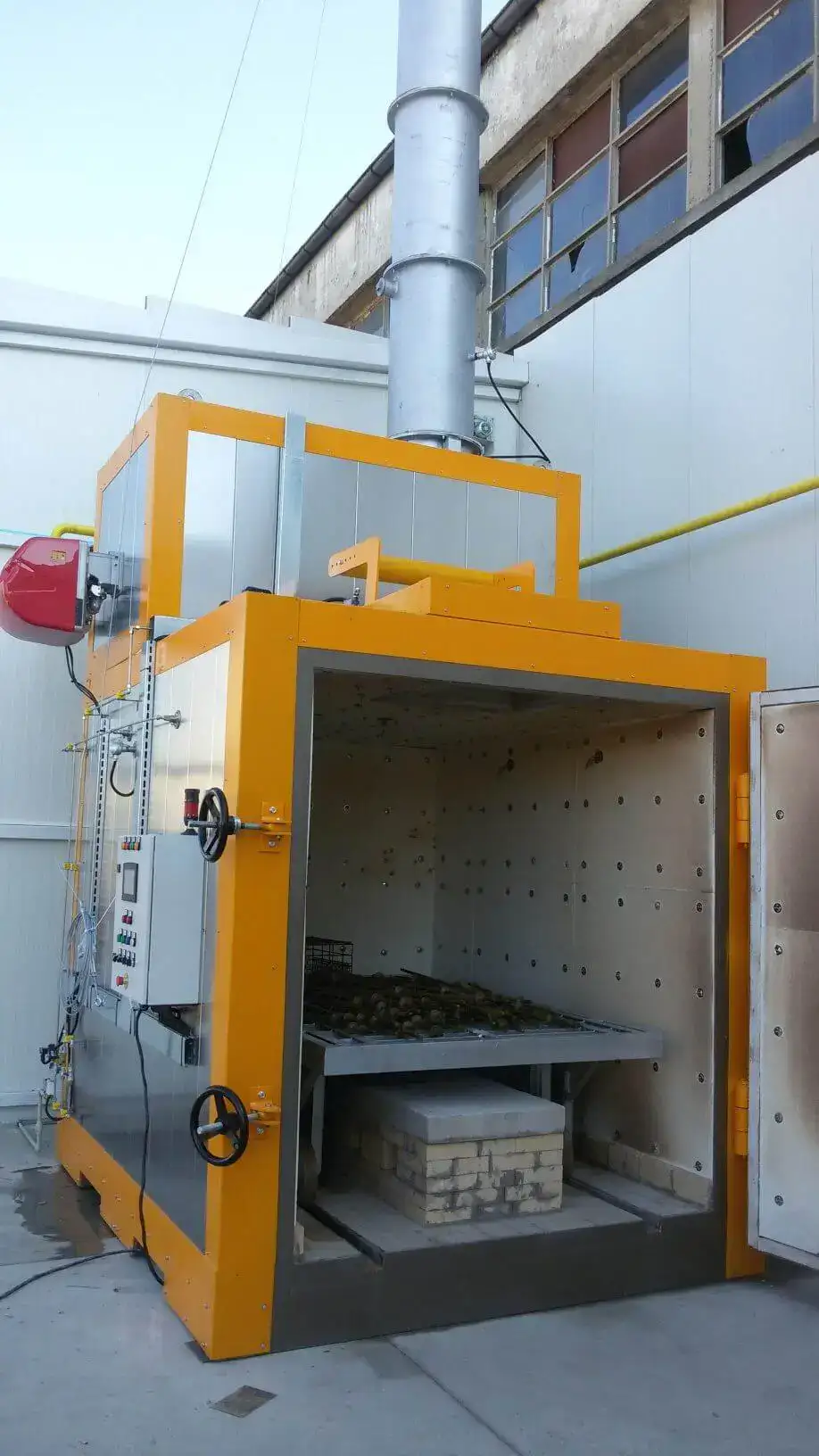
Heat cleaning oven plays a crucial role in the powder coating process, ensuring the effective removal of contaminants from metal surfaces before the application of powder coatings. This thermal cleaning method, often referred to as burn-off or heat cleaning, utilizes elevated temperatures to break down and eliminate unwanted residues, such as paint, grease, and other organic materials.
Heat Cleaning Oven
- Temperature Control: Heat cleaning ovens are designed to achieve and sustain high temperatures, typically ranging from 800°F to 1200°F (427°C to 649°C). This elevated temperature is essential for the thermal decomposition of organic substances adhering to the metal substrate.
- Combustion Process: During the heat cleaning cycle, the oven creates an oxygen-controlled environment to prevent excessive oxidation of the metal substrate. This controlled atmosphere facilitates the combustion of organic contaminants without causing damage to the underlying material.
- Residue Conversion: Organic contaminants undergo pyrolysis, a process where high temperatures cause the breakdown of complex molecules into simpler compounds. This results in the conversion of paints, coatings, and other residues into ash or gaseous byproducts, leaving the metal substrate clean and ready for the powder coating application.
Heat Cleaning Oven Key Features:
- Insulation: Heat cleaning ovens are equipped with high-quality insulation materials to minimize heat loss and ensure energy efficiency. This insulation helps maintain the required elevated temperatures throughout the cleaning cycle.
- Temperature Uniformity: Advanced oven designs incorporate mechanisms to ensure uniform temperature distribution within the heating chamber. This feature prevents localized overheating or underheating, guaranteeing consistent and reliable cleaning results across the entire metal surface.
- Control Systems: Modern heat cleaning ovens are equipped with sophisticated control systems that allow operators to precisely set and monitor temperature profiles. This ensures optimal cleaning conditions for different types of contaminants and substrates.
- Safety Measures: Safety is paramount in heat cleaning operations. Ovens are equipped with safety interlocks and monitoring systems to prevent overheating, ensure proper ventilation, and secure the working environment during the cleaning process.
Heat Cleaning Oven Advantages:
- Efficient Contaminant Removal: Heat cleaning offers a highly efficient method for removing a wide range of contaminants, including paints, varnishes, oils, and adhesives, from metal surfaces. This thorough cleaning is essential for achieving strong adhesion of powder coatings.
- Reduced Environmental Impact: Unlike chemical stripping methods, heat cleaning generates minimal waste and does not involve hazardous chemicals. This makes it an environmentally friendly option, aligning with sustainable and eco-conscious manufacturing practices.
- Cost-Effective Operation: Although the initial investment in a heat cleaning oven may be significant, the long-term cost-effectiveness is evident through reduced reliance on chemical stripping agents, decreased waste disposal costs, and increased operational efficiency.
Conclusion:
Heat cleaning ovens play a pivotal role in preparing metal surfaces for powder coating applications, offering a reliable and environmentally friendly method for removing contaminants. The combination of precise temperature control, advanced safety features, and energy-efficient designs makes these ovens indispensable in modern powder coating facilities, ensuring the durability and quality of coated products.
Heat Cleaning Oven
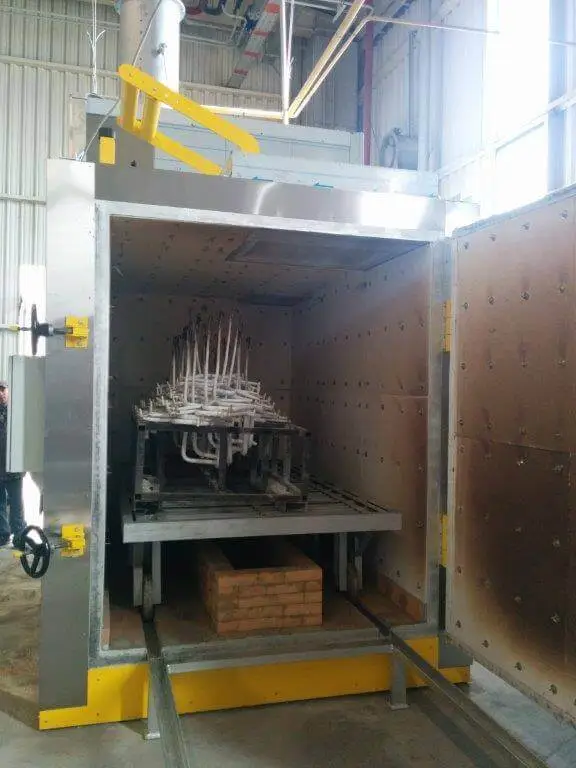
Heat cleaning ovens represent a pivotal component in the realm of industrial surface preparation, particularly in the context of powder coating applications. These specialized ovens are designed to employ elevated temperatures for the thorough removal of contaminants from metal surfaces, ensuring an optimal substrate for subsequent powder coating processes.
Operating Principle:
The fundamental principle underlying the function of a heat cleaning oven involves subjecting metal surfaces to controlled high temperatures, typically ranging between 800°F and 1200°F (427°C to 649°C). This temperature range is carefully selected to induce the pyrolysis of organic residues, such as paints, coatings, adhesives, and other substances adhering to the metal substrate.
Construction and Components:
Heat cleaning ovens are meticulously constructed to withstand the extreme temperatures involved in the cleaning process. They are equipped with robust insulation materials to minimize heat loss and maintain efficiency. The heating chamber is designed to facilitate uniform temperature distribution, ensuring that every inch of the metal surface undergoes the cleaning process consistently.
Control panels with advanced temperature regulation systems are integral components, allowing operators to set precise temperature profiles tailored to the specific cleaning requirements of different contaminants and substrates.
Safety Measures:
Safety is paramount in heat cleaning operations, and these ovens are equipped with sophisticated safety interlocks. These interlocks prevent issues such as overheating, ensuring the well-being of the equipment and the personnel involved. Additionally, proper ventilation systems are incorporated to manage any gaseous byproducts generated during the cleaning process.
Advantages:
The advantages of employing a heat cleaning oven are multifaceted. First and foremost, this method offers unparalleled efficiency in removing a diverse range of contaminants, contributing to the enhancement of powder coating adhesion. Moreover, it is an environmentally friendly alternative, as the process generates minimal waste compared to chemical stripping methods.
Conclusion:
In conclusion, the heat cleaning oven stands as a crucial asset in the powder coating industry, providing a reliable and efficient means of preparing metal surfaces for coating applications. Through precise temperature control, advanced safety features, and energy-efficient designs, these ovens contribute significantly to the overall quality and longevity of coated products in modern manufacturing environments.
Heat Cleaning Oven for Powder Coating
Powder coating is a widely adopted method in the realm of surface finishing, offering a durable and aesthetically pleasing alternative to traditional liquid paint. This process involves the application of a dry powder onto a substrate, followed by curing to create a robust and attractive finish. It has become a preferred choice in various industries due to its numerous advantages over conventional coating methods.
Application Process:
The powder coating process begins with the application of a finely ground powder onto the surface of a substrate, typically metal. This can be achieved through various methods, including electrostatic spray guns, fluidized beds, or even manual application for intricate or smaller parts. The charged powder particles adhere to the grounded substrate, forming a uniform coating.
Curing and Fusion:
After the powder is applied, the coated substrate is subjected to a curing process, usually conducted in a curing oven. During this stage, the powder particles melt and fuse to the substrate, creating a continuous and durable film. The curing process involves raising the temperature to a specific level for a predetermined period, allowing the powder to flow and react, resulting in a smooth and resilient coating.
Advantages of Powder Coating:
- Durability: Powder coatings are renowned for their exceptional durability, offering resistance to chipping, cracking, and other forms of wear and tear.
- Environmental Friendliness: Unlike liquid paints, powder coatings contain no solvents, reducing the release of volatile organic compounds (VOCs) into the atmosphere. This makes powder coating an environmentally friendly option.
- Color Options and Finish Variety: Powder coatings provide a vast array of color options and finish types, including glossy, matte, and textured finishes, allowing for versatility in design.
- Uniform Coating: The electrostatic application of powder ensures a uniform coating, even on complex shapes and surfaces, resulting in a high-quality finish.
