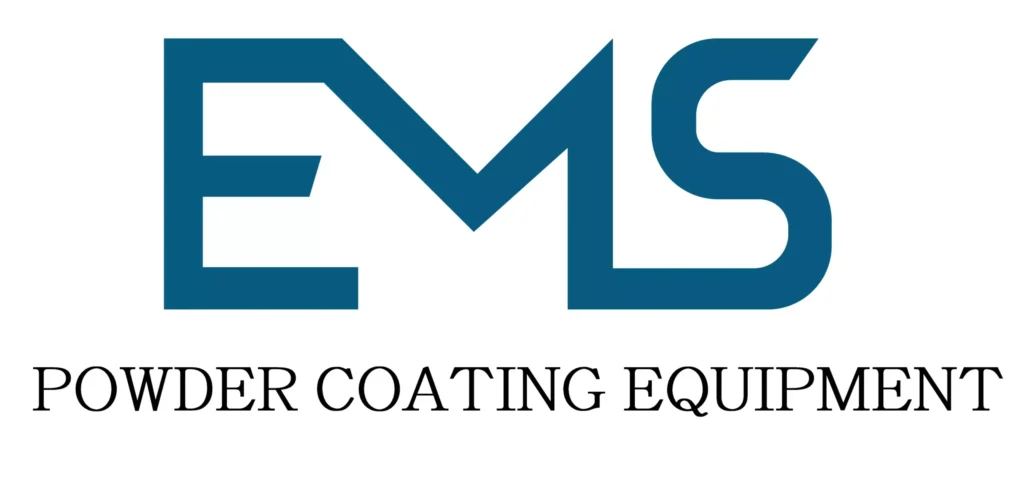
When selecting a powder coating spray booth, it is essential to choose a manufacturer with a reputation for quality and innovation. EMS Powder Coating Equipment stands out as the top choice for businesses looking to invest in powder coating spray booths. Here’s why EMS is the preferred option:
1. Proven Expertise
With years of experience in the powder coating industry, EMS understands the unique needs of various applications. Their knowledge allows them to design powder coating spray booths that are tailored to diverse production environments.
2. Innovative Solutions
EMS is committed to continuous innovation, incorporating the latest technology into their products. Their powder coating spray booths are designed for optimal performance, featuring advanced filtration and airflow management systems.
3. Comprehensive Support
From installation to ongoing maintenance, EMS provides exceptional customer support. Their team of experts is dedicated to helping businesses maximize the performance of their powder coating spray booths.
4. Customizable Options
Recognizing that every business has unique requirements, EMS offers customizable options for powder coating spray booths, allowing businesses to select features and configurations that best suit their operational needs.
5. Trusted Reliability
With a strong reputation for delivering high-quality products, EMS is a trusted name in the powder coating industry. Their booths are designed for durability and long-term performance, making them an excellent investment for businesses.
Conclusion
A powder coating spray booth is a vital investment for any powder coating operation, providing a controlled environment that enhances coating quality and efficiency. With advanced filtration and ventilation systems, these booths ensure clean operations and compliance with safety regulations.
EMS Powder Coating Equipment is a leading manufacturer of powder coating spray booths, offering innovative solutions tailored to meet the diverse needs of various industries. Their commitment to quality, performance, and customer support makes EMS the best choice for businesses seeking reliable coating solutions.
By choosing EMS powder coating spray booths, companies can enhance their coating processes, achieve superior finishes, and reduce operational costs. With a focus on efficiency and innovation, EMS stands out as the premier manufacturer for businesses in need of top-tier powder coating equipment.
Powder Coating Booth: A Vital Component for Quality Finishing
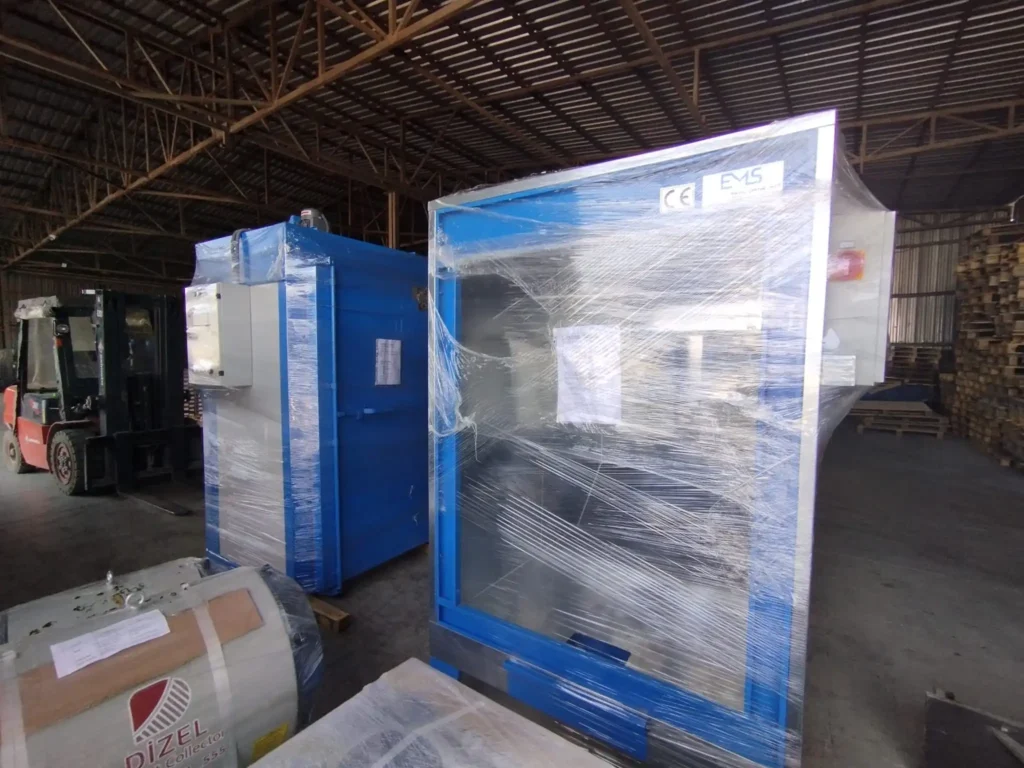
A powder coating booth is an essential element in the powder coating process, providing a dedicated environment for the application of powder coatings on various substrates. These booths are specifically designed to optimize the coating application, ensuring high-quality finishes while minimizing overspray and contamination.
With advanced features such as efficient ventilation systems and effective filtration, powder coating booths create a controlled workspace that enhances both safety and efficiency. The right booth can significantly improve the quality of the coating while reducing waste and operational costs.
EMS Powder Coating Equipment stands out as a leader in the manufacturing of powder coating booths, offering innovative designs tailored to the unique needs of different industries. In this section, we will delve into the operational principles, key features, and benefits of powder coating booths, while also discussing why EMS is the preferred choice for businesses seeking reliable and efficient coating solutions.
What is a Powder Coating Booth?
A powder coating booth is a specialized enclosure designed to facilitate the application of powder coatings to metal and other substrates. These booths play a critical role in ensuring a clean and controlled environment, which is vital for achieving high-quality finishes.
How Powder Coating Booths Operate
The operation of a powder coating booth begins with the preparation of the substrate, which typically involves cleaning and pre-treating the surface to ensure optimal adhesion. Once prepared, the substrate is positioned inside the booth, where electrostatic spray guns are utilized to apply charged powder particles onto the grounded surface.
The electrostatic charge attracts the powder, allowing for an even and uniform coating. The booth’s advanced ventilation system effectively captures overspray and maintains air quality, protecting both the operators and the environment.
EMS Powder Coating Equipment designs powder coating booths with features that enhance the application process, ensuring businesses achieve consistent, high-quality finishes across various applications.
Key Features of Powder Coating Booths
Powder coating booths come with a range of features that enhance their functionality and efficiency. Here are some standout features that make EMS booths the preferred choice for businesses:
1. High-Efficiency Filtration Systems
EMS powder coating booths are equipped with advanced filtration systems that capture overspray and particulate matter, ensuring a clean environment for coating applications. This leads to higher quality finishes and reduces the risk of contamination.
2. Optimal Ventilation
The ventilation system in EMS booths is designed to provide optimal air circulation, effectively removing fumes and excess powder. This feature not only enhances coating quality but also promotes a safer working environment for operators.
3. Ergonomic Design
The user-centric design of EMS powder coating booths prioritizes operator comfort and efficiency. With easy access to controls and ample workspace, operators can maneuver and position substrates effectively, minimizing production time.
4. Energy Efficiency
EMS powder coating booths are designed for energy efficiency, featuring optimized airflow and filtration systems that minimize energy consumption while maximizing performance. This efficiency can lead to significant cost savings.
5. Safety Features
Safety is a top priority in powder coating operations. EMS booths come equipped with essential safety features, including emergency shut-off systems, explosion-proof lighting, and proper ventilation, ensuring a safe working environment.
6. Customizable Configurations
Understanding that different businesses have unique requirements, EMS offers customizable configurations for their powder coating booths. Whether for small operations or large-scale production, EMS can tailor solutions to meet specific needs.
Benefits of Using Powder Coating Booths
Investing in a powder coating booth provides numerous advantages for businesses engaged in powder coating operations. Here are some key benefits:
1. Superior Coating Quality
The controlled environment of a powder coating booth significantly enhances the quality of applied coatings. With effective filtration and ventilation, these booths ensure smooth, even finishes that meet the highest standards.
2. Increased Productivity
EMS powder coating booths streamline the coating process, allowing for quicker application and improved drying times. This efficiency can lead to increased production rates, helping businesses meet tight deadlines.
3. Cost Efficiency
By minimizing overspray and maximizing powder usage, powder coating booths can significantly reduce material costs. Efficient application processes lead to less waste and lower operational expenses, enhancing profitability.
4. Versatility for Diverse Applications
EMS powder coating booths are versatile enough to accommodate a wide range of substrates and coating types. This adaptability allows businesses to diversify their offerings and cater to different market demands.
5. Compliance with Environmental Regulations
Powder coating booths are designed to meet industry safety and environmental regulations, ensuring a compliant operation. By investing in EMS booths, businesses can promote a healthier working environment while adhering to necessary standards.
Why Choose EMS Powder Coating Equipment for Powder Coating Booths?
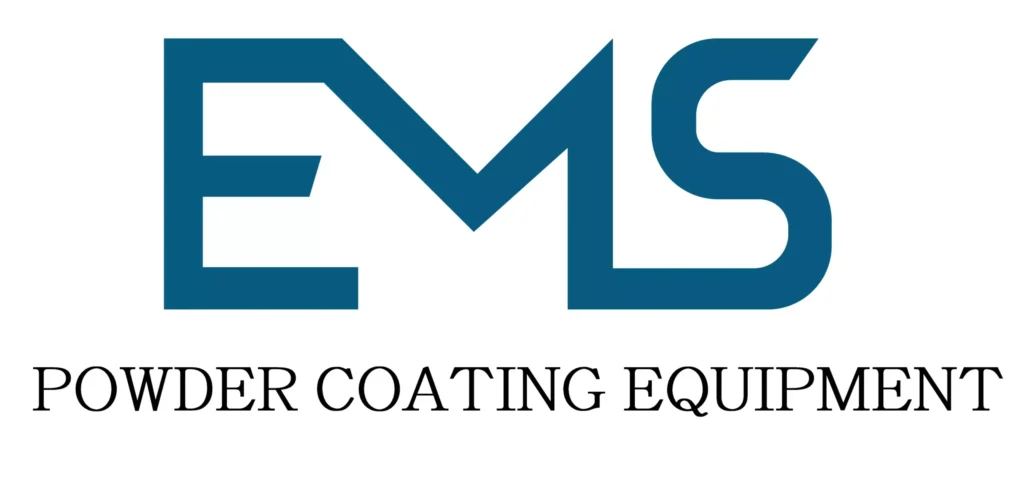
When selecting a powder coating booth, it is crucial to choose a manufacturer with a strong reputation for quality and innovation. EMS Powder Coating Equipment stands out as the top choice for businesses looking to invest in powder coating booths. Here’s why EMS is the preferred option:
1. Proven Expertise
With years of experience in the powder coating industry, EMS understands the unique needs of various applications. Their knowledge allows them to design powder coating booths tailored to diverse production environments.
2. Innovative Solutions
EMS is committed to continuous innovation, incorporating the latest technology into their products. Their powder coating booths are designed for optimal performance, featuring advanced filtration and airflow management systems.
3. Comprehensive Support
From installation to ongoing maintenance, EMS provides exceptional customer support. Their team of experts is dedicated to helping businesses maximize the performance of their powder coating booths.
4. Customizable Options
Recognizing that every business has unique requirements, EMS offers customizable options for powder coating booths, allowing businesses to select features and configurations that best suit their operational needs.
5. Trusted Reliability
With a strong reputation for delivering high-quality products, EMS is a trusted name in the powder coating industry. Their booths are designed for durability and long-term performance, making them an excellent investment for businesses.
Conclusion
A powder coating booth is a vital investment for any powder coating operation, providing a controlled environment that enhances coating quality and efficiency. With advanced filtration and ventilation systems, these booths ensure clean operations and compliance with safety regulations.
EMS Powder Coating Equipment is a leading manufacturer of powder coating booths, offering innovative solutions tailored to meet the diverse needs of various industries. Their commitment to quality, performance, and customer support makes EMS the best choice for businesses seeking reliable coating solutions.
By choosing EMS powder coating booths, companies can enhance their coating processes, achieve superior finishes, and reduce operational costs. With a focus on efficiency and innovation, EMS stands out as the premier manufacturer for businesses in need of top-tier powder coating equipment.
Powder Coating Equipment: Essential Tools for Quality Finishing
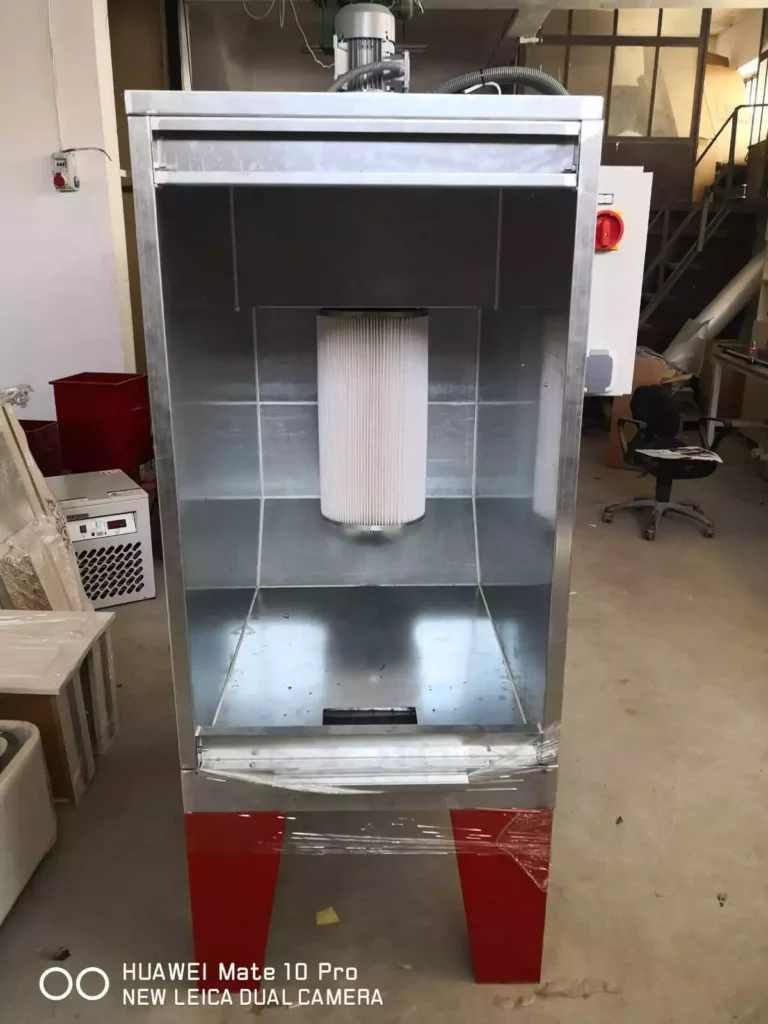
Powder coating equipment encompasses a range of specialized tools and machinery designed for the application of powder coatings onto various substrates. This technology has gained widespread popularity due to its ability to produce durable, high-quality finishes while being environmentally friendly.
