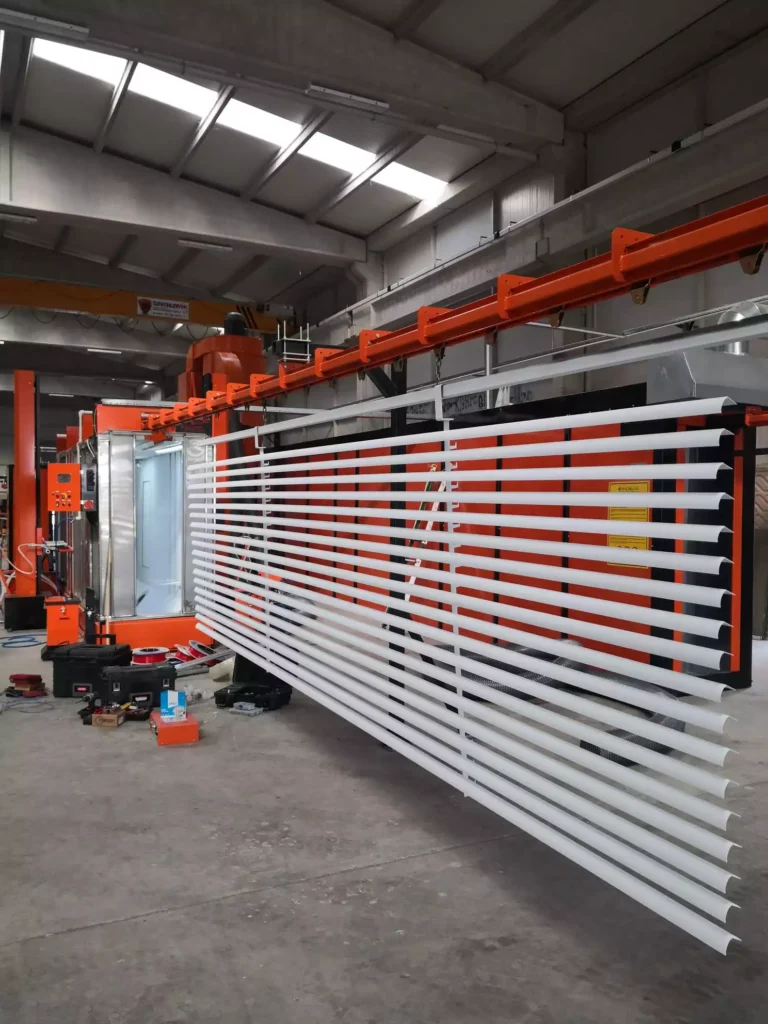
The Paint Shop Conveyor System process is a crucial step in the powder coating workflow, ensuring that the substrate is adequately prepared to receive the powder coat. Among various methods, Dip Pre-treatment stands out as an effective technique, particularly for metal surfaces. This method involves immersing the metal components into a series of chemical baths, each designed to perform a specific function—cleaning, rinsing, and applying conversion coatings.
Dip Pre-treatment ensures that contaminants such as oils, dirt, and oxides are removed from the metal surface, allowing for better adhesion of the powder coat. This process is especially vital for Sheet Metal Pre-treatment, where the quality of surface preparation directly impacts the durability and appearance of the final product. Properly pre-treated surfaces resist corrosion and other environmental damages better than untreated ones.
In the context of Pretreatment Process for Powder Coating, the dip method offers several advantages:
- Thorough Coverage: Immersion allows for complete surface coverage, even in complex geometries.
- Consistency: Ensures uniform treatment across all parts.
- Efficiency: Often faster and more cost-effective compared to spray or manual cleaning methods.
However, the dip pre-treatment process must be carefully controlled. Factors such as bath temperature, immersion time, and chemical concentration need to be optimized to avoid issues like over-etching or inadequate cleaning. Failure to maintain these parameters can lead to defects in the final powder coat, such as poor adhesion or uneven finishes.
Sheet Metal Pre-treatment

Sheet metal is a common material used in various industries, particularly in automotive and appliance manufacturing. Proper pre-treatment of sheet metal is essential for achieving a high-quality finish during powder coating. The Sheet Metal Pre-treatment process typically involves multiple stages, including degreasing, pickling, phosphating, and rinsing.
- Degreasing: This initial step removes oils and greases from the metal surface. Degreasing can be accomplished using alkaline cleaners or solvents, depending on the type of contamination.
- Pickling: Involves the use of acid baths to remove oxides and scale from the metal surface. This step is crucial for ensuring that the surface is chemically clean and ready for further treatment.
- Phosphating: A chemical conversion process that deposits a thin layer of phosphate crystals on the metal surface. This layer enhances corrosion resistance and improves the adhesion of the powder coat.
- Rinsing: Multiple rinsing stages are used to remove any residual chemicals from the surface, ensuring that the metal is clean and free of contaminants.
For industries requiring high-performance coatings, such as automotive or aerospace, the Pretreatment Process for Powder Coating must be meticulously controlled. Advances in technology have introduced automated systems that can precisely manage these stages, reducing human error and ensuring consistent quality across batches.
The importance of Dip Pre-treatment and Sheet Metal Pre-treatment cannot be overstated in the context of modern manufacturing. These processes lay the groundwork for the entire coating process, ensuring that the finished product meets the stringent requirements of durability, appearance, and performance.
Great! Let’s continue with Section 2, where we’ll dive into the Coating Equipment Production Line. This section will explore the machinery and systems that play crucial roles in the powder coating process.
Section 2: Coating Equipment Production Line
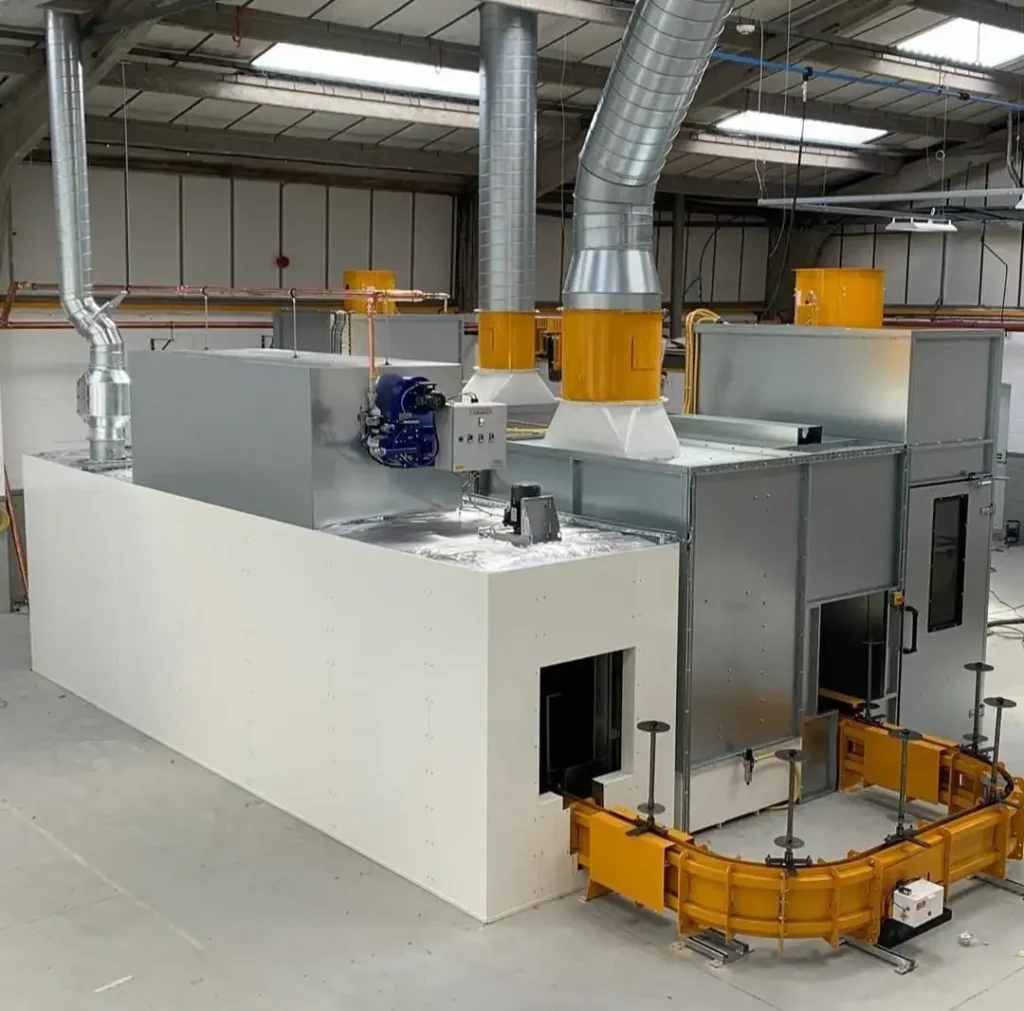
In modern manufacturing, the coating equipment production line is a complex, well-coordinated system designed to deliver high-quality finishes on various products. From large-scale industrial applications to smaller setups, these lines are composed of several critical components, each contributing to the efficiency and quality of the coating process. This section explores the key equipment used in these production lines, with a focus on their functionality, importance, and integration.
Overview of a Coating Equipment Production Line
A Coating Equipment Production Line is an assembly of machines and systems engineered to apply protective and decorative coatings to products. The line typically includes pre-treatment stations, coating booths, curing ovens, and conveyor systems, all working in unison to ensure that products move smoothly through each stage of the coating process.
The production line’s design is tailored to the specific needs of the manufacturing process, taking into account factors like the type of material being coated, the required finish, and the production volume. For instance, in high-volume operations such as automotive manufacturing, an Automatic Painting Line is essential to achieve the speed and consistency required to meet demand.
Powdercoat Equipment
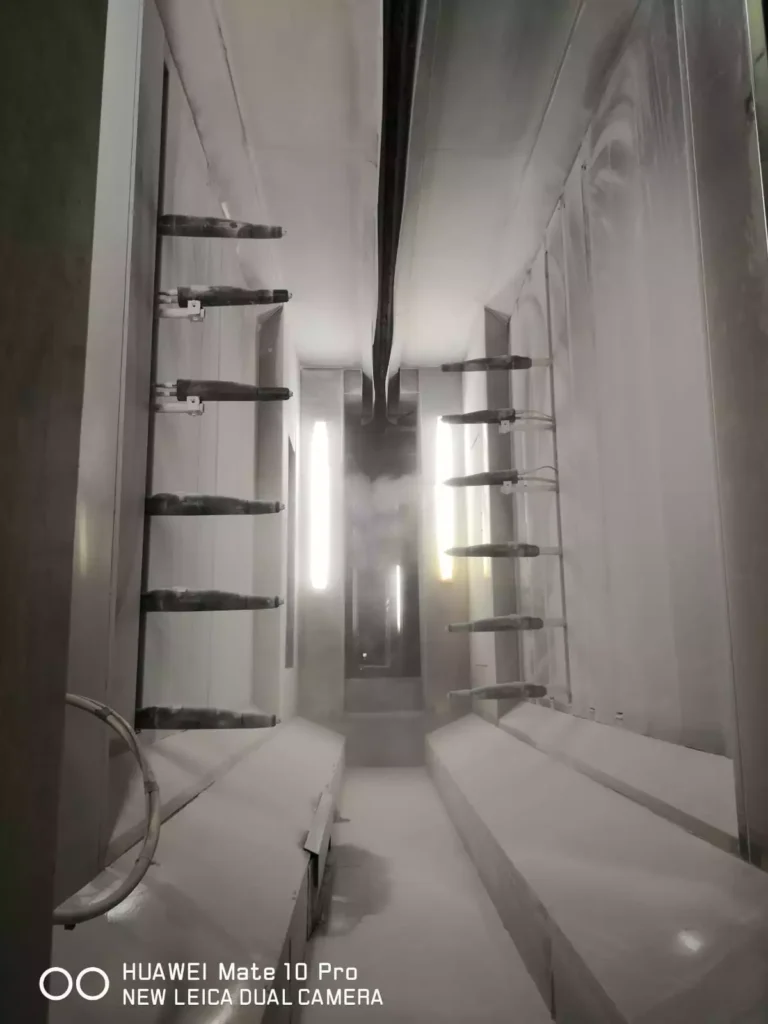
Powdercoat Equipment forms the backbone of any powder coating production line. This equipment is designed to apply a powder coating to the surface of a product, which is then cured to form a hard, durable finish. The powder coating process is widely used due to its environmental benefits, cost-effectiveness, and the superior finish it provides.
Key components of Powdercoat Equipment include:
- Powder Feed Systems: These systems deliver the powder to the spray guns. They are designed to handle different powder types and provide consistent feed rates for uniform application.
- Spray Guns: Used to apply the powder to the substrate. They come in various designs, including manual and automatic options, depending on the production requirements.
- Powder Recovery Systems: These systems collect and recycle overspray powder, improving efficiency and reducing waste.
Advanced Powdercoat Equipment includes features like electrostatic spray guns, which use an electric charge to attract the powder to the metal surface, ensuring even coverage and reducing material wastage. The integration of automation and control systems further enhances the precision and repeatability of the powder application process, making it suitable for industries with stringent quality requirements.
Spray Coating Equipment
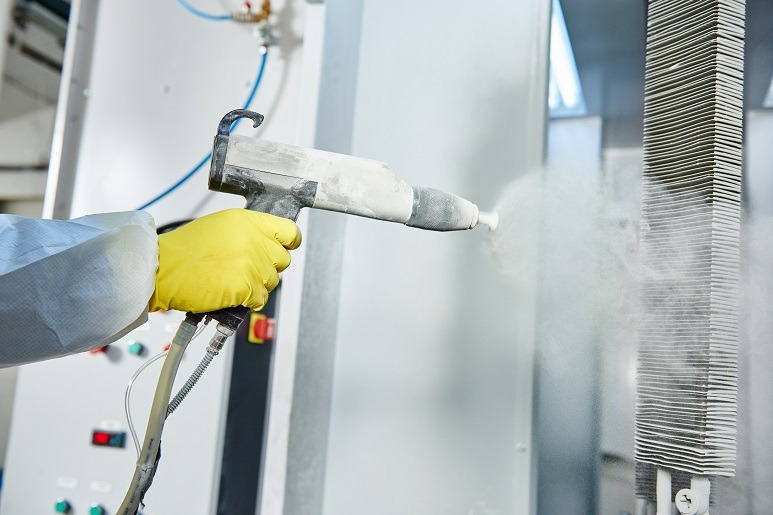
Spray Coating Equipment plays a vital role in the application of various coatings, from liquid paints to powder coatings. This equipment is engineered to deliver a fine, even spray of the coating material onto the product surface, ensuring a smooth finish without defects such as runs, sags, or orange peel.
There are different types of Spray Coating Equipment depending on the coating material and application method:
- Airless Sprayers: These use high pressure to atomize the paint, allowing for thick coatings and fast application rates. They are commonly used in industrial settings where large surfaces need to be coated quickly.
- Electrostatic Sprayers: These are designed for powder coating and some liquid coatings. They charge the coating particles, which are then attracted to the grounded substrate, ensuring an even coating with minimal overspray.
- HVLP (High Volume Low Pressure) Sprayers: These are ideal for precision work, as they deliver a softer spray, reducing overspray and ensuring a fine finish.
The choice of Spray Coating Equipment depends on several factors, including the type of coating material, the surface being coated, and the required finish. In an Automatic Painting Line, spray coating equipment is often integrated with robotic arms and conveyor systems to automate the coating process, ensuring consistent results and high throughput.
