Powder coating machine for screw heads are specialized pieces of equipment designed to efficiently and effectively coat screw heads with a durable, protective layer of powder. These machines are widely used in manufacturing settings, particularly those that produce screws and fasteners for various applications.
A bolt, fastener, and screw heads powder coating machine is a specialized piece of equipment designed to provide a durable, aesthetic, and protective coating to small mechanical components. This type of machine is crucial in industries such as automotive, aerospace, construction, and electronics, where high-quality finishes are required to ensure both functionality and longevity of parts. Powder coating, as a process, involves applying a dry, free-flowing, thermoplastic or thermoset powder to a surface, which is then cured under heat or with ultraviolet light to form a tough, continuous film.
The machine typically consists of multiple components, each contributing to the efficiency and precision of the coating process. The first stage involves surface preparation, which is critical to ensure proper adhesion of the powder coating. This may include cleaning, degreasing, and sandblasting the bolt, fastener, or screw head surfaces to remove contaminants like oils, dirt, or oxides. Some machines are equipped with automated pre-treatment chambers that handle these processes efficiently.
Once the parts are prepped, they move to the coating application area. Here, the powder is applied using an electrostatic spray gun. This tool charges the powder particles as they are sprayed onto the grounded metal parts, creating a strong electrostatic attraction that ensures even and thorough coverage. For small components like bolt and screw heads, the machine often features specialized fixtures or holders that can rotate or reposition the parts during the spraying process, enabling consistent coverage even in hard-to-reach areas.
After the powder application, the parts are transferred to a curing oven, where the coating is baked to achieve its final properties. The temperature and duration of the curing process depend on the type of powder used, with thermosetting powders typically requiring higher temperatures. The curing oven in these machines is designed to accommodate the small size of bolts and screws while ensuring even heat distribution for uniform curing. In advanced machines, infrared curing systems may be used for faster processing and energy efficiency.
To handle the high-volume requirements of industrial applications, these machines often operate in a continuous or semi-continuous manner. A conveyor system moves the parts through the various stages of the process, ensuring smooth and uninterrupted production. For flexibility, some machines are equipped with adjustable speed controls and modular designs, allowing manufacturers to customize the setup according to specific production needs.
Quality control is an integral part of the powder coating process for bolt, fastener, and screw heads. Machines are often equipped with sensors and monitoring systems to ensure consistent application thickness and detect any defects in real-time. In some setups, an integrated inspection system may use cameras or other imaging technologies to check for surface imperfections, missed spots, or uneven coating.
Environmental considerations are also addressed in modern powder coating machines. Unlike liquid coatings, powder coating produces minimal volatile organic compound (VOC) emissions, making it an eco-friendly option. Additionally, these machines are designed to minimize powder waste by incorporating recovery systems. Excess powder from the spraying process is collected, filtered, and reused, contributing to cost savings and sustainability.
Ergonomics and safety are other important features of these machines. Operators are protected from powder exposure through the use of enclosures, extraction systems, and personal protective equipment. Maintenance is also simplified with features like quick-release components and easy-to-clean designs.
In summary, a bolt, fastener, and screw heads powder coating machine is a highly specialized system engineered for precision, efficiency, and quality. Its components work together seamlessly to deliver a robust and aesthetically pleasing finish, meeting the stringent demands of modern manufacturing while adhering to environmental and safety standards. This technology exemplifies the integration of advanced engineering with practical functionality, ensuring that even the smallest components perform optimally in their intended applications.
Bolt, Fastener and Screw Heads Powder Coating Machine
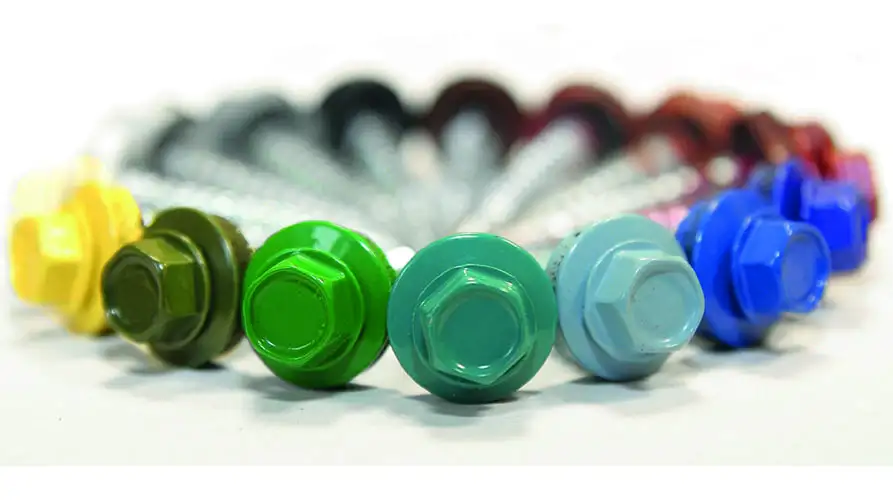
A bolt, fastener, and screw heads powder coating machine is an essential tool in industries where high-quality finishes and protective coatings are required for small mechanical components. Powder coating offers durability, corrosion resistance, and an attractive finish, making it a preferred method for coating hardware items used in sectors like automotive, aerospace, electronics, and construction. This document outlines the key features, processes, and benefits of these machines.
Surface Preparation
Surface preparation is the foundation of a successful powder coating process. The machine begins by ensuring that the parts are free from contaminants such as oils, grease, dirt, or rust. Common pre-treatment methods include:
- Cleaning and Degreasing: Removes oils and residues using chemical solutions or ultrasonic cleaners.
- Sandblasting: Abrasive blasting techniques provide a roughened surface for better powder adhesion.
- Chemical Etching: Enhances the surface properties for specific applications.
Many modern machines feature automated pre-treatment chambers to ensure consistency and efficiency during this stage.
Powder Application
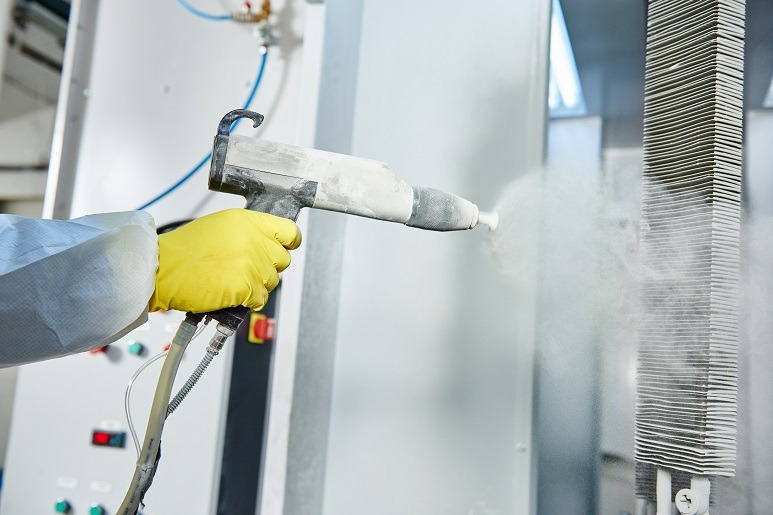
Once the components are pre-treated, they proceed to the coating application stage. The key features of this stage include:
- Electrostatic Spray Gun: The powder is charged electrostatically and sprayed onto the grounded parts, ensuring even distribution.
- Specialized Fixtures: Rotating or repositioning holders secure bolt, fastener, and screw heads, allowing complete coverage of all surfaces, including hard-to-reach areas.
- Adjustable Settings: Operators can modify the spray pressure, powder flow, and other parameters to accommodate different component sizes and coating requirements.
Powder application in the coating process is a critical step that ensures a uniform and durable finish on the surface of components such as bolts, fasteners, and screw heads. The process begins with the introduction of powder material into an application system, most commonly an electrostatic spray gun. This gun is designed to impart an electrostatic charge to the powder particles as they are propelled towards the grounded workpiece. The charged particles are attracted to the surface of the metal parts due to the electrostatic force, ensuring that the powder adheres evenly across the component. This technique is highly efficient, minimizing waste and ensuring comprehensive coverage, even on intricate geometries like threaded sections and recessed areas of small mechanical parts.
The application system often includes mechanisms to control the flow rate of the powder, the spray pressure, and the distribution pattern, allowing precise adjustments to achieve the desired thickness and quality of the coating. The equipment may also incorporate automated positioning fixtures or rotating holders to manipulate the parts during the spraying process. These fixtures are particularly important for complex shapes, as they allow the spray gun to access all areas of the component without missing spots or creating uneven layers. In addition to precision, the use of automation reduces human error and increases consistency, which is vital in high-volume production environments.
Modern powder application machines often feature multi-stage systems to optimize efficiency. For example, the initial spray stage applies the bulk of the coating, while a secondary touch-up stage ensures that all areas are properly covered. Advanced machines might include integrated sensors to monitor the application process in real-time, detecting issues such as uneven distribution, insufficient coating, or contamination. These systems alert operators to potential problems, enabling immediate corrections and minimizing defects in the final product.
The powder used in this process is typically composed of thermoplastic or thermosetting resins mixed with pigments, leveling agents, and other additives to enhance performance and appearance. These powders are free of solvents, which makes the process environmentally friendly, as it produces minimal volatile organic compound emissions. Excess powder that does not adhere to the component is not wasted; instead, it is collected in a recovery system, filtered, and reused in subsequent applications. This not only reduces material costs but also minimizes waste, contributing to the overall sustainability of the operation.
In industrial applications, powder application systems are designed for speed and scalability. Conveyor systems transport components through the application chamber, allowing continuous or semi-continuous operation to meet high production demands. Adjustable conveyor speeds provide flexibility to adapt to different coating requirements, ensuring optimal results for both small and large batches. Moreover, the equipment can be customized to handle various sizes and shapes of components, making it versatile for different industries and applications.
