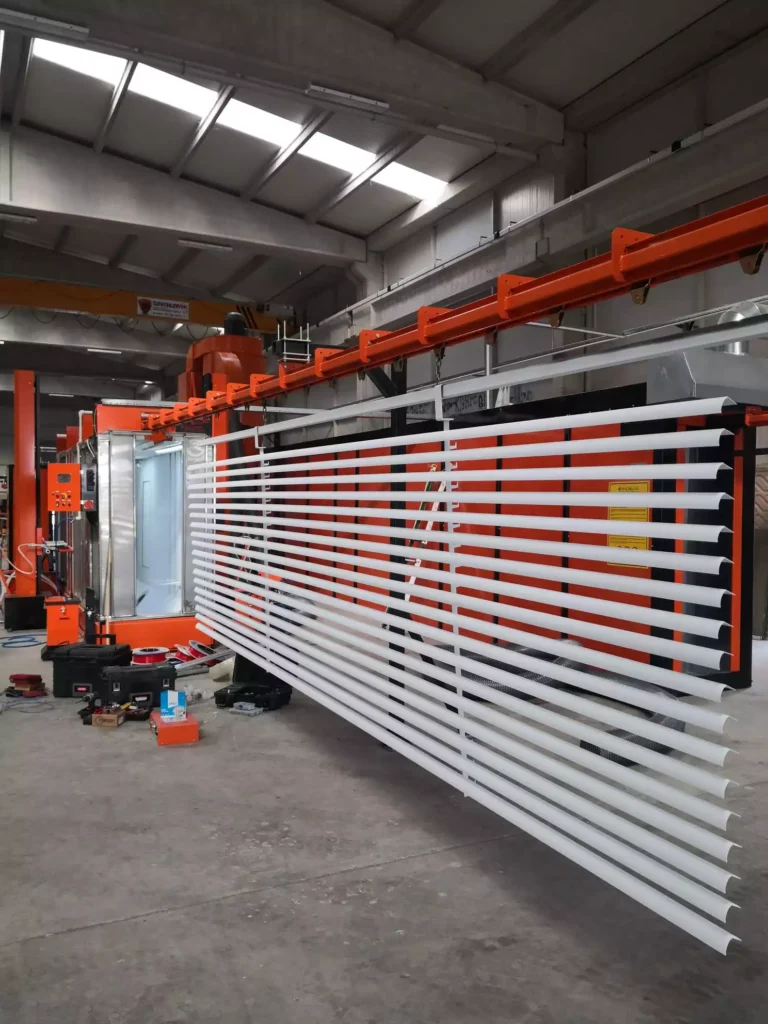
Powder coating equipment is a set of tools and machines used to apply powder coating to a variety of surfaces. The equipment includes:
- Powder coating guns: Powder coating guns are used to spray powder coating onto the surface of the part being coated.
- Powder coating booth: The powder coating booth is a ventilated enclosure that contains the powder coating gun and the part being coated. It helps to collect overspray powder coating and prevent it from contaminating the environment.
- Powder coating oven: The powder coating oven is used to cure the powder coating and make it durable.
- Conveyor belt: The conveyor belt transports the part through the powder coating booth and the powder coating oven.
- Agitator: The agitator mixes the powder coating in the hopper to ensure that it is evenly distributed.
- Hopper: The hopper stores the powder coating until it is needed.
- Filter: The filter removes dust and debris from the powder coating before it is applied to the part.
In addition to these basic pieces of equipment, there are also a number of other accessories that can be used with powder coating equipment, such as:
- Powder coating robots: Powder coating robots are used to automate the powder coating process.
- Powder coating dryers: Powder coating dryers are used to remove moisture from the powder coating before it is applied to the part.
- Powder coating reclaimers: Powder coating reclaimers are used to recover overspray powder coating and recycle it back into the powder coating process.
Powder coating equipment can be used to coat a wide variety of materials, including metal, plastic, wood, and glass. It is a versatile and durable coating that offers a number of benefits, such as:
- Durability: Powder coating is a very durable coating that can withstand a variety of environmental conditions.
- Corrosion resistance: Powder coating is resistant to corrosion, making it ideal for use in outdoor applications.
- Chemical resistance: Powder coating is resistant to a variety of chemicals, making it ideal for use in industrial applications.
- Heat resistance: Powder coating is resistant to heat, making it ideal for use in applications where the part will be exposed to high temperatures.
- Color variety: Powder coating is available in a wide variety of colors, making it possible to create custom finishes.
Powder coating equipment is a valuable tool for businesses that need to coat parts for durability, corrosion resistance, chemical resistance, heat resistance, and color variety.
We manufacture and supply powder coating equipment Germany for our customers in Germany, Austria, and Switzerland. A powder coating oven, powder coating gun, and powder coating machine is used in many different types of powder coating plant. Industrial powder coating is becoming more and more popular in Europe as the needs of companies that need powder coating services to have specific requests. Not every powder coating supplier can provide this service at the quality level that the companies need.
Powder Coating Equipment Germany
Powder coating equipment encompasses a range of machinery and tools used to apply and cure powder coatings onto various substrates. This equipment plays a crucial role in various industries, including automotive, appliance, furniture, electronics, construction, and aerospace.
Essential Components of Powder Coating Equipment
A typical powder coating setup involves several key components:
- Pre-Treatment System: This system prepares the workpiece surface for powder adhesion by removing contaminants like grease, oil, and rust. It may involve degreasing, etching, and phosphating.
- Powder Booth: The booth provides a controlled environment for applying the powder coating, preventing overspray and contamination of the surrounding environment.
- Powder Coating Guns: These guns apply the powder onto the workpieces using electrostatic or mechanical principles. Electrostatic guns impart a charge to the powder particles, attracting them to the grounded workpiece, while mechanical guns rely on air pressure to atomize and propel the powder.
- Reciprocator or Robot Arm: This device moves the powder coating guns back and forth over the workpieces, ensuring uniform and consistent powder distribution. Reciprocators are typically used for flat or evenly shaped workpieces, while robot arms offer greater flexibility for complex shapes.
- Curing Oven: The curing oven cures the applied powder coating, transforming it into a durable and hard finish. It heats the powder particles to a specific temperature for a specified time, allowing them to melt, flow, and crosslink.
- Workpiece Handling System: This system transports the workpieces through the various stages of the powder coating process, maintaining proper positioning and orientation. It may involve conveyor belts, rotating turntables, or automated robotic systems.
- Control System: The control system oversees the entire powder coating process, coordinating the operation of the different components, regulating the powder application, and monitoring the curing parameters.
Types of Powder Coating Equipment
Powder coating equipment can be categorized into different types based on the application method, automation level, and workpiece size and shape:
- Manual Powder Coating Equipment: This setup involves manual application of powder using handheld guns, making it suitable for small-scale or low-volume production.
- Automatic Powder Coating Equipment: This system automates the powder application process, significantly increasing production rates and achieving consistent coating quality.
- Reciprocating Powder Coating Systems: These systems utilize a reciprocator to move the powder coating guns over the workpieces, ensuring uniform powder distribution and high-quality finishes.
- Robotic Powder Coating Systems: These systems employ robot arms to move the powder coating guns, offering exceptional flexibility and precision, particularly for complex workpieces or intricate coating requirements.
- Batch Powder Coating Systems: These systems are designed for batch processing, where a batch of workpieces is moved through the powder coating stages simultaneously.
- Continuous Powder Coating Systems: These systems are suitable for high-volume production, continuously feeding workpieces into the powder coating process.
- Powder Coating Equipment for Specific Applications: There are specialized powder coating systems tailored to specific applications, such as automotive, appliance, and furniture coating.
- Powder Recovery Systems: These systems collect and recycle overspray powder, reducing waste and minimizing environmental impact.
Selection Criteria for Powder Coating Equipment
The choice of powder coating equipment depends on several factors:
- Production Volume: For high-volume production, automatic systems are essential.
- Workpiece Size and Shape: Complex workpieces may require robotic systems, while reciprocating systems are suitable for flat or evenly shaped workpieces.
- Desired Coating Quality: Automation and advanced guns ensure consistent coating quality.
- Budget: Manual systems are cost-effective for small-scale operations, while automated systems offer higher productivity and quality for larger volumes.
- Environmental Considerations: Powder recovery systems minimize environmental impact.
Conclusion
Powder coating equipment plays a crucial role in achieving high-quality, durable, and environmentally friendly finishes for a wide range of products. By selecting the appropriate equipment, optimizing the powder coating process, and maintaining proper maintenance, manufacturers can enhance their production efficiency, reduce costs, and deliver superior powder-coated products to their customers.
Powder coating guns

Powder coating guns are used to spray powder coating onto the surface of the part being coated. There are two main types of powder coating guns: electrostatic guns and tribo guns.
Electrostatic guns use a high voltage charge to attract the powder coating particles to the part being coated. This results in a more even and efficient application of the powder coating.
Tribo guns use friction to charge the powder coating particles. This is a simpler and less expensive technology than electrostatic guns, but it is not as efficient and can result in a less even application of the powder coating.
Powder coating booths
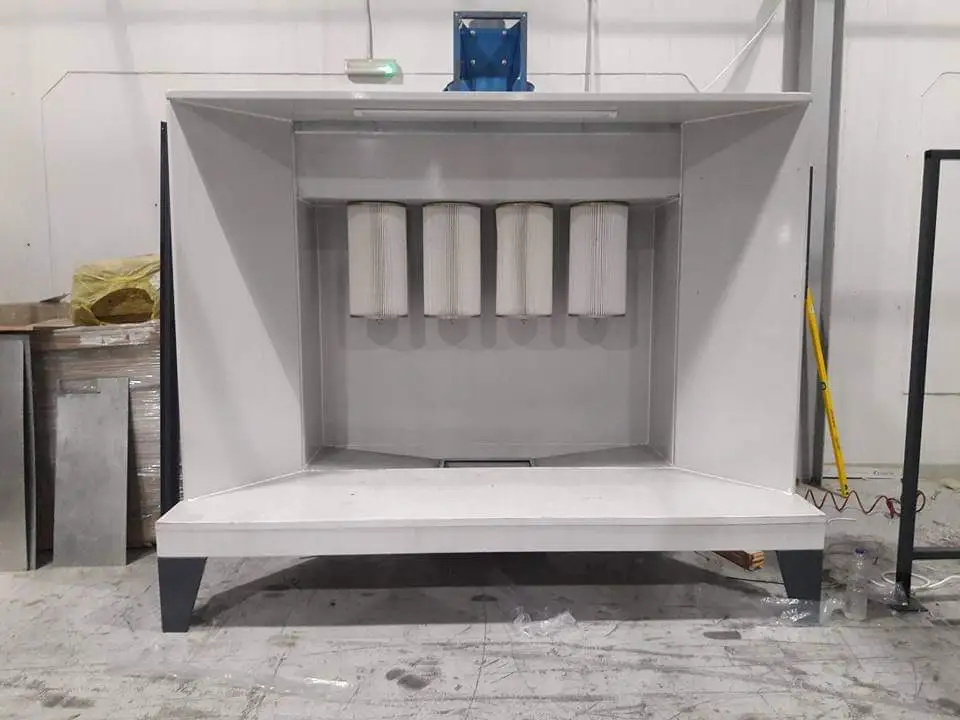
Powder coating booths are ventilated enclosures that contain the powder coating gun and the part being coated. They help to collect overspray powder coating and prevent it from contaminating the environment.
Powder coating booths typically have a number of features to help protect workers and the environment from overspray powder coating, such as:
- Exhaust fans: Exhaust fans remove overspray powder coating from the air inside the booth.
- Filters: Filters remove dust and debris from the air inside the booth.
- Interlocks: Interlocks prevent the powder coating gun from being operated if the booth is not properly ventilated.
Powder coating ovens
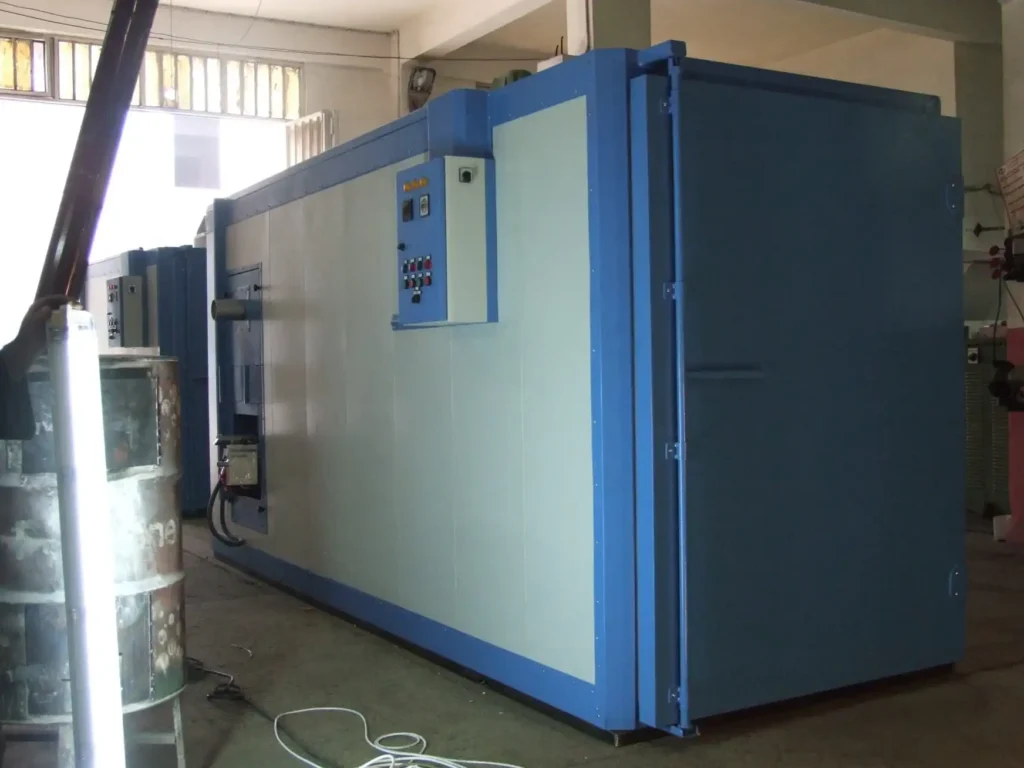
Powder coating ovens are used to cure the powder coating and make it durable. Powder coating ovens typically operate at temperatures of 180-200 degrees Celsius (350-400 degrees Fahrenheit).
There are two main types of powder coating ovens: batch ovens and conveyor ovens.
Batch ovens are used for small-scale powder coating operations. The parts to be coated are loaded into the oven and cured all at once.
Conveyor ovens are used for large-scale powder coating operations. The parts to be coated are loaded onto a conveyor belt and transported through the oven.
Conveyor ovens are more efficient than batch ovens, but they are also more expensive.
Conveyor belts
Conveyor belts are used to transport the part through the powder coating booth and the powder coating oven. Conveyor belts are typically made of a durable material, such as steel or stainless steel.
Agitators
Agitators are used to mix the powder coating in the hopper to ensure that it is evenly distributed. Agitators are typically powered by an electric motor.
Hoppers
Hoppers are used to store the powder coating until it is needed. Hoppers are typically made of a durable material, such as steel or stainless steel.
Filters
Filters are used to remove dust and debris from the powder coating before it is applied to the part. Filters are typically made of a paper or fabric material.
Powder coating robots

Powder coating robots are used to automate the powder coating process. Powder coating robots can be used to spray the powder coating, transport the parts through the powder coating booth and the powder coating oven, and unload the coated parts.
Powder coating robots can help to improve the efficiency and quality of the powder coating process, but they are also very expensive.
Powder coating dryers
Powder coating dryers are used to remove moisture from the powder coating before it is applied to the part. Powder coating dryers are typically used in conjunction with powder coating robots.
Powder coating dryers can help to improve the quality of the powder coating finish by preventing the formation of bubbles and craters.
Powder coating reclaimers
Powder coating reclaimers are used to recover overspray powder coating and recycle it back into the powder coating process. Powder coating reclaimers can help to reduce costs and improve the environmental impact of the powder coating process.
Conclusion
Powder coating equipment is a complex system of tools and machines that is used to apply a durable and decorative finish to a variety of surfaces. Powder coating equipment can be used in a wide variety of industries, including automotive, aerospace, appliance, and general manufacturing.
When choosing powder coating equipment, it is important to consider the specific needs of your application. Factors to consider include the type of material being coated, the desired finish, and the production volume.
Powder coating equipment can be a significant investment, but it is a valuable tool for businesses that need to coat parts for durability, corrosion resistance, chemical resistance, heat resistance, and color variety.
Powder Coating Equipment Germany
As a powder coating plant manufacturer, we manufacture the following coating equipment:
- Powder Spray Booth Germany
- Powder Coating Oven Germany
- Powder Spray Machine Germany
The powder spray booth for our german customers is at its best for the coating industry. The spray booths are designed for a better spray coating. Because of the increasing powder coating prices, we more and more advise the closed-type booth as below

As this spray booth is closed from 5 sides, it is more convenient for coating machines used for powder coating alloy wheels for instance. The surfaces of the spray booth are powder painted. The powder coating powder we use in our production is CE certified.
For the industry coating, there is also a second type for the powder coating spray booth with 3 sides closed for powder coating of more extensive parts. In this spray booth, there is no limitation for the length of the part to be coated. This powder booth also has filters and it is designed for a better manual powder coating.
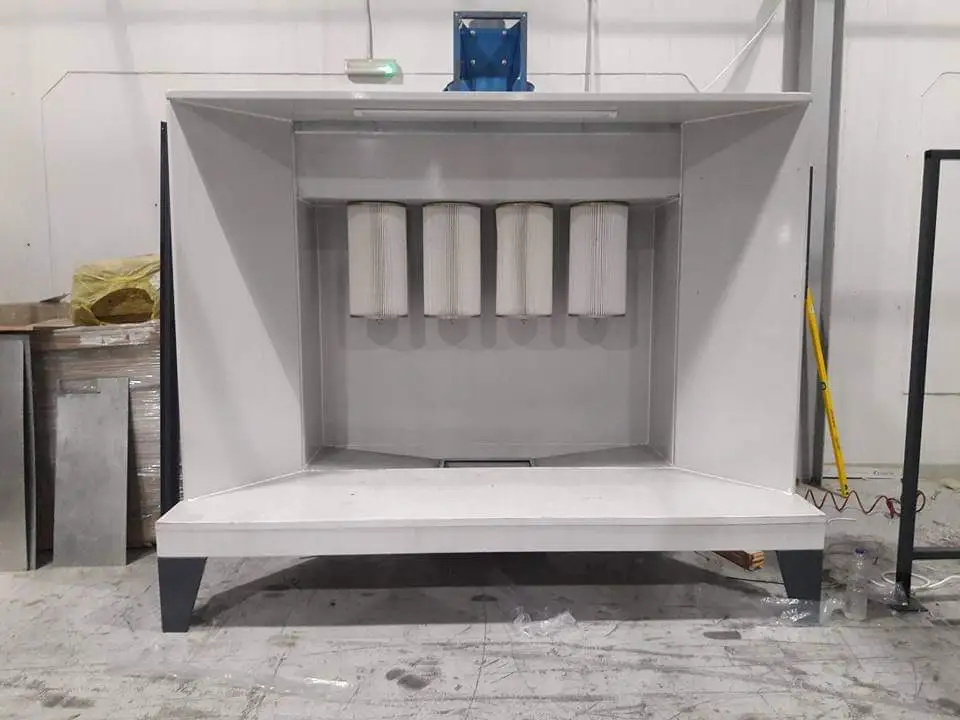
The powder spray paint is applied with powder coating spray equipment. The spray gun for powder coating is used in this case for bigger parts, which cannot fit in a close powder spray booth. The powder quality is the same in both types of powder coating booths.
Powder Coating Spray Booth Design
The powder coating spray booth design in Germany is usually chosen as the open type. Here it is also possible to make powder coating over powder coating. This method is also called as spraying over powder coating and usually used for parts that need to have a longer service life.
The powder paint booth is designed according to the inner space and we have the following options for our powder paint booths:
- 2 Filter Booth dims in mm: 1200(W) x 1500(D) x 2250(H)
- 3 Filter Booth dims in mm: 1500(W) x 1500(D) x 2250(H)
- 4 Filter Booth dims in mm: 2000(W) x 1500(D) x 2250(H)
- 5 Filter Booth dims in mm: 3000(W) x 1500(D) x 2250(H)
- 6 Filter Booth dims in mm: 4000(W) x 1500(D) x 2250(H)
- 8 Filter Booth dims in mm: 5000(W) x 1500(D) x 2250(H)
- 10 Filter Booth dims in mm: 6000(W) x 1500(D)x 2250(H)
Automatic Powder Coating Equipment Germany
Automatic powder coating equipment is used to automate the powder coating process, from the application of the powder to the curing of the coating. This type of equipment is typically used for high-volume powder coating applications, such as in the automotive and appliance industries.
Automatic powder coating equipment typically includes the following components:
Automatic powder coating equipment typically includes the following components:
- Powder coating gun: The powder coating gun is used to spray powder coating onto the surface of the part being coated. Automatic powder coating guns are typically equipped with sensors that help to ensure a uniform application of powder coating.
- Powder coating booth: The powder coating booth is a ventilated enclosure that contains the powder coating gun and the part being coated. The booth helps to collect overspray powder coating and prevent it from contaminating the environment.
- Powder coating oven: The powder coating oven is used to cure the powder coating and make it durable. Automatic powder coating ovens are typically equipped with conveyor belts that transport the parts through the oven.
- Control system: The control system controls the operation of the powder coating gun, the powder coating booth, and the powder coating oven. The control system also ensures that the parts are coated properly and that the powder coating process is efficient.
Automatic powder coating equipment offers a number of advantages over manual powder coating equipment, including:
- Increased efficiency: Automatic powder coating equipment can coat parts much faster than manual powder coating equipment. This can lead to significant productivity gains.
- Improved quality: Automatic powder coating equipment can help to improve the quality of the powder coating finish by ensuring that the powder coating is applied evenly and consistently.
- Reduced costs: Automatic powder coating equipment can help to reduce labor costs and reduce the amount of wasted powder coating.
Applications of automatic powder coating equipment
Automatic powder coating equipment is used in a wide variety of industries, including:
- Automotive: Automatic powder coating equipment is used to coat automotive parts, such as wheels, bumpers, and chassis components.
- Appliance: Automatic powder coating equipment is used to coat appliance components, such as washing machine drums and refrigerator doors.
- Electronics: Automatic powder coating equipment is used to coat electronic components, such as circuit boards and enclosures.
- General manufacturing: Automatic powder coating equipment is used to coat a wide variety of parts in the general manufacturing industry.
Safety considerations for automatic powder coating equipment
Automatic powder coating equipment is safe to operate when used properly. However, there are a few safety considerations to keep in mind:
- Ventilate the oven area: Automatic powder coating equipment can produce fumes from the powder coating process. Be sure to ventilate the oven area properly to remove these fumes.
- Wear safety gear: When operating automatic powder coating equipment, be sure to wear appropriate safety gear, such as gloves, safety glasses, and a respirator.
- Keep the booth clean: Automatic powder coating booths can accumulate dust and debris over time. Be sure to clean the booth regularly to prevent this from happening.
- Inspect the equipment regularly: Inspect the equipment regularly for any signs of damage. If you find any damage, have it repaired immediately.
- Follow the manufacturer’s instructions: Be sure to follow the manufacturer’s instructions for operating and maintaining the automatic powder coating equipment.
By following these safety precautions, you can help to prevent accidents and injuries when using automatic powder coating equipment.
Conclusion
Automatic powder coating equipment is a valuable tool for businesses that need to coat parts quickly, efficiently, and with high quality. By choosing the right automatic powder coating equipment and using it properly, you can improve productivity, quality, and safety.
As a powder coating equipment manufacturer, we manufacture and assembly complete coating systems including:
- Surface Pretreatment for Powder Coating
- Powder Drying Oven
- Powder Coating Spray Booth
- Powder Curing Oven
- Conveyor Lines
Powder Coating Equipment Germany
Powder coating equipment is used to apply a powder coating to a metal surface. Powder coating is a dry finishing process that is used to create a durable and long-lasting finish on metal products.
The typical powder coating equipment setup consists of the following components:
- Powder coating gun: The powder coating gun is used to apply the powder to the metal surface. The gun uses compressed air to atomize the powder and spray it onto the surface.
- Powder coating booth: The powder coating booth is a ventilated enclosure where the powder is applied to the metal surface. The booth is typically equipped with a system for collecting and filtering the excess powder.
- Powder coating oven: The powder coating oven is used to cure the powder coating. The oven heats the powder coating to a temperature that causes it to melt and flow. Once the powder coating has melted and flowed, it cools and hardens to form a durable finish.
In addition to these basic components, powder coating equipment can also include a variety of other equipment, such as:
- Conveyor belt: The conveyor belt is used to carry the parts through the powder coating booth and oven. This is especially useful for high-volume production applications.
- Curing chamber: The curing chamber is a separate enclosure that is used to cure powder coated parts. This can help to improve the quality of the finish and reduce the overall curing time.
- Powder coating feed system: The powder coating feed system supplies powder to the powder coating gun.
- Powder coating recovery system: The powder coating recovery system collects and filters the excess powder from the powder coating booth.
- Control system: The control system monitors and controls the operation of the entire powder coating system.
Powder coating equipment is available in a variety of sizes and configurations to meet the needs of different industries and applications. Manual powder coating equipment is typically used for low-volume production applications, while automatic powder coating equipment is typically used for high-volume production applications.
Here are some examples of powder coating equipment:
- Powder coating guns: There are a variety of powder coating guns available, including manual guns, automatic guns, and electrostatic guns.
- Powder coating booths: Powder coating booths are available in a variety of sizes and configurations, including downdraft booths, updraft booths, and crossdraft booths.
- Powder coating ovens: Powder coating ovens are available in a variety of sizes and configurations, including batch ovens, conveyor ovens, and curing chambers.
When choosing powder coating equipment, it is important to consider the following factors:
- The size and type of parts you will be coating
- The volume of parts you will be coating
- Your budget
It is also important to make sure that the equipment you choose is compatible with the type of powder coating you will be using.
If you are new to powder coating, it is a good idea to consult with a qualified supplier to get help choosing the right equipment for your needs.
Powder coating
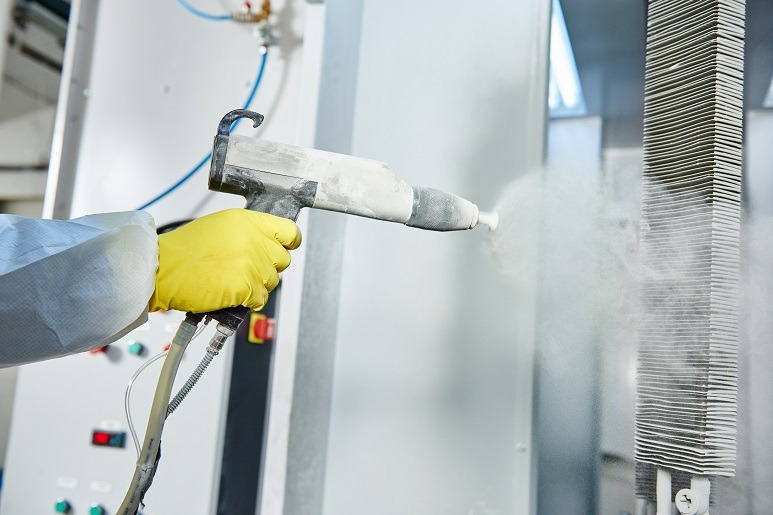
Powder coating is a widely used finishing process in manufacturing, characterized by its ability to produce a high-quality, durable finish. The process involves the application of dry powder to a surface, which is then cured under heat to form a solid, protective coating. This process is favored in many industries due to its efficiency and environmental benefits compared to traditional liquid paint. Essential to the powder coating process are various pieces of equipment, including the Powder Coating Equipment, Powder Coating Booth, Powder Coating Spray Booth, Small Powder Coating Booth, and Powder Paint Booth with Filters.
Powder Coating Equipment Overview
Powder Coating Equipment encompasses a wide range of tools and machinery designed to facilitate the powder coating process. These include spray guns, booths, ovens, and automated systems. Each component plays a crucial role in ensuring the quality and efficiency of the coating process. For instance, Automatic Powder Coating Equipment is often used in large-scale operations where precision and consistency are paramount.
Powder Coating Booths
A Powder Coating Booth is a controlled environment where powder is applied to the substrate. These booths are designed to contain overspray, minimize contamination, and ensure even coating application. There are various types of booths, including the Small Powder Coating Booth, which is ideal for limited-space operations or for coating smaller parts. For larger operations, a Powder Coating Spray Booth is typically used, which allows for greater flexibility and efficiency.
Small Powder Coating Booths and Applications
Small Powder Coating Booths are specifically designed for operations that require a compact setup. These booths are particularly useful in small workshops or for businesses that specialize in coating small parts, such as Alloy Wheel Powder Coating. A Small Powder Coating Booth is typically paired with a Small Powder Coating Oven or a combined Small Powder Coating Booth and Oven to streamline the coating and curing processes.
Automated Powder Coating Systems
For businesses that require high throughput and consistent quality, an Automated Powder Coating System is often the best choice. These systems integrate various components of the powder coating process, including automated spray guns, conveyor systems, and curing ovens. By automating these processes, manufacturers can achieve a higher level of efficiency and reduce the potential for human error.
Ovens in Powder Coating
Curing ovens are an essential part of the powder coating process. They provide the heat necessary to cure the powder and form a durable coating. There are different types of ovens, including Gas Powder Coating Oven, Diesel Powder Coating Oven, and Portable Powder Coating Oven. Each type of oven offers distinct advantages depending on the application. For instance, a Gas Powder Coating Oven is known for its energy efficiency and consistent temperature control, while a Diesel Powder Coating Oven is favored in environments where gas supply is limited or where diesel is more readily available.