The main components of powder coating equipment include spray guns, powder coating booths, curing ovens, and other essential tools that facilitate the coating process. Together, these components work seamlessly to create an efficient production line, resulting in coatings that are not only aesthetically pleasing but also resistant to corrosion, chemicals, and wear.
EMS Powder Coating Equipment is recognized as a leader in the manufacture of powder coating equipment, offering innovative solutions that cater to the unique needs of different industries. In this section, we will delve into the different types of powder coating equipment, their functionalities, and the advantages they provide, while highlighting why EMS is the preferred choice for businesses looking for reliable and effective coating solutions.
Types of Powder Coating Equipment
Powder coating equipment consists of several key components, each playing a crucial role in the coating process. Here’s an overview of the primary types of equipment involved:
1. Powder Coating Spray Guns
Powder coating spray guns are essential for applying the powder to the substrate. These guns utilize electrostatic technology, which charges the powder particles as they are sprayed. This charge causes the powder to adhere uniformly to the grounded surface, ensuring even coverage.
There are various types of spray guns available, including manual, automatic, and robotic systems. EMS Powder Coating Equipment offers a range of spray guns designed for efficiency and precision, making it easier for operators to achieve high-quality finishes.
2. Powder Coating Booths
Powder coating booths provide a controlled environment for the application of powder coatings. These booths are equipped with ventilation and filtration systems that capture overspray and maintain air quality. By minimizing contamination, EMS powder coating booths ensure superior coating quality.
3. Curing Ovens
After application, the coated substrate must be cured in an oven to achieve a durable finish. Curing ovens, whether electric, gas, or diesel-powered, heat the coated items to the necessary temperature for the powder to melt and form a solid bond with the substrate. EMS provides a variety of curing ovens to suit different production needs.
4. Powder Paint Booths with Filters
These booths are specifically designed for the application of powder coatings, featuring advanced filtration systems to capture overspray and particulates. This helps to maintain a clean working environment and enhances the overall quality of the coating application.
5. Powder Coating Accessories
In addition to the primary equipment, various accessories, such as hooks, racks, and conveyor systems, are vital for efficient operation. These accessories assist in transporting substrates through the coating process, ensuring smooth workflow and maximizing productivity.
Benefits of Using Powder Coating Equipment
Investing in high-quality powder coating equipment offers numerous advantages for businesses engaged in coating operations. Here are some key benefits:
1. Superior Durability
Powder coatings are known for their exceptional durability and resistance to chipping, scratching, and fading. The equipment designed for powder coating applications ensures that these qualities are maximized, resulting in long-lasting finishes.
2. Environmentally Friendly
Unlike traditional liquid coatings, powder coatings contain little to no volatile organic compounds (VOCs). This makes them a more environmentally friendly option, aligning with modern regulations and sustainability goals.
3. Cost Efficiency
By minimizing overspray and maximizing powder utilization, powder coating equipment can lead to significant cost savings. Efficient application processes result in less waste and lower operational costs, which enhance overall profitability.
4. Versatile Applications
Powder coating equipment can be used for a wide range of substrates, including metals, plastics, and wood. This versatility allows businesses to expand their offerings and cater to diverse market demands.
5. Enhanced Quality Control
With advanced features such as electrostatic application and controlled environments, powder coating equipment helps maintain high standards of quality. Businesses can achieve consistent finishes, reducing the likelihood of defects and rework.
6. Increased Productivity
Modern powder coating equipment is designed for efficiency, allowing for quicker application, curing, and turnaround times. This boost in productivity enables businesses to meet tight deadlines and increase production rates.
Why Choose EMS Powder Coating Equipment?
When selecting powder coating equipment, it is essential to choose a manufacturer known for quality, reliability, and innovation. EMS Powder Coating Equipment stands out as the top choice for businesses seeking powder coating solutions. Here’s why EMS is the preferred option:
1. Industry Expertise
With years of experience in the powder coating industry, EMS understands the unique requirements of various applications. Their expertise allows them to design equipment that meets the needs of diverse production environments.
2. Innovative Technologies
EMS is committed to continuous improvement and innovation, incorporating the latest technologies into their products. Their powder coating equipment features advanced design elements that enhance performance and efficiency.
3. Comprehensive Customer Support
From initial consultation to ongoing maintenance, EMS provides exceptional customer support. Their team of experts is dedicated to helping businesses optimize their powder coating operations.
4. Customizable Solutions
Recognizing that every business has unique needs, EMS offers customizable options for their powder coating equipment. This allows businesses to select features and configurations that align with their operational requirements.
5. Proven Reliability
With a strong reputation for delivering high-quality products, EMS is a trusted name in the powder coating industry. Their equipment is built for durability and long-term performance, making it an excellent investment for businesses.
Conclusion
Powder coating equipment is a crucial investment for any business involved in powder coating operations. By providing superior durability, cost efficiency, and environmentally friendly solutions, this equipment enhances the overall quality of the coating process.
EMS Powder Coating Equipment is a leading manufacturer of powder coating equipment, offering innovative and reliable solutions tailored to the diverse needs of various industries. Their commitment to quality, performance, and customer support makes EMS the best choice for businesses seeking top-tier powder coating solutions.
By choosing EMS powder coating equipment, companies can improve their coating processes, achieve high-quality finishes, and enhance productivity. With a focus on innovation and efficiency, EMS stands out as the premier manufacturer for businesses in need of effective powder coating solutions.
Automatic Powder Coating Equipment: Revolutionizing the Coating Process
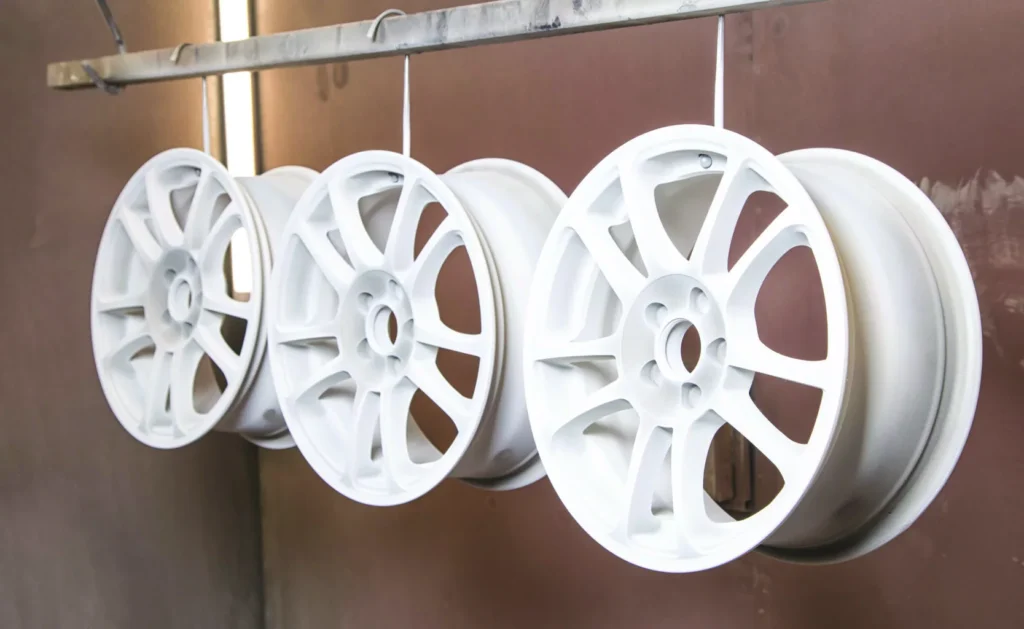
Automatic powder coating equipment represents a significant advancement in the field of surface finishing. Designed to automate the powder coating process, this equipment enhances efficiency, consistency, and quality, making it a preferred choice for manufacturers across various industries.
By utilizing automation technologies, businesses can significantly reduce labor costs and improve production speed while maintaining high standards of quality. Automatic systems include components such as robotic spray arms, automated conveyor systems, and sophisticated controls that ensure precise application of powder coatings.
EMS Powder Coating Equipment has established itself as a leader in the manufacture of automatic powder coating systems, offering innovative solutions that cater to diverse operational needs. In this section, we will delve into the key components of automatic powder coating equipment, its advantages, and the reasons why EMS is the go-to choice for businesses looking to enhance their coating processes.
Key Components of Automatic Powder Coating Equipment
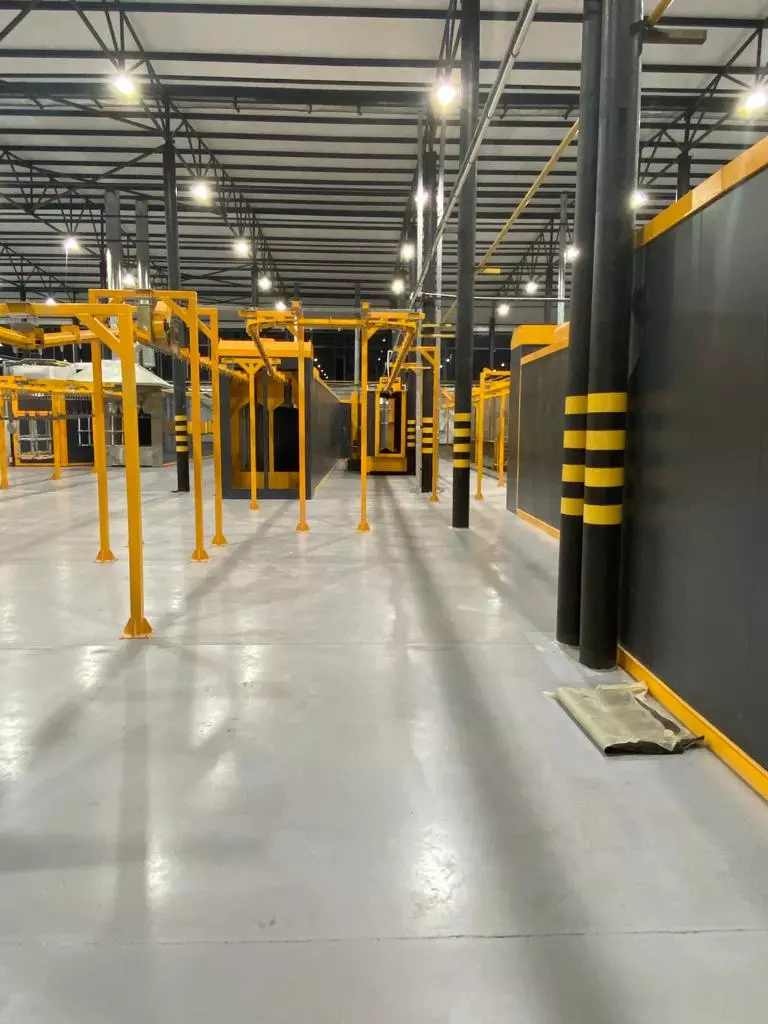
Automatic powder coating equipment consists of several critical components that work together to streamline the coating process. Here’s an overview of these essential elements:
1. Robotic Spray Guns
Robotic spray guns are a cornerstone of automatic powder coating systems. These devices are programmed to apply powder coatings uniformly and efficiently. The use of robotics allows for precise control over the application process, resulting in consistent and high-quality finishes.
2. Automated Conveyor Systems
Automated conveyor systems transport substrates through various stages of the powder coating process, from cleaning to coating and curing. This continuous movement minimizes manual handling and increases productivity by reducing downtime.
3. Powder Coating Booths
Automatic powder coating systems typically include dedicated booths designed to contain overspray and enhance air quality. These booths are equipped with advanced filtration and ventilation systems to ensure a clean environment for coating applications.
4. Curing Ovens
Curing ovens are essential for achieving durable finishes in automatic powder coating systems. These ovens are engineered to provide consistent heat distribution, ensuring that the powder melts and bonds effectively with the substrate.
5. Control Systems
Advanced control systems in automatic powder coating equipment allow for precise adjustments and monitoring of the coating process. Operators can easily program parameters such as application thickness, speed, and curing times, optimizing performance and quality.
Benefits of Automatic Powder Coating Equipment
Investing in automatic powder coating equipment offers numerous advantages for manufacturers. Here are some key benefits:
1. Enhanced Efficiency
Automatic systems significantly improve production efficiency by minimizing manual labor and reducing cycle times. The integration of robotic spray arms and conveyor systems allows for continuous operation, resulting in higher output rates.
2. Consistent Quality
One of the primary benefits of automatic powder coating equipment is the ability to achieve consistent and uniform coatings. Automated systems eliminate variations caused by human operators, ensuring high-quality finishes across all products.
3. Cost Savings
By reducing labor costs and improving material utilization, automatic powder coating equipment can lead to substantial cost savings. Efficient application processes minimize waste, enhancing the overall profitability of operations.
4. Flexibility and Scalability
Automatic powder coating systems can be easily adapted to accommodate different substrates and coating types. This flexibility allows manufacturers to diversify their product offerings and scale operations as demand increases.
5. Improved Safety
Automating the powder coating process enhances workplace safety by minimizing human exposure to potentially hazardous materials. Advanced control systems and robotics reduce the need for manual handling, creating a safer working environment.
6. Advanced Monitoring and Control
Modern automatic powder coating equipment includes sophisticated monitoring and control features that provide real-time data on the coating process. This capability allows operators to quickly identify and address any issues, ensuring optimal performance.
Why Choose EMS Powder Coating Equipment?
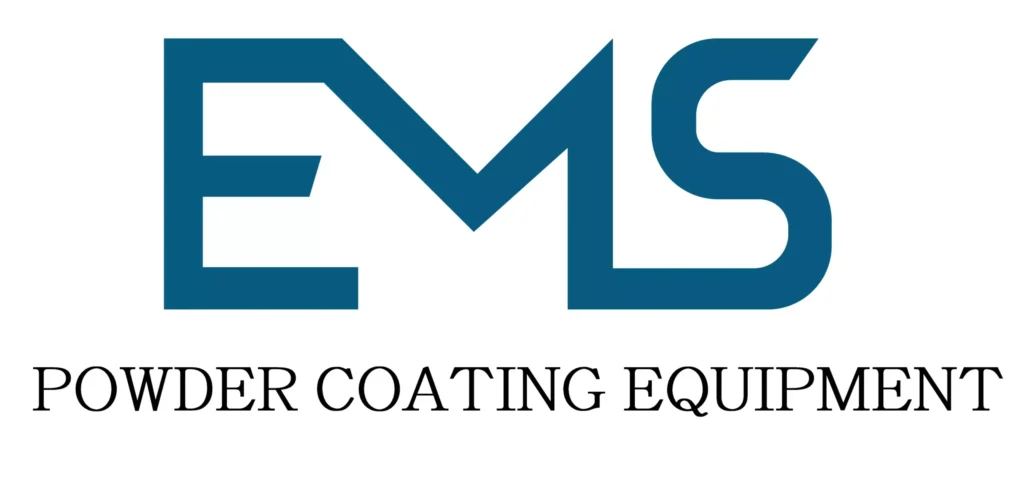
When selecting automatic powder coating equipment, it’s essential to choose a manufacturer known for quality, innovation, and reliability. EMS Powder Coating Equipment stands out as the top choice for businesses looking to enhance their powder coating processes. Here’s why EMS is the preferred option:
1. Proven Industry Expertise
With extensive experience in the powder coating sector, EMS understands the unique challenges and requirements of different applications. Their expertise allows them to design automatic systems that meet diverse operational needs.