Automated Paint Systems

Automated Paint Systems have revolutionized the coating industry by providing consistent, high-quality finishes while reducing labor costs and production times. These systems are designed to handle various tasks, from surface preparation to final coating, with minimal human intervention.
Key features of Automated Paint Systems include:
- Robotic Applicators: These robots are programmed to apply paint or powder coatings with precision. They can be adjusted for different product shapes and sizes, ensuring uniform coverage across the entire surface.
- Conveyor Systems: These systems move products through the various stages of the coating process, from pre-treatment to curing. Power Free Conveyor Systems are particularly useful as they allow for the independent movement of products, enabling flexible production schedules.
- Control Systems: These systems monitor and adjust various parameters, such as spray pressure, conveyor speed, and oven temperature, to ensure that the coating process remains within specified tolerances.
Automated Paint Systems are particularly beneficial in industries where high volumes and tight tolerances are required. For instance, in automotive manufacturing, these systems ensure that every vehicle receives a flawless finish, meeting both aesthetic and protective standards.
Paint Shop Conveyor System
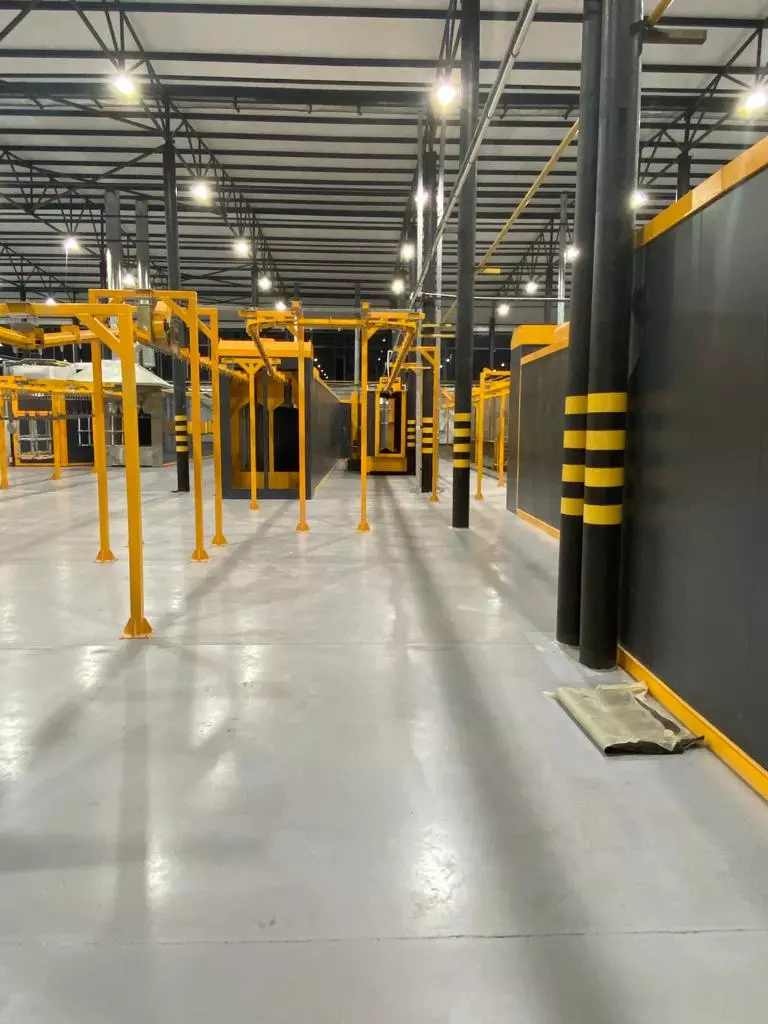
A Paint Shop Conveyor System is a critical component of a coating equipment production line, ensuring the smooth movement of products through each stage of the coating process. These conveyor systems are designed to handle various product sizes and weights, providing a flexible and efficient means of transporting products from one stage to the next.
There are several types of Paint Shop Conveyor Systems used in the industry:
- Overhead Conveyors: These are commonly used in automotive and large-scale manufacturing settings. They allow products to be transported through different stages of the coating process, including pre-treatment, coating, and curing.
- Belt Conveyors: These are used for transporting smaller items or flat products. They offer a continuous flow of products, ensuring a steady production rate.
- Power Free Conveyor Systems: These systems provide greater flexibility, as they allow for the independent movement of products. This is particularly useful in processes where products need to be paused or rerouted for additional treatments or inspections.
The choice of a Paint Shop Conveyor System depends on the specific requirements of the production line, including the size and weight of the products, the layout of the facility, and the desired production rate. The integration of these conveyor systems with other equipment, such as Spray Coating Equipment and curing ovens, is essential for achieving a streamlined and efficient production process.
Powder Coating Line
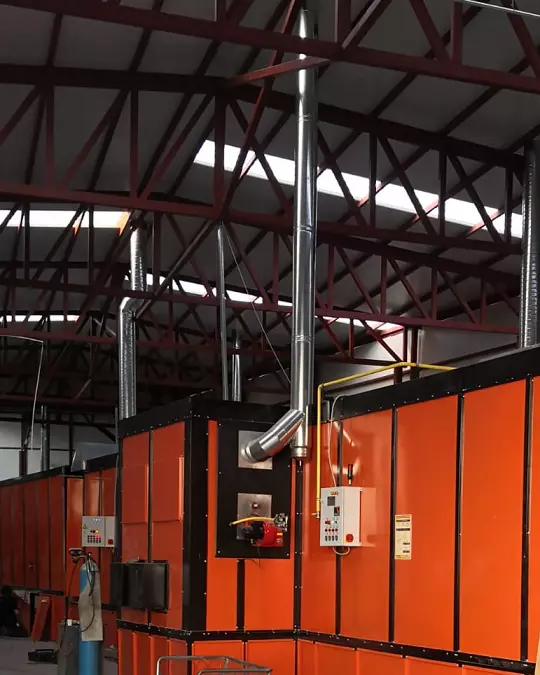
A Powder Coating Line is a specialized production line designed to apply powder coatings to products. These lines are used in various industries, including automotive, aerospace, and consumer goods, to provide durable, high-quality finishes that protect against corrosion and wear.
The Powder Coating Line typically includes the following stages:
- Pre-treatment: The product undergoes a pre-treatment process to remove contaminants and prepare the surface for coating. This stage may involve cleaning, rinsing, and applying conversion coatings.
- Coating Application: The powder coating is applied using Spray Coating Equipment or Powdercoat Equipment. The powder adheres to the surface due to the electrostatic charge applied during spraying.
- Curing: After the powder is applied, the product is transferred to a curing oven, where the powder melts and flows to form a continuous, durable coating.
- Cooling: Once the coating is cured, the product is cooled before it can be handled or packaged.
An example of an effective Powder Coating Line can be found in Istanbul, where advanced systems have been implemented to meet the demands of various industries. The Powder Coating Line Istanbul is known for its efficiency, quality, and ability to handle a wide range of products, from small components to large assemblies.
For smaller operations or startups, a Small Powder Coating Setup can be a cost-effective solution. These setups typically include compact equipment designed for lower production volumes, making them ideal for custom or limited-run projects.
Challenges in setting up a Powder Coating Line can include space constraints, equipment selection, and process optimization. However, with the right planning and equipment, these challenges can be overcome, resulting in a highly efficient and profitable operation.
Section 3: Ovens in Coating and Curing
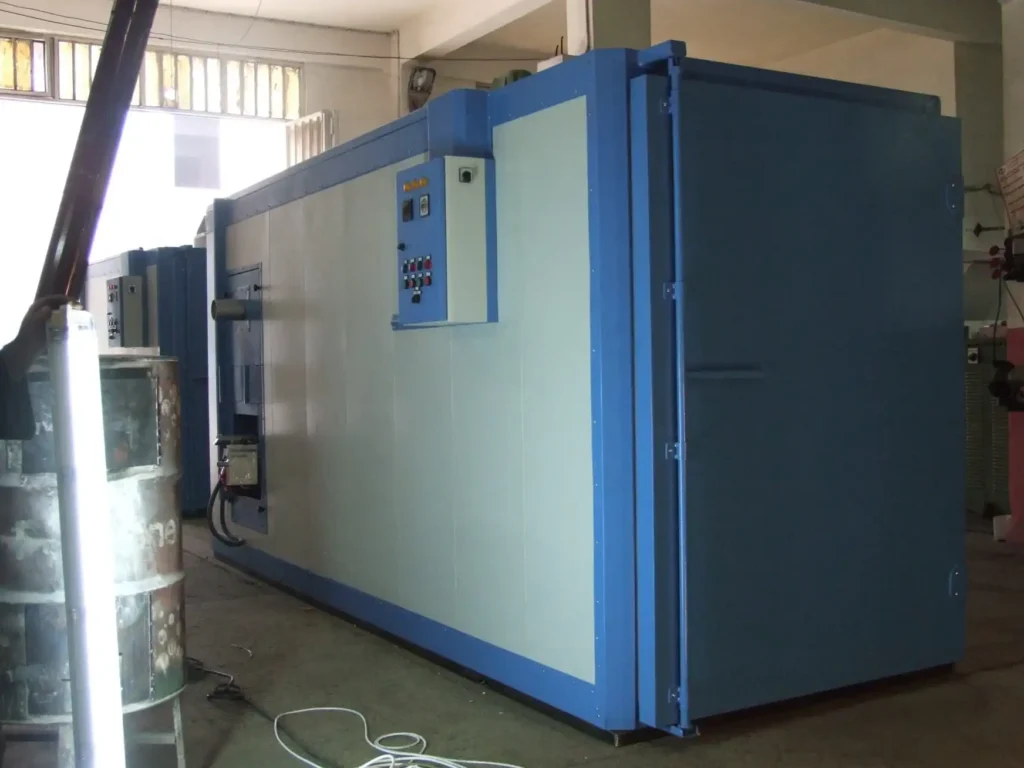
In the world of industrial coatings, ovens play a crucial role in the curing process, which is essential for transforming applied coatings into durable, resilient finishes. The right choice of ovens ensures that coatings achieve their intended properties, such as hardness, resistance to chemicals, and aesthetic appeal. This section delves into the various types of ovens used in coating and curing, highlighting their specific applications and benefits.
Curing Ovens
Curing Ovens are a fundamental component of any coating process, designed to provide the controlled heat required to cure coatings. The curing process involves heating the coated product to a specific temperature for a set period, causing the powder or liquid coating to melt, flow, and harden into a smooth, durable finish.
Types of Curing Ovens
There are several types of curing ovens, each suited to different production needs:
- Electric Curing Ovens: These ovens are powered by electricity and are commonly used in industries where precise temperature control is critical. An Electric Curing Ovens Factory typically produces ovens with advanced features such as programmable controllers, which allow operators to set and maintain exact curing conditions.
- Gas Curing Ovens: These ovens use natural gas or propane as a fuel source. Gas Curing Ovens are favored in high-volume production environments due to their efficiency and lower operating costs compared to electric ovens. A Gas Curing Ovens Factory specializes in designing ovens that are energy-efficient and capable of handling large batches.
- Infrared Curing Ovens: These ovens use infrared radiation to heat the coating directly, rather than the surrounding air. This method allows for faster curing times and is ideal for thin coatings or heat-sensitive substrates.
- Convection Curing Ovens: These ovens use forced air to circulate heat evenly throughout the curing chamber. Convection ovens are versatile and can be used for various coating materials and product sizes.
Importance of Curing Ovens
The role of Curing Ovens in the coating process cannot be overstated. Proper curing is essential to achieve the desired properties of the coating, such as:
- Durability: Cured coatings are resistant to wear, scratches, and environmental factors.
- Adhesion: The curing process ensures that the coating bonds effectively with the substrate, preventing peeling or flaking.
- Finish Quality: Curing helps to eliminate surface defects, resulting in a smooth, glossy finish.
Without proper curing, coatings may fail prematurely, leading to costly rework and dissatisfied customers. Therefore, selecting the right curing oven is crucial for ensuring product quality and meeting industry standards.
Custom Burn-off Ovens
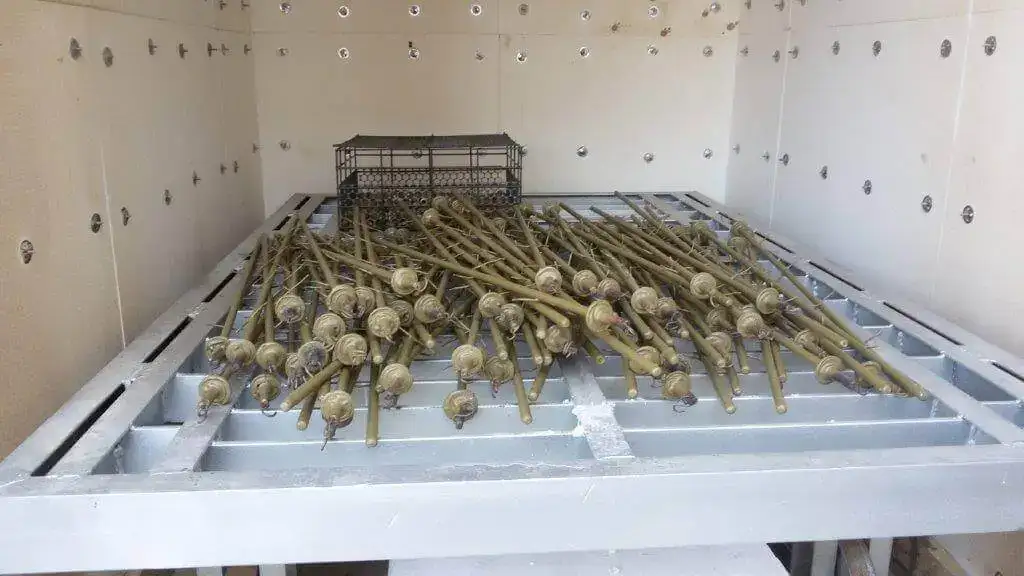
Custom Burn-off Ovens are specialized ovens used to remove old coatings, paint, or contaminants from metal parts. These ovens are designed to safely and efficiently burn off unwanted materials, leaving the metal substrate clean and ready for recoating or other processes.
Applications of Custom Burn-off Ovens
Burn-off ovens are commonly used in industries such as automotive, aerospace, and manufacturing, where metal parts need to be stripped of old coatings before being refinished. Custom Burn-off Ovens are tailored to meet the specific needs of the operation, taking into account factors such as:
- Size of Parts: Large parts may require oversized ovens with high-capacity burners.
- Type of Contaminants: The oven’s temperature and burn-off process can be adjusted based on the materials being removed, such as paint, powder coat, or grease.
- Safety Requirements: Custom ovens are designed with safety features like afterburners to ensure that harmful emissions are minimized during the burn-off process.
For smaller operations, a Small Burn-off Oven can be a practical solution. These ovens are compact and designed for lower volume usage, making them ideal for workshops or businesses that handle smaller parts or have limited space.
Advantages of Custom Burn-off Ovens
The main advantage of using a Custom Burn-off Oven is its ability to be tailored to specific requirements, ensuring efficient and safe operation. These ovens provide several benefits, including:
- Extended Equipment Life: Regular burn-off processes can help extend the life of coating equipment by removing build-up and preventing clogging.
- Improved Coating Quality: By removing old coatings, burn-off ovens help ensure that new coatings adhere properly and achieve the desired finish.
- Environmental Compliance: Custom ovens can be equipped with afterburners or other technologies to reduce emissions, helping businesses meet environmental regulations.
