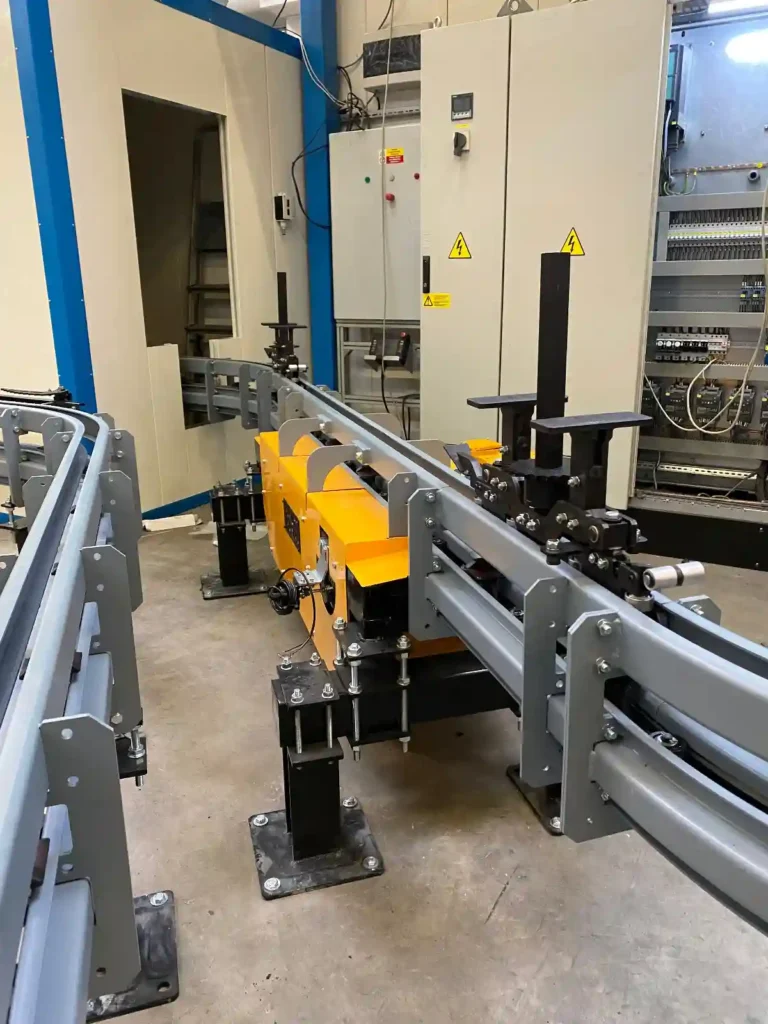
Designing a conveyor system for alloy wheels involves several considerations to ensure efficient and safe transportation of the wheels throughout the manufacturing process. Here’s a general guideline on how to design such a system:
- Initial Assessment: Understand the manufacturing process of alloy wheels including casting, machining, painting, and inspection. Identify the points where conveyors will be needed.
- Conveyor Types:
- Roller Conveyor: Suitable for moving heavy alloy wheels between different manufacturing stages.
- Belt Conveyor: Useful for transporting alloy wheels along inclines or declines.
- Overhead Conveyor: Ideal for moving alloy wheels through painting or coating processes without touching the ground.
- Size and Capacity: Determine the size and weight of the alloy wheels to select appropriate conveyor sizes and capacities. Ensure the conveyor system can handle the heaviest wheel expected in the manufacturing process.
- Material Handling: Consider the material of the conveyor belts or rollers. For alloy wheels, which can be heavy and have smooth surfaces, belts with high grip or roller coatings to prevent slippage are necessary.
- Control System: Implement sensors and control systems to regulate the speed and movement of the conveyor system. This can include start/stop sensors, speed controllers, and emergency stop mechanisms.
- Safety Features: Incorporate safety features such as guards, emergency stops, and safety interlocks to protect workers and prevent accidents.
- Space Optimization: Design the layout of the conveyor system to optimize floor space and facilitate smooth flow of alloy wheels between manufacturing stages.
- Maintenance Accessibility: Ensure easy access to all parts of the conveyor system for maintenance and repair tasks.
- Integration with Manufacturing Equipment: Coordinate with suppliers of casting machines, machining centers, painting booths, and inspection stations to seamlessly integrate the conveyor system into the overall manufacturing process.
- Testing and Optimization: Before full deployment, conduct thorough testing of the conveyor system to identify any issues or inefficiencies. Optimize the system based on the test results to ensure smooth operation.
- Scalability: Design the conveyor system with scalability in mind to accommodate future increases in production capacity or changes in manufacturing processes.
- Energy Efficiency: Consider energy-efficient components and designs to minimize energy consumption and reduce operating costs.
- Regulatory Compliance: Ensure the conveyor system complies with relevant safety and environmental regulations.
- Training: Provide comprehensive training to operators and maintenance personnel on the operation and maintenance of the conveyor system.
By carefully considering these factors and designing a conveyor system tailored to the specific requirements of alloy wheel manufacturing, you can optimize efficiency, safety, and productivity in the production process.