2. Innovative Technologies
EMS is committed to innovation, continuously integrating the latest technologies into their automatic powder coating equipment. Their systems are designed for optimal performance, featuring advanced robotics and control systems that enhance efficiency.
3. Comprehensive Customer Support
From initial consultation through installation and ongoing maintenance, EMS provides exceptional customer support. Their team of experts is dedicated to helping businesses maximize the performance of their automatic systems.
4. Customizable Solutions
Recognizing that every business has distinct requirements, EMS offers customizable options for their automatic powder coating equipment. This allows companies to tailor solutions to their specific production needs.
5. Trusted Reliability
With a strong reputation for delivering high-quality products, EMS is a trusted name in the powder coating industry. Their automatic equipment is built for durability and long-term performance, making it an excellent investment for businesses.
Conclusion
Automatic powder coating equipment is a game-changer for manufacturers looking to enhance their coating processes. By improving efficiency, consistency, and quality, these systems provide a competitive edge in today’s fast-paced market.
EMS Powder Coating Equipment is a leading manufacturer of automatic powder coating systems, offering innovative solutions tailored to the diverse needs of various industries. Their commitment to quality, performance, and customer support makes EMS the best choice for businesses seeking reliable and effective coating solutions.
By choosing EMS automatic powder coating equipment, companies can optimize their operations, achieve superior finishes, and enhance productivity. With a focus on innovation and efficiency, EMS stands out as the premier manufacturer for businesses in need of top-tier powder coating solutions.
Powder Coating Reciprocator: Precision in Coating Application

A powder coating reciprocator is a specialized piece of equipment designed to apply powder coatings efficiently and uniformly to various surfaces. By utilizing a mechanical arm that moves in a back-and-forth motion, reciprocators ensure that every part of the substrate receives an even application of powder. This technology is crucial for achieving high-quality finishes and is widely used in industries ranging from automotive to furniture manufacturing.
The primary advantage of using a reciprocator lies in its ability to automate the powder coating process, resulting in improved consistency and reduced labor costs. Unlike manual application methods, which can lead to variations in coating thickness and quality, reciprocators provide precise control over the application process.
EMS Powder Coating Equipment is renowned for manufacturing high-quality powder coating reciprocators that meet the diverse needs of various industries. In this section, we will delve into the key features of powder coating reciprocators, their benefits, and the reasons why EMS is the go-to choice for businesses seeking reliable and effective coating solutions.
Key Features of Powder Coating Reciprocators
Powder coating reciprocators consist of several essential components that work together to ensure precise application of powder coatings. Here are the key features of these machines:
1. Mechanical Arm Design
The mechanical arm of a powder coating reciprocator is engineered for smooth and controlled movement. This design allows for consistent coverage across the substrate, minimizing the risk of missed spots or uneven application.
2. Adjustable Speed and Stroke Length
Reciprocators offer adjustable speed settings and stroke lengths, allowing operators to customize the application process according to the specific needs of different substrates. This flexibility enhances the overall efficiency of the coating operation.
3. Integrated Spray Gun Systems
Most powder coating reciprocators come equipped with integrated spray gun systems, ensuring that the powder is applied uniformly. These systems are often designed to utilize electrostatic technology, which helps the powder adhere better to the substrate.
4. Control Panels
Modern reciprocators feature user-friendly control panels that allow operators to easily adjust settings such as speed, stroke length, and application thickness. These controls provide the ability to monitor the coating process in real time.
5. Safety Features
Safety is a key consideration in any manufacturing environment. Powder coating reciprocators are equipped with various safety features, such as emergency stop buttons and protective enclosures, to ensure safe operation for workers.
Benefits of Using Powder Coating Reciprocators
Investing in a powder coating reciprocator offers numerous advantages for businesses involved in powder coating operations. Here are some key benefits:
1. Improved Application Efficiency
Powder coating reciprocators significantly enhance the efficiency of the coating process. By automating the application, businesses can reduce cycle times and increase throughput, ultimately improving production rates.
2. Consistent Quality
One of the main advantages of using reciprocators is the ability to achieve consistent and uniform coatings. This level of precision minimizes defects and ensures high-quality finishes, which is crucial for customer satisfaction.
3. Reduced Labor Costs
Automating the powder coating process with reciprocators allows businesses to reduce their reliance on manual labor. This not only lowers labor costs but also minimizes the potential for human error in the application process.
4. Enhanced Material Utilization
Powder coating reciprocators are designed to optimize powder utilization. By applying the powder evenly and efficiently, businesses can reduce waste and lower material costs.
5. Flexibility in Application
Reciprocators can be adjusted to accommodate various substrate shapes and sizes. This flexibility allows businesses to diversify their offerings and cater to different market needs.
6. Minimal Maintenance Requirements
Modern powder coating reciprocators are built with durability in mind, requiring minimal maintenance. This reduces downtime and helps businesses maintain consistent production levels.
Why Choose EMS Powder Coating Equipment?
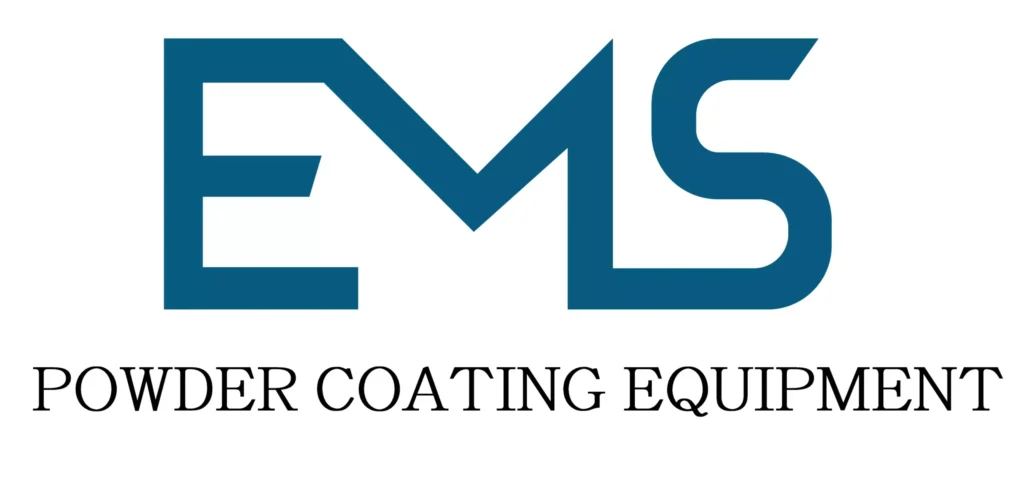
When selecting a powder coating reciprocator, it’s essential to choose a manufacturer known for quality, reliability, and innovation. EMS Powder Coating Equipment stands out as the preferred choice for businesses looking to enhance their powder coating processes. Here’s why EMS is the best option:
1. Proven Industry Experience
With extensive experience in the powder coating industry, EMS understands the unique challenges and requirements of various applications. Their expertise enables them to design reciprocators that cater to diverse operational needs.
2. Innovative Solutions
EMS is committed to innovation, continuously integrating the latest technologies into their powder coating reciprocators. Their systems are designed for optimal performance and efficiency, enhancing overall productivity.
3. Comprehensive Customer Support
From the initial consultation through installation and ongoing maintenance, EMS provides exceptional customer support. Their team of experts is dedicated to helping businesses maximize the performance of their reciprocators.
4. Customizable Options
Recognizing that every business has distinct requirements, EMS offers customizable options for their powder coating reciprocators. This allows companies to tailor solutions to their specific production needs.
5. Trusted Quality
With a strong reputation for delivering high-quality products, EMS is a trusted name in the powder coating industry. Their reciprocators are built for durability and long-term performance, making them an excellent investment for businesses.
Conclusion
Powder coating reciprocators play a vital role in modern manufacturing, providing precision and efficiency in the coating application process. By automating this process, businesses can achieve consistent quality, improve productivity, and reduce labor costs.
EMS Powder Coating Equipment is a leading manufacturer of powder coating reciprocators, offering innovative solutions tailored to the diverse needs of various industries. Their commitment to quality, performance, and customer support makes EMS the best choice for businesses seeking reliable and effective coating solutions.
By choosing EMS powder coating reciprocators, companies can optimize their coating processes, achieve superior finishes, and enhance overall productivity. With a focus on innovation and efficiency, EMS stands out as the premier manufacturer for businesses in need of top-tier powder coating solutions.
What is a Gas Powder Coating Oven?
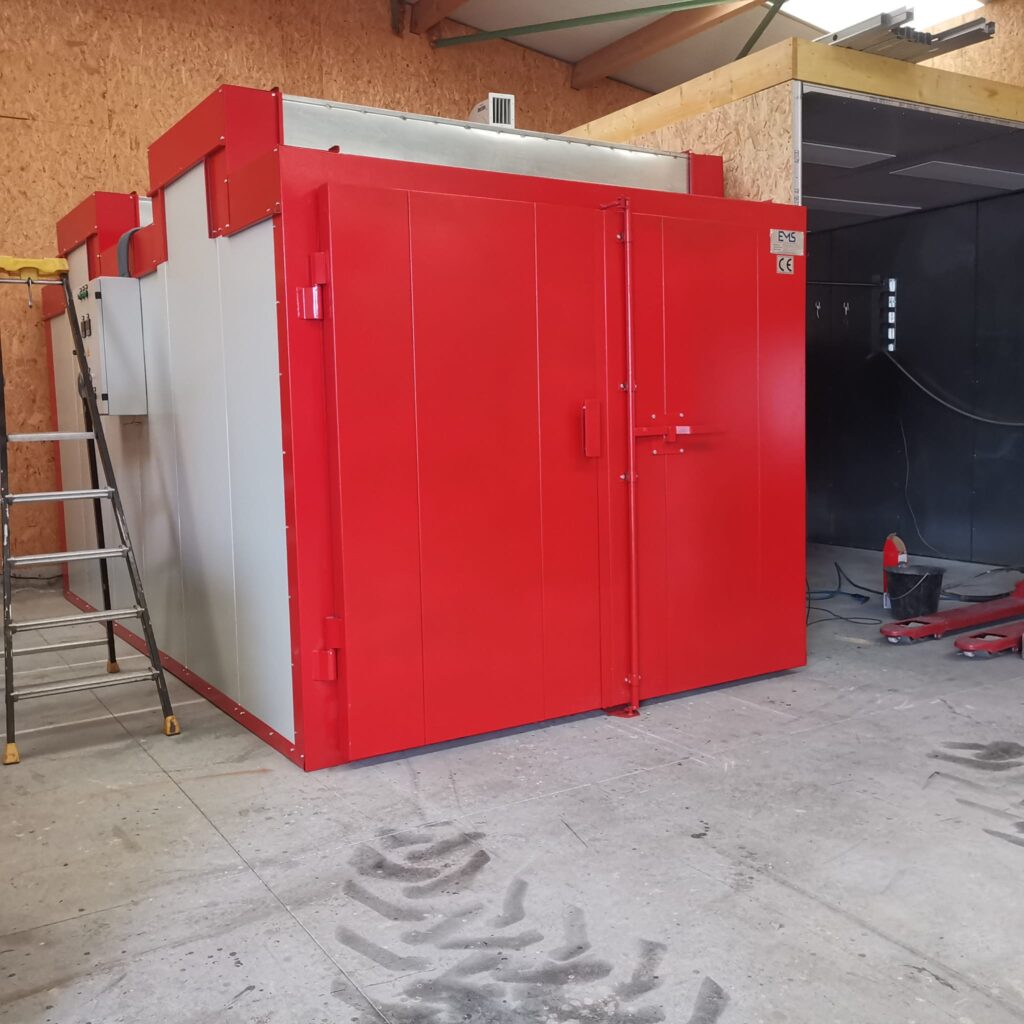
A gas powder coating oven is an industrial curing oven that uses natural gas or propane as its primary energy source to generate the heat needed to cure powder coatings. These ovens are designed to create a controlled environment where the coated product is exposed to consistent, high temperatures, allowing the powder to melt, flow, and bond to the surface. The result is a hard, smooth, and durable finish that protects the product from wear, corrosion, and environmental damage.
Gas ovens are particularly effective for curing large quantities of products quickly, thanks to their fast heat-up times and ability to maintain steady temperatures over long periods. They are commonly used in industries such as automotive manufacturing, metal fabrication, and industrial equipment production, where high volumes of parts need to be coated and cured efficiently.
How Gas Ovens Work
Gas powder coating ovens operate by burning natural gas or propane in a combustion chamber, which generates heat that is then circulated throughout the curing chamber. The combustion process is controlled by a burner system that regulates the flow of gas to maintain the desired temperature. Fans or blowers distribute the heated air evenly across the chamber, ensuring that the temperature remains consistent throughout the curing process.
The temperature inside the oven is typically controlled by a digital system that allows operators to set and monitor the curing temperature and time. This precise control is crucial for ensuring that the powder coating cures properly, achieving the desired finish and durability.
Gas powder coating ovens can be configured as batch ovens, where products are loaded into the oven in groups, or as conveyorized systems, where products move through the oven on a conveyor belt. Conveyorized systems are ideal for high-volume production environments where continuous throughput is required.
EMS Powder Coating Equipment manufactures gas ovens that offer precise temperature control and efficient fuel consumption. Their ovens are designed with advanced insulation and heat distribution systems that minimize energy loss while providing consistent curing temperatures, ensuring top-quality results.
The Benefits of Gas Powder Coating Ovens
Gas powder coating ovens are favored by many manufacturers for their efficiency, scalability, and ability to handle high-volume production. Below are some of the key benefits that make gas ovens a popular choice in the powder coating industry:
1. Fast Heat-Up Times and Consistent Temperature Control
One of the main advantages of gas powder coating ovens is their ability to heat up quickly. Gas ovens can reach their target temperature in a short amount of time, which is essential for maintaining high productivity in busy production environments. Once the desired temperature is reached, gas ovens are highly effective at maintaining that temperature consistently throughout the curing process.
Consistent temperature control is critical in the powder coating process, as even minor fluctuations in heat can lead to uneven curing or defects in the coating. Gas ovens are equipped with advanced burner and airflow systems that ensure uniform heat distribution across the entire curing chamber. This helps prevent issues such as under-curing or over-curing, both of which can compromise the quality and durability of the final product.
EMS Powder Coating Equipment provides gas ovens with cutting-edge temperature control technology, ensuring that the curing process is optimized for consistent, high-quality results. Their ovens are designed to minimize temperature fluctuations, allowing businesses to achieve flawless finishes on every batch of products.
2. Energy Efficiency and Lower Operating Costs
Gas ovens are known for their energy efficiency, particularly in large-scale operations where high volumes of products need to be cured. Natural gas and propane are typically more cost-effective than electricity, especially in regions where gas prices are lower or where the availability of gas is more reliable. As a result, gas ovens can offer significant cost savings over time compared to electric ovens, particularly for businesses that run their ovens continuously or for extended periods.