Portable Powder Coating Ovens
Portable Powder Coating Ovens are a versatile solution for businesses that require mobility in their operations. These ovens can be moved easily to different locations, making them ideal for on-site jobs or businesses with limited space. Despite their portability, these ovens are capable of delivering high-quality curing results comparable to their stationary counterparts.
Specialized Coating Applications: Alloy Wheel Powder Coating
Alloy Wheel Powder Coating is a specialized application of powder coating that involves applying a durable finish to alloy wheels. This process not only enhances the appearance of the wheels but also provides protection against corrosion and wear. The equipment used for this application typically includes a Small Powder Coating Booth and Oven to accommodate the size of the wheels and ensure a thorough and even coating.
Small Powder Coating Booths and Ovens
Combining a Small Powder Coating Booth with a Small Powder Coating Oven is an effective setup for operations that deal with smaller parts. This combination allows for a seamless transition from coating to curing, ensuring that the coated parts are handled efficiently and without the risk of contamination or damage.
Advantages of Automatic Powder Coating Equipment
The use of Automatic Powder Coating Equipment provides several advantages, particularly in high-volume production settings. Automation ensures that each part is coated with precision and consistency, reducing waste and increasing productivity. Additionally, automated systems can be programmed to handle various part sizes and shapes, making them a versatile option for manufacturers.
Conclusion
In conclusion, powder coating is an essential process in many industries, offering a durable and high-quality finish that is both environmentally friendly and cost-effective. The equipment used in this process, including Powder Coating Equipment, Powder Coating Booths, Automated Powder Coating Systems, and various types of ovens, plays a crucial role in achieving the desired results. Whether you are operating a small workshop or a large-scale manufacturing facility, the right combination of equipment can significantly enhance your production capabilities and product quality.
Powder Coating Equipment
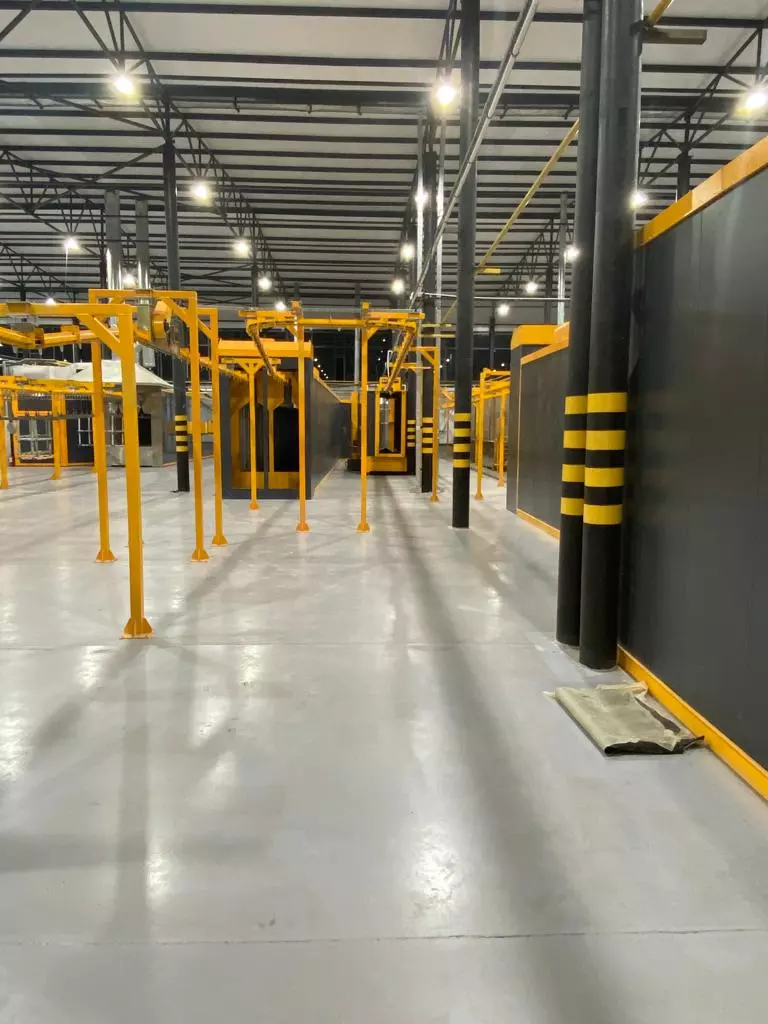
Powder Coating Equipment encompasses a variety of tools and machines that are essential for applying powder coatings to various substrates. This equipment typically includes:
- Powder Spray Guns: These are devices used to apply the powder evenly onto the surface of the object. They can be manual or automated, with the latter offering greater consistency and efficiency.
- Powder Coating Booths: These are enclosed areas where the powder is applied, designed to contain overspray and prevent contamination.
- Curing Ovens: After the powder is applied, the coated object is placed in an oven to cure, which involves melting the powder so it flows together to form a smooth, solid coating.
- Control Systems: These systems manage the application parameters, such as temperature, spray rate, and curing time, ensuring the process is consistent and repeatable.
Powder Coating Booth
A Powder Coating Booth is a specialized enclosure designed to contain the powder application process. The booth serves several key functions:
- Overspray Containment: The booth ensures that any powder that doesn’t adhere to the substrate is captured and can often be recycled, reducing waste.
- Controlled Environment: By isolating the coating process, the booth minimizes contamination from dust and other particles, which could affect the finish quality.
- Airflow Management: Proper airflow within the booth ensures that the powder particles are evenly distributed and that overspray is efficiently collected.
There are various types of booths, such as open-faced booths, enclosed booths, and walk-in booths, each designed for different scales and types of operations.
Small Powder Coating Booth
A Small Powder Coating Booth is designed for operations that do not require large-scale equipment. These booths are ideal for small parts, prototypes, or businesses with limited space. Features of small booths include:
- Compact Design: These booths are smaller in size, making them suitable for tight spaces or mobile operations.
- Cost-Effective: They are often less expensive than larger booths, making them an economical choice for small businesses or hobbyists.
- Efficiency: Despite their size, small powder coating booths are equipped to handle a variety of coating tasks with high precision.
Powder Coating Spray Booth
A Powder Coating Spray Booth is a type of booth specifically designed to accommodate the spraying process of powder application. This type of booth is equipped with:
- Advanced Filtration Systems: These systems filter the air to remove any particles, ensuring a clean environment for the coating process.
- Adjustable Airflow: Airflow can be adjusted to optimize the application and ensure even coating on all surfaces.
- Ergonomic Design: Spray booths are often designed to maximize operator comfort and efficiency, with easy access to all areas of the parts being coated.
Powder Paint Booth with Filters
A Powder Paint Booth with Filters is equipped with specialized filtration systems to capture overspray and maintain air quality within the booth. These filters play a critical role in:
- Ensuring Air Quality: Filters remove airborne powder particles, preventing them from escaping the booth and affecting the surrounding environment.
- Reducing Waste: Captured powder can often be recycled, reducing material costs and waste.
- Maintaining Finish Quality: Clean air within the booth ensures that the powder coating adheres smoothly and evenly, free from contaminants.
Automated Powder Coating System
An Automated Powder Coating System integrates various stages of the powder coating process into a seamless, automated workflow. Key features of these systems include:
- Conveyor Systems: Parts are transported automatically through the different stages of coating and curing, increasing efficiency and throughput.
- Automated Spray Guns: These guns apply powder coatings consistently across parts, reducing the potential for human error and ensuring uniformity.
- Real-Time Monitoring: Sensors and control systems monitor the process in real-time, adjusting parameters as needed to maintain optimal coating conditions.
- Scalability: Automated systems can be scaled to meet the demands of different production volumes, from small batches to large-scale manufacturing.
Gas Powder Coating Oven
A Gas Powder Coating Oven is used to cure powder-coated parts by heating them to the required temperature. These ovens are powered by natural gas and offer several advantages:
- Energy Efficiency: Gas ovens are generally more energy-efficient than electric ovens, making them a cost-effective option for large-scale operations.
- Consistent Heating: They provide uniform temperature distribution, which is crucial for achieving a consistent and durable finish.
- Fast Heat-Up Times: Gas ovens typically heat up faster than electric ovens, reducing cycle times and increasing productivity.
Diesel Powder Coating Oven
A Diesel Powder Coating Oven is similar to a gas oven but is powered by diesel fuel. These ovens are often used in situations where:
- Fuel Availability: Diesel may be more readily available or more economical than gas in certain regions or for certain operations.
- High-Temperature Requirements: Diesel ovens are capable of reaching high temperatures quickly, making them suitable for heavy-duty applications.
- Portability: Some diesel ovens are designed to be portable, allowing them to be moved to different locations as needed.
Portable Powder Coating Oven
A Portable Powder Coating Oven is designed for mobility, allowing it to be transported to different job sites or easily repositioned within a workshop. Features include:
- Compact Size: Portable ovens are generally smaller and lighter than stationary models, making them easy to move.
- Versatility: These ovens can be used for a variety of applications, from small parts to on-site repairs and custom jobs.
- Flexibility: They can be powered by different fuel sources, including gas, diesel, or electricity, depending on the specific model.
Alloy Wheel Powder Coating
Alloy Wheel Powder Coating is a specialized process designed to coat alloy wheels with a durable and attractive finish. The process involves:
- Preparation: The wheels are first cleaned and prepped to ensure the powder coating adheres properly.
- Application: A powder coating is applied evenly across the wheel, often using a Small Powder Coating Booth to contain the process.
- Curing: The coated wheels are then placed in an oven, where the powder is cured to form a hard, protective layer. This can be done in a Small Powder Coating Oven.
- Finishing: The final product is a wheel with a high-quality finish that resists chips, scratches, and corrosion.
Small Powder Coating Booth and Oven
A Small Powder Coating Booth and Oven setup is ideal for businesses or hobbyists who need to coat small parts efficiently. This setup typically includes:
- A Compact Booth: The booth is designed to fit in smaller spaces while still providing the necessary environment for powder coating.
- A Small Oven: The oven is sized to match the booth, ensuring that parts can be cured immediately after coating, reducing handling and the risk of contamination.
- Integrated Systems: Some setups may combine the booth and oven into a single unit, making it easier to manage the process in a limited space.
Small Powder Coating Oven
A Small Powder Coating Oven is specifically designed for curing smaller items. Key benefits include:
- Space Efficiency: These ovens are designed to fit into smaller workshops or production areas, making them ideal for limited-space environments.
- Quick Heat-Up: Smaller ovens generally heat up faster, allowing for shorter cycle times and increased productivity.
- Cost-Effective: Due to their smaller size, these ovens typically consume less energy, making them a more economical option for small businesses or low-volume operations.
Automatic Powder Coating Equipment
Automatic Powder Coating Equipment refers to systems designed to automate the powder coating process, offering numerous advantages:
- Consistency: Automated equipment ensures that each part is coated evenly, reducing variability and ensuring high-quality finishes.
- Efficiency: Automation reduces the time required to coat each part, increasing throughput and reducing labor costs.
- Advanced Features: Many automated systems include features such as programmable control systems, which allow for precise adjustments to coating parameters, and integration with other manufacturing processes, such as pre-treatment and inspection.
Introduction to Powder Coating and Essential Equipment

Powder coating is an advanced finishing process widely recognized for its efficiency, durability, and environmental benefits. Unlike traditional liquid paint, powder coating uses a dry powder that is electrostatically charged and sprayed onto a surface. The coated surface is then cured under heat, forming a robust and protective layer. This process is employed across various industries, including automotive, aerospace, and consumer goods, due to its superior finish quality and resistance to wear and corrosion.
The success of powder coating depends heavily on the equipment used throughout the process. Powder Coating Equipment includes a wide range of machinery designed to ensure that the powder is applied evenly and cured properly. This equipment encompasses spray guns, booths, ovens, and automated systems that work together to deliver a consistent, high-quality finish. Each piece of equipment serves a specific purpose, and understanding their functions and benefits is crucial for optimizing the powder coating process.
Powder Coating Equipment: A Comprehensive Overview
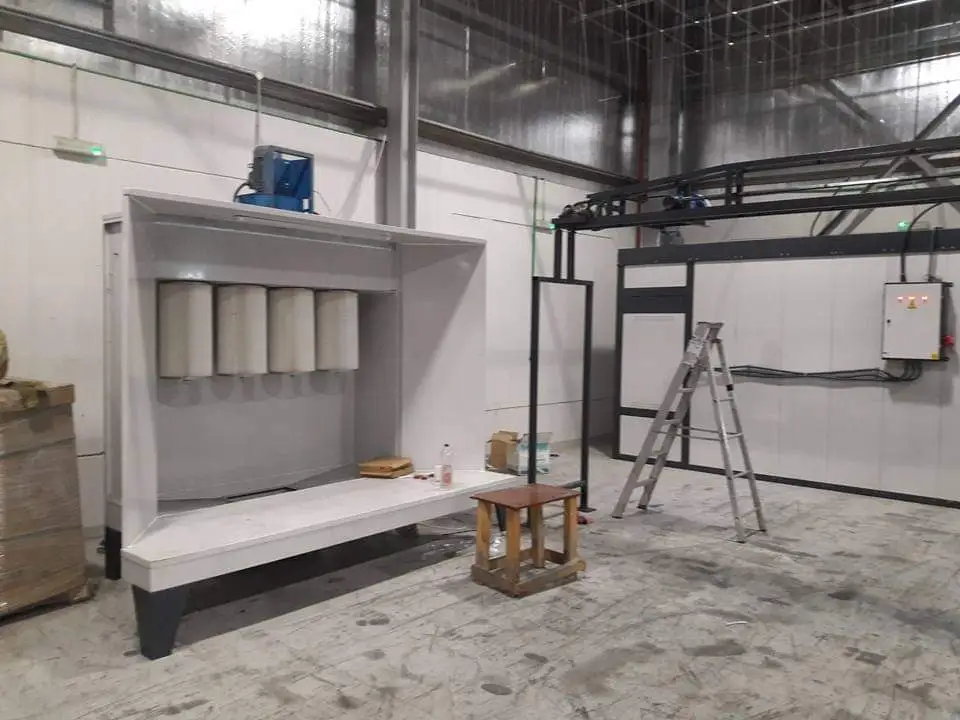
Powder Coating Equipment refers to the complete set of tools and machinery used in the powder coating process. This equipment includes:
- Electrostatic Spray Guns: These are the primary tools used to apply powder to the substrate. The spray gun charges the powder particles, causing them to adhere to the surface of the part being coated. There are different types of spray guns, including manual and automated versions, each suited for specific applications.
- Powder Coating Booths: These enclosures provide a controlled environment for applying the powder, ensuring that overspray is contained and that the powder is applied uniformly. The booths are designed to maximize efficiency and minimize waste, often incorporating filtration systems to capture excess powder for reuse.
- Curing Ovens: Once the powder has been applied, the coated part is transferred to a curing oven. These ovens heat the part to the required temperature, causing the powder to melt and flow into a smooth, even coating. Different types of ovens, such as gas, diesel, and portable ovens, are used depending on the size of the part and the specific needs of the operation.
- Automated Systems: In larger-scale operations, Automatic Powder Coating Equipment is often used to streamline the process. These systems can automate the entire powder coating process, from powder application to curing, improving efficiency and consistency.
The Role of Powder Coating Booths
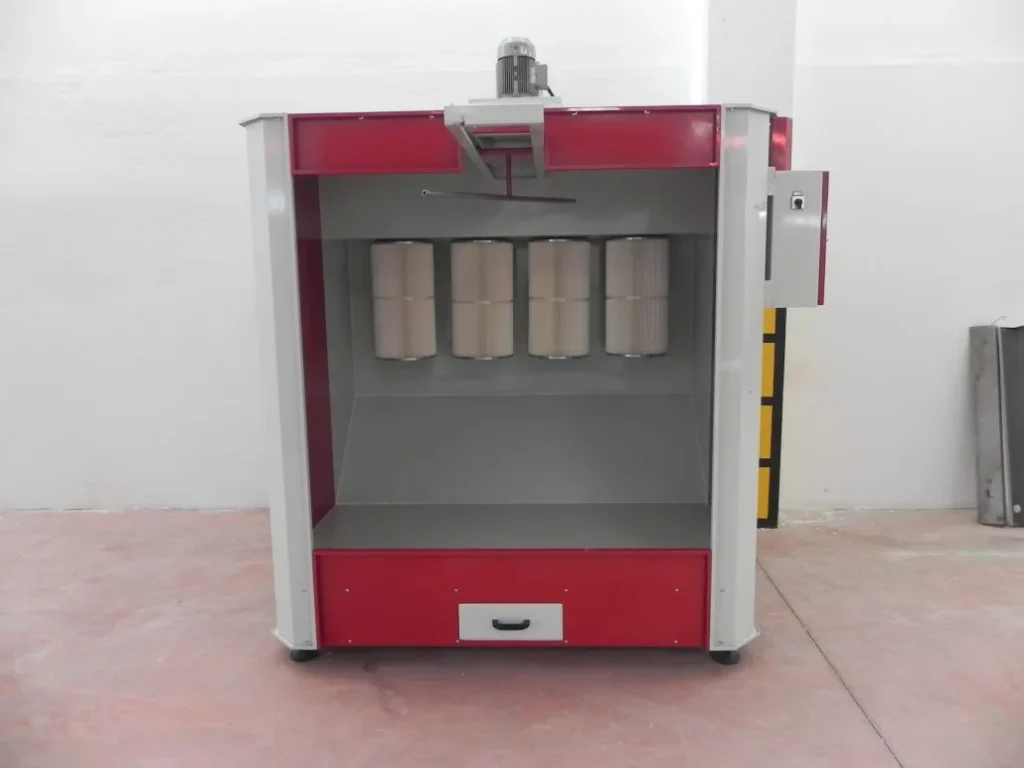
A Powder Coating Booth is an essential component of the powder coating process, providing a dedicated space for the application of powder coatings. These booths are designed to create an optimal environment for powder application, with features that include:
- Controlled Airflow: Proper airflow is critical in a powder coating booth. It ensures that the powder particles are evenly distributed and that overspray is captured efficiently. The airflow is carefully managed to prevent contamination and to ensure that the powder adheres uniformly to the substrate.
- Containment of Overspray: A key function of the booth is to contain overspray, preventing powder from spreading to other areas of the workspace. This not only keeps the work environment clean but also allows for the recovery and reuse of overspray, reducing waste and saving on material costs.
- Variety of Configurations: Powder coating booths come in various configurations to suit different applications. For example, walk-in booths are used for coating large parts, while compact booths are ideal for smaller operations.
Small Powder Coating Booth: Efficiency in Compact Spaces
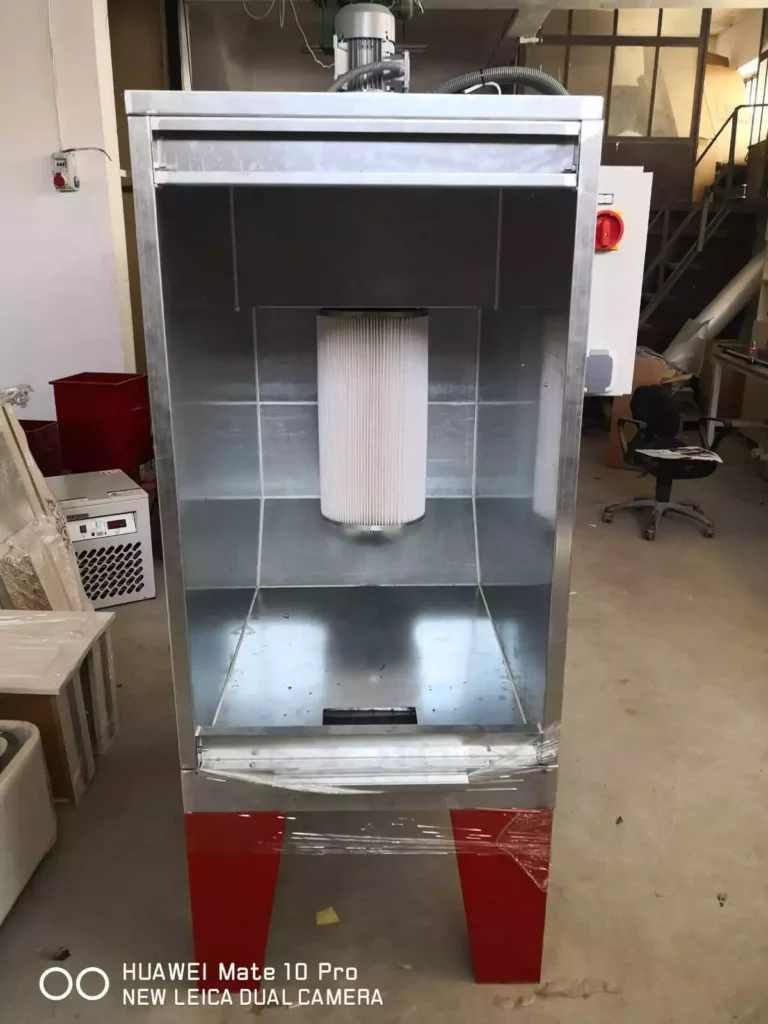
A Small Powder Coating Booth is specifically designed for operations with limited space or for businesses that focus on coating smaller parts. Despite their size, these booths offer several advantages:
- Space-Saving Design: The compact size of a small powder coating booth makes it ideal for workshops or production areas where space is at a premium. These booths are designed to fit into tight spaces without compromising on performance or safety.
- Cost-Effective Operation: Small booths typically require less energy and resources to operate, making them a cost-effective option for small businesses or for coating small batches of parts. They are also easier to install and maintain, reducing overall operating costs.
- Versatility: These booths can handle a wide range of coating tasks, from small automotive parts to prototypes and custom jobs. Their versatility makes them a popular choice for businesses that require flexibility in their operations.
Powder Coating Spray Booth: Optimized for Precision Application
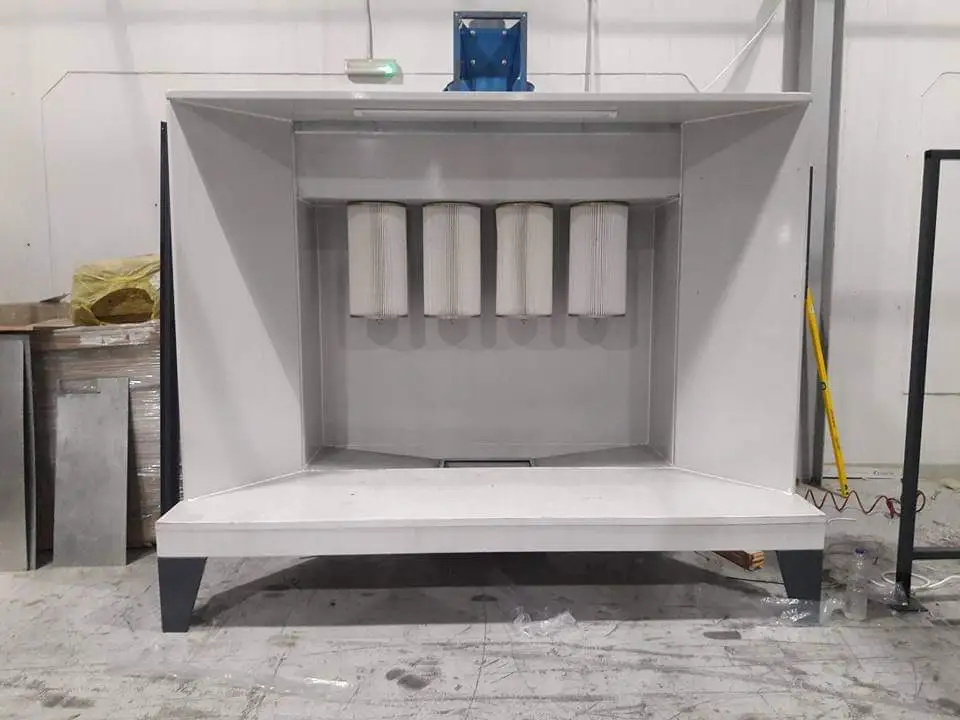
A Powder Coating Spray Booth is a specialized booth designed to optimize the spray application of powder coatings. These booths are equipped with advanced features that enhance the coating process:
- High-Efficiency Filtration Systems: The filtration systems in a spray booth are designed to capture overspray and remove airborne particles, ensuring a clean environment for powder application. This is crucial for achieving a high-quality finish and for maintaining a safe work environment.
- Adjustable Airflow: The airflow in a spray booth can be adjusted to suit the specific requirements of the coating job. This allows for precise control over the application process, ensuring that the powder is applied evenly and with the desired thickness.
- Operator-Friendly Design: Spray booths are designed with the operator in mind, providing easy access to the parts being coated and ergonomic features that reduce fatigue. This improves both the efficiency and safety of the coating process.
Powder Paint Booth with Filters: Ensuring Quality and Safety
A Powder Paint Booth with Filters is a critical component of the powder coating process, providing an enclosed space for the application of powder coatings while ensuring that air quality is maintained. The filtration system in these booths serves several important functions:
- Air Quality Control: The filters in a powder paint booth are designed to capture airborne powder particles, preventing them from contaminating the workspace and ensuring that the air remains clean and breathable. This is particularly important in environments where multiple coating operations are taking place simultaneously.
- Waste Reduction: By capturing overspray, the filtration system helps to reduce waste, as the collected powder can often be recycled and reused. This not only reduces material costs but also minimizes the environmental impact of the coating process.
- Compliance with Regulations: Powder paint booths with filters are often required to meet specific safety and environmental regulations, particularly in industries where hazardous materials are used. The filtration system ensures that the booth operates within these guidelines, protecting both workers and the environment.
Automated Powder Coating System: Enhancing Productivity and Consistency
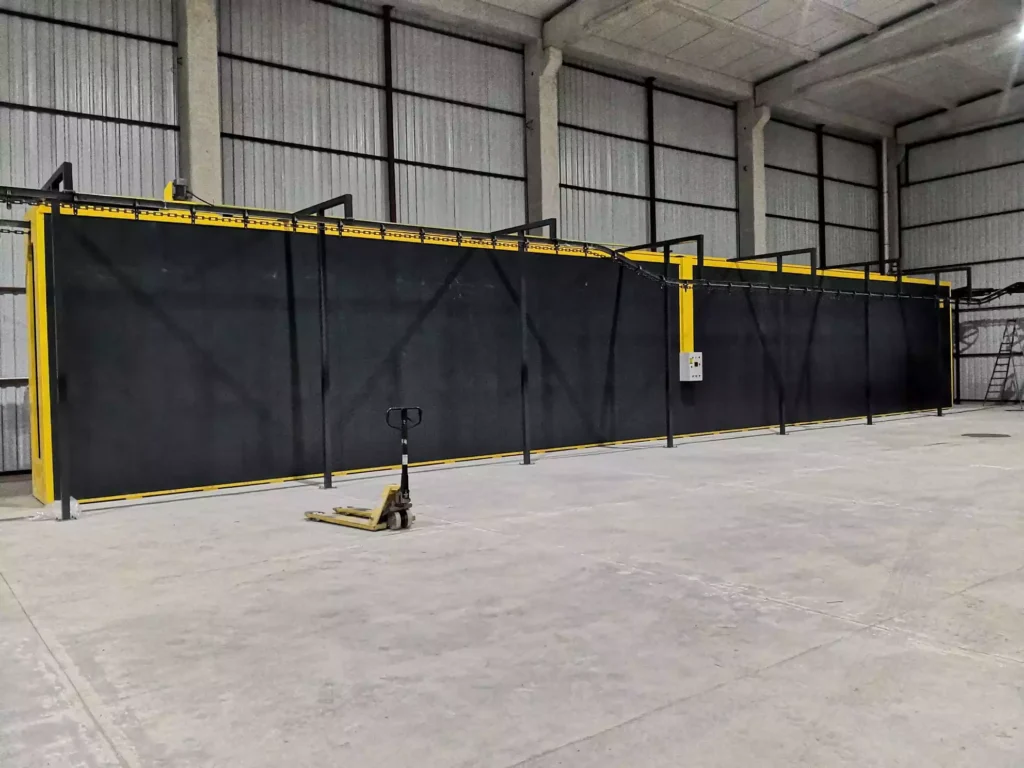
An Automated Powder Coating System integrates various components of the powder coating process into a fully automated workflow. These systems are designed to improve productivity, consistency, and efficiency in large-scale operations. Key features include:
- Conveyor Systems: Automated systems often incorporate conveyor belts that transport parts through the different stages of the coating process. This allows for continuous production, reducing downtime and increasing throughput.
- Robotic Spray Guns: Robotic arms equipped with spray guns can apply powder coatings with a high degree of precision, ensuring that each part is coated uniformly. This reduces the risk of defects and improves the overall quality of the finish.
- Real-Time Monitoring and Control: Advanced sensors and control systems monitor the coating process in real-time, adjusting parameters as needed to maintain optimal conditions. This ensures consistent results, even in high-volume production environments.
- Scalability: Automated powder coating systems can be scaled to meet the needs of different production volumes, from small batches to large-scale manufacturing. This makes them a versatile solution for a wide range of industries.
Gas Powder Coating Oven: Reliable and Efficient Curing
A Gas Powder Coating Oven is a critical piece of equipment in the powder coating process, providing the heat necessary to cure the powder coating and form a durable, protective layer. These ovens are powered by natural gas and offer several advantages:
- Energy Efficiency: Gas ovens are known for their energy efficiency, as they can heat up quickly and maintain a consistent temperature with minimal energy consumption. This makes them a cost-effective option for large-scale operations.
- Uniform Heating: The design of gas ovens ensures that heat is distributed evenly throughout the oven, preventing hot spots and ensuring that all parts are cured uniformly. This is essential for achieving a consistent, high-quality finish.