Conveyor System for Alloy Wheels
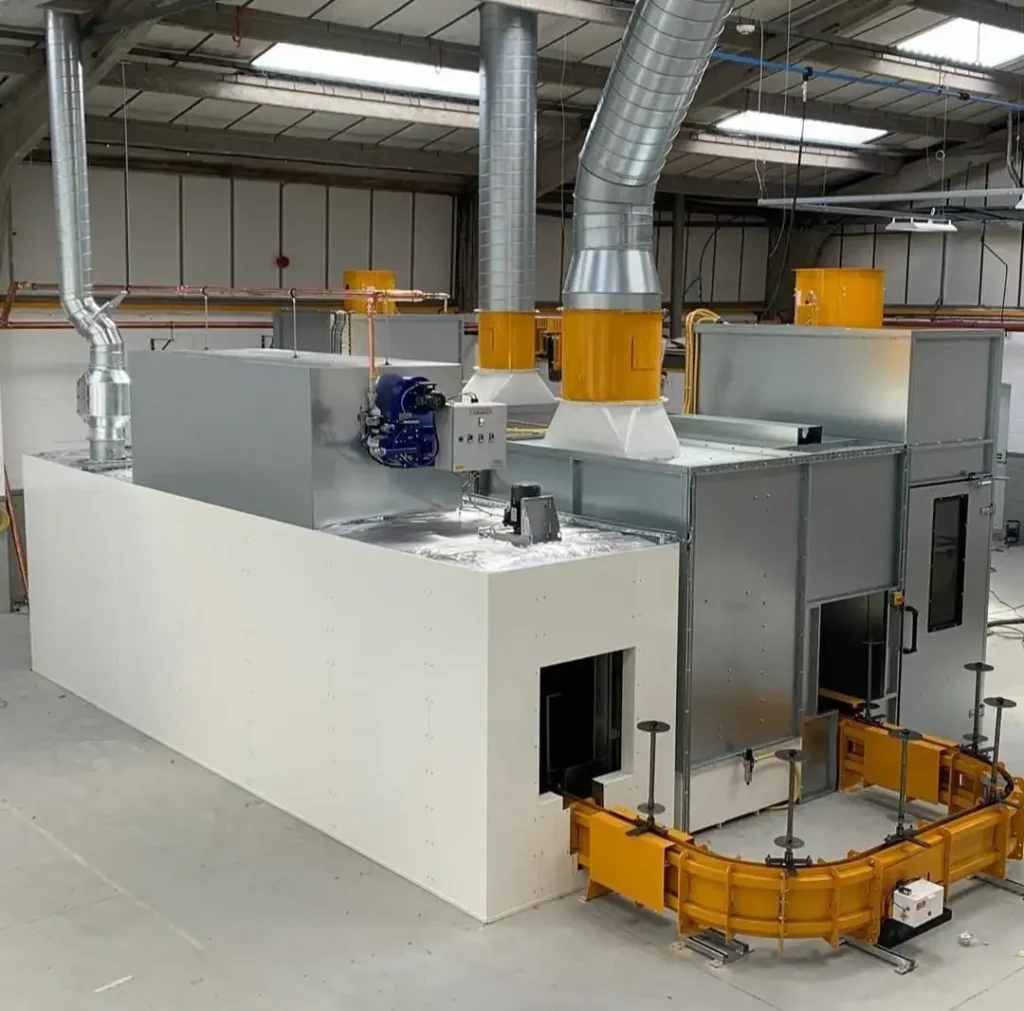
For transporting alloy wheels in a manufacturing facility, several types of conveyors can be utilized based on the specific requirements of the process. Here are some conveyor types commonly used for handling alloy wheels:
- Roller Conveyor:
- Description: Roller conveyors consist of rollers mounted on a frame, allowing items to be moved along the conveyor by the force of gravity or by a motorized system.
- Application: Roller conveyors are suitable for transporting heavy alloy wheels between different manufacturing stages, such as moving them from casting to machining or from machining to painting.
- Belt Conveyor:
- Description: Belt conveyors use belts to transport items along a continuous loop of material, offering a smooth and consistent movement.
- Application: Belt conveyors can be useful for moving alloy wheels along inclines or declines, as well as for transporting them through processes where a smooth and continuous motion is required, such as painting or coating.
- Overhead Conveyor:
- Description: Overhead conveyors are mounted above the production floor, typically utilizing either chains or enclosed tracks to move items along a specified path.
- Application: Overhead conveyors are ideal for transporting alloy wheels through processes such as painting or coating, where it’s important to keep the wheels off the ground to prevent contamination or damage.
- Slat Conveyor:
- Description: Slat conveyors use slats or plates to transport items along a path, providing a sturdy surface for heavy loads.
- Application: Slat conveyors can be suitable for moving alloy wheels through processes where a rugged and durable conveyor surface is necessary, such as during casting or heavy machining operations.
- Power-and-Free Conveyor:
- Description: Power-and-free conveyors consist of two tracks—one for moving the items (power track) and another for controlling the movement (free track), allowing for accumulation and indexing of items along the conveyor line.
- Application: Power-and-free conveyors can be beneficial for transporting alloy wheels through complex manufacturing processes with multiple assembly stations or where buffering and sequencing of wheels are required.
- Gravity Conveyor:
- Description: Gravity conveyors utilize a downward slope to move items along the conveyor without the need for external power, relying on gravity for movement.
- Application: Gravity conveyors can be employed for simple and cost-effective transportation of alloy wheels over short distances or between processes with minimal elevation changes.
Choosing the most suitable conveyor type for handling alloy wheels depends on factors such as the weight and size of the wheels, the layout of the manufacturing facility, the required throughput, and the specific processes involved. Integrating a combination of conveyor types may also be necessary to optimize efficiency and productivity in alloy wheel manufacturing.
Roller Conveyor
A roller conveyor system is a popular choice for transporting heavy items such as alloy wheels within manufacturing facilities. Here’s a more detailed look at roller conveyors and how they can be applied specifically to handling alloy wheels:
Roller Conveyor Overview:
- Design: Roller conveyors consist of a series of cylindrical rollers mounted on a frame. The rollers can be either powered by a motorized system or left free-spinning, relying on gravity or external force to move items along the conveyor.
- Types:
- Gravity Roller Conveyor: Relies on the weight of the items being conveyed and gravity to move them along the conveyor.
