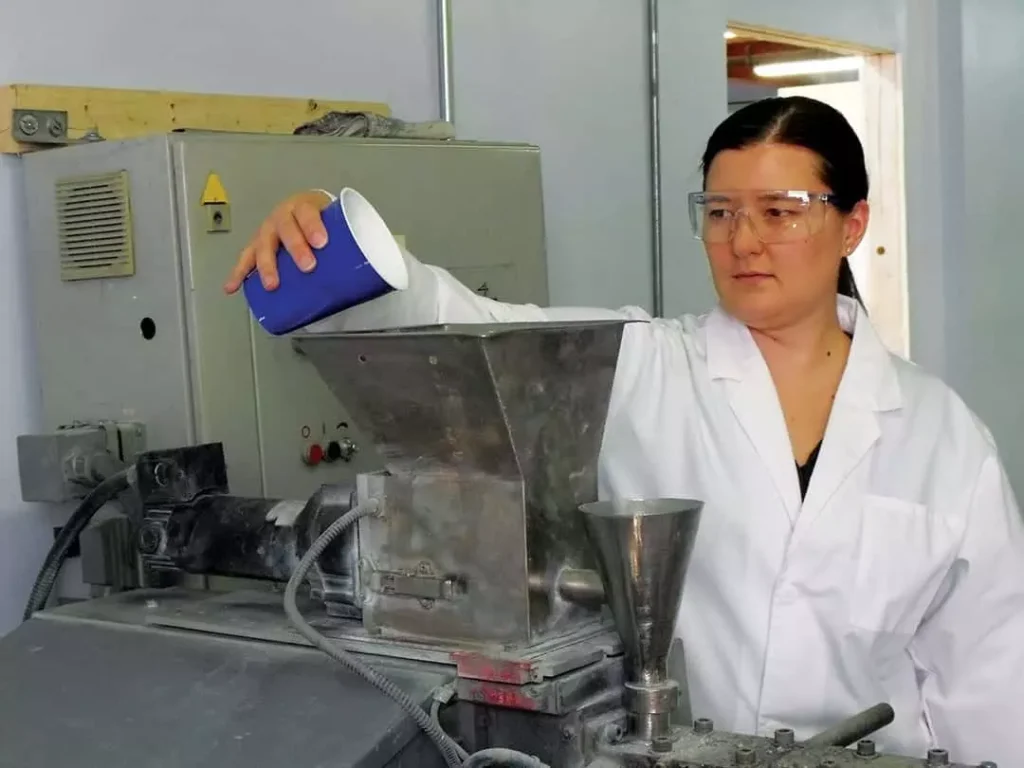
The requirements of the particular heating applications in powder coating must be thoroughly studied and these matched with the capabilities and design principles of available ovens. Such a thorough investigation of all aspects of the heating components of a powder finishing line is critical to achieving an efficient, effective and satisfactory operation that will produce a high-quality product.
Powder coating is increasingly accepted as the preferred finishing process for many applications. Increasingly stringent environmental regulations, rising costs in all areas, and demands by consumers for better quality and more durable products are among the challenges facing today’s finishers. Powder coatings provide a solution to these challenges and others. Powder coating is the technique of applying dry paint to the component.
The powdered paint is normally applied by using a powder feed system and gun to electrostatically charge and spray the powder onto the part. For some applications, the part being coated is dipped into a fluidized bed of powder. The coated part is then heated in an oven, or via infrared panels, to melt and cure the paint. During the curing process, a chemical cross-linking reaction is triggered and it is this chemical reaction that gives the powder coatings many of their desirable properties.
Heating Applications In Powder Coating
Heating is a critical step in the powder coating process, as it is responsible for curing the powder and creating a durable, long-lasting finish. The specific type of heating used will depend on the type of powder being used, the desired finish, and the size and shape of the part being coated.
Types of Heating
There are four main types of heating used in powder coating:
- Convection: This is the most common type of heating, and it involves circulating hot air around the part being coated. Convection is a good choice for parts that have a uniform shape and surface area.