Standard Batch Oven – Batch Oven
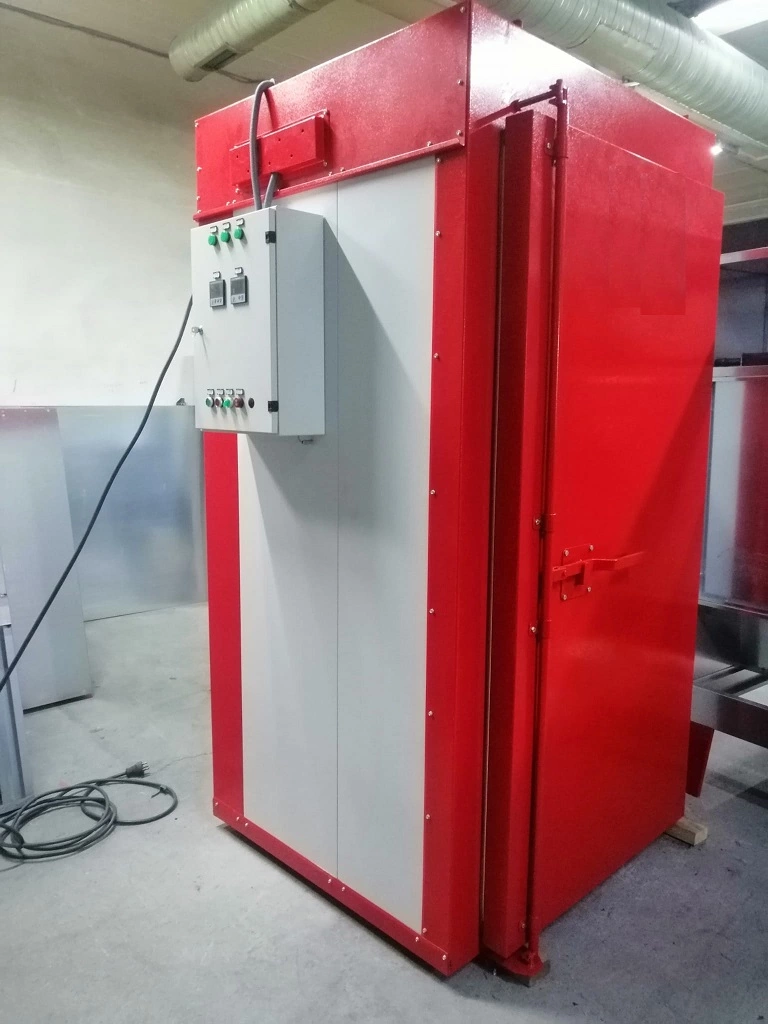
A Standard Batch Oven, often referred to as a Batch Oven, is a versatile and widely used type of industrial oven. These ovens are designed to process one batch of parts at a time, making them ideal for operations that require flexibility and frequent changes in production.
Applications of Standard Batch Ovens
Batch Ovens are used in various industries for processes such as:
- Curing: As discussed earlier, batch ovens are commonly used to cure powder coatings, liquid paints, and other types of coatings.
- Drying: Batch ovens can be used to dry parts after washing or pre-treatment processes.
- Baking: In some manufacturing processes, batch ovens are used to bake parts to achieve specific material properties.
Curing & Drying Ovens are a specific type of batch oven designed to handle both the curing and drying stages within the same unit. This dual functionality makes them highly efficient for small to medium-sized operations.
Advantages of Batch Ovens
The Standard Batch Oven offers several advantages, including:
- Flexibility: Batch ovens are ideal for operations that produce a variety of parts in different sizes and materials. The oven can be easily adjusted to accommodate different batches.
- Cost-Effectiveness: For businesses that do not require continuous production, batch ovens offer a cost-effective solution, as they do not need to be kept running when not in use.
- Precision: Batch ovens allow for precise control of temperature and time, ensuring consistent quality across all parts in a batch.
However, Batch Ovens also have limitations, particularly in high-volume production environments where continuous ovens may be more efficient. Despite this, they remain a popular choice for many manufacturers due to their versatility and reliability.
Gas Fired Ovens
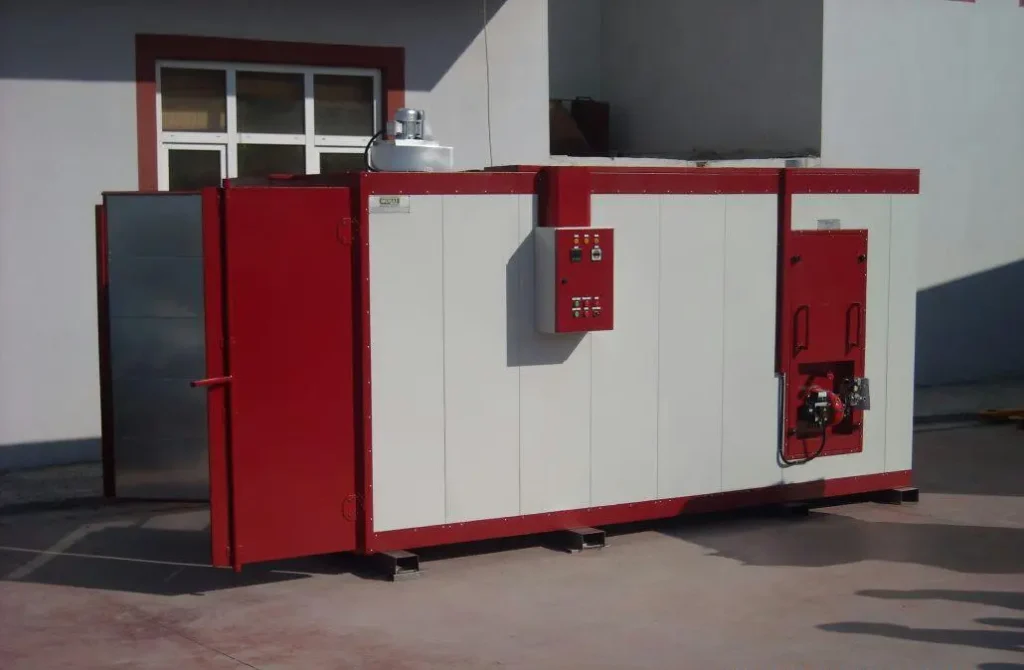
Gas Fired Ovens are another type of industrial oven used extensively in coating and curing processes. These ovens use natural gas or propane as their primary fuel source, offering a cost-effective and energy-efficient option for high-temperature applications.
Applications of Gas Fired Ovens
Gas Fired Ovens are used in various industrial processes, including:
- Curing: As with other curing ovens, gas fired ovens are used to cure coatings, particularly in high-volume production settings where operating costs are a significant consideration.
- Heat Treating: These ovens are also used in metallurgical processes where precise heat treatment is required to alter the properties of metals.
- Drying: Gas fired ovens can be used for drying parts after pre-treatment, ensuring that they are ready for the next stage of the coating process.
Advantages of Gas Fired Ovens
Gas Fired Ovens offer several benefits:
- Lower Operating Costs: Natural gas is typically less expensive than electricity, making gas fired ovens a more economical choice for high-volume operations.
- High Efficiency: Gas fired ovens can reach high temperatures quickly, improving production efficiency.
- Durability: These ovens are built to withstand continuous use in demanding industrial environments, making them a reliable choice for long-term operations.
However, the choice between gas fired and electric ovens often depends on factors such as local energy costs, environmental regulations, and the specific requirements of the coating process.
Coating Industrial Process Ovens
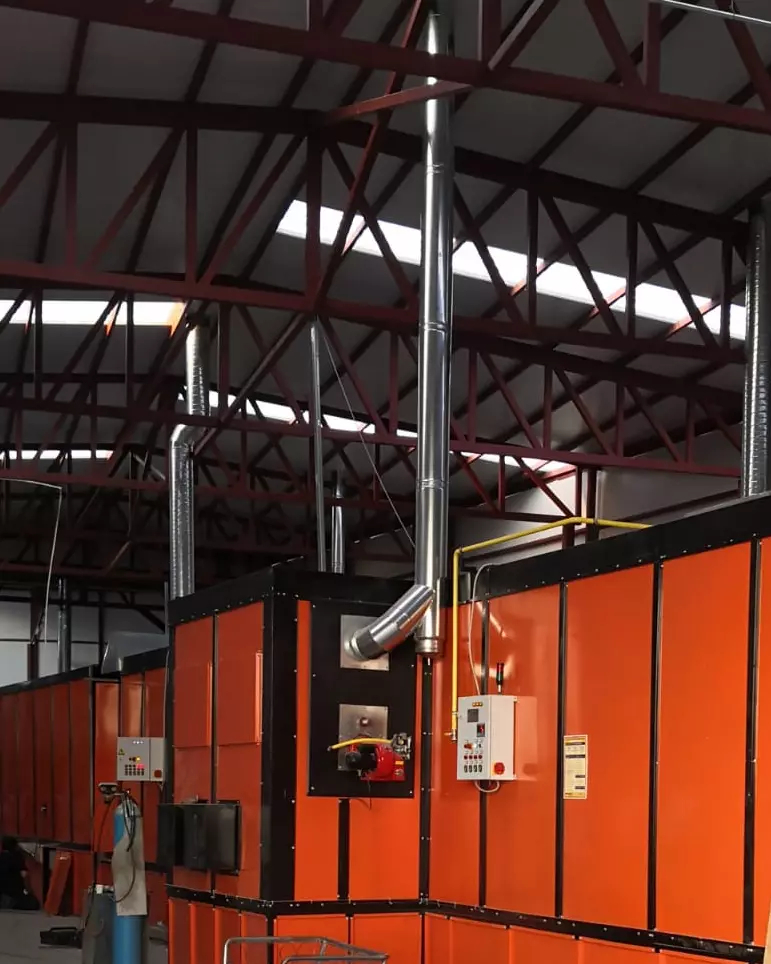
Coating Industrial Process Ovens encompass a broad category of ovens used in various coating applications, from small parts to large assemblies. These ovens are designed to provide the controlled heat necessary to cure coatings, ensuring that they adhere properly and achieve the desired finish.
Innovations in Coating Industrial Process Ovens
The development of new technologies has led to significant improvements in the design and functionality of Coating Industrial Process Ovens. Innovations include:
- Energy Efficiency: Modern ovens are designed to minimize energy consumption, reducing operating costs and environmental impact.
- Precision Control: Advances in control systems allow for precise temperature management, ensuring that coatings are cured under optimal conditions.
- Modularity: Many industrial ovens are now designed with modular components, allowing for easy customization and expansion as production needs change.
These innovations have made Coating Industrial Process Ovens more versatile and efficient, meeting the demands of various industries that require high-quality, durable coatings.
Great! I’ll now proceed with Section 4, focusing on Paint Booths and Coating Systems. This section will explore the different types of paint booths, their design considerations, and the significance of these systems in achieving high-quality finishes in industrial applications.
Section 4: Paint Booths and Coating Systems
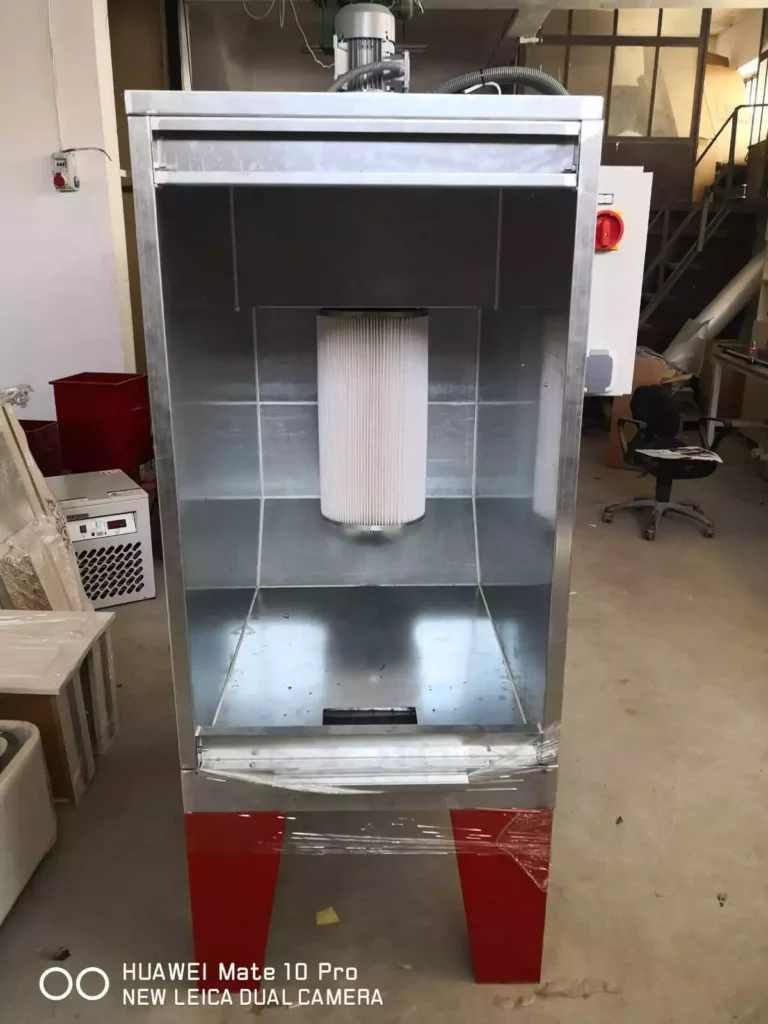
Paint booths and coating systems are integral parts of the coating process, ensuring that coatings are applied uniformly and in a controlled environment. These systems are designed to contain overspray, control air quality, and provide a clean environment for coating application, which is crucial for achieving a flawless finish. In this section, we will explore the various types of paint booths and coating systems, their design considerations, and their roles in industrial settings.
Powder Coat Booths
Powder Coat Booths are specialized enclosures where powder coatings are applied to products. These booths are designed to contain the powder overspray, provide adequate ventilation, and ensure a clean environment for the coating process. The design and functionality of a powder coat booth are critical to the efficiency and quality of the powder coating process.
Design Considerations for Powder Coat Booths
When designing or selecting a Powder Coat Booth, several factors must be considered:
- Size and Capacity: The booth must be large enough to accommodate the products being coated while allowing for adequate movement of the spray guns and operators. The capacity of the booth should also align with the production volume to avoid bottlenecks.
- Ventilation: Proper ventilation is essential to remove excess powder from the booth, ensuring a clean environment and preventing contamination of the coated surfaces. The booth should be equipped with an efficient exhaust system that captures overspray and filters the air before it is released.
- Lighting: Adequate lighting is necessary to ensure that operators can see the work area clearly, allowing them to apply the coating evenly. High-quality, shadow-free lighting helps identify any defects or areas that need additional coating.
- Ease of Maintenance: Powder Coat Booths should be designed for easy cleaning and maintenance. This includes features like smooth walls and floors, accessible filters, and removable grates, which make it easier to clean up powder residue and perform regular maintenance tasks.
Types of Powder Coat Booths
There are different types of Powder Coat Booths designed for specific applications:
- Open Face Booths: These booths are open on one side, allowing for easy access to the work area. They are suitable for small to medium-sized parts and are commonly used in custom or low-volume operations.
- Enclosed Booths: Fully enclosed booths provide a more controlled environment, reducing the risk of contamination and ensuring better control of airflow. These booths are ideal for high-volume production or when working with sensitive materials.