Safety and ergonomics are also key considerations in powder application systems. Operators are protected from inhaling powder particles through the use of enclosed workspaces, extraction systems, and personal protective equipment. The equipment is engineered for easy maintenance, with features such as quick-access panels and self-cleaning components to streamline routine cleaning and reduce downtime.
In conclusion, the powder application process is a sophisticated and highly efficient method for applying protective and decorative finishes to metal components. By leveraging advanced technology, automation, and environmentally friendly practices, this process ensures high-quality, durable coatings that meet the stringent requirements of modern manufacturing.
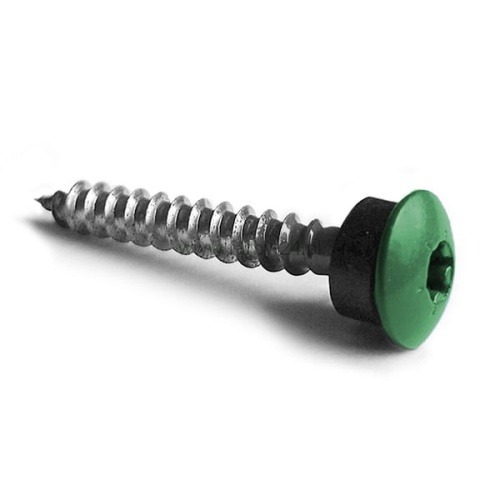
The success of the powder application process is rooted in its ability to achieve uniform coverage and strong adhesion while minimizing waste and environmental impact. The electrostatic nature of the process ensures that the charged powder particles are drawn to every accessible area of the component, including edges, corners, and recessed sections. This precision is especially critical for small and intricate parts like bolts, fasteners, and screw heads, where any inconsistency in coating thickness can compromise both appearance and performance. A properly applied powder coat not only enhances the component’s resistance to corrosion, wear, and impact but also provides an appealing finish that can be tailored to aesthetic preferences through a wide range of available colors and textures.
Temperature and humidity control within the application environment are additional factors that influence the quality of the powder application. Excessive humidity can cause powder particles to clump together, reducing their ability to disperse evenly and adhere effectively to the surface. Similarly, temperature variations can affect the charging process and the flow properties of the powder, potentially leading to uneven coating. Modern powder application systems are designed with environmental control features, such as dehumidifiers and temperature regulators, to ensure consistent performance regardless of external conditions.
One of the remarkable advantages of the powder application process is its efficiency and sustainability. Unlike liquid coatings, which often involve solvents and produce significant waste, powder coatings are solvent-free and designed to minimize excess material. The recovery systems integrated into powder application machines are highly effective, capturing overspray and returning it to the powder feed system for reuse. This closed-loop approach not only conserves resources but also reduces operational costs and waste disposal requirements. Additionally, the absence of solvents eliminates volatile organic compound (VOC) emissions, making powder coating an environmentally friendly option that complies with stringent regulatory standards.
The versatility of powder application systems further enhances their appeal. These systems can be configured to handle a wide range of component sizes, shapes, and production volumes. Whether the requirement is for a small batch of custom parts or a large-scale production run, the flexibility of the equipment ensures that manufacturers can adapt to diverse needs without compromising quality or efficiency. Customization options such as interchangeable spray nozzles, programmable coating patterns, and adjustable conveyor speeds allow for fine-tuning of the process to meet specific application requirements.
Innovation continues to drive advancements in powder application technology. For instance, some modern systems incorporate robotics to automate the movement of spray guns and component holders, achieving unprecedented levels of precision and repeatability. Others employ artificial intelligence and machine learning algorithms to optimize the application process by analyzing data from sensors and making real-time adjustments to parameters such as powder flow, gun positioning, and spray duration. These innovations not only enhance the quality and efficiency of the process but also reduce the need for manual intervention, further streamlining operations.
The safety and ergonomic aspects of powder application machines are designed with operators in mind. Enclosed application chambers and advanced ventilation systems prevent the escape of powder particles into the workspace, protecting operators from exposure. In addition, automated cleaning systems simplify maintenance by reducing the need for manual intervention in cleaning spray guns, recovery systems, and conveyors. These features contribute to a safer and more comfortable working environment, improving overall productivity.
In essence, the powder application process represents a seamless integration of science, engineering, and sustainability. It is a cornerstone of modern manufacturing, enabling industries to produce high-quality, durable, and aesthetically pleasing components while adhering to environmental and economic constraints. The continued evolution of this technology promises even greater efficiencies, broader applications, and enhanced capabilities, solidifying its position as a preferred coating method across a wide range of industries.
Electrostatic Spray Gun
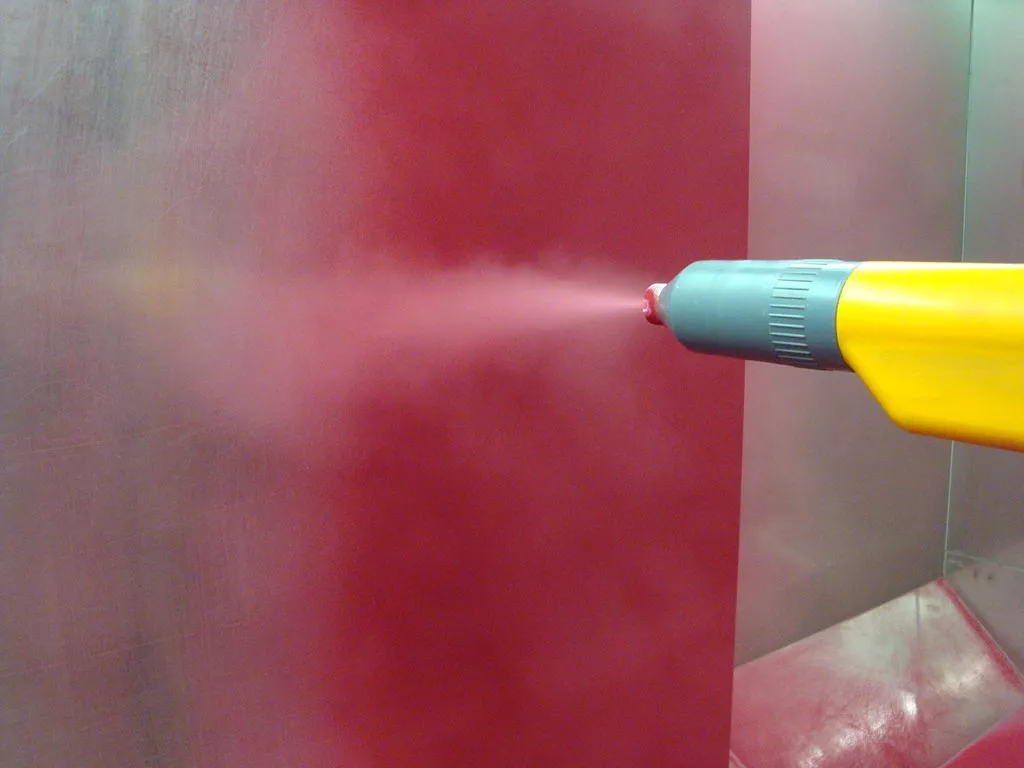
The electrostatic spray gun is a central component in the powder coating process, designed to deliver precise, efficient, and uniform application of powder to a variety of surfaces. This tool operates on the principle of electrostatics, where the powder particles are given an electrical charge as they pass through the gun. The components being coated are grounded, creating an electrostatic attraction between the charged powder and the surface of the component. This mechanism ensures that the powder adheres effectively, even to complex geometries and hard-to-reach areas, minimizing waste and maximizing coverage.
The electrostatic spray gun consists of several key components that work together to achieve optimal performance. The powder feed system supplies a consistent stream of powder to the gun, which is then propelled forward using compressed air. Inside the gun, the particles are charged either by a corona discharge mechanism or by triboelectric charging. In corona discharge systems, a high-voltage electrode at the nozzle tip generates an electric field that imparts a charge to the powder. In triboelectric systems, the powder is charged through friction as it moves through the gun’s internal pathways. Each method has its specific applications, with corona systems being more commonly used due to their versatility and efficiency.
The design of the spray nozzle plays a crucial role in determining the distribution and coverage of the powder. Adjustable nozzles allow operators to control the shape and size of the spray pattern, accommodating different component sizes and shapes. For small and intricate parts like bolts, fasteners, and screw heads, precision nozzles are used to direct the powder accurately, ensuring that even the smallest details are coated evenly. Advanced spray guns may also feature multi-port nozzles that can spray powder in various directions simultaneously, reducing the need for repositioning components during the process.
Modern electrostatic spray guns often incorporate features that enhance efficiency and reduce downtime. For example, many systems include automatic cleaning functions that remove residual powder from the gun and nozzle between coating sessions, preventing clogs and ensuring consistent performance. Some guns are also equipped with real-time monitoring sensors that measure variables such as powder flow rate, charge level, and spray pattern consistency. These sensors provide valuable feedback to operators, enabling them to make immediate adjustments and maintain high-quality results.
One of the most significant advantages of using an electrostatic spray gun is its ability to minimize material waste. The electrostatic attraction ensures that a high percentage of the powder adheres to the component, while any overspray is collected in a recovery system for reuse. This not only reduces costs but also contributes to the sustainability of the process. The solvent-free nature of powder coating, combined with the efficiency of the spray gun, makes it an environmentally friendly alternative to liquid coatings, which often involve significant waste and volatile organic compound (VOC) emissions.
