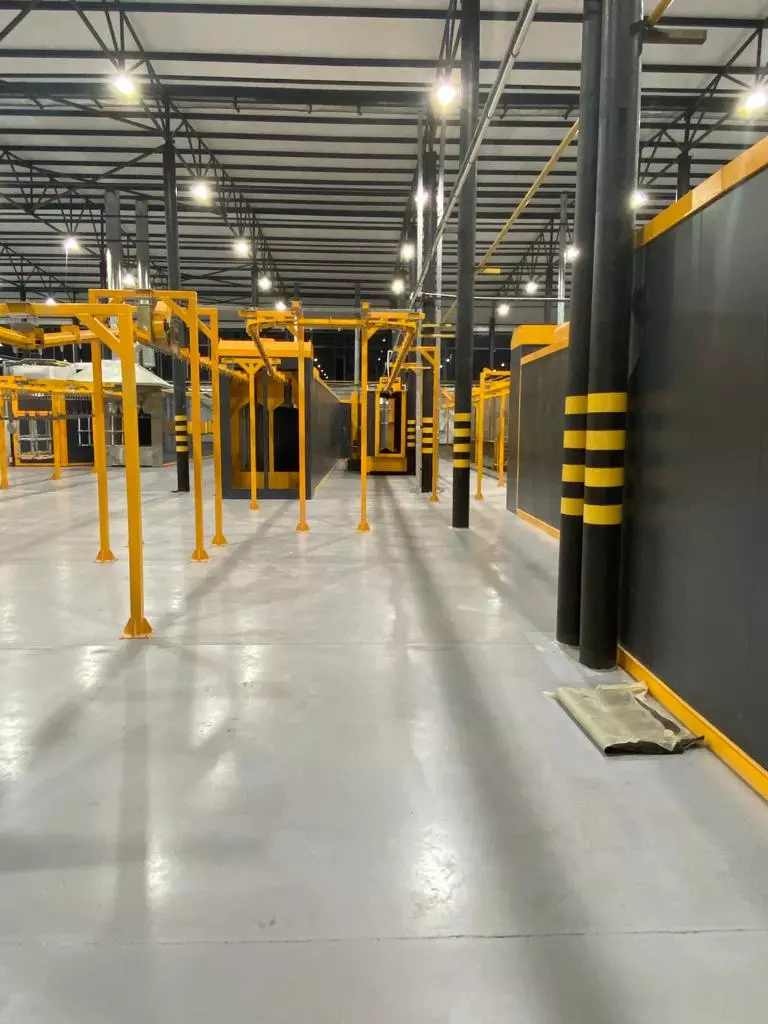
Powder coating is a versatile and efficient method of applying a durable finish to various surfaces, and automatic powder coating equipment plays a pivotal role in streamlining this process. At its core, powder coating involves the electrostatic application of finely ground particles onto a substrate, creating a protective and visually appealing coating. The automatic equipment used in this context encompasses a range of sophisticated technologies and components.
Automatic Powder Coating Equipment
The heart of the system lies in its ability to provide a consistent and uniform application of the powder. Through conveyorized or batch processing, these automated setups ensure an even distribution of the coating material, optimizing efficiency and minimizing waste. The electrostatic nature of the process enhances adhesion, as charged powder particles are attracted to grounded substrates, resulting in a more robust and long-lasting finish.
Pretreatment is a critical step facilitated by automatic powder coating equipment, involving the application of various chemicals to prepare surfaces for optimal adhesion. This can include cleaning, phosphating, or other treatments, enhancing the coating’s durability and corrosion resistance. The equipment also integrates cure ovens, where the coated items are subjected to controlled heat to achieve a durable and resilient finish.
Key components, such as programmable logic controllers (PLCs) and human-machine interfaces (HMIs), provide operators with precise control over the coating process. Automation technology ensures repeatability and accuracy, contributing to consistent coating thickness and quality. Powder recovery systems play a pivotal role in sustainability by capturing excess powder for reuse, minimizing waste and environmental impact.
The powder application itself is facilitated by advanced guns with precise control mechanisms. These guns deliver the powder efficiently, and reciprocators or automated systems ensure comprehensive coverage of complex geometries. Coating efficiency is further optimized through features like adjustable spray patterns, allowing for customization based on specific requirements.
Automatic Powder Coating Lines
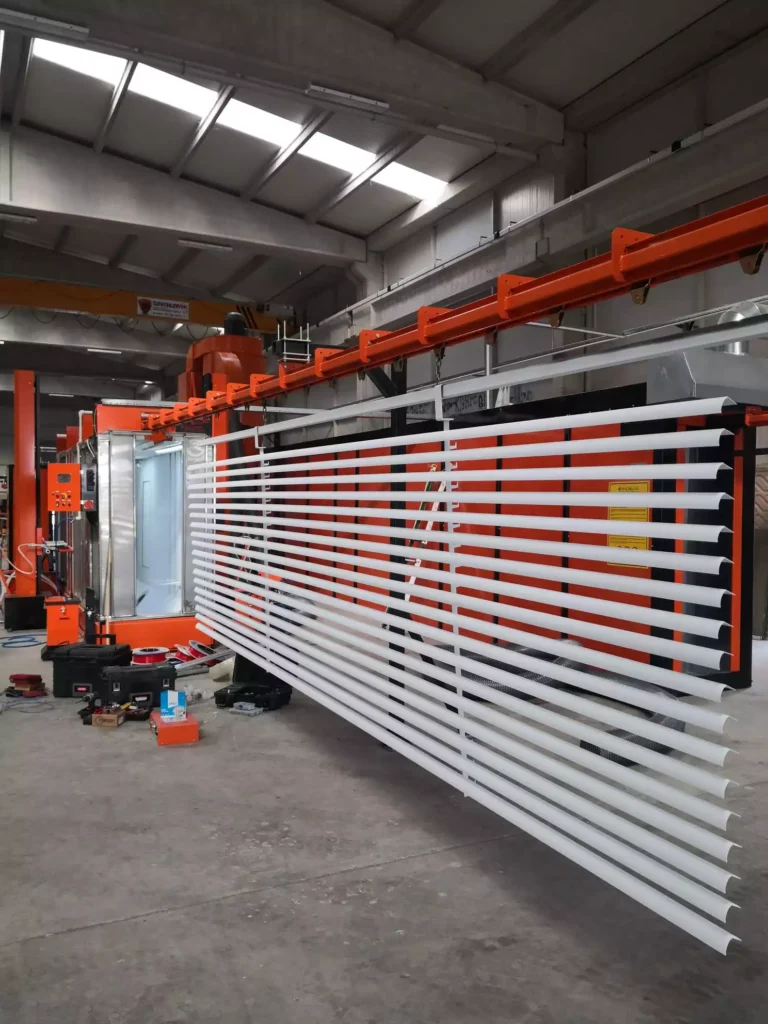
Powder coating lines, equipped with conveyors and tracking systems, enable seamless movement of items through the process. The automation extends to part hanging mechanisms, ensuring that items are positioned optimally for uniform coating. Grounding systems and controls are implemented to manage electrostatic charge, enhancing both safety and the effectiveness of the coating process.
In essence, automatic powder coating equipment integrates a multitude of technologies to create a streamlined, efficient, and high-quality coating process. From initial substrate preparation to final curing, each component works in harmony to produce durable, visually appealing finishes across a variety of applications. As industries increasingly prioritize efficiency and sustainability, the role of automatic powder coating equipment becomes ever more crucial in achieving these objectives.
Automatic powder coating equipment, represented by its advanced electrostatic application methods, stands as a cornerstone in modern surface finishing processes. At the heart of this technology is the nuanced interplay of elements, encapsulating the powder application process (2), the electrostatic principles governing it (3), and the conveyorized or batch processing systems that embody efficiency (4) and consistency (5).
The electrostatic nature of powder coating (3) is a defining feature that sets it apart from traditional liquid coatings. As powdered particles are charged, they exhibit a unique affinity for grounded substrates, creating a robust bond that translates into enhanced adhesion and a uniform coating thickness. This inherent electrostatic charge is precisely harnessed by automatic powder coating equipment, ensuring an even distribution of the powder for optimal coverage.
The powder application process (2) is a focal point where advanced technologies come into play. Automated guns, a hallmark of modern powder coating equipment, provide precise control over the application, allowing for customizable spray patterns and coating thickness. Reciprocators or robotic systems further refine this process, ensuring comprehensive coverage even on intricate or complex geometries. The result is a consistent and high-quality finish across a diverse range of surfaces.
Efficiency (4) is a driving force behind the adoption of automatic powder coating equipment. These systems are designed for conveyorized or batch processing, enabling a seamless flow of items through the coating line. Conveyor speed, part hanging mechanisms, and tracking systems contribute to a streamlined process, minimizing downtime and optimizing throughput. This efficiency is not only a testament to technological advancements but also a practical consideration for industries seeking to maximize productivity.
Consistency (5) is another hallmark of automatic powder coating equipment. Through programmable logic controllers (PLCs) and human-machine interfaces (HMIs), operators exercise precise control over the coating process. This control extends to factors such as powder delivery, gun settings, and cure oven parameters. The result is a reproducible and uniform coating quality, essential for industries where product aesthetics and durability are paramount.
In essence, the synergy of powder application, electrostatic principles, efficiency, and consistency defines the realm of automatic powder coating equipment. This technology not only revolutionizes surface finishing but also addresses key industry demands for precision, speed, and sustainability. As manufacturing landscapes evolve, the role of these advanced systems becomes increasingly pivotal in meeting the stringent requirements of diverse applications.
Automatic Powder Coating Equipment
Automatic powder coating equipment, characterized by its sophisticated electrostatic application methods, plays a pivotal role in modern surface finishing processes. At the core of this technology lies the intricate interplay of elements, incorporating the powder application process (2), electrostatic principles (3), conveyorized or batch processing systems emphasizing efficiency (4), and the crucial aspect of consistency (5). Together, these components contribute to a transformative approach in achieving superior finishes across a spectrum of materials and industries.
The powder application process (2) is a multifaceted aspect where cutting-edge technologies converge. The automated guns, integral to modern powder coating equipment, exemplify precision in powder delivery. These guns not only allow for adjustable spray patterns but also ensure uniform coating thickness, responding to the diverse requirements of substrates and end-product specifications. This precision is further complemented by reciprocators or robotic systems, facilitating a meticulous and comprehensive application even on intricate or three-dimensional surfaces.
The electrostatic principles (3) governing powder coating represent a paradigm shift from traditional liquid coatings. The charged powder particles exhibit a unique attraction to grounded substrates, resulting in superior adhesion and coating uniformity. Automatic powder coating equipment harnesses these principles with finesse, optimizing the electrostatic charge to achieve an efficient and effective application process. This inherent property enhances the durability and longevity of the applied coating.
Efficiency (4) stands as a cornerstone in the design and functionality of automatic powder coating equipment. The systems are adept at conveyorized or batch processing, ensuring a seamless flow of items through the coating line. Conveyor speed, part hanging mechanisms, and tracking systems contribute to a streamlined process, minimizing downtime and maximizing throughput. This efficiency not only improves productivity but also aligns with the growing emphasis on resource optimization and sustainable manufacturing practices.
Consistency (5) is a hallmark feature meticulously addressed by automatic powder coating equipment. Through the integration of programmable logic controllers (PLCs) and human-machine interfaces (HMIs), operators exert precise control over the entire coating process. From regulating powder delivery to adjusting gun settings and managing cure oven parameters, this level of control results in reproducible and uniform coating quality. Consistency is paramount in industries where product aesthetics and durability are critical factors.
In conclusion, the amalgamation of advanced powder application techniques, mastery of electrostatic principles, efficiency, and unwavering consistency defines the landscape of automatic powder coating equipment. This transformative technology not only elevates surface finishing standards but also positions itself at the forefront of meeting the evolving demands of diverse applications, where precision, speed, and sustainability are non-negotiable elements.
Automatic powder coating equipment, distinguished by its advanced electrostatic application methods, serves as a cornerstone in the realm of surface finishing. Within this intricate ecosystem, the powder application process (2), electrostatic principles (3), efficiency (4), consistency (5), and conveyorized or batch processing systems collaboratively shape an innovative approach to achieving high-quality finishes across various materials and industries.
Delving into the electrostatic principles (3) underpinning powder coating reveals a fundamental shift in surface finishing dynamics. The charged powder particles exhibit an inherent attraction to grounded substrates, fostering robust adhesion and uniform coating thickness. Automatic powder coating equipment masterfully navigates these principles, optimizing the electrostatic charge to deliver an efficient and effective application process. This inherent property not only enhances the durability of coatings but also contributes to the environmental sustainability of the overall finishing process.
Efficiency (4) emerges as a driving force behind the design and functionality of automatic powder coating equipment. The systems are adept at both conveyorized and batch processing, orchestrating a seamless flow of items through the coating line. Conveyor speed, intelligently designed part hanging mechanisms, and precision tracking systems contribute to a streamlined process, minimizing downtime and maximizing throughput. This efficiency not only improves overall productivity but aligns with contemporary manufacturing practices emphasizing resource optimization and sustainable operational footprints.
Consistency (5) stands as a hallmark feature meticulously addressed by automatic powder coating equipment. By integrating programmable logic controllers (PLCs) and human-machine interfaces (HMIs), operators exert precise control over the entire coating process. From regulating powder delivery and adjusting gun settings to managing cure oven parameters, this level of control ensures reproducible and uniform coating quality. In industries where product aesthetics and durability are paramount, this commitment to consistency translates into enhanced product reliability and customer satisfaction.
Conveyorized or batch processing systems (4) represent the logistical backbone of automatic powder coating equipment. These systems are engineered to handle diverse production scales and accommodate varying part sizes and geometries. The seamless flow of items through the coating line, coupled with intelligent tracking mechanisms, not only optimizes efficiency but also contributes to a standardized and controlled manufacturing environment. This adaptability positions automatic powder coating equipment as a versatile solution for industries with dynamic production demands.
In conclusion, the intricate synergy of advanced powder application techniques, mastery of electrostatic principles, efficiency, consistency, and adaptable processing systems defines the landscape of automatic powder coating equipment. This transformative technology not only elevates surface finishing standards but also positions itself at the forefront of meeting the evolving demands of diverse applications, where precision, speed, sustainability, and adaptability are paramount considerations.
Automatic powder coating equipment, with its sophisticated electrostatic application methods, is a linchpin in contemporary surface finishing. Within this intricate ecosystem, the powder application process (2), electrostatic principles (3), efficiency (4), consistency (5), and conveyorized or batch processing systems collaborate harmoniously, defining an innovative paradigm for achieving impeccable finishes across diverse materials and industries.
Efficiency (4) emerges as a driving force, shaping the very design and functionality of automatic powder coating equipment. The systems, adept at both conveyorized and batch processing, orchestrate a seamless flow of items through the coating line. Conveyor speed, intelligently designed part hanging mechanisms, and precision tracking systems contribute to a streamlined process, minimizing downtime and maximizing throughput. This efficiency not only improves overall productivity but aligns seamlessly with contemporary manufacturing practices that prioritize resource optimization and sustainable operational footprints.
Consistency (5), a hallmark feature meticulously addressed by automatic powder coating equipment, is a linchpin in ensuring the reliability and uniformity of coated products. Integration of programmable logic controllers (PLCs) and human-machine interfaces (HMIs) empowers operators with precise control over the entire coating process. From regulating powder delivery and adjusting gun settings to managing cure oven parameters, this meticulous control ensures reproducible and uniform coating quality. In industries where product aesthetics and durability are paramount, this commitment to consistency translates into enhanced product reliability and heightened customer satisfaction.
Conveyorized or batch processing systems (4) represent the logistical backbone of automatic powder coating equipment. Engineered to handle diverse production scales and accommodate varying part sizes and geometries, these systems contribute to the adaptability of the equipment. The seamless flow of items through the coating line, coupled with intelligent tracking mechanisms, not only optimizes efficiency but also fosters a standardized and controlled manufacturing environment. This adaptability positions automatic powder coating equipment as a versatile solution for industries with dynamic production demands.