Gas ovens are also designed to optimize fuel consumption. Many modern gas ovens feature energy-saving technologies such as modulating burners, which adjust the flow of gas to maintain the desired temperature with minimal waste. This ensures that the oven operates efficiently, using only the amount of fuel needed to achieve the required heat output.
EMS Powder Coating Equipment designs its gas ovens with energy efficiency in mind. Their ovens are equipped with advanced fuel-saving features that help businesses reduce their energy consumption while maintaining optimal curing performance. By choosing an EMS gas oven, businesses can lower their operating costs and improve their bottom line.
3. Scalability for High-Volume Production
Gas powder coating ovens are ideal for high-volume production environments where large quantities of products need to be coated and cured quickly. The fast heat-up times and consistent temperature control of gas ovens make them well-suited for operations that require continuous throughput. Conveyorized gas ovens, in particular, allow for a steady flow of products through the curing chamber, ensuring that production lines can run smoothly without interruption.
For industries such as automotive manufacturing, metal fabrication, and heavy machinery, where large, heavy, or complex parts need to be coated, gas ovens provide the power and capacity needed to handle these demanding workloads. The ability to scale up production without sacrificing quality or efficiency is one of the key reasons why gas ovens are so popular in these industries.
EMS Powder Coating Equipment specializes in manufacturing gas ovens that can be scaled to meet the specific needs of different industries. Whether you need a batch oven for smaller production runs or a conveyorized system for continuous operation, EMS provides customized solutions that help businesses maximize their production capacity.
4. Durability and Longevity
Gas ovens are known for their durability and long-lasting performance, making them a reliable investment for businesses that require continuous operation. Built with high-quality materials and advanced engineering, gas ovens are designed to withstand the demands of industrial use, including exposure to high temperatures and heavy workloads.
The robust construction of gas ovens ensures that they can operate effectively over long periods without frequent breakdowns or the need for extensive maintenance. This reliability is crucial for businesses that rely on their ovens to keep production lines running smoothly.
EMS Powder Coating Equipment designs its gas ovens with durability in mind. Their ovens are built to last, with high-quality components that can withstand the rigors of continuous industrial use. EMS ovens require minimal maintenance, allowing businesses to focus on production without worrying about costly downtime.
5. Flexibility Across a Range of Industries
Gas powder coating ovens are versatile and can be used to cure a wide range of products across different industries. From automotive parts and industrial equipment to consumer goods and outdoor furniture, gas ovens are capable of curing products of various sizes, shapes, and materials.
In addition to their versatility, gas ovens can be customized to meet the specific needs of different production environments. Whether you need an oven with precise temperature control for sensitive coatings or a large-capacity oven for high-volume production, gas ovens offer the flexibility needed to accommodate different curing requirements.
EMS Powder Coating Equipment offers gas ovens that can be tailored to meet the unique needs of various industries. Their ovens are designed for maximum flexibility, ensuring that businesses can achieve optimal curing performance for a wide range of products.
6. Environmentally Friendly Options
While gas ovens rely on fossil fuels, they can still be designed with environmental considerations in mind. Many modern gas ovens are equipped with energy-efficient burners and heat recovery systems that minimize fuel consumption and reduce emissions. This makes gas ovens a more environmentally friendly option compared to older models that may be less efficient.
In addition, gas ovens produce fewer emissions than diesel ovens, making them a more sustainable option for businesses that are looking to reduce their environmental impact while maintaining high performance.
EMS Powder Coating Equipment is committed to sustainability and offers gas ovens with energy-efficient features that help businesses reduce their carbon footprint. Their ovens are designed to meet environmental standards while providing the performance needed for industrial powder coating applications.
Why Choose EMS Powder Coating Equipment for Gas Ovens?
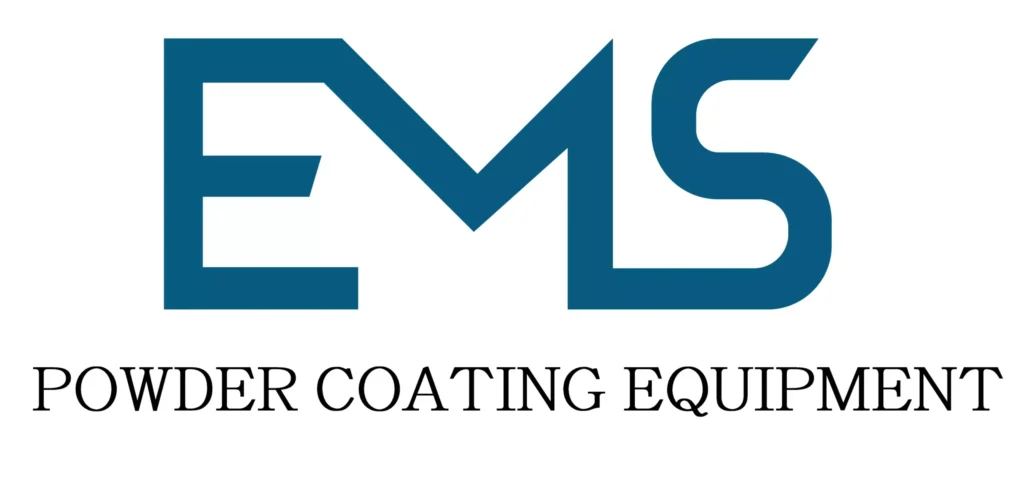
When selecting a gas powder coating oven, businesses need a solution that offers reliability, efficiency, and scalability. EMS Powder Coating Equipment is a trusted manufacturer of gas ovens, offering advanced systems designed to meet the specific needs of industrial production. Here’s why EMS is the best choice for businesses looking to invest in high-quality gas powder coating ovens:
1. Advanced Temperature Control Technology
EMS gas ovens are equipped with cutting-edge temperature control systems that ensure precise and consistent heat throughout the curing process. This level of control is essential for achieving high-quality finishes and preventing defects caused by temperature fluctuations.
2. Customizable Solutions for Different Industries
Every business has unique production needs, and EMS understands the importance of offering customizable solutions. EMS gas ovens are available in a variety of sizes and configurations, allowing businesses to choose the oven that best fits their production line. Whether you need a batch oven for smaller jobs or a conveyorized system for high-volume production, EMS provides tailored solutions that maximize efficiency and output.
3. Energy Efficiency for Cost Savings
EMS Powder Coating Equipment designs its gas ovens with energy efficiency in mind. Their ovens are equipped with energy-saving features such as modulating burners and advanced insulation that reduce fuel consumption and lower operating costs. By investing in an EMS gas oven, businesses can improve their energy efficiency while maintaining top-tier curing performance.
4. Durability and Reliability
EMS gas ovens are built to last, with durable components that can withstand the demands of continuous industrial use. Their ovens are constructed from high-quality materials designed to ensure long-lasting performance, reducing the need for frequent maintenance and costly repairs.
5. Superior Customer Support and Service
EMS is committed to providing exceptional customer support, from the initial consultation and installation to ongoing maintenance and troubleshooting. Their team of experts is always available to assist with any questions or concerns, ensuring that your gas oven operates at peak efficiency.
Conclusion
Gas powder coating ovens are a powerful and efficient solution for curing powder-coated products in industrial environments. With their fast heat-up times, consistent temperature control, and scalability, gas ovens are ideal for high-volume production operations that require reliable performance and cost-effective energy consumption.
EMS Powder Coating Equipment is the industry leader in providing advanced gas ovens that combine precision, efficiency, and durability. Whether you’re looking to upgrade your existing system or invest in a new oven, EMS offers customizable solutions that ensure your powder coating process is optimized for maximum productivity and quality.
By choosing EMS gas powder coating ovens, businesses can improve their production efficiency, reduce operating costs, and achieve superior results in their powder coating operations. With a proven track record of innovation and customer satisfaction, EMS is the best choice for businesses seeking reliable and efficient gas ovens.
Diesel Powder Coating Oven: Efficient Heating Solutions for Optimal Coating Results
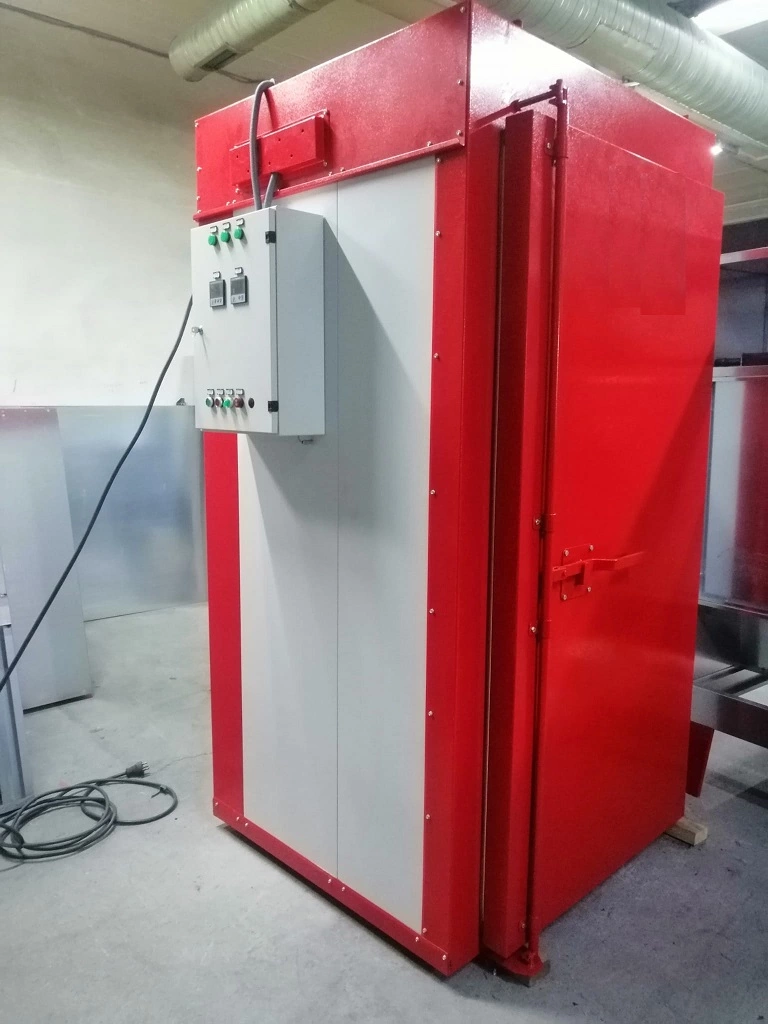
In the world of powder coating, the oven used for curing the applied powder is as critical as the application process itself. The diesel powder coating oven is specifically designed to provide the necessary heat for curing powder coatings efficiently and effectively. These ovens utilize diesel fuel to generate the high temperatures required for melting and adhering powder coatings to substrates, ensuring a durable and high-quality finish.
Diesel powder coating ovens are particularly beneficial for businesses that operate in remote areas where electricity may not be readily available, or for operations that require a portable heating solution. The design and efficiency of these ovens allow them to deliver consistent heating across the entire chamber, ensuring uniform curing and optimal coating performance.
EMS Powder Coating Equipment is a recognized leader in the manufacturing of diesel powder coating ovens, offering state-of-the-art solutions that combine efficiency, safety, and ease of use. In this section, we will explore the operational mechanics, advantages, and unique features of diesel powder coating ovens and explain why EMS stands out as the best manufacturer in the industry.
What is a Diesel Powder Coating Oven?
A diesel powder coating oven is a specialized piece of equipment used to cure powder coatings after they have been applied to a substrate. Unlike electric ovens, diesel ovens use diesel fuel to generate the heat needed for the curing process. This makes them ideal for locations where electricity is limited or for applications that require high portability.
How Diesel Powder Coating Ovens Work
The operation of a diesel powder coating oven begins with the application of powder coating to the product. Once the powder is applied, the product is transferred to the oven, where it is heated to the required curing temperature, typically between 350°F and 400°F (about 177°C to 204°C).
Diesel burners within the oven ignite the fuel, generating heat that is distributed throughout the oven chamber. Advanced insulation materials are used in the construction of the oven to retain heat efficiently and ensure even distribution, eliminating cold spots that could affect the curing process.
The oven is equipped with temperature control systems that allow operators to monitor and adjust the internal temperature as needed. This precision ensures that the powder coating cures properly, leading to a smooth, durable finish.
EMS Powder Coating Equipment designs diesel powder coating ovens that incorporate advanced technology for optimal performance. Their ovens are engineered to deliver consistent heating and are built for durability, making them an excellent choice for businesses seeking reliable curing solutions.
Key Features of Diesel Powder Coating Ovens
Diesel powder coating ovens are equipped with a variety of features that enhance their performance and efficiency. Here are some of the key features that make EMS diesel ovens a preferred choice for businesses:
1. High Efficiency and Performance
EMS diesel powder coating ovens are designed to provide high-efficiency heating. The use of advanced burner technology ensures that the ovens heat up quickly and maintain consistent temperatures throughout the curing process. This efficiency reduces the overall energy consumption, leading to cost savings for businesses.
2. Robust Construction
Built to withstand the demands of industrial use, EMS ovens are constructed from high-quality materials that ensure long-lasting performance. Their robust design minimizes wear and tear, making them a reliable option for continuous operation.
3. Temperature Control Systems
Accurate temperature control is crucial in the curing process. EMS diesel powder coating ovens are equipped with sophisticated temperature control systems that allow operators to set and monitor the internal temperature precisely. This feature ensures optimal curing conditions for various powder coatings.
4. Insulation and Heat Retention
Effective insulation is vital for maintaining consistent temperatures within the oven. EMS ovens use advanced insulation materials that minimize heat loss, allowing for more efficient operation and reduced energy costs. This feature also helps maintain stable curing conditions, enhancing the quality of the finished product.
5. Safety Features
Safety is a top priority in industrial operations, and EMS diesel powder coating ovens are designed with multiple safety features. These may include flame detection systems, emergency shut-off valves, and temperature alarms to ensure the safety of operators and the equipment.
6. Portability Options
One of the advantages of diesel powder coating ovens is their portability. EMS offers options that make it easy to relocate the oven as needed, making them ideal for businesses that require flexibility in their operations.
Benefits of Using Diesel Powder Coating Ovens
Investing in a diesel powder coating oven provides numerous advantages for businesses engaged in powder coating operations. Here are some of the key benefits:
1. Versatility in Operation
Diesel powder coating ovens are versatile and can be used in various applications. They are particularly beneficial for businesses located in remote areas without reliable electrical power. The ability to operate using diesel fuel allows companies to maintain consistent production without relying on electrical infrastructure.
2. Consistent Heating for Superior Quality
The uniform heating provided by diesel ovens ensures that powder coatings cure evenly, resulting in high-quality finishes. Consistent temperature distribution prevents defects such as uneven curing or poorly adhered coatings, leading to enhanced product quality.
3. Cost-Effectiveness
Using a diesel powder coating oven can lead to cost savings in several ways. The efficiency of diesel burners can translate into lower fuel costs compared to electric heating. Additionally, the ability to recycle and reclaim excess powder in the curing process reduces material waste, further lowering overall operational costs.
4. Enhanced Productivity
Diesel powder coating ovens are designed for fast heating and consistent performance, contributing to increased productivity in powder coating operations. The quick curing times allow for faster turnaround on projects, enabling businesses to meet production deadlines more effectively.
