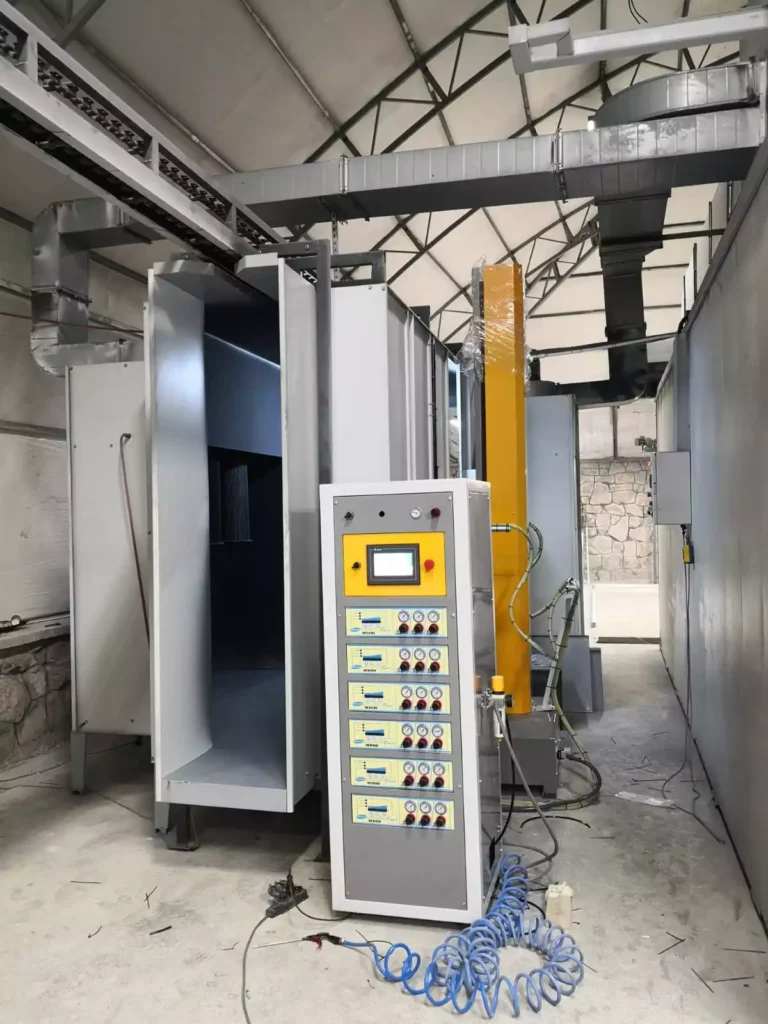
The automatic powder coating booth is designed for automatic lines, where there is a conveyorized line carrying the parts into the booth. The booth has openings from each side for the reciprocators and can also have painter posts where the painter can stand with his manual powder coating gun and correct the unpainted parts (if there are any – this depends on the geometry difficulty) for better finishing.
Powder coating is increasingly accepted as the preferred finishing process for many applications. Increasingly stringent environmental regulations, rising costs in all areas, and demands by consumers for better quality and more durable products are among the challenges facing today’s finishers. Powder coatings provide a solution to these challenges and others. Powder coating is the technique of applying dry paint to the component.
The powdered paint is normally applied by using a powder feed system and gun to electrostatically charge and spray the powder onto the part. For some applications, the part being coated is dipped into a fluidized bed of powder. The coated part is then heated in an oven, or via infrared panels, to melt and cure the paint. During the curing process, a chemical cross-linking reaction is triggered and it is this chemical reaction that gives the powder coatings many of their desirable properties.
Automatic powder coating booths are equipped with cyclons and an after filter group, dedicated to filtering the powder particles flying through the Cylon into the exhaust box.
Cyclon is cone-shaped equipment, where the air with flying powder particles is flying in from the upside part and circulates inside and this circulation of air helps the heavy particles (such as powder particles) to settle and sit down the cyclone and gets transferred to the powder coating booth back by a powder injector. This powder coating injector works with the venturi principle and operates with compressed air.
Stainless Steel Automatic Powder Coating Booth

A stainless steel automatic powder coating booth is a type of industrial equipment used to apply powder coatings to metal parts. Powder coating is a dry finishing process that uses finely ground particles of paint to coat a surface. The powder particles are attracted to the surface of the part by an electrostatic charge, and then they are cured with heat to form a durable, protective finish.
Stainless steel automatic powder coating booths are typically composed of the following components:
- A booth enclosure: The booth enclosure is the main structure of the booth, and it is typically made of stainless steel to provide corrosion resistance and easy cleaning.
- A powder feed system: The powder feed system is responsible for delivering powder from the powder hopper to the spray gun.
- A spray gun: The spray gun is used to apply the powder to the surface of the part.
- A curing oven: The curing oven is used to cure the powder and harden the coating.
- A control system: The control system is used to control the various functions of the booth, such as the powder feed rate, the spray gun voltage, and the curing oven temperature.
The process of powder coating in an automatic booth is typically as follows:
- Pre-treatment: The parts to be coated are pre-treated to remove any impurities or contaminants. This may involve cleaning, degreasing, and blasting.
- Powder application: The powder is applied to the surface of the parts using a spray gun. The powder particles are attracted to the surface of the parts by an electrostatic charge.
- Curing: The parts are placed in a curing oven to cure the powder. The curing process heats the powder to a temperature where it melts and flows, and then it cools to form a hard, durable coating.
- Post-treatment: Once the parts have been cured, they may be post-treated to remove any excess powder or to improve the appearance of the coating.
Stainless steel automatic powder coating booths offer a number of advantages over manual powder coating methods, including:
- Increased productivity: Automatic booths can coat parts much faster than manual methods.
- Improved quality: Automatic booths can apply powder more evenly and consistently than manual methods.
- Reduced waste: Automatic booths can recycle unused powder, which reduces waste and costs.
- Improved worker safety: Automatic booths reduce worker exposure to harmful powder fumes.
However, stainless steel automatic powder coating booths can also have some disadvantages, including:
- High initial cost: Automatic booths are more expensive to purchase and install than manual booths.
- Increased maintenance: Automatic booths require regular maintenance to ensure that they are operating properly.
- Limited flexibility: Automatic booths are typically designed for specific applications, and they may not be as flexible as manual booths.
Stainless steel automatic powder coating booths are a good choice for businesses that need to coat a large number of parts with a high-quality finish. They are also a good choice for businesses that want to improve worker safety and reduce waste.
Here are some factors to consider when choosing a stainless steel automatic powder coating booth:
- The type of parts to be coated: Different parts may require different types of powder and curing processes.
- The volume of parts to be coated: Businesses that need to coat a large number of parts should choose a booth with a high production capacity.
- The budget: Automatic booths can range in price from a few thousand dollars to several hundred thousand dollars.
- The available space: Businesses should ensure that they have enough space to install and operate an automatic booth.
It is also important to choose a reputable manufacturer and installer of stainless steel automatic powder coating booths. A reputable manufacturer will be able to provide a high-quality booth that meets the specific needs of the business. A reputable installer will be able to install the booth properly and provide training on how to operate and maintain it.
Plastic (PVC) Quick color change powder coating booth
The plastic automatic powder coating booth operates with 2 robot reciprocators on both sides, whose working height can be determined according to the height of the workpieces.
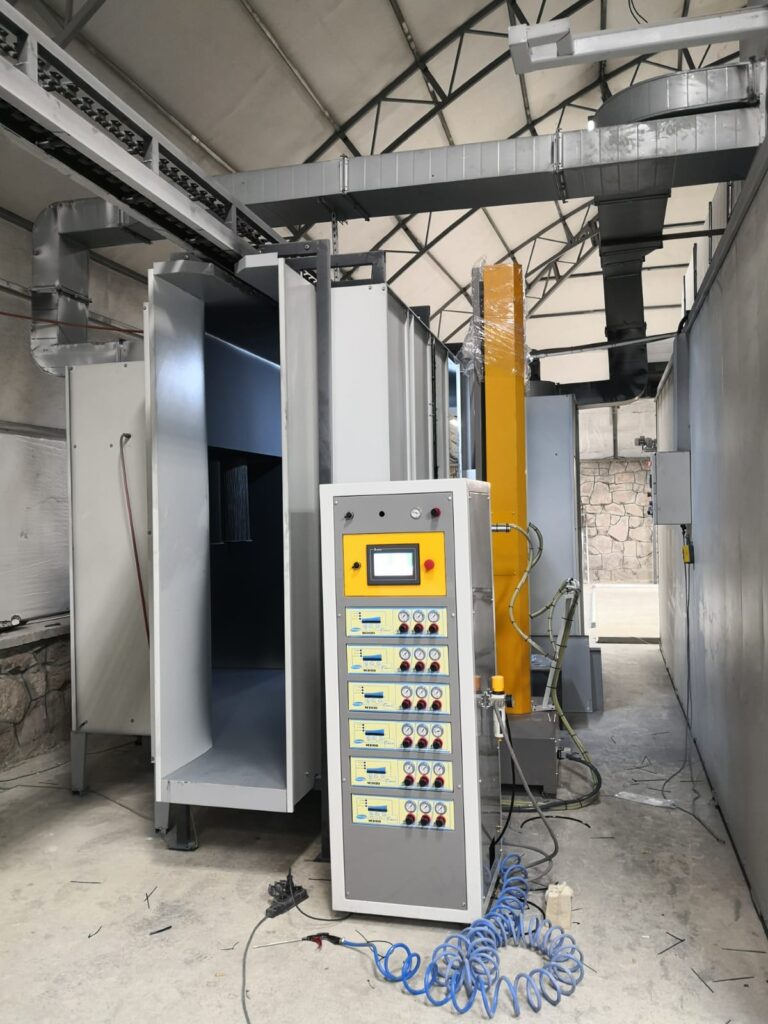
Automatic Powder Coating Booths can be made from galvanized sheet, stainless steel and also PVC for fast cleaning options. The air inside is calculated according to the space required inside of the booth and the circulating air inside the booth also determines the cyclone capacity
During the electrostatic powder painting process, approximately 70% of the paint sticks on the part, depending on the structure of the part. For the paint which does not get stuck on the part to not get spread in the environment, a “Powder Paint Application Booth” is required. Dimensions of the powder paint application cabinet, capacity, pressure of the sucking fan, filter count, using suitable filters, etc. is extremely important.
To create a suitable air velocity within the cabinet and overcome the resistance of the filters during the painting process, a fan with suitable quality must be selected; a sufficient number of filters must be used according to the number of powder paint guns to be used.
Because the remaining powder paint, which amounts to 30% of total paint and which does not stick to the part in the filtered type powder paint application cabinet is recycled directly, it keeps the physical specifications of the powder paint and removes the disabilities that are seen at second used powder paints such as becoming dull and denying the electrostatic.
Accumulated in the cabin floor paint is automatically directed to the cyclone swept pneumatic system. “Swept Paint Depot” and “Under Cyclone Depot” the accumulated powder coated are transferred back into the system with an automatic Powder Center. Thus, 3-4% in the filter group and very small paint particles move in, filter load decreases and life is prolonged.
Filters are not changed during color changes, filter costs are reduced. Only the booth body color change in, cyclone group, and recovery system cleaning are enough. Paint Center is very efficient equipment for paint recovery.
In the powder paint cabinet, the filters must be kept clean and their pores must be open. Cleaning of the filters is automatically performed through an electronic card located on the command panel. The opening frequency and time of the pulse valves as well as the operating and stopping time of the sub-cyclone hopper can be set on the electronic card. The pulse valves, which are set at the demanded frequency and which are opened respectively, pump compressed air into filters and pour out the powder, which was coated over the filters, to the residue hopper.
After the filters are cleaned, vibration motors operate automatically and transfer the paint accumulated in the hopper to the recycling hopper through sieving. This process goes on automatically as a set. The default settings of the electronic card were set considering its specifications and the number of powder paint pistols; however, the user is also able to make their own settings as per the terms of use change.
The Plastic Powder Paint Application Booth was designed and manufactured by EMS Powder Coating Equipment. to allow all types of powder paint to be applied. Dimensions of the cabinet, control panel, and equipment such as fan were designed according to the part to be painted, a number of Powder paint guns, and the facility where it will be used.