- Powered Roller Conveyor: Utilizes motorized rollers to drive the movement of items along the conveyor, providing more control over speed and direction.
- Versatility: Roller conveyors are versatile and can be customized to fit various layouts and requirements. They can handle a wide range of loads, including heavy and irregularly shaped items like alloy wheels.
- Low Friction: Roller conveyors typically have low rolling resistance, making them suitable for transporting heavy loads with minimal effort.
- Modularity: Roller conveyor systems are modular, allowing for easy installation, modification, and expansion as manufacturing needs change.
Application to Alloy Wheels:
- Transportation between Manufacturing Stages:
- Roller conveyors can efficiently move alloy wheels between different stages of the manufacturing process, such as transferring them from casting to machining or from machining to painting.
- Buffering and Accumulation:
- In cases where there might be variations in production rates between manufacturing stages, roller conveyors can provide buffering and accumulation zones to ensure a smooth flow of alloy wheels through the process.
- Loading and Unloading Stations:
- Roller conveyors can be integrated with loading and unloading stations where alloy wheels are placed onto or removed from the conveyor system, either manually or using automated equipment.
- Integration with Inspection Stations:
- Inspection stations can be positioned along the roller conveyor line to check the quality of alloy wheels as they move through the manufacturing process.
- Painting and Coating Processes:
- Roller conveyors can be utilized in painting or coating processes, facilitating the movement of alloy wheels through spray booths or drying ovens.
- Customization for Specific Requirements:
- Roller conveyor systems for handling alloy wheels can be customized with features such as adjustable roller spacing, guardrails, and special coatings to ensure the safe and efficient transportation of the wheels.
Overall, roller conveyors offer a robust and reliable solution for transporting alloy wheels within manufacturing facilities, providing flexibility, efficiency, and control over the production process.
Application to Alloy Wheels
When applying roller conveyors specifically to handling alloy wheels within a manufacturing setting, there are several considerations and applications to keep in mind:
- Transportation between Manufacturing Stages:
- Roller conveyors are essential for transferring alloy wheels between different stages of the manufacturing process. This can include moving wheels from casting to machining, machining to painting, painting to inspection, and so on.
- Loading and Unloading Stations:
- Roller conveyors can be integrated with loading and unloading stations where alloy wheels are placed onto or removed from the conveyor system. This could involve manual loading/unloading or automated systems such as robotic arms.
- Buffering and Accumulation:
- Roller conveyors can create buffering and accumulation zones to manage variations in production rates between different stages of manufacturing. This ensures a smooth flow of alloy wheels through the process and prevents bottlenecks.
- Integration with Inspection Stations:
- Inspection stations can be strategically positioned along the roller conveyor line to check the quality of alloy wheels as they move through the manufacturing process. Defective wheels can be diverted for rework or rejection.
- Painting and Coating Processes:
- Roller conveyors are commonly used in painting or coating processes for alloy wheels. They facilitate the movement of wheels through spray booths, drying ovens, and curing stations, ensuring uniform coating application.
- Customization for Alloy Wheel Characteristics:
- Roller conveyor systems can be customized to accommodate the specific characteristics of alloy wheels. This includes considerations such as wheel size, weight, surface finish, and any special handling requirements.
- Alignment and Orientation:
- Specialized roller conveyor systems can be designed to ensure proper alignment and orientation of alloy wheels as they move through the manufacturing process. This is particularly important for precision machining and assembly operations.
- Safety Features:
- Incorporating safety features such as guards, emergency stops, and sensors is crucial to protect workers and prevent accidents, especially considering the weight and potential hazards associated with alloy wheels.
- Maintenance and Durability:
- Roller conveyors should be designed for ease of maintenance and durability to withstand the demands of continuous operation in a manufacturing environment. This includes using high-quality materials and components resistant to corrosion and wear.
- Integration with Overall Manufacturing Layout:
- The design of roller conveyor systems should consider the overall layout of the manufacturing facility to optimize space utilization, minimize material handling distances, and streamline the production flow for efficiency.
By carefully considering these applications and requirements, roller conveyors can effectively facilitate the handling and transportation of alloy wheels throughout the manufacturing process, contributing to improved productivity, quality, and safety.
Transportation between Manufacturing Stages
Transportation between manufacturing stages is a critical application of roller conveyors in handling alloy wheels. Here’s how roller conveyors facilitate the smooth movement of alloy wheels between different stages of the manufacturing process:
- Casting to Machining:
- After the alloy wheels are cast, roller conveyors can transport them from the casting area to machining stations where they are shaped, drilled, and finished to meet specifications.
- Machining to Painting/Coating:
- Once machining is complete, roller conveyors transfer the wheels to the painting or coating area. This may involve cleaning and surface preparation steps before applying the paint or coating.
- Painting/Coating to Curing:
- After painting or coating, roller conveyors transport the wheels through curing ovens or drying chambers to set the finish and ensure it adheres properly to the alloy surface.
- Curing to Inspection:
- Following curing, alloy wheels move along roller conveyors to inspection stations where they undergo quality checks for defects, dimensional accuracy, and surface finish.
- Inspection to Packaging:
- Alloy wheels that pass inspection are conveyed to packaging stations where they are prepared for shipment. This may involve wrapping, boxing, labeling, and palletizing the wheels for distribution.
- Rejection or Rework Loop:
- In cases where alloy wheels do not meet quality standards during inspection, roller conveyors provide a loopback route for diverting defective wheels to rework areas or rejection bins.
- Interstage Buffering:
- Roller conveyors can incorporate buffering zones between manufacturing stages to accommodate variations in production rates and prevent bottlenecks. This ensures a continuous flow of wheels through the process.
- Integration with Automated Systems:
- Roller conveyors can be seamlessly integrated with automated systems such as robotic arms, sensors, and PLC controls to optimize the flow of alloy wheels between manufacturing stages and improve efficiency.