- Cost-Effectiveness: Powder coating is a cost-effective solution due to minimal waste generation, high transfer efficiency, and the absence of solvent-related disposal issues.
Industries and Applications:
Powder coating finds widespread use across various industries, including automotive, architecture, furniture, appliances, and more. It is applied to items ranging from vehicle components and household appliances to outdoor furniture and architectural structures.
Conclusion:
Powder coating stands as a superior finishing method, combining durability, environmental responsibility, and aesthetic versatility. The synergy between powder coating and heat cleaning ovens ensures the preparation of surfaces that not only meet but exceed the stringent quality standards expected in modern manufacturing and design.
Thermal Cleaning with Heat Cleaning Oven
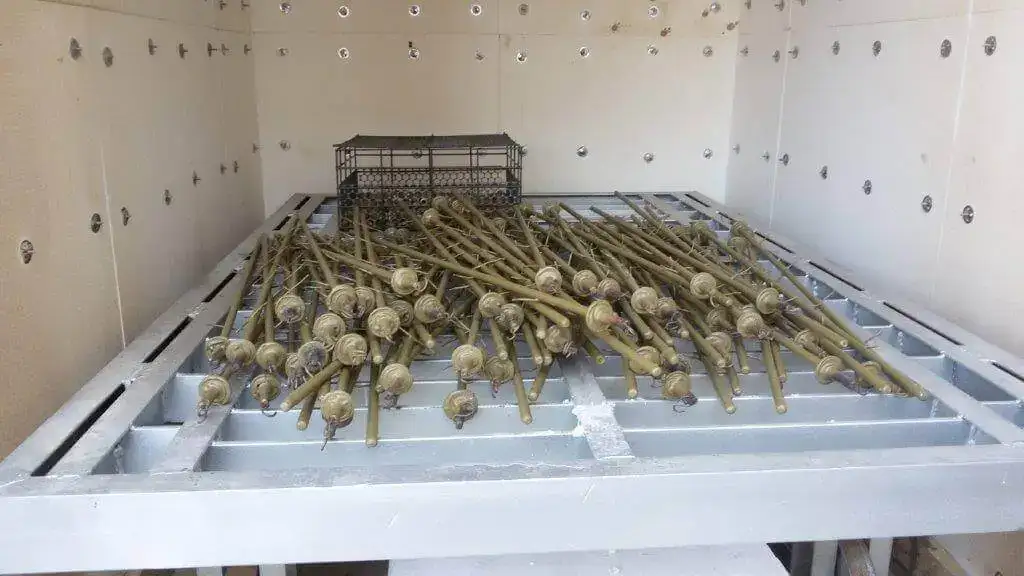
Thermal cleaning, often referred to as burn-off or heat cleaning, represents a specialized method employed in industrial processes to remove contaminants, coatings, and organic residues from various surfaces. This technique relies on elevated temperatures to induce the breakdown and decomposition of unwanted materials, ensuring a clean and pristine substrate for subsequent applications such as powder coating.
Mechanism of Thermal Cleaning:
The fundamental principle underlying thermal cleaning involves subjecting the contaminated surface to temperatures high enough to initiate pyrolysis. Pyrolysis is a chemical process where the application of heat causes organic compounds to decompose into simpler substances, often leaving behind ash or gaseous byproducts. In the context of thermal cleaning, this process effectively disintegrates paints, coatings, and other contaminants, leaving the substrate free of unwanted residues.
Applications in Industrial Settings:
- Coating Removal: Thermal cleaning is extensively utilized for the removal of coatings, including paints, varnishes, and adhesives, from a diverse range of substrates. This is particularly crucial in industries such as aerospace and automotive, where precise surface preparation is essential for subsequent manufacturing processes.
- Polymer Cleanup: In the realm of polymer processing, thermal cleaning proves effective in removing residual polymer buildup on extrusion dies, molds, and other equipment. This ensures optimal performance and longevity of the equipment in polymer manufacturing.
- Industrial Maintenance: Thermal cleaning plays a vital role in maintenance activities, facilitating the cleaning of components, machinery, and tools in various industrial settings. This not only extends the lifespan of equipment but also enhances overall operational efficiency.
Key Advantages:
- Environmentally Friendly: Thermal cleaning is often considered an environmentally friendly method as it doesn’t involve the use of harsh chemicals or generate hazardous waste. The process primarily relies on heat, making it a cleaner and more sustainable option.
- Efficiency and Precision: The precision and efficiency of thermal cleaning make it a preferred choice for industries requiring meticulous surface preparation. It ensures thorough cleaning without compromising the integrity of the underlying substrate.
- Energy-Efficient: While the process involves high temperatures, modern thermal cleaning methods incorporate energy-efficient designs and insulation to optimize energy consumption and reduce operational costs.
Conclusion:
Thermal cleaning stands as a versatile and efficient technique in various industrial applications, providing a means to achieve pristine surfaces for subsequent manufacturing processes. Whether used in the removal of coatings, polymer cleanup, or general industrial maintenance, thermal cleaning plays a vital role in ensuring the quality, efficiency, and sustainability of industrial operations.
Burn-Off Oven – Heat Cleaning Oven
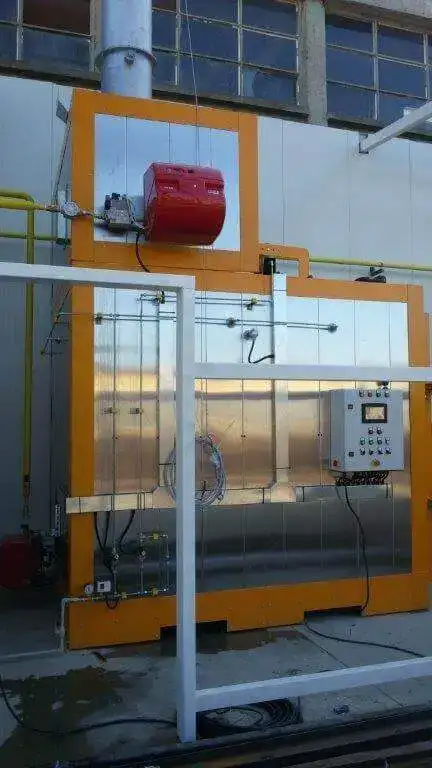
A burn-off oven, also known as a pyrolysis oven, is a specialized piece of equipment designed for the thermal cleaning of various objects, particularly those in industrial settings. This type of oven utilizes high temperatures to perform a burn-off process, effectively removing coatings, paints, and contaminants from surfaces. The burn-off oven is a crucial component in industries where precise and thorough cleaning is paramount, such as in preparation for powder coating applications.
Operating Principles:
- Temperature Range: Burn-off ovens are designed to achieve and maintain elevated temperatures, typically ranging from 800°F to 1200°F (427°C to 649°C). This temperature range is carefully selected to induce pyrolysis, breaking down organic compounds into simpler substances.
- Controlled Atmosphere: The oven creates a controlled atmosphere to prevent excessive oxidation of the metal substrate during the cleaning process. This controlled environment ensures that the organic contaminants undergo combustion without causing damage to the underlying material.
- Heating Chamber Design: The heating chamber of a burn-off oven is constructed with high-quality insulation materials to minimize heat loss and ensure energy efficiency. It is designed to provide uniform temperature distribution, guaranteeing consistent cleaning results across the entire surface of the objects being processed.
Applications:
- Coating Removal: Burn-off ovens are extensively used for the removal of coatings, including paints, varnishes, and adhesives, from a variety of substrates. This is crucial in industries such as automotive manufacturing, where components need to be free of any contaminants before further processing.
- Tool and Equipment Cleaning: In industrial maintenance, burn-off ovens are employed to clean tools, molds, and equipment by efficiently removing accumulated coatings or residues. This ensures the optimal performance and longevity of the tools and machinery.
Safety Features:
- Safety Interlocks: Burn-off ovens are equipped with safety interlocks to prevent issues such as overheating and to ensure the safety of personnel during the cleaning process.
- Ventilation Systems: Proper ventilation systems are incorporated to manage any gaseous byproducts generated during the burn-off process, contributing to a safe working environment.
Advantages:
- Efficient Contaminant Removal: Burn-off ovens offer a highly efficient method for removing a wide range of contaminants, providing a clean and well-prepared surface for subsequent processes like powder coating.
- Energy-Efficient Design: Advanced designs incorporate energy-efficient features, optimizing the consumption of energy during the cleaning cycle.
Conclusion:
In conclusion, the burn-off oven is a critical tool in industrial settings, providing an efficient and precise method for the removal of coatings and contaminants. Whether used in manufacturing processes or industrial maintenance, the burn-off oven ensures that surfaces are thoroughly cleaned, contributing to the overall quality and reliability of the products and equipment in various industries.
Pyrolysis with Heat Cleaning Oven
Pyrolysis is a chemical process integral to thermal cleaning methods, including those employed in burn-off ovens. This process involves the application of high temperatures to organic compounds, leading to their decomposition into simpler substances without the presence of oxygen. In the context of burn-off ovens used for cleaning applications, pyrolysis is a key mechanism driving the breakdown of coatings, paints, and contaminants on surfaces.
Pyrolysis Mechanism:
- Thermal Decomposition: Pyrolysis occurs when organic compounds are subjected to elevated temperatures, typically ranging from 800°F to 1200°F (427°C to 649°C) in the context of burn-off ovens. The heat causes the complex organic molecules to break down into simpler compounds without undergoing combustion.
- Oxygen-Free Environment: A crucial aspect of pyrolysis in burn-off ovens is that it takes place in an oxygen-controlled environment. The absence of oxygen prevents the complete combustion of organic materials, ensuring that the breakdown results in non-toxic gaseous byproducts or ash residues.
Applications in Thermal Cleaning:
- Coating Removal: Pyrolysis is at the core of the thermal cleaning process in burn-off ovens. The application of high temperatures in an oxygen-free environment induces the pyrolysis of coatings, paints, and other contaminants, facilitating their efficient removal from various surfaces.
- Polymer Cleanup: In polymer processing equipment, pyrolysis is utilized to remove residual polymer buildup on dies, molds, and other components. The controlled breakdown of polymers ensures the thorough cleaning of equipment, maintaining optimal performance.
Environmental Considerations:
- Low Emission of Hazardous Compounds: The controlled nature of pyrolysis in burn-off ovens results in the low emission of hazardous compounds. This aligns with environmental considerations, making the process more sustainable compared to alternative methods involving harsh chemicals.
- Waste Reduction: Pyrolysis contributes to waste reduction in cleaning processes. By breaking down organic contaminants into simpler compounds or ash residues, it minimizes the volume of waste generated during the thermal cleaning cycle.
Challenges and Considerations:
- Optimization of Temperature: Achieving the optimal temperature for pyrolysis is crucial for the efficiency of thermal cleaning processes. Too low a temperature may not effectively break down contaminants, while excessively high temperatures can risk damage to the substrate.
- Energy Consumption: The energy-intensive nature of pyrolysis processes necessitates the incorporation of energy-efficient designs in burn-off ovens to minimize operational costs.
Conclusion:
Pyrolysis stands as a fundamental chemical process in burn-off ovens, driving the thermal cleaning of surfaces in various industrial applications. Its controlled and oxygen-free nature contributes to efficient contaminant removal while addressing environmental considerations in the realm of industrial surface preparation.
Contaminant Removal with Heat Cleaning Oven
Contaminant removal is a critical aspect of industrial processes, particularly in applications like powder coating where the quality and durability of the coating rely on the cleanliness of the substrate. Various methods are employed for efficient contaminant removal, with thermal cleaning techniques, such as those performed in burn-off ovens, being integral to achieving thorough and reliable results.
Types of Contaminants:
- Coatings and Paints: Contaminants often include existing coatings, paints, and finishes on metal surfaces. These materials must be effectively removed to ensure proper adhesion and bonding of subsequent coatings.