Electrostatic spray guns are designed with safety and ergonomics in mind. The gun’s lightweight and balanced design reduce operator fatigue during prolonged use, while insulated handles protect users from the high-voltage currents used in the charging process. Many systems also include safety interlocks and grounding checks to prevent accidental discharges or improper operation. Additionally, enclosed spraying chambers and advanced ventilation systems protect operators from exposure to airborne powder particles, ensuring a safe working environment.
The versatility of electrostatic spray guns allows them to be used across a wide range of industries and applications. From small-scale operations requiring precise coatings for intricate components to large-scale industrial production lines demanding high throughput, these tools can be adapted to meet various needs. They are compatible with different types of powders, including thermosetting and thermoplastic materials, and can achieve a variety of finishes, such as matte, glossy, textured, or metallic.
In recent years, advancements in technology have further enhanced the capabilities of electrostatic spray guns. Automation and robotics have been integrated into the spraying process, allowing for consistent and repeatable coating of components with minimal manual intervention. Some systems utilize artificial intelligence to optimize parameters like powder flow, charge levels, and nozzle positioning in real-time, ensuring superior results and reducing waste. Portable and compact designs have also made these tools more accessible for on-site applications, expanding their usability beyond traditional factory settings.
In summary, the electrostatic spray gun is a sophisticated and indispensable tool in the powder coating process. Its ability to deliver precise, uniform, and efficient powder application while minimizing waste and environmental impact makes it a cornerstone of modern manufacturing. With continued innovation and improvements in design, the electrostatic spray gun will remain a critical component in achieving high-quality finishes for a wide range of products.
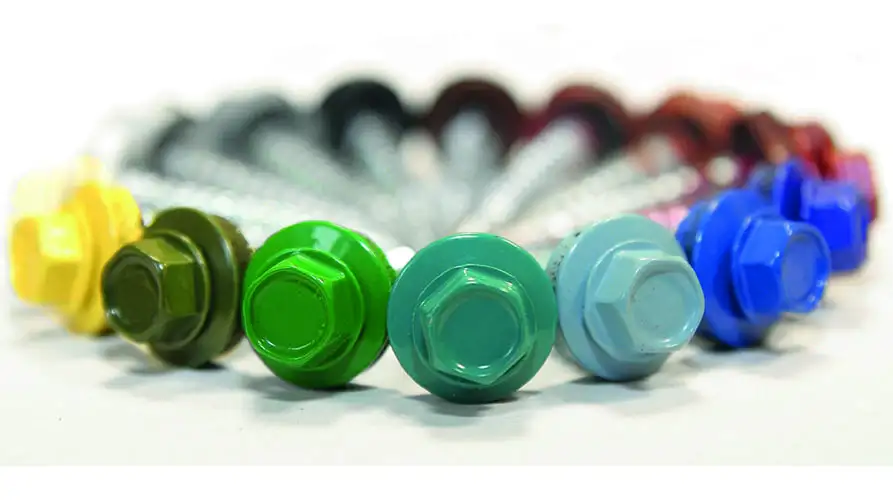
The electrostatic spray gun continues to evolve, incorporating new technologies and design improvements that further enhance its functionality and efficiency. One notable area of advancement is the development of smart systems that integrate sensors, data analytics, and connectivity features. These smart guns can communicate with other components in the coating line, such as the conveyor system or curing oven, to optimize the overall process. For instance, by analyzing data from environmental sensors, the gun can adjust parameters like powder charge intensity or spray velocity to compensate for changes in temperature or humidity. This level of adaptability ensures consistent coating quality even under variable operating conditions.
Another significant innovation in electrostatic spray guns is the use of modular designs. Modular systems allow for easy customization and upgrading of the spray gun to meet specific application requirements. Operators can switch out nozzles, powder pathways, or charging mechanisms to tailor the gun for different coating projects. This flexibility is particularly valuable in industries that handle a wide variety of components with unique shapes, sizes, and material requirements. For example, a single modular system can be configured to coat both large flat surfaces and intricate threaded components like screw heads or fasteners.
Energy efficiency is also a key focus in modern electrostatic spray gun designs. By optimizing the power usage of the charging system and airflow control mechanisms, manufacturers have been able to reduce the energy consumption of these tools without compromising performance. Some advanced guns utilize high-efficiency powder transport systems that minimize the compressed air required to propel the powder, further lowering energy demands. This not only reduces operational costs but also aligns with the growing emphasis on sustainable manufacturing practices.
The introduction of multi-axis robotic systems has revolutionized the way electrostatic spray guns are used in automated production lines. These robotic arms, equipped with electrostatic guns, can perform precise and repeatable spraying motions that are difficult to achieve manually. With the ability to program complex paths and angles, robotic systems ensure comprehensive coverage even for components with intricate designs. Moreover, they can operate continuously without fatigue, increasing productivity and reducing the likelihood of human error. This automation is particularly beneficial in high-volume industries like automotive or consumer electronics, where consistency and speed are paramount.
In addition to robotic integration, portable and compact electrostatic spray guns have gained popularity for specialized applications and on-site operations. These lightweight tools are designed for maximum mobility, enabling operators to perform precision coating in hard-to-reach or confined spaces. For instance, in the aerospace or construction sectors, where certain components must be coated after assembly, portable spray guns provide a practical and efficient solution. Despite their smaller size, these portable models often include many of the advanced features found in larger systems, such as adjustable spray patterns, real-time monitoring, and self-cleaning capabilities.
The compatibility of electrostatic spray guns with a wide range of powder materials further enhances their versatility. Thermoset powders, such as epoxy, polyester, and hybrid formulations, are commonly used for their durability and resistance to environmental factors. Thermoplastic powders, like nylon or polyethylene, offer additional benefits such as flexibility and chemical resistance, making them suitable for specialized applications. The ability to handle diverse powders enables manufacturers to achieve specific performance characteristics and aesthetic effects, from high-gloss finishes to textured coatings that provide additional grip or decorative appeal.
Training and user support have also improved significantly with the advent of digital interfaces and augmented reality tools. Many modern electrostatic spray guns are equipped with intuitive control panels or touchscreens that guide operators through setup and operation. Some systems offer virtual tutorials or augmented reality overlays that help users understand the optimal gun settings, nozzle positioning, and spraying techniques for different tasks. This not only reduces the learning curve for new operators but also helps experienced users refine their skills and achieve better results.
Looking to the future, the electrostatic spray gun is poised to become even more integrated with smart manufacturing ecosystems. As Industry 4.0 technologies become more widespread, these tools will likely feature enhanced connectivity, enabling them to share data with central control systems, monitor their performance remotely, and even receive over-the-air updates to improve functionality. This level of integration will further streamline the coating process, reduce downtime, and ensure that manufacturers can maintain the highest standards of quality and efficiency.
In conclusion, the electrostatic spray gun remains at the forefront of powder coating technology, combining precision, efficiency, and sustainability in a single tool. Its ability to adapt to diverse applications, coupled with ongoing innovations in design and functionality, ensures its continued relevance in a rapidly changing industrial landscape. As manufacturers seek to optimize their processes and reduce environmental impact, the electrostatic spray gun will remain an indispensable asset in achieving these goals.
Curing Process
After powder application, the coated components enter a curing oven. This stage is critical for fusing the powder into a hard, durable finish. The curing process includes:
- Temperature Control: Ensures the proper curing temperature is maintained, which typically ranges between 160°C and 220°C, depending on the powder type.
- Infrared or Convection Systems: Advanced ovens may use infrared technology for faster heating and energy efficiency.
- Even Heat Distribution: Essential for ensuring uniform curing, especially for small components with intricate shapes.
The curing process is a critical stage in the powder coating workflow, transforming the applied powder into a durable, uniform, and aesthetically pleasing finish. Once the powder has been electrostatically applied to the surface of a component, the coated part is transferred to a curing oven, where heat triggers a chemical reaction that bonds the powder particles into a continuous, hardened layer. This process ensures the coating adheres firmly to the substrate, delivering the desired performance characteristics such as corrosion resistance, abrasion resistance, and an attractive appearance.
Curing begins with the introduction of coated parts into a temperature-controlled oven. The type of oven used depends on the size, shape, and production volume of the components being coated. Convection ovens are the most common type, using circulating hot air to evenly heat the parts and melt the powder. For faster heating and greater efficiency, infrared (IR) ovens are often employed, as they directly heat the surface of the components without significantly warming the surrounding air. Some advanced systems use a combination of convection and IR technologies to optimize energy usage and curing time.
The curing process typically involves two key phases: the melting phase and the cross-linking phase. In the melting phase, the powder particles soften and flow into a uniform layer. This is followed by the cross-linking phase, during which chemical reactions occur, fusing the powder into a solid, durable coating. Thermoset powders, the most commonly used in industrial applications, undergo a chemical curing reaction that permanently sets the coating. This reaction is triggered at specific temperatures, usually between 160°C and 220°C, depending on the powder formulation. Once cured, thermoset coatings cannot be melted or reformed, providing excellent stability and resistance to environmental factors.
Maintaining consistent temperature and airflow within the oven is crucial for achieving high-quality results. Uneven heating can lead to defects such as orange peel texture, uneven gloss, or incomplete curing, which can compromise both the appearance and performance of the coating. Modern curing ovens are equipped with advanced temperature control systems and sensors that monitor and adjust heat distribution in real time. These systems ensure that all parts, regardless of their size or placement within the oven, receive uniform heat exposure.
The duration of the curing process varies based on the powder type, thickness of the coating, and the thermal conductivity of the substrate. Most curing cycles range from 10 to 30 minutes, though some rapid-curing powders allow for shorter times, improving overall production efficiency. For components with complex geometries or materials with low thermal conductivity, specialized ovens or extended curing times may be required to ensure complete curing.
