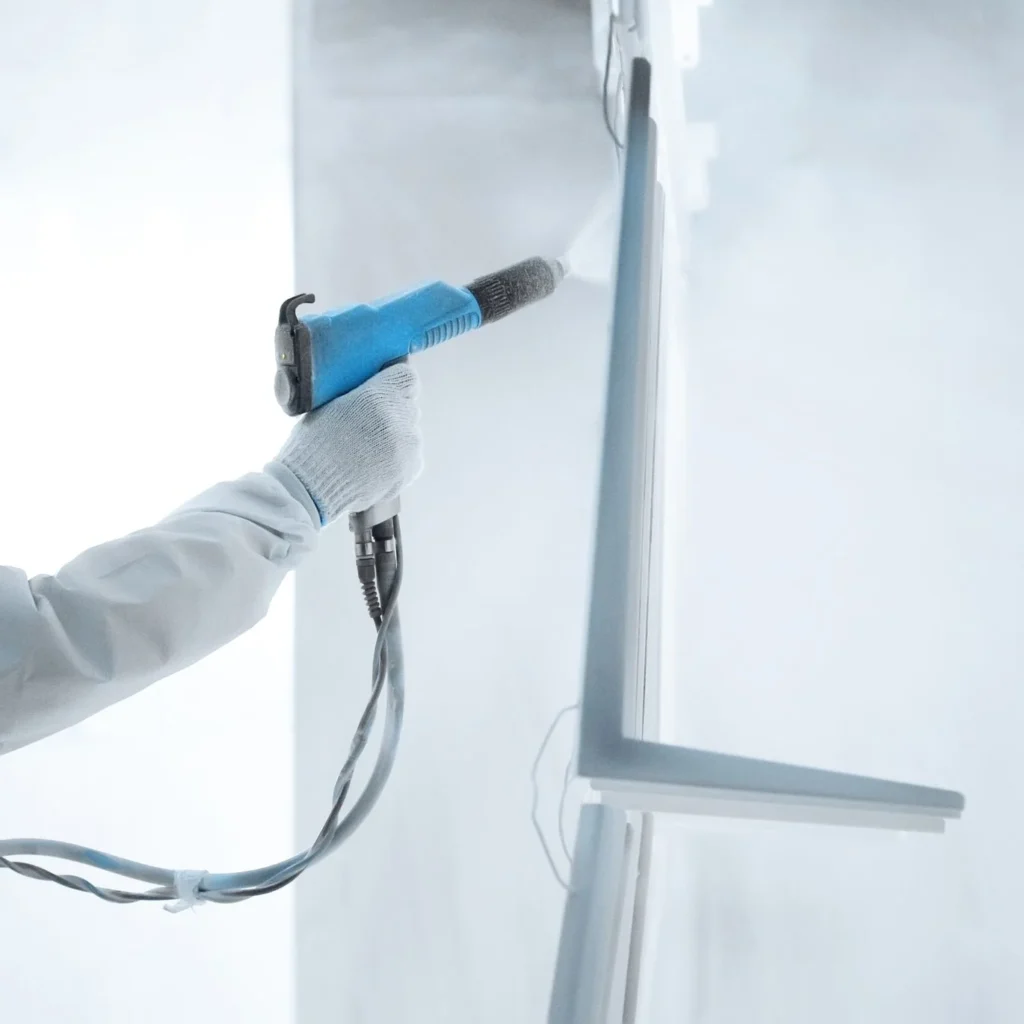
We manufacture Electrostatic Powder Coating Machine with high quality and low prices. Check link below for the Manual and Automatic Powder Coating Machine for sale
Electrostatic powder coating machines are used to apply powder coating to a variety of products, including metal, plastic, and wood. They are particularly well-suited for coating products that are exposed to harsh environments, such as automotive parts and outdoor furniture.
Electrostatic powder coating machines work by charging the powder coating particles with a positive electrical charge. The product to be coated is then grounded, so that the powder coating particles are attracted to it. The powder coating particles then adhere to the product and form a uniform coating.
Electrostatic powder coating machines are typically used in conjunction with a powder coating booth. The powder coating booth collects excess powder coating from the air and returns it to the powder feeder. This helps to reduce waste and improve efficiency.
Electrostatic powder coating machines offer a number of advantages over other coating methods, including:
- Durability: Powder coatings are very durable and can withstand harsh weather conditions and chemicals.
- Color options: Powder coatings are available in a wide variety of colors and finishes.
- Environmentally friendly: Powder coatings are more environmentally friendly than liquid coatings because they do not contain volatile organic compounds (VOCs).
However, electrostatic powder coating machines also have some disadvantages, including:
- High initial investment: Electrostatic powder coating machines can be expensive to purchase.
- Complex operation: Electrostatic powder coating machines can be complex to operate and require trained operators.
- Safety concerns: Electrostatic powder coating machines can generate dust and fumes, so it is important to operate them in a well-ventilated area and to wear personal protective equipment (PPE).
Overall, electrostatic powder coating machines offer a number of advantages over other coating methods. They are durable, versatile, and environmentally friendly. However, they can be expensive to purchase and operate, and they require trained operators to operate safely.
Here are some safety tips for operating an electrostatic powder coating machine:
- Always wear personal protective equipment (PPE), such as a respirator, gloves, and safety glasses.
- Be aware of the electrostatic charge generated by the machine. Do not touch the product while it is still charged.
- Use only powder coating materials that are approved for use with electrostatic powder coating machines.
- Be careful not to overspray the product. Excess powder coating can be difficult to remove and can ruin the finish.
- Make sure that the powder coating booth is properly ventilated.
- Clean up any spills or leaks immediately.
If you are operating an electrostatic powder coating machine for the first time, it is important to read the manufacturer’s instructions carefully. They will provide you with specific safety instructions for the type of machine you are using.
Electrostatic Powder Coating Machine – Electrostatic Painting
Electrostatic painting is a coating process that uses electrostatics to apply paint to a surface. The paint is first charged with a positive electrical charge, and the surface to be coated is grounded. This creates an electrostatic attraction between the paint particles and the surface, causing the paint to adhere to the surface evenly.
Electrostatic painting is a versatile process that can be used to coat a wide variety of materials, including metal, plastic, and wood. It is also a very durable coating process, and the finished product is often resistant to chipping, peeling, and corrosion.
Electrostatic painting has a number of advantages over other coating processes, including:
- High transfer efficiency: Electrostatic painting has a very high transfer efficiency, meaning that most of the paint that is applied to the surface actually adheres to it. This reduces waste and saves money on materials.
- Uniform coating: Electrostatic painting can produce a very uniform coating, even on complex shapes. This is because the electrostatic attraction ensures that the paint particles are distributed evenly over the surface.
- Durable finish: Electrostatic paint finishes are very durable and resistant to chipping, peeling, and corrosion. This makes them ideal for applications where the coating needs to withstand harsh conditions.
However, electrostatic painting also has some disadvantages, including:
- High initial investment: Electrostatic painting equipment can be expensive to purchase.
- Complex operation: Electrostatic painting equipment can be complex to operate and requires trained operators.
- Safety concerns: Electrostatic painting equipment can generate dust and fumes, so it is important to operate it in a well-ventilated area and to wear personal protective equipment (PPE).
Overall, electrostatic painting is a versatile and durable coating process that offers a number of advantages over other coating processes. However, it is important to weigh the costs and benefits before deciding whether or not to use electrostatic painting for a particular application.
Here are some examples of products that are commonly coated using electrostatic painting:
- Automotive parts: Electrostatic painting is used to coat a wide variety of automotive parts, including bumpers, fenders, and trim.
- Appliance parts: Electrostatic painting is used to coat a variety of appliance parts, including refrigerator doors, dishwasher fronts, and stovetops.
- Furniture: Electrostatic painting is used to coat a variety of furniture pieces, including chairs, tables, and cabinets.
- Outdoor equipment: Electrostatic painting is used to coat a variety of outdoor equipment, including lawnmowers, grills, and patio furniture.
Electrostatic painting is a versatile and durable coating process that can be used to coat a wide variety of products. It is a good choice for applications where a durable and uniform finish is required.
Powder Coating Gun:
A powder coating gun is an essential tool used in the powder coating process to apply a fine powder coating material onto a surface. It operates on the principle of electrostatic attraction, where the powder particles are charged and then attracted to the grounded workpiece, resulting in a uniform and even coating. Let’s delve deeper into the technical aspects of a powder coating gun:
Components: A powder coating gun comprises several key components, each playing a crucial role in the application process:
- Gun Body: The main housing of the gun, which houses the internal components and provides a grip for the operator.
- Powder Hopper: A container that holds the powder coating material, typically located at the rear of the gun. The hopper can vary in size depending on the volume of powder needed for the application.
- Fluidizing Plate: Located at the bottom of the powder hopper, the fluidizing plate helps maintain a consistent flow of powder by introducing air to fluidize the powder particles.
- Powder Pump: Responsible for transporting the powder from the hopper to the gun’s nozzle. The pump can be pneumatic or electrostatically driven.
- Nozzle: The nozzle is the outlet through which the powder is expelled onto the workpiece. It can be interchangeable to accommodate different spray patterns and powder particle sizes.
- Electrostatic Charging System: This system charges the powder particles as they pass through the gun, creating a negative charge on the particles and ensuring they adhere to the positively charged workpiece.
- Control Panel: Some powder coating guns feature a control panel that allows operators to adjust various parameters such as powder flow rate, air pressure, and electrostatic charge.
Operating Principle: The operation of a powder coating gun involves several steps:
- Powder Feed: The powder coating material is loaded into the hopper of the gun.
- Fluidization: Air is introduced through the fluidizing plate, creating a fluidized bed of powder particles and ensuring consistent flow.
- Charging: The powder particles pass through the charging system, where they acquire a negative charge.
- Spraying: The charged powder particles are expelled from the gun’s nozzle and propelled towards the grounded workpiece.
- Adhesion: The electrostatic attraction between the charged powder particles and the grounded workpiece causes the particles to adhere to the surface, forming a uniform coating.
- Curing: After the coating is applied, the workpiece is transferred to a curing oven where the powder coating is melted and fused into a durable finish.
Applications: Powder coating guns are widely used across various industries for coating a wide range of materials, including metal, plastic, and wood. Common applications include:
- Automotive parts
- Household appliances
- Furniture
- Architectural components
- Machinery and equipment
In summary, a powder coating gun is a versatile and indispensable tool in the powder coating process, offering precision, efficiency, and flexibility in applying high-quality coatings to a variety of surfaces. Its electrostatic application method ensures excellent coverage and adhesion, making it a preferred choice for many industrial coating applications.
Spray Booth:
A spray booth is a controlled environment designed for the application of various coatings, including powder coatings, paints, and finishes. It provides a safe and efficient space for coating processes by containing overspray, controlling ventilation, and ensuring worker safety. Let’s delve into the technical details of a spray booth:
Components: A spray booth comprises several key components, each playing a critical role in the coating process:
- Enclosure: The enclosure of the spray booth consists of walls, a ceiling, and a floor, creating a contained space for coating operations. It is typically constructed from durable materials such as metal or fiberglass to withstand the chemicals and solvents used in coatings.
- Exhaust System: The exhaust system consists of fans, ductwork, and filters designed to remove overspray and fumes from the spray booth. It maintains a safe working environment by preventing the buildup of flammable vapors and ensuring proper ventilation.
- Airflow Control: Airflow within the spray booth is carefully controlled to direct overspray away from the workpiece and towards the exhaust filters. This is typically achieved through the strategic placement of intake and exhaust vents, as well as the use of airflow control devices such as baffles or curtains.
- Lighting: Adequate lighting is essential for visibility during the coating process. Spray booths are equipped with bright, uniform lighting fixtures positioned to minimize shadows and provide optimal illumination of the workpiece.
- Filtration System: Filters, such as high-efficiency particulate air (HEPA) filters or paint arrestors, capture overspray and contaminants suspended in the air, preventing them from escaping into the surrounding environment.
- Control Panel: Some spray booths feature a control panel that allows operators to monitor and adjust various parameters such as airflow, temperature, and lighting.
Types of Spray Booths: Spray booths come in various configurations to accommodate different coating processes and application requirements:
- Open-Faced Spray Booth: Also known as a single-wall booth, an open-faced spray booth has three enclosed sides and an open front, allowing easy access for operators and workpieces.
- Enclosed Spray Booth: An enclosed spray booth has four enclosed sides, providing a fully contained environment for coating operations. It offers greater control over airflow and overspray containment compared to open-faced booths.
- Downdraft Spray Booth: In a downdraft spray booth, air is drawn downward through a grated floor or pit, capturing overspray and fumes and directing them away from the workpiece and operator.
- Crossdraft Spray Booth: In a crossdraft spray booth, airflow moves horizontally across the workpiece, carrying overspray and contaminants towards exhaust filters located on the opposite side of the booth.
- Semi-Downraft Spray Booth: A semi-downraft spray booth combines elements of downdraft and crossdraft airflow, offering a compromise between the two configurations.
Applications: Spray booths are used in a wide range of industries and applications, including:
- Automotive refinishing
- Aerospace manufacturing
- Furniture production
- Metal fabrication
- Woodworking
- Electronics assembly
In summary, a spray booth is an essential piece of equipment for coating operations, providing a controlled environment for the application of various coatings. Its design and configuration play a crucial role in ensuring worker safety, environmental compliance, and coating quality. By containing overspray, controlling ventilation, and maintaining proper airflow, a spray booth facilitates efficient and effective coating processes across a diverse range of industries.
Powder Coating Oven
A powder coating oven is a specialized heating chamber used in the powder coating process to cure and harden powder coatings applied to workpieces. It plays a crucial role in transforming the powder coating material from a dry powder into a durable and attractive finish. Let’s explore the technical aspects of a powder coating oven:
Construction and Design: Powder coating ovens are typically constructed from durable materials such as steel or stainless steel to withstand high temperatures and chemical exposure. They feature insulated walls, ceiling, and floor to minimize heat loss and maintain consistent temperatures throughout the curing process. The oven chamber may be lined with insulation materials such as ceramic fiber or mineral wool to improve energy efficiency and reduce operating costs.
The design of a powder coating oven can vary depending on the specific requirements of the application. Common designs include:
- Batch Ovens: Batch ovens are designed to cure a single batch of workpieces at a time. They feature a stationary chamber where workpieces are loaded manually or with the help of racks or carts. Batch ovens offer flexibility and versatility for small to medium production runs.
- Continuous Ovens: Continuous ovens are designed for high-volume production processes where workpieces are continuously fed through the oven on a conveyor system. They feature a long chamber with a conveyor belt or chain to transport workpieces through the heating zone. Continuous ovens offer high throughput and efficiency for large-scale production operations.
Heating System: Powder coating ovens utilize various heating methods to provide the necessary heat for curing the powder coating material. Common heating systems include:
- Electric Heating: Electric ovens use electric heating elements, such as resistance coils or rods, to generate heat within the oven chamber. Electric heating offers precise temperature control and uniform heating, making it ideal for powder coating applications.
- Gas Heating: Gas ovens use gas-fired burners to generate heat, typically fueled by natural gas or propane. Gas heating systems offer fast heat-up times and high energy efficiency, making them suitable for high-temperature curing applications.
- Infrared Heating: Infrared ovens use infrared radiation to heat the workpieces directly, rather than heating the surrounding air. Infrared heating systems offer rapid heat transfer and energy savings, making them suitable for specific curing applications.
Temperature Control and Monitoring: Temperature control is critical in powder coating ovens to ensure proper curing of the powder coating material. Ovens are equipped with temperature control systems, including thermocouples, controllers, and PID algorithms, to regulate the oven temperature to the precise level required for curing. Temperature sensors are strategically placed throughout the oven chamber to monitor temperature uniformity and provide feedback to the control system.
Safety Features: Powder coating ovens are equipped with various safety features to ensure safe operation and protect against hazards. Common safety features include:
- Overheat Protection: Automatic shut-off systems are installed to prevent the oven from overheating in case of a malfunction or temperature excursion.
- Ventilation Systems: Ventilation systems remove fumes and gases generated during the curing process, ensuring a safe working environment for operators.
- Interlocks: Interlock systems prevent the oven door from being opened while the oven is in operation, minimizing the risk of accidental exposure to high temperatures.
Applications: Powder coating ovens are used in a wide range of industries and applications, including automotive, aerospace, furniture, metal fabrication, and electronics. They are essential for curing powder-coated finishes on various substrates such as metal, plastic, and wood, providing durability, corrosion resistance, and aesthetic appeal to finished products.
In summary, a powder coating oven is a critical component of the powder coating process, providing controlled heating to cure and harden powder coatings applied to workpieces. Its construction, design, heating system, temperature control, and safety features play a crucial role in ensuring efficient and effective curing operations across a diverse range of industrial applications.
Infrared Oven:
An infrared oven is a type of heating chamber used in industrial processes, including powder coating, to cure coatings and materials using infrared radiation. Unlike traditional convection ovens that heat the surrounding air, infrared ovens emit infrared radiation directly onto the surface of the workpiece, resulting in rapid and efficient heat transfer. Let’s explore the technical aspects of an infrared oven:
Principle of Operation: Infrared ovens operate on the principle of electromagnetic radiation, specifically in the infrared spectrum. The oven contains heating elements, typically made of quartz or ceramic, that emit infrared radiation when energized. This radiation penetrates the surface of the workpiece and is converted into heat, raising the temperature of the material and causing curing or drying to occur. Unlike convection heating, which relies on heating the air around the workpiece, infrared radiation heats the object directly, resulting in faster heating and reduced energy consumption.
Types of Infrared Heating: Infrared ovens can utilize different types of infrared heating elements, each offering unique advantages and applications:
- Quartz Tubes: Quartz tube heaters are commonly used in infrared ovens due to their high efficiency and rapid heat-up times. These tubes contain coiled resistance wire elements surrounded by a quartz tube, which emits infrared radiation when heated. Quartz tubes are durable, long-lasting, and provide uniform heating across the workpiece.
- Ceramic Panels: Ceramic panels consist of ceramic elements embedded in a metal housing. They emit infrared radiation when heated and are suitable for applications requiring high temperatures and precise control. Ceramic panels offer excellent heat distribution and can be customized to meet specific heating requirements.
- Gas Infrared Burners: Gas infrared burners use combustion to produce infrared radiation, typically fueled by natural gas or propane. They offer high heat output and are suitable for large-scale heating applications. Gas burners provide rapid heat-up times and can be easily controlled to achieve the desired temperature profile.
Advantages of Infrared Heating: Infrared ovens offer several advantages over traditional convection ovens and other heating methods:
- Faster Heating: Infrared radiation heats the workpiece directly, resulting in faster heating rates and reduced cycle times compared to convection heating.
- Energy Efficiency: Infrared heating is highly efficient, as it targets the object being heated rather than heating the surrounding air. This reduces energy consumption and operating costs.
- Uniform Heating: Infrared ovens provide uniform heating across the entire surface of the workpiece, minimizing temperature variations and ensuring consistent curing or drying results.
- Versatility: Infrared heating can be tailored to suit a wide range of materials and applications, from thin films and coatings to thick substrates and composites.
- Compact Design: Infrared ovens are often more compact than convection ovens, making them suitable for installations where space is limited.
Applications: Infrared ovens are used in various industries and applications, including:
- Powder coating curing
- Paint drying and curing
- Adhesive bonding
- Plastic welding and thermoforming
- Food processing
- Semiconductor manufacturing
In summary, infrared ovens are versatile and efficient heating solutions used in industrial processes such as powder coating. Their ability to provide rapid and uniform heating makes them ideal for curing coatings and materials, while their energy efficiency and compact design offer advantages in terms of cost and space savings.
Hybrid Oven:
A hybrid oven combines multiple heating technologies, such as convection, infrared, and/or gas heating, to provide versatile and efficient heating solutions for industrial processes like powder coating. By integrating different heating methods, hybrid ovens offer enhanced flexibility, energy efficiency, and control over the curing process. Let’s delve into the technical details of a hybrid oven:
Principle of Operation: Hybrid ovens leverage the strengths of different heating technologies to achieve optimal heating performance. For example, a hybrid oven may combine convection heating for uniform heat distribution with infrared heating for rapid heat transfer to the workpiece’s surface. By integrating multiple heating methods, hybrid ovens can provide precise temperature control, fast heat-up times, and consistent curing results across a wide range of applications.
Components: The components of a hybrid oven can vary depending on the specific heating technologies integrated into the system. However, common components may include:
- Heating Elements: Hybrid ovens may incorporate electric heating elements, gas-fired burners, infrared lamps, or a combination of these to provide the necessary heat for curing the powder coating material.
- Control System: A sophisticated control system regulates the operation of the heating elements and monitors various parameters such as temperature, airflow, and conveyor speed to ensure optimal curing conditions.
- Insulation: Hybrid ovens are typically insulated to minimize heat loss and maintain consistent temperatures throughout the curing process. Insulation materials such as ceramic fiber or mineral wool may be used to line the oven walls, ceiling, and floor.
- Airflow System: Convection-based hybrid ovens feature an airflow system comprising fans, ductwork, and baffles to distribute heated air evenly throughout the oven chamber, ensuring uniform curing of the powder coating material.
- Conveyor System: In continuous hybrid ovens, a conveyor system transports workpieces through the oven at a controlled speed, allowing for efficient and consistent curing of large volumes of parts.
Advantages of Hybrid Ovens: Hybrid ovens offer several advantages over single-heating technology ovens:
- Versatility: Hybrid ovens can accommodate a wide range of heating requirements and material types by leveraging multiple heating technologies. This versatility allows for greater flexibility in process optimization and product customization.
- Energy Efficiency: By combining different heating methods, hybrid ovens can optimize energy usage and reduce operating costs compared to traditional single-heating technology ovens.
- Enhanced Performance: Hybrid ovens provide superior heating performance, including faster heat-up times, precise temperature control, and consistent curing results, leading to improved productivity and product quality.
- Process Optimization: The ability to adjust and combine heating technologies allows for fine-tuning of the curing process to meet specific application requirements, resulting in optimized throughput and coating performance.
- Space Savings: Hybrid ovens can often replace multiple single-heating technology ovens, resulting in space savings and simplified equipment layout in the production facility.
Applications: Hybrid ovens find application in various industries and processes requiring precise and efficient curing of coatings and materials. Some common applications include:
- Powder coating curing
- Paint drying and curing
- Composite curing
- Annealing and heat treatment
- Food processing
- Pharmaceutical manufacturing
In summary, hybrid ovens offer versatile and efficient heating solutions for industrial processes like powder coating, combining the strengths of different heating technologies to achieve optimal performance and productivity. Their ability to provide precise temperature control, fast heat-up times, and consistent curing results makes them an ideal choice for a wide range of applications across various industries.
Continuous Oven
A continuous oven is a type of industrial heating chamber designed to cure coatings, including powder coatings, on a continuous basis. Unlike batch ovens that process workpieces in discrete batches, continuous ovens feature a conveyor system that continuously transports workpieces through the heating chamber, allowing for high-volume production with minimal downtime. Let’s explore the technical aspects of a continuous oven:
Operating Principle: Continuous ovens utilize a conveyor system to transport workpieces through the heating chamber at a constant speed. As workpieces enter the oven, they are exposed to controlled heat, typically provided by gas-fired burners, infrared lamps, or electric heating elements. The heat cures the coating material, transforming it from a powder into a durable finish. The conveyor system ensures a continuous flow of workpieces through the oven, maximizing production throughput and efficiency.
Components: The components of a continuous oven may vary depending on the specific application and heating requirements. However, common components include:
- Conveyor System: The conveyor system consists of a conveyor belt or chain that moves workpieces through the oven at a controlled speed. Conveyor belts are typically made of stainless steel or other heat-resistant materials to withstand the curing temperatures.
- Heating System: Continuous ovens utilize various heating methods, such as gas-fired burners, infrared lamps, or electric heating elements, to provide the necessary heat for curing the coating material. The heating system is designed to deliver uniform heat distribution across the entire length of the oven chamber.
- Insulation: Continuous ovens are insulated to minimize heat loss and maintain consistent temperatures throughout the curing process. Insulation materials such as ceramic fiber or mineral wool may be used to line the oven walls, ceiling, and floor.
- Control System: A control system regulates the operation of the heating elements and conveyor system, monitoring various parameters such as temperature, conveyor speed, and airflow to ensure optimal curing conditions.
- Exhaust System: An exhaust system removes fumes and gases generated during the curing process, ensuring a safe working environment for operators and preventing the buildup of flammable vapors.
Advantages of Continuous Ovens: Continuous ovens offer several advantages over batch ovens and other curing methods:
- High Throughput: Continuous ovens can process a large volume of workpieces continuously, resulting in higher production throughput and efficiency compared to batch processing.
- Consistent Quality: The continuous flow of workpieces through the oven ensures consistent curing conditions and coating quality, minimizing variations in finished product quality.
- Reduced Labor Costs: Continuous ovens require less operator intervention and manual handling compared to batch ovens, resulting in lower labor costs and increased productivity.
- Space Savings: Continuous ovens have a smaller footprint compared to batch ovens processing the same volume of workpieces, resulting in space savings and more efficient use of floor space in the production facility.
- Energy Efficiency: Continuous ovens can be designed with energy-efficient features such as insulated chambers, heat recovery systems, and precise temperature control, reducing energy consumption and operating costs.
Applications: Continuous ovens find application in a wide range of industries and processes requiring high-volume curing of coatings and materials. Some common applications include:
- Automotive part manufacturing
- Aerospace component production
- Metal fabrication
- Glass and ceramic manufacturing
- Electronics assembly
- Food processing
In summary, continuous ovens offer efficient and cost-effective solutions for curing coatings on a large scale. Their ability to provide high throughput, consistent quality, and energy efficiency makes them an ideal choice for industries requiring continuous production of coated products.
Gas Oven:
A gas oven is a type of industrial heating chamber used for various applications, including powder coating curing, where heat is generated using gas-fired burners fueled by natural gas or propane. Gas ovens offer efficient and reliable heating solutions, making them popular in industrial settings. Let’s delve into the technical aspects of a gas oven:
Operating Principle: Gas ovens operate on the principle of combustion, where a mixture of fuel (natural gas or propane) and air is ignited in burners to produce heat. The heat generated by the burners is circulated within the oven chamber to cure coatings, dry materials, or perform other heating processes. Gas ovens may utilize different burner configurations, such as atmospheric burners, radiant tube burners, or infrared burners, depending on the specific application requirements.
Components: Gas ovens consist of several key components, including:
- Burners: The burners are responsible for combusting the fuel-air mixture to generate heat. They are typically located at strategic locations within the oven chamber to ensure uniform heat distribution.
- Combustion System: The combustion system includes components such as gas valves, ignition systems, and flame monitoring devices to control the combustion process and ensure safe and efficient operation of the oven.
- Heat Exchangers: Heat exchangers transfer heat from the combustion gases to the circulating air within the oven chamber. They may be located within the oven walls or as separate units depending on the oven design.
- Air Circulation System: Gas ovens feature fans or blowers that circulate heated air within the oven chamber to ensure uniform heating of the workpieces.
- Control System: A control system regulates the operation of the gas burners, combustion system, and air circulation system, monitoring various parameters such as temperature, airflow, and gas pressure to maintain optimal curing conditions.
Advantages of Gas Ovens: Gas ovens offer several advantages over other types of heating systems:
- Fast Heat-Up Times: Gas ovens can reach operating temperatures quickly, resulting in shorter heat-up times and increased productivity.
- Precise Temperature Control: Gas ovens provide precise temperature control, allowing operators to maintain consistent curing conditions and achieve desired coating properties.
- High Efficiency: Gas-fired burners are highly efficient at converting fuel into heat energy, resulting in lower operating costs compared to electric heating systems.
- Versatility: Gas ovens can accommodate a wide range of applications and materials, making them suitable for various industrial processes beyond powder coating curing.
- Reliability: Gas ovens are known for their reliability and durability, requiring minimal maintenance and providing consistent performance over time.
