Automatic Rivet Painting Machine: An Automatic Rivet Coating Machine is a specialized industrial device designed to streamline the process of applying coatings, such as adhesives, paints, or protective layers, onto rivets used in various manufacturing sectors. This machine integrates advanced automation technology to ensure uniformity, precision, and efficiency, which are crucial for maintaining the quality and durability of riveted joints. By automating the coating process, manufacturers can significantly reduce labor costs, minimize material wastage, and enhance production throughput, making the system ideal for large-scale operations.
The machine typically consists of several key components, including a feeding mechanism, a coating applicator, a drying or curing system, and a control panel. The feeding mechanism is responsible for the seamless and continuous supply of rivets to the coating applicator. It uses a combination of vibratory feeders, conveyor belts, or robotic arms to align and transport rivets to the application area. This alignment is critical, as even slight misplacements can result in uneven coatings, potentially compromising the functionality of the rivet in its final application.
The coating applicator is the core of the machine, employing various techniques such as spraying, dipping, or brushing to apply the desired material onto the rivet surface. The choice of technique depends on the type of coating material and the specific requirements of the rivet’s application. For instance, adhesive coatings may require a precise, controlled application to ensure optimal bonding, while protective coatings like corrosion-resistant layers might necessitate full immersion to achieve complete coverage. The applicator’s design ensures that the coating is uniformly distributed, eliminating defects such as drips, streaks, or bubbles that could affect performance.
Once coated, the rivets pass through a drying or curing system, which solidifies or stabilizes the applied layer. Depending on the coating material, this system may involve thermal ovens, UV curing units, or air-drying chambers. The drying process is carefully calibrated to avoid overheating or under-curing, both of which could degrade the coating’s properties. Additionally, modern machines are equipped with real-time monitoring systems to track parameters like temperature, humidity, and curing time, ensuring consistency and adherence to quality standards.
The control panel serves as the interface between the operator and the machine, offering features like programmable settings, fault detection, and operational feedback. Advanced models incorporate sensors and machine learning algorithms to optimize performance and reduce downtime. For example, sensors can detect variations in rivet size or coating viscosity, automatically adjusting the applicator settings to maintain uniformity. Machine learning algorithms analyze production data to predict maintenance needs or suggest improvements, enhancing overall efficiency.
An Automatic Rivet Coating Machine is designed with safety and environmental considerations in mind. Safety features include protective enclosures, emergency stop buttons, and interlock systems to prevent accidental injuries. Environmentally, these machines aim to reduce the environmental impact of the coating process by incorporating features like solvent recovery systems, low-energy drying technologies, and the use of eco-friendly materials. Such measures align with growing regulatory pressures and consumer demand for sustainable manufacturing practices.
The versatility of these machines makes them suitable for a wide range of industries, including aerospace, automotive, construction, and electronics. In aerospace, for instance, rivets require precise coatings to withstand extreme conditions and prevent galvanic corrosion. Similarly, in the automotive industry, rivet coatings contribute to vehicle safety and longevity by enhancing the strength and durability of joints exposed to vibrations, heat, and moisture.
In conclusion, an Automatic Rivet Coating Machine represents a critical advancement in manufacturing technology, offering unmatched precision, efficiency, and adaptability. By automating and optimizing the rivet coating process, these machines enable manufacturers to meet stringent quality requirements while reducing costs and environmental impact. Their integration into production lines not only boosts productivity but also ensures that rivets are consistently coated to the highest standards, enhancing the reliability and performance of the end products.
Automatic Rivet Coating Machine
The future of Automatic Rivet Coating Machines lies in the incorporation of cutting-edge technologies to further enhance performance, flexibility, and sustainability. As manufacturing continues to adopt Industry 4.0 principles, these machines are increasingly equipped with smart capabilities, such as IoT connectivity and data analytics. IoT-enabled rivet coating machines allow operators to monitor and control operations remotely, accessing real-time data on production rates, coating consistency, and machine health. This connectivity enables predictive maintenance, where potential issues are identified before they lead to downtime, reducing operational disruptions and extending the machine’s lifespan.
Another promising development is the integration of artificial intelligence (AI) to refine the coating process. AI can analyze patterns in production data to optimize parameters like coating thickness, curing time, and material usage. By learning from historical data, AI-driven machines can adapt to variations in raw materials or environmental conditions, ensuring consistent output quality without manual intervention. This adaptability is particularly valuable in industries that demand high precision, such as medical device manufacturing or microelectronics, where even minor defects can have significant consequences.
Energy efficiency is another area of focus for the evolution of these machines. Advanced drying and curing systems now utilize energy-saving technologies, such as infrared or microwave-based drying, to reduce power consumption while maintaining effectiveness. These systems target only the coated area, minimizing heat loss and shortening cycle times. Additionally, efforts are being made to develop low-energy applicators that use precision-engineered nozzles or electrostatic coating methods to achieve maximum material coverage with minimal waste.
Environmental sustainability is becoming a critical consideration, driving innovations in eco-friendly coating materials and processes. Manufacturers are exploring water-based coatings and bio-degradable adhesives that reduce the environmental footprint without compromising performance. Automatic Rivet Coating Machines are also being designed to handle these newer materials effectively, incorporating features like material compatibility sensors and non-reactive surfaces to prevent contamination. Closed-loop systems for solvent recovery and material recycling further enhance the environmental profile of these machines, aligning them with global sustainability goals.
Customization is another significant trend, as manufacturers increasingly seek machines tailored to their specific production requirements. Modular designs allow for easy adaptation of the machine’s components to accommodate different rivet sizes, shapes, and coating types. For instance, a manufacturer producing rivets for both aerospace and automotive applications can configure the machine to handle the stringent specifications of aerospace coatings while switching seamlessly to the more robust coatings required for automotive parts. This flexibility reduces the need for multiple machines, lowering capital expenditure and simplifying maintenance.
Human-machine interaction is also being enhanced through the use of intuitive interfaces and augmented reality (AR) tools. Modern control panels feature touchscreens with user-friendly interfaces, making it easier for operators to adjust settings, troubleshoot issues, and monitor performance. AR tools enable operators to visualize machine components and processes in real time, facilitating faster training and more efficient maintenance. For example, AR headsets can guide technicians step-by-step through the replacement of parts or the calibration of applicators, reducing downtime and error rates.
In terms of scalability, Automatic Rivet Coating Machines are being developed to cater to both small-scale operations and large industrial setups. Compact models are available for small businesses or specialized production lines, offering the same level of precision and efficiency as their larger counterparts but at a reduced footprint and cost. For high-volume manufacturers, machines with multiple applicators, high-speed conveyors, and integrated quality control systems ensure that production goals are met without sacrificing quality.
Quality assurance remains a cornerstone of these machines, with advanced inspection systems integrated into the production line. High-resolution cameras, laser scanners, and ultrasonic sensors can detect even the slightest imperfections in the coating layer, ensuring that only flawless rivets proceed to the next stage of manufacturing. These systems are capable of inspecting rivets at high speeds, maintaining throughput without compromising accuracy. Additionally, detailed reports generated by the inspection systems provide valuable insights into production trends, helping manufacturers identify areas for improvement.
In summary, the evolution of Automatic Rivet Coating Machines reflects the broader trends in modern manufacturing: a commitment to precision, efficiency, sustainability, and adaptability. By embracing new technologies and innovative design principles, these machines continue to set new benchmarks for performance, enabling manufacturers to meet the ever-increasing demands of global markets. As industries evolve and new challenges arise, the role of these machines will only grow more critical, solidifying their place as an indispensable tool in advanced manufacturing.
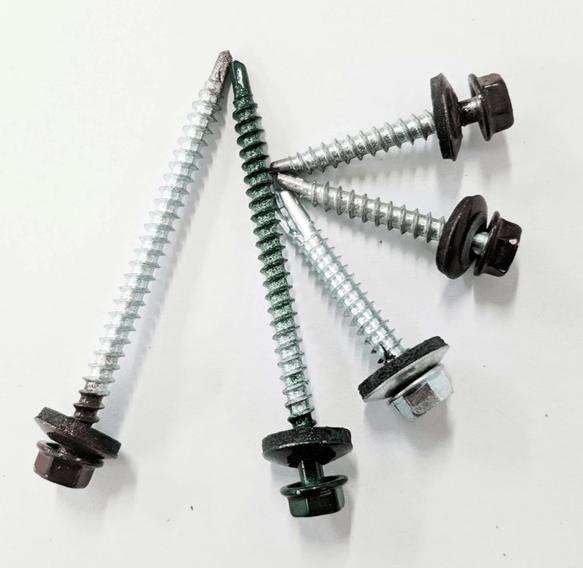
The versatility and adaptability of Automatic Rivet Coating Machines also make them pivotal in emerging industries and applications where unique requirements call for innovative solutions. For instance, in the renewable energy sector, components like wind turbine blades and solar panel mounting systems often rely on riveted assemblies. These components are exposed to harsh environmental conditions, such as high winds, temperature fluctuations, and moisture. Coatings applied by automatic rivet coating machines ensure that the rivets used in these assemblies maintain their integrity and resist corrosion, thereby extending the lifespan and reliability of renewable energy systems.
In the medical field, rivets are used in specialized equipment and devices where hygiene and biocompatibility are paramount. Coatings applied to these rivets often include antimicrobial layers or biocompatible materials that must adhere to stringent regulatory standards. Automatic rivet coating machines are designed to handle such delicate and precise tasks, providing the consistency required to meet medical-grade specifications. The integration of cleanroom-compatible designs ensures that the coating process does not introduce contaminants, a critical factor in this highly regulated industry.
Military and defense applications also benefit significantly from the precision and reliability of these machines. Rivets used in defense equipment, such as armored vehicles, aircraft, and naval vessels, must withstand extreme conditions, including high impact, temperature extremes, and exposure to corrosive environments. The coatings applied to these rivets often involve specialized materials, such as thermal barriers or stealth coatings, which demand meticulous application processes. Automatic rivet coating machines are engineered to accommodate these challenging requirements, ensuring that every rivet meets the rigorous standards of defense manufacturing.
Looking ahead, the development of hybrid rivet coating systems could revolutionize the field. These systems would combine the capabilities of automatic coating machines with additional functionalities, such as rivet assembly or inspection, creating an all-in-one solution. By integrating processes that are currently performed separately, such systems would further streamline production lines, reduce setup times, and enhance overall efficiency. For instance, a hybrid machine could coat, inspect, and sort rivets in a single automated workflow, eliminating the need for multiple stations and reducing the risk of handling-related defects.
Another avenue of innovation lies in the use of advanced materials and nanotechnology in coatings. Nanocoatings, which involve ultra-thin layers of material applied at the nanoscale, offer exceptional properties such as superhydrophobicity, self-healing capabilities, and enhanced durability. Automatic rivet coating machines are being adapted to handle these advanced materials, incorporating precise application systems and controlled environments to ensure the integrity of nanocoatings. These advancements open up new possibilities for rivet applications in cutting-edge technologies, such as aerospace exploration and advanced electronics.
Additionally, global economic and regulatory trends are shaping the development and adoption of these machines. With an increasing emphasis on reducing carbon footprints and adhering to environmental regulations, manufacturers are seeking greener production solutions. Automatic rivet coating machines equipped with energy-efficient systems, waste recycling capabilities, and support for eco-friendly coatings align perfectly with these goals. Governments and industry bodies are also offering incentives for adopting sustainable technologies, further driving the demand for modern, environmentally conscious coating machines.
Training and workforce development are also critical to maximizing the potential of these machines. As technology evolves, operators need to be well-versed in the use of sophisticated features such as AI algorithms, IoT interfaces, and real-time monitoring tools. Manufacturers of automatic rivet coating machines are addressing this need by offering comprehensive training programs, virtual simulations, and user-friendly manuals. The incorporation of augmented reality (AR) training modules provides an interactive way for operators to learn machine operations, maintenance procedures, and troubleshooting techniques, significantly reducing the learning curve.
In conclusion, the ongoing advancements in Automatic Rivet Coating Machines underscore their importance as a cornerstone of modern manufacturing. From enhancing product quality and production efficiency to supporting sustainability and innovation, these machines are pivotal in meeting the demands of an ever-evolving industrial landscape. As new materials, applications, and challenges emerge, the flexibility and technological sophistication of these machines will continue to expand, ensuring their relevance and value for decades to come. By investing in such advanced systems, manufacturers position themselves at the forefront of industry innovation, ready to tackle future challenges with confidence and precision.
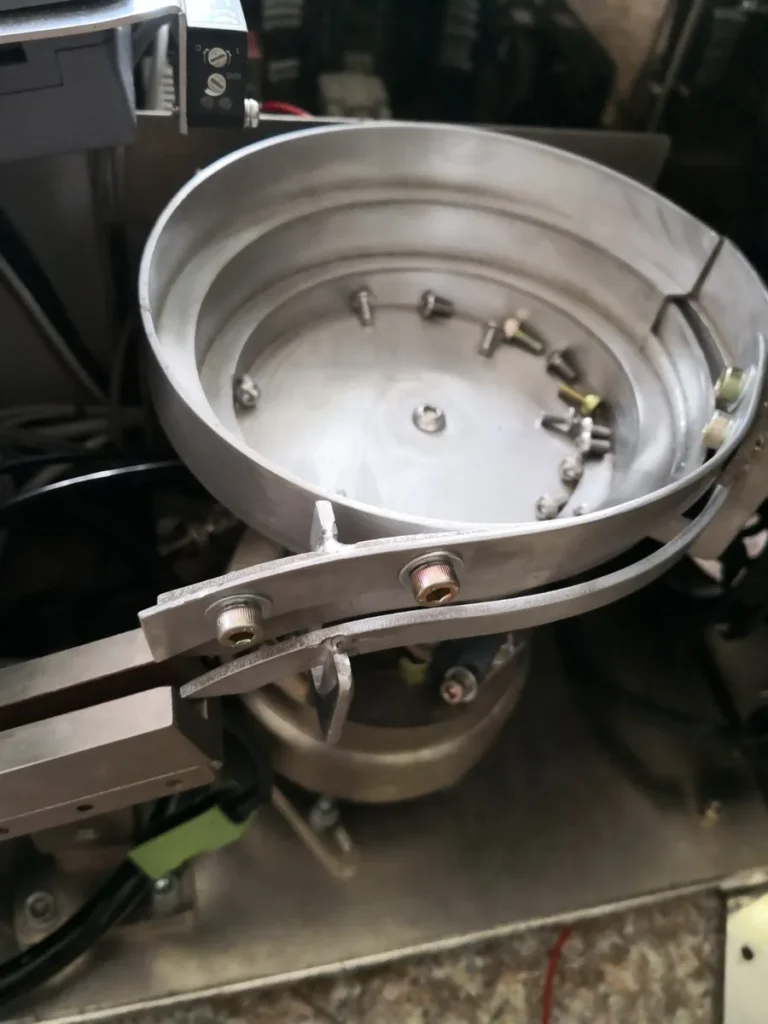
As the industrial landscape continues to evolve, the integration of Automatic Rivet Coating Machines into smart manufacturing ecosystems is becoming increasingly prevalent. These machines are no longer isolated units but are part of interconnected production environments that leverage data to optimize processes across the entire assembly line. This interconnectedness is facilitated by technologies such as digital twins, which create virtual replicas of physical systems. In the context of rivet coating machines, digital twins can simulate the coating process, predict outcomes, and suggest optimizations, enabling manufacturers to fine-tune operations without interrupting production.
The role of data analytics in these systems cannot be overstated. Rivet coating machines equipped with advanced sensors generate a wealth of data related to performance metrics, such as coating thickness, material consumption, and production speed. By analyzing this data in real-time, manufacturers can identify trends, diagnose inefficiencies, and implement corrective measures swiftly. For example, if data reveals that a certain batch of rivets consistently requires more coating material, the machine can automatically adjust its settings or alert operators to inspect the rivets for irregularities. This level of responsiveness ensures consistent product quality and minimizes waste.
Customization through software advancements is another area where significant strides are being made. Modern automatic rivet coating machines allow users to create and store multiple operational profiles tailored to specific production needs. These profiles can include parameters such as coating material type, application method, drying time, and rivet dimensions. With a simple selection on the control interface, operators can switch between profiles, enabling rapid transitions between different production runs. This capability is especially valuable for manufacturers who produce diverse product lines or frequently change designs.
The impact of these machines on production economics is substantial. By automating the rivet coating process, manufacturers achieve higher throughput and lower per-unit costs. Moreover, the precision and repeatability of automated systems significantly reduce material wastage, contributing to cost savings and environmental sustainability. For example, an automated spray applicator ensures that only the required amount of coating material is used, eliminating over-spray and the associated cleanup costs. Additionally, the reduction in human labor requirements allows companies to allocate workforce resources more strategically, focusing on tasks that require creativity or critical thinking.
Another exciting development is the use of robotic arms and collaborative robots (cobots) in conjunction with rivet coating machines. Robotic arms enhance the flexibility and precision of the coating process, especially for complex geometries or hard-to-reach areas. Cobots, designed to work safely alongside humans, allow for semi-automated systems where operators and machines collaborate seamlessly. For instance, an operator might handle the initial setup and quality inspection, while the cobot performs the repetitive task of feeding rivets into the machine. This hybrid approach combines the strengths of human ingenuity with the efficiency of automation.
The adoption of these machines is also fostering a shift in the supply chain dynamics. With the ability to achieve consistent and high-quality coatings in-house, manufacturers are less reliant on external suppliers for coated rivets. This reduction in outsourcing not only lowers costs but also shortens lead times and enhances supply chain resilience. In industries where time-to-market is critical, such as consumer electronics or automotive manufacturing, this capability provides a significant competitive advantage.
In terms of research and development, efforts are being directed toward enhancing the durability and functionality of coatings applied by these machines. Innovations in material science are yielding new coating formulations with properties such as self-lubrication, enhanced thermal resistance, or even electrical conductivity. These advancements are expanding the scope of rivet applications, enabling their use in cutting-edge fields like aerospace propulsion systems or next-generation electronic devices. Automatic rivet coating machines, equipped with precise and adaptable applicators, are essential for successfully deploying these advanced materials.
Global competition and regulatory standards are also influencing the design and functionality of these machines. In regions with strict environmental regulations, manufacturers are increasingly investing in machines with low emissions and energy-efficient systems. Furthermore, international standards for quality and safety, such as ISO certifications, are driving the adoption of automated systems that can consistently meet stringent requirements. Manufacturers of automatic rivet coating machines are responding to these demands by incorporating compliance-focused features, such as traceability modules that document every step of the coating process for auditing purposes.