Energy efficiency is a significant consideration in the design of curing ovens. Advanced systems often include features such as zoned heating, which allows specific areas of the oven to be heated only as needed, reducing energy consumption. Insulated oven walls and doors minimize heat loss, while exhaust systems capture and recycle heat for reuse in the curing process or other facility operations. These measures not only lower operating costs but also contribute to the sustainability of the powder coating process.
Safety is another critical aspect of the curing process. High temperatures and volatile by-products generated during curing necessitate robust ventilation and exhaust systems to maintain a safe working environment. Modern ovens are designed with built-in safety features, such as temperature limiters, automatic shut-off mechanisms, and fire suppression systems, to prevent overheating and other potential hazards. Operators are also trained to handle components carefully during the curing process, as the parts can become extremely hot.
The curing process plays a pivotal role in determining the final properties of the coated component. A properly cured coating exhibits excellent adhesion to the substrate, forming a protective barrier against environmental factors like moisture, UV radiation, and chemical exposure. The coating’s mechanical properties, such as flexibility, hardness, and impact resistance, are also enhanced during curing. In addition, the curing process helps achieve a consistent finish, whether it is glossy, matte, or textured, depending on the powder formulation.
Automation and monitoring systems are increasingly being integrated into curing processes to improve efficiency and quality control. Sensors and cameras installed within curing ovens can detect anomalies such as uneven temperatures or improperly loaded parts, allowing for immediate corrective actions. Data from these monitoring systems can also be analyzed to optimize curing parameters and reduce energy usage, contributing to cost savings and process improvements.
The versatility of the curing process enables its application across a wide range of industries and products. From small, intricate components like bolts and fasteners to large automotive parts and industrial equipment, curing ovens can be customized to accommodate various sizes, shapes, and production requirements. Batch ovens are often used for small-scale operations, while continuous conveyor ovens are ideal for high-volume production lines, ensuring seamless integration with other stages of the coating process.
In summary, the curing process is the final and indispensable step in the powder coating workflow, converting applied powder into a durable and aesthetically pleasing finish. Through precise temperature control, efficient energy usage, and advanced monitoring systems, curing ovens ensure that coatings meet the highest standards of quality and performance. As technology continues to advance, the curing process is becoming faster, more energy-efficient, and increasingly adaptable, solidifying its role as a cornerstone of modern powder coating systems.
The curing process’s continued evolution ensures its alignment with modern manufacturing demands, including increased production speeds, sustainability, and the ability to handle diverse material requirements. Innovations in curing technology are transforming how industries approach this critical step, with advancements such as ultra-fast curing powders, hybrid curing systems, and intelligent process optimization.
Ultra-Fast Curing Powders
One of the most significant advancements in the curing process is the development of ultra-fast curing powders. These formulations require shorter curing times and lower temperatures, which reduces energy consumption and enhances throughput. These powders are particularly advantageous in high-volume industries such as automotive or consumer goods manufacturing, where production speed is a key metric of efficiency. Additionally, these powders can be used on heat-sensitive materials, such as plastics or composites, expanding the range of substrates that can be effectively powder-coated.
Hybrid Curing Systems
Hybrid curing systems combine multiple heat sources, such as infrared (IR), convection, and ultraviolet (UV) light, to optimize the curing process. Each heat source addresses specific challenges: IR provides rapid surface heating, convection ensures deep and even heating, and UV light offers instantaneous curing for specific powder formulations. This hybrid approach is especially useful for complex parts with varying material thicknesses, as it ensures uniform curing without overexposing thinner sections or undercuring thicker ones. Hybrid systems also enhance energy efficiency by allowing selective heating, focusing energy only where needed.
Intelligent Process Optimization
The integration of artificial intelligence (AI) and machine learning in curing systems is revolutionizing process control. Intelligent curing ovens use data from sensors, cameras, and environmental monitors to dynamically adjust curing parameters such as temperature, airflow, and cycle time. AI-driven algorithms analyze historical data and real-time inputs to predict and prevent potential issues, such as uneven curing or excessive energy usage. These systems can also suggest optimizations for future production runs, improving overall efficiency and reducing waste.
Sustainability in Curing
The environmental impact of the curing process has become a focal point for manufacturers. Energy-efficient ovens, combined with renewable energy sources, significantly reduce the carbon footprint of powder coating operations. Additionally, innovations such as heat recovery systems allow facilities to capture waste heat from the curing process and repurpose it for other functions, such as preheating incoming components or maintaining facility temperatures. Low-temperature curing powders also contribute to sustainability by reducing the energy required for curing.
Modular and Scalable Curing Systems
Modern curing systems are designed with scalability and flexibility in mind. Modular ovens can be easily expanded or reconfigured to accommodate changes in production volume or product size. For manufacturers working with a variety of products, this adaptability ensures they can meet evolving demands without significant capital investment. Scalable systems are especially beneficial for small and medium-sized enterprises looking to grow their production capabilities incrementally.
Industry-Specific Applications
The curing process has been tailored to meet the unique requirements of various industries. In the automotive sector, curing systems must handle large components like car bodies while ensuring precision for smaller parts such as brackets and fasteners. In the electronics industry, the focus is on achieving highly consistent and thin coatings for delicate components. For the construction and architectural sectors, curing systems are optimized to handle oversized parts, such as panels and frames, while maintaining efficiency.
Advanced Coating Properties Achieved Through Curing
The curing process is pivotal in unlocking advanced properties in powder coatings. Beyond durability and aesthetics, specific formulations can impart additional benefits such as anti-microbial properties, electrical insulation, or enhanced thermal conductivity. For example, components used in medical devices or food processing equipment often require coatings with anti-bacterial finishes, which are activated and solidified during the curing phase. Similarly, coatings for electronic components may require exacting dielectric properties achieved only through precise curing.
Challenges and Future Directions
While the curing process has seen remarkable advancements, challenges remain. Achieving consistent results with large or geometrically complex parts requires careful planning and advanced equipment. Additionally, as industries increasingly adopt lightweight and composite materials, curing technologies must adapt to handle these substrates without compromising coating performance. Research into alternative curing methods, such as microwave or induction-based systems, promises to address some of these challenges by offering faster and more localized heating.
In conclusion, the curing process is the keystone of the powder coating system, where applied powder transitions into a robust, high-performance finish. Through innovations in technology, energy efficiency, and adaptability, the curing process continues to meet the needs of modern industries while aligning with sustainability goals. As technology progresses, curing systems will become even more precise, efficient, and versatile, ensuring their integral role in manufacturing for decades to come.
Conveyor and Automation
To meet industrial production demands, these machines often integrate conveyor systems for continuous or semi-continuous operations. Key aspects include:
- Conveyor Systems: Automatically move parts through pre-treatment, coating, and curing stages.
- Modular Design: Machines can be configured or expanded to meet specific production needs.
- Speed Adjustments: Allows for flexible processing times based on the size and complexity of the components.
Quality Control
Ensuring the quality of the coating is critical for achieving optimal performance and aesthetics. Modern machines often include:
- Thickness Monitoring: Sensors measure the thickness of the powder layer for consistency.
- Defect Detection: Cameras or imaging systems identify imperfections such as uneven coating or missed spots.
- Inspection Systems: Automated inspection ensures that all components meet quality standards before packaging.
Environmental Considerations
Powder coating is an eco-friendly alternative to traditional liquid coatings, producing minimal waste and reducing environmental impact. Features addressing sustainability include:
- Low VOC Emissions: Powder coating releases negligible volatile organic compounds compared to liquid paints.
- Powder Recovery Systems: Excess powder is collected, filtered, and reused, minimizing material waste.
- Energy Efficiency: Advanced curing ovens and systems reduce overall energy consumption.
Ergonomics and Safety
The design of these machines prioritizes operator safety and ease of use. Key features include:
- Enclosed Work Areas: Protect operators from exposure to powder particles.
- Ventilation and Extraction Systems: Ensure a safe and clean working environment.
- User-Friendly Maintenance: Quick-release components and accessible designs simplify cleaning and servicing.
Applications and Benefits
Powder coating machines for bolt, fastener, and screw heads offer numerous advantages:
- Durability: Provides a tough, long-lasting finish resistant to corrosion, abrasion, and impact.
- Aesthetics: Achieves a consistent, high-quality appearance with a range of color options.
- Cost-Effectiveness: Reduced material waste and minimal maintenance costs enhance profitability.
- Versatility: Suitable for various industries and adaptable to different production volumes.
Conclusion
Bolt, fastener, and screw heads powder coating machines represent a perfect blend of precision engineering and advanced coating technology. By integrating efficient processes, automation, and environmental safeguards, these machines deliver superior-quality finishes that meet the rigorous demands of modern manufacturing. Their versatility, reliability, and sustainability make them indispensable tools for producing high-performance hardware components.