Applications: Gas ovens find application in numerous industries and processes, including:
- Powder coating curing
- Paint drying and curing
- Heat treatment and annealing
- Food processing
- Glass manufacturing
- Metal fabrication
In summary, gas ovens are versatile and efficient heating solutions used in industrial applications such as powder coating curing. Their ability to provide fast heat-up times, precise temperature control, and high efficiency makes them well-suited for various heating processes across a wide range of industries.
Electric Oven
An electric oven is a type of industrial heating chamber used for curing coatings, such as powder coatings, and other heat treatment processes. Unlike gas ovens that rely on combustion to generate heat, electric ovens utilize electrical resistance heating elements to produce the required heat. Let’s delve into the technical aspects of an electric oven:
Operating Principle: Electric ovens operate on the principle of electrical resistance heating, where electrical energy is converted into heat when an electric current passes through resistive heating elements. These heating elements are typically made of materials with high electrical resistance, such as nichrome or Kanthal wire, which generate heat when subjected to an electric current. The heat generated by the heating elements is circulated within the oven chamber to cure coatings or perform other heating processes.
Components: Electric ovens consist of several key components, including:
- Heating Elements: The heating elements are the primary components responsible for generating heat within the oven chamber. They may be located along the walls, ceiling, or floor of the oven, depending on the specific design and heating requirements.
- Temperature Control System: A temperature control system regulates the operation of the heating elements to maintain the desired curing temperature within the oven chamber. It typically includes temperature sensors, controllers, and relays to monitor and adjust the oven temperature as needed.
- Air Circulation System: Electric ovens feature fans or blowers that circulate heated air within the oven chamber to ensure uniform heating of the workpieces. Proper air circulation is essential for achieving consistent curing results and preventing hot spots.
- Insulation: Electric ovens are insulated to minimize heat loss and maintain consistent temperatures throughout the curing process. Insulation materials such as ceramic fiber or mineral wool may be used to line the oven walls, ceiling, and floor.
- Control Panel: A control panel allows operators to monitor and adjust various parameters, such as temperature, airflow, and conveyor speed, to optimize curing conditions and ensure product quality.
Advantages of Electric Ovens: Electric ovens offer several advantages over other types of heating systems:
- Cleaner Operation: Electric ovens do not produce combustion by-products or emissions, making them suitable for applications where cleanliness is important, such as food processing or electronics manufacturing.
- Precise Temperature Control: Electric ovens provide precise temperature control, allowing operators to maintain consistent curing conditions and achieve desired coating properties.
- Energy Efficiency: Electric ovens can be highly efficient, as they convert electrical energy directly into heat with minimal energy loss. They may also incorporate energy-saving features such as insulation and programmable controllers to optimize energy usage.
- Versatility: Electric ovens can accommodate a wide range of applications and materials, making them suitable for various industrial processes beyond powder coating curing.
- Safety: Electric ovens are generally considered safer to operate than gas-fired ovens, as they do not involve combustion or the use of flammable gases.
Applications: Electric ovens find application in numerous industries and processes, including:
- Powder coating curing
- Paint drying and curing
- Heat treatment and annealing
- Semiconductor manufacturing
- Pharmaceutical production
- Laboratory testing
In summary, electric ovens are versatile and efficient heating solutions used in various industrial processes, including powder coating curing. Their ability to provide precise temperature control, energy efficiency, and cleanliness makes them well-suited for a wide range of applications across different industries.
Convection Oven:
A convection oven is a type of heating chamber used for curing coatings, such as powder coatings, by circulating heated air throughout the oven chamber. Convection ovens utilize fans or blowers to distribute heated air evenly, ensuring uniform heating of the workpieces and consistent curing results. Let’s explore the technical aspects of a convection oven:
Operating Principle: Convection ovens operate on the principle of convection heating, where heated air is circulated within the oven chamber to transfer heat to the workpieces. The oven contains heating elements, typically located along the walls or ceiling, which generate heat. Fans or blowers then circulate the heated air throughout the chamber, ensuring uniform distribution of heat and promoting efficient curing of the coatings.
Components: Convection ovens consist of several key components, including:
- Heating Elements: The heating elements are responsible for generating heat within the oven chamber. They may be electric resistance heating elements, gas-fired burners, or infrared lamps, depending on the specific design and heating requirements.
- Fan or Blower: A fan or blower circulates heated air within the oven chamber to ensure uniform heating of the workpieces. The fan may be located inside the oven chamber or in a separate compartment, depending on the oven design.
- Air Circulation System: Convection ovens feature an air circulation system that directs heated air evenly throughout the chamber. This ensures uniform heating of the workpieces and prevents hot spots.
- Insulation: Convection ovens are insulated to minimize heat loss and maintain consistent temperatures throughout the curing process. Insulation materials such as ceramic fiber or mineral wool may be used to line the oven walls, ceiling, and floor.
- Control System: A control system regulates the operation of the heating elements, fan or blower, and temperature settings to maintain optimal curing conditions. It may include temperature sensors, controllers, and timers to monitor and adjust the curing process as needed.
Advantages of Convection Ovens: Convection ovens offer several advantages over other types of heating systems:
- Uniform Heating: Convection ovens provide uniform heating of the workpieces by circulating heated air throughout the chamber. This ensures consistent curing results and prevents variations in coating quality.
- Fast Heat-Up Times: Convection ovens can reach operating temperatures quickly, resulting in shorter heat-up times and increased productivity.
- Energy Efficiency: Convection ovens are typically more energy-efficient than other heating methods, as they utilize fans or blowers to distribute heat evenly, reducing heat loss and energy consumption.
- Versatility: Convection ovens can accommodate a wide range of applications and materials, making them suitable for various industrial processes beyond powder coating curing.
- Ease of Operation: Convection ovens are relatively easy to operate and maintain, requiring minimal operator intervention and manual handling.
Applications: Convection ovens find application in numerous industries and processes, including:
- Powder coating curing
- Paint drying and curing
- Food baking and cooking
- Pharmaceutical production
- Semiconductor manufacturing
- Textile drying
In summary, convection ovens are versatile and efficient heating solutions used in various industrial processes, including powder coating curing. Their ability to provide uniform heating, fast heat-up times, and energy efficiency makes them well-suited for a wide range of applications across different industries.
Infrared Convection Oven:
An infrared convection oven combines the heating principles of both infrared radiation and convection heating to provide efficient and precise curing of coatings, such as powder coatings, in industrial applications. This type of oven utilizes infrared lamps or heating elements to emit infrared radiation, coupled with a convection system that circulates heated air throughout the oven chamber. Let’s explore the technical aspects of an infrared convection oven:
Operating Principle: An infrared convection oven operates by combining two heating methods: infrared radiation and convection heating. Infrared lamps or heating elements emit infrared radiation, which penetrates the surface of the workpieces and heats them directly. At the same time, a convection system consisting of fans or blowers circulates heated air throughout the oven chamber, ensuring uniform heating and promoting efficient curing of the coatings. This dual heating approach results in faster heat transfer and more consistent curing compared to using infrared or convection heating alone.
Components: The components of an infrared convection oven typically include:
- Infrared Lamps or Heating Elements: Infrared lamps or heating elements are used to generate infrared radiation, which heats the workpieces directly. These lamps or elements may be located above, below, or alongside the conveyor belt or workpiece support system.
- Convection System: A convection system comprising fans or blowers circulates heated air within the oven chamber to ensure uniform heating of the workpieces. The convection system may include ductwork, baffles, and other components to optimize airflow and heat distribution.
- Temperature Control System: A temperature control system regulates the operation of the heating elements, fans or blowers, and other components to maintain the desired curing temperature within the oven chamber. It may include temperature sensors, controllers, and programmable settings to monitor and adjust the curing process as needed.
- Insulation: Infrared convection ovens are typically insulated to minimize heat loss and maintain consistent temperatures throughout the curing process. Insulation materials such as ceramic fiber or mineral wool may be used to line the oven walls, ceiling, and floor.
- Conveyor System: Infrared convection ovens designed for continuous operation may feature a conveyor system to transport workpieces through the oven chamber at a controlled speed. The conveyor system ensures a continuous flow of workpieces for efficient curing.
Advantages of Infrared Convection Ovens: Infrared convection ovens offer several advantages over single-heating method ovens:
- Faster Curing: The combination of infrared radiation and convection heating results in faster heat transfer to the workpieces, reducing curing times and increasing productivity.
- Uniform Heating: Infrared convection ovens provide uniform heating of the workpieces, ensuring consistent curing results and preventing variations in coating quality.
- Energy Efficiency: By combining infrared radiation with convection heating, these ovens can achieve efficient heat transfer with minimal energy consumption, resulting in lower operating costs.
- Versatility: Infrared convection ovens can accommodate a wide range of coatings and materials, making them suitable for various industrial processes beyond powder coating curing.
- Controlled Process: The temperature control system allows operators to precisely control the curing temperature and monitor the curing process in real-time, ensuring optimal results and product quality.
Applications: Infrared convection ovens find application in numerous industries and processes, including:
- Powder coating curing
- Paint drying and curing
- Food baking and cooking
- Semiconductor manufacturing
- Aerospace component production
- Pharmaceutical production
In summary, infrared convection ovens offer efficient, precise, and versatile heating solutions for curing coatings in industrial applications. Their ability to combine infrared radiation with convection heating results in faster curing, uniform heating, and energy efficiency, making them well-suited for a wide range of coating processes across various industries.
Batch Oven:
A batch oven is a type of heating chamber used in industrial processes, including powder coating curing, where workpieces are cured in discrete batches. Unlike continuous ovens that process workpieces continuously, batch ovens are loaded with a batch of workpieces, cured for a specific duration, and then unloaded before the next batch is processed. Let’s explore the technical aspects of a batch oven:
Operating Principle: Batch ovens operate on the principle of batch processing, where workpieces are loaded into the oven chamber manually or using a material handling system. Once the oven is loaded, the heating elements are energized to generate heat, raising the temperature within the chamber to the desired curing temperature. The workpieces remain in the oven for a predetermined duration, allowing the coating material to cure fully. After the curing cycle is complete, the oven is cooled, and the cured workpieces are unloaded before the next batch is processed.
Components: The components of a batch oven typically include:
- Oven Chamber: The oven chamber is the enclosed space where the workpieces are placed for curing. It is constructed from heat-resistant materials such as steel or aluminum and may be insulated to minimize heat loss and maintain consistent temperatures.
- Heating Elements: Batch ovens utilize heating elements, such as electric resistance heaters or gas-fired burners, to generate heat within the oven chamber. The heating elements may be located along the walls, ceiling, or floor of the chamber, depending on the specific design and heating requirements.
- Control System: A control system regulates the operation of the heating elements and monitors various parameters such as temperature, airflow, and curing time to ensure optimal curing conditions. It may include temperature sensors, controllers, and timers to control the curing process accurately.
- Insulation: Batch ovens are typically insulated to minimize heat loss and maintain consistent temperatures throughout the curing process. Insulation materials such as ceramic fiber or mineral wool may be used to line the oven walls, ceiling, and floor.
- Material Handling System: In some cases, batch ovens may feature a material handling system, such as carts, racks, or trays, to facilitate the loading and unloading of workpieces into the oven chamber. This system helps streamline the curing process and improve productivity.
Advantages of Batch Ovens: Batch ovens offer several advantages over continuous ovens and other curing methods:
- Flexibility: Batch ovens are highly flexible and can accommodate a wide range of workpiece sizes, shapes, and materials, making them suitable for various applications and production requirements.
- Customization: Batch ovens allow for customization of the curing process, as each batch can be tailored to meet specific curing requirements, such as temperature, time, and airflow settings.
- Cost-Effectiveness: Batch ovens are typically more cost-effective than continuous ovens for small to medium-sized production runs, as they require less upfront investment and have lower operating costs.
- Ease of Maintenance: Batch ovens are relatively simple in design and require minimal maintenance compared to continuous ovens, resulting in reduced downtime and increased productivity.
- Energy Efficiency: Batch ovens can be designed with energy-efficient features such as insulation and programmable controllers to optimize energy usage and reduce operating costs.
Applications: Batch ovens find application in numerous industries and processes, including:
- Powder coating curing
- Paint drying and curing
- Heat treatment and annealing
- Food baking and cooking
- Laboratory testing
- Pharmaceutical production
In summary, batch ovens offer flexible, customizable, and cost-effective solutions for curing coatings and performing other heating processes in industrial applications. Their ability to accommodate various workpiece sizes and materials makes them well-suited for small to medium-sized production runs across different industries.
Hydrostatic Testing:
Hydrostatic testing is a non-destructive method used to determine the integrity and strength of pressure vessels, such as pipelines, storage tanks, and cylinders. This testing method involves pressurizing the vessel with a liquid, usually water, to a specified pressure level for a predetermined duration, while monitoring for any leaks or deformations. Let’s delve into the technical details of hydrostatic testing:
Operating Principle: Hydrostatic testing operates on the principle of applying a controlled internal pressure to a pressure vessel and observing its response. The vessel is filled with a test medium, typically water, which is non-compressible. The pressure is gradually increased to a predetermined level, usually a percentage higher than the vessel’s maximum operating pressure. The vessel is then held at this pressure for a specified duration, during which time it is inspected for leaks, bulges, or other signs of failure.
Procedure: The hydrostatic testing procedure typically involves the following steps:
- Preparation: The pressure vessel is prepared by cleaning and draining it of any residual fluids or contaminants. All openings, such as valves and fittings, are securely closed to prevent leakage.
- Filling: The vessel is filled with the test medium, usually water, until it is completely submerged. Care is taken to remove any trapped air to ensure accurate test results.
- Pressurization: The test medium is pressurized using a pump or other pressure-generating device. The pressure is gradually increased to the specified test pressure, typically following a predetermined ramp-up rate to minimize sudden stress on the vessel.
- Hold Period: Once the test pressure is reached, the vessel is held at this pressure for a specified duration, often ranging from several minutes to several hours. During this time, the vessel is monitored for any signs of leakage, deformation, or other abnormalities.
- Inspection: After the hold period, the vessel is carefully inspected for leaks, bulges, or other indications of failure. Visual inspection, dye penetrant testing, or other non-destructive testing methods may be used to detect defects.
- Depressurization: Once the test is complete and the vessel passes inspection, the pressure is gradually released, and the test medium is drained from the vessel. The vessel is then returned to service if it meets the specified safety criteria.
Safety Considerations: Hydrostatic testing involves high pressures and potential safety hazards, so strict safety precautions must be followed. These may include:
- Ensuring proper training and certification for personnel conducting the test.
- Using appropriate personal protective equipment (PPE), such as safety glasses, gloves, and hearing protection.
- Performing the test in a controlled environment with adequate ventilation and emergency procedures in place.
- Following established procedures for pressure control, including pressure relief devices and emergency shutdown protocols.
Applications: Hydrostatic testing is commonly used in various industries and applications, including:
- Pressure vessel manufacturing
- Pipeline construction and maintenance
- Storage tank inspection and certification
- Fire extinguisher testing
- Aerospace component testing
- Hydraulic system testing
In summary, hydrostatic testing is a crucial method for assessing the integrity and safety of pressure vessels and other components subjected to internal pressure. By subjecting the vessel to controlled pressure levels and monitoring its response, hydrostatic testing helps ensure compliance with safety standards and regulatory requirements, reducing the risk of catastrophic failure and ensuring safe operation.
Electrostatic Powder Coating
Electrostatic powder coating is a surface finishing process used to apply a durable and decorative coating to various substrates, such as metal, plastic, and wood. This method involves applying charged powder particles to an oppositely charged workpiece, creating an electrostatic attraction that ensures uniform coverage and adhesion. Let’s explore the technical details of electrostatic powder coating:
Operating Principle: Electrostatic powder coating operates on the principle of electrostatic attraction between charged particles and a grounded workpiece. The process typically involves the following steps:
- Powder Application: The powder coating material, consisting of finely ground pigment and resin particles, is electrostatically charged using a spray gun or applicator. The powder particles acquire a positive charge as they are ejected from the gun.
- Substrate Preparation: The workpiece to be coated is thoroughly cleaned and pretreated to remove any contaminants and improve adhesion. It is then grounded to provide an electrical connection.
- Coating Application: The charged powder particles are attracted to the grounded workpiece, forming a uniform coating layer. The electrostatic attraction ensures that the powder particles adhere evenly to all surfaces, including recesses and corners.
- Curing: After the coating is applied, the workpiece is transferred to a curing oven, where it is heated to a specific temperature to melt and fuse the powder particles into a smooth and durable finish. The curing process typically takes place at temperatures between 150°C and 200°C for a predetermined duration.
Components: The components of an electrostatic powder coating system typically include:
- Powder Coating Gun: The powder coating gun is used to apply the charged powder particles to the workpiece. It consists of a spray nozzle, electrode, and control unit for adjusting the powder flow and electrostatic charge.
- Powder Supply System: The powder supply system stores and delivers the powder coating material to the spray gun. It may include a hopper, feed mechanism, and fluidizing bed to maintain consistent powder flow.
- Grounding System: The grounding system ensures that the workpiece is electrically grounded to provide a path for the electrostatic charge. This prevents the accumulation of static electricity and ensures effective coating application.
- Curing Oven: The curing oven is used to heat the coated workpiece to the required curing temperature, allowing the powder particles to melt and form a smooth, durable finish. The oven may be electrically or gas heated and may incorporate conveyor systems for continuous production.
- Control System: A control system regulates the operation of the powder coating equipment, monitoring parameters such as powder flow, voltage, and curing temperature to ensure consistent coating quality and performance.
Advantages of Electrostatic Powder Coating: Electrostatic powder coating offers several advantages over conventional liquid painting methods:
- High Efficiency: Electrostatic powder coating allows for high transfer efficiency, with up to 98% of the powder particles adhering to the workpiece, minimizing waste and reducing material costs.
- Uniform Coverage: The electrostatic attraction ensures uniform coverage of the coating material, even on complex-shaped or irregular surfaces, resulting in a smooth and consistent finish.
- Durable Finish: Powder coatings are highly resistant to chipping, scratching, and fading, providing long-lasting protection and aesthetic appeal to the coated surfaces.
- Environmentally Friendly: Electrostatic powder coating produces minimal volatile organic compounds (VOCs) and hazardous air pollutants (HAPs), making it an environmentally friendly coating option compared to solvent-based paints.
- Versatility: Powder coating can be applied to a wide range of substrates, including metals, plastics, and composites, making it suitable for various industrial and architectural applications.
Applications: Electrostatic powder coating is used in a variety of industries and applications, including:
- Automotive and transportation
- Architectural and building construction
- Furniture and fixtures
- Appliances and consumer goods
- Aerospace and aviation
- Metal fabrication and manufacturing
In summary, electrostatic powder coating is a highly efficient and versatile surface finishing process used to apply durable and decorative coatings to a wide range of substrates. Its ability to provide uniform coverage, durability, and environmental sustainability makes it a preferred choice for many industrial and commercial applications.
Powder Coating Booth:
A powder coating booth is an essential component of the powder coating process, providing a controlled environment for the application of powder coatings to various workpieces. It is designed to contain overspray, capture airborne powder particles, and ensure uniform coating coverage while minimizing waste and ensuring operator safety. Let’s explore the technical details of a powder coating booth:
Operating Principle: A powder coating booth operates on the principle of creating a controlled environment where powder coating material can be applied to workpieces efficiently and safely. The booth typically consists of an enclosed space with walls, a ceiling, and a floor, designed to contain the overspray generated during the coating process. Airflow is carefully managed to capture and filter airborne powder particles, ensuring a clean working environment and preventing contamination of adjacent areas.
Components: The components of a powder coating booth typically include:
- Enclosure: The booth enclosure provides a contained space where the powder coating process can take place. It is constructed from materials such as steel or aluminum and may feature access doors, viewing windows, and lighting fixtures for ease of use and visibility.
- Powder Collection System: The powder collection system captures overspray generated during the coating process and directs it to a collection point, such as a recovery hopper or filter system. This prevents waste and ensures efficient use of the powder coating material.
- Airflow System: The airflow system controls the movement of air within the booth, directing it in a specific pattern to capture and contain airborne powder particles. It typically includes exhaust fans, air ducts, and filters to ensure proper ventilation and filtration.
- Filters: Filters are used to remove powder particles from the airflow before it is discharged from the booth. Common types of filters include cartridge filters, pleated filters, and HEPA filters, depending on the specific requirements of the application.
- Lighting: Lighting fixtures provide illumination within the booth, allowing operators to see the workpieces clearly and ensure proper coating coverage. LED lights are commonly used due to their energy efficiency and long lifespan.
Advantages of Powder Coating Booths: Powder coating booths offer several advantages over open-air or makeshift coating environments:
- Containment: Booths provide a contained environment where overspray can be captured and controlled, minimizing waste and preventing contamination of surrounding areas.
- Operator Safety: Booths help protect operators from exposure to airborne powder particles, reducing the risk of respiratory issues and other health hazards associated with powder coating materials.
- Uniform Coating: By controlling airflow and powder deposition, booths ensure uniform coating coverage on workpieces, resulting in consistent and high-quality finishes.
- Environmental Protection: Booths help prevent the release of powder coating materials into the environment, reducing air pollution and contamination of soil and water sources.
- Compliance: Many industries have regulations and standards governing powder coating operations, and booths help ensure compliance with these requirements by providing a controlled and safe working environment.
Applications: Powder coating booths are used in various industries and applications, including:
- Automotive and transportation
- Metal fabrication and manufacturing
- Aerospace and aviation
- Furniture and fixtures
- Appliances and consumer goods
- Architectural and building construction
In summary, powder coating booths are essential components of the powder coating process, providing a controlled environment for efficient, safe, and high-quality coating applications. Their ability to contain overspray, capture airborne particles, and ensure uniform coating coverage makes them indispensable in many industrial and commercial settings.
Powder Coating Gun
A powder coating gun is a handheld or automated device used to apply powder coating material onto various surfaces, providing a uniform and durable finish. It is a crucial component of the powder coating process, allowing for precise control over the application of the coating material. Let’s delve into the technical details of a powder coating gun:
Operating Principle: Powder coating guns operate on the principle of electrostatic attraction, where charged powder particles are applied to grounded workpieces. The gun typically consists of a nozzle, electrode, and control unit. The powder coating material is electrostatically charged as it passes through the gun, creating an electrostatic field between the gun and the grounded workpiece. This electrostatic attraction ensures that the powder particles adhere evenly to the surface of the workpiece, resulting in a uniform coating.
Components: The components of a powder coating gun may vary depending on the specific design and application requirements. However, some common components include:
- Nozzle: The nozzle is the part of the gun through which the powder coating material is ejected. It controls the pattern and velocity of the powder spray, allowing for precise application onto the workpiece.
- Electrode: The electrode is responsible for imparting an electrostatic charge to the powder particles as they pass through the gun. It may be located near the nozzle or integrated into the gun body, depending on the design.
- Control Unit: The control unit regulates various parameters of the powder coating process, such as powder flow rate, electrostatic charge, and gun settings. It may include adjustable dials, digital displays, and programmable features for precise control over the coating application.
- Trigger: In handheld powder coating guns, a trigger mechanism is used to initiate the powder spraying process. The operator can control the flow of powder by pressing or releasing the trigger.
- Hopper: Some powder coating guns are equipped with a hopper or reservoir for storing and dispensing the powder coating material. The hopper may have a capacity ranging from a few pounds to several kilograms, depending on the application requirements.
- Grounding Cable: To ensure proper electrostatic attraction, the workpiece being coated must be grounded. Some powder coating guns come with a grounding cable or attachment to facilitate this connection.
Types of Powder Coating Guns: There are several types of powder coating guns available, each with its own unique features and capabilities:
- Manual Guns: Manual powder coating guns are handheld devices operated by an operator. They offer flexibility and control but require manual operation for coating application.
- Automatic Guns: Automatic powder coating guns are mounted on robotic arms or automated systems for continuous and precise coating application. They are suitable for high-volume production environments.
- Tribo Guns: Tribocharging powder coating guns use friction to charge the powder particles, rather than electrostatic methods. They are suitable for coating materials that are difficult to charge electrostatically.
- Corona Guns: Corona charging powder coating guns use a high-voltage corona discharge to charge the powder particles as they pass through the gun. They are commonly used in industrial powder coating applications.
Advantages of Powder Coating Guns: Powder coating guns offer several advantages over other coating methods, including:
- High Efficiency: Powder coating guns provide high transfer efficiency, with up to 98% of the powder material adhering to the workpiece, minimizing waste and reducing material costs.
- Uniform Coating: The electrostatic attraction ensures uniform coverage of the coating material, even on complex-shaped or irregular surfaces, resulting in a smooth and consistent finish.
- Durable Finish: Powder coatings are highly resistant to chipping, scratching, and fading, providing long-lasting protection and aesthetic appeal to the coated surfaces.
- Environmentally Friendly: Powder coating guns produce minimal volatile organic compounds (VOCs) and hazardous air pollutants (HAPs), making them an environmentally friendly coating option compared to solvent-based paints.
- Versatility: Powder coating guns can be used to apply a wide range of coating materials, including epoxy, polyester, acrylic, and hybrid powders, making them suitable for various industrial and commercial applications.
Applications: Powder coating guns are used in numerous industries and applications, including:
- Automotive and transportation
- Metal fabrication and manufacturing
- Aerospace and aviation
- Furniture and fixtures
- Appliances and consumer goods
- Architectural and building construction
In summary, powder coating guns are essential tools for applying powder coating material onto various surfaces, providing a durable, uniform, and environmentally friendly finish. Their versatility, efficiency, and precision make them indispensable in many industrial and commercial coating applications.
Curing Oven
A curing oven is a crucial component of the powder coating process, designed to thermally cure powder coatings applied to various substrates, such as metal, plastic, and wood. It provides controlled heat and airflow to melt and fuse the powder particles, forming a durable and protective finish on the workpieces. Let’s delve into the technical details of a curing oven:
Operating Principle: Curing ovens operate on the principle of applying heat to the coated workpieces to melt and fuse the powder coating material into a smooth and durable finish. The oven chamber is heated to the specified curing temperature, typically between 150°C and 200°C, depending on the type of powder coating material used. During the curing process, the powder particles melt, flow, and chemically cross-link to form a continuous film, providing adhesion and protection to the substrate.
Components: The components of a curing oven may vary depending on the specific design and application requirements. However, some common components include:
- Oven Chamber: The oven chamber is the enclosed space where the curing process takes place. It is constructed from materials such as steel or aluminum and may be insulated to minimize heat loss and maintain consistent temperatures.
- Heating System: The heating system provides the necessary heat to raise the temperature within the oven chamber to the desired curing temperature. It may consist of electric resistance heaters, gas-fired burners, or infrared lamps, depending on the specific requirements of the application.
- Airflow System: The airflow system controls the movement of air within the oven chamber, ensuring uniform heating and circulation of heat around the coated workpieces. It may include fans, blowers, and ductwork to distribute heat evenly and minimize temperature gradients.
- Temperature Control System: A temperature control system regulates the operation of the heating elements and monitors the temperature within the oven chamber to ensure precise control over the curing process. It may include temperature sensors, controllers, and programmable settings to maintain the desired curing temperature.
- Conveyor System: In continuous curing ovens, a conveyor system is used to transport the coated workpieces through the oven chamber at a controlled speed. The conveyor system ensures a consistent curing time and temperature profile for each workpiece, resulting in uniform coating quality.
- Exhaust System: An exhaust system removes excess heat and fumes from the oven chamber, maintaining a safe working environment and preventing the buildup of combustible gases. It may include exhaust fans, vents, and filters to capture particulate matter and contaminants.
Advantages of Curing Ovens: Curing ovens offer several advantages over alternative curing methods, such as air drying or solvent evaporation:
- Fast Curing: Curing ovens provide rapid and efficient curing of powder coatings, reducing production cycle times and increasing productivity.