In summary, the evolution of Automatic Rivet Coating Machines is a testament to the broader trends of innovation and efficiency in manufacturing. By embracing automation, data-driven insights, and advanced materials, these machines are not just meeting current industrial demands but are also setting the stage for future possibilities. Whether it’s enhancing sustainability, enabling customization, or integrating into smart factories, these machines represent a critical link in the chain of modern manufacturing. Their continued development will undoubtedly shape the future of rivet applications, driving progress across industries and supporting the creation of high-performance, reliable, and cost-effective products.
Automatic Rivet Painting Machine
An Automatic Rivet Painting Machine is a highly specialized piece of equipment designed to apply paint or other protective coatings to rivets with precision, efficiency, and consistency. These machines play a critical role in industries where rivets serve as structural or decorative elements, ensuring that they not only perform their mechanical function but also meet aesthetic and protective requirements. By automating the painting process, these machines provide a reliable solution for high-volume production while reducing labor costs, material waste, and production time.
The machine typically comprises several essential components, including a rivet feeding system, a painting application unit, a drying or curing system, and a control interface. The rivet feeding system is responsible for organizing and transporting rivets into the painting zone. This system often employs vibratory bowls, conveyor belts, or robotic arms to align and position rivets for seamless and continuous operation. The precision of the feeding mechanism ensures that each rivet is properly oriented, a critical factor in achieving uniform paint coverage.
The painting application unit is the heart of the machine, utilizing advanced techniques such as spray painting, electrostatic painting, or dip coating to apply a uniform layer of paint onto the rivets. The choice of painting method depends on the specific requirements of the rivets, such as the desired thickness, finish, and type of paint being used. Spray painting is commonly employed for its versatility, allowing for smooth and even coverage on rivets of varying shapes and sizes. Electrostatic painting, on the other hand, is ideal for achieving high-efficiency paint transfer and minimizing overspray, making it particularly suitable for large-scale operations.
Once the paint is applied, the rivets move into the drying or curing system. This system is designed to solidify the paint layer and ensure its durability. Depending on the type of paint used, the drying process may involve heat curing in ovens, infrared drying, or air-drying chambers. Modern machines incorporate precise temperature and airflow controls to optimize the drying process, preventing issues like bubbling, cracking, or uneven finishes. In addition, real-time monitoring systems ensure consistent drying conditions, maintaining high-quality output.
The control interface of an Automatic Rivet Painting Machine is user-friendly and equipped with advanced features for customization and monitoring. Operators can set parameters such as paint type, application speed, and drying time, tailoring the machine’s operation to specific production needs. High-end models often include touchscreen interfaces, programmable logic controllers (PLCs), and IoT connectivity, enabling remote operation and monitoring. These features provide real-time feedback on machine performance, production rates, and maintenance requirements, ensuring smooth and uninterrupted operation.
Quality assurance is an integral aspect of the machine’s functionality. Integrated inspection systems, such as cameras or sensors, verify the uniformity and consistency of the paint layer. These systems detect defects like uneven coverage, drips, or missed areas, allowing for immediate corrective action. By maintaining stringent quality control, these machines reduce the likelihood of defective rivets reaching subsequent stages of production or final assembly.
The versatility of Automatic Rivet Painting Machines makes them suitable for a wide range of industries, including automotive, aerospace, construction, and consumer goods. In the automotive sector, for example, painted rivets contribute to both the structural integrity and aesthetic appeal of vehicles. They are often used in visible areas, such as trim or paneling, where a flawless finish is essential. Similarly, in the aerospace industry, painted rivets are critical for corrosion resistance and maintaining the integrity of aircraft structures exposed to extreme environmental conditions.
Environmental sustainability is a growing priority in the development and operation of these machines. Manufacturers are increasingly incorporating eco-friendly features, such as low-energy drying systems, solvent recovery units, and support for water-based or low-VOC paints. These advancements align with global efforts to reduce the environmental impact of industrial processes, helping manufacturers meet regulatory standards and improve their sustainability profile. Additionally, automated systems minimize paint waste through precise application and efficient material usage, further reducing the environmental footprint.
The future of Automatic Rivet Painting Machines lies in the integration of advanced technologies to enhance performance and adaptability. IoT-enabled machines allow for real-time data collection and analysis, enabling predictive maintenance, process optimization, and remote troubleshooting. For instance, sensors embedded in the machine can monitor paint viscosity, ambient conditions, and production rates, providing valuable insights for fine-tuning operations. Artificial intelligence (AI) is also being explored to optimize painting parameters dynamically, adapting to variations in rivet materials, shapes, or environmental factors.
Customization is another emerging trend, with machines being designed to handle diverse requirements across industries. Modular systems allow manufacturers to configure the machine for different rivet sizes, shapes, or paint types, enabling quick and easy transitions between production runs. This flexibility is particularly valuable for manufacturers producing rivets for multiple applications, such as decorative rivets for consumer goods and functional rivets for industrial equipment.
Robotics and automation are further enhancing the capabilities of these machines. Robotic arms can be integrated to handle rivet loading, unloading, or repositioning, ensuring seamless operation even for complex or non-standard rivet geometries. Collaborative robots, or cobots, enable hybrid systems where human operators and automated machines work together efficiently, combining the precision of automation with the adaptability of human oversight.
In summary, Automatic Rivet Painting Machines are indispensable tools in modern manufacturing, providing a highly efficient, precise, and reliable solution for applying paint to rivets. By leveraging advanced technologies and incorporating sustainable practices, these machines meet the demands of high-quality production while supporting environmental and economic goals. Their adaptability, scalability, and integration into smart manufacturing ecosystems position them as a cornerstone of industrial innovation. As industries evolve and new challenges arise, the role of these machines will continue to expand, ensuring their relevance and importance in the future of manufacturing.
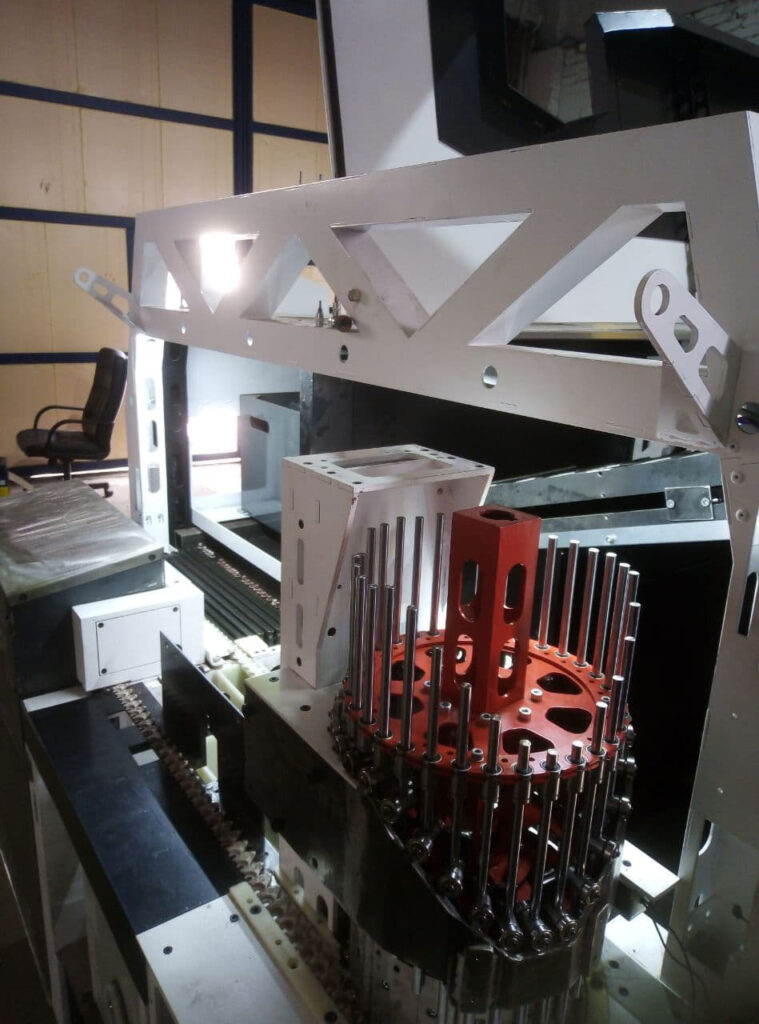
The integration of Automatic Rivet Painting Machines into advanced manufacturing processes is paving the way for further innovation and efficiency. These machines are becoming a key component of Industry 4.0 ecosystems, where interconnected systems communicate and collaborate to optimize production workflows. By incorporating sensors, data analytics, and AI-driven algorithms, rivet painting machines are now capable of self-optimization, enhancing their precision, speed, and adaptability. This advancement enables manufacturers to meet the rising demands for custom solutions and rapid production turnaround times without compromising quality.
In smart factories, these machines operate as part of an interconnected network, exchanging data with other systems such as assembly lines, quality control units, and inventory management systems. For example, a rivet painting machine can automatically adjust its operation based on real-time feedback from upstream processes, such as changes in rivet sizes or batch requirements. This level of integration not only streamlines production but also minimizes errors and delays, ensuring that the entire manufacturing process is efficient and cost-effective.
One notable area of development is the incorporation of machine learning to improve the painting process. With machine learning algorithms, rivet painting machines can analyze historical data to identify patterns and predict optimal painting conditions. This capability allows the machine to dynamically adjust parameters like paint flow rate, nozzle pressure, and drying temperature to achieve consistent results, even when external conditions or input materials vary. Over time, the system becomes more efficient, reducing material waste and energy consumption while maintaining or even improving output quality.
Energy efficiency is a critical focus in the evolution of these machines, particularly as industries strive to reduce their carbon footprints. Modern rivet painting machines are equipped with energy-efficient components such as high-performance motors, LED-based curing systems, and low-energy ventilation setups. Infrared and ultraviolet curing technologies are increasingly used to accelerate paint drying while consuming less energy than traditional methods. These systems precisely target the painted rivet surface, reducing heat loss and ensuring uniform drying across all rivets.
Customization and scalability are becoming central to the design philosophy of Automatic Rivet Painting Machines. Manufacturers increasingly demand equipment that can adapt to a wide range of production scenarios, from small-scale bespoke projects to high-volume industrial runs. To address this, machine developers are creating modular designs that allow for the addition or removal of components based on specific requirements. For instance, a manufacturer might start with a single painting unit and later expand to include multiple units for higher throughput. This flexibility not only reduces initial capital investment but also allows businesses to scale their operations as needed.
In the realm of coatings, advancements in material science are expanding the possibilities for rivet painting applications. Beyond traditional paints, these machines are now capable of applying specialized coatings such as anti-corrosive layers, thermal barriers, or decorative finishes with unique textures and colors. This versatility makes them invaluable in industries such as aerospace, where rivets must withstand extreme temperatures and pressures, or consumer electronics, where aesthetic appeal is paramount. Nanotechnology is also making its mark, enabling the application of ultra-thin, highly durable coatings that enhance performance without adding significant weight.
Quality assurance remains a top priority, and advancements in inspection technologies are enhancing the reliability of these machines. High-resolution cameras, laser scanners, and spectroscopic sensors are now commonly integrated into rivet painting systems to detect even the slightest imperfections in real time. These systems can identify defects such as uneven paint distribution, color mismatches, or surface irregularities, ensuring that only rivets meeting stringent quality standards proceed to the next stage of production. Additionally, the data collected during inspections can be analyzed to identify recurring issues and refine the painting process.
The role of human operators is evolving alongside these technological advancements. While the machines handle the precision painting tasks, operators are increasingly focused on overseeing operations, analyzing performance data, and conducting maintenance. To support this shift, manufacturers of rivet painting machines are investing in user-friendly interfaces and training programs. Augmented reality (AR) tools are becoming a popular choice for training and troubleshooting, allowing operators to visualize machine components, simulate processes, and perform guided repairs. This approach reduces downtime and enhances the overall productivity of the manufacturing facility.
The environmental impact of Automatic Rivet Painting Machines is also being addressed through innovations in waste management and material usage. Many machines now include features such as closed-loop paint recycling systems, which capture and reuse excess paint, reducing material waste and lowering operational costs. Additionally, advancements in paint formulations, such as water-based and low-VOC (volatile organic compound) options, are making the painting process more environmentally friendly. These eco-conscious features help manufacturers comply with strict environmental regulations and appeal to customers prioritizing sustainability.
Looking to the future, the development of fully autonomous rivet painting systems is a tantalizing possibility. These systems would combine advanced robotics, AI, and IoT technologies to operate without human intervention, from rivet feeding to final quality inspection. Such systems could adapt in real time to changing production requirements, integrate seamlessly with other manufacturing equipment, and continuously optimize their processes based on data-driven insights. This level of automation would represent a significant leap forward in manufacturing efficiency, allowing companies to achieve unprecedented levels of precision, speed, and scalability.
In conclusion, Automatic Rivet Painting Machines are at the forefront of modern manufacturing innovation. By embracing cutting-edge technologies, sustainable practices, and advanced customization options, these machines are transforming how rivets are painted across industries. Their ability to deliver high-quality results at scale, coupled with their adaptability to diverse applications, ensures their relevance in a rapidly changing industrial landscape. As new challenges and opportunities arise, these machines will continue to evolve, driving progress and enabling manufacturers to meet the demands of the future with confidence and precision.
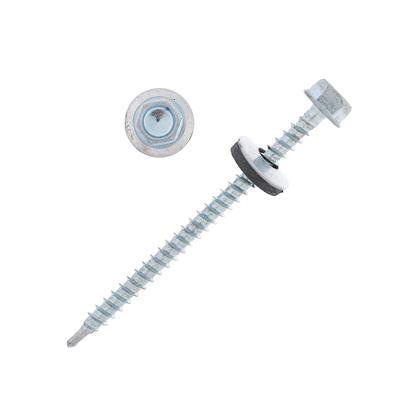
As Automatic Rivet Painting Machines continue to evolve, their influence extends beyond operational efficiency to broader implications for industrial innovation and competitiveness. Their integration into manufacturing ecosystems not only streamlines production but also fosters innovation in product design, enabling the creation of components with enhanced functionality and aesthetics. For instance, painted rivets can now serve dual purposes, acting as both structural elements and design features in industries like consumer electronics, automotive, and luxury goods. This convergence of utility and artistry highlights the transformative potential of these machines.
The adaptability of modern rivet painting machines is particularly significant for industries undergoing rapid technological change, such as aerospace and defense. In these sectors, rivets are subjected to extreme environmental stresses, including high temperatures, corrosive atmospheres, and mechanical loads. Advanced coatings applied by these machines provide critical protective layers that extend the lifespan and performance of riveted assemblies. For example, heat-resistant paints can be precisely applied to rivets used in jet engines, while anti-corrosion coatings are essential for maritime and military applications.
In the automotive industry, the rise of electric vehicles (EVs) is creating new demands for rivet painting machines. EVs require lightweight, corrosion-resistant components to maximize energy efficiency and durability. Painted rivets play a crucial role in ensuring the longevity of battery enclosures, chassis assemblies, and exterior panels. Additionally, the aesthetic requirements for visible rivets on EVs align with consumer preferences for sleek and modern designs. Automatic rivet painting machines, with their ability to deliver flawless finishes and consistent quality, are well-equipped to meet these challenges.
The role of automation and robotics in rivet painting processes continues to expand, with collaborative robots (cobots) gaining traction in semi-automated systems. Cobots enhance flexibility by working alongside human operators, handling repetitive tasks such as rivet feeding and positioning while leaving quality inspections and adjustments to human expertise. This hybrid approach balances the precision and speed of automation with the adaptability and problem-solving capabilities of human workers. Furthermore, cobots can be reprogrammed for different tasks, making them a versatile addition to rivet painting operations.
Digitalization is another transformative trend, with manufacturers increasingly adopting digital twins and advanced monitoring systems to optimize rivet painting machines. Digital twins provide a virtual representation of the machine and its operations, enabling engineers to simulate different scenarios, predict potential issues, and implement optimizations without disrupting production. Real-time monitoring systems, often powered by IoT sensors, collect data on variables such as paint viscosity, ambient temperature, and machine performance. This data is then analyzed to detect anomalies, forecast maintenance needs, and ensure consistent output quality.
Sustainability remains a core consideration in the development and operation of rivet painting machines. Manufacturers are prioritizing energy efficiency, waste reduction, and the use of environmentally friendly materials. For example, some machines now incorporate advanced filtration systems to capture paint overspray and prevent harmful emissions. Others are designed to support biodegradable or water-based paints, reducing the environmental impact of the coating process. These eco-friendly features not only comply with regulatory standards but also resonate with customers and stakeholders committed to sustainable practices.
The application of nanotechnology in rivet coatings is a cutting-edge area that holds significant promise. Nanocoatings, characterized by their ultra-thin and highly durable properties, offer unique advantages such as enhanced scratch resistance, hydrophobicity, and self-cleaning capabilities. Automatic rivet painting machines are being adapted to apply these advanced coatings with the precision and consistency required for nanoscale applications. Industries such as medical devices and electronics, where performance and miniaturization are critical, are likely to benefit greatly from these advancements.
The economic implications of investing in Automatic Rivet Painting Machines are substantial. By automating the painting process, manufacturers achieve significant cost savings through reduced labor requirements, minimized material waste, and faster production cycles. The initial investment in these machines is often offset by long-term benefits, including increased throughput, improved product quality, and enhanced competitiveness in the market. Furthermore, the ability to handle diverse production needs—from small custom orders to large-scale manufacturing—makes these machines a strategic asset for businesses looking to expand their capabilities.
In terms of workforce development, the rise of these advanced machines is reshaping the skills required in manufacturing. Operators are transitioning from manual painting tasks to roles focused on machine programming, data analysis, and system maintenance. Training programs and certifications are evolving to equip workers with the technical knowledge needed to manage and optimize these sophisticated systems. The integration of augmented reality (AR) and virtual reality (VR) tools into training modules is making it easier for operators to learn complex procedures and troubleshoot issues in a virtual environment, reducing downtime and enhancing productivity.
Looking ahead, the development of next-generation Automatic Rivet Painting Machines will likely emphasize greater autonomy, adaptability, and integration with broader manufacturing systems. Fully autonomous machines, capable of managing every aspect of the painting process without human intervention, represent the ultimate goal in automation. These machines would use advanced AI algorithms to make real-time decisions, dynamically adjust to changing conditions, and self-diagnose maintenance needs. Additionally, the integration of blockchain technology for traceability could ensure that every rivet’s coating history is recorded, providing transparency and accountability in industries where quality and safety are paramount.