- Flexible Operation: Gas powder coating ovens can be used for a wide range of applications, from small parts to large assemblies. They are also available in various sizes and configurations, making them adaptable to different production needs.
Diesel Powder Coating Oven: Power and Portability
A Diesel Powder Coating Oven is similar to a gas oven but is powered by diesel fuel. These ovens are often used in situations where gas is not readily available or where diesel is more economical. The key benefits of diesel ovens include:
- High Heat Output: Diesel ovens are capable of reaching high temperatures quickly, making them ideal for heavy-duty applications that require fast curing times.
- Portability: Many diesel ovens are designed to be portable, allowing them to be easily moved to different locations as needed. This makes them a flexible option for businesses that need to perform coating operations on-site or in remote locations.
- Durability: Diesel ovens are built to withstand harsh conditions and are often used in industrial settings where durability and reliability are critical.
Portable Powder Coating Oven: Versatility on the Move
A Portable Powder Coating Oven offers the flexibility of being moved to different job sites or repositioned within a workshop. These ovens are ideal for operations that require mobility or for businesses with limited space. Key features of portable ovens include:
- Compact and Lightweight Design: Portable ovens are designed to be easily transported, with a compact size and lightweight construction that makes them easy to move and set up.
Powder coating is a popular method for applying a protective and decorative finish to metal surfaces. The process involves applying a dry powder that is then cured under heat to form a durable, high-quality coating. Here’s an overview of the equipment used in powder coating:
1. Powder Coating Gun
- Function: The gun is used to apply the powder onto the metal surface. It uses an electrostatic charge to attract the powder particles to the grounded workpiece.
- Types:
- Corona Guns: The most common type, which applies a high voltage to charge the powder.
- Triboelectric Guns: These use friction to charge the powder.
2. Powder Booth
- Function: The booth is where the powder is applied to the workpiece. It provides a controlled environment to minimize contamination and optimize the application process.
- Types:
- Open Face Booths: For simple, low-volume jobs.
- Enclosed Booths: These are more effective for high-efficiency powder recovery.
3. Powder Recovery System
- Function: This system recycles unused powder. It usually involves a combination of filters and cyclonic separation to capture the excess powder that didn’t stick to the workpiece.
- Key Components:
- Cyclone: Separates the powder from the air.
- Filters: Help remove any airborne powder particles.
4. Curing Oven
- Function: After the powder is applied, the workpiece must be heated to a specific temperature for the powder to cure and form a solid, durable finish.
- Types:
- Batch Ovens: Used for smaller volumes, where items are placed inside and baked.
- Conveyor Ovens: Used for high-volume production, where parts move through the oven on a conveyor belt.
5. Pre-treatment System
- Function: Prior to coating, surfaces must be cleaned to ensure the powder adheres properly. This system involves chemical cleaning or abrasive methods such as sandblasting.
- Components:
- Wash Stations: For removing grease, oils, and other contaminants.
- Phosphating: Adds a layer that enhances powder adhesion.
6. Air Compressor
- Function: Provides the necessary air pressure for the powder coating gun, recovery system, and curing oven. Proper air quality is important to avoid contamination of the coating process.
7. Powder Coating Curing Systems
- These include:
- Infrared (IR) Curing: Cures the powder using infrared radiation.
- Convection Ovens: Uses hot air to cure the coating.
- Hybrid Systems: Combines both infrared and convection methods for faster curing.
8. Cooling System
- After curing, parts may need to be cooled rapidly to prevent warping or distortion. A cooling system, such as a blow-off system or a cooling tunnel, is used for this purpose.
9. Control Systems
- Modern powder coating systems often come with digital controllers that monitor and adjust key parameters like temperature, humidity, powder flow, and oven speed. These ensure consistent quality and efficiency.
Maintenance and Safety
- Maintenance: Regular cleaning and maintenance of guns, booths, and recovery systems are critical to ensure smooth operation and high-quality finishes.
- Safety: Powder coating involves the use of chemicals and high temperatures, so personal protective equipment (PPE) like gloves, goggles, and proper ventilation is necessary.
Powder coating is a highly efficient and durable finishing process, widely used in industries like automotive, construction, and appliances. The equipment involved in powder coating ensures that the coating is applied uniformly and cures effectively to form a tough, resistant finish.
The powder coating gun is one of the essential pieces of equipment. It uses electrostatic forces to apply a dry powder to the surface of the item being coated. The powder is charged and then attracted to the grounded metal surface, ensuring even coverage. The process typically uses a high-voltage corona gun or, in some cases, a triboelectric gun that relies on friction for charging the powder. This application process is done inside a powder booth, a controlled environment designed to minimize contamination. These booths can range from simple open-faced models for small jobs to fully enclosed booths with advanced filtration systems for high-efficiency powder recovery.
To make sure the powder that doesn’t stick to the workpiece is not wasted, a recovery system is used. This system captures the excess powder and recycles it for future use, making the process more cost-effective. The recovery system typically involves cyclonic separation and filter systems to remove the powder from the air, preventing any loss of material and keeping the environment clean.
Once the powder is applied, the coated parts need to be cured in a curing oven. The heat causes the powder to melt and bond to the surface, forming a solid, durable coating. There are two primary types of curing ovens: batch ovens, which are used for smaller runs and where parts are placed individually for curing, and conveyor ovens, which are designed for high-volume production with parts moving through the oven continuously on a belt. The curing process must be precisely controlled, with attention to both temperature and time, to ensure a perfect finish. Some systems also use infrared radiation or convection to speed up the curing process.
Before powder coating can be applied, the parts must go through a pre-treatment process to ensure proper adhesion. This typically involves cleaning and surface preparation, which may include washing with chemicals or sandblasting to remove oils, grease, and rust. For some applications, a phosphate layer might also be applied to further enhance adhesion and corrosion resistance.
The air compressor plays a crucial role throughout the process, providing the necessary pressure for the gun, recovery system, and sometimes even the curing oven. The air quality must be carefully controlled to prevent contaminants from affecting the coating process.
After the parts are cured, they may require a cooling phase to avoid warping or distortion, which can be achieved through blow-off systems or cooling tunnels. Modern powder coating systems often come with advanced control systems, allowing operators to monitor and adjust parameters such as temperature, powder flow, and curing time to ensure consistent results.
Lastly, maintenance of the equipment is vital for consistent performance. This includes regular cleaning of the guns, booths, recovery systems, and ovens to avoid build-up that could affect the coating quality. In addition, safety is a key consideration. The process involves working with high-voltage equipment and high temperatures, so protective gear such as gloves, goggles, and proper ventilation is essential to ensure the safety of the operators.
In essence, the combination of precise application, efficient powder recovery, effective curing, and safety protocols makes powder coating a highly effective and sustainable finishing process.
Expanding further on the powder coating process, the equipment setup is designed to work harmoniously, ensuring both efficiency and quality in the final product. The key to the success of powder coating lies not just in the equipment but also in the operational environment, including temperature, humidity, and cleanliness of the workspace. Powder coating is known for its environmental benefits since it typically produces fewer VOCs (volatile organic compounds) than liquid paints, making it a more eco-friendly option.
Another important aspect of powder coating equipment is its adaptability to different production scales. In smaller operations or when custom work is required, batch ovens and manual powder application guns are often used. However, for large-scale manufacturing, automated systems with conveyor belts are more common. These systems allow continuous movement of parts through the powder application booth and curing oven, leading to faster turnaround times and higher volumes of production. Automated systems also reduce the chances of human error and provide consistent finishes, especially in environments where high precision is required, like in the automotive or appliance industries.
The evolution of powder coating technology has also led to more advanced methods of curing the powder. In addition to traditional convection ovens, some newer systems utilize infrared (IR) curing, which is more energy-efficient because it heats the parts directly, rather than relying on air circulation. This can reduce curing times, making the process even more efficient. Hybrid curing systems that combine IR and convection also exist, giving manufacturers the ability to balance speed and energy usage, depending on the specific needs of the job.
For some applications, especially in industries where aesthetics and durability are critical, custom finishes can be achieved by using various types of powders. These range from standard polyester and epoxy powders to more advanced options like urethane, hybrid, or epoxy-polyester powders. These variations allow for specific properties such as greater resistance to UV degradation, chemical exposure, or extreme temperatures. Additionally, powders can be customized to create different textures or effects, such as matte, gloss, or metallic finishes, to meet aesthetic demands.
Technology has also introduced sophisticated control and monitoring systems that make it easier for operators to maintain precise conditions throughout the process. These systems allow users to track parameters such as temperature, powder thickness, and air pressure in real-time, providing a high level of control over the final result. Some advanced systems can even adjust settings automatically to compensate for variations in temperature or powder flow, further enhancing the quality and consistency of the coating.
As the powder coating industry continues to evolve, the focus is also shifting toward sustainability. Many manufacturers are exploring ways to minimize waste, such as using more efficient powder recovery systems and ensuring that any overspray or waste materials are properly disposed of or recycled. Advances in powder formulation have also led to the development of low-temperature curing powders that can be used on a broader range of substrates, reducing energy consumption and making powder coating even more versatile.
Moreover, research into new types of powders has expanded the range of materials that can be coated, including plastics and other non-metal surfaces. This opens up new opportunities for industries that require coatings on a variety of substrates beyond metal, expanding the potential applications for powder coating across fields like furniture manufacturing, electronics, and even automotive parts that use plastic components.
Lastly, as industries demand greater customization and faster turnaround times, many companies are investing in digital powder coating solutions. These solutions include sophisticated software that allows operators to precisely control coating parameters, ensuring that each product meets specific requirements. The future of powder coating equipment likely includes even more automation and integration with Industry 4.0 technologies, where real-time data analysis, machine learning, and predictive maintenance systems will play a key role in optimizing the powder coating process.
In summary, powder coating equipment is at the heart of creating durable, high-quality finishes for a wide variety of industries. Its evolution continues to focus on efficiency, sustainability, and adaptability to meet the increasing demands for customization, precision, and speed in the production process.
Expanding on the advancements and trends in powder coating, the ongoing improvements in equipment and techniques continue to shape the industry. As manufacturing processes become more sophisticated and as demands for efficiency, quality, and sustainability increase, several key innovations are driving the future of powder coating.
One significant trend is the increasing emphasis on automation. Automated powder coating systems are becoming more common, particularly in high-volume manufacturing environments. These systems use robotic arms or conveyor systems to apply the powder and move the parts through the curing process. Robotic powder coating offers multiple advantages, such as consistency in application, the ability to handle complex geometries, and improved safety by reducing human exposure to high-voltage equipment and hot surfaces. Automated systems can also optimize the powder application process, reducing waste and ensuring that parts are coated uniformly.
In tandem with automation, there has been an increasing push toward integrating smart technology into powder coating processes. This includes the use of sensors and control systems to monitor and adjust various parameters in real-time. For example, humidity and temperature sensors can ensure that the environment inside the powder booth is ideal for coating, while automated systems can track and adjust the flow of powder to minimize overspray and waste. Additionally, many modern systems now include data logging and analysis capabilities, which provide manufacturers with detailed insights into the coating process. These insights can help operators identify and resolve issues quickly, leading to less downtime and higher-quality finishes.
Another exciting development is the advancement in coating materials. Powder manufacturers are continually innovating to offer powders with improved properties, including enhanced durability, better resistance to UV light, and improved chemical resistance. There has also been a rise in the use of customized powder formulations for specific applications. For example, coatings with improved adhesion properties are being developed for use on challenging surfaces such as plastics, wood, or non-ferrous metals. This broadens the potential applications for powder coating, allowing manufacturers to achieve a durable, consistent finish on a wider variety of substrates. Some coatings even include anti-microbial properties, making them suitable for medical or food industry applications where cleanliness is paramount.
In addition to these advancements, the sustainability of the powder coating process is continually being improved. A major benefit of powder coating is that it produces fewer volatile organic compounds (VOCs) compared to traditional liquid coatings, but companies are going further to minimize their environmental footprint. New low-temperature curing powders are being developed to reduce energy consumption in the curing phase, which can account for a significant portion of energy use in powder coating operations. These powders can be cured at lower temperatures, which not only saves energy but also allows for the coating of a broader range of materials, including heat-sensitive substrates.
Recycling and waste reduction are also critical areas of focus. Modern powder coating systems include improved recovery systems that capture nearly all overspray and recycle it back into the process. In addition, some companies have implemented closed-loop systems where excess powder is recovered, cleaned, and reused, significantly reducing material waste. The adoption of these systems not only lowers operating costs but also aligns with the growing emphasis on sustainable manufacturing practices.
There is also growing interest in the development of water-based powder coatings. While traditional powder coatings are solvent-free, water-based versions use water as the primary carrier for the powder, rather than relying on chemical solvents. These coatings are particularly attractive for use in industries where solvent emissions and health concerns are top priorities. While still relatively new, water-based powder coatings offer a promising solution to the need for even more eco-friendly coating options.
As the powder coating industry moves forward, high-efficiency powder recovery systems are being developed to further reduce waste and improve sustainability. These systems not only capture overspray more effectively but also help reclaim finer powders that would have traditionally been lost in the process. By using cyclonic separation, electrostatic filters, or more advanced air filtration systems, recovery rates have improved significantly, making the process even more economical and environmentally friendly.
Customization is another area where powder coating is advancing. In today’s market, many industries require a wide range of colors, textures, and finishes to meet customer demands. Manufacturers are now able to create specialty finishes that include unique effects such as metallic, textured, or hammertone finishes, giving products more aesthetic appeal. The ability to produce customized coatings is especially important in industries like automotive and consumer goods, where design and branding are essential.
The future of powder coating also lies in its potential to be integrated with smart factories. As part of Industry 4.0, powder coating systems are increasingly connected to larger manufacturing ecosystems. This allows manufacturers to monitor production in real-time, using predictive maintenance and remote diagnostics to minimize downtime and improve overall efficiency. By connecting powder coating systems with other processes like assembly or packaging, manufacturers can ensure smoother workflows and optimize the entire production line.
Lastly, innovation in curing technology continues to progress. Traditional convection ovens have been complemented by new curing technologies like infrared, ultraviolet (UV), and even induction curing. These methods provide faster curing times and reduced energy consumption, helping companies meet production deadlines while reducing operating costs.
In conclusion, the powder coating industry is on the brink of significant advancements, driven by technological innovation, sustainability goals, and a demand for more customization. As automated systems, smart technology, and more efficient materials continue to evolve, powder coating will remain a highly relevant and growing method of coating for industries ranging from automotive to electronics and beyond. The shift toward eco-friendly processes, faster production, and customization promises a bright future for powder coating in a wide variety of applications.
Automatic Powder Coating Equipment
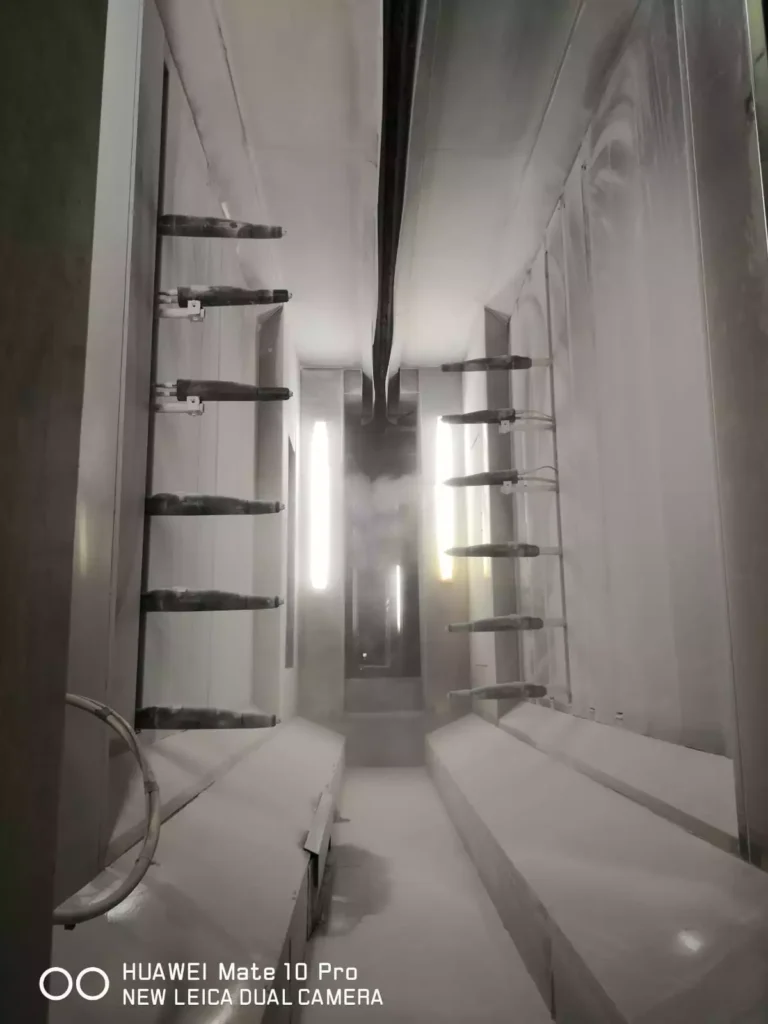
Automatic powder coating equipment is designed to streamline and enhance the powder coating process by using automation to apply powder and cure parts with minimal human intervention. These systems are especially beneficial for high-volume production, as they increase efficiency, ensure consistent quality, and reduce labor costs. Here’s an overview of the key components and features of automatic powder coating equipment:
Key Components of Automatic Powder Coating Equipment:
- Automated Powder Coating Guns:
- These guns are designed to apply powder to parts automatically. In an automated system, robotic arms or conveyors are used to move the workpieces to and from the coating area. The guns apply a uniform layer of powder, using an electrostatic charge to ensure the powder adheres to the grounded workpiece.
- Types of Guns:
- Corona guns: These are the most common type of automatic guns, applying high voltage to create an electrostatic charge that attracts the powder.
- Triboelectric guns: These use friction to charge the powder, which can be advantageous in certain applications where high-efficiency coating is required.
- Robotic Arms and Conveyors:
- Robotic arms: In an automated setup, robotic arms are often used to apply powder to parts in a controlled and precise manner. These robots can handle intricate geometries, ensuring even coverage and consistent coating thickness. Robotic arms also help in moving parts through different stages of the process, such as powder application, curing, and cooling.
- Conveyor systems: Conveyor belts are used to move parts through various stages of the coating process, including the application booth, curing oven, and cooling stations. Automated conveyors reduce manual handling and speed up the production process by allowing parts to be continuously processed.
- Automatic Powder Recovery Systems:
- An automatic powder recovery system captures the excess powder that doesn’t adhere to the part during the application process. The recovery system uses cyclonic separation or filtration to remove powder from the air, collect it, and return it to the powder hopper for reuse.
- The system ensures that there is minimal waste, as unused powder is cleaned and recycled. In automated systems, this process is fully integrated, allowing for continuous use of recovered powder without operator intervention.
- Automatic Pre-treatment Systems:
- Pre-treatment is an essential step in preparing parts for powder coating. Automatic pre-treatment systems typically consist of wash stations, chemical treatments, or sandblasting equipment that remove contaminants such as oils, grease, rust, and dirt.
- These systems ensure that the surface is clean and properly prepared for the powder coating process, improving adhesion and coating quality.
- Automated Curing Ovens:
- After the powder is applied, it needs to be cured in an oven to form a solid, durable finish. In automated systems, curing ovens are designed to handle multiple parts at once, with automated conveyor systems moving parts through the oven at the correct speed and temperature.
- Batch ovens: These are used for smaller, custom runs, where parts are placed individually in the oven.
- Conveyor ovens: These are more common in high-volume production, where parts move continuously through the oven.
- Advanced curing ovens may use technologies like infrared (IR) radiation or hybrid curing systems that combine infrared and convection methods for faster curing times and energy efficiency.
- Automatic Powder Coating Booths:
- Automatic powder coating booths are equipped with systems that apply powder uniformly to the workpiece. The booth is designed to create a controlled environment that minimizes contamination and powder waste. Some automatic systems are enclosed and equipped with advanced filtration and air management systems to capture and recycle powder.
- The booth is also typically designed with an efficient ventilation system to remove excess powder from the air, ensuring a clean working environment.
- Control Systems and Monitoring:
- Modern automatic powder coating systems include integrated control systems that manage various parameters such as powder flow, voltage, and coating thickness. These systems provide real-time data and feedback to operators, allowing them to monitor the performance of the system and ensure consistent results.
- In more advanced systems, the control system may feature a touchscreen interface that allows operators to adjust settings remotely, monitor equipment performance, and troubleshoot any issues that arise during the coating process.
Benefits of Automatic Powder Coating Equipment:
- Improved Efficiency:
- Automation reduces the need for manual intervention, speeding up the production process. Parts can be processed continuously, and the system can operate for longer periods without breaks, increasing throughput.
- Consistent Quality:
- Automatic systems ensure that each part receives a consistent, even coating, which is difficult to achieve with manual application. The automated powder guns and robotic arms are programmed to apply powder precisely, minimizing variations in coating thickness and finish.
- Reduced Waste:
- The recovery systems in automatic powder coating equipment significantly reduce the amount of powder waste, which is both environmentally friendly and cost-effective. Powder that does not adhere to the part is collected, cleaned, and reused, making the process more sustainable.
- Faster Turnaround:
- The use of automated systems, such as conveyors and robotic arms, reduces handling time and allows parts to move quickly through each stage of the process. This results in faster turnaround times, which is especially important in industries with tight production deadlines.
- Enhanced Safety:
- Automation reduces the need for human operators to be in direct contact with high-voltage equipment and high-temperature ovens, which improves overall safety in the work environment. Robots and automated systems handle the repetitive and potentially hazardous tasks.
- Reduced Labor Costs:
- With automation, the need for manual labor is significantly reduced, leading to lower labor costs. The system can operate with minimal human intervention, allowing operators to focus on overseeing the process rather than performing manual tasks.
- Scalability:
- Automatic powder coating systems are highly scalable. As production demands increase, the system can be expanded with additional guns, robots, or conveyors to accommodate higher volumes without compromising on quality.
- Flexibility:
- Many automated powder coating systems are adaptable, allowing manufacturers to adjust the powder application process for different types of parts and finishes. The system can handle a variety of sizes and shapes of parts, making it suitable for a wide range of industries, from automotive to electronics.
Conclusion:
Automatic powder coating equipment offers significant advantages in terms of speed, efficiency, quality, and cost-effectiveness. By integrating robotic arms, automated guns, conveyors, recovery systems, and curing ovens, manufacturers can achieve consistent and high-quality finishes while reducing waste and increasing production capacity. As technology continues to advance, the future of automatic powder coating systems will likely include even more sophisticated control systems, greater automation, and integration with Industry 4.0 technologies to further optimize the process.
Automatic powder coating equipment is designed to automate the entire powder coating process, making it faster, more efficient, and less dependent on manual labor. These systems are particularly beneficial in high-volume production environments where consistency and speed are critical. By automating the application of powder, the pre-treatment of parts, and the curing process, manufacturers can significantly improve the quality of the coating while reducing waste and production time.
The powder coating process begins with automated powder guns, which are equipped to apply a uniform layer of powder onto the workpiece. These guns are integrated with robotic arms or conveyor systems that transport parts through the process. The guns are often equipped with electrostatic charge technology to attract powder particles to the grounded surface, ensuring an even and consistent coating. These automated guns can be programmed to apply the right amount of powder in a controlled manner, reducing the likelihood of overspray and ensuring that the coating thickness is uniform across all parts.
Automated robotic arms are used to handle and move parts throughout the coating process. They can navigate complex part geometries, ensuring precise and accurate powder application. These robotic systems are programmed to follow a set path, which guarantees consistent coverage on each piece. Conveyor belts, on the other hand, transport parts automatically through different stages, such as the powder application booth and the curing oven. This continuous movement eliminates the need for manual intervention, allowing parts to be processed faster and more efficiently.
In addition to powder application, automated systems are equipped with powder recovery systems. These systems capture any powder that doesn’t adhere to the part during the application process and return it to the system for reuse. This is achieved through methods like cyclonic separation or filtration, which help remove the powder from the air and clean it so it can be recycled. The integration of these recovery systems is essential in reducing waste, lowering material costs, and improving the overall sustainability of the powder coating process.
The pre-treatment of parts, which is a crucial step in ensuring proper powder adhesion, is also automated in many advanced systems. This might involve washing stations that use chemical treatments or abrasive blasting to clean parts before coating. Automated pre-treatment systems ensure that the surface is properly prepared, leading to better adhesion of the powder and a more durable finish. The pre-treatment process is often monitored through sensors to ensure that it meets the required standards before the parts move to the coating stage.
Once the powder has been applied, parts are automatically transported to the curing oven, where the powder is heated to a high temperature, causing it to melt and bond to the surface. In automated systems, conveyor belts are used to move parts through the oven, ensuring a continuous process. The curing time and temperature are carefully controlled to ensure the coating forms a smooth, durable finish. Some automated systems use advanced curing technologies like infrared radiation or hybrid systems that combine convection and infrared heating. These technologies speed up the curing process, improve energy efficiency, and allow for more precise control over the curing process.
Automatic powder coating systems come equipped with sophisticated control and monitoring systems, which enable operators to oversee the entire process. These systems allow operators to monitor important variables like powder flow, temperature, and coating thickness in real-time. Some systems are even equipped with sensors that automatically adjust these parameters, ensuring optimal results with minimal intervention. The use of control systems also helps operators identify any issues or inconsistencies during the process, allowing them to quickly address problems and reduce downtime.
The benefits of automatic powder coating equipment are numerous. The most obvious advantage is the increased efficiency and speed of production. Automation significantly reduces the need for manual labor, which not only cuts down on labor costs but also reduces the potential for human error. Parts are moved through the coating process more quickly, and with robotic arms and automated systems applying the powder, the quality is consistent across all parts. This consistency is particularly important in industries where a high-quality finish is required, such as automotive, appliances, and electronics.
Another key benefit is the reduction of powder waste. Automatic recovery systems capture unused powder, which can be cleaned and recycled back into the process. This is both cost-effective and environmentally friendly, as it reduces the amount of waste generated and ensures that the material is used efficiently. By minimizing overspray and optimizing powder usage, automatic systems help to lower the overall cost of the coating process.
Automatic powder coating systems also improve safety. The use of robots and automated systems reduces human involvement in potentially hazardous tasks, such as handling high-voltage equipment or working near high-temperature ovens. This minimizes the risk of injury to workers and creates a safer work environment. Additionally, automated systems can operate for long periods with little downtime, ensuring that production can continue without interruption.
The scalability of automatic powder coating systems is another major advantage. As production demands increase, the system can be expanded with additional robotic arms, guns, and conveyor systems to meet the needs of larger production runs. This flexibility ensures that the system can grow with the business, providing the capacity to handle a variety of production volumes without compromising on quality or efficiency.
Customization is another area where automatic powder coating systems shine. These systems are adaptable and can be programmed to apply different types of powders, finishes, and colors depending on the specific requirements of the parts being coated. Whether it’s a glossy, matte, textured, or metallic finish, automated systems can handle the job with precision and consistency. This ability to customize finishes makes automatic powder coating systems particularly useful in industries that require specialized coatings, such as automotive or consumer electronics.
In conclusion, automatic powder coating equipment is transforming the way products are finished in a wide range of industries. The automation of powder application, pre-treatment, curing, and recovery systems not only boosts efficiency and reduces waste but also ensures a consistent, high-quality finish across all parts. By reducing manual labor, increasing safety, and offering greater flexibility and scalability, these systems provide manufacturers with a competitive edge, allowing them to meet growing demand while maintaining high standards of quality and sustainability.
The continued evolution of automatic powder coating equipment introduces even more advanced capabilities and refinements that further streamline the coating process. One major advancement is the increasing integration of Industry 4.0 technologies into automatic powder coating systems. This includes data-driven insights from sensors, automated monitoring systems, and the use of predictive analytics to optimize production schedules and improve quality control. By incorporating real-time data into the coating process, manufacturers can make immediate adjustments to improve efficiency, reduce downtime, and avoid production errors before they occur.
For example, sensors embedded in the system can detect any deviations from the optimal coating conditions, such as incorrect powder flow, temperature fluctuations, or curing inconsistencies. These sensors provide feedback to the central control system, which automatically adjusts the process parameters to compensate for any changes, ensuring that the coating is applied consistently across all parts. With the help of these technologies, predictive maintenance can also be implemented, enabling operators to identify and address potential issues with the equipment before they lead to failures or production stoppages.
Another exciting development is the further automation of the pre-treatment process. As surface preparation is crucial for the success of powder coating, the automation of this step can drastically improve efficiency and reduce human error. Automated pre-treatment systems are now being designed with enhanced robotic washing stations and chemical baths, capable of handling large batches of parts with minimal oversight. These systems can also monitor and adjust chemical concentrations in real time, ensuring that parts are treated optimally for adhesion, which can lead to a more durable finish.
Advanced powder coating guns are also becoming more sophisticated. Newer technologies in electrostatic application allow for better control of powder distribution, even in areas that are difficult to reach, such as deep cavities or complex geometries. These new-generation guns offer better powder adhesion, improved transfer efficiency, and the ability to apply coatings at much lower voltages, reducing the energy consumption of the system while maintaining high-quality finishes. The reduction in energy use is especially important in industries where energy efficiency is a key concern, such as in the automotive and appliance sectors.
Moreover, low-temperature curing technologies are increasingly integrated into automatic powder coating equipment. These advancements allow parts to be cured at lower temperatures, which can be advantageous for coating substrates that might be damaged by high heat, such as certain plastics or heat-sensitive materials. This allows for greater versatility in the range of materials that can be coated using powder coating, broadening the scope of applications. By curing at lower temperatures, manufacturers also see a reduction in overall energy consumption, aligning with sustainability goals.
