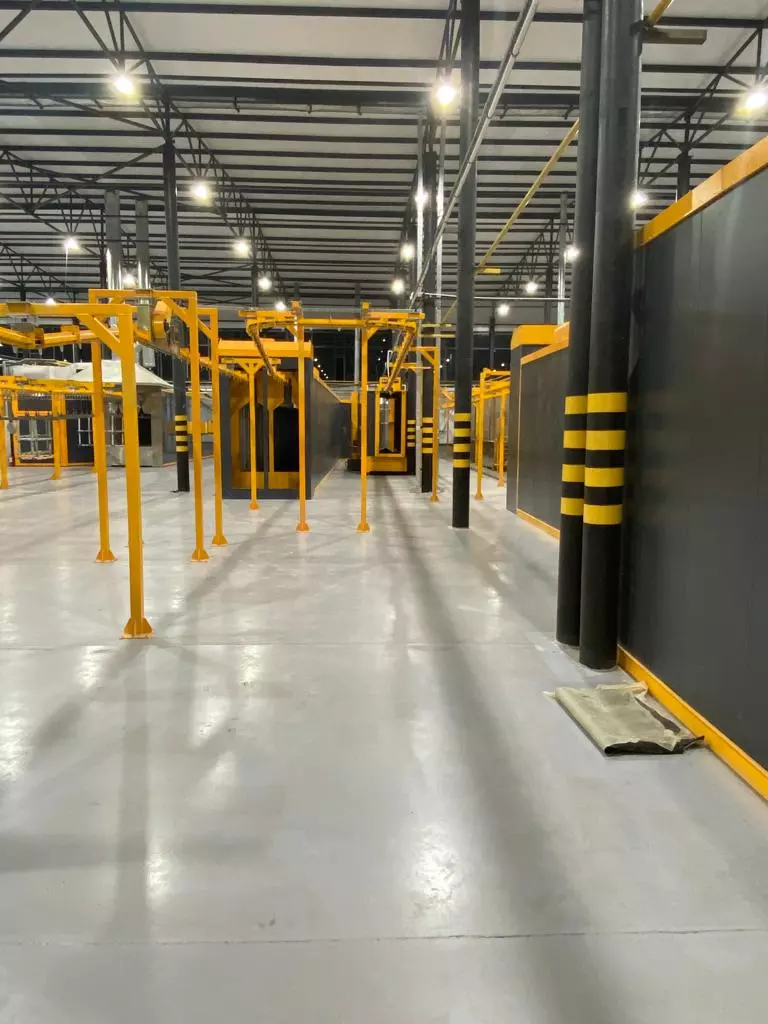
Industrial coating systems are complex processes involving machinery and specialized equipment to apply protective or decorative coatings to various substrates, primarily metal. These systems ensure consistent, high-quality finishes while optimizing production efficiency.
Key Components of Industrial Coating Systems
- Pre-treatment: Prepares the substrate by cleaning, degreasing, and often applying a conversion coating.
- Coating Application: Applies the coating material, which can be liquid, powder, or vaporized.
- Curing or Drying: Cures or dries the applied coating through heat, UV light, or chemical reactions.
- Conveyor Systems: Transport substrates through the coating process.
- Environmental Control: Maintains safe and clean working conditions.
Types of Industrial Coating Systems
- Liquid Coating Systems: Utilize paints, varnishes, or other liquid coatings.
- Powder Coating Systems: Employ dry powder coatings cured in an oven.
- Electroplating Systems: Deposit a metal coating through an electrolytic process.
- PVD (Physical Vapor Deposition) Systems: Create thin coatings in a vacuum environment.
- CVD (Chemical Vapor Deposition) Systems: Deposit coatings through chemical reactions in a gaseous state.
Industries Utilizing Industrial Coating Systems
- Automotive
- Aerospace
- Electronics
- Construction
- Appliances
- Metal fabrication
Automated Spray Coating Systems
Spray coating systems operate on a few basic principles that govern the way coatings are applied. Here are some key aspects:
- Basics of Spray Coating Technology: Spray coating involves atomizing a coating material into fine droplets and directing them towards a target surface. The goal is to create a uniform layer of material with the desired thickness and properties.
- Types of Spray Coating: There are several methods of spray coating, each with its unique characteristics:
- Air Spray: Utilizes compressed air to atomize the coating material. It’s suitable for fine finishes but can be less efficient due to overspray.
- Airless Spray: Uses high pressure to atomize the coating without the need for compressed air, reducing overspray and improving transfer efficiency.
- Electrostatic Spray: Charges the coating particles, which are attracted to the grounded target surface, enhancing transfer efficiency and providing a more even coating.
- Components of a Typical Spray Coating System: An automated spray coating system typically includes the following components:
- Spray Gun: The device that atomizes and applies the coating material.
- Control Unit: Manages the operation of the spray gun and other components.
- Material Supply System: Provides the coating material to the spray gun.
- Automation Equipment: Includes robotic arms, conveyor systems, or other machinery that positions the workpiece for coating.
3. Types of Automated Spray Coating Systems
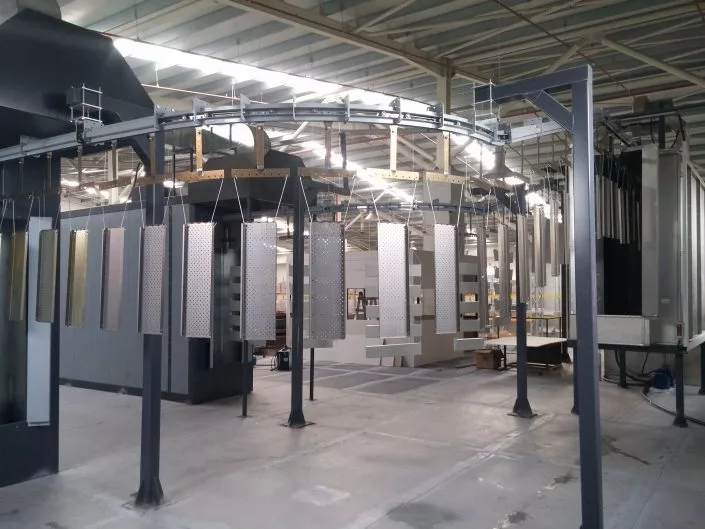
The choice of an automated spray coating system depends on several factors, including the type of products being coated, production volume, and specific quality requirements. Here are some common types:
- Robotic Spray Systems: These systems utilize robotic arms to apply coatings, offering precise control over spray patterns and allowing for complex geometries. They are ideal for high-volume production environments where consistency is critical.
- Conveyorized Spray Systems: Often used in continuous production lines, these systems transport parts through a spray booth on a conveyor belt, allowing for efficient coating of multiple items simultaneously.
- Spray Booths: Enclosed areas where spray coating takes place, designed to contain overspray and provide a controlled environment for application. Spray booths can be configured in various ways, such as open-face or downdraft designs, depending on the specific needs of the process.
4. Advantages of Automated Spray Coating Systems
Automated spray coating systems offer numerous benefits that make them an attractive option for manufacturers:
- Enhanced Efficiency and Productivity: Automation reduces the need for manual labor, speeding up the coating process and allowing for higher production rates.
- Consistent and High-Quality Finish: Automated systems provide precise control over the application process, resulting in a more uniform coating with fewer defects.
- Reduced Material Waste and Environmental Impact: Improved transfer efficiency minimizes overspray and waste, reducing the environmental impact of the coating process and lowering material costs.
- Improved Worker Safety: Automation reduces workers’ exposure to potentially hazardous materials and conditions, enhancing safety in the workplace.
5. Applications of Automated Spray Coating Systems
Automated spray coating systems are used across a wide range of industries, each with unique requirements and challenges:
- Automotive Industry: Spray coating is used for painting vehicle bodies, applying protective coatings, and finishing interior components. Automated systems ensure a high-quality finish that meets strict automotive standards.
- Aerospace Industry: Precision and reliability are paramount in aerospace applications. Automated spray systems are used for applying coatings to aircraft components, providing corrosion resistance, and improving aerodynamics.
- Electronics and Electrical Components: Coatings are applied to protect sensitive electronics from moisture, dust, and other environmental factors. Automated systems ensure a consistent application without damaging delicate components.
- Furniture and Woodworking: Spray coating is used to apply finishes to furniture and wooden products, enhancing their appearance and durability. Automation allows for efficient coating of complex shapes and large surfaces.
- Industrial Machinery and Equipment: Protective coatings are applied to machinery and equipment to prevent corrosion and wear. Automated systems provide a durable finish that extends the life of industrial assets.
6. Technological Advancements in Spray Coating
Recent advancements in technology have driven significant improvements in automated spray coating systems:
- Innovations in Robotics and Automation: Modern robotic systems offer greater precision and flexibility, enabling more complex applications and improved efficiency.
- Use of AI and Machine Learning: Artificial intelligence is used to optimize spray patterns, reduce waste, and improve the quality of the finished product. Machine learning algorithms analyze data from the coating process to make real-time adjustments.
- Smart Sensors and IoT Integration: Sensors monitor various parameters, such as temperature, humidity, and material flow, to ensure optimal coating conditions. IoT connectivity allows for remote monitoring and control of the spray system.
- Development of Eco-Friendly Coating Materials: Advances in materials science have led to the creation of environmentally friendly coatings that reduce VOC emissions and improve sustainability.
7. Challenges and Considerations
While automated spray coating systems offer numerous benefits, there are challenges and considerations to keep in mind:
- Initial Setup Costs and ROI: The cost of implementing an automated system can be high, but the long-term benefits often outweigh the initial investment. Calculating the return on investment is crucial for justifying the expense.
- Maintenance and Operational Challenges: Regular maintenance is necessary to ensure optimal performance and prevent downtime. Training staff to operate and maintain the system is also important.
- Regulatory Compliance and Safety Standards: Ensuring compliance with industry regulations and safety standards is critical, particularly when dealing with hazardous materials.
8. Choosing the Right System for Your Needs
Selecting the appropriate automated spray coating system involves several key considerations:
- Factors to Consider: Evaluate the type of material being coated, the surface area, production volume, and specific quality requirements to determine the best system for your needs.
- Customization and Scalability Options: Many systems offer customization options to meet specific production needs. Scalability is also important for accommodating future growth.
- Vendor Selection and Support Services: Choose a reputable vendor with a track record of quality and reliability. Consider the level of support and service they offer, including training and maintenance assistance.
9. Case Studies and Success Stories
Examining real-world examples of automated spray coating systems in action can provide valuable insights:
- Example 1: An automotive manufacturer implemented a robotic spray system to paint vehicle bodies, resulting in a 30% reduction in paint waste and a 25% increase in production speed.
- Example 2: An electronics company used automated spray coating to apply protective coatings to circuit boards, achieving a 15% reduction in defects and improving product reliability.
- Example 3: A furniture manufacturer adopted an automated spray booth for finishing wooden products, increasing production capacity by 40% and enhancing the quality of the finish.
10. Future Trends in Automated Spray Coating
The future of automated spray coating systems is bright, with several trends shaping the industry:
- Emerging Technologies: Continued advancements in robotics, AI, and materials science are expected to drive further improvements in spray coating systems.
- Sustainability and Environmental Considerations: The development of eco-friendly coatings and more efficient application methods will reduce the environmental impact of spray coating processes.
- Industry 4.0 Influence: The integration of automated spray coating systems with Industry 4.0 technologies, such as IoT and data analytics, will enable smarter and more efficient manufacturing processes.
11. Conclusion
Automated spray coating systems are transforming the way manufacturers apply coatings to products, offering numerous benefits in terms of efficiency, quality, and sustainability. As technology continues to evolve, these systems will play an increasingly important role in modern manufacturing, helping companies meet the demands of a rapidly changing market.
Key Components of Automated Spray Coating Systems
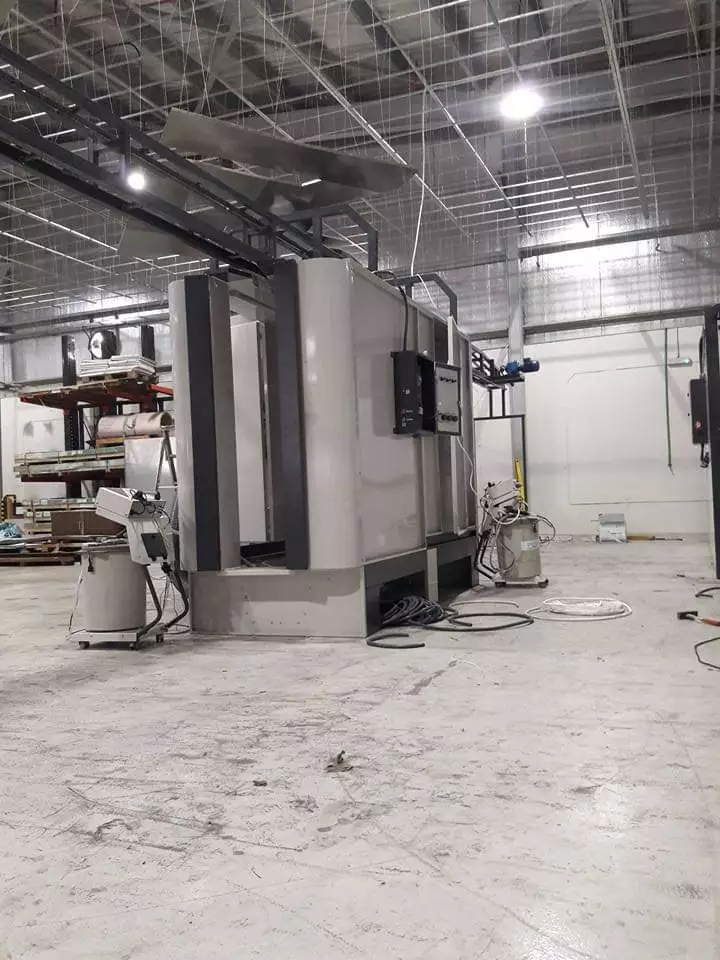
Automated spray coating systems are sophisticated setups consisting of multiple components that work together to achieve efficient and precise application of coatings. Here’s an in-depth look at the key components of these systems:
- Spray Gun
- Function: The spray gun is responsible for atomizing the coating material into fine droplets and directing them onto the target surface. It is the primary tool for applying the coating.
- Types:
- Conventional Air Spray Gun: Uses compressed air to atomize the coating. It’s ideal for achieving fine finishes but can lead to overspray.
- Airless Spray Gun: Utilizes high pressure to atomize the coating, resulting in less overspray and more efficient material use.
- Electrostatic Spray Gun: Charges the particles of the coating, allowing them to adhere more uniformly to the target surface.
- Material Supply System
- Function: Provides a continuous and controlled supply of coating material to the spray gun. Ensures consistent application and minimizes downtime.
- Components:
- Material Reservoir: Stores the coating material before it is fed into the system.
- Pumps: Move the material from the reservoir to the spray gun. Pumps can be pneumatic or electric, depending on the system.
- Hoses and Fittings: Transport the coating material from the reservoir to the spray gun.
- Control Unit
- Function: The control unit manages and coordinates the operation of the entire spray system, ensuring that each component functions correctly.
- Features:
- User Interface: Allows operators to adjust settings such as spray pressure, flow rate, and pattern.
- Automation Controls: Provides options for programming and automating the spray process, including start/stop functions and cycle times.
- Monitoring Systems: Includes sensors and feedback mechanisms to ensure optimal performance and alert operators to any issues.
- Automation Equipment
- Function: Positions and moves the workpieces through the spray coating process, ensuring precise and consistent application.
- Components:
- Robotic Arms: Used for intricate and precise spray applications. They offer flexibility and can handle complex geometries.
- Conveyor Systems: Transport parts through the spray booth in a continuous or indexed manner, ideal for high-volume production.
- Rotary Tables and Fixtures: Hold and manipulate workpieces, allowing for complete and even coverage.
- Spray Booth
- Function: Provides a controlled environment for the spray coating process, minimizing contamination and overspray.
- Types:
- Open-Face Booth: Suitable for smaller operations with lower volumes. Provides basic containment for overspray.
- Downdraft Booth: Features air filtration and ventilation systems to manage overspray and maintain air quality.
- Enclosed Booths: Offer complete containment for the spray process, with advanced ventilation and filtration systems.
- Ventilation and Filtration Systems
- Function: Maintain a safe and clean working environment by controlling the flow of air and removing overspray and fumes.
- Components:
- Air Filters: Capture overspray particles and contaminants, preventing them from escaping the booth.
- Exhaust Fans: Draw air through the booth, ensuring proper ventilation and maintaining air quality.
- Air Makeup Units: Supply fresh air to replace exhausted air, maintaining balanced airflow within the booth.
- Drying and Curing Equipment
- Function: Facilitate the drying and curing of coatings to achieve the desired finish and properties.
- Types:
- Infrared Ovens: Use infrared radiation to quickly and evenly cure coatings, ideal for heat-sensitive materials.
- Convection Ovens: Utilize heated air to cure coatings, suitable for high-temperature applications.
- UV Curing Systems: Employ ultraviolet light to cure certain coatings, providing rapid curing times and energy efficiency.
- Safety and Compliance Equipment
- Function: Ensure safe operation and compliance with regulatory standards.
- Components:
- Personal Protective Equipment (PPE): Includes respirators, gloves, and protective clothing for operators.
- Fire Suppression Systems: Detect and extinguish fires, ensuring safety in the event of an accident.
- Emergency Shutdown Systems: Allow operators to quickly stop the system in case of an emergency.
Integration of Components
The integration of these components into a cohesive system requires careful planning and engineering. The following considerations are crucial for optimal performance:
- System Design and Layout: The layout should facilitate efficient workflow and minimize bottlenecks. Proper spacing and positioning of equipment are essential for safety and accessibility.
- Programming and Automation: Automation software should be configured to optimize the spray process, including precise control over spray patterns, pressures, and cycle times.
- Maintenance and Calibration: Regular maintenance and calibration are necessary to ensure consistent performance and prolong the lifespan of the equipment. This includes cleaning spray guns, checking hoses and fittings, and replacing worn parts.
- Training and Safety Protocols: Operators should be thoroughly trained in system operation and safety protocols. This includes understanding the controls, recognizing potential hazards, and responding to emergencies.
Customization and Scalability
Automated spray coating systems can be customized to meet the specific needs of different industries and applications:
- Customization Options:
- Spray Pattern and Coverage: Adjustments can be made to the spray pattern to accommodate different shapes and sizes of workpieces.
- Material Compatibility: Systems can be configured to handle a wide range of coating materials, from paints and varnishes to specialized coatings.
- Automation Levels: From basic automated systems to fully integrated robotic solutions, the level of automation can be tailored to production requirements.
- Scalability:
- Modular Design: Many systems are designed with modular components, allowing for easy expansion and upgrades as production needs grow.
- Flexible Configurations: Systems can be reconfigured to accommodate changes in product lines or production volumes, providing adaptability in dynamic manufacturing environments.
Conclusion
The components of automated spray coating systems work together to deliver precise, efficient, and high-quality coatings. By understanding the roles and functions of each component, manufacturers can select and configure systems that meet their specific needs, ensuring optimal performance and a competitive edge in the market. These systems are integral to modern manufacturing, offering solutions that enhance productivity, quality, and sustainability.
Overview of the Coating Operation
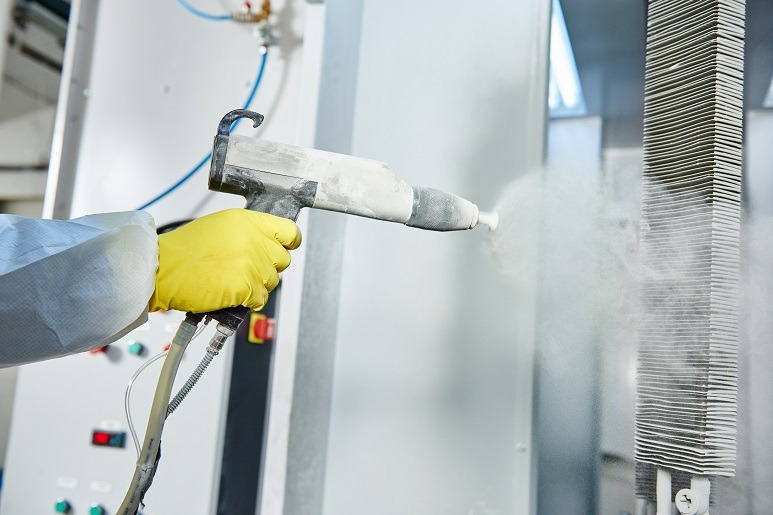
The coating operation in automated spray coating systems is a complex process involving multiple stages and sophisticated technology to ensure high-quality finishes. This operation is critical for industries that require precise and uniform application of coatings, such as automotive, aerospace, electronics, and more. Here’s an in-depth look at the coating operation process:
The coating operation involves several steps, from preparation and setup to the actual application of the coating and post-processing. Each step is crucial to achieving the desired quality and efficiency.
Key Steps in the Coating Operation
- Preparation and Setup
- Surface Preparation: Proper surface preparation is essential for achieving good adhesion and a high-quality finish. This may include cleaning, sanding, or chemical treatments to remove contaminants and create a suitable surface for coating.
- Cleaning: Removes dust, grease, oil, and other contaminants.
- Sanding: Smoothens the surface and increases mechanical adhesion.
- Chemical Treatments: Include degreasing or etching to enhance adhesion.
- Material Selection: The choice of coating material depends on the desired properties, such as color, texture, durability, and environmental resistance. Factors influencing material selection include:
- Type of Substrate: Different materials require specific coatings (e.g., metal, plastic, wood).
- Environmental Conditions: Considerations for UV resistance, moisture resistance, etc.
- Application Requirements: Performance characteristics, such as hardness, flexibility, and chemical resistance.
- Equipment Setup: Ensure that all equipment, including spray guns, material supply systems, and automation equipment, is correctly set up and calibrated.
- Calibration: Adjust spray guns for optimal pressure, flow rate, and pattern.
- System Checks: Inspect hoses, fittings, and automation systems for any leaks or malfunctions.
- Safety Precautions: Verify that all safety equipment is in place, including ventilation systems and personal protective equipment (PPE).
- Surface Preparation: Proper surface preparation is essential for achieving good adhesion and a high-quality finish. This may include cleaning, sanding, or chemical treatments to remove contaminants and create a suitable surface for coating.
- Coating Application
- Atomization Process: The spray gun atomizes the coating material into fine droplets and propels them onto the target surface. The goal is to achieve a uniform coating with the desired thickness and finish.
- Spray Patterns: Adjusting the pattern to suit the shape and size of the workpiece.
- Droplet Size: Controlling the size of the droplets to achieve the desired finish (e.g., fine finish for smooth surfaces).
- Transfer Efficiency: Maximizing the amount of material that adheres to the surface, minimizing overspray and waste.
- Automation and Control: Automated systems use robotics and computer controls to apply coatings with precision and consistency.
- Robotic Arms: Programmed to follow specific paths and angles, ensuring even coverage and reaching complex geometries.
- Control Systems: Monitor and adjust parameters in real-time, such as spray pressure, flow rate, and distance from the surface.
- Feedback Loops: Sensors provide feedback to adjust the process dynamically, compensating for variations in material or environmental conditions.
- Atomization Process: The spray gun atomizes the coating material into fine droplets and propels them onto the target surface. The goal is to achieve a uniform coating with the desired thickness and finish.
- Drying and Curing
- Drying Process: After application, the coating must dry to allow solvents or carriers to evaporate. This step is crucial for achieving the desired properties and finish.
- Air Drying: Natural evaporation, suitable for water-based or solvent-based coatings.
- Forced Drying: Using heated air or infrared heaters to speed up the drying process.
- Flash Off: A brief period before curing where solvents are allowed to evaporate, preventing defects like blistering.
- Curing Process: Involves chemical reactions that solidify the coating, enhancing its mechanical properties and adhesion.
- Thermal Curing: Using ovens or heated air to cure coatings, suitable for high-temperature materials.
- UV Curing: Employs ultraviolet light to cure specific coatings, providing rapid curing and energy efficiency.
- Time and Temperature Control: Precise control of curing time and temperature to achieve optimal hardness, adhesion, and durability.
- Drying Process: After application, the coating must dry to allow solvents or carriers to evaporate. This step is crucial for achieving the desired properties and finish.
- Quality Inspection and Control
- Inspection Techniques: Ensure that the coating meets the desired quality standards and specifications.
- Visual Inspection: Check for defects like runs, sags, and uneven coverage.
- Thickness Measurement: Use tools like micrometers or ultrasonic gauges to measure coating thickness.
- Adhesion Testing: Assess the bond strength between the coating and substrate using tests like cross-hatch or pull-off tests.
- Quality Control Systems: Automated systems use sensors and cameras to monitor the coating process and detect defects in real-time.
- Real-Time Monitoring: Track parameters such as temperature, humidity, and coating thickness during application.
- Defect Detection: Identify defects and deviations from specifications, allowing for immediate corrective action.
- Data Logging and Analysis: Collect and analyze data for continuous improvement and process optimization.
- Inspection Techniques: Ensure that the coating meets the desired quality standards and specifications.
- Post-Processing and Finishing
- Post-Processing Steps: Additional steps may be required to achieve the desired finish and properties.
- Buffing and Polishing: Enhance the surface finish and appearance.
- Secondary Coatings: Apply additional layers for added protection or aesthetics.
- Packaging and Handling: Ensure proper handling to avoid damage to the coated surface.
- Finishing Techniques: Final adjustments and treatments to meet specific requirements.
- Texturing: Creating specific textures or patterns on the surface.
- Gloss and Matte Finishes: Adjusting the surface to achieve the desired level of gloss or matte.
- Special Effects: Applying effects like metallic, pearlescent, or iridescent finishes.
- Post-Processing Steps: Additional steps may be required to achieve the desired finish and properties.
Factors Influencing the Coating Operation
Several factors influence the success and efficiency of the coating operation:
- Environmental Conditions: Temperature, humidity, and air quality can affect the coating process and final finish.
- Controlled Environment: Maintain stable conditions within the spray booth to ensure consistent results.
- Humidity Control: Prevent issues like blushing or orange peel caused by excessive moisture.
- Material Characteristics: The properties of the coating material, such as viscosity, drying time, and chemical composition, impact the application process.
- Viscosity Control: Adjust the viscosity of the material for optimal atomization and coverage.
- Compatibility: Ensure compatibility between the coating material and substrate to prevent issues like delamination or cracking.
- Equipment Performance: The performance and reliability of the equipment, including spray guns, automation systems, and curing equipment, are crucial for achieving high-quality coatings.
- Regular Maintenance: Perform routine maintenance and calibration to ensure equipment operates at peak efficiency.
- Operator Training: Ensure operators are trained in equipment use, troubleshooting, and safety protocols.
Conclusion
The coating operation in automated spray coating systems is a multi-step process that requires careful planning, execution, and control. By understanding the key steps and factors influencing the operation, manufacturers can achieve high-quality coatings that meet industry standards and customer expectations. With the integration of advanced technologies and continuous improvement, automated spray coating systems continue to provide solutions that enhance productivity, quality, and sustainability in modern manufacturing.
Powder Coating Process
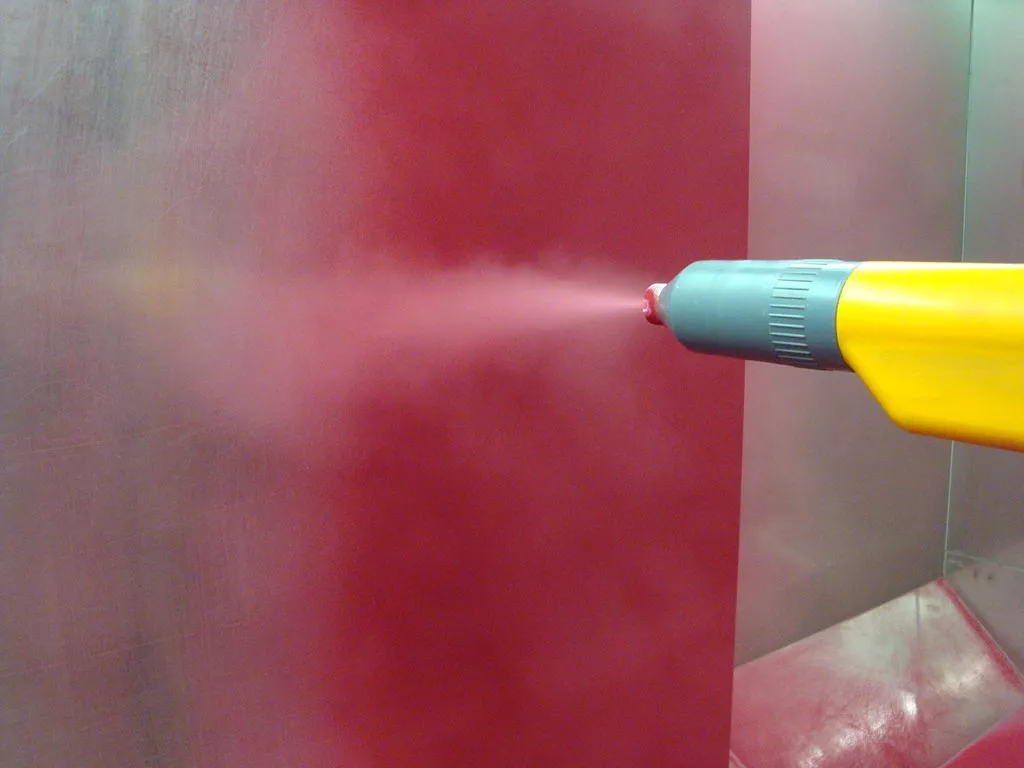
Powder coating is a widely used method for applying a durable and high-quality finish to metal and other surfaces. Unlike traditional liquid paint, powder coating involves the use of dry powder, which is electrostatically charged and then cured under heat to form a solid layer. Here’s an in-depth look at how powder coating melts and coats parts, including the key steps and processes involved.
The powder coating process consists of several key steps, including preparation, application, and curing. Each step is critical to achieving the desired finish and performance characteristics.
1. Surface Preparation
Proper surface preparation is essential for ensuring good adhesion and a high-quality finish. This involves cleaning, degreasing, and pre-treating the surface to remove any contaminants that could interfere with the coating process.
- Cleaning: Surfaces are cleaned to remove dirt, grease, oil, and other contaminants. This can be done using solvents, detergents, or abrasive blasting.
- Degreasing: Chemical degreasers may be used to eliminate oils and residues that could affect adhesion.
- Pre-treatment: Chemical treatments such as phosphating or chromating are often used to enhance corrosion resistance and improve adhesion. This step is particularly important for metal substrates.
2. Powder Application
The application of powder coating involves several steps, including electrostatic charging, spraying, and depositing the powder onto the workpiece.
- Electrostatic Charging: The powder particles are electrostatically charged using a spray gun. This is achieved by passing the powder through an electric field, which imparts a positive or negative charge to the particles.
- Spraying: The charged powder is sprayed onto the grounded workpiece using a powder spray gun. The electrostatic charge causes the powder particles to be attracted to the workpiece, allowing them to adhere uniformly to the surface.
- Powder Deposition: The powder forms a uniform layer on the surface due to the electrostatic attraction. The thickness of the coating can be controlled by adjusting the spray parameters, such as voltage, powder flow rate, and distance from the workpiece.
3. Curing and Melting
The curing process is where the powder coating melts and transforms into a continuous, durable film. This step involves the application of heat to melt the powder and initiate a chemical reaction that cross-links the particles, forming a solid layer.
- Heating: The coated workpieces are placed in an oven where they are heated to a specific temperature, typically between 350°F and 450°F (177°C and 232°C). The temperature and duration of the heating process depend on the type of powder used and the desired properties of the finish.
- Melting: As the temperature rises, the powder particles begin to melt, flowing together to form a smooth, uniform layer over the surface of the workpiece.
- Cross-linking: The heat initiates a chemical reaction (polymerization) within the powder particles, causing them to cross-link and form a continuous, hard film. This step is crucial for achieving the desired mechanical properties, such as hardness, adhesion, and chemical resistance.
- Cooling: After the curing process is complete, the workpieces are allowed to cool, solidifying the coating and forming a durable, finished surface.
Advantages of Powder Coating
Powder coating offers several advantages over traditional liquid coatings, making it a popular choice in many industries:
- Durability: Powder coatings are known for their exceptional durability, providing resistance to chipping, scratching, and corrosion.
- Environmental Friendliness: Powder coatings do not contain solvents or volatile organic compounds (VOCs), making them an environmentally friendly option compared to liquid paints.
- Efficiency: The electrostatic application process results in minimal overspray and waste, improving material efficiency and reducing costs.
- Variety of Finishes: Powder coatings are available in a wide range of colors, textures, and finishes, including matte, gloss, metallic, and specialty effects.
- Uniformity: The electrostatic application ensures a consistent and uniform coating thickness, reducing the risk of runs or sags.
Applications of Powder Coating
Powder coating is used across a variety of industries due to its versatility and performance characteristics. Some common applications include:
- Automotive: Powder coating is widely used for automotive parts, including wheels, chassis components, and body panels, due to its durability and corrosion resistance.
- Appliances: Many household appliances, such as refrigerators, washing machines, and ovens, are powder-coated to provide a durable and aesthetically pleasing finish.
- Furniture: Powder coating is used for outdoor and indoor furniture, providing a weather-resistant and durable finish that can withstand the elements.
- Architecture: Architectural elements, such as window frames, railings, and cladding, are often powder-coated to provide a long-lasting and visually appealing finish.
- Industrial Equipment: Powder coating is used for a variety of industrial equipment, including machinery, tools, and enclosures, to provide protection against wear and corrosion.
Considerations and Challenges
While powder coating offers many benefits, there are some considerations and challenges to keep in mind:
- Surface Preparation: Proper surface preparation is critical for achieving good adhesion and preventing defects. Inadequate preparation can lead to poor adhesion and coating failure.
- Curing Requirements: The curing process requires precise control of temperature and time to achieve the desired properties. Variations in curing conditions can affect the final finish and performance.
- Material Limitations: Powder coating is best suited for metallic substrates that can withstand the curing temperatures. It may not be suitable for heat-sensitive materials, such as certain plastics or composites.
- Equipment Costs: The initial investment in powder coating equipment can be significant, though the long-term benefits often outweigh the initial costs.
Conclusion
Powder coating is a highly efficient and environmentally friendly method for applying durable finishes to a wide range of products. By understanding the process of how powder coating melts and coats parts, manufacturers can achieve high-quality finishes that meet industry standards and customer expectations. The combination of durability, efficiency, and versatility makes powder coating a preferred choice for many applications, offering solutions that enhance both performance and aesthetics.
Paint Line Conveyor Systems
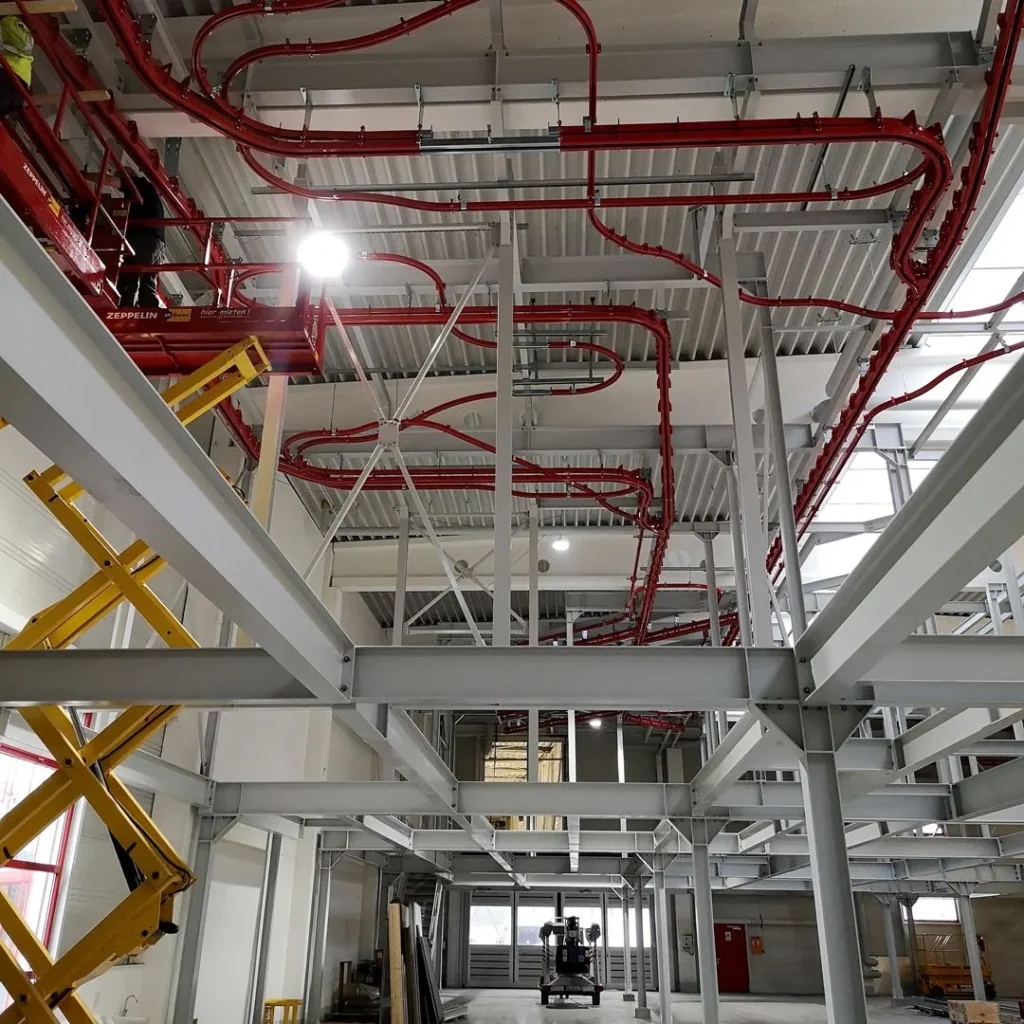
Paint line conveyor systems are integral components of modern manufacturing and finishing processes. These systems are designed to automate the movement of parts through various stages of painting, including surface preparation, coating application, curing, and cooling. The use of conveyor systems in paint lines enhances efficiency, consistency, and productivity, making them essential for industries such as automotive, aerospace, appliances, and more. This article explores the key aspects of paint line conveyor systems, including their components, types, advantages, applications, and design considerations.
Paint line conveyor systems are used to transport parts or products through a series of processing stations within a paint line. The primary goal is to automate the movement of parts, ensuring a smooth and continuous flow through each stage of the painting process. This automation minimizes manual handling, reduces cycle times, and improves the overall quality and consistency of the finished products.
Key Components of Paint Line Conveyor Systems
1. Conveyor Track
The conveyor track serves as the backbone of the system, guiding parts through the various stages of the paint line.
- Types of Tracks:
- Monorail Tracks: Single-rail systems where parts are suspended from a continuous loop of track.
- Dual-Rail Tracks: Two-rail systems that provide more stability and allow for larger or heavier parts.
2. Carriers or Hangers
Carriers or hangers are used to suspend parts from the conveyor track, allowing them to move freely through the paint line.
- Design Considerations:
- Weight Capacity: Must be capable of supporting the weight of the parts being transported.
- Versatility: Designed to accommodate different part shapes and sizes.
- Ease of Loading/Unloading: Facilitates quick and efficient loading and unloading of parts.
3. Drive System
The drive system powers the movement of the conveyor, ensuring a consistent and controlled speed throughout the paint line.
- Components:
- Motors: Provide the necessary power to move the conveyor.
- Gearboxes: Adjust the speed and torque of the drive system.
- Control Systems: Manage the speed, direction, and timing of the conveyor.
4. Loading and Unloading Stations
These stations are where parts are loaded onto and unloaded from the conveyor system, typically at the beginning and end of the paint line.
- Automated Loading/Unloading: Robotic systems or automated machinery can be used to load and unload parts, minimizing manual labor.
- Manual Loading/Unloading: In some systems, operators manually load and unload parts, especially for smaller or more complex items.
5. Processing Stations
These stations are where the various stages of the painting process take place, including cleaning, coating, curing, and cooling.
- Cleaning Stations: Parts are cleaned and pre-treated to remove contaminants and prepare them for coating.
- Coating Stations: Automated spray guns or powder coating equipment apply the desired finish to the parts.
- Curing Stations: Ovens or other curing equipment are used to dry and cure the coatings.
- Cooling Stations: Parts are allowed to cool after curing to solidify the coating and facilitate handling.