Conveyor and Automation
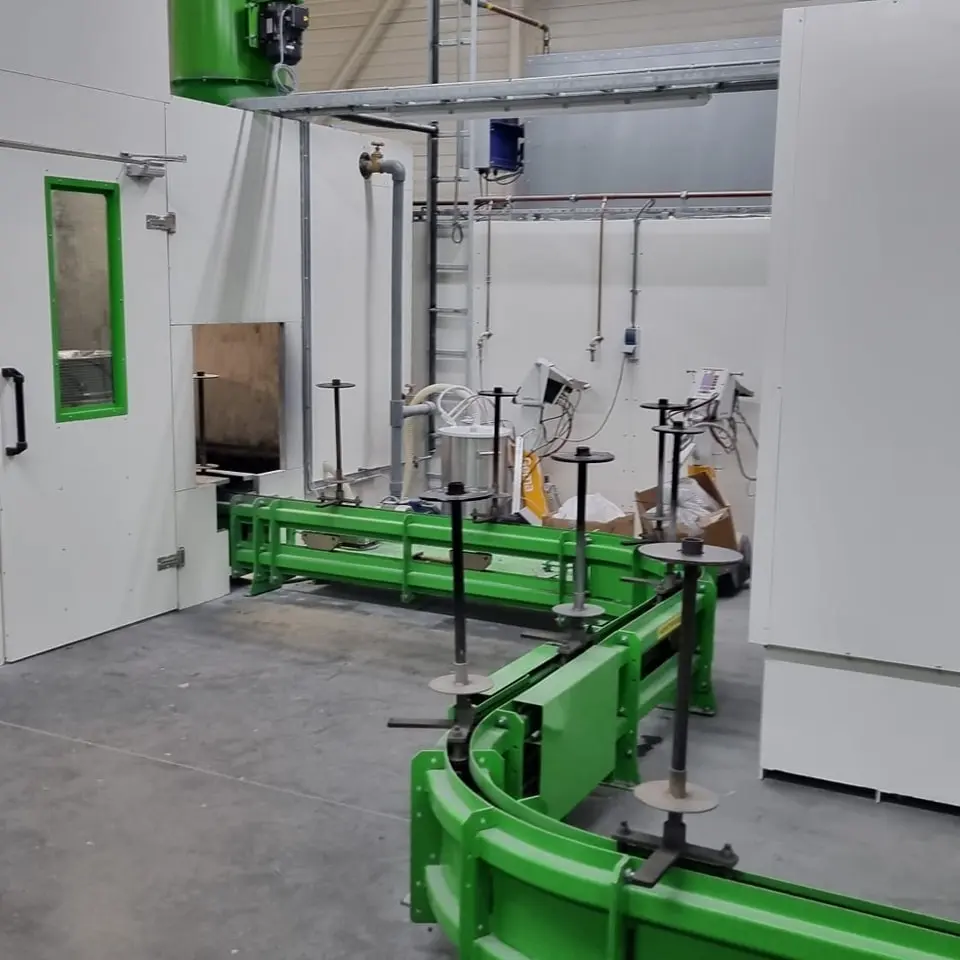
The conveyor and automation systems in powder coating processes play a vital role in ensuring efficiency, consistency, and scalability in modern manufacturing. These systems facilitate the seamless movement of components through various stages of the coating process, from pre-treatment and powder application to curing and cooling. By integrating conveyors with automation technologies, manufacturers can achieve higher throughput, reduce labor costs, and maintain consistent quality across production runs.
Conveyors are the backbone of automated powder coating lines, providing a reliable means of transporting parts. The type of conveyor used depends on the production requirements and the nature of the components being coated. Overhead conveyors are among the most common, with parts suspended on hooks or fixtures that travel along a guided path. These systems are ideal for high-volume operations and are particularly suited for irregularly shaped components. Floor-mounted conveyors, such as belt or roller systems, are used for larger or heavier parts, ensuring stability during transport.
One of the key benefits of using conveyors in powder coating is the ability to achieve continuous production. Components move steadily through each stage of the process, minimizing idle time and ensuring a smooth workflow. Conveyor systems are often equipped with variable speed controls, allowing operators to adjust the pace based on production needs. For instance, slower speeds may be used for complex parts that require precise coating, while higher speeds accommodate simpler items in bulk.
Automation enhances the functionality of conveyor systems by integrating advanced technologies such as programmable logic controllers (PLCs), sensors, and robotics. PLCs manage the movement and timing of conveyors, ensuring that components arrive at each stage of the process at the right time. Sensors placed along the conveyor track monitor the position and condition of parts, providing real-time feedback to the system. This level of control ensures that each component receives the correct pre-treatment, coating, and curing time, regardless of variations in size or shape.
Robotics play a significant role in automated powder coating lines, particularly in tasks that require precision and repeatability. Robotic arms equipped with electrostatic spray guns can follow programmed paths to coat components uniformly, even in areas that are difficult to reach manually. These systems are especially beneficial for complex geometries, such as fasteners, screw heads, or intricate automotive parts, where manual application might result in uneven coating or overspray. By working in tandem with conveyor systems, robots can coat components as they move through the line, increasing both speed and accuracy.
Customization is a hallmark of modern conveyor and automation systems. Manufacturers can design lines tailored to their specific needs, incorporating features such as multi-level conveyors for space-saving vertical layouts or looped tracks that allow parts to pass through the system multiple times for additional coating layers. Modular conveyor designs provide flexibility, enabling manufacturers to expand or reconfigure their systems as production demands evolve.
Safety and ergonomics are also critical considerations in conveyor and automation systems. Modern conveyors are equipped with safety features such as emergency stop mechanisms, anti-jam systems, and load sensors to prevent accidents and equipment damage. Automated systems reduce the need for manual handling of parts, minimizing the risk of injury and fatigue for workers. Additionally, the consistent movement of parts through automated systems ensures uniform exposure to each stage of the process, reducing the likelihood of defects caused by human error.
Energy efficiency is another area where automation contributes to the overall effectiveness of powder coating lines. By coordinating the operation of conveyors with other equipment, such as spray booths and curing ovens, automation systems can minimize energy waste. For instance, sensors can detect when no parts are on the conveyor and temporarily pause the system, conserving energy during idle periods. Additionally, predictive maintenance algorithms monitor the condition of conveyor components, alerting operators to potential issues before they result in downtime or inefficiency.
The integration of Industry 4.0 technologies is transforming conveyor and automation systems into smart manufacturing tools. Connected systems equipped with the Internet of Things (IoT) enable real-time data collection and analysis, providing insights into production efficiency, equipment health, and process optimization. Operators can access dashboards that display key performance indicators (KPIs) such as throughput rates, energy usage, and defect rates, allowing for proactive decision-making. Advanced systems can even use machine learning to predict and prevent bottlenecks or equipment failures, ensuring uninterrupted production.
Conveyor and automation systems are designed to accommodate a wide range of component sizes, shapes, and materials, making them suitable for diverse industries. In the automotive sector, these systems handle everything from small brackets and fasteners to large body panels. In consumer electronics, precision and speed are paramount, as small parts require delicate handling. In heavy industries, robust conveyors transport large, heavy components such as machinery housings, while maintaining stability and efficiency.
The flexibility of conveyor systems also extends to the ability to handle mixed production runs. With automated tracking and sorting mechanisms, parts of different sizes or specifications can be processed simultaneously, reducing the need for batch processing and increasing overall efficiency. Barcodes, RFID tags, or other identification methods allow the system to recognize each part and adjust the coating parameters accordingly.
In summary, conveyors and automation are integral to modern powder coating systems, providing the foundation for efficient, consistent, and scalable operations. By integrating advanced technologies, these systems enhance productivity, reduce costs, and ensure high-quality results across a wide range of applications. As automation technologies continue to evolve, conveyor systems will become even more sophisticated, incorporating AI-driven optimization, predictive maintenance, and greater flexibility to meet the demands of an ever-changing manufacturing landscape.
As conveyor and automation systems continue to advance, several emerging trends and innovations are further shaping the future of powder coating operations. These advancements promise to improve not only the speed and efficiency of the coating process but also its adaptability, precision, and sustainability.
Advanced Robotics and AI Integration
The role of robotics in automated powder coating lines is becoming increasingly sophisticated. In addition to traditional tasks such as spraying and coating, robots are now capable of performing complex tasks like component inspection, quality control, and even cleaning. Equipped with advanced vision systems, AI-driven robots can detect defects in the coating, such as uneven thickness or flaws, and make real-time adjustments to the spray patterns or application techniques. This closed-loop feedback system allows for continuous improvement in the coating process, leading to higher-quality results and reduced waste.
Furthermore, the integration of AI and machine learning algorithms enables robots to learn from past production data and adapt to changing conditions. For example, robots can adjust their spray patterns based on the specific geometry of each part, optimizing material usage and ensuring uniform coverage. This level of adaptability allows manufacturers to handle a wider variety of parts with minimal downtime or reconfiguration, making it easier to switch between different production runs without sacrificing quality or efficiency.
Predictive Maintenance and Smart Monitoring
One of the most significant benefits of automation in powder coating systems is the ability to implement predictive maintenance. Sensors embedded in conveyors, robotic arms, and other key equipment collect real-time data on their performance, including factors such as vibration, temperature, and usage patterns. Machine learning algorithms analyze this data to predict potential failures before they occur, allowing operators to schedule maintenance activities during non-peak hours and avoid costly downtime.
Smart monitoring systems also allow for remote access, enabling operators to monitor the performance of the entire powder coating line from anywhere in the world. Dashboards and mobile apps provide real-time insights into system status, allowing for proactive decision-making and immediate response to issues that may arise. This level of connectivity ensures optimal uptime and helps to maximize the efficiency of the entire system.
Enhanced Flexibility with Modular Automation Systems
Modular automation systems are gaining traction as they offer manufacturers the flexibility to adapt to changing production needs. These systems consist of interchangeable components such as conveyor sections, robotic arms, spray booths, and curing ovens, which can be easily swapped out or reconfigured based on specific requirements. Manufacturers can scale their production lines up or down, customize configurations for new products, or incorporate new technologies without significant infrastructure changes.
For example, a modular system might include a robotic arm that can be easily adjusted to coat a variety of parts, from small fasteners to large automotive panels. Conveyor systems can be expanded or contracted to accommodate varying production volumes. Modular systems provide a cost-effective way for businesses to remain agile in the face of fluctuating demand, new product lines, or market trends.
Sustainable Automation Solutions
As sustainability becomes a priority in manufacturing, the demand for eco-friendly automation solutions is increasing. Conveyor and automation systems are evolving to minimize their environmental impact through energy-saving features and the reduction of material waste. Conveyor systems equipped with energy-efficient motors and smart controls can reduce power consumption by optimizing speed and load. For example, systems may automatically adjust speed based on production volume or idle time, reducing energy consumption during non-operational periods.