- Uniform Heating: The controlled airflow and temperature distribution within the oven chamber ensure uniform heating of the coated workpieces, resulting in consistent coating quality and performance.
- Durable Finish: Curing ovens facilitate the complete cross-linking of powder coating materials, resulting in a durable and protective finish that resists chipping, scratching, and fading.
- Energy Efficiency: Curing ovens can be designed with energy-efficient features such as insulation, recirculating air systems, and programmable controllers to optimize energy usage and reduce operating costs.
- Versatility: Curing ovens can accommodate a wide range of powder coating materials and workpiece sizes, making them suitable for various industrial and commercial applications.
Applications: Curing ovens are used in numerous industries and applications, including:
- Automotive and transportation
- Metal fabrication and manufacturing
- Aerospace and aviation
- Furniture and fixtures
- Appliances and consumer goods
- Architectural and building construction
In summary, curing ovens are essential components of the powder coating process, providing controlled heat and airflow to cure powder coatings applied to various substrates. Their ability to facilitate rapid, uniform, and durable curing makes them indispensable in many industrial and commercial coating applications.
Powder Coating Booth Filters:
Powder coating booth filters play a crucial role in maintaining a clean and efficient working environment during the powder coating process. These filters are designed to capture overspray particles generated during the coating operation, ensuring that the surrounding air remains free from contaminants and that the powder coating material is efficiently utilized. Let’s explore the technical details of powder coating booth filters:
Operating Principle: Powder coating booth filters operate on the principle of mechanical filtration, where airborne particles are captured and retained by the filter media as air passes through. The filters are strategically positioned within the booth to intercept overspray particles generated during the coating process. As the air flows through the booth, the filters trap the powder particles while allowing clean air to exit the booth, thus maintaining a clean and controlled working environment.
Types of Filters: Several types of filters are commonly used in powder coating booths, each offering specific filtration capabilities and efficiency levels:
- Pleated Filters: Pleated filters consist of a pleated media material, such as polyester or cellulose, folded accordion-style to increase the surface area for particle capture. They offer high filtration efficiency and can capture a wide range of particle sizes.
- Cartridge Filters: Cartridge filters are cylindrical in shape and feature a pleated or non-pleated filter media enclosed within a perforated metal or plastic housing. They provide excellent filtration efficiency and are easy to install and replace.
- Panel Filters: Panel filters are flat or rectangular filters typically made from fiberglass, polyester, or synthetic media. They are suitable for applications with lower air volume and can capture larger particles effectively.
- HEPA Filters: High-efficiency particulate air (HEPA) filters are designed to capture particles as small as 0.3 microns with 99.97% efficiency. They are used in applications where strict air quality standards must be met, such as cleanrooms and sensitive manufacturing environments.
- Activated Carbon Filters: Activated carbon filters are used to adsorb odors, gases, and volatile organic compounds (VOCs) generated during the powder coating process. They are often used in conjunction with other filter types to improve air quality and remove airborne contaminants.
Installation and Maintenance: Proper installation and maintenance of powder coating booth filters are essential to ensure optimal filtration performance and longevity. Filters should be installed according to the manufacturer’s recommendations and replaced regularly to prevent clogging and maintain airflow. Routine inspection and cleaning of filters can help extend their service life and prevent contamination of the booth environment.
Advantages of Powder Coating Booth Filters: Powder coating booth filters offer several advantages for powder coating operations:
- Air Quality: By capturing overspray particles, booth filters help maintain clean and breathable air within the work environment, protecting operators from exposure to airborne contaminants.
- Environmental Compliance: Booth filters help prevent the release of powder coating material into the atmosphere, ensuring compliance with environmental regulations and reducing the risk of pollution.
- Efficiency: High-quality filters can capture a high percentage of overspray particles, maximizing the efficiency of powder coating material usage and minimizing waste.
- Equipment Protection: By preventing overspray buildup on booth surfaces and equipment, filters help extend the lifespan of powder coating equipment and reduce maintenance requirements.
- Versatility: Booth filters are available in various sizes, shapes, and filtration efficiencies to accommodate different booth configurations and coating applications.
Applications: Powder coating booth filters are used in various industries and applications where powder coating operations are performed, including:
- Automotive and transportation
- Metal fabrication and manufacturing
- Aerospace and aviation
- Furniture and fixtures
- Appliances and consumer goods
- Architectural and building construction
In summary, powder coating booth filters are essential components of powder coating booths, helping to maintain a clean and efficient working environment while ensuring compliance with air quality standards and environmental regulations. Their ability to capture overspray particles effectively contributes to the overall quality, efficiency, and sustainability of powder coating operations.
Powder Coating Oven Temperature Control:
Powder coating oven temperature control is a critical aspect of the powder coating process, ensuring that the coated workpieces are cured at the optimal temperature for the required duration. Proper temperature control is essential to achieve uniform curing, optimal adhesion, and a durable finish. Let’s delve into the technical details of powder coating oven temperature control:
Operating Principle: Powder coating oven temperature control operates on the principle of regulating the temperature within the oven chamber to the specified curing temperature range for the powder coating material being used. The oven chamber is heated using electric resistance heaters, gas-fired burners, or infrared lamps, and the temperature is monitored and controlled using temperature sensors and controllers. The goal is to achieve and maintain a consistent temperature profile throughout the curing process to ensure uniform curing of the powder coating material.
Components: The components involved in powder coating oven temperature control include:
- Temperature Sensors: Temperature sensors, such as thermocouples or resistance temperature detectors (RTDs), are used to measure the temperature within the oven chamber. They are strategically positioned to provide accurate temperature readings at various locations to ensure uniform heating.
- Temperature Controllers: Temperature controllers regulate the operation of the heating elements based on the temperature readings from the sensors. They maintain the oven temperature within the desired curing temperature range by adjusting the power output to the heating elements.
- Heating Elements: Heating elements, such as electric resistance heaters, gas-fired burners, or infrared lamps, generate the heat required to raise the temperature within the oven chamber to the curing temperature range. The heating elements are controlled by the temperature controllers to achieve and maintain the desired temperature profile.
- Airflow System: An airflow system consisting of fans, blowers, and ductwork helps distribute heat evenly throughout the oven chamber, ensuring uniform heating of the coated workpieces. Proper airflow management is essential to prevent temperature gradients and ensure consistent curing.
Temperature Control Methods: Powder coating ovens utilize various temperature control methods to achieve precise temperature regulation and uniform curing:
- On/Off Control: In on/off control, the heating elements are cycled on and off based on the temperature setpoint and hysteresis value. This method provides basic temperature control but may result in temperature fluctuations and overshoot.
- Proportional Control: Proportional control adjusts the power output to the heating elements based on the difference between the measured temperature and the setpoint. This method provides more precise temperature control by modulating the heating intensity in proportion to the temperature error.
- PID Control: Proportional-Integral-Derivative (PID) control is a more advanced temperature control algorithm that combines proportional, integral, and derivative actions to achieve optimal temperature regulation. PID control continuously adjusts the heating element power output based on the present error, past error, and future error predictions, resulting in fast response times and minimal overshoot.
- Ramp/Soak Control: Ramp/soak control allows for gradual temperature ramp-up and precise temperature soaking at the curing temperature for a specified duration. This method is commonly used for heat-sensitive coatings or complex curing profiles requiring multiple temperature stages.
Advantages of Temperature Control: Proper temperature control in powder coating ovens offers several advantages:
- Uniform Curing: Precise temperature control ensures that the coated workpieces are cured evenly, resulting in consistent coating quality and performance.
- Optimal Adhesion: Curing at the correct temperature promotes optimal adhesion between the powder coating material and the substrate, ensuring long-term durability and resistance to chipping and peeling.
- Energy Efficiency: Efficient temperature control minimizes energy consumption by preventing overheating and unnecessary heat loss, resulting in cost savings and reduced environmental impact.
- Process Stability: Stable temperature control contributes to overall process stability, reducing the likelihood of defects and rework and improving production efficiency and throughput.
Applications: Powder coating oven temperature control is used in various industries and applications where powder coating operations are performed, including:
- Automotive and transportation
- Metal fabrication and manufacturing
- Aerospace and aviation
- Furniture and fixtures
- Appliances and consumer goods
- Architectural and building construction
In summary, powder coating oven temperature control is essential for achieving consistent and high-quality curing of powder coatings, ensuring optimal adhesion, durability, and performance of the coated workpieces. Proper temperature regulation contributes to the overall efficiency, stability, and success of powder coating operations in various industrial and commercial applications.
Powder Coating Booth Lighting:
Powder coating booth lighting is an essential component of the powder coating process, providing illumination within the booth to ensure visibility and accuracy during coating application and inspection. Proper lighting is crucial for achieving uniform coverage, identifying defects, and ensuring quality control throughout the coating process. Let’s explore the technical details of powder coating booth lighting:
Operating Principle: Powder coating booth lighting operates on the principle of providing adequate illumination within the booth to facilitate coating application, inspection, and quality control. The lighting fixtures are strategically positioned to minimize shadows and glare, ensuring uniform lighting coverage across the work area. Various types of lighting sources, such as fluorescent tubes, LED lights, and halogen lamps, may be used depending on the specific requirements of the application.
Components: The components involved in powder coating booth lighting include:
- Lighting Fixtures: Lighting fixtures, such as overhead lights, task lights, and inspection lights, provide illumination within the booth. They are typically enclosed in protective housings to prevent damage from overspray and airborne contaminants.
- Light Bulbs or Lamps: Light bulbs or lamps are the sources of illumination within the lighting fixtures. They may be fluorescent tubes, LED bulbs, halogen lamps, or other types of lighting sources, chosen based on factors such as brightness, color rendering index (CRI), and energy efficiency.
- Reflectors: Reflectors are used to direct and focus the light emitted by the bulbs or lamps, maximizing the efficiency of the lighting system and minimizing light loss.
- Ballasts and Drivers: Ballasts (for fluorescent lights) and drivers (for LED lights) regulate the electrical current supplied to the bulbs or lamps, ensuring stable and consistent operation.
- Mounting Hardware: Mounting hardware, such as brackets, tracks, and clamps, secure the lighting fixtures to the booth structure and allow for adjustable positioning to achieve optimal lighting coverage.
Types of Lighting Sources: Several types of lighting sources are commonly used in powder coating booths, each offering specific advantages and considerations:
- Fluorescent Lights: Fluorescent lights are cost-effective and provide diffuse, even lighting. However, they may have limited color rendering properties and may require frequent replacement of bulbs and ballasts.
- LED Lights: LED lights are energy-efficient, long-lasting, and offer excellent color rendering properties. They produce minimal heat and are more resistant to vibration and impact, making them well-suited for industrial applications.
- Halogen Lamps: Halogen lamps provide bright, white light with good color rendering properties. However, they consume more energy and generate more heat than fluorescent or LED lights, requiring adequate ventilation and heat dissipation.
Considerations for Booth Lighting: When selecting and designing lighting for a powder coating booth, several factors should be considered to ensure optimal performance and safety:
- Brightness: The lighting system should provide sufficient brightness to illuminate the work area and allow for accurate coating application and inspection.
- Color Rendering: High color rendering index (CRI) lighting sources are preferable for accurately assessing color and finish quality during coating application and inspection.
- Durability: Lighting fixtures should be durable and resistant to damage from overspray, airborne contaminants, and environmental factors typically found in powder coating environments.
- Energy Efficiency: Energy-efficient lighting sources, such as LED lights, can help reduce operating costs and minimize environmental impact while providing adequate illumination.
- Safety: Lighting fixtures should be designed and installed in compliance with relevant safety standards to minimize the risk of electrical hazards and ensure operator safety.
Applications: Powder coating booth lighting is used in various industries and applications where powder coating operations are performed, including:
- Automotive and transportation
- Metal fabrication and manufacturing
- Aerospace and aviation
- Furniture and fixtures
- Appliances and consumer goods
- Architectural and building construction
In summary, powder coating booth lighting plays a crucial role in ensuring visibility, accuracy, and quality control throughout the coating process. Properly designed and installed lighting systems contribute to the overall efficiency, safety, and success of powder coating operations in various industrial and commercial applications.
Powder Coating Booth Ventilation System:
A powder coating booth ventilation system is a critical component of the powder coating process, responsible for controlling airflow within the booth to ensure operator safety, environmental compliance, and coating quality. Proper ventilation helps remove overspray particles, volatile organic compounds (VOCs), and airborne contaminants generated during the coating operation, maintaining a clean and safe working environment. Let’s delve into the technical details of a powder coating booth ventilation system:
Operating Principle: Powder coating booth ventilation systems operate on the principle of controlling airflow to capture and remove overspray particles and airborne contaminants from the booth environment. The ventilation system consists of intake and exhaust components that regulate the flow of air into and out of the booth, creating a controlled airflow pattern to contain and capture the contaminants effectively. By controlling airflow direction, velocity, and volume, the ventilation system helps maintain a clean and safe working environment for operators while ensuring compliance with environmental regulations.
Components: The components involved in a powder coating booth ventilation system include:
- Intake Plenum: The intake plenum is a chamber located at the entrance of the booth, where clean air is drawn into the booth environment. It may feature filters or baffles to remove large particles and contaminants from the incoming air.
- Exhaust Plenum: The exhaust plenum is a chamber located at the exit of the booth, where contaminated air is expelled from the booth environment. It may be equipped with filters or separators to capture overspray particles before releasing the air into the atmosphere.
- Exhaust Fans: Exhaust fans are used to create negative pressure within the booth, drawing contaminated air out of the booth and expelling it through the exhaust plenum. The size and capacity of the exhaust fans are selected based on the booth size, airflow requirements, and regulatory standards.
- Ductwork: Ductwork consists of pipes or channels that transport air between the booth, exhaust fans, and external exhaust stack or filtration system. Properly designed ductwork ensures efficient airflow distribution and minimizes pressure losses.
- Filters: Filters, such as cartridge filters or bag filters, are used to capture overspray particles and contaminants from the exhaust air before it is discharged into the atmosphere. They help prevent pollution and comply with environmental regulations.
- Control System: A control system regulates the operation of the ventilation system, including fan speed, airflow direction, and pressure differential. It may include manual switches, variable frequency drives (VFDs), or automated controls for precise adjustment of ventilation parameters.
Types of Ventilation Systems: Several types of ventilation systems are commonly used in powder coating booths, each offering specific advantages and considerations:
- Crossdraft Ventilation: Crossdraft ventilation systems draw air horizontally across the workpiece, from the intake side to the exhaust side of the booth. They are simple and cost-effective but may result in uneven airflow distribution and overspray accumulation on booth surfaces.
- Downdraft Ventilation: Downdraft ventilation systems draw air vertically downward over the workpiece, capturing overspray particles and contaminants as they settle. They offer superior containment and capture efficiency but may require additional floor space and installation costs.
- Semi-Downdraft Ventilation: Semi-downdraft ventilation systems combine elements of both crossdraft and downdraft systems, drawing air at an angle over the workpiece. They offer a compromise between containment efficiency and installation costs.
- Reverse Flow Ventilation: Reverse flow ventilation systems reverse the direction of airflow periodically to prevent overspray buildup on booth surfaces. They are commonly used in large-scale powder coating operations with high production volumes.
Advantages of Ventilation Systems: Powder coating booth ventilation systems offer several advantages for powder coating operations:
- Operator Safety: Ventilation systems help remove hazardous fumes, VOCs, and airborne contaminants from the booth environment, protecting operators from exposure and respiratory issues.
- Environmental Compliance: By capturing overspray particles and pollutants, ventilation systems prevent air and water pollution, ensuring compliance with environmental regulations and standards.
- Coating Quality: Proper ventilation ensures uniform airflow and prevents overspray accumulation, resulting in consistent coating quality, adhesion, and finish.
- Equipment Protection: By controlling humidity and temperature, ventilation systems help prevent corrosion, rust, and damage to powder coating equipment and booth surfaces.
- Energy Efficiency: Energy-efficient ventilation systems, such as variable speed fans and air recirculation systems, help minimize energy consumption and operating costs while maintaining optimal airflow and contaminant capture.
Applications: Powder coating booth ventilation systems are used in various industries and applications where powder coating operations are performed, including:
- Automotive and transportation
- Metal fabrication and manufacturing
- Aerospace and aviation
- Furniture and fixtures
- Appliances and consumer goods
- Architectural and building construction
In summary, powder coating booth ventilation systems are essential for maintaining a clean, safe, and environmentally compliant working environment during powder coating operations. Properly designed and operated ventilation systems contribute to the overall efficiency, quality, and success of powder coating processes in various industrial and commercial applications.
Powder Coating Booth Design:
Powder coating booth design plays a pivotal role in the efficiency, safety, and quality of the powder coating process. A well-designed booth ensures proper containment of overspray, effective ventilation, operator safety, and compliance with environmental regulations. Let’s explore the technical aspects of powder coating booth design:
Operating Principle: Powder coating booth design revolves around creating a controlled environment where powder coating materials can be applied to workpieces efficiently and safely. The primary objectives of booth design include containing overspray, providing adequate ventilation, ensuring operator safety, and maintaining environmental compliance. The design considers factors such as booth size, configuration, airflow pattern, lighting, filtration, and material handling capabilities.
Key Design Considerations: Several critical factors influence powder coating booth design:
- Booth Size and Configuration: The size and layout of the booth are determined based on the size and volume of workpieces, production requirements, available floor space, and workflow considerations. Booth configurations may include open-face booths, enclosed booths, walk-in booths, or custom-designed configurations to suit specific application requirements.
- Airflow Pattern: The airflow pattern within the booth, such as crossdraft, downdraft, semi-downdraft, or reverse flow, is selected based on containment efficiency, ventilation requirements, and coating application considerations. Proper airflow design ensures uniform distribution of overspray and contaminants and facilitates effective capture and removal by the ventilation system.
- Ventilation System: The ventilation system comprises intake and exhaust components, including plenums, fans, ductwork, and filters, designed to control airflow and remove overspray particles and contaminants from the booth environment. The ventilation system is sized and configured to meet airflow requirements, maintain operator safety, and comply with environmental regulations.
- Lighting: Adequate lighting within the booth is essential for visibility, accuracy, and quality control during coating application and inspection. Lighting fixtures are strategically positioned to minimize shadows and glare, ensuring uniform illumination across the work area and facilitating accurate coating application and defect detection.
- Filtration: Filtration systems, such as intake and exhaust filters, are installed to capture overspray particles and contaminants and prevent their release into the atmosphere. Filters may include pre-filters, final filters, HEPA filters, or activated carbon filters, selected based on filtration efficiency, maintenance requirements, and environmental compliance considerations.
- Material Handling: Booth design may include provisions for material handling equipment, such as conveyors, hoists, or racks, to facilitate loading, unloading, and movement of workpieces within the booth. Material handling systems are designed to optimize workflow efficiency, minimize operator fatigue, and ensure proper positioning for coating application and curing.
- Safety Features: Safety features, such as fire suppression systems, explosion venting, interlocks, emergency stops, and personal protective equipment (PPE), are incorporated into booth design to protect operators, equipment, and the surrounding environment from hazards associated with powder coating operations.
Advantages of Proper Booth Design: Proper powder coating booth design offers several advantages:
- Enhanced Efficiency: Well-designed booths streamline coating operations, optimize workflow efficiency, and minimize downtime, resulting in increased productivity and cost savings.
- Improved Quality: Effective containment, ventilation, and lighting contribute to consistent coating quality, adhesion, and finish, reducing rework and waste and enhancing customer satisfaction.
- Operator Safety: Booths designed with safety features and ergonomic considerations protect operators from exposure to hazardous fumes, chemicals, and airborne contaminants, ensuring a safe working environment.
- Environmental Compliance: Booths designed with efficient ventilation and filtration systems prevent pollution and comply with environmental regulations, minimizing air and water emissions and reducing the ecological footprint of powder coating operations.
- Flexibility and Adaptability: Modular booth designs and customizable features allow for easy reconfiguration and adaptation to changing production requirements, enabling manufacturers to accommodate different workpieces, coatings, and process parameters.
Applications: Powder coating booth design is used in various industries and applications where powder coating operations are performed, including:
- Automotive and transportation
- Metal fabrication and manufacturing
- Aerospace and aviation
- Furniture and fixtures
- Appliances and consumer goods
- Architectural and building construction
In summary, powder coating booth design is a multifaceted process that involves careful consideration of numerous technical, operational, and regulatory factors to create a safe, efficient, and compliant environment for powder coating operations. Properly designed booths contribute to the overall success, quality, and sustainability of powder coating processes in diverse industrial and commercial applications.
Powder Coating Booth Construction:
Powder coating booth construction is a crucial aspect of creating a controlled environment for powder coating operations. The construction materials, layout, and assembly of the booth significantly impact its performance, durability, and safety. Let’s delve into the technical details of powder coating booth construction:
Materials:
- Frame: Powder coating booth frames are typically constructed from durable materials such as steel or aluminum to provide structural support and stability. The frame is designed to withstand the weight of the booth components, resist vibrations, and maintain dimensional stability.
- Panels: Booth panels are constructed from rigid materials such as galvanized steel, stainless steel, or aluminum to provide enclosure and containment of overspray. The panels may feature smooth, non-porous surfaces for easy cleaning and maintenance.
- Insulation: Insulation materials, such as fiberglass or foam board, may be incorporated into the booth construction to provide thermal insulation and noise reduction. Insulated panels help maintain consistent temperature levels within the booth and improve energy efficiency.
- Flooring: Booth flooring is typically constructed from non-combustible materials such as concrete, steel grating, or metal decking to withstand heavy loads and prevent the accumulation of powder coating material. Anti-slip coatings or textures may be applied to enhance safety and facilitate cleaning.
- Doors: Booth doors are constructed from sturdy materials such as steel or aluminum and may feature reinforced hinges, locks, and seals to provide secure closure and containment. Doors may be hinged, sliding, or roll-up, depending on space constraints and operational requirements.
Assembly:
- Modular Design: Many powder coating booths feature a modular design, allowing for easy assembly, disassembly, and reconfiguration. Modular components, such as panels, frames, and doors, can be prefabricated off-site and assembled on-site using standard fasteners and connectors.
- Bolt-together Construction: Booth components are often designed for bolt-together construction, where panels, frames, and other structural elements are connected using bolts, screws, or rivets. Bolt-together construction facilitates quick installation and allows for easy modification or expansion of the booth.
- Sealing and Gasketing: Sealing and gasketing materials, such as silicone seals, foam gaskets, or rubber strips, are used to ensure airtight and weatherproof connections between booth components. Proper sealing prevents air leaks, contamination, and energy loss.
- Welding: In some cases, booth components may be welded together to create a rigid and seamless structure. Welding provides strong, permanent connections and enhances structural integrity but may require specialized equipment and skilled labor.
- Finishing: After assembly, powder coating booths may undergo finishing processes such as painting, powder coating, or galvanizing to enhance durability, corrosion resistance, and aesthetic appearance. Finishing materials and techniques are selected based on environmental conditions, operational requirements, and budget considerations.
Safety Features:
- Fire Suppression Systems: Powder coating booths may be equipped with fire suppression systems, such as sprinklers, fire extinguishers, or automated fire suppression systems, to mitigate the risk of fires caused by combustible powder coating materials or electrical malfunctions.
- Explosion Venting: Explosion venting panels or devices may be installed in the booth walls or roof to safely release pressure in the event of an explosion caused by powder cloud ignition or accumulation of flammable vapors.
- Emergency Exits: Booths are equipped with emergency exits, such as doors or access panels, to provide quick evacuation routes for personnel in the event of an emergency, such as fire, explosion, or equipment malfunction.
- Safety Interlocks: Safety interlock systems may be installed to prevent unauthorized access to hazardous areas of the booth, such as the spray area or curing oven, and to ensure that equipment is safely shut down during maintenance or emergencies.
- Personal Protective Equipment (PPE): Operators are required to wear appropriate PPE, such as respirators, gloves, goggles, and protective clothing, to protect against exposure to hazardous fumes, chemicals, and airborne contaminants generated during powder coating operations.
Applications: Powder coating booth construction is used in various industries and applications where powder coating operations are performed, including:
- Automotive and transportation
- Metal fabrication and manufacturing
- Aerospace and aviation
- Furniture and fixtures
- Appliances and consumer goods
- Architectural and building construction
In summary, powder coating booth construction involves the careful selection of materials, assembly techniques, and safety features to create a robust and reliable environment for powder coating operations. Properly constructed booths ensure operator safety, environmental compliance, and high-quality coating results in diverse industrial and commercial applications.
Powder Coating Booth Maintenance:
Powder coating booth maintenance is essential for ensuring optimal performance, safety, and longevity of the equipment. Regular maintenance activities help prevent downtime, reduce operating costs, and ensure compliance with safety and environmental regulations. Let’s delve into the technical aspects of powder coating booth maintenance:
Cleaning and Inspection:
- Interior Surfaces: Regularly clean the interior surfaces of the booth, including walls, floors, and filters, to remove overspray, debris, and contaminants. Use appropriate cleaning agents and equipment to prevent buildup and maintain airflow efficiency.
- Exhaust Filters: Inspect and replace exhaust filters as needed to ensure proper capture and removal of overspray particles and contaminants. Dirty or clogged filters can restrict airflow and reduce ventilation efficiency.
- Lighting Fixtures: Clean and inspect lighting fixtures regularly to ensure adequate illumination within the booth. Replace bulbs or fixtures that are damaged or malfunctioning to maintain visibility and safety.
- Ventilation System: Check the ventilation system components, including intake and exhaust plenums, ductwork, fans, and filters, for signs of wear, damage, or malfunction. Clean or replace filters, lubricate moving parts, and repair or replace worn-out components to maintain airflow efficiency and compliance with environmental regulations.
- Electrical Systems: Inspect electrical components, such as wiring, switches, controls, and safety devices, for signs of damage, corrosion, or overheating. Tighten connections, replace damaged components, and perform routine maintenance to prevent electrical hazards and ensure safe operation.
- Fire Suppression Systems: Test and inspect fire suppression systems, such as sprinklers, fire extinguishers, and alarms, according to manufacturer recommendations and regulatory requirements. Ensure that equipment is properly installed, functional, and readily accessible in case of emergency.
Equipment Calibration and Adjustment:
- Temperature Controls: Calibrate temperature controllers, thermocouples, and heating elements regularly to ensure accurate temperature regulation and uniform curing of powder coatings. Adjust settings as needed to maintain optimal curing conditions for different coating materials and workpiece specifications.
- Airflow Management: Verify airflow patterns, velocities, and pressures within the booth using airflow meters, anemometers, or manometers. Adjust dampers, fans, and ductwork as needed to optimize airflow distribution, containment efficiency, and ventilation performance.
- Spray Equipment: Inspect and calibrate spray guns, nozzles, pumps, and hoses regularly to ensure consistent coating application and minimize overspray. Clean or replace worn-out components, adjust spray settings, and perform maintenance according to manufacturer recommendations to achieve optimal coating quality and efficiency.
- Material Handling Systems: Check material handling equipment, such as conveyors, hoists, and racks, for proper alignment, operation, and safety. Lubricate moving parts, tighten fasteners, and perform preventive maintenance to minimize wear and ensure smooth material flow throughout the coating process.
Safety and Compliance:
- Personal Protective Equipment (PPE): Provide and enforce the use of appropriate PPE, such as respirators, gloves, goggles, and protective clothing, for operators and maintenance personnel working in or around the powder coating booth. Ensure that PPE is properly fitted, maintained, and used according to safety guidelines and regulatory requirements.
- Hazardous Materials Handling: Properly handle, store, and dispose of hazardous materials, such as powder coating materials, solvents, and cleaning agents, in accordance with safety regulations and environmental best practices. Train personnel on safe handling procedures, spill response protocols, and emergency evacuation routes to minimize risks and ensure compliance.
- Emergency Preparedness: Develop and implement emergency response plans, including fire evacuation procedures, spill containment measures, and medical emergency protocols. Conduct regular drills and training exercises to familiarize personnel with emergency procedures and ensure readiness to respond effectively to accidents or incidents.