Types of Paint Line Conveyor Systems
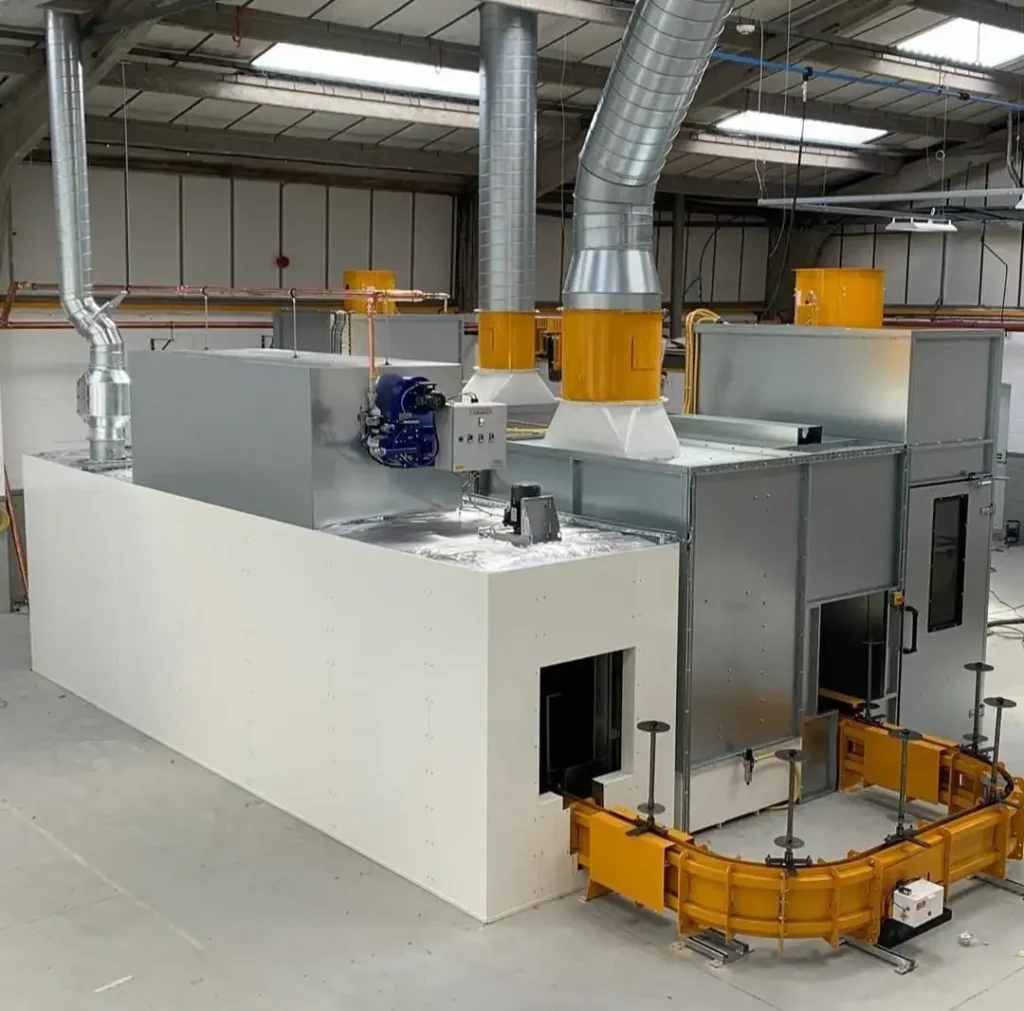
There are several types of conveyor systems used in paint lines, each with its unique features and applications:
1. Overhead Conveyor Systems
Overhead conveyor systems are commonly used in paint lines due to their space-saving design and flexibility.
- Features:
- Space Efficiency: Utilizes overhead space, freeing up floor space for other operations.
- Flexibility: Can be configured in complex layouts to accommodate various production requirements.
- Versatility: Suitable for a wide range of part sizes and shapes.
2. Power and Free Conveyor Systems
Power and free conveyor systems offer greater flexibility and control by allowing individual carriers to be stopped, started, or rerouted as needed.
- Features:
- Independent Movement: Carriers can move independently of one another, enabling precise control over the flow of parts.
- Buffering Capabilities: Parts can be temporarily stored or buffered within the system, allowing for greater flexibility in scheduling and production.
- Complex Layouts: Capable of handling complex layouts with multiple processing stations and routes.
3. Chain Conveyor Systems
Chain conveyor systems are robust and durable, making them suitable for heavy-duty applications and large parts.
- Features:
- High Load Capacity: Capable of transporting heavy parts or products.
- Durability: Designed to withstand harsh environments and demanding conditions.
- Simple Design: Easy to install and maintain, with minimal moving parts.
4. Floor Conveyor Systems
Floor conveyor systems are used when overhead space is limited or when parts are too large to be suspended.
- Features:
- Floor-Level Installation: Parts are transported on the floor, eliminating the need for overhead space.
- Stability: Provides stable transport for large or heavy parts.
- Easy Access: Operators can easily access parts for inspection, adjustment, or maintenance.
Advantages of Paint Line Conveyor Systems
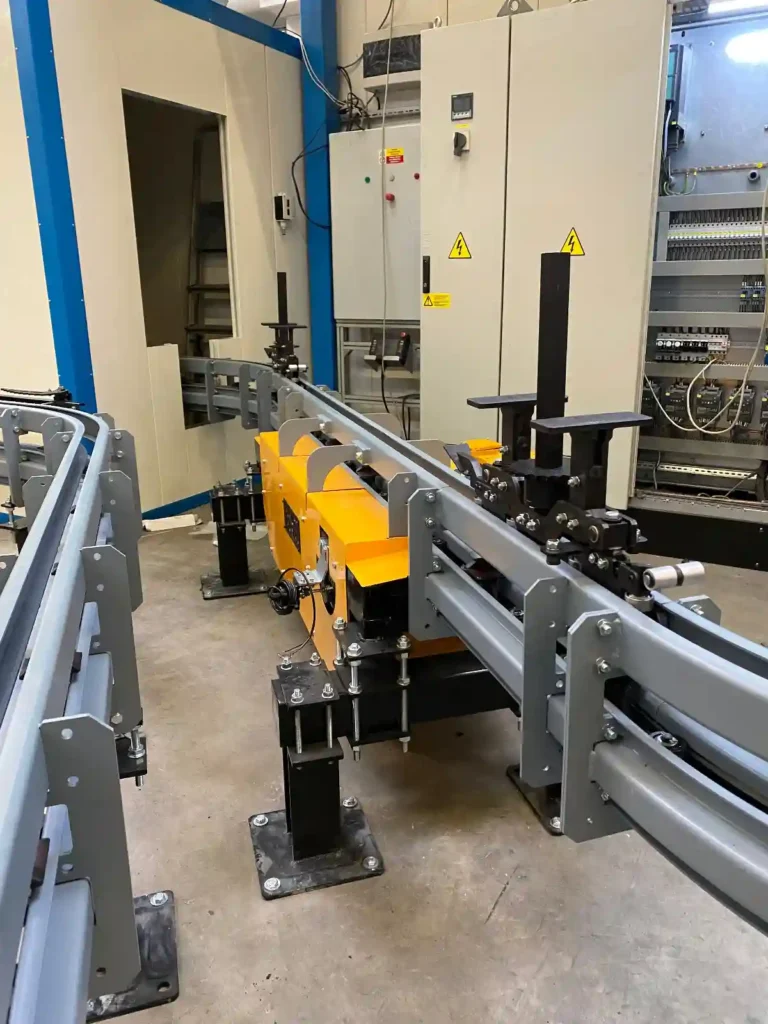
Paint line conveyor systems offer numerous advantages that enhance efficiency, productivity, and quality:
1. Increased Efficiency
- Automation: Reduces the need for manual handling, speeding up the production process.
- Continuous Flow: Ensures a smooth and continuous flow of parts through the paint line, minimizing downtime and bottlenecks.
2. Consistent Quality
- Precision: Automated systems provide precise control over the painting process, ensuring consistent and uniform coatings.
- Reduced Human Error: Minimizes the risk of human error and variability in the application of coatings.
3. Improved Safety
- Reduced Manual Handling: Minimizes the need for manual lifting and handling, reducing the risk of injuries.
- Controlled Environment: Automated systems maintain a controlled environment for painting, reducing exposure to hazardous materials.
4. Cost Savings
- Material Efficiency: Automated systems minimize overspray and waste, reducing material costs.
- Labor Savings: Automation reduces the need for manual labor, lowering labor costs and increasing productivity.
Applications of Paint Line Conveyor Systems
Paint line conveyor systems are used across various industries due to their versatility and efficiency:
1. Automotive Industry
- Applications: Painting vehicle bodies, parts, and components.
- Benefits: High-quality finishes, improved production speed, and reduced labor costs.
2. Aerospace Industry
- Applications: Coating aircraft components and assemblies.
- Benefits: Precision and consistency in coatings, enhanced corrosion resistance, and reduced waste.
3. Appliance Industry
- Applications: Finishing appliances such as refrigerators, ovens, and washing machines.
- Benefits: Durable finishes, reduced environmental impact, and cost-effective production.
4. Furniture Industry
- Applications: Coating furniture components and assemblies.
- Benefits: Consistent quality, increased production speed, and reduced manual labor.
5. Industrial Equipment
- Applications: Painting machinery, tools, and equipment.
- Benefits: Improved durability, protection against corrosion, and enhanced aesthetics.
Design Considerations for Paint Line Conveyor Systems
Designing an effective paint line conveyor system requires careful consideration of several factors:
1. Part Size and Weight
- Considerations: The system must accommodate the size and weight of the parts being transported, ensuring stability and smooth movement.
- Customization: Custom carriers or hangers may be required for unique or complex part shapes.
2. Production Volume
- Considerations: The system should be designed to handle the desired production volume, ensuring sufficient capacity and throughput.
- Scalability: The system should be scalable to accommodate future growth or changes in production requirements.
3. Coating Requirements
- Considerations: The system should be compatible with the desired coating materials and processes, including any specific application or curing requirements.
- Flexibility: The system should offer flexibility to accommodate different coatings or finishes as needed.
4. Space Constraints
- Considerations: The layout of the system should take into account available space, ensuring efficient use of the facility.
- Space Utilization: Overhead or floor-level systems may be chosen based on space availability and constraints.
5. Environmental Considerations
- Considerations: The system should comply with environmental regulations and standards, minimizing emissions and waste.
- Sustainability: Energy-efficient components and processes should be incorporated to reduce the environmental impact.
Conclusion
Paint line conveyor systems are essential for modern manufacturing and finishing processes, providing efficient and consistent movement of parts through various stages of painting. By automating the transport of parts, these systems enhance productivity, quality, and safety while reducing costs and environmental impact. With a wide range of applications across industries, paint line conveyor systems continue to play a vital role in achieving high-quality finishes and meeting the demands of today’s competitive markets.
Overview of Industrial Coating Systems
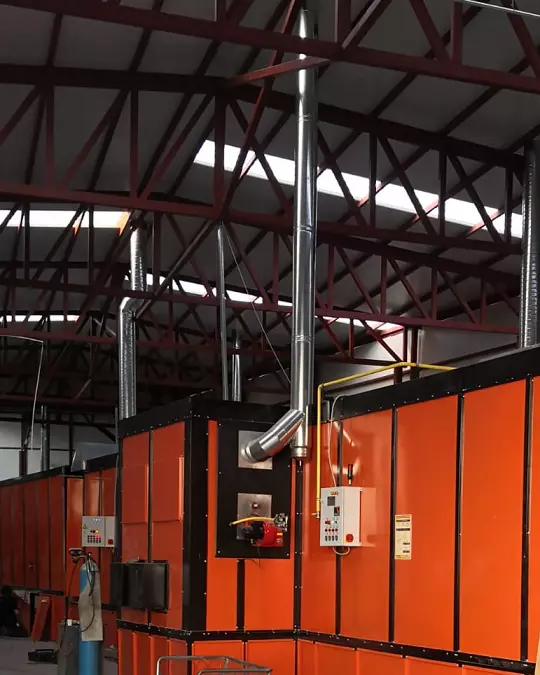
Industrial coating systems are essential components of the manufacturing process, providing protective and decorative finishes to a wide range of products and surfaces. These systems are used in various industries, including automotive, aerospace, construction, and electronics, to enhance durability, aesthetics, and performance. This comprehensive guide covers the types of industrial coating systems, their applications, advantages, and key considerations in selecting the right system for specific needs.
Industrial coating systems involve the application of various types of coatings to substrates for protection, aesthetics, or functional purposes. These coatings can be applied using different methods, each tailored to specific materials, environments, and performance requirements.
Key Objectives of Industrial Coating Systems
- Protection: Shielding surfaces from corrosion, abrasion, chemicals, and environmental factors.
- Aesthetics: Enhancing the appearance of products with color, texture, and gloss.
- Functionality: Providing additional properties such as electrical conductivity, insulation, or anti-fouling.
Types of Industrial Coating Systems
Industrial coating systems can be categorized based on the type of coating material used and the application method. Here are some of the most common types:
1. Liquid Coating Systems
Liquid coatings are applied in liquid form and cured to form a solid film. They can be water-based, solvent-based, or high-solids coatings, each with its own properties and benefits.
- Water-Based Coatings:
- Properties: Environmentally friendly, low VOC emissions, easy cleanup.
- Applications: Suitable for industries with stringent environmental regulations, such as automotive and electronics.
- Solvent-Based Coatings:
- Properties: High durability, excellent adhesion, wide range of finishes.
- Applications: Commonly used in harsh environments where durability is critical, such as marine and industrial equipment.
- High-Solids Coatings:
- Properties: High coverage with minimal VOC emissions, thicker film builds.
- Applications: Ideal for heavy-duty protection in industries like construction and oil & gas.
2. Powder Coating Systems
Powder coating involves applying a dry powder to a surface and curing it under heat to form a hard, durable finish. This method is popular for its environmental benefits and excellent finish quality.
- Properties:
- Durability: High resistance to chipping, scratching, and corrosion.
- Environmentally Friendly: No solvents, minimal waste, and recyclable overspray.
- Variety: Available in a wide range of colors, textures, and finishes.
- Applications:
- Automotive: Coating wheels, frames, and other components.
- Appliances: Finishing refrigerators, ovens, and washing machines.
- Furniture: Coating metal and wood furniture for durability and aesthetics.
3. Electrostatic Coating Systems
Electrostatic coating systems use an electrostatic charge to attract the coating material to the substrate, ensuring a uniform and efficient application.
- Properties:
- Efficiency: High transfer efficiency reduces waste and overspray.
- Uniform Finish: Even coating thickness and coverage.
- Versatility: Suitable for complex shapes and hard-to-reach areas.
- Applications:
- Aerospace: Coating aircraft components for corrosion resistance and aerodynamics.
- Automotive: Painting vehicle bodies and parts for a smooth finish.
- Industrial Equipment: Applying protective coatings to machinery and tools.
4. Thermal Spray Coating Systems
Thermal spray coatings involve spraying melted or heated materials onto a surface to create a coating with specific properties, such as wear resistance or thermal insulation.
- Types of Thermal Sprays:
- Plasma Spraying: Uses a plasma torch to melt materials for coating.
- Flame Spraying: Involves melting materials using a flame for application.
- HVOF (High-Velocity Oxy-Fuel): Uses high-pressure combustion to apply coatings with high density and bond strength.
- Applications:
- Aerospace: Coating turbine blades and engine components for heat resistance.
- Oil & Gas: Protecting pipelines and equipment from corrosion and wear.
- Industrial Machinery: Enhancing wear resistance on components like bearings and gears.
5. Dip Coating Systems
Dip coating involves immersing parts into a liquid coating solution and then withdrawing them to form a uniform coating layer. This method is suitable for batch processing and high-volume production.
- Properties:
- Uniform Coverage: Provides consistent coating thickness across surfaces.
- Efficient for Simple Shapes: Ideal for parts with simple geometries and large surface areas.
- Cost-Effective: Suitable for high-volume production with lower setup costs.
- Applications:
- Automotive: Coating fasteners, springs, and small components.
- Electronics: Applying protective coatings to circuit boards and components.
- Textiles: Coating fabrics for water resistance and durability.
6. UV Curing Coating Systems
UV curing coatings use ultraviolet light to rapidly cure the coating material, resulting in a durable and high-quality finish. This method is known for its energy efficiency and fast processing times.
- Properties:
- Fast Curing: Rapid processing speeds, ideal for high-volume production.
- Environmentally Friendly: Low VOC emissions and energy consumption.
- High Durability: Provides excellent resistance to chemicals and wear.
- Applications:
- Electronics: Coating circuit boards and components for protection.
- Automotive: Finishing interior and exterior components.
- Woodworking: Applying clear coats and finishes to wood products.
Advantages of Industrial Coating Systems
Industrial coating systems offer numerous benefits that enhance product performance, aesthetics, and longevity:
1. Corrosion Protection
- Barrier Protection: Coatings provide a physical barrier between the substrate and the environment, preventing corrosion and rust.
- Chemical Resistance: Many coatings offer resistance to chemicals, acids, and solvents, protecting surfaces from damage.
2. Aesthetic Enhancement
- Color and Finish Options: Coatings are available in a wide range of colors, textures, and finishes, allowing for customization and branding.
- Improved Appearance: Coatings enhance the visual appeal of products, making them more attractive to consumers.
3. Increased Durability
- Wear and Abrasion Resistance: Coatings protect surfaces from wear, abrasion, and impact, extending the lifespan of products.
- UV and Weather Resistance: Many coatings offer protection against UV radiation and environmental factors, reducing fading and degradation.
4. Functional Properties
- Electrical Insulation or Conductivity: Some coatings provide electrical insulation or conductivity for specific applications.
- Thermal Insulation: Coatings can offer thermal insulation, protecting surfaces from heat and reducing energy consumption.
- Anti-Fouling and Anti-Microbial Properties: Specialized coatings prevent fouling and microbial growth on surfaces.
Applications of Industrial Coating Systems
Industrial coating systems are used across a wide range of industries, each with unique requirements and challenges:
1. Automotive Industry
- Applications: Painting vehicle bodies, frames, wheels, and components.
- Benefits: Enhanced durability, corrosion resistance, and aesthetics.
2. Aerospace Industry
- Applications: Coating aircraft components, engines, and structures.
- Benefits: Improved aerodynamics, heat resistance, and protection against harsh environments.
3. Construction Industry
- Applications: Coating structural steel, bridges, and infrastructure.
- Benefits: Protection against corrosion, weathering, and wear.
4. Electronics Industry
- Applications: Coating circuit boards, components, and enclosures.
- Benefits: Protection against moisture, chemicals, and electrical interference.
5. Marine Industry
- Applications: Coating ships, boats, and offshore structures.
- Benefits: Protection against saltwater corrosion, fouling, and UV exposure.
6. Oil & Gas Industry
- Applications: Coating pipelines, tanks, and equipment.
- Benefits: Corrosion resistance, chemical protection, and wear resistance.
Key Considerations in Selecting Industrial Coating Systems
Choosing the right industrial coating system involves several key considerations, including material properties, application requirements, and environmental factors:
1. Substrate Material
- Compatibility: Ensure the coating is compatible with the substrate material, whether it’s metal, plastic, wood, or composite.
- Adhesion Properties: Select coatings that provide strong adhesion to the substrate, preventing delamination or peeling.
2. Environmental Conditions
- Exposure: Consider environmental factors such as humidity, temperature, UV exposure, and chemical exposure that the coated surface will face.
- Corrosion Resistance: Choose coatings that offer protection against specific environmental threats, such as saltwater or industrial pollutants.
3. Performance Requirements
- Durability: Evaluate the expected lifespan and wear resistance of the coating for the intended application.
- Aesthetic Properties: Consider color, gloss, and texture requirements to achieve the desired appearance.
4. Application Method
- Coating Process: Select the most suitable coating method based on part size, shape, production volume, and available equipment.
- Cost and Efficiency: Assess the cost-effectiveness and efficiency of the chosen coating process, including labor, material, and equipment costs.
5. Regulatory Compliance
- Environmental Regulations: Ensure compliance with environmental regulations regarding VOC emissions, waste disposal, and safety.
- Industry Standards: Adhere to industry-specific standards and specifications for coating performance and quality.
Conclusion
Industrial coating systems play a vital role in modern manufacturing, providing essential protection, aesthetics, and functionality to a wide range of products and surfaces. By understanding the types of coatings, their applications, and key considerations, manufacturers can select the most suitable coating system to meet their specific needs and challenges. With advancements in coating technologies and processes, industrial coating systems continue to evolve, offering improved performance, sustainability, and versatility in an ever-changing market.
Overview of Industrial Powder Coating
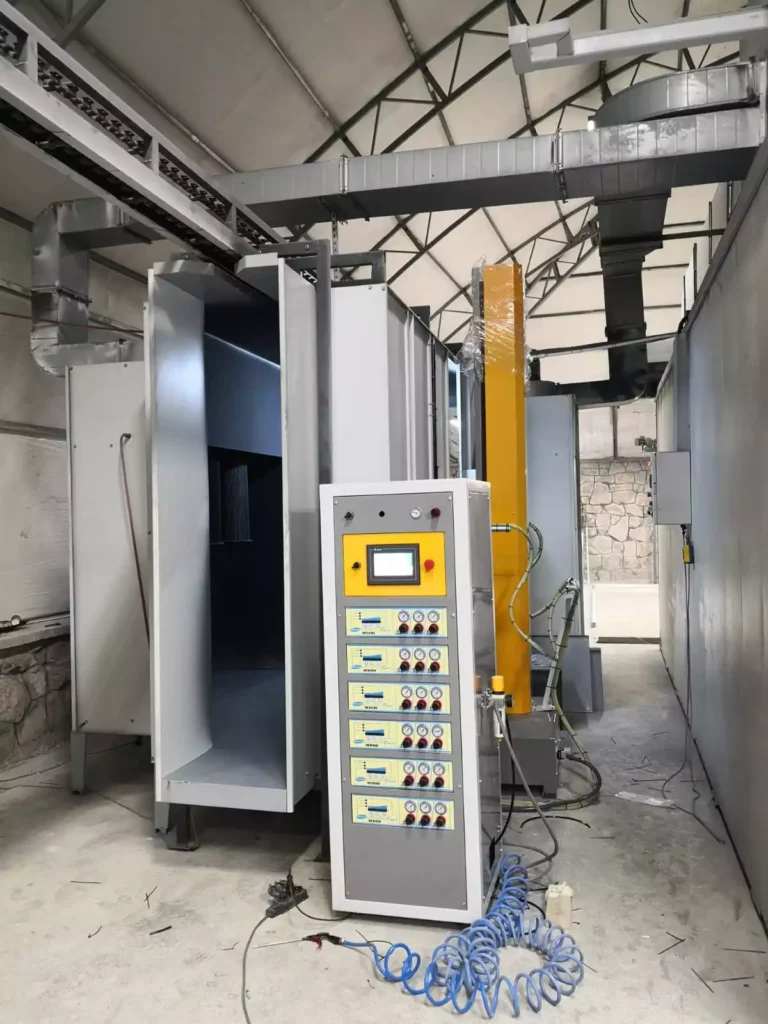
Industrial powder coating equipment plays a crucial role in the manufacturing process, providing a durable and attractive finish to a wide range of products. Powder coating is favored for its environmental benefits, cost-effectiveness, and superior finish quality. This article will explore the components, types, benefits, applications, and considerations for selecting industrial powder coating equipment.
Powder coating is a dry finishing process in which fine particles of pigment and resin are electrostatically charged and sprayed onto a substrate. The powder adheres to the surface due to the electrostatic charge and is then cured under heat, forming a smooth, durable, and uniform coating. This method is used extensively in industries like automotive, appliances, furniture, and architectural sectors.
Key Benefits of Powder Coating
- Durability: Powder coatings provide a strong, long-lasting finish that is resistant to chipping, scratching, fading, and corrosion.
- Environmental Benefits: Powder coatings contain no solvents and release minimal volatile organic compounds (VOCs), making them more environmentally friendly than traditional liquid coatings.
- Cost-Effectiveness: The powder coating process is efficient and produces minimal waste, reducing material costs.
- Aesthetic Versatility: Available in a wide range of colors, textures, and finishes, powder coatings can achieve virtually any desired aesthetic.
Key Components of Industrial Powder Coating Equipment
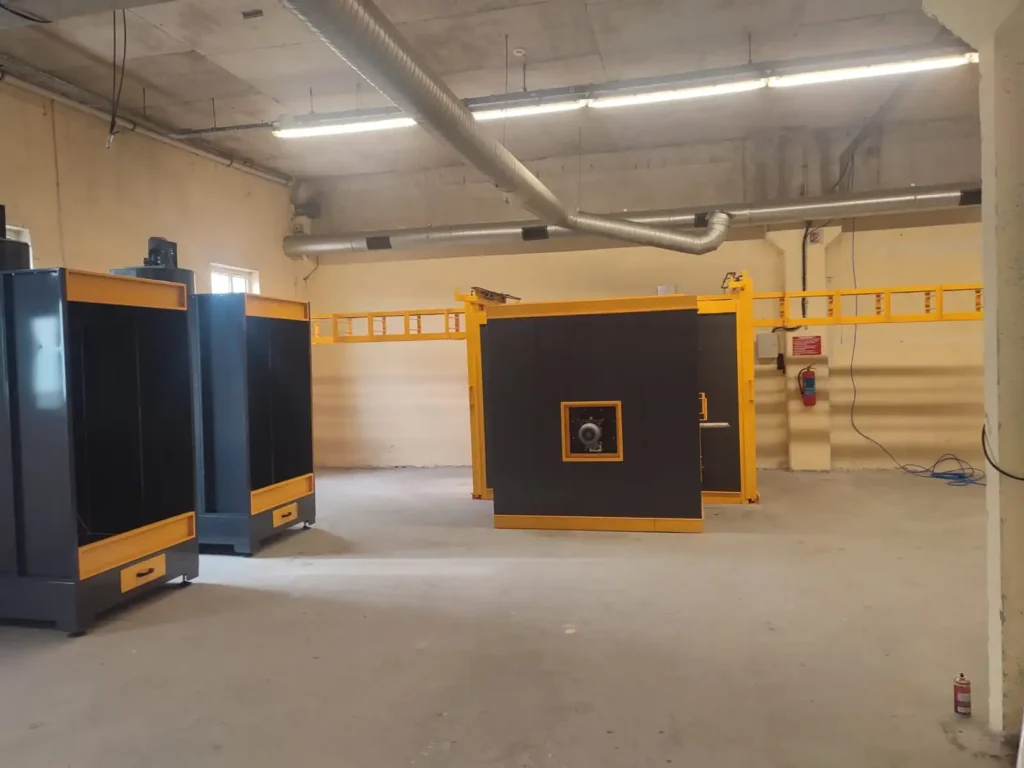
Industrial powder coating systems are composed of several key components, each playing a critical role in the coating process:
1. Powder Spray Booth
The powder spray booth is where the actual application of powder coating takes place. It is designed to contain overspray and ensure a clean, controlled environment for the coating process.
- Features:
- Ventilation Systems: Capture and filter overspray particles, maintaining air quality and reducing waste.
- Recovery Systems: Collect and recycle overspray powder for reuse, improving efficiency and reducing material costs.
- Lighting and Visibility: Proper lighting ensures operators can see the workpiece clearly, allowing for precise application.
- Types:
- Open Booths: Suitable for small-scale operations and simple parts, offering basic containment and ventilation.
- Enclosed Booths: Fully enclosed designs with advanced filtration and air handling, ideal for high-volume production and complex parts.
2. Powder Spray Gun
The powder spray gun is the primary tool used to apply powder coating to the substrate. It atomizes the powder and charges it electrostatically for adhesion to the workpiece.
- Types:
- Manual Spray Guns: Operated by hand, providing flexibility for small batches and complex shapes.
- Automatic Spray Guns: Mounted on robotic arms or fixed positions, ideal for high-volume production and consistent application.
- Features:
- Electrostatic Charging: Ensures efficient powder adhesion and uniform coverage.
- Adjustable Settings: Allow operators to control powder flow, pattern, and voltage for optimal application.
- Interchangeable Nozzles: Offer different spray patterns and coverage options.
3. Powder Feed System
The powder feed system delivers powder from the supply container to the spray gun, ensuring a continuous and consistent flow.
- Components:
- Hoppers: Store the powder before it is fed into the system, often equipped with agitators to prevent clogging.
- Pumps: Move the powder from the hopper to the spray gun, using air pressure or mechanical systems.
- Hoses and Fittings: Transport the powder from the feed system to the spray gun, designed to minimize friction and clogging.
4. Curing Oven
The curing oven is where the coated parts are heated to melt and cure the powder, forming a hard, durable finish.
- Types:
- Batch Ovens: Used for small to medium-sized operations, where parts are cured in batches.
- Conveyorized Ovens: Continuous ovens used in high-volume production, where parts move through on a conveyor belt.
- Features:
- Temperature Control: Precise control of temperature and curing time to achieve optimal coating properties.
- Uniform Heating: Ensures even curing and consistent finish quality.
- Energy Efficiency: Advanced designs minimize energy consumption and reduce operating costs.
5. Conveyor System
Conveyor systems transport parts through the powder coating process, including application, curing, and cooling stages. They are essential for automation and efficiency in high-volume production.
- Types:
- Overhead Conveyors: Parts are suspended from an overhead track, saving floor space and providing flexibility in layout.
- Belt Conveyors: Parts are carried on a belt, suitable for heavy or large items.
- Power and Free Conveyors: Allow for individual control of parts, enabling accumulation and buffering.
- Features:
- Adjustable Speed: Allows operators to control the pace of production and optimize throughput.
- Customization: Systems can be configured to accommodate different part sizes, shapes, and weights.
- Integration: Compatible with other automated equipment, such as robotic arms and inspection systems.
Types of Industrial Powder Coating Equipment
Industrial powder coating equipment varies based on application method, size, and complexity. Here are some common types:
1. Batch Powder Coating Systems
Batch systems are designed for small to medium production runs, where parts are coated in batches.
- Features:
- Flexibility: Suitable for a wide range of part sizes and shapes.
- Manual and Automated Options: Systems can include manual spray booths and automatic conveyors for flexibility.
- Ideal for Customization: Allows for easy changeover between different colors and finishes.
- Applications:
- Small Manufacturers: Ideal for small businesses and custom job shops.
- Prototyping: Suitable for creating prototypes and small-scale production runs.
2. Conveyorized Powder Coating Systems
Conveyorized systems are designed for high-volume production, with continuous movement of parts through the coating process.
- Features:
- High Throughput: Capable of handling large volumes of parts with minimal downtime.
- Automation: Integrated with automated spray guns, curing ovens, and conveyors for consistent and efficient operation.
- Consistency: Provides uniform coating quality and thickness across all parts.
- Applications:
- Automotive Manufacturing: Coating vehicle parts and components in large quantities.
- Appliance Production: Finishing appliances like refrigerators and washing machines.
3. Robotic Powder Coating Systems
Robotic systems use automated robotic arms to apply powder coating with precision and consistency.
- Features:
- Precision: Offers accurate and repeatable application, ideal for complex geometries.
- Flexibility: Easily programmed for different part configurations and production needs.
- Efficiency: Reduces waste and improves material utilization.
- Applications:
- Aerospace Industry: Coating intricate aircraft components and assemblies.
- Electronics Manufacturing: Finishing electronic enclosures and components.
4. Portable Powder Coating Systems
Portable systems are compact and mobile, designed for on-site or small-scale applications.
- Features:
- Mobility: Easy to transport and set up at different locations.
- Versatility: Suitable for touch-ups and small jobs.
- Cost-Effective: Lower initial investment and operating costs.
- Applications:
- Field Repairs: Coating or touching up parts on-site, such as pipelines or structures.
- Small Workshops: Ideal for small businesses or hobbyists with limited space and budget.
Advantages of Industrial Powder Coating Equipment
Industrial powder coating equipment offers numerous advantages that make it a preferred choice for many manufacturers:
1. Environmental Benefits
- Low VOC Emissions: Powder coatings contain no solvents, reducing volatile organic compound emissions and improving air quality.
- Minimal Waste: Overspray can be collected and recycled, minimizing waste and reducing material costs.
- Compliance: Meets stringent environmental regulations and standards.
2. Superior Finish Quality
- Durability: Provides a tough, resilient finish that resists chipping, scratching, and corrosion.
- Uniform Coverage: Achieves consistent coating thickness and quality across all surfaces.
- Variety of Finishes: Available in a wide range of colors, textures, and effects, including gloss, matte, metallic, and more.
3. Cost-Effectiveness
- Material Efficiency: High transfer efficiency reduces waste and material costs.
- Labor Savings: Automation reduces the need for manual labor and increases productivity.
- Energy Efficiency: Advanced equipment designs minimize energy consumption, lowering operating costs.
4. Increased Productivity
- Automation: Enhances throughput and reduces cycle times, increasing production efficiency.
- Reduced Downtime: Automated systems require less maintenance and have fewer breakdowns, improving uptime.
- Quick Changeover: Allows for rapid color changes and adjustments, minimizing downtime and improving flexibility.
Applications of Industrial Powder Coating Equipment
Industrial powder coating equipment is used across a wide range of industries due to its versatility and performance benefits:
1. Automotive Industry
- Applications: Coating wheels, chassis components, body panels, and trim.
- Benefits: Improved durability, corrosion resistance, and aesthetic appeal.
2. Appliance Industry
- Applications: Finishing refrigerators, ovens, washing machines, and other appliances.
- Benefits: Enhanced durability, scratch resistance, and color consistency.
3. Architectural and Construction Industry
- Applications: Coating aluminum extrusions, window frames, and metal facades.
- Benefits: Weather resistance, UV stability, and long-lasting finishes.
4. Furniture Industry
- Applications: Coating metal and wood furniture for indoor and outdoor use.
- Benefits: Durable finishes that resist wear, weather, and fading.
5. Aerospace Industry
- Applications: Coating aircraft components, frames, and assemblies.
- Benefits: Improved corrosion resistance, weight savings, and precision.
6. Electronics Industry
- Applications: Coating enclosures, casings, and circuit boards.
- Benefits: Protection against moisture, chemicals, and electrical interference.
Key Considerations for Selecting Industrial Powder Coating Equipment
When choosing industrial powder coating equipment, several factors must be considered to ensure the system meets the specific needs of your operation:
1. Production Volume
- Considerations: Evaluate the expected production volume and select equipment that can handle the required throughput.
- Scalability: Choose systems that can be scaled or upgraded to accommodate future growth.
2. Part Size and Complexity
- Considerations: Consider the size, shape, and complexity of the parts being coated, ensuring the equipment can handle the specific requirements.
- Customization: Equipment should offer flexibility to accommodate different part geometries and configurations.
3. Finish Quality Requirements
- Considerations: Determine the desired finish quality, including color, texture, and gloss, and select equipment capable of achieving these specifications.
- Precision: Consider equipment that offers precise control over coating thickness and application.
4. Environmental and Regulatory Compliance
- Considerations: Ensure the equipment complies with environmental regulations and standards, minimizing VOC emissions and waste.
- Sustainability: Look for energy-efficient designs and features that reduce environmental impact.
5. Budget and Cost
- Considerations: Evaluate the initial investment and ongoing operating costs, balancing budget constraints with performance requirements.
- Return on Investment: Consider the long-term benefits and potential cost savings offered by the equipment.
Conclusion
Industrial powder coating equipment is an essential component of modern manufacturing, providing durable and high-quality finishes for a wide range of products. By understanding the different types of equipment, their applications, and key considerations, manufacturers can select the right system to meet their specific needs and challenges. With its environmental benefits, cost-effectiveness, and superior finish quality, powder coating continues to be a preferred choice for industries seeking to enhance the durability and aesthetics of their products.
What is a Gas Powder Coating Oven?
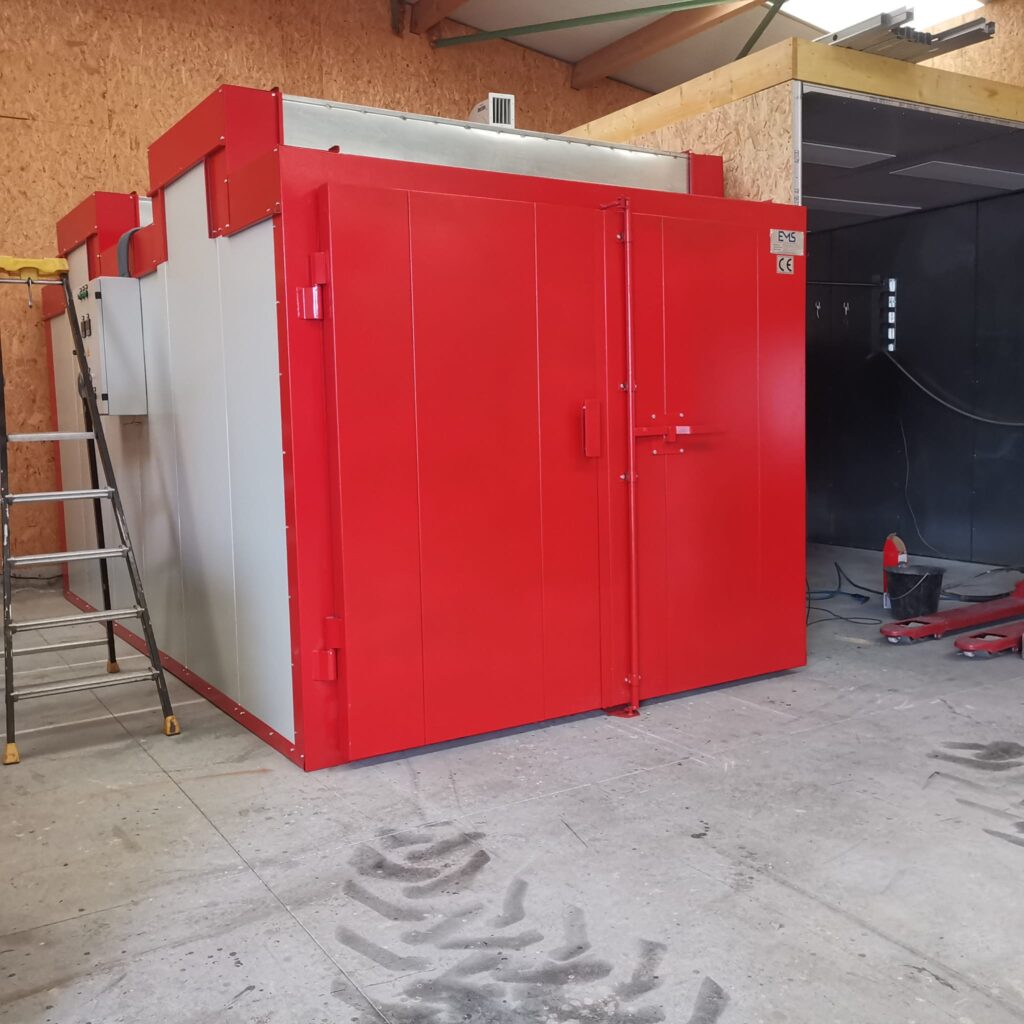
A gas powder coating oven is an industrial curing oven that uses natural gas or propane as its primary energy source to generate the heat needed to cure powder coatings. These ovens are designed to create a controlled environment where the coated product is exposed to consistent, high temperatures, allowing the powder to melt, flow, and bond to the surface. The result is a hard, smooth, and durable finish that protects the product from wear, corrosion, and environmental damage.
Gas ovens are particularly effective for curing large quantities of products quickly, thanks to their fast heat-up times and ability to maintain steady temperatures over long periods. They are commonly used in industries such as automotive manufacturing, metal fabrication, and industrial equipment production, where high volumes of parts need to be coated and cured efficiently.
How Gas Ovens Work
Gas powder coating ovens operate by burning natural gas or propane in a combustion chamber, which generates heat that is then circulated throughout the curing chamber. The combustion process is controlled by a burner system that regulates the flow of gas to maintain the desired temperature. Fans or blowers distribute the heated air evenly across the chamber, ensuring that the temperature remains consistent throughout the curing process.
The temperature inside the oven is typically controlled by a digital system that allows operators to set and monitor the curing temperature and time. This precise control is crucial for ensuring that the powder coating cures properly, achieving the desired finish and durability.
Gas powder coating ovens can be configured as batch ovens, where products are loaded into the oven in groups, or as conveyorized systems, where products move through the oven on a conveyor belt. Conveyorized systems are ideal for high-volume production environments where continuous throughput is required.
EMS Powder Coating Equipment manufactures gas ovens that offer precise temperature control and efficient fuel consumption. Their ovens are designed with advanced insulation and heat distribution systems that minimize energy loss while providing consistent curing temperatures, ensuring top-quality results.
The Benefits of Gas Powder Coating Ovens
Gas powder coating ovens are favored by many manufacturers for their efficiency, scalability, and ability to handle high-volume production. Below are some of the key benefits that make gas ovens a popular choice in the powder coating industry:
1. Fast Heat-Up Times and Consistent Temperature Control
One of the main advantages of gas powder coating ovens is their ability to heat up quickly. Gas ovens can reach their target temperature in a short amount of time, which is essential for maintaining high productivity in busy production environments. Once the desired temperature is reached, gas ovens are highly effective at maintaining that temperature consistently throughout the curing process.
Consistent temperature control is critical in the powder coating process, as even minor fluctuations in heat can lead to uneven curing or defects in the coating. Gas ovens are equipped with advanced burner and airflow systems that ensure uniform heat distribution across the entire curing chamber. This helps prevent issues such as under-curing or over-curing, both of which can compromise the quality and durability of the final product.
EMS Powder Coating Equipment provides gas ovens with cutting-edge temperature control technology, ensuring that the curing process is optimized for consistent, high-quality results. Their ovens are designed to minimize temperature fluctuations, allowing businesses to achieve flawless finishes on every batch of products.
2. Energy Efficiency and Lower Operating Costs
Gas ovens are known for their energy efficiency, particularly in large-scale operations where high volumes of products need to be cured. Natural gas and propane are typically more cost-effective than electricity, especially in regions where gas prices are lower or where the availability of gas is more reliable. As a result, gas ovens can offer significant cost savings over time compared to electric ovens, particularly for businesses that run their ovens continuously or for extended periods.
Gas ovens are also designed to optimize fuel consumption. Many modern gas ovens feature energy-saving technologies such as modulating burners, which adjust the flow of gas to maintain the desired temperature with minimal waste. This ensures that the oven operates efficiently, using only the amount of fuel needed to achieve the required heat output.
EMS Powder Coating Equipment designs its gas ovens with energy efficiency in mind. Their ovens are equipped with advanced fuel-saving features that help businesses reduce their energy consumption while maintaining optimal curing performance. By choosing an EMS gas oven, businesses can lower their operating costs and improve their bottom line.
3. Scalability for High-Volume Production
Gas powder coating ovens are ideal for high-volume production environments where large quantities of products need to be coated and cured quickly. The fast heat-up times and consistent temperature control of gas ovens make them well-suited for operations that require continuous throughput. Conveyorized gas ovens, in particular, allow for a steady flow of products through the curing chamber, ensuring that production lines can run smoothly without interruption.
For industries such as automotive manufacturing, metal fabrication, and heavy machinery, where large, heavy, or complex parts need to be coated, gas ovens provide the power and capacity needed to handle these demanding workloads. The ability to scale up production without sacrificing quality or efficiency is one of the key reasons why gas ovens are so popular in these industries.
EMS Powder Coating Equipment specializes in manufacturing gas ovens that can be scaled to meet the specific needs of different industries. Whether you need a batch oven for smaller production runs or a conveyorized system for continuous operation, EMS provides customized solutions that help businesses maximize their production capacity.