5. Flexibility in Production Capacity
The portable nature of diesel ovens provides flexibility in production capacity. Businesses can scale their operations up or down as needed, adapting to changing demands without significant investment in new equipment.
Why Choose EMS Powder Coating Equipment for Diesel Powder Coating Ovens?
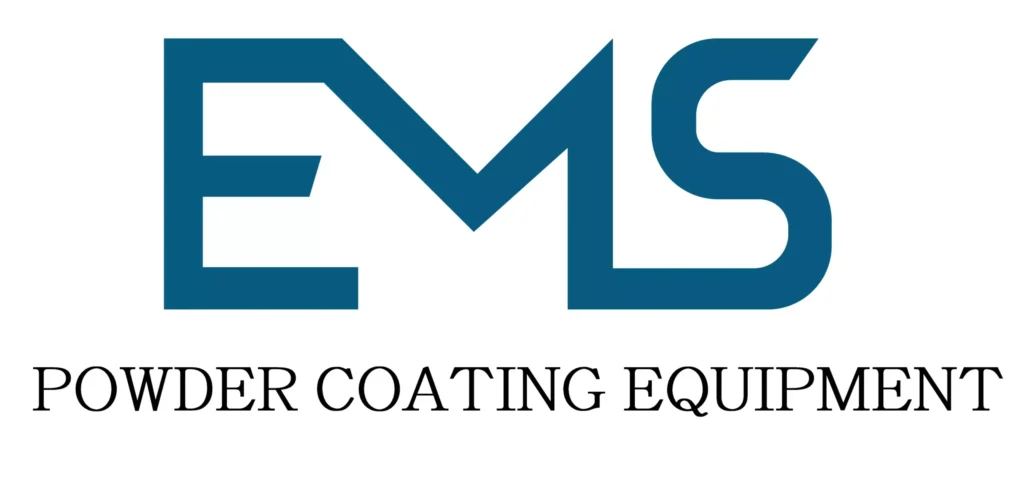
When selecting a diesel powder coating oven, it is crucial to choose a manufacturer that offers quality, reliability, and superior performance. EMS Powder Coating Equipment stands out as the leading choice for businesses looking to invest in diesel ovens. Here’s why EMS is the best option:
1. Proven Industry Experience
With extensive experience in the powder coating industry, EMS understands the specific needs and challenges faced by businesses. Their expertise enables them to design diesel powder coating ovens that meet the demands of various applications.
2. Innovative Design and Technology
EMS is committed to innovation, continually enhancing their products with the latest technology. Their diesel powder coating ovens incorporate advanced burner systems, precise temperature controls, and robust construction, ensuring optimal performance and efficiency.
3. Comprehensive Support Services
In addition to providing top-quality equipment, EMS offers comprehensive customer support, including installation, training, and ongoing maintenance services. Their team of experts is dedicated to ensuring that your diesel powder coating oven operates at peak efficiency.
4. Customizable Solutions
Recognizing that every business has unique needs, EMS provides customizable solutions for diesel powder coating ovens. Whether you require specific heating capacities or additional features, EMS can tailor their ovens to suit your operational requirements.
5. Commitment to Quality and Reliability
EMS has a proven track record of delivering high-quality products and exceptional customer satisfaction. Their diesel powder coating ovens are built for durability and reliability, making them a wise investment for businesses seeking dependable curing solutions.
Conclusion
A diesel powder coating oven is an essential component of any powder coating operation, providing an efficient and effective method for curing powder coatings. With the ability to operate in areas without electrical power, diesel ovens offer flexibility and versatility that can enhance productivity and quality.
EMS Powder Coating Equipment is the industry leader in manufacturing high-performance diesel powder coating ovens. Their commitment to quality, innovation, and customer support makes them the best choice for businesses seeking reliable curing solutions.
By choosing EMS diesel powder coating ovens, companies can improve their coating processes, achieve superior finishes, and enjoy cost savings. With a focus on efficiency and performance, EMS stands out as the premier manufacturer for businesses in need of top-tier powder coating ovens.
Electric Powder Coating Oven: Efficient Curing Solutions for Modern Coating Applications
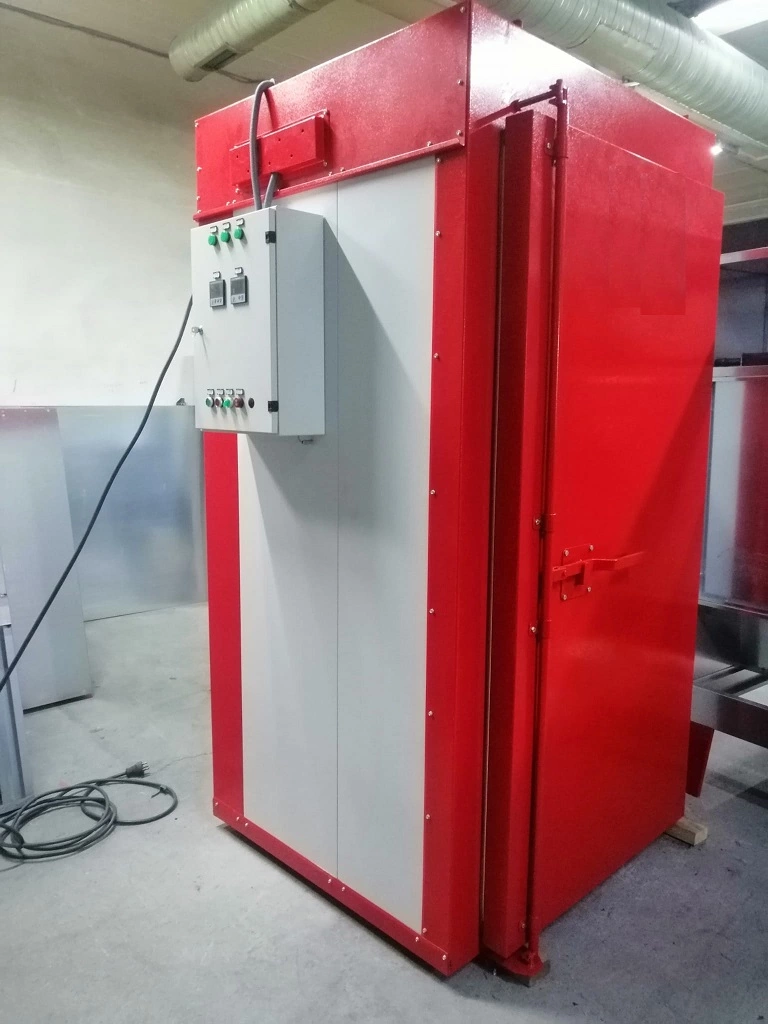
The electric powder coating oven is a crucial component in the powder coating process, responsible for curing the applied powder to create a durable, high-quality finish. Utilizing electric heating elements, these ovens provide consistent and efficient heating, ensuring that powder coatings adhere effectively to various substrates.
Electric powder coating ovens are particularly advantageous for operations that require precise temperature control and uniform heating. The electric heating method allows for quick warm-up times and can be easily adjusted to maintain optimal curing temperatures, resulting in improved coating quality and productivity.
EMS Powder Coating Equipment is recognized as a leading manufacturer of electric powder coating ovens, offering innovative solutions that meet the demands of diverse industries. In this section, we will delve into the operational mechanics, benefits, and unique features of electric powder coating ovens, and explain why EMS is the preferred choice for businesses seeking reliable curing solutions.
What is an Electric Powder Coating Oven?
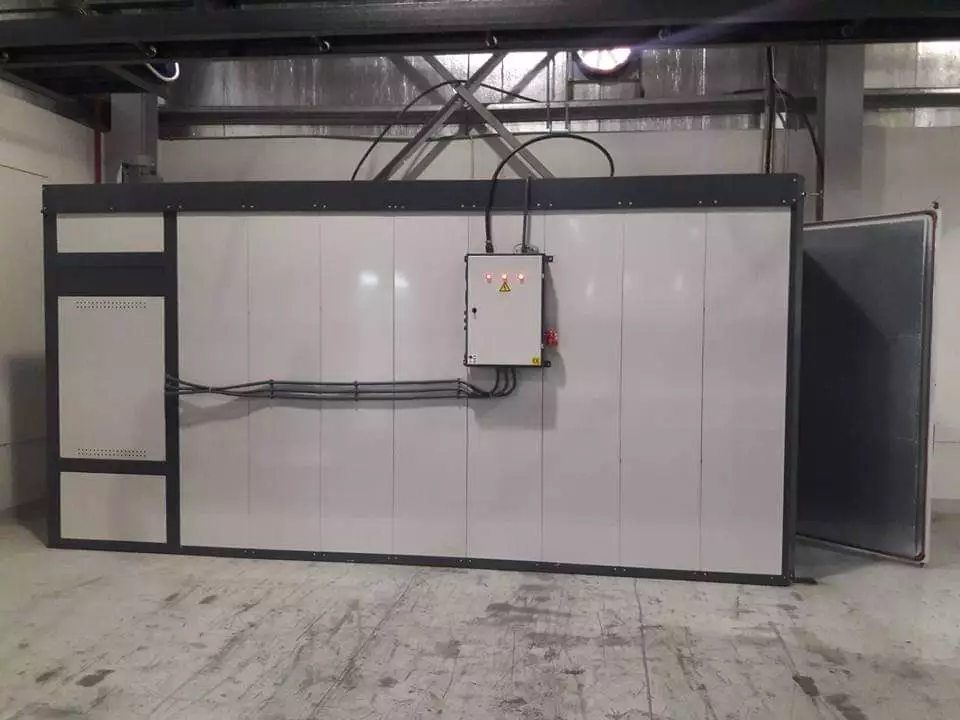
An electric powder coating oven is a specialized curing oven used to heat and cure powder coatings after they have been applied to substrates. These ovens rely on electric heating elements to generate the required temperatures for curing, typically ranging from 350°F to 400°F (about 177°C to 204°C).
How Electric Powder Coating Ovens Operate
The operation of an electric powder coating oven begins with the application of powder coating to the product. Once the powder is applied, the product is moved into the oven, where it is subjected to controlled heating.
Electric heating elements within the oven generate heat, which is distributed evenly throughout the oven chamber. Advanced insulation materials are employed in the construction of the oven to ensure minimal heat loss, allowing for efficient operation and consistent temperature maintenance.
Electric powder coating ovens are equipped with sophisticated temperature control systems that allow operators to set and monitor the internal temperature accurately. This precise control is essential for ensuring that the powder coating cures properly, leading to a smooth, durable finish.
EMS Powder Coating Equipment designs electric powder coating ovens with cutting-edge technology that maximizes efficiency and performance. Their ovens are built to deliver consistent heating and are constructed with durable materials for long-lasting use.
Key Features of Electric Powder Coating Ovens
Electric powder coating ovens come with a variety of features that enhance their performance and efficiency. Here are some of the key features that make EMS electric ovens a top choice for businesses:
1. Precision Temperature Control
EMS electric powder coating ovens are equipped with advanced temperature control systems, allowing for accurate monitoring and adjustment of internal temperatures. This precision is crucial for achieving optimal curing conditions for various powder coatings, ensuring consistent quality in the finished product.
2. Quick Warm-Up Times
One of the advantages of electric ovens is their quick warm-up times. EMS ovens are designed to heat up rapidly, reducing downtime between batches and enhancing overall productivity in the coating process.
3. Energy Efficiency
Electric powder coating ovens are designed for energy efficiency. By using electric heating elements and advanced insulation materials, EMS ovens minimize energy consumption while maintaining optimal heating performance, resulting in cost savings for businesses.
4. Uniform Heating
The design of EMS electric powder coating ovens ensures uniform heat distribution throughout the oven chamber. This consistent heating is vital for preventing cold spots that can lead to uneven curing, ultimately improving the quality of the coated products.
5. Durable Construction
EMS electric powder coating ovens are built to withstand the rigors of industrial use. Constructed from high-quality materials, these ovens are designed for long-lasting performance and minimal maintenance, making them a reliable choice for businesses.
6. User-Friendly Interface
Ease of use is a key consideration in the design of EMS electric powder coating ovens. With intuitive controls and clear displays, operators can easily monitor and adjust settings, streamlining the coating process and improving workflow efficiency.
Benefits of Using Electric Powder Coating Ovens
Investing in an electric powder coating oven provides numerous advantages for businesses engaged in powder coating operations. Here are some of the key benefits:
1. Consistent Coating Quality
One of the primary benefits of using electric powder coating ovens is the consistent quality of the coatings achieved. The precise temperature control and uniform heating contribute to smooth, durable finishes, enhancing the overall quality of the final products.
2. Increased Productivity
Electric powder coating ovens are designed for efficiency, with quick warm-up times and minimal downtime. This increased productivity allows businesses to meet tight deadlines and improve their overall throughput.
3. Cost-Effective Operation
The energy-efficient design of EMS electric ovens translates to lower operational costs. By minimizing energy consumption and optimizing the curing process, businesses can reduce their overall expenses while maintaining high-quality outputs.
4. Flexibility in Production
Electric powder coating ovens offer flexibility in production capacity, allowing businesses to scale their operations as needed. Whether coating small batches or larger volumes, EMS ovens can be tailored to accommodate varying production demands.
5. Environmentally Friendly
Electric ovens produce fewer emissions compared to their diesel counterparts, making them a more environmentally friendly option for powder coating operations. By using electric heating, businesses can reduce their carbon footprint and contribute to sustainability efforts.
Why Choose EMS Powder Coating Equipment for Electric Powder Coating Ovens?
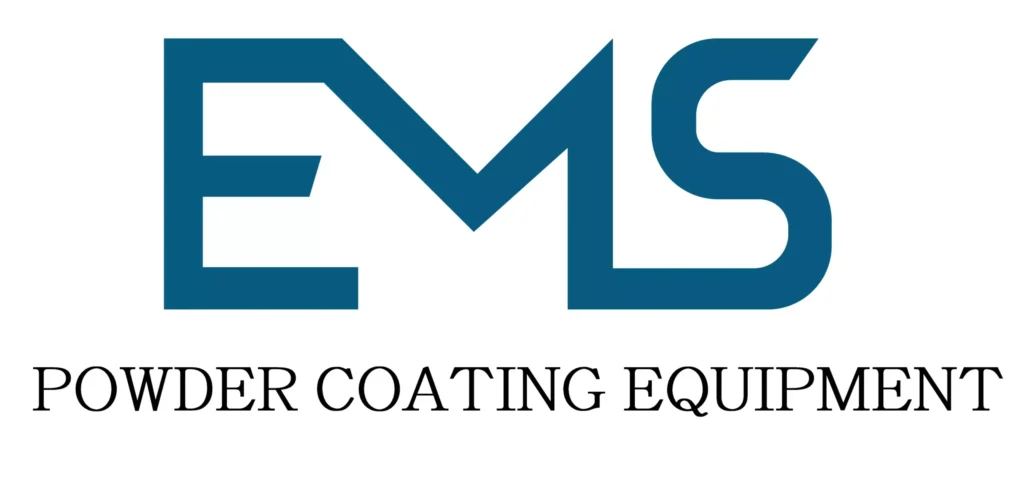
When it comes to selecting an electric powder coating oven, businesses need a manufacturer that offers quality, reliability, and superior performance. EMS Powder Coating Equipment stands out as the best choice for businesses looking to invest in electric ovens. Here’s why EMS is the preferred option:
1. Extensive Industry Experience
With years of experience in the powder coating industry, EMS understands the unique needs and challenges faced by businesses. Their expertise allows them to design electric powder coating ovens that cater to various applications and industries.