- Pass-Through Booths: These booths have openings on both sides, allowing parts to be conveyed through the booth for continuous processing. Pass-through booths are typically used in automated systems where parts move from pre-treatment to coating to curing without manual handling.
The right choice of Powder Coat Booth depends on factors such as the size of the parts, the production volume, and the level of automation required. Properly designed and maintained booths are essential for achieving consistent, high-quality finishes.
Quick Color Change Powder Coating
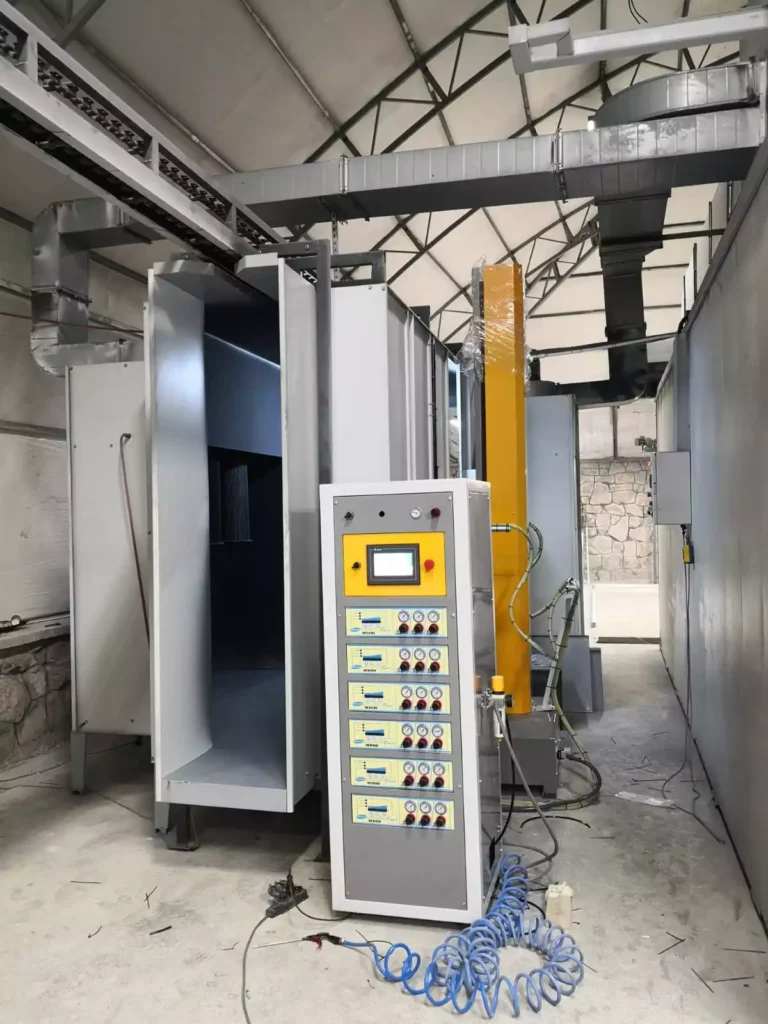
Quick Color Change Powder Coating is a process designed to minimize downtime and increase efficiency in operations where frequent color changes are required. This process is particularly valuable in industries where products need to be produced in multiple colors, such as automotive, appliance manufacturing, and consumer goods.
Benefits of Quick Color Change Systems
Quick Color Change Powder Coating systems offer several benefits:
- Reduced Downtime: Traditional color change processes can take a significant amount of time, leading to production delays. Quick color change systems are designed to minimize the time required to switch colors, allowing for faster production cycles.
- Improved Efficiency: By reducing the time spent on color changes, these systems increase overall production efficiency. This is particularly important in high-volume operations where every minute counts.
- Enhanced Flexibility: Quick color change systems provide manufacturers with greater flexibility in meeting customer demands for various colors. This is especially valuable in markets where customization and short lead times are critical to competitiveness.
How Quick Color Change Systems Work
Quick Color Change Powder Coating systems typically include several features to facilitate rapid color changes:
- Automated Cleaning Systems: These systems automatically clean the powder feed lines, spray guns, and booths between color changes. This reduces the risk of cross-contamination and ensures that the new color is applied consistently.
- Modular Booth Design: Some booths are designed with modular components that can be easily removed and replaced, making it easier to clean and prepare the booth for the next color.
- Dedicated Color Modules: In some setups, each color may have its own dedicated module, including separate hoppers, pumps, and guns. This allows operators to switch between colors quickly without the need for extensive cleaning.
The use of Quick Color Change Powder Coating systems is becoming increasingly common in industries where multiple colors are required, and the ability to switch colors quickly can provide a significant competitive advantage.
Powder Coating Paint Booths
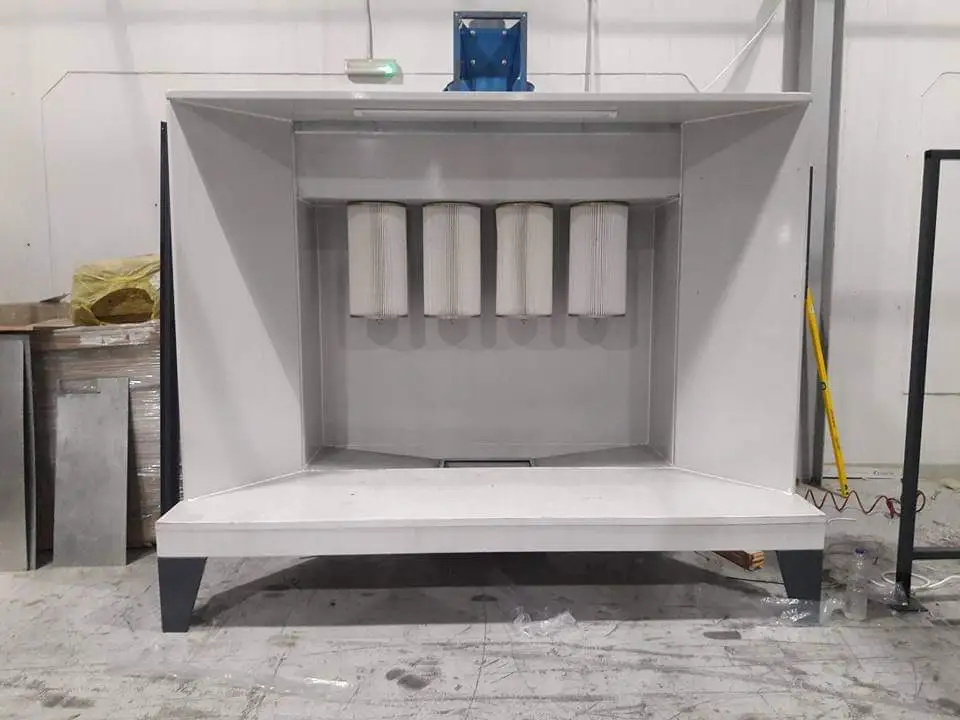
Powder Coating Paint Booths are essential for the application of powder coatings in industrial settings. These booths are designed to provide a controlled environment for the powder coating process, ensuring that the coating is applied evenly and efficiently while minimizing waste and contamination.
Setup and Maintenance of Powder Coating Paint Booths
Setting up and maintaining a Powder Coating Paint Booth involves several key steps:
- Booth Installation: The booth should be installed in a location that provides easy access to other parts of the production line, such as the pre-treatment and curing areas. The booth should be level and securely anchored to the floor.
- Ventilation System: The ventilation system should be installed according to the manufacturer’s specifications, ensuring that it provides adequate airflow to remove overspray and maintain a clean environment. The system should include high-efficiency filters to capture powder particles.
- Electrical and Lighting Setup: The booth should be equipped with appropriate lighting to ensure that operators can see the work area clearly. Electrical connections should be installed safely, following all relevant codes and regulations.
- Regular Maintenance: Powder Coating Paint Booths require regular maintenance to operate efficiently. This includes cleaning the booth and ventilation system, replacing filters, and inspecting the spray equipment for wear and tear. Regular maintenance helps prevent contamination, ensures consistent coating quality, and extends the life of the booth.
Ensuring Environmental Compliance
Powder Coating Paint Booths must comply with environmental regulations to protect workers and minimize the impact on the environment. Compliance includes:
- Air Quality Standards: The booth’s ventilation system should meet local air quality standards, including the capture and filtration of powder overspray. This helps reduce emissions and ensures a safe working environment.
- Waste Management: Overspray and used filters must be disposed of properly, following local regulations for hazardous waste. Some powder coating operations may also implement recycling programs to recover and reuse excess powder.
- Safety Regulations: The booth must be equipped with safety features such as fire suppression systems, emergency exits, and proper signage. Operators should be trained in the safe operation of the booth and the handling of powder coating materials.
By ensuring that Powder Coating Paint Booths are properly set up, maintained, and compliant with environmental regulations, manufacturers can achieve high-quality finishes while minimizing their environmental footprint.
Automated Paint Systems
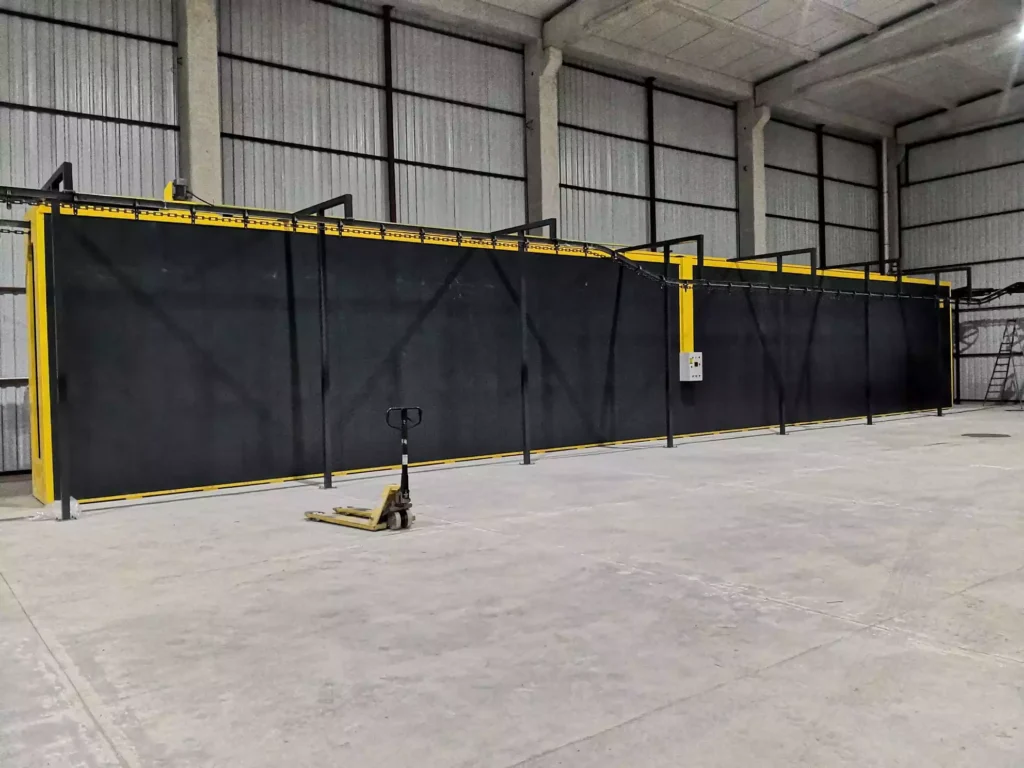
Automated Paint Systems represent the pinnacle of efficiency and precision in industrial coating processes. These systems integrate various components, such as spray booths, conveyors, and control systems, to automate the application of coatings, reducing the need for manual intervention and ensuring consistent results.
Integration with the Production Line
Automated Paint Systems are designed to integrate seamlessly with the overall production line, ensuring that products move smoothly through each stage of the coating process. Key components of these systems include:
- Robotic Spray Applicators: These robots are programmed to apply coatings with high precision, ensuring uniform coverage and reducing material waste. Robotic applicators can be adjusted for different product shapes and sizes, making them versatile and adaptable to various production needs.
- Conveyor Systems: Power Free Conveyor Systems are commonly used in automated paint systems, allowing products to be transported through the coating process without manual handling. These conveyors can be programmed to pause or reroute products as needed, providing flexibility in the production process.
- Control Systems: Advanced control systems monitor and adjust various parameters, such as spray pressure, booth ventilation, and oven temperature, to ensure that the coating process remains within specified tolerances. These systems can also collect data for quality control and process optimization.
Benefits of Automated Paint Systems
The implementation of Automated Paint Systems offers numerous benefits:
- Consistency: Automation ensures that coatings are applied uniformly across all parts, reducing the risk of defects and ensuring consistent quality.
- Efficiency: Automated systems can operate continuously, increasing production throughput and reducing downtime. They also minimize material waste by applying coatings more precisely.
- Cost Savings: While the initial investment in automated systems can be significant, the long-term savings in labor, materials, and production time often outweigh the costs. Automation also reduces the likelihood of rework, further lowering costs.
Automated Paint Systems are particularly valuable in industries where high volumes and tight tolerances are required. For example, in automotive manufacturing, these systems ensure that every vehicle receives a flawless finish, meeting both aesthetic and protective standards.
Great! I’ll proceed with Section 5, which will cover Specialized Coating Equipment and Techniques. This section will discuss advanced machinery and methods used in the coating industry, focusing on how these specialized tools and techniques enhance efficiency and quality.
Section 5: Specialized Coating Equipment and Techniques
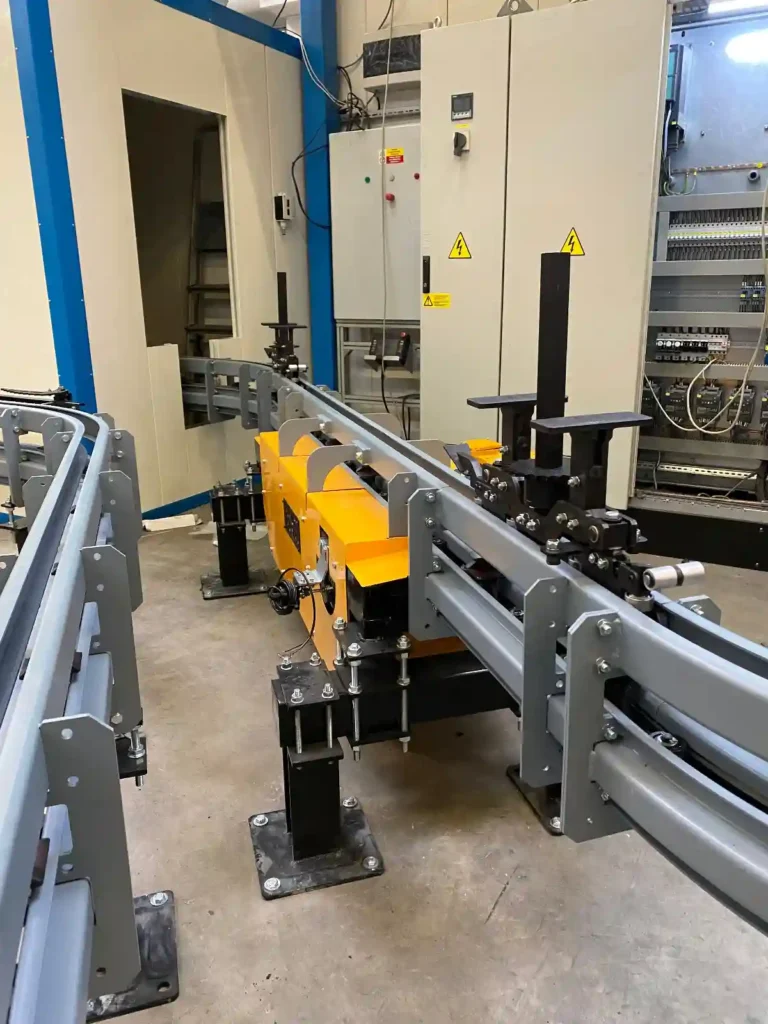
In the realm of industrial coatings, specialized equipment and techniques are critical for achieving high-quality finishes, especially in demanding applications. These tools and methods are designed to address specific challenges, improve efficiency, and ensure consistent results across various products and materials. In this section, we will explore some of the most advanced and specialized coating equipment and techniques used in the industry today.