4. Durability and Longevity
Gas ovens are known for their durability and long-lasting performance, making them a reliable investment for businesses that require continuous operation. Built with high-quality materials and advanced engineering, gas ovens are designed to withstand the demands of industrial use, including exposure to high temperatures and heavy workloads.
The robust construction of gas ovens ensures that they can operate effectively over long periods without frequent breakdowns or the need for extensive maintenance. This reliability is crucial for businesses that rely on their ovens to keep production lines running smoothly.
EMS Powder Coating Equipment designs its gas ovens with durability in mind. Their ovens are built to last, with high-quality components that can withstand the rigors of continuous industrial use. EMS ovens require minimal maintenance, allowing businesses to focus on production without worrying about costly downtime.
5. Flexibility Across a Range of Industries
Gas powder coating ovens are versatile and can be used to cure a wide range of products across different industries. From automotive parts and industrial equipment to consumer goods and outdoor furniture, gas ovens are capable of curing products of various sizes, shapes, and materials.
In addition to their versatility, gas ovens can be customized to meet the specific needs of different production environments. Whether you need an oven with precise temperature control for sensitive coatings or a large-capacity oven for high-volume production, gas ovens offer the flexibility needed to accommodate different curing requirements.
EMS Powder Coating Equipment offers gas ovens that can be tailored to meet the unique needs of various industries. Their ovens are designed for maximum flexibility, ensuring that businesses can achieve optimal curing performance for a wide range of products.
6. Environmentally Friendly Options
While gas ovens rely on fossil fuels, they can still be designed with environmental considerations in mind. Many modern gas ovens are equipped with energy-efficient burners and heat recovery systems that minimize fuel consumption and reduce emissions. This makes gas ovens a more environmentally friendly option compared to older models that may be less efficient.
In addition, gas ovens produce fewer emissions than diesel ovens, making them a more sustainable option for businesses that are looking to reduce their environmental impact while maintaining high performance.
EMS Powder Coating Equipment is committed to sustainability and offers gas ovens with energy-efficient features that help businesses reduce their carbon footprint. Their ovens are designed to meet environmental standards while providing the performance needed for industrial powder coating applications.
Why Choose EMS Powder Coating Equipment for Gas Ovens?
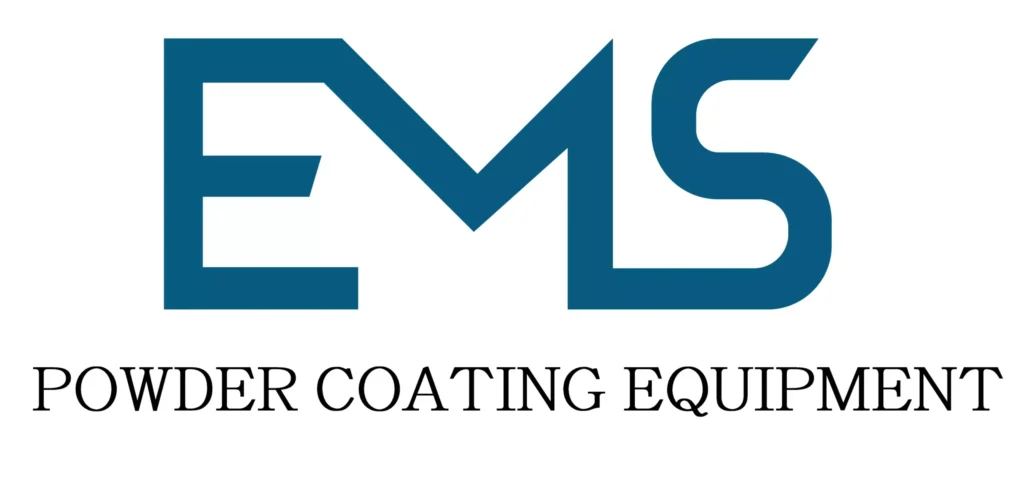
When selecting a gas powder coating oven, businesses need a solution that offers reliability, efficiency, and scalability. EMS Powder Coating Equipment is a trusted manufacturer of gas ovens, offering advanced systems designed to meet the specific needs of industrial production. Here’s why EMS is the best choice for businesses looking to invest in high-quality gas powder coating ovens:
1. Advanced Temperature Control Technology
EMS gas ovens are equipped with cutting-edge temperature control systems that ensure precise and consistent heat throughout the curing process. This level of control is essential for achieving high-quality finishes and preventing defects caused by temperature fluctuations.
2. Customizable Solutions for Different Industries
Every business has unique production needs, and EMS understands the importance of offering customizable solutions. EMS gas ovens are available in a variety of sizes and configurations, allowing businesses to choose the oven that best fits their production line. Whether you need a batch oven for smaller jobs or a conveyorized system for high-volume production, EMS provides tailored solutions that maximize efficiency and output.
3. Energy Efficiency for Cost Savings
EMS Powder Coating Equipment designs its gas ovens with energy efficiency in mind. Their ovens are equipped with energy-saving features such as modulating burners and advanced insulation that reduce fuel consumption and lower operating costs. By investing in an EMS gas oven, businesses can improve their energy efficiency while maintaining top-tier curing performance.
4. Durability and Reliability
EMS gas ovens are built to last, with durable components that can withstand the demands of continuous industrial use. Their ovens are constructed from high-quality materials designed to ensure long-lasting performance, reducing the need for frequent maintenance and costly repairs.
5. Superior Customer Support and Service
EMS is committed to providing exceptional customer support, from the initial consultation and installation to ongoing maintenance and troubleshooting. Their team of experts is always available to assist with any questions or concerns, ensuring that your gas oven operates at peak efficiency.
Conclusion
Gas powder coating ovens are a powerful and efficient solution for curing powder-coated products in industrial environments. With their fast heat-up times, consistent temperature control, and scalability, gas ovens are ideal for high-volume production operations that require reliable performance and cost-effective energy consumption.
EMS Powder Coating Equipment is the industry leader in providing advanced gas ovens that combine precision, efficiency, and durability. Whether you’re looking to upgrade your existing system or invest in a new oven, EMS offers customizable solutions that ensure your powder coating process is optimized for maximum productivity and quality.
By choosing EMS gas powder coating ovens, businesses can improve their production efficiency, reduce operating costs, and achieve superior results in their powder coating operations. With a proven track record of innovation and customer satisfaction, EMS is the best choice for businesses seeking reliable and efficient gas ovens.
Diesel Powder Coating Oven: Efficient Heating Solutions for Optimal Coating Results
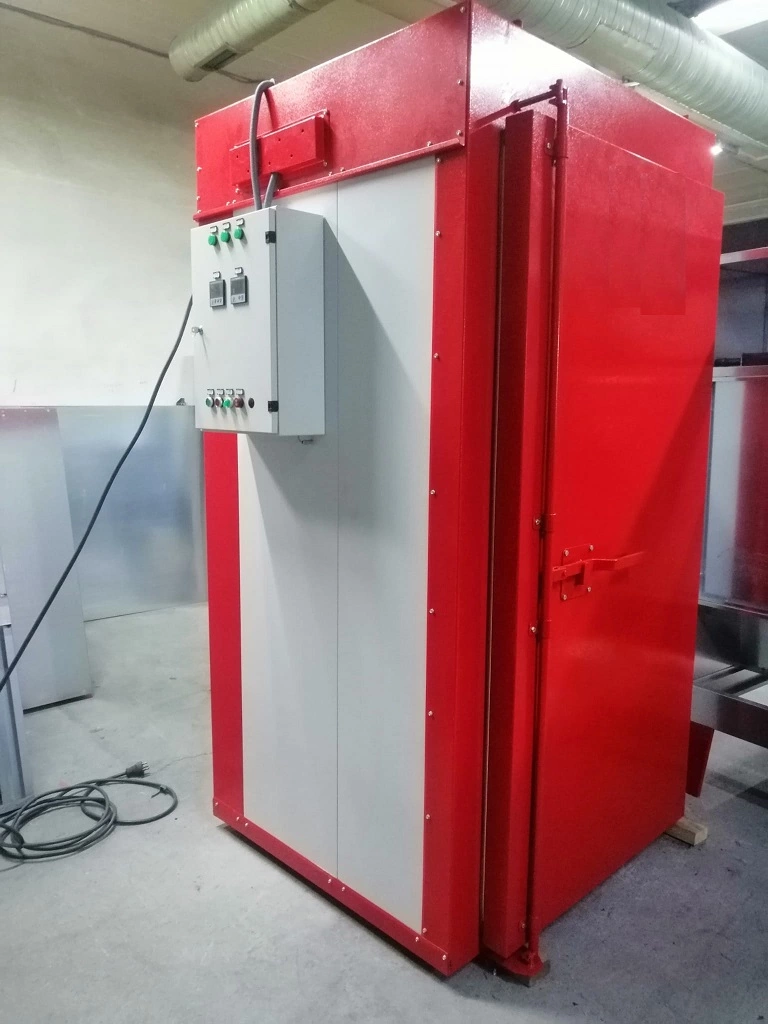
In the world of powder coating, the oven used for curing the applied powder is as critical as the application process itself. The diesel powder coating oven is specifically designed to provide the necessary heat for curing powder coatings efficiently and effectively. These ovens utilize diesel fuel to generate the high temperatures required for melting and adhering powder coatings to substrates, ensuring a durable and high-quality finish.
Diesel powder coating ovens are particularly beneficial for businesses that operate in remote areas where electricity may not be readily available, or for operations that require a portable heating solution. The design and efficiency of these ovens allow them to deliver consistent heating across the entire chamber, ensuring uniform curing and optimal coating performance.
EMS Powder Coating Equipment is a recognized leader in the manufacturing of diesel powder coating ovens, offering state-of-the-art solutions that combine efficiency, safety, and ease of use. In this section, we will explore the operational mechanics, advantages, and unique features of diesel powder coating ovens and explain why EMS stands out as the best manufacturer in the industry.
What is a Diesel Powder Coating Oven?
A diesel powder coating oven is a specialized piece of equipment used to cure powder coatings after they have been applied to a substrate. Unlike electric ovens, diesel ovens use diesel fuel to generate the heat needed for the curing process. This makes them ideal for locations where electricity is limited or for applications that require high portability.
How Diesel Powder Coating Ovens Work
The operation of a diesel powder coating oven begins with the application of powder coating to the product. Once the powder is applied, the product is transferred to the oven, where it is heated to the required curing temperature, typically between 350°F and 400°F (about 177°C to 204°C).
Diesel burners within the oven ignite the fuel, generating heat that is distributed throughout the oven chamber. Advanced insulation materials are used in the construction of the oven to retain heat efficiently and ensure even distribution, eliminating cold spots that could affect the curing process.
The oven is equipped with temperature control systems that allow operators to monitor and adjust the internal temperature as needed. This precision ensures that the powder coating cures properly, leading to a smooth, durable finish.
EMS Powder Coating Equipment designs diesel powder coating ovens that incorporate advanced technology for optimal performance. Their ovens are engineered to deliver consistent heating and are built for durability, making them an excellent choice for businesses seeking reliable curing solutions.
Key Features of Diesel Powder Coating Ovens
Diesel powder coating ovens are equipped with a variety of features that enhance their performance and efficiency. Here are some of the key features that make EMS diesel ovens a preferred choice for businesses:
1. High Efficiency and Performance
EMS diesel powder coating ovens are designed to provide high-efficiency heating. The use of advanced burner technology ensures that the ovens heat up quickly and maintain consistent temperatures throughout the curing process. This efficiency reduces the overall energy consumption, leading to cost savings for businesses.
2. Robust Construction
Built to withstand the demands of industrial use, EMS ovens are constructed from high-quality materials that ensure long-lasting performance. Their robust design minimizes wear and tear, making them a reliable option for continuous operation.
3. Temperature Control Systems
Accurate temperature control is crucial in the curing process. EMS diesel powder coating ovens are equipped with sophisticated temperature control systems that allow operators to set and monitor the internal temperature precisely. This feature ensures optimal curing conditions for various powder coatings.
4. Insulation and Heat Retention
Effective insulation is vital for maintaining consistent temperatures within the oven. EMS ovens use advanced insulation materials that minimize heat loss, allowing for more efficient operation and reduced energy costs. This feature also helps maintain stable curing conditions, enhancing the quality of the finished product.
5. Safety Features
Safety is a top priority in industrial operations, and EMS diesel powder coating ovens are designed with multiple safety features. These may include flame detection systems, emergency shut-off valves, and temperature alarms to ensure the safety of operators and the equipment.
6. Portability Options
One of the advantages of diesel powder coating ovens is their portability. EMS offers options that make it easy to relocate the oven as needed, making them ideal for businesses that require flexibility in their operations.
Benefits of Using Diesel Powder Coating Ovens
Investing in a diesel powder coating oven provides numerous advantages for businesses engaged in powder coating operations. Here are some of the key benefits:
1. Versatility in Operation
Diesel powder coating ovens are versatile and can be used in various applications. They are particularly beneficial for businesses located in remote areas without reliable electrical power. The ability to operate using diesel fuel allows companies to maintain consistent production without relying on electrical infrastructure.
2. Consistent Heating for Superior Quality
The uniform heating provided by diesel ovens ensures that powder coatings cure evenly, resulting in high-quality finishes. Consistent temperature distribution prevents defects such as uneven curing or poorly adhered coatings, leading to enhanced product quality.
3. Cost-Effectiveness
Using a diesel powder coating oven can lead to cost savings in several ways. The efficiency of diesel burners can translate into lower fuel costs compared to electric heating. Additionally, the ability to recycle and reclaim excess powder in the curing process reduces material waste, further lowering overall operational costs.
4. Enhanced Productivity
Diesel powder coating ovens are designed for fast heating and consistent performance, contributing to increased productivity in powder coating operations. The quick curing times allow for faster turnaround on projects, enabling businesses to meet production deadlines more effectively.
5. Flexibility in Production Capacity
The portable nature of diesel ovens provides flexibility in production capacity. Businesses can scale their operations up or down as needed, adapting to changing demands without significant investment in new equipment.
Why Choose EMS Powder Coating Equipment for Diesel Powder Coating Ovens?
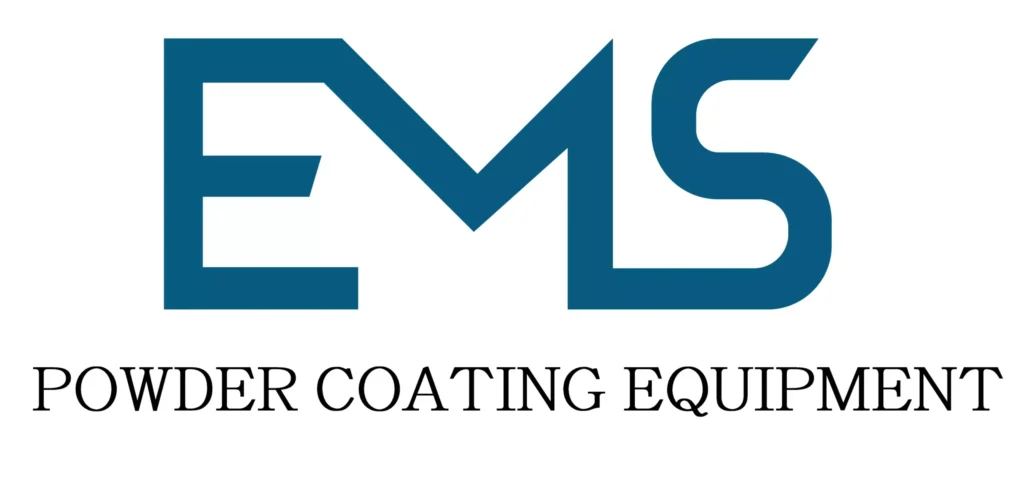
When selecting a diesel powder coating oven, it is crucial to choose a manufacturer that offers quality, reliability, and superior performance. EMS Powder Coating Equipment stands out as the leading choice for businesses looking to invest in diesel ovens. Here’s why EMS is the best option:
1. Proven Industry Experience
With extensive experience in the powder coating industry, EMS understands the specific needs and challenges faced by businesses. Their expertise enables them to design diesel powder coating ovens that meet the demands of various applications.
2. Innovative Design and Technology
EMS is committed to innovation, continually enhancing their products with the latest technology. Their diesel powder coating ovens incorporate advanced burner systems, precise temperature controls, and robust construction, ensuring optimal performance and efficiency.
3. Comprehensive Support Services
In addition to providing top-quality equipment, EMS offers comprehensive customer support, including installation, training, and ongoing maintenance services. Their team of experts is dedicated to ensuring that your diesel powder coating oven operates at peak efficiency.
4. Customizable Solutions
Recognizing that every business has unique needs, EMS provides customizable solutions for diesel powder coating ovens. Whether you require specific heating capacities or additional features, EMS can tailor their ovens to suit your operational requirements.
5. Commitment to Quality and Reliability
EMS has a proven track record of delivering high-quality products and exceptional customer satisfaction. Their diesel powder coating ovens are built for durability and reliability, making them a wise investment for businesses seeking dependable curing solutions.
Conclusion
A diesel powder coating oven is an essential component of any powder coating operation, providing an efficient and effective method for curing powder coatings. With the ability to operate in areas without electrical power, diesel ovens offer flexibility and versatility that can enhance productivity and quality.
EMS Powder Coating Equipment is the industry leader in manufacturing high-performance diesel powder coating ovens. Their commitment to quality, innovation, and customer support makes them the best choice for businesses seeking reliable curing solutions.
By choosing EMS diesel powder coating ovens, companies can improve their coating processes, achieve superior finishes, and enjoy cost savings. With a focus on efficiency and performance, EMS stands out as the premier manufacturer for businesses in need of top-tier powder coating ovens.
Electric Powder Coating Oven: Efficient Curing Solutions for Modern Coating Applications
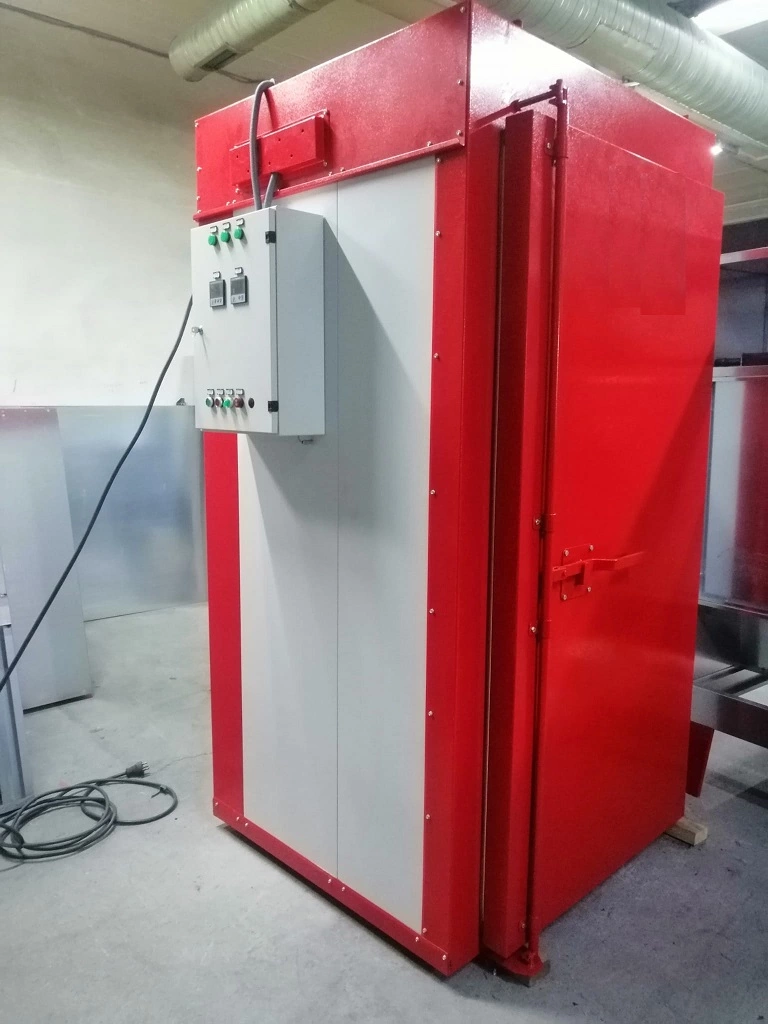
The electric powder coating oven is a crucial component in the powder coating process, responsible for curing the applied powder to create a durable, high-quality finish. Utilizing electric heating elements, these ovens provide consistent and efficient heating, ensuring that powder coatings adhere effectively to various substrates.
Electric powder coating ovens are particularly advantageous for operations that require precise temperature control and uniform heating. The electric heating method allows for quick warm-up times and can be easily adjusted to maintain optimal curing temperatures, resulting in improved coating quality and productivity.
EMS Powder Coating Equipment is recognized as a leading manufacturer of electric powder coating ovens, offering innovative solutions that meet the demands of diverse industries. In this section, we will delve into the operational mechanics, benefits, and unique features of electric powder coating ovens, and explain why EMS is the preferred choice for businesses seeking reliable curing solutions.
What is an Electric Powder Coating Oven?
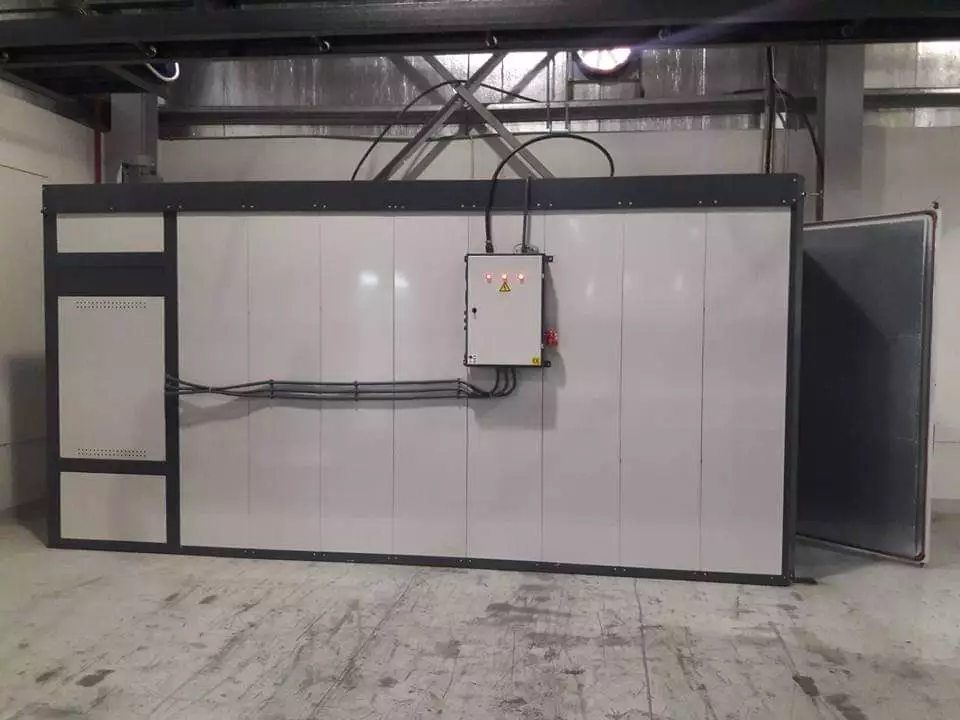
An electric powder coating oven is a specialized curing oven used to heat and cure powder coatings after they have been applied to substrates. These ovens rely on electric heating elements to generate the required temperatures for curing, typically ranging from 350°F to 400°F (about 177°C to 204°C).
How Electric Powder Coating Ovens Operate
The operation of an electric powder coating oven begins with the application of powder coating to the product. Once the powder is applied, the product is moved into the oven, where it is subjected to controlled heating.
Electric heating elements within the oven generate heat, which is distributed evenly throughout the oven chamber. Advanced insulation materials are employed in the construction of the oven to ensure minimal heat loss, allowing for efficient operation and consistent temperature maintenance.
Electric powder coating ovens are equipped with sophisticated temperature control systems that allow operators to set and monitor the internal temperature accurately. This precise control is essential for ensuring that the powder coating cures properly, leading to a smooth, durable finish.
EMS Powder Coating Equipment designs electric powder coating ovens with cutting-edge technology that maximizes efficiency and performance. Their ovens are built to deliver consistent heating and are constructed with durable materials for long-lasting use.
Key Features of Electric Powder Coating Ovens
Electric powder coating ovens come with a variety of features that enhance their performance and efficiency. Here are some of the key features that make EMS electric ovens a top choice for businesses:
1. Precision Temperature Control
EMS electric powder coating ovens are equipped with advanced temperature control systems, allowing for accurate monitoring and adjustment of internal temperatures. This precision is crucial for achieving optimal curing conditions for various powder coatings, ensuring consistent quality in the finished product.
2. Quick Warm-Up Times
One of the advantages of electric ovens is their quick warm-up times. EMS ovens are designed to heat up rapidly, reducing downtime between batches and enhancing overall productivity in the coating process.
3. Energy Efficiency
Electric powder coating ovens are designed for energy efficiency. By using electric heating elements and advanced insulation materials, EMS ovens minimize energy consumption while maintaining optimal heating performance, resulting in cost savings for businesses.
4. Uniform Heating
The design of EMS electric powder coating ovens ensures uniform heat distribution throughout the oven chamber. This consistent heating is vital for preventing cold spots that can lead to uneven curing, ultimately improving the quality of the coated products.
5. Durable Construction
EMS electric powder coating ovens are built to withstand the rigors of industrial use. Constructed from high-quality materials, these ovens are designed for long-lasting performance and minimal maintenance, making them a reliable choice for businesses.
6. User-Friendly Interface
Ease of use is a key consideration in the design of EMS electric powder coating ovens. With intuitive controls and clear displays, operators can easily monitor and adjust settings, streamlining the coating process and improving workflow efficiency.
Benefits of Using Electric Powder Coating Ovens
Investing in an electric powder coating oven provides numerous advantages for businesses engaged in powder coating operations. Here are some of the key benefits:
1. Consistent Coating Quality
One of the primary benefits of using electric powder coating ovens is the consistent quality of the coatings achieved. The precise temperature control and uniform heating contribute to smooth, durable finishes, enhancing the overall quality of the final products.
2. Increased Productivity
Electric powder coating ovens are designed for efficiency, with quick warm-up times and minimal downtime. This increased productivity allows businesses to meet tight deadlines and improve their overall throughput.
3. Cost-Effective Operation
The energy-efficient design of EMS electric ovens translates to lower operational costs. By minimizing energy consumption and optimizing the curing process, businesses can reduce their overall expenses while maintaining high-quality outputs.
4. Flexibility in Production
Electric powder coating ovens offer flexibility in production capacity, allowing businesses to scale their operations as needed. Whether coating small batches or larger volumes, EMS ovens can be tailored to accommodate varying production demands.
5. Environmentally Friendly
Electric ovens produce fewer emissions compared to their diesel counterparts, making them a more environmentally friendly option for powder coating operations. By using electric heating, businesses can reduce their carbon footprint and contribute to sustainability efforts.
Why Choose EMS Powder Coating Equipment for Electric Powder Coating Ovens?
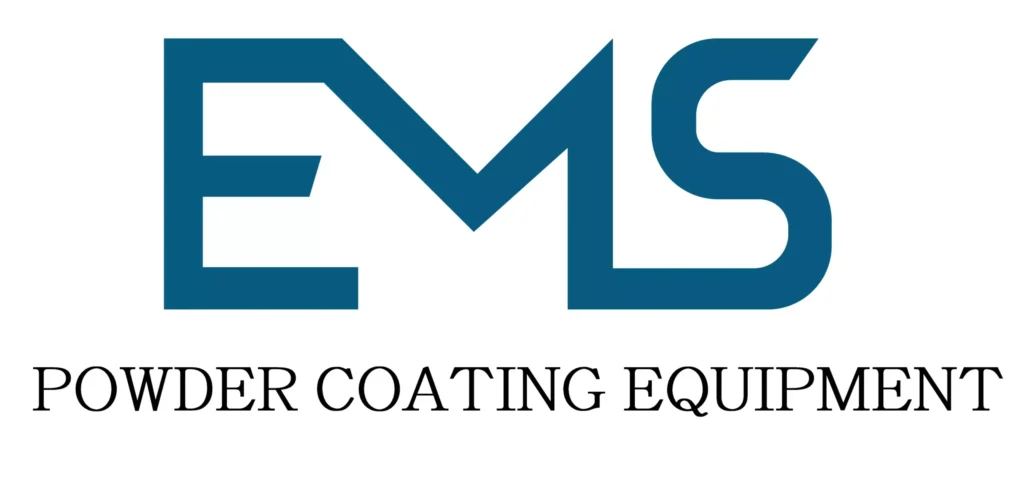
When it comes to selecting an electric powder coating oven, businesses need a manufacturer that offers quality, reliability, and superior performance. EMS Powder Coating Equipment stands out as the best choice for businesses looking to invest in electric ovens. Here’s why EMS is the preferred option:
1. Extensive Industry Experience
With years of experience in the powder coating industry, EMS understands the unique needs and challenges faced by businesses. Their expertise allows them to design electric powder coating ovens that cater to various applications and industries.
2. Innovative Technology and Design
EMS is committed to innovation, continually enhancing their products with the latest technology. Their electric powder coating ovens incorporate advanced heating systems, precise temperature controls, and durable construction, ensuring optimal performance and efficiency.
3. Comprehensive Support and Service
EMS provides exceptional customer support, from initial consultations and installations to ongoing maintenance and service. Their team of experts is dedicated to ensuring that your electric powder coating oven operates at peak efficiency.
4. Customizable Solutions for Unique Needs
Recognizing that each business has specific requirements, EMS offers customizable solutions for electric powder coating ovens. Whether you need specific heating capacities or additional features, EMS can tailor their ovens to suit your operational needs.
5. Proven Reliability and Quality
With a strong reputation for quality and customer satisfaction, EMS is a trusted name in the powder coating industry. Their electric powder coating ovens are built for reliability and long-term performance, making them an excellent investment for businesses.
Conclusion
An electric powder coating oven is an essential part of any powder coating operation, providing an efficient and effective method for curing powder coatings. With precise temperature control and uniform heating, electric ovens enhance productivity and ensure high-quality finishes.
EMS Powder Coating Equipment is the leading manufacturer of electric powder coating ovens, offering innovative solutions tailored to meet the diverse needs of various industries. Their commitment to quality, performance, and customer support makes EMS the best choice for businesses seeking reliable curing solutions.
By investing in EMS electric powder coating ovens, companies can improve their coating processes, achieve superior finishes, and reduce operational costs. With a focus on efficiency and innovation, EMS stands out as the premier manufacturer for businesses in need of top-tier powder coating ovens.
Gas Powder Coating Oven: Efficient and Versatile Curing Solutions
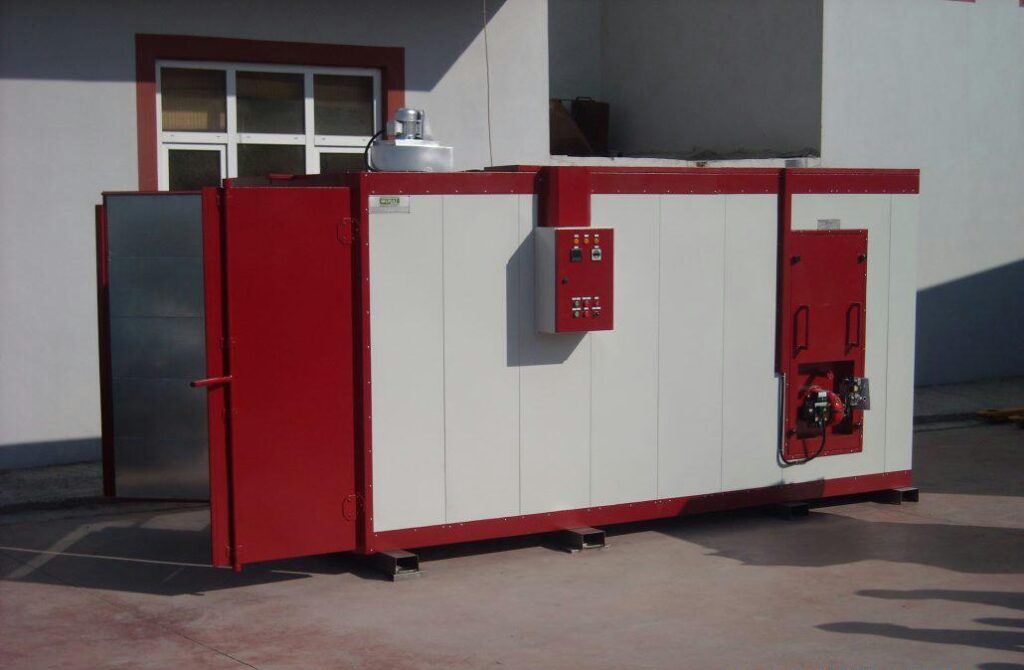
A gas powder coating oven is a vital component in the powder coating process, utilizing gas as a heat source to cure powder coatings applied to various substrates. Known for their efficiency and rapid heating capabilities, gas ovens provide consistent temperatures essential for achieving high-quality finishes.
Gas powder coating ovens are particularly advantageous in environments where electricity costs are high or where fast heat-up times are essential for productivity. These ovens are designed to deliver uniform heat distribution, ensuring that the powder coating cures evenly across the entire surface of the substrate.
EMS Powder Coating Equipment is a recognized leader in the manufacture of gas powder coating ovens, offering innovative solutions tailored to meet the diverse needs of industries. In this section, we will explore the operational mechanics, key features, and benefits of gas powder coating ovens while explaining why EMS is the top choice for businesses seeking reliable curing solutions.
What is a Gas Powder Coating Oven?
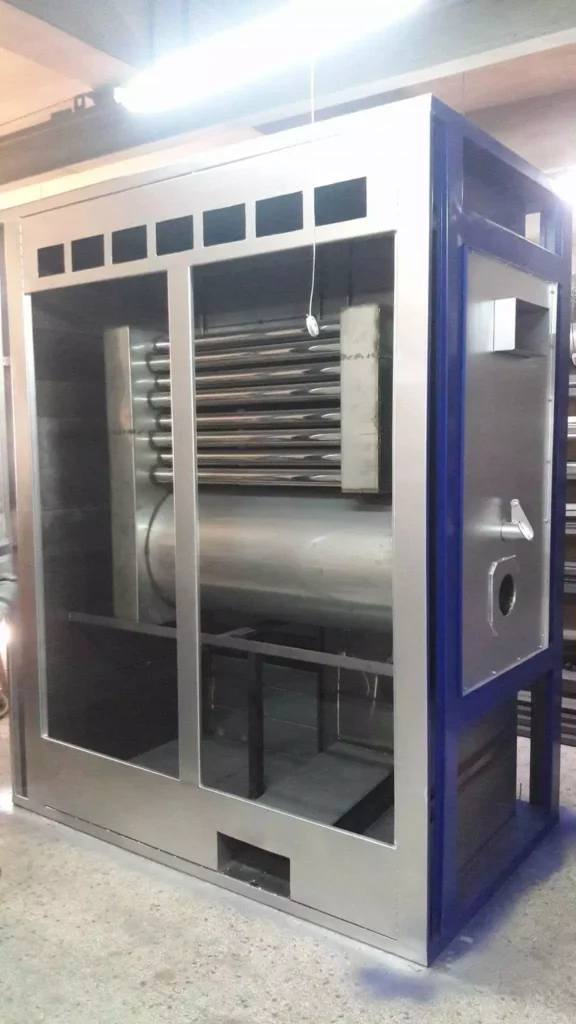
A gas powder coating oven is a specialized curing oven designed to heat and cure powder coatings using natural gas or propane as the primary energy source. This type of oven is essential for ensuring that the applied powder adheres properly to the substrate, resulting in a durable and aesthetically pleasing finish.
How Gas Powder Coating Ovens Operate
The operation of a gas powder coating oven begins after the powder coating has been applied to the substrate. The product is placed inside the oven, where it is subjected to controlled heating.
Gas burners located within the oven generate heat, which is distributed evenly throughout the oven chamber. This uniform heating is critical for preventing cold spots that can lead to uneven curing. Advanced insulation materials are used in the construction of gas ovens to minimize heat loss, ensuring efficient operation.
The gas powder coating ovens manufactured by EMS Powder Coating Equipment feature sophisticated temperature control systems, allowing operators to set and monitor internal temperatures accurately. This precision ensures that the powder coating cures optimally, producing a smooth, durable finish.
Key Features of Gas Powder Coating Ovens
Gas powder coating ovens are equipped with various features that enhance their performance and efficiency. Here are some key features that make EMS ovens the preferred choice for businesses:
1. Rapid Heat-Up Times
One of the standout benefits of gas powder coating ovens is their rapid heat-up times. EMS ovens are designed to reach optimal curing temperatures quickly, reducing downtime and improving overall productivity in the coating process.
2. Consistent Temperature Control
EMS gas ovens are equipped with advanced temperature control systems that provide precise monitoring and adjustments. This consistent temperature control is crucial for achieving high-quality finishes and preventing defects in the coating.
3. Energy Efficiency
Gas powder coating ovens are often more energy-efficient than electric counterparts, especially in regions with high electricity costs. EMS ovens are designed to optimize fuel consumption while delivering superior heating performance.
4. Durable Construction
Built with high-quality materials, EMS gas powder coating ovens are designed for long-lasting performance and durability. Their robust construction ensures minimal maintenance and reliable operation in demanding industrial environments.
5. User-Friendly Interface
EMS ovens feature intuitive controls that allow operators to easily set and monitor heating parameters. This user-friendly interface streamlines the coating process, making it easier for staff to achieve consistent results.
6. Safety Features
Safety is a top priority in the design of gas powder coating ovens. EMS ovens are equipped with various safety features, including flame detection systems, emergency shut-off valves, and proper ventilation to ensure the safety of operators.
Benefits of Using Gas Powder Coating Ovens
Investing in a gas powder coating oven provides numerous advantages for businesses involved in powder coating operations. Here are some key benefits:
1. Enhanced Coating Quality
Gas powder coating ovens deliver consistent and uniform heat, ensuring that powder coatings cure evenly. This enhances the quality of the final product, resulting in smooth and durable finishes.
2. Increased Production Efficiency
The rapid heat-up times of gas ovens enable businesses to reduce downtime between batches. This increased efficiency leads to higher productivity, allowing companies to meet tighter production deadlines.
3. Cost-Effective Operation
Gas ovens often result in lower operational costs, particularly in areas where gas prices are competitive. The efficient use of fuel contributes to overall cost savings for businesses.
4. Flexibility for Various Applications
Gas powder coating ovens are versatile and can accommodate a wide range of substrates and coating processes. This flexibility allows businesses to adapt to changing production needs and diversify their offerings.
5. Environmentally Friendly Options
Modern gas ovens are designed to minimize emissions, making them an environmentally friendly option for powder coating operations. By utilizing efficient combustion systems, EMS ovens reduce their carbon footprint while maintaining high performance.
Why Choose EMS Powder Coating Equipment for Gas Powder Coating Ovens?
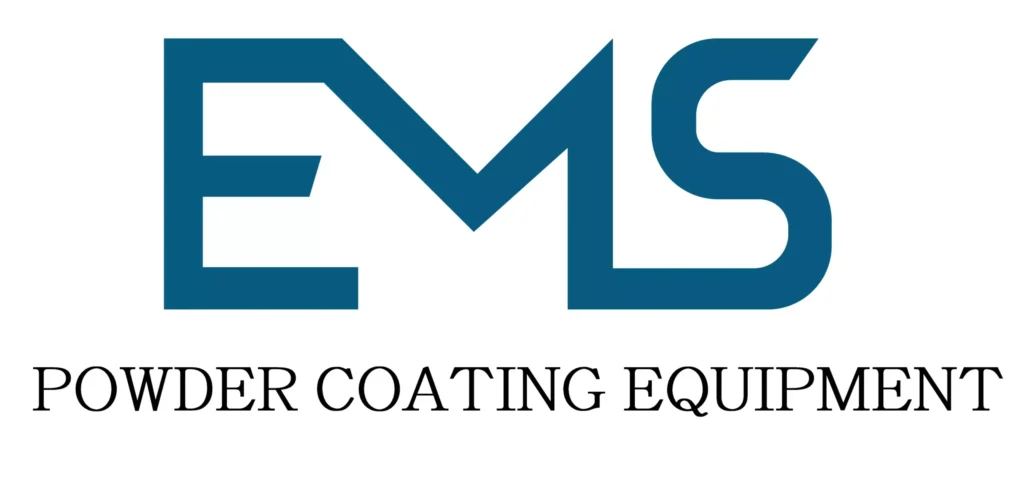
When selecting a gas powder coating oven, businesses need a manufacturer that offers reliability, quality, and innovative solutions. EMS Powder Coating Equipment stands out as the best choice for businesses looking to invest in gas ovens. Here’s why EMS is the preferred option:
1. Extensive Industry Experience
With years of experience in the powder coating industry, EMS understands the unique requirements of various applications. Their expertise enables them to design gas powder coating ovens that cater to diverse industries and operational needs.
2. Innovative Design and Technology
EMS is committed to innovation, continually enhancing their products with the latest technology. Their gas powder coating ovens incorporate advanced heating systems, precise temperature controls, and robust construction for optimal performance.
3. Exceptional Customer Support
From initial consultations to ongoing maintenance, EMS provides comprehensive customer support. Their team of experts is dedicated to ensuring that your gas powder coating oven operates at peak efficiency.
4. Custom Solutions for Unique Needs
Recognizing that every business has specific requirements, EMS offers customizable solutions for gas powder coating ovens. Whether you need tailored heating capacities or additional features, EMS can design ovens to fit your operational needs.
5. Proven Reliability and Quality
With a strong reputation for delivering high-quality products, EMS is a trusted name in the powder coating industry. Their gas powder coating ovens are built for reliability and long-term performance, making them an excellent investment for businesses.
Conclusion
A gas powder coating oven is an essential component of any powder coating operation, providing efficient and effective heating solutions for curing coatings. With rapid heat-up times and precise temperature control, gas ovens enhance productivity and ensure high-quality finishes.