Furthermore, the automation of powder coating processes contributes to sustainability by minimizing material waste. Automated spray guns with precise control mechanisms reduce overspray, ensuring that powder is applied only where it is needed. This not only lowers material costs but also reduces the environmental impact associated with powder waste. Some advanced systems even incorporate powder recovery technologies that capture unused powder from the air and return it to the system, allowing for recycling and reducing the amount of waste generated.
Integration with Other Manufacturing Processes
The future of automation in powder coating is closely tied to broader trends in smart manufacturing. As industries adopt Industry 4.0 technologies, the automation of powder coating lines will become increasingly integrated with other stages of the manufacturing process. For example, conveyors and robots may be connected to upstream processes such as assembly lines or material handling systems, allowing for a fully automated production flow from start to finish.
In highly automated environments, conveyor and automation systems can communicate with inventory management systems to track the status of components throughout the entire production cycle. This level of integration helps manufacturers streamline operations, reduce inventory holding costs, and optimize production schedules. Additionally, data collected from the coating process can be shared with other parts of the business, including quality control, logistics, and customer service departments, to ensure that production runs meet customer specifications and deadlines.
Collaborative Robotics for Flexibility and Safety
Collaborative robots, or cobots, are becoming increasingly popular in powder coating operations. Unlike traditional industrial robots, cobots are designed to work alongside human operators, providing a level of flexibility that traditional robots do not. These robots are often equipped with sensors that allow them to detect human presence and adjust their actions accordingly, ensuring a safe and efficient working environment.
In the context of powder coating, cobots can assist with tasks such as manual part loading or unloading, inspecting coated parts, or even adjusting coating parameters. By working in tandem with human operators, cobots can take on repetitive or physically demanding tasks, freeing up workers to focus on more complex or high-value activities. This collaboration enhances both productivity and worker safety, as the cobots can handle hazardous tasks like coating in confined spaces or managing high-temperature components in the curing process.
Future Prospects of Conveyor and Automation Systems
Looking ahead, the potential for innovation in conveyor and automation systems for powder coating is vast. As the demand for faster production cycles, higher-quality coatings, and more sustainable processes grows, the technology will continue to evolve. The integration of advanced sensors, AI, and robotics will allow for greater precision and flexibility, while predictive maintenance systems will ensure maximum uptime and operational efficiency.
Moreover, as manufacturers strive for greater sustainability, automation systems will likely incorporate renewable energy sources, such as solar or wind power, to further reduce their environmental impact. The ability to reduce energy consumption, material waste, and emissions while increasing productivity will be crucial in meeting both economic and environmental goals in the coming years.
In conclusion, conveyor and automation systems are central to the efficiency, flexibility, and scalability of modern powder coating processes. With continued advancements in robotics, AI, sustainability, and modular design, these systems will play an even greater role in shaping the future of manufacturing. As technology continues to progress, the ability to seamlessly integrate these systems into the broader context of smart manufacturing will ensure that powder coating lines remain at the forefront of industrial innovation.
Components of a Powder Coating Machine for Screw Heads:
- Screw Feeder: A hopper or reservoir that feeds screws into the coating process, ensuring a consistent supply of fasteners for even coating.
- Pre-cleaning System: A cleaning stage that removes dirt, grease, or other contaminants from the screw heads before coating, ensuring a clean surface for optimal adhesion.
- Electrostatic Powder Feeder: A powder feeder that supplies a fine layer of charged powder particles to the screw heads, utilizing electrostatic forces to attract the powder to the metal surface.
- Rotating Disk: A rotating disk that holds the screw heads in place, ensuring that they are evenly coated with powder as they pass through the spray zone.
- Curing Oven: A curing oven that heats the coated screw heads to a specific temperature for a predetermined time, curing the powder and hardening the coating.
- Cooling System: A cooling system that gradually cools the coated screw heads to prevent thermal shock and ensure a smooth, durable finish.
Types of Powder Coating Machines for Screw Heads:
- Manual Powder Coating Machines: Operated by hand, suitable for small-scale production or custom coating projects.
- Semi-automatic Powder Coating Machines: Incorporate some automated functions, such as screw feeding and powder application, suitable for medium-scale production runs.
- Automatic Powder Coating Machines: Highly automated, with integrated processes for screw handling, pre-cleaning, powder application, curing, and cooling, suitable for high-volume production environments.
Advantages of Powder Coating Machines for Screw Heads:
- Efficiency: Automated systems provide consistent and efficient coating of screw heads, reducing labor costs and increasing productivity.
- Quality Control: Precise powder application and curing ensure consistent coating thickness and high-quality finishes.
- Durability: Powder coating provides a durable, long-lasting finish that protects screw heads from corrosion, wear, and abrasion.
- Environmental Impact: Powder coating reduces solvent emissions and waste compared to traditional wet painting methods.
- Versatility: Can accommodate a variety of screw head sizes and shapes, including pan head, Phillips, and hex screw heads.
Applications of Powder Coating Machines for Screw Heads:
- Manufacturing of Screws and Fasteners: Coating screw heads for various applications, including automotive, construction, and appliance manufacturing.
- Production of Hardware Components: Coating hardware components for furniture, machinery, and electronic devices.
- Custom Coating Projects: Providing custom coating services for screw heads used in unique applications.
- Repair and Restoration: Coating screw heads during repair or restoration projects to enhance appearance and protection.
Tips for Using Powder Coating Machines for Screw Heads:
- Proper Preparation: Ensure screw heads are clean and free of contaminants before coating to achieve optimal adhesion.
- Powder Selection: Choose powder formulations suitable for the intended application and environment to ensure durability and performance.
- Powder Application: Adjust the powder feeder and rotating disk settings to achieve consistent and uniform powder coating.
- Curing Parameters: Follow the recommended curing temperature and time for the specific powder type to ensure proper curing and finish.
- Regular Maintenance: Maintain the equipment regularly to ensure optimal performance and extend its lifespan.
Screw Powder Coating Equipment – Powder Coating Machine
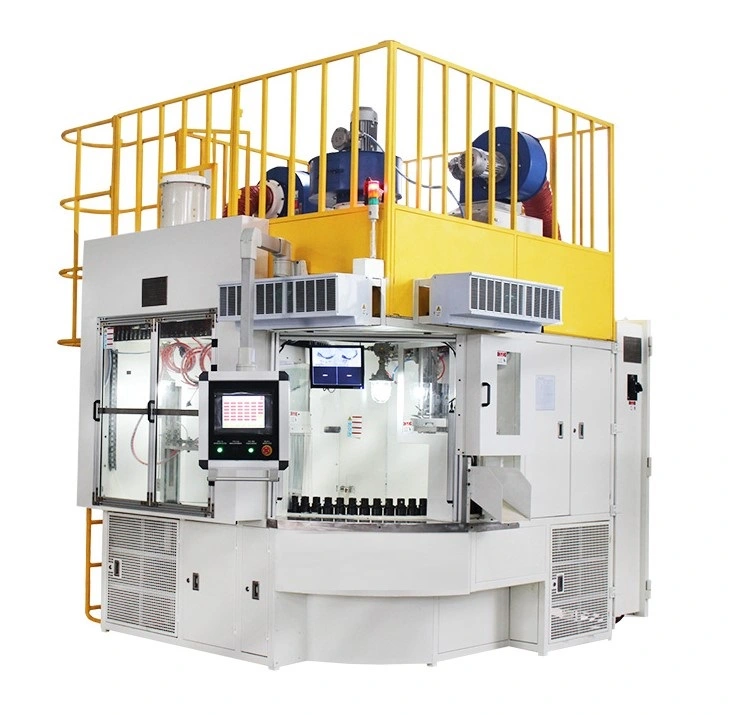
Screw powder coating equipment is a specialized type of powder coating machine that is specifically designed for coating screws and other small fasteners. It is typically used in manufacturing environments where high-quality, durable finishes are required for screws and other hardware components.
Components of Screw Powder Coating Equipment:
- Screw Feeder: A hopper or reservoir feeds screws to the coating process, ensuring a consistent supply of fasteners for even coating.
- Pre-cleaning System: A cleaning stage removes dirt, grease, or other contaminants from the screws before coating, ensuring a clean surface for optimal adhesion.
- Electrostatic Powder Feeder: A powder feeder supplies a fine layer of charged powder particles to the screws, utilizing electrostatic forces to attract the powder to the metal surface.
- Fluidized Bed: A fluidized bed suspends the screws in a stream of air, allowing the powder particles to evenly coat the entire surface of the screws.
- Curing Oven: A curing oven heats the coated screws to a specific temperature for a predetermined time, curing the powder and hardening the coating.
- Cooling System: A cooling system gradually cools the coated screws to prevent thermal shock and ensure a smooth, durable finish.
Types of Screw Powder Coating Equipment:
- Manual Screw Powder Coating Equipment: Operated by hand, suitable for small-scale production or custom coating projects.
- Semi-automatic Screw Powder Coating Equipment: Incorporates some automated functions, such as screw feeding and powder application, suitable for medium-scale production runs.
- Automatic Screw Powder Coating Equipment: Highly automated, with integrated processes for screw handling, pre-cleaning, powder application, curing, and cooling, suitable for high-volume production environments.
Advantages of Screw Powder Coating Equipment:
- Efficiency: Automated systems provide consistent and efficient coating of screws, reducing labor costs and increasing productivity.
- Quality Control: Precise powder application and curing ensure consistent coating thickness and high-quality finishes.
- Durability: Powder coating provides a durable, long-lasting finish that protects screws from corrosion, wear, and abrasion.
- Environmental Impact: Powder coating reduces solvent emissions and waste compared to traditional wet painting methods.
- Versatility: Can accommodate a variety of screw sizes and shapes, including pan head, Phillips, and hex screws.