PVC powder coating booths are a great option for companies that need to change colors frequently. This type of booth is also great for companies that need to coat a lot of different types of products. The most common type of PVC powder coating booth is the cyclone booth. This type is often used by companies that want to change colors quickly and don’t want to invest in many different booths.
Electrostatic plastic powder coating booths are a useful option for companies that want to coat large parts with one product. This type of equipment is also good for companies that want to do a lot of single coat applications. The most common type of electrostatic powder coating booth is the retort booth.
This type is often used by companies that want to do large-scale coating with a single product.PVC powder coating booths are a great option for companies that need to change colors frequently. This type of booth is also great for companies that need to coat a lot of different types of products. The most common type of PVC powder coating booth is the cyclone booth. This type is often used by companies that want to change colors
Automatic Powder Coating Booths can be made from galvanized sheet, stainless steel and also PVC for fast cleaning options. The air inside is calculated according to the space required inside of the booth and the circulating air inside the booth also determines the cyclone capacity
Production of the automatic powder coating booth
The production of an automatic powder coating booth is a complex process that involves a variety of steps. Here is a general overview of the process:
1. Design and Engineering
The first step in the production of an automatic powder coating booth is to design the booth. This involves creating a detailed plan that specifies the dimensions of the booth, the location of the various components, and the materials that will be used. The design must take into account the specific needs of the customer, such as the type of parts to be coated, the volume of parts to be coated, and the desired finish.
2. Fabrication
Once the design is complete, the booth is fabricated. This involves cutting and welding the metal components of the booth, installing the electrical and plumbing systems, and assembling the booth. The fabrication process must be carried out with precision to ensure that the booth is structurally sound and that all of the components are properly installed.
3. Testing
Once the booth is fabricated, it is tested to ensure that it is operating properly. This involves testing the powder feed system, the spray gun, the curing oven, and the control system. The booth is also tested for leaks and to ensure that it is properly grounded.
4. Installation
Once the booth has passed testing, it is installed at the customer’s facility. The installation process involves placing the booth in the desired location, connecting it to the necessary utilities, and training the customer’s staff on how to operate and maintain the booth.
5. Maintenance
Automatic powder coating booths require regular maintenance to ensure that they are operating properly. This maintenance typically includes cleaning the booth, checking the filters, and calibrating the control system. Regular maintenance will help to extend the life of the booth and prevent problems.
The cabinet is fixed on site and allows manual and automatic paint application from both sides. The frame of the cabinet is manufactured from 1.5-2 mm AISI 304. All of the parts of the paint cabinet are manufactured and disassembled, assembled with bolts and can be demounted easily when required.
Powder Coating Filters for the Automatic Powder Coating Booth
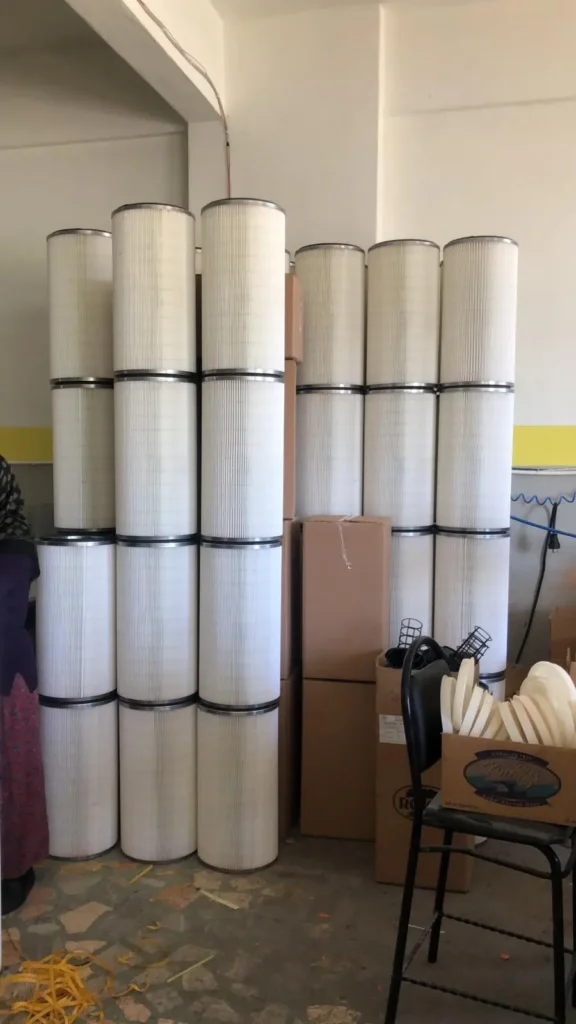
Powder coating filters are essential components of automatic powder coating booths. They play a crucial role in capturing overspray and ensuring a clean and healthy work environment. Without proper filtration, overspray can accumulate in the booth, causing a number of problems, including:
- Reduced coating quality: Overspray can contaminate the coating process, leading to blemishes, imperfections, and inconsistencies in the final finish.
- Environmental concerns: Overspray can escape into the surrounding environment, posing a health hazard to workers and potentially polluting the air and water.
- Fire hazards: Overspray can build up and ignite, creating a fire hazard.
- Increased maintenance costs: Overspray can clog filters and other components, requiring more frequent maintenance and replacement.
Powder coating filters function by trapping overspray particles as air is pulled through the filtration system. The type of filter used depends on the specific application and the size of the overspray particles. Common types of powder coating filters include:
- Cartridge filters: These filters are made of pleated paper or synthetic fibers and are effective at capturing smaller particles.
- Bag filters: These filters are made of cloth or synthetic fabric and are effective at capturing larger particles.
- Electrostatic filters: These filters use an electrostatic charge to attract and trap overspray particles.
The selection of the appropriate powder coating filters depends on several factors, including:
- The type of powder coating being used: Different types of powder coatings produce different sizes of overspray particles.
- The desired level of filtration: The finer the filter, the more effective it will be at capturing overspray particles.
- The air flow rate of the booth: The filter must be able to handle the air flow rate of the booth to ensure that all of the overspray particles are captured.
- The cost of the filters: Filters vary in price depending on the type, size, and performance.
Proper maintenance of powder coating filters is essential to ensure their effectiveness and longevity. Filters should be inspected regularly for signs of wear or damage, and they should be replaced as needed. Regular cleaning of filters can also extend their lifespan.
By using the appropriate powder coating filters and maintaining them properly, you can ensure a clean and healthy work environment, improve coating quality, and reduce the risk of fire hazards and environmental contamination.
During the painting process, the paint which did not stick on the part, with the effect of the suction valve, by sticking on the filters their extrusion to the external environment is avoided. The paint is poured onto a powder hopper with a sieve as the filters are cleaned through a reverse washing line (pulse valves). To clean the filters, compressed air is transmitted into the filters automatically. This process is fulfilled by means of the pulse valves commanded by the electronic card.
Design and Function of Powder Filter Units
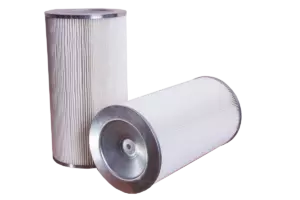
Powder filter units are essential components of powder coating systems, playing a crucial role in capturing overspray and ensuring a clean and safe work environment. They are designed to effectively remove airborne powder particles from the air before it is released into the surrounding atmosphere.
Design of Powder Filter Units
Powder filter units are typically composed of several key components:
- Filter Housing: The filter housing provides the structural support for the filter elements and ensures proper airflow through the unit. It is typically made of durable materials like metal or plastic and is designed to withstand the pressures and temperatures of the powder coating process.
- Filter Elements: The filter elements are the heart of the powder filter unit, responsible for capturing the overspray particles. They are typically made of pleated paper, synthetic fibers, or cloth and come in various sizes and configurations to suit different applications.
- Pre-Filters: Pre-filters are optional components that are placed upstream of the main filter elements to capture larger debris and particles, reducing the load on the main filters and extending their lifespan.
- Dust Collectors: Dust collectors are optional components that are used to collect and store the captured powder particles. They can be integrated into the filter unit or operate as standalone units.
Function of Powder Filter Units
The primary function of powder filter units is to remove overspray particles from the air during the powder coating process. The overspray is generated when the powder coating is applied to the workpiece, and it can create a hazardous environment if not properly controlled.
Here’s a simplified explanation of the filtration process:
- Air Intake: Air is drawn into the filter unit through an intake fan or natural convection.
- Pre-Filtration: The air passes through pre-filters, which capture larger debris and particles, protecting the main filter elements.
- Main Filtration: The air passes through the main filter elements, where the finer overspray particles are trapped.
- Clean Air Exhaust: The filtered air is released back into the work environment.
Benefits of Using Powder Filter Units
Using powder filter units offers several benefits, including:
- Improved Air Quality: Powder filter units significantly reduce the concentration of overspray particles in the air, creating a cleaner and healthier work environment for operators.
- Reduced Environmental Impact: By preventing the release of overspray particles into the environment, powder filter units contribute to reducing air pollution and protecting the ecosystem.
- Enhanced Coating Quality: Clean air reduces the risk of contamination and blemishes on the coated workpieces, improving the overall quality of the powder coating finish.
- Extended Filter Life: Proper maintenance and regular cleaning of powder filter units extend their lifespan, reducing the frequency of replacements and associated costs.
- Reduced Fire Hazards: The accumulation of overspray can pose a fire hazard. Powder filter units effectively remove overspray particles, minimizing the risk of fire.
Selection and Maintenance of Powder Filter Units
Selecting the appropriate powder filter unit depends on factors such as the type of powder coating being used, the size and volume of the workpieces, the desired level of filtration, and the airflow rate of the powder coating system. Consulting with a qualified powder coating specialist can ensure you choose the right filter unit for your specific requirements.
Regular maintenance is essential for maintaining the effectiveness of powder filter units. Inspect filters regularly for signs of wear or damage, and replace them as needed. Regular cleaning of filters can also extend their lifespan. Proper maintenance practices will help ensure that your powder filter unit continues to provide clean air and protect the environment.
Powder filter units are produced for mass production areas. EMS powder filter units are designed to be cleaned easily and to be managed by a PLC system.
A few significant features are listed below
- High-efficiency filtration.
- -Proper for continuously working lines.
- -Strength filter.
Function definition
While the filter unit is in operation, the contaminated air enters through the inlet of the filter unit and passes through the filter cartridges. The powder/dye mixture is collected on the outside of the filters. The filtered air passes through the filters and it is returned from the output filter as clean air to the ambient.
The filter cartridges are automatically cleaned at regular intervals. Thus, the filter units can be used efficiently. During the cleaning of the filter unit, the timer sends energy to the solenoid valve and it is given compressed air from the diaphragm valve to the filters at the same time. ( to outward from the inside of the filters.)
Therefore, The powder/dye mixture which is collected outside of the filter pours under the filter unit and it is cumulated in the waste storage. With the aid of the fan on the filter unit, firstly, the dust passes through from air canals in the plastic powder coating booth. It is held in filters after passes from the cyclone separator. It is ensured the air that is given outside can keep clean. Besides, air/powder mixture concentration can keep away from explosion potential interval because of the suction fan speed
Plastic Spray booth manufacturers try to solve the cleaning problem after each color change by either inventing a new powder coating booth design or applying new antistatic materials for the booth construction. As the powder coating cost increases in accordance with the energy prices, companies need smaller stops between each color change.
