
Powder coating equipment is used to apply a protective layer of powder to metal surfaces. The powder is applied using an electrostatic gun, which applies a negative charge to the powder particles. The metal surface is then grounded, which attracts the negatively charged powder particles. The powder is then cured using heat, which melts the powder and forms a smooth, durable coating.
There are many different types of powder coating equipment available, including manual guns, automated guns, booths, and ovens. The type of equipment you need will depend on the size and complexity of your project.
Manual guns are the simplest and most affordable type of powder coating equipment. They are typically used for small projects or for touch-ups.
Automated guns are more expensive than manual guns, but they can be used to coat larger projects more quickly and evenly.
If you are considering purchasing powder coating equipment, it is important to do your research and find the right equipment for your needs. You should also consider the cost of the equipment, the cost of maintenance, and the learning curve for using the equipment.
Powder coating is increasingly accepted as the preferred finishing process for many applications. Increasingly stringent environmental regulations, rising costs in all areas, and demands by consumers for better quality and more durable products are among the challenges facing today’s finishers. Powder coatings provide a solution to these challenges and others. Powder coating is the technique of applying dry paint to the component.
The powdered paint is normally applied by using a powder feed system and gun to electrostatically charge and spray the powder onto the part. For some applications, the part being coated is dipped into a fluidized bed of powder. The coated part is then heated in an oven, or via infrared panels, to melt and cure the paint. During the curing process, a chemical cross-linking reaction is triggered and it is this chemical reaction that gives the powder coatings many of their desirable properties.
Here are some of the benefits of using powder coating equipment:
- Powder coating is a very durable finish that can withstand harsh weather conditions and abrasion.
- Powder coating is a very environmentally friendly finish, as it does not use any solvents or VOCs.
- Powder coating is a very versatile finish that can be used on a variety of different materials, including metal, plastic, and wood.
- Powder coating is a very cost-effective finish, as it can be applied quickly and easily.
If you are looking for a durable, environmentally friendly, and versatile finish, then powder coating is a great option for you.
Powder Coating Application
- Surface preparation: The metal surface to be coated must be clean and free of rust, grease, and other contaminants. The surface can be cleaned using a variety of methods, such as sandblasting, solvent cleaning, or alkaline cleaning.
- Powder application: The powder is applied to the metal surface using an electrostatic gun. The gun applies a negative charge to the powder particles, which are then attracted to the grounded metal surface.
- Curing: The powder is cured using heat, which melts the powder and forms a smooth, durable coating. The curing time and temperature will vary depending on the type of powder being used.
Benefits of Powder Coating
- Durability: Powder coating is a very durable finish that can withstand harsh weather conditions and abrasion.
- Environmental friendliness: Powder coating is a very environmentally friendly finish, as it does not use any solvents or VOCs.
- Versatility: Powder coating is a very versatile finish that can be used on a variety of different materials, including metal, plastic, and wood.
- Cost-effectiveness: Powder coating is a very cost-effective finish, as it can be applied quickly and easily.
Drawbacks of Powder Coating
- Initial investment: Powder coating equipment can be expensive to purchase.
- Learning curve: There is a learning curve associated with using powder coating equipment.
- Limited color selection: The color selection for powder coating is not as wide as the color selection for other types of finishes, such as paint.
Overall, powder coating is a great option for those who are looking for a durable, environmentally friendly, and versatile finish.
Here are some additional things to keep in mind when choosing powder coating equipment:
- The size and complexity of your project: If you are only going to be coating small projects, then a manual gun may be all you need. However, if you are going to be coating larger projects, then you will need an automated gun.
- The type of material you are coating: Powder coating can be used on a variety of different materials, but some materials are more difficult to coat than others. For example, aluminum can be difficult to coat with powder coating because it is a heat-sensitive material.
- The budget: Powder coating equipment can range in price from a few hundred dollars to several thousand dollars. It is important to set a budget before you start shopping for equipment.
- The learning curve: There is a learning curve associated with using powder coating equipment. It is important to be willing to take the time to learn how to use the equipment properly before you start using it on your project.
Powder Coating Equipment

Manual powder coating equipment is the most basic type of powder coating system. It consists of a powder hopper, a feed pump, a spray gun, and a compressed air supply. The operator manually controls the powder flow and spray pattern. Automatic powder coating equipment is more complex than manual equipment and is typically used for larger production runs. It consists of a powder hopper, a feed pump, a spray gun, a control unit, and a compressed air supply. The control unit automatically controls the powder flow and spray pattern.
We manufacture 2 different types of manual powder coating equipment (with hopper and multicolor) and also automatic powder coating equipment
Here is a table that summarizes the key differences between manual and automatic powder coating equipment:
Feature | Manual | Automatic |
---|---|---|
Control | Manual | Automatic |
Production rate | Lower | Higher |
Cost | Lower | Higher |
Flexibility | More flexible | Less flexible |
Quality | Can be good, but is more dependent on operator skill | More consistent |
Manual powder coating equipment is a good choice for small to medium-sized businesses that do not have a high volume of production. It is also a good choice for businesses that need a flexible system that can be used to coat a variety of products.
Automatic powder coating equipment is a good choice for large businesses that have a high volume of production. It is also a good choice for businesses that need a consistent and high-quality finish.
Ultimately, the best type of powder coating equipment for your business will depend on your specific needs and budget.
Here are some additional factors to consider when choosing between manual and automatic powder coating equipment:
- The size and complexity of your products
- The desired finish quality
- The production volume
- The budget
- The available labor
If you are not sure which type of powder coating equipment is right for your business, you should consult with a qualified professional.
Manual Hand Guns

Manual powder coating guns are used to apply a fine layer of powder coating to a surface. The powder is typically electrostatically charged, which helps it to adhere to the surface. The gun is then triggered, and the powder is released from the gun in a fine mist. The powder coats the surface evenly and dries quickly.
A manual powder coating gun consists of several components, including:
- Gun body: The gun body houses the other components of the gun.
- Trigger: The trigger is used to release the powder from the gun.
- Nozzle: The nozzle is the opening through which the powder is released.
- Powder feed system: The powder feed system supplies the powder to the nozzle.
- Air supply system: The air supply system supplies the air that is used to atomize the powder.
- Electrical system: The electrical system charges the powder particles and provides power to the gun’s other components.
Types of Manual Powder Coating Guns
There are two main types of manual powder coating guns:
- Corona gun: Corona guns use a high-voltage corona to charge the powder particles. This type of gun is typically used to apply powder coatings to metal surfaces.
- Tribo gun: Tribo guns use friction to charge the powder particles. This type of gun is typically used to apply powder coatings to non-metal surfaces.
Benefits of Using Manual Powder Coating Guns
There are several benefits to using manual powder coating guns, including:
- They are easy to use and operate.
- They are relatively inexpensive.
- They are versatile and can be used to apply a wide variety of powder coatings.
- They are less messy than other methods of applying powder coatings.
- They produce a high-quality finish.
How to Use a Manual Powder Coating Gun
To use a manual powder coating gun, follow these steps:
- Prepare the surface to be coated. The surface should be clean, dry, and free of oils and grease.
- Mask off any areas that you do not want to be coated.
- Fill the powder hopper with powder.
- Connect the gun to the air supply and the electrical supply.
- Adjust the gun settings. The settings will vary depending on the type of powder coating and the surface being coated.
- Trigger the gun and move it back and forth over the surface. The gun should be held about 6-12 inches from the surface.
- Allow the powder to dry completely.
- Cure the powder coating. The curing process will vary depending on the type of powder coating.
Tips for Using a Manual Powder Coating Gun
Here are a few tips for using a manual powder coating gun:
- Use a light touch when triggering the gun.
- Move the gun back and forth evenly over the surface.
- Overlap the strokes slightly.
- Do not apply too much powder.
- Allow the powder to dry completely before curing.
- Wear a respirator when using a powder coating gun.
Safety Precautions
When using a manual powder coating gun, it is important to take the following safety precautions:
- Wear safety glasses, gloves, and a respirator.
- Work in a well-ventilated area.
- Do not smoke or use open flames near the powder coating gun.
- Store powder in a cool, dry place.
- Keep powder out of reach of children.
Conclusion
Manual powder coating guns are a versatile and easy-to-use tool that can be used to apply a high-quality finish to a variety of surfaces. With proper care and maintenance, a manual powder coating gun can last for many years
The Manual powder Gun EMS Powder Coating Equipment with a High voltage generator is designed to apply electrostatically chargeable powder on grounded work pieces. The gun is designed with state of the art of technology. The parts are assembled in a simple manner which guarantees easy maintenance and repair. The guns produce 100KV high voltage and it is therefore absolutely necessary to read the instruction manual carefully before starting to operate.
This Manual coating equipment is for use with organic powders coating electrostatically grounded objects.
Manual Powder Coating Equipment Parts

Manual powder coating guns are widely used for various applications in different industries, including automotive, manufacturing, and construction. Powder coating is a method of applying a dry paint powder to a surface using an electrostatic charge. The powder is then cured by heat, resulting in a durable, colorful finish.
Here are some of the parts of a manual powder coating gun:
- Gun body: The gun body houses the other components of the gun.
- Trigger: The trigger is used to release the powder from the gun
- Nozzle: The nozzle is the opening through which the powder is released
- Powder feed system: The powder feed system supplies the powder to the nozzle.
- Air supply system: The air supply system supplies the air that is used to atomize the powder.
- Electrical system: The electrical system charges the powder particles and provides power to the gun’s other components.
- Powder hopper: The powder hopper stores the powder that is to be sprayed.
- Fluidizing plate: The fluidizing plate helps to keep the powder in the hopper fluidized, so that it can be easily transported to the nozzle
- Electrode: The electrode charges the powder particles, so that they are attracted to the surface being coated
- Barrel: The barrel houses the electrode and the nozzle.
- Grip: The grip is the part of the gun that is held by the operator.
- Different brands and models of manual powder coating guns may have some additional parts or features. It is important to consult the manual for the specific gun that you are using to learn more about its parts and features.
- Here are some additional tips for using a manual powder coating gun:
- Always wear safety glasses, gloves, and a respirator when using a powder coating gun.
- Make sure that the gun is properly grounded to prevent electrical shock.
- Use the correct air pressure for the type of powder that you are using.
- Hold the gun at a consistent distance from the surface being coated.
- Move the gun back and forth slowly and evenly.
- Overlap the strokes slightly to ensure even coverage.
- Allow the powder to dry completely before curing.
- Follow the manufacturer’s instructions for cleaning and maintaining the gun.
EMS manual coating equipment – Structure
- Gun control unit
- Manual powder gun
- Injector
- Suction tube
- Filter Unit
Electrical data
The electrical data of a manual powder coating gun can vary depending on the specific model and manufacturer. However, some common electrical specifications for manual powder coating guns include:
- Voltage: 220-240V AC
- Current: 5-10A
- Power: 1-2kW
- Frequency: 50-60Hz
It is important to always check the electrical data for the specific gun that you are using before plugging it in. Using the wrong voltage or current can damage the gun or cause a safety hazard.
Here are some additional electrical safety tips for using a manual powder coating gun:
- Always use a grounded outlet.
- Do not use the gun if the cord is damaged.
- Do not unplug the gun by pulling on the cord.
- Do not operate the gun in wet or dusty conditions.
- Do not touch the electrode or any other electrical components of the gun while it is plugged in.
By following these electrical safety tips, you can help to prevent accidents and injuries while using a manual powder coating gun.
EMS Manual Powder Coating Equipment Electrical Features:
- Nominal input voltage 100-240 VAC
- Frequency 50-60 Hz
- Connected load 40 VA
- Nominal output voltage (to the gun) eff.10 V
- Nominal output current (to the gun) max. 1.2 A
- Connection and output for a vibrator (on Aux output)
- 110/230 VAC max. 100 W
- Connection for rinsing function (valve) 24 VDC max. 3 W
- Temperature range 0 °C – +40 °C (+32 °F – +104 °F)
- Max. operating temperature 100 °C (+212 °F)
Pneumatic data
The pneumatic data of a manual powder coating gun includes the pressure, flow, and volume of air required to operate the gun. The specific values of these parameters will vary depending on the manufacturer and model of the gun. However, some typical values are as follows:
- Air pressure: 40-60 psi (2.76-4.14 bar)
- Air flow: 5-10 cfm (0.14-0.28 m³/min)
- Air volume: 0.5-1.0 cubic feet (0.014-0.028 m³)
The air pressure is used to atomize the powder, which means breaking it down into fine particles so that it can be evenly coated onto the surface. The air flow is used to transport the powder particles from the hopper to the nozzle. The air volume is the total amount of air that is used by the gun.
It is important to use the correct air pressure for the type of powder that you are using. Using too much air pressure can cause the powder to be sprayed too forcefully, which can damage the surface being coated. Using too little air pressure can cause the powder to clump together and not adhere to the surface properly.
Here are some additional pneumatic tips for using a manual powder coating gun:
- Use a clean, dry air supply.
- Use a pressure regulator to adjust the air pressure to the correct level.
- Use an air filter to remove dust and moisture from the air supply.
- Use an air dryer to remove moisture from the air supply if necessary.
EMS Manual Powder Coating Equipment
Max. input pressure 10 bar
Min. input pressure 6 bar
Input pressure (Based on pressure regulator setting) 5.5 bar/80 psi
Max. water vapor content of the compressed air 1,3 g/m³
Max. oil vapor content of the compressed air 0,1 mg/m³
Max. compressed air consumption 8 Nm³/h
Dimensions
- Width 333 mm
- Depth 460 mm
- Height 697 mm
- Weight 33 kg
Processible powders
- Plastic powder yes
- Metallic powder yes
- Enamel powder yes
General conditions for the Injector
- Powder type Epoxy/polyester
- Powder hose length (m) 6
- Powder hose Ø (mm) 10
- Power hose type POE with guide strips
- Input pressure (bar) 5,5
- Conveying air nozzle Ø (mm) 1,6
- Correction value C0 Powder output zeroing adjustment
The EMS manual coating equipment must be connected in accordance with the setup and connection instructions (Please also review the operating instructions for the manual gun control unit).
When a color change takes place, the individual components of the manual coating equipment must be cleaned carefully. All powder particles of the former color must be removed during this process! The following describes an ‘extreme’ color change (light to dark).
Multicolor Quick color change option

A multicolor quick color change option is a feature of some powder coating equipment that allows the operator to quickly change the color of the powder being applied. This can be done without having to shut down the equipment or clean the hopper.
There are two main ways to achieve quick color change:
- Using multiple hoppers: This option involves having a separate hopper for each color of powder. The operator can then select the desired color by opening the valve on the corresponding hopper.
Quick color change can be a valuable feature for powder coating applications that require frequent color changes. It can save time and improve productivity.
Here are some of the benefits of using a multicolor quick color change option:
- Reduced downtime: Quick color change can help to reduce downtime by eliminating the need to shut down the equipment or clean the hopper.
- Improved productivity: Quick color change can help to improve productivity by allowing the operator to change colors quickly and easily.
- Increased flexibility: Quick color change can give the operator more flexibility to experiment with different colors and shades.
- Reduced waste: Quick color change can help to reduce waste by eliminating the need to dispose of unused powder.
If you are considering adding a powder coating system to your business, it is important to consider whether a multicolor quick color change option is right for you. This option can be a valuable asset for businesses that require frequent color changes.
Here are some additional factors to consider when choosing a powder coating system with a multicolor quick color change option:
- The number of colors you need to use: If you only need to use a few colors, a system with multiple hoppers may be a good option. However, if you need to use a wider range of colors, a system with a color blender may be a better choice.
- The frequency of color changes: If you need to change colors frequently, a system with a quick color change option can save you time and improve productivity.
- Your budget: Systems with multicolor quick color change options can be more expensive than systems without this feature. However, the cost savings from reduced downtime and improved productivity may offset the initial investment.
Automatic Powder Coating Equipment

Automatic powder coating equipment is powder spray equipment typically used to powder coat parts on a conveyor line. Here the automatic spray guns are triggered continuously and they coat the parts without delay and pause. Here the capacity is high and all the automatic powder coating equipment in the booth is all arranged with the same parameters.
An automatic powder coating gun is a device used to apply a dry paint powder to a surface using an electrostatic charge. The powder is then cured by heat, resulting in a durable, colorful finish.
Automatic powder coating guns are typically used in industrial applications where a high-quality finish is required. They are often used to coat metal parts, such as car bodies, appliances, and machinery.
Advantages of using automatic powder coating guns
There are many advantages to using automatic powder coating guns, including:
- High-quality finish: Automatic powder coating guns can produce a high-quality finish that is durable, colorful, and resistant to scratches and fading.
- Consistent results: Automatic powder coating guns can produce consistent results, even with complex shapes and geometries.
- Reduced waste: Automatic powder coating guns can reduce waste by efficiently applying the powder to the surface.
- Improved efficiency: Automatic powder coating guns can improve efficiency by automating the coating process.
- Reduced labor costs: Automatic powder coating guns can reduce labor costs by automating the coating process.
Components of automatic powder coating guns
Automatic powder coating guns typically consist of the following components:
- Powder hopper: The powder hopper stores the powder that is to be sprayed
- Electrode: The electrode charges the powder particles, so that they are attracted to the surface being coated
- Nozzle: The nozzle is the opening through which the powder is released
- Air supply system: The air supply system supplies the air that is used to atomize the powder.
- Control system: The control system controls the operation of the gun, including the powder feed rate, air pressure, and voltage.
How to use automatic powder coating guns
To use an automatic powder coating gun, follow these steps:
- Prepare the surface to be coated. The surface should be clean, dry, and free of oils and grease.
- Mask off any areas that you do not want to be coated.
- Fill the powder hopper with powder.
- Set the powder feed rate, air pressure, and voltage.
- Position the gun over the surface to be coated.
- Trigger the gun to start the coating process.
- Move the gun back and forth over the surface.
- Allow the powder to dry completely before curing.
- Cure the powder coating. The curing process will vary depending on the type of powder coating.
Safety precautions when using automatic powder coating guns
It is important to follow safety precautions when using automatic powder coating guns, including:
- Wear safety glasses, gloves, and a respirator.
- Work in a well-ventilated area.
- Do not smoke or use open flames near the powder coating gun.
- Store powder in a cool, dry place.
- Keep powder out of reach of children.
Automatic powder coating guns are a versatile and efficient tool that can be used to apply a high-quality finish to a variety of surfaces. With proper care and maintenance, an automatic powder coating gun can last for many years.