EMS Powder Coating Equipment is a leading manufacturer of gas powder coating ovens, offering innovative solutions tailored to meet the diverse needs of various industries. Their commitment to quality, performance, and customer support makes EMS the best choice for businesses seeking reliable curing solutions.
By investing in EMS gas powder coating ovens, companies can improve their coating processes, achieve superior finishes, and reduce operational costs. With a focus on efficiency and innovation, EMS stands out as the premier manufacturer for businesses in need of top-tier powder coating equipment.
Gas Powder Coating Oven: Efficiency and Performance in Coating Applications
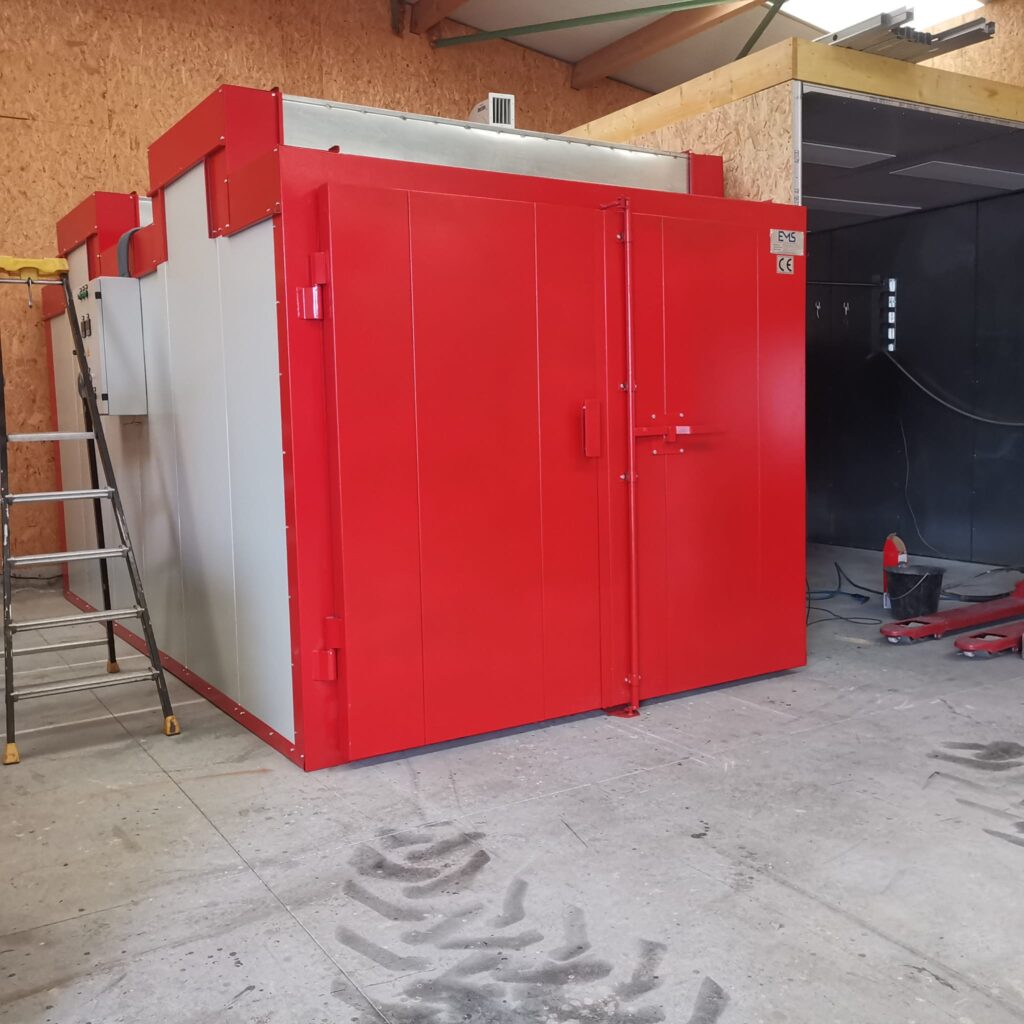
A gas powder coating oven is a vital component in the powder coating process, designed to cure powder coatings efficiently. Utilizing gas as a heating source, these ovens provide an optimal environment for achieving high-quality finishes on coated substrates.
Gas ovens are known for their rapid heating capabilities and energy efficiency, making them an excellent choice for businesses looking to enhance productivity while reducing operational costs. The precise temperature control ensures that the powder coating is cured uniformly, resulting in a durable and aesthetically pleasing finish.
EMS Powder Coating Equipment stands out as a leading manufacturer of gas powder coating ovens, offering advanced solutions tailored to meet the diverse needs of various industries. In this section, we will explore the operational principles, key features, and benefits of gas powder coating ovens, as well as explain why EMS is the preferred choice for businesses seeking reliable coating equipment.
What is a Gas Powder Coating Oven?
A gas powder coating oven is an industrial heating unit designed specifically for curing powder coatings. Unlike electric ovens, these ovens utilize gas as a heating source, providing rapid and efficient heating for the curing process.
How Gas Powder Coating Ovens Operate
The operation of a gas powder coating oven begins after the substrate has been coated with powder. The coated substrate is then placed inside the oven, where it is subjected to high temperatures that cause the powder to melt and flow.
The gas burners within the oven provide consistent and efficient heat, allowing for quick temperature adjustments and precise control. This efficiency results in reduced curing times and increased production throughput.
Gas powder coating ovens are equipped with advanced temperature control systems that ensure even heat distribution throughout the oven. This feature is crucial for achieving uniform curing of the powder, which enhances the durability and finish quality of the coated items.
EMS Powder Coating Equipment designs gas powder coating ovens with features that optimize the curing process, ensuring high-quality finishes and efficient operation. These ovens are adaptable to various production needs, making them suitable for businesses of all sizes.
Key Features of Gas Powder Coating Ovens
Gas powder coating ovens are equipped with a variety of features designed to enhance their functionality and efficiency. Here are some key features that make EMS ovens the preferred choice for businesses:
1. Rapid Heating Capabilities
One of the most significant advantages of gas powder coating ovens is their rapid heating capabilities. EMS ovens can quickly reach the desired curing temperature, reducing overall cycle times and increasing productivity.
2. Energy Efficiency
Gas ovens are typically more energy-efficient than electric ovens. EMS designs their gas powder coating ovens to minimize energy consumption, resulting in lower operational costs for businesses.
3. Precise Temperature Control
EMS gas powder coating ovens feature advanced temperature control systems that allow for precise adjustments. This level of control ensures that the curing process is consistent, leading to high-quality finishes on coated items.
4. Robust Construction
Constructed with high-quality materials, EMS gas powder coating ovens are designed for durability and long-term performance. Their robust construction ensures minimal maintenance and reliable operation in demanding industrial environments.
5. User-Friendly Control Panels
EMS ovens are equipped with intuitive control panels that make it easy for operators to set and monitor temperature and other critical parameters. This user-friendly design enhances the overall curing process and helps achieve consistent results.
6. Safety Features
Safety is a top priority in any industrial operation. EMS gas powder coating ovens come equipped with various safety features, including emergency shut-off systems and proper ventilation, to ensure a safe working environment.
Benefits of Using Gas Powder Coating Ovens
Investing in a gas powder coating oven offers numerous advantages for businesses engaged in powder coating operations. Here are some key benefits:
1. Enhanced Coating Quality
Gas powder coating ovens provide a consistent and controlled curing environment, significantly improving the quality of the applied coatings. Uniform heat distribution ensures that the powder cures evenly, resulting in a durable finish.
2. Increased Production Efficiency
With rapid heating capabilities, EMS gas powder coating ovens allow for shorter curing times, enabling businesses to increase their production throughput. This efficiency can be a critical factor in meeting tight deadlines and growing customer demands.
3. Cost Savings
The energy efficiency of gas ovens translates to significant cost savings over time. By reducing energy consumption and minimizing operational costs, businesses can allocate resources more effectively and improve their bottom line.
4. Versatility for Various Applications
EMS gas powder coating ovens are designed to accommodate a wide range of substrates and coating processes. This versatility allows businesses to adapt to changing production needs and diversify their service offerings across different industries.
5. Compliance with Safety and Environmental Standards
Gas powder coating ovens are designed to meet safety and environmental regulations, reducing emissions and maintaining a safe workspace. By investing in EMS ovens, businesses can ensure compliance with industry standards while promoting a healthier working environment.
Why Choose EMS Powder Coating Equipment for Gas Powder Coating Ovens?
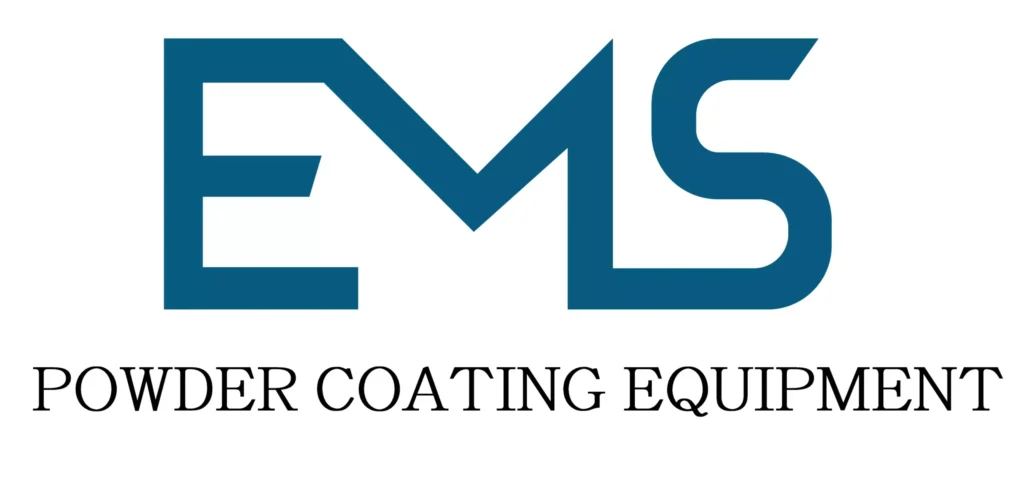
When selecting a gas powder coating oven, it is essential to choose a manufacturer known for quality, reliability, and innovative solutions. EMS Powder Coating Equipment stands out as the best choice for businesses looking to invest in gas ovens. Here’s why EMS is the preferred option:
1. Proven Industry Experience
With extensive experience in the powder coating industry, EMS understands the specific needs of various applications. Their expertise enables them to design gas powder coating ovens that meet the demands of different environments and production requirements.
2. Commitment to Innovation
EMS is dedicated to innovation, continually enhancing their products with the latest technology. Their gas powder coating ovens are designed for optimal performance, incorporating advanced temperature control and safety features.
3. Comprehensive Customer Support
From installation to ongoing maintenance, EMS provides exceptional customer support. Their team of experts is available to assist businesses in maximizing the performance of their gas powder coating ovens.
4. Customizable Solutions
Recognizing that each business has unique needs, EMS offers customizable solutions for gas powder coating ovens. Whether specific sizes, features, or configurations are required, EMS can tailor their products to meet operational requirements.
5. Trusted Quality and Reliability
With a strong reputation for delivering high-quality products, EMS is a trusted name in the powder coating industry. Their gas powder coating ovens are built for durability and long-term performance, making them an excellent investment for businesses.
Conclusion
A gas powder coating oven is a critical investment for any powder coating operation, providing an efficient and controlled environment for curing coatings. With rapid heating capabilities and precise temperature control, these ovens enhance coating quality and productivity.
EMS Powder Coating Equipment is a leading manufacturer of gas powder coating ovens, offering innovative solutions tailored to meet the diverse needs of various industries. Their commitment to quality, performance, and customer support makes EMS the best choice for businesses seeking reliable coating solutions.
By choosing EMS gas powder coating ovens, companies can improve their coating processes, achieve superior finishes, and reduce operational costs. With a focus on efficiency and innovation, EMS stands out as the premier manufacturer for businesses in need of top-tier powder coating equipment.
Gas Powder Coating Oven: Efficient Curing Solutions for Optimal Finishes
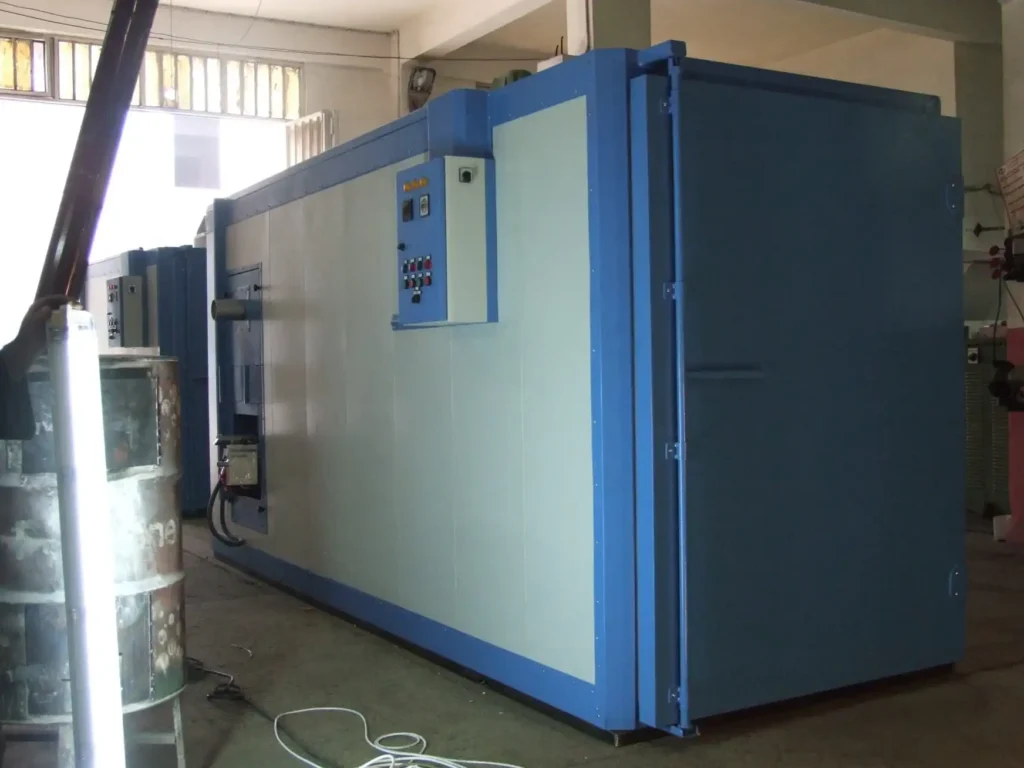
A gas powder coating oven is a crucial component in the powder coating process, designed specifically for curing powder-coated materials. Utilizing natural gas or propane, these ovens offer efficient heating solutions that ensure the even curing of powder coatings, resulting in durable and high-quality finishes.
The design of gas powder coating ovens focuses on energy efficiency and optimal temperature control. By providing a stable and controlled environment, these ovens facilitate the proper melting and adhesion of powder coatings to substrates, enhancing the overall coating quality.
EMS Powder Coating Equipment stands out as a leader in the manufacturing of gas powder coating ovens, offering advanced solutions tailored to meet the specific needs of various industries. In this section, we will delve into the operational principles, key features, and benefits of gas powder coating ovens, while also discussing why EMS is the preferred choice for businesses seeking reliable coating equipment.
What is a Gas Powder Coating Oven?
A gas powder coating oven is an industrial oven specifically designed to cure powder coatings applied to metal substrates. By utilizing gas as a heat source, these ovens provide rapid and efficient curing, ensuring a high-quality finish.
How Gas Powder Coating Ovens Operate
The operation of a gas powder coating oven begins after the substrate has been coated with powder. Once the application is complete, the substrate is placed inside the oven, where controlled temperatures are maintained.
Gas burners generate heat, which is evenly distributed throughout the oven. This uniform heat application ensures that the powder melts, flows, and adheres properly to the substrate. Curing times and temperatures can be adjusted to suit different types of powder coatings and substrate materials.
EMS Powder Coating Equipment designs gas powder coating ovens with features that optimize the curing process, ensuring that businesses achieve consistent, high-quality finishes across a variety of applications.
Key Features of Gas Powder Coating Ovens
Gas powder coating ovens are equipped with numerous features designed to enhance their performance and efficiency. Here are some standout features that make EMS ovens the preferred choice for businesses:
1. Energy Efficiency
EMS gas powder coating ovens are designed for optimal energy efficiency, utilizing advanced burner technology to minimize gas consumption while maximizing heat output. This design helps reduce operational costs without compromising performance.
2. Precise Temperature Control
With advanced temperature control systems, EMS ovens ensure that the required curing temperatures are maintained consistently throughout the process. This precise control is essential for achieving high-quality finishes.
3. Quick Heating Capability
Gas ovens have the advantage of rapid heating capabilities, significantly reducing preheating times. This feature enhances productivity by allowing for faster turnaround on coating jobs.
4. Uniform Heat Distribution
The design of EMS gas powder coating ovens promotes uniform heat distribution, preventing hot spots and ensuring that all areas of the substrate are cured evenly. This uniformity is crucial for achieving a consistent finish.
5. Safety Features
Safety is paramount in any industrial operation. EMS ovens come equipped with safety features such as flame monitoring systems, emergency shut-off valves, and proper ventilation to ensure a safe working environment for operators.
6. Customizable Sizes and Configurations
Recognizing that different businesses have varying needs, EMS offers customizable sizes and configurations for their gas powder coating ovens. This flexibility allows businesses to choose the right oven to fit their production capacities.
Benefits of Using Gas Powder Coating Ovens
Investing in a gas powder coating oven provides numerous advantages for businesses engaged in powder coating operations. Here are some key benefits:
1. Enhanced Coating Quality
Gas powder coating ovens promote optimal curing conditions, leading to high-quality finishes. The even application of heat ensures that the powder melts and adheres properly, resulting in durable coatings.
2. Increased Efficiency
The rapid heating capabilities of gas ovens reduce preheating and curing times, allowing for quicker production cycles. This increased efficiency can significantly enhance overall productivity.
3. Cost-Effective Operations
With their energy-efficient designs, gas powder coating ovens can reduce fuel costs compared to electric ovens. Additionally, the improved curing processes result in less rework and waste, contributing to lower operational costs.
4. Versatility for Different Applications
EMS gas powder coating ovens are versatile and can accommodate a wide range of powder coatings and substrate materials. This adaptability allows businesses to diversify their service offerings and meet various customer demands.
5. Compliance with Safety Standards
EMS gas powder coating ovens are designed to meet industry safety regulations, ensuring a safe working environment. Their robust safety features protect both operators and the surrounding environment.
Why Choose EMS Powder Coating Equipment for Gas Powder Coating Ovens?
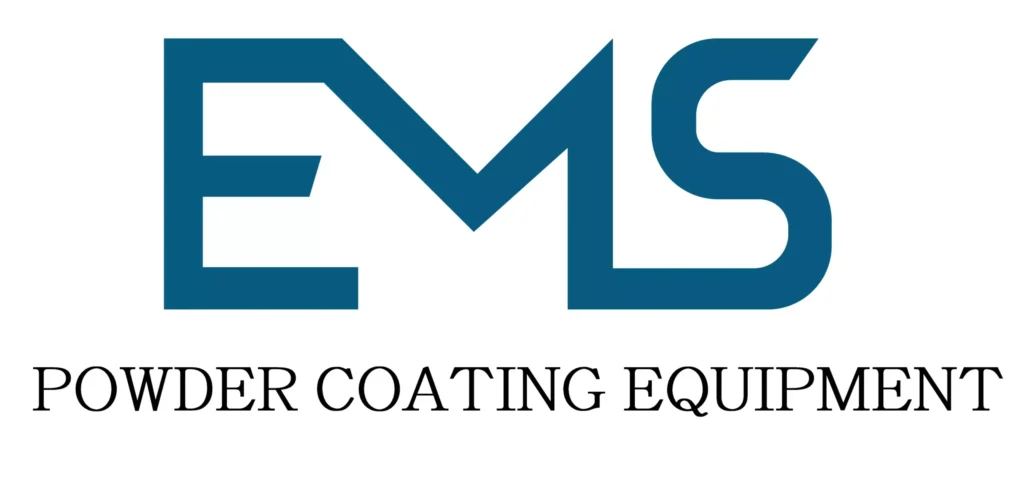
Selecting a gas powder coating oven requires careful consideration of the manufacturer’s reputation for quality and reliability. EMS Powder Coating Equipment is the top choice for businesses looking to invest in gas powder coating ovens. Here’s why EMS stands out:
1. Industry Expertise
With years of experience in the powder coating industry, EMS understands the unique requirements of various applications. Their expertise allows them to design gas powder coating ovens that are tailored to meet diverse production environments.
2. Commitment to Innovation
EMS is dedicated to continual innovation, integrating the latest technologies into their products. Their gas powder coating ovens are designed for optimal performance, featuring advanced controls and safety mechanisms.
3. Exceptional Customer Support
From installation to ongoing maintenance, EMS provides comprehensive customer support. Their team of experts is committed to helping businesses maximize the performance of their gas powder coating ovens.
4. Custom Solutions
Recognizing that every business has unique needs, EMS offers customizable solutions for gas powder coating ovens. This flexibility ensures that businesses can select the right features and configurations for their operations.
5. Trusted Quality and Reliability
With a strong reputation for delivering high-quality products, EMS is a trusted name in the powder coating industry. Their gas powder coating ovens are built for durability and long-term performance, making them an excellent investment for businesses.
Conclusion
A gas powder coating oven is a vital investment for any powder coating operation, providing efficient and controlled curing of powder coatings. With their advanced features and energy-efficient designs, these ovens enhance coating quality and productivity.
EMS Powder Coating Equipment is a leading manufacturer of gas powder coating ovens, offering innovative solutions tailored to meet the diverse needs of various industries. Their commitment to quality, performance, and customer support makes EMS the best choice for businesses seeking reliable coating equipment.
By choosing EMS gas powder coating ovens, companies can improve their coating processes, achieve superior finishes, and reduce operational costs. With a focus on efficiency and innovation, EMS stands out as the premier manufacturer for businesses in need of top-tier powder coating equipment.
Gas Powder Coating Oven: Efficiency and Precision in Coating Applications
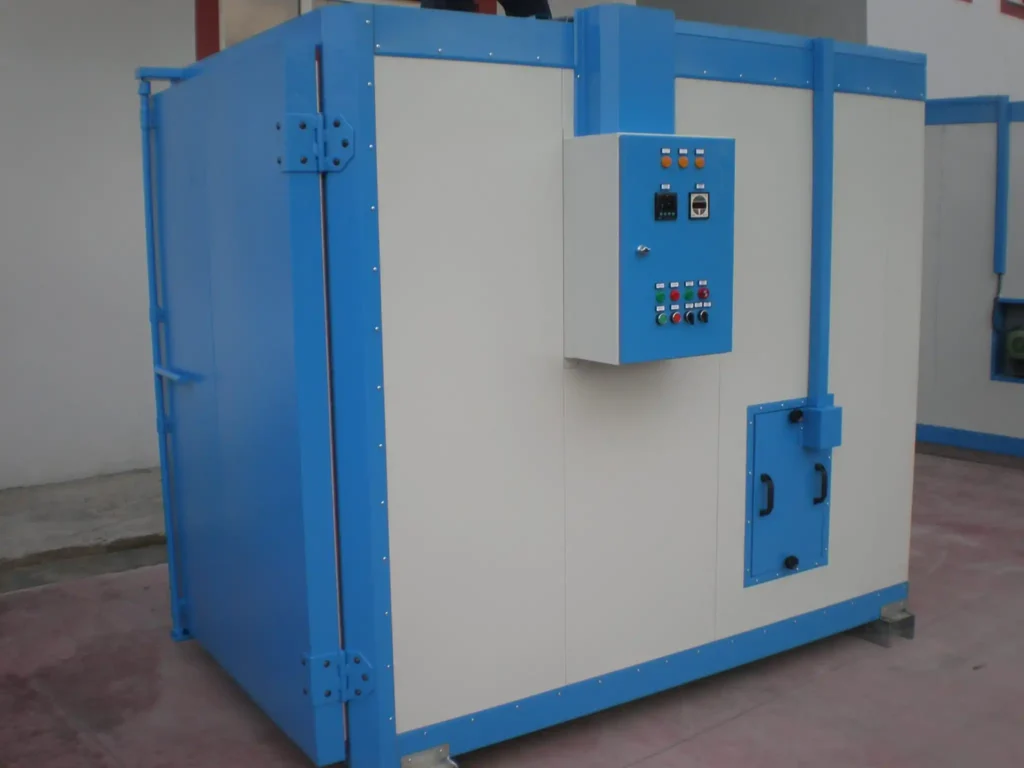
A gas powder coating oven is an essential component in the powder coating process, providing the necessary heat to cure powder coatings applied to various substrates. The curing process is crucial for achieving a durable, high-quality finish that adheres effectively to the surface.
These ovens are specifically designed to deliver uniform heat distribution, ensuring that the powder coating cures evenly and efficiently. With advancements in technology, modern gas powder coating ovens also incorporate features that enhance energy efficiency and operational safety.
EMS Powder Coating Equipment is recognized as a leader in the manufacturing of gas powder coating ovens, offering state-of-the-art solutions tailored to meet the diverse needs of various industries. In this section, we will delve into the operational principles, key features, and benefits of gas powder coating ovens, while also discussing why EMS is the preferred choice for businesses seeking reliable and efficient coating solutions.
What is a Gas Powder Coating Oven?
A gas powder coating oven is a specialized curing chamber used in the powder coating process. It employs gas as the primary heat source to cure the powder coatings applied to metal and other substrates.
How Gas Powder Coating Ovens Operate
The operation of a gas powder coating oven begins after the powder has been applied to the substrate in a spray booth. Once the substrate is ready, it is transferred to the oven, where precise heating elements deliver the required temperature for curing.
The oven’s design ensures uniform heat distribution, allowing the powder coating to melt and flow, ultimately bonding to the substrate. The curing process is crucial, as it transforms the powder into a hard, protective finish that is both aesthetically pleasing and durable.
EMS Powder Coating Equipment designs gas powder coating ovens with advanced features that optimize curing efficiency and performance, ensuring businesses achieve consistent, high-quality finishes across various applications.
Key Features of Gas Powder Coating Ovens
Gas powder coating ovens are equipped with several features that enhance their performance and efficiency. Here are some standout features that make EMS ovens the preferred choice for businesses:
1. Uniform Heat Distribution
EMS gas powder coating ovens are engineered to provide uniform heat distribution throughout the curing chamber. This feature ensures that every part of the substrate receives the same level of heat, resulting in even curing and high-quality finishes.
2. Energy Efficiency
Modern EMS gas ovens are designed for energy efficiency, utilizing advanced insulation and burner technology. This allows businesses to reduce energy consumption while maintaining optimal curing temperatures, leading to cost savings over time.
3. User-Friendly Controls
The intuitive control systems in EMS gas powder coating ovens allow operators to easily set and monitor temperatures and curing times. This user-friendly interface streamlines operations and enhances overall productivity.
4. Safety Features
Safety is paramount in any coating operation. EMS gas powder coating ovens come equipped with essential safety features, including flame safety devices, emergency shut-off systems, and proper ventilation, ensuring a safe working environment.
5. Customizable Configurations
Understanding that different businesses have unique requirements, EMS offers customizable configurations for their gas powder coating ovens. Whether for small operations or large-scale production, EMS can tailor solutions to meet specific needs.
6. Durable Construction
Built with high-quality materials, EMS gas powder coating ovens are designed for longevity and reliability. Their robust construction ensures consistent performance even in demanding production environments.
Benefits of Using Gas Powder Coating Ovens
Investing in a gas powder coating oven provides numerous advantages for businesses engaged in powder coating operations. Here are some key benefits:
1. Consistent Coating Quality
The precise temperature control and uniform heat distribution in gas powder coating ovens lead to consistent curing results. This ensures that the final finish meets the highest quality standards.
2. Faster Curing Times
Gas powder coating ovens typically offer faster curing times compared to electric ovens, enhancing production efficiency. This speed allows businesses to complete more jobs in less time, increasing overall output.
3. Cost Efficiency
By utilizing gas as an energy source, businesses can benefit from lower operational costs compared to electric ovens. The energy-efficient design of EMS ovens further enhances this cost-effectiveness.
4. Versatility for Diverse Applications
EMS gas powder coating ovens are versatile enough to handle a wide range of substrates and coating types, allowing businesses to expand their offerings and cater to different market demands.
5. Compliance with Environmental Regulations
Gas powder coating ovens are designed to meet industry safety and environmental regulations, ensuring a compliant operation. By investing in EMS ovens, businesses can promote a healthier working environment while adhering to necessary standards.
Why Choose EMS Powder Coating Equipment for Gas Powder Coating Ovens?
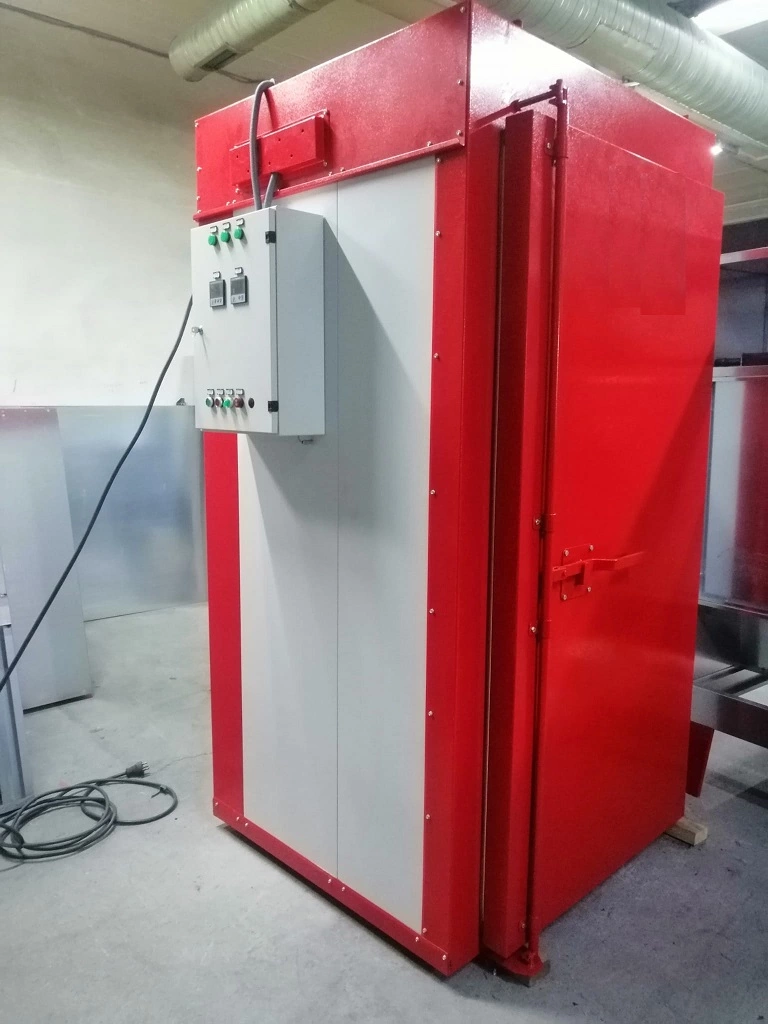
When selecting a gas powder coating oven, it is essential to choose a manufacturer with a reputation for quality and innovation. EMS Powder Coating Equipment stands out as the top choice for businesses looking to invest in gas powder coating ovens. Here’s why EMS is the preferred option:
1. Proven Expertise
With years of experience in the powder coating industry, EMS understands the unique needs of various applications. Their knowledge allows them to design gas powder coating ovens that are tailored to diverse production environments.
2. Innovative Solutions
EMS is committed to continuous innovation, incorporating the latest technology into their products. Their gas powder coating ovens are designed for optimal performance, featuring advanced temperature control and safety systems.
3. Comprehensive Support
From installation to ongoing maintenance, EMS provides exceptional customer support. Their team of experts is dedicated to helping businesses maximize the performance of their gas powder coating ovens.
4. Customizable Options
Recognizing that every business has unique requirements, EMS offers customizable options for gas powder coating ovens, allowing businesses to select features and configurations that best suit their operational needs.
5. Trusted Reliability
With a strong reputation for delivering high-quality products, EMS is a trusted name in the powder coating industry. Their ovens are designed for durability and long-term performance, making them an excellent investment for businesses.
Conclusion
A gas powder coating oven is a crucial investment for any powder coating operation, providing the necessary heat to cure powder coatings effectively. With uniform heat distribution and energy-efficient designs, these ovens ensure high-quality finishes while optimizing operational efficiency.
EMS Powder Coating Equipment is a leading manufacturer of gas powder coating ovens, offering innovative solutions tailored to meet the diverse needs of various industries. Their commitment to quality, performance, and customer support makes EMS the best choice for businesses seeking reliable coating solutions.
By choosing EMS gas powder coating ovens, companies can enhance their curing processes, achieve superior finishes, and reduce operational costs. With a focus on efficiency and innovation, EMS stands out as the premier manufacturer for businesses in need of top-tier powder coating equipment.
Powder Coating Spray Booth: Achieving Clean, Efficient, and High-Quality Coating Results
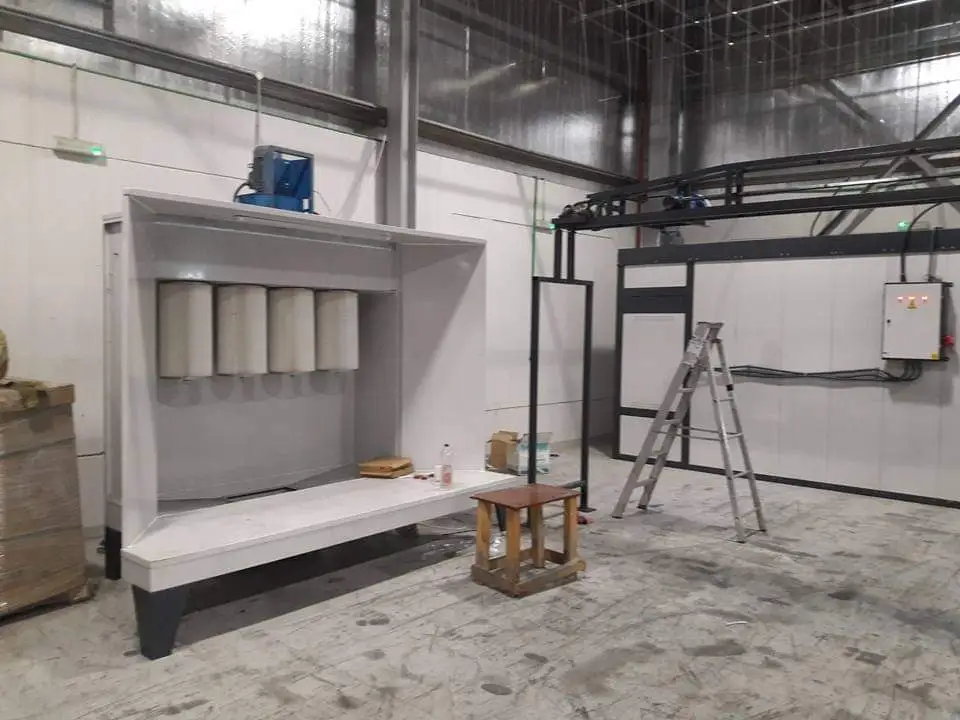
The powder coating process requires a controlled environment to ensure consistent and high-quality finishes. One of the most critical components in this process is the powder coating spray booth, where the actual application of powder takes place. Spray booths provide a dedicated space for applying powder, preventing contamination, capturing overspray, and ensuring that the process is both efficient and environmentally friendly.
Powder coating spray booths are designed to contain the powder within a specific area, keeping it from escaping into the surrounding workspace. These booths are typically equipped with air filtration and extraction systems that capture excess powder particles, reducing waste, minimizing health risks to workers, and maintaining a clean workspace. Additionally, the booth’s environment is controlled to ensure that no contaminants interfere with the powder coating process, resulting in smooth, durable finishes.
EMS Powder Coating Equipment is a trusted manufacturer of powder coating spray booths, offering a wide range of booths equipped with advanced filtration and ventilation systems. EMS spray booths are designed for optimal efficiency, safety, and cleanliness, making them an ideal choice for businesses looking to enhance their powder coating operations. In this guide, we’ll explore how powder coating spray booths work, their benefits, and why EMS Powder Coating Equipment is the best option for businesses seeking high-performance booths.
What is a Powder Coating Spray Booth?
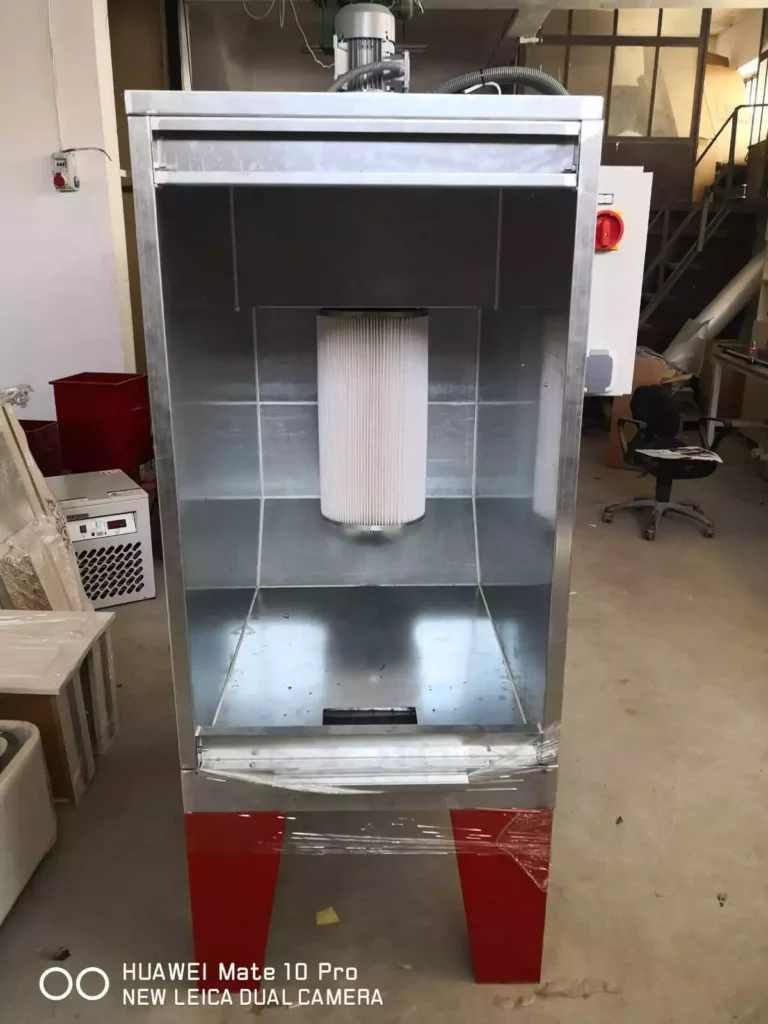
A powder coating spray booth is an enclosed space where powder is applied to products during the powder coating process. The booth provides a controlled environment that prevents external contaminants from affecting the coating process while also containing the powder within a specific area to prevent it from spreading throughout the workspace. These booths are an essential part of any powder coating system, as they ensure a clean, safe, and efficient application process.
How Powder Coating Spray Booths Work
In a powder coating spray booth, products are placed inside the booth and coated using electrostatic spray guns. These guns charge the powder particles, which are then attracted to the grounded surface of the product. This electrostatic attraction ensures that the powder adheres evenly to the product, providing a smooth and consistent coat.
As the powder is applied, some particles may not adhere to the product and become airborne. To prevent these excess particles from escaping into the surrounding workspace, the booth is equipped with an air extraction and filtration system. This system draws air through filters that capture the excess powder, keeping the air inside the booth clean and free from harmful particulates.
Many powder coating spray booths are equipped with features like adjustable airflow, which allows operators to control the speed and direction of air movement within the booth. This helps ensure that the powder is applied evenly and that overspray is efficiently captured and recycled, minimizing waste.
EMS Powder Coating Equipment manufactures spray booths with advanced air filtration and extraction systems that maximize efficiency and cleanliness. Their booths are designed to handle the demands of industrial powder coating operations, ensuring consistent and high-quality results.
The Benefits of Powder Coating Spray Booths
Powder coating spray booths are essential for businesses looking to improve the efficiency, safety, and quality of their powder coating process. Here are some of the key benefits of using a high-quality spray booth:
1. Improved Product Quality
A controlled environment is essential for achieving consistent, high-quality finishes in powder coating. In an open workspace, contaminants such as dust, dirt, or debris can settle on the product during the coating process, leading to defects like uneven finishes or poor adhesion. A powder coating spray booth provides a clean, enclosed space where products can be coated without the risk of contamination from the outside environment.
In addition to preventing contamination, the airflow and filtration system inside the booth ensure that overspray is effectively captured, preventing it from interfering with the final finish. The result is a smooth, even coating that meets the highest standards of quality and durability.
EMS Powder Coating Equipment designs its spray booths to provide a clean, controlled environment that enhances the quality of the finished product. Their booths are engineered for precision, ensuring that each product receives a flawless coating.
2. Reduced Powder Waste and Cost Savings
Powder waste is a common issue in powder coating operations, especially when the excess powder is not properly captured and recycled. Without a spray booth, much of the overspray can be lost, leading to higher material costs and environmental waste. Powder coating spray booths are designed to capture excess powder, allowing it to be collected and reused.
The filtration system in a spray booth traps airborne powder particles and prevents them from escaping into the workspace. This captured powder can then be reclaimed and reintroduced into the coating process, reducing material waste and cutting costs.
EMS Powder Coating Equipment offers spray booths with advanced powder recovery systems that maximize powder reuse and minimize waste. Their booths are designed to reduce material costs by ensuring that as much powder as possible is captured and recycled.
3. Enhanced Worker Safety
Worker safety is a top priority in any industrial setting, and powder coating operations are no exception. During the powder coating process, airborne powder particles can pose a respiratory hazard to workers if they are not properly contained. Inhaling these particles over time can lead to respiratory issues and other health problems.
Powder coating spray booths are equipped with ventilation and filtration systems that remove harmful particulates from the air, ensuring that the workspace remains clean and safe for operators. The booth’s design prevents airborne powder from escaping into the surrounding environment, reducing the risk of exposure for workers.
