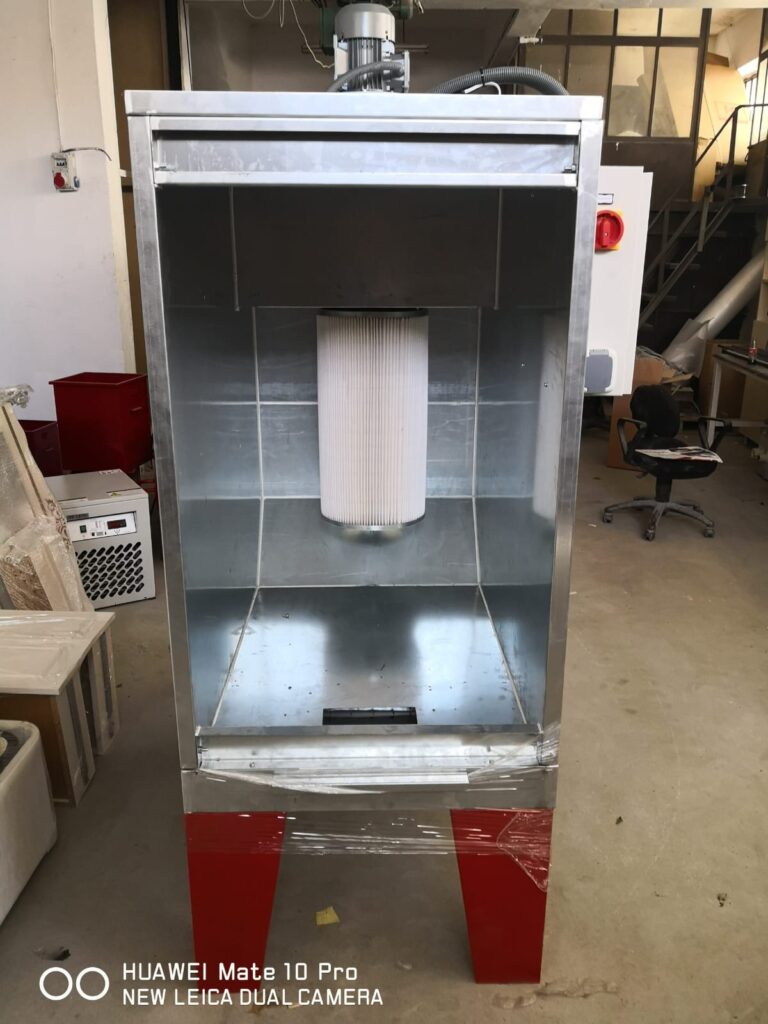
A small powder coating booth is the easiest solutions for powder coating applications when you don’t have many colors and you don’t need to change colors often. Our manual powder coating spray booths are designed and manufactured either from galvanized sheets or mild steel sheets which are then painted.
There is an inside space for the painter to hang his parts and paint with his powder coating gun, while filters suck and clean the air in the medium and blow off the paint gathered on the filters once in a while.
Manual powder coating booths can be made starting from 1 filter and 2,3,4,5,6 and 8 filters maximum. We use 32x60cm cellulose powder coating filters in our booths. There is an electrical board, to control the blow-off valves to clean the filters and lights inside for the operator to see and check the painting quality
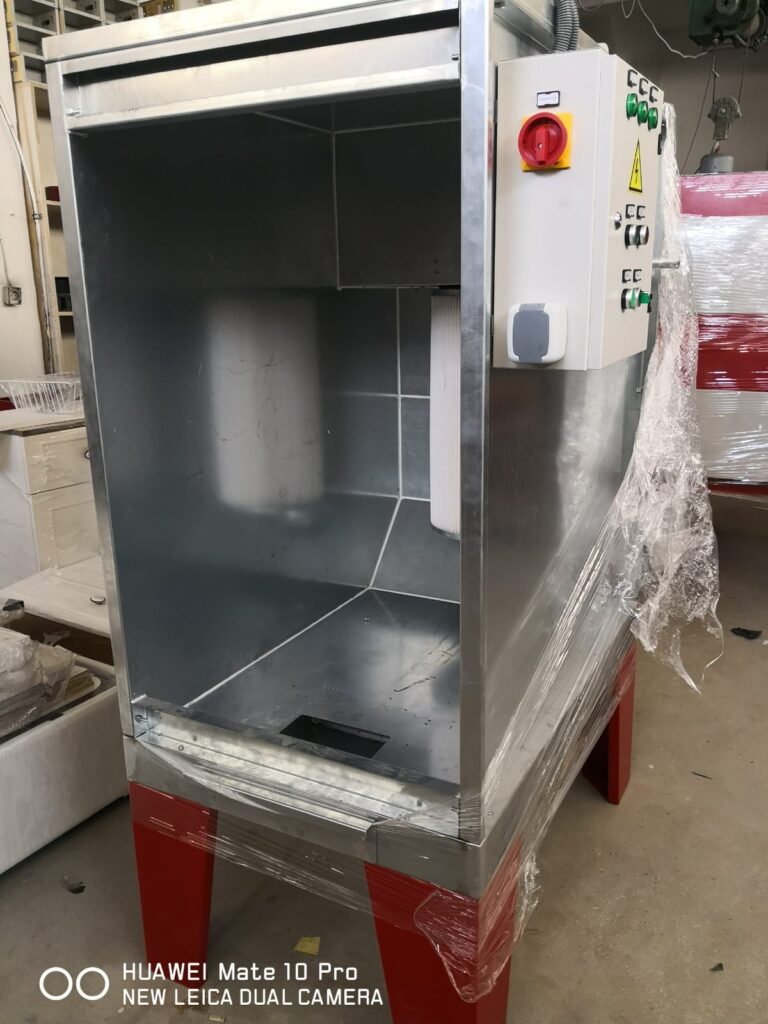
Filtration is achieved by using cartridge filters in an open compartment. The filtered clean air (now devoid of powder particles) then passes through a sealed plenum chamber and via the centrifugal extraction fan back into the factory atmosphere. The system avoids any explosion risk that may be caused by passing powder-laden unfiltered air into a sealed chamber.
Sound Level Due to the level of airflow required the noise level determines that ear defenders are required.
Small Powder Coating Booth
Small powder coating booths are compact and versatile enclosures designed for applying powder coatings to smaller workpieces or for low-volume production. They offer a cost-effective solution for businesses that require powder coating capabilities without investing in large, industrial-scale booths.
Advantages of Small Powder Coating Booths
- Space Efficiency: Small booths occupy minimal space, making them suitable for smaller workshops or limited production areas.
- Cost-Effectiveness: The smaller size and simpler design of these booths translate into lower initial investment costs.
- Versatility: Small booths can accommodate a variety of workpiece sizes and shapes, catering to diverse production needs.
- Portability: Some smaller booths are designed to be portable, allowing for easy relocation and temporary setups.
- Energy Efficiency: Smaller booths require less energy to operate, reducing energy consumption and costs.
Components of Small Powder Coating Booths
- Enclosure: The enclosure provides a controlled environment for applying powder coating and preventing overspray contamination. It typically includes walls, a ceiling, a floor grate, and an exhaust system.
- Powder Coating Guns: Powder coating guns apply the powder onto the workpieces. Electrostatic guns are commonly used in small booths due to their efficient powder distribution.
- Powder Recovery System: A powder recovery system collects overspray powder, reducing waste and allowing for powder reuse. It may involve cyclones, filters, or a combination of both.
- Air Circulation System: The air circulation system ensures even distribution of powder and removal of overspray. It consists of fans, ducts, and plenums.
- Control System: The control system regulates the operation of the booth, including powder delivery, air circulation, and powder recovery. It may involve timers, sensors, and control panels.
Applications of Small Powder Coating Booths
- Small-Scale Production: Small booths are ideal for low-volume production of powder-coated parts.
- Prototyping and Testing: Small booths provide a convenient and cost-effective setup for prototyping and testing new powder coating applications.
- Customizing and Repairing: Small booths can be used for customizing or repairing smaller items, such as bicycle frames, motorcycle parts, or hardware components.
- Powder Coating Services: Small booths are suitable for businesses offering powder coating services to individual customers or small businesses.
- Educational and Training Purposes: Small booths can be used in educational settings or training centers to teach powder coating techniques.
Considerations When Choosing a Small Powder Coating Booth
- Workpiece Size and Volume: Select a booth that can accommodate the size and volume of your typical workpieces.
- Ventilation Requirements: Ensure the booth has adequate ventilation to handle the amount of powder being used and comply with local regulations.
- Filter Efficiency: Choose filters that are appropriate for the type of powder being used and provide the necessary level of filtration.
- Safety Features: Ensure the booth has safety features such as emergency shut-off switches, grounding connections, and proper lighting.
- Ease of Use: Consider the booth’s design and controls for ease of operation and maintenance.
Conclusion
Small powder coating booths offer a practical and cost-effective solution for smaller-scale powder coating applications. By selecting the appropriate booth, considering ventilation and safety requirements, and ensuring proper maintenance, businesses can achieve high-quality powder coating results while maximizing space efficiency and resource utilization.
Powder Coating Booth Design
The powder coating spray booth design in the EU countries is usually chosen as the open type. Here it is also possible to make powder coating over powder coating. This method is also called spraying over powder coating and is usually used for parts that need to have a longer service life.
The powder paint booth is designed according to the inner space and we have the following options for our powder paint booths:
- 2 Filter Booth inner dimensions in mm: 1200(W) x 1500(D) x 2250(H)
- 3 Filter Booth inner dimensions in mm: 1500(W) x 1500(D) x 2250(H)
- 4 Filter Booth inner dimensions in mm: 2000(W) x 1500(D) x 2250(H)
- 5 Filter Booth inner dimensions in mm: 3000(W) x 1500(D) x 2250(H)
- 6 Filter Booth inner dimensions in mm: 4000(W) x 1500(D) x 2250(H)
- 8 Filter Booth inner dimensions in mm: 5000(W) x 1500(D) x 2250(H)
- 10 Filter Booth inner dimensions in mm: 6000(W) x 1500(D)x 2250(H)
A small powder coating booth, often referred to as a small powder coating enclosure or mini powder coating booth, is a compact and enclosed workspace designed for applying powder coatings to small or medium-sized workpieces. These booths are commonly used in settings such as small manufacturing operations, custom coating shops, automotive garages, and hobbyist workshops. Here are the key features and considerations for a small powder coating booth:
- Enclosure Size: Small powder coating booths are designed to accommodate workpieces of various sizes, but they are generally smaller in scale compared to larger industrial booths. The booth’s dimensions can vary, but they are typically designed to fit within limited workshop or garage spaces.
- Powder Containment: Like larger booths, small powder coating booths are designed to contain overspray powder during the coating process. This containment prevents powder from escaping into the surrounding environment.
- Exhaust and Ventilation: Proper ventilation and exhaust systems are critical in small powder coating booths to remove excess powder and maintain a clean and safe working environment. Adequate airflow helps in controlling airborne particles and fumes.
- Powder Recovery: Some small booths may include a powder recovery system, such as a simple filter unit, to collect and reclaim overspray powder. This reduces material waste and lowers operating costs.
- Lighting: Adequate lighting is essential for operators to see and inspect the workpieces during the coating process. Good visibility ensures consistent and even powder application.
- Access Doors: Access doors or openings allow for the placement and retrieval of workpieces. These doors should be easy to open and close, ensuring efficient workflow.
- Powder Coating Gun: Small booths typically use manual powder coating guns for their versatility and ease of use. The choice of gun can vary depending on the specific application requirements.
- Control Panel: A control panel with basic controls for adjusting powder flow rate and fan speed may be included, allowing for some customization of the coating process.
- Workpiece Handling: Small booths may have racks, hooks, or hangers to hold and suspend workpieces during coating. The design should maximize space usage within the limited booth size.
- Safety Features: Safety features such as grounding mechanisms, emergency shut-off switches, and safety interlocks should be integrated into the booth to ensure operator safety.
- Compliance: Small powder coating booths should adhere to safety regulations and standards specific to the region and industry in which they are used.
Small powder coating booths are suitable for a range of applications, including coating automotive parts, motorcycle components, bicycles, small appliances, and various metal or plastic objects. They offer the advantage of space efficiency and are often more affordable than larger industrial booths. However, they are best suited for projects that do not require high production volumes or oversized workpieces.
Small Powder Coating Booth for Alloy Wheel Painting
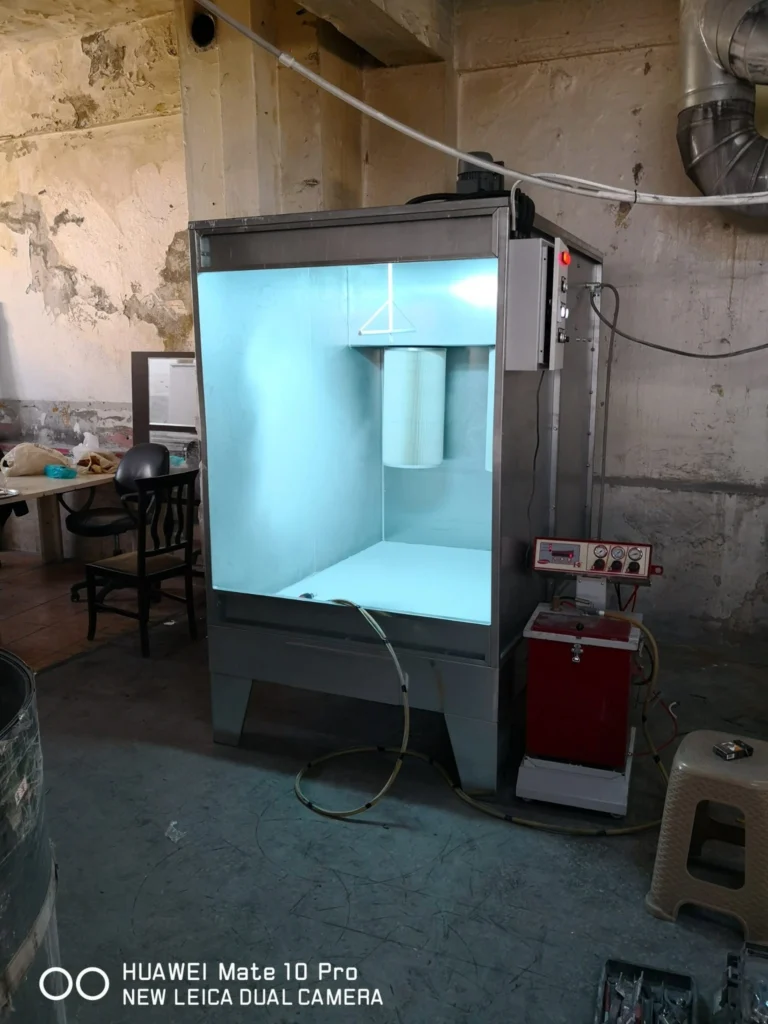
A small powder coating booth for alloy wheel painting is an essential piece of equipment for any business that powder coats alloy wheels. A small powder coating booth is typically designed to accommodate one or two alloy wheels at a time. This makes it ideal for small businesses or businesses that only need to powder coat a small number of alloy wheels per day.
Benefits of Using a Small Powder Coating Booth for Alloy Wheel Painting
There are many benefits to using a small powder coating booth for alloy wheel painting, including:
- Affordability: Small powder coating booths are typically more affordable than larger booths.
- Portability: Small powder coating booths are typically portable, making them easy to move and install in different locations.
- Ease of use: Small powder coating booths are typically easy to use, even for beginners.
- Efficiency: Small powder coating booths can powder coat alloy wheels quickly and efficiently.
- High-quality finish: Small powder coating booths can produce a high-quality finish on alloy wheels.
Features of a Small Powder Coating Booth for Alloy Wheel Painting
A small powder coating booth for alloy wheel painting typically has the following features:
- Compact size: Small powder coating booths are typically designed to fit in small spaces.
- Powder coating spray gun: A powder coating spray gun is used to apply the powder coating to the alloy wheels.
- Powder coating recovery system: A powder coating recovery system collects the overspray powder and returns it to the powder coating hopper for reuse.
- Ventilation system: A ventilation system removes the powder coating dust from the booth.
- Lighting system: A lighting system provides adequate lighting for the powder coating process.
How to Choose a Small Powder Coating Booth for Alloy Wheel Painting
When choosing a small powder coating booth for alloy wheel painting, it is important to consider the following factors:
- The size of the alloy wheels you need to powder coat: Make sure to choose a booth that is large enough to accommodate the largest alloy wheels you need to coat.
- The type of powder coating you are using: Some types of powder coating require different booth conditions. Choose a booth that is compatible with the type of powder coating you are using.
- The production volume: If you need to powder coat a high volume of alloy wheels, you will need a booth that is fast enough to keep up with the demand. Choose a booth with a high capacity and fast curing times.
- The budget: Small powder coating booths can range in price from a few thousand dollars to tens of thousands of dollars. Choose a booth that fits your budget.
Operating and Maintaining a Small Powder Coating Booth for Alloy Wheel Painting
Once you have chosen a small powder coating booth for alloy wheel painting, it is important to learn how to operate and maintain it properly. This will help to ensure that the booth produces a high-quality finish and lasts for many years.
Here are some tips for operating and maintaining a small powder coating booth for alloy wheel painting:
- Clean the booth regularly: Powder coating dust can build up inside the booth over time, which can reduce the quality of the finish. Clean the booth regularly to remove any dust buildup.
- Inspect the booth regularly: Inspect the booth regularly for any signs of wear or damage. If you find any problems, have them repaired immediately.
- Calibrate the booth’s powder coating system regularly: The booth’s powder coating system should be calibrated regularly to ensure that the system is applying the powder coating correctly.
- Follow the manufacturer’s instructions: Be sure to follow the manufacturer’s instructions for operating and maintaining your small powder coating booth for alloy wheel painting.
Safety Precautions
Small powder coating booths for alloy wheel painting can be dangerous if not used properly. Here are some safety precautions to follow when using a small powder coating booth for alloy wheel painting:
- Wear personal protective equipment (PPE): Wear PPE, such as a respirator, gloves, and goggles, when using a small powder coating booth for alloy wheel painting. This will help to protect you from the powder coating dust and fumes.
- Ventilate the area: Make sure that the area where you are using the booth is well ventilated. This will help to remove the powder coating dust and fumes from the air.
- Keep the booth clean: Keep the booth clean to prevent powder coating dust from building up.
- Follow the manufacturer’s instructions: Be sure to follow the manufacturer’s instructions for safely operating and maintaining your small powder coating booth for alloy wheel painting.
Conclusion
A small powder coating booth for alloy wheel painting is an essential piece of equipment for any business that powder coats alloy wheels. By choosing the right booth and operating and maintaining it properly, you can ensure that
Small Powder Coating Booth
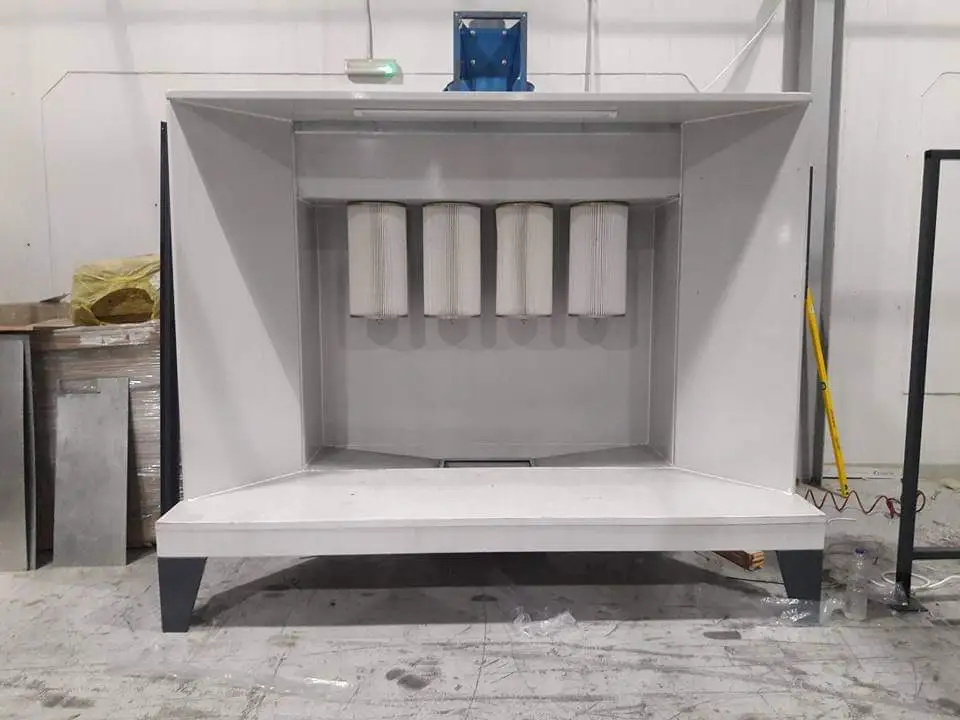
A small powder coating booth is a controlled environment where the process of powder coating is carried out. Powder coating is a type of coating that is applied as a dry powder and then cured to form a hard finish. The booth provides a contained space for the application of the powder, ensuring a clean and efficient process. Here are some key elements and considerations for a small powder coating booth:
- Enclosure:
- The booth should be enclosed to contain the powder overspray and prevent it from spreading to the surrounding area.
- Walls and ceiling materials should be easy to clean to maintain a clean working environment.
- Ventilation:
- Proper ventilation is crucial to remove airborne powder particles and ensure a safe working environment.
- An exhaust system with adequate airflow is necessary to capture and filter the powder particles.
- Filtration System:
- Install a high-quality filtration system to capture and filter out the powder particles from the air. This helps maintain air quality and prevent environmental contamination.
- Filters may include primary and secondary filters, and they should be regularly checked and replaced.
- Lighting:
- Adequate lighting is essential for accurate application of the powder coating.
- Ensure that the lighting is positioned to minimize shadows and provide uniform illumination.
- Grounding and Static Control:
- Implement measures to control static electricity, as it can interfere with the powder coating process.
- Proper grounding of the booth, equipment, and personnel is critical to prevent electrostatic discharge.
- Size and Layout:
- Design the booth to accommodate the size and shape of the parts you will be coating.
- Consider the layout for efficient workflow and ease of movement.
- Powder Application Equipment:
- Install a powder coating gun and related equipment suitable for the scale of your operations.
- Ensure that the equipment is properly maintained for consistent and quality coatings.
- Curing Oven:
- Depending on the type of powder used, a curing oven may be necessary to bake the powder-coated parts and achieve the desired finish.
- The oven should be appropriately sized for the parts being coated.
- Safety Measures:
- Implement safety features such as emergency stop buttons, fire suppression systems, and proper personal protective equipment for operators.
- Compliance with Regulations:
- Ensure that the booth complies with local environmental and safety regulations related to powder coating operations.
When setting up a small powder coating booth, it’s important to carefully plan and design the space to meet your specific requirements and comply with industry standards and regulations. Additionally, training operators on proper powder coating techniques and safety procedures is essential for successful and safe operations.
Parts of the Small Powder Coating Booth
Certainly, when referring to the components or parts of a small powder coating booth, here are the key elements typically found in such a setup:
- Booth Enclosure:
- Walls, ceiling, and floor materials designed to contain overspray and maintain a clean environment.
- Ventilation System:
- Exhaust fan(s) to facilitate airflow and remove airborne powder particles.
- Ductwork to direct air and contaminants outside the booth.
- Air intake system to maintain a balanced airflow.
- Filtration System:
- Primary and secondary filters to capture and remove powder particles from the air.
- Filter housing and frames.
- Lighting:
- Light fixtures strategically placed to illuminate the work area effectively.
- Grounding and Static Control:
- Grounding wires and rods to prevent static buildup.
- Anti-static flooring or grounding straps for personnel.
- Powder Application Equipment:
- Powder coating gun: The device used to apply the powder to the workpiece.
- Control unit for adjusting voltage, current, and airflow.
- Powder delivery system, including hoses and nozzles.
- Recovery System:
- Booth-mounted or external powder recovery system to collect oversprayed powder for reuse.
- Curing Oven:
- Oven or heating system for curing the powder-coated parts.
- Temperature control system.
- Safety Features:
- Emergency stop buttons or switches.
- Fire suppression system.
- Proper signage indicating safety protocols.
- Control Panel:
- Central control panel for managing various aspects of the powder coating process, such as fan speed, temperature, and safety features.
- Personnel Protection:
- Personal protective equipment (PPE) for operators, including gloves, masks, and aprons.
- Access Doors:
- Doors for entry and exit, designed to prevent powder leakage.
- Powder Storage Area:
- If applicable, a designated area for storing different types and colors of powder.
- Compliance Equipment:
- Devices for monitoring and ensuring compliance with environmental and safety regulations.
- Cleanout System:
- System for cleaning and maintaining the booth, such as vacuum systems for removing accumulated powder.
- Workpiece Handling Equipment:
- Racks, hooks, or other fixtures for holding and moving the workpieces through the coating process.
When setting up a small powder coating booth, it’s important to ensure that each component is appropriately sized and installed to facilitate an efficient and safe powder coating process. Additionally, regular maintenance and adherence to safety protocols are essential for optimal performance and operator well-being.
Booth Enclosure
The booth enclosure in a powder coating setup serves as the physical structure that contains the powder coating process, preventing overspray and maintaining a controlled environment. Here are key aspects of the booth enclosure:
- Material:
- Walls, ceiling, and floor of the booth are typically constructed using materials that are easy to clean and resist the build-up of powder residue. Common materials include galvanized steel, stainless steel, or other non-porous surfaces.
- Construction:
- The booth is constructed to be sturdy and durable, providing a secure space for the powder coating process.
- Modular construction is common, allowing for flexibility in booth size and configuration.
- Seals and Gaskets:
- Seals and gaskets are used at joints and openings to ensure that the booth is airtight. This prevents the escape of powder particles and maintains proper airflow within the booth.
- Access Doors:
- The booth typically includes access doors for personnel to enter and exit. These doors should have proper sealing mechanisms to prevent powder leakage.
- Windows and Viewing Panels:
- Some booths have windows or viewing panels to allow operators to monitor the coating process without opening the doors, minimizing the risk of powder escaping.
- Lighting:
- Adequate lighting is crucial for operators to see and inspect the workpieces. Light fixtures are strategically placed within the booth to provide uniform illumination.
- Exhaust Openings:
- Exhaust openings are strategically located to facilitate the capture and removal of airborne powder particles. These openings are connected to the ventilation system.
- Hanger System:
- If applicable, a system for hanging or supporting the workpieces during the coating process. This may include hooks, racks, or other fixtures.
- Grounding Points:
- Grounding points are installed to dissipate static electricity, reducing the risk of electrostatic discharge during the coating process.
- Cleaning Accessibility:
- Design features that facilitate easy cleaning of the booth, including smooth surfaces and removable panels for access to all areas.
- Fire Safety Measures:
- The booth may be equipped with fire safety features such as fire-resistant materials and fire suppression systems to ensure operator safety.
- Compliance with Regulations:
- Booth construction and materials should comply with local regulations and safety standards related to powder coating operations.
When designing and setting up a powder coating booth enclosure, it’s crucial to consider the size and type of workpieces to be coated, the volume of coating operations, and environmental and safety regulations. Regular maintenance and cleaning of the booth are essential to ensure consistent and high-quality powder coating results.
Ventilation System
The ventilation system in a powder coating booth is a critical component designed to control airflow, remove airborne powder particles, and maintain a safe and efficient working environment. Here are the key aspects of a ventilation system in a powder coating booth:
- Exhaust Fan(s):
- Powerful exhaust fans are installed to create a controlled airflow within the booth.
- The fans are strategically positioned to capture overspray and direct it towards the filtration system.
- Airflow Design:
- The ventilation system is designed to ensure a consistent and controlled airflow pattern throughout the booth.
- The goal is to prevent the escape of powder particles and direct them toward the exhaust system.
- Ductwork:
- Ducts are used to transport the air from the booth to the exterior or to a filtration system.
- Properly designed ductwork ensures efficient and effective removal of contaminants.
- Air Intake System:
- An intake system is incorporated to balance the airflow within the booth.
- It helps prevent negative pressure, which can affect the performance of the exhaust system.
- Balancing Airflow:
- The ventilation system is designed to balance the airflow to avoid turbulence and ensure consistent coating application.
- Variable Airflow Control:
- Some systems may have variable speed controls to adjust the airflow based on the specific coating requirements and workpiece sizes.
- Air Velocity Control:
- Control mechanisms may be in place to adjust the speed and direction of the airflow, allowing for optimization based on the coating process.
- Exhaust Openings:
- Exhaust openings or outlets are strategically positioned to capture overspray and direct it out of the booth.
- These openings are connected to the ductwork leading to the exhaust fan(s).
- Air Filters:
- Air filters are part of the ventilation system and are designed to capture and remove powder particles from the air.
- Primary and secondary filters may be used, and they should be regularly checked and replaced to maintain efficiency.
- Positive Pressure Zones:
- In some systems, positive pressure zones may be created to prevent outside air, contaminants, or ambient humidity from entering the booth.
- Environmentally Controlled Systems:
- Some advanced systems may include features to control temperature and humidity within the booth for optimal coating conditions.
- Compliance with Regulations:
- The ventilation system design should comply with local environmental and safety regulations governing powder coating operations.
Properly designed and maintained ventilation systems are crucial for the safety of operators, the quality of powder coating applications, and compliance with environmental regulations. Regular inspections, cleaning, and filter replacements are essential for the continued effectiveness of the ventilation system.