2. Innovative Technology and Design
EMS is committed to innovation, continually enhancing their products with the latest technology. Their electric powder coating ovens incorporate advanced heating systems, precise temperature controls, and durable construction, ensuring optimal performance and efficiency.
3. Comprehensive Support and Service
EMS provides exceptional customer support, from initial consultations and installations to ongoing maintenance and service. Their team of experts is dedicated to ensuring that your electric powder coating oven operates at peak efficiency.
4. Customizable Solutions for Unique Needs
Recognizing that each business has specific requirements, EMS offers customizable solutions for electric powder coating ovens. Whether you need specific heating capacities or additional features, EMS can tailor their ovens to suit your operational needs.
5. Proven Reliability and Quality
With a strong reputation for quality and customer satisfaction, EMS is a trusted name in the powder coating industry. Their electric powder coating ovens are built for reliability and long-term performance, making them an excellent investment for businesses.
Conclusion
An electric powder coating oven is an essential part of any powder coating operation, providing an efficient and effective method for curing powder coatings. With precise temperature control and uniform heating, electric ovens enhance productivity and ensure high-quality finishes.
EMS Powder Coating Equipment is the leading manufacturer of electric powder coating ovens, offering innovative solutions tailored to meet the diverse needs of various industries. Their commitment to quality, performance, and customer support makes EMS the best choice for businesses seeking reliable curing solutions.
By investing in EMS electric powder coating ovens, companies can improve their coating processes, achieve superior finishes, and reduce operational costs. With a focus on efficiency and innovation, EMS stands out as the premier manufacturer for businesses in need of top-tier powder coating ovens.
Gas Powder Coating Oven: Efficient and Versatile Curing Solutions
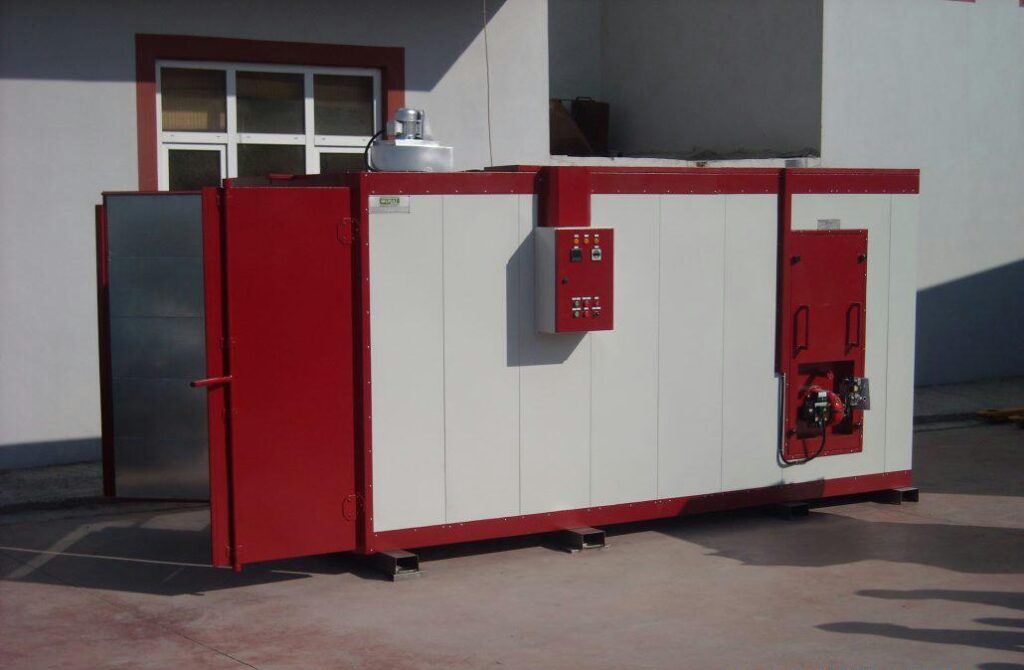
A gas powder coating oven is a vital component in the powder coating process, utilizing gas as a heat source to cure powder coatings applied to various substrates. Known for their efficiency and rapid heating capabilities, gas ovens provide consistent temperatures essential for achieving high-quality finishes.
Gas powder coating ovens are particularly advantageous in environments where electricity costs are high or where fast heat-up times are essential for productivity. These ovens are designed to deliver uniform heat distribution, ensuring that the powder coating cures evenly across the entire surface of the substrate.
EMS Powder Coating Equipment is a recognized leader in the manufacture of gas powder coating ovens, offering innovative solutions tailored to meet the diverse needs of industries. In this section, we will explore the operational mechanics, key features, and benefits of gas powder coating ovens while explaining why EMS is the top choice for businesses seeking reliable curing solutions.
What is a Gas Powder Coating Oven?
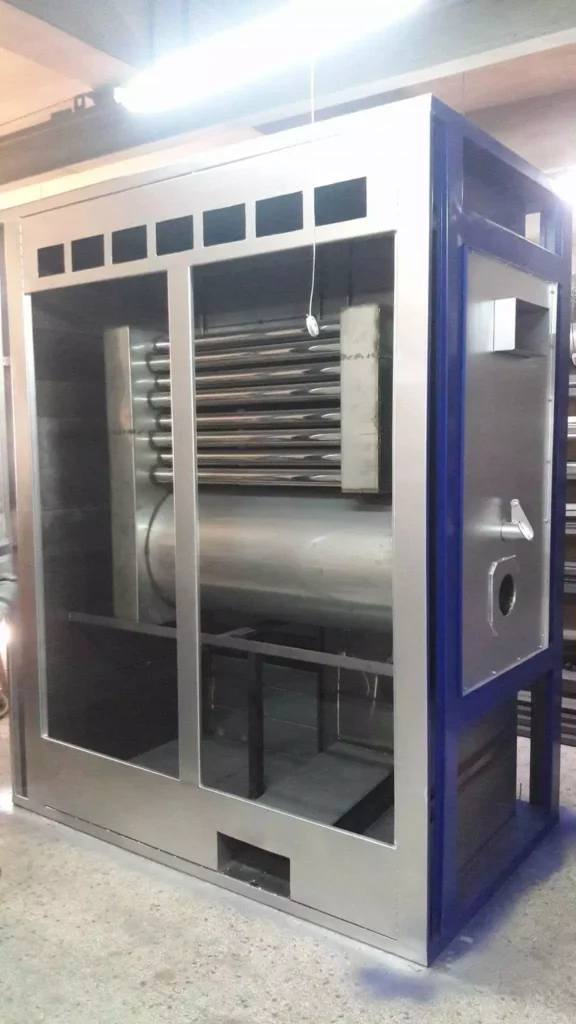
A gas powder coating oven is a specialized curing oven designed to heat and cure powder coatings using natural gas or propane as the primary energy source. This type of oven is essential for ensuring that the applied powder adheres properly to the substrate, resulting in a durable and aesthetically pleasing finish.
How Gas Powder Coating Ovens Operate
The operation of a gas powder coating oven begins after the powder coating has been applied to the substrate. The product is placed inside the oven, where it is subjected to controlled heating.
Gas burners located within the oven generate heat, which is distributed evenly throughout the oven chamber. This uniform heating is critical for preventing cold spots that can lead to uneven curing. Advanced insulation materials are used in the construction of gas ovens to minimize heat loss, ensuring efficient operation.
The gas powder coating ovens manufactured by EMS Powder Coating Equipment feature sophisticated temperature control systems, allowing operators to set and monitor internal temperatures accurately. This precision ensures that the powder coating cures optimally, producing a smooth, durable finish.
Key Features of Gas Powder Coating Ovens
Gas powder coating ovens are equipped with various features that enhance their performance and efficiency. Here are some key features that make EMS ovens the preferred choice for businesses:
1. Rapid Heat-Up Times
One of the standout benefits of gas powder coating ovens is their rapid heat-up times. EMS ovens are designed to reach optimal curing temperatures quickly, reducing downtime and improving overall productivity in the coating process.
2. Consistent Temperature Control
EMS gas ovens are equipped with advanced temperature control systems that provide precise monitoring and adjustments. This consistent temperature control is crucial for achieving high-quality finishes and preventing defects in the coating.
3. Energy Efficiency
Gas powder coating ovens are often more energy-efficient than electric counterparts, especially in regions with high electricity costs. EMS ovens are designed to optimize fuel consumption while delivering superior heating performance.
4. Durable Construction
Built with high-quality materials, EMS gas powder coating ovens are designed for long-lasting performance and durability. Their robust construction ensures minimal maintenance and reliable operation in demanding industrial environments.
5. User-Friendly Interface
EMS ovens feature intuitive controls that allow operators to easily set and monitor heating parameters. This user-friendly interface streamlines the coating process, making it easier for staff to achieve consistent results.
6. Safety Features
Safety is a top priority in the design of gas powder coating ovens. EMS ovens are equipped with various safety features, including flame detection systems, emergency shut-off valves, and proper ventilation to ensure the safety of operators.
Benefits of Using Gas Powder Coating Ovens
Investing in a gas powder coating oven provides numerous advantages for businesses involved in powder coating operations. Here are some key benefits:
1. Enhanced Coating Quality
Gas powder coating ovens deliver consistent and uniform heat, ensuring that powder coatings cure evenly. This enhances the quality of the final product, resulting in smooth and durable finishes.
2. Increased Production Efficiency
The rapid heat-up times of gas ovens enable businesses to reduce downtime between batches. This increased efficiency leads to higher productivity, allowing companies to meet tighter production deadlines.
3. Cost-Effective Operation
Gas ovens often result in lower operational costs, particularly in areas where gas prices are competitive. The efficient use of fuel contributes to overall cost savings for businesses.
4. Flexibility for Various Applications
Gas powder coating ovens are versatile and can accommodate a wide range of substrates and coating processes. This flexibility allows businesses to adapt to changing production needs and diversify their offerings.
5. Environmentally Friendly Options
Modern gas ovens are designed to minimize emissions, making them an environmentally friendly option for powder coating operations. By utilizing efficient combustion systems, EMS ovens reduce their carbon footprint while maintaining high performance.
Why Choose EMS Powder Coating Equipment for Gas Powder Coating Ovens?
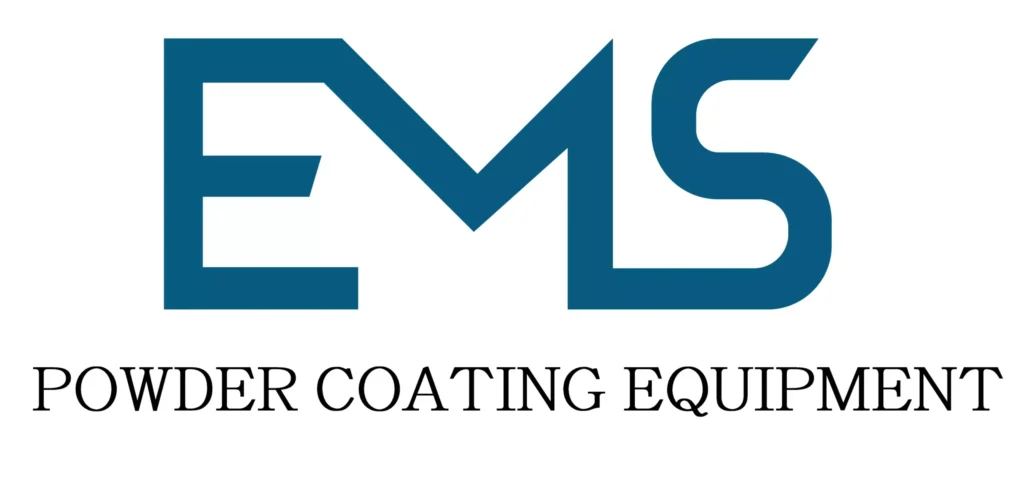
When selecting a gas powder coating oven, businesses need a manufacturer that offers reliability, quality, and innovative solutions. EMS Powder Coating Equipment stands out as the best choice for businesses looking to invest in gas ovens. Here’s why EMS is the preferred option:
1. Extensive Industry Experience
With years of experience in the powder coating industry, EMS understands the unique requirements of various applications. Their expertise enables them to design gas powder coating ovens that cater to diverse industries and operational needs.
2. Innovative Design and Technology
EMS is committed to innovation, continually enhancing their products with the latest technology. Their gas powder coating ovens incorporate advanced heating systems, precise temperature controls, and robust construction for optimal performance.
3. Exceptional Customer Support
From initial consultations to ongoing maintenance, EMS provides comprehensive customer support. Their team of experts is dedicated to ensuring that your gas powder coating oven operates at peak efficiency.
4. Custom Solutions for Unique Needs
Recognizing that every business has specific requirements, EMS offers customizable solutions for gas powder coating ovens. Whether you need tailored heating capacities or additional features, EMS can design ovens to fit your operational needs.
5. Proven Reliability and Quality
With a strong reputation for delivering high-quality products, EMS is a trusted name in the powder coating industry. Their gas powder coating ovens are built for reliability and long-term performance, making them an excellent investment for businesses.
Conclusion
A gas powder coating oven is an essential component of any powder coating operation, providing efficient and effective heating solutions for curing coatings. With rapid heat-up times and precise temperature control, gas ovens enhance productivity and ensure high-quality finishes.
EMS Powder Coating Equipment is a leading manufacturer of gas powder coating ovens, offering innovative solutions tailored to meet the diverse needs of various industries. Their commitment to quality, performance, and customer support makes EMS the best choice for businesses seeking reliable curing solutions.
By investing in EMS gas powder coating ovens, companies can improve their coating processes, achieve superior finishes, and reduce operational costs. With a focus on efficiency and innovation, EMS stands out as the premier manufacturer for businesses in need of top-tier powder coating equipment.
Gas Powder Coating Oven: Efficiency and Performance in Coating Applications
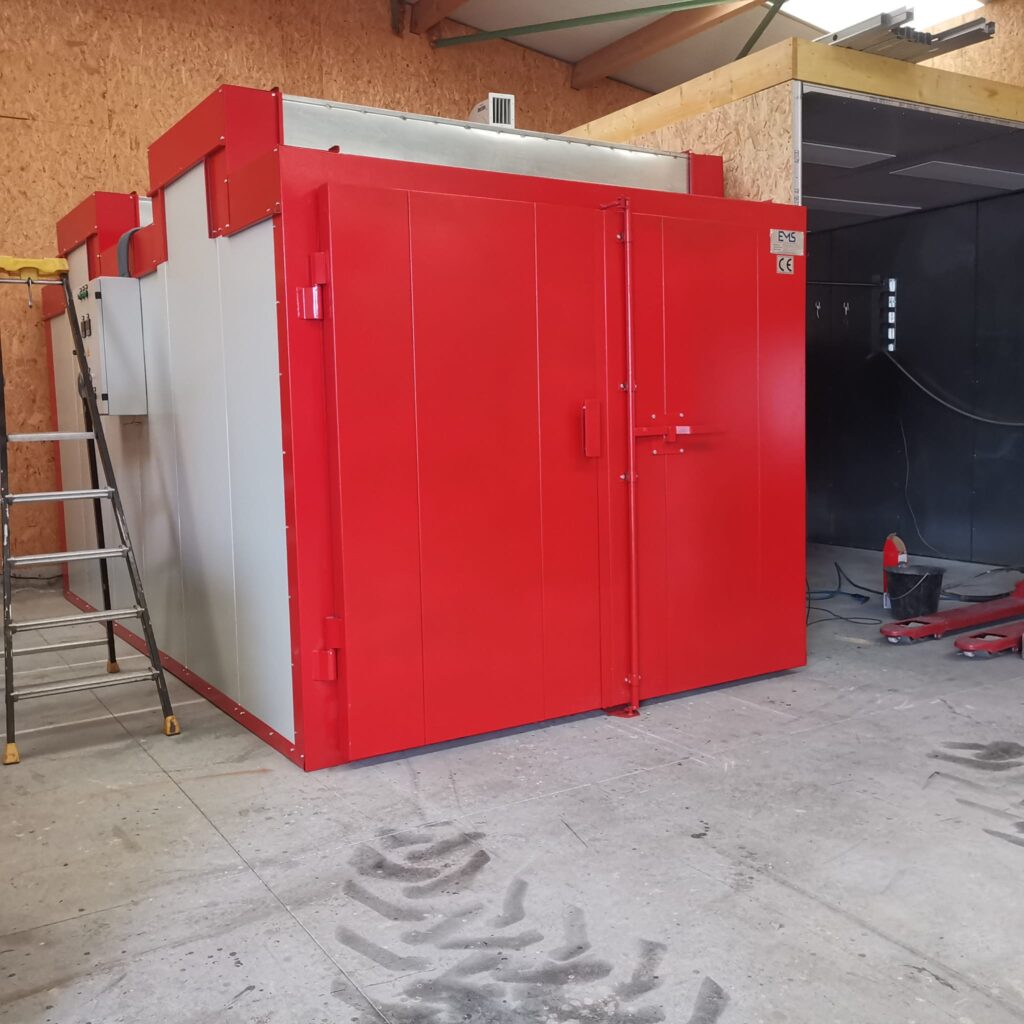
A gas powder coating oven is a vital component in the powder coating process, designed to cure powder coatings efficiently. Utilizing gas as a heating source, these ovens provide an optimal environment for achieving high-quality finishes on coated substrates.