The powder recovery systems in automatic setups are becoming even more efficient. As technology improves, recovery systems are able to capture smaller particles of powder that were once difficult to reuse, increasing overall powder utilization and further reducing material waste. New advanced filtration systems, such as nano-filtration and electrostatic filtering, are making these recovery systems even more effective at cleaning and reusing powder with minimal loss. These improvements not only save money but also contribute to a greener, more sustainable process by reducing the amount of excess powder that ends up in landfills.
In addition to operational enhancements, there has been a shift toward greater flexibility in coating finishes. Automated systems now support a broader range of finishes, from highly decorative to functional coatings, making it easier for manufacturers to produce parts with the specific visual or performance characteristics needed. The ability to apply multi-layer coatings with varying textures, colors, or even specialized finishes—like anti-microbial or UV-resistant coatings—has become easier through the automation of powder coating systems.
Furthermore, some systems now include the ability to handle dual or multi-color powder coatings, enabling manufacturers to create more intricate designs or customized color schemes without the need for extensive manual intervention. This is particularly useful in industries where aesthetic appeal is critical, such as the furniture, consumer electronics, and automotive sectors, where brands demand high-quality, unique finishes.
The integration of robotic finishing systems also extends to the post-coating process, where the parts are automatically cooled, inspected, and even packaged, ready for shipment. This is especially beneficial in industries that require high-throughput production, such as automotive parts or consumer goods. Cooling tunnels, for instance, can now be automated to ensure that parts cool down at an optimal rate, preventing warping or distortion of parts after curing. Automated inspection systems use cameras and sensors to assess the quality of the coating, ensuring that no defects—such as runs, sags, or missed spots—are present. This enhances product quality and reduces the need for manual inspection.
Additionally, integrating the entire powder coating process into a single automated line ensures a seamless workflow, from part loading to coating and curing, all the way through to packaging. This type of integrated system minimizes the need for manual handling, reduces potential contamination, and improves overall process speed. The entire process, from coating to curing to cooling, is executed in one continuous flow, making it more efficient and reducing downtime between steps.
The customizability of automatic powder coating systems is another key benefit that continues to evolve. Manufacturers can program their systems to handle specific coating requirements, including adjustments to the type of powder used, the speed of conveyor belts, curing temperature, and even the flow of recovery powder. This level of customization makes it possible to create highly specialized coatings tailored to the needs of a variety of industries, from aerospace to heavy machinery, to consumer products.
Looking to the future, the role of artificial intelligence (AI) and machine learning is likely to become more prominent in automatic powder coating systems. AI can be used to analyze data from sensors and monitoring systems to detect patterns, predict potential failures, and optimize system performance. Machine learning algorithms can analyze historical data to suggest improvements in the coating process, helping manufacturers make adjustments that improve efficiency, quality, and sustainability.
In summary, the future of automatic powder coating equipment is poised to be marked by greater integration of smart technology, more sophisticated materials and coatings, and an increasing focus on sustainability and energy efficiency. With automation continuing to play a central role in enhancing production speed and consistency, the industry is heading toward even more advanced, high-quality, and environmentally responsible coating solutions. As technology advances, automatic powder coating systems will become more versatile, efficient, and capable of meeting the evolving needs of industries around the world.
As automatic powder coating systems continue to evolve, manufacturers are placing a stronger emphasis on sustainability and resource efficiency, in response to growing environmental concerns and regulatory pressures. The future of these systems will see even greater strides toward eco-friendly practices, such as reduced energy consumption, improved powder recovery rates, and the use of biodegradable or non-toxic coatings. The need for a circular economy—where waste is minimized and materials are reused—is increasingly becoming a focal point, and advancements in powder coating technology align with this goal.
The integration of low-emission technologies is one area where significant improvements are expected. By using advanced curing methods that operate at lower temperatures, such as infrared (IR) and ultraviolet (UV) curing, manufacturers can reduce the energy required to heat the curing ovens. These technologies heat parts directly, bypassing the need to heat large volumes of air within the oven, which reduces both energy consumption and production time. This results in a lower carbon footprint for the powder coating process, contributing to sustainability goals and decreasing operating costs. For example, UV curing allows for faster curing times, meaning products are ready for use more quickly, increasing throughput while using less energy.
Waste reduction and recycling are also a major part of the drive for more sustainable powder coating systems. Modern powder recovery technologies have advanced to the point where almost all of the excess powder can be captured and reused. By utilizing techniques like cyclonic separation, filtration, and electrostatic powder recovery, automated systems can recover fine powder particles that would have previously been discarded, leading to minimal waste. The powder that is collected can be filtered, cleaned, and recycled back into the coating process, lowering material costs and reducing the environmental impact of discarded coatings. This is a huge benefit for manufacturers, as it not only lowers costs but also supports environmentally conscious practices.
Another promising trend in sustainability is the development of green powder coatings. These coatings are made from raw materials that are non-toxic, contain fewer harmful chemicals, and offer reduced emissions during curing. Manufacturers are increasingly shifting toward water-based or low-VOC (volatile organic compounds) powder coatings, which are safer for workers and more environmentally friendly. This reduces the release of harmful substances into the atmosphere and minimizes the need for hazardous waste disposal.
On the manufacturing floor, smarter inventory management will help further reduce waste. Automated systems can track and manage inventory in real time, ensuring that the right amount of powder is ordered, stored, and used. This reduces overstocking, which leads to wasted material, and ensures that the powder coating process is as efficient as possible. With precise tracking, manufacturers can minimize their environmental footprint by using only what is necessary and eliminating the need for excess stock or shipping.
In terms of improving operational performance, there is a trend toward incorporating augmented reality (AR) and virtual reality (VR) technologies to assist operators in troubleshooting and system maintenance. These immersive technologies allow workers to virtually inspect the coating process, identify potential issues in real time, and even simulate repairs or process adjustments. AR glasses or VR interfaces can provide detailed, on-the-spot information about equipment status, coating parameters, and predictive maintenance needs, helping to reduce downtime and keep the systems running at peak efficiency.
The next generation of automatic powder coating systems will likely feature more advanced process optimization algorithms that rely on AI and machine learning. These systems will analyze real-time data from the coating process to fine-tune application parameters such as powder flow rates, electrostatic charge levels, and curing temperatures. By continuously learning from each batch, the system can automatically adjust to ensure the best coating quality with minimal waste and downtime. This approach would allow for greater flexibility and adaptability to varying production runs, enabling manufacturers to maintain high standards of quality while optimizing their resources.
The smart factory concept will be fully integrated with automatic powder coating systems in the near future. This integration allows powder coating equipment to communicate with other manufacturing processes and machines, creating a seamless, fully automated production environment. Parts can be loaded, coated, cured, and packaged with minimal human involvement, all managed by an overarching central system that optimizes the entire workflow. This interconnected system enables manufacturers to synchronize their powder coating operations with other stages of production, such as assembly, quality control, and packaging, creating a just-in-time manufacturing environment that reduces inventory costs and accelerates time-to-market.
In addition to operational improvements, the introduction of robotic process automation (RPA) in powder coating systems will further drive the industry’s evolution. RPA systems can automate tasks that were previously considered too complex or detailed for traditional automation, such as adjusting the powder flow based on the surface geometry of the part being coated or handling the nuances of multi-color or multi-layer finishes. These advanced robotic systems will work in tandem with AI to provide precise, high-quality coatings on a wide range of products, from delicate electronic parts to heavy-duty industrial machinery.
There’s also the growing potential for 3D printing to complement or even replace traditional powder coating processes in certain applications. With 3D printing technologies improving rapidly, manufacturers are exploring the possibility of coating 3D-printed parts directly with powder to create a uniform and durable finish. This could revolutionize industries like aerospace or medical devices, where lightweight, complex parts require high-performance coatings.
Looking further ahead, personalized coating solutions may become more common in industries like consumer goods and automotive, where specific coatings are needed to achieve desired aesthetic effects or functional properties. With advanced customization capabilities, customers could have direct input into the coatings applied to their products, from colors and textures to special properties such as scratch resistance or thermal protection.
In summary, the future of automatic powder coating equipment will be defined by greater efficiency, sustainability, and smart technology integration. Manufacturers will continue to benefit from improved automation, energy-saving technologies, advanced recovery systems, and better process optimization. The adoption of AI, machine learning, AR/VR, and smart factory concepts will pave the way for increasingly flexible, scalable, and eco-friendly powder coating operations. These advancements will help manufacturers meet the growing demands for high-quality coatings while reducing their environmental footprint, ultimately driving a more sustainable and innovative future for the industry.
Powder Coating Reciprocator

A powder coating reciprocator is a key component in the automatic powder coating process. It is a mechanical or robotic device used to move powder coating guns back and forth across the surface of a part to ensure even and consistent application of the powder. The reciprocator’s movement is typically controlled by a computer or PLC (programmable logic controller) and is carefully programmed to ensure precise powder coverage, especially for complex or intricate part geometries.
How a Powder Coating Reciprocator Works:
The reciprocator is designed to move the powder coating spray guns in a controlled path, usually in horizontal or vertical directions, to ensure even distribution of the powder over the part. This movement can be linear, with the guns moving back and forth across the part, or in some cases, a more complex pattern is used depending on the design of the part being coated.
- Movement and Speed Control: The reciprocator’s movement can be precisely controlled in terms of speed, stroke length, and direction. This helps ensure that the powder coating is applied evenly and without overlap. By adjusting the speed and direction of the reciprocator, operators can optimize the coating process for different part shapes and sizes.
- Spray Guns: The powder coating guns are mounted on the reciprocator, and they can be adjusted to different angles or distances from the part being coated. These guns are typically electrostatic, charging the powder particles to attract them to the grounded part, ensuring even powder distribution.
- Control Systems: Modern reciprocators are often integrated with advanced control systems that can adjust the movement based on factors such as part size, geometry, or coating requirements. The control system may automatically adjust the speed and stroke length of the reciprocator to ensure the powder is applied correctly, and it can even stop or pause in certain areas where more coverage is required.
- Automated Functions: In fully automated powder coating systems, the reciprocator can be part of a continuous production line where parts are moved through various stages, including pre-treatment, coating, curing, and cooling. The reciprocator plays a crucial role in the coating step, as it moves the powder guns consistently and accurately to coat the parts.
Benefits of Powder Coating Reciprocators:
- Uniform Coating Application: The primary benefit of using a reciprocator is its ability to apply a uniform layer of powder over the surface of the part. The controlled, repetitive motion ensures that no spots are missed and that the powder adheres evenly across the part’s surface.
- Enhanced Speed and Efficiency: Reciprocators increase the speed and efficiency of the powder coating process, as they eliminate the need for manual application, which can be inconsistent and slow. The automated movement of the guns ensures faster cycle times, leading to higher production throughput.
- Improved Powder Recovery: As reciprocators are often part of a more sophisticated powder coating system, they are integrated with powder recovery technologies that allow unused powder to be captured and recycled. This reduces waste and lowers material costs, making the entire process more cost-effective and environmentally friendly.
- Better Finish Quality: Automated reciprocators can provide higher-quality finishes compared to manual methods, as the even distribution of powder leads to fewer imperfections, such as streaks, runs, or uneven thickness. This is particularly important in industries where aesthetics and durability are crucial.
- Flexibility for Complex Parts: Reciprocators are versatile enough to handle a wide range of part sizes and geometries, from flat surfaces to intricate shapes. Their adjustable parameters make them suitable for a variety of applications, whether it’s a simple part with few curves or a more complex shape with deep recesses or edges.
- Reduced Labor Costs: By automating the powder coating process with a reciprocator, the need for manual labor is greatly reduced. This not only cuts down on labor costs but also reduces the risk of human error, leading to a more consistent and predictable coating result.
- Customization: Modern reciprocators can be programmed to apply different types of powder coatings, whether it’s a single color or a multi-layer, textured, or special finish. The ability to easily switch between different coating styles adds to the system’s flexibility, especially for manufacturers that need to produce parts with varying aesthetic or functional coatings.
Types of Powder Coating Reciprocators:
- Manual Reciprocators: These are simple, basic systems where the operator manually adjusts the movement of the spray gun. They are typically less expensive but also less efficient and precise than automated systems.
- Semi-Automatic Reciprocators: These systems involve some level of automation, where the operator can set up the movement parameters, but the machine still requires some manual input, such as loading and unloading parts. Semi-automatic systems can provide better consistency and efficiency than manual ones.
- Fully Automatic Reciprocators: In fully automatic systems, the reciprocator is integrated into a complete automated powder coating line. These systems are programmable and are capable of adjusting to different part types and sizes automatically, ensuring optimal powder application without human intervention.
Maintenance of Powder Coating Reciprocators:
To maintain the proper functioning of a powder coating reciprocator, regular maintenance is essential. This includes:
- Cleaning: Powder buildup on the reciprocator’s moving parts can cause irregular motion or inefficient powder distribution. Regular cleaning of the spray guns, control mechanisms, and conveyor tracks is crucial.
- Lubrication: The reciprocator’s moving parts, such as gears, rails, and bearings, should be regularly lubricated to prevent wear and tear.
- Inspection: Routine inspections to check for wear on mechanical components and electrical systems help ensure that the reciprocator operates smoothly.
- Calibration: Over time, the reciprocator may require recalibration to ensure that the movement parameters remain accurate, which can be done using the machine’s control system or manual adjustments.
Applications of Powder Coating Reciprocators:
Powder coating reciprocators are widely used in various industries, including:
- Automotive: For coating car parts, rims, and other components.
- Appliances: Such as washers, dryers, refrigerators, and ovens.
- Metal Fabrication: Coating metal components in construction, agriculture, and industrial machinery.
- Furniture: Applying durable, aesthetic finishes to office furniture and outdoor furniture.
- Electronics: Coating parts like housings, cases, and panels for consumer electronics.
In conclusion, the powder coating reciprocator is an essential part of modern powder coating systems, providing consistency, speed, and high-quality finishes. Whether used in manual, semi-automatic, or fully automatic systems, it helps manufacturers achieve uniform powder distribution, reduce waste, and enhance overall process efficiency. With continued advancements in automation and control technology, the role of reciprocators in powder coating systems will only grow in importance, supporting industries that require high-quality and durable coatings.
Advanced Features of Powder Coating Reciprocators:
- Programmable Movement: Modern powder coating reciprocators are equipped with advanced controllers that allow for precise programming of the movement patterns. This means that users can set specific speed, stroke length, and direction for the spray guns based on the type of part being coated. These programmable settings allow for optimal coverage, ensuring that the part is coated uniformly and efficiently, reducing the chances of uneven powder application.
- Electrostatic Control Integration: Many powder coating reciprocators are integrated with electrostatic powder application technology. This system charges the powder particles, which are then attracted to the grounded part, allowing for a more consistent application. The reciprocator works in tandem with the electrostatic system to ensure that powder is distributed evenly and sticks to the surface of the part, even in areas that may otherwise be difficult to coat.
- Variable Speed Control: Some advanced reciprocators offer variable speed control, allowing users to adjust the speed of the reciprocator’s movement based on the specific part characteristics. Faster speeds may be ideal for simpler, flat parts, while slower speeds can ensure more coverage on complex or intricate parts with deep crevices or hard-to-reach areas. Variable speed control ensures that the coating process is optimized for each specific job, improving both the quality of the finish and the efficiency of the operation.
- Vertical and Horizontal Adjustments: For complex geometries, vertical and horizontal adjustments in the reciprocator’s movement may be necessary. This allows for greater flexibility in coating parts of different shapes, such as those with irregular contours or tall, narrow features. These adjustments can also optimize the angle of the powder spray, ensuring that every part of the part is coated uniformly, including undercuts and hard-to-reach areas.
- Multi-Gun Configuration: Some reciprocators allow for multi-gun configurations, where multiple spray guns can be mounted on the same reciprocator arm or on separate arms that work in parallel. This setup is particularly useful for large parts that need to be coated quickly. Multi-gun systems enable better coverage and speed up the process, as each gun applies a portion of the coating, allowing for a faster overall coating time.
Benefits of Advanced Features:
- Increased Flexibility and Precision: The combination of programmable movement, electrostatic control, and multi-gun configurations allows for higher precision in the powder coating process, especially when dealing with complex part shapes and sizes.
- Enhanced Speed and Throughput: With variable speed control and multi-gun configurations, reciprocators can apply coatings faster, allowing for higher throughput in manufacturing operations. This is particularly valuable in high-volume industries such as automotive and appliances.
- Reduced Waste: Advanced systems with optimized movement and electrostatic charge help reduce the amount of powder that misses the part or is over-applied. This minimizes waste, reduces material costs, and contributes to more sustainable operations by ensuring maximum powder efficiency.
Integration with Other Systems:
Powder coating reciprocators can also be integrated with automated handling systems to create fully integrated powder coating lines. These systems can automatically load and unload parts, move them through pre-treatment stages, and transport them through the coating and curing process without requiring manual intervention. When combined with robotic arms or conveyor systems, the reciprocator can ensure that each part receives consistent coverage as it moves through the coating process.
For example, in a fully automated powder coating line, the part is loaded onto a conveyor belt, where it moves into the coating zone. Here, the reciprocator moves the powder spray guns over the part while adjusting the spray pattern and coverage area to match the part’s shape. After coating, the part is moved into a curing oven where it is baked at a specific temperature, and then cooled before being unloaded and packaged.
Impact on Quality Control:
Quality control is a critical aspect of powder coating, and the reciprocator plays a key role in ensuring consistent and high-quality finishes. Automated systems with built-in monitoring features can provide real-time feedback on coating thickness, uniformity, and powder usage. For example:
- Coating Thickness Measurement: Some systems are equipped with sensors that measure the thickness of the applied powder layer in real-time, ensuring that it meets specified standards.
- Automated Inspection: Vision systems or cameras can be integrated with the reciprocator to monitor the application process and ensure there are no defects, such as powder streaks, inconsistencies, or missed areas. If an issue is detected, the system can automatically adjust the movement or pause the process to prevent further defects.
- Feedback Loops: In some advanced systems, real-time data collected from the coating process can be fed back to the system’s control software. If irregularities are detected, adjustments can be made on the fly to optimize the coating process, ensuring that defects are minimized and quality is maintained.
Conclusion:
The powder coating reciprocator is a crucial part of modern powder coating systems, offering significant advantages in terms of speed, efficiency, precision, and quality. With continued advancements in technology, reciprocators are becoming more versatile and adaptable to a wide range of applications. Whether it’s for small, intricate parts or large-scale, high-volume production, the reciprocator ensures that powder coatings are applied consistently and evenly. By integrating with automated lines, multi-gun systems, and advanced control technologies, reciprocators help manufacturers meet the growing demands for high-quality, durable finishes while reducing waste, improving throughput, and contributing to sustainability.
The integration of powder coating reciprocators into automated systems has further enhanced their capabilities. These advancements not only improve coating consistency but also enable a more seamless and efficient workflow across the entire coating process. By automating the movement of the spray guns, the reciprocator removes much of the human error that can occur in manual applications. This level of consistency is critical in industries where appearance and durability are paramount, such as automotive and appliance manufacturing.
As the powder coating industry continues to evolve, the demand for greater precision and faster processing speeds is pushing the boundaries of what reciprocators can achieve. Some of the latest systems include features like motion sensors and adaptive learning algorithms that allow the reciprocator to adjust its movements based on the specific shape and orientation of each part. This adaptive feature helps ensure that even the most complex parts are coated evenly, regardless of their geometry.
Moreover, the modern reciprocator’s role in improving overall resource efficiency cannot be overlooked. By fine-tuning the powder flow rate and minimizing overspray, it contributes significantly to reducing material waste. The electrostatic process already ensures that most of the powder is attracted to the part, but by optimizing the reciprocator’s path and speed, companies can reclaim a larger portion of the unused powder for reuse, thus reducing costs and minimizing environmental impact.
Another important consideration is the relationship between reciprocators and energy consumption. In powder coating, the curing process typically requires the part to be baked in an oven, and the energy used in this stage can account for a significant portion of the overall energy consumption. While the reciprocator itself doesn’t directly affect the curing process, its role in streamlining the coating stage helps shorten cycle times. This reduction in time spent on coating parts can lead to a decrease in the total energy required for each part, as the oven can process parts more quickly. Additionally, with improved automation and synchronization between coating and curing, manufacturers can optimize their oven loads, further improving energy efficiency.
Advancements in smart manufacturing technologies are also beginning to integrate with reciprocator systems. These systems, powered by the Internet of Things (IoT), allow for real-time monitoring and remote diagnostics, making it easier to spot potential issues and fix them before they become major problems. Operators can access detailed performance data on the reciprocator, such as movement patterns, speed, and coating coverage, from a central control room or via mobile devices, allowing them to make adjustments on the fly. This level of connectivity ensures that the powder coating process remains agile and responsive to changing production requirements.
The flexibility of modern reciprocators is also increasing. These machines can be easily adapted to handle various part sizes and shapes. The ability to adjust the coating path or the number of guns used allows for a wider range of applications, from simple geometries to highly complex, custom parts. In industries like aerospace or medical device manufacturing, where part designs can be highly intricate, the ability to use a reciprocator that can adjust its path dynamically ensures that the coating is applied uniformly, regardless of the part’s complexity.
Lastly, the continued push toward sustainability in manufacturing means that powder coating reciprocators are being designed with eco-friendly features. As the coating process moves toward greener solutions, such as low-VOC or water-based powders, reciprocators are being engineered to work with these new materials. The improved powder recovery systems built into these devices also play a critical role in reducing waste and conserving materials. As environmental regulations become stricter, the powder coating industry is increasingly focusing on ways to minimize its environmental footprint, and reciprocators are key to meeting these goals.
In conclusion, the evolution of powder coating reciprocators reflects a broader trend in manufacturing toward higher precision, greater automation, and improved sustainability. As they continue to integrate advanced technologies like adaptive control systems, energy-efficient designs, and smart monitoring, reciprocators are becoming even more essential to industries seeking efficient, high-quality, and environmentally friendly coating solutions. These machines are no longer just part of the process; they are the backbone of modern powder coating lines that help businesses meet the growing demands of speed, quality, and sustainability.
The next generation of powder coating reciprocators will likely see even more profound shifts, influenced by ongoing advancements in robotics, artificial intelligence (AI), and machine learning (ML). These technologies will significantly enhance the precision and flexibility of reciprocators, making them even more adaptable to complex manufacturing needs and pushing the boundaries of what is possible in terms of coating quality and process optimization.
One of the most exciting prospects is the integration of AI-driven predictive analytics into reciprocator systems. This would allow for the monitoring of various variables—such as part geometry, powder flow, and environmental factors—that can influence the coating process. By analyzing real-time data, AI systems can predict and correct potential inconsistencies in the coating application before they occur, reducing the likelihood of defects and ensuring that every part meets the desired quality standards. For instance, if the system detects a slight variation in powder thickness or flow rate, it could automatically adjust the reciprocator’s speed, spray angle, or distance from the part to compensate.
With the combination of machine learning and advanced computer vision, powder coating reciprocators could be equipped with the ability to “see” the parts they are coating in real time. Cameras or imaging systems would allow the reciprocator to scan the part’s surface and identify areas that may require more powder or areas where the application is excessive. By continuously analyzing the part’s shape and surface, the system could adjust in real time, ensuring that every nook and cranny is evenly coated without overspray or missed spots. This technology would be especially beneficial for highly intricate or geometrically complex parts, where traditional reciprocators might struggle to achieve consistent coverage.
In addition to quality control, AI and machine learning could also contribute to process optimization by analyzing historical data to determine the most efficient coating parameters. For example, based on the past performance of specific powder types or part geometries, the system could automatically adjust the reciprocator’s settings to optimize the application process, reducing waste, energy consumption, and curing time. Over time, the system would “learn” the ideal settings for a variety of production scenarios, continuously improving the coating process as more data is collected.
The integration of robotic arms and collaborative robots (cobots) with powder coating reciprocators is another area of significant growth. These advanced robots would provide even greater flexibility and precision in powder coating applications. Cobots, in particular, are designed to work alongside human operators, providing added support while ensuring safety. These systems could be used to coat parts with irregular shapes, move components through different stages of the process, or even handle delicate items with minimal risk of damage. Their ability to adapt to different tasks and environments would make them invaluable for industries that produce diverse parts requiring varied coating techniques.
The future of powder coating reciprocators will also likely feature increased integration with other manufacturing technologies within the factory. This includes the ability to communicate seamlessly with automated guided vehicles (AGVs) that transport parts, as well as integration with Enterprise Resource Planning (ERP) systems that help manage production schedules, inventory, and overall factory workflow. Such connectivity would ensure that the coating process is always synchronized with the rest of the manufacturing line, enhancing overall operational efficiency and reducing downtime.
Sustainability will continue to be a key driving factor in the evolution of reciprocator technology. Future designs will likely emphasize energy efficiency, utilizing lower-power motors and advanced power management systems. This is important not only to reduce operational costs but also to align with global efforts to reduce carbon footprints. Additionally, improvements in powder recovery and waste management technologies will further minimize the environmental impact of powder coating. New methods for capturing and reusing overspray, for example, could lead to even higher recovery rates, ensuring that powder material is utilized to its fullest potential.
In terms of coating materials, we are seeing the development of more sustainable and specialized powder formulations that offer better performance with less environmental impact. These include water-based powders, low-VOC coatings, and biodegradable materials. Reciprocators will need to adapt to these new materials, ensuring they can apply them efficiently while maintaining the high-quality finish expected in industries such as automotive, architecture, and consumer goods.
Furthermore, customization will become more important as consumers and businesses alike demand more tailored solutions. Reciprocators of the future will likely offer even more flexible capabilities, allowing for custom color blending, texture creation, and the application of multiple coating layers in a single pass. This could revolutionize sectors like high-end consumer goods and luxury products, where the ability to offer bespoke finishes can set brands apart.
The ongoing development of smart factories will also shape the future of reciprocators. In these advanced environments, manufacturing equipment is interconnected through IoT sensors, creating a highly responsive and data-driven production system. In such settings, reciprocators will play a crucial role in ensuring that the powder coating process is seamlessly integrated with other steps, from material handling to packaging, and that the entire production line operates with maximum efficiency. For instance, real-time data from the reciprocator can be used to dynamically adjust oven temperatures, curing times, or conveyor speeds to optimize the overall process.
Finally, the concept of remote monitoring and control will become even more prominent. Manufacturers will be able to oversee and control their powder coating systems from virtually anywhere, thanks to cloud-based interfaces and mobile applications. This would allow operators to monitor performance, adjust settings, and troubleshoot issues without needing to be physically present on the factory floor, improving flexibility and response times.
In conclusion, the future of powder coating reciprocators is incredibly exciting, with developments in AI, robotics, sustainability, and smart manufacturing technologies shaping the next generation of systems. These advancements will not only improve the quality and efficiency of the coating process but also contribute to a more sustainable and agile manufacturing environment. As these technologies continue to evolve, reciprocators will become even more integral to the success of modern manufacturing, enabling companies to meet the growing demands for high-quality, customized, and environmentally responsible products.
Powder Coating Machine
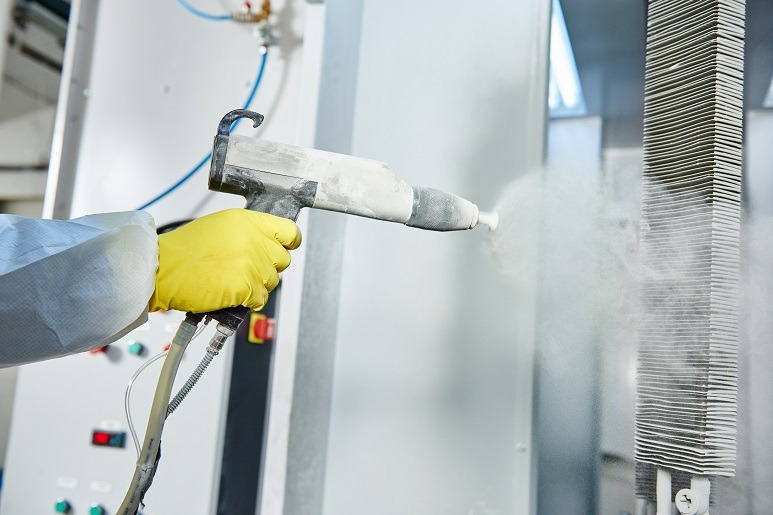
A powder coating machine is a critical piece of equipment in the powder coating process, used to apply a dry powder to metal or other materials in order to create a durable, high-quality finish. Powder coating is a more environmentally friendly alternative to traditional liquid paints because it doesn’t require solvents and produces fewer emissions. The machine works by spraying electrostatically charged powder particles onto a part, which is then cured in an oven to form a solid, long-lasting coating.
Key Components of a Powder Coating Machine:
- Powder Spray Gun: The spray gun is the heart of the powder coating machine, used to apply the powder to the surface of the object being coated. The gun works by charging the powder particles electrostatically, causing them to be attracted to the grounded part. This process ensures even coverage and efficient use of the powder. Spray guns may come in different types:
- Corona guns: The most common type, where the powder is charged by the corona discharge created by a high-voltage electrode.
- Tribo guns: These work by using friction to charge the powder particles as they move through the gun.
- Powder Booth: The powder booth is the enclosed area where the coating process takes place. It is designed to contain the overspray powder, ensuring that it doesn’t contaminate the surrounding environment. Powder booths may include features like:
- Filtered airflow to prevent the escape of powder particles.
- Recirculation systems to collect and reuse unused powder.
- Efficient ventilation to capture and filter out excess powder and maintain a clean working environment.
- Powder Recovery System: One of the advantages of powder coating is the ability to reclaim unused powder, reducing waste and material costs. The recovery system consists of:
- Cyclone separators or filters that capture airborne powder particles.
- Suction and vacuum systems to remove the excess powder from the air within the booth and direct it into storage containers for reuse.