- Infrared (IR): IR heating uses electromagnetic waves to heat the part. IR is a good choice for parts that have a complex shape or that are made of a material that is not a good conductor of heat.
- Ultraviolet (UV): UV heating uses ultraviolet light to cure the powder. UV is a good choice for parts that require a high-gloss finish or that are made of a material that is sensitive to heat.
- Induction: Induction heating uses a magnetic field to heat the part. Induction is a good choice for parts that are made of metal.
Temperature and Time
The temperature and time required for curing will vary depending on the type of powder being used, the desired finish, and the size and shape of the part being coated. However, in general, the part must be heated to a temperature between 300°F and 450°F for a period of 10 to 20 minutes.
Controlling the Heat
It is important to carefully control the heat during the curing process. If the part is heated too quickly, it can warp or crack. If the part is not heated hot enough or for the correct amount of time, the powder will not cure properly and will not be durable.
Applications
Powder coating is used in a wide variety of applications, including:
- Automotive: Powder coating is used on car exteriors, interiors, and wheels.
- Appliance: Powder coating is used on refrigerators, stoves, dishwashers, and washing machines.
- Furniture: Powder coating is used on metal furniture, such as chairs, tables, and desks.
- Industrial: Powder coating is used on a wide variety of industrial equipment, such as machinery, tools, and pipes.
Benefits
Powder coating has several benefits over other types of finishes, including:
- Durability: Powder coating is a very durable finish that can withstand scratches, chips, and fading.
- Environmentally friendly: Powder coating is a more environmentally friendly finish than liquid paint because it does not emit volatile organic compounds (VOCs).
- Cost-effective: Powder coating is a cost-effective finish that can be applied quickly and easily.
Conclusion
Heating is a critical step in the powder coating process, and it must be carefully controlled to ensure that the part is cured properly. Powder coating is a durable, environmentally friendly, and cost-effective finish that is used in a wide variety of applications.
Preheating
Parts on their way to the coating application area are preheated and were required to dry off any moisture remaining from previous cleaning or conditioning steps. Such heating must only be adequate to accomplish this simple function. Temperatures -at most – can be in the range of 190 F (88C) and can be attained with any number of available ovens. Ventilation of the area is of little significance and only the time dryness relationship is of importance.
Preheating also is needed to raise the temperature of parts that are to be coated by processes requiring that the powder fuse on the part upon contact. This requires the establishment of a temperature-time coating cycle so that coating thickness can be reproduced. The hotter the part, the more the amount of material adhered before the temperature falls below the fusion point. The temperature-time curve for such ovens must be known and reproducible.
Generally, such ovens need not be ventilated beyond that required by safety considerations. These conditions can easily be met by any number of commercial ovens. Parts generally preheated for application reasons are items such as glass bottles, plastic pens, MDF, certain woods, and sometimes castings.