Turning attention to the powder application process (2), it is the very essence of automatic powder coating. Advanced guns, pivotal components in this process, ensure precision in powder delivery. Adjustable spray patterns and uniform coating thickness are achieved through these automated guns. Reciprocators or robotic systems further refine the application, guaranteeing comprehensive coverage even on intricate or three-dimensional surfaces. This level of precision underscores the commitment of automatic powder coating equipment to delivering high-quality finishes consistently.
The electrostatic principles (3) governing powder coating underscore its departure from traditional liquid coatings. The charged powder particles exhibit a unique affinity for grounded substrates, resulting in superior adhesion and coating uniformity. Automatic powder coating equipment navigates these principles adeptly, optimizing the electrostatic charge to achieve an efficient and effective application process. This inherent property enhances the durability of coatings and contributes to the sustainability of the overall finishing process.
In conclusion, the intricate interplay of advanced powder application techniques, mastery of electrostatic principles, efficiency, consistency, and adaptable processing systems defines the landscape of automatic powder coating equipment. This transformative technology not only elevates surface finishing standards but also positions itself at the forefront of meeting the evolving demands of diverse applications, where precision, speed, sustainability, and adaptability are paramount considerations.
Automatic powder coating equipment, standing at the forefront of modern surface finishing, seamlessly integrates a myriad of technologies to optimize the powder application process (2), leverage electrostatic principles (3), enhance efficiency (4), ensure consistency (5), and employ conveyorized or batch processing systems for a comprehensive and sophisticated approach.
Consistency (5), a hallmark of automatic powder coating equipment, is meticulously maintained throughout the entire coating process. The integration of programmable logic controllers (PLCs) and human-machine interfaces (HMIs) empowers operators to exert precise control over various parameters. From regulating powder delivery and adjusting gun settings to managing cure oven parameters, this meticulous control ensures reproducible and uniform coating quality. Industries prioritizing product aesthetics and durability benefit immensely from the commitment to consistency, resulting in heightened product reliability and customer satisfaction.
Conveyorized or batch processing systems (4) form the logistical backbone of automatic powder coating equipment, contributing to both efficiency and adaptability. These systems are engineered to handle diverse production scales and accommodate varying part sizes and geometries. The seamless flow of items through the coating line, coupled with intelligent tracking mechanisms, not only optimizes efficiency but also fosters a standardized and controlled manufacturing environment. The adaptability of these processing systems positions automatic powder coating equipment as a versatile solution for industries with dynamic production demands.
Efficiency (4) remains a driving force in the design and functionality of automatic powder coating equipment. The systems, proficient in both conveyorized and batch processing, orchestrate a seamless flow of items through the coating line. Conveyor speed, intelligently designed part hanging mechanisms, and precision tracking systems contribute to a streamlined process, minimizing downtime and maximizing throughput. This efficiency not only improves overall productivity but aligns seamlessly with contemporary manufacturing practices that prioritize resource optimization and sustainable operational footprints.
Exploring the powder application process (2) reveals the intricate dance of advanced technologies within automatic powder coating equipment. The automated guns, central to this process, ensure precision in powder delivery. Adjustable spray patterns and uniform coating thickness are achieved through these cutting-edge components. Reciprocators or robotic systems further refine the application, guaranteeing comprehensive coverage even on intricate or three-dimensional surfaces. This level of precision underscores the commitment of automatic powder coating equipment to delivering consistently high-quality finishes.
The electrostatic principles (3) governing powder coating are fundamental to its superiority over traditional liquid coatings. The charged powder particles exhibit a unique attraction to grounded substrates, resulting in superior adhesion and coating uniformity. Automatic powder coating equipment adeptly harnesses these principles, optimizing the electrostatic charge to achieve an efficient and effective application process. This inherent property not only enhances the durability of coatings but also contributes to the sustainability of the overall finishing process.
In conclusion, the intricate interplay of advanced powder application techniques, mastery of electrostatic principles, efficiency, consistency, and adaptable processing systems defines the landscape of automatic powder coating equipment. This transformative technology not only elevates surface finishing standards but also positions itself at the forefront of meeting the evolving demands of diverse applications, where precision, speed, sustainability, and adaptability are paramount considerations.
In the realm of automatic powder coating equipment, the interplay of various components, including the powder application process (2), electrostatic principles (3), efficiency (4), consistency (5), conveyorized or batch processing systems (6), contributes to a cutting-edge approach in achieving superior surface finishes across diverse materials and industries.
Conveyorized or batch processing systems (6) stand as pivotal elements, shaping the logistical backbone of automatic powder coating equipment. Engineered for versatility, these systems seamlessly handle diverse production scales and accommodate varying part sizes and geometries. The seamless flow of items through the coating line, coupled with intelligent tracking mechanisms, optimizes efficiency and fosters a standardized and controlled manufacturing environment. The adaptability of these processing systems positions automatic powder coating equipment as a versatile solution for industries with dynamic production demands, ensuring a tailored approach to various manufacturing scenarios.
Efficiency (4) remains a cornerstone in the design and functionality of automatic powder coating equipment, with conveyorized or batch processing systems playing a crucial role. Proficient in both configurations, the systems orchestrate a seamless flow of items through the coating line. Conveyor speed, intelligently designed part hanging mechanisms, and precision tracking systems contribute to a streamlined process, minimizing downtime and maximizing throughput. This efficiency not only improves overall productivity but aligns seamlessly with contemporary manufacturing practices emphasizing resource optimization and sustainable operational footprints.
Consistency (5), as an inherent attribute of automatic powder coating equipment, underscores its commitment to delivering reliable and uniform coating quality. The integration of programmable logic controllers (PLCs) and human-machine interfaces (HMIs) empowers operators to exert precise control over the entire coating process. From regulating powder delivery and adjusting gun settings to managing cure oven parameters, meticulous control ensures reproducible and uniform coating quality. Industries prioritizing product aesthetics and durability benefit immensely from this commitment to consistency, ensuring a reliable and predictable outcome in each production cycle.
Exploring the powder application process (2) reveals the technological prowess within automatic powder coating equipment. Automated guns, central to this process, ensure precision in powder delivery. Adjustable spray patterns and uniform coating thickness are achieved through these cutting-edge components. Reciprocators or robotic systems further refine the application, guaranteeing comprehensive coverage even on intricate or three-dimensional surfaces. This level of precision underscores the commitment of automatic powder coating equipment to delivering consistently high-quality finishes, meeting the stringent demands of various industries.
The electrostatic principles (3) governing powder coating represent a fundamental departure from traditional liquid coatings. The charged powder particles exhibit a unique attraction to grounded substrates, resulting in superior adhesion and coating uniformity. Automatic powder coating equipment adeptly harnesses these principles, optimizing the electrostatic charge to achieve an efficient and effective application process. This inherent property not only enhances the durability of coatings but also contributes to the sustainability of the overall finishing process, aligning with contemporary environmental and efficiency standards.
In conclusion, the intricate interplay of advanced powder application techniques, mastery of electrostatic principles, efficiency, consistency, conveyorized or batch processing systems, and adaptable technology defines the landscape of automatic powder coating equipment. This transformative technology not only elevates surface finishing standards but also positions itself at the forefront of meeting the evolving demands of diverse applications, where precision, speed, sustainability, and adaptability are paramount considerations.
In the dynamic landscape of automatic powder coating equipment, the synthesis of cutting-edge technologies, including the powder application process (2), electrostatic principles (3), efficiency (4), consistency (5), conveyorized or batch processing systems (6), and powder recovery (7), creates a paradigm shift in surface finishing, offering a comprehensive solution for diverse materials and industries.
Powder recovery (7) emerges as a pivotal aspect, contributing to both efficiency and sustainability in the powder coating process. Automatic powder coating equipment integrates sophisticated powder recovery systems that capture and reclaim excess powder for reuse. This not only minimizes waste but also enhances resource efficiency, aligning with the growing emphasis on sustainable manufacturing practices. Powder recovery systems, such as cyclone separators, efficiently separate powder particles from the air, ensuring that a significant portion of the powder is recycled and utilized in subsequent coating cycles.
Efficiency (4) remains a foundational element, intricately linked with powder recovery in automatic powder coating equipment. The systems, designed for conveyorized or batch processing, orchestrate a seamless flow of items through the coating line. Conveyor speed, part hanging mechanisms, and precision tracking systems contribute to a streamlined process, minimizing downtime and maximizing throughput. The integration of efficient powder recovery systems not only enhances environmental sustainability but also ensures that valuable coating material is utilized optimally.
Consistency (5) continues to be a hallmark feature, meticulously maintained through the integration of programmable logic controllers (PLCs) and human-machine interfaces (HMIs). Operators exert precise control over the entire coating process, regulating powder delivery, adjusting gun settings, managing cure oven parameters, and overseeing powder recovery operations. This level of control ensures reproducible and uniform coating quality, contributing to the reliability and predictability of the finishing process.
Conveyorized or batch processing systems (6) further underscore the adaptability and efficiency of automatic powder coating equipment. Engineered to handle diverse production scales and accommodate varying part sizes and geometries, these systems optimize the utilization of resources. The seamless flow of items through the coating line, coupled with intelligent tracking mechanisms, fosters a standardized and controlled manufacturing environment. This adaptability positions automatic powder coating equipment as a versatile solution for industries with dynamic production demands, where efficient processing and resource management are paramount.
Exploring the powder application process (2) unveils the technological precision within automatic powder coating equipment. Advanced guns, central to this process, ensure precision in powder delivery. Adjustable spray patterns and uniform coating thickness are achieved through these cutting-edge components. Reciprocators or robotic systems further refine the application, guaranteeing comprehensive coverage even on intricate or three-dimensional surfaces. This level of precision underscores the commitment of automatic powder coating equipment to delivering consistently high-quality finishes, meeting the stringent demands of various industries.
The electrostatic principles (3) governing powder coating represent a fundamental departure from traditional liquid coatings. The charged powder particles exhibit a unique attraction to grounded substrates, resulting in superior adhesion and coating uniformity. Automatic powder coating equipment adeptly harnesses these principles, optimizing the electrostatic charge to achieve an efficient and effective application process. This inherent property not only enhances the durability of coatings but also contributes to the sustainability of the overall finishing process, aligning with contemporary environmental and efficiency standards.
In conclusion, the intricate interplay of advanced powder application techniques, mastery of electrostatic principles, efficiency, consistency, conveyorized or batch processing systems, powder recovery, and adaptable technology defines the landscape of automatic powder coating equipment. This transformative technology not only elevates surface finishing standards but also positions itself at the forefront of meeting the evolving demands of diverse applications, where precision, speed, sustainability, and resource efficiency are paramount considerations.
In the realm of automatic powder coating equipment, where innovation and precision converge, the integration of advanced technologies, including the powder application process (2), electrostatic principles (3), efficiency (4), consistency (5), conveyorized or batch processing systems (6), powder recovery (7), and pretreatment (8), defines a comprehensive solution for achieving impeccable finishes across diverse materials and industries.
Pretreatment (8) emerges as a crucial prelude to the powder coating process, emphasizing the importance of surface preparation for optimal adhesion and longevity of the applied coating. Automatic powder coating equipment incorporates sophisticated pretreatment systems that apply chemical treatments to surfaces before the powder application. These treatments, which may include cleaning, phosphating, or other preparatory steps, enhance the substrate’s receptivity to the powder coating, ensuring a robust and enduring finish. This attention to pretreatment aligns with the overarching goal of delivering coatings that not only exhibit visual appeal but also withstand the rigors of various environmental conditions.
Efficiency (4) remains a driving force, intricately linked with both pretreatment and the subsequent powder coating process in automatic powder coating equipment. The systems, designed for conveyorized or batch processing, orchestrate a seamless flow of items through the coating line. Conveyor speed, part hanging mechanisms, and precision tracking systems contribute to a streamlined process, minimizing downtime and maximizing throughput. Integrated pretreatment and efficient powder recovery systems not only enhance environmental sustainability but also ensure that valuable coating material is utilized optimally, further contributing to overall efficiency.
Consistency (5) continues to be a hallmark feature meticulously maintained through the integration of programmable logic controllers (PLCs) and human-machine interfaces (HMIs). Operators exert precise control over the entire coating process, regulating powder delivery, adjusting gun settings, managing cure oven parameters, and overseeing both pretreatment and powder recovery operations. This meticulous control ensures reproducible and uniform coating quality, contributing to the reliability and predictability of the finishing process, from surface preparation to the final coating.
Conveyorized or batch processing systems (6) underscore the adaptability and efficiency of automatic powder coating equipment, ensuring a seamless transition from pretreatment to the powder coating application. Engineered to handle diverse production scales and accommodate varying part sizes and geometries, these systems optimize the utilization of resources. The seamless flow of items through the coating line, coupled with intelligent tracking mechanisms, fosters a standardized and controlled manufacturing environment. This adaptability positions automatic powder coating equipment as a versatile solution for industries with dynamic production demands, where efficient processing, resource management, and comprehensive surface treatment are paramount.
Exploring the powder application process (2) unveils the technological precision within automatic powder coating equipment. Advanced guns, central to this process, ensure precision in powder delivery. Adjustable spray patterns and uniform coating thickness are achieved through these cutting-edge components. Reciprocators or robotic systems further refine the application, guaranteeing comprehensive coverage even on intricate or three-dimensional surfaces. This level of precision underscores the commitment of automatic powder coating equipment to delivering consistently high-quality finishes, meeting the stringent demands of various industries.
The electrostatic principles (3) governing powder coating represent a fundamental departure from traditional liquid coatings. The charged powder particles exhibit a unique attraction to grounded substrates, resulting in superior adhesion and coating uniformity. Automatic powder coating equipment adeptly harnesses these principles, optimizing the electrostatic charge to achieve an efficient and effective application process. This inherent property not only enhances the durability of coatings but also contributes to the sustainability of the overall finishing process, aligning with contemporary environmental and efficiency standards.
In conclusion, the intricate interplay of advanced powder application techniques, mastery of electrostatic principles, efficiency, consistency, conveyorized or batch processing systems, powder recovery, pretreatment, and adaptable technology defines the landscape of automatic powder coating equipment. This transformative technology not only elevates surface finishing standards but also positions itself at the forefront of meeting the evolving demands of diverse applications, where precision, speed, sustainability, resource efficiency, and comprehensive surface treatment are paramount considerations.
Within the realm of automatic powder coating equipment, where technological finesse meets industrial precision, the integration of advanced processes, including the powder application (2), electrostatic principles (3), efficiency (4), consistency (5), conveyorized or batch processing systems (6), powder recovery (7), pretreatment (8), and curing (9), encapsulates a holistic solution for achieving impeccable surface finishes across a myriad of materials and industries.
Curing (9), a pivotal step in the powder coating process, takes center stage as the applied powder is subjected to controlled heat in specialized ovens. Automatic powder coating equipment seamlessly incorporates curing mechanisms to solidify the coating, ensuring durability and longevity. The curing process completes the transformation from powder to a resilient finish, enhancing the coated item’s resistance to environmental factors. This meticulous attention to the curing phase aligns with the overarching goal of delivering coatings that not only exhibit visual appeal but also withstand the test of time.
Efficiency (4) remains a driving force, intricately linked with curing and other facets of the powder coating process in automatic powder coating equipment. The systems, designed for conveyorized or batch processing, orchestrate a seamless flow of items through the coating line. Conveyor speed, part hanging mechanisms, precision tracking systems, and integrated curing mechanisms contribute to a streamlined process, minimizing downtime and maximizing throughput. This efficiency not only improves overall productivity but also aligns seamlessly with contemporary manufacturing practices emphasizing resource optimization and sustainable operational footprints.
Consistency (5) remains a hallmark feature meticulously maintained through the integration of programmable logic controllers (PLCs) and human-machine interfaces (HMIs). Operators exert precise control over the entire coating process, regulating powder delivery, adjusting gun settings, managing cure oven parameters, and overseeing both pretreatment and powder recovery operations. This meticulous control ensures reproducible and uniform coating quality, contributing to the reliability and predictability of the finishing process, from surface preparation to the final cured coating.