Filtration System

The filtration system in a powder coating booth plays a crucial role in capturing and removing powder particles from the air, ensuring a clean and safe working environment. Here are the key components and considerations for a filtration system in a powder coating booth:
- Primary Filters:
- Primary filters are the first line of defense and capture larger particles of overspray.
- They prevent these particles from reaching the more sensitive secondary filters, extending the life of the entire filtration system.
- Secondary Filters:
- Secondary filters are designed to capture finer particles that may pass through the primary filters.
- These filters provide higher efficiency in removing smaller particles from the air.
- Filter Housing and Frames:
- The filtration system includes housings and frames to securely hold the filters in place.
- Well-designed frames ensure a proper seal to prevent air bypass and maximize filtration efficiency.
- Filter Media:
- Filters are made of media that is specifically designed to capture and retain powder particles.
- Common filter media includes polyester, fiberglass, or other materials with high particle retention capabilities.
- Filter Replacement Indicators:
- Some systems are equipped with indicators to signal when filters need replacement.
- Regularly replacing filters is essential for maintaining optimal airflow and filtration efficiency.
- Accessibility for Maintenance:
- The filtration system should be designed for easy access to facilitate regular maintenance tasks such as filter replacement and cleaning.
- Air-to-Cloth Ratio:
- The air-to-cloth ratio is a key consideration in filter design and refers to the volume of air that can be filtered per unit of filter surface area.
- Properly balancing this ratio is crucial for efficient filtration.
- Filter Efficiency Rating:
- Filters are assigned an efficiency rating based on their ability to capture particles of a certain size.
- High-efficiency filters are important for maintaining air quality and complying with environmental regulations.
- Filter Type:
- Depending on the specific requirements and regulations, different types of filters may be used, such as bag filters, cartridge filters, or panel filters.
- Environmental Compliance:
- The filtration system must comply with local environmental regulations regarding the control of airborne contaminants generated during powder coating.
- Filter Disposal:
- Proper disposal methods for used filters must be followed to adhere to environmental guidelines.
- Filter Cleaning or Replacement Schedule:
- Establishing a regular schedule for filter maintenance, cleaning, or replacement is essential to ensure consistent performance.
- Pressure Drop Monitoring:
- Monitoring the pressure drop across the filters helps identify when they are becoming clogged and need replacement.
Regular inspection and maintenance of the filtration system are critical to the overall performance of the powder coating booth. It not only ensures a clean working environment but also contributes to the longevity and efficiency of the entire powder coating system.
Grounding and Static Control
Grounding and static control are crucial aspects of a powder coating booth to prevent the buildup of static electricity, which can interfere with the coating process and pose safety risks. Here are the key components and considerations for grounding and static control in a powder coating booth:
- Grounding Wires and Rods:
- Grounding wires are strategically installed to create a path for the dissipation of static electricity.
- Grounding rods may be driven into the ground outside the booth to provide a secure grounding connection.
- Grounding Points:
- Various components within the booth, such as the workpiece hangers, powder coating gun, and booth structure, should be equipped with grounding points.
- These points ensure that static charges are safely and efficiently grounded.
- Grounding Straps for Personnel:
- Operators and personnel working in the booth may use grounding straps or wrist straps to ensure that they are grounded and prevent the buildup of static charges on their bodies.
- Anti-Static Flooring:
- The booth floor may be constructed with anti-static or conductive flooring materials.
- Anti-static flooring helps dissipate static charges and provides a safe working environment for personnel.
- Ionization Systems:
- Ionization systems release ions into the air, neutralizing static charges on surfaces.
- These systems can be installed at various points in the booth to minimize the risk of electrostatic discharge.
- Conductive Equipment:
- Powder coating guns, workpiece hangers, and other equipment used in the booth may be designed with conductive materials to aid in grounding.
- Proper Workpiece Grounding:
- Ensuring that workpieces are properly grounded before the coating process begins is essential to prevent the attraction of airborne powder particles due to static charges.
- Static Control Devices:
- Devices such as static control bars or brushes may be installed along the conveyor system or in areas where workpieces move to reduce static charges.
- Humidity Control:
- Maintaining a controlled level of humidity in the booth can help reduce the buildup of static electricity.
- Humidity acts as a natural conductor and can enhance the effectiveness of static control measures.
- Operator Training:
- Proper training for operators on the importance of grounding and static control measures is essential for maintaining a safe working environment.
- Monitoring Systems:
- Implementing monitoring systems to regularly check the effectiveness of grounding and static control measures.
- Alarms or indicators may be included to alert operators if static electricity levels become a concern.
- Compliance with Safety Standards:
- Ensuring that the grounding and static control measures comply with relevant safety standards and regulations.
Proper grounding and static control measures are essential to prevent electrostatic discharge, which can negatively impact the quality of powder coating applications and pose safety risks to both personnel and equipment. Regular checks and maintenance of these measures are critical for their ongoing effectiveness.
Powder Application Equipment
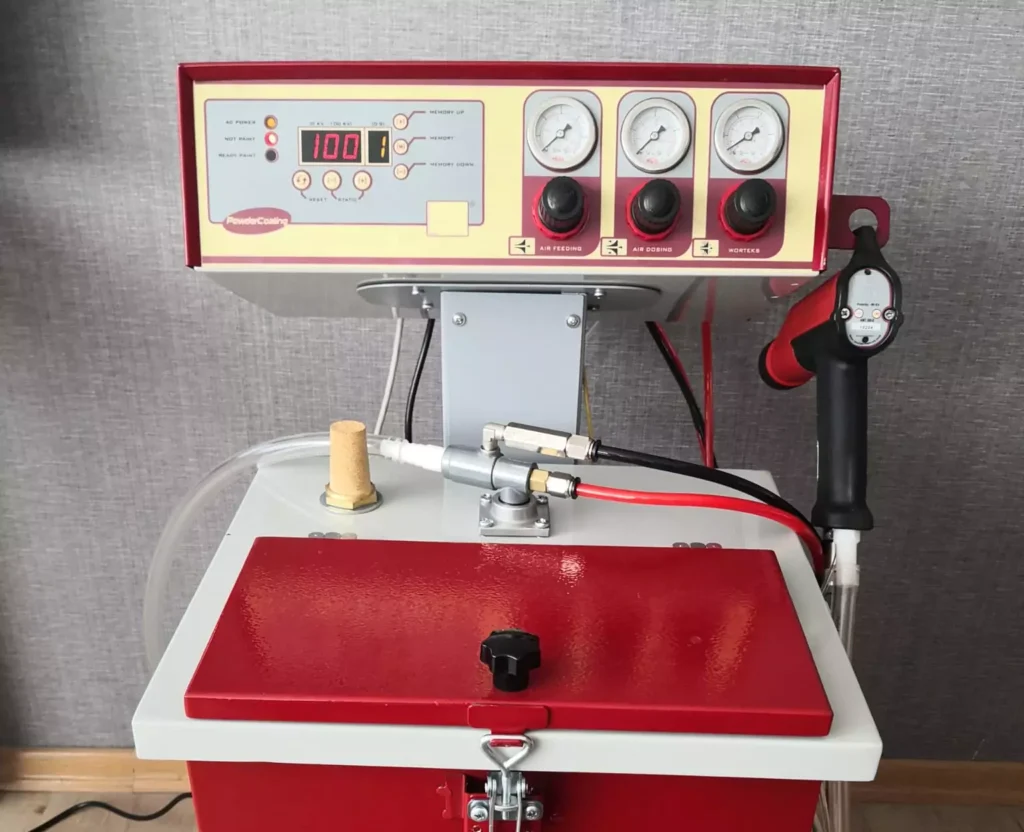
Powder application equipment is a critical component of a powder coating system, responsible for applying the dry powder to the surface of the workpieces. The key element in this equipment is the powder coating gun. Here are the primary components and considerations for powder application equipment:
- Powder Coating Gun:
- The powder coating gun is the primary tool used to apply the dry powder to the workpiece.
- It features a nozzle through which the powder is electrostatically charged and sprayed onto the grounded workpiece.
- Control Unit:
- The control unit is responsible for adjusting and regulating various parameters of the powder coating process.
- It typically includes controls for voltage, current, and airflow to optimize the powder coating application.
- Powder Delivery System:
- The powder delivery system consists of hoses and tubes that transport the dry powder from the powder container to the powder coating gun.
- Properly designed delivery systems ensure a consistent and controlled flow of powder.
- Fluidizing Hopper or Powder Container:
- The powder is stored in a fluidizing hopper or a powder container equipped with a fluidizing system.
- The fluidizing system ensures that the powder remains in a suspended, fluid-like state for consistent feeding to the powder gun.
- Powder Sieve:
- A powder sieve is used to remove any clumps or impurities from the powder before it enters the powder gun.
- This ensures a smooth and even powder flow.
- Nozzles and Electrodes:
- Nozzles are a crucial part of the powder gun, determining the spray pattern and particle size.
- Electrodes within the gun charge the powder particles, enabling them to adhere to the grounded workpiece.
- Powder Cups or Containers:
- Some powder coating guns come with small powder cups or containers for easy color changes or testing.
- Gun Movers and Automation:
- In automated powder coating systems, gun movers or robots may be used to precisely control the movement of the powder coating gun for consistent coverage.
- Gun Cleaning Systems:
- Systems for purging and cleaning the powder coating gun, preventing cross-contamination of colors and ensuring the longevity of the equipment.
- Voltage Multipliers:
- Some powder coating guns feature voltage multipliers to generate higher electrostatic charges, improving powder transfer efficiency.
- Powder Recirculation Systems:
- In some setups, powder recirculation systems may be employed to reclaim and reuse excess powder that does not adhere to the workpiece.
- Compliance with Coating Requirements:
- The powder coating equipment should be selected based on the specific requirements of the coating process, including the type of powder used and the characteristics of the workpieces.
- Grounding Devices:
- The powder coating gun and associated equipment should have proper grounding devices to prevent electrostatic discharge.
- Operator Training:
- Proper training of operators on the correct use, maintenance, and troubleshooting of the powder application equipment is crucial for optimal performance.
When choosing powder application equipment, it’s essential to consider factors such as the type of powder, desired finish, production volume, and the characteristics of the workpieces. Regular maintenance and cleaning of the equipment are also necessary to ensure consistent and high-quality powder coating applications.
Recovery System

The recovery system in a powder coating booth is responsible for capturing and reclaiming excess powder particles that do not adhere to the workpieces during the coating process. This system helps minimize waste, reduce environmental impact, and optimize the use of powder materials. Here are the key components and considerations for a powder recovery system:
- Powder Recovery Booth or Module:
- A designated area within the powder coating booth or a separate module where the recovery process takes place.
- The booth or module is designed to contain the overspray and facilitate efficient powder recovery.
- Collector Modules or Filters:
- Collector modules or filters are positioned within the recovery system to capture oversprayed powder particles.
- These filters are designed to allow the powder to adhere while allowing clean air to pass through.
- Reclaiming Hopper or Cyclone Separator:
- The collected powder is directed to a reclaiming hopper or a cyclone separator where separation of the powder from the air occurs.
- The hopper or cyclone uses gravity or centrifugal force to separate the powder from the airflow.
- Recovery Fan:
- A dedicated recovery fan assists in creating the necessary airflow to transport the oversprayed powder from the booth to the recovery system.
- The fan aids in moving the powder through the collection process.
- Powder Recovery Pump:
- In some systems, a powder recovery pump may be employed to assist in transporting the collected powder to the reclaiming hopper or cyclone.
- Fluidizing System:
- A fluidizing system within the reclaiming hopper ensures that the collected powder remains in a fluid-like state for ease of transport and application.
- Powder Storage System:
- The recovered powder is directed to a storage system, which may include bins or containers.
- Properly designed storage systems allow for easy retrieval and reuse of the reclaimed powder.
- Sieves or Filters for Reclaimed Powder:
- Sieves or filters may be used to further refine the reclaimed powder, removing any impurities or larger particles before it is reused.
- Powder Pumps and Feeders:
- Powder pumps and feeders assist in transporting the reclaimed powder from the storage system to the powder application equipment.
- These components ensure a consistent and controlled flow of powder for subsequent coating processes.
- Monitoring and Control Systems:
- Monitoring systems are often integrated to track the performance of the recovery system.
- Control systems may adjust parameters such as fan speed or reclaiming hopper operation for optimal efficiency.
- Compliance with Environmental Regulations:
- The recovery system should comply with local environmental regulations related to the handling and reuse of powder materials.
- Regular Maintenance:
- Regular cleaning and maintenance of the recovery system components are crucial for its efficient operation and longevity.
Implementing an effective recovery system is essential for reducing powder waste, minimizing costs, and promoting sustainable powder coating practices. Regular maintenance and monitoring ensure that the system operates optimally and contributes to overall efficiency in the powder coating process.
Curing Oven
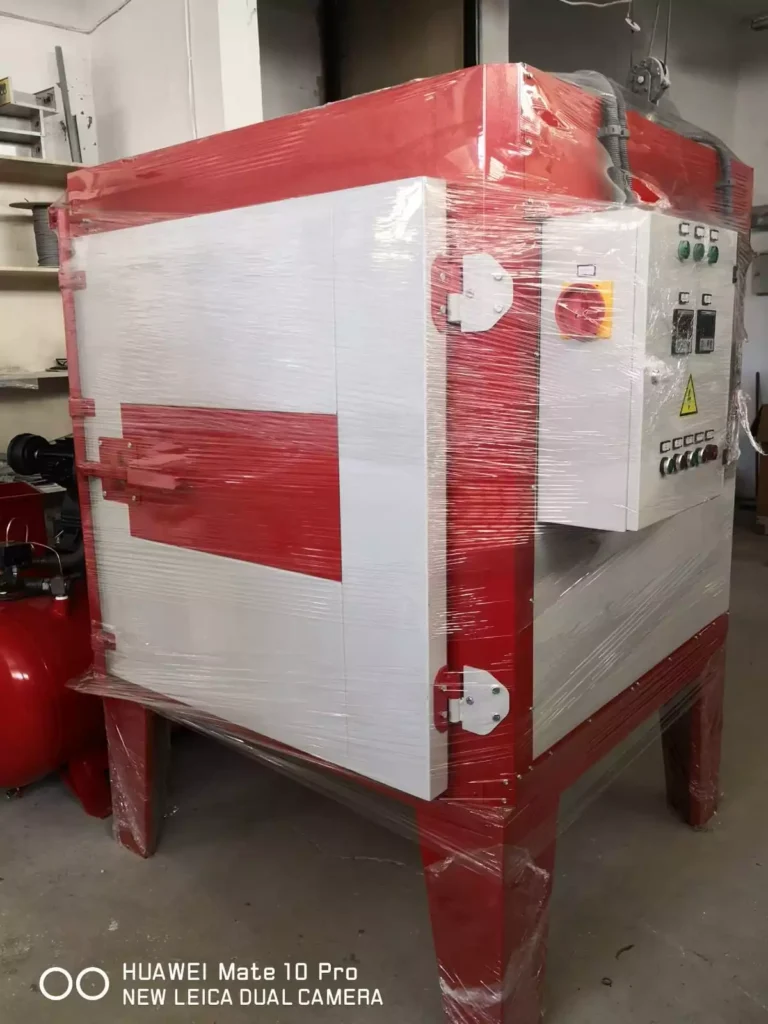
A curing oven is an essential component in the powder coating process, responsible for baking or curing the applied powder coating on the workpieces. The curing process transforms the powder into a durable and protective finish. Here are the key components and considerations for a curing oven in a powder coating system:
- Oven Chamber:
- The oven chamber is the enclosed space where the curing process takes place.
- It is constructed with materials that can withstand the curing temperatures and maintain a consistent temperature throughout the chamber.
- Heating Elements:
- Electric, gas, or infrared heating elements are used to provide the necessary heat for curing the powder coating.
- The type of heating elements depends on the specific requirements of the coating process.
- Temperature Control System:
- A temperature control system regulates the oven temperature to achieve and maintain the desired curing temperature.
- Precise temperature control is crucial for achieving a quality finish and avoiding over-curing or under-curing.
- Conveyor System:
- In continuous powder coating lines, a conveyor system is often integrated to move workpieces through the curing oven.
- The conveyor system ensures a consistent and controlled dwell time within the oven.
- Air Circulation System:
- Fans or blowers are used to circulate heated air within the oven chamber.
- Proper air circulation ensures uniform heat distribution and consistent curing across all surfaces of the workpieces.
- Insulation:
- The oven is insulated to minimize heat loss and maintain a stable internal temperature.
- Insulation materials are chosen to withstand high temperatures and provide energy efficiency.
- Exhaust System:
- An exhaust system may be integrated to remove any fumes or by-products generated during the curing process.
- Proper ventilation helps maintain a safe working environment.
- Cooling Zone:
- Some curing ovens include a cooling zone where workpieces gradually cool down after the curing process.
- Controlled cooling helps prevent damage to the cured coating and ensures a durable finish.
- Timer and Dwell Time Control:
- A timer system allows operators to set and control the dwell time, ensuring that workpieces remain in the oven for the required duration for complete curing.
- Monitoring and Safety Systems:
- Monitoring systems may be incorporated to track and display temperature, conveyor speed, and other critical parameters.
- Safety features such as emergency stop buttons and temperature alarms enhance the overall safety of the curing process.
- Compliance with Regulations:
- The curing oven design and operation should comply with local safety and environmental regulations associated with powder coating operations.
- Accessibility for Maintenance:
- Design features that facilitate easy access for maintenance tasks, such as cleaning or replacing heating elements and inspecting insulation.
- Heat Recovery Systems:
- In some cases, heat recovery systems may be implemented to capture and reuse excess heat, improving overall energy efficiency.
Properly designed and maintained curing ovens are crucial for achieving high-quality powder coating finishes. They play a significant role in ensuring the durability, adhesion, and appearance of the cured powder coating on the workpieces. Regular maintenance and adherence to safety protocols contribute to the longevity and effectiveness of the curing oven.
Powder coating
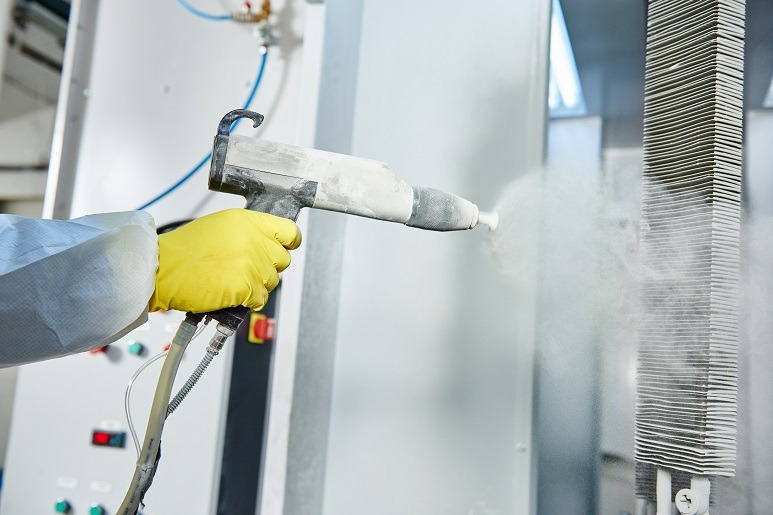
Powder coating is a widely used finishing process in manufacturing, characterized by its ability to produce a high-quality, durable finish. The process involves the application of dry powder to a surface, which is then cured under heat to form a solid, protective coating. This process is favored in many industries due to its efficiency and environmental benefits compared to traditional liquid paint. Essential to the powder coating process are various pieces of equipment, including the Powder Coating Equipment, Powder Coating Booth, Powder Coating Spray Booth, Small Powder Coating Booth, and Powder Paint Booth with Filters.
Powder Coating Equipment Overview
Powder Coating Equipment encompasses a wide range of tools and machinery designed to facilitate the powder coating process. These include spray guns, booths, ovens, and automated systems. Each component plays a crucial role in ensuring the quality and efficiency of the coating process. For instance, Automatic Powder Coating Equipment is often used in large-scale operations where precision and consistency are paramount.
Powder Coating Booths
A Powder Coating Booth is a controlled environment where powder is applied to the substrate. These booths are designed to contain overspray, minimize contamination, and ensure even coating application. There are various types of booths, including the Small Powder Coating Booth, which is ideal for limited-space operations or for coating smaller parts. For larger operations, a Powder Coating Spray Booth is typically used, which allows for greater flexibility and efficiency.
Small Powder Coating Booths and Applications
Small Powder Coating Booths are specifically designed for operations that require a compact setup. These booths are particularly useful in small workshops or for businesses that specialize in coating small parts, such as Alloy Wheel Powder Coating. A Small Powder Coating Booth is typically paired with a Small Powder Coating Oven or a combined Small Powder Coating Booth and Oven to streamline the coating and curing processes.
Automated Powder Coating Systems
For businesses that require high throughput and consistent quality, an Automated Powder Coating System is often the best choice. These systems integrate various components of the powder coating process, including automated spray guns, conveyor systems, and curing ovens. By automating these processes, manufacturers can achieve a higher level of efficiency and reduce the potential for human error.
Ovens in Powder Coating
Curing ovens are an essential part of the powder coating process. They provide the heat necessary to cure the powder and form a durable coating. There are different types of ovens, including Gas Powder Coating Oven, Diesel Powder Coating Oven, and Portable Powder Coating Oven. Each type of oven offers distinct advantages depending on the application. For instance, a Gas Powder Coating Oven is known for its energy efficiency and consistent temperature control, while a Diesel Powder Coating Oven is favored in environments where gas supply is limited or where diesel is more readily available.
Portable Powder Coating Ovens
Portable Powder Coating Ovens are a versatile solution for businesses that require mobility in their operations. These ovens can be moved easily to different locations, making them ideal for on-site jobs or businesses with limited space. Despite their portability, these ovens are capable of delivering high-quality curing results comparable to their stationary counterparts.
Specialized Coating Applications: Alloy Wheel Powder Coating
Alloy Wheel Powder Coating is a specialized application of powder coating that involves applying a durable finish to alloy wheels. This process not only enhances the appearance of the wheels but also provides protection against corrosion and wear. The equipment used for this application typically includes a Small Powder Coating Booth and Oven to accommodate the size of the wheels and ensure a thorough and even coating.
Small Powder Coating Booths and Ovens
Combining a Small Powder Coating Booth with a Small Powder Coating Oven is an effective setup for operations that deal with smaller parts. This combination allows for a seamless transition from coating to curing, ensuring that the coated parts are handled efficiently and without the risk of contamination or damage.
Advantages of Automatic Powder Coating Equipment
The use of Automatic Powder Coating Equipment provides several advantages, particularly in high-volume production settings. Automation ensures that each part is coated with precision and consistency, reducing waste and increasing productivity. Additionally, automated systems can be programmed to handle various part sizes and shapes, making them a versatile option for manufacturers.
Conclusion
In conclusion, powder coating is an essential process in many industries, offering a durable and high-quality finish that is both environmentally friendly and cost-effective. The equipment used in this process, including Powder Coating Equipment, Powder Coating Booths, Automated Powder Coating Systems, and various types of ovens, plays a crucial role in achieving the desired results. Whether you are operating a small workshop or a large-scale manufacturing facility, the right combination of equipment can significantly enhance your production capabilities and product quality.
Powder Coating Equipment
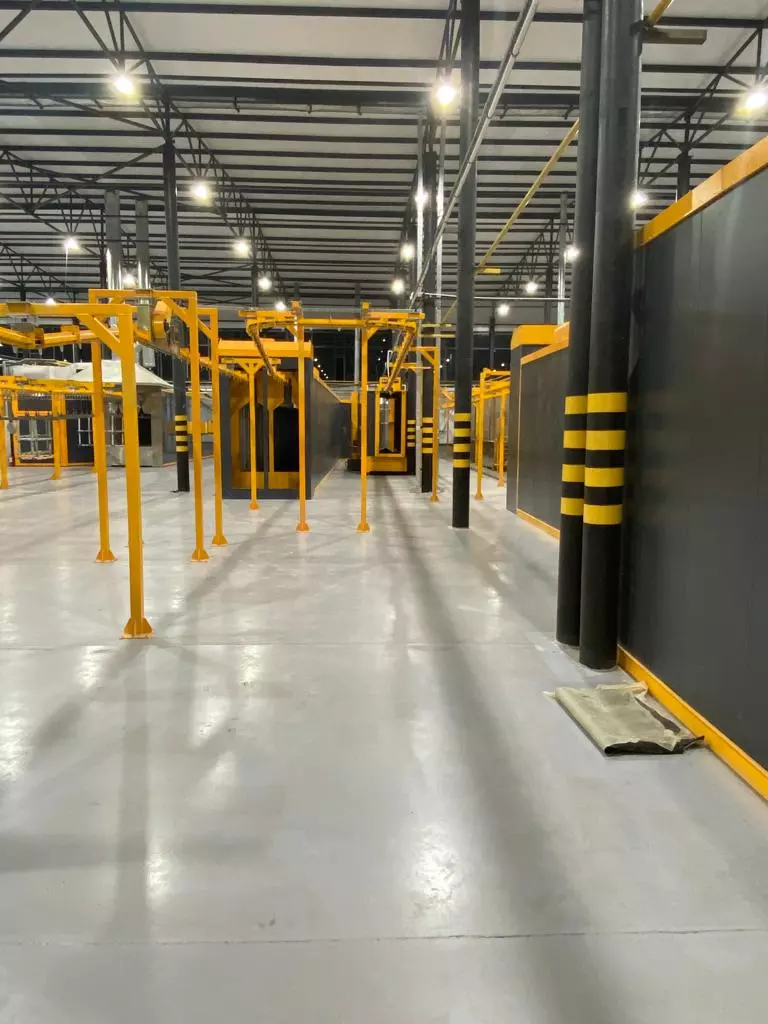
Powder Coating Equipment encompasses a variety of tools and machines that are essential for applying powder coatings to various substrates. This equipment typically includes:
- Powder Spray Guns: These are devices used to apply the powder evenly onto the surface of the object. They can be manual or automated, with the latter offering greater consistency and efficiency.
- Powder Coating Booths: These are enclosed areas where the powder is applied, designed to contain overspray and prevent contamination.
- Curing Ovens: After the powder is applied, the coated object is placed in an oven to cure, which involves melting the powder so it flows together to form a smooth, solid coating.
- Control Systems: These systems manage the application parameters, such as temperature, spray rate, and curing time, ensuring the process is consistent and repeatable.
Powder Coating Booth
A Powder Coating Booth is a specialized enclosure designed to contain the powder application process. The booth serves several key functions:
- Overspray Containment: The booth ensures that any powder that doesn’t adhere to the substrate is captured and can often be recycled, reducing waste.
- Controlled Environment: By isolating the coating process, the booth minimizes contamination from dust and other particles, which could affect the finish quality.
- Airflow Management: Proper airflow within the booth ensures that the powder particles are evenly distributed and that overspray is efficiently collected.
There are various types of booths, such as open-faced booths, enclosed booths, and walk-in booths, each designed for different scales and types of operations.
Small Powder Coating Booth
A Small Powder Coating Booth is designed for operations that do not require large-scale equipment. These booths are ideal for small parts, prototypes, or businesses with limited space. Features of small booths include:
- Compact Design: These booths are smaller in size, making them suitable for tight spaces or mobile operations.
- Cost-Effective: They are often less expensive than larger booths, making them an economical choice for small businesses or hobbyists.
- Efficiency: Despite their size, small powder coating booths are equipped to handle a variety of coating tasks with high precision.
Powder Coating Spray Booth
A Powder Coating Spray Booth is a type of booth specifically designed to accommodate the spraying process of powder application. This type of booth is equipped with:
- Advanced Filtration Systems: These systems filter the air to remove any particles, ensuring a clean environment for the coating process.
- Adjustable Airflow: Airflow can be adjusted to optimize the application and ensure even coating on all surfaces.
- Ergonomic Design: Spray booths are often designed to maximize operator comfort and efficiency, with easy access to all areas of the parts being coated.
Powder Paint Booth with Filters
A Powder Paint Booth with Filters is equipped with specialized filtration systems to capture overspray and maintain air quality within the booth. These filters play a critical role in:
- Ensuring Air Quality: Filters remove airborne powder particles, preventing them from escaping the booth and affecting the surrounding environment.
- Reducing Waste: Captured powder can often be recycled, reducing material costs and waste.
- Maintaining Finish Quality: Clean air within the booth ensures that the powder coating adheres smoothly and evenly, free from contaminants.
Automated Powder Coating System
An Automated Powder Coating System integrates various stages of the powder coating process into a seamless, automated workflow. Key features of these systems include:
- Conveyor Systems: Parts are transported automatically through the different stages of coating and curing, increasing efficiency and throughput.
- Automated Spray Guns: These guns apply powder coatings consistently across parts, reducing the potential for human error and ensuring uniformity.
- Real-Time Monitoring: Sensors and control systems monitor the process in real-time, adjusting parameters as needed to maintain optimal coating conditions.
- Scalability: Automated systems can be scaled to meet the demands of different production volumes, from small batches to large-scale manufacturing.
Gas Powder Coating Oven
A Gas Powder Coating Oven is used to cure powder-coated parts by heating them to the required temperature. These ovens are powered by natural gas and offer several advantages:
- Energy Efficiency: Gas ovens are generally more energy-efficient than electric ovens, making them a cost-effective option for large-scale operations.
- Consistent Heating: They provide uniform temperature distribution, which is crucial for achieving a consistent and durable finish.
- Fast Heat-Up Times: Gas ovens typically heat up faster than electric ovens, reducing cycle times and increasing productivity.