- Adhesives and Sealants: Residues of adhesives and sealants pose challenges to surface preparation. Efficient contaminant removal is crucial to achieving a clean and receptive substrate.
- Oils and Greases: Industrial processes often involve the application of oils and greases, which can adhere to surfaces and hinder proper coating adhesion. Thorough removal is necessary for optimal performance.
Importance in Powder Coating:
- Enhanced Adhesion: Contaminant-free surfaces contribute to improved adhesion of powder coatings. This is vital for the longevity and durability of the final product, preventing issues such as peeling or delamination.
- Quality Finish: The removal of contaminants ensures a smooth and uniform surface, essential for achieving a high-quality finish in powder coating. Any remaining residues can lead to defects in the coated surface.
Thermal Cleaning in Contaminant Removal:
- Pyrolysis of Organic Residues: In the context of burn-off ovens, thermal cleaning employs pyrolysis to break down organic contaminants. The elevated temperatures induce the decomposition of coatings, paints, adhesives, and other residues into simpler substances, allowing for their efficient removal.
- Minimization of Residual Ash: The controlled nature of pyrolysis minimizes the residue left after contaminant breakdown. This ensures that the cleaned surface is free from unwanted remnants, ready for subsequent coating applications.
Considerations for Efficient Contaminant Removal:
- Temperature Control: Precise temperature control in burn-off ovens is crucial for optimizing the contaminant removal process. Different contaminants may require specific temperature profiles for effective breakdown.
- Uniform Heating: Ensuring uniform heating across the entire surface is essential for consistent contaminant removal. Modern burn-off ovens incorporate designs to achieve uniform temperature distribution.
Conclusion:
Contaminant removal is a foundational step in achieving high-quality powder-coated products. Thermal cleaning methods, particularly those involving burn-off ovens and pyrolysis, play a pivotal role in ensuring efficient and thorough removal of contaminants, setting the stage for impeccable surface preparation in diverse industrial applications.
High Temperatures with Heat Cleaning Oven
High temperatures are a fundamental element in thermal cleaning processes, particularly in burn-off ovens utilized for contaminant removal in industrial settings. The application of elevated temperatures is a key factor in inducing pyrolysis, a chemical process that plays a central role in breaking down and eliminating organic contaminants, coatings, and residues from various surfaces.
Temperature Ranges in Thermal Cleaning:
- Optimal Cleaning Temperatures: Burn-off ovens are designed to reach temperatures ranging from 800°F to 1200°F (427°C to 649°C) during the cleaning cycle. These temperatures are carefully chosen to achieve the necessary level of thermal energy required for the effective pyrolysis of different contaminants.
- Material Compatibility: The selection of temperature ranges is also influenced by the material compatibility of the substrate being cleaned. Ensuring that the temperature is sufficient to induce pyrolysis while avoiding damage to the base material is crucial.
Importance of High Temperatures:
- Pyrolysis Induction: High temperatures are essential for initiating pyrolysis, the process by which organic compounds undergo thermal decomposition. Pyrolysis facilitates the breakdown of complex organic molecules into simpler substances, such as gases or ash, allowing for efficient contaminant removal.
- Uniform Heating: Achieving and maintaining high temperatures uniformly across the entire surface is critical for consistent and thorough contaminant removal. Modern burn-off ovens incorporate advanced designs to ensure uniform temperature distribution.
Energy Efficiency:
- Insulation Materials: To optimize energy efficiency, burn-off ovens are constructed with high-quality insulation materials. These materials minimize heat loss, allowing the oven to reach and sustain the required high temperatures while conserving energy.
- Controlled Atmosphere: The creation of a controlled atmosphere within the oven is another factor influencing energy efficiency. By regulating the oxygen content, burn-off ovens prevent excessive oxidation, ensuring that the energy is primarily utilized for the pyrolysis process.
Challenges and Considerations:
- Substrate Sensitivity: Sensitivity to high temperatures varies among different substrates. It’s essential to tailor the thermal cleaning process to the specific requirements of the material to avoid any adverse effects.
- Energy Consumption: While high temperatures are necessary for effective contaminant removal, there is a need to balance this requirement with energy consumption considerations. Efficient designs and insulation contribute to minimizing energy usage.
Conclusion:
High temperatures are a cornerstone in the thermal cleaning process, particularly in burn-off ovens. They enable the induction of pyrolysis, a crucial mechanism for breaking down contaminants. Careful consideration of temperature ranges, material compatibility, and energy efficiency ensures that the thermal cleaning process is both effective and environmentally sustainable in diverse industrial applications.
Organic Residues
Organic residues encompass a broad category of materials, often found adhering to surfaces in industrial settings. In the context of thermal cleaning processes, such as those performed in burn-off ovens, the efficient removal of organic residues is essential for preparing surfaces for subsequent applications like powder coating. These residues can include various substances, each presenting unique challenges in terms of removal.
Types of Organic Residues:
- Paints and Coatings: Old or unwanted paints and coatings on surfaces can leave organic residues that need thorough removal. Burn-off ovens are particularly effective in breaking down and eliminating these layers.
- Adhesives and Sealants: Residues from adhesives and sealants can be resilient and challenging to remove. The controlled high temperatures in burn-off ovens induce pyrolysis, breaking down these adhesive materials for efficient cleaning.
- Oils and Greases: Industrial processes often involve the application of oils and greases. Residues from these substances can accumulate on surfaces and hinder proper adhesion of coatings. Thermal cleaning methods effectively address the removal of such residues.
Pyrolysis of Organic Residues:
- Chemical Decomposition: Pyrolysis, a chemical process induced by high temperatures, plays a central role in the breakdown of organic residues. This process involves the decomposition of complex organic molecules into simpler compounds, such as gases or ash, rendering them easier to remove.
- Complete Combustion Avoidance: In the controlled environment of burn-off ovens, pyrolysis occurs without the presence of oxygen, preventing complete combustion. This controlled breakdown minimizes the generation of ash residues and facilitates cleaner surfaces.
Challenges in Organic Residue Removal:
- Residue Diversity: The diverse nature of organic residues requires careful consideration of temperature profiles and cleaning cycles to ensure effective removal without damaging the substrate.
- Substrate Sensitivity: Different substrates may have varying sensitivities to high temperatures. The cleaning process needs to be tailored to the specific material to prevent unintended consequences.
Quality Surface Preparation:
- Enhanced Powder Coating Adhesion: The removal of organic residues ensures a pristine surface, contributing to enhanced adhesion of powder coatings. This is crucial for achieving a durable and long-lasting finish.
- Surface Uniformity: Thorough removal of organic residues results in a uniform surface, free from contaminants. This uniformity is vital for the consistent application and appearance of coatings.
Conclusion:
Efficient removal of organic residues through thermal cleaning processes, such as those performed in burn-off ovens, is imperative for achieving optimal surface preparation. The controlled pyrolysis of these residues ensures a clean and receptive substrate, laying the foundation for high-quality powder coating applications in diverse industrial scenarios.
Uniform Temperature
Uniform temperature distribution is a critical factor in thermal cleaning processes, particularly in burn-off ovens, where precision is essential for achieving consistent and thorough contaminant removal. Maintaining a uniform temperature across the entire surface being treated ensures that the cleaning process is effective and reliable.
Importance of Uniform Temperature:
- Consistent Contaminant Removal: Uniform temperature ensures that all areas of the substrate experience the same level of heat treatment. This consistency is vital for the simultaneous breakdown and removal of contaminants, including paints, coatings, and organic residues.
- Prevention of Hot Spots: Hot spots, areas with excessively high temperatures, can lead to uneven cleaning and potential damage to the substrate. Uniform temperature distribution mitigates the risk of hot spots, ensuring a controlled and safe cleaning process.
Achieving Uniform Temperature:
- Oven Design and Insulation: Modern burn-off ovens are designed with features that promote uniform temperature distribution. High-quality insulation materials and well-engineered oven designs help minimize heat loss and ensure even heating throughout the chamber.
- Advanced Control Systems: Burn-off ovens are equipped with advanced control systems that monitor and regulate temperature profiles. These systems enable precise control over heating elements, ensuring that the desired temperature is maintained consistently.
Benefits of Uniform Temperature:
- Efficient Contaminant Breakdown: Uniform temperature distribution contributes to the efficient breakdown of contaminants through pyrolysis. Each part of the substrate receives the required thermal energy for the simultaneous decomposition of organic residues.
- Optimal Cleaning Results: Consistent temperature ensures optimal cleaning results, preventing underheated or overheated areas that may compromise the quality of the surface preparation. This is particularly crucial in industries where stringent cleanliness standards are imperative.
Challenges and Considerations:
- Material Sensitivity: Some substrates may be sensitive to high temperatures. Achieving uniform temperature requires careful consideration of the material being treated to avoid any adverse effects.
- Energy Efficiency: While uniform temperature is crucial, energy efficiency is also a consideration. Modern ovens strive to balance uniformity with energy conservation, incorporating insulation and control systems to optimize overall efficiency.
Conclusion:
Uniform temperature distribution is a cornerstone in thermal cleaning processes, ensuring that contaminants are consistently and thoroughly removed from surfaces. In burn-off ovens, where precise surface preparation is essential for subsequent applications like powder coating, achieving and maintaining uniform temperatures is paramount for reliable and high-quality results.
Combustion Process
The combustion process is a fundamental aspect of thermal cleaning methodologies, particularly in burn-off ovens utilized for contaminant removal in industrial applications. This controlled combustion is integral to breaking down and eliminating organic contaminants, coatings, and residues adhering to various surfaces, ensuring a clean substrate for subsequent processes like powder coating.
Principles of the Combustion Process:
- Oxygen-Controlled Environment: Burn-off ovens create an oxygen-controlled environment during the cleaning cycle. This controlled atmosphere prevents complete combustion of organic materials, allowing them to undergo pyrolysis—thermal decomposition without the presence of oxygen.
- Temperature Optimization: The combustion process is optimized within a specific temperature range, typically between 800°F to 1200°F (427°C to 649°C). This range is carefully chosen to induce pyrolysis efficiently, breaking down complex organic molecules into simpler compounds.
Stages of the Combustion Process:
- Heating Phase: The initial phase involves heating the contaminated substrate to the desired temperature. This process ensures uniform temperature distribution across the entire surface.
- Pyrolysis: Once the required temperature is reached, pyrolysis occurs. This is the chemical process where organic compounds decompose into simpler substances, such as gases or ash. The absence of oxygen prevents complete combustion.
- Contaminant Breakdown: The breakdown of contaminants during pyrolysis results in the conversion of paints, coatings, adhesives, and other residues into forms that are easier to remove, leaving the substrate clean.
Advantages of the Combustion Process:
- Efficient Organic Residue Removal: The combustion process efficiently removes organic residues through controlled pyrolysis, ensuring thorough contaminant breakdown and subsequent removal.
- Minimized Residue Generation: By preventing complete combustion, the process minimizes the generation of ash residues, contributing to cleaner surfaces and reducing the need for additional cleaning steps.
Safety Considerations:
- Controlled Atmosphere: The controlled environment in burn-off ovens ensures safety by preventing uncontrolled combustion and minimizing the risk of fire hazards.
- Ventilation Systems: Proper ventilation systems are incorporated to manage any gaseous byproducts generated during the combustion process, contributing to a safe working environment.
Challenges and Considerations:
- Temperature Control: Precise control of the combustion process is crucial to prevent substrate damage and ensure efficient contaminant removal. Advanced control systems in burn-off ovens play a significant role in achieving this precision.
- Energy Efficiency: While achieving optimal temperatures, maintaining energy efficiency is essential. Modern burn-off oven designs incorporate insulation and energy-efficient features to balance the need for high temperatures with operational sustainability.
Conclusion:
The combustion process in burn-off ovens is a carefully controlled and essential step in thermal cleaning, ensuring effective contaminant removal and the preparation of surfaces for subsequent industrial applications. By harnessing controlled pyrolysis, this process contributes to the efficiency, safety, and environmental sustainability of thermal cleaning operations.