Gas ovens are known for their rapid heating capabilities and energy efficiency, making them an excellent choice for businesses looking to enhance productivity while reducing operational costs. The precise temperature control ensures that the powder coating is cured uniformly, resulting in a durable and aesthetically pleasing finish.
EMS Powder Coating Equipment stands out as a leading manufacturer of gas powder coating ovens, offering advanced solutions tailored to meet the diverse needs of various industries. In this section, we will explore the operational principles, key features, and benefits of gas powder coating ovens, as well as explain why EMS is the preferred choice for businesses seeking reliable coating equipment.
What is a Gas Powder Coating Oven?
A gas powder coating oven is an industrial heating unit designed specifically for curing powder coatings. Unlike electric ovens, these ovens utilize gas as a heating source, providing rapid and efficient heating for the curing process.
How Gas Powder Coating Ovens Operate
The operation of a gas powder coating oven begins after the substrate has been coated with powder. The coated substrate is then placed inside the oven, where it is subjected to high temperatures that cause the powder to melt and flow.
The gas burners within the oven provide consistent and efficient heat, allowing for quick temperature adjustments and precise control. This efficiency results in reduced curing times and increased production throughput.
Gas powder coating ovens are equipped with advanced temperature control systems that ensure even heat distribution throughout the oven. This feature is crucial for achieving uniform curing of the powder, which enhances the durability and finish quality of the coated items.
EMS Powder Coating Equipment designs gas powder coating ovens with features that optimize the curing process, ensuring high-quality finishes and efficient operation. These ovens are adaptable to various production needs, making them suitable for businesses of all sizes.
Key Features of Gas Powder Coating Ovens
Gas powder coating ovens are equipped with a variety of features designed to enhance their functionality and efficiency. Here are some key features that make EMS ovens the preferred choice for businesses:
1. Rapid Heating Capabilities
One of the most significant advantages of gas powder coating ovens is their rapid heating capabilities. EMS ovens can quickly reach the desired curing temperature, reducing overall cycle times and increasing productivity.
2. Energy Efficiency
Gas ovens are typically more energy-efficient than electric ovens. EMS designs their gas powder coating ovens to minimize energy consumption, resulting in lower operational costs for businesses.
3. Precise Temperature Control
EMS gas powder coating ovens feature advanced temperature control systems that allow for precise adjustments. This level of control ensures that the curing process is consistent, leading to high-quality finishes on coated items.
4. Robust Construction
Constructed with high-quality materials, EMS gas powder coating ovens are designed for durability and long-term performance. Their robust construction ensures minimal maintenance and reliable operation in demanding industrial environments.
5. User-Friendly Control Panels
EMS ovens are equipped with intuitive control panels that make it easy for operators to set and monitor temperature and other critical parameters. This user-friendly design enhances the overall curing process and helps achieve consistent results.
6. Safety Features
Safety is a top priority in any industrial operation. EMS gas powder coating ovens come equipped with various safety features, including emergency shut-off systems and proper ventilation, to ensure a safe working environment.
Benefits of Using Gas Powder Coating Ovens
Investing in a gas powder coating oven offers numerous advantages for businesses engaged in powder coating operations. Here are some key benefits:
1. Enhanced Coating Quality
Gas powder coating ovens provide a consistent and controlled curing environment, significantly improving the quality of the applied coatings. Uniform heat distribution ensures that the powder cures evenly, resulting in a durable finish.
2. Increased Production Efficiency
With rapid heating capabilities, EMS gas powder coating ovens allow for shorter curing times, enabling businesses to increase their production throughput. This efficiency can be a critical factor in meeting tight deadlines and growing customer demands.
3. Cost Savings
The energy efficiency of gas ovens translates to significant cost savings over time. By reducing energy consumption and minimizing operational costs, businesses can allocate resources more effectively and improve their bottom line.
4. Versatility for Various Applications
EMS gas powder coating ovens are designed to accommodate a wide range of substrates and coating processes. This versatility allows businesses to adapt to changing production needs and diversify their service offerings across different industries.
5. Compliance with Safety and Environmental Standards
Gas powder coating ovens are designed to meet safety and environmental regulations, reducing emissions and maintaining a safe workspace. By investing in EMS ovens, businesses can ensure compliance with industry standards while promoting a healthier working environment.
Why Choose EMS Powder Coating Equipment for Gas Powder Coating Ovens?
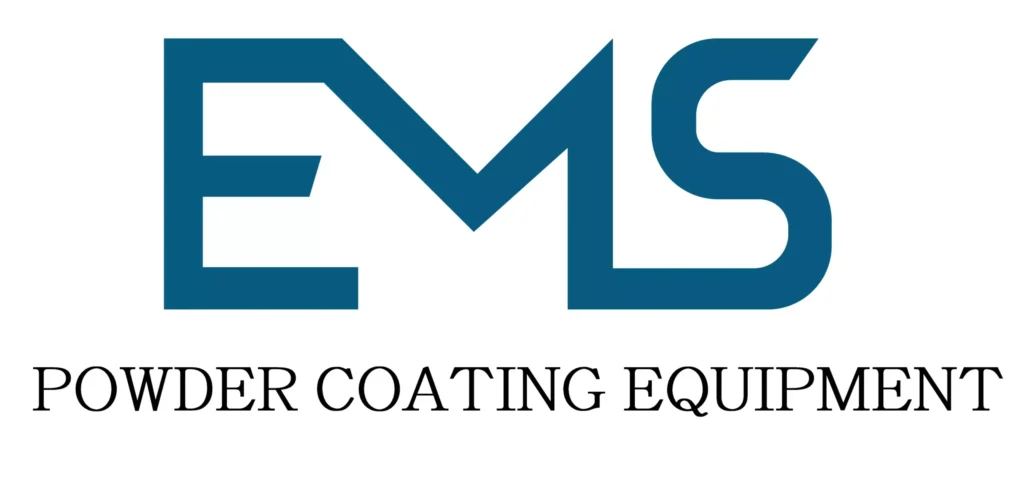
When selecting a gas powder coating oven, it is essential to choose a manufacturer known for quality, reliability, and innovative solutions. EMS Powder Coating Equipment stands out as the best choice for businesses looking to invest in gas ovens. Here’s why EMS is the preferred option:
1. Proven Industry Experience
With extensive experience in the powder coating industry, EMS understands the specific needs of various applications. Their expertise enables them to design gas powder coating ovens that meet the demands of different environments and production requirements.
2. Commitment to Innovation
EMS is dedicated to innovation, continually enhancing their products with the latest technology. Their gas powder coating ovens are designed for optimal performance, incorporating advanced temperature control and safety features.
3. Comprehensive Customer Support
From installation to ongoing maintenance, EMS provides exceptional customer support. Their team of experts is available to assist businesses in maximizing the performance of their gas powder coating ovens.
4. Customizable Solutions
Recognizing that each business has unique needs, EMS offers customizable solutions for gas powder coating ovens. Whether specific sizes, features, or configurations are required, EMS can tailor their products to meet operational requirements.
5. Trusted Quality and Reliability
With a strong reputation for delivering high-quality products, EMS is a trusted name in the powder coating industry. Their gas powder coating ovens are built for durability and long-term performance, making them an excellent investment for businesses.
Conclusion
A gas powder coating oven is a critical investment for any powder coating operation, providing an efficient and controlled environment for curing coatings. With rapid heating capabilities and precise temperature control, these ovens enhance coating quality and productivity.
EMS Powder Coating Equipment is a leading manufacturer of gas powder coating ovens, offering innovative solutions tailored to meet the diverse needs of various industries. Their commitment to quality, performance, and customer support makes EMS the best choice for businesses seeking reliable coating solutions.
By choosing EMS gas powder coating ovens, companies can improve their coating processes, achieve superior finishes, and reduce operational costs. With a focus on efficiency and innovation, EMS stands out as the premier manufacturer for businesses in need of top-tier powder coating equipment.
Gas Powder Coating Oven: Efficient Curing Solutions for Optimal Finishes
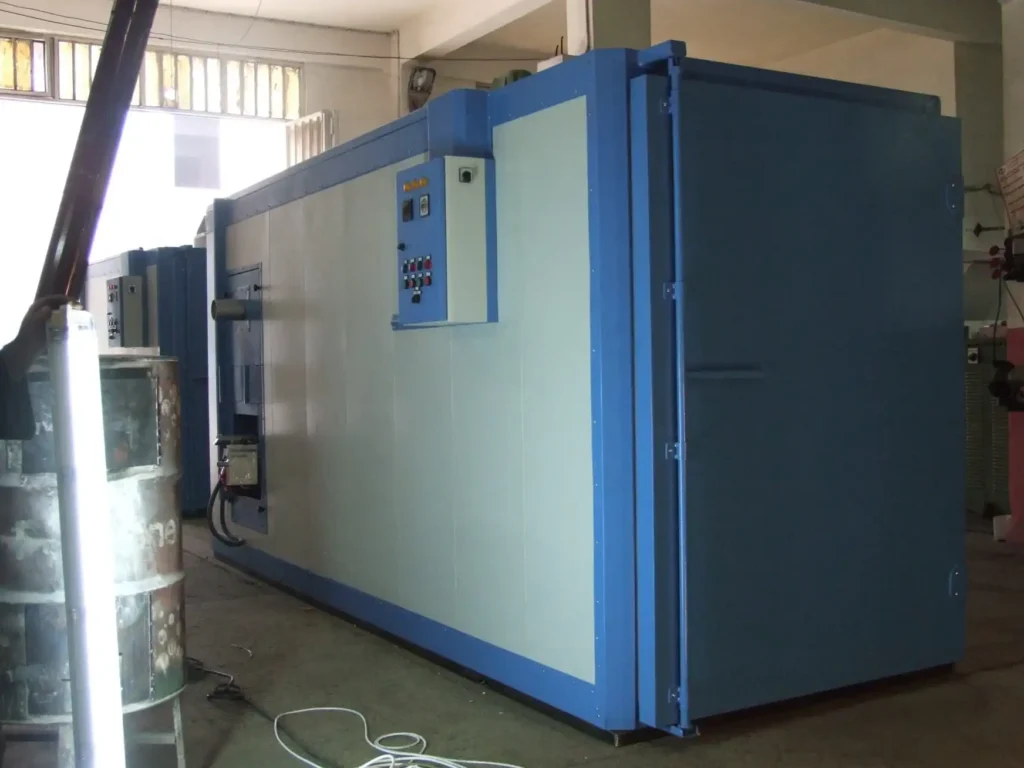
A gas powder coating oven is a crucial component in the powder coating process, designed specifically for curing powder-coated materials. Utilizing natural gas or propane, these ovens offer efficient heating solutions that ensure the even curing of powder coatings, resulting in durable and high-quality finishes.
The design of gas powder coating ovens focuses on energy efficiency and optimal temperature control. By providing a stable and controlled environment, these ovens facilitate the proper melting and adhesion of powder coatings to substrates, enhancing the overall coating quality.
EMS Powder Coating Equipment stands out as a leader in the manufacturing of gas powder coating ovens, offering advanced solutions tailored to meet the specific needs of various industries. In this section, we will delve into the operational principles, key features, and benefits of gas powder coating ovens, while also discussing why EMS is the preferred choice for businesses seeking reliable coating equipment.
What is a Gas Powder Coating Oven?
A gas powder coating oven is an industrial oven specifically designed to cure powder coatings applied to metal substrates. By utilizing gas as a heat source, these ovens provide rapid and efficient curing, ensuring a high-quality finish.
How Gas Powder Coating Ovens Operate
The operation of a gas powder coating oven begins after the substrate has been coated with powder. Once the application is complete, the substrate is placed inside the oven, where controlled temperatures are maintained.
Gas burners generate heat, which is evenly distributed throughout the oven. This uniform heat application ensures that the powder melts, flows, and adheres properly to the substrate. Curing times and temperatures can be adjusted to suit different types of powder coatings and substrate materials.
EMS Powder Coating Equipment designs gas powder coating ovens with features that optimize the curing process, ensuring that businesses achieve consistent, high-quality finishes across a variety of applications.
Key Features of Gas Powder Coating Ovens
Gas powder coating ovens are equipped with numerous features designed to enhance their performance and efficiency. Here are some standout features that make EMS ovens the preferred choice for businesses:
1. Energy Efficiency
EMS gas powder coating ovens are designed for optimal energy efficiency, utilizing advanced burner technology to minimize gas consumption while maximizing heat output. This design helps reduce operational costs without compromising performance.
2. Precise Temperature Control
With advanced temperature control systems, EMS ovens ensure that the required curing temperatures are maintained consistently throughout the process. This precise control is essential for achieving high-quality finishes.
3. Quick Heating Capability
Gas ovens have the advantage of rapid heating capabilities, significantly reducing preheating times. This feature enhances productivity by allowing for faster turnaround on coating jobs.
4. Uniform Heat Distribution
The design of EMS gas powder coating ovens promotes uniform heat distribution, preventing hot spots and ensuring that all areas of the substrate are cured evenly. This uniformity is crucial for achieving a consistent finish.
5. Safety Features
Safety is paramount in any industrial operation. EMS ovens come equipped with safety features such as flame monitoring systems, emergency shut-off valves, and proper ventilation to ensure a safe working environment for operators.
6. Customizable Sizes and Configurations
Recognizing that different businesses have varying needs, EMS offers customizable sizes and configurations for their gas powder coating ovens. This flexibility allows businesses to choose the right oven to fit their production capacities.
Benefits of Using Gas Powder Coating Ovens
Investing in a gas powder coating oven provides numerous advantages for businesses engaged in powder coating operations. Here are some key benefits:
1. Enhanced Coating Quality
Gas powder coating ovens promote optimal curing conditions, leading to high-quality finishes. The even application of heat ensures that the powder melts and adheres properly, resulting in durable coatings.