- Curing Oven: Once the powder has been applied to the part, it needs to be cured to form a solid coating. The curing oven is heated to a specific temperature (typically between 160°C and 200°C, depending on the powder material), which causes the powder to melt, flow, and chemically bond to the substrate, creating a hard, durable finish. There are different types of curing ovens:
- Convection ovens, where hot air circulates around the parts.
- Infrared ovens, which use radiant heat to cure the powder more quickly.
- Hybrid ovens, which combine convection and infrared technologies.
- Conveyor System: In larger systems, parts are often transported through the powder coating process via a conveyor system. This helps to automate the process and ensures parts are consistently moved through the spray booth and curing oven. Conveyor systems can be manual or automated, depending on the size and requirements of the production line.
- Control Panel: A control panel is used to adjust the settings for the powder coating machine. It includes controls for the spray gun settings (such as voltage and airflow), curing oven temperature and time, and conveyor speed. The control panel allows operators to fine-tune the process based on the specific material and type of finish required.
Types of Powder Coating Machines:
- Manual Powder Coating Machine: A manual powder coating system involves a spray gun operated by an individual who manually applies the powder to the part. This system is often used for small batches or customized items. Manual machines are typically more affordable but may be less efficient and consistent compared to automated systems.
- Automatic Powder Coating Machine: In an automatic system, the spray guns and other components of the powder coating process are automated to improve efficiency and consistency. Parts are usually loaded onto a conveyor system, where they are transported through the powder booth and curing oven. Automatic machines are ideal for high-volume production and larger manufacturing facilities, where consistency, speed, and quality are crucial.
- Robotic Powder Coating Machine: Robotic powder coating systems are highly advanced, using robotic arms to move spray guns over parts. These systems can be programmed to coat complex parts with high precision, ensuring an even coat and reducing the chances of human error. Robotic systems are commonly used in industries such as automotive and aerospace, where part geometries are complex, and high-quality finishes are required.
Powder Coating Process with a Powder Coating Machine:
- Preparation: Before the powder coating can be applied, the part must be cleaned and pretreated to ensure proper adhesion of the powder. This may involve processes such as:
- Cleaning: Removing oils, dirt, or other contaminants from the surface.
- Pretreatment: Applying a phosphate or chromate coating to enhance powder adhesion and corrosion resistance.
- Drying: Ensuring that the part is dry before powder application.
- Powder Application: The part is placed in the powder booth, where it is sprayed with an electrostatically charged powder from the spray gun. The charged powder particles adhere to the grounded part, forming a thin, uniform layer. The amount of powder applied is controlled by adjusting the settings on the gun, such as voltage, airflow, and the distance from the part.
- Curing: After the powder is applied, the part is moved into the curing oven, where heat causes the powder to melt, flow, and chemically bond to the surface of the part. The curing process typically lasts for 10-20 minutes, depending on the type of powder and the part’s size and thickness.
- Cooling: Once the curing process is complete, the part is removed from the oven and allowed to cool. This cooling period solidifies the coating, giving the part a durable, smooth, and uniform finish.
- Inspection and Finishing: After cooling, the coated part may undergo inspection for quality control purposes. If necessary, touch-ups can be made to address any imperfections. Some machines may have automated inspection systems that check for coating thickness and consistency, ensuring that each part meets the required specifications.
Advantages of Powder Coating Machines:
- Durability: Powder coatings are highly durable, providing resistance to scratches, chipping, fading, and corrosion. This makes powder coating machines ideal for industrial applications where long-lasting finishes are required.
- Environmentally Friendly: Powder coating does not require solvents or chemicals, which reduces the environmental impact associated with traditional liquid coatings. The process produces fewer emissions and waste, making it a more sustainable option.
- Efficiency: Powder coating is more efficient than liquid painting because it produces less waste and allows for faster application. The electrostatic process ensures that most of the powder sticks to the part, and unused powder can be recycled.
- Variety of Finishes: Powder coating machines can produce a wide range of finishes, including matte, gloss, textured, and even custom colors. The flexibility in finish types makes it suitable for various industries, from automotive to home appliances to architectural elements.
- Cost-Effective: While initial setup costs for a powder coating system can be higher, the reduced need for solvents, faster curing times, and the ability to recycle unused powder make the process cost-effective in the long run.
Applications of Powder Coating Machines:
- Automotive: Powder coating is widely used to coat car parts, wheels, bumpers, and trim components due to its durability and resistance to the elements.
- Appliances: Items such as refrigerators, washing machines, and ovens often receive powder coatings for their durability and aesthetic appeal.
- Architectural Components: Aluminum window frames, door handles, and other exterior components are often powder-coated for both aesthetic and protective reasons.
- Metal Furniture: Furniture pieces like tables, chairs, and filing cabinets benefit from the durable finish offered by powder coating.
Conclusion:
Powder coating machines are essential for achieving high-quality, durable finishes on a wide variety of materials, particularly metals. They offer numerous advantages, such as durability, environmental sustainability, efficiency, and cost-effectiveness. Whether used in manual, automatic, or robotic systems, powder coating machines have become indispensable in industries that require long-lasting, aesthetically pleasing coatings on metal parts. As technology continues to improve, the capabilities of powder coating machines will continue to evolve, providing even better performance and flexibility for manufacturers.
Powder coating machines play a crucial role in providing high-quality, durable finishes for a wide range of materials, particularly metals, by utilizing a process that is both efficient and environmentally friendly. These machines ensure that products like automotive parts, appliances, and metal furniture receive a uniform and lasting coat that not only enhances their appearance but also protects them from the elements, wear, and tear.
The process begins with a thorough cleaning and pretreatment of the part to ensure that the coating adheres properly. This step may involve the removal of oils, grease, and contaminants, followed by the application of a chemical treatment to improve adhesion. Once the surface is prepped, the powder coating machine applies the dry powder using an electrostatic spray gun. The powder particles are electrically charged and then attracted to the grounded part. This application method helps ensure even coverage, reducing the amount of waste powder that would otherwise be lost in the air. The excess powder that doesn’t stick to the part is captured by the powder recovery system and can be recycled for future use, which helps reduce material costs and environmental impact.
After the powder is applied, the part is transferred to a curing oven where it is heated to the required temperature. This heat causes the powder to melt, flow, and chemically bond to the surface, creating a smooth, hard finish that provides excellent durability and resistance to scratches, corrosion, fading, and chipping. The curing process is critical to ensuring the final product meets the desired quality standards. Once the part has been properly cured, it is allowed to cool, solidifying the coating and making the part ready for inspection.
The ability to recycle unused powder is a major advantage of the powder coating process. Not only does this reduce waste, but it also minimizes the cost of materials, which can be a significant expense for high-volume production lines. Additionally, because powder coatings do not require solvents or chemicals, the environmental impact is much lower than that of traditional liquid coatings. This makes powder coating an attractive option for manufacturers seeking sustainable solutions.
Powder coating machines are versatile, and their use extends across a variety of industries. In the automotive sector, they are used to coat car parts such as wheels, bumpers, and trim components, where durability and resistance to harsh conditions are critical. The appliance industry also benefits from powder coating technology, as items like refrigerators, ovens, and washing machines often require tough, long-lasting finishes to withstand everyday use and exposure to moisture. The architectural industry relies on powder coating for items like window frames, door handles, and other exterior components, as the coating provides both aesthetic appeal and protection against the elements. Similarly, metal furniture manufacturers use powder coating to ensure their products are both attractive and durable.
One of the advantages of powder coating machines is their ability to produce a variety of finishes, including matte, glossy, textured, and even custom colors. This flexibility allows manufacturers to meet the demands of different applications and consumer preferences. While the initial investment in a powder coating system may be higher than traditional liquid painting equipment, the long-term savings in material costs, environmental compliance, and energy efficiency make it a cost-effective solution in high-volume production settings.
As technology continues to advance, powder coating machines are becoming more sophisticated, with improvements in automation and robotic systems. Automated systems, in particular, increase efficiency and ensure consistent application, especially in high-volume settings. Robotic powder coating machines can be programmed to move spray guns over parts with great precision, ensuring that even complex geometries receive an even coat of powder. This level of automation allows for faster turnaround times and reduces the potential for human error.
The ongoing integration of IoT and AI technologies into powder coating systems is transforming how these machines operate. Real-time monitoring of the process allows for predictive maintenance, and advanced sensors can detect variations in powder thickness, ensuring that the finish is consistently applied to meet stringent quality standards. Smart systems can automatically adjust spray gun settings, curing times, and oven temperatures, ensuring that every part is coated according to the exact specifications required.
The flexibility of powder coating machines continues to grow, allowing them to handle a wider range of part shapes and sizes. With innovations in conveyor systems, robotic arms, and automated processes, these machines can accommodate a variety of production environments, from small-batch custom work to large-scale manufacturing operations. As industries continue to push for higher quality, faster production times, and more sustainable practices, the powder coating machine will remain a key player in achieving these goals.
In conclusion, powder coating machines are essential for delivering high-performance finishes across many industries, from automotive and appliances to architectural components and metal furniture. Their ability to produce durable, high-quality coatings, combined with their environmental benefits and efficiency, makes them a preferred solution for many manufacturers. As technology continues to advance, these machines will only become more powerful, capable, and adaptable, further solidifying their role in modern manufacturing processes.
As the powder coating industry continues to evolve, the technology behind powder coating machines is advancing to meet the increasing demands for higher precision, better efficiency, and more eco-friendly solutions. One of the most notable trends in the development of powder coating machines is the integration of automation and robotics, which is transforming the powder coating process across various industries. The automation of tasks like powder application, part handling, and curing significantly reduces labor costs while improving consistency and throughput. Automated powder coating systems can quickly adjust to changes in part size or shape, making them ideal for high-volume manufacturing environments where consistent quality is essential.
Moreover, robotic powder coating machines offer an unprecedented level of control and precision. These systems utilize robotic arms that can be programmed to coat parts in complex or difficult-to-reach areas, ensuring an even and consistent coating across the entire surface. Robotic systems can be paired with advanced vision systems, enabling the machine to “see” the part, evaluate its geometry, and adjust the spray pattern accordingly. This level of adaptability ensures that parts with intricate shapes, such as automotive components or custom-designed products, receive a uniform coat that traditional manual or non-robotic systems might struggle to achieve.
Alongside robotic automation, there is also a growing focus on data-driven technologies in powder coating systems. With the advent of smart manufacturing, powder coating machines are increasingly equipped with sensors, cameras, and IoT connectivity to monitor and adjust the coating process in real-time. This allows manufacturers to track every stage of the coating process, from powder application to curing, ensuring that parts are coated consistently and defects are minimized. By collecting and analyzing this data, manufacturers can identify trends, optimize their processes, and even predict when maintenance is required, reducing downtime and increasing operational efficiency.
Incorporating AI into powder coating systems further enhances their capabilities. For instance, AI-driven algorithms can optimize powder usage, automatically adjusting the spray gun settings based on part geometry, powder type, and environmental conditions. By improving the accuracy of powder application and reducing waste, these intelligent systems help manufacturers cut costs and reduce their environmental footprint. The use of machine learning also enables the system to adapt to new materials and processes as they are introduced, making it highly versatile and future-proof.
As environmental concerns continue to rise, powder coating systems are becoming more sustainable. The demand for greener manufacturing practices is driving the development of energy-efficient powder coating machines that minimize power consumption while maintaining high-quality finishes. New technologies in curing ovens, such as infrared curing, have made it possible to reduce the energy required for the curing process. This is particularly important in industries with strict sustainability goals, as energy-efficient systems can significantly lower operating costs and reduce the carbon footprint of production lines.
Another environmentally friendly development in powder coating is the use of low-VOC (volatile organic compound) or water-based powders, which produce fewer harmful emissions compared to traditional solvents. These innovations are part of a broader trend toward eco-friendly coating materials, which are less harmful to workers and the environment while maintaining the same high standards of finish and durability. The powder coating process itself, which eliminates the need for solvents, already offers a greener alternative to liquid coatings, and these new materials further enhance the environmental benefits of the process.
As the global market for customized products continues to grow, powder coating machines are also becoming more adaptable to the needs of diverse industries. From high-end automotive finishes to customized metal furniture and appliances, the ability to create unique colors, textures, and finishes is in high demand. Powder coating machines are now capable of producing specialized effects, such as metallic finishes, textured coatings, and multi-layered coatings, giving manufacturers the flexibility to meet these bespoke requirements. This customization capability is particularly beneficial for industries like luxury goods, where product differentiation is key to attracting consumers.
At the same time, the growing trend of shorter production cycles and on-demand manufacturing is also influencing powder coating technologies. Manufacturers are increasingly expected to produce smaller batches of products, often with quick turnaround times. To accommodate this, powder coating systems are being designed to be more flexible, allowing for fast changeovers between different parts and finishes. Quick color change systems and automated part loading/unloading systems are examples of technologies that enable powder coating machines to be more versatile and responsive to rapidly changing production schedules.
As demand for higher throughput continues to grow, manufacturers are also looking for ways to streamline the powder coating process. Innovations in conveyor systems and batch processing allow parts to be coated more quickly and efficiently. For instance, modular conveyor systems can be configured to handle various part sizes and shapes, optimizing part flow and reducing the time it takes for parts to go through the entire coating process. This flexibility is essential for industries that deal with a wide range of parts, from small custom components to large mass-produced items.
In addition to improving efficiency and sustainability, the powder coating industry is also benefiting from innovations in advanced coating materials. New formulations of powder coatings are offering improved properties, such as better corrosion resistance, increased UV stability, and greater flexibility for demanding applications. These new coatings are enabling manufacturers to expand the range of products that can be powder-coated, including those exposed to harsher environmental conditions, such as marine and outdoor applications.
As the technology behind powder coating systems advances, the cost of ownership for manufacturers continues to decrease. Automation, energy-efficient systems, and material recovery technologies are all contributing to a lower total cost of ownership. Furthermore, the recyclability of powder coating material itself reduces waste and makes the process more cost-effective in the long term. Manufacturers who invest in these advanced systems benefit from improved quality, reduced waste, and enhanced operational efficiencies, making powder coating a more attractive option for a wide variety of industries.
In conclusion, the future of powder coating machines is marked by advancements in automation, sustainability, data-driven optimization, and customization. As these machines continue to evolve, they will offer even greater precision, efficiency, and flexibility, enabling manufacturers to meet the increasing demands of modern production environments. With improvements in energy efficiency, environmental sustainability, and the ability to handle customized finishes, powder coating systems are poised to remain a crucial part of manufacturing processes across a broad range of industries. As technology progresses, powder coating machines will continue to play an integral role in delivering high-quality, durable finishes while meeting the growing need for eco-friendly, cost-effective solutions.
The next wave of advancements in powder coating machines will likely focus on further enhancing automation and digital integration, which will continue to drive the evolution of the industry toward higher efficiency and greater precision. Smart factories equipped with interconnected systems and data-sharing capabilities will be able to monitor every aspect of the powder coating process in real-time, leading to more intelligent decision-making and less human intervention.
Predictive maintenance is one of the key benefits of this digital transformation. With the integration of IoT sensors, machines will be able to detect anomalies in real-time and predict when certain components, such as motors or spray guns, will need maintenance or replacement. By analyzing historical data and recognizing patterns, these systems can help prevent breakdowns, extend the life of equipment, and minimize downtime. Manufacturers will no longer have to rely on a fixed maintenance schedule or wait for an issue to arise before making repairs. This predictive approach reduces costs and boosts operational uptime, making powder coating machines more reliable and cost-effective over the long term.
Additionally, the use of artificial intelligence (AI) and machine learning will enable powder coating machines to continuously learn from the data they collect during the production process. AI algorithms will be able to automatically adjust key variables, such as spray gun settings, airflow, and oven curing times, based on real-time performance data. This means that the machines can continuously improve their own efficiency and output without the need for human intervention. This will lead to a new era of self-optimizing systems where the machines themselves are responsible for fine-tuning their processes to achieve the best possible results. The increased accuracy will not only improve product quality but will also reduce material waste and energy consumption.
Another exciting development in the future of powder coating systems will be the advancement of powder materials themselves. Innovations in powder formulations will continue to improve the quality and performance of powder coatings. For instance, nano-coatings could provide an even more durable and resistant finish, offering additional benefits such as enhanced corrosion resistance, higher scratch resistance, or even self-healing properties. This is particularly important in industries where parts are exposed to extreme environments, such as marine, automotive, or industrial applications. New materials may also enable powder coatings to be used on a broader range of substrates, expanding their potential applications even further.
In addition to improved performance characteristics, new powder coatings will likely focus on expanding the color and texture options available to manufacturers. Custom color-matching technologies, using advanced spectrophotometers and AI algorithms, will enable manufacturers to more easily replicate specific color shades, offering greater precision in meeting client demands. In addition to color, textured finishes like metallic, matte, and satin coatings will continue to gain popularity. New technologies may even allow for the creation of interactive finishes that change appearance depending on the angle of the light, offering a dynamic visual appeal.
The future of powder coating machines will also be shaped by advances in sustainability. With the continued push toward greener manufacturing practices, there will be more demand for low-emission powder coating systems that limit harmful pollutants and reduce the environmental impact of industrial operations. Emerging trends in zero-waste and circular manufacturing will influence the design of powder coating systems, encouraging greater recycling of excess powder, water-based and non-toxic powder formulations, and more energy-efficient curing processes. Powder coating machines will become key enablers of circular economies where waste and by-products are minimized, and materials are reused as much as possible.
Energy-efficient curing technologies will play a significant role in making powder coating systems more sustainable. New infrared curing ovens and hybrid curing systems, which combine infrared radiation with conventional convection heating, are expected to reduce energy consumption and increase throughput. Infrared curing, for example, can heat parts more quickly by directly applying heat to the substrate, making the process faster and more energy-efficient. With the rise of renewable energy sources, manufacturers will also have the opportunity to power their powder coating systems with cleaner energy, further reducing their carbon footprint.
Moreover, the growing trend of customization in manufacturing will continue to shape the powder coating market. As consumers increasingly demand unique and personalized products, powder coating systems will need to accommodate small batch runs and quick changes between coatings. The rise of on-demand manufacturing and just-in-time production means that manufacturers will require machines that can quickly adjust to different parts, finishes, and colors, all while maintaining consistent quality. This increased demand for flexibility will push powder coating systems to evolve, with more modular systems and fast-changeover technologies that make switching between coatings faster and more efficient.
The integration of robotics and artificial intelligence will also enable even more precise and intricate designs to be coated. With advancements in 3D printing and additive manufacturing, there will be an increase in the use of powder coating for parts with complex geometries and detailed surfaces. Robotic arms and automated spray guns will be able to follow the contours of these parts with a high degree of accuracy, ensuring that the coating is applied evenly and consistently, even on intricate or non-standard shapes. This will open up new possibilities for industries such as aerospace, medical devices, and custom automotive, where precision is critical, and the need for customization is high.
In summary, the future of powder coating machines is full of potential. Advances in automation, artificial intelligence, energy efficiency, and sustainable practices will continue to transform how powder coating systems operate. As manufacturers demand more customized solutions and faster production cycles, these machines will evolve to meet these challenges, with better precision, improved material handling, and greater adaptability. With the continued development of new powder formulations, smarter technologies, and environmentally friendly innovations, powder coating will remain a cutting-edge solution for achieving high-performance, durable finishes across a wide range of industries.
Powder Coating Equipment
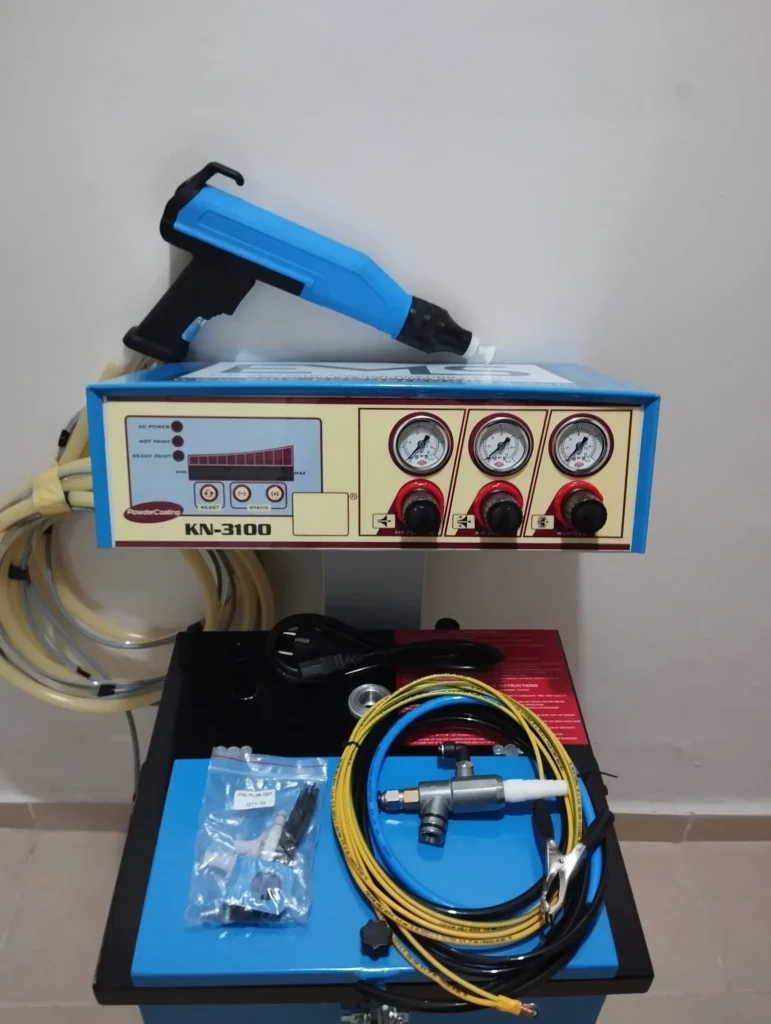
Powder coating equipment is a key component in the powder coating process, which is used to apply a durable, high-quality finish to various products, particularly metal parts, while minimizing environmental impact. Powder coating equipment ensures that the powder is evenly applied and properly cured, resulting in a smooth, durable finish. Below is an overview of the main components and types of powder coating equipment used in industrial applications:
Key Components of Powder Coating Equipment
- Powder Coating Spray Gun
- The spray gun is the central tool in powder coating equipment. It uses electrostatic charging to apply powder to the surface of the part. The powder particles are given a negative charge, while the part is grounded, causing the powder to be attracted to the surface. There are different types of spray guns, such as manual, automatic, and robotic spray guns, each suited for different production needs.
- Manual spray guns are used in smaller operations and for custom parts. Operators manually direct the spray nozzle over the part.
- Automatic spray guns are used in automated systems and are designed to apply powder coatings with precision for consistent finishes.
- Robotic spray guns provide high precision and can handle complex geometries, typically found in large-scale manufacturing settings.
- Powder Booth
- The powder booth is where the parts are coated with powder. It provides a controlled environment to ensure that the powder is applied evenly. Powder booths come with an integrated airflow system to keep the powder in suspension and prevent overspray.
- These booths are designed with filters to capture excess powder, which can be reused, ensuring efficient use of materials and reducing waste.
- Advanced booths may include recapture systems to collect the unused powder and send it back to the powder feed system for reuse.
- Powder Recovery System
- A powder recovery system captures excess or oversprayed powder that doesn’t adhere to the part. This system typically includes filters, cyclonic separators, and sieving equipment. The recovered powder is sent back into the powder supply for reuse, reducing waste and improving cost-efficiency.
- These systems are essential in high-volume manufacturing environments, where minimizing material waste is crucial for profitability and environmental sustainability.
- Curing Oven
- The curing oven is used to bake the coated parts at a specific temperature to melt the powder and bond it to the surface. Curing is a critical step in powder coating, as it ensures that the coating hardens to form a tough, durable finish.
- There are various types of curing ovens, such as convection ovens, infrared ovens, and hybrid ovens. The choice of oven depends on the type of powder coating used, part size, and production requirements.
- Modern curing ovens are often designed for energy efficiency, reducing operating costs while maintaining uniform heat distribution for consistent results.
- Conveyor System
- The conveyor system is responsible for moving parts through the powder coating process. Conveyor systems can be manual, automated, or robotically controlled, depending on the scale of production.
- Automated conveyor systems improve efficiency by providing consistent part movement, reducing handling time, and minimizing errors.
- Overhead conveyors and flat-bed conveyors are commonly used to transport parts from one stage of the process to another, such as from pre-treatment to coating and then to curing.
- Pre-Treatment System
- Before powder coating, parts must be pre-treated to ensure proper adhesion of the coating. Pre-treatment systems are used to clean, degrease, and sometimes chemically etch the surface of parts.
- Common pre-treatment methods include phosphating, abrasive blasting, or acid pickling, which remove oils, dirt, and rust from metal surfaces.
- Pre-treatment is critical in industries such as automotive and aerospace, where durability and adhesion are vital for product performance.
- Powder Feed System
- The powder feed system is responsible for delivering the correct amount of powder to the spray gun. The system ensures a constant flow of powder, which is important for achieving uniform coating coverage.
- The powder can be supplied through gravity-fed hoppers, pressure pots, or fluidized beds, each providing a different method for maintaining a steady powder supply.
- Control and Automation Systems
- Advanced powder coating systems often include automated control systems that monitor and adjust various aspects of the process, including spray gun parameters, oven temperature, and curing times.
- PLC (Programmable Logic Controllers) and HMI (Human Machine Interface) systems are used to integrate and control the entire powder coating line. These systems ensure that the coating process remains consistent, reducing human error and improving overall productivity.
Types of Powder Coating Equipment
- Manual Powder Coating Equipment
- Manual powder coating equipment includes handheld spray guns, powder booths, and basic curing ovens. It is typically used in smaller-scale operations, custom work, and low-volume production.
- This type of equipment offers flexibility and lower upfront costs but may not be as efficient for large-scale production runs due to the higher labor requirements.
- Automatic Powder Coating Equipment
- Automatic systems are ideal for high-volume production and large part runs. These systems use robotic arms, automatic spray guns, and conveyor belts to coat parts without the need for human intervention during the application process.
- Automatic equipment can increase throughput, improve consistency, and reduce labor costs, making it ideal for industries like automotive and appliance manufacturing.
- Batch Powder Coating Systems
- Batch systems are used for small to medium-sized parts that are coated in smaller quantities or in a non-continuous manner. These systems are highly customizable and can be configured for a variety of parts with different geometries.
- While not as high-output as automated systems, batch powder coating systems are efficient for custom or low-volume production.
- Robotic Powder Coating Systems
- Robotic systems are used in applications that require high precision and flexibility in coating complex geometries. These systems are highly automated and use robotic arms to apply powder to parts with consistent and accurate results.
- Robotic systems are especially useful in industries like automotive, aerospace, and electronics, where parts have intricate shapes or where the need for a uniform coating is paramount.
- Hybrid Powder Coating Systems
- Hybrid systems combine the benefits of both manual and automatic systems, allowing manufacturers to switch between batch processing and continuous production. This adaptability is useful for companies that need both flexibility and efficiency in their powder coating processes.
- Hybrid systems can be customized to meet specific production needs, making them suitable for medium to high-volume runs that involve different part types and coatings.
Benefits of Powder Coating Equipment
- Durability: Powder-coated surfaces are resistant to scratches, fading, corrosion, and chipping, making them ideal for harsh environments and heavy-use applications.
- Environmental Benefits: Powder coating produces less waste compared to traditional liquid coatings. Additionally, the process doesn’t require solvents, making it more environmentally friendly.
- Cost-Effectiveness: The ability to recycle unused powder reduces material costs, and the durability of powder coatings extends the life of products, reducing long-term replacement costs.
- Customization: Powder coating equipment allows for a wide variety of textures, finishes, and colors, making it suitable for many industries where aesthetics are important.
- High Efficiency: Automated systems and robotic arms improve throughput, minimize downtime, and ensure consistency across large production runs.
In conclusion, powder coating equipment is crucial for ensuring the efficient, high-quality, and environmentally friendly application of durable coatings to various parts. The choice of equipment, whether manual, automatic, or robotic, depends on the scale of production, type of parts, and specific requirements of the industry. With ongoing advancements in technology, powder coating equipment is becoming more efficient, customizable, and eco-friendly, ensuring that it remains a popular choice in manufacturing across many sectors.
Powder coating equipment plays a crucial role in ensuring that a wide range of products, particularly metal parts, receive durable and high-quality finishes. These systems are designed to efficiently apply powder coatings to products while minimizing waste and environmental impact. One of the most important components in powder coating equipment is the spray gun. This tool uses electrostatic charge to apply powder to a part, ensuring that the powder adheres evenly to the surface. Powder coating systems typically come with either manual or automated spray guns, depending on the scale and precision required. For large-scale operations, automatic and robotic spray guns are increasingly being used as they provide high precision and consistency, allowing for faster and more efficient coating with minimal human intervention.
The powder is applied inside a powder booth, where a controlled airflow helps keep the powder suspended and ensures an even distribution. Advanced booths come with integrated systems to capture oversprayed powder, which is then recycled for reuse, reducing waste and making the process more cost-effective. The recovered powder is directed back to the powder feed system, which supplies the spray gun with a constant stream of powder during the application process. These systems can include gravity-fed hoppers, pressure pots, or fluidized beds, each chosen based on the production requirements.
After the powder is applied to the parts, they are moved into a curing oven. The oven heats the parts to a specific temperature, causing the powder to melt and bond to the surface, resulting in a smooth and durable coating. Infrared ovens and hybrid curing ovens are becoming more popular as they provide energy-efficient solutions and faster curing times. The choice of oven depends on the type of powder coating being used and the specific needs of the production process.
To facilitate smooth movement through the process, a conveyor system is often used to transport parts between different stages, such as pre-treatment, coating, and curing. These conveyor systems can be manual or automated, with overhead conveyors and flat-bed conveyors being the most common types. The use of automated conveyors increases efficiency and ensures parts are handled consistently throughout the coating process.