Energy Efficiency
Energy efficiency is a crucial consideration in the design and operation of burn-off ovens used for thermal cleaning processes. Balancing the need for high temperatures with optimal energy consumption is essential to ensure the cost-effectiveness and sustainability of the cleaning operation.
Insulation Materials:
- High-Quality Insulation: Burn-off ovens are constructed with high-quality insulation materials to minimize heat loss. This insulation helps maintain elevated temperatures within the oven, improving energy efficiency by reducing the amount of energy required to achieve and sustain the desired temperature.
- Minimized Heat Loss: Effective insulation minimizes heat loss to the surroundings, allowing the oven to operate at peak efficiency. This not only conserves energy but also contributes to a controlled and uniform temperature distribution across the entire heating chamber.
Controlled Atmosphere and Oxygen:
- Optimizing Oxygen Levels: Burn-off ovens create a controlled atmosphere to optimize the combustion process during thermal cleaning. This controlled environment, including carefully managed oxygen levels, ensures efficient pyrolysis without unnecessary energy consumption.
- Preventing Excessive Oxidation: By preventing excessive oxidation of the metal substrate, the controlled atmosphere minimizes unnecessary energy consumption, contributing to the overall energy efficiency of the cleaning process.
Advanced Control Systems:
- Precision Temperature Control: Modern burn-off ovens are equipped with advanced control systems that allow operators to precisely set and monitor temperature profiles. This precision in temperature control ensures that the oven operates at the optimal temperature for efficient contaminant removal while minimizing energy waste.
- Automation for Efficiency: Automation features in control systems can optimize energy efficiency by adjusting parameters based on real-time conditions. This includes factors such as load size, material type, and process stage.
Sustainability Considerations:
- Reduced Environmental Impact: Energy-efficient burn-off ovens contribute to reduced environmental impact by lowering overall energy consumption. This aligns with sustainable manufacturing practices and minimizes the carbon footprint associated with thermal cleaning processes.
- Cost-Effective Operation: Energy efficiency not only benefits the environment but also contributes to cost-effective operation. By optimizing energy usage, manufacturers can reduce operational costs associated with thermal cleaning processes.
Challenges and Innovations:
- Balancing Energy Intensity: Achieving a balance between the high temperatures required for effective thermal cleaning and energy efficiency remains a challenge. Ongoing innovations in oven design and control systems aim to address this balance, optimizing both performance and energy consumption.
- Integration of Renewable Energy: Some facilities explore the integration of renewable energy sources to power burn-off ovens, further reducing their environmental impact and dependence on non-renewable resources.
Conclusion:
Energy efficiency in burn-off ovens is a multifaceted consideration, encompassing insulation, controlled atmospheres, and advanced control systems. By prioritizing energy-efficient designs and operations, manufacturers can enhance the sustainability and cost-effectiveness of thermal cleaning processes while meeting the stringent requirements of industrial applications.
Environmental-Friendly Practices
The adoption of environmentally friendly practices in burn-off ovens is integral to aligning industrial operations with sustainable and responsible manufacturing. By minimizing environmental impact, these practices contribute to a cleaner and more ecologically sound industrial landscape.
Minimization of Hazardous Waste:
- Reduced Chemical Usage: Burn-off ovens, in their thermal cleaning process, eliminate the need for harsh chemical stripping agents. This minimizes the usage of chemicals that may pose environmental hazards and reduces the generation of hazardous waste.
- Lower Volatile Organic Compounds (VOCs): Compared to chemical stripping methods, thermal cleaning in burn-off ovens produces lower levels of volatile organic compounds (VOCs). This reduction contributes to improved air quality and reduces the environmental footprint of the cleaning process.
Energy Efficiency and Conservation:
- Optimized Energy Consumption: The integration of energy-efficient designs in burn-off ovens optimizes energy consumption, contributing to reduced greenhouse gas emissions and overall energy conservation.
- Renewable Energy Integration: Some facilities explore the integration of renewable energy sources to power burn-off ovens, further enhancing the environmental-friendliness of the thermal cleaning process.
Waste Reduction Strategies:
- Ash Residue Management: The controlled combustion and pyrolysis in burn-off ovens result in ash residues. Environmentally friendly practices involve the proper management and disposal of these residues to minimize their impact on ecosystems.
- Efficient Contaminant Breakdown: By efficiently breaking down contaminants into simpler forms during the cleaning process, burn-off ovens contribute to waste reduction. This is particularly relevant in industries where strict waste disposal regulations are in place.
Sustainability Certifications:
- Adherence to Standards: Facilities using burn-off ovens may pursue certifications and adhere to industry standards that emphasize sustainable and environmentally friendly practices. Compliance with these standards demonstrates a commitment to responsible manufacturing.
- Life Cycle Assessment: Conducting life cycle assessments helps evaluate the environmental impact of burn-off ovens from production to disposal. This holistic approach aids in identifying areas for improvement in sustainability practices.
Challenges and Continuous Improvement:
- Emission Control: Managing and controlling emissions, including any byproducts from the burn-off process, remains a challenge. Ongoing research and development focus on addressing these challenges to enhance the environmental performance of burn-off ovens.
- Material Sensitivity: Balancing the need for high temperatures in burn-off ovens with the sensitivity of certain materials is an ongoing consideration. Innovations in oven design and control systems aim to optimize thermal cleaning processes while minimizing environmental impact.
Conclusion:
Adopting environmentally friendly practices in burn-off ovens is a proactive step toward sustainable industrial processes. By prioritizing waste reduction, energy efficiency, and adherence to environmental standards, manufacturers can contribute to a greener and more responsible approach to thermal cleaning in various industrial applications.
Safety Interlocks
Safety interlocks are crucial components integrated into burn-off ovens to ensure the well-being of both personnel and equipment during the thermal cleaning process. These interlocks play a pivotal role in preventing potential hazards, mitigating risks, and maintaining a secure working environment.
Preventing Overheating:
- Temperature Monitoring: Safety interlocks incorporate advanced temperature monitoring systems to ensure that the oven operates within safe temperature limits. This prevents overheating, which could lead to equipment damage or compromise the quality of the cleaning process.
- Automatic Shut-Off: In the event of temperature anomalies or deviations beyond preset safety thresholds, safety interlocks trigger automatic shut-off mechanisms. This rapid response helps prevent accidents, protect personnel, and safeguard the integrity of the burn-off oven.
Personnel Protection:
- Access Control Systems: Safety interlocks are often linked to access control systems, ensuring that the oven remains inaccessible during operation. This prevents accidental exposure of personnel to high temperatures and potential hazards associated with the thermal cleaning process.
- Emergency Stop Features: Emergency stop features are integrated into safety interlocks, allowing immediate cessation of oven operations in case of unforeseen circumstances or emergencies. This rapid response capability enhances overall workplace safety.
Ventilation and Gas Management:
- Exhaust System Monitoring: Safety interlocks monitor the performance of ventilation and exhaust systems. Proper functioning of these systems is critical for managing gaseous byproducts generated during the combustion process, contributing to a safe working environment.
- Gas Detection Systems: Advanced safety interlocks may include gas detection systems to monitor the presence of any potentially harmful gases. Rapid detection and response mechanisms are essential to prevent the accumulation of hazardous substances in the workspace.
Equipment Protection:
- Overload Protection: Safety interlocks incorporate overload protection features to safeguard the burn-off oven from excessive stress or load. This ensures the longevity and reliability of the equipment while minimizing the risk of malfunctions.
- Fault Diagnosis Systems: In the event of equipment malfunctions or faults, safety interlocks may include diagnostic systems that provide real-time information. This aids in identifying issues promptly, facilitating timely maintenance and repairs.
Compliance with Standards:
- Regulatory Compliance: Burn-off ovens equipped with safety interlocks adhere to industry standards and regulations for occupational safety. Compliance ensures that manufacturing facilities meet stringent safety requirements and create a secure working environment.
- Certifications: Some safety interlock systems may come with certifications that validate their adherence to recognized safety standards. These certifications instill confidence in users regarding the reliability and effectiveness of the safety features.
Conclusion:
Safety interlocks are integral elements in burn-off ovens, contributing to a secure and controlled thermal cleaning process. By preventing overheating, ensuring personnel protection, monitoring ventilation systems, and safeguarding equipment, these interlocks play a vital role in maintaining safety standards and minimizing risks associated with industrial thermal cleaning operations.
Ventilation Systems
Ventilation systems are essential components of burn-off ovens, playing a critical role in managing air quality, controlling emissions, and ensuring a safe working environment during the thermal cleaning process. These systems are designed to effectively handle the byproducts generated during the combustion and pyrolysis stages.
Controlling Gaseous Byproducts:
- Gaseous Emissions: During thermal cleaning, the combustion of organic contaminants results in the generation of gaseous byproducts. Ventilation systems are responsible for efficiently extracting and managing these emissions to prevent their accumulation in the workspace.
- Gas Treatment and Filtration: Ventilation systems often incorporate gas treatment and filtration mechanisms to remove pollutants and particulate matter from the exhaust gases. This ensures compliance with environmental standards and minimizes the impact on air quality.
Creating a Controlled Atmosphere:
- Oxygen Regulation: Ventilation systems contribute to maintaining a controlled atmosphere within the burn-off oven by regulating oxygen levels. This controlled environment is crucial for optimizing the combustion process while preventing excessive oxidation of the metal substrate.
- Preventing Uncontrolled Combustion: Effective ventilation prevents uncontrolled combustion and minimizes the risk of fire hazards. By regulating the oxygen supply, the ventilation system ensures that the combustion of contaminants occurs in a controlled and safe manner.
Worker Safety:
- Fume Extraction: Ventilation systems include fume extraction mechanisms to prevent the inhalation of potentially harmful gases by personnel. This is vital for ensuring a safe working environment and minimizing health risks associated with exposure to combustion byproducts.
- Exhaust Hood Design: The design of exhaust hoods in burn-off ovens is optimized to capture and remove emissions efficiently. Well-engineered exhaust systems contribute to the overall safety of workers by preventing the escape of hazardous substances.
Environmental Compliance:
- Emission Monitoring: Ventilation systems may incorporate emission monitoring devices to measure and track the levels of pollutants released during the thermal cleaning process. This data ensures compliance with environmental regulations and allows for continuous improvement in emission control.
- Efficient Gaseous Disposal: Properly designed ventilation systems facilitate the efficient disposal of gaseous byproducts, minimizing their impact on the environment. This aligns with sustainable and environmentally friendly practices in industrial operations.
Regular Maintenance and Inspection:
- System Integrity Checks: Regular maintenance and inspection of ventilation systems are essential to ensure their integrity and effectiveness. This proactive approach helps identify and address potential issues, maintaining the reliability of the system.
- Filter Replacement: Routine replacement of filters within the ventilation system is necessary to optimize gas treatment and filtration. This practice ensures that the system continues to meet air quality standards and effectively removes contaminants.
Conclusion:
Ventilation systems are integral to the safe and environmentally responsible operation of burn-off ovens. By effectively managing gaseous byproducts, creating a controlled atmosphere, prioritizing worker safety, and ensuring environmental compliance, these systems contribute to the overall efficiency and sustainability of thermal cleaning processes in industrial settings.
Catalyst Integration
Catalyst integration in burn-off ovens represents an innovative approach to enhance the efficiency and environmental performance of thermal cleaning processes. Catalysts play a crucial role in facilitating and optimizing the combustion and pyrolysis of organic contaminants, offering benefits such as improved energy efficiency and reduced emissions.
Catalyst Functionality:
- Acceleration of Pyrolysis: Catalysts are substances that accelerate chemical reactions without being consumed in the process. In burn-off ovens, catalysts can enhance the pyrolysis of organic contaminants, promoting faster and more efficient breakdown.