In conclusion, Automatic Rivet Painting Machines are a cornerstone of modern manufacturing, offering unparalleled efficiency, precision, and versatility. Their ability to adapt to diverse applications, integrate into smart manufacturing ecosystems, and support sustainable practices ensures their continued relevance and importance. As industries evolve and new challenges emerge, these machines will remain at the forefront of innovation, empowering manufacturers to achieve higher standards of quality, efficiency, and environmental stewardship. The ongoing advancements in technology and materials will only expand their potential, solidifying their role as indispensable tools in the future of industrial production.
Automatic Steel Nail Painting Machine
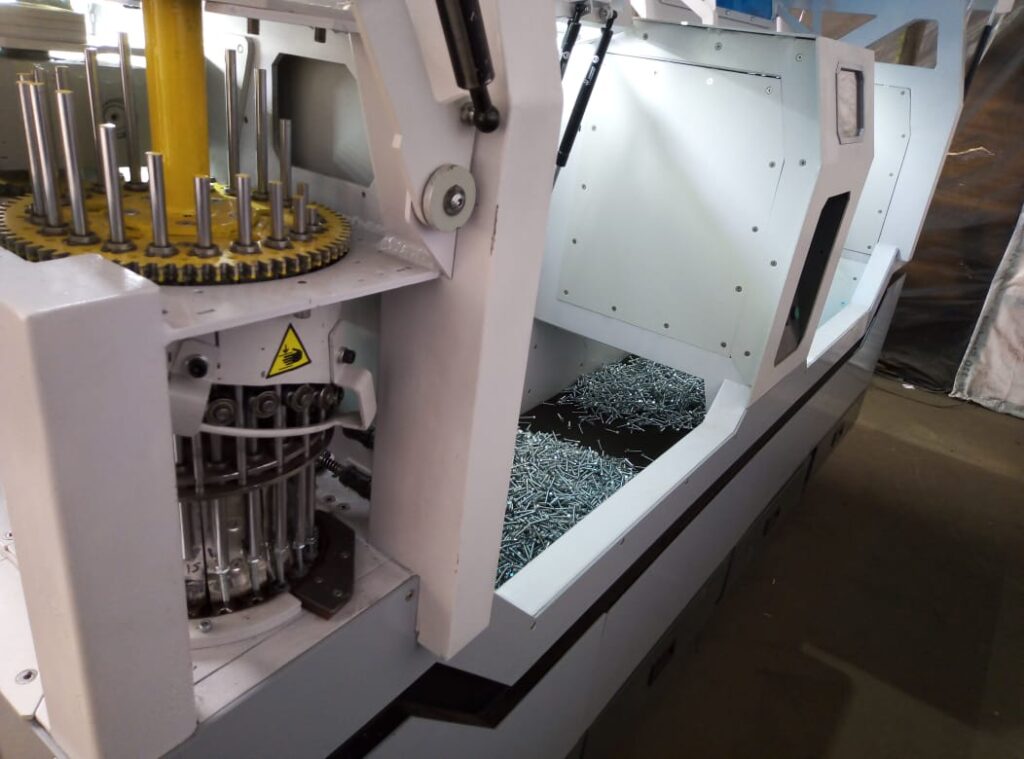
An Automatic Steel Nail Painting Machine is a highly specialized piece of industrial equipment designed to coat steel nails with paint or protective finishes in a precise, efficient, and consistent manner. These machines are essential in manufacturing environments where steel nails must meet strict quality and aesthetic standards. They are widely used in construction, furniture manufacturing, and other industries where nails play both functional and decorative roles. By automating the painting process, these machines enhance production efficiency, reduce labor costs, minimize waste, and ensure a uniform, high-quality finish on every nail.
The machine operates through a series of well-coordinated systems, including a nail feeding mechanism, a paint application unit, a drying or curing system, and a control interface. The feeding mechanism is designed to sort and align steel nails of various sizes and shapes, transporting them seamlessly into the painting unit. This process is achieved using components such as vibratory feeders, conveyors, or custom-designed robotic systems. Precise alignment ensures that each nail is correctly positioned for uniform paint application, a critical factor in achieving consistent quality.
The paint application unit is the core component of the machine, responsible for applying paint or other coatings to the nails. Common techniques include spray painting, dip coating, or electrostatic coating. Spray painting is a versatile method suitable for nails of varying shapes and sizes, ensuring even coverage. Dip coating involves immersing the nails in a paint bath, making it ideal for achieving complete coverage, particularly for nails with complex geometries. Electrostatic coating, where paint particles are electrically charged and attracted to the nails, ensures minimal overspray and high material efficiency.
After the paint is applied, the nails proceed to the drying or curing system. Depending on the type of paint or coating, the drying process may involve air drying, heat curing in ovens, or ultraviolet (UV) curing. Advanced machines are equipped with precise temperature and airflow controls to ensure the paint dries uniformly, preventing defects like drips, bubbles, or surface inconsistencies. UV curing is particularly efficient, providing rapid hardening of specialized coatings, thereby increasing throughput without compromising quality.
The control interface of the machine enables operators to adjust and monitor various parameters such as paint type, application speed, drying temperature, and nail dimensions. Modern machines often feature touchscreen interfaces, programmable logic controllers (PLCs), and IoT connectivity, allowing for remote monitoring and operation. These advanced controls provide real-time feedback on machine performance, production rates, and potential issues, empowering operators to make data-driven decisions and maintain optimal performance.
Quality assurance is a built-in feature of these machines, with integrated inspection systems that verify the uniformity and consistency of the coating. High-resolution cameras or sensors can detect defects such as uneven paint application, missed spots, or surface imperfections. Any anomalies are flagged for corrective action, ensuring that only nails meeting stringent quality standards move on to packaging or assembly. This automated inspection process minimizes waste and reduces the need for manual quality checks.
The versatility of Automatic Steel Nail Painting Machines allows them to handle a wide range of nail types, including common nails, finishing nails, roofing nails, and specialty nails. This adaptability makes them indispensable in industries that require nails with specific coatings for enhanced performance or aesthetic appeal. For example, construction nails may need anti-corrosive coatings to withstand outdoor conditions, while decorative nails used in furniture or interior design may require precise color matching and a flawless finish.
Environmental sustainability is a significant consideration in the design and operation of these machines. Manufacturers are increasingly incorporating eco-friendly features, such as systems for capturing and recycling paint overspray, reducing emissions, and supporting the use of water-based or low-VOC (volatile organic compound) paints. These innovations help manufacturers comply with environmental regulations and reduce their ecological footprint while maintaining cost efficiency.
The integration of advanced technologies is driving continuous improvements in the functionality and efficiency of these machines. IoT-enabled sensors and data analytics provide real-time insights into machine performance, paint consumption, and production trends. This data can be used to optimize operations, identify inefficiencies, and implement predictive maintenance strategies, reducing downtime and extending the machine’s lifespan. Artificial intelligence (AI) is also being explored to enhance the precision of the painting process, with algorithms that dynamically adjust parameters based on nail size, shape, or environmental conditions.
Customization is another critical feature of modern steel nail painting machines. Manufacturers can configure machines to accommodate various production requirements, such as different nail sizes, paint types, or finishes. Modular designs allow for the addition or removal of components, enabling scalability and flexibility in production. For instance, a machine may start with a single painting unit and later expand to include multiple units for higher throughput, providing a cost-effective solution for growing businesses.
Robotics and automation further enhance the capabilities of these machines. Robotic arms can be integrated to handle tasks such as nail feeding, positioning, or unloading, ensuring seamless operation even for complex production setups. Collaborative robots (cobots) allow for hybrid systems where human operators work alongside automated systems, leveraging the precision of machines and the adaptability of human oversight. This approach is particularly beneficial for custom or small-batch production runs, where manual adjustments and quality checks are essential.
The economic benefits of Automatic Steel Nail Painting Machines are substantial. By automating the painting process, manufacturers achieve higher production rates and lower per-unit costs. The precision of automated systems reduces material waste, and the ability to operate continuously minimizes downtime. These efficiencies translate into significant cost savings and a competitive edge in the market. Moreover, the consistent quality achieved by these machines enhances customer satisfaction and brand reputation.
Looking to the future, the development of next-generation steel nail painting machines will likely focus on greater automation, sustainability, and integration into smart manufacturing ecosystems. Fully autonomous machines equipped with AI and advanced robotics could handle every aspect of the painting process, from nail feeding to final inspection, with minimal human intervention. Blockchain technology may also be employed for traceability, ensuring a transparent record of the coating process for industries with stringent quality and safety standards.
In conclusion, Automatic Steel Nail Painting Machines represent a cornerstone of modern manufacturing, providing efficient, precise, and versatile solutions for coating steel nails. Their ability to adapt to diverse applications, integrate advanced technologies, and support sustainable practices ensures their continued relevance in a rapidly evolving industrial landscape. As industries demand higher standards of quality, efficiency, and environmental responsibility, these machines will remain at the forefront of innovation, empowering manufacturers to meet current and future challenges with confidence. Their continued evolution will undoubtedly shape the future of nail production and coating, driving progress across multiple industries.
As the demand for precision and efficiency grows across industries, Automatic Steel Nail Painting Machines are positioned to play an increasingly pivotal role in modern manufacturing. They not only address the immediate needs for high-volume production but also cater to specialized requirements, such as custom finishes, rapid prototyping, and environmentally friendly operations. By bridging the gap between traditional manufacturing practices and cutting-edge technology, these machines are transforming how steel nails are produced, finished, and utilized in various applications.
One of the key trends shaping the development of these machines is the incorporation of intelligent automation. Machine learning algorithms and artificial intelligence (AI) are being leveraged to enhance the adaptability and self-optimization capabilities of nail painting systems. For example, AI-driven sensors can monitor the viscosity and flow of paint in real time, adjusting parameters dynamically to ensure consistent application. These systems can also predict potential issues, such as paint clogs or irregular nail feeding, before they occur, reducing downtime and maintenance costs.
Another area of advancement is the development of multifunctional machines capable of handling multiple stages of production. Modern nail painting machines are being designed to integrate additional processes, such as surface preparation, cleaning, and even packaging. By consolidating these steps into a single automated workflow, manufacturers can achieve greater efficiency and reduce the complexity of their production lines. For instance, nails could pass through a pre-cleaning station to remove contaminants before entering the painting unit, followed by a drying process and automated sorting for packaging.
The role of coatings is expanding as industries demand nails with advanced functional properties. Beyond traditional paints, these machines can now apply specialized coatings such as anti-corrosion layers, thermal barriers, and decorative finishes with metallic or matte effects. In the construction industry, nails with weather-resistant coatings are essential for outdoor applications, while in the furniture and interior design sectors, aesthetically appealing finishes are increasingly important. These diverse capabilities make Automatic Steel Nail Painting Machines indispensable across a wide range of markets.
Sustainability is driving significant innovation in the design and operation of these machines. Paint recovery and recycling systems are becoming standard features, capturing excess paint during the application process and reintroducing it into the system to minimize waste. Low-VOC and water-based paints are increasingly used to reduce environmental impact and comply with stringent emissions regulations. Additionally, energy-efficient components, such as LED-based curing systems and variable-speed motors, are being incorporated to lower the overall energy consumption of the machines.
Customization and modularity remain central to the appeal of Automatic Steel Nail Painting Machines. Manufacturers can tailor these systems to their specific production needs, whether they require high-speed operations for large-scale manufacturing or precise control for small-batch production. Modular designs enable businesses to start with a basic setup and expand as their needs evolve, adding features such as additional painting units, advanced drying systems, or enhanced inspection capabilities. This scalability ensures that the machines remain relevant and cost-effective over time.
Digital twins and simulation technologies are becoming integral to the operation and optimization of these machines. By creating a virtual replica of the machine and its processes, manufacturers can simulate different scenarios, identify potential bottlenecks, and implement improvements without disrupting actual production. This capability is particularly valuable for industries that require rapid adaptation to changing market demands or regulatory requirements. Real-time data collected from the machines can be fed into the digital twin, providing a comprehensive view of performance and enabling continuous optimization.
The integration of these machines into smart factories is another exciting development. Connected to broader manufacturing ecosystems via IoT (Internet of Things) networks, they can communicate with other equipment, such as nail production lines, assembly units, and quality control systems. This level of integration ensures seamless coordination across the production process, reducing inefficiencies and enabling just-in-time manufacturing. For example, the painting machine could automatically adjust its settings based on the specifications of nails being produced upstream, ensuring a smooth and error-free operation.
The human-machine interface is also undergoing significant enhancements to improve user experience and operational efficiency. Advanced touchscreen controls, voice commands, and augmented reality (AR) tools are being introduced to simplify machine setup, monitoring, and troubleshooting. AR applications, in particular, allow operators to visualize machine components, access step-by-step guides for maintenance tasks, and diagnose issues in real time. These innovations reduce downtime, enhance productivity, and empower operators to manage complex systems with ease.
Looking ahead, the evolution of Automatic Steel Nail Painting Machines is likely to be driven by emerging technologies such as robotics, AI, and advanced materials. Fully autonomous systems that require minimal human intervention could become the norm, leveraging AI to make real-time decisions and optimize performance. Robotics may further enhance precision and flexibility, enabling machines to handle increasingly complex tasks and adapt to a wider range of nail types and coatings. Additionally, breakthroughs in material science could lead to the development of new coatings with unprecedented properties, such as self-healing surfaces or ultra-thin protective layers.
The global push for sustainability and energy efficiency will continue to influence the design and operation of these machines. Manufacturers will prioritize features that reduce resource consumption, minimize waste, and support the use of environmentally friendly materials. This focus not only helps businesses comply with regulations but also aligns with consumer and industry trends toward greener practices. Machines equipped with energy recovery systems, smart power management, and eco-friendly paint technologies will set the standard for sustainable manufacturing.
In conclusion, Automatic Steel Nail Painting Machines are at the forefront of innovation in manufacturing technology. Their ability to deliver high-quality finishes, adapt to diverse applications, and integrate with advanced production systems makes them invaluable across industries. As technology continues to advance, these machines will evolve to meet new challenges and opportunities, driving progress and enabling manufacturers to achieve greater efficiency, precision, and sustainability. Whether through enhanced automation, advanced coatings, or smarter integration, these machines are shaping the future of nail production and setting new benchmarks for industrial excellence.
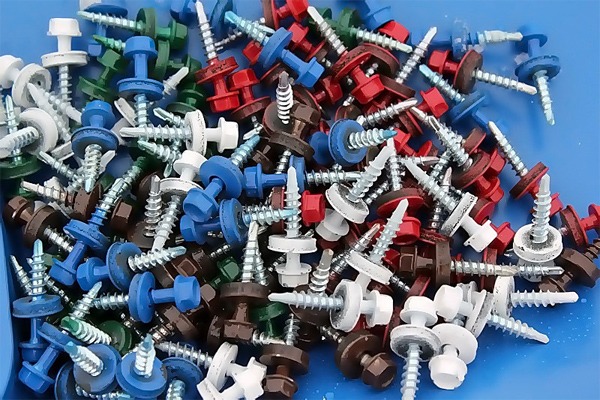
As Automatic Steel Nail Painting Machines continue to advance, their influence extends into the broader context of industrial manufacturing, where innovation and adaptability are paramount. These machines exemplify the convergence of automation, precision engineering, and sustainable practices, addressing the demands of modern industries while paving the way for future advancements. Their impact goes beyond efficiency, touching upon areas such as product differentiation, environmental stewardship, and global competitiveness.
One significant avenue of development lies in the refinement of automated inspection and quality control systems. As industries increasingly adopt zero-defect manufacturing philosophies, the integration of high-precision optical and sensor-based inspection systems in nail painting machines becomes critical. These systems can detect minute imperfections, such as uneven coatings, color deviations, or surface contaminants, ensuring that only nails meeting exacting standards proceed to market. Combined with machine learning algorithms, these inspection systems can also learn and adapt over time, improving their accuracy and efficiency with each production cycle.
The customization potential of nail finishes is also expanding, driven by advancements in paint chemistry and application technology. Manufacturers are exploring ways to produce nails with gradient finishes, textured coatings, or multi-layer protective films, all of which can be achieved using state-of-the-art painting machines. Gradient finishes, for instance, offer aesthetic appeal in decorative applications, while multi-layer coatings can provide a combination of properties, such as corrosion resistance and thermal insulation, tailored to specific industry needs.
Collaborative efforts between equipment manufacturers and paint suppliers are fostering innovations in coating materials. By developing paints specifically designed for automated application, these partnerships are improving the performance and efficiency of nail painting machines. For example, paints with optimized viscosity and drying times allow for faster application and curing, reducing production bottlenecks. Similarly, advancements in paint adhesion technology ensure that coatings remain durable under harsh conditions, such as extreme temperatures or high humidity, broadening the scope of applications for painted nails.
The application of smart coatings is another exciting frontier for steel nail painting machines. Smart coatings, which respond to environmental changes such as temperature, light, or pressure, are finding increasing use in specialized industries. For example, nails coated with thermochromic paints can change color based on temperature, providing visual indicators for safety or performance monitoring. Similarly, self-cleaning or anti-microbial coatings are becoming popular in sectors like healthcare and food processing, where hygiene and cleanliness are critical.
In manufacturing environments where flexibility is key, hybrid systems that combine manual oversight with automated operations are gaining traction. These systems allow for seamless transitions between different production modes, such as high-speed automated runs for standard nails and slower, more customized processes for specialty products. By incorporating features like quick-change tooling and adjustable settings, hybrid systems enable manufacturers to meet diverse customer demands without compromising efficiency or quality.
From an economic perspective, the return on investment (ROI) of Automatic Steel Nail Painting Machines is becoming increasingly attractive. With shorter payback periods resulting from reduced labor costs, minimized waste, and higher throughput, these machines represent a strategic investment for manufacturers looking to enhance their competitive edge. Additionally, their ability to handle complex and high-value applications opens up new revenue streams, enabling businesses to diversify their offerings and target niche markets.
The role of training and workforce development is also evolving alongside the adoption of these machines. As operators transition from manual painting tasks to overseeing automated systems, there is a growing need for specialized training programs that focus on areas such as machine programming, troubleshooting, and data analysis. Virtual reality (VR) and augmented reality (AR) technologies are being incorporated into training modules, providing immersive and interactive learning experiences that improve knowledge retention and operator confidence.