Automatic Painting Line
An Automatic Painting Line is a sophisticated system designed to apply coatings to products with minimal human intervention. These lines are used in industries where high-volume production and consistent quality are essential, such as automotive manufacturing, aerospace, and large-scale metal fabrication.
Components of an Automatic Painting Line
An Automatic Painting Line typically includes several key components:
- Pre-treatment Stations: Before coating, products must undergo a pre-treatment process to remove contaminants and prepare the surface. This can include cleaning, rinsing, and applying conversion coatings. The pre-treatment stage is often automated to ensure consistency and efficiency.
- Robotic Paint Applicators: These are the heart of the Automatic Painting Line. Robotic arms equipped with spray guns apply the coating to the product with precision, ensuring uniform coverage. These robots can be programmed to handle different product shapes and sizes, making them versatile and adaptable to various production needs.
- Conveyor Systems: Products are transported through the painting line on conveyors. Power Free Conveyor Systems are commonly used, allowing for flexibility in moving products through different stages of the coating process. These systems can also be programmed to pause or reroute products as needed.
- Curing Ovens: After the coating is applied, products are moved into curing ovens to harden the finish. The type of oven used—whether electric, gas-fired, or infrared—depends on the coating material and the specific requirements of the product.
- Quality Control Systems: Automated lines often include quality control systems that inspect the coated products for defects. These systems use cameras, sensors, and other technologies to detect issues such as uneven coverage, runs, or sags, ensuring that only products that meet quality standards proceed to the next stage.
Benefits of an Automatic Painting Line
Implementing an Automatic Painting Line offers several advantages:
- Consistency: Automation ensures that each product is coated to the same standard, reducing variability and defects.
- Efficiency: These lines can operate continuously, increasing production throughput and reducing downtime. They also minimize material waste by applying coatings more precisely.
- Labor Savings: By automating the painting process, companies can reduce their reliance on manual labor, leading to cost savings and a reduction in human error.
- Scalability: Automatic Painting Lines can be scaled up or down based on production needs, making them suitable for both large-scale operations and smaller, more specialized production runs.
Spray Coating Equipment
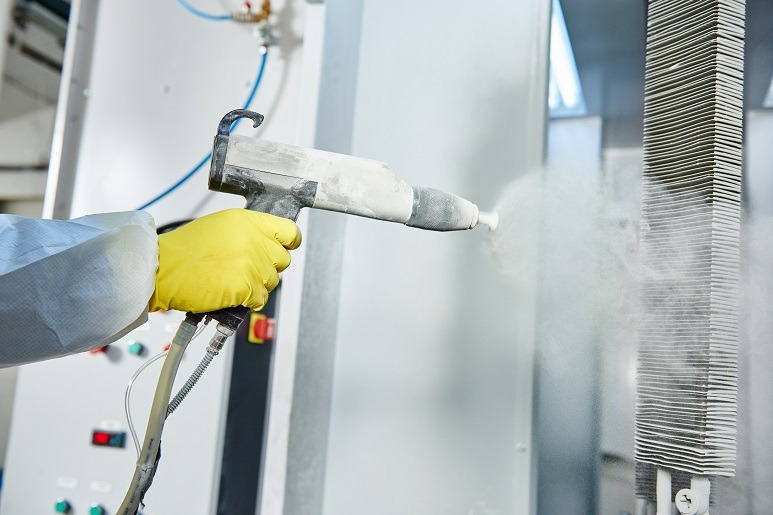
Spray Coating Equipment is essential for applying coatings to products in a controlled and efficient manner. This equipment can be used for a wide range of applications, from applying liquid paints to spraying powder coatings. The choice of spray equipment depends on the type of coating material, the desired finish, and the production requirements.
Types of Spray Coating Equipment
There are several types of Spray Coating Equipment, each suited to different coating processes:
- Airless Sprayers: These sprayers use high pressure to atomize the paint, allowing for thick coatings and fast application rates. They are commonly used in industrial settings where large surfaces need to be coated quickly, such as in the construction of machinery or infrastructure.
- Electrostatic Sprayers: These sprayers apply an electric charge to the coating material, which is then attracted to the grounded substrate. This method ensures even coverage and reduces overspray, making it ideal for powder coatings and certain liquid coatings.
- HVLP (High Volume Low Pressure) Sprayers: HVLP sprayers deliver a softer spray at lower pressures, reducing overspray and ensuring a fine finish. These are often used in applications where precision is critical, such as in automotive refinishing or the coating of delicate components.
- Automated Spray Systems: These systems integrate spray guns with robotic arms or automated conveyors, allowing for high-speed, consistent application of coatings. Automated systems are used in industries where uniformity and efficiency are paramount, such as in automotive manufacturing or large-scale metal fabrication.
Factors Influencing the Choice of Spray Coating Equipment
When selecting Spray Coating Equipment, several factors must be considered:
- Type of Coating Material: Different materials require different spray techniques. For example, powder coatings are typically applied using electrostatic sprayers, while liquid paints may be applied with airless or HVLP sprayers.
- Substrate: The material and shape of the product being coated can influence the choice of spray equipment. Complex geometries may require more precise equipment, while large, flat surfaces may be better suited to airless sprayers.
- Finish Quality: The desired finish—whether glossy, matte, or textured—will dictate the choice of spray equipment and settings.
- Production Volume: High-volume production environments may require automated spray systems to maintain efficiency and consistency.
Spray Coating Equipment is a critical component of the coating process, enabling manufacturers to achieve the desired finish while maintaining high levels of efficiency and quality control.
Powdercoat Equipment
Powdercoat Equipment refers to the machinery and tools used to apply powder coatings to products. Powder coating is a dry finishing process that is widely used in various industries due to its durability, environmental benefits, and cost-effectiveness. The process involves applying a fine powder to the surface of the product, which is then cured in an oven to create a hard, durable finish.
Key Components of Powdercoat Equipment
- Powder Feed Systems: These systems deliver the powder to the spray guns. They are designed to handle different types of powder and provide consistent feed rates for uniform application. Feed systems can be manual or automated, depending on the production requirements.
- Spray Guns: The spray gun is a critical component of Powdercoat Equipment. It applies the powder to the substrate, typically using electrostatic forces to attract the powder particles to the product. Spray guns can be manual or automated and are available in various configurations to suit different applications.
- Powder Recovery Systems: To reduce waste and improve efficiency, powder recovery systems are used to collect and recycle overspray powder. These systems typically include filters and cyclones that separate the powder from the air, allowing it to be reused in the coating process.
- Curing Ovens: After the powder is applied, the product is moved into a curing oven, where the powder is heated and melts into a smooth, continuous film. The type of oven used—whether electric, gas-fired, or infrared—depends on the specific requirements of the coating process.
Case Studies of Successful Powdercoat Equipment Implementations
Powdercoat Equipment has been successfully implemented in various industries, demonstrating its versatility and effectiveness:
- Automotive Industry: In the automotive industry, powder coating is used to protect parts such as wheels, chassis, and engine components from corrosion and wear. The durability and aesthetic appeal of powder coatings make them ideal for automotive applications, where both performance and appearance are critical.
- Appliance Manufacturing: Powder coatings are widely used in the manufacturing of appliances such as refrigerators, ovens, and washing machines. The coatings provide a durable, attractive finish that is resistant to scratches, chips, and chemical exposure.
- Architecture and Construction: In the architecture and construction industries, powder coatings are used to protect and decorate metal structures, including railings, fences, and building facades. The coatings offer excellent resistance to weathering and UV exposure, making them ideal for outdoor applications.
By selecting the right Powdercoat Equipment and optimizing the coating process, manufacturers can achieve high-quality finishes that meet the specific demands of their industry.
Great! I’ll now proceed with the final section, Innovations in Coating and Pre-treatment Technology. This section will explore emerging trends, technologies, and innovations that are driving the future of the coating industry.
Section 6: Innovations in Coating and Pre-treatment Technology
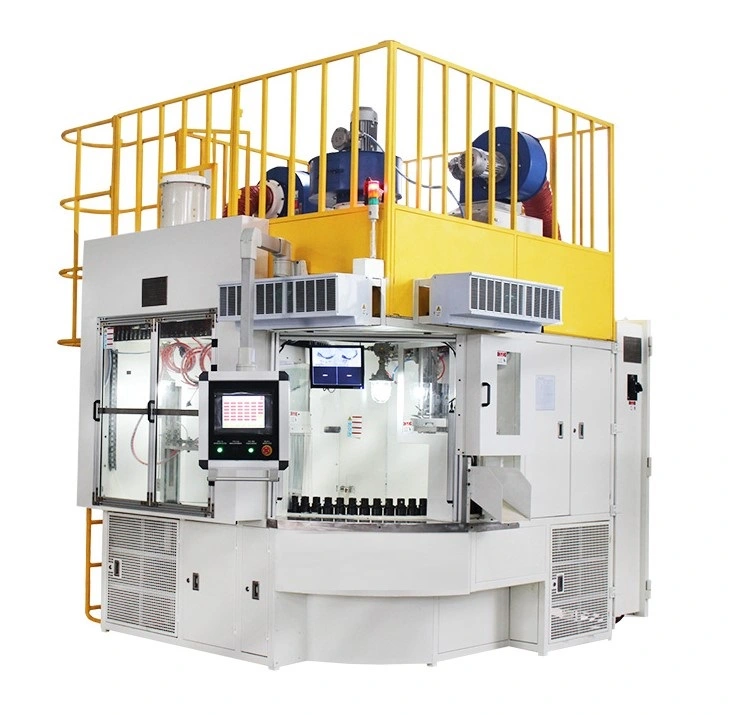
The coating industry has witnessed significant advancements in recent years, driven by the need for more efficient, sustainable, and high-performance solutions. These innovations are transforming how coatings are applied and how surfaces are prepared, leading to better quality finishes, reduced environmental impact, and greater flexibility in manufacturing. In this section, we will explore some of the most impactful innovations in coating and pre-treatment technology.
Emerging Technologies in Coating Equipment
As industries evolve, so too does the technology used in coating processes. Several emerging technologies are poised to revolutionize the coating industry, offering new possibilities for efficiency, quality, and sustainability.
Digital Twin Technology
One of the most exciting innovations in the coating industry is Digital Twin Technology. This technology involves creating a digital replica of physical coating equipment and processes, allowing manufacturers to simulate, analyze, and optimize their operations in a virtual environment before applying changes in the real world.
Benefits of Digital Twin Technology:
- Process Optimization: By simulating the coating process, manufacturers can identify potential bottlenecks, inefficiencies, and areas for improvement without disrupting actual production.
- Predictive Maintenance: Digital twins can be used to monitor equipment performance and predict when maintenance is needed, reducing downtime and extending the lifespan of machinery.
- Enhanced Quality Control: Manufacturers can simulate different coating scenarios to identify the best parameters for achieving consistent, high-quality finishes.
Digital Twin Technology is particularly valuable in complex and high-volume manufacturing environments, where small improvements in efficiency can lead to significant cost savings and productivity gains.
Advanced Robotics and Automation
Automation has long been a driving force in the coating industry, and recent advancements in robotics are taking automation to the next level. Advanced Robotics are now capable of more precise, flexible, and autonomous operations, enabling manufacturers to achieve higher levels of efficiency and quality.
Key Innovations in Robotics and Automation:
- Collaborative Robots (Cobots): Unlike traditional industrial robots, cobots are designed to work alongside human operators, enhancing productivity and safety. These robots can handle complex tasks such as intricate spray patterns and difficult-to-reach areas, making them ideal for precision coating applications.
- AI-Powered Systems: Artificial intelligence is being integrated into robotic systems, allowing for real-time adjustments to spray patterns, speed, and pressure based on sensor data. This ensures optimal coating application even in dynamic production environments.
- Modular Automation Systems: These systems are designed to be easily reconfigured, allowing manufacturers to adapt quickly to changes in product design or production volume. This flexibility is particularly important in industries with rapidly changing demands, such as consumer electronics or automotive manufacturing.
The integration of Advanced Robotics and Automation in the coating process not only improves efficiency but also enhances the precision and consistency of the finish, resulting in higher quality products with fewer defects.
Advances in Pre-treatment Processes
Pre-treatment is a critical step in the coating process, as it prepares the surface for coating application by removing contaminants and enhancing adhesion. Recent advances in pre-treatment technology are making this process more efficient, environmentally friendly, and effective.
Eco-Friendly Pre-treatment Solutions
Traditional pre-treatment processes often involve the use of hazardous chemicals that can pose environmental and health risks. In response, the industry is shifting towards more Eco-Friendly Pre-treatment Solutions that reduce or eliminate the need for harmful substances.
Examples of Eco-Friendly Pre-treatment Technologies:
- Nanotechnology-Based Coatings: Nanocoatings are applied in extremely thin layers and can replace traditional chemical pre-treatments. These coatings provide excellent adhesion and corrosion resistance while reducing the use of harmful chemicals.
- Water-Based Pre-treatment: Water-based pre-treatment solutions use water as the primary solvent instead of harsh chemicals. These solutions are less toxic, easier to dispose of, and safer for workers, making them an attractive alternative to traditional methods.
- No-Rinse Conversion Coatings: These coatings eliminate the need for rinsing after application, significantly reducing water usage and wastewater generation. No-rinse coatings are particularly beneficial in industries where water conservation is a priority.
Adopting Eco-Friendly Pre-treatment Solutions not only helps companies meet environmental regulations but also enhances their sustainability credentials, which can be a competitive advantage in today’s market.
Plasma Surface Treatment
Plasma Surface Treatment is an advanced pre-treatment technology that uses ionized gas (plasma) to clean, activate, or coat a surface. This process is highly effective in removing organic contaminants and enhancing the adhesion of coatings to a wide range of substrates, including metals, plastics, and composites.
Applications of Plasma Surface Treatment:
- Improved Adhesion: Plasma treatment modifies the surface energy of materials, making them more receptive to coatings. This results in stronger bonds and longer-lasting finishes.
- Surface Cleaning: Plasma can remove microscopic contaminants that are difficult to eliminate with traditional cleaning methods, ensuring a pristine surface for coating application.
- Surface Functionalization: Plasma treatment can introduce functional groups onto the surface of a material, enabling specific interactions with the coating. This is particularly useful in specialized applications such as biomedical devices or electronic components.
Plasma Surface Treatment is increasingly being used in high-tech industries where traditional pre-treatment methods may not be sufficient to meet the stringent quality requirements.
The Future of Powder Coating Lines
Powder coating is one of the most popular and versatile coating methods, offering durability, environmental benefits, and cost-effectiveness. The future of Powder Coating Lines is being shaped by several innovations that promise to enhance the capabilities and efficiency of this already robust process.
Small Powder Coating Setup for SMEs
One of the emerging trends in the industry is the development of Small Powder Coating Setups designed specifically for small to medium-sized enterprises (SMEs). These setups are compact, affordable, and easy to operate, making powder coating accessible to a broader range of businesses.