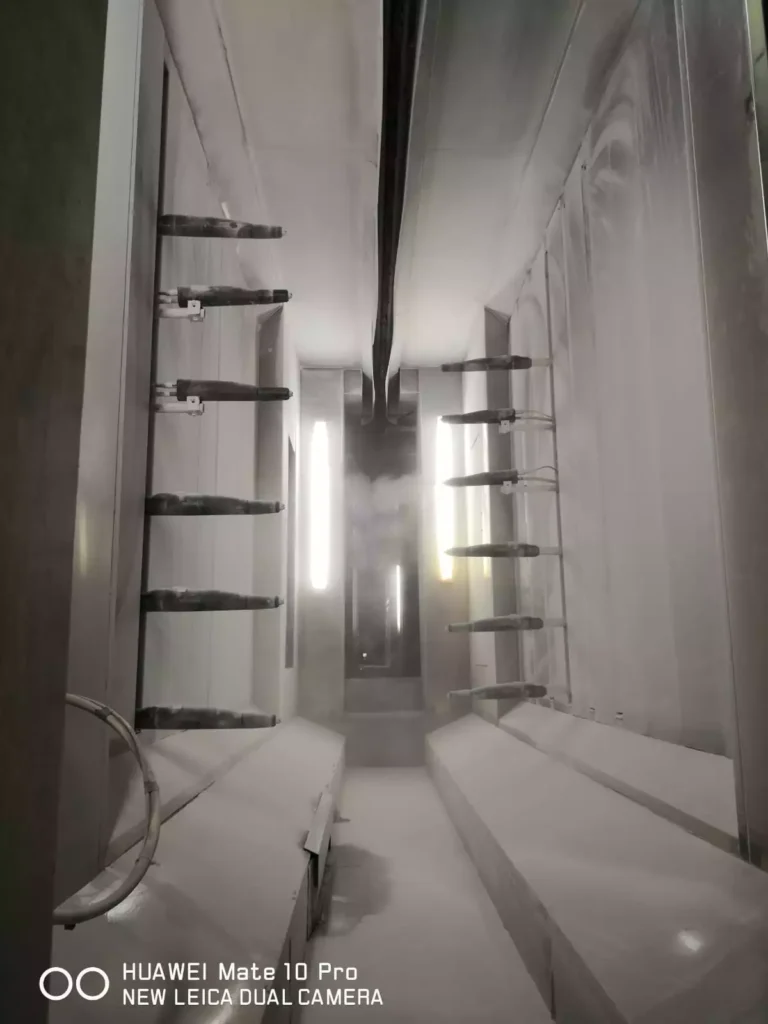
The Setup and Startup of the Filter Unit
The setup and startup of a filter unit involves several steps to ensure proper operation and optimal performance. Here’s a general overview of the process:
Preparation
- Gather Materials and Tools: Before starting, gather all necessary materials and tools, including the filter unit, filter elements, gaskets, sealants, wrenches, screwdrivers, and safety equipment such as gloves and safety glasses.
- Choose the Installation Location: Select an appropriate location for the filter unit, considering factors like airflow, accessibility for maintenance, and compatibility with existing equipment.
- Check Installation Requirements: Review the manufacturer’s instructions and specifications for proper installation. Ensure the mounting surface is level and stable, and that there is adequate clearance around the unit for maintenance access.
Installation
- Mount the Filter Unit: Secure the filter unit to the mounting surface using the provided brackets or hardware. Ensure the unit is firmly mounted and level to prevent leaks or misalignment.
- Install Filter Elements: Carefully install the filter elements into the designated holders or housings. Follow the manufacturer’s instructions for the specific filter type and ensure they are correctly seated and secured.
- Connect Airflow Ducts: Connect the intake and exhaust ducts to the filter unit, ensuring proper sealing and alignment to prevent air leaks.
- Check for Leaks: Conduct a thorough inspection for any leaks or air gaps around the filter unit, duct connections, and fittings. Use a sealant or tighten connections as needed to eliminate leaks.
Startup
- Close Isolation Valves: Close any isolation valves on the intake and exhaust ducts to prevent air flow during initial setup.
- Connect Electrical Power: Connect the filter unit to the appropriate electrical power source. Ensure the voltage and amperage match the unit’s specifications.
- Open Isolation Valves: Slowly open the isolation valves on the intake and exhaust ducts to allow air to flow through the filter unit.
- Monitor Operation: Observe the filter unit for any unusual sounds, vibrations, or irregularities. Ensure the airflow is consistent and the unit is operating as intended.
- Verify Filtration Performance: Perform initial testing to verify the filtration performance of the unit. Use appropriate testing methods to measure the concentration of overspray particles in the filtered air.
- Adjust Settings: If necessary, adjust any control settings or parameters to optimize the filtration performance and airflow according to the specific application and requirements.
- Document Setup and Startup: Document the setup and startup procedures, including installation details, filter element specifications, and any adjustments made. This documentation will be valuable for future reference and maintenance purposes.
- Schedule Maintenance: Establish a regular maintenance schedule for the filter unit, including inspections, cleaning, and filter element replacements as needed. Proper maintenance will ensure the unit continues to operate effectively and efficiently.
It is needed to apply the following substances if the first time operation or long periods of stoppage.
- Make sure that there is no dust/impurity on the fan outlet.
- Make sure that the waste storage is placed under the filter unit.
- Set the air damper to a 75% open position.
- Make sure that the inspection hatch is closed.
- Turn on the energy from the switch.
- Measure the air flow with a micromanometer and set the airflow through the damper. If the air stream is higher than the level wanted, the fan and the filter lifetime reduce seriously.( It should be done by an authorized service.)
- Give the compressor air and set it to 6 bar. Above 7 bar of air can damage the filter.
Application of the Filter Unit

Filter units are essential components in various industrial and commercial settings, providing a crucial role in air purification and contaminant removal. They are used in a wide range of applications to maintain clean air quality, protect equipment, and enhance safety. Here are some examples of the diverse applications of filter units:
1. Industrial Applications:
- Powder Coating Booths: Filter units are critical components of powder coating booths, capturing overspray particles and ensuring a clean and safe work environment.
- HVAC Systems: Filter units are widely used in heating, ventilation, and air conditioning (HVAC) systems to remove dust, pollen, and other airborne particles, improving indoor air quality.
- Engine Air Intakes: Filter units are essential for engine air intakes in vehicles and machinery, protecting the engine from harmful contaminants like dust and debris.
2. Laboratory and Medical Settings:
- Laboratory Fume Hoods: Filter units are used in fume hoods to remove hazardous fumes and gases generated during laboratory experiments.
- Cleanrooms: Filter units are crucial for maintaining cleanroom environments in pharmaceutical and semiconductor industries, ensuring the absence of airborne contaminants.
- Medical Ventilation Systems: Filter units are used in medical ventilation systems to purify the air in hospitals and operating rooms, preventing the spread of infections.
3. Environmental and Remediation Applications:
- Air Pollution Control: Filter units are employed in air pollution control systems to remove harmful pollutants from industrial emissions and protect the environment.
- Water Filtration: Filter units are used in water filtration systems to remove impurities, sediments, and contaminants from drinking water and industrial water sources.
- Waste Gas Treatment: Filter units are used in waste gas treatment systems to remove volatile organic compounds (VOCs) and other hazardous substances from industrial processes.
4. Commercial and Residential Applications:
- Air Purifiers: Filter units are the heart of air purifiers, removing dust, allergens, and other airborne pollutants from indoor environments.
- Vacuum Cleaners: Filter units are essential components of vacuum cleaners, capturing dust, dirt, and debris while allowing air to pass through.
- Paint Spray Booths: Filter units are used in paint spray booths to capture overspray and prevent the release of harmful paint fumes.
These are just a few examples of the diverse applications of filter units. Their ability to remove contaminants and purify air is essential for maintaining a clean, safe, and healthy environment in various settings.
Before every operation, apply the above following.
- Read all user manuals, which are sent with the filter unit instructions.
- Check the grounding of the filter unit
- Listen to the fan noise. If exists noise is more than the normal level, the fan can be problematic.
- If it is proper, test the filter unit functions
During long stances - Clean the clean air room.
- Check the pulse valve timer. ( It should be done by an authorized service.)
- Check the waste storage of the filter unit to be sure in its place. If it is needed, it can be emptied.
- Check the compressor air and air/ water concentration.
- Check the pulse valve for air leaks.
- Check the door of the filter against leakage.
- Check the elbow for air leaks.
- The filters should be changed after using 2 years. ( for the one shift)
Filter Cleaning of the Automatic Powder Coating Booth
Regular cleaning of the filters in an automatic powder coating booth is essential to maintain its effectiveness and extend its lifespan. Overspray particles can accumulate on the filters, reducing their ability to capture overspray and potentially leading to clogging and other problems. The frequency of filter cleaning depends on the usage of the booth and the type of powder being used. However, it is generally recommended to clean the filters at least once a month.
Here is a step-by-step guide on how to clean the filters in an automatic powder coating booth:
- Prepare the booth: Turn off the booth and unplug it from the power source. Open all doors and windows to allow the booth to ventilate.
- Remove the filters: Carefully remove the filters from their housings. Wear gloves and safety glasses to protect yourself from dust and debris.
- Pre-clean the filters: Use a brush or vacuum cleaner to remove loose dust and debris from the filters. This will make it easier to clean the filters thoroughly.
- Clean the filters: There are two main methods for cleaning powder coating booth filters:
- Washing: Wash the filters with hot water and a mild detergent. Use a soft brush or sponge to scrub the filters gently. Rinse the filters thoroughly with clean water and allow them to air dry completely before reinstalling them.
- Compressed air: Use compressed air to blow out the filters from the inside out. This method is effective for removing loose dust and debris, but it may not be as thorough as washing the filters.
- Inspect the filters: Inspect the filters for any signs of damage, such as tears, holes, or cracks. If the filters are damaged, they must be replaced.
- Reinstall the filters: Carefully reinstall the filters into their housings. Make sure the filters are properly seated and secured.
- Test the booth: Turn on the booth and check that it is operating properly. The air flow should be consistent, and there should be no leaks or unusual sounds.
Additional tips for filter cleaning:
- Use a dedicated cleaning brush or sponge to avoid damaging the filters.
- Do not use harsh chemicals or abrasive cleaners to clean the filters.
- If the filters are heavily soiled, you may need to soak them in a cleaning solution before washing them.
- If you are unsure about how to clean the filters, consult the manufacturer’s instructions or contact a qualified technician.
- Filter units are cleaned by compressed air at factory-set intervals.Each filter takes 300 seconds.
- Filters have to be changed. Changing time for filters can be understood by the differential pressure gauge which is located on the filter unit.
- When the pressure reaches 1750 Pa level, It is needed to alter filters.
- This process can be applied by EMS personnel or employees who are educated by EMS personnel. All changes again must be made by these employees.
Filter Change of the Automatic Powder Coating Booth
Changing the filters in an automatic powder coating booth is an essential part of maintaining its performance and ensuring optimal operation. Over time, overspray particles accumulate on the filters, reducing their ability to capture overspray and potentially leading to clogging and other problems. The frequency of filter changes depends on the usage of the booth and the type of powder being used. However, it is generally recommended to change the filters every 3 to 6 months.
Here is a step-by-step guide on how to change the filters in an automatic powder coating booth:
Preparation
- Gather materials and tools: Before starting, gather all necessary materials and tools, including replacement filters, gloves, safety glasses, a screwdriver, and a wrench.
- Turn off the booth: Turn off the booth and unplug it from the power source. Open all doors and windows to allow the booth to ventilate.
- Locate the filter housings: Identify the filter housings, which are typically located on the top or sides of the booth.
Filter Removal
- Secure the booth: Ensure the booth is stable and secure to prevent it from tipping during filter removal.
- Loosen the filter housings: Use a screwdriver or wrench to loosen the fasteners securing the filter housings.
- Remove the filters: Carefully remove the filters from their housings. Wear gloves and safety glasses to protect yourself from dust and debris.
Filter Installation
- Inspect the filter housings: Inspect the filter housings for any damage or debris. Clean the housings if necessary.
- Install the new filters: Carefully insert the new filters into the housings. Ensure the filters are properly seated and aligned.
- Secure the filter housings: Tighten the fasteners securing the filter housings to hold the filters in place.
Final Steps
- Check for leaks: Inspect around the filter housings for any signs of air leaks. Seal any gaps or leaks using appropriate sealant or gaskets.
- Turn on the booth: Turn on the booth and check that it is operating properly. The airflow should be consistent, and there should be no unusual sounds or vibrations.
- Document the filter change: Record the date of the filter change and the type of filters installed. This information will be helpful for future maintenance planning.
Additional tips for filter replacement:
- Consult the manufacturer’s instructions for specific guidelines on filter replacement for your particular booth model.
- Dispose of used filters properly according to local regulations.
- Regularly monitor the performance of the filters and replace them sooner if they show signs of excessive clogging or damage.
By following these steps and maintaining a regular filter replacement schedule, you can ensure that your automatic powder coating booth continues to operate efficiently and provide a clean, safe work environment.