Globalization is influencing the deployment and capabilities of nail painting machines, with manufacturers catering to regional preferences and regulatory requirements. For instance, certain markets may prioritize environmentally friendly coatings, while others focus on aesthetics or durability. By designing machines that can be easily adapted to different regional needs, equipment manufacturers are enabling businesses to operate effectively in diverse global markets. Moreover, the rise of export-oriented manufacturing necessitates machines that can produce nails meeting international quality standards.
Looking toward the future, the integration of blockchain technology may play a role in enhancing the traceability and accountability of coated nails. By creating a digital ledger that records every step of the production process, from raw material sourcing to final coating, manufacturers can ensure transparency and build trust with customers and stakeholders. This level of traceability is particularly valuable in industries where quality and compliance are critical, such as aerospace, automotive, and construction.
As industries embrace Industry 4.0, the concept of connected manufacturing ecosystems is reshaping the way nail painting machines are utilized. These machines are becoming integral components of smart factories, where data flows seamlessly between equipment, operators, and management systems. Predictive maintenance, enabled by real-time monitoring and advanced analytics, ensures that machines operate at peak efficiency with minimal downtime. Furthermore, the ability to remotely monitor and control these machines via cloud-based platforms allows for greater operational flexibility and responsiveness.
In conclusion, Automatic Steel Nail Painting Machines are more than just tools for applying paint—they are sophisticated systems that embody the principles of modern manufacturing. Their ability to adapt to emerging technologies, meet diverse industry requirements, and support sustainable practices positions them as key enablers of innovation and progress. As these machines continue to evolve, they will play an increasingly vital role in shaping the future of industrial production, setting new standards for quality, efficiency, and environmental responsibility. By leveraging their capabilities, manufacturers can not only enhance their operations but also contribute to a more sustainable and technologically advanced industrial landscape.
Automatic Steel Nail Coating Machine
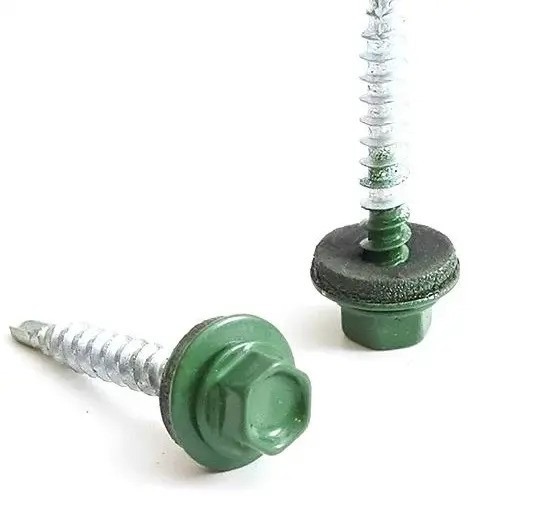
An Automatic Steel Nail Coating Machine is a vital piece of equipment used in industrial manufacturing to apply protective or decorative coatings to steel nails. The primary purpose of these machines is to enhance the nails’ performance characteristics, such as corrosion resistance, durability, and appearance, by applying coatings made of various materials, such as zinc, epoxy, PVC, or other specialty coatings. These machines streamline the coating process, making it faster, more consistent, and more efficient, compared to traditional manual methods. They play a crucial role in industries like construction, automotive, furniture manufacturing, and hardware production, where nails must meet stringent quality and functional requirements.
The automatic steel nail coating machine typically consists of several key components: a nail feeding system, a coating application unit, a curing or drying system, and a quality control system. These components work in harmony to ensure that each nail is coated evenly and efficiently, maintaining the highest standards of quality throughout the production process. The nail feeding system is responsible for sorting, aligning, and transporting the nails to the coating unit, where they will be coated with the chosen material. Automation ensures that the nails are fed into the system continuously, reducing the need for manual intervention and improving production speed.
The coating application unit is the heart of the machine and determines the quality of the final coating. There are various methods of applying coatings, each suited to different types of materials and desired outcomes. Common methods include electroplating, dip coating, powder coating, and spray coating. Electroplating is widely used for applying zinc coatings to nails, providing them with excellent corrosion resistance. Dip coating involves immersing the nails in a liquid coating material, such as PVC or a polymer resin, to create a protective layer. Powder coating, which uses dry powder applied electrostatically and then cured with heat, results in a durable and aesthetically appealing finish. Spray coating is often used for more decorative finishes or when a thinner coating is required.
Once the coating is applied, the nails move to the curing or drying system, where the coating is set or hardened. Depending on the type of coating, this process may involve air drying, heat curing, or UV curing. Heat curing, often used in powder coating processes, involves subjecting the nails to high temperatures in an oven to melt and bond the coating material to the surface. UV curing, used for coatings that are sensitive to ultraviolet light, provides a rapid drying process that is energy-efficient and effective at curing coatings in a short time.
In addition to the core components, Automatic Steel Nail Coating Machines are equipped with an integrated quality control system to ensure that every nail meets the required specifications. Visual and sensor-based inspection systems can check for uniformity in coating thickness, surface defects, and other quality metrics. These systems reduce the need for manual inspection and minimize the risk of defects slipping through to the final product. Some machines even feature real-time feedback systems, where data from sensors or cameras is used to adjust the machine’s settings dynamically, ensuring consistent quality throughout the entire batch of nails.
One of the key advantages of an automatic coating system is its ability to handle a high volume of production with minimal human intervention. This results in faster processing times, increased throughput, and a more consistent output. By automating the coating process, manufacturers can achieve uniform coatings on large quantities of nails, eliminating variations that might occur with manual labor. Additionally, automation reduces the likelihood of human error and helps maintain the precision required to meet strict industry standards.
These machines also offer significant improvements in cost-effectiveness. Through automation, manufacturers can lower labor costs, reduce material waste, and increase production efficiency. The precise control of coating thickness ensures that the correct amount of material is applied, reducing over-application and waste. In addition, the machines’ ability to operate continuously without frequent downtime improves production output, making them an attractive investment for companies looking to increase profitability and efficiency.
As industries continue to prioritize sustainability, manufacturers of automatic steel nail coating machines are incorporating eco-friendly features into their designs. For example, many machines now include paint recovery and overspray filtration systems that capture excess coating material, reducing waste and making the process more environmentally responsible. Additionally, the use of low-VOC (volatile organic compound) and water-based coatings further minimizes the environmental impact of the coating process. These machines can also be equipped with energy-efficient curing systems, such as LED-based UV curing, which consume less energy and produce fewer emissions compared to traditional curing methods.
The versatility of automatic steel nail coating machines allows them to handle various types of nails and coatings, making them suitable for a wide range of applications. For instance, nails used in construction may require heavy-duty corrosion-resistant coatings, such as zinc or galvanized coatings, to withstand outdoor exposure. On the other hand, nails used in the furniture industry might need to be coated with decorative finishes or protective layers that enhance their appearance and durability. The ability to easily switch between different coating materials or application methods is a significant benefit for manufacturers that produce a variety of products.
In addition to their versatility, these machines are designed for ease of use and maintenance. Many models feature user-friendly interfaces that allow operators to adjust settings such as coating thickness, application speed, and curing temperature. Touchscreen controls, programmable logic controllers (PLCs), and remote monitoring capabilities make it easier for operators to manage and troubleshoot the machines, reducing the learning curve and downtime associated with machine operation. Predictive maintenance systems, often equipped with sensors that monitor the machine’s performance and detect potential issues before they occur, help reduce unexpected maintenance costs and ensure consistent uptime.
In industries where quality assurance and traceability are critical, such as automotive or aerospace manufacturing, automatic steel nail coating machines can integrate with existing enterprise resource planning (ERP) systems to provide detailed records of the coating process. Data such as batch numbers, coating materials, and curing parameters can be stored digitally and accessed for traceability and reporting. This level of documentation helps meet regulatory requirements and provides assurance to customers that the nails have been manufactured to the highest standards.
As the demand for customization and product differentiation grows, manufacturers of automatic steel nail coating machines are developing new technologies to meet these needs. Innovations such as multi-layer coatings, textured finishes, and color-changing coatings are becoming more common, allowing manufacturers to offer a broader range of nail products with distinct features. The ability to apply multiple coatings or create unique surface finishes using automated systems opens up new possibilities for design and functionality in applications ranging from home décor to industrial machinery.
Looking ahead, the future of automatic steel nail coating machines will likely involve further advancements in automation, artificial intelligence, and smart manufacturing technologies. Fully automated systems that require minimal human intervention, coupled with artificial intelligence to optimize coating quality and predict maintenance needs, could redefine the standards of efficiency and precision. The ongoing integration of Internet of Things (IoT) technology will allow for greater connectivity between machines, providing operators with real-time data and enabling predictive analytics for process optimization.
In conclusion, Automatic Steel Nail Coating Machines are indispensable in modern manufacturing, offering unparalleled efficiency, precision, and versatility. By automating the coating process, these machines reduce labor costs, minimize waste, and ensure consistent, high-quality finishes on steel nails. Their ability to adapt to different types of coatings and production requirements makes them valuable across a wide array of industries, from construction to consumer goods. As technology continues to advance, these machines will remain at the forefront of innovation, enabling manufacturers to meet evolving market demands, enhance sustainability, and maintain competitiveness in a rapidly changing industrial landscape.
Automatic Painting Machine for Fasteners
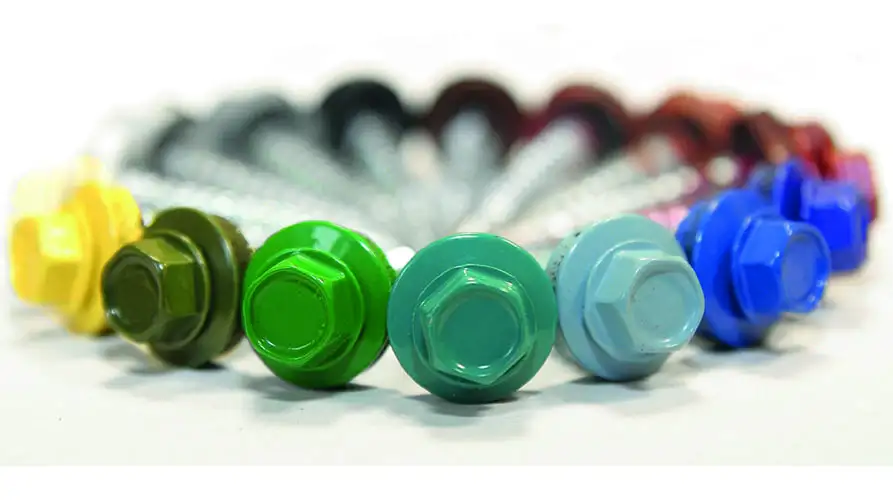
As the future of Automatic Steel Nail Coating Machines continues to evolve, the focus will increasingly be on enhancing automation, connectivity, and sustainability. These advancements will further transform how manufacturers approach production, allowing for smarter, more flexible, and resource-efficient processes. The rise of Industry 4.0, where machines are integrated into a smart, interconnected manufacturing environment, is likely to be a defining factor in the next generation of nail coating machines.
One promising development is the growing integration of Artificial Intelligence (AI) and machine learning (ML) technologies into the operation of these machines. These technologies can help optimize various aspects of the coating process, such as adjusting coating thickness, speed, and curing conditions based on real-time data. By using sensors and data analysis, AI can detect subtle variations in coating application and make immediate adjustments to ensure a consistent and high-quality finish. Over time, AI algorithms can “learn” from past production data, improving their accuracy and efficiency, which can lead to significant reductions in scrap rates and product defects.
Moreover, AI-driven systems can facilitate predictive maintenance, which is becoming increasingly important in high-demand production environments. By monitoring key components such as pumps, conveyors, and curing systems, the system can predict when a part is likely to fail or when maintenance is needed, reducing the risk of unexpected downtime. This approach extends the lifespan of the machine, minimizes unplanned stops, and helps manufacturers avoid costly repairs and disruptions in production schedules. Operators are alerted to issues well before they become critical, allowing for timely interventions and boosting overall machine reliability.
Another aspect of automation that will continue to gain traction is the implementation of robots in the coating process. Robotic arms, for example, can assist in material handling, such as picking up and positioning nails for coating application. This reduces labor costs and improves the precision of the coating application. Robots can also be used in post-coating tasks, like sorting, inspecting, or packaging the finished nails, further streamlining the entire process. Automation of these tasks not only improves the efficiency of the production line but also reduces the potential for human error, resulting in more consistent quality and higher throughput.
Connectivity is another area of future development for these machines. The incorporation of Internet of Things (IoT) technology enables Automatic Steel Nail Coating Machines to be part of a broader smart factory ecosystem. IoT sensors can track parameters such as temperature, humidity, and coating thickness in real time, providing operators with instant feedback on the performance of the machine. This data can also be accessed remotely, allowing operators and managers to monitor production progress, troubleshoot issues, and make informed decisions from virtually anywhere. In addition, IoT systems can help optimize resource usage, such as energy and raw materials, by analyzing usage patterns and identifying opportunities for cost savings.
The increasing emphasis on sustainability will continue to shape the design and functionality of these machines. The use of environmentally friendly coatings, such as water-based or low-VOC (volatile organic compounds) options, is becoming more common. These coatings are less harmful to both the environment and the workers handling them, aligning with stricter environmental regulations and growing consumer demand for greener products. In addition, automatic steel nail coating machines are incorporating systems that minimize waste, such as paint recovery units, which capture excess material during the application process and recycle it for future use. This not only reduces the environmental impact but also lowers operating costs by conserving valuable coating materials.
Energy efficiency will also play a significant role in the future of these machines. Modern curing systems, such as LED-based UV curing, are far more energy-efficient compared to traditional heat-based methods. LED UV curing uses less power and provides faster curing times, leading to increased throughput and reduced energy consumption. Similarly, the implementation of energy-efficient motors and intelligent power management systems will help reduce the overall carbon footprint of the production process.
Furthermore, advancements in coating materials are likely to influence the capabilities of steel nail coating machines. For example, the development of self-healing or nanocoatings could lead to even more durable and long-lasting products. Self-healing coatings, which are capable of repairing minor scratches or cracks automatically, could extend the life of nails in demanding applications, such as in harsh outdoor environments. Additionally, the use of nanotechnology in coatings could result in ultra-thin, highly protective layers that do not compromise the nail’s mechanical properties. These innovations will require corresponding advances in coating machines to handle new materials and application methods.
Customization will continue to be a significant factor in the evolution of these machines. Manufacturers are increasingly looking for ways to offer tailored products, whether it is in terms of coating colors, finishes, or functional properties. Automatic steel nail coating machines of the future will likely feature more flexible designs, allowing for quick changes between different coating types, application methods, and production volumes. This flexibility will enable manufacturers to cater to niche markets and offer products with unique characteristics that set them apart from competitors.
The role of quality control systems will also expand as technology advances. In addition to visual inspection cameras and sensors, future machines may incorporate more sophisticated AI-powered inspection systems capable of detecting defects that are invisible to the naked eye. These systems can analyze coating adhesion, detect micro-cracks, and measure the exact coating thickness, ensuring that every nail meets the highest quality standards. The real-time data provided by these systems can also be used to fine-tune the machine’s settings, further improving production accuracy.
Lastly, the increasing global demand for steel nails in diverse industries, ranging from construction and automotive to furniture and consumer goods, will continue to drive innovation in the field. As manufacturers seek to meet the needs of a wide variety of markets, automatic steel nail coating machines will play a central role in ensuring the efficient production of high-quality, reliable nails. The adaptability and precision offered by these machines will make them indispensable for companies striving to maintain a competitive edge in an increasingly complex and demanding manufacturing landscape.
In conclusion, Automatic Steel Nail Coating Machines are poised for continued innovation, with advancements in automation, AI, IoT connectivity, sustainability, and customization. These machines will become even more efficient, flexible, and capable of handling a broader range of coating materials and production requirements. By embracing these technological advancements, manufacturers will be able to meet the growing demand for high-quality, durable, and environmentally friendly steel nails, while staying competitive in a rapidly changing global market. The future of automatic steel nail coating machines is bright, with potential to revolutionize the industry and pave the way for smarter, more sustainable manufacturing practices.
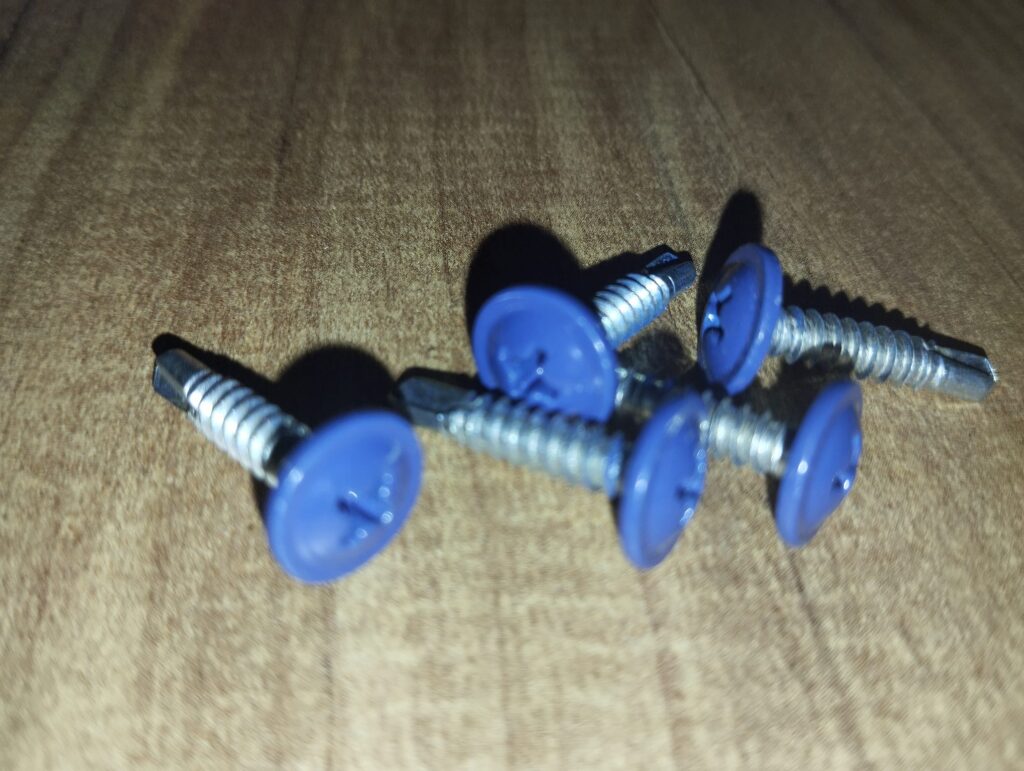
As the evolution of Automatic Steel Nail Coating Machines progresses, the focus will also shift toward further enhancing the user experience and improving the overall integration of the machines into existing production lines. The ability of these machines to seamlessly integrate with other manufacturing systems will be a key driver of their continued success. This integration allows for the creation of highly efficient, end-to-end production workflows, where automated steel nail coating is just one part of a larger, interconnected process.