Characteristics of Automatic Powder Coating Equipment
Description of EMS Automatic Powder Coating Equipment
- Lifetime finish quality
- Long-life cascade durability and HV performance
- Efficient powder transfer
- Reduced downtime: Quick gun change in less than 1-minute
- Performance
- Easy and accurate settings for voltage and current
- Constant and stable spray for a smooth and even application
- Our technology offers a high-quality finish
- Our technology offers a high-quality finish
- Fast color change without cross-contamination
- Productivity
- High transfer efficiency to reduce additional manual work
- Wide range of adapted nozzles for optimal application
- Powerful cascade providing a strong wraparound effect
- Advanced HV control for excellent penetration in recessed areas
- Modular gun design for an easy integration Sustainability
- Highly abrasion-resistant nozzles
- Heavy-duty electrostatic cascade
- Quick disconnect in 1 minute, only 1 operator needed to change gun
- Robust design
- 2-year warranty
Powder Coating Equipment in Use
Powder coating equipment is used to apply a dry paint powder to a surface using an electrostatic charge. The powder is then cured by heat, resulting in a durable, colorful finish.
Powder coating is a rapidly growing industry, and there are many different types of powder coating equipment available. The most common type of powder coating equipment is a manual powder coating gun. Manual powder coating guns are relatively inexpensive and easy to use, but they can be slow and inefficient.
For high-volume production, automatic powder coating equipment is a better option. Automatic powder coating equipment is more expensive than manual powder coating guns, but it can apply powder much faster and more efficiently.
Powder coating equipment is used in a variety of industries, including automotive, appliance, furniture, and manufacturing. Powder coating is a popular choice for these industries because it is a durable, environmentally friendly, and cost-effective way to finish a product.
Here are some of the benefits of using powder coating equipment:
- Durable: Powder coating finishes are very durable and can withstand a variety of harsh conditions.
- Environmentally friendly: Powder coating does not use solvents, so it is a more environmentally friendly way to finish a product than traditional painting.
- Cost-effective: Powder coating is a cost-effective way to finish a product because it is a one-step process that does not require primers or sealers.
- Versatile: Powder coating can be used to finish a variety of surfaces, including metal, plastic, wood, and MDF.
Here are some of the drawbacks of using powder coating equipment:
- Expensive: Powder coating equipment can be expensive, especially automated powder coating equipment.
- Requires training: Powder coating requires some training to operate properly.
- Not suitable for all surfaces: Powder coating is not suitable for all surfaces, such as fabrics and porous materials.
If you are considering using powder coating equipment, there are a few things you should keep in mind:
- The type of surface you are coating: Make sure that the powder coating equipment you choose is compatible with the type of surface you are coating.
- The size and shape of the product you are coating: Make sure that the powder coating equipment you choose is large enough to coat the product you are coating.
- The volume of products you are coating: If you are coating a high volume of products, you may want to consider investing in automated powder coating equipment.
With careful planning and consideration, you can choose the right powder coating equipment for your needs and achieve the high-quality, durable finish you desire.
Here are some additional tips for using powder coating equipment:
- Always wear safety glasses, gloves, and a respirator when using powder coating equipment.
- Work in a well-ventilated area.
- Follow the manufacturer’s instructions carefully.
- Clean and maintain your powder coating equipment regularly.
The automatic powder coating equipment is used with a pair of reciprocators, holding the guns and reciprocating them vertically while the conveyor is moving through the powder spray booth. The parameters of the equipment is arranged by the control unit in the control board on the left side of the picture above
As a manufacturer of powder coating equipment, we supply spare parts for life long time and 2 years guarantee for our powder coating equipment
Technical safety regulations for electrostatic powder spraying equipment
- All equipment and parts within a reach of 5m from the spray gun have to be earthed.
- The floor of the place the operator is standing has to be conductive.
- The operator has to wear conductive shoes. Leather shoes are recommended.
- The operator has to handle the gun with bare hands or with conductive gloves.
- The earth wire (green/yellow) has to be connected with the earth screw of the electrostatic powder coating unit. The earth wire has to have a solid metallic connection with the booth, the recovery system, the conveyor chain as well as the objects to be coated.
- The electric cables as well as the powder hoses leading to the guns have to be handled in such a way that they are protected against mechanical damage.
- Only when the recovery system has been put into operation the powder coating unit be switched on.
- Electric wires as well as powder hoses have to be controlled at least once a week.
- The earth of all conductive parts and equipment within the reach of 5m from the spray area has to be checked at least once a week.
- The control panel has to be switched off when cleaning the guns or changing the nozzles or extensions.
- As a general rule for all powder spraying installations, persons with pacemakers should never enter high-voltage areas or areas with electromagnetic fields.
- Each person responsible for the assembly, start-up, operation, service, and repair of powder spraying equipment must have read and understood the operating instructions and the “Safety regulations”-chapter. The operator must ensure that the user has had the appropriate training for powder spraying equipment and is aware of the possible sources of danger.
Pulse coating system
-High quality of the coating.
-Reduction in coating material consumption.
-Effective coating in corners.
-Effective recoating.
-Decrease in orange peel.
-3pre programmed mode
-Gun and Earth connectivity detector
The Function of High voltage generation
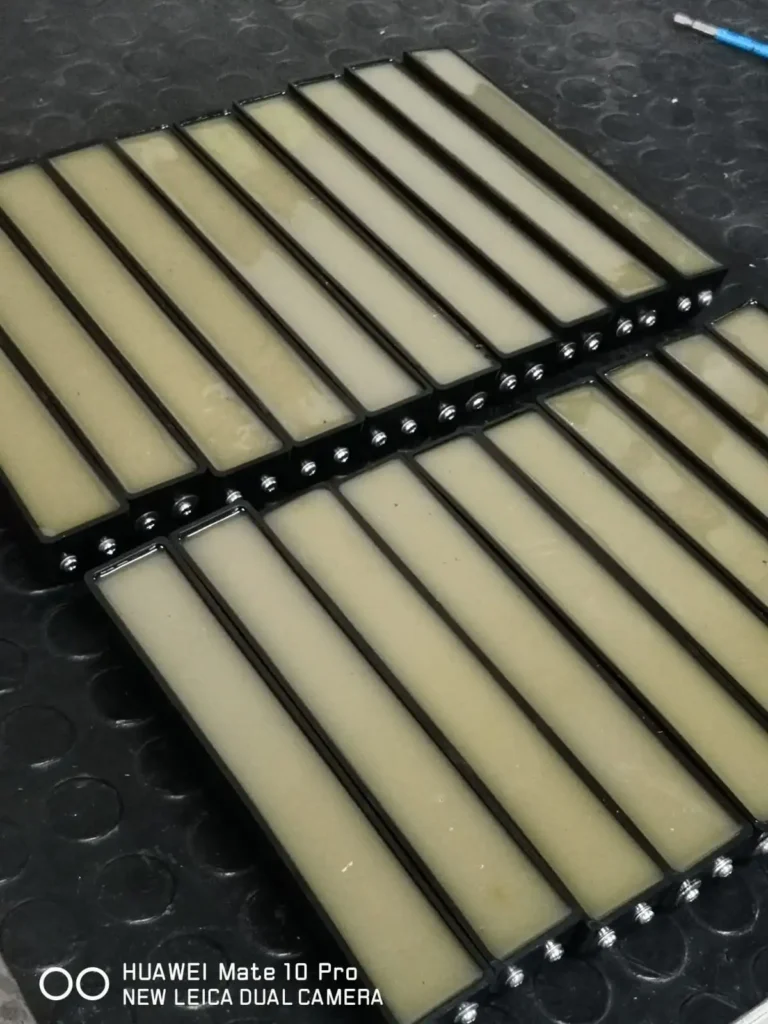
In powder coating guns, high voltage generation plays a crucial role in achieving a consistent, high-quality finish. The high voltage generates an electrostatic charge that attracts the powder particles to the surface being coated. This electrostatic force ensures that the powder particles are evenly distributed and adhere firmly to the surface, resulting in a durable and aesthetically pleasing finish.
Here’s a more detailed explanation of the function of high voltage generation in powder coating guns:
- Electrostatic Charging of Powder Particles: The high voltage generates an electrostatic field around the powder nozzle. As the powder particles pass through this field, they become positively charged.
- Attraction to the Grounded Surface: The surface being coated is grounded, creating a negative electrostatic charge. The positively charged powder particles are attracted to this negative charge, causing them to deposit uniformly on the surface.
- Efficient Powder Transfer: The electrostatic force ensures that the powder particles are transferred efficiently from the gun to the surface, minimizing overspray and waste.
- Improved Adhesion: The electrostatic charge helps the powder particles adhere firmly to the surface, resulting in a durable and long-lasting finish.
- Consistent Coating Thickness: The high voltage ensures that the electrostatic field is consistent, leading to a uniform coating thickness across the entire surface.
- Reduced Overspray and Waste: The electrostatic attraction minimizes overspray, reducing powder waste and environmental impact.
- Adaptability to Complex Shapes: The electrostatic force allows for even coating on complex shapes and corners, ensuring a consistent finish even in intricate areas.
In summary, high voltage generation is an essential component of powder coating guns, enabling efficient and effective powder transfer, consistent coating thickness, and durable adhesion. It plays a critical role in achieving high-quality finishes on a wide range of surfaces.
The control unit supplies a high-frequency low-voltage signal of approximately 10 V rms. This voltage is fed through the gun cable to the high voltage cascade in the gun body. In the high voltage cascade, the low voltage is high-transformed in the first step.
This primary high voltage is subsequently rectified and multiplied in the high voltage cascade in a second step until the required high voltage is obtained at the end (approx. 100 kV). The high voltage is now fed to the electrode within the spray nozzle.
Circuit
In addition to the modulated low voltage needed for high voltage generation, there are signal lines fed troughs the gun cable. The control signals are used for monitoring gun trigger status and gun remote control functions. The gun is released by a reed switch, which is operated by a magnet in the trigger. The control unit switches the modulated low voltage, powder conveying, and the rinsing air on.
The Powder Coating Gun
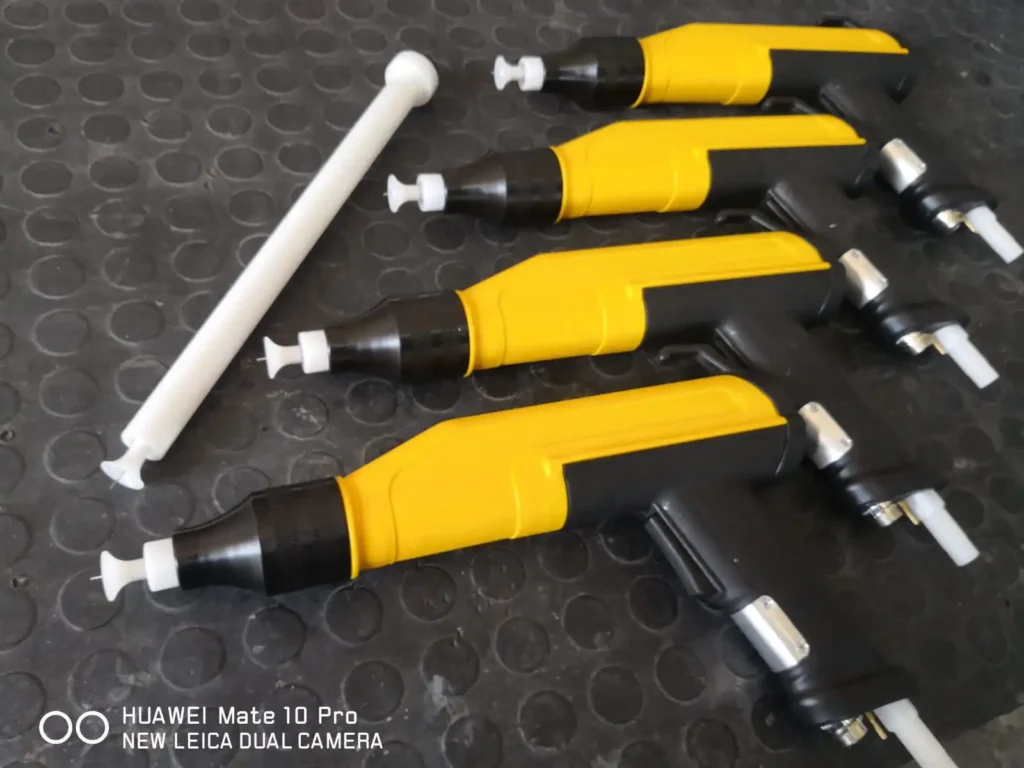
A powder coating gun is a device that applies a dry paint powder to a surface using an electrostatic charge. The powder is then cured by heat, resulting in a durable, colorful finish. Powder coating guns are used in a variety of industries, including automotive, appliance, furniture, and manufacturing.
Types of Powder Coating Guns
There are two main types of powder coating guns:
- Manual powder coating guns: Manual powder coating guns are relatively inexpensive and easy to use, but they can be slow and inefficient.
- Automatic powder coating guns: Automatic powder coating guns are more expensive than manual powder coating guns, but they can apply powder much faster and more efficiently.
Components of a Powder Coating Gun
A powder coating gun typically consists of the following components:
- Powder hopper: The powder hopper stores the powder that is to be sprayed.
- Electrode: The electrode charges the powder particles, so that they are attracted to the surface being coated.
- Nozzle: The nozzle is the opening through which the powder is released.
- Air supply system: The air supply system supplies the air that is used to atomize the powder.
- Control system: The control system controls the operation of the gun, including the powder feed rate, air pressure, and voltage.
Powder Hopper
The powder hopper is a container that holds the powder that is to be sprayed. The hopper is typically made of metal or plastic and has a capacity of a few pounds to several hundred pounds. The powder hopper is connected to the gun by a hose or tube.
Electrode
The electrode is a charged metal rod that is located near the nozzle. The electrode charges the powder particles as they pass through the air, so that they are attracted to the surface being coated. The electrode is connected to a high-voltage power supply.
Nozzle
The nozzle is the opening through which the powder is released. The nozzle is typically made of metal or ceramic and has a diameter of a few millimeters. The nozzle is connected to the powder hopper by a hose or tube.
Air Supply System
The air supply system supplies the air that is used to atomize the powder. The air supply system typically consists of an air compressor, a regulator, and a filter. The air compressor provides the compressed air, the regulator controls the air pressure, and the filter removes dust and moisture from the air. The air supply system is connected to the gun by a hose or tube.
Control System
The control system controls the operation of the gun, including the powder feed rate, air pressure, and voltage. The control system is typically located on the gun itself or on a remote control unit. The control system is connected to the powder hopper, electrode, nozzle, and air supply system by wires or cables.
How to Use a Powder Coating Gun
To use a powder coating gun, follow these steps:
- Prepare the surface to be coated. The surface should be clean, dry, and free of oils and grease.
- Mask off any areas that you do not want to be coated.
- Fill the powder hopper with powder.
- Set the powder feed rate, air pressure, and voltage.
- Position the gun over the surface to be coated.
- Trigger the gun to start the coating process.
- Move the gun back and forth over the surface.
- Allow the powder to dry completely before curing.
- Cure the powder coating. The curing process will vary depending on the type of powder coating.
Safety Precautions When Using a Powder Coating Gun
It is important to follow safety precautions when using a powder coating gun, including:
- Wear safety glasses, gloves, and a respirator.
- Work in a well-ventilated area.
- Do not smoke or use open flames near the powder coating gun.
- Store powder in a cool, dry place.
- Keep powder out of reach of children.
Conclusion
Powder coating guns are a versatile and efficient tool that can be used to apply a high-quality finish to a variety of surfaces. With proper care and maintenance, a powder coating gun can last for many years.
Length of gun: 340mm
Gun weight: 420gr
Output voltage: 100K V approx
Max output current: 140µA
Frequency: 32KHz approx
Polarity: negative
Max powder injection: 500g/min
Length of cable: 5m
Packing size: 240 x 320 x 60 mm
The injector of the Powder Coating Equipment
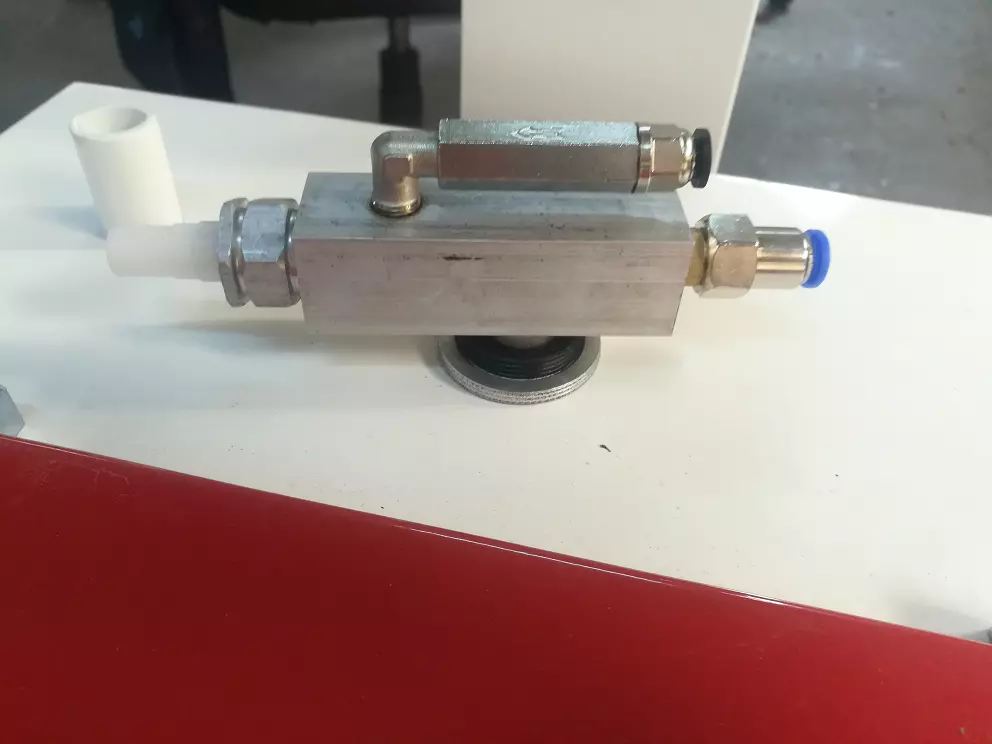
The injector of the powder coating equipment is a device that transports powder from the powder hopper to the powder coating gun. It is an essential component of the powder coating system, as it ensures that a consistent flow of powder is delivered to the gun.
There are two main types of injectors used in powder coating equipment:
- Volumetric injectors: Volumetric injectors measure the powder by volume, and they deliver a consistent amount of powder with each stroke.
- Gravimetric injectors: Gravimetric injectors measure the powder by weight, and they deliver a consistent amount of powder regardless of the powder density.
Volumetric injectors are typically used for low-volume applications, while gravimetric injectors are typically used for high-volume applications.
