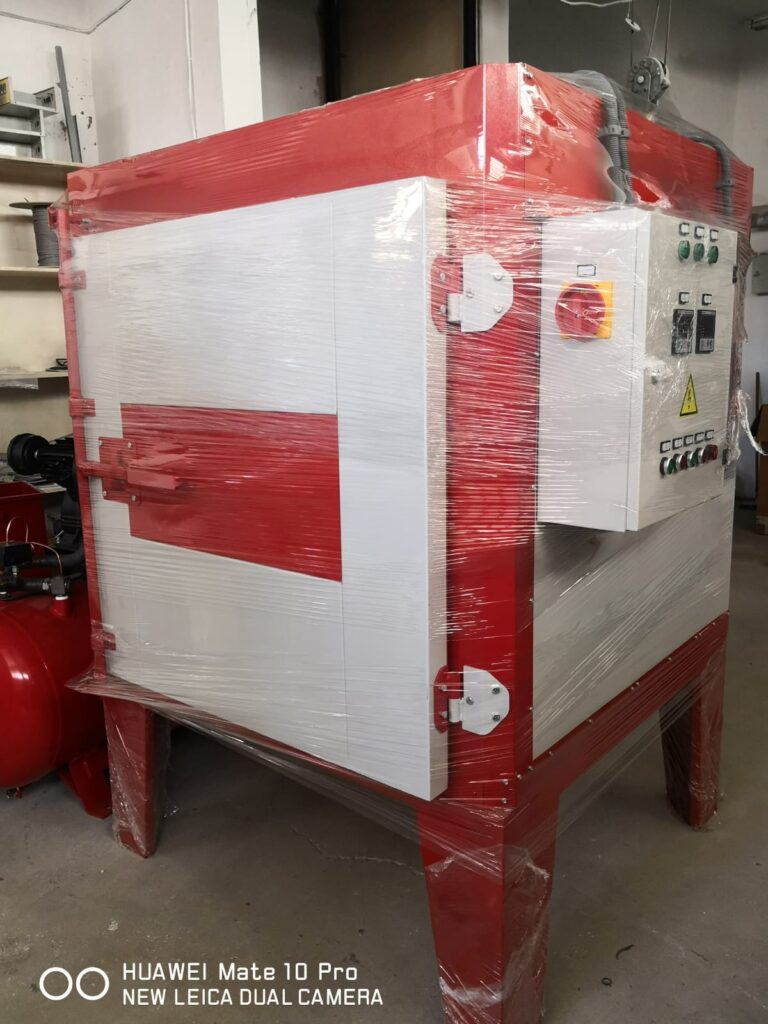
After the coating of the powder in the booth, the powder on the parts needs to be cured in a small powder coating oven, where the inside temperature will be 200 C for 20 minutes.
We believe this is one of the best-selling powder curing ovens, with hundreds of our ovens being used throughout the world. The success of this oven is down to the superb design and our high-quality construction process. The design of our ovens has been perfected over many years supplying the powder coating industry. Customers in Australia, India, Africa, Iceland, and throughout Europe are currently using our ovens.
Latest design improvement – Burnerbox at side
In order to make servicing and maintenance easier and safer, we now situate the burner box at ground level. The burner box can be situated at either side or at the back to suit your individual requirements. This modification is of particular benefit in a self-build situation.
Small Powder Coating Oven
Small powder coating ovens are compact and versatile heating units designed for curing powder coatings applied to smaller workpieces or for low-volume production. They offer a cost-effective and space-efficient solution for businesses that require powder coating capabilities without investing in large, industrial-scale ovens.
Advantages of Small Powder Coating Ovens
- Space Efficiency: Small ovens occupy minimal space, making them suitable for smaller workshops or limited production areas.
- Cost-Effectiveness: The smaller size and simpler design of these ovens translate into lower initial investment costs.
- Versatility: Small ovens can accommodate a variety of workpiece sizes and shapes, catering to diverse production needs.
- Energy Efficiency: Smaller ovens require less energy to operate, reducing energy consumption and costs.
- Precise Temperature Control: Small ovens typically offer precise temperature control, ensuring consistent curing results.
Components of Small Powder Coating Ovens
- Heating Elements: The heating elements provide the heat source for the curing process. They may be electric resistance heaters, infrared (IR) emitters, or a combination of both.
- Heat Exchanger (Optional): A heat exchanger transfers heat from the heating elements to the circulating air, ensuring uniform heat distribution within the oven chamber.
- Temperature Control System: The temperature control system regulates the temperature within the curing oven, ensuring the powder particles are heated to the correct temperature range for optimal curing. It may involve thermocouples, controllers, and feedback loops.
- Workpiece Handling System: The workpiece handling system transports the powder-coated workpieces through the curing oven, maintaining proper positioning and exposure to the heat source. It may involve conveyor belts, rotating turntables, or manual loading and unloading.
- Ventilation System (Optional): A ventilation system removes fumes and gases generated during the curing process, maintaining a safe and comfortable working environment. It may include fans, ducts, and filtration systems.
Applications of Small Powder Coating Ovens
- Small-Scale Production: Small ovens are ideal for low-volume production of powder-coated parts.
- Prototyping and Testing: Small ovens provide a convenient and cost-effective setup for prototyping and testing new powder coating applications.
- Customizing and Repairing: Small ovens can be used for customizing or repairing smaller items, such as bicycle frames, motorcycle parts, or hardware components.
- Powder Coating Services: Small ovens are suitable for businesses offering powder coating services to individual customers or small businesses.
- Educational and Training Purposes: Small ovens can be used in educational settings or training centers to teach powder coating techniques.
Considerations When Choosing a Small Powder Coating Oven
- Workpiece Size and Volume: Select an oven that can accommodate the size and volume of your typical workpieces.
- Curing Temperature Requirements: Ensure the oven can reach the curing temperature specified for the powder coating you are using.
- Uniformity of Heat Distribution: Choose an oven that provides even heat distribution within the chamber to achieve consistent curing results.
- Safety Features: Ensure the oven has safety features such as emergency shut-off switches, grounding connections, and proper insulation.
- Ease of Use: Consider the oven’s design and controls for ease of operation and maintenance.
Conclusion
Small powder coating ovens offer a practical and cost-effective solution for smaller-scale powder coating applications. By selecting the appropriate oven, considering temperature and safety requirements, and ensuring proper maintenance, businesses can achieve high-quality powder coating results while maximizing space efficiency and resource utilization.
Electric Curing Oven Features
Electric curing ovens are used to cure powder coating finishes on metal parts. They use electricity to heat the parts to a temperature that causes the powder coating to melt and flow, forming a hard, durable finish.
Electric curing ovens offer a number of advantages over other types of curing ovens, including:
- Cleanliness: Electric curing ovens do not produce any emissions, making them a clean and environmentally friendly way to cure powder coatings.
- Precision: Electric curing ovens can be programmed to maintain a precise temperature, ensuring that the powder coating is cured properly.
- Efficiency: Electric curing ovens are very efficient, and they can cure powder coatings quickly and evenly.
Some of the key features of electric curing ovens include:
- Temperature range: Electric curing ovens typically have a temperature range of up to 500 degrees Fahrenheit (260 degrees Celsius). This is sufficient to cure most powder coatings.
- Temperature controller: Electric curing ovens are typically equipped with a temperature controller that allows the user to set and maintain a precise temperature.
- Ventilation system: Electric curing ovens typically have a ventilation system that removes fumes and smoke from the oven.
- Safety features: Electric curing ovens typically have safety features such as over-temperature protection and automatic shutdown.
In addition to these basic features, some electric curing ovens may also have additional features, such as:
- Programmable cycles: Some electric curing ovens can be programmed to run different curing cycles, which can be useful for curing different types of powder coatings.
- Data logging: Some electric curing ovens can log data such as temperature and time, which can be useful for quality control purposes.
- Remote monitoring: Some electric curing ovens can be monitored remotely, which can be useful for businesses that need to monitor multiple ovens or that have ovens in remote locations.
Electric curing ovens are an essential piece of equipment for any business that applies powder coatings. By choosing the right electric curing oven for your needs, you can ensure that your powder coatings are cured properly, efficiently, and consistently.
Here are some examples of applications for electric curing ovens:
- Automotive parts: Electric curing ovens are used to cure powder coatings on automotive parts such as wheels, bumpers, and frames.
- Aerospace parts: Electric curing ovens are used to cure powder coatings on aircraft parts such as landing gear, engine components, and wings.
- Industrial machinery parts: Electric curing ovens are used to cure powder coatings on industrial machinery parts such as pumps, valves, and compressors.
- Consumer goods: Electric curing ovens are used to cure powder coatings on consumer goods such as appliances, electronics, and furniture.
- Medical devices: Electric curing ovens are used to cure powder coatings on medical devices such as implants, surgical instruments, and hospital equipment.
- Sporting goods: Electric curing ovens are used to cure powder coatings on sporting goods such as bicycles, golf clubs, and fishing rods.
If you are considering purchasing an electric curing oven, be sure to do your research and compare different models before making a decision. It is also important to consider your specific needs and budget when choosing an oven.
- Internal size starts from 1 M wide x 1M deep x 1 M high
- Will hold 2 alloy wheels
- 14 kw heater
- 380v
- 100mm thick Glasswool + 50 mm thick Rockwool isolation
- Fully digital temperature control
Small Powder Coating Oven for Industry
Small powder coating ovens are ideal for businesses that need to powder coat small batches of parts or parts that are too large or complex to be coated on an automatic line. Small powder coating ovens are typically less expensive than larger ovens, but they are also slower and less efficient.
Applications of Small Powder Coating Ovens for Industry
Small powder coating ovens are used in a variety of industries, including:
- Automotive
- Aerospace
- Industrial machinery
- Consumer goods
- Medical devices
- Sporting goods
Features of Small Powder Coating Ovens for Industry
Small powder coating ovens for industry typically have the following features:
- Compact size: Small powder coating ovens are typically smaller than larger systems, making them ideal for small businesses or industries with limited space.
- Affordability: Small powder coating ovens are typically more affordable than larger systems.
- Ease of use: Small powder coating ovens are typically easy to use, even for beginners.
- Durability: Small powder coating ovens are typically made of durable materials and can last for many years with proper care and maintenance.
- Adjustable temperature: Small powder coating ovens typically have an adjustable temperature range so that you can cure different types of powder coatings.
- Digital controller: Small powder coating ovens typically have a digital controller that allows you to set and monitor the temperature precisely.
- Safety features: Small powder coating ovens typically have safety features such as over-temperature protection and automatic shutdown.
Benefits of Using Small Powder Coating Ovens for Industry
There are many benefits to using small powder coating ovens for industry, including:
- Versatility: Small powder coating ovens can be used to powder coat a wide variety of parts, from small electronic components to large automotive parts.
- Efficiency: Small powder coating ovens are very efficient and can cure powder coatings quickly and evenly.
- Consistency: Small powder coating ovens produce consistent results, ensuring that your powder coatings are cured properly every time.
- Durability: Small powder coating ovens produce durable finishes that can withstand the elements.
- Environmental friendliness: Small powder coating ovens are environmentally friendly and do not produce any emissions.
How to Choose a Small Powder Coating Oven for Industry
When choosing a small powder coating oven for industry, it is important to consider the following factors:
- Size: Choose an oven that is large enough to accommodate the parts you need to powder coat.
- Temperature range: Choose an oven with a temperature range that is high enough to cure the powder coatings you are using.
- Features: Consider which features are important to you, such as a digital controller, safety features, and programmability.
- Price: Set a budget before you start shopping and choose an oven that fits your budget.
If you are looking for a versatile, efficient, and durable powder coating oven for your industry, a small powder coating oven is a great option to consider.
Our small powder coating oven products are manufactured in our own facility in Turkey and have 20 cm of rockwool and 5 cm of glasswool a total of 25 cm isolation material covered with galvanized sheets from both sides and compressed into 15 cm. Our powder coating ovens have isolation also in the floor wall panels and have a minimized loss of heat during operation
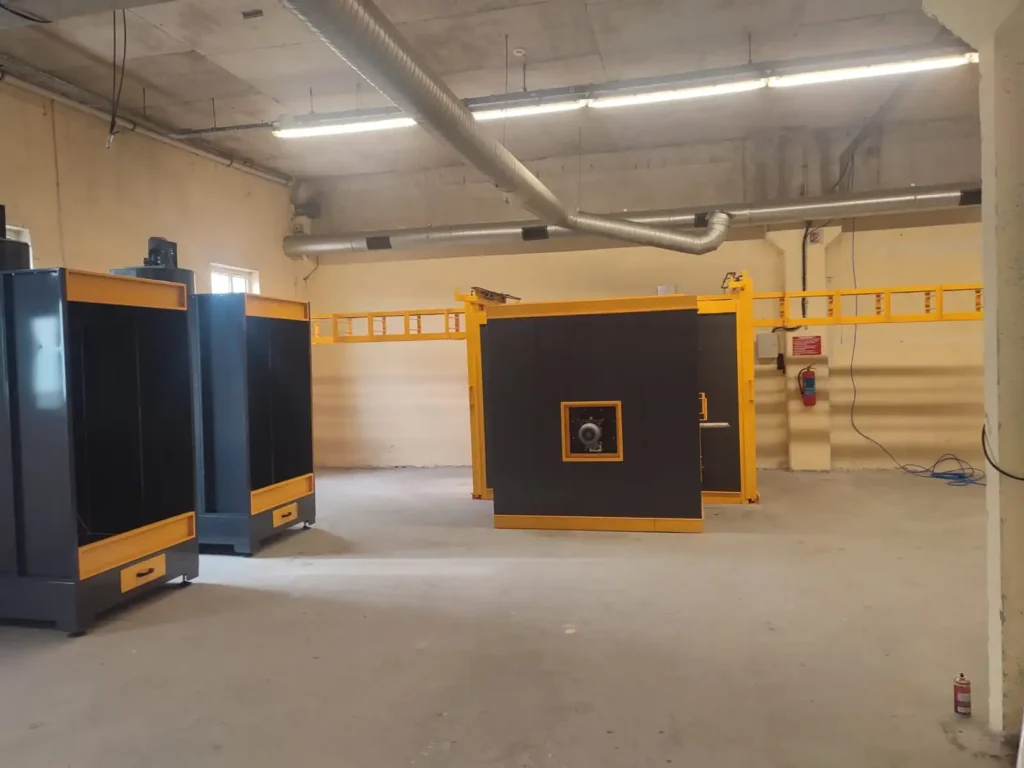
Our small powder coating ovens are mostly used for alloy wheel or rim painting as decorative purposes. The ovens are operated either with electricity or gas, depending on the customer.
Small Powder Coating Oven for Sale
A small powder coating oven is a specialized piece of equipment used in the powder coating process. It provides a controlled environment for curing or baking powder-coated items, allowing the powder to melt and create a durable and attractive finish. Here are some key features and considerations regarding small powder coating ovens:
- Size and Capacity: Small powder coating ovens come in various sizes, with interior dimensions suitable for processing smaller items. The capacity of the oven is determined by its dimensions and can vary from a few cubic feet to several cubic feet.
- Construction: Powder coating ovens are typically constructed with insulated walls to retain heat efficiently and ensure even heat distribution. The interior is often made of metal to withstand the curing temperatures.
- Heating System: The oven’s heating system is responsible for raising the temperature to the desired curing level. Electric heating elements or gas burners are commonly used as heating sources. Electric ovens are suitable for smaller setups, while gas ovens are preferred for larger or industrial applications.
- Temperature Control: Precise temperature control is essential for achieving the correct curing process. Small powder coating ovens should have a reliable temperature control system that allows you to set and maintain the desired temperature throughout the curing process.
- Air Circulation: Proper air circulation within the oven ensures uniform heating and curing of the powder-coated items. Some ovens are equipped with fans or blowers to promote even heat distribution.
- Timer and Alarms: Ovens often come with built-in timers that allow you to set the curing time. Some models also feature alarms or notifications to signal the end of the curing cycle.
- Safety Features: Safety is a priority in any industrial process. Look for ovens with safety features such as over-temperature protection, ventilation systems to expel fumes, and safety interlocks to prevent the door from opening during operation.
- Energy Efficiency: Energy-efficient ovens are designed to minimize heat loss and maximize energy utilization. Good insulation and well-sealed doors contribute to energy efficiency.
- Mobility: Some small powder coating ovens are designed with casters or wheels, making them easy to move and position as needed in your workspace.
- Compliance: Depending on your location and industry, your powder coating oven may need to meet specific safety and environmental standards. Ensure that the chosen oven complies with relevant regulations.
- Accessories: Additional accessories such as racks, hooks, and shelves can help optimize the oven’s capacity and allow for efficient arrangement of coated items.
When choosing a small powder coating oven, consider your specific needs, the size of items you’ll be coating, and the available space in your workshop. It’s also advisable to consult with experts or manufacturers in the powder coating industry to ensure you select the right oven for your requirements.
Size and Capacity
The size and capacity of a small powder coating oven can vary based on the manufacturer, model, and intended applications. Here’s a general overview of size and capacity considerations for small powder coating ovens:
- Interior Dimensions: Small powder coating ovens typically have interior dimensions that are suitable for processing smaller to medium-sized items. The interior dimensions may range from approximately 2 feet in width, 2 feet in height, and 2 feet in depth to larger sizes depending on the specific model.
- Cubic Feet Capacity: The capacity of the oven is often measured in cubic feet. Small ovens might have a capacity of around 8 to 20 cubic feet. This capacity allows for the coating of various items such as small parts, components, tools, or even moderate-sized products.
- Rack Arrangement: The interior of the oven is designed to accommodate racks, hooks, or shelves for hanging or placing items to be coated. The arrangement of these racks will affect the overall capacity and how efficiently items can be coated.
- Weight Capacity: Along with cubic feet capacity, manufacturers often provide weight capacity specifications. This indicates the maximum weight of the items that the oven can handle. It’s essential to consider the weight of the items you plan to coat to ensure they can be accommodated safely.
- Loading Accessibility: The oven’s dimensions should also consider how easily items can be loaded and unloaded. The size of the oven’s opening and its design (such as swing or lift-up doors) play a role in this.
- Application Variability: Small powder coating ovens can cater to a variety of applications, from smaller components to larger parts. Some ovens are designed with flexibility in mind, allowing for the coating of different sizes and shapes.
When choosing a small powder coating oven, it’s important to assess your specific needs and the sizes of the items you intend to coat. Consider both the interior dimensions and the weight capacity to ensure that the oven can handle your production requirements. Manufacturers and suppliers can provide detailed specifications to help you make an informed decision based on your application’s demands.
Construction
The construction of a small powder coating oven is a critical aspect that determines its durability, efficiency, and performance. Here are the key construction considerations for such an oven:
- Material: The exterior of the oven is often made of sturdy materials like steel to provide structural integrity and protection from environmental factors. The interior is usually made of stainless steel or other heat-resistant materials that can withstand high temperatures without corroding or degrading.
- Insulation: Good insulation is crucial to maintaining a consistent and efficient temperature inside the oven. Adequate insulation helps prevent heat loss, reduces energy consumption, and ensures uniform heat distribution. Common insulation materials include ceramic fiber, mineral wool, and high-temperature insulation blankets.
- Doors and Seals: The oven doors should be well-sealed to prevent heat leakage and maintain temperature stability. Gasket seals around the door frame help create an airtight seal, preventing heat from escaping and cold air from entering.
- Heating Elements: The type and placement of heating elements play a significant role in even heat distribution. Electric heating elements or gas burners are commonly used. They are strategically positioned to provide uniform heat throughout the oven.
- Air Circulation: Proper air circulation is essential for uniform curing. Some ovens are equipped with fans or blowers that ensure consistent air movement, preventing hotspots and cold spots inside the oven.
- Control Panel: The control panel houses temperature controllers, timers, and other components necessary for operating and monitoring the oven. It should be easily accessible and designed for user-friendly operation.
- Exhaust System: An exhaust system helps remove fumes, smoke, and potentially hazardous gases generated during the curing process. It’s important for worker safety and environmental compliance.
- Safety Features: Safety is paramount. Ovens may include features like over-temperature protection, emergency stop buttons, and interlock systems that prevent the oven from operating when the door is open.
- Finish: The exterior of the oven may have a protective finish that enhances its durability and resistance to environmental factors.
- Portability: Some smaller ovens are designed with mobility in mind, featuring wheels or casters for easy movement within the workspace.
- Ventilation: Adequate ventilation around the oven is important to dissipate excess heat and prevent overheating of surrounding equipment or structures.
- Electrical and Gas Connections: The oven should be designed with proper electrical and gas connections that adhere to safety standards and regulations.
When selecting a small powder coating oven, it’s advisable to choose from reputable manufacturers who provide detailed information about the construction materials and design. Paying attention to the quality of construction ensures that the oven is reliable, safe, and capable of delivering consistent results over time.
Small powder coating oven for small items and alloy wheels

A small powder coating oven for small items and alloy wheels is a great investment for any business or hobbyist that needs to powder coat small parts. These ovens are typically compact and affordable, making them ideal for small spaces and budgets.
Benefits of small powder coating ovens
Small powder coating ovens offer a number of benefits, including:
- Compact size: Small powder coating ovens are typically smaller than larger systems, making them ideal for small businesses or hobbyists.
- Affordability: Small powder coating ovens are typically more affordable than larger systems.
- Ease of use: Small powder coating ovens are typically easy to use, even for beginners.
- Durability: Small powder coating ovens are typically made of durable materials and can last for many years with proper care and maintenance.
Applications of small powder coating ovens for small items and alloy wheels
Small powder coating ovens for small items and alloy wheels can be used to powder coat a variety of small parts, including:
- Alloy wheels
- Bicycle parts
- Motorcycle parts
- Hand tools
- Power tools
- Electronic components
- Electrical components
- Medical devices
- Sporting goods
- Hobby projects
Choosing a small powder coating oven for small items and alloy wheels
When choosing a small powder coating oven for small items and alloy wheels, it is important to consider the following factors:
- Size: Make sure to choose an oven that is large enough to accommodate the parts you need to powder coat.
- Temperature range: Make sure to choose an oven with a temperature range that is high enough to cure the powder coating you are using.
- Features: Some small powder coating ovens come with additional features, such as timers, temperature controllers, and built-in racks. Consider which features are important to you and choose an oven that has them.
- Price: Small powder coating ovens range in price from a few hundred dollars to a few thousand dollars. Set a budget before you start shopping and choose an oven that fits your budget.
Conclusion
Small powder coating ovens for small items and alloy wheels are a great option for businesses and hobbyists that need to powder coat small parts. These ovens are compact, affordable, easy to use, and durable. When choosing a small powder coating oven, be sure to consider the size, temperature range, features, and price.
Small Powder Coating Oven
A small powder coating oven is a piece of equipment used to cure or bake powdered coatings onto the surface of objects. Powder coating is a dry finishing process where a fine powder is applied to a substrate (such as metal) and then cured at high temperatures. The result is a durable and attractive finish. Here are some key considerations for a small powder coating oven:
- Size and Capacity:
- Determine the size of the objects you plan to coat. The oven should have enough space to accommodate the items you’ll be working with.
- Consider the dimensions of the oven, both in terms of the internal chamber size and the external footprint.
- Heat Source:
- Powder coating ovens typically use electric heaters or natural gas burners for heat. Electric ovens are more common for smaller setups due to their ease of use and cleaner operation.
- Temperature Control:
- The oven should have precise temperature control capabilities to ensure that the curing process is done accurately. Look for an oven with a digital temperature controller for better accuracy.
- Air Circulation:
- Adequate air circulation is crucial for even curing. Convection ovens are commonly used for powder coating, as they circulate hot air throughout the chamber.
- Insulation:
- Good insulation is essential to maintain a consistent temperature inside the oven and improve energy efficiency.
- Rack or Hooks:
- Consider the design of the interior. Some ovens come with racks or hooks to hang parts, facilitating an even coating and curing process.
- Ease of Use:
- Look for user-friendly features, such as easy controls, programmable settings, and safety features like overheat protection.
- Power Requirements:
- Check the power requirements of the oven and ensure that it matches the electrical supply available in your workspace.
- Ventilation:
- Adequate ventilation is important to remove any fumes generated during the curing process. Ensure that your workspace has proper ventilation, and consider installing an exhaust system if needed.
- Durability:
- Invest in a well-built oven made from durable materials, especially if you plan to use it frequently.
- Cost:
- Consider your budget and look for a powder coating oven that meets your requirements without exceeding your financial constraints.
Before purchasing a small powder coating oven, carefully assess your specific needs and the types of items you’ll be coating. Additionally, always follow safety guidelines and precautions when operating any industrial equipment, including powder coating ovens.
Size and Capacity
The size and capacity of a small powder coating oven can vary depending on the manufacturer and model. However, I can provide you with a general idea of what you might find in the market for small powder coating ovens:
- Internal Chamber Size:
- Small powder coating ovens may have internal chamber dimensions ranging from approximately 2 feet by 2 feet to 4 feet by 4 feet or slightly larger. These dimensions provide enough space for coating smaller items or batches of smaller items.
- Height:
- The height of the oven chamber can vary, but it’s typically designed to accommodate objects of varying heights. Some ovens may have adjustable racks or hanging hooks to maximize vertical space.
- External Footprint:
- The overall size of the oven, including its external dimensions, is also a consideration, especially if you have limited space in your workshop or facility. Make sure to account for the external dimensions when planning for installation.
- Capacity:
- The capacity of a small powder coating oven is often measured in terms of the weight or number of parts it can accommodate. It can range from a few pounds to a few hundred pounds, depending on the specific model. Consider the weight and size of the items you plan to coat to ensure they fit within the oven’s capacity.
When selecting a small powder coating oven, it’s crucial to match the internal chamber size and capacity with the size and quantity of items you intend to coat. Always check the specifications provided by the manufacturer for precise details on dimensions, capacity, and any other relevant features. If possible, consult with the manufacturer or supplier to ensure that the oven meets your specific requirements.
Heat Source
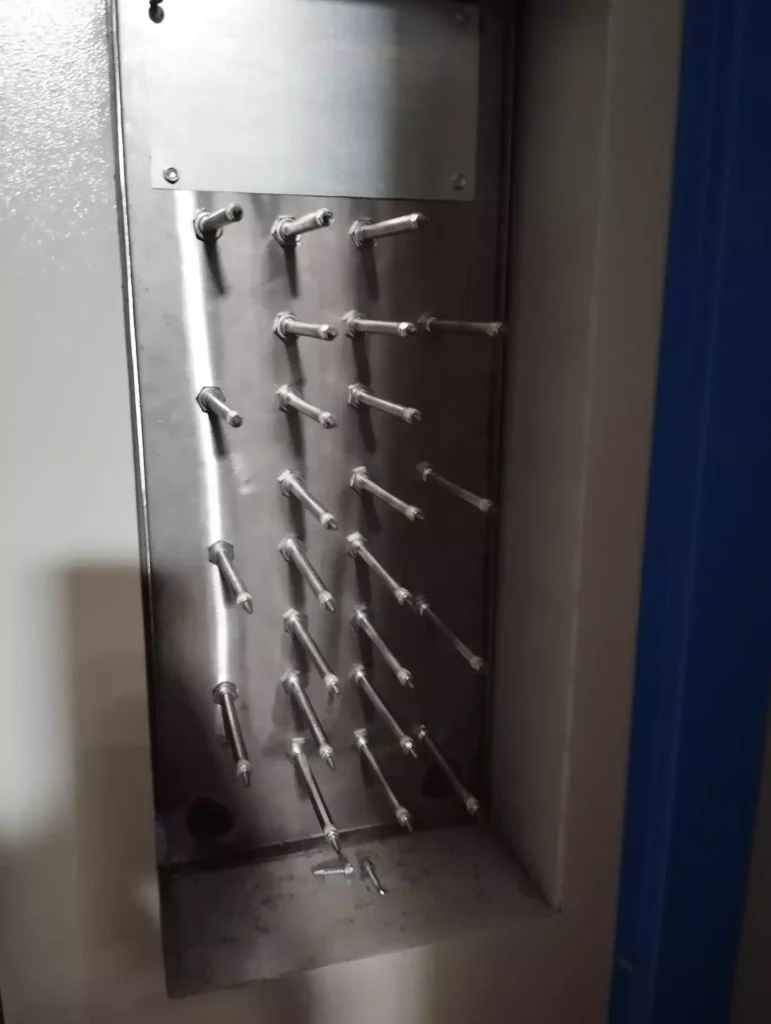
The heat source in a powder coating oven is a critical component that plays a key role in the curing process. The two primary types of heat sources used in powder coating ovens are electric heaters and natural gas burners. Here’s a brief overview of each:
- Electric Heaters:
- Advantages:
- Clean Operation: Electric heaters do not produce combustion byproducts, making them a cleaner option.
- Precision Control: Electric ovens often have precise temperature control, allowing for accurate and consistent curing.
- Considerations:
- Operating Cost: Electricity costs can be higher than natural gas in some regions, so consider the operating cost based on your local energy prices.
- Initial Cost: Electric powder coating ovens may have a higher initial cost compared to gas ovens.
- Advantages:
- Natural Gas Burners:
- Advantages:
- Cost-Efficient: Natural gas is often less expensive than electricity, making gas ovens more cost-effective for larger operations.
- Faster Heating: Gas ovens can achieve higher temperatures more quickly than electric ovens.
- Considerations:
- Combustion Byproducts: Gas burners produce combustion byproducts, so adequate ventilation is necessary to remove fumes from the curing process.
- Control: While modern gas ovens have good temperature control, electric ovens generally offer more precise temperature control.
- Advantages:
When choosing between electric and gas heat sources for your powder coating oven, consider factors such as your budget, energy costs in your area, the size of your operation, and the specific requirements of your coating process. Both electric and gas ovens are widely used in the industry, so the choice ultimately depends on your preferences and the practical considerations of your workshop or facility. Always follow safety guidelines and ensure proper ventilation when using gas-powered equipment.