Conveyorized or batch processing systems (6) underscore the adaptability and efficiency of automatic powder coating equipment, ensuring a seamless transition from curing to the powder coating application. Engineered to handle diverse production scales and accommodate varying part sizes and geometries, these systems optimize the utilization of resources. The seamless flow of items through the coating line, coupled with intelligent tracking mechanisms, fosters a standardized and controlled manufacturing environment. This adaptability positions automatic powder coating equipment as a versatile solution for industries with dynamic production demands, where efficient processing, resource management, and comprehensive surface treatment are paramount.
Exploring the powder application process (2) unveils the technological precision within automatic powder coating equipment. Advanced guns, central to this process, ensure precision in powder delivery. Adjustable spray patterns and uniform coating thickness are achieved through these cutting-edge components. Reciprocators or robotic systems further refine the application, guaranteeing comprehensive coverage even on intricate or three-dimensional surfaces. This level of precision underscores the commitment of automatic powder coating equipment to delivering consistently high-quality finishes, meeting the stringent demands of various industries.
The electrostatic principles (3) governing powder coating represent a fundamental departure from traditional liquid coatings. The charged powder particles exhibit a unique attraction to grounded substrates, resulting in superior adhesion and coating uniformity. Automatic powder coating equipment adeptly harnesses these principles, optimizing the electrostatic charge to achieve an efficient and effective application process. This inherent property not only enhances the durability of coatings but also contributes to the sustainability of the overall finishing process, aligning with contemporary environmental and efficiency standards.
In conclusion, the intricate interplay of advanced powder application techniques, mastery of electrostatic principles, efficiency, consistency, conveyorized or batch processing systems, powder recovery, pretreatment, curing, and adaptable technology defines the landscape of automatic powder coating equipment. This transformative technology not only elevates surface finishing standards but also positions itself at the forefront of meeting the evolving demands of diverse applications, where precision, speed, sustainability, resource efficiency, and comprehensive surface treatment are paramount considerations.
In the dynamic arena of automatic powder coating equipment, where technological prowess converges with industrial precision, the integration of advanced processes, including the powder application (2), electrostatic principles (3), efficiency (4), consistency (5), conveyorized or batch processing systems (6), powder recovery (7), pretreatment (8), curing (9), robotics (10), and quality control (11), encapsulates a comprehensive solution for achieving impeccable surface finishes across diverse materials and industries.
Robotic systems (10) stand out as a transformative addition to the landscape of automatic powder coating equipment. These automated marvels play a pivotal role in refining the powder application process, ensuring unparalleled precision and coverage. Equipped with advanced programming and sensing capabilities, robotic systems contribute to the uniformity of coatings, especially on intricate or three-dimensional surfaces. Their integration further enhances the adaptability of the equipment, allowing for customization based on specific requirements, and aligns seamlessly with the modernization trends driving manufacturing industries toward increased automation.
Quality control (11), a critical facet in the powder coating process, becomes paramount in automatic powder coating equipment. As technology advances, integrated quality control mechanisms monitor and assess every stage of the coating process, from pretreatment to curing. Automated inspections, in conjunction with human oversight, ensure that the coatings meet stringent quality standards. This meticulous approach to quality control not only guarantees the reliability of the finished products but also contributes to the overall efficiency of the manufacturing process.
Efficiency (4) remains a driving force, intricately linked with robotic systems, quality control, and other facets of the powder coating process in automatic powder coating equipment. The systems, designed for conveyorized or batch processing, orchestrate a seamless flow of items through the coating line. Conveyor speed, part hanging mechanisms, precision tracking systems, integrated curing and robotic systems contribute to a streamlined process, minimizing downtime and maximizing throughput. This efficiency not only improves overall productivity but also aligns seamlessly with contemporary manufacturing practices emphasizing resource optimization and sustainable operational footprints.
Consistency (5) continues to be a hallmark feature meticulously maintained through the integration of programmable logic controllers (PLCs) and human-machine interfaces (HMIs). Operators exert precise control over the entire coating process, regulating powder delivery, adjusting gun settings, managing cure oven parameters, and overseeing both pretreatment, powder recovery, robotic systems, and quality control operations. This meticulous control ensures reproducible and uniform coating quality, contributing to the reliability and predictability of the finishing process, from surface preparation to the final cured coating.
Conveyorized or batch processing systems (6) underscore the adaptability and efficiency of automatic powder coating equipment, ensuring a seamless transition from curing to the powder coating application. Engineered to handle diverse production scales and accommodate varying part sizes and geometries, these systems optimize the utilization of resources. The seamless flow of items through the coating line, coupled with intelligent tracking mechanisms, fosters a standardized and controlled manufacturing environment. This adaptability positions automatic powder coating equipment as a versatile solution for industries with dynamic production demands, where efficient processing, resource management, and comprehensive surface treatment are paramount.
Exploring the powder application process (2) unveils the technological precision within automatic powder coating equipment. Advanced guns, central to this process, ensure precision in powder delivery. Adjustable spray patterns and uniform coating thickness are achieved through these cutting-edge components. Reciprocators, robotic systems, and other automated technologies further refine the application, guaranteeing comprehensive coverage even on intricate or three-dimensional surfaces. This level of precision underscores the commitment of automatic powder coating equipment to delivering consistently high-quality finishes, meeting the stringent demands of various industries.
The electrostatic principles (3) governing powder coating represent a fundamental departure from traditional liquid coatings. The charged powder particles exhibit a unique attraction to grounded substrates, resulting in superior adhesion and coating uniformity. Automatic powder coating equipment adeptly harnesses these principles, optimizing the electrostatic charge to achieve an efficient and effective application process. This inherent property not only enhances the durability of coatings but also contributes to the sustainability of the overall finishing process, aligning with contemporary environmental and efficiency standards.
Powder recovery (7), an essential aspect in efficient resource utilization, is seamlessly integrated into automatic powder coating equipment. Advanced recovery systems, such as cyclone separators, capture and reclaim excess powder for reuse. This not only minimizes waste but also enhances resource efficiency, aligning with the growing emphasis on sustainable manufacturing practices. Powder recovery systems, working in conjunction with robotic systems, further contribute to the overall efficiency and environmental sustainability of the powder coating process.
Pretreatment (8) emerges as a crucial prelude to the powder coating process, emphasizing the importance of surface preparation for optimal adhesion and longevity of the applied coating. Automatic powder coating equipment incorporates sophisticated pretreatment systems that apply chemical treatments to surfaces before the powder application. These treatments enhance the substrate’s receptivity to the powder coating, ensuring a robust and enduring finish. This attention to pretreatment aligns with the overarching goal of delivering coatings that not only exhibit visual appeal but also withstand the rigors of various environmental conditions.
Curing (9), a pivotal step in the powder coating process, takes center stage as the applied powder is subjected to controlled heat in specialized ovens. Automatic powder coating equipment seamlessly incorporates curing mechanisms to solidify the coating, ensuring durability and longevity. The curing process completes the transformation from powder to a resilient finish, enhancing the coated item’s resistance to environmental factors. This meticulous attention to the curing phase aligns with the overarching goal of delivering coatings that not only exhibit visual appeal but also withstand the test of time.
In conclusion, the intricate interplay of advanced powder application techniques, mastery of electrostatic principles, efficiency, consistency, conveyorized or batch processing systems, powder recovery, pretreatment, curing, robotic systems, and quality control defines the landscape of automatic powder coating equipment. This transformative technology not only elevates surface finishing standards but also positions itself at the forefront of meeting the evolving demands of diverse applications, where precision, speed, sustainability, resource efficiency, and comprehensive surface treatment are paramount considerations.
Powder Coating: An In-Depth Guide to Equipment and Processes
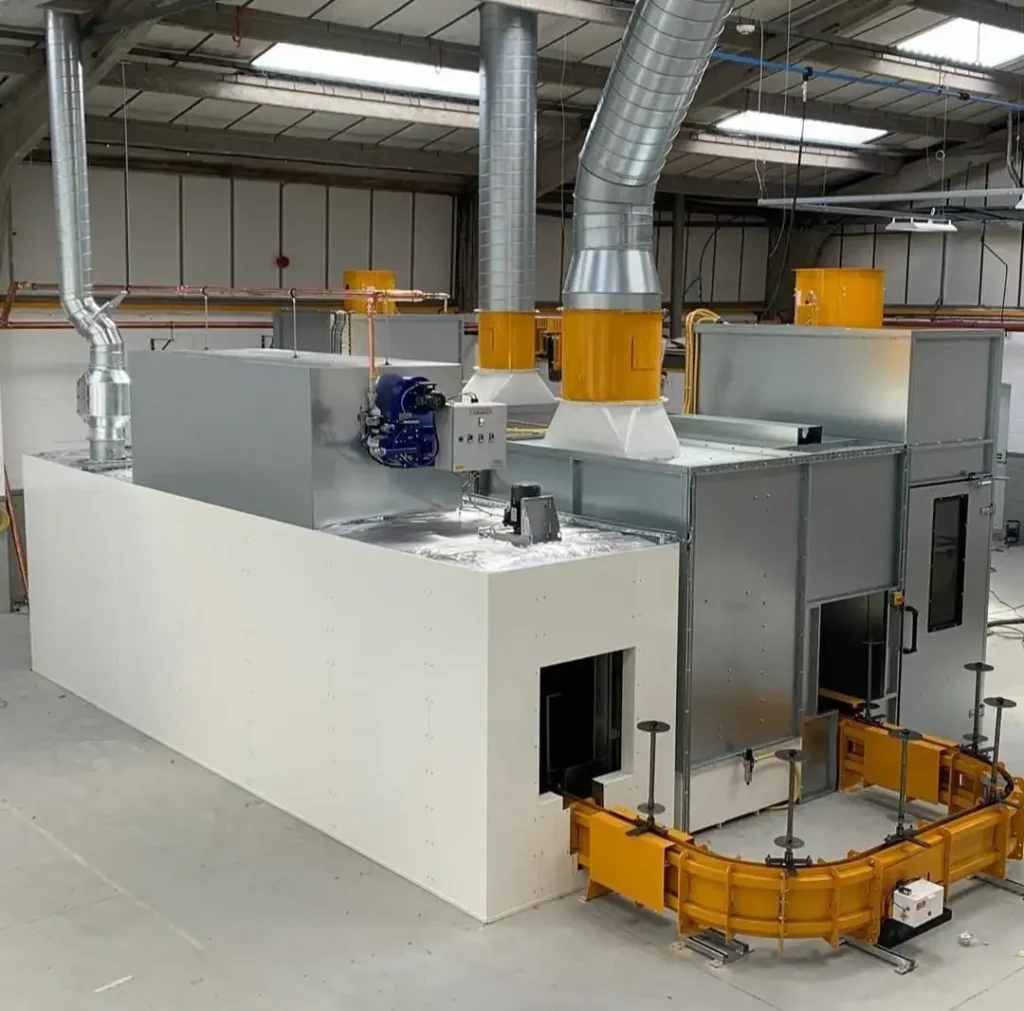
Introduction
Powder coating is a popular finishing process used across various industries to apply a durable and protective layer to metal surfaces. Unlike traditional liquid paint, powder coating uses a dry powder that is electrostatically charged and applied to the surface, which is then cured in a high-temperature oven. This process results in a hard finish that is more resistant to chipping, scratching, and fading.
In this guide, we’ll explore the different components of a powder coating system, including ovens, machines, equipment, and entire production lines. Understanding these elements is crucial for businesses looking to enhance their production capabilities with powder coating technology.
Powder Coating Ovens
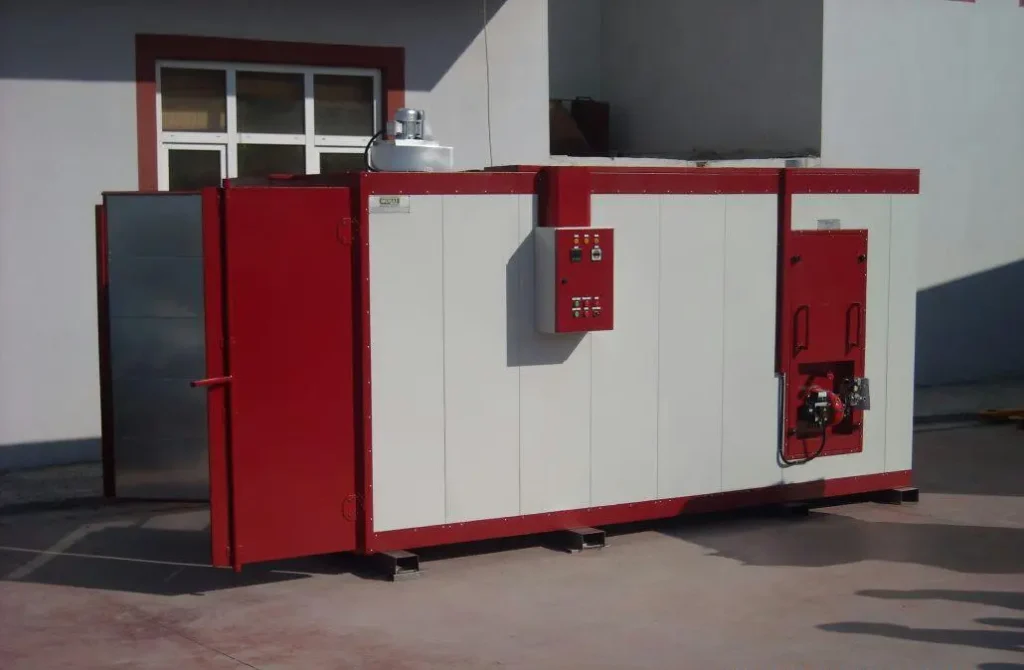
Definition and Purpose:
Powder coating ovens are essential for the curing process, where the powder adheres to the surface and forms a smooth, hard finish. These ovens provide the necessary heat to melt the powder, ensuring even and thorough coating.
Types of Powder Coating Ovens:
- Batch Ovens:
- Ideal for small to medium-sized production runs
- Flexibility to handle various part sizes
- Suitable for businesses with diverse product lines
- Conveyor Ovens:
- Designed for continuous production
- Higher throughput and efficiency
- Suitable for large-scale operations
Features and Specifications:
- Temperature Range: Typically between 325°F to 450°F
- Heating Source: Options include electric, gas, or infrared
- Size and Capacity: Varies based on production needs
- Energy Efficiency: Consider models with advanced insulation and airflow systems
How to Choose the Right Oven:
- Evaluate production volume and part sizes
- Consider energy consumption and operating costs
- Assess available space and installation requirements
- Consult with manufacturers for customized solutions
Powder Coating Machines
Overview of Different Machines Used:
Powder coating machines are used to apply the powder to the surface. They vary in complexity and functionality, catering to different production needs.
Manual vs. Automated Machines:
- Manual Machines:
- Suitable for small-scale operations
- Offers flexibility and control
- Requires skilled operators
- Automated Machines:
- Ideal for high-volume production
- Consistent and uniform application
- Reduced labor costs
Key Features and Specifications:
- Voltage and Power Requirements: Ensure compatibility with your facility
- Control Systems: Look for user-friendly interfaces and programmable settings
- Spray Gun Options: Different nozzles and gun types for various applications
Selecting the Right Machine for Your Needs:
- Determine the scale and complexity of your operations
- Evaluate budget constraints and long-term ROI
- Seek advice from industry experts and suppliers
Powder Coating Equipment
Essential Equipment for Powder Coating:
- Powder Coating Booths: Enclosed areas for applying powder
- Powder Recovery Systems: Capture and reuse overspray powder
- Air Compressors and Dryers: Ensure consistent airflow for optimal coating
Optional Equipment for Enhanced Performance:
- Pre-Treatment Systems: Clean and prepare surfaces before coating
- Curing Lamps: Speed up the curing process with infrared or UV lamps
Maintenance and Safety Considerations:
- Regularly inspect and clean equipment
- Train staff on proper handling and safety protocols
- Adhere to industry standards and regulations
Powder Coating Lines and Plants
Explanation of Powder Coating Lines:
Powder coating lines are integrated systems that automate the entire powder coating process, from pre-treatment to curing.