- Customized Conveyor Design:
- Depending on the specific requirements of the manufacturing process, roller conveyors can be customized with features such as adjustable roller spacing, diverter gates, and accumulation zones to suit the handling needs of alloy wheels.
- Safety Measures:
- Throughout transportation between manufacturing stages, safety measures such as guardrails, emergency stops, and interlocks are implemented to protect workers and prevent accidents involving heavy alloy wheels.
By efficiently transporting alloy wheels between manufacturing stages, roller conveyors play a crucial role in streamlining the production process, reducing cycle times, and ensuring consistent quality in alloy wheel manufacturing.
Loading and Unloading Stations
Loading and unloading stations are key components in a manufacturing facility where alloy wheels are handled. These stations ensure smooth integration of alloy wheels into and out of the manufacturing process. Roller conveyors play a vital role in facilitating loading and unloading operations. Here’s how loading and unloading stations are utilized:
Loading Stations:
- Manual Loading:
- In some cases, workers manually load alloy wheels onto the roller conveyor system. This may involve lifting wheels from pallets or carts and placing them onto the conveyor.
- Automated Loading:
- Automated loading systems, such as robotic arms or pick-and-place mechanisms, can be integrated with the roller conveyor system to load alloy wheels onto the conveyor. This improves efficiency and reduces manual labor.
- Loading Chutes:
- Loading chutes or ramps may be installed at loading stations to facilitate the transition of alloy wheels from static storage areas or pallets onto the moving roller conveyor. These chutes ensure a smooth transfer without causing damage to the wheels.
- Orientation Control:
- Loading stations can incorporate mechanisms to ensure proper orientation of alloy wheels before they are placed onto the roller conveyor. This ensures that wheels are aligned correctly for downstream processes.
- Quality Checks:
- Before loading alloy wheels onto the conveyor system, operators may perform visual inspections or quality checks to ensure that the wheels meet the required standards for the next manufacturing stage.
Unloading Stations:
- Manual Unloading:
- At manual unloading stations, workers remove alloy wheels from the roller conveyor system. This may involve transferring wheels to carts, pallets, or other transport containers for further processing or packaging.
- Automated Unloading:
- Automated unloading systems, such as robotic arms or conveyor diverters, can be employed to automatically remove alloy wheels from the roller conveyor system. This improves efficiency and reduces manual labor.
- Diverters and Sorters:
- Unloading stations may incorporate diverters or sorters to direct alloy wheels to different downstream processes based on predetermined criteria. For example, wheels may be sorted based on size, color, or quality.
- Integration with Downstream Equipment:
- Unloading stations are often integrated with downstream equipment such as machining centers, painting booths, or inspection stations. This ensures a seamless transition of alloy wheels from the conveyor system to the next stage of the manufacturing process.
- Packaging Preparation:
- At certain unloading stations, alloy wheels may be prepared for packaging or shipment. This may involve wrapping, labeling, or palletizing the wheels before they are transferred to the packaging area.
- Quality Checks:
- Before alloy wheels are unloaded from the conveyor system, operators may conduct final quality checks or inspections to ensure that the wheels meet the required standards for the next manufacturing stage or shipment.
By effectively managing loading and unloading operations, roller conveyor systems contribute to the overall efficiency, productivity, and quality of alloy wheel manufacturing processes.
Buffering and Accumulation
Buffering and accumulation zones are critical features in a manufacturing environment where there might be variations in production rates or processing times between different stages of the manufacturing process. Roller conveyors can be strategically designed to incorporate buffering and accumulation capabilities, ensuring a smooth flow of alloy wheels through the production line. Here’s how buffering and accumulation zones are utilized with roller conveyors:
Buffering Zones:
- Purpose:
- Buffering zones are designed to temporarily store alloy wheels during peak production periods or when there’s a delay at downstream processes. They help prevent disruptions in the production flow and minimize the risk of bottlenecks.
- Location:
- Buffering zones are typically positioned between manufacturing stages where there’s a potential for uneven production rates or processing times. This allows for the creation of a buffer to absorb fluctuations in the production process.
- Design:
- Buffering zones can be implemented by creating sections of the roller conveyor line where alloy wheels can accumulate without hindering the movement of wheels in the upstream stages. These zones may consist of extended conveyor sections or accumulation beds.
- Control:
- Buffering zones are controlled using sensors, actuators, or programmable logic controllers (PLCs) to monitor the level of inventory and regulate the flow of alloy wheels. When downstream processes are ready to receive more wheels, wheels are released from the buffer zone.
- Benefits:
- Buffering zones help optimize the overall efficiency of the manufacturing process by ensuring a continuous flow of alloy wheels, even during fluctuations in production rates. They also provide flexibility to handle unexpected delays or disruptions.
Accumulation Zones:
- Purpose:
- Accumulation zones are designed to temporarily hold alloy wheels as they wait for processing at downstream stages. Unlike buffering zones, accumulation zones are intended for longer-term storage of wheels until they can be processed further.
- Configuration:
- Accumulation zones are configured to allow alloy wheels to accumulate without interrupting the movement of wheels upstream. This may involve creating gaps between rollers or using specialized accumulation conveyors that can hold wheels in place.
- Control:
- Accumulation zones are controlled using sensors and control systems that regulate the spacing between alloy wheels. Wheels are allowed to accumulate in the zone until there’s space available for them to move forward.
- Flexibility:
- Accumulation zones provide flexibility in managing the flow of alloy wheels through the production line, allowing for adjustments to accommodate changes in production schedules or unexpected downtime at downstream processes.
- Preventing Jams:
- By allowing alloy wheels to accumulate in a controlled manner, accumulation zones help prevent jams and blockages in the conveyor system, ensuring smooth operation and minimizing the risk of damage to the wheels or equipment.