The injector is typically located near the powder hopper, and it is connected to the powder coating gun by a hose or tube. The injector is controlled by a motor or an air cylinder, and it meters the powder out of the hopper and into the hose or tube.
The powder is then transported to the powder coating gun, where it is atomized and sprayed onto the surface being coated.
Here are some of the benefits of using an injector in powder coating equipment:
- Consistent powder delivery: The injector ensures that a consistent flow of powder is delivered to the powder coating gun, which results in a consistent coating thickness.
- Reduced waste: The injector helps to reduce waste by delivering the correct amount of powder to the gun, which minimizes overspray.
- Improved efficiency: The injector helps to improve efficiency by automating the powder delivery process.
Overall, the injector is an essential component of the powder coating system, as it ensures that a consistent flow of powder is delivered to the powder coating gun. This results in a consistent coating thickness, reduced waste, and improved efficiency.
Here are some additional tips for using an injector in powder coating equipment:
- Keep the injector clean: Regularly clean the injector to prevent the buildup of powder, which can interfere with its performance.
- Inspect the injector regularly: Regularly inspect the injector for signs of wear or damage.
- Calibrate the injector regularly: Regularly calibrate the injector to ensure that it is delivering the correct amount of powder.
By following these tips, you can help to ensure that your powder coating injector is operating properly and delivering consistent results.
The injector is used to convey normal organic powders between the powder hopper and the powder gun. The injector is supplied with a Teflon insert sleeve as standard. If air flows through the nozzle into the cavity, a vacuum is created in the cavity. This vacuum causes the powder to be drawn up the suction tube and into the cavity. A powder/air mixture is created.
The forward air velocity at the nozzle conveys the powder/air mixture through to the powder hose to the gun. The concentration of the powder/air mixture, and with it, the powder output depends on the conveying air pressure and supplementary air pressure, the quality of the powder, the length of the powder hose, the diameter of the powder hose, and the difference in the height between the gun and injector, and the type of nozzle. The condition of the insert sleeve is of great importance because wear causes the powder output to sink drastically.
Color Change
When a color change takes place, the individual components of the manual coating equipment must be cleaned carefully.
- Empty the powder hopper and clean thoroughly
- Clean the powder hose
- Strip the powder hose from the hose connection on the injector
- Point the gun into the booth
- Blow through the hose manually with a compressed air gun
- Fit the powder hose again to the hose connection on the Injector
- Dismantle and clean the powder gun
- Clean the injector
- Prepare the manual coating equipment with new powder for start-up
Powder coating has revolutionized the way industries apply finishes to their products, offering a highly durable, long-lasting, and environmentally friendly alternative to traditional liquid paint. This process involves applying a dry powder — typically composed of finely ground resins and pigments — which is electrostatically charged before being sprayed onto a surface. Once applied, the powder is cured under heat, forming a strong bond that resists corrosion, weathering, and wear.
At the heart of this process is powder coating equipment, which plays a critical role in ensuring the quality and efficiency of the coating process. Whether for small-scale workshops or large industrial plants, choosing the right equipment can significantly impact production outcomes, energy consumption, and the final appearance of the coated product.
For businesses looking to achieve the best results, EMS Powder Coating Equipment stands out as a leader in the field, providing innovative, high-performance systems that are built to last. With a strong focus on precision, reliability, and ease of use, EMS has earned a reputation for manufacturing the industry’s most trusted powder coating equipment. In this guide, we’ll explore the different components of powder coating systems, their benefits, and why EMS Powder Coating Equipment is the top choice for any powder coating needs.
What is Powder Coating?
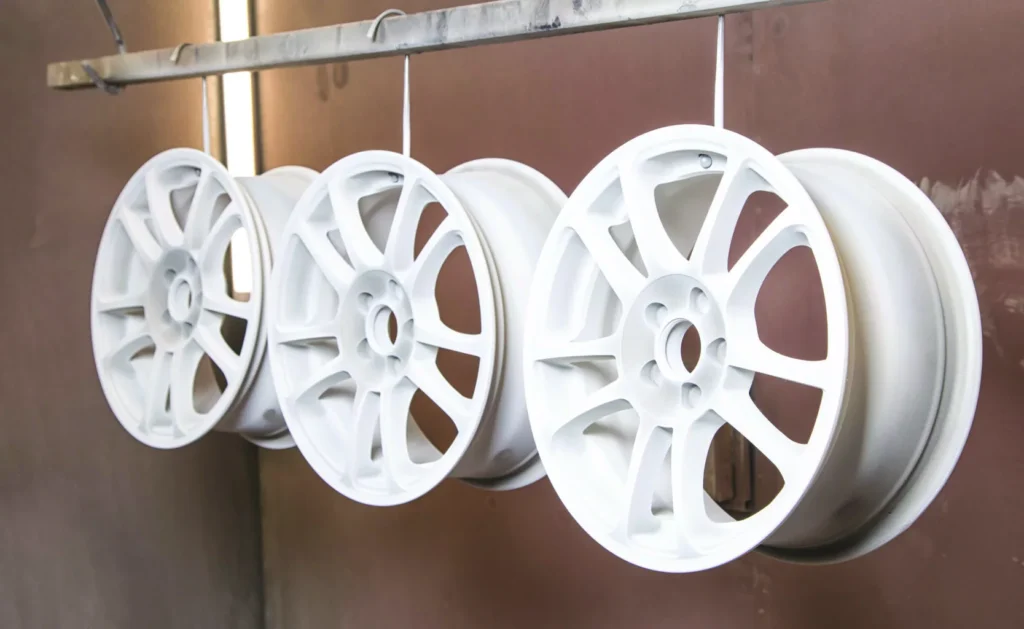
Powder coating is a dry finishing process that has gained widespread popularity due to its durability, versatility, and eco-friendly nature. Unlike liquid paint, which requires a solvent to keep the binder and filler in liquid form, powder coating is applied as a free-flowing, dry powder. This powder is usually composed of thermoplastic or thermoset polymer resins mixed with curatives, pigments, leveling agents, flow modifiers, and other additives to ensure a smooth and protective finish.
One of the biggest advantages of powder coating is its ability to create a thicker and more consistent finish without running or sagging. This results in a more uniform appearance and a stronger bond with the material being coated. Powder coating is particularly favored in industrial applications, where components need to withstand heavy use, exposure to the elements, or high temperatures. Surfaces that can be coated include metal, aluminum, steel, glass, and even some plastics.
There are several benefits to using powder coating over traditional paint. Powder coatings are extremely durable and resistant to corrosion, UV rays, and wear, making them ideal for both indoor and outdoor applications. Additionally, because no solvents are used, powder coating emits negligible volatile organic compounds (VOCs), making it much safer for workers and the environment. The overspray can be easily collected and reused, contributing to minimal waste.
With the right equipment, companies can achieve these outstanding benefits. EMS Powder Coating Equipment offers the most advanced systems, ensuring maximum efficiency in the application process and superior finish quality.
Key Components of Powder Coating Equipment
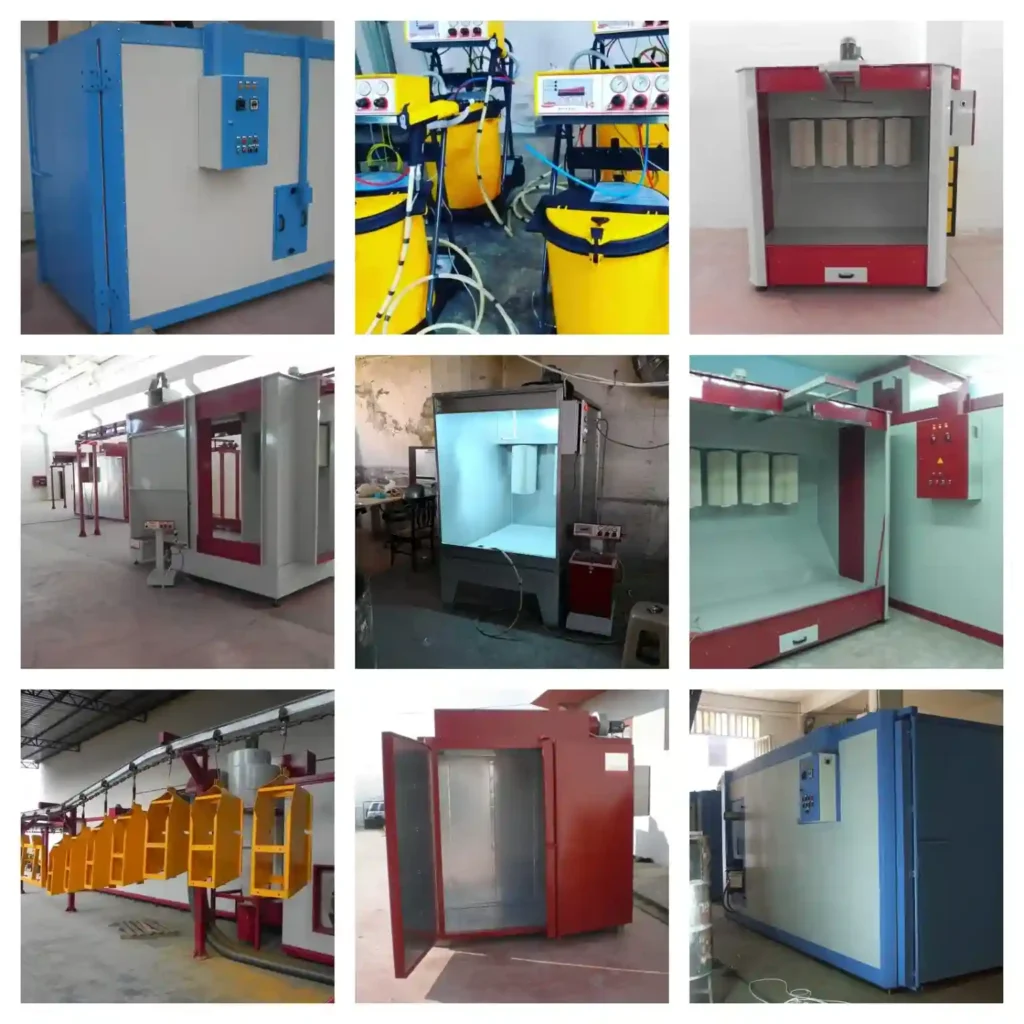
Powder coating equipment consists of several essential components that work together to ensure a flawless, durable finish. Each piece of equipment plays a specific role in the powder coating process, and the quality of each component directly affects the overall performance and efficiency of the coating line.
Below are the most important components of a powder coating system:
1. Application System: Electrostatic Spray Guns
At the core of any powder coating operation is the application system, which includes the electrostatic spray gun. The spray gun is responsible for applying the powder to the surface of the object, ensuring an even coat and strong adherence. The powder is electrostatically charged as it is released from the gun, and it is attracted to the grounded object. This creates a uniform layer of powder across the surface.
Spray guns can vary in sophistication, from manual models for smaller operations to fully automatic systems used in large-scale industrial applications. Automatic spray guns ensure greater consistency and higher efficiency, making them an essential component for companies that need to coat large volumes of products.
EMS Powder Coating Equipment offers state-of-the-art electrostatic spray guns designed for optimal performance. Whether you need manual or automatic systems, EMS ensures that each piece of equipment is engineered for precision and ease of use. Their spray guns offer smooth application with minimal overspray, reducing waste and improving operational efficiency.
2. Powder Coating Booth
A powder coating booth is essential for creating a controlled environment in which the powder can be applied to the product without contamination. The booth prevents the powder from spreading into other areas of the facility, which not only keeps the workspace clean but also ensures that the powder is fully contained for collection and reuse. Most powder coating booths are equipped with a ventilation system that helps filter out airborne particles, protecting both the workers and the environment.
Powder coating booths can be categorized into two main types: open-front and closed-front booths. Open-front booths are typically used for smaller projects and are easy to set up and operate. On the other hand, closed-front booths are often used in high-volume industrial settings because they provide more controlled conditions and reduce the risk of contamination.
EMS Powder Coating Equipment provides high-quality powder coating booths tailored to the specific needs of your operation. Their booths are designed for maximum efficiency, with advanced filtration systems that keep the workspace safe and reduce powder loss. EMS booths are also easy to clean and maintain, ensuring minimal downtime between shifts.
3. Curing Ovens
Once the powder has been applied to the surface, the object must be cured in an oven to allow the powder to melt, flow, and form a continuous coating. Curing ovens are vital to the powder coating process, as they ensure that the powder bonds correctly to the substrate, resulting in a hard, smooth, and durable finish. There are several types of curing ovens available, including convection ovens, infrared ovens, and hybrid ovens.
- Convection Ovens: These are the most common type of curing ovens used in powder coating. Convection ovens use hot air to raise the temperature of the coated object, allowing the powder to cure. They are highly efficient and work well with a variety of materials, making them a popular choice for many manufacturers.
- Infrared Ovens: These ovens use infrared energy to heat the powder coating. Infrared ovens can provide rapid heating and are particularly useful for objects that have complex shapes or are made from materials that are sensitive to high temperatures.
- Hybrid Ovens: Hybrid ovens combine both convection and infrared technologies, providing the benefits of both systems. They offer fast heating and uniform curing, making them ideal for high-precision applications.
EMS Powder Coating Equipment manufactures curing ovens that are optimized for fast and even curing, ensuring that each product has a perfect finish. Whether you need a gas-powered or electric oven, EMS provides custom solutions that meet the specific needs of your production line.
Types of Powder Coating Equipment
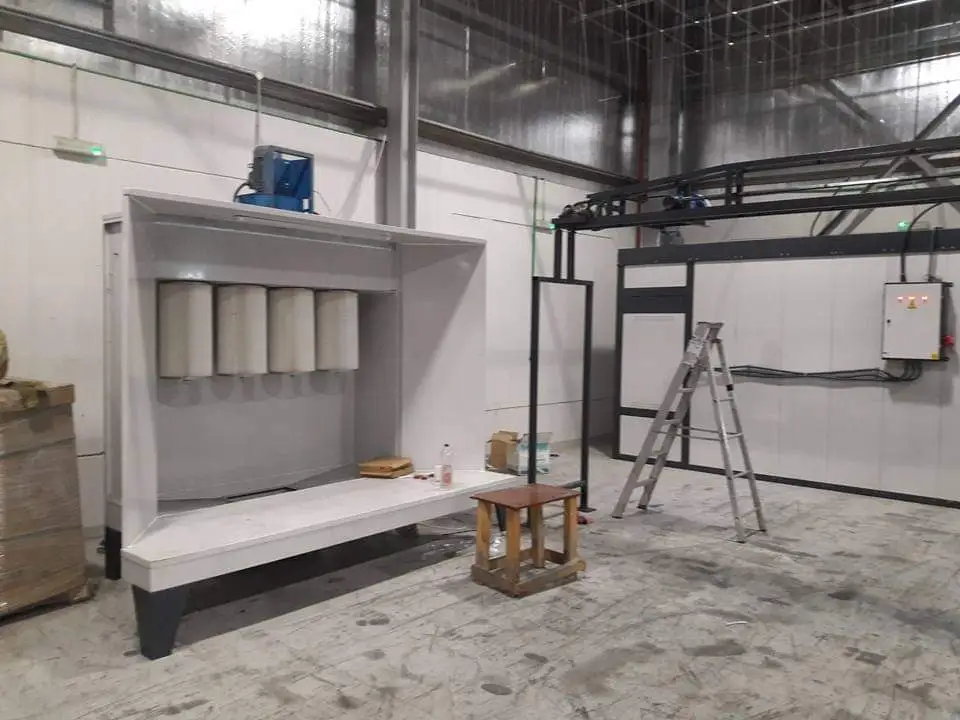
Powder coating systems can be categorized into several types based on their level of automation, the type of operation they support, and their specific functions. Understanding the differences between these systems can help businesses select the right equipment for their needs.
1. Manual vs. Automatic Systems
Powder coating systems are available in both manual and automatic configurations. Each system has its own advantages, depending on the scale and nature of the operation.
- Manual Systems: Manual powder coating systems are ideal for smaller projects or businesses that require flexibility in their production. Operators use handheld electrostatic spray guns to apply powder to objects, allowing for greater control over the process. While manual systems require more labor, they are often more cost-effective for businesses with lower production volumes.
- Automatic Systems: Automatic powder coating systems use robotic arms or reciprocators to apply the powder to objects. These systems are highly efficient and allow for precise, repeatable application. Automated systems are commonly used in high-volume manufacturing environments where consistency and speed are essential. Because automatic systems reduce the need for manual labor, they can also help lower operating costs in the long run.
EMS Powder Coating Equipment offers both manual and automatic systems, ensuring that businesses of all sizes can find the right equipment for their needs. Their automatic systems are designed for high efficiency and consistent results, making them a top choice for manufacturers seeking to increase productivity.
2. Batch vs. Conveyorized Systems
Another important distinction in powder coating equipment is between batch and conveyorized systems.
- Batch Systems: In a batch system, objects are coated one at a time or in small groups. After the powder is applied, the objects are placed in a curing oven. Batch systems are ideal for smaller production runs or when flexibility is required. They allow operators to handle various parts and products in small quantities.
- Conveyorized Systems: Conveyorized systems are used in large-scale production environments. In this system, objects move through the powder coating line on a conveyor belt, passing through the spray booth and curing oven without the need for manual handling. Conveyorized systems are highly efficient and are the best choice for high-volume operations that need to coat large quantities of parts consistently and quickly.
EMS Powder Coating Equipment provides robust batch and conveyorized systems tailored to different production needs. Whether you need a flexible batch system for custom work or a conveyorized system for high-speed production, EMS offers solutions that enhance productivity and ensure high-quality finishes.
Why Choose EMS Powder Coating Equipment?
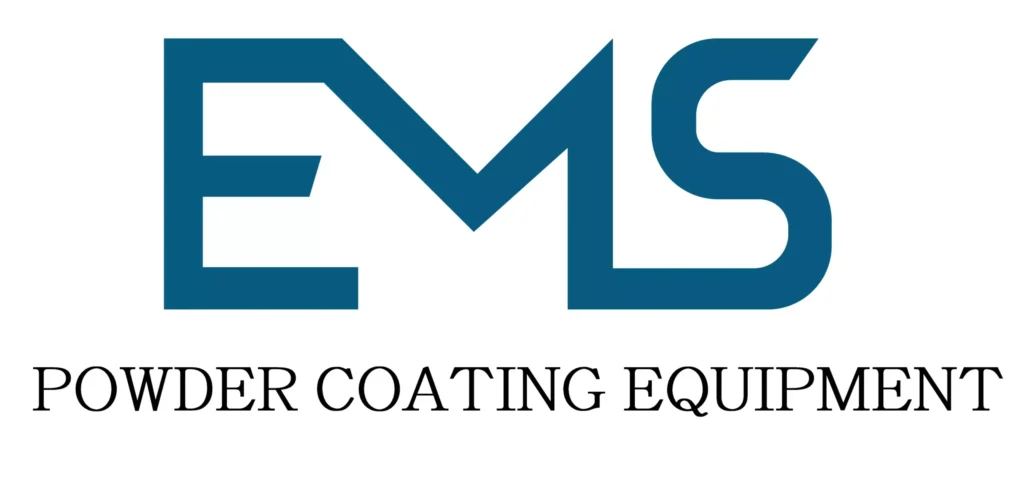
When it comes to selecting powder coating equipment, businesses must consider multiple factors such as efficiency, reliability, ease of use, and cost-effectiveness. EMS Powder Coating Equipment excels in all of these areas, offering top-of-the-line solutions that meet the needs of various industries. Below are several reasons why EMS is regarded as the best manufacturer of powder coating equipment.