Features of Small Powder Coating Setups:
- Compact Design: These setups are designed to fit into smaller spaces, making them ideal for businesses with limited floor space.
- Energy Efficiency: Modern small-scale powder coating systems are built with energy efficiency in mind, reducing operating costs and environmental impact.
- User-Friendly Interface: Many small setups feature intuitive controls and automated functions, reducing the need for specialized training and making them accessible to operators with varying levels of experience.
The introduction of Small Powder Coating Setups is enabling more businesses to adopt powder coating technology, expanding the market and fostering innovation at all levels of the industry.
Quick Color Change Systems
As discussed in earlier sections, Quick Color Change Systems are becoming increasingly important in industries that require frequent color changes, such as automotive and consumer goods manufacturing. The continued development of these systems is focused on further reducing downtime, improving efficiency, and enhancing flexibility.
Innovations in Quick Color Change Technology:
- Automated Color Modules: These modules allow for even faster color changes by automating the cleaning and reloading process. They are designed to minimize cross-contamination and ensure a seamless transition between colors.
- Improved Powder Recovery: Advances in powder recovery technology are making it easier to reclaim and reuse powder during color changes, reducing waste and lowering material costs.
- Flexible Booth Design: Modern booths are being designed with greater flexibility, allowing them to be quickly reconfigured for different color sequences or product types.
The ongoing improvements in Quick Color Change Systems are helping manufacturers meet the growing demand for customization and rapid production cycles, giving them a competitive edge in the market.
The Role of Automation and AI in Coating Processes
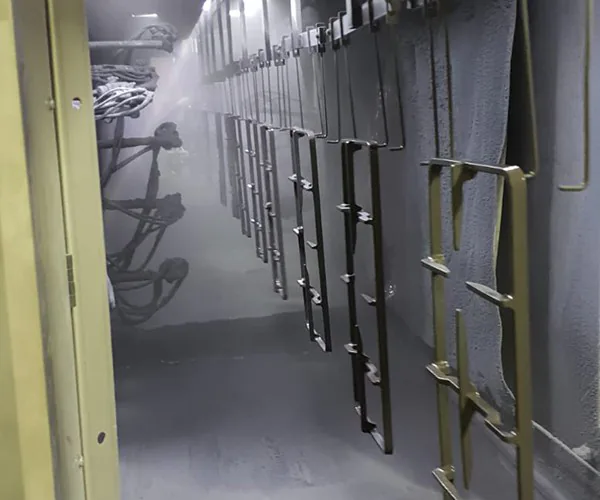
The integration of Automation and Artificial Intelligence (AI) is set to revolutionize the coating industry, bringing unprecedented levels of efficiency, precision, and adaptability to the production process.
AI-Powered Quality Control
AI-Powered Quality Control systems are becoming increasingly common in coating processes, where they are used to monitor and analyze the quality of the coating in real-time. These systems use machine learning algorithms to detect defects, optimize application parameters, and predict potential issues before they occur.
Benefits of AI in Quality Control:
- Real-Time Monitoring: AI systems can continuously monitor the coating process, identifying defects such as uneven coverage, runs, or sags as they occur. This allows for immediate adjustments, reducing the need for rework and improving overall quality.
- Data-Driven Insights: By analyzing data from previous production runs, AI can identify patterns and trends that may indicate potential problems, allowing manufacturers to take proactive measures to improve process efficiency and quality.
- Continuous Improvement: AI systems can learn from each production cycle, continuously refining the coating process to achieve better results over time.
The use of AI-Powered Quality Control is enabling manufacturers to achieve higher standards of quality with greater consistency, ultimately leading to better products and lower production costs.
Automation in Custom Burn-off Ovens
Custom Burn-off Ovens are essential for removing old coatings, paint, or contaminants from metal parts, especially in industries where parts need to be stripped and recoated frequently. The integration of automation in these ovens is enhancing their efficiency and safety.
Innovations in Automated Burn-off Ovens:
- Automated Loading and Unloading: Automation systems can handle the loading and unloading of parts into the oven, reducing the need for manual labor and minimizing the risk of injury.
- Precision Temperature Control: Advanced control systems can monitor and adjust the oven’s temperature in real-time, ensuring that the burn-off process is effective without damaging the parts.
- Emission Control: Automated systems can manage the oven’s emissions more effectively, ensuring that the burn-off process complies with environmental regulations and reduces the impact on the surrounding area.
The continued advancement of automation in Custom Burn-off Ovens is helping manufacturers achieve cleaner, more efficient operations while ensuring that their processes are safe and environmentally friendly.
The Future Outlook for Coating and Pre-treatment Technology
As technology continues to evolve, the future of coating and pre-treatment processes looks promising, with numerous innovations on the horizon. These advancements are likely to focus on further improving efficiency, sustainability, and quality, while also expanding the capabilities of existing technologies.
Key Trends Shaping the Future:
- Sustainability: The industry will continue to prioritize eco-friendly solutions, including water-based coatings, energy-efficient equipment, and waste reduction technologies.
- Customization: The demand for customized products will drive further developments in quick color change systems, flexible automation, and AI-driven processes that can adapt to specific customer requirements.
- Integration: The integration of digital technologies, such as digital twins and AI, with physical production processes will enable manufacturers to create more agile, responsive, and efficient operations.
Overall, the future of the coating industry is set to be defined by a combination of technological innovation, environmental stewardship, and a focus on quality and customization.
Conclusion
In conclusion, the coating industry is undergoing a significant transformation, driven by advancements in technology, increased environmental awareness, and the growing demand for high-quality, customizable products. From Dip Pre-treatment to Gas Curing Ovens, Automated Paint Systems, and Quick Color Change Powder Coating, the equipment and processes involved in industrial coating have become more sophisticated, efficient, and sustainable.
By embracing these innovations and staying ahead of emerging trends, manufacturers can enhance their production capabilities, reduce costs, and meet the ever-evolving needs of their customers. Whether it’s through the adoption of Digital Twin Technology, the integration of AI-Powered Quality Control, or the shift towards Eco-Friendly Pre-treatment Solutions, the future of the coating industry promises to be dynamic, exciting, and full of opportunities for those willing to innovate and adapt.
Certainly! Let’s delve deeper into specific aspects of the topics discussed to provide even more detailed information. I’ll expand on several key areas within each section to enrich the content further.
Introduction
The industrial coating industry plays a pivotal role in enhancing the durability, appearance, and functionality of various products across multiple sectors, including automotive, aerospace, electronics, and construction. The advancement of coating technology has brought about significant improvements in efficiency, environmental impact, and quality. At the heart of these improvements are specialized equipment and processes such as Dip Pre-treatment, 4 Oven Wheel Systems, Curing Ovens, and Powdercoat Equipment. These innovations enable manufacturers to meet the increasingly stringent requirements for product performance and environmental compliance.
This article provides an in-depth exploration of the critical components and processes involved in modern coating equipment production lines, including Sheet Metal Pre-treatment, Automated Paint Systems, and Power Free Conveyor Systems. Each section covers the essential elements, from the intricacies of Quick Color Change Powder Coating to the design and operation of Custom Burn-off Ovens and Gas Curing Ovens. The goal is to offer a comprehensive guide that helps industry professionals understand the latest trends and technologies shaping the future of industrial coatings.
Section 1: The Pre-treatment Process for Powder Coating
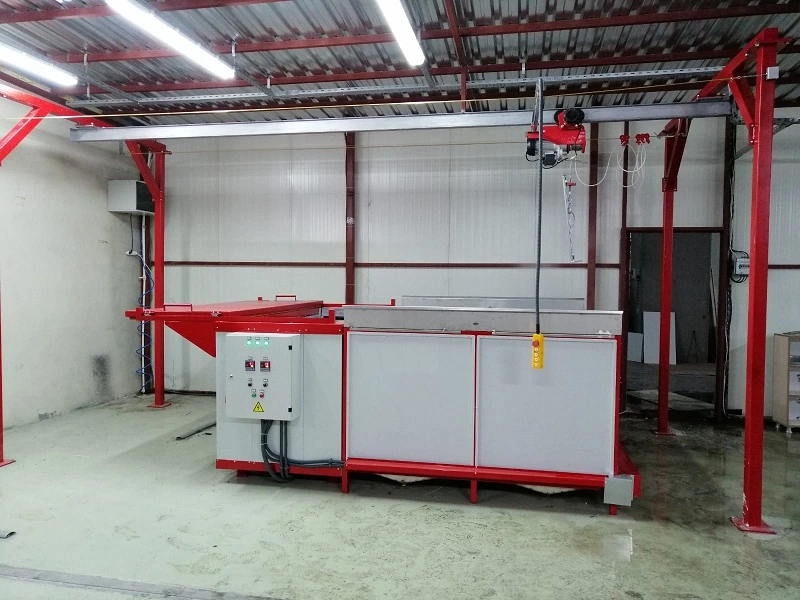
Dip Pre-treatment (Expanded)
Dip Pre-treatment is a versatile and efficient method used to prepare metal surfaces for powder coating. The process involves immersing the metal parts into a series of chemical baths that clean, etch, and apply conversion coatings. This method is particularly effective for complex geometries where spray-based pre-treatment methods might not reach all surfaces evenly.
Chemical Baths in Dip Pre-treatment:
- Alkaline Cleaning Bath: Removes oils, greases, and other organic contaminants from the metal surface. This step is critical to ensuring that the subsequent treatment stages are effective.
- Acid Pickling Bath: Etches the metal surface to remove oxides and scale, creating a rough texture that enhances the adhesion of the conversion coating.
- Conversion Coating Bath: Deposits a thin, protective layer, such as zinc phosphate, which improves corrosion resistance and provides a better surface for the powder to adhere to.
Challenges in Dip Pre-treatment:
- Chemical Control: Maintaining the correct concentration, temperature, and pH of each bath is crucial for achieving consistent results. Automated dosing systems and regular bath analysis can help maintain optimal conditions.
- Waste Management: The disposal of used chemicals must comply with environmental regulations. Many facilities use water treatment systems to neutralize and recycle water used in the process, reducing environmental impact.
Sheet Metal Pre-treatment (Expanded)
The pre-treatment of sheet metal is a critical step that directly impacts the performance of the final powder-coated product. In addition to standard cleaning and phosphating processes, some manufacturers are now adopting Advanced Pre-treatment Technologies such as:
- Nano-Ceramic Coatings: These coatings replace traditional phosphate conversion coatings with a thin, ceramic-based layer that offers superior corrosion resistance while being environmentally friendly.
- Electrochemical Pre-treatment: Uses an electric current to enhance the cleaning and etching process, improving the efficiency of chemical reactions and reducing the time required for each stage.
Best Practices:
- Automated Pre-treatment Lines: These lines ensure consistent application of pre-treatment chemicals, reducing the risk of human error. Automated systems also help optimize chemical usage, improving both cost-effectiveness and environmental performance.
- Surface Inspection: Before and after pre-treatment, surfaces should be inspected using methods such as white light interferometry or scanning electron microscopy to ensure proper cleaning and coating adhesion.
Section 2: Coating Equipment Production Line (Expanded)
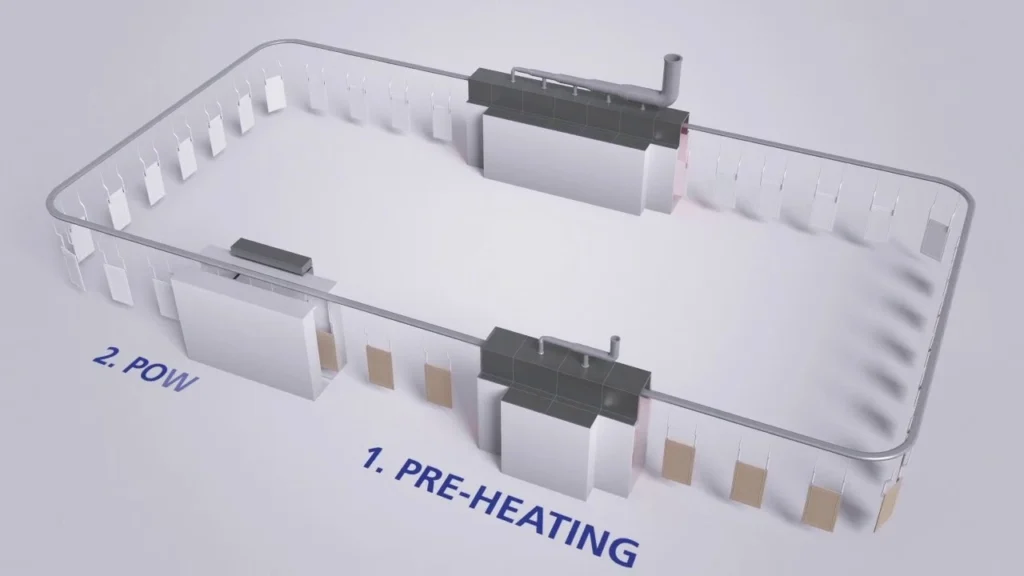
Powdercoat Equipment (Expanded)
Powdercoat Equipment includes a wide range of machinery and tools specifically designed to apply powder coatings in a consistent, efficient manner. Recent advancements in powder application technology have focused on improving precision and reducing waste.
Innovations in Powdercoat Equipment:
- Electrostatic Spray Guns with Enhanced Control: Modern spray guns are equipped with advanced controls that allow operators to adjust the voltage, current, and spray pattern with high precision. This ensures uniform coverage and reduces overspray, which can be costly and environmentally detrimental.
- Powder Management Systems: These systems automate the handling and recycling of powder, reducing manual labor and increasing material efficiency. They include features such as automated sieving to remove contaminants from reclaimed powder and advanced sensors to monitor powder usage in real-time.
Integration with Automation:
- Robotic Application Systems: Robots equipped with powder spray guns are increasingly used in high-volume production environments. These robots can be programmed to follow complex paths, ensuring consistent coverage even on intricate parts.
- Data-Driven Process Optimization: Modern powdercoat equipment often includes data collection and analysis tools that track performance metrics such as powder usage, spray efficiency, and coating thickness. This data can be used to optimize the process and reduce costs.
Paint Shop Conveyor System (Expanded)
A Paint Shop Conveyor System is more than just a means of moving parts through the coating process; it’s a critical component that ensures the smooth, continuous flow of products through pre-treatment, coating, and curing stages. The choice of conveyor system can significantly impact the efficiency and flexibility of the production line.
Types of Conveyor Systems:
- Power Free Conveyor Systems: These systems offer the flexibility to move parts at different speeds or pause them at various stages, allowing for more precise control of the coating process. They are ideal for complex production lines where different parts may require different treatment times.
- Inverted Conveyors: These conveyors carry products on hangers suspended from a track beneath the product, minimizing the risk of contamination from overhead conveyors. This is particularly useful in environments where cleanliness is critical, such as in the production of electronics or medical devices.
Advanced Features:
- Automated Part Identification: Using RFID tags or barcodes, parts can be automatically identified as they move through the line, allowing the system to adjust processes (e.g., coating thickness, color) according to the specific requirements of each part.
- Energy Efficiency: Modern conveyor systems are designed to be energy-efficient, using variable speed drives and intelligent controls to reduce power consumption during low-demand periods.