Diesel Powder Coating Oven
A Diesel Powder Coating Oven is similar to a gas oven but is powered by diesel fuel. These ovens are often used in situations where:
- Fuel Availability: Diesel may be more readily available or more economical than gas in certain regions or for certain operations.
- High-Temperature Requirements: Diesel ovens are capable of reaching high temperatures quickly, making them suitable for heavy-duty applications.
- Portability: Some diesel ovens are designed to be portable, allowing them to be moved to different locations as needed.
Portable Powder Coating Oven
A Portable Powder Coating Oven is designed for mobility, allowing it to be transported to different job sites or easily repositioned within a workshop. Features include:
- Compact Size: Portable ovens are generally smaller and lighter than stationary models, making them easy to move.
- Versatility: These ovens can be used for a variety of applications, from small parts to on-site repairs and custom jobs.
- Flexibility: They can be powered by different fuel sources, including gas, diesel, or electricity, depending on the specific model.
Alloy Wheel Powder Coating
Alloy Wheel Powder Coating is a specialized process designed to coat alloy wheels with a durable and attractive finish. The process involves:
- Preparation: The wheels are first cleaned and prepped to ensure the powder coating adheres properly.
- Application: A powder coating is applied evenly across the wheel, often using a Small Powder Coating Booth to contain the process.
- Curing: The coated wheels are then placed in an oven, where the powder is cured to form a hard, protective layer. This can be done in a Small Powder Coating Oven.
- Finishing: The final product is a wheel with a high-quality finish that resists chips, scratches, and corrosion.
Small Powder Coating Booth and Oven
A Small Powder Coating Booth and Oven setup is ideal for businesses or hobbyists who need to coat small parts efficiently. This setup typically includes:
- A Compact Booth: The booth is designed to fit in smaller spaces while still providing the necessary environment for powder coating.
- A Small Oven: The oven is sized to match the booth, ensuring that parts can be cured immediately after coating, reducing handling and the risk of contamination.
- Integrated Systems: Some setups may combine the booth and oven into a single unit, making it easier to manage the process in a limited space.
Small Powder Coating Oven
A Small Powder Coating Oven is specifically designed for curing smaller items. Key benefits include:
- Space Efficiency: These ovens are designed to fit into smaller workshops or production areas, making them ideal for limited-space environments.
- Quick Heat-Up: Smaller ovens generally heat up faster, allowing for shorter cycle times and increased productivity.
- Cost-Effective: Due to their smaller size, these ovens typically consume less energy, making them a more economical option for small businesses or low-volume operations.
Automatic Powder Coating Equipment
Automatic Powder Coating Equipment refers to systems designed to automate the powder coating process, offering numerous advantages:
- Consistency: Automated equipment ensures that each part is coated evenly, reducing variability and ensuring high-quality finishes.
- Efficiency: Automation reduces the time required to coat each part, increasing throughput and reducing labor costs.
- Advanced Features: Many automated systems include features such as programmable control systems, which allow for precise adjustments to coating parameters, and integration with other manufacturing processes, such as pre-treatment and inspection.
Introduction to Powder Coating and Essential Equipment

Powder coating is an advanced finishing process widely recognized for its efficiency, durability, and environmental benefits. Unlike traditional liquid paint, powder coating uses a dry powder that is electrostatically charged and sprayed onto a surface. The coated surface is then cured under heat, forming a robust and protective layer. This process is employed across various industries, including automotive, aerospace, and consumer goods, due to its superior finish quality and resistance to wear and corrosion.
The success of powder coating depends heavily on the equipment used throughout the process. Powder Coating Equipment includes a wide range of machinery designed to ensure that the powder is applied evenly and cured properly. This equipment encompasses spray guns, booths, ovens, and automated systems that work together to deliver a consistent, high-quality finish. Each piece of equipment serves a specific purpose, and understanding their functions and benefits is crucial for optimizing the powder coating process.
Powder Coating Equipment: A Comprehensive Overview
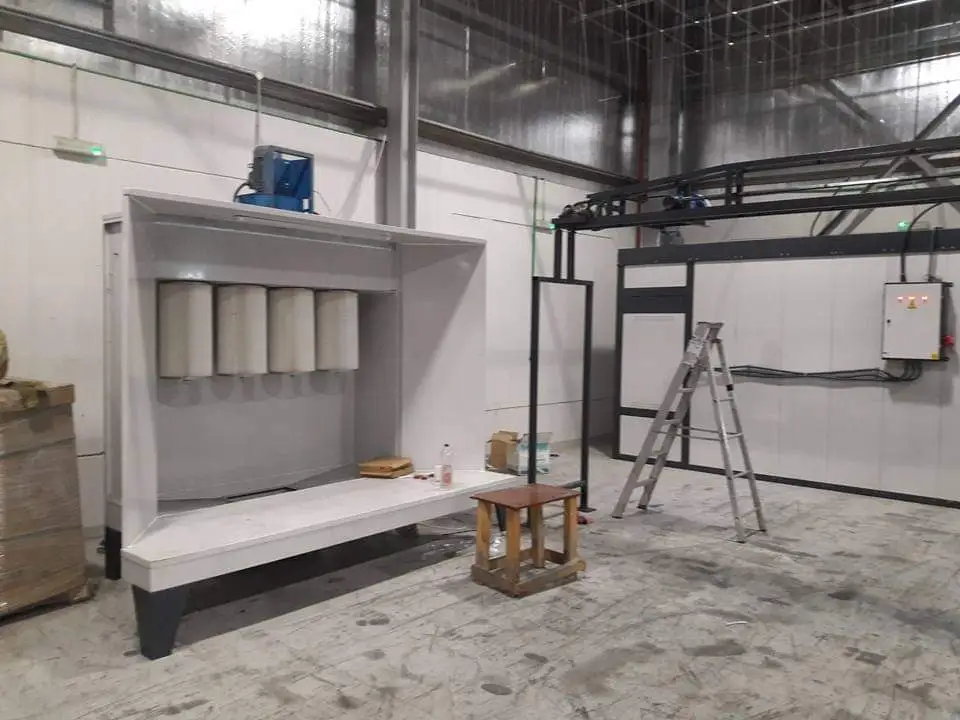
Powder Coating Equipment refers to the complete set of tools and machinery used in the powder coating process. This equipment includes:
- Electrostatic Spray Guns: These are the primary tools used to apply powder to the substrate. The spray gun charges the powder particles, causing them to adhere to the surface of the part being coated. There are different types of spray guns, including manual and automated versions, each suited for specific applications.
- Powder Coating Booths: These enclosures provide a controlled environment for applying the powder, ensuring that overspray is contained and that the powder is applied uniformly. The booths are designed to maximize efficiency and minimize waste, often incorporating filtration systems to capture excess powder for reuse.
- Curing Ovens: Once the powder has been applied, the coated part is transferred to a curing oven. These ovens heat the part to the required temperature, causing the powder to melt and flow into a smooth, even coating. Different types of ovens, such as gas, diesel, and portable ovens, are used depending on the size of the part and the specific needs of the operation.
- Automated Systems: In larger-scale operations, Automatic Powder Coating Equipment is often used to streamline the process. These systems can automate the entire powder coating process, from powder application to curing, improving efficiency and consistency.
The Role of Powder Coating Booths
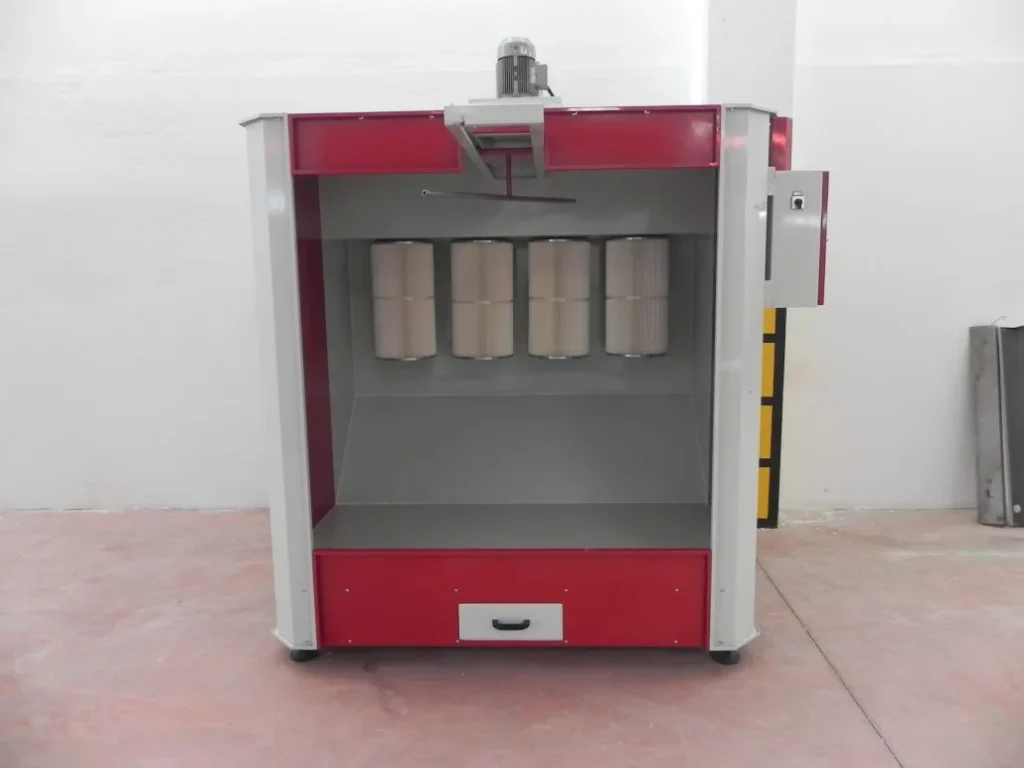
A Powder Coating Booth is an essential component of the powder coating process, providing a dedicated space for the application of powder coatings. These booths are designed to create an optimal environment for powder application, with features that include:
- Controlled Airflow: Proper airflow is critical in a powder coating booth. It ensures that the powder particles are evenly distributed and that overspray is captured efficiently. The airflow is carefully managed to prevent contamination and to ensure that the powder adheres uniformly to the substrate.
- Containment of Overspray: A key function of the booth is to contain overspray, preventing powder from spreading to other areas of the workspace. This not only keeps the work environment clean but also allows for the recovery and reuse of overspray, reducing waste and saving on material costs.
- Variety of Configurations: Powder coating booths come in various configurations to suit different applications. For example, walk-in booths are used for coating large parts, while compact booths are ideal for smaller operations.
Small Powder Coating Booth: Efficiency in Compact Spaces
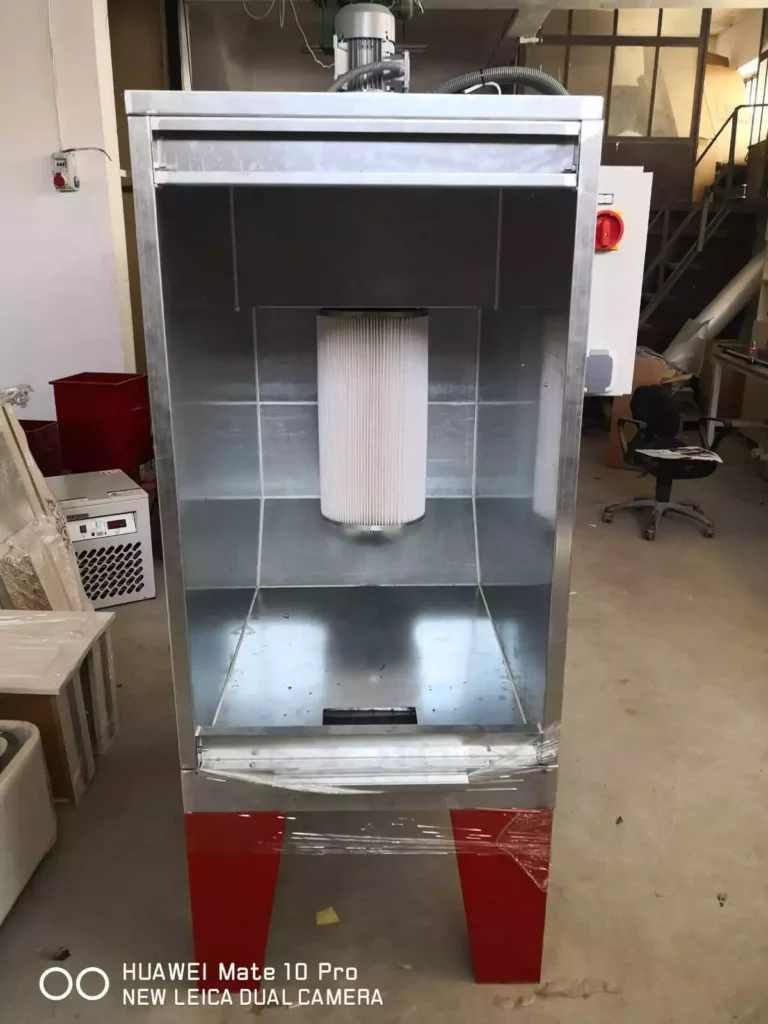
A Small Powder Coating Booth is specifically designed for operations with limited space or for businesses that focus on coating smaller parts. Despite their size, these booths offer several advantages:
- Space-Saving Design: The compact size of a small powder coating booth makes it ideal for workshops or production areas where space is at a premium. These booths are designed to fit into tight spaces without compromising on performance or safety.
- Cost-Effective Operation: Small booths typically require less energy and resources to operate, making them a cost-effective option for small businesses or for coating small batches of parts. They are also easier to install and maintain, reducing overall operating costs.
- Versatility: These booths can handle a wide range of coating tasks, from small automotive parts to prototypes and custom jobs. Their versatility makes them a popular choice for businesses that require flexibility in their operations.
Powder Coating Spray Booth: Optimized for Precision Application
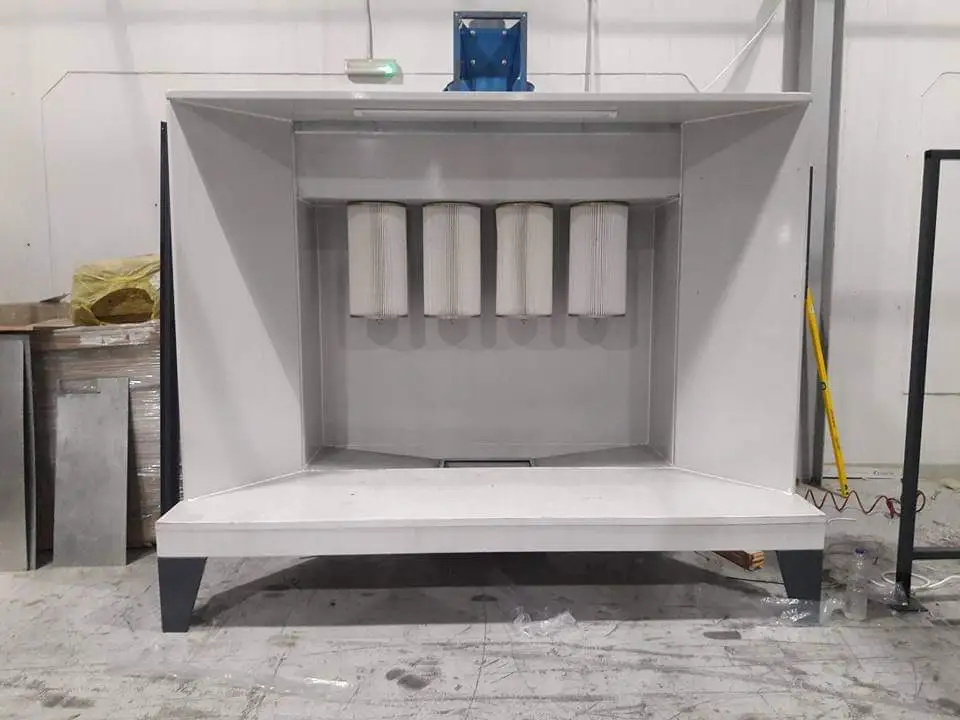
A Powder Coating Spray Booth is a specialized booth designed to optimize the spray application of powder coatings. These booths are equipped with advanced features that enhance the coating process:
- High-Efficiency Filtration Systems: The filtration systems in a spray booth are designed to capture overspray and remove airborne particles, ensuring a clean environment for powder application. This is crucial for achieving a high-quality finish and for maintaining a safe work environment.
- Adjustable Airflow: The airflow in a spray booth can be adjusted to suit the specific requirements of the coating job. This allows for precise control over the application process, ensuring that the powder is applied evenly and with the desired thickness.
- Operator-Friendly Design: Spray booths are designed with the operator in mind, providing easy access to the parts being coated and ergonomic features that reduce fatigue. This improves both the efficiency and safety of the coating process.
Powder Paint Booth with Filters: Ensuring Quality and Safety
A Powder Paint Booth with Filters is a critical component of the powder coating process, providing an enclosed space for the application of powder coatings while ensuring that air quality is maintained. The filtration system in these booths serves several important functions:
- Air Quality Control: The filters in a powder paint booth are designed to capture airborne powder particles, preventing them from contaminating the workspace and ensuring that the air remains clean and breathable. This is particularly important in environments where multiple coating operations are taking place simultaneously.
- Waste Reduction: By capturing overspray, the filtration system helps to reduce waste, as the collected powder can often be recycled and reused. This not only reduces material costs but also minimizes the environmental impact of the coating process.
- Compliance with Regulations: Powder paint booths with filters are often required to meet specific safety and environmental regulations, particularly in industries where hazardous materials are used. The filtration system ensures that the booth operates within these guidelines, protecting both workers and the environment.
Automated Powder Coating System: Enhancing Productivity and Consistency
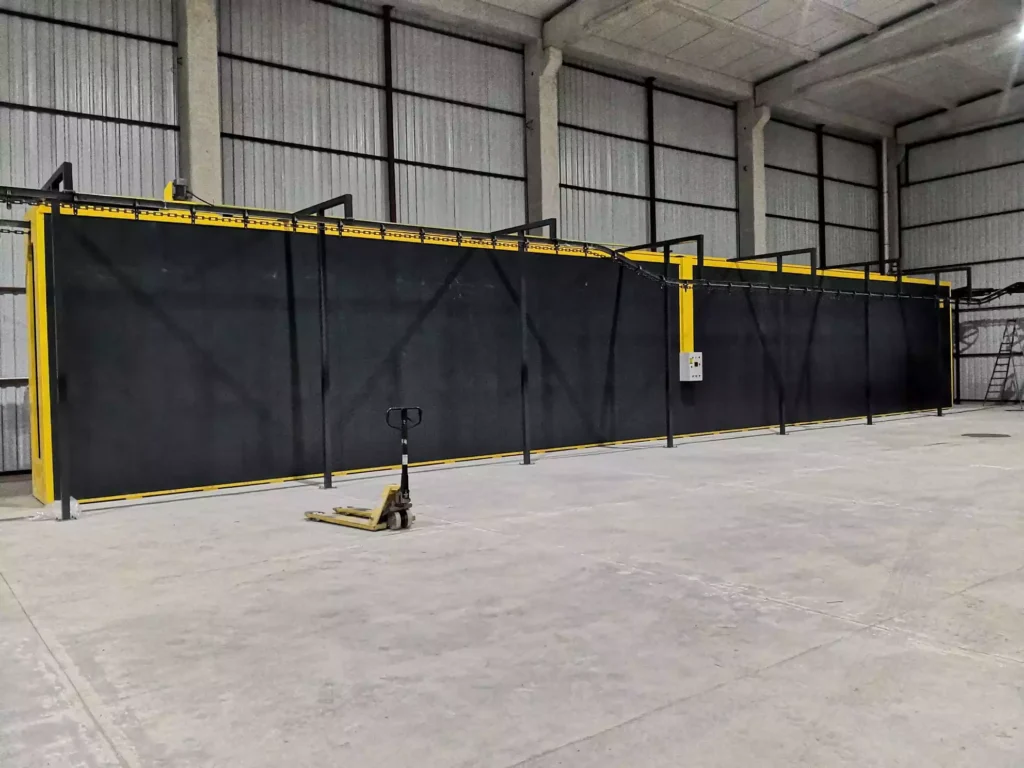
An Automated Powder Coating System integrates various components of the powder coating process into a fully automated workflow. These systems are designed to improve productivity, consistency, and efficiency in large-scale operations. Key features include:
- Conveyor Systems: Automated systems often incorporate conveyor belts that transport parts through the different stages of the coating process. This allows for continuous production, reducing downtime and increasing throughput.
- Robotic Spray Guns: Robotic arms equipped with spray guns can apply powder coatings with a high degree of precision, ensuring that each part is coated uniformly. This reduces the risk of defects and improves the overall quality of the finish.
- Real-Time Monitoring and Control: Advanced sensors and control systems monitor the coating process in real-time, adjusting parameters as needed to maintain optimal conditions. This ensures consistent results, even in high-volume production environments.
- Scalability: Automated powder coating systems can be scaled to meet the needs of different production volumes, from small batches to large-scale manufacturing. This makes them a versatile solution for a wide range of industries.
Gas Powder Coating Oven: Reliable and Efficient Curing
A Gas Powder Coating Oven is a critical piece of equipment in the powder coating process, providing the heat necessary to cure the powder coating and form a durable, protective layer. These ovens are powered by natural gas and offer several advantages:
- Energy Efficiency: Gas ovens are known for their energy efficiency, as they can heat up quickly and maintain a consistent temperature with minimal energy consumption. This makes them a cost-effective option for large-scale operations.
- Uniform Heating: The design of gas ovens ensures that heat is distributed evenly throughout the oven, preventing hot spots and ensuring that all parts are cured uniformly. This is essential for achieving a consistent, high-quality finish.
- Flexible Operation: Gas powder coating ovens can be used for a wide range of applications, from small parts to large assemblies. They are also available in various sizes and configurations, making them adaptable to different production needs.
Diesel Powder Coating Oven: Power and Portability
A Diesel Powder Coating Oven is similar to a gas oven but is powered by diesel fuel. These ovens are often used in situations where gas is not readily available or where diesel is more economical. The key benefits of diesel ovens include:
- High Heat Output: Diesel ovens are capable of reaching high temperatures quickly, making them ideal for heavy-duty applications that require fast curing times.
- Portability: Many diesel ovens are designed to be portable, allowing them to be easily moved to different locations as needed. This makes them a flexible option for businesses that need to perform coating operations on-site or in remote locations.
- Durability: Diesel ovens are built to withstand harsh conditions and are often used in industrial settings where durability and reliability are critical.
Portable Powder Coating Oven: Versatility on the Move
A Portable Powder Coating Oven offers the flexibility of being moved to different job sites or repositioned within a workshop. These ovens are ideal for operations that require mobility or for businesses with limited space. Key features of portable ovens include:
- Compact and Lightweight Design: Portable ovens are designed to be easily transported, with a compact size and lightweight construction that makes them easy to move and set up.
Powder Coating Spray Booth: Achieving Clean, Efficient, and High-Quality Coating Results
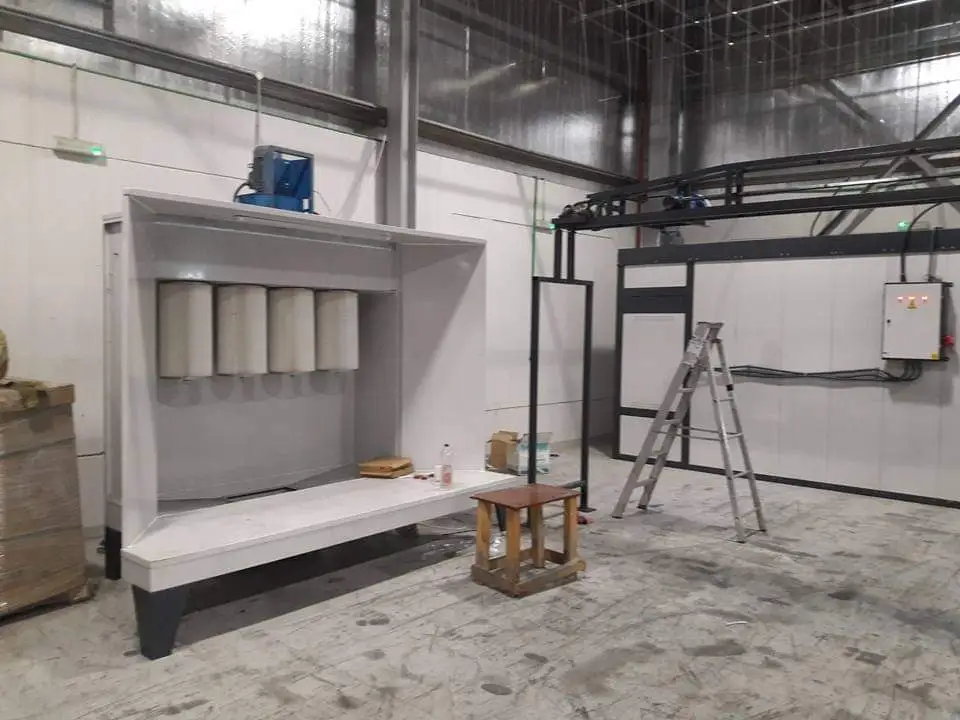
The powder coating process requires a controlled environment to ensure consistent and high-quality finishes. One of the most critical components in this process is the powder coating spray booth, where the actual application of powder takes place. Spray booths provide a dedicated space for applying powder, preventing contamination, capturing overspray, and ensuring that the process is both efficient and environmentally friendly.
Powder coating spray booths are designed to contain the powder within a specific area, keeping it from escaping into the surrounding workspace. These booths are typically equipped with air filtration and extraction systems that capture excess powder particles, reducing waste, minimizing health risks to workers, and maintaining a clean workspace. Additionally, the booth’s environment is controlled to ensure that no contaminants interfere with the powder coating process, resulting in smooth, durable finishes.
EMS Powder Coating Equipment is a trusted manufacturer of powder coating spray booths, offering a wide range of booths equipped with advanced filtration and ventilation systems. EMS spray booths are designed for optimal efficiency, safety, and cleanliness, making them an ideal choice for businesses looking to enhance their powder coating operations. In this guide, we’ll explore how powder coating spray booths work, their benefits, and why EMS Powder Coating Equipment is the best option for businesses seeking high-performance booths.
What is a Powder Coating Spray Booth?
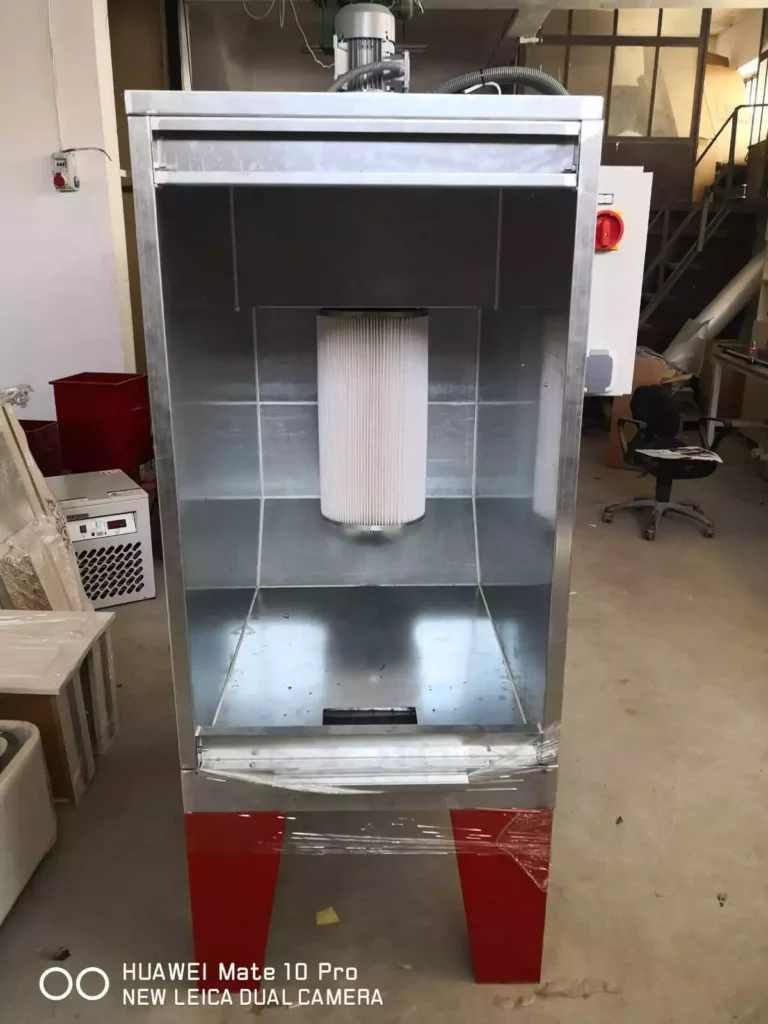
A powder coating spray booth is an enclosed space where powder is applied to products during the powder coating process. The booth provides a controlled environment that prevents external contaminants from affecting the coating process while also containing the powder within a specific area to prevent it from spreading throughout the workspace. These booths are an essential part of any powder coating system, as they ensure a clean, safe, and efficient application process.
How Powder Coating Spray Booths Work
In a powder coating spray booth, products are placed inside the booth and coated using electrostatic spray guns. These guns charge the powder particles, which are then attracted to the grounded surface of the product. This electrostatic attraction ensures that the powder adheres evenly to the product, providing a smooth and consistent coat.
As the powder is applied, some particles may not adhere to the product and become airborne. To prevent these excess particles from escaping into the surrounding workspace, the booth is equipped with an air extraction and filtration system. This system draws air through filters that capture the excess powder, keeping the air inside the booth clean and free from harmful particulates.