- Regulatory Compliance: Stay informed about applicable safety, environmental, and industry regulations governing powder coating operations, including OSHA standards, NFPA codes, EPA regulations, and local ordinances. Maintain accurate records of equipment maintenance, inspections, training, and compliance documentation to demonstrate adherence to regulatory requirements and facilitate audits or inspections by regulatory authorities.
Continuous Improvement:
- Feedback and Evaluation: Solicit feedback from operators, maintenance technicians, and other stakeholders to identify opportunities for improvement in equipment performance, workflow efficiency, and safety protocols. Conduct regular evaluations and performance reviews to assess the effectiveness of maintenance practices and identify areas for optimization or enhancement.
- Training and Education: Provide ongoing training and education for operators, maintenance personnel, and other employees involved in powder coating operations. Offer training programs, workshops, and certifications to enhance skills, knowledge, and competency in equipment operation, maintenance, safety procedures, and regulatory compliance.
- Technology and Innovation: Stay abreast of advancements in powder coating equipment, materials, and technologies to leverage new tools, techniques, and best practices for improved performance, quality, and sustainability. Invest in upgrades, retrofits, or automation solutions to enhance productivity, reduce waste, and achieve greater operational efficiency over time.
In summary, powder coating booth maintenance is a comprehensive process that encompasses cleaning, inspection, calibration, safety compliance, and continuous improvement initiatives to ensure the reliable and sustainable operation of powder coating equipment. By implementing proactive maintenance practices and fostering a culture of safety and excellence, organizations can optimize equipment performance, minimize downtime, and achieve long-term success in powder coating operations.
Powder Coating Booth Filtration System:
The powder coating booth filtration system is a critical component responsible for capturing overspray particles and contaminants generated during the coating process, ensuring a clean and safe working environment and compliance with environmental regulations. Let’s explore the technical details of powder coating booth filtration systems:
Operating Principle: The filtration system operates on the principle of capturing and removing overspray particles and contaminants from the booth environment before they are discharged into the atmosphere. It consists of intake and exhaust filters that trap airborne particles, volatile organic compounds (VOCs), and other pollutants generated during the coating process. The filtered air is then either recirculated back into the booth or expelled safely into the environment.
Components:
- Intake Filters: Intake filters are installed in the intake plenum of the powder coating booth to capture incoming overspray particles and contaminants. They prevent debris from entering the booth environment and help maintain clean air quality for coating operations.
- Exhaust Filters: Exhaust filters are located in the exhaust plenum of the booth to capture overspray particles and contaminants before they are expelled into the atmosphere. They prevent pollution and ensure compliance with environmental regulations by capturing and containing hazardous materials.
- Filter Media: Filter media are the materials used in intake and exhaust filters to capture and retain overspray particles. Common filter media include fiberglass, polyester, cellulose, and synthetic fibers, selected based on filtration efficiency, airflow resistance, and environmental compatibility.
- Filter Housing: Filter housings provide structural support and containment for the filter media, ensuring proper alignment and sealing within the intake and exhaust plenums. They are designed to withstand airflow pressure, temperature variations, and exposure to powder coating materials.
- Seals and Gaskets: Seals and gaskets are used to create airtight and leak-proof connections between filter housings, plenums, ductwork, and booth components. They prevent air bypass and ensure that all airflow passes through the filters for effective capture and containment of overspray.
- Filter Retention Devices: Filter retention devices, such as clips, springs, or clamps, secure the filters in place within the filter housings and prevent them from dislodging or shifting during operation. They ensure proper filter alignment and prevent bypass of unfiltered air.
- Filter Monitoring Systems: Filter monitoring systems, such as differential pressure gauges or alarms, provide real-time feedback on filter performance and indicate when filters need to be cleaned or replaced. They help maintain optimal filtration efficiency and prolong the service life of filters.
Types of Filters:
- Pre-Filters: Pre-filters are installed upstream of the main intake filters to capture large particles and debris before they reach the primary filtration media. They extend the service life of the main filters and improve overall filtration efficiency by removing coarse contaminants.
- Final Filters: Final filters, also known as high-efficiency particulate air (HEPA) filters or ultra-low penetration air (ULPA) filters, are installed downstream of the pre-filters to capture fine particles and contaminants. They provide high filtration efficiency and ensure compliance with stringent environmental standards.
- Activated Carbon Filters: Activated carbon filters are used to adsorb and neutralize odors, VOCs, and other gaseous pollutants generated during the coating process. They complement mechanical filtration and enhance air quality by removing airborne chemicals and volatile organic compounds.
Maintenance and Replacement:
- Regular Inspection: Inspect intake and exhaust filters regularly for signs of damage, clogging, or degradation. Check for tears, holes, or discoloration in the filter media and ensure that seals and gaskets are intact and properly seated.
- Cleaning: Clean intake and exhaust filters as needed to remove accumulated overspray particles and contaminants. Use compressed air, vacuuming, or washing with mild detergents to restore airflow and filtration efficiency.
- Replacement: Replace intake and exhaust filters at recommended intervals to maintain optimal filtration performance. Follow manufacturer guidelines for filter selection, installation, and disposal to ensure compatibility and compliance with regulatory requirements.
- Filter Upgrades: Consider upgrading to higher efficiency filters or adding additional filtration stages to improve capture efficiency and air quality. Evaluate the cost-effectiveness and benefits of advanced filtration technologies, such as electrostatic precipitators or multi-stage filtration systems, for specific application requirements.
Advantages of Filtration Systems:
- Environmental Compliance: Filtration systems prevent air and water pollution by capturing overspray particles and contaminants before they are released into the atmosphere. They help organizations comply with environmental regulations and minimize their ecological footprint.
- Operator Safety: Clean air quality and reduced exposure to airborne contaminants improve operator safety and minimize health risks associated with powder coating operations. Filtration systems protect operators from respiratory issues, skin irritation, and other occupational hazards.
- Equipment Protection: By removing overspray particles from the booth environment, filtration systems help protect powder coating equipment, surfaces, and components from damage, corrosion, and contamination. They prolong equipment life and reduce maintenance costs.
- Quality Control: Effective filtration ensures consistent airflow and coating application conditions, resulting in uniform coating thickness, adhesion, and finish quality. Filtration systems contribute to enhanced product quality and customer satisfaction.
- Energy Efficiency: Well-designed filtration systems with optimized airflow and filtration media help minimize energy consumption and operating costs. They maintain airflow efficiency while reducing the load on ventilation equipment and prolonging filter service life.
Applications: Powder coating booth filtration systems are used in various industries and applications where powder coating operations are performed, including:
- Automotive and transportation
- Metal fabrication and manufacturing
- Aerospace and aviation
- Furniture and fixtures
- Appliances and consumer goods
- Architectural and building construction
In summary, powder coating booth filtration systems are essential for maintaining a clean, safe, and environmentally compliant working environment during powder coating operations. Properly designed and maintained filtration systems contribute to the overall efficiency, safety, and success of powder coating processes
Powder Coating Booth Ventilation System:
The ventilation system of a powder coating booth is a crucial component responsible for controlling airflow, removing overspray particles and contaminants, maintaining a safe working environment, and ensuring compliance with environmental regulations. Let’s explore the technical aspects of powder coating booth ventilation systems:
Operating Principle: The ventilation system operates on the principle of creating controlled airflow patterns within the powder coating booth to capture overspray particles and contaminants and exhaust them safely out of the environment. It consists of intake and exhaust components designed to control airflow direction, velocity, and distribution throughout the booth.
Components:
- Intake Plenum: The intake plenum is the chamber or ductwork located at the entrance of the booth, where clean air is drawn into the booth environment. It distributes fresh air evenly across the booth width and directs it towards the workpiece being coated.
- Exhaust Plenum: The exhaust plenum is the chamber or ductwork located at the rear or top of the booth, where contaminated air and overspray particles are extracted from the booth environment. It collects and removes air and contaminants efficiently to prevent their re-entry into the workspace.
- Fans: Fans or blowers are installed in the exhaust plenum to create negative pressure within the booth and facilitate the extraction of contaminated air. They generate airflow by drawing air through the intake filters, across the workpiece, and into the exhaust filters before discharging it outside the booth.
- Ductwork: Ductwork connects the intake and exhaust plenums to the booth enclosure, facilitating the transfer of air and contaminants between the booth interior and the external environment. It is designed to minimize airflow resistance, turbulence, and pressure drop to optimize ventilation efficiency.
- Dampers: Dampers are adjustable valves or louvers installed in the ductwork to regulate airflow direction, volume, and distribution within the booth. They control the balance between intake and exhaust airflow rates, adjust air velocities, and maintain proper pressure differentials for effective containment and ventilation.
- Airflow Control Devices: Airflow control devices, such as baffles, diffusers, or curtains, are installed within the booth to manipulate airflow patterns and velocities, distribute air uniformly across the workpiece, and minimize turbulence and overspray drift.
- Ventilation Filters: Ventilation filters, located in the exhaust plenum, capture overspray particles and contaminants before they are expelled into the atmosphere. They prevent pollution and ensure compliance with environmental regulations by removing hazardous materials from the exhaust air stream.
Types of Ventilation Systems:
- Crossdraft: In a crossdraft ventilation system, airflow moves horizontally across the width of the booth, from the intake side to the exhaust side. Crossdraft systems are simple and cost-effective but may result in uneven airflow distribution and overspray accumulation.
- Downdraft: In a downdraft ventilation system, airflow moves vertically downward from the ceiling to the floor of the booth, capturing overspray particles and contaminants as they settle onto the workpiece and floor surfaces. Downdraft systems offer efficient containment and capture of overspray but require a deeper booth design and may be more expensive to install and operate.
- Semi-Downdraft: A semi-downdraft ventilation system combines elements of both crossdraft and downdraft systems, with airflow directed diagonally downward across the workpiece. Semi-downdraft systems offer a compromise between containment efficiency and cost-effectiveness, suitable for a wide range of applications.
- Reverse Flow: In a reverse flow ventilation system, airflow moves from the exhaust side to the intake side of the booth, reversing the direction of conventional airflow patterns. Reverse flow systems may be used to prevent overspray accumulation on the workpiece or to accommodate specific coating application requirements.
Design Considerations:
- Airflow Rate: The airflow rate, expressed in cubic feet per minute (CFM), is determined based on booth size, configuration, production requirements, and coating application parameters. Proper airflow rates ensure effective capture and containment of overspray particles and contaminants and maintain a clean working environment.
- Air Velocity: Air velocity, measured in feet per minute (FPM), determines the speed at which air moves through the booth and across the workpiece surface. It influences overspray control, drying/curing times, and coating quality and should be optimized for specific coating materials and application processes.
- Pressure Differentials: Pressure differentials between the intake and exhaust sides of the booth are critical for creating airflow patterns and ensuring proper containment and capture of overspray. Positive pressure on the intake side and negative pressure on the exhaust side help prevent overspray leakage and maintain booth integrity.
- Air Distribution: Air distribution within the booth should be uniform and consistent to ensure even coverage and drying/curing of powder coatings. Properly designed airflow control devices, such as baffles, diffusers, or curtains, help distribute air evenly across the workpiece and minimize overspray drift and accumulation.
- Environmental Considerations: Ventilation system design should consider environmental factors such as temperature, humidity, air quality, and regulatory requirements. Proper filtration, exhaust, and emission controls minimize air pollution, energy consumption, and ecological impact while ensuring compliance with environmental standards.
Maintenance and Monitoring:
- Filter Replacement: Regularly inspect and replace intake and exhaust filters as needed to maintain optimal filtration efficiency and airflow performance. Follow manufacturer guidelines for filter selection, installation, and replacement intervals to ensure compliance with regulatory requirements.
- Fan Maintenance: Inspect fans and blowers for signs of wear, damage, or malfunction and perform preventive maintenance, such as lubrication, bearing replacement, and motor alignment, to ensure reliable operation and prolong equipment life.
- Ductwork Inspection: Check ductwork for leaks, obstructions, or damage that may affect airflow distribution and ventilation efficiency. Repair or replace damaged ducts, seals, and connections to prevent air leaks and maintain proper containment.
- Airflow Monitoring: Monitor airflow rates, velocities, and pressure differentials within the booth using airflow meters, anemometers, or pressure gauges. Adjust dampers, fans, and airflow control devices as needed to optimize ventilation performance and maintain safe operating conditions.
- System Testing: Conduct periodic testing and commissioning of the ventilation system to verify compliance with design specifications, regulatory requirements, and performance standards. Perform smoke tests, airflow measurements, and pressure tests to identify and rectify any deficiencies or anomalies in the system.
Advantages of Ventilation Systems:
- Overspray Control: Ventilation systems capture and remove overspray particles and contaminants from the booth environment, ensuring a clean working environment, minimizing airborne pollution, and preventing contamination of finished products.
- Operator Safety: Proper ventilation reduces exposure to hazardous fumes, chemicals, and airborne contaminants generated during the coating process, protecting operators from respiratory issues, skin irritation, and other health hazards.
- Compliance: Ventilation systems help organizations comply with safety, environmental, and industry regulations governing powder coating operations, including OSHA standards, NFPA codes, EPA regulations, and local ordinances.
- Quality Assurance: Effective ventilation ensures consistent airflow conditions, coating application parameters, and curing/drying times, resulting in uniform coating thickness, adhesion, and finish quality. It contributes to enhanced product quality, customer satisfaction, and brand reputation.
- Energy Efficiency: Well-designed ventilation systems with optimized airflow rates and filtration efficiency minimize energy consumption, operating costs
Powder Coating Booth Lighting System:
The lighting system in a powder coating booth plays a critical role in providing adequate illumination for operators, enhancing visibility during coating operations, ensuring quality control, and maintaining a safe working environment. Let’s delve into the technical details of powder coating booth lighting systems:
Operating Principle: The lighting system operates on the principle of providing uniform and glare-free illumination throughout the powder coating booth to facilitate coating application, inspection, and quality control. It consists of lighting fixtures strategically positioned to maximize light coverage and minimize shadowing and glare.
Components:
- Lighting Fixtures: Lighting fixtures, such as fluorescent tubes, LED panels, or high-intensity discharge (HID) lamps, provide the primary source of illumination within the powder coating booth. They are designed to withstand harsh operating conditions, including exposure to powder coating materials, high temperatures, and corrosive chemicals.
- Enclosures: Lighting fixtures may be housed in protective enclosures or housings made from durable materials such as steel or aluminum to shield them from overspray, dust, and debris. Enclosures prevent contamination of light bulbs and electrical components and ensure safe operation in hazardous environments.
- Reflectors: Reflectors or diffusers may be installed behind lighting fixtures to redirect and diffuse light rays, minimize glare, and enhance light distribution within the booth. Reflectors improve lighting efficiency and uniformity by directing light towards the workpiece and reducing shadows and dark spots.
- Mounting Hardware: Mounting hardware, such as brackets, clamps, or chains, secures lighting fixtures to the booth structure or ceiling and allows for adjustable positioning and alignment. It ensures proper fixture orientation and coverage of the work area without obstructing airflow or interfering with coating operations.
- Ballasts and Controls: Lighting fixtures may be equipped with ballasts, starters, or electronic control systems to regulate voltage, current, and power consumption and ensure stable and reliable operation. Advanced control systems allow for dimming, zoning, or remote monitoring of lighting levels for energy savings and customization.
Types of Lighting:
- Fluorescent Lighting: Fluorescent tubes are commonly used in powder coating booths due to their energy efficiency, long lifespan, and uniform light output. They provide bright, white light with minimal heat generation and are suitable for general illumination and color inspection tasks.
- LED Lighting: LED panels or fixtures are increasingly popular for powder coating booth lighting due to their high efficiency, durability, and versatility. LEDs offer instant startup, adjustable brightness, and customizable color temperatures, making them ideal for precise color matching and quality control.
- HID Lighting: High-intensity discharge (HID) lamps, such as metal halide or high-pressure sodium bulbs, provide high-output, high-intensity illumination for large powder coating booths or applications requiring maximum brightness. HID lamps offer long lamp life and excellent color rendering properties but may require longer warm-up times and higher maintenance.
- UV Lighting: UV lamps or black lights are used for curing UV-curable powder coatings or coatings containing photoinitiators. UV lighting accelerates curing times and enhances coating adhesion and durability, especially for complex or heat-sensitive substrates.
Design Considerations:
- Lighting Uniformity: Ensure uniform distribution of light across the work area to minimize shadows, glare, and color variation during coating application and inspection. Position lighting fixtures strategically to cover all angles and surfaces of the workpiece and eliminate dark spots or uneven illumination.
- Color Rendering: Choose lighting fixtures with high color rendering index (CRI) ratings to accurately represent colors and surface finishes and facilitate color matching and quality control. CRI values above 80 ensure natural color appearance and consistent coating results under different lighting conditions.
- Heat Management: Select lighting fixtures with efficient heat dissipation mechanisms to prevent overheating and premature failure in high-temperature environments. LED lighting generates minimal heat output compared to fluorescent or HID lamps, reducing the risk of heat-related damage to fixtures and electrical components.
- Durability and Safety: Install lighting fixtures with rugged construction, shatterproof enclosures, and sealed electrical components to withstand exposure to powder coating materials, chemical vapors, and mechanical impact. Ensure compliance with safety standards and regulations for hazardous locations, electrical wiring, and fixture mounting.
- Energy Efficiency: Optimize lighting system design for energy efficiency by selecting energy-efficient lamps, ballasts, and controls, such as dimmers or motion sensors, to minimize power consumption and operating costs. LED lighting offers the highest energy efficiency and long-term savings compared to traditional lighting technologies.
Maintenance and Inspection:
- Regular Cleaning: Clean lighting fixtures and lenses regularly to remove dust, dirt, and overspray buildup that may reduce light output and visibility. Use non-abrasive cleaners and soft cloths to avoid scratching or damaging light bulbs and reflectors.
- Bulb Replacement: Replace burned-out or damaged light bulbs promptly to maintain consistent illumination levels and prevent disruptions to coating operations. Follow manufacturer recommendations for bulb types, wattages, and replacement intervals to ensure compatibility and performance.
- Fixture Inspection: Inspect lighting fixtures, enclosures, and mounting hardware for signs of wear, corrosion, or damage caused by exposure to powder coating materials or environmental conditions. Tighten loose connections, replace damaged components, and repair or replace fixtures as needed to ensure safe and reliable operation.
- Electrical Safety: Perform routine electrical inspections and testing to identify and address wiring faults, insulation breakdown, or electrical hazards that may pose risks to personnel or equipment. Check for proper grounding, voltage stability, and compliance with electrical codes and regulations governing hazardous locations.
- Emergency Lighting: Install emergency lighting systems or backup power sources to provide illumination in the event of a power outage or emergency situation. Emergency lighting ensures safe evacuation routes, visibility of safety equipment, and continuity of coating operations during unforeseen disruptions.
Advantages of Proper Lighting:
- Enhanced Visibility: Adequate lighting improves operator visibility, reduces eye strain, and enhances color perception during coating application, inspection, and quality control tasks. It enables operators to detect defects, inconsistencies, and imperfections in coatings more
Powder Coating Booth Control Panel:
The control panel of a powder coating booth serves as the central command center for monitoring and regulating various booth functions, including airflow, temperature, humidity, lighting, and coating application parameters. Let’s delve into the technical aspects of powder coating booth control panels:
Operating Principle: The control panel operates on the principle of providing operators with intuitive interfaces and controls to manage and optimize powder coating booth performance. It integrates sensors, actuators, switches, displays, and communication interfaces to facilitate real-time monitoring, adjustment, and automation of booth operations.
Components:
- Control Console: The control console houses the main interface and control components, including switches, knobs, buttons, touchscreens, or digital displays, for accessing and adjusting booth settings and parameters. It provides operators with real-time feedback and status updates on booth conditions and performance.
- Sensors and Transducers: Sensors and transducers are used to measure and monitor various environmental and process parameters, such as airflow velocity, temperature, humidity, pressure differentials, and coating thickness. They provide input signals to the control system for closed-loop feedback and control.
- Actuators: Actuators, such as fans, dampers, valves, heaters, and lighting fixtures, are controlled by the control panel to regulate airflow, temperature, humidity, and other booth parameters. They respond to commands from the control system to maintain desired setpoints and operating conditions.
- PLC or Programmable Logic Controller: A PLC is an industrial-grade computing device used to automate and control complex processes and machinery, including powder coating booths. It executes control algorithms, logic sequences, and safety interlocks programmed by the operator or system integrator to ensure safe and efficient operation.
- HMI or Human-Machine Interface: The HMI is the user-friendly interface that allows operators to interact with the control system and access critical information, such as operating modes, setpoints, alarms, and diagnostic messages. It may consist of a touchscreen display, graphical user interface (GUI), or physical control panel with intuitive controls.
- Communication Interfaces: Communication interfaces, such as Ethernet, Modbus, Profibus, or RS-485, enable connectivity and data exchange between the control panel and external devices, such as PLCs, sensors, actuators, and supervisory control systems. They facilitate remote monitoring, data logging, and integration with higher-level automation systems.
- Power Distribution: Power distribution components, such as circuit breakers, relays, contactors, and terminal blocks, distribute electrical power from the main supply to individual components and subsystems within the booth. They ensure safe and reliable operation by protecting against overloads, short circuits, and electrical faults.
Control Strategies:
- Open-Loop Control: In open-loop control, the control system operates based on predefined setpoints and control parameters without feedback from sensors or external conditions. It provides basic control functionality but lacks the ability to adapt to changing environmental or process conditions.
- Closed-Loop Control: Closed-loop control utilizes feedback from sensors to continuously monitor and adjust booth parameters in real-time to maintain desired setpoints and operating conditions. It improves accuracy, responsiveness, and stability by compensating for disturbances, variations, and deviations from the target values.
- PID Control: PID control, or proportional-integral-derivative control, is a common control algorithm used in powder coating booth control panels to regulate airflow, temperature, and other process variables. It adjusts control outputs based on proportional, integral, and derivative terms to minimize errors and achieve optimal performance.
- Cascade Control: Cascade control is a multi-loop control strategy that hierarchically sequences and coordinates multiple control loops to achieve tighter regulation and faster response times. It enables more precise control of complex processes with interdependent variables, such as airflow and temperature.
- Fuzzy Logic Control: Fuzzy logic control is a rule-based control method that mimics human reasoning and decision-making by defining linguistic rules and fuzzy sets to handle uncertainty and imprecision in control systems. It is particularly useful for adaptive control and nonlinear processes with variable operating conditions.
Integration and Automation:
- Data Logging: The control panel may include data logging capabilities to record and store historical data on booth performance, operating parameters, alarms, and events. Data logging enables trend analysis, performance monitoring, and troubleshooting to optimize booth operation and maintenance.
- Alarm Management: The control panel can generate visual or audible alarms to alert operators to abnormal conditions, faults, or safety hazards in the booth. Alarms may indicate deviations from setpoints, sensor failures, equipment malfunctions, or system errors that require immediate attention or corrective action.
- Remote Monitoring: Remote monitoring allows operators to access and control the powder coating booth from a centralized location, such as a control room or office, using networked computers, tablets, or smartphones. Remote access enables real-time monitoring, troubleshooting, and adjustment of booth parameters without onsite presence.
- Process Automation: Process automation involves the use of advanced control algorithms, scheduling routines, and optimization techniques to automate routine tasks, minimize manual intervention, and improve productivity and efficiency in powder coating operations. Automation increases throughput, reduces labor costs, and ensures consistent coating quality.
Safety and Compliance:
- Safety Interlocks: The control panel may incorporate safety interlocks and emergency stop buttons to halt booth operation in the event of unsafe conditions, equipment malfunction, or personnel hazards. Safety interlocks prevent unauthorized access, equipment damage, and accidents during maintenance or troubleshooting.
- Compliance Standards: Powder coating booth control panels must comply with relevant safety, electrical, and environmental standards, such as NFPA 33, NFPA 70 (NEC), UL 508A, CE, and OSHA regulations. Compliance ensures the safe design, installation, operation, and maintenance of control systems to protect personnel, property, and the environment.
Advantages of Control Panels:
- Precision Control: Control panels provide precise and reliable control over powder coating booth parameters, ensuring consistent and high-quality coating results. Operators can adjust setpoints, monitor performance, and optimize operating conditions for maximum efficiency and productivity.
- Automation and Integration: Control panels automate routine tasks, streamline workflow, and integrate with other equipment and systems, such as powder coating guns, conveyors, and curing ovens, to create a seamless and efficient coating process. Automation reduces manual labor, minimizes errors, and enhances overall system performance.
- Safety and Compliance: Control panels incorporate safety features, alarms, and interlocks to protect personnel, equipment, and the environment from hazards and ensure compliance with safety standards and regulations. They provide operators with real-time feedback and alerts to respond promptly to abnormal conditions or emergencies.
- Remote Monitoring and Access: Control panels enable remote monitoring and access to powder coating booth operations, allowing operators to oversee and control the process from anywhere with internet connectivity. Remote access improves responsiveness, enables proactive maintenance, and facilitates troubleshooting to minimize downtime and optimize uptime.
In summary, the control panel of a powder coating booth serves as the nerve center of the operation, providing operators with the tools and information they need to monitor, regulate, and optimize booth performance for consistent, high-quality coating results. Its integration, automation, and safety features enhance productivity, efficiency, and compliance in powder coating operations.
Powder Coating Booth Filtration System:
The filtration system of a powder coating booth is essential for capturing overspray particles, maintaining air quality, and ensuring compliance with environmental regulations. Let’s explore the technical details of powder coating booth filtration systems:
Operating Principle: The filtration system operates on the principle of removing overspray particles and contaminants from the airflow within the powder coating booth. It consists of filters designed to capture and retain particles while allowing clean air to pass through, thereby preventing pollution and maintaining a safe working environment.
Components:
- Intake Filters: Intake filters are located in the intake plenum of the powder coating booth and serve to capture airborne contaminants and particulate matter before they enter the booth environment. They consist of porous media, such as fiberglass, polyester, or synthetic fibers, with high particle retention efficiency and low airflow resistance.
- Exhaust Filters: Exhaust filters are installed in the exhaust plenum of the booth to capture overspray particles and contaminants from the airflow before it is discharged into the atmosphere. They are designed to trap fine particles and prevent their release into the environment, ensuring compliance with air quality standards and regulations.
- Filter Media: Filter media come in various types and configurations, including panel filters, cartridge filters, bag filters, and HEPA (high-efficiency particulate air) filters, each offering specific benefits in terms of filtration efficiency, airflow capacity, service life, and cost-effectiveness.
- Filter Housing: Filter housings or frames provide structural support and sealing for filters, ensuring proper fit and alignment within the booth plenums. They are typically made of metal, plastic, or composite materials and feature gaskets or seals to prevent air bypass and maintain filtration integrity.
- Filter Retention Systems: Filter retention systems secure filters in place within the booth plenums and prevent them from dislodging or shifting during operation. Retention systems may include clips, brackets, frames, or locking mechanisms that hold filters securely in position and facilitate easy installation and replacement.
- Pre-filters: Pre-filters are coarse-grade filters installed upstream of main filters to capture large particles, dust, and debris and prevent them from reaching and clogging the primary filtration media. Pre-filters extend the service life of main filters, improve airflow efficiency, and reduce maintenance requirements.
- Diffusion Media: Diffusion media, such as filter blankets, pads, or screens, are sometimes used in conjunction with main filters to promote uniform airflow distribution and minimize turbulence and overspray drift within the booth. Diffusion media help improve filtration efficiency and capture overspray particles more effectively.
Types of Filters:
- Fiberglass Filters: Fiberglass filters are commonly used as intake and exhaust filters in powder coating booths due to their high dust-holding capacity, low pressure drop, and cost-effectiveness. They offer excellent filtration efficiency for capturing overspray particles while maintaining optimal airflow rates.
- Polyester Filters: Polyester filters are preferred for their durability, washability, and resistance to moisture and chemicals. They provide reliable performance in demanding powder coating applications, with long service life and minimal maintenance requirements.