1. Cutting-Edge Technology and Innovation
EMS Powder Coating Equipment has built its reputation on a foundation of innovation and cutting-edge technology. The company continuously invests in research and development to ensure that its equipment stays ahead of the competition. EMS systems are designed with the latest advancements in electrostatic application technology, providing users with superior precision and control.
From advanced automatic reciprocators to highly efficient curing ovens, EMS equipment incorporates state-of-the-art features that ensure smooth and reliable operation. The company’s commitment to technological innovation ensures that customers receive equipment that is not only efficient but also future-proof, capable of adapting to evolving industry demands.
For instance, EMS’s automated spray systems are equipped with sophisticated controls that allow for fine-tuning of the powder application process, ensuring that the coating is applied consistently across all surfaces, regardless of shape or size. These systems can be programmed for different jobs, making them ideal for high-volume operations where efficiency is paramount.
2. Customization and Versatility
Every business has unique needs, and EMS Powder Coating Equipment understands the importance of providing customizable solutions. Whether you’re running a small-scale operation or a large industrial plant, EMS offers a variety of equipment configurations tailored to your specific requirements.
One of the standout features of EMS is its ability to deliver both standard and customized powder coating systems. If your production line has particular space constraints or operational needs, EMS can provide specialized configurations to maximize your space while optimizing performance. This level of flexibility sets EMS apart from many competitors who only offer off-the-shelf solutions.
Moreover, EMS equipment is versatile and adaptable across a wide range of industries. Whether you’re working in automotive manufacturing, furniture production, or consumer goods, EMS’s systems can handle different materials and product sizes with ease. This versatility ensures that businesses investing in EMS Powder Coating Equipment are making a long-term investment that will pay dividends across various projects.
3. Durability and Reliability
Powder coating equipment represents a significant investment for any business, so it’s crucial that the systems you choose are built to last. EMS Powder Coating Equipment is renowned for the durability and reliability of its products. All equipment is designed with high-quality materials that can withstand the rigors of daily industrial use, ensuring minimal maintenance and long service life.
EMS takes pride in manufacturing powder coating systems that are not only highly efficient but also reliable under continuous operation. This means fewer breakdowns, less downtime, and reduced maintenance costs, all of which contribute to increased productivity and profitability for businesses.
The reliability of EMS systems is backed by rigorous quality control measures. Each piece of equipment undergoes thorough testing before being delivered to customers, ensuring that it meets the highest standards of performance and safety.
4. Energy Efficiency
Energy consumption is a critical consideration for any business, particularly in industries with high operational costs. EMS Powder Coating Equipment is designed to maximize energy efficiency without compromising performance. This focus on energy conservation helps businesses reduce their operational expenses while also minimizing their environmental footprint.
EMS offers high-efficiency curing ovens that use innovative technology to ensure uniform heat distribution and rapid curing times. These ovens consume less energy compared to traditional models, helping businesses cut down on utility costs. Additionally, EMS systems are designed to reduce powder waste, allowing operators to reclaim and reuse powder that is not deposited on the substrate, further boosting cost savings and sustainability.
5. Exceptional Customer Support and After-Sales Service
Another significant factor that sets EMS Powder Coating Equipment apart is the company’s commitment to customer support. Purchasing industrial equipment is a long-term investment, and EMS ensures that customers receive ongoing support throughout the life of their equipment.
From the initial consultation to installation and training, EMS offers comprehensive support to ensure that businesses get the most out of their systems. The company also provides maintenance and repair services, ensuring that any issues are addressed promptly to avoid prolonged downtime. This dedication to after-sales service gives EMS customers peace of mind, knowing that their equipment is backed by a team of experts ready to assist at any time.
6. Proven Track Record and Global Reach
With years of experience and a global client base, EMS Powder Coating Equipment has established itself as a leading manufacturer in the industry. The company has successfully partnered with businesses across the world, delivering equipment that has helped manufacturers improve their processes and quality.
EMS’s extensive portfolio of clients includes companies from a wide range of industries, including automotive, aerospace, furniture, and consumer goods. This broad industry experience ensures that EMS understands the specific needs of different sectors and can tailor solutions accordingly.
Trends and Innovations in Powder Coating Equipment
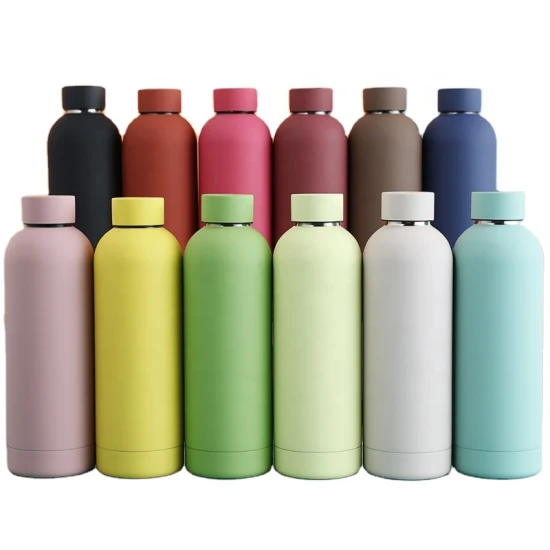
The powder coating industry is constantly evolving, with new technologies and trends shaping the way businesses operate. EMS Powder Coating Equipment stays at the forefront of these developments, ensuring that its customers benefit from the latest innovations in the field. Below are some of the key trends currently influencing powder coating technology:
1. Automation and Industry 4.0 Integration
Automation is becoming increasingly prevalent in the powder coating industry, with businesses looking for ways to improve efficiency and reduce labor costs. Automated systems, such as EMS’s powder coating reciprocators, allow for more consistent application and faster production times. Industry 4.0 integration, including the use of smart sensors and data analytics, is also making it easier for manufacturers to monitor and optimize their powder coating operations in real-time.
EMS has embraced these trends by offering equipment that can be fully integrated into modern manufacturing systems. This allows businesses to streamline their operations and improve overall productivity while maintaining high levels of quality.
2. Sustainability and Eco-Friendly Solutions
As industries become more focused on sustainability, the demand for environmentally friendly powder coating solutions continues to grow. Powder coating is inherently eco-friendly because it produces minimal waste and contains no solvents, which reduces VOC emissions. However, EMS has taken sustainability a step further by designing energy-efficient systems that consume less power while maintaining optimal performance.
These innovations make EMS Powder Coating Equipment the ideal choice for businesses seeking to reduce their environmental impact without sacrificing quality or efficiency.
3. Advanced Material Compatibility
New advances in powder coating materials are allowing manufacturers to coat a wider range of substrates, including plastics and composites. EMS’s powder coating systems are designed to handle these advanced materials, providing businesses with the flexibility to expand their product offerings.
Conclusion
Powder coating has become a cornerstone in modern manufacturing, providing businesses with a durable, environmentally friendly, and cost-effective way to protect their products. However, achieving the best results requires investing in high-quality equipment.
EMS Powder Coating Equipment stands out as the industry leader, offering advanced technology, customization options, and exceptional reliability. Whether you are looking for manual systems for small-scale operations or automated systems for large industrial plants, EMS provides tailored solutions that meet your specific needs. Their commitment to innovation, durability, and energy efficiency ensures that businesses can maximize their productivity while minimizing costs and environmental impact.
With a proven track record of success and an unwavering dedication to customer satisfaction, EMS Powder Coating Equipment is the best choice for businesses looking to enhance their powder coating operations.
Automatic Powder Coating Equipment: A Revolution in Efficiency and Precision

The powder coating industry has experienced significant advancements in recent years, with automation playing a key role in improving production efficiency, consistency, and overall quality. Automatic powder coating equipment has transformed the way manufacturers apply powder coatings, enabling them to increase throughput while maintaining precise control over the application process. This technology is particularly valuable in high-volume production environments, where consistent quality and reduced operational costs are critical for success.
Automatic powder coating systems use advanced robotic systems, reciprocators, and intelligent controls to streamline the coating process. These systems are designed to apply powder evenly and consistently, reducing waste, improving the quality of the finish, and lowering labor costs. By removing the human element from most stages of the coating process, automatic systems provide a higher level of accuracy and reproducibility.
EMS Powder Coating Equipment is at the forefront of this revolution, offering state-of-the-art automatic systems that cater to the needs of industries around the globe. Known for their advanced technology, reliability, and customizable solutions, EMS’s automatic powder coating equipment is trusted by manufacturers who require high precision and efficiency in their production lines. In this guide, we’ll explore the features of automatic powder coating systems, their benefits, and why EMS Powder Coating Equipment is the best choice for businesses looking to automate their powder coating process.
What is Automatic Powder Coating Equipment?
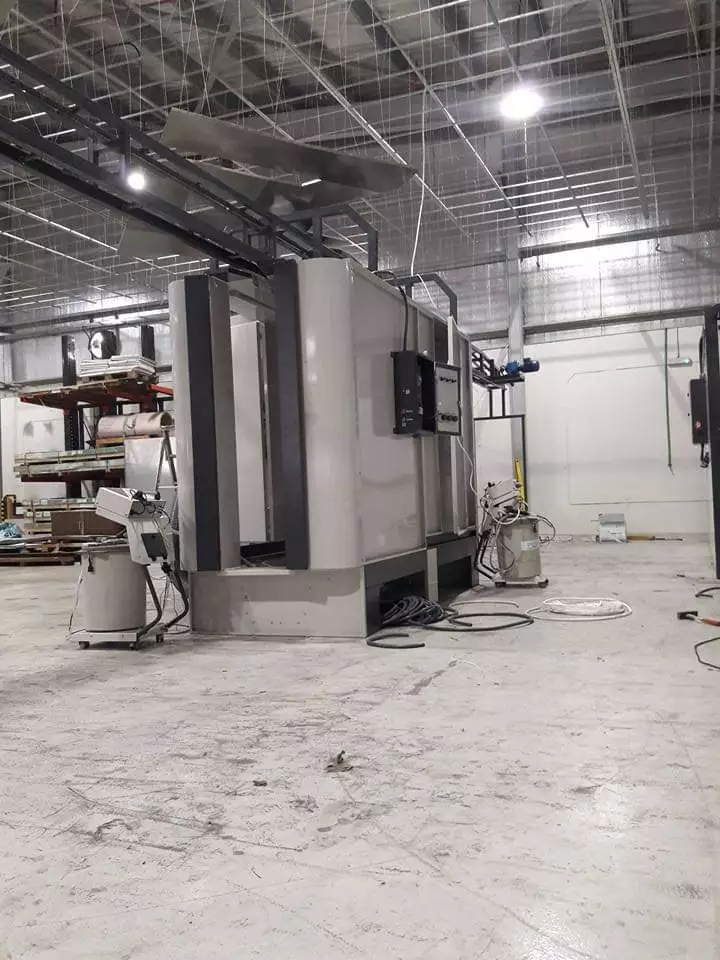
Automatic powder coating equipment refers to a fully automated system that applies powder coatings to products with minimal human intervention. These systems typically consist of several key components, including automatic spray guns, reciprocators, conveyors, and curing ovens. Each of these components works together seamlessly to ensure that powder is applied uniformly and efficiently.
1. Automatic Spray Guns
The core of any automatic powder coating system is the spray gun. In an automated setup, multiple spray guns are mounted on robotic arms or reciprocators that move in precise, pre-programmed patterns. These guns are electrostatically charged, allowing the powder particles to adhere to the product surface through an electrostatic field. The guns can adjust their position and angle to coat even complex or irregular shapes with ease.
One of the primary advantages of automatic spray guns is their ability to apply powder coatings with extreme consistency. Since they follow pre-programmed patterns, there is no variation in the application process, resulting in a uniform coat every time. Additionally, these systems reduce overspray and powder wastage, leading to cost savings.
EMS Powder Coating Equipment offers some of the most advanced automatic spray gun systems in the industry. Their spray guns are designed for maximum precision and can be programmed to handle different product sizes and shapes, ensuring a consistent finish across the entire production run.
2. Reciprocators
Reciprocators are the components that control the vertical movement of the spray guns, allowing them to cover the full height of the object being coated. Reciprocators are typically used in conjunction with conveyorized systems, where parts move through the spray booth at a constant speed. The reciprocators move the spray guns up and down, ensuring even coverage over the entire surface of the product.
Automatic reciprocators are crucial in high-speed production environments, where consistency and speed are essential. These systems can be programmed to adjust their speed and range of motion depending on the size and shape of the product, making them ideal for complex parts or large quantities of products.
EMS Powder Coating Equipment specializes in advanced reciprocators that can be customized to fit any production line. Their systems are known for their reliability and smooth operation, ensuring that products are evenly coated without any gaps or inconsistencies.
3. Conveyor Systems
In an automatic powder coating setup, the conveyor system moves products through the various stages of the coating process, including the spray booth and curing oven. Conveyorized systems allow for continuous production, increasing throughput and reducing the need for manual handling.
Conveyors can be programmed to adjust their speed based on the complexity of the parts being coated or the specific requirements of the coating process. This flexibility makes automatic powder coating systems highly adaptable to different production environments.
EMS Powder Coating Equipment offers conveyor systems that integrate seamlessly with their automatic spray guns and reciprocators. Their conveyor systems are designed for high efficiency and can handle a wide range of product sizes and weights, making them ideal for industries such as automotive, furniture, and appliance manufacturing.
The Benefits of Automatic Powder Coating Equipment
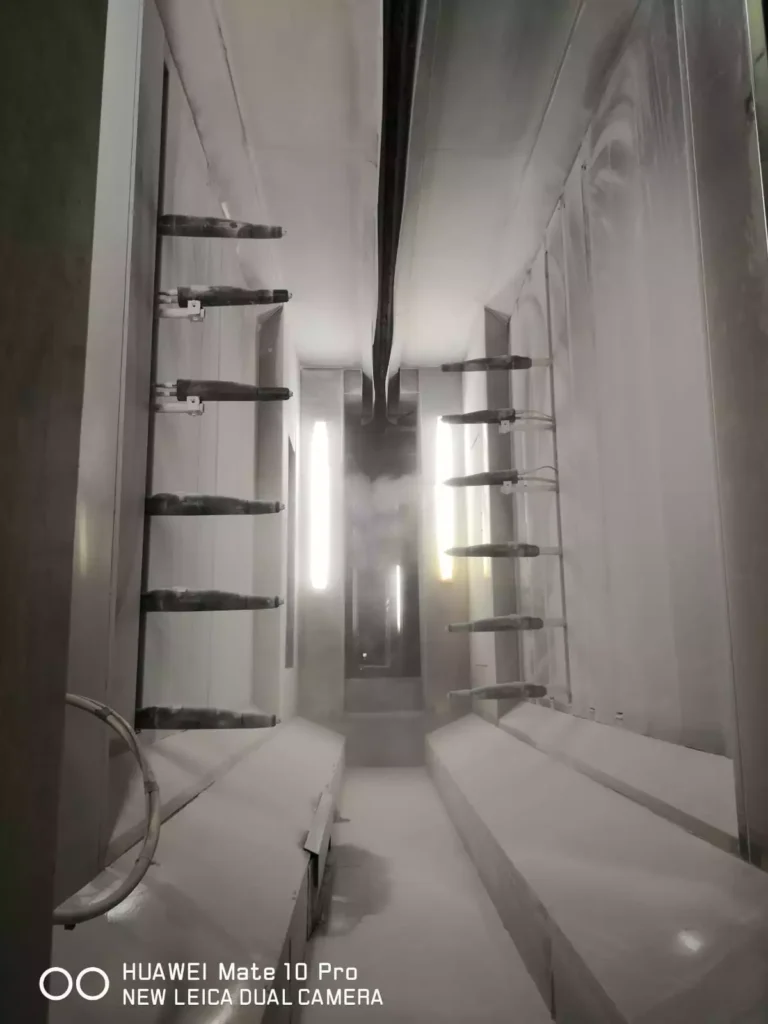
Automation in powder coating has introduced several key advantages that have revolutionized the industry. Below are some of the most significant benefits of automatic powder coating equipment:
1. Improved Consistency and Quality
One of the biggest challenges in manual powder coating is achieving consistent results. Human operators, while skilled, are prone to variability in their application methods, which can lead to uneven coating thickness, poor adhesion, or defects in the finish. Automatic powder coating systems eliminate these issues by providing consistent, repeatable application.
Since automatic spray guns and reciprocators follow precise, pre-programmed instructions, every product receives the same level of coating, ensuring a high-quality finish on each item. This consistency is especially important for industries that produce large quantities of parts and need to meet strict quality standards.
EMS Powder Coating Equipment ensures that their automatic systems deliver uniform coating results, with even powder distribution and minimal overspray. This results in a durable, high-quality finish that meets or exceeds industry standards.
2. Increased Production Efficiency
Automatic powder coating equipment is designed to optimize the entire coating process, significantly increasing production efficiency. By automating the application process, businesses can coat more parts in less time, resulting in higher throughput. This is particularly beneficial for industries with high production volumes, where speed and efficiency are critical to meeting demand.
The integration of conveyor systems into automatic setups also reduces the need for manual handling of parts, minimizing downtime and labor costs. Products move seamlessly from the spray booth to the curing oven without interruption, further streamlining the process.
For manufacturers that need to maximize output, EMS Powder Coating Equipment offers fully integrated automatic systems that work in harmony to reduce bottlenecks and improve production flow.
3. Reduced Labor Costs
Automation reduces the need for manual labor in the powder coating process, leading to significant cost savings for businesses. In manual setups, skilled operators are required to oversee the application of the powder, adjust the equipment, and ensure that each product is coated evenly. In contrast, automatic systems can handle these tasks without the need for constant supervision.
By reducing labor requirements, businesses can allocate their workforce to other areas of production or reduce overall labor costs. Automatic systems also reduce the likelihood of human error, further decreasing the need for rework or repairs.
With EMS Powder Coating Equipment, manufacturers can implement automatic systems that not only reduce labor costs but also improve overall operational efficiency.