Before the powder is applied, parts must go through a pre-treatment process, which may involve cleaning, degreasing, and sometimes etching the surface to ensure proper adhesion. Common pre-treatment methods include phosphating and abrasive blasting, which remove dirt, oils, and rust from the metal surface. The pre-treatment ensures that the powder adheres properly, resulting in a high-quality and durable finish that can withstand environmental stresses such as corrosion, fading, and wear.
As manufacturers seek greater efficiency, more powder coating systems are being integrated with advanced control and automation technologies. Programmable controllers (PLCs) and human-machine interfaces (HMIs) allow operators to control and monitor the coating process from start to finish, ensuring that the machines run smoothly and consistently. These systems can adjust spray parameters, curing times, and oven temperatures based on real-time data, further enhancing the efficiency and quality of the finished product.
One of the key advantages of powder coating equipment is the ability to recycle excess powder, which significantly reduces waste. With powder recovery systems that capture overspray, manufacturers can reuse powder that does not adhere to the part, making the process more sustainable and cost-effective. This recovery system is often integrated into the powder booth, where filters and cyclonic separators collect unused powder for reintroduction into the process.
Powder coating equipment is highly customizable, and there are systems available for different production volumes and part types. Manual systems are ideal for smaller production runs, offering flexibility for custom parts, while automatic systems are better suited for large-scale, high-volume production. Automated systems use robotic arms and conveyors to move parts through the coating process, improving throughput and consistency. Hybrid systems allow manufacturers to combine manual and automated processes, providing flexibility for small to medium-sized runs with varying part types and finishes.
The powder coating process itself is highly efficient and environmentally friendly compared to traditional liquid coatings. Since it doesn’t require solvents, powder coating generates fewer volatile organic compounds (VOCs) and reduces the environmental impact. Additionally, the durability of powder coatings means that parts require less frequent maintenance or replacement, further contributing to sustainability.
In terms of energy efficiency, the development of more advanced curing ovens has made it possible to reduce the energy consumption of the powder coating process. Infrared curing ovens, for example, directly apply heat to the parts, allowing for faster curing times and reducing the overall energy required to achieve a high-quality finish. This energy-efficient technology is particularly beneficial for manufacturers looking to lower operating costs and reduce their carbon footprint.
Looking forward, the trend in powder coating equipment will continue to focus on automation and smart technologies. The integration of IoT sensors, AI, and machine learning into powder coating systems will allow for more precise control of the coating process. These technologies will be able to monitor the process in real time, making adjustments to optimize powder application, curing time, and temperature, ensuring a consistent, high-quality finish every time. Predictive maintenance capabilities powered by AI will also reduce downtime by anticipating equipment failures before they happen, extending the life of machines and minimizing the risk of production delays.
Powder coating equipment is also becoming more flexible and adaptable to meet the increasing demand for custom finishes. As industries require more specialized coatings—such as metallic, textured, or multi-layer finishes—powder coating systems are evolving to accommodate these diverse needs. Advances in color-matching technology and interactive finishes that change appearance depending on lighting or viewing angle will enable manufacturers to create unique and high-end products that appeal to modern consumers.
With growing demand for eco-friendly manufacturing practices, powder coating systems will continue to embrace sustainability. New powder formulations that are low-VOC or even water-based will reduce harmful emissions, while increased focus on material recovery will ensure that waste is minimized. These systems will also be designed to handle shorter production cycles and on-demand manufacturing, which are increasingly important in industries that need flexibility and speed in response to customer demands.
Overall, the evolution of powder coating equipment is focused on improving efficiency, quality, sustainability, and customization. With innovations in automation, smart technologies, and energy-efficient systems, powder coating is becoming an even more attractive solution for a wide variety of industries, from automotive to appliance manufacturing, offering durable, eco-friendly, and cost-effective finishes. As technology advances, the future of powder coating equipment looks set to deliver even greater precision, speed, and sustainability.
As powder coating equipment continues to evolve, there will be a further push toward intelligent manufacturing with an emphasis on data integration and real-time monitoring. The adoption of smart systems that are interconnected within the production line will enhance the ability to collect, analyze, and leverage data throughout the entire coating process. By integrating technologies like Internet of Things (IoT) sensors and cloud computing, manufacturers can gain deep insights into every step of the coating process—from powder application to curing—and make instant adjustments to optimize efficiency and quality.
The implementation of predictive analytics will take the maintenance and operational performance of powder coating equipment to the next level. Using historical data and sensor inputs, these systems will be able to predict when a machine or part is likely to fail, allowing for proactive maintenance that reduces unplanned downtime and minimizes production disruptions. These predictive systems will also help identify inefficiencies in the coating process, allowing manufacturers to fine-tune their operations and reduce waste, which will further lower costs and improve overall sustainability.
One of the major areas of innovation in powder coating equipment will be in the development of next-generation powder formulations. New powders with improved adhesion properties, enhanced resistance to UV degradation, and superior chemical resistance will enable manufacturers to meet the increasingly complex demands of industries like automotive, aerospace, and electronics. These advanced formulations may also offer benefits such as self-healing capabilities, allowing the coating to recover from minor scratches or damage without requiring touch-ups.
There will also be an increased demand for specialized finishes that go beyond traditional solid colors. As design aesthetics become more important, manufacturers will look for ways to incorporate metallic, pearlescent, and textured finishes with greater precision. Powder coating systems will need to adapt to these demands, allowing for easy customization and the ability to seamlessly switch between different powder types and finishes without sacrificing efficiency. Automated systems will be able to detect the specific coating requirements for each batch, ensuring that the correct powder is applied, and the coating is consistent.
Another significant area of focus will be in improving the energy efficiency of the entire powder coating process. Hybrid ovens, which combine traditional convection with advanced infrared or UV curing technologies, are being developed to reduce energy consumption and curing times. By applying energy more directly to the parts being coated, these systems will enable faster throughput and a reduced environmental footprint, helping manufacturers meet increasingly stringent sustainability goals. Moreover, the integration of solar power and other renewable energy sources into the curing process could help reduce the reliance on conventional energy, making powder coating even more eco-friendly.
The industry will also continue to explore automated robotic solutions that enhance both the precision and efficiency of the powder coating process. With advancements in robotics, systems are now capable of coating highly complex or delicate parts with intricate geometries, which was once difficult to achieve with traditional manual or automated spray methods. Collaborative robots (cobots), which work alongside human operators, will become more common in powder coating lines. These cobots can be deployed to assist in delicate tasks, such as fine-tuning spray patterns or handling smaller, custom-coated components that require human oversight.
In addition to increased automation, there will be a growing trend toward customized powder coating systems tailored to meet the needs of specific industries. Modular systems will allow manufacturers to configure their equipment based on the requirements of each job. Whether it’s a batch system for smaller runs, an automated conveyor system for high-volume production, or a hybrid solution that combines both, manufacturers will be able to tailor their powder coating equipment for maximum flexibility and efficiency.
Sustainability will continue to be a major driver of change within the powder coating industry. As consumers and governments place greater emphasis on environmental responsibility, powder coating will see further advancements in reduced environmental impact and resource efficiency. From low-emission curing ovens to waterborne and non-toxic powder formulations, the focus on creating coatings that are safer for both the environment and human health will shape the direction of the industry.
The future of powder coating also holds the potential for faster production cycles and just-in-time manufacturing. As industries demand quicker turnaround times and more agile production lines, powder coating equipment will need to adapt to meet these challenges. Future systems will likely feature enhanced fast-changeover capabilities that allow for quick switches between colors and coatings, minimizing downtime and maximizing throughput. This is particularly important in industries like automotive, where rapid customization of parts and finishes is key to meeting consumer demand.
Another important aspect of the future of powder coating equipment will be enhanced precision and quality control. Advances in machine vision, automated inspection systems, and augmented reality (AR) technologies will be integrated into the powder coating process to ensure that every part is coated to the highest standards. These systems will use advanced sensors and cameras to detect any coating defects, such as missed spots, uneven application, or contamination. This data will be fed into automated systems, allowing for immediate adjustments to the coating process and preventing defects before they occur.
Finally, as powder coating technology continues to advance, the market for powder-coated products will expand. More industries are adopting powder coating for its combination of durability, environmental friendliness, and aesthetic appeal. Consumer goods, such as electronics, home appliances, and furniture, are increasingly being powder coated due to the unique finish options, long-lasting durability, and low environmental impact compared to traditional painting methods.
In conclusion, the future of powder coating equipment is poised for major advancements driven by automation, sustainability, customization, and digitalization. Manufacturers will benefit from systems that offer greater flexibility, improved efficiency, and the ability to meet the evolving needs of a diverse range of industries. With the continued development of innovative powder formulations, eco-friendly technologies, and cutting-edge robotic solutions, powder coating will remain a key process for producing high-quality, durable, and sustainable finishes on a wide range of products.
Automated Powder Coating System
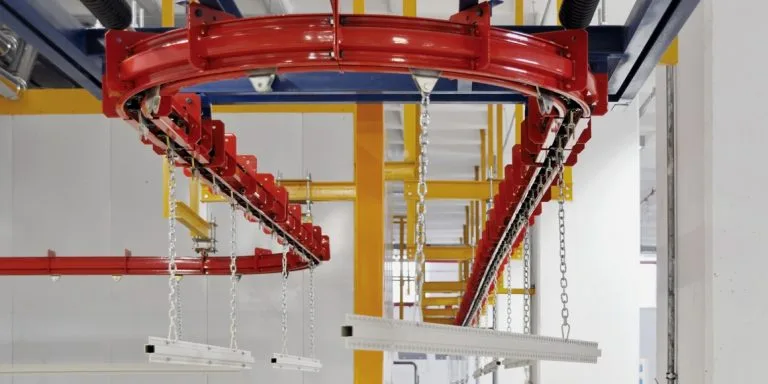
An Automated Powder Coating System is designed to apply a uniform, durable powder coating to parts with minimal manual intervention. This system is particularly valuable for high-volume production environments where efficiency, consistency, and quality are essential. Automated powder coating systems integrate advanced technologies to streamline the coating process, improving precision, reducing waste, and enhancing productivity. Below is a comprehensive overview of the components and benefits of automated powder coating systems.
Key Components of an Automated Powder Coating System
- Automatic Powder Coating Guns
- Automatic spray guns are central to the automated coating process. These guns are programmed to apply powder to parts with consistent coverage. They use electrostatic charge to ensure that the powder is attracted to the surface of the part, resulting in even coverage. The spray guns are controlled by robotic arms or conveyors that move them around the part to apply the powder uniformly.
- Spray gun types may include automatic reciprocators, which move back and forth, or robotic spray arms that allow for precise application over complex geometries.
- Robotic Systems
- Robotic arms are often integrated into automated powder coating systems to provide high precision in powder application. The robots are programmed to move the spray guns in a manner that ensures even and consistent powder deposition on every part, regardless of its shape.
- Articulated robotic arms can reach all areas of the part, ensuring that every surface is coated. Robots can work with multiple guns simultaneously to increase the speed of the process.
- These systems are capable of handling complex shapes and configurations, making them ideal for industries such as automotive, aerospace, and electronics.
- Powder Feed System
- The powder feed system delivers the powder to the spray guns in a controlled manner. It typically uses gravity-fed hoppers, pressure pots, or fluidized beds to provide a steady flow of powder to the guns.
- The system is integrated with the powder recovery unit, ensuring that any excess powder is collected and sent back into the feed system for reuse, reducing material waste and improving cost-effectiveness.
- Powder Booth
- The powder booth is a dedicated area where the powder is sprayed onto the parts. Automated powder coating booths are designed to minimize powder loss and ensure an even application across all parts. They typically feature airflow systems that keep the powder suspended, preventing overspray from settling in unwanted areas.
- Advanced booths come with recapture systems that collect unused powder and send it back into the system for reuse, making the process more environmentally friendly and economical.
- Filtration systems within the booth help keep the air clean by removing excess powder, which is important for worker safety and for maintaining a clean working environment.
- Conveyor System
- A conveyor system is used to move parts through the various stages of the powder coating process, from pre-treatment and coating to curing. Automated conveyors help reduce the need for manual handling, which increases throughput and reduces the potential for contamination or errors in handling.
- These conveyors can be overhead, flat-belt, or monorail systems, depending on the layout of the production line and the size of the parts being coated.
- Curing Oven
- After the powder is applied, the parts are moved into a curing oven, where the powder is baked at a specific temperature. The heat causes the powder to melt and form a durable, protective finish on the part.
- Infrared curing ovens and hybrid curing ovens are often used in automated systems to speed up the curing process and improve energy efficiency. These ovens ensure that all parts receive uniform heat to create a consistent finish.
- The curing oven can be integrated with automated conveyors, ensuring that parts are moved through the oven at the correct speed and temperature for optimal curing.
- Powder Recovery and Filtration System
- Powder recovery systems are designed to capture excess or oversprayed powder. The recovered powder is sent back to the powder feed system for reuse, reducing material waste and improving efficiency.
- The system typically includes cyclonic separators, filters, and sieving equipment to remove contaminants from the powder before it is reused.
- High-efficiency filters are crucial to maintaining clean air in the powder booth and ensuring that recovered powder meets the required quality standards.
- Control and Automation System
- A central control system is used to monitor and manage the entire automated powder coating process. This includes controlling the operation of spray guns, robotic arms, conveyor systems, curing ovens, and powder recovery systems.
- Programmable Logic Controllers (PLCs) and Human-Machine Interfaces (HMIs) are used to control and adjust key parameters such as spray gun speed, powder feed rates, oven temperature, and curing time.
- Modern systems often feature data logging and real-time monitoring capabilities, enabling manufacturers to track performance, detect issues, and make adjustments quickly to optimize the process.
Benefits of Automated Powder Coating Systems
- Increased Efficiency
- Automated systems significantly increase the speed and efficiency of the powder coating process. By reducing manual intervention, parts can be coated more quickly, allowing for faster production cycles and higher throughput. This is especially beneficial for industries with high-volume production needs, such as automotive or appliance manufacturing.
- Consistency and Quality Control
- Automation ensures that powder coating is applied uniformly, reducing the likelihood of defects such as inconsistent coverage, overspray, or uneven coating thickness. With robotic arms and automated spray guns, the system can apply coatings with a high degree of precision, resulting in a consistent finish across all parts.
- Cost Savings
- While the initial investment in automated powder coating equipment can be significant, the long-term savings are substantial. The ability to recycle unused powder, reduce labor costs, and minimize material waste makes automated systems a cost-effective solution over time.
- Reduced labor costs, faster production times, and fewer defects all contribute to overall cost savings in the production process.
- Environmental Benefits
- Automated systems are designed to minimize waste and improve material recovery. The use of powder recovery systems allows for the reuse of oversprayed powder, significantly reducing waste and lowering material costs.
- Moreover, powder coating is an environmentally friendly process compared to traditional liquid coating methods. It does not require solvents, reducing the emission of volatile organic compounds (VOCs) and creating a safer, more sustainable working environment.
- Improved Safety
- Automation reduces the amount of direct human involvement in the coating process, which can be hazardous due to the chemicals and heat involved. The use of robotic systems and automated conveyors minimizes the risk of worker exposure to harmful substances, improving workplace safety.
- Flexibility and Customization
- Automated systems can be programmed to coat parts of various sizes and shapes, providing flexibility for different types of production runs. Modern automated powder coating systems often feature easy changeover capabilities, allowing manufacturers to switch between different powder colors or finishes quickly and with minimal downtime.
- Increased Precision
- The integration of robotic arms and automatic spray guns enhances precision and enables the coating of complex geometries. Robotic systems are capable of adjusting their spray patterns and angles to ensure that every part is coated evenly, even in hard-to-reach areas.
- Reduced Downtime
- Automated powder coating systems can operate continuously, with minimal intervention required. This leads to reduced downtime and increased uptime in production. Furthermore, predictive maintenance systems powered by AI and IoT sensors can anticipate equipment failures before they happen, minimizing unplanned outages.
Applications of Automated Powder Coating Systems
Automated powder coating systems are used across various industries due to their efficiency and versatility. Some key applications include:
- Automotive Industry: Powder coating is used for car parts, including wheels, bumpers, and chassis components. The automated system ensures that these parts receive a durable, high-quality finish that withstands wear, corrosion, and exposure to the elements.
- Appliance Manufacturing: Household appliances such as refrigerators, washing machines, and ovens benefit from powder coating, as it provides a tough, attractive finish. Automated systems are ideal for coating large quantities of parts consistently.
- Metal Fabrication: Automated systems are used to coat metal furniture, structural components, and other metal products. The precision of robotic systems ensures a uniform finish on metal surfaces.
- Electronics: Some electronic components are coated with powder to enhance durability, protect against corrosion, and provide an aesthetic finish.
- Architectural Coatings: Powder coating is used to finish architectural components like window frames, door frames, and decorative metalwork. Automated systems provide a consistent and high-quality finish for these products, which are often exposed to harsh environmental conditions.
In conclusion, automated powder coating systems are a game-changer for industries looking to improve production efficiency, reduce costs, and maintain consistent quality. With their ability to handle complex geometries, provide precision coating, and recycle materials for minimal waste, these systems are essential for manufacturers aiming to meet the growing demands of high-volume production, sustainability, and product quality.
Automated powder coating systems have revolutionized the coating process by increasing efficiency, precision, and consistency, particularly for high-volume manufacturing. These systems are essential for industries that require rapid production cycles and top-notch finish quality, such as automotive, aerospace, and appliance manufacturing. By incorporating robotic systems, automated powder coating equipment can achieve unparalleled consistency in powder application, ensuring uniform coverage and reducing the risk of defects like missed spots or uneven coating thickness. Additionally, the use of advanced spray guns and robotic arms ensures that even parts with intricate shapes or difficult-to-reach areas receive a consistent, durable finish.
One of the most significant advantages of these automated systems is their ability to reduce material waste. Through the use of powder recovery systems, excess powder is captured and sent back into the system, allowing it to be reused. This closed-loop system minimizes waste, making powder coating a more environmentally friendly option than traditional liquid coatings that require solvents. The ability to recycle powder is a significant cost-saving feature for manufacturers, as it reduces the amount of new powder needed for production. Furthermore, automated systems often come with built-in filtration and separation systems, ensuring that only high-quality powder is applied to the parts, which further enhances the final product’s durability and finish.
Another key benefit of automated powder coating systems is their speed. These systems are designed to run continuously with minimal downtime, which is especially important for industries that rely on large-scale, high-volume production. Automated systems can also handle multiple parts simultaneously, dramatically increasing throughput while maintaining quality. The integration of robotic systems with conveyor systems ensures that parts move seamlessly through each stage of the coating process, from application to curing, without manual handling. This reduces the chances of contamination or defects caused by human error and significantly increases production efficiency.
Moreover, automated powder coating systems are increasingly integrated with smart technologies like IoT sensors and machine learning algorithms. These innovations allow manufacturers to monitor the process in real-time, track performance, and make immediate adjustments if necessary. For example, a system could automatically adjust spray parameters or curing times based on real-time data, ensuring optimal results every time. These systems can also provide valuable insights into maintenance needs, enabling predictive maintenance that helps reduce downtime by addressing issues before they cause equipment failure.
With the ability to customize the finish and adapt to various parts, automated systems can handle a wide range of coating requirements. Whether applying a simple solid color or a complex texture, automated powder coating systems offer the flexibility to meet diverse customer demands. In fact, many systems today feature easy changeover capabilities, allowing manufacturers to switch between colors or coatings quickly without significant downtime. This level of customization makes these systems ideal for industries that require both high-volume production and flexibility, such as automotive manufacturing, where part designs and finishes can vary.
The curing process is another area where automation adds value. After powder is applied, parts are moved to a curing oven, where the powder melts and bonds to the surface. Automated curing ovens are often equipped with advanced technologies, such as infrared heating and hybrid curing systems, that reduce energy consumption and speed up curing times. These ovens are often integrated with the automated conveyor system, ensuring that parts are heated to the correct temperature for the right amount of time, leading to consistent results.
In terms of cost-effectiveness, while the initial investment in automated systems may be high, the return on investment is significant due to reduced labor costs, faster production times, and lower material waste. The precision of automated systems minimizes the need for manual touch-ups or rework, which can be both time-consuming and costly. Additionally, by reducing waste and increasing throughput, automated systems help manufacturers achieve higher profit margins and remain competitive in a rapidly changing market.
Another notable advantage of automated systems is their environmental impact. Compared to traditional liquid coatings that contain solvents and volatile organic compounds (VOCs), powder coating is a much cleaner process. It produces little to no harmful emissions, making it an attractive option for companies looking to reduce their environmental footprint. The ability to recover and reuse powder further contributes to the system’s eco-friendliness, as it limits material waste and reduces the need for raw materials.
The versatility of automated powder coating systems means they can be used across a broad spectrum of industries. For example, in the automotive sector, powder coating is used for a variety of components, from chassis parts to wheels. The durability and corrosion resistance of the coating make it ideal for parts exposed to harsh weather conditions. In appliance manufacturing, products like refrigerators, washing machines, and microwaves benefit from the smooth, long-lasting finish that automated powder coating provides. Furthermore, the system’s ability to handle large volumes of parts at once ensures that manufacturers can meet the high demands of these industries.
Electronics is another area where automated powder coating systems have proven valuable. Components like circuit boards or metal enclosures require powder coatings that offer protection from wear, corrosion, and even electromagnetic interference (EMI). Automated systems ensure that these delicate components receive the proper coating thickness and uniformity, preventing defects and ensuring reliability.
In terms of future advancements, automated powder coating systems will likely continue to integrate more sophisticated technologies, such as machine vision for automated quality control. By using cameras and sensors, these systems can detect defects in real-time and make immediate adjustments to the coating process to ensure that all parts meet the required standards. In addition, artificial intelligence and big data analytics will play an increasingly important role in optimizing the powder coating process, predicting maintenance needs, and improving the overall quality and efficiency of the system.
Looking ahead, there will also be a greater emphasis on sustainability. With growing pressure to reduce environmental impact, the powder coating industry will likely see more innovations in low-emission systems, eco-friendly powders, and energy-efficient curing ovens. As demand for custom finishes continues to rise, automated systems will evolve to handle a broader range of finishes, such as textured coatings, metallic finishes, and specialty effects, without compromising speed or efficiency.
Overall, automated powder coating systems represent the future of coating technology, offering manufacturers an efficient, cost-effective, and sustainable solution for high-quality finishes. With their ability to handle large production runs, deliver consistent results, and minimize waste, these systems are essential in meeting the evolving demands of industries seeking to improve their operations and produce top-tier products. As technology continues to advance, automated powder coating systems will become even more precise, flexible, and energy-efficient, helping manufacturers stay competitive while achieving the highest standards of quality and sustainability.
As automated powder coating systems continue to evolve, there will be an even greater push toward integration with Industry 4.0 technologies. The shift towards smart manufacturing will see automated powder coating systems leveraging big data analytics, cloud computing, and real-time data exchange to enable a fully connected production environment. These systems will not only monitor the coating process but also provide detailed insights into machine performance, environmental factors, and product quality throughout the entire production cycle. Manufacturers will be able to analyze data from the system in real-time, adjusting parameters to optimize output, prevent defects, and reduce waste without halting production.
In the near future, predictive maintenance will become even more sophisticated, utilizing AI-driven algorithms to predict potential failures or malfunctions before they happen. By analyzing patterns in sensor data, such as temperature, pressure, and powder usage, AI can forecast when parts or components of the system may need maintenance. This will reduce the risk of unexpected downtime, helping manufacturers avoid costly production interruptions. Predictive maintenance systems will also optimize service schedules, ensuring that parts are replaced or repaired only when necessary, further reducing costs and increasing the efficiency of the production line.
Furthermore, machine vision will play an increasingly important role in quality control within automated powder coating systems. Advanced visual inspection technologies will be able to detect even the smallest defects in the coating process, such as uneven powder distribution, inconsistent thickness, or contaminants in the coating. Cameras and imaging systems will work in real-time to provide instant feedback to the system, allowing for adjustments to the spray guns, curing temperatures, or conveyor speed. This will not only improve the consistency of the coating process but also reduce the need for manual inspection, which can be time-consuming and prone to human error.
To complement these advancements, augmented reality (AR) may be used to assist operators in monitoring and controlling the automated systems. By wearing AR glasses or using tablets, operators could access real-time data and analytics, viewing the status of various components, such as powder flow, gun settings, or oven temperatures, in an intuitive interface. AR could also provide troubleshooting guidance, with step-by-step visual instructions for maintenance or repair tasks, helping operators respond to issues more quickly and accurately.
The energy efficiency of automated powder coating systems will also continue to improve. As manufacturers look for ways to reduce their environmental footprint, the use of renewable energy sources, such as solar power, could become more common in curing ovens or auxiliary heating systems. Additionally, advanced energy recovery technologies will help optimize the use of energy during the curing process, reducing consumption and lowering operating costs. Some systems may even incorporate heat recovery systems to capture and reuse heat generated during the curing process, further improving overall energy efficiency.
Customization and flexibility will also be key drivers in the development of future automated powder coating systems. As consumer demands for personalized products increase, manufacturers will need systems that can easily switch between various powder types, colors, and finishes. Modular systems will allow manufacturers to reconfigure their powder coating setups based on the specific needs of a production run, providing a high degree of flexibility without sacrificing efficiency. These systems will be capable of handling a wide variety of finishes, including matte, glossy, metallic, and textured coatings, enabling manufacturers to meet diverse customer preferences.
Automation will also enable faster changeovers between production runs, reducing downtime and increasing the responsiveness of manufacturing operations. Automated powder coating systems will be equipped with quick-change features, such as powder delivery systems that can be rapidly cleaned and reconfigured, minimizing the time required to switch between different powder types. This is particularly important in industries where rapid turnaround times and custom finishes are required, such as the automotive and consumer electronics sectors.
Another potential development in automated powder coating is the integration of advanced coatings that offer enhanced performance characteristics, such as self-healing properties, anti-microbial coatings, or coatings with superhydrophobic (water-repellent) properties. These innovative coatings would open up new markets for automated powder coating systems, allowing manufacturers to meet the increasing demand for specialized finishes in industries like medical devices, food processing, and consumer goods. Automated systems would need to be adapted to handle these new types of powders, which may have different application requirements compared to traditional coatings.
The focus on sustainability will continue to drive innovations in powder coating technologies. As companies seek to meet stricter environmental regulations and achieve net-zero emissions goals, powder coating systems will evolve to become even more environmentally responsible. Water-based powder coatings, which are free from harmful solvents, will become more widely used, and manufacturers will look for ways to reduce the carbon footprint of their operations. For instance, systems may include features that enable the use of bio-based or recycled powders, further reducing the environmental impact of the coating process.
In conclusion, the future of automated powder coating systems is bright, with continued advancements that promise to improve efficiency, precision, flexibility, and sustainability. As manufacturers seek to meet the challenges of increasing production demands, customization, and environmental responsibility, automated powder coating systems will continue to evolve. With greater integration of smart technologies, energy efficiency improvements, and the ability to handle specialized coatings, these systems will remain a cornerstone of modern manufacturing, providing high-quality, cost-effective solutions for a wide range of industries. The continued development of these technologies will enable manufacturers to stay competitive in an increasingly demanding and environmentally conscious market.
As the demand for high-quality finishes and sustainable practices increases, the role of automated powder coating systems will expand further, enabling manufacturers to deliver precision-engineered products with greater consistency and lower environmental impact. Future developments in this field will increasingly focus on integrating cutting-edge technologies such as artificial intelligence (AI), machine learning (ML), and Internet of Things (IoT), which will further enhance the capabilities of automated systems in several ways.
One of the key advantages of AI and ML integration into automated powder coating systems will be the ability to optimize the application process in real-time. These systems will learn from historical data, environmental variables, and process feedback, adjusting settings like spray gun pressure, powder feed rates, and curing oven temperatures to ensure the most efficient and high-quality results with every application. The continuous learning capabilities of AI-powered systems will reduce the need for manual intervention and increase the adaptability of systems to handle a wider range of coatings, surfaces, and production demands. This kind of adaptive, data-driven approach will lead to minimized defects and optimized material usage, creating a smarter, more sustainable manufacturing process.
IoT integration will enable better communication between equipment and the central control system, providing real-time monitoring of production parameters such as humidity, temperature, and powder flow rates. The ability to collect and transmit data from connected sensors allows manufacturers to make proactive decisions on equipment maintenance, energy consumption, and operational adjustments. IoT will also facilitate better traceability and compliance reporting, as data collected throughout the powder coating process can be analyzed and stored for later review, ensuring quality assurance standards are met and products adhere to industry regulations.
Remote monitoring and control will become more prevalent in automated powder coating systems, offering manufacturers greater flexibility and control over their production lines. Operators will be able to access data and make adjustments from remote locations, reducing the need for on-site supervision. This could also help businesses scale production across multiple sites, allowing for centralized oversight of various manufacturing processes. Additionally, cloud-based platforms will play an important role in storing large amounts of production data, which can then be analyzed and accessed from anywhere in the world, fostering collaboration and informed decision-making.
As energy costs continue to rise and environmental concerns grow, energy-efficient technologies will be a major focus for automated powder coating systems. Future systems may incorporate more advanced heat recovery technologies in curing ovens, reducing energy consumption by capturing and reusing heat that would otherwise be wasted. Additionally, the use of low-energy curing methods such as infrared radiation or UV curing could reduce overall energy consumption and shorten curing times, further optimizing the process. Manufacturers will increasingly rely on sustainable energy sources, like solar or wind power, to fuel their operations, reducing the carbon footprint of powder coating systems.
Hybrid curing technologies will also gain traction, combining multiple curing methods to achieve superior results while reducing energy use. For example, a combination of infrared heat and convection ovens could allow for faster curing times and better energy efficiency, without compromising the quality of the finish. Manufacturers are likely to seek solutions that balance high-performance coating with sustainability goals, driving further innovations in curing technologies.