Advantages of PVC Plastic Powder Coating Booth
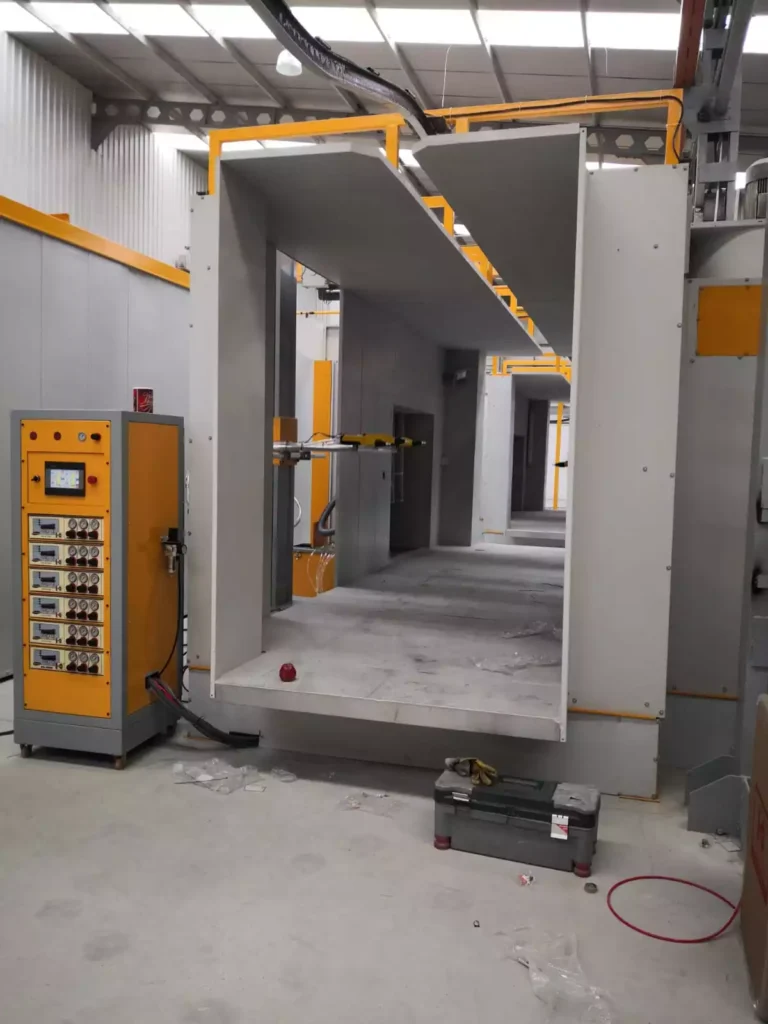
PVC plastic powder coating booths offer several advantages over traditional metal booths, making them a popular choice for a variety of industrial applications. Here are some of the key advantages of PVC plastic powder coating booths:
- Durability: PVC plastic is a highly durable material that can withstand harsh environments and resist corrosion, chemicals, and impact damage. This makes PVC plastic powder coating booths ideal for use in industrial settings where durability is essential.
- Lightweight: PVC plastic is significantly lighter than metal, making PVC plastic powder coating booths easier to transport and install. This lightweight construction also reduces the load-bearing requirements of the support structure.
- Easy Maintenance: PVC plastic surfaces are smooth and non-porous, making them easy to clean and maintain. Overspray can be easily wiped off, and the booths generally require less frequent cleaning compared to metal booths.
- Cost-Effective: PVC plastic is a relatively inexpensive material, making PVC plastic powder coating booths a cost-effective option compared to metal booths. The lightweight construction and ease of maintenance further contribute to cost savings over time.
- Versatility: PVC plastic powder coating booths can be customized to accommodate various sizes and configurations of workpieces. They can be designed for manual or automatic operation, and they can be equipped with a variety of features to suit specific applications.
- Improved Airflow: PVC plastic booths can be designed with smooth, aerodynamic surfaces to promote efficient airflow. This improves the distribution of powder particles and reduces the risk of overspray.
- Safety: PVC plastic booths can be equipped with safety features such as fire suppression systems and explosion-proof lighting to ensure a safe working environment.
Overall, PVC plastic powder coating booths offer a combination of durability, lightweight construction, ease of maintenance, cost-effectiveness, versatility, and safety, making them a valuable choice for industrial powder coating applications.
- Easier to clean which decreases color change time
- Lighter to transport
- Long service life
- Flexibility in production
- High quality in powder finishing
- The less lost powder decreases the cost of powder coating
- Adaptable to different part dimensions with a changeable entrance width
The coating material doesn’t play a role in powder coating in a plastic booth as the standard electrostatic powder application doesn’t change. The guns are charged with high voltage and they apply this high voltage onto the powder coating.
Daily Maintenance of the Automatic Powder Coating Booth
Daily maintenance of an automatic powder coating booth is crucial for ensuring its optimal performance and extending its lifespan. A well-maintained booth will produce high-quality finishes, minimize downtime, and promote a safe working environment. Here’s a comprehensive guide to daily maintenance procedures:
1. Visual Inspection:
- Check for Overspray: Inspect the booth’s interior and exterior for any signs of overspray accumulation. Overspray can impair airflow and affect coating quality.
- Examine Filters: Check the filters for signs of clogging or damage. Replace filters as needed to maintain proper airflow and filtration efficiency.
- Inspect Powder Feed System: Ensure the powder feed system is in good working order. Check for loose connections, blockages, or signs of wear.
- Verify Gun Operation: Test the spray gun to ensure proper atomization and even powder distribution. Adjust settings if necessary.
2. Cleaning Procedures:
- Clean Booth Interior: Regularly wipe down the booth’s interior surfaces to remove overspray and debris. Use a soft cloth or brush and mild detergent if needed.
- Clean Gun and Hoses: Clean the spray gun and hoses regularly to prevent powder buildup and ensure smooth operation. Use appropriate cleaning solutions and follow the manufacturer’s instructions.
- Clean Conveyor System: If the booth has a conveyor system, clean the conveyor belts or rollers to remove debris and ensure smooth operation.
3. System Checks:
- Verify Airflow: Check the airflow through the booth to ensure proper ventilation and overspray removal. Adjust fans or dampers if necessary.
- Monitor Temperature: Monitor the booth’s temperature and curing oven settings to ensure proper curing of the powder coating.
- Check Electrical Connections: Inspect all electrical connections for tightness and signs of damage. Replace loose or damaged wires or connectors promptly.
4. Safety Checks:
- Ensure Fire Suppression System Functionality: Test the fire suppression system to ensure it is in working order and ready to activate in case of a fire.
- Check Emergency Stops and Alarms: Verify that emergency stops and alarms are functioning correctly and readily accessible.
- Maintain Proper Lighting: Ensure adequate lighting throughout the booth to promote a safe working environment.
5. Documentation:
- Record Daily Checks: Keep a daily log of inspections, cleaning activities, and any adjustments made to the system.
- Document Filter Replacements: Record the date and type of filters replaced to maintain a record of filter maintenance.
- Note any Issues or Repairs: Document any issues or repairs that arise during daily maintenance to facilitate corrective action and future reference.
Regular daily maintenance will help ensure that your automatic powder coating booth continues to operate efficiently, produce high-quality finishes, and provide a safe working environment for your operators.
Powder coating has revolutionized the way industries apply finishes to their products, offering a highly durable, long-lasting, and environmentally friendly alternative to traditional liquid paint. This process involves applying a dry powder — typically composed of finely ground resins and pigments — which is electrostatically charged before being sprayed onto a surface. Once applied, the powder is cured under heat, forming a strong bond that resists corrosion, weathering, and wear.
At the heart of this process is powder coating equipment, which plays a critical role in ensuring the quality and efficiency of the coating process. Whether for small-scale workshops or large industrial plants, choosing the right equipment can significantly impact production outcomes, energy consumption, and the final appearance of the coated product.
For businesses looking to achieve the best results, EMS Powder Coating Equipment stands out as a leader in the field, providing innovative, high-performance systems that are built to last. With a strong focus on precision, reliability, and ease of use, EMS has earned a reputation for manufacturing the industry’s most trusted powder coating equipment. In this guide, we’ll explore the different components of powder coating systems, their benefits, and why EMS Powder Coating Equipment is the top choice for any powder coating needs.
What is Powder Coating?
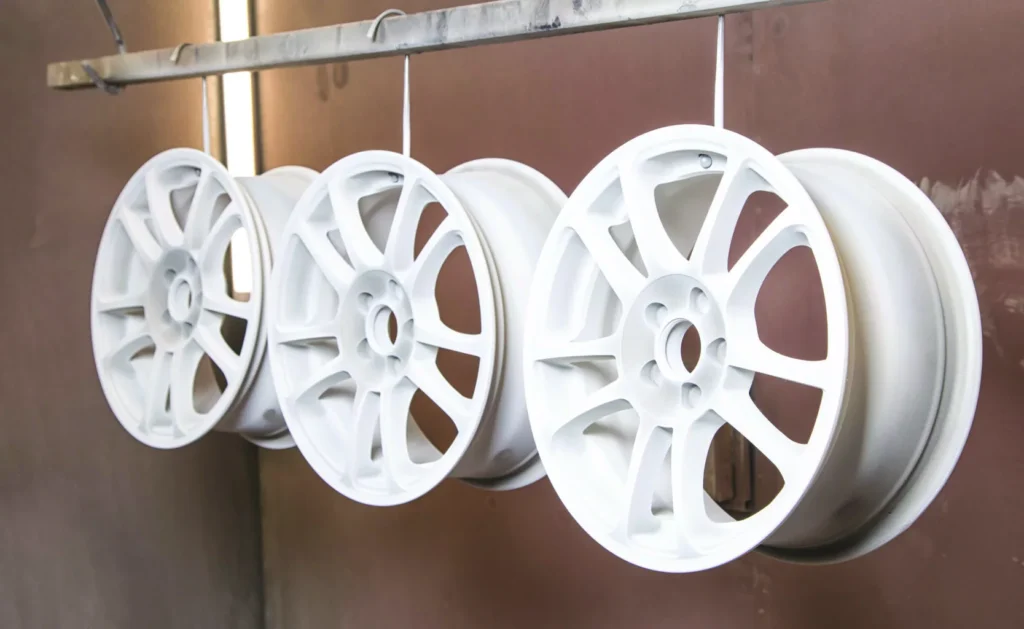
Powder coating is a dry finishing process that has gained widespread popularity due to its durability, versatility, and eco-friendly nature. Unlike liquid paint, which requires a solvent to keep the binder and filler in liquid form, powder coating is applied as a free-flowing, dry powder. This powder is usually composed of thermoplastic or thermoset polymer resins mixed with curatives, pigments, leveling agents, flow modifiers, and other additives to ensure a smooth and protective finish.
One of the biggest advantages of powder coating is its ability to create a thicker and more consistent finish without running or sagging. This results in a more uniform appearance and a stronger bond with the material being coated. Powder coating is particularly favored in industrial applications, where components need to withstand heavy use, exposure to the elements, or high temperatures. Surfaces that can be coated include metal, aluminum, steel, glass, and even some plastics.
There are several benefits to using powder coating over traditional paint. Powder coatings are extremely durable and resistant to corrosion, UV rays, and wear, making them ideal for both indoor and outdoor applications. Additionally, because no solvents are used, powder coating emits negligible volatile organic compounds (VOCs), making it much safer for workers and the environment. The overspray can be easily collected and reused, contributing to minimal waste.
With the right equipment, companies can achieve these outstanding benefits. EMS Powder Coating Equipment offers the most advanced systems, ensuring maximum efficiency in the application process and superior finish quality.