Temperature Control
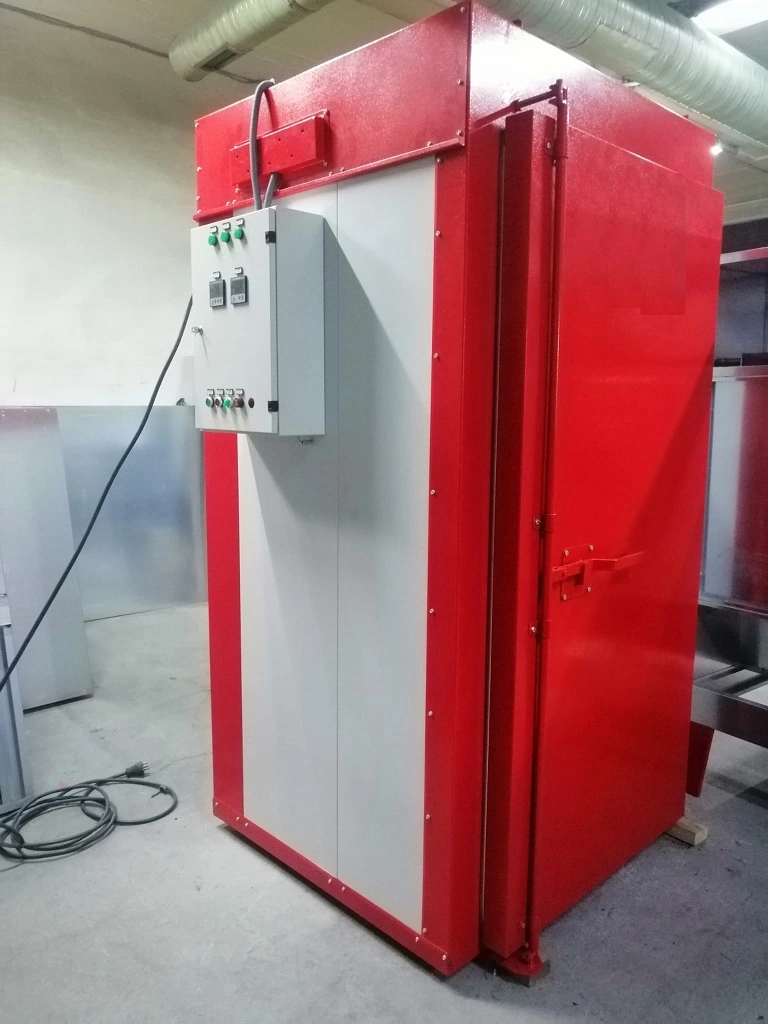
Temperature control is a crucial aspect of a powder coating oven to ensure that the curing process is carried out accurately and consistently. Here are some considerations regarding temperature control in a powder coating oven:
- Digital Temperature Controller:
- Many modern powder coating ovens come equipped with digital temperature controllers. These controllers offer precise and reliable temperature regulation.
- Setpoint and Actual Temperature Display:
- A good temperature controller should allow you to set the desired temperature (setpoint) and display the actual temperature inside the oven. This feature enables you to monitor and adjust the temperature as needed.
- Temperature Range:
- Consider the temperature range of the oven, ensuring it covers the temperatures required for the curing process of the specific powder coating material you are using. Standard curing temperatures often range from around 300°F (149°C) to 450°F (232°C).
- Ramp-Up and Soak Capability:
- Some advanced controllers offer ramp-up and soak features. Ramp-up allows the oven to gradually reach the desired temperature, and soak maintains the temperature for a specified duration. This capability can be beneficial for achieving optimal curing results.
- Thermocouples or Temperature Probes:
- Temperature controllers typically rely on thermocouples or temperature probes to measure the actual temperature inside the oven. Ensure that the oven is equipped with reliable and accurate sensors.
- Uniform Heating:
- The oven should be designed to provide uniform heating throughout the entire chamber. This helps ensure that all coated items receive consistent heat, leading to an even cure.
- Over-Temperature Protection:
- Look for ovens with built-in over-temperature protection features. These features automatically shut off or adjust the heat if the temperature exceeds a safe limit, preventing damage to the coated items and the oven.
- User-Friendly Interface:
- A user-friendly interface on the temperature controller can simplify operation and make it easier to set and monitor temperatures.
Before purchasing a powder coating oven, review the specifications provided by the manufacturer to understand the temperature control features. Ensure that the oven’s temperature control capabilities align with the requirements of your specific powder coating process. If possible, consult with the manufacturer or supplier for guidance on selecting the right oven for your needs.
Air Circulation
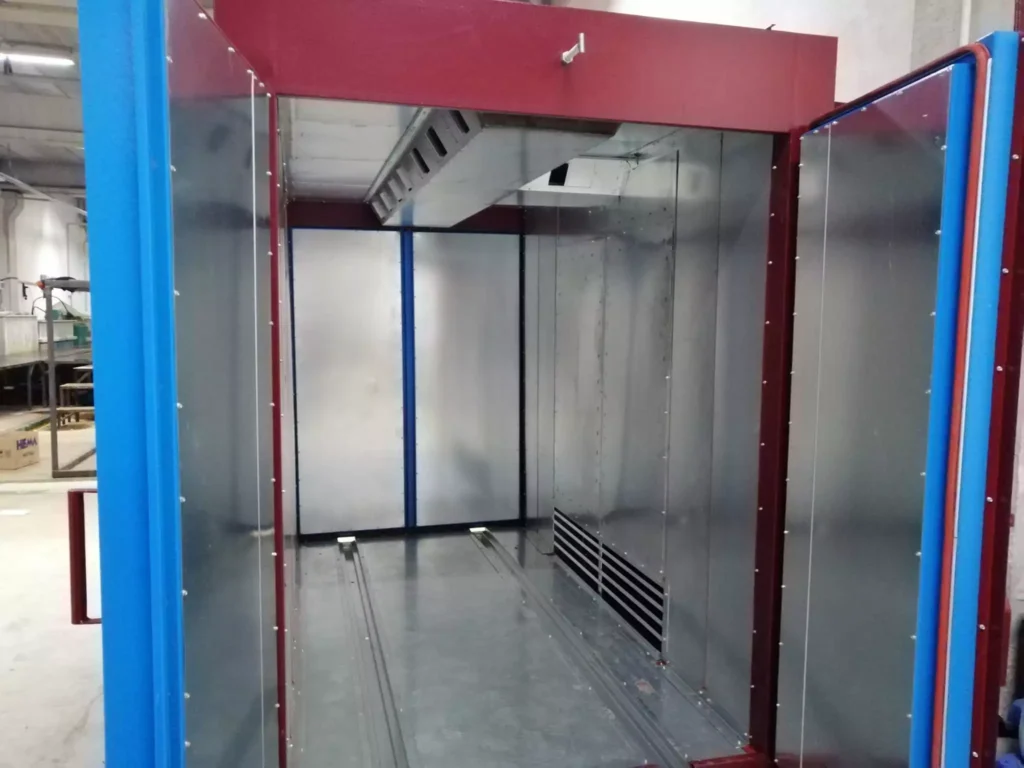
Air circulation is a critical factor in the performance of a powder coating oven. Proper and consistent air circulation ensures that heat is distributed evenly throughout the oven chamber, leading to uniform curing of the powder coating on the items being processed. Here are some considerations related to air circulation in a powder coating oven:
- Convection Ovens:
- Many powder coating ovens utilize convection heating, where a fan circulates hot air throughout the oven chamber. Convection ovens are effective in providing uniform heat distribution, ensuring that all coated items receive the same level of heat.
- Fan Placement:
- The placement and design of the fan or fans in the oven are crucial. They should be strategically located to promote efficient airflow and prevent hotspots within the chamber.
- Variable Speed Fans:
- Some advanced powder coating ovens may have variable speed fans. Adjusting the fan speed can help optimize the curing process for different types of coated items or varying production requirements.
- Ducting and Ventilation:
- Ensure that the oven has well-designed ducting to guide the airflow and that there’s proper ventilation to expel any fumes generated during the curing process.
- Even Heat Distribution:
- The goal is to achieve even heat distribution across all parts of the oven. This is essential for consistent curing, preventing issues like uneven coatings or incomplete curing.
- Airflow Patterns:
- Manufacturers may design ovens with specific airflow patterns to enhance efficiency. Understanding these patterns and ensuring they align with your coating requirements is important.
- Adjustable Airflow:
- In some ovens, you may have the option to adjust the airflow. This can be beneficial for optimizing the curing process based on the size, shape, or density of the coated items.
- Insulation:
- Adequate insulation helps maintain a stable internal temperature and reduces heat loss. Insulation contributes to the efficiency of the oven and its ability to sustain consistent air circulation.
- Regular Maintenance:
- Regularly clean and maintain the oven’s ventilation system and fans to ensure optimal performance over time.
When selecting a powder coating oven, inquire about the air circulation system and features related to convection heating. Understanding how air circulation is managed in the oven will help you make an informed decision based on your specific coating requirements and production needs.
Insulation
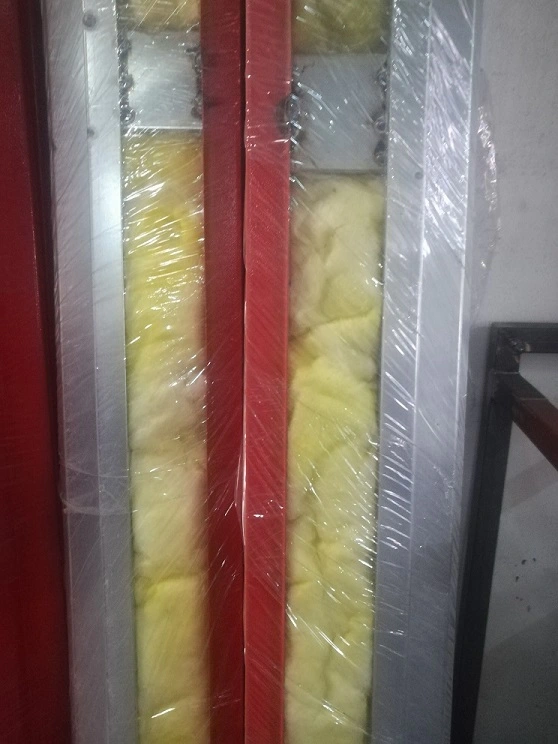
Insulation is a crucial element in a powder coating oven, as it helps maintain a stable and consistent temperature inside the oven chamber. Proper insulation is essential for energy efficiency, even heat distribution, and preventing heat loss. Here are some key considerations regarding insulation in a powder coating oven:
- Material:
- Powder coating ovens typically use insulation materials that can withstand high temperatures. Common insulation materials include ceramic fiber, mineral wool, and high-temperature fiberglass. The chosen material should provide effective thermal resistance.
- Thickness:
- The thickness of the insulation layer can impact the overall performance of the oven. Thicker insulation is generally more effective in preventing heat transfer and maintaining a stable internal temperature.
- Double-Walled Construction:
- Some ovens feature a double-walled construction with insulation between the inner and outer walls. This design enhances insulation efficiency by reducing heat transfer to the external surfaces of the oven.
- Seamless Construction:
- Ensure that the insulation is installed seamlessly without gaps or compression, as any inconsistencies can compromise its effectiveness.
- Door Insulation:
- Pay attention to the insulation around the oven door, as this is a critical area for preventing heat loss. Ovens with well-insulated doors contribute to overall energy efficiency.
- Heat Reflective Coatings:
- Some ovens may have heat-reflective coatings or materials on the inner surfaces to enhance heat retention and distribution within the chamber.
- Energy Efficiency:
- Effective insulation contributes to energy efficiency by reducing the amount of heat that escapes from the oven. This not only lowers energy costs but also helps maintain a consistent curing environment.
- Temperature Stability:
- A well-insulated oven contributes to stable and consistent temperature control. This is crucial for achieving uniform curing results across all coated items.
- Maintenance:
- Regularly inspect and maintain the insulation to ensure its integrity. Any damage or deterioration should be promptly addressed to preserve the efficiency of the oven.
When considering a powder coating oven, inquire about the type and quality of insulation used, as well as any additional features that enhance insulation effectiveness. Well-designed insulation contributes to the overall performance and reliability of the oven, ensuring that it meets the temperature requirements for successful powder coating processes.
Power Requirements
Understanding the power requirements of a powder coating oven is crucial to ensure proper operation and integration into your facility. Here are key considerations regarding power requirements:
- Voltage and Phase:
- Check the voltage and phase requirements of the powder coating oven. Common voltages for industrial equipment include 208V, 240V, 380V, 415V, and 480V. Additionally, ovens may operate on single-phase or three-phase power. Ensure that the electrical supply in your facility matches the oven’s requirements.
- Amperage:
- Verify the amperage requirements of the oven. This information is essential for sizing the electrical circuit and determining the capacity of the electrical service needed.
- Total Power Consumption:
- Understand the total power consumption of the powder coating oven, usually measured in kilowatts (kW) or kilovolt-amperes (kVA). This information helps estimate energy costs and ensures that your facility’s electrical infrastructure can support the oven.
- Installation by a Qualified Electrician:
- The installation of the powder coating oven should be carried out by a qualified electrician to ensure compliance with electrical codes and safety standards.
- Dedicated Electrical Circuit:
- It’s often recommended to have a dedicated electrical circuit for the powder coating oven to prevent overloading shared circuits and to ensure consistent power supply.
- Power Factor:
- Consider the power factor of the oven. A high power factor indicates efficient use of electrical power. Some industrial equipment may incorporate power factor correction to optimize energy efficiency.
- Generator Compatibility:
- If your facility uses backup generators, check if the powder coating oven is compatible with generator power. Some equipment may require modifications or additional features for reliable operation on generator power.
- Start-Up Surge:
- Be aware of the initial start-up surge or inrush current that the oven may draw when powering up. This information is important for sizing circuit breakers and ensuring that the electrical system can handle the temporary increase in load.
- Energy Efficiency Considerations:
- Evaluate the energy efficiency features of the oven, such as insulation and temperature control systems. A more energy-efficient oven can help reduce overall power consumption and operational costs.
Always refer to the manufacturer’s specifications and guidelines for accurate information on the power requirements of the specific powder coating oven model you are considering. If in doubt, consult with the manufacturer or a qualified electrician to ensure that the oven can be safely and effectively integrated into your facility’s electrical infrastructure.
Ventilation
Proper ventilation is essential when operating a powder coating oven to ensure a safe working environment and to expel any fumes or byproducts generated during the curing process. Here are key considerations regarding ventilation for a powder coating oven:
- Exhaust System:
- Powder coating ovens should be equipped with an effective exhaust system to remove fumes and prevent the accumulation of potentially hazardous gases. The exhaust system typically includes fans and ducting.
- Ventilation Rate:
- Determine the required ventilation rate based on the size of the oven and the type of coating material being used. The ventilation system should be capable of exchanging the air within the oven chamber at a rate that ensures the removal of fumes.
- Ventilation Design:
- The design of the ventilation system should promote efficient airflow, drawing fumes away from the oven and safely expelling them outside the facility. Consider consulting with ventilation system professionals to ensure optimal design.
- Airflow Direction:
- Establish a clear direction for airflow within the workspace. Ensure that the exhaust system effectively captures and removes fumes without creating areas of stagnant air.
- Ducting:
- Use proper ducting to direct fumes from the oven to the outside. Ducting materials should be suitable for high-temperature applications and resistant to the corrosive effects of any byproducts.
- Stack or Chimney:
- Depending on local regulations, the exhaust system may terminate in a stack or chimney that releases the fumes safely into the atmosphere. Ensure compliance with environmental and safety standards.
- Make-up Air:
- Consider the need for make-up air to replace the air being exhausted. This helps maintain a balanced airflow within the facility and prevents negative pressure, which can affect the efficiency of the exhaust system.
- Environmental Compliance:
- Ensure that the ventilation system complies with local environmental regulations. Some areas have specific requirements for the treatment and release of air emissions.
- Regular Maintenance:
- Regularly inspect and maintain the ventilation system to ensure its proper functioning. Clean or replace filters as needed, and address any issues promptly to avoid compromising the effectiveness of the system.
- Safety Features:
- Consider safety features such as alarms or monitoring systems that can alert operators to ventilation issues or malfunctions.
Always adhere to local regulations and safety standards when designing and operating a ventilation system for a powder coating oven. Consulting with ventilation experts or environmental health and safety professionals can help ensure that your system meets all necessary requirements for a safe and compliant workspace.
Powder coating
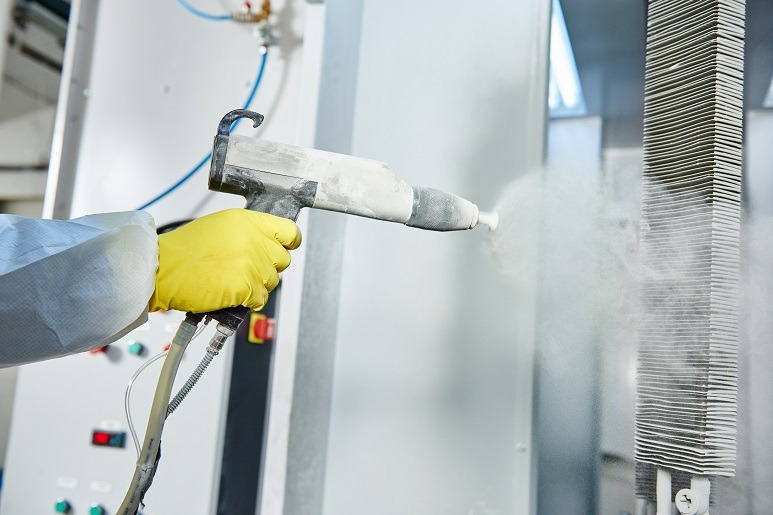
Powder coating is a widely used finishing process in manufacturing, characterized by its ability to produce a high-quality, durable finish. The process involves the application of dry powder to a surface, which is then cured under heat to form a solid, protective coating. This process is favored in many industries due to its efficiency and environmental benefits compared to traditional liquid paint. Essential to the powder coating process are various pieces of equipment, including the Powder Coating Equipment, Powder Coating Booth, Powder Coating Spray Booth, Small Powder Coating Booth, and Powder Paint Booth with Filters.
Powder Coating Equipment Overview
Powder Coating Equipment encompasses a wide range of tools and machinery designed to facilitate the powder coating process. These include spray guns, booths, ovens, and automated systems. Each component plays a crucial role in ensuring the quality and efficiency of the coating process. For instance, Automatic Powder Coating Equipment is often used in large-scale operations where precision and consistency are paramount.
Powder Coating Booths
A Powder Coating Booth is a controlled environment where powder is applied to the substrate. These booths are designed to contain overspray, minimize contamination, and ensure even coating application. There are various types of booths, including the Small Powder Coating Booth, which is ideal for limited-space operations or for coating smaller parts. For larger operations, a Powder Coating Spray Booth is typically used, which allows for greater flexibility and efficiency.
Small Powder Coating Booths and Applications
Small Powder Coating Booths are specifically designed for operations that require a compact setup. These booths are particularly useful in small workshops or for businesses that specialize in coating small parts, such as Alloy Wheel Powder Coating. A Small Powder Coating Booth is typically paired with a Small Powder Coating Oven or a combined Small Powder Coating Booth and Oven to streamline the coating and curing processes.
Automated Powder Coating Systems
For businesses that require high throughput and consistent quality, an Automated Powder Coating System is often the best choice. These systems integrate various components of the powder coating process, including automated spray guns, conveyor systems, and curing ovens. By automating these processes, manufacturers can achieve a higher level of efficiency and reduce the potential for human error.
Ovens in Powder Coating
Curing ovens are an essential part of the powder coating process. They provide the heat necessary to cure the powder and form a durable coating. There are different types of ovens, including Gas Powder Coating Oven, Diesel Powder Coating Oven, and Portable Powder Coating Oven. Each type of oven offers distinct advantages depending on the application. For instance, a Gas Powder Coating Oven is known for its energy efficiency and consistent temperature control, while a Diesel Powder Coating Oven is favored in environments where gas supply is limited or where diesel is more readily available.
Portable Powder Coating Ovens
Portable Powder Coating Ovens are a versatile solution for businesses that require mobility in their operations. These ovens can be moved easily to different locations, making them ideal for on-site jobs or businesses with limited space. Despite their portability, these ovens are capable of delivering high-quality curing results comparable to their stationary counterparts.
Specialized Coating Applications: Alloy Wheel Powder Coating
Alloy Wheel Powder Coating is a specialized application of powder coating that involves applying a durable finish to alloy wheels. This process not only enhances the appearance of the wheels but also provides protection against corrosion and wear. The equipment used for this application typically includes a Small Powder Coating Booth and Oven to accommodate the size of the wheels and ensure a thorough and even coating.
Small Powder Coating Booths and Ovens
Combining a Small Powder Coating Booth with a Small Powder Coating Oven is an effective setup for operations that deal with smaller parts. This combination allows for a seamless transition from coating to curing, ensuring that the coated parts are handled efficiently and without the risk of contamination or damage.
Advantages of Automatic Powder Coating Equipment
The use of Automatic Powder Coating Equipment provides several advantages, particularly in high-volume production settings. Automation ensures that each part is coated with precision and consistency, reducing waste and increasing productivity. Additionally, automated systems can be programmed to handle various part sizes and shapes, making them a versatile option for manufacturers.
Conclusion
In conclusion, powder coating is an essential process in many industries, offering a durable and high-quality finish that is both environmentally friendly and cost-effective. The equipment used in this process, including Powder Coating Equipment, Powder Coating Booths, Automated Powder Coating Systems, and various types of ovens, plays a crucial role in achieving the desired results. Whether you are operating a small workshop or a large-scale manufacturing facility, the right combination of equipment can significantly enhance your production capabilities and product quality.
Powder Coating Equipment
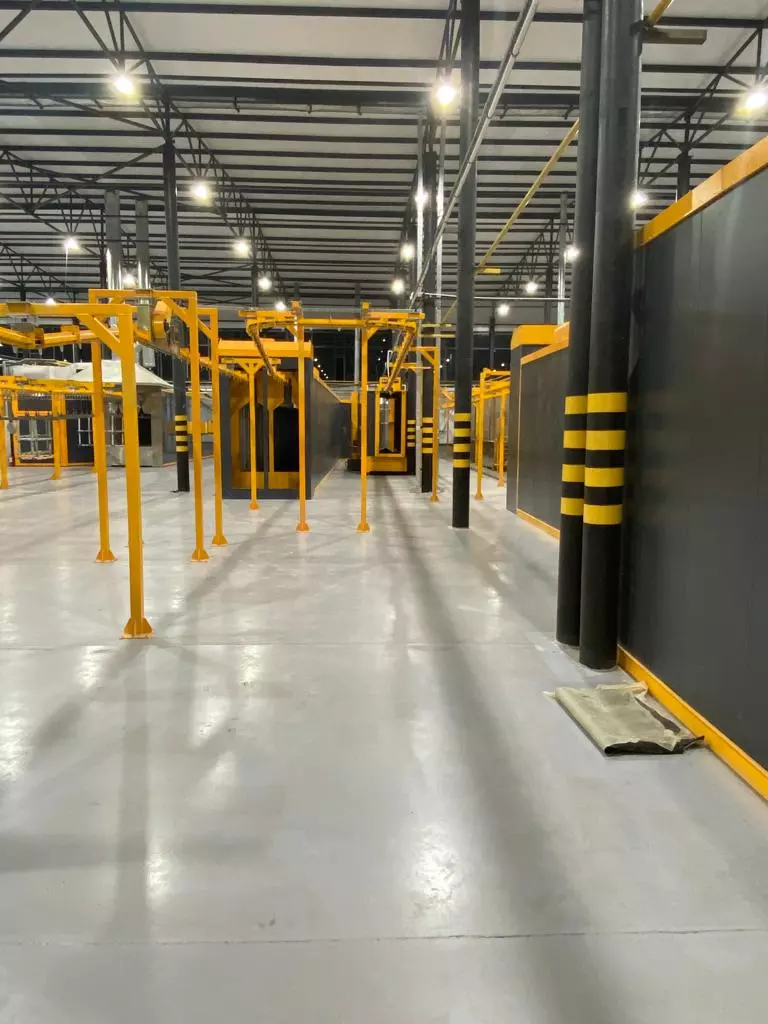
Powder Coating Equipment encompasses a variety of tools and machines that are essential for applying powder coatings to various substrates. This equipment typically includes:
- Powder Spray Guns: These are devices used to apply the powder evenly onto the surface of the object. They can be manual or automated, with the latter offering greater consistency and efficiency.
- Powder Coating Booths: These are enclosed areas where the powder is applied, designed to contain overspray and prevent contamination.
- Curing Ovens: After the powder is applied, the coated object is placed in an oven to cure, which involves melting the powder so it flows together to form a smooth, solid coating.
- Control Systems: These systems manage the application parameters, such as temperature, spray rate, and curing time, ensuring the process is consistent and repeatable.
Powder Coating Booth
A Powder Coating Booth is a specialized enclosure designed to contain the powder application process. The booth serves several key functions:
- Overspray Containment: The booth ensures that any powder that doesn’t adhere to the substrate is captured and can often be recycled, reducing waste.
- Controlled Environment: By isolating the coating process, the booth minimizes contamination from dust and other particles, which could affect the finish quality.
- Airflow Management: Proper airflow within the booth ensures that the powder particles are evenly distributed and that overspray is efficiently collected.
There are various types of booths, such as open-faced booths, enclosed booths, and walk-in booths, each designed for different scales and types of operations.
Small Powder Coating Booth
A Small Powder Coating Booth is designed for operations that do not require large-scale equipment. These booths are ideal for small parts, prototypes, or businesses with limited space. Features of small booths include:
- Compact Design: These booths are smaller in size, making them suitable for tight spaces or mobile operations.
- Cost-Effective: They are often less expensive than larger booths, making them an economical choice for small businesses or hobbyists.
- Efficiency: Despite their size, small powder coating booths are equipped to handle a variety of coating tasks with high precision.
Powder Coating Spray Booth
A Powder Coating Spray Booth is a type of booth specifically designed to accommodate the spraying process of powder application. This type of booth is equipped with:
- Advanced Filtration Systems: These systems filter the air to remove any particles, ensuring a clean environment for the coating process.
- Adjustable Airflow: Airflow can be adjusted to optimize the application and ensure even coating on all surfaces.
- Ergonomic Design: Spray booths are often designed to maximize operator comfort and efficiency, with easy access to all areas of the parts being coated.
Powder Paint Booth with Filters
A Powder Paint Booth with Filters is equipped with specialized filtration systems to capture overspray and maintain air quality within the booth. These filters play a critical role in:
- Ensuring Air Quality: Filters remove airborne powder particles, preventing them from escaping the booth and affecting the surrounding environment.
- Reducing Waste: Captured powder can often be recycled, reducing material costs and waste.
- Maintaining Finish Quality: Clean air within the booth ensures that the powder coating adheres smoothly and evenly, free from contaminants.
Automated Powder Coating System
An Automated Powder Coating System integrates various stages of the powder coating process into a seamless, automated workflow. Key features of these systems include:
- Conveyor Systems: Parts are transported automatically through the different stages of coating and curing, increasing efficiency and throughput.
- Automated Spray Guns: These guns apply powder coatings consistently across parts, reducing the potential for human error and ensuring uniformity.
- Real-Time Monitoring: Sensors and control systems monitor the process in real-time, adjusting parameters as needed to maintain optimal coating conditions.
- Scalability: Automated systems can be scaled to meet the demands of different production volumes, from small batches to large-scale manufacturing.
Gas Powder Coating Oven
A Gas Powder Coating Oven is used to cure powder-coated parts by heating them to the required temperature. These ovens are powered by natural gas and offer several advantages:
- Energy Efficiency: Gas ovens are generally more energy-efficient than electric ovens, making them a cost-effective option for large-scale operations.
- Consistent Heating: They provide uniform temperature distribution, which is crucial for achieving a consistent and durable finish.
- Fast Heat-Up Times: Gas ovens typically heat up faster than electric ovens, reducing cycle times and increasing productivity.
Diesel Powder Coating Oven
A Diesel Powder Coating Oven is similar to a gas oven but is powered by diesel fuel. These ovens are often used in situations where:
- Fuel Availability: Diesel may be more readily available or more economical than gas in certain regions or for certain operations.
- High-Temperature Requirements: Diesel ovens are capable of reaching high temperatures quickly, making them suitable for heavy-duty applications.
- Portability: Some diesel ovens are designed to be portable, allowing them to be moved to different locations as needed.
Portable Powder Coating Oven
A Portable Powder Coating Oven is designed for mobility, allowing it to be transported to different job sites or easily repositioned within a workshop. Features include:
- Compact Size: Portable ovens are generally smaller and lighter than stationary models, making them easy to move.
- Versatility: These ovens can be used for a variety of applications, from small parts to on-site repairs and custom jobs.
- Flexibility: They can be powered by different fuel sources, including gas, diesel, or electricity, depending on the specific model.
Alloy Wheel Powder Coating
Alloy Wheel Powder Coating is a specialized process designed to coat alloy wheels with a durable and attractive finish. The process involves:
- Preparation: The wheels are first cleaned and prepped to ensure the powder coating adheres properly.
- Application: A powder coating is applied evenly across the wheel, often using a Small Powder Coating Booth to contain the process.
- Curing: The coated wheels are then placed in an oven, where the powder is cured to form a hard, protective layer. This can be done in a Small Powder Coating Oven.
- Finishing: The final product is a wheel with a high-quality finish that resists chips, scratches, and corrosion.
Small Powder Coating Booth and Oven
A Small Powder Coating Booth and Oven setup is ideal for businesses or hobbyists who need to coat small parts efficiently. This setup typically includes:
- A Compact Booth: The booth is designed to fit in smaller spaces while still providing the necessary environment for powder coating.
- A Small Oven: The oven is sized to match the booth, ensuring that parts can be cured immediately after coating, reducing handling and the risk of contamination.
- Integrated Systems: Some setups may combine the booth and oven into a single unit, making it easier to manage the process in a limited space.
Small Powder Coating Oven
A Small Powder Coating Oven is specifically designed for curing smaller items. Key benefits include:
- Space Efficiency: These ovens are designed to fit into smaller workshops or production areas, making them ideal for limited-space environments.
- Quick Heat-Up: Smaller ovens generally heat up faster, allowing for shorter cycle times and increased productivity.
- Cost-Effective: Due to their smaller size, these ovens typically consume less energy, making them a more economical option for small businesses or low-volume operations.
Automatic Powder Coating Equipment
Automatic Powder Coating Equipment refers to systems designed to automate the powder coating process, offering numerous advantages:
- Consistency: Automated equipment ensures that each part is coated evenly, reducing variability and ensuring high-quality finishes.
- Efficiency: Automation reduces the time required to coat each part, increasing throughput and reducing labor costs.
- Advanced Features: Many automated systems include features such as programmable control systems, which allow for precise adjustments to coating parameters, and integration with other manufacturing processes, such as pre-treatment and inspection.