By incorporating buffering and accumulation zones into roller conveyor systems, manufacturers can improve the overall efficiency, flexibility, and reliability of their alloy wheel manufacturing processes, enabling smoother production flow and better resource utilization.
Integration with Inspection Stations
Integration with inspection stations is crucial in ensuring the quality of alloy wheels throughout the manufacturing process. Roller conveyors play a key role in facilitating the movement of wheels through inspection stations efficiently and effectively. Here’s how integration with inspection stations works:
1. Positioning of Inspection Stations:
- Inspection stations are strategically placed along the roller conveyor line at critical points in the manufacturing process, such as after machining, painting/coating, or assembly.
- Each inspection station is equipped with the necessary tools, equipment, and personnel to conduct specific quality checks on the alloy wheels.
2. Roller Conveyor Design:
- Roller conveyors leading to and from inspection stations are designed to accommodate the flow of alloy wheels seamlessly.
- The conveyor system should ensure a smooth and steady movement of wheels to prevent damage or disruption during inspection.
3. Controlled Speed and Stop:
- Roller conveyors can be equipped with sensors and control systems to regulate the speed of the conveyor as wheels approach the inspection station.
- Automatic stopping mechanisms can be activated to halt the movement of wheels precisely at the inspection station for thorough examination.
4. Inspection Procedures:
- At the inspection station, trained personnel perform visual inspections and use specialized equipment to check various aspects of the alloy wheels, including dimensional accuracy, surface finish, structural integrity, and adherence to specifications.
- Automated inspection technologies such as machine vision systems may also be integrated with the conveyor system to enhance inspection efficiency and accuracy.
5. Decision Making:
- Based on the inspection results, decisions are made regarding the acceptance, rejection, or further processing of alloy wheels.
- Defective wheels may be flagged for rework, repair, or scrap, while compliant wheels proceed to the next stage of the manufacturing process.
6. Integration with Sorting and Diverting Systems:
- Roller conveyors can be integrated with sorting and diverting systems to route alloy wheels based on inspection outcomes.
- Wheels that pass inspection continue along the main conveyor line, while those requiring further attention are diverted to designated areas for rework or rejection.
7. Data Logging and Traceability:
- Inspection stations may include systems for logging inspection results and tracking the status of each alloy wheel throughout the production process.
- This data helps maintain traceability, identify trends in quality issues, and support continuous improvement efforts.
8. Safety Measures:
- Safety features such as guards, emergency stops, and interlocks are implemented to protect personnel and equipment at inspection stations.
- Workers are trained on proper inspection procedures and safety protocols to ensure a safe working environment.
By integrating roller conveyors with inspection stations, manufacturers can maintain stringent quality standards for alloy wheels, identify and address defects in a timely manner, and uphold customer satisfaction. This integration enhances overall process efficiency and contributes to the production of high-quality products.
Painting and Coating Processes
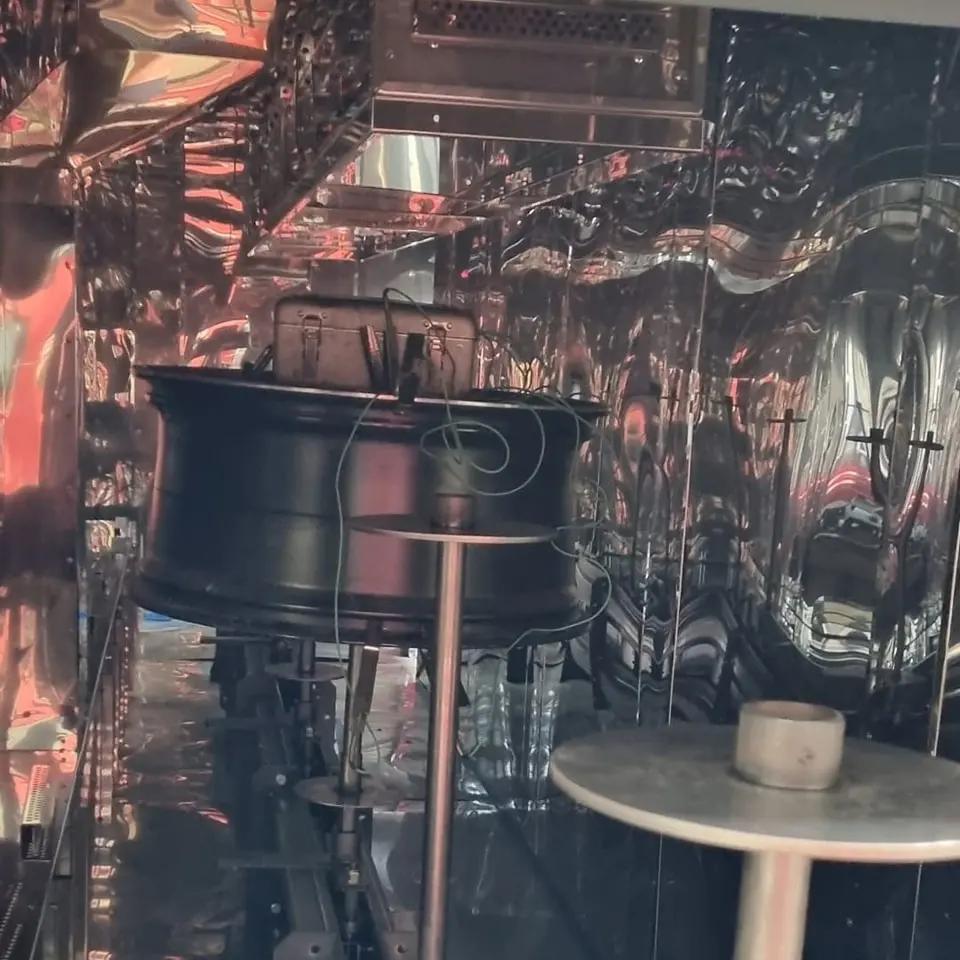
Integration of roller conveyors with painting and coating processes is essential for efficiently handling alloy wheels during surface finishing operations. Here’s how roller conveyors are utilized in the painting and coating processes for alloy wheels:
1. Pre-treatment:
- Before painting or coating, alloy wheels may undergo pre-treatment processes such as cleaning, degreasing, and surface preparation. Roller conveyors transport the wheels through pre-treatment stations where these processes are carried out.