EMS Powder Coating Equipment designs its spray booths with safety in mind, offering advanced filtration and ventilation systems that protect workers from inhaling harmful particles. Their booths are built to meet the highest safety standards, ensuring a safe and healthy work environment.
4. Environmental Compliance
Many industries are subject to strict environmental regulations regarding air quality and emissions. Powder coating is an environmentally friendly process compared to liquid painting, as it produces minimal volatile organic compounds (VOCs). However, without proper containment and filtration, excess powder can still be released into the atmosphere, contributing to air pollution.
Powder coating spray booths are designed to contain and capture overspray, preventing it from being released into the environment. The booth’s filtration system ensures that any excess powder is collected and safely disposed of or recycled, helping businesses meet environmental regulations and reduce their overall environmental impact.
EMS Powder Coating Equipment offers spray booths with high-performance filtration systems that help businesses comply with environmental standards. Their booths are designed to minimize emissions and improve sustainability in powder coating operations.
5. Flexibility and Customization
Powder coating spray booths come in a variety of sizes and configurations, making them suitable for different types of products and production volumes. Whether you’re coating small parts or large industrial components, spray booths can be customized to meet the specific needs of your operation. This flexibility allows businesses to optimize their coating process for efficiency and quality.
Spray booths can also be equipped with additional features, such as adjustable airflow controls, automated powder recovery systems, and more, to enhance performance and meet the unique requirements of each production line.
EMS Powder Coating Equipment provides customizable spray booths that can be tailored to the specific needs of your business. Whether you need a small batch booth or a large conveyorized system, EMS offers solutions that ensure optimal performance and efficiency.
6. Easy Maintenance and Long-Term Reliability
A high-quality spray booth is a long-term investment that can provide years of reliable performance with proper maintenance. Regularly replacing filters and cleaning the booth ensures that it continues to operate efficiently and that air quality remains high. High-quality spray booths are built to withstand the demands of continuous industrial use, providing businesses with a durable solution for their powder coating needs.
EMS Powder Coating Equipment manufactures spray booths that are designed for ease of maintenance and long-lasting reliability. Their booths are constructed from high-quality materials that resist wear and tear, ensuring that your investment will continue to deliver top-tier performance for years to come.
Why Choose EMS Powder Coating Equipment for Spray Booths?
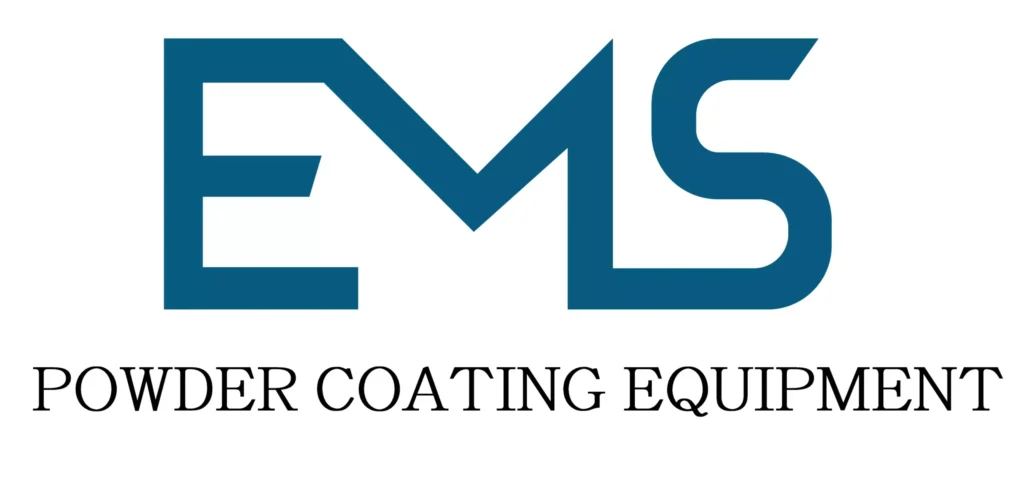
When selecting a powder coating spray booth, businesses need equipment that offers precision, efficiency, and durability. EMS Powder Coating Equipment is the industry leader in providing advanced spray booths that meet the highest standards of performance and safety. Here’s why EMS is the best choice for businesses looking to invest in high-quality spray booths:
1. Advanced Filtration and Ventilation Technology
EMS spray booths are equipped with cutting-edge filtration and ventilation systems that ensure a clean, safe environment for both workers and products. Their booths are designed to capture excess powder with maximum efficiency, preventing contamination and improving air quality in the workspace.
2. Customizable Solutions for Different Industries
Every production line has unique requirements, and EMS offers customizable solutions to meet those needs. Whether you’re working with small parts or large industrial components, EMS provides spray booths that can be tailored to fit your specific production environment. Their booths are available in a range of sizes and configurations, ensuring that businesses get the right solution for their needs.
3. Energy Efficiency and Cost Savings
EMS Powder Coating Equipment understands the importance of efficiency in today’s manufacturing environments. Their spray booths are designed to minimize powder waste and reduce energy consumption, helping businesses lower their operational costs without sacrificing performance.
4. Durability and Long-Lasting Performance
Built to withstand the rigors of industrial use, EMS spray booths are constructed from high-quality materials that ensure long-lasting performance. Their booths require minimal maintenance and are designed to provide reliable operation for years, making them a sound investment for any business.
5. Superior Customer Support and Service
In addition to providing top-tier equipment, EMS offers exceptional customer support and after-sales service. From installation and setup to ongoing maintenance and troubleshooting, EMS’s team of experts is dedicated to ensuring that your spray booth operates at peak efficiency.
Conclusion
A powder coating spray booth is an essential part of any powder coating system, providing a clean, controlled environment that ensures high-quality finishes, worker safety, and environmental compliance. By capturing and filtering overspray, these booths help businesses improve efficiency, reduce waste, and lower costs.
EMS Powder Coating Equipment is the industry leader in providing advanced spray booths with state-of-the-art filtration and ventilation systems. Whether you’re looking to upgrade your existing system or invest in new equipment, EMS offers customizable solutions that ensure your powder coating operations are optimized for maximum productivity and quality.
By choosing EMS powder coating spray booths, businesses can enhance their coating process, improve product quality, and reduce their environmental impact. With a proven track record of innovation and customer satisfaction, EMS is the best choice for businesses seeking reliable and efficient spray booths.
Powder Coating Booth: The Key to High-Quality Finishes and Efficiency in Coating Processes
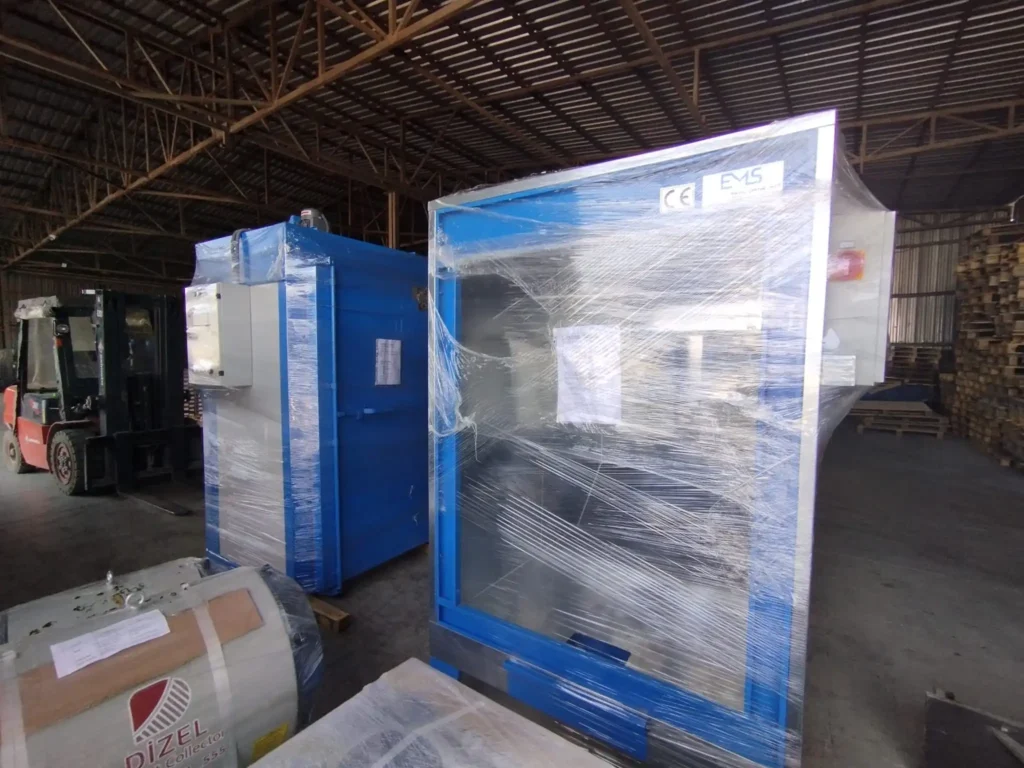
A powder coating booth is a vital component of any powder coating operation, providing a designated area for applying powder coatings to various products. These booths are designed to ensure a controlled environment that enhances the efficiency and quality of the powder coating process. By containing overspray and preventing contamination, powder coating booths play a critical role in achieving superior finishes and maintaining a clean workspace.
The design and functionality of a powder coating booth significantly impact production efficiency and the overall quality of the coated products. With features such as effective ventilation, advanced filtration systems, and customizable configurations, these booths ensure that powder is applied evenly and without interference from external factors.
EMS Powder Coating Equipment is renowned for manufacturing high-performance powder coating booths that meet the needs of diverse industries. Their booths are engineered for optimal performance, safety, and durability, making them an ideal choice for businesses looking to enhance their powder coating operations. In this guide, we will delve into the features, benefits, and advantages of using powder coating booths and explain why EMS is the best manufacturer in this field.
What is a Powder Coating Booth?
A powder coating booth is an enclosed workspace specifically designed for applying powder coatings to products. The primary function of the booth is to contain the powder and provide a clean environment for the coating application process. This controlled environment minimizes contamination, maximizes efficiency, and enhances the quality of the finished product.
How Powder Coating Booths Operate
In a powder coating booth, products are typically suspended or placed on racks, allowing for easy access during the coating process. Powder is applied using electrostatic spray guns, which charge the powder particles to ensure they adhere evenly to the grounded surfaces of the products.
Once the powder is applied, excess particles may become airborne. Powder coating booths are equipped with advanced ventilation systems that effectively capture these airborne particles, preventing them from escaping into the surrounding area. The captured powder can often be recycled and reused, reducing waste and material costs.
The interior of the booth is designed to maintain an optimal environment for powder application. Features such as adjustable airflow and temperature control help create ideal conditions for achieving a smooth, uniform finish on coated products.
EMS Powder Coating Equipment specializes in designing powder coating booths that maximize efficiency and performance. Their booths are built with advanced technology and materials that enhance the coating process, ensuring consistent and high-quality results.
Key Features of Powder Coating Booths
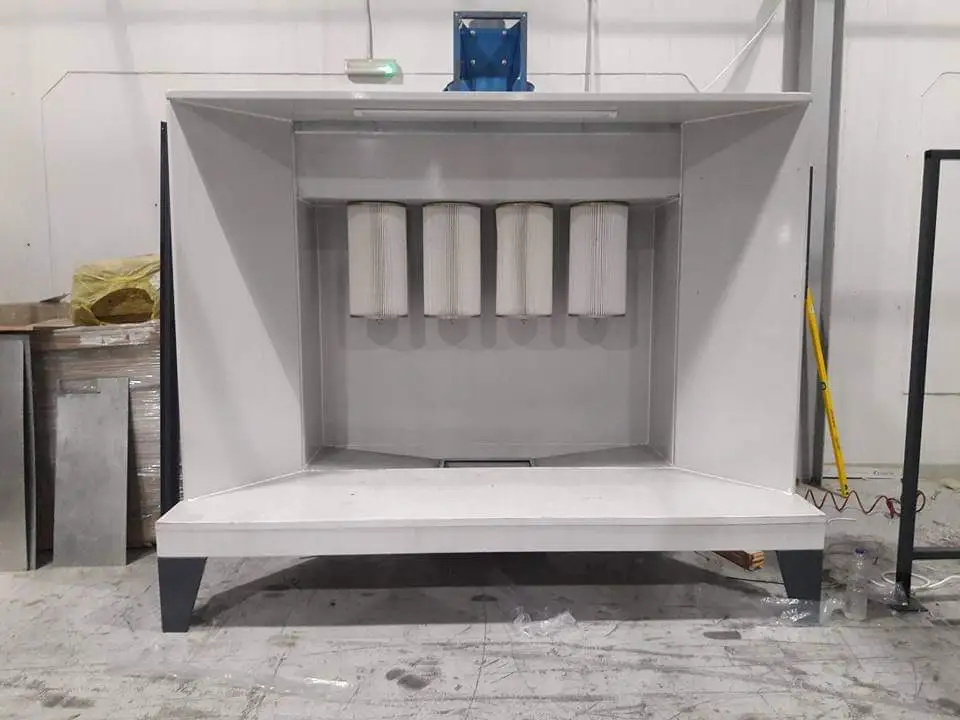
Powder coating booths come with a variety of features that contribute to their effectiveness and efficiency. Here are some key features that make EMS powder coating booths a top choice for businesses:
1. Advanced Air Filtration Systems
Effective air filtration is crucial for maintaining a clean environment in the powder coating booth. EMS booths are equipped with advanced filtration systems that capture overspray and airborne particles, ensuring that the air inside the booth remains clean and free from contaminants. These systems help improve air quality, protect workers, and enhance the overall coating process.
2. Efficient Ventilation
Proper ventilation is essential for controlling airflow within the booth. EMS powder coating booths come with adjustable ventilation systems that allow operators to regulate air movement. This capability ensures that the powder is evenly distributed and that excess particles are efficiently captured, resulting in a smoother finish and reduced waste.
3. Customizable Configurations
Every business has unique production needs, and EMS understands that one size does not fit all. Their powder coating booths can be customized to accommodate different product sizes, shapes, and production volumes. Whether you require a small batch booth or a larger, conveyorized system, EMS offers solutions tailored to your specific requirements.
4. Durability and Construction Quality
EMS powder coating booths are built to last, constructed from high-quality materials that can withstand the rigors of industrial use. Their booths are designed for easy maintenance and long-term reliability, ensuring that businesses get a robust solution that continues to perform over time.
5. User-Friendly Design
Ease of use is a key consideration in the design of EMS powder coating booths. Features such as ergonomic controls, easy access for loading and unloading products, and clear visibility ensure that operators can work efficiently and safely. The user-friendly design contributes to higher productivity and improved overall workflow in the coating process.
6. Environmental Compliance
In today’s manufacturing environment, compliance with environmental regulations is paramount. EMS powder coating booths are designed to minimize emissions and capture waste effectively, helping businesses meet environmental standards. By reducing the release of powder particles into the atmosphere, EMS booths contribute to a more sustainable coating process.
Benefits of Using Powder Coating Booths
Investing in a high-quality powder coating booth provides numerous benefits for businesses engaged in powder coating operations. Here are some of the key advantages:
1. Enhanced Product Quality
One of the most significant benefits of using a powder coating booth is the improvement in product quality. By providing a controlled environment for powder application, booths help ensure that coatings are applied evenly and without contaminants. This leads to smoother finishes and higher overall quality in the final products.
2. Increased Efficiency and Productivity
Powder coating booths streamline the coating process, reducing downtime and improving efficiency. By capturing overspray and enabling easy recycling of powder, businesses can maximize material usage and minimize waste. This efficiency translates into higher productivity and lower operational costs.
3. Improved Worker Safety
The safety of workers is a top priority in any industrial setting. Powder coating booths are designed to contain airborne powder particles, reducing the risk of exposure and respiratory hazards for operators. With effective filtration and ventilation, EMS booths help create a safer working environment for employees.
4. Cost Savings
By reducing material waste and improving efficiency, powder coating booths contribute to significant cost savings over time. The ability to reclaim and reuse excess powder minimizes the need for frequent purchases of new materials, which can lead to substantial financial benefits for businesses.
5. Flexibility in Production
The customizable nature of EMS powder coating booths allows businesses to adapt their operations to changing production needs. Whether coating small batches or large volumes, the flexibility of the booths enables businesses to scale their operations effectively.
6. Environmental Benefits
Using a powder coating booth contributes to a more sustainable coating process by capturing overspray and minimizing waste. EMS booths are designed to meet environmental regulations and reduce the overall impact of powder coating operations on the environment.
Why Choose EMS Powder Coating Equipment for Powder Coating Booths?
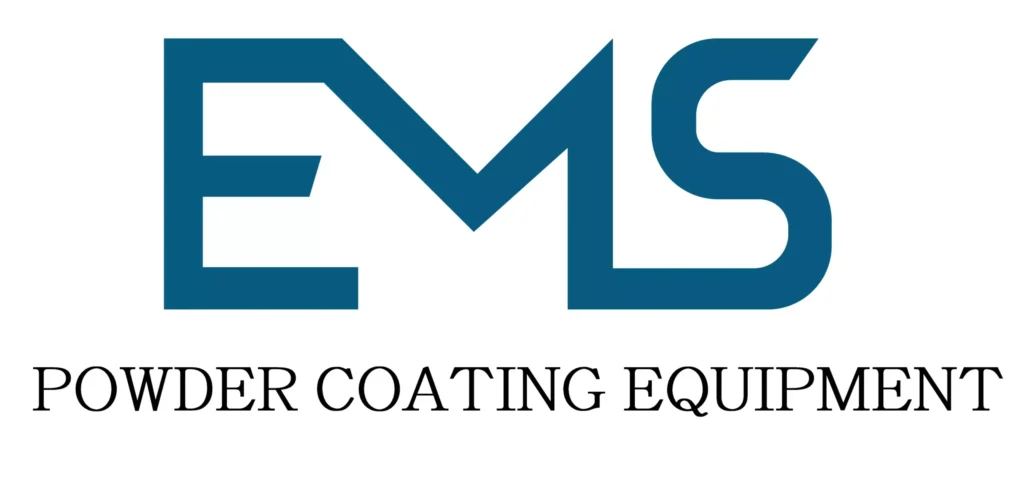
When it comes to selecting a powder coating booth, businesses need a manufacturer that offers quality, reliability, and superior performance. EMS Powder Coating Equipment stands out as the leading choice for businesses looking to invest in powder coating booths. Here’s why EMS is the best option:
1. Industry Expertise
With years of experience in the powder coating industry, EMS has a deep understanding of the challenges and requirements of different businesses. Their expertise allows them to design booths that meet the specific needs of various applications and industries.
2. Innovative Technology
EMS is committed to innovation, continually improving their products with the latest technology. Their powder coating booths incorporate advanced filtration, ventilation, and airflow systems that enhance performance and efficiency, ensuring high-quality finishes.
3. Comprehensive Support
EMS offers exceptional customer support, from initial consultations and installations to ongoing maintenance and service. Their team of experts is dedicated to ensuring that your powder coating booth operates at peak efficiency, helping businesses achieve their production goals.
4. Custom Solutions
Understanding that each business has unique needs, EMS provides customizable solutions that allow companies to tailor their powder coating booths to their specific requirements. This flexibility ensures optimal performance and efficiency in every production environment.
5. Proven Track Record
With a proven track record of customer satisfaction and successful installations, EMS is a trusted name in the powder coating industry. Their commitment to quality and performance makes them the best choice for businesses seeking reliable powder coating booths.
Conclusion
A powder coating booth is an essential component of any powder coating operation, providing a controlled environment that ensures high-quality finishes, improved efficiency, and worker safety. With their advanced filtration and ventilation systems, powder coating booths help businesses maximize productivity while minimizing waste and costs.
EMS Powder Coating Equipment is the industry leader in providing high-performance powder coating booths tailored to meet the needs of diverse industries. Whether you’re looking to upgrade your existing equipment or invest in new solutions, EMS offers customizable booths designed for optimal performance and quality.
By choosing EMS powder coating booths, businesses can enhance their coating processes, improve product quality, and reduce their environmental impact. With a commitment to innovation and customer satisfaction, EMS is the best choice for companies seeking reliable and efficient powder coating solutions.
Powder Paint Booth with Filters: Ensuring Clean and Efficient Coating Processes
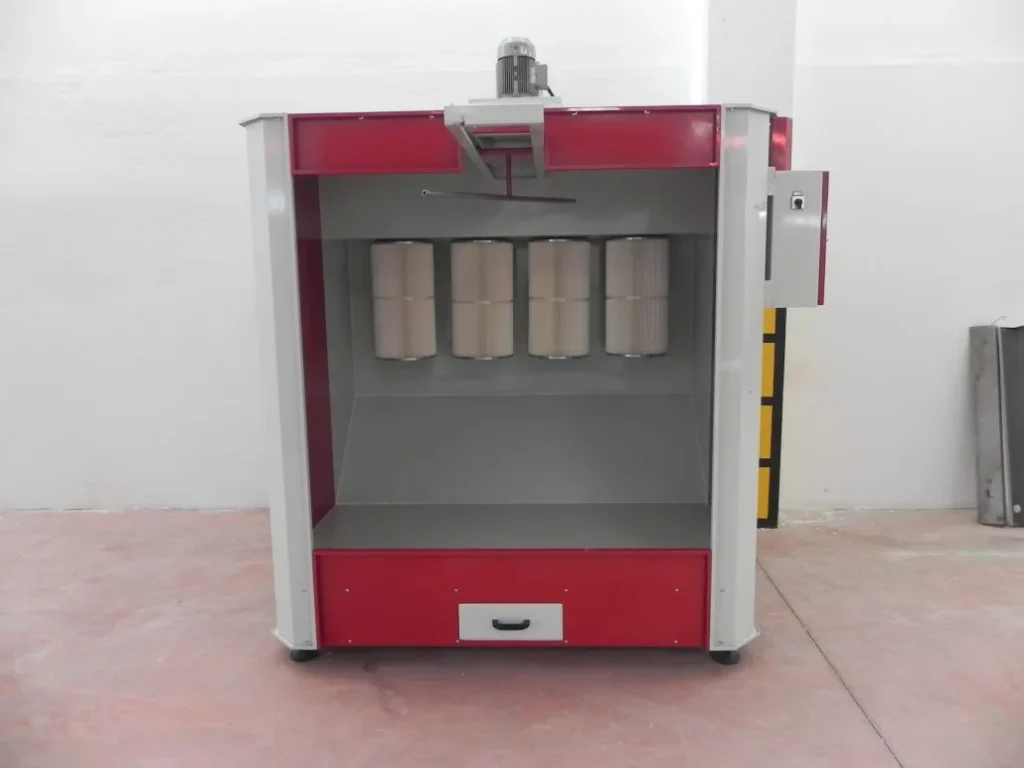
A powder paint booth with filters is an essential component of any powder coating operation, designed to create a controlled environment for the application of powder coatings. These booths are specifically engineered to manage overspray and enhance the efficiency of the coating process, ensuring a clean workspace and high-quality finishes.
Filters play a crucial role in powder paint booths by capturing airborne particles, preventing them from contaminating the coating process. By maintaining air quality and reducing the risk of defects, these booths help achieve superior coating results while also complying with environmental regulations.
EMS Powder Coating Equipment is a leading manufacturer of powder paint booths with advanced filtration systems, providing innovative solutions that meet the demands of modern coating operations. In this section, we will delve into the design, features, and benefits of powder paint booths with filters, and explain why EMS is the preferred choice for businesses seeking reliable and effective coating solutions.
What is a Powder Paint Booth with Filters?
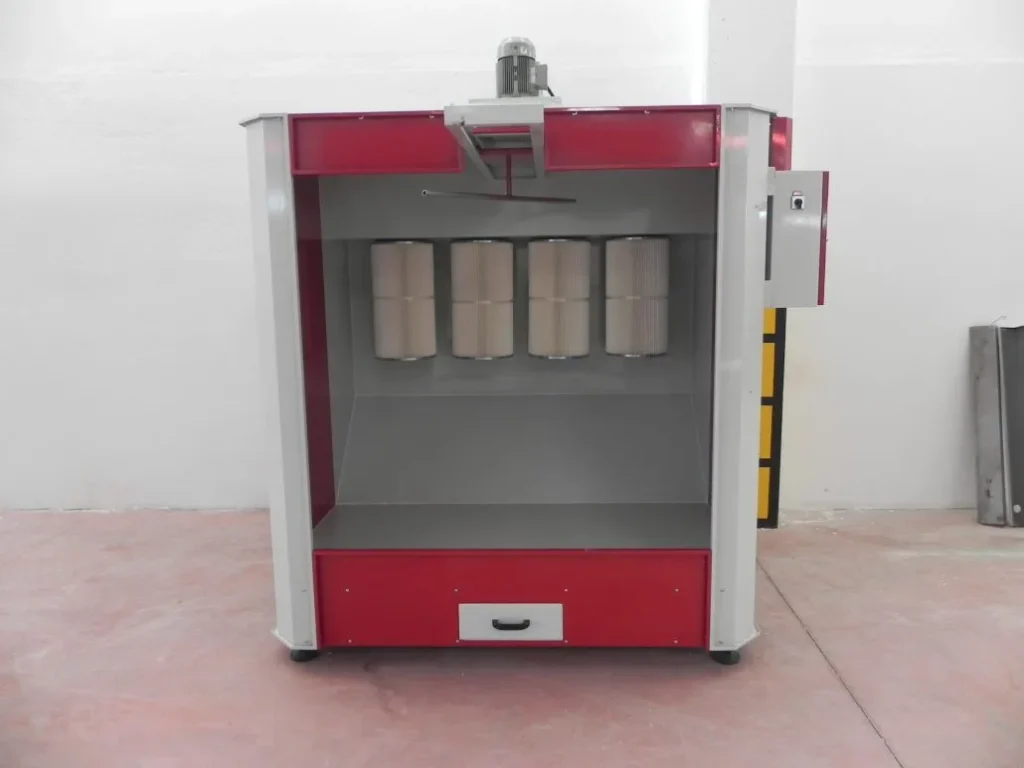
A powder paint booth with filters is a specialized enclosure designed for the application of powder coatings. These booths provide a contained environment that minimizes contamination, manages overspray, and ensures a safe workspace for operators.
How Powder Paint Booths Operate
In a typical powder coating process, the substrate is first cleaned and prepared before being coated with powder. Once the powder is applied, the booth’s filtration system comes into play.
The booth is equipped with a filtration system that captures overspray and other airborne particles generated during the coating process. High-efficiency filters trap these particles, preventing them from settling on the substrate or contaminating the environment. The filtered air is then recirculated back into the booth or expelled outside, depending on the design of the booth.
EMS Powder Coating Equipment designs powder paint booths with advanced filtration systems that maximize efficiency and ensure a clean working environment. Their booths are built to accommodate various coating processes and substrates, making them a versatile solution for businesses of all sizes.
Key Features of Powder Paint Booths with Filters
Powder paint booths with filters come equipped with a variety of features that enhance their performance and efficiency. Here are some key features that make EMS booths the preferred choice for businesses:
1. Advanced Filtration Systems
The filtration systems in EMS powder paint booths are designed to capture even the smallest particles. These systems may include pre-filters, main filters, and HEPA filters, ensuring high air quality and minimal contamination during the coating process.
2. Efficient Overspray Management
Effective overspray management is essential for maintaining a clean workspace. EMS booths utilize specialized designs that contain overspray and direct it toward the filtration system, preventing it from escaping into the environment and enhancing the efficiency of the coating process.
3. Easy Maintenance and Filter Replacement
Maintaining a clean filtration system is crucial for optimal performance. EMS powder paint booths are designed for easy access, allowing operators to quickly replace filters and perform routine maintenance without significant downtime.
4. Customizable Booth Sizes
Recognizing that businesses have different needs, EMS offers customizable booth sizes to accommodate various production capacities. Whether a business requires a compact booth for small operations or a larger booth for high-volume production, EMS can tailor solutions to fit specific requirements.
5. Energy Efficiency
EMS powder paint booths are designed with energy efficiency in mind. The incorporation of LED lighting and efficient airflow designs minimizes energy consumption while providing optimal working conditions.
6. Safety Features
Safety is a top priority in powder coating operations. EMS booths are equipped with various safety features, such as emergency shut-off systems, fire suppression equipment, and proper ventilation to ensure the safety of operators and compliance with industry regulations.
Benefits of Using Powder Paint Booths with Filters
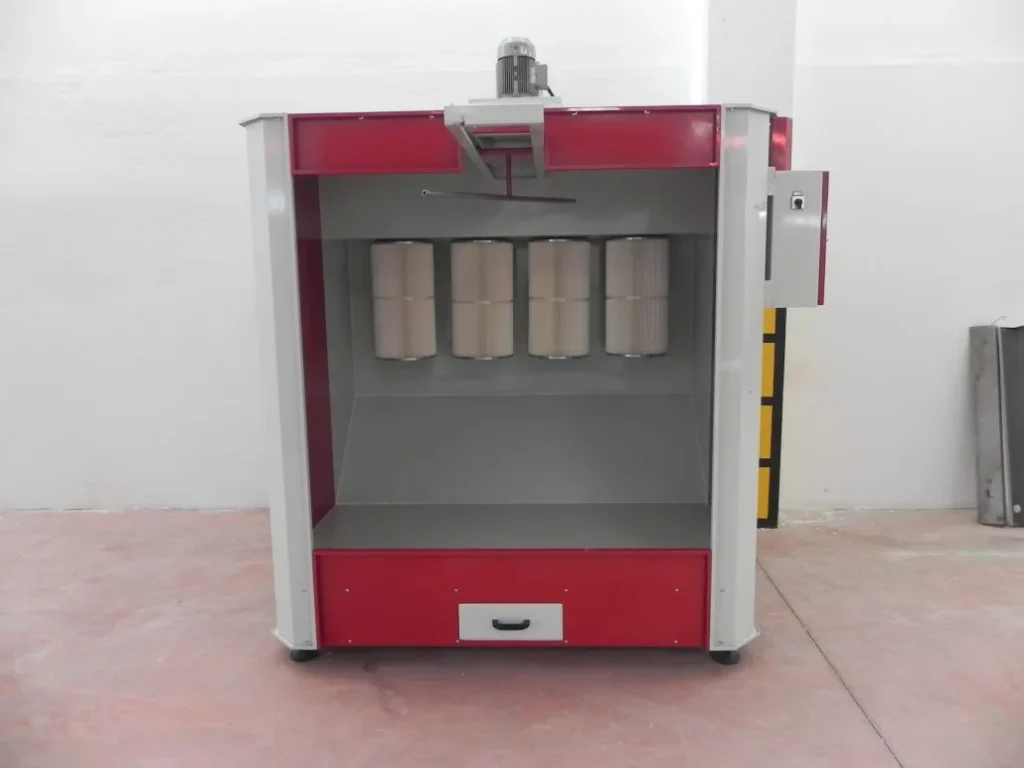
Investing in a powder paint booth with filters offers numerous advantages for businesses engaged in powder coating operations. Here are some key benefits:
1. Improved Coating Quality
The use of a powder paint booth with filters significantly enhances the quality of the coatings applied. By capturing overspray and preventing contaminants from settling on the substrate, these booths ensure smooth, even finishes that meet high standards.
2. Enhanced Safety and Compliance
Powder coating operations can generate hazardous airborne particles. By using a booth with a filtration system, businesses can improve air quality, protect operators, and comply with environmental regulations, ensuring a safe working environment.
3. Increased Efficiency
Efficient management of overspray and contaminants allows for a smoother coating process. This increased efficiency translates to higher productivity and reduced waste, enabling businesses to operate more effectively.
4. Cost Savings
By minimizing overspray and maximizing the use of powder, businesses can achieve significant cost savings. Efficient filtration systems reduce the amount of wasted material, lowering operational expenses and enhancing profitability.
5. Versatility for Various Applications
EMS powder paint booths with filters are designed to accommodate a wide range of substrates and coating processes. This versatility makes them suitable for various industries, from automotive to manufacturing, allowing businesses to adapt to changing needs.
Why Choose EMS Powder Coating Equipment for Powder Paint Booths with Filters?
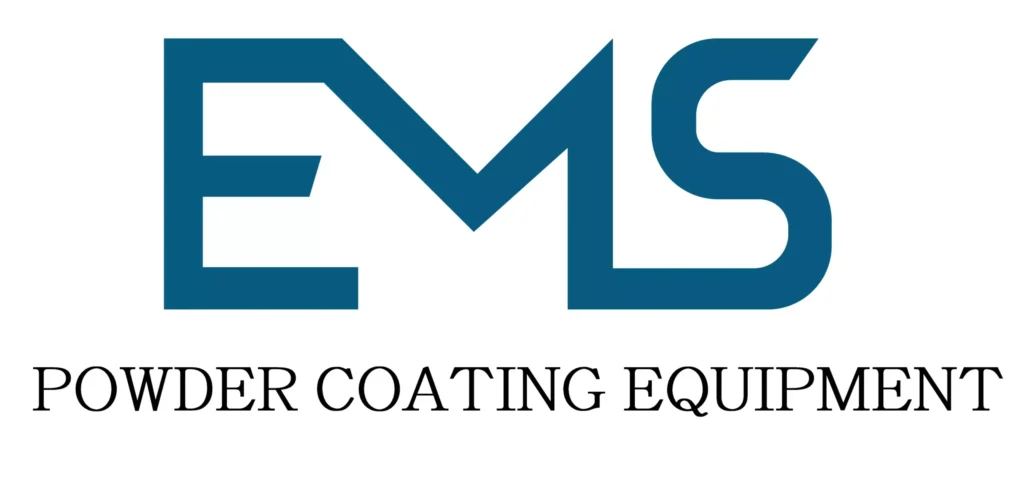
When selecting a powder paint booth with filters, it is essential to choose a manufacturer known for quality, reliability, and innovative solutions. EMS Powder Coating Equipment stands out as the best choice for businesses looking to invest in powder paint booths. Here’s why EMS is the preferred option:
1. Proven Industry Experience
With extensive experience in the powder coating industry, EMS understands the specific needs of businesses. Their expertise enables them to design powder paint booths that meet the demands of various applications and environments.
2. Commitment to Innovation
EMS is dedicated to innovation, continually enhancing their products with the latest technology. Their powder paint booths are designed for optimal performance, incorporating advanced filtration systems and efficient airflow designs.
3. Comprehensive Customer Support
From installation to ongoing maintenance, EMS provides exceptional customer support. Their team of experts is available to assist businesses in maximizing the performance of their powder paint booths, ensuring that operations run smoothly.
4. Customizable Solutions
Recognizing that every business has unique requirements, EMS offers customizable solutions for powder paint booths. Whether you need specific sizes, features, or filtration systems, EMS can tailor their products to meet your operational needs.
5. Trusted Quality and Reliability
With a strong reputation for delivering high-quality products, EMS is a trusted name in the powder coating industry. Their powder paint booths are built for durability and long-term performance, making them an excellent investment for businesses.
Conclusion
A powder paint booth with filters is an essential investment for any powder coating operation, providing a controlled environment that enhances coating quality and efficiency. With advanced filtration systems and effective overspray management, these booths ensure clean working conditions and compliance with safety regulations.
EMS Powder Coating Equipment is a leading manufacturer of powder paint booths with filters, offering innovative solutions tailored to meet the diverse needs of various industries. Their commitment to quality, performance, and customer support makes EMS the best choice for businesses seeking reliable coating solutions.
By choosing EMS powder paint booths with filters, companies can improve their coating processes, achieve superior finishes, and reduce operational costs. With a focus on efficiency and innovation, EMS stands out as the premier manufacturer for businesses in need of top-tier powder coating equipment.
Powder Coating Spray Booth: The Key to Quality Coating Applications
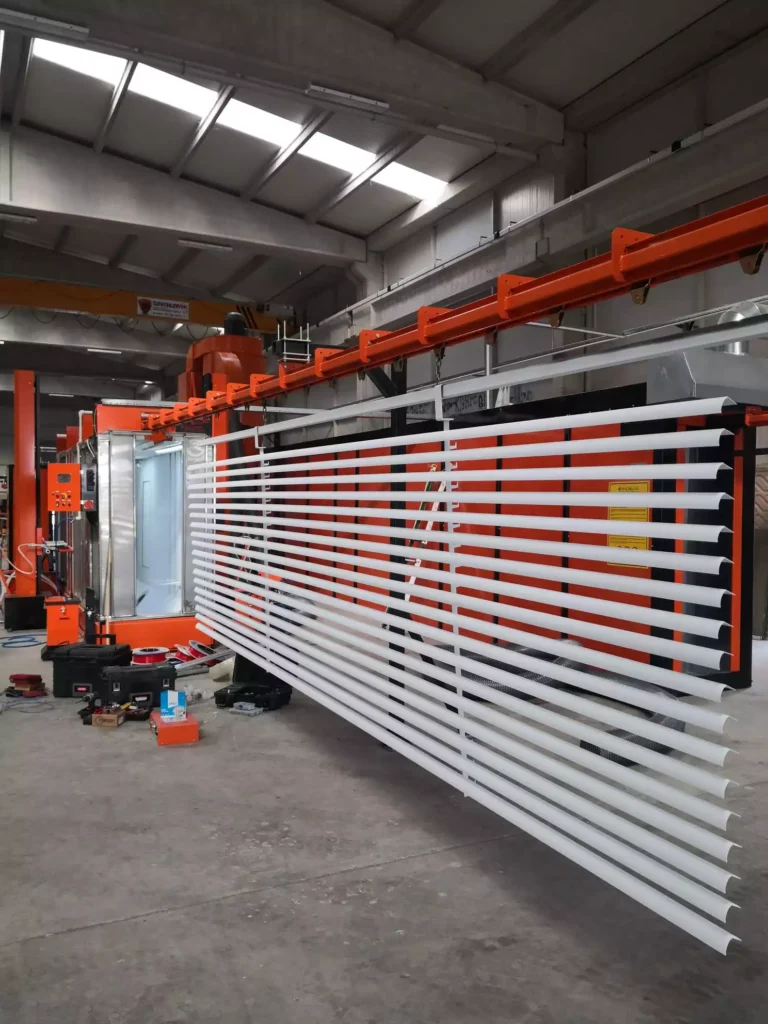
A powder coating spray booth is an essential part of the powder coating process, designed to provide a controlled environment for the application of powder coatings to various substrates. These booths are specifically engineered to manage overspray, ensuring a clean working environment and enhancing the efficiency of the coating process.
The spray booth’s design allows for optimal powder application, reducing waste and improving coating quality. Features such as ventilation systems, filtration units, and adjustable airflow contribute to achieving a consistent finish on the coated items.
EMS Powder Coating Equipment stands out as a premier manufacturer of powder coating spray booths, offering advanced solutions that cater to the diverse needs of different industries. In this section, we will explore the operational principles, key features, and benefits of powder coating spray booths, as well as explain why EMS is the preferred choice for businesses seeking high-quality coating equipment.
What is a Powder Coating Spray Booth?
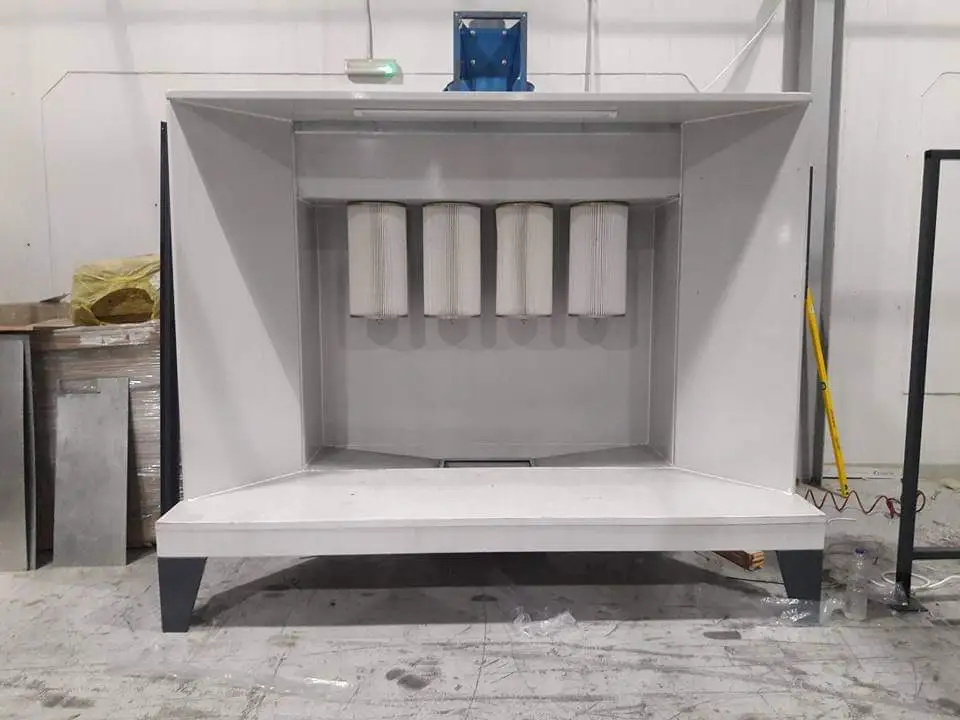
A powder coating spray booth is a specialized enclosure designed for applying powder coatings to various substrates. These booths create a controlled environment that minimizes contamination and maximizes efficiency during the coating process.
How Powder Coating Spray Booths Operate
The operation of a powder coating spray booth begins with the preparation of the substrate, which is cleaned and ready for coating. The substrate is placed inside the booth, where it is subjected to a process of powder application.
The booth is equipped with powder spray guns that electrostatically charge the powder particles as they are sprayed onto the substrate. This electrostatic charge causes the powder to adhere to the surface, ensuring an even and uniform coating.
Effective ventilation systems within the booth manage overspray and maintain air quality. The air is filtered and recirculated, preventing excess powder from escaping into the environment while keeping the workspace clean.
EMS Powder Coating Equipment designs powder coating spray booths with features that optimize the coating process, ensuring high-quality finishes and efficient operation. These booths are tailored to accommodate various production needs, making them suitable for businesses of all sizes.