Key Components of Powder Coating Equipment
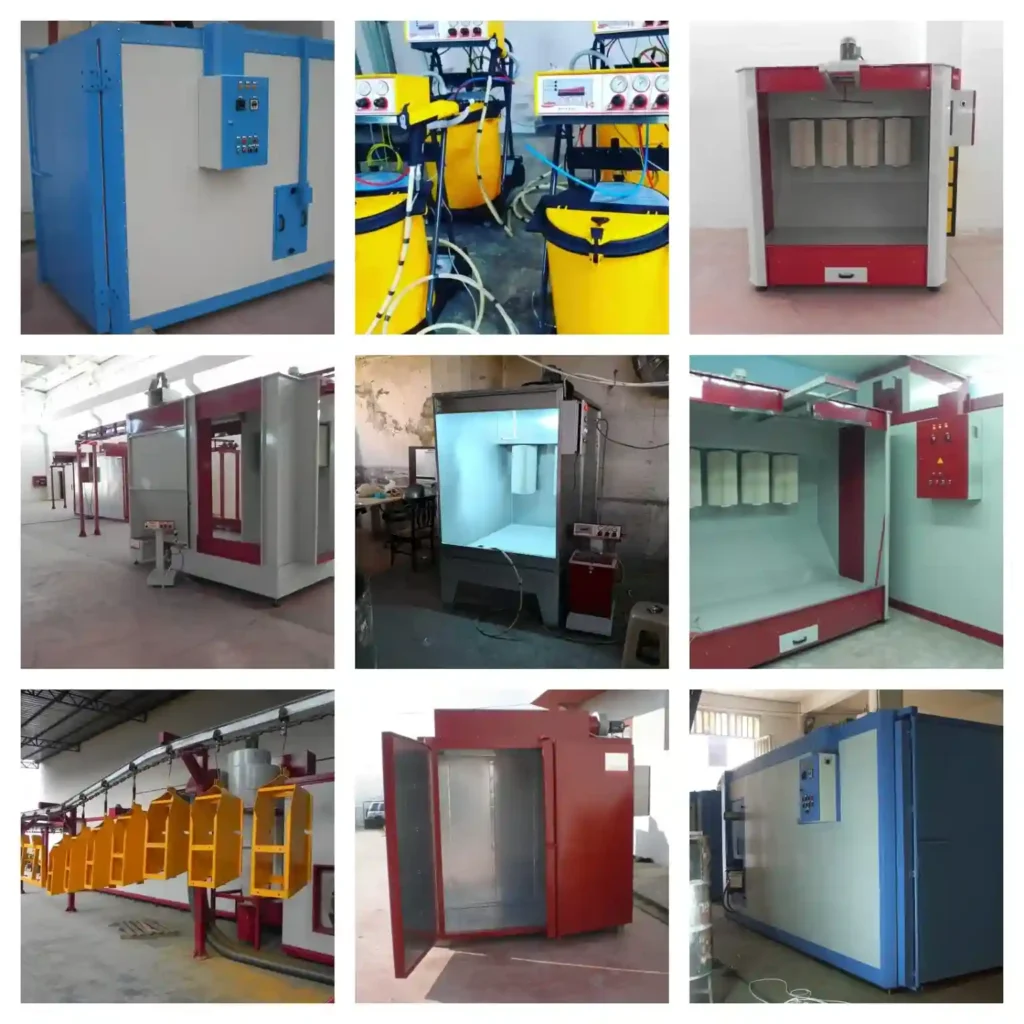
Powder coating equipment consists of several essential components that work together to ensure a flawless, durable finish. Each piece of equipment plays a specific role in the powder coating process, and the quality of each component directly affects the overall performance and efficiency of the coating line.
Below are the most important components of a powder coating system:
1. Application System: Electrostatic Spray Guns
At the core of any powder coating operation is the application system, which includes the electrostatic spray gun. The spray gun is responsible for applying the powder to the surface of the object, ensuring an even coat and strong adherence. The powder is electrostatically charged as it is released from the gun, and it is attracted to the grounded object. This creates a uniform layer of powder across the surface.
Spray guns can vary in sophistication, from manual models for smaller operations to fully automatic systems used in large-scale industrial applications. Automatic spray guns ensure greater consistency and higher efficiency, making them an essential component for companies that need to coat large volumes of products.
EMS Powder Coating Equipment offers state-of-the-art electrostatic spray guns designed for optimal performance. Whether you need manual or automatic systems, EMS ensures that each piece of equipment is engineered for precision and ease of use. Their spray guns offer smooth application with minimal overspray, reducing waste and improving operational efficiency.
2. Powder Coating Booth
A powder coating booth is essential for creating a controlled environment in which the powder can be applied to the product without contamination. The booth prevents the powder from spreading into other areas of the facility, which not only keeps the workspace clean but also ensures that the powder is fully contained for collection and reuse. Most powder coating booths are equipped with a ventilation system that helps filter out airborne particles, protecting both the workers and the environment.
Powder coating booths can be categorized into two main types: open-front and closed-front booths. Open-front booths are typically used for smaller projects and are easy to set up and operate. On the other hand, closed-front booths are often used in high-volume industrial settings because they provide more controlled conditions and reduce the risk of contamination.
EMS Powder Coating Equipment provides high-quality powder coating booths tailored to the specific needs of your operation. Their booths are designed for maximum efficiency, with advanced filtration systems that keep the workspace safe and reduce powder loss. EMS booths are also easy to clean and maintain, ensuring minimal downtime between shifts.
3. Curing Ovens
Once the powder has been applied to the surface, the object must be cured in an oven to allow the powder to melt, flow, and form a continuous coating. Curing ovens are vital to the powder coating process, as they ensure that the powder bonds correctly to the substrate, resulting in a hard, smooth, and durable finish. There are several types of curing ovens available, including convection ovens, infrared ovens, and hybrid ovens.
- Convection Ovens: These are the most common type of curing ovens used in powder coating. Convection ovens use hot air to raise the temperature of the coated object, allowing the powder to cure. They are highly efficient and work well with a variety of materials, making them a popular choice for many manufacturers.
- Infrared Ovens: These ovens use infrared energy to heat the powder coating. Infrared ovens can provide rapid heating and are particularly useful for objects that have complex shapes or are made from materials that are sensitive to high temperatures.
- Hybrid Ovens: Hybrid ovens combine both convection and infrared technologies, providing the benefits of both systems. They offer fast heating and uniform curing, making them ideal for high-precision applications.
EMS Powder Coating Equipment manufactures curing ovens that are optimized for fast and even curing, ensuring that each product has a perfect finish. Whether you need a gas-powered or electric oven, EMS provides custom solutions that meet the specific needs of your production line.
Types of Powder Coating Equipment
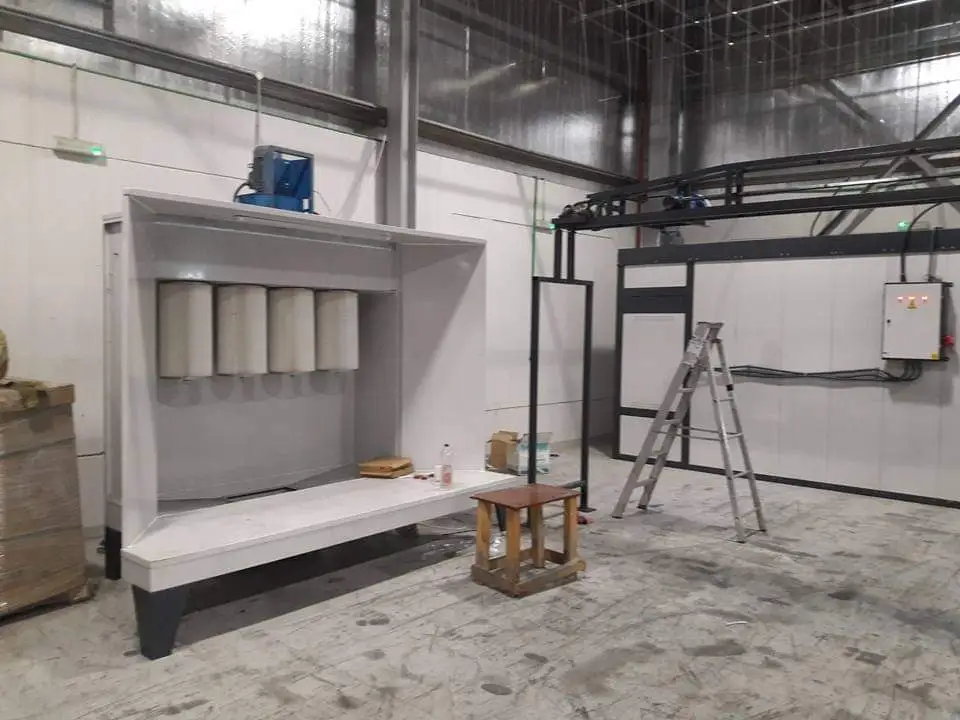
Powder coating systems can be categorized into several types based on their level of automation, the type of operation they support, and their specific functions. Understanding the differences between these systems can help businesses select the right equipment for their needs.
1. Manual vs. Automatic Systems
Powder coating systems are available in both manual and automatic configurations. Each system has its own advantages, depending on the scale and nature of the operation.
- Manual Systems: Manual powder coating systems are ideal for smaller projects or businesses that require flexibility in their production. Operators use handheld electrostatic spray guns to apply powder to objects, allowing for greater control over the process. While manual systems require more labor, they are often more cost-effective for businesses with lower production volumes.
- Automatic Systems: Automatic powder coating systems use robotic arms or reciprocators to apply the powder to objects. These systems are highly efficient and allow for precise, repeatable application. Automated systems are commonly used in high-volume manufacturing environments where consistency and speed are essential. Because automatic systems reduce the need for manual labor, they can also help lower operating costs in the long run.
EMS Powder Coating Equipment offers both manual and automatic systems, ensuring that businesses of all sizes can find the right equipment for their needs. Their automatic systems are designed for high efficiency and consistent results, making them a top choice for manufacturers seeking to increase productivity.
2. Batch vs. Conveyorized Systems
Another important distinction in powder coating equipment is between batch and conveyorized systems.
- Batch Systems: In a batch system, objects are coated one at a time or in small groups. After the powder is applied, the objects are placed in a curing oven. Batch systems are ideal for smaller production runs or when flexibility is required. They allow operators to handle various parts and products in small quantities.
- Conveyorized Systems: Conveyorized systems are used in large-scale production environments. In this system, objects move through the powder coating line on a conveyor belt, passing through the spray booth and curing oven without the need for manual handling. Conveyorized systems are highly efficient and are the best choice for high-volume operations that need to coat large quantities of parts consistently and quickly.
EMS Powder Coating Equipment provides robust batch and conveyorized systems tailored to different production needs. Whether you need a flexible batch system for custom work or a conveyorized system for high-speed production, EMS offers solutions that enhance productivity and ensure high-quality finishes.
Why Choose EMS Powder Coating Equipment?
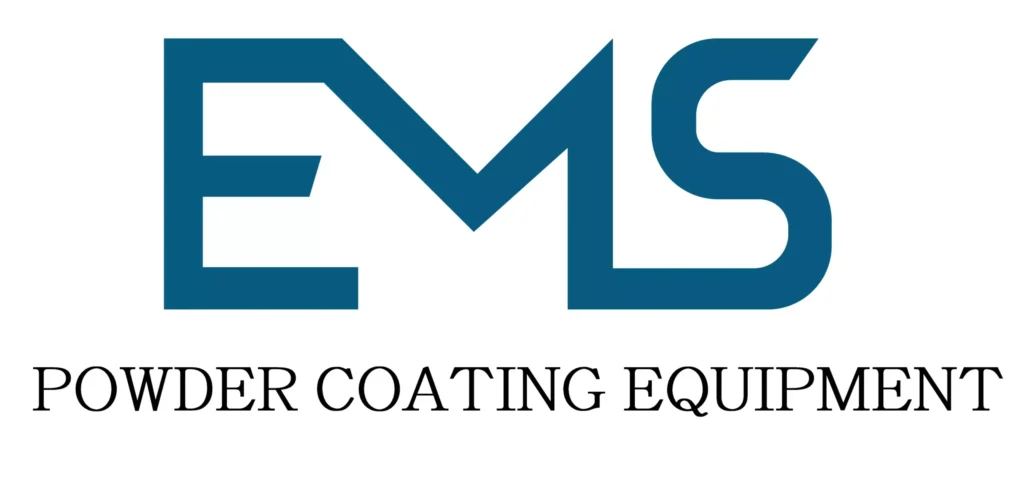
When it comes to selecting powder coating equipment, businesses must consider multiple factors such as efficiency, reliability, ease of use, and cost-effectiveness. EMS Powder Coating Equipment excels in all of these areas, offering top-of-the-line solutions that meet the needs of various industries. Below are several reasons why EMS is regarded as the best manufacturer of powder coating equipment.
1. Cutting-Edge Technology and Innovation
EMS Powder Coating Equipment has built its reputation on a foundation of innovation and cutting-edge technology. The company continuously invests in research and development to ensure that its equipment stays ahead of the competition. EMS systems are designed with the latest advancements in electrostatic application technology, providing users with superior precision and control.