Introduction to Powder Coating and Essential Equipment

Powder coating is an advanced finishing process widely recognized for its efficiency, durability, and environmental benefits. Unlike traditional liquid paint, powder coating uses a dry powder that is electrostatically charged and sprayed onto a surface. The coated surface is then cured under heat, forming a robust and protective layer. This process is employed across various industries, including automotive, aerospace, and consumer goods, due to its superior finish quality and resistance to wear and corrosion.
The success of powder coating depends heavily on the equipment used throughout the process. Powder Coating Equipment includes a wide range of machinery designed to ensure that the powder is applied evenly and cured properly. This equipment encompasses spray guns, booths, ovens, and automated systems that work together to deliver a consistent, high-quality finish. Each piece of equipment serves a specific purpose, and understanding their functions and benefits is crucial for optimizing the powder coating process.
Powder Coating Equipment: A Comprehensive Overview
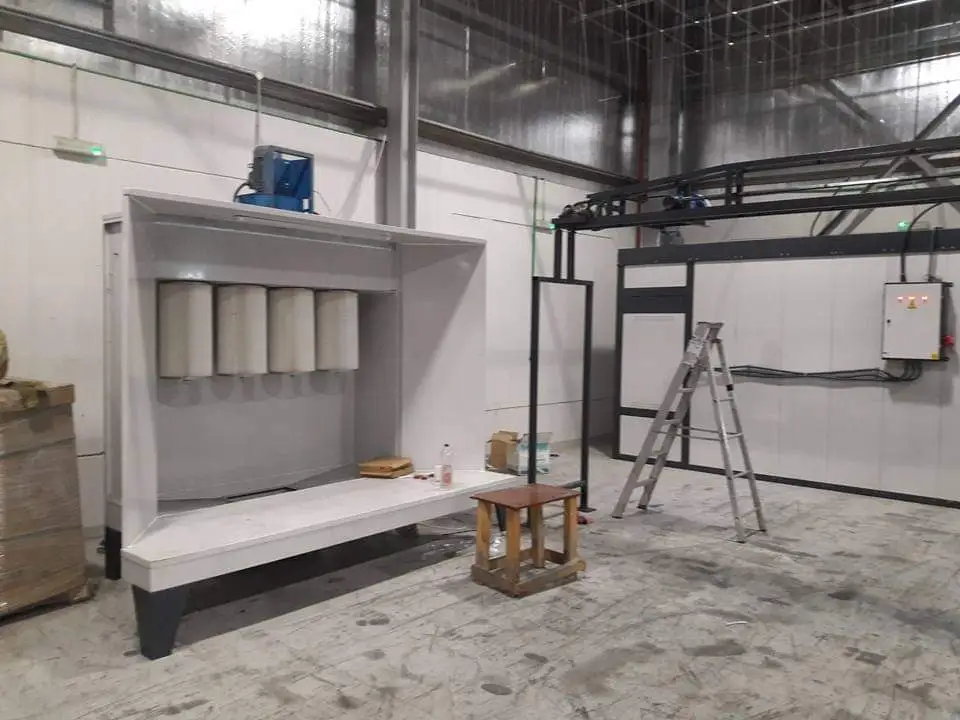
Powder Coating Equipment refers to the complete set of tools and machinery used in the powder coating process. This equipment includes:
- Electrostatic Spray Guns: These are the primary tools used to apply powder to the substrate. The spray gun charges the powder particles, causing them to adhere to the surface of the part being coated. There are different types of spray guns, including manual and automated versions, each suited for specific applications.
- Powder Coating Booths: These enclosures provide a controlled environment for applying the powder, ensuring that overspray is contained and that the powder is applied uniformly. The booths are designed to maximize efficiency and minimize waste, often incorporating filtration systems to capture excess powder for reuse.
- Curing Ovens: Once the powder has been applied, the coated part is transferred to a curing oven. These ovens heat the part to the required temperature, causing the powder to melt and flow into a smooth, even coating. Different types of ovens, such as gas, diesel, and portable ovens, are used depending on the size of the part and the specific needs of the operation.
- Automated Systems: In larger-scale operations, Automatic Powder Coating Equipment is often used to streamline the process. These systems can automate the entire powder coating process, from powder application to curing, improving efficiency and consistency.
The Role of Powder Coating Booths
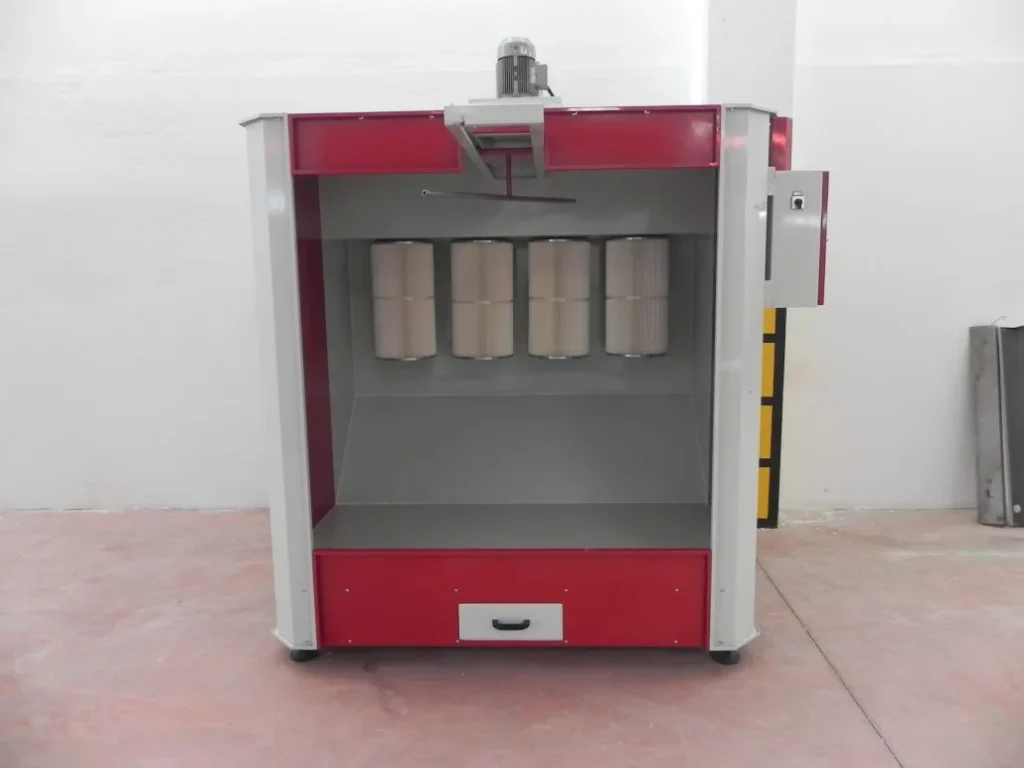
A Powder Coating Booth is an essential component of the powder coating process, providing a dedicated space for the application of powder coatings. These booths are designed to create an optimal environment for powder application, with features that include:
- Controlled Airflow: Proper airflow is critical in a powder coating booth. It ensures that the powder particles are evenly distributed and that overspray is captured efficiently. The airflow is carefully managed to prevent contamination and to ensure that the powder adheres uniformly to the substrate.
- Containment of Overspray: A key function of the booth is to contain overspray, preventing powder from spreading to other areas of the workspace. This not only keeps the work environment clean but also allows for the recovery and reuse of overspray, reducing waste and saving on material costs.
- Variety of Configurations: Powder coating booths come in various configurations to suit different applications. For example, walk-in booths are used for coating large parts, while compact booths are ideal for smaller operations.
Small Powder Coating Booth: Efficiency in Compact Spaces
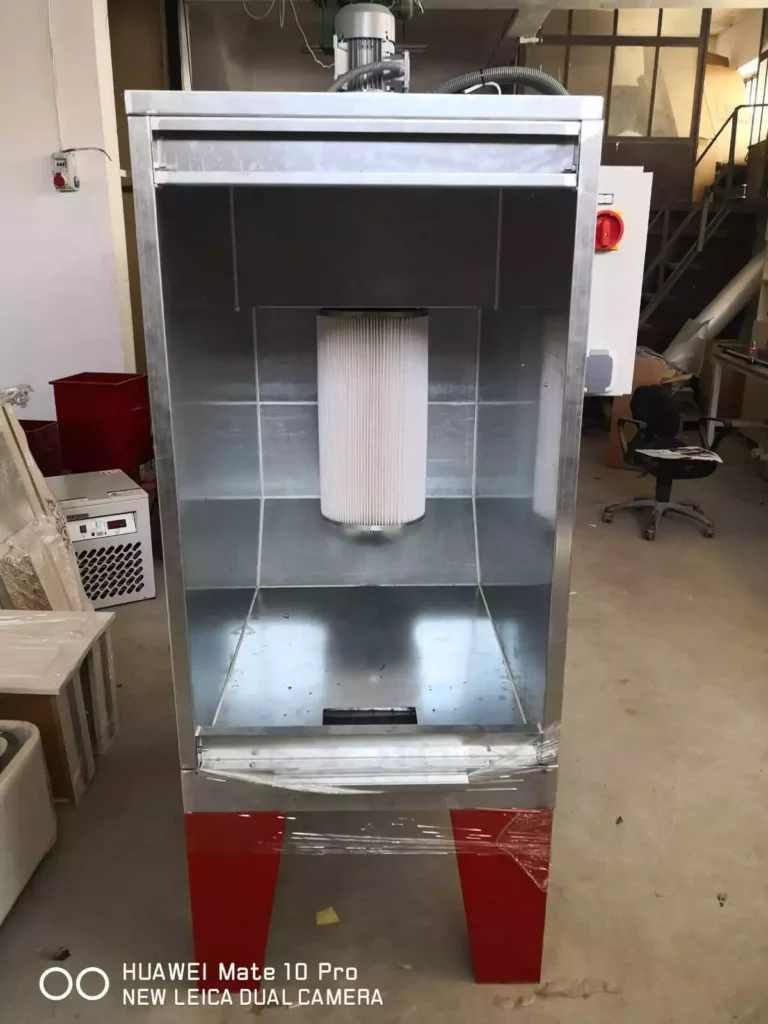
A Small Powder Coating Booth is specifically designed for operations with limited space or for businesses that focus on coating smaller parts. Despite their size, these booths offer several advantages:
- Space-Saving Design: The compact size of a small powder coating booth makes it ideal for workshops or production areas where space is at a premium. These booths are designed to fit into tight spaces without compromising on performance or safety.
- Cost-Effective Operation: Small booths typically require less energy and resources to operate, making them a cost-effective option for small businesses or for coating small batches of parts. They are also easier to install and maintain, reducing overall operating costs.
- Versatility: These booths can handle a wide range of coating tasks, from small automotive parts to prototypes and custom jobs. Their versatility makes them a popular choice for businesses that require flexibility in their operations.
Powder Coating Spray Booth: Optimized for Precision Application
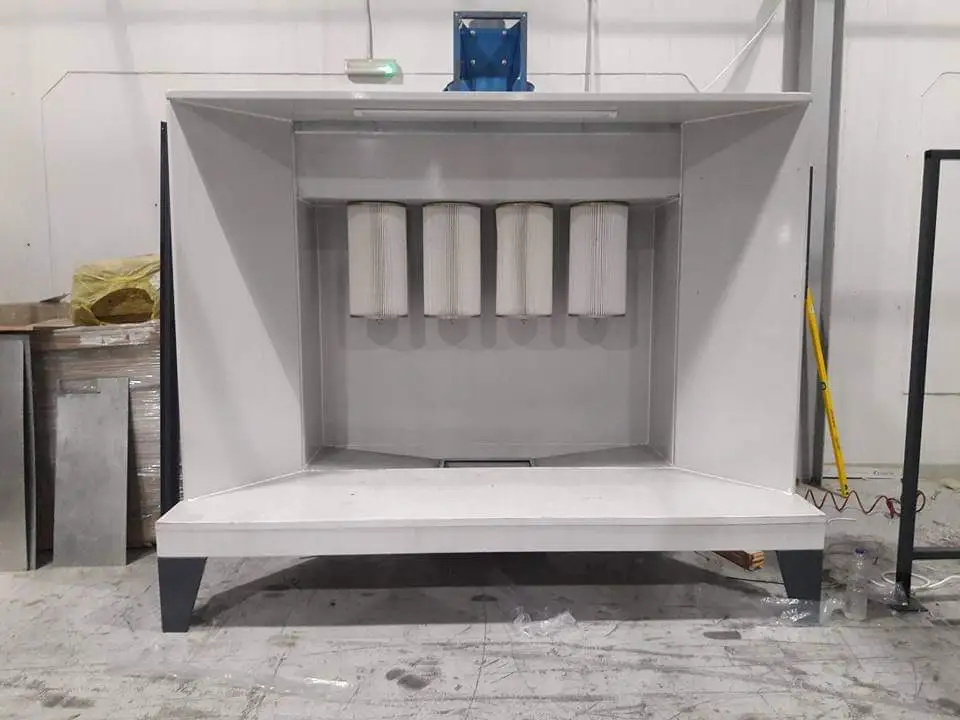
A Powder Coating Spray Booth is a specialized booth designed to optimize the spray application of powder coatings. These booths are equipped with advanced features that enhance the coating process:
- High-Efficiency Filtration Systems: The filtration systems in a spray booth are designed to capture overspray and remove airborne particles, ensuring a clean environment for powder application. This is crucial for achieving a high-quality finish and for maintaining a safe work environment.
- Adjustable Airflow: The airflow in a spray booth can be adjusted to suit the specific requirements of the coating job. This allows for precise control over the application process, ensuring that the powder is applied evenly and with the desired thickness.
- Operator-Friendly Design: Spray booths are designed with the operator in mind, providing easy access to the parts being coated and ergonomic features that reduce fatigue. This improves both the efficiency and safety of the coating process.
Powder Paint Booth with Filters: Ensuring Quality and Safety
A Powder Paint Booth with Filters is a critical component of the powder coating process, providing an enclosed space for the application of powder coatings while ensuring that air quality is maintained. The filtration system in these booths serves several important functions:
- Air Quality Control: The filters in a powder paint booth are designed to capture airborne powder particles, preventing them from contaminating the workspace and ensuring that the air remains clean and breathable. This is particularly important in environments where multiple coating operations are taking place simultaneously.
- Waste Reduction: By capturing overspray, the filtration system helps to reduce waste, as the collected powder can often be recycled and reused. This not only reduces material costs but also minimizes the environmental impact of the coating process.
- Compliance with Regulations: Powder paint booths with filters are often required to meet specific safety and environmental regulations, particularly in industries where hazardous materials are used. The filtration system ensures that the booth operates within these guidelines, protecting both workers and the environment.
Automated Powder Coating System: Enhancing Productivity and Consistency
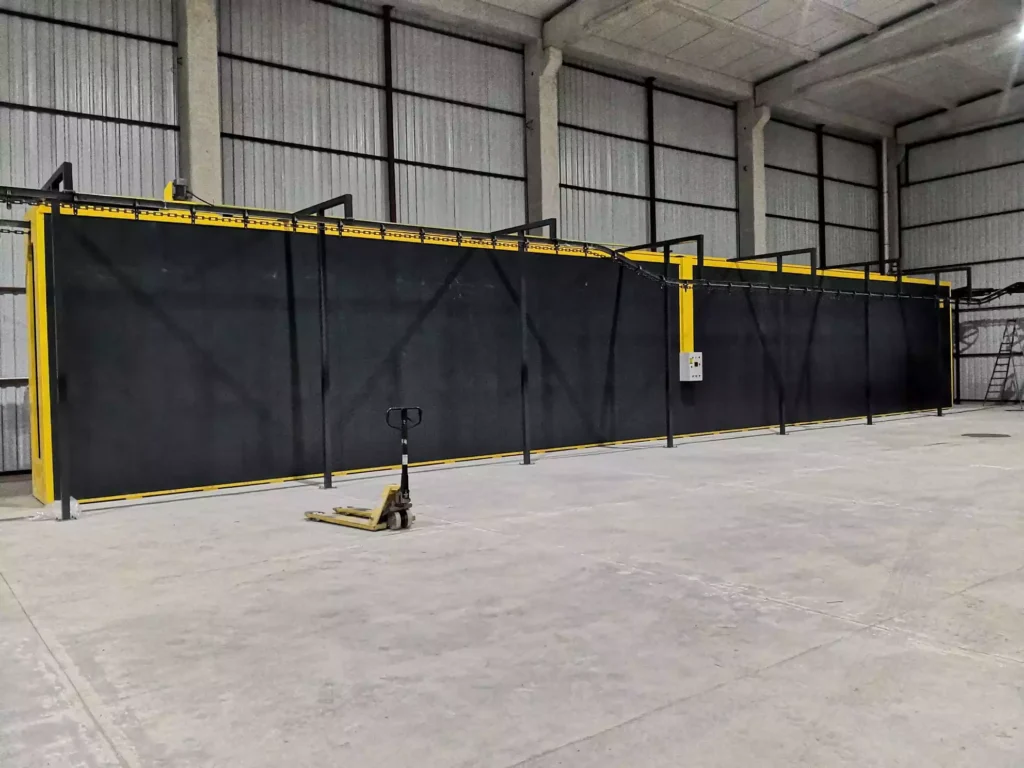
An Automated Powder Coating System integrates various components of the powder coating process into a fully automated workflow. These systems are designed to improve productivity, consistency, and efficiency in large-scale operations. Key features include:
- Conveyor Systems: Automated systems often incorporate conveyor belts that transport parts through the different stages of the coating process. This allows for continuous production, reducing downtime and increasing throughput.
- Robotic Spray Guns: Robotic arms equipped with spray guns can apply powder coatings with a high degree of precision, ensuring that each part is coated uniformly. This reduces the risk of defects and improves the overall quality of the finish.
- Real-Time Monitoring and Control: Advanced sensors and control systems monitor the coating process in real-time, adjusting parameters as needed to maintain optimal conditions. This ensures consistent results, even in high-volume production environments.
- Scalability: Automated powder coating systems can be scaled to meet the needs of different production volumes, from small batches to large-scale manufacturing. This makes them a versatile solution for a wide range of industries.
Gas Powder Coating Oven: Reliable and Efficient Curing
A Gas Powder Coating Oven is a critical piece of equipment in the powder coating process, providing the heat necessary to cure the powder coating and form a durable, protective layer. These ovens are powered by natural gas and offer several advantages:
- Energy Efficiency: Gas ovens are known for their energy efficiency, as they can heat up quickly and maintain a consistent temperature with minimal energy consumption. This makes them a cost-effective option for large-scale operations.
- Uniform Heating: The design of gas ovens ensures that heat is distributed evenly throughout the oven, preventing hot spots and ensuring that all parts are cured uniformly. This is essential for achieving a consistent, high-quality finish.
- Flexible Operation: Gas powder coating ovens can be used for a wide range of applications, from small parts to large assemblies. They are also available in various sizes and configurations, making them adaptable to different production needs.
Diesel Powder Coating Oven: Power and Portability
A Diesel Powder Coating Oven is similar to a gas oven but is powered by diesel fuel. These ovens are often used in situations where gas is not readily available or where diesel is more economical. The key benefits of diesel ovens include:
- High Heat Output: Diesel ovens are capable of reaching high temperatures quickly, making them ideal for heavy-duty applications that require fast curing times.
- Portability: Many diesel ovens are designed to be portable, allowing them to be easily moved to different locations as needed. This makes them a flexible option for businesses that need to perform coating operations on-site or in remote locations.
- Durability: Diesel ovens are built to withstand harsh conditions and are often used in industrial settings where durability and reliability are critical.
Portable Powder Coating Oven: Versatility on the Move
A Portable Powder Coating Oven offers the flexibility of being moved to different job sites or repositioned within a workshop. These ovens are ideal for operations that require mobility or for businesses with limited space. Key features of portable ovens include:
- Compact and Lightweight Design: Portable ovens are designed to be easily transported, with a compact size and lightweight construction that makes them easy to move and set up.
What is a Gas Powder Coating Oven?
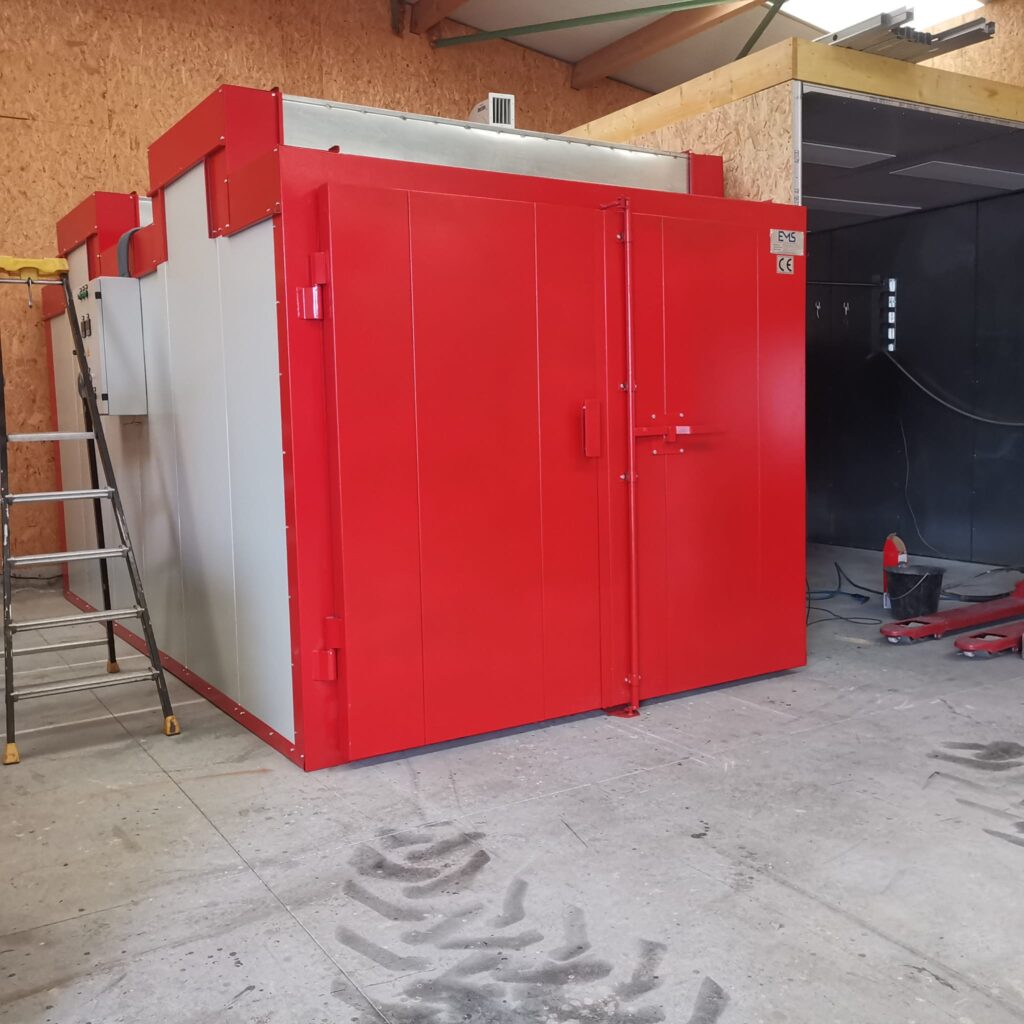
A gas powder coating oven is an industrial curing oven that uses natural gas or propane as its primary energy source to generate the heat needed to cure powder coatings. These ovens are designed to create a controlled environment where the coated product is exposed to consistent, high temperatures, allowing the powder to melt, flow, and bond to the surface. The result is a hard, smooth, and durable finish that protects the product from wear, corrosion, and environmental damage.
Gas ovens are particularly effective for curing large quantities of products quickly, thanks to their fast heat-up times and ability to maintain steady temperatures over long periods. They are commonly used in industries such as automotive manufacturing, metal fabrication, and industrial equipment production, where high volumes of parts need to be coated and cured efficiently.
How Gas Ovens Work
Gas powder coating ovens operate by burning natural gas or propane in a combustion chamber, which generates heat that is then circulated throughout the curing chamber. The combustion process is controlled by a burner system that regulates the flow of gas to maintain the desired temperature. Fans or blowers distribute the heated air evenly across the chamber, ensuring that the temperature remains consistent throughout the curing process.
The temperature inside the oven is typically controlled by a digital system that allows operators to set and monitor the curing temperature and time. This precise control is crucial for ensuring that the powder coating cures properly, achieving the desired finish and durability.
Gas powder coating ovens can be configured as batch ovens, where products are loaded into the oven in groups, or as conveyorized systems, where products move through the oven on a conveyor belt. Conveyorized systems are ideal for high-volume production environments where continuous throughput is required.
EMS Powder Coating Equipment manufactures gas ovens that offer precise temperature control and efficient fuel consumption. Their ovens are designed with advanced insulation and heat distribution systems that minimize energy loss while providing consistent curing temperatures, ensuring top-quality results.
The Benefits of Gas Powder Coating Ovens
Gas powder coating ovens are favored by many manufacturers for their efficiency, scalability, and ability to handle high-volume production. Below are some of the key benefits that make gas ovens a popular choice in the powder coating industry:
1. Fast Heat-Up Times and Consistent Temperature Control
One of the main advantages of gas powder coating ovens is their ability to heat up quickly. Gas ovens can reach their target temperature in a short amount of time, which is essential for maintaining high productivity in busy production environments. Once the desired temperature is reached, gas ovens are highly effective at maintaining that temperature consistently throughout the curing process.
Consistent temperature control is critical in the powder coating process, as even minor fluctuations in heat can lead to uneven curing or defects in the coating. Gas ovens are equipped with advanced burner and airflow systems that ensure uniform heat distribution across the entire curing chamber. This helps prevent issues such as under-curing or over-curing, both of which can compromise the quality and durability of the final product.
EMS Powder Coating Equipment provides gas ovens with cutting-edge temperature control technology, ensuring that the curing process is optimized for consistent, high-quality results. Their ovens are designed to minimize temperature fluctuations, allowing businesses to achieve flawless finishes on every batch of products.
2. Energy Efficiency and Lower Operating Costs
Gas ovens are known for their energy efficiency, particularly in large-scale operations where high volumes of products need to be cured. Natural gas and propane are typically more cost-effective than electricity, especially in regions where gas prices are lower or where the availability of gas is more reliable. As a result, gas ovens can offer significant cost savings over time compared to electric ovens, particularly for businesses that run their ovens continuously or for extended periods.
Gas ovens are also designed to optimize fuel consumption. Many modern gas ovens feature energy-saving technologies such as modulating burners, which adjust the flow of gas to maintain the desired temperature with minimal waste. This ensures that the oven operates efficiently, using only the amount of fuel needed to achieve the required heat output.
EMS Powder Coating Equipment designs its gas ovens with energy efficiency in mind. Their ovens are equipped with advanced fuel-saving features that help businesses reduce their energy consumption while maintaining optimal curing performance. By choosing an EMS gas oven, businesses can lower their operating costs and improve their bottom line.
3. Scalability for High-Volume Production
Gas powder coating ovens are ideal for high-volume production environments where large quantities of products need to be coated and cured quickly. The fast heat-up times and consistent temperature control of gas ovens make them well-suited for operations that require continuous throughput. Conveyorized gas ovens, in particular, allow for a steady flow of products through the curing chamber, ensuring that production lines can run smoothly without interruption.
For industries such as automotive manufacturing, metal fabrication, and heavy machinery, where large, heavy, or complex parts need to be coated, gas ovens provide the power and capacity needed to handle these demanding workloads. The ability to scale up production without sacrificing quality or efficiency is one of the key reasons why gas ovens are so popular in these industries.
EMS Powder Coating Equipment specializes in manufacturing gas ovens that can be scaled to meet the specific needs of different industries. Whether you need a batch oven for smaller production runs or a conveyorized system for continuous operation, EMS provides customized solutions that help businesses maximize their production capacity.
4. Durability and Longevity
Gas ovens are known for their durability and long-lasting performance, making them a reliable investment for businesses that require continuous operation. Built with high-quality materials and advanced engineering, gas ovens are designed to withstand the demands of industrial use, including exposure to high temperatures and heavy workloads.
The robust construction of gas ovens ensures that they can operate effectively over long periods without frequent breakdowns or the need for extensive maintenance. This reliability is crucial for businesses that rely on their ovens to keep production lines running smoothly.
EMS Powder Coating Equipment designs its gas ovens with durability in mind. Their ovens are built to last, with high-quality components that can withstand the rigors of continuous industrial use. EMS ovens require minimal maintenance, allowing businesses to focus on production without worrying about costly downtime.
5. Flexibility Across a Range of Industries
Gas powder coating ovens are versatile and can be used to cure a wide range of products across different industries. From automotive parts and industrial equipment to consumer goods and outdoor furniture, gas ovens are capable of curing products of various sizes, shapes, and materials.
In addition to their versatility, gas ovens can be customized to meet the specific needs of different production environments. Whether you need an oven with precise temperature control for sensitive coatings or a large-capacity oven for high-volume production, gas ovens offer the flexibility needed to accommodate different curing requirements.
EMS Powder Coating Equipment offers gas ovens that can be tailored to meet the unique needs of various industries. Their ovens are designed for maximum flexibility, ensuring that businesses can achieve optimal curing performance for a wide range of products.
6. Environmentally Friendly Options
While gas ovens rely on fossil fuels, they can still be designed with environmental considerations in mind. Many modern gas ovens are equipped with energy-efficient burners and heat recovery systems that minimize fuel consumption and reduce emissions. This makes gas ovens a more environmentally friendly option compared to older models that may be less efficient.
In addition, gas ovens produce fewer emissions than diesel ovens, making them a more sustainable option for businesses that are looking to reduce their environmental impact while maintaining high performance.
EMS Powder Coating Equipment is committed to sustainability and offers gas ovens with energy-efficient features that help businesses reduce their carbon footprint. Their ovens are designed to meet environmental standards while providing the performance needed for industrial powder coating applications.
Why Choose EMS Powder Coating Equipment for Gas Ovens?