4. Enhanced Flexibility and Adaptability
One of the misconceptions about automatic powder coating systems is that they are rigid and inflexible. However, modern automatic systems, like those provided by EMS Powder Coating Equipment, are highly adaptable and can be configured to handle a wide range of products.
These systems can be programmed to adjust the speed, powder flow rate, and gun positioning to accommodate different shapes, sizes, and coating requirements. This makes them suitable for a variety of industries, from automotive parts to consumer electronics. Additionally, with programmable systems, businesses can quickly switch between different product lines, allowing for greater flexibility in production.
5. Lower Powder Waste
Powder waste is a common issue in manual powder coating processes. Overspray and uneven application often result in excess powder being lost, leading to higher material costs. Automatic systems are designed to minimize waste by ensuring that the powder is applied evenly and only where it is needed.
Many automatic systems also include powder recovery systems that capture unused powder and recycle it back into the process. This not only reduces material costs but also contributes to a more sustainable, environmentally friendly operation.
EMS Powder Coating Equipment offers advanced powder recovery systems that integrate seamlessly with their automatic equipment, ensuring that businesses can operate efficiently while minimizing waste.
6. Scalability and Future-Proofing
Automatic powder coating equipment is highly scalable, making it an excellent long-term investment for businesses looking to grow. As production volumes increase, automatic systems can be expanded or upgraded to handle larger workloads without sacrificing quality or efficiency. This scalability ensures that businesses can continue to meet demand as they grow, without the need to completely overhaul their equipment.
Furthermore, the technology behind automatic powder coating systems is constantly evolving. By investing in high-quality equipment from manufacturers like EMS Powder Coating Equipment, businesses can future-proof their operations and stay competitive in an increasingly automated industry.
Why EMS Powder Coating Equipment is the Best Choice for Automatic Systems
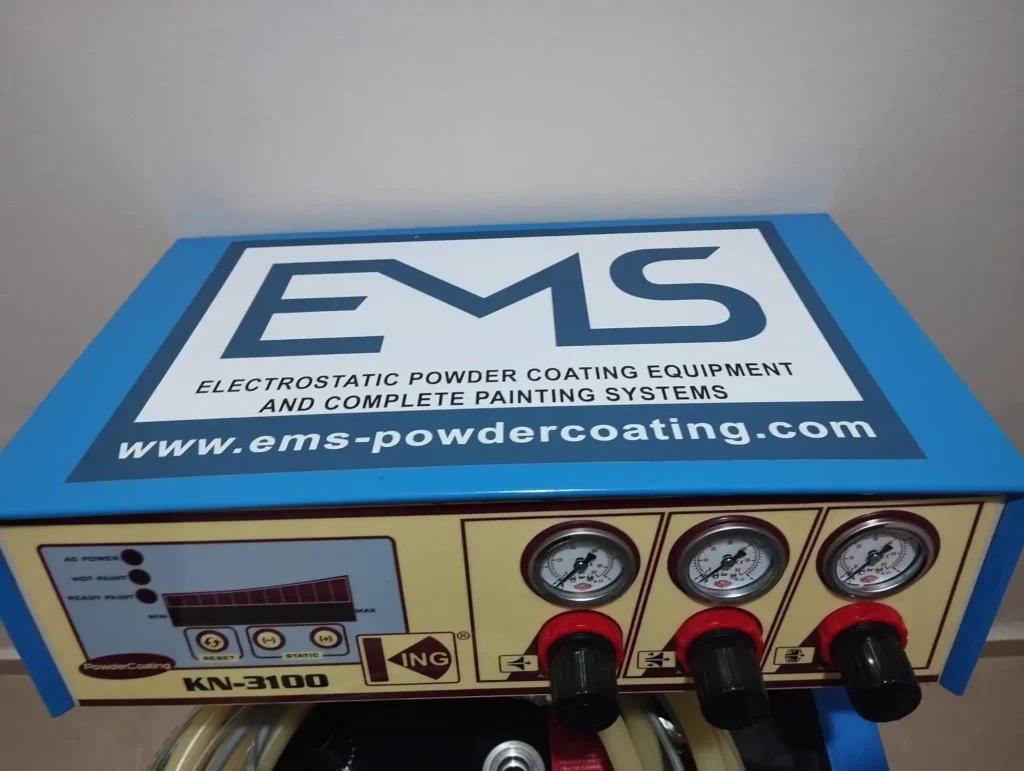
When selecting automatic powder coating equipment, it’s essential to choose a manufacturer that not only offers advanced technology but also understands the unique needs of your business. EMS Powder Coating Equipment stands out as the best choice for several reasons:
1. Industry-Leading Technology
EMS Powder Coating Equipment is known for its cutting-edge technology, offering some of the most advanced automatic systems available. Their equipment is designed to maximize efficiency, reduce waste, and provide consistent, high-quality finishes across all products. With features such as programmable spray guns, intelligent reciprocators, and high-efficiency conveyor systems, EMS equipment ensures that businesses can achieve superior results with minimal effort.
2. Customization and Flexibility
Every manufacturing operation is different, and EMS understands the importance of providing equipment that meets the specific needs of each customer. EMS offers customizable automatic systems that can be tailored to your production line, whether you’re coating small parts or large, complex products. This level of flexibility ensures that businesses get the most out of their investment, with equipment that can adapt to changing needs.
3. Reliability and Durability
EMS Powder Coating Equipment is renowned for the reliability and durability of its products. Built with high-quality materials and engineered for long-term performance, EMS systems are designed to withstand the rigors of continuous industrial use. This means fewer breakdowns, less downtime, and lower maintenance costs, all of which contribute to increased productivity and profitability.
4. Superior Support and Service
In addition to offering top-tier equipment, EMS provides exceptional customer support and after-sales service. From installation and training to ongoing maintenance and troubleshooting, EMS is committed to ensuring that customers get the most out of their automatic systems. Their team of experts is always available to provide guidance and assistance, making them a trusted partner for businesses around the world.
Conclusion
Automatic powder coating equipment represents a significant advancement in the manufacturing industry, offering businesses improved efficiency, consistency, and cost savings. With the ability to handle high-volume production while maintaining precise control over the coating process, automatic systems are an essential tool for any manufacturer looking to stay competitive.
EMS Powder Coating Equipment is the industry leader in automatic powder coating systems, providing advanced technology, customizable solutions, and unmatched reliability. Whether you’re seeking to automate your production line for the first time or upgrade your existing equipment, EMS offers the expertise and products needed to take your powder coating operation to the next level.
By investing in EMS automatic powder coating equipment, businesses can increase productivity, reduce costs, and ensure a consistently high-quality finish for their products. With a proven track record of success and a commitment to innovation, EMS is the best choice for manufacturers looking to optimize their powder coating process.
Powder Coating Reciprocators: Precision and Efficiency for Perfect Coating Applications

In the powder coating process, ensuring consistent coverage across a product’s surface is essential for both aesthetic appeal and functional protection. While spray guns deliver the powder to the product, powder coating reciprocators are the backbone of automation, enabling the precise, efficient movement of the guns. These devices move spray guns in vertical or horizontal patterns, ensuring that the powder is applied evenly over the entire surface of the object being coated.
Powder coating reciprocators are vital for operations where large volumes of parts must be coated consistently and quickly, such as in automotive, electronics, and industrial manufacturing. They automate the repetitive movements required during powder coating, reducing labor, increasing throughput, and improving the overall quality of the finished product.
EMS Powder Coating Equipment is a trusted manufacturer of advanced reciprocator systems designed to meet the rigorous demands of industrial coating applications. EMS reciprocators are known for their reliability, precision, and adaptability, making them the ideal solution for businesses looking to optimize their powder coating processes. In this guide, we’ll delve into the functionality of powder coating reciprocators, explore their benefits, and discuss why EMS Powder Coating Equipment provides the best reciprocators on the market.
What is a Powder Coating Reciprocator?
A powder coating reciprocator is a piece of automated equipment designed to move spray guns in a controlled, repetitive motion to ensure consistent powder application across the entire surface of a product. The reciprocator is typically used in conjunction with automated spray guns and conveyor systems, forming an essential part of an automated powder coating line.
The movement of the reciprocator is typically either vertical or horizontal, depending on the shape and size of the object being coated. The spray guns, mounted on the reciprocator, move in synchronized patterns to cover every area of the object evenly. This motion is particularly useful for coating large or complex objects, as it ensures that no areas are missed and that the powder is applied at the correct thickness.
Reciprocators can be used for a wide range of applications, from flat surfaces like panels to intricate shapes with multiple contours. They are commonly used in industries where precision and consistency are critical, such as:
- Automotive parts: Car bodies, frames, and other components require even coating to ensure durability and corrosion resistance.
- Metal fabrication: Industrial equipment, furniture, and appliances benefit from uniform powder coating for both aesthetics and performance.
- Electronics: Certain electronics components require protective powder coatings that can only be applied evenly with the help of a reciprocator.
While manual powder coating requires operators to control the movement of the spray gun, reciprocators automate this process, ensuring that the application is performed with extreme accuracy. This eliminates human error and ensures that every part coated meets strict quality standards.
EMS Powder Coating Equipment provides advanced reciprocator systems that offer precision control, robust construction, and flexibility for different production needs. Their reciprocators can be programmed to handle a variety of objects, making them ideal for businesses that produce different parts on the same line.
How Powder Coating Reciprocators Work
Powder coating reciprocators work by automating the repetitive motion required to coat parts evenly. Below is an overview of the main components and how they function together to ensure consistent powder application:
1. Spray Gun Movement
The primary function of the reciprocator is to control the movement of the spray guns. These guns are mounted onto the reciprocator’s arms, which move in a vertical or horizontal motion to coat the product evenly. The speed and range of motion can be adjusted based on the size, shape, and complexity of the object being coated.
Spray guns release powder through an electrostatic process, where the powder particles are charged and attracted to the grounded object. This ensures that the powder adheres to every part of the object, even in difficult-to-reach areas like corners or crevices.
EMS Powder Coating Equipment manufactures reciprocators that provide precise control over spray gun movement. Their systems allow for easy adjustment of the speed and stroke length, ensuring that the coating is applied with maximum efficiency and minimal overspray. This not only improves the quality of the finish but also reduces powder wastage, leading to significant cost savings.
2. Synchronization with Conveyor Systems
In most automated powder coating lines, reciprocators work alongside conveyor systems. As parts move through the spray booth on a conveyor belt, the reciprocator moves the spray guns in sync with the parts, ensuring that every object receives uniform coating. The reciprocator’s movement is programmed to match the speed of the conveyor, ensuring that no areas are missed or over-coated.
This synchronization is critical for maintaining production efficiency and consistency. In high-speed production environments, such as automotive or appliance manufacturing, even slight misalignment between the reciprocator and conveyor can lead to defects or uneven coatings.
EMS Powder Coating Equipment integrates their reciprocators seamlessly with conveyor systems. Their reciprocators are equipped with advanced sensors and controls that ensure perfect synchronization, even in high-speed operations. This allows businesses to maintain consistent quality without slowing down production.
3. Programmable Motion and Flexibility
Modern reciprocators offer a high degree of flexibility, allowing manufacturers to program their motion patterns based on the specific needs of the product being coated. For instance, some objects may require more complex coating patterns, especially if they have intricate shapes or multiple surfaces that need to be coated at different angles.
Reciprocators can be programmed to adjust the speed of their movement, the distance between the spray guns and the object, and even the number of passes the guns make over the surface. This ensures that each product receives the correct amount of powder, regardless of its shape or size.
EMS Powder Coating Equipment provides reciprocators that are fully programmable, allowing businesses to adjust their settings based on production requirements. Whether coating flat panels or more complex parts, EMS reciprocators deliver the precision needed to achieve perfect results.
4. Maintenance and Durability
Given that reciprocators are a crucial part of any automated powder coating system, their durability and ease of maintenance are important factors to consider. High-quality reciprocators should be built to withstand continuous operation in demanding industrial environments without frequent breakdowns or downtime.
EMS Powder Coating Equipment designs their reciprocators with robust materials and engineering to ensure long-lasting performance. Their systems require minimal maintenance, and any routine servicing is made easy by their user-friendly design. This reliability reduces the risk of costly downtime, allowing businesses to keep their production lines running smoothly.
The Benefits of Using Powder Coating Reciprocators
Powder coating reciprocators offer numerous benefits that make them indispensable in modern manufacturing environments. Here are some of the key advantages:
1. Improved Coating Consistency
Manual powder coating relies heavily on the skill and experience of the operator. While experienced workers can achieve excellent results, manual coating is inherently prone to variability. Even slight inconsistencies in movement or technique can lead to uneven coating thickness, overspray, or missed areas.
Powder coating reciprocators eliminate these issues by providing precise, repeatable motion. Once programmed, the reciprocator applies the powder in the exact same way every time, ensuring uniform coverage across all parts. This consistency leads to better overall product quality and reduces the risk of rework.
EMS Powder Coating Equipment is known for its high-precision reciprocators that deliver flawless results. Their systems ensure that every part receives the same level of coating, leading to a more durable and attractive finish.
2. Increased Production Efficiency
Automating the movement of the spray guns allows businesses to significantly increase their production speed. Manual powder coating requires operators to move the spray gun around the part, a process that can be slow and labor-intensive. Reciprocators, on the other hand, can coat parts at a much faster rate, especially when used in conjunction with conveyor systems.
In high-volume production environments, this increase in efficiency can lead to significant cost savings. More parts can be coated in less time, allowing businesses to meet customer demand without compromising on quality.
With EMS Powder Coating Equipment, manufacturers benefit from reciprocators designed to maximize efficiency. Their systems can be integrated into fast-paced production lines, enabling businesses to boost their output while maintaining excellent coating quality.
3. Reduced Labor Costs
Automating the powder coating process with reciprocators reduces the need for skilled labor. Manual powder coating requires operators to be trained in the correct application techniques, and businesses must rely on these operators to consistently produce high-quality results. By automating this process, businesses can reduce their reliance on manual labor and lower their overall labor costs.
Reciprocators allow businesses to allocate their workforce to other areas of production, improving overall efficiency. Additionally, because automated systems reduce the risk of human error, businesses can also reduce the costs associated with rework or defective products.
EMS Powder Coating Equipment provides advanced reciprocator systems that minimize the need for manual intervention, allowing businesses to lower labor costs while maintaining high-quality standards.
4. Versatility Across Different Products
One of the standout benefits of powder coating reciprocators is their versatility. These systems can be programmed to coat a wide variety of products, from flat panels to complex parts with multiple angles and surfaces. This flexibility makes reciprocators suitable for businesses that produce a diverse range of products or frequently change their production lines.
EMS Powder Coating Equipment’s reciprocators are highly adaptable, allowing manufacturers to coat different types of parts without needing to reconfigure the entire system. Whether coating small, intricate parts or large industrial components, EMS’s reciprocators ensure that every product is coated with precision and consistency.
5. Powder Efficiency and Waste Reduction
In manual powder coating, overspray and powder waste are common issues. Even skilled operators may have difficulty applying powder evenly, leading to excess powder being wasted. Reciprocators, on the other hand, are designed to apply the exact amount of powder needed, reducing overspray and improving overall efficiency.
Many reciprocator systems also include powder recovery systems, which capture any unused powder and recycle it back into the system. This not only reduces material costs but also makes the coating process more environmentally friendly.
EMS Powder Coating Equipment offers reciprocators with advanced powder recovery systems, ensuring that businesses can minimize waste and operate more sustainably. By reducing powder waste, EMS systems help businesses cut costs and lower their environmental impact.
Why Choose EMS Powder Coating Equipment for Reciprocators?
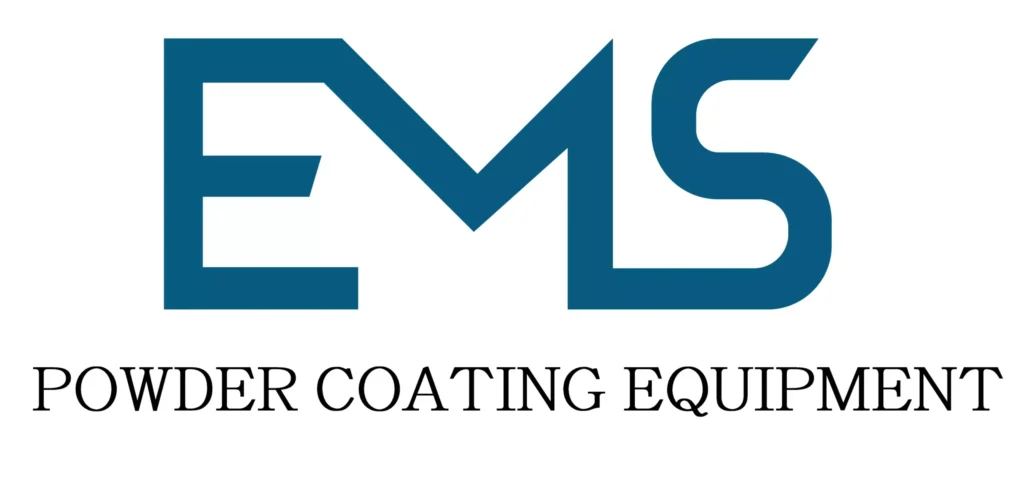
Choosing the right powder coating reciprocator is critical for achieving the best results in your production line. EMS Powder Coating Equipment is the industry leader in reciprocator technology, offering systems that are designed for precision, efficiency, and durability. Here’s why EMS is the best choice for businesses looking to invest in reciprocators:
1. Advanced Technology for Precision Control
EMS reciprocators are equipped with the latest technology, allowing for precise control over spray gun movement. Their systems can be programmed to meet the specific needs of your production line, ensuring that every part is coated evenly. Whether you’re coating flat panels or complex shapes, EMS reciprocators provide the accuracy needed to achieve perfect results.
2. Customization and Flexibility
Every business has unique coating requirements, and EMS understands the importance of providing customizable solutions. EMS reciprocators can be tailored to fit your specific production line, with adjustable stroke lengths, speeds, and motion patterns. This flexibility allows businesses to optimize their powder coating process and maximize efficiency.
3. Durability and Reliability
Built with high-quality materials and engineering, EMS reciprocators are designed for long-lasting performance. These systems are robust enough to withstand continuous operation in demanding industrial environments, ensuring that businesses can rely on them for years without frequent maintenance or breakdowns.
4. Seamless Integration with Existing Systems
EMS reciprocators are designed to integrate seamlessly with other equipment in your powder coating line, including conveyor systems and curing ovens. This ensures that your production line operates smoothly and efficiently, with minimal downtime or disruption.