Components of a Powder Coating Line:
- Conveyor Systems: Move parts through the line efficiently
- Pre-Treatment Stations: Clean and prepare surfaces
- Powder Application Booths: Enclosed areas for powder coating
- Curing Ovens: Finalize the coating process
Design and Layout Considerations:
- Optimize workflow and space utilization
- Consider future scalability and expansion
- Ensure compliance with safety and environmental regulations
Scalability and Customization Options:
- Modular designs for easy expansion
- Custom configurations to meet specific production needs
Benefits of Powder Coating
Environmental Advantages:
- Low VOC emissions compared to liquid paints
- Overspray can be recycled, reducing waste
- Complies with environmental regulations
Durability and Longevity:
- Resistant to corrosion, fading, and wear
- Suitable for outdoor and high-traffic applications
- Provides a high-quality, professional finish
Cost-Effectiveness:
- Reduces long-term maintenance and repainting costs
- Efficient use of materials minimizes waste
- High throughput and automation lower labor expenses
Considerations for Setting Up a Powder Coating Plant
Initial Investment and ROI:
- Assess capital requirements for equipment and infrastructure
- Calculate potential returns based on production capacity and demand
- Explore financing options and incentives
Regulatory Compliance:
- Adhere to industry standards and local regulations
- Implement safety protocols and employee training
- Monitor environmental impact and waste management
Market Trends and Future Outlook:
- Growing demand for eco-friendly coatings
- Advancements in automation and technology
- Increasing adoption in automotive, aerospace, and consumer goods sectors
Conclusion
Powder coating offers numerous advantages over traditional liquid painting methods, making it an attractive option for industries seeking durable and environmentally friendly finishes. By investing in the right equipment and understanding the intricacies of powder coating processes, businesses can enhance their production capabilities and meet the growing demand for high-quality coated products.
When setting up a powder coating plant, it’s essential to carefully consider your needs, budget, and long-term goals. Collaborating with experienced suppliers and industry experts can help you make informed decisions and achieve success in the competitive world of powder coating.
This comprehensive guide should provide valuable insights for your website visitors and help position your business as a knowledgeable and reliable source in the powder coating industry.
Installation process steps
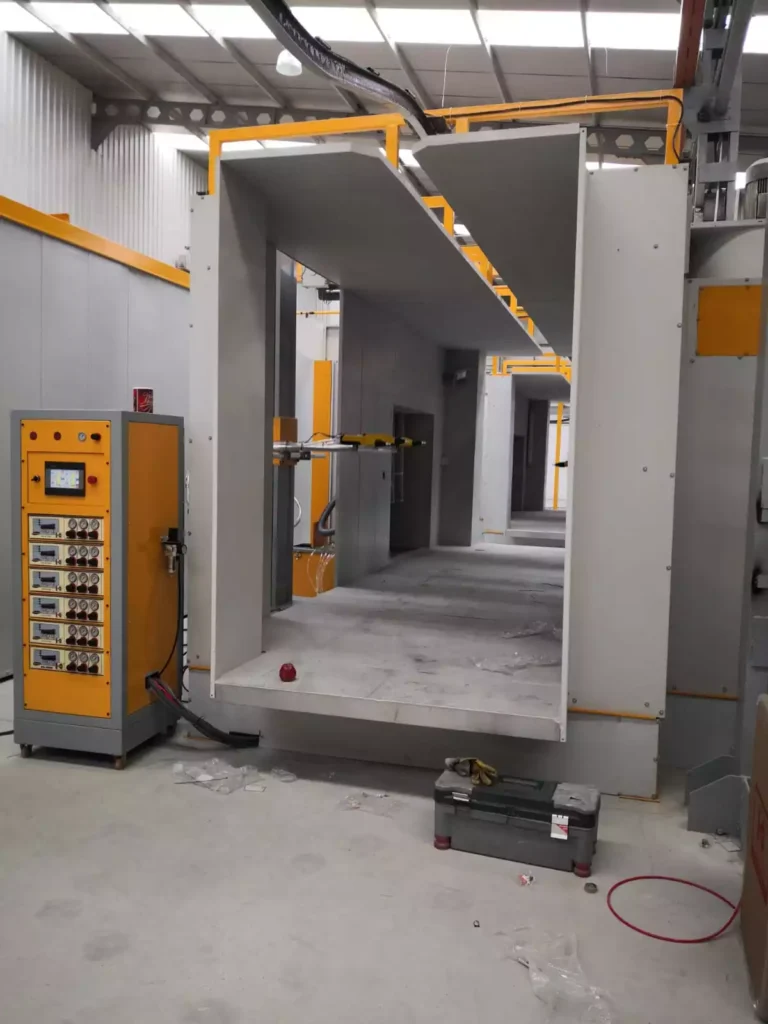
To provide a comprehensive guide on the installation process for powder coating systems, we’ll cover each step involved in setting up a powder coating plant. This includes planning, selecting equipment, site preparation, installation, testing, and staff training. Here’s a detailed outline and content for this section:
Outline for Installation Process Steps
- Planning and Design
- Assessing needs and capacity
- Layout and design considerations
- Budget and timeline
- Equipment Selection
- Choosing the right ovens, machines, and equipment
- Consulting with manufacturers and suppliers
- Site Preparation
- Preparing the facility for installation
- Ensuring compliance with regulations
- Installation Process
- Step-by-step installation guide
- Safety protocols and considerations
- System Testing and Calibration
- Testing each component
- Ensuring optimal performance
- Training and Support
- Staff training on operation and safety
- Ongoing maintenance and support
- Post-Installation Considerations
- Regular inspections and maintenance
- Upgrades and scalability
Installation Process Steps for Powder Coating Systems
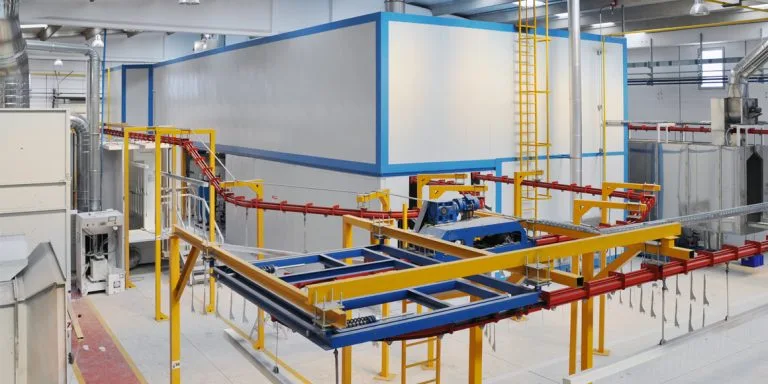
Setting up a powder coating plant involves careful planning and execution to ensure a successful installation. Here’s a step-by-step guide to help you navigate the process:
1. Planning and Design
Assessing Needs and Capacity:
- Identify Production Requirements: Determine the types and sizes of parts you will be coating, and estimate your production volume.
- Analyze Workflow: Consider how materials will move through the plant, from pre-treatment to curing.
- Evaluate Space Requirements: Ensure adequate space for equipment, storage, and workflow efficiency.
Layout and Design Considerations:
- Optimize Workflow: Design a layout that minimizes bottlenecks and maximizes efficiency.
- Future Scalability: Plan for potential expansion or upgrades.
- Compliance with Safety Standards: Ensure the layout meets all safety and regulatory requirements.
Budget and Timeline:
- Create a Detailed Budget: Account for equipment, installation, training, and operational costs.
- Establish a Timeline: Set realistic milestones for each phase of the installation process.
2. Equipment Selection
Choosing the Right Ovens, Machines, and Equipment:
- Powder Coating Ovens: Select between batch or conveyor ovens based on production needs.
- Powder Coating Machines: Choose manual or automated systems that match your operational scale.
- Additional Equipment: Consider powder booths, recovery systems, and pre-treatment stations.
Consulting with Manufacturers and Suppliers:
- Leverage Expertise: Work with manufacturers to choose equipment tailored to your specific requirements.
- Request Demonstrations: Evaluate equipment performance through demos or site visits.
- Negotiate Contracts: Ensure favorable terms and warranties with suppliers.
3. Site Preparation
Preparing the Facility for Installation:
- Infrastructure Readiness: Ensure adequate power supply, ventilation, and environmental controls.
- Space Optimization: Clear and organize the installation area for easy access and efficient workflow.
Ensuring Compliance with Regulations:
- Local Permits and Licenses: Obtain necessary permits and ensure compliance with zoning regulations.
- Safety Standards: Adhere to occupational health and safety standards.
4. Installation Process
Step-by-Step Installation Guide:
- Site Inspection: Conduct a final inspection of the site to verify readiness.
- Delivery and Unpacking: Receive and unpack equipment carefully, checking for any damage.
- Positioning Equipment: Install each piece of equipment according to the layout plan.
- Electrical and Plumbing Connections: Ensure all electrical and plumbing connections are correctly made and tested.
- Calibration and Setup: Configure equipment settings and calibrate machinery to specifications.
Safety Protocols and Considerations:
- Install Safety Features: Implement necessary safety features such as emergency stops and protective barriers.
- Personal Protective Equipment (PPE): Ensure that all personnel have access to required PPE.
5. System Testing and Calibration
Testing Each Component:
- Conduct Trial Runs: Test each component individually and as part of the integrated system.
- Check for Performance Issues: Identify and resolve any performance or operational issues.
Ensuring Optimal Performance:
- Fine-Tune Settings: Adjust equipment settings for optimal coating quality.
- Document Results: Record all testing results and adjustments for future reference.
6. Training and Support
Staff Training on Operation and Safety:
- Conduct Training Sessions: Provide comprehensive training on equipment operation and safety protocols.
- Create Training Materials: Develop manuals and guides for ongoing staff reference.
Ongoing Maintenance and Support:
- Establish a Maintenance Schedule: Set up regular maintenance checks to ensure equipment longevity.
- Vendor Support: Engage with suppliers for ongoing support and troubleshooting.
7. Post-Installation Considerations
Regular Inspections and Maintenance:
- Implement Routine Inspections: Regularly inspect equipment and systems for wear and tear.
- Schedule Maintenance: Adhere to the maintenance schedule to prevent downtime and extend equipment life.
Upgrades and Scalability:
- Monitor Technological Advancements: Stay informed about new technologies and equipment improvements.
- Plan for Upgrades: Budget for future upgrades and expansion as business needs grow.
Conclusion
The installation of a powder coating system is a multi-step process that requires meticulous planning and execution. By following these steps, businesses can ensure a smooth setup and operation, maximizing efficiency and product quality. It’s crucial to work closely with experienced manufacturers and suppliers to tailor the installation process to your specific needs and to provide ongoing training and support for staff.
Installation cost estimate
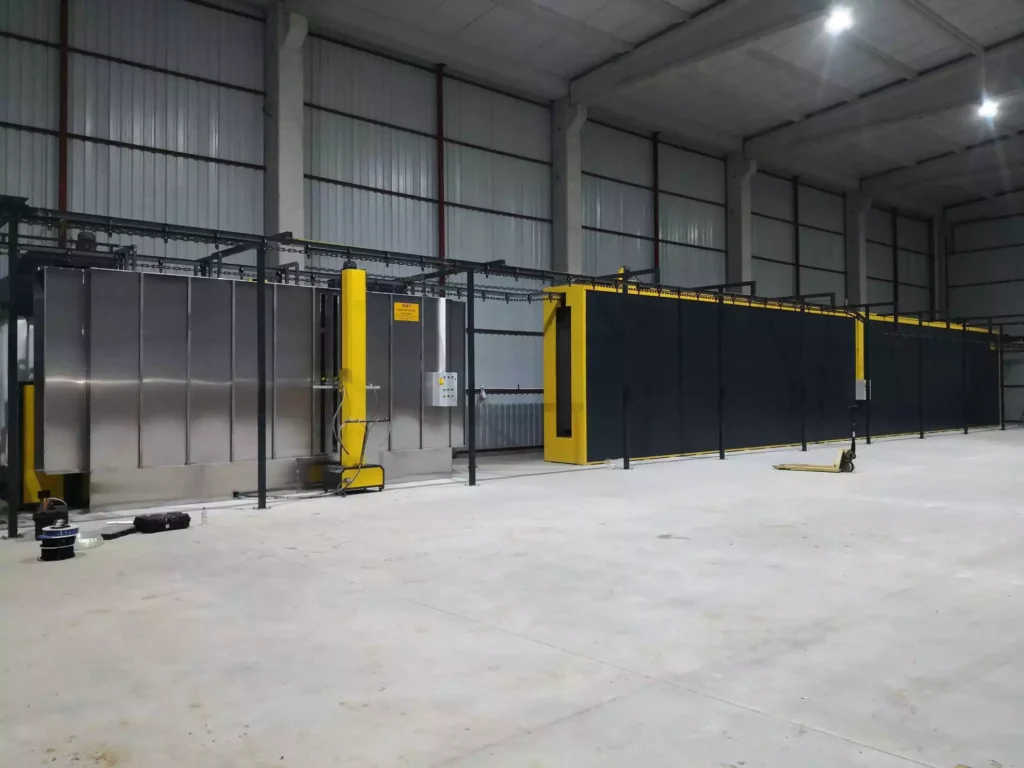
Estimating the installation cost of a powder coating system involves considering various factors, such as the size of the operation, the type of equipment, facility modifications, labor, and additional costs like permits and training. Here’s a detailed breakdown to help you understand the potential costs involved in setting up a powder coating plant.
Installation Cost Estimate for Powder Coating Systems
Factors Influencing Costs
- Type of Equipment and Technology
- Powder coating ovens (batch vs. conveyor)
- Coating machines (manual vs. automated)
- Auxiliary equipment (booths, recovery systems, pre-treatment stations)
- Scale and Capacity of the Operation
- Production volume
- Facility size and space requirements
- Facility Modifications
- Infrastructure updates (electrical, ventilation, plumbing)
- Space optimization and layout design
- Labor and Installation Services
- Skilled labor for installation
- Equipment calibration and testing
- Additional Costs
- Permits and regulatory compliance
- Staff training and support
- Maintenance and contingency expenses
Estimated Costs
Below is a general estimate of the costs associated with installing a powder coating system. Note that prices can vary significantly based on location, vendor, and specific requirements.
1. Equipment Costs
- Powder Coating Ovens:
- Batch Ovens: $1,000 – $50,000
- Conveyor Ovens: $10,000 – $200,000
- Powder Coating Machines:
- Manual Machines: $1,000 – $20,000
- Automated Systems: $20,000 – $100,000
- Auxiliary Equipment:
- Powder Booths: $2,000 – $30,000
- Recovery Systems: $3,000 – $15,000
- Pre-Treatment Systems: $10,000 – $50,000
2. Facility Modifications
- Electrical and Ventilation Upgrades: $10,000 – $50,000
- Space Optimization and Layout Design: $5,000 – $20,000
3. Labor and Installation Services
- Installation Labor: $10,000 – $30,000
- Calibration and Testing: $5,000 – $10,000
4. Additional Costs
- Permits and Compliance: $2,000 – $10,000
- Training and Support: $2,000 – $5,000
- Maintenance and Contingency: $5,000 – $15,000
Total Estimated Cost
The total estimated cost for installing a powder coating system can range from $70,000 to $500,000, depending on the size, complexity, and specific requirements of the operation. Here’s a breakdown by scale:
- Small-Scale Operations: $20,000 – $50,000
- Medium-Scale Operations: $50,000 – $100,000
- Large-Scale Operations: $100,000 – $500,000
Tips for Cost Management
- Conduct a Detailed Assessment:
- Evaluate your specific needs and choose equipment accordingly.
- Consider future scalability to avoid unnecessary upgrades later.
- Get Multiple Quotes:
- Request quotes from multiple vendors to compare prices and services.
- Negotiate terms and warranties to get the best deal.
- Plan for Contingencies:
- Set aside a contingency budget for unexpected expenses during installation.
- Regularly review and adjust your budget as the project progresses.
- Focus on Energy Efficiency:
- Invest in energy-efficient equipment to reduce long-term operational costs.
- Evaluate the potential return on investment (ROI) for each piece of equipment.