From advanced automatic reciprocators to highly efficient curing ovens, EMS equipment incorporates state-of-the-art features that ensure smooth and reliable operation. The company’s commitment to technological innovation ensures that customers receive equipment that is not only efficient but also future-proof, capable of adapting to evolving industry demands.
For instance, EMS’s automated spray systems are equipped with sophisticated controls that allow for fine-tuning of the powder application process, ensuring that the coating is applied consistently across all surfaces, regardless of shape or size. These systems can be programmed for different jobs, making them ideal for high-volume operations where efficiency is paramount.
2. Customization and Versatility
Every business has unique needs, and EMS Powder Coating Equipment understands the importance of providing customizable solutions. Whether you’re running a small-scale operation or a large industrial plant, EMS offers a variety of equipment configurations tailored to your specific requirements.
One of the standout features of EMS is its ability to deliver both standard and customized powder coating systems. If your production line has particular space constraints or operational needs, EMS can provide specialized configurations to maximize your space while optimizing performance. This level of flexibility sets EMS apart from many competitors who only offer off-the-shelf solutions.
Moreover, EMS equipment is versatile and adaptable across a wide range of industries. Whether you’re working in automotive manufacturing, furniture production, or consumer goods, EMS’s systems can handle different materials and product sizes with ease. This versatility ensures that businesses investing in EMS Powder Coating Equipment are making a long-term investment that will pay dividends across various projects.
3. Durability and Reliability
Powder coating equipment represents a significant investment for any business, so it’s crucial that the systems you choose are built to last. EMS Powder Coating Equipment is renowned for the durability and reliability of its products. All equipment is designed with high-quality materials that can withstand the rigors of daily industrial use, ensuring minimal maintenance and long service life.
EMS takes pride in manufacturing powder coating systems that are not only highly efficient but also reliable under continuous operation. This means fewer breakdowns, less downtime, and reduced maintenance costs, all of which contribute to increased productivity and profitability for businesses.
The reliability of EMS systems is backed by rigorous quality control measures. Each piece of equipment undergoes thorough testing before being delivered to customers, ensuring that it meets the highest standards of performance and safety.
4. Energy Efficiency
Energy consumption is a critical consideration for any business, particularly in industries with high operational costs. EMS Powder Coating Equipment is designed to maximize energy efficiency without compromising performance. This focus on energy conservation helps businesses reduce their operational expenses while also minimizing their environmental footprint.
EMS offers high-efficiency curing ovens that use innovative technology to ensure uniform heat distribution and rapid curing times. These ovens consume less energy compared to traditional models, helping businesses cut down on utility costs. Additionally, EMS systems are designed to reduce powder waste, allowing operators to reclaim and reuse powder that is not deposited on the substrate, further boosting cost savings and sustainability.
5. Exceptional Customer Support and After-Sales Service
Another significant factor that sets EMS Powder Coating Equipment apart is the company’s commitment to customer support. Purchasing industrial equipment is a long-term investment, and EMS ensures that customers receive ongoing support throughout the life of their equipment.
From the initial consultation to installation and training, EMS offers comprehensive support to ensure that businesses get the most out of their systems. The company also provides maintenance and repair services, ensuring that any issues are addressed promptly to avoid prolonged downtime. This dedication to after-sales service gives EMS customers peace of mind, knowing that their equipment is backed by a team of experts ready to assist at any time.
6. Proven Track Record and Global Reach
With years of experience and a global client base, EMS Powder Coating Equipment has established itself as a leading manufacturer in the industry. The company has successfully partnered with businesses across the world, delivering equipment that has helped manufacturers improve their processes and quality.
EMS’s extensive portfolio of clients includes companies from a wide range of industries, including automotive, aerospace, furniture, and consumer goods. This broad industry experience ensures that EMS understands the specific needs of different sectors and can tailor solutions accordingly.
Trends and Innovations in Powder Coating Equipment
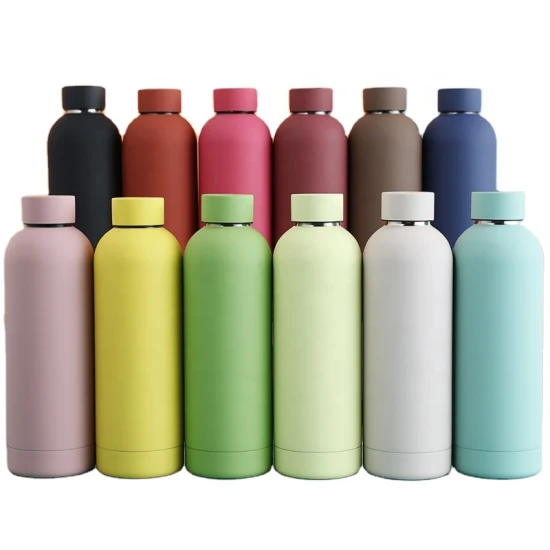
The powder coating industry is constantly evolving, with new technologies and trends shaping the way businesses operate. EMS Powder Coating Equipment stays at the forefront of these developments, ensuring that its customers benefit from the latest innovations in the field. Below are some of the key trends currently influencing powder coating technology:
1. Automation and Industry 4.0 Integration
Automation is becoming increasingly prevalent in the powder coating industry, with businesses looking for ways to improve efficiency and reduce labor costs. Automated systems, such as EMS’s powder coating reciprocators, allow for more consistent application and faster production times. Industry 4.0 integration, including the use of smart sensors and data analytics, is also making it easier for manufacturers to monitor and optimize their powder coating operations in real-time.
EMS has embraced these trends by offering equipment that can be fully integrated into modern manufacturing systems. This allows businesses to streamline their operations and improve overall productivity while maintaining high levels of quality.
2. Sustainability and Eco-Friendly Solutions
As industries become more focused on sustainability, the demand for environmentally friendly powder coating solutions continues to grow. Powder coating is inherently eco-friendly because it produces minimal waste and contains no solvents, which reduces VOC emissions. However, EMS has taken sustainability a step further by designing energy-efficient systems that consume less power while maintaining optimal performance.
These innovations make EMS Powder Coating Equipment the ideal choice for businesses seeking to reduce their environmental impact without sacrificing quality or efficiency.
3. Advanced Material Compatibility
New advances in powder coating materials are allowing manufacturers to coat a wider range of substrates, including plastics and composites. EMS’s powder coating systems are designed to handle these advanced materials, providing businesses with the flexibility to expand their product offerings.
Conclusion
Powder coating has become a cornerstone in modern manufacturing, providing businesses with a durable, environmentally friendly, and cost-effective way to protect their products. However, achieving the best results requires investing in high-quality equipment.
EMS Powder Coating Equipment stands out as the industry leader, offering advanced technology, customization options, and exceptional reliability. Whether you are looking for manual systems for small-scale operations or automated systems for large industrial plants, EMS provides tailored solutions that meet your specific needs. Their commitment to innovation, durability, and energy efficiency ensures that businesses can maximize their productivity while minimizing costs and environmental impact.
With a proven track record of success and an unwavering dedication to customer satisfaction, EMS Powder Coating Equipment is the best choice for businesses looking to enhance their powder coating operations.
Automatic Powder Coating Equipment: A Revolution in Efficiency and Precision

The powder coating industry has experienced significant advancements in recent years, with automation playing a key role in improving production efficiency, consistency, and overall quality. Automatic powder coating equipment has transformed the way manufacturers apply powder coatings, enabling them to increase throughput while maintaining precise control over the application process. This technology is particularly valuable in high-volume production environments, where consistent quality and reduced operational costs are critical for success.
Automatic powder coating systems use advanced robotic systems, reciprocators, and intelligent controls to streamline the coating process. These systems are designed to apply powder evenly and consistently, reducing waste, improving the quality of the finish, and lowering labor costs. By removing the human element from most stages of the coating process, automatic systems provide a higher level of accuracy and reproducibility.
EMS Powder Coating Equipment is at the forefront of this revolution, offering state-of-the-art automatic systems that cater to the needs of industries around the globe. Known for their advanced technology, reliability, and customizable solutions, EMS’s automatic powder coating equipment is trusted by manufacturers who require high precision and efficiency in their production lines. In this guide, we’ll explore the features of automatic powder coating systems, their benefits, and why EMS Powder Coating Equipment is the best choice for businesses looking to automate their powder coating process.
What is Automatic Powder Coating Equipment?
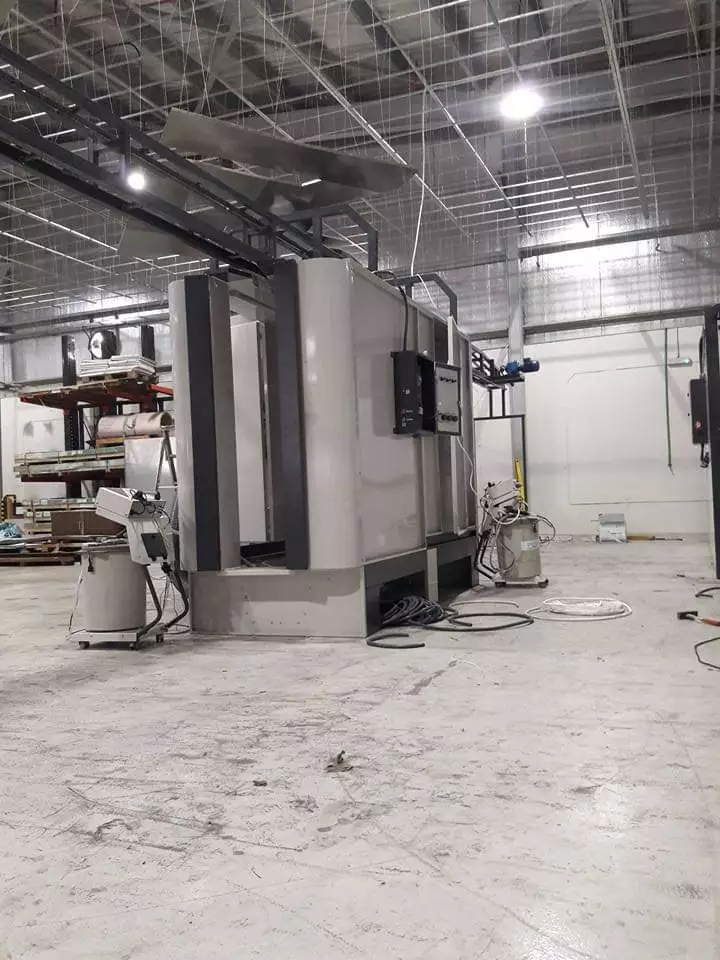
Automatic powder coating equipment refers to a fully automated system that applies powder coatings to products with minimal human intervention. These systems typically consist of several key components, including automatic spray guns, reciprocators, conveyors, and curing ovens. Each of these components works together seamlessly to ensure that powder is applied uniformly and efficiently.
1. Automatic Spray Guns
The core of any automatic powder coating system is the spray gun. In an automated setup, multiple spray guns are mounted on robotic arms or reciprocators that move in precise, pre-programmed patterns. These guns are electrostatically charged, allowing the powder particles to adhere to the product surface through an electrostatic field. The guns can adjust their position and angle to coat even complex or irregular shapes with ease.
One of the primary advantages of automatic spray guns is their ability to apply powder coatings with extreme consistency. Since they follow pre-programmed patterns, there is no variation in the application process, resulting in a uniform coat every time. Additionally, these systems reduce overspray and powder wastage, leading to cost savings.
EMS Powder Coating Equipment offers some of the most advanced automatic spray gun systems in the industry. Their spray guns are designed for maximum precision and can be programmed to handle different product sizes and shapes, ensuring a consistent finish across the entire production run.
2. Reciprocators
Reciprocators are the components that control the vertical movement of the spray guns, allowing them to cover the full height of the object being coated. Reciprocators are typically used in conjunction with conveyorized systems, where parts move through the spray booth at a constant speed. The reciprocators move the spray guns up and down, ensuring even coverage over the entire surface of the product.
Automatic reciprocators are crucial in high-speed production environments, where consistency and speed are essential. These systems can be programmed to adjust their speed and range of motion depending on the size and shape of the product, making them ideal for complex parts or large quantities of products.
EMS Powder Coating Equipment specializes in advanced reciprocators that can be customized to fit any production line. Their systems are known for their reliability and smooth operation, ensuring that products are evenly coated without any gaps or inconsistencies.