The integration of these machines with other automated systems, such as sorting, packaging, and labeling machines, will further streamline production. This level of automation reduces manual handling, improves consistency across the entire production cycle, and reduces the chances of human error. For example, a nail coating machine could be linked to a sorting system that categorizes nails by size and then directs them to the appropriate coating process. After the nails are coated and cured, they could then move directly to packaging systems, where they are automatically wrapped, labeled, and prepared for shipment. Such fully integrated systems not only optimize efficiency but also reduce labor costs and time spent on manual tasks, offering manufacturers a significant competitive advantage.
Furthermore, the continuous improvement of machine interfaces will make these systems easier for operators to manage and monitor. In the future, we can expect to see more advanced user interfaces that are intuitive, providing operators with real-time feedback and actionable insights. These interfaces might include features such as touchscreens with detailed graphical representations of the machine’s performance, predictive maintenance alerts, and access to production data analytics. With such tools, operators can make quick, informed decisions on-the-fly, minimizing downtime and ensuring smooth operation throughout shifts.
The shift toward more advanced user interfaces will also go hand in hand with the trend of remote monitoring and operation. The increased connectivity of steel nail coating machines via the Internet of Things (IoT) will allow for remote diagnostics and adjustments. Using cloud-based platforms, managers and operators will be able to monitor machine performance from anywhere in the world, making it possible to quickly address issues, optimize production processes, and even adjust production settings in real time. This remote capability also allows for improved support services, as manufacturers can provide troubleshooting and maintenance assistance without needing to be on-site, further reducing downtime.
Additionally, as part of the growing trend of sustainable manufacturing practices, the development of environmentally responsible coatings will likely continue to drive innovation in automatic steel nail coating machines. Innovations in water-based coatings, bio-based materials, and low-toxicity formulations will further align with stricter environmental regulations and growing consumer demand for eco-friendly products. In response, coating machines may be designed to work with these emerging materials, ensuring that the machine remains versatile and adaptable in meeting changing industry requirements. The eco-conscious trend could also encourage the development of waste management systems within the machines that capture overspray and recycle unused materials to minimize environmental impact.
The integration of carbon footprint tracking and resource optimization within the machines will likely be another focus in the near future. By measuring the energy consumed during coating, curing, and other production stages, manufacturers can better understand and reduce the environmental impact of their operations. Many future automatic steel nail coating machines may be equipped with sensors that track resource consumption and provide insights into ways to reduce energy use, water consumption, and material waste. These machines could also feature adaptive systems that optimize energy use based on real-time conditions, such as adjusting curing times or temperatures to achieve the best results with the least energy consumption.
The rise of additive manufacturing, or 3D printing, may also play a role in the evolution of automatic steel nail coating machines. As the demand for customized products grows, 3D printing technology could enable the creation of bespoke coating solutions for nails. For example, additive manufacturing could be used to print specialized coatings that have unique properties, such as anti-corrosive or anti-bacterial features, which are tailored to meet specific customer or industry needs. In combination with traditional coating processes, 3D printing could offer an additional layer of customization, enabling manufacturers to cater to niche markets with high-value or specialized products.
In response to the growing demand for faster, more efficient production methods, manufacturers of these coating machines are likely to develop higher-speed models capable of processing larger volumes of nails in shorter time frames. Advances in conveyor technology, integrated feeding systems, and high-speed curing processes will all contribute to a more efficient production cycle. This will be particularly important as global demand for steel nails in industries like construction, infrastructure, and DIY markets continues to rise. Meeting these demands will require faster, more capable machines, capable of scaling production quickly without compromising quality or consistency.
Moreover, innovations in coating techniques will continue to improve the functional properties of coated nails. New coating technologies such as anti-microbial coatings, self-healing coatings, or even coatings that provide enhanced friction resistance will push the boundaries of what nails can be used for. These innovations will be valuable in industries that require specialized nails for unique applications. For instance, self-healing coatings, which can repair small damage to the coating, will be in high demand for applications where nails are exposed to harsh conditions, like outdoor furniture or automotive manufacturing. Similarly, anti-microbial coatings may find a growing market in sectors such as healthcare or food production, where cleanliness and hygiene are critical.
As industries evolve and the demand for quality assurance increases, the trend toward data-driven manufacturing will become even more significant. Automatic steel nail coating machines will likely include more advanced data collection systems, capable of tracking and storing detailed production data. This data can be used for process optimization, troubleshooting, and compliance documentation, helping manufacturers maintain high levels of quality control. Additionally, real-time data can help predict when maintenance is needed or when components are starting to show signs of wear, which can prevent costly breakdowns and unplanned downtimes.
In summary, the future of Automatic Steel Nail Coating Machines is poised to be shaped by advances in automation, connectivity, sustainability, and customization. These machines will continue to evolve, becoming faster, smarter, and more versatile while aligning with the ever-changing demands of global manufacturing industries. Their role in the efficient production of high-quality nails with diverse coatings will be central to ensuring that manufacturers meet the increasing expectations for performance, quality, and sustainability. As they become more integrated into the smart factories of the future, these machines will not only streamline the production process but also contribute to more sustainable, data-driven, and high-performance manufacturing practices that can meet the challenges of an increasingly interconnected and environmentally conscious world.
Automatic Self Drilling Screw Painting Machine
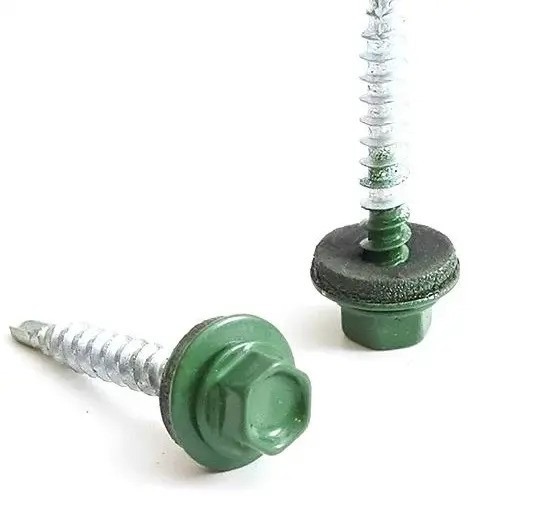
An Automatic Self Drilling Screw Painting Machine is a specialized industrial piece of equipment used to apply coatings to self-drilling screws, enhancing their appearance, durability, and resistance to environmental factors. These machines are essential in industries where screws need to be protected from corrosion, wear, or extreme conditions, such as construction, automotive, and manufacturing. Self-drilling screws, known for their ability to drill their own pilot hole while fastening, often require coatings that improve their performance and extend their lifespan, especially when used in outdoor or harsh environments. The automatic nature of these machines ensures a high level of efficiency, consistency, and quality control during the painting process.
The machine is typically made up of several key components that work together to efficiently coat self-drilling screws. These components include a screw feeding system, a coating application unit, a drying or curing system, and a quality control system. Each component plays a vital role in ensuring that the screws are consistently coated with the required finish, and that the final product meets high standards for both function and appearance.
The screw feeding system is responsible for collecting, aligning, and feeding the screws into the painting process. Depending on the design of the machine, this can be achieved through vibratory bowls, conveyor belts, or automated feeders that ensure screws are consistently fed into the system without jamming or misalignment. The feeding mechanism ensures that screws are oriented in the correct position before being exposed to the coating application process.
The coating application unit is where the painting process takes place. This unit can employ various methods for applying the coating material, such as electrostatic spray coating, dip coating, or liquid spray coating. Electrostatic spray coating is particularly effective for self-drilling screws, as it uses an electric charge to attract the paint to the screw surface, ensuring an even and uniform coating. This method is particularly useful for applying powder coatings, which are known for their durability and resistance to wear. Dip coating, where screws are immersed in a liquid coating solution, is another technique that provides excellent coverage, especially for screws with irregular shapes or deep threads. Liquid spray coating is commonly used for applying a thin, even layer of paint or other coatings, ensuring a smooth and consistent finish.
Once the coating is applied, the screws move to a drying or curing system. The type of curing process depends on the coating material used. If powder coating is applied, the screws are passed through a curing oven, where heat is used to melt and bond the coating to the surface, creating a durable and smooth finish. For liquid coatings, drying systems may use air drying or infrared lamps to speed up the curing process. UV curing is also becoming increasingly common, especially for coatings that cure quickly under ultraviolet light, offering a more energy-efficient and environmentally friendly alternative to traditional heat curing. The curing or drying process ensures that the coating hardens properly, providing the screw with the necessary protection and finish.
Quality control is an essential part of the automatic self-drilling screw painting machine. To ensure that every screw meets the required specifications, machines often include integrated inspection systems. These systems can include visual inspection cameras, thickness measurement tools, and sensors that check for coating defects, such as bubbles, drips, or uneven application. Some systems are equipped with artificial intelligence (AI) to analyze the screws’ surface and detect defects that might be missed by human operators. With real-time feedback from these quality control systems, operators can make adjustments to the machine settings to address any issues before they affect large quantities of screws, ensuring that only high-quality products are sent to the next stage of the production line.
One of the main advantages of an automatic self-drilling screw painting machine is its ability to handle large volumes of screws quickly and efficiently. These machines are capable of operating continuously, reducing the need for manual intervention and significantly increasing production capacity. As a result, manufacturers can produce a high number of painted screws in a relatively short amount of time, which is essential for meeting the demands of high-volume industries like construction, automotive, and electronics.
The automation of the painting process also leads to greater consistency in coating application. With manual painting methods, there is often variability in the thickness and coverage of the coating, which can lead to defects or inconsistent performance. By automating the process, the machine ensures that each screw receives an even and uniform coating, improving the overall quality of the finished product and ensuring that screws perform reliably in their intended applications.
In addition to speed and consistency, automatic painting machines also offer cost savings. By reducing the need for labor-intensive manual processes, companies can cut down on labor costs. The automation of the coating process also reduces the amount of material waste, as the machine is able to apply the right amount of coating to each screw, eliminating the over-application that often occurs in manual processes. The ability to recycle coating materials, such as paint or powder, also helps to further reduce material costs and minimize waste, contributing to a more sustainable production process.
Sustainability is becoming an increasingly important focus for manufacturers, and many automatic self-drilling screw painting machines are designed with eco-friendly features. For example, the use of low-VOC (volatile organic compound) coatings and energy-efficient curing systems helps reduce the environmental impact of the painting process. Furthermore, systems for capturing overspray and recycling coating materials help minimize waste and reduce the amount of harmful chemicals released into the environment. By implementing these eco-conscious features, manufacturers can meet regulatory standards and appeal to environmentally-conscious consumers and industries.
The versatility of automatic self-drilling screw painting machines allows them to handle a wide range of screw sizes and coating types, making them suitable for various industries. For example, in the construction industry, screws often require coatings that provide strong corrosion resistance, such as zinc or galvanized coatings. These coatings protect screws from rust and degradation when exposed to outdoor elements. In contrast, screws used in the automotive industry may require coatings that are not only corrosion-resistant but also aesthetically pleasing, such as colored or textured finishes. The ability of automatic painting machines to accommodate different types of coatings and production needs makes them invaluable to manufacturers that need to meet diverse customer requirements.
Another key feature of these machines is their adaptability to different production scales. Whether a manufacturer is producing large quantities of screws for mass production or smaller batches of specialized screws for custom applications, the machine can be adjusted to accommodate different production volumes. The ability to switch between different coating materials or production speeds without significant downtime is a significant advantage in a competitive market where demand can fluctuate.
In the future, automatic self-drilling screw painting machines are likely to incorporate more advanced technologies, including AI, machine learning, and enhanced connectivity. These technologies will improve the machines’ efficiency, productivity, and adaptability. For instance, AI-driven systems could predict and adjust for changes in coating material properties, environmental conditions, or screw specifications, further optimizing the painting process. Machine learning algorithms can be used to track production data over time, enabling the machine to “learn” from past batches and optimize settings for future runs, reducing waste and increasing efficiency.
The integration of IoT (Internet of Things) technology will also allow automatic self-drilling screw painting machines to be part of a broader smart manufacturing ecosystem. With IoT, operators can monitor the machine’s performance in real time, track production progress, and receive alerts about potential maintenance issues or operational inefficiencies. Data collected from the machine can also be used for predictive maintenance, which can identify parts that may need attention before they cause problems, minimizing downtime and reducing repair costs.
In conclusion, Automatic Self Drilling Screw Painting Machines are integral to the modern manufacturing of coated screws. By automating the coating process, these machines provide high-speed, consistent, and cost-effective solutions to industries that require self-drilling screws with durable, protective, and aesthetically pleasing coatings. Their versatility, efficiency, and quality control features make them indispensable for companies seeking to produce large quantities of high-quality screws. As technology continues to advance, these machines will become even more sophisticated, incorporating AI, IoT, and other innovations that will further improve their performance and sustainability. With these ongoing advancements, automatic self-drilling screw painting machines will continue to play a critical role in the global manufacturing landscape.
As the demand for automation and efficiency in manufacturing continues to grow, the future of Automatic Self Drilling Screw Painting Machines will likely be shaped by innovations in several key areas, including further automation, smarter integration, enhanced sustainability features, and the evolution of coating materials and technologies.
Enhanced Automation and Process Integration
One significant direction for future developments is the further integration of automation within the production line. As the industry moves toward a more interconnected manufacturing environment, automatic self-drilling screw painting machines will become even more seamlessly integrated with other systems, including screw sorting, feeding, and packaging systems. This integration will reduce the need for manual intervention, streamline workflows, and increase overall production speed. Automated sorting and alignment systems, which ensure screws are oriented correctly for optimal coating application, will become more sophisticated, using advanced sensors and AI algorithms to enhance accuracy and minimize errors.
Furthermore, as these machines become part of smart manufacturing systems, they will not only communicate with other machines on the production line but also with central management systems, providing real-time data on production rates, efficiency, and quality. This data-driven approach will allow manufacturers to quickly adjust production processes based on changing demands, ensuring greater flexibility and responsiveness in their operations. For example, if a particular coating type is required for a special order, the system can automatically adjust parameters for the coating application, drying, or curing process to accommodate the change without requiring manual intervention.
Integration of Artificial Intelligence (AI) and Machine Learning
The integration of AI and machine learning into automatic self-drilling screw painting machines will continue to evolve, allowing these systems to become increasingly intelligent and adaptable. AI algorithms can analyze production data in real time to predict the optimal coating application parameters, reducing waste and improving coating consistency. For example, by learning from previous runs, AI can optimize spray patterns, paint viscosity, and curing times based on the specific characteristics of the coating material and environmental conditions.
Machine learning can also help detect and correct issues during production before they become visible defects. By analyzing data from sensors and cameras, the system can identify potential quality issues, such as irregular paint thickness or adhesion problems, and make automatic adjustments to correct the issue without stopping production. This proactive approach to quality control will minimize waste, reduce rework, and ensure that every screw meets the required standards.
Sustainability and Environmental Impact
Sustainability remains a critical concern in the manufacturing industry, and automatic self-drilling screw painting machines are being designed with eco-friendly features to help manufacturers reduce their environmental footprint. One area of focus is the continued development of environmentally friendly coatings. The shift toward water-based coatings and low-VOC (volatile organic compound) options has already gained traction, and this trend will likely continue as industries push for more sustainable and safer alternatives to traditional solvent-based paints.
In addition to using eco-friendly coatings, the machines themselves are being designed with energy efficiency in mind. The incorporation of energy-saving technologies in curing systems, such as LED-based UV curing and infrared lamps, will help reduce the overall energy consumption during the painting process. These technologies offer faster curing times and require less power than traditional heat-based curing methods, making them not only more energy-efficient but also more environmentally friendly.
Automatic self-drilling screw painting machines will also feature enhanced waste reduction capabilities. By incorporating advanced recycling systems, such as paint recovery units that capture overspray and unused materials, these machines will minimize material waste. The recovered coatings can be recycled and reused in future production runs, reducing the amount of raw material needed and contributing to a more sustainable manufacturing process.
Additionally, the use of data analytics will help manufacturers optimize their use of resources, identifying opportunities to reduce energy consumption, material waste, and water usage. These systems will track and analyze production data in real time, offering insights into potential areas for improvement, such as reducing idle time, optimizing coating thickness, and minimizing downtime, all of which contribute to a greener, more cost-efficient operation.
Advancements in Coating Materials and Application Technologies
The future of automatic self-drilling screw painting machines will also be driven by advancements in coating materials and application technologies. One emerging trend is the use of advanced coatings, such as self-healing or nano-coatings, which offer improved durability and performance. Self-healing coatings are designed to repair minor damage, such as scratches or chips, automatically, extending the lifespan of coated screws and making them ideal for applications exposed to harsh environmental conditions.
Nanotechnology is another promising area of development in coating materials. Nanocoatings offer enhanced properties, such as increased corrosion resistance, water repellency, and improved mechanical strength, all while maintaining a thin and lightweight profile. These coatings may be particularly beneficial for screws used in industries like automotive, aerospace, and construction, where performance and durability are critical.
As new materials and application techniques emerge, automatic self-drilling screw painting machines will need to adapt to handle these innovations. Machines will be designed to accommodate a wider range of coating materials, such as liquid coatings, powder coatings, or specialty formulations that require precise temperature and humidity control. The ability to quickly switch between different coating types and adjust application parameters to suit the material will be a key feature of future machines, allowing manufacturers to meet the growing demand for customized solutions.
Increased Customization and Production Flexibility
The trend toward customization in manufacturing is gaining momentum, and automatic self-drilling screw painting machines will play a central role in enabling this shift. As customer demands become more specific, manufacturers will need machines that can quickly adapt to different screw sizes, coating colors, finishes, and functional properties.
Future machines will be equipped with flexible feeding systems, advanced coating application technologies, and customizable curing options that allow for quick and easy changes between production runs. This adaptability will enable manufacturers to handle a wide variety of screws and coatings without significant downtime, making it easier to meet diverse customer requirements. Whether producing small batches of specialty screws with unique coatings or large volumes of standard screws, the machine will be able to scale production efficiently while maintaining high levels of quality and consistency.