- Leverage Financing Options:
- Explore financing options, grants, or incentives available for industrial upgrades.
Conclusion
Setting up a powder coating plant requires a significant investment, but careful planning and strategic decision-making can help manage costs effectively. By considering your specific needs, working with experienced suppliers, and planning for the future, you can ensure a successful installation and operation of your powder coating system.
Let me know if you need further details or specific cost estimates tailored to your project!
Components of a Powder Coating Plant
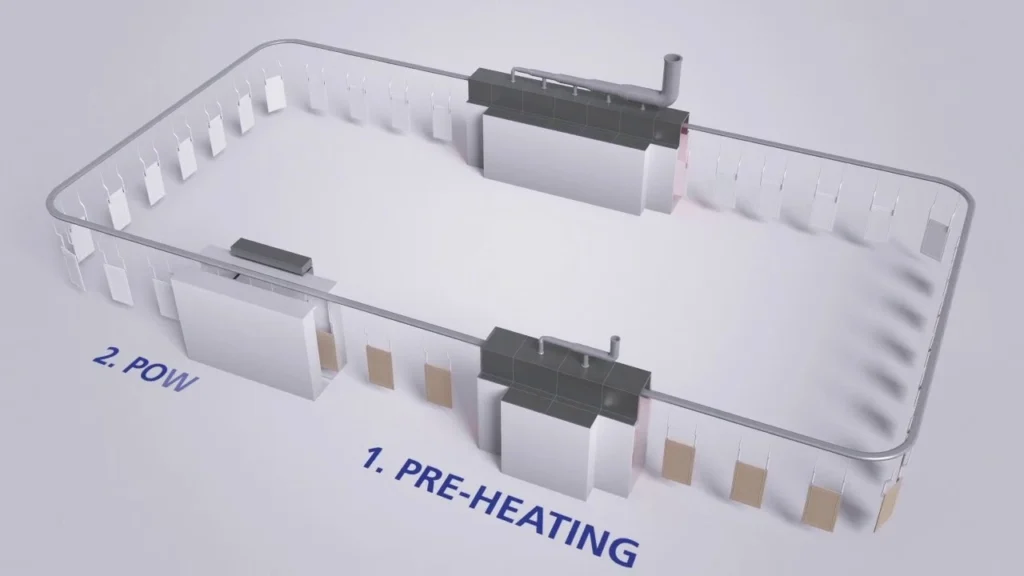
A powder coating plant consists of various components that work together to facilitate the coating process, from preparation to application and curing. Understanding these components is crucial for designing an efficient and effective system tailored to specific production needs. Below is a detailed overview of the key components of a powder coating plant:
Key Components of a Powder Coating Plant
- Pre-Treatment System
- Purpose: Cleans and prepares surfaces for powder coating to ensure adhesion and finish quality.
- Components:
- Washing Stations: Use chemical solutions to remove contaminants like grease, oil, dirt, and rust.
- Rinse Stations: Remove residual chemicals from the surface.
- Drying Ovens: Dry the parts after washing and rinsing to prepare them for powder application.
- Powder Coating Booths
- Purpose: Enclosed area where the powder is applied to the parts.
- Types:
- Manual Booths: Operators manually apply powder using spray guns. Ideal for small or custom jobs.
- Automatic Booths: Equipped with automated spray guns and reciprocators for high-volume production.
- Features:
- Ventilation Systems: Ensure proper airflow to capture overspray and maintain a clean environment.
- Powder Recovery Systems: Collect overspray powder for reuse, improving material efficiency.
- Powder Application Equipment
- Purpose: Applies the powder to the surfaces using electrostatic spray guns.
- Components:
- Electrostatic Spray Guns: Charge the powder particles and spray them onto the grounded parts.
- Control Units: Adjust settings like voltage, powder flow rate, and air pressure to ensure uniform coverage.
- Conveyor System
- Purpose: Transports parts through various stages of the powder coating process.
- Types:
- Overhead Conveyors: Hang parts from hooks or racks for continuous production.
- Floor Conveyors: Suitable for heavier or larger parts that cannot be suspended.
- Features:
- Variable Speed Control: Adjusts the speed of the conveyor to match production needs and curing times.
- Loading and Unloading Stations: Facilitate the movement of parts onto and off the conveyor system.
- Powder Coating Ovens
- Purpose: Cures the powder coating by melting and fusing it to the surface, forming a durable finish.
- Types:
- Batch Ovens: Suitable for smaller production runs and varied part sizes.
- Conveyor Ovens: Designed for continuous, high-volume production.
- Features:
- Temperature Control Systems: Ensure precise and consistent heating for optimal curing.
- Energy Efficiency: Incorporate insulation and heat recovery systems to minimize energy consumption.
- Cooling and Inspection Stations
- Purpose: Cool the parts after curing and inspect them for quality assurance.
- Components:
- Cooling Zones: Allow parts to cool gradually to avoid warping or defects.
- Inspection Areas: Check for coating consistency, thickness, and finish quality before packaging or assembly.
- Control and Monitoring Systems
- Purpose: Manage and monitor the entire powder coating process for efficiency and quality control.
- Components:
- PLC Systems (Programmable Logic Controllers): Automate and synchronize various plant operations.
- Data Logging and Analysis Tools: Record production metrics and identify areas for improvement.
- Safety and Environmental Controls
- Purpose: Ensure the safety of workers and compliance with environmental regulations.
- Components:
- Fire Suppression Systems: Protect against powder fires or explosions in booths and ovens.
- Ventilation and Filtration Systems: Maintain air quality by removing dust, fumes, and volatile organic compounds (VOCs).
- Personal Protective Equipment (PPE): Provide workers with necessary safety gear, such as masks, gloves, and goggles.
Optional and Auxiliary Components
- Advanced Pre-Treatment Systems: Utilize additional technologies like ultrasonic cleaning or nanotechnology for improved surface preparation.
- Curing Lamps: Use infrared or UV lamps for faster curing times and energy savings.
- Automated Robotic Systems: Enhance precision and efficiency in powder application and handling.
- Quality Control Instruments: Use advanced tools like thickness gauges, gloss meters, and adhesion testers for detailed quality assessment.
Layout and Design Considerations
- Workflow Optimization: Design the plant layout to minimize bottlenecks and ensure smooth transitions between stages.
- Space Utilization: Efficiently allocate space for equipment, storage, and movement of materials.
- Scalability: Plan for future expansion or upgrades to accommodate growing production demands.
Conclusion
A well-designed powder coating plant integrates these components to create an efficient, high-quality coating process. Understanding each element and its role in the system is crucial for businesses looking to enhance their powder coating capabilities. By investing in the right equipment and technology, companies can achieve superior finishes, increased productivity, and long-term success in the powder coating industry.
Detailed Components of a Powder Coating Plant
Certainly! To provide a detailed understanding of each component within a powder coating plant, we’ll delve into the technical specifications, functions, types, and key considerations for each element. This comprehensive breakdown will cover everything from the initial pre-treatment to the final inspection.
1. Pre-Treatment System
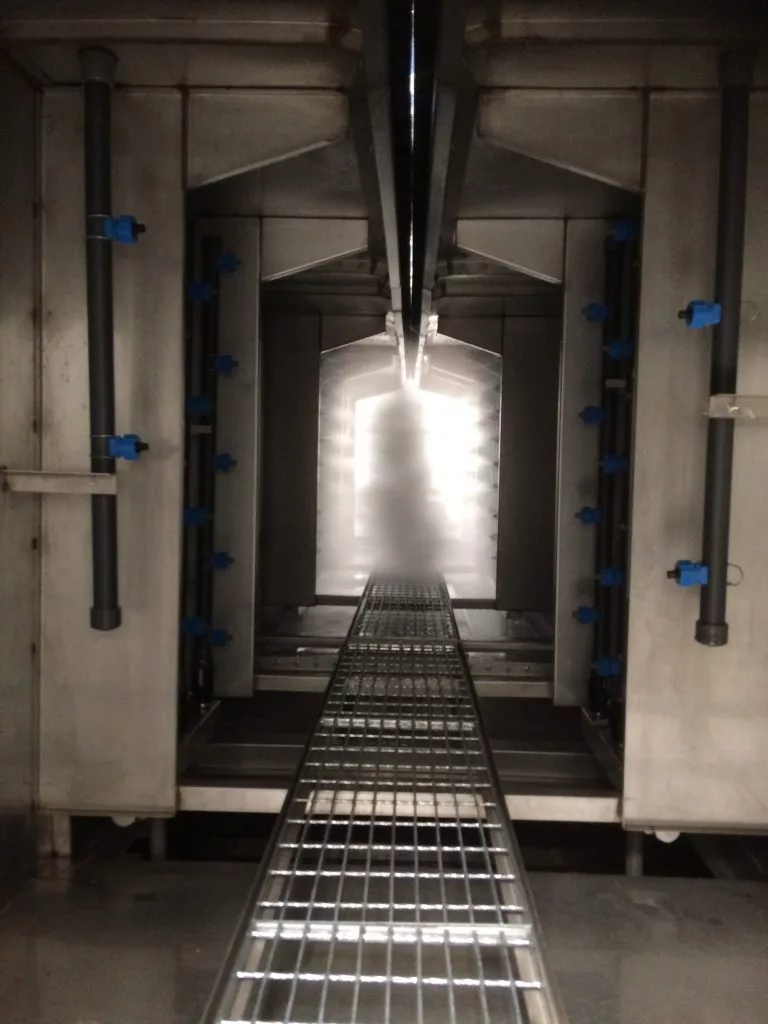
Overview
The pre-treatment system is crucial in ensuring that surfaces are properly cleaned and prepared for powder coating. This step enhances adhesion, improves finish quality, and increases the longevity of the coating.
Components and Process
1.1. Cleaning and Degreasing Stations
- Purpose: Remove oils, grease, and other contaminants from the surface.
- Methods:
- Alkaline Cleaning: Uses alkaline solutions to break down grease and oils.
- Solvent Cleaning: Employs organic solvents to dissolve contaminants.
- Ultrasonic Cleaning: Utilizes high-frequency sound waves for deep cleaning, especially effective for complex shapes.
- Equipment:
- Tanks and spray systems
- Heating elements to improve cleaning efficiency
- Agitation systems for even cleaning
1.2. Rinse Stations
- Purpose: Eliminate residual chemicals and contaminants from the cleaning stage.
- Types of Rinse:
- Freshwater Rinse: Basic water rinse to remove chemicals.
- Deionized Water Rinse: Prevents mineral deposits and spots on surfaces.
- Equipment:
- Spray bars and nozzles for thorough rinsing
- Closed-loop systems to recycle water and reduce waste
1.3. Surface Conditioning
- Purpose: Prepare the surface for subsequent conversion coating.
- Processes:
- Acid Etching: Removes oxides and prepares metal surfaces.
- Descaling: Removes scale and rust from the surface.
- Equipment:
- Immersion tanks or spray booths
- Automated dosing systems for precise chemical application
1.4. Conversion Coating
- Purpose: Apply a chemical layer that enhances powder adhesion and corrosion resistance.
- Types:
- Phosphate Coating: Iron or zinc phosphate for steel surfaces.
- Chromate Coating: Used for aluminum and zinc surfaces.
- Nano-Ceramic Coatings: Environmentally friendly option with superior adhesion and corrosion resistance.
- Equipment:
- Spray or immersion systems
- Temperature control for optimal reaction conditions
1.5. Drying Ovens
- Purpose: Remove moisture from parts to prevent defects in the powder coating.
- Features:
- Adjustable temperature settings
- Air circulation systems for even drying
- Equipment:
- Batch ovens for smaller production
- Conveyor ovens for continuous processing
Key Considerations
- Chemical Management: Ensure proper handling, storage, and disposal of chemicals used in pre-treatment.
- Environmental Compliance: Adhere to local regulations for effluent discharge and waste management.
- Maintenance: Regular cleaning and inspection of tanks and nozzles to prevent contamination.
2. Powder Coating Booths
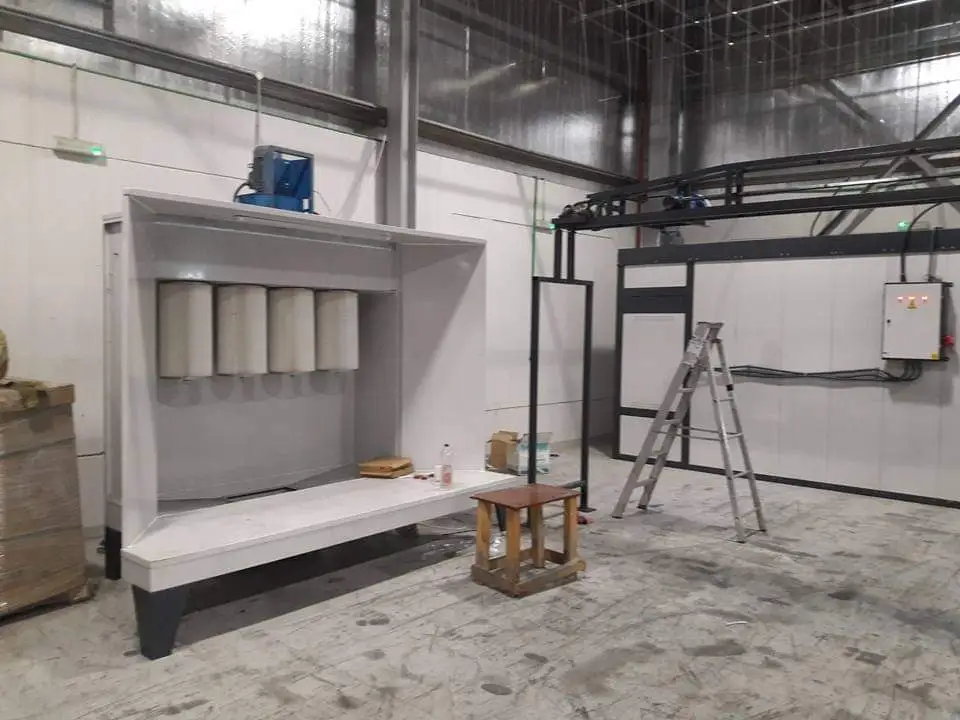
Overview
Powder coating booths provide a controlled environment for applying the powder. They ensure that the powder is applied evenly and that any overspray is efficiently managed and collected for reuse.
Types and Features
2.1. Manual Powder Coating Booths
- Purpose: Allow operators to manually apply powder using handheld spray guns.
- Applications: Suitable for small batches, custom jobs, and intricate parts.
- Features:
- Ventilation Systems: Maintain air quality and remove overspray.
- Lighting: Ensure visibility for precise application.
- Ergonomic Design: Facilitate operator comfort and efficiency.
2.2. Automatic Powder Coating Booths
- Purpose: Use automated systems to apply powder to parts, ideal for high-volume production.
- Applications: Suitable for standard parts and large-scale operations.
- Features:
- Robotic Arms and Reciprocators: Ensure consistent application across parts.
- Programmable Settings: Customize application parameters for different parts.
- Rapid Color Change Systems: Allow quick and efficient color changes with minimal downtime.
2.3. Powder Recovery Systems
- Purpose: Capture and recycle overspray powder to improve efficiency and reduce waste.
- Types:
- Cyclone Separators: Use centrifugal force to separate powder from the air.
- Cartridge Filters: Trap fine powder particles for reuse.
- Baghouse Filters: Employ fabric bags to capture powder, suitable for larger particles.
Key Considerations
- Airflow Management: Ensure proper ventilation to prevent contamination and maintain a clean environment.
- Color Change Efficiency: Invest in systems that allow quick and easy color changes to minimize downtime.
- Safety: Implement explosion-proof designs and fire suppression systems to prevent hazards.