- Pleated Filters: Pleated filters feature an extended surface area folded into a pleated configuration to maximize particle capture and airflow capacity. They offer higher efficiency and dust-holding capacity compared to flat-panel filters, reducing filter replacement frequency and operating costs.
- Cartridge Filters: Cartridge filters consist of cylindrical filter elements housed in a cartridge configuration for easy installation and replacement. They are ideal for applications requiring high filtration efficiency, compact design, and quick filter changeouts, such as automated powder coating systems.
- Bag Filters: Bag filters utilize a bag-shaped filter media housed in a rigid frame or housing to capture overspray particles while allowing airflow to pass through. They offer high filtration efficiency, ease of installation, and versatility for various booth configurations and airflow rates.
- HEPA Filters: HEPA filters are highly efficient filters capable of capturing particles as small as 0.3 microns with a minimum efficiency of 99.97%. They are used in critical applications requiring ultra-clean air, such as pharmaceutical, semiconductor, or cleanroom environments, where strict particulate control is essential.
Design Considerations:
- Filtration Efficiency: Select filters with appropriate filtration efficiency ratings to capture overspray particles and contaminants effectively while maintaining optimal airflow rates and booth performance. Higher efficiency filters may be required for fine or hazardous particles to meet regulatory requirements.
- Airflow Capacity: Ensure filters are sized and rated for the airflow capacity of the powder coating booth to prevent airflow restrictions, pressure drop, or filter bypass. Calculate the required filter area and velocity based on booth dimensions, airflow rates, and coating application parameters.
- Service Life: Consider the service life and replacement intervals of filters when designing the filtration system to minimize downtime, maintenance costs, and filter disposal. Choose filters with long-lasting media and durable construction to withstand the rigors of powder coating operations.
- Filter Maintenance: Implement a proactive filter maintenance program to inspect, clean, and replace filters regularly to ensure optimal filtration performance and booth efficiency. Schedule filter maintenance based on operating conditions, production volumes, and filter loading to prevent oversaturation and pressure drop.
- Filter Disposal: Dispose of used filters properly in accordance with local regulations and environmental guidelines for handling hazardous waste materials. Consider recycling options for filters containing reusable materials or exploring alternative disposal methods, such as incineration or landfilling, with proper permits and approvals.
Advantages of Filtration Systems:
- Environmental Protection: Filtration systems prevent overspray particles and contaminants from escaping into the atmosphere, reducing air pollution, environmental impact, and regulatory compliance risks. They help organizations comply with air quality standards and emission limits governing powder coating operations.
- Worker Safety: Filtration systems maintain a clean and safe working environment for operators by removing hazardous particulates, fumes, and odors generated during the coating process. They protect workers from respiratory issues, skin irritation, and other health hazards associated with exposure to airborne contaminants.
- Equipment Protection: Filtration systems prolong the service life of powder coating equipment, such as fans, ductwork, and heating elements, by preventing fouling, corrosion, and mechanical damage caused by overspray buildup. They minimize maintenance requirements, downtime, and repair costs for booth components and accessories.
- Quality Assurance: Filtration systems contribute to consistent coating quality and finish by removing overspray particles and contaminants that could cause defects, blemishes, or adhesion issues on finished products. They ensure clean air circulation and contamination-free coating environments for optimal performance and customer satisfaction.
- Regulatory Compliance: Filtration systems help organizations meet regulatory requirements and industry standards governing air emissions, workplace safety, and environmental protection. They demonstrate commitment to responsible manufacturing practices and sustainability initiatives by minimizing air pollution and environmental footprint.
In summary, the filtration system of a powder coating booth is a critical component for maintaining air quality, protecting workers and equipment, and ensuring compliance with environmental regulations. Proper selection, installation, and maintenance of filters are essential for achieving optimal booth performance, coating quality, and operational efficiency.
Powder Coating Booth Airflow System:
The airflow system of a powder coating booth is designed to control the movement of air within the booth environment, ensuring proper ventilation, overspray capture, and operator safety. Let’s delve into the technical aspects of powder coating booth airflow systems:
Operating Principle: The airflow system operates on the principle of creating a controlled airflow pattern within the powder coating booth to capture overspray particles, direct them towards filtration media, and maintain a clean working environment. It involves the strategic placement of intake and exhaust components to optimize airflow efficiency and booth performance.
Components:
- Intake Plenum: The intake plenum is located at the front or sides of the powder coating booth and serves as the entry point for fresh air into the booth environment. It distributes incoming air evenly across the width of the booth and directs it towards the workpiece, creating a uniform airflow pattern for effective overspray capture.
- Exhaust Plenum: The exhaust plenum is positioned at the rear or top of the booth and serves as the exit point for contaminated air and overspray particles. It collects air from the booth interior and channels it towards the filtration system, where overspray particles are captured and removed before the air is discharged into the atmosphere.
- Fan or Blower: Fans or blowers are used to generate airflow within the powder coating booth by drawing in fresh air from the intake plenum, circulating it through the booth interior, and exhausting it through the exhaust plenum. They are typically centrifugal or axial flow types, selected based on airflow requirements, static pressure, and motor power.
- Ductwork: Ductwork consists of a network of pipes, ducts, and fittings that distribute airflow from the fan to the intake plenum and from the exhaust plenum to the filtration system. It ensures proper airflow distribution, pressure balance, and system efficiency by minimizing air leaks, turbulence, and resistance.
- Airflow Controls: Airflow controls, such as dampers, louvers, or adjustable vents, are installed in the intake and exhaust plenums to regulate airflow rates, velocities, and directions within the powder coating booth. They allow operators to adjust airflow patterns based on coating application requirements, part geometry, and booth configuration.
- Airflow Sensors: Airflow sensors, such as anemometers or differential pressure gauges, monitor airflow velocities, pressures, and directions within the booth and provide feedback to the control system for real-time adjustment and optimization. They ensure proper ventilation, overspray capture, and operator safety by detecting airflow anomalies or restrictions.
- Air Filters: Air filters, located in the intake and exhaust plenums, capture overspray particles and contaminants from the airflow before they are discharged into the atmosphere. Filters prevent environmental pollution, maintain air quality, and protect downstream equipment and personnel from exposure to hazardous substances.
- Baffles or Baffles: Baffles or baffles are installed in the intake and exhaust plenums to promote uniform airflow distribution, minimize turbulence, and enhance overspray capture efficiency. They direct airflow towards filtration media, prevent overspray drift, and reduce pressure drop and energy consumption.
Airflow Patterns:
- Crossflow: In a crossflow airflow pattern, fresh air enters the booth from one side (intake plenum), flows horizontally across the workpiece, and exits through the opposite side (exhaust plenum). Crossflow patterns are suitable for wide or shallow booths and provide uniform coverage for large workpieces.
- Downward Flow: In a downward flow airflow pattern, fresh air is introduced from the top of the booth (ceiling) and directed downward towards the workpiece, creating a vertical airflow path. Downward flow patterns are effective for capturing overspray particles and preventing contamination of surrounding areas.
- Upward Flow: In an upward flow airflow pattern, fresh air enters the booth from the bottom (floor) and rises vertically towards the top (ceiling), carrying overspray particles and contaminants away from the workpiece. Upward flow patterns are beneficial for minimizing overspray drift and maintaining a clean working environment.
Design Considerations:
- Airflow Rate: Determine the required airflow rate based on booth size, configuration, coating application parameters, and regulatory requirements for overspray capture and ventilation. Calculate airflow velocity and volume to achieve optimal airflow patterns and capture efficiency while minimizing energy consumption and operating costs.
- Airflow Distribution: Design intake and exhaust plenums, ductwork, and airflow controls to ensure uniform distribution of airflow across the booth width and height. Position fans, dampers, and filters strategically to optimize airflow patterns and minimize turbulence, dead zones, and overspray buildup.
- Air Velocity: Maintain adequate airflow velocities within the powder coating booth to prevent overspray drift, achieve proper particle capture, and ensure operator safety. Monitor airflow velocities using sensors and adjust airflow controls as needed to maintain optimal conditions for coating application and booth operation.
- Pressure Balance: Balance airflow rates between intake and exhaust plenums to maintain pressure equilibrium within the powder coating booth and prevent air leakage or infiltration. Use airflow sensors and dampers to adjust airflow rates and pressure differentials to achieve desired airflow patterns and booth performance.
- Air Filtration: Select air filters with appropriate filtration efficiency ratings, pressure drop characteristics, and service life for capturing overspray particles and maintaining air quality within the booth. Choose filter media and configurations based on coating material properties, particle size distribution, and environmental considerations.
- Energy Efficiency: Design airflow systems for maximum energy efficiency by minimizing pressure drop, optimizing fan selection and placement, and incorporating variable speed drives or frequency converters for fan control. Implement energy-saving measures, such as heat recovery systems or recirculation loops, to reduce operating costs and environmental impact.
Advantages of Airflow Systems:
- Overspray Capture: Airflow systems effectively capture overspray particles and contaminants, preventing their release into the atmosphere and minimizing environmental pollution. They ensure compliance with air quality standards and regulatory requirements governing powder coating operations.
- Worker Safety: Proper ventilation and airflow control protect workers from exposure to hazardous substances, fumes, and airborne contaminants generated during the coating process. Airflow systems maintain a clean and safe working environment, reducing the risk of respiratory issues, skin irritation, and other health hazards.
- Coating Quality: Controlled airflow patterns and ventilation promote consistent coating quality and finish by minimizing overspray drift, contamination, and defects. They ensure uniform coverage, adhesion, and curing of coatings on workpieces, enhancing product aesthetics and performance.
- Equipment Protection: Airflow systems prolong the service life of powder coating equipment, such as fans, filters, and ductwork, by preventing fouling, corrosion, and mechanical damage caused by overspray buildup and contamination. They minimize maintenance requirements, downtime, and repair costs for booth components and accessories.
- Regulatory Compliance: Airflow systems help organizations meet regulatory requirements and industry standards governing air emissions, workplace safety, and environmental protection. They demonstrate commitment to responsible manufacturing practices and sustainability initiatives by minimizing air pollution and environmental footprint.
In summary, the airflow system of a powder coating booth is essential for maintaining air quality, overspray capture efficiency, and operator safety. Proper design, installation, and operation of airflow systems are critical for achieving optimal booth performance, coating quality, and regulatory compliance in powder coating operations
Powder Coating Booth Lighting System:
The lighting system of a powder coating booth plays a crucial role in providing visibility, safety, and quality control during the coating process. Let’s explore the technical details of powder coating booth lighting systems:
Operating Principle: The lighting system operates on the principle of providing uniform and sufficient illumination within the powder coating booth to ensure accurate color matching, defect detection, and operator safety. It consists of light fixtures strategically positioned to minimize shadows, glare, and color distortion while maximizing visibility and productivity.
Components:
- Light Fixtures: Light fixtures, such as fluorescent tubes, LED lamps, or metal halide bulbs, are installed inside the powder coating booth to provide illumination for coating application, inspection, and quality control. They are designed to withstand the harsh operating conditions of powder coating environments, including high temperatures, humidity, and chemical exposure.
- Fixture Housing: Fixture housings or enclosures protect light bulbs and electrical components from dust, overspray, and mechanical damage within the powder coating booth. They are typically made of corrosion-resistant materials, such as stainless steel or aluminum, and feature sealed gaskets or lenses to prevent ingress of contaminants.
- Mounting Hardware: Mounting hardware, such as brackets, arms, or hooks, secure light fixtures to the walls, ceiling, or structure of the powder coating booth. They ensure proper alignment, stability, and positioning of fixtures to achieve optimal lighting coverage and visibility for coating application and inspection tasks.
- Ballasts or Drivers: Ballasts or drivers regulate the electrical current flowing to fluorescent or HID (high-intensity discharge) lamps, ensuring consistent light output and stable operation. Electronic ballasts or drivers are preferred for their energy efficiency, flicker-free performance, and compatibility with dimming controls.
- Reflectors: Reflectors or diffusers are used to direct and diffuse light emitted from fixtures to minimize glare, shadows, and hotspots within the powder coating booth. They improve light distribution, uniformity, and color rendering for accurate visual inspection and defect detection.
- Controls: Lighting controls, such as switches, dimmers, timers, or motion sensors, allow operators to adjust light intensity, timing, and activation based on coating application requirements, workpiece geometry, and operator preferences. They optimize energy usage, extend lamp life, and enhance user comfort and productivity.
- Emergency Lighting: Emergency lighting systems provide backup illumination in the event of power outages or emergencies, ensuring continued visibility and safety for operators to evacuate the powder coating booth safely. Emergency lights may feature battery backup, self-testing, and remote monitoring capabilities for reliable operation and compliance with safety regulations.
Types of Lighting:
- Fluorescent Lighting: Fluorescent lamps are commonly used in powder coating booths for their energy efficiency, long life, and broad spectrum of visible light. They provide uniform illumination with minimal heat generation and are available in various color temperatures to match different coating materials and substrates.
- LED Lighting: LED (light-emitting diode) lamps offer several advantages over traditional lighting technologies, including higher energy efficiency, longer lifespan, instant startup, and superior color rendering. LED fixtures are durable, compact, and environmentally friendly, making them ideal for powder coating applications requiring high-quality illumination.
- HID Lighting: HID (high-intensity discharge) lamps, such as metal halide or high-pressure sodium bulbs, produce intense light output with excellent color rendition and visibility. They are suitable for large powder coating booths or areas requiring high-intensity lighting but may have higher operating costs and shorter lifespans compared to fluorescent or LED lamps.
Design Considerations:
- Lighting Intensity: Determine the required lighting intensity based on coating application tasks, workpiece size, coating material properties, and operator preferences. Calculate illumination levels in foot-candles or lux to ensure adequate visibility and color accuracy for coating application, inspection, and quality control.
- Color Temperature: Select light sources with appropriate color temperature ratings to match the spectral characteristics of coating materials and substrates. Choose cool-white or daylight lamps for accurate color rendering and color matching, especially for automotive or industrial coatings requiring precise color consistency.
- Uniformity and Distribution: Design lighting layouts to achieve uniform illumination and minimize shadows, hotspots, and glare within the powder coating booth. Position light fixtures evenly across the booth walls, ceiling, and workpiece surfaces to ensure consistent lighting coverage and visibility from all angles.
- Heat Management: Minimize heat buildup from light fixtures to prevent overheating, thermal degradation, or discoloration of coating materials and substrates. Use low-heat-emitting lamps, such as LEDs or fluorescent tubes, and incorporate thermal management features, such as heat sinks or ventilation, to dissipate excess heat and maintain comfortable working conditions.
- Energy Efficiency: Optimize energy usage and operating costs by selecting energy-efficient lighting fixtures, such as LED lamps with high efficacy ratings and dimming capabilities. Install lighting controls, such as timers or motion sensors, to automatically adjust light levels based on occupancy or usage patterns and reduce unnecessary energy consumption.
- Maintenance and Accessibility: Choose light fixtures with easy-to-access components and tool-free maintenance features to facilitate lamp replacement, cleaning, and troubleshooting. Ensure adequate clearance and accessibility around fixtures for safe and efficient servicing without disrupting coating operations or workflow.
Advantages of Lighting Systems:
- Visibility and Safety: Lighting systems provide operators with clear visibility and illumination for accurate coating application, inspection, and quality control. They enhance operator safety by reducing the risk of accidents, errors, and injuries associated with poor lighting conditions or obscured workpiece visibility.
- Quality Control: Proper lighting ensures consistent color rendering, finish quality, and defect detection during the powder coating process. It enables operators to identify imperfections, surface irregularities, or coating defects early in the production cycle and take corrective action to maintain product quality and customer satisfaction.
- Productivity and Efficiency: Well-designed lighting systems improve operator comfort, productivity, and efficiency by reducing eye strain, fatigue, and errors caused by inadequate or inconsistent lighting. They enable faster and more accurate coating application, inspection, and rework tasks, leading to higher throughput and reduced rejections.
- Regulatory Compliance: Lighting systems help organizations comply with workplace safety regulations and industry standards governing lighting levels, visibility, and color rendering in powder coating operations. They demonstrate commitment to employee health and safety, environmental stewardship, and responsible manufacturing practices.
- Environmental Impact: Energy-efficient lighting technologies, such as LEDs, minimize energy consumption, greenhouse gas emissions, and environmental footprint associated with powder coating booth operations. They contribute to sustainability goals, resource conservation, and cost savings by reducing electricity usage and carbon emissions.
In summary, the lighting system of a powder coating booth is essential for ensuring visibility, safety, and quality control during the coating process. Proper selection, design, and maintenance of lighting systems are critical for achieving optimal illumination levels, color accuracy, and operator comfort in powder coating operations.
Powder Coating Booth Control Panel:
The control panel of a powder coating booth serves as the central hub for monitoring, regulating, and controlling various operational parameters and functions of the booth system. Let’s explore the technical details of powder coating booth control panels:
Operating Principle: The control panel operates on the principle of integrating electrical, pneumatic, and electronic components to manage and coordinate the operation of powder coating booth equipment, including fans, lights, conveyors, and spray guns. It provides operators with intuitive interfaces and feedback mechanisms for real-time monitoring, adjustment, and troubleshooting of booth functions.
Components:
- Main Control Unit: The main control unit houses the primary control circuitry, power distribution components, and interface modules for connecting and controlling peripheral devices and systems within the powder coating booth. It includes a microprocessor or programmable logic controller (PLC) for executing control algorithms, logic sequences, and operator inputs.
- HMI (Human-Machine Interface): The HMI is a user-friendly interface that allows operators to interact with the control panel and access system information, status indicators, and control functions. It typically consists of a touchscreen display, push buttons, indicator lights, and status indicators for displaying operating parameters, alarms, and diagnostics.
- Control Devices: Control devices, such as switches, relays, contactors, and solenoid valves, are used to initiate, stop, or regulate the operation of equipment and systems within the powder coating booth. They provide manual or automated control inputs based on operator commands, process signals, or programmed logic sequences.
- Input/Output Modules: Input/output (I/O) modules interface with external sensors, actuators, and devices to monitor input signals, such as temperature, pressure, flow rate, and position, and generate output signals to control equipment operation, such as fans, lights, and conveyor motors. They convert analog and digital signals into compatible formats for processing and communication with the control unit.
- Communication Interfaces: Communication interfaces, such as Ethernet, RS-232, RS-485, or Modbus protocols, enable the control panel to communicate with external devices, systems, or networked platforms for data exchange, remote monitoring, and integration with enterprise or supervisory control systems. They facilitate real-time data acquisition, analysis, and decision-making for optimizing booth performance and productivity.
- Power Supply: The power supply unit converts incoming AC power from the mains supply into DC power for powering control circuitry, electronic components, and peripherals within the powder coating booth control panel. It provides stable and regulated voltage levels to ensure reliable operation and protection against power surges or fluctuations.
- Safety Devices: Safety devices, such as emergency stop buttons, interlocks, and safety relays, are integrated into the control panel to safeguard operators, equipment, and the environment from potential hazards, accidents, or malfunctions. They provide failsafe mechanisms for shutting down equipment, activating alarms, and triggering emergency procedures in response to abnormal conditions or operator interventions.
Control Functions:
- Fan Speed Control: The control panel regulates the speed of fans or blowers within the powder coating booth to maintain desired airflow rates, pressure differentials, and ventilation conditions. It adjusts fan speeds based on process requirements, airflow sensors, or feedback signals to ensure proper overspray capture, air circulation, and operator comfort.
- Lighting Control: The control panel manages the operation of lighting fixtures within the powder coating booth, including on/off switching, dimming, and scheduling functions. It controls light levels, color temperatures, and illumination patterns to optimize visibility, color rendering, and energy efficiency during coating application, inspection, and quality control tasks.
- Conveyor Control: If the powder coating booth is equipped with a conveyor system for transporting workpieces through the coating process, the control panel coordinates conveyor speed, direction, and indexing functions. It synchronizes conveyor movement with coating application, curing cycles, and part handling operations for efficient and seamless production flow.
- Spray Gun Control: For automated powder coating systems, the control panel interfaces with spray gun controllers to regulate powder flow, gun positioning, and triggering functions. It coordinates spray gun movements, powder delivery rates, and coating parameters based on part geometry, coating profiles, and process requirements for consistent and uniform coating application.
- Temperature Control: The control panel monitors and controls temperature levels within the powder coating booth, including ambient temperature, oven temperature, and substrate temperature. It adjusts heating elements, airflow rates, and insulation levels to achieve and maintain desired temperature profiles for coating curing, film formation, and thermal stability.
- Alarm and Diagnostics: The control panel provides alarm notifications, diagnostic messages, and status indicators to alert operators to abnormal conditions, equipment faults, or system malfunctions. It logs event data, error codes, and performance metrics for troubleshooting, maintenance, and process optimization purposes, ensuring reliable and efficient booth operation.
- Data Logging and Reporting: The control panel records process data, operating parameters, and performance metrics over time for analysis, trending, and reporting purposes. It stores data in internal memory or external storage devices and generates reports, graphs, or charts to visualize trends, identify anomalies, and track process improvements or deviations.
Design Considerations:
- User Interface Design: Design an intuitive and ergonomic user interface for the control panel to facilitate operator interaction, navigation, and feedback. Use graphical displays, icons, and color-coding schemes to convey information, status, and alarms effectively and enhance user experience and productivity.
- Modularity and Expandability: Design the control panel with modular architecture and expandable capabilities to accommodate future upgrades, expansions, or modifications to the powder coating booth system. Use standardized interfaces, connectors, and protocols to facilitate integration with third-party devices or systems and ensure compatibility and interoperability.
- Reliability and Redundancy: Ensure the reliability and redundancy of critical components, such as power supplies, controllers, and communication interfaces, to prevent system failures, downtime, or data loss. Implement backup systems, redundant pathways, and fault-tolerant designs to maintain continuity of operations and minimize disruptions in case of component failures or maintenance activities.
- Safety Compliance: Design the control panel to comply with applicable safety standards, regulations, and guidelines governing electrical, mechanical, and functional aspects of powder coating booth control systems. Incorporate safety features, such as emergency stop circuits, interlocks, and protective enclosures, to mitigate risks and ensure operator and equipment safety during operation.
- Environmental Considerations: Select components, materials, and enclosures for the control panel that can withstand the harsh operating conditions of powder coating environments, including temperature extremes, humidity, vibration, and chemical exposure. Ensure ingress protection (IP) ratings for dust and moisture resistance and corrosion-resistant finishes for long-term durability and reliability.
- Ease of Maintenance: Design the control panel with accessibility, serviceability, and ease of maintenance in mind to facilitate troubleshooting, repair, and replacement of components. Provide clear labeling, wiring diagrams, and documentation for quick identification of components, connections, and functions, and minimize downtime and disruption to production.
Advantages of Control Panels:
- Automation and Efficiency: Control panels automate and streamline powder coating booth operations, reducing manual intervention, errors, and cycle times. They improve process efficiency, throughput, and productivity by optimizing equipment utilization, resource allocation, and workflow management.
- Precision and Accuracy: Control panels provide precise and accurate control over critical parameters, such as airflow rates, lighting
Powder Coating Booth Filtration System:
The filtration system of a powder coating booth is responsible for capturing overspray particles and contaminants generated during the coating process, ensuring environmental compliance, air quality, and equipment protection. Let’s delve into the technical details of powder coating booth filtration systems:
Operating Principle: The filtration system operates on the principle of mechanically capturing overspray particles and contaminants from the airflow within the powder coating booth, preventing their release into the atmosphere. It consists of filtration media, such as filters or cartridges, strategically positioned to intercept and collect overspray particles before clean air is discharged.
Components:
- Filter Media: Filter media, such as polyester, fiberglass, or paper, serve as the primary mechanism for capturing overspray particles from the airflow within the powder coating booth. They feature high-efficiency particulate arrestance (HEPA) or electrostatic properties to attract and retain fine particles, ensuring clean air emission and compliance with regulatory standards.
- Filter Cartridges: Filter cartridges, also known as filter elements or filter bags, are cylindrical structures containing pleated or woven filter media for increased surface area and particle retention capacity. They are installed in filter housings or frames within the powder coating booth to capture overspray particles and contaminants from the airflow efficiently.
- Filter Housings: Filter housings or frames provide structural support and containment for filter cartridges within the powder coating booth. They ensure proper alignment, sealing, and integrity of filters to prevent bypass leakage, overspray buildup, and contamination of downstream equipment or surfaces.
- Filter Mounting System: The filter mounting system secures filter cartridges to the filter housings or frames and facilitates easy installation, replacement, and maintenance. It may include clamps, gaskets, retainers, or fasteners designed to withstand the rigors of powder coating environments and ensure airtight sealing and particle capture efficiency.
- Pre-Filters: Pre-filters, such as fiberglass pads, foam media, or wire mesh screens, are installed upstream of primary filters to capture larger particles and debris before they reach the main filtration media. Pre-filters prolong the service life of primary filters, reduce maintenance frequency, and enhance filtration efficiency by removing coarse contaminants.
- Filter Cleaning System: Some powder coating booth filtration systems feature a filter cleaning mechanism, such as reverse pulse-jet cleaning or mechanical shaking, to dislodge accumulated overspray particles from filter surfaces and restore airflow capacity. Filter cleaning systems improve filter longevity, reduce pressure drop, and minimize downtime for maintenance.
- Filter Monitoring Devices: Filter monitoring devices, such as differential pressure gauges or pressure sensors, measure the pressure drop across filter media and provide feedback to the control system for real-time monitoring of filter condition and performance. They trigger alarms or alerts when filter saturation or airflow restriction exceeds predefined thresholds, indicating the need for filter replacement or cleaning.
- Exhaust Plenum: The exhaust plenum collects filtered air from the filtration system and directs it towards the exhaust stack or outlet for discharge into the atmosphere. It ensures proper containment and containment of overspray particles and contaminants within the powder coating booth and prevents their release into the surrounding environment.
Filtration Efficiency:
- Particulate Removal: The filtration system effectively removes overspray particles, dust, and contaminants from the airflow within the powder coating booth, preventing their release into the atmosphere and minimizing environmental pollution. High-efficiency filtration media, such as HEPA filters or electrostatic precipitators, achieve particle removal efficiencies exceeding 99% for fine and ultrafine particles.
- Air Quality: The filtration system ensures clean air emission and compliance with air quality standards, regulations, and permits governing powder coating operations. It minimizes emissions of volatile organic compounds (VOCs), hazardous air pollutants (HAPs), and particulate matter, protecting public health, environmental resources, and regulatory compliance.
- Worker Safety: Proper filtration reduces exposure of powder coating booth operators to airborne contaminants, fumes, and respirable particles generated during the coating process. It maintains a clean and safe working environment, reducing the risk of respiratory issues, skin irritation, and occupational hazards associated with prolonged exposure to hazardous substances.
- Equipment Protection: Filtration systems protect downstream equipment, such as fans, ductwork, and heating elements, from fouling, corrosion, and mechanical damage caused by overspray buildup and contamination. They extend the service life of equipment, minimize maintenance requirements, and ensure reliable operation and performance of powder coating booth components.
- Environmental Compliance: The filtration system helps organizations comply with environmental regulations and permit requirements governing air emissions, pollution control, and workplace safety in powder coating facilities. It demonstrates commitment to responsible manufacturing practices, sustainability initiatives, and community stewardship by minimizing environmental impact and protecting natural resources.
Maintenance and Replacement:
- Filter Inspection: Regularly inspect filters for signs of damage, clogging, or degradation, such as tears, holes, or discoloration. Check filter housings, seals, and connections for leaks, gaps, or deterioration that may compromise filtration efficiency and air quality.
- Filter Replacement: Replace filters according to manufacturer recommendations, service intervals, or pressure drop limits to maintain optimal filtration performance and airflow capacity. Use compatible replacement filters with the same specifications, dimensions, and filtration ratings to ensure proper fit and function within the powder coating booth.