2. Painting/Coating Application:
- Roller conveyors carry alloy wheels into the painting or coating booths where automated or manual application of paint or coating takes place. Conveyors ensure a smooth and consistent movement of wheels through the application area.
- Powder coating equipment is used to apply a thin layer of powder over a metal surface. This type of coating is applied by an electrostatic process and is a very popular method for finishing metal parts.
- This type of equipment can be divided into two main categories: automatic and manual. Automatic booths are more popular because they provide better production rates, but they are also more expensive.
- A powder booth is an enclosure in which the powder-coating process takes place. Powder-coating equipment includes an oven where the parts are heated to activate the powder, a gun that sprays or brushes on the powder, a conveyor belt that moves parts through the oven, and cartridge-type guns for applying thicker coatings with less overspray.
- Powder coating is a technique that is used to provide a finish to metal parts. This technique has been in use for many years and it is still one of the most popular techniques today.
- Powder coating equipment consists of booths, ovens, guns, machines, lines and conveyors. A booth can be either automatic or manual. An automatic booth is more expensive than a manual booth but it is also faster and more efficient.
3. Drying/Curing:
- After painting or coating, alloy wheels are conveyed through drying or curing ovens to cure the applied paint or coating. Roller conveyors facilitate the movement of wheels through the ovens at controlled speeds and temperatures for proper curing.
4. Inspection:
- Roller conveyors transport alloy wheels to inspection stations after the drying/curing process. Visual inspections and quality checks are performed to ensure the applied paint or coating meets the required standards.
5. Cooling and Handling:
- Once the inspection is completed, roller conveyors may transport alloy wheels through cooling zones to reduce their temperature before further handling or packaging. This helps prevent damage to the wheels and ensures proper curing of the paint or coating.
6. Rejection/Reprocessing:
- If alloy wheels fail inspection due to defects in the paint or coating, roller conveyors can divert them to rework or rejection areas for necessary touch-ups, repairs, or stripping and recoating.
7. Packaging and Shipping:
- Roller conveyors can deliver finished alloy wheels to packaging stations where they are prepared for shipment. This may involve wrapping, labeling, and palletizing the wheels before they are transferred to storage or shipping areas.
8. Conveyor Design Considerations:
- Roller conveyors used in painting and coating processes must be designed to withstand the potentially harsh environments of these operations, including exposure to paint overspray and chemical fumes.
- Conveyor rollers and frames may be coated with corrosion-resistant materials to ensure longevity and minimize maintenance requirements.
9. Integration with Painting Equipment:
- Roller conveyors are integrated with painting equipment such as spray booths, drying ovens, and curing chambers to ensure seamless operation and efficient material flow throughout the painting and coating process.
10. Safety Measures:
- Safety features such as guards, emergency stops, and interlocks are implemented to protect workers and prevent accidents during painting and coating operations. Proper ventilation systems are also essential to maintain air quality and worker safety.
By integrating roller conveyors with painting and coating processes, manufacturers can achieve consistent and high-quality surface finishes on alloy wheels while optimizing production efficiency and throughput. This integration ensures smooth material flow, reduces handling errors, and minimizes production downtime.
Pre-treatment of Alloy wheels on a conveyor
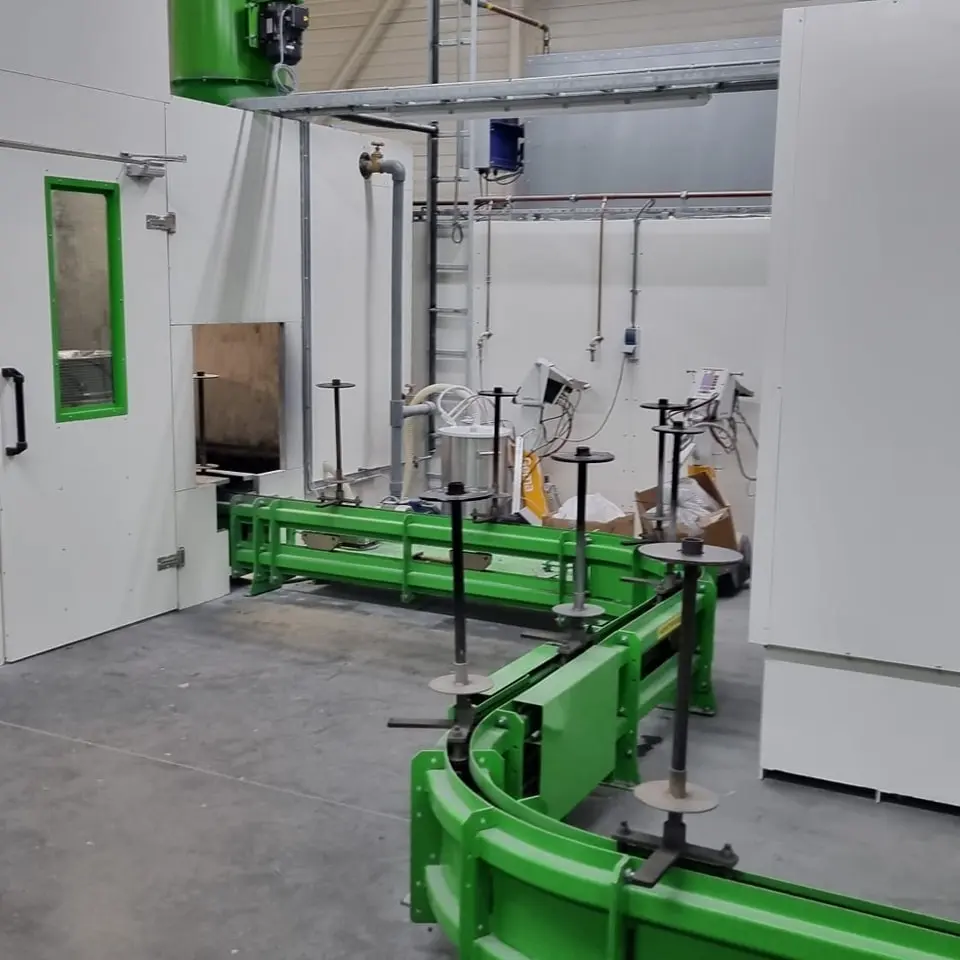
Pre-treatment of alloy wheels is a crucial step in the painting and coating process to ensure proper adhesion and durability of the applied finish. Here’s how pre-treatment is typically conducted on alloy wheels using a conveyor system:
1. Cleaning:
- Alloy wheels are transported on roller conveyors through a cleaning station where they undergo thorough cleaning to remove dirt, grease, oil, and other contaminants from the surface.