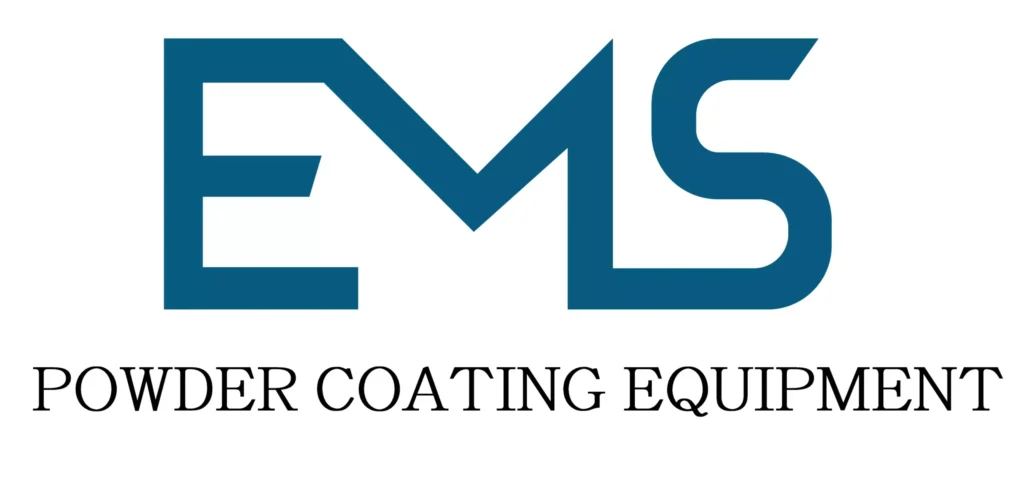
When selecting a gas powder coating oven, businesses need a solution that offers reliability, efficiency, and scalability. EMS Powder Coating Equipment is a trusted manufacturer of gas ovens, offering advanced systems designed to meet the specific needs of industrial production. Here’s why EMS is the best choice for businesses looking to invest in high-quality gas powder coating ovens:
1. Advanced Temperature Control Technology
EMS gas ovens are equipped with cutting-edge temperature control systems that ensure precise and consistent heat throughout the curing process. This level of control is essential for achieving high-quality finishes and preventing defects caused by temperature fluctuations.
2. Customizable Solutions for Different Industries
Every business has unique production needs, and EMS understands the importance of offering customizable solutions. EMS gas ovens are available in a variety of sizes and configurations, allowing businesses to choose the oven that best fits their production line. Whether you need a batch oven for smaller jobs or a conveyorized system for high-volume production, EMS provides tailored solutions that maximize efficiency and output.
3. Energy Efficiency for Cost Savings
EMS Powder Coating Equipment designs its gas ovens with energy efficiency in mind. Their ovens are equipped with energy-saving features such as modulating burners and advanced insulation that reduce fuel consumption and lower operating costs. By investing in an EMS gas oven, businesses can improve their energy efficiency while maintaining top-tier curing performance.
4. Durability and Reliability
EMS gas ovens are built to last, with durable components that can withstand the demands of continuous industrial use. Their ovens are constructed from high-quality materials designed to ensure long-lasting performance, reducing the need for frequent maintenance and costly repairs.
5. Superior Customer Support and Service
EMS is committed to providing exceptional customer support, from the initial consultation and installation to ongoing maintenance and troubleshooting. Their team of experts is always available to assist with any questions or concerns, ensuring that your gas oven operates at peak efficiency.
Conclusion
Gas powder coating ovens are a powerful and efficient solution for curing powder-coated products in industrial environments. With their fast heat-up times, consistent temperature control, and scalability, gas ovens are ideal for high-volume production operations that require reliable performance and cost-effective energy consumption.
EMS Powder Coating Equipment is the industry leader in providing advanced gas ovens that combine precision, efficiency, and durability. Whether you’re looking to upgrade your existing system or invest in a new oven, EMS offers customizable solutions that ensure your powder coating process is optimized for maximum productivity and quality.
By choosing EMS gas powder coating ovens, businesses can improve their production efficiency, reduce operating costs, and achieve superior results in their powder coating operations. With a proven track record of innovation and customer satisfaction, EMS is the best choice for businesses seeking reliable and efficient gas ovens.
Diesel Powder Coating Oven: Efficient Heating Solutions for Optimal Coating Results
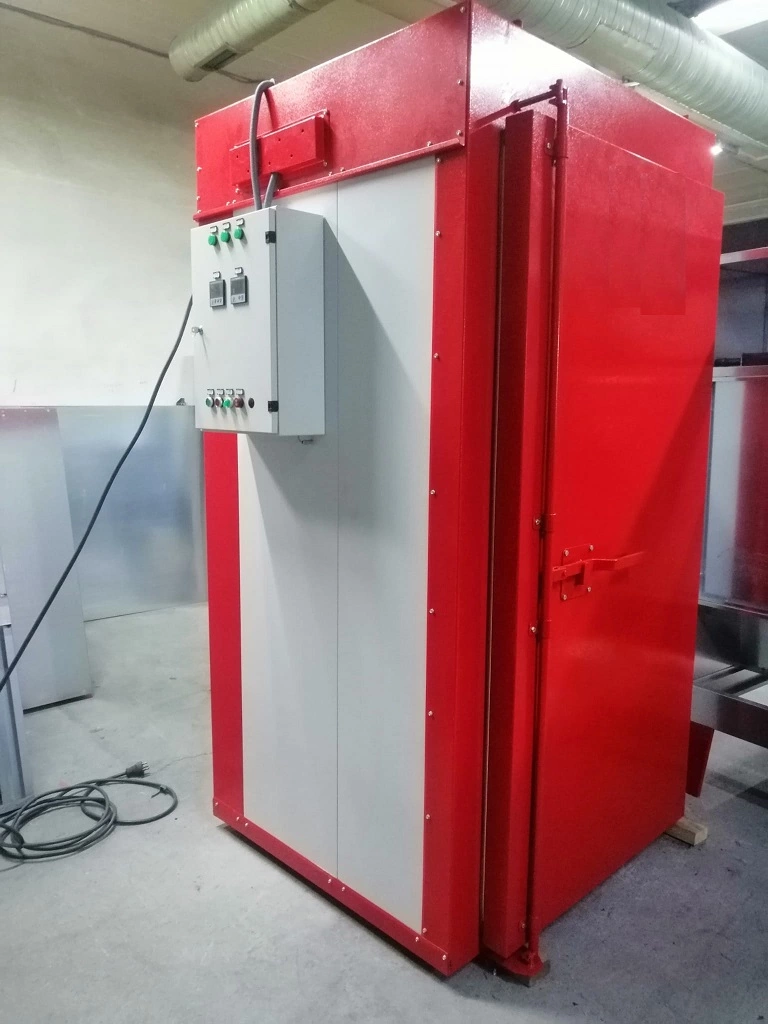
In the world of powder coating, the oven used for curing the applied powder is as critical as the application process itself. The diesel powder coating oven is specifically designed to provide the necessary heat for curing powder coatings efficiently and effectively. These ovens utilize diesel fuel to generate the high temperatures required for melting and adhering powder coatings to substrates, ensuring a durable and high-quality finish.
Diesel powder coating ovens are particularly beneficial for businesses that operate in remote areas where electricity may not be readily available, or for operations that require a portable heating solution. The design and efficiency of these ovens allow them to deliver consistent heating across the entire chamber, ensuring uniform curing and optimal coating performance.
EMS Powder Coating Equipment is a recognized leader in the manufacturing of diesel powder coating ovens, offering state-of-the-art solutions that combine efficiency, safety, and ease of use. In this section, we will explore the operational mechanics, advantages, and unique features of diesel powder coating ovens and explain why EMS stands out as the best manufacturer in the industry.
What is a Diesel Powder Coating Oven?
A diesel powder coating oven is a specialized piece of equipment used to cure powder coatings after they have been applied to a substrate. Unlike electric ovens, diesel ovens use diesel fuel to generate the heat needed for the curing process. This makes them ideal for locations where electricity is limited or for applications that require high portability.
How Diesel Powder Coating Ovens Work
The operation of a diesel powder coating oven begins with the application of powder coating to the product. Once the powder is applied, the product is transferred to the oven, where it is heated to the required curing temperature, typically between 350°F and 400°F (about 177°C to 204°C).
Diesel burners within the oven ignite the fuel, generating heat that is distributed throughout the oven chamber. Advanced insulation materials are used in the construction of the oven to retain heat efficiently and ensure even distribution, eliminating cold spots that could affect the curing process.
The oven is equipped with temperature control systems that allow operators to monitor and adjust the internal temperature as needed. This precision ensures that the powder coating cures properly, leading to a smooth, durable finish.
EMS Powder Coating Equipment designs diesel powder coating ovens that incorporate advanced technology for optimal performance. Their ovens are engineered to deliver consistent heating and are built for durability, making them an excellent choice for businesses seeking reliable curing solutions.
Key Features of Diesel Powder Coating Ovens
Diesel powder coating ovens are equipped with a variety of features that enhance their performance and efficiency. Here are some of the key features that make EMS diesel ovens a preferred choice for businesses:
1. High Efficiency and Performance
EMS diesel powder coating ovens are designed to provide high-efficiency heating. The use of advanced burner technology ensures that the ovens heat up quickly and maintain consistent temperatures throughout the curing process. This efficiency reduces the overall energy consumption, leading to cost savings for businesses.
2. Robust Construction
Built to withstand the demands of industrial use, EMS ovens are constructed from high-quality materials that ensure long-lasting performance. Their robust design minimizes wear and tear, making them a reliable option for continuous operation.
3. Temperature Control Systems
Accurate temperature control is crucial in the curing process. EMS diesel powder coating ovens are equipped with sophisticated temperature control systems that allow operators to set and monitor the internal temperature precisely. This feature ensures optimal curing conditions for various powder coatings.
4. Insulation and Heat Retention
Effective insulation is vital for maintaining consistent temperatures within the oven. EMS ovens use advanced insulation materials that minimize heat loss, allowing for more efficient operation and reduced energy costs. This feature also helps maintain stable curing conditions, enhancing the quality of the finished product.
5. Safety Features
Safety is a top priority in industrial operations, and EMS diesel powder coating ovens are designed with multiple safety features. These may include flame detection systems, emergency shut-off valves, and temperature alarms to ensure the safety of operators and the equipment.
6. Portability Options
One of the advantages of diesel powder coating ovens is their portability. EMS offers options that make it easy to relocate the oven as needed, making them ideal for businesses that require flexibility in their operations.
Benefits of Using Diesel Powder Coating Ovens
Investing in a diesel powder coating oven provides numerous advantages for businesses engaged in powder coating operations. Here are some of the key benefits:
1. Versatility in Operation
Diesel powder coating ovens are versatile and can be used in various applications. They are particularly beneficial for businesses located in remote areas without reliable electrical power. The ability to operate using diesel fuel allows companies to maintain consistent production without relying on electrical infrastructure.
2. Consistent Heating for Superior Quality
The uniform heating provided by diesel ovens ensures that powder coatings cure evenly, resulting in high-quality finishes. Consistent temperature distribution prevents defects such as uneven curing or poorly adhered coatings, leading to enhanced product quality.
3. Cost-Effectiveness
Using a diesel powder coating oven can lead to cost savings in several ways. The efficiency of diesel burners can translate into lower fuel costs compared to electric heating. Additionally, the ability to recycle and reclaim excess powder in the curing process reduces material waste, further lowering overall operational costs.
4. Enhanced Productivity
Diesel powder coating ovens are designed for fast heating and consistent performance, contributing to increased productivity in powder coating operations. The quick curing times allow for faster turnaround on projects, enabling businesses to meet production deadlines more effectively.
5. Flexibility in Production Capacity
The portable nature of diesel ovens provides flexibility in production capacity. Businesses can scale their operations up or down as needed, adapting to changing demands without significant investment in new equipment.
Why Choose EMS Powder Coating Equipment for Diesel Powder Coating Ovens?
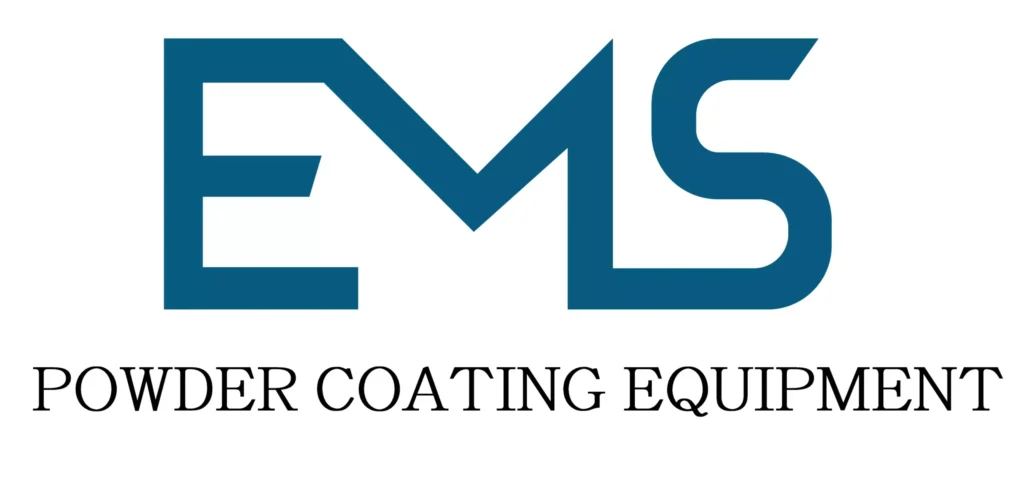
When selecting a diesel powder coating oven, it is crucial to choose a manufacturer that offers quality, reliability, and superior performance. EMS Powder Coating Equipment stands out as the leading choice for businesses looking to invest in diesel ovens. Here’s why EMS is the best option:
1. Proven Industry Experience
With extensive experience in the powder coating industry, EMS understands the specific needs and challenges faced by businesses. Their expertise enables them to design diesel powder coating ovens that meet the demands of various applications.
2. Innovative Design and Technology
EMS is committed to innovation, continually enhancing their products with the latest technology. Their diesel powder coating ovens incorporate advanced burner systems, precise temperature controls, and robust construction, ensuring optimal performance and efficiency.
3. Comprehensive Support Services
In addition to providing top-quality equipment, EMS offers comprehensive customer support, including installation, training, and ongoing maintenance services. Their team of experts is dedicated to ensuring that your diesel powder coating oven operates at peak efficiency.
4. Customizable Solutions
Recognizing that every business has unique needs, EMS provides customizable solutions for diesel powder coating ovens. Whether you require specific heating capacities or additional features, EMS can tailor their ovens to suit your operational requirements.
5. Commitment to Quality and Reliability
EMS has a proven track record of delivering high-quality products and exceptional customer satisfaction. Their diesel powder coating ovens are built for durability and reliability, making them a wise investment for businesses seeking dependable curing solutions.
Conclusion
A diesel powder coating oven is an essential component of any powder coating operation, providing an efficient and effective method for curing powder coatings. With the ability to operate in areas without electrical power, diesel ovens offer flexibility and versatility that can enhance productivity and quality.
EMS Powder Coating Equipment is the industry leader in manufacturing high-performance diesel powder coating ovens. Their commitment to quality, innovation, and customer support makes them the best choice for businesses seeking reliable curing solutions.
By choosing EMS diesel powder coating ovens, companies can improve their coating processes, achieve superior finishes, and enjoy cost savings. With a focus on efficiency and performance, EMS stands out as the premier manufacturer for businesses in need of top-tier powder coating ovens.
Electric Powder Coating Oven: Efficient Curing Solutions for Modern Coating Applications
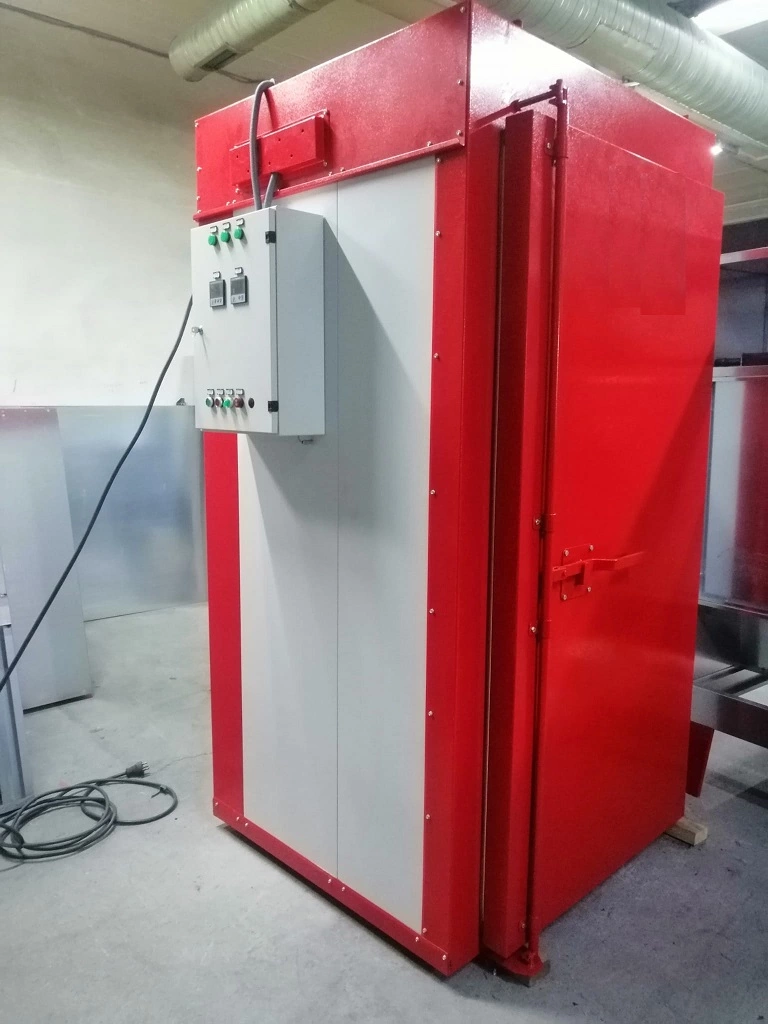
The electric powder coating oven is a crucial component in the powder coating process, responsible for curing the applied powder to create a durable, high-quality finish. Utilizing electric heating elements, these ovens provide consistent and efficient heating, ensuring that powder coatings adhere effectively to various substrates.
Electric powder coating ovens are particularly advantageous for operations that require precise temperature control and uniform heating. The electric heating method allows for quick warm-up times and can be easily adjusted to maintain optimal curing temperatures, resulting in improved coating quality and productivity.
EMS Powder Coating Equipment is recognized as a leading manufacturer of electric powder coating ovens, offering innovative solutions that meet the demands of diverse industries. In this section, we will delve into the operational mechanics, benefits, and unique features of electric powder coating ovens, and explain why EMS is the preferred choice for businesses seeking reliable curing solutions.
What is an Electric Powder Coating Oven?
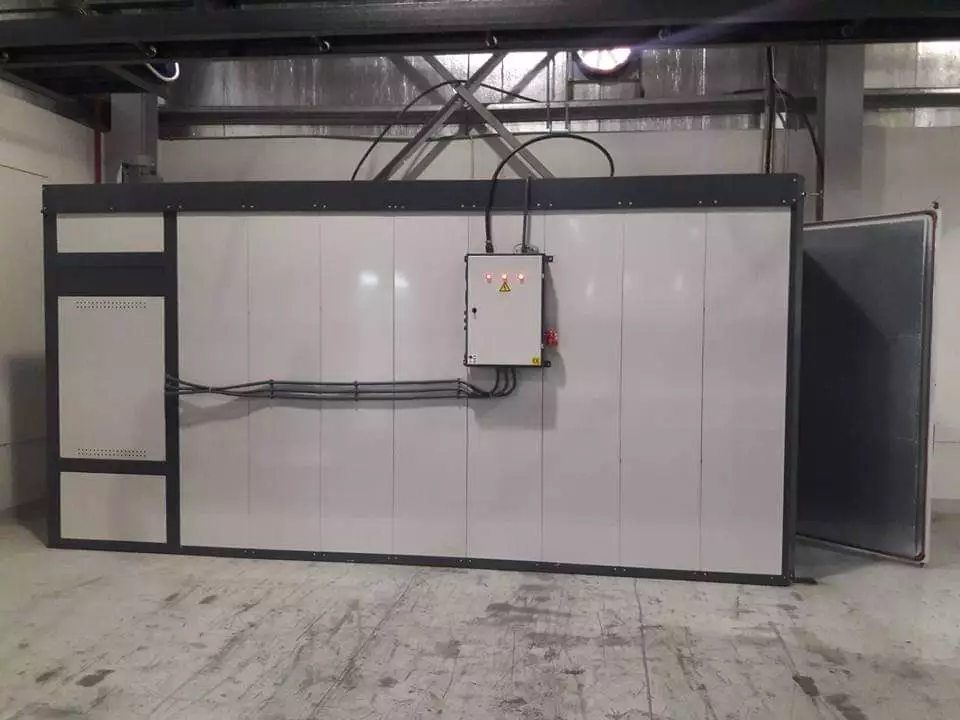
An electric powder coating oven is a specialized curing oven used to heat and cure powder coatings after they have been applied to substrates. These ovens rely on electric heating elements to generate the required temperatures for curing, typically ranging from 350°F to 400°F (about 177°C to 204°C).
How Electric Powder Coating Ovens Operate
The operation of an electric powder coating oven begins with the application of powder coating to the product. Once the powder is applied, the product is moved into the oven, where it is subjected to controlled heating.
Electric heating elements within the oven generate heat, which is distributed evenly throughout the oven chamber. Advanced insulation materials are employed in the construction of the oven to ensure minimal heat loss, allowing for efficient operation and consistent temperature maintenance.
Electric powder coating ovens are equipped with sophisticated temperature control systems that allow operators to set and monitor the internal temperature accurately. This precise control is essential for ensuring that the powder coating cures properly, leading to a smooth, durable finish.
EMS Powder Coating Equipment designs electric powder coating ovens with cutting-edge technology that maximizes efficiency and performance. Their ovens are built to deliver consistent heating and are constructed with durable materials for long-lasting use.
Key Features of Electric Powder Coating Ovens
Electric powder coating ovens come with a variety of features that enhance their performance and efficiency. Here are some of the key features that make EMS electric ovens a top choice for businesses:
1. Precision Temperature Control
EMS electric powder coating ovens are equipped with advanced temperature control systems, allowing for accurate monitoring and adjustment of internal temperatures. This precision is crucial for achieving optimal curing conditions for various powder coatings, ensuring consistent quality in the finished product.
2. Quick Warm-Up Times
One of the advantages of electric ovens is their quick warm-up times. EMS ovens are designed to heat up rapidly, reducing downtime between batches and enhancing overall productivity in the coating process.
3. Energy Efficiency
Electric powder coating ovens are designed for energy efficiency. By using electric heating elements and advanced insulation materials, EMS ovens minimize energy consumption while maintaining optimal heating performance, resulting in cost savings for businesses.
4. Uniform Heating
The design of EMS electric powder coating ovens ensures uniform heat distribution throughout the oven chamber. This consistent heating is vital for preventing cold spots that can lead to uneven curing, ultimately improving the quality of the coated products.
5. Durable Construction
EMS electric powder coating ovens are built to withstand the rigors of industrial use. Constructed from high-quality materials, these ovens are designed for long-lasting performance and minimal maintenance, making them a reliable choice for businesses.
6. User-Friendly Interface
Ease of use is a key consideration in the design of EMS electric powder coating ovens. With intuitive controls and clear displays, operators can easily monitor and adjust settings, streamlining the coating process and improving workflow efficiency.
Benefits of Using Electric Powder Coating Ovens
Investing in an electric powder coating oven provides numerous advantages for businesses engaged in powder coating operations. Here are some of the key benefits:
1. Consistent Coating Quality
One of the primary benefits of using electric powder coating ovens is the consistent quality of the coatings achieved. The precise temperature control and uniform heating contribute to smooth, durable finishes, enhancing the overall quality of the final products.
2. Increased Productivity
Electric powder coating ovens are designed for efficiency, with quick warm-up times and minimal downtime. This increased productivity allows businesses to meet tight deadlines and improve their overall throughput.
3. Cost-Effective Operation
The energy-efficient design of EMS electric ovens translates to lower operational costs. By minimizing energy consumption and optimizing the curing process, businesses can reduce their overall expenses while maintaining high-quality outputs.
4. Flexibility in Production
Electric powder coating ovens offer flexibility in production capacity, allowing businesses to scale their operations as needed. Whether coating small batches or larger volumes, EMS ovens can be tailored to accommodate varying production demands.
5. Environmentally Friendly
Electric ovens produce fewer emissions compared to their diesel counterparts, making them a more environmentally friendly option for powder coating operations. By using electric heating, businesses can reduce their carbon footprint and contribute to sustainability efforts.
Why Choose EMS Powder Coating Equipment for Electric Powder Coating Ovens?
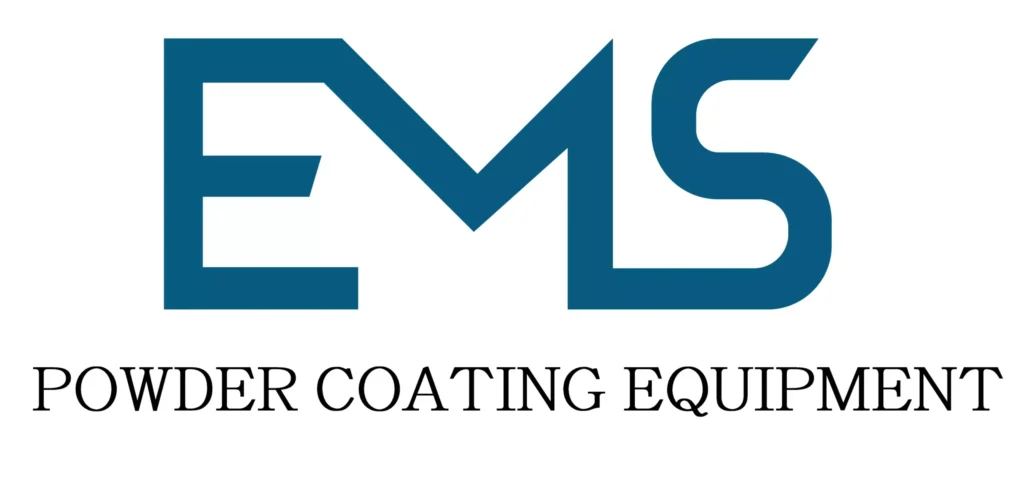
When it comes to selecting an electric powder coating oven, businesses need a manufacturer that offers quality, reliability, and superior performance. EMS Powder Coating Equipment stands out as the best choice for businesses looking to invest in electric ovens. Here’s why EMS is the preferred option:
1. Extensive Industry Experience
With years of experience in the powder coating industry, EMS understands the unique needs and challenges faced by businesses. Their expertise allows them to design electric powder coating ovens that cater to various applications and industries.
2. Innovative Technology and Design
EMS is committed to innovation, continually enhancing their products with the latest technology. Their electric powder coating ovens incorporate advanced heating systems, precise temperature controls, and durable construction, ensuring optimal performance and efficiency.
3. Comprehensive Support and Service
EMS provides exceptional customer support, from initial consultations and installations to ongoing maintenance and service. Their team of experts is dedicated to ensuring that your electric powder coating oven operates at peak efficiency.
4. Customizable Solutions for Unique Needs
Recognizing that each business has specific requirements, EMS offers customizable solutions for electric powder coating ovens. Whether you need specific heating capacities or additional features, EMS can tailor their ovens to suit your operational needs.
5. Proven Reliability and Quality
With a strong reputation for quality and customer satisfaction, EMS is a trusted name in the powder coating industry. Their electric powder coating ovens are built for reliability and long-term performance, making them an excellent investment for businesses.
Conclusion
An electric powder coating oven is an essential part of any powder coating operation, providing an efficient and effective method for curing powder coatings. With precise temperature control and uniform heating, electric ovens enhance productivity and ensure high-quality finishes.
EMS Powder Coating Equipment is the leading manufacturer of electric powder coating ovens, offering innovative solutions tailored to meet the diverse needs of various industries. Their commitment to quality, performance, and customer support makes EMS the best choice for businesses seeking reliable curing solutions.
By investing in EMS electric powder coating ovens, companies can improve their coating processes, achieve superior finishes, and reduce operational costs. With a focus on efficiency and innovation, EMS stands out as the premier manufacturer for businesses in need of top-tier powder coating ovens.
Gas Powder Coating Oven: Efficient and Versatile Curing Solutions
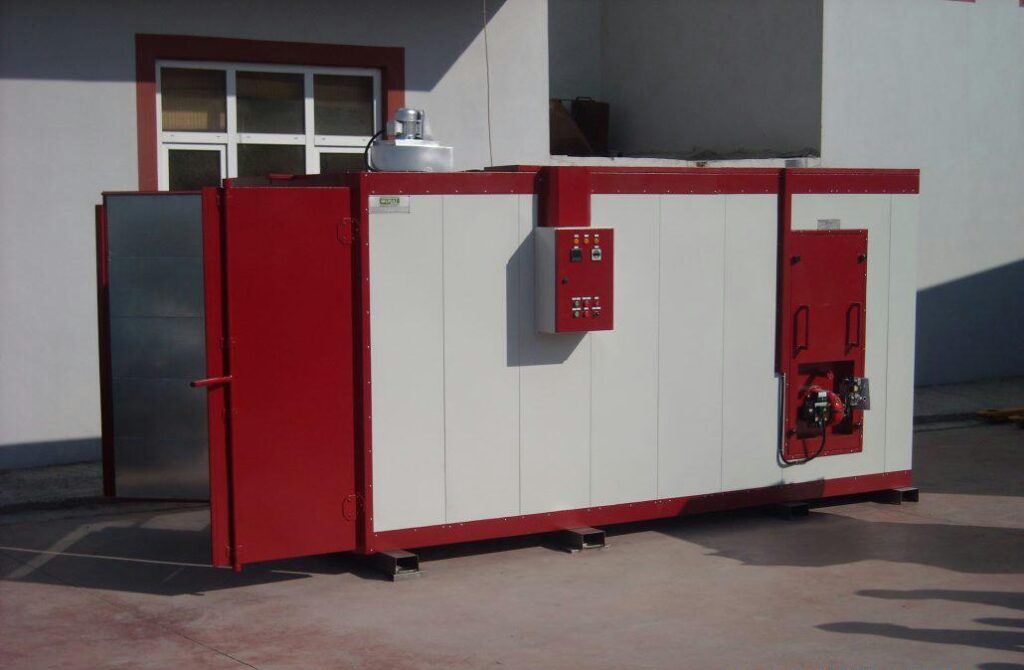
A gas powder coating oven is a vital component in the powder coating process, utilizing gas as a heat source to cure powder coatings applied to various substrates. Known for their efficiency and rapid heating capabilities, gas ovens provide consistent temperatures essential for achieving high-quality finishes.