The ability to apply customized coatings, such as color matching, special textures, or functional coatings with specific properties (e.g., corrosion resistance, anti-microbial, or flame retardant), will make automatic self-drilling screw painting machines even more versatile. This versatility will be especially valuable in industries where screws need to meet strict specifications or perform in challenging environments.
Integration with Smart Factory Systems
As Industry 4.0 continues to transform manufacturing, automatic self-drilling screw painting machines will become part of interconnected, data-driven smart factories. These machines will be equipped with IoT (Internet of Things) sensors that provide real-time data on machine performance, production efficiency, and material usage. Operators and managers will be able to monitor and control the painting process remotely, making adjustments to improve productivity, troubleshoot issues, and reduce downtime.
Advanced data analytics will play a key role in this process, allowing manufacturers to analyze production data and identify trends or potential issues before they affect production. Predictive maintenance systems will monitor key machine components, alerting operators to potential problems before they lead to breakdowns. This proactive approach will reduce maintenance costs and improve machine reliability, ensuring consistent and efficient production.
The integration of AI-driven analytics with IoT systems will also provide valuable insights into optimizing production schedules, reducing waste, and improving overall production efficiency. These smart factory systems will be able to automatically adjust machine settings based on real-time data, making continuous improvements to the painting process and enabling manufacturers to stay competitive in an increasingly fast-paced and dynamic market.
Conclusion
The future of Automatic Self Drilling Screw Painting Machines is poised to be shaped by innovations in automation, connectivity, sustainability, and coating technology. As manufacturers seek to improve production efficiency, reduce costs, and meet increasing demands for customization and high-quality products, these machines will evolve to become more flexible, intelligent, and environmentally friendly. With advancements in AI, machine learning, sustainable coatings, and smart factory integration, these machines will continue to play a vital role in producing high-performance self-drilling screws for a wide range of industries. By embracing these developments, manufacturers will be able to meet the evolving demands of the global marketplace while contributing to a more sustainable and efficient manufacturing ecosystem.
As the industry evolves, future Automatic Self Drilling Screw Painting Machines will increasingly incorporate even more advanced technological innovations, aligning with broader trends in manufacturing, sustainability, and customization. This continued evolution will significantly impact how these machines are used, enabling more efficient, smarter, and eco-friendly production methods.
Future Trends in Automation and Robotics
One of the most exciting future developments in automatic self-drilling screw painting machines is the incorporation of advanced robotics and automation technologies. While these machines already utilize automated systems for feeding, painting, and curing screws, future advancements in robotics will enable even more sophisticated handling and processing.
For instance, robotic arms could be used for more complex screw manipulation, including precise placement on moving conveyors or even sorting screws by size, type, or coating requirements. The integration of machine vision and advanced robotics will ensure a higher degree of flexibility in handling various screw geometries and sizes, minimizing the risk of jams, misplacements, or misalignments. This will allow manufacturers to further scale their operations without having to worry about manual reconfiguration or adjustments, ensuring that even the smallest batch sizes or the most intricate coating patterns can be handled with ease.
Additionally, collaborative robots (cobots) could be used alongside human operators, creating a more interactive and efficient working environment. These robots would assist with tasks that require flexibility, adaptability, and precision, while still allowing for human oversight when necessary. As a result, the collaboration between humans and robots will improve both the speed and the consistency of the coating process, ensuring high-quality results across production runs.
Integration of Augmented Reality (AR) for Maintenance and Troubleshooting
Augmented Reality (AR) is another technology that will likely be incorporated into the future of automatic self-drilling screw painting machines. With AR tools, maintenance technicians and operators will be able to visualize real-time diagnostics directly on their mobile devices or smart glasses, overlaying digital information on the physical machine. This real-time assistance will be crucial for troubleshooting and preventing downtime by allowing quick identification of issues, whether mechanical, electrical, or process-related.
For example, if an operator notices a slight deviation in coating quality, AR systems could provide step-by-step guidance on how to adjust machine settings or identify the source of the issue. Maintenance teams can also use AR to receive remote support, where experts from the manufacturer or supplier can guide them through troubleshooting and repairs from any location. This will reduce machine downtime and ensure continuous, uninterrupted production.
Advanced Customization of Coatings
The future of automatic self-drilling screw painting machines will also witness enhanced capabilities for coating customization. As demand for specialized screws with unique finishes and properties continues to rise, these machines will evolve to accommodate a broader variety of coatings, including smart coatings and multi-layer finishes.
Smart coatings, which react to environmental changes such as temperature, humidity, or UV exposure, could become a common feature in screws used in advanced applications like electronics, aerospace, or renewable energy systems. For instance, screws used in solar panel installations may require coatings that adjust their properties based on weather conditions, providing extra corrosion resistance or thermal conductivity when needed.
Additionally, multi-layer coatings could be applied in a more automated and efficient manner, allowing for the application of complex combinations of coatings in a single pass. This would be particularly beneficial for screws intended for industries with demanding performance specifications. With multi-layer coatings, manufacturers could enhance the screw’s resistance to corrosion, UV degradation, and wear, all while maintaining a sleek appearance.
These advanced coating capabilities will be made possible through ongoing research and development in both the application techniques and materials used. As new coating formulations emerge, the machine’s application units will be equipped with more sophisticated nozzles, electrostatic systems, or dip tanks that can handle diverse materials. Machines will also be able to automatically detect and adjust to the specific needs of each screw based on its application and desired properties, ensuring optimal performance in the final product.
Further Enhancements in Sustainability
Sustainability will continue to be a driving force in the development of automatic self-drilling screw painting machines. The focus on reducing environmental impact will not only drive the adoption of eco-friendly coatings but also influence the design of the machines themselves.
Future machines may be designed to operate with minimal environmental impact, including the integration of more energy-efficient motors, air filtration systems to capture any hazardous fumes or particulate matter, and water-saving systems that recycle rinse water used during the coating process. Enhanced filtration and ventilation systems will ensure that emissions from spray painting processes are minimized, while the machine’s cooling systems could be optimized to reduce energy consumption.
The use of closed-loop systems will also reduce the amount of waste generated during the painting process. For example, by capturing overspray and recycling it back into the system, the machine can reduce both material and coating waste. This closed-loop system will be coupled with advanced tracking and measurement systems that allow manufacturers to monitor their resource consumption more accurately, helping them identify areas where they can reduce waste or improve material use efficiency.
These sustainability measures will not only help manufacturers comply with increasingly stringent environmental regulations but will also support their goals to reduce carbon footprints and enhance their corporate social responsibility (CSR) profiles.
High-Speed, High-Volume Production
As global demand for self-drilling screws continues to increase, manufacturers will require faster and more efficient coating machines to keep up with production schedules. Future automatic self-drilling screw painting machines will be designed to meet the demands of high-volume production, offering faster processing times without sacrificing the quality of the final product.
One possible advancement will be the ability of machines to handle higher throughput with multiple lanes or larger, faster conveyors, enabling them to coat a larger number of screws simultaneously. Additionally, the application units will be optimized for faster, more precise coating applications, utilizing advanced spray technologies or robotic arms that can cover more surface area in less time.
Furthermore, manufacturers will be able to fine-tune the curing process for even greater efficiency. High-speed curing systems could be implemented to accelerate the drying or curing phase, whether through improved ovens, UV curing systems, or infrared technologies, allowing for quicker turnaround times while maintaining the quality of the coating.
Real-Time Data and Predictive Analytics
The use of real-time data analytics will become more pervasive in the management of automatic self-drilling screw painting machines. Sensors embedded within the machines will continually gather data on machine performance, coating quality, energy consumption, and material usage. Advanced analytics platforms will use this data to optimize the production process by identifying inefficiencies, predicting maintenance needs, and providing operators with detailed insights into production trends.
For example, predictive analytics could signal when a part of the machine is starting to wear down, allowing operators to schedule maintenance before a breakdown occurs, thus preventing downtime. Additionally, real-time monitoring could track changes in coating quality, alerting operators to potential issues such as inconsistencies in thickness or curing, enabling them to make adjustments on the fly.
Machine learning could also help optimize the coating process over time. By analyzing historical data, the system could learn which parameters result in the best coating quality and adjust settings automatically to improve consistency. This means that as production continues, the system can refine its process to ensure better overall performance with each batch of screws produced.
Conclusion
As automatic self-drilling screw painting machines continue to evolve, their role in modern manufacturing will become more central and indispensable. From further automation and robotics to enhanced customization, sustainability, and smart technologies, the future of these machines holds immense potential. Manufacturers will benefit from increased efficiency, faster production times, and improved quality control, all while being able to meet the growing demand for specialized coatings and environmentally responsible manufacturing practices.
By embracing these innovations, automatic self-drilling screw painting machines will not only keep up with the demands of an increasingly complex and competitive global marketplace but will also help companies become more sustainable and agile in responding to customer needs. These developments will lead to a smarter, more efficient production process that ensures high-quality products with minimal environmental impact.
Automatic Self Drilling Screw Coating Machine
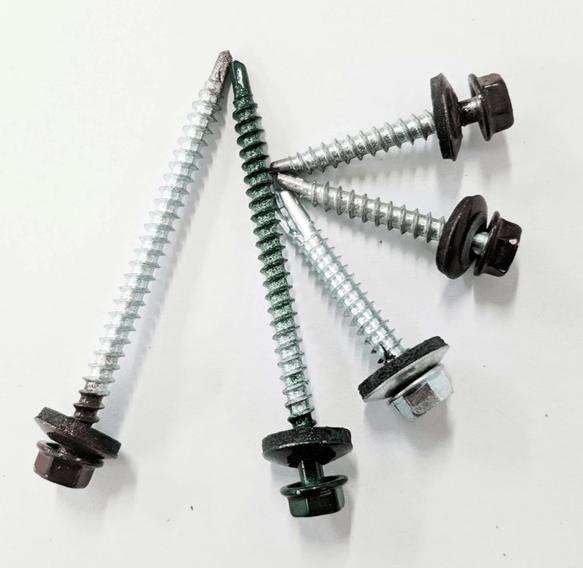
The Automatic Self Drilling Screw Coating Machine plays a vital role in enhancing the durability and performance of self-drilling screws, particularly for industries where these screws are subjected to harsh environmental conditions. These machines automate the application of protective coatings to screws, providing uniform coverage that improves the screws’ resistance to corrosion, wear, and other forms of degradation. As manufacturing technologies continue to advance, the future of automatic self-drilling screw coating machines will likely be shaped by several key trends, including greater automation, advanced material usage, sustainability, and the integration of smart technologies.
Future Trends in Automation and Robotic Integration
Automation will continue to be the cornerstone of future self-drilling screw coating machines, driven by the need for greater production efficiency, precision, and minimal manual intervention. As these machines become increasingly automated, they will integrate advanced robotics for tasks such as screw handling, feeding, sorting, and even quality control checks.
Robotic arms equipped with machine vision will be able to handle the screws at various stages of the coating process, ensuring they are placed on the conveyor correctly for consistent coating coverage. These robots will also allow for precise control over the application of the coating, ensuring that screws of varying sizes and geometries are coated uniformly. With automation, manufacturers will be able to reduce the risk of human error, minimize downtime, and achieve higher levels of productivity.
In addition, machine learning and AI integration will allow the system to continuously learn and adapt based on historical production data, optimizing the coating process. AI-driven algorithms could adjust parameters such as coating thickness, curing time, and spray patterns based on real-time data, ensuring consistent results even during high-volume production runs.
Enhanced Coating Technologies
One of the most significant areas of development in automatic self-drilling screw coating machines is the advancement of coating technologies. In response to growing demand for more durable and versatile screw coatings, manufacturers will likely develop new coating materials that offer superior protection, such as nano-coatings and self-healing coatings.
Nano-coatings are made up of ultra-thin layers of material, often incorporating nanoparticles that improve the mechanical properties of the coating. These coatings offer enhanced corrosion resistance, hardness, and scratch resistance, making them ideal for screws used in automotive, aerospace, and construction applications where durability is crucial.
Self-healing coatings are designed to repair minor scratches or chips in the coating, significantly extending the lifespan of the screws and reducing maintenance needs. This technology will become increasingly important for industries where screws are exposed to harsh weather conditions, chemicals, or other environmental factors that typically accelerate corrosion.
Automatic self-drilling screw coating machines will evolve to accommodate these advanced coating materials by incorporating more sophisticated application technologies. For instance, machines may utilize electrostatic spray systems, which apply an electric charge to the coating material, ensuring more efficient adhesion to the screw surface and reducing overspray waste. This technology allows for finer control over coating thickness and uniformity, even with complex or specialty materials.
Sustainability and Eco-friendly Coatings
As with other manufacturing sectors, there is increasing pressure to adopt sustainable practices in the production of coated screws. Manufacturers are transitioning away from harmful solvents and VOCs (volatile organic compounds) traditionally used in coating processes, opting for water-based and low-VOC coatings that are safer for both workers and the environment. The shift toward these eco-friendly coatings will drive future advancements in automatic self-drilling screw coating machines, as they will need to be optimized for new materials that may require different application techniques or curing methods.
In addition, automatic coating machines will incorporate energy-efficient technologies to reduce the overall environmental footprint of the coating process. For example, advanced curing systems, such as UV curing or infrared (IR) curing, are becoming more prevalent as they use less energy compared to traditional heat-based curing ovens. These systems allow for faster curing times and are more environmentally friendly due to their reduced energy consumption.
Further enhancements in sustainability will also involve the reduction of material waste. Automatic self-drilling screw coating machines will increasingly feature closed-loop systems for coating material recovery. These systems capture overspray and excess coatings, which can then be filtered, recycled, and reused in the production process. This not only reduces the amount of raw materials needed but also helps lower disposal costs, making the entire process more sustainable.
High-Speed Production and Flexibility
As global demand for self-drilling screws grows, automatic coating machines will be expected to handle higher production volumes while maintaining consistent quality. Future machines will incorporate high-speed conveyor systems and multi-lane designs that allow for simultaneous coating of multiple screws, improving throughput without sacrificing quality.
Moreover, flexibility will be a key feature of next-generation machines. They will be designed to easily switch between different screw sizes, types, and coatings with minimal downtime. The ability to change coating formulations quickly will become increasingly important as industries demand customized solutions, such as screws with specific colors, textures, or functional coatings. This could be achieved through the use of advanced multi-function nozzles or automated mixing systems that can accommodate various coating materials on demand.
For example, some machines may offer the ability to apply dual-layer coatings, which combine two different materials for enhanced performance. This could be used in applications requiring both aesthetic appeal and increased durability, such as screws for decorative products or those used in extreme outdoor environments.
Integration with Smart Manufacturing and Data Analytics
The Industry 4.0 movement, which emphasizes smart, connected manufacturing, will heavily influence the future development of automatic self-drilling screw coating machines. These machines will become part of an interconnected network, where they share real-time production data with other systems on the factory floor, including inventory management, packaging, and quality control systems.
Sensors embedded in the machines will monitor variables such as temperature, humidity, coating thickness, and spray efficiency. The data generated will be analyzed by advanced data analytics platforms that provide operators with insights into the performance of the coating process. Predictive analytics could identify trends or abnormalities in the coating process, alerting operators to potential issues before they become serious problems.
For example, if the system detects a change in coating consistency or quality, it can automatically adjust parameters like spray pressure or coating speed. These adjustments will ensure that every screw receives the exact treatment it requires, resulting in consistently high-quality products with minimal waste.
Additionally, cloud-based platforms will allow manufacturers to monitor their production lines remotely, enabling them to make real-time adjustments to machine settings, track production efficiency, and even schedule predictive maintenance. This will improve overall equipment effectiveness (OEE) and reduce downtime, contributing to more efficient and cost-effective operations.
Customization and Product Specialization
As demand for customized products continues to rise, automatic self-drilling screw coating machines will need to accommodate a broader range of specifications and applications. Manufacturers will increasingly require machines capable of applying coatings with specialized properties, such as anti-microbial, fire-retardant, or heat-resistant coatings.
These coatings will be essential in industries like healthcare, where screws are used in medical devices, or in construction, where screws may need to withstand high temperatures or exposure to chemicals. Future coating machines will be designed to apply these coatings quickly and efficiently while maintaining consistent quality.
In addition, color matching and aesthetic coatings will become more important, especially in industries like furniture and home decor. Automatic coating machines will be able to apply custom colors, textures, and finishes with greater precision, allowing manufacturers to meet the growing consumer demand for aesthetically appealing and durable screws.
Predictive Maintenance and Reduced Downtime
The integration of predictive maintenance technologies will play a crucial role in enhancing the reliability of automatic self-drilling screw coating machines. By using IoT (Internet of Things) sensors and machine learning algorithms, these systems will continuously monitor machine health and performance, predicting potential failures before they occur. This proactive approach to maintenance will allow manufacturers to schedule maintenance during planned downtimes, avoiding unplanned stops and reducing the overall cost of repairs.
For example, sensors could monitor the condition of critical components, such as nozzles, pumps, and motors, and alert operators when wear or damage is detected. This data would be analyzed to determine the optimal time for part replacement, ensuring that production continues without interruption and machine lifespan is maximized.
Conclusion
The future of automatic self-drilling screw coating machines promises exciting developments in automation, coating technology, sustainability, and smart manufacturing. As these machines evolve, they will become more efficient, adaptable, and environmentally friendly, meeting the growing demand for high-quality screws with specialized coatings. Advances in robotics, AI, and machine learning will enhance production speed, reduce waste, and ensure greater customization, allowing manufacturers to stay competitive in an increasingly demanding market.
With ongoing innovations in coating materials, such as nano-coatings, self-healing layers, and multi-functional coatings, these machines will offer even more durable and specialized solutions to meet the needs of industries ranging from automotive to construction. Additionally, the shift toward smarter, data-driven production lines will streamline operations, reduce downtime, and enhance overall product quality.
In summary, automatic self-drilling screw coating machines will play a central role in driving the future of screw manufacturing, ensuring that products meet the highest standards of durability, functionality, and sustainability while keeping pace with industry trends.
Integration with Sustainable Practices and Green Manufacturing
The future of automatic self-drilling screw coating machines will be increasingly aligned with green manufacturing principles. As global environmental concerns grow and regulations become stricter, there will be a heightened emphasis on reducing waste, emissions, and energy consumption throughout the production process. The coating industry is already seeing a shift towards more sustainable practices, and these will continue to evolve in the coming years.