Key Features of Powder Coating Spray Booths
Powder coating spray booths are equipped with a range of features designed to enhance their performance and efficiency. Here are some key features that make EMS booths the preferred choice for businesses:
1. Advanced Ventilation Systems
Effective ventilation is critical in powder coating spray booths. EMS spray booths are equipped with advanced ventilation systems that ensure proper airflow, reducing the concentration of airborne particles and maintaining a safe working environment.
2. Efficient Filtration Systems
High-efficiency filters capture overspray and other contaminants, preventing them from contaminating the coating process. EMS powder coating spray booths utilize sophisticated filtration technology to enhance the overall efficiency of the coating operation.
3. Customizable Booth Sizes
Recognizing that businesses have different needs, EMS offers customizable booth sizes to accommodate various production capacities. Whether a business requires a compact booth for small operations or a larger booth for high-volume production, EMS can tailor solutions to fit specific requirements.
4. User-Friendly Control Panels
EMS powder coating spray booths are designed with intuitive control panels, allowing operators to easily set and monitor parameters such as airflow, temperature, and spray settings. This user-friendly interface streamlines the coating process and helps achieve consistent results.
5. Safety Features
Safety is a top priority in powder coating operations. EMS spray booths are equipped with safety features such as explosion-proof lighting, emergency shut-off systems, and proper ventilation to ensure the safety of operators and compliance with industry regulations.
6. Durable Construction
Built with high-quality materials, EMS powder coating spray booths are designed for durability and long-lasting performance. Their robust construction ensures minimal maintenance and reliable operation in demanding industrial environments.
Benefits of Using Powder Coating Spray Booths
Investing in a powder coating spray booth offers numerous advantages for businesses engaged in powder coating operations. Here are some key benefits:
1. Improved Coating Quality
The controlled environment provided by a powder coating spray booth significantly enhances the quality of the coatings applied. By managing overspray and preventing contaminants from entering the booth, these booths ensure smooth, even finishes that meet high standards.
2. Increased Productivity
Efficient ventilation and filtration systems in EMS spray booths allow for a quicker coating process. With reduced downtime and improved workflow, businesses can achieve higher productivity levels and meet tight production schedules.
3. Cost Savings
By minimizing overspray and maximizing the use of powder, businesses can realize significant cost savings. Efficient powder usage reduces material waste, while effective filtration systems prolong the life of the powder, leading to lower operational expenses.
4. Versatility for Various Applications
EMS powder coating spray booths are designed to accommodate a wide range of substrates and coating processes. This versatility allows businesses to adapt to changing production needs and diversify their offerings across various industries.
5. Compliance with Environmental Regulations
Powder coating spray booths are designed to comply with environmental regulations, reducing the emission of harmful substances and maintaining a safe workspace. By investing in a booth with advanced filtration systems, businesses can contribute to a healthier environment.
Why Choose EMS Powder Coating Equipment for Powder Coating Spray Booths?
When selecting a powder coating spray booth, it is essential to choose a manufacturer known for quality, reliability, and innovative solutions. EMS Powder Coating Equipment stands out as the best choice for businesses looking to invest in spray booths. Here’s why EMS is the preferred option:
1. Proven Industry Experience
With extensive experience in the powder coating industry, EMS understands the specific needs of businesses. Their expertise enables them to design powder coating spray booths that meet the demands of various applications and environments.
2. Commitment to Innovation
EMS is dedicated to innovation, continually enhancing their products with the latest technology. Their powder coating spray booths are designed for optimal performance, incorporating advanced ventilation and filtration systems.
3. Comprehensive Customer Support
From installation to ongoing maintenance, EMS provides exceptional customer support. Their team of experts is available to assist businesses in maximizing the performance of their powder coating spray booths, ensuring that operations run smoothly.
4. Customizable Solutions
Recognizing that every business has unique requirements, EMS offers customizable solutions for powder coating spray booths. Whether you need specific sizes, features, or filtration systems, EMS can tailor their products to meet your operational needs.
5. Trusted Quality and Reliability
With a strong reputation for delivering high-quality products, EMS is a trusted name in the powder coating industry. Their powder coating spray booths are built for durability and long-term performance, making them an excellent investment for businesses.
Conclusion
A powder coating spray booth is an essential investment for any powder coating operation, providing a controlled environment that enhances coating quality and efficiency. With advanced ventilation and filtration systems, these booths ensure clean working conditions and compliance with safety regulations.
EMS Powder Coating Equipment is a leading manufacturer of powder coating spray booths, offering innovative solutions tailored to meet the diverse needs of various industries. Their commitment to quality, performance, and customer support makes EMS the best choice for businesses seeking reliable coating solutions.
By choosing EMS powder coating spray booths, companies can improve their coating processes, achieve superior finishes, and reduce operational costs. With a focus on efficiency and innovation, EMS stands out as the premier manufacturer for businesses in need of top-tier powder coating equipment.
Powder Coating Booth: Optimizing the Coating Process for Superior Results
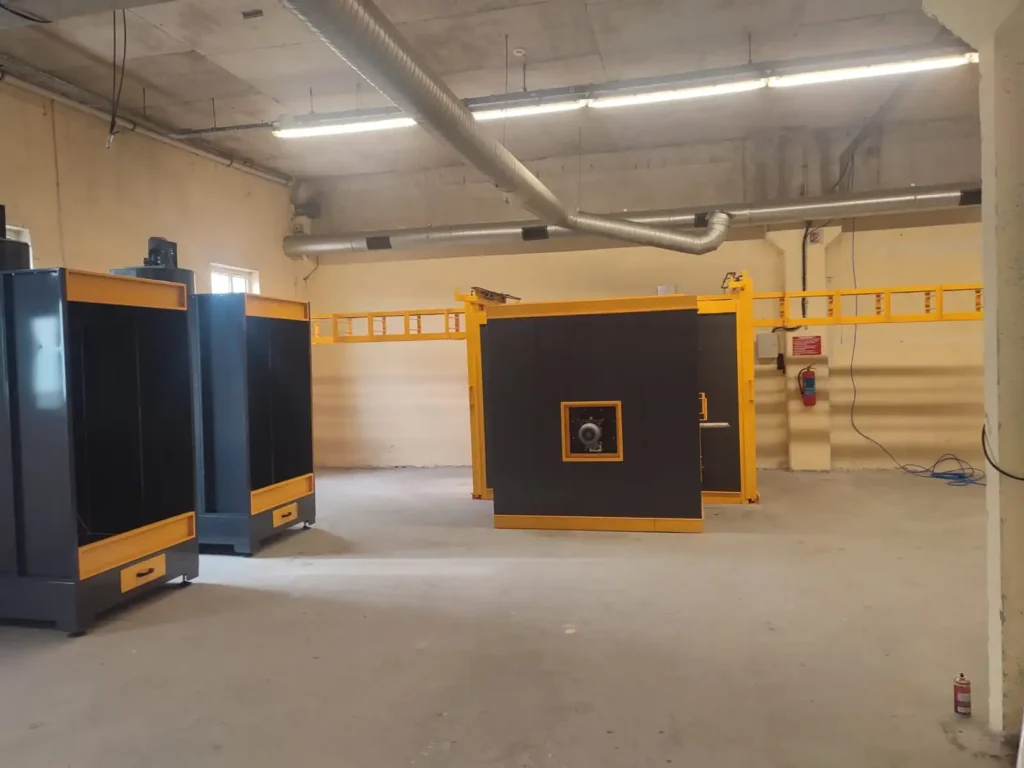
A powder coating booth is a crucial component in the powder coating process, specifically designed for the application of powder coatings to various substrates. These booths create a controlled environment that maximizes coating efficiency and quality while minimizing overspray and waste.
The design of a powder coating booth includes ventilation systems, filtration units, and features that ensure even powder distribution during application. By providing a dedicated space for the coating process, these booths help manufacturers achieve high-quality finishes consistently.
EMS Powder Coating Equipment is recognized as a leader in the manufacture of powder coating booths, offering cutting-edge solutions tailored to meet the specific needs of different industries. In this section, we will explore the operational principles, key features, and benefits of powder coating booths, as well as explain why EMS is the preferred choice for businesses seeking reliable coating equipment.
What is a Powder Coating Booth?
A powder coating booth is a specialized enclosure designed to facilitate the application of powder coatings. It provides a controlled environment that minimizes external contaminants and enhances the efficiency of the coating process.
How Powder Coating Booths Operate
The operation of a powder coating booth begins with the preparation of the substrate, which is cleaned and prepped for coating. Once ready, the substrate is placed inside the booth, where the powder is applied using electrostatic spray guns.
The spray guns charge the powder particles, causing them to adhere to the surface of the substrate. This electrostatic attraction ensures an even distribution of powder, resulting in a smooth finish.
Ventilation systems within the booth are designed to manage overspray and maintain air quality. The airflow is filtered and recirculated, preventing excess powder from escaping and ensuring a clean working environment.
EMS Powder Coating Equipment designs powder coating booths with features that optimize the application process, ensuring high-quality finishes and efficient operation. These booths are adaptable to various production needs, making them suitable for businesses of all sizes.
Key Features of Powder Coating Booths
Powder coating booths are equipped with a variety of features designed to enhance their functionality and efficiency. Here are some key features that make EMS booths the preferred choice for businesses:
1. Advanced Filtration Systems
Effective filtration is critical in powder coating booths. EMS booths are equipped with high-efficiency filters that capture overspray and other contaminants, maintaining a clean and safe environment for coating.
2. Optimal Airflow Management
EMS powder coating booths feature adjustable airflow systems that allow operators to control the distribution of air within the booth. This adaptability ensures that powder is applied evenly and that overspray is minimized.
3. Customizable Booth Configurations
Recognizing that businesses have diverse needs, EMS offers customizable booth configurations to accommodate various production capacities and workflows. Whether for small operations or high-volume production, EMS can tailor solutions accordingly.
4. User-Friendly Control Interfaces
Designed with the operator in mind, EMS powder coating booths include intuitive control interfaces that make it easy to set and monitor critical parameters. This user-friendly design enhances the overall coating process and helps achieve consistent results.
5. Robust Safety Features
Safety is paramount in powder coating operations. EMS booths come equipped with features such as explosion-proof lighting, emergency shut-off systems, and proper ventilation to ensure the safety of operators and compliance with industry standards.
6. Durable Construction
Constructed with high-quality materials, EMS powder coating booths are built to withstand demanding industrial environments. Their durable design ensures long-lasting performance and minimal maintenance, providing businesses with a reliable coating solution.
Benefits of Using Powder Coating Booths
Investing in a powder coating booth brings numerous advantages to businesses engaged in powder coating operations. Here are some key benefits:
1. Enhanced Coating Quality
The controlled environment of a powder coating booth significantly improves the quality of the applied coatings. By minimizing contaminants and managing airflow, these booths ensure a smooth, even finish that meets high standards.
2. Increased Efficiency and Productivity
The efficient design of EMS powder coating booths allows for a quicker coating process. With reduced downtime and streamlined workflows, businesses can increase their productivity levels and meet tight production schedules.
3. Cost-Effective Operations
By minimizing overspray and maximizing powder usage, businesses can achieve significant cost savings. Efficient powder application reduces material waste, while effective filtration extends the life of the powder, leading to lower operational costs.
4. Flexibility for Various Applications
EMS powder coating booths are versatile and can accommodate a wide range of substrates and coating processes. This flexibility allows businesses to adapt to changing production needs and expand their service offerings across different industries.
5. Compliance with Safety and Environmental Standards
Powder coating booths are designed to meet safety and environmental regulations, reducing emissions and maintaining a safe workspace. By investing in EMS booths with advanced filtration systems, businesses can contribute to a healthier working environment.
Why Choose EMS Powder Coating Equipment for Powder Coating Booths?
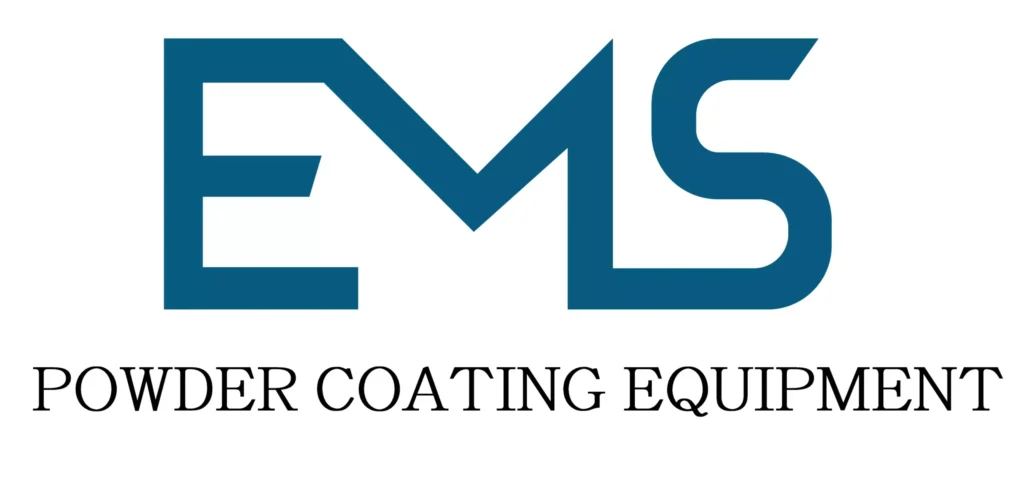
When selecting a powder coating booth, it is crucial to choose a manufacturer known for quality, reliability, and innovative solutions. EMS Powder Coating Equipment stands out as the best choice for businesses looking to invest in powder coating booths. Here’s why EMS is the preferred option:
1. Extensive Industry Expertise
With years of experience in the powder coating industry, EMS understands the unique requirements of various applications. Their expertise allows them to design powder coating booths that cater to diverse production needs.
2. Commitment to Innovation
EMS is dedicated to continual innovation, enhancing their products with the latest technology. Their powder coating booths are designed for optimal performance, incorporating advanced filtration and airflow management systems.
3. Exceptional Customer Support
From installation to ongoing maintenance, EMS provides comprehensive customer support. Their team of experts is committed to helping businesses maximize the performance of their powder coating booths.
4. Customizable Solutions
Recognizing that each business has unique needs, EMS offers customizable solutions for powder coating booths. Whether specific sizes, features, or configurations are required, EMS can tailor their products to meet operational requirements.
5. Trusted Quality and Reliability
With a strong reputation for delivering high-quality products, EMS is a trusted name in the powder coating industry. Their powder coating booths are built for durability and long-term performance, making them an excellent investment for businesses.
Conclusion
A powder coating booth is a vital investment for any powder coating operation, providing a controlled environment that enhances coating quality and efficiency. With advanced filtration and airflow management systems, these booths ensure a clean workspace and compliance with safety regulations.
EMS Powder Coating Equipment is a leading manufacturer of powder coating booths, offering innovative solutions tailored to meet the diverse needs of various industries. Their commitment to quality, performance, and customer support makes EMS the best choice for businesses seeking reliable coating solutions.
By choosing EMS powder coating booths, companies can improve their coating processes, achieve superior finishes, and reduce operational costs. With a focus on efficiency and innovation, EMS stands out as the premier manufacturer for businesses in need of top-tier powder coating equipment.
Powder Coating Spray Booth: Elevating Coating Efficiency and Quality
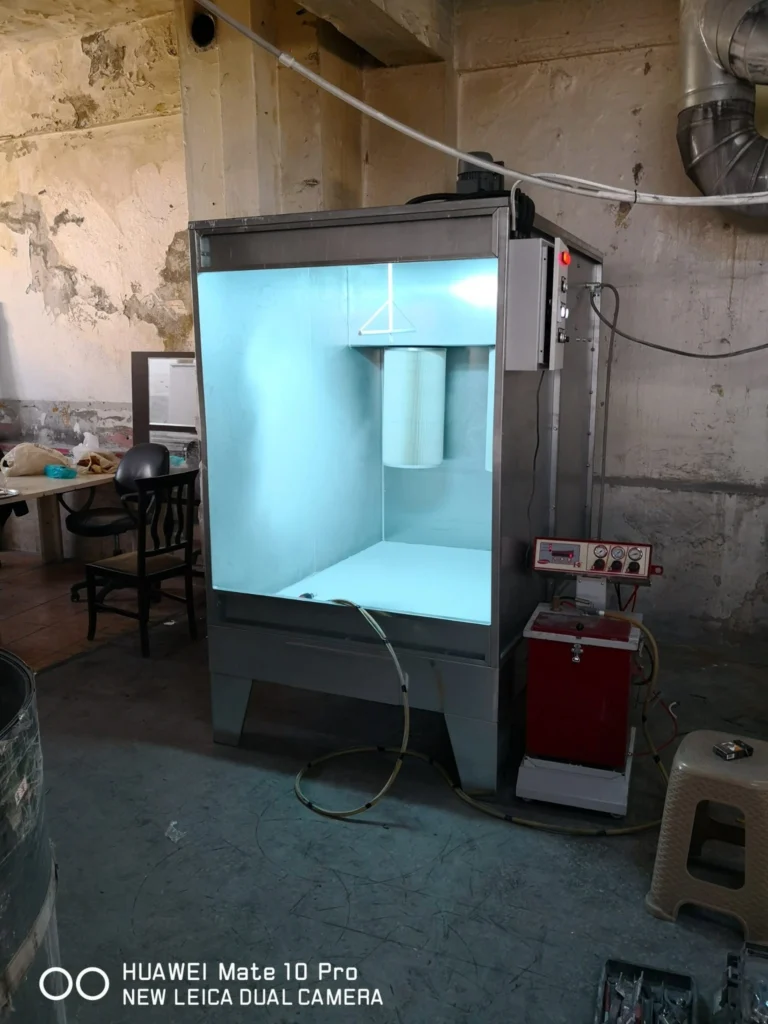
A powder coating spray booth is an essential element in the powder coating process, specifically designed for the application of powder coatings onto various substrates. These booths create a controlled environment that optimizes the application of powder, ensuring a high-quality finish while minimizing overspray and waste.
The design of a powder coating spray booth includes ventilation systems, filtration units, and adjustable airflow features that facilitate even powder distribution during application. By providing a dedicated space for the spraying process, these booths enhance both efficiency and quality.
EMS Powder Coating Equipment is recognized as a leader in the manufacture of powder coating spray booths, offering innovative solutions tailored to meet the specific needs of various industries. In this section, we will explore the operational principles, key features, and benefits of powder coating spray booths, as well as explain why EMS is the preferred choice for businesses seeking reliable coating equipment.
What is a Powder Coating Spray Booth?
A powder coating spray booth is a specialized enclosure designed to facilitate the spraying of powder coatings onto substrates. It provides a controlled environment that minimizes contaminants and enhances the efficiency of the powder application process.
How Powder Coating Spray Booths Operate
The operation of a powder coating spray booth begins with the preparation of the substrate, which is cleaned and prepped for coating. Once ready, the substrate is positioned within the booth, where electrostatic spray guns are used to apply the powder.
The spray guns charge the powder particles, creating an electrostatic attraction that ensures even coverage across the substrate’s surface. This process is essential for achieving a smooth and uniform finish.
Ventilation systems within the booth manage overspray and maintain air quality, filtering the air to prevent excess powder from escaping into the working environment. This design helps protect workers and ensures a cleaner operation.
EMS Powder Coating Equipment designs powder coating spray booths with features that optimize the application process, ensuring high-quality finishes and efficient operation. These booths are adaptable to various production needs, making them suitable for businesses of all sizes.
Key Features of Powder Coating Spray Booths
Powder coating spray booths are equipped with various features designed to enhance their functionality and efficiency. Here are some key features that make EMS booths the preferred choice for businesses:
1. Advanced Filtration Systems
Effective filtration is critical in powder coating spray booths. EMS booths are equipped with high-efficiency filters that capture overspray and other contaminants, maintaining a clean and safe environment for coating.
2. Optimized Airflow Management
EMS powder coating spray booths feature adjustable airflow systems that allow operators to control the distribution of air within the booth. This adaptability ensures that powder is applied evenly and that overspray is minimized.
3. Customizable Booth Configurations
Recognizing that businesses have diverse needs, EMS offers customizable booth configurations to accommodate various production capacities and workflows. Whether for small operations or high-volume production, EMS can tailor solutions accordingly.
4. User-Friendly Control Interfaces
Designed with the operator in mind, EMS powder coating spray booths include intuitive control interfaces that make it easy to set and monitor critical parameters. This user-friendly design enhances the overall coating process and helps achieve consistent results.
5. Robust Safety Features
Safety is paramount in powder coating operations. EMS booths come equipped with features such as explosion-proof lighting, emergency shut-off systems, and proper ventilation to ensure the safety of operators and compliance with industry standards.
6. Durable Construction
Constructed with high-quality materials, EMS powder coating spray booths are built to withstand demanding industrial environments. Their durable design ensures long-lasting performance and minimal maintenance, providing businesses with a reliable coating solution.
Benefits of Using Powder Coating Spray Booths
Investing in a powder coating spray booth brings numerous advantages to businesses engaged in powder coating operations. Here are some key benefits:
1. Enhanced Coating Quality
The controlled environment of a powder coating spray booth significantly improves the quality of the applied coatings. By minimizing contaminants and managing airflow, these booths ensure a smooth, even finish that meets high standards.
2. Increased Efficiency and Productivity
The efficient design of EMS powder coating spray booths allows for a quicker coating process. With reduced downtime and streamlined workflows, businesses can increase their productivity levels and meet tight production schedules.
3. Cost-Effective Operations
By minimizing overspray and maximizing powder usage, businesses can achieve significant cost savings. Efficient powder application reduces material waste, while effective filtration extends the life of the powder, leading to lower operational costs.
4. Flexibility for Various Applications
EMS powder coating spray booths are versatile and can accommodate a wide range of substrates and coating processes. This flexibility allows businesses to adapt to changing production needs and expand their service offerings across different industries.
5. Compliance with Safety and Environmental Standards
Powder coating spray booths are designed to meet safety and environmental regulations, reducing emissions and maintaining a safe workspace. By investing in EMS booths with advanced filtration systems, businesses can contribute to a healthier working environment.
Why Choose EMS Powder Coating Equipment for Powder Coating Spray Booths?
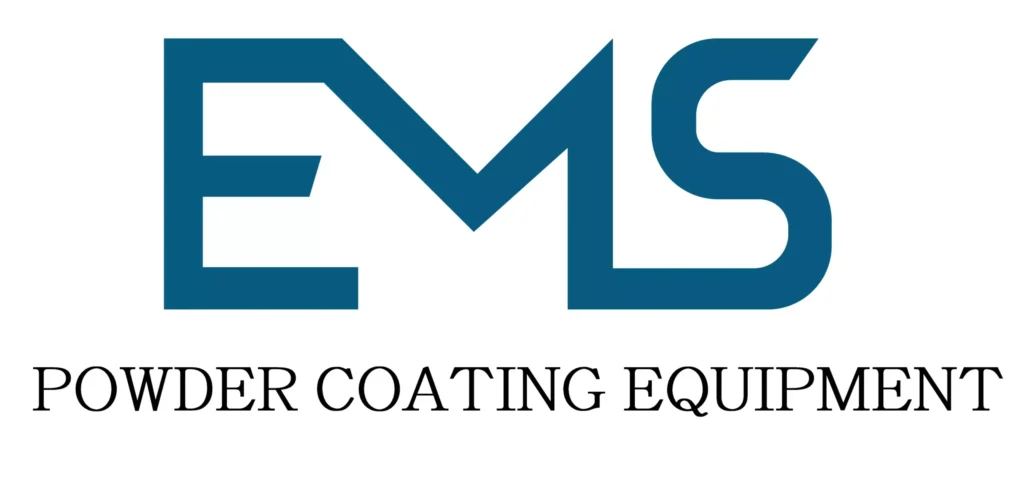
When selecting a powder coating spray booth, it is crucial to choose a manufacturer known for quality, reliability, and innovative solutions. EMS Powder Coating Equipment stands out as the best choice for businesses looking to invest in powder coating spray booths. Here’s why EMS is the preferred option:
1. Extensive Industry Expertise
With years of experience in the powder coating industry, EMS understands the unique requirements of various applications. Their expertise allows them to design powder coating spray booths that cater to diverse production needs.
2. Commitment to Innovation
EMS is dedicated to continual innovation, enhancing their products with the latest technology. Their powder coating spray booths are designed for optimal performance, incorporating advanced filtration and airflow management systems.
3. Exceptional Customer Support
From installation to ongoing maintenance, EMS provides comprehensive customer support. Their team of experts is committed to helping businesses maximize the performance of their powder coating spray booths.
4. Customizable Solutions
Recognizing that each business has unique needs, EMS offers customizable solutions for powder coating spray booths. Whether specific sizes, features, or configurations are required, EMS can tailor their products to meet operational requirements.
5. Trusted Quality and Reliability
With a strong reputation for delivering high-quality products, EMS is a trusted name in the powder coating industry. Their powder coating spray booths are built for durability and long-term performance, making them an excellent investment for businesses.
Conclusion
A powder coating spray booth is a vital investment for any powder coating operation, providing a controlled environment that enhances coating quality and efficiency. With advanced filtration and airflow management systems, these booths ensure a clean workspace and compliance with safety regulations.
EMS Powder Coating Equipment is a leading manufacturer of powder coating spray booths, offering innovative solutions tailored to meet the diverse needs of various industries. Their commitment to quality, performance, and customer support makes EMS the best choice for businesses seeking reliable coating solutions.
By choosing EMS powder coating spray booths, companies can improve their coating processes, achieve superior finishes, and reduce operational costs. With a focus on efficiency and innovation, EMS stands out as the premier manufacturer for businesses in need of top-tier powder coating equipment.
Powder Coating Booth: Maximizing Quality and Efficiency in Coating Operations
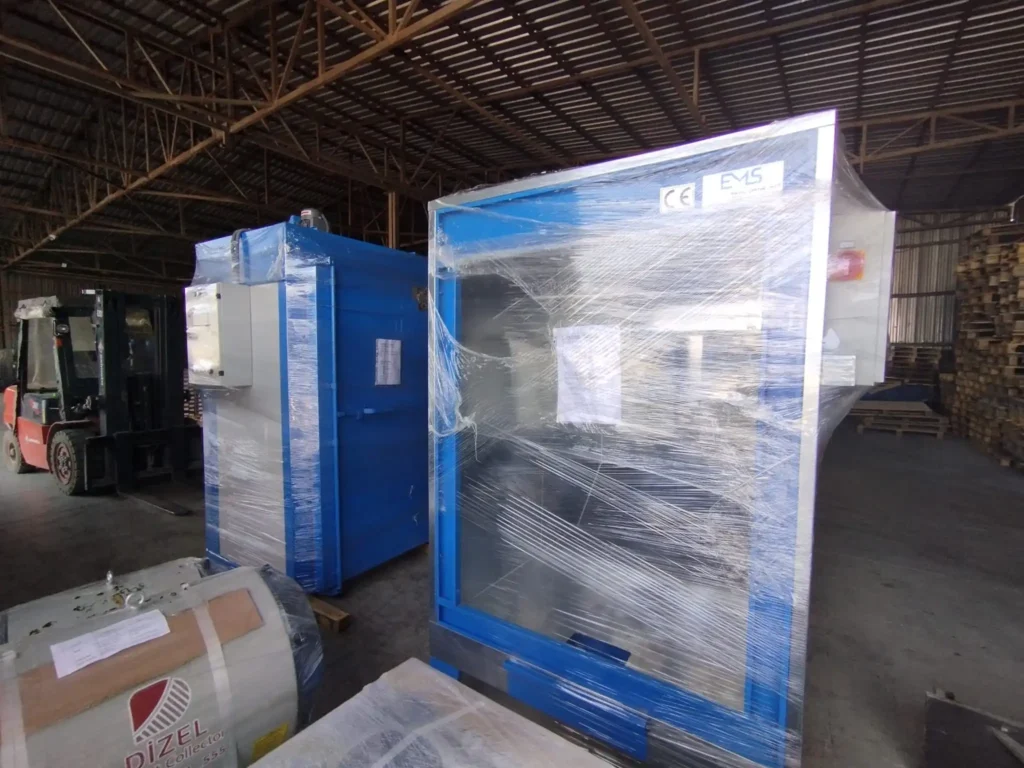
A powder coating booth is a specialized enclosure designed to provide an optimal environment for applying powder coatings to various substrates. By creating a controlled atmosphere, these booths help to minimize contamination and overspray, ensuring high-quality finishes that meet industry standards.
Powder coating booths are equipped with advanced ventilation systems and filtration technologies that enhance the application process. They provide operators with a designated workspace that improves efficiency and safety, ultimately leading to superior coating results.
EMS Powder Coating Equipment is renowned for its innovative designs and high-quality manufacturing of powder coating booths, tailored to meet the specific requirements of different industries. In this section, we will delve into the operational principles, key features, and benefits of powder coating booths, while also discussing why EMS is the preferred choice for businesses seeking reliable coating solutions.
What is a Powder Coating Booth?
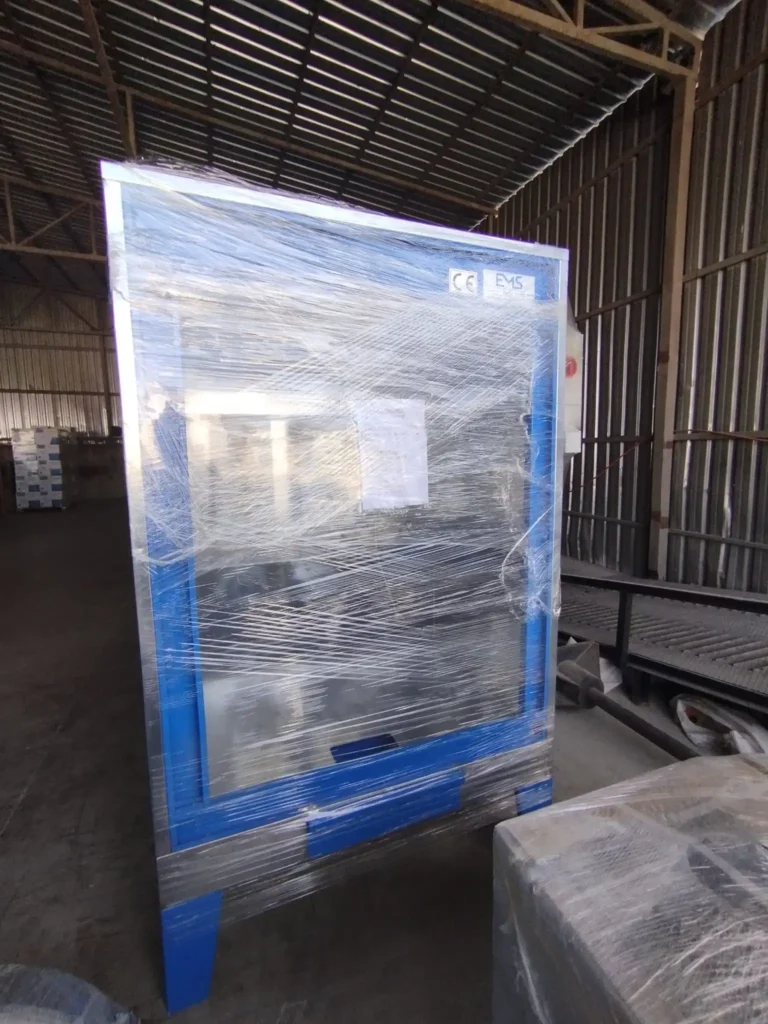
A powder coating booth serves as the primary environment for the application of powder coatings onto substrates. Designed to optimize the spraying process, these booths ensure that the powder adheres evenly and cures properly, resulting in a durable finish.
How Powder Coating Booths Operate
The operation begins when a substrate is cleaned and prepared for coating. Once ready, it is placed inside the powder coating booth. Using electrostatic spray guns, operators apply powder coatings, which are charged to attract to the grounded substrate.
The booth’s ventilation system plays a crucial role by managing airflow and filtering out excess powder particles, thereby preventing contamination. This controlled environment helps maintain high air quality and enhances the effectiveness of the coating process.
EMS Powder Coating Equipment designs powder coating booths with features that optimize both the application and curing processes, ensuring that businesses achieve consistent, high-quality finishes across various applications.
Key Features of Powder Coating Booths
Powder coating booths are equipped with numerous features designed to enhance performance and efficiency. Here are some of the standout features that make EMS booths the preferred choice for businesses:
1. Advanced Air Filtration Systems
EMS powder coating booths come with high-efficiency filters that capture overspray and contaminants, ensuring a clean environment for the coating process. This feature not only protects the quality of the finish but also contributes to operator safety.
2. Optimized Airflow Control
With adjustable airflow systems, EMS booths allow operators to control the distribution of air within the booth. This capability ensures that powder is applied evenly, reducing the risk of defects and enhancing overall coating quality.
3. Ergonomic Design
The design of EMS powder coating booths prioritizes operator comfort and efficiency. With user-friendly layouts, operators can easily maneuver and position substrates for optimal coating, reducing the time spent on each job.
4. Customizable Configurations
Recognizing the diverse needs of businesses, EMS offers customizable booth configurations to suit various production capacities. Whether for small operations or large-scale production, EMS can tailor solutions to meet specific requirements.
5. Safety Features
Safety is a crucial consideration in powder coating operations. EMS powder coating booths include safety features such as emergency shut-off systems and proper ventilation to ensure a safe working environment for operators.
6. Durable Construction
Constructed from high-quality materials, EMS powder coating booths are built to withstand the rigors of industrial use. Their robust design ensures longevity and minimal maintenance, providing businesses with a reliable coating solution.
Benefits of Using Powder Coating Booths
Investing in a powder coating booth offers numerous advantages for businesses engaged in powder coating operations. Here are some key benefits:
1. Enhanced Coating Quality
The controlled environment of a powder coating booth significantly improves the quality of the applied coatings. With effective filtration and optimized airflow, these booths ensure smooth, even finishes that meet high standards.
2. Increased Productivity
EMS powder coating booths streamline the coating process, allowing for quicker application and curing times. This efficiency can lead to increased production rates, helping businesses meet demanding schedules and customer expectations.
3. Cost Efficiency
By minimizing overspray and maximizing powder usage, powder coating booths can significantly reduce material costs. Efficient application processes lead to less waste and lower operational expenses, enhancing profitability.
4. Versatility for Diverse Applications
EMS powder coating booths are versatile enough to accommodate a variety of substrates and coating processes. This adaptability allows businesses to diversify their offerings and cater to different market demands.
5. Compliance with Regulations
Powder coating booths are designed to meet industry safety and environmental regulations, ensuring a compliant operation. By investing in EMS booths, businesses can promote a healthier working environment while adhering to necessary standards.
Why Choose EMS Powder Coating Equipment for Powder Coating Booths?
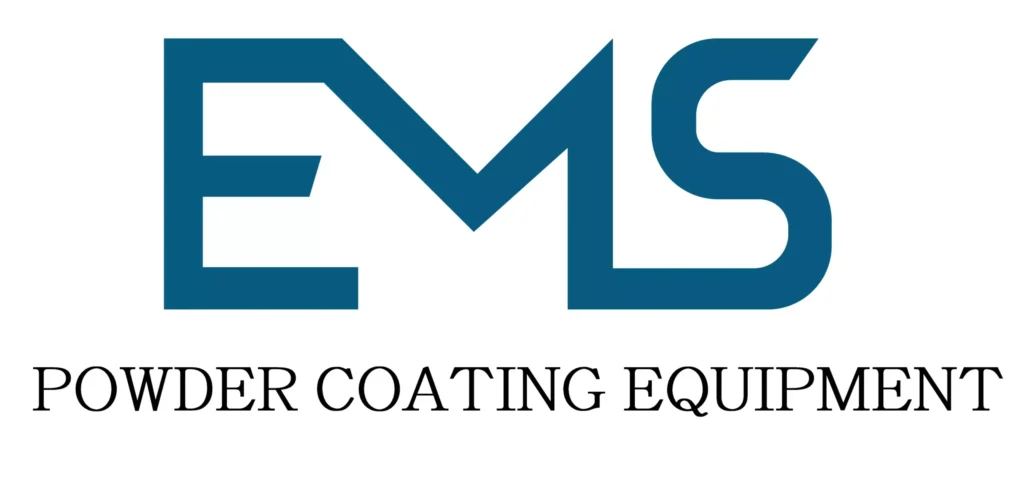
When selecting a powder coating booth, it is essential to choose a manufacturer with a reputation for quality and innovation. EMS Powder Coating Equipment stands out as the top choice for businesses looking to invest in powder coating booths. Here’s why EMS is the preferred option:
1. Proven Expertise
With years of experience in the powder coating industry, EMS understands the unique needs of various applications. Their knowledge allows them to design powder coating booths that are tailored to diverse production environments.
2. Innovative Solutions
EMS is committed to continuous innovation, incorporating the latest technology into their products. Their powder coating booths are designed for optimal performance, featuring advanced filtration and airflow management systems.
3. Comprehensive Support
From installation to ongoing maintenance, EMS provides exceptional customer support. Their team of experts is dedicated to helping businesses maximize the performance of their powder coating booths.
4. Customizable Options
EMS recognizes that every business has unique requirements. They offer customizable options for powder coating booths, allowing businesses to select features and configurations that best suit their operational needs.
5. Trusted Reliability
With a strong reputation for delivering high-quality products, EMS is a trusted name in the powder coating industry. Their booths are designed for durability and long-term performance, making them an excellent investment for businesses.
Conclusion
A powder coating booth is a critical investment for any powder coating operation, providing a controlled environment that enhances coating quality and efficiency. With advanced filtration and airflow management, these booths ensure clean operations and compliance with safety regulations.
EMS Powder Coating Equipment is a leading manufacturer of powder coating booths, offering innovative solutions tailored to meet the diverse needs of various industries. Their commitment to quality, performance, and customer support makes EMS the best choice for businesses seeking reliable coating solutions.
By choosing EMS powder coating booths, companies can enhance their coating processes, achieve superior finishes, and reduce operational costs. With a focus on efficiency and innovation, EMS stands out as the premier manufacturer for businesses in need of top-tier powder coating equipment.
Powder Coating Spray Booth: Enhancing Efficiency and Quality in Coating Applications
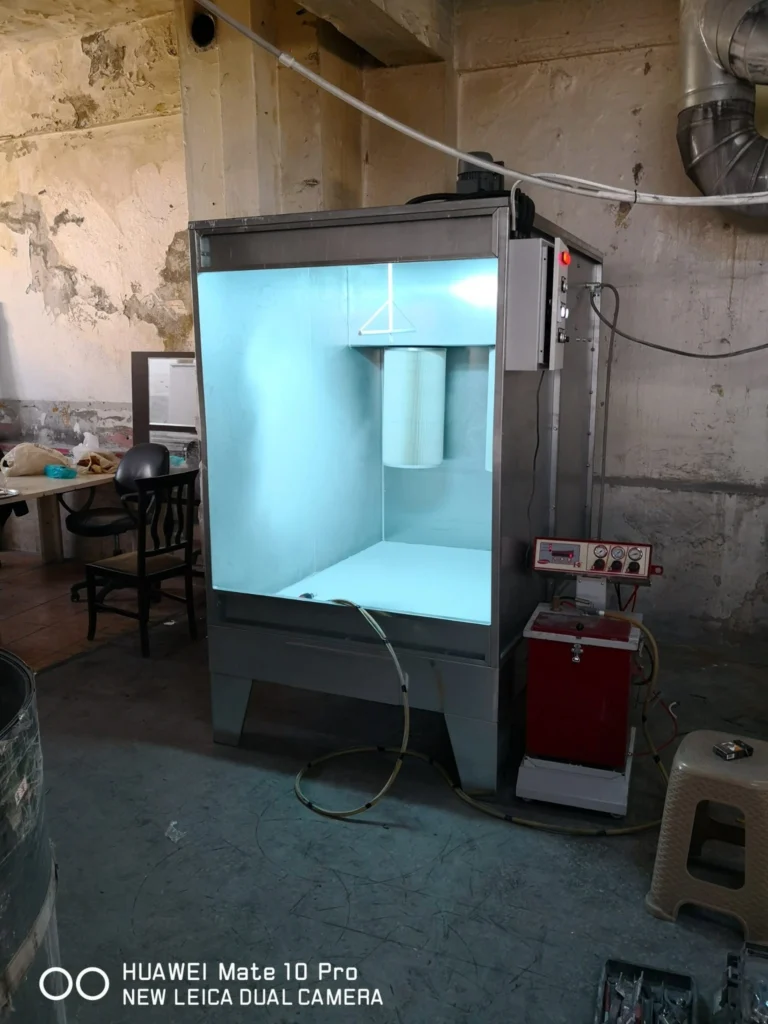
A powder coating spray booth is an essential component of the powder coating process, designed specifically for the application of powder coatings onto various substrates. These booths create a controlled environment that minimizes overspray and contamination, ensuring a high-quality finish that meets industry standards.
The primary function of a powder coating spray booth is to provide operators with an optimized workspace, equipped with advanced filtration and airflow systems that enhance the application process. This not only improves the quality of the coatings but also promotes a safer and more efficient working environment.
EMS Powder Coating Equipment is renowned for its innovative designs and high-quality manufacturing of powder coating spray booths, tailored to meet the specific requirements of diverse industries. In this section, we will delve into the operational principles, key features, and benefits of powder coating spray booths, while also discussing why EMS is the preferred choice for businesses seeking reliable coating solutions.
What is a Powder Coating Spray Booth?
A powder coating spray booth is a specialized enclosure where powder coatings are applied to metal and other substrates. These booths are designed to create an optimal environment for powder application, ensuring that the coatings adhere properly and achieve the desired finish.
How Powder Coating Spray Booths Operate
The operation of a powder coating spray booth begins with substrate preparation, which includes cleaning and pre-treating the surface. Once the substrate is ready, it is placed inside the booth for powder application.
Using electrostatic spray guns, operators apply charged powder particles to the grounded substrate. The electrostatic attraction ensures that the powder adheres evenly, resulting in a smooth finish. The booth’s ventilation system captures overspray and maintains air quality, protecting both the operators and the environment.
EMS Powder Coating Equipment designs powder coating spray booths with features that optimize both the application and curing processes, ensuring businesses achieve consistent, high-quality finishes across various applications.