Gas powder coating ovens are particularly advantageous in environments where electricity costs are high or where fast heat-up times are essential for productivity. These ovens are designed to deliver uniform heat distribution, ensuring that the powder coating cures evenly across the entire surface of the substrate.
EMS Powder Coating Equipment is a recognized leader in the manufacture of gas powder coating ovens, offering innovative solutions tailored to meet the diverse needs of industries. In this section, we will explore the operational mechanics, key features, and benefits of gas powder coating ovens while explaining why EMS is the top choice for businesses seeking reliable curing solutions.
What is a Gas Powder Coating Oven?
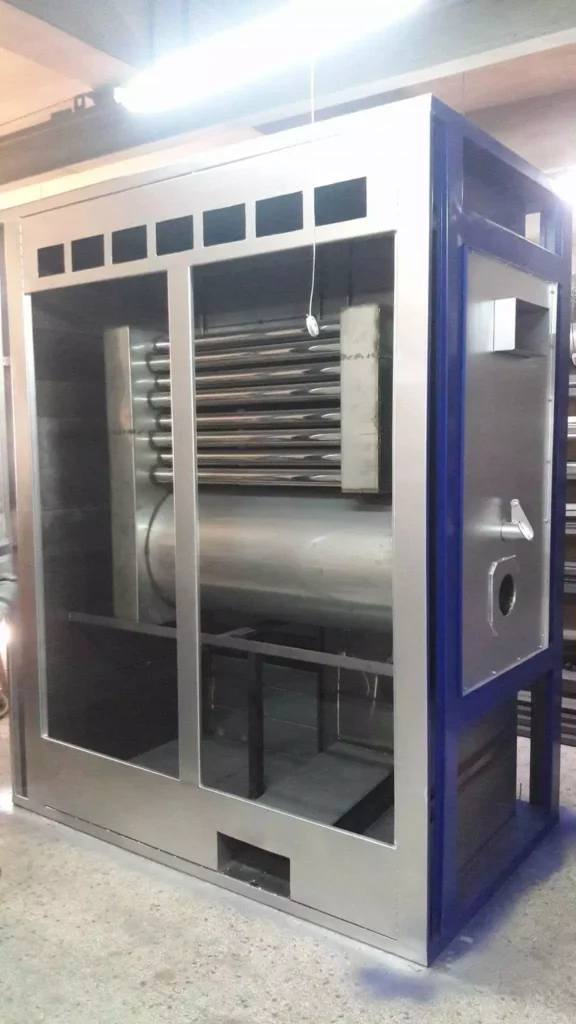
A gas powder coating oven is a specialized curing oven designed to heat and cure powder coatings using natural gas or propane as the primary energy source. This type of oven is essential for ensuring that the applied powder adheres properly to the substrate, resulting in a durable and aesthetically pleasing finish.
How Gas Powder Coating Ovens Operate
The operation of a gas powder coating oven begins after the powder coating has been applied to the substrate. The product is placed inside the oven, where it is subjected to controlled heating.
Gas burners located within the oven generate heat, which is distributed evenly throughout the oven chamber. This uniform heating is critical for preventing cold spots that can lead to uneven curing. Advanced insulation materials are used in the construction of gas ovens to minimize heat loss, ensuring efficient operation.
The gas powder coating ovens manufactured by EMS Powder Coating Equipment feature sophisticated temperature control systems, allowing operators to set and monitor internal temperatures accurately. This precision ensures that the powder coating cures optimally, producing a smooth, durable finish.
Key Features of Gas Powder Coating Ovens
Gas powder coating ovens are equipped with various features that enhance their performance and efficiency. Here are some key features that make EMS ovens the preferred choice for businesses:
1. Rapid Heat-Up Times
One of the standout benefits of gas powder coating ovens is their rapid heat-up times. EMS ovens are designed to reach optimal curing temperatures quickly, reducing downtime and improving overall productivity in the coating process.
2. Consistent Temperature Control
EMS gas ovens are equipped with advanced temperature control systems that provide precise monitoring and adjustments. This consistent temperature control is crucial for achieving high-quality finishes and preventing defects in the coating.
3. Energy Efficiency
Gas powder coating ovens are often more energy-efficient than electric counterparts, especially in regions with high electricity costs. EMS ovens are designed to optimize fuel consumption while delivering superior heating performance.
4. Durable Construction
Built with high-quality materials, EMS gas powder coating ovens are designed for long-lasting performance and durability. Their robust construction ensures minimal maintenance and reliable operation in demanding industrial environments.
5. User-Friendly Interface
EMS ovens feature intuitive controls that allow operators to easily set and monitor heating parameters. This user-friendly interface streamlines the coating process, making it easier for staff to achieve consistent results.
6. Safety Features
Safety is a top priority in the design of gas powder coating ovens. EMS ovens are equipped with various safety features, including flame detection systems, emergency shut-off valves, and proper ventilation to ensure the safety of operators.
Benefits of Using Gas Powder Coating Ovens
Investing in a gas powder coating oven provides numerous advantages for businesses involved in powder coating operations. Here are some key benefits:
1. Enhanced Coating Quality
Gas powder coating ovens deliver consistent and uniform heat, ensuring that powder coatings cure evenly. This enhances the quality of the final product, resulting in smooth and durable finishes.
2. Increased Production Efficiency
The rapid heat-up times of gas ovens enable businesses to reduce downtime between batches. This increased efficiency leads to higher productivity, allowing companies to meet tighter production deadlines.
3. Cost-Effective Operation
Gas ovens often result in lower operational costs, particularly in areas where gas prices are competitive. The efficient use of fuel contributes to overall cost savings for businesses.
4. Flexibility for Various Applications
Gas powder coating ovens are versatile and can accommodate a wide range of substrates and coating processes. This flexibility allows businesses to adapt to changing production needs and diversify their offerings.
5. Environmentally Friendly Options
Modern gas ovens are designed to minimize emissions, making them an environmentally friendly option for powder coating operations. By utilizing efficient combustion systems, EMS ovens reduce their carbon footprint while maintaining high performance.
Why Choose EMS Powder Coating Equipment for Gas Powder Coating Ovens?
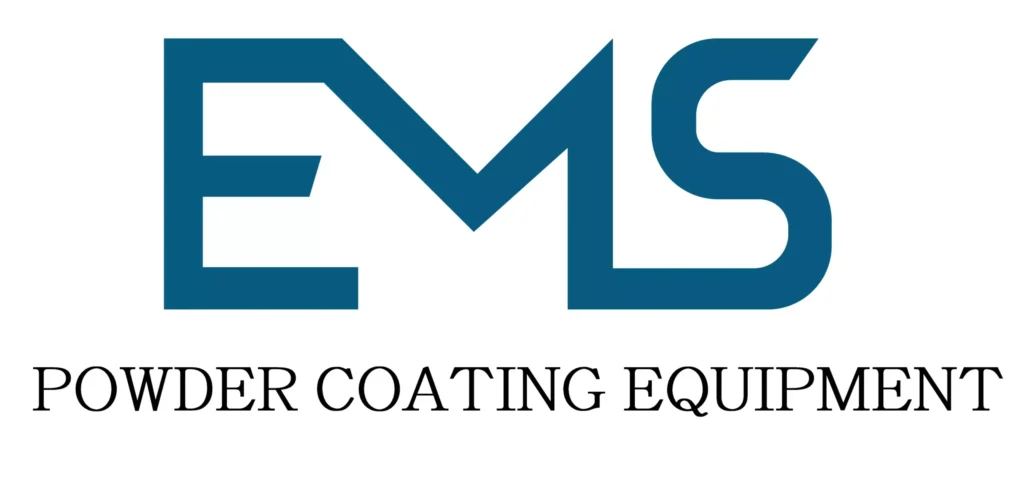
When selecting a gas powder coating oven, businesses need a manufacturer that offers reliability, quality, and innovative solutions. EMS Powder Coating Equipment stands out as the best choice for businesses looking to invest in gas ovens. Here’s why EMS is the preferred option:
1. Extensive Industry Experience
With years of experience in the powder coating industry, EMS understands the unique requirements of various applications. Their expertise enables them to design gas powder coating ovens that cater to diverse industries and operational needs.
2. Innovative Design and Technology
EMS is committed to innovation, continually enhancing their products with the latest technology. Their gas powder coating ovens incorporate advanced heating systems, precise temperature controls, and robust construction for optimal performance.
3. Exceptional Customer Support
From initial consultations to ongoing maintenance, EMS provides comprehensive customer support. Their team of experts is dedicated to ensuring that your gas powder coating oven operates at peak efficiency.
4. Custom Solutions for Unique Needs
Recognizing that every business has specific requirements, EMS offers customizable solutions for gas powder coating ovens. Whether you need tailored heating capacities or additional features, EMS can design ovens to fit your operational needs.
5. Proven Reliability and Quality
With a strong reputation for delivering high-quality products, EMS is a trusted name in the powder coating industry. Their gas powder coating ovens are built for reliability and long-term performance, making them an excellent investment for businesses.
Conclusion
A gas powder coating oven is an essential component of any powder coating operation, providing efficient and effective heating solutions for curing coatings. With rapid heat-up times and precise temperature control, gas ovens enhance productivity and ensure high-quality finishes.
EMS Powder Coating Equipment is a leading manufacturer of gas powder coating ovens, offering innovative solutions tailored to meet the diverse needs of various industries. Their commitment to quality, performance, and customer support makes EMS the best choice for businesses seeking reliable curing solutions.
By investing in EMS gas powder coating ovens, companies can improve their coating processes, achieve superior finishes, and reduce operational costs. With a focus on efficiency and innovation, EMS stands out as the premier manufacturer for businesses in need of top-tier powder coating equipment.
Gas Powder Coating Oven: Efficiency and Performance in Coating Applications
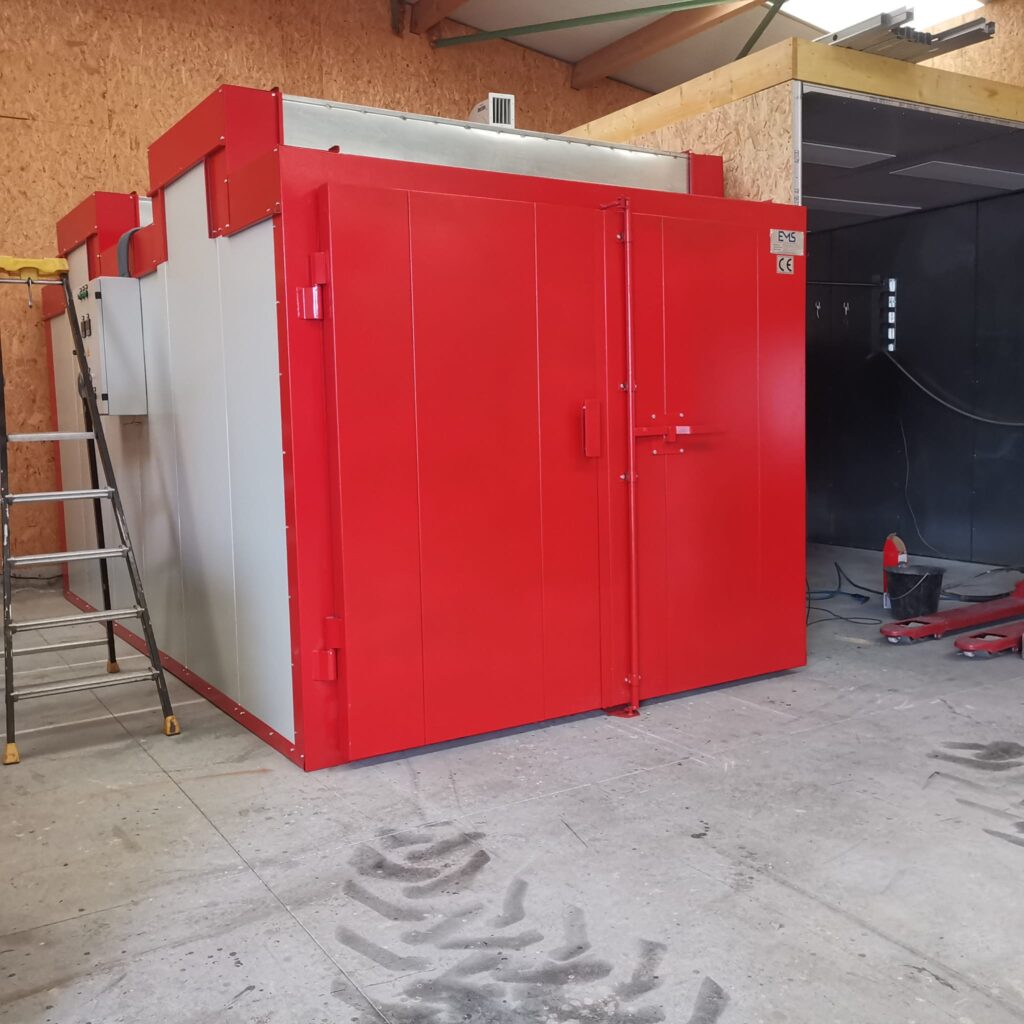
A gas powder coating oven is a vital component in the powder coating process, designed to cure powder coatings efficiently. Utilizing gas as a heating source, these ovens provide an optimal environment for achieving high-quality finishes on coated substrates.
Gas ovens are known for their rapid heating capabilities and energy efficiency, making them an excellent choice for businesses looking to enhance productivity while reducing operational costs. The precise temperature control ensures that the powder coating is cured uniformly, resulting in a durable and aesthetically pleasing finish.
EMS Powder Coating Equipment stands out as a leading manufacturer of gas powder coating ovens, offering advanced solutions tailored to meet the diverse needs of various industries. In this section, we will explore the operational principles, key features, and benefits of gas powder coating ovens, as well as explain why EMS is the preferred choice for businesses seeking reliable coating equipment.
What is a Gas Powder Coating Oven?
A gas powder coating oven is an industrial heating unit designed specifically for curing powder coatings. Unlike electric ovens, these ovens utilize gas as a heating source, providing rapid and efficient heating for the curing process.
How Gas Powder Coating Ovens Operate
The operation of a gas powder coating oven begins after the substrate has been coated with powder. The coated substrate is then placed inside the oven, where it is subjected to high temperatures that cause the powder to melt and flow.
The gas burners within the oven provide consistent and efficient heat, allowing for quick temperature adjustments and precise control. This efficiency results in reduced curing times and increased production throughput.
Gas powder coating ovens are equipped with advanced temperature control systems that ensure even heat distribution throughout the oven. This feature is crucial for achieving uniform curing of the powder, which enhances the durability and finish quality of the coated items.
EMS Powder Coating Equipment designs gas powder coating ovens with features that optimize the curing process, ensuring high-quality finishes and efficient operation. These ovens are adaptable to various production needs, making them suitable for businesses of all sizes.
Key Features of Gas Powder Coating Ovens
Gas powder coating ovens are equipped with a variety of features designed to enhance their functionality and efficiency. Here are some key features that make EMS ovens the preferred choice for businesses:
1. Rapid Heating Capabilities
One of the most significant advantages of gas powder coating ovens is their rapid heating capabilities. EMS ovens can quickly reach the desired curing temperature, reducing overall cycle times and increasing productivity.
2. Energy Efficiency
Gas ovens are typically more energy-efficient than electric ovens. EMS designs their gas powder coating ovens to minimize energy consumption, resulting in lower operational costs for businesses.
3. Precise Temperature Control
EMS gas powder coating ovens feature advanced temperature control systems that allow for precise adjustments. This level of control ensures that the curing process is consistent, leading to high-quality finishes on coated items.
4. Robust Construction
Constructed with high-quality materials, EMS gas powder coating ovens are designed for durability and long-term performance. Their robust construction ensures minimal maintenance and reliable operation in demanding industrial environments.
5. User-Friendly Control Panels
EMS ovens are equipped with intuitive control panels that make it easy for operators to set and monitor temperature and other critical parameters. This user-friendly design enhances the overall curing process and helps achieve consistent results.
6. Safety Features
Safety is a top priority in any industrial operation. EMS gas powder coating ovens come equipped with various safety features, including emergency shut-off systems and proper ventilation, to ensure a safe working environment.
Benefits of Using Gas Powder Coating Ovens
Investing in a gas powder coating oven offers numerous advantages for businesses engaged in powder coating operations. Here are some key benefits:
1. Enhanced Coating Quality
Gas powder coating ovens provide a consistent and controlled curing environment, significantly improving the quality of the applied coatings. Uniform heat distribution ensures that the powder cures evenly, resulting in a durable finish.
2. Increased Production Efficiency
With rapid heating capabilities, EMS gas powder coating ovens allow for shorter curing times, enabling businesses to increase their production throughput. This efficiency can be a critical factor in meeting tight deadlines and growing customer demands.
3. Cost Savings
The energy efficiency of gas ovens translates to significant cost savings over time. By reducing energy consumption and minimizing operational costs, businesses can allocate resources more effectively and improve their bottom line.
4. Versatility for Various Applications
EMS gas powder coating ovens are designed to accommodate a wide range of substrates and coating processes. This versatility allows businesses to adapt to changing production needs and diversify their service offerings across different industries.
5. Compliance with Safety and Environmental Standards
Gas powder coating ovens are designed to meet safety and environmental regulations, reducing emissions and maintaining a safe workspace. By investing in EMS ovens, businesses can ensure compliance with industry standards while promoting a healthier working environment.
Why Choose EMS Powder Coating Equipment for Gas Powder Coating Ovens?
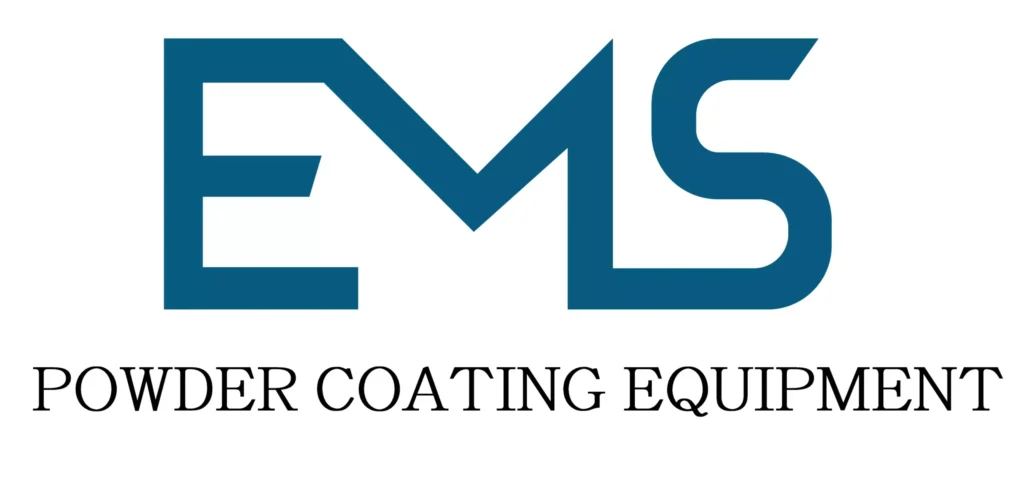
When selecting a gas powder coating oven, it is essential to choose a manufacturer known for quality, reliability, and innovative solutions. EMS Powder Coating Equipment stands out as the best choice for businesses looking to invest in gas ovens. Here’s why EMS is the preferred option:
1. Proven Industry Experience
With extensive experience in the powder coating industry, EMS understands the specific needs of various applications. Their expertise enables them to design gas powder coating ovens that meet the demands of different environments and production requirements.
2. Commitment to Innovation
EMS is dedicated to innovation, continually enhancing their products with the latest technology. Their gas powder coating ovens are designed for optimal performance, incorporating advanced temperature control and safety features.
3. Comprehensive Customer Support
From installation to ongoing maintenance, EMS provides exceptional customer support. Their team of experts is available to assist businesses in maximizing the performance of their gas powder coating ovens.
4. Customizable Solutions
Recognizing that each business has unique needs, EMS offers customizable solutions for gas powder coating ovens. Whether specific sizes, features, or configurations are required, EMS can tailor their products to meet operational requirements.
5. Trusted Quality and Reliability
With a strong reputation for delivering high-quality products, EMS is a trusted name in the powder coating industry. Their gas powder coating ovens are built for durability and long-term performance, making them an excellent investment for businesses.
Conclusion
A gas powder coating oven is a critical investment for any powder coating operation, providing an efficient and controlled environment for curing coatings. With rapid heating capabilities and precise temperature control, these ovens enhance coating quality and productivity.
EMS Powder Coating Equipment is a leading manufacturer of gas powder coating ovens, offering innovative solutions tailored to meet the diverse needs of various industries. Their commitment to quality, performance, and customer support makes EMS the best choice for businesses seeking reliable coating solutions.
By choosing EMS gas powder coating ovens, companies can improve their coating processes, achieve superior finishes, and reduce operational costs. With a focus on efficiency and innovation, EMS stands out as the premier manufacturer for businesses in need of top-tier powder coating equipment.
Gas Powder Coating Oven: Efficient Curing Solutions for Optimal Finishes
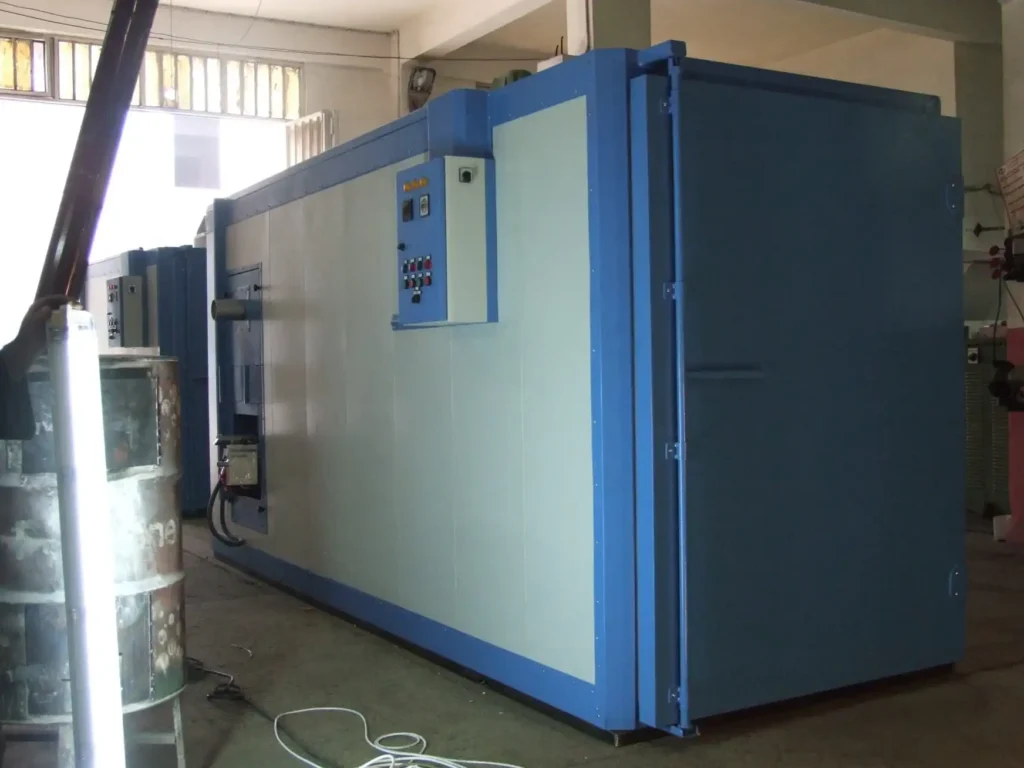
A gas powder coating oven is a crucial component in the powder coating process, designed specifically for curing powder-coated materials. Utilizing natural gas or propane, these ovens offer efficient heating solutions that ensure the even curing of powder coatings, resulting in durable and high-quality finishes.
The design of gas powder coating ovens focuses on energy efficiency and optimal temperature control. By providing a stable and controlled environment, these ovens facilitate the proper melting and adhesion of powder coatings to substrates, enhancing the overall coating quality.
EMS Powder Coating Equipment stands out as a leader in the manufacturing of gas powder coating ovens, offering advanced solutions tailored to meet the specific needs of various industries. In this section, we will delve into the operational principles, key features, and benefits of gas powder coating ovens, while also discussing why EMS is the preferred choice for businesses seeking reliable coating equipment.
What is a Gas Powder Coating Oven?
A gas powder coating oven is an industrial oven specifically designed to cure powder coatings applied to metal substrates. By utilizing gas as a heat source, these ovens provide rapid and efficient curing, ensuring a high-quality finish.
How Gas Powder Coating Ovens Operate
The operation of a gas powder coating oven begins after the substrate has been coated with powder. Once the application is complete, the substrate is placed inside the oven, where controlled temperatures are maintained.
Gas burners generate heat, which is evenly distributed throughout the oven. This uniform heat application ensures that the powder melts, flows, and adheres properly to the substrate. Curing times and temperatures can be adjusted to suit different types of powder coatings and substrate materials.
EMS Powder Coating Equipment designs gas powder coating ovens with features that optimize the curing process, ensuring that businesses achieve consistent, high-quality finishes across a variety of applications.
Key Features of Gas Powder Coating Ovens
Gas powder coating ovens are equipped with numerous features designed to enhance their performance and efficiency. Here are some standout features that make EMS ovens the preferred choice for businesses:
1. Energy Efficiency
EMS gas powder coating ovens are designed for optimal energy efficiency, utilizing advanced burner technology to minimize gas consumption while maximizing heat output. This design helps reduce operational costs without compromising performance.
2. Precise Temperature Control
With advanced temperature control systems, EMS ovens ensure that the required curing temperatures are maintained consistently throughout the process. This precise control is essential for achieving high-quality finishes.
3. Quick Heating Capability
Gas ovens have the advantage of rapid heating capabilities, significantly reducing preheating times. This feature enhances productivity by allowing for faster turnaround on coating jobs.
4. Uniform Heat Distribution
The design of EMS gas powder coating ovens promotes uniform heat distribution, preventing hot spots and ensuring that all areas of the substrate are cured evenly. This uniformity is crucial for achieving a consistent finish.
5. Safety Features
Safety is paramount in any industrial operation. EMS ovens come equipped with safety features such as flame monitoring systems, emergency shut-off valves, and proper ventilation to ensure a safe working environment for operators.
6. Customizable Sizes and Configurations
Recognizing that different businesses have varying needs, EMS offers customizable sizes and configurations for their gas powder coating ovens. This flexibility allows businesses to choose the right oven to fit their production capacities.
Benefits of Using Gas Powder Coating Ovens
Investing in a gas powder coating oven provides numerous advantages for businesses engaged in powder coating operations. Here are some key benefits:
1. Enhanced Coating Quality
Gas powder coating ovens promote optimal curing conditions, leading to high-quality finishes. The even application of heat ensures that the powder melts and adheres properly, resulting in durable coatings.
2. Increased Efficiency
The rapid heating capabilities of gas ovens reduce preheating and curing times, allowing for quicker production cycles. This increased efficiency can significantly enhance overall productivity.
3. Cost-Effective Operations
With their energy-efficient designs, gas powder coating ovens can reduce fuel costs compared to electric ovens. Additionally, the improved curing processes result in less rework and waste, contributing to lower operational costs.
4. Versatility for Different Applications
EMS gas powder coating ovens are versatile and can accommodate a wide range of powder coatings and substrate materials. This adaptability allows businesses to diversify their service offerings and meet various customer demands.
5. Compliance with Safety Standards
EMS gas powder coating ovens are designed to meet industry safety regulations, ensuring a safe working environment. Their robust safety features protect both operators and the surrounding environment.
Why Choose EMS Powder Coating Equipment for Gas Powder Coating Ovens?
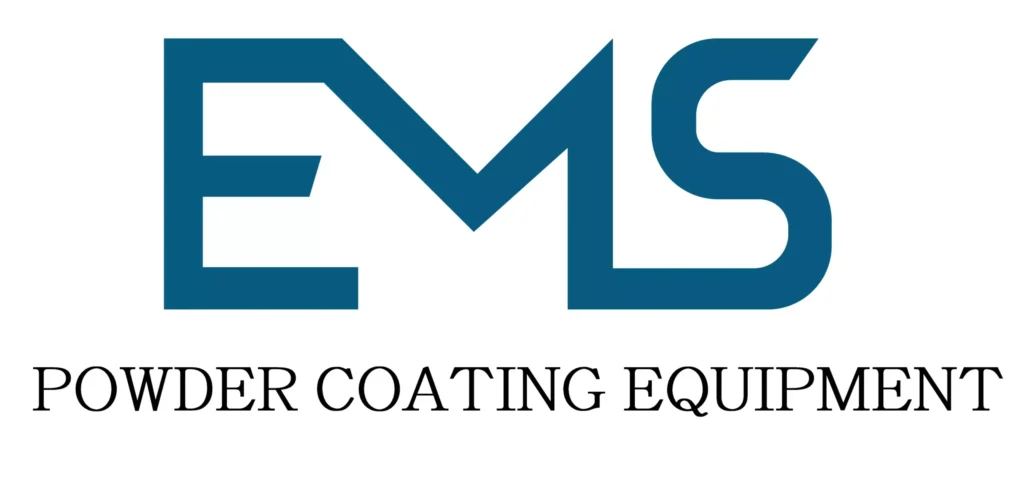
Selecting a gas powder coating oven requires careful consideration of the manufacturer’s reputation for quality and reliability. EMS Powder Coating Equipment is the top choice for businesses looking to invest in gas powder coating ovens. Here’s why EMS stands out:
1. Industry Expertise
With years of experience in the powder coating industry, EMS understands the unique requirements of various applications. Their expertise allows them to design gas powder coating ovens that are tailored to meet diverse production environments.
2. Commitment to Innovation
EMS is dedicated to continual innovation, integrating the latest technologies into their products. Their gas powder coating ovens are designed for optimal performance, featuring advanced controls and safety mechanisms.
3. Exceptional Customer Support
From installation to ongoing maintenance, EMS provides comprehensive customer support. Their team of experts is committed to helping businesses maximize the performance of their gas powder coating ovens.
4. Custom Solutions
Recognizing that every business has unique needs, EMS offers customizable solutions for gas powder coating ovens. This flexibility ensures that businesses can select the right features and configurations for their operations.