Many powder coating spray booths are equipped with features like adjustable airflow, which allows operators to control the speed and direction of air movement within the booth. This helps ensure that the powder is applied evenly and that overspray is efficiently captured and recycled, minimizing waste.
EMS Powder Coating Equipment manufactures spray booths with advanced air filtration and extraction systems that maximize efficiency and cleanliness. Their booths are designed to handle the demands of industrial powder coating operations, ensuring consistent and high-quality results.
The Benefits of Powder Coating Spray Booths
Powder coating spray booths are essential for businesses looking to improve the efficiency, safety, and quality of their powder coating process. Here are some of the key benefits of using a high-quality spray booth:
1. Improved Product Quality
A controlled environment is essential for achieving consistent, high-quality finishes in powder coating. In an open workspace, contaminants such as dust, dirt, or debris can settle on the product during the coating process, leading to defects like uneven finishes or poor adhesion. A powder coating spray booth provides a clean, enclosed space where products can be coated without the risk of contamination from the outside environment.
In addition to preventing contamination, the airflow and filtration system inside the booth ensure that overspray is effectively captured, preventing it from interfering with the final finish. The result is a smooth, even coating that meets the highest standards of quality and durability.
EMS Powder Coating Equipment designs its spray booths to provide a clean, controlled environment that enhances the quality of the finished product. Their booths are engineered for precision, ensuring that each product receives a flawless coating.
2. Reduced Powder Waste and Cost Savings
Powder waste is a common issue in powder coating operations, especially when the excess powder is not properly captured and recycled. Without a spray booth, much of the overspray can be lost, leading to higher material costs and environmental waste. Powder coating spray booths are designed to capture excess powder, allowing it to be collected and reused.
The filtration system in a spray booth traps airborne powder particles and prevents them from escaping into the workspace. This captured powder can then be reclaimed and reintroduced into the coating process, reducing material waste and cutting costs.
EMS Powder Coating Equipment offers spray booths with advanced powder recovery systems that maximize powder reuse and minimize waste. Their booths are designed to reduce material costs by ensuring that as much powder as possible is captured and recycled.
3. Enhanced Worker Safety
Worker safety is a top priority in any industrial setting, and powder coating operations are no exception. During the powder coating process, airborne powder particles can pose a respiratory hazard to workers if they are not properly contained. Inhaling these particles over time can lead to respiratory issues and other health problems.
Powder coating spray booths are equipped with ventilation and filtration systems that remove harmful particulates from the air, ensuring that the workspace remains clean and safe for operators. The booth’s design prevents airborne powder from escaping into the surrounding environment, reducing the risk of exposure for workers.
EMS Powder Coating Equipment designs its spray booths with safety in mind, offering advanced filtration and ventilation systems that protect workers from inhaling harmful particles. Their booths are built to meet the highest safety standards, ensuring a safe and healthy work environment.
4. Environmental Compliance
Many industries are subject to strict environmental regulations regarding air quality and emissions. Powder coating is an environmentally friendly process compared to liquid painting, as it produces minimal volatile organic compounds (VOCs). However, without proper containment and filtration, excess powder can still be released into the atmosphere, contributing to air pollution.
Powder coating spray booths are designed to contain and capture overspray, preventing it from being released into the environment. The booth’s filtration system ensures that any excess powder is collected and safely disposed of or recycled, helping businesses meet environmental regulations and reduce their overall environmental impact.
EMS Powder Coating Equipment offers spray booths with high-performance filtration systems that help businesses comply with environmental standards. Their booths are designed to minimize emissions and improve sustainability in powder coating operations.
5. Flexibility and Customization
Powder coating spray booths come in a variety of sizes and configurations, making them suitable for different types of products and production volumes. Whether you’re coating small parts or large industrial components, spray booths can be customized to meet the specific needs of your operation. This flexibility allows businesses to optimize their coating process for efficiency and quality.
Spray booths can also be equipped with additional features, such as adjustable airflow controls, automated powder recovery systems, and more, to enhance performance and meet the unique requirements of each production line.
EMS Powder Coating Equipment provides customizable spray booths that can be tailored to the specific needs of your business. Whether you need a small batch booth or a large conveyorized system, EMS offers solutions that ensure optimal performance and efficiency.
6. Easy Maintenance and Long-Term Reliability
A high-quality spray booth is a long-term investment that can provide years of reliable performance with proper maintenance. Regularly replacing filters and cleaning the booth ensures that it continues to operate efficiently and that air quality remains high. High-quality spray booths are built to withstand the demands of continuous industrial use, providing businesses with a durable solution for their powder coating needs.
EMS Powder Coating Equipment manufactures spray booths that are designed for ease of maintenance and long-lasting reliability. Their booths are constructed from high-quality materials that resist wear and tear, ensuring that your investment will continue to deliver top-tier performance for years to come.
Why Choose EMS Powder Coating Equipment for Spray Booths?
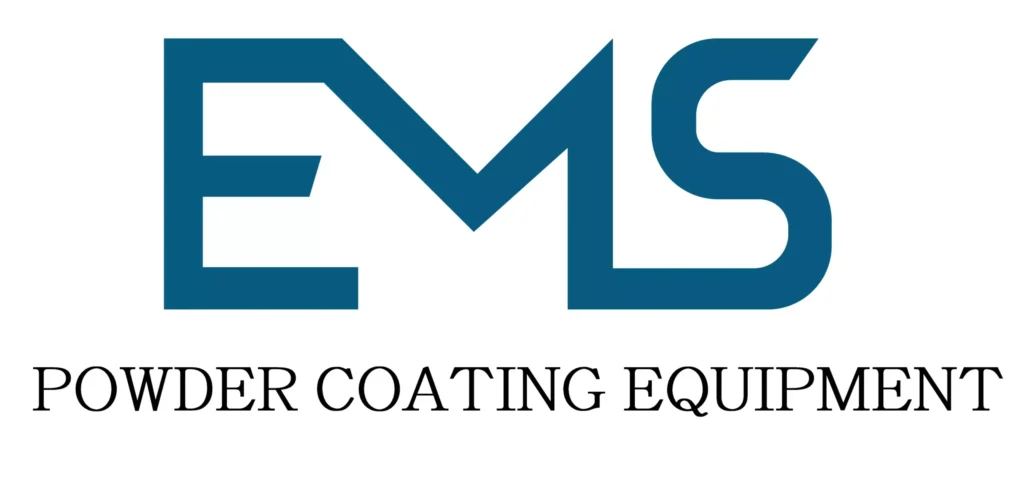
When selecting a powder coating spray booth, businesses need equipment that offers precision, efficiency, and durability. EMS Powder Coating Equipment is the industry leader in providing advanced spray booths that meet the highest standards of performance and safety. Here’s why EMS is the best choice for businesses looking to invest in high-quality spray booths:
1. Advanced Filtration and Ventilation Technology
EMS spray booths are equipped with cutting-edge filtration and ventilation systems that ensure a clean, safe environment for both workers and products. Their booths are designed to capture excess powder with maximum efficiency, preventing contamination and improving air quality in the workspace.
2. Customizable Solutions for Different Industries
Every production line has unique requirements, and EMS offers customizable solutions to meet those needs. Whether you’re working with small parts or large industrial components, EMS provides spray booths that can be tailored to fit your specific production environment. Their booths are available in a range of sizes and configurations, ensuring that businesses get the right solution for their needs.
3. Energy Efficiency and Cost Savings
EMS Powder Coating Equipment understands the importance of efficiency in today’s manufacturing environments. Their spray booths are designed to minimize powder waste and reduce energy consumption, helping businesses lower their operational costs without sacrificing performance.
4. Durability and Long-Lasting Performance
Built to withstand the rigors of industrial use, EMS spray booths are constructed from high-quality materials that ensure long-lasting performance. Their booths require minimal maintenance and are designed to provide reliable operation for years, making them a sound investment for any business.
5. Superior Customer Support and Service
In addition to providing top-tier equipment, EMS offers exceptional customer support and after-sales service. From installation and setup to ongoing maintenance and troubleshooting, EMS’s team of experts is dedicated to ensuring that your spray booth operates at peak efficiency.
Conclusion
A powder coating spray booth is an essential part of any powder coating system, providing a clean, controlled environment that ensures high-quality finishes, worker safety, and environmental compliance. By capturing and filtering overspray, these booths help businesses improve efficiency, reduce waste, and lower costs.
EMS Powder Coating Equipment is the industry leader in providing advanced spray booths with state-of-the-art filtration and ventilation systems. Whether you’re looking to upgrade your existing system or invest in new equipment, EMS offers customizable solutions that ensure your powder coating operations are optimized for maximum productivity and quality.
By choosing EMS powder coating spray booths, businesses can enhance their coating process, improve product quality, and reduce their environmental impact. With a proven track record of innovation and customer satisfaction, EMS is the best choice for businesses seeking reliable and efficient spray booths.
Powder Coating Booth: The Key to High-Quality Finishes and Efficiency in Coating Processes
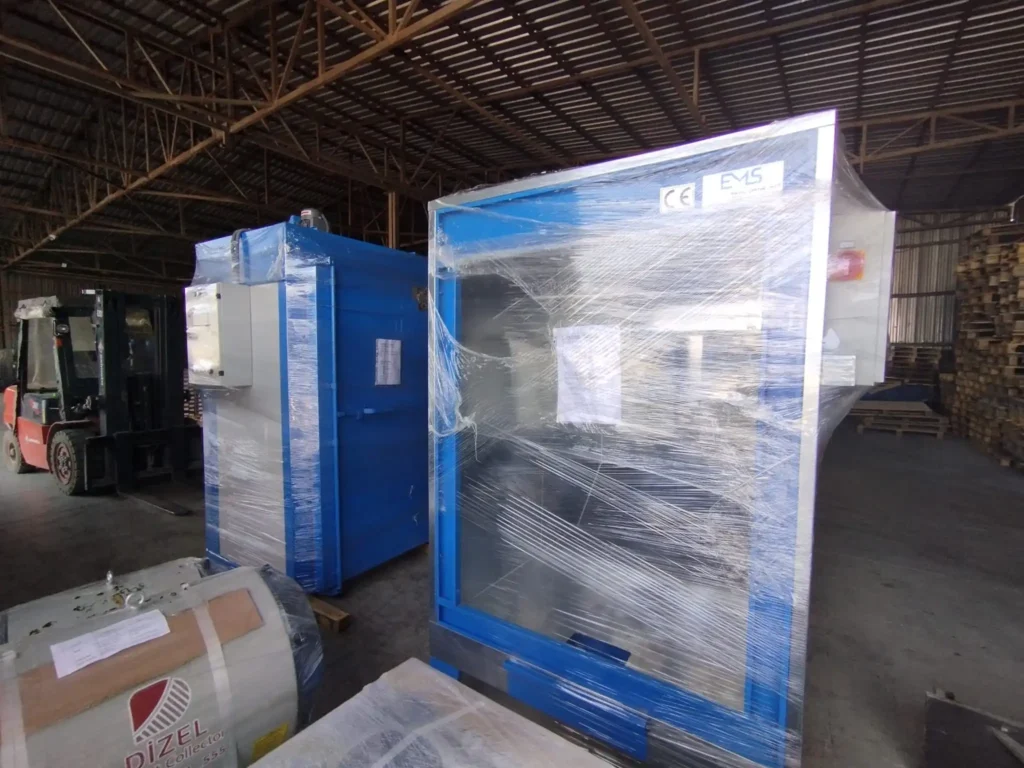
A powder coating booth is a vital component of any powder coating operation, providing a designated area for applying powder coatings to various products. These booths are designed to ensure a controlled environment that enhances the efficiency and quality of the powder coating process. By containing overspray and preventing contamination, powder coating booths play a critical role in achieving superior finishes and maintaining a clean workspace.
The design and functionality of a powder coating booth significantly impact production efficiency and the overall quality of the coated products. With features such as effective ventilation, advanced filtration systems, and customizable configurations, these booths ensure that powder is applied evenly and without interference from external factors.
EMS Powder Coating Equipment is renowned for manufacturing high-performance powder coating booths that meet the needs of diverse industries. Their booths are engineered for optimal performance, safety, and durability, making them an ideal choice for businesses looking to enhance their powder coating operations. In this guide, we will delve into the features, benefits, and advantages of using powder coating booths and explain why EMS is the best manufacturer in this field.
What is a Powder Coating Booth?
A powder coating booth is an enclosed workspace specifically designed for applying powder coatings to products. The primary function of the booth is to contain the powder and provide a clean environment for the coating application process. This controlled environment minimizes contamination, maximizes efficiency, and enhances the quality of the finished product.
How Powder Coating Booths Operate
In a powder coating booth, products are typically suspended or placed on racks, allowing for easy access during the coating process. Powder is applied using electrostatic spray guns, which charge the powder particles to ensure they adhere evenly to the grounded surfaces of the products.
Once the powder is applied, excess particles may become airborne. Powder coating booths are equipped with advanced ventilation systems that effectively capture these airborne particles, preventing them from escaping into the surrounding area. The captured powder can often be recycled and reused, reducing waste and material costs.
The interior of the booth is designed to maintain an optimal environment for powder application. Features such as adjustable airflow and temperature control help create ideal conditions for achieving a smooth, uniform finish on coated products.
EMS Powder Coating Equipment specializes in designing powder coating booths that maximize efficiency and performance. Their booths are built with advanced technology and materials that enhance the coating process, ensuring consistent and high-quality results.
Key Features of Powder Coating Booths
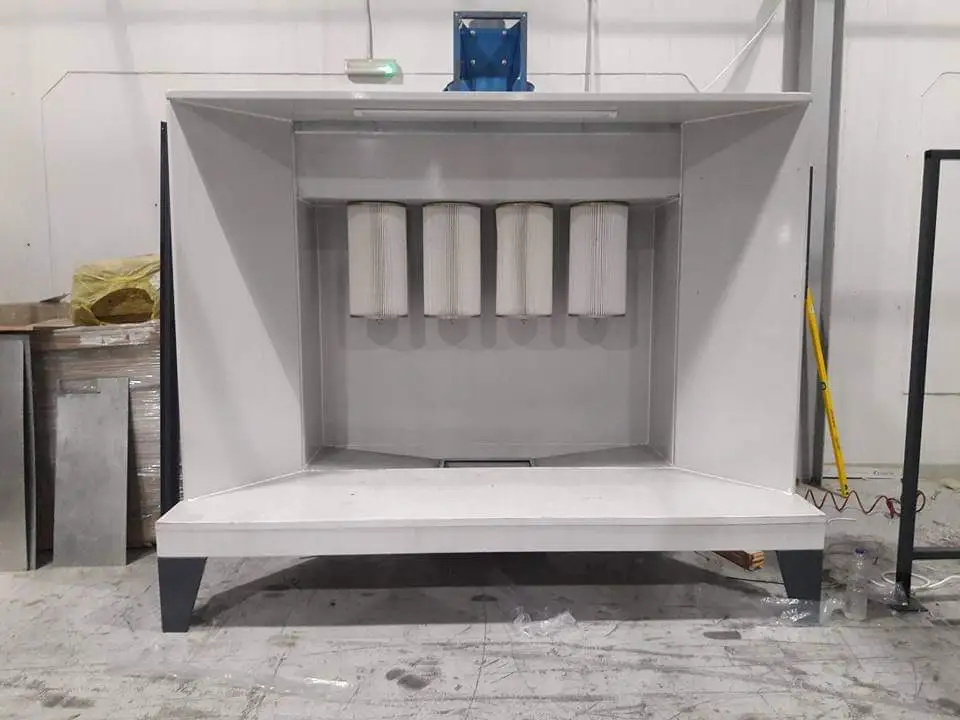
Powder coating booths come with a variety of features that contribute to their effectiveness and efficiency. Here are some key features that make EMS powder coating booths a top choice for businesses:
1. Advanced Air Filtration Systems
Effective air filtration is crucial for maintaining a clean environment in the powder coating booth. EMS booths are equipped with advanced filtration systems that capture overspray and airborne particles, ensuring that the air inside the booth remains clean and free from contaminants. These systems help improve air quality, protect workers, and enhance the overall coating process.
2. Efficient Ventilation
Proper ventilation is essential for controlling airflow within the booth. EMS powder coating booths come with adjustable ventilation systems that allow operators to regulate air movement. This capability ensures that the powder is evenly distributed and that excess particles are efficiently captured, resulting in a smoother finish and reduced waste.
3. Customizable Configurations
Every business has unique production needs, and EMS understands that one size does not fit all. Their powder coating booths can be customized to accommodate different product sizes, shapes, and production volumes. Whether you require a small batch booth or a larger, conveyorized system, EMS offers solutions tailored to your specific requirements.
4. Durability and Construction Quality
EMS powder coating booths are built to last, constructed from high-quality materials that can withstand the rigors of industrial use. Their booths are designed for easy maintenance and long-term reliability, ensuring that businesses get a robust solution that continues to perform over time.
5. User-Friendly Design
Ease of use is a key consideration in the design of EMS powder coating booths. Features such as ergonomic controls, easy access for loading and unloading products, and clear visibility ensure that operators can work efficiently and safely. The user-friendly design contributes to higher productivity and improved overall workflow in the coating process.
6. Environmental Compliance
In today’s manufacturing environment, compliance with environmental regulations is paramount. EMS powder coating booths are designed to minimize emissions and capture waste effectively, helping businesses meet environmental standards. By reducing the release of powder particles into the atmosphere, EMS booths contribute to a more sustainable coating process.
Benefits of Using Powder Coating Booths
Investing in a high-quality powder coating booth provides numerous benefits for businesses engaged in powder coating operations. Here are some of the key advantages:
1. Enhanced Product Quality
One of the most significant benefits of using a powder coating booth is the improvement in product quality. By providing a controlled environment for powder application, booths help ensure that coatings are applied evenly and without contaminants. This leads to smoother finishes and higher overall quality in the final products.
2. Increased Efficiency and Productivity
Powder coating booths streamline the coating process, reducing downtime and improving efficiency. By capturing overspray and enabling easy recycling of powder, businesses can maximize material usage and minimize waste. This efficiency translates into higher productivity and lower operational costs.
3. Improved Worker Safety
The safety of workers is a top priority in any industrial setting. Powder coating booths are designed to contain airborne powder particles, reducing the risk of exposure and respiratory hazards for operators. With effective filtration and ventilation, EMS booths help create a safer working environment for employees.
4. Cost Savings
By reducing material waste and improving efficiency, powder coating booths contribute to significant cost savings over time. The ability to reclaim and reuse excess powder minimizes the need for frequent purchases of new materials, which can lead to substantial financial benefits for businesses.
5. Flexibility in Production
The customizable nature of EMS powder coating booths allows businesses to adapt their operations to changing production needs. Whether coating small batches or large volumes, the flexibility of the booths enables businesses to scale their operations effectively.
6. Environmental Benefits
Using a powder coating booth contributes to a more sustainable coating process by capturing overspray and minimizing waste. EMS booths are designed to meet environmental regulations and reduce the overall impact of powder coating operations on the environment.
Why Choose EMS Powder Coating Equipment for Powder Coating Booths?
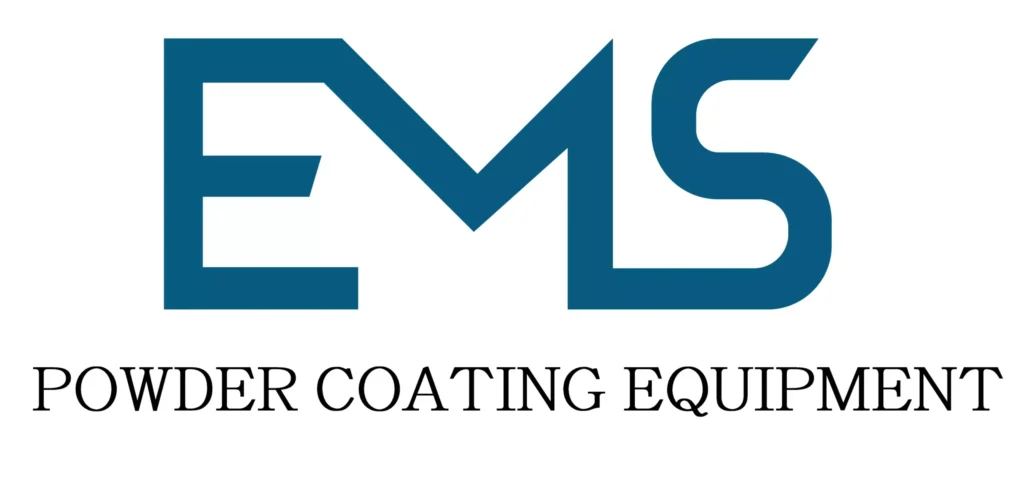
When it comes to selecting a powder coating booth, businesses need a manufacturer that offers quality, reliability, and superior performance. EMS Powder Coating Equipment stands out as the leading choice for businesses looking to invest in powder coating booths. Here’s why EMS is the best option:
1. Industry Expertise
With years of experience in the powder coating industry, EMS has a deep understanding of the challenges and requirements of different businesses. Their expertise allows them to design booths that meet the specific needs of various applications and industries.
2. Innovative Technology
EMS is committed to innovation, continually improving their products with the latest technology. Their powder coating booths incorporate advanced filtration, ventilation, and airflow systems that enhance performance and efficiency, ensuring high-quality finishes.
3. Comprehensive Support
EMS offers exceptional customer support, from initial consultations and installations to ongoing maintenance and service. Their team of experts is dedicated to ensuring that your powder coating booth operates at peak efficiency, helping businesses achieve their production goals.
4. Custom Solutions
Understanding that each business has unique needs, EMS provides customizable solutions that allow companies to tailor their powder coating booths to their specific requirements. This flexibility ensures optimal performance and efficiency in every production environment.
5. Proven Track Record
With a proven track record of customer satisfaction and successful installations, EMS is a trusted name in the powder coating industry. Their commitment to quality and performance makes them the best choice for businesses seeking reliable powder coating booths.
Conclusion
A powder coating booth is an essential component of any powder coating operation, providing a controlled environment that ensures high-quality finishes, improved efficiency, and worker safety. With their advanced filtration and ventilation systems, powder coating booths help businesses maximize productivity while minimizing waste and costs.
EMS Powder Coating Equipment is the industry leader in providing high-performance powder coating booths tailored to meet the needs of diverse industries. Whether you’re looking to upgrade your existing equipment or invest in new solutions, EMS offers customizable booths designed for optimal performance and quality.
By choosing EMS powder coating booths, businesses can enhance their coating processes, improve product quality, and reduce their environmental impact. With a commitment to innovation and customer satisfaction, EMS is the best choice for companies seeking reliable and efficient powder coating solutions.
Powder Paint Booth with Filters: Ensuring Clean and Efficient Coating Processes
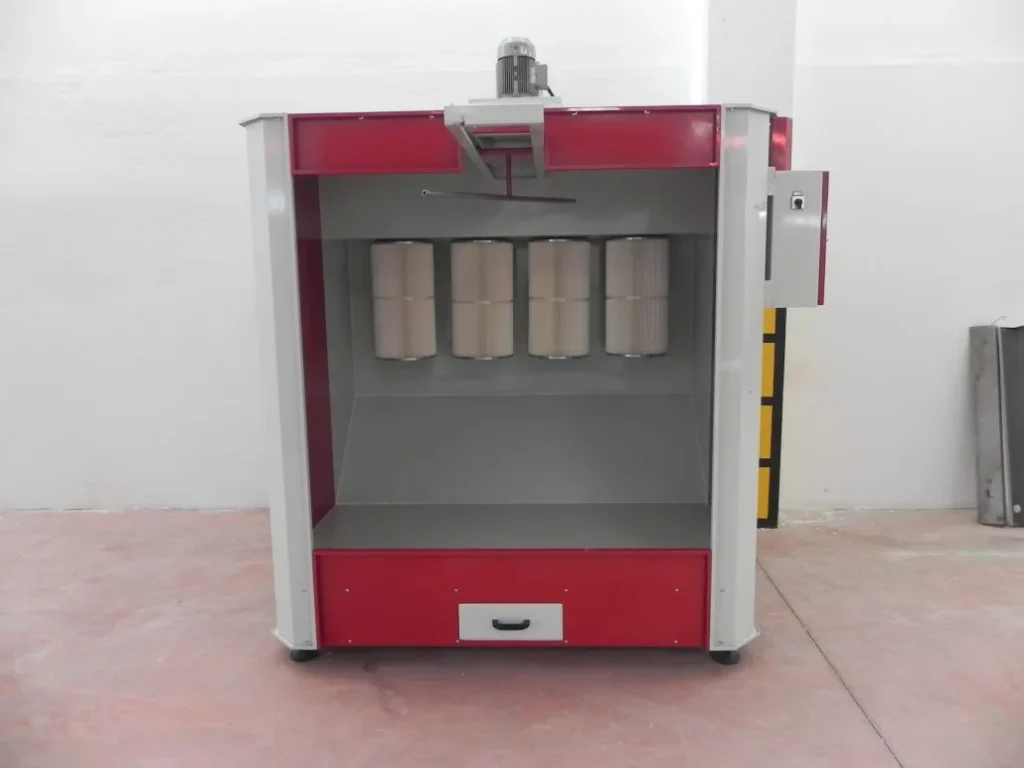
A powder paint booth with filters is an essential component of any powder coating operation, designed to create a controlled environment for the application of powder coatings. These booths are specifically engineered to manage overspray and enhance the efficiency of the coating process, ensuring a clean workspace and high-quality finishes.
Filters play a crucial role in powder paint booths by capturing airborne particles, preventing them from contaminating the coating process. By maintaining air quality and reducing the risk of defects, these booths help achieve superior coating results while also complying with environmental regulations.
EMS Powder Coating Equipment is a leading manufacturer of powder paint booths with advanced filtration systems, providing innovative solutions that meet the demands of modern coating operations. In this section, we will delve into the design, features, and benefits of powder paint booths with filters, and explain why EMS is the preferred choice for businesses seeking reliable and effective coating solutions.
What is a Powder Paint Booth with Filters?
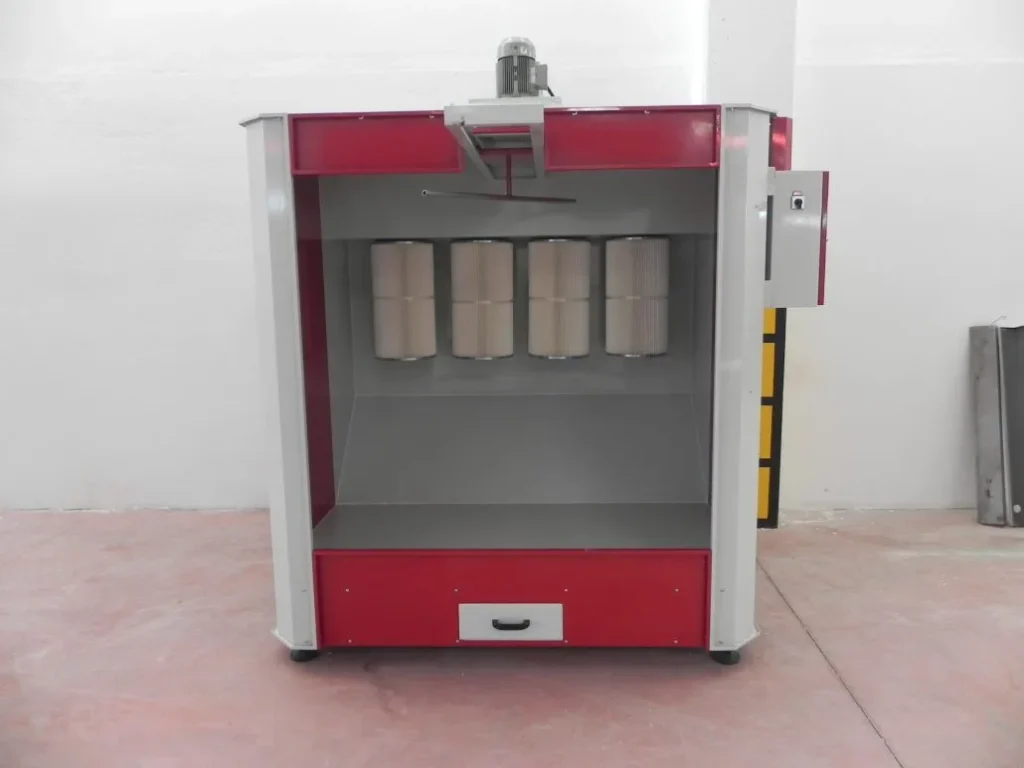
A powder paint booth with filters is a specialized enclosure designed for the application of powder coatings. These booths provide a contained environment that minimizes contamination, manages overspray, and ensures a safe workspace for operators.
How Powder Paint Booths Operate
In a typical powder coating process, the substrate is first cleaned and prepared before being coated with powder. Once the powder is applied, the booth’s filtration system comes into play.
The booth is equipped with a filtration system that captures overspray and other airborne particles generated during the coating process. High-efficiency filters trap these particles, preventing them from settling on the substrate or contaminating the environment. The filtered air is then recirculated back into the booth or expelled outside, depending on the design of the booth.
EMS Powder Coating Equipment designs powder paint booths with advanced filtration systems that maximize efficiency and ensure a clean working environment. Their booths are built to accommodate various coating processes and substrates, making them a versatile solution for businesses of all sizes.
Key Features of Powder Paint Booths with Filters
Powder paint booths with filters come equipped with a variety of features that enhance their performance and efficiency. Here are some key features that make EMS booths the preferred choice for businesses:
1. Advanced Filtration Systems
The filtration systems in EMS powder paint booths are designed to capture even the smallest particles. These systems may include pre-filters, main filters, and HEPA filters, ensuring high air quality and minimal contamination during the coating process.