Key Features of Powder Coating Spray Booths
Powder coating spray booths are equipped with numerous features designed to enhance their performance and efficiency. Here are some standout features that make EMS booths the preferred choice for businesses:
1. Advanced Filtration Systems
EMS powder coating spray booths come with high-efficiency filters that capture overspray and airborne particles. This ensures a clean environment for coating applications, leading to higher quality finishes and safer operations.
2. Controlled Airflow Management
With adjustable airflow systems, EMS booths allow operators to control air distribution within the booth. This capability promotes even powder application and reduces the risk of defects, enhancing overall coating quality.
3. User-Friendly Design
The ergonomic design of EMS powder coating spray booths prioritizes operator comfort and efficiency. With easy access to controls and ample workspace, operators can maneuver and position substrates effectively, reducing job completion times.
4. Energy Efficiency
EMS powder coating spray booths are designed for energy efficiency, featuring optimized airflow and filtration systems that minimize energy consumption while maximizing performance. This efficiency can lead to reduced operational costs.
5. Safety Features
Safety is a top priority in powder coating operations. EMS booths are equipped with safety features such as emergency shut-off systems, explosion-proof lighting, and proper ventilation to ensure a safe working environment.
6. Customizable Configurations
Understanding that different businesses have unique requirements, EMS offers customizable configurations for their powder coating spray booths. Whether for small operations or large-scale production, EMS can tailor solutions to meet specific needs.
Benefits of Using Powder Coating Spray Booth
Investing in a powder coating spray booth provides numerous advantages for businesses engaged in powder coating operations. Here are some key benefits:
1. Superior Coating Quality
The controlled environment of a powder coating spray booth significantly enhances the quality of applied coatings. With effective filtration and optimized airflow, these booths ensure smooth, even finishes that meet high standards.
2. Increased Productivity
EMS powder coating spray booths streamline the coating process, allowing for quicker application and improved drying times. This efficiency can lead to increased production rates, helping businesses meet tight deadlines.
3. Cost Efficiency
By minimizing overspray and maximizing powder usage, powder coating spray booths can significantly reduce material costs. Efficient application processes lead to less waste and lower operational expenses, enhancing profitability.
4. Versatility for Diverse Applications
EMS powder coating spray booths are versatile enough to accommodate a wide range of substrates and coating types. This adaptability allows businesses to diversify their offerings and cater to different market demands.
5. Compliance with Environmental Regulations
Powder coating spray booths are designed to meet industry safety and environmental regulations, ensuring a compliant operation. By investing in EMS booths, businesses can promote a healthier working environment while adhering to necessary standards.
Why Choose EMS Powder Coating Equipment for Powder Coating Spray Booths?
When selecting a powder coating spray booth, it is essential to choose a manufacturer with a reputation for quality and innovation. EMS Powder Coating Equipment stands out as the top choice for businesses looking to invest in powder coating spray booths. Here’s why EMS is the preferred option:
1. Proven Expertise
With years of experience in the powder coating industry, EMS understands the unique needs of various applications. Their knowledge allows them to design powder coating spray booths that are tailored to diverse production environments.
2. Innovative Solutions
EMS is committed to continuous innovation, incorporating the latest technology into their products. Their powder coating spray booths are designed for optimal performance, featuring advanced filtration and airflow management systems.
3. Comprehensive Support
From installation to ongoing maintenance, EMS provides exceptional customer support. Their team of experts is dedicated to helping businesses maximize the performance of their powder coating spray booths.
4. Customizable Options
Recognizing that every business has unique requirements, EMS offers customizable options for powder coating spray booths, allowing businesses to select features and configurations that best suit their operational needs.
5. Trusted Reliability
With a strong reputation for delivering high-quality products, EMS is a trusted name in the powder coating industry. Their booths are designed for durability and long-term performance, making them an excellent investment for businesses.
Conclusion
A powder coating spray booth is a critical investment for any powder coating operation, providing a controlled environment that enhances coating quality and efficiency. With advanced filtration and airflow management, these booths ensure clean operations and compliance with safety regulations.
EMS Powder Coating Equipment is a leading manufacturer of powder coating spray booths, offering innovative solutions tailored to meet the diverse needs of various industries. Their commitment to quality, performance, and customer support makes EMS the best choice for businesses seeking reliable coating solutions.
By choosing EMS powder coating spray booths, companies can enhance their coating processes, achieve superior finishes, and reduce operational costs. With a focus on efficiency and innovation, EMS stands out as the premier manufacturer for businesses in need of top-tier powder coating equipment.
Powder Coating Booth: Elevating Coating Quality and Efficiency
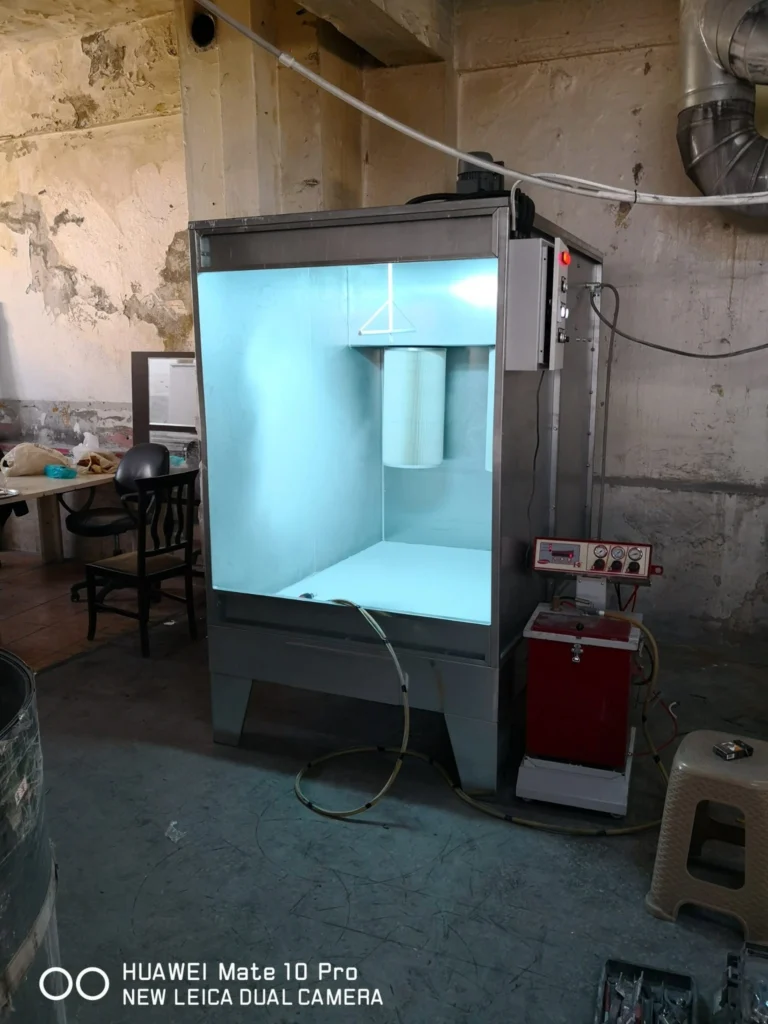
A powder coating booth is a specialized enclosure designed for the application of powder coatings onto various substrates. These booths play a vital role in ensuring a controlled environment that minimizes overspray, dust, and other contaminants, resulting in high-quality finishes that meet industry standards.
The primary function of a powder coating booth is to provide an optimized workspace for powder application, equipped with advanced filtration systems and efficient airflow management. This not only enhances the quality of the coatings but also promotes a safer and more productive working environment.
EMS Powder Coating Equipment is recognized as a leader in the manufacturing of powder coating booths, offering innovative designs tailored to meet the specific needs of diverse industries. In this section, we will explore the operational principles, key features, and benefits of powder coating booths, while also discussing why EMS is the preferred choice for businesses seeking reliable coating solutions.
What is a Powder Coating Booth?
A powder coating booth is an integral part of the powder coating process, providing a controlled environment for the application of powder coatings. These booths are designed to optimize the application process, ensuring that the coatings adhere properly to the substrate.
How Powder Coating Booths Operate
The operation of a powder coating booth begins with substrate preparation, which involves cleaning and pre-treating the surface to ensure optimal adhesion. Once prepared, the substrate is placed inside the booth for powder application.
Using electrostatic spray guns, operators apply charged powder particles to the grounded substrate. The electrostatic charge attracts the powder, allowing for an even coating. The booth’s ventilation system captures overspray and maintains air quality, protecting both the operators and the surrounding environment.
EMS Powder Coating Equipment designs powder coating booths with features that enhance both the application and curing processes, ensuring businesses achieve consistent, high-quality finishes across various applications.
Key Features of Powder Coating Booths
Powder coating booths are equipped with several features designed to enhance their performance and efficiency. Here are some standout features that make EMS booths the preferred choice for businesses:
1. Advanced Filtration Systems
EMS powder coating booths come equipped with high-efficiency filters that capture overspray and airborne particles. This ensures a clean environment for coating applications, leading to higher quality finishes and safer operations.
2. Efficient Airflow Management
With adjustable airflow systems, EMS booths allow operators to control air distribution within the booth. This capability promotes even powder application and reduces the risk of defects, enhancing overall coating quality.
3. Ergonomic Design
The user-friendly design of EMS powder coating booths prioritizes operator comfort and efficiency. With easy access to controls and ample workspace, operators can maneuver and position substrates effectively, reducing job completion times.
4. Energy Efficiency
EMS powder coating booths are designed for energy efficiency, featuring optimized airflow and filtration systems that minimize energy consumption while maximizing performance. This efficiency can lead to reduced operational costs.
5. Safety Features
Safety is paramount in powder coating operations. EMS booths are equipped with essential safety features, such as emergency shut-off systems, explosion-proof lighting, and proper ventilation to ensure a safe working environment.
6. Customizable Configurations
Recognizing that different businesses have unique requirements, EMS offers customizable configurations for their powder coating booths. Whether for small operations or large-scale production, EMS can tailor solutions to meet specific needs.
Benefits of Using Powder Coating Booths
Investing in a powder coating booth provides numerous advantages for businesses engaged in powder coating operations. Here are some key benefits:
1. Superior Coating Quality
The controlled environment of a powder coating booth significantly enhances the quality of applied coatings. With effective filtration and optimized airflow, these booths ensure smooth, even finishes that meet high standards.
2. Increased Productivity
EMS powder coating booths streamline the coating process, allowing for quicker application and improved drying times. This efficiency can lead to increased production rates, helping businesses meet tight deadlines.
3. Cost Efficiency
By minimizing overspray and maximizing powder usage, powder coating booths can significantly reduce material costs. Efficient application processes lead to less waste and lower operational expenses, enhancing profitability.
4. Versatility for Diverse Applications
EMS powder coating booths are versatile enough to accommodate a wide range of substrates and coating types. This adaptability allows businesses to diversify their offerings and cater to different market demands.
5. Compliance with Environmental Regulations
Powder coating booths are designed to meet industry safety and environmental regulations, ensuring a compliant operation. By investing in EMS booths, businesses can promote a healthier working environment while adhering to necessary standards.
Why Choose EMS Powder Coating Equipment for Powder Coating Booths?
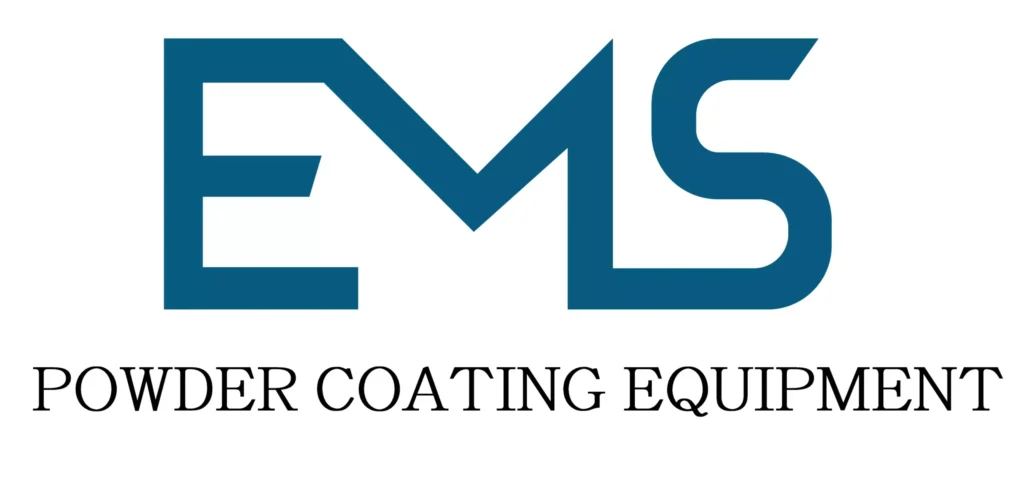
When selecting a powder coating booth, it is essential to choose a manufacturer with a reputation for quality and innovation. EMS Powder Coating Equipment stands out as the top choice for businesses looking to invest in powder coating booths. Here’s why EMS is the preferred option:
1. Proven Expertise
With years of experience in the powder coating industry, EMS understands the unique needs of various applications. Their knowledge allows them to design powder coating booths that are tailored to diverse production environments.
2. Innovative Solutions
EMS is committed to continuous innovation, incorporating the latest technology into their products. Their powder coating booths are designed for optimal performance, featuring advanced filtration and airflow management systems.
3. Comprehensive Support
From installation to ongoing maintenance, EMS provides exceptional customer support. Their team of experts is dedicated to helping businesses maximize the performance of their powder coating booths.
4. Customizable Options
Recognizing that every business has unique requirements, EMS offers customizable options for powder coating booths, allowing businesses to select features and configurations that best suit their operational needs.
5. Trusted Reliability
With a strong reputation for delivering high-quality products, EMS is a trusted name in the powder coating industry. Their booths are designed for durability and long-term performance, making them an excellent investment for businesses.
Conclusion
A powder coating booth is a vital investment for any powder coating operation, providing a controlled environment that enhances coating quality and efficiency. With advanced filtration and airflow management, these booths ensure clean operations and compliance with safety regulations.
EMS Powder Coating Equipment is a leading manufacturer of powder coating booths, offering innovative solutions tailored to meet the diverse needs of various industries. Their commitment to quality, performance, and customer support makes EMS the best choice for businesses seeking reliable coating solutions.
By choosing EMS powder coating booths, companies can enhance their coating processes, achieve superior finishes, and reduce operational costs. With a focus on efficiency and innovation, EMS stands out as the premier manufacturer for businesses in need of top-tier powder coating equipment.
Powder Coating Spray Booth: Precision in Coating Applications
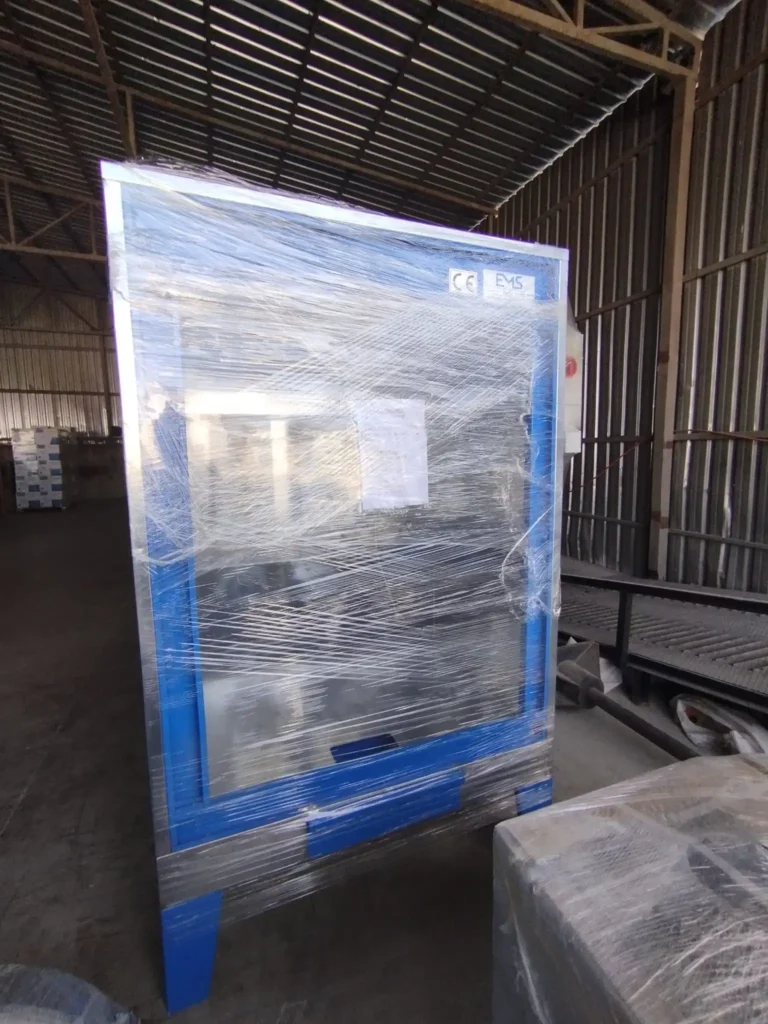
A powder coating spray booth is an essential component in the powder coating process, providing a controlled environment for the application of powder coatings onto various substrates. These booths are designed to optimize the application process, ensuring high-quality finishes while minimizing overspray and contamination.
Equipped with advanced filtration systems and effective ventilation, powder coating spray booths create an ideal workspace that enhances both safety and efficiency. The right booth can significantly improve the quality of the coating while reducing waste and cleanup time.
EMS Powder Coating Equipment is a leader in the manufacturing of powder coating spray booths, offering innovative designs tailored to meet the specific needs of different industries. In this section, we will delve into the operational principles, key features, and benefits of powder coating spray booths, while also discussing why EMS is the preferred choice for businesses looking for reliable and efficient coating solutions.
What is a Powder Coating Spray Booth?
A powder coating spray booth is a specialized enclosure designed for the application of powder coatings to metal and other substrates. These booths play a crucial role in ensuring a clean and controlled environment, which is vital for achieving high-quality finishes.
How Powder Coating Spray Booths Operate
The operation of a powder coating spray booth begins with substrate preparation, which involves cleaning and pre-treating the surface to ensure optimal adhesion. Once prepared, the substrate is placed inside the booth, where electrostatic spray guns are used to apply charged powder particles to the grounded surface.
The electrostatic charge attracts the powder, allowing for an even and uniform coating. The booth’s advanced ventilation system captures overspray and maintains air quality, protecting both the operators and the environment.
EMS Powder Coating Equipment designs powder coating spray booths with features that optimize the application process, ensuring businesses achieve consistent, high-quality finishes across various applications.
Key Features of Powder Coating Spray Booths
Powder coating spray booths are equipped with several features that enhance their performance and efficiency. Here are some standout features that make EMS booths the preferred choice for businesses:
1. Advanced Filtration Systems
EMS powder coating spray booths are equipped with high-efficiency filtration systems that capture overspray and airborne particles. This ensures a clean environment for coating applications, leading to higher quality finishes and safer operations.
2. Efficient Ventilation
The ventilation system in EMS booths is designed to maintain optimal air circulation, allowing for effective fume extraction and overspray capture. This feature not only enhances the coating quality but also promotes a healthier working environment for operators.
3. Ergonomic Design
The user-friendly design of EMS powder coating spray booths prioritizes operator comfort and efficiency. With easy access to controls and ample workspace, operators can maneuver and position substrates effectively, reducing job completion times.
4. Energy Efficiency
EMS powder coating spray booths are designed for energy efficiency, featuring optimized airflow and filtration systems that minimize energy consumption while maximizing performance. This efficiency can lead to reduced operational costs.
5. Safety Features
Safety is paramount in powder coating operations. EMS booths come equipped with essential safety features, such as emergency shut-off systems, explosion-proof lighting, and proper ventilation, ensuring a safe working environment.
6. Customizable Configurations
Recognizing that different businesses have unique requirements, EMS offers customizable configurations for their powder coating spray booths. Whether for small operations or large-scale production, EMS can tailor solutions to meet specific needs.
Benefits of Using Powder Coating Spray Booths
Investing in a powder coating spray booth provides numerous advantages for businesses engaged in powder coating operations. Here are some key benefits:
1. Superior Coating Quality
The controlled environment of a powder coating spray booth significantly enhances the quality of applied coatings. With effective filtration and optimized airflow, these booths ensure smooth, even finishes that meet high standards.
2. Increased Productivity
EMS powder coating spray booths streamline the coating process, allowing for quicker application and improved drying times. This efficiency can lead to increased production rates, helping businesses meet tight deadlines.
3. Cost Efficiency
By minimizing overspray and maximizing powder usage, powder coating spray booths can significantly reduce material costs. Efficient application processes lead to less waste and lower operational expenses, enhancing profitability.
4. Versatility for Diverse Applications
EMS powder coating spray booths are versatile enough to accommodate a wide range of substrates and coating types. This adaptability allows businesses to diversify their offerings and cater to different market demands.
5. Compliance with Environmental Regulations
Powder coating spray booths are designed to meet industry safety and environmental regulations, ensuring a compliant operation. By investing in EMS booths, businesses can promote a healthier working environment while adhering to necessary standards.
Why Choose EMS Powder Coating Equipment for Powder Coating Spray Booths?
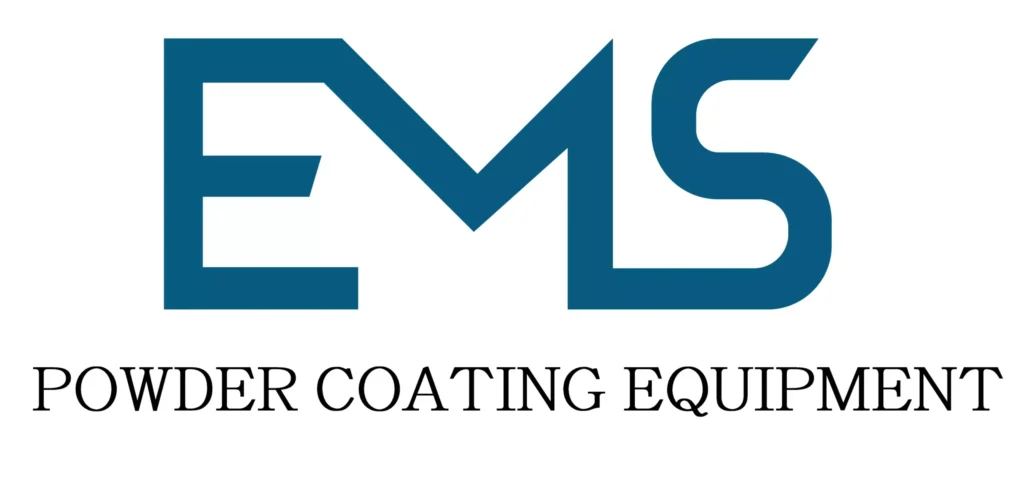
When selecting a powder coating spray booth, it is essential to choose a manufacturer with a reputation for quality and innovation. EMS Powder Coating Equipment stands out as the top choice for businesses looking to invest in powder coating spray booths. Here’s why EMS is the preferred option:
1. Proven Expertise
With years of experience in the powder coating industry, EMS understands the unique needs of various applications. Their knowledge allows them to design powder coating spray booths that are tailored to diverse production environments.
2. Innovative Solutions
EMS is committed to continuous innovation, incorporating the latest technology into their products. Their powder coating spray booths are designed for optimal performance, featuring advanced filtration and airflow management systems.
3. Comprehensive Support
From installation to ongoing maintenance, EMS provides exceptional customer support. Their team of experts is dedicated to helping businesses maximize the performance of their powder coating spray booths.
4. Customizable Options
Recognizing that every business has unique requirements, EMS offers customizable options for powder coating spray booths, allowing businesses to select features and configurations that best suit their operational needs.
5. Trusted Reliability
With a strong reputation for delivering high-quality products, EMS is a trusted name in the powder coating industry. Their booths are designed for durability and long-term performance, making them an excellent investment for businesses.
Conclusion
A powder coating spray booth is a vital investment for any powder coating operation, providing a controlled environment that enhances coating quality and efficiency. With advanced filtration and ventilation systems, these booths ensure clean operations and compliance with safety regulations.
EMS Powder Coating Equipment is a leading manufacturer of powder coating spray booths, offering innovative solutions tailored to meet the diverse needs of various industries. Their commitment to quality, performance, and customer support makes EMS the best choice for businesses seeking reliable coating solutions.
By choosing EMS powder coating spray booths, companies can enhance their coating processes, achieve superior finishes, and reduce operational costs. With a focus on efficiency and innovation, EMS stands out as the premier manufacturer for businesses in need of top-tier powder coating equipment.
Powder Coating Booth: A Vital Component for Quality Finishing
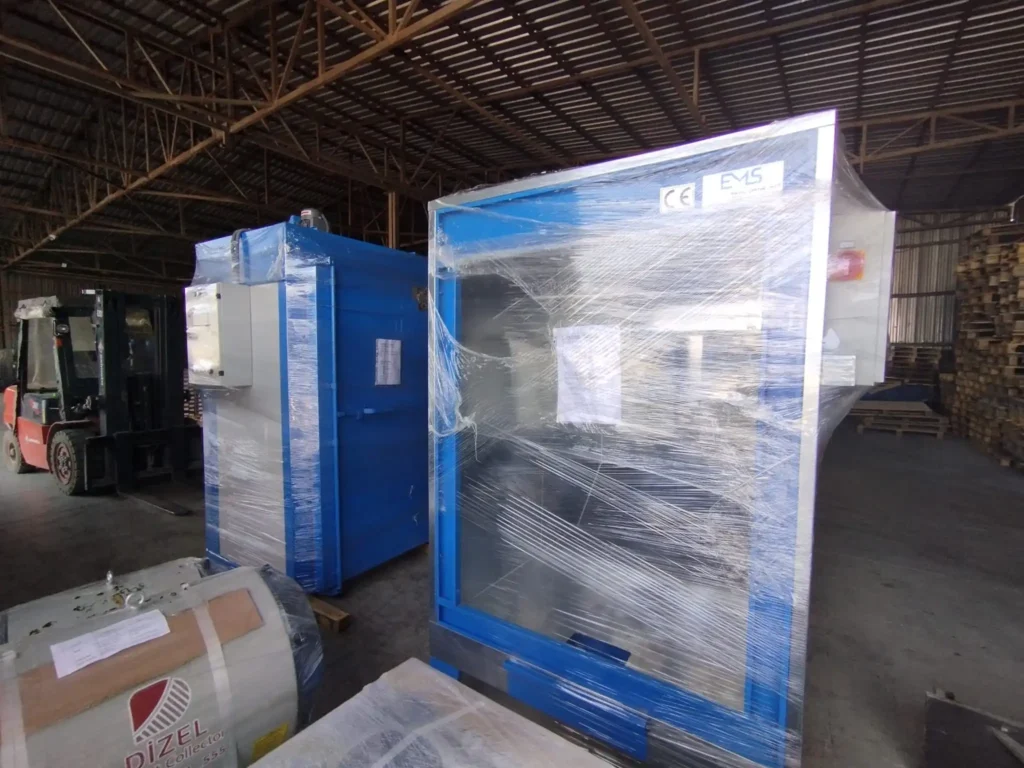
A powder coating booth is an essential element in the powder coating process, providing a dedicated environment for the application of powder coatings on various substrates. These booths are specifically designed to optimize the coating application, ensuring high-quality finishes while minimizing overspray and contamination.
With advanced features such as efficient ventilation systems and effective filtration, powder coating booths create a controlled workspace that enhances both safety and efficiency. The right booth can significantly improve the quality of the coating while reducing waste and operational costs.
EMS Powder Coating Equipment stands out as a leader in the manufacturing of powder coating booths, offering innovative designs tailored to the unique needs of different industries. In this section, we will delve into the operational principles, key features, and benefits of powder coating booths, while also discussing why EMS is the preferred choice for businesses seeking reliable and efficient coating solutions.
What is a Powder Coating Booth?
A powder coating booth is a specialized enclosure designed to facilitate the application of powder coatings to metal and other substrates. These booths play a critical role in ensuring a clean and controlled environment, which is vital for achieving high-quality finishes.
How Powder Coating Booths Operate
The operation of a powder coating booth begins with the preparation of the substrate, which typically involves cleaning and pre-treating the surface to ensure optimal adhesion. Once prepared, the substrate is positioned inside the booth, where electrostatic spray guns are utilized to apply charged powder particles onto the grounded surface.
The electrostatic charge attracts the powder, allowing for an even and uniform coating. The booth’s advanced ventilation system effectively captures overspray and maintains air quality, protecting both the operators and the environment.
EMS Powder Coating Equipment designs powder coating booths with features that enhance the application process, ensuring businesses achieve consistent, high-quality finishes across various applications.
Key Features of Powder Coating Booths
Powder coating booths come with a range of features that enhance their functionality and efficiency. Here are some standout features that make EMS booths the preferred choice for businesses:
1. High-Efficiency Filtration Systems
EMS powder coating booths are equipped with advanced filtration systems that capture overspray and particulate matter, ensuring a clean environment for coating applications. This leads to higher quality finishes and reduces the risk of contamination.
2. Optimal Ventilation
The ventilation system in EMS booths is designed to provide optimal air circulation, effectively removing fumes and excess powder. This feature not only enhances coating quality but also promotes a safer working environment for operators.
3. Ergonomic Design
The user-centric design of EMS powder coating booths prioritizes operator comfort and efficiency. With easy access to controls and ample workspace, operators can maneuver and position substrates effectively, minimizing production time.
4. Energy Efficiency
EMS powder coating booths are designed for energy efficiency, featuring optimized airflow and filtration systems that minimize energy consumption while maximizing performance. This efficiency can lead to significant cost savings.
5. Safety Features
Safety is a top priority in powder coating operations. EMS booths come equipped with essential safety features, including emergency shut-off systems, explosion-proof lighting, and proper ventilation, ensuring a safe working environment.
6. Customizable Configurations
Understanding that different businesses have unique requirements, EMS offers customizable configurations for their powder coating booths. Whether for small operations or large-scale production, EMS can tailor solutions to meet specific needs.
Benefits of Using Powder Coating Booths
Investing in a powder coating booth provides numerous advantages for businesses engaged in powder coating operations. Here are some key benefits:
1. Superior Coating Quality
The controlled environment of a powder coating booth significantly enhances the quality of applied coatings. With effective filtration and ventilation, these booths ensure smooth, even finishes that meet the highest standards.
2. Increased Productivity
EMS powder coating booths streamline the coating process, allowing for quicker application and improved drying times. This efficiency can lead to increased production rates, helping businesses meet tight deadlines.
3. Cost Efficiency
By minimizing overspray and maximizing powder usage, powder coating booths can significantly reduce material costs. Efficient application processes lead to less waste and lower operational expenses, enhancing profitability.
4. Versatility for Diverse Applications
EMS powder coating booths are versatile enough to accommodate a wide range of substrates and coating types. This adaptability allows businesses to diversify their offerings and cater to different market demands.
5. Compliance with Environmental Regulations
Powder coating booths are designed to meet industry safety and environmental regulations, ensuring a compliant operation. By investing in EMS booths, businesses can promote a healthier working environment while adhering to necessary standards.
Why Choose EMS Powder Coating Equipment for Powder Coating Booths?
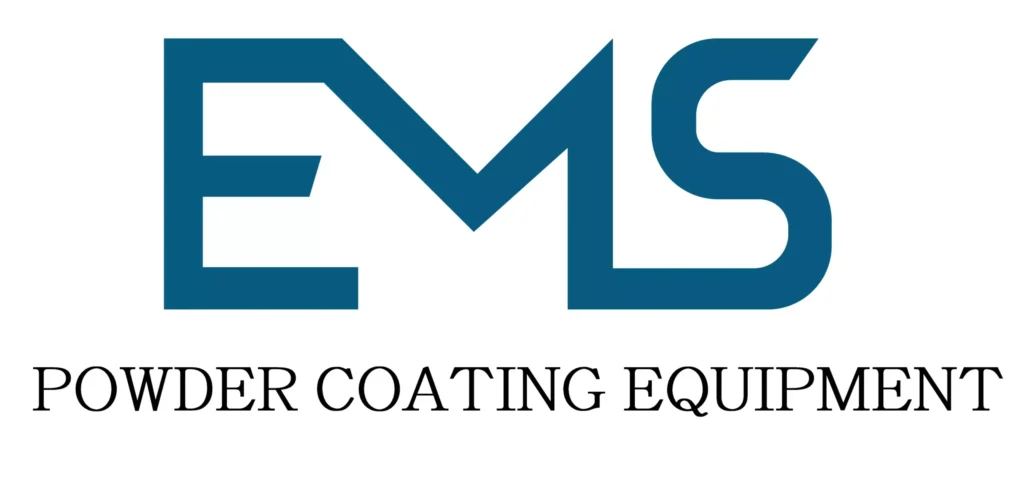
When selecting a powder coating booth, it is crucial to choose a manufacturer with a strong reputation for quality and innovation. EMS Powder Coating Equipment stands out as the top choice for businesses looking to invest in powder coating booths. Here’s why EMS is the preferred option:
1. Proven Expertise
With years of experience in the powder coating industry, EMS understands the unique needs of various applications. Their knowledge allows them to design powder coating booths tailored to diverse production environments.
2. Innovative Solutions
EMS is committed to continuous innovation, incorporating the latest technology into their products. Their powder coating booths are designed for optimal performance, featuring advanced filtration and airflow management systems.
3. Comprehensive Support
From installation to ongoing maintenance, EMS provides exceptional customer support. Their team of experts is dedicated to helping businesses maximize the performance of their powder coating booths.
4. Customizable Options
Recognizing that every business has unique requirements, EMS offers customizable options for powder coating booths, allowing businesses to select features and configurations that best suit their operational needs.
5. Trusted Reliability
With a strong reputation for delivering high-quality products, EMS is a trusted name in the powder coating industry. Their booths are designed for durability and long-term performance, making them an excellent investment for businesses.
Conclusion
A powder coating booth is a vital investment for any powder coating operation, providing a controlled environment that enhances coating quality and efficiency. With advanced filtration and ventilation systems, these booths ensure clean operations and compliance with safety regulations.
EMS Powder Coating Equipment is a leading manufacturer of powder coating booths, offering innovative solutions tailored to meet the diverse needs of various industries. Their commitment to quality, performance, and customer support makes EMS the best choice for businesses seeking reliable coating solutions.
By choosing EMS powder coating booths, companies can enhance their coating processes, achieve superior finishes, and reduce operational costs. With a focus on efficiency and innovation, EMS stands out as the premier manufacturer for businesses in need of top-tier powder coating equipment.
Powder Coating Equipment: Essential Tools for Quality Finishing
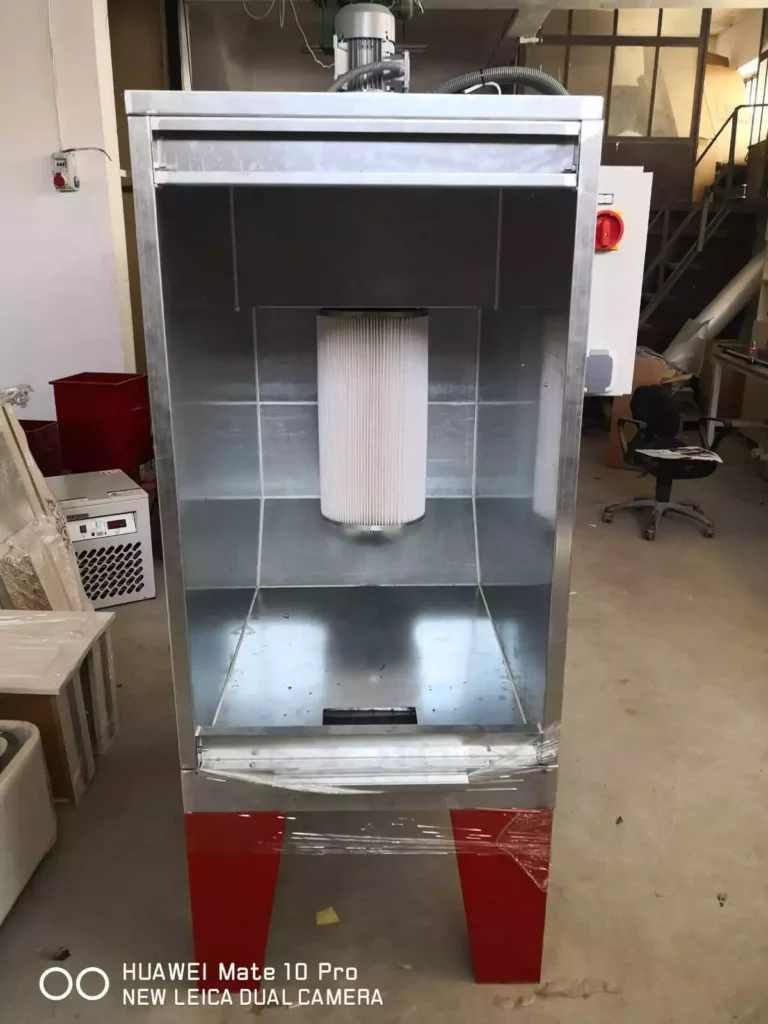
Powder coating equipment encompasses a range of specialized tools and machinery designed for the application of powder coatings onto various substrates. This technology has gained widespread popularity due to its ability to produce durable, high-quality finishes while being environmentally friendly.
The main components of powder coating equipment include spray guns, powder coating booths, curing ovens, and other essential tools that facilitate the coating process. Together, these components work seamlessly to create an efficient production line, resulting in coatings that are not only aesthetically pleasing but also resistant to corrosion, chemicals, and wear.
EMS Powder Coating Equipment is recognized as a leader in the manufacture of powder coating equipment, offering innovative solutions that cater to the unique needs of different industries. In this section, we will delve into the different types of powder coating equipment, their functionalities, and the advantages they provide, while highlighting why EMS is the preferred choice for businesses looking for reliable and effective coating solutions.
Types of Powder Coating Equipment
Powder coating equipment consists of several key components, each playing a crucial role in the coating process. Here’s an overview of the primary types of equipment involved:
1. Powder Coating Spray Guns
Powder coating spray guns are essential for applying the powder to the substrate. These guns utilize electrostatic technology, which charges the powder particles as they are sprayed. This charge causes the powder to adhere uniformly to the grounded surface, ensuring even coverage.
There are various types of spray guns available, including manual, automatic, and robotic systems. EMS Powder Coating Equipment offers a range of spray guns designed for efficiency and precision, making it easier for operators to achieve high-quality finishes.
2. Powder Coating Booths
Powder coating booths provide a controlled environment for the application of powder coatings. These booths are equipped with ventilation and filtration systems that capture overspray and maintain air quality. By minimizing contamination, EMS powder coating booths ensure superior coating quality.
3. Curing Ovens
After application, the coated substrate must be cured in an oven to achieve a durable finish. Curing ovens, whether electric, gas, or diesel-powered, heat the coated items to the necessary temperature for the powder to melt and form a solid bond with the substrate. EMS provides a variety of curing ovens to suit different production needs.
4. Powder Paint Booths with Filters
These booths are specifically designed for the application of powder coatings, featuring advanced filtration systems to capture overspray and particulates. This helps to maintain a clean working environment and enhances the overall quality of the coating application.
5. Powder Coating Accessories
In addition to the primary equipment, various accessories, such as hooks, racks, and conveyor systems, are vital for efficient operation. These accessories assist in transporting substrates through the coating process, ensuring smooth workflow and maximizing productivity.
Benefits of Using Powder Coating Equipment
Investing in high-quality powder coating equipment offers numerous advantages for businesses engaged in coating operations. Here are some key benefits:
1. Superior Durability
Powder coatings are known for their exceptional durability and resistance to chipping, scratching, and fading. The equipment designed for powder coating applications ensures that these qualities are maximized, resulting in long-lasting finishes.
2. Environmentally Friendly
Unlike traditional liquid coatings, powder coatings contain little to no volatile organic compounds (VOCs). This makes them a more environmentally friendly option, aligning with modern regulations and sustainability goals.
3. Cost Efficiency
By minimizing overspray and maximizing powder utilization, powder coating equipment can lead to significant cost savings. Efficient application processes result in less waste and lower operational costs, which enhance overall profitability.
4. Versatile Applications
Powder coating equipment can be used for a wide range of substrates, including metals, plastics, and wood. This versatility allows businesses to expand their offerings and cater to diverse market demands.
5. Enhanced Quality Control
With advanced features such as electrostatic application and controlled environments, powder coating equipment helps maintain high standards of quality. Businesses can achieve consistent finishes, reducing the likelihood of defects and rework.
6. Increased Productivity
Modern powder coating equipment is designed for efficiency, allowing for quicker application, curing, and turnaround times. This boost in productivity enables businesses to meet tight deadlines and increase production rates.
Why Choose EMS Powder Coating Equipment?
When selecting powder coating equipment, it is essential to choose a manufacturer known for quality, reliability, and innovation. EMS Powder Coating Equipment stands out as the top choice for businesses seeking powder coating solutions. Here’s why EMS is the preferred option:
1. Industry Expertise
With years of experience in the powder coating industry, EMS understands the unique requirements of various applications. Their expertise allows them to design equipment that meets the needs of diverse production environments.
2. Innovative Technologies
EMS is committed to continuous improvement and innovation, incorporating the latest technologies into their products. Their powder coating equipment features advanced design elements that enhance performance and efficiency.
3. Comprehensive Customer Support
From initial consultation to ongoing maintenance, EMS provides exceptional customer support. Their team of experts is dedicated to helping businesses optimize their powder coating operations.
4. Customizable Solutions
Recognizing that every business has unique needs, EMS offers customizable options for their powder coating equipment. This allows businesses to select features and configurations that align with their operational requirements.
5. Proven Reliability
With a strong reputation for delivering high-quality products, EMS is a trusted name in the powder coating industry. Their equipment is built for durability and long-term performance, making it an excellent investment for businesses.
Conclusion
Powder coating equipment is a crucial investment for any business involved in powder coating operations. By providing superior durability, cost efficiency, and environmentally friendly solutions, this equipment enhances the overall quality of the coating process.