5. Trusted Quality and Reliability
With a strong reputation for delivering high-quality products, EMS is a trusted name in the powder coating industry. Their gas powder coating ovens are built for durability and long-term performance, making them an excellent investment for businesses.
Conclusion
A gas powder coating oven is a vital investment for any powder coating operation, providing efficient and controlled curing of powder coatings. With their advanced features and energy-efficient designs, these ovens enhance coating quality and productivity.
EMS Powder Coating Equipment is a leading manufacturer of gas powder coating ovens, offering innovative solutions tailored to meet the diverse needs of various industries. Their commitment to quality, performance, and customer support makes EMS the best choice for businesses seeking reliable coating equipment.
By choosing EMS gas powder coating ovens, companies can improve their coating processes, achieve superior finishes, and reduce operational costs. With a focus on efficiency and innovation, EMS stands out as the premier manufacturer for businesses in need of top-tier powder coating equipment.
Gas Powder Coating Oven: Efficiency and Precision in Coating Applications
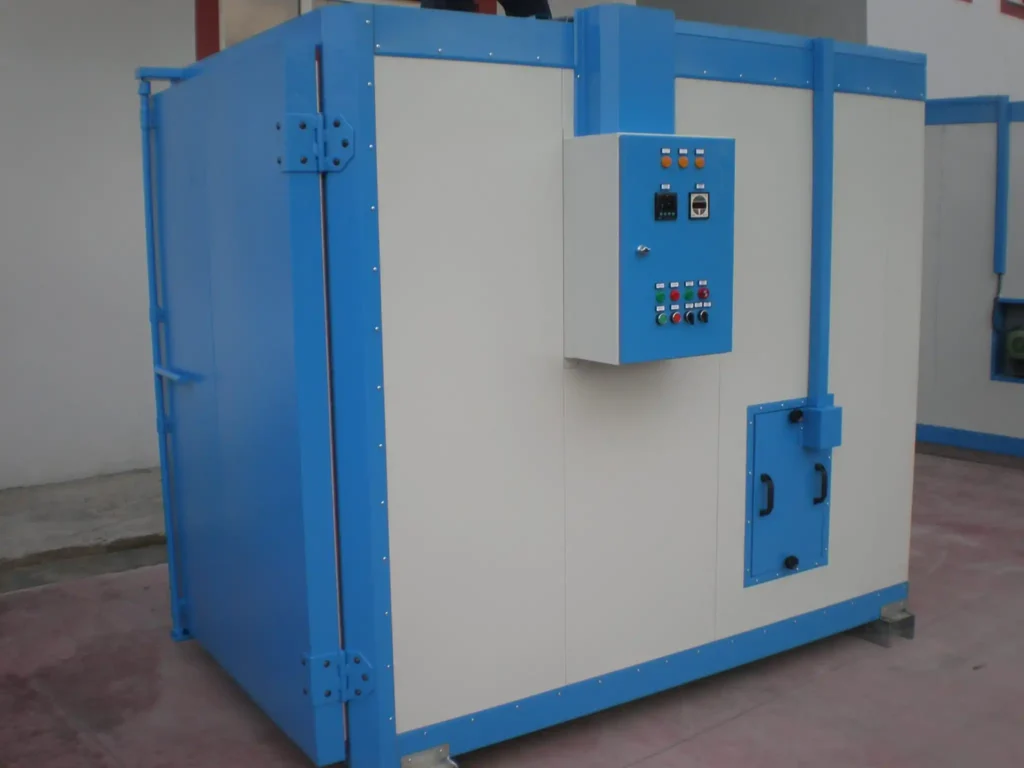
A gas powder coating oven is an essential component in the powder coating process, providing the necessary heat to cure powder coatings applied to various substrates. The curing process is crucial for achieving a durable, high-quality finish that adheres effectively to the surface.
These ovens are specifically designed to deliver uniform heat distribution, ensuring that the powder coating cures evenly and efficiently. With advancements in technology, modern gas powder coating ovens also incorporate features that enhance energy efficiency and operational safety.
EMS Powder Coating Equipment is recognized as a leader in the manufacturing of gas powder coating ovens, offering state-of-the-art solutions tailored to meet the diverse needs of various industries. In this section, we will delve into the operational principles, key features, and benefits of gas powder coating ovens, while also discussing why EMS is the preferred choice for businesses seeking reliable and efficient coating solutions.
What is a Gas Powder Coating Oven?
A gas powder coating oven is a specialized curing chamber used in the powder coating process. It employs gas as the primary heat source to cure the powder coatings applied to metal and other substrates.
How Gas Powder Coating Ovens Operate
The operation of a gas powder coating oven begins after the powder has been applied to the substrate in a spray booth. Once the substrate is ready, it is transferred to the oven, where precise heating elements deliver the required temperature for curing.
The oven’s design ensures uniform heat distribution, allowing the powder coating to melt and flow, ultimately bonding to the substrate. The curing process is crucial, as it transforms the powder into a hard, protective finish that is both aesthetically pleasing and durable.
EMS Powder Coating Equipment designs gas powder coating ovens with advanced features that optimize curing efficiency and performance, ensuring businesses achieve consistent, high-quality finishes across various applications.
Key Features of Gas Powder Coating Ovens
Gas powder coating ovens are equipped with several features that enhance their performance and efficiency. Here are some standout features that make EMS ovens the preferred choice for businesses:
1. Uniform Heat Distribution
EMS gas powder coating ovens are engineered to provide uniform heat distribution throughout the curing chamber. This feature ensures that every part of the substrate receives the same level of heat, resulting in even curing and high-quality finishes.
2. Energy Efficiency
Modern EMS gas ovens are designed for energy efficiency, utilizing advanced insulation and burner technology. This allows businesses to reduce energy consumption while maintaining optimal curing temperatures, leading to cost savings over time.
3. User-Friendly Controls
The intuitive control systems in EMS gas powder coating ovens allow operators to easily set and monitor temperatures and curing times. This user-friendly interface streamlines operations and enhances overall productivity.
4. Safety Features
Safety is paramount in any coating operation. EMS gas powder coating ovens come equipped with essential safety features, including flame safety devices, emergency shut-off systems, and proper ventilation, ensuring a safe working environment.
5. Customizable Configurations
Understanding that different businesses have unique requirements, EMS offers customizable configurations for their gas powder coating ovens. Whether for small operations or large-scale production, EMS can tailor solutions to meet specific needs.
6. Durable Construction
Built with high-quality materials, EMS gas powder coating ovens are designed for longevity and reliability. Their robust construction ensures consistent performance even in demanding production environments.
Benefits of Using Gas Powder Coating Ovens
Investing in a gas powder coating oven provides numerous advantages for businesses engaged in powder coating operations. Here are some key benefits:
1. Consistent Coating Quality
The precise temperature control and uniform heat distribution in gas powder coating ovens lead to consistent curing results. This ensures that the final finish meets the highest quality standards.
2. Faster Curing Times
Gas powder coating ovens typically offer faster curing times compared to electric ovens, enhancing production efficiency. This speed allows businesses to complete more jobs in less time, increasing overall output.
3. Cost Efficiency
By utilizing gas as an energy source, businesses can benefit from lower operational costs compared to electric ovens. The energy-efficient design of EMS ovens further enhances this cost-effectiveness.
4. Versatility for Diverse Applications
EMS gas powder coating ovens are versatile enough to handle a wide range of substrates and coating types, allowing businesses to expand their offerings and cater to different market demands.
5. Compliance with Environmental Regulations
Gas powder coating ovens are designed to meet industry safety and environmental regulations, ensuring a compliant operation. By investing in EMS ovens, businesses can promote a healthier working environment while adhering to necessary standards.
Why Choose EMS Powder Coating Equipment for Gas Powder Coating Ovens?
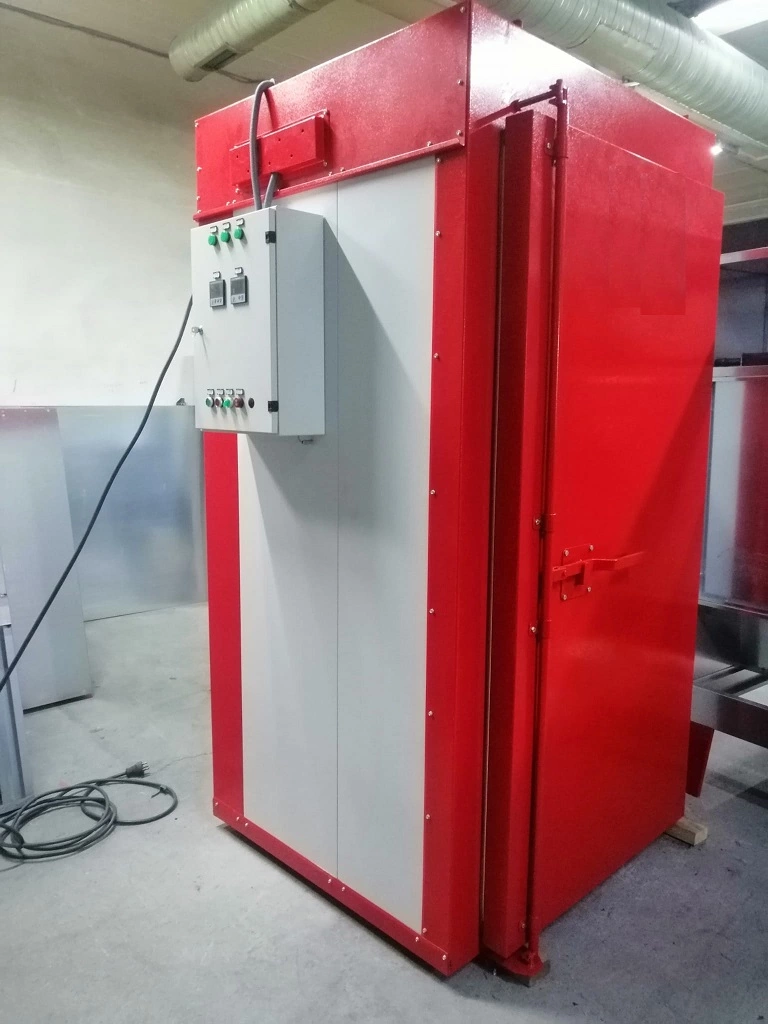
When selecting a gas powder coating oven, it is essential to choose a manufacturer with a reputation for quality and innovation. EMS Powder Coating Equipment stands out as the top choice for businesses looking to invest in gas powder coating ovens. Here’s why EMS is the preferred option:
1. Proven Expertise
With years of experience in the powder coating industry, EMS understands the unique needs of various applications. Their knowledge allows them to design gas powder coating ovens that are tailored to diverse production environments.
2. Innovative Solutions
EMS is committed to continuous innovation, incorporating the latest technology into their products. Their gas powder coating ovens are designed for optimal performance, featuring advanced temperature control and safety systems.
3. Comprehensive Support
From installation to ongoing maintenance, EMS provides exceptional customer support. Their team of experts is dedicated to helping businesses maximize the performance of their gas powder coating ovens.
4. Customizable Options
Recognizing that every business has unique requirements, EMS offers customizable options for gas powder coating ovens, allowing businesses to select features and configurations that best suit their operational needs.
5. Trusted Reliability
With a strong reputation for delivering high-quality products, EMS is a trusted name in the powder coating industry. Their ovens are designed for durability and long-term performance, making them an excellent investment for businesses.
A powder coating oven is a specialized piece of equipment used to cure powder coating applied to metal or other surfaces. The process involves electrostatically applying a dry powder—typically a thermoset polymer or thermoplastic—to a part, then heating it in the oven to melt and form a durable, protective finish. These ovens are designed to maintain consistent temperatures, usually between 350°F and 450°F (175°C to 232°C), depending on the powder type and curing requirements, ensuring a smooth, uniform coating that’s tougher than conventional paint.
They come in various forms, like batch ovens for smaller or custom jobs and conveyorized ovens for high-volume production. Key features often include thick insulation (e.g., 6-inch walls with mineral wool or ceramic fiber), precise temperature controls, and efficient airflow to prevent powder blow-off and ensure even curing. You’ll find electric or gas-powered options—electric tends to be simpler and cheaper upfront, while gas can be more cost-effective for larger operations over time due to lower operating costs.
For a practical example, a small electric oven (say, 4’x4’x6’) might suit hobbyists coating wheels or motorcycle frames, while industrial setups could handle parts up to 120 feet long. Costs vary widely—a DIY build might run $1,000-$1,400, while commercial units start around $5,000 and climb into the tens of thousands for custom configurations.
A powder coating oven is an essential tool in the finishing industry, designed to transform a dry, electrostatically applied powder into a hard, durable coating that adheres seamlessly to a variety of surfaces—most commonly metals like steel, aluminum, or galvanized alloys, though some non-metallic substrates like MDF can also be coated with specialized powders. The process starts outside the oven: a part is cleaned, often via sandblasting or chemical pretreatment, to remove rust, oils, or contaminants, ensuring the powder bonds properly. Then, using a spray gun, the powder—typically a mix of finely ground resin, pigment, and curing agents—is given an electrostatic charge, causing it to cling to the grounded workpiece. Once coated, the part enters the oven, where heat triggers a chemical reaction (for thermoset powders) or simply melts the material (for thermoplastics), forming a tough, uniform skin that resists corrosion, chipping, and UV damage far better than traditional liquid paints.
The ovens themselves are engineered for precision and efficiency. Temperatures typically range from 350°F to 450°F (175°C to 232°C), though some low-cure powders work as low as 250°F (121°C) for heat-sensitive materials. Curing times vary—10 to 30 minutes is standard, depending on the powder’s spec sheet and the part’s mass and thickness. The design of the oven plays a huge role in the outcome. Batch ovens, for instance, are box-like units with doors, perfect for small shops or custom jobs like coating car rims, motorcycle frames, or patio furniture. They’re often compact—think 4’x4’x6’ for a garage setup—but can scale up to 10’x10’x20’ for bigger projects. Conveyorized ovens, on the other hand, are the workhorses of industrial lines, moving parts through on racks or overhead tracks, sometimes stretching 100 feet or more to handle massive volumes, like automotive parts or architectural beams.
Construction-wise, these ovens are built to trap heat and distribute it evenly. Walls are typically 6 to 8 inches thick, packed with high-grade insulation—mineral wool, fiberglass, or ceramic fiber—to minimize energy loss. Heating elements or burners (electric coils, infrared panels, or gas-fired systems) kick things off, while fans or ductwork ensure hot air circulates consistently, preventing cold spots that could lead to uneven curing or defects like orange peel texture. Electric ovens dominate smaller setups due to their simplicity and lower upfront cost—think $1,500 for a basic unit—while gas ovens, using natural gas or propane, shine in larger operations where fuel efficiency slashes long-term expenses. Some high-end models even offer programmable controllers, letting you ramp up heat gradually or hold specific temps for tricky powders.
For a real-world sense, consider a DIY enthusiast rigging up an old electric oven with extra insulation and a PID controller for under $1,000—good enough for bike frames or toolboxes. Compare that to a commercial batch oven, like a $10,000 Wisconsin Oven model with 8-foot ceilings and dual-zone heating, or a full-on $50,000+ conveyor system from Gema or Nordson, built for coating hundreds of parts daily. The powder itself matters too—polyester powders are popular for outdoor durability, while epoxy excels indoors for chemical resistance. Cure schedules are precise; a typical polyester might need 400°F for 20 minutes post-flow-out, meaning the oven’s accuracy is non-negotiable.
Safety’s a factor as well—powder’s flammable when airborne, so good ventilation and grounding are critical to avoid sparks or dust explosions. Maintenance is straightforward: clean filters, check thermocouples, and watch for wear on seals. If you’re sizing one up, think about part dimensions, throughput, and energy costs. A small shop might run a 6 kW electric oven for $50 a month, while a gas-fired beast could sip $200 worth of propane for heavier use.
Powder coating ovens are a fascinating blend of engineering and chemistry, bridging the gap between raw materials and a finished product that’s both functional and aesthetically sharp. The process they enable—powder coating—has surged in popularity since the 1960s, when it emerged as a greener alternative to solvent-heavy liquid paints, cutting down on volatile organic compounds (VOCs) and waste. Today, it’s a go-to for industries ranging from automotive to aerospace, furniture to heavy machinery, thanks to its versatility and the sheer toughness of the end result. At the heart of it all is the oven, which doesn’t just heat things up—it orchestrates a transformation that’s as much about precision as it is about durability.
Let’s break it down further. Once a part’s coated with powder—say, a steel bracket or an aluminum extrusion—it’s the oven’s job to take that loose, chalky layer and turn it into something rock-solid. For thermoset powders, like polyester or epoxy, heat triggers cross-linking, a chemical reaction where polymer chains bond into a tight, irreversible matrix. Thermoplastics, like nylon or polyethylene, skip the chemistry and simply melt into a cohesive film, cooling back into shape. Either way, the oven has to hit the sweet spot: too cool, and the powder won’t fully cure, leaving a brittle or sticky mess; too hot, and you risk burning it, yellowing the finish, or warping the part. Most powders come with a data sheet spelling out the cure window—say, 375°F for 15 minutes at temperature (not counting ramp-up)—and the oven’s got to nail it, every time.
Design-wise, these ovens are a study in heat management. Take a typical batch oven: you’ve got a steel shell, double-walled with 6 to 10 inches of insulation—think Rockwool or Kaowool—rated to handle 500°F+ without breaking a sweat. Inside, heating elements (electric resistance coils or gas burners) crank up the temp, while a blower system—often a squirrel-cage fan—pushes air through ducts or baffles to keep it even. Airflow’s a big deal; if it’s too weak, you get hot spots, and if it’s too aggressive, it can blow uncured powder off the part before it melts. High-end ovens might use infrared panels for faster, targeted heating, especially on complex shapes with nooks and crannies. Conveyor ovens up the ante, with zones—preheat, soak, and cool-down—linked by tracks or belts, churning out parts like an assembly-line beast. A 60-foot conveyor might process 500 car doors a day, each hanging from hooks, curing as it glides through.
Powering these ovens is a choice between electric and gas, and it’s a trade-off. Electric’s plug-and-play—hook it to a 240V line, and you’re off. A 6’x6’x8’ unit might pull 12 kW, costing $0.15 per kWh in the U.S., or about $1.80 an hour to run. Gas ovens—natural gas or propane—need venting and fuel lines, bumping up installation costs (maybe $2,000 extra), but they’re cheaper per BTU over time. A 100,000 BTU gas oven might burn $0.50 of fuel hourly, depending on local rates. For small shops, electric’s king; for factories, gas often wins. Hybrid systems exist too, blending infrared with convection for speed and efficiency, though they’re pricier—think $20,000 versus $8,000 for a basic setup.
Practical examples paint the picture. A hot-rodder might convert an old kitchen oven, adding a $100 controller and $200 in insulation, to coat valve covers for $5 a pop in electricity. A mid-tier shop could grab a Reliant 8’x8’x10’ batch oven for $12,000, curing 50 bike frames a week. Big players—like a trailer manufacturer—might drop $75,000 on a custom Gema conveyor system, powder-coating 200 chassis daily, with reclaim booths to recycle overspray and slash powder costs by 30%. Powder choice ties in too: a UV-resistant polyester for outdoor grills (Sherwin-Williams Powdura, $10/lb) versus a high-gloss epoxy for indoor toolboxes ($8/lb). Each needs its own cure profile, so the oven’s versatility matters.
Beyond the tech, there’s a craft to it. Preheat the part to 200°F to outgas trapped air, or you’ll get pinholes. Hang parts vertically to avoid sagging. Clean the oven floor—stray powder can ignite. Safety’s non-negotiable: ground everything to dodge static sparks, and vent fumes to keep air quality sane. Maintenance? Swap filters quarterly, calibrate thermocouples yearly, and watch for burner clogs or coil burnout. Costs scale with use—a hobbyist might spend $100 yearly, a factory $5,000.
Small Powder Coating Oven
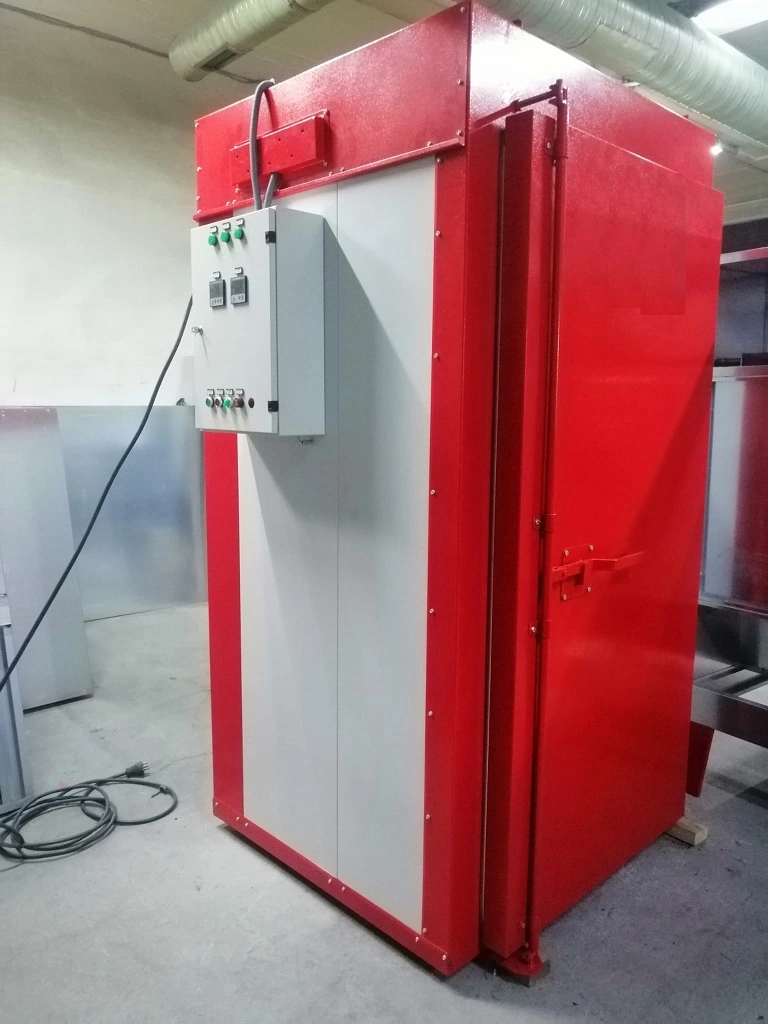
A small powder coating oven is a compact, practical solution for hobbyists, small businesses, or anyone looking to coat modest-sized parts—like car wheels, motorcycle frames, bicycle components, or even custom metal crafts—without needing the footprint or expense of industrial-scale equipment. These ovens typically range from about 2’x2’x2’ up to 6’x6’x8’ internally, offering enough space for single or small batches of items while fitting into a garage, workshop, or shed. They’re designed to cure powder coating—turning that dry, electrostatically applied powder into a tough, glossy finish—using controlled heat, usually between 350°F and 450°F (175°C to 232°C), for 10 to 30 minutes per cycle, depending on the powder and part.
Construction-wise, small ovens keep it simple but effective. You’re looking at a steel box—often 14- or 16-gauge—with 4 to 6 inches of insulation, like fiberglass or mineral wool, to hold heat and cut energy waste. Most are electric, powered by standard 240V household circuits, drawing 6 to 12 kW depending on size. Heating comes from coiled elements mounted on the walls or floor, paired with a fan—sometimes a basic centrifugal blower—to circulate hot air evenly. Temperature control is key; entry-level models might use a manual thermostat, while better ones sport digital PID controllers (around $50-$150 extra) to lock in precise temps, avoiding under- or over-curing. A 4’x4’x6’ oven, for instance, might weigh 300-500 lbs, sit on legs or casters, and feature a single swing door or double doors for easy access.
For a real-world example, picture a DIY setup: an old electric oven (like a $50 Craigslist find) retrofitted with $200 in insulation and a $100 PID controller. Total cost? Under $400, and it’ll cure a set of 17-inch rims at 400°F for 20 minutes, sipping maybe $1 in electricity per run (at $0.15/kWh). Compare that to a purpose-built small oven, like a $1,500 HotCoat from Eastwood—3’x3’x4’, 8 kW, with a prewired control box and racks. It’s plug-and-play, fits in a corner, and handles parts up to 50 lbs comfortably. For a step up, a $3,000 Reliant or Dura-Bake 4’x4’x6’ model offers thicker walls, better airflow, and maybe 10 kW of juice—perfect for a side hustle coating 5-10 pieces a day.
Operation’s straightforward but has quirks. You’d prep your part—blast it clean, hang it on hooks or a rack (wire or steel, $20-$50)—then spray it with powder (say, $10/lb polyester from Prismatic Powders). Roll it into the oven on a cart, set 375°F, and wait. The powder melts in 5-10 minutes, then cures fully after 15-20 total. Airflow matters—too little, and you get uneven finishes; too much, and powder blows off before it sets. A small fan (500-1000 CFM) usually does the trick. Outgassing’s another gotcha: preheat aluminum parts to 200°F first, or trapped gases bubble through the finish.
Cost-wise, small ovens are approachable. DIY builds hit $500-$1,000, factoring in materials like sheet metal ($200), elements ($100), and wiring. Off-the-shelf units start at $1,200-$2,000 for basic models, climbing to $5,000 for semi-pro rigs with extras like timers or dual elements. Running costs? A 6 kW oven at 400°F for an hour burns about $0.90-$1.20, depending on local rates. Powder’s cheap—$10 coats a few wheels—and overspray’s reusable with a $200 reclaim booth. Maintenance is light: clean the interior, check elements yearly, swap a $20 filter now and then.
They’re not perfect, though. Size limits you—forget coating a full car frame—and heat-up takes 20-40 minutes from cold. Electric bills creep up if you’re batching all day. Still, for a small shop or enthusiast, it’s a sweet spot: affordable, manageable, and capable of pro-grade finishes.
A small powder coating oven is a game-changer for anyone dipping their toes into powder coating or running a low-volume operation, offering a balance of affordability, compactness, and performance that’s tough to beat. These units are tailored for parts that don’t demand sprawling industrial setups—think alloy wheels, valve covers, metal signs, or even custom knife blades. Typically, they max out at around 6’x6’x8’ internally, though most hover in the 3’x3’x4’ to 4’x4’x6’ range, making them ideal for a garage corner or a small workshop with standard 8-foot ceilings. They’re built to do one thing well: heat powder-coated parts to 350°F-450°F (175°C-232°C), melting and curing the powder into a hard, vibrant finish that laughs off rust, scratches, and UV rays better than any spray paint.
Let’s dig into the nuts and bolts. A small oven’s frame is usually welded steel—14-gauge for lighter models, 12-gauge for sturdier ones—wrapped in a double-wall design stuffed with 4 to 6 inches of insulation. That’s often fiberglass batting or mineral wool, rated for 600°F+, keeping heat in and your electric bill sane. Heating’s almost always electric—gas is rare at this scale due to venting hassles—using coiled nichrome elements (like giant toaster wires) pulling 6 to 12 kW on a 240V, 30-50 amp circuit. A 4’x4’x4’ oven might have two 4 kW elements, one top, one bottom, kicking out 36,000 BTUs total. Air moves via a small blower—500-1000 CFM—pushing heat through simple ducts or an open chamber. Cheap models skimp with a basic dial thermostat ($20), but spend $100-$200 more, and you get a PID controller with a thermocouple, holding temps within 5°F for flawless cures.
Take a practical case: a 3’x3’x4’ Eastwood HotCoat oven, $1,500 new, weighs 250 lbs, rolls on casters, and fits through a standard door. Plug it into a 240V outlet (dryer-style, 30 amps), and it hits 400°F in 30 minutes, drawing 8 kW—about $1.20/hour at $0.15/kWh. Load it with a pair of 18-inch rims, hung on $10 wire hooks, coated in $8 worth of gloss black polyester powder. Set it to 375°F, wait 20 minutes after flow-out (when the powder turns glossy), and you’ve got a mirror finish that’ll outlast the car. DIYers go cheaper—an old 30-inch kitchen oven, gutted and relined with $150 in Rockwool, plus a $90 Inkbird PID, totals $300-$500. It’ll cure a motorcycle tank for $0.80 a pop, though heat-up’s slower and capacity’s tight.
The workflow’s simple but finicky. Start with a clean part—sandblast ($50 for a cheap harbor freight gun) or chemically strip it ($10 in degreaser). Spray powder with a $100 Wagner gun hooked to a compressor; the electrostatic charge makes it stick like magic. Roll the part in on a $50 cart (Harbor Freight again), shut the door, and fire it up. Powder melts in 5-10 minutes, cures in 15-25 total—check the powder’s spec sheet (e.g., Tiger Drylac’s 49/12345 needs 390°F for 18 minutes). Watch for pitfalls: skip preheating cast aluminum, and pinholes pop from outgassing; overload the rack, and airflow chokes, leaving dull spots. A $30 infrared thermometer helps spot-check.
Cost breaks down nicely. A turnkey small oven runs $1,200-$3,000—say, a Dura-Bake 4’x4’x6’ at $2,800 with a digital panel. DIY cuts that to $500-$1,000: $200 for steel, $100 for elements, $150 for insulation, $50 for a fan, plus elbow grease. Powder’s $8-$15/lb, coating 10-20 sq ft; a 5-lb box does a dozen small jobs. Electricity’s the big variable—a 10 kW oven at 400°F for 1.5 hours (including warmup) costs $2-$3 daily. Add $50/year for filters and upkeep. Compare that to outsourcing: $50-$100 per wheel versus $10-$15 DIY.
Limits? You’re capped at parts under 6 feet—think fenders, not bumpers—and batch size tops out at 5-10 pieces before cooldowns slow you down. Electric-only means no gas savings, and a cold start eats 20-40 minutes. Still, for a small gig—coating Etsy crafts or hot-rod bits—it’s gold.