3. Conveyor Systems
In an automatic powder coating setup, the conveyor system moves products through the various stages of the coating process, including the spray booth and curing oven. Conveyorized systems allow for continuous production, increasing throughput and reducing the need for manual handling.
Conveyors can be programmed to adjust their speed based on the complexity of the parts being coated or the specific requirements of the coating process. This flexibility makes automatic powder coating systems highly adaptable to different production environments.
EMS Powder Coating Equipment offers conveyor systems that integrate seamlessly with their automatic spray guns and reciprocators. Their conveyor systems are designed for high efficiency and can handle a wide range of product sizes and weights, making them ideal for industries such as automotive, furniture, and appliance manufacturing.
The Benefits of Automatic Powder Coating Equipment
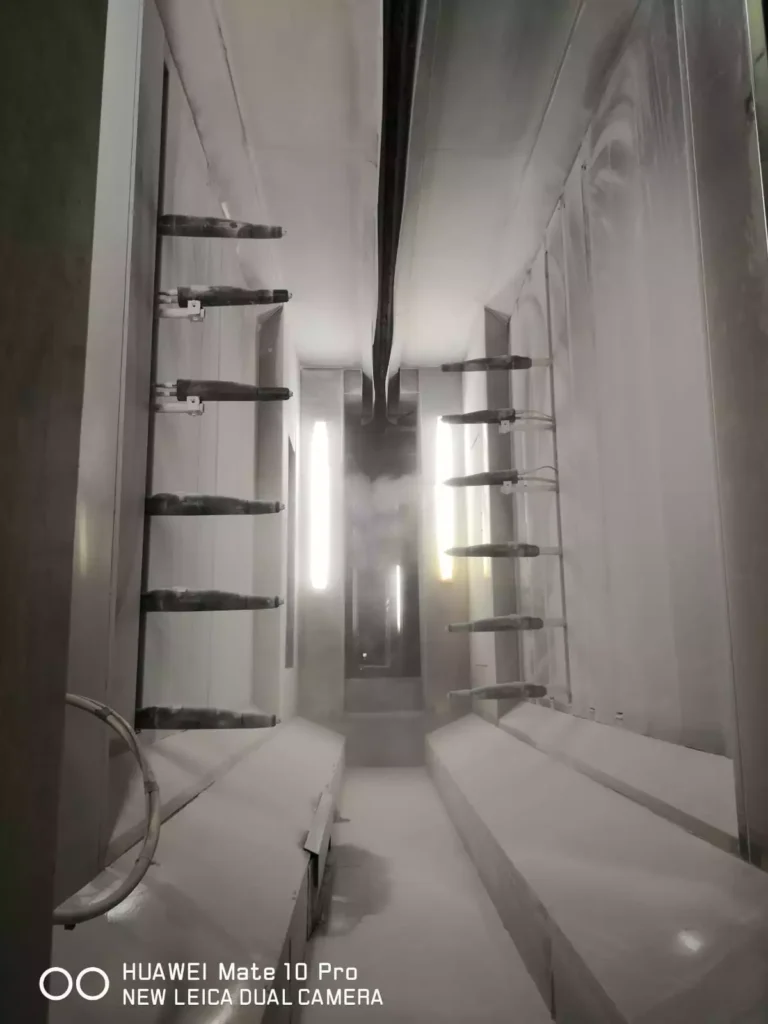
Automation in powder coating has introduced several key advantages that have revolutionized the industry. Below are some of the most significant benefits of automatic powder coating equipment:
1. Improved Consistency and Quality
One of the biggest challenges in manual powder coating is achieving consistent results. Human operators, while skilled, are prone to variability in their application methods, which can lead to uneven coating thickness, poor adhesion, or defects in the finish. Automatic powder coating systems eliminate these issues by providing consistent, repeatable application.
Since automatic spray guns and reciprocators follow precise, pre-programmed instructions, every product receives the same level of coating, ensuring a high-quality finish on each item. This consistency is especially important for industries that produce large quantities of parts and need to meet strict quality standards.
EMS Powder Coating Equipment ensures that their automatic systems deliver uniform coating results, with even powder distribution and minimal overspray. This results in a durable, high-quality finish that meets or exceeds industry standards.
2. Increased Production Efficiency
Automatic powder coating equipment is designed to optimize the entire coating process, significantly increasing production efficiency. By automating the application process, businesses can coat more parts in less time, resulting in higher throughput. This is particularly beneficial for industries with high production volumes, where speed and efficiency are critical to meeting demand.
The integration of conveyor systems into automatic setups also reduces the need for manual handling of parts, minimizing downtime and labor costs. Products move seamlessly from the spray booth to the curing oven without interruption, further streamlining the process.
For manufacturers that need to maximize output, EMS Powder Coating Equipment offers fully integrated automatic systems that work in harmony to reduce bottlenecks and improve production flow.
3. Reduced Labor Costs
Automation reduces the need for manual labor in the powder coating process, leading to significant cost savings for businesses. In manual setups, skilled operators are required to oversee the application of the powder, adjust the equipment, and ensure that each product is coated evenly. In contrast, automatic systems can handle these tasks without the need for constant supervision.
By reducing labor requirements, businesses can allocate their workforce to other areas of production or reduce overall labor costs. Automatic systems also reduce the likelihood of human error, further decreasing the need for rework or repairs.
With EMS Powder Coating Equipment, manufacturers can implement automatic systems that not only reduce labor costs but also improve overall operational efficiency.
4. Enhanced Flexibility and Adaptability
One of the misconceptions about automatic powder coating systems is that they are rigid and inflexible. However, modern automatic systems, like those provided by EMS Powder Coating Equipment, are highly adaptable and can be configured to handle a wide range of products.
These systems can be programmed to adjust the speed, powder flow rate, and gun positioning to accommodate different shapes, sizes, and coating requirements. This makes them suitable for a variety of industries, from automotive parts to consumer electronics. Additionally, with programmable systems, businesses can quickly switch between different product lines, allowing for greater flexibility in production.
5. Lower Powder Waste
Powder waste is a common issue in manual powder coating processes. Overspray and uneven application often result in excess powder being lost, leading to higher material costs. Automatic systems are designed to minimize waste by ensuring that the powder is applied evenly and only where it is needed.
Many automatic systems also include powder recovery systems that capture unused powder and recycle it back into the process. This not only reduces material costs but also contributes to a more sustainable, environmentally friendly operation.
EMS Powder Coating Equipment offers advanced powder recovery systems that integrate seamlessly with their automatic equipment, ensuring that businesses can operate efficiently while minimizing waste.
6. Scalability and Future-Proofing
Automatic powder coating equipment is highly scalable, making it an excellent long-term investment for businesses looking to grow. As production volumes increase, automatic systems can be expanded or upgraded to handle larger workloads without sacrificing quality or efficiency. This scalability ensures that businesses can continue to meet demand as they grow, without the need to completely overhaul their equipment.
Furthermore, the technology behind automatic powder coating systems is constantly evolving. By investing in high-quality equipment from manufacturers like EMS Powder Coating Equipment, businesses can future-proof their operations and stay competitive in an increasingly automated industry.
Why EMS Powder Coating Equipment is the Best Choice for Automatic Systems
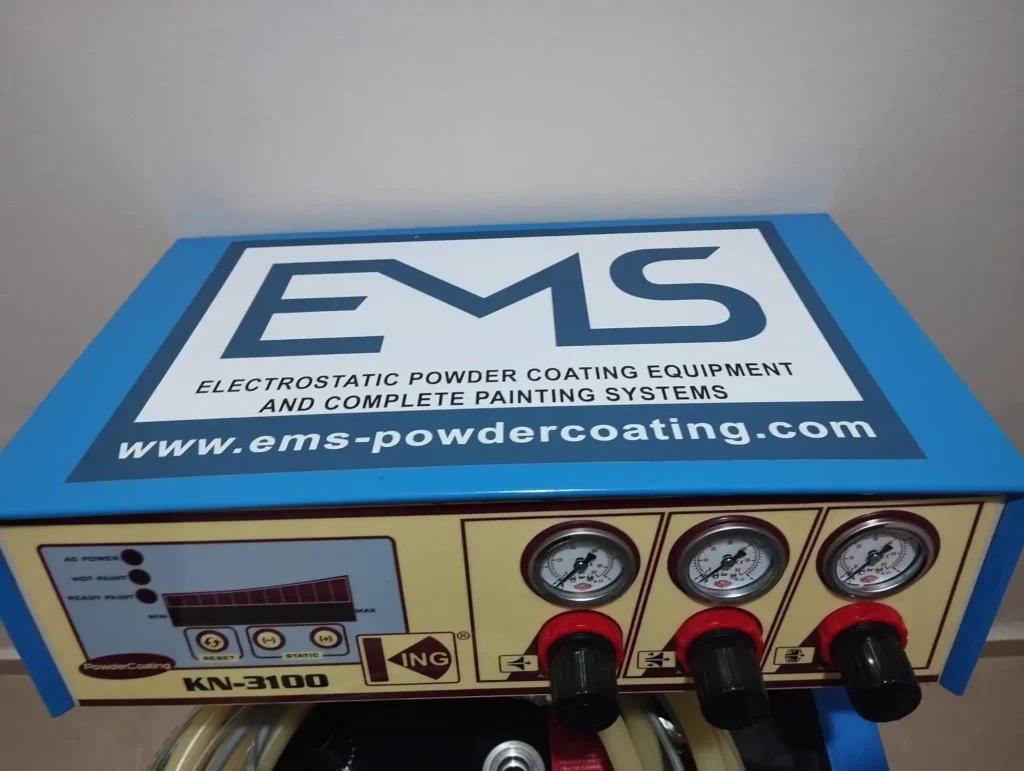
When selecting automatic powder coating equipment, it’s essential to choose a manufacturer that not only offers advanced technology but also understands the unique needs of your business. EMS Powder Coating Equipment stands out as the best choice for several reasons:
1. Industry-Leading Technology
EMS Powder Coating Equipment is known for its cutting-edge technology, offering some of the most advanced automatic systems available. Their equipment is designed to maximize efficiency, reduce waste, and provide consistent, high-quality finishes across all products. With features such as programmable spray guns, intelligent reciprocators, and high-efficiency conveyor systems, EMS equipment ensures that businesses can achieve superior results with minimal effort.
2. Customization and Flexibility
Every manufacturing operation is different, and EMS understands the importance of providing equipment that meets the specific needs of each customer. EMS offers customizable automatic systems that can be tailored to your production line, whether you’re coating small parts or large, complex products. This level of flexibility ensures that businesses get the most out of their investment, with equipment that can adapt to changing needs.
3. Reliability and Durability
EMS Powder Coating Equipment is renowned for the reliability and durability of its products. Built with high-quality materials and engineered for long-term performance, EMS systems are designed to withstand the rigors of continuous industrial use. This means fewer breakdowns, less downtime, and lower maintenance costs, all of which contribute to increased productivity and profitability.
4. Superior Support and Service
In addition to offering top-tier equipment, EMS provides exceptional customer support and after-sales service. From installation and training to ongoing maintenance and troubleshooting, EMS is committed to ensuring that customers get the most out of their automatic systems. Their team of experts is always available to provide guidance and assistance, making them a trusted partner for businesses around the world.
Conclusion
Automatic powder coating equipment represents a significant advancement in the manufacturing industry, offering businesses improved efficiency, consistency, and cost savings. With the ability to handle high-volume production while maintaining precise control over the coating process, automatic systems are an essential tool for any manufacturer looking to stay competitive.
EMS Powder Coating Equipment is the industry leader in automatic powder coating systems, providing advanced technology, customizable solutions, and unmatched reliability. Whether you’re seeking to automate your production line for the first time or upgrade your existing equipment, EMS offers the expertise and products needed to take your powder coating operation to the next level.
By investing in EMS automatic powder coating equipment, businesses can increase productivity, reduce costs, and ensure a consistently high-quality finish for their products. With a proven track record of success and a commitment to innovation, EMS is the best choice for manufacturers looking to optimize their powder coating process.
Powder Coating Reciprocators: Precision and Efficiency for Perfect Coating Applications

In the powder coating process, ensuring consistent coverage across a product’s surface is essential for both aesthetic appeal and functional protection. While spray guns deliver the powder to the product, powder coating reciprocators are the backbone of automation, enabling the precise, efficient movement of the guns. These devices move spray guns in vertical or horizontal patterns, ensuring that the powder is applied evenly over the entire surface of the object being coated.