- Filter Cleaning: If equipped with a filter cleaning system, follow manufacturer instructions and safety guidelines for performing filter cleaning procedures. Use appropriate tools, equipment, and protective gear to remove accumulated overspray particles and restore filter airflow capacity without damaging filter media or components.
- Filter Disposal: Dispose of used filters in accordance with local regulations, waste management practices, and environmental guidelines for handling hazardous or contaminated materials. Follow proper disposal procedures to prevent environmental contamination, pollution, or health risks associated with exposure to overspray residues or contaminants.
- Documentation: Maintain records of filter maintenance activities, replacement schedules, and performance data for compliance, auditing, and quality assurance purposes. Document filter specifications, part numbers, and suppliers for future reference and procurement of replacement filters.
Advantages of Filtration Systems:
- Environmental Protection: Filtration systems prevent release of overspray particles and contaminants into the atmosphere, reducing environmental pollution and minimizing air emissions from powder coating operations. They help organizations comply with regulatory requirements, mitigate environmental risks, and protect natural resources and ecosystems.
- Worker Health and Safety: Proper filtration improves air quality and reduces exposure of powder coating booth operators to hazardous substances, fumes, and airborne particles. It promotes a clean and safe working environment, minimizing health risks, respiratory issues, and occupational hazards associated with inhalation or contact with contaminants.
- Process Efficiency: Efficient filtration systems maintain consistent airflow rates, ventilation conditions, and overspray capture efficiency within the powder coating booth, ensuring optimal coating application and curing conditions. They enhance process efficiency, productivity, and product quality by minimizing defects, rework, and material waste.
- Equipment Reliability: Filtration systems protect downstream equipment and components from fouling, corrosion, and mechanical damage caused by overspray buildup and contamination. They extend the service life of fans, motors, ductwork, and heating elements, reducing maintenance requirements, downtime, and repair costs for powder coating booth systems.
- Compliance and Reputation: By investing in advanced filtration technologies and sustainable practices, organizations demonstrate commitment to regulatory compliance, environmental stewardship, and corporate responsibility. Effective filtration systems enhance brand reputation
Powder Coating Booth Exhaust System:
The exhaust system of a powder coating booth plays a critical role in removing overspray particles, volatile organic compounds (VOCs), and contaminants generated during the coating process, ensuring air quality, environmental compliance, and operator safety. Let’s explore the technical aspects of powder coating booth exhaust systems:
Operating Principle: The exhaust system operates on the principle of extracting contaminated air from the powder coating booth and discharging it safely into the atmosphere or through appropriate pollution control measures. It creates negative pressure within the booth to induce airflow and capture overspray particles, fumes, and pollutants before they escape into the surrounding environment.
Components:
- Exhaust Fan: The exhaust fan is the primary component of the exhaust system responsible for generating airflow within the powder coating booth. It creates suction or negative pressure to draw contaminated air from the booth interior through filters and ductwork for subsequent discharge or treatment. Exhaust fans are available in various sizes, capacities, and configurations to accommodate different booth sizes, airflow requirements, and operating conditions.
- Ductwork: Ductwork comprises a network of pipes, channels, and fittings that convey contaminated air from the powder coating booth to the exhaust fan for extraction and discharge. It distributes airflow evenly, minimizes pressure drop, and ensures efficient capture and removal of overspray particles and pollutants from the booth interior. Ductwork materials may include galvanized steel, stainless steel, or PVC depending on corrosion resistance, durability, and budget considerations.
- Stack or Exhaust Outlet: The stack or exhaust outlet is the final point of discharge for contaminated air exiting the powder coating booth exhaust system. It directs exhaust air vertically or horizontally away from the facility to prevent recirculation or re-entry of pollutants into the workspace. Exhaust outlets may feature weatherproof louvers, dampers, or diffusers to control airflow direction, dispersion, and noise levels.
- Exhaust Filters: Exhaust filters, such as high-efficiency particulate arrestance (HEPA) filters or activated carbon adsorption media, remove overspray particles, VOCs, and odors from the exhaust air stream before discharge into the atmosphere. They capture fine particles and contaminants, ensuring compliance with air quality standards, regulatory limits, and environmental regulations. Exhaust filters may be installed upstream or downstream of the exhaust fan, depending on filtration requirements and system configuration.
- Inlet Louvers or Hoods: Inlet louvers or hoods located at the entrance of the powder coating booth facilitate airflow capture and containment, preventing overspray particles and contaminants from escaping into the surrounding environment. They guide airflow into the booth interior, create uniform airflow patterns, and enhance overspray capture efficiency during coating application and curing processes.
- Pressure Sensors or Gauges: Pressure sensors or gauges monitor the pressure differential across the exhaust system, providing real-time feedback on airflow velocity, static pressure, and system performance. They alert operators to abnormal conditions, airflow restrictions, or filter clogging, indicating the need for maintenance, adjustment, or troubleshooting to ensure proper operation and compliance with ventilation requirements.
- Control Panel: The control panel interfaces with the exhaust system to monitor, regulate, and control fan speed, airflow direction, and system operation. It provides operators with intuitive interfaces, status indicators, and alarm notifications for monitoring exhaust performance, detecting faults, and initiating corrective actions to maintain air quality and compliance with regulatory standards.
Design Considerations:
- Airflow Requirements: Determine the required airflow rates, velocities, and exchange rates based on booth size, coating processes, and regulatory requirements for ventilation and pollution control. Calculate airflow volumes in cubic feet per minute (CFM) or cubic meters per hour (m³/h) to ensure adequate capture and removal of overspray particles and contaminants from the booth interior.
- Ductwork Layout: Design ductwork layouts to minimize pressure drop, turbulence, and airflow restrictions while maximizing airflow uniformity and efficiency. Use smooth, straight duct runs with gradual bends, transitions, and expansion joints to reduce friction losses, minimize energy consumption, and optimize airflow distribution throughout the system.
- Fan Selection: Select exhaust fans with appropriate capacities, efficiencies, and static pressure ratings to meet airflow requirements and overcome resistance from filters, ductwork, and system components. Choose fan types, such as centrifugal or axial fans, based on operating conditions, space constraints, and noise considerations to achieve optimal performance and energy efficiency.
- Filter Media: Choose exhaust filters with high-efficiency particulate arrestance (HEPA) or activated carbon adsorption media to capture overspray particles, VOCs, and odors effectively. Select filter media and configurations based on filtration efficiency, pressure drop, service life, and compatibility with coating materials, substrates, and environmental regulations.
- Exhaust Outlet Location: Position exhaust outlets or stacks away from building entrances, air intakes, and occupied areas to prevent re-entry of contaminants into the facility and minimize exposure risks to personnel and neighboring properties. Consider wind direction, prevailing weather conditions, and dispersion patterns when determining exhaust outlet locations to prevent air recirculation or nuisance odors.
- Noise Control: Implement noise control measures, such as acoustic enclosures, vibration isolation mounts, or sound attenuators, to mitigate noise emissions from exhaust fans and ductwork. Design exhaust systems with proper fan placement, airflow baffles, and noise barriers to minimize occupational noise exposure and comply with noise regulations and workplace safety standards.
Advantages of Exhaust Systems:
- Air Quality Improvement: Exhaust systems remove overspray particles, VOCs, and contaminants from the powder coating booth environment, ensuring clean air emission and compliance with air quality standards and regulatory limits. They protect public health, environmental resources, and worker safety by minimizing exposure risks and pollution impacts associated with coating operations.
- Environmental Compliance: By capturing and controlling airborne pollutants, exhaust systems help organizations comply with environmental regulations, permits, and emissions limits governing powder coating activities. They demonstrate commitment to sustainable practices, pollution prevention, and corporate responsibility by minimizing environmental impact and protecting air quality.
- Operator Safety: Proper ventilation and exhaust systems maintain a clean and safe working environment for powder coating booth operators, reducing exposure risks to hazardous substances, fumes, and respiratory irritants. They promote employee health, well-being, and productivity by minimizing occupational hazards, respiratory issues, and chemical exposures during coating processes.
- Equipment Protection: Exhaust systems protect downstream equipment, such as fans, motors, and heating elements, from contamination, fouling, and corrosion caused by overspray buildup and airborne particles. They extend the service life of equipment, reduce maintenance requirements, and ensure reliable operation and performance of powder coating booth components.
- Process Efficiency: Efficient exhaust systems maintain consistent airflow rates, ventilation conditions, and overspray capture efficiency within the powder coating booth, optimizing coating application and curing processes. They enhance process efficiency, throughput, and product quality by minimizing defects, rework, and material waste associated with poor air circulation and contamination.
Maintenance and Operation:
- Regular Inspection: Conduct regular inspections of exhaust fans, ductwork, filters, and components for signs of wear, damage, or degradation. Check for leaks, blockages, or corrosion that may affect airflow performance and system integrity.
- Filter Replacement: Replace exhaust filters according to manufacturer recommendations, service intervals, or pressure drop limits to maintain filtration efficiency and airflow capacity. Use compatible replacement filters with
Oven Heating Elements
Heating elements are crucial components of powder coating ovens, responsible for generating the necessary heat to cure the applied powder coating on the workpieces. Let’s delve into the technical details of oven heating elements:
Operating Principle: Heating elements operate on the principle of converting electrical energy into heat energy through resistance heating. When an electric current passes through the heating element, it encounters resistance, leading to the generation of heat. This heat is then transferred to the surrounding air within the oven, raising the temperature to the desired curing level.
Components:
- Resistance Wire: The core component of heating elements is the resistance wire, typically made from materials such as nichrome (nickel-chromium alloy) or Kanthal (iron-chromium-aluminum alloy). These alloys offer high resistance to electrical current, allowing them to generate substantial heat when energized. The resistance wire is coiled or formed into specific shapes to maximize surface area and heat output.
- Insulation: Heating elements are often insulated to prevent heat loss and improve energy efficiency. Insulation materials, such as ceramic fiber, mica, or fiberglass, are wrapped around or embedded within the resistance wire to minimize heat transfer to the surrounding structure and maintain uniform heating within the oven chamber.
- Support Structure: Heating elements are supported by a framework or mounting system to maintain their position and ensure proper alignment within the oven chamber. The support structure may consist of metal brackets, rods, or frames that secure the heating elements in place and facilitate installation, maintenance, and replacement as needed.
- Terminal Connections: Terminal connections provide electrical connections between the heating elements and the power supply source. They typically consist of metal terminals, connectors, or lead wires attached to the ends of the resistance wire, allowing for easy connection to electrical cables or bus bars within the oven.
- Protective Sheath (Optional): In some applications, heating elements may be encased in a protective sheath or tube to shield them from mechanical damage, corrosive environments, or contamination. Sheaths are typically made from stainless steel, Incoloy, or other heat-resistant alloys, providing durability and longevity in harsh operating conditions.
Types of Heating Elements:
- Coil Elements: Coil heating elements consist of resistance wire wound into coils or spirals, providing a large surface area for heat generation. They are commonly used in convection ovens and batch ovens, where uniform heating is required across the entire oven chamber. Coil elements offer flexibility in design and installation, allowing for customization to fit various oven configurations and heating requirements.
- Rod Elements: Rod heating elements consist of straight or bent resistance wire encased in ceramic or metal tubes. They are often used in infrared ovens and radiant ovens, where direct or focused heat is needed for rapid curing of powder coatings. Rod elements offer high heat transfer efficiency and precise temperature control, making them ideal for applications requiring fast curing times and energy savings.
- Tubular Elements: Tubular heating elements consist of resistance wire enclosed within metal tubes or sheaths, providing robust construction and durability. They are commonly used in industrial ovens and conveyor ovens, where high temperatures, heavy loads, and continuous operation are required. Tubular elements offer versatility in design, allowing for easy integration into existing oven systems and configurations.
- Flat Panel Elements: Flat panel heating elements consist of resistance wire embedded within ceramic or metal plates, offering a compact and low-profile design. They are often used in infrared curing ovens and custom-built ovens, where space is limited, and precise heat distribution is essential. Flat panel elements provide uniform heating across large surface areas, ensuring consistent curing results and high-quality finishes.
Key Considerations:
- Temperature Range: Heating elements must be capable of reaching and maintaining the required curing temperature for powder coatings, typically ranging from 300°F to 450°F (150°C to 230°C) for standard thermoset powders. Select heating elements with temperature ratings and performance specifications suitable for the desired curing process and coating materials.
- Heat Distribution: Choose heating elements that provide uniform heat distribution across the entire oven chamber to ensure consistent curing of powder coatings on workpieces. Optimize element placement, spacing, and configuration to minimize hot spots, cold zones, and uneven curing, resulting in high-quality finishes and reduced rework.
- Energy Efficiency: Consider the energy efficiency of heating elements to minimize operating costs and environmental impact. Select elements with high heat transfer efficiency, low heat loss, and fast response times to reduce energy consumption, cycle times, and overall curing process duration.
- Durability and Reliability: Choose heating elements with durable construction, corrosion resistance, and long service life to withstand the rigors of industrial powder coating operations. Select materials and designs that can withstand high temperatures, thermal cycling, mechanical stress, and chemical exposure without degradation or performance deterioration.
- Maintenance Requirements: Assess the maintenance requirements of heating elements, including cleaning, inspection, and replacement procedures. Choose elements that are easy to access, clean, and maintain to minimize downtime and ensure continuous operation of the powder coating oven. Implement regular preventive maintenance practices to extend the life of heating elements and optimize oven performance.
Advantages of Quality Heating Elements:
- Uniform Heating: Quality heating elements ensure uniform heat distribution within the oven chamber, resulting in consistent curing of powder coatings and high-quality finishes on workpieces. They minimize variations in temperature, reduce defects, and improve overall coating performance and aesthetics.
- Energy Efficiency: Efficient heating elements optimize energy utilization and reduce operating costs by minimizing heat loss, cycle times, and energy consumption during the curing process. They contribute to sustainable practices and environmental stewardship by conserving resources and reducing carbon emissions associated with powder coating operations.
- Process Control: Reliable heating elements enable precise temperature control and process monitoring, allowing operators to achieve desired curing profiles, cure times, and coating properties. They enhance process repeatability, productivity, and quality assurance, leading to improved customer satisfaction and competitiveness in the market.
- Longevity and Reliability: Quality heating elements exhibit durability, longevity, and resistance to wear, corrosion, and thermal degradation, ensuring reliable performance over extended operating periods. They minimize downtime, maintenance requirements, and replacement costs, maximizing uptime and productivity of powder coating oven systems.
- Compatibility and Versatility: High-quality heating elements are compatible with a wide range of powder coating materials, substrates, and part geometries, offering versatility and flexibility in curing applications. They accommodate diverse curing requirements, production volumes, and coating specifications, allowing for efficient and cost-effective processing of various workpieces and formulations.
In summary, heating elements are essential components of powder coating ovens, providing the necessary heat energy for curing powder coatings on workpieces. By selecting quality heating elements and optimizing their design, operation, and maintenance, powder coating manufacturers can achieve uniform curing, energy efficiency, process control, and
Temperature Controllers in Powder Coating Ovens:
Temperature controllers are pivotal components within powder coating ovens, responsible for regulating and maintaining precise temperature levels throughout the curing process. Let’s explore the technical intricacies of temperature controllers in powder coating ovens:
Operating Principle: Temperature controllers operate on the principle of monitoring the actual temperature inside the oven chamber and comparing it to the desired setpoint temperature. Based on this comparison, the controller adjusts the heat output of the heating elements to achieve and maintain the target temperature within a narrow tolerance range.
Components:
- Temperature Sensor: The temperature sensor, typically a thermocouple or resistance temperature detector (RTD), measures the actual temperature inside the oven chamber. It converts temperature changes into electrical signals that are transmitted to the temperature controller for processing and feedback control.
- Control Algorithm: The control algorithm is the logic implemented within the temperature controller to calculate the required adjustment to the heating elements based on the deviation between the actual temperature and the setpoint temperature. Common control algorithms include proportional-integral-derivative (PID) control, which dynamically adjusts the heat output to minimize temperature errors and achieve stable and precise control.
- Output Device: The output device of the temperature controller modulates the power supplied to the heating elements to achieve the desired temperature setpoint. It may use relays, solid-state switches (such as silicon-controlled rectifiers or SSRs), or proportional control valves to regulate the heat output based on the control algorithm’s instructions.
- User Interface: The user interface provides operators with a means to set the desired temperature setpoint, monitor the actual temperature, and configure control parameters. It may consist of a digital display, push buttons, and status indicators for intuitive operation and troubleshooting of the temperature control system.
- Safety Features: Temperature controllers may incorporate safety features such as high-temperature alarms, over-temperature protection, and fault detection mechanisms to prevent overheating, equipment damage, or process deviations. These features ensure safe and reliable operation of the powder coating oven and protect personnel and products from harm.
Types of Temperature Controllers:
- On/Off Controllers: On/off controllers, also known as simple or bang-bang controllers, operate by switching the heating elements on or off based on the deviation between the actual temperature and the setpoint temperature. They provide basic temperature regulation but may result in temperature overshoots and oscillations due to their binary control action.
- PID Controllers: PID controllers offer advanced temperature control capabilities by dynamically adjusting the heat output of the heating elements based on proportional, integral, and derivative control actions. They continuously analyze temperature errors and adjust the control output to achieve precise and stable temperature control with minimal overshoot and settling time.
- Programmable Controllers: Programmable controllers allow for the implementation of complex temperature profiles and ramp/soak sequences to accommodate various curing processes and part geometries. They offer flexibility and customization options for optimizing curing cycles, ramp rates, hold times, and cooling phases to achieve desired coating properties and performance characteristics.
Key Features and Considerations:
- Temperature Accuracy: Temperature controllers should provide accurate temperature measurement and control within a tight tolerance range to ensure consistent and repeatable curing results. High-resolution sensors, calibration procedures, and temperature profiling capabilities contribute to precise temperature regulation and uniform heating across the oven chamber.
- Response Time: Temperature controllers should have fast response times to quickly adjust the heat output of the heating elements in response to temperature deviations or setpoint changes. Rapid response times minimize temperature fluctuations, reduce process variability, and improve productivity by accelerating curing cycles and minimizing cycle times.
- Stability and Reliability: Temperature controllers should exhibit stability and reliability in maintaining consistent temperature levels over prolonged curing cycles. Robust construction, reliable components, and advanced control algorithms contribute to stable and dependable performance, ensuring uninterrupted operation and minimal downtime for maintenance or adjustments.
- Integration and Compatibility: Temperature controllers should be compatible with the heating elements, sensors, and control systems of the powder coating oven. They should support standard communication protocols, such as Modbus, Ethernet, or analog signals, for seamless integration with supervisory control systems, data acquisition systems, and factory automation platforms.
- User-Friendly Interface: Temperature controllers should feature an intuitive and user-friendly interface for easy setup, programming, and operation by operators and maintenance personnel. Clear displays, menu-driven navigation, and status indicators enhance usability and facilitate monitoring, troubleshooting, and configuration of temperature control parameters.
- Safety and Alarms: Temperature controllers should incorporate safety features such as high-temperature alarms, temperature limits, and emergency shutdowns to prevent overheating, equipment damage, or process deviations. Alarms, alerts, and diagnostic messages provide early warnings of abnormal conditions and prompt operators to take corrective actions or initiate preventive measures.
Advantages of Temperature Controllers:
- Precise Temperature Control: Temperature controllers ensure precise and stable temperature control within the powder coating oven, minimizing temperature variations, hot spots, and cold zones. They enable consistent curing results, uniform coating properties, and high
Airflow Control Systems in Powder Coating Booths:
Airflow control systems are essential components of powder coating booths, regulating the airflow patterns to optimize overspray capture, air quality, and coating application efficiency. Let’s explore the technical aspects of airflow control systems in powder coating booths:
Operating Principle: Airflow control systems operate on the principle of creating and directing airflow patterns within the powder coating booth to capture overspray particles, contaminants, and volatile organic compounds (VOCs) generated during the coating process. By controlling airflow velocity, direction, and distribution, these systems ensure uniform coating coverage, minimize overspray waste, and maintain a clean working environment.
Components:
- Exhaust Fans: Exhaust fans create suction or negative pressure within the powder coating booth, drawing contaminated air and overspray particles towards the filtration system for capture and removal. They provide the primary airflow force to establish proper ventilation and overspray containment within the booth.
- Inlet Plenums: Inlet plenums distribute clean, filtered air evenly across the width and height of the powder coating booth, creating uniform airflow patterns and reducing turbulence. They ensure consistent coating application and overspray capture efficiency by maintaining stable airflow velocities and minimizing air recirculation within the booth.
- Exhaust Plenums: Exhaust plenums collect contaminated air and overspray particles from the booth interior and direct them towards the filtration system for capture and removal. They prevent overspray escape, re-entrainment, or recirculation by creating localized suction zones and guiding airflow towards exhaust ducts or filters.
- Airflow Dampers: Airflow dampers regulate the airflow volume, velocity, and distribution within the powder coating booth by adjusting the opening or closing of ductwork dampers, louvers, or diffusers. They provide fine-tuning of airflow patterns to match coating requirements, part geometries, and process conditions for optimal performance and efficiency.
- Variable Frequency Drives (VFDs): VFDs control the speed of exhaust fans and airflow motors to modulate airflow rates and adapt to changing process conditions, production demands, or coating parameters. They offer energy savings, noise reduction, and flexibility in airflow adjustment, allowing for precise control and optimization of ventilation systems.
- Airflow Monitoring Devices: Airflow monitoring devices, such as velocity sensors, pressure gauges, or flow meters, measure airflow velocity, differential pressure, and volume within the powder coating booth. They provide real-time feedback on airflow conditions, filter performance, and ventilation efficiency for process optimization, troubleshooting, and quality assurance.
- Adjustable Airfoils or Baffles: Adjustable airfoils or baffles located along the walls or ceiling of the powder coating booth help control airflow patterns, turbulence, and overspray dispersion. They direct airflow towards the workpieces, minimize overspray drift, and improve coating transfer efficiency by optimizing airflow distribution and containment within the booth.
- Automatic Control Systems: Automatic control systems integrate sensors, actuators, and controllers to automate airflow regulation and adjustment based on preset parameters, coating profiles, or environmental conditions. They offer hands-free operation, self-monitoring, and adaptive control features to optimize coating processes, minimize energy consumption, and ensure consistent quality and productivity.
Types of Airflow Control:
- Crossdraft Systems: Crossdraft airflow systems direct airflow horizontally across the width of the powder coating booth, from the inlet side to the exhaust side. They provide simple and cost-effective airflow control, suitable for small to medium-sized booths and batch coating applications.
- Downdraft Systems: Downdraft airflow systems direct airflow vertically downward from the ceiling to the floor of the powder coating booth, creating a downward airflow pattern that captures overspray particles and contaminants efficiently. They offer superior overspray containment, airflow uniformity, and operator safety, making them ideal for large booths, automated lines, and high-production environments.
- Semi-Downdraft Systems: Semi-downdraft airflow systems combine elements of crossdraft and downdraft airflow patterns, directing airflow at an angle from the ceiling towards the rear exhaust plenum or ductwork. They provide a compromise between overspray containment, airflow uniformity, and installation flexibility, suitable for medium to large-sized booths with varying coating requirements.
Key Considerations:
- Airflow Velocity: Control airflow velocity to achieve optimal overspray capture, coating transfer efficiency, and ventilation effectiveness within the powder coating booth. Maintain recommended airflow velocities based on coating specifications, part geometries, and process conditions to minimize overspray drift, bounce-back, and re-entrainment.
- Airflow Distribution: Ensure uniform airflow distribution across the width, height, and depth of the powder coating booth to achieve consistent coating application and curing results. Control inlet and exhaust airflow rates, damper positions, and baffle configurations to minimize turbulence, dead zones, and uneven coating coverage.
- Airflow Balancing: Balance airflow rates between inlet and exhaust plenums to maintain pressure differentials, airflow velocities, and capture velocities within the powder coating booth. Adjust damper settings, fan speeds, or ductwork configurations to achieve desired airflow balance and optimize ventilation performance for maximum overspray capture and containment.
- Energy Efficiency: Optimize airflow control systems for energy efficiency by minimizing pressure drop, fan power consumption, and operating costs associated with ventilation and exhaust systems. Use variable frequency drives (VFDs), energy-efficient motors, and airflow optimization strategies to reduce energy waste and carbon emissions while maintaining process performance and air quality.
- Process Flexibility: Design airflow control systems with flexibility and adaptability to accommodate diverse coating processes, part sizes, and production requirements. Incorporate adjustable components, modular designs, and automated controls to facilitate quick setup, reconfiguration, and adaptation to changing coating conditions or part geometries.
- Maintenance and Calibration: Implement regular maintenance and calibration procedures for airflow control systems to ensure proper operation, accuracy, and reliability. Clean filters, inspect dampers, and calibrate sensors regularly to prevent airflow restrictions, deviations, or equipment failures that may impact coating quality, production efficiency, or worker safety.
Advantages of Airflow Control Systems:
- Overspray Capture Efficiency: Airflow control systems optimize overspray capture efficiency by directing airflow patterns towards the workpieces, minimizing overspray drift, and maximizing coating transfer efficiency. They ensure uniform coating coverage, reduce material waste, and improve finishing quality for enhanced productivity and profitability.
- Air Quality Improvement: Airflow control systems enhance air quality within the powder coating booth by capturing and containing overspray particles, VOCs, and contaminants generated during the coating process. They mitigate environmental pollution, reduce health risks, and ensure regulatory compliance with air quality standards and emissions limits.
- Process Consistency: Airflow control systems provide consistent and repeatable coating application and curing results by maintaining stable airflow patterns, velocities, and distribution within the powder coating booth. They minimize variations in coating thickness, color consistency, and finish appearance, ensuring product quality and customer satisfaction.
- Worker Safety: Airflow control systems create a clean and safe working environment for powder coating booth operators by minimizing exposure to airborne contaminants, fumes, and respiratory irritants. They protect personnel from health hazards, respiratory issues, and occupational risks associated with prolonged exposure to hazardous substances during coating operations.
- Energy Efficiency: Airflow control systems optimize energy consumption and operating costs by reducing fan power requirements, pressure drop losses, and heating/cooling loads associated with ventilation and exhaust systems. They
Advantages of Automated Conveyor Systems in Powder Coating Lines:
Automated conveyor systems offer numerous benefits in powder coating lines, enhancing productivity, efficiency, and quality while reducing costs and manual labor. Let’s explore the advantages of automated conveyor systems:
- Increased Productivity: Automated conveyor systems enable continuous and uninterrupted material flow through the powder coating process, maximizing throughput and production rates. They eliminate manual material handling, loading, and unloading tasks, allowing operators to focus on value-added activities and process optimization.
- Improved Efficiency: Automated conveyor systems optimize workflow management and resource utilization by streamlining material flow, reducing cycle times, and minimizing idle time between process steps. They synchronize coating, curing, and cooling processes for seamless integration and efficient use of equipment, manpower, and floor space.
- Consistent Quality: Automated conveyor systems ensure consistent and uniform coating application, curing, and finish quality across all workpieces, eliminating variations and defects associated with manual handling or batch processing. They maintain precise control over process parameters, such as line speed, conveyor spacing, and coating thickness, to achieve desired coating properties and performance characteristics.
- Enhanced Flexibility: Automated conveyor systems offer versatility and adaptability to accommodate various part sizes, shapes, and configurations within the powder coating line. They support quick changeovers, setup adjustments, and product customization without disrupting production schedules or requiring extensive retooling or downtime.
- Reduced Labor Costs: Automated conveyor systems reduce dependency on manual labor for material handling, transport, and processing tasks, leading to labor cost savings and workforce reallocation. They minimize labor-intensive tasks, ergonomic risks, and repetitive motions associated with manual loading/unloading, allowing personnel to focus on skilled tasks and process supervision.
- Optimized Space Utilization: Automated conveyor systems optimize floor space utilization by compactly arranging equipment, workstations, and processing zones within the powder coating line layout. They minimize footprint requirements, aisle widths, and buffer zones, maximizing available space for production equipment, storage, and facility expansion.