One of the primary areas of focus will be the reduction of harmful chemicals in coatings. Manufacturers will increasingly move towards solvent-free coatings, which eliminate the need for volatile organic compounds (VOCs) that contribute to air pollution and pose health risks to workers. New innovations in water-based coatings or coatings that use environmentally friendly solvents will be incorporated into coating machines, requiring modifications to accommodate different application methods and curing techniques.
Further advancements will likely involve biodegradable coatings. These environmentally friendly options are gaining popularity, especially in industries like construction, where screws and fasteners are exposed to outdoor conditions. The ability to apply biodegradable coatings to self-drilling screws via automatic coating machines will reduce the environmental impact of waste products and enhance sustainability in industries that require large volumes of screws.
In addition to reducing emissions and chemical exposure, energy efficiency will become a central focus of coating machine development. Energy consumption during the curing phase, where screws are dried or hardened, can be substantial. Future coating machines will incorporate advanced energy-saving technologies, such as solar-powered curing systems or regenerative heat recovery systems, that capture and reuse heat energy. This will help reduce energy consumption and operating costs while also making the manufacturing process more eco-friendly.
Integration of Advanced Coating Curing Technologies
As coating materials evolve, the methods for curing these materials will also become more advanced. In the future, automatic self-drilling screw coating machines may incorporate ultraviolet (UV) curing or electron beam curing to replace traditional heat-based curing systems. These technologies offer faster curing times and require significantly less energy, making them more efficient and environmentally friendly.
UV curing is particularly advantageous because it allows for instant curing under UV light, which can be done at lower temperatures than conventional heat-based systems. This technology works well with specific types of coatings, including UV-cured varnishes and resins, which will likely see increased use due to their ability to offer superior protection against wear, UV degradation, and corrosion. UV curing also produces fewer emissions, making it a cleaner option for factories and reducing the overall environmental impact of the coating process.
Electron beam curing, on the other hand, uses high-energy electrons to cure coatings instantly, even at lower temperatures. It is an innovative technique that is suitable for various types of coatings, including those used in harsh industrial environments. This curing method is extremely efficient, and because it eliminates the need for solvents or heat, it significantly reduces the environmental footprint of the coating process.
As these curing technologies become more widely available and cost-effective, automatic self-drilling screw coating machines will integrate them to meet the growing demand for environmentally friendly and energy-efficient production processes. Manufacturers will increasingly rely on these advanced curing systems to keep pace with industry trends and consumer preferences for more sustainable products.
Smart Quality Control and Inspection
The introduction of smart quality control systems in automatic self-drilling screw coating machines will further refine the coating process and ensure consistent, high-quality results. These systems will rely heavily on machine vision, AI algorithms, and real-time data analytics to continuously monitor the coating application.
For instance, integrated cameras and sensors can detect defects such as uneven coating thickness, missed spots, or coating imperfections in real-time. Using machine vision, the system can analyze each screw as it moves along the production line, checking for inconsistencies that could compromise performance or appearance. If a defect is detected, the machine can automatically adjust the spray nozzles or coating application speed to ensure the correct amount of material is applied.
AI-driven algorithms can also optimize the application process by adjusting parameters such as spray pressure, nozzle angle, and curing time. These real-time adjustments will help maintain a consistent level of coating quality across a high volume of production, minimizing waste and maximizing product reliability.
In addition, robotic arms equipped with advanced sensors will handle screws during quality control phases. These robots can perform tasks like rotating screws for a 360-degree inspection or carefully sorting out screws that don’t meet quality standards. This level of automation ensures that only the best-quality screws proceed to the next production stages, improving overall product consistency.
Scalability for Increased Production Demand
The global demand for self-drilling screws is likely to continue growing across industries such as construction, automotive, electronics, and home improvement. In response, future automatic self-drilling screw coating machines will be designed for scalability, enabling manufacturers to meet higher production volumes without compromising on coating quality or consistency.
Machines will be able to handle larger batches of screws at higher speeds while maintaining flexibility to switch between different screw sizes, coating types, and configurations. For example, a multi-lane conveyor system may be employed, with separate lanes dedicated to different types of screws or coatings. This would allow the machine to process multiple orders simultaneously, drastically reducing production time and improving throughput.
Furthermore, modular systems will become more common, allowing manufacturers to expand their coating lines as needed. If a production line experiences increased demand or new product requirements, machines can be upgraded by adding additional coating stations or incorporating new technologies, without requiring a full system overhaul. This modularity helps manufacturers adapt to changing market conditions while minimizing capital expenditure.
Customization for Specialized Coatings and Applications
As industries continue to demand specialized coatings for specific applications, automatic self-drilling screw coating machines will become more adaptable and versatile. These machines will be capable of handling a wide variety of coatings, including anti-corrosion, heat-resistant, electrostatic coatings, and decorative finishes.
For example, in industries like aerospace and automotive, screws may require specialized coatings to withstand extreme temperatures, humidity, and environmental wear. Coating machines will be designed to precisely apply these coatings to ensure maximum protection and performance. The ability to produce screws with multiple coatings—such as an anti-corrosion base layer followed by a heat-resistant finish—will be critical in meeting industry-specific standards.
Additionally, with the rise of customized aesthetics in consumer products, self-drilling screws used in furniture or electronics will require color-matching and decorative finishes. Automatic self-drilling screw coating machines will be equipped with the capability to apply custom colors and textures, allowing manufacturers to meet diverse customer demands for visually appealing screws without sacrificing durability.
Conclusion: The Future of Automatic Self Drilling Screw Coating Machines
The future of automatic self-drilling screw coating machines is poised for significant transformation, driven by advancements in technology, sustainability, and the evolving demands of various industries. As automation, robotics, and AI continue to shape the manufacturing landscape, these machines will become faster, more efficient, and capable of producing high-quality coated screws for a wide range of applications.
With increasing demand for eco-friendly practices, the adoption of green manufacturing technologies will be a central focus, ensuring that coating processes are not only more efficient but also environmentally responsible. In parallel, the development of new, advanced coating materials and curing technologies will further enhance the durability and functionality of screws, expanding their use in a broader array of industries.
By embracing these innovations, automatic self-drilling screw coating machines will continue to meet the ever-growing need for high-performance, sustainable, and aesthetically pleasing screws. As manufacturers adapt to new challenges and market demands, these machines will remain integral to ensuring product quality, reducing production costs, and supporting sustainability goals across industries worldwide.
Future Challenges and Opportunities in Automatic Self-Drilling Screw Coating Machines
While the future of automatic self-drilling screw coating machines is promising, it is not without challenges. These challenges will require innovative solutions and present opportunities for continued growth and development in the industry.
1. Adapting to Diverse Industry Requirements
One of the significant challenges faced by automatic self-drilling screw coating machines is meeting the diverse and evolving demands across various industries. Different sectors—such as construction, automotive, aerospace, medical devices, and electronics—often require screws with unique coating properties, such as high corrosion resistance, biocompatibility, or aesthetic finishes. The need for customized coatings that can withstand specific environmental conditions (e.g., extreme temperatures, exposure to chemicals, UV radiation, etc.) can complicate production processes.
To address this challenge, automatic self-drilling screw coating machines will need to incorporate more versatile and adaptive coating systems that can easily switch between different materials and application techniques. This could involve the use of multi-chamber coating systems or modular units that allow for quick changes in the coating process based on customer requirements. The flexibility to switch between coatings like anti-corrosion layers, heat-resistant finishes, or decorative coatings on the same production line will be crucial for manufacturers aiming to stay competitive.
2. Maintaining High Throughput While Ensuring Quality
As the demand for self-drilling screws grows, manufacturers will face the challenge of balancing high production throughput with consistent quality control. In industries with tight production schedules, there is often pressure to meet high-volume demands without compromising on the performance or aesthetics of the screws. However, increasing production speed can lead to quality issues such as uneven coatings, contamination, or insufficient curing.
The solution lies in advanced automation, real-time quality monitoring, and predictive maintenance. Automatic self-drilling screw coating machines will need to incorporate real-time sensors, machine vision systems, and AI-driven quality control algorithms to monitor each screw during the coating process. This enables the system to detect defects immediately, apply adjustments automatically, and maintain high-quality standards throughout the production run. Additionally, predictive maintenance systems will help avoid machine failures and downtime, ensuring that production schedules are met without compromising the quality of the screws.
3. Scaling for Global Production Demands
With the continued globalization of manufacturing, there will be an increased demand for automatic self-drilling screw coating machines capable of handling large-scale operations. Manufacturers will require machines that not only operate at high speeds but also adapt to regional differences in coating requirements, local environmental conditions, and regulatory standards. For instance, screws used in automotive applications in one region may need different coatings than those used in construction in another region.
To meet these global demands, coating machines will need to be scalable and customizable to handle different types of coatings, screw sizes, and production volumes. Modular designs that allow manufacturers to expand or adjust their production lines based on varying demand will be crucial. Additionally, multi-lingual interfaces, cloud connectivity, and the ability to integrate with local regulatory requirements will be important features for international manufacturers.
4. Addressing Environmental and Regulatory Pressures
As global environmental concerns intensify, manufacturers will face increased pressure to comply with stricter environmental regulations related to the coating process. Governments worldwide are implementing stricter VOC limits, emissions standards, and waste disposal regulations for industrial processes, including coatings. These regulations will require manufacturers to adopt cleaner, more sustainable processes.
In response, the development of low-VOC, water-based, and non-toxic coatings will be essential. Additionally, coating machines will need to be designed with closed-loop systems for material recovery and recycling, ensuring minimal waste. The integration of eco-friendly curing technologies (such as UV curing and electron beam curing) will further reduce energy consumption and the release of harmful emissions. Manufacturers that prioritize sustainability in their operations will not only reduce environmental impact but also benefit from increased consumer demand for eco-friendly products.
5. Incorporating Smart Technology for Predictive Analytics
The integration of smart technologies such as IoT sensors, big data analytics, and cloud-based platforms will be vital in improving operational efficiency and minimizing downtime. As manufacturing plants become more connected, coating machines will be able to collect and share real-time data with other machines, providing manufacturers with valuable insights into production efficiency, coating quality, and maintenance needs.
For instance, predictive analytics powered by machine learning algorithms can forecast when a machine will require maintenance or when coating material may need to be replenished. By analyzing historical data, the system can optimize machine settings for each production run, reducing waste and improving throughput. These technologies also enable real-time troubleshooting, allowing operators to resolve issues remotely and minimizing the need for manual intervention.
6. Ensuring Compatibility with Industry 4.0
As part of the ongoing Industry 4.0 revolution, automatic self-drilling screw coating machines will be required to seamlessly integrate with other factory automation systems, such as inventory management, quality control, and supply chain monitoring. The goal is to create a fully interconnected production ecosystem that allows for the continuous flow of data and real-time decision-making across all aspects of the manufacturing process.
Incorporating cloud-based systems and AI into coating machines will allow for real-time monitoring of production parameters and enable automatic adjustments based on fluctuations in the environment, material properties, or production demand. This will ensure consistent quality and speed in a highly dynamic production environment.
7. Focus on Cost-Effectiveness and Return on Investment (ROI)
Despite the increasing demand for advanced technologies in automatic self-drilling screw coating machines, manufacturers will face continued pressure to keep costs down while ensuring a high return on investment (ROI). The cost of raw materials, energy consumption, machine operation, and maintenance must all be carefully managed to remain competitive in the market.
Manufacturers will seek to maximize the efficiency of their coating machines by incorporating energy-efficient technologies, automation, and predictive maintenance systems. These investments in advanced technologies will ultimately lead to long-term cost savings by reducing waste, optimizing production schedules, and extending the lifespan of the machinery.
8. Enhancing Worker Safety and Ergonomics
As the automation of coating machines progresses, there will be an increased focus on worker safety and ergonomics. Although automation reduces the need for manual labor, operators will still need to monitor and maintain the machines. As such, the design of the machines will prioritize user-friendly interfaces, safety features, and ergonomic considerations to ensure a safe and comfortable working environment.
Advanced machine vision and AI systems can be integrated into the machines to ensure that workers are alerted to potential hazards, such as malfunctioning equipment, excessive heat, or unsafe handling procedures. Additionally, remote monitoring and virtual interfaces will allow operators to oversee multiple machines at once, minimizing the need for on-site intervention and reducing the risk of accidents.
Conclusion: A Bright Future for Automatic Self-Drilling Screw Coating Machines
The future of automatic self-drilling screw coating machines is bright, with rapid technological advancements paving the way for more efficient, sustainable, and customizable solutions. As industries demand higher-quality, more durable, and eco-friendly products, these machines will continue to evolve to meet those needs. With the integration of automation, AI, robotics, and sustainable coating technologies, manufacturers will be able to deliver superior self-drilling screws while reducing waste and environmental impact.
At the same time, the global manufacturing landscape will continue to require machines that can scale with increasing production demands, meet diverse industry requirements, and comply with strict environmental regulations. As manufacturers address these challenges through innovation and smart technology integration, the future of self-drilling screw coating will remain pivotal in ensuring the durability, performance, and sustainability of fasteners used in a wide range of applications across the globe.
By embracing these technological advancements, automatic self-drilling screw coating machines will not only improve the quality and efficiency of screw manufacturing but will also contribute to the broader goal of creating a more sustainable and innovative manufacturing industry.
Not only do we manufacture our powder coating equipment, we also ship them worldwide to your facility with care
We’re not just the manufacturers of your powder coating equipment, we’re also your worldwide delivery partners.
At EMS Powder Coating Equipment, we understand that getting your powder coating equipment to you quickly and safely is just as important as manufacturing it to the highest standards. That’s why we offer worldwide delivery services to all of our customers.
We work with a network of experienced and reliable shipping partners to ensure that your equipment arrives on time and in perfect condition. We also offer a variety of shipping options to fit your budget and needs.
Whether you need your equipment shipped to a local address or to an international destination, we can help. We’ll work with you to choose the best shipping option for your needs and to keep you updated on the status of your shipment every step of the way.
So when you choose EMS for your powder coating equipment, you’re not just getting the best products on the market, you’re also getting the best possible delivery experience.
Contact us today to learn more about our worldwide delivery services.