3. Powder Application Equipment
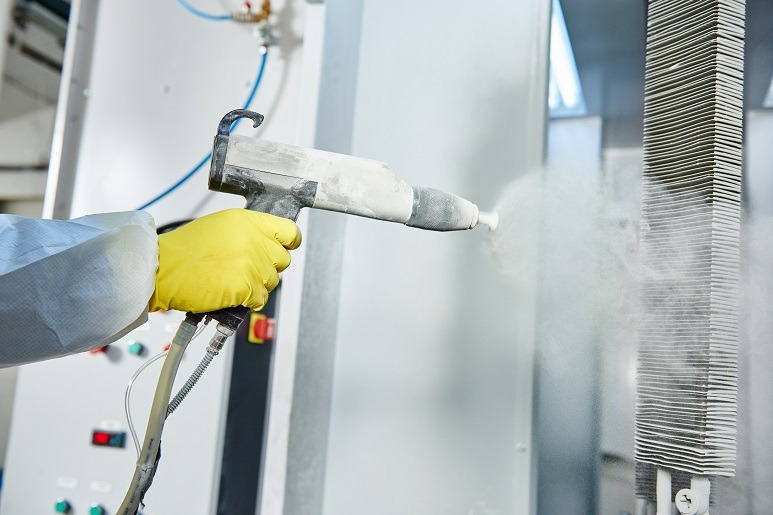
Overview
Powder application equipment is responsible for applying the powder coating to the parts. This equipment uses electrostatic principles to ensure uniform coverage and strong adhesion.
Components and Features
3.1. Electrostatic Spray Guns
- Purpose: Apply powder to the parts using an electrostatic charge.
- Types:
- Corona Guns: Use a high-voltage electrode to charge the powder.
- Tribo Guns: Charge the powder through friction, suitable for specific applications.
- Features:
- Adjustable Voltage and Current: Control the electrostatic charge for optimal coverage.
- Interchangeable Nozzles: Provide different spray patterns for various applications.
- Lightweight and Ergonomic Design: Ensure operator comfort during manual application.
3.2. Control Units
- Purpose: Manage and adjust the settings of the powder application equipment.
- Features:
- Digital Displays: Provide real-time feedback on settings and performance.
- Programmable Settings: Allow customization for different parts and powder types.
- Data Logging: Record application parameters for quality control and traceability.
3.3. Fluidized Bed Systems
- Purpose: Coat parts by dipping them into a bed of fluidized powder, typically used for thicker coatings.
- Applications: Suitable for specific applications requiring a thick and even coating.
- Features:
- Uniform Airflow: Ensure consistent fluidization of powder particles.
- Temperature Control: Maintain optimal conditions for coating.
Key Considerations
- Powder Compatibility: Ensure equipment is compatible with different powder formulations.
- Operator Training: Provide comprehensive training for operators to ensure efficient and safe use.
- Maintenance: Regularly clean and maintain spray guns and control units to prevent clogging and ensure consistent performance.
4. Conveyor System
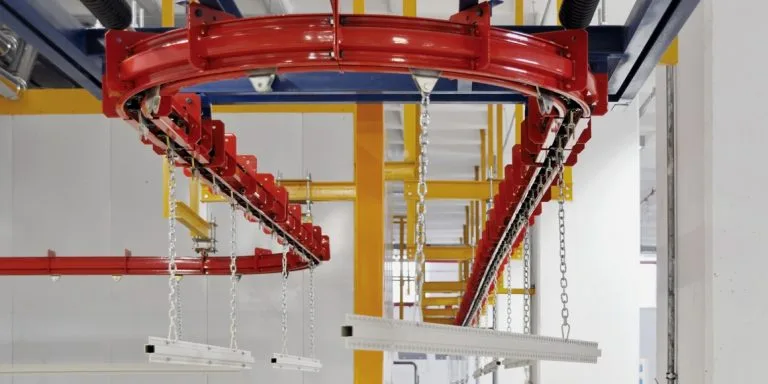
Overview
The conveyor system is the backbone of the powder coating plant, transporting parts through each stage of the process, from pre-treatment to curing.
Types and Features
4.1. Overhead Conveyors
- Purpose: Transport parts by suspending them from hooks or racks, ideal for continuous production.
- Types:
- Monorail Systems: Simple looped tracks for straightforward applications.
- Power and Free Systems: Offer more flexibility with multiple paths and stopping points.
- Features:
- Variable Speed Control: Adjust the speed to match production needs and curing times.
- Load Capacity: Designed to handle different part sizes and weights.
- Integration with Other Systems: Seamlessly integrate with pre-treatment, application, and curing systems.
4.2. Floor Conveyors
- Purpose: Transport heavier or larger parts that cannot be suspended, suitable for specific applications.
- Types:
- Belt Conveyors: Use belts to move parts horizontally or on an incline.
- Roller Conveyors: Employ rollers to facilitate the movement of parts.
- Features:
- Heavy-Duty Construction: Designed to support large or heavy parts.
- Customizable Configurations: Adapt to different plant layouts and processes.
Key Considerations
- Layout Design: Plan the conveyor layout to optimize workflow and minimize bottlenecks.
- Load and Speed Requirements: Ensure the conveyor system meets production demands for speed and capacity.
- Safety Features: Implement safety measures such as guards, emergency stops, and regular inspections.
5. Powder Coating Ovens
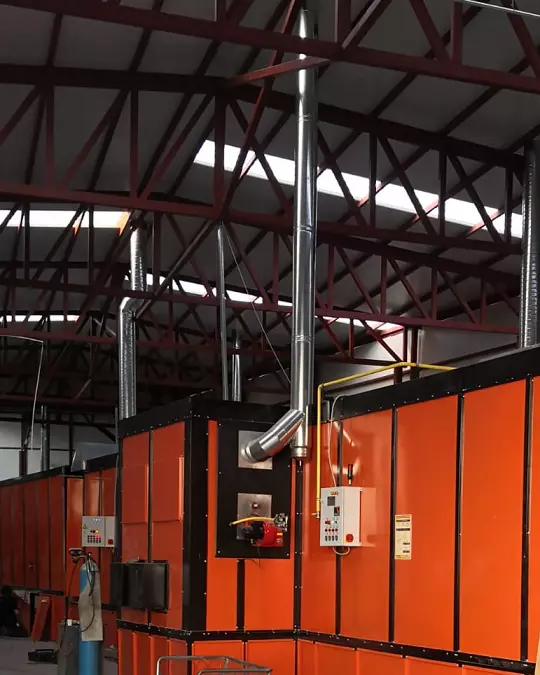
Overview
Powder coating ovens are responsible for curing the powder coating by melting and fusing it to the surface, resulting in a durable and attractive finish.
Types and Features
5.1. Batch Ovens
- Purpose: Cure parts in small batches, suitable for varied part sizes and low-volume production.
- Applications: Ideal for custom jobs, small businesses, and prototyping.
- Features:
- Adjustable Temperature Control: Precise control of curing conditions.
- Flexible Configuration: Accommodate different part sizes and shapes.
- Insulated Construction: Minimize heat loss and improve energy efficiency.
5.2. Conveyor Ovens
- Purpose: Designed for continuous production, curing parts as they move through the oven.
- Applications: Suitable for high-volume production and standardized parts.
- Features:
- Consistent Temperature Distribution: Ensure even curing across all parts.
- Variable Conveyor Speed: Match curing times with production speed.
- Energy Efficiency: Incorporate heat recovery systems and advanced insulation.
Key Considerations
- Oven Size and Capacity: Choose an oven that meets production demands without excessive energy use.
- Heating Source: Decide between electric, gas, or infrared heating based on cost and efficiency.
- Temperature Uniformity: Ensure consistent heat distribution to prevent defects in the finish.
6. Cooling and Inspection Stations
Overview
Cooling and inspection stations are crucial for ensuring the quality and consistency of the finished products. Cooling prevents defects, while inspection verifies the coating quality.
Components and Features
6.1. Cooling Zones
- Purpose: Gradually cool parts after curing to prevent warping or defects.
- Features:
- Controlled Airflow: Ensure even cooling and avoid thermal shock.
- Adjustable Cooling Rates: Customize settings for different materials and part sizes.
6.2. Inspection Areas
- Purpose: Conduct quality checks on coated parts to ensure consistency and adherence to standards.
- Features:
- Lighting and Magnification: Facilitate detailed visual inspections.
- Measurement Tools: Use instruments like thickness gauges and gloss meters for precise evaluation.
- Defect Detection Systems: Implement automated systems for detecting coating defects, such as thin spots or uneven coverage.
Key Considerations
- Quality Assurance Protocols: Establish standards and procedures for inspections to ensure consistent product quality.
- Training for Inspectors: Provide training to staff on recognizing defects and using inspection tools effectively.
- Feedback Loop: Use inspection data to inform process improvements and address recurring issues.
7. Control and Monitoring Systems
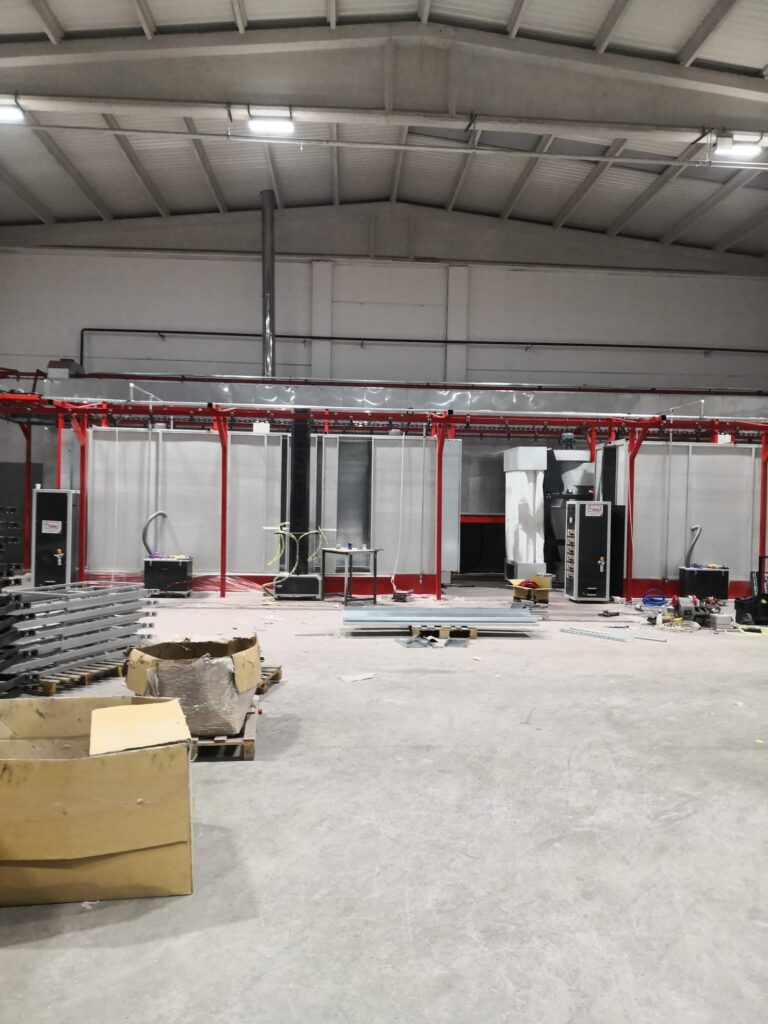
Overview
Control and monitoring systems automate and synchronize various plant operations, ensuring efficiency, consistency, and quality in the powder coating process.
Components and Features
7.1. PLC Systems (Programmable Logic Controllers)
- Purpose: Automate and control equipment functions throughout the plant.
- Features:
- Centralized Control: Manage multiple systems from a single interface.
- Real-Time Monitoring: Track performance metrics and adjust settings as needed.
- Data Logging: Record operational data for analysis and process optimization.
7.2. Data Logging and Analysis Tools
- Purpose: Collect and analyze production data to improve efficiency and quality.
- Features:
- Trend Analysis: Identify patterns and trends in production metrics.
- Performance Dashboards: Visualize key performance indicators (KPIs) for easy monitoring.
- Predictive Maintenance: Use data to anticipate equipment maintenance needs and prevent downtime.
Key Considerations
- System Integration: Ensure seamless integration with existing equipment and software.
- User Interface: Provide intuitive and user-friendly interfaces for operators.
- Cybersecurity: Implement security measures to protect sensitive data and control systems.
8. Safety and Environmental Controls
Overview
Safety and environmental controls are essential for protecting workers and ensuring compliance with regulations. These systems manage hazards and minimize environmental impact.
Components and Features
8.1. Fire Suppression Systems
- Purpose: Prevent and control powder fires or explosions in booths and ovens.
- Features:
- Automatic Detection and Suppression: Quickly identify and extinguish fires.
- Integration with Control Systems: Automatically shut down equipment in case of fire.
- Regular Testing and Maintenance: Ensure systems are operational and compliant with safety standards.
8.2. Ventilation and Filtration Systems
- Purpose: Maintain air quality by removing dust, fumes, and volatile organic compounds (VOCs).
- Features:
- High-Efficiency Particulate Air (HEPA) Filters: Capture fine particles and contaminants.
- Exhaust Fans and Ductwork: Ensure proper airflow and ventilation.
- Regular Filter Replacement: Maintain efficiency and prevent clogs.
8.3. Personal Protective Equipment (PPE)
- Purpose: Provide workers with necessary safety gear to protect against hazards.
- Components:
- Respirators and Masks: Protect against inhalation of powder particles and fumes.
- Safety Glasses and Goggles: Shield eyes from dust and chemical splashes.
- Gloves and Protective Clothing: Prevent skin contact with chemicals and powders.
Key Considerations
- Compliance with Regulations: Adhere to local and international safety and environmental standards.
- Safety Training: Conduct regular training sessions on safety protocols and emergency procedures.
- Continuous Improvement: Regularly review and update safety measures to address emerging risks and regulations.
Conclusion
Each component of a powder coating plant plays a vital role in ensuring a successful and efficient coating process. By understanding the details and functions of these components, businesses can design and operate a plant that meets their specific needs and production goals. Investing in the right equipment and systems, along with proper training and maintenance, will lead to high-quality finishes, increased productivity, and long-term success in the powder coating industry.
Installation time estimate
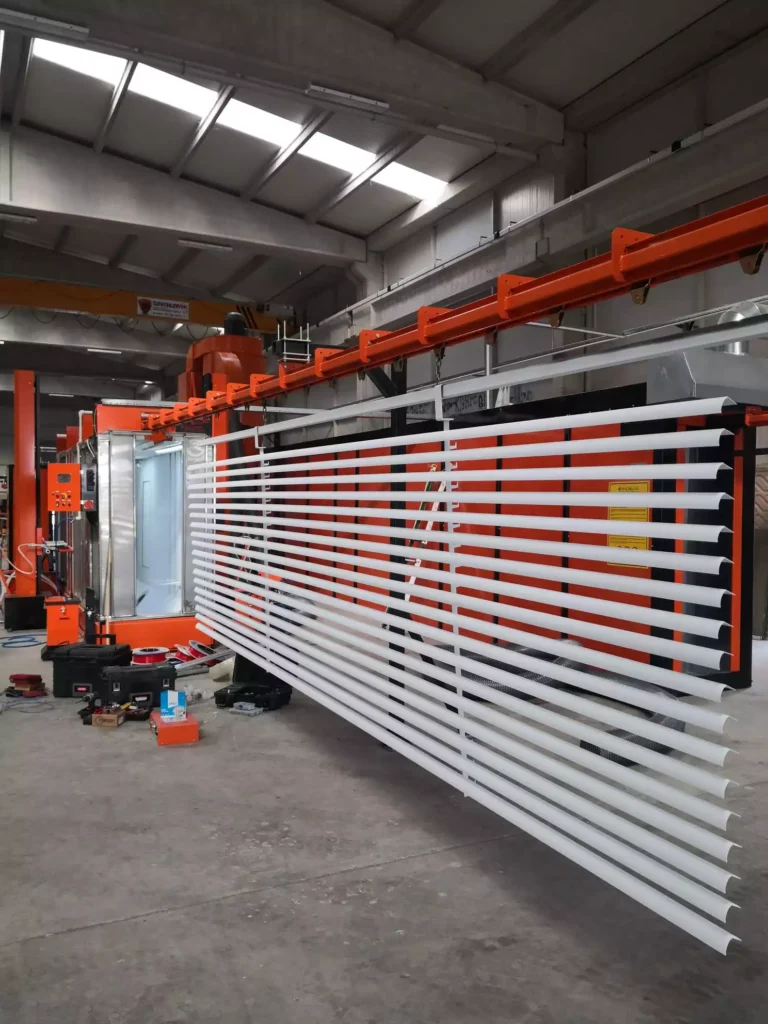
Estimating the installation time for a powder coating plant involves considering several factors such as the size of the operation, complexity of the equipment, facility preparation, and the efficiency of the installation team. Below is a detailed breakdown of the installation time estimate, including factors that can influence the timeline and strategies to ensure a smooth installation process.