- Improved Safety: Automated conveyor systems enhance workplace safety by reducing manual handling hazards, heavy lifting, and ergonomic strains associated with material transport and processing. They incorporate safety features such as interlocks, guards, and emergency stops to prevent accidents, collisions, and operator injuries during operation.
- Real-time Monitoring and Control: Automated conveyor systems integrate sensors, actuators, and control systems to monitor and control material flow, process parameters, and equipment status in real-time. They provide operators with visibility into production metrics, performance indicators, and quality assurance data for process optimization, troubleshooting, and continuous improvement.
- Energy Efficiency: Automated conveyor systems optimize energy consumption and operating costs by minimizing idle time, equipment downtime, and energy waste during powder coating operations. They utilize energy-efficient motors, variable frequency drives (VFDs), and automation strategies to reduce power consumption, carbon emissions, and environmental impact.
- Scalability and Expansion: Automated conveyor systems offer scalability and scalability, enabling gradual expansion, capacity upgrades, and future-proofing of powder coating lines to accommodate growing production demands and changing market trends. They support modular construction, equipment integration, and system reconfiguration for seamless expansion and adaptation to evolving business needs.
In summary, automated conveyor systems play a pivotal role in enhancing productivity, efficiency, and quality in powder coating lines. They enable continuous material flow, consistent coating application, and optimized resource utilization while reducing labor costs, manual errors, and process variability. By investing in automated conveyor systems, manufacturers can achieve competitive advantages, operational excellence, and sustainable growth in the powder coating industry.
Automatic Powder Guns
Automatic powder guns are critical components in powder coating equipment, offering precise and efficient powder application onto various workpieces. Here’s an in-depth exploration of automatic powder guns:
Operating Principle: Automatic powder guns operate on the principle of electrostatic attraction and pneumatic powder delivery. They use electrostatic charge to positively charge powder particles and attract them to the negatively charged workpiece surface. The guns are connected to a powder feed system that delivers the powder to the gun’s nozzle, where it is charged and dispersed onto the parts.
Components:
- Powder Feed System: The powder feed system comprises a powder hopper, feeder, and delivery tubes that transport the powder from the storage container to the gun. It ensures a continuous supply of powder to the gun during the coating process, allowing for uninterrupted operation and consistent powder flow.
- Electrostatic Charging System: The electrostatic charging system generates and maintains a high-voltage electrostatic charge on the powder particles as they pass through the gun. It consists of high-voltage power supplies, electrodes, and charging electrodes located near the gun’s nozzle to impart a positive charge to the powder particles.
- Powder Gun Body: The powder gun body houses the powder delivery system, charging components, and controls. It typically includes a trigger or button for activating the gun, an adjustable nozzle for controlling the spray pattern and powder flow, and a handle for comfortable grip and maneuverability.
- Control Unit: The control unit regulates the powder gun’s operation, including voltage settings, powder flow rate, and spray pattern adjustments. It may feature digital displays, control knobs, and interface panels for user-friendly operation and programming of coating parameters.
- Air Supply: Automatic powder guns require compressed air for powder atomization and delivery. The air supply system includes an air compressor, hoses, regulators, and filters to deliver clean and dry compressed air to the powder gun at the required pressure and flow rate.
- Nozzle and Electrodes: The nozzle directs the powder flow and disperses it onto the workpiece surface, while the charging electrodes impart an electrostatic charge to the powder particles. The design and configuration of the nozzle and electrodes influence the spray pattern, transfer efficiency, and coating quality.
- Grounding System: A grounding system ensures proper electrostatic grounding of the workpieces to prevent electrostatic discharge, powder waste, and coating defects. It typically includes grounding cables, hooks, or contact points that establish a conductive path between the workpieces and the ground.
Operation Modes:
- Automatic Mode: In automatic mode, the powder gun is integrated into an automated powder coating line or system, where it moves along a predetermined path and applies powder to the workpieces as they pass through the coating process. The gun’s operation is synchronized with conveyor speed, part positioning, and coating parameters for consistent and efficient powder application.
- Manual Mode: In manual mode, the powder gun is operated by an operator who manually aims and controls the powder application onto the workpieces. The operator adjusts powder flow, spray pattern, and gun movement based on part geometry, coating requirements, and visual inspection to achieve desired coating coverage and quality.
Advantages:
- High Efficiency: Automatic powder guns offer high application efficiency and transfer rates, ensuring maximum powder utilization and minimal waste. They provide uniform coating thickness and coverage across complex part geometries, recesses, and surfaces, resulting in optimized material usage and cost savings.
- Consistent Coating Quality: Automatic powder guns deliver consistent and repeatable coating quality, free from inconsistencies, streaks, or overspray. They maintain precise control over powder flow, spray pattern, and electrostatic charge distribution, resulting in high-quality finishes and enhanced product aesthetics.
- Increased Productivity: Automatic powder guns improve productivity and throughput in powder coating operations by enabling continuous, high-speed coating of parts on automated conveyor lines. They reduce cycle times, manual labor, and production bottlenecks, allowing for faster turnaround times and increased output capacity.
- Versatility and Flexibility: Automatic powder guns are versatile and adaptable to various part sizes, shapes, and materials, making them suitable for a wide range of powder coating applications. They support quick changeovers, reconfigurations, and programming adjustments to accommodate diverse production requirements and coating specifications.
- Operator Safety: Automatic powder guns enhance operator safety by minimizing direct contact with powder particles, chemical exposure, and ergonomic strains associated with manual powder application. They eliminate manual handling of powder containers, reduce airborne dust, and mitigate health risks in the workplace.
- Process Control and Monitoring: Automatic powder guns incorporate advanced control and monitoring features, allowing for real-time adjustment of coating parameters, troubleshooting, and quality assurance. They provide feedback on powder flow, coating thickness, and gun performance, enabling operators to fine-tune process settings and optimize coating results.
Applications: Automatic powder guns are used in various industries for powder coating applications, including automotive, aerospace, appliances, furniture, and architectural components. They are suitable for coating metal, plastic, wood, and composite substrates, offering corrosion protection, durability, and decorative finishes.
In summary, automatic powder guns are essential tools in powder coating operations, offering high efficiency, consistent quality, and enhanced productivity. With their advanced features, versatility, and reliability, they contribute to cost-effective, sustainable, and high-performance powder coating solutions in diverse industrial applications.
Batch Powder Coating Ovens
Batch powder coating ovens play a crucial role in the curing process of powder-coated materials, providing controlled heating environments to melt and cure the powder coating onto workpieces. Here’s a detailed overview of batch powder coating ovens:
Operating Principle: Batch powder coating ovens operate based on the principle of convection heating, where heated air circulates within the oven chamber to transfer heat energy to the coated workpieces. The oven’s heating elements, typically electric resistance heaters or gas burners, generate heat that is evenly distributed throughout the chamber, ensuring uniform heating and curing of the powder coating.
Components:
- Oven Chamber: The oven chamber is the enclosed space where the curing process takes place. It is constructed of insulated walls, floor, and ceiling to minimize heat loss and maintain consistent temperatures. The chamber is designed to accommodate various sizes and quantities of workpieces, with adjustable racks, shelves, or trays for optimal loading and airflow distribution.
- Heating Elements: Heating elements, such as electric resistance heaters or gas burners, generate heat energy within the oven chamber. They are strategically positioned along the walls or ceiling to provide uniform heating and temperature control throughout the curing cycle. Heating elements may feature temperature sensors and control systems to regulate heat output and prevent overheating.
- Air Circulation System: An air circulation system facilitates the movement of heated air within the oven chamber, ensuring even distribution of heat and consistent curing temperatures across all workpieces. It typically includes fans, blowers, or recirculation systems that circulate air from the bottom to the top of the chamber, maintaining uniform airflow patterns and minimizing temperature gradients.
- Temperature Control System: The temperature control system regulates the oven’s heating elements to achieve and maintain the desired curing temperature throughout the process. It may incorporate thermostats, temperature controllers, or programmable logic controllers (PLCs) that monitor temperature sensors and adjust heating output accordingly to ensure precise temperature control and cycle repeatability.
- Insulation: Insulation materials, such as ceramic fiber, mineral wool, or fiberglass, line the interior walls, floor, and ceiling of the oven chamber to reduce heat loss and improve energy efficiency. Insulation minimizes heat transfer to the external environment, conserving energy and maintaining stable operating temperatures within the oven.
- Exhaust System: An exhaust system removes excess heat, moisture, and volatile organic compounds (VOCs) from the oven chamber during the curing process. It may include exhaust fans, ductwork, and filters that vent air to the outside environment or recirculate it through an air purification system to maintain air quality and prevent buildup of contaminants.
- Safety Features: Batch powder coating ovens incorporate safety features such as overheat protection, flame detectors, and emergency shutdowns to prevent equipment damage, fire hazards, or personnel injuries. Safety interlocks, alarms, and monitoring systems ensure compliance with safety regulations and provide early warning of abnormal conditions or malfunctions.
Operation Modes:
- Batch Processing: In batch processing mode, workpieces are loaded into the oven chamber on racks, shelves, or trays, and the curing cycle is initiated. The oven heats up to the specified temperature, and the powder coating melts and flows onto the workpieces, forming a durable and uniform finish. Once the curing cycle is complete, the workpieces are unloaded, inspected, and prepared for further processing or finishing operations.
- Manual Operation: Batch powder coating ovens may be operated manually by operators who set the temperature, cycle time, and other parameters based on coating requirements and workpiece specifications. Manual operation allows for flexibility and customization of curing cycles but requires active monitoring and supervision to ensure proper curing and quality control.
Advantages:
- Versatility: Batch powder coating ovens offer versatility in accommodating various part sizes, shapes, and production volumes. They can handle small batches or large quantities of workpieces with customizable racks, shelves, or trays to optimize loading density and airflow distribution.
- Cost-Effective: Batch powder coating ovens are cost-effective solutions for small to medium-scale powder coating operations, offering lower upfront investment costs and operational expenses compared to continuous or automated systems. They require less infrastructure, maintenance, and energy consumption, making them suitable for start-ups or low-volume production.
- Quality Assurance: Batch powder coating ovens ensure consistent and repeatable curing results, with precise temperature control and uniform heat distribution across all workpieces. They minimize coating defects, inconsistencies, and rework, resulting in high-quality finishes and enhanced product aesthetics.
- Flexibility: Batch powder coating ovens allow for flexibility in process control, customization, and experimentation with different curing parameters and coating formulations. Operators can fine-tune curing cycles, temperature profiles, and dwell times to optimize coating performance and meet specific application requirements.
- Ease of Maintenance: Batch powder coating ovens are relatively simple to maintain, with fewer moving parts and components compared to continuous or automated systems. They require routine cleaning, inspection, and calibration of temperature sensors, heating elements, and ventilation systems to ensure optimal performance and longevity.
- Space Efficiency: Batch powder coating ovens offer space-efficient solutions for powder coating operations, with compact footprints and modular designs that maximize floor space utilization. They can be installed in existing facilities or integrated into production lines with minimal disruption to workflow and layout.
Applications: Batch powder coating ovens are used in various industries for curing powder-coated materials, including automotive, aerospace, furniture, appliances, and architectural components. They are suitable for coating metal, plastic, wood, and composite substrates, offering corrosion protection, durability, and decorative finishes.
In summary, batch powder coating ovens are essential equipment in powder coating operations, providing efficient and cost-effective solutions for curing powder-coated materials. With their versatility, reliability, and quality assurance capabilities, they contribute to the success and competitiveness of powder coating businesses in diverse industrial applications.
Continuous Powder Coating Ovens
Continuous powder coating ovens are integral components of automated powder coating lines, providing continuous and uniform heat treatment to powder-coated materials as they pass through the oven conveyor system. Let’s delve into the technical details of continuous powder coating ovens:
Operating Principle: Continuous powder coating ovens operate based on the principle of convection heating, where heated air is circulated within the oven chamber to transfer heat energy to the coated workpieces. The oven’s heating elements generate heat, which is evenly distributed throughout the chamber, ensuring consistent heating and curing of the powder coating as the parts move along the conveyor.
Components:
- Conveyor System: The conveyor system transports workpieces through the oven chamber in a continuous manner, ensuring consistent processing and optimal throughput. It typically consists of a conveyor belt or chain, drive mechanism, and supporting rollers or guides that move the workpieces at a controlled speed through the oven.
- Oven Chamber: The oven chamber is an insulated enclosure where the curing process takes place. It is constructed of insulated walls, floor, and ceiling to minimize heat loss and maintain stable operating temperatures. The chamber is designed to accommodate various part sizes and configurations, with adjustable conveyor speeds and loading configurations.
- Heating Elements: Heating elements, such as electric resistance heaters or gas burners, generate heat within the oven chamber. They are strategically positioned along the walls or ceiling to provide uniform heating and temperature control throughout the curing process. Heating elements may feature temperature sensors and control systems to regulate heat output and ensure precise temperature control.
- Air Circulation System: An air circulation system facilitates the movement of heated air within the oven chamber, ensuring uniform distribution of heat and consistent curing temperatures across all workpieces. It typically includes fans, blowers, or recirculation systems that circulate air from the bottom to the top of the chamber, maintaining uniform airflow patterns and minimizing temperature differentials.
- Temperature Control System: The temperature control system regulates the oven’s heating elements to achieve and maintain the desired curing temperature throughout the process. It may incorporate thermostats, temperature controllers, or programmable logic controllers (PLCs) that monitor temperature sensors and adjust heating output accordingly to ensure precise temperature control and cycle repeatability.
- Insulation: Insulation materials line the interior walls, floor, and ceiling of the oven chamber to minimize heat loss and improve energy efficiency. Insulation materials, such as ceramic fiber, mineral wool, or fiberglass, reduce heat transfer to the external environment, conserving energy and maintaining stable operating temperatures within the oven.
- Exhaust System: An exhaust system removes excess heat, moisture, and volatile organic compounds (VOCs) from the oven chamber during the curing process. It may include exhaust fans, ductwork, and filters that vent air to the outside environment or recirculate it through an air purification system to maintain air quality and prevent buildup of contaminants.
- Safety Features: Continuous powder coating ovens incorporate safety features such as overheat protection, flame detectors, and emergency shutdowns to prevent equipment damage, fire hazards, or personnel injuries. Safety interlocks, alarms, and monitoring systems ensure compliance with safety regulations and provide early warning of abnormal conditions or malfunctions.
Operation Modes:
- Continuous Processing: In continuous processing mode, workpieces are loaded onto the conveyor at one end of the oven and transported through the oven chamber at a controlled speed. The oven heats up to the specified curing temperature, and the powder coating melts and cures onto the workpieces as they move along the conveyor. Once the curing cycle is complete, the finished parts are unloaded from the conveyor at the other end of the oven.
- Automated Operation: Continuous powder coating ovens may be integrated into automated powder coating lines, where they operate in conjunction with other equipment such as powder booths, pretreatment systems, and cooling stations. Automated operation allows for seamless material flow, process synchronization, and real-time monitoring and control of curing parameters to optimize production efficiency and quality.
Advantages:
- High Throughput: Continuous powder coating ovens offer high throughput and productivity by enabling continuous processing of workpieces at a consistent speed. They eliminate the need for manual loading and unloading between curing cycles, reducing idle time and maximizing production output.
- Consistent Quality: Continuous powder coating ovens ensure consistent and uniform curing of powder coatings across all workpieces, with precise temperature control and airflow distribution. They minimize variations in coating thickness, color consistency, and finish appearance, resulting in high-quality finishes and enhanced product aesthetics.
- Energy Efficiency: Continuous powder coating ovens optimize energy consumption and operating costs by minimizing heat loss, idle time, and energy waste during the curing process. They utilize insulation materials, recirculation systems, and energy-efficient heating elements to conserve energy and reduce environmental impact.
- Process Control and Monitoring: Continuous powder coating ovens incorporate advanced control and monitoring features, allowing for real-time adjustment of curing parameters, troubleshooting, and quality assurance. They provide feedback on temperature profiles, conveyor speed, and oven performance, enabling operators to fine-tune process settings and optimize coating results.
- Space Efficiency: Continuous powder coating ovens offer space-efficient solutions for powder coating operations, with compact footprints and modular designs that maximize floor space utilization. They can be integrated into existing production lines or custom-built to fit specific facility layouts and production requirements.
- Flexibility: Continuous powder coating ovens provide flexibility in processing various part sizes, shapes, and materials, allowing for quick changeovers and customization of curing parameters. They support a wide range of coating applications and production volumes, making them suitable for diverse industrial applications and market demands.
Applications: Continuous powder coating ovens are used in various industries for curing powder-coated materials, including automotive, aerospace, appliances, furniture, and architectural components. They are suitable for coating metal, plastic, wood, and composite substrates, offering corrosion protection, durability, and decorative finishes.
In summary, continuous powder coating ovens are essential equipment in automated powder coating lines, providing efficient, high-throughput solutions for curing powder-coated materials. With their advanced features, versatility, and reliability, they contribute to the success and competitiveness of powder coating businesses in diverse industrial applications.
Powder Coating Curing Process:
The curing process in powder coating is a crucial step that transforms the applied powder into a durable, protective, and aesthetically pleasing finish. Here’s an in-depth explanation of the powder coating curing process:
1. Preheating Stage: The curing process typically begins with a preheating stage, where the coated workpieces are gradually heated to the desired curing temperature. Preheating removes moisture from the surface of the powder coating and promotes the flow and adhesion of the powder particles to the substrate. This stage helps prevent defects such as pinholes, blisters, and orange peel texture in the final finish.
2. Gelation Stage: Once the workpieces reach the curing temperature, the powder coating undergoes a gelation stage where the resin particles within the powder begin to melt and flow together. This creates a semi-liquid state where the powder coating forms a continuous film over the substrate. During gelation, the powder coating becomes tacky and begins to adhere firmly to the substrate surface.
3. Crosslinking Stage: In the crosslinking stage, chemical reactions occur between the resin molecules within the powder coating, resulting in the formation of crosslinks or bonds between adjacent polymer chains. These crosslinks enhance the mechanical strength, chemical resistance, and durability of the powder coating, improving its adhesion to the substrate and resistance to abrasion, corrosion, and UV degradation.
4. Curing Stage: The curing stage is where the powder coating fully cures and hardens to form a durable finish. It involves maintaining the workpieces at the specified curing temperature for a predetermined duration, allowing the crosslinking reactions to proceed to completion. Curing times vary depending on factors such as powder chemistry, substrate material, coating thickness, and curing temperature.
5. Cooling Stage: After the curing stage is complete, the workpieces are gradually cooled down to room temperature to solidify the powder coating and stabilize its properties. Cooling may occur naturally by allowing the workpieces to air-cool within the curing oven or through forced air circulation or water quenching for rapid cooling. Proper cooling helps prevent thermal stress, distortion, or adhesion issues in the finished coating.
6. Post-Curing or Heat Aging (Optional): In some cases, a post-curing or heat aging process may be employed to further enhance the performance and properties of the powder coating. Post-curing involves subjecting the cured workpieces to elevated temperatures for an extended period, typically at a lower temperature than the initial curing stage. This additional heat treatment helps promote additional crosslinking and improves coating adhesion, chemical resistance, and outdoor durability.
Advantages of Powder Coating Curing Process:
- Durable Finish: The powder coating curing process produces a durable and resilient finish that resists chipping, cracking, fading, and peeling, even under harsh environmental conditions.
- Excellent Adhesion: Cured powder coatings form strong bonds with the substrate surface, providing excellent adhesion and long-term performance.
- Uniform Coverage: The curing process ensures uniform coverage and thickness of the powder coating, resulting in consistent appearance and quality across all coated surfaces.
- Environmental Benefits: Powder coating is an environmentally friendly finishing process that produces minimal waste, emissions, and hazardous pollutants compared to liquid coatings. The curing process does not involve solvents or VOCs, reducing environmental impact and regulatory compliance costs.
- Versatility: The powder coating curing process is versatile and adaptable to a wide range of substrates, including metal, plastic, wood, and composite materials. It can be tailored to meet specific application requirements and performance criteria for various industries and end-use applications.
In summary, the powder coating curing process is a critical step in achieving high-quality, durable finishes with excellent adhesion and performance characteristics. By understanding the stages and principles of curing, manufacturers can optimize their powder coating processes for enhanced productivity, efficiency, and product quality.
Powder Coating Pretreatment:
Powder coating pretreatment is a preparatory step that enhances the adhesion, corrosion resistance, and durability of powder coatings by properly cleaning and treating the substrate surface before the powder application. Here’s a detailed explanation of powder coating pretreatment:
1. Surface Cleaning: The pretreatment process begins with thorough surface cleaning to remove contaminants such as dirt, grease, oil, rust, and oxides from the substrate surface. Cleaning is typically done using chemical cleaners, alkaline degreasers, solvent wipes, or mechanical methods such as sandblasting or shot blasting. Proper surface cleaning ensures optimal adhesion and coating performance by eliminating barriers that can interfere with coating adhesion.
2. Surface Preparation: After cleaning, the substrate surface may undergo surface preparation techniques to improve adhesion and promote coating uniformity. Surface preparation methods include mechanical abrasion, etching, or chemical treatments to create a profile or roughness on the surface, providing a mechanical anchor for the powder coating. Abrasive blasting, phosphating, chromating, or conversion coating processes are commonly used to prepare metal substrates for powder coating.
3. Phosphating or Conversion Coating: Phosphating or conversion coating is a chemical treatment process that forms a thin, protective layer of phosphate or chromate compounds on the substrate surface. Phosphating enhances adhesion and corrosion resistance by promoting chemical bonding between the substrate and the powder coating. It also provides a clean and uniform surface for improved coating coverage and appearance.
4. Rinse and Drying: After surface cleaning and preparation, the substrate is rinsed with clean water to remove any remaining cleaning agents or contaminants. Proper rinsing prevents residue buildup and ensures the effectiveness of subsequent treatment steps. After rinsing, the substrate is dried thoroughly to remove moisture and prevent water spots or surface defects in the powder coating. Drying may be done using air blowers, ovens, or drying tunnels to achieve complete drying of the substrate surface.
5. Surface Activation (Optional): In some cases, the pretreatment process may include surface activation treatments to further enhance coating adhesion and performance. Surface activation methods include chemical primers, adhesion promoters, or plasma treatment techniques that modify the surface chemistry or morphology to improve bonding between the substrate and the powder coating. Surface activation treatments are particularly beneficial for challenging substrates such as plastics or non-metallic materials.
6. Quality Control and Inspection: Throughout the pretreatment process, quality control measures are implemented to ensure the effectiveness of surface cleaning, preparation, and treatment steps. Visual inspection, adhesion testing, surface profiling, and chemical analysis are performed to verify substrate cleanliness, adhesion strength, coating uniformity, and corrosion resistance. Any deviations or defects are identified and corrected to maintain the integrity of the pretreatment process and ensure optimal coating performance.
Advantages of Powder Coating Pretreatment:
- Improved Adhesion: Proper pretreatment enhances the adhesion of powder coatings to the substrate surface, ensuring durable and long-lasting adhesion under various environmental conditions.
- Corrosion Protection: Pretreatment processes such as phosphating or conversion coating provide corrosion resistance by forming a protective barrier on the substrate surface, preventing moisture and corrosive agents from reaching the underlying metal substrate.
- Enhanced Durability: Pretreatment improves the durability and performance of powder coatings by promoting chemical bonding, reducing coating defects, and enhancing resistance to chipping, scratching, and abrasion.
- Surface Cleanliness: Pretreatment removes contaminants and residues from the substrate surface, ensuring a clean and uniform surface for optimal coating adhesion and appearance.
- Environmental Compliance: Powder coating pretreatment is environmentally friendly and compliant with regulations, as it minimizes the use of hazardous chemicals, VOC emissions, and waste generation compared to traditional pretreatment methods such as chromating or solvent cleaning.
In summary, powder coating pretreatment plays a critical role in achieving high-quality, durable powder coating finishes with excellent adhesion, corrosion resistance, and performance characteristics. By properly cleaning, preparing, and treating the substrate surface, manufacturers can ensure the success and longevity of powder coating applications in various industries and applications.
Powder Coating Booth:
A powder coating booth is an essential piece of equipment used in the powder coating process to apply powder coatings onto workpieces efficiently and uniformly. Here’s an in-depth look at powder coating booths:
1. Enclosed Structure: A powder coating booth is typically an enclosed structure designed to contain overspray, minimize powder wastage, and create a controlled environment for powder application. It features walls, a ceiling, and a floor constructed of durable materials such as galvanized steel, stainless steel, or powder-coated aluminum to withstand the rigors of powder coating operations.
2. Extraction System: The booth is equipped with an extraction system, which consists of one or more fans or blowers that create negative pressure within the booth, drawing air and overspray particles away from the workpieces and towards a filtration system. The extraction system ensures proper containment and removal of overspray, preventing powder buildup and maintaining a clean working environment.
3. Filtration System: The extracted air and overspray particles pass through a filtration system, which typically includes filters or cartridges designed to capture and retain powder particles while allowing clean air to be discharged back into the environment or recirculated within the booth. Filtration systems may utilize various types of filter media, such as polyester, fiberglass, or high-efficiency particulate air (HEPA) filters, to achieve efficient powder capture and filtration.
4. Lighting and Visibility: Powder coating booths are equipped with lighting fixtures, such as fluorescent or LED lights, to provide adequate illumination and visibility for operators during the coating process. Proper lighting ensures uniform coverage, precise application, and quality control inspection of the powder coating onto the workpieces. Lighting fixtures are strategically positioned to minimize shadows and glare and optimize visibility across the booth.
5. Operator Accessibility: Powder coating booths are designed to facilitate operator accessibility and mobility for efficient powder application and coating inspection. They may feature access doors, entry ports, or removable panels that allow operators to enter the booth, load and unload workpieces, and perform coating tasks comfortably and safely. Booth configurations may vary depending on the size, layout, and workflow requirements of the powder coating operation.
6. Grounding System: To prevent electrostatic discharge and ensure safe powder application, powder coating booths are equipped with grounding systems that dissipate electrostatic charges from the workpieces and powder particles. Grounding devices, such as conductive flooring, grounding rods, or cables, provide a path for static electricity to flow safely to ground, reducing the risk of ignition or explosion in potentially hazardous environments.
7. Control Panel and Monitoring: Powder coating booths may include a control panel or interface where operators can monitor and adjust booth parameters such as airflow, filtration efficiency, lighting intensity, and extraction system operation. Control panels may feature digital displays, touchscreens, or manual switches for easy operation and control of booth functions, ensuring optimal performance and safety during powder coating operations.
Advantages of Powder Coating Booths:
- Efficient Powder Application: Powder coating booths provide a controlled environment for precise and uniform application of powder coatings onto workpieces, minimizing overspray, waste, and rework.
- Environmental Protection: By containing overspray and capturing powder particles, powder coating booths help protect the environment from air pollution, contamination, and waste generation associated with powder coating operations.
- Improved Quality Control: Powder coating booths facilitate quality control inspection by providing adequate lighting, visibility, and accessibility for operators to monitor coating application, coverage, and finish quality in real-time.
- Operator Safety: Powder coating booths enhance operator safety by containing powder particles, minimizing exposure to airborne contaminants, and incorporating safety features such as grounding systems, ventilation, and filtration to prevent hazardous conditions.
- Versatility and Customization: Powder coating booths are available in various sizes, configurations, and configurations to accommodate different part sizes, shapes, and production volumes. They can be customized with additional features such as conveyor systems, recovery systems, or process controls to meet specific application requirements and workflow needs.
In summary, powder coating booths are essential components of powder coating operations, providing a controlled environment for efficient, uniform, and environmentally friendly application of powder coatings onto workpieces. By incorporating advanced features and safety measures, powder coating booths contribute to the success, quality, and sustainability of powder coating businesses in diverse industrial applications.