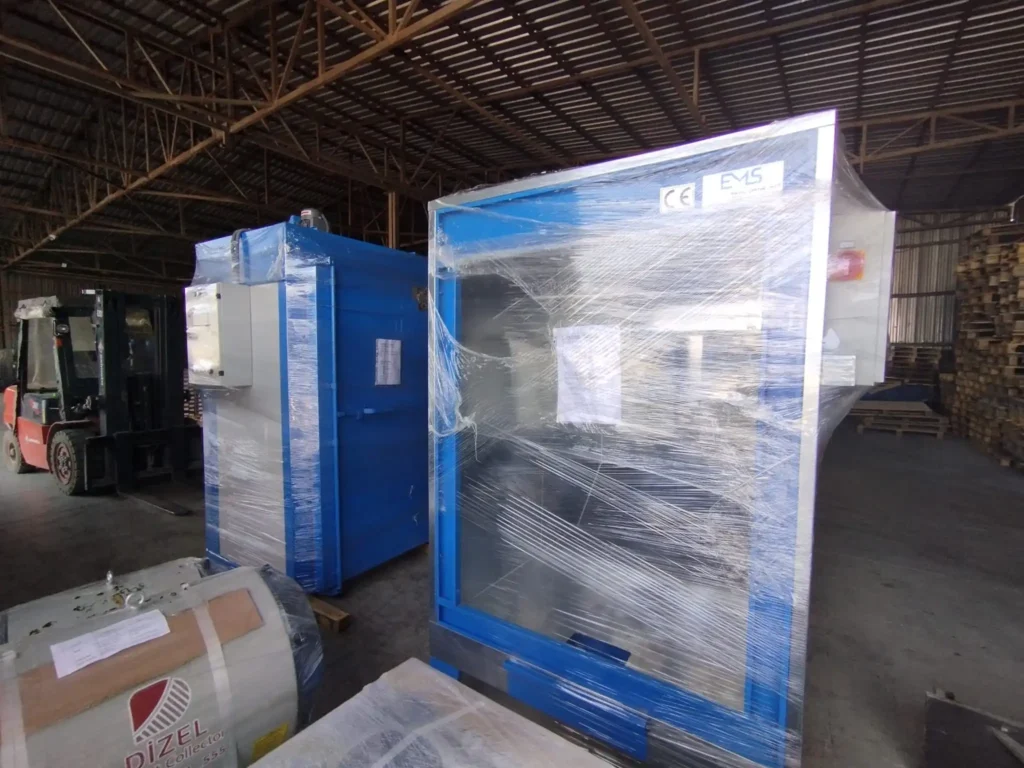
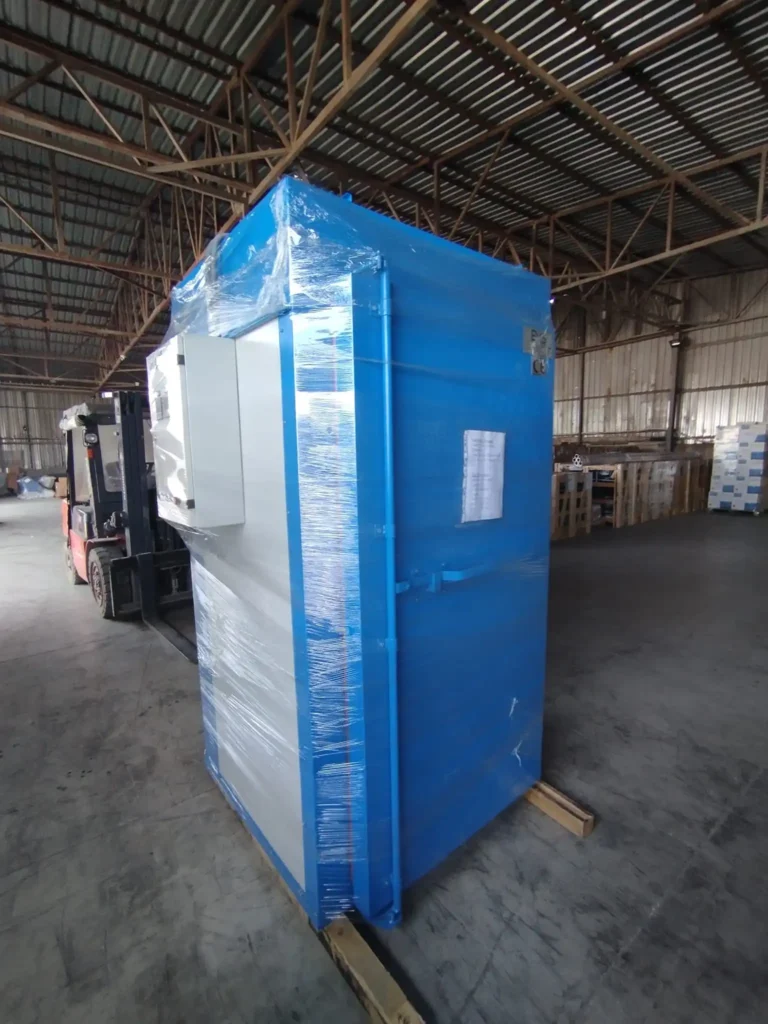
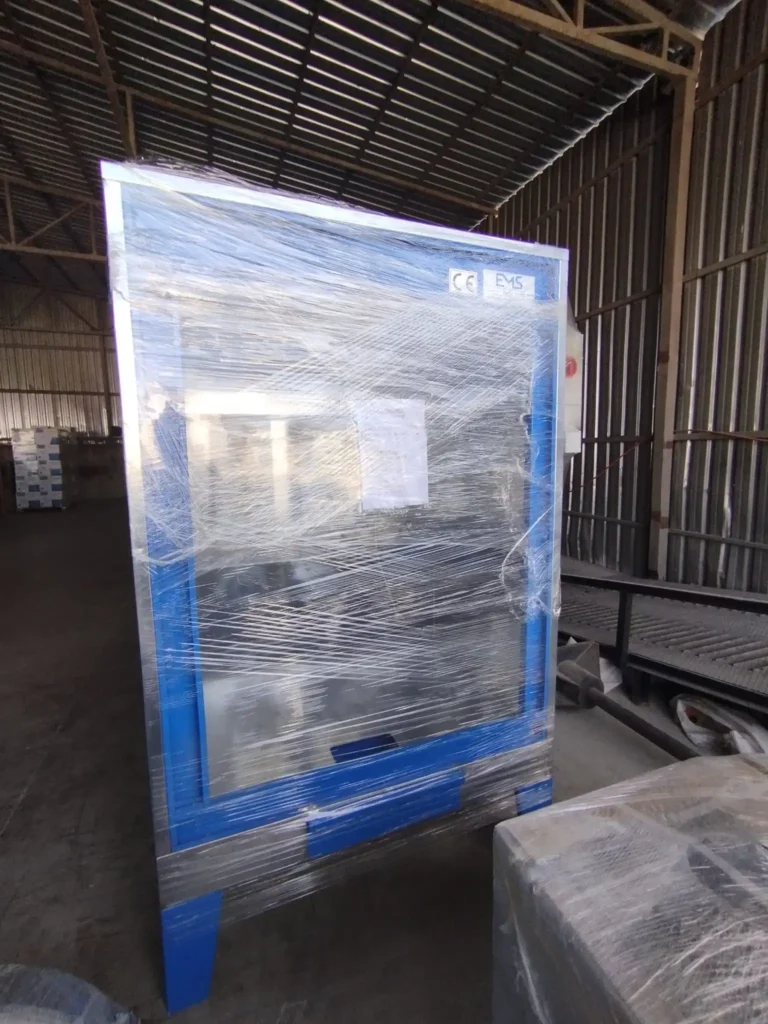
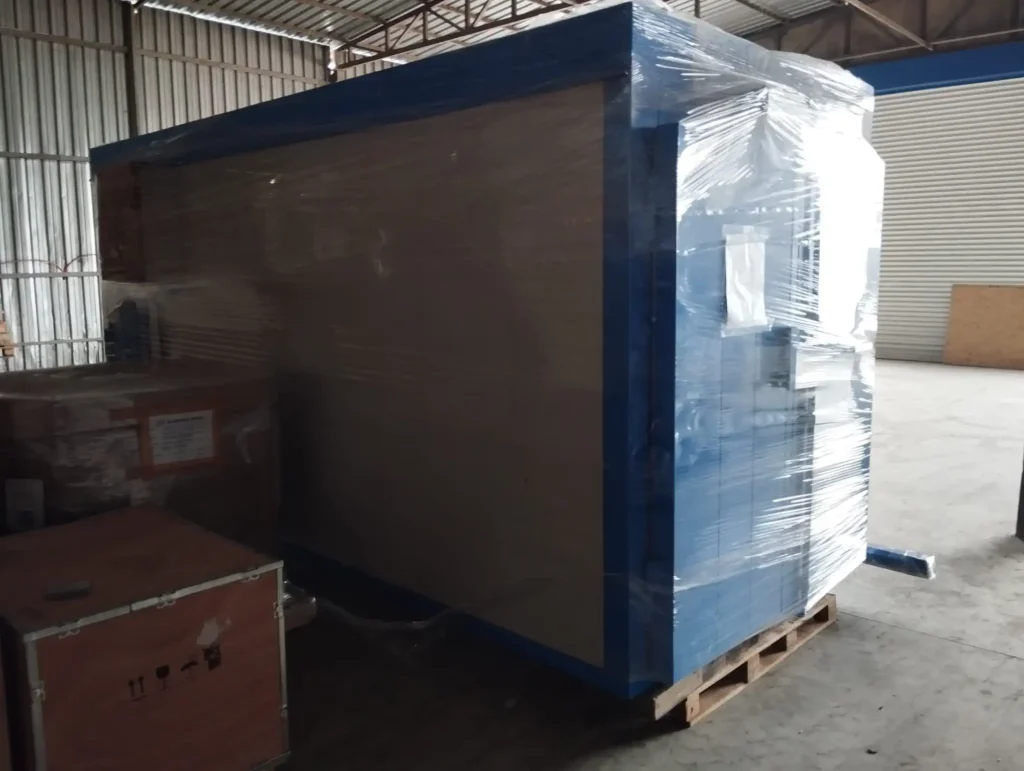
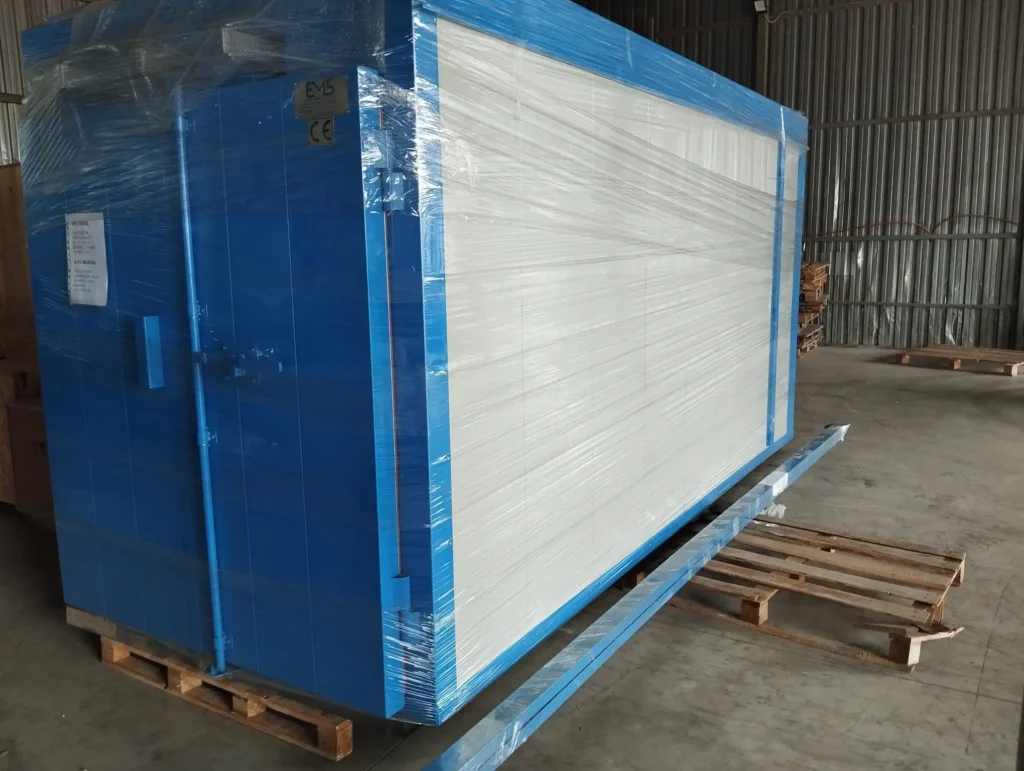
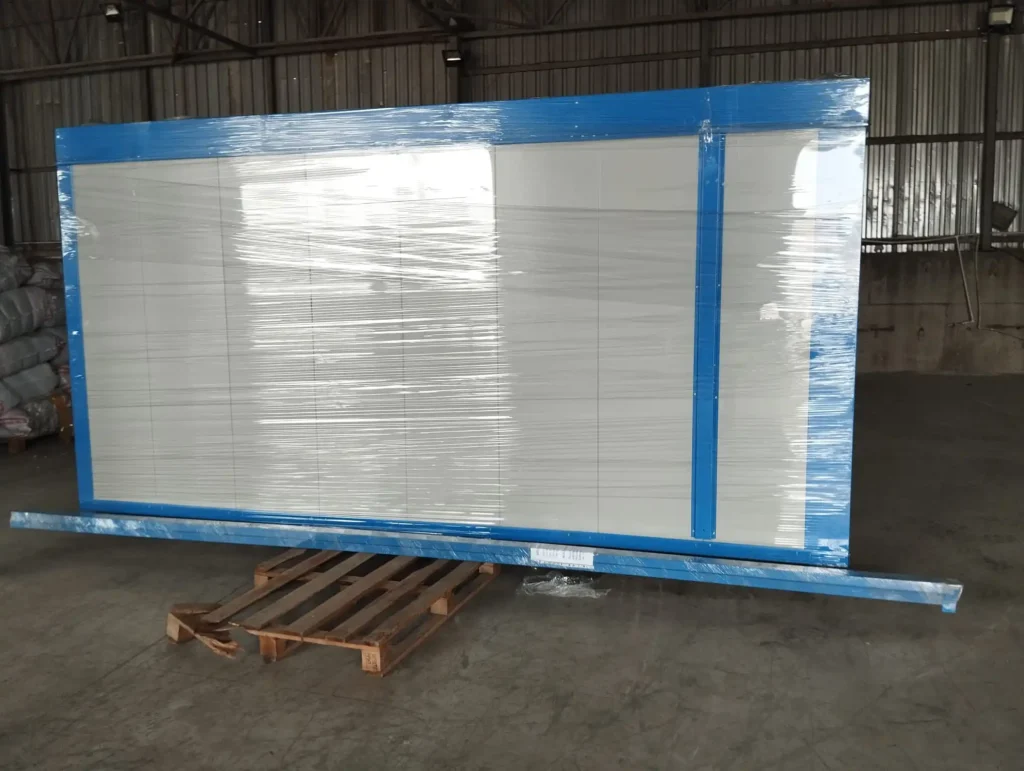
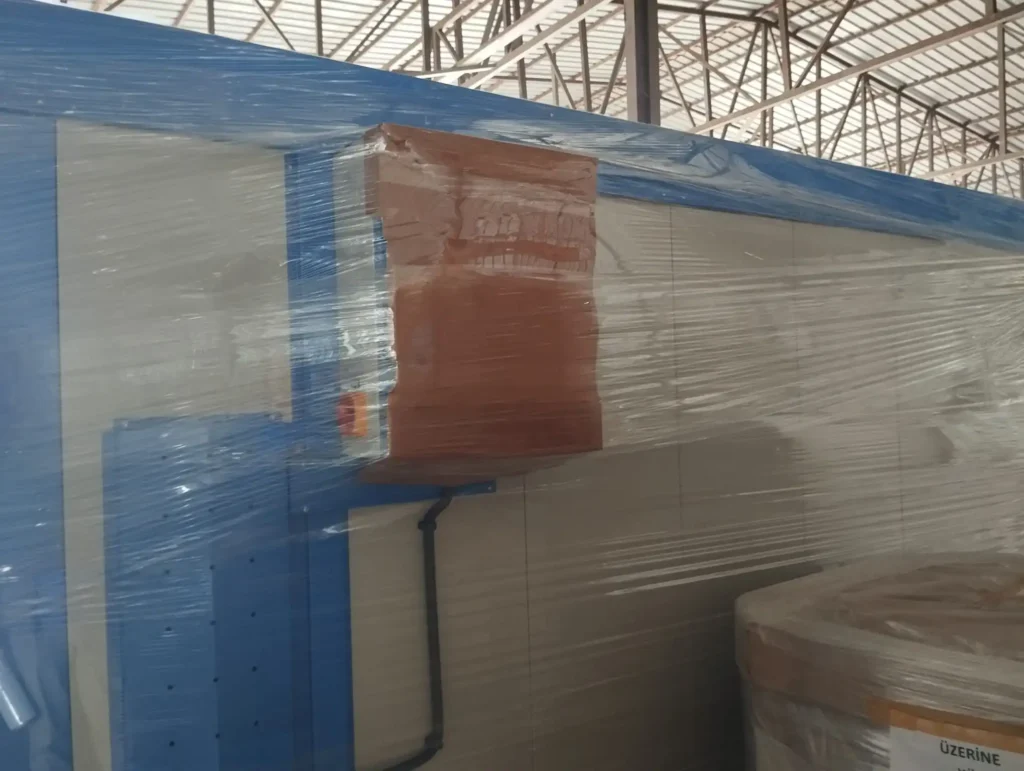
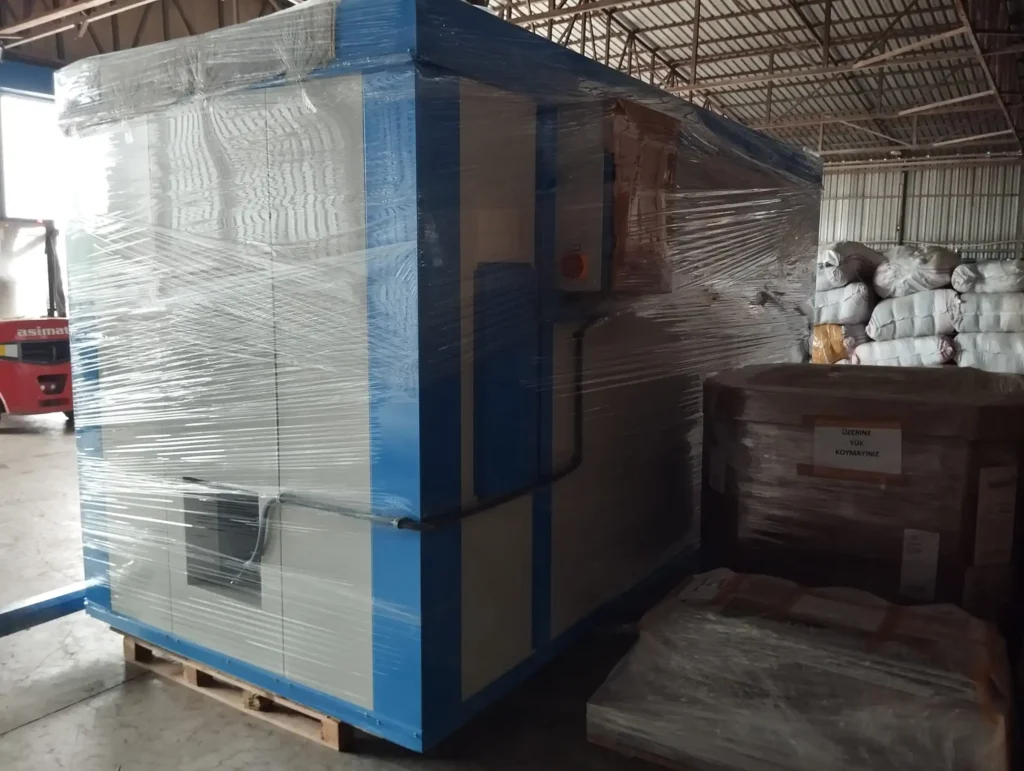
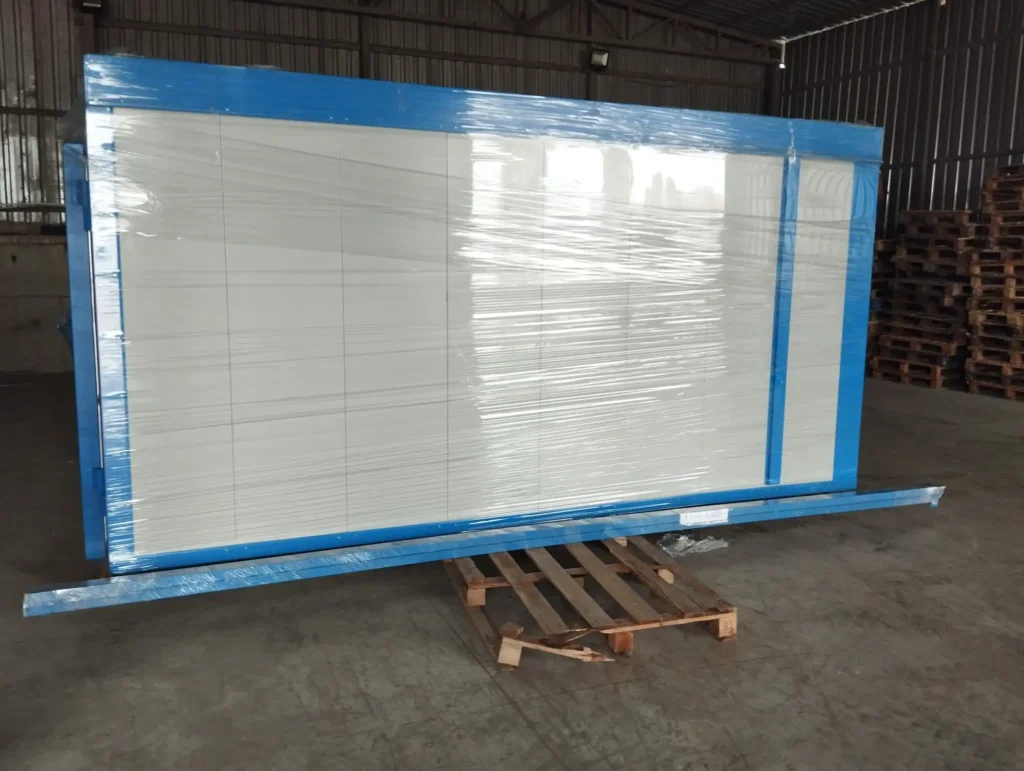