EMS Powder Coating Equipment is a leading manufacturer of powder coating equipment, offering innovative and reliable solutions tailored to the diverse needs of various industries. Their commitment to quality, performance, and customer support makes EMS the best choice for businesses seeking top-tier powder coating solutions.
By choosing EMS powder coating equipment, companies can improve their coating processes, achieve high-quality finishes, and enhance productivity. With a focus on innovation and efficiency, EMS stands out as the premier manufacturer for businesses in need of effective powder coating solutions.
Automatic Powder Coating Equipment: Revolutionizing the Coating Process
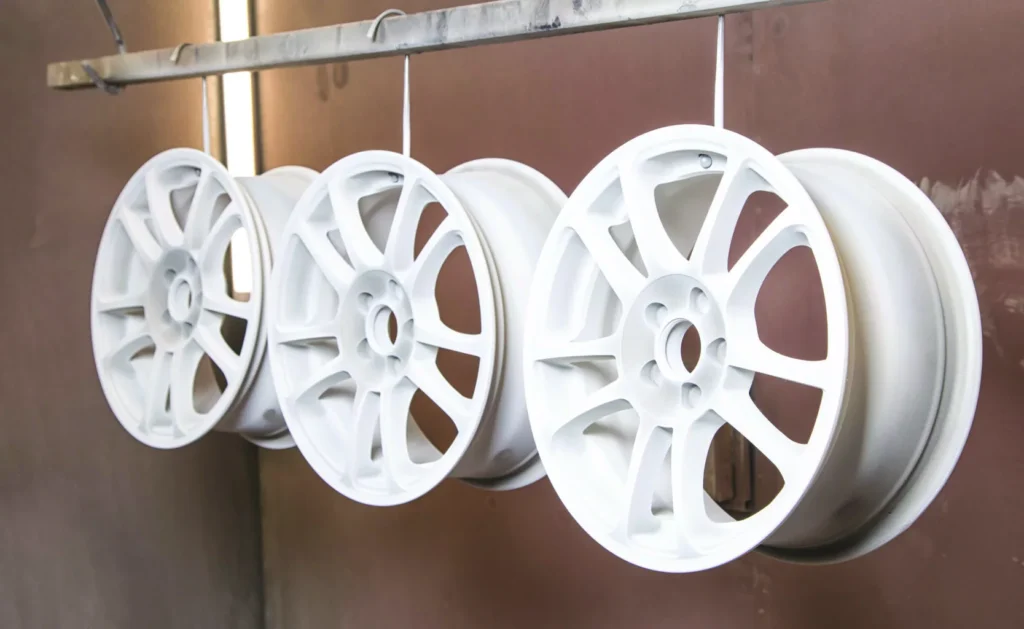
Automatic powder coating equipment represents a significant advancement in the field of surface finishing. Designed to automate the powder coating process, this equipment enhances efficiency, consistency, and quality, making it a preferred choice for manufacturers across various industries.
By utilizing automation technologies, businesses can significantly reduce labor costs and improve production speed while maintaining high standards of quality. Automatic systems include components such as robotic spray arms, automated conveyor systems, and sophisticated controls that ensure precise application of powder coatings.
EMS Powder Coating Equipment has established itself as a leader in the manufacture of automatic powder coating systems, offering innovative solutions that cater to diverse operational needs. In this section, we will delve into the key components of automatic powder coating equipment, its advantages, and the reasons why EMS is the go-to choice for businesses looking to enhance their coating processes.
Key Components of Automatic Powder Coating Equipment
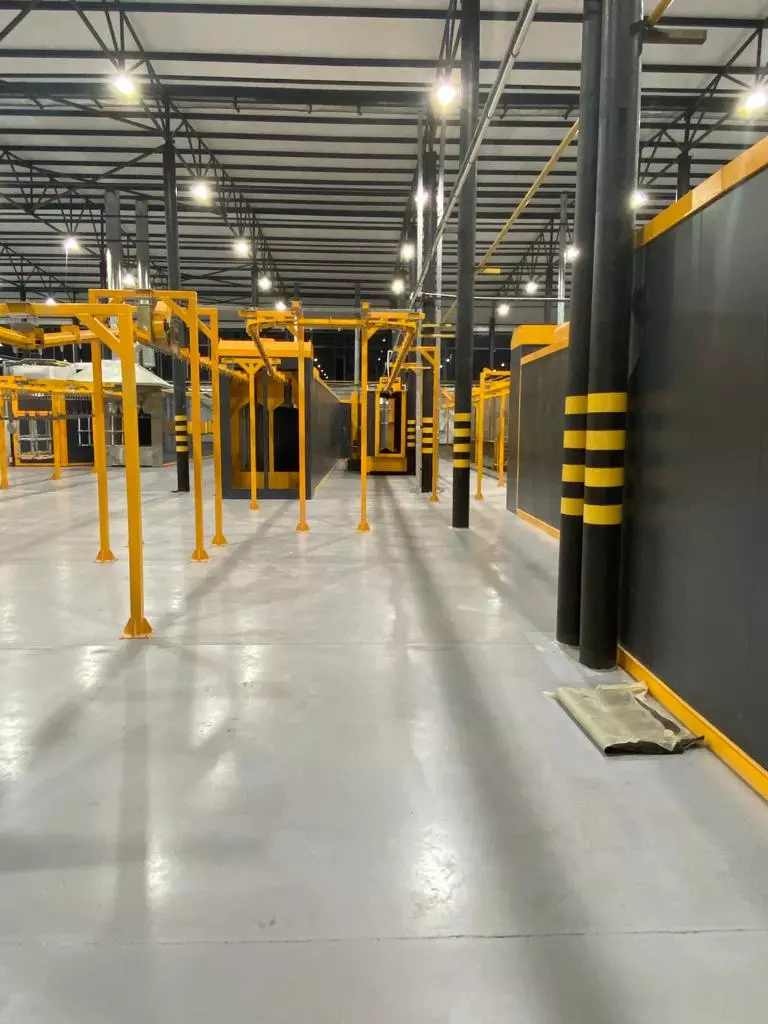
Automatic powder coating equipment consists of several critical components that work together to streamline the coating process. Here’s an overview of these essential elements:
1. Robotic Spray Guns
Robotic spray guns are a cornerstone of automatic powder coating systems. These devices are programmed to apply powder coatings uniformly and efficiently. The use of robotics allows for precise control over the application process, resulting in consistent and high-quality finishes.
2. Automated Conveyor Systems
Automated conveyor systems transport substrates through various stages of the powder coating process, from cleaning to coating and curing. This continuous movement minimizes manual handling and increases productivity by reducing downtime.
3. Powder Coating Booths
Automatic powder coating systems typically include dedicated booths designed to contain overspray and enhance air quality. These booths are equipped with advanced filtration and ventilation systems to ensure a clean environment for coating applications.
4. Curing Ovens
Curing ovens are essential for achieving durable finishes in automatic powder coating systems. These ovens are engineered to provide consistent heat distribution, ensuring that the powder melts and bonds effectively with the substrate.
5. Control Systems
Advanced control systems in automatic powder coating equipment allow for precise adjustments and monitoring of the coating process. Operators can easily program parameters such as application thickness, speed, and curing times, optimizing performance and quality.
Benefits of Automatic Powder Coating Equipment
Investing in automatic powder coating equipment offers numerous advantages for manufacturers. Here are some key benefits:
1. Enhanced Efficiency
Automatic systems significantly improve production efficiency by minimizing manual labor and reducing cycle times. The integration of robotic spray arms and conveyor systems allows for continuous operation, resulting in higher output rates.
2. Consistent Quality
One of the primary benefits of automatic powder coating equipment is the ability to achieve consistent and uniform coatings. Automated systems eliminate variations caused by human operators, ensuring high-quality finishes across all products.
3. Cost Savings
By reducing labor costs and improving material utilization, automatic powder coating equipment can lead to substantial cost savings. Efficient application processes minimize waste, enhancing the overall profitability of operations.
4. Flexibility and Scalability
Automatic powder coating systems can be easily adapted to accommodate different substrates and coating types. This flexibility allows manufacturers to diversify their product offerings and scale operations as demand increases.
5. Improved Safety
Automating the powder coating process enhances workplace safety by minimizing human exposure to potentially hazardous materials. Advanced control systems and robotics reduce the need for manual handling, creating a safer working environment.
6. Advanced Monitoring and Control
Modern automatic powder coating equipment includes sophisticated monitoring and control features that provide real-time data on the coating process. This capability allows operators to quickly identify and address any issues, ensuring optimal performance.
Why Choose EMS Powder Coating Equipment?
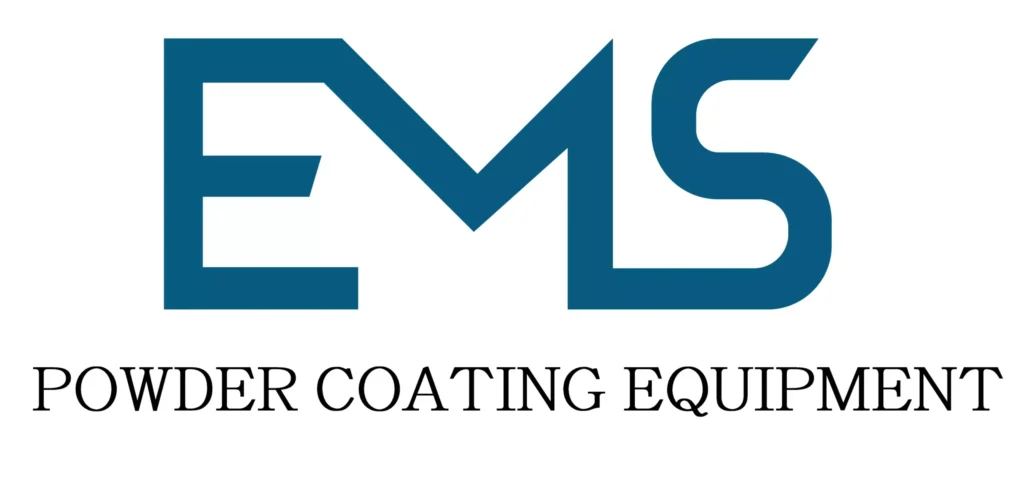
When selecting automatic powder coating equipment, it’s essential to choose a manufacturer known for quality, innovation, and reliability. EMS Powder Coating Equipment stands out as the top choice for businesses looking to enhance their powder coating processes. Here’s why EMS is the preferred option:
1. Proven Industry Expertise
With extensive experience in the powder coating sector, EMS understands the unique challenges and requirements of different applications. Their expertise allows them to design automatic systems that meet diverse operational needs.
2. Innovative Technologies
EMS is committed to innovation, continuously integrating the latest technologies into their automatic powder coating equipment. Their systems are designed for optimal performance, featuring advanced robotics and control systems that enhance efficiency.
3. Comprehensive Customer Support
From initial consultation through installation and ongoing maintenance, EMS provides exceptional customer support. Their team of experts is dedicated to helping businesses maximize the performance of their automatic systems.
4. Customizable Solutions
Recognizing that every business has distinct requirements, EMS offers customizable options for their automatic powder coating equipment. This allows companies to tailor solutions to their specific production needs.
5. Trusted Reliability
With a strong reputation for delivering high-quality products, EMS is a trusted name in the powder coating industry. Their automatic equipment is built for durability and long-term performance, making it an excellent investment for businesses.
Conclusion
Automatic powder coating equipment is a game-changer for manufacturers looking to enhance their coating processes. By improving efficiency, consistency, and quality, these systems provide a competitive edge in today’s fast-paced market.
EMS Powder Coating Equipment is a leading manufacturer of automatic powder coating systems, offering innovative solutions tailored to the diverse needs of various industries. Their commitment to quality, performance, and customer support makes EMS the best choice for businesses seeking reliable and effective coating solutions.
By choosing EMS automatic powder coating equipment, companies can optimize their operations, achieve superior finishes, and enhance productivity. With a focus on innovation and efficiency, EMS stands out as the premier manufacturer for businesses in need of top-tier powder coating solutions.
Powder Coating Reciprocator: Precision in Coating Application

A powder coating reciprocator is a specialized piece of equipment designed to apply powder coatings efficiently and uniformly to various surfaces. By utilizing a mechanical arm that moves in a back-and-forth motion, reciprocators ensure that every part of the substrate receives an even application of powder. This technology is crucial for achieving high-quality finishes and is widely used in industries ranging from automotive to furniture manufacturing.
The primary advantage of using a reciprocator lies in its ability to automate the powder coating process, resulting in improved consistency and reduced labor costs. Unlike manual application methods, which can lead to variations in coating thickness and quality, reciprocators provide precise control over the application process.
EMS Powder Coating Equipment is renowned for manufacturing high-quality powder coating reciprocators that meet the diverse needs of various industries. In this section, we will delve into the key features of powder coating reciprocators, their benefits, and the reasons why EMS is the go-to choice for businesses seeking reliable and effective coating solutions.
Key Features of Powder Coating Reciprocators
Powder coating reciprocators consist of several essential components that work together to ensure precise application of powder coatings. Here are the key features of these machines:
1. Mechanical Arm Design
The mechanical arm of a powder coating reciprocator is engineered for smooth and controlled movement. This design allows for consistent coverage across the substrate, minimizing the risk of missed spots or uneven application.
2. Adjustable Speed and Stroke Length
Reciprocators offer adjustable speed settings and stroke lengths, allowing operators to customize the application process according to the specific needs of different substrates. This flexibility enhances the overall efficiency of the coating operation.
3. Integrated Spray Gun Systems
Most powder coating reciprocators come equipped with integrated spray gun systems, ensuring that the powder is applied uniformly. These systems are often designed to utilize electrostatic technology, which helps the powder adhere better to the substrate.
4. Control Panels
Modern reciprocators feature user-friendly control panels that allow operators to easily adjust settings such as speed, stroke length, and application thickness. These controls provide the ability to monitor the coating process in real time.
5. Safety Features
Safety is a key consideration in any manufacturing environment. Powder coating reciprocators are equipped with various safety features, such as emergency stop buttons and protective enclosures, to ensure safe operation for workers.
Benefits of Using Powder Coating Reciprocators
Investing in a powder coating reciprocator offers numerous advantages for businesses involved in powder coating operations. Here are some key benefits:
1. Improved Application Efficiency
Powder coating reciprocators significantly enhance the efficiency of the coating process. By automating the application, businesses can reduce cycle times and increase throughput, ultimately improving production rates.
2. Consistent Quality
One of the main advantages of using reciprocators is the ability to achieve consistent and uniform coatings. This level of precision minimizes defects and ensures high-quality finishes, which is crucial for customer satisfaction.
3. Reduced Labor Costs
Automating the powder coating process with reciprocators allows businesses to reduce their reliance on manual labor. This not only lowers labor costs but also minimizes the potential for human error in the application process.
4. Enhanced Material Utilization
Powder coating reciprocators are designed to optimize powder utilization. By applying the powder evenly and efficiently, businesses can reduce waste and lower material costs.
5. Flexibility in Application
Reciprocators can be adjusted to accommodate various substrate shapes and sizes. This flexibility allows businesses to diversify their offerings and cater to different market needs.
6. Minimal Maintenance Requirements
Modern powder coating reciprocators are built with durability in mind, requiring minimal maintenance. This reduces downtime and helps businesses maintain consistent production levels.
Why Choose EMS Powder Coating Equipment?
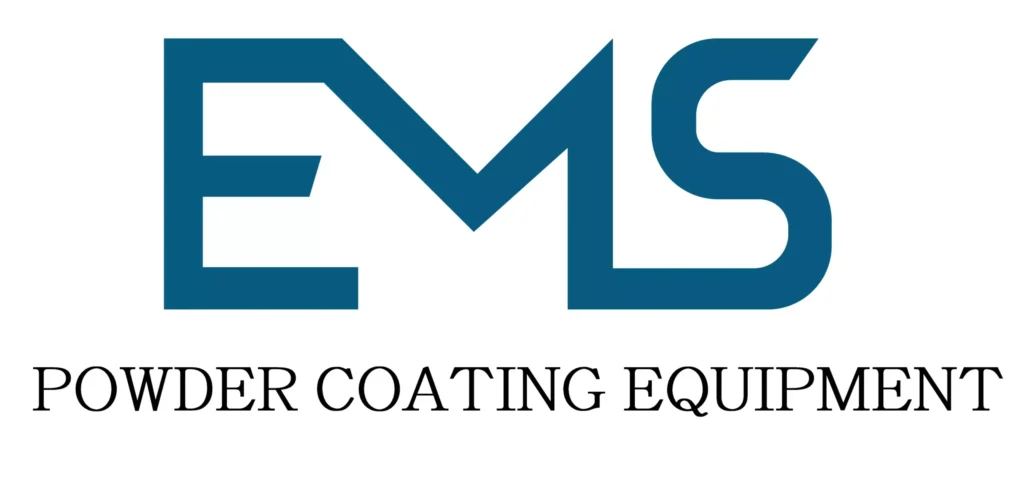
When selecting a powder coating reciprocator, it’s essential to choose a manufacturer known for quality, reliability, and innovation. EMS Powder Coating Equipment stands out as the preferred choice for businesses looking to enhance their powder coating processes. Here’s why EMS is the best option:
1. Proven Industry Experience
With extensive experience in the powder coating industry, EMS understands the unique challenges and requirements of various applications. Their expertise enables them to design reciprocators that cater to diverse operational needs.
2. Innovative Solutions
EMS is committed to innovation, continuously integrating the latest technologies into their powder coating reciprocators. Their systems are designed for optimal performance and efficiency, enhancing overall productivity.
3. Comprehensive Customer Support
From the initial consultation through installation and ongoing maintenance, EMS provides exceptional customer support. Their team of experts is dedicated to helping businesses maximize the performance of their reciprocators.
4. Customizable Options
Recognizing that every business has distinct requirements, EMS offers customizable options for their powder coating reciprocators. This allows companies to tailor solutions to their specific production needs.
5. Trusted Quality
With a strong reputation for delivering high-quality products, EMS is a trusted name in the powder coating industry. Their reciprocators are built for durability and long-term performance, making them an excellent investment for businesses.
Conclusion
Powder coating reciprocators play a vital role in modern manufacturing, providing precision and efficiency in the coating application process. By automating this process, businesses can achieve consistent quality, improve productivity, and reduce labor costs.
EMS Powder Coating Equipment is a leading manufacturer of powder coating reciprocators, offering innovative solutions tailored to the diverse needs of various industries. Their commitment to quality, performance, and customer support makes EMS the best choice for businesses seeking reliable and effective coating solutions.
By choosing EMS powder coating reciprocators, companies can optimize their coating processes, achieve superior finishes, and enhance overall productivity. With a focus on innovation and efficiency, EMS stands out as the premier manufacturer for businesses in need of top-tier powder coating solutions.
Not only do we manufacture our powder coating equipment, we also ship them worldwide to your facility with care
We’re not just the manufacturers of your powder coating equipment, we’re also your worldwide delivery partners.
At EMS Powder Coating Equipment, we understand that getting your powder coating equipment to you quickly and safely is just as important as manufacturing it to the highest standards. That’s why we offer worldwide delivery services to all of our customers.
We work with a network of experienced and reliable shipping partners to ensure that your equipment arrives on time and in perfect condition. We also offer a variety of shipping options to fit your budget and needs.
Whether you need your equipment shipped to a local address or to an international destination, we can help. We’ll work with you to choose the best shipping option for your needs and to keep you updated on the status of your shipment every step of the way.
So when you choose EMS for your powder coating equipment, you’re not just getting the best products on the market, you’re also getting the best possible delivery experience.
Contact us today to learn more about our worldwide delivery services.
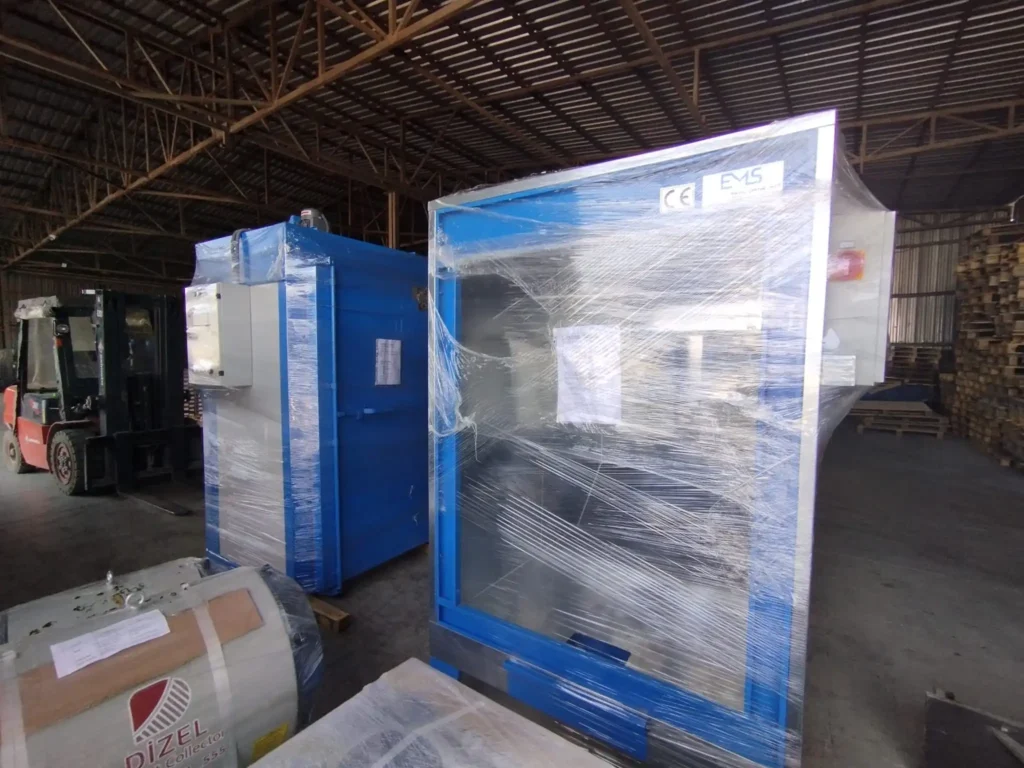
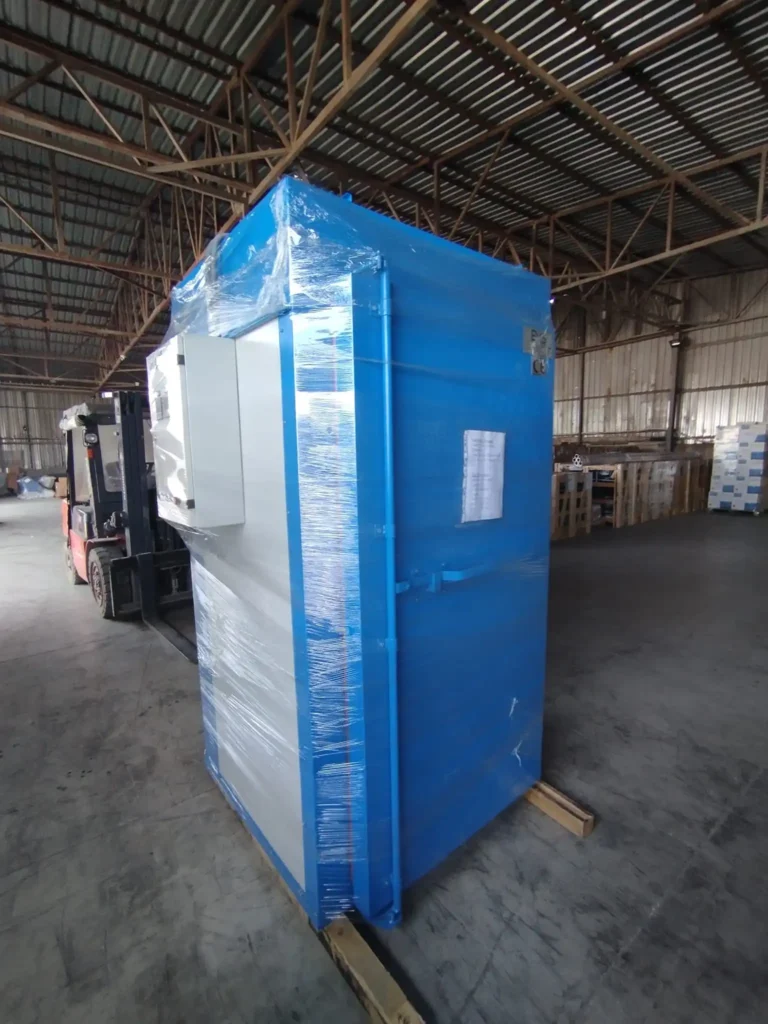
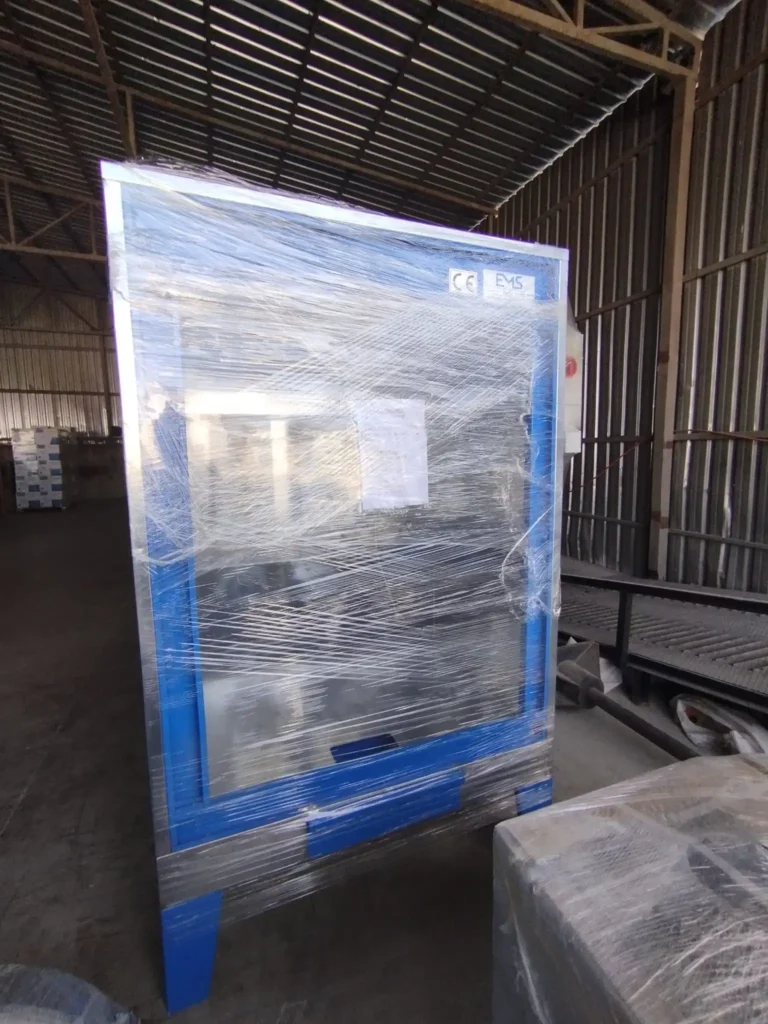
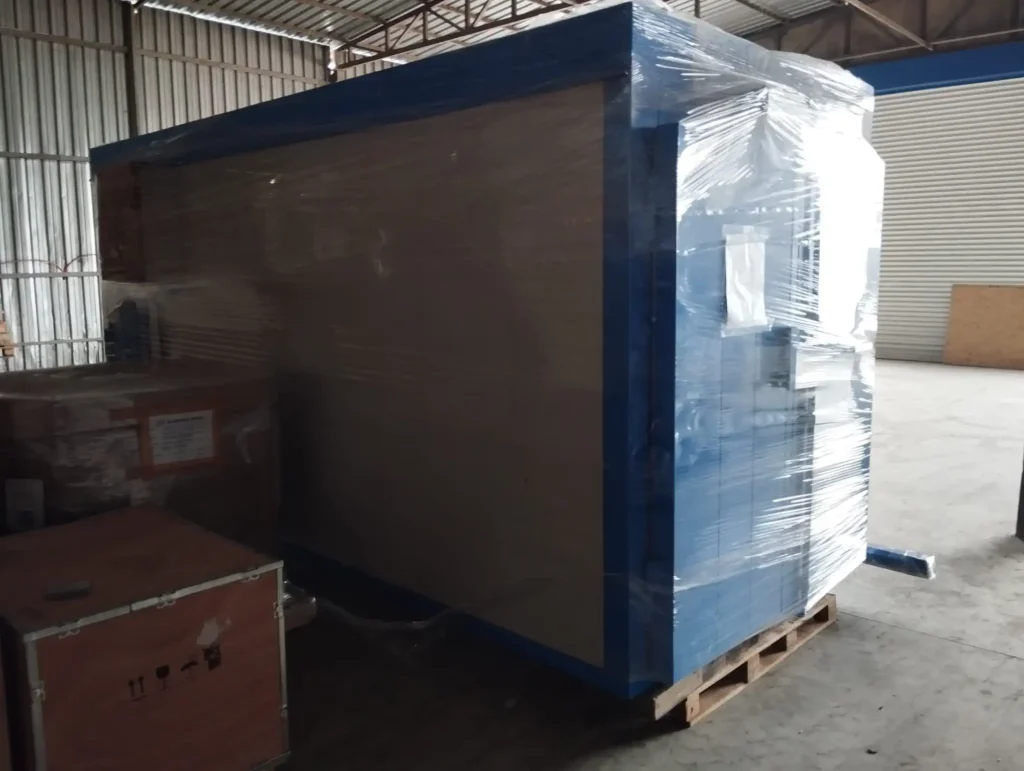
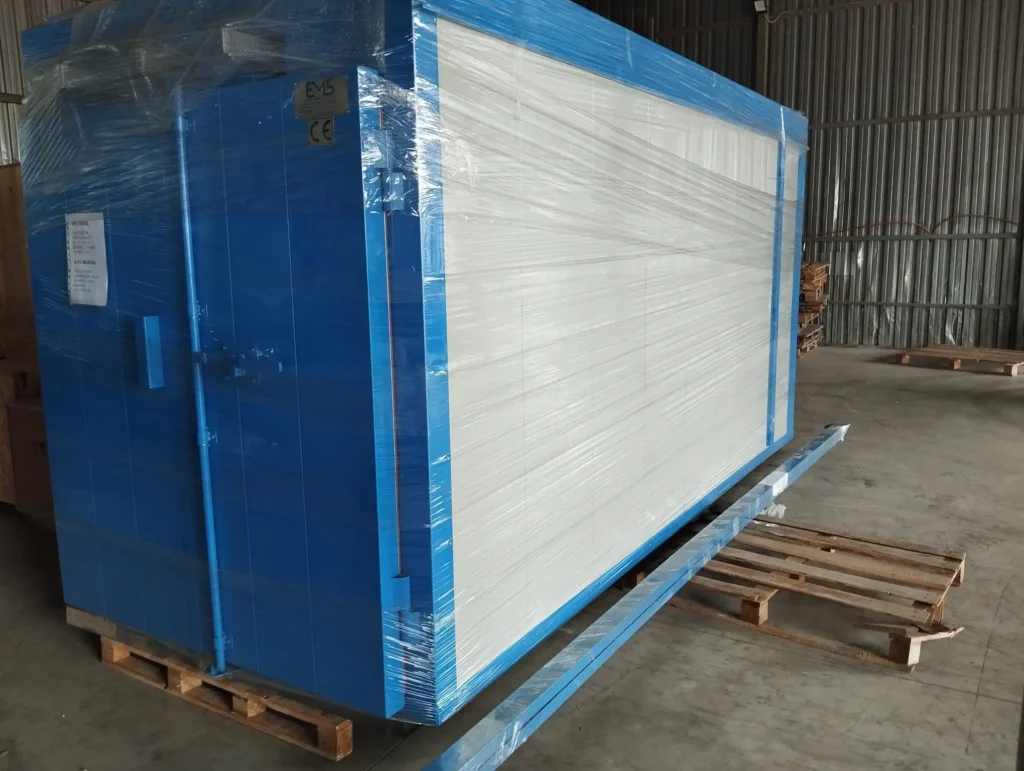
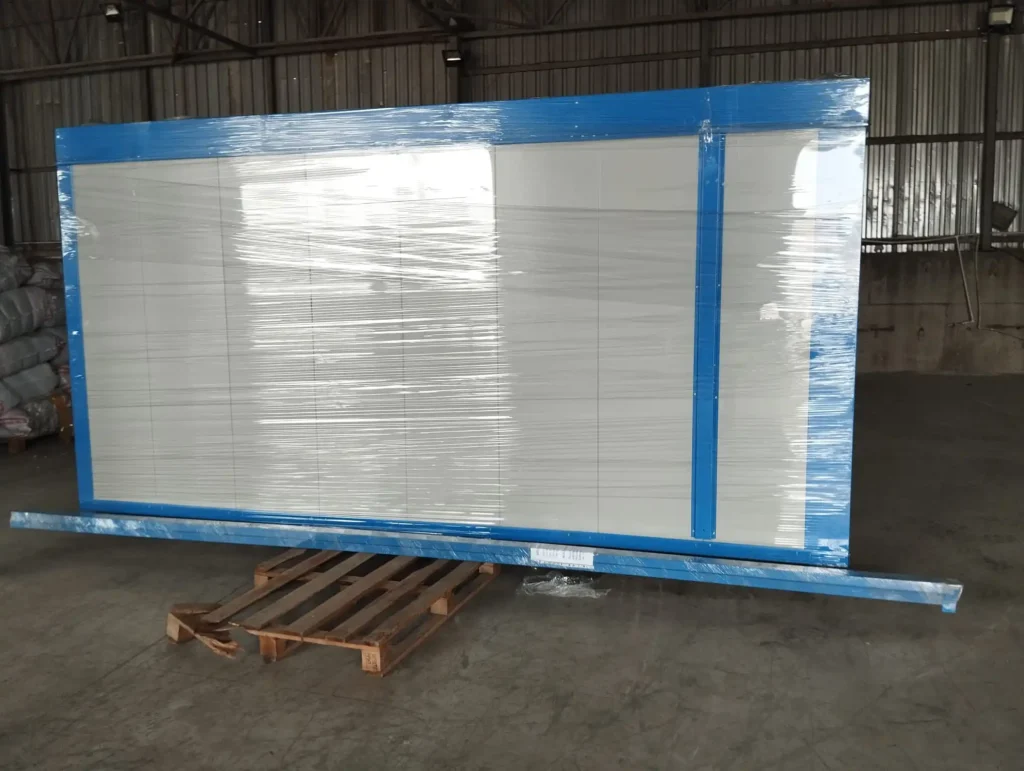
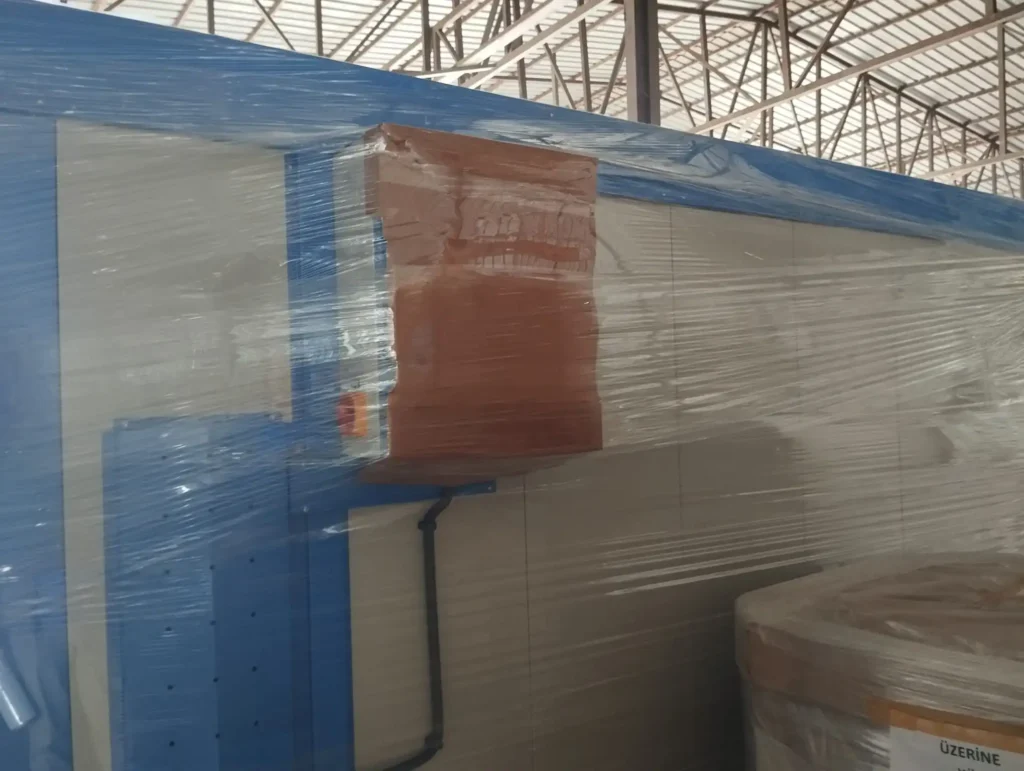
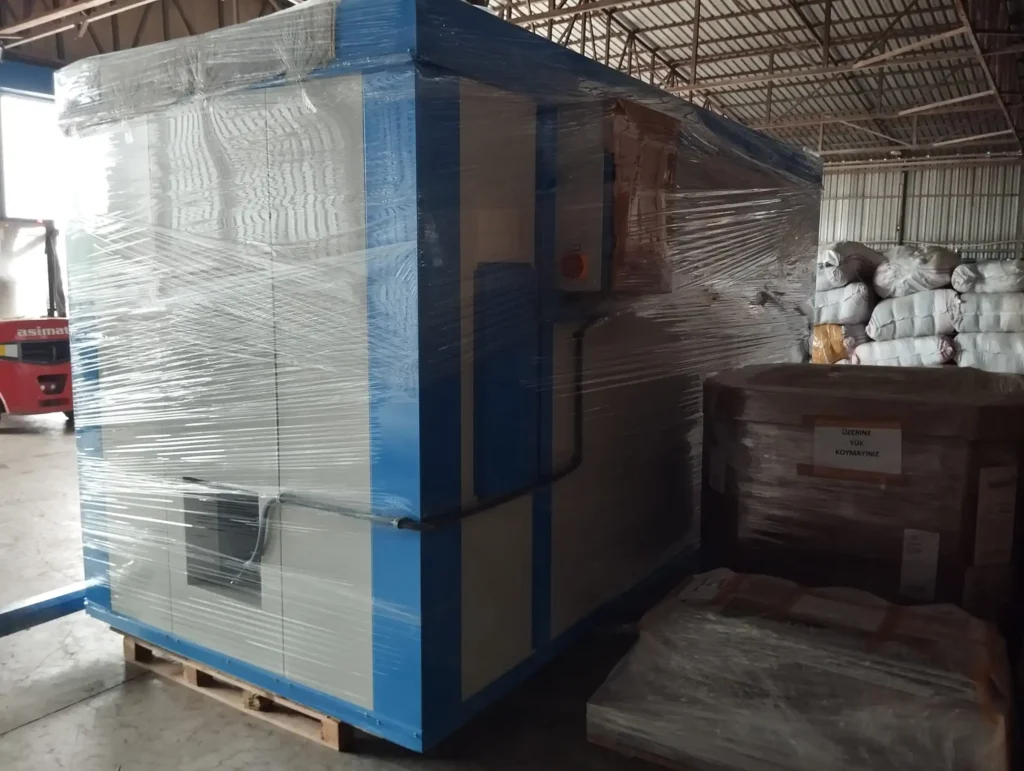
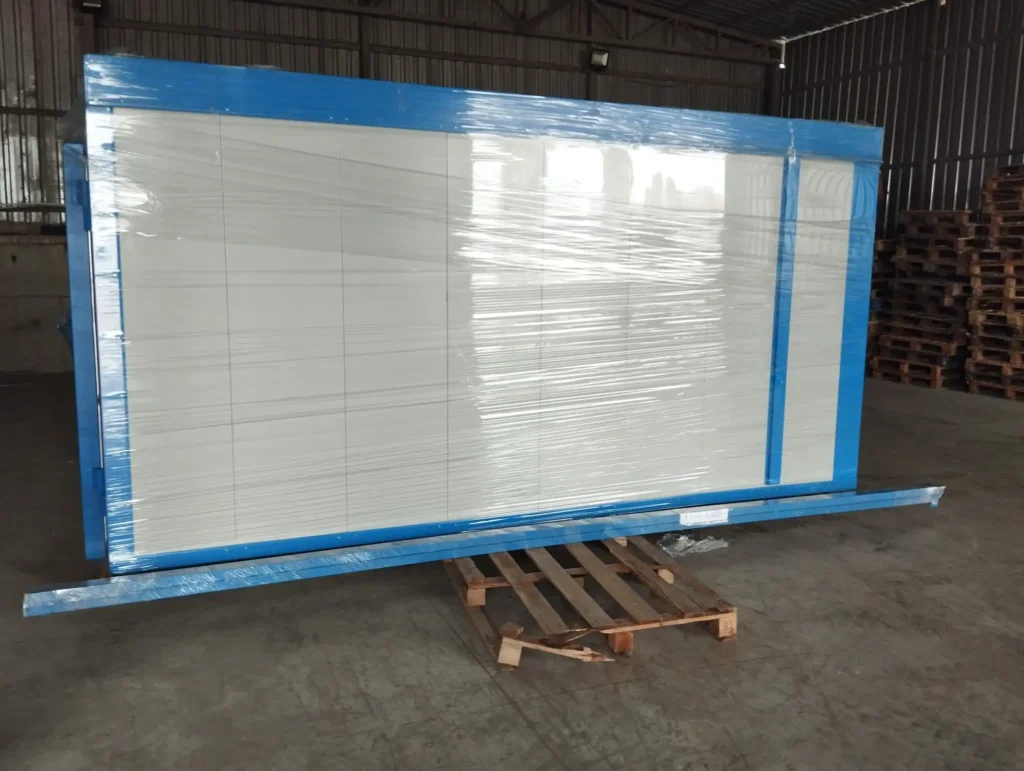