The demand for custom finishes will continue to grow as consumers seek more personalized products, leading to innovations in powder coating formulas. In the future, powder coatings may be designed to offer advanced properties such as scratch resistance, self-cleaning surfaces, or anti-fingerprint qualities. Automated powder coating systems will need to adapt to these more specialized formulations, which may require modifications in the powder delivery systems, spray techniques, and curing processes to accommodate new types of powder materials.
Customization in automated systems will not just be limited to finishes and formulations but will also extend to the flexibility of the equipment itself. As manufacturing processes become more diverse, automated systems will need to be reconfigurable to handle a range of part sizes, shapes, and materials. Modular systems will allow for easy reconfiguration of spray gun setups, curing oven temperatures, and conveyor speeds to adapt to changing production requirements. This level of flexibility will ensure that automated powder coating systems remain relevant in an ever-changing production landscape.
With the rise of global supply chains and just-in-time (JIT) manufacturing, automation will help meet the increasing pressure to deliver high-quality products quickly and efficiently. The future of powder coating will see systems designed to maximize throughput while maintaining consistency in the finish. As demand increases, especially for industries like automotive, electronics, and consumer goods, automated systems will need to scale up without sacrificing the precision and quality of the coating. The ability to quickly switch between different part types, colors, or finishes will allow manufacturers to stay agile in a competitive marketplace.
The shift toward eco-friendly coatings will continue to influence the design and development of powder coating equipment. Waterborne powder coatings and bio-based powders are gaining popularity for their reduced environmental impact. As the demand for non-toxic, low-VOC, and solvent-free coatings rises, manufacturers will need to adopt technologies that can handle these new formulations, ensuring compatibility with automated coating processes. Additionally, regulatory pressures to reduce environmental impact will push for further innovations in powder coatings that are not only high-performing but also sustainable.
Another area of development will be the integration of smart maintenance solutions. The ability to predict when maintenance is needed based on machine learning algorithms and real-time performance data will extend the life of equipment and reduce downtime. Automated powder coating systems will be equipped with self-diagnostic tools that can detect issues like wear and tear, clogged nozzles, or temperature fluctuations in real-time. These diagnostic tools will alert operators to potential issues before they become critical, allowing for preemptive action and minimizing disruptions to the production schedule.
Finally, collaboration between suppliers and manufacturers will play a critical role in advancing powder coating technologies. Suppliers of powders, curing equipment, and automation systems will continue to innovate together to create synergistic solutions that improve both the process and the final product. These partnerships will help manufacturers implement the most advanced powder coating solutions available, keeping them competitive while meeting the growing demand for high-quality, customizable, and sustainable coatings.
In conclusion, the future of automated powder coating systems is poised for continuous evolution, driven by advancements in AI, IoT, energy efficiency, and sustainability. Manufacturers will benefit from systems that are increasingly data-driven, customizable, and environmentally responsible, allowing them to meet the demands of a rapidly changing market. As automation becomes more integrated into smart manufacturing environments, powder coating systems will play a critical role in delivering high-quality, cost-effective, and eco-friendly coatings for a wide range of industries.
Alloy Wheel Powder Coating
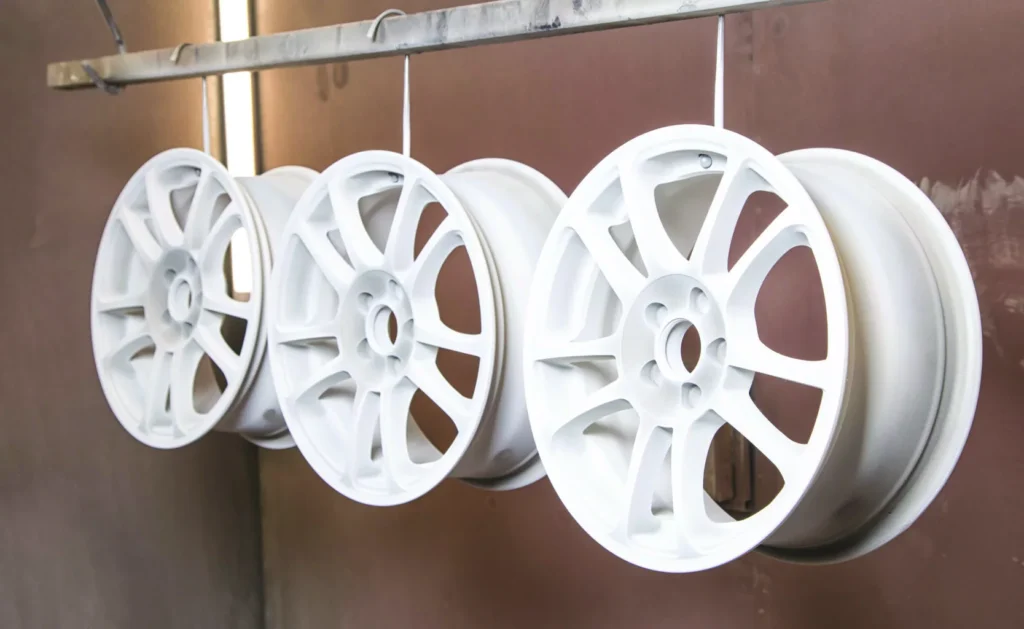
Alloy wheel powder coating is a popular and effective method used to enhance the appearance, durability, and protection of alloy wheels. The process involves applying a dry powder coating to the surface of the alloy wheels, which is then cured under heat to form a hard, protective finish. This method is preferred over traditional liquid painting for several reasons, including better durability, corrosion resistance, and a more uniform, smooth finish.
Key Benefits of Alloy Wheel Powder Coating
- Durability: Powder coating provides a more durable and long-lasting finish compared to traditional liquid paint. The coating forms a strong bond with the wheel surface, making it resistant to scratches, chips, fading, and wear. This is especially important for alloy wheels, which are exposed to harsh conditions such as road debris, salt, and UV rays.
- Corrosion Resistance: Alloy wheels are often exposed to moisture, salt, and chemicals, which can lead to corrosion and rusting. Powder coating acts as a protective barrier that prevents these elements from damaging the wheel’s surface, ensuring that the wheels maintain their appearance and structural integrity for a longer period.
- Aesthetic Appeal: Powder coating offers a wide range of finishes and colors, from matte and glossy to metallic and textured coatings. This allows car owners to customize their wheels to match the vehicle’s design and style. It also ensures a consistent and smooth finish, without the runs or sags that can occur with liquid paint.
- Eco-friendly: Powder coating is considered more environmentally friendly than traditional liquid painting because it contains no solvents and low levels of volatile organic compounds (VOCs). This makes it a safer and more sustainable option for both manufacturers and consumers.
- Cost-Effective: While the initial cost of powder coating may be higher than traditional painting, it is more cost-effective in the long run due to its durability and the fact that it requires fewer touch-ups or repairs. Additionally, the powder recovery system in many automated powder coating processes reduces material waste, making it more economical.
- Heat Resistance: Alloy wheels are exposed to high temperatures from the braking system. Powder coatings can withstand these higher temperatures without losing their structural integrity, unlike some traditional paints, which may break down or discolor under heat.
Powder Coating Process for Alloy Wheels
The process of powder coating alloy wheels is relatively straightforward, but it involves several key steps to ensure a high-quality finish:
- Cleaning and Preparation: The first step is to thoroughly clean the alloy wheel surface to remove any dirt, grease, or contaminants. This can be done using abrasive blasting (sandblasting), chemical cleaning agents, or other methods. The goal is to create a clean, smooth surface for the powder coating to adhere to.
- Surface Treatment: After cleaning, the wheels may undergo a treatment process to improve the adhesion of the powder coating. This often includes an acid etching or phosphating process that roughens the surface slightly, providing better bonding for the coating.
- Powder Application: Once the wheels are prepped, the powder is applied using an electrostatic spray gun. The powder particles are electrically charged and sprayed onto the wheel’s surface. The electrostatic charge ensures that the powder adheres evenly to the surface, creating a consistent layer of coating.
- Curing: After the powder is applied, the wheels are placed in a curing oven, where they are heated to a specific temperature (usually around 180-200°C or 356-392°F) for a set amount of time. During this process, the powder melts, flows, and chemically bonds to the surface, forming a hard, smooth finish. Curing is a critical step in ensuring the powder coating’s durability and performance.
- Cooling and Inspection: Once the curing process is complete, the wheels are allowed to cool down before being inspected for defects. Any imperfections, such as bubbles or inconsistencies, are identified and corrected. The wheels are then ready for reassembly and installation.
Types of Powder Coatings for Alloy Wheels
- Polyester Powder Coating: This is the most commonly used powder coating for alloy wheels due to its durability, weather resistance, and excellent finish. It is highly resistant to UV light, ensuring that the coating does not fade or discolor over time.
- Epoxy Powder Coating: Epoxy powder coatings offer excellent adhesion and corrosion resistance, making them ideal for wheels exposed to harsh conditions. However, they are not as resistant to UV degradation as polyester-based coatings, so they may be more prone to fading if exposed to direct sunlight over time.
- Hybrid Powder Coating: Hybrid powders combine the properties of both epoxy and polyester, offering a balance of durability, corrosion resistance, and UV stability. These coatings are well-suited for alloy wheels because they provide an excellent combination of protection and aesthetic appeal.
- Textured Finishes: In addition to glossy and matte finishes, alloy wheels can be powder-coated with textured finishes such as wrinkle, hammered, or pebble textures. These finishes not only enhance the visual appeal but also help to mask minor imperfections in the wheel’s surface.
- Metallic and Gloss Finishes: For a more striking look, metallic and gloss finishes can be applied. These finishes offer a high-shine effect and can include special metallic powders that add a glittering effect, giving the wheels a premium, customized look.
Common Applications of Alloy Wheel Powder Coating
- Automotive Industry: The most common application of powder coating is in the automotive industry, where it is used to coat alloy wheels of cars, trucks, and motorcycles. Powder-coated wheels offer superior protection against corrosion, road salts, and grime, which are particularly important for vehicles driven in areas with harsh winters or coastal climates.
- Motorcycle and Bicycle Wheels: Powder coating is also used on motorcycle and bicycle wheels, offering a durable finish that can withstand the wear and tear associated with outdoor use, including impacts, UV exposure, and moisture.
- Aftermarket Wheel Customization: Many aftermarket wheel suppliers offer powder coating as a customization service, allowing customers to choose from a range of colors, finishes, and textures. This allows vehicle owners to personalize their vehicles while also adding an extra layer of protection to their wheels.
- Off-Road Vehicles: Off-road vehicles, such as 4x4s and ATVs, often use powder-coated wheels due to the harsh conditions they are exposed to, including dirt, mud, and exposure to the elements. Powder coating helps to protect the wheels from corrosion, which is especially important when driving through water, snow, or off-road terrain.
Conclusion
Alloy wheel powder coating is an excellent way to enhance the durability, appearance, and longevity of wheels, offering significant advantages over traditional liquid paint. It provides superior protection against corrosion, chips, and UV degradation while offering a wide range of finishes and colors to suit various styles. Whether for OEM manufacturers or aftermarket customization, powder coating remains one of the most popular and effective ways to coat alloy wheels, ensuring they maintain their performance and aesthetic appeal for years.
Alloy wheel powder coating is a popular and effective way to enhance the appearance, durability, and protection of wheels, making them more resistant to corrosion, scratches, and wear. This method provides a superior finish compared to traditional liquid paint, making it the preferred choice for automotive, motorcycle, and bicycle wheels, as well as for off-road vehicles.
The powder coating process begins with thorough cleaning and preparation of the wheel’s surface. This ensures that any dirt, grease, or contaminants are removed, which could otherwise affect the adhesion of the coating. Once the wheel is clean, a surface treatment is applied to improve the bonding between the powder coating and the wheel. After this, the powder is applied using an electrostatic spray gun, where the powder particles are charged and adhere evenly to the wheel’s surface. The coating is then cured in an oven at high temperatures to form a hard, durable finish that is resistant to UV rays, weathering, and harsh chemicals.
Powder coating offers numerous advantages over traditional liquid paint. One of the main benefits is its durability; powder coating forms a much tougher bond with the wheel’s surface, making it more resistant to impacts, chips, and abrasions. Additionally, powder coating is less prone to fading or discoloration due to UV exposure, which is a common issue with liquid paints. Another significant advantage is corrosion resistance; alloy wheels are often exposed to water, road salts, and other environmental factors that can lead to rust and deterioration. Powder coating acts as a barrier, protecting the wheels from these elements and extending their lifespan.
Aesthetic appeal is another area where powder coating excels. With a variety of finishes and colors available, it allows car and bike owners to fully customize their wheels to match the look of their vehicles. Whether opting for a matte, glossy, or metallic finish, the powder coating process delivers a smooth and consistent surface. Custom finishes such as textured coatings are also available, offering unique visual effects and additional functionality, such as masking small imperfections on the wheel’s surface.
In terms of eco-friendliness, powder coating is a cleaner option compared to traditional liquid painting. It contains no solvents and emits little to no volatile organic compounds (VOCs), making it safer for both the environment and the workers applying the coating. Furthermore, powder coating produces less waste, as any excess powder can be collected and reused in the process.
Alloy wheel powder coating also provides a cost-effective long-term solution. While the initial investment may be higher than liquid painting, the durability of powder coating means fewer touch-ups or repaints are necessary. The overall life cycle of the coating is longer, which reduces maintenance costs and prolongs the overall performance and appearance of the wheels. This is particularly important for vehicles that are frequently exposed to harsh conditions, such as off-road vehicles or cars used in coastal areas with high salt content.
In the future, we can expect even more advancements in the alloy wheel powder coating process. With the integration of smart technologies, powder coating systems could become more efficient and adaptive, using data analytics and real-time monitoring to optimize the application and curing process. Additionally, the growing demand for sustainable practices may lead to further innovations, such as more eco-friendly powders, enhanced curing techniques that consume less energy, and further reduction in the environmental impact of powder coating systems.
Overall, alloy wheel powder coating remains one of the most effective and versatile methods for enhancing and protecting alloy wheels. Its combination of durability, aesthetic appeal, and environmental benefits makes it a preferred choice for both manufacturers and consumers alike. With continued innovation, it is likely that powder coating will continue to evolve, offering even greater protection and customization options in the future.
As alloy wheel powder coating continues to grow in popularity, several key advancements are on the horizon that will further enhance the performance and versatility of this coating method. One major trend is the development of advanced powder formulations that can offer even more specialized benefits. For instance, there is growing interest in self-healing powder coatings, which are designed to repair minor scratches or surface damage on their own when exposed to heat or sunlight. These coatings could significantly increase the longevity of powder-coated alloy wheels, as they would be able to “heal” from small chips and scratches that typically occur during everyday use.
Another area of focus is the advancement in color technology. While there are already numerous color options available for powder-coated wheels, manufacturers are increasingly pushing the boundaries to offer more sophisticated and unique color effects. Chameleon and pearlescent powders are becoming more popular, allowing for multi-dimensional finishes that change color depending on the angle of the light. This trend is being driven by consumer demand for highly customized and attention-grabbing designs. Additionally, metallic finishes that feature small reflective particles are being refined to offer a more brilliant, eye-catching shine without compromising durability.
Sustainability in powder coating is also expected to become a more prominent focus. As environmental regulations tighten and consumers become more eco-conscious, the powder coating industry is turning to bio-based and recycled powders. These alternatives use materials derived from renewable resources or recycled plastic and rubber to create the powders used in coating alloy wheels. This reduces the reliance on traditional raw materials and further diminishes the environmental impact of the coating process. Manufacturers may also begin to incorporate water-based powders as a greener alternative to conventional powder formulations, which are solvent-free but may still contain petrochemical components.
Additionally, with the increasing integration of digital technologies, powder coating processes are becoming more efficient and customizable. For example, 3D printing could allow for the production of custom powder-coated wheels with intricate patterns or shapes, enhancing the aesthetic appeal of the wheels and offering unique designs that were not previously possible. The use of artificial intelligence (AI) and machine learning (ML) could also play a role in automating the process of detecting imperfections or inconsistencies in the coating. AI could help fine-tune the application parameters, ensuring an even and flawless finish, while also monitoring the curing process to guarantee that the correct conditions are met.
The rise of smart manufacturing technologies will enable more flexible and automated powder coating systems that can adapt to a wide range of production needs. Automated systems equipped with sensors and machine vision could precisely monitor the wheel’s surface before, during, and after the coating application. These systems can detect small defects or contamination, alert operators in real time, and even make automatic adjustments to ensure the highest possible quality. Furthermore, IoT (Internet of Things) connectivity will allow real-time tracking of production data and remote monitoring of the powder coating process. Operators and managers will have access to key performance metrics and maintenance alerts, improving overall efficiency and reducing downtime.
Heat-resistant coatings will also continue to be a focal point for alloy wheel powder coating, especially as vehicles with performance-based needs become more prevalent. High-performance vehicles, such as sports cars and off-road trucks, generate more heat during driving, which can affect the integrity of traditional coatings. Advances in heat-resistant powder formulations will ensure that these wheels remain protected under high temperatures, preventing degradation, discoloration, or damage caused by the intense heat generated during high-speed driving or heavy braking.
In addition to improving the durability and appearance of alloy wheels, there is a growing trend to incorporate functional coatings. For example, powder coatings that include anti-microbial properties are being tested and could be incorporated into alloy wheels to offer additional benefits. This type of coating could be particularly useful for vehicles used in public transportation or shared vehicle fleets, where hygiene is a concern. Similarly, powder coatings with anti-fingerprint or hydrophobic properties are becoming more popular, as these finishes prevent oils and water from sticking to the surface, making the wheels easier to clean and maintain.
Energy-efficient curing processes are another key area for innovation. Traditional curing methods, which rely on large ovens, consume a significant amount of energy. However, newer methods, such as infrared curing or UV curing, can reduce energy consumption and cure the powder faster, improving the overall efficiency of the process. These alternative curing methods may also help reduce the environmental footprint of alloy wheel powder coating by lowering overall energy demand.
The global demand for customized and durable alloy wheels will continue to drive innovation in powder coating techniques. With an increasing number of car owners seeking personalized looks for their vehicles, powder coating offers an ideal solution for creating unique designs. Whether opting for a bold color, metallic finish, or a custom pattern, alloy wheels coated with high-quality powder provide the flexibility to meet diverse aesthetic preferences while maintaining their protective properties.
As technology advances and consumer demands shift, the future of alloy wheel powder coating promises to be even more exciting. With innovative materials, enhanced efficiency, eco-friendly practices, and customization options, the powder coating process will continue to evolve, offering better performance, improved sustainability, and even more beautiful results for alloy wheels in the years to come.
Looking ahead, the future of alloy wheel powder coating is poised to be shaped by further integration of advanced technologies, particularly in the areas of automation, sustainability, and customization. These innovations will not only improve the functional performance of the coating but also open up new possibilities for creativity and adaptability in the automotive industry.
One of the most promising areas of development is the continued refinement of automation in the powder coating process. Automation will likely take center stage in the evolution of alloy wheel coating, with increased use of robotic arms, automated conveyor systems, and AI-powered systems that can handle large-scale production with minimal human intervention. These technologies will enable manufacturers to coat wheels faster and more consistently, while reducing the likelihood of human error. Additionally, robots equipped with precision spray technology can ensure that each wheel receives a perfectly uniform coat, even in complex or intricate wheel designs.
With AI and machine learning, automated systems will be able to learn from past performance, optimizing the application process in real-time and adjusting parameters such as powder flow rate, spray gun position, and curing times to adapt to changing conditions or specific requirements. This increased precision will also reduce material waste, as the powder coating can be applied more efficiently, ensuring that only the necessary amount of coating is used. This is particularly important as manufacturers seek to meet sustainability goals while maintaining the quality of the product.
Sustainability will remain a driving force in the future of powder coating. As environmental concerns become more pressing and regulations around waste reduction and energy efficiency tighten, the industry will continue to innovate in ways that reduce its environmental footprint. In particular, low-energy curing technologies will become more widespread, allowing powder coatings to be cured at lower temperatures and in shorter times. This reduction in energy consumption will lower operational costs and minimize carbon emissions, aligning the powder coating process with global efforts to combat climate change.
Furthermore, recyclable and bio-based powder formulations will continue to gain traction. As the demand for more sustainable materials increases, powder coatings made from renewable resources or recycled materials will become more commonplace. These eco-friendly powders will help reduce reliance on petrochemical-derived products, offering manufacturers a greener alternative that aligns with sustainability goals. The development of closed-loop recycling systems for powder coatings could also reduce material waste, as excess powder can be reclaimed and reused in the production process.
Additionally, green chemistry innovations in the production of powder coatings will likely result in coatings with fewer hazardous chemicals, improving both the safety of workers and the environmental impact. This aligns with growing global concerns over harmful chemical exposure and the need for safer industrial processes. There is also potential for non-toxic additives to be developed, improving the safety and eco-friendliness of powder coatings without compromising performance.
The demand for customization in the automotive industry is expected to continue to rise, with consumers increasingly seeking more personalized designs for their vehicles. Powder coating offers a wide range of color options and finishes, but the future will see an even broader selection of unique textures, patterns, and finishes that can be applied to alloy wheels. Technologies like 3D printing and laser etching could be used to create intricate, custom designs on alloy wheels, allowing car owners to express their individuality in new ways. Matte, satin, and glossy finishes will continue to evolve, and new technologies may even enable the creation of dynamic finishes that change based on light exposure or viewing angle.
Smart coatings will also play an important role in the future of alloy wheel powder coating. These coatings, which are designed to respond to environmental changes, could offer enhanced functionalities such as self-cleaning, anti-fingerprint, or self-healing capabilities. For instance, wheels coated with hydrophobic (water-repellent) coatings will be easier to clean and maintain, while anti-fingerprint coatings will help keep wheels looking pristine for longer. Moreover, self-healing coatings could repair minor surface scratches, extending the lifespan of the coating and maintaining the appearance of the wheels even in the face of daily wear and tear.
Advanced curing techniques will continue to improve as well, with UV curing and infrared curing becoming more widely adopted. These methods allow for faster curing times and lower energy usage, making the coating process more efficient. As the technology matures, manufacturers may even be able to introduce localized curing methods that target specific areas of the wheel with precision, reducing overall curing times and energy consumption.
The globalization of the powder coating industry is another factor that will influence future trends. As more countries and regions adopt powder coating technology due to its cost-effectiveness, durability, and eco-friendly nature, the demand for high-quality coatings will increase. Manufacturers will need to ensure that their products meet a diverse set of standards and regulations in various markets while still offering a consistent, high-quality finish. This could drive the development of more universal powder coatings that are adaptable to different environmental conditions and requirements.
Moreover, the use of Internet of Things (IoT) technology in powder coating systems will allow for real-time monitoring and remote management. IoT sensors will track data points such as temperature, humidity, and curing times, providing operators with valuable insights that can help prevent defects and ensure optimal coating quality. Additionally, IoT-enabled systems will allow manufacturers to predict maintenance needs, reducing downtime and improving the overall efficiency of the powder coating process.
As the automotive and transportation industries continue to evolve, alloy wheel powder coating will play a central role in improving the performance and aesthetics of vehicles. Whether it’s through advancements in automation, the development of sustainable practices, the exploration of new textures and finishes, or the integration of smart technologies, the future of powder coating promises even more opportunities to create durable, high-quality, and customizable wheels. The combination of innovation, environmental consciousness, and consumer demand for personalization will drive this evolution, ensuring that alloy wheels continue to be coated with coatings that offer long-lasting protection and striking visual appeal.
Powder Coating Plant Manufacturing
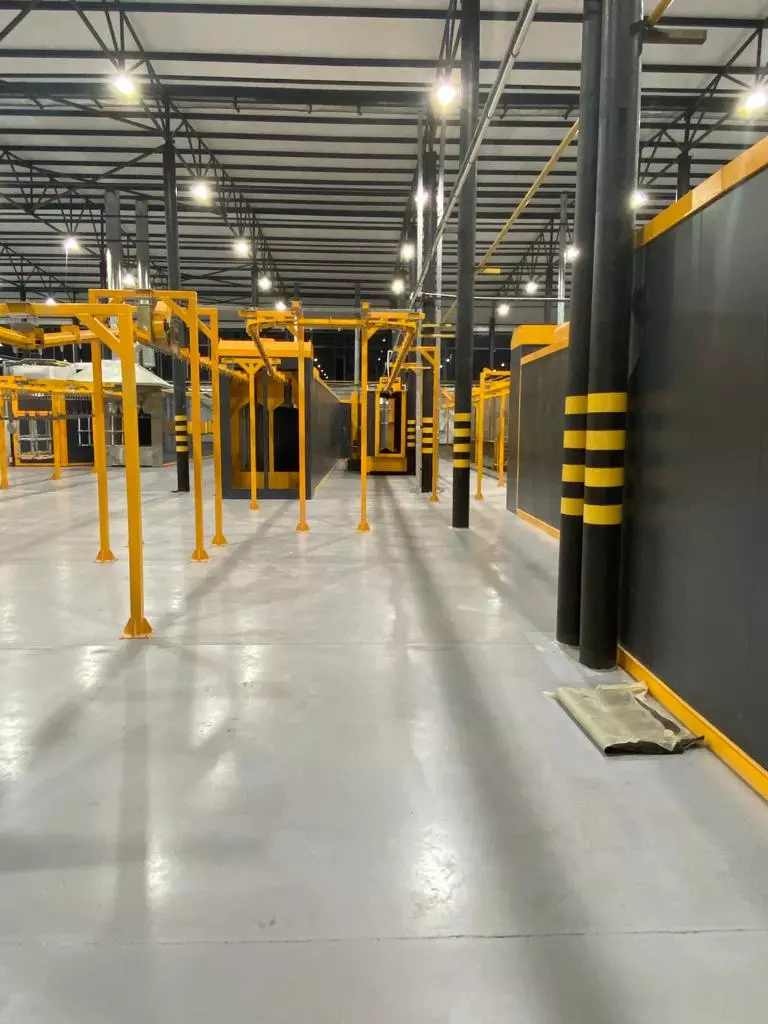
Powder coating plant manufacturing involves the design, construction, and operation of facilities dedicated to applying powder coatings to various products, such as metal parts, automotive components, and other substrates. A powder coating plant typically consists of a range of equipment, including application systems, curing ovens, and surface preparation tools, to ensure that the coating process is efficient, environmentally friendly, and produces high-quality finishes.
Here’s a detailed breakdown of the process involved in manufacturing a powder coating plant:
Key Components of a Powder Coating Plant
- Surface Preparation Equipment: The first step in any powder coating process is proper surface preparation. Clean surfaces are essential for good adhesion of the powder coating. Surface preparation equipment may include:
- Shot Blasting or Sand Blasting Machines: These machines are used to clean the metal surface by propelling abrasive particles at high speeds to remove contaminants like rust, dirt, and old coatings.
- Chemical Cleaning Stations: These systems use chemical solutions to clean and degrease the parts. This is often followed by a rinse to remove any residues and ensure the surface is clean.
- Phosphating or Chromating: Chemical treatment to increase corrosion resistance and improve the adhesion of the coating.
- Powder Application Systems: After surface preparation, the parts need to be coated with powder. This is typically done using electrostatic powder coating guns:
- Electrostatic Spray Guns: These are the primary tools used for applying the powder to the parts. The gun charges the powder particles electrostatically, causing them to adhere to the surface of the part. The powder is then evenly distributed over the object.
- Automatic and Manual Spray Booths: In an automated plant, robotic arms or conveyor systems may apply the coating, while manual spray booths are used for smaller or more intricate items. The powder is applied uniformly and evenly to achieve the desired finish.
- Curing Ovens: Once the powder is applied, it must be cured or baked to bond it to the surface of the part. Curing ovens are an essential component of a powder coating plant, where the coated items are subjected to heat to melt the powder and form a solid, durable coating. There are several types of curing ovens:
- Convection Ovens: These use hot air to cure the powder, providing an even distribution of heat throughout the oven.
- Infrared Ovens: These use infrared radiation to heat the surface of the parts more quickly than convection ovens, reducing curing times and energy consumption.
- Hybrid Ovens: Some modern systems use a combination of both convection and infrared heating to achieve more efficient curing.
- Cooling Systems: After the items are cured, they must be cooled to allow the coating to harden fully. Cooling systems typically use forced air or water cooling methods to rapidly lower the temperature of the coated items, ensuring they reach a stable, hardened state before handling or packaging.
- Powder Recovery and Filtration Systems: Powder coating systems are designed to minimize waste. Powder recovery systems are used to collect overspray, which can then be reused, reducing material costs and increasing efficiency. These systems generally include:
- Cyclone Systems: These are used to collect and separate excess powder from the air, returning it to the powder reservoir for reuse.
- Filters and Airflow Systems: These systems ensure that the powder particles do not pollute the environment, filtering out excess powder and maintaining a clean working atmosphere.
- Quality Control Stations: Ensuring a high-quality powder coating is crucial. A powder coating plant will typically include stations where finished parts are inspected for defects such as:
- Coating Thickness: Using tools like dry film thickness gauges to ensure the coating is applied evenly and to the correct thickness.
- Visual Inspection: Workers inspect the finished parts for imperfections such as runs, sags, or uneven coverage.
- Adhesion Tests: Methods like the crosshatch test or tape test may be used to assess how well the coating adheres to the surface.
- Material Handling Systems: Efficient movement of parts throughout the powder coating process is critical for both throughput and quality. Powder coating plants often use automated conveyor systems, hanging racks, and trolleys to transport parts from one station to the next, ensuring that the entire process runs smoothly and efficiently.
Design Considerations for Powder Coating Plant Manufacturing
- Capacity and Throughput: The design of a powder coating plant must be scalable to meet production demands. Whether it’s a small facility handling a limited volume of parts or a large operation processing thousands of items daily, the plant’s equipment should be sized to handle the required output.