Installation Time Estimate for a Powder Coating Plant
Factors Influencing Installation Time
- Scale and Complexity of the Plant
- Size and layout of the facility
- Number and type of equipment components
- Type of Equipment
- Manual vs. automated systems
- Batch vs. continuous production lines
- Site Preparation
- Existing infrastructure readiness
- Facility modifications needed
- Installation Team and Expertise
- Experience and skills of the installation crew
- Availability of necessary resources and tools
- Regulatory Compliance and Inspections
- Time required for permits and approvals
- Safety inspections and certifications
- Coordination and Scheduling
- Coordination between vendors, contractors, and stakeholders
- Availability of equipment and personnel
Estimated Installation Time by Component
Here is an approximate installation timeline for each major component of a powder coating plant. These estimates are generalized and may vary depending on specific project requirements.
1. Pre-Treatment System
- Time Estimate: 1 to 3 weeks
- Activities:
- Delivery and setup of washing, rinsing, and drying stations
- Plumbing and drainage installations
- Testing and calibration of chemical dosing systems
2. Powder Coating Booths
- Time Estimate: 1 to 2 weeks
- Activities:
- Assembly and installation of booth structures
- Integration of ventilation and powder recovery systems
- Setup of lighting and electrical connections
3. Powder Application Equipment
- Time Estimate: 1 to 2 weeks
- Activities:
- Installation of electrostatic spray guns and control units
- Calibration of application settings and nozzles
- Testing for uniform powder distribution
4. Conveyor System
- Time Estimate: 2 to 4 weeks
- Activities:
- Layout design and track installation
- Assembly of conveyor components and drives
- Testing for load capacity and speed control
5. Powder Coating Ovens
- Time Estimate: 2 to 3 weeks
- Activities:
- Installation of oven structures and insulation
- Setup of heating systems and temperature controls
- Testing for temperature uniformity and energy efficiency
6. Cooling and Inspection Stations
- Time Estimate: 1 to 2 weeks
- Activities:
- Installation of cooling systems and airflow management
- Setup of inspection stations and quality control tools
- Training staff on inspection procedures
7. Control and Monitoring Systems
- Time Estimate: 1 to 2 weeks
- Activities:
- Installation of PLC systems and control panels
- Integration with other equipment components
- Testing and validation of automation processes
8. Safety and Environmental Controls
- Time Estimate: 1 to 2 weeks
- Activities:
- Installation of fire suppression and ventilation systems
- Setup of safety barriers and emergency stops
- Safety audits and compliance checks
Total Estimated Installation Time
The total estimated installation time for a powder coating plant can range from 8 to 18 weeks, depending on the scale and complexity of the project. Here’s a breakdown by plant size:
- Small-Scale Operations: 8 to 10 weeks
- Medium-Scale Operations: 10 to 14 weeks
- Large-Scale Operations: 14 to 18 weeks
Strategies for Reducing Installation Time
- Detailed Planning and Coordination
- Develop a comprehensive project plan with clear timelines and milestones.
- Coordinate with vendors, contractors, and stakeholders to align schedules and resources.
- Pre-Fabrication and Pre-Assembly
- Opt for pre-fabricated components to reduce on-site assembly time.
- Pre-assemble equipment off-site where possible to minimize installation complexity.
- Experienced Installation Team
- Hire experienced professionals familiar with powder coating systems and processes.
- Conduct regular training and briefings to ensure the team is well-prepared.
- Efficient Site Preparation
- Ensure the facility is ready for installation before equipment arrives.
- Complete necessary infrastructure upgrades and modifications in advance.
- Streamlined Permitting and Inspections
- Obtain permits and approvals early in the project timeline.
- Schedule inspections and certifications to avoid delays.
- Contingency Planning
- Identify potential risks and develop contingency plans to address unforeseen issues.
- Allocate buffer time in the schedule for unexpected challenges.
Conclusion
The installation of a powder coating plant is a complex process that requires careful planning and coordination. By understanding the factors that influence installation time and implementing strategies to streamline the process, businesses can achieve a successful setup that meets their production goals and timelines.
Maintenance schedule tips
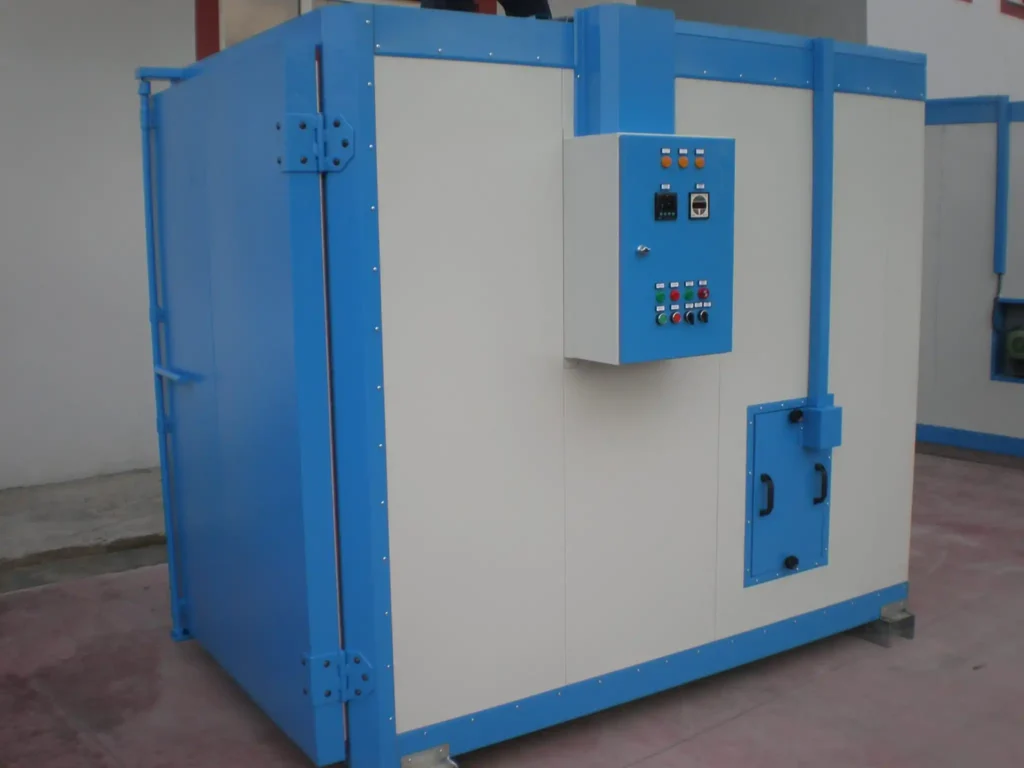
Creating a maintenance schedule for a powder coating plant is essential for ensuring efficient operation, minimizing downtime, and extending the lifespan of your equipment. A well-structured maintenance plan should address the needs of each component, including pre-treatment systems, powder coating booths, application equipment, conveyors, ovens, and safety controls. Here are some tips and guidelines to help you develop an effective maintenance schedule.
Tips for Creating a Maintenance Schedule for a Powder Coating Plant
1. Understand Equipment Requirements
- Read Manufacturer Guidelines: Start by reviewing the maintenance recommendations provided by the equipment manufacturers. These guidelines offer valuable insights into the specific needs and intervals for each component.
- Identify Critical Components: Prioritize maintenance for critical components that directly impact production quality and efficiency, such as spray guns, ovens, and conveyors.
2. Develop a Comprehensive Maintenance Plan
- Routine Inspections: Schedule regular inspections to identify wear and tear, leaks, or potential issues before they escalate. Inspections should cover all plant components, including electrical, mechanical, and safety systems.
- Preventive Maintenance: Implement a preventive maintenance schedule that includes tasks such as cleaning, lubrication, calibration, and parts replacement. This helps prevent unexpected breakdowns and maintains optimal performance.
- Predictive Maintenance: Utilize data analytics and monitoring tools to predict equipment failures and schedule maintenance based on condition and usage patterns.
3. Create a Detailed Maintenance Schedule
- Daily Maintenance Tasks:
- Check air pressure and filtration systems.
- Inspect spray guns and nozzles for clogs or wear.
- Clean work areas and remove powder buildup.
- Weekly Maintenance Tasks:
- Inspect conveyor systems for alignment and wear.
- Lubricate moving parts such as bearings and chains.
- Check temperature settings and calibrate sensors.
- Monthly Maintenance Tasks:
- Conduct a thorough inspection of pre-treatment systems.
- Inspect and clean ventilation and exhaust systems.
- Test and recalibrate control systems.
- Quarterly Maintenance Tasks:
- Perform a detailed inspection of the ovens for heat distribution and insulation integrity.
- Replace worn-out components such as belts and filters.
- Review and update safety protocols.
- Annual Maintenance Tasks:
- Conduct a comprehensive review of the entire plant.
- Audit compliance with safety and environmental regulations.
- Plan for equipment upgrades or replacements as needed.
4. Document Maintenance Activities
- Record Keeping: Maintain detailed records of all maintenance activities, including dates, tasks performed, and any issues identified. This documentation helps track equipment performance and identifies recurring problems.
- Use Digital Tools: Consider using computerized maintenance management systems (CMMS) to schedule, track, and analyze maintenance activities. Digital tools can provide reminders, automate scheduling, and generate reports.
5. Train and Empower Staff
- Employee Training: Train employees on the importance of maintenance and proper procedures. Ensure they understand how to identify and report issues and perform routine tasks.
- Empowerment: Encourage staff to take ownership of their equipment and be proactive in reporting potential problems.
6. Monitor Key Performance Indicators (KPIs)
- Track KPIs: Monitor KPIs such as equipment uptime, mean time between failures (MTBF), and maintenance costs to evaluate the effectiveness of your maintenance program.
- Continuous Improvement: Use KPI data to identify areas for improvement and make data-driven decisions to enhance maintenance strategies.
7. Plan for Spare Parts and Inventory
- Spare Parts Management: Maintain an inventory of critical spare parts to minimize downtime during repairs. Track usage patterns to ensure adequate stock levels.
- Vendor Relationships: Build strong relationships with equipment suppliers to ensure quick access to parts and technical support.
8. Evaluate and Adjust the Maintenance Plan
- Regular Reviews: Periodically review and update the maintenance schedule based on equipment performance, technological advancements, and changing production needs.
- Feedback Loop: Encourage feedback from maintenance staff and operators to identify pain points and improve processes.
Sample Maintenance Schedule Template
Here’s a sample template to help you structure your maintenance schedule:
Frequency | Task | Details |
---|---|---|
Daily | Check air pressure | Ensure proper airflow for spray guns and equipment. |
Inspect spray guns | Look for clogs, wear, and powder buildup. | |
Clean work areas | Remove excess powder and debris from booths and equipment. | |
Weekly | Inspect conveyor systems | Check alignment and wear of belts and chains. |
Lubricate moving parts | Apply lubrication to bearings, chains, and gears. | |
Calibrate temperature settings | Ensure accurate temperature readings in ovens. | |
Monthly | Inspect pre-treatment systems | Check tanks, pumps, and chemical levels. |
Clean ventilation systems | Remove dust and powder buildup in filters and ducts. | |
Test control systems | Verify functionality and accuracy of control units. | |
Quarterly | Inspect oven heat distribution | Check for even heat distribution and insulation integrity. |
Replace worn components | Swap out belts, filters, and other wear-prone parts. | |
Review safety protocols | Update safety measures and conduct training if needed. | |
Annually | Conduct plant-wide inspection | Evaluate overall condition and performance. |
Audit compliance with regulations | Ensure adherence to safety and environmental standards. | |
Plan equipment upgrades | Assess the need for new equipment or technology upgrades. |
Conclusion
Implementing a well-structured maintenance schedule is vital for the smooth operation and longevity of your powder coating plant. By focusing on preventive and predictive maintenance, documenting activities, and involving your team, you can reduce downtime, improve efficiency, and maintain high-quality production standards.
Powder Coating Oven Types
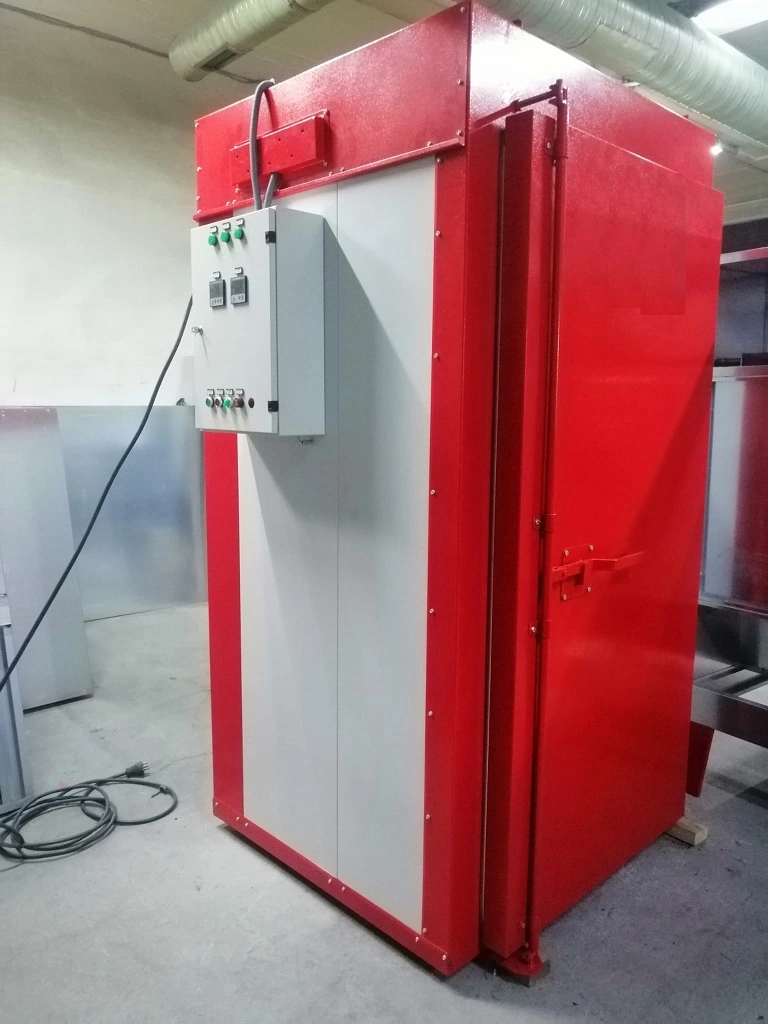
Powder coating ovens are a critical component of the powder coating process, providing the heat necessary to cure the powder and ensure a durable finish. There are several types of powder coating ovens, each designed to meet different production needs and efficiency levels. This guide will cover the various types of powder coating ovens, their features, benefits, and applications, helping you choose the right oven for your specific requirements.
Types of Powder Coating Ovens
1. Batch Ovens
Batch ovens are designed to cure powder coatings for small to medium-sized production runs. They are ideal for operations that require flexibility in coating different part sizes and types.
Features:
- Flexibility: Accommodates various part sizes and shapes.
- Energy Efficiency: Often includes insulation and heat recovery systems to reduce energy consumption.
- Manual or Semi-Automatic Operation: Suitable for low to moderate production volumes.
Benefits:
- Cost-Effective: Lower initial investment compared to continuous ovens.
- Versatile: Can handle a variety of coating tasks, including custom and complex shapes.
- Ease of Use: Simple to operate and maintain.
Applications:
- Small businesses and job shops
- Custom and prototype work
- Low to medium production volumes
Common Types of Batch Ovens:
- Walk-In Ovens: Large enough for operators to enter and load parts, suitable for oversized items.