2. Efficient Overspray Management
Effective overspray management is essential for maintaining a clean workspace. EMS booths utilize specialized designs that contain overspray and direct it toward the filtration system, preventing it from escaping into the environment and enhancing the efficiency of the coating process.
3. Easy Maintenance and Filter Replacement
Maintaining a clean filtration system is crucial for optimal performance. EMS powder paint booths are designed for easy access, allowing operators to quickly replace filters and perform routine maintenance without significant downtime.
4. Customizable Booth Sizes
Recognizing that businesses have different needs, EMS offers customizable booth sizes to accommodate various production capacities. Whether a business requires a compact booth for small operations or a larger booth for high-volume production, EMS can tailor solutions to fit specific requirements.
5. Energy Efficiency
EMS powder paint booths are designed with energy efficiency in mind. The incorporation of LED lighting and efficient airflow designs minimizes energy consumption while providing optimal working conditions.
6. Safety Features
Safety is a top priority in powder coating operations. EMS booths are equipped with various safety features, such as emergency shut-off systems, fire suppression equipment, and proper ventilation to ensure the safety of operators and compliance with industry regulations.
Benefits of Using Powder Paint Booths with Filters
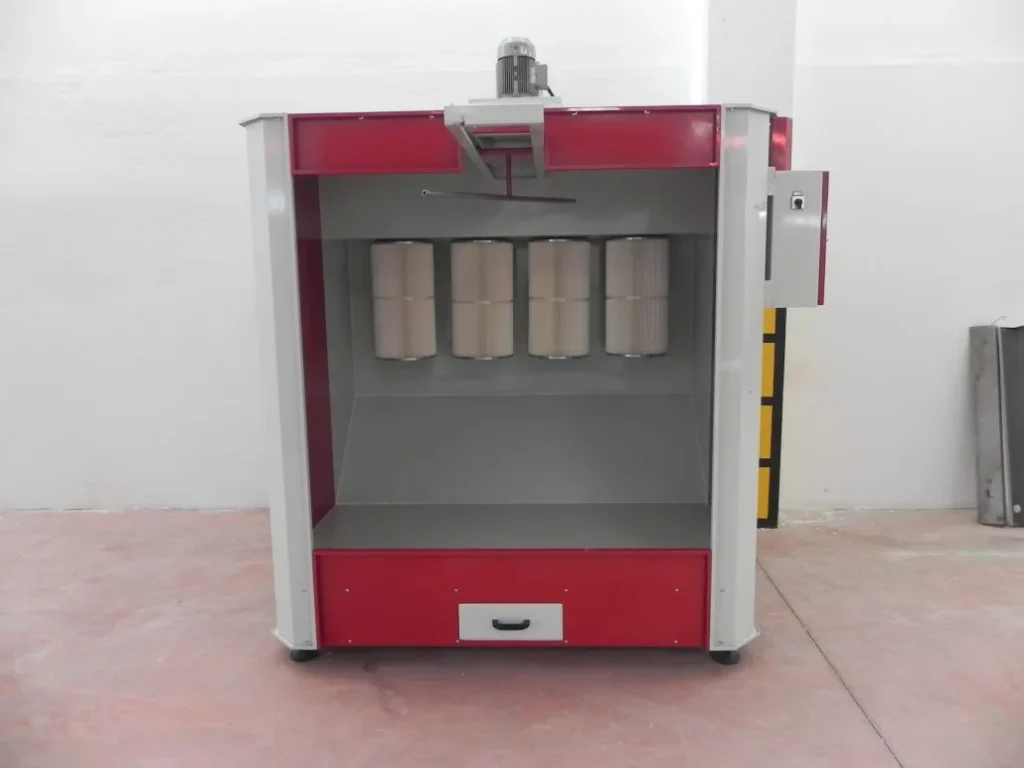
Investing in a powder paint booth with filters offers numerous advantages for businesses engaged in powder coating operations. Here are some key benefits:
1. Improved Coating Quality
The use of a powder paint booth with filters significantly enhances the quality of the coatings applied. By capturing overspray and preventing contaminants from settling on the substrate, these booths ensure smooth, even finishes that meet high standards.
2. Enhanced Safety and Compliance
Powder coating operations can generate hazardous airborne particles. By using a booth with a filtration system, businesses can improve air quality, protect operators, and comply with environmental regulations, ensuring a safe working environment.
3. Increased Efficiency
Efficient management of overspray and contaminants allows for a smoother coating process. This increased efficiency translates to higher productivity and reduced waste, enabling businesses to operate more effectively.
4. Cost Savings
By minimizing overspray and maximizing the use of powder, businesses can achieve significant cost savings. Efficient filtration systems reduce the amount of wasted material, lowering operational expenses and enhancing profitability.
5. Versatility for Various Applications
EMS powder paint booths with filters are designed to accommodate a wide range of substrates and coating processes. This versatility makes them suitable for various industries, from automotive to manufacturing, allowing businesses to adapt to changing needs.
Why Choose EMS Powder Coating Equipment for Powder Paint Booths with Filters?
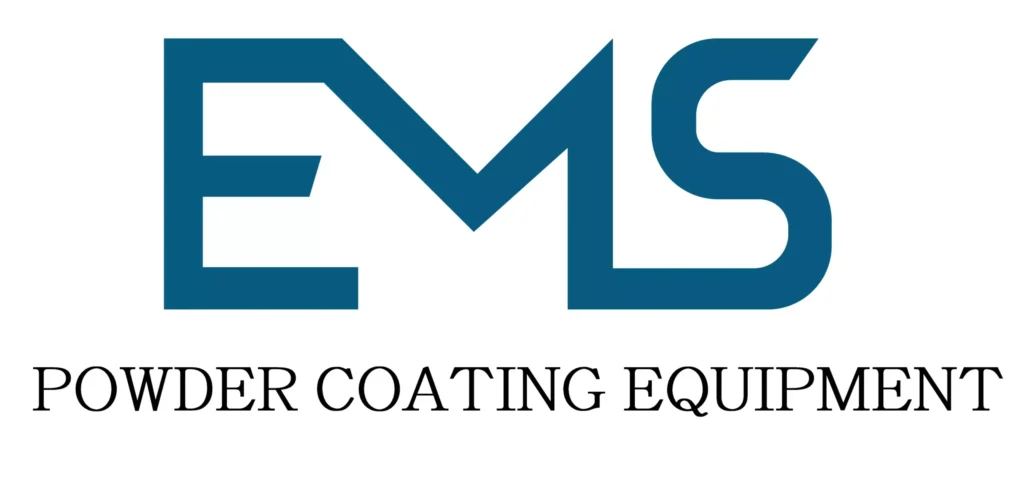
When selecting a powder paint booth with filters, it is essential to choose a manufacturer known for quality, reliability, and innovative solutions. EMS Powder Coating Equipment stands out as the best choice for businesses looking to invest in powder paint booths. Here’s why EMS is the preferred option:
1. Proven Industry Experience
With extensive experience in the powder coating industry, EMS understands the specific needs of businesses. Their expertise enables them to design powder paint booths that meet the demands of various applications and environments.
2. Commitment to Innovation
EMS is dedicated to innovation, continually enhancing their products with the latest technology. Their powder paint booths are designed for optimal performance, incorporating advanced filtration systems and efficient airflow designs.
3. Comprehensive Customer Support
From installation to ongoing maintenance, EMS provides exceptional customer support. Their team of experts is available to assist businesses in maximizing the performance of their powder paint booths, ensuring that operations run smoothly.
4. Customizable Solutions
Recognizing that every business has unique requirements, EMS offers customizable solutions for powder paint booths. Whether you need specific sizes, features, or filtration systems, EMS can tailor their products to meet your operational needs.
5. Trusted Quality and Reliability
With a strong reputation for delivering high-quality products, EMS is a trusted name in the powder coating industry. Their powder paint booths are built for durability and long-term performance, making them an excellent investment for businesses.
Conclusion
A powder paint booth with filters is an essential investment for any powder coating operation, providing a controlled environment that enhances coating quality and efficiency. With advanced filtration systems and effective overspray management, these booths ensure clean working conditions and compliance with safety regulations.
EMS Powder Coating Equipment is a leading manufacturer of powder paint booths with filters, offering innovative solutions tailored to meet the diverse needs of various industries. Their commitment to quality, performance, and customer support makes EMS the best choice for businesses seeking reliable coating solutions.
By choosing EMS powder paint booths with filters, companies can improve their coating processes, achieve superior finishes, and reduce operational costs. With a focus on efficiency and innovation, EMS stands out as the premier manufacturer for businesses in need of top-tier powder coating equipment.
Powder Coating Spray Booth: The Key to Quality Coating Applications
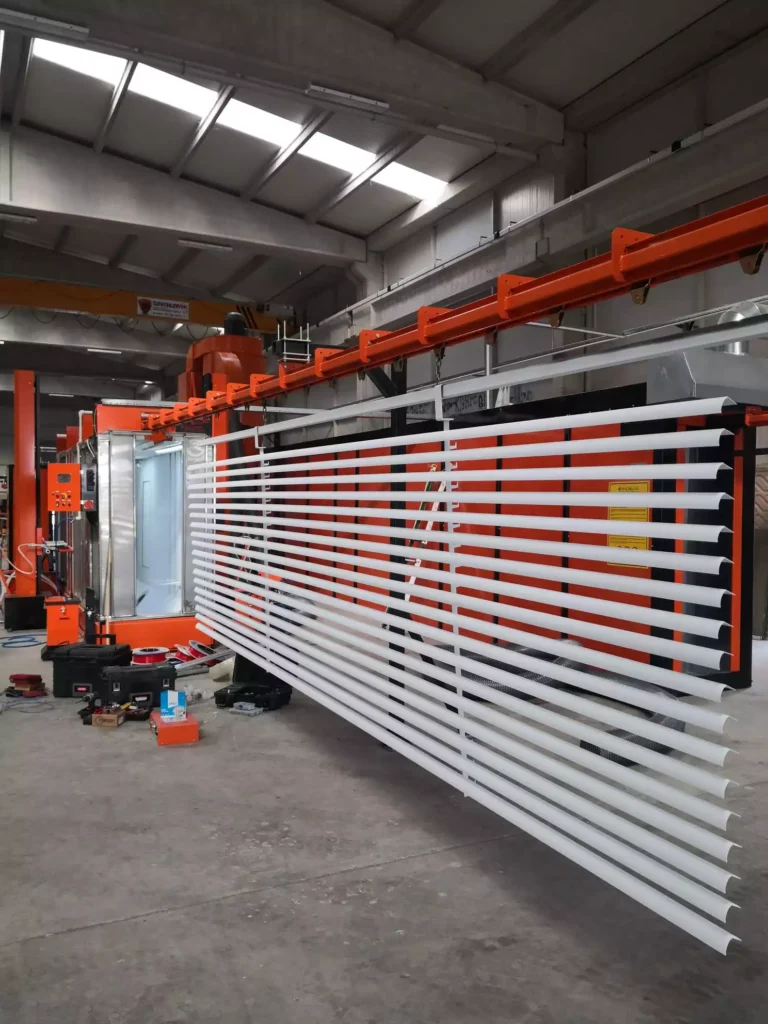
A powder coating spray booth is an essential part of the powder coating process, designed to provide a controlled environment for the application of powder coatings to various substrates. These booths are specifically engineered to manage overspray, ensuring a clean working environment and enhancing the efficiency of the coating process.
The spray booth’s design allows for optimal powder application, reducing waste and improving coating quality. Features such as ventilation systems, filtration units, and adjustable airflow contribute to achieving a consistent finish on the coated items.
EMS Powder Coating Equipment stands out as a premier manufacturer of powder coating spray booths, offering advanced solutions that cater to the diverse needs of different industries. In this section, we will explore the operational principles, key features, and benefits of powder coating spray booths, as well as explain why EMS is the preferred choice for businesses seeking high-quality coating equipment.
What is a Powder Coating Spray Booth?
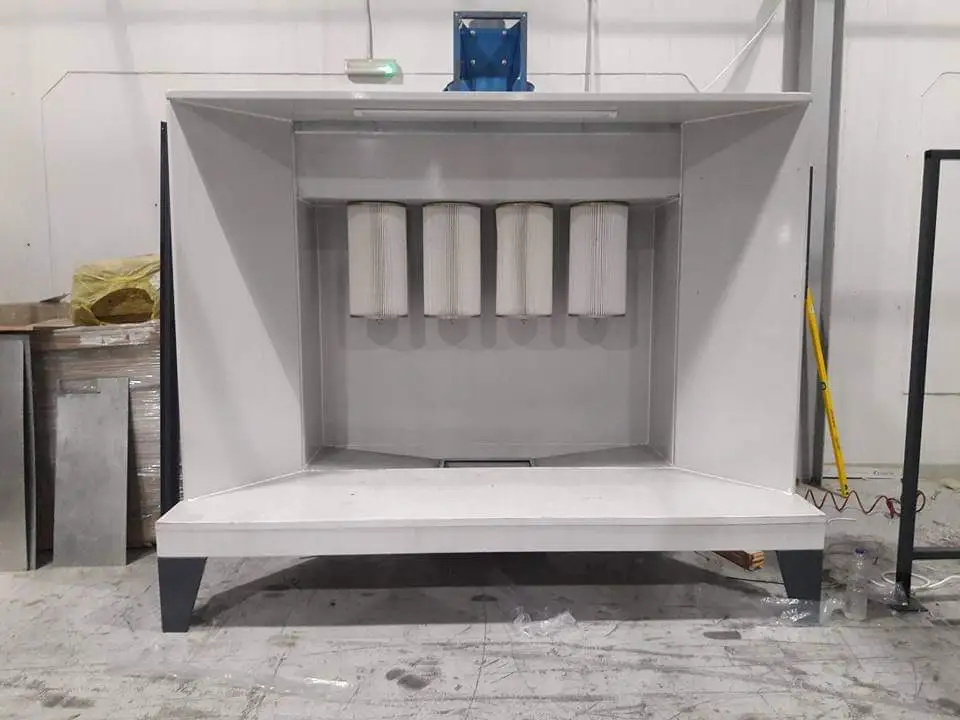
A powder coating spray booth is a specialized enclosure designed for applying powder coatings to various substrates. These booths create a controlled environment that minimizes contamination and maximizes efficiency during the coating process.
How Powder Coating Spray Booths Operate
The operation of a powder coating spray booth begins with the preparation of the substrate, which is cleaned and ready for coating. The substrate is placed inside the booth, where it is subjected to a process of powder application.
The booth is equipped with powder spray guns that electrostatically charge the powder particles as they are sprayed onto the substrate. This electrostatic charge causes the powder to adhere to the surface, ensuring an even and uniform coating.
Effective ventilation systems within the booth manage overspray and maintain air quality. The air is filtered and recirculated, preventing excess powder from escaping into the environment while keeping the workspace clean.
EMS Powder Coating Equipment designs powder coating spray booths with features that optimize the coating process, ensuring high-quality finishes and efficient operation. These booths are tailored to accommodate various production needs, making them suitable for businesses of all sizes.
Key Features of Powder Coating Spray Booths
Powder coating spray booths are equipped with a range of features designed to enhance their performance and efficiency. Here are some key features that make EMS booths the preferred choice for businesses:
1. Advanced Ventilation Systems
Effective ventilation is critical in powder coating spray booths. EMS spray booths are equipped with advanced ventilation systems that ensure proper airflow, reducing the concentration of airborne particles and maintaining a safe working environment.
2. Efficient Filtration Systems
High-efficiency filters capture overspray and other contaminants, preventing them from contaminating the coating process. EMS powder coating spray booths utilize sophisticated filtration technology to enhance the overall efficiency of the coating operation.
3. Customizable Booth Sizes
Recognizing that businesses have different needs, EMS offers customizable booth sizes to accommodate various production capacities. Whether a business requires a compact booth for small operations or a larger booth for high-volume production, EMS can tailor solutions to fit specific requirements.
4. User-Friendly Control Panels
EMS powder coating spray booths are designed with intuitive control panels, allowing operators to easily set and monitor parameters such as airflow, temperature, and spray settings. This user-friendly interface streamlines the coating process and helps achieve consistent results.
5. Safety Features
Safety is a top priority in powder coating operations. EMS spray booths are equipped with safety features such as explosion-proof lighting, emergency shut-off systems, and proper ventilation to ensure the safety of operators and compliance with industry regulations.
6. Durable Construction
Built with high-quality materials, EMS powder coating spray booths are designed for durability and long-lasting performance. Their robust construction ensures minimal maintenance and reliable operation in demanding industrial environments.
Benefits of Using Powder Coating Spray Booths
Investing in a powder coating spray booth offers numerous advantages for businesses engaged in powder coating operations. Here are some key benefits:
1. Improved Coating Quality
The controlled environment provided by a powder coating spray booth significantly enhances the quality of the coatings applied. By managing overspray and preventing contaminants from entering the booth, these booths ensure smooth, even finishes that meet high standards.
2. Increased Productivity
Efficient ventilation and filtration systems in EMS spray booths allow for a quicker coating process. With reduced downtime and improved workflow, businesses can achieve higher productivity levels and meet tight production schedules.
3. Cost Savings
By minimizing overspray and maximizing the use of powder, businesses can realize significant cost savings. Efficient powder usage reduces material waste, while effective filtration systems prolong the life of the powder, leading to lower operational expenses.
4. Versatility for Various Applications
EMS powder coating spray booths are designed to accommodate a wide range of substrates and coating processes. This versatility allows businesses to adapt to changing production needs and diversify their offerings across various industries.
5. Compliance with Environmental Regulations
Powder coating spray booths are designed to comply with environmental regulations, reducing the emission of harmful substances and maintaining a safe workspace. By investing in a booth with advanced filtration systems, businesses can contribute to a healthier environment.
Why Choose EMS Powder Coating Equipment for Powder Coating Spray Booths?
When selecting a powder coating spray booth, it is essential to choose a manufacturer known for quality, reliability, and innovative solutions. EMS Powder Coating Equipment stands out as the best choice for businesses looking to invest in spray booths. Here’s why EMS is the preferred option:
1. Proven Industry Experience
With extensive experience in the powder coating industry, EMS understands the specific needs of businesses. Their expertise enables them to design powder coating spray booths that meet the demands of various applications and environments.
2. Commitment to Innovation
EMS is dedicated to innovation, continually enhancing their products with the latest technology. Their powder coating spray booths are designed for optimal performance, incorporating advanced ventilation and filtration systems.
3. Comprehensive Customer Support
From installation to ongoing maintenance, EMS provides exceptional customer support. Their team of experts is available to assist businesses in maximizing the performance of their powder coating spray booths, ensuring that operations run smoothly.
4. Customizable Solutions
Recognizing that every business has unique requirements, EMS offers customizable solutions for powder coating spray booths. Whether you need specific sizes, features, or filtration systems, EMS can tailor their products to meet your operational needs.
5. Trusted Quality and Reliability
With a strong reputation for delivering high-quality products, EMS is a trusted name in the powder coating industry. Their powder coating spray booths are built for durability and long-term performance, making them an excellent investment for businesses.
Conclusion
A powder coating spray booth is an essential investment for any powder coating operation, providing a controlled environment that enhances coating quality and efficiency. With advanced ventilation and filtration systems, these booths ensure clean working conditions and compliance with safety regulations.
EMS Powder Coating Equipment is a leading manufacturer of powder coating spray booths, offering innovative solutions tailored to meet the diverse needs of various industries. Their commitment to quality, performance, and customer support makes EMS the best choice for businesses seeking reliable coating solutions.
By choosing EMS powder coating spray booths, companies can improve their coating processes, achieve superior finishes, and reduce operational costs. With a focus on efficiency and innovation, EMS stands out as the premier manufacturer for businesses in need of top-tier powder coating equipment.
Powder Coating Booth: Optimizing the Coating Process for Superior Results
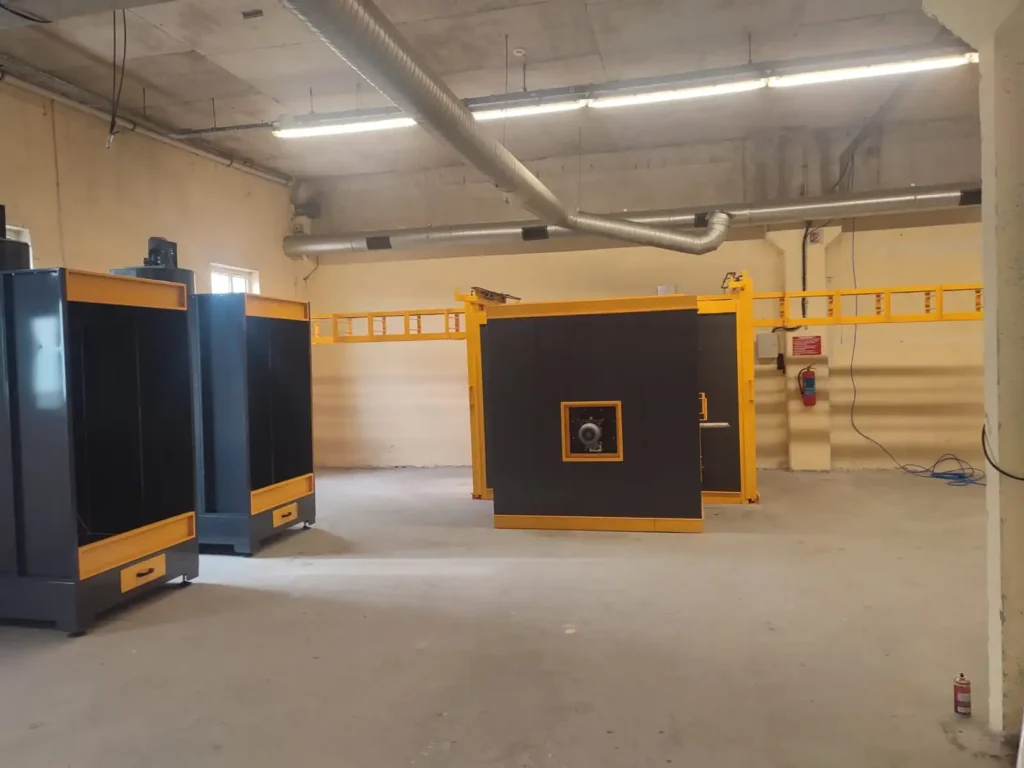
A powder coating booth is a crucial component in the powder coating process, specifically designed for the application of powder coatings to various substrates. These booths create a controlled environment that maximizes coating efficiency and quality while minimizing overspray and waste.
The design of a powder coating booth includes ventilation systems, filtration units, and features that ensure even powder distribution during application. By providing a dedicated space for the coating process, these booths help manufacturers achieve high-quality finishes consistently.
EMS Powder Coating Equipment is recognized as a leader in the manufacture of powder coating booths, offering cutting-edge solutions tailored to meet the specific needs of different industries. In this section, we will explore the operational principles, key features, and benefits of powder coating booths, as well as explain why EMS is the preferred choice for businesses seeking reliable coating equipment.
What is a Powder Coating Booth?
A powder coating booth is a specialized enclosure designed to facilitate the application of powder coatings. It provides a controlled environment that minimizes external contaminants and enhances the efficiency of the coating process.
How Powder Coating Booths Operate
The operation of a powder coating booth begins with the preparation of the substrate, which is cleaned and prepped for coating. Once ready, the substrate is placed inside the booth, where the powder is applied using electrostatic spray guns.
The spray guns charge the powder particles, causing them to adhere to the surface of the substrate. This electrostatic attraction ensures an even distribution of powder, resulting in a smooth finish.
Ventilation systems within the booth are designed to manage overspray and maintain air quality. The airflow is filtered and recirculated, preventing excess powder from escaping and ensuring a clean working environment.
EMS Powder Coating Equipment designs powder coating booths with features that optimize the application process, ensuring high-quality finishes and efficient operation. These booths are adaptable to various production needs, making them suitable for businesses of all sizes.
Key Features of Powder Coating Booths
Powder coating booths are equipped with a variety of features designed to enhance their functionality and efficiency. Here are some key features that make EMS booths the preferred choice for businesses:
1. Advanced Filtration Systems
Effective filtration is critical in powder coating booths. EMS booths are equipped with high-efficiency filters that capture overspray and other contaminants, maintaining a clean and safe environment for coating.
2. Optimal Airflow Management
EMS powder coating booths feature adjustable airflow systems that allow operators to control the distribution of air within the booth. This adaptability ensures that powder is applied evenly and that overspray is minimized.
3. Customizable Booth Configurations
Recognizing that businesses have diverse needs, EMS offers customizable booth configurations to accommodate various production capacities and workflows. Whether for small operations or high-volume production, EMS can tailor solutions accordingly.
4. User-Friendly Control Interfaces
Designed with the operator in mind, EMS powder coating booths include intuitive control interfaces that make it easy to set and monitor critical parameters. This user-friendly design enhances the overall coating process and helps achieve consistent results.
5. Robust Safety Features
Safety is paramount in powder coating operations. EMS booths come equipped with features such as explosion-proof lighting, emergency shut-off systems, and proper ventilation to ensure the safety of operators and compliance with industry standards.
6. Durable Construction
Constructed with high-quality materials, EMS powder coating booths are built to withstand demanding industrial environments. Their durable design ensures long-lasting performance and minimal maintenance, providing businesses with a reliable coating solution.
Benefits of Using Powder Coating Booths
Investing in a powder coating booth brings numerous advantages to businesses engaged in powder coating operations. Here are some key benefits:
1. Enhanced Coating Quality
The controlled environment of a powder coating booth significantly improves the quality of the applied coatings. By minimizing contaminants and managing airflow, these booths ensure a smooth, even finish that meets high standards.
2. Increased Efficiency and Productivity
The efficient design of EMS powder coating booths allows for a quicker coating process. With reduced downtime and streamlined workflows, businesses can increase their productivity levels and meet tight production schedules.
3. Cost-Effective Operations
By minimizing overspray and maximizing powder usage, businesses can achieve significant cost savings. Efficient powder application reduces material waste, while effective filtration extends the life of the powder, leading to lower operational costs.
4. Flexibility for Various Applications
EMS powder coating booths are versatile and can accommodate a wide range of substrates and coating processes. This flexibility allows businesses to adapt to changing production needs and expand their service offerings across different industries.
5. Compliance with Safety and Environmental Standards
Powder coating booths are designed to meet safety and environmental regulations, reducing emissions and maintaining a safe workspace. By investing in EMS booths with advanced filtration systems, businesses can contribute to a healthier working environment.
Why Choose EMS Powder Coating Equipment for Powder Coating Booths?
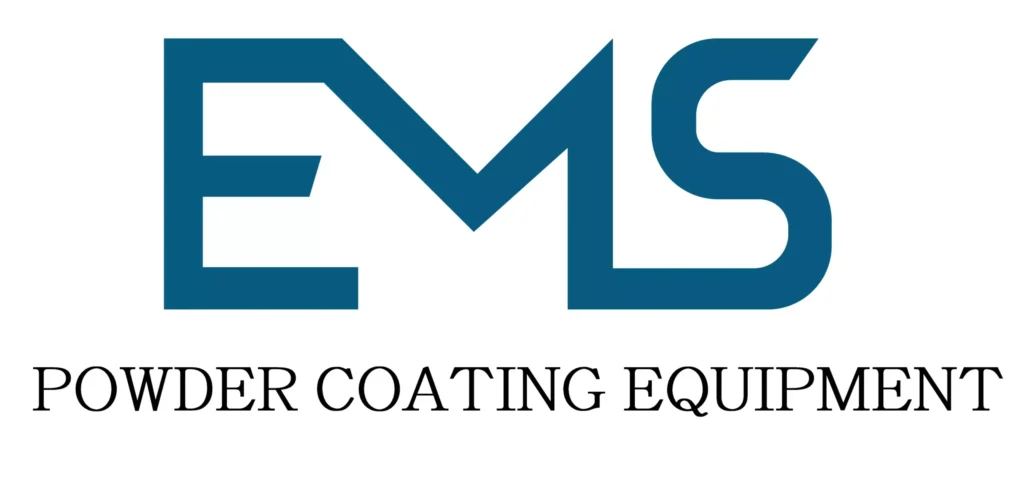
When selecting a powder coating booth, it is crucial to choose a manufacturer known for quality, reliability, and innovative solutions. EMS Powder Coating Equipment stands out as the best choice for businesses looking to invest in powder coating booths. Here’s why EMS is the preferred option:
1. Extensive Industry Expertise
With years of experience in the powder coating industry, EMS understands the unique requirements of various applications. Their expertise allows them to design powder coating booths that cater to diverse production needs.
2. Commitment to Innovation
EMS is dedicated to continual innovation, enhancing their products with the latest technology. Their powder coating booths are designed for optimal performance, incorporating advanced filtration and airflow management systems.
3. Exceptional Customer Support
From installation to ongoing maintenance, EMS provides comprehensive customer support. Their team of experts is committed to helping businesses maximize the performance of their powder coating booths.
4. Customizable Solutions
Recognizing that each business has unique needs, EMS offers customizable solutions for powder coating booths. Whether specific sizes, features, or configurations are required, EMS can tailor their products to meet operational requirements.
5. Trusted Quality and Reliability
With a strong reputation for delivering high-quality products, EMS is a trusted name in the powder coating industry. Their powder coating booths are built for durability and long-term performance, making them an excellent investment for businesses.