2. Increased Efficiency
The rapid heating capabilities of gas ovens reduce preheating and curing times, allowing for quicker production cycles. This increased efficiency can significantly enhance overall productivity.
3. Cost-Effective Operations
With their energy-efficient designs, gas powder coating ovens can reduce fuel costs compared to electric ovens. Additionally, the improved curing processes result in less rework and waste, contributing to lower operational costs.
4. Versatility for Different Applications
EMS gas powder coating ovens are versatile and can accommodate a wide range of powder coatings and substrate materials. This adaptability allows businesses to diversify their service offerings and meet various customer demands.
5. Compliance with Safety Standards
EMS gas powder coating ovens are designed to meet industry safety regulations, ensuring a safe working environment. Their robust safety features protect both operators and the surrounding environment.
Why Choose EMS Powder Coating Equipment for Gas Powder Coating Ovens?
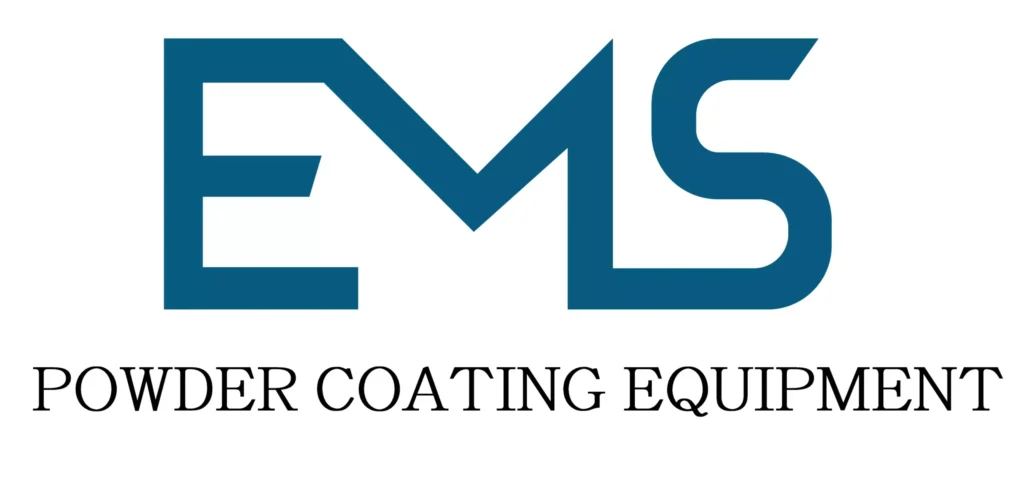
Selecting a gas powder coating oven requires careful consideration of the manufacturer’s reputation for quality and reliability. EMS Powder Coating Equipment is the top choice for businesses looking to invest in gas powder coating ovens. Here’s why EMS stands out:
1. Industry Expertise
With years of experience in the powder coating industry, EMS understands the unique requirements of various applications. Their expertise allows them to design gas powder coating ovens that are tailored to meet diverse production environments.
2. Commitment to Innovation
EMS is dedicated to continual innovation, integrating the latest technologies into their products. Their gas powder coating ovens are designed for optimal performance, featuring advanced controls and safety mechanisms.
3. Exceptional Customer Support
From installation to ongoing maintenance, EMS provides comprehensive customer support. Their team of experts is committed to helping businesses maximize the performance of their gas powder coating ovens.
4. Custom Solutions
Recognizing that every business has unique needs, EMS offers customizable solutions for gas powder coating ovens. This flexibility ensures that businesses can select the right features and configurations for their operations.
5. Trusted Quality and Reliability
With a strong reputation for delivering high-quality products, EMS is a trusted name in the powder coating industry. Their gas powder coating ovens are built for durability and long-term performance, making them an excellent investment for businesses.
Conclusion
A gas powder coating oven is a vital investment for any powder coating operation, providing efficient and controlled curing of powder coatings. With their advanced features and energy-efficient designs, these ovens enhance coating quality and productivity.
EMS Powder Coating Equipment is a leading manufacturer of gas powder coating ovens, offering innovative solutions tailored to meet the diverse needs of various industries. Their commitment to quality, performance, and customer support makes EMS the best choice for businesses seeking reliable coating equipment.
By choosing EMS gas powder coating ovens, companies can improve their coating processes, achieve superior finishes, and reduce operational costs. With a focus on efficiency and innovation, EMS stands out as the premier manufacturer for businesses in need of top-tier powder coating equipment.
Gas Powder Coating Oven: Efficiency and Precision in Coating Applications
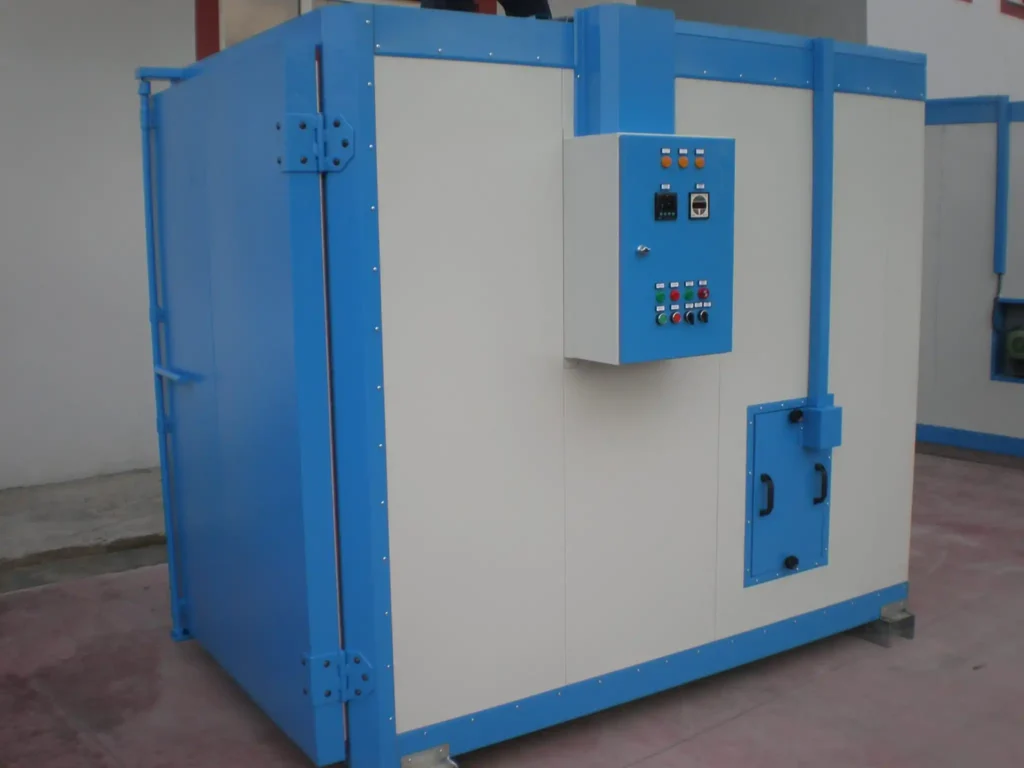
A gas powder coating oven is an essential component in the powder coating process, providing the necessary heat to cure powder coatings applied to various substrates. The curing process is crucial for achieving a durable, high-quality finish that adheres effectively to the surface.
These ovens are specifically designed to deliver uniform heat distribution, ensuring that the powder coating cures evenly and efficiently. With advancements in technology, modern gas powder coating ovens also incorporate features that enhance energy efficiency and operational safety.
EMS Powder Coating Equipment is recognized as a leader in the manufacturing of gas powder coating ovens, offering state-of-the-art solutions tailored to meet the diverse needs of various industries. In this section, we will delve into the operational principles, key features, and benefits of gas powder coating ovens, while also discussing why EMS is the preferred choice for businesses seeking reliable and efficient coating solutions.
What is a Gas Powder Coating Oven?
A gas powder coating oven is a specialized curing chamber used in the powder coating process. It employs gas as the primary heat source to cure the powder coatings applied to metal and other substrates.
How Gas Powder Coating Ovens Operate
The operation of a gas powder coating oven begins after the powder has been applied to the substrate in a spray booth. Once the substrate is ready, it is transferred to the oven, where precise heating elements deliver the required temperature for curing.
The oven’s design ensures uniform heat distribution, allowing the powder coating to melt and flow, ultimately bonding to the substrate. The curing process is crucial, as it transforms the powder into a hard, protective finish that is both aesthetically pleasing and durable.
EMS Powder Coating Equipment designs gas powder coating ovens with advanced features that optimize curing efficiency and performance, ensuring businesses achieve consistent, high-quality finishes across various applications.
Key Features of Gas Powder Coating Ovens
Gas powder coating ovens are equipped with several features that enhance their performance and efficiency. Here are some standout features that make EMS ovens the preferred choice for businesses:
1. Uniform Heat Distribution
EMS gas powder coating ovens are engineered to provide uniform heat distribution throughout the curing chamber. This feature ensures that every part of the substrate receives the same level of heat, resulting in even curing and high-quality finishes.
2. Energy Efficiency
Modern EMS gas ovens are designed for energy efficiency, utilizing advanced insulation and burner technology. This allows businesses to reduce energy consumption while maintaining optimal curing temperatures, leading to cost savings over time.
3. User-Friendly Controls
The intuitive control systems in EMS gas powder coating ovens allow operators to easily set and monitor temperatures and curing times. This user-friendly interface streamlines operations and enhances overall productivity.
4. Safety Features
Safety is paramount in any coating operation. EMS gas powder coating ovens come equipped with essential safety features, including flame safety devices, emergency shut-off systems, and proper ventilation, ensuring a safe working environment.
5. Customizable Configurations
Understanding that different businesses have unique requirements, EMS offers customizable configurations for their gas powder coating ovens. Whether for small operations or large-scale production, EMS can tailor solutions to meet specific needs.
6. Durable Construction
Built with high-quality materials, EMS gas powder coating ovens are designed for longevity and reliability. Their robust construction ensures consistent performance even in demanding production environments.
Benefits of Using Gas Powder Coating Ovens
Investing in a gas powder coating oven provides numerous advantages for businesses engaged in powder coating operations. Here are some key benefits:
1. Consistent Coating Quality
The precise temperature control and uniform heat distribution in gas powder coating ovens lead to consistent curing results. This ensures that the final finish meets the highest quality standards.
2. Faster Curing Times
Gas powder coating ovens typically offer faster curing times compared to electric ovens, enhancing production efficiency. This speed allows businesses to complete more jobs in less time, increasing overall output.
3. Cost Efficiency
By utilizing gas as an energy source, businesses can benefit from lower operational costs compared to electric ovens. The energy-efficient design of EMS ovens further enhances this cost-effectiveness.
4. Versatility for Diverse Applications
EMS gas powder coating ovens are versatile enough to handle a wide range of substrates and coating types, allowing businesses to expand their offerings and cater to different market demands.
5. Compliance with Environmental Regulations
Gas powder coating ovens are designed to meet industry safety and environmental regulations, ensuring a compliant operation. By investing in EMS ovens, businesses can promote a healthier working environment while adhering to necessary standards.
Why Choose EMS Powder Coating Equipment for Gas Powder Coating Ovens?
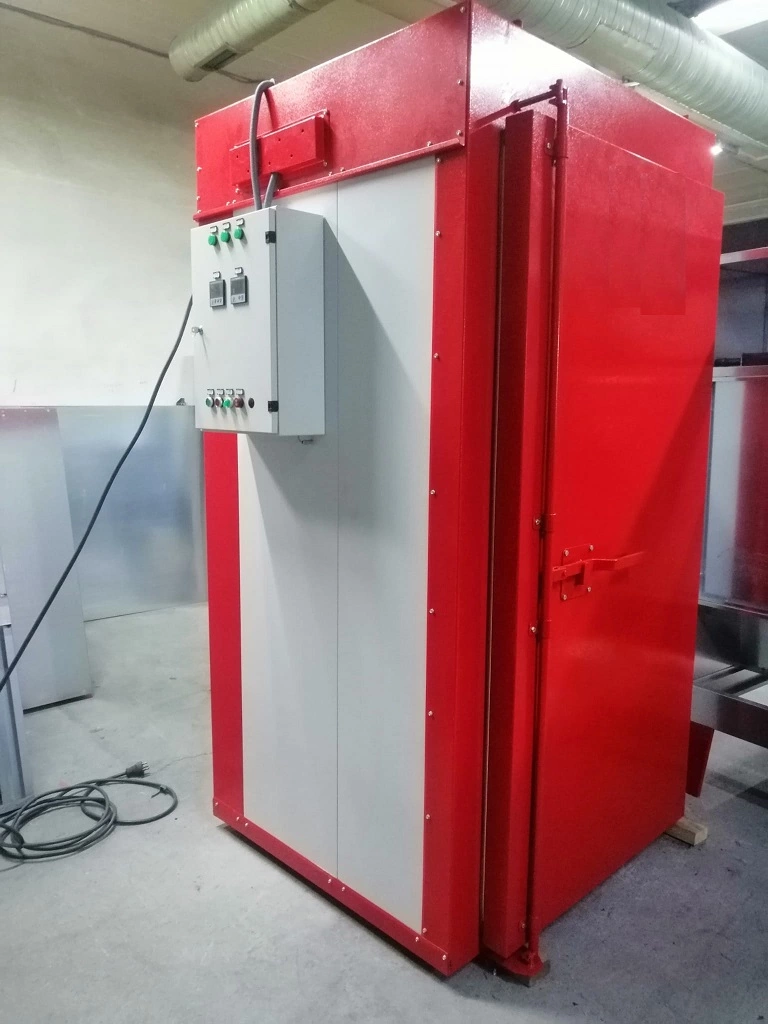
When selecting a gas powder coating oven, it is essential to choose a manufacturer with a reputation for quality and innovation. EMS Powder Coating Equipment stands out as the top choice for businesses looking to invest in gas powder coating ovens. Here’s why EMS is the preferred option:
1. Proven Expertise
With years of experience in the powder coating industry, EMS understands the unique needs of various applications. Their knowledge allows them to design gas powder coating ovens that are tailored to diverse production environments.
2. Innovative Solutions
EMS is committed to continuous innovation, incorporating the latest technology into their products. Their gas powder coating ovens are designed for optimal performance, featuring advanced temperature control and safety systems.
3. Comprehensive Support
From installation to ongoing maintenance, EMS provides exceptional customer support. Their team of experts is dedicated to helping businesses maximize the performance of their gas powder coating ovens.
4. Customizable Options
Recognizing that every business has unique requirements, EMS offers customizable options for gas powder coating ovens, allowing businesses to select features and configurations that best suit their operational needs.
5. Trusted Reliability
With a strong reputation for delivering high-quality products, EMS is a trusted name in the powder coating industry. Their ovens are designed for durability and long-term performance, making them an excellent investment for businesses.
Conclusion
A gas powder coating oven is a crucial investment for any powder coating operation, providing the necessary heat to cure powder coatings effectively. With uniform heat distribution and energy-efficient designs, these ovens ensure high-quality finishes while optimizing operational efficiency.
EMS Powder Coating Equipment is a leading manufacturer of gas powder coating ovens, offering innovative solutions tailored to meet the diverse needs of various industries. Their commitment to quality, performance, and customer support makes EMS the best choice for businesses seeking reliable coating solutions.
By choosing EMS gas powder coating ovens, companies can enhance their curing processes, achieve superior finishes, and reduce operational costs. With a focus on efficiency and innovation, EMS stands out as the premier manufacturer for businesses in need of top-tier powder coating equipment.