Large Powder Coat Oven
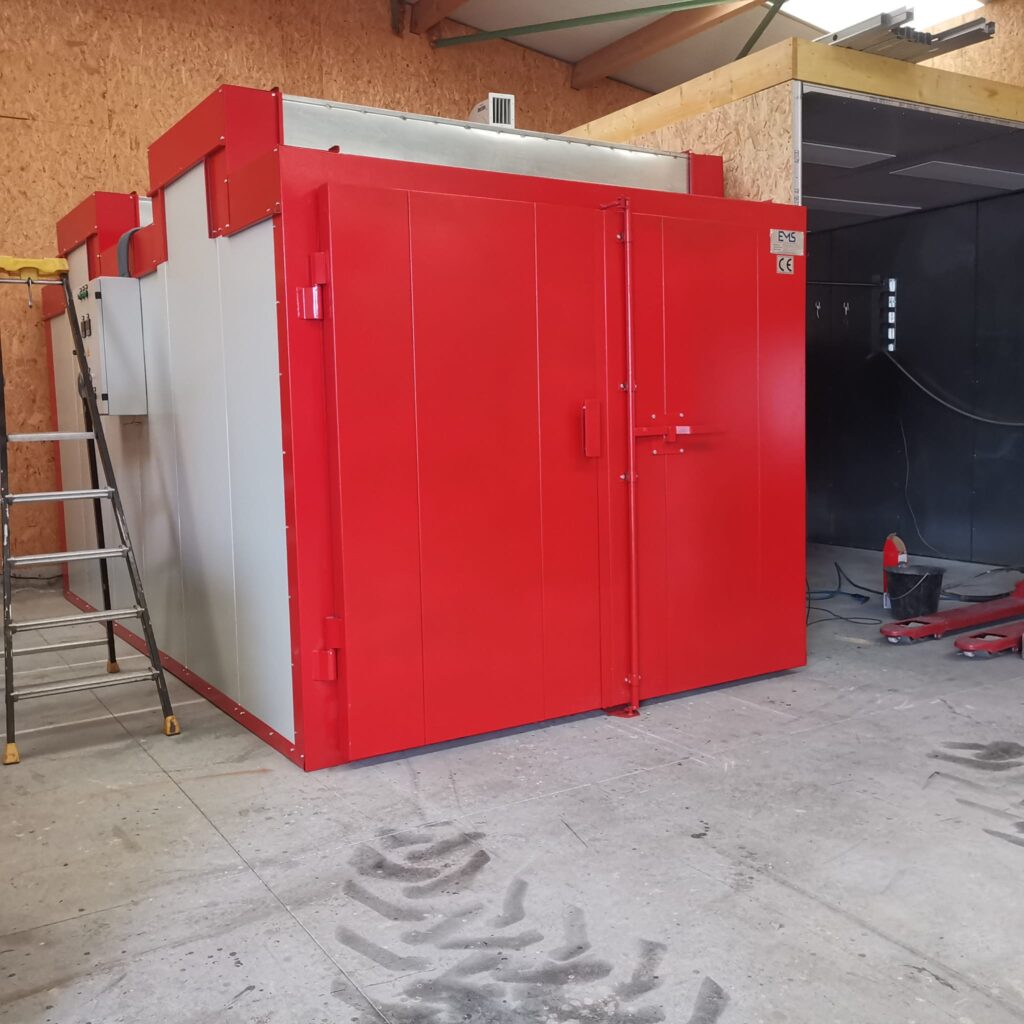
A large powder coating oven is a heavy-duty beast built for high-volume or oversized parts, catering to industrial shops, manufacturers, or serious custom operations that need to coat everything from truck frames and industrial machinery components to architectural beams and massive batches of smaller items. These ovens typically start at 8’x8’x10’ and can stretch to 20’x20’x50’ or beyond, often paired with conveyor systems for continuous production. They’re engineered to cure powder at 350°F-450°F (175°C-232°C), turning that dry, electrostatically applied coating into a rugged, uniform finish that stands up to corrosion, impact, and weathering—ideal for parts too big or numerous for small batch ovens.
Construction is robust. You’re looking at 12- or 10-gauge steel walls, double-layered with 6 to 10 inches of high-grade insulation—think ceramic fiber or mineral wool, rated for 1000°F+—to trap heat across a cavernous interior. Heating options split between electric and gas. Electric models might pack 50-100 kW of coiled elements, wired to a 480V three-phase supply, while gas-fired units—natural gas or propane—crank out 500,000 to 1,000,000 BTUs via burners, vented through a stack. Airflow’s critical at this scale; industrial blowers (2000-5000 CFM) and ducted systems ensure even heat, avoiding cold spots on a 15-foot-long chassis. Controls are sophisticated—programmable PLCs or touchscreen PIDs ($500-$2,000) tied to multiple thermocouples, holding temps within 2°F for consistent cures.
Picture a real-world setup: a 10’x10’x20’ batch oven from Wisconsin Oven, $25,000-$35,000, with 75 kW electric heat or 750,000 BTU gas burners. It’s got double doors, a reinforced floor for 5,000-lb loads, and carts on rails to roll in a trailer frame. At 400°F, it cures a polyester powder in 25 minutes, drawing $11/hour electric (75 kW at $0.15/kWh) or $3/hour gas (at $1/therm). For continuous flow, a 60’x10’x10’ conveyor oven from Gema—$75,000-$150,000—moves parts on an overhead track, curing 200 wheel rims hourly. Gas-powered at 1.2 million BTUs, it sips $5/hour, with zones (preheat, soak, cool) for efficiency. Both can handle 10-20 ft parts, coated in $50-$100 of powder per load.
Operation scales up the small-oven playbook. Parts—say, a 12-foot steel railing—get blasted clean (industrial blaster, $2,000), hung on racks or a conveyor (custom-built, $1,000-$5,000), and sprayed with a $500 Nordson gun. The oven preheats to 200°F to outgas, then ramps to 400°F. A big oven might take 45-60 minutes to hit temp from cold, but once hot, it cycles fast—20-30 minutes per batch. Powder choice matters: a UV-tough polyester (Sherwin-Williams, $12/lb) for outdoor gear, or epoxy ($10/lb) for indoor durability. Airflow’s a beast to manage—too weak, and a 15-foot part cures patchy; too strong, and powder drifts off. Dampers and baffles fine-tune it.
Costs reflect the scale. A large batch oven starts at $20,000-$50,000; conveyor systems hit $100,000-$500,000 with bells like powder reclaim ($10,000 extra) or quick-color-change booths. Installation adds $5,000-$20,000 for wiring (480V, 200 amps) or gas lines. Running it? A 100 kW electric oven at 400°F for 2 hours costs $30/day; a 1 million BTU gas unit, $10-$15/day. Powder for a 20-foot part might run $50-$150, though reclaim cuts that 30%. Maintenance climbs—$1,000-$5,000 yearly for filters, burner tune-ups, and element swaps. A crew of 2-4 runs it, versus 1 for a small oven.
Trade-offs are real. These ovens guzzle energy—electric bills can hit $500/month for heavy use, though gas slashes that to $200. Space is a factor; a 20’x20’x20’ unit needs 1,000 sq ft, plus clearance. Heat-up lags—1-2 hours cold—but throughput (50-500 parts/day) justifies it. Safety’s tighter: ground everything, vent fumes (OSHA-grade exhaust, $2,000), and train for dust hazards. For a factory coating 100 frames daily or a shop doing 10 oversized jobs, it’s unmatched—small ovens can’t touch it.
A large powder coating oven is a powerhouse tailored for serious production, built to handle oversized parts or massive batches with the kind of efficiency and durability that small ovens can only dream of. These units are the backbone of industries like automotive manufacturing, construction, aerospace, and heavy equipment, where you’re coating things like 20-foot-long steel beams, tractor chassis, or hundreds of smaller components in a single shift. They typically kick off at dimensions like 8’x8’x10’ for big batch ovens and can sprawl to 20’x20’x50’ or more for conveyorized systems, designed to cure powder at 350°F-450°F (175°C-232°C) into a finish that’s tough as nails—resistant to corrosion, abrasion, and the elements, with a uniformity that’s critical for high-stakes applications.
The build is industrial-grade. Picture a shell of 10- or 12-gauge steel, welded tight, with walls 8 to 12 inches thick, packed with top-tier insulation—ceramic fiber, mineral wool, or even rigid foam boards—rated for 1000°F+ to keep heat loss minimal across a huge volume. Heating splits two ways: electric ovens might wield 50-150 kW of elements, wired to a 480V three-phase grid (think 100-200 amps), while gas ovens—natural gas or propane—blast 500,000 to 2 million BTUs through burners, vented via a chimney or exhaust stack. Airflow’s a science here; massive blowers (3000-10,000 CFM) and intricate ductwork or plenums push hot air evenly, critical when curing a 15-foot-wide part. Controls are pro-level—PLCs ($1,000-$5,000) with touchscreens, tied to a dozen thermocouples, let you program ramp-up, soak, and cooldown cycles, holding temps within 1-2°F for zero defects.
Take a 12’x12’x20’ batch oven—say, a $40,000 model from Precision Quincy. It’s got 100 kW electric heat (or 1 million BTU gas), a floor rated for 10,000 lbs, and double doors wide enough for a forklift. Load it with a 16-foot aluminum extrusion, coated in $75 of polyester powder, and it hits 400°F in 60 minutes from cold, curing in 25 minutes more—$15/run electric ($0.15/kWh) or $4 gas ($1/therm). Scale up to a 100’x10’x10’ conveyor oven from Nordson—$200,000-$300,000—with 1.5 million BTUs, rolling 300 car hoods hourly through preheat (300°F), cure (400°F), and cool zones. Gas costs $6/hour, and powder reclaim saves $500/day. These beasts handle parts 20-30 feet long, coated in $100-$300 of powder per cycle.
Running one’s a process. Parts—say, a 20-foot I-beam—get prepped with a $5,000 industrial blaster or $200 in chemical wash, hung on custom racks ($2,000) or a conveyor chain ($10,000). A $1,000 Gema spray system coats it, then it’s in the oven. Preheat to 200°F for outgassing (castings especially), then cure at 390°F for 30 minutes (per powder specs, like Axalta’s 10-15 minute flow-out). Airflow’s dialed—5,000 CFM ensures no dead zones, but dampers tweak it to avoid blowing powder off edges. Powder choice is strategic: epoxy-polyester hybrids ($11/lb) for indoor machinery, super-durable fluoropolymers ($20/lb) for outdoor bridges. Overspray’s gold—reclaim booths ($15,000) recycle 40%, slashing costs.
The price tag’s steep. A big batch oven runs $30,000-$75,000; conveyor systems, $150,000-$500,000+, depending on length, zones, and automation. Installation’s another $10,000-$30,000—480V power drops, gas piping, exhaust stacks (10-20 ft, $5,000). Operating costs scale: a 150 kW electric oven at 400°F for 8 hours eats $180/day; a 2 million BTU gas unit, $40-$50/day. Powder for a 20×20 ft batch might hit $500, halved with reclaim. Maintenance is $5,000-$15,000 yearly—burners clog, elements fail, filters ($50 each) swap quarterly. Labor’s 3-5 people: one blasting, one spraying, one loading, plus a supervisor.
Challenges stack up. Heat-up’s 1-2 hours cold, eating time unless you run 24/7. Energy’s a beast—$1,000/month electric, $300 gas for heavy use. Space? A 20’x20’x20’ oven needs 1,500 sq ft, plus staging. Safety’s strict: ground all racks (static sparks ignite powder dust), vent fumes (10,000 CFM exhaust, $10,000), and train for confined-space risks. Payoff’s huge, though—50-1,000 parts/day, flawless finishes, and economies of scale small ovens can’t touch.
A large powder coating oven is the industrial titan of the finishing world, built to tackle the biggest, toughest, or most numerous parts with a level of throughput and precision that transforms raw metal into coated perfection at scale. These ovens are the go-to for manufacturers churning out semi-truck frames, wind turbine components, or architectural cladding, as well as shops handling dozens of oversized custom jobs daily. They start at sizes like 10’x10’x12’ for batch processing and can balloon to 30’x20’x100’ for conveyorized lines, curing powder at 350°F-450°F (175°C-232°C) to deliver finishes that shrug off rust, dents, and decades of wear. Whether it’s a single 25-foot-long steel girder or 500 smaller brackets an hour, these ovens are engineered for volume, durability, and consistency.
The construction is a marvel of heavy engineering. The frame’s thick—10-gauge steel or heavier—welded into a fortress, with double walls 8 to 12 inches deep, stuffed with premium insulation like ceramic fiber blankets or high-density Rockwool, rated for 1200°F+ to keep heat locked in across a massive chamber. Heating’s a choice: electric ovens pack 100-300 kW of elements—think banks of glowing coils—tied to a 480V, 200-400 amp three-phase feed, while gas ovens roar with 1-3 million BTU burners, fueled by natural gas or propane, vented through a 20-foot stack. Airflow’s a beast—10,000-20,000 CFM blowers, paired with adjustable ducts or perforated plenums, blast hot air evenly, crucial for curing a 20-foot-wide part without streaks or soft spots. Controls are cutting-edge: PLCs ($2,000-$10,000) with HMI screens, networked thermocouples, and zoned heating let you tweak every inch, holding temps within 1°F for aerospace-grade results.
Imagine a 15’x15’x30’ batch oven—say, a $60,000 unit from Global Finishing Solutions. It’s got 150 kW electric heat (or 1.5 million BTU gas), a floor for 15,000-lb loads, and sliding doors for a crane to drop in a bulldozer blade. At 400°F, it cures $150 of UV-resistant polyester powder in 30 minutes, costing $22/run electric ($0.15/kWh) or $6 gas ($1/therm). Now picture a 120’x12’x12’ conveyor oven from L&L Oven Co.—$400,000—with 2 million BTUs, rolling 1,000 bike frames daily through three zones: 250°F preheat, 400°F cure, 200°F cool. Gas runs $8/hour, and a $20,000 reclaim system recycles $1,000 of powder daily. These can swallow 30-foot extrusions or coat 50 sq ft/minute, dwarfing small-oven output.
The process is a production dance. A 25-foot steel truss gets blasted ($10,000 walk-in booth), hung on a $5,000 motorized rack or $20,000 conveyor, and sprayed with a $2,000 Wagner system—$200 of powder per piece. The oven preheats to 200°F (outgassing for 15 minutes), then hits 390°F for 35 minutes (per specs, like PPG’s 20-minute flow-out). Airflow’s dialed—15,000 CFM, with baffles to balance it—because a cold corner means rework. Powder’s picked for the job: epoxy ($10/lb) for indoor generators, fluoropolymer ($25/lb) for coastal railings. Reclaim’s standard—40-60% recovery—turning $500 of overspray into $200 of savings per batch.
Costs are industrial too. A large batch oven runs $50,000-$100,000; conveyor systems, $250,000-$1 million, factoring automation, length, and extras like IR boosters ($50,000). Installation’s $20,000-$50,000—think 480V transformers ($5,000), gas mains ($10,000), and 30-foot exhausts ($15,000). Operating? A 200 kW electric oven at 400°F for 10 hours eats $300/day; a 3 million BTU gas unit, $75-$100/day. Powder for a 30×20 ft load hits $1,000, halved with reclaim. Maintenance is $10,000-$25,000 yearly—burners need tuning, elements burn out, blowers ($2,000) wear. Crew’s 5-10: blasters, sprayers, loaders, and a tech for the PLC.
It’s not flawless. Cold-start’s 2-3 hours, so you run hot or lose time. Energy’s a monster—$2,000/month electric, $600 gas for 24/7 use. Space? A 30’x20’x20’ oven demands 2,000 sq ft, plus staging and booths. Safety’s intense: ground every hook (dust explosions hit 50 psi), vent 20,000 CFM ($20,000 system), and monitor CO. But the upside? 100-5,000 parts/day, finishes that last 20 years, and costs per piece drop to pennies at scale—small ovens can’t compete.
Gas Powder Coating Oven
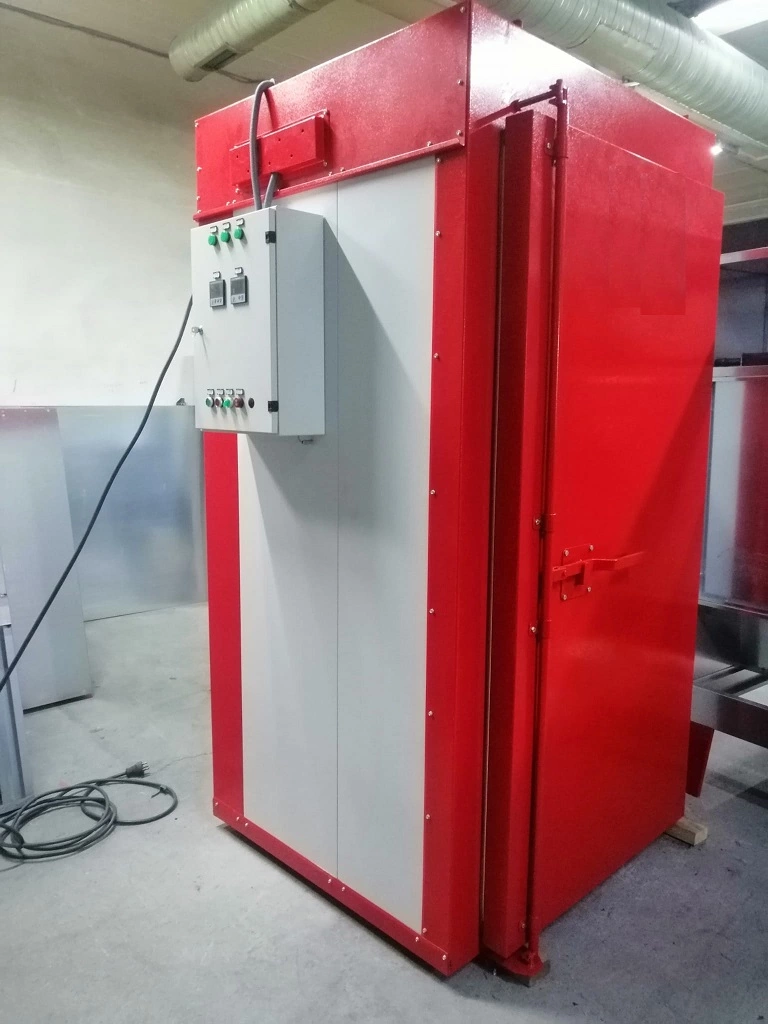
A gas powder coating oven is a high-efficiency workhorse that uses natural gas or propane to cure powder coatings, offering a cost-effective alternative to electric models, especially for larger operations or high-throughput needs. These ovens are designed to heat parts to 350°F-450°F (175°C-232°C), melting and curing electrostatically applied powder into a durable, protective finish that outperforms liquid paint in toughness and longevity. Popular in industrial settings, small shops, and even some DIY builds, gas ovens shine where fuel costs beat electricity rates or where massive heat output—measured in BTUs rather than kilowatts—is a must for big parts or continuous production.
The build is rugged and heat-focused. The frame’s typically 12- or 10-gauge steel, double-walled with 6 to 12 inches of insulation—ceramic fiber or mineral wool, rated for 1000°F+—to keep energy loss low. The heart is the burner system: a gas-fired unit, often modulating for precision, pumping out 100,000 to 3 million BTUs depending on size. A small 4’x4’x6’ oven might use a 100,000 BTU burner, while a 20’x20’x50’ conveyor beast could hit 2-3 million BTUs. Heat’s delivered via direct-fired burners (flame in the chamber) or indirect-fired heat exchangers (cleaner air, pricier), with blowers—1,000-20,000 CFM—circulating it through ducts or open space. Exhaust stacks (10-30 ft) vent combustion gases, and controls range from basic thermostats ($50) to PLCs ($1,000-$5,000) with thermocouples for tight temp regulation.
Take a 6’x6’x8’ batch oven—say, a $5,000-$10,000 custom job. A 250,000 BTU natural gas burner heats it to 400°F in 30-45 minutes, curing a set of truck rims in 20 minutes post-flow-out. At $1/therm (100,000 BTU), it burns $0.50-$0.75/hour—compare that to a 12 kW electric oven at $1.80/hour ($0.15/kWh). Scale up to a 15’x15’x30’ industrial unit—$50,000-$75,000—with 1.5 million BTUs, curing a 20-foot trailer frame for $3-$4/hour. A 100’x10’x10’ conveyor oven—$200,000-$400,000—might pack 2 million BTUs, coating 500 parts/hour at $5-$6/hour, with zones for preheat (250°F) and cure (400°F). Gas trims costs over electric by 50-70% at scale.
Operation mirrors other ovens with a fuel twist. Parts—say, a steel gate—get blasted, hung on racks ($500-$5,000), and sprayed with a $500 gun ($50 powder/load). The oven fires up—burners ignite via a pilot or spark—and preheats to 200°F for outgassing, then hits 390°F for 25-35 minutes (e.g., Prismatic Powders’ spec: 15 minutes at temp). Airflow’s key—5,000 CFM for a big oven, adjusted via dampers—since gas heat can stratify without circulation. Powder choice fits the job: polyester ($12/lb) for outdoor durability, epoxy ($10/lb) for indoor grit. Reclaim systems ($10,000-$20,000) catch overspray, saving 40% on powder.
Costs lean on fuel efficiency. A small gas oven starts at $5,000-$15,000; large batch units, $50,000-$100,000; conveyors, $200,000-$500,000. Installation adds $2,000-$15,000—gas lines ($500-$5,000), venting ($1,000-$10,000), and a 120V control circuit. Running costs? A 500,000 BTU oven at 400°F for 8 hours uses 4-5 therms ($4-$5/day); a 2 million BTU unit, 16-20 therms ($16-$20/day)—versus $50-$150/day for equivalent electric. Maintenance is $1,000-$10,000 yearly—burners need tuning, flues clog, filters swap ($50-$100 each). Propane’s pricier ($2-$3/gallon, 91,000 BTU), but portable for off-grid shops.
Gas has edge and quirks. It’s cheaper long-term—$100-$500/month versus $500-$2,000 electric—but needs venting (OSHA rules) and a steady fuel supply. Heat-up’s fast—20-60 minutes—but direct-fired can taint finishes with combustion byproducts unless indirect ($5,000 extra). Safety’s tighter: vent 10,000 CFM, ground everything (powder dust ignites at 50 psi), and monitor CO. For a shop coating 50-1,000 parts/day or a factory with 20-foot jobs, gas wins on cost and scale—electric struggles to match.
A gas powder coating oven is a fuel-driven titan that leverages natural gas or propane to deliver the heat needed to cure powder coatings, making it a standout choice for anyone prioritizing operating cost savings, high heat output, or large-scale production over the simplicity of electric models. These ovens are built to hit that sweet spot of 350°F-450°F (175°C-232°C), transforming dry powder—applied electrostatically to parts like steel frames, aluminum panels, or industrial machinery—into a rock-solid finish that resists corrosion, chipping, and UV damage with a durability liquid paint can’t touch. From small shops coating custom grills to factories churning out miles of coated pipe, gas ovens thrive where efficiency and scale matter most.
The design is all about harnessing combustion. The shell’s heavy-duty—10- or 12-gauge steel—double-walled with 8 to 12 inches of insulation like ceramic fiber or high-temp fiberglass, rated for 1200°F+ to keep heat where it belongs. The burner’s the star: a gas-fired unit, often modulating (adjusting flame dynamically), delivering 100,000 BTUs for a compact 4’x4’x6’ oven up to 3-5 million BTUs for a 30’x20’x100’ conveyor monster. Direct-fired burners shoot flame into the chamber—cheap and efficient—while indirect-fired use a heat exchanger for cleaner air, adding $5,000-$20,000 to the price. Blowers (1,000-25,000 CFM) and ductwork—sometimes with adjustable louvers—spread heat evenly, vital for curing a 20-foot part without hot or cold patches. Exhaust stacks (10-40 ft, $1,000-$15,000) vent fumes, and controls range from $50 thermostats to $5,000-$10,000 PLCs with zoned sensors for pinpoint accuracy.
Picture a 8’x8’x10’ batch oven—$15,000-$25,000—with a 500,000 BTU natural gas burner. It hits 400°F in 30 minutes, curing a stack of ATV frames in 25 minutes for $1-$1.50/hour ($1/therm)—versus $5/hour for a 30 kW electric equivalent. Step up to a 20’x20’x40’ batch oven—$75,000-$125,000—with 2 million BTUs, coating a 30-foot steel beam for $4-$5/hour. For continuous flow, a 150’x12’x12’ conveyor oven—$500,000-$750,000—with 3 million BTUs runs 1,000 car parts/hour at $7-$9/hour, with preheat (300°F), cure (400°F), and cool zones. Pair it with a $30,000 reclaim booth, and you save $2,000/day on powder. These ovens handle 50-foot extrusions or 100 sq ft/minute, fueled by gas’s raw power.
The workflow’s industrial but familiar. A 15-foot railing gets blasted ($5,000 booth), hung on a $2,000 rack or $25,000 conveyor, and sprayed with a $1,000 Gema gun—$100 of powder. The burner kicks on—pilot-lit or spark-ignited—preheating to 200°F (15-20 minutes) to outgas, then curing at 390°F for 30-40 minutes (e.g., Tiger Drylac’s 20-minute spec). Airflow’s critical—10,000 CFM, tuned with dampers—since gas heat rises, risking uneven cures. Powder’s job-specific: polyester-epoxy ($11/lb) for indoor durability, polyurethane ($15/lb) for outdoor gloss. Reclaim recycles 50%, turning $200 of overspray into $100 of profit.
Costs hinge on fuel’s edge. Small gas ovens start at $5,000-$20,000; large batch, $50,000-$150,000; conveyors, $300,000-$1 million+, with extras like IR assist ($50,000) or multi-zone burners. Installation’s $5,000-$25,000—gas piping ($1,000-$10,000), venting ($2,000-$15,000), and 120V controls. Running costs shine: a 1 million BTU oven at 400°F for 10 hours uses 10 therms ($10-$12/day); a 3 million BTU unit, 30 therms ($30-$36/day)—versus $100-$300/day electric. Propane’s $2-$3/gallon (91,000 BTU), doubling costs but freeing remote setups. Maintenance is $2,000-$15,000 yearly—burners need annual service ($500), flues corrode, blowers wear ($3,000).
Gas rules efficiency but demands respect. It slashes energy bills—$200-$600/month versus $1,000-$3,000 electric—but requires venting (10-20,000 CFM, $10,000-$30,000) and fuel infrastructure. Heat-up’s quick—20-90 minutes—but direct-fired risks soot (1-2% finish rejection) unless indirect’s used. Safety’s non-negotiable: ground all metal (dust explodes at 0.02 oz/ft³), vent CO (detectors, $100), and train for gas leaks. For 100-10,000 parts/day or oversized jobs, gas ovens dominate—electric can’t match the BTU bang for the buck.
A gas powder coating oven is a fuel-powered juggernaut that harnesses the raw energy of natural gas or propane to cure powder coatings, delivering a blend of cost efficiency, scalability, and brute thermal force that makes it a favorite for everything from small custom shops to sprawling industrial lines. These ovens are engineered to hit that critical 350°F-450°F (175°C-232°C) range, melting and bonding powder—electrostatically sprayed onto parts like steel pipes, aluminum extrusions, or heavy machinery—into a finish that’s tougher than nails, shrugging off rust, impacts, and harsh weather. Gas ovens excel where high heat demand meets long run times, offering a cheaper-per-BTU alternative to electric models, especially for large parts or nonstop production.
The build is a fortress of heat management. The structure’s beefy—10-gauge steel or thicker—double-walled with 8 to 12 inches of insulation, often ceramic fiber or mineral wool, rated for 1200°F+ to trap every calorie of combustion. The burner’s the muscle: a gas-fired system, typically modulating for fine control, churning out 100,000 BTUs for a modest 4’x4’x6’ oven up to 5 million BTUs for a 40’x20’x150’ conveyor beast. Direct-fired burners blast flame straight in—simple, affordable, 90%+ efficient—while indirect-fired use a stainless-steel heat exchanger ($10,000-$30,000 extra) for cleaner air, dodging combustion byproducts. Blowers—2,000-30,000 CFM—paired with ducts, baffles, or plenums, push heat evenly, a must for curing a 30-foot beam without flaws. Exhaust stacks (15-50 ft, $2,000-$20,000) vent CO and water vapor, and controls span $50 thermostats to $10,000 PLCs with multi-zone sensors, locking temps within 1-2°F.
Picture a 10’x10’x15’ batch oven—$25,000-$40,000—with a 750,000 BTU natural gas burner. It hits 400°F in 40 minutes, curing a stack of 10-foot railings in 25 minutes for $1.50-$2/hour ($1/therm)—versus $7/hour for a 50 kW electric rig. Jump to a 25’x20’x60’ batch oven—$100,000-$175,000—with 2.5 million BTUs, coating a 50-foot windmill shaft for $5-$6/hour. For high volume, a 200’x15’x12’ conveyor oven—$750,000-$1.2 million—with 4 million BTUs runs 2,000 parts/hour at $9-$12/hour, with staged zones: 200°F preheat, 400°F cure, 150°F cool. Add a $50,000 reclaim system, and you’re banking $5,000/day on powder savings. These ovens swallow 60-foot monsters or coat 150 sq ft/minute, fueled by gas’s relentless output.
The process is a production symphony. A 20-foot steel girder gets blasted ($10,000 booth), hung on a $5,000 rack or $50,000 conveyor, and sprayed with a $2,000 Nordson gun—$150 powder. The burner roars—spark-ignited or pilot-lit—preheating to 200°F (20 minutes) to outgas, then curing at 390°F for 35-45 minutes (e.g., AkzoNobel’s 25-minute spec). Airflow’s dialed—15,000 CFM, with adjustable vents—since gas heat stratifies, risking top-heavy cures. Powder’s tailored: polyurethane ($15/lb) for glossy trailers, fluoropolymer ($25/lb) for coastal bridges. Reclaim grabs 50-60% overspray, turning $300 waste into $150 profit.
Costs spotlight gas’s thrift. Small ovens start at $10,000-$25,000; large batch, $75,000-$200,000; conveyors, $500,000-$2 million+, with options like dual burners ($20,000) or IR assist ($75,000). Installation’s $10,000-$50,000—gas mains ($2,000-$15,000), venting ($5,000-$25,000), and 120V/240V controls. Operating shines: a 1.5 million BTU oven at 400°F for 12 hours uses 18 therms ($18-$22/day); a 4 million BTU unit, 48 therms ($48-$60/day)—versus $200-$500/day electric. Propane’s $2.50/gallon (91,000 BTU), so a 1 million BTU run costs $27/day—rural-ready but pricier. Maintenance is $5,000-$20,000 yearly—burners tune ($1,000), heat exchangers crack ($5,000), blowers die ($5,000).
Gas dominates efficiency but brings baggage. It cuts energy costs—$300-$1,000/month versus $2,000-$5,000 electric—but demands infrastructure: 20,000 CFM vents ($20,000-$50,000), gas meters ($1,000), and permits. Heat-up’s brisk—30-120 minutes—but direct-fired can speckle finishes with soot (1-3% rework) unless indirect’s spec’d. Safety’s ironclad: ground everything (dust ignites at 430°F), vent CO (alarms, $200), and leak-test lines. For 200-20,000 parts/day or 50-foot jobs, gas ovens rule—electric’s wattage wilts in comparison.