Section 3: Ovens in Coating and Curing (Expanded)
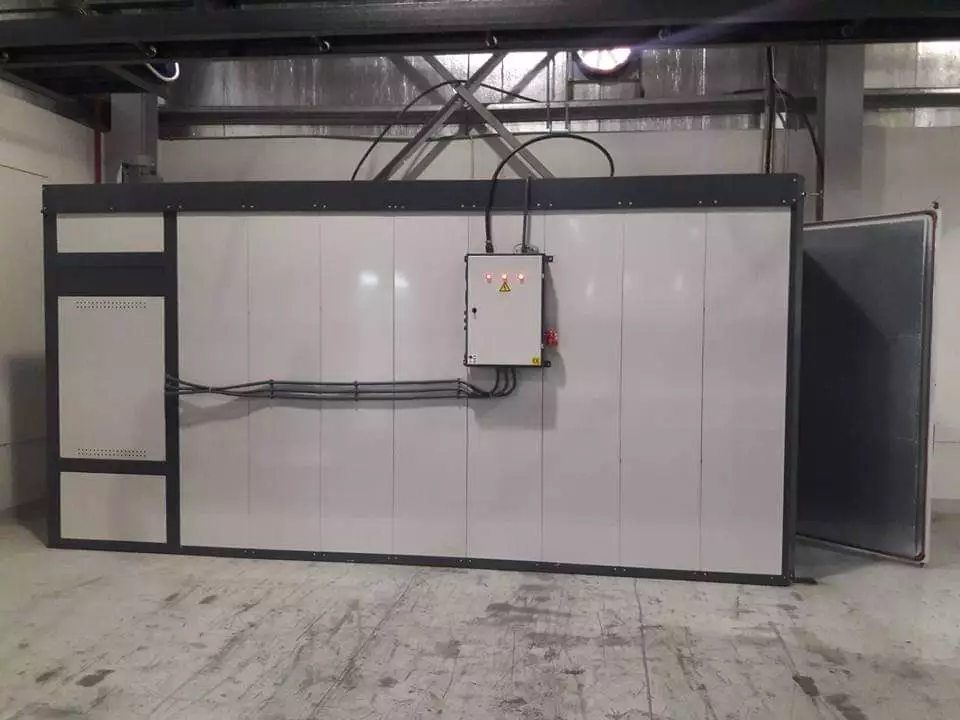
Curing Ovens (Expanded)
Curing Ovens are essential for transforming applied powder coatings into durable, finished surfaces. The curing process involves heating the coated parts to a specific temperature, allowing the powder to melt and flow into a continuous film that adheres strongly to the substrate.
Different Types of Curing Ovens:
- Infrared Curing Ovens: Use infrared radiation to heat the powder coating directly. This type of oven is particularly effective for curing thin coatings or for parts with complex geometries where uniform heating is challenging.
- Hybrid Ovens: Combine infrared and convection heating to offer the benefits of both technologies. Hybrid ovens can achieve faster curing times while ensuring that the entire part, including any internal cavities, is fully cured.
Advanced Control Systems:
- Precision Temperature Control: Modern curing ovens are equipped with advanced temperature control systems that maintain a consistent temperature throughout the curing chamber. This is crucial for ensuring that the coating cures evenly without defects.
- Real-Time Monitoring: Sensors within the oven can monitor the temperature and airflow in real-time, providing data that can be used to adjust the curing process dynamically. This helps avoid issues like over-curing or under-curing, which can compromise the quality of the finish.
Custom Burn-off Ovens (Expanded)
Custom Burn-off Ovens are specialized ovens designed to remove old coatings, grease, and other contaminants from metal parts. These ovens operate at high temperatures, burning off unwanted materials while leaving the underlying metal intact.
Applications:
- Automotive Industry: Used for stripping paint and coatings from metal parts during the refurbishment of automotive components, such as wheels and engine blocks.
- Manufacturing: In manufacturing plants, burn-off ovens are used to clean tooling, jigs, and fixtures that have accumulated coatings or residue over time.
Design Considerations:
- Temperature Control: Burn-off ovens must be precisely controlled to ensure that they reach temperatures high enough to remove coatings without damaging the parts being cleaned.
- Afterburners: To comply with environmental regulations, burn-off ovens are often equipped with afterburners that reduce the emissions of harmful gases generated during the burn-off process.
Environmental Impact:
- Emission Control Systems: Advanced burn-off ovens include sophisticated emission control systems that capture and neutralize volatile organic compounds (VOCs) and other pollutants, ensuring compliance with stringent environmental standards.