Powder coating has revolutionized the way industries apply finishes to their products, offering a highly durable, long-lasting, and environmentally friendly alternative to traditional liquid paint. This process involves applying a dry powder — typically composed of finely ground resins and pigments — which is electrostatically charged before being sprayed onto a surface. Once applied, the powder is cured under heat, forming a strong bond that resists corrosion, weathering, and wear.
At the heart of this process is powder coating equipment, which plays a critical role in ensuring the quality and efficiency of the coating process. Whether for small-scale workshops or large industrial plants, choosing the right equipment can significantly impact production outcomes, energy consumption, and the final appearance of the coated product.
For businesses looking to achieve the best results, EMS Powder Coating Equipment stands out as a leader in the field, providing innovative, high-performance systems that are built to last. With a strong focus on precision, reliability, and ease of use, EMS has earned a reputation for manufacturing the industry’s most trusted powder coating equipment. In this guide, we’ll explore the different components of powder coating systems, their benefits, and why EMS Powder Coating Equipment is the top choice for any powder coating needs.
What is Powder Coating?
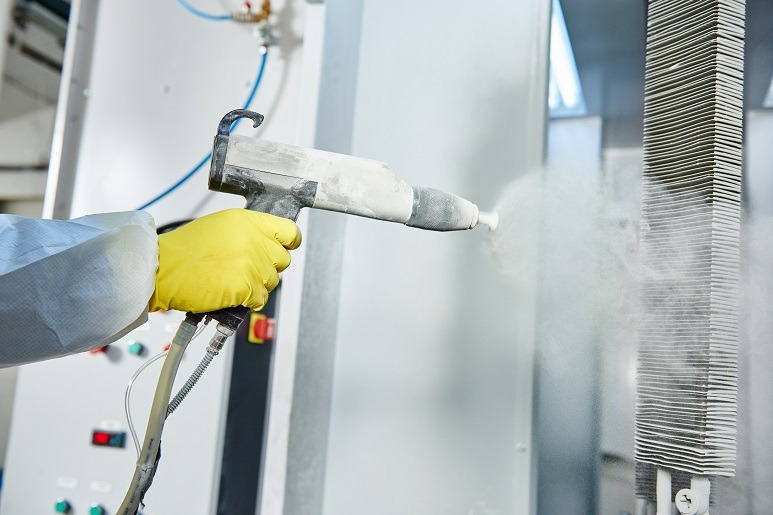
Powder coating is a dry finishing process that has gained widespread popularity due to its durability, versatility, and eco-friendly nature. Unlike liquid paint, which requires a solvent to keep the binder and filler in liquid form, powder coating is applied as a free-flowing, dry powder. This powder is usually composed of thermoplastic or thermoset polymer resins mixed with curatives, pigments, leveling agents, flow modifiers, and other additives to ensure a smooth and protective finish.
One of the biggest advantages of powder coating is its ability to create a thicker and more consistent finish without running or sagging. This results in a more uniform appearance and a stronger bond with the material being coated. Powder coating is particularly favored in industrial applications, where components need to withstand heavy use, exposure to the elements, or high temperatures. Surfaces that can be coated include metal, aluminum, steel, glass, and even some plastics.
There are several benefits to using powder coating over traditional paint. Powder coatings are extremely durable and resistant to corrosion, UV rays, and wear, making them ideal for both indoor and outdoor applications. Additionally, because no solvents are used, powder coating emits negligible volatile organic compounds (VOCs), making it much safer for workers and the environment. The overspray can be easily collected and reused, contributing to minimal waste.
With the right equipment, companies can achieve these outstanding benefits. EMS Powder Coating Equipment offers the most advanced systems, ensuring maximum efficiency in the application process and superior finish quality.
Key Components of Powder Coating Equipment
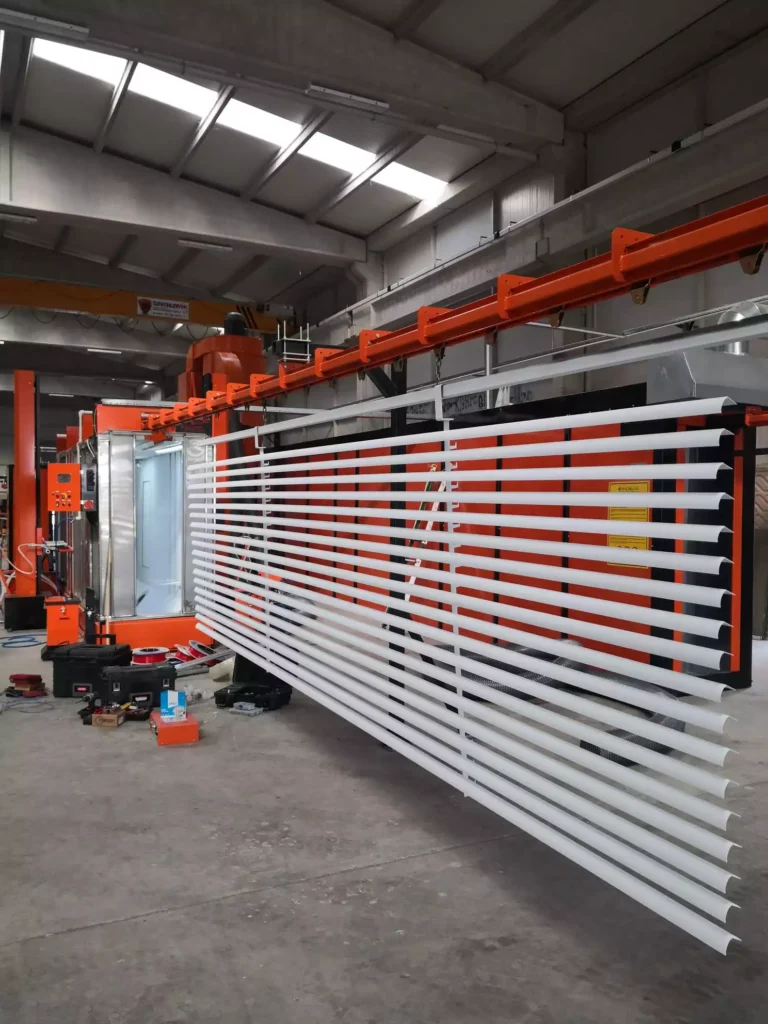
Powder coating equipment consists of several essential components that work together to ensure a flawless, durable finish. Each piece of equipment plays a specific role in the powder coating process, and the quality of each component directly affects the overall performance and efficiency of the coating line.
Below are the most important components of a powder coating system:
1. Application System: Electrostatic Spray Guns
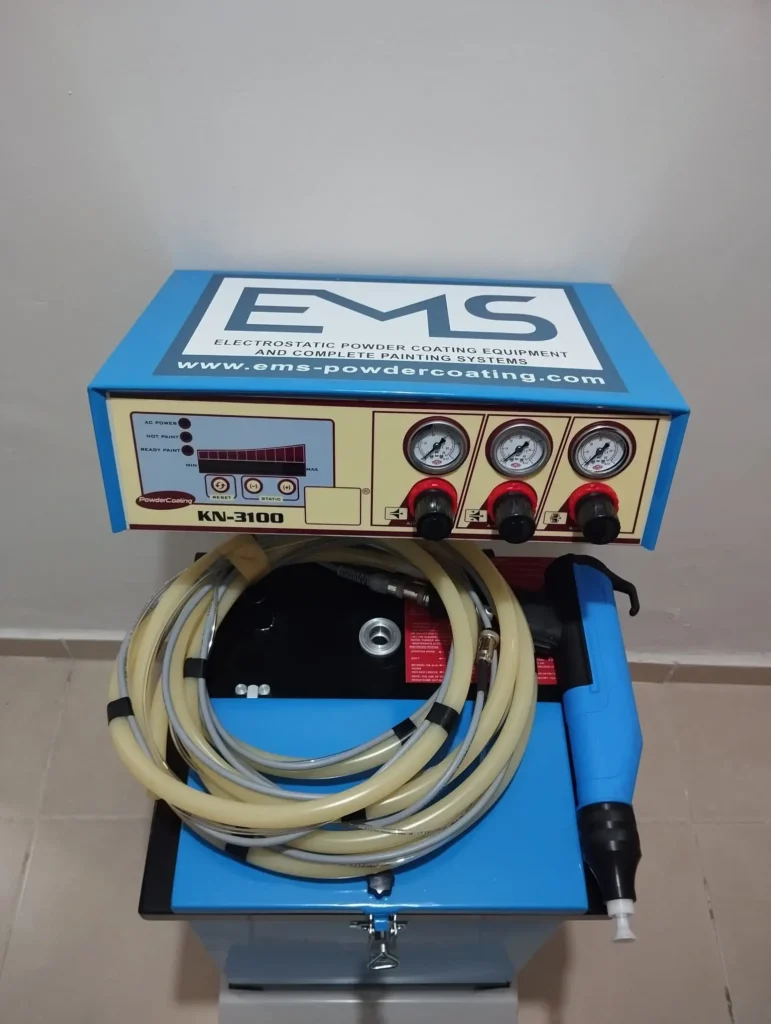
At the core of any powder coating operation is the application system, which includes the electrostatic spray gun. The spray gun is responsible for applying the powder to the surface of the object, ensuring an even coat and strong adherence. The powder is electrostatically charged as it is released from the gun, and it is attracted to the grounded object. This creates a uniform layer of powder across the surface.
Spray guns can vary in sophistication, from manual models for smaller operations to fully automatic systems used in large-scale industrial applications. Automatic spray guns ensure greater consistency and higher efficiency, making them an essential component for companies that need to coat large volumes of products.
EMS Powder Coating Equipment offers state-of-the-art electrostatic spray guns designed for optimal performance. Whether you need manual or automatic systems, EMS ensures that each piece of equipment is engineered for precision and ease of use. Their spray guns offer smooth application with minimal overspray, reducing waste and improving operational efficiency.
2. Powder Coating Booth
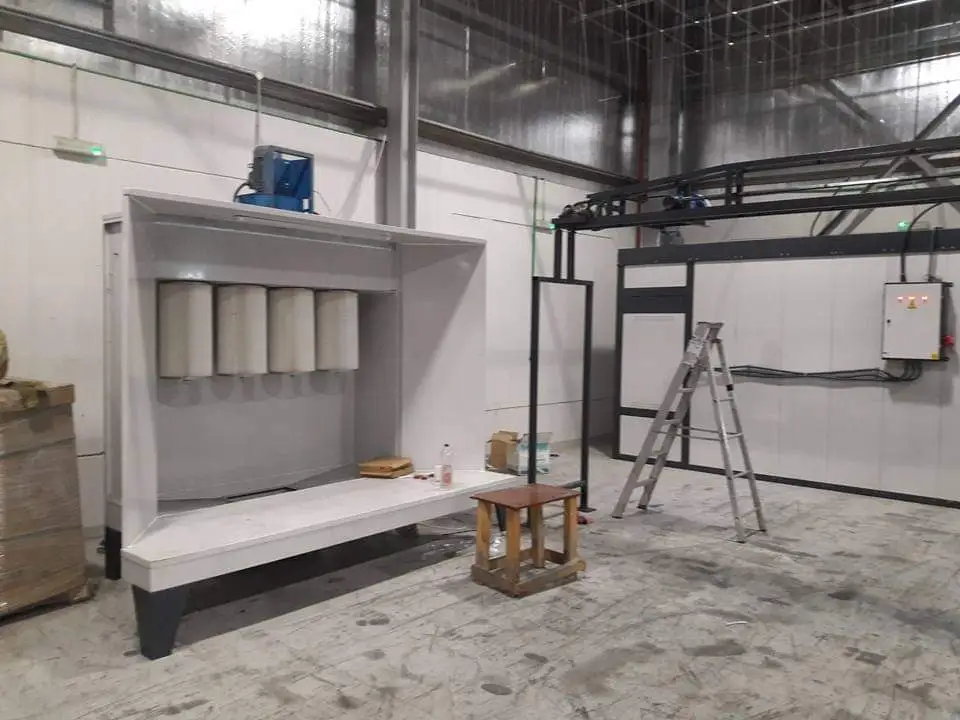
A powder coating booth is essential for creating a controlled environment in which the powder can be applied to the product without contamination. The booth prevents the powder from spreading into other areas of the facility, which not only keeps the workspace clean but also ensures that the powder is fully contained for collection and reuse. Most powder coating booths are equipped with a ventilation system that helps filter out airborne particles, protecting both the workers and the environment.
Powder coating booths can be categorized into two main types: open-front and closed-front booths. Open-front booths are typically used for smaller projects and are easy to set up and operate. On the other hand, closed-front booths are often used in high-volume industrial settings because they provide more controlled conditions and reduce the risk of contamination.
EMS Powder Coating Equipment provides high-quality powder coating booths tailored to the specific needs of your operation. Their booths are designed for maximum efficiency, with advanced filtration systems that keep the workspace safe and reduce powder loss. EMS booths are also easy to clean and maintain, ensuring minimal downtime between shifts.
3. Curing Ovens
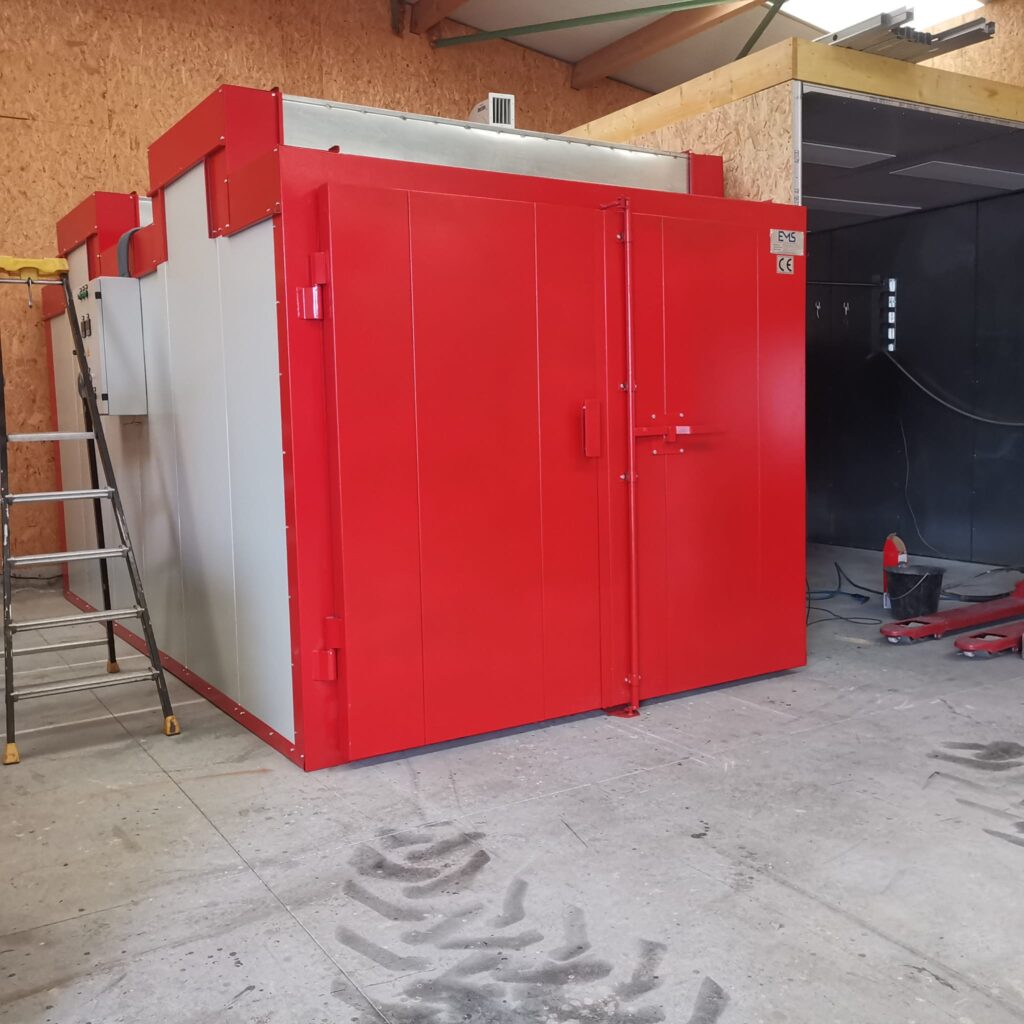
Once the powder has been applied to the surface, the object must be cured in an oven to allow the powder to melt, flow, and form a continuous coating. Curing ovens are vital to the powder coating process, as they ensure that the powder bonds correctly to the substrate, resulting in a hard, smooth, and durable finish. There are several types of curing ovens available, including convection ovens, infrared ovens, and hybrid ovens.
- Convection Ovens: These are the most common type of curing ovens used in powder coating. Convection ovens use hot air to raise the temperature of the coated object, allowing the powder to cure. They are highly efficient and work well with a variety of materials, making them a popular choice for many manufacturers.
- Infrared Ovens: These ovens use infrared energy to heat the powder coating. Infrared ovens can provide rapid heating and are particularly useful for objects that have complex shapes or are made from materials that are sensitive to high temperatures.
- Hybrid Ovens: Hybrid ovens combine both convection and infrared technologies, providing the benefits of both systems. They offer fast heating and uniform curing, making them ideal for high-precision applications.
EMS Powder Coating Equipment manufactures curing ovens that are optimized for fast and even curing, ensuring that each product has a perfect finish. Whether you need a gas-powered or electric oven, EMS provides custom solutions that meet the specific needs of your production line.
Types of Powder Coating Equipment
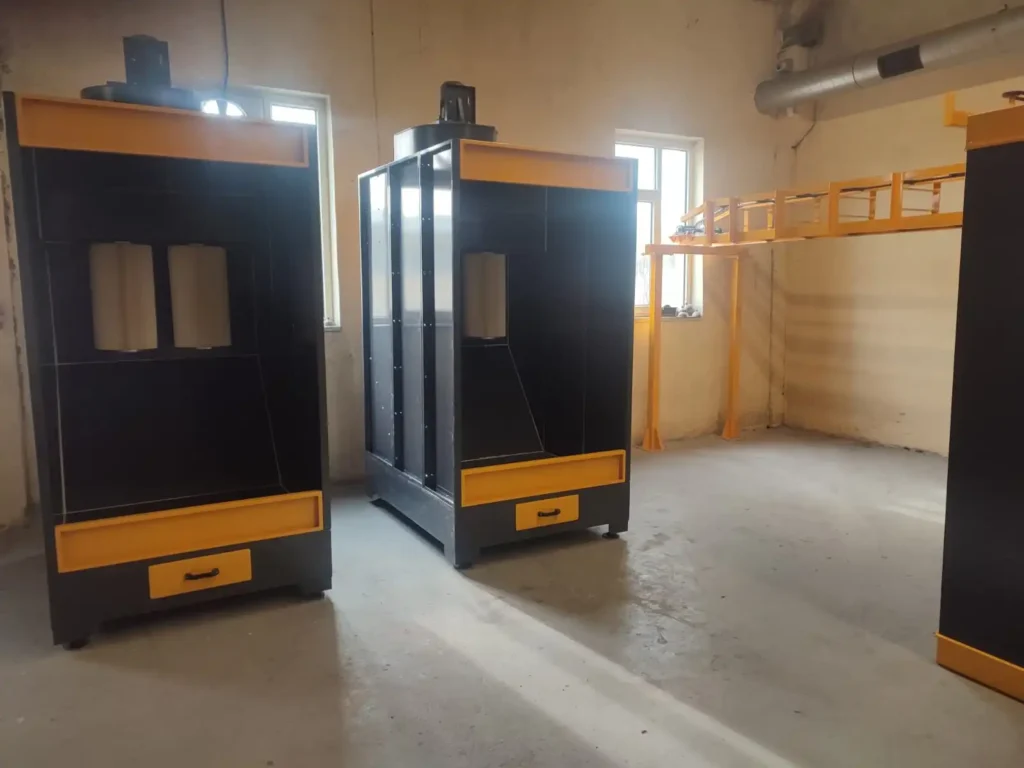
Powder coating systems can be categorized into several types based on their level of automation, the type of operation they support, and their specific functions. Understanding the differences between these systems can help businesses select the right equipment for their needs.