Post heating – Product Cure
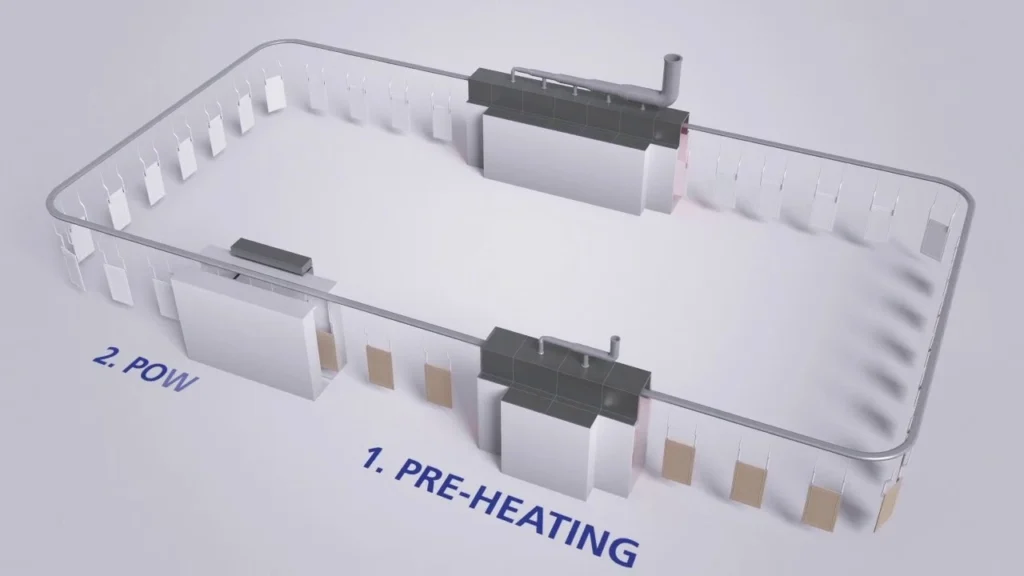
Post heating operations on a powder finishing line are perhaps the most critical. They are used to melt, flow and cure the powder which has been applied to the part at ambient temperature as with the use of the electrostatic spraying process.
This application of heat has to be very carefully controlled because the temperature-fluidity characteristics of a particular powder are peculiar to that powder and it is this relationship that determines how the flow of the material will take place as the temperature is raised.
Most materials cross-link and become more viscous with time at a given temperature so this, for thermosetting materials further complicates the control. The final properties of the coating can only be acquired uniformly over the part if parts of the coating are treated in thermally equivalent conditions. The post-heat ovens for this reason again must be of high quality and be equipped with adequate controls to insure reproducibility.
Post heating – Process Considerations in Heating Applications in Powder Coating
Many elements and variables must be considered and studied when selecting ovens for the powder coating line. Of utmost importance are:
- Product. Size, Configuration, Mass, Temperature limitations.
- Conveyor. Method, Product holder, Line speeds.
- Powder. Formulation type, Thickness, Cure profile, Color, Gloss, Cure test.
All parameters should be defined and communicated to equipment and powder suppliers are involved to insure that an integrated system and successful installation are achieved
Post heating – Hot Air, Gas, or Electric Convection Cure as Heating Applications in Powder Coating
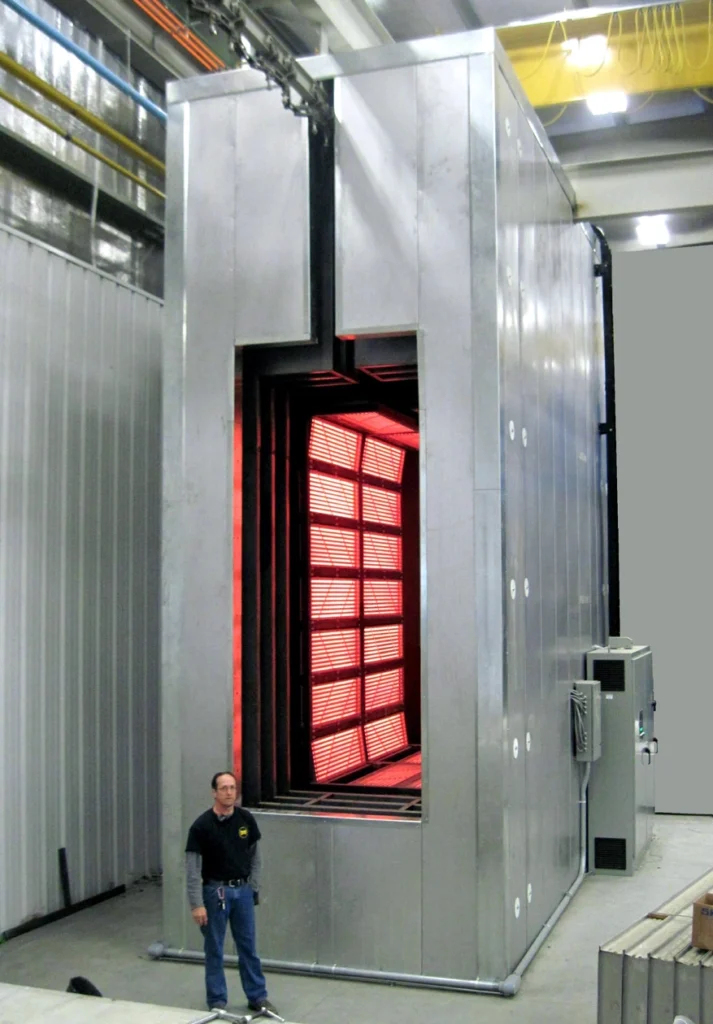
Convection heating uses a medium such as air to transfer heat from the energy source to the product. Many convection systems use a fired source (gas flame or steam) which provides heated air circulation in the oven chamber. Using a combustion chamber, the oven atmosphere can contain combustion products, solvent vapors, and possibly traces of unburned fuel.