- Temperature Reduction: Catalysts can lower the temperature at which pyrolysis occurs. This reduction in the required temperature contributes to energy savings and allows for more controlled thermal cleaning processes.
Environmental Benefits:
- Emission Reduction: Catalysts aid in the more complete combustion of organic materials, reducing the emission of pollutants. This leads to cleaner exhaust gases and aligns with environmental goals by minimizing the impact on air quality.
- Lower Carbon Footprint: Improved combustion efficiency, facilitated by catalysts, results in a lower carbon footprint associated with thermal cleaning operations. This aligns with sustainability objectives and regulatory standards for industrial processes.
Energy Efficiency:
- Optimized Energy Consumption: Catalyst integration can contribute to optimizing energy consumption in burn-off ovens. By promoting more efficient pyrolysis at lower temperatures, the overall energy requirements for the thermal cleaning process may be reduced.
- Enhanced Heat Transfer: Catalysts can enhance heat transfer efficiency within the oven, ensuring that thermal energy is effectively utilized for the breakdown of contaminants. This contributes to both energy savings and improved cleaning performance.
Application Considerations:
- Catalyst Selection: The choice of catalyst depends on the specific contaminants being processed. Different catalysts may be more effective for certain types of organic materials, and careful selection is crucial for optimal performance.
- Integration with Control Systems: Catalyst integration should be well-coordinated with the control systems of burn-off ovens. This ensures that catalysts are applied judiciously and in response to real-time conditions for maximum effectiveness.
Continuous Improvement:
- Research and Development: Ongoing research and development efforts focus on identifying and developing catalysts tailored for use in burn-off ovens. These efforts aim to continually enhance the efficiency and environmental performance of thermal cleaning processes.
- Adaptation to Industry Needs: The adaptability of catalyst integration to various industry needs is an area of exploration. Continuous improvements and adaptations to different contaminants and materials contribute to the versatility of catalyst-enhanced burn-off ovens.
Conclusion:
Catalyst integration in burn-off ovens represents an innovative strategy to improve the efficiency, environmental impact, and energy performance of thermal cleaning processes. By accelerating pyrolysis, reducing emissions, and optimizing energy consumption, catalysts contribute to more sustainable and effective industrial surface preparation.
Real-Time Monitoring Systems
Real-time monitoring systems in burn-off ovens are advanced technological solutions designed to provide instantaneous insights into various aspects of the thermal cleaning process. These systems enhance control, efficiency, and safety by continuously collecting and analyzing data during the operation of the burn-off oven.
Temperature Monitoring:
- Precision Temperature Control: Real-time monitoring systems enable precise control over the temperature within the burn-off oven. This ensures that the cleaning process operates at the optimal temperature range for effective contaminant breakdown without risking damage to the substrate.
- Immediate Anomaly Detection: These systems have the capability to detect temperature anomalies in real-time. Any deviations from preset thresholds trigger immediate alerts or corrective actions, preventing potential issues such as overheating.
Load and Capacity Management:
- Optimized Loading: Real-time monitoring allows for optimized loading of materials into the oven. The system can assess the current load and recommend adjustments to ensure uniform heating and efficient contaminant removal.
- Capacity Utilization: By continuously monitoring the oven’s capacity and performance, these systems help operators maximize the utilization of the burn-off oven, enhancing overall efficiency and productivity.
Emission Control:
- Gas Composition Monitoring: Real-time monitoring systems track the composition of gases emitted during the thermal cleaning process. This data helps ensure compliance with environmental standards and allows for prompt adjustments to minimize emissions.
- Efficient Ventilation Control: Integration with ventilation systems enables efficient control of air circulation and extraction, contributing to the effective removal of gaseous byproducts. Real-time adjustments can be made to maintain a safe working environment.
Predictive Maintenance:
- Equipment Health Monitoring: These systems monitor the health of critical components in real-time. By analyzing equipment performance data, predictive maintenance can be implemented to address potential issues before they lead to downtime or malfunctions.
- Diagnostic Alerts: In case of equipment malfunctions or faults, real-time monitoring systems generate diagnostic alerts. These alerts provide insights into the nature of the issue, facilitating swift troubleshooting and resolution.
Data Logging and Reporting:
- Comprehensive Data Logging: Real-time monitoring systems continuously log data related to temperature profiles, gas emissions, and equipment performance. This comprehensive data set serves as a valuable resource for process analysis and optimization.
- Customizable Reporting: Operators can generate customizable reports based on real-time data. These reports provide a detailed overview of the thermal cleaning process, facilitating decision-making, process improvement, and compliance documentation.
Integration with Automation:
- Automated Control Adjustments: Real-time monitoring systems often integrate with automation features in burn-off ovens. This allows for automated adjustments to temperature, ventilation, and other parameters based on real-time data, enhancing operational efficiency.
- Remote Monitoring and Control: Remote monitoring capabilities enable operators to access real-time data and control the burn-off oven from a centralized location. This feature enhances flexibility and allows for quick responses to changing conditions.
Conclusion:
Real-time monitoring systems play a transformative role in burn-off ovens, providing continuous insights into temperature control, load management, emission control, and equipment health. By harnessing real-time data, these systems contribute to enhanced efficiency, safety, and the overall effectiveness of thermal cleaning processes in industrial applications.
Automated Loading and Unloading Systems:
Automated loading and unloading systems are integral components in modern burn-off ovens, revolutionizing the efficiency and productivity of thermal cleaning processes. These systems leverage automation to streamline the handling of materials, enhancing overall operational effectiveness.
Load Optimization:
- Consistent Loading: Automated systems ensure consistent and uniform loading of materials into the burn-off oven. This helps maintain even heat distribution, contributing to thorough contaminant removal across the entire surface.
- Optimized Capacity Utilization: These systems assess the available space within the oven and optimize the loading process to maximize capacity. This leads to efficient use of resources and increased productivity.
Time and Labor Savings:
- Reduced Manual Intervention: Automated loading and unloading systems minimize the need for manual labor in these repetitive tasks. This not only reduces the risk of operator fatigue but also results in significant time savings.
- Continuous Operation: Automation enables continuous loading and unloading processes, allowing burn-off ovens to operate seamlessly without extended downtime. This continuous operation contributes to higher throughput and improved efficiency.
Precision and Accuracy:
- Positioning Accuracy: Automated systems ensure precise positioning of materials within the oven. This accuracy is crucial for achieving uniform heating and contaminant removal, especially in complex geometries.
- Load Monitoring: Sensors and monitoring devices integrated into these systems provide real-time feedback on the load status. This information allows for immediate adjustments and ensures that the oven operates within optimal conditions.
Safety Enhancement:
- Reduced Operator Exposure: By minimizing manual handling of materials, automated systems reduce operator exposure to potentially hazardous conditions, such as high temperatures or contaminants. This contributes to improved workplace safety.
- Emergency Stop Features: Automated systems include emergency stop features that can halt the loading or unloading process in case of unforeseen circumstances. This enhances overall safety and prevents accidents.
Integration with Control Systems:
- Seamless Coordination: Automated loading and unloading systems seamlessly integrate with the overall control systems of burn-off ovens. This coordination ensures that the automation process aligns with temperature profiles, ventilation settings, and other operational parameters.
- Customization and Flexibility: These systems offer customization options to adapt to different material types and sizes. The flexibility provided by automated systems allows for versatile use in various industrial applications.
Remote Monitoring and Control:
- Centralized Operation: Automated systems often feature remote monitoring and control capabilities. This allows operators to oversee the loading and unloading processes from a centralized location, improving overall efficiency and flexibility.
- Data Logging and Analysis: Integration with automation systems enables data logging and analysis. This data can be used to assess performance, identify optimization opportunities, and enhance the overall efficiency of burn-off oven operations.
Conclusion:
Automated loading and unloading systems represent a significant advancement in the field of burn-off ovens. By optimizing load distribution, saving time and labor, ensuring precision, enhancing safety, and integrating seamlessly with control systems, these systems contribute to streamlined and efficient thermal cleaning processes in diverse industrial applications.
Advanced Control Systems
Advanced control systems are pivotal components of modern burn-off ovens, providing sophisticated functionalities to optimize and fine-tune thermal cleaning processes. These systems leverage cutting-edge technologies to enhance precision, efficiency, and overall performance in industrial applications.
Temperature Control Precision:
- PID Controllers: Proportional-Integral-Derivative (PID) controllers are often integrated into advanced control systems to precisely regulate the temperature within burn-off ovens. This level of control ensures that the oven operates at the optimal temperature for effective contaminant breakdown.
- Multi-Zone Temperature Management: Advanced systems enable multi-zone temperature management, allowing different areas of the oven to be controlled independently. This is particularly beneficial for applications with diverse material types and geometries.
Dynamic Process Optimization:
- Adaptive Control Algorithms: Adaptive control algorithms continuously analyze real-time data to make dynamic adjustments during the thermal cleaning process. This adaptability enhances the efficiency and effectiveness of contaminant removal.
- Machine Learning Integration: Some advanced control systems incorporate machine learning algorithms. By learning from historical data and adapting to changing conditions, these systems optimize thermal cleaning operations for improved outcomes.
Integration with Sensors and Monitoring Devices:
- Real-Time Data Acquisition: Advanced control systems integrate seamlessly with sensors and monitoring devices to acquire real-time data on temperature, load status, emissions, and other critical parameters. This data forms the basis for informed decision-making.
- Smart Sensors for Process Feedback: Smart sensors provide detailed process feedback, allowing the control system to adjust parameters based on actual conditions. This ensures that the thermal cleaning process remains within specified parameters for optimal results.
Energy Efficiency:
- Optimized Energy Consumption: Advanced control systems contribute to energy efficiency by fine-tuning the operation of burn-off ovens. This includes adjusting temperature profiles, optimizing ventilation, and minimizing energy waste during the cleaning process.
- Predictive Energy Management: Some systems employ predictive energy management strategies, forecasting energy requirements based on the current load and historical data. This proactive approach enhances overall energy efficiency.
Comprehensive Data Logging and Analysis:
- Historical Data Storage: Advanced control systems facilitate comprehensive data logging, storing historical data on temperature profiles, load characteristics, and system performance. This information serves as a valuable resource for analysis and optimization.
- Performance Metrics and Reporting: Operators can generate performance metrics and reports through the control system. This data-driven approach allows for continuous improvement, identification of efficiency bottlenecks, and documentation for compliance purposes.
Remote Monitoring and Diagnostics:
- Remote Access Capabilities: Advanced control systems often offer remote monitoring capabilities. This allows operators to oversee burn-off oven operations, make real-time adjustments, and address issues from a centralized location.
- Diagnostic Tools for Troubleshooting: In case of malfunctions or deviations, the control system provides diagnostic tools for troubleshooting. This aids in rapid problem resolution, minimizing downtime and optimizing overall operational efficiency.
Conclusion:
Advanced control systems play a transformative role in optimizing burn-off ovens for thermal cleaning processes. Through precise temperature control, dynamic process optimization, integration with sensors, energy efficiency enhancements, comprehensive data analysis, and remote monitoring capabilities, these systems contribute to efficient, intelligent, and adaptive thermal cleaning operations in diverse industrial settings.
Robotics and Automation Integration
The integration of robotics and automation technologies in burn-off ovens represents a paradigm shift in thermal cleaning processes. These advanced systems bring a new level of efficiency, precision, and versatility to industrial surface preparation, revolutionizing the way contaminants are removed from various materials.
Robotic Handling and Manipulation:
- Automated Loading and Unloading: Robotics enable fully automated loading and unloading of materials into and out of burn-off ovens. This not only reduces manual labor but also ensures consistent and optimized loading for efficient thermal cleaning.
- Material Positioning and Orientation: Robotic systems can precisely position and orient materials within the oven. This level of accuracy is crucial for achieving uniform heating and contaminant removal, especially for complex geometries.