- The cleaning process may involve the use of chemical cleaners, high-pressure water jets, or ultrasonic cleaning baths, depending on the level of contamination and the specific requirements of the application.
2. Degreasing:
- After cleaning, alloy wheels are conveyed through a degreasing station where any residual oils or grease are removed from the surface.
- Degreasing agents are applied to the wheels either through spray nozzles or immersion tanks to ensure complete removal of contaminants that could interfere with the adhesion of the coating.
3. Surface Preparation:
- Following cleaning and degreasing, alloy wheels may undergo surface preparation to enhance the adhesion of the coating.
- This may involve processes such as etching, sandblasting, or chemical treatment to create a roughened surface texture or promote chemical bonding with the coating material.
4. Rinse:
- After surface preparation, alloy wheels are conveyed through a rinsing station to remove any remaining cleaning or treatment chemicals from the surface.
- The rinse may involve spraying the wheels with clean water or immersion in a rinse bath to ensure thorough removal of residues.
5. Drying:
- Once rinsed, alloy wheels are transported through a drying station to remove moisture from the surface before proceeding to the painting or coating process.
- Drying can be accomplished using hot air blowers, infrared heaters, or other drying methods to ensure the wheels are completely dry and free of moisture.
6. Quality Control:
- Throughout the pre-treatment process, quality checks may be performed to ensure that each alloy wheel meets the required cleanliness and surface condition standards before proceeding to the next stage of production.
7. Conveyor Design Considerations:
- The conveyor system used for pre-treatment of alloy wheels must be designed to withstand exposure to cleaning chemicals, water, and high temperatures.
- Conveyor rollers and frames should be constructed from corrosion-resistant materials to ensure longevity and minimize maintenance requirements.
8. Integration with Painting/Coating Process:
- The pre-treatment process is seamlessly integrated with the subsequent painting or coating process to ensure proper adhesion and durability of the applied finish.
- Roller conveyors facilitate the smooth transition of alloy wheels from the pre-treatment stations to the painting or coating booths, ensuring efficient material flow and production throughput.
By utilizing a conveyor system for pre-treatment of alloy wheels, manufacturers can ensure that the wheels are properly cleaned, degreased, and prepared for painting or coating, ultimately resulting in high-quality finished products with excellent durability and appearance.
Painting/Coating Application of Alloy wheels on a conveyor
Painting and coating application of alloy wheels on a conveyor involves a systematic process to ensure consistent and high-quality finishes. Here’s how this process typically unfolds using a conveyor system:
1. Preparation:
- Alloy wheels are transported on roller conveyors to the painting or coating area. Before entering the application zone, the wheels may undergo pre-treatment processes such as cleaning, degreasing, and surface preparation to ensure optimal adhesion of the paint or coating.
2. Application Booths:
- Roller conveyors carry alloy wheels into enclosed application booths where the paint or coating is applied. These booths are designed to contain overspray and maintain a controlled environment for optimal coating application.
- Depending on the specific requirements and equipment, the painting or coating may be applied manually by operators using spray guns, or it may be automated using robotic systems for precision and consistency.
3. Spraying:
- Alloy wheels move through the painting or coating booths on the roller conveyors, where they are exposed to a fine mist or spray of paint or coating material. The application process ensures even coverage of the entire wheel surface.
4. Coating Thickness Control:
- In automated systems, sensors or cameras may be integrated with the conveyor system to monitor and control the thickness of the applied paint or coating. This ensures uniformity and adherence to specifications.
5. Drying/Curing:
- After the paint or coating is applied, alloy wheels are transported through drying or curing ovens on the roller conveyors. These ovens facilitate the drying or curing process to ensure proper adhesion and durability of the finish.
- Drying ovens may use heat, infrared radiation, or air circulation to accelerate the drying process and remove solvent or water from the applied paint or coating.
6. Quality Control:
- Throughout the painting or coating process, quality checks may be performed to inspect the finish for defects such as runs, sags, or uneven coverage. Any defects detected are addressed before the wheels proceed further in the production process.
7. Cooling:
- Once the drying or curing process is complete, alloy wheels are transported through cooling zones on the roller conveyors to reduce their temperature before handling or packaging. This prevents damage to the finish and ensures it sets properly.