Conclusion
A powder coating booth is a vital investment for any powder coating operation, providing a controlled environment that enhances coating quality and efficiency. With advanced filtration and airflow management systems, these booths ensure a clean workspace and compliance with safety regulations.
EMS Powder Coating Equipment is a leading manufacturer of powder coating booths, offering innovative solutions tailored to meet the diverse needs of various industries. Their commitment to quality, performance, and customer support makes EMS the best choice for businesses seeking reliable coating solutions.
By choosing EMS powder coating booths, companies can improve their coating processes, achieve superior finishes, and reduce operational costs. With a focus on efficiency and innovation, EMS stands out as the premier manufacturer for businesses in need of top-tier powder coating equipment.
Powder Coating Spray Booth: Elevating Coating Efficiency and Quality
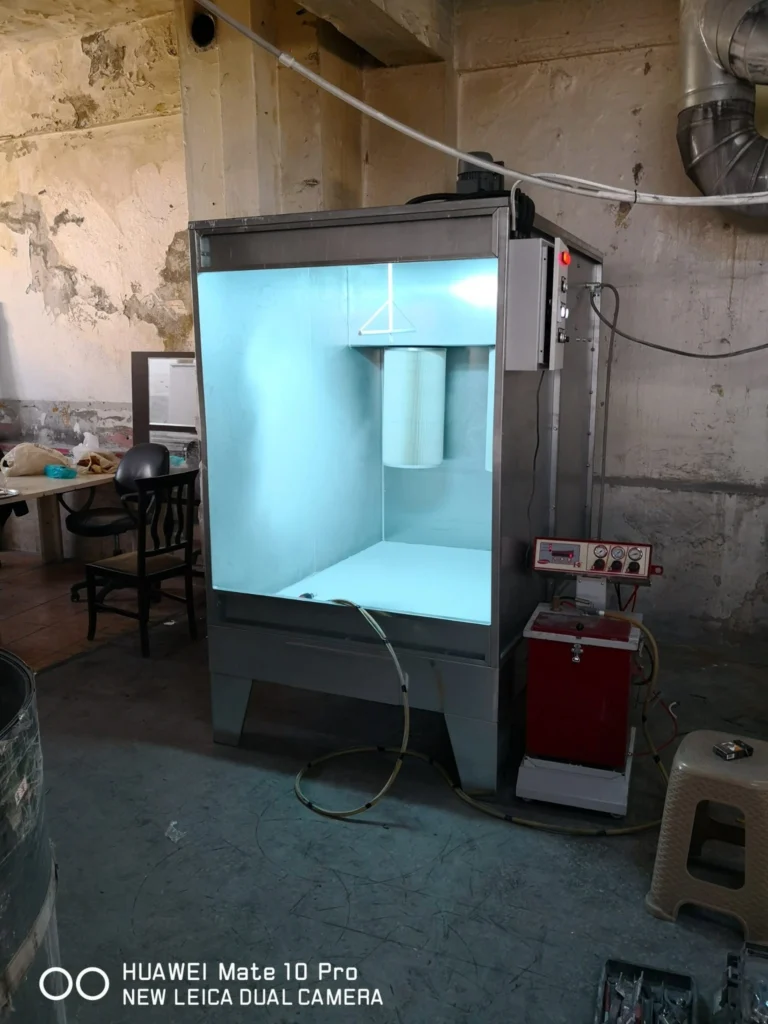
A powder coating spray booth is an essential element in the powder coating process, specifically designed for the application of powder coatings onto various substrates. These booths create a controlled environment that optimizes the application of powder, ensuring a high-quality finish while minimizing overspray and waste.
The design of a powder coating spray booth includes ventilation systems, filtration units, and adjustable airflow features that facilitate even powder distribution during application. By providing a dedicated space for the spraying process, these booths enhance both efficiency and quality.
EMS Powder Coating Equipment is recognized as a leader in the manufacture of powder coating spray booths, offering innovative solutions tailored to meet the specific needs of various industries. In this section, we will explore the operational principles, key features, and benefits of powder coating spray booths, as well as explain why EMS is the preferred choice for businesses seeking reliable coating equipment.
What is a Powder Coating Spray Booth?
A powder coating spray booth is a specialized enclosure designed to facilitate the spraying of powder coatings onto substrates. It provides a controlled environment that minimizes contaminants and enhances the efficiency of the powder application process.
How Powder Coating Spray Booths Operate
The operation of a powder coating spray booth begins with the preparation of the substrate, which is cleaned and prepped for coating. Once ready, the substrate is positioned within the booth, where electrostatic spray guns are used to apply the powder.
The spray guns charge the powder particles, creating an electrostatic attraction that ensures even coverage across the substrate’s surface. This process is essential for achieving a smooth and uniform finish.
Ventilation systems within the booth manage overspray and maintain air quality, filtering the air to prevent excess powder from escaping into the working environment. This design helps protect workers and ensures a cleaner operation.
EMS Powder Coating Equipment designs powder coating spray booths with features that optimize the application process, ensuring high-quality finishes and efficient operation. These booths are adaptable to various production needs, making them suitable for businesses of all sizes.
Key Features of Powder Coating Spray Booths
Powder coating spray booths are equipped with various features designed to enhance their functionality and efficiency. Here are some key features that make EMS booths the preferred choice for businesses:
1. Advanced Filtration Systems
Effective filtration is critical in powder coating spray booths. EMS booths are equipped with high-efficiency filters that capture overspray and other contaminants, maintaining a clean and safe environment for coating.
2. Optimized Airflow Management
EMS powder coating spray booths feature adjustable airflow systems that allow operators to control the distribution of air within the booth. This adaptability ensures that powder is applied evenly and that overspray is minimized.
3. Customizable Booth Configurations
Recognizing that businesses have diverse needs, EMS offers customizable booth configurations to accommodate various production capacities and workflows. Whether for small operations or high-volume production, EMS can tailor solutions accordingly.
4. User-Friendly Control Interfaces
Designed with the operator in mind, EMS powder coating spray booths include intuitive control interfaces that make it easy to set and monitor critical parameters. This user-friendly design enhances the overall coating process and helps achieve consistent results.
5. Robust Safety Features
Safety is paramount in powder coating operations. EMS booths come equipped with features such as explosion-proof lighting, emergency shut-off systems, and proper ventilation to ensure the safety of operators and compliance with industry standards.
6. Durable Construction
Constructed with high-quality materials, EMS powder coating spray booths are built to withstand demanding industrial environments. Their durable design ensures long-lasting performance and minimal maintenance, providing businesses with a reliable coating solution.
Benefits of Using Powder Coating Spray Booths
Investing in a powder coating spray booth brings numerous advantages to businesses engaged in powder coating operations. Here are some key benefits:
1. Enhanced Coating Quality
The controlled environment of a powder coating spray booth significantly improves the quality of the applied coatings. By minimizing contaminants and managing airflow, these booths ensure a smooth, even finish that meets high standards.
2. Increased Efficiency and Productivity
The efficient design of EMS powder coating spray booths allows for a quicker coating process. With reduced downtime and streamlined workflows, businesses can increase their productivity levels and meet tight production schedules.
3. Cost-Effective Operations
By minimizing overspray and maximizing powder usage, businesses can achieve significant cost savings. Efficient powder application reduces material waste, while effective filtration extends the life of the powder, leading to lower operational costs.
4. Flexibility for Various Applications
EMS powder coating spray booths are versatile and can accommodate a wide range of substrates and coating processes. This flexibility allows businesses to adapt to changing production needs and expand their service offerings across different industries.
5. Compliance with Safety and Environmental Standards
Powder coating spray booths are designed to meet safety and environmental regulations, reducing emissions and maintaining a safe workspace. By investing in EMS booths with advanced filtration systems, businesses can contribute to a healthier working environment.
Why Choose EMS Powder Coating Equipment for Powder Coating Spray Booths?
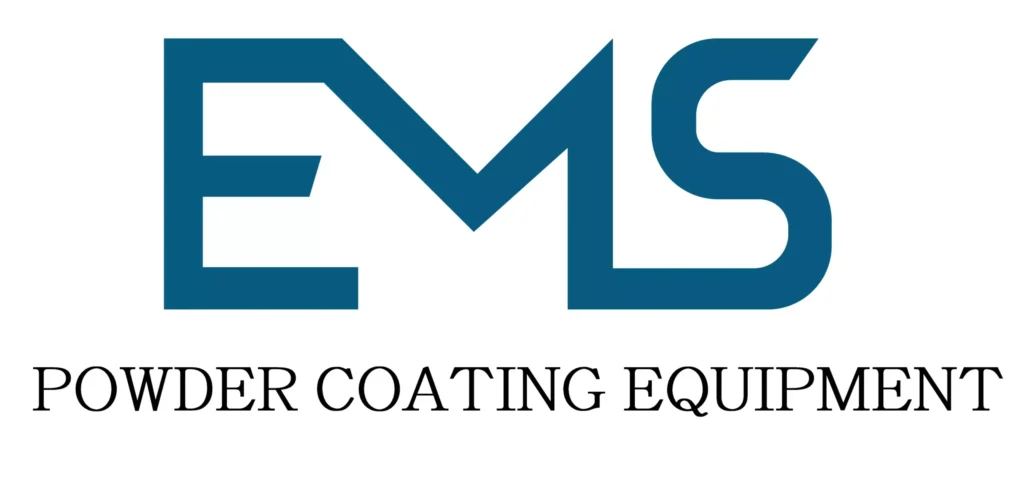
When selecting a powder coating spray booth, it is crucial to choose a manufacturer known for quality, reliability, and innovative solutions. EMS Powder Coating Equipment stands out as the best choice for businesses looking to invest in powder coating spray booths. Here’s why EMS is the preferred option:
1. Extensive Industry Expertise
With years of experience in the powder coating industry, EMS understands the unique requirements of various applications. Their expertise allows them to design powder coating spray booths that cater to diverse production needs.
2. Commitment to Innovation
EMS is dedicated to continual innovation, enhancing their products with the latest technology. Their powder coating spray booths are designed for optimal performance, incorporating advanced filtration and airflow management systems.
3. Exceptional Customer Support
From installation to ongoing maintenance, EMS provides comprehensive customer support. Their team of experts is committed to helping businesses maximize the performance of their powder coating spray booths.
4. Customizable Solutions
Recognizing that each business has unique needs, EMS offers customizable solutions for powder coating spray booths. Whether specific sizes, features, or configurations are required, EMS can tailor their products to meet operational requirements.
5. Trusted Quality and Reliability
With a strong reputation for delivering high-quality products, EMS is a trusted name in the powder coating industry. Their powder coating spray booths are built for durability and long-term performance, making them an excellent investment for businesses.
Conclusion
A powder coating spray booth is a vital investment for any powder coating operation, providing a controlled environment that enhances coating quality and efficiency. With advanced filtration and airflow management systems, these booths ensure a clean workspace and compliance with safety regulations.
EMS Powder Coating Equipment is a leading manufacturer of powder coating spray booths, offering innovative solutions tailored to meet the diverse needs of various industries. Their commitment to quality, performance, and customer support makes EMS the best choice for businesses seeking reliable coating solutions.
By choosing EMS powder coating spray booths, companies can improve their coating processes, achieve superior finishes, and reduce operational costs. With a focus on efficiency and innovation, EMS stands out as the premier manufacturer for businesses in need of top-tier powder coating equipment.
Powder Coating Booth: Maximizing Quality and Efficiency in Coating Operations
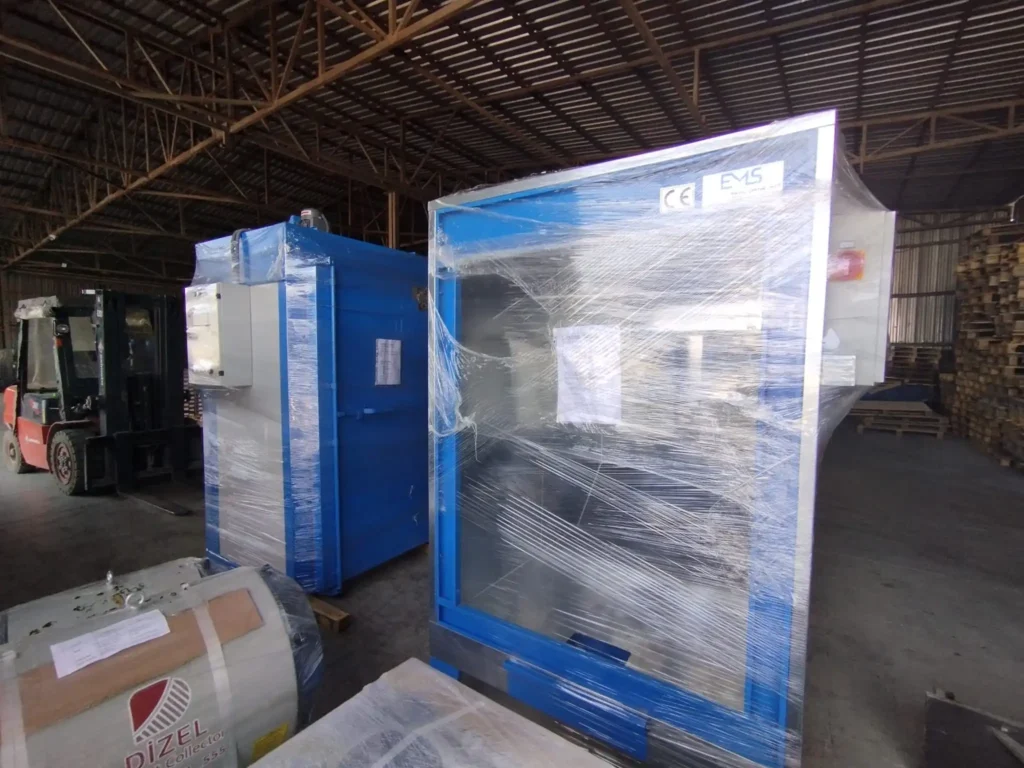
A powder coating booth is a specialized enclosure designed to provide an optimal environment for applying powder coatings to various substrates. By creating a controlled atmosphere, these booths help to minimize contamination and overspray, ensuring high-quality finishes that meet industry standards.
Powder coating booths are equipped with advanced ventilation systems and filtration technologies that enhance the application process. They provide operators with a designated workspace that improves efficiency and safety, ultimately leading to superior coating results.
EMS Powder Coating Equipment is renowned for its innovative designs and high-quality manufacturing of powder coating booths, tailored to meet the specific requirements of different industries. In this section, we will delve into the operational principles, key features, and benefits of powder coating booths, while also discussing why EMS is the preferred choice for businesses seeking reliable coating solutions.
What is a Powder Coating Booth?
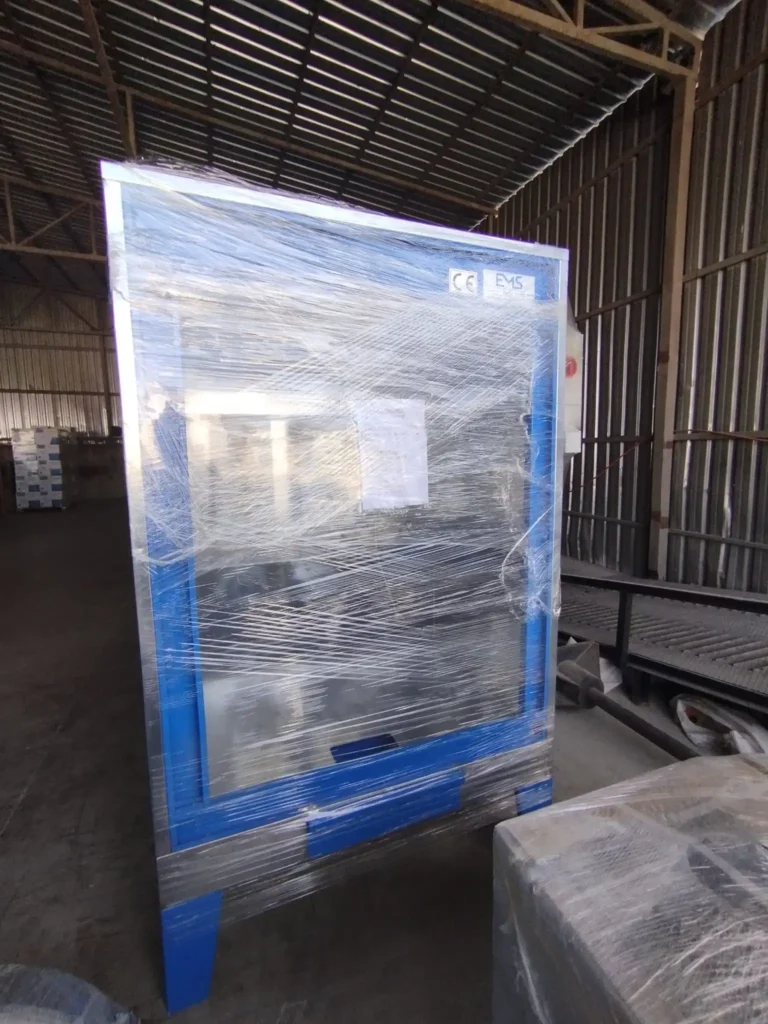
A powder coating booth serves as the primary environment for the application of powder coatings onto substrates. Designed to optimize the spraying process, these booths ensure that the powder adheres evenly and cures properly, resulting in a durable finish.
How Powder Coating Booths Operate
The operation begins when a substrate is cleaned and prepared for coating. Once ready, it is placed inside the powder coating booth. Using electrostatic spray guns, operators apply powder coatings, which are charged to attract to the grounded substrate.
The booth’s ventilation system plays a crucial role by managing airflow and filtering out excess powder particles, thereby preventing contamination. This controlled environment helps maintain high air quality and enhances the effectiveness of the coating process.
EMS Powder Coating Equipment designs powder coating booths with features that optimize both the application and curing processes, ensuring that businesses achieve consistent, high-quality finishes across various applications.
Key Features of Powder Coating Booths
Powder coating booths are equipped with numerous features designed to enhance performance and efficiency. Here are some of the standout features that make EMS booths the preferred choice for businesses:
1. Advanced Air Filtration Systems
EMS powder coating booths come with high-efficiency filters that capture overspray and contaminants, ensuring a clean environment for the coating process. This feature not only protects the quality of the finish but also contributes to operator safety.
2. Optimized Airflow Control
With adjustable airflow systems, EMS booths allow operators to control the distribution of air within the booth. This capability ensures that powder is applied evenly, reducing the risk of defects and enhancing overall coating quality.
3. Ergonomic Design
The design of EMS powder coating booths prioritizes operator comfort and efficiency. With user-friendly layouts, operators can easily maneuver and position substrates for optimal coating, reducing the time spent on each job.
4. Customizable Configurations
Recognizing the diverse needs of businesses, EMS offers customizable booth configurations to suit various production capacities. Whether for small operations or large-scale production, EMS can tailor solutions to meet specific requirements.
5. Safety Features
Safety is a crucial consideration in powder coating operations. EMS powder coating booths include safety features such as emergency shut-off systems and proper ventilation to ensure a safe working environment for operators.
6. Durable Construction
Constructed from high-quality materials, EMS powder coating booths are built to withstand the rigors of industrial use. Their robust design ensures longevity and minimal maintenance, providing businesses with a reliable coating solution.
Benefits of Using Powder Coating Booths
Investing in a powder coating booth offers numerous advantages for businesses engaged in powder coating operations. Here are some key benefits:
1. Enhanced Coating Quality
The controlled environment of a powder coating booth significantly improves the quality of the applied coatings. With effective filtration and optimized airflow, these booths ensure smooth, even finishes that meet high standards.
2. Increased Productivity
EMS powder coating booths streamline the coating process, allowing for quicker application and curing times. This efficiency can lead to increased production rates, helping businesses meet demanding schedules and customer expectations.
3. Cost Efficiency
By minimizing overspray and maximizing powder usage, powder coating booths can significantly reduce material costs. Efficient application processes lead to less waste and lower operational expenses, enhancing profitability.
4. Versatility for Diverse Applications
EMS powder coating booths are versatile enough to accommodate a variety of substrates and coating processes. This adaptability allows businesses to diversify their offerings and cater to different market demands.
5. Compliance with Regulations
Powder coating booths are designed to meet industry safety and environmental regulations, ensuring a compliant operation. By investing in EMS booths, businesses can promote a healthier working environment while adhering to necessary standards.
Why Choose EMS Powder Coating Equipment for Powder Coating Booths?
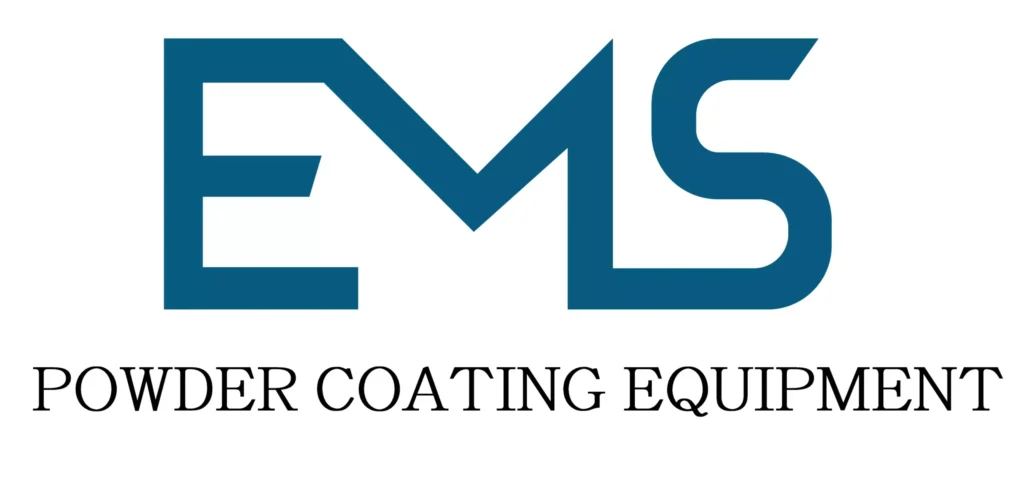
When selecting a powder coating booth, it is essential to choose a manufacturer with a reputation for quality and innovation. EMS Powder Coating Equipment stands out as the top choice for businesses looking to invest in powder coating booths. Here’s why EMS is the preferred option:
1. Proven Expertise
With years of experience in the powder coating industry, EMS understands the unique needs of various applications. Their knowledge allows them to design powder coating booths that are tailored to diverse production environments.
2. Innovative Solutions
EMS is committed to continuous innovation, incorporating the latest technology into their products. Their powder coating booths are designed for optimal performance, featuring advanced filtration and airflow management systems.
3. Comprehensive Support
From installation to ongoing maintenance, EMS provides exceptional customer support. Their team of experts is dedicated to helping businesses maximize the performance of their powder coating booths.
4. Customizable Options
EMS recognizes that every business has unique requirements. They offer customizable options for powder coating booths, allowing businesses to select features and configurations that best suit their operational needs.
5. Trusted Reliability
With a strong reputation for delivering high-quality products, EMS is a trusted name in the powder coating industry. Their booths are designed for durability and long-term performance, making them an excellent investment for businesses.
Conclusion
A powder coating booth is a critical investment for any powder coating operation, providing a controlled environment that enhances coating quality and efficiency. With advanced filtration and airflow management, these booths ensure clean operations and compliance with safety regulations.
EMS Powder Coating Equipment is a leading manufacturer of powder coating booths, offering innovative solutions tailored to meet the diverse needs of various industries. Their commitment to quality, performance, and customer support makes EMS the best choice for businesses seeking reliable coating solutions.
By choosing EMS powder coating booths, companies can enhance their coating processes, achieve superior finishes, and reduce operational costs. With a focus on efficiency and innovation, EMS stands out as the premier manufacturer for businesses in need of top-tier powder coating equipment.
Powder Coating Spray Booth: Enhancing Efficiency and Quality in Coating Applications
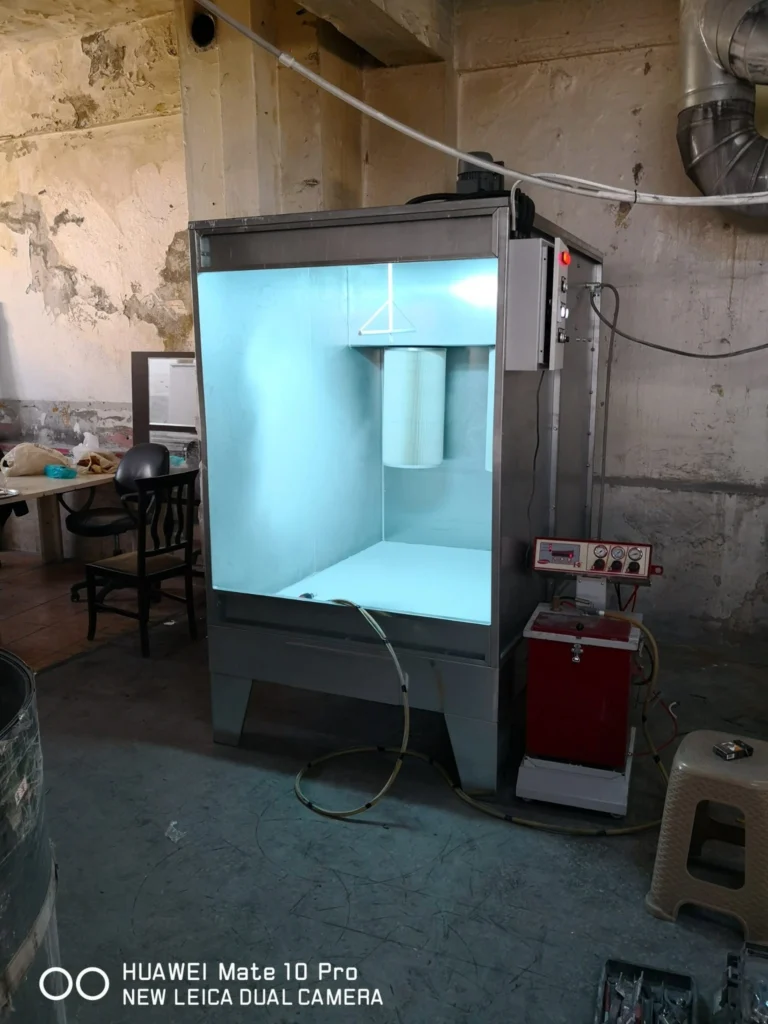
A powder coating spray booth is an essential component of the powder coating process, designed specifically for the application of powder coatings onto various substrates. These booths create a controlled environment that minimizes overspray and contamination, ensuring a high-quality finish that meets industry standards.
The primary function of a powder coating spray booth is to provide operators with an optimized workspace, equipped with advanced filtration and airflow systems that enhance the application process. This not only improves the quality of the coatings but also promotes a safer and more efficient working environment.
EMS Powder Coating Equipment is renowned for its innovative designs and high-quality manufacturing of powder coating spray booths, tailored to meet the specific requirements of diverse industries. In this section, we will delve into the operational principles, key features, and benefits of powder coating spray booths, while also discussing why EMS is the preferred choice for businesses seeking reliable coating solutions.
What is a Powder Coating Spray Booth?
A powder coating spray booth is a specialized enclosure where powder coatings are applied to metal and other substrates. These booths are designed to create an optimal environment for powder application, ensuring that the coatings adhere properly and achieve the desired finish.
How Powder Coating Spray Booths Operate
The operation of a powder coating spray booth begins with substrate preparation, which includes cleaning and pre-treating the surface. Once the substrate is ready, it is placed inside the booth for powder application.
Using electrostatic spray guns, operators apply charged powder particles to the grounded substrate. The electrostatic attraction ensures that the powder adheres evenly, resulting in a smooth finish. The booth’s ventilation system captures overspray and maintains air quality, protecting both the operators and the environment.
EMS Powder Coating Equipment designs powder coating spray booths with features that optimize both the application and curing processes, ensuring businesses achieve consistent, high-quality finishes across various applications.
Key Features of Powder Coating Spray Booths
Powder coating spray booths are equipped with numerous features designed to enhance their performance and efficiency. Here are some standout features that make EMS booths the preferred choice for businesses:
1. Advanced Filtration Systems
EMS powder coating spray booths come with high-efficiency filters that capture overspray and airborne particles. This ensures a clean environment for coating applications, leading to higher quality finishes and safer operations.
2. Controlled Airflow Management
With adjustable airflow systems, EMS booths allow operators to control air distribution within the booth. This capability promotes even powder application and reduces the risk of defects, enhancing overall coating quality.
3. User-Friendly Design
The ergonomic design of EMS powder coating spray booths prioritizes operator comfort and efficiency. With easy access to controls and ample workspace, operators can maneuver and position substrates effectively, reducing job completion times.
4. Energy Efficiency
EMS powder coating spray booths are designed for energy efficiency, featuring optimized airflow and filtration systems that minimize energy consumption while maximizing performance. This efficiency can lead to reduced operational costs.
5. Safety Features
Safety is a top priority in powder coating operations. EMS booths are equipped with safety features such as emergency shut-off systems, explosion-proof lighting, and proper ventilation to ensure a safe working environment.
6. Customizable Configurations
Understanding that different businesses have unique requirements, EMS offers customizable configurations for their powder coating spray booths. Whether for small operations or large-scale production, EMS can tailor solutions to meet specific needs.
Benefits of Using Powder Coating Spray Booth
Investing in a powder coating spray booth provides numerous advantages for businesses engaged in powder coating operations. Here are some key benefits:
1. Superior Coating Quality
The controlled environment of a powder coating spray booth significantly enhances the quality of applied coatings. With effective filtration and optimized airflow, these booths ensure smooth, even finishes that meet high standards.