Vision Systems for Enhanced Precision:
- 3D Vision Technology: Vision systems integrated into robotics utilize 3D imaging technology to accurately perceive the shape and dimensions of materials. This information is used to guide robotic movements and optimize the positioning of items within the oven.
- Quality Inspection and Recognition: Vision systems can perform real-time quality inspections, recognizing features and characteristics of materials. This capability ensures that only suitable items are processed, contributing to the overall quality of thermal cleaning.
Flexible Automation for Various Materials:
- Adaptability to Material Types: Robotic systems are adaptable to a wide range of material types, including metals, plastics, and composites. The flexibility of automation allows for the processing of diverse materials with varying shapes and sizes.
- Programmable Operations: Automation systems are programmable to handle different materials and load configurations. This flexibility enables manufacturers to optimize thermal cleaning processes for specific applications and production requirements.
Precision in Contaminant Removal:
- Targeted Cleaning Movements: Robotics enable targeted and precise movements during the thermal cleaning process. This level of control ensures that contaminants are effectively removed without causing damage to the substrate.
- Customizable Cleaning Paths: Automation systems can follow customizable cleaning paths based on the geometry of the material. This adaptability ensures that even intricate or irregularly shaped items undergo thorough and uniform cleaning.
Data-Driven Decision-Making:
- Integration with Control Systems: Robotic and automation systems seamlessly integrate with control systems. This integration allows for data-driven decision-making, where real-time information on temperature, load status, and other parameters influences robotic actions.
- Continuous Process Optimization: Automation systems continuously optimize the thermal cleaning process based on data feedback. This iterative improvement contributes to enhanced efficiency, reduced energy consumption, and overall process optimization.
Safety Features and Emergency Response:
- Collision Detection and Avoidance: Robotic systems include safety features such as collision detection and avoidance mechanisms. These features prevent unintended collisions and ensure the safety of both the equipment and personnel.
- Emergency Stop Protocols: In emergency situations or malfunctions, automation systems are equipped with emergency stop protocols. This rapid response capability enhances overall safety in the working environment.
Conclusion:
The integration of robotics and automation technologies in burn-off ovens brings unprecedented efficiency, precision, and adaptability to thermal cleaning processes. Through automated handling, vision systems, flexibility in material processing, precision in contaminant removal, data-driven decision-making, and enhanced safety features, these advanced systems redefine the landscape of industrial surface preparation, setting new standards for productivity and quality.
Industry 4.0 Integration
The integration of Industry 4.0 concepts in burn-off ovens signifies a transformative shift towards smart, connected, and data-driven thermal cleaning processes. Industry 4.0 technologies leverage the power of the Internet of Things (IoT), artificial intelligence (AI), and data analytics to enhance efficiency, monitoring, and decision-making in industrial applications.
IoT-Enabled Sensors and Connectivity:
- Sensor Networks: Burn-off ovens equipped with IoT-enabled sensors create a network of interconnected devices. These sensors monitor various parameters such as temperature, load status, and equipment health, providing real-time data.
- Connectivity and Data Exchange: Industry 4.0 integration ensures seamless connectivity between burn-off oven components. This facilitates data exchange and enables a holistic view of the thermal cleaning process, allowing for informed decision-making.
Predictive Maintenance:
- Condition Monitoring: IoT sensors continuously monitor the condition of critical components in burn-off ovens. This real-time condition monitoring forms the basis for predictive maintenance, helping to address potential issues before they lead to downtime.
- Machine Learning Algorithms: Industry 4.0 integration often incorporates machine learning algorithms that analyze historical data to predict equipment failures. This predictive capability enhances the reliability of burn-off ovens and reduces unplanned maintenance.
Cloud-Based Data Analytics:
- Centralized Data Storage: Data generated by burn-off ovens, including temperature profiles, energy consumption, and process efficiency, can be stored centrally in the cloud. This centralized data storage facilitates accessibility and analysis from any location.
- Advanced Analytics for Optimization: Cloud-based analytics platforms leverage advanced algorithms to analyze large datasets. This analysis provides insights into process optimization, energy efficiency, and potential areas for improvement in thermal cleaning operations.
Remote Monitoring and Control:
- Real-Time Visibility: Industry 4.0 integration enables real-time visibility into burn-off oven operations through remote monitoring. Operators can access comprehensive data on the thermal cleaning process and make informed decisions from anywhere with an internet connection.
- Remote Control Capabilities: With remote control capabilities, Industry 4.0-connected burn-off ovens allow operators to adjust parameters, initiate maintenance tasks, and optimize settings without physical presence at the oven location.
Cyber-Physical Systems:
- Integration of Digital and Physical Processes: Industry 4.0 seamlessly integrates digital and physical processes in burn-off ovens. This cyber-physical integration results in a more responsive and adaptive system that aligns with real-world conditions.
- Automated Decision-Making: Advanced control systems within Industry 4.0-connected burn-off ovens can make automated decisions based on real-time data. This automated decision-making enhances efficiency, reduces human intervention, and minimizes errors.
Cybersecurity Measures:
- Data Security Protocols: Industry 4.0 integration includes robust cybersecurity measures to protect sensitive data generated by burn-off ovens. Encryption, access controls, and secure data transmission protocols ensure the integrity and confidentiality of information.
- Continuous Monitoring for Threats: Cybersecurity measures also involve continuous monitoring for potential threats to the connected system. This proactive approach helps prevent unauthorized access and ensures the stability of burn-off oven operations.
Conclusion:
The integration of Industry 4.0 concepts in burn-off ovens heralds a new era of smart and connected thermal cleaning processes. Through IoT-enabled sensors, predictive maintenance, cloud-based analytics, remote monitoring and control, cyber-physical systems, and cybersecurity measures, Industry 4.0-connected burn-off ovens offer a holistic, efficient, and data-driven approach to industrial surface preparation.
Powder Coating Machinery At Competitive Prices
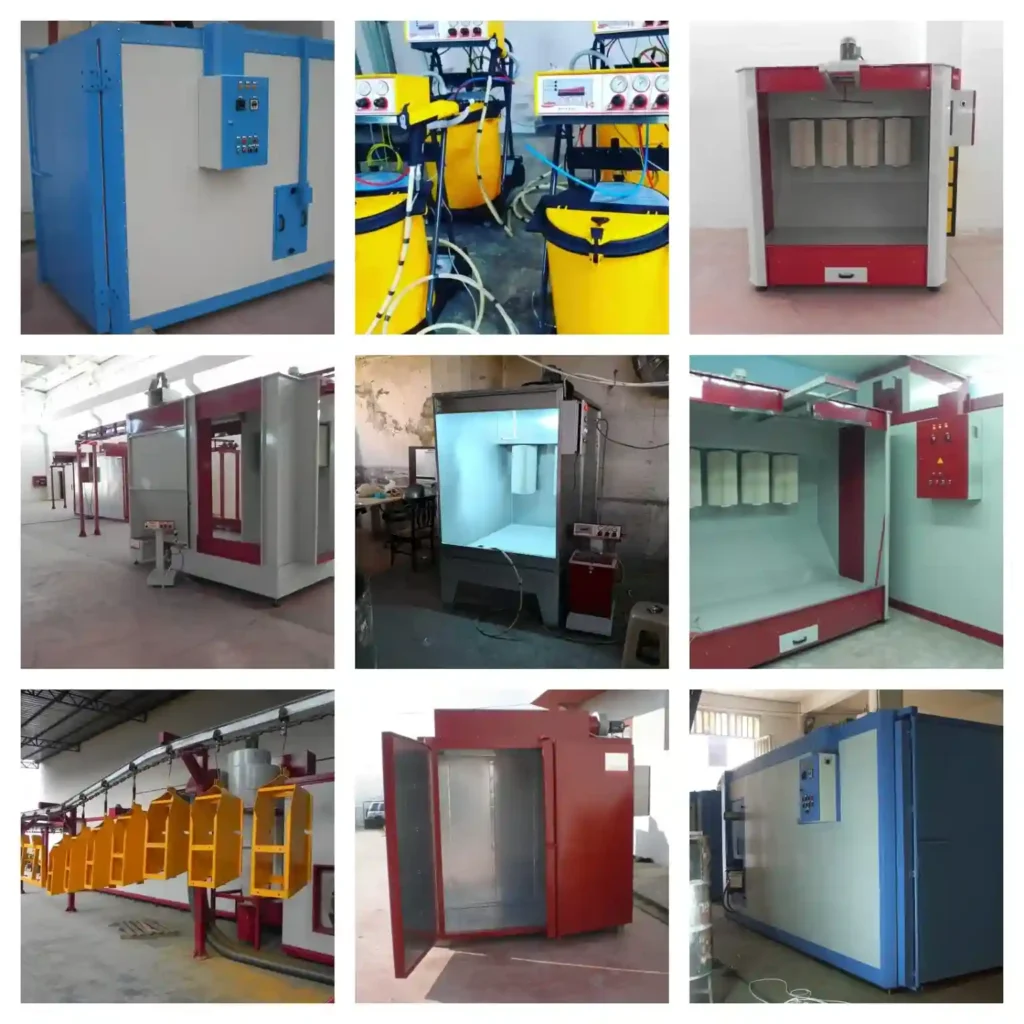
Powder coating equipment is used to apply a thin layer of powder over a metal surface. This type of coating is applied by an electrostatic process and is a very popular method for finishing metal parts.
This type of equipment can be divided into two main categories: automatic and manual. Automatic booths are more popular because they provide better production rates, but they are also more expensive.
A powder booth is an enclosure in which the powder-coating process takes place. Powder-coating equipment includes an oven where the parts are heated to activate the powder, a gun that sprays or brushes on the powder, a conveyor belt that moves parts through the oven, and cartridge-type guns for applying thicker coatings with less overspray.
Powder coating is a technique that is used to provide a finish to metal parts. This technique has been in use for many years and it is still one of the most popular techniques today.
Powder coating equipment consists of booths, ovens, guns, machines, lines and conveyors. A booth can be either automatic or manual. An automatic booth is more expensive than a manual booth but it is also faster and more efficient.
Thermoset powder: Thermoset powders are the most common type of powder coating. They undergo an irreversible chemical reaction during the curing process, forming a hard, crosslinked network that is highly resistant to heat, chemicals, and scratches.
Thermoplastic powder: Thermoplastic powders do not undergo a chemical reaction during the curing process. Instead, they simply melt and fuse together when heated. This makes them less durable than thermoset powders, but they are also more re-flowable, which can be useful for certain applications.
Epoxy powder: Epoxy powders are known for their excellent corrosion resistance and chemical resistance. They are also very hard and durable. However, they can be brittle and are not as UV resistant as some other types of powder coating.
Polyester powder: Polyester powders are the most versatile type of powder coating. They offer a good balance of properties, including durability, corrosion resistance, UV resistance, and chemical resistance. They are also available in a wide range of colors and finishes.
Polyurethane powder: Polyurethane powders are known for their flexibility and toughness. They are also very resistant to abrasion and impact. However, they are not as heat resistant as some other types of powder coating.
Acrylic powder: Acrylic powders are known for their excellent UV resistance and weather resistance. They are also very glossy and have a high scratch resistance. However, they are not as chemically resistant as some other types of powder coating.
Nylon powder: Nylon powders are known for their excellent chemical resistance and abrasion resistance. They are also very flexible and impact resistant. However, they are not as heat resistant as some other types of powder coating.
Fluorocarbon powder: Fluorocarbon powders are known for their excellent chemical resistance, UV resistance, and non-stick properties. They are also very durable and easy to clean. However, they are relatively expensive.
Silica powder: Silica powders are used as fillers and extenders in powder coatings. They can help to improve the adhesion, flow, and leveling of the coating.
Metal flake powder: Metal flake powders are used to create decorative finishes. They can be used to add sparkle, shine, or a metallic look to a powder coating.
Not only do we manufacture our powder coating equipment, we also ship them worldwide to your facility with care
We’re not just the manufacturers of your powder coating equipment, we’re also your worldwide delivery partners.