Applications of Screw Powder Coating Equipment:
- Manufacturing of Screws and Fasteners: Coating screws and fasteners for various applications, including automotive, construction, and appliance manufacturing.
- Production of Hardware Components: Coating hardware components for furniture, machinery, and electronic devices.
- Custom Coating Projects: Providing custom coating services for screws and fasteners used in unique applications.
- Repair and Restoration: Coating screws and fasteners during repair or restoration projects to enhance appearance and protection.
Tips for Using Screw Powder Coating Equipment:
- Proper Preparation: Ensure screws are clean and free of contaminants before coating to achieve optimal adhesion.
- Powder Selection: Choose powder formulations suitable for the intended application and environment to ensure durability and performance.
- Powder Application: Adjust the powder feeder and fluidized bed settings to achieve consistent and uniform powder coating.
- Curing Parameters: Follow the recommended curing temperature and time for the specific powder type to ensure proper curing and finish.
- Regular Maintenance: Maintain the equipment regularly to ensure optimal performance and extend its lifespan.
Vibratory Bowl Feeder for Screw Coating
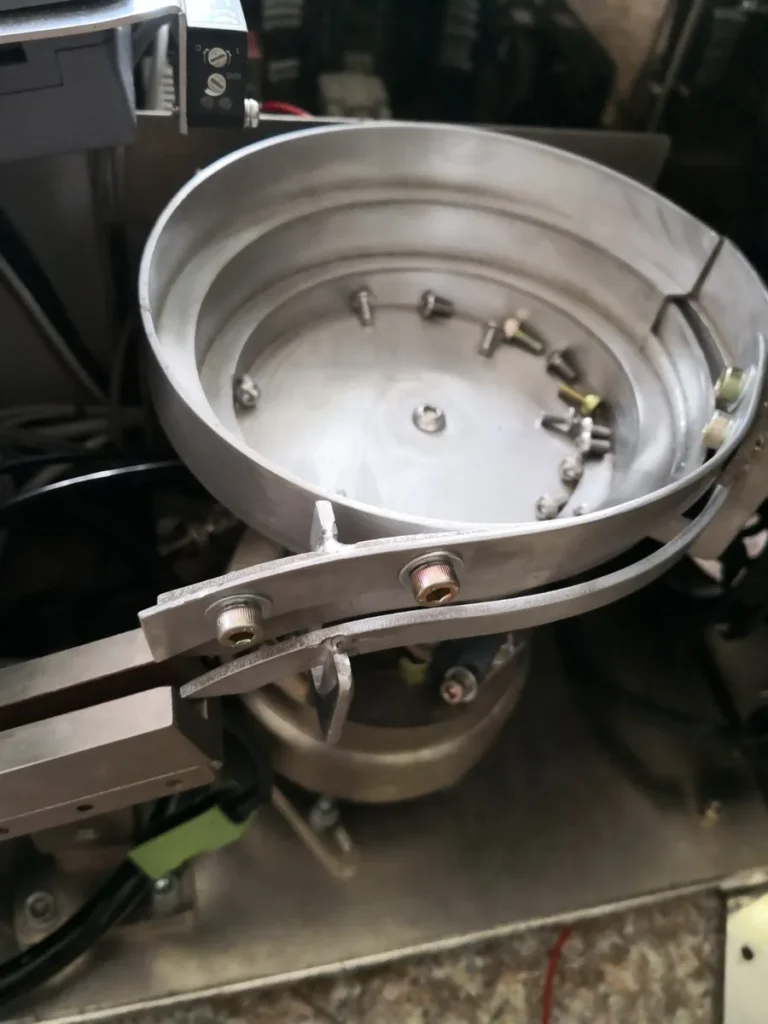
A vibratory bowl feeder is an effective solution for automatically sorting, orienting, and feeding screws in a production line. Here’s a detailed guide on how to design and implement a vibratory bowl feeder for screws:
1. Components and Functionality
1.1. Bowl feeder for Screw
- Shape: Typically conical or cylindrical with a spiral track.
- Material: Stainless steel or other durable materials to withstand wear and tear.
- Coating: Can be added to reduce noise and protect the screws from damage.
1.2. Drive Unit
- Vibration Mechanism: Uses electromagnetic or pneumatic drives to create vibrations.
- Frequency and Amplitude: Adjustable to control the speed and movement of the screws.
1.3. Control System
- Controller: Manages the vibration frequency and amplitude.
- Sensors: Monitor screw levels and detect jams or blockages.
1.4. Orienting Mechanism
- Orienting Rails: Guide the screws into the correct orientation (head up) as they travel up the spiral track.
- Gates and Traps: Mechanisms to reject misoriented screws back into the bowl.
1.5. Escapement Mechanism
- Purpose: Ensures that screws are released one at a time to the next stage of the process.
- Types: Pneumatic or mechanical gates.
1.6. Feeding Mechanism
- Linear Track: Transfers oriented screws from the bowl feeder to the next station.
- Buffers and Presenters: Ensure a steady flow of screws.
2. Design Considerations for Screw and Bolt Painting
2.1. Screw Specifications
- Size and Shape: Tailor the bowl and orienting mechanisms to the specific screw dimensions.
- Material: Consider the material of the screws to select the appropriate bowl coating.
2.2. Capacity
- Bowl Size: Select a bowl size that matches the production requirements and the volume of screws needed.
- Feeding Rate: Ensure the feeder can supply screws at the rate required by the painting machine.
2.3. Orientation Accuracy
- Orientation Efficiency: Design orienting rails and mechanisms to achieve high accuracy in screw orientation.
- Adjustment: Provide adjustments to handle different screw sizes and types.
3. Implementation Steps
3.1. Design and Fabrication
- Custom Bowl Design: Design the bowl with a spiral track and orienting mechanisms tailored to the screws.
- Material Selection: Choose appropriate materials for durability and compatibility with screw material.
- Drive Unit Specification: Select a drive unit capable of providing adjustable vibration settings.
3.2. Installation
- Mounting: Secure the bowl feeder on a stable base to prevent movement.
- Connection to Control System: Integrate the feeder with a PLC or other control system for synchronized operation.
3.3. Testing and Calibration
- Initial Testing: Run the feeder with a batch of screws to observe performance.
- Calibration: Adjust the vibration frequency, amplitude, and orienting mechanisms for optimal performance.
- Error Handling: Implement sensors and controls to detect and address misfeeds or jams.
3.4. Integration with Painting Machine
- Synchronization: Ensure the feeder is synchronized with the painting machine’s cycle.
- Feeding Mechanism: Connect the linear track to the painting station to deliver screws consistently.
4. Maintenance and Troubleshooting of Screw Coating
4.1. Regular Maintenance
- Cleaning: Regularly clean the bowl and tracks to prevent buildup of debris.
- Inspection: Periodically inspect the drive unit, sensors, and mechanical parts for wear and tear.
4.2. Troubleshooting
- Jams and Blockages: Check for and clear any jams in the bowl or tracks.
- Vibration Issues: Adjust the frequency and amplitude if screws are not moving correctly.
Electrostatic Powder Coating Unit
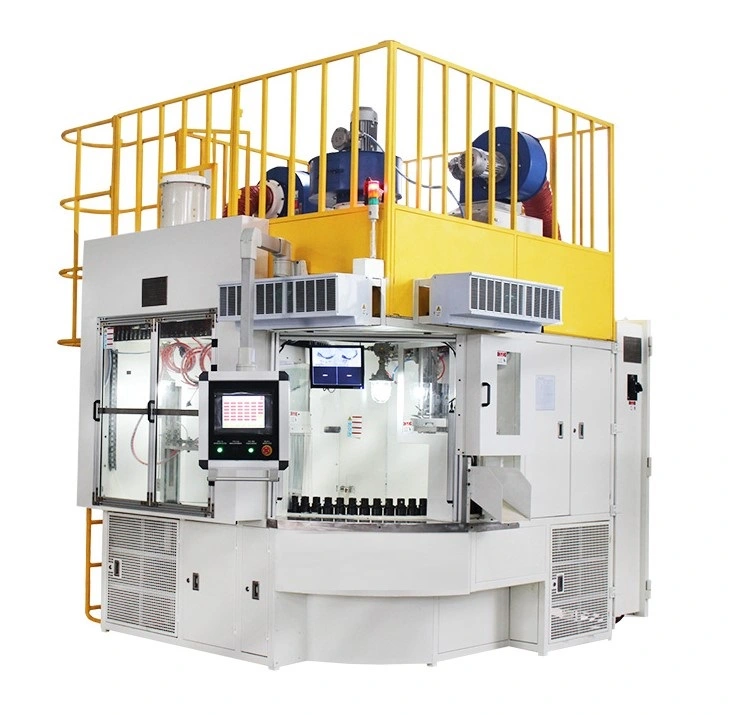
Designing an electrostatic powder coating unit for screws involves several critical components and steps to ensure uniform and efficient coating. Here’s a detailed guide on how to set up and operate such a unit:
Components of an Electrostatic Powder Coating Unit
1. Powder Coating Booth
- Purpose: Encloses the coating process to contain overspray and ensure a clean environment.
- Construction: Made of non-conductive materials; equipped with proper ventilation and filters.
2. Powder Feed System
- Powder Hopper: Stores the powder coating material.
- Powder Pump: Transports powder from the hopper to the spray gun.
3. Electrostatic Spray Gun
- Corona or Tribo Charging: Ionizes the powder particles to create an electrostatic charge.
- Nozzle: Designed to provide an even spray pattern and efficient transfer of powder to screws.
4. Conveyor System
- Purpose: Moves screws through the coating booth at a controlled speed.
- Types: Can be a chain, belt, or rotary conveyor depending on production requirements.