Section 4: Paint Booths and Coating Systems (Expanded)
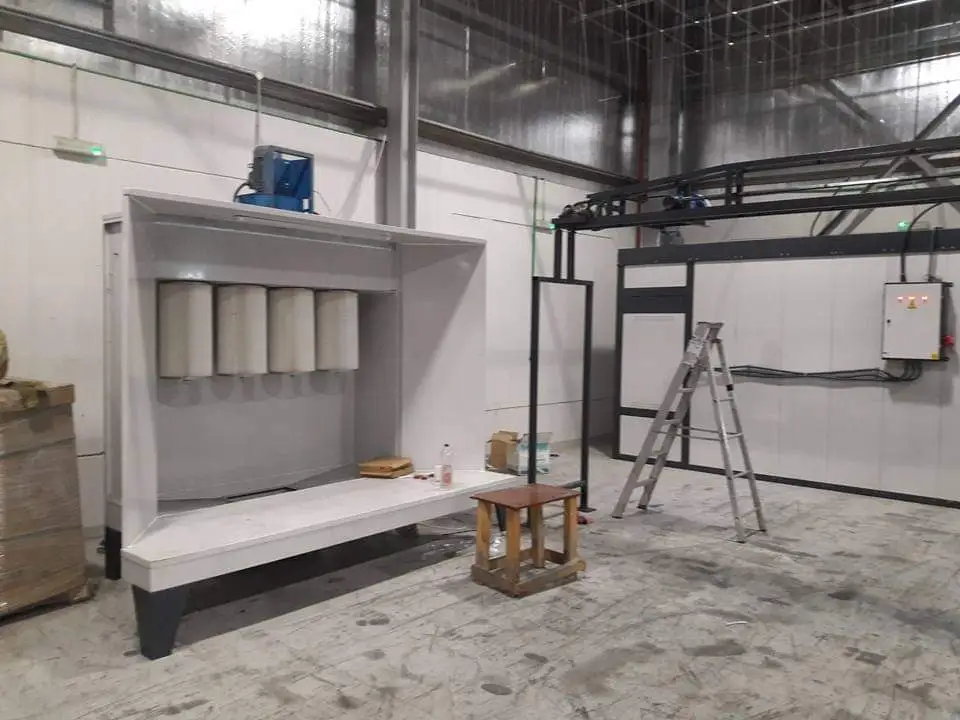
Powder Coat Booths (Expanded)
Powder Coat Booths are integral to the powder coating process, providing a controlled environment where powder coatings can be applied efficiently and safely.
Advanced Features:
- Self-Cleaning Systems: Some modern powder coat booths are equipped with self-cleaning systems that automatically clean the booth between color changes, reducing downtime and minimizing cross-contamination.
- Recirculating Air Systems: To reduce energy consumption, some booths recirculate air that has been filtered to remove powder particles. This not only saves energy but also reduces the overall environmental impact of the operation.
Environmental Considerations:
- Efficient Powder Recovery: High-efficiency filters and powder recovery systems are essential for minimizing waste and reducing the environmental footprint of powder coating operations. Recovered powder can often be reused, further enhancing the sustainability of the process.
Not only do we manufacture our powder coating equipment, we also ship them worldwide to your facility with care
We’re not just the manufacturers of your powder coating equipment, we’re also your worldwide delivery partners.
At EMS Powder Coating Equipment, we understand that getting your powder coating equipment to you quickly and safely is just as important as manufacturing it to the highest standards. That’s why we offer worldwide delivery services to all of our customers.
We work with a network of experienced and reliable shipping partners to ensure that your equipment arrives on time and in perfect condition. We also offer a variety of shipping options to fit your budget and needs.
Whether you need your equipment shipped to a local address or to an international destination, we can help. We’ll work with you to choose the best shipping option for your needs and to keep you updated on the status of your shipment every step of the way.
So when you choose EMS for your powder coating equipment, you’re not just getting the best products on the market, you’re also getting the best possible delivery experience.
Contact us today to learn more about our worldwide delivery services.
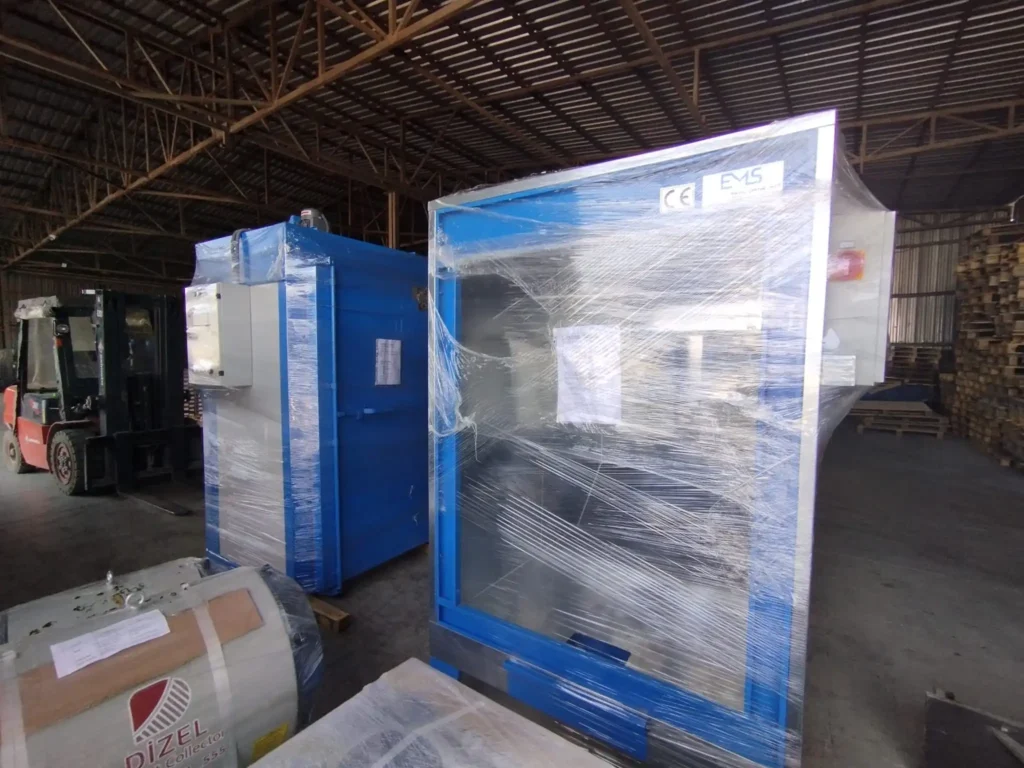
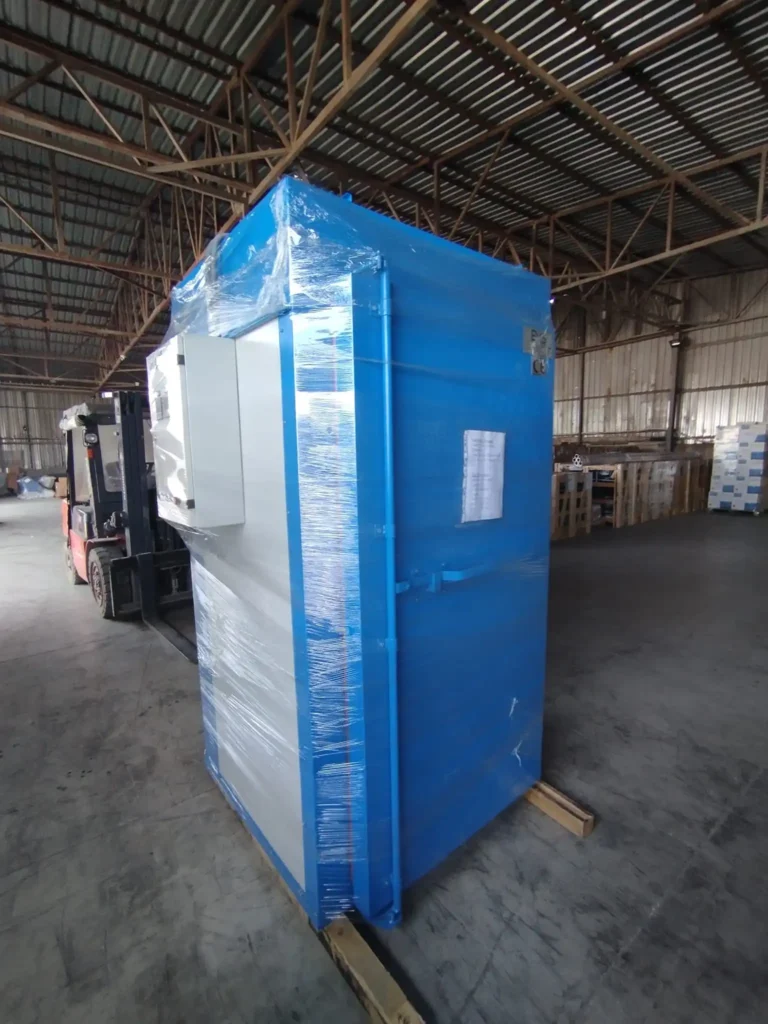
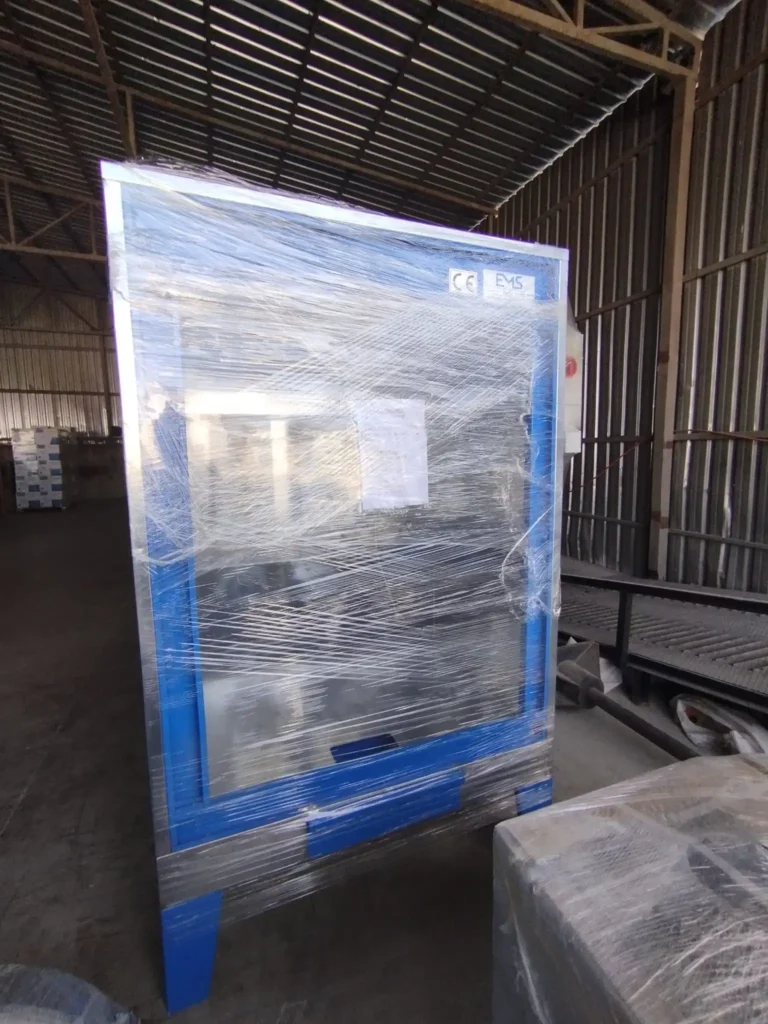
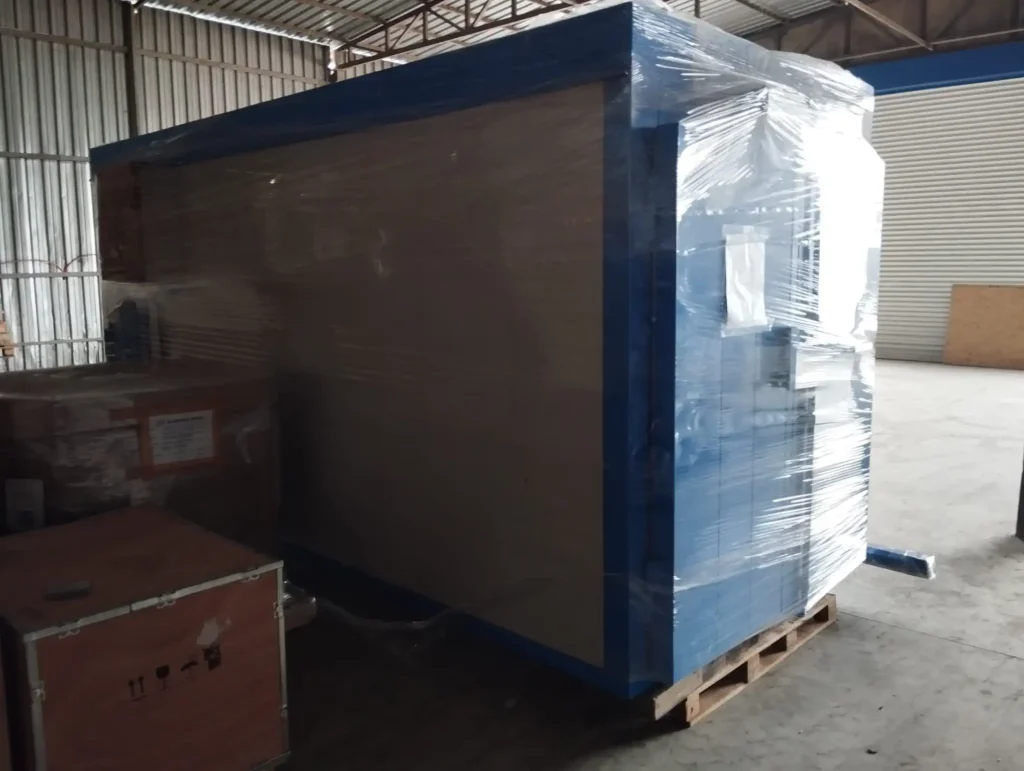
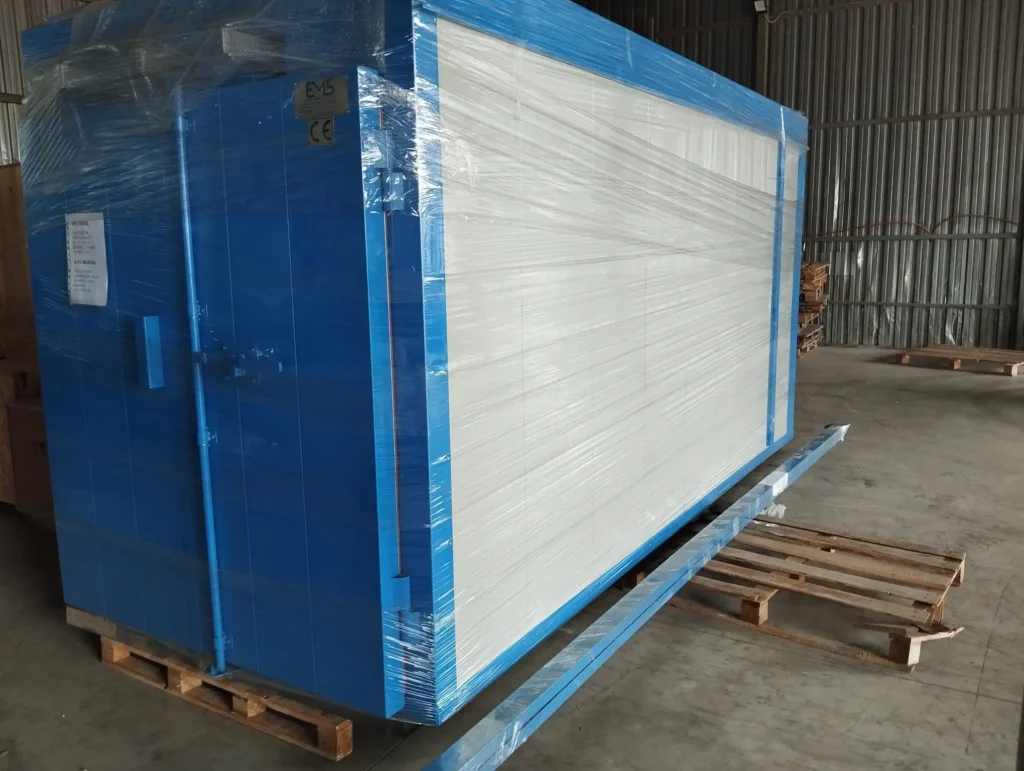
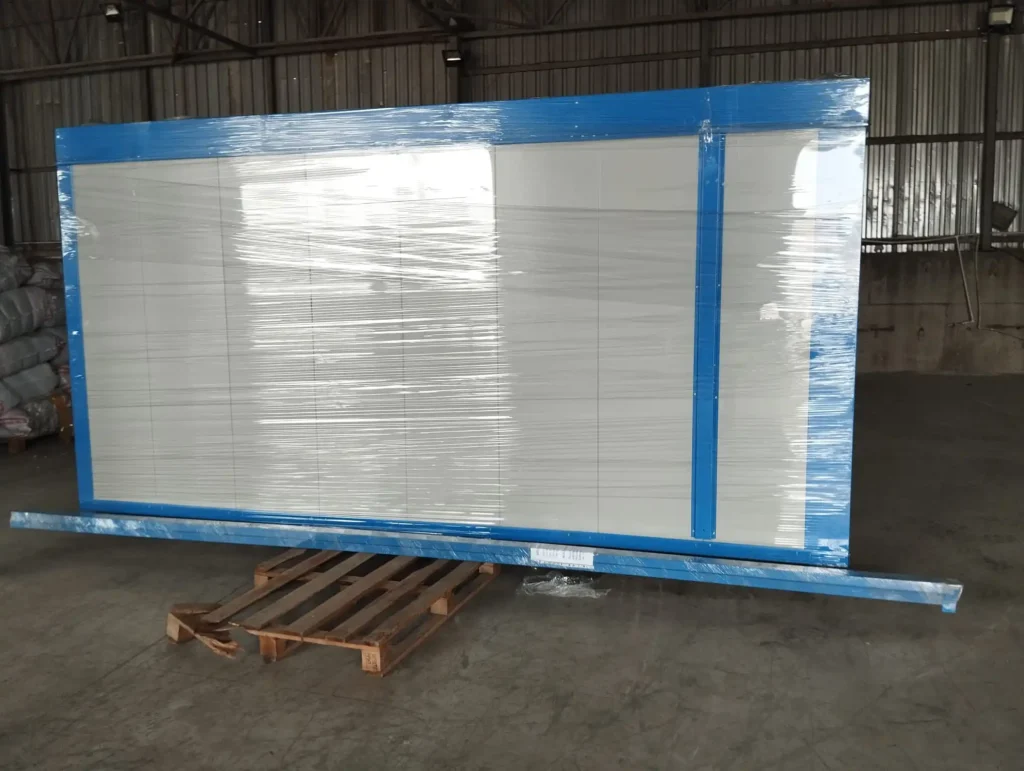
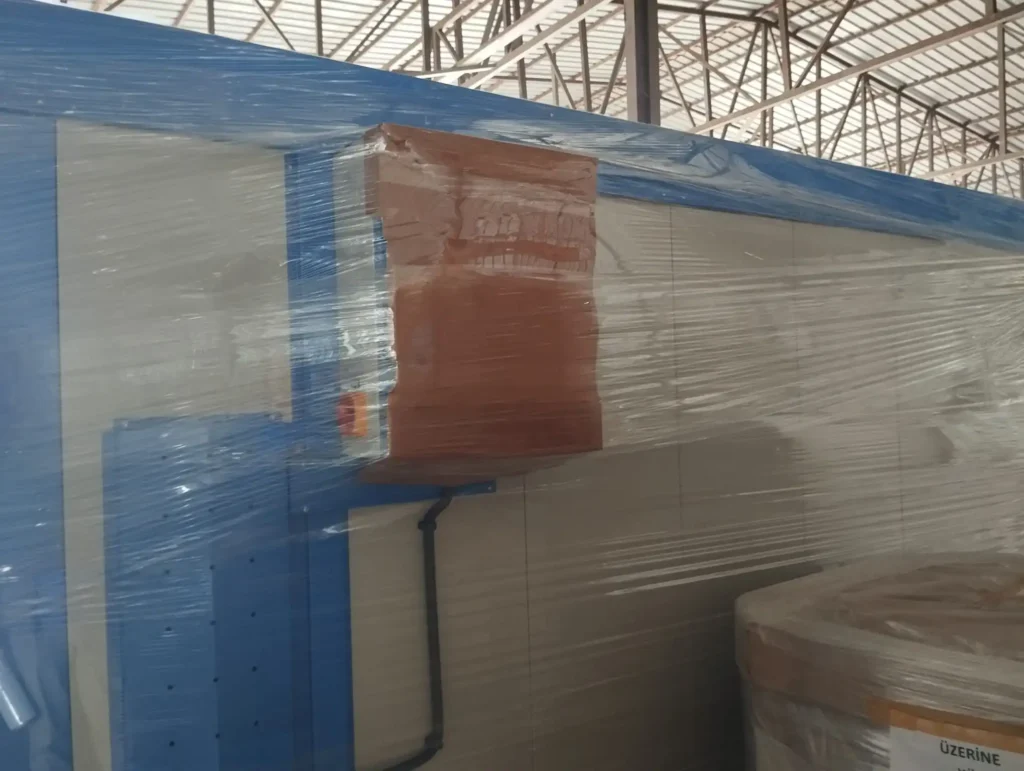
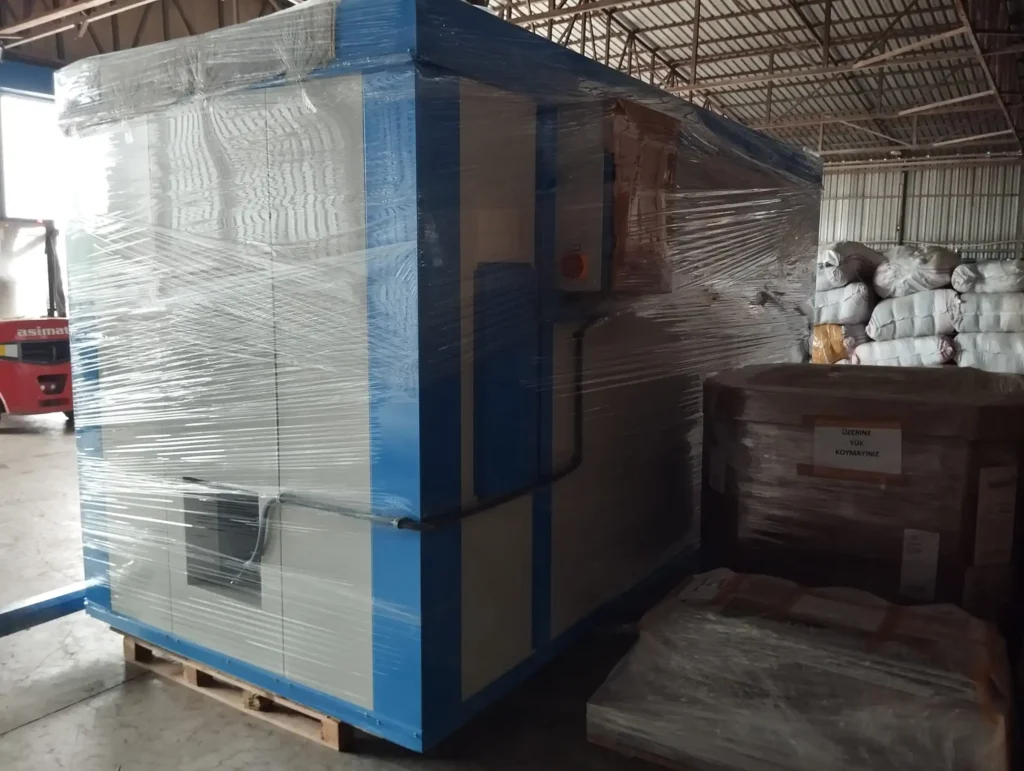
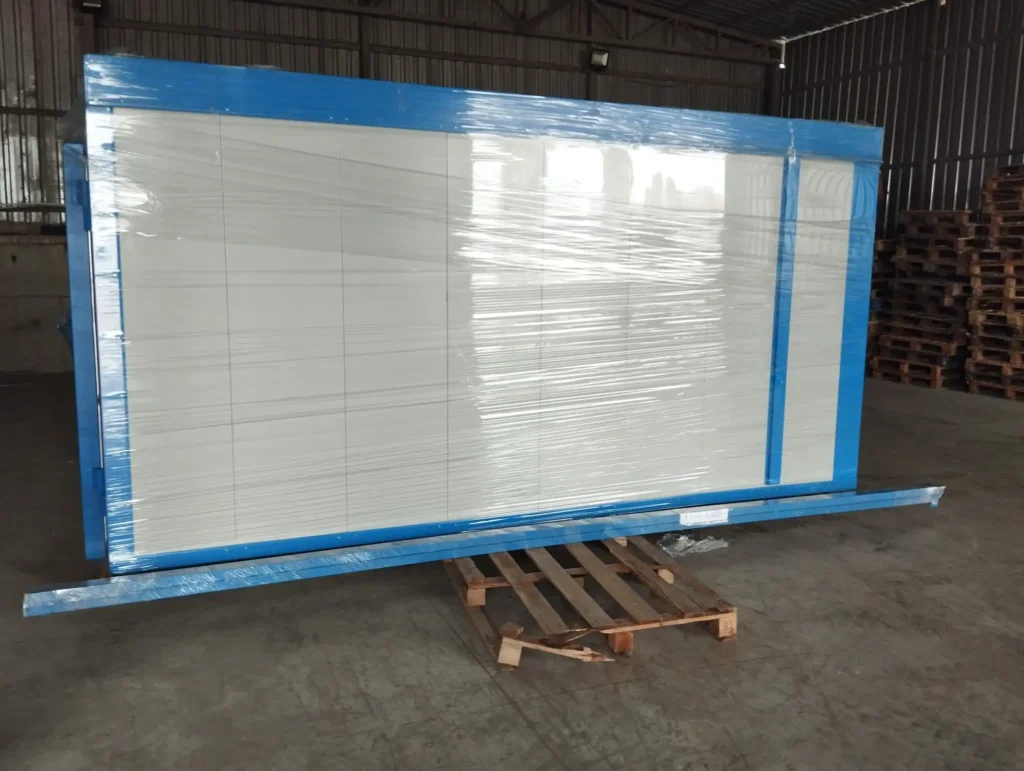