Powder coating reciprocators are vital for operations where large volumes of parts must be coated consistently and quickly, such as in automotive, electronics, and industrial manufacturing. They automate the repetitive movements required during powder coating, reducing labor, increasing throughput, and improving the overall quality of the finished product.
EMS Powder Coating Equipment is a trusted manufacturer of advanced reciprocator systems designed to meet the rigorous demands of industrial coating applications. EMS reciprocators are known for their reliability, precision, and adaptability, making them the ideal solution for businesses looking to optimize their powder coating processes. In this guide, we’ll delve into the functionality of powder coating reciprocators, explore their benefits, and discuss why EMS Powder Coating Equipment provides the best reciprocators on the market.
What is a Powder Coating Reciprocator?
A powder coating reciprocator is a piece of automated equipment designed to move spray guns in a controlled, repetitive motion to ensure consistent powder application across the entire surface of a product. The reciprocator is typically used in conjunction with automated spray guns and conveyor systems, forming an essential part of an automated powder coating line.
The movement of the reciprocator is typically either vertical or horizontal, depending on the shape and size of the object being coated. The spray guns, mounted on the reciprocator, move in synchronized patterns to cover every area of the object evenly. This motion is particularly useful for coating large or complex objects, as it ensures that no areas are missed and that the powder is applied at the correct thickness.
Reciprocators can be used for a wide range of applications, from flat surfaces like panels to intricate shapes with multiple contours. They are commonly used in industries where precision and consistency are critical, such as:
- Automotive parts: Car bodies, frames, and other components require even coating to ensure durability and corrosion resistance.
- Metal fabrication: Industrial equipment, furniture, and appliances benefit from uniform powder coating for both aesthetics and performance.
- Electronics: Certain electronics components require protective powder coatings that can only be applied evenly with the help of a reciprocator.
While manual powder coating requires operators to control the movement of the spray gun, reciprocators automate this process, ensuring that the application is performed with extreme accuracy. This eliminates human error and ensures that every part coated meets strict quality standards.
EMS Powder Coating Equipment provides advanced reciprocator systems that offer precision control, robust construction, and flexibility for different production needs. Their reciprocators can be programmed to handle a variety of objects, making them ideal for businesses that produce different parts on the same line.
How Powder Coating Reciprocators Work
Powder coating reciprocators work by automating the repetitive motion required to coat parts evenly. Below is an overview of the main components and how they function together to ensure consistent powder application:
1. Spray Gun Movement
The primary function of the reciprocator is to control the movement of the spray guns. These guns are mounted onto the reciprocator’s arms, which move in a vertical or horizontal motion to coat the product evenly. The speed and range of motion can be adjusted based on the size, shape, and complexity of the object being coated.
Spray guns release powder through an electrostatic process, where the powder particles are charged and attracted to the grounded object. This ensures that the powder adheres to every part of the object, even in difficult-to-reach areas like corners or crevices.
EMS Powder Coating Equipment manufactures reciprocators that provide precise control over spray gun movement. Their systems allow for easy adjustment of the speed and stroke length, ensuring that the coating is applied with maximum efficiency and minimal overspray. This not only improves the quality of the finish but also reduces powder wastage, leading to significant cost savings.
2. Synchronization with Conveyor Systems
In most automated powder coating lines, reciprocators work alongside conveyor systems. As parts move through the spray booth on a conveyor belt, the reciprocator moves the spray guns in sync with the parts, ensuring that every object receives uniform coating. The reciprocator’s movement is programmed to match the speed of the conveyor, ensuring that no areas are missed or over-coated.
This synchronization is critical for maintaining production efficiency and consistency. In high-speed production environments, such as automotive or appliance manufacturing, even slight misalignment between the reciprocator and conveyor can lead to defects or uneven coatings.
EMS Powder Coating Equipment integrates their reciprocators seamlessly with conveyor systems. Their reciprocators are equipped with advanced sensors and controls that ensure perfect synchronization, even in high-speed operations. This allows businesses to maintain consistent quality without slowing down production.
3. Programmable Motion and Flexibility
Modern reciprocators offer a high degree of flexibility, allowing manufacturers to program their motion patterns based on the specific needs of the product being coated. For instance, some objects may require more complex coating patterns, especially if they have intricate shapes or multiple surfaces that need to be coated at different angles.
Reciprocators can be programmed to adjust the speed of their movement, the distance between the spray guns and the object, and even the number of passes the guns make over the surface. This ensures that each product receives the correct amount of powder, regardless of its shape or size.
EMS Powder Coating Equipment provides reciprocators that are fully programmable, allowing businesses to adjust their settings based on production requirements. Whether coating flat panels or more complex parts, EMS reciprocators deliver the precision needed to achieve perfect results.
4. Maintenance and Durability
Given that reciprocators are a crucial part of any automated powder coating system, their durability and ease of maintenance are important factors to consider. High-quality reciprocators should be built to withstand continuous operation in demanding industrial environments without frequent breakdowns or downtime.
EMS Powder Coating Equipment designs their reciprocators with robust materials and engineering to ensure long-lasting performance. Their systems require minimal maintenance, and any routine servicing is made easy by their user-friendly design. This reliability reduces the risk of costly downtime, allowing businesses to keep their production lines running smoothly.
The Benefits of Using Powder Coating Reciprocators
Powder coating reciprocators offer numerous benefits that make them indispensable in modern manufacturing environments. Here are some of the key advantages:
1. Improved Coating Consistency
Manual powder coating relies heavily on the skill and experience of the operator. While experienced workers can achieve excellent results, manual coating is inherently prone to variability. Even slight inconsistencies in movement or technique can lead to uneven coating thickness, overspray, or missed areas.
Powder coating reciprocators eliminate these issues by providing precise, repeatable motion. Once programmed, the reciprocator applies the powder in the exact same way every time, ensuring uniform coverage across all parts. This consistency leads to better overall product quality and reduces the risk of rework.
EMS Powder Coating Equipment is known for its high-precision reciprocators that deliver flawless results. Their systems ensure that every part receives the same level of coating, leading to a more durable and attractive finish.
2. Increased Production Efficiency
Automating the movement of the spray guns allows businesses to significantly increase their production speed. Manual powder coating requires operators to move the spray gun around the part, a process that can be slow and labor-intensive. Reciprocators, on the other hand, can coat parts at a much faster rate, especially when used in conjunction with conveyor systems.
In high-volume production environments, this increase in efficiency can lead to significant cost savings. More parts can be coated in less time, allowing businesses to meet customer demand without compromising on quality.
With EMS Powder Coating Equipment, manufacturers benefit from reciprocators designed to maximize efficiency. Their systems can be integrated into fast-paced production lines, enabling businesses to boost their output while maintaining excellent coating quality.
3. Reduced Labor Costs
Automating the powder coating process with reciprocators reduces the need for skilled labor. Manual powder coating requires operators to be trained in the correct application techniques, and businesses must rely on these operators to consistently produce high-quality results. By automating this process, businesses can reduce their reliance on manual labor and lower their overall labor costs.
Reciprocators allow businesses to allocate their workforce to other areas of production, improving overall efficiency. Additionally, because automated systems reduce the risk of human error, businesses can also reduce the costs associated with rework or defective products.
EMS Powder Coating Equipment provides advanced reciprocator systems that minimize the need for manual intervention, allowing businesses to lower labor costs while maintaining high-quality standards.
4. Versatility Across Different Products
One of the standout benefits of powder coating reciprocators is their versatility. These systems can be programmed to coat a wide variety of products, from flat panels to complex parts with multiple angles and surfaces. This flexibility makes reciprocators suitable for businesses that produce a diverse range of products or frequently change their production lines.
EMS Powder Coating Equipment’s reciprocators are highly adaptable, allowing manufacturers to coat different types of parts without needing to reconfigure the entire system. Whether coating small, intricate parts or large industrial components, EMS’s reciprocators ensure that every product is coated with precision and consistency.
5. Powder Efficiency and Waste Reduction
In manual powder coating, overspray and powder waste are common issues. Even skilled operators may have difficulty applying powder evenly, leading to excess powder being wasted. Reciprocators, on the other hand, are designed to apply the exact amount of powder needed, reducing overspray and improving overall efficiency.
Many reciprocator systems also include powder recovery systems, which capture any unused powder and recycle it back into the system. This not only reduces material costs but also makes the coating process more environmentally friendly.
EMS Powder Coating Equipment offers reciprocators with advanced powder recovery systems, ensuring that businesses can minimize waste and operate more sustainably. By reducing powder waste, EMS systems help businesses cut costs and lower their environmental impact.
Why Choose EMS Powder Coating Equipment for Reciprocators?
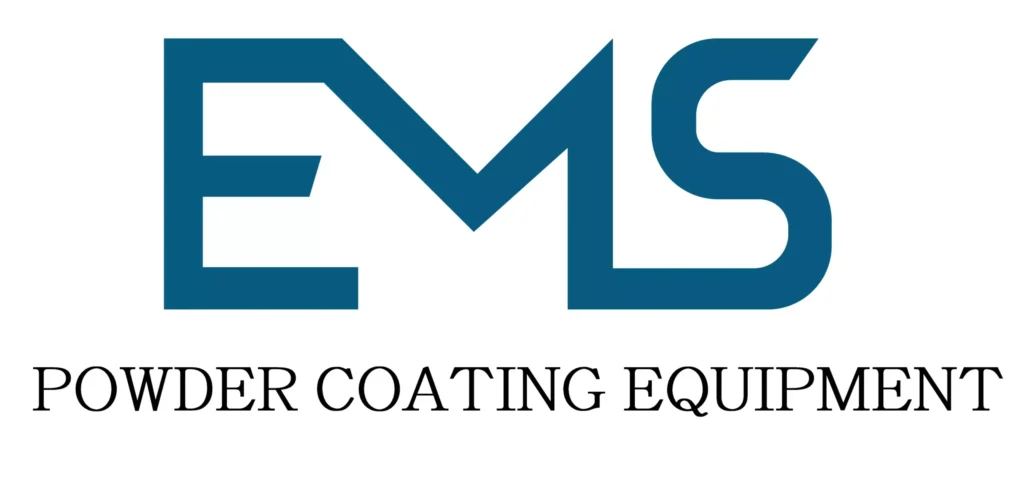
Choosing the right powder coating reciprocator is critical for achieving the best results in your production line. EMS Powder Coating Equipment is the industry leader in reciprocator technology, offering systems that are designed for precision, efficiency, and durability. Here’s why EMS is the best choice for businesses looking to invest in reciprocators:
1. Advanced Technology for Precision Control
EMS reciprocators are equipped with the latest technology, allowing for precise control over spray gun movement. Their systems can be programmed to meet the specific needs of your production line, ensuring that every part is coated evenly. Whether you’re coating flat panels or complex shapes, EMS reciprocators provide the accuracy needed to achieve perfect results.
2. Customization and Flexibility
Every business has unique coating requirements, and EMS understands the importance of providing customizable solutions. EMS reciprocators can be tailored to fit your specific production line, with adjustable stroke lengths, speeds, and motion patterns. This flexibility allows businesses to optimize their powder coating process and maximize efficiency.
3. Durability and Reliability
Built with high-quality materials and engineering, EMS reciprocators are designed for long-lasting performance. These systems are robust enough to withstand continuous operation in demanding industrial environments, ensuring that businesses can rely on them for years without frequent maintenance or breakdowns.
4. Seamless Integration with Existing Systems
EMS reciprocators are designed to integrate seamlessly with other equipment in your powder coating line, including conveyor systems and curing ovens. This ensures that your production line operates smoothly and efficiently, with minimal downtime or disruption.
Conclusion
Powder coating reciprocators are a key component of any automated coating system, providing the precision and efficiency needed to produce consistent, high-quality finishes. By automating the movement of spray guns, reciprocators ensure that every product is coated evenly, reducing the risk of defects and improving overall production efficiency.
EMS Powder Coating Equipment offers the best reciprocators on the market, designed to meet the needs of businesses in a wide range of industries. With advanced technology, customizable solutions, and a commitment to durability and reliability, EMS ensures that your powder coating process is optimized for maximum efficiency and quality.
Whether you’re looking to automate your production line for the first time or upgrade your existing equipment, EMS Powder Coating Equipment provides the expertise and products needed to take your powder coating operation to the next level.