- Space Planning and Layout: The layout of the powder coating plant is critical to ensuring efficient workflow and minimizing the risk of contamination. Equipment must be arranged in a logical flow, from surface preparation to powder application, curing, cooling, and final inspection. Adequate space for handling, storage, and inventory is also essential to maintain smooth operations.
- Energy Efficiency: Given that powder coating processes require significant energy, especially for curing, manufacturers focus on incorporating energy-efficient technologies into the plant. This includes using energy-saving ovens, optimizing airflow, and employing efficient powder recovery systems.
- Environmental Control: Powder coating plants must be designed to meet environmental regulations regarding emissions, waste disposal, and air quality. Ventilation systems, dust collection systems, and proper waste management are necessary to ensure that the plant operates in an environmentally responsible manner.
- Safety Considerations: The plant must comply with health and safety standards to protect workers from the potential hazards associated with powder coating. This includes proper ventilation to avoid inhalation of powder particles, fire safety measures due to the flammability of certain powders, and the use of personal protective equipment (PPE) for operators.
- Automation and Control Systems: Advanced powder coating plants may incorporate automated control systems to manage the entire process, from surface preparation to coating application and curing. These systems can monitor and adjust parameters in real-time, ensuring consistency, quality, and efficiency. Automation reduces human error and increases production speed, while also improving safety.
Trends in Powder Coating Plant Manufacturing
- Customization and Flexibility: As industries like automotive, aerospace, and consumer goods demand more customization, powder coating plants are increasingly incorporating flexible systems that can handle a wide range of part sizes, shapes, and finishes. Automated systems are becoming more adaptable, allowing for quick changes in production and customized coatings based on customer requirements.
- Sustainability: As companies strive to reduce their environmental footprint, many powder coating plants are being designed with sustainability in mind. This includes using eco-friendly powder formulations, reducing energy consumption through more efficient equipment, and recycling materials to minimize waste. Plants are also being built to comply with stricter environmental standards and regulations.
- Digitalization and Industry 4.0: The rise of digital technologies is having a significant impact on powder coating plant manufacturing. Sensors, IoT devices, and data analytics are being used to monitor equipment performance, track production efficiency, and predict maintenance needs. This approach allows for real-time data-driven decisions that improve quality control and reduce downtime.
- Advanced Curing Technologies: The demand for faster and more efficient curing processes has led to the development of new curing technologies, including UV curing and infrared curing, which use less energy and reduce curing times compared to traditional convection ovens.
- Lean Manufacturing Principles: Many powder coating plants are adopting lean manufacturing principles to optimize their operations. This includes improving workflows, reducing waste, and minimizing downtime by streamlining processes and implementing just-in-time production strategies.
Conclusion
Powder coating plant manufacturing is a complex, highly specialized field that requires advanced equipment, precise process control, and efficient operations to ensure the production of high-quality coated products. The plant’s design must accommodate the entire coating process, from surface preparation to final inspection, while also considering factors like automation, energy efficiency, and environmental responsibility. With the ongoing advancements in technology and growing demand for customizable, sustainable finishes, powder coating plant manufacturing will continue to evolve to meet the needs of various industries, offering solutions that improve both performance and aesthetic appeal.
Powder coating plant manufacturing is a highly specialized process that involves designing, constructing, and operating facilities dedicated to applying powder coatings to various products. The primary goal is to create durable, aesthetically appealing finishes that provide protection against corrosion, wear, and environmental exposure. Manufacturing a powder coating plant requires understanding the components of the coating process, including surface preparation, powder application, curing, and recovery systems, as well as the layout and design considerations necessary for efficient and effective operation.
At the heart of the process is the surface preparation phase, which is crucial for ensuring proper adhesion of the powder coating to the substrate. Surface preparation equipment, such as shot blasters or sandblasting machines, removes rust, dirt, grease, and old coatings, while chemical cleaning stations and phosphate treatments enhance corrosion resistance and coating adhesion. After cleaning, the powder application system takes over, where electrostatic spray guns charge the powder particles and apply them to the parts. Automated and manual spray booths help achieve even, uniform coverage. Once the powder is applied, the parts move to the curing ovens where heat is used to melt and bond the powder into a durable coating. These ovens can be convection, infrared, or hybrid, depending on the needs of the operation.
Following curing, a cooling system is used to lower the temperature of the parts to room temperature, ensuring the coating fully hardens. Powder recovery systems ensure efficiency and cost savings by collecting overspray, which can then be reused, reducing material waste. Filtration systems are also essential for maintaining a clean working environment and preventing contamination during the application process.
In terms of design, the layout of a powder coating plant is critical for ensuring smooth and efficient operation. The plant must be organized to allow for the logical flow of materials from surface preparation to application, curing, cooling, and inspection. Material handling systems, including automated conveyors, racks, and trolleys, are often incorporated to streamline the movement of parts and maintain workflow.
Another significant factor is energy efficiency, especially in curing processes, which can be energy-intensive. Incorporating energy-efficient ovens and optimizing energy use across the plant reduces operational costs and minimizes the plant’s environmental footprint. Moreover, with an increased emphasis on sustainability, many plants are moving toward eco-friendly powder formulations that are free from hazardous chemicals, while adopting practices that focus on minimizing waste and emissions.
The quality control process within a powder coating plant ensures that finished products meet the required standards. Tools for measuring coating thickness, performing visual inspections, and conducting adhesion tests are crucial for maintaining high product quality. New technologies, such as AI-powered systems, help improve consistency and reduce human error in the coating process by automating adjustments based on real-time data.
Advanced automation is increasingly becoming a defining feature of powder coating plants. Robotic arms and conveyors are used to apply powder coatings uniformly and efficiently, while automated curing systems and quality control stations help ensure that the process runs smoothly and consistently. The rise of Industry 4.0 technologies, such as IoT and data analytics, has also enabled powder coating plants to operate with greater precision. Real-time monitoring of equipment performance, predictive maintenance, and production data tracking help optimize operations and reduce downtime.
As environmental concerns continue to grow, the powder coating industry is embracing sustainable practices. Plants are incorporating systems that reduce energy consumption, recycle materials, and use environmentally friendly powders. The development of low-energy curing methods, such as UV and infrared curing, also helps reduce the plant’s environmental impact. Additionally, the use of bio-based powders and other sustainable materials will likely continue to increase, as manufacturers seek to reduce their carbon footprint and meet regulatory standards.
Customization is a growing trend in the automotive and consumer goods industries, and powder coating plants are evolving to meet the demand for more personalized finishes. Advances in coating technologies, such as self-healing, anti-fingerprint, and hydrophobic coatings, provide additional functionality and aesthetic appeal. Furthermore, innovations in color technology have opened up new possibilities for custom finishes, including metallic, pearlescent, and chameleon effects that change with light angles.
The future of powder coating plant manufacturing will continue to be influenced by advancements in automation, sustainability, and customization. As the industry evolves, the demand for more efficient, flexible, and environmentally friendly solutions will drive the development of innovative technologies that improve both product quality and production efficiency. The ongoing focus on energy efficiency, waste reduction, and customization will ensure that powder coating remains a vital and growing sector in manufacturing. With these improvements, the powder coating process will continue to deliver high-quality, durable finishes while meeting the ever-increasing demands for sustainability and performance.
Thermoplastic Powder Coating Equipment
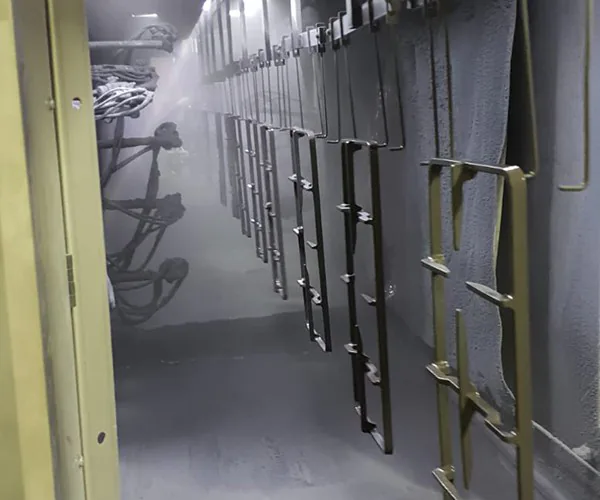
Thermoplastic powder coating equipment is specialized machinery designed to apply thermoplastic powder coatings to various substrates, primarily metals, to create durable, high-performance finishes. Unlike thermoset powders, which cure through chemical reactions during the baking process, thermoplastic powders melt and flow when heated and solidify again once cooled, without undergoing any chemical change. This characteristic makes thermoplastic powder coatings more suitable for products that require flexibility, high impact resistance, and the ability to be reworked or repaired.
The equipment used for thermoplastic powder coating is similar to that used for thermoset powder coating, but there are some distinct considerations given the different properties of thermoplastic materials. Here’s a breakdown of the essential components of thermoplastic powder coating equipment:
1. Powder Coating Application Systems
The application of thermoplastic powders typically involves an electrostatic spray gun that charges the powder particles, making them adhere to the surface of the part. The thermoplastic powder is applied in a manner similar to thermoset powder coating but requires careful control to ensure even coverage and the proper thickness of the coating. Some key considerations for thermoplastic powder application include:
- Electrostatic Spray Guns: These guns charge the powder particles and spray them onto the part, ensuring uniform coverage. In thermoplastic coatings, the gun setup must maintain a steady powder flow while avoiding over-spraying, as thermoplastic powders tend to be more prone to clumping compared to thermoset powders.
- Automatic and Manual Application: Depending on the production volume, thermoplastic powder coating can be applied using automatic robots or manual spray booths. Automated systems allow for faster, more uniform application, especially when parts have complex geometries.
2. Pre-Heating Systems
Thermoplastic powders need to be preheated before application to ensure they flow properly when they are sprayed onto the part. Pre-heating equipment, often integrated with the coating system, helps achieve the ideal temperature for the powder. This is an important step because if the powder is not heated sufficiently, it may not adhere well to the substrate.
3. Curing Ovens
Curing ovens are used to heat the coated parts after the thermoplastic powder has been applied. The key difference in curing for thermoplastic coatings is that it involves melt flow rather than a chemical curing reaction. As such, the oven must be carefully controlled to allow for uniform heat distribution and to achieve the desired thickness and finish. There are several considerations for thermoplastic powder curing:
- Temperature Control: The curing temperature must be sufficient to melt the thermoplastic powder but not so high as to degrade it. Typically, the curing temperature for thermoplastic coatings is lower than for thermoset coatings.
- Curing Time: Unlike thermoset coatings that require a longer time to cure, thermoplastic coatings usually cure more quickly once the material melts. Therefore, ovens are designed to ensure uniform heating and adequate time for the material to melt, flow, and bond to the substrate.
4. Cooling Systems
After the thermoplastic powder has been melted and adhered to the part, it must be cooled in order to solidify and form the final coating. Cooling systems use either forced air or water-cooling systems to quickly lower the temperature of the parts and solidify the thermoplastic material. Rapid cooling is necessary to maintain the desired coating finish and prevent defects like surface imperfections or an uneven finish.
5. Powder Recovery Systems
Thermoplastic powders are often more expensive than thermoset powders due to their properties and performance characteristics. To minimize waste, powder recovery systems are used to collect overspray during the application process. These systems include:
- Cyclone Recovery Units: These units separate excess powder from the air and funnel it back into the powder supply for reuse.
- Filters: The powder recovery system often includes filters that capture fine powder particles to ensure that the air remains clean and safe.
6. Surface Preparation Equipment
As with all powder coating processes, proper surface preparation is essential for ensuring a strong bond between the coating and the substrate. Thermoplastic powder coating equipment will typically include systems for cleaning, degreasing, and treating parts before they are coated. This may involve:
- Shot Blasting: To clean the surface and prepare it for coating by removing rust, scale, or old coatings.
- Chemical Cleaning Stations: These remove oils, dirt, or grease from the surface.
- Phosphating or Pretreatment: To enhance corrosion resistance and improve the bonding of the coating.
7. Quality Control Systems
The quality of thermoplastic powder coatings must be carefully monitored to ensure uniformity and durability. Key quality control features include:
- Thickness Measurement: Tools like dry film thickness gauges are used to measure the coating’s thickness, ensuring that it meets specifications for durability.
- Visual Inspection: To check for uniform coverage, color consistency, and the absence of defects like pinholes, runs, or sags.
- Adhesion Testing: Various methods such as crosshatch testing may be used to assess how well the coating adheres to the substrate.
8. Material Handling Systems
Efficient material handling systems are essential to move parts through the powder coating process. These systems include:
- Conveyor Systems: Automated conveyor systems move parts through different stages of the coating process, from cleaning to powder application and curing.
- Racking Systems: Racks are used to hold parts in place during coating and curing. In a thermoplastic powder coating system, these racks must be able to withstand the heat used during the curing process.
Advantages of Thermoplastic Powder Coating Equipment
Thermoplastic powder coating equipment offers several advantages, particularly when flexibility, impact resistance, and reworkability are essential:
- Reworkability: Since thermoplastic powders melt upon heating and solidify again once cooled, parts can be reheated and recoated if defects are found or if a different finish is required. This reworkability is ideal for applications where future modifications or repairs are necessary.
- Durability: Thermoplastic powder coatings are known for their high impact resistance, excellent flexibility, and better resistance to abrasion and wear compared to thermoset powders.
- Chemical Resistance: Thermoplastic coatings can provide better resistance to certain chemicals, making them suitable for applications in harsh environments.
- Environmental Benefits: Like thermoset powder coating, thermoplastic powder coatings do not require solvents, making the process cleaner and more environmentally friendly than traditional liquid coatings.
Challenges and Considerations
While thermoplastic powder coating has many benefits, there are challenges that need to be considered when designing and operating the equipment:
- Powder Flow and Application: Thermoplastic powders tend to be more challenging to apply uniformly compared to thermoset powders due to their tendency to clump together. Special care must be taken to ensure an even application without excess powder buildup.
- Curing Time: The curing time for thermoplastic powder coatings is typically shorter than thermoset powders, which may require more advanced or optimized curing systems to ensure the coating bonds properly.
- Material Costs: Thermoplastic powders tend to be more expensive than thermoset powders, so powder recovery systems must be well designed to reduce waste and make the process cost-effective.
Conclusion
Thermoplastic powder coating equipment is specialized for applying thermoplastic powders to substrates, providing products with enhanced flexibility, impact resistance, and reworkability. The key components of thermoplastic powder coating systems include surface preparation equipment, electrostatic spray guns, curing ovens, powder recovery systems, and material handling systems. While thermoplastic coatings offer excellent durability and resistance to wear and chemicals, the equipment must be designed to handle the unique challenges associated with their application, such as the need for uniform powder flow and effective curing. With the right setup, thermoplastic powder coating equipment can deliver high-quality finishes suitable for a wide range of applications in industries like automotive, industrial machinery, and consumer goods.
Thermoplastic powder coating equipment is designed to apply powder coatings that melt and fuse when heated, forming a durable, flexible, and long-lasting finish. The process involves several key steps to ensure uniform application and high-quality results. The equipment required for thermoplastic powder coating includes systems for surface preparation, powder application, curing, cooling, and powder recovery. Each of these components plays a crucial role in producing a reliable and aesthetically pleasing finish.
In the powder application phase, electrostatic spray guns are used to charge the thermoplastic powder particles, making them adhere to the surface of the part. This process ensures an even coat across the substrate, but special care must be taken to control the flow of powder, as thermoplastic powders can be more prone to clumping than thermoset powders. Whether the application is automated or manual depends on the scale of production, with automated systems offering faster, more consistent coverage for high-volume production.
Once the powder is applied, the parts are moved to the curing oven. The curing process for thermoplastic coatings is different from that of thermoset coatings; instead of chemical curing, thermoplastic powders melt and flow at a specific temperature. The oven must be calibrated to the correct temperature to allow the powder to melt and form a smooth, solid coating without causing any degradation to the material. Curing times are generally shorter for thermoplastic powders compared to thermoset powders, which makes temperature and time control in the oven critical for the proper adhesion and finish of the coating.
After curing, parts are cooled, often using air or water cooling systems, which helps the coating solidify quickly. This ensures that the finish is both durable and hard enough to withstand handling without marring the surface. The cooling process also ensures that the coating does not retain excess heat that could lead to deformation or other defects. Efficient cooling systems are designed to handle the volume of parts being processed and to ensure a smooth transition from the high heat of the curing oven to ambient temperatures.
One of the advantages of thermoplastic powder coating is its ability to be reworked. Because the coating simply melts and does not undergo a chemical curing process, damaged or imperfect parts can be reheated, and the coating can be reapplied. This makes it an ideal solution for products that may require future modifications or repairs. The reworkability aspect also means that overspray from the application process is not wasted. Powder recovery systems, which include cyclone recovery units and filtration systems, capture excess powder from the air and return it to the supply, ensuring minimal waste and reducing material costs.
The surface preparation phase, which includes cleaning and treating the substrate before the powder application, is crucial for achieving good adhesion and long-lasting performance of the coating. Equipment for shot blasting, chemical cleaning, and phosphating is used to remove dirt, grease, rust, and other contaminants from the part. This ensures that the thermoplastic powder bonds effectively to the surface, creating a strong and durable finish.
As with any industrial coating process, quality control is essential to ensuring that the finished products meet the required standards. Thickness gauges, visual inspections, and adhesion tests are performed to ensure uniform coating, good coverage, and the durability of the finished product. Thermoplastic coatings are often chosen for their impact resistance, flexibility, and ability to resist abrasion and wear. These coatings are also well-suited for applications where the coated parts will be exposed to chemicals or harsh environments.
Material handling systems, including conveyors, racks, and automated systems, are used to move parts through the various stages of the powder coating process. These systems ensure that the parts are consistently and efficiently processed, minimizing downtime and handling time. The design of the material handling system must accommodate the specific requirements of thermoplastic coating, such as the need for precise temperature control during curing and cooling.
Thermoplastic powders tend to be more expensive than thermoset powders, which makes the efficient use of materials critical. Powder recovery and recycling systems are employed to capture overspray, reducing waste and making the process more cost-effective. This is especially important in high-production environments where the cost of raw materials can significantly impact the overall production costs.
Overall, thermoplastic powder coating equipment must be designed to handle the unique properties of thermoplastic materials, including their melting point, flow characteristics, and reworkability. With proper application, curing, cooling, and recovery systems, thermoplastic powder coating provides a high-quality, durable finish suitable for a wide range of industries, including automotive, appliances, and industrial applications. The combination of flexibility, durability, and reworkability makes thermoplastic powder coating an attractive choice for products that require long-lasting performance under demanding conditions.
The thermoplastic powder coating process offers several unique advantages, which can make it particularly attractive for various industries. Since thermoplastic coatings can be re-melted and re-coated, they offer flexibility and a level of adaptability that is often not possible with thermoset coatings. This reworkability means that if a coating is damaged, it can simply be heated and re-applied, eliminating the need to strip off the old layer and start from scratch. This feature is valuable in situations where the coating might need to be adjusted or when parts are prone to wear and tear during their lifecycle.
Thermoplastic coatings also provide excellent impact resistance due to their inherent flexibility. The nature of the thermoplastic material means it can absorb impacts without cracking or chipping, making it ideal for high-wear environments like automotive parts, machinery components, and outdoor applications. Furthermore, thermoplastic coatings typically offer superior abrasion resistance, which is essential for items that are subjected to friction or rough handling.
Because thermoplastic powders do not cure chemically but instead undergo a melting process, they tend to exhibit better chemical resistance in many cases. This makes thermoplastic powder coatings ideal for parts that will be exposed to harsh chemicals, oils, or other corrosive materials. They also provide strong weather resistance, with many thermoplastic coatings performing well under UV exposure, temperature fluctuations, and extreme environmental conditions.
Thermoplastic coatings can be customized with various specialty additives to enhance certain properties. For example, thermoplastic coatings can be formulated with anti-static, anti-microbial, or fire-retardant properties, depending on the needs of the product or industry. Additives can also be incorporated to achieve a range of aesthetic finishes, including high gloss, matte, metallic, or textured looks.
In terms of sustainability, thermoplastic coatings offer some environmental advantages. Like all powder coatings, they are free from solvents, reducing the risk of harmful emissions. Furthermore, they typically involve minimal waste, as any overspray can be recovered and reused. This can be a significant benefit in reducing the environmental impact of the coating process. Given the rising demand for eco-friendly solutions in manufacturing, the ability to recover and reuse powder in thermoplastic systems contributes to a more sustainable and cost-efficient operation.
The powder recovery systems in thermoplastic powder coating processes are crucial for minimizing waste and maintaining consistent coating quality. Cyclone separators, filtration systems, and fluidized bed recovery units are commonly used to collect overspray and return it to the process. The ability to reuse excess powder significantly reduces material costs and waste, making the overall process more efficient. However, thermoplastic powder recovery systems must be carefully calibrated to handle the unique properties of thermoplastic powders, which may behave differently from thermoset powders in terms of flow and handling characteristics.
In terms of equipment considerations, thermoplastic powder coating systems must be designed with proper heat management. Since the powder requires careful temperature control during both the application and curing phases, having precise control systems for the curing oven is critical. Overheating can cause degradation of the coating material, while insufficient heating may result in poor adhesion or incomplete fusing. Customizable temperature zones within the curing oven, along with accurate thermostats, are essential for achieving the best results.
Automation also plays a key role in improving efficiency and consistency. Robotic arms and automated powder spray booths can achieve more consistent powder application, reducing human error and increasing throughput. Automated systems ensure that the coating is applied evenly across all parts, even those with complex geometries, which would be more challenging for manual operators to coat uniformly. Advanced technology also enables real-time monitoring, allowing for adjustments to be made to the coating process instantly. For instance, if the powder thickness is not within specification, automated systems can make adjustments to ensure that the required thickness is achieved.
For larger-scale operations, material handling becomes a crucial consideration. Conveyor systems, overhead tracks, and rotating racks are commonly used to move parts through the various stages of the powder coating process. Automated handling systems not only improve throughput but also reduce the physical strain on workers and minimize the chances of damage to parts during transit. Parts are often coated while suspended in racks or on conveyors, which must be designed to withstand the temperature of curing ovens and ensure the part is securely held during the entire coating cycle.
As demand for customization and aesthetic variety continues to grow, thermoplastic powder coatings can be tailored to achieve specific colors, textures, and finishes. Color consistency is critical, and with the right equipment, manufacturers can ensure that each batch of powder coating matches the desired hue and finish, whether it is for a matte, glossy, or even metallic look. Advances in powder formulation allow manufacturers to create a wide range of finishes, including highly reflective surfaces, textured coatings for improved grip, and even coatings that change appearance depending on the viewing angle.
The versatility of thermoplastic coatings makes them suitable for industries ranging from automotive manufacturing (where flexibility, impact, and chemical resistance are vital) to consumer electronics (where coatings may need to offer not only protection but also an appealing finish). Outdoor furniture, appliances, and industrial equipment also benefit from thermoplastic coatings’ ability to resist environmental wear and tear, ensuring products maintain their appearance and functionality for longer periods.
The future of thermoplastic powder coating is expected to continue evolving with advancements in automation, sustainability, and performance. Automation technologies will continue to reduce costs, increase precision, and improve the speed of production. At the same time, there is growing interest in eco-friendly alternatives and bio-based thermoplastic powders, which offer more sustainable coatings for industries looking to reduce their environmental footprint. These trends are driving the development of even more efficient and cost-effective powder coating systems that deliver high-quality results while meeting the increasing demands for sustainability and customization.
In conclusion, thermoplastic powder coating equipment is an integral part of a wide variety of manufacturing processes, providing a highly durable, flexible, and reworkable finish. By incorporating advanced technologies for application, curing, recovery, and quality control, manufacturers can produce parts with excellent impact resistance, chemical protection, and aesthetic appeal. As industries demand higher performance, more customization, and environmentally responsible solutions, thermoplastic powder coating will continue to evolve, offering new opportunities for manufacturers looking to enhance the durability and appearance of their products.
Thermoplastic powder coating continues to expand its reach and application across various industries, driven by the evolving demands for better performance, environmental sustainability, and aesthetic flexibility. As industries like automotive, aerospace, electronics, and consumer goods push for more durable and visually appealing coatings, thermoplastic powder coating systems are being adapted and optimized to meet these needs.
One of the key benefits of thermoplastic powder coatings is their superior adhesion properties. The ability of thermoplastic coatings to form strong bonds with substrates makes them especially useful in applications that require long-lasting finishes under extreme conditions. This characteristic is especially valuable in sectors such as automotive and industrial machinery, where parts are exposed to harsh environments, chemicals, and physical wear. In automotive manufacturing, thermoplastic coatings are used to provide durable finishes for both functional and aesthetic parts, including bumpers, trim pieces, and wheels. These coatings can withstand impact, resist abrasions, and maintain their appearance over time, even in outdoor conditions.
The flexibility of thermoplastic coatings makes them ideal for a variety of part geometries. Parts with intricate shapes or hard-to-reach areas can still receive uniform coverage, especially when automated systems like robotic arms or conveyor-based spray systems are used. These systems ensure that even complex shapes receive consistent and complete coating coverage, reducing the potential for imperfections that could arise from manual spraying. This capability is particularly important when coating parts with highly detailed surfaces or those that require specialized finishes.
In addition to their physical durability, thermoplastic coatings also offer aesthetic versatility. Manufacturers are increasingly focusing on providing customizable finishes to meet specific design requirements. Whether it’s a matte finish for a more industrial or understated look, a glossy finish for a high-end aesthetic, or a metallic finish for a premium appearance, thermoplastic powder coatings can be tailored to achieve a wide range of visual effects. The ability to incorporate metallic flake, pearlescent pigments, or color-shifting effects allows brands to offer products with unique looks that stand out in the marketplace.
Thermoplastic powder coating is also favored for its environmental benefits. Unlike liquid coatings, thermoplastic powders contain no solvents, which significantly reduces the emission of volatile organic compounds (VOCs). This is an important consideration as industries work to comply with increasingly stringent environmental regulations. The absence of solvents not only reduces harmful emissions but also enhances worker safety by minimizing exposure to toxic fumes that are typically released during the application of solvent-based coatings.
The ability to reuse oversprayed powder also contributes to the sustainability of the process. Advanced powder recovery systems, such as cyclone separators and fluidized bed systems, allow for the efficient capture and reuse of excess powder, minimizing waste and maximizing material utilization. This process makes thermoplastic powder coating more cost-effective, particularly in large-scale production environments, where the cost of raw materials can be a significant concern.
Energy efficiency is another area where thermoplastic powder coating has made strides. By optimizing curing ovens and controlling the temperature and duration of the curing cycle, manufacturers can reduce energy consumption while still achieving high-quality finishes. Innovations in oven technology, such as multi-zone ovens with precise temperature control, allow for better energy management, ensuring that the process uses only the necessary amount of energy while maintaining consistent coating quality.
Another trend in thermoplastic powder coating is the growing adoption of smart technologies to monitor and control the coating process. Real-time monitoring systems, which use sensors and data analytics, allow manufacturers to adjust variables like powder flow, spray gun settings, oven temperature, and curing time. These technologies enable manufacturers to maintain consistent product quality, reduce defects, and improve operational efficiency. Additionally, smart systems can collect data on the coating process, providing valuable insights that can help optimize workflows, troubleshoot issues, and predict maintenance needs.
Customization is becoming a more prominent feature of thermoplastic powder coatings. Manufacturers are increasingly using custom formulations to achieve specific performance characteristics in the coating. These formulations can include special additives that enhance corrosion resistance, increase chemical resistance, improve scratch resistance, or even add anti-bacterial properties. Customization also extends to the color matching process, which is essential for industries like consumer electronics and automotive manufacturing, where visual consistency and branding are critical.
As innovation in coating technologies continues to progress, bio-based and sustainable powder coatings are gaining traction. Companies are beginning to experiment with bio-derived resins and other environmentally friendly materials to create thermoplastic powders that are less reliant on petroleum-based products. These eco-friendly coatings offer similar performance characteristics as traditional thermoplastics but with a reduced environmental impact, aligning with global sustainability goals.
Thermoplastic coatings’ reparability is one of the key differentiators from thermoset powder coatings. This feature is particularly useful for industries that deal with parts that experience high wear or damage over time. For instance, in automotive and heavy equipment manufacturing, parts that are coated with thermoplastic powders can be repaired without the need for completely stripping and re-coating the surface. This ability to rework the coating by simply reheating the part allows manufacturers to maintain high-quality finishes while minimizing downtime and repair costs.
As the global focus on sustainability continues to grow, thermoplastic powder coating is well-positioned to benefit from these trends. The ability to produce low-VOC, solvent-free coatings that can be easily recycled makes thermoplastic powder coating an increasingly preferred choice for manufacturers committed to reducing their environmental impact. In industries like construction, furniture manufacturing, and consumer goods, where long-lasting, high-performance finishes are essential, the thermoplastic coating process offers an attractive combination of durability, aesthetics, and environmental friendliness.
The ongoing research and development efforts in the field of thermoplastic powder coatings will likely lead to even further innovations. As the demand for high-performance, eco-friendly coatings grows, manufacturers are likely to develop new formulations that offer enhanced properties, such as increased scratch resistance, self-healing capabilities, and advanced corrosion resistance. This continuous improvement will likely expand the applications of thermoplastic coatings into new industries and markets, making them an even more versatile and indispensable technology for modern manufacturing.
In conclusion, thermoplastic powder coating equipment is a key enabler in producing coatings that combine exceptional durability, flexibility, and aesthetic appeal. The combination of advanced application systems, customizable formulations, and sustainable practices makes thermoplastic powder coating an ideal choice for a wide range of industries, from automotive to industrial machinery. As technology continues to evolve and industries push for more sustainable, high-performance products, thermoplastic powder coating will undoubtedly remain a core technology in the future of surface finishing.