- Cabinet Ovens: Smaller units ideal for small parts or lower-volume production.
- Truck-In Ovens: Designed for loading parts on racks or carts that can be rolled into the oven.
2. Conveyor Ovens
Conveyor ovens are designed for high-volume production and continuous processing. They automate the curing process, improving efficiency and consistency.
Features:
- Continuous Operation: Ideal for high production rates and large-scale operations.
- Automated Conveyor Systems: Transport parts through the oven for consistent curing.
- Variable Speed Control: Allows adjustment of conveyor speed to match curing requirements.
Benefits:
- High Throughput: Capable of processing large quantities of parts quickly.
- Consistent Quality: Ensures uniform curing across all parts.
- Reduced Labor Costs: Automation reduces the need for manual intervention.
Applications:
- Automotive and aerospace industries
- High-volume manufacturing plants
- Standardized parts production
Common Types of Conveyor Ovens:
- Monorail Ovens: Parts are hung from an overhead conveyor and pass through the oven in a linear path.
- Chain-On-Edge Ovens: Parts are attached to fixtures on a conveyor chain, suitable for heavier items.
- Flat-Belt Ovens: Use a flat conveyor belt to transport parts, ideal for lightweight or flat components.
3. Infrared Ovens
Infrared ovens use infrared radiation to cure powder coatings, offering a fast and energy-efficient alternative to conventional ovens. They are often used in combination with other oven types to optimize curing.
Features:
- Fast Heating: Infrared radiation provides rapid heat-up and curing times.
- Energy Efficiency: Direct heating reduces energy consumption compared to convection ovens.
- Compact Size: Smaller footprint compared to traditional ovens.
Benefits:
- Quick Curing: Significantly reduces curing times, increasing throughput.
- Targeted Heating: Infrared heat can be focused on specific areas, reducing overall energy use.
- Improved Finish: Provides smooth and even curing, minimizing defects.
Applications:
- Automotive and consumer electronics
- Applications requiring quick turnaround
- Parts with complex shapes or heat-sensitive materials
Common Types of Infrared Ovens:
- Short-Wave Infrared Ovens: Provide intense heat for fast curing, suitable for thicker coatings.
- Medium-Wave Infrared Ovens: Balance between heat intensity and penetration, ideal for general applications.
- Long-Wave Infrared Ovens: Gentle heat suitable for heat-sensitive substrates.
4. Gas-Fired Ovens
Gas-fired ovens use natural gas or propane as a heat source. They are popular for large-scale operations due to their efficiency and cost-effectiveness.
Features:
- High Heat Output: Efficiently generates high temperatures for rapid curing.
- Cost-Effective: Generally lower operating costs compared to electric ovens.
- Robust Construction: Designed to handle heavy-duty industrial use.
Benefits:
- Reduced Operating Costs: Lower energy costs compared to electric ovens, especially for large volumes.
- Reliable Performance: Consistent heating for uniform curing.
- Scalability: Suitable for large-scale production and expansion.
Applications:
- Automotive and heavy equipment manufacturing
- Large industrial operations
- High-volume powder coating lines
Common Types of Gas-Fired Ovens:
- Direct-Fired Ovens: Burners directly heat the air inside the oven chamber, providing fast and efficient heating.
- Indirect-Fired Ovens: Heat exchangers separate combustion gases from the oven air, offering cleaner operation.
5. Electric Ovens
Electric ovens use electrical heating elements to generate heat for curing powder coatings. They are commonly used in smaller operations due to their ease of use and installation.
Features:
- Precise Temperature Control: Offers accurate and consistent temperature settings.
- Easy Installation: No need for gas lines or combustion venting.
- Low Maintenance: Fewer moving parts compared to gas-fired ovens.
Benefits:
- Safe and Clean: No combustion gases, reducing emissions and improving air quality.
- Consistent Performance: Stable temperature control ensures uniform curing.
- Versatile: Suitable for various applications and materials.
Applications:
- Small to medium-sized businesses
- Custom and low-volume production
- Applications with strict environmental regulations
Common Types of Electric Ovens:
- Forced-Air Convection Ovens: Use fans to circulate heated air for uniform temperature distribution.
- Static Ovens: Rely on natural convection, suitable for delicate or sensitive parts.
6. Combination Ovens
Combination ovens integrate multiple heating methods, such as infrared and convection, to provide flexibility and optimize curing processes.
Features:
- Multi-Mode Operation: Allows switching between or combining different heating methods.
- Optimized Curing: Adjusts curing methods based on part size, shape, and material.
- Flexible Configuration: Customizable to meet specific production needs.
Benefits:
- Versatility: Capable of handling a wide range of parts and coatings.
- Improved Efficiency: Combines the strengths of different heating methods for optimal results.
- Enhanced Finish Quality: Provides tailored curing conditions to minimize defects.
Applications:
- Complex parts with varying geometries
- Industries requiring rapid production changes
- Specialized coating applications
Considerations for Choosing the Right Powder Coating Oven
When selecting a powder coating oven, consider the following factors:
- Production Volume:
- Choose batch ovens for low to medium production and conveyor ovens for high-volume operations.
- Part Size and Shape:
- Consider the size, weight, and geometry of the parts to determine the appropriate oven type.
- Energy Efficiency:
- Evaluate energy consumption and costs, especially for large-scale operations.
- Temperature Requirements:
- Ensure the oven can maintain consistent temperatures for your specific powder coatings.
- Space and Layout:
- Consider the available space and how the oven will fit into your production line layout.
- Budget and Cost:
- Balance initial investment with long-term operating costs and return on investment.
- Regulatory Compliance:
- Ensure the oven meets local safety and environmental regulations.
Conclusion
Selecting the right powder coating oven is crucial for achieving high-quality finishes and efficient production. By understanding the features, benefits, and applications of each oven type, businesses can make informed decisions that align with their production needs and goals. Investing in the right oven will enhance productivity, reduce costs, and ensure a durable, attractive finish on your coated products.
Powder coating oven maintenance tips
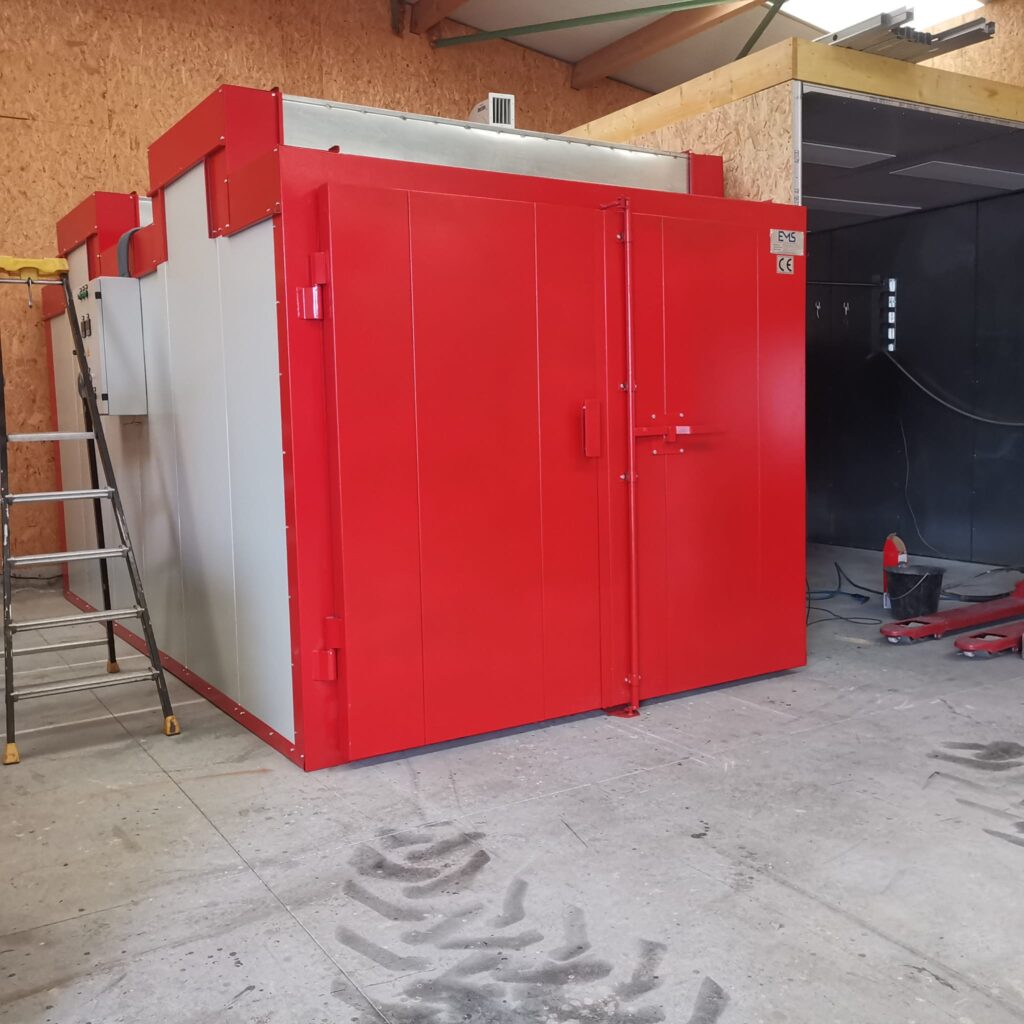
Proper maintenance of powder coating ovens is crucial to ensure efficient operation, consistent curing quality, and the longevity of the equipment. A well-maintained oven minimizes downtime, reduces energy consumption, and prevents costly repairs. Below are comprehensive tips and guidelines for maintaining powder coating ovens effectively.
Powder Coating Oven Maintenance Tips
1. Regular Cleaning
Keeping the oven clean is essential to prevent powder buildup, which can affect performance and finish quality.
Cleaning Tips:
- Daily Cleaning:
- Inspect and Clean Interior Surfaces: Remove any powder buildup on oven walls, floors, and ceilings.
- Clean Heating Elements: Check and clean heating elements to ensure efficient heat transfer.
- Vacuum or Sweep the Floor: Remove any loose powder or debris from the oven floor.
- Weekly Cleaning:
- Clean Air Ducts and Vents: Ensure proper airflow and ventilation by cleaning ducts and vents regularly.
- Wipe Down Doors and Seals: Clean door seals and check for any damage that could affect insulation.
- Monthly Cleaning:
- Deep Clean Oven Interior: Use a non-abrasive cleaner to deep clean the oven interior and remove any stubborn residue.
- Inspect and Clean Exhaust Systems: Check and clean exhaust fans and filters to prevent blockages.
2. Routine Inspections
Regular inspections help identify potential issues before they become major problems, ensuring the oven operates at peak efficiency.
Inspection Tips:
- Daily Inspections:
- Check Temperature Settings: Verify that the oven reaches and maintains the correct curing temperature.
- Monitor Airflow: Ensure that fans and blowers are functioning correctly for even heat distribution.
- Inspect Doors and Seals: Check for gaps or damage that could lead to heat loss.
- Weekly Inspections:
- Inspect Electrical Components: Check wiring, connections, and control panels for signs of wear or damage.
- Check for Unusual Noises: Listen for any unusual noises that might indicate mechanical issues.
- Monthly Inspections:
- Inspect Insulation: Check oven insulation for any damage or wear that could reduce energy efficiency.
- Examine Conveyor Systems: For conveyor ovens, inspect belts, chains, and rollers for wear and alignment.
3. Calibration and Testing
Regular calibration and testing ensure that the oven operates at the correct temperature and settings, maintaining coating quality.
Calibration Tips:
- Temperature Calibration:
- Use Thermocouples: Place thermocouples at various points in the oven to verify temperature uniformity.
- Adjust Temperature Controllers: Calibrate controllers to maintain consistent curing temperatures across the oven.
- Testing Performance:
- Conduct Cure Tests: Perform test runs with sample parts to ensure that coatings are cured properly.
- Check Heating Elements: Test heating elements for consistent output and replace any that are faulty.
4. Preventive Maintenance
Implementing a preventive maintenance schedule helps prevent unexpected breakdowns and extends the life of the oven.
Preventive Maintenance Tips:
- Lubrication:
- Lubricate Moving Parts: Apply lubrication to bearings, chains, and other moving parts to reduce friction and wear.
- Component Replacement:
- Replace Worn Parts: Regularly check and replace parts like belts, seals, and filters that show signs of wear.
- Fan and Blower Maintenance:
- Inspect and Clean Fans: Check fans for balance and clean them to prevent vibration and noise.
- Replace Worn Bearings: Replace any bearings that are noisy or show signs of wear.
5. Safety and Compliance
Ensuring safety and regulatory compliance is critical for protecting workers and meeting industry standards.
Safety Tips:
- Fire Safety:
- Check Fire Suppression Systems: Ensure that fire suppression systems are operational and regularly serviced.
- Install Smoke Detectors: Regularly test smoke detectors and alarms to ensure they are functional.
- Electrical Safety:
- Inspect Wiring and Connections: Regularly check electrical wiring and connections for signs of wear or damage.
- Conduct Safety Audits: Perform regular safety audits to ensure compliance with safety regulations.
6. Documentation and Record Keeping
Keeping detailed records of maintenance activities helps track oven performance and identify trends or recurring issues.
Documentation Tips:
- Maintain a Maintenance Log: Record all maintenance activities, including inspections, cleaning, and repairs.
- Track Performance Metrics: Monitor metrics such as energy consumption, downtime, and repair frequency.
7. Staff Training and Awareness
Proper training ensures that staff are equipped to perform maintenance tasks safely and effectively.
Training Tips:
- Provide Comprehensive Training: Train staff on oven operation, maintenance procedures, and safety protocols.
- Encourage Proactive Maintenance: Empower staff to identify and report potential issues promptly.
Sample Maintenance Schedule for Powder Coating Ovens
Below is a sample maintenance schedule to help you organize and plan oven maintenance tasks:
Frequency | Task | Details |
---|---|---|
Daily | Clean interior surfaces | Remove powder buildup from oven walls, floors, and ceilings. |
Check temperature settings | Verify that the oven reaches the correct curing temperature. | |
Inspect doors and seals | Look for gaps or damage that could lead to heat loss. | |
Weekly | Clean air ducts and vents | Ensure proper airflow and ventilation. |
Inspect electrical components | Check wiring, connections, and control panels for wear. | |
Lubricate moving parts | Apply lubrication to bearings, chains, and other components. | |
Monthly | Deep clean oven interior | Use non-abrasive cleaner to remove stubborn residue. |
Calibrate temperature controllers | Verify and adjust temperature settings for consistency. | |
Inspect insulation and conveyor systems | Check insulation integrity and conveyor alignment. | |
Quarterly | Test heating elements and fans | Ensure consistent output and replace faulty components. |
Review safety protocols and systems | Update safety measures and test fire suppression systems. | |
Annually | Conduct comprehensive performance review | Evaluate overall condition and plan for upgrades. |
Audit compliance with regulations | Ensure adherence to safety and environmental standards. |
Conclusion
Regular maintenance of powder coating ovens is essential for achieving high-quality finishes, maintaining production efficiency, and ensuring equipment longevity. By implementing a structured maintenance plan, conducting regular inspections, and training staff, businesses can minimize downtime, reduce costs, and maintain a safe working environment.
EMS Powder Coating Equipment
Powder coating equipment is used to apply a thin layer of powder over a metal surface. This type of coating is applied by an electrostatic process and is a very popular method for finishing metal parts.
This type of equipment can be divided into two main categories: automatic and manual. Automatic booths are more popular because they provide better production rates, but they are also more expensive.
A powder booth is an enclosure in which the powder-coating process takes place. Powder-coating equipment includes an oven where the parts are heated to activate the powder, a gun that sprays or brushes on the powder, a conveyor belt that moves parts through the oven, and cartridge-type guns for applying thicker coatings with less overspray.
Powder coating is a technique that is used to provide a finish to metal parts. This technique has been in use for many years and it is still one of the most popular techniques today.
Powder coating equipment consists of booths, ovens, guns, machines, lines and conveyors. A booth can be either automatic or manual. An automatic booth is more expensive than a manual booth but it is also faster and more efficient.