Powder Coating Recovery System:
A powder coating recovery system is an integral part of a powder coating booth or line, designed to collect and reclaim oversprayed powder particles for reuse, thereby minimizing material waste and optimizing powder usage. Here’s an in-depth look at powder coating recovery systems:
1. Cyclone Separator: A cyclone separator is a primary component of powder coating recovery systems, responsible for separating oversprayed powder particles from the airflow within the booth or recovery chamber. The cyclone utilizes centrifugal force to separate heavier powder particles from the air stream, causing them to spiral downward and collect in a hopper or collection bin for reuse.
2. Filter Cartridges or Bags: After passing through the cyclone separator, the air stream containing finer powder particles is filtered through filter cartridges or bags to capture and retain the remaining powder particles. Filter cartridges or bags provide high-efficiency filtration and ensure clean air discharge or recirculation within the powder coating system. They may utilize various filter media such as polyester, fiberglass, or PTFE membrane to achieve optimal powder capture and filtration efficiency.
3. Reverse Pulse Cleaning System: To maintain the effectiveness of filter cartridges or bags and prevent powder buildup, powder coating recovery systems often incorporate a reverse pulse cleaning system. This system periodically releases compressed air pulses or blasts into the filter cartridges or bags, dislodging accumulated powder particles and restoring airflow and filtration efficiency. Reverse pulse cleaning helps extend the lifespan of filter media and ensures continuous operation of the recovery system with minimal downtime for maintenance.
4. Recovery Hopper or Collection System: Collected oversprayed powder particles are deposited into a recovery hopper or collection system located beneath the cyclone separator or filter cartridges/bags. The recovery hopper may feature a fluidized bed or vibration mechanism to facilitate powder fluidization and transfer for recycling. Powder recovered from the hopper can be reintroduced into the powder coating process for reuse, reducing material waste and production costs.
5. Sieving and Screening Equipment: To ensure the quality and consistency of reclaimed powder, powder coating recovery systems may include sieving or screening equipment to remove contaminants, agglomerates, or oversized particles from the recovered powder stream. Sieving or screening equipment separates fine powder particles from larger particles or foreign objects, resulting in a purified powder stream suitable for reuse in powder coating applications.
6. Powder Feed System: Reclaimed powder from the recovery system is reintroduced into the powder coating process through a powder feed system. The powder feed system delivers reclaimed powder to the powder coating gun or application equipment, where it is combined with fresh powder and electrostatically charged for uniform application onto workpieces. Powder feed systems may utilize gravity feed hoppers, fluidized beds, or pneumatic conveyors to transport and meter powder into the coating process.
7. Monitoring and Control: Powder coating recovery systems may incorporate monitoring and control features to optimize system performance, efficiency, and powder quality. Control systems may include sensors, gauges, and programmable logic controllers (PLCs) that monitor airflow, filter pressure, powder flow rates, and system status. Operators can adjust system parameters, set cleaning intervals, and troubleshoot issues to ensure smooth operation and maximum powder recovery efficiency.
Advantages of Powder Coating Recovery Systems:
- Reduced Material Waste: Powder coating recovery systems minimize material waste by reclaiming oversprayed powder particles for reuse, reducing powder consumption and disposal costs.
- Cost Savings: By recycling and reusing recovered powder, powder coating recovery systems help lower material costs and improve overall process economics, resulting in significant cost savings for powder coating operations.
- Environmental Benefits: Powder coating recovery systems promote environmental sustainability by reducing powder waste, energy consumption, and emissions associated with powder coating processes, contributing to a cleaner and greener manufacturing environment.
- Enhanced Efficiency: Recovery systems optimize powder usage and production efficiency by maximizing the utilization of powder particles and minimizing downtime for manual cleaning or maintenance, ensuring continuous operation and productivity.
- Improved Powder Quality: By filtering, sieving, and purifying recovered powder, recovery systems maintain powder quality and consistency, ensuring uniform coating application, adhesion, and finish quality on coated workpieces.
In summary, powder coating recovery systems play a vital role in optimizing powder usage, minimizing waste, and enhancing sustainability in powder coating operations. By reclaiming and recycling oversprayed powder, these systems help manufacturers achieve cost-effective, environmentally friendly, and high-quality powder coating finishes in diverse industrial applications.
Powder Coating Gun:
The powder coating gun is a fundamental tool used in powder coating operations to apply a uniform and consistent layer of powder coating onto workpieces. Here’s a detailed explanation of the powder coating gun:
1. Electrostatic Charging: The powder coating gun utilizes an electrostatic charging process to impart a positive charge to the powder particles as they are ejected from the gun’s nozzle. This electrostatic charge causes the powder particles to become attracted to the grounded workpiece, resulting in uniform coating deposition and adhesion.
2. Powder Delivery System: The powder coating gun features a powder delivery system that delivers a controlled flow of powder particles to the gun’s nozzle for application onto the workpiece. The powder is typically fed into the gun from a fluidized hopper, gravity feed hopper, or pressure pot, where it is fluidized, metered, and transported to the gun via air pressure or gravity.
3. Nozzle Design: The nozzle of the powder coating gun is designed to disperse the powder particles in a uniform and consistent spray pattern onto the workpiece surface. Nozzle designs may vary depending on the application requirements and powder characteristics, with options for adjustable spray patterns, fan widths, and powder flow rates to accommodate different part geometries and coating thicknesses.
4. Electrostatic Spray Process: During the powder coating process, the powder coating gun applies an electrostatic charge to the powder particles as they pass through the gun’s charging electrode. The charged powder particles are then accelerated and propelled towards the grounded workpiece, where they adhere to the surface due to electrostatic attraction. This electrostatic spray process ensures uniform coating coverage and adhesion, even on complex-shaped or irregular surfaces.
5. Control and Adjustability: Powder coating guns offer control and adjustability features that allow operators to customize coating parameters such as powder flow rate, spray pattern, and electrostatic charge intensity. Control knobs, switches, or digital interfaces on the gun provide operators with precise control over coating parameters, enabling them to optimize coating quality, thickness, and efficiency for different application requirements.
6. Ergonomic Design: Modern powder coating guns are ergonomically designed to enhance operator comfort, productivity, and safety during coating operations. They feature lightweight and balanced designs, ergonomic handles, and adjustable trigger controls that reduce operator fatigue and strain during prolonged use. Comfortable grip surfaces, trigger locks, and safety interlocks further enhance operator convenience and control.
7. Powder Recovery and Reclamation: Some powder coating guns may incorporate powder recovery and reclamation features that allow for efficient collection and reuse of oversprayed powder particles. These guns may include built-in suction or vacuum systems that capture overspray during the coating process, directing it back into the powder coating system for recycling and reuse, minimizing material waste and optimizing powder usage.
8. Maintenance and Cleaning: Proper maintenance and cleaning of the powder coating gun are essential to ensure consistent performance and prolong its lifespan. Guns should be regularly inspected, cleaned, and lubricated according to manufacturer recommendations to prevent clogging, buildup, or malfunction. Routine maintenance tasks may include nozzle cleaning, electrode inspection, and replacement of worn or damaged components.
Advantages of Powder Coating Guns:
- Uniform Coating Application: Powder coating guns provide uniform and consistent coating application, resulting in high-quality finishes with excellent coverage and adhesion.
- Efficient Powder Usage: By utilizing electrostatic charging and precise control features, powder coating guns optimize powder usage, minimizing waste and material costs.
- Versatility: Powder coating guns are versatile tools that can accommodate a wide range of part sizes, shapes, and geometries, making them suitable for diverse coating applications in various industries.
- Ergonomic and User-Friendly: With ergonomic designs and intuitive controls, powder coating guns are easy to use, comfortable to handle, and conducive to safe and efficient coating operations.
- Environmental Friendliness: Powder coating guns offer environmental benefits by eliminating the use of solvents, reducing VOC emissions, and promoting recycling and reuse of oversprayed powder particles, contributing to sustainable coating practices.
In summary, powder coating guns are essential equipment in powder coating operations, offering precise and efficient coating application with uniform coverage, adhesion, and finish quality. With their advanced features, versatility, and environmental benefits, powder coating guns play a critical role in achieving high-quality, durable powder coating finishes in various industrial applications.
Powder Coating Oven:
A powder coating oven is a specialized heating chamber used in the powder coating process to cure and finish coated workpieces by applying heat to the powder coating material, causing it to melt, flow, and cure into a durable and protective finish. Here’s an in-depth explanation of powder coating ovens:
1. Heating Chamber: A powder coating oven consists of a heating chamber or enclosure designed to accommodate coated workpieces and provide controlled heating conditions for the curing process. Ovens are typically constructed of insulated panels or walls made from materials such as steel, aluminum, or fiberglass to retain heat and minimize heat loss during operation.
2. Heating Elements: Heating elements, such as electric resistance heaters or gas-fired burners, are installed within the oven chamber to generate and distribute heat evenly throughout the enclosure. Heating elements may be located on the walls, ceiling, or floor of the oven, depending on the design and configuration of the oven system. They are controlled by temperature sensors and thermostats to maintain precise curing temperatures for optimal coating performance.
3. Temperature Control System: Powder coating ovens are equipped with temperature control systems that monitor and regulate the temperature inside the oven chamber during the curing process. Temperature controllers, thermocouples, and PID (proportional-integral-derivative) algorithms are used to maintain the desired curing temperature within tight tolerances, ensuring consistent and uniform curing of the powder coating across all coated surfaces.
4. Air Circulation System: To facilitate heat transfer and uniform curing of the powder coating, powder coating ovens feature air circulation systems that circulate heated air evenly throughout the oven chamber. Fans or blowers distribute hot air from the heating elements to all areas of the enclosure, ensuring uniform temperature distribution and curing across the coated workpieces. Proper air circulation minimizes hot spots, cold spots, and curing defects in the finished coating.
5. Insulation: Powder coating ovens are insulated to minimize heat loss and improve energy efficiency during the curing process. Insulation materials such as fiberglass, ceramic fiber, or mineral wool are installed within the oven walls, ceiling, and door to provide thermal resistance and prevent heat transfer to the surrounding environment. Effective insulation helps maintain stable curing temperatures, reduce energy consumption, and ensure consistent coating quality.
6. Conveyor System (Optional): In automated powder coating systems, powder coating ovens may incorporate conveyor systems to transport coated workpieces through the curing process continuously. Conveyor systems consist of conveyors, rollers, or chains that move workpieces into and out of the oven chamber at a controlled pace, allowing for high-volume production and efficient curing of large quantities of parts.
7. Cooling Zone (Optional): Some powder coating ovens may include a cooling zone or chamber at the exit end of the oven to gradually cool down cured workpieces to ambient temperature before removal. Cooling zones may feature ambient air blowers, water misting systems, or forced air circulation to accelerate cooling and stabilize the powder coating finish without causing thermal shock or distortion to the workpieces.
8. Safety Features: Powder coating ovens are equipped with safety features to protect operators, equipment, and workpieces during operation. Safety features may include temperature alarms, overheat protection, ventilation systems, and interlocks to prevent overheating, combustion, or exposure to hazardous fumes. Proper ventilation and exhaust systems ensure a safe working environment and compliance with regulatory standards for occupational health and safety.
Advantages of Powder Coating Ovens:
- Durable and Uniform Coating: Powder coating ovens provide controlled heating conditions for uniform curing of powder coatings, resulting in durable finishes with excellent adhesion, coverage, and appearance.
- High Efficiency: With efficient heating elements, insulation, and air circulation systems, powder coating ovens offer high energy efficiency and productivity, allowing for fast curing times and increased throughput in powder coating operations.
- Versatility: Powder coating ovens are versatile and adaptable to a wide range of part sizes, shapes, and coating requirements, making them suitable for diverse applications in industries such as automotive, aerospace, furniture, and appliances.
- Quality Control: Temperature control systems and monitoring features ensure precise curing temperatures and consistent coating quality, enabling manufacturers to achieve high standards of performance and reliability in their powder coating processes.
- Cost Savings: By minimizing rework, rejects, and material waste, powder coating ovens help reduce production costs and improve overall process economics, providing a cost-effective solution for finishing coated workpieces.
In summary, powder coating ovens are essential equipment in powder coating operations, providing the controlled heating conditions necessary for curing powder coatings into durable and high-quality finishes. With their advanced features, efficiency, and versatility, powder coating ovens play a critical role in achieving optimal coating performance and production efficiency in various industrial applications.
Powder Coating Batch System:
A powder coating batch system refers to a type of powder coating equipment setup designed for small-scale or batch production of coated parts. This system allows for efficient coating of individual or limited quantities of parts within a controlled environment. Here’s an in-depth explanation of the powder coating batch system:
1. Oven and Booth Integration: In a powder coating batch system, the powder coating booth and oven are typically integrated into a single unit or workstation. This integration allows for seamless transfer of coated parts from the booth to the oven for curing without the need for manual handling or transportation between separate equipment.
2. Booth Configuration: The powder coating booth in a batch system is configured to accommodate the size and shape of the parts being coated. It may feature adjustable spray nozzles, movable racks, or fixtures to hold the parts securely in place during the coating process. The booth is equipped with overspray collection and filtration systems to capture and contain powder overspray for recycling or disposal.
3. Powder Application: Powder coating batch systems utilize powder coating guns or manual application equipment to apply powder coatings onto the parts. Operators manually apply the powder coating using handheld guns or applicators, ensuring uniform coverage and adhesion on all surfaces of the parts. The powder is electrostatically charged to facilitate adhesion to the grounded parts.
4. Operator Control and Monitoring: Operators have control over the powder coating process, including powder flow rate, gun settings, and coating parameters. They monitor the coating process visually to ensure proper coverage and quality. Some batch systems may incorporate monitoring devices or sensors to measure powder thickness, coating adhesion, or cure temperature for quality assurance purposes.
5. Curing Process: After the parts are coated, they are transferred directly from the booth to the integrated oven for curing. The oven is preheated to the required curing temperature, and the parts are placed on racks or trays inside the oven for uniform heating and curing. The curing process typically involves heating the parts to a specific temperature for a predetermined time to melt and cure the powder coating, forming a durable finish.
6. Cooling and Unloading: Once the curing cycle is complete, the parts are allowed to cool inside the oven or in a designated cooling area before unloading. Cooling may be accelerated using ambient air circulation or fans to reduce cycle times. After cooling, operators remove the cured parts from the oven and inspect them for quality and adherence to specifications.
7. Quality Control and Finishing: Quality control checks are performed on the finished parts to ensure they meet the required standards for adhesion, appearance, and performance. Any defects or imperfections are addressed through touch-up or rework processes as needed. Finished parts may undergo additional finishing steps such as cleaning, masking, or packaging before shipment or assembly.
8. Flexibility and Efficiency: Powder coating batch systems offer flexibility and efficiency for small-scale or customized production runs. They allow for quick changeovers between different parts or colors, enabling manufacturers to meet varying customer requirements with minimal downtime. Batch systems are well-suited for job shops, prototyping, or specialized applications where flexibility and adaptability are paramount.
Advantages of Powder Coating Batch Systems:
- Customization: Batch systems allow for customized coating of individual parts or small batches, making them ideal for prototyping, custom work, or specialty applications.
- Quick Turnaround: Batch systems offer fast turnaround times for small production runs, enabling manufacturers to respond quickly to customer demands and reduce lead times.
- Cost-Effectiveness: Batch systems are cost-effective solutions for small-scale production, as they require less investment in equipment and infrastructure compared to larger automated systems.
- Versatility: Batch systems can accommodate a wide range of part sizes, shapes, and materials, providing flexibility for diverse coating applications in various industries.
- Quality Assurance: Operators have greater control over the coating process in batch systems, allowing for real-time monitoring and adjustment to ensure consistent quality and performance in finished parts.
In summary, powder coating batch systems offer a flexible and efficient solution for small-scale or customized powder coating operations. With their integrated design, operator control, and quick turnaround times, batch systems provide manufacturers with the versatility and agility to meet diverse coating requirements while maintaining high standards of quality and performance.
Powder Coating Conveyor System:
A powder coating conveyor system is a specialized type of equipment used in powder coating operations to transport coated parts through various stages of the coating process. These systems are designed to improve efficiency, productivity, and consistency in powder coating operations. Here’s an in-depth explanation of the powder coating conveyor system:
1. Conveyor Design: Powder coating conveyor systems consist of a series of interconnected conveyors, rollers, or belts arranged in a linear or loop configuration. The conveyor design may vary depending on the layout of the powder coating line, the size and shape of the parts being coated, and the production volume requirements. Common conveyor types include overhead conveyors, monorail conveyors, belt conveyors, and chain conveyors.
2. Part Fixturing and Hanging: Parts to be coated are fixtured or hung onto the conveyor system using hooks, racks, or fixtures designed to securely hold the parts in place during the coating process. Fixturing options may include adjustable hooks, clamps, or custom-designed carriers tailored to the specific requirements of the parts being coated. Proper part fixturing ensures uniform coating coverage and prevents parts from shifting or falling off the conveyor during transport.
3. Coating Application Zone: In the coating application zone, powder coating guns or automated applicators apply powder coatings onto the parts as they pass along the conveyor system. The conveyor speed and part spacing are carefully controlled to optimize coating coverage and ensure uniform application across all surfaces of the parts. Operators may adjust coating parameters such as powder flow rate, gun settings, and spray patterns to meet specific coating requirements.
4. Curing Oven Integration: Powder coating conveyor systems are often integrated with curing ovens to facilitate the curing process immediately after coating application. After being coated, the parts are transported directly from the coating application zone to the entrance of the curing oven via the conveyor system. This seamless integration minimizes handling and transfer time, streamlining the overall coating process and improving production efficiency.
5. Temperature Control and Monitoring: Curing ovens integrated into powder coating conveyor systems feature temperature control systems that regulate the oven temperature according to the curing requirements of the powder coatings being used. Temperature sensors and controllers monitor the oven temperature continuously to ensure precise control within the desired range. This temperature control and monitoring system ensures consistent curing results and prevents overcuring or undercuring of the powder coatings.
6. Cooling Zone (Optional): Some powder coating conveyor systems may include a cooling zone or chamber at the exit end of the curing oven to gradually cool down cured parts to ambient temperature before unloading. The cooling zone may utilize ambient air blowers, fans, or forced air circulation to accelerate cooling and stabilize the powder coating finish without causing thermal shock or distortion to the parts.
7. Automated Control and Integration: Powder coating conveyor systems can be equipped with automated control systems and integration capabilities to synchronize the operation of the conveyor, coating equipment, curing oven, and other components of the powder coating line. Programmable logic controllers (PLCs), sensors, and HMI (human-machine interface) panels enable operators to monitor and control the entire coating process from a centralized control station, ensuring seamless operation and coordination of system components.
8. Versatility and Customization: Powder coating conveyor systems offer versatility and customization options to accommodate a wide range of part sizes, shapes, and production requirements. Conveyor speed, part spacing, and fixturing configurations can be adjusted to optimize throughput, coating quality, and efficiency for different coating applications and production scenarios.
Advantages of Powder Coating Conveyor Systems:
- Increased Efficiency: Conveyor systems streamline the powder coating process by automating part transport, reducing manual handling, and improving production throughput and efficiency.
- Consistent Coating Quality: Conveyor systems ensure uniform coating application and curing across all parts, resulting in consistent coating quality, appearance, and performance.
- Space Optimization: By integrating multiple process stages into a single conveyor system, powder coating lines can be compactly designed, maximizing floor space utilization and efficiency in production facilities.
- Reduced Labor Costs: Automated conveyor systems minimize the need for manual labor in part handling and transport, reducing labor costs and improving operator safety and ergonomics.
- Scalability and Flexibility: Powder coating conveyor systems can be scaled up or modified to accommodate changing production volumes, part sizes, and coating requirements, providing flexibility and adaptability for future growth and expansion.
In summary, powder coating conveyor systems are essential equipment in powder coating operations, offering efficient, automated, and customizable solutions for transporting coated parts through the coating process. With their integration capabilities, control features, and performance advantages, conveyor systems play a critical role in optimizing productivity, quality, and efficiency in powder coating applications across various industries
Powder Coating Pretreatment System:
A powder coating pretreatment system is a crucial component of powder coating operations designed to prepare and clean substrates before the application of powder coatings. This system helps improve coating adhesion, corrosion resistance, and overall finish quality by removing contaminants, promoting surface adhesion, and enhancing coating performance. Here’s an in-depth explanation of the powder coating pretreatment system:
1. Cleaning Stage: The pretreatment process typically begins with a cleaning stage, where substrates are subjected to various cleaning methods to remove surface contaminants such as dirt, grease, oil, rust, and scale. Common cleaning methods include solvent cleaning, alkaline cleaning, acid cleaning, degreasing, and water-based cleaning. Cleaning solutions are applied using spray nozzles, brushes, or immersion tanks to ensure thorough removal of contaminants from the substrate surface.
2. Surface Activation: After cleaning, the substrate surface may undergo surface activation to improve adhesion and promote bonding between the substrate and the powder coating. Surface activation methods include mechanical abrasion, sandblasting, shot blasting, or chemical treatments such as phosphating, chromating, or etching. These processes roughen the surface and create microscopic features or chemical bonding sites that enhance the adhesion of the powder coating to the substrate.
3. Rinsing Stage: Following cleaning and surface activation, substrates are rinsed with clean water to remove residual cleaning agents, chemicals, and contaminants from the surface. Rinsing helps prevent contamination of subsequent process stages and ensures the effectiveness of subsequent pretreatment treatments. Water rinse tanks, spray rinsers, or immersion tanks may be used to thoroughly rinse the substrates before proceeding to the next pretreatment stage.
4. Conversion Coating: In some pretreatment systems, substrates undergo a conversion coating process to further improve adhesion and corrosion resistance properties. Conversion coatings chemically react with the substrate surface to form a thin, protective layer that enhances the bonding of the powder coating and provides additional corrosion protection. Common conversion coating methods include phosphating (iron phosphate, zinc phosphate), chromating (chromate conversion coating), and zirconium-based coatings.
5. Drying Stage: After pretreatment treatments are complete, substrates are dried to remove moisture and prepare them for powder coating application. Drying may be accomplished using forced air ovens, infrared heaters, or convection dryers that apply heat to evaporate water from the substrate surface. Proper drying ensures that substrates are free from moisture, contaminants, and surface defects before powder coating application.
6. Inspection and Quality Control: Throughout the pretreatment process, substrates are inspected for cleanliness, surface condition, and adherence to pretreatment specifications. Quality control checks may include visual inspection, adhesion testing, surface profile measurement, and chemical analysis to ensure that pretreatment treatments meet the required standards for coating performance and durability.
7. Environmental Considerations: Powder coating pretreatment systems must comply with environmental regulations and guidelines regarding the use, handling, and disposal of cleaning agents, chemicals, and wastewater. Pretreatment processes may incorporate environmentally friendly practices such as water recycling, solvent recovery, and waste minimization to reduce environmental impact and ensure compliance with regulatory requirements.
8. Process Optimization and Automation: Advanced powder coating pretreatment systems may incorporate process optimization and automation features to improve efficiency, consistency, and productivity. Automation technologies such as programmable logic controllers (PLCs), sensors, and feedback control systems enable precise control of process parameters, monitoring of process variables, and adjustment of pretreatment treatments in real-time to optimize performance and quality.
Advantages of Powder Coating Pretreatment Systems:
- Improved Coating Adhesion: Pretreatment systems enhance coating adhesion by removing surface contaminants, promoting surface adhesion, and improving the bonding between the substrate and the powder coating.
- Enhanced Corrosion Resistance: Conversion coatings provide additional corrosion protection by forming a protective layer on the substrate surface, increasing the durability and longevity of powder coating finishes.
- Consistent Finish Quality: Pretreatment systems ensure consistent and uniform surface preparation, resulting in high-quality powder coating finishes with excellent adhesion, appearance, and performance.
- Environmental Compliance: Pretreatment processes are designed to comply with environmental regulations and standards, minimizing environmental impact and ensuring safe handling and disposal of chemicals, wastewater, and waste products.
- Process Efficiency: Automated pretreatment systems improve process efficiency, productivity, and repeatability by optimizing process parameters, reducing manual labor, and minimizing cycle times, leading to increased throughput and reduced production costs.
In summary, powder coating pretreatment systems play a critical role in preparing substrates for powder coating applications, ensuring proper adhesion, corrosion resistance, and finish quality. With their cleaning, surface activation, conversion coating, and drying processes, pretreatment systems optimize substrate preparation and enhance the performance and durability of powder coating finishes in various industrial applications.
Powder Coating Reciprocator:
A powder coating reciprocator is a mechanical device used in powder coating operations to automate the movement of powder coating guns or applicators along multiple axes, typically horizontally and vertically, to ensure uniform and consistent coating application on workpieces. Here’s an in-depth explanation of the powder coating reciprocator:
1. Horizontal Movement: The powder coating reciprocator moves the powder coating gun horizontally along a predefined path or trajectory across the surface of the workpiece being coated. Horizontal movement ensures that the powder coating is applied evenly across the entire width of the workpiece, covering all areas with consistent thickness and coating quality.
2. Vertical Movement: In addition to horizontal movement, the powder coating reciprocator may also control the vertical movement of the powder coating gun, allowing it to adjust the distance between the gun and the workpiece surface. Vertical movement enables the coating of parts with varying heights or contours, ensuring uniform coating application even on complex-shaped or irregular surfaces.
3. Programmable Control: Powder coating reciprocators are equipped with programmable control systems that allow operators to define and customize coating parameters such as stroke length, speed, acceleration, and dwell time. These parameters can be adjusted to optimize coating coverage, thickness, and quality for different part geometries and coating requirements.
4. Precision and Accuracy: Powder coating reciprocators offer precise and accurate movement control, ensuring that the powder coating gun follows the specified path or trajectory with minimal deviation or error. This precision allows for consistent coating application and uniform coverage across all areas of the workpiece, reducing the risk of overcoating, undercoating, or coating defects.
5. Speed and Efficiency: By automating the movement of the powder coating gun, reciprocators improve the speed and efficiency of the coating process, allowing for faster throughput and increased productivity. Automated movement eliminates the need for manual handling and positioning of the coating gun, reducing labor costs and cycle times in powder coating operations.
6. Multi-Axis Movement: Some powder coating reciprocators feature multi-axis movement capabilities, allowing for simultaneous control of horizontal, vertical, and rotational movements of the coating gun. Multi-axis movement provides greater flexibility and versatility in coating applications, enabling the coating of parts with complex geometries or intricate details from multiple angles and orientations.
7. Integration with Conveyor Systems: Powder coating reciprocators can be integrated with conveyor systems to synchronize the movement of the coating gun with the movement of coated parts along the conveyor line. Integration ensures proper timing and alignment between the coating process and part transport, facilitating continuous and uninterrupted production flow in powder coating operations.
8. Safety Features: Powder coating reciprocators are equipped with safety features such as emergency stop buttons, safety interlocks, and protective guards to ensure operator safety during operation. Safety features prevent accidents, injuries, or damage to equipment by immediately halting movement in case of emergencies or abnormal conditions.
Advantages of Powder Coating Reciprocators:
- Uniform Coating Application: Reciprocators ensure uniform and consistent coating application across all areas of the workpiece, resulting in high-quality finishes with excellent coverage and adhesion.
- Increased Productivity: Automated movement of the coating gun improves process efficiency, throughput, and productivity, allowing for faster coating cycles and higher production volumes.
- Versatility and Flexibility: Reciprocators offer versatility and flexibility in coating applications, accommodating a wide range of part sizes, shapes, and geometries with customizable movement parameters.
- Precision Control: Precise movement control enables accurate positioning and coating of parts, minimizing wastage, rework, and coating defects in powder coating operations.
- Cost Savings: By reducing labor costs, cycle times, and material wastage, reciprocators contribute to cost savings and improved overall efficiency in powder coating operations.
In summary, powder coating reciprocators are essential equipment in powder coating operations, providing automated movement control to ensure uniform, efficient, and precise coating application on workpieces. With their programmable control, multi-axis movement, and integration capabilities, reciprocators optimize coating quality, productivity, and cost-effectiveness in various industrial applications.