8. Conveyor Design Considerations:
- Roller conveyors used in the painting or coating application process must be designed to withstand exposure to paint overspray, chemicals, and high temperatures.
- Conveyor rollers and frames should be constructed from corrosion-resistant materials to ensure durability and minimize maintenance requirements.
9. Integration with Downstream Processes:
- After painting or coating, alloy wheels are conveyed to downstream processes such as inspection, assembly, or packaging. Roller conveyors facilitate the smooth transition of wheels between production stages, ensuring efficient material flow.
By utilizing a conveyor system for painting or coating application of alloy wheels, manufacturers can achieve consistent and high-quality finishes while optimizing production efficiency and throughput. This integration ensures smooth material flow, reduces handling errors, and minimizes production downtime.
Drying/Curing of Alloy wheels on a conveyor
Drying and curing of alloy wheels after painting or coating is a critical step to ensure the durability and quality of the finish. Roller conveyors are commonly used to transport alloy wheels through drying and curing ovens in a controlled manner. Here’s how the drying/curing process typically occurs on a conveyor system:
1. Transition to Drying/Curing Area:
- After the painting or coating application process, alloy wheels are transported on roller conveyors to the drying/curing area. This area typically consists of drying or curing ovens designed specifically for the type of paint or coating being used.
2. Drying Process:
- Alloy wheels enter the drying oven on the roller conveyors, where they are subjected to controlled heat and airflow to evaporate solvents and accelerate the drying process.
- Depending on the type of paint or coating used, drying temperatures and durations are carefully controlled to ensure proper curing without damaging the finish.
3. Curing Process:
- For certain types of paints or coatings that require curing, alloy wheels continue through the drying oven to the curing section. Curing may involve exposure to specific temperatures and durations to chemically cross-link the molecules in the finish, resulting in a durable and resilient coating.
- Infrared lamps, UV lights, or other curing methods may be employed depending on the requirements of the paint or coating material.
4. Conveyor Speed Control:
- Roller conveyors are equipped with speed control mechanisms to regulate the movement of alloy wheels through the drying/curing oven. This ensures that wheels spend the appropriate amount of time in the oven to achieve thorough drying and curing.
5. Cooling Zone:
- After completing the drying/curing process, alloy wheels are conveyed through a cooling zone on the roller conveyors. This allows the wheels to gradually cool down to room temperature before further handling or packaging.
6. Quality Checks:
- Throughout the drying/curing process, quality checks may be performed to inspect the finish for defects such as runs, sags, or improper curing. Any defects detected are addressed before the wheels proceed further in the production process.
7. Conveyor Design Considerations:
- Roller conveyors used in the drying/curing process must be designed to withstand exposure to high temperatures and potential chemical residues from the paint or coating material.
- Conveyor rollers and frames should be constructed from heat-resistant materials to ensure durability and minimize maintenance requirements.
8. Integration with Downstream Processes:
- After completing the drying/curing process, alloy wheels are conveyed to downstream processes such as inspection, assembly, or packaging. Roller conveyors facilitate the smooth transition of wheels between production stages, ensuring efficient material flow.
By utilizing roller conveyors for drying and curing of alloy wheels, manufacturers can ensure that the paint or coating finish is properly cured and dried, resulting in durable, high-quality products. This integration helps optimize production efficiency and throughput while maintaining consistent quality standards.
Cooling and Handling of alloy wheels on a conveyor
Cooling and handling of alloy wheels after the drying or curing process are critical steps to ensure the quality and integrity of the finished product. Roller conveyors play a significant role in efficiently transporting alloy wheels through cooling zones and facilitating their subsequent handling. Here’s how cooling and handling typically occur on a conveyor system:
1. Cooling Zone:
- After the drying or curing process, alloy wheels are transported on roller conveyors through a designated cooling zone. This zone allows the wheels to gradually cool down to ambient temperature before further handling or packaging.
- Cooling zones may utilize ambient air or controlled airflow to facilitate the cooling process. The duration of time spent in the cooling zone can vary depending on factors such as the temperature of the wheels and the ambient conditions.
2. Temperature Monitoring:
- Temperature sensors may be installed within the cooling zone to monitor the temperature of alloy wheels as they pass through. This ensures that the wheels reach a safe handling temperature before proceeding to the next stage of production.
3. Inspection:
- While alloy wheels are cooling on the conveyor, visual inspections may be conducted to check for any defects or abnormalities in the finish. Any defects detected can be addressed before the wheels move on to subsequent processes.
4. Handling:
- Once alloy wheels have sufficiently cooled, they are ready for handling. Roller conveyors facilitate the smooth transition of wheels to the next stage of production, whether it involves assembly, inspection, or packaging.
- Handling may involve transferring the wheels from the conveyor to carts, pallets, or other transport containers for further processing or packaging.
5. Conveyor Design Considerations:
- Roller conveyors used for cooling and handling alloy wheels must be designed to withstand the weight and dimensions of the wheels, as well as the temperature variations in the cooling zone.
- Conveyor rollers and frames should be constructed from durable materials capable of withstanding the environmental conditions in the cooling zone and the demands of continuous operation.
6. Integration with Downstream Processes:
- After completing the cooling process, alloy wheels are conveyed to downstream processes such as inspection, assembly, or packaging. Roller conveyors facilitate the smooth transition of wheels between production stages, ensuring efficient material flow.
7. Safety Measures:
- Safety features such as guards, emergency stops, and interlocks are implemented along the conveyor system to protect workers and prevent accidents during cooling and handling operations.
By utilizing roller conveyors for cooling and handling alloy wheels, manufacturers can ensure that the wheels are properly cooled and prepared for subsequent processing or packaging. This integration helps optimize production efficiency, maintain product quality, and ensure worker safety.