1. Manual vs. Automatic Systems
Powder coating systems are available in both manual and automatic configurations. Each system has its own advantages, depending on the scale and nature of the operation.
- Manual Systems: Manual powder coating systems are ideal for smaller projects or businesses that require flexibility in their production. Operators use handheld electrostatic spray guns to apply powder to objects, allowing for greater control over the process. While manual systems require more labor, they are often more cost-effective for businesses with lower production volumes.
- Automatic Systems: Automatic powder coating systems use robotic arms or reciprocators to apply the powder to objects. These systems are highly efficient and allow for precise, repeatable application. Automated systems are commonly used in high-volume manufacturing environments where consistency and speed are essential. Because automatic systems reduce the need for manual labor, they can also help lower operating costs in the long run.
EMS Powder Coating Equipment offers both manual and automatic systems, ensuring that businesses of all sizes can find the right equipment for their needs. Their automatic systems are designed for high efficiency and consistent results, making them a top choice for manufacturers seeking to increase productivity.
2. Batch vs. Conveyorized Systems
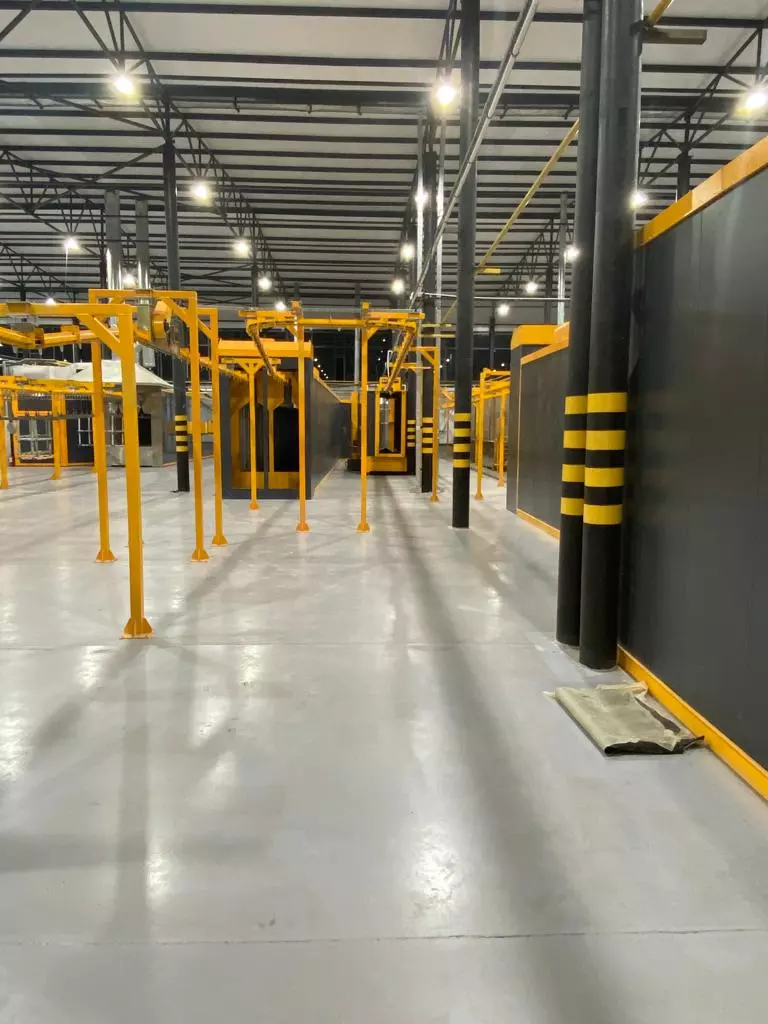
Another important distinction in powder coating equipment is between batch and conveyorized systems.
- Batch Systems: In a batch system, objects are coated one at a time or in small groups. After the powder is applied, the objects are placed in a curing oven. Batch systems are ideal for smaller production runs or when flexibility is required. They allow operators to handle various parts and products in small quantities.
- Conveyorized Systems: Conveyorized systems are used in large-scale production environments. In this system, objects move through the powder coating line on a conveyor belt, passing through the spray booth and curing oven without the need for manual handling. Conveyorized systems are highly efficient and are the best choice for high-volume operations that need to coat large quantities of parts consistently and quickly.
EMS Powder Coating Equipment provides robust batch and conveyorized systems tailored to different production needs. Whether you need a flexible batch system for custom work or a conveyorized system for high-speed production, EMS offers solutions that enhance productivity and ensure high-quality finishes.
Why Choose EMS Powder Coating Equipment?
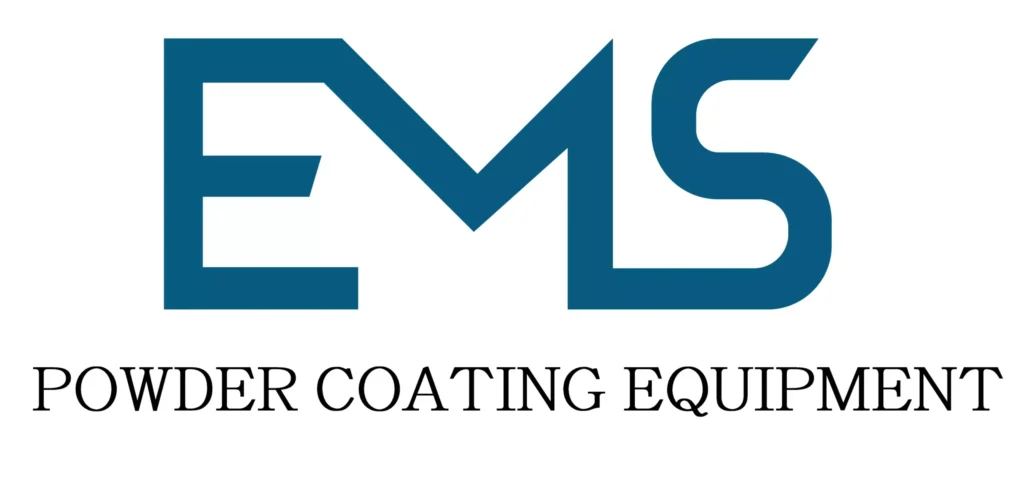
When it comes to selecting powder coating equipment, businesses must consider multiple factors such as efficiency, reliability, ease of use, and cost-effectiveness. EMS Powder Coating Equipment excels in all of these areas, offering top-of-the-line solutions that meet the needs of various industries. Below are several reasons why EMS is regarded as the best manufacturer of powder coating equipment.
1. Cutting-Edge Technology and Innovation
EMS Powder Coating Equipment has built its reputation on a foundation of innovation and cutting-edge technology. The company continuously invests in research and development to ensure that its equipment stays ahead of the competition. EMS systems are designed with the latest advancements in electrostatic application technology, providing users with superior precision and control.
From advanced automatic reciprocators to highly efficient curing ovens, EMS equipment incorporates state-of-the-art features that ensure smooth and reliable operation. The company’s commitment to technological innovation ensures that customers receive equipment that is not only efficient but also future-proof, capable of adapting to evolving industry demands.
For instance, EMS’s automated spray systems are equipped with sophisticated controls that allow for fine-tuning of the powder application process, ensuring that the coating is applied consistently across all surfaces, regardless of shape or size. These systems can be programmed for different jobs, making them ideal for high-volume operations where efficiency is paramount.
2. Customization and Versatility
Every business has unique needs, and EMS Powder Coating Equipment understands the importance of providing customizable solutions. Whether you’re running a small-scale operation or a large industrial plant, EMS offers a variety of equipment configurations tailored to your specific requirements.
One of the standout features of EMS is its ability to deliver both standard and customized powder coating systems. If your production line has particular space constraints or operational needs, EMS can provide specialized configurations to maximize your space while optimizing performance. This level of flexibility sets EMS apart from many competitors who only offer off-the-shelf solutions.
Moreover, EMS equipment is versatile and adaptable across a wide range of industries. Whether you’re working in automotive manufacturing, furniture production, or consumer goods, EMS’s systems can handle different materials and product sizes with ease. This versatility ensures that businesses investing in EMS Powder Coating Equipment are making a long-term investment that will pay dividends across various projects.
3. Durability and Reliability
Powder coating equipment represents a significant investment for any business, so it’s crucial that the systems you choose are built to last. EMS Powder Coating Equipment is renowned for the durability and reliability of its products. All equipment is designed with high-quality materials that can withstand the rigors of daily industrial use, ensuring minimal maintenance and long service life.
EMS takes pride in manufacturing powder coating systems that are not only highly efficient but also reliable under continuous operation. This means fewer breakdowns, less downtime, and reduced maintenance costs, all of which contribute to increased productivity and profitability for businesses.
The reliability of EMS systems is backed by rigorous quality control measures. Each piece of equipment undergoes thorough testing before being delivered to customers, ensuring that it meets the highest standards of performance and safety.
4. Energy Efficiency
Energy consumption is a critical consideration for any business, particularly in industries with high operational costs. EMS Powder Coating Equipment is designed to maximize energy efficiency without compromising performance. This focus on energy conservation helps businesses reduce their operational expenses while also minimizing their environmental footprint.
EMS offers high-efficiency curing ovens that use innovative technology to ensure uniform heat distribution and rapid curing times. These ovens consume less energy compared to traditional models, helping businesses cut down on utility costs. Additionally, EMS systems are designed to reduce powder waste, allowing operators to reclaim and reuse powder that is not deposited on the substrate, further boosting cost savings and sustainability.
5. Exceptional Customer Support and After-Sales Service
Another significant factor that sets EMS Powder Coating Equipment apart is the company’s commitment to customer support. Purchasing industrial equipment is a long-term investment, and EMS ensures that customers receive ongoing support throughout the life of their equipment.
From the initial consultation to installation and training, EMS offers comprehensive support to ensure that businesses get the most out of their systems. The company also provides maintenance and repair services, ensuring that any issues are addressed promptly to avoid prolonged downtime. This dedication to after-sales service gives EMS customers peace of mind, knowing that their equipment is backed by a team of experts ready to assist at any time.
6. Proven Track Record and Global Reach
With years of experience and a global client base, EMS Powder Coating Equipment has established itself as a leading manufacturer in the industry. The company has successfully partnered with businesses across the world, delivering equipment that has helped manufacturers improve their processes and quality.
EMS’s extensive portfolio of clients includes companies from a wide range of industries, including automotive, aerospace, furniture, and consumer goods. This broad industry experience ensures that EMS understands the specific needs of different sectors and can tailor solutions accordingly.
Trends and Innovations in Powder Coating Equipment
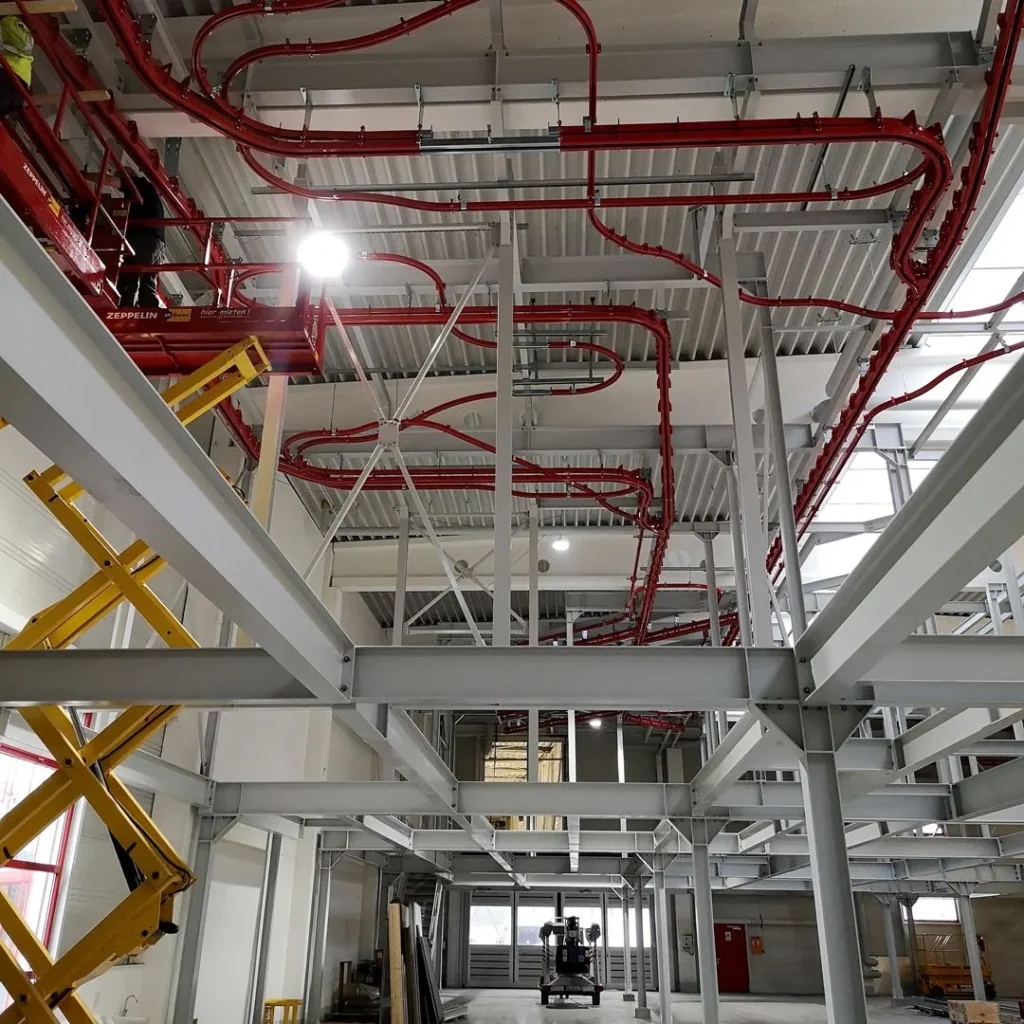
The powder coating industry is constantly evolving, with new technologies and trends shaping the way businesses operate. EMS Powder Coating Equipment stays at the forefront of these developments, ensuring that its customers benefit from the latest innovations in the field. Below are some of the key trends currently influencing powder coating technology:
1. Automation and Industry 4.0 Integration
Automation is becoming increasingly prevalent in the powder coating industry, with businesses looking for ways to improve efficiency and reduce labor costs. Automated systems, such as EMS’s powder coating reciprocators, allow for more consistent application and faster production times. Industry 4.0 integration, including the use of smart sensors and data analytics, is also making it easier for manufacturers to monitor and optimize their powder coating operations in real-time.
EMS has embraced these trends by offering equipment that can be fully integrated into modern manufacturing systems. This allows businesses to streamline their operations and improve overall productivity while maintaining high levels of quality.
2. Sustainability and Eco-Friendly Solutions
As industries become more focused on sustainability, the demand for environmentally friendly powder coating solutions continues to grow. Powder coating is inherently eco-friendly because it produces minimal waste and contains no solvents, which reduces VOC emissions. However, EMS has taken sustainability a step further by designing energy-efficient systems that consume less power while maintaining optimal performance.
These innovations make EMS Powder Coating Equipment the ideal choice for businesses seeking to reduce their environmental impact without sacrificing quality or efficiency.
3. Advanced Material Compatibility
New advances in powder coating materials are allowing manufacturers to coat a wider range of substrates, including plastics and composites. EMS’s powder coating systems are designed to handle these advanced materials, providing businesses with the flexibility to expand their product offerings.
Conclusion
Powder coating has become a cornerstone in modern manufacturing, providing businesses with a durable, environmentally friendly, and cost-effective way to protect their products. However, achieving the best results requires investing in high-quality equipment.
EMS Powder Coating Equipment stands out as the industry leader, offering advanced technology, customization options, and exceptional reliability. Whether you are looking for manual systems for small-scale operations or automated systems for large industrial plants, EMS provides tailored solutions that meet your specific needs. Their commitment to innovation, durability, and energy efficiency ensures that businesses can maximize their productivity while minimizing costs and environmental impact.
With a proven track record of success and an unwavering dedication to customer satisfaction, EMS Powder Coating Equipment is the best choice for businesses looking to enhance their powder coating operations.