5. Curing Oven
- Purpose: Heats coated screws to cure the powder, forming a hard, durable finish.
- Temperature Control: Precisely controls the temperature to match the powder’s curing requirements.
6. Control System
- PLC (Programmable Logic Controller): Automates the coating process, controlling the conveyor, spray gun, and curing oven.
- Sensors and Timers: Ensure consistent application and curing.
7. Recovery System
- Cyclone Separator or Filters: Captures overspray powder for reuse, improving efficiency and reducing waste.
Design Considerations
1. Screw Specifications
- Size and Shape: Adapt the system to handle various screw sizes and shapes.
- Material: Ensure compatibility of screws with the electrostatic process and powder material.
2. Coating Uniformity
- Spray Gun Positioning: Position guns to ensure even coverage from all angles.
- Conveyor Speed: Adjust speed to match the spray rate and ensure complete coverage.
3. Powder Material
- Type: Choose powder based on desired properties such as color, finish, and durability.
- Compatibility: Ensure powder is suitable for the screws’ application environment.
Implementation Steps
1. Setup and Installation
- Booth Installation: Set up the powder coating booth with proper ventilation and filtration systems.
- Conveyor System: Install and calibrate the conveyor system for smooth and consistent movement of screws.
- Spray Gun and Powder Feed System: Set up and calibrate the spray gun and feed system for optimal performance.
2. Testing and Calibration
- Initial Testing: Run a batch of screws through the system to test for even coating and proper curing.
- Adjustments: Adjust spray gun settings, conveyor speed, and oven temperature as needed.
3. Operation
- Loading Screws: Feed screws onto the conveyor system, ensuring they are properly spaced for even coating.
- Spraying: Operate the spray guns to apply powder to the screws as they pass through the booth.
- Curing: Pass coated screws through the curing oven to bake the powder onto the surface.
- Cooling and Inspection: Allow screws to cool and inspect for coating quality.
4. Maintenance and Troubleshooting
- Regular Cleaning: Clean the booth, guns, and recovery system to prevent powder buildup.
- Equipment Check: Regularly inspect and maintain all components to ensure smooth operation.
- Troubleshooting: Address issues such as uneven coating, powder clumping, or curing defects promptly.
Example Process Flow
- Loading: Screws are loaded onto the conveyor system.
- Powder Application: Screws pass through the powder coating booth where the electrostatic spray gun applies the powder.
- Curing: Coated screws enter the curing oven where the powder is baked onto the screws.
- Cooling: Screws are cooled and then inspected for quality.
- Unloading: Finished screws are collected from the conveyor system.
Conclusion
Setting up an electrostatic powder coating unit for screws requires careful planning and consideration of various factors, including screw specifications, coating uniformity, and material compatibility. By following the steps and ensuring proper maintenance and calibration, you can achieve a high-quality, efficient coating process for screws.
Curing Oven for Painted Screw, Fasteners and Bolts
Designing and implementing a curing oven for painted screws, fasteners, and bolts involves several critical factors to ensure efficient curing and high-quality finishes. Here’s a comprehensive guide on setting up a curing oven for these components:
1. Types of Curing Ovens for Screw Coating
1.1. Batch Ovens
- Description: Suitable for smaller production runs or varied parts. Components are loaded into the oven in batches.
- Advantages: Flexibility, lower initial cost.
- Disadvantages: Lower throughput, more labor-intensive.
1.2. Continuous Ovens
- Description: Designed for high-volume production. Parts move continuously through the oven on a conveyor system.
- Advantages: High throughput, consistent processing.
- Disadvantages: Higher initial cost, less flexibility.
2. Key Design Considerations
2.1. Temperature Control
- Uniformity: Ensure even temperature distribution to prevent uneven curing.
- Control System: Use precise temperature controllers to maintain the desired curing temperature, typically between 150-200°C (300-400°F) depending on the coating material.
2.2. Airflow and Ventilation
- Forced Air Circulation: Ensures uniform heat distribution and efficient curing.
- Ventilation: Proper ventilation to remove volatile organic compounds (VOCs) and ensure a safe working environment.
2.3. Conveyor System
- Material Handling: Design the conveyor to handle the weight and size of screws, fasteners, and bolts.
- Speed Control: Adjustable speed to match the curing time required for the coating material.
2.4. Oven Size and Capacity
- Sizing: Design the oven size based on production volume and part dimensions.
- Capacity: Ensure the oven can handle peak production loads without compromising performance.
2.5. Insulation
- Energy Efficiency: Use high-quality insulation materials to minimize heat loss and reduce energy consumption.
- Safety: Ensure exterior surfaces remain safe to touch during operation.
3. Implementation Steps
3.1. Design and Fabrication
- Oven Chamber: Design the chamber with appropriate dimensions, insulation, and airflow mechanisms.
- Heating Elements: Choose suitable heating elements (electric, gas, or infrared) based on energy availability and cost considerations.
- Control Systems: Integrate PLC or microprocessor-based controllers for precise temperature and conveyor speed control.
3.2. Installation
- Site Preparation: Ensure adequate space, ventilation, and safety measures at the installation site.
- Electrical and Gas Connections: Ensure proper and safe connections to power sources.
- Conveyor Setup: Install and calibrate the conveyor system for smooth operation.
3.3. Testing and Calibration
- Initial Testing: Run the oven with a sample batch to verify temperature uniformity and curing efficiency.
- Calibration: Adjust temperature settings, conveyor speed, and airflow to optimize performance.
3.4. Operation
- Loading Parts: Load screws, fasteners, and bolts onto the conveyor or into the batch oven.
- Curing Process: Monitor the curing process to ensure consistent temperature and curing time.
- Unloading and Inspection: Unload cured parts and inspect for coating quality.
3.5. Maintenance and Troubleshooting
- Regular Maintenance: Schedule regular inspections and maintenance of heating elements, conveyor system, and control units.
- Cleaning: Regularly clean the oven interior to prevent buildup of coating material.
- Troubleshooting: Address issues such as uneven curing, temperature fluctuations, or mechanical failures promptly.
Why Choose EMS Powder Coating Equipment for Reciprocators?
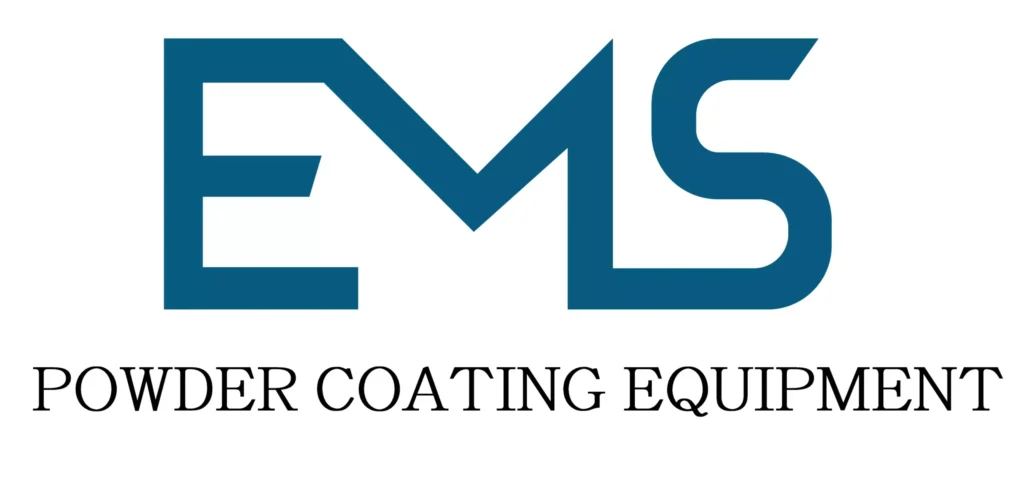
Choosing the right powder coating reciprocator is critical for achieving the best results in your production line. EMS Powder Coating Equipment is the industry leader in reciprocator technology, offering systems that are designed for precision, efficiency, and durability. Here’s why EMS is the best choice for businesses looking to invest in reciprocators:
1. Advanced Technology for Precision Control
EMS reciprocators are equipped with the latest technology, allowing for precise control over spray gun movement. Their systems can be programmed to meet the specific needs of your production line, ensuring that every part is coated evenly. Whether you’re coating flat panels or complex shapes, EMS reciprocators provide the accuracy needed to achieve perfect results.
2. Customization and Flexibility
Every business has unique coating requirements, and EMS understands the importance of providing customizable solutions. EMS reciprocators can be tailored to fit your specific production line, with adjustable stroke lengths, speeds, and motion patterns. This flexibility allows businesses to optimize their powder coating process and maximize efficiency.
3. Durability and Reliability
Built with high-quality materials and engineering, EMS reciprocators are designed for long-lasting performance. These systems are robust enough to withstand continuous operation in demanding industrial environments, ensuring that businesses can rely on them for years without frequent maintenance or breakdowns.
4. Seamless Integration with Existing Systems
EMS reciprocators are designed to integrate seamlessly with other equipment in your powder coating line, including conveyor systems and curing ovens. This ensures that your production line operates smoothly and efficiently, with minimal downtime or disruption.
Conclusion
Powder coating reciprocators are a key component of any automated coating system, providing the precision and efficiency needed to produce consistent, high-quality finishes. By automating the movement of spray guns, reciprocators ensure that every product is coated evenly, reducing the risk of defects and improving overall production efficiency.
EMS Powder Coating Equipment offers the best reciprocators on the market, designed to meet the needs of businesses in a wide range of industries. With advanced technology, customizable solutions, and a commitment to durability and reliability, EMS ensures that your powder coating process is optimized for maximum efficiency and quality.
Whether you’re looking to automate your production line for the first time or upgrade your existing equipment, EMS Powder Coating Equipment provides the expertise and products needed to take your powder coating operation to the next level.