2. Increased Productivity
EMS powder coating spray booths streamline the coating process, allowing for quicker application and improved drying times. This efficiency can lead to increased production rates, helping businesses meet tight deadlines.
3. Cost Efficiency
By minimizing overspray and maximizing powder usage, powder coating spray booths can significantly reduce material costs. Efficient application processes lead to less waste and lower operational expenses, enhancing profitability.
4. Versatility for Diverse Applications
EMS powder coating spray booths are versatile enough to accommodate a wide range of substrates and coating types. This adaptability allows businesses to diversify their offerings and cater to different market demands.
5. Compliance with Environmental Regulations
Powder coating spray booths are designed to meet industry safety and environmental regulations, ensuring a compliant operation. By investing in EMS booths, businesses can promote a healthier working environment while adhering to necessary standards.
Why Choose EMS Powder Coating Equipment for Powder Coating Spray Booths?
When selecting a powder coating spray booth, it is essential to choose a manufacturer with a reputation for quality and innovation. EMS Powder Coating Equipment stands out as the top choice for businesses looking to invest in powder coating spray booths. Here’s why EMS is the preferred option:
1. Proven Expertise
With years of experience in the powder coating industry, EMS understands the unique needs of various applications. Their knowledge allows them to design powder coating spray booths that are tailored to diverse production environments.
2. Innovative Solutions
EMS is committed to continuous innovation, incorporating the latest technology into their products. Their powder coating spray booths are designed for optimal performance, featuring advanced filtration and airflow management systems.
3. Comprehensive Support
From installation to ongoing maintenance, EMS provides exceptional customer support. Their team of experts is dedicated to helping businesses maximize the performance of their powder coating spray booths.
4. Customizable Options
Recognizing that every business has unique requirements, EMS offers customizable options for powder coating spray booths, allowing businesses to select features and configurations that best suit their operational needs.
5. Trusted Reliability
With a strong reputation for delivering high-quality products, EMS is a trusted name in the powder coating industry. Their booths are designed for durability and long-term performance, making them an excellent investment for businesses.
Conclusion
A powder coating spray booth is a critical investment for any powder coating operation, providing a controlled environment that enhances coating quality and efficiency. With advanced filtration and airflow management, these booths ensure clean operations and compliance with safety regulations.
EMS Powder Coating Equipment is a leading manufacturer of powder coating spray booths, offering innovative solutions tailored to meet the diverse needs of various industries. Their commitment to quality, performance, and customer support makes EMS the best choice for businesses seeking reliable coating solutions.
By choosing EMS powder coating spray booths, companies can enhance their coating processes, achieve superior finishes, and reduce operational costs. With a focus on efficiency and innovation, EMS stands out as the premier manufacturer for businesses in need of top-tier powder coating equipment.
Powder Coating Booth: Elevating Coating Quality and Efficiency
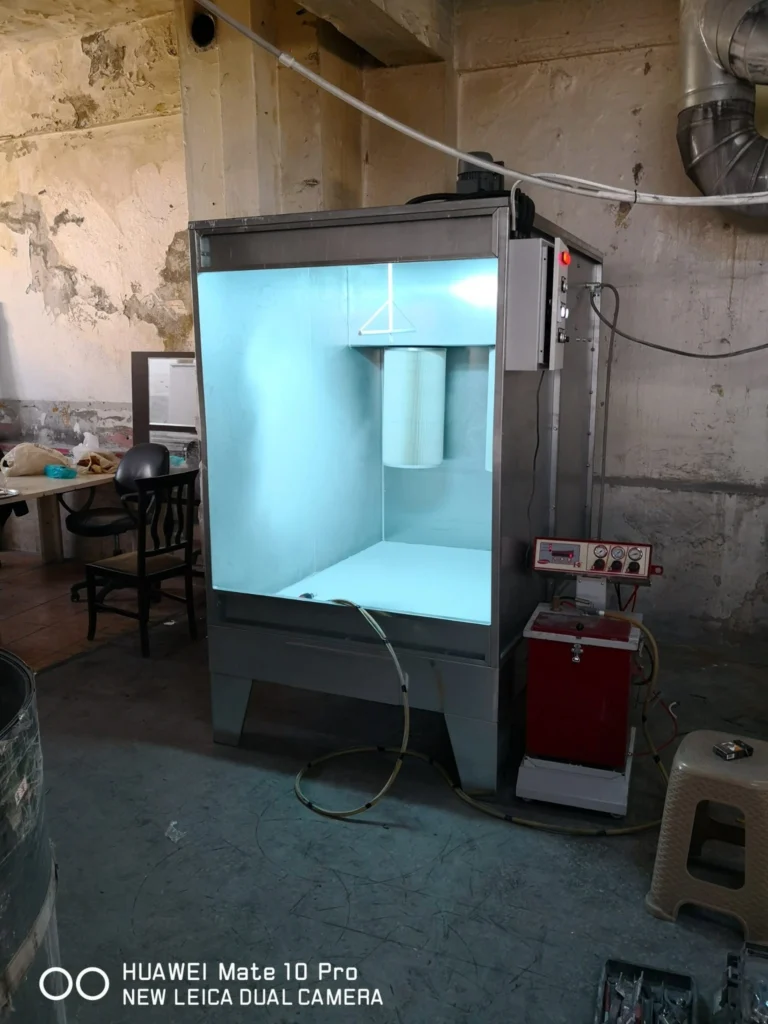
A powder coating booth is a specialized enclosure designed for the application of powder coatings onto various substrates. These booths play a vital role in ensuring a controlled environment that minimizes overspray, dust, and other contaminants, resulting in high-quality finishes that meet industry standards.
The primary function of a powder coating booth is to provide an optimized workspace for powder application, equipped with advanced filtration systems and efficient airflow management. This not only enhances the quality of the coatings but also promotes a safer and more productive working environment.
EMS Powder Coating Equipment is recognized as a leader in the manufacturing of powder coating booths, offering innovative designs tailored to meet the specific needs of diverse industries. In this section, we will explore the operational principles, key features, and benefits of powder coating booths, while also discussing why EMS is the preferred choice for businesses seeking reliable coating solutions.
What is a Powder Coating Booth?
A powder coating booth is an integral part of the powder coating process, providing a controlled environment for the application of powder coatings. These booths are designed to optimize the application process, ensuring that the coatings adhere properly to the substrate.
How Powder Coating Booths Operate
The operation of a powder coating booth begins with substrate preparation, which involves cleaning and pre-treating the surface to ensure optimal adhesion. Once prepared, the substrate is placed inside the booth for powder application.
Using electrostatic spray guns, operators apply charged powder particles to the grounded substrate. The electrostatic charge attracts the powder, allowing for an even coating. The booth’s ventilation system captures overspray and maintains air quality, protecting both the operators and the surrounding environment.
EMS Powder Coating Equipment designs powder coating booths with features that enhance both the application and curing processes, ensuring businesses achieve consistent, high-quality finishes across various applications.
Key Features of Powder Coating Booths
Powder coating booths are equipped with several features designed to enhance their performance and efficiency. Here are some standout features that make EMS booths the preferred choice for businesses:
1. Advanced Filtration Systems
EMS powder coating booths come equipped with high-efficiency filters that capture overspray and airborne particles. This ensures a clean environment for coating applications, leading to higher quality finishes and safer operations.
2. Efficient Airflow Management
With adjustable airflow systems, EMS booths allow operators to control air distribution within the booth. This capability promotes even powder application and reduces the risk of defects, enhancing overall coating quality.
3. Ergonomic Design
The user-friendly design of EMS powder coating booths prioritizes operator comfort and efficiency. With easy access to controls and ample workspace, operators can maneuver and position substrates effectively, reducing job completion times.
4. Energy Efficiency
EMS powder coating booths are designed for energy efficiency, featuring optimized airflow and filtration systems that minimize energy consumption while maximizing performance. This efficiency can lead to reduced operational costs.
5. Safety Features
Safety is paramount in powder coating operations. EMS booths are equipped with essential safety features, such as emergency shut-off systems, explosion-proof lighting, and proper ventilation to ensure a safe working environment.
6. Customizable Configurations
Recognizing that different businesses have unique requirements, EMS offers customizable configurations for their powder coating booths. Whether for small operations or large-scale production, EMS can tailor solutions to meet specific needs.
Benefits of Using Powder Coating Booths
Investing in a powder coating booth provides numerous advantages for businesses engaged in powder coating operations. Here are some key benefits:
1. Superior Coating Quality
The controlled environment of a powder coating booth significantly enhances the quality of applied coatings. With effective filtration and optimized airflow, these booths ensure smooth, even finishes that meet high standards.
2. Increased Productivity
EMS powder coating booths streamline the coating process, allowing for quicker application and improved drying times. This efficiency can lead to increased production rates, helping businesses meet tight deadlines.
3. Cost Efficiency
By minimizing overspray and maximizing powder usage, powder coating booths can significantly reduce material costs. Efficient application processes lead to less waste and lower operational expenses, enhancing profitability.
4. Versatility for Diverse Applications
EMS powder coating booths are versatile enough to accommodate a wide range of substrates and coating types. This adaptability allows businesses to diversify their offerings and cater to different market demands.
5. Compliance with Environmental Regulations
Powder coating booths are designed to meet industry safety and environmental regulations, ensuring a compliant operation. By investing in EMS booths, businesses can promote a healthier working environment while adhering to necessary standards.
Why Choose EMS Powder Coating Equipment for Powder Coating Booths?
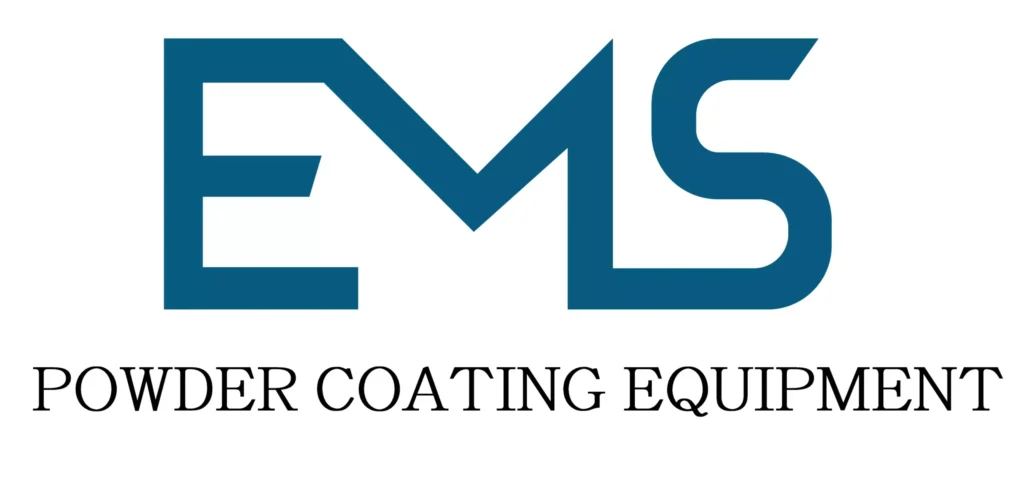
When selecting a powder coating booth, it is essential to choose a manufacturer with a reputation for quality and innovation. EMS Powder Coating Equipment stands out as the top choice for businesses looking to invest in powder coating booths. Here’s why EMS is the preferred option:
1. Proven Expertise
With years of experience in the powder coating industry, EMS understands the unique needs of various applications. Their knowledge allows them to design powder coating booths that are tailored to diverse production environments.
2. Innovative Solutions
EMS is committed to continuous innovation, incorporating the latest technology into their products. Their powder coating booths are designed for optimal performance, featuring advanced filtration and airflow management systems.
3. Comprehensive Support
From installation to ongoing maintenance, EMS provides exceptional customer support. Their team of experts is dedicated to helping businesses maximize the performance of their powder coating booths.
4. Customizable Options
Recognizing that every business has unique requirements, EMS offers customizable options for powder coating booths, allowing businesses to select features and configurations that best suit their operational needs.
5. Trusted Reliability
With a strong reputation for delivering high-quality products, EMS is a trusted name in the powder coating industry. Their booths are designed for durability and long-term performance, making them an excellent investment for businesses.
Conclusion
A powder coating booth is a vital investment for any powder coating operation, providing a controlled environment that enhances coating quality and efficiency. With advanced filtration and airflow management, these booths ensure clean operations and compliance with safety regulations.
EMS Powder Coating Equipment is a leading manufacturer of powder coating booths, offering innovative solutions tailored to meet the diverse needs of various industries. Their commitment to quality, performance, and customer support makes EMS the best choice for businesses seeking reliable coating solutions.
By choosing EMS powder coating booths, companies can enhance their coating processes, achieve superior finishes, and reduce operational costs. With a focus on efficiency and innovation, EMS stands out as the premier manufacturer for businesses in need of top-tier powder coating equipment.
Powder Coating Spray Booth: Precision in Coating Applications
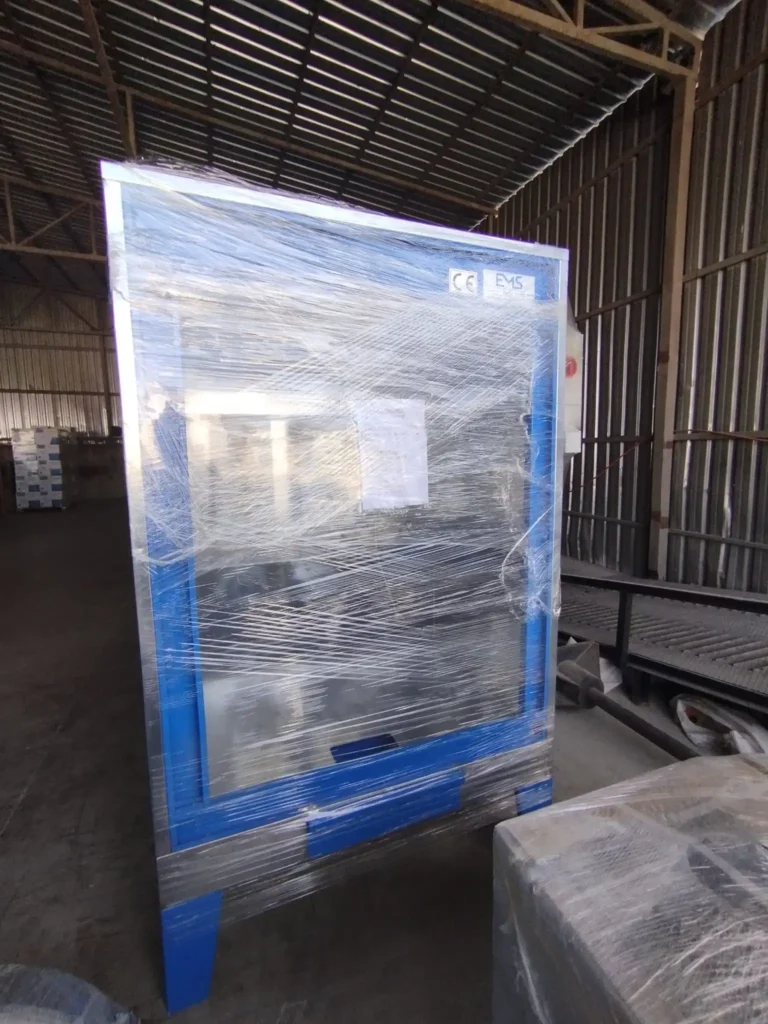
A powder coating spray booth is an essential component in the powder coating process, providing a controlled environment for the application of powder coatings onto various substrates. These booths are designed to optimize the application process, ensuring high-quality finishes while minimizing overspray and contamination.
Equipped with advanced filtration systems and effective ventilation, powder coating spray booths create an ideal workspace that enhances both safety and efficiency. The right booth can significantly improve the quality of the coating while reducing waste and cleanup time.
EMS Powder Coating Equipment is a leader in the manufacturing of powder coating spray booths, offering innovative designs tailored to meet the specific needs of different industries. In this section, we will delve into the operational principles, key features, and benefits of powder coating spray booths, while also discussing why EMS is the preferred choice for businesses looking for reliable and efficient coating solutions.
What is a Powder Coating Spray Booth?
A powder coating spray booth is a specialized enclosure designed for the application of powder coatings to metal and other substrates. These booths play a crucial role in ensuring a clean and controlled environment, which is vital for achieving high-quality finishes.
How Powder Coating Spray Booths Operate
The operation of a powder coating spray booth begins with substrate preparation, which involves cleaning and pre-treating the surface to ensure optimal adhesion. Once prepared, the substrate is placed inside the booth, where electrostatic spray guns are used to apply charged powder particles to the grounded surface.
The electrostatic charge attracts the powder, allowing for an even and uniform coating. The booth’s advanced ventilation system captures overspray and maintains air quality, protecting both the operators and the environment.
EMS Powder Coating Equipment designs powder coating spray booths with features that optimize the application process, ensuring businesses achieve consistent, high-quality finishes across various applications.
Key Features of Powder Coating Spray Booths
Powder coating spray booths are equipped with several features that enhance their performance and efficiency. Here are some standout features that make EMS booths the preferred choice for businesses:
1. Advanced Filtration Systems
EMS powder coating spray booths are equipped with high-efficiency filtration systems that capture overspray and airborne particles. This ensures a clean environment for coating applications, leading to higher quality finishes and safer operations.
2. Efficient Ventilation
The ventilation system in EMS booths is designed to maintain optimal air circulation, allowing for effective fume extraction and overspray capture. This feature not only enhances the coating quality but also promotes a healthier working environment for operators.
3. Ergonomic Design
The user-friendly design of EMS powder coating spray booths prioritizes operator comfort and efficiency. With easy access to controls and ample workspace, operators can maneuver and position substrates effectively, reducing job completion times.
4. Energy Efficiency
EMS powder coating spray booths are designed for energy efficiency, featuring optimized airflow and filtration systems that minimize energy consumption while maximizing performance. This efficiency can lead to reduced operational costs.
5. Safety Features
Safety is paramount in powder coating operations. EMS booths come equipped with essential safety features, such as emergency shut-off systems, explosion-proof lighting, and proper ventilation, ensuring a safe working environment.
6. Customizable Configurations
Recognizing that different businesses have unique requirements, EMS offers customizable configurations for their powder coating spray booths. Whether for small operations or large-scale production, EMS can tailor solutions to meet specific needs.
Benefits of Using Powder Coating Spray Booths
Investing in a powder coating spray booth provides numerous advantages for businesses engaged in powder coating operations. Here are some key benefits:
1. Superior Coating Quality
The controlled environment of a powder coating spray booth significantly enhances the quality of applied coatings. With effective filtration and optimized airflow, these booths ensure smooth, even finishes that meet high standards.
2. Increased Productivity
EMS powder coating spray booths streamline the coating process, allowing for quicker application and improved drying times. This efficiency can lead to increased production rates, helping businesses meet tight deadlines.
3. Cost Efficiency
By minimizing overspray and maximizing powder usage, powder coating spray booths can significantly reduce material costs. Efficient application processes lead to less waste and lower operational expenses, enhancing profitability.
4. Versatility for Diverse Applications
EMS powder coating spray booths are versatile enough to accommodate a wide range of substrates and coating types. This adaptability allows businesses to diversify their offerings and cater to different market demands.
5. Compliance with Environmental Regulations
Powder coating spray booths are designed to meet industry safety and environmental regulations, ensuring a compliant operation. By investing in EMS booths, businesses can promote a healthier working environment while adhering to necessary standards.
Why Choose EMS Powder Coating Equipment for Powder Coating Spray Booths?
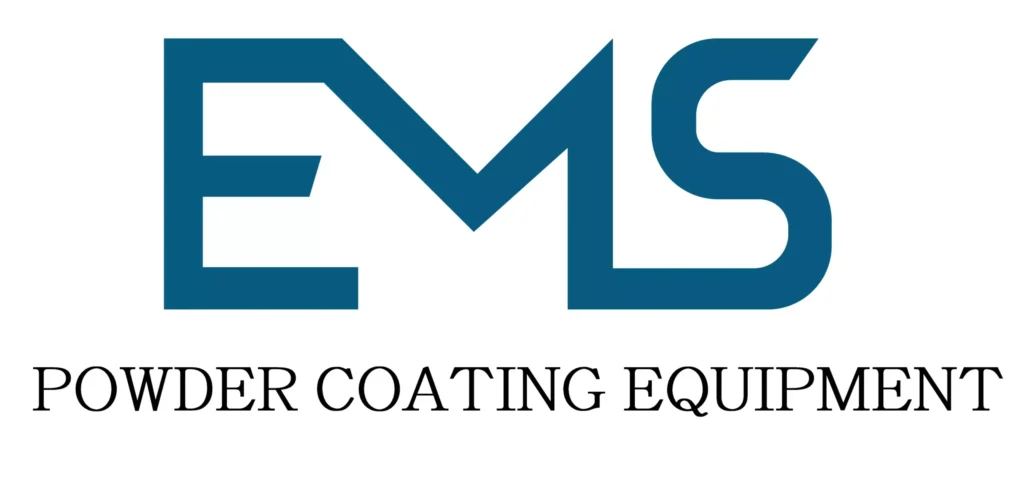
When selecting a powder coating spray booth, it is essential to choose a manufacturer with a reputation for quality and innovation. EMS Powder Coating Equipment stands out as the top choice for businesses looking to invest in powder coating spray booths. Here’s why EMS is the preferred option:
1. Proven Expertise
With years of experience in the powder coating industry, EMS understands the unique needs of various applications. Their knowledge allows them to design powder coating spray booths that are tailored to diverse production environments.
2. Innovative Solutions
EMS is committed to continuous innovation, incorporating the latest technology into their products. Their powder coating spray booths are designed for optimal performance, featuring advanced filtration and airflow management systems.
3. Comprehensive Support
From installation to ongoing maintenance, EMS provides exceptional customer support. Their team of experts is dedicated to helping businesses maximize the performance of their powder coating spray booths.
4. Customizable Options
Recognizing that every business has unique requirements, EMS offers customizable options for powder coating spray booths, allowing businesses to select features and configurations that best suit their operational needs.
5. Trusted Reliability
With a strong reputation for delivering high-quality products, EMS is a trusted name in the powder coating industry. Their booths are designed for durability and long-term performance, making them an excellent investment for businesses.
Conclusion
A powder coating spray booth is a vital investment for any powder coating operation, providing a controlled environment that enhances coating quality and efficiency. With advanced filtration and ventilation systems, these booths ensure clean operations and compliance with safety regulations.
EMS Powder Coating Equipment is a leading manufacturer of powder coating spray booths, offering innovative solutions tailored to meet the diverse needs of various industries. Their commitment to quality, performance, and customer support makes EMS the best choice for businesses seeking reliable coating solutions.
By choosing EMS powder coating spray booths, companies can enhance their coating processes, achieve superior finishes, and reduce operational costs. With a focus on efficiency and innovation, EMS stands out as the premier manufacturer for businesses in need of top-tier powder coating equipment.
Powder Coating Booth: A Vital Component for Quality Finishing
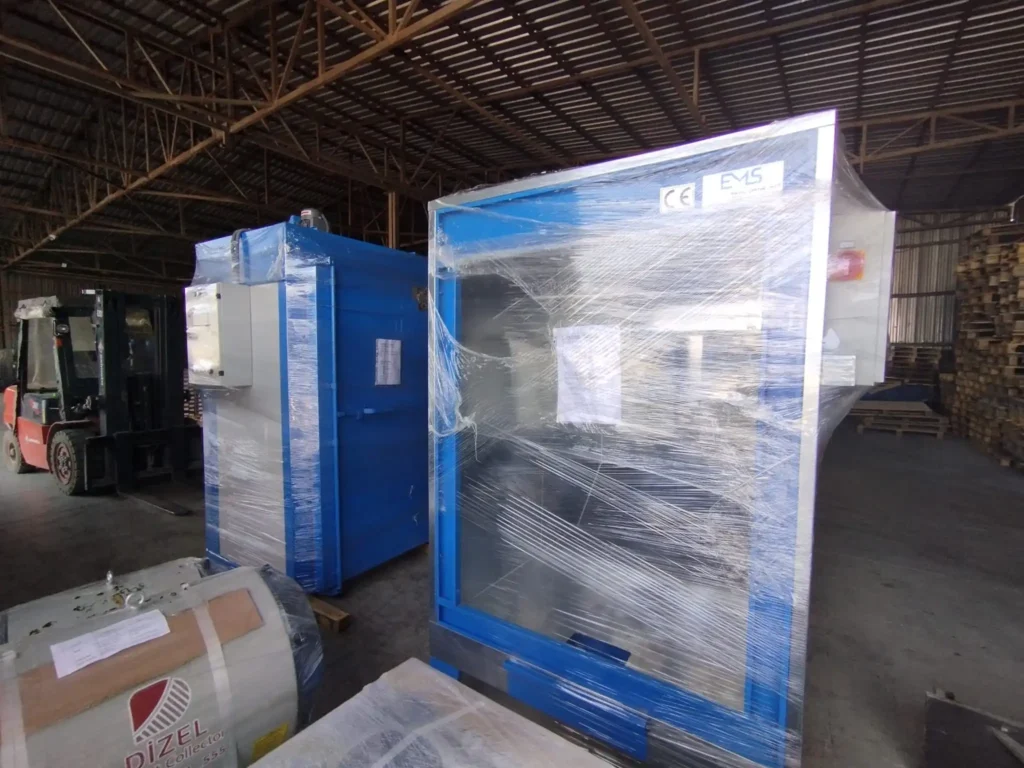
A powder coating booth is an essential element in the powder coating process, providing a dedicated environment for the application of powder coatings on various substrates. These booths are specifically designed to optimize the coating application, ensuring high-quality finishes while minimizing overspray and contamination.
With advanced features such as efficient ventilation systems and effective filtration, powder coating booths create a controlled workspace that enhances both safety and efficiency. The right booth can significantly improve the quality of the coating while reducing waste and operational costs.
EMS Powder Coating Equipment stands out as a leader in the manufacturing of powder coating booths, offering innovative designs tailored to the unique needs of different industries. In this section, we will delve into the operational principles, key features, and benefits of powder coating booths, while also discussing why EMS is the preferred choice for businesses seeking reliable and efficient coating solutions.
What is a Powder Coating Booth?
A powder coating booth is a specialized enclosure designed to facilitate the application of powder coatings to metal and other substrates. These booths play a critical role in ensuring a clean and controlled environment, which is vital for achieving high-quality finishes.
How Powder Coating Booths Operate
The operation of a powder coating booth begins with the preparation of the substrate, which typically involves cleaning and pre-treating the surface to ensure optimal adhesion. Once prepared, the substrate is positioned inside the booth, where electrostatic spray guns are utilized to apply charged powder particles onto the grounded surface.
The electrostatic charge attracts the powder, allowing for an even and uniform coating. The booth’s advanced ventilation system effectively captures overspray and maintains air quality, protecting both the operators and the environment.
EMS Powder Coating Equipment designs powder coating booths with features that enhance the application process, ensuring businesses achieve consistent, high-quality finishes across various applications.
Key Features of Powder Coating Booths
Powder coating booths come with a range of features that enhance their functionality and efficiency. Here are some standout features that make EMS booths the preferred choice for businesses:
1. High-Efficiency Filtration Systems
EMS powder coating booths are equipped with advanced filtration systems that capture overspray and particulate matter, ensuring a clean environment for coating applications. This leads to higher quality finishes and reduces the risk of contamination.
2. Optimal Ventilation
The ventilation system in EMS booths is designed to provide optimal air circulation, effectively removing fumes and excess powder. This feature not only enhances coating quality but also promotes a safer working environment for operators.
3. Ergonomic Design
The user-centric design of EMS powder coating booths prioritizes operator comfort and efficiency. With easy access to controls and ample workspace, operators can maneuver and position substrates effectively, minimizing production time.
4. Energy Efficiency
EMS powder coating booths are designed for energy efficiency, featuring optimized airflow and filtration systems that minimize energy consumption while maximizing performance. This efficiency can lead to significant cost savings.
5. Safety Features
Safety is a top priority in powder coating operations. EMS booths come equipped with essential safety features, including emergency shut-off systems, explosion-proof lighting, and proper ventilation, ensuring a safe working environment.
6. Customizable Configurations
Understanding that different businesses have unique requirements, EMS offers customizable configurations for their powder coating booths. Whether for small operations or large-scale production, EMS can tailor solutions to meet specific needs.
Benefits of Using Powder Coating Booths
Investing in a powder coating booth provides numerous advantages for businesses engaged in powder coating operations. Here are some key benefits:
1. Superior Coating Quality
The controlled environment of a powder coating booth significantly enhances the quality of applied coatings. With effective filtration and ventilation, these booths ensure smooth, even finishes that meet the highest standards.
2. Increased Productivity
EMS powder coating booths streamline the coating process, allowing for quicker application and improved drying times. This efficiency can lead to increased production rates, helping businesses meet tight deadlines.
3. Cost Efficiency
By minimizing overspray and maximizing powder usage, powder coating booths can significantly reduce material costs. Efficient application processes lead to less waste and lower operational expenses, enhancing profitability.
4. Versatility for Diverse Applications
EMS powder coating booths are versatile enough to accommodate a wide range of substrates and coating types. This adaptability allows businesses to diversify their offerings and cater to different market demands.
5. Compliance with Environmental Regulations
Powder coating booths are designed to meet industry safety and environmental regulations, ensuring a compliant operation. By investing in EMS booths, businesses can promote a healthier working environment while adhering to necessary standards.
Why Choose EMS Powder Coating Equipment for Powder Coating Booths?