Automatic powder coating equipment
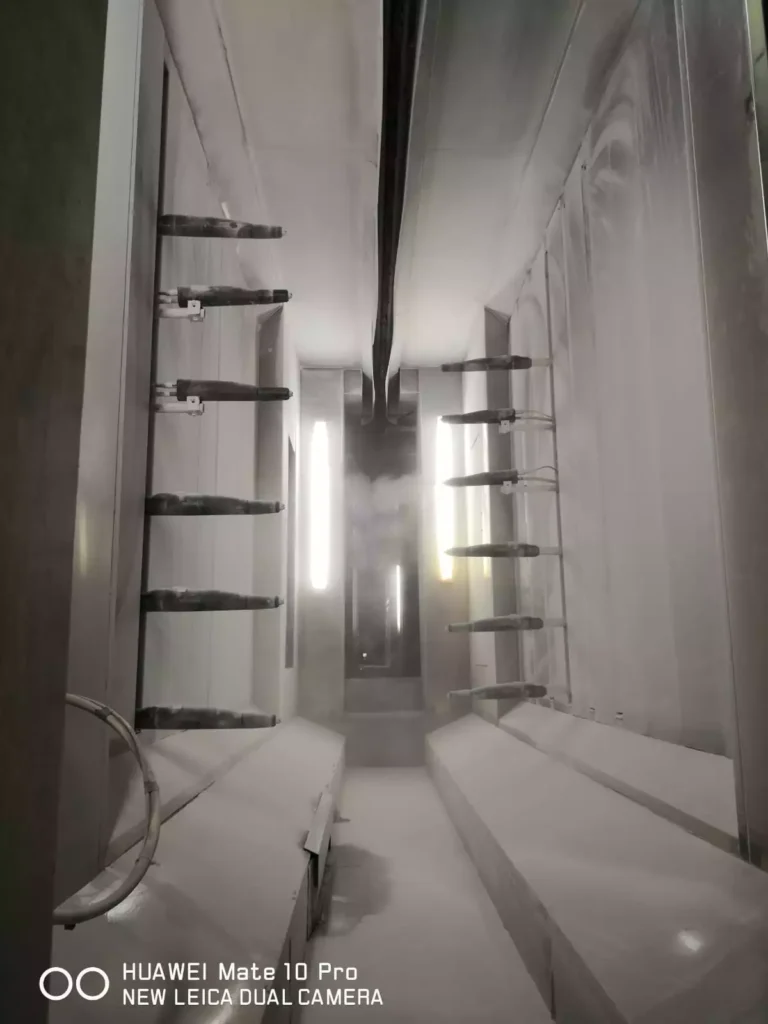
The powder coating industry has experienced significant advancements in recent years, with automation playing a key role in improving production efficiency, consistency, and overall quality. Automatic powder coating equipment has transformed the way manufacturers apply powder coatings, enabling them to increase throughput while maintaining precise control over the application process. This technology is particularly valuable in high-volume production environments, where consistent quality and reduced operational costs are critical for success.
Automatic powder coating systems use advanced robotic systems, reciprocators, and intelligent controls to streamline the coating process. These systems are designed to apply powder evenly and consistently, reducing waste, improving the quality of the finish, and lowering labor costs. By removing the human element from most stages of the coating process, automatic systems provide a higher level of accuracy and reproducibility.
EMS Powder Coating Equipment is at the forefront of this revolution, offering state-of-the-art automatic systems that cater to the needs of industries around the globe. Known for their advanced technology, reliability, and customizable solutions, EMS’s automatic powder coating equipment is trusted by manufacturers who require high precision and efficiency in their production lines. In this guide, we’ll explore the features of automatic powder coating systems, their benefits, and why EMS Powder Coating Equipment is the best choice for businesses looking to automate their powder coating process.
What is Automatic Powder Coating Equipment?
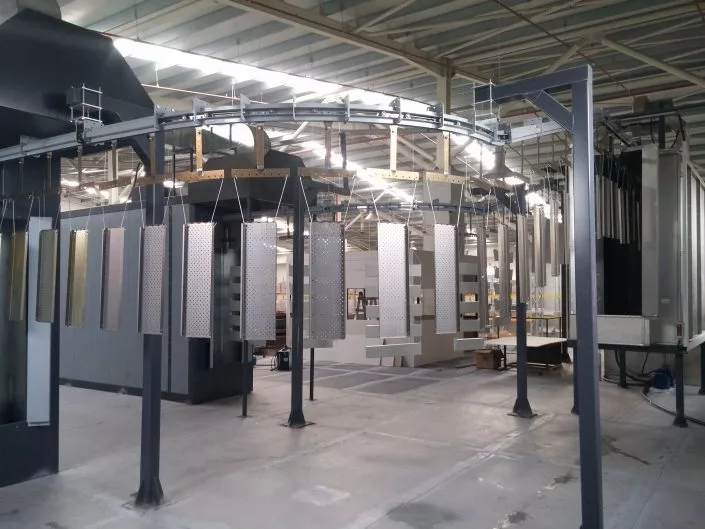
Automatic powder coating equipment refers to a fully automated system that applies powder coatings to products with minimal human intervention. These systems typically consist of several key components, including automatic spray guns, reciprocators, conveyors, and curing ovens. Each of these components works together seamlessly to ensure that powder is applied uniformly and efficiently.
1. Automatic Spray Guns

The core of any automatic powder coating system is the spray gun. In an automated setup, multiple spray guns are mounted on robotic arms or reciprocators that move in precise, pre-programmed patterns. These guns are electrostatically charged, allowing the powder particles to adhere to the product surface through an electrostatic field. The guns can adjust their position and angle to coat even complex or irregular shapes with ease.
One of the primary advantages of automatic spray guns is their ability to apply powder coatings with extreme consistency. Since they follow pre-programmed patterns, there is no variation in the application process, resulting in a uniform coat every time. Additionally, these systems reduce overspray and powder wastage, leading to cost savings.
EMS Powder Coating Equipment offers some of the most advanced automatic spray gun systems in the industry. Their spray guns are designed for maximum precision and can be programmed to handle different product sizes and shapes, ensuring a consistent finish across the entire production run.
2. Reciprocators

Reciprocators are the components that control the vertical movement of the spray guns, allowing them to cover the full height of the object being coated. Reciprocators are typically used in conjunction with conveyorized systems, where parts move through the spray booth at a constant speed. The reciprocators move the spray guns up and down, ensuring even coverage over the entire surface of the product.
Automatic reciprocators are crucial in high-speed production environments, where consistency and speed are essential. These systems can be programmed to adjust their speed and range of motion depending on the size and shape of the product, making them ideal for complex parts or large quantities of products.
EMS Powder Coating Equipment specializes in advanced reciprocators that can be customized to fit any production line. Their systems are known for their reliability and smooth operation, ensuring that products are evenly coated without any gaps or inconsistencies.
3. Conveyor Systems
In an automatic powder coating setup, the conveyor system moves products through the various stages of the coating process, including the spray booth and curing oven. Conveyorized systems allow for continuous production, increasing throughput and reducing the need for manual handling.
Conveyors can be programmed to adjust their speed based on the complexity of the parts being coated or the specific requirements of the coating process. This flexibility makes automatic powder coating systems highly adaptable to different production environments.
EMS Powder Coating Equipment offers conveyor systems that integrate seamlessly with their automatic spray guns and reciprocators. Their conveyor systems are designed for high efficiency and can handle a wide range of product sizes and weights, making them ideal for industries such as automotive, furniture, and appliance manufacturing.
The Benefits of Automatic Powder Coating Equipment
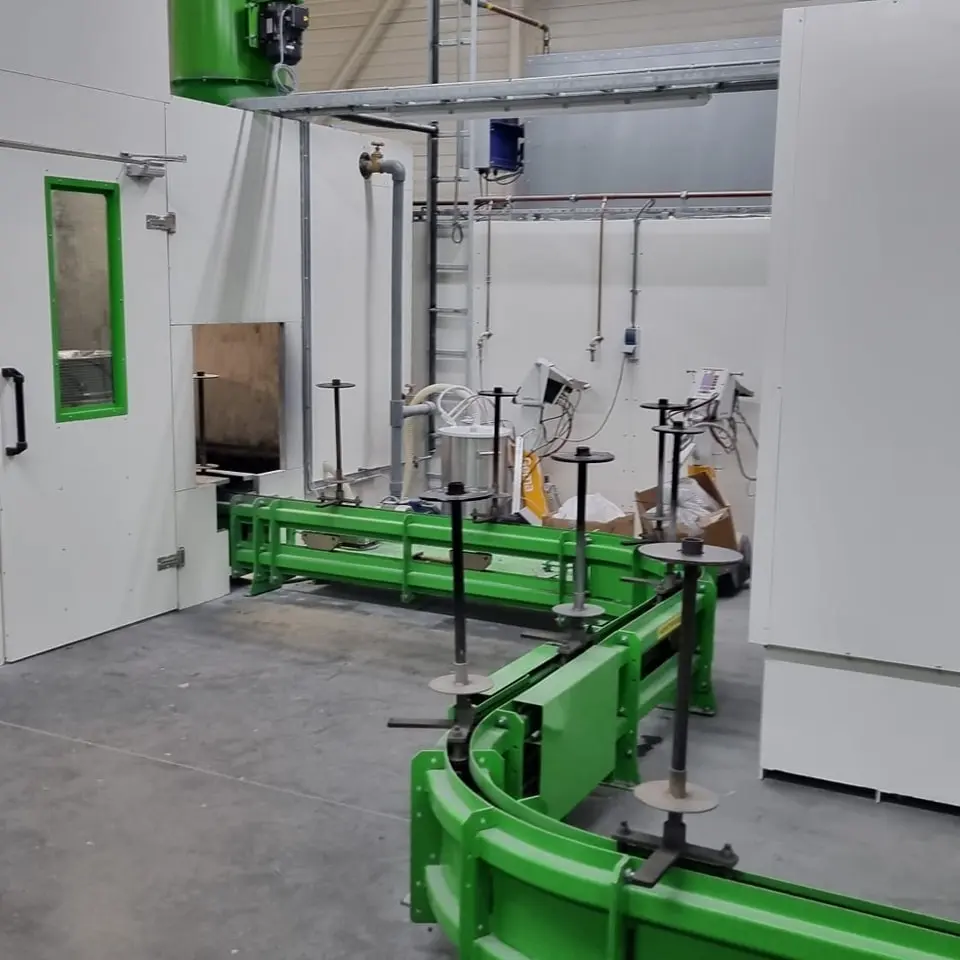
Automation in powder coating has introduced several key advantages that have revolutionized the industry. Below are some of the most significant benefits of automatic powder coating equipment:
1. Improved Consistency and Quality
One of the biggest challenges in manual powder coating is achieving consistent results. Human operators, while skilled, are prone to variability in their application methods, which can lead to uneven coating thickness, poor adhesion, or defects in the finish. Automatic powder coating systems eliminate these issues by providing consistent, repeatable application.
Since automatic spray guns and reciprocators follow precise, pre-programmed instructions, every product receives the same level of coating, ensuring a high-quality finish on each item. This consistency is especially important for industries that produce large quantities of parts and need to meet strict quality standards.
EMS Powder Coating Equipment ensures that their automatic systems deliver uniform coating results, with even powder distribution and minimal overspray. This results in a durable, high-quality finish that meets or exceeds industry standards.
2. Increased Production Efficiency
Automatic powder coating equipment is designed to optimize the entire coating process, significantly increasing production efficiency. By automating the application process, businesses can coat more parts in less time, resulting in higher throughput. This is particularly beneficial for industries with high production volumes, where speed and efficiency are critical to meeting demand.
The integration of conveyor systems into automatic setups also reduces the need for manual handling of parts, minimizing downtime and labor costs. Products move seamlessly from the spray booth to the curing oven without interruption, further streamlining the process.
For manufacturers that need to maximize output, EMS Powder Coating Equipment offers fully integrated automatic systems that work in harmony to reduce bottlenecks and improve production flow.
3. Reduced Labor Costs
Automation reduces the need for manual labor in the powder coating process, leading to significant cost savings for businesses. In manual setups, skilled operators are required to oversee the application of the powder, adjust the equipment, and ensure that each product is coated evenly. In contrast, automatic systems can handle these tasks without the need for constant supervision.
By reducing labor requirements, businesses can allocate their workforce to other areas of production or reduce overall labor costs. Automatic systems also reduce the likelihood of human error, further decreasing the need for rework or repairs.
With EMS Powder Coating Equipment, manufacturers can implement automatic systems that not only reduce labor costs but also improve overall operational efficiency.
4. Enhanced Flexibility and Adaptability
One of the misconceptions about automatic powder coating systems is that they are rigid and inflexible. However, modern automatic systems, like those provided by EMS Powder Coating Equipment, are highly adaptable and can be configured to handle a wide range of products.
These systems can be programmed to adjust the speed, powder flow rate, and gun positioning to accommodate different shapes, sizes, and coating requirements. This makes them suitable for a variety of industries, from automotive parts to consumer electronics. Additionally, with programmable systems, businesses can quickly switch between different product lines, allowing for greater flexibility in production.
5. Lower Powder Waste
Powder waste is a common issue in manual powder coating processes. Overspray and uneven application often result in excess powder being lost, leading to higher material costs. Automatic systems are designed to minimize waste by ensuring that the powder is applied evenly and only where it is needed.
Many automatic systems also include powder recovery systems that capture unused powder and recycle it back into the process. This not only reduces material costs but also contributes to a more sustainable, environmentally friendly operation.
EMS Powder Coating Equipment offers advanced powder recovery systems that integrate seamlessly with their automatic equipment, ensuring that businesses can operate efficiently while minimizing waste.
6. Scalability and Future-Proofing
Automatic powder coating equipment is highly scalable, making it an excellent long-term investment for businesses looking to grow. As production volumes increase, automatic systems can be expanded or upgraded to handle larger workloads without sacrificing quality or efficiency. This scalability ensures that businesses can continue to meet demand as they grow, without the need to completely overhaul their equipment.
Furthermore, the technology behind automatic powder coating systems is constantly evolving. By investing in high-quality equipment from manufacturers like EMS Powder Coating Equipment, businesses can future-proof their operations and stay competitive in an increasingly automated industry.
Why EMS Powder Coating Equipment is the Best Choice for Automatic Systems
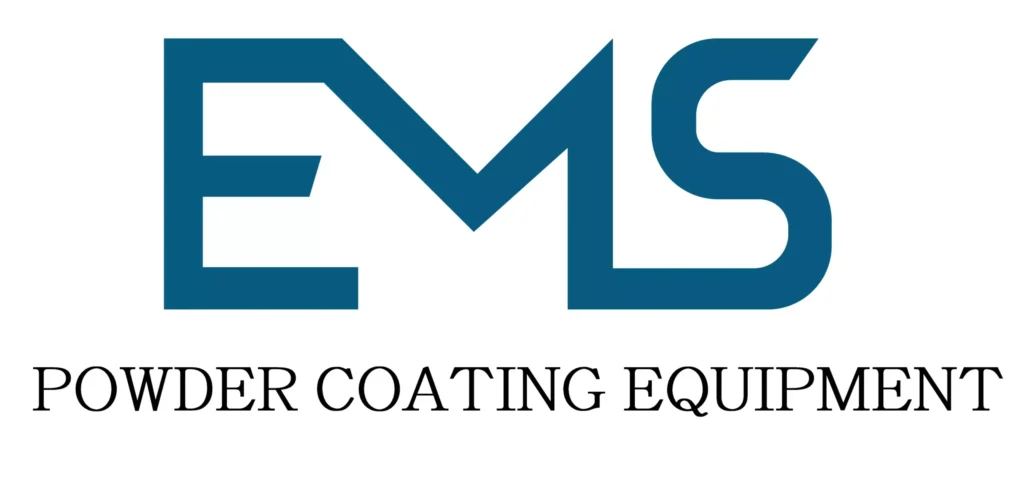
When selecting automatic powder coating equipment, it’s essential to choose a manufacturer that not only offers advanced technology but also understands the unique needs of your business. EMS Powder Coating Equipment stands out as the best choice for several reasons:
1. Industry-Leading Technology
EMS Powder Coating Equipment is known for its cutting-edge technology, offering some of the most advanced automatic systems available. Their equipment is designed to maximize efficiency, reduce waste, and provide consistent, high-quality finishes across all products. With features such as programmable spray guns, intelligent reciprocators, and high-efficiency conveyor systems, EMS equipment ensures that businesses can achieve superior results with minimal effort.
2. Customization and Flexibility
Every manufacturing operation is different, and EMS understands the importance of providing equipment that meets the specific needs of each customer. EMS offers customizable automatic systems that can be tailored to your production line, whether you’re coating small parts or large, complex products. This level of flexibility ensures that businesses get the most out of their investment, with equipment that can adapt to changing needs.
3. Reliability and Durability
EMS Powder Coating Equipment is renowned for the reliability and durability of its products. Built with high-quality materials and engineered for long-term performance, EMS systems are designed to withstand the rigors of continuous industrial use. This means fewer breakdowns, less downtime, and lower maintenance costs, all of which contribute to increased productivity and profitability.
4. Superior Support and Service
In addition to offering top-tier equipment, EMS provides exceptional customer support and after-sales service. From installation and training to ongoing maintenance and troubleshooting, EMS is committed to ensuring that customers get the most out of their automatic systems. Their team of experts is always available to provide guidance and assistance, making them a trusted partner for businesses around the world.
Conclusion
Automatic powder coating equipment represents a significant advancement in the manufacturing industry, offering businesses improved efficiency, consistency, and cost savings. With the ability to handle high-volume production while maintaining precise control over the coating process, automatic systems are an essential tool for any manufacturer looking to stay competitive.
EMS Powder Coating Equipment is the industry leader in automatic powder coating systems, providing advanced technology, customizable solutions, and unmatched reliability. Whether you’re seeking to automate your production line for the first time or upgrade your existing equipment, EMS offers the expertise and products needed to take your powder coating operation to the next level.
By investing in EMS automatic powder coating equipment, businesses can increase productivity, reduce costs, and ensure a consistently high-quality finish for their products. With a proven track record of success and a commitment to innovation, EMS is the best choice for manufacturers looking to optimize their powder coating process.
Powder Coating Reciprocators: Precision and Efficiency for Perfect Coating Applications

In the powder coating process, ensuring consistent coverage across a product’s surface is essential for both aesthetic appeal and functional protection. While spray guns deliver the powder to the product, powder coating reciprocators are the backbone of automation, enabling the precise, efficient movement of the guns. These devices move spray guns in vertical or horizontal patterns, ensuring that the powder is applied evenly over the entire surface of the object being coated.
Powder coating reciprocators are vital for operations where large volumes of parts must be coated consistently and quickly, such as in automotive, electronics, and industrial manufacturing. They automate the repetitive movements required during powder coating, reducing labor, increasing throughput, and improving the overall quality of the finished product.
EMS Powder Coating Equipment is a trusted manufacturer of advanced reciprocator systems designed to meet the rigorous demands of industrial coating applications. EMS reciprocators are known for their reliability, precision, and adaptability, making them the ideal solution for businesses looking to optimize their powder coating processes. In this guide, we’ll delve into the functionality of powder coating reciprocators, explore their benefits, and discuss why EMS Powder Coating Equipment provides the best reciprocators on the market.
Conclusion
Powder coating reciprocators are a key component of any automated coating system, providing the precision and efficiency needed to produce consistent, high-quality finishes. By automating the movement of spray guns, reciprocators ensure that every product is coated evenly, reducing the risk of defects and improving overall production efficiency.
EMS Powder Coating Equipment offers the best reciprocators on the market, designed to meet the needs of businesses in a wide range of industries. With advanced technology, customizable solutions, and a commitment to durability and reliability, EMS ensures that your powder coating process is optimized for maximum efficiency and quality.
Whether you’re looking to automate your production line for the first time or upgrade your existing equipment, EMS Powder Coating Equipment provides the expertise and products needed to take your powder coating operation to the next level.