Electric Ovens for Powder Coating
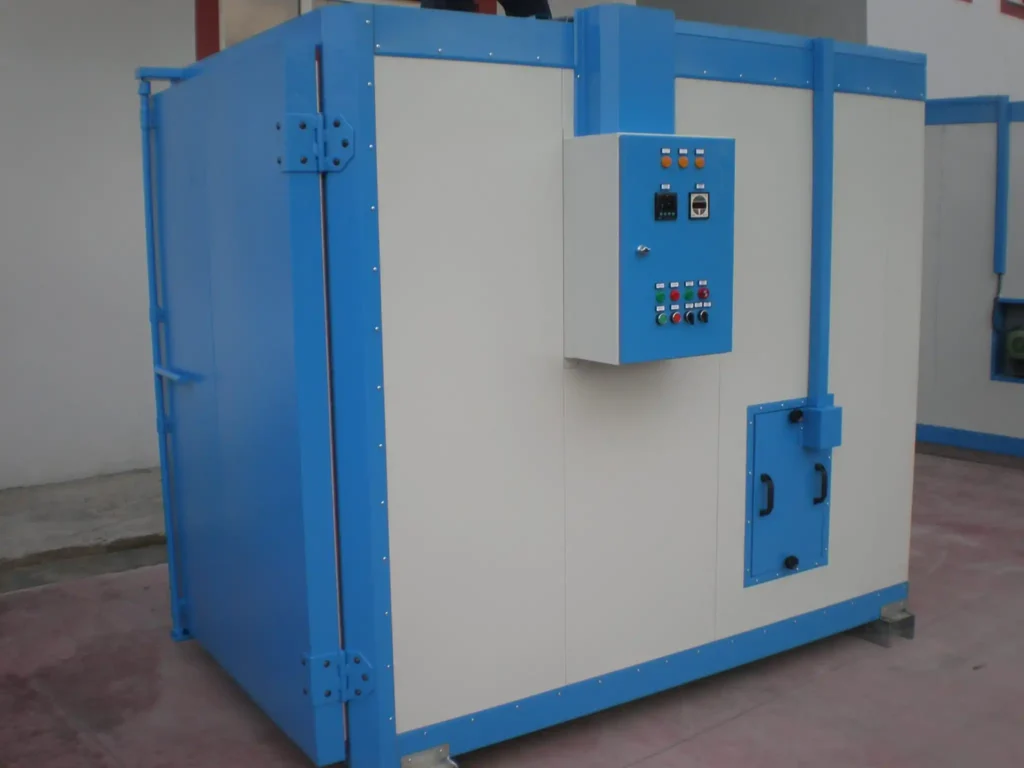
Electric ovens for powder coating are a straightforward, versatile option that use electrical resistance heating to cure powder coatings, making them a go-to for small shops, hobbyists, and even some industrial setups where simplicity and precision outweigh fuel cost concerns. These ovens heat parts to the standard 350°F-450°F (175°C-232°C) range, transforming electrostatically applied powder into a tough, uniform finish that beats out traditional paint for durability, corrosion resistance, and aesthetics. They’re prized for their ease of installation, clean operation, and tight temperature control, shining in spaces where gas lines or venting aren’t practical—think garages, urban workshops, or facilities with strict emissions rules.
The design is all about efficiency and accessibility. The frame’s typically 14- or 12-gauge steel, double-walled with 4 to 12 inches of insulation—fiberglass, mineral wool, or ceramic fiber, rated for 600°F+—to keep heat in and energy costs manageable. Heating comes from electric elements—nichrome coils or rods—mounted on walls, floor, or ceiling, delivering 6 kW for a small 4’x4’x6’ oven up to 200-300 kW for a 20’x20’x40’ industrial unit. Power’s usually 240V single-phase for smaller models (30-50 amps) or 480V three-phase for big ones (100-400 amps). Blowers—500-20,000 CFM—circulate air via ducts or open chambers, ensuring even cures. Controls range from $20 dial thermostats to $200-$2,000 PID controllers or PLCs, holding temps within 2-5°F—crucial for flawless finishes.
Take a small 4’x4’x6’ oven—say, an Eastwood HotCoat, $1,500-$2,000—with 10 kW of elements. It hits 400°F in 30 minutes on a 240V, 50-amp circuit, curing a set of motorcycle wheels in 20 minutes for $1.50/hour ($0.15/kWh)—plug-and-play in a garage. Scale up to a 10’x10’x15’ batch oven—$20,000-$30,000—with 60 kW, curing a car frame for $9/hour. For volume, a 50’x10’x10’ conveyor oven—$100,000-$250,000—with 150 kW runs 200 parts/hour at $22/hour, often with zoned heating (preheat at 300°F, cure at 400°F). These handle 20-foot parts or 50 sq ft/minute, powered by electricity’s steady hum.
Operation’s clean and simple. A steel bracket gets blasted ($50 gun), hung on a $20 rack or $10,000 conveyor, and sprayed with a $100 gun—$10 powder. The oven powers up—elements glow red—preheating to 200°F (10-15 minutes) for outgassing, then curing at 390°F for 20-30 minutes (e.g., Powder Buy the Pound’s 15-minute spec). Airflow’s key—2,000 CFM for a mid-size oven, tuned with baffles—since electric heat can pool without movement. Powder’s job-matched: polyester ($12/lb) for outdoor chairs, epoxy ($10/lb) for indoor tools. Reclaim ($5,000-$20,000) grabs 40% overspray, saving $5-$50/load.
Costs reflect electricity’s price. Small ovens start at $1,000-$5,000; mid-size batch, $15,000-$50,000; conveyors, $100,000-$500,000+, with extras like IR panels ($10,000) or multi-zone controls ($5,000). Installation’s light—$500-$5,000 for 240V/480V wiring, no venting needed. Running costs? A 20 kW oven at 400°F for 8 hours uses 160 kWh ($24/day); a 200 kW unit, 1,600 kWh ($240/day)—steep versus gas’s $10-$50/day. Maintenance is $500-$5,000 yearly—elements burn out ($100-$1,000), blowers wear ($1,000), filters swap ($20-$50).
Electric ovens win on simplicity. They’re vent-free—perfect for tight spaces—and start instantly, no flame lag. Heat’s clean—no soot risk—and control’s precise, ideal for small batches or sensitive parts. Downsides? Energy’s pricier—$500-$2,000/month versus gas’s $200-$600—and max output tops out (300 kW vs. 5 million BTUs), limiting scale. Safety’s easier: ground for static (dust ignites at 430°F), but no CO or gas leaks. For 1-500 parts/day or 20-foot jobs, electric’s a champ—gas only pulls ahead at high volume.
Electric ovens for powder coating are a sleek, no-fuss solution that lean on electrical resistance to cure powder coatings, delivering a reliable, clean, and precise heating option for everything from DIY projects to mid-tier industrial jobs. These ovens crank up to that essential 350°F-450°F (175°C-232°C) range, turning dry, electrostatically applied powder into a hard, vibrant finish that outclasses liquid paint in durability, scratch resistance, and longevity. They’re a favorite for small workshops, urban facilities, or anyone dodging the complexity of gas—offering plug-in simplicity, no emissions headaches, and tight temperature control that’s perfect for everything from bike frames to batches of automotive parts.
The build is streamlined yet robust. The shell’s typically 14- or 12-gauge steel—sometimes 10-gauge for bigger units—double-walled with 4 to 12 inches of insulation like fiberglass batting, mineral wool, or ceramic fiber, rated for 600°F-1000°F+ to minimize heat bleed. Heating’s all electric: nichrome or kanthal elements—coils, rods, or panels—wired to deliver 6 kW for a compact 3’x3’x4’ oven up to 300-500 kW for a 25’x20’x60’ industrial rig. Small ovens run on 240V single-phase (20-60 amps), while large ones tap 480V three-phase (200-600 amps). Blowers—500-25,000 CFM—push air through ducts, baffles, or open chambers, keeping heat even across a 15-foot part. Controls vary: $20 thermostats for basic models, $100-$500 PIDs for hobbyists, or $2,000-$10,000 PLCs with zoned sensors for pro-grade precision, nailing temps within 1-3°F.
Picture a 5’x5’x7’ batch oven—say, a $3,000-$5,000 Dura-Bake model—with 15 kW of elements. It hits 400°F in 35 minutes on a 240V, 60-amp line, curing a set of alloy wheels in 20 minutes for $2.25/hour ($0.15/kWh)—ideal for a garage hustle. Jump to a 12’x12’x20’ oven—$30,000-$50,000—with 80 kW, curing a truck bed for $12/hour. For volume, a 75’x12’x10’ conveyor oven—$150,000-$350,000—with 200 kW coats 300 parts/hour at $30/hour, with staged zones: 250°F preheat, 400°F cure, 200°F cool. These tackle 25-foot extrusions or 75 sq ft/minute, driven by electricity’s steady pulse.
The process is clean-cut. A steel panel gets blasted ($100 gun), hung on a $50 rack or $15,000 conveyor, and sprayed with a $200 Wagner gun—$20 powder. Elements fire up—glowing orange—preheating to 200°F (10-20 minutes) to outgas, then curing at 390°F for 20-35 minutes (e.g., Sherwin-Williams’ 15-minute spec). Airflow’s critical—5,000 CFM for a big oven, with adjustable vents—since electric heat can stagnate, risking dull spots. Powder’s picked for purpose: epoxy-polyester ($11/lb) for indoor cabinets, super-durable polyester ($14/lb) for patio sets. Reclaim ($10,000-$30,000) snags 40-50% overspray, saving $10-$100/load.
Costs tie to power rates. Small ovens run $1,000-$10,000; mid-size batch, $20,000-$75,000; conveyors, $150,000-$750,000+, with add-ons like IR boosters ($20,000) or touchscreen controls ($5,000). Installation’s cheap—$500-$10,000 for wiring (240V breaker or 480V drop), no stacks or pipes. Operating? A 30 kW oven at 400°F for 10 hours uses 300 kWh ($45/day); a 300 kW unit, 3,000 kWh ($450/day)—pricey versus gas’s $15-$75/day. Maintenance is $1,000-$10,000 yearly—elements fail ($200-$2,000), blowers wear ($2,000), filters clog ($30-$100).
Electric ovens shine in simplicity. They’re vent-free—great for tight urban spots—and start instantly, no burner warm-up. Heat’s pure—no combustion residue—and control’s razor-sharp, perfect for small runs or delicate substrates. Trade-offs? Electricity’s costly—$1,000-$5,000/month versus gas’s $300-$1,000—and output caps at 500 kW (1.7 million BTUs), paling next to gas’s 5 million BTU ceiling. Safety’s lighter: ground for static (dust sparks at 0.02 oz/ft³), but no gas hazards. For 1-1,000 parts/day or 25-foot jobs, electric holds strong—gas only wins at extreme scale.
Electric ovens for powder coating are a sleek, electrified backbone for curing powder coatings, relying on resistance heating to deliver a clean, controlled, and accessible solution for hobbyists, small businesses, and even some industrial players. These ovens heat up to that critical 350°F-450°F (175°C-232°C) window, melting and curing electrostatically applied powder into a finish that’s tough, vibrant, and built to last—outpacing liquid paint in resistance to corrosion, abrasion, and fading. They’re the darling of setups where gas isn’t an option—think home garages, city workshops, or plants with strict air quality rules—offering easy setup, no fumes, and precision that’s hard to beat for small-to-mid-scale jobs.
The construction is a study in practical engineering. The shell’s typically 14- or 12-gauge steel—10-gauge for heavyweights—double-walled with 4 to 12 inches of insulation like fiberglass, mineral wool, or ceramic fiber, rated for 600°F-1200°F+ to keep heat loss low. Heating’s pure electric: nichrome or kanthal elements—coils snaking along walls or rods in panels—pumping out 6 kW for a tiny 3’x3’x3’ oven up to 400-600 kW for a 30’x20’x80’ industrial giant. Small units plug into 240V single-phase (20-60 amps), while big ones demand 480V three-phase (200-800 amps). Blowers—500-30,000 CFM—drive air through ducts, plenums, or open space, ensuring even cures across a 20-foot part. Controls range from $20 dial thermostats to $500 PIDs for DIYers, up to $10,000-$20,000 PLCs with multi-zone sensors, pinning temps within 1-2°F for pro finishes.
Imagine a 6’x6’x8’ batch oven—say, a $5,000-$10,000 Reliant model—with 20 kW of elements. It hits 400°F in 40 minutes on a 240V, 100-amp circuit, curing a batch of bike frames in 25 minutes for $3/hour ($0.15/kWh)—perfect for a small shop. Step up to a 15’x15’x25’ oven—$50,000-$80,000—with 100 kW, curing a trailer chassis for $15/hour. For high throughput, a 100’x12’x12’ conveyor oven—$250,000-$500,000—with 250 kW runs 500 parts/hour at $37/hour, with zones: 200°F preheat, 400°F cure, 150°F cool. These handle 30-foot extrusions or 100 sq ft/minute, powered by electricity’s quiet reliability.
The workflow’s smooth and sterile. A steel fender gets blasted ($200 blaster), hung on a $100 rack or $20,000 conveyor, and sprayed with a $300 gun—$30 powder. Elements kick on—glowing steadily—preheating to 200°F (15-25 minutes) to outgas, then curing at 390°F for 25-40 minutes (e.g., Axalta’s 20-minute spec). Airflow’s vital—10,000 CFM for a big oven, with adjustable baffles—since electric heat can settle, risking uneven gloss. Powder’s purpose-driven: epoxy ($10/lb) for indoor machinery, polyester-urethane ($15/lb) for outdoor grills. Reclaim ($15,000-$50,000) catches 50% overspray, saving $20-$200/load.
Costs are tied to the grid. Small ovens start at $1,000-$15,000; mid-size batch, $30,000-$100,000; conveyors, $200,000-$1 million+, with options like IR assist ($30,000) or programmable zones ($10,000). Installation’s a breeze—$1,000-$15,000 for wiring (240V panel or 480V feed), no venting or fuel lines. Operating? A 50 kW oven at 400°F for 12 hours uses 600 kWh ($90/day); a 400 kW unit, 4,800 kWh ($720/day)—steep versus gas’s $20-$100/day. Maintenance is $1,000-$15,000 yearly—elements corrode ($300-$3,000), blowers fail ($3,000), filters clog ($50-$150).
Electric ovens excel in ease. They’re emission-free—ideal for urban or residential spots—and fire up instantly, no burner delays. Heat’s pristine—no combustion quirks—and control’s surgical, perfect for 1-10 parts or heat-sensitive jobs. Drawbacks? Power’s pricey—$1,500-$10,000/month versus gas’s $500-$2,000—and output peaks at 600 kW (2 million BTUs), dwarfed by gas’s 5-10 million BTU potential. Safety’s simpler: ground for static (dust flashes at 430°F), but no CO or fuel risks. For 1-2,000 parts/day or 30-foot jobs, electric’s a star—gas only trumps it at massive scale.
Electric ovens for powder coating are a refined, electricity-driven cornerstone of the coating world, using resistance heating to cure powder into a resilient, high-quality finish that’s a cut above traditional paint in toughness, adhesion, and resistance to wear. These ovens reliably hit the 350°F-450°F (175°C-232°C) sweet spot, melting and bonding powder—electrostatically sprayed onto parts like aluminum wheels, steel furniture, or industrial fixtures—into a seamless, durable layer. They’re the pick for setups valuing simplicity, cleanliness, and precision, from basement tinkerers to mid-sized factories, especially where gas infrastructure’s a hassle or emissions are a no-go—think suburban garages, downtown shops, or regulated plants.
The design blends efficiency with practicality. The frame’s typically 14- or 12-gauge steel—10-gauge for the big leagues—double-walled with 4 to 12 inches of insulation like fiberglass, mineral wool, or ceramic fiber, rated for 600°F-1200°F+ to curb heat escape. Heating’s all about electric elements—nichrome coils weaving through walls or kanthal rods in panels—delivering 6 kW for a small 3’x3’x4’ oven up to 500-800 kW for a 30’x20’x100’ industrial titan. Small units run on 240V single-phase (20-80 amps), while large ones tap 480V three-phase (300-1000 amps). Blowers—500-40,000 CFM—circulate air via ducts, plenums, or open chambers, ensuring uniform cures across a 25-foot span. Controls span $20 thermostats for basic rigs, $200-$1,000 PIDs for enthusiasts, to $10,000-$25,000 PLCs with zoned sensors and touchscreens, locking temps within 1-2°F for zero-defect finishes.
Picture a 4’x4’x6’ batch oven—say, a $2,000-$3,000 HotCoat model—with 12 kW of elements. It hits 400°F in 30 minutes on a 240V, 60-amp line, curing a set of valve covers in 20 minutes for $1.80/hour ($0.15/kWh)—a DIY dream. Scale to a 15’x15’x30’ oven—$60,000-$100,000—with 120 kW, curing a 20-foot railing for $18/hour. For volume, a 120’x15’x12’ conveyor oven—$300,000-$600,000—with 300 kW runs 1,000 parts/hour at $45/hour, with staged zones: 200°F preheat, 400°F cure, 100°F cool. These tackle 40-foot extrusions or 120 sq ft/minute, fueled by electricity’s consistent buzz.
The process is polished and predictable. A steel toolbox gets blasted ($150 blaster), hung on a $50 rack or $25,000 conveyor, and sprayed with a $300 gun—$15 powder. Elements hum to life—glowing evenly—preheating to 200°F (15-30 minutes) to outgas, then curing at 390°F for 25-40 minutes (e.g., PPG’s 20-minute spec). Airflow’s crucial—15,000 CFM for a big oven, with adjustable vents—since electric heat can stagnate, risking matte patches. Powder’s task-specific: epoxy-polyester ($11/lb) for indoor shelves, fluoropolymer ($25/lb) for coastal signs. Reclaim ($20,000-$60,000) snags 50-60% overspray, saving $15-$300/load.
Costs are grid-dependent. Small ovens start at $1,000-$20,000; mid-size batch, $40,000-$150,000; conveyors, $250,000-$1.5 million+, with extras like IR panels ($40,000) or multi-zone controls ($15,000). Installation’s minimal—$1,000-$20,000 for wiring (240V breaker or 480V transformer), no stacks or gas lines. Operating? A 40 kW oven at 400°F for 10 hours uses 400 kWh ($60/day); a 500 kW unit, 5,000 kWh ($750/day)—steep versus gas’s $25-$150/day. Maintenance is $1,000-$20,000 yearly—elements burn out ($500-$5,000), blowers wear ($5,000), filters clog ($50-$200).
Electric ovens thrive on ease. They’re vent-free—perfect for tight or regulated spaces—and start on a dime, no flame warm-up. Heat’s spotless—no burner residue—and control’s surgical, ideal for 1-20 parts or delicate jobs. Downsides? Electricity’s a wallet-drainer—$2,000-$15,000/month versus gas’s $500-$3,000—and output maxes at 800 kW (2.7 million BTUs), paling next to gas’s 10 million BTU ceiling. Safety’s straightforward: ground for static (dust ignites at 0.02 oz/ft³), but no CO or fuel leaks. For 1-5,000 parts/day or 40-foot jobs, electric’s a powerhouse—gas only dominates at extreme volume.
Benchtop Curing Oven
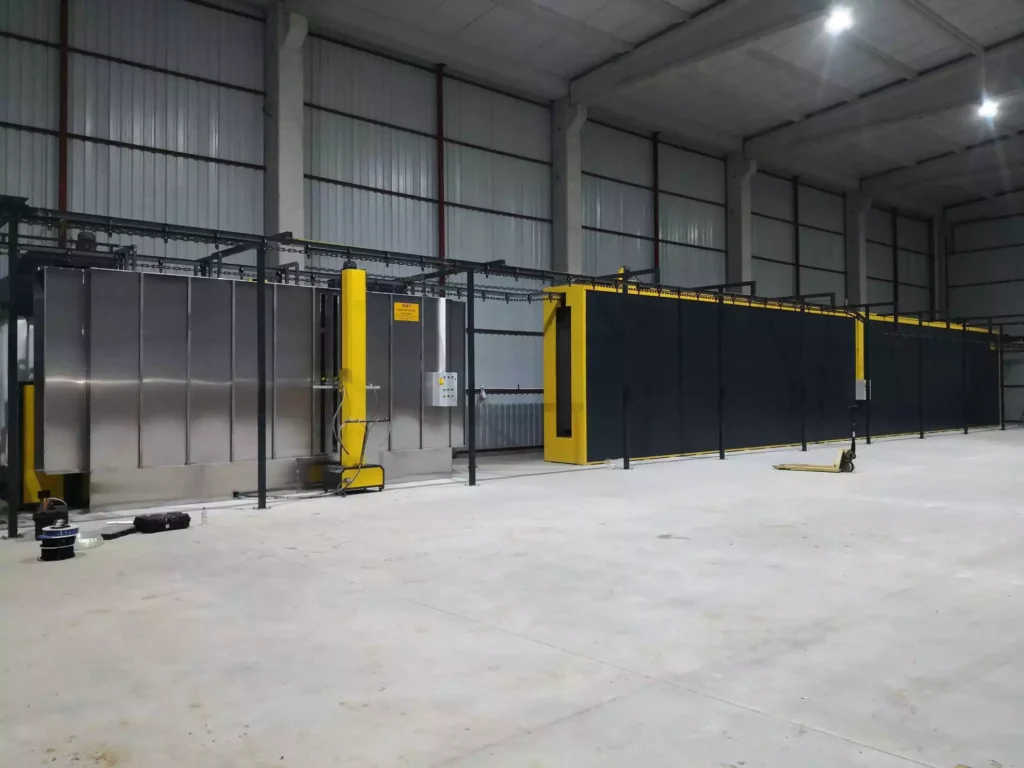
A benchtop curing oven is a compact, tabletop-sized unit designed for small-scale powder coating, ideal for hobbyists, DIY enthusiasts, or small businesses curing parts like jewelry, model components, custom tools, or batches of small automotive bits. These ovens typically operate at 350°F-450°F (175°C-232°C), the sweet spot for melting and curing electrostatically applied powder into a tough, durable finish that outshines liquid paint in hardness, corrosion resistance, and longevity. Built to fit on a workbench or sturdy table, they’re perfect for tight spaces—garages, basements, or craft rooms—offering an entry-level solution that’s affordable, portable, and easy to use without sacrificing quality.
The design is all about efficiency in a small footprint. The shell’s usually 16- or 14-gauge steel—sometimes stainless for durability—double-walled with 2 to 4 inches of insulation like fiberglass or mineral wool, rated for 500°F+ to keep heat contained. Heating comes from electric elements—nichrome coils or small rods—delivering 1-6 kW, powered by a standard 120V household outlet (10-20 amps) or 240V (20-30 amps) for slightly larger models. Interior sizes range from 1’x1’x1’ (1 cu ft) up to 2’x2’x3’ (12 cu ft), with a single hinged door or slide-out tray. Airflow’s modest—100-500 CFM via a small fan—circulating heat evenly in tight quarters. Controls are simple: $20 dial thermostats for basic units, $50-$200 PIDs with a thermocouple for precision, holding temps within 5-10°F.
Take a 18”x18”x18” oven—say, a $300-$500 Eastwood benchtop model—with 2 kW of elements. It hits 400°F in 15-20 minutes on 120V, curing a set of knife scales in 20 minutes for $0.30/hour ($0.15/kWh)—small enough to sit on a garage bench. Or a 2’x2’x2’ DIY build—$200-$400—using an old toaster oven, $100 in insulation, and a $50 PID, curing a motorcycle bracket for $0.45/hour on 240V, 3 kW. For a step up, a 2’x2’x3’ pro-grade unit—$800-$1,500, like a HotCoat Elite—with 4 kW cures small batches (e.g., 10-20 sq in) at $0.60/hour. These max out at parts under 2-3 feet, ideal for low-volume precision work.
Operation’s a breeze. A steel gear gets blasted ($50 handheld gun), hung on a $10 wire rack or skewer, and sprayed with a $100 gun—$5 powder. The oven powers up—elements glowing—preheating to 200°F (5-10 minutes) to outgas, then curing at 390°F for 15-25 minutes (e.g., Prismatic Powders’ 10-minute spec). Airflow’s light—200 CFM—but enough for small parts; too much risks blowing powder off. Powder’s tailored: epoxy ($10/lb) for indoor tools, polyester ($12/lb) for outdoor trinkets. No reclaim at this scale—overspray’s minimal ($1-$2 lost).
Costs are wallet-friendly. Benchtop ovens start at $200-$500 for basic or DIY; pro models hit $800-$2,000 with digital controls or extra capacity. Installation’s zero—plug into a 120V/240V outlet, maybe $50 for a dedicated circuit. Operating? A 2 kW oven at 400°F for 1 hour uses 2 kWh ($0.30/day); a 4 kW unit, 4 kWh ($0.60/day)—cheap versus gas’s setup overhead. Maintenance is $50-$200 yearly—elements fail ($20-$50), fans wear ($50), filters swap ($10). Powder’s $5-$10/job, coating 5-20 sq ft.
Benchtop ovens shine in simplicity. They’re portable—20-50 lbs, no venting—and start fast, perfect for 1-5 parts/run. Heat’s clean, control’s decent, and they fit anywhere with power. Limits? Size caps at 2-3 feet—think knobs, not fenders—and output’s low (6 kW max, 20,000 BTUs), dwarfed by gas or big electric. Safety’s basic: ground for static (dust sparks at 430°F), keep it ventilated. For small runs or tight spaces, they’re unbeatable—scale up, and you’re into batch territory.
A benchtop curing oven is a pint-sized powerhouse tailored for small-scale powder coating, delivering the heat needed to cure powder into a robust, professional-grade finish in a package that sits comfortably on a workbench or sturdy table. These ovens operate at the standard 350°F-450°F (175°C-232°C), melting and bonding electrostatically applied powder onto parts like custom jewelry, model car pieces, small tools, or batches of hardware—think bolts, brackets, or fishing lures—into a coating that’s tougher, more corrosion-resistant, and longer-lasting than any spray paint. They’re the darling of hobbyists, crafters, and small-scale entrepreneurs who need quality results without the space or budget for full-sized ovens, fitting seamlessly into garages, sheds, or even apartment workshops.
The design is compact yet purposeful. The shell’s typically 16- or 14-gauge steel—sometimes stainless for longevity—double-walled with 2 to 4 inches of insulation like fiberglass batting or mineral wool, rated for 500°F-600°F+ to keep heat tight in a small volume. Heating’s all electric: nichrome coils or compact rods, wired for 1-6 kW, running off 120V household power (10-20 amps) for the smallest units or 240V (20-30 amps) for slightly beefier ones. Interior dimensions span 12”x12”x12” (1 cu ft) to 24”x24”x36” (12 cu ft), with a single swing door, slide-out shelf, or top hatch. Airflow’s gentle—100-500 CFM from a small centrifugal fan—circulating heat evenly across tiny parts. Controls are user-friendly: $20 dial thermostats for budget builds, $50-$200 PIDs with thermocouples for precision, holding temps within 5-10°F—good enough for flawless small cures.
Imagine a 16”x16”x16” oven—say, a $250-$400 basic model from Amazon—with 1.5 kW of elements. It hits 400°F in 15 minutes on 120V, curing a handful of custom keychains in 20 minutes for $0.23/hour ($0.15/kWh)—small enough to tuck under a shelf. Or a DIY 20”x20”x20” rig—$150-$300—using a thrift-store toaster oven, $80 in insulation, and a $50 PID, curing a small exhaust manifold for $0.45/hour on 240V, 3 kW. For a pro touch, a 24”x24”x30” unit—$1,000-$2,000, like a Quincy Lab model—with 5 kW cures batches (e.g., 15-30 sq in) at $0.75/hour. These cap at parts under 2-3 feet, perfect for low-volume, high-detail work.
The process is simple and intimate. A brass fitting gets blasted ($30 handheld gun), hung on a $5 wire hook or skewer, and sprayed with a $100 Wagner gun—$3 powder. The oven hums awake—elements glowing—preheating to 200°F (5-15 minutes) to outgas, then curing at 390°F for 15-25 minutes (e.g., Tiger Drylac’s 10-minute spec). Airflow’s light—150 CFM—but sufficient; too strong, and powder drifts off tiny edges. Powder’s picked for the gig: epoxy ($10/lb) for indoor gears, polyester ($12/lb) for outdoor ornaments. Overspray’s negligible ($0.50-$2 lost)—reclaim’s overkill at this scale.
Costs stay lean. Benchtop ovens range from $150-$500 for DIY or entry-level; pro units hit $800-$2,500 with digital controls or extra depth. Installation’s nothing—plug into a 120V/240V socket, maybe $20-$50 for a breaker upgrade. Operating? A 1 kW oven at 400°F for 1 hour uses 1 kWh ($0.15/day); a 6 kW unit, 6 kWh ($0.90/day)—pennies compared to gas’s setup costs. Maintenance is $50-$300 yearly—elements burn out ($20-$60), fans falter ($50-$100), filters swap ($5-$15). Powder’s $3-$10/job, coating 3-25 sq ft.
Benchtop ovens excel in accessibility. They’re lightweight—15-60 lbs, no venting—and heat up fast, ideal for 1-10 parts/run. Heat’s clean, control’s solid, and they squeeze into any powered nook. Downsides? Size limits—2-3 feet max, think knobs, not doors—and power tops out at 6 kW (20,000 BTUs), a fraction of gas or big electric. Safety’s minimal: ground for static (dust flashes at 430°F), keep air moving. For small batches or tight quarters, they’re gold—scale up, and you’re into full batch ovens.
Conclusion
A gas powder coating oven is a crucial investment for any powder coating operation, providing the necessary heat to cure powder coatings effectively. With uniform heat distribution and energy-efficient designs, these ovens ensure high-quality finishes while optimizing operational efficiency.
EMS Powder Coating Equipment is a leading manufacturer of gas powder coating ovens, offering innovative solutions tailored to meet the diverse needs of various industries. Their commitment to quality, performance, and customer support makes EMS the best choice for businesses seeking reliable coating solutions.
By choosing EMS gas powder coating ovens, companies can enhance their curing processes, achieve superior finishes, and reduce operational costs. With a focus on efficiency and innovation, EMS stands out as the premier manufacturer for businesses in need of top-tier powder coating equipment.