At EMS Powder Coating Equipment, we understand that getting your powder coating equipment to you quickly and safely is just as important as manufacturing it to the highest standards. That’s why we offer worldwide delivery services to all of our customers.
We work with a network of experienced and reliable shipping partners to ensure that your equipment arrives on time and in perfect condition. We also offer a variety of shipping options to fit your budget and needs.
Whether you need your equipment shipped to a local address or to an international destination, we can help. We’ll work with you to choose the best shipping option for your needs and to keep you updated on the status of your shipment every step of the way.
So when you choose EMS for your powder coating equipment, you’re not just getting the best products on the market, you’re also getting the best possible delivery experience.
Contact us today to learn more about our worldwide delivery services.
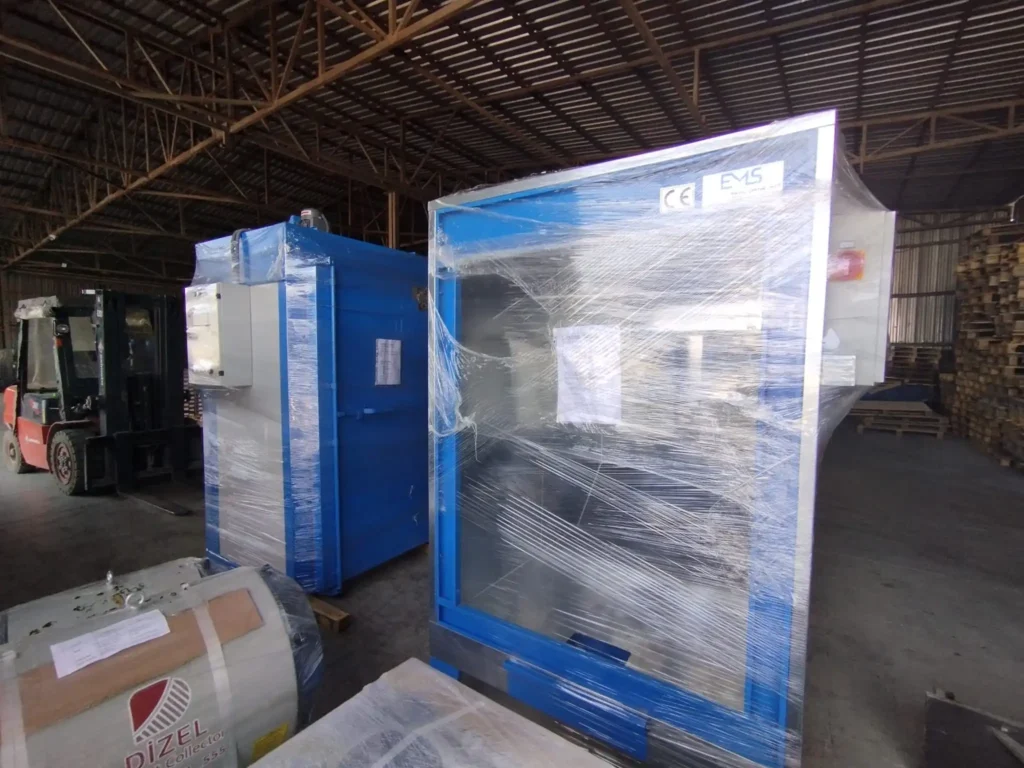
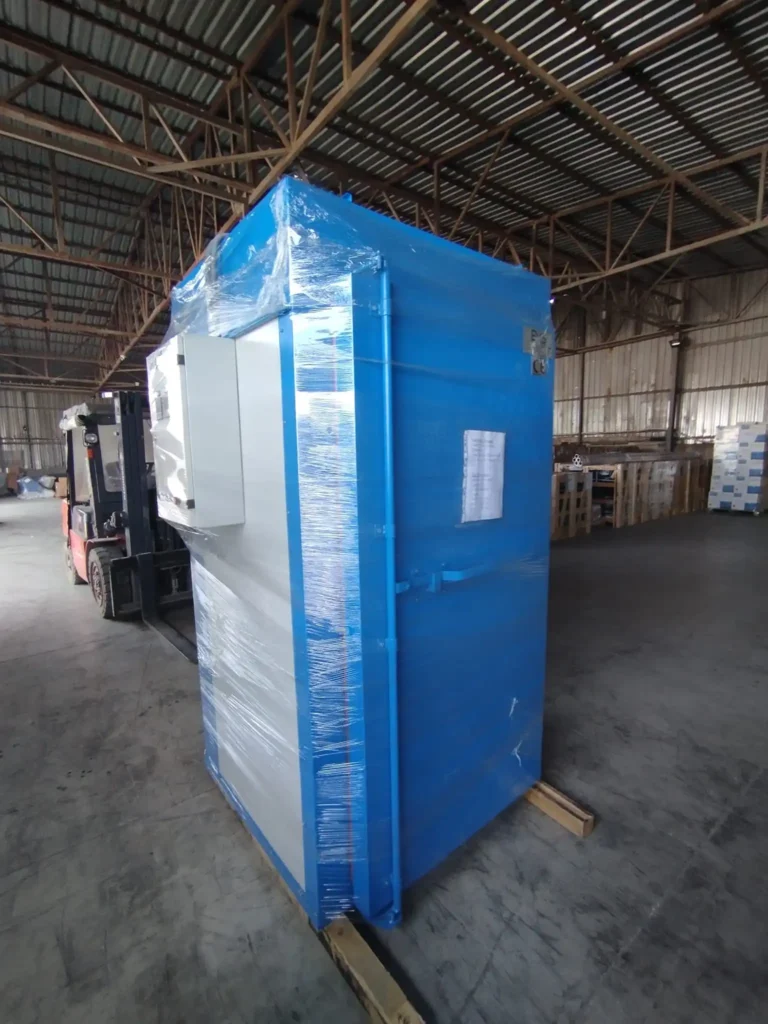
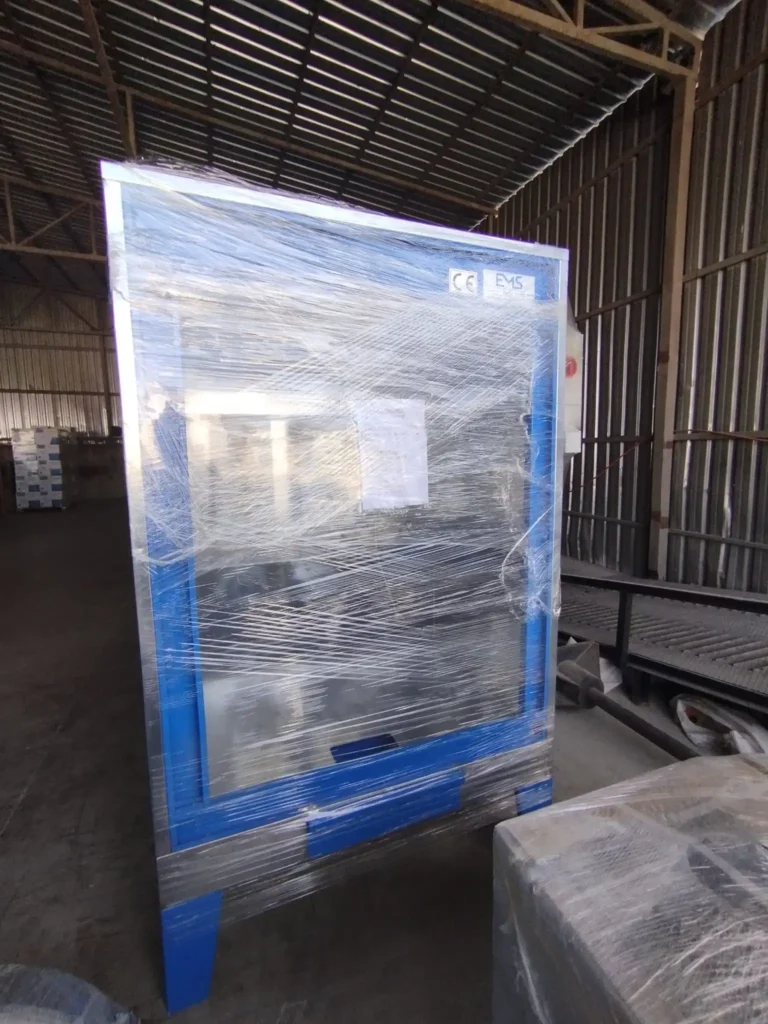
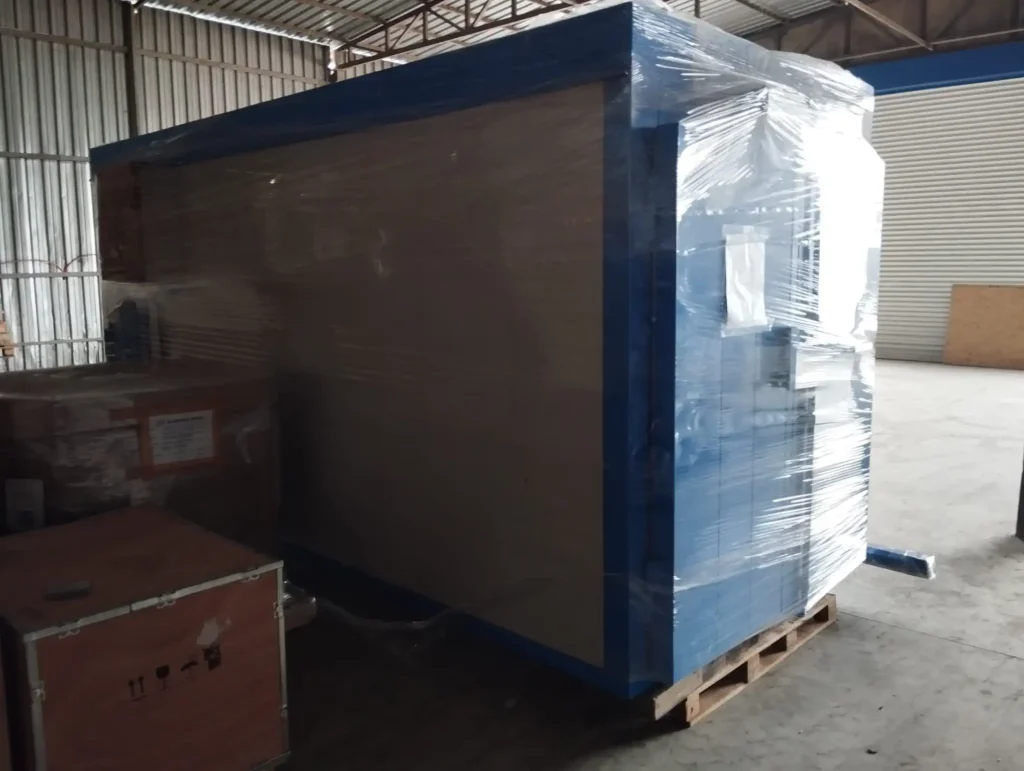
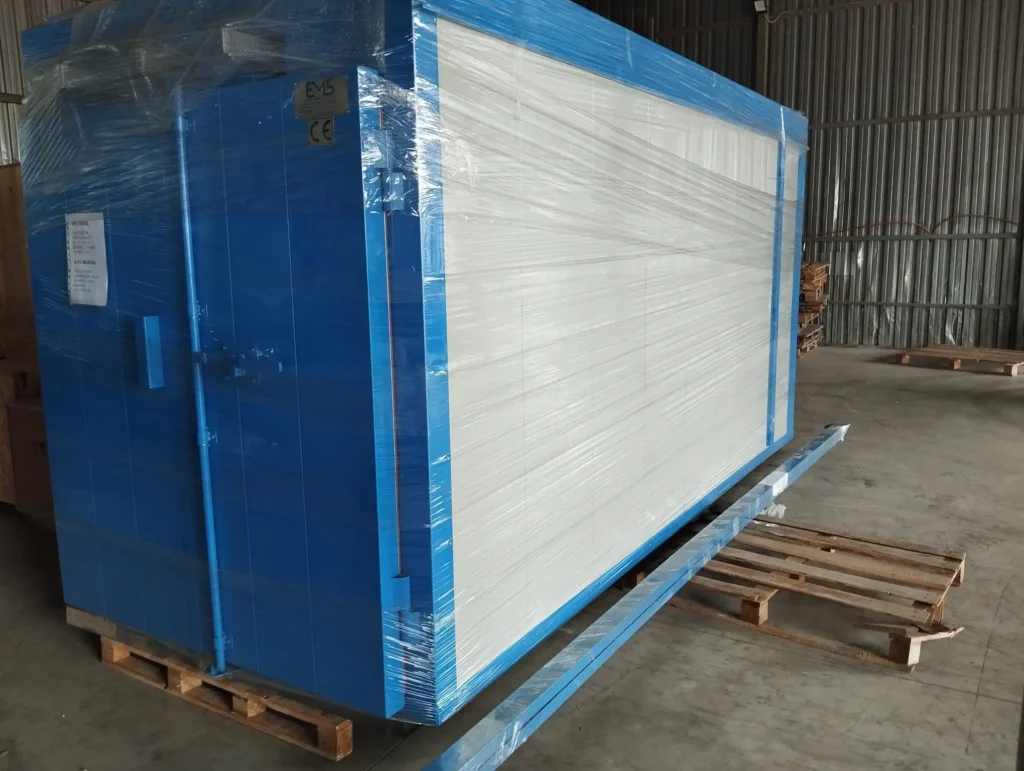
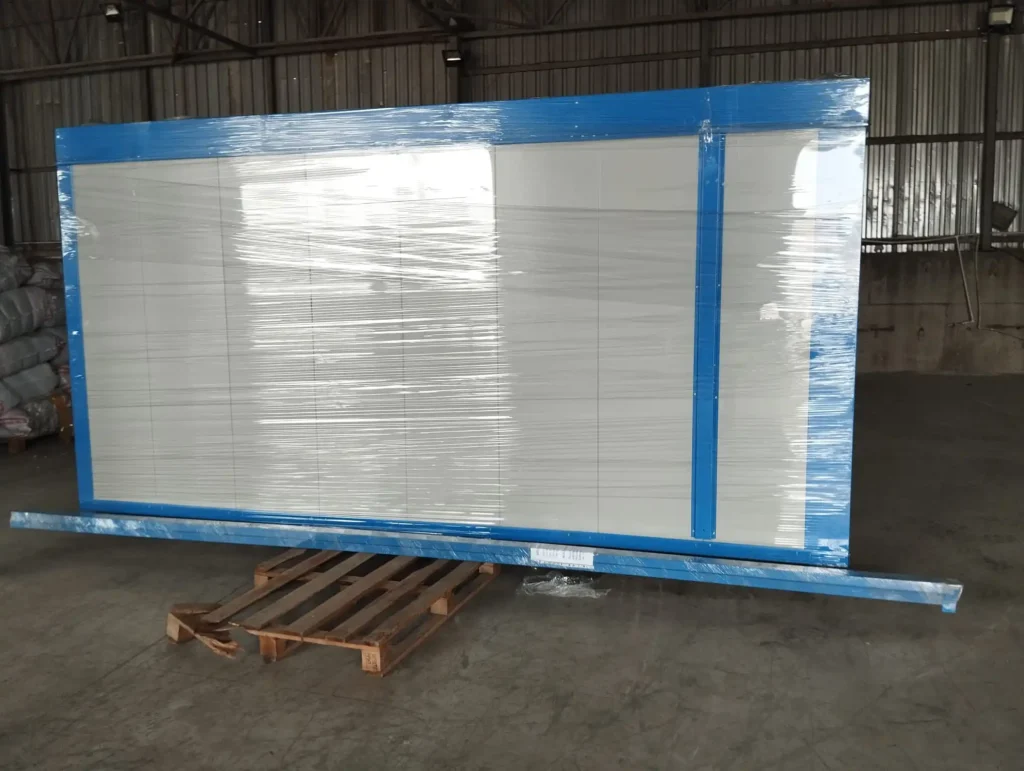
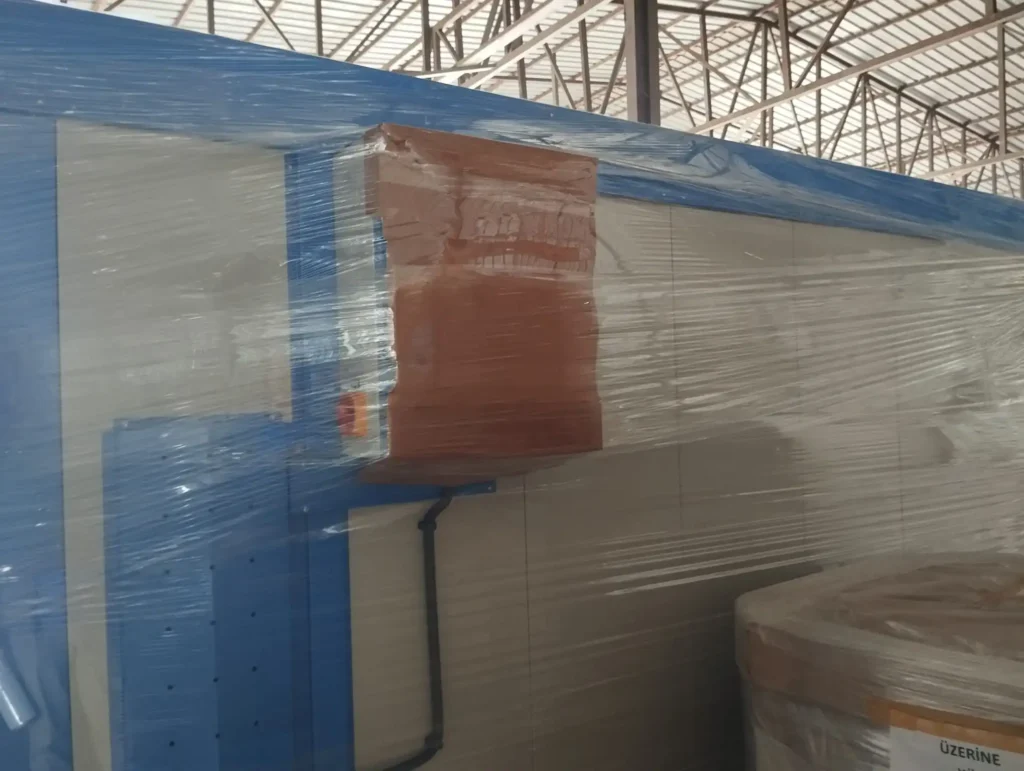
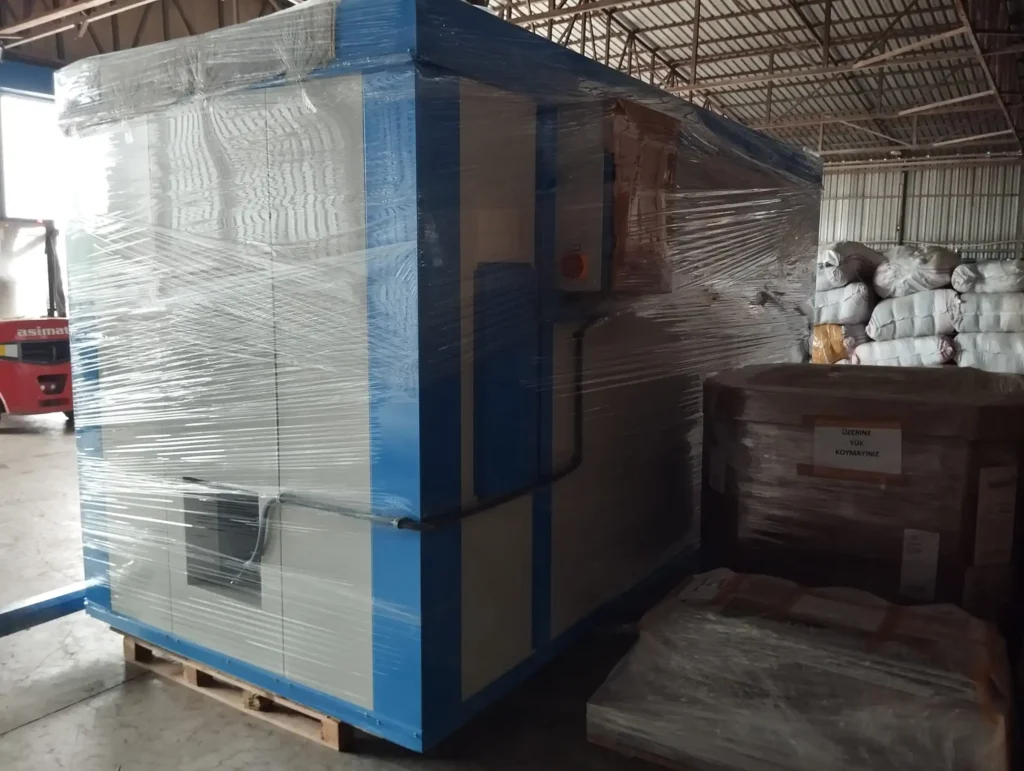
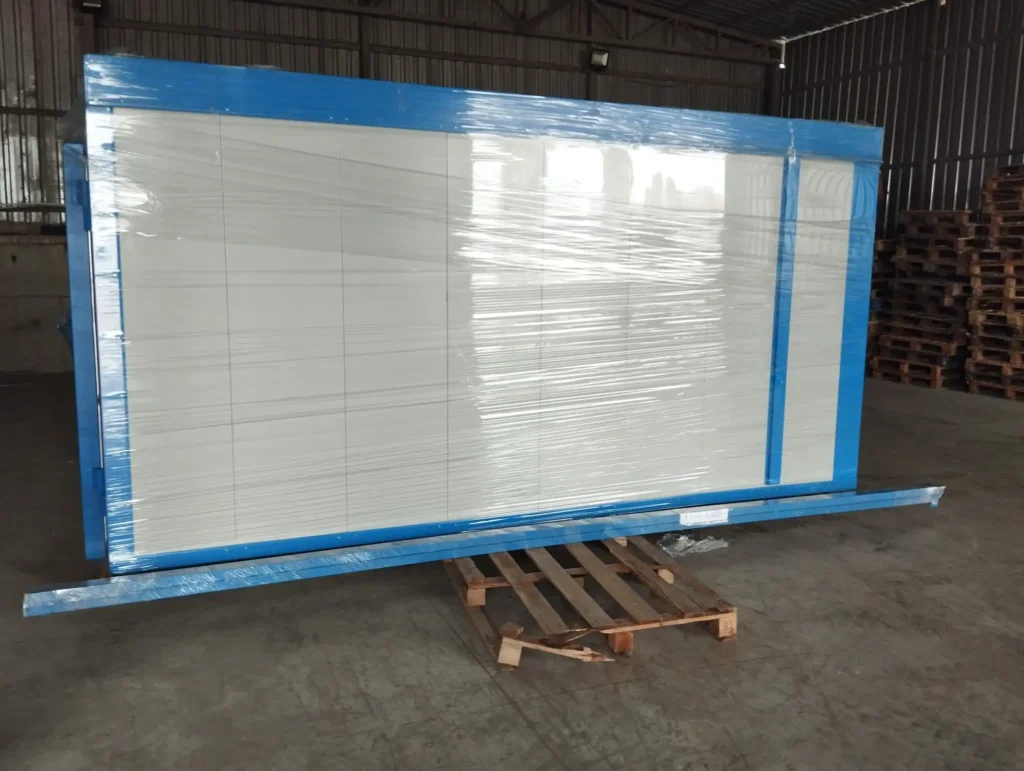