Other convection ovens utilize electric low-intensity infrared elements (calrods, resistance emitters) to provide a clean, safe method of convection heating.
The time required to bring the powder deposited on a part to its cure temperature is largely a function of the mass of the part and the rate at which the part accepts heat using convection heating. Large metal objects may require from 30 minutes to 60 minutes or more to reach the desired cure temperature, while smaller parts can be brought to temperature much more rapidly.
This heat absorption by the part is a waste of heat energy as far as powder curing is concerned. But considering all of the process requirements, such as part configuration, products with varying size and dimensions, and processes where products of similar configuration cannot be batched. This may be the most flexible and efficient method of curing. The temperature response time of a large convection oven is not particularly rapid, often taking up to an hour or more for the oven to reach operating temperature.
They require considerable floor space and routine cleaning if good finishes at high production rates are to be obtained. Despite these limitations, convection ovens are currently the most popular for industrial painting curing. Energy and operating costs however are often high and users should be aware of alternative methods for their production lines
Post heating – Infrared Radiation as Heat Applications in Powder Coating
Short, Medium, and Longwave, high-intensity infrared heating utilizes electrical energy to provide a direct, radiant method of heating. Infrared is transmitted directly from emitter to product via electromagnetic waves traveling at the speed of light (186,000 miles per second). Different from convection heating, high-intensity infrared requires no medium to be heated for heat transfer to take place.
Heated energy is transferred quickly, cleanly, and efficiently typically in tungsten quartz infrared lamps. These can be electric or gas-fired. High-intensity infrared can have a fast temperature time response. Curing ovens using this method of radiation heating are compact in size and can be zoned to match exact product configuration and size.
Oven start-up times of 10-15 minutes or less are common. Savings in energy, space, and time can be realized with high-intensity infrared. Infrared radiation is best used with products of consistent shape produced on dedicated lines in large volumes. A direct line of sight and heater to the object surface is needed for proper powder cure, and cure is affected by object distance.
Rotating the coated product during the infrared cure for the round to cylindrical shape product produces uniform heating with consistent cure results. Reflow and cure times range from 10 seconds to 120 seconds using high-intensity infrared.
- Infrared also permits horizontal and vertical zone control for varying
part profiles. - It is possible to shut off, or turn down, zones to save energy.
- Infrared is 3 times more efficient on average than convection.
Post heating – Ultraviolet Light & Electron Beam as Heating Applications in Powder Coating
UV cure relies on the penetration of UV light through the coating while EB uses accelerated electrons that can penetrate even pigmented coatings. This supplied energy causes a rapid chemical and physical change brought on by the energies agitation, or excitement, of photoinitiators formulated into the product.
This technology is very dependent upon line of sight cure and end uses with three-dimensional parts are limited. In fact, worldwide use of this technology is limited to a handful of companies. A UV powder paint line is suited to powder coating heat-sensitive materials. A typical cure range would be 2-3 minutes at 175F to 230F.