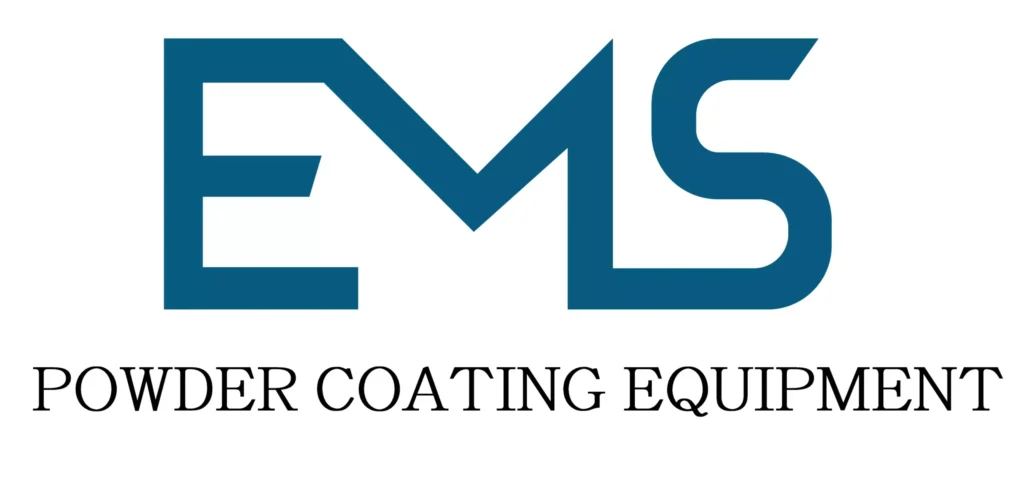
When selecting a powder coating booth, it is crucial to choose a manufacturer with a strong reputation for quality and innovation. EMS Powder Coating Equipment stands out as the top choice for businesses looking to invest in powder coating booths. Here’s why EMS is the preferred option:
1. Proven Expertise
With years of experience in the powder coating industry, EMS understands the unique needs of various applications. Their knowledge allows them to design powder coating booths tailored to diverse production environments.
2. Innovative Solutions
EMS is committed to continuous innovation, incorporating the latest technology into their products. Their powder coating booths are designed for optimal performance, featuring advanced filtration and airflow management systems.
3. Comprehensive Support
From installation to ongoing maintenance, EMS provides exceptional customer support. Their team of experts is dedicated to helping businesses maximize the performance of their powder coating booths.
4. Customizable Options
Recognizing that every business has unique requirements, EMS offers customizable options for powder coating booths, allowing businesses to select features and configurations that best suit their operational needs.
5. Trusted Reliability
With a strong reputation for delivering high-quality products, EMS is a trusted name in the powder coating industry. Their booths are designed for durability and long-term performance, making them an excellent investment for businesses.
Conclusion
A powder coating booth is a vital investment for any powder coating operation, providing a controlled environment that enhances coating quality and efficiency. With advanced filtration and ventilation systems, these booths ensure clean operations and compliance with safety regulations.
EMS Powder Coating Equipment is a leading manufacturer of powder coating booths, offering innovative solutions tailored to meet the diverse needs of various industries. Their commitment to quality, performance, and customer support makes EMS the best choice for businesses seeking reliable coating solutions.
By choosing EMS powder coating booths, companies can enhance their coating processes, achieve superior finishes, and reduce operational costs. With a focus on efficiency and innovation, EMS stands out as the premier manufacturer for businesses in need of top-tier powder coating equipment.
Powder Coating Equipment: Essential Tools for Quality Finishing
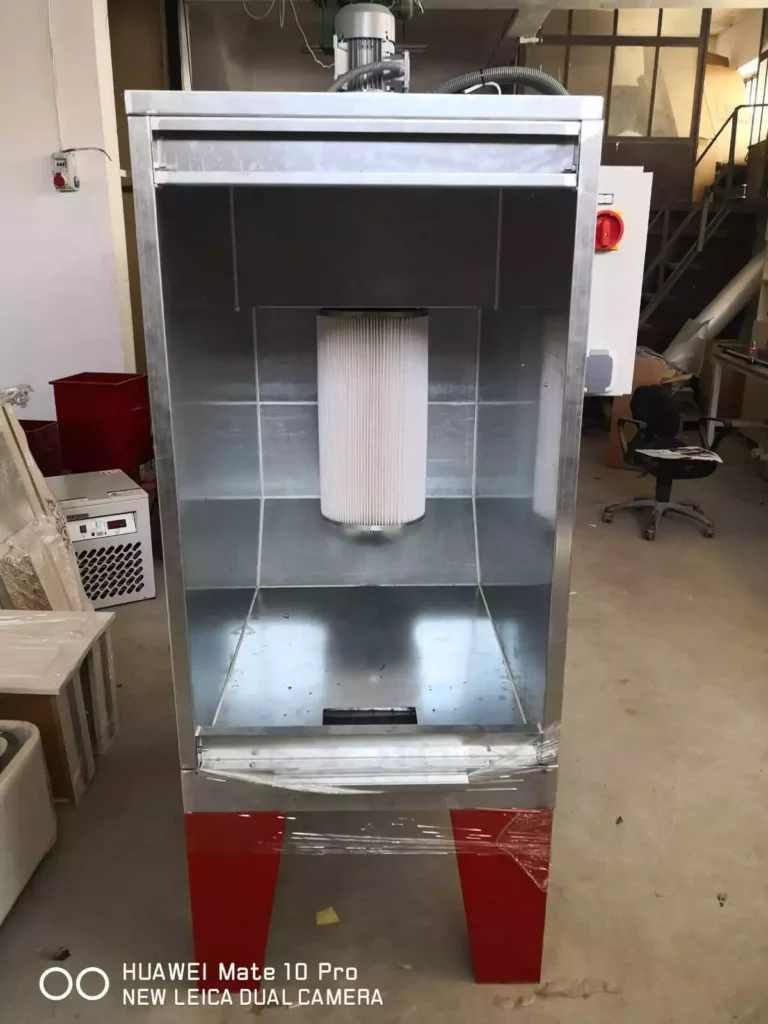
Powder coating equipment encompasses a range of specialized tools and machinery designed for the application of powder coatings onto various substrates. This technology has gained widespread popularity due to its ability to produce durable, high-quality finishes while being environmentally friendly.
The main components of powder coating equipment include spray guns, powder coating booths, curing ovens, and other essential tools that facilitate the coating process. Together, these components work seamlessly to create an efficient production line, resulting in coatings that are not only aesthetically pleasing but also resistant to corrosion, chemicals, and wear.
EMS Powder Coating Equipment is recognized as a leader in the manufacture of powder coating equipment, offering innovative solutions that cater to the unique needs of different industries. In this section, we will delve into the different types of powder coating equipment, their functionalities, and the advantages they provide, while highlighting why EMS is the preferred choice for businesses looking for reliable and effective coating solutions.
Types of Powder Coating Equipment
Powder coating equipment consists of several key components, each playing a crucial role in the coating process. Here’s an overview of the primary types of equipment involved:
1. Powder Coating Spray Guns
Powder coating spray guns are essential for applying the powder to the substrate. These guns utilize electrostatic technology, which charges the powder particles as they are sprayed. This charge causes the powder to adhere uniformly to the grounded surface, ensuring even coverage.
There are various types of spray guns available, including manual, automatic, and robotic systems. EMS Powder Coating Equipment offers a range of spray guns designed for efficiency and precision, making it easier for operators to achieve high-quality finishes.
2. Powder Coating Booths
Powder coating booths provide a controlled environment for the application of powder coatings. These booths are equipped with ventilation and filtration systems that capture overspray and maintain air quality. By minimizing contamination, EMS powder coating booths ensure superior coating quality.
3. Curing Ovens
After application, the coated substrate must be cured in an oven to achieve a durable finish. Curing ovens, whether electric, gas, or diesel-powered, heat the coated items to the necessary temperature for the powder to melt and form a solid bond with the substrate. EMS provides a variety of curing ovens to suit different production needs.
4. Powder Paint Booths with Filters
These booths are specifically designed for the application of powder coatings, featuring advanced filtration systems to capture overspray and particulates. This helps to maintain a clean working environment and enhances the overall quality of the coating application.
5. Powder Coating Accessories
In addition to the primary equipment, various accessories, such as hooks, racks, and conveyor systems, are vital for efficient operation. These accessories assist in transporting substrates through the coating process, ensuring smooth workflow and maximizing productivity.
Benefits of Using Powder Coating Equipment
Investing in high-quality powder coating equipment offers numerous advantages for businesses engaged in coating operations. Here are some key benefits:
1. Superior Durability
Powder coatings are known for their exceptional durability and resistance to chipping, scratching, and fading. The equipment designed for powder coating applications ensures that these qualities are maximized, resulting in long-lasting finishes.
2. Environmentally Friendly
Unlike traditional liquid coatings, powder coatings contain little to no volatile organic compounds (VOCs). This makes them a more environmentally friendly option, aligning with modern regulations and sustainability goals.
3. Cost Efficiency
By minimizing overspray and maximizing powder utilization, powder coating equipment can lead to significant cost savings. Efficient application processes result in less waste and lower operational costs, which enhance overall profitability.
4. Versatile Applications
Powder coating equipment can be used for a wide range of substrates, including metals, plastics, and wood. This versatility allows businesses to expand their offerings and cater to diverse market demands.
5. Enhanced Quality Control
With advanced features such as electrostatic application and controlled environments, powder coating equipment helps maintain high standards of quality. Businesses can achieve consistent finishes, reducing the likelihood of defects and rework.
6. Increased Productivity
Modern powder coating equipment is designed for efficiency, allowing for quicker application, curing, and turnaround times. This boost in productivity enables businesses to meet tight deadlines and increase production rates.
Why Choose EMS Powder Coating Equipment?
When selecting powder coating equipment, it is essential to choose a manufacturer known for quality, reliability, and innovation. EMS Powder Coating Equipment stands out as the top choice for businesses seeking powder coating solutions. Here’s why EMS is the preferred option:
1. Industry Expertise
With years of experience in the powder coating industry, EMS understands the unique requirements of various applications. Their expertise allows them to design equipment that meets the needs of diverse production environments.
2. Innovative Technologies
EMS is committed to continuous improvement and innovation, incorporating the latest technologies into their products. Their powder coating equipment features advanced design elements that enhance performance and efficiency.
3. Comprehensive Customer Support
From initial consultation to ongoing maintenance, EMS provides exceptional customer support. Their team of experts is dedicated to helping businesses optimize their powder coating operations.
4. Customizable Solutions
Recognizing that every business has unique needs, EMS offers customizable options for their powder coating equipment. This allows businesses to select features and configurations that align with their operational requirements.
5. Proven Reliability
With a strong reputation for delivering high-quality products, EMS is a trusted name in the powder coating industry. Their equipment is built for durability and long-term performance, making it an excellent investment for businesses.
Conclusion
Powder coating equipment is a crucial investment for any business involved in powder coating operations. By providing superior durability, cost efficiency, and environmentally friendly solutions, this equipment enhances the overall quality of the coating process.
EMS Powder Coating Equipment is a leading manufacturer of powder coating equipment, offering innovative and reliable solutions tailored to the diverse needs of various industries. Their commitment to quality, performance, and customer support makes EMS the best choice for businesses seeking top-tier powder coating solutions.
By choosing EMS powder coating equipment, companies can improve their coating processes, achieve high-quality finishes, and enhance productivity. With a focus on innovation and efficiency, EMS stands out as the premier manufacturer for businesses in need of effective powder coating solutions.
Automatic Powder Coating Equipment: Revolutionizing the Coating Process
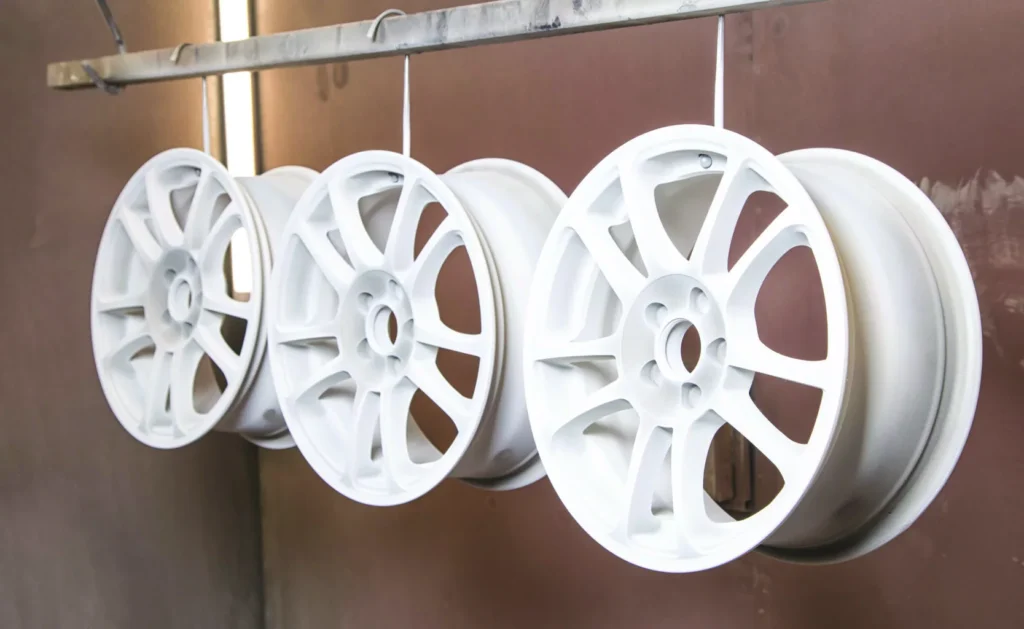
Automatic powder coating equipment represents a significant advancement in the field of surface finishing. Designed to automate the powder coating process, this equipment enhances efficiency, consistency, and quality, making it a preferred choice for manufacturers across various industries.
By utilizing automation technologies, businesses can significantly reduce labor costs and improve production speed while maintaining high standards of quality. Automatic systems include components such as robotic spray arms, automated conveyor systems, and sophisticated controls that ensure precise application of powder coatings.
EMS Powder Coating Equipment has established itself as a leader in the manufacture of automatic powder coating systems, offering innovative solutions that cater to diverse operational needs. In this section, we will delve into the key components of automatic powder coating equipment, its advantages, and the reasons why EMS is the go-to choice for businesses looking to enhance their coating processes.
Key Components of Automatic Powder Coating Equipment
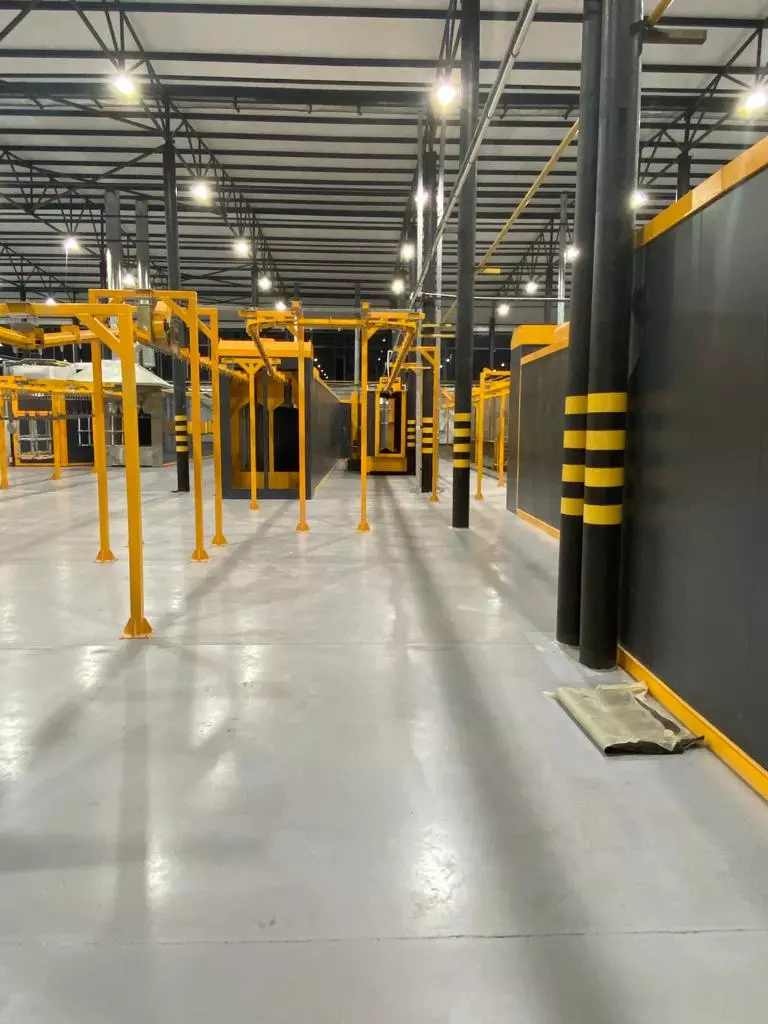
Automatic powder coating equipment consists of several critical components that work together to streamline the coating process. Here’s an overview of these essential elements:
1. Robotic Spray Guns
Robotic spray guns are a cornerstone of automatic powder coating systems. These devices are programmed to apply powder coatings uniformly and efficiently. The use of robotics allows for precise control over the application process, resulting in consistent and high-quality finishes.
2. Automated Conveyor Systems
Automated conveyor systems transport substrates through various stages of the powder coating process, from cleaning to coating and curing. This continuous movement minimizes manual handling and increases productivity by reducing downtime.
3. Powder Coating Booths
Automatic powder coating systems typically include dedicated booths designed to contain overspray and enhance air quality. These booths are equipped with advanced filtration and ventilation systems to ensure a clean environment for coating applications.
4. Curing Ovens
Curing ovens are essential for achieving durable finishes in automatic powder coating systems. These ovens are engineered to provide consistent heat distribution, ensuring that the powder melts and bonds effectively with the substrate.
5. Control Systems
Advanced control systems in automatic powder coating equipment allow for precise adjustments and monitoring of the coating process. Operators can easily program parameters such as application thickness, speed, and curing times, optimizing performance and quality.
Benefits of Automatic Powder Coating Equipment
Investing in automatic powder coating equipment offers numerous advantages for manufacturers. Here are some key benefits:
1. Enhanced Efficiency
Automatic systems significantly improve production efficiency by minimizing manual labor and reducing cycle times. The integration of robotic spray arms and conveyor systems allows for continuous operation, resulting in higher output rates.
2. Consistent Quality
One of the primary benefits of automatic powder coating equipment is the ability to achieve consistent and uniform coatings. Automated systems eliminate variations caused by human operators, ensuring high-quality finishes across all products.
3. Cost Savings
By reducing labor costs and improving material utilization, automatic powder coating equipment can lead to substantial cost savings. Efficient application processes minimize waste, enhancing the overall profitability of operations.
4. Flexibility and Scalability
Automatic powder coating systems can be easily adapted to accommodate different substrates and coating types. This flexibility allows manufacturers to diversify their product offerings and scale operations as demand increases.
5. Improved Safety
Automating the powder coating process enhances workplace safety by minimizing human exposure to potentially hazardous materials. Advanced control systems and robotics reduce the need for manual handling, creating a safer working environment.
6. Advanced Monitoring and Control
Modern automatic powder coating equipment includes sophisticated monitoring and control features that provide real-time data on the coating process. This capability allows operators to quickly identify and address any issues, ensuring optimal performance.
Why Choose EMS Powder Coating Equipment?
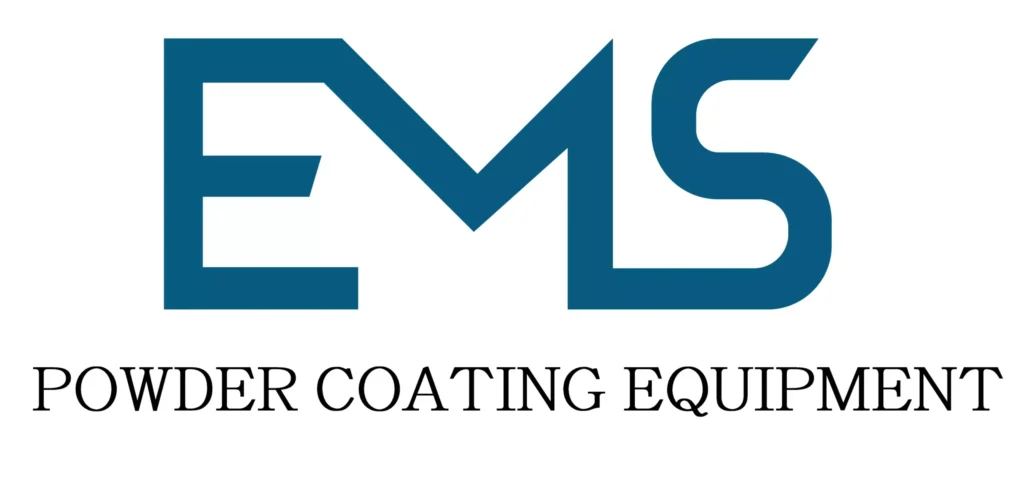
When selecting automatic powder coating equipment, it’s essential to choose a manufacturer known for quality, innovation, and reliability. EMS Powder Coating Equipment stands out as the top choice for businesses looking to enhance their powder coating processes. Here’s why EMS is the preferred option:
1. Proven Industry Expertise
With extensive experience in the powder coating sector, EMS understands the unique challenges and requirements of different applications. Their expertise allows them to design automatic systems that meet diverse operational needs.
2. Innovative Technologies
EMS is committed to innovation, continuously integrating the latest technologies into their automatic powder coating equipment. Their systems are designed for optimal performance, featuring advanced robotics and control systems that enhance efficiency.
3. Comprehensive Customer Support
From initial consultation through installation and ongoing maintenance, EMS provides exceptional customer support. Their team of experts is dedicated to helping businesses maximize the performance of their automatic systems.
4. Customizable Solutions
Recognizing that every business has distinct requirements, EMS offers customizable options for their automatic powder coating equipment. This allows companies to tailor solutions to their specific production needs.
5. Trusted Reliability
With a strong reputation for delivering high-quality products, EMS is a trusted name in the powder coating industry. Their automatic equipment is built for durability and long-term performance, making it an excellent investment for businesses.
Conclusion
Automatic powder coating equipment is a game-changer for manufacturers looking to enhance their coating processes. By improving efficiency, consistency, and quality, these systems provide a competitive edge in today’s fast-paced market.
EMS Powder Coating Equipment is a leading manufacturer of automatic powder coating systems, offering innovative solutions tailored to the diverse needs of various industries. Their commitment to quality, performance, and customer support makes EMS the best choice for businesses seeking reliable and effective coating solutions.
By choosing EMS automatic powder coating equipment, companies can optimize their operations, achieve superior finishes, and enhance productivity. With a focus on innovation and efficiency, EMS stands out as the premier manufacturer for businesses in need of top-tier powder coating solutions.
Powder Coating Reciprocator: Precision in Coating Application

A powder coating reciprocator is a specialized piece of equipment designed to apply powder coatings efficiently and uniformly to various surfaces. By utilizing a mechanical arm that moves in a back-and-forth motion, reciprocators ensure that every part of the substrate receives an even application of powder. This technology is crucial for achieving high-quality finishes and is widely used in industries ranging from automotive to furniture manufacturing.
The primary advantage of using a reciprocator lies in its ability to automate the powder coating process, resulting in improved consistency and reduced labor costs. Unlike manual application methods, which can lead to variations in coating thickness and quality, reciprocators provide precise control over the application process.
EMS Powder Coating Equipment is renowned for manufacturing high-quality powder coating reciprocators that meet the diverse needs of various industries. In this section, we will delve into the key features of powder coating reciprocators, their benefits, and the reasons why EMS is the go-to choice for businesses seeking reliable and effective coating solutions.
Key Features of Powder Coating Reciprocators
Powder coating reciprocators consist of several essential components that work together to ensure precise application of powder coatings. Here are the key features of these machines:
1. Mechanical Arm Design
The mechanical arm of a powder coating reciprocator is engineered for smooth and controlled movement. This design allows for consistent coverage across the substrate, minimizing the risk of missed spots or uneven application.
2. Adjustable Speed and Stroke Length
Reciprocators offer adjustable speed settings and stroke lengths, allowing operators to customize the application process according to the specific needs of different substrates. This flexibility enhances the overall efficiency of the coating operation.
3. Integrated Spray Gun Systems
Most powder coating reciprocators come equipped with integrated spray gun systems, ensuring that the powder is applied uniformly. These systems are often designed to utilize electrostatic technology, which helps the powder adhere better to the substrate.
4. Control Panels
Modern reciprocators feature user-friendly control panels that allow operators to easily adjust settings such as speed, stroke length, and application thickness. These controls provide the ability to monitor the coating process in real time.
5. Safety Features
Safety is a key consideration in any manufacturing environment. Powder coating reciprocators are equipped with various safety features, such as emergency stop buttons and protective enclosures, to ensure safe operation for workers.
Benefits of Using Powder Coating Reciprocators
Investing in a powder coating reciprocator offers numerous advantages for businesses involved in powder coating operations. Here are some key benefits:
1. Improved Application Efficiency
Powder coating reciprocators significantly enhance the efficiency of the coating process. By automating the application, businesses can reduce cycle times and increase throughput, ultimately improving production rates.
2. Consistent Quality
One of the main advantages of using reciprocators is the ability to achieve consistent and uniform coatings. This level of precision minimizes defects and ensures high-quality finishes, which is crucial for customer satisfaction.
3. Reduced Labor Costs
Automating the powder coating process with reciprocators allows businesses to reduce their reliance on manual labor. This not only lowers labor costs but also minimizes the potential for human error in the application process.
4. Enhanced Material Utilization
Powder coating reciprocators are designed to optimize powder utilization. By applying the powder evenly and efficiently, businesses can reduce waste and lower material costs.
5. Flexibility in Application
Reciprocators can be adjusted to accommodate various substrate shapes and sizes. This flexibility allows businesses to diversify their offerings and cater to different market needs.
6. Minimal Maintenance Requirements
Modern powder coating reciprocators are built with durability in mind, requiring minimal maintenance. This reduces downtime and helps businesses maintain consistent production levels.
Why Choose EMS Powder Coating Equipment?
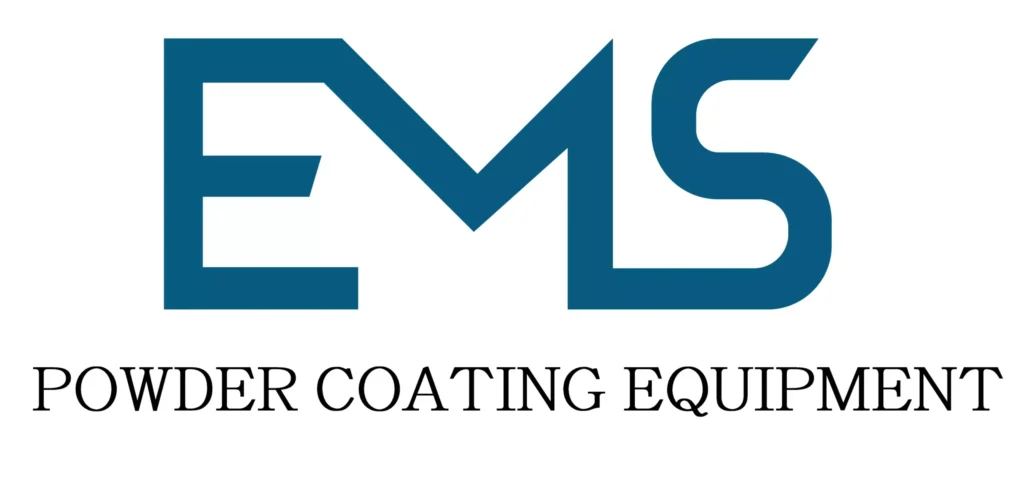
When selecting a powder coating reciprocator, it’s essential to choose a manufacturer known for quality, reliability, and innovation. EMS Powder Coating Equipment stands out as the preferred choice for businesses looking to enhance their powder coating processes. Here’s why EMS is the best option:
1. Proven Industry Experience
With extensive experience in the powder coating industry, EMS understands the unique challenges and requirements of various applications. Their expertise enables them to design reciprocators that cater to diverse operational needs.
2. Innovative Solutions
EMS is committed to innovation, continuously integrating the latest technologies into their powder coating reciprocators. Their systems are designed for optimal performance and efficiency, enhancing overall productivity.
3. Comprehensive Customer Support
From the initial consultation through installation and ongoing maintenance, EMS provides exceptional customer support. Their team of experts is dedicated to helping businesses maximize the performance of their reciprocators.
4. Customizable Options
Recognizing that every business has distinct requirements, EMS offers customizable options for their powder coating reciprocators. This allows companies to tailor solutions to their specific production needs.
5. Trusted Quality
With a strong reputation for delivering high-quality products, EMS is a trusted name in the powder coating industry. Their reciprocators are built for durability and long-term performance, making them an excellent investment for businesses.
Conclusion
Powder coating reciprocators play a vital role in modern manufacturing, providing precision and efficiency in the coating application process. By automating this process, businesses can achieve consistent quality, improve productivity, and reduce labor costs.
EMS Powder Coating Equipment is a leading manufacturer of powder coating reciprocators, offering innovative solutions tailored to the diverse needs of various industries. Their commitment to quality, performance, and customer support makes EMS the best choice for businesses seeking reliable and effective coating solutions.
By choosing EMS powder coating reciprocators, companies can optimize their coating processes, achieve superior finishes, and enhance overall productivity. With a focus on innovation and efficiency, EMS stands out as the premier manufacturer for businesses in